Thermal Dynamics ULTRA-CUT 100, 200, 300, 400 XT Mode d'emploi
PDF
Download
Document
® MAX PUISSANCE MAX PUISSANCE 100 200 A A MAX PUISSANCE MAX PUISSANCE 300 400 A ALIMENTATION D'ENTRÉE PHASÉ A TENSION 400V ULTRA-CUT 100, 200, 300, 400 XT ™ GENERATEUR DE COUPAGE À L’ARC PLASMA Manuel d’instructions Rév.: AK Date: 5 janvier 2017 Manuel n°: 0-5264FR Thermal-Dynamics.com ® NOUS SOMMES HEUREUX DE VOUS COMPTER PARMI NOS CLIENTS ! Félicitations pour votre nouveau produit Thermal Dynamics. Nous sommes fiers de vous compter au nombre de nos clients et ferons tout notre possible pour vous fournir un service et une fiabilité sans égal dans notre secteur. Ce produit bénéficie d'une garantie étendue et d’un réseau de service après-vente mondial. Pour trouver un distributeur ou un service après-vente local, veuillez appeler le numéro suivant 1-800-752-7622 ou vous rendre sur notre site web : www.thermal-dynamics.com. Le présent manuel d’instructions a été rédigé pour vous fournir des informations sur les conditions de fonctionnement et d’exploitation du produit Thermal Dynamics que vous avez acheté. Parce que nous attachons une importance toute particulière à l'exploitation sécurisée du produit et à la satisfaction que vous en retirerez, nous vous demandons de bien vouloir prendre le temps de lire l’intégralité de ce manuel, notamment les « consignes de sécurité », afin d’éviter les risques potentiels qui pourraient surgir lors de l’utilisation du produit. VOUS ETES EN BONNE COMPAGNIE ! La marque de choix des entrepreneurs et des constructeurs dans le monde entier. Thermal Dynamics est une marque internationale de produits de coupage manuel et automatique à l’arc plasma de Thermal Dynamics Corporation. Nous nous démarquons de nos concurrents grâce à la fiabilité de nos produits qui se sont hissés au premier rang du marché et ont fait leurs preuves au fil des ans. L’innovation technique, des prix concurrentiels, des délais de livraison hors pair, un niveau supérieur de service après-vente et d'assistance technique, ainsi que l'expérience appréciable de nos équipes de vente et de marketing, font l’objet de notre fierté. Mais par dessus tout, nous nous engageons à mettre au point des produits de pointe sur le plan technologique afin d’assurer un environnement de travail plus sûr dans le secteur du soudage. ! MISE EN GARDE Merci de lire et de bien comprendre l’intégralité de ce manuel ainsi que les procédures de sécurité sur le lieu de travail avant d'installer, d'exploiter et de réparer ce produit. Si les informations contenues dans ce manuel reflètent le discernement du fabricant, celui-ci décline toute responsabilité quant à son utilisation. Générateur de coupage à l’arc plasma, Ultra-Cut XT™ 100/200/300/400 Manuel d’instructions n° 0-5264FR Publié par : Thermal Dynamics Corporation. 2800 Airport Rd. Denton, Texas 76207 www.thermal-dynamics.com © Copyright 2013, 2014, 2015, 2016 par Thermal Dynamics Corporation Tous droits réservés. Il est interdit de reproduire cet ouvrage, intégralement ou partiellement, sans l’autorisation écrite de l’éditeur. L’éditeur décline par la présente toute responsabilité à l’égard de tiers en cas de perte ou de dommages provoqués par une quelconque erreur ou une quelconque ommission dans ce manuel, que lesdites erreurs soient le résultat d’une négligence, d'un accident ou de toute autre cause. Pour l'impression Caractéristiques des matériaux se référer au document 47x1922. Date de publication : 18 avril 2013 Date de révision : 5 janvier 2017 Noter les renseignements suivants aux fins de la garantie : Lieu d’achat : ___________________________________ Date d’achat :______________________________________ N° de série du générateur :_______________________________ N° de série de la torche :_______________________________________ ASSUREZ-VOUS QUE CE DOCUMENT D’INFORMATION EST DISTRIBUÉ À L’OPÉRATEUR. DES COPIES SUPPLÉMENTAIRES SONT DISPONIBLES CHEZ VOTRE FOURNISSEUR. ATTENTION Les INSTRUCTIONS suivantes sont destinées aux opérateurs qualifiés seulement. Si vous n’avez pas une connaissance approfondie des principes de fonctionnement et des règles de sécurité applicables au soudage à l’arc et à l’équipement de coupage, nous vous suggérons de lire notre brochure « Précautions et pratiques de sécurité pour le soudage à l’arc, le coupage et le gougeage », Formulaire 52-529. Ne permettez PAS aux personnes non qualifiées d’installer, d’utiliser ou d’effectuer des opérations de maintenance sur cet équipement cet équipement. Ne tentez PAS d’installer ou d’utiliser cet équipement avant d’avoir lu et bien compris ces instructions. Si vous ne comprenez pas bien les instructions, renseignez-vous auprès de votre fournisseur. Assurez-vous de lire les Règles de Sécurité avant d’installer ou d’utiliser cet équipement. RESPONSABILITÉS DE L’UTILISATEUR Cet équipement fonctionnera conformément à la description contenue dans ce manuel, les étiquettes d’accompagnement et/ou les feuillets d’information à condition d’être installé, utilisé, entretenu et réparé selon les instructions fournies. L’équipement doit être contrôlé de manière périodique. Ne jamais utiliser un équipement qui ne fonctionne correctement bien ou n’est pas bien entretenu. Les pièces qui sont brisées, usées, déformées ou contaminées doivent être remplacées immédiatement. Dans le cas où une réparation ou un remplacement est nécessaire, e fabricant recommande de faire une demande de conseil de service écrite ou par téléphone auprès du distributeur agréé où l’équipement a été acheté. Cet équipement ou ses pièces ne doivent pas être modifiés sans permission préalable écrite du fabricant. L’utilisateur de l’équipement sera le seul responsable de toute défaillance résultant de toute utilisation, maintenance, réparation incorrectes, de dommages ou encore de modification apportées par une personne autre que le fabricant ou un centre de service désigné par ce dernier. ! ASSUREZ-VOUS DE LIRE ET DE COMPRENDRE LE MANUEL D’UTILISATION AVANT D’INSTALLER OU D’UTILISER L’UNITÉ. PROTÉGEZ-VOUS ET LES AUTRES! Declaration of Conformity We of Thermal Dynamics 2800 Airport Road Denton, TX 76207 U.S.A. in accordance with the following Directive(s): 2006/95/EC The Low Voltage Directive 2004/108/EC The Electromagnetic Compatibility Directive hereby declare that: Equipment: Plasma Cutting Controller Model Name/Number: Ultra-Cut 100, 200, 300 and 400 XT Market Release Date: April 18, 2013 is in conformity with the applicable requirements of the following harmonized standards: CENELEC EN61010-1 Ed:3 Safety Requirements for Electrical Equipment for Measurement, Control, and Laboratory Use Part 1: General Requirements Classification: The equipment described in this document is Class A and intended for industrial use. ! WARNING This Class A equipment is not intended for use in residential locations where the electrical power is provided by the public low-voltage supply system. There may be potential difficulties in ensuring electromagnetic compatibility in those locations, due to conducted as well as radiated disturbances. Manufacturer’s Authorized Representative Steve Ward V.P. Europe and General Manager Address:Victor Technologies International Inc. Europa Building Chorley N Industrial Park Chorley, Lancashire, England PR6 7BX Date: April 8, 2015 (Signature) Steve Ward Full Name V.P. Europe and General Manager (Position) ! WARNING This Class A equipment is not intended for use in residential locations where the electrical power is provided by the public low-voltage supply system. There may be potential difficulties in ensuring electromagnetic compatibility in those locations, due to conducted as well as radiated disturbances. TABLE DES MATIÈRES CHAPITRE 1 : INFORMATIONS GÉNÉRALES............................................................. 1-1 1.02 Précautions de sécurité................................................................................... 1-1 CHAPITRE 2 : CARACTÉRISTIQUES...................................................................... 2-1 2.01 Description générale du système..................................................................... 2-1 2.02 Générateur à l’arc plasma................................................................................ 2-1 2.03 Une amorce d’arc à distance............................................................................ 2-1 2.04 Un module de commande du gaz.................................................................... 2-1 2.05 Une torche de coupage à l’arc plasma de précision......................................... 2-1 2.06 Spécifications et caractéristiques électriques.................................................. 2-2 2.07 Dimensions du générateur............................................................................... 2-4 2.08 Fonctions du panneau arrière du générateur.................................................... 2-5 2.09 Caractéristiques du gaz.................................................................................... 2-6 2.10 Applications du gaz.......................................................................................... 2-8 2.11 Spécifications de torche XT ............................................................................ 2-9 CHAPITRE 3 : INSTALLATION............................................................................. 3-1 3.01 Conditions d’installation.................................................................................. 3-1 3.02 Schéma du système 100 - 200 A .................................................................... 3-2 3.03 Schéma du système 300 A.............................................................................. 3-3 3.04 Schéma du système 400 A.............................................................................. 3-3 3.05 Tuyau recommandé pour l’alimentation en gaz................................................ 3-4 3.06 Fils et câbles toutes intensités......................................................................... 3-4 3.07 Levage du générateur...................................................................................... 3-5 3.08 Raccorder les câbles de l’alimentation et de masse......................................... 3-6 3.09 Connexion du câble de mise à la terre, de l’arc pilote et des câbles négatifs... 3-7 3.10 Connexions de masse...................................................................................... 3-8 3.11 Raccordement des câbles du liquide de refroidissement............................... 3-11 3.12 Connection des câbles pour CNC, allumage de l’arc à distance, GCM et HE400........................................................................................................ 3-12 3.13 Manipulation et installation de fibres optiques............................................... 3-13 3.14 Configuration des interrupteurs du module de commande - contrôle............ 3-15 3.15 Raccordements de contrôle de la hauteur...................................................... 3-17 3.16 Installation du module de contrôle des gaz.................................................... 3-17 3.17 Installation du câble à fibre optique............................................................... 3-19 3.18 Module de contrôle du gaz : Connexions de contrôle, d’entrée et de sortie.. 3-21 3.19 Système de refroidissement HE400............................................................... 3-22 3.20 Installation de l’amorce d’arc à distance........................................................ 3-24 3.21 Installation de la soupape de la torche........................................................... 3-32 3.22 Raccordement de la torche............................................................................ 3-33 3.23 Installation des consommables de la torche.................................................. 3-35 3.24 Diviseur de tension (« V-D ») pour contrôler la hauteur de torche iHC.......... 3-37 3.25 Fin de l’installation......................................................................................... 3-39 TABLE DES MATIÈRES CHAPITRE 4 : FONCTIONNEMENT........................................................................ 4-1 4.01 Panneau de commande du générateur............................................................. 4-1 4.02 Fonctionnement du système............................................................................ 4-2 4.03 Sélection du gaz............................................................................................... 4-4 4.04 Fonctionnement du module de contrôle de gaz GCM 2010.............................. 4-6 4.05 Initialisation de GCM 2010 pour adapter le contrôle des gaz à la longueur des conduites....................................................................................................... 4-10 4.06 Séquence de fonctionnement du GCM 2010.................................................. 4-10 4.07 Codes de fonctionnement du générateur....................................................... 4-12 4.08 Résolution des problèmes pour l’allumage d’arc à distance.......................... 4-21 CHAPITRE 5 : ENTRETIEN................................................................................. 5-1 5.01 Entretien général.............................................................................................. 5-1 5.02 Procédure de nettoyage du filtre externe du liquide de refroidissement.......... 5-1 5.03 Procédure de remplacement du liquide de refroidissement............................. 5-2 CHAPITRE 6 : ÉLÉMENTS ET PIÈCES DE RECHANGE.................................................. 6-1 6.01 Générateur de rechange................................................................................... 6-1 6.02 Schéma du système 100 - 200 A..................................................................... 6-2 6.03 Schéma du système 300 A.............................................................................. 6-2 6.04 Schéma du système 400 A.............................................................................. 6-3 6.05 Tuyau d’alimentation du gaz recommandé....................................................... 6-3 6.06 Fils et câbles toutes intensités......................................................................... 6-4 6.07 Pièces de rechange externes pour le générateur.............................................. 6-6 6.08 Pièces de rechange d’alimentation électrique - Côté supérieur droit................ 6-7 6.09 Pièces de rechange d’alimentation électrique - Côté inférieur droit................. 6-8 6.10 Pièces de rechange d’alimentation électrique - Panneau arrière...................... 6-9 6.11 Pièces de rechange d’alimentation électrique - Côté gauche.......................... 6-10 6.12 Gas Control Module (GCM-2010) Replacement Parts.................................... 6-11 6.13 Pièces de rechange du module de commande du gaz (GCM-2010)............... 6-12 6.14 Amorce d’arc à distance (RAS-1000 XT) Pièces de rechange........................ 6-13 6.15 Pièces de rechange de l’échangeur de chaleur HE 400.................................. 6-14 6.16 Torche XTL distributeur de pièces externes................................................... 6-15 6.17 Torche XTL distributeur de pièces de remplacement interne.......................... 6-16 CHAPITRE 7 : TORCHE ENTRETIEN....................................................................... 7-1 7.01 Enlèvement des consommables....................................................................... 7-1 7.02 Lubrification du joint torique............................................................................ 7-2 7.03 Usure des pièces............................................................................................. 7-2 7.04 Installation des consommables de la torche.................................................... 7-3 7.05 Dépannage en cas de fuite du liquide de refroidissement................................ 7-5 ANNEXE 1 : SCHÉMA DU DÉMARREUR À DISTANCE DE L’ARC...................................... A-1 ANNEXE 2 : SCHÉMA DE COMMANDE DE GAZ ET DE SOUPAPE DE LA TORCHE .................. A-2 ANNEXE 3 : SCHÉMA DE PLOMBERIE DU MODULE DE COMMANDE DU GAZ...................... A-4 ANNEXE 4 : DISPOSITION DU CIRCUIT IMPRIMÉ DU MODULE DE COMMANDE DU GAZ........ A-5 TABLE DES MATIÈRES ANNEXE 5 : DISPOSITION DU CIRCUIT IMPRIMÉ DU MODULE D’AFFICHAGE DE COMMANDE DU GAZ................................................................................. A-6 ANNEXE 6 : CNC - CONNEXIONS DU CIRCUIT IMPRIMÉ DU MODULE DE COMMANDE........... A-7 ANNEXE 7 : CNC ............................................................................................ A-8 Fonctionnalités CNC....................................................................................................... A-8 Description de l’entrée/de la sortie de la CNC.............................................................. A-10 Circuit simplifié CNC.................................................................................................... A-12 Connexions CNC.......................................................................................................... A-14 Code couleurs du câble CNC........................................................................................ A-15 ANNEXE 8 : COMMUNICATIONS DE SÉRIE.............................................................A-16 A8.01 Paramètres des câbles et des interrupteurs pour 2 et 4 fils .......................... A-16 ANNEXE 9 : DISPOSITION CIRCUIT IMPRIMÉ UC CCM..............................................A-18 ANNEXE 10 : DISPOSITION CIRCUIT IMPRIMÉ E/S CCM............................................A-20 ANNEXE 11 : DISPOSITION DU CIRCUIT DU PILOTE.................................................A-22 ANNEXE 12 : DISPOSITION DU CIRCUIT DU DU RELAIS ET DE L’INTERFACE....................A-24 ANNEXE 13 : AFFICHER LA DISPOSITION DES CIRCUITS IMPRIMÉS.............................A-26 ANNEXE 14 : DISPOSITION DU CIRCUIT DE LA POLARISATION DU SYSTÈME...................A-28 ANNEXE 15 : DISPOSITION DU CIRCUIT INFÉRIEUR DU HÂCHEUR PRINCIPAL..................A-30 ANNEXE 16 : DISPOSITION DU CIRCUIT SUPÉRIEUR DU HÂCHEUR PRINCIPAL.................A-32 ANNEXE 17 : DISPOSITION CIRCUITS IMPRIMÉS DE COMMANDE ET DE DÉFAUT..............A-34 ANNEXE 18 : DISPOSITION DU CIRCUIT IMPRIMÉ DU CONDENSATEUR INFÉRIEUR BIAS.....A-36 ANNEXE 19 : DISPOSITION DU CIRCUIT IMPRIMÉ DU CONDENSATEUR SUPÉRIEUR BIAS....A-37 ANNEXE 20 : DISPOSITION DU CIRCUIT DE PROTECTION DE CONTACT..........................A-38 ANNEXE 21 : SCHÉMA DE REFROIDISSEMENT.......................................................A-39 ANNEXE 22 : SCHÉMA DE PRINCIPE 100A, 380-415V PG 1..........................................A-40 ANNEXE 23 : SCHÉMA DE PRINCIPE 100A, 380-415V PG 2..........................................A-42 ANNEXE 24 : SCHÉMA DE PRINCIPE 200A, 380-415V PG 1..........................................A-44 ANNEXE 25 : SCHÉMA DE PRINCIPE 200A, 380-415V PG 2..........................................A-46 ANNEXE 26 : SCHÉMA DE PRINCIPE 300A, 380-415V PG 1..........................................A-48 ANNEXE 27 : SCHÉMA DE PRINCIPE 300A, 380-415V PG 2..........................................A-50 ANNEXE 28 : SCHÉMA DE PRINCIPE 400A, 380-415V PG 1..........................................A-52 ANNEXE 29 : SCHÉMA DE PRINCIPE 400A, 380-415V PG 2..........................................A-54 ANNEXE 30 : DÉPANNAGE AVANCÉ.....................................................................A-56 TABLE DES MATIÈRES ANNEXE 31 : SL100 INTERCONNECTION............................................................. A-102 ANNEXE 32 : HE 400 XT CONNECTION............................................................... A-104 ANNEXE 33 : SL100 TORCH EN OPTION.............................................................. A-105 ANNEXE 34 : HISTORIQUE DE PUBLICATION........................................................ A-112 DÉCLARATION DE GARANTIE....................................... L'INTÉRIEUR DE LA PAGE ARRIÈRE INFORMATIONS DE CONTACT INTERNATIONAL........................................ PAGE ARRIÈRER ULTRA-CUT 100 XT/200 XT/300 XT/400 XT CHAPITRE 1 : INFORMATIONS GÉNÉRALES 1.02 Précautions de sécurité AVERTISSEMENT : Ces règles de sécurité ont pour but d’assurer votre protection. Ils récapitulent les informations de précaution provenant des références dans la section des Informations de sécurité supplémentaires. Avant de procéder à l’installation ou d’utiliser l’unité, assurez-vous de lire et de suivre les précautions de sécurité ci-dessous, dans les manuels, les fiches d’information sur la sécurité du matériel et sur les étiquettes, etc. Tout défaut d’observer ces précautions de sécurité peut entraîner des blessures graves ou mortelles. ! PROTÉGEZ-VOUS -- Les processus de soudage, de coupage et de gougeage produisent un niveau de bruit élevé et exige l’emploi d’une protection auditive. L’arc, tout comme le soleil, émet des rayons ultraviolets en plus d’autre rayons qui peuvent causer des blessures à la peau et les yeux. Le métal incandescent peut causer des brûlures. Une formation reliée à l’usage des processus et de l’équipement est essentielle pour prévenir les accidents. Par conséquent: 1. 2. 3. 4. 5. 6. 1. 2. 3. 4. 5. 6. 7. 0-5264FR Portez des lunettes protectrices munies d’écrans latéraux lorsque vous êtes dans l’aire de travail, même si vous devez porter un casque de soudeur, un écran facial ou des lunettes étanches. Portez un écran facial muni de verres filtrants et de plaques protectrices appropriées afin de protéger vos yeux, votre visage, votre cou et vos oreilles des étincelles et des rayons de l’arc lors d’une opération ou lorsque vous observez une opération. Avertissez les personnes se trouvant à proximité de ne pas regarder l’arc et de ne pas s’exposer aux rayons de l’arc électrique ou le métal incandescent. Portez des gants ignifugiés à crispin, une chemise épaisse à manches longues, des pantalons sans rebord et des chaussures montantes afin de vous protéger des rayons de l’arc, des étincelles et du métal incandescent, en plus d’un casque de soudeur ou casquette pour protéger vos cheveux. Il est également recommandé de porter un tablier ininflammable afin de vous protéger des étincelles et de la chaleur par rayonnement. Les étincelles et les projections de métal incandescent risquent de se loger dans les manches retroussées, les rebords de pantalons ou les poches. Il est recommandé de garder boutonnés le col et les manches et de porter des vêtements sans poches en avant. Protégez toute personne se trouvant à proximité des étincelles et des rayons de l’arc à l’aide d’un rideau ou d’une cloison ininflammable. Portez des lunettes étanches par dessus vos lunettes de sécurité lors des opérations d’écaillage ou de meulage du laitier. Les écailles de laitier incandescent peuvent être projetées à des distances considérables. Les personnes se trouvant à proximité doivent également porter des lunettes étanches par dessus leur lunettes de sécurité. INCENDIES ET EXPLOSIONS -- La chaleur provenant des flammes ou de l’arc peut provoquer un incendie. Le laitier incandescent ou les étincelles peuvent également provoquer un incendie ou une explosion. Par conséquent : Éloignez suffisamment tous les matériaux combustibles de l’aire de travail et recouvrez les matériaux avec un revêtement protecteur ininflammable. Les matériaux combustibles incluent le bois, les vêtements, la sciure, le gaz et les liquides combustibles, les solvants, les peintures et les revêtements, le papier, etc. Les étincelles et les projections de métal incandescent peuvent tomber dans les fissures dans les planchers ou dans les ouvertures des murs et déclencher un incendie couvant à l’étage inférieur Assurez-vous que ces ouvertures sont bien protégées des étincelles et du métal incandescent. N’exécutez pas de soudure, de coupe ou autre travail à chaud avant d’avoir complètement nettoyé la surface de la pièce à traiter de façon à ce qu’il n’ait aucune substance présente qui pourrait produire des vapeurs inflammables ou toxiques. N’exécutez pas de travail à chaud sur des contenants fermés car ces derniers pourraient exploser. Assurez-vous qu’un équipement d’extinction d’incendie est disponible et prêt à servir, tel qu’un tuyau d’arrosage, un seau d’eau, un seau de sable ou un extincteur portatif. Assurez-vous d’être bien instruit par rapport à l’usage de cet équipement. Assurez-vous de ne pas excéder la capacité de l’équipement. Par exemple, un câble de soudage surchargé peut surchauffer et provoquer un incendie. Une fois les opérations terminées, inspectez l’aire de travail pour assurer qu’aucune étincelle ou projection de métal incandescent ne risque de provoquer un incendie ultérieurement. Employez des guetteurs d’incendie au besoin. Pour obtenir des informations supplémentaires, consultez le NFPA Standard 51B, “Fire Prevention in Use of Cutting and Welding Processes”, disponible au National Fire Protection Association, Batterymarch Park, Quincy, MA 02269. INSTRUCTIONS DE SÉCURITÉ 1-1 ULTRA-CUT 100 XT/200 XT/300 XT/400 XT CHOC ÉLECTRI QUE -- Le contact avec des pièces électriques ou les pièces de mise à la terre sous tension peut causer des blessures graves ou mortelles. NE PAS utiliser un courant de soudage c.a. dans un endroit humide, en espace restreint ou si un danger de chute se pose. 1. 2. 3. 4. 5. Assurez-vous que le châssis de la source d’alimentation est branché au système de mise à la terre de l’alimentation d’entrée. Branchez la pièce à traiter à une bonne mise de terre électrique. Branchez le câble de masse à la pièce à traiter et assurez une bonne connexion afin d’éviter le risque de choc électrique mortel. Utilisez toujours un équipement correctement entretenu. Remplacez les câbles usés ou endommagés. Veillez à garder votre environnement sec, incluant les vêtements, l’aire de travail, les câbles, le porteélectrode/torche et la source d’alimentation. 6. Assurez-vous que tout votre corps est bien isolé de la pièce à traiter et des pièces de la mise à la terre. 7. Si vous devez effectuer votre travail dans un espace restreint ou humide, ne tenez vous pas directement sur le métal ou sur la terre; tenez-vous sur des planches sèches ou une plate-forme isolée et portez des chaussures à semelles de caoutchouc. 8. Avant de mettre l’équipement sous tension, isolez vos mains avec des gants secs et sans trous. 9. Mettez l’équipement hors tension avant d’enlever vos gants. 10. Consultez ANSI/ASC Standard Z49.1 (listé à la page suivante) pour des recommandations spécifiques concernant les procédures de mise à la terre. Ne pas confondre le câble de masse avec le câble de mise à la terre. CHAMPS ÉLECTRIQUES ET MAGNÉTIQUES — comportent un risque de danger. Le courant électrique qui passe dans n’importe quel conducteur produit des champs électriques et magnétiques localisés. Le soudage et le courant de coupage créent des champs électriques et magnétiques autour des câbles de soudage et l’équipement. Par conséquent : 1. Un soudeur ayant un stimulateur cardiaque doit consulter son médecin avant d’entreprendre une opération de soudage. Les champs électriques et magnétiques peuvent causer des ennuis pour certains stimulateurs cardiaques. 2. L’exposition à des champs électriques et magnétiques peut avoir des effets néfastes inconnus pour la santé. 3. Les soudeurs doivent suivre les procédures suivantes pour minimiser l’exposition aux champs électriques et magnétiques : A. Acheminez l’électrode et les câbles de masse ensemble. Fixez-les à l’aide d’une bande adhésive lorsque possible. B. Ne jamais enrouler la torche ou le câble de masse autour de votre corps. C. Ne jamais vous placer entre la torche et les câbles de masse. Acheminez tous les câbles sur le même côté de votre corps. D. Branchez le câble de masse à la pièce à traiter le plus près possible de la section à souder. E. Veillez à garder la source d’alimentation pour le soudage et les câbles à une distance appropriée de votre corps. LES VAPEURS ET LES GAZ -- peuvent causer un malaise ou des dommages corporels, plus particulièrement dans les espaces restreints. Ne respirez pas les vapeurs et les gaz. Le gaz de protection risque de causer l’asphyxie. Par conséquent : 1. Assurez en permanence une ventilation adéquate dans l’aire de travail en maintenant une ventilation naturelle ou à l’aide de moyens mécanique. N’effectuez jamais de travaux de soudage, de coupage ou de gougeage sur des matériaux tels que l’acier galvanisé, l’acier inoxydable, le cuivre, le zinc, le plomb, le berylliym ou le cadmium en l’absence de moyens mécaniques de ventilation efficaces. Ne respirez pas les vapeurs de ces matériaux. 2. N’effectuez jamais de travaux à proximité d’une opération de dégraissage ou de pulvérisation. Lorsque la chaleur ou le rayonnement de l’arc entre en contact avec les vapeurs d’hydrocarbure chloré, ceci peut déclencher la formation de phosgène ou d’autres gaz irritants, tous extrêmement toxiques. 3. Une irritation momentanée des yeux, du nez ou de la gorge au cours d’une opération indique que la ventilation n’est pas adéquate. Cessez votre travail afin de prendre les mesures nécessaires pour améliorer la ventilation dans l’aire de travail. Ne poursuivez pas l’opération si le malaise persiste. 4. Consultez ANSI/ASC Standard Z49.1 (à la page suivante) pour des recommandations spécifiques concernant la ventilation. 5. AVERTISSEMENT : Ce produitcontient des produits chimiques, notamment du plomb, reconnu par l’Étatde la Californie pour causerdes malformations congénitaleset d’autresdommages touchant le système reproductif. Se laver les mainsaprès manipulation. 1-2 INSTRUCTIONS DE SÉCURITÉ 0-5264FR ULTRA-CUT 100 XT/200 XT/300 XT/400 XT MANIPULATION DES CYLINDRES -- La manipulation d’un cylindre, sans observer les précautions nécessaires, peut produire des fissures et un échappement dangereux des gaz. Une brisure soudaine du cylindre, de la soupape ou du dispositif de surpression peut causer des blessures graves ou mortelles. Par conséquent : 1. 2. 3. 4. 5. ! 1. Utilisez toujours le gaz prévu pour une opération et le détendeur approprié conçu pour utilisation sur les cylindres de gaz comprimé. N’utilisez jamais d’adaptateur. Maintenez en bon état les tuyaux et les raccords. Observez les instructions d’opération du fabricant pour assembler le détendeur sur un cylindre de gaz comprimé. Fixez les cylindres dans une position verticale, à l’aide d’une chaîne ou une sangle, sur un chariot manuel, un châssis de roulement, un banc, un mur, une colonne ou un support convenable. Ne fixez jamais un cylindre à un poste de travail ou toute autre dispositif faisant partie d’un circuit électrique. Lorsque les cylindres ne servent pas, gardez les soupapes fermées. Si le détendeur n’est pas branché, assurez-vous que le bouchon de protection de la soupape est bien en place. Fixez et déplacez les cylindres à l’aide d’un chariot manuel approprié. Toujours manipuler les cylindres avec soin. Placez les cylindres à une distance appropriée de toute source de chaleur, des étincelles et des flammes. Ne jamais amorcer l’arc sur un cylindre. Pour de l’information supplémentaire, consultez CGA Standard P-1, “Precautions for Safe Handling of Compressed Gases in Cylinders”, mis à votre disposition par le Compressed Gas Association, 1235 Jefferson Davis Highway, Arlington, VA 22202. ENTRETIEN DE L’ÉQUIPEMENT -- Un équipement entretenu de façon défectueuse ou inadéquate peut causer des blessures graves ou mortelles. Par conséquent : 5. 6. Efforcez-vous de toujours confier les tâches d’installation, de dépannage et d’entretien à un personnel qualifié. N’effectuez aucune réparation électrique à moins d’être qualifié à cet effet. Avant de procéder à une tâche d’entretien à l’intérieur de la source d’alimentation, débranchez l’alimentation électrique. Maintenez les câbles, les fils de mise à la terre, les branchements, le cordon d’alimentation et la source d’alimentation en bon état. N’utilisez jamais un équipement s’il présente une défectuosité quelconque. N’utilisez pas l’équipement de façon abusive. Gardez l’équipement à l’écart de toute source de chaleur, notamment des fours, de l’humidité, des flaques d’eau, de l’huile ou de la graisse, des atmosphères corrosives et des intempéries. Laissez en place tous les dispositifs de sécurité et tous les panneaux de la console et maintenez-les en bon état. Utilisez l’équipement conformément à son usage prévu et n’effectuez aucune modification. ! INFORMATIONS SUPPLÉMENTAIRES RELATI VES À LA SÉCURITÉ -- Pour obtenir de l’information supplémentaire sur les règles de sécurité à observer pour l’équipement de soudage à l’arc électrique et le coupage, demandez un exemplaire du livret “Precautions and Safe Practices for Arc Welding, Cutting and Gouging”, Form 52-529. 2. 3. 4. Les publications suivantes sont également recommandées et mises à votre disposition par l’American Welding Society, 550 N.W. LeJuene Road, Miami, FL 33126 : 1. 2. 3. 4. 5. 6. 7. 8. 0-5264FR ANSI/ASC Z49.1 - “Safety in Welding and Cutting”. AWS C5.1 - “Recommended Practices for Plasma Arc Welding”. AWS C5.2 - “Recommended Practices for Plasma Arc Cutting”. AWS C5.3 - “Recommended Practices for Air Carbon Arc Gouging and Cutting”. AWS C5.5 - “Recommended Practices for Gas Tungsten Arc Welding“. AWS C5.6 - “Recommended Practices for Gas Metal Arc Welding”. AWS SP - “Safe Practices” - Reprint, Welding Handbook. ANSI/AWS F4.1, “Recommended Safe Practices for Welding and Cutting of Containers That Have Held Hazardous Substances.” INSTRUCTIONS DE SÉCURITÉ 1-3 ULTRA-CUT 100 XT/200 XT/300 XT/400 XT 9. CSA Standard - W117.2 = Safety in Welding, Cutting and Allied Processes. ! SIGNIFICATION DES SYMBOLES - Ce symbole, utilisé partout dans ce manuel, signifie “Attention” ! Soyez vigilant ! Votre sécurité est en jeu. DANGER ATTENTION DANGER Signifie un danger immédiat. La situation peut entraîner des blessures graves ou mortelles. Signifie un danger potentiel qui peut entraîner des blessures graves ou mortelles. Signifie un danger qui peut entraîner des blessures corporelles mineures. Classe de protection de l’enveloppe L’indice de protection (codification IP) indique la classe de protection de l’enveloppe, c’est-à-dire, le degré de protection contre les corps solides étrangers ou l’eau. L’enveloppe protège contre le toucher, la pénétration d’objets solides dont le diamètre dépasse 12 mm et contre l’eau pulvérisée à un angle de jusqu’à 60 degrés de la verticale. Les équipements portant la marque IP21S peuvent être entreposés à l’extérieur, mais ne sont pas conçus pour être utilisés à l’extérieur pendant une précipitation à moins d’être à l’abri. ATTENTION Ce produit a été conçu pour la découpe au plasma seulement. Toute autre utilisation pourrait causer des blessures et/ou endommager l’appareil. ATTENTION L’équipement pourrait basculer s’il est placé sur une surface dont la pente dépasse 15°. Vous pourriez vous blesser ou endommager l’équipement de façon importante. 1-4 INSTRUCTIONS DE SÉCURITÉ 0-5264FR ULTRA-CUT 100 XT/200 XT/300 XT/400 XT 15° Art# A-12726 Art# A-12736 ATTENTION Soulevez à l’aide de la méthode et des points d’attache illustrés afin d’éviter de vous blesser ou d’endommager l’équipement. 0-5264FR INSTRUCTIONS DE SÉCURITÉ 1-5 ULTRA-CUT 100 XT/200 XT/300 XT/400 XT Cette page est intentionnellement vierge. 1-6 INSTRUCTIONS DE SÉCURITÉ 0-5264FR ULTRA-CUT 100 XT/200 XT/300 XT/400 XT CHAPITRE 2 : CARACTÉRISTIQUES 2.01 Description générale du système Une configuration type du système Ultra-Cut XT comprend : MD • Un bloc d’alimentation • Une amorce d’arc à distance • Un module de commande du gaz • Une valve de torche • Une torche de coupage à l’arc plasma de précision • Un ensemble de câbles de raccordement • Un kit de pièces détachées pour la torche Les composants sont raccordés lors de l’installation. 2.02 Générateur à l’arc plasma Le générateur fournit le courant nécessaire pour les opérations de coupage. Le générateur supervise également les performances du système et il refroidit et fait circuler le liquide de refroidissement pour la torche et les câbles. 2.03 Une amorce d’arc à distance Cet appareil produit une impulsion HF temporaire pour amorcer l’arc pilote. L’arc pilote crée un sillon de façon à ce que l’arc principal puisse être transféré sur la pièce. Quand l’arc principal est établi, l’arc pilote se coupe. 2.04 Un module de commande du gaz Ce module permet de configurer à distance la sélection du gaz, les pressions et les débits ainsi que de configurer le courant de coupage. 2.05 Une torche de coupage à l’arc plasma de précision La torche fourni le courant contrôlé à la pièce par l’intermédiaire de l’arc principal, ce qui permet de couper le métal. 0-5264FR 2-1 SPÉCIFICATIONS ULTRA-CUT 100 XT/200 XT/300 XT/400 XT 2.06 Spécifications et caractéristiques électriques Conception et spécifications de l’Ultra-Cut 100 XTMD Système 100 A OCV max (U0) 425 VCC Courant de sortie minimum 5A Courant de sortie max 100 A Tension de sortie 60 - 180 VCC Caractéristique du facteur de marche 100% à 100A, 200V, (20kW), Température ambiante pour la caractéristique du facteur de marche 104°F (40°C) Plage de fonctionnement De 14°F à 122°F (de -10°C à +50°C) Facteur de puissance 0.94 à 100 A sortie CC Refroidissement Liquide de refroidissement et air forcé (Classe F) Conception et spécifications de l’Ultra-Cut 200 XTMD Système 200 A OCV max (U0) 425 VCC Courant de sortie minimum 5A Courant de sortie max 200 A Tension de sortie 60 - 180 VCC Caractéristique du facteur de marche 100% à 200A, 200V, (40kW), Température ambiante pour la caractéristique du facteur de marche 104°F (40°C) Plage de fonctionnement De 14°F à 122°F (de -10°C à +50°C) Facteur de puissance 0.94 à 200 A sortie CC Refroidissement Liquide de refroidissement et air forcé (Classe F) Conception et spécifications de l’Ultra-Cut 300 XTMD Système 300 A OCV max (U0) 425 VCC Courant de sortie minimum 5A Courant de sortie max 300 A Tension de sortie / IEC 60 - 180 VCC / 60 - 200 VCC Caractéristique du facteur de marche 100% à 300A, 200V, (60kW), Température ambiante pour la caractéristique du facteur de marche 104°F (40°C) Plage de fonctionnement De 14°F à 122°F (de -10°C à +50°C) Facteur de puissance 0.94 à 300 A sortie CC Refroidissement Liquide de refroidissement et air forcé (Classe F) Conception et spécifications de l’Ultra-Cut 400 XTMD Système 400 A OCV max (U0) 425 VCC Courant de sortie minimum 5A Courant de sortie max 400 A Tension de sortie 60 - 200 VCC Caractéristique du facteur de marche 100% à 400A, 200V, (80kW), Température ambiante pour la caractéris- 104°F (40°C) tique du facteur de marche SPÉCIFICATIONS Plage de fonctionnement De 14°F à 122°F (de -10°C à +50°C) Facteur de puissance 0.94 à 400 A sortie CC Refroidissement Liquide de refroidissement et air forcé (Classe F) 2-2 0-5264FR ULTRA-CUT 100 XT/200 XT/300 XT/400 XT Générateur Ultra-Cut 100 XTMD Entrée Puissance absorbée Intensité Tailles conseillées (Voir Remarque) Tension Fréquence Triphasée Triphasée Fusible (A) Fil (AWG) Fil (mm2) (Volts) (Hz) (kVA) (A) Triphasée Triphasée Triphasée 400 50/60 21 31 40-45 #12 4 Générateur Ultra-Cut 200 XTMD Entrée Puissance absorbée Intensité Tailles conseillées (Voir Remarque) Tension Fréquence Triphasée Triphasée Fusible (A) Fil (AWG) Fil (mm2) (Volts) (Hz) (kVA) (A) Triphasée Triphasée Triphasée 400 50/60 42 62 100 #6 16 Générateur Ultra-Cut 300 XTMD Entrée Puissance absorbée Intensité Tailles conseillées (Voir Remarque) Tension Fréquence Triphasée Triphasée Fusible (A) Fil (AWG) Fil (mm2) (Volts) (Hz) (kVA) (A) Triphasée Triphasée Triphasée 400 50/60 63 93 150 #4 25 400 50/60 72 106 150 #4 25 IEC Générateur Ultra-Cut 400 XTMD Entrée Puissance absorbée Intensité Tailles conseillées (Voir Remarque) Tension Fréquence Triphasée Triphasée Fusible (A) Fil (AWG) Fil (mm2) (Volts) (Hz) (kVA) (A) Triphasée Triphasée Triphasée 400 50/60 93 137 200 #1 50 REMARQUE ! * La taille suggérée pour les câbles est basée sur le code national d’électricité américain NFPA 70 édition 2011, publiée par la National Fire Prevention Association. Les listes sont issues du tableau 400.5(A)(2) pour les cordons souples de certains types étalonnés pour 75°C à température ambiante atteignant jusqu’à 30°C. Utiliser des câbles à faible cote de température ou des types différents d’isolation peut exiger des tailles de câblage plus grandes. Réduire la valeur nominale des températures ambiantes plus élevées. Il s’agit uniquement de suggestions. Référez-vous toujours à vos législations locales et nationales qui s’appliquent à votre région pour la détermination finale du bon type et de la bonne taille de câblage 0-5264FR 2-3 SPÉCIFICATIONS ULTRA-CUT 100 XT/200 XT/300 XT/400 XT 2.07 Dimensions du générateur 1213 mm 47,77 Pouce 914 mm 35,97 Pouce 701 mm 27,6 Pouce 100A 420 lb / 190 kg 200A 465 lb / 211 kg 300A 560 lb / 254 kg 400A 580 lb / 263 kg Art # A-11487FR_AB SPÉCIFICATIONS 2-4 0-5264FR ULTRA-CUT 100 XT/200 XT/300 XT/400 XT 2.08 Fonctions du panneau arrière du générateur TSC/Comm Clients ports en option Disjoncteurs Connecteur GCM Connecteur CNC J55 - GCM USER INPUT Retour du liquide de refroidissement C.C.M. J15 - CNC HEIGHT CONTROL Alimentation du liquide de refroidissement J54 - TSC /COMM Connecteur de l’amorce d’arc J59 - RAS CB2 - 5A 120 VAC Voyant alimentation CA CB3 - 5A 24 VAC J70 - HE Connecteur à 7 broches CB4 - 5A 120 VAC F1 - 8A SB 230 VAC F2 - 8A SB 230 VAC Fusible Câble de l’arc pilote Ports d'entrée d'alimentation Câble de mise à la terre Rendement négatif Filtre du liquide de refroidissement Art # A-11842FEU 0-5264FR 2-5 SPÉCIFICATIONS ULTRA-CUT 100 XT/200 XT/300 XT/400 XT 2.09 Caractéristiques du gaz Le client fournira tous les gaz et les régulateurs de pression. Les gaz doivent être de haute qualité. Les régulateurs de pression doivent être à double étage et installés à moins de 3 mètres de la console du gaz. Générateur Ultra-Cut 100 XT™ : caractéristiques de qualité, débits et pressions du gaz Gaz Qualité Pression minimale Flow O2 (Oxygène) 99.5% Pureté (Liquide recommandé) 120 psi 8.3 bar / 827 kPa 70 scfh (2000 l/h) N2 (Azote) 99.5% Pureté (Liquide recommandé) <1000 ppm O2, <32 ppm H2O) 120 psi 8.3 bar / 827 kPa 200 scfh (5700 l/h) Air en bouteille ou comprimé Propre, sec, Exempt d’huile (Consultez remarque 1) 120 psi 8.3 bar / 827 kPa 250 scfh (7000 l/h) H35 (Argon-Hydrogène) H35 = 35% Hydrogène, 65% Argon 99.995% Pureté (gaz recommandé) 120 psi 8.3 bar / 827 kPa 90 scfh (2550 l/h) H2O (Eau) Consultez remarque 2 50 psi (3.5 bar) 10 gph (38 lph) REMARQUE 1 : La source d’air doit être correctement filtrée afin d’éliminer toute trace d’huile ou de graisse. La contamination d’huile ou de graisse provenant de l’air comprimé ou en bouteille peut provoquer des incendies quand elle s’accompagne de la présence d’oxygène. Pour le filtrage, un filtre coalescent capable de filtrer jusqu’à 0,01 microns devrait être placé le plus près possible des orifices de gaz sur le module de commande du gaz. REMARQUE 2 : L’eau du robinet n’a pas besoin d’être déionisée mais dans les systèmes à l’eau avec un contenu minéral extrêmement élevé, il est recommandé d’utiliser un adoucisseur d’eau. L’eau du robinet présentant des niveaux élevés de particules doit être filtrée. REMARQUE 3 : Le régulateur de la pression de l’eau n° 8-6118 est recommandé pour garantir une pression correcte de l’eau. Générateur Ultra-Cut 200 XT™ : caractéristiques de qualité, débits et pressions du gaz Gaz Qualité Pression minimale Flow O2 (Oxygène) 99.5% Pureté (Liquide recommandé) 120 psi 8.3 bar / 827 kPa 200 scfh (5700 l/h) N2 (Azote) 99.5% Pureté (Liquide recommandé) <1000 ppm O2, <32 ppm H2O) 120 psi 8.3 bar / 827 kPa 200 scfh (5700 l/h) Air en bouteille ou comprimé Propre, sec, Exempt d’huile (Consultez remarque 1) 120 psi 8.3 bar / 827 kPa 450 scfh (12700 l/h) H35 (Argon-Hydrogène) H35 = 35% Hydrogène, 65% Argon 99.995% Pureté (gaz recommandé) 120 psi 8.3 bar / 827 kPa 200 scfh (5700 l/h) H2O (Eau) Consultez remarque 2 50 psi (3.5 bar) 10 gph (38 lph) REMARQUE 1 : La source d’air doit être correctement filtrée afin d’éliminer toute trace d’huile ou de graisse. La contamination d’huile ou de graisse provenant de l’air comprimé ou en bouteille peut provoquer des incendies quand elle s’accompagne de la présence d’oxygène. Pour le filtrage, un filtre coalescent capable de filtrer jusqu’à 0,01 microns devrait être placé le plus près possible des orifices de gaz sur le module de commande du gaz. REMARQUE 2 : L’eau du robinet n’a pas besoin d’être déionisée mais dans les systèmes à l’eau avec un contenu minéral extrêmement élevé, il est recommandé d’utiliser un adoucisseur d’eau. L’eau du robinet présentant des niveaux élevés de particules doit être filtrée. REMARQUE 3 : Le régulateur de la pression de l’eau n° 8-6118 est recommandé pour garantir une pression correcte de l’eau. SPÉCIFICATIONS 2-6 0-5264FR ULTRA-CUT 100 XT/200 XT/300 XT/400 XT Générateur Ultra-Cut 300 XT™ : caractéristiques de qualité, débits et pressions du gaz Gaz Qualité Pression minimale Flow O2 (Oxygène) 99.5% Pureté (Liquide recommandé) 120 psi 8.3 bar / 827 kPa 200 scfh (5700 l/h) N2 (Azote) 99.5% Pureté (Liquide recommandé) <1000 ppm O2, <32 ppm H2O) 120 psi 8.3 bar / 827 kPa 300 scfh (8496 l/h) Air en bouteille ou comprimé Propre, sec, Exempt d’huile (Consultez remarque 1) 120 psi 8.3 bar / 827 kPa 450 scfh (12743 l/h) H35 (Argon-Hydrogène) H35 = 35% Hydrogène, 65% Argon 99.995% Pureté (gaz recommandé) 120 psi 8.3 bar / 827 kPa 200 scfh (5664 l/h) H2O (Eau) Consultez remarque 2 50 psi (3.5 bar) 10 gph (38 lph) REMARQUE 1 : La source d’air doit être correctement filtrée afin d’éliminer toute trace d’huile ou de graisse. La contamination d’huile ou de graisse provenant de l’air comprimé ou en bouteille peut provoquer des incendies quand elle s’accompagne de la présence d’oxygène. Pour le filtrage, un filtre coalescent capable de filtrer jusqu’à 0,01 microns devrait être placé le plus près possible des orifices de gaz sur le module de commande du gaz. REMARQUE 2 : L’eau du robinet n’a pas besoin d’être déionisée mais dans les systèmes à l’eau avec un contenu minéral extrêmement élevé, il est recommandé d’utiliser un adoucisseur d’eau. L’eau du robinet présentant des niveaux élevés de particules doit être filtrée. REMARQUE 3 : Le régulateur de la pression de l’eau n° 8-6118 est recommandé pour garantir une pression correcte de l’eau. Générateur Ultra-Cut 400 XT™ : caractéristiques de qualité, débits et pressions du gaz Gaz Qualité Pression minimale Flow O2 (Oxygène) 99.5% Pureté (Liquide recommandé) 120 psi 8.3 bar / 827 kPa 200 scfh (5700 l/h) N2 (Azote) 99.5% Pureté (Liquide recommandé) <1000 ppm O2, <32 ppm H2O) 120 psi 8.3 bar / 827 kPa 300 scfh (8496 l/h) Air en bouteille ou comprimé Propre, sec, Exempt d’huile (Consultez remarque 1) 120 psi 8.3 bar / 827 kPa 500 scfh (14158 l/h) H35 (Argon-Hydrogène) H35 = 35% Hydrogène, 65% Argon 99.995% Pureté (gaz recommandé) 120 psi 8.3 bar / 827 kPa 200 scfh (5700 l/h) H17 17.5% Hydrogène 32.5% Argon 50% Azote 99.995% Pureté (gaz recommandé) 120 psi 8.3 bar / 827 kPa 200 scfh (5700 l/h) Ar (Argon) 99.995% Pureté (gaz recommandé) 120 psi 8.3 bar / 827 kPa 150 scfh (4200 l/h) H2O (Eau) Consultez remarque 2 50 psi (3.5 bar) 10 gph (38 lph) REMARQUE 1 : La source d’air doit être correctement filtrée afin d’éliminer toute trace d’huile ou de graisse. La contamination d’huile ou de graisse provenant de l’air comprimé ou en bouteille peut provoquer des incendies quand elle s’accompagne de la présence d’oxygène. Pour le filtrage, un filtre coalescent capable de filtrer jusqu’à 0,01 microns devrait être placé le plus près possible des orifices de gaz sur le module de commande du gaz. REMARQUE 2 : L’eau du robinet n’a pas besoin d’être déionisée mais dans les systèmes à l’eau avec un contenu minéral extrêmement élevé, il est recommandé d’utiliser un adoucisseur d’eau. L’eau du robinet présentant des niveaux élevés de particules doit être filtrée. REMARQUE 3 : Le régulateur de la pression de l’eau n° 8-6118 est recommandé pour garantir une pression correcte de l’eau. 0-5264FR 2-7 SPÉCIFICATIONS ULTRA-CUT 100 XT/200 XT/300 XT/400 XT 2.10 Applications du gaz MATÉRIAU FONCTIONNEMENT 30A Cut 50A Cut 70A Cut 100A Cut 150A Cut 200A Cut 250A Cut 300A Cut SPÉCIFICATIONS ACIER INOXYDABLE Aluminium TYPE DE GAZ TYPE DE GAZ TYPE DE GAZ PREFLOW PLASMA SHIELD PREFLOW PLASMA SHIELD PREFLOW PLASMA SHIELD Air O2 O2 Air Air Air Air Air Air N2 N2 H20 N2 N2 H20 Air Air Air Air Air Air N2 N2 H20 N2 N2 H20 Air Air Air Air Air Air N2 N2 H20 N2 N2 H20 N2 H35 N2 N2 H35 N2 N2 N2 H20 N2 N2 H20 N2 H35 N2 N2 H35 N2 N2 N2 H20 N2 N2 H20 Air Air Air Air Air O2 O2 O2 O2 O2 Air Air Air Air Air Air O2 Air Air O2 Air Air 400A Cut ACIER DOUX O2 Air N2 H35 N2 N2 H35 N2 N2 N2 H20 N2 N2 H20 N2 H35 N2 N2 H35 N2 N2 N2 H20 N2 N2 H20 N2 H35 N2 N2 H35 N2 N2 N2 H20 N2 N2 H20 N2 H17 N2 N2 H17 N2 2-8 0-5264FR 0-5264FR 2.7" 69.6 mm 1.6" 40. mm Tube plongeur Capuchon 2-9 1.49" 37.8 mm 2.4" 61 mm 2.0" 50.8 mm 2.25" 57.15 mm 6.6” 4.3” 109.1 mm 168.5 mm Base 100 A dimensions de la torche 3.98" 101.1 mm 6.3" 160.1 mm 15.5" 393.8 mm 19" 482.7 mm Art # A-09534FEU 1.4” 34.5 mm 70° .5” 12.7 mm 2.4” 61 mm 2” 50.8 mm ULTRA-CUT 100 XT/200 XT/300 XT/400 XT 2.11 Spécifications de torche XT A. Dimensions de la torche Base 400 A dimensions de la torche SPÉCIFICATIONS ULTRA-CUT 100 XT/200 XT/300 XT/400 XT B. Longueur de câblage de la torche Montage de la tuyauterie de la torche Longueurs Pieds Mètres 10 3.05 15 4.6 25 7.6 50 15.2 75 22.9 100 30.4 C. Pièces de la torche (pièces génériques montrées) Distributeur du gaz plasmagène Distributeur du gaz de protection Art # A-04741 Coiffe de protection Tuyère Electrode Jupe Cartouche D. Pièces - en - place (PIP) La torche est conçue pour être utilisée avec un générateur qui détecte le débit de retour du liquide de refroidissement pour confirmer que les pièces de la torche sont en place. Si le débit de retour du liquide de refroidissement vers le générateur est absent ou insuffisant le générateur ne fournira pas de courant à la torche. Les fuites de liquide de refroidissement au niveau de la torche indiquent également que des pièces de la torche sont mancantes ou mal installées. E. Type de refroidissement Un mélange de flux de gaz à travers la torche et de liquide de refroidissement. F. Données de la torche XT Étalonnage de la torche XT pour utilisation avec l’alimentation électrique d’Ultra-Cut 400 XT™ Température ambiante 104° F 40° C Facteur de marche 100% à 400 A Intensité maximale 400 A Tension (Vpeak) 500V Tension d’amorçage d’arc 10kV Intensité Jusqu’à 400 A, DC,Polarité directe Spécifications de la torche à gaz XT SPÉCIFICATIONS Gaz à plasma Air comprimé, Oxygène, Azote, H35, H17, Ar Gaz d’écran : Air comprimé, Oxygène, Azote, Eau, H35 Pression de fonctionnement 125 psi ± 10 psi 8,6 bar ± 0,7 bar Pression maximale en entrée 135 psi / 9.3 bar Débit de gaz 10 - 500 scfh 2-10 0-5264FR ULTRA-CUT 100 XT/200 XT/300 XT/400 XT CHAPITRE 3 : installation 3.01 Conditions d’installation Alimentation électrique Le réseau d’alimentation électrique, le système d’alimentation en gaz et en eau doivent respecter les normes de sécurité locales. Du personnel qualifié contrôlera cette conformité. Alimentation électrique Ultra-Cut 100 XT™ Entrée Puissance absorbée Intensité Tailles conseillées (Voir Remarque) Tension Fréquence Triphasée Triphasée Fusible (A) Fil (AWG) Fil (mm2) (Volts) (Hz) (kVA) (A) Triphasée Triphasée Triphasée 400 50/60 21 31 40-45 #12 4 Ultra-Cut 200 XT™ Power Supply Entrée Puissance absorbée Intensité Tailles conseillées (Voir Remarque) Tension Fréquence Triphasée Triphasée Fusible (A) Fil (AWG) Fil (mm2) (Volts) (Hz) (kVA) (A) Triphasée Triphasée Triphasée 400 50/60 42 62 100 #6 16 Alimentation électrique Ultra-Cut 300 XT™ Entrée Puissance absorbée Intensité Tailles conseillées (Voir Remarque) Tension Fréquence Triphasée Triphasée Fusible (A) Fil (AWG) Fil (mm2) (Volts) (Hz) (kVA) (A) Triphasée Triphasée Triphasée 400 50/60 63 93 150 #4 25 400 50/60 72 106 150 #4 25 IEC Alimentation électrique Ultra-Cut 400 XT™ Entrée Puissance absorbée Intensité Tailles conseillées (Voir Remarque) Tension Fréquence Triphasée Triphasée Fusible (A) Fil (AWG) Fil (mm2) (Volts) (Hz) (kVA) (A) Triphasée Triphasée Triphasée 400 50/60 93 137 200 #1 50 REMARQUE ! * La taille suggérée pour les câbles est basée sur le code national d’électricité américain NFPA 70 édition 2011, publiée par la National Fire Prevention Association. Les listes sont issues du tableau 400.5(A)(2) pour les cordons souples de certains types étalonnés pour 75°C à température ambiante atteignant jusqu’à 30°C. Utiliser des câbles à faible cote de température ou des types différents d’isolation peut exiger des tailles de câblage plus grandes. Réduire la valeur nominale des températures ambiantes plus élevées. Il s’agit uniquement de suggestions. Référez-vous toujours à vos législations locales et nationales qui s’appliquent à votre région pour la détermination finale du bon type et de la bonne taille de câblage. 0-5264FR 3-1 INSTALLATION ULTRA-CUT 100 XT/200 XT/300 XT/400 XT Alimentation en gaz Le client doit fournir tous les gaz et les régulateurs de pression. Les gaz doivent être de haute qualité. Les régulateurs de pression doivent être à double étage et être installés le plus près possible de la console de gaz. Le gaz contaminé peut provoquer un ou plusieurs des problèmes suivants : • Une vitesse de coupe réduite • Une mauvaise qualité de coupe • Une mauvaise précision de coupe • Une durée de vie réduite des consommables • La contamination d’huile ou de graisse provenant de l’air comprimé ou en bouteille peut provoquer des incendies quand elle est accompagnée d’oxygène. Caractéristiques du système de refroidissement Le liquide de refroidissement doit être ajouté au système lors de l’installation. La quantité requise varie en fonction de la longueur des câbles de la torche. Thermal Dynamics recommande d’utiliser ses liquides de refroidissement 7-3580 et 7-3581 (pour les basses températures). Capacités du liquide de refroidissement Numéro de la catégorie et mélange Mélange 7-3580 ‘Extra-Cool™’ 25 / 75 7-3581 ‘Ultra-Cool™’ 50 / 50 7-3582 ‘Extreme Cool™’ Concentré* TM * Pour être mélangé avec D-I Cool 7-3583 Protège jusqu’à 10° F / -12° C -27° F / -33° C -76° F / -60° C 3.02 Schéma du système 100 - 200 A cf. § 3.05 et 3.06 pour les connexions de raccordement à la terre et les câbles de raccordement à la terre. 175’ / 53.3 m Longueur maximale 125’ / 38.1 m Longueur maximale Négatif Puissance principale CNC A Retour de l’arc pilote F1 Générateur Ultra Cut XT P 100’ / 30.5 m Longueur maximale C Retour du liquide D Câble de commande F1 Câble de commande Amorce de l’arc à distance Module de commande du gaz INSTALLATION Retour du liquide Coiffe H Gaz de protection Q Gaz du flux préliminaire R Câble de commande S Rideau d’eau T Câble de mise à la terre Art # A-11941FEU Alimentation du liquide E Gaz plasmagène L K F Coiffe B Alimentation du liquide Câble à fibre optique Retour de l’arc pilote Valve de torche Gaz plasmagène I Gaz de protection J G Tube plongeur Torche O Pièce 175’ / 53.3 m Longueur maximale 3-2 0-5264FR ULTRA-CUT 100 XT/200 XT/300 XT/400 XT 3.03 Schéma du système 300 A Cf. section 3.08 et 3.10 pour les raccordements à la terre et les câbles associés. 175’ / 53.3 m Longueur maximale 125’ / 38.1 m Longueur maximale A Retour de l’arc pilote F1 Négatif Puissance principale CNC 50’ / 15.25 m Longueur maximale Générateur Ultra Cut XT Coiffe B Alimentation du liquide C Retour du liquide D Câble de commande L Câble de commande K Module de commande du gaz F Amorce de l’arc à distance Alimentation du liquide Retour du liquide Coiffe E F1 Câble à fibre optique P Retour de l’arc pilote Gaz plasmagène H Gaz plasmagène I Gaz de protection Q Gaz de protection J Gaz du flux préliminaire R Câble de commande S Rideau d’eau T Ensemble de la valve de la torche Tube plongeur Torche Câble de mise à la terre Art # A-12026FEU G Pièce O 175’ / 53.3 m Longueur maximale 3.04 Schéma du système 400 A Cf. section 3.08 et 3.10 pour les raccordements à la terre et les câbles associés. 175’ / 53.3 m Longueur maximale 50’ / 15.25 m Longueur maximale 125’ / 38.1 m Longueur maximale F1 Retour de l’arc pilote #8 A Câble négatif B Câble de commande Puissance principale Alimentation du liquide 10’ C Retour du liquide 10’ D Câble de commande Y Générateur Ultra Cut XT CNC P Câble à fibre optique Câble de commande K F Module de commande du gaz Coiffe E Échangeur de chaleur HE 400 L Retour de l’arc pilote Alimentation du liquide C Retour du liquide D Amorce de l’arc à distance Alimentation du liquide Retour du liquide Coiffe F1 Gaz plasmagène H Gaz de protection Q Gaz du flux préliminaire R Câble de commande S Rideau d’eau T Gaz plasmagène I Gaz de protection J Valve de torche G Tube plongeur Torche Art # A-11940FEU Câble de mise à la terre Pièce 175’ / 53.3 m Longueur maximale 0-5264FR 3-3 INSTALLATION ULTRA-CUT 100 XT/200 XT/300 XT/400 XT 3.05 Tuyau recommandé pour l’alimentation en gaz Article n° Qté Description Catalogue # 1 Tuyau 3/8” Gris Synflex Aucun raccordement inclus. Numéro de catalogue par pied9-3616 3.06 Fils et câbles toutes intensités Retour de l’arc pilote, du générateur à l’amorce de l’arc Câble 3/0 AWG (95 mm2 ) Câble négatif, du générateur à l’amorce de l’arc B Art # A-11873FEU Câble AWG n° 8 A C Vert Vert Câble d’alimentation du liquide de refroidissement, du générateur à l’amorce de l’arc D Rouge Rouge Câble de retour du liquide de refroidissement, du générateur à l’amorce de l’arc E - Câble de commande, du générateur à l’amorce de l’arc E,Y 14/7 Y - De câble de commande à l’échangeur de chaleur Câble de masse AWG n° 4 vert / jaune F Câble de masse, de l’amorce de l’arc à distance à la mise à la terre 1/0 vert / jaune (50 mm 2) F1 G Câble de la torche blindé, de l’amorce de l’arc à distance à la torche I Câble du gaz plasmagène, de la valve de la torche à la torche J Câble du gaz de protection, de la valve de la torche à la torche K Câble de commande, du générateur au module de commande du gaz 37 Câble à fibre optique, du générateur au module de commande du gaz L H, Q, R, S,T Câble 3/0 (95 mm 2) O P Câble de mise à la terre 37 INSTALLATION Câble CNC (37 fil) 3-4 0-5264FR ULTRA-CUT 100 XT/200 XT/300 XT/400 XT 3.07 Levage du générateur MISE EN GARDE Ne pas toucher les composants électriques sous tension. Débrancher les conducteurs de courant de la ligne d’alimentation hors tension avant de déplacer l’appareil. TOUTE CHUTE DE MATERIEL peut entraîner des lésions corporelles graves et endommager le matériel. Utiliser un chariot élévateur, une grue ou un treuil pour soulever l’appareil de la palette d’expédition comme cela est montré. Maintenir le générateur stable et à la verticale. Ne pas le soulever plus que nécessaire pour dégager la palette d’expédition. S’assurer que tous les panneaux et les vis soient bien fixés avant d’effectuer le levage. Art # A-11531_AC Placer le générateur sur une surface solide et plane. L’installateur peut attacher le générateur au sol ou à une fixation de soutien avec un élément passant à travers les pièces horizontales des pieds du générateur. 0-5264FR 3-5 INSTALLATION ULTRA-CUT 100 XT/200 XT/300 XT/400 XT 3.08 Raccorder les câbles de l’alimentation et de masse Raccorder les câbles de l’alimentation et de masse du système 1. Enlever le couvercle de l’alimentation en entrée à droite du filtre à liquide de refroidissement à l’arrière de l’alimentation électrique. Pour ce faire, enlever les deux vis puis soulever le couvercle et l’enlever. 2. Couper soigneusement la gaine extérieur du câble de l’alimentation principale pour dénuder les différents fils. Réduire l’isolation sur les différents fils. Orienter le câble vers le haut à travers le port d’alimentation en entrée en bas du panneau. 2 plaques supplémentaires sont incluses à l’entrée du câble. En jeter une ou les deux permet de changer la taille d’ouverture pour admettre de plus gros câbles / manchons. 3. Placer l’extrémité dénudée des fils triphasés sur le bornier L1, L2 et L3. Raccorder les différents câbles comme cela est montré. 4. Raccorder le cordon de masse du câble d’alimentation au bornier de mise à la terre. 5. Orienter un câble de raccordement à la terre (F1) à travers la dernière ouverture dans le panneau de support du couvercle de connexion à côté du câble d’alimentation en entrée. Raccorder le câble au bornier de terre sur le panneau arrière d’alimentation électrique. Cf. section Raccordement à la terre pour les détails et les procédures de raccordement à la terre. Bornes de terre Masse Alimentation Art # A-11942FEU INSTALLATION 3-6 0-5264FR ULTRA-CUT 100 XT/200 XT/300 XT/400 XT 3.09 Connexion du câble de mise à la terre, de l’arc pilote et des câbles négatifs 1. Enlever le couvercle de l’alimentation en sortie à gauche du filtre à liquide de refroidissement à l’arrière de l’alimentation électrique. Pour ce faire, enlever les deux vis puis soulever le couvercle et l’enlever. 2. Orienter les extrémités du câble de travail, pilote et négative/fils de la torche vers le haut à travers le manchon en bas du panneau arrière gauche. 3. Se reporter à l’illustration. Raccorder les câbles comme cela est indiqué. Bien serrer. Ne trop serrez pas. + - Pilote Câble de mise à la terre Art # A-11533FEU Torche 4. Réinstaller le couvercle sur l’alimentation électrique. Fixer le matériel à la main. Ne trop serrez pas. 0-5264FR 3-7 INSTALLATION ULTRA-CUT 100 XT/200 XT/300 XT/400 XT 3.10 Connexions de masse Masse étoilée sur la table de découpe Amorce d’arc à distance (RAS-1000) Machine de découpe / passerelle Lifter Torch Emplacement principal du module de commande du gaz Générateur #4 AWG Ground Remarque : The module de commande du gaz peut être montée au sommet du générateur. Si c’est le cas, elle peut être mise à la terre directement au niveau du générateur avec la mise à la terre AWG n° 4 (F). Tout emplacement requiert la mise à la terre du générateur au niveau de la masse « étoilée » avec le câble de masse 1/0 (F1). iCNC Câble de masse 1/0 (F1) Table de découpe Piquet de terre Câble de masse 1/0 fourni par le client Une bonne masse sera inférieure à 3 ohm. Idéalement 1. Idéal 0 - 10 ft (0 - 3 m) Maximum 20 ft (6 m) Câble de mise à la terre 3/0 Câble de masse 1/0 Masse ‘étoilée’ Art # A-11875FR_AC A. Interférence électromagnétique (EMI) L’amorçage de l’arc pilote génère une certaine quantité d’interférence électromagnétique (EMI), couramment appelée bruit RF. Ce bruit RF peut interférer avec d’autres équipements électroniques tels que les contrôleurs de la CNC, les télécommandes, les contrôleurs de hauteur, etc. Pour réduire au minimum l’interférence RF, suivre ces procédures de mises à la terre lors de l’installation de systèmes mécanisés : B. Mise à la terre 1. La disposition de mise à la terre préférée est la mise à la terre en un point unique ou « étoilée ». Le point unique, habituellement sur la table de découpe, est raccordé avec un fil AWG 1/0 (Européen 50 mm2) ou plus grand à une bonne masse (mesurant moins de 3 ohm ; une masse idéale mesure 1 ohm ou moins). Se reporter au paragraphe ‘C’, Création d’une masse. Le piquet de terre doit être le plus près possible de la table de découpe, de préférence à moins de 10 ft (3,0 m) mais pas à plus de 20 ft (6,1 m) de la table de découpe. REMARQUE ! Tous les fils de garde doivent être les plus courts possible. Les longs fils possèdent une plus grande résistance vis-à-vis des fréquences RF. Un fil d’un diamètre inférieur possède une résistance majeure vis-à-vis des fréquences RF, il vaut donc mieux utiliser un fil de diamètre plus élevé. 2. La mise à la terre pour les composants montés sur la table de découpe (contrôleurs de la CNC, contrôleurs de hauteur, télécommandes au plasma, etc.) devrait respecter les recommandations du fabricant pour la section du fil, le type et les emplacements du point de connexion. Pour les composants Thermal Dynamics (à l’exception de l’amorce d’arc à distance et du module de commande du gaz), il est recommandé d’utiliser un minimum de câble AWG 10 (européen 6 mm2) ou une tresse en cuivre plate avec une section supérieure ou égale au câble AWG 10 raccordé au châssis de la table de découpe. L’amorce d’arc à distance utilise un fil de garde 1/0 et le module de commande du gaz devrait utiliser un câble AWG 4 minimum. Le point de connexion doit être en métal nu ; la rouille et la peinture portent à de mauvaises connexions. Pour tous les composants, des fils plus grands que le minimum recommandé peuvent être utilisés et peuvent améliorer la protection sonore. 3. Le châssis de la machine de découpe est alors raccordé au point « étoilé » au moyen d’un câble AWG 1/0 (européen 50 mm2) ou plus grand. INSTALLATION 3-8 0-5264FR ULTRA-CUT 100 XT/200 XT/300 XT/400 XT 4. Le câble du générateur au plasma (voir Remarque) est raccordé à la table de découpe au niveau de la mise à la terre « étoilée » en un point unique. REMARQUE ! Ne pas raccorder le câble de mise à la terre directement au piquet de terre. Ne pas enrouler trop de câble de terre ou d’alimentation électrique. Couper à la bonne longueur et remonter la borne à l’extrémité nouvellement créée. 5. S’assurer que le câble de mise à la terre et les câbles de masse soient raccordés correctement. Le câble de mise à la terre doit avoir un raccordement solide à la table de découpe. Les raccordements de mise à la terre et de masse doivent être exempts de rouille, saleté, graisse, huile et peinture. Si cela s’avère nécessaire, affiler ou sabler jusqu’à ce qu’on atteigne le métal nu. Utiliser des rondelles d’arrêt pour que les raccordements soient serrés. Il est également recommandé d’utiliser une pâte à joint électrique pour prévenir la corrosion. 6. Le châssis du générateur au plasma est raccordé à la masse du système de distribution du courant selon les prescriptions des codes électriques. Si l’alimentation au plasma est proche de la table de découpe (voir Remarque), il n’est normalement pas nécessaire d’avoir un deuxième piquet de terre. En fait, il pourrait être néfaste car il peut porter à une boucle de masse qui provoque des interférences. Quand le générateur au plasma est loin du piquet de terre et qu’il y a des interférences, il peut être utile d’installer un deuxième piquet de terre à côté du générateur au plasma. Le châssis du générateur au plasma devrait alors être raccordé à ce piquet de terre. REMARQUE ! Il est recommandé que l’alimentation électrique du plasma soit entre 20 - 30 ft (6,1 – 9,1 m) de la table de découpe, si possible. 7. Le câble de commande du plasma devrait être blindé avec une protection raccordée uniquement à l’extrémité de la machine de découpe. Si l’on raccorde la protection aux deux extrémités, cela permettra la création d’une boucle de masse qui peut provoquer plus d’interférences que quand il n’y a aucune protection. La création d’une masse de terre 1. Pour créer un solide, faible résistance, la terre, le lecteur a 1/2 in (12 mm) ou plus de diamètre tige au sol recouverts de cuivre au moins 6 - 8 ft (1,8 - 2,4 m) dans la terre de sorte que la tige des contacts du sol humide sur la plus grande partie de sa longueur. Selon l’endroit, une plus grande profondeur peut être nécessaire pour obtenir une résistance faible masse (voir la Remarque). La masse des tiges, généralement 10 ft (3,0 m) de long, peuvent être soudés bout à bout Pour plus longues. Localisez la tige aussi près que possible de la table de travail. Installer un fil de masse, 1/0 AWG (European 50 mm2) ou supérieur, entre la tige de mise à la terre et le point de mise à la masse en étoile sur la table de découpe. REMARQUE ! Idéalement, une tige de mise à la terre installé correctement aura une résistance de 3 ohms ou moins. D. Tige de test de mise à la terre de faible coût 1. Un composant clé des EMI réduites est une bonne tige de mise à la terre au sol de faible résistance. Il existe plusieurs instruments très dispendieux pour mesurer le sol, mais leur coût varie de plusieurs centaines à quelques milliers de dollars. Une solution de rechange à faible coût pouvant être fabriquée par du personnel qualifié familier avec les pratiques de Construction électrique et de sécurité établies est présentée ci-après. La méthode antérieurement suggérée utilisant une ampoule incandescente ne fonctionnera pas avec les prises de disjoncteur de fuite de terre qui sont de plus en plus utilisées alors que les ampoules deviennent désuètes.. 2. Cette méthode, ainsi que la méthode de l’ampoule et certains des instruments dispendieux, assume que le sol des services publics est parfait (zéro ohm). Elle permet de brancher la tige à tester en série avec le sol des services publics et de mesurer la résistance des deux en série. Si le sol des services publics n’est pas de zéro ohm, peu importe la qualité de votre tige, vous n’obtiendrez aucune basse lecture en raison de la résistance plus élevée du sol des services publics. Heureusement, cela se produit rarement. Aussi, si votre tige est tout près d’une autre structure mise à la terre au sol, vous pourriez obtenir une fausse lecture plus basse de la résistance seulement entre cette structure et votre tige plutôt que vers le sol. 0-5264FR 3-9 INSTALLATION ULTRA-CUT 100 XT/200 XT/300 XT/400 XT REMARQUE ! Aux États-Unis, la plupart des prises c.a. sont de 120 VCA, 60 Hz. Ailleurs, la plupart des prises sont de 220 VCA, 50 Hz. 3. Obtenez un transformateur d’au moins 25 VA offrant une tension primaire et une fréquence concordant avec vos prises normalisées. Le transformateur doit avoir un enroulement secondaire isolé soit de 220 VCA (220 à 240) ou de 120 VCA (110 à 120) et doit être d’au moins 100 mA. Le transformateur peut également avoir des enroulements primaires doubles de 115 VCA en série pour le 220 V ou en parallèle pour le 120 VCA. Le Triad N-68X, montré ci-dessous, classé 50 VA, 50/60 Hz, en est un exemple. Obtenez une résistance de fortes puissances soit de 1 200 ohms (1,2 K), 15 à 25 W min., si vous utilisez un enroulement primaire de 120 V ou de 2 200 ohms (2,2 K), 25 à 30 W pour un enroulement secondaire de 220 V. 4. Assemblez le transformateur et la résistance de fortes puissances dans une boîte métallique. Branchez un cordon d’alimentation à 3 fils (avec mise à la terre), avec le fil de mise à la terre fixé à une boîte métallique pour en assurer la sécurité. Si une boîte de plastique est utilisé à la place, connectez le noyau du transformateur et la résistance se monte sur le cordon d’alimentation Câble de masse. Il doit y avoir un fusible, de 0,25 à 0,5 A, en série avec l’enroulement primaire du transformateur. Depuis l’enroulement secondaire du transformateur, branchez un fil de terre de sécurité des services publics, ce qui pourrait être le bâti de la table à découper, la borne de mise à la terre de la prise de 120 ou 220 VCA ou la boîte de test si mise à la terre comme indiqué. Un sol excellent mesure 1 ohm ou moins. Un sol donnant jusqu’à 3 ohms est souvent acceptable. Une valeur plus élevée réduit l’efficacité de la suppression EMI. R = 1.2K, 15W (2.2K, 25W pour 220 V c.a.) Triad N-68X Triad N-68X 0.1 V c.a. = 1 OHM, 0.3 V c.a. = 3 OHM, etc. 115 V c.a. 115 V c.a. 115 V c.a. Masse 220 V c.a. F 115 V c.a. 115 V c.a. F Tige de mise à la terre avec d'autres connexions supprimé Masse 120 V c.a. Utility (bâtiment), masse Art # A-12710FR 5. Accroître la longueur de tige de terre au-delà de 20 - 30 ft (6.1 - 9.1 m) n’a pas généralement d’accroître l’efficacité de la tige de mise à la terre. Une tige de diamètre plus grand qui a plus de surface peut vous aider. Parfois, pour garder la terre autour de la tige de mise à la terre humide en exécutant, en continu, une petite quantité d’eau dans il travaillera. L’ajout de sel dans le sol en faisant tremper dans l’eau salée peut également réduire sa résistance. Vous pouvez également essayer une tige de masse chimique périphérique. Lorsque ces méthodes sont utilisées, le contrôle périodique de la résistance de terre est nécessaire pour s’assurer que le sol est encore bonne. E. Acheminement des câbles de la Torche 1. Pour minimiser les interférences RF, torche position mène aussi loin que possible de tout CNC, les moteurs d’entraînement, composants de câbles de commande, ou les lignes d’alimentation primaire. Si les câbles doivent passer plus de chalumeau conduit, le faire à un angle. Ne pas faire fonctionner la commande de plasma ou d’autres câbles de commande en parallèle avec la torche mène au pouvoir tracts. 2. Gardez torch mène propre. Les saletés et les particules de métal purger l’énergie, qui cause démarrage difficile et risque accru d’interférence RF. INSTALLATION 3-10 0-5264FR ULTRA-CUT 100 XT/200 XT/300 XT/400 XT 3.11 Raccordement des câbles du liquide de refroidissement 1. Raccorder les tuyaux du liquide de refroidissement avec le codage couleur aux raccordements du liquide de refroidissement sur le panneau arrière du générateur. La ligne d’alimentation (externe) est verte tandis que la ligne de retour (interne) est rouge. J55 - GCM USER INPUT J15 - CNC HEIGHT CONTROL J54 - TSC /COMM J59 - RAS CB2 - 5A 120 VAC CB3 - 5A 24 VAC J70 - HE CB4 - 5A 120 VAC F1 - 8A SB 230 VAC F2 - 8A SB 230 VAC COOLANT RETURN SUPPLY ROUGE Connexions du liquide de refroidissement VERT Vers l’amorce d’arc RAS 1000 ou l’échangeur de chaleur HE-400 si elle est utilisée Art # A-11534FEU 0-5264FR 3-11 INSTALLATION ULTRA-CUT 100 XT/200 XT/300 XT/400 XT 3.12 Connection des câbles pour CNC, allumage de l’arc à distance, GCM et HE400 1. Raccorder une extrémité de chaque câble au générateur. 2. Raccorder l’autre extrémité du câble CNC à la CNC. 3. Le blindage du câble CNC doit être attaché à la terre à l’extrémité CNC. J55 vers GCM J55 - GCM USER INPUT J15 - CNC HEIGHT CONTROL J54 - TSC /COMM J15 vers la commande de la CNC J59 - RAS CB2 - 5A 120 VAC CB3 - 5A 24 VAC J70 - HE CB4 - 5A 120 VAC F1 - 8A SB 230 VAC F2 - 8A SB 230 VAC J54 TSC/ Comm J59 vers l’amorce d’arc à distance J70 vers l’échangeur de chaleur Art # A-11971FEU INSTALLATION 3-12 0-5264FR ULTRA-CUT 100 XT/200 XT/300 XT/400 XT 3.13 Manipulation et installation de fibres optiques INFORMATIONS GÉNÉRALES Ce kit est destiné à la manipulation et la bonne installation de câbles à fibres optiques utilisés dans les boîtiers à gaz automatisés Thermal Dynamics Ultra-Cut® et les modules de contrôle des gaz. Le câble à fibres optiques s’utilise en lieu et place d’un câble car il offre une immunité très supérieure au bruit électromagnétique, mais il est plus délicat et exige d’être manipulé avec précautions. Avec les fibres optiques, les signaux électriques sont convertis en lumière par un transmetteur LED. La lumière traverse la longueur de la fibre avant d’être reconvertie en signal électrique au niveau du récepteur. Tout dommage à la fibre par suite d’une forte courbure ou d’une traction de nature à distendre la fibre peut réduire sa capacité à transmettre la lumière. Nous faisons courir la fibre dans un tuyau sur l’essentiel de la longueur afin de la protéger de l’abrasion, des brûlures au contact de métal chaud et des courbures aiguës, mais ses extrémités restent exposées et doivent être manipulées avec précautions. Art # A-09416FEU Réducteur de tension Tuyau Fibre Connecteur avec verrouillage Fin housses de protection Enlever le revêtement et les bouchons aux extrémités de la fibre optique. Art # A-12015 MISE EN GARDE Déconnecter l’alimentation électrique primaire à la source. Éviter les points suivants : 1. Si vous avez besoin de tirer le câble à travers un circuit d’alimentation, ne pas replier la fibre sur elle-même au risque de créer un angle aigu en sortie du tuyau. Art # A-09417 2. N’accrochez pas la fibre pour extraire le câble. Art # A-09418 3. Une fois le câble à fibre optique installé dans le CCM ou le contrôle des gaz, vérifier que l’écrou du manchon est bien serré sur le tuyau pour que l’on ne puisse pas arracher le tuyau comme : 0-5264FR 3-13 INSTALLATION ULTRA-CUT 100 XT/200 XT/300 XT/400 XT Tuyau n'est pas fixé dans la décharge de traction. Art # A-09677FEU Installation correcte : La bonne façon de tirer le câble consiste à utiliser un câble multi-canaux, un fil ou un autre câble et de bien l’attacher au tuyau derrière le manchon. Ensuite, fixer le connecteur à fibres à l’appareil de tirage de fil, en laissant un peu de mou à la fibre. Laisser le couvercle de protection en bout de fibre jusqu’à ce que vous soyez prêt à la raccorder au PCB dans le CCM ou le contrôle des gaz. Art # A-09420 Une bonne installation dans un CCM ou un contrôle des gaz laisse une boucle de fibre, de sorte qu’il n’y ait pas de tension mécanique dans la fibre là où elle sort du connecteur ou du tuyau. CCM Aucun No des sharp courbures bends Art # A-12014FEU INSTALLATION 3-14 0-5264FR ULTRA-CUT 100 XT/200 XT/300 XT/400 XT 3.14 Configuration des interrupteurs du module de commande - contrôle Enlever l’alimentation électrique en haut à droite. Configurer les interrupteurs du CCM (module de commande et de contrôle) selon les illustrations. Les réglages des interrupteurs et les détails de connexion sont fournis en annexe. Tout changement nécessite de redémarrer l’alimentation électrique. ATTENTION Les circuits imprimés du module de commande et de contrôle sont sensibles à l’électricité statique. Évacuer toute accumulation d’électricité statique dans votre corps ou l’environnement avant de toucher les circuits imprimés. O N 1 SW8 2 3 4 1 SW5 SW9 1 Utilisation future SW1 4 1 2 3 2 Switches shown in OFF position USB 2 SW9 SW4 O N SW3 SW4 SW5 2 SW1 1 SW8 SW3 1 O N 2 2 3 4 1 4 1 2 3 2 1 1 2 Commutateurs sont représentés en position OFF 2 1 2 O N 1 Orientation réelle SW 8-1: Temps de l’arc pilote 1 = ETEINT = Court (85 ms) (paramètre défini en usine). 1 = ALLUME = Long (3 s) SW 8-2: Courant à distance 1 = ETEINT = Désactivé (paramètre défini en usine). 1 = ALLUME = (Commande du courant analogique à distance) *SW 8-3: Nouvel essai de 1 = ETEINT = Permet jusqu’à 3 essais (paramètre défini en usine). transfert automatique 1 = ALLUME = Désactivé SW 8-4: OFF = ETEINT = Désactivé (paramètre défini en usine). ALLUME = Marquage à distance SW habilité à TB3-1&2 SW-1-1: Redémarrage de l’arc pilote automatique. 1 = ALLUME = Fonction de l’arc pilote automatique habilitée. 1 = ETEINT = Fonction de l’arc pilote automatique désactivée (Paramètre défini en usine). SW-1-2: Retard de l’arc pilote 2 = ETEINT, 3 = ETEINT, 4 = ETEINT : 0 seconde (paramètre défini en usine) SW-1-3: Retard de l’arc pilote 2 = ALLUME, 3 = ETEINT, 4 = ETEINT : 0,1 seconde SW-1-4: Retard de l’arc pilote 2 = ETEINT, 3 = ALLUME, 4 = ETEINT : 0,2 seconde 2 = ALLUME, 3 = ALLUME, 4 = ETEINT : 0,4 seconde 2 = ETEINT, 3 = ETEINT, 4 = ALLUME : 0,8 seconde 2 = ALLUME, 3 = ETEINT, 4 = ALLUME : 1,0 seconde 2 = ETEINT, 3 = ALLUME, 4 = ALLUME : 1,5 seconde 2 = ALLUME, 3 = ALLUME, 4 = ALLUME : 2,0 secondes SW-5-1: Economiseur de tuyère SW-5-2: hors patin SW-4: Temps après le flux Réservé pour une utilisation en usine Réservé pour une utilisation en usine 1 = OFF, 2 = OFF: 1 = ETEINT, 2 = ETEINT : 10 secondes (paramètre défini en usine) 1 = ALLUME, 2 = ETEINT : 20 secondes 1 = ETEINT, 2 = ALLUME : 5 secondes 1 = ALLUME, 2 = ALLUME : 0 seconde SW-3: Temps du flux préliminaire 0-5264FR Foncionement seulement quand SW-1-1 est ALLUME 1 = ETEINT, 2 = ETEINT : 3 secondes 1 = ALLUME, 2 = ETEINT : 4 secondes 1 = ETEINT, 2 = ALLUME : 6 secondes 1 = ALLUME, 2 = ALLUME : 8 secondes 3-15 Art # A-11890FEU INSTALLATION ULTRA-CUT 100 XT/200 XT/300 XT/400 XT ATTENTION Les circuits imprimés du module de commande et de contrôle sont sensibles à l’électricité statique. Évacuer toute accumulation d’électricité statique dans votre corps ou l’environnement avant de toucher les circuits imprimés. SW6 SW12 SW13 SW-6: Déplacement autorisé : SW-12-1/2/3/4: Fermeture du contact, 120 VCA à 1 A (paramètre défini en usine) ou CC Volts (16-18 VCC jusqu’à 100 mA) Signal de l’arc divisé Tous = ETEINT = 50:1 (paramètre défini en usine) 1 = ALLUME = 16.6:1 2 = ALLUME = 30:1 3 = ALLUME = 40:1 4 = ALLUME = 25:1 Un seul à la fois Art # A-12016FEU ON 1 2 3 4 SW13: Positions de l’Ultra-Cut SW13 (Noter que les positions 3-4 ne sont pas encore utilisées) INSTALLATION 3-16 0-5264FR ULTRA-CUT 100 XT/200 XT/300 XT/400 XT 3.15 Raccordements de contrôle de la hauteur La barrette de raccordement fournit des connexions au fil négatif de l’arc (torche ou électrode), à la pointe (pilote) et à la pièce d’usinage. Elles servent pour un contrôle de la hauteur qui requiert la connexion à la tension d’arc non-divisée complète. La plaque à bornes présente également les valeurs 120 VCA (120,0) et 24 VCA (24, 0). Remarquer que les deux 0 ne sont pas communs. L’appel de courant admissible est de 100 mA à 120 VCA et 1 A à 24 VCA. Art # A-11900 TB4 1 2 24 VCA à1A 3 4 5 6 7 120 VCA Travail à 100 mA Astuce les tensions (Pilote) Tension d’arc (Torche) Art # A-11954FEU REMARQUE ! Il y a également un trou ajouté sur le panneau arrière au-dessus du réceptacle pour le câblage du client. On le préfèrera à celui situé dans le CCM pour le câblage du client ajouté (et le réducteur de tension) pour les raccordements aux commandes de hauteur, etc. 3.16 Installation du module de contrôle des gaz Il faut installer le module de contrôle des gaz à un endroit adéquat, où il sera facilement accessible pour l’opérateur du système. L’appareil doit être monté sur une surface plane horizontale. Si le module est monté sur un portique ou sur n’importe quel autre support sujet à vibrations ou aux mouvements, l’installateur doit fixer le module au support. Le module doit être situé aussi loin que possible de l’allumage de l’arc en raison des interférences électromagnétiques. Il est possible de placer le câble de contrôle dans le même support que les câbles de l’allumage de l’arc. Le module comprend des pieds qui rehaussent le panneau du fond par rapport à la surface de montage. Il y a des orifices de ventilation sur le panneau inférieur ; l’espace entre le panneau inférieur et la surface de montage doit rester ouvert à l’air de ventilation qui doit accéder au module. Buses d’aération à l’arrière du panneau du module doit rester également débloqués, pour le libre passage de l’air de ventilation. Dimensions de montage REMARQUE ! La hauteur qui n’est pas montrée est de 14.125” (359 mm). 0-5264FR 3-17 INSTALLATION ULTRA-CUT 100 XT/200 XT/300 XT/400 XT Boîte de gaz 410.97mm 16.18” 347.47mm 7.14mm 13.68” 0.28” 279.40mm 11.00” 215.90mm 8.50” Art # A-07962FEU REMARQUE ! L’appareil doit être monté de façon que les débitmètres soient d’aplomb. Si les débitmètres ne sont pas d’aplomb, il peut en résulter de mauvais affichages des valeurs de débit. Préparation 1. Enlever les vis fixant le panneau du couvercle sur le module. 2. Enlever délicatement le couvercle du module en notant la présence du fil de terre rattaché. Enlever le fil de terre si nécessaire. Couvercle du module de commande du gaz Retirer fil de terre Ne retirez pas Art # A-06882FEU Enlèvement du couvercle INSTALLATION 3-18 0-5264FR ULTRA-CUT 100 XT/200 XT/300 XT/400 XT 3.17 Installation du câble à fibre optique 1. Installer la protection du câble à fibre optique pour son passage à travers l’orifice du panneau de connexion à l’arrière du module. 2. Faire passer le connecteur du câble à fibre optique à travers l’orifice du panneau de connexion à l’arrière du module. Faire passer assez de câble dans le module pour lui permettre de faire une boucle vers le haut comme illustré ici. ATTENTION Eviter de faire des noeuds, de tordre ou de concentrer le câble à fibre optique. Le câble peut être endommagé lorsqu’on le force à tourner avec des angles serrés. Carte de circuit 2 3 Câble à fibre optique MM CO J56 J57 A SM PLA T OU H2O ER POW LY PP F5 SU TVA W FLO PRE UT O H35 UTS INP N2 O2 AIR 1 LD SHIET OU MM CO J56 J57 LOW MA LD SHIE H2 O D SHIEL PLAS H2O TVA H35 PREF UTS INP N2 R WE PO LY PP F5 SU O2 AIR Art # A-04772FEU 3. Insérer le connecteur du câble à fibre optique dans le réceptacle sur la carte montée verticalement comme illustré ici. Le câble doit se fixer en place d’un coup sec. 0-5264FR 3-19 INSTALLATION ULTRA-CUT 100 XT/200 XT/300 XT/400 XT Carte de circuit Câble à fibre optique Art # A-04773FEU 4. Serrer la protection de passage à travers l’orifice pour le câble à fibre optique en utilisant des outils à main. 5. Réinstaller le couvercle en vous assurant que le raccordement à la terre est bien attaché. INSTALLATION 3-20 0-5264FR ULTRA-CUT 100 XT/200 XT/300 XT/400 XT 3.18 Module de contrôle du gaz : Connexions de contrôle, d’entrée et de sortie 1. Effectuer toutes les autres connexions à l’arrière du module. Les connexions sont étiquetées. Le module doit être relié à la terre ; le terminal de raccordement à la terre est marqué Utiliser un fil n°10 AWG (Européen 6 mm 2 ) (ou plus épais) pour le raccordement à la terre. Le fil de terre doit être aussi court que possible. 2. Positionner le module sur une surface de montage plane et horizontale. 3. S’assurer que les débitmètres soient d’aplomb. 4. Fixer le module à la surface de montage. 5. Connecter toutes les entrées de gaz / eau au panneau arrière du module. 6. Connecter les câbles de contrôle adéquats aux bornes marquées «TVA» (torch valve assembly - soupape de la torche) et «power supply» (alimentation électrique). Vers le générateur Vers l’ensemble de la valve de la torche SHIELD PLASMA When Cutting With O2 Plasma Air MUST BE Connected H 2O SHIELD J56 J57 COMM PREFLOW TVA INPUTS H2O AIR F5 H35 POWER SUPPLY O2 N2 Gaz et eau entrées (Clapets de non-retour) Borne de masse Vers l’ensemble de la valve de la torche Panneau arrière de la boîte de commande du gaz SHIELD PLASMA When Cutting With O2 Plasma Air MUST BE Connected Panneau de connexion H 2O SHIELD J56 J57 PREFLOW INPUTS H 2O AIR N2 TVA H35 F5 COMM POWER SUPPLY O2 Art # A-06881FEU 0-5264FR 3-21 INSTALLATION ULTRA-CUT 100 XT/200 XT/300 XT/400 XT 3.19 Système de refroidissement HE400 Utilisé en série avec le système de refroidissement existant de l’alimentation électrique série Ultra-Cut XT™, le Système de refroidissement HE400 fournit le refroidissement d’eau supplémentaire nécessaire à la tête de la torche pour une découpe à plus de 300 A. Le ventilateur HE400 est contrôlé thermiquement pour fonctionner quand le ventilateur de l’Ultra-Cut et la pompe fonctionnent et la température est supérieure à un niveau prédéterminé. Cela peut se produire n’importe quand quand la pompe principale fonctionne. ! MISE EN GARDE Ne pas démonter le système de refroidissement s’il est sous tension ou si le liquide de refroidissement circule. Dangereux : présence de tension 220 V C.A. et de liquide sous haute pression. Disposer le système de refroidissement de façon à avoir une ventilation suffisante devant et derrière l’appareil ; ne rien disposer ni empiler sur l’appareil. 0,6 m (2’) 76 mm (3”) 76 mm (3”) 0,6 m (2’) Art # A-12813FR INSTALLATION 3-22 0-5264FR ULTRA-CUT 100 XT/200 XT/300 XT/400 XT REMARQUE ! Vérifier que les quatre lignes de liquide de refroidissement décrites ci-dessous sont raccordées et ne fuient pas avant de brancher l’alimentation électrique sur J71. Accorder les couleurs des tuyaux avec l’étiquette du panneau avant. Les lignes d’alimentation sont en vert, les lignes de retour sont en rouge. Avec l’appareil vu comme sur la figure ci-dessous, les connexions de gauche vont à l’alimentations électrique de l’Ultra-Cut XT™, les connexions de droite vont à l’allumage de l’arc RAS1000. ATTENTION NE PAS CROISER les lignes de refroidissement : cela n’assurerait pas le refroidissement de la torche à plasma XT™ telle qu’elle est conçue, et annulerait la garantie. Attacher et serrer toutes les fixations n°6 JIC avec une clef 11/16” (18 mm). Ne pas trop serrer : cela risquerait d’user la surface du filetages des fixations et déboucherait sur une fuite. Ne pas démarrer l’Ultra-Cut XT™ sans liquide de refroidissement dans le réservoir. Un gallon supplémentaire (3,78 l) de liquide de refroidissement est nécessaire pour compenser la présence du HE400 attaché au système. Contrôler le niveau de liquide quand vous remplissez l’Ultra Cut XT. Ne pas laisser le niveau du réservoir de liquide de refroidissement descendre sous le minimum. Art # A-09624_AB Attacher le câble J71 une fois établi que le système de refroidissement et les conduites de fluide de refroidissement ne fuient pas. En conditions de découpe avec un plasma de faible puissance, le HE400 peut ne pas se mettre en marche. C’est le mode normal de fonctionnement. Vérifier périodiquement que rien ne vient boucher le radiateur ; si besoin, passer l’aspirateur sur les ventilateurs. Ne pas utiliser de produits nettoyants ni de liquides pour éliminer les débris : ils peuvent endommager le radiateur. 0-5264FR 3-23 INSTALLATION ULTRA-CUT 100 XT/200 XT/300 XT/400 XT 3.20 Installation de l’amorce d’arc à distance Emplacement du site Sélectionner un endroit sec et propre avec une bonne ventilation et un espace de travail approprié autour de tous les composants. Examiner les consignes de sécurité au début de ce manuel pour vérifier que l’endroit respecte toutes les exigences en matière de sécurité. Les câbles d’interconnexion et les tuyaux se fixent à l’amorce d’arc. Il doit y avoir un espace adéquat autour de l’amorce d’arc pour ces connexions sans sertissage. Dimensions de montage REMARQUE ! La hauteur qui n’est pas montrée est de 7.375” (187 mm). 190.50mm 7.50in 38.10mm 1.50in 50.80mm 2.00in 203.20mm 8.00in 50.80mm 2.00in 38.10mm 1.50in Art # A-12058 Installation L’amorce d’arc à distance doit être installée dans un endroit approprié près du corps de la torche. Si l’amorce d’arc est montée sur une passerelle ou tout autre support sujet à des mouvements ou des vibrations, bien attacher l’amorce d’arc au support. 1. Desserrer, mais sans les enlever, les vis inférieures fixant le couvercle à l’amorce d’arc. Enlever les vis supérieures fixant le panneau du couvercle à l’amorce d’arc. REMARQUE ! Un fil de garde connecte le couvercle à la base de l’amorce d’arc. Ce fil doit rester en place. INSTALLATION 3-24 0-5264FR ULTRA-CUT 100 XT/200 XT/300 XT/400 XT 2. Enlever le panneau du couvercle de l’amorce d’arc. Vis supérieures (2 de chaque côté) Couvercle Fil de garde Vis inférieures (2 de chaque côté) Art # A-09625FEU Enlèvement du couvercle 3. Placer l’amorce d’arc sur une surface de montage horizontale et plane. 4. Utiliser des trous pré-forés dans au moins deux des pieds au fond de l’amorce d’arc pour fixer l’amorce d’arc à la surface de montage. Minimum de 2 Art # A-09626FR 0-5264FR 3-25 INSTALLATION ULTRA-CUT 100 XT/200 XT/300 XT/400 XT Connexions d’entrée 1. Se reporter aux illustrations. Effectuer les connexions d’entrée suivantes au niveau de l’amorce d’arc. • Tuyaux d’alimentation en liquide de refroidissement et de retour (de l’échanteur de chaleur HE400). Les tuyaux et les connecteurs possèdent un code couleur ; rouge pour le retour et vert pour l’alimentation. Art # A-09627FEU Retour Alimentation Alimentation en liquide de refroidissement et tuyaux de retour (provenant du générateur) Art # A-09628FEU Rouge Retour du liquide de refroidissement (rouge) Vert Alimentation en liquide de refroidissement (vert) INSTALLATION 3-26 0-5264FR ULTRA-CUT 100 XT/200 XT/300 XT/400 XT Plaque en cuivre Art # A-09629FEU Câble négatif provenant du générateur Câbles négatifs (provenant du panneau arrière du générateur) Art # A-09630FEU Câble de retour de l’arc pilote provenant du générateur Câble de retour de l’ARC PILOTE (provenant du panneau arrière du générateur) 0-5264FR 3-27 INSTALLATION ULTRA-CUT 100 XT/200 XT/300 XT/400 XT Art # A-09631 Câble de commande provenant du panneau arrière du générateur Connexions de sortie 1. Se reporter aux illustrations. Effectuer les connexions de sortie suivantes au niveau de l’amorce d’arc. REMARQUE ! Pour les câbles les plus récents avec un seul fil noir, celui-ci doit être branché au retour de l’arc pilote. Il n’y pas de câbles de garde internes. Câble de l’arc pilote Art # A-09632FEU Détail de la connexion du câble de l’arc pilote Câble de retour de l’arc pilote et câble blindé interne (provenant des câbles de la torche) INSTALLATION 3-28 0-5264FR ULTRA-CUT 100 XT/200 XT/300 XT/400 XT Art # A-09633FEU Certains éléments sont enlevés pour rendre le dessin plus compréhensible Raccord du retour du liquide de refroidissement (avec une étiquette rouge) Raccord de l’alimentation en liquide de refroidissement (avec une étiquette verte) Alimentation en liquide de refroidissement (vert) vers la torche Retour du liquide de refroidissement (rouge) provenant de la torche Alimentation en liquide de refroidissement et tuyaux de retour (provenant de la torche) Remonter le couvercle de l’amorce d’arc. S’assurer que le fil de garde n’est pas plié entre le couvercle et la base. Vis supérieures (2 de chaque côté) Couvercle Fil de garde Vis inférieures (2 de chaque côté) Art # A-09625FEU L’amorce d’arc doit être mise à la terre ; la borne de mise à la terre est indiquée par cédent pour plus de détails sur la mise à la terre. 0-5264FR 3-29 . Se reporter au paragraphe pré- INSTALLATION ULTRA-CUT 100 XT/200 XT/300 XT/400 XT Art # A-04758 Câblage de la torche 1 écrou et 1 rondelle restent en place • Câble de masse Utiliser un collier pour fixer la tresse de la protection du câblage de la torche à la porte présente sur l’amorce d’arc à distance comme cela est montré. Art # A-04759 Protection du câblage de la torche Collier de protection Câblage du liquide de refoidissement et de l’arc pilote vers l’ensemble de la valve de la torche INSTALLATION 3-30 0-5264FR ULTRA-CUT 100 XT/200 XT/300 XT/400 XT Raccordement du câble de commande 1. Raccorder le câble de l’amorce d’arc à distance au réceptacle de l’amorce d’arc à distance. J55 - GCM USER INPUT J15 - CNC HEIGHT CONTROL J54 - TSC /COMM J59 - RAS CB2 - 5A 120 VAC CB3 - 5A 24 VAC J70 - HE CB4 - 5A 120 VAC F1 - 8A SB 230 VAC F2 - 8A SB 230 VAC Art # A-11540_AB 0-5264FR 3-31 INSTALLATION ULTRA-CUT 100 XT/200 XT/300 XT/400 XT 3.21 Installation de la soupape de la torche INFORMATIONS GÉNÉRALES Ce montage doit se faire aussi près que possible de la tête de la torche. Il reçoit les gaz de pré-écoulement, de plasma et d’écran du module de contrôle des gaz et les envoie à la torche. Montage 113.03 mm 4.450” 6.63 mm .261” Dia. 36.83 mm 1.450” Art # A-07648 1. Monter le kit de soupape aussi près que possible de la torche. Le kit de soupape peut se monter dans n’importe quelle position pratique, pourvu que le côté de sortie (avec deux fixations) soit plus proche de la torche que le côté d’entrée (avec trois fixations et un connecteur de câble de contrôle). 2. Connecter les sorties du kit de soupape aux conduites de la torche comme illustré ici. (figuration de XTL) Ne pas retirer les bouchons en laiton frontal et latéral Côté sortie Art # A-07645FEU Filetage vers le gauche: Pour raccord de gaz torche à plasma Filetage vers la droite: Pour raccord de gaz protecteur de la flamme INSTALLATION 3-32 0-5264FR ULTRA-CUT 100 XT/200 XT/300 XT/400 XT 3. Connecter les lignes d’alimentation en gaz et le connecteur du câble de contrôle depuis le module de contrôle des gaz vers le kit de soupape comme illustré ici. Maintenir les soupapes de contrôle stationnaires en attachant les lignes de gaz. (figuration de XTL) Silencieux d'échappement Câble de commande Entrée du WMS™ Entrée du gaz de protection Entrée du gaz du flux préliminaire Entrée du gaz plasmagène Art # A-07646FEU ATTENTION Maintenir les fixations stationnaires en attachant les tuyaux - sinon, risque de fuites. La pression latérale peut briser les soupapes de contrôle ou affaiblir leur raccordement à la soupape de la torche. Contrôler sur toutes les connexions qu’il n’y ait pas de fuite avant de continuer. 3.22 Raccordement de la torche Raccorder la torche comme suit : Câblage d’alimentation en liquide de refroidissement, de retour du liquide de refroidissement et de l’arc pilote Couvercle du câblage Capuchon du câblage de la torche Gaz de protection (filetage vers la droite) Encoche pour le joint torique Tube plongeur Câble de l’arc pilote Joint torique Gaz plasmagène (filetage vers la gauche) Vers la valve de la torche Câblage de courant et d’alimentation en liquide de refroidissement (-) Connecteur du câble de l’arc pilote Corps de la torche Art # A-09198FEU 1. Disposer le câblage de la torche sur une surface de travail propre et sèche. 0-5264FR 3-33 INSTALLATION ULTRA-CUT 100 XT/200 XT/300 XT/400 XT 2. Tenir le capuchon du câblage de la torche afin qu’il soit immobile. Tirer environ 18” (0,5 m) de câblage à traver le capuchon. 3. Enlever et jeter les capuchons de protection du tube plongeur. 4. Placer le joint torique dans la rainure au niveau de l’extrémité supérieure du tube plongeur. 5. Installer le tube plongeur comme suit : a. Positionner le tube plongeur à l’extrémité du câblage comme cela est montré. b. Faire glisser le tube plongeur vers le haut sur le câblage. c. Appuyer l’extrémité supérieure du tube plongeur dans l’extrémité inférieure du capuchon du câblage de la torche. S’assurer que le joint torique sur le tube entre dans la rainure d’appui à l’intérieur du capuchon du câblage de la torche. d. S’assurer que le tube plongeur peut tourner librement à l’intérieur du capuchon du câblage de la torche. 6. Raccorder le câblage du gaz et du liquide de refroidissement au corps de la torche. a. Les raccordements de retour et d’alimentation en liquide de refroidissement vers le corps de la torche sont de différentes longueurs. b. Les raccordements du gaz plasmagène et du gaz secondaire vers le corps de la torche ont des filetages différents ; le raccordement du gaz plasmagène présente un filetage vers le gauche tandis que le raccordement du gaz de protection présente un filetage vers la droite. c. Tenir les connecteurs du câblage du corps de la torche immobiles ; tourner les raccords du câblage avec une clé pour bien fixer le câblage au corps de la torche. Serrer sans trop forcer. ATTENTION Le câblage du gaz et du liquide de refroidissement comprennent des raccords de compression. Ne pas utiliser de pâte d’étanchéité sur ces connexions. Mettre lentement sous pression les lignes du gaz. Contrôler sur toutes les connexions qu’il n’y ait pas de fuite avant de continuer. S’il n’y a pas de fuites, couper les alimentations en gaz et continuer l’installation. 7. Raccorder le câblage de l’arc pilote au corps de la torche. Bien appuyer les deux extrémités du connecteur ensemble. Enfiler le connecteur/couvercle du câblage en plastique sur le connecteur du corps de la torche d’appui. 8. Appuyer le corps de la torche vers le haut pour le connecter au tube plongeur. Tirer le câblage vers l’arrière suffisamment pour garantir un bon positionnement à travers le tube plongeur et le capuchon du câblage de la torche. Tenir le corps de la torche immobile ; faire tourner le tube plongeur pour l’enfiler sur le corps de la torche. ATTENTION S’assurer que le câblage ne s’entortille pas à l’intérieur du tube plongeur. Le câblage doit se présenter comme sur le schéma d’installation. 9. L’extrémité inférieure du tube plongeur comprend quatre trous filetés. Placer une vis à tête creuse dans l’un des trous filetés pour fixer le corps de la torche au tube plongeur. 10. Installer les consommables appropriés comme cela est montré dans les pages suivantes. Le manuel de la torche comprend des diagrammes montrant les pièces correctes à installer, en fonction du métal à découper et des gaz utilisés. INSTALLATION 3-34 0-5264FR ULTRA-CUT 100 XT/200 XT/300 XT/400 XT 3.23 Installation des consommables de la torche Installer les consommables comme suit afin de garantir un fonctionnement correct. Ces étapes aideront à garantir que les pièces soient placées correctement. MISES EN GARDE Ne pas placer de consommables dans la cartouche quand celle-ci est fixée au corps de la torche. Faire en sorte qu’aucun matériau étranger ne pénètre dans les consommables et la cartouche. Manipuler soigneusement toutes les pièces afin d’éviter de les endommager car cela pourrait affecter les performances de la torche. Art # A-03887FR 1. Contrôler le tableau de coupe approprié pour connaître la bonne combinaison de pièces pour l’application de coupage 2. Uniquement pour les pièces 200 A, enfiler le dispositif de retenue de protection sur la jupe. 3. Empiler les consommables ensemble. he uc rto Ca de tro ec El D ga istri z p bu las teu m rd ag u èn e uy èr e Jupe C pr oiffe ot d ec e tio n Dispositif de retenue D ga istri z d bu e p teu ro r d te u ct io n T Art # A-08303FEU B A 1 - Assembler « A » 200 A uniquement. 2 - Assembler « B ». 3 - Assembler « B .sur « C ». C 4 - Assembler « A » sur le bloc « B-C ». 4. Introduire la pile de consommables dans la cartouche. S’assurer que le grand joint torique sur la tuyère de la torche entre entièrement dans la cartouche. Si une partie du joint torique dépasse de la cartouche, cela veut dire que les pièces ne sont pas positionnées correctement. 5. Utiliser l’outil de la cartouche pour tenir l’ensemble de la cartouche, tout en tournant la jupe (et le dispositif de retenue pour les pièces 200 A) sur l’ensemble de la cartouche. Pour les pièces 300 A tourner le dispositif de retenue sur la jupe maintenant. Quand ce groupe est entièrement monté, la protection devrait dépasser de l’avant de la jupe ou du dispositif de retenue. S’il ne dépasse pas, cela veut dire que la jupe n’est pas bien serrée sur la cartouche. 6. Enlever l’outil de la cartouche de la cartouche. Monter la cartouche sur le corps de la torche. La bague « Speed Lok » devrait s’encliqueter et la cartouche devrait toucher le grand joint torique sur la torche. Corps de torche Joint torique du corps de torche Saillie de 0.063 0.083" (1,6 – 2,1 mm) Art # A-08300_AB Installation de la cartouche sur le corps de torche 7. Faire glisser la borne du capteur ohmique sur la jupe si l’on utilise la détection de la hauteur de la torche ohmique. 0-5264FR 3-35 INSTALLATION ULTRA-CUT 100 XT/200 XT/300 XT/400 XT Montage des pièces 30 - 100 A 2: Appuyer la cartouche contre les pièces empilées 1: Empiler les pièces Electrode Distributeur du gaz plasmagène Joint torique supérieur sur la tuyère Aucun vide entre les pièces Tuyère Distributeur du gaz de protection La cartouche couvre le joint torique supérieur sur la tuyère de la torche Coiffe de protection 3: Enfiler la jupe sur la cartouche 4: Contrôler que la jupe dépasse Jupe Bouclier cap La coiffe de protection dépasse de 0.063-0.083" (1.6 - 2.1 mm) Art # A-04873FC Installation de la cartouche sur le corps de torche 7. Raccorder le câblage de l’altimètre à la borne du capteur ohmique si l’on utilise la détection de la hauteur de la torche ohmique. Borne du capteur ohmique A-03393 REMARQUE ! La détection de la hauteur ohmique n’est pas recommandée avec une feuille d’étanchéité. L’eau sur la plaque interfère électriquement avec le circuit de détection ohmique. INSTALLATION 3-36 0-5264FR ULTRA-CUT 100 XT/200 XT/300 XT/400 XT 3.24 Diviseur de tension (« V-D ») pour contrôler la hauteur de torche iHC Pour obtenir les meilleures performances de découpe au plasma, il est nécessaire de maintenir une hauteur (distance de dégagement) constante au-dessus du métal pendant la coupe. Les tables de découpe utilisent un contrôle de la hauteur de torche (THC), également appelé contrôle sur l’axe Z, et la plupart d’entre elles se basent sur une rétroaction de la tension d’arc pour ajuster la hauteur. Plusieurs de ces dispositifs de contrôle, y compris l’iHC (contrôle de hauteur interne), qui fait partie du contrôleur CNC Victor Technologies XT, sont munis d’un circuit imprimé diviseur de tension (« carte V-D », pour « Voltage-Divider » en anglais) qui doit être installé à l’intérieur de l’alimentation du plasma pour abaisser la tension d’arc et qui sera utilisé par les circuits de commande. Un espace est prévu pour le montage de la carte V-D, sur la partie supérieure d’un panneau vertical interne situé près de l’arrière de l’alimentation. Des trous pré-percés permettent le montage de la carte V-D iHT, ou d’un autre circuit fréquemment utilisé de commande de hauteur. MISE EN GARDE Si vous utilisez une autre carte, qui ne s’aligne pas avec les trous existants, retirez le panneau avant d’en percer d’autres. Si ce n’est pas possible, toutes les précautions doivent être prises pour empêcher la limaille de se déposer à l’intérieur de l’alimentation. Installation de la carte V-D. 1. Localisez la carte V-D qui devrait être avec l’iCNC. 2. À l’intérieur de l’alimentation, localisez et retirez les 2 vis et le panneau de la plaque de montage. 3. Installez les entretoises de la carte V-D et la carte elle-même, en provenance de l’iCNC du XT, puis revissez le panneau avec les 2 vis de fixation, ce qui sécurise la carte V-D. Si vous utilisez une autre carte V-D, suivez les instructions fournies pour l’installer à ce même endroit. Jeu pour V-D carte Ouverture du borne du capteur ohmique installé V-D Board carte Art # A-12079FR Raccordement du V-D carte La carte V-D est illustrée avec le faisceau de câbles en option pour le contrôleur iHC 0-5264FR 3-37 INSTALLATION ULTRA-CUT 100 XT/200 XT/300 XT/400 XT Câble de contrôle. La carte iHC peut être livrée avec un faisceau de câbles et le connecteur correspondant (voir image précédente), qui doivent être installés dans le trou du panneau arrière portant la mention « Height Control » (contrôle de la hauteur). Le connecteur se branche sur un câble de l’iHC. Si vous utilisez une autre carte V-D pour le contrôle de la hauteur, vous pouvez installer un serre-câbles dans ce trou. Reportez-vous à l’annexe pour le schéma de câblage. Ouverture du borne du capteur ohmique J55 - GCM USER INPUT J15 - CNC HEIGHT CONTROL Raccordement du V-D carte J54 - TSC /COMM J59 - RAS CB2 - 5A 120 VAC CB3 - 5A 24 VAC J70 - HE CB4 - 5A 120 VAC F1 - 8A SB 230 VAC F2 - 8A SB 230 VAC Art # A-12080FR Connexions de tension d’arc. Le XT plasma présente un bornier TB4, sur le côté droit à l’avant du module CCM pour les connexions à Arc-V (Torch) [torche], Tip V (Pilot) [pilote] et Arc V + (Work) [travail]. Au cas où la carte V-D nécessite une alimentation séparée, des bornes à 24 VCA et 120 VCA sont disponibles sur le bornier TB4. Reportez-vous au schéma de câblage en annexe pour plus d’informations. TB4 1 2 24 VCA à1A 3 4 5 6 7 120 VCA Travail à 100 mA Astuce les tensions (Pilote) Tension d’arc (Torche) Art # A-11954FEU Câble « Ohmique » ou de buse. Certains contrôles de hauteur, y compris l’iHC, détectent la plaque en utilisant une mesure de contact électrique ou de résistance, c’est-à-dire « ohmique », le contact entre l’extrémité conductrice de la torche et le métal ou « plaque » étant coupé. Un fil métallique, généralement un câble unique hautement flexible capable de résister à la chaleur d’arc réfléchie, relie la carte V-D à la buse de la torche. La torche XT comprend une pince à ressort métallique qui se glisse dans une rainure de la buse permettant d’enlever facilement les pièces à changer. Le fil ohmique peut être connecté à cette pince par une borne femelle de ¼ po (6,35 mm) à pression. Une quantité importante d’énergie à haute fréquence (HF), provoquant des interférences électromagnétiques (EMI), peut être transmise par ce fil, en raison de son couplage serré avec la torche. C’est la raison pour laquelle la carte V-D est placée loin du CCM et à proximité du panneau arrière, où le fil ohmique n’a pas besoin de passer à proximité d’autres appareils électroniques sensibles. Il est particulièrement recommandé de ne pas faire passer le fil ohmique à proximité du module CCM ou le long des câbles de la torche. Reportez-vous à l’annexe pour le schéma de câblage. Noyaux de ferrite. Il est recommandé d’enrouler le fil de détection ohmique autour d’un noyau de ferrite en faisant plusieurs tours, au minimum 3 et de préférence davantage, pour atténuer l’énergie transférée à la carte V-D et à l’alimentation du plasma. Le noyau de ferrite doit être placé sur le fil à l’endroit où il entre dans l’alimentation du plasma. Un deuxième noyau de ferrite ajouté à environ 2 m (plusieurs pieds) de la torche permettra de réduire davantage les interférences dans le fil, qui peuvent être transmises à d’autres câbles/fils et provoquer des interférences ailleurs. Reportez-vous à l’annexe pour le schéma de câblage. INSTALLATION 3-38 0-5264FR ULTRA-CUT 100 XT/200 XT/300 XT/400 XT 3.25 Fin de l’installation 1. Enlever le bouchon du réservoir du liquide de refroidissement. Remplir le réservoir du liquide de refroidissement jusqu’au niveau indiqué avec du liquide de refroidissement Thermal Dynamics. Le niveau du liquide de refroidissement est visible à travers le réservoir translucide. La quantité de liquide de refroidissement requise varie en fonction de la longueur des câbles de la torche. Capacités du liquide de refroidissement Numéro de la catégorie et mélange Mélange Protège jusqu’à 7-3580 ‘Extra-CoolTM’ 25 / 75 10° F / -12° C 7-3581 ‘Ultra-CoolTM’ 50 / 50 27° F / -33° C 7-3582 ‘Extreme CoolTM’ Concentré* -65° F / -51° C * Pour être mélangé avec D-I CoolTM 7-3583 Réservoir du liquide de refroidissement Plage de remplissage Art # A-11536FEU 2. Quand l’ensemble du système a été installé, contrôler que le liquide de refroidissement a été pompé à travers le système comme suit (voir Remarque) : REMARQUE ! En fonction de la longueur du câblage de la torche, le système peut avoir besoin de plus de liquide de refroidissement après avoir allumé pour la première fois le système. a. Placer l’interrupteur Marche/Arrêt sur Marche. b. Au bout de 30 secondes environ, le système peut se couper si le câblage n’est pas rempli de liquide de refroidissement. a. Placer l’interrupteur Marche/Arrêt sur Arrêt. d. Au bout de 10 secondes, mettre à nouveau l’interrupteur Marche/Arrêt sur Marche. e. Répéter les étapes de ‘b’ à ‘d’ jusqu’à ce que le système cesse de se couper. Selon la longueur du câblage de la torche, il peut être nécessaire de répéter de trois à cinq fois cette séquence. 0-5264FR 3-39 INSTALLATION ULTRA-CUT 100 XT/200 XT/300 XT/400 XT f. Quand le système reste opérationnel, laisser la pompe fonctionner pendant dix minutes afin de purger correctement l’air des lignes du liquide de refroidissement avant d’utiliser le système. 3. Remplir à nouveau le réservoir et remettre le bouchon du produit de remplissage. 4. Purger le liquide de refroidissement dans la torche avant d’allumer celle-ci. S’assurer qu’il n’y ait pas de fuite avant de l’utiliser. Si des fuites sont évidentes, consulter le guide de dépannage pour les fuites de liquide de refroidissement dans le paragraphe d’entretien de ce manuel. INSTALLATION 3-40 0-5264FR ULTRA-CUT 100 XT/200 XT/300 XT/400 XT Page volontairement laissée vierge. 0-5264FR 3-41 INSTALLATION ULTRA-CUT 100 XT/200 XT/300 XT/400 XT Page volontairement laissée vierge. INSTALLATION 3-42 0-5264FR ULTRA-CUT 100 XT/200 XT/300 XT/400 XT CHAPITRE 4 : FONCTIONNEMENT 4.01 Panneau de commande du générateur Témoin d’alimentation CA A/ Témoin de gaz Témoin de température Témoin de fonctionnement Témoin d’alimentation CC A/ Art # A-11541FEU Témoin d’alimentation CA Il indique que l’alimentation CA est fournie aux inverseurs quand l’interrupteur Marche/Arrêt est sur la position Marche. Quand l’interrupteur est d’abord mis sur Marche, le témoin reste éteint jusqu’à ce que le cycle d’irruption soit terminé et que la tension correcte soit confirmée. Témoin de température : Il est normalement éteint. Le témoin s’allume quand les capteurs de la température interne détectent des températures supérieures aux limites normales. Laisser l’équipement refroidir avant de poursuivre les opérations. Témoin de gaz : ON pendant le démarrage de la purge de gaz / amorçage de la pompe, puis quand le gaz s’écoule. Indique la pression de gaz adéquate pour le fonctionnement. Témoin d’alimentation CC : Indique que le générateur produit une tension CC de sortie. A/ Témoin de fonctionnement : Montre la version du code CCM au démarrage, suivie du réglage de contrôle d’intensité électrique et du statut du système. Cf. section 4.05 et Code de statut pour plus de détails. Lampe d’alimentation électrique C.A. du panneau arrière Indique que l’appareil est sous tension C.A. 0-5264FR 4-1 FONCTIONNEMENT ULTRA-CUT 100 XT/200 XT/300 XT/400 XT 4.02 Fonctionnement du système Ce chapitre contient des informations sur le fonctionnement qui sont spécifiques à l’alimentation électrique. MISE EN GARDE ! Passer en revue les précautions de sécurité de la section 1. Si le cordon d’alimentation électrique comporte une prise ou n’est pas connecté de façon permanente sur l’alimentation électrique, s’assurer que la sortie est déconnectée au moment du branchement. Déconnecter l’alimentation électrique primaire à la source avant d’assembler ou de désassembler l’alimentation électrique, des pièces de la torche, ou des montages de la torche et de ses fils, ou d’ajouter du liquide de refroidissement. Il ne suffit pas de positionner l’interrupteur Marche/Arrêt de l’appareil sur Arrêt quand les opérations de découpe sont terminées. Ouvrir toujours l’interrupteur de déconnexion de l’alimentation électrique cinq minutes après la fin de la dernière découpe. REMARQUE ! Avant de faire démarrer le système, déterminer le procédé à utiliser. Le procédé est déterminé par le type et l’épaisseur du métal à découper. Sélectionner et installer les consommables nécessaires, connecter les gaz nécessaires au système. 1. Raccorder le système à la source de courant principale. Un indicateur s’allume sur le panneau arrière quand l’appareil est sous tension C.A. Sur le GCM 2010, placer l’interrupteur (coin supérieur droit) en position “Activé”. 2. Mettre l’interrupteur MARCHE / ARRET sur MARCHE (haut). Le système passe par la séquence de démarrage”. • Pendant environ 10 secondes, les décimales de l’affichage à 4 chiffres clignotent de droite à gauche. • Ensuite, les 4 LED rectangulaires indicatrices et les 4 chiffres d’affichage de statut s’allument entièrement à titre de test. • Ensuite, pendant environ 6 secondes, l’écran affiche la lettre “C” (code) suivie de la version du code CCM. Exemple “C1.2.0”. Pendant ce temps, divers tests de tension en entrée sont effectués. Si une panne est détectée, son code s’affiche et la séquence de démarrage s’arrête. Les pannes s’affichent par “E” ou “L”. Si le plasma n’a pas encore été activé à ce moment, E101 s’affiche et la séquence de démarrage ne débute pas. • La pompe à liquide de refroidissement démarre et l’indicateur de présence de gaz clignote en affichant E304, tandis que les gaz de découpe sont purgés. La durée de purge varie en fonction de la longueur des conduites de la torche et du procédé de découpe. cf. section 4.05 pour régler la longueur de la conduite sur le GCM 2010. • Une fois qu’un écoulement du liquide de refroidissement est détecté, habituellement dans les 5 secondes après le démarrage de la pompe, le(s) contact(s) d’entrée W1 (W2) se ferme(nt) et l’indicateur C.A. s’allume. POWER I ON OFF O O OFF O OFF O OFF Art # A-11542 3. Régler la pression de gaz du GCM 2010 a. Placer l’interrupteur de mode en mode SET PREFLOW. Régler la pression de pré-écoulement selon ce qui est nécessaire au procédé de découpe. b. Régler l’interrupteur de mode en position SET PLASMA & SHIELD. Régler les régulateurs de pression de plasma et d’écran aux bonnes valeurs. c. Régler les débitmètres de plasma et l’écran (si le procédé nécessite de régler l’écoulement d’écran) aux bonnes valeurs. d. Ramener l’interrupteur de mode en position RUN. 4. Régler l’intensité électrique de découpe. a. Régler l’intensité électrique de découpe avec le bouton tournant AMPERAGE SET_UP et l’écran LCD sur le GCM 2010. FONCTIONNEMENT 4-2 0-5264FR ULTRA-CUT 100 XT/200 XT/300 XT/400 XT 5. Préparer la découpe. a. Protéger vos yeux et vos oreilles. b. Positionner la torche à la bonne distance de transfert au-dessus de la pièce de travail. 6. Appuyer sur DÉMARRER. • Lorsque l’indicateur de gaz clignote, le pré-écoulement de gaz commence. • Lors du pré-écoulement de gaz, l’alimentation est mise en marche. La lampe DC s’allume. 7. L’arc pilote • À la fin du pré-écoulement, l’inflammation se produit (feux pour démarreur d’arc) et l’arc pilote est fixé. 8. Transfert • Si la torche est correctement positionnée, l’arc pilote la transfert presque immédiatement au service et elle devient un arc de coupe (transféré). • Le niveau du courant augmente rapidement jusqu’au niveau fixé par la commande de courant et l’arc passe à travers le métal. • La fonction ‘OK pour déplacer’ devient active et la torche se déplace pour effectuer la coupe. 9. Fin de la coupe. • Lorsque le signal DÉMARRER est désactivé, le courant baisse et ne passe plus. • Les gaz continuent de s’écouler pendant la période post-écoulement sélectionnée, puis s’arrêtent. • La pompe se met en marche pendant 4 minutes, puis s’arrête. 10. Pour effectuer une coupe supplémentaire, répéter les étapes 5-9. Une fois la première coupe achevée, il est possible de démarrer une deuxième. 11. Arrêt du système. a. Régler le commutateur MARCHE / ARRÊT, situé sur le panneau avant de l’appareil, sur ARRÊT. MISE EN GARDE ! L’alimentation C.A. traverse encore l’appareil. • Le système de ventilation et la pompe, ainsi que tous les indicateurs, arrêtent de fonctionner. • L’écran peut afficher un code d’erreur pendant un moment : c’est une étape normale de l’arrêt d’alimentation et cela n’indique pas une panne. b. Activer (désactiver) l’alimentation principale. L’appareil perd alors toute son énergie. • L’indicateur C.A du panneau arrière s’arrête. Suggestions opérationnelles 1. Attendre quatre minutes avant de régler l’interrupteur Marche/Arrêt sur Arrêt après utilisation. Cela permet aux ventilateur de refroidissement de fonctionner afin de dissiper la valeur de l’alimentation électrique. 2. Pour maximiser la durée de vie des pièces, ne pas faire fonctionner l’arc pilote plus longtemps que nécessaire. 3. Faire attention en manipulant le câblage de la torche et le protéger de tout dommage. 4. Si vous utilisez de l’eau comme écran, notez les points suivants : • Utiliser de l’eau du robinet potable de bonne qualité pour contribuer à empêcher tout colmatage par des particules dans la plomberie de l’écran du système. • Une contamination par des particules et un colmatage peuvent réduire la durée de vie des consommables et faire tomber prématurément la torche en panne. • Un filtre à particules de type cartouche peut aider à optimiser les performances de découpe. 0-5264FR 4-3 FONCTIONNEMENT ULTRA-CUT 100 XT/200 XT/300 XT/400 XT 4.03 Sélection du gaz A. Gaz plasmagènes 1. Plasma à l’air • Le plus souvent utilisé sur les matériaux ferreux ou à base de carbone pour une bonne qualité avec des vitesses de coupe plus rapides. • Le plasma à l’air est normalement utilisé avec un rideau d’air. • Il est recommandé de n’utiliser que de l’air propre et sec avec le gaz plasmagène. Toute présence d’huile ou d’humidité dans l’air réduira considérablement la durée de vie des pièces de la torche. • Fournit des résultats satisfaisants sur les matériaux non-ferreux et une soudabilité réduite sur les matériaux ferreux. 2. Plasma à l’argon/azote (H35) • Recommendé pour une utilisation sur l’acier inoxydable d’une épaisseur de 3/4 in (19 mm) et plus. Recommandé sur les matériaux non-ferreux d’une épaisseur de 1/2 inch (12 mm) et plus. Le Ar/H2 n’est normalement pas utilisé sur les matériaux non-ferreux plus fins car des gaz moins coûteux peuvent obtenir une qualité de coupe similaire. • Mauvaise qualité de coupe sur les matériaux ferreux. • Fournit des vitesses de coupe plus rapide et une qualité de coupe élevée sur les matériaux plus épais pour compenser les coûts supérieurs. • Un mélange de 65% d’argon et de 35% d’azote devrait être utilisé. 3. Plasma à l’oxygène (O2) • L’oxygène est recommandé pour le coupage des matériaux ferreux. • Fournit des vitesses de coupe plus rapides. • Fournit des finitions très lisses et réduit au minimum les dépôts de nitrure sur la surface de découpe (les dépôts de nitrure peuvent provoquer des problèmes lors de la production de soudures de grande qualité s’ils ne sont pas enlevés). 4. Plasma à l’azote (N2) • Fournit une meilleure qualité de coupe sur les matériaux non-ferreux comme l’acier inoxydable et l’aluminium. • Peut être utilisé à la place du plasma à l’air avec un rideau d’air. • De l’azote avec un bon degré de soudage devrait être utilisé. • Si vous utilisez secondairement un brouillard d’eau, vous obtiendrez des vitesses supérieures de découpe et une meilleure qualité de découpe sur l’inox et l’aluminium. 5. Plasma H17 (17,5% Hydrogène / 32,5% Argon / 50% Azote) • Recommandé pour les matériaux non-ferreux de ½” (12 mm) d’épaisseur et plus. Normalement, ne pas utiliser H17 pour les matériaux non-ferreux plus minces, car il est possible d’obtenir une qualité de découpe similaire avec des gaz moins coûteux. • Alternatives au plasma H35 Donne des vitesses de découpe légèrement supérieures et une qualité de découpe similaire. • Lors de l’utilisation de H17, il faut alimenter le système en gaz par le port d’alimentation en gaz marqué “H35”. • Mauvaise qualité de découpe sur les matériaux ferreux. B. Gaz de protection 1. Rideau d’air comprimé • Un rideau d’air est normalement utilisé quand on opère avec du plasma à l’air. • Améliore la qualité de coupe sur certains matériaux ferreux. • Economique - frais d’exploitation réduits. 2. Protection avec de l’azote (N2) • La protection avec de l’azote est utilisée avec le plasma à l’Ar/H2 (H35). FONCTIONNEMENT 4-4 0-5264FR ULTRA-CUT 100 XT/200 XT/300 XT/400 XT • Fournit des finitions lisses sur les matériaux non-ferreux. • Peut réduire la fumée quand il est utilisé avec le plasma à l’Ar/H2. 3. Rideau d’eau • Normalement utilisé avec l’azote. • Fournit une surface de coupe très lisse. • Réduit la fumée et la chaleur au niveau de la pièce à usiner. • Efficace en cas d’utilisation avec N2 jusqu’à 2” (50 mm) maximum d’épaisseur de matériau. • L’eau du robinet permet un coût réduit. 0-5264FR 4-5 FONCTIONNEMENT ULTRA-CUT 100 XT/200 XT/300 XT/400 XT 4.04 Fonctionnement du module de contrôle de gaz GCM 2010 Aperçu du fonctionnement Le module de contrôle des gaz fournit la sélection du plasma et des gaz secondaires et l’instrumentation de contrôle. Il existe divers contrôles et indicateurs qui servent à régler les pressions et débits des gaz. O2 - AIR O2 - O2 RUN ENABLE H35 - N2 SET PREFLOW F5 - N2 SET PLASMA & SHIELD AIR - AIR TEST DISABLE N2 - H20 N2 - N2 PLASMA POWER SUPPLY GAS MODE O2 - AIR O2 - O2 RUN F5 - N2 SET PLASMA & SHIELD TEST MODE PREFLOW ENABLE H35 - N2 SET PREFLOW AIR - AIR DISABLE N2 - H20 GAS N2 - N2 AMPERAGE SET-UP PLASMA 9 2010 H20 MIST PRESSURE PRESSURE GAS GAS FLOW Art # A-04771FE_AC FONCTIONNEMENT AMPERAGE SET-UP SHIELD 9 GCM PLASMA POWER SUPPLY 4-6 FLOW 0-5264FR ULTRA-CUT 100 XT/200 XT/300 XT/400 XT Module de contrôle des gaz GCM 2010 : 1. Interrupteur de sélection de mode RUN SET PREFLOW SET PLASMA & SHIELD TEST MODE O2 - AIR O2 - O2 H35 -N2 F5 - N2 AIR - AIR N 2 - H2 O N2 - N2 RUN SET PREFLOW SET PLASMA & SHIELD TEST GAS MODE PREFLOW ENABLE DISABLE High Precision Plasma Cutting System PLASMA POWER SUPPLY SHIELD PLASMA 9 9 GCM H2O MIST PRESSURE GAS FLOW 2010 Art # A-04765FE_AB • Normalement en position RUN quand la torche fonctionne. • En position SET PREFLOW, le gaz de pré-écoulement ou de pilotage (Air ou N2 ) s’écoule vers la torche, ce qui permet à l’opérateur de régler la pression. Le gaz se coupe automatiquement après 2 minutes si l’on reste en position SET PREFLOW. • En position SET PLASMA & SHIELD, les gaz de découpe choisis s’écoulent vers la torche pour permettre à l’opérateur de régler la pression (régulateur & jauge) et le débit (bouton en haut du débitmètre). Le gaz se coupe automatiquement après 2 minutes si l’on reste en position SET PLASMA & SHIELD. GCM 2010 et plus incluent des capteurs de pression en entrée. En position SET PLASMA & SHIELD, le LCD affiche alternativement les pressions d’entrée du plasma et de l’écran. Si l’une de ces deux pressions est hors de sa gamme de valeurs acceptables, et si l’écran affiche «PSI low» ou «PSI high», c’est que la pression est inférieur ou respectivement supérieure à la limite. • En position TEST, les gaz de découpe sélectionnés s’écoulent aussi vers la torche. La pression du plasma en sortie (la pression arrivant à la torche) s’affiche. • Pour GCM 2010 ou plus, l’interrupteur de sélection de mode inclut une fonction cachée utilisée à l’initialisation pour configurer le contrôle des gaz selon la longueur de la conduite des gaz. cf. Séquence de fonctionnement, initialisation 0-5264FR 4-7 FONCTIONNEMENT ULTRA-CUT 100 XT/200 XT/300 XT/400 XT 2. Interrupteur de sélection de gaz Sélectionne les combinaisons de gaz de plasma et d’écran. O2 - AIR O2 - O2 H35 -N2 F5 - N2 AIR - AIR N2 - H2O N2 - N2 GAS O2 - AIR O2 - O2 H35 -N2 F5 - N2 AIR - AIR N2 - H2O N2 - N2 RUN SET PREFLOW SET PLASMA & SHIELD TEST GAS MODE PREFLOW ENABLE DISABLE High Precision Plasma Cutting System PLASMA POWER SUPPLY SHIELD PLASMA 9 9 GCM 2010 H2O MIST PRESSURE GAS FLOW Art # A-04766FE_AB 3. Écran LCD L’écran LED affiche le statut de contrôle des gaz, comme en Attente de communication (Waiting for Communication), Désactivation (Plasma Power Supply Disabled), Initialisation (Initializing), Purge (Purging) et réglage de l’intensité en sortie (Output Current setting). Il affiche aussi des états opératoires, comme Pré-écoulement (Preflow), Pilotage (Piloting), Découpe (Cutting) et Post-écoulement (Postflow). De plus, il existe quelques erreurs CANBus bas niveau qui sont indiquées par des messages ^E#. ^E4 = erreur CANBus message non-reconnu ^E5 = erreur CANBus Bus désactivé ^E6 = erreur CANBus délai de communication dépassé FONCTIONNEMENT 4-8 0-5264FR ULTRA-CUT 100 XT/200 XT/300 XT/400 XT 4. Contrôle d’intensité électrique Règle l’intensité en sortie de l’alimentation électrique. High Precision Plasma Cutting System O2 - AIR O2 - O2 H35 -N2 F5 - N2 AIR - AIR N2 - H2O N2 - N2 RUN SET PREFLOW SET PLASMA & SHIELD TEST GAS MODE PREFLOW AMPERAGE SET-UP ENABLE DISABLE High Precision Plasma Cutting System PLASMA PLASMA POWER SUPPLY SHIELD 9 9 GCM AMPERAGE SET-UP H2O MIST PRESSURE GAS FLOW 2010 Art # A-04767FE_AC 5. Interrupteur d’activation/désactivation de l’alimentation électrique du plasma Le position DISABLE coupe l’alimentation électrique des onduleurs, désactive la pompe à fluide de refroidissement et le ventilateur, le contacteur pilote & HF et coupe l’alimentation C.A. des solénoïdes de contrôle de gaz, ce qui coupe tous les écoulements de gaz. Quand l’interrupteur repasse en position ENABLE, une purge automatique démarre, puis le système retourne en fonctionnement normal sous le contrôle des appareils CNC. 6. Bouton tournant de contrôle de PRÉ-ÉCOULEMENT et jauge de pression Sert à régler la pression et le débit du gaz en pré-écoulement. L’interrupteur MODE doit être en position SET PREFLOW. 7. Boutons tournants de contrôle du PLASAME et du SHIELD, jauges de pression et débitmètre Servent à régler les pressions et débits de gaz du plasma et de l’écran. L’interrupteur de mode doit être en position SET PLASMA & SHIELD. 8. Interrupteur d’écoulement de pression de gaz Aux faibles débits, commencer par régler la pression du gaz d’écran selon les paramètres de découpe, puis régler l’écoulement grâce au débitmètre avec l’interrupteur des gaz en position FLOW. Certaines pièces de torches nécessitent des débits qui dépassent la capacité du débitmètre. Dans ce cas, mettre l’interrupteur des gaz en position PRESSURE et utiliser le régulateur et la jauge pour régler la pression selon les paramètres de découpe quand n’est affiché aucun réglage «Ball». 9. Bouton rotatif de contrôle de brume H2O et débitmètre Sert à régler le débit d’eau. L’interrupteur de mode doit être en position SET PLASMA & SHIELD. L’interrupteur de sélection des gaz doit être en position N2 -H2O. REMARQUE ! Ne pas utiliser le brouillard d’eau dans toutes les applications. 0-5264FR 4-9 FONCTIONNEMENT ULTRA-CUT 100 XT/200 XT/300 XT/400 XT 4.05 Initialisation de GCM 2010 pour adapter le contrôle des gaz à la longueur des conduites Pour l’initialisation du GCM2010 avec la version du logiciel 2.1 ou plus. 1. Avant de mettre l’appareil sous tension, mettre l’interrupteur ACTIVER/DÉSACTIVER sur l’alimentation électrique du module de contrôle des gaz sur DÉSACTIVER . 2. Régler l’interrupteur de sélection des gaz dans la bonne position pour le procédé de découpe utilisé. 3. Mettre l’appareil sous tension et mettre l’interrupteur ACTIVER/DÉSACTIVER de l’alimentation électrique sur ACTIVER. Après un bref délai pour établir la communication, le contrôle de gaz initie une purge et la séquence d’amorçage. (si la torche et les conduites de refroidissement n’étaient pas déjà pleines de fluide de refroidissement, vous pouvez être amené à répéter ce cycle de mise sous tension et ajouter le liquide de refroidissement jusqu’à ce que l’amorçage soit effectué). 4. Une fois la séquence de purge terminée, régler l’interrupteur de mode entre Run et Set Precharge. L’écran affiche : «SET HOSE LENGTH» à la première ligne et LENGTH xxx FEET à la deuxième ligne. xxx a probablement pour valeur la valeur par défaut 175, qui est le maximum du système. 5. Maintenir enfoncé le bouton rotatif de contrôle d’intensité électrique. L’écran passe à SELECT HOSE LENGTH en première ligne et la deuxième ligne decrémente de 175’ à 50’ par pas de 25’. Dès que la bonne longueur s’affiche, relâcher le bouton. 6. Ramener l’interrupteur de mode sur Run. 7. L’initialisation est terminée ; inutile de la refaire par la suite, sauf en cas de remplacement du contrôle des gaz ou du panneau principal du PC. 4.06 Séquence de fonctionnement du GCM 2010 Pour la première utilisation, reportez-vous aux étapes précédentes «Initialisation..» 1. Régler l’interrupteur d’ Activation / Désactivation de l’alimentation électrique du plasma sur Désactivation. MISE EN GARDE ! Il faut couper l’alimentation électrique en entrée du système avant de changer ou d’inspecter des pièces de la torche. a. Changer les pièces de la torche si nécessaire. b. Régler l’interrupteur d’ Activation / Désactivation de l’alimentation électrique du plasma (sur le module de contrôle des gaz) sur Activation . Le module effectue des purges de 15 secondes, 11 secondes et encore une de 11 secondes. Cela élimine l’eau de la torche. 2. Sélectionner le gaz que vous désirez pour le plasma et l’écran en réglant l’interrupteur de sélection de gaz sur la position désirée. 2 secondes après la sélection du gaz, le module purge le ou les nouveau(x) gaz dans les conduites. 3. Réglage de la pression du gaz de pré-écoulement. a. Régler l’interrupteur de mode sur SET PREFLOW. b. Utiliser le bouton rotatif de contrôle de PRÉ-ÉCOULEMENT poru régler la pression du gaz de pré-écoulement. Reportez-vous au manuel de la torche pour les réglages de pression. 4. Régler les pressions et débits de gaz du plasma et de l’écran. a. Régler l’interrupteur de mode en position SET PLASMA & SHIELD. b. Utiliser le bouton rotatif de contrôle du PLASAME et de l’ÉCRAN, les jauges de pression et les débitmètres pour régler les pressions et débits du gaz de plasma et d’écran. Reportez-vous au manuel de la torche pour les réglages de pression. c. Dans les installations qui utilisent un écran d’eau, utiliser le bouton de contrôle H2O MIST et le débitmètre pour régler le débit de l’eau. Reportez-vous au manuel de la torche pour les réglages de débit. FONCTIONNEMENT 4-10 0-5264FR ULTRA-CUT 100 XT/200 XT/300 XT/400 XT 5. Utiliser le bouton rotatif de contrôle AMPERAGE SET-UP pour régler l’intensité électrique désirée en sortie. Le module actualisera l’intensité électrique toutes les 2 secondes après le dernier réglage du bouton rotatif. Le module garde en mémoire le point de consigne. 6. Placer l’interrupteur de mode en position RUN. 7. Régler l’interrupteur d’ Activation / Désactivation de l’alimentation électrique du plasma (sur le module de contrôle des gaz) sur ACTIVATION . Le module effectue des purges de 15 secondes, 11 secondes et encore une de 11 secondes. Cela élimine l’eau de la torche. REMARQUE ! Si vous changez de gaz entre deux opérations, laisser assez de temps de purge pour évacuer le gaz précédent des conduites de la torche. ATTENTION Bien que rien n’empêche l’opérateur de changer de gaz pendant le pilotage ou la découpe, ce n’est pas recommandé. Si l’opérateur change de gaz pendant le pilotage ou la découpe, l’alimentation électrique finira la découpe avec le premier gaz choisi. Ensuite, le contrôle des gaz passera au nouveau gaz. Changer de gaz pendant le pilotage ou la découpe peut endommager certaines pièces de la torche, ses conduites, le module de contrôle ou la pièce que vous découpez. Qualité de découpe Les exigences de qualité de découpe diffèrent en fonction de l’application. En l’occurrence, l’accumulation de nitrures et l’angle de biseau peuvent être des facteurs majeurs quand la surface doit être soudée après découpe. Une découpe sans mattes est importante quand on désire une bonne qualité de la finition de découpe pour éviter une opération de nettoyage secondaire. La qualité de la découpe varie selon les matériaux et leur épaisseur. Largeur de saignée Angle de coupe du flanc gauche Angle du chanfrein de la surface de coupe Perles sur le bord supérieur Angle de coupe du flanc droit Arrondi de l’arête supérieure Formation d’écume A-00512FC Rayures de la surface de la coupe A-00007FC Surface de découpe L’état (lisse ou rugueux) de la face de découpe. Angle de biseau L’angle entre la surface de découpe et un plan perpendiculaire à la surface de la plaque. Une découpe parfaitement perpendiculaire donnera un angle de biseau de 0°C. Arrondi de l’angle supérieur Arrondi sur le bord supérieur d’une découpe dû à l’usure par le contact initial de l’arc à plasma sur la pièce d’usinage. Accumulation de matte et éclaboussure supérieure La matte est du matériau fondu qui n’est pas expulsé de la zone de découpe et qui se resolidifie sur la plaque. Les éclaboussures supérieures sont de la matte qui s’accumule sur la surface supérieure de la pièce d’usinage. Un excès de matte peut nécessiter des opérations de nettoyage secondaire après découpe. Largeur de coupe La largeur du matériau enlevé pendant la découpe. 0-5264FR 4-11 FONCTIONNEMENT ULTRA-CUT 100 XT/200 XT/300 XT/400 XT Accumulation de nitrures Des dépôts de nitrure qui peuvent rester sur l’angle de découpe d’un acier au carbone quand de l’azote est présent dans le jet de gaz du plasma. Des accumulations de nitrures peuvent poser des problèmes si l’acier doit être soudé après découpe. Direction de découpe Le jet de gaz plasma tourbillonne en sortant de la torche en maintenant une colonne de gaz régulière. Cet effet de tourbillon a pour effet qu’un côté de la découpe est plus carré que l’autre. Vu suivant la direction de déplacement, le côté droit de la découpe est plus carré que le gauche. Angle de coupe du flanc gauche Dans le sens des aiguilles d'une montre Angle de coupe du flanc droit Chute Dans le sens contraire des aiguilles d'une montre Chute Objet A-00512FC Art # A-04182FC Effet de tourbillonnement sur les caractéristiques des côtés de découpe Pour faire une coupe carrée le long du diamètre interne d’un cercle, la torche doit se déplacer dans le sens inverse des aiguilles d’une montre le long du cercle. Pour maintenir l’angle carré le long du diamètre externe d’une découpe, la torche doit se déplacer dans le sens des aiguilles d’une montre. Découpe sous l’eau Il n’est pas recommandé d’effectuer des découpes à l’eau, que ce soit sous l’eau ou avec de l’eau en contact avec la plaque ou avec un système d’amortissement à eau. Si vous utilisez un système de découpe à eau, le niveau d’eau doit être d’un minimum de 4 pouces (10 cm) au-dessus du fond de la plaque. Ne pas suivre cette recommandation peut entraîner une mauvaise qualité de découpe et une réduction de la durée de vie des pièces. Capteur ohmique de hauteur La détection de la hauteur ohmique n’est pas recommandée avec une feuille d’étanchéité. L’eau sur la plaque interfère électriquement avec le circuit de détection ohmique. 4.07 Codes de fonctionnement du générateur Lors du démarrage et durant le fonctionnement, la circuiterie de commande du générateur effectue différents tests. Si la circuiterie détecte une situation nécessitant l’attention de l’opérateur, le statut qui s’affiche sur le panneau avant affiche un code de 3 chiffres précédé par la lettre «E» (erreur active) ou la lettre «L» (erreur récente ou loquet) signifiant qu’une erreur est survenue lors du processus mais n’est pas active. Certaines conditions peuvent être actives indéfiniment tandis que d’autres sont momentanées. Le générateur verrouille les conditions momentanées ; certaines conditions momentanées peuvent couper le système. Le témoin peut montrer des conditions multiples en séquence ; il est important de reconnaître toutes les conditions possibles qui peuvent être affichées. REMARQUE ! Il n’y a pas de codes de statut numéroté de groupe 5 (500) avec le système GCM 2010. Ces tableaux couvrent les appareils jusqu’à 400 A ; les appareils à plus basse intensité n’ont pas tous les onduleurs auxquels il est fait référence dans le groupe 2. Toutefois, les codes pour ces sections ne devraient pas apparaître. FONCTIONNEMENT 4-12 0-5264FR ULTRA-CUT 100 XT/200 XT/300 XT/400 XT Code de fonctionnement CCM Message Code Remède / Commentaire Groupe 1 -- Procédé plasma 101 102 Plasma désactivé Activation plasma éteinte ; Désactivation actionnée sur le GCM 2010 ou interrupteur externe actionné (CNC); cavalier CCM TB1-1&2 manquant ; câble ruban du circuit 40 circuit entre le relais PCB et le CCM déconnecté ou défectueux ; L’arc pilote n’a pas démarré dans les 15 secondes. Les consommables de la torche sont-ils usés ? Vérifier que Échec de l’allumage du pilote le bon procédé a été sélectionné ou que le réglage manuel, y compris le réglage de contrôle d’intensité électrique, correspond aux consommables ; pression du plasma trop élevée ; amorce d’arc défectueuse ; pilote PCB défectueux ; onduleur défectueux section 1A. Câbles rubans inversés sur les sections INV1 1A et 1B. Pilote perdu Le pilote est parti après démarrage. Les consommables de la torche sont-ils usés ? Vérifier que le procédé de découpe ou que le réglage du contrôle d’intensité électrique correspond aux consommables ; pression de plasma trop élevée ; 104 Transfert perdu L’arc a été transféré sur la pièce d’usinage puis est parti après démarrage. L’arc a perdu contact avec la pièce d’usinage (a dépassé la bordure, est passé sur un orifice, etc. ; sécurité trop élevée ; vérifier que le procédé de découpe ou les réglages manuels (contrôle d’intensité électrique, pressions des gaz) correspond aux consommables. 105 Non utilisé 103 106 Réservé pour le produit de legs Expiration de délai pilote, pas Le transfert du pilote à l’arc de découpe doit se faire sous 0,085 s (SW8-1 OFF) ou sous 3 s (SW8-1 ON). de transfert Sécurité trop élevée ou vide pendant le travail sous la torche ; sélection d’un mauvais procédé de découpe ou mauvais réglages manuels (contrôle d’intensité électrique réglé trop bas ou mauvaise pression des gaz). 107 Non utilisé Réservé pour le produit de legs 108 Mauvaise tension entre la pointe et l’électrode. La tension de la pointe est trop proche de celle de l’électrode ; consommables de la torche usés ; mauvais consommables installés provoquant un court-circuit entre la pointe et l’électrode ; sélection d’un mauvais procédé ou mauvais réglage manuel du gaz de plasma ou de l’intensité de découpe ; fuite dans le tuyau de plasma vers la torche ; pilote PCB défectueux ; court-circuit au niveau du corps de la torche. 109 Procédé non configuré. S’applique uniquement au contrôle automatique des gaz DFC 3000. Sélectionner et charger un procédé de découpe. 110 Non utilisé Réservé pour le produit de legs Code de fonctionnement CCM Code Message Remède / Commentaire Groupe 2 -- Alimentation électrique du plasma 201 Phase C.A. manquante Fusible mural disjoncté ; fusible de l’appareil F1 ou F2 ou du panneau arrière disjoncté ; mauvaise connexion du câble d’alimentation ; système Bias PCB défectueux. 202 Non utilisé Réservé pour le produit de legs 203 Non utilisé Réservé pour le produit de legs 204 Non utilisé Réservé pour le produit de legs 205 Sortie DC faible Inférieure à 60 V c. c. ; court-circuit du fil négatif vers la pièce d’usinage ou la terre ; onduleur défectueux (court-circuit en sortie) ; tension CCM (J24) déconnectée ou fil rompu ; CCM défectueux. 206 Non utilisé Réservé pour le produit de legs 207 Intensité inattendue dans le Intensité supérieure à 8 A dans le fil d’usinage avant l’allumage ou le transfert du pilote. Court-circuit du fil négatif à fil d’usinage la terre ou au châssis de l’allumage de l’arc ; fil d’usinage de l’ampèremètre HCT1 défectueux ; relais PCB défectueux. 0-5264FR 4-13 FONCTIONNEMENT ULTRA-CUT 100 XT/200 XT/300 XT/400 XT Code Message Remède / Commentaire 208 Intensité supérieure à 6 A dans le circuit du pilote avant allumage. Consommables mauvais ou mal appariés causant Intensité inattendue dans le un court-circuit entre la pointe et l’électrode ; court-circuit entre le fil du pilote au pôle négatif du tube de la torche ; circuit du pilote relais PCB défectueux ; court-circuit possible au niveau de la torche. 209 Non utilisé Réservé pour le produit de legs 210 Intensité de travail trop élevée Intensité de travail détectée supérieure de 16% à la consigne de procédé. Possibilité de défaut de l’ampèremètre HCT1 ou du relais PCB ; CCM défectueux. 211 Intensité de travail trop basse Intensité de travail détectée inférieure de 16% à la consigne de procédé. Possibilité de défaut de l’ampèremètre HCT1 ou du relais PCB ; possibilité de défaut du pilote PCB (court-circuit de l’IGBT) 212 Intensité de travail du plasma basse pendant la découpe et attribuée à une intensité basse en sortie de la section A du Intensité basse en sortie de module onduleur 1 ; sortie de l’onduleur déconnectée ; possibilité de câble ruban défectueux ; si le problème persiste, l’onduleur 1A remplacer le module onduleur 1. 213 Intensité basse en sortie de Intensité de travail du plasma basse pendant la découpe et attribuée à une intensité basse en sortie de la section B du module onduleur 1 ; sortie de l’onduleur déconnectée ; possibilité de câble ruban défectueux ; si le problème persiste, l’onduleur 1B remplacer le module onduleur 1. 214 Intensité de travail du plasma basse pendant la découpe et attribuée à une intensité basse en sortie de la section A du Intensité basse en sortie de module onduleur 2 ; sortie de l’onduleur déconnectée ; possibilité de câble ruban défectueux ; si le problème persiste, l’onduleur 2A remplacer le module onduleur 2. 215 Intensité basse en sortie de Intensité de travail du plasma basse pendant la découpe et attribuée à une intensité basse en sortie de la section B du module onduleur 2 ; sortie de l’onduleur déconnectée ; possibilité de câble ruban défectueux ; si le problème persiste, l’onduleur 2B remplacer le module onduleur 2. 216 Intensité de travail du plasma basse pendant la découpe et attribuée à une intensité basse en sortie de la section A du Intensité basse en sortie de module onduleur 3 ; sortie de l’onduleur déconnectée ; possibilité de câble ruban défectueux ; si le problème persiste, l’onduleur 3A remplacer le module onduleur 3. 217 Intensité basse en sortie de Intensité de travail du plasma basse pendant la découpe et attribuée à une intensité basse en sortie de la section B du module onduleur 3 ; sortie de l’onduleur déconnectée ; possibilité de câble ruban défectueux ; si le problème persiste, l’onduleur 3B remplacer le module onduleur 2. 218 Intensité haute en sortie de Intensité de travail du plasma haute pendant la découpe et attribuée à une intensité haute en sortie de la section A du l’onduleur 1A module onduleur 1 ; si le problème persiste, remplacer le module onduleur 1. 219 Intensité haute en sortie de Intensité de travail du plasma haute pendant la découpe et attribuée à une intensité haute en sortie de la section B du l’onduleur 1B module onduleur 1 ; si le problème persiste, remplacer le module onduleur 1. 220 Intensité haute en sortie de Intensité de travail du plasma haute pendant la découpe et attribuée à une intensité haute en sortie de la section A du l’onduleur 2A module onduleur 2 ; si le problème persiste, remplacer le module onduleur 2. 221 Intensité haute en sortie de Intensité de travail du plasma haute pendant la découpe et attribuée à une intensité haute en sortie de la section B du l’onduleur 2B module onduleur 2 ; si le problème persiste, remplacer le module onduleur 2. 222 Intensité haute en sortie de Intensité de travail du plasma haute pendant la découpe et attribuée à une intensité haute en sortie de la section A du l’onduleur 3A module onduleur 3 ; si le problème persiste, remplacer le module onduleur 2. 223 Intensité haute en sortie de Intensité de travail du plasma haute pendant la découpe et attribuée à une intensité haute en sortie de la section B du l’onduleur 3B module onduleur 3 ; si le problème persiste, remplacer le module onduleur 2. 224 Onduleur 1 introuvable Module onduleur 1 section A nécessaire au pilotage ; mauvaise connexion du câble ruban CCM J31 au module onduleur 1 section A. 225 Révision incompatible de l’onduleur 1A Révision de l’onduleur non supportée ; câble ruban CCM J31 au module onduleur 1 section A endommagé ; version du code CCM incompatible avec la révision ou le modèle de l’onduleur FONCTIONNEMENT 4-14 0-5264FR ULTRA-CUT 100 XT/200 XT/300 XT/400 XT Code Message Remède / Commentaire 226 Révision incompatible de l’onduleur 1B Révision de l’onduleur non supportée ; câble ruban CCM J32 au module onduleur 1 section B endommagé ; version du code CCM incompatible avec la révision ou le modèle de l’onduleur 227 Révision incompatible de l’onduleur 2A Révision de l’onduleur non supportée ; câble ruban CCM J33 au module onduleur 2 section A endommagé ; version du code CCM incompatible avec la révision ou le modèle de l’onduleur 228 Révision incompatible de l’onduleur 2B Révision de l’onduleur non supportée ; câble ruban CCM J34 au module onduleur 2 section B endommagé ; version du code CCM incompatible avec la révision ou le modèle de l’onduleur 229 Révision incompatible de l’onduleur 3A Révision de l’onduleur non supportée ; câble ruban CCM J35 au module onduleur 3 section A endommagé ; version du code CCM incompatible avec la révision ou le modèle de l’onduleur 230 Révision incompatible de l’onduleur 3B Révision de l’onduleur non supportée ; câble ruban CCM J36 au module onduleur 3 section B endommagé ; version du code CCM incompatible avec la révision ou le modèle de l’onduleur 231 Mauvais appariement de l’onduleur 1A V C.A. Étalonnage de tension de l’onduleur C.A. incompatible avec l’étalonnage de la tension d’alimentation ; mauvaise connexion du câble ruban CCM J31 au module onduleur 1 section A ; mauvaise tension installée sur le module onduleur 1 ; module onduleur défectueux 232 Mauvais appariement de l’onduleur 1B V C.A. Étalonnage de tension de l’onduleur C.A. incompatible avec l’étalonnage de la tension d’alimentation ; mauvaise connexion du câble ruban CCM J32 au module onduleur 1 section B ; mauvaise tension installée sur le module onduleur 1 ; module onduleur défectueux 233 Mauvais appariement de l’onduleur 2A V C.A. Étalonnage de tension de l’onduleur C.A. incompatible avec l’étalonnage de la tension d’alimentation ; mauvaise connexion du câble ruban CCM J33 au module onduleur 2 section A ; mauvaise tension installée sur le module onduleur 2 ; module onduleur défectueux 234 Mauvais appariement de l’onduleur 2B V C.A. Étalonnage de tension de l’onduleur C.A. incompatible avec l’étalonnage de la tension d’alimentation ; mauvaise connexion du câble ruban CCM J34 au module onduleur 2 section A ; mauvaise tension installée sur le module onduleur 2 ; module onduleur défectueux 235 Mauvais appariement de l’onduleur 3A V C.A. Étalonnage de tension de l’onduleur C.A. incompatible avec l’étalonnage de la tension d’alimentation ; mauvaise connexion du câble ruban CCM J35 au module onduleur 3 section A ; mauvaise tension installée sur le module onduleur 3 ; module onduleur défectueux 236 Mauvais appariement de l’onduleur 3B V C.A. Étalonnage de tension de l’onduleur C.A. incompatible avec l’étalonnage de la tension d’alimentation ; mauvaise connexion du câble ruban CCM J36 au module onduleur 2 section B ; mauvaise tension installée sur le module onduleur 3 ; module onduleur défectueux 237 Pas assez d’onduleurs trouvés Il faut au moins deux sections d’onduleurs pour fonctionner ; câble ruban CCM à la section d’onduleur endommagé ou déconnecté 238 BIAS V C.A. Invalide Sélection de tension C.A. invalide ; connexion endommagée ou détachée de J61 de l’alimentation électrique du système Bias ; système Bias PCB défectueux 239 Tension C.A. haute La tension détectée sur le système Bias PCB est supérieure à la tension d’étalonnage de l’alimentation électrique ; connexion de sélection de tension J61 de l’alimentation du système Bias endommagée ou déconnectée ; système Bias PCB défectueux ; CCM défectueux 240 Tension C.A. basse La tension détectée sur le système Bias PCB est inférieure à la tension d’étalonnage de l’alimentation électrique ; connexion de sélection de tension J61 de l’alimentation du système Bias endommagée ou déconnectée ; système Bias PCB défectueux ; CCM défectueux 241 Défaut de tension en entrée d’onduleur ; tension hors limites ou phase manquante à l’entrée C.A. du module onduleur Erreur de tension d’entrée de 1 section A ; mauvaise qualité de l’alimentation C.A. ; contact W1 défectueux ; connexion détachée ou ouverte l’onduleur 1A entre les bornes d’entrée et le contact W1 ou entre le contact et l’entrée de la section d’onduleur ; module onduleur défectueux 242 Défaut de tension en entrée d’onduleur ; tension hors limites ou phase manquante à l’entrée C.A. du module onduleur Erreur de tension d’entrée de 1 section B ; mauvaise qualité de l’alimentation C.A. ; contact W1 défectueux ; connexion détachée ou ouverte entre l’onduleur 1B les bornes d’entrée et le contact W1 ou entre le contact et l’entrée de la section d’onduleur ; module onduleur défectueux 0-5264FR 4-15 FONCTIONNEMENT ULTRA-CUT 100 XT/200 XT/300 XT/400 XT Code Message Remède / Commentaire 243 Défaut de tension en entrée d’onduleur ; tension hors limites ou phase manquante à l’entrée C.A. du module onduleur Erreur de tension d’entrée de 2 section A ; mauvaise qualité de l’alimentation C.A. ; contact W1 défectueux ; connexion détachée ou ouverte l’onduleur 2A entre les bornes d’entrée et le contact W1 ou entre le contact et l’entrée de la section d’onduleur ; module onduleur défectueux 244 Défaut de tension en entrée d’onduleur ; tension hors limites ou phase manquante à l’entrée C.A. du module onduleur Erreur de tension d’entrée de 2 section B ; mauvaise qualité de l’alimentation C.A. ; contact W2 défectueux ; connexion détachée ou ouverte entre l’onduleur 2B les bornes d’entrée et le contact W2 ou entre le contact et l’entrée de la section d’onduleur ; module onduleur défectueux 245 Défaut de tension en entrée d’onduleur ; tension hors limites ou phase manquante à l’entrée C.A. du module onduleur Erreur de tension d’entrée de 3 section A ; mauvaise qualité de l’alimentation C.A. ; contact W2 défectueux ; connexion détachée ou ouverte l’onduleur 3A entre les bornes d’entrée et le contact W2 ou entre le contact et l’entrée de la section d’onduleur ; module onduleur défectueux 246 Défaut de tension en entrée d’onduleur ; tension hors limites ou phase manquante à l’entrée C.A. du module onduleur Erreur de tension d’entrée de 3 section B ; mauvaise qualité de l’alimentation C.A. ; contact W2 défectueux ; connexion détachée ou ouverte entre l’onduleur 3B les bornes d’entrée et le contact W2 ou entre le contact et l’entrée de la section d’onduleur ; module onduleur défectueux 247 Circuit de l’onduleur 1A défectueux Le module onduleur 1 section A a détecté un défaut dans le circuit ; module onduleur 1 endommagé 248 Circuit de l’onduleur 1B défectueux Le module onduleur 1 section B a détecté un défaut dans le circuit ; module onduleur 1 endommagé 249 Circuit de l’onduleur 2A défectueux Le module onduleur 2 section A a détecté un défaut dans le circuit ; module onduleur 2 endommagé 250 Circuit de l’onduleur 2B défectueux Le module onduleur 2 section B a détecté un défaut dans le circuit ; module onduleur 2 endommagé 251 Circuit de l’onduleur 3A défectueux Le module onduleur 3 section A a détecté un défaut dans le circuit ; module onduleur 3 endommagé 252 Circuit de l’onduleur 3B défectueux Le module onduleur 3 section B a détecté un défaut dans le circuit ; module onduleur 3 endommagé 253 Température excessive de l’onduleur 1A La température du module onduleur 1 section A est excessive ; enlever les panneaux latéraux pour travailler, vérifier que rien n’entrave l’écoulement d’air ni ne bouche le radiateur ; ventilateur défectueux ; si le problème persiste, remplacer le module onduleur. 254 Température excessive de l’onduleur 1B La température du module onduleur 1 section B est excessive ; enlever les panneaux latéraux pour travailler, vérifier que rien n’entrave l’écoulement d’air ni ne bouche le radiateur ; ventilateur défectueux ; si le problème persiste, remplacer le module onduleur. 255 Température excessive de l’onduleur 2A La température du module onduleur 2 section A est excessive ; enlever les panneaux latéraux pour travailler, vérifier que rien n’entrave l’écoulement d’air ni ne bouche le radiateur ; ventilateur défectueux ; si le problème persiste, remplacer le module onduleur. 256 Température excessive de l’onduleur 2B La température du module onduleur 2 section B est excessive ; enlever les panneaux latéraux pour travailler, vérifier que rien n’entrave l’écoulement d’air ni ne bouche le radiateur ; ventilateur défectueux ; si le problème persiste, remplacer le module onduleur. 257 Température excessive de l’onduleur 3A La température du module onduleur 3 section A est excessive ; enlever les panneaux latéraux pour travailler, vérifier que rien n’entrave l’écoulement d’air ni ne bouche le radiateur ; ventilateur défectueux ; si le problème persiste, remplacer le module onduleur. 258 Température excessive de l’onduleur 3B La température du module onduleur 3 section B est excessive ; enlever les panneaux latéraux pour travailler, vérifier que rien n’entrave l’écoulement d’air ni ne bouche le radiateur ; ventilateur défectueux ; si le problème persiste, remplacer le module onduleur. 259 La température du circuit de l’onduleur est excessive, probablement parce que la température ambiante est supérieure Température ambiante à 40°C ; réduire l’alimentation électrique du cycle de découpe ; réduire la température ambiante ; ajouter un refroidisexcessive pour l’onduleur 1A seur auxiliaire. FONCTIONNEMENT 4-16 0-5264FR ULTRA-CUT 100 XT/200 XT/300 XT/400 XT Code Message Remède / Commentaire 260 La température du circuit de l’onduleur est excessive, probablement parce que la température ambiante est supérieure Température ambiante à 40°C ; réduire l’alimentation électrique du cycle de découpe ; réduire la température ambiante ; ajouter un refroidisexcessive pour l’onduleur 1B seur auxiliaire. 261 La température du circuit de l’onduleur est excessive, probablement parce que la température ambiante est supérieure Température ambiante à 40°C ; réduire l’alimentation électrique du cycle de découpe ; réduire la température ambiante ; ajouter un refroidisexcessive pour l’onduleur 2A seur auxiliaire. 262 La température du circuit de l’onduleur est excessive, probablement parce que la température ambiante est supérieure Température ambiante à 40°C ; réduire l’alimentation électrique du cycle de découpe ; réduire la température ambiante ; ajouter un refroidisexcessive pour l’onduleur 2B seur auxiliaire. 263 La température du circuit de l’onduleur est excessive, probablement parce que la température ambiante est supérieure Température ambiante à 40°C ; réduire l’alimentation électrique du cycle de découpe ; réduire la température ambiante ; ajouter un refroidisexcessive pour l’onduleur 3A seur auxiliaire. 264 La température du circuit de l’onduleur est excessive, probablement parce que la température ambiante est supérieure Température ambiante à 40°C ; réduire l’alimentation électrique du cycle de découpe ; réduire la température ambiante ; ajouter un refroidisexcessive pour l’onduleur 3B seur auxiliaire. 265 Onduleur 1A Pas d’alimenta- La section d’onduleur peut ne pas avoir d’alimentation électrique en entrée. Contact W1 non fermé ; contact défection électrique en entrée tueux ou CB4 déclenché ; entrée de la section d’onduleur non connectée ; onduleur défectueux. 266 Onduleur 1B Pas d’alimenta- La section d’onduleur peut ne pas avoir d’alimentation électrique en entrée. Contact W1 non fermé ; contact défection électrique en entrée tueux ou CB4 déclenché ; entrée de la section d’onduleur non connectée ; onduleur défectueux. 267 Onduleur 2A Pas d’alimenta- La section d’onduleur peut ne pas avoir d’alimentation électrique en entrée. Contact W1 non fermé ; contact défection électrique en entrée tueux ou CB4 déclenché ; entrée de la section d’onduleur non connectée ; onduleur défectueux. 268 Onduleur 2B Pas d’alimenta- La section d’onduleur peut ne pas avoir d’alimentation électrique en entrée. Contact W2 non fermé ; contact défection électrique en entrée tueux ou CB4 déclenché ; entrée de la section d’onduleur non connectée ; onduleur défectueux. 269 Onduleur 3A Pas d’alimenta- La section d’onduleur peut ne pas avoir d’alimentation électrique en entrée. Contact W2 non fermé ; contact défection électrique en entrée tueux ou CB4 déclenché ; entrée de la section d’onduleur non connectée ; onduleur défectueux. 270 Onduleur 3B Pas d’alimenta- La section d’onduleur peut ne pas avoir d’alimentation électrique en entrée. Contact W2 non fermé ; contact défection électrique en entrée tueux ou CB4 déclenché ; entrée de la section d’onduleur non connectée ; onduleur défectueux. 271 Erreur de lecture de ID de l’onduleur 0-5264FR CCM a trouvé des valeurs ID incohérentes pendant la lecture. Ruban du CCM à une section d’onduleur endommagé ou déconnecté ; mauvais routage du câble ruban. 4-17 FONCTIONNEMENT ULTRA-CUT 100 XT/200 XT/300 XT/400 XT Code de fonctionnement CCM Code Message Remède / Commentaire Groupe 3 -- Statut & Protocole du contrôleur de gaz 301 Défaut de communication du contrôle des gaz Problème avec le câble à fibres optiques vers le GCM 2010 ; saleté aux extrémités de la fibre ou dans les connecteurs ; la souffler avec de l’air propre et sec. Le fibre n’est pas verrouillée dans le connecteur ; fortes courbures dans le câble de la fibre ; fibre défectueuse ; circuit imprimé du GCM 2010 défectueux ; 302 Défaut de réponse du contrôle des gaz Problème avec le câble à fibres optiques vers le GCM 2010 ; saleté aux extrémités de la fibre ou dans les connecteurs ; la souffler avec de l’air propre et sec. Le fibre n’est pas verrouillée dans le connecteur ; fortes courbures dans le câble de la fibre ; fibre défectueuse ; circuit imprimé du GCM 2010 défectueux ; 303 Pression d’alimentation en gaz hors Pression basse en entrée du plasma ou de l’écran du GCM 2010 ou manomèters PS3 & PS4 défectueux limites. ; circuit imprimé du GCM 2010 défectueux. 304 Purge du contrôle des gaz 305 Erreur de protocole de contrôle des Vérifier que la version du logiciel est compatible avec le GCM 2010 gaz 306 Non utilisé 307 Erreur de séquence de contrôle des gaz Vérifier que la version du logiciel est compatible avec le GCM 2010 308 Mauvais appariement dans le contrôle des gaz Mauvais CCM (Auto-Cut ou Pak 200 ?) pour Ultra-Cut ; installer un bon CMM 309 Défaut de commande du contrôle des gaz Vérifier que la version du logiciel est compatible avec le GCM 2010; Interférences électromagnétiques avec l’allumage de l’arc ; vérifier le raccordement à la terre, la métallisation et l’isolation FONCTIONNEMENT Cela est normal après la mise sous tension ou la remise en service après désactivation du plasma. Attendre la fin de la purge. Réservé à une utilisation ultérieure 4-18 0-5264FR ULTRA-CUT 100 XT/200 XT/300 XT/400 XT Code de fonctionnement CCM Code Message Remède / Commentaire Groupe 4 -- Système de refroidissement de la torche 401 Bas niveau de liquide de refroi- Vérifier le niveau de liquide de refroidissement ; en rajouter si nécessaire. Capteur de niveau défectueux ou dissement débranché. 402 Le débit de liquide de refroidissement tel que mesuré par le débitmètre FS1 est inférieur à 0,7 gpm (2,65 l/ Faible débit du liquide de refroi- min) ; filtre bouché ; restriction dans la tuyauterie ou la tête de la torche ; mauvais type de consommables dissement ; tube de refroidissement ou vanne de contrôle de la torche rompu ou défectueux ; pompe ou soupape de dérivation. 403 La température d’alimentation en liquide de refroidissement a dépassé 75°C (167°F). Ouvrir ou enlever Surchauffe du liquide de refroile panneau latéral pour travailler ; arrivée d’air bouchée en entrée de l’alimentation électrique ; panne du dissement ventilateur de refroidissement ; radiateur encrassé. 404 Un débit de liquide de refroidissement de 0,7 gpm (2,65 l/min) tel que mesuré par le débitmètre FS1 n’a pas été obtenu pendant l’amorçage, jusqu’à 4 minutes. Une nouvelle installation peut nécessiter un ou plusieurs cycles supplémentaires d’amorçage pour remplir les tuyaux de liquide de refroidissement ; éteindre Système de refroidissement pas et rallumer l’appareil pour redémarrer l’amorçage ; les tuyaux de liquide de refroidissement et de la torche prêt. ont été inversés ; le filtre du liquide de refroidissement est obstrué ; restriction dans la conduite ou la tête de la torche ; mauvais type de consommables ; tube de refroidissement ou soupape de dérivation rompu ou défectueux ; débitmètre FS1 défectueux ou déconnecté ; pompe ou soupape de dérivation défectueuse. 405 Alarme de bas niveau du liquide Un bas niveau de liquide de refroidissement n’interrompra pas la découpe. Ajouter du liquide de refroidisde refroidissement sement si nécessaire. 406 Cette alarme n’interrompt pas le fonctionnement du système. Le débit de liquide de refroidissement est inférieur aux prévisions. Cela peut résulter de bulles introduites dans le liquide de refroidissement ou de Alarme de bas débit de liquide de consommables mauvais, mal assortis ou usés, de joints défectueux de la cartouche ou du corps de la torche, refroidissement. d’un filtre à liquide de refroidissement bouché, d’une restriction de la conduite ou de la tête de la torche, ou d’un débitmètre FL1 défectueux ou déconnecté. 407 Surchauffe du liquide de refroidissement, température ambiante excessive La température du circuit de refroidissement dépasse 75°C (167°F), probablement parce que la température ambiante est supérieure à 40°C (104°F) ; réduire le cycle de découpe ; réduirela température ambiante ; ajouter un système séparé de refroidissement du liquide. Il n’y a pas de codes de statut numéroté de groupe 5 (500) avec le système GCM 2010. 0-5264FR 4-19 FONCTIONNEMENT ULTRA-CUT 100 XT/200 XT/300 XT/400 XT Code de fonctionnement CCM Code Message Remède / Commentaire Groupe 6 -- CCM 601 Erreur de tension analogique CCM défectueux, remplacez. 602 Erreur ADC ou D C.A. CCM défectueux, remplacez. 603 Réservé Aucune information disponible ; Contactez le service de client 604 Erreur de mémoire CCM défectueux, remplacez. 605 Défaut de mémoire du programme CCM défectueux, remplacez. 606 Bas niveau +5V Logic CCM défectueux, remplacez. 607 Température excessive du processeur Réduire la température ambiante ; CCM défectueux ; le remplacer 608 Alimentation 5 V faible pour communicaCCM défectueux, remplacez. tion RS 485/422. 609 Erreur matérielle d’actualisation du logiciel CCM défectueux ; remplacez 610 Erreur de protocole d’actualisation du logiciel CCM défectueux ; remplacez 611 Défaut du contrôleur USB CCM défectueux ; remplacez 612 Défaut d’alimentation USB Appareil USB défectueux branché sur le port USB ; l’enlever ; CCM défectueux Défaut de création de log USB Impossible de créer un fichier de connexion sur le lecteur USB Flash ; dernière tentative d’actualisation du logiciel ; utiliser un autre lecteur USB Flash ou reformater Pas de fichier USF Fichier VTCCMFW.USF manquant dans le lecteur Flash ; ajouter des fichiers adéquats au lecteur Flash pour actualiser le logiciel ; utiliser un autre lecteur USB Flash ou reformater Pas de fichier d’actualisation CCM Logiciel CCM spécifié dans VTCCMFW.USF introuvable ; ajouter les fichiers adéquats au lecteur Flash pour actualiser le logiciel Défaut d’actualisation DPC Une panne est survenue en essayant d’actualiser le logiciel DPC ; ajouter les fichiers adéquats au lecteur USB Flash pour actualiser le logiciel ; reportez-vous à CCM_LOG.TXT sur le lecteur Flash pour plus de détails Défaut d’actualisation DMC Une panne est survenue en essayant d’actualiser le logiciel DMC ; ajouter les fichiers adéquats au lecteur USB Flash pour actualiser le logiciel ; reportez-vous à CCM_LOG.TXT sur le lecteur Flash pour plus de détails 618 Défaut d’étalonnage ADC Étalonnage trop large de l’ADC ; si la panne persiste, le CCM est défectueux ; 619 Panne de débitmètre Le débitmètre rapporte un débit de liquide de refroidissement quand la pompe est coupée ; Erreur mémoire ROM Le stockage de mémoire ROM a été corrompu et écrasé ; si la panne persiste, le CCM est défectueux. 613 614 615 616 617 620 FONCTIONNEMENT 4-20 0-5264FR ULTRA-CUT 100 XT/200 XT/300 XT/400 XT 4.08 Résolution des problèmes pour l’allumage d’arc à distance Résolution des problèmes de l’allumage de l’arc Symptôme Pas d’allumage du pilote : l’indicateur au néon sur le panneau du couvercle s’allume, mais il n’y a pas d’allumage. Pas d’allumage du pilote : Indicateur au néon non allumé. Fuites de liquide de refroidissement Pas ou pas assez de refroidissement : Pas d’écoulement de liquide de refroidissement Comportement erratique du système (interférence EMI) 0-5264FR Cause Check Solution Le câblage de retour du pilote n’est pas connecté à la tête de la torche ou est rompu dans la conduite de la torche Inspection visuelle, contrôle de continuité Connecter le câblage ou remplacer les conduites. Le liquide de refroidissement est devenu conducteur Utiliser un conductimètre Purger le système, remplacer le liquide de refroidissement. Le couvercle haute fréquence (C4 sur le circuit) est peut-être ouvert ; câbles déconnectés. Utiliser un capacimètre Reconnecter ou remplacer. Le câble d’alimentation négatif n’est pas bien connecté Inspection visuelle Raccordez Le câble de retour du pilote n’est pas ou mal connecté dans l’allumage de l’arc. Inspection visuelle Brancher le câble. Pas d’alimentation 120 V, CB4 du plasma sur le panneau arrière déclenché Réinitialiser le coupe-circuit ; vérifier l’alimentation 120 V C.A. aux bornes 115 V du module pendant l’allumage. Vérifier si un câble est court-circuit, si le coupe-circuit est défectueux, si l’entrée du module d’allumage est court-circuité (reportez-vous au symptôme suivant) Module d’allumage électronique courtcircuité en entrée Mesure de résistance : les bonnes mesures de résistance sont aux alentours de 45 Ω Remplacer un module défectueux Pas d’alimentation 120 V, CB4 non déclenché Vérifier l’alimentation électrique 120 V C.A. sur les connecteurs J59-7 & 9 du panneau arrière d’alimentation en plasma pendant la période d’allumage. 120 V présent - câble de contrôle ouvert ; 120 V absent - défaut d’alimentation électrique du plasma Module d’allumage électronique défectueux Vérifier la tension 120 V C.A. au niveau des bornes 115 V des modules pendant la phase d’allumage du pilote En cas de présence de la tension 120 V C.A. mais si le néon n’est pas allumé, le module est défectueux ; remplacer le module Mauvaise(s) fixation(s) Inspection visuelle Resserrer les fixations. Ligne(s) de liquide de refroidissement endommagée(s) ou percée(s). Inspection visuelle Remplacer les lignes de refroidissement Les tuyaux d’alimentation et de retour ont Inspection visuelle des connexions codées été intervertis par couleurs Colmatage dans les tuyaux d’alimentation/retour Desserrer légèrement le raccordement et vérifier que le liquide de refroidissement s’écoule Assortir les couleurs des connexions de liquide de refroidissementà celles des connexions de l’allumage de l’arc. Purger le système ou remplacer le tuyau bouché. Raccordement à la terre manquant ou mal Inspection visuelle du fil de terre de l’alluconnecté mage de l’arc Connecter ou resserrer les connexions à la terre. Écran de la torche pas ou mal connecté. Câble F1 GND non connecté Rebrancher / serrer les connecteurs. Inspection visuelle de l’attache de l’écran à l’allumage de l’arc La vis de raccordement à la terre du panneau des couvercles est manquante ou Inspection visuelle mal serrée. Serrer ou remplacer. Couvercle C5 ou C7 (sur le circuit) ouvert ou fils déconnectés vers le panneau. Remplacer le circuit. Inspection visuelle / mesure de capacité 4-21 FONCTIONNEMENT ULTRA-CUT 100 XT/200 XT/300 XT/400 XT Page volontairement laissée vierge. FONCTIONNEMENT 4-22 0-5264FR ULTRA-CUT 100 XT/200 XT/300 XT/400 XT CHAPITRE 5 : ENTRETIEN 5.01 Entretien général Effectuez périodiquement les contrôles suivants afin de garantir des performances correctes du système. Planning d’entretien du générateur Chaque jour Contrôler le niveau du liquide de refroidissement, en ajouter le cas échéant. Contrôler les raccordements des tuyaux du gaz et les pressions. Calendrier d’entretien Chaque mois Contrôler le ventilateur de refroidissement et le radiateur ; les nettoyer le cas échéant Contrôler les tuyaux du gaz pour vérifier qu’ils ne présentent pas de fissures, de fuites ou d’abrasion. Remplacer si besoin est. Vérifiez toutes les connexions électriquespour y repérer fissures et abrasions. Remplacez-les si nécessaire. Tous les 6 mois Nettoyez ou remplacez le filtre externe du liquide de refroidissement. Nettoyer le réservoir du liquide de refroidissement. Evacuer tout dépôt de poussière présent à l’intérieur du générateur. 5.02 Procédure de nettoyage du filtre externe du liquide de refroidissement Le nettoyage périodique du filtre du liquide de refroidissement garantit l’efficacité maximale du débit de liquide de refroidissement. Un mauvais débit du liquide de refroidissement provoque un refroidissement inefficace des pièces de la torche, ce qui porte à une usure plus rapide des consommables. Nettoyer le filtre du liquide de refroidissement comme suit : 1. Débrancher le système de l’alimentation principale. 2. Dévisser et enlever la cuve du filtre à la main. Grand réservoir situé à l’arrière de l’alimentation électrique. Veiller à conserver le joint torique. 3. Inspectez et remplacez le filtre si nécessaire. Remettre la cuve en la serrant à la main. Veiller à ce que le joint torique soit en place. 4. Allumer le système et contrôler s’il y a des fuites. 0-5264FR 5-1 ENTRETIEN ULTRA-CUT 100 XT/200 XT/300 XT/400 XT 5.03 Procédure de remplacement du liquide de refroidissement Remplacer le liquide de refroidissement comme suit : 1. Débrancher le système de l’alimentation principale. 2. Enlevez les deux panneaux du côté droit. 3. Repérez l’accouplement dans la ligne de refroidissement qui part du fond du réservoir de liquide de refroidissement, n°1 dans l’illustration suivante. Déconnectez la ligne de refroidissement au niveau de ce raccordement et drainez le liquide de refroidissement dans un réservoir jetable de taille suffisante. Rappelez-vous que vous drainerez plus que le contenu du réservoir de liquide de refroidissement. 4. Lorsque le liquide de refroidissement est en cors de drainage, débranchez le couplage du tuyau gris n°2 dans l’illustration ci-dessous. Laissez s’écouler le liquide de refroidissement en excès, puis appliquez un maximum de 5 psi pour purger les lignes. ATTENTION Appliquer plus de 5 psi de pression d’air peut entraîner des dommages à l’appareillage. Faites particulièrement attention quand vous effectuez ce travail. 2 1 Art # A11689 5. Rebranchez ces deux raccordements puis enlevez le boîtier à filtre du réservoir à l’arrière de l’alimentation électrique. Déversez le reliquat du liquide de refroidissement dans le réservoir et remettez le boîtier à filtre en place. REMARQUE ! S’il vous faut encore remplacer le liquide de refroidissement restant dans les conduites, débranchez-les de l’alimentation électrique et drainez-les manuellement. 6. Remplissez le réservoir de liquide de refroidissement jusqu’au niveau indiqué ; vérifiez qu’il n’y a pas de fuites. 7. Allumez l’appareillage, laissez-le fonctionnement quelques minutes et vérifiez le niveau de liquide de refroidissement ; remettez-en si nécessaire. Se référer aux sections 3 :24 Effectuer l’installation pour connaître la procédure. 8. Installez les panneaux latéraux. ENTRETIEN 5-2 0-5264FR ULTRA-CUT 100 XT/200 XT/300 XT/400 XT CHAPITRE 6 : ÉLÉMENTS ET PIÈCES DE RECHANGE 6.01 Générateur de rechange Unité complète / Composant Numéro du catalogue Générateur Ultra-Cut 100 XT™, 400V +10 -15% 3-8116-4 Générateur Ultra-Cut 200 XT™, 400V +10 -15% 3-8119-4 Générateur Ultra-Cut 300 XT™, 400V +10 -15% 3-8118-4 Générateur Ultra-Cut 400 XT™, 400V +10 -15% 3-8120-4 Générateur Ultra-Cut 100 XT™, 400V +10 -15% avec l’interface SL100 3-8116-4T Générateur Ultra-Cut 200 XT , 400V +10 -15% avec l’interface SL100 3-8119-4T Générateur Ultra-Cut 300 XT , 400V +10 -15% avec l’interface SL100 3-8118-4T Générateur Ultra-Cut 400 XT , 400V +10 -15% avec l’interface SL100 3-8120-4T Module de commande des gaz (GCM-2010) avec montage de valve pour la torche XTL 3-9131 Module de commande des gaz (GCM-2010) seulement 7-4000 Pièce de rechange d’origine pour la réparation du montage de valve de la torche uniquement 4-3049 Montage de valve de la torche XTL uniquement 4-3054 ™ ™ ™ (nécessite le logiciel GCM 2010 version 3.1 ou plus récente) Amorce d’arc à distance (RAS-1000 XT) 3-9130E EQUIPEMENT EN OPTION : Kit de roues 0-5264FR Liste des pièces détachées 9-7378 6-1 ULTRA-CUT 100 XT/200 XT/300 XT/400 XT 6.02 Schéma du système 100 - 200 A Se référer aux section 3.08 et 3.10 pour les connexions de raccordement à la terre et les câbles de raccordement à la terre. 175’ / 53.3 m Longueur maximale 125’ / 38.1 m Longueur maximale A Retour de l’arc pilote F1 Négatif Puissance principale CNC 100’ / 30.5 m Longueur maximale Générateur Ultra Cut XT C Retour du liquide D Câble de commande F1 Câble de commande Coiffe B Alimentation du liquide Câble à fibre optique P Retour de l’arc pilote Module de commande du gaz F Retour du liquide Coiffe H Gaz de protection Q Gaz du flux préliminaire R Câble de commande S Rideau d’eau T Valve de torche Gaz plasmagène I Gaz de protection J G Tube plongeur Torche Câble de mise à la terre Art # A-11941FEU Alimentation du liquide E Gaz plasmagène L K Amorce de l’arc à distance Pièce O 175’ / 53.3 m Longueur maximale 6.03 Schéma du système 300 A Se référer aux section 3.08 et 3.10 pour les connexions de raccordement à la terre et les câbles de raccordement à la terre. 175’ / 53.3 m Longueur maximale 125’ / 38.1 m Longueur maximale Négatif Puissance principale CNC A Retour de l’arc pilote F1 Générateur Ultra Cut XT P 50’ / 15.25 m Longueur maximale C Retour du liquide D Câble de commande F1 Câble de commande L K F Coiffe B Alimentation du liquide Câble à fibre optique Retour de l’arc pilote Module de commande du gaz Amorce de l’arc à distance 6-2 Retour du liquide Coiffe E Gaz plasmagène H Gaz plasmagène I Gaz de protection Q Gaz de protection J Gaz du flux préliminaire R Câble de commande S Rideau d’eau T Câble de mise à la terre Art # A-12026FEU Alimentation du liquide Ensemble de la valve de la torche G Tube plongeur Torche O Pièce 175’ / 53.3 m Longueur maximale Liste des pièces détachées 0-5264FR ULTRA-CUT 100 XT/200 XT/300 XT/400 XT 6.04 Schéma du système 400 A Se référer aux section 3.08 et 3.10 pour les connexions de raccordement à la terre et les câbles de raccordement à la terre. 175’ / 53.3 m Longueur maximale 50’ / 15.25 m Longueur maximale 125’ / 38.1 m Longueur maximale F1 Retour de l’arc pilote #8 A Câble négatif B Câble de commande Puissance principale Alimentation du liquide 10’ C Retour du liquide 10’ D Câble de commande Y Générateur Ultra Cut XT CNC Câble à fibre optique P Câble de commande K F Module de commande du gaz Coiffe E Échangeur de chaleur HE 400 L Retour de l’arc pilote Alimentation du liquide C Retour du liquide D Amorce de l’arc à distance Alimentation du liquide Retour du liquide Coiffe F1 Gaz plasmagène H Gaz de protection Q Gaz du flux préliminaire R Câble de commande S Rideau d’eau T Gaz plasmagène I Gaz de protection J Valve de torche G Tube plongeur Torche Art # A-11940FEU Câble de mise à la terre Pièce 175’ / 53.3 m Longueur maximale 6.05 Tuyau d’alimentation du gaz recommandé N°comp. Qté 1 0-5264FR Description Numéro du catalogue Tuyau Synflex gris 3/8” Pas de raccords inclus. Numéro du catalogue par pied Liste des pièces détachées 9-3616 6-3 ULTRA-CUT 100 XT/200 XT/300 XT/400 XT 6.06 Fils et câbles toutes intensités Retour de l’arc pilote, du générateur à l’amorce de l’arc Câble 3/0 AWG (95 mm2 ) Câble négatif, du générateur à l’amorce de l’arc B Art # A-11873FEU Câble AWG n° 8 A C Vert Vert Câble d’alimentation du liquide de refroidissement, du générateur à l’amorce de l’arc D Rouge Rouge Câble de retour du liquide de refroidissement, du générateur à l’amorce de l’arc E - Câble de commande, du générateur à l’amorce de l’arc E,Y 14/7 Y - De câble de commande à l’échangeur de chaleur AWG n° 4 vert / jaune F 1/0 vert / jaune (50 mm 2) F1 Câble de masse Câble de masse, de l’amorce de l’arc à distance à la mise à la terre G Câble de la torche blindé, de l’amorce de l’arc à distance à la torche I Câble du gaz plasmagène, de la valve de la torche à la torche J Câble du gaz de protection, de la valve de la torche à la torche K Câble de commande, du générateur au module de commande du gaz 37 Câble à fibre optique, du générateur au module de commande du gaz L H, Q, R, S,T Câble 3/0 (95 mm 2) O P 6-4 37 Câble de mise à la terre Câble CNC (37 fil) Liste des pièces détachées 0-5264FR 0-5264FR 10 pi 3.05 m 15 pi 4.5 m 9-7368 4-3037 9-4941 9-4916 9-4917 9-4923 9-3333 9-3334 Câble de contrôle à l’allumage d’arc Fil de garde, du générateur au module de commande du gaz Fil de garde, de l’amorce d’arc à distance à la terre Ensemble, câblage de la torche Câblage du plasma Câblage de protection Câble de contrôle, PS à GCM Câble de commande, fibre optique Câble de mise à la terre Câble de commande, de la CNC au générateur Ensemble de câblage du gaz, (Voir Remarque 2) E F F1 G I J K L O P H,Q,R,S,T Liste des pièces détachées 9-4933 9-9428 9-9425 9-9424 9-7360 9-9426 4-3100 35 pi 10.6 m 40 pi 12 m 9-4934 9-4926 9-4942 9-4816 9-4808 9-7361 9-4792 4-3101 50 pi 15.2 m Câble de commande Rideau d’eau S T 9-6988 9-6996 9-6992 9-4755 9-4756 9-4757 9-4758 9-4759 4-3205 4-3203 4-3202 4-3201 4-3200 4-3105 60 pi 18.3 m 9-6993 9-4760 9-6964 9-7282 9-7272 4-3039 9-7370 9-7353 9-4902 9-4911 4-3016 9-4935 9-4927 9-4943 9-4817 9-4809 9-7362 9-4793 4-3102 75 pi 22.8 m 9-7073 9-4761 9-7080 9-7283 9-7273 4-3040 9-7371 9-4903 9-4912 9-4936 9-4928 9-4944 9-4818 9-4810 9-7363 9-4794 4-3103 100 pi 30.5 m 9-7074 9-7075 9-7076 9-4879 9-4880 9-4881 9-7081 9-4876 9-4877 9-7284 9-7285 9-7286 9-7274 9-7275 9-7276 4-3041 4-3042 4-3043 9-7372 9-4904 9-4905 9-4906 9-4913 9-4914 9-4937 9-4938 9-4929 9-4930 9-4922 9-4820 9-4812 9-7364 9-4796 4-3104 125 pi 150 pi 175 pi 38.1 m 45.7 m 53.3 m REMARQUE 2 : Les ensembles de câblage du gaz automatique comprennent le tuyau du gaz plasmagène, le tuyau du gaz de protection, le tuyau de gaz du flux préliminaire, le tuyau du rideau d’eau,le câble à fibre optique, le tuyau du marquage et le câble de command REMARQUE 1 : Les ensembles de câblage d’alimentation comprennent le câble de retour de l’arc pilote, le câble négatif, les tuyaux de retour et d’alimentation du liquide de refroidissement ainsi que le câble de commande 9-6985 9-6986 9-4878 9-4753 9-6956 9-6957 9-6958 9-6959 9-6960 9-6961 9-6962 9-6963 9-7281 Tuyau du gaz de l’arc pilote/du flux préliminaire 9-7280 R 9-7279 9-7271 9-7277 9-7278 9-7270 4-3038 9-7369 9-7352 9-4901 9-4910 Tuyau du gaz de protection 8-0149 4-3051 9-9335 9-9332 Q 9-7103 9-7104 9-7351 9-4900 9-4909 Orifice de gaz de plasma 4-3035 4-3036 9-7350 9-4899 9-4908 4-5200 4-5201 4-5202 4-5203 4-5204 4-5205 4-5206 4-5207 9-4932 9-4925 9-4918 30 pi 9.1 m H 9-4898 9-4907 9-4931 9-4815 Tuyau, retour du liquide de refroidis9-4813 9-4889 9-4814 semen D 9-4924 9-4807 9-4805 9-4887 9-4806 C 9-7359 9-7356 9-7357 9-7358 Tuyau, alimentation du liquidede refroidissement 9-4791 4-3099 25 pi 7.6 m Câble négatif 20 pi 6m B 9-4890 9-4891 9-4790 4-3096 4-3097 4-3098 4 pi 1.2 m Câble de retour de l’arc pilote Ensemble de câblage d’alimentation,(Voir Remarque 1) Description A A,B,C,D,E Touche Ultra-Cut XT Fils 100-200-300-400 XT ULTRA-CUT 100 XT/200 XT/300 XT/400 XT 6-5 ULTRA-CUT 100 XT/200 XT/300 XT/400 XT 6.07 Pièces de rechange externes pour le générateur N°comp. Qté Description Numéro du catalogue 1 1 Couvercle des câbles d’alimentation et des fils 9-7346 2 1 Panneau supérieur, 9-7300 3 1 Couvercles supérieurs 9-7301 4 1 Panneau inférieur gauche 9-7304 5 1 Panneau inférieur droit 300 A / 400 A 9-7344 6 1 Panneau inférieur droit 100 A / 200 A 9-7302 7 1 Anneau de levage 9-9373 Art # A-11543FEU 1 2 1 7 3 3 5 Agrandir 300/400A 6 Petit 100/200A 4 6-6 Liste des pièces détachées 0-5264FR ULTRA-CUT 100 XT/200 XT/300 XT/400 XT 6.08 Pièces de rechange d’alimentation électrique - Côté supérieur droit N°comp. Qté Description Ref. Des. Numéro du catalogue 1 1 Circuit imprimé du système Bias 9-9253 2 1 Circuit imprimé du pilote 9-9250 3 1 Montage CCM 9-7335 4 1 Relais, Pompe / Ventilateur MC3 / MC2 9-7314 5 1 Relais, Contrôle de surintensité K1 9-7336 6 1 Relais, Démarrage MC1 9-7337 7 1 Résistance, Démarrage R2 9-7376 8 1 Circuit imprimé de l’écran d’affichage 9-9252 9 1 Transformateur auxiliaire T1 9-7315 10 1 Coupe-circuit Marche/Arrêt CB1 9-7316 11 1 Circuit imprimé Relais et Interface 9-9251 1 2 11 10 9 8 3 7 6 5 4 Art # A-11546_AB 0-5264FR Liste des pièces détachées 6-7 ULTRA-CUT 100 XT/200 XT/300 XT/400 XT 6.09 Pièces de rechange d’alimentation électrique - Côté inférieur droit N°comp. Qté Description Ref. Des. Numéro du catalogue 1 1 Couvercle du réservoir de liquide de refroidissement 8-5142 2 1 Réservoir du liquide de refroidissement 9-7306 3 1 Capteur de niveau de liquide de refroidissement 9-7307 4 1 Pompe, Liquide de refroidissement, Montage 9-7309 1 Pump, Coolant, Assembly (no motor) 9-7422 5 1 Motor, Pump (motor only) 9-7424 6 1 Ventilateur(s) de refroidissement 9-7348 7 1 Radiateur Systèmes 300 A / 400 A 9-7349 Systèmes 100 A / 200 A 9-7311 8 1 Écoulement, Interrupteur (Non illustré) FS1 9-7310 9 1 Capteur de débit (bulle) (Non illustré) FL1 9-9297 10 1 Transducteur de courant, 300A HCT1 W7005324 (non illustré utilisé sur toutes les intensités en entrant) Art # A-11984_AB 1 2 3 4 7 8 5 6 6-8 Liste des pièces détachées 0-5264FR ULTRA-CUT 100 XT/200 XT/300 XT/400 XT 6.10 Pièces de rechange d’alimentation électrique - Panneau arrière N°comp. Qté Description Calibredudisjoncteur Calibreducircuit Ref. Des. Numéro du catalogue 1 1 Montage du filtre à liquide de refroidissement 9-7320 2 1 Filtre à liquide de refroidissement 9-7321 3 1 Fusible, 8A SB 500 V C.A. 9-7377 1 J55 - GCM USER INPUT J15 - CNC HEIGHT CONTROL 2 J54 - TSC /COMM J59 - RAS CB2 - 5A 120 VAC CB3 - 5A 24 VAC J70 - HE CB4 - 5A 120 VAC F1 - 8A SB 500 VAC F2 - 8A SB 500 VAC 3 Art # A-11549_AC 0-5264FR Liste des pièces détachées 6-9 ULTRA-CUT 100 XT/200 XT/300 XT/400 XT 6.11 Pièces de rechange d’alimentation électrique - Côté gauche N°comp. Qté 1 2 3 1 1 1 Description Ref. Des. Numéro du catalogue Circuit de suppression C.A. Contact principal (2 au total) W1, W2 Module onduleur, complet 380-415 V C.A. (les systèmes 100 et 200 A en utilisent 1) (le système 300 A en utilise 2) (le système 400 A en utilise 3) 9-9254 9-7318 9-7317 4 1 Module onduleur, partiel 380-415 V C.A. (pour 200 A et 300 A SEULEMENT) 9-7319 5 1 Carte Filtre EMI 9-9264 (Système 100 A en utilisent 1) (Système 200 A en utilisent 2) (Système 300 A en utilisent 3) (Système 400 A en utilisent 4) 400 A d'alimentation 200 A d'alimentation 1 2 4 5 5 3 Art # A-11943FEU 6-10 Liste des pièces détachées 0-5264FR ULTRA-CUT 100 XT/200 XT/300 XT/400 XT 6.12 Gas Control Module (GCM-2010) Replacement Parts N°comp. Qté 1 2 3 4 5 6 7 8 9 10 11 12 13 14 Non illustré : Description Numéro du catalogue 6 1 1 1 1 1 1 1 1 1 3 1 1 2 Solénoïde 7 W pour utilisation avec O2 Montage du manifold de sélection de gaz Valve de contrôle, 1/4 NPT .5 PSI Montage du commutateur de mode Montage du commutateur de sélection de gaz Panneau d’interface PC LCD Encodeur rotatif (interrupteur) Commutateur Panneau Solénoïde / Logique PC Couvercle Jauge, 0-160 psi Régulateur Manomètre et faisceau de câblage 100 PSI Manomètre et faisceau de câblage 250 PSI 9-9393 9-9391 9-9390 9-9406 9-9403 9-9408 9-9398 9-3426 9-9409 9-9410 8-6800 8-3223 9-9407 9-9508 1 1 1 1 1 1 Faisceau de câblage du montage de valve de la torche (J13 à J57) Faisceau de câblage de connexion de l’alimentation électrique (J3 & J5 à J56) Faisceau de câblage du panneau d’interface PC LCD Faisceau de câblage de l’encodeur rotatif (interrupteur) Faisceau de câblage de la commande de solénoïde A (J12 aux solénoïdes 1-6) Faisceau de câblage de la commande de solénoïde B (J1 aux solénoïdes 7-12) 9-9399 9-9400 9-9401 9-9402 9-9404 9-9405 7 12 11 11 6 5 12 11 12 13 4 8 9 1 10 14 8 1 1 1 1 1 14 3 0-5264FR 3 3 Liste des pièces détachées 2 Art # A-07030_AB 6-11 ULTRA-CUT 100 XT/200 XT/300 XT/400 XT 6.13 Pièces de rechange du module de commande du gaz (GCM-2010) N°comp. Qté Description Numéro du catalogue 1 1 Bouton rotatif noir 1” de l’instrument 9-4233 2 1 Débitmètre d’eau avec valve 9-7005 3 1 Commutateur 2 positions SPDT 9-3426 4 1 Manomètre, 2” de diamètre 8-6800 5 1 Manomètre, 2” de diamètre 8-4313 6 1 Débitmètre 8-6801 Non illustré Montage de valve 9-9382 Tube 9-9383 Bouton rotatif 9-9384 7 1 Lentille de protection d’écran (seulement) 9-9395 1 O2 - AIR O2 - O2 H35 -N2 F5 - N2 AIR - AIR N2 - H2O N2 - N2 RUN SET PREFLOW SET PLASMA & SHIELD 4 7 1 TEST GAS MODE PREFLOW 1 ENABLE DISABLE High Precision Plasma Cutting System AMPERAGE SET-UP 3 PLASMA POWER SUPPLY SHIELD PLASMA 9 9 H 2O MIST 4 2 GCM PRESSURE GAS FLOW 2010 6 3 6 Art # A-04814FR_AB 6-12 Liste des pièces détachées 0-5264FR ULTRA-CUT 100 XT/200 XT/300 XT/400 XT 6.14 Amorce d’arc à distance (RAS-1000 XT) Pièces de rechange N°comp. Qté Description Numéro du catalogue 1 1 Montage RAS 1000 XT complet 3-9130E 2 1 Montage du couvercle du pilote 9-7341 3 1 Module d’allumage électronique 9-7342 4 1 Bobine toroïdale 9-7343 1 2 3 4 Art # A-12066 0-5264FR Liste des pièces détachées 6-13 ULTRA-CUT 100 XT/200 XT/300 XT/400 XT 6.15 Pièces de rechange de l’échangeur de chaleur HE 400 N°comp. Qté Description Numéro du catalogue 1 1 Montage, Échangeur de chaleur HE 400XT 9-9416 2 1 Ventilateur 9-7348 3 1 Radiateur 9-7349 4 1 Condensateur 9-1059 5 1 Commutateur thermique 9-1448 1 2 4 3 5 Art # A-12672 6-14 Liste des pièces détachées 0-5264FR ULTRA-CUT 100 XT/200 XT/300 XT/400 XT 6.16 Torche XTL distributeur de pièces externes REMARQUE! L’ensemble soupape de torche XTL nécessite les versions de firmware 3.2 ou supérieur pour la C.C.M. et 3.1 ou supérieur pour le GCM 2010. Il exige aussi la réinitialisation d’interrupteurs DIP dans le C.C.M. N°comp. Qté Description Numéro du catalogue 1 1 Montage de soupape de la torche 4-3054 2 1 Faisceau de torche 9-9413 3 1 Fiche, Circuit 14 9-3294 4 1 Vérifier la soupape 8-4512 5 3 Vérifier la soupape 9-7006 6 1 STR 1/8 NPT. Raccord en T 8-0352 7 1 Le coude de la rue (bague) 8-3369 8 1 Couvercle supérieur 9-3324 9 1 Capot avant 9-3323 1 8 7 2 4 9 3 5 6 Art # A-07650 0-5264FR Liste des pièces détachées 6-15 ULTRA-CUT 100 XT/200 XT/300 XT/400 XT 6.17 Torche XTL distributeur de pièces de remplacement interne REMARQUE! L’ensemble soupape de torche XTL nécessite les versions de firmware 3.2 ou supérieur pour la C.C.M. et 3.1 ou supérieur pour le GCM 2010. Il exige aussi la réinitialisation d’interrupteurs DIP dans le C.C.M. N°comp. Qté Description Numéro du catalogue 1 1 Silencieux d’échappement 9-3321 2 2 Solénoïde 9-9550 3 3 Solénoïde 9-9392 1 2 SO SO L19 L18 Art # A-07651 3 6-16 Liste des pièces détachées 0-5264FR ULTRA-CUT 100 XT/200 XT/300 XT/400 XT CHAPITRE 7 : TORCHE ENTRETIEN 7.01 Enlèvement des consommables 1. Utiliser l’outil de retrait pour tenir immobile l’ensemble formé de la jupe et de la cartouche. Tourner la jupe pour l’enlever de la cartouche. Outil pour la cartouche Cartouche montée Art # A-04344 Jupe 2. Utiliser l’outil de retrait pour tenir immobile l’ensemble formé de la jupe et de la cartouche. Tourner la jupe pour l’enlever de la cartouche. Outil pour la cartouche Cartouche Art # A-04345 0-5264FR INFORMATIONS RELATIVES À LA TORCHE 7-1 ULTRA-CUT 100 XT/200 XT/300 XT/400 XT 7.02 Lubrification du joint torique Lubrifier les trois joints toriques sur la cartouche et les trois joints toriques sur le corps de la torche périodiquement avec le lubrifiant pour joint torique fourni. Enlever le circlip de la cartouche et faire glisser la bague de serrage vers le bas pour accéder au joint torique en dessous de la bague de serrage. Joint torique interne (n° cat. 8-0545) Emplacement (sous la bague de serrage) Joint torique, n° cat. 8-0544 Joint torique, n° cat. 8-0540 Joints toriques Corps de torche N° cat. 9-9041 N° cat. 8-0524 Cartouche N° cat. 9-3026 Circlip N° cat. 9-3025 Art # A-04071 N° cat. 9-9429 Art # A-04066FR_AE ! ATTENTION N’utiliser que du lubrifiant pour joint torique Thermal Dynamics n° 9-4893 (Christo Lube MCG-129) avec cette pièce de la torche. L’utilisation d’autres lubrifiants peut provoquer des dégâts irréparables à la torche. 7.03 Usure des pièces Remplacer le distributeur de gaz s’il est carbonisé ou fissuré. Remplacer le distributeur de gaz si la bride est endommagée. Remplacer la tuyère et/ou l’électrode si elles sont usées. Tuyère usagée Tuyère en bon état Electrode en bon état Electrode usagée Art # A-04745 7-2 INFORMATIONS RELATIVES À LA TORCHE 0-5264FR ULTRA-CUT 100 XT/200 XT/300 XT/400 XT 7.04 Installation des consommables de la torche MISES EN GARDE Ne pas placer de consommables dans la cartouche quand celle-ci est fixée au corps de la torche. Faire en sorte qu’aucun matériau étranger ne pénètre dans les consommables et la cartouche. Manipuler soigneusement toutes les pièces afin d’éviter de les endommager car cela pourrait affecter les performances de la torche. Art # A-03887 1. Installer les consommables comme suit : 1: Empiler les pièces 2: Appuyer la cartouche contre les pièces empilées Electrode Distributeur du gaz plasmagène Joint torique supérieur sur la tuyère Aucun vide entre les pièces Tuyère Distributeur du gaz de protection La cartouche couvre le joint torique supérieur sur la tuyère de la torche Coiffe de protection 3: Enfiler la jupe sur la cartouche 4: Contrôler que la jupe dépasse Jupe Bouclier cap La coiffe de protection dépasse de 0.063-0.083" (1,6 – 2,1 mm) Art # A-04716FR 2. Enlever l’outil de retrait de la cartouche et monter la cartouche assemblée sur le corps de torche. 0-5264FR INFORMATIONS RELATIVES À LA TORCHE 7-3 ULTRA-CUT 100 XT/200 XT/300 XT/400 XT ! ATTENTION La cartouche doit couvrir le joint torique sur le corps de torche. Ne pas forcer sur la cartouche si elle ne se serre pas entièrement. Enlever la cartouche et nettoyer délicatement les filets sur le corps de torche avec une brosse métallique. Appliquer un lubrifiant compatible avec l’oxygène (fourni avec la torche) sur les filets. Corps de torche Joint torique du corps de torche Saillie de 0.063 - 0.083" (1,6 – 2,1 mm) Art # A-07202 Installation de la cartouche sur le corps de torche 3. Faire glisser la borne du capteur ohmique sur la jupe si l’on utilise la détection de la hauteur de la torche ohmique. REMARQUE! La détection de la hauteur ohmique n’est pas recommandée avec une feuille d’étanchéité. L’eau sur la plaque interfère électriquement avec le circuit de détection ohmique. Borne du capteur ohmique A-03393 4. Raccorder le câblage de l’altimètre à la borne du capteur ohmique. 7-4 INFORMATIONS RELATIVES À LA TORCHE 0-5264FR ULTRA-CUT 100 XT/200 XT/300 XT/400 XT 7.05 Dépannage en cas de fuite du liquide de refroidissement Ne jamais faire fonctionner le système s’il y a des fuites de liquide de refroidissement provenant de la torche. Un écoulement stable indique que les pièces de la torche sont endommagées ou mal installées. Si l’on utilise le système dans ces conditions, on risque d’endommager le corps de torche. Se reporter au tableau suivant pour avoir des instructions en cas de fuite du liquide de refroidissement provenant du corps de torche. La torche fuit Les consommables de la torche sont-ils montés ? Non Fuite provenant de l’alimentation ou du retour du liquide de refroidissement ? Alimentation Oui Les pièces sontelles neuves ou utilisées ? Retour Commander le kit du clapet de non-retour du liquide de refroidissement 9-4846 Commander le kit de rechange du tube du liquide de refroidissement Les pièces sont probablement usagées. Consulter le tableau pour connaître la durée de vie moyenne. Usagé Il se peut que la torche soit endommagée. Voir la page pour déterminer si le corps a été endommagé. Neuf Les pièces sontelles entièrement montées dans la torche ? Oui La torche est-elle endommagée ? Non Vous n’êtes pas sûr ? Enlever et lubrifier tous les joints toriques sur le corps de torche, la cartouche de consommables et les consommables. Remonter la torche. Fuit-elle encore ? Oui Oui Démonter entièrement et remonter la torche correctement. Consulter le manuel d’installation. Remplacer le corps de torche Oui Remplacer la cartouche des consomambles et la jupe. La torche fuit-elle encore ? Art # A-09638FEU 0-5264FR INFORMATIONS RELATIVES À LA TORCHE 7-5 ULTRA-CUT 100 XT/200 XT/300 XT/400 XT Électrodes de torche Art # A-09653FEU Intensité du courant 30 50 70 85 100 150 200 250 300 400 7-6 Gaz plasmagène Profondeur d’usure recommandée pour le remplacement Inch mm O2 0.04 1 Air 0.04 1 N2 0.04 1 O2 0.04 1 Air 0.08 2 N2 0.04 1 O2 0.04 1 Air 0.08 2 N2 0.04 1 Air 0.08 2 O2 0.04 1 H35 0.08 2 N2 0.08 2 O2 0.06 1.5 H35 0.08 2 N2 0.08 2 O2 0.06 1.5 H35 0.08 2 N2 0.08 2 O2 0.06 1.5 O2 0.06 1.5 H35 0.08 2 N2 0.08 2 O2 0.08 2 H17 0.08 2 H35 0.08 2 N2 0.08 2 INFORMATIONS RELATIVES À LA TORCHE 0-5264FR ULTRA-CUT 100 XT/200 XT/300 XT/400 XT ANNEXE 1 : Schéma du démarreur à distance de l’arc 1 2 Fil de pontage au câble à ID est connecté. Démarrage d'Arc Bloc d'alimentation en plasma A 3 J59-RAS 1 2 3 4 5 6 7 8 9 10 11 12 13 14 GND 4 RAS 1000 XT 5 6 A Dispositif d'allumage SIG 4.5 J58 Chassis Gnd (masse) 120 VAC 120 VAC RET 1 2 3 4 5 6 7 8 9 10 11 12 13 14 15 16 115 Vac GND 115 Vac RET Ho Hb (99) (98) (49) (52) Bouclier de la torche NEG 0.047 uf CGND GND PU 100K 0.047 uf B RAS Condensateur électrique PCB 0.1 uf Neon (-) Électrode NEG Bague en laiton NEG B PLT PILOTE (+) PILOTE L1 TORCHE Embout MASSE (+) GND MASSE C C Art # A-12071_AC Revision Rev AA By ECO B2487 Date Thermal Dynamics Corporation RWH 07/30/2013 2800 Airport Rd. Denton, Texas 76207 USA D Date Printed 7/30/2013 Drawn Date Revised 7/30/2013 Date The information contained herein is proprietary to Thermal Dynamics. Not for release, reproduction or distribution without written consent. Size Sheet Title Drawing Number DAT SCHEMATIC 0-5264FR 2 3 4 ANNEXE 03/13/2013 1 of 1 042X1361 RAS 1000 XT Arc Starter 1 A D 5 6 A-1 ULTRA-CUT 100 XT/200 XT/300 XT/400 XT ANNEXE 2 : Schéma de commande de gaz et de soupape de la torche 5 4 ULTRACUT SW2 GAS D 1 2 3 4 5 6 7 A GCM 2010 GAS CONTROL SW3 MODE O2 - AIR O2 - O2 H35 - N2 F5 - N2 AIR - AIR N2 - H2O N2 - N2 A 1 2 3 4 RUN SET PREFLOW SET CUTFLOW TEST (10) To CCM (1) (13) (3) (4) (5) (6) (7) (8) (9) (14) (15) PLASMA ENABLE SW6 2 1 DISABLE (50) J5 3 1 ENABLE SW7 SHIELD FLOW / PRESSURE2 (51) 3 3 4 (55) 24 VAC RET 120 VAC 120 VAC RET Shield 5 5 4 3 2 1 9 8 10 7 6 5 4 3 D25 GREEN 8 PLASMA ENABLE + PLASMA ENABLE - 2 - 9 10 F20 1A 11 (56) FERRITE CORE 12 (57) 13 14 (58) (58) 15 (59) D13 16 16 PIN GREEN Safety Gnd (low freq) - 2 E-STOP + E-STOP 24 VAC 24 VAC RET E-STOP F18 1.6A 120 VAC 120 VAC RET J3 120 VAC to SOLENOIDS 120 VAC (60) F19 1A 5 15 VDC RET 1 2 3 4 5 6 7 8 9 10 11 12 13 14 15 16 17 18 19 20 21 22 23 24 25 26 27 28 29 30 31 32 33 34 35 36 37 7 1 +15 VDC 1 2 3 4 5 6 7 8 9 10 11 12 13 14 15 16 17 18 19 20 21 22 23 24 25 26 27 28 29 30 31 32 33 34 35 36 37 1 + 4 + 24 VAC J56 5 PIN PLASMA ENABLE 6 4 E-STOP J55 J7 U36 U35 5 (54) POWER SUPPLY 10 PIN 2 (52) FLOW PRESSURE 1 (53) C 1 J11 2 FIBEROPTIC 120 VAC to BOARD POWER 1 2 (61) 3 RF Gnd (Shield) (16) (17) (18) (19) SOL3 SOL1 SOL2 (20) 13 14 15 16 17 18 19 20 12 11 10 9 8 7 6 5 4 3 1 J12 2 B (21) SOL5 SOL4 SOL6 (22) (23) (24) (25) (26) (27) 18 PIN SOLENOID LOCATIONS SOLENOID MANIFOLD (from rear) PS3 A 1 AIR 2 N2 3 O2 FRONT PANEL (rear) SHIELD < 8 AIR 9 N2 10 O2 Shield Flow PREFLOW < 6 AIR 7 N2 PLASMA < 13 PS4 4 H35 5 F5 Art # A-04837_AC 5 A-2 17 12 H2O Shield Shield Press 11 Plasma Precharge / Bypass 4 ANNEXE 0-5264FR ULTRA-CUT 100 XT/200 XT/300 XT/400 XT 3 2 LCD Display Assembly 1 19X2220 D LCD DISPLAY ENCODER w/SW 15 16 1 2 3 4 5 6 7 8 9 10 11 12 13 14 INTERFACE BOARD PS1 Plasma Outlet Pressure 34 34 33 32 32 31 30 30 29 28 28 27 26 26 25 24 24 23 22 22 21 20 20 19 18 18 17 16 16 15 14 14 9 12 12 13 10 10 7 8 11 6 5 4 8 3 1 2 6 4 3 2 1 JP1 33 31 29 27 25 23 21 19 17 15 13 11 9 7 5 1 3 (62) (63) (64) (65) (66) (67) 4 3 34 DUAL RIBBON HEADER ENCODER 2 { J8 1 2 3 4 5 6 4 J1 RIBBON CABLE 2 34 DUAL RIBBON HEADER J10 1 1 2 3 4 5 6 BA J16 J6 18 +5VDC +5VDC 17 LCD DISPLAY CONNECTOR 16 15 +5VDC 14 13 12 11 CURRENT CONTROL (Thumbwheel) optional 10 9 J9 F1 F2 F3 F4 F5 F6 F7 F8 F9 F10 F11 F12 F13 F14 F15 F16 F17 F18 F19 F20 0.125A 0.125A 0.125A 0.125A 0.125A 0.125A 0.125A 0.125A 0.125A 0.125A 0.125A 0.125A 0.125A 0.250A 0.250A 0.125A 0.125A 1.6A 1A ( 1A ( SW1 C 8 1 4 SOL1 1 SOL2 2 2 3 SOL3 3 BOTH SECTIONS ON FOR OPERATION SOL4 4 OFF ONLY FOR PROGRAMMING 5 SOL5 6 SOL6 SOL7 IN-CIRCUIT SERIAL SOL8 PROGRAMMING SOL9 SOL10 SOL11 SOL12 SOL13 SOL14 * SOL15 * SOL16 SOL17 ( 120 VAC to Solenoids) 120 VAC to Low Voltage Power Supply) to E-Stop Relay) 7 6 5 4 3 2 1 18 PIN +5VDC PS3 Plasma Inlet Pressure 1 JP3 1 2 2 4 3 * 19X2219_AG and earlier F14 & 15 are 0.125A 4 Inlet sensors in 19X2219 PCB (rev AG or later) 3 1 +5VDC PS4 Shield Inlet Pressure JP4 1 2 2 4 3 4 B ULTRACUT TORCH VALVE ASSEMBLY (TVA or TVA-XTL) 12 13 14 15 16 11 10 9 8 7 6 5 4 3 2 J13 1 13 14 15 16 17 18 12 11 10 9 8 7 6 5 4 3 1 2 3 J1 J57 (40) (46) (28) SOL7 (29) (30) (31) (32) (33) (42) SOL13 (44) (47) (40) SOL11 SOL9 (41) SOL17 FERRITE CORE (49) (40) SOL8 SOL10 SOL12 (48) J60 1 1 2 2 3 3 4 4 5 5 6 6 7 7 8 8 9 10 11 12 13 14 9 10 11 12 13 14 SOL16 TVA SHIELD SOL14 TVA PLASMA CUTFLOW SOL18 * PLASMA EXAUST 1 Normally Open (42) (34) (43) (35) (36) (44) (37) SOL15 TVA PLASMA PREFLOW SOL19 * PLASMA EXAUST 2 Normally Open (38) (39) (45) 18 PIN Safety Gnd (low freq) RF Gnd (Shield) * Additional Solenoids used in TVA-XTL Vent TVA-XTL TVA 18 Plasma 19 A 14 Plasma Plasma 14 Art # A-04837_AD Preflow 15 Plasma Preflow Shield Gas Shield Revisions AA ECO-B214 AB ECO-B367 AC ECO-B587 15 16 Rev By Date Shield NOTE: UNLESS OTHERWISE SPECIFIED 1. RESISTOR VALUES ARE EXPRESSED IN OHMS, 1/4W 5%. 2. CAPACITOR VALUES ARE EXPRESSED IN MICROFARADS (uF). 16 Last Modified: Monday, January 29, 2007 13:57:13 Supersedes Date: Wednesday, January 26, 2005 Drawn: DAT References Chk: App: Size DWG No: D 1 Sheet of 1 42X1202 1 2 0-5264FR SCHEMATIC, Ultracut GCM 2010 Gas Control & TVA TITLE: H2O Shield 3 Assy No: Scale Information Proprietary to THERMAL DYNAMICS CORPORATION. Not For Release, Reproduction, or Distribution without Written Consent. H2O Shield Gas Shield PCB No: DAT 07/26/06 RWH 01/29/07 RWH 01/06/08 ANNEXE A-3 ULTRA-CUT 100 XT/200 XT/300 XT/400 XT ANNEXE 3 : Schéma de plomberie du module de commande du gaz Plasma nouveau capteur de pression d'admission SOL5 SOL11 F5 H35 TVA & XTL-TVA Atmosphère SOL4 PLASMA SOL19 SOL18 SOL1 SOL2 Capteur de pression SOL3 SOL14 PLASMA SOL6 FLUX PRÉLIMINAIRE AIR SOL15 SOL16 COIFFE N2 SOL7 O2 SOL12 SOL8 SOL9 SOL 18 & 19 dans XTL-TVA seulement. SOL10 SOL13 MANIFOLD DE GAZ Protection nouveau capteur de pression d'admission H2O SOL 18 & 19 normal ouverte. Fonctionner en parallèle avec normalement fermé SOL 14 & 15 COIFFE SOL17 EAU Art # A-07577FEU A-4 ANNEXE 0-5264FR ULTRA-CUT 100 XT/200 XT/300 XT/400 XT ANNEXE 4 : Disposition du circuit imprimé du module de commande du gaz F10 F12 F8 F17 J1 F9 F11 F15 F16 F7 J13 J13 F13 F14 J3 F19 F18 TP4 J12 F5 F3 F1 TP3 TP2 F2 F4 F6 TP7 F20 J5 TP8 JP1 TP9 TP5 TP10 TP6 TP1 TP11 Art # A-07621 J6 0-5264FR TP12 J7 J11 TP15 TP13 TP14 ANNEXE TP16 TP19 J8 J10 TP18 A-5 ULTRA-CUT 100 XT/200 XT/300 XT/400 XT ANNEXE 5 : Disposition du circuit imprimé du module d’affichage de commande du gaz J1 D15 69 R24 D11 D13 D12 D26 D25 D20 C2 C1 D10 D9 R1 R2 R3 R4 R5 R6 R7 R8 R9 R10 R11 R22 R21 R20 R19 R18 R17 R16 R15 R14 R13 R12 19X2220 REVAB LCD INTERFACE TDC C 2005 R23 72 + D24 D8 D7 D23 D6 D22 D5 D19 D16 D14 D2 D4 D3 D18 D1 J1 34 33 D21 2 1 D17 70 1 16 68 Art # A-06904 A-6 ANNEXE 0-5264FR ULTRA-CUT 100 XT/200 XT/300 XT/400 XT ANNEXE 6 : CNC - Connexions du circuit imprimé du module de commande TB1 (LV) Déplacement autorisé 2 12 élevé +10V 10K 11 Commande du courant analogique 10 essuie-glace / entrée faible(-) Volts de l’arc divisé Sortie Entrée démarrage/arrêt 9 (+) 8 (-) 7 (+) 6 (-) 5 Arrêt (NC) 4 (LV) Déplacement autorisé 2 3 (+) 2 (-) 1 CNC enable plasma TB2 Déplacement autorisé (+) 12 SW6 11 DC 10 9 8 Sortie de l’arc pilote activée (Contacts) Flux préliminaire activée Retenir le démarrage 7 6 5 (+) 4 (-) 3 (+) 2 Art # A-11512FEU (-) 1 TB3 Rechange # 2 sorties contacts normalement ouverts 12 Rechange #2 sorties contacts normalement fermés 10 Rechange #1 sorties contacts normalement fermés 8 23X5560_AB Métal déployé 0-5264FR Réduction du courant d'angle Marquage plasma à distance 11 9 7 (-) 6 (+) 5 (-) 4 + 3 (-) 2 (+) 1 ANNEXE A-7 ULTRA-CUT 100 XT/200 XT/300 XT/400 XT ANNEXE 7 : CNC Fonctionnalités CNC Les circuits E/S de la CNC fournissent au moins 1 000 v d’isolation galvanique à partir du bloc d’alimentation au plasma. Bien que les circuits CNC soient isolés de l’alimentation électrique, beaucoup de retours de signaux sur J15 et TB1, TB2 & TB3 sont communs. Les broches 12 du J15 et le TB2-10 sont également raccordés aux autres lorsque le SW6 est réglé pour la tension (avec « OK pour déplacement » sélectionné). Connecteur J15 de la CNC du panneau arrière : Standard distant du circuit 37 (A CPC) : Il existe également des doubles sur le TB1, le TB2 et le TB3. Utiliser l’un ou l’autre et non les deux. Masse (pour blindage SC-11) 1 Start/Stop 3 (+); 4 (-) Ok pour déplacement (contacts ou tension 1) 12(-); 14 (+) Tensions d’arc divisé (rapport au choix 50:1; 40:1; 30:1; 16.6:1, 25:1) 5 (-); 6 (+) PreFlow ON 7 (+); 9 (-) Réduction du courant à l’angle 10 (+); 11 (-) Interr. circuit isolé (pour SC-11) 8 Terre du châssis13 Prise pour clavier15 Retenir le démarrage 16(+); 17 (-) Repère plasma 21 (+); 22 (-) Coupe de métal déployé 23 (+); 24 (-) Activation de plasma CNC2 25 (+); 26 (-) Contrôle le courant analogique à distance 3 29 (+); 30 (signal); 31 (-) Arrêt (Verrouillé) Int. 4 32 (+); 33 (-)(comm.) Pilote en marche (contacts) 34; 35 Rechange (contact) 36; 37 A-8 ANNEXE 0-5264FR ULTRA-CUT 100 XT/200 XT/300 XT/400 XT Raccordements internes à la CNC. TB1, TB2 et TB3 sur le module du CCM. Les raccordements sont fournis sur les plaques à bornes TB1, TB2 et TB3 du module du CCM y compris la plupart des fonctions du panneau arrière plus certaines fonctions supplémentaires. Tous ces signaux sont isolés du générateur à plasma mais les signaux marqués (comm.) et (-) sont communs à chacun. Les utilisateurs sont censés installer leur propre câble CNC sur ces raccordements. Le trou d’expulsion est fourni dans le panneau arrière du module du CCM. L’utilisateur doit fournir le réducteur de tension pour le câble installé par l’utilisateur. TB1 FonctionConnexion Activer/Désactiver CNC TB1-2 (+), TB1-1(-)(comm.) OK to Move 2 Contacts TB1-3 & TB1-12 seulement, étalonné 1A @ 28 V C.A./ c. c. Arrêt verrouillé (NC) 4 TB1-4 (+) & TB1-5 (-) (comm.) utilisé avec Démarrage verrouillé Démarrage/Arrêt Ret 4 TB1-6 (+), TB1-5 (-) (comm.) TB1-6 (+), TB1-5 (-) (comm.) utilisé avec Arrêt verrouillé ou Démarrage verrouillé (NO) 4 Tensions d’arc divisé TB1-8 (+), TB1-7 (-) comm. Contrôle le courant analogique à distance TB1-9 analogique Comm. (-) ou 10K Pot. c.c bas TB1-10 analogique en (+) ou pour le balai du potentiomètre c.c TB1-11 10K Pot. c.c haut (+10V @ 1 mA Supply) TB2 FonctionConnexion Retenir le démarrage TB2-2 (+),TB2-1 (-) (comm. ) Preflow ON TB2-4 (+), TB2-3 (-) (comm.) Pilote en marche (contacts) TB2-6, TB2-8 rated 1A @ 120 VAC or 28 V c.c. OK pour déplacement (contacts ou tension c.c.)5 TB2-12 (+), TB2-10 (-) TB3 FonctionConnexion Marquage plasmaTB3-2(+), TB3-1(-) (comm.) Réduction du courant à l’angle TB-4(+), TB3-3(-)(comm.) Coupe de métal déployé TB3-6(+), TB3-5(-)(comm.) Contact NO de rechange TB3-7, TB3-8 Contact NC de rechange TB3-9, TB3-10 Contact NO de rechange TB3-11, TB3-12 1 L’interrupteur SW6 sur le circuit imprimé d’E/S du CCM sélectionne OK pour déplacement pour la fermeture des contacts isolés ou la tension V c.c. (15-18 V) à moins de 100 mA Lors du réglage pour les contacts, le circuit ‘OK pour déplacer’ est étalonné pour 120 V c.a. / 28 V c.c. Enlever le cavalier installé en usine de TB1-1 et 2 si utilisation d’Activation du plasma CNC en J15. 2 3-5 Voir ci-dessous. 0-5264FR ANNEXE A-9 ULTRA-CUT 100 XT/200 XT/300 XT/400 XT Description de l’entrée/de la sortie de la CNC Entrée E-Stop — Nécessite un raccordement fermé pour 35 mA à 20 VCC pour l’appareil à utiliser. Le cavalier installé en usine entre le TB1-1 et 2 doit être enlevé lors du raccordement du circuit E-Stop fourni par l’utilisateur. 4 Entrée démarrage/arrêt—Interrupteur (momentané ou soutenu) de 35 mA à 20 VCC. Configuration du circuit Démarrage / Arrêt. L’arrêt/le démarrage momentané (verrouillé) n’est disponible que pour le TB1. DÉMARRAGE / ARRÊT SOUTENU DÉMARRAGE / ARRÊT TB1-5 TB1-6 DÉMARRAGE / ARRÊT MOMENTAN ARRÊT TB1-4 TB1-5 DÉMARRAGE TB1-6 Tension d’arc divisé — Le signal de la tension d’arc est isolé du générateur à plasma, néanmoins (-) est courant avec d’autres signaux de la CNC isolés. Le niveau du signal de la tension d’arc divisée maximum dépend du rapport de division des délais de la tension d’arc effective, néanmoins il ne peut dépasser 12 V environ. Analog Molette de commande du courant input— La commande du courant analogique comprend le module d’isolation analogique, un module d’isolation séparé qui n’est habituellement pas requis même si sa faible entrée est commune aux autres entrées de la CNC isolées. La mise à l’échelle de l’entrée de la commande du courant analogique est 0 V = 0 A, 10 V. = sortie maximum et elle est linéaire au milieu. Néanmoins la sortie minimale est de 5 A. L’utilisateur est responsable pour la configuration de la tension analogique correcte afin de maintenir une sortie d’au moins 5 A. Pour utiliser la commande du courant analogique sur le PCB E/S réglé sur SW11 sur la position en bas et sur le PCB de l’UC réglé sur SW8-2 activé (haut). 3 Entrée Retenir le démarrage —Normalement ouvert, fermé pour retenir le démarrage. Calibre du circuit 10 ma. @ 20 V c.c.. Retarde l’allumage du pilote, le flux préliminaire du gaz continue. Utilisé par certains contrôles de hauteur pour faire circuler du gaz durant l’ajustement de la hauteur. Sert également à synchroniser les démarrages lorsque plusieurs alimentations en plasma sont utilisées sur la même table de coupe. L’utilisateur fournit le circuit pour conserver les entrées « Retenir le démarrage » actives jusqu’à ce que toutes les torches trouvent leur hauteur. Utilisé avec DÉMARRAGE CNC. Appuyer sur DÉMARRER (START) pour démarrer la circulation du gaz. Appuyer sur HOLD en même temps pour retarder l’amorçage jusqu’à ce que la hauteur soit réglée. Supprimer HOLD pour allumer le pilote et démarrer l’arc. Entrée flux préliminaire activée — Normalement ouverte, fermée pour démarrer le flux préliminaire avant le signal de DEMARRAGE normal. La valeur nominale du circuit est de 10 mA à 20 VCC Les commandes de la hauteur de torche (THC) émettent normalement le signal de DEMARRAGE pour l’alimentation en plasma quand la hauteur de torche a été trouvée. Ensuite, le plasma prend 1-2 secondes (ou plus) pour effectuer le pré-débit avant l’amorçage du pilote. Certaines commandes de la hauteur de torche (THC) disposent d’une sortie leur permettant de commencer le pré-débit plus tôt, pendant la recherche des hauteurs, permettant ainsi de gagner 1 ou 2 secondes sur chaque coupe. PRÉ-DÉBIT EN MARCHE (Preflow On) devrait rester actif pendant au moins une seconde après l’appui sur DÉMARRAGE CNC. Il n’y a pas de problème si cette option reste active jusqu’à la fin de la coupe. Il faut la désactiver et la réactiver pour lancer un autre pré-débit avant d’appuyer sur START pour démarrer l’opération de coupe suivante. Sortie Pilote en marche - contacts du relais de 1 A @ 120 V c.a. / 28 V c.c. Les contacts se ferment lorsque le pilote est en marche. Peut être câblé en parallèle avec les contacts possibles à déplacer pour amorcer le mouvement de la machine lorsque le pilote est établi. Utilisé lors du démarrage sur les trous. Pour démarrer sur des trous, il faut régler le SW8-1 sur MARCHE (haut) sur le circuit CPU pendant une durée du pilote prolongée. L’utilisation prolongée du temps pilote pour démarrer ou pour couper sur les trous réduira la durée de vie des pièces. Sortie Déplacement autorisé — Active quand l’arc de coupage est établi, l’arc est transféré. Utilisé pour dire à la table de découpe de démarrer le mouvement X-Y. Les contacts du relais ont une valeur nominale de 1 A à 120 VCA ou 28 VCC quand le SW6 est configuré pour les contacts. Quand le SW6 est configuré pour le VCC, la sortie fournit 15-18 V.CC à 100 mA. Il peut être câble en parallèle avec l’arc pilote activé pour démarrer le mouvement de la machine de découpe dès que l’arc pilote est établi. Déplacement autorisé 2 – Fournit un deuxième ensemble de contacts N.O. qui se ferment lors de la détection du transfert d’arc. Les contacts ont une valeur nominale maximale de 24 VCA/CC à 1 A. Circuit de la CNC simplifié. 5 A-10 ANNEXE 0-5264FR ULTRA-CUT 100 XT/200 XT/300 XT/400 XT +10V @ 10ma. Pour Pot. C.C à distance – Dans les versions antérieures du CCM, si quelqu’un voulait utiliser un potentiomètre pour l’entrée de commande de courant (C.C) analogique à distance, il fallait une alimentation externe de 10 V pour Pot. élevé.. Maintenant, une alimentation 10 V isolée (des circuits plasma principaux) est fournie. La valeur recommandée du potentiomètre est de 5 k ou de 10 k. 5 TB1 Ext. +10V 11 +10V 10 ESSUIE-GLACE 9 Art # A-09246FEU Sélection du marquage au plasma (à distance) – Le marquage au plasma, disponible uniquement avec le DFC 3000, peut être activé avec une fermeture du contact entre TB3-1 et TB3-2 si le SW8-4, l’interrupteur DIP sur la carte de l’UC (plus petite que les 2 cartes CCM) est également activé. L’ouverture de la connexion entre le TB3-1 et le TB3-2 permet de revenir au mode de coupage normal. Pour les générateurs Ultracut, il est bon de laisser le SW8-4 activé que l’on effectue le marquage ou non. 5 Les fonctions suivantes peuvent toutefois ne pas être disponibles sur votre système. * *Réduction du courant à l’angle (entrée) --- Lorsque cette entrée est activée, normalement à partir de l’angle du contrôleur de la table ou d’un signal d’inhibition de commande de la hauteur, montrant la réduction de la vitesse de coupe pour passer un angle ou un petit rayon, le courant de coupe est réduit à une valeur fixe à un niveau prédéterminé pour une meilleure coupe à une vitesse inférieure. *Coupe de métal déployé (entrée)---En général, le bloc d’alimentation au plasma est optimal pour la découpe par perforage, une grande hauteur de perforage au-dessus du métal à découper, un temps pilote court, etc. L’activation de cette entrée permet d’ajuster le bloc d’alimentation au plasma pour optimiser ses paramètres de coupe du métal déployé ou perforé, le démarrage depuis le bord, etc. Parmi les autres changements, l’on peut citer une égalisation de la hauteur de transfert avec la hauteur de coupe. En plus de l’activation, l’interrupteur SW1-1 de l’entrée CCM de coupe du métal déployé doit être mis en marche automatiquement, il faut redémarrer le pilote et régler SW8-1 sur un temps pilote plus long. *Contacts de rechange --- . 0-5264FR ANNEXE A-11 ULTRA-CUT 100 XT/200 XT/300 XT/400 XT Circuit simplifié CNC TB2 12 11 10 9 8 7 6 5 4 3 2 1 5 - +10V 5 6 8 V OL TA GE D IV IDER G ND AL L SW SW1 2 A ( SW1 2 B ( SW1 2 C ( TB2 Spare #2 NO 12 11 4 (+) (-) (+) (-) + 4 SW 12D Prefl ow ON Prefl ow ON Hol d Start Hol d Start B 3 PILOT is ON 3 SW 12C PILOT is ON OK SW6B 1 OK to M OV E (-) C ONTA CT S SW 12A OK to M OV E (+) SW6A D C VO LT S 7 OK2 (cont act) 12 +10V (CC Pot Hi ) 11 CC Pot W iper 10 CC Pot L ow 9 Di v A rc V (+) 8 Di v A rc V (-) 7 /Start - Stop (+) 6 /Start - Stop (-) 5 Stop Mo m NC 4 OK2 (cont act) 3 / CNC Enabl e (+) 2 / CNC Enabl e (-) 1 +18VDC 2 TB1 OK TO MOV E SELECT 18 V D C or Con tacts SW 12B Ult racut X T Simplified CNC OFF f o r 1 ) ON = 2 ) ON = 3 ) ON = 50: 16. 30: 40: 1 ( def aul t ) 7 : 1 ( SC- 1 1 ) 1 1 Spare #2 NC 10 Spare #1b NO / Cut Ex panded M etal (-) / Cut Ex panded M etal (+) / Corner Current Reducti on (-) / Corner Current Reducti on (+) / Plasma M arki ng (-) / Plasma M arki ng (+) 9 8 7 6 5 4 3 2 1 PSR Art # A-11579 A-12 ANNEXE 0-5264FR ULTRA-CUT 100 XT/200 XT/300 XT/400 XT J54 - Rem ote HM I & CN C CO M M (100) (101) (102) Harness to Relay PCB (109) (108) (115) Harness to CPU PCB 1 2 3 4 5 6 7 8 9 10 11 12 13 14 15 16 17 18 G ND SPA RE #1a (142) (116) (117) (118) (119) (120) (133) (134) (137) (139) (138) (143) J22 C hassi s (140) (141) (136) (135) (132) (153) (133) (134) (135) (136) (137) (138) (139) (140) (141) (142) (143) (144) (145) (144) (145) (146) (147) (148) (149) (150) (151) (146) (147) (148) (149) (150) (151) (152) (154) (155) (132) (152) (153) (154) (155) (156) (157) (158) (159) (156) (157) (158) (159) J15-1 to chassis used f or SC-11 cable shield 1 - 24 V AC 2 - 24 V AC Re t 3- Jumper to 24 V AC 5-H M I Pl asma Enabl e SW 6-H M I Pl asma Enabl e SW 7 - K ey Pl ug 8 - Tx + 9 - GND RS 485 10 - GN D / 422 12 - Tx 13 - Rx + 14 - Rx - Comm J15-CNC J21 1 2 3 4 5 6 7 8 9 10 11 12 13 14 15 16 17 18 19 20 1 2 3 4 5 6 7 8 9 10 11 12 13 14 The COM M Ref at pin 8 is also f or the SC-11 J15-13 connects SC-11 chassis to PS chassis. 1 2 3 4 5 6 7 8 9 10 11 12 13 14 15 16 17 18 19 20 21 22 23 24 25 26 27 28 29 30 31 32 33 34 35 36 37 3- / CNC Start (+) 4- / CNC Start (-) 5- D ivided A rc V (-) 6- D ivided A rc V (+) 7- / Preflow ON (+) 8- COM M Ref (1K Ohm) 9- / Preflow ON (-) 12- OK to M ove (-) 14- OK to M ove (+) 15 - K ey Plug 16- / H old Start (+) 17- / H old Start (-) 21- / Plasma M ark (+) 22- / Plasma M ark (-) 23- / Cut Expanded M etal (+) 24- / Cut Expanded M etal (-) 25- / CNC Plasma Enable (+) 26- / CNC Plasma Enable (-) 29- Remote CC Pot H igh 30- Remote CC (analog) 31- Remote CC Pot L ow 32- Stop SW (momentary) * 33- Stop SW Ret 34- Pilot is ON (a) 35- Pilot is ON (b) 36- Spare OU T #1 (a) 37- Spare OU T #1 (b) * Used with Mom en tary C NC St art SW Art # A-11579 0-5264FR ANNEXE A-13 ULTRA-CUT 100 XT/200 XT/300 XT/400 XT Connexions CNC Machine de découpe Câble CNC Générateur J15 1 2 ( 2) DÉMARRAGE/ARRÊT (3) (4) ( 5) (6) ( 7) Commencez mouvement (Déplacement autorisé) { 3 4 5 6 7 8 9 10 11 (9) (10) (11) (12) * NC .......... ... Arc divisée V (-) .......... Arc divisée V (+) .......... Flux préliminaire activé (+) .......... Flux préliminaire activé (-) .......... ... Réduction du courant d'angle (+) 12 13 * (14) 14 (16) 15 16 (17) Source, 16 VDC, 10 ma. Réduction du courant d'angle (-) Déplacement autorisé Contacts DCV (-) de relais ou (1 A à DCV (+) SW6 120 VCA ( 15 - 18 VCC .......... /Retenir le ou 28 VCC) jusqu’à 100 mA) démarrage(+) .......... /Retenir le démarrage(-) DC (+) * (1) 17 18 19 20 21 .......... /Note plasma (+) 22 .......... /Note plasma (-) 23 .......... /Couper métal déployé (+) 24 .......... /Couper métal déployé (-) 25 .......... /CNC enable plasma (+) 26 .......... /CNC enable plasma (-) (21) (22) (23) (24) (25) (26) 27 28 29 30 31 32 33 34 35 (29) (30) (31) (32) (33) (34) (35) 10 K (36) (37) 36 37 .......... .......... .......... .......... .......... .......... .......... Télécommande pot de haute CC (+10VDC) Éloigné CC 0-10V Signal ou essuie-glace de pot Pot de CC à distance faible (-) Arrêter SW (momentané) Arrêter SW Ret Pilote est sur ON (a) Contact relais 1 A à 120 VCA / 28 Pilote est sur ON (b) .......... Rechange OUT #1 (a) .......... Rechange OUT #1 (b) Coiffe ** Représente interrupteur, relais, transistor à collecteur ouvert, etc A-14 * GND de l'alimentation n'est pas utilisée pour le câble CNC Ne pas connecter le fil n ° 1 à rien. ** Câble fil de drain blindage doit être relié à la terre à la machine à découper. Art # A-11901FEU ANNEXE 0-5264FR ULTRA-CUT 100 XT/200 XT/300 XT/400 XT Code couleurs du câble CNC Tableau 1 : Tableau des codes de couleurs de l'article no 4 du câble Emplacement de la broche COULEUR 3 4 5 6 7 8 9 10 11 12 14 16 17 21 22 23 24 25 26 29 30 31 32 33 34 35 36 37 BLANC/BLEU BLANC/VIOLET BLANC/MARRON/VIOLET BLANC/MARRON JAUNE VERT BLANC/NOIR/MARRON BLANC/MARRON/BLEU BLANC/NOIR NOIR BLEU BLANC/MARRON/JAUNE BLANC/MARRON/VERT BLANC/NOIR/ORANGE BLANC/NOIR/ROUGE BLANC/MARRON/ORANGE ORANGE ROUGE MARRON BLANC/MARRON ROUGE BLANC GRIS VIOLET BLANC/NOIR/JAUNE BLANC/NOIR/GRIS BLANC/NOIR/VIOLET BLANC/NOIR/BLEU BLANC/NOIR/VERT Description du signal DÉMARRER LE CNC (+) DÉMARRER LE CNC (-) DIV ARC (-) DIV ARC (+) FLUX PRÉLIMINAIRE EN MARCHE (+) COMM 1K FLUX PRÉLIMINAIRE EN MARCHE (-) COIN CR (+) COIN CR (-) OK POUR DÉPLACER (-) OK POUR DÉPLACER (+) /RETENIR LE DÉMARRAGE (+) /RETENIR LE DÉMARRAGE (-) /MARQUAGE PLASMA (+) /MARQUAGE PLASMA (-) /DÉCOUPE DE MÉTAL EXPANSÉ (+) /DÉCOUPE DE MÉTAL EXPANSÉ (-) /ACTIVÉ AU PLASMA CNC (+) /ACTIVÉ AU PLASMA CNC (-) CC À DISTANCE, POT. ÉLEVÉ CC À DISTANCE (ANALOGIQUE) CC À DISTANCE, POT. BAS ARRÊTER LE SW (MOMENTANÉMENT) ARRÊTER LE RETOUR DU SW PILOTE EN MARCHE (A) PILOTE EN MARCHE (B) PIÈCE DE RECHANGE MANQUANTE NO 1 (A) PIÈCE DE RECHANGE MANQUANTE NO 1 (B) BROCHE 1 Art # A-12757FR 0-5264FR ANNEXE A-15 ULTRA-CUT 100 XT/200 XT/300 XT/400 XT ANNEXE 8 : COMMUNICATIONS DE SÉRIE A8.01 Paramètres des câbles et des interrupteurs pour 2 et 4 fils Le CCM communique avec le TSC 3000 (panneau à écran tactile HMI) à l’aide de RS 485 (2 fils, semi-duplex). Lorsqu’un contrôleur CNC est utilisé à la place du TSC, le CCM peut être reconfiguré pour RS 422 (4 fils, semi-duplex) s’il est pris en charge par le CNC. RS 422 est normalement en duplex intégral, mais le CCM n’est compatible qu’avec le semi-duplex. RS 232 n’est pas directement compatible. Des convertisseurs sont disponibles de diverses sources pour convertir RS 232 à RS 485/422. When possible, the 4 wire ConfigurationisIl est recommandé d’utiliser la Configuration à 4 fils si possible pour faciliter le dépannage. Le port de communication série du CCM a une isolation de 3KV sur le reste du circuit du bloc d’alimentation au plasma. Câblage RS 485 (2 fils, semi-duplex) Module de CCM de CCM pour 2 FILS (RS485 uniquement) utiliser Data +, Data -, Gnd. J54 J14 4W 2W COMMUTATEUR Données+ Données- TERMINAISON SW14 DE LIGNE (line termination) normalement allumée (voir mode d'emploi) CÂBLE ENTRE LE TSC À DISTANCE ET LE CCM (V): J61 (W) 1 2 3 4 5 6 7 8 9 10 11 12 13 14 (R) (BK) (OR) (GN) (OR / W) (W / BL) (BL / W) (W / OR) (GN / W) (W / GN) Les fils multicolores sont torsadés par paires. OR / W = file orange avec ligne blanche. 1 2 3 4 5 6 7 8 9 10 11 12 13 14 15 16 TSC 3000 Activation de plasma Art # A-09481FR CCM à TSC 3000 est RS 485 - 2 fils. Câblage RS 422 (4 fils, semi-duplex) (également appelé RS 485 4 fils) CAVALIER pour 4 FILS, utiliser TX+, TX-, RX+, RXJ14 CÂBLES DE COMMUNICATIONS ET DE COMMANDE (W) CNC à CCM J54 4W 2W 1 2 3 4 5 6 COMMUTATEUR 7 Tx+ 8 9 10 SW14 11 Tx- 12 Rx+ 13 Rx- 14 SW14 - TERMINAISON DE LIGNE (line termination) normalement allumée (voir mode d'emploi) (W) (R) (BK) #1 #2 #3 (OR) (GN) #5 #6 (OR / W) (W / BL) (BL / W) #8 #9 #10 (W / OR) #12 GN / W) #13 (W / GN) #14 Normalement ouvert (NO) pour PLASMA ENABLE (activation de plasma) (fermer pour activer), cavalier de 1 à 3, brancher l'interrupteur sur les nº5 et 6 à la place du cavalier. Fermé normalement (NC) PLASMA ENABLE (activation plasma) (ouvrir pour activer), mettre l'interrupteur sur les nº1 et 3 à la place du cavalier. Pas de cavalier requis. #1 #3 ACTIVATION DU PLASMA NC (ouvrir interrupteur pour activer) ACTIVATION DU PLASMA No (utilisé avec le cavalier) à CNC Rx+ Terre du signal à CNC RxLes fils multicolores sont torsadés par paires. à CNC Tx+ à CNC Tx- Bouclier 2 Bouclier 1 OR / W = file orange avec ligne blanche. Connectez les deux protections à la prise de terre à l’extrémité CNC du câble. Art # A-09482FR_AB Module de CCM Il est recommandé d’utiliser les 4 fils si possible, ce qui facilite le dépannage en cas de problème. Note that CCM Tx+ connects to CNC Rx+ and CCM TX- connects to CNC RX- for 4 wire half duplex. En cas d’utilisation d’un RS 485 à deux fils, connecter le CCM Tx+ (aussi appelé D+ ou Data +) au CNC Tx+ et le CCM Tx- (aussi appelé D- ou Data-) au CNC Tx-. Les fils Rx ne sont pas utilisés pour 2 fils. A-16 ANNEXE 0-5264FR ULTRA-CUT 100 XT/200 XT/300 XT/400 XT Terminaison de ligne : RS 485 and RS 422 are both “multi-drop protocols, that is there can be multiple devices on the same line. Nous ne prenons pas actuellement en charge plus d’un CCM. Jusqu’à ce que nous le fassions, la terminaison des lignes doit toujours être sur ON. Pour RS 485, il est recommandé de couper les lignes de communication à chaque extrémité avec l’impédance caractéristique de la ligne. Pour RS 422, il est recommandé de couper la ligne de communication au niveau du récepteur. Le CCM comporte un interrupteur de terminaison de ligne SW14 dont la position par défaut est sur MARCHE. Pour les CCM qui ne sont pas en bout de ligne (comme CCM 1 et 2, ci-dessous), couper SW14. RS 485 avec de multiples CCM : TSC 3000 (HMI) ou CNC utilisant RS 485 à deux fils La terre (GND) du signal est également requise, mais n'apparaît pas. Données+ 120 Données- SW14 ARRÊT 120 SW14 ARRÊT SW14 MARCHE CCM #1 CCM #2 CCM # (dernier sur la ligne) Art # A-09483FR RS 422 4 fils semi-duplex : CNC avec semi-duplex RS 422 La terre (GND) du signal est également requise, mais n'apparaît pas. Tx+ Tx120 Rx+ Rx- Rx Tx SW14 ARRÊT CCM #1 Art # A-09484FR_AB Rx Tx SW14 ARRÊT CCM #2 Rx 120 Tx SW14 MARCHE CCM # (dernier sur la ligne) Adresse de CCM : Lorsque plus d’un appareil est monté en parallèle sur une ligne de communication série, chacun doit avoir une adresse unique. Le CCM comporte un interrupteur SW10 pour définir l’adresse de chaque CCM. The “0” Réglage en usine is correct for system with one plasma (one CCM). Nous ne prenons pas actuellement en charge de CCM en parallèle. Lorsque cela se présente, les détails pour définir d’autres adresses seront inclus dans un manuel à jour expliquant l’installation et la mise en marche des systèmes parallèles. 0-5264FR ANNEXE A-17 ULTRA-CUT 100 XT/200 XT/300 XT/400 XT ANNEXE 9 : Disposition circuit imprimé UC CCM = Test Point = Test Point Art # A-11675_AC A-18 ANNEXE 0-5264FR ULTRA-CUT 100 XT/200 XT/300 XT/400 XT CCM CPU PCB Points de test TP1 GND TP2 ISO +5.0V TP3 +24V TP4 +3.3V TP5 ISO GND TP6 +5.0V TP7 DEMANDE TOTALE 3,3 V = 400 A TP9 /WR TP10 /RD TP11 DÉTECTION DE TEMPÉRATURE D’UC TP12 +3.3VA TP13 -15VDAC TP14 PC2 TP15 +15VDAC TP16 CLKO TP18 OSC_CLOCK Référence DEL D2 Rouge RXD D3 Rouge TXD D4 Rouge Sortie de fibre 2 D7 Rouge Sortie de fibre 1 D11 Vert Usage ultérieur D17 Vert Usage ultérieur 0-5264FR ANNEXE A-19 ULTRA-CUT 100 XT/200 XT/300 XT/400 XT ANNEXE 10 : Disposition circuit imprimé E/S CCM = Test Point Art # A-11676_AD = Test Point A-20 ANNEXE 0-5264FR ULTRA-CUT 100 XT/200 XT/300 XT/400 XT CCM I/O PCB Connecteurs J Points de test J21CNC DE BASE TP1 GND J22 CNC PROLONGÉ TP2 /VENTILATEURS DE REFROIDISSEMENT ON J23CARTE RELAIS - D’INTERFACE TP3 /POMPE DE LA TORCHE ON J24ARC / TIP VOLTS (VOLTS ARC/POINTE) TP4 FAIBLE DÉBIT DU LIQUIDE DE REFROIDISSEMENT (INT.) J25 TEST TP5 SIGNAL DU DÉBIT DU LIQUIDE DE REFROIDISSEMENT (IMPULSION) TP6 +15 V ISOLÉ TP7 -15V ISOLÉ TP8 +18 V ISOLÉ TP9 CONTRÔLE DU COURANT ANALOGIQUE 0-3,3 V TP10 MISE À LA TERRE ISOLÉE TP11 /ACTIVATION DU PILOTE TP12 +5 V c.c. TP13 -15 V c.c. TP14 +15 V c.c. TP15 24 V c.c. TP18 +5V ISOLÉ TP19 COURANT DE SERVICE J26BOÎTIER À GAZ J28VERS L’UNITÉ CENTRALE J29VERS L’UNITÉ CENTRALE Référence DEL D2 Vert ACTIVATION DE PLASMA D3 Vert E-STOP_PS D4 Vert GAS ON D6 Vert CNC MARCHE D8 Vert HOLD START D12 Vert PREFLOW ON D13 Vert CSD D18 Vert MARK D20 Vert SPARE1 D25 Vert EXP METAL D33 Vert OK TO MOVE D37 Vert PSR D41 RAIN 2 Vert PIÈCE DE RECHANGE DE SORTIE POUR LE TER- D43 RAIN 1 Vert PIÈCE DE RECHANGE DE SORTIE POUR LE TER- 0-5264FR ANNEXE A-21 ULTRA-CUT 100 XT/200 XT/300 XT/400 XT ANNEXE 11 : Disposition du circuit du pilote = Test Point = Test Point Art # A-11677_AB A-22 ANNEXE 0-5264FR ULTRA-CUT 100 XT/200 XT/300 XT/400 XT Points de test du circuit du pilote TP1 GND TP2 PORTAIL DU PILOTE TP3 +5V TP4 POINTE Référence DEL D2 Vert ACTIVATION DU PILOTE D11 Vert +5V 0-5264FR ANNEXE A-23 ULTRA-CUT 100 XT/200 XT/300 XT/400 XT ANNEXE 12 : Disposition du circuit du du relais et de l’interface = Test Point = Test Point Art # A-11678_AB A-24 ANNEXE 0-5264FR ULTRA-CUT 100 XT/200 XT/300 XT/400 XT Points de test du circuit du relais et de l’interface TP1 GND TP2 -15V TP3 +5 V c.c. TP4 +12V TP5 +24V TP6 +15V TP7 +5 V c.c. Référence DEL D2 Vert 1GAZ DE LA TORCHE ALLUMÉ D7 Vert ACTIVATION DU PILOTE D11 Vert COURANT DU PILOTE DÉTECTÉ D12 Vert COURANT DE SERVICE DÉTECTÉ D22 Vert CONTACTEURS EN MARCHE D23 Vert RF ON D24 Vert VENTILATEURS EN MARCHE D25 Vert PLASMA ACTIVÉ D26 Vert 1TORCHE ALLUMÉE D27 Vert LIQUIDE DE REFROIDISSEMENT DE LA TORCHE EN MARCHE 0-5264FR ANNEXE A-25 ULTRA-CUT 100 XT/200 XT/300 XT/400 XT ANNEXE 13 : Afficher la disposition des circuits imprimés = Test Point = Test Point Art # A-11679 A-26 ANNEXE 0-5264FR ULTRA-CUT 100 XT/200 XT/300 XT/400 XT Afficher les points de test de circuit imprimé TP1 GND TP2 +5 V c.c. TP3 +24 V c.c. 0-5264FR ANNEXE A-27 ULTRA-CUT 100 XT/200 XT/300 XT/400 XT ANNEXE 14 : Disposition du circuit de la polarisation du système = Test Point = Test Point Art # A-11680_AB A-28 ANNEXE 0-5264FR ULTRA-CUT 100 XT/200 XT/300 XT/400 XT Points de tests du circuit de la polarisation du système TP1 GND TP2 24 V c.c. TP3 ENTRÉE POSITIVE C.C. TP4 V c.c. 1 TP5 V c.c. 2 TP6 PORTAILAIL TP7 MISE À LA TERRE PRIMAIRE TP8 +12V PRIMAIRE TP9 P_ISOL_GND TP10 SENS POSITIF C.C. Référence DEL D3 Rouge PHASE MANQUANTE D4 Rouge TENSION CA ÉLEVÉE D14 Rouge TENSION CA BASSE D15 Vert VAC_IDA D26 Vert +12V PRIMAIRE D27 Vert VAC_IDB D30 Vert 24 V c.c. D44 Vert TRANSFORMATEUR EN MARCHE 0-5264FR ANNEXE A-29 ULTRA-CUT 100 XT/200 XT/300 XT/400 XT ANNEXE 15 : Disposition du circuit inférieur du hâcheur principal A-30 Art # A-11681_AC = Test Point = Test Point ANNEXE 0-5264FR ULTRA-CUT 100 XT/200 XT/300 XT/400 XT Points de test du circuit inférieur du hâcheur principal TP1 GND TP2 PORTAIL 2A TP3 PORTAIL 1A TP4 PORTAIL 3A TP5 PORTAIL 4A TP6 PORTAIL 2B TP7 PORTAIL 1B TP8 PORTAIL 4B TP9 PORTAIL 3B TP10 +12VP TP11 +12 V c.c. TP12 CÔTÉ THERMISTANCE A TP13 CÔTÉ THERMISTANCE B TP14 +5 V c.c. TP15 PGND Référence DEL D3 Rouge DÉSÉQUILIBRE DU CONDENSATEUR D4 Vert 0-5264FR PRÊT ANNEXE A-31 ULTRA-CUT 100 XT/200 XT/300 XT/400 XT ANNEXE 16 : Disposition du circuit supérieur du hâcheur principal A-32 Art # A-11682_AC = Test Point = Test Point ANNEXE 0-5264FR ULTRA-CUT 100 XT/200 XT/300 XT/400 XT Points de test du circuit supérieur du hâcheur principal TP1 GND TP2 PORTAIL 2A TP3 PORTAIL 1A TP4 PORTAIL 3A TP5 PORTAIL 4A TP6 PORTAIL 2B TP7 PORTAIL 1B TP8 PORTAIL 4B TP9 PORTAIL 3B TP10 +12VP TP11 +12 V c.c. TP12 CÔTÉ THERMISTANCE A TP13 CÔTÉ THERMISTANCE B TP14 +5 V c.c. TP15 PGND Référence DEL D3 Rouge DÉSÉQUILIBRE DU CONDENSATEUR D4 Vert 0-5264FR PRÊT ANNEXE A-33 ULTRA-CUT 100 XT/200 XT/300 XT/400 XT ANNEXE 17 : Disposition circuits imprimés de commande et de défaut = Test Point = Test Point Art # A-11683_AC A-34 ANNEXE 0-5264FR ULTRA-CUT 100 XT/200 XT/300 XT/400 XT Points de test des circuits imprimés de commande et de défaut TP1 GND TP22 +12 V c.c. TP23 +5 V c.c. TP24 PORTAIL 1+ TP25 A_OUT1 TP26 B_OUT1 TP27 PORTAIL 1- TP28 I_SNS1 TP29 PORTAIL 2+ TP30 I_DMD1 0,5 V-6,7 V TP31 PORTAIL 2- TP32 -12 V c.c. TP33 MARCHE 2 TP34 SHDN TP35 ACTIVÉ TP36 ENTRÉE PRÊTE TP37 SORTIE PRÊTE Référence DEL D1 Rouge INV FLT D14 Rouge TEMPÉRATURE EXCESSIVE D24 Vert D32 Rouge PRI OC 0-5264FR PWM ON ANNEXE A-35 ULTRA-CUT 100 XT/200 XT/300 XT/400 XT ANNEXE 18 : Disposition du circuit imprimé du condensateur inférieur Bias Art # A-11685_AC A-36 ANNEXE 0-5264FR ULTRA-CUT 100 XT/200 XT/300 XT/400 XT ANNEXE 19 : Disposition du circuit imprimé du condensateur supérieur Bias Art # A-11686_AC 0-5264FR ANNEXE A-37 ULTRA-CUT 100 XT/200 XT/300 XT/400 XT ANNEXE 20 : Disposition du circuit de protection de contact Art # A-11684_AC A-38 ANNEXE 0-5264FR 0-5264FR ANNEXE Art # A-12268FR Trop-plein Alimentation Réservoir du liquide de refroidissement Plaque de refroidissement 1 Plaque de refroidissement 2 Plaque de refroidissement 3 Pompe Interrupteur de niveau Retour du liquide de refroidissement Radiateur HS1 Capteur de température Débit Débit Détecteur de bulles Interrupteur de débit DESCRIPTION ECO B2502 Torch Coolant Supply Torch Coolant Return Filter 1 REV AA APPROVED AJR XT-300 RAS 1000 **FOR 400 AMP SYSTEMS HE400 DATE 8-8-2013 ULTRA CUT XT POWER SUPPLIES 100A-400A ULTRA-CUT 100 XT/200 XT/300 XT/400 XT ANNEXE 21 : Schéma de refroidissement A-39 ULTRA-CUT 100 XT/200 XT/300 XT/400 XT ANNEXE 22 : SCHÉMA DE PRINCIPE 100A, 380-415V PG 1 1 2 3 4 5 A L1 1 L2 1 L3 1 INVERTER MODULE (IM) #`1 (bottom) W1A 1 2 IN1 EMI FILTER PCB 2 1 IN2 1 2 IN3 (1) (22) 2 1 1 2 Toriod Core 019x502700 MAIN PCB LEDS D3, RED, CAP IMBALANCE D4, GREEN, READY CAP BIAS PCB LEDS D6, GREEN, -12V D11, GREEN, +12VP D13, GREEN, +12V IM #1 Section B (upper) CONTROL PCB LEDS D1, RED, INV FLT D14, RED, OVER TEMP D24, GREEN, PWM ON D32, RED, PRI OC OUT3 CHASSIS GND (2) J103B (9) W1C OUT2 GND2B 1 2 (8) (21) 2 1 1 2 AC INPUT 1 2 J104B W1B OUT1 J105B L5 (7) (20) (3-22) (2-21) (1-20) B 380-415 VAC INPUT (Customer supplied power cord must pass through ferrite core assembly.) (7) J105A L4 IM #1 Section A (lower) AC INPUT 1 2 J104A (3) (8) 1 2 (9) J103A 1 2 Earth Toriod Core 1 WORK (+) 019x502000 C CHASSIS GND AC SUPPRESSION J50 PCB J51 019X504000 (1) (2) (3) 18 AWG wire both in and out of CB1 (1-20) (2-21) (3-22) (26) (27A&B) (28) CB1 (11) (12) J52 LT2 1 2 3 4 GND Component Locations (not including PCB components) (13) INTERNAL AC INDICATOR C4 CB1 LT1 & LT2 INPUT POWER NEON INDICATORS Rear Panel & Internal CHASSIS GND ON / OFF 16 A LT1 PANEL AC INDICATOR AC LINE D (10) 1 2 3 4 1 2 3 4 5 6 7 8 9 10 11 12 13 14 To J27 on CCM I/O PCB F1 (Sht 2, E3) SYSTEM BIAS SUPPLY PCB +24VDC 8A, 500V, SB 8A, 500V, SB J62 019X501900 F2 1 2 +V 3 4 AC INPUT E (85A) (86B) (27B) (85B) 5 6 7 8 9 11 12 13 14 J63 F 1 2 3 4 5 6 7 8 9 10 11 12 J60 J63 = Mini-Fit Jr goes to J12 on T1 primary 400 VAC -- Single 18 AWG in pins 1 & 12 480 VAC -- Single 18 AWG in pins 1 & 12 230 VAC -- 18 AWG wires in pins 1, 6, 7, 12 A-40 (29) (30) (31) (32) (33) (34) (35) (36) (37) (38) (39) (40) (41) (42) 230V 400V 480V ERR /VAC_IDAb 0 1 0 1 /VAC_IDBb 0 0 1 1 Measure relative to TP1 (24VDC_RET) "0" = 10-12V "1" = 24V J61 VOLTAGE SELECTION TO AUX TRANSFORMER Wire #48 from J61-1 to: J61-2 for 208-230 VAC J61-3 for 400 VAC J61-4 for 480 VAC System Bias LEDs & Test Points (48) (44A) (43A) TO J12 T1 PRIMARY (Sht 2, A1) Art # A-11959_AD 1 10 GND 480V-ID 400V-ID 208-230V-ID COM (27A) 1 2 3 4 5 6 7 8 9 10 11 12 13 14 15 16 17 18 4 3 2 1 (86A) 24 VDC 24 VDC MISSING PHASE a MISSING PHASE b AC V HIGH a AC V HIGH b AC V LOW a 24 VDC_RET 24 VDC_RET AC V LOW b VAC_IDA a / VAC_IDA b VAC_IDB a / VAC_IDB b 2 LEDS D3, RED, MISSING PHASE D4, RED, AC V HIGH D14, RED, AC V LOW D26, GREEN, +12V PRI D30, GREEN, 24VDC D44, GREEN, T1 ON Capacitor, fan starting, 8uf 440VAC (Sht 2, E1) Circuit Breaker /ON/OFF SW, 15A 480V (Sht 1, E1) CB2-4 Circuit Breaker, 5A, 250V (Sht 2, B3) F1, 2 Fuse, 8A, 500V, S.B. (Sht 1,E1) FAN1,2 Fan, Heat Exchanger , 230 VAC (Sht 2, D2) FL1 Flow meter, pulse output (Sht 2, B2) FS1 Flow SW, 0.5 GPM (3.8 lpm), N.O. (Sht 2, A2) HCT1 Current Sensor, Hall Effect 200A, Work Lead (Sht 1, C8) K1 Relay, 24VAC, Inrush Control, (Sht2, B9) L1 Inductor, (Sht 1, B7) L3-5 Toriod Core Common Mode Ind (Sht1 B8, B&C3) LS1 Level Switch, Coolant Tank (Sht 2, A3) LT1, LT2 Indicator, Neon, 250V, AC Volts Present (Sht 1, B2 & C2) M1 Motor, Pump, ½ hp 230VAC, 50/60 Hz, 1Ph (Sht 2, C2) MC1 Relay, 120VAC, Inrush, coil (Sht2, B9) contact (Sht2, A1) MC2 Relay, 120 VAC, Fan Control, coil (Coil at Sht 2, A7)(Contacts at Sht 2, D1) MC3 Relay, 120 VAC, Pump Motor Control, coil (Coil at Sht 2, A7)(Contacts at Sht 2, C1) R2 Inrush, 4.7 Ohm, 30W (Sht2, A1) R3,4 Ext RC, 100 ohm 55W (Sht1, A7) SA1-3 Snubber, Contactor & Relay coils (Sht 2, A8 & A9) T1 Aux Transformer (Sht 2, B2) TB4 Terminal Block (Sht 1, C9) TS1 Temperature Sensor, NTC, Coolant Return (Sht 2, A5) TS2 Temperature Sensor, NTC, Ambient (Sht 2, A5) W1 Contactor , Input (Coil Sht 2, A8), (Contacts C2) TEST POINTS TP1 SECONDARY GND TP2 24VDC TP3 DC INPUT POSITIVE TP4 VCC1 TP5 VCC2 TP6 GATE TP7 PRIMARY GND TP8 +12V PRIMARY TP9 P ISOL GND 3 ANNEXE 4 0-5264FR ULTRA-CUT 100 XT/200 XT/300 XT/400 XT 6 7 8 9 10 TORCH To TB4-7 TORCH (49) 1 A TEST POINTS TP1 GND TP2 PILOT GATE TP3 +5V PILOT BOARD LED'S D2 PILOT ENABLE D11 +5V L3 (49) RAS PILOT 1 J43 ELECTRODE To TB4-6 TIP PILOT PCB J58A 1 J44 (52) J41 (J87) 2 1 1 R3 & R4 CHASSIS GND ELECTRODE (-) 4 3 2 1 WORK (+) 2 1 INVERTER L1 J42 TIP To / From Optional 1 Torch Module (Refer to 1 Torch section for details.) J45 10 ckt Ribbon (51B) (+) B Tip WORK (53) TO J3 on RELAY PCB (Sht 2, A5) OUTPUT (-) CHASSIS GND 019X501600 1 2 3 4 5 6 7 8 J102B (49B) 5 SHIELD (52) 1 2 1 2 3 4 5 6 7 8 9 10 J100 -- 30 CKT RIBBON J40 2 1 J46-F J46-M (Sht 2, C3) J41 5 4 3 2 1 Electrode J58C (50) TO CCM CPU PCB J32 Work 1 (+) TIP VOLTS TO CCM CPU PCB J31 To J24 on I-O PCB (Sht 2, C3) (Sht 2, D3) (51) WORK ARC VOLTS (55) J100 -- 30 CKT RIBBON J102A (49A) HCT1 (50) Hall Effect Sensor (51) 3 4 2 C 4 J16 (51) (51) 1 OUTPUT 3 (51) 2 WORK (+) 1 5 4 3 2 1 ELECTRODE (-) TO J1 on RELAY PCB (Sht 2, B9) COMMON SIG (+) -15 VDC +15 VDC TB4 TORCH (Sht 1, A9) TIP (Sht 1, A9) (56) o AC 120V- TB4-4 (57) b AC 120V- Ret- TB4-3 (58) g (59) AC 24V-TB4-2 w AC 24V- Ret -TB4-1 (49) (52) (51) (60) 7 ARC VOLTS (TORCH) 6 TIP VOLTS (PILOT) 5 WORK 4 (61) 3 (62) 120 VAC @ 100 ma. 2 (63) 1 24 VAC @ 1A (J10 Sht 2, B8) RIBBON CABLE 40 ckt CCM (J23) - RELAY PCB (J4) 32 COMMON 1 COMMON 33 -15 VDC 2 /1TORCH START * 34 COMMON 3 NA 35 24 VDC 4 /1TORCH GAS SOL ON * 36 COMMON 5 /MAIN TORCH IDLE * 37 24 VDC 6 /1TORCH PRESS OK * 38 COMMON 7 FLOW SENSOR (pulses) 39 24 VDC 8 LOW COOLANT FLOW 40 COMMON 9 COOLANT LEVEL OK 10 COMMON 11 NA RIBBON CABLE 16 ckt 12 /PLASMA ENABLE-HMI CCM ( J37) - DISPLAY 13 /COOLANT PUMP ON PCB (J17) 14 COMMON 1,3,5,7 24 VDC 15 /PILOT ENABLE 2,4,6,8 COMMON 16 /RAS ON 9,10 NC 17 /CONTACTORS ON 11-16 SERIAL DATA 18 COMMON 19 /COOLANT FANS ON 20 /1TORCH CONTACTOR ON * RIBBON CABLE 10 ckt 21 /PLASMA ENABLE RELAY RELAY PCB (J3) – PILOT PCB (J42) 22 COMMON 23 PILOT CURRENT SIG1,2 24 VDC 24 NC 3,4,7,10 COMMON 25 PILOT CURRENT SIG+ 5 PILOT ENABLE + 26 COMMON 6 PILOT ENABLE – 27 WORK CURRENT SIG8 PILOT CURRENT SIG – 28 WORK CURRENT SIG+ 9 PILOT CURRENT SIG + 29 NC 30 AMBIENT TEMP 31 COOLANT TEMP * Used with 1 Torch O ption RIBBON CABLE 30 ckt. CCM (J31& 32) - INVERTER (J100) 1 2 3 4 5 6 7 8 9 10 11 12 13 14 15 16 17 18 19 20 21 22 23 24 25 26 27 28 29 30 READY + READY INVERTER_FLT + INVERTER_FLT OVERTEMP_FLT + OVERTEMP_FLT PWR_PRESENT + PWR_PRESENT OUT_COM (+3 to 5VDC) VAC_SELA VAC_SELB IS_IDA IS_IDB IS_IDC ENABLE + ENABLE START2 + START2 SPARE SYNC_IN + SYNC_IN NC NC 47 OHM to COMM DEMAND + DEMAND 47 OHM to COMM CURRENT + CURRENT 47 OHM to COMM D E Art # A-11959_AD Revision Rev 00 Initial Design DAT AA AB By DAT ECO-B2687 DAT Date Revision Rev By Date Thermal Dynamics Corporation 2800 Airport Rd. Denton, Texas 76207 USA 10/03/2012 9 /1 6 /2 0 1 4 F Date Printed Date Revised 11/20/2014 12/16/2014 Drawn Date 10/17/2014 Size Drawing Number SCHEMATIC Ultra-Cut XT 100A CE 380-415 VAC 5 0-5264FR 6 7 8 ANNEXE 10 10/03/2012 DAT The information contained herein is proprietary to Thermal Dynamics. Not for release, reproduction or distribution without written consent. Title C Sheet 1 of 2 042X1354 9 A-41 ULTRA-CUT 100 XT/200 XT/300 XT/400 XT ANNEXE 23 : SCHÉMA DE PRINCIPE 100A, 380-415V PG 2 3 J12 = Mini-Fit Jr 400 VAC -- Single 18 AWG in pins 1 & 4 480 VAC -- Single 18 AWG in pins 1 & 8 230 VAC -- 18 AWG wires in pins 1,5,2,6 1 LS1 COOLANT LEVEL (89) COOLANT MC1A J74 (84) 1 2 (83) COOLANT TS2 (59) (58) (57) (56) FS1 (44A) 4 J71 AMBIENT (92) TS1 (93) COMMON SIG (+) -15 VDC +15 VDC A 5 (90) 2 3 From Sys Bias J63 (Sht 1, F2) (43A) 4 (Sht 1, C8) 2 TO HCT1 (Work) 1 0.7 GPM (94) (95) 3 T1 1 2 3 4 (81) (82) J49 460V 24V RET (79) BLUE 6 RED 24V B BLUE 4 3 RED 2 YELLOW 120V_2 220V 5 YELLOW 120V_2 RET 400V J6 120V-1 RET 1 (77) (74) (71) 12 11 10 9 8 7 6 5 4 3 2 1 (78) CB2 5 A (76) (75) CB3 5 A (73) CB4 5 A (72) J9 J14 120V_1 120VAC_2 24VAC MC3A J16 (66) BIAS TRANSFORMER J72 (69) (65A) (64A) FAN1 1 2 3 (70) MC2B D 230 VAC _ SW _ RET (A9) FAN2 1 2 3 230 VAC _ SW (A9) R J72 1 2 3 E C4 BK FAN1 BN BL R 6 5 4 3 2 1 1 2 J33 - 30 CKT RIBBON J34 - 30 CKT RIBBON N/C N/C J35 - 30 CKT RIBBON J36 - 30 CKT RIBBON J84 J85 CPU PCB (CCM ) J28 30 CKT RECEPTACLE - BOTTOM ENTRY I-O PCB (CCM) (55) 1 2 3 4 5 6 7 8 230 VAC_SW goes to J70 for HE 400 I / O PCB TEST POINTS ------------------------------------TP1 PCB COMMON TP2 COOLANT FANS ON TP3 PUMP ON TP4 LOW FLOW (SW) TP5 FLOW SIGNAL (pulse, Ultracut only) TP6 +15VDC_ISO (ref to TP10) TP7 -15VDC_ISO (ref to TP10) TP8 +16-18 VDC_ISO (ref to TP10) TP9 ANALOG CURRENT SIGNAL (remote & Autocut only) TP10 ISOLATED VOLTAGE COMMON TP11 1 TORCH CONTACTOR ON TP12 +5 VDC TP13 -15 VDC TP14 +15 VDC TP15 +24 VDC TP18 +5 VDC_ISO (ref to TP10) Harness from System Bias PCB J62 (Sht 1, E3) 24 VDC 24 VDC MISSING PHASE a MISSING PHASE b AC V HIGH a AC V HIGH b AC V LOW a 24 VDC_RET 24 VDC_RET AC V LOW b VAC_IDA a / VAC_IDA b VAC_IDB a / VAC_IDB b (29) (30) (31) (32) (33) (34) (35) (36) (37) (38) (39) (40) (41) (42) 1 2 3 4 5 6 7 8 9 10 11 12 13 14 J27 . 230V 400V 480V ERR J62-12 (/VAC_IDAb) 0 1 0 1 J62-14 (/VAC_IDBb) 0 0 1 1 J28 30 CKT PIN HEADER I / O PCB LEDS ---------------------------------------------D2 CNC PLASMA ENABLE D3 E-STOP_PS D4 GAS ON (Auto-cut, PAK) D6 CNC START D8 HOLD START D12 PREFLOW ON D13 CSD (corner current reduction) D18 MARK D20 SPARE D25 EXP METAL D33 OK_CNC D37 PSR D41 SPARE OUT 2 D43 SPARE OUT 1 CHASSIS GND Alternate fan. 100 & 200A units may use either this single larger fan (same as 300 & 400A units) or the 2 smaller fans shown above. 3 N/C J24 (70) J32 - 30 CKT RIBBON N/C (53) (51) J73 (69) (70) TIP VOLTS 230 VAC (69) MC2A (Sht 1, B8) WORK (67) (64B) 019X501700 J11 Harness from Pilot PCB J45 Torch Coolant Pump ARC VOLTS J13 to CB5 and to MC2 & MC3, also J14, J16 all 18 AWG 4 1 TORCH INTERFACE M1 1 2 3 CHASSIS GND Test Points TP1, GND TP2, -15V TP3, +5VDC TP4, +12V TP5, +24V TP6, +15V TP7, +5VDC Refer to 1 Torch Module Schematic for Details 19X501100 MC3B TEMP SENSOR D2, GREEN, 1TORCH GAS ON D7, GREEN, PILOT ENABLED D11, GREEN, PILOT CURRENT D12, GREEN, WORK CURRENT D22, GREEN, CONTACTORS ON D23, GREEN, RF ON D24, GREEN, FANS ON D25, GREEN, PLASMA ENABLED D26, GREEN, 1TORCH ON D27, GREEN, COOLANT ON 120VAC_1 1 2 3 (64A) (64B) (65A) (65B) 4 SIGNAL (pulse) TORCH FLOW SENSOR J31 - 30 CKT RIBBON Mini-Fit C J2 RELAY & INTERFACE PCB +5VDC To J100 of IM #1B To J100 of IM #1A (Sht 1, B&C- 5&6) 0V J13 J1 WORK CURRENT SENSOR 14 13 12 11 10 9 8 7 6 5 4 3 2 1 1 2 3 4 5 6 7 8 1 2 3 4 LEVEL SENSORS 3 2 1 2 J7 COOLANT FLOW SW (80) 5 4 3 2 1 r b g 1 1 5 2 6 3 7 4 8 J12 J5 FL1 Mini-Fit Jr 8 7 6 5 4 3 2 1 4.7 30W (87) 2 1 R2 19X501200 I / O PCB DIP SW --------------------------------------------SW6 OK TO MOVE (CONTACTS, VOLTS) SW11 ANALOG CC SOURCE SW12 DIVIDED ARC VOLTAGE (50:1, 16.7:1, 30:1, 40:1, 25:1) Measure relative to TP1 (24VDC_RET) "0" = 10-12V "1" = 24V F Art # A-11960_AD 1 A-42 2 3 ANNEXE 4 0-5264FR ULTRA-CUT 100 XT/200 XT/300 XT/400 XT 6 7 TO PILOT PCB (Sht 1, B8) (161) SA3 (162) MC3 SA4 SA1 ARC_SUPPRESSOR (60) CONTROL OUTPUTS 120 VAC_1 HMI/GCM (101) (102) (103) (104) (106) AC 24V GCM2 (62) AC 120V - GCM (60) (108) (109) (110) (111) (113) (61) AC 24V - RET - GCM2 AC 120V- Ret- GCM AC 120V- Ret- TB4-3 (63) (62) 1 J10 1 2 3 4 PROG USB IC J18 J29 30 CKT RECEPTACLE - BOTTOM ENTRY GND GND J19 RxTx+ Rx+ Tx- 4 WIRE 1 2 3 4 5 6 7 8 9 10 11 12 120 VAC Ret (98) 1 2 3 4 5 6 5 (101) (102) AC 24V-TB4-2 (109) AC 120V- TB4-4 (108) (115) AC 24V Ret- GCM1 (116) (117) Harness AC 24V- Ret -TB4-1 (118) K1 2 3 (119) (120) (107) PLAS_ENABLE SW PLAS_ EN_SW_RET / GAS PRESS OK / BASIC ID TB1 OK2 (contact) +10V (CC Pot Hi) CC Pot Wiper CC Pot Low Div Arc V (+) Div Arc V (-) /Start - Stop (+) /Start - Stop (-) Stop Mom NC OK2 (contact) / CNC Enable (+) / CNC Enable (-) CPU PCB TEST POINTS -------------------------------------------TP1 GND (PCB common) TP2 +5V_ISO (REF TP5) TP3 +24 VDC TP4 +3.3V TP5 GND_ISO TP6 +5.0 V TP7 TOTAL DEMAND (3.3V = 400A) TP9 /WR TP10 /RD TP11 CPU TEMP SENSE TP12 +3.3VA TP13 -15VDAC TP14 PC2 TP15 +15VDAC TP16 CLKO TP18 OSC_CLOCK 12 11 10 9 8 7 6 5 4 3 2 1 12 11 10 9 8 7 6 5 4 3 2 1 OK to MOVE (-) PILOT is ON PILOT is ON Preflow ON (+) Preflow ON (-) Hold Start (+) Hold Start (-) CPU PCB DIP SW --------------------------------------------SW1 AUTO PILOT RESTART SW3 PREFLOW TIME SW4 POSTFLOW TIME SW5 FUNCTION SW8 SYSTEM CONTROL (pilot time, etc.) SW9 RESERVED (future) SW10 ADDRESS (default = 0) SW13 UNIT TYPE (AC / UC) SW14 LINE TERMINATION (serial comm.) 1 2 3 4 5 6 7 8 9 10 11 12 13 14 15 16 GND 1 2 3 4 5 6 7 8 9 10 11 12 13 14 15 16 17 18 TB2 OK to MOVE (+) +10V GND GND TB3 12 11 10 9 Spare #1b NO 8 7 6 Spare 5 Digital 4 Inputs 3 / Plasma Marking (-) 2 / Plasma Marking (+) 1 PSR SPARE #1a 00 Initial Design AA AB By DAT DAT ECO-B2687 DAT Date Revision Rev 16 CKT RIBBON (121) (122) (123) (124) (125) (126) (127) (128) (129) (130) (131) (130) (131) (112) (114) (121) (122) (124) (129) (128) (123) AC 24V Ret - GCM1 AC 24V-GCM2 AC 24V Ret-GCM2 (111) J69 2 1 (133) (134) (137) (139) (138) (143) (104) (166) (125) (126) (127) (142) (112) (114) (103) (110) AC 24V-GCM1 AC 120V - GCM AC 120V- Ret- GCM (167) (106) (113) CHASSIS GND (133) (134) (135) (136) (137) (138) (139) (140) (141) (142) (140) (141) (136) (135) (132) (153) (143) (144) (145) (144) (145) (146) (147) (148) (149) (150) (151) (146) (147) (148) (149) (150) (151) (152) (154) (155) (132) (152) (153) (154) (155) (156) (157) (158) (159) (156) (157) (158) (159) J22 By Date 0-5264FR 6 J55 - GCM 1- PLAS_ENABLE SW * 2- PLAS_ EN_SW_RET 3- GAS PRESS OK RET 4- / GAS PRESS OK 5- POT HIGH (GCM 1000) 6- POT WIPER (GCM 1000) 7- POT LOW (GCM 1000) 8- BASIC ID RET 9- / BASIC ID ** 1011GCM 1000 XT Jumper 1415- 24 VAC - RET 1 2 3 4 5 6 7 8 9 10 11 12 13 14 15 16 17 18 19 20 21 22 23 24 25 26 27 28 29 30 31 32 33 34 35 36 37 * Plasma Enable SW in GCM 2010. Jumpered in GCM 1000 XT and DMC 3000. ** Jumper in GCM 1000 XT 27- GAS SEL SW RET 28- GAS SEL SW D J15-1 to chassis used for SC-11 cable shield J15-13 connects SC-11 chassis to PS chassis. J15-CNC 1 2 3 4 5 6 7 8 9 10 11 12 13 14 15 16 17 18 19 20 21 22 23 24 25 26 27 28 29 30 31 32 33 34 35 36 37 C The COMM Ref at pin 8 is also for the SC-11 3- / CNC Start (+) 4- / CNC Start (-) 5- Divided Arc V (-) 6- Divided Arc V (+) 7- / Preflow ON (+) 8- COMM Ref (1K Ohm) 9- / Preflow ON (-) 10- / Spare Digital Input (+) 11- / Spare Digital Input (-) 12- OK to Move (-) 14- OK to Move (+) 15 - Key Plug 16- / Hold Start (+) 17- / Hold Start (-) E 21- / Plasma Mark (+) 22- / Plasma Mark (-) 23- / Spare Digital Input(+) 24- / Spare Digital Input (-) 25- / CNC Plasma Enable (+) 26- / CNC Plasma Enable (-) 29- Remote CC Pot High 30- Remote CC (analog) 31- Remote CC Pot Low 32- Stop SW (momentary) * 33- Stop SW Ret 34- Pilot is ON (a) 35- Pilot is ON (b) 36- Spare OUT #1 (a) 37- Spare OUT #1 (b) * Used with Momentary CNC Start SW Thermal Dynamics Corporation 10/03/2012 2800 Airport Rd. Denton, Texas 76207 USA 9 /1 6 /2 0 1 4 F Date Printed Date Revised 12/16/2014 11/20/2014 Drawn Date 10/17/2014 Size Drawing Number SCHEMATIC 7 8 ANNEXE 9 10/3/2012 DAT The information contained herein is proprietary to Thermal Dynamics. Not for release, reproduction or distribution without written consent. Title Ultra-Cut XT 100A CE 380-415 VAC 5 12 - Tx13 - Rx+ 14 - Rx- Harness Art # A-11960_AD Revision Rev B Comm Display PCB J21 1 2 3 4 5 6 7 8 9 10 11 12 13 14 15 16 17 18 19 20 Spare Digital Inputs 5-HMI Plasma Enable SW 6-HMI Plasma Enable SW 7 - Key Plug 8 - Tx+ 9 - GND RS 485 10 - GND / 422 J17 J26 OK 1 - 24 VAC 2 - 24 VAC Ret 3- Jumper to 24 VAC 2 3 4 5 6 7 8 9 10 11 12 13 14 (61) GAS ON ENABLE 3 - Key Plug 019X501800 J37 J23- 40 ckt ribbon cable A (61) J20 J29 30 CKT PIN HEADER CPU PCB LEDs ---------------------------D2 RXD (red) D3 TXD (red) D4 CAN BUS (slave) D7 CAN BUS (MAIN) D11 5 VDC POWER D17 STATUS CODE D18 INITIALIZING / PROGRAMMING (red) 1 2 3 4 5 6 7 8 9 10 11 12 13 14 J54 - Remote HMI & CNC COMM (100) 1 AC 24V GCM1 INRUSH CONTROL (116) (117) (120) (115) (119) (118) J30 2 WIRE 1 2 3 4 5 6 1 2 3 4 5 6 7 8 9 10 11 12 NORMAL PROGRAM RS 232 D-SUB SERIAL PROG PORT (63) J47 1 2 3 4 1 2 3 4 5 6 7 8 9 J39 USB PORT (99) (107) 4 USB Cable to Front Panel J38 MC1 120 VAC to RAS 120VAC (100) 18 17 16 15 14 13 12 11 10 9 8 7 6 5 4 3 2 1 120 VAC_2 J4 -- 40 CKT RIBBON CABLE J59 - RAS (97) (96) (98) (99) (97) 24 VAC 1 2 3 4 5 6 7 CHASSIS GND 24 VDC GND (70) ( 69) W1 16 15 14 13 12 11 10 9 8 7 6 5 4 3 2 1 2 1 4 3 J8 230 VAC Ret ( 69) J70 - HE (D2) (96) Pump Motor Control (163) (160) 10 CKT RIBBON / PILOT ENABLE / PILOT ENABLE RET 5 6 7 PILOT A SIG Vin+ PILOT A SIG Vin8 9 10 (D2) 230 VAC _ SW _ RET 10 230 VAC to HE 400 (70) 230 VAC _ SW ARC_SUPPRESSOR PILOT PCB 9 MC2 Fan Control ARC_SUPPRESSOR J3 8 C Sheet 2 of 2 042X1354 10 A-43 ULTRA-CUT 100 XT/200 XT/300 XT/400 XT ANNEXE 24 : SCHÉMA DE PRINCIPE 200A, 380-415V PG 1 1 2 3 4 5 A INVERTER 1/2 MODULE (IM) #2 (top) (1) 1 2 IN1 (2) EMI FILTER PCB 1 2 (21) 2 1 IN2 (3) (20) 2 1 OUT1 1 2 OUT2 IM #2 Section A (lower) AC INPUT 1 2 (8) OUT3 IN3 1 2 J104A (22) 2 1 GND2B J105A L6 (7) J103A (9) 1 2 Toriod Core CHASSIS GND 019x502000 B IN2 C 1 L2 1 L3 1 Earth OUT2 IN3 (1) 1 2 (8) J103B (9) 1 2 Toriod Core (7) J105A L4 1 2 CHASSIS GND 1 2 3 4 5 6 7 8 9 10 11 12 13 14 (1) 380-415 VAC INPUT (Customer supplied power cord must pass through ferrite core assembly.) (2) (3) 019X504000 (10) J51 1 2 3 4 LT1 & LT2 INPUT POWER NEON INDICATORS (11) (12) GND Component Locations (not including PCB components) C4 CB1 LT2Rear Panel & Internal 1 2 3 4 (13) INTERNAL AC INDICATOR CHASSIS GND (3-22) (2-21) (1-20) 18 AWG wire both in and out of CB1 (FRONT PANEL) (28) (26) (27A&B) To J27 on CCM I/O PCB SYSTEM BIAS SUPPLY PCB F2 J62 019X501900 8A, 500V, SB +24VDC 1 2 +V E (85A) (86B) (27B) (85B) AC INPUT 4 1 2 3 4 5 6 7 8 9 10 11 12 13 14 15 16 17 18 5 6 7 8 9 GND 13 K1B 1 2 3 4 5 6 7 8 9 10 11 12 J63 F TO AUX TRANSFORMER A-44 14 (48) J61 VOLTAGE SELECTION (44A) (43A) TO J12 T1 PRIMARY (Sht 2, A1) Art # A-11961_AD 1 11 12 K1A J60 J63 = Mini-Fit Jr goes to J12 on T1 primary 400 VAC -- Single 18 AWG in pins 1 & 12 480 VAC -- Single 18 AWG in pins 1 & 12 230 VAC -- 18 AWG wires in pins 1, 6, 7, 12 10 480V-ID 400V-ID 208-230V-ID COM (27A) 3 4 3 2 1 (86A) 2 WORK (+) 019x502000 LT1 PANEL AC INDICATOR IM #1 Section A (lower) AC INPUT 1 2 D F1 CONTROL PCB LEDS D1, RED, INV FLT D14, RED, OVER TEMP D24, GREEN, PWM ON D32, RED, PRI OC 1 2 Toriod Core J52 AC LINE 8A, 500V, SB D6, GREEN, -12V D11, GREEN, +12VP D13, GREEN, +12V IM #1 Section B (upper) J103A (9) AC SUPPRESSION PCB J50 CB1 019x502700 MAIN PCB LEDS D3, RED, CAP IMBALANCE D4, GREEN, READY CAP BIAS PCB LEDS J104A (8) (3) 1 ON / OFF 16 A AC INPUT 1 2 OUT3 CHASSIS GND (2) J105B L5 J104B W1C (22) 2 1 GND2B (3-22) L1 (21) 2 1 1 2 W1B OUT1 1 2 (7) (20) 2 1 (1-20) IN1 INVERTER MODULE (IM) #`1 (bottom) W1A EMI FILTER PCB (2-21) 1 2 (Sht 2, E3) 24 VDC 24 VDC MISSING PHASE a MISSING PHASE b AC V HIGH a AC V HIGH b AC V LOW a 24 VDC_RET 24 VDC_RET AC V LOW b VAC_IDA a / VAC_IDA b VAC_IDB a / VAC_IDB b (29) (30) (31) (32) (33) (34) (35) (36) (37) (38) (39) (40) (41) (42) 230V 400V 480V ERR /VAC_IDAb 0 1 0 1 /VAC_IDBb 0 0 1 1 Capacitor, fan starting, 8uf 440VAC (Sht 2, E1) Circuit Breaker /ON/OFF SW, 15A 480V (Sht 1, E1) CB2-4 Circuit Breaker, 5A, 250V (Sht 2, B3) F1, 2 Fuse, 8A, 500V, S.B. (Sht 1,E1) FAN1,2 Fan, Heat Exchanger , 230 VAC (Sht 2, D2) FL1 Flow meter, pulse output (Sht 2, B2) FS1 Flow SW, 0.5 GPM (3.8 lpm), N.O. (Sht 2, A2) HCT1 Current Sensor, Hall Effect 200A, Work Lead (Sht 1, C8) K1 Relay, 24VAC, Inrush Control, (Sht2, B9) L1 Inductor, (Sht 1, B7) L3-5 Toriod Core Common Mode Ind (Sht1 B8, B&C3) LS1 Level Switch, Coolant Tank (Sht 2, A3) LT1, LT2 Indicator, Neon, 250V, AC Volts Present (Sht 1, B2 & C2) M1 Motor, Pump, ½ hp 230VAC, 50/60 Hz, 1Ph (Sht 2, C2) MC1 Relay, 120VAC, Inrush, coil (Sht2, B9) contact (Sht2, A1) MC2 Relay, 120 VAC, Fan Control, coil (Coil at Sht 2, A7)(Contacts at Sht 2, D1) MC3 Relay, 120 VAC, Pump Motor Control, coil (Coil at Sht 2, A7)(Contacts at Sht 2, C1) R2 Inrush, 4.7 Ohm, 30W (Sht2, A1) R3,4 Ext RC, 100 ohm 55W (Sht1, A7) SA1-3 Snubber, Contactor & Relay coils (Sht 2, A8 & A9) T1 Aux Transformer (Sht 2, B2) TB4 Terminal Block (Sht 1, C9) TS1 Temperature Sensor, NTC, Coolant Return (Sht 2, A5) TS2 Temperature Sensor, NTC, Ambient (Sht 2, A5) W1 Contactor , Input (Coil Sht 2, A8), (Contacts C2) Measure relative to TP1 (24VDC_RET) "0" = 10-12V "1" = 24V Wire #48 from J61-1 to: J61-2 for 208-230 VAC J61-3 for 400 VAC J61-4 for 480 VAC System Bias LEDs & Test Points LEDS D3, RED, MISSING PHASE D4, RED, AC V HIGH D14, RED, AC V LOW D26, GREEN, +12V PRI D30, GREEN, 24VDC D44, GREEN, T1 ON TEST POINTS TP1 SECONDARY GND TP2 24VDC TP3 DC INPUT POSITIVE TP4 VCC1 TP5 VCC2 TP6 GATE TP7 PRIMARY GND TP8 +12V PRIMARY TP9 P ISOL GND 3 ANNEXE 4 0-5264FR ULTRA-CUT 100 XT/200 XT/300 XT/400 XT 6 7 8 9 10 TORCH To TB4-7 TEST POINTS TP1 GND TP2 PILOT GATE TP3 +5V D2 PILOT ENABLE D11 +5V J43 ELECTRODE CHASSIS GND (51C) OUTPUT TO CCM CPU PCB J32 2 1 (51F) J42 WORK (+) OUTPUT To / From Optional 1 Torch Module (Refer to 1 Torch section for details.) J45 10 ckt Ribbon (51B) Tip WORK B SHIELD Work 1 (+) TIP VOLTS To J24 on I-O PCB WORK (Sht 2, D3) 4 3 2 1 (+) (53) TO J3 on RELAY PCB (Sht 2, A5) J102B (49B) 5 ELECTRODE (-) 019X501600 INVERTER (Sht 2, C3) J100 -- 30 CKT RIBBON TIP J40 SHIELD (-) CHASSIS GND 1 2 2 1 J46-F J46-M WORK (+) J41 5 4 3 2 1 1 2 3 4 5 6 7 8 9 10 4 3 2 1 1 2 3 4 5 6 7 8 (50) J102A (49C) 5 ELECTRODE (-) J58C Electrode (Sht 2, C3) J100 -- 30 CKT RIBBON 1 2 1 J41 (J87) RAS PILOT (52) 1 R3 & R4 TO CCM CPU PCB J33 A To TB4-6 TIP J44 PILOT PCB J58A 1 L3 (49) 1 PILOT BOARD LED'S TORCH (49) (49) (51) ARC VOLTS (55) L1 TO CCM CPU PCB J31 HCT1 (Sht 2, C3) (51) (51) Hall Effect Sensor TO J1 on RELAY PCB (Sht 2, B9) 3 4 3 4 SIG (+) OUTPUT C TB4 COMMON 2 +15 VDC 1 J16 (50) 2 5 4 3 2 1 WORK (+) -15 VDC J102A (49A) ELECTRODE (-) 1 J100 -- 30 CKT RIBBON TORCH (Sht 1, A9) TIP (Sht 1, A9) (56) o AC 120V- TB4-4 (57) b AC 120V- Ret- TB4-3 (58) g (59) AC 24V-TB4-2 w AC 24V- Ret -TB4-1 (49) (52) (51) (60) 7 ARC VOLTS (TORCH) 6 TIP VOLTS (PILOT) 5 WORK 4 (61) 3 (62) 2 (63) 1 120 VAC @ 100 ma. 24 VAC @ 1A (J10 Sht 2, B8) RIBBON CABLE 30 ckt. CCM (J31-36) - INVERTER (J100) 1 2 3 4 5 6 7 8 9 10 11 12 13 14 15 16 17 18 19 20 21 22 23 24 25 26 27 28 29 30 RIBBON CABLE 40 ckt CCM (J23) - RELAY PCB (J4) 32 COMMON 1 COMMON 33 -15 VDC 2 /1TORCH START * 34 COMMON 3 NA 35 24 VDC 4 /1TORCH GAS SOL ON * 36 COMMON 5 /MAIN TORCH IDLE * 37 24 VDC 6 /1TORCH PRESS OK * 38 COMMON 7 FLOW SENSOR (pulses) 39 24 VDC 8 LOW COOLANT FLOW 40 COMMON 9 COOLANT LEVEL OK 10 COMMON 11 NA 12 /PLASMA ENABLE-HMI 13 /COOLANT PUMP ON 14 COMMON 15 /PILOT ENABLE 16 /RAS ON 17 /CONTACTORS ON 18 COMMON 19 /COOLANT FANS ON 20 /1TORCH CONTACTOR ON * 21 /PLASMA ENABLE RELAY 22 COMMON 23 PILOT CURRENT SIG24 NC 25 PILOT CURRENT SIG+ 26 COMMON 27 WORK CURRENT SIG28 WORK CURRENT SIG+ 29 NC 30 AMBIENT TEMP 31 COOLANT TEMP * Used with 1 Torch Option READY + READY INVERTER_FLT + INVERTER_FLT OVERTEMP_FLT + OVERTEMP_FLT PWR_PRESENT + PWR_PRESENT OUT_COM (+3 to 5VDC) VAC_SELA VAC_SELB IS_IDA IS_IDB IS_IDC ENABLE + ENABLE START2 + START2 SPARE SYNC_IN + SYNC_IN NC NC 47 OHM to COMM DEMAND + DEMAND 47 OHM to COMM CURRENT + CURRENT 47 OHM to COMM D RIBBON CABLE 16 ckt CCM ( J37) - DISPLAY PCB (J17) 1,3,5,7 2,4,6,8 9,10 11-16 24 VDC COMMON NC SERIAL DATA RIBBON CABLE 10 ckt RELAY PCB (J3) – PILOT PCB (J42) 1,2 3,4,7,10 5 6 8 9 E 24 VDC COMMON PILOT ENABLE + PILOT ENABLE – PILOT CURRENT SIG – PILOT CURRENT SIG + Art # A-11961_AD Revision Rev 00 Initial Design DAT AA AB By ECO-B2687 Date Revision Rev By Date Thermal Dynamics Corporation 10/03/2012 DAT 9 /1 6 /2 0 1 4 DAT 10/17/2014 2800 Airport Rd. Denton, Texas 76207 USA The information contained herein is proprietary to Thermal Dynamics. Not for release, reproduction or distribution without written consent. Size Drawing Number SCHEMATIC 0-5264FR 6 7 8 ANNEXE 9 10/04/2012 DAT Title Ultra-Cut XT 200A CE 380-415 VAC 5 F Date Printed Date Revised 11/20/2014 12/16/2014 Drawn Date C Sheet 1 of 2 042X1353 10 A-45 ULTRA-CUT 100 XT/200 XT/300 XT/400 XT ANNEXE 25 : SCHÉMA DE PRINCIPE 200A, 380-415V PG 2 (89) 2 3 T1 1 2 3 4 (81) (82) J49 460V 1 2 3 4 5 6 7 8 24V RET 6 RED 24V B BLUE 220V 4 (74) 3 RED 2 YELLOW 120V_2 (77) 5 YELLOW 120V_2 RET 400V J6 (79) BLUE 120V-1 RET (71) 1 12 11 10 9 8 7 6 5 4 3 2 1 (78) CB2 5 A (76) (75) CB3 5 A (73) CB4 5 A (72) J9 J14 120V_1 MC3A J16 (66) M1 1 2 3 J72 (69) (64A) 230 VAC _ SW _ RET (A9) 8 7 6 5 4 3 2 1 120VAC_2 24VAC FAN2 1 2 3 1 TORCH INTERFACE BIAS TRANSFORMER J32 - 30 CKT RIBBON J34 - 30 CKT RIBBON J35 - 30 CKT RIBBON J36 - 30 CKT RIBBON J84 J85 CPU PCB (CPU) J28 30 CKT RECEPTACLE - BOTTOM ENTRY CHASSIS GND C4 (55) 1 2 3 4 5 6 7 8 I / O PCB TEST POINTS ------------------------------------TP1 PCB COMMON TP2 COOLANT FANS ON TP3 PUMP ON TP4 LOW FLOW (SW) TP5 FLOW SIGNAL (pulse, Ultracut only) TP6 +15VDC_ISO (ref to TP10) TP7 -15VDC_ISO (ref to TP10) TP8 +16-18 VDC_ISO (ref to TP10) TP9 ANALOG CURRENT SIGNAL (remote & Autocut only) TP10 ISOLATED VOLTAGE COMMON TP11 1 TORCH CONTACTOR ON TP12 +5 VDC TP13 -15 VDC TP14 +15 VDC TP15 +24 VDC TP18 +5 VDC_ISO (ref to TP10) 230 VAC_SW goes to J70 for HE 400 (Sht 1 F2) 24 VDC 24 VDC MISSING PHASE a MISSING PHASE b AC V HIGH a AC V HIGH b AC V LOW a 24 VDC_RET 24 VDC_RET AC V LOW b VAC_IDA a / VAC_IDA b VAC_IDB a / VAC_IDB b FAN1 BN BL R (29) (30) (31) (32) (33) (34) (35) (36) (37) (38) (39) (40) (41) (42) 1 2 3 4 5 6 7 8 9 10 11 I / O PCB DIP SW --------------------------------------------SW6 OK TO MOVE (CONTACTS, VOLTS) SW11 ANALOG CC SOURCE SW12 DIVIDED ARC VOLTAGE (50:1, 16.7:1, 30:1, 40:1, 25:1) 12 13 14 J27 . 230V 400V 480V ERR J62-12 (/VAC_IDAb) 0 1 0 1 J62-14 (/VAC_IDBb) 0 0 1 1 J28 30 CKT PIN HEADER I / O PCB LEDS ---------------------------------------------D2 CNC PLASMA ENABLE D3 E-STOP_PS D4 GAS ON (Auto-cut, PAK) D6 CNC START D8 HOLD START D12 PREFLOW ON D13 CSD (corner current reduction) D18 MARK D20 SPARE D25 EXP METAL D33 OK_CNC D37 PSR D41 SPARE OUT 2 D43 SPARE OUT 1 Harness from System Bias PCB Alternate fan. 100 & 200A units may use either this single larger fan (same as 300 & 400A units) or the 2 smaller fans shown above. BK I-O PCB (CCM) 230 VAC _ SW (A9) 1 2 3 019X501700 J33 - 30 CKT RIBBON J24 (70) E Test Points TP1, GND TP2, -15V TP3, +5VDC TP4, +12V TP5, +24V TP6, +15V TP7, +5VDC Refer to 1 Torch Module Schematic for Details 120VAC_1 (53) (51) J73 (69) (70) R FAN1 1 2 3 (70) MC2B (Sht 1, B8) TIP VOLTS (69) MC2A (65A) Harness from Pilot PCB J45 WORK 230 VAC Torch Coolant Pump (67) ARC VOLTS CHASSIS GND (64B) J72 TEMP SENSORS D2, GREEN, 1TORCH GAS ON D7, GREEN, PILOT ENABLED D11, GREEN, PILOT CURRENT D12, GREEN, WORK CURRENT D22, GREEN, CONTACTORS ON D23, GREEN, RF ON D24, GREEN, FANS ON D25, GREEN, PLASMA ENABLED D26, GREEN, 1TORCH ON D27, GREEN, COOLANT ON 1 2 3 (64A) (64B) (65A) (65B) 4 TORCH FLOW SENSOR 19X501100 D J2 WORK CURRENT SENSOR RELAY & INTERFACE PCB SIGNAL (pulse) J31 - 30 CKT RIBBON MC3B J13 to CB5 and to MC2 & MC3, also J14, J16 all 18 AWG J1 (95) J11 To J100 of IM #2A (Sht 1, B,C6) C LEVEL SENSORS +5VDC To J100 of IM #1B To J100 of IM #1A (Sht 1, C,D6) 0V J13 J7 COOLANT FLOW SW (80) 1 2 3 4 (94) 3 2 1 r b g 1 1 5 2 6 3 7 4 8 J12 J5 FL1 (87) (93) 14 13 12 11 10 9 8 7 6 5 4 3 2 1 4.7 30W 2 1 0.7 GPM R2 (92) 5 4 3 2 1 (83) TS1 6 5 4 3 2 1 (84) 1 2 1 J74 (59) (58) (57) (56) COOLANT MC1A COOLANT TS2 COMMON SIG (+) -15 VDC +15 VDC FS1 (44A) 4 J71 AMBIENT Sht 1, C8) COOLANT LEVEL (43A) (90) 2 3 From Sys Bias J63 (Sht 1, F2) TO HCT1 (Work) 1 LS1 5 2 J12 = Mini-Fit Jr 400 VAC -- Single 18 AWG in pins 1 & 4 480 VAC -- Single 18 AWG in pins 1 & 8 230 VAC -- 18 AWG wires in pins 1,5,2,6 A 4 3 3 2 4 1 19X501200 Measure relative to TP1 (24VDC_RET) "0" = 10-12V "1" = 24V F Art # A-11962_AD 1 A-46 2 3 ANNEXE 4 5 0-5264FR ULTRA-CUT 100 XT/200 XT/300 XT/400 XT 6 (162) / PILOT ENABLE / PILOT ENABLE RET (161) MC3 SA4 J8 (96) (98) (99) (97) J59 - RAS HMI/GCM J4 -- 40 CKT RIBBON CABLE (106) (113) (61) (62) AC 120V - GCM (60) AC 24V - RET - GCM2 AC 120V- Ret- GCM AC 120V- Ret- TB4-3 1 2 3 4 J18 4 WIRE RxTx+ Rx+ Tx- (116) (117) Harness (118) (119) (120) 2 J37 Display PCB Harness 019X501800 16 CKT RIBBON (121) (122) (123) (124) (125) (126) (127) (128) (129) (130) (131) J29 30 CKT RECEPTACLE - BOTTOM ENTRY GAS ON J29 30 CKT PIN HEADER J23- 40 ckt ribbon cable CPU PCB LEDs ---------------------------D2 RXD (red) D3 TXD (red) D4 CAN BUS (slave) D7 CAN BUS (MAIN) D11 5 VDC POWER D17 STATUS CODE D18 INITIALIZING / PROGRAMMING (red) ENABLE PLAS_ENABLE SW PLAS_ EN_SW_RET / GAS PRESS OK / BASIC ID TB1 OK2 (contact) +10V (CC Pot Hi) CC Pot Wiper CC Pot Low Div Arc V (+) Div Arc V (-) /Start - Stop (+) /Start - Stop (-) Stop Mom NC OK2 (contact) / CNC Enable (+) / CNC Enable (-) CPU PCB TEST POINTS -------------------------------------------TP1 GND (PCB common) TP2 +5V_ISO (REF TP5) TP3 +24 VDC TP4 +3.3V TP5 GND_ISO TP6 +5.0 V TP7 TOTAL DEMAND (3.3V = 400A) TP9 /WR TP10 /RD TP11 CPU TEMP SENSE TP12 +3.3VA TP13 -15VDAC TP14 PC2 TP15 +15VDAC TP16 CLKO TP18 OSC_CLOCK 12 11 10 9 8 7 6 5 4 3 2 1 GND 1 2 3 4 5 6 7 8 9 10 11 12 13 14 15 16 17 18 TB2 12 11 10 9 8 7 6 5 4 3 2 1 OK to MOVE (-) PILOT is ON PILOT is ON Preflow ON (+) Preflow ON (-) Hold Start (+) Hold Start (-) CPU PCB DIP SW --------------------------------------------SW1 AUTO PILOT RESTART SW3 PREFLOW TIME SW4 POSTFLOW TIME SW5 FUNCTION SW8 SYSTEM CONTROL (pilot time, etc.) SW9 RESERVED (future) SW10 ADDRESS (default = 0) SW13 UNIT TYPE (AC / UC) SW14 LINE TERMINATION (serial comm.) 1 2 3 4 5 6 7 8 9 10 11 12 13 14 15 16 (130) (131) (112) (114) (121) (122) (124) (129) (128) (123) AC 24V Ret - GCM1 AC 24V-GCM2 AC 24V Ret-GCM2 +10V GND GND TB3 12 11 10 9 Spare #1b NO 8 7 6 Spare 5 Digital 4 Inputs 3 / Plasma Marking (-) 2 / Plasma Marking (+) 1 PSR SPARE #1a (167) (106) AC 120V - GCM (113) AC 120V- Ret- GCM CHASSIS GND (133) (134) (135) (136) (137) (138) (139) (140) (141) (142) (140) (141) (136) (135) (132) (153) J21 (143) 1 2 3 4 5 6 7 8 9 10 11 12 13 14 15 16 17 18 19 20 Spare Digital Inputs (111) J69 2 1 (133) (134) (137) (139) (138) (143) (104) (166) (125) (126) (127) (142) (112) (114) (103) (110) AC 24V-GCM1 J26 OK OK to MOVE (+) (144) (145) (144) (145) (146) (147) (148) (149) (150) (151) (146) (147) (148) (149) (150) (151) (152) (154) (155) (132) (152) (153) (154) (155) (156) (157) (158) (159) (156) (157) (158) (159) J22 Art # A-11962_AD Revision Rev 00 Initial Design AA AB By DAT DAT ECO-B2687 DAT Date Revision Rev By Date 0-5264FR J55 - GCM 1- PLAS_ENABLE SW * 2- PLAS_ EN_SW_RET 3- GAS PRESS OK RET 4- / GAS PRESS OK 5- POT HIGH (GCM 1000) 6- POT WIPER (GCM 1000) 7- POT LOW (GCM 1000) 8- BASIC ID RET 9- / BASIC ID ** 1011- 1 2 3 4 5 6 7 8 9 10 11 12 13 14 15 16 17 18 19 20 21 22 23 24 25 26 27 28 29 30 31 32 33 34 35 36 37 GCM 1000 XT Jumper 1415- 24 VAC - RET * Plasma Enable SW in GCM 2010. Jumpered in GCM 1000 XT and DMC 3000. ** Jumper in GCM 1000 XT 27- GAS SEL SW RET 28- GAS SEL SW D J15-1 to chassis used for SC-11 cable shield J15-13 connects SC-11 chassis to PS chassis. J15-CNC 1 2 3 4 5 6 7 8 9 10 11 12 13 14 15 16 17 18 19 20 21 22 23 24 25 26 27 28 29 30 31 32 33 34 35 36 37 C The COMM Ref at pin 8 is also for the SC-11 3- / CNC Start (+) 4- / CNC Start (-) 5- Divided Arc V (-) 6- Divided Arc V (+) 7- / Preflow ON (+) 8- COMM Ref (1K Ohm) 9- / Preflow ON (-) 10- / Spare Digital Input (+) 11- / Spare Digital Input (-) 12- OK to Move (-) 14- OK to Move (+) 15 - Key Plug 16- / Hold Start (+) 17- / Hold Start (-) E 21- / Plasma Mark (+) 22- / Plasma Mark (-) 23- / Spare Digital Input(+) 24- / Spare Digital Input (-) 25- / CNC Plasma Enable (+) 26- / CNC Plasma Enable (-) 29- Remote CC Pot High 30- Remote CC (analog) 31- Remote CC Pot Low 32- Stop SW (momentary) * 33- Stop SW Ret 34- Pilot is ON (a) 35- Pilot is ON (b) 36- Spare OUT #1 (a) 37- Spare OUT #1 (b) * Used with Momentary CNC Start SW Thermal Dynamics Corporation 10/03/2012 2800 Airport Rd. Denton, Texas 76207 USA 9 /1 6 /2 0 1 4 F Date Printed Date Revised 11/20/2014 12/16/2014 Drawn Date 10/17/2014 Size Drawing Number SCHEMATIC 7 8 ANNEXE 9 10/4/2012 DAT The information contained herein is proprietary to Thermal Dynamics. Not for release, reproduction or distribution without written consent. Title Ultra-Cut XT 200A CE 380-415 VAC 6 B Comm 12 - Tx13 - Rx+ 14 - Rx- J17 J20 J19 5-HMI Plasma Enable SW 6-HMI Plasma Enable SW 7 - Key Plug 8 - Tx+ 9 - GND RS 485 10 - GND / 422 3 INRUSH CONTROL (116) (117) (120) (115) (119) (118) 1 2 3 4 5 6 J30 2 WIRE NORMAL PROGRAM PROG USB IC GND GND 1 2 3 4 5 6 7 8 9 10 11 12 (115) AC 24V- Ret -TB4-1 (63) 5 J47 1 2 3 4 1 2 3 4 5 6 7 8 9 1 2 3 4 5 6 1 2 3 4 5 6 7 8 9 10 11 12 (108) K1 1 - 24 VAC 2 - 24 VAC Ret 3- Jumper to 24 VAC 2 3 4 5 6 7 8 9 10 11 12 13 14 (109) AC 24V Ret- GCM1 (62) 1 3 - Key Plug J54 - Remote HMI & CNC COMM (100) 1 (101) (102) AC 120V- TB4-4 (63) A 4 USB Cable to Front Panel RS 232 D-SUB SERIAL PROG PORT (98) AC 24V-TB4-2 J10 J39 USB PORT 120 VAC Ret AC 24V GCM1 AC 24V GCM2 (108) (109) (110) (111) (99) MC1 (101) (102) (103) (104) 120 VAC to RAS 120VAC (100) 18 17 16 15 14 13 12 11 10 9 8 7 6 5 4 3 2 1 120 VAC_1 1 2 3 4 5 6 7 8 9 10 11 12 13 14 ARC_SUPPRESSOR (60) 120 VAC_2 J38 1 2 3 4 5 6 7 ( 69) 230 VAC Ret W1 CONTROL OUTPUTS 24 VAC (70) 230 VAC to HE 400 ( 69) CHASSIS GND 24 VDC GND 10 J70 - HE (D2) SA1 Pump Motor Control 16 15 14 13 12 11 10 9 8 7 6 5 4 3 2 1 2 1 4 3 5 6 PILOT A SIG Vin+ PILOT A SIG Vin- 7 8 9 10 (D2) (163) (160) 10 CKT RIBBON SA3 (70) 230 VAC _ SW 230 VAC _ SW _ RET ARC_SUPPRESSOR PILOT PCB 9 MC2 Fan Control ARC_SUPPRESSOR J3 8 7 TO PILOT PCB Sht 1, B8) C Sheet 2 of 2 042X1353 10 A-47 ULTRA-CUT 100 XT/200 XT/300 XT/400 XT ANNEXE 26 : SCHÉMA DE PRINCIPE 300A, 380-415V PG 1 1 2 (1) 1 2 IN1 (2) 2 1 IN2 OUT2 1 2 IN1 (2) B 380-415 VAC INPUT (Customer supplied power cord must pass through ferrite core assembly.) L1 Earth OUT1 (3) 1 2 W2B (5) 2 1 IN2 (7) (7) (8) (8) (9) OUT2 2 1 GND2B 1 2 019X502700 J105A L8 1 2 1 2 J103A 1 2 Toriod Core 019X502000 CHASSIS GND INVERTER MODULE (IM) #2 (middle) AC SUPPRESSION PCB J50 1 2 3 4 5 6 7 8 9 10 11 12 13 14 1 1 1 (3) 1 019X504000 (10) J51 1 2 3 4 LT1 (11) PANEL AC INDICATOR (12) J52 LT2 1 2 3 4 GND (23) (13) C 1 2 AC INPUT 1 2 J103A 1 2 Toriod Core 019x502000 W1A (1) 1 2 IN1 (2) EMI FILTER PCB OUT1 1 2 1 2 W1B (21) 2 1 IN2 (3) OUT2 GND2B IN3 INVERTER MODULE (IM) #`1 (bottom) (20) 2 1 (22) 2 1 W1C (23) (23) (24) (24) (25) (25) (1) 1 2 IN1 (2) EMI FILTER PCB (23) 1 2 OUT1 GND2B 2 1 TEST POINTS TP1 SECONDARY GND TP2 24VDC TP3 DC INPUT POSITIVE TP4 VCC1 TP5 VCC2 TP6 GATE TP7 PRIMARY GND TP8 +12V PRIMARY TP9 P ISOL GND J62 SYSTEM BIAS SUPPLY PCB 8A, 500V, SB +24VDC (85A) (86B) (27B) (85B) 3 AC INPUT 4 1 2 3 4 5 6 7 8 9 10 11 12 13 14 15 16 17 18 5 6 7 8 9 10 GND 11 12 13 K1A K1B J63 1 2 3 4 5 6 7 8 9 10 11 12 J60 F 2 14 480V-ID 400V-ID 208-230V-ID COM (27A) 1 +V 019X501900 (86A) Art # A-11963_AD 1 A-48 CONTROL PCB LEDS D1, RED, INV FLT D14, RED, OVER TEMP D24, GREEN, PWM ON D32, RED, PRI OC 1 2 IM #1 Section A (lower) AC INPUT 1 2 J103A 1 2 LEDS D3, RED, MISSING PHASE D4, RED, AC V HIGH D14, RED, AC V LOW D26, GREEN, +12V PRI D30, GREEN, 24VDC D44, GREEN, T1 ON (Sht 2, E3) 24 VDC 24 VDC MISSING PHASE a MISSING PHASE b AC V HIGH a AC V HIGH b AC V LOW a 24 VDC_RET 24 VDC_RET AC V LOW b VAC_IDA a / VAC_IDA b VAC_IDB a / VAC_IDB b TO AUX TRANSFORMER TO J12 (44A) T1 PRIMARY (Sht 2, A1) (48) (29) (30) (31) (32) (33) (34) (35) (36) (37) (38) (39) (40) (41) (42) 230V 400V 480V ERR /VAC_IDAb 0 1 0 1 /VAC_IDBb 0 0 1 1 J61 Measure relative to TP1 (24VDC_RET) "0" = 10-12V "1" = 24V VOLTAGE SELECTION (43A) D6, GREEN, -12V D11, GREEN, +12VP D13, GREEN, +12V IM #1 Section B (upper) J104A System Bias LEDs & Test Points OUT3 4 3 2 1 (28) (26) F1 J105A L4 To J27 on CCM I/O PCB F2 019x502700 MAIN PCB LEDS D3, RED, CAP IMBALANCE D4, GREEN, READY CAP BIAS PCB LEDS WORK (+) 019x502000 (FRONT PANEL) 8A, 500V, SB 1 2 Toriod Core (1-20) (2-21) (3-22) (27A&B) E J103B (25) CHASSIS GND CB1 1 2 OUT2 IN3 ON / OFF 16 A J104B (24) 2 1 2 1 IN2 AC INPUT 1 2 OUT3 1 2 (3) J105B L5 Toriod Core CHASSIS GND D IM #2 Section A (lower) J104A (25) LT1 & LT2 INPUT POWER NEON INDICATORS Rear Panel & Internal CHASSIS GND J105A L6 (24) INTERNAL AC INDICATOR AC LINE CHASSIS GND IM #3 Section A AC INPUT J104A (9) W2C (6) OUT3 IN3 (2) L3 2 1 1 2 (1) L2 EMI FILTER PCB 1 2 Toriod Core W2A (4) IM #3 Section B AC INPUT J103B (9) CHASSIS GND (1) 1 2 J104B (8) OUT3 IN3 J105B L9 (7) (6) 2 1 GND2B 5 INVERTER MODULE (IM) #3 (top) (5) 2 1 1 2 4 3 (4) OUT1 1 2 (3) A EMI FILTER PCB Wire #48 from J61-1 to: J61-2 for 208-230 VAC J61-3 for 400 VAC J61-4 for 480 VAC 2 3 ANNEXE Component Locations (not including PCB components) C4 CB1 Capacitor, fan starting, 8uf 440VAC (Sht 2, D2) Circuit Breaker /ON/OFF SW, 15A 480V (Sht 1, E1) CB2-4 Circuit Breaker, 5A, 250V (Sht 2, B3) F1, 2 Fuse, 8A, 500V, S.B. (Sht 1,E1) FAN1 Fan, Heat Exchanger , 230 VAC (Sht 2, D2) FL1 Flow meter, pulse output (Sht 2, B2) FS1 Flow SW, 0.5 GPM (3.8 lpm), N.O. (Sht 2, A2) HCT1 Current Sensor, Hall Effect 200A, Work Lead (Sht 1, C8) K1 Relay, 24VAC, Inrush Control, (Sht2, B9) L1 Inductor, (Sht 1, B7) L3-9 Toriod Core Common Mode Ind (Sht1 B8, A-D3) LS1 Level Switch, Coolant Tank (Sht 2, A3) LT1, LT2 Indicator, Neon, 250V, AC Volts Present (Sht 1, B2 & C2) M1 Motor, Pump, ½ hp 230VAC, 50/60 Hz, 1Ph (Sht 2, C2) MC1 Relay, 120VAC, Inrush, coil (Sht2, B9) contact (Sht2, A1) MC2 Relay, 120 VAC, Fan Control, coil (Coil at Sht 2, A7)(Contacts at Sht 2, D1) MC3 Relay, 120 VAC, Pump Motor Control, coil (Coil at Sht 2, A7)(Contacts at Sht 2, C1) R2 Inrush, 4.7 Ohm, 30W (Sht2, A1) R3,4 Ext RC, 100 ohm 55W (Sht1, A7) SA1-4 Snubber, Contactor & Relay coils (Sht 2, A8 & A9) T1 Aux Transformer (Sht 2, B2) TB4 Terminal Block (Sht 1, C9) TS1 Temperature Sensor, NTC, Coolant Return (Sht 2, A5) TS2 Temperature Sensor, NTC, Ambient (Sht 2, A5) W1 Contactor , Input (Coil Sht 2, A8), (Contacts C2) W2 Contactor , Input (Coil Sht 2, A8), (Contacts A2) 4 5 0-5264FR ULTRA-CUT 100 XT/200 XT/300 XT/400 XT 7 6 8 9 10 TO CCM CPU PCB J36 (Sht 2, C3) TORCH To TB4-7 (49F) D2 PILOT ENABLE D11 +5V J102B TO CCM CPU PCB J35 OUTPUT J44 J41 (J87) (51E) CHASSIS GND J58C (50) J41 5 4 3 2 1 J102A TIP J40 INVERTER 019X501600 To / From Optional 1 Torch Module (Refer to 1 Torch section for details.) J45 10 ckt Ribbon TO J3 on RELAY PCB (Sht 2, A5) To J24 on I-O PCB (Sht 2, D3) TO CCM CPU PCB J33 (+) SHIELD Tip WORK Work 1 (53) B (+) TIP VOLTS (51) WORK ARC VOLTS (55) L1 (Sht 2, C3) HCT1 2 3 4 3 4 Hall Effect Sensor 1 (51) (51) 4 3 2 1 2 (51C) J102A (49C) 5 1 WORK (+) (-) CHASSIS GND 1 2 J42 ELECTRODE (-) 1 (52) 1 (51F) J100 -- 30 CKT RIBBON RAS PILOT To TB4-6 TIP PILOT PCB R3 & R4 (49E) A Electrode WORK (+) 5 4 3 2 1 J43 ELECTRODE 1 L3 (49) J58A (Sht 2, C3) J100 -- 30 CKT RIBBON ELECTRODE (-) TEST POINTS TP1 GND TP2 PILOT GATE TP3 +5V PILOT BOARD LED'S 2 1 OUTPUT (51F) TORCH (49) 1 WORK (+) 5 4 3 2 1 1 2 3 4 5 6 7 8 9 10 ELECTRODE (-) (49) 1 2 3 4 5 6 7 8 J100 -- 30 CKT RIBBON OUTPUT ELECTRODE (-) WORK (+) OUTPUT 4 3 2 1 TO J1 on RELAY PCB (Sht 2, B9) SIG (+) -15 VDC J46-F AC 120V- TB4-4 (57) b AC 120V- Ret- TB4-3 (58) g AC 24V-TB4-2 (59) w AC 24V- Ret -TB4-1 (49) (52) (51) (60) 7 ARC VOLTS (TORCH) 6 TIP VOLTS (PILOT) 5 WORK 4 (61) 3 (62) 2 (63) 1 120 VAC @ 100 ma. 24 VAC @ 1A (J10 Sht 2, B8) (Sht 2, C3) RIBBON CABLE 30 ckt. CCM (J31-36) - INVERTER (J100) J100 -- 30 CKT RIBBON J102A (49A) WORK (+) TORCH (Sht 1, A9) TIP (Sht 1, A9) (56) o TO CCM CPU PCB J31 ELECTRODE (-) COMMON J102B (49B) 5 +15 VDC 2 1 (Sht 2, C3) C TB4 J46-M (51B) J100 -- 30 CKT RIBBON 2 1 J16 TO CCM CPU PCB J32 5 4 3 2 1 1 2 3 4 5 6 7 8 9 10 11 12 13 14 15 16 17 18 19 20 21 22 23 24 25 26 27 28 29 30 (50) OUTPUT RIBBON CABLE 40 ckt CCM (J23) - RELAY PCB (J4) 32 COMMON 1 COMMON 33 -15 VDC 2 /1TORCH START * 34 COMMON 3 NA 35 24 VDC 4 /1TORCH GAS SOL ON * 36 COMMON 5 /MAIN TORCH IDLE * 37 24 VDC 6 /1TORCH PRESS OK * 38 COMMON 7 FLOW SENSOR (pulses) 39 24 VDC 8 LOW COOLANT FLOW 40 COMMON 9 COOLANT LEVEL OK 10 COMMON RIBBON CABLE 16 ckt 11 NA CCM ( J37) - DISPLAY 12 /PLASMA ENABLE-HMI PCB (J17) 13 /COOLANT PUMP ON 14 COMMON 1,3,5,7 24 VDC 15 /PILOT ENABLE 2,4,6,8 COMMON 16 /RAS ON 9,10 NC 17 /CONTACTORS ON 11-16 SERIAL DATA 18 COMMON 19 /COOLANT FANS ON 20 /1TORCH CONTACTOR ON * RIBBON CABLE 10 ckt 21 /PLASMA ENABLE RELAY RELAY PCB (J3) – PILOT PCB (J42) 22 COMMON 23 PILOT CURRENT SIG24 NC 1,2 24 VDC 25 PILOT CURRENT SIG+ 3,4,7,10 COMMON 26 COMMON 5 PILOT ENABLE + 27 WORK CURRENT SIG6 PILOT ENABLE – 28 WORK CURRENT SIG+ 8 PILOT CURRENT SIG – 29 NC 9 PILOT CURRENT SIG + 30 AMBIENT TEMP 31 COOLANT TEMP * Used with 1 Torch Option READY + READY INVERTER_FLT + INVERTER_FLT OVERTEMP_FLT + OVERTEMP_FLT PWR_PRESENT + PWR_PRESENT OUT_COM (+3 to 5VDC) VAC_SELA VAC_SELB IS_IDA IS_IDB IS_IDC ENABLE + ENABLE START2 + START2 SPARE SYNC_IN + SYNC_IN NC NC 47 OHM to COMM DEMAND + DEMAND 47 OHM to COMM CURRENT + CURRENT 47 OHM to COMM D E Art # A-11963_AD Revision Rev 00 Initial Design DAT AA AB By ECO 1 Torch Option Date Revision Rev By Date Thermal Dynamics Corporation 10/03/2012 DAT 9 /1 6 /2 0 1 4 DAT 10/17/2014 2800 Airport Rd. Denton, Texas 76207 USA The information contained herein is proprietary to Thermal Dynamics. Not for release, reproduction or distribution without written consent. Size Drawing Number SCHEMATIC 0-5264FR 7 8 9 ANNEXE 10/04/2012 DAT Title Ultra-Cut XT 300A CE 380-415 VAC 6 F Date Printed Date Revised 10/20/2014 12/16/2014 Drawn Date C Sheet 1 of 2 042X1352 10 A-49 ULTRA-CUT 100 XT/200 XT/300 XT/400 XT ANNEXE 27 : SCHÉMA DE PRINCIPE 300A, 380-415V PG 2 (89) 2 3 T1 1 2 3 4 (81) (82) J49 24V RET (79) BLUE 6 RED 24V B BLUE 220V 4 (74) 3 RED 2 YELLOW 120V_2 (77) 5 YELLOW 120V_2 RET 400V J6 120V-1 RET (71) 1 12 11 10 9 8 7 6 5 4 3 2 1 (78) CB2 5 A (76) (75) CB3 5 A (73) CB4 5 A (72) J9 J14 TORCH FLOW SENSOR 120VAC_2 24VAC J16 (66) M1 1 2 3 J72 (69) (65A) MC2B (64A) 230 VAC _ SW _ RET (A9) 1 TORCH INTERFACE BIAS TRANSFORMER FAN2 1 2 3 J35 - 30 CKT RIBBON J36 - 30 CKT RIBBON CHASSIS GND J85 CPU PCB (CPU) (55) 1 2 3 4 5 6 7 8 I / O PCB TEST POINTS ------------------------------------TP1 PCB COMMON TP2 COOLANT FANS ON TP3 PUMP ON TP4 LOW FLOW (SW) TP5 FLOW SIGNAL (pulse, Ultracut only) TP6 +15VDC_ISO (ref to TP10) TP7 -15VDC_ISO (ref to TP10) TP8 +16-18 VDC_ISO (ref to TP10) TP9 ANALOG CURRENT SIGNAL (remote & Autocut only) TP10 ISOLATED VOLTAGE COMMON TP11 1 TORCH CONTACTOR ON TP12 +5 VDC TP13 -15 VDC TP14 +15 VDC TP15 +24 VDC TP18 +5 VDC_ISO (ref to TP10) 230 VAC_SW goes to J70 for HE 400 (Sht 1 F2) 24 VDC 24 VDC MISSING PHASE a MISSING PHASE b AC V HIGH a AC V HIGH b AC V LOW a 24 VDC_RET 24 VDC_RET AC V LOW b VAC_IDA a / VAC_IDA b VAC_IDB a / VAC_IDB b FAN1 BN BL R (29) (30) (31) (32) (33) (34) (35) (36) (37) (38) (39) (40) (41) (42) 1 2 3 4 5 6 7 8 9 10 11 I / O PCB DIP SW --------------------------------------------SW6 OK TO MOVE (CONTACTS, VOLTS) SW11 ANALOG CC SOURCE SW12 DIVIDED ARC VOLTAGE (50:1, 16.7:1, 30:1, 40:1, 25:1) 12 13 14 J27 . 230V 400V 480V ERR J62-12 (/VAC_IDAb) 0 1 0 1 J62-14 (/VAC_IDBb) 0 0 1 1 J28 30 CKT PIN HEADER I / O PCB LEDS ---------------------------------------------D2 CNC PLASMA ENABLE D3 E-STOP_PS D4 GAS ON (Auto-cut, PAK) D6 CNC START D8 HOLD START D12 PREFLOW ON D13 CSD (corner current reduction) D18 MARK D20 SPARE D25 EXP METAL D33 OK_CNC D37 PSR D41 SPARE OUT 2 D43 SPARE OUT 1 Harness from System Bias PCB Alternate fan. 100 & 200A units may use either this single larger fan (same as 300 & 400A units) or the 2 smaller fans shown above. 1 2 3 J84 J28 30 CKT RECEPTACLE - BOTTOM ENTRY I-O PCB (CCM) 230 VAC _ SW (A9) C4 J32 - 30 CKT RIBBON J34 - 30 CKT RIBBON J24 (70) J72 019X501700 J33 - 30 CKT RIBBON (53) (51) J73 (69) (70) BK FAN1 1 2 3 (70) (Sht 1, B8) TIP VOLTS (69) MC2A Harness from Pilot PCB J45 WORK 230 VAC Torch Coolant Pump (67) ARC VOLTS CHASSIS GND (64B) E Test Points TP1, GND TP2, -15V TP3, +5VDC TP4, +12V TP5, +24V TP6, +15V TP7, +5VDC Refer to 1 Torch Module Schematic for Details 120VAC_1 19X501100 R D2, GREEN, 1TORCH GAS ON D7, GREEN, PILOT ENABLED D11, GREEN, PILOT CURRENT D12, GREEN, WORK CURRENT D22, GREEN, CONTACTORS ON D23, GREEN, RF ON D24, GREEN, FANS ON D25, GREEN, PLASMA ENABLED D26, GREEN, 1TORCH ON D27, GREEN, COOLANT ON 1 2 3 4 (64A) (64B) (65A) (65B) MC3A MC3B D TEMP SENSORS RELAY & INTERFACE PCB +5VDC SIGNAL (pulse) J31 - 30 CKT RIBBON To J100 of IM #2A (Sht 1, B,C6) J13 to CB5 and to MC2 & MC3, also J14, J16 all 18 AWG J2 J11 0V C J1 (95) WORK CURRENT SENSOR To J100 of IM #1B To J100 of IM #1A (Sht 1, C,D6) 120V_1 J13 LEVEL SENSORS (94) 14 13 12 11 10 9 8 7 6 5 4 3 2 1 460V 1 2 3 4 5 6 7 8 J7 COOLANT FLOW SW (80) 1 2 3 4 (93) 3 2 1 r b g 1 1 5 2 6 3 7 4 8 J12 J5 FL1 (87) 8 7 6 5 4 3 2 1 R2 2 1 0.7 GPM 4.7 30W (92) 5 4 3 2 1 (83) TS1 6 5 4 3 2 1 (84) 1 2 1 J74 (59) (58) (57) (56) COOLANT MC1A COOLANT TS2 COMMON SIG (+) -15 VDC +15 VDC FS1 (44A) 4 J71 AMBIENT Sht 1, C8) COOLANT LEVEL (43A) (90) 2 3 From Sys Bias J63 (Sht 1, F2) A 1 LS1 2 J12 = Mini-Fit Jr 400 VAC -- Single 18 AWG in pins 1 & 4 480 VAC -- Single 18 AWG in pins 1 & 8 230 VAC -- 18 AWG wires in pins 1,5,2,6 5 4 TO HCT1 (Work) 3 3 2 4 1 19X501200 Measure relative to TP1 (24VDC_RET) "0" = 10-12V "1" = 24V F Art # A-11964_AD 1 A-50 2 3 ANNEXE 4 0-5264FR ULTRA-CUT 100 XT/200 XT/300 XT/400 XT 6 7 TO PILOT PCB Sht 1, B8) (162) / PILOT ENABLE / PILOT ENABLE RET (D2) (161) MC3 J8 SA4 J59 - RAS CHASSIS GND (96) (98) (99) (97) 120 VAC_2 HMI/GCM J4 -- 40 CKT RIBBON CABLE (106) (113) (61) (62) AC 120V - GCM AC 120V- Ret- GCM AC 120V- Ret- TB4-3 J18 GND GND J19 4 WIRE RxTx+ Rx+ Tx- (119) (120) 2 1 2 3 4 5 6 J37 Harness 019X501800 16 CKT RIBBON (121) (122) (123) (124) (125) (126) (127) (128) (129) (130) (131) GAS ON J23- 40 ckt ribbon cable ENABLE PLAS_ENABLE SW PLAS_ EN_SW_RET / GAS PRESS OK / BASIC ID TB1 OK2 (contact) +10V (CC Pot Hi) CC Pot Wiper CC Pot Low Div Arc V (+) Div Arc V (-) /Start - Stop (+) /Start - Stop (-) Stop Mom NC OK2 (contact) / CNC Enable (+) / CNC Enable (-) CPU PCB TEST POINTS -------------------------------------------TP1 GND (PCB common) TP2 +5V_ISO (REF TP5) TP3 +24 VDC TP4 +3.3V TP5 GND_ISO TP6 +5.0 V TP7 TOTAL DEMAND (3.3V = 400A) TP9 /WR TP10 /RD TP11 CPU TEMP SENSE TP12 +3.3VA TP13 -15VDAC TP14 PC2 TP15 +15VDAC TP16 CLKO TP18 OSC_CLOCK 12 11 10 9 8 7 6 5 4 3 2 1 GND 1 2 3 4 5 6 7 8 9 10 11 12 13 14 15 16 17 18 TB2 12 11 10 9 8 7 6 5 4 3 2 1 OK to MOVE (-) PILOT is ON PILOT is ON Preflow ON (+) Preflow ON (-) Hold Start (+) Hold Start (-) CPU PCB DIP SW --------------------------------------------SW1 AUTO PILOT RESTART SW3 PREFLOW TIME SW4 POSTFLOW TIME SW5 FUNCTION SW8 SYSTEM CONTROL (pilot time, etc.) SW9 RESERVED (future) SW10 ADDRESS (default = 0) SW13 UNIT TYPE (AC / UC) SW14 LINE TERMINATION (serial comm.) 1 2 3 4 5 6 7 8 9 10 11 12 13 14 15 16 (130) (131) (112) (114) (121) (122) (124) (129) (128) (123) AC 24V Ret - GCM1 AC 24V-GCM2 AC 24V Ret-GCM2 +10V GND GND TB3 12 11 10 9 Spare #1b NO 8 7 6 Spare 5 Digital 4 Inputs 3 / Plasma Marking (-) 2 / Plasma Marking (+) 1 PSR SPARE #1a AC 120V - GCM AC 120V- Ret- GCM (167) (106) (113) CHASSIS GND (133) (134) (135) (136) (137) (138) (139) (140) (141) (142) (140) (141) (136) (135) (132) (153) J21 (143) 1 2 3 4 5 6 7 8 9 10 11 12 13 14 15 16 17 18 19 20 Spare Digital Inputs (111) J69 2 1 (133) (134) (137) (139) (138) (143) (104) (166) (125) (126) (127) (142) (112) (114) (103) (110) AC 24V-GCM1 J26 OK OK to MOVE (+) (144) (145) (144) (145) (146) (147) (148) (149) (150) (151) (146) (147) (148) (149) (150) (151) (152) (154) (155) (132) (152) (153) (154) (155) (156) (157) (158) (159) (156) (157) (158) (159) J22 Art # A-11964_AD Revision Rev 00 Initial Design AA AB By DAT DAT ECO-B2687 DAT Date Revision Rev By Date 6 0-5264FR J55 - GCM 1- PLAS_ENABLE SW * 2- PLAS_ EN_SW_RET 3- GAS PRESS OK RET 4- / GAS PRESS OK 5- POT HIGH (GCM 1000) 6- POT WIPER (GCM 1000) 7- POT LOW (GCM 1000) 8- BASIC ID RET 9- / BASIC ID ** 1011- 1 2 3 4 5 6 7 8 9 10 11 12 13 14 15 16 17 18 19 20 21 22 23 24 25 26 27 28 29 30 31 32 33 34 35 36 37 1 2 3 4 5 6 7 8 9 10 11 12 13 14 15 16 17 18 19 20 21 22 23 24 25 26 27 28 29 30 31 32 33 34 35 36 37 C GCM 1000 XT Jumper 1415- 24 VAC - RET * Plasma Enable SW in GCM 2010. Jumpered in GCM 1000 XT and DMC 3000. ** Jumper in GCM 1000 XT 27- GAS SEL SW RET 28- GAS SEL SW D J15-1 to chassis used for SC-11 cable shield J15-13 connects SC-11 chassis to PS chassis. J15-CNC The COMM Ref at pin 8 is also for the SC-11 3- / CNC Start (+) 4- / CNC Start (-) 5- Divided Arc V (-) 6- Divided Arc V (+) 7- / Preflow ON (+) 8- COMM Ref (1K Ohm) 9- / Preflow ON (-) 10- / Spare Digital Input (+) 11- / Spare Digital Input (-) 12- OK to Move (-) 14- OK to Move (+) 15 - Key Plug 16- / Hold Start (+) 17- / Hold Start (-) E 21- / Plasma Mark (+) 22- / Plasma Mark (-) 23- / Spare Digital Input(+) 24- / Spare Digital Input (-) 25- / CNC Plasma Enable (+) 26- / CNC Plasma Enable (-) 29- Remote CC Pot High 30- Remote CC (analog) 31- Remote CC Pot Low 32- Stop SW (momentary) * 33- Stop SW Ret 34- Pilot is ON (a) 35- Pilot is ON (b) 36- Spare OUT #1 (a) 37- Spare OUT #1 (b) * Used with Momentary CNC Start SW Thermal Dynamics Corporation 2800 Airport Rd. Denton, Texas 76207 USA 10/03/2012 9 /1 6 /2 0 1 4 F Date Printed Date Revised 11/20/2014 12/16/2014 Drawn Date 10/17/2014 Size Drawing Number SCHEMATIC 7 8 ANNEXE 9 10/4/2012 DAT The information contained herein is proprietary to Thermal Dynamics. Not for release, reproduction or distribution without written consent. Title Ultra-Cut XT 200A CE 380-415 VAC 5 12 - Tx13 - Rx+ 14 - Rx- Display PCB J20 J29 30 CKT PIN HEADER B Comm J17 J29 30 CKT RECEPTACLE - BOTTOM ENTRY CPU PCB LEDs ---------------------------D2 RXD (red) D3 TXD (red) D4 CAN BUS (slave) D7 CAN BUS (MAIN) D11 5 VDC POWER D17 STATUS CODE D18 INITIALIZING / PROGRAMMING (red) 5-HMI Plasma Enable SW 6-HMI Plasma Enable SW 7 - Key Plug 8 - Tx+ 9 - GND RS 485 10 - GND / 422 3 INRUSH CONTROL (116) (117) (120) (115) (119) (118) J30 2 WIRE PROG USB IC (118) K1 (63) 5 J47 1 2 3 4 5 6 7 8 9 10 11 12 NORMAL PROGRAM 1 2 3 4 5 6 1 2 3 4 5 6 7 8 9 10 11 12 (115) (116) (117) Harness 1 - 24 VAC 2 - 24 VAC Ret 3- Jumper to 24 VAC 4 1 2 3 4 1 2 3 4 1 2 3 4 5 6 7 8 9 RS 232 D-SUB SERIAL PROG PORT (108) AC 24V- Ret -TB4-1 (62) 1 3 - Key Plug 2 3 4 5 6 7 8 9 10 11 12 13 14 (109) AC 24V Ret- GCM1 (63) A J54 - Remote HMI & CNC COMM (100) 1 (101) (102) AC 120V- TB4-4 J10 J39 USB PORT (98) AC 24V-TB4-2 (60) AC 24V - RET - GCM2 USB Cable to Front Panel J38 120 VAC Ret AC 24V GCM1 AC 24V GCM2 (108) (109) (110) (111) (99) MC1 (101) (102) (103) (104) 120 VAC to RAS 120VAC (100) 18 17 16 15 14 13 12 11 10 9 8 7 6 5 4 3 2 1 120 VAC_1 1 2 3 4 5 6 7 8 9 10 11 12 13 14 ARC_SUPPRESSOR (60) 24 VDC 24 VAC 1 2 3 4 5 6 7 ( 69) 230 VAC Ret W1 CONTROL OUTPUTS GND ( 69) (D2) SA1 Pump Motor Control 16 15 14 13 12 11 10 9 8 7 6 5 4 3 2 1 2 1 4 3 5 6 7 PILOT A SIG Vin+ PILOT A SIG Vin8 9 10 230 VAC _ SW 10 J70 - HE (70) 230 VAC to HE 400 (163) (160) 10 CKT RIBBON SA3 (70) 230 VAC _ SW _ RET ARC_SUPPRESSOR PILOT PCB 9 MC2 Fan Control ARC_SUPPRESSOR J3 8 C Sheet 2 of 2 042X1353 10 A-51 ULTRA-CUT 100 XT/200 XT/300 XT/400 XT ANNEXE 28 : SCHÉMA DE PRINCIPE 400A, 380-415V PG 1 1 2 (1) 1 2 IN1 (2) 2 1 IN2 OUT2 GND2B CHASSIS GND (1) 1 2 IN1 (2) B 380-415 VAC INPUT (Customer supplied power cord must pass through ferrite core assembly.) L1 1 2 Earth (5) 2 1 (6) OUT3 1 2 Toriod Core W2B (7) (7) (8) (8) (9) OUT2 GND2B IN3 J105A L8 1 2 J103A 1 2 Toriod Core 019X502000 INVERTER MODULE (IM) #2 (middle) AC SUPPRESSION PCB J50 019X504000 J51 1 2 3 4 5 6 7 8 9 10 11 12 13 14 1 1 1 (3) 1 LT1 (23) (13) 019X502700 J105A L6 AC INPUT 1 2 1 2 J103A 1 2 Toriod Core 019x502000 W1A (1) 1 2 IN1 (2) EMI FILTER PCB OUT1 1 2 1 2 OUT2 GND2B IN3 W1B (21) 2 1 IN2 (3) INVERTER MODULE (IM) #`1 (bottom) (20) 2 1 (22) 2 1 W1C (23) (23) (24) (24) (25) (25) (1) 1 2 IN1 (2) EMI FILTER PCB (23) 2 1 OUT1 2 1 IN2 1 2 OUT2 GND2B IN3 2 1 (20) (21) TEST POINTS TP1 SECONDARY GND TP2 24VDC TP3 DC INPUT POSITIVE TP4 VCC1 TP5 VCC2 TP6 GATE TP7 PRIMARY GND TP8 +12V PRIMARY TP9 P ISOL GND SYSTEM BIAS SUPPLY PCB 8A, 500V, SB +24VDC (27B) (85B) AC INPUT 4 1 2 3 4 5 6 7 8 9 10 11 12 13 14 15 16 17 18 5 6 7 8 9 11 12 13 14 1 2 3 4 5 6 7 8 9 10 11 12 J63 Art # A-11965_AD 1 IM #1 Section B (upper) CONTROL PCB LEDS D1, RED, INV FLT D14, RED, OVER TEMP D24, GREEN, PWM ON D32, RED, PRI OC IM #1 Section A (lower) AC INPUT 1 2 J104A 1 2 J103A 1 2 LEDS D3, RED, MISSING PHASE D4, RED, AC V HIGH D14, RED, AC V LOW D26, GREEN, +12V PRI D30, GREEN, 24VDC D44, GREEN, T1 ON WORK (+) Component Locations (not including PCB components) (Sht 2, E3) 24 VDC 24 VDC MISSING PHASE a MISSING PHASE b AC V HIGH a AC V HIGH b AC V LOW a 24 VDC_RET 24 VDC_RET AC V LOW b VAC_IDA a / VAC_IDA b VAC_IDB a / VAC_IDB b (29) (30) (31) (32) (33) (34) (35) (36) (37) (38) (39) (40) (41) (42) 230V 400V 480V ERR /VAC_IDAb 0 1 0 1 /VAC_IDBb 0 0 1 1 J61 Measure relative to TP1 (24VDC_RET) "0" = 10-12V "1" = 24V VOLTAGE SELECTION (43A) A-52 10 GND J60 F 2 3 480V-ID 400V-ID 208-230V-ID COM (86B) 1 +V 019X501900 (85A) L4 System Bias LEDs & Test Points OUT3 J62 (27A) 019x502700 J105A To J27 on CCM I/O PCB F2 (86A) 1 2 MAIN PCB LEDS D3, RED, CAP IMBALANCE D4, GREEN, READY CAP BIAS PCB LEDS D6, GREEN, -12V D11, GREEN, +12VP D13, GREEN, +12V 019x502000 (22) 4 3 2 1 (28) (26) F1 8A, 500V, SB J103B Toriod Core (FRONT PANEL) (27A&B) E 1 2 (25) (1-20) (2-21) (3-22) ON / OFF 16 A J104B (24) CHASSIS GND CB1 AC INPUT 1 2 OUT3 1 2 (3) J105B L5 Toriod Core CHASSIS GND D IM #2 Section A (lower) J104A (25) LT1 & LT2 INPUT POWER NEON INDICATORS Rear Panel & Internal C 1 2 (24) INTERNAL AC INDICATOR CHASSIS GND J103B LT2 1 2 3 4 GND 1 2 Toriod Core (12) IM #2 Section B J104B (9) (11) AC INPUT 1 2 (8) PANEL AC INDICATOR J52 J105B L7 (7) (10) 1 2 3 4 AC LINE CHASSIS GND IM #3 Section A AC INPUT 1 2 J104A (9) W2C 019X502700 CHASSIS GND (2) L3 OUT1 2 1 IN2 (3) (4) 2 1 1 2 (1) L2 EMI FILTER PCB 1 2 J103B (9) W2A IM #3 Section B AC INPUT 1 2 J104B (8) OUT3 IN3 J105B L9 (7) (6) 2 1 5 INVERTER MODULE (IM) #3 (top) (5) 2 1 1 2 4 3 (4) OUT1 1 2 (3) A EMI FILTER PCB TO AUX TRANSFORMER TO J12 T1 PRIMARY (Sht 2, A1) 2 (44A) (48) Wire #48 from J61-1 to: J61-2 for 208-230 VAC J61-3 for 400 VAC J61-4 for 480 VAC C4 CB1 Capacitor, fan starting, 8uf 440VAC (Sht 2, D2) Circuit Breaker /ON/OFF SW, 15A 480V (Sht 1, E1) CB2-4 Circuit Breaker, 5A, 250V (Sht 2, B3) F1, 2 Fuse, 8A, 500V, S.B. (Sht 1,E1) FAN1 Fan, Heat Exchanger , 230 VAC (Sht 2, D2) FL1 Flow meter, pulse output (Sht 2, B2) FS1 Flow SW, 0.5 GPM (3.8 lpm), N.O. (Sht 2, A2) HCT1 Current Sensor, Hall Effect 200A, Work Lead (Sht 1, C8) K1 Relay, 24VAC, Inrush Control, (Sht2, B9) L1 Inductor, (Sht 1, B7) L3-9 Toriod Core Common Mode Ind (Sht1 B8, A-D3) LS1 Level Switch, Coolant Tank (Sht 2, A3) LT1, LT2 Indicator, Neon, 250V, AC Volts Present (Sht 1, B2 & C2) M1 Motor, Pump, ½ hp 230VAC, 50/60 Hz, 1Ph (Sht 2, C2) MC1 Relay, 120VAC, Inrush, coil (Sht2, B9) contact (Sht2, A1) MC2 Relay, 120 VAC, Fan Control, coil (Coil at Sht 2, A7)(Contacts at Sht 2, D1) Relay, 120 VAC, Pump Motor Control, coil MC3 (Coil at Sht 2, A7)(Contacts at Sht 2, C1) R2 Inrush, 4.7 Ohm, 30W (Sht2, A1) R3,4 Ext RC, 100 ohm 55W (Sht1, A7) SA1-4 Snubber, Contactor & Relay coils (Sht 2, A8 & A9) T1 Aux Transformer (Sht 2, B2) TB4 Terminal Block (Sht 1, C9) TS1 Temperature Sensor, NTC, Coolant Return (Sht 2, A5) TS2 Temperature Sensor, NTC, Ambient (Sht 2, A5) W1 Contactor , Input (Coil Sht 2, A8), (Contacts C2) W2 Contactor , Input (Coil Sht 2, A8), (Contacts A2) 4 3 ANNEXE 5 0-5264FR ULTRA-CUT 100 XT/200 XT/300 XT/400 XT 6 8 7 9 10 TO CCM CPU PCB J36 (Sht 2, C3) TORCH To TB4-7 J100 -- 30 CKT RIBBON J41 (J87) J58C (50) J100 -- 30 CKT RIBBON (51D) B Work 1 2 3 4 5 6 7 8 1 WORK (+) (51) ARC VOLTS (55) HCT1 Hall Effect Sensor 4 4 3 2 1 (51) (51) 3 J102A (49C) 5 4 WORK (+) Tip WORK L1 (51C) ELECTRODE (-) SHIELD TIP VOLTS (Sht 2, D3) TO CCM CPU PCB J33 (+) (53) To J24 on I-O PCB J102B To / From Optional 1 Torch Module (Refer to 1 Torch section for details.) J45 TO I/O BOARD 10 ckt Ribbon TO J3 on RELAY PCB (Sht 2, A5) (Sht 2, C3) J100 -- 30 CKT RIBBON J42 3 OUTPUT 5 4 3 2 1 TIP 019X501600 INVERTER (51F) (-) CHASSIS GND 1 2 J40 (Sht 2, C3) WORK (+) J41 5 4 3 2 1 Electrode (51E) CHASSIS GND J102A (49D) 1 (52) 1 R3 & R4 TO CCM CPU PCB J34 ELECTRODE (-) J44 (49E) 2 OUTPUT RAS PILOT To TB4-6 TIP PILOT PCB J58A 1 WORK (+) 5 4 3 2 1 J43 ELECTRODE A 2 1 J102B 1 L3 (49) 1 D2 PILOT ENABLE D11 +5V (Sht 2, C3) ELECTRODE (-) TEST POINTS TP1 GND TP2 PILOT GATE TP3 +5V PILOT BOARD LED'S TO CCM CPU PCB J35 J100 -- 30 CKT RIBBON TORCH (49) (51F) 2 OUTPUT (49F) 1 WORK (+) 5 4 3 2 1 1 2 3 4 5 6 7 8 9 10 ELECTRODE (-) OUTPUT WORK (+) OUTPUT 4 3 2 1 TO J1 on RELAY PCB (Sht 2, B9) TO CCM CPU PCB J31 (Sht 2, C3) WORK (+) SIG (+) -15 VDC (56) o AC 120V- TB4-4 (57) b AC 120V- Ret- TB4-3 (58) g AC 24V-TB4-2 (59) w AC 24V- Ret -TB4-1 (49) (52) (51) (60) 7 ARC VOLTS (TORCH) 6 TIP VOLTS (PILOT) 5 WORK 4 (61) 3 (62) 2 (63) 1 120 VAC @ 100 ma. 24 VAC @ 1A RIBBON CABLE 40 ckt CCM (J23) - RELAY PCB (J4) RIBBON CABLE 30 ckt. CCM (J31-36) - INVERTER (J100) J102A (49A) 5 4 3 2 1 TORCH (Sht 1, A9) TIP (Sht 1, A9) (J10 Sht 2, B8) J100 -- 30 CKT RIBBON ELECTRODE (-) COMMON J102B (49B) 5 J46-F (51B) ELECTRODE (-) 2 1 (Sht 2, C3) J100 -- 30 CKT RIBBON C TB4 J46-M +15 VDC 2 1 J16 TO CCM CPU PCB J32 1 2 3 4 5 6 7 8 9 10 11 12 13 14 15 16 17 18 19 20 21 22 23 24 25 26 27 28 29 30 (50) OUTPUT 32 33 34 35 36 37 38 39 40 1 COMMON 2 /1TORCH START * 3 NA 4 /1TORCH GAS SOL ON * 5 /MAIN TORCH IDLE * 6 /1TORCH PRESS OK * 7 FLOW SENSOR (pulses) 8 LOW COOLANT FLOW 9 COOLANT LEVEL OK 10 COMMON 11 NA 12 /PLASMA ENABLE-HMI 13 /COOLANT PUMP ON 14 COMMON 15 /PILOT ENABLE 16 /RAS ON 17 /CONTACTORS ON 18 COMMON 19 /COOLANT FANS ON 20 /1TORCH CONTACTOR ON * 21 /PLASMA ENABLE RELAY 22 COMMON 23 PILOT CURRENT SIG24 NC 25 PILOT CURRENT SIG+ 26 COMMON 27 WORK CURRENT SIG28 WORK CURRENT SIG+ 29 NC 30 AMBIENT TEMP 31 COOLANT TEMP * Used with 1 Torch Option READY + READY INVERTER_FLT + INVERTER_FLT OVERTEMP_FLT + OVERTEMP_FLT PWR_PRESENT + PWR_PRESENT OUT_COM (+3 to 5VDC) VAC_SELA VAC_SELB IS_IDA IS_IDB IS_IDC ENABLE + ENABLE START2 + START2 SPARE SYNC_IN + SYNC_IN NC NC 47 OHM to COMM DEMAND + DEMAND 47 OHM to COMM CURRENT + CURRENT 47 OHM to COMM COMMON -15 VDC COMMON 24 VDC COMMON 24 VDC COMMON 24 VDC COMMON D RIBBON CABLE 16 ckt CCM ( J37) - DISPLAY PCB (J17) 1,3,5,7 2,4,6,8 9,10 11-16 24 VDC COMMON NC SERIAL DATA RIBBON CABLE 10 ckt RELAY PCB (J3) – PILOT PCB (J42) 1,2 3,4,7,10 5 6 8 9 E 24 VDC COMMON PILOT ENABLE + PILOT ENABLE – PILOT CURRENT SIG – PILOT CURRENT SIG + Art # A-11965_AD Rev 00 Revision Initial Design AA AB By DAT DAT ECO-B2687 DAT Date Revision Rev By Date Thermal Dynamics Corporation 2800 Airport Rd. Denton, Texas 76207 USA 10/03/2012 9 /1 6 /2 0 1 4 10/17/2014 Size Drawing Number SCHEMATIC 0-5264FR 8 7 ANNEXE 9 10/03/2012 DAT The information contained herein is proprietary to Thermal Dynamics. Not for release, reproduction or distribution without written consent. Title Ultra-Cut XT 400A CE 380-415 VAC 6 F Date Printed Date Revised 11/20/2014 12/16/2014 Drawn Date C Sheet 1 of 2 042X1341 10 A-53 ULTRA-CUT 100 XT/200 XT/300 XT/400 XT ANNEXE 29 : SCHÉMA DE PRINCIPE 400A, 380-415V PG 2 1 3 2 (1) 1 2 IN1 (2) 2 1 (5) 2 1 IN2 1 2 OUT2 GND2B 1 2 IN1 (2) B 380-415 VAC INPUT (Customer supplied power cord must pass through ferrite core assembly.) L1 L3 OUT1 (3) (5) 2 1 IN2 1 2 1 2 J103B 2 1 (6) OUT3 1 2 Toriod Core W2A W2B (7) (7) (8) (8) (9) OUT2 GND2B IN3 J105A L8 1 2 J103A 1 2 Toriod Core 019X502000 INVERTER MODULE (IM) #2 (middle) AC SUPPRESSION PCB J50 019X504000 J51 1 2 3 4 5 6 7 8 9 10 11 12 13 14 1 1 1 (3) 1 LT1 (23) (13) 019X502700 J105A L6 AC INPUT 1 2 1 2 J103A 1 2 Toriod Core 019x502000 W1A (1) 1 2 IN1 (2) EMI FILTER PCB OUT1 1 2 1 2 OUT2 GND2B IN3 W1B (21) 2 1 IN2 (3) INVERTER MODULE (IM) #`1 (bottom) (20) 2 1 (22) 2 1 W1C (23) (23) (24) (24) (25) (25) (1) 1 2 IN1 (2) EMI FILTER PCB (23) 2 1 OUT1 2 1 IN2 1 2 OUT2 GND2B IN3 2 1 (20) (21) TEST POINTS TP1 SECONDARY GND TP2 24VDC TP3 DC INPUT POSITIVE TP4 VCC1 TP5 VCC2 TP6 GATE TP7 PRIMARY GND TP8 +12V PRIMARY TP9 P ISOL GND SYSTEM BIAS SUPPLY PCB 8A, 500V, SB +24VDC (27B) (85B) AC INPUT 4 1 2 3 4 5 6 7 8 9 10 11 12 13 14 15 16 17 18 5 6 7 8 9 11 12 13 14 1 2 3 4 5 6 7 8 9 10 11 12 J63 Art # A-11966_AD 1 CONTROL PCB LEDS D1, RED, INV FLT D14, RED, OVER TEMP D24, GREEN, PWM ON D32, RED, PRI OC IM #1 Section A (lower) AC INPUT 1 2 1 2 J103A 1 2 LEDS D3, RED, MISSING PHASE D4, RED, AC V HIGH D14, RED, AC V LOW D26, GREEN, +12V PRI D30, GREEN, 24VDC D44, GREEN, T1 ON (Sht 2, E3) 24 VDC 24 VDC MISSING PHASE a MISSING PHASE b AC V HIGH a AC V HIGH b AC V LOW a 24 VDC_RET 24 VDC_RET AC V LOW b VAC_IDA a / VAC_IDA b VAC_IDB a / VAC_IDB b (29) (30) (31) (32) (33) (34) (35) (36) (37) (38) (39) (40) (41) (42) 230V 400V 480V ERR /VAC_IDAb 0 1 0 1 /VAC_IDBb 0 0 1 1 J61 Measure relative to TP1 (24VDC_RET) "0" = 10-12V "1" = 24V VOLTAGE SELECTION (43A) A-54 10 GND J60 F 2 3 480V-ID 400V-ID 208-230V-ID COM (86B) 1 +V 019X501900 (85A) D6, GREEN, -12V D11, GREEN, +12VP D13, GREEN, +12V IM #1 Section B (upper) J104A WORK (+) Component Locations (not including PCB components) To J27 on CCM I/O PCB F2 (27A) 019x502700 J105A L4 System Bias LEDs & Test Points OUT3 J62 (86A) 1 2 MAIN PCB LEDS D3, RED, CAP IMBALANCE D4, GREEN, READY CAP BIAS PCB LEDS 019x502000 (22) 4 3 2 1 (28) (26) F1 8A, 500V, SB J103B Toriod Core (FRONT PANEL) (27A&B) E 1 2 (25) (1-20) (2-21) (3-22) CB1 J104B (24) CHASSIS GND ON / OFF 16 A AC INPUT 1 2 OUT3 1 2 (3) J105B L5 Toriod Core CHASSIS GND D IM #2 Section A (lower) J104A (25) LT1 & LT2 INPUT POWER NEON INDICATORS Rear Panel & Internal C 1 2 (24) INTERNAL AC INDICATOR CHASSIS GND J103B LT2 1 2 3 4 GND 1 2 Toriod Core (12) IM #2 Section B J104B (9) (11) AC INPUT 1 2 (8) PANEL AC INDICATOR J52 J105B L7 (7) (10) 1 2 3 4 AC LINE CHASSIS GND IM #3 Section A AC INPUT 1 2 J104A (9) W2C 019X502700 CHASSIS GND (2) Earth 2 1 1 2 (1) L2 EMI FILTER PCB (4) IM #3 Section B AC INPUT 1 2 (9) CHASSIS GND (1) 5 J104B (8) (6) 2 1 J105B L9 (7) OUT3 IN3 4 INVERTER MODULE (IM) #3 (top) (4) OUT1 1 2 (3) A EMI FILTER PCB TO AUX TRANSFORMER TO J12 T1 PRIMARY (Sht 2, A1) 2 (44A) (48) Wire #48 from J61-1 to: J61-2 for 208-230 VAC J61-3 for 400 VAC J61-4 for 480 VAC 3 C4 CB1 Capacitor, fan starting, 8uf 440VAC (Sht 2, D2) Circuit Breaker /ON/OFF SW, 15A 480V (Sht 1, E1) CB2-4 Circuit Breaker, 5A, 250V (Sht 2, B3) F1, 2 Fuse, 8A, 500V, S.B. (Sht 1,E1) FAN1 Fan, Heat Exchanger , 230 VAC (Sht 2, D2) FL1 Flow meter, pulse output (Sht 2, B2) FS1 Flow SW, 0.5 GPM (3.8 lpm), N.O. (Sht 2, A2) HCT1 Current Sensor, Hall Effect 200A, Work Lead (Sht 1, C8) K1 Relay, 24VAC, Inrush Control, (Sht2, B9) L1 Inductor, (Sht 1, B7) L3-9 Toriod Core Common Mode Ind (Sht1 B8, A-D3) LS1 Level Switch, Coolant Tank (Sht 2, A3) LT1, LT2 Indicator, Neon, 250V, AC Volts Present (Sht 1, B2 & C2) M1 Motor, Pump, ½ hp 230VAC, 50/60 Hz, 1Ph (Sht 2, C2) MC1 Relay, 120VAC, Inrush, coil (Sht2, B9) contact (Sht2, A1) MC2 Relay, 120 VAC, Fan Control, coil (Coil at Sht 2, A7)(Contacts at Sht 2, D1) Relay, 120 VAC, Pump Motor Control, coil MC3 (Coil at Sht 2, A7)(Contacts at Sht 2, C1) R2 Inrush, 4.7 Ohm, 30W (Sht2, A1) R3,4 Ext RC, 100 ohm 55W (Sht1, A7) SA1-4 Snubber, Contactor & Relay coils (Sht 2, A8 & A9) T1 Aux Transformer (Sht 2, B2) TB4 Terminal Block (Sht 1, C9) TS1 Temperature Sensor, NTC, Coolant Return (Sht 2, A5) TS2 Temperature Sensor, NTC, Ambient (Sht 2, A5) W1 Contactor , Input (Coil Sht 2, A8), (Contacts C2) W2 Contactor , Input (Coil Sht 2, A8), (Contacts A2) 4 ANNEXE 5 0-5264FR ULTRA-CUT 100 XT/200 XT/300 XT/400 XT 6 8 7 9 10 TO CCM CPU PCB J36 (Sht 2, C3) TORCH To TB4-7 J100 -- 30 CKT RIBBON PILOT BOARD LED'S D2 PILOT ENABLE D11 +5V CHASSIS GND (50) J100 -- 30 CKT RIBBON (51D) B Work 1 2 3 4 5 6 7 8 1 (+) (51) WORK (55) ARC VOLTS HCT1 4 3 2 1 Hall Effect Sensor (51) (51) 4 J102A (49C) 5 3 WORK (+) Tip WORK L1 (51C) ELECTRODE (-) SHIELD TIP VOLTS (Sht 2, D3) (Sht 2, C3) J100 -- 30 CKT RIBBON (+) (53) To J24 on I-O PCB J102B TO CCM CPU PCB J33 To / From Optional 1 Torch Module (Refer to 1 Torch section for details.) J45 TO I/O BOARD 10 ckt Ribbon TO J3 on RELAY PCB (Sht 2, A5) 4 OUTPUT 5 4 3 2 1 J42 3 WORK (+) TIP 019X501600 INVERTER (51F) (-) CHASSIS GND 1 2 J40 TO CCM CPU PCB J34 (49D) J41 5 4 3 2 1 J102A Electrode J58C (Sht 2, C3) ELECTRODE (-) (52) J41 (J87) (49E) 2 OUTPUT 1 1 1 WORK (+) 5 4 3 2 1 J44 R3 & R4 (51E) ELECTRODE (-) RAS PILOT To TB4-6 TIP PILOT PCB J58A (Sht 2, C3) J100 -- 30 CKT RIBBON J43 ELECTRODE A 2 1 J102B TO CCM CPU PCB J35 1 L3 (49) 1 (51F) 2 OUTPUT TORCH (49) TEST POINTS TP1 GND TP2 PILOT GATE TP3 +5V 1 WORK (+) 5 4 3 2 1 1 2 3 4 5 6 7 8 9 10 ELECTRODE (-) (49F) OUTPUT ELECTRODE (-) WORK (+) OUTPUT 4 3 2 1 TO J1 on RELAY PCB (Sht 2, B9) TO CCM CPU PCB J31 (Sht 2, C3) WORK (+) SIG (+) -15 VDC (56) o AC 120V- TB4-4 (57) b AC 120V- Ret- TB4-3 (58) g AC 24V-TB4-2 (59) w AC 24V- Ret -TB4-1 (49) (52) (51) (60) 7 ARC VOLTS (TORCH) 6 TIP VOLTS (PILOT) 5 WORK 4 (61) 3 (62) 2 (63) 1 120 VAC @ 100 ma. 24 VAC @ 1A RIBBON CABLE 40 ckt CCM (J23) - RELAY PCB (J4) RIBBON CABLE 30 ckt. CCM (J31-36) - INVERTER (J100) J102A (49A) 5 4 3 2 1 TORCH (Sht 1, A9) TIP (Sht 1, A9) (J10 Sht 2, B8) J100 -- 30 CKT RIBBON ELECTRODE (-) COMMON J102B (49B) 5 J46-F (51B) J100 -- 30 CKT RIBBON 2 1 (Sht 2, C3) C TB4 J46-M +15 VDC 2 1 J16 TO CCM CPU PCB J32 1 2 3 4 5 6 7 8 9 10 11 12 13 14 15 16 17 18 19 20 21 22 23 24 25 26 27 28 29 30 (50) OUTPUT 32 33 34 35 36 37 38 39 40 1 COMMON 2 /1TORCH START * 3 NA 4 /1TORCH GAS SOL ON * 5 /MAIN TORCH IDLE * 6 /1TORCH PRESS OK * 7 FLOW SENSOR (pulses) 8 LOW COOLANT FLOW 9 COOLANT LEVEL OK 10 COMMON 11 NA 12 /PLASMA ENABLE-HMI 13 /COOLANT PUMP ON 14 COMMON 15 /PILOT ENABLE 16 /RAS ON 17 /CONTACTORS ON 18 COMMON 19 /COOLANT FANS ON 20 /1TORCH CONTACTOR ON * 21 /PLASMA ENABLE RELAY 22 COMMON 23 PILOT CURRENT SIG24 NC 25 PILOT CURRENT SIG+ 26 COMMON 27 WORK CURRENT SIG28 WORK CURRENT SIG+ 29 NC 30 AMBIENT TEMP 31 COOLANT TEMP * Used with 1 Torch Option READY + READY INVERTER_FLT + INVERTER_FLT OVERTEMP_FLT + OVERTEMP_FLT PWR_PRESENT + PWR_PRESENT OUT_COM (+3 to 5VDC) VAC_SELA VAC_SELB IS_IDA IS_IDB IS_IDC ENABLE + ENABLE START2 + START2 SPARE SYNC_IN + SYNC_IN NC NC 47 OHM to COMM DEMAND + DEMAND 47 OHM to COMM CURRENT + CURRENT 47 OHM to COMM COMMON -15 VDC COMMON 24 VDC COMMON 24 VDC COMMON 24 VDC COMMON D RIBBON CABLE 16 ckt CCM ( J37) - DISPLAY PCB (J17) 1,3,5,7 2,4,6,8 9,10 11-16 24 VDC COMMON NC SERIAL DATA RIBBON CABLE 10 ckt RELAY PCB (J3) – PILOT PCB (J42) 1,2 3,4,7,10 5 6 8 9 E 24 VDC COMMON PILOT ENABLE + PILOT ENABLE – PILOT CURRENT SIG – PILOT CURRENT SIG + Art # A-11966_AD Rev 00 Revision Initial Design DAT AA AB By ECO-B2687 Date Revision Rev By Date Thermal Dynamics Corporation 2800 Airport Rd. Denton, Texas 76207 USA 10/03/2012 DAT 9 /1 6 /2 0 1 4 DAT 10/17/2014 The information contained herein is proprietary to Thermal Dynamics. Not for release, reproduction or distribution without written consent. Size Drawing Number SCHEMATIC 0-5264FR 8 7 ANNEXE 9 10/03/2012 DAT Title Ultra-Cut XT 400A CE 380-415 VAC 6 F Date Printed Date Revised 11/20/2014 12/16/2014 Drawn Date C Sheet 1 of 2 042X1341 10 A-55 ULTRA-CUT 100 XT/200 XT/300 XT/400 XT ANNEXE 30 : DÉPANNAGE AVANCÉ Présentation de System Les alimentations Auto-Cut 200 et 300 XT, PAK200i, et Ultra-Cut 100, 200, 300 & 400 XT comprennent un, deux ou trois modules onduleurs. Chaque MO peut avoir une ou deux sections d’onduleur désignées sections A ou B. Les modules onduleurs sont montés l’un sur l’autre numérotés de bas en haut. Les sections sont également nommées de bas en haut avec la section A se trouvant sur la partie inférieure de chaque module. Un MO avec une section est considéré comme un demi-module ou un module partiel avec la section supérieure (« B ») manquante. Les demi-modules sont utilisés avec les alimentations 200 A et 300 A et seront toujours en position centrale. Les MO avec 2 sections sont considérés comme des modules « pleins ». Chaque section d’onduleur peut fournir jusqu’à 67 A, mais pas dans toutes les configurations : Une unité 400 A utilise 6 sections. 400 A / 6 = 66,67 A par section. Une unité 300 A utilise 5 sections. 300 A / 5 = 60 A par section. Une unité 200 A utilise 3 sections. 200/3 = 66,67 A par section. Une unité 100 A utilise 2 sections. 100/2=50 A par section. Configurations de l’appareil Art # 12299 À l’exception de l’AC 200 XT et du PAK200i, toutes les autres unités ont le même châssis, avec suffisamment de place pour jusqu’à 3 modules d’onduleur. Les zones non utilisées ont des panneaux vierges occupant des emplacements vides qui sont requis pour le flux d’air. Un système 100 A utilise un 1 MO complet; le système 200 A utilise un module et demi, avec un module complet à l’arrière et un demi-module en position centrale. Une unité 300 A a des modules pleins en haut et en bas, avec un demi-module en position centrale. L’AC 200, le XT et le PAK200i ne comportent que les emplacements de module du bas et du milieu. Un démarreur d’arc interne et le contrôle des gaz sont situés à la place du 3e MO (supérieur). Refroidissement du module de l’onduleur. Les semi-conducteurs de puissance des modules onduleurs sont refroidis par liquide, ce qui nous permet d’obtenir plus de puissance dans une zone plus petite et à moindre coût. Chaque MO a un puits thermique refroidi par liquide ou une « plaque de refroidissement » partagée par les 2 sections d’onduleur. Les composants, les transformateurs et les inducteurs magnétiques sont refroidis par air et montés sur le côté arrière du module onduleur où ils sont exposés à des volumes élevés de flux d’air des ventilateurs de refroidissement dont l’air refroidit également le liquide de refroidissement dans l’échangeur de chaleur ou radiateur. Il est important que le panneau inférieur droit soit bien en place, sinon le flux d’air ne circulera pas correctement pour refroidir les composantes magnétiques. Contrôle de l’onduleur. Les sections de l’onduleur fonctionnent comme des onduleurs séparés dont les sorties sont montées en parallèle. Ils sont contrôlés indépendamment du module de commande et de contrôle (CCM) qui est le « cerveau » du système. Chaque section d’onduleur est connectée à un câble plat distinct provenant du CCM, qui a 6 connecteurs, J31 – J36, A-56 ANNEXE À INV 1A À INV 1B À INV 2A À INV 2B À INV 3A À INV 3B Art # 12300FR 0-5264FR ULTRA-CUT 100 XT/200 XT/300 XT/400 XT correspondant aux sections d’onduleur 1A à 3B. Les câbles plats sont étiquetés sur les extrémités de l’onduleur comme INV et comporte le numéro et la section (INV 1A, 1B INV, etc.). Une unité de 100 A ne comportera que des câbles plats dans J31 et J32 ; dans une unité de 200 A, J31 à J33 seront occupés et les autres emplacements vides. Pour 300 A, J34 sera absent et les autres seront occupés. Les autres cartes dans le système sont le System Bias Supply (alimentation de polarisation système), le Relay & Interface PCB (circuit relais et interface), le Display PCB (circuit d’affichage), le Pilot PCB (pilote PCB). et l’AC Suppression PCB (circuit de suppression AC) Le CCM comporte 2 cartes, à savoir la carte E/S (entrée/ sortie) et la carte CPU (unité centrale). Les unités CE auront également un ou plusieurs cartes filtres d’interférences électromagnétique sur la puissance d’entrée. La carte d’alimentation du System Bias est alimentée à partir de l’entrée alternative triphasée et fonctionne à environ 150V à plus de 600V couvrant toutes les plages de tension normales. Il peut opérer sur 2 phases (monophasé) afin de pouvoir fournir une alimentation polarisée et peut signaler un défaut s’il manque l’une des phases. La sortie de l’alimentation est de 24 V CC, qui alimente la carte de relais, l’affichage, la carte pilote et les deux carte du CCM. System Bias comporte également des circuits permettant de détecter la phase manquante et de déterminer si la tension alternative est dans la bonne plage, ni trop haut ni trop bas. Il signale aussi au CCM pour quel voltage l’unité est configurée. Le circuit imprimé d’alimentation de la polarisation comprend un relais, K1, qui ne met sous tension le primaire du transformateur auxiliaire, T1, que lorsque la tension d’entrée se situe dans la plage correcte. La carte relais et l’interface accepte et répartit à la sortie du transformateur auxiliaire. Il a pour contrôler le relais de pompe, ventilateurs, contacteurs d’entrée, l’Arc démarreur et le relais de courant d’appel. Un circuit sur la carte de relais accepte l’entrée du capteur de courant d’usinage, HCT1, et le capteur de courant du pilote (sur le PCB du pilote) et envoie le signal Activer aux commutateurs IGBT des cartes du pilote via le câble plat J3 à J42. Les autres entrées sur la carte Relay (relais) comprennent le Negative Temperature Coefficient (coefficient négatif de température, NTC) des capteurs de température ambiante et de liquide de refroidissement. Le commutateur de niveau du réservoir de liquide de refroidissement et de circulation du liquide de refroidissement, qui détermine si l’écoulement est supérieur au taux minimum requis, envoie aussi des signaux à la carte de relais. Les modèles Ultra-Cut sont munis d’un capteur de débit dont la sortie de la carte de relais est une série d’impulsions dont la fréquence indique le débit et permet de détecter la présence de bulles de gaz dans le liquide de refroidissement. Tous ces signaux passent au CCM via un câble plat à 40 conducteurs menant à la carte E/S du CCM. Le tableau d’affichage comporte des LED pour AC, TEMP, GAS & DC. Il a également un affichage de 7 segments à 4 caractères pour indiquer les renseignements de défaut ou de statut. La DEL a.c. indique que les contacteurs d’entrée aux onduleurs ont reçu l’ordre de se fermer, mais pas qu’ils sont fermés. TEMP signifie qu’un ou plusieurs onduleurs ou le liquide de refroidissement a dépassé la température autorisée. GAS signifie que le gaz s’écoule et que l’écoulement de liquide de refroidissement sont corrects. DC signifie que la tension de sortie de l’onduleur est supérieure à 60 Vcc. Le premier chiffre de l’affichage à 7 segments indique la lettre « C »; « E »; « L » ou est vide. Pendant séquence de démarrage initiale, la lettre « C » suivie de 3 autres chiffres indique la révision du code du CCM. Les codes d’état ou de défaut qui peuvent apparaître lors de la séquence d’allumage, ou à tout autre moment, sont précédés par la lettre « E » pour un défaut actif ou par un « L » pour un défaut « verrouillé » ou « passé », qui a arrêté le processus, mais qui n’est plus actif. Lorsqu’il n’y a pas de défaut ou de code d’état actif, le courant de sortie actuel est affiché avec le premier chiffre absent. Si le système est un Ultra-Cut XT avec un contrôle des gaz automatique, DFC 3000, l’affichage montre « 0 » jusqu’à ce qu’un processus ait été chargé. Si l’écran indique une défaillance ou un autre statut, il alternera entre le réglage actuel et la défaillance.. La carte pilote contient une paire de transistors IGBT parallèles qui fonctionnent comme un commutateur électronique pour brancher et débrancher la pointe de la torche de la 1ère section de l’onduleur. Lorsque le commutateur électronique pilote est fermé et le pilote est allumé par le démarreur d’arc, le courant à partir de la 1ère section passe entre l’électrode et la pointe. Ensuite, à mesure que le transfert commence, un petit courant du 2e onduleur circule de l’électrode pour fonctionner. Lorsque le transfert est détecté, le commutateur de pilote est ouvert et le courant de la 1ère section est libre de circulation à l’ouvrage à travers la diode qui est également sur le carte pilote. Le PAK200i et l’option 1Torch font exception en ce que la deuxième section n’est pas activée lors de l’établissement du pilote. Le pilote et le transfert initial sont assurés par la première section. Les autres sections sont introduites progressivement à mesure que l’intensité s’accroît jusqu’au niveau final. La carte pilote comporte également un capteur de courant pilote pour détecter et mesurer le niveau de courant pilote. Des circuits résistance/capacité (RC) additionnels sur le PCB du pilote aident et stabilisent le pilote et les arcs transférés. 0-5264FR ANNEXE A-57 ULTRA-CUT 100 XT/200 XT/300 XT/400 XT Interrupteur pilote (IGBT) 1e section du hâcheur (INV 1 A) Électrode 2e section du hâcheur (INV 1 B) (+) Pointe Pièce Art # 12301FR (+) La carte antiparasite alternative a des condensateurs et autres composants antiparasites transitoires pour protéger le système contre les transitoires sur les lignes à courant alternatif. Il fournit également l’alimentation pour les voyants au néon qui signalent la présence du courant alternatif (CA), en s’allumant lorsque l’alimentation secteur est connectée même lorsque le commutateur MARCHE/ARRÊT, CB1, est ouvert. Différences entre divers modèles. Les unités Auto-Cut 200, PAK 200i et XT 300 utilisent les circuits de base d’amorçage de l’arc et de commande du gaz, qui comprennent des entrées de gaz simples, une pour le plasma et une autre pour le gaz de protection. Une troisième entrée, fournissant de l’eau pour le brouillard de protection H2O, est également comprise dans l’Auto-Cut 300 XT et disponible en option pour l’Auto-Cut 200XT. Il existe un régulateur de pression et un manomètre pour chaque entrée de gaz et compteur / contrôle de débit d’eau lorsque l’option H2O Mist est utilisée. Les trois sont allumés/éteints avec des solénoïdes de commande. Changer les types de gaz exige de connecter différents gaz sur le panneau arrière et régler l’interrupteur de gaz sur le panneau arrière pour le faire correspondre au type de gaz plasma. Il n’existe pas de gaz (de débit anticipé) pilote à ce moment. L’éclateur de l’Auto-Cut 200 XT, de l’Auto-Cut 300 XT et du PAK 200i est un éclateur de type classique avec bobine refroidie à l’eau, que nous utilisons depuis plusieurs années Ce démarreur d’arc injecte le HF sur l’électrode de la torche à travers le fil négatif avec le retour par le fil de la pointe et du pilote. Les unités Ultra-Cut XT utilisent le démarreur d’arc à distance, RAS 1000 XT. Au lieu d’un éclateur, le RAS 1000 XT utilise un module d’allumage transistorisé pour créer les pulsations HF qui sont injectées dans l’embout et retournent par l’électrique, dans la direction opposée à celle utilisée dans l’Auto-Cut, l’Auto-Cut XT et le modèle plus ancien RAS 1000 utilisé avec les unités Ultra-Cut. L’AC 200 XT et le PAK200i avait une commande de gaz et un démarreur d’arc intégrés dans le boîtier principal dans la zone qui est utilisée pour le module supérieur de l’onduleur dans d’autres unités de cette famille. L’AC 300 XT a une commande de gaz / un démarreur d’arc distinct qui repose au-dessus du boîtier principal très similaire à la GCM 1000 de nos précédents modèles Auto-Cut. Il s’appelle de fait un GCM 1000 XT. Les deux modèles Auto-Cut XT ont une commande de courant analogique (potentiomètre). Sur le panneau avant de l’unité principale pour l’AC 200 XT comme ceux de PAK 200i et sur le boîtier principal, le GCM 1000 XT, pour la version AC 300 XT. Dans chacun des cas, l’ampérage est affiché sur l’écran numérique du panneau avant. Les deux modèles Auto-Cut ont un sélecteur de mode de gaz à l’arrière, pour le AC 300 XT près des admissions de gaz du GCM 1000 XT. Sur l’AC 200 XT il se situe près des connecteurs, des fusibles et des disjoncteurs. Le commutateur doit être réglé en fonction du type de gaz, d’AIR/O2 or N2, H35 ou autres gaz non oxydants utilisés pour le plasma. Le PAK200i n’est pas muni de ce commutateur. Dans l’AC XT 200 et le PAK200i, le circuit du pilote est monté sur la partie supérieure du deuxième module de l’onduleur (IM#2), le demi-module, à la place de la deuxième section (section « B ») que comporterait un module complet. L’AC 300 XT et tous les modèles Ultra-Cut XT ont la carte pilote sur le côté opposé des onduleurs, le côté « disjoncteur », dans la partie supérieure arrière derrière le module CCM. Reportez-vous à la section Pièces de rechange (pièces de rechange) du mode d’emploi pour trouver les illustrations indiquant les différents emplacements. Les modèles Ultra-Cut XT, ainsi que les modèles 100, 200, 300 et 400A peuvent tous utiliser soit une commande de gaz « manuel » GCM 2010 ou la commande de gaz Aut DFC 3000. Ces commandes de gaz restent inchangés par rapport aux anciens appareils Ultra-Cut. Les modèles Ultra-Cut XT utilisent le même interrupteur de débit, FS1, tout comme les modèles Auto-Cut XT, pour détecter et empêcher le fonctionnement lorsque le débit du liquide de refroidissement est inférieur au minimum de 0,75 GPM (2,8 l/m). Néanmoins, les Ultra-Cut XT comprennent un détecteur d’écoulement de liquide de refroidissement, FL1, qui mesure aussi l’écoulement et peut détecter la présence de bulles de gaz dans le liquide de refroidissement, ces bulles pouvant réA-58 ANNEXE 0-5264FR ULTRA-CUT 100 XT/200 XT/300 XT/400 XT duire la durée de vie des consommables. La détection de bulles ou d’un faible écoulement au niveau de FL1 n’empêchera PAS la coupe, mais un code avertissant la présence d’une anomalie s’affichera. Le code est E406. Les modèles Ultra-Cut XT ont des consommables standards pour les courants de découpe plus faibles que celles utilisées pour Auto-Cut XT, 15A vs. 55A, ainsi qu’un marquage à des courants plus faibles. Pour améliorer le fonctionnement à ces niveaux de courant très faibles, un inducteur de sortie supplémentaire, L1, est ajoutée en série à la première section d’onduleur (Module onduleur# 1A).. Module 1Torch en option À partir du début 2015, tous les modèles d’Auto-Cut 300 XT et d’Ultra-Cut XT pourront être commandés en usine munis d’un module en option permettant la connexion d’une SL100 « 1Torch » qui effectue des coupes à alimentation fixe de 100 A. Ce module est intégré dans le panneau avant d’alimentation du XT, juste au-dessus du couvercle du remplissage du réservoir de liquide de refroidissement. En connectant une alimentation d’air de l’atelier et une torche SL100, vous pouvez utiliser cette torche avec ses consommables de coût relativement faible pour couper de la ferraille à la main ou n’importe quoi d’autre, sans consommer les fournitures plus chères de la torche XT. Codes d’état. Les codes de l’alimentation sont affichés sur l’écran numérique à 4 chiffre de la carte d’affichage. Certains codes concernent les commandes du gaz, mais plus de détails sont indiqués sur les codes de commande de gaz sur chacune des commandes. Les commandes de gaz utilisées avec la famille XT de fourniture de plasma n’ont pas changé. Ils ont leur propre ensemble de codes d’état qui seront abordés dans une autre section. Ce guide suppose que vous avez d’abord consulté les tableaux de code d’état dans la section Fonctionnement du manuel de l’appareil. Les codes individuels indiquent différentes sections de l’onduleur, mais dans ce guide, les codes similaires sont regroupés. Par exemple, un code E (ou L) 249 indique une défaillance de l’onduleur à l’onduleur 2A. Ce guide traite des codes 247-252 en une section puisqu’ils sont tous les mêmes, la seule différence étant l’onduleur et la section auxquels ils se rapportent. Les codes sont séparés en 7 groupes. Groupe 1 Procédé plasma -- Concerne les voltages du pilote, du transfert, de la torche, etc. Groupe 2 Alimentation électrique du plasma -- Surtout les sections de l’onduleur Groupe 3 Interface avec les Gas controls (contrôles du gaz) - DFC 3000 principalement Groupe 4 Système de refroidissement -- Système de refroidissement par liquide pour la torcheet les onduleurs Groupe 5 CCM -- Port de communications aux contrôles de gaz Groupe 6 CCM – État Groupe 7 Accessoires – 1Torch Pour les unités XT, nous utilisons un code à trois chiffres avec les codes du groupe 1 dans les 100, du groupe 2 dans les 200, etc. Ceux-ci correspondent aux anciens codes utilisés dans les appareils passés, où 1-1 est maintenant 101. Pour la plupart, les codes ont la même signification. Lorsqu’un ancien code n’est plus appliqué au système XT nous ne l’utilisons pas, mais l’avons laissé réservé pour éviter toute confusion. Par exemple, le code 204 (2- 4), qui signifie que le module d’onduleur n’était pas prêt. Nous détectons maintenant cette erreur d’une manière différente, qui a un sens quelque peu différent si nous avons réservé le code 204.. Tandis que la plupart des codes indiquent qu’une erreur est survenue, quelques-uns d’entre eux, tels que 304 (anciennement 3 - 4), renvoient simplement à l’état actuel. 304 indique soit l’« amorce », où la pompe remplît le système avec du liquide de refroidissement, ou plus souvent la « purge », au cours de laquelle le gaz s’écoule pour sécher les consommables après les avoir remplacés ou la purge des conduites de gaz lorsqu’un type de gaz différent a été sélectionné. Dépannage (généralités) Souvent, lorsque la cause indiquée est un câble ou un fil débranché, celui-ci pourrait être mal branché ou endommagé. Tous les câbles plats ont un réceptacle supplémentaire à une extrémité pour mesurer les signaux sur ce câble. 0-5264FR ANNEXE A-59 ULTRA-CUT 100 XT/200 XT/300 XT/400 XT Plusieurs des mesures nécessiteront de sonder certains petits connecteurs ou de mesurer le signal sur les câbles plats. Pour inspecter les petits connecteurs, des sondes de mesure standard sont généralement trop grosses. Nous vous suggérons de faire quelques sondes en utilisant un fil d’acier. Le fil bus en cuivre n’est pas suffisamment rigide. Un trombone et un peu trop gros. Une idée est de prendre une prise d’un Amp Mate-N-Lok ou connecteur similaire sur lequel vous pourrez brancher la sonde et glisser un fil d’acier très fin, (0,020 à 0,025” dia. ; (0,5-0,6 mm) est idéal), là où le fil doit normalement être inséré. Le fil doit être soudé et serti. Le fil d’acier peut être disponible dans les magasins de modélisme qui satisfont aux besoins de conception de modèles. Art # 12302 Art # 12303 Isolez entièrement le câble en laissant seulement les extrémités libres, puis insérez-les dans votre sonde. Si votre voltmètre a des adaptateurs de pince crocodile, vous pouvez tenir le fil dans ces adaptateurs aussi, assurez-vous qu’ils ne font pas court-circuit. Les problèmes ne sont pas tous provoqués par le système de plasma. Lorsque des fils supplémentaires ou d’autres composants ont été ajoutés au système d’origine, retirez-les si c’est possible, pour voir s’ils sont à l’origine du problème. Les branchements au bornier TB4 ou aux autres borniers TB sur le CCM peuvent générer du bruit ou créer des chemins de courant inattendus qui changent la façon dont le système fonctionne. Problèmes qui ne déclenchent pas de codes d’état ou de défaut : Problèmes de liquide de refroidissement : 1. Voyant gaz clignotant. À l’allumage, le voyant GAZ sur le panneau avant clignote sans s’arrêter. Aucun code ne s’affiche. Le problème réel est une circulation du liquide de refroidissement faible ou nulle, mais il faut 4 minutes avant que le code ne soit généré et la plupart des gens n’attentent pas aussi longtemps. Reportez-vous au code 404 pour le dépannage. 2. La pompe ne démarre pas. La résistance R2 est ouverte, ce qui empêche la mise sous tension du transformateur T1. Cela empêche la pompe de démarrer. Cela va également générer un code 404 après 4 minutes, mais la plupart des gens n’attendent pas aussi longtemps. Problèmes avec le pilote. 3. Échec de démarrage du pilote. En fait, ce problème définit un code de défaillance 102 au bout de 15 à 18 secondes, mais si vous n’attendez pas assez longtemps, il donne l’impression de ne pas générer de code. Reportez-vous au code 102 pour le dépannage. 4. Un pilote faible qui ne s’établit que lorsque la torche est très proche de la pièce, peut être provoqué par une inversion des câbles plats à 30 broches sur les sections A et B de l’onduleur 1. Problèmes de démarrage rapportés également comme des problèmes de défaillance du pilote. 5. Pas de réponse au démarreur CNC ou à la gâchette de la torche Pak200i. Regardez sur le circuit d’entrée sortie CCM si la DEL D6 CNC START est allumée en permanence. Si c’est le cas, soit le signal de démarrage externe CNC est activé, soit le CCM est défectueux. Débranchez le câble CNC de J15, ou, si le signal d’amorçage passe par le bornier du CCM, débranchez celui-ci. Si D6 est toujours allumé, remplacez le CCM. 6. Pas de réponse à la gâchette en option 1Torch (démarrage). Reportez-vous au début du groupe de code 700 pour le dépannage. Problèmes avec les communications. 7. Les pannes de communication avec le TSC 3000 ou le contrôleur de table de coupe sur le RS 485 peuvent être dues à une mauvaise position du cavalier J14_4W ou J14_2W (respectivement pour 4 ou 2 fils). Le TSC 3000 nécessite le 2 W. Le contrôleur iCNC nécessite le 4 W. Reportez-vous à la section _____ du manuel. A-60 ANNEXE 0-5264FR ULTRA-CUT 100 XT/200 XT/300 XT/400 XT Power Supply Status Codes (codes d’état de l’alimentation électrique) Groupe 1, Codes de processus 101 Activation de plasma désactivé Le code 101 est activé soit par un circuit ouvert entre TB1-1 et 2 sur le PCB E/S du CCM soir par une activation plasma éteinte sur le GCM 2010 ou sur le TSC 3000. TB1-1 et 2 sort d’usine avec un cavalier installé. Un installateur peut retirer le cavalier et connecter un commutateur d’activation plasma distinct ou utiliser les fils d’activation plasma inclus dans le câble CNC à 37 broches utilisé avec le Ultra-Cut XT & Auto-Cut 300XT. L’Auto-Cut 200XT qui utilise la CNC du terminal 12 n’a pas le Plasma Actif dans le câble. Ils peuvent être utilisés pour se brancher à l’interrupteur E-Stop de la table de découpe. Dans tous les cas de figure, le cavalier doit être retiré des TB1-1 et 2. 101 n’est pas un code verrouillé, il disparaît dès que la situation est réglée. Causes du code 101 en dehors des commutateurs d’activation hors tension (voir descriptions détaillées ci-dessous) : • Câble de contrôle des gaz de J55 au contrôle des gaz non connecté. • Tension d’entrée trop élevée, GCM 2010 restant hors tension. • Le câble plat connectant la carte Relay (relais) à la carte I/O n’est pas branché. • Le câble CNC n’est pas connecté (si vous utilisez un commutateur d’activation plasma ou la sortie de la table de découpe ou du robot). • PCB de relais défectueux • CCM défectueux I/O PCB Cas particulier : l’écran alterne entre E101 et ----. Cela arrive lorsque une phase est manquante et l’activation au plasma est éteinte. C’est probablement un bug dans le code, il devrait afficher E101 et E201 (code de phase manquante). Nous corrigerons probablement ce problème dans une publication de codes ultérieure, mais prenez-en conscience pour l’instant. La condition « Tension d’entrée trop élevée » est détectée sur le circuit imprimé de polarisation qui allume le voyant D4 (DEL rouge) et laisse le relais K1 relais hors tension, de sorte que le transformateur T1 n’est pas alimenté, laissant sans alimentation tous les composants alimentés en courant alternatif, y compris les commandes de gaz. Cela peut entraîner que le GCM 2010 ne réponde pas correctement au circuit d’activation du plasma et rapporte un code de panne erroné (E101). La DEL D2 ACTIVATION PLASMA externe ou du CNC n’est pas allumée. • La LED D2 sur le CCM sera allumée si l’entrée est validée avec soit avec le cavalier en TB1 - 1 et 2 ou, soit avec un interrupteur externe ou CNC. Si le cavalier est en place et que la DEL n’est pas allumée, le CCM est très probablement défectueux. • Si le cavalier à CCM TB1-1 et 2 a été retiré pour utiliser un commutateur externe, installez un cavalier omme test. Si D2 s’allume, le problème réside dans le commutateur ou son câblage. • Si l’activation de plasma est connectée avec le câble CNC, enlevez le câble et les broches 25 et 26 du cavalier J15. Si D2 ne s’allume toujours pas, il pourrait y avoir un problème dans le câble dans l’alimentation.. Activation du plasma de la commande du gaz ou du TSC 3000 Si l’activation plasma externe ou CNC est satisfaite, D2 est allumée, un relais K7 sur le PCB E/S du CCM énergise, fournissant +15 V à un autre relais K1 sur la carte E/S. Un faible signal actif, /HMI activation plasma, provient du commutateur d’activation plasma TSC 3000 via le PCB de relais ou, si TSC 3000 n’est pas installé, le signal provient du PCB de relais. Ce signal effectue la mise au sol du relais K1 l’activant et allumant la LED, D3 sur la carte E/S. Les contacts de K1 retournent à la carte Relay (relais) et au COMMANDE DU GAZ connector (connecteur de contrôle du gaz) J55 afin de pouvoir démarrer les relais et les solénoïdes sur ces appareils. L’AC 200 XT n’utilise pas la commande du gaz séparé ou le TSC 3000. 0-5264FR ANNEXE A-61 ULTRA-CUT 100 XT/200 XT/300 XT/400 XT Schéma simplifié, tous les connecteurs ne sont pas indiqués. Se reporter au schéma de l'unité pour plus de détails. Lorsque le circuit entre J54-1 &AMP; 3 est fermé (volant, etc.) \K7 est excité et nécessite une activation plasma SW ou équivalent pour activer le plasma. Avec J54-1 &AMP; 3 Ouvrez K7 est désexcitée et c'est les contacts NF terminer le plasma enable-circuit HMI. Bloc d'alimentation XT CCM I/O PCB 1 K6 2 D2 Vert +15VDC Circuit relais 4 3 5 24 VAC K1 Activation de plasma CNC 1 2 3 4 D3 Vert PS_ACTIVÉ 24 VAC 5 8 6 7 Activation de plasma À la carte relais Pour la commande de gaz 1 5 K7 J54 -1 J61 -1 -3 -3 GND 2 -6 -6 4 -5 -5 TSC 3000 J54 -1 J25 -3 Activation de plasma SW iCNC XT 2 & XT 242 J54 -1 J30 iCNC XT 211 -3 -6 -22 -6 -25 -5 -15 -5 -20 3 GCM 2010 GCM 1000 XT (AC 300 XT DMC 3000) (ou cavalier dans d’autres systèmes de contrôle des gaz) DÉRIVATION D’ACTIVATION PLASMA HMI /Activation de plasma- HMI J26-6 J55 -1 J56 -1 J26-7 -2 -2 Activation de plasma SW J56 -1 -2 Cavalier à AC200 XT Art # 12304FR Si un TSC 3000 n’est pas connecté ou si l’unité est une Auto-Cut, K7 sur le PCB de relais est réénergisé et GND est connecté par ses contacts normalement fermés. Si le TSC est déconnecté, 24 Vca à travers un cavalier dans le TSC 3000 énergise K7, ouvrant son contact NC et le GND se connecte maintenant à travers le commutateur d’activation du plasma du TDC 3000. Le GND obtenu par l’une des voies passe à travers un commutateur de validation à plasma ou un cavalier de GCM 2010 (J56-1 de J56-2) présent dans les autres commandes de gaz (GCM 1000 XT ou DMC 3000) et est connecté à la bobine de K1 sur la carte E/S. Si l’activation plasma CNC est aussi activée (D2 allumée) +15 V sera connecté à la bobine de K1 par le relais K7 sur le PCB E/S. Cela met sous tension K1 et active D3, LED activée au plasma. Les contacts de K1 reviennent à la carte à relais et à la commande de gaz pour permettre l’alimentation des relais et solénoïdes dans ces composants. Dépannage : 1. Si D2 et D3 sont allumées et que vous avez toujours une erreur 101, remplacez le CCM. Dans le cas contraire, passez à l’étape 2, à moins que le modèle soit un AC 200 XT, auquel cas, passez à l’étape 4. 2. Si D3 n’est pas allumé et qu’il y a un TSC 3000 utilisé, déconnectez son câble de J54. K7 sur la carte du relais se déchargera et répondra au critère d’Activation plasma de K1. Si D3 est maintenant allumé, le problème résidait dans le TSC 3000 ou son câble. Dans le cas contraire, rebranchez le câble. 3. Pour un Ultra-Cut avec DFC 3000 ou GCM 2010 ou un Auto-Cut 300 avec GCM 1000 XT, retirez le câble de J55, le connecteur du contrôle des gaz et les broches de cavalier 1 et 2. Si D3 est allumé, le problème réside dans le contrôle des gaz ou son câble. Si D3 n’est toujours pas allumé, remplacez le câble du contrôle des gaz. 4. Si aucune des étapes précédentes ne fonctionne, sur la carte E/S du CCM, cavalier J26-7 à GND (TP1 sur E/S). Si D2 est allumée et que D3 continue de ne pas s’allumer, remplacez le CCM. 5. Si D3 s’allume à l’étape précédente, trouvez le câble plat à 40 broches branché sur le dessus du CCM. Vérifiez qu’il est connecté au CCM et à la carte de relais et que les languettes de connecteur sont fixées en place. À l’aide du réceptacle de rechange, mesurez maintenant le voltage entre le GND (terre) (TP1 sur I/O) et la broche 12 du câble plat. Il doit être de zéro V. Dans le cas contraire, si elle se situe entre 10 et 15 Vcc, le câble plat est ouvert ou la carte de relais est défectueuse. A-62 ANNEXE 0-5264FR ULTRA-CUT 100 XT/200 XT/300 XT/400 XT ACTIVATION DU PLASMA / CIRCUIT D’ARRÊT D’URGENCE SIMPLIFIÉ DU GCM 2010 l'alimentation au plasma de XT Circuit relais AC24V GCM1 AC24V Ret - GCM1 15 GCM 2010 COMMANDE DE GAZ 7 CÂBLE DE CONTRÔLE DU GAZ J10 E/S du CCM (103) 3 K1 (112) (110) Activation de plasma 4 (114) J26 GCM 2010 TABLEAU DE COMMANDE 16 16 14 14 17 13 15 15 J56 J55 (56) (58) (57) (59) F20 1A 12 15 13 16 J5 1 K? D13 Vert 4 5 2 E-STOP Art # 12306FR 102 Échec de l’allumage du pilote Le code 102 est activé lorsqu’il n’y a pas de courant de pilote 15 secondes après avoir lancé le démarreur d’arc. L’allumage du pilote nécessite l’activation de la carte Pilot (pilote), l’enclenchement de l’interrupteur pilote (IGBT) et des pulsations à haute tension (HF) du démarreur d’arc (qui peut être le Remote Arc Starter RAS 1000 XT, le GCM 1000 XT ou le démarreur d’arc intégré sur l’AC 200 XT) envoyées entre la pointe et l’électrode de la torche. Causes possibles pour un code 102 : Torche XT automatisée SEULEMENT : • Pas de HF sur la torche à cause d’un branchement endommagé au niveau des fils de la torche. • Pas de HF sur la torche à cause d’un défaut sur l’Arc Starter (démarreur de l’arc). • Le démarreur d’arc n’est pas alimenté. Torche XT ou 1Torch en option : • Carte Pilot (pilot) non activée. • Carte Pilot (pilote) défectueuse. • Carte relais défectueuse • Capteur de courant du câble de masse défectueux. • CCM défectueux. • Le W4, contacteur d’isolation de la pointe, n’est pas mis sous tension pour la coupe automatique, reportezvous au groupe de codes 700. 1Torch UNIQUEMENT : • Le W5, contacteur d’isolation de la 1Torch, n’est pas mis sous tension pour la coupe avec 1Torch, reportezvous au groupe de codes 700. Dépannage : 1. Déterminez si le problème est l’absence de HF (démarreur d’arc) ou s’il est attribuable au circuit du pilote. Le démarreur d’arc Auto-cut XT (à l’intérieur du châssis principal pour AC200 XT; dans le GCM1000XT pour AC300XT) contient un éclateur ouvert. S’il y a amorçage dans l’éclateur, celui-ci est alimenté. Quelques-unes des premières unités Ultra-Cut XT ont été expédiées avec le démarreur d’arc RAS1000. Résolvez les problèmes de la même manière que le GCM1000XT ci-dessous. La plupart des unités Ultra-Cut XT utilisent désormais l’Arc Starter (démarreur de l’arc) RAS1000XT qui n’utilise pas d’éclateur; celui-ci est décrit dans le chapitre suivant. 0-5264FR ANNEXE A-63 ULTRA-CUT 100 XT/200 XT/300 XT/400 XT Démarreur d’arc avec éclateur (Auto-Cut) Pas d’étincelle au niveau de l’éclateur 1. Vérifiez que l’éclateur est réglé à 1,6 mm +/- 0,05 mm (0,062” +/- 0,002”). Si l’écart est trop important, il pourrait ne pas y avoir une tension suffisante venant de T1 pour combler l’écart. 2. Vérifiez l’alimentation vers le transformateur haute fréquence (HF) (T2 dans AC 200 XT; T1 dans GCM1000XT) pendant 15 secondes après le pré-écoulement (phase d’allumage). L’alimentation du démarreur d’arc provient du disjoncteur du panneau arrière CB4, assurez-vous que celui-ci ne soit pas ouvert. a. Pour le GCM1000XT (AC300XT), 120 Vca de J59-7 et 9 sur le panneau arrière de l’alimentation se connecte au J58-7 et 9 sur le GCM 1000XT. Voir le diagramme ci-dessous. Du J58 sur le GCM1000XT, il va directement au filtre de ligne et passe à travers le filtre au principal de T1. Pendant la phase d’allumage, vérifiez qu’il y a 120 Vca du côté T1 du filtre de ligne. b. Pour AC200XT, le transformateur T2 a un clip faston isolé sur ses fils principaux. Déconnectez-les et vérifiez que le côté harnais a 120 Vca pendant la phase d’allumage. 3. S’il n’y a pas 120 Vca, passez à l’étape 4. a. S’il y a 120 Vca, mais toujours pas d’étincelle, T1 (T2 sur AC200XT) pourrait être défectueux. Débranchez l’alimentation électrique et mesurez la résistance du T1 (T2 sur l’AC2000XT) primaire et secondaire. Le premier devrait mesurer environ 3 - 7 ohms. Le deuxième est d’environ 25 - 35 K ohms. Si aucune des mesures n’est correcte, remplacez T1 (T2 sur AC200XT). b. Si les mesures de T1 (T2 dans AC200XT) sont OK, vérifiez la présence de courts-circuits au niveau des condensateurs C1-C3 (très peu probable). 4. Pas de 120 VCA sur le T1 (T2 pour le modèle AC200XT) lors de la phase d’allumage (15 secondes après le Preflow(pré-écoulement), vérifiez la présence de 120 VCA dans le filtre de ligne (GCM1000XT uniquement). Si tel est le cas, remplacez le filtre. S’il n’y a pas 120 Vca au niveau du filtre de ligne ou pour un AC 200XT, passez à l’étape 5 à la section Tout démarreur d’arc, ci-dessous. Démarreur d’arc sans éclateur (Ultra-Cut) 1. Vérifiez l’alimentation au module d’allumage du RAS 1000XT pendant 15 secondes après le pré-écoulement (phase d’allumage). L’alimentation du démarreur d’arc provient du disjoncteur du panneau arrière CB4, assurez-vous que celui-ci ne soit pas ouvert.. a. Pendant la phase d’allumage, vérifiez qu’il y a 120 Vca au niveau des bornes d’entrée marquées 120 Vcc sur le module d’allumage, un rectangle gris avec des bornes à vis d’un côté. AVERTISSEMENT Ne laissez pas les sondes de mesure (ou vos mains) entrer en contact avec les autres bornes marquées Hb et Ho ou l’autre extrémité des fils auxquels ils sont connectés. Ceux-ci peuvent avoir des impulsions de 10.000 volts pouvant causer des dommages physiques et endommager votre appareil. 2. S’il n’y a pas 120 Vca, passez à l’étape 3. a. S’il y a 120 Vca, mais toujours pas d’étincelle, le module d’allumage pourrait être défectueux. 3. 120 Vca au démarreur d’arc à distance vient de J59-7 et 9 sur le panneau arrière de l’alimentation et se connecte au J58-7 et 9 sur RAS1000XT. Retirez le câble du J59 et, au cours de la phase d’allumage, mesurez la tension à 120 CA entre les broches 7 et 9. a. S’il y a 120 Vca, le problème réside dans le câble au RAS 1000 XT ou au connecteur J58 et le faisceau interne dans le démarreur d’arc. b. S’il y a 120 Vca, passez à l’étape suivante. 4. 120 Vca à J59 vient de la carte de relais J8-3 avec un retour sur la broche 11. Sur la carte Relay (relais), la LED RF ON, D23, doit s’éclairer au cours de la phase d’allumage. Dans le cas contraire, passez à l’étape suivante. a. Si D23 est allumée et qu’il n’y a pas 120 Vca à J8-3 et 11, alors la carte de relais est défectueuse. A-64 ANNEXE 0-5264FR ULTRA-CUT 100 XT/200 XT/300 XT/400 XT Tout démarreur d’arc 5. Signal /RAS ON désactivé. Le CCM envoie un signal faible actif « /RAS ON » via le câble plat à 40 broches sur la broche 16 sur la carte de relais et d’interface. Sur la carte Relay (relais), le relais RAS Control (contrôle RAS) (K2) se ferme (LED RF ON, D23, allumé), envoyant un voltage de 120 VCA sur J8-3 avec un retour sur J8-11. De là, il va soit au transformateur HF T2 (AC200XT) ou au J59 tel que décrit ci-dessus. a. Mesurez le signal « /RAS ON » sur la broche 16 du câble plat à 40 broches correspondant au TP1, soit au niveau de la carte CCM I/O soit sur la carte Relay (relais). Si elle est basse (inférieure à 1 V), passez à l’étape 6. Dans le cas contraire, continuez cette étape. REMARQUE ! Si le CCM pense qu’il y a déjà un pilote, il n’activera pas le HF. La carte Pilot (pilote) est équipée d’un capteur de courant qui envoie un signal de niveau de courant analogique du pilote sur la carte Relay (relais), qui passe à son tour le signal au CCM. Sur la carte Relay (relais), la LED D11 « COURANT DU PILOTE DÉTECTÉ » (courant du pilote détecté), ou tout simplement « PILOT », s’éclaire si elle reçoit un signal de la carte pilote. Raisons pour lesquelles le relais RAS Control (contrôle RAS) ne ferme pas : 6. Le courant pilote circule. Un courant pilote devrait circuler quelque part. Aussi improbable que cela paraît, il devrait normalement régler le défaut 208, mais nous devons l’exclure. a. Déconnectez J41 de la carte du pilote, si HF ne s’allume toujours pas et que la DEL de la carte de relais du pilote, D11, est toujours allumée, l’erreur est attribuable à une défaillance dans les circuits de détection. 7. Circuit de détection défectueux. Il n’y a pas de courant pilote, mais une panne dans les circuits mesurant le courant pilote indique que le courant est présent. a. Mesurez entre les broches 8 (-) et 9 (+) sur le câble plat du Pilot (pilote), entre la carte Relay (relais) J3 et la carte Pilot (pilote) J42. S’il n’y a pas de courant de pilote, il devrait être de zéro. Tout autre résultat indique que le capteur de courant de la carte du pilote est défectueux, ce qui entraîne l’allumage de la DEL D11 sur la carte de relais. Remplacez l’assemblage de la carte Pilot (pilote). b. Si le signal du courant du pilote sur le câble plat du pilote était de zéro, mesurez le courant entre les broches 23 (-) et 25 (+) sur le câble plat à 40 broches entre la carte de relais et le CCM. Cela serait aussi normalement égale à zéro en l’absence de courant pilote. Tout autre résultat indiquerait que la carte de relais est défectueuse. Carte relais et d'interface À LA CARTE RELAIS / RAS ON TP1 Masse 0-5264FR 1 2 3 4 5 6 7 8 9 10 11 12 13 14 15 16 17 18 19 20 21 22 23 24 25 26 27 28 29 30 31 32 33 34 35 36 37 38 39 40 J4 1 2 3 4 5 6 7 8 9 10 11 12 13 14 15 16 17 18 19 20 21 22 23 24 25 26 27 28 29 30 31 32 33 34 35 36 37 38 39 40 120 VAC_RET 120 VAC_1 À partir de J9-7 À partir de J9-1 From I/O PCB 24VDC_SW D21 1 K2 3 D23 4 Vert RF ON 120 VAC RET J23 120 VAC E/S du CCM 120 VAC à RAS 5 J8 16 15 14 13 12 11 10 9 8 7 6 5 4 3 2 1 J59 - RAS (Panneau arrière) 1 2 3 4 5 6 7 8 9 10 11 12 13 14 (99) (98) Commande RAS (99) T2 6.5K 1W (98) AC200XT Seulement 6.5K 1W 120 / 6000 VAC TP1 Masse Art # 12307FR ANNEXE A-65 ULTRA-CUT 100 XT/200 XT/300 XT/400 XT 8. Si le signal « /RAS ON » est bas à la broche 16 du câble plat à 40 broches, relativement à TP1 sur la carte E/S du CCM, pendant le délai d’allumage, nous devons alors déterminer si la carte de relais est défectueuse. Si le signal « /RAS ON » n’est pas bas, le CCM ou le câble plat à 40 broches pourrait être défectueux. a. Si la DEL RF ON de la carte de relais, D23, n’est pas allumée lorsque le signal /RAS ON est bas, alors la carte de relais est défectueuse. b. Si la D23 est allumée, mesurez la tension 120 VCA de J8-3 à J8-11. Si tel n’est pas le cas, la carte de relais est défectueuse. c. S’il y a 120 Vca à J8 pendant la période d’allumage, retournez aux étapes 2 à 4. Résolution des problèmes de la carte pilote : 1. La carte pilote se trouve derrière le CCM dans l’AC 300 XT et tous les Ultra-Cut XT ou sur la section supérieure du deuxième module onduleur dans une 200 XT AC et comporte deux LED. Le premier, D11, une LED verte, indique que la carte a une puissance de polarisation et devrait l’avoir en tout temps lorsque l’appareil est sous tension. La deuxième LED, D2, aussi vert, est allumée lorsque le pilote est activé, c’est-à-dire que le commutateur IGBT du pilote est activé. Le pilote est activé à la fin du temps de de flux anticipé et reste allumé jusqu’à ce que le transfert soit établi ou pendant 15 secondes, après lesquelles un code 102 est affiché. Si D2 fonctionne comme prévu, vous savez que le CCM, la carte de relais et le capteur de courant d’usinage ne sont pas la source du problème. 2. Testez le fonctionnement du pilote IGBT. Si D2 est allumé, le pilote est activé, mais vous ne savez pas si le commutateur du pilote (le transistor IGBT) ferme réellement le circuit. Pour le tester, posez un cavalier de calibre 18 AWG ou plus comme suit : a. Ultra-Cut XT ou Auto-Cut 300 XT : connectez un cavalier de TB4-7 (tension de l’arc) à TB4-6 (tension de la pointe). b. Auto-Cut 200 ou Pak200i : connectez un cavalier entre la barre bus négative à côté de la bobine HF et l’endroit où les fils du pilote s’attachent au branchement du gaz sur le panneau des connexions de la torche. Appuyez sur CNC Start. Si le commutateur du pilote se ferme comme il se doit, vous verrez un code de panne 106 ou 208 au bout de 3 à 5 secondes. Si ce n’est pas le cas, maintenir CNC Start pour un maximum de 20 secondes. L’afficheur à DEL CC du panneau avant restera allumé pendant 15 secondes avant d’afficher de nouveau le code 102. Cela indique vraisemblablement que le circuit intégré pilote est défectueux, mais si l’approvisionnement du XT inclut l’option 1Torch il pourrait s’agir d’un mauvais contact du W4. Consultez les instructions du groupe 700 pour contourner le contacteur W4. 3. Si D11 sur la carte du pilote n’est pas allumée, vérifiez si le câble plat à 10 broches est connecté entre la carte du pilote (J42) et la carte de relais (J3). Assurez-vous que la tension soit bien de 24 VCC sur les broches 2 (+) et 10 (-) du connecteur de test du câble plat du Pilot (pilote). S’il y a 24 V et que les DEL D11 et D2 ne s’allument pas, la carte du pilote pourrait être défectueuse. Le côté carte Pilot (pilot) du câble plat pourrait également être à l’origine du problème. Ce qui devrait arriver sur la carte relais est LEDs D12, Courant de service détecté et D11, Courant pilote actuel détecté doit être éteint. Lorsque vous appliquez START après 2 secondes (temps de débit avancé) D7, ACTIVATION DU PILOTE, devrait être activé. De même D23, RF ON, devrait indiquer que le démarreur d’arc est activé. Normalement, le D23 doit être seulement allumé momentanément, jusqu’à ce que le courant du pilote soit détecté. Puis, D11 serait activé (et D23 désactivé) jusqu’au transfert à l’arc ou délai de pilote (15 sec.) Si un pilote n’a pas été détecté, D11 ne devrait pas être activé. 4. Si le capteur de courant d’usinage est défectueux, il pourrait dire à la carte de relais (et donc au CCM) qu’il y a déjà un arc transféré et que le pilote n’est donc pas nécessaire. D12, une DEL verte sur la carte de relais, est allumée si un courant d’usinage est détecté. Si D12 n’est pas allumée, passez à l’étape 5, sinon déconnectez J1, le connecteur du capteur de courant d’usinage. Si D12 est toujours allumée, la carte de relais est défectueuse. 5. Si D12 s’éteint lorsque J1 est déconnecté, rebranchez-le et mesurez la tension de TP1 (commun) à J1-1, elle devrait être positive, entre 12- 15 Vcc. Mesurez maintenant J1-2, le voltage doit être de 12-15 VCC négatifs. Mesurez maintenant J1-3, le voltage doit être de 0+/-0,05 V. Si un d’entre eux est erroné, déconnectez J1 et mesurez de nouveau (sur la carte de relais, pas sur le faisceau). Si l’erreur persiste, la carte de relais est défectueuse. Dans le cas contraire, il s’agit du capteur de travail. 6. Le signal ACTIVATION DU PILOTE (activation du pilote) arrive en provenance du CCM sur la broche 15 du câble plat à 40 broches entre la carte Relay (relais) (J4) et le CCM (J23). Il doit être faible, moins que 2 V par rapport au TP1, soit sur la carte CCM I/O, soit sur la carte Relay (relais). Vous pouvez également mesurer cela sur TP11 de la carte A-66 ANNEXE 0-5264FR ULTRA-CUT 100 XT/200 XT/300 XT/400 XT E/S. Si le signal ne baisse pas quand le pilote devrait être activé à la fin du délai de pré-écoulement, alors le CCM est probablement défectueux. Vous pouvez également vérifier le cavalier TP11 sur l’E/S CCM pour TP1, également sur l’E/S, pour voir si cela va activer D7, le LED d’activation de pilote, sur la carte de relais. Si tel est le cas, cela confirme que le CCM est défectueux. Si contourner TP11 pour TP1 ne fait pas s’allumer D7 sur la carte de relais, le problème réside probablement dans la carte de relais ou, éventuellement, le câble plat. 103 Pilote perdu Le code 103 se produit lorsque le pilote a été allumé tel que détecté par le capteur de courant de pilote sur la carte du pilote, mais s’est éteint tout seul alors que le démarrage CNC est toujours actif avant le délai d’expiration du pilote (85 ms ou 3 s). Causes possibles : • La pression du gaz de pré-écoulement est trop élevée, pour les contrôles manuels du gaz, vérifiez les diagrammes de découpe pour effectuer correctement le réglage. Pour DFC 3000, vérifiez que le processus est correct pour les consommables. • Courant de coupe réglé trop bas pour les parties de torche utilisées. Le niveau du courant pilote est réglé automatiquement sur la base du courant de découpe. Un faible courant de coupe entraîne un courant de pilote inférieur qui pourrait ne pas être en mesure d’alimenter un pilote pour les portions supérieures de la torche à courant. • Si les interrupteurs de Contrôle l’intensité analogique à distance (contrôle à distance de la tension analogique) sont mal réglés, le courant du pilote peut s’avérer plus faible que prévu. Voir le chapitre sur les réglages de cet interrupteur dans le prochain chapitre traitant du code 104. • Câble de pilote de torche rompu. • Un module d’onduleur défectueux émet moins de courant que ce pour quoi il a été réglé. 104 Transfert annulé L’arc a été transféré au métal pendant au moins 50 ms puis s’est éteint. Causes du code 104 : • Demande de coupe réglée bien en dessous de la valeur recommandée pour les parties de torche, à savoir 100 A, il y a des consommables dans la torche, mais le courant de coupe réglé à 30 ou à 50 A (ou zéro). Le courant pourrait être trop faible pour maintenir l’arc. • Distance de retrait de torche trop élevée pour le processus de coupe en cours. • Le gaz plasma s’écoule trop lentement en raison d’une fuite située entre le régulateur de plasma ou le DPC 3000 et la torche. Vérifiez s’il y a des fuites. • La circulation de liquide de refroidissement diminue excessivement, à la suite de quoi l’unité coupe l’arc. Cela devrait normalement entraîner un code de panne 402, mais pour des raisons actuellement inconnues, le code est parfois 104. o Une des causes possibles de cette faible circulation est un joint torique défectueux dans l’ensemble clapet antiretour de la torche. Le remplacement du joint torique résout le problème. • Interrupteurs de contrôle l’intensité analogique à distance mal réglés. o Si le contrôle de courant analogique à distance est utilisé, SW8-2 (PCB de CPU du CCM) est allumé et SW11 (PCB E/S du CCM) est en position « A » (basse), mais aucune tension analogique n’est connectée à TB1-10 ou J15-30 (câble CNC), alors la demande de coupe sera zéro, le pilote sera faible, selon la hauteur de torche, il pourrait continuer de transférer, mais il s’arrêtera immédiatement. o Si le contrôle de courant analogique à distance n’est pas utilisé, mais que soit SW11 est en position basse soit SW8-2 est allumé, cela entraîne aussi une demande de coupe de zéro. o Si le système est un Auto-Cut XT, le contrôle de courant est une tension analogue du potentiomètre du panneau frontal du GCM 1000 XT ou du AC 200 XT. Le réglage de la commande actuelle sera affiché sur le panneau d’affichage avant à 4 chiffres. Le SW8-2 doit être éteint et le SW11 doit être réglé en position. Avec le pot au max, vérifiez s’il y a une tension 3,3 V sur la carte E/S CCM TP9 (TP1 commun). En tournant le pot vers TP9 au minimum, la tension doit varier linéairement jusqu’à zéro V. 0-5264FR ANNEXE A-67 ULTRA-CUT 100 XT/200 XT/300 XT/400 XT GCM 1000 XT (AC 300 XT) R1 10K J56 J55 1 2 3 4 5 6 7 8 9 10 11 12 13 14 15 16 1 2 3 4 5 6 7 8 9 10 11 12 13 14 15 16 l'alimentation au plasma de Auto-Cut XT J26 (125) (126) (127) AC 200 XT R1 10K Art # 12309FR 16 15 14 13 12 11 10 9 8 7 6 5 4 3 2 1 CCM +10.0V Diviser par 3 1 SW11 3 TP9 2 0-3.3VDC TP1 Masse Masse 105 Non utilisé. Ceci est l’un des codes réservés des produits antérieurs. 106 Délai de pilote, pas de transfert Depuis la commande de courant analogique à distance Masse Le temps du pilote est limité soit à 0,085 secondes (85 ms) avec le CCM SW8-1 désactivé (par défaut pour le début du perçage), soit à 3 secondes avec le SW8-1 activé (utilisé pour coupe par-dessus les trous, pour le métal déployé, etc.) L’arc doit être transféré avant que le délai du pilote se termine. Le code 106 est déclenché si aucun transfert d’arc (courant dans le fil d’usinage) n’a été détecté avant le délai d’expiration du pilote. Si l’unité ne détecte pas de courant de pilote, l’éclateur fonctionne pendant un maximum de 15 secondes puis déclenche le code 102. Si vous obtenez l’erreur 106, il y a un courant de pilote quelque part. S’il est invisible, il pourrait être à l’intérieur des consommables ou suivre une autre pièce. Causes du code 106 : No Pilot Visible (pas de pilote visible) : • Pilote dans les consommables Pilote visible : • En commençant par l’évidence, assurez-vous que le fil d’usinage est connecté à l’alimentation et à la pièce. Assurez-vous aussi que la pièce elle-même a un bon contact électrique avec la table de découpe. Avec du métal rouillé ou peint, vous pourriez devoir nettoyer une zone et fixer le fil d’usinage directement sur le métal. • Torche trop loin du travail. • Courant de coupe réglé trop bas pour les parties de torche utilisées. Le courant pilote est réglé selon le courant de découpe. Si le courant de coupe est trop faible, le courant du pilote sera inférieur et pourrait ne pas transférer à la hauteur utilisée pour les consommables de courant plus élevés. • Pression du pré-écoulement ou écoulement trop faible. • Si les interrupteurs de Contrôle l’intensité analogique à distance (contrôle à distance de la tension analogique) sont mal réglés, le courant du pilote peut s’avérer plus faible que prévu. Voir le chapitre sur les réglages de cet interrupteur dans le chapitre traitant du code 104. • Circuit de capteur de courant du fil d’usinage défectueux. Si le transfert n’est pas détecté, le courant de coupe reste au niveau initial inférieur, et la minuterie du pilote (85 ms ou 3 s) expirera. 107 Panne du dispositif de protection de la pointe pour Pak200i seulement. Les torches avec pointe exposée peuvent être endommagées si la pointe touche la pièce pendant la coupe. Le dispositif de protection de la pointe réduit le courant à un niveau que la pointe peut supporter pendant un certain temps. Sur la torche Pak200i, cette panne se produit si la pointe est restée en contact avec la pièce pendant plus de 15 secondes. Sur la 1Torch équipée du dispositif de protection, la pointe peut rester au contact de la pièce sans limite de temps. 108 Pointe pour défaut de tension d’électrode. La tension pilote, mesurée entre la pointe et l’électrode, varie en fonction de différents types de courant et de gaz, du débit et de la conception des consommables. A-68 ANNEXE 0-5264FR ULTRA-CUT 100 XT/200 XT/300 XT/400 XT Une fois que l’arc est transféré, l’interrupteur pilote s’ouvre, laissant la pointe pratiquement flotter. La tension est alors déterminée par la capacité de la barrière contre les gaz froid à entourer l’arc. Courant excessif ou gaz insuffisant et l’arc commence à entrer en contact avec la pointe, réduisant ainsi la différence de tension entre la pointe et l’électrode, entrainant une double arc qui détruit les consommables. Le CCM mesure à la fois la tension de l’électrode et de la pointe, et calcule l’écart. Si la différence entre l’extrémité et l’électrode se révèle inférieure à une tension minimum, la coupe est arrêtée et un code d’erreur 108 s’affiche. La pointe normale à la tension de l’électrode est différente pour différents processus de sorte que la valeur minimum pour chaque processus est intégré dans les tableaux de coupe lors de l’utilisation du DFC 3000 ou dans le code de CCM lors de l’utilisation du GCM 2010 ou des commandes de gaz Auto-Cut XT (GCM 1000XT ou celui intégré dans l’AC 200 XT). Nouveauté pour les unités Auto-Cut XT, un interrupteur situé à l’arrière de l’alimentation électrique, et qui doit être positionné selon le gaz plasma. Si vous utilisez un gaz comburant (O2 ou air), réglez-le tel qu’indiqué pour ces gaz (à gauche pour AC 200 XT ou en haut pour AC300XT), tandis que pour un gaz non comburant (N2, H35 ou un autre gaz inerte), réglez-le à droite ou en bas, tel qu’indiqué pour ces types de gaz. Ce commutateur permet de régler la plage de tension du type de gaz afin de mieux protéger la torche. Un réglage erroné pourrait entraîner le faux déclenchement du code 108. Pendant le pilotage et l’augmentation (le délai entre le transfert et l’atteinte du courant de coupe complet), nous réduisons la tension autorisée de l’extrémité à l’électrode à environ 80 % de la tension autorisée pendant la coupe, car le courant et l’écoulement de gaz sont inférieurs pendant cette période. Causes du code 108 : • Pression/écoulement de gaz trop faible pour que les parties consommables soient utilisées. o Si la pression de la source de gaz n’est pas bien régulée, il est possible que la pression parfois OK puis qu’elle devienne insuffisante d’autres fois, par exemple pendant une coupe. o Une fuite dans le pré-écoulement/gaz plasma après le contrôle de pression/débit (GCM 2010, DPC, GCM 1000 XT) peut réduire la pression/le débit vers la torche, parce qu’une certaine quantité de gaz contourne la torche, tout en semblant avoir suffisamment de pression/de débit au niveau de la commande de gaz. • Courant de coupe réglé trop haut pour les parties consommables utilisées. • Avec DFC 3000, un composant défectueux devrait définir un code de défaut soit dans le DPC soit dans le DMC. Néanmoins, si un processus erroné ne correspondant pas au type de consommable est choisi ou si on utilise un processus personnalisé dans lequel la pression a été définie trop basse ou le courant a été défini trop élevé, cela pourrait entraîner une erreur 108 sans entraîner d’erreur dans le DFC 3000. • Un fil de pilote brisé dans le faisceau de torche faisant un contact intermittent peut permettre le pilotage ou, parfois, la torche ne peut transférer qu’à HF (haute fréquence). Cette connexion intermittente bouleversera la mesure de la tension de pointe et peut se traduire par le code 108. Le symptôme est le suivant - il peut s’arrêter pendant une brève période, puis tomber en panne. Vérifiez s’il n’y a pas un fil de pilote de faisceau de torche ouvert ou brisé. • Corps de la torche court-circuité physique entre l’anode (pointe) et la cathode (électrode). Le défaut entraînant le code 108 est mesurée pendant l’arrêt. C’est le plus souvent un court-circuit au niveau du corps de la torche, selon la résistance du court-circuit, il va déclencher le code 208 (Unwanted Current (courant non désiré)), étant mesuré avant le court-circuit de départ. Cependant, il faut considérer ceci comme une solution de dernier recours. 109 Procédé non configuré. Cela représente un état, pas un défaut. Ceci est utilisé avec le DFC 3000 uniquement. Cela signifie que l’opérateur n’a pas chargé la procédure de découpe des TSC 3000 ou du programme intégré dans le contrôleur CNC de la table de coupe. La solution est de charger un processus. Le code continuera de s’afficher jusqu’à ce que le Démarrage de la CNC est appliqué, après lequel le code s’effacera. 110 Appareil verrouillé. Cela signifie que le DPC ou le DMC est encore en train de télécharger un nouveau processus de coupe. Ce code ne devrait se produire pour le DFC 3000 que si vous appuyez sur CNC Start avant la fin du téléchargement. L’option 1Torch peut être démarrée alors que le processus d’automatisation est en cours de téléchargement. 0-5264FR ANNEXE A-69 ULTRA-CUT 100 XT/200 XT/300 XT/400 XT Groupe 2 – Alimentation électrique du plasma codes Généralités : LEDS Plusieurs LED sont utilisées à titre d’indicateurs sur les différentes cartes de module de l’onduleur. Les LED ROUGES indiquent un défaut. Les DEL vertes devraient être allumées la plupart du temps. Les DEL vertes sont : Sur la carte principale, D4-PRÊT; sur la carte Cap BIAS, D6, -12V, D11 +12VP (référence principale), D13, +12V; sur la carte de contrôle D24, PWM ne sera allumé que lorsque l’onduleur est activé et son intensité varie avec le cycle de travail du PWM. Signaux : Description générale de certains signaux d’onduleur passés au CCM qui peuvent générer des codes d’erreur du groupe 2. « Prêt » aussi appelé AC IN FLT (D4, DEL PRÊT, verte, sur la carte du convertisseur principal) Sur la carte principale de l’onduleur, nous mesurons le voltage d’entrée. Les 3 phases sont rectifiées et légèrement filtrées pour atteindre une tension moyenne. En raison du filtrage de la lumière, une phase manquante réduira aussi la tension moyenne et sera donc détectée. La tension dans la plage correcte allume READY LED D4 (à l’extrême gauche des cartes principales, dans la partie supérieure de la section « B » ou la partie inférieure de la section « A »). Tension hors de la plage correcte ou la phase manquante mettra D4 à l’arrêt. Une défaillance d’entrée a.c. en soi (aucune autre défaillance se produisant en même temps) déclenchera les codes du groupe 241-246 selon l’onduleur sur lequel le problème s’est produit. INV FLT (D1, DEL rouge INV FLT, sur le circuit de commande et de surveillance de l’onduleur) Plusieurs causes peuvent entraîner un Inv Flt (Inverter Fault, défaut de l’onduleur). L’Inverter Fault (défaut de l’onduleur) est indiqué par une LED, no. D1 sur la carte Inverter Control and Fault (contrôle et défaut de l’onduleur). L’Inverter Fault (défaut de l’onduleur), lorsqu’il se produit, est verrouillé. Le verrouillage est réinitialisé la prochaine fois que l’onduleur est activé à moins qu’il ne soit actif, auquel cas il est immédiatement verrouillé à nouveau. L’Inverter Fault (défaut de l’onduleur) déclenchera les codes 247-252 à moins qu’il ait lieu en conjonction avec un autre défaut, auquel cas le code de ce dernier apparaîtra. Situations pouvant régler les défauts de l’onduleur : • L’emplacement (de l’onduleur) + l’alimentation de polarisation 12V et -12V hors de tolérance. Il existe des LED sur la carte Cap / Bias qui s’allument indiquant que ces alimentations de polarisation sont présents, mais ne vérifiez pas qu’ils sont dans la tolérance. Il est peu probable que cela se produise. Il est plus probable que pour un défaut lié au +/-12 V, l’alimentation vienne à manquer et la LED ne s’allume pas. • Déséquilibre de capacités. En état de déséquilibre du condensateur, D3, la DEL rouge sur la carte mère (coin inférieur gauche dans la section inférieure ou « A » et coin supérieur gauche de la section supérieure ou « B »), se verrouillera. • Surtension primaire Ceci est une surintensité de la tension primaire du transformateur du commutateur principal. Cela se verrouillera, mais sera supprimé lorsque l’onduleur est activé à moins qu’il ne soit actif, auquel cas il est immédiatement reverrouillé. • La surchauffe de l’onduleur déclenche le signal et la LED de défaut, mais a également son propre signal de défaut au CCM. Voir OT Flt ci-dessous. OT FLT (D14, OT FLT, carte Inverter Control and Fault (contrôle et défaut de l’onduleur) • La surchauffe de l’onduleur allume la diode LED D14 sur la carte de contrôle et de défaut de l’onduleur, et verrouille le signal de défaut et la LED correspondante, mais a également son propre défaut, afin de pouvoir être signalée avec un code situé entre 253-258 ou 259-264. PWR Present • Lorsque l’alimentation est d’abord appliquée à l’onduleur (contacteur fermé) CCM vérifie la présence d’une polarisation de + 12V sur la carte de commande et de défaut de l’onduleur. Si tel n’est pas le cas, les codes définis seront entre 265-270. A-70 ANNEXE 0-5264FR ULTRA-CUT 100 XT/200 XT/300 XT/400 XT 201 Phase CA absent La carte d’alimentation du System Bias comporte des circuits permettant de détecter si l’une des trois phases d’entrée CA est manquante. Il peut de plus détecter si le voltage a.c. est trop faible ou trop élevé. Une tension triphasée est fournie des bornes d’entrée en passant par le commutateur ON/OFF/disjoncteur CB1 à la carte du System Bias. Le System Bias peut fonctionner sur 2 des 3 phases fournir une énergie de réglage et une détection de défauts. I/O PCB Circuit imprimé de polarisation du système J62 +V CB1 F1 J60-9,18 triphasée AC J60-5,14 F2 J60-1,10 MARCHE / ARRÊT Masse 1 2 3 4 5 6 7 8 9 10 11 12 13 14 J27 Phase Manquante A Phase Manquante B 1 2 3 4 5 6 7 8 9 10 11 12 13 14 1 U? 2 4 Phase Manquante 3 HCPL-817 À CPU PCB J29-16 Masse Art # 12310FR Normalement, lorsque la phase n’est pas manquante, le transistor est allumé, ce qui démarre l’opto-isolateur, rendant le signal « PHASE MANQUANTE » (phase manquante) faible. Causes du code 201, absence de la phase : Les codes sont affichés de deux façons différentes, avec un « L » pour « Latched » (verrouillé) ou « Last » (dernier), avant le chiffre, ce qui signifie qu’il est incorrect actuellement ou avec un « E », ce qui révèle la présence d’un problème. L201 : Plus vraisemblablement, la cause est un problème intermittent avec l’alimentation électrique, ou du jeu au niveau du branchement du câble d’alimentation à l’arrière de l’alimentation plasma de l’Ultra-Cut ou de l’Auto-Cut. E201: • Phase manquante au niveau de la boîte de fusible sur le mur, fusible grillé. • Fusibles à fusion lente F1 ou F2, 8 A 500 V brûlés. • CB1 une phase ouverte. • Carte du System Bias défectueuse. • Carte E/S défectueuse. Dépannage : 1. La carte de System Bias a une LED rouge, D3, qui s’allume lorsqu’elle détecte une phase manquante. Si D3 est allumé, vérifiez J60 pour les trois phases. a. Si les trois phases ne sont pas présentes à J60, vérifiez l’alimentation d’entrée, puis les fusibles F1 et F2. Finalement le CB1. b. Si les trois phases sont présentes et ont environ la même tension, changez alors la carte BIAS du système. 2. SI D3, la DEL de phase manquante, n’est pas allumée, vérifiez la tension à J27-3 et 4 sur le CCM. Voltage normal, sans phase manquante, sur le J27 (ou J62 sur la carte System Bias (polarisation système) broche 3 et broche 4, correspondant à la terre du circuit I/O. (TP1) devrait être entre 10-14 Vcc, la broche 3 ayant quelques voltes de plus que la broche 4. Si elle est normale, le problème pourrait résider dans le CCM. 3. Si la tension aux bornes 3 et 4 de J27 est supérieure à 10-14 Vcc et jusqu’à 20-24 Vcc, faites les mêmes mesures à la broche 4 de J62. Si elle est toujours élevée et que vous avez confirmé que les trois phases sont présentes à J60, c’est le BIAS système qui est défectueux. 4. Si la tension à la broche 4 de J62 n’est pas élevée, les fils entre J27 et J62 pourraient être brisés. 202-204 205 Non utilisé. Codes réservés dans la version précédente du produit. Sortie c.c. faible 0-5264FR ANNEXE A-71 ULTRA-CUT 100 XT/200 XT/300 XT/400 XT Une faible sortie de DC (tension) signifie qu’une ou plusieurs sections d’onduleur sont activées, mais la tension de sortie est inférieure à une tension prédéfinie. Peu après avoir reçu le signal Start (démarrage) du CNC, mais avant la fin du pré-écoulement, les deux sections de l’IM#1 sont activées, et le CCM mesure le voltage de sortie de l’alimentation électrique entre le pôle négatif (Torch) et le pôle position (Travail) sur les terminaux de sortie. Si elle est inférieure à une valeur définie pendant le pré-écoulement ou si, à n’importe quel moment pendant le pilotage ou la coupe, elle descend plus bas que cette valeur pendant une courte période, les onduleurs sont éteints et le code 205 s’affiche. 205 apparaîtra presque toujours sous forme d’erreur « L » plutôt que « E » puisque les onduleurs sont arrêtés et ne présentent donc plus d’erreur de tension de sortie basse. Actuellement, la valeur de basse tension est de -60 Vcc. Les causes du code 205 peuvent comprendre des courts-circuits à l’extérieur de l’alimentation plasma, des courts-circuits à l’intérieur de l’alimentation plasma et des erreurs de mesure. a. Court-circuit externe à l’alimentation électrique du plasma : • Le fil négatif va de l’arrière de l’alimentation au démarreur d’arc à distance ou au GCM 1000 XT dans le cas de l’AC 3000 XT. o Câble pincé dans le rail ou sortant du rail o Court-circuit à l’intérieur de l’Arc Starter (démarreur de l’arc), comme un fil détaché qui provoque la mise à la terre à travers le châssis. o Court-circuit à l’intérieur du tube de montage de la torche. • Résolvez le problème de court-circuit du fil négatif externe en enlevant le fil à l’arrière de l’alimentation et essayez de démarrer. Il ne démarrera, mais si vous obtenez le même code 205, cela signifie que le problème se situe à l’intérieur de la machine. b. Court-circuit à l’intérieur de l’alimentation : • Toutes les sorties d’onduleur sauf celle du IM1A sont en parallèle. Si la sortie de tout onduleur est raccourcie, elle apparaîtra comme un court-circuit sur la sortie de l’alimentation générale. Résolvez les problèmes en enlevant tous (ou un à la fois) les connecteurs de sortie de l’onduleur, sauf ceux sur le module onduleur 1A. Ensuite, appliquez Démarrer à l’appareil. Si elle démarre maintenant, un des autres onduleurs avait une sortie court-circuitée. Pour trouver la pièce défectueuse reconnectez chacune à la fois jusqu’à ce que le défaut réapparaît. 206 Non utilisé. Codes réservés dans la version précédente du produit. 207 Courant inattendu dans le fil d’usinage. HCT1, un capteur de courant à effet Hall sur le positif (jeu de barres d’usinage), mesure le courant du fil d’usinage. La section 1A de l’onduleur est activée au cours du pré-débit, mais il ne doit pas y avoir de courant électrique dans le câble de travail avant que le pilote ne s’allume et avant que l’arc ne soit transféré au travail. Si un courant supérieur à 8 A est détecté avant ou pendant le pré-écoulement, il y a un problème. 1. Code 207 avant l’application de DÉMARRAGE : • Capteur de courant d’usinage, HCT1, défectueux. • PCB de relais défectueux • CCM défectueux Capteur défectueux • Le capteur de courant de service, HCT1, reçoit une alimentation, + 15 VCC et -15 VCC de la carte relais. Les deux doivent être présents pour que le capteur fonctionne correctement. Assurez-vous que la tension soit bien de +15 VCC entre le TP1 du Circuit relais (circuit relais) (ou J1-4) et le J1-1, et de -15 VCC vers le J1-2. • S’il n’y a pas plus ou moins 15 Vcc, enlevez le connecteur J1 et répétez la mesure à J1-1 et 2 sur la carte de relais. Si la tension est maintenant présente, le capteur est défectueux ou court-circuité (le faisceau pourrait être court-circuité). Si la tension n’est toujours pas présente, la carte de relais est défectueuse. Circuit relais • La LED D12 de la carte relais, COURANT DE TRAVAIL DÉTECTÉ (courant de travail détecté), s’allume si le signale du capteur de courant dépasse 0,05 V. Si D12 est allumée, mesurez le signal de sortie du capteur à J1-3 avec le signal commun à J1-1. Ce signal doit être de 0 V +/- 0,04 VCC. S’il est supérieur à +/- 0,04 Vcc sans courant de fil A-72 ANNEXE 0-5264FR ULTRA-CUT 100 XT/200 XT/300 XT/400 XT d’usinage, le capteur est défectueux. Si la tension du signal est dans les limites et que D12 est allumée, alors la carte de relais est défectueuse. • Si D12 n’est pas allumée et que le code 207 est toujours actif, soit la carte de relais soit le CCM sont défectueux. CCM or câble plat • Le signal de courant de service provenant de la carte relais est sur le câble-ruban à 40 contacts (relais J4 à CCM J23 ) contacts 27 (-) et 28 (+). Si la tension à cet endroit dépasse 0,1 Vcc sans courant d’usinage, la carte de relais est probablement défectueuse. Il est aussi possible que dans le câble plat à 40 broches, la broche 27 ou 28 fasse un court-circuit avec une broche adjacente. Dans le cas contraire, le CCM est défectueux. 2. Code 207 après l’application de DÉMARRAGE (pendant le pré-écoulement) : • Court-circuit entre la sortie négative de l’alimentation électrique et le circuit de travail. • Court-circuit entre la sortie négative de l’alimentation électrique et la mise à la terre. • Équipement fourni par l’utilisateur défectueux ou mal installé, comme des contrôles de hauteur de torche qui établissent des connexions avec la sortie de l’alimentation électrique. Les courts-circuits risquent de provoquer une baisse du voltage continu de sortie (code 205) Néanmoins, si le court-circuit a suffisamment de résistance, il est possible que le code 207 s’affiche. Pour tester, retirez le câble de la sortie négative et réactivez Start. Si le code 207 ne s’affiche pas, le problème est un court-circuit quelque part à l’extérieur de l’alimentation. Équipement d’utilisateur installé Pour que l’équipement installé par l’utilisateur provoque un code 207, il faut qu’il soit connecté à la sortie (à l’arrière) des capteurs de courant. Pour tester, débranchez l’équipement de l’utilisateur et activez CNC START. Si le code 207 a disparu, l’équipement de l’utilisateur était défectueux ou mal connecté. 208 Courant inattendu dans le circuit de pilote Le carte pilote comporte un capteur de courant pour mesurer le courant du pilote. Il ne devrait pas y avoir de courant pilote jusqu’à ce que les onduleurs et la carte pilote soient activés et le démarreur d’arc ait démarré pour allumer le pilote. Le courant du pilote ou le signal indiquant le courant du pilote ne doivent pas être présents tant que le démarreur de l’arc n’a pas été déclenché. Un signal de courant indésirable dû au capteur défectueux ou aux cartes de circuits défectueux sera probablement présent dès que la séquence de démarrage est complète et sera indiqué comme une défaut actif, E208. Il n’y aura pas de véritable court-circuit permettant au courant réel de circuler dans le circuit du pilote tant que l’onduleur et la carte du pilote sont activés près de la fin du pré-écoulement. Cela va entrainer l’arrêt immédiat des onduleurs et faire en sorte qu’ils affichent un défaut « dernier » ou « verrouillé », L208. Une DEL, D2, sur la carte du pilote s’allume lorsque la carte du pilote est activée. 1. Code 208 avant l’application de DÉMARRAGE : • Carte de pilote défectueuse (circuit de capteur de courant). • PCB de relais défectueux • CCM défectueux Circuit imprimé du pilote Le signal indiquant le courant du pilote est situé sur la broche 10 du câble plat (pilote J42, circuit relais J3) entre les broches 8 (-) et 9 (+) En l’absence de courant, le signal devrait être de zéro +/- 0,05 V. De même, la carte de relais a une DEL, D11, « Courant de pilote détecté », qui s’allume si le signal de courant de pilote dépasse 0,15 V. Si le signal n’est pas de zéro V, le PCB du pilote est vraisemblablement la cause du problème. Pour être sûr, débranchez le câble-ruban de la carte pilote de la carte relais à J3. Si D11 s’éteint, la carte du pilote était la cause. Vérifiez deux fois en mesurant les broches 8 et 9 de nouveau. Si c’est zéro V. la carte Pilot (pilote) est maintenant défectueuse. Si D11 est toujours allumée ou si la tension des broches 8 et 9 est toujours élevée, vérifiez la carte de relais. Carte relais or CCM Si D11 sur le PCB de relais est toujours allumée après les tests précédents, mesurez la sortie au CCM sur le câble plat à 40 broches (relais J4 à CCM J23) entre les broches 23 (-) et 25 (+). Il doit être inférieur à 0,1 V. Si tel n’est pas le cas, la carte de relais est défectueuse. Si la tension est de zéro, alors le CCM est défectueux. 0-5264FR ANNEXE A-73 ULTRA-CUT 100 XT/200 XT/300 XT/400 XT 2. Le code 208 apparaît pendant le pré-écoulement : Le MO 1 et la carte de pilote sont activés près de la fin du pré-écoulement. Pour avoir un courant indésirable il doit y avoir un chemin (court) pour le passage du courant entre la sortie négative de l’onduleur (électrode négative du câble/ de la torche) et le retour/la pointe pilote avant que le démarreur d’arc ne soit activé pour l’allumage du pilote. Les causes possibles sont : • Court-circuit entre l’électrode et la pointe à cause d’une disparité de consommables, de consommables endommagés ou de corps étranger entre la pointe et l’électrode. Une électrode en fin de vie pourrait perdre du matériel qui peut provoquer un court-circuit entre l’électrode et l’embout. • Équipement fourni par l’utilisateur défectueux ou mal installé, comme des contrôles de hauteur de torche qui établissent des connexions avec la sortie de l’alimentation électrique. • Court-circuit entre la sortie négative de l’alimentation électrique et le câble du pilote. • Corps de torche court-circuité. Dépannage : 1. Retirez et isolez (risque de haute tension) le câble du pilote de l’arrière de l’unité. Essayez de piloter. Si aucun code 208 ne s’affiche, cela confirme que le problème ne réside pas dans l’alimentation. 2. Retirez et vérifiez que le consommable n’est pas endommagé, manquant ou sale (distribution de gaz, etc.) ou de mauvais composants. 3. Déconnectez l’équipement fourni par l’utilisateur et vérifiez si le problème persiste. 4. Inspectez l’Arc Starter (démarreur de l’arc) pour déceler tout câble endommagé/débranché, ou toute trace de brûlure sur les composants. 5. Inspectez l’intérieur du tube de montage de la torche pour déceler tout court-circuit. 6. Si toutes les autres solutions ont échoué, déconnectez le fil du pilote à l’arrière de la tête de torche. Veillez à bien l’isoler et à le tenir éloigné de toute matière métallique, car il peut encore être chargé de courant HF (haute fréquence) lorsque vous le démarrerez. Essayez de démarrer, si le 208 est maintenant résolu, la tête de torche est court-circuitée. 209 Non utilisé. Codes réservés dans la version précédente du produit. 210–211 (211). Le courant de sortie, mesuré par l’ampèremètre du fil d’usinage, est trop élevé (210) ou trop bas Ce sont des Avertissements et ils n’arrêtent pas le processus mais peuvent expliquer la mauvaise qualité de coupe ou le mauvais état des pièces. Les sections individuelles de l’onduleur ont leurs propres capteurs de tension et le câble de travail a un capteur de tension dont le signal doit correspondre à la somme des différentes sections de l’onduleur. Chaque section est réglée pour fournir un certain courant selon son signal de « demande ». Si le courant diffère de la « demande » totale, la somme des demandes individuelles, les sections individuelles sont vérifiées pour déterminer si leur sortie est correcte comparativement à leurs signaux de demande. Si les sections individuelles sont correctes, mais que le signal du capteur du courant d’usinage diffère de la demande totale de plus de 16 %, le code 210 (trop élevé) ou 211 (trop faible) s’affiche. Si une section individuelle d’onduleur se révèle défectueuse, ce qui entraîne une erreur du courant total, un code différent s’affichera entre 212 et 223, selon la section défaillante. Causes possibles pour un signal de courant de travail trop élevé : • HCT1 Work Capteur de courant • Circuit relais • CCM La cause possible pour un courant de travail trop faible. • Toutes les causes précédentes plus un court-circuit au châssis provoqués par : A-74 ANNEXE 0-5264FR ULTRA-CUT 100 XT/200 XT/300 XT/400 XT o L’équipement d’utilisateur installé se connecte derrière le capteur de courant qui établit une connexion pour travailler ou mettre à la terre permettant le passage du courant par le capteur de travail de dérivation. o Onduleur + sortie court-circuités sur le châssis. Dépannage : 1. Pour le courant trop faible en raison d’un court-circuit, déconnectez le fil d’usinage à l’arrière de l’unité. Vérifiez la continuité vers le châssis, il ne devrait pas en avoir. Inspectez l’équipement de l’utilisateur pour vérifier l’intégrité des branchements. 2. En l’absence de courts-circuits ou si l’erreur était un signal de courant trop élevé, voyez la section sur le code 207 pour une Description détaillée des parcours de l’alimentation et des signaux pour le capteur de courant du fil d’usinage. 3. Dans la section correspondante au code 207 pour le Circuit relais (circuit relais), la manière de mesurer le signal du capteur de courant lorsque il n’y a pas de courant est décrite. Le signal doit être zéro et nous supposons que c’est le cas, autrement vous devriez avoir obtenu le code 207. Si le signal de courant zéro est correct, mais qu’il y a une erreur lors de la coupe, mesurez le signal aux broches 27 (-) et 28 (+) du câble plat à 40 broches (carte de relais J4 à CCM J23). La tension du signal doit être égale au courant de coupe * 0,0266. Par exemple, pour 100 A (100*0,0266) =2,66V. • Si ce signal est correct, le CCM est défectueux • S’il est erroné, l’erreur pourrait être dans la carte de relais ou le capteur. Suivez les instructions du code 207 pour mesurer la tension vers le capteur de courant et le signal vers le capteur de courant à J1 sur la carte de relais. La tension du signal doit être égale au courant de coupe * 0,0133. Par exemple, pour 100 A (100*0,0133) =1,33 V. Pour 400A serait 400*0,013 3= 5.33V. • Si l’alimentation et le signal sont corrects, la carte de relais est défectueuse. S’ils sont incorrects, le capteur de courant d’usinage HCT1 est défectueux. 212-223 Sortie incorrecte d’une section d’onduleur. Courant de service élevé ou faible en raison de mauvaise sortie d’une section de l’onduleur. Le code individuel indique la section concernée. Les causes peuvent être : • Le connecteur de sortie de la section de l’onduleur nommé, J102 A ou B, n’est pas branché ou est endommagé. • Mauvaise connexion du câble plat, celui-ci n’est peut-être pas correctement enfoncé du côté de l’onduleur ou du CCM. • Section d’onduleur défectueuse. Dépannage : 1. S’il signale que le courant d’une section d’onduleur individuelle est trop élevé, le problème réside dans l’onduleur. 2. Si le rapport est actuellement trop bas (y compris l’absence de courant), vérifiez les connexions. 3. Le câble plat de la première section de l’onduleur (Module onduleur # 1A) doit se raccorder uniquement à cette section, mais s’il existe 2 sections supplémentaires, l’unité est 200A ou plus, permutez le câble plat allant dans ces sections. a. S’il est indiqué qu’une section différente est défectueuse, celle dont le câble a été déplacé, alors la section originale était défectueuse. b. Si elle indique maintenant la section originale, le câble plat ou le CCM sont défectueux (peu probable). c. Permutez les deux extrémités du câble-ruban avec celles du câble-ruban se trouvant à proximité. S’il indique toujours la section originale, alors le problème réside dans le CCM ou le câble plat. 4. Si c’est la première section d’onduleur ou une unité 100 A, il n’y a aucun autre onduleur avec lequel échanger de câble, remplacez donc l’onduleur. Conseil additionnel : Les PCB de contrôle d’onduleur ont une DEL verte, D24, MID ON, qui s’allume quand cette section est activée et a un signal de demande. La luminosité des LED est relative à la sortie et peut donc être très faible si le débit est faible. Si la DEL ne s’allume pas, cela pourrait indiquer un onduleur défectueux (carte du contrôleur). 0-5264FR ANNEXE A-75 ULTRA-CUT 100 XT/200 XT/300 XT/400 XT 224 Onduleur 1 introuvable. Un onduleur doit être connecté à la première section, 1A, pour être en mesure de piloter. Pendant la séquence de démarrage, avant que les onduleurs soient alimentés, le CCM effectue un test de continuité pour vérifier si le câble plat de sa section 1C (J31 sur le CCM) est connecté. Causes et dépannage : • Étant donné qu’il s’agit simplement d’un test de continuité, il est très improbable que ce soit un onduleur défectueux. Plus vraisemblablement, un mauvais branchement, ou un câble plat défectueux. o Vérifiez les connexions du câble plat aux deux extrémités de INV1A avec le câble CCM J31 (1A). Assurez-vous qu’il soit branché sur J31, le connecteur du haut, sur le CCM. o Branchez un autre câble d’onduleur dans le J31, peu importe les besoins du test, du moment qu’il est branché à un onduleur à l’autre extrémité. Si le code 224 s’affiche toujours, « Onduleur 1 non trouvé », le CCM est défectueux. Dans le cas contraire, il s’agit du câble plat. 225-230 Révision de l’onduleur et incompatibilité avec le CCM. Si à l’avenir, nous étions amenés à faire un changement à l’onduleur qui le rendrait incompatible avec un CCM plus ancien, nous avons inclus une clé matérielle qui changerait pour signaler la situation. Pendant la séquence de démarrage, avant que les onduleurs soient alimentés, le CCM effectue un test de continuité pour déterminer la configuration matérielle clé. La clé utilise 3 lignes du CCM au câble-ruban de l’onduleur qui sont nommées IS_ID_A, IS_ID_B, IS_ID_C (sur les terminaux 12, 13 et 14) et vérifie la continuité de la 4e ligne OUTCOM (terminal 9). L’essai consiste à appliquer une tension à OUTCOM et à chercher à ce que cette tension revienne sur les terminaux à 3 ID. La configuration actuelle a tous les 3 lignes connectées à OUTCOM; ainsi toutes les 3 lignes devraient être élevées. Pour obtenir le code 225-230 maintenant que nous ne disposons pas de révisions incompatibles, ce serait probablement une mauvaise connexion du câble plat entre le CCM et l’onduleur ou un CCM défectueux (peu probable). • Sur la section de l’onduleur, intervertissez le câble plat avec celui d’une autre section de l’onduleur. Si l’erreur ne change pas et continue de faire référence à la section de l’onduleur originale, le problème réside dans le câble plat ou le CCM. • Du côté de l’onduleur, remettez les câbles plats dans leur position initiale. Intervertissez maintenant le câble plat suspect avec un autre câble sur le CCM. Si l’erreur passe à une section différente, le câble plat est défectueux. Si elle reste avec la section originale, le problème réside dans le CCM. 231-236 Décalage du Vca de l’onduleur. Différents modules d’onduleur sont fabriqués pour les tensions d’usinage de 480 Vca, de 380-415 Vca et de 208-230 Vca. Il existe une clé, appelée ID onduleur, qui lit le câble-ruban de l’onduleur, afin d’identifier les plages de tension pour lesquelles l’onduleur est conçu. L’appareil est lui-même câblé différemment pour les différentes tensions d’entrée, et une partie de ces tensions comprend un cavalier à J61 sur la carte du System Bias qui indique à la carte du System Bias la tension à laquelle l’appareil est relié pour accepter. Lors de l’allumage, la carte BIAS système mesure la tension d’entrée, détermine dans quelle fourchette de tension elle se situe et envoie l’information sur cette fourchette au CCM. Avant d’appliquer l’alimentation aux onduleurs en mettant en marche les contacteurs d’entrée, le CCM vérifie que chaque modulateur connecté a la tension correcte correspondant à celle de la carte BIAS système. Les ID de l’onduleur sont lus à partir de la section la plus basse à la plus haute, de sorte que dans tous les cas s’il s’agit vraiment d’un onduleur de tension incorrecte, il doit faire appel à la section A dont le code est lu en premier. Un décalage de Vca d’une section B est vraisemblablement un autre problème. Causes possibles : • Mauvaise tension de l’onduleur (très peu probable, mais facile à vérifier). • Cavalier J61 de la carte du System Bias défaillant - (peu probable, mais facile à vérifier) • Onduleur défectueux. • Câble plat • CCM • Carte du System Bias défectueuse. A-76 ANNEXE 0-5264FR ULTRA-CUT 100 XT/200 XT/300 XT/400 XT Dépannage : 1. Si la carte BIAS système a soit le mauvais cavalier ou est défectueuse, il signale la première section de l’onduleur, code 231, parce que tous les onduleurs ne correspondront pas au signal incorrect et 1A est vérifiée en premier. a. Pour le cavalier, le fil #48 devrait être connecté depuis J61-1 à : i. J61-2 pour 208-230 VAC ii. J61-3 pour 400 VAC iii. J61-4 pour 480 VAC Vérifiez que les connexions et la continuité sont adéquates. b. Le System Bias peut être défectueuse, indiquant une ID de tension erronée. Sur la sortie de la carte System Bias (polarisation système) sur le J62 faites la mesure correspondante au TP1 ou (J62-8, 24VDC_RET) ou au J62-12 pour déceler un signal/VAC-IDAb, et J62-14 pour déceler un signal/VAC_IDB. Ces deux signaux doivent indiquer, selon la table suivante : « 0 » = 10-12 V ; « 1 » = 24 V ; signal 230V 400V 480V ERR /VAC_IDAb 0 1 0 1 /VAC_IDBb 0 0 1 1 2. Onduleur, câble plat ou CCM défectueux. a. Sur la section de l’onduleur, intervertissez le câble plat de la section de l’onduleur qui présente un défaut avec le câble d’une autre section de l’onduleur. Si l’erreur ne change pas et continue de faire référence à la section de l’onduleur originale, le problème réside dans le câble plat ou le CCM. Si l’erreur passe à une autre section, celle dont le câble plat a été échangé, alors c’est l’onduleur qui est défectueux. b. Si l’erreur n’a pas changé à l’étape A, du côté de l’onduleur, remettez les câbles plats dans leur position d’origine. Intervertissez maintenant le câble plat suspect avec un autre câble sur le CCM. Si l’erreur passe à une section différente, le câble plat est défectueux. Si elle reste avec la section originale, le problème réside dans le CCM. 237 Pas assez d’onduleurs trouvés Au moins 2 sections de l’onduleur doivent être présentes pour fonctionner. Nous savons que le câble-ruban pour la section 1A de l’onduleur est connecté ou bien nous aurions le code 224. Pendant la séquence de démarrage, avant que les onduleurs soient alimentés, le CCM effectue un test de continuité par un câble plat pour vérifier si un onduleur est connecté. S’il ne voit pas la continuité avec au moins un autre onduleur, il suppose qu’aucun onduleur n’est connecté. Causes possibles : • Câble plat débranché ou défectueux. • Onduleur défectueux • CCM défectueux. Dépannage : 1. Vérifiez que tous les câbles sont connectés, les loquets fermés, aux extrémités de l’onduleur et du CCM. 2. Si la défaillance se produit, c’est le plus probablement sur une unité 100 A qui a une section (1B) en plus de la section 1A. S’il y avait deux sections supplémentaires ou plus, il est extrêmement peu probable que tous les câbles plats ou les connecteurs CCM soient défectueux. a. Permutez les câbles-rubans de la section d’onduleur 1A et 1B. Si l’erreur ne change pas et reste 237, le problème réside dans le câble plat ou le CCM. Si l’erreur passe de 237 à 224, indiquant que la section l’onduleur 1A est manquante, alors c’est l’onduleur qui est défectueux. b. Si l’erreur n’a pas changé à l’étape A, du côté de l’onduleur, remettez les câbles plats dans leur position d’origine. Intervertissez maintenant les câbles plats suspects sur le CCM. Si l’erreur change, le câble plat est défectueux. Si elle ne change pas, c’est le CCM. 0-5264FR ANNEXE A-77 ULTRA-CUT 100 XT/200 XT/300 XT/400 XT c. S’il y a deux câbles plats ou plus en plus de celui de la section 1A, alors le CCM ne voit aucun d’entre eux connecté, ce qui indique que le CCM est défectueux. 238 Identification de la tension de polarisation du système non valide. Lors de l’allumage, la carte BIAS système mesure la tension d’entrée et envoie des signaux au CCM, indiquant quelle fourchette de tension elle a détectée. Voir les chapitres 231-236 pour obtenir plus de renseignements. Si une des trois fourchettes de tension, 208-230 V, 380-415 V ou 480 V, n’est pas identifiée, alors les deux signaux ID sont élevés, ce qui entraîne un signal non valide. Causes possibles : • L’appareil est connecté à une tension en dessous de la plage 208-230V ou au-dessus de la plage 480V. (Peu probable à moins qu’il y a un problème avec la tension d’entrée.) • Carte BIAS système défectueuse • Mauvaise connexion entre la sortie BIAS système J62 et l’entrée CCM J27 sur la carte E/S. • CCM défectueux Dépannage : 1. Mesurez les 3 phases de voltage d’entrée et confirmez qu’ils sont tous les trois dans les limites de tolérances indiquées dans le mode d’emploi de l’unité. 2. Reportez-vous à la section 231-235 Inverter VAC Mismatch (disparité de voltage alternatif sur l’onduleur) et effectuez le dépannage décrit à l’étape 1.b. Si les deux signaux ne correspondent pas à la tension d’entrée, s’ils sont tous les deux élevés, alors le BIAS système est défectueux. 3. Si l’étape 2 était OK, faites la même mesure à J27 sur le PCB E/S du CCM. Si elle est OK ici, le CCM est défectueux. Dans le cas contraire, inspectez les connexions sur J62 et J27. 239 Tension CA élevée Tension Normal - Au démarrage, la carte du System Bias mesure la tension d’entrée et détermine si elle est dans la plage de tension définie par le cavalier J16. Voir les chapitres 231-236 Inverter VAC Mismatch Troubleshooting (dépannage de la disparité de voltage alternatif sur l’onduleur) étape 1.a pour obtenir plus de détails concernant le cavalier. Normalement, lorsque le voltage d’entrée est OK, la carte System Bias (polarisation système) allume un relais K1 sur le côté gauche de la carte pour alimenter l’Transformateur auxiliaire (transformateur auxiliaire) T1. D44, une DEL verte « TRANSFORMATEUR EN MARCHE », s’allume lorsque K1 est sous tension. T1 alimente les commandes de gaz et le TSC 3000 ainsi que les pompes et les ventilateurs. Tension élevée - Si la tension CA est établie comme étant trop élevée, il allume D4, ACV HIGH, une LED rouge sur la carte system Bias, et met le signal “VAC HIGH b” sur J62-6 à « élevé » à environ 24 VCC (normal pour un « faible » ici est 10-14 VDC). Pour éviter la possibilité qu’une tension excessive soit appliquée à plusieurs éléments (commandes de gaz, pompes, ventilateurs, etc.) K1 est ouvert supprimant l’alimentation de T1, et D44 s’éteint. Si c’est plus qu’une déformation passagère, les contrôles des gaz et le TSC 3000 (le cas échéant) seront réinitialisés. La communication avec la table de découpe peut être interrompue. Avec la commande de gaz Auto DFC 3000 et éventuellement le contrôle de la table de coupe, le processus devra être rechargé. D4 est allumé et le signal « AC V HIGH b » est élevé uniquement lorsque la tension est réellement élevée. Le signal “AC V HIGH b” ne se verrouille pas. Si l’erreur est E239, cela signifie qu’il est actuellement actif, c’est-à-dire que la tension est détectée actuellement comme étant trop élevée. Si c’est L239, cela signifie que la tension était trop élevée auparavant, mais qu’il n’est plus trop élevé. Appliquer DÉMARRER supprimera la défaillance, sauf si celle-ci se réactive. La tension qui déclenche un défaut de tension CA élevé est au-dessus de 550V pour une ligne de 480 VCA; au-dessus de 470V pour une ligne nominale de 415V, 380V, 400V ou; au-dessus de 270V pour une ligne 208 VCA ou 230 VCA. Causes possibles : • La tension d’alimentation est ou était trop élevée. • Mauvaise connexion à J62 ou J27 A-78 ANNEXE 0-5264FR ULTRA-CUT 100 XT/200 XT/300 XT/400 XT • Mauvaise connexion au cavalier J61 • Carte du System Bias défectueuse • CCM défectueux. Dépannage : 1. Si l’erreur est L239, appliquer DÉMARRER supprimera la défaillance, sauf si celle-ci se réactive. Un problème occasionnel peut être provoqué par des pics de tension d’entrée (hausses de tension durant d’un demi-cycle à jusqu’à une minute). Habituellement, si le plasma est défectueux, le problème sera présent tout le temps. 2. Il est peu probable qu’une connexion ouverte sur le cavalier J61 entraîne un défaut 239, la cause est plus vraisemblablement un défaut de Voltage Mismatch (disparité de voltage). Néanmoins, si l’erreur est intermittente au même moment exactement, éventuellement parce qu’il n’est pas entièrement connecté, elle pourrait s’afficher avec le code 239. Vérifiez J61. 3. Si la tension d’entrée est OK et que le problème persiste, il pourrait être attribuable à la carte BIAS système, au CCM ou à la connexion entre J62 et J27. a. Si la tension d’entrée est OK et que D4 est allumée ou que le signal « AC V HIGH b » sur J62-6 est « élevé » (au sujet de 24 Vcc, par rapport à TP1 ou J62-8), la carte BIAS système est défectueuse. b. Si D4 n’est pas allumée et que le signal « AC V HIGH b » sur J62-6 est « low » (environ 10-14 Vcc, par rapport à TP1 ou J62-8), alors le BIAS du système est OK et le problème réside dans le CCM. c. Si J62-6 est proche de zéro volte, il pourrait y avoir une mauvaise connexion entre J62-6 et J27-6 ou J62-7 et J27-6. 240 Tensions AC faible Reportez-vous au premier paragraphe dans la section du code 239 pour trouver l’explication de ce qui doit se produire lorsque le voltage d’entrée est correct. Basse tension - Si la carte System Bias détermine la tension CA est trop faible, il allume une LED rouge, D14, ACV LOW, et met le signal “V AC Low B” sur J62-10 à « haut », à propos de 24 VCC (normal pour « faible » ici est 10-14 VCC). L’alimentation n’a pas encore été enlevée dans le T1, vu qu’un faible voltage ne risque pas d’endommager les composants. Cependant, si le courant reste trop faible pour une durée trop longue, certains composants comme les contacteurs, les solénoïdes CA, les contrôles de gaz ou le TSC 3000 pourrait cesser de fonctionner. Un faible voltage, s’il est suffisamment faible, peut aussi allumer D3, la DEL rouge de phase manquante. Cela n’indique pas effectivement la phase manquante. La tension qui déclenche un défaut de tension CA bas est de 380V pour une ligne nominale de 480 VCA; 300 V pour une ligne nominale de 380 VCA, 400 VCA ou 415 VCA; 175 V pour une ligne de 208 VCA ou 230 VCA; Causes possibles : • La tension d’alimentation est actuellement, ou a été, trop faible. o Fils de distribution électrique ou câble d’alimentation trop courts pour la charge. o Une connexion qui a du jeu ou à haute résistance à un endroit dans la distribution d’alimentation ou au niveau du branchement du câble d’alimentation. • Mauvaise connexion à J62 sur la carte BIAS système ou à J27 sur le CCM. • Mauvaise connexion au cavalier J61 sur la carte BIAS système. • Carte du System Bias défectueuse. • CCM défectueux. Dépannage : 1. Si l’erreur est L240, appliquer DÉMARRER supprimera la défaillance, sauf si celle-ci se réactive. Un problème occasionnel peut être provoqué par des creux de tension d’entrée (chutes de tension durant d’un demi-cycle à jusqu’à une minute). Habituellement, si le plasma est défectueux, le problème sera présent tout le temps. Après avoir 0-5264FR ANNEXE A-79 ULTRA-CUT 100 XT/200 XT/300 XT/400 XT écarté toute autre cause, nous pourrions devoir fixer un moniteur à l’alimentation électrique pour déterminer si c’est la cause du problème. 2. La tension peut être normale lorsque l’appareil ne coupe pas ou coupe à des courants plus faibles, mais lorsqu’il coupe à un niveau de courant plus élevé, beaucoup trop de tension peut être perdue à cause d’un cordon d’alimentation ou des fils faibles. a. Mesurez le voltage en coupant à un courant plus élevé, afin de déterminer si la baisse est excessive. b. Vérifiez que toutes les connexions électriques sont propres et sécurisés. c. Vérifiez que la taille des fils est appropriée pour la consommation de courant selon les recommandations de notre manuel ainsi que les codes électriques locaux. 3. Il est peu probable qu’une connexion ouverte sur le cavalier J61 entraîne un défaut 240, la cause est plus vraisemblablement un défaut de Voltage Mismatch (disparité de voltage). Néanmoins, si l’erreur est intermittente au même moment exactement, éventuellement parce qu’il n’est pas entièrement connecté, elle pourrait s’afficher avec le code 240. Vérifiez le cavalier à J61. 4. Si la tension d’entrée est OK et que le problème persiste, il pourrait être attribuable au BIAS système, au CCM ou à la connexion entre J62 et J27. a. Si la tension d’entrée est OK et que D14, ACV LOW, est allumée ou que le signal « AC V LOW b » sur J62-10 est « élevé » (au sujet de 24 Vcc, par rapport à TP1 ou J62-8), la carte BIAS système est défectueuse. b. Si D14 n’est pas allumée et que le signal « AC V HIGH b » sur J62-10 est « low » (environ 10-14 Vcc, par rapport à TP1 ou J62-8), alors le BIAS du système est OK et le problème réside dans le CCM. c. Si J62-10 est proche de zéro volte, il pourrait y avoir une mauvaise connexion entre J62-10 et J27-10 ou J62-7 et J27-7. 241-246 Erreur de la tension d’entrée de la section de l’onduleur. Le carte du System Bias contrôle si la tension d’entrée est haute, basse ou manquante sur une phase de l’alimentation provenant du cordon d’alimentation. Il est peu probable, mais pas impossible, qu’un problème avec l’alimentation électrique entraîne des codes 241-246. Les codes 241-246 codes indique plus probablement des problèmes d’alimentation dans une section de l’onduleur unique ou, dans le cas de la phase manquante, il peut s’agir du contacteur qui alimente jusqu’à 3 sections de l’onduleur. Une fois que les contacteurs d’entrée se ferment, applique le voltage aux onduleurs, des tests sont effectués pour déceler si la tension est trop élevée ou trop faible, et si une phase est manquante. Lorsque la tension d’entrée est dans la plage correcte, une LED verte, D4, nommé READY, s’allume sur le côté gauche de la carte principale de l’onduleur. Si D4 n’est pas allumé, soit la tension d’entrée est en dehors de la plage ou l’onduleur est défectueux. Vous pouvez toujours obtenir le code 241-246 avec une phase manquante et la READY LED activé. La LED s’allumera et s’éteindra rapidement, mais aura l’air d’être allumée à l’œil. Dans ce cas de figure, vous pouvez mesurer le signal sur le câble plat. Le signal précédemment appelé READY est maintenant appelé AC_INPUT_FLT. Il s’agit d’un signal différentiel sur les broches 1(+) et 2(-) du câble plat à 30 broches de l’onduleur. Si l’entrée CA est correcte, vous devriez lire 5-6 V entre les broches. Si AC_INPUT_FLT est une tension continue, les broches 1 et 2 auront moins de 2 V. Plusieurs autres défauts, comme Inverter Fault (défaut de l’onduleur) et Over Temperature (surchauffe), déclenchent également le défaut AC_INPUT_FLT (not Ready (pas prêt). Néanmoins, ils verrouilleront les DEL associées ou définiront différents codes d’erreur. Dans le cas d’un Voltage d’entrée Fault (défaut de tension d’alimentation), le CCM ne supprime pas l’alimentation électrique présente dans l’onduleur. Situations pouvant causer les codes de défaut de tension d’entrée : 1. Baisse intermittente de l’alimentation sur une ou plusieurs phases pour 1 ms au moins, une perte d’une durée plus longue devrait provoquer un autre genre d’erreur. Si c’est l’alimentation d’entrée, ce ne sera probablement pas toujours le même onduleur. 2. Phase manquante ou intermittente sur un onduleur spécifique, le défaut indiquera toujours l’onduleur concerné A-80 ANNEXE 0-5264FR ULTRA-CUT 100 XT/200 XT/300 XT/400 XT 3. Connexions intermittentes sur le signal de défaut à l’intérieur de l’onduleur 247-252 Défaillance de l’onduleur Une fois que les contacteurs d’entrée se ferment, appliquant le voltage aux onduleurs, différents tests sont effectués. Le signal de défaut d’onduleur se ferme, de sorte que même si la cause disparaît, vous pouvez voir qu’il y avait un défaut, indiquée par la LED rouge D1, INV FLT sur le contrôle de l’onduleur et la carte défaut. Il sera réinitialisé en déclenchant le signal de démarrage ou en redémarrant l’alimentation. Si l’erreur est toujours présente, elle se rallume. Situations pouvant causer les défauts de l’onduleur : • Une ou plusieurs alimentations de polarisation locales (+/-12 VCC) ont rencontré une panne ou sont non conformes. Les DEL vertes sur la carte Cap BIAS indiquant +12V (D13) et -12V (D6) indiquent que les fournitures sont présentes, mais pas nécessairement qu’elles sont dans la zone de tolérance. • Un déséquilibre de voltage du condensateur électrique d’entrée indiqué par la LED D3 DÉSÉQUILIBRE DU COUVERCLE (déséquilibre du couvercle) (rouge) sur le côté gauche de la carte principale de l’onduleur. S’applique aux unités avec des capacités connectées en série (unités de 380-480 V). • Courant excessif dans la tension primaire du transformateur (transformateur du commuteur), D32, PRI OC LED (rouge), la carte de commande de l’onduleur. INV_FLT est un signal différentiel sur les broches 3(+) et 4(-) du câble plat à 30 broches de l’onduleur. En l’absence de défaillance, vous devriez lire 5-6 V entre les deux broches. Si INV_FLT est une tension continue, les broches 3 et 4 auront moins de 2 V. 253-258 Surchauffe de l’onduleur. Chaque section d’onduleur (SO) contient un ou plusieurs capteurs de température. Si un de ces capteurs détecte une surchauffe, il active le signal « OVERTEMP_FLT » vers le CCM sur le câble plat des sections d’onduleur. Les semi-conducteurs des onduleurs (transistors et diodes) sont refroidis par liquide. Tout élément qui augmente trop la température du liquide de refroidissement peut provoquer une surchauffe des onduleurs. Le magnétisme des onduleurs (transformateurs et inducteurs) est refroidi par air par le(s) même(s) ventilateur(s) qui refroidissent le liquide. Causes possibles : • Ventilateur(s) de refroidissement non fonctionnel(s). • Écoulement d’air perturbé. • Module d’onduleur défectueux. • Problème de connexion du câble plat de l’onduleur. • CCM défectueux. À l’origine, les unités 100 et 200 A avaient 2 ventilateurs plus petits, alors que le 300 et le 400 A utilisaient un ventilateur unique plus puissant, avec un radiateur plus grand. Plus récemment, le ventilateur simple, plus puissant, peut être également utilisé sur le 100 et le 200 A. Les ventilateurs de rechange pour toutes les unités sont contenus dans une trousse unique. Dépannage : 1. Vérifiez que l’air est évacué du haut (ventilateur supérieur) et du bas (ventilateur inférieur sur les unités à 2 ventilateurs) dans l’orifice sur le panneau du côté droit. Le ou les ventilateurs étant derrière le radiateur, il est difficile de les voir pour confirmer s’ils tournent, mais vous pourriez utiliser un miroir d’inspection. Reportez-vous à la section du code 403 pour dépanner les ventilateurs défectueux. 0-5264FR ANNEXE A-81 ULTRA-CUT 100 XT/200 XT/300 XT/400 XT ! AVERTISSEMENT Les lames de ventilateur peuvent être en mouvement et un contact accidentel avec un miroir ou un autre dispositif d’inspection pourrait provoquer des lésions corporelles ou endommager la machine. 2. Le fait de laisser les panneaux latéraux et le couvercle démontés, en particulier le côté inférieur gauche et le couvercle supérieur, entraîne une réduction du flux d’air. De même, si les ailettes du radiateur sont bouchées par de la poussière, cela réduira l’écoulement d’air. Nettoyez périodiquement le radiateur en soufflant de l’air à l’intérieur pour éliminer la poussière des ailettes. 259-264 Surchauffe de l’onduleur attribuable à une température ambiante élevée. Le CCM mesure la température ambiante, lorsque l’air de refroidissement entre dans les déflecteurs sur le côté gauche du panneau avant. Si l’onduleur surchauffe et que nous avons déterminé que la température ambiante dépasse 40 degrés Celcius, nous obtiendrons un ou plusieurs codes de température ambiante élevée (252-264). Le capteur, TS2, est un NTC (coefficient de température négatif ) dont la résistance varie avec la température. Il est monté à l’intérieur du panneau avant, à côté des fentes d’aération sur la gauche. Pour y accéder, il faut enlever un ou plusieurs modules d’onduleur. Si la température ambiante est élevée, mais qu’aucun onduleur n’est trop chaud, il n’y a pas de défaillance. Causes possibles : • La température ambiante est trop élevée. • Ventilateur(s) de refroidissement non fonctionnel(s). • Écoulement d’air perturbé. • Capteur de température ambiante, TS2, court-circuité (très peu probable) ou autrement défectueux. • Carte de relais défectueuse. • CCM défectueux. • Carte de relais défectueuse. Dépannage : 1. Si la température de la pièce dépasse 40 degrés Celcius, rafraîchissez la pièce ou utilisez l’unité à un cycle de travail réduit ou à un courant inférieur. 2. Vérifiez que l’air est évacué par l’ouverture sur le panneau du côté droit. Le ou les ventilateurs étant derrière le radiateur, il est difficile de les voir pour confirmer s’ils tournent, mais vous pourriez utiliser un miroir d’inspection. Assurez-vous de ne pas mettre le miroir ou vos mains dans les lames. Les unités 100 et 200 A ont 2 ventilateurs plus petits, les unités 300 et 400 A en ont un plus grand. 3. Il est peu probable que ces codes de température ambiante élevée se déclenchent avant tout autre code de température, mais dans ce cas, nous pouvons noter qu’en retirant le couvercle et les panneaux latéraux, en particulier le panneau inférieur gauche et le panneau supérieur, on réduit le flux d’air. De même, des ailettes du radiateur bouchées par de la poussière réduiront l’écoulement d’air. 4. Pour tester TS2, enlevez J2 de la carte relais et mesurez la résistance entre les broches 4 et 6 du connecteur du faisceau J2. La résistance varie d’environ 33K ohms à 0°C à environ 12K ohms à 20°C à 5,3K ohms à 40°C. 5. Si TS2 est dans la gamme correcte, le problème pourrait résider dans la carte de relais ou le CCM. a. La sortie de la carte de relais allant à la CCM est sur le terminal 30 du câble-ruban à 40 contacts (J4 de la carte de relais à J23 de la carte E/S du CCM). Son voltage est analogique et devrait se situer entre 0,44 V à 0°C et 1,6 V à 40°C S’il est confirmé que la température ambiante de la pièce n’est pas supérieure à 40 degrés Celcius et que le signal de température ambiante à la broche 30 est supérieur à 1,6 V, alors la carte de relais est défectueuse. b. Si le signal de température ambiante à la broche 30 est correcte, inférieure à 1,6 V, et que la température ambiante de la pièce n’est pas supérieure à 40 degrés Celcius, alors le CCM est défectueux. 265-270 Inverter No Alimentation d’entrée Il existe plusieurs signaux numériques sur les câbles plats entre les sections de l’onduleur et le CCM qui nécessitent un certain niveau de tension. Ces comprennent AC_INPUT_FLT\, inverseur _FLT\, surchauffe_FLT\ et power_présents. A-82 ANNEXE 0-5264FR ULTRA-CUT 100 XT/200 XT/300 XT/400 XT Normalement, toutes ces valeurs doivent être élevées. Avant d’appliquer l’alimentation à l’onduleur, le CCM a déjà effectué une vérification de continuité pour s’assurer que cette section est en place et que le câble plat est connecté (code 224 et 237). Dès que l’alimentation est appliquée aux modules d’onduleur, le CCM vérifie ces 4 signaux et, si la présence de l’onduleur a déjà été confirmée, quel câble plat est connecté. S’il trouve qu’aucun des signaux n’a de tension, il suppose qu’il n’y a pas d’alimentation dans la section ou qu’il y a un problème au niveau de l’alimentation BIAS de la section de l’onduleur. Causes possibles : • Les 3 phases d’entrée, J103-105, de cette section de l’onduleur ne sont pas connectées. • Le disjoncteur CB2 fournissant une alimentation de 120 Vac au contacteur (et au démarreur d’arc à distance) est déclenché. • Le contacteur qui alimente cette section (et les autres) est défectueux. • Carte relais défectueuse • Onduleur défectueux. • CCM défectueux. Dépannage : 1. Vérifiez que les câbles d’alimentation secteur sont connectés aux onduleurs. 2. Vérifiez si le contacteur pour cette section (W1 pour 1A, 1B, 2A; W2 pour 2B, 3A, 3B) est sous tension. a. Il existe une section rectangulaire, au milieu de chaque sommet du contacteur pouvant être utilisé pour fixer les contacts auxiliaires. Cela peut également être un indicateur de fonctionnement du contacteur puisqu’il s’arrête lorsque le contacteur est sous tension. b. Vérifiez si le CB2 est ouvert sur le panneau arrière. Le bouton blanc marqué “5”, indiquant qu’il est 5 ampères, apparaîtra s’il est déclenché. Réinitialisez-le, et si un autre problème survient (la bobine du contacteur?) peut être court-circuité. c. Mesurez s’il y a bien 120 VCA de tension au niveau de la bobine du contacteur. Si tel est le cas, mais que le contacteur n’est pas tiré, c’est probablement un contacteur défectueux. 3. Sur la carte Relay (relais), la LED D22 CONTACTOR ON LED (verte) située à côté du relais K1 s’allume si elle reçoit l’ordre de s’activer. a. S’il est allumé, vérifiez qu’il y a 120 Vca entre J8-1 et J8-9. Si tel n’est pas le cas, la carte de relais est OK. b. Si D22 est allumée, mais qu’il n’y a pas 120 Vca à J8-1 et J8-9 (assurez-vous que le voltmètre est réglé à Vca), alors la carte de relais est défectueuse. c. D22 n’est pas allumée, allez au connecteur de test de câble plat à 40 broches et mesurez la tension sur la broche 17 (relativement à TP1 soit sur la carte de relais soit sur la carte E/S du CCM). Il doit être faible, moins de 1 volt. Si c’est le cas, la carte de relais est probablement défectueuse. Si elle est élevée, environ 24 Vcc, alors le CCM peut être défectueux et ne pas indiquer au contacteur de s’allumer. 4. La section de l’onduleur peut être défectueuse à cause d’une mauvaise alimentation de polarisation. Permutez l’extrémité de l’onduleur du câble-ruban avec celle de l’onduleur de câble-ruban se trouvant à proximité. a. Si un code différent est maintenant affiché, celui de l’onduleur avec lequel il a été échangé, alors la section originale est défectueuse. b. Si elle continue d’indiquer la même section même si le câble plat a été changé, le CCM est défectueux. 271 Faute de lecture de l’identifiant de l’onduleur. Reportez-vous à la section pour les codes 225-230 pour la Description des signaux ID. Si ce code s’affiche, cela signifie qu’un de ces signaux ID s’est corrompu peu après l’allumage. Causes possibles : • Un câble plat intermittent ou un non entièrement fixé. • EMI. 0-5264FR ANNEXE A-83 ULTRA-CUT 100 XT/200 XT/300 XT/400 XT Dépannage : 1. Tout d’abord, réenclenchez l’alimentation pour vérifier si la défaillance est toujours présente. Il peut désormais afficher un code entre 225-230, ce qui permet de déterminer l’onduleur en question. 2. Déterminez quand le code s’affiche. Si c’est l’EMI, cela pourrait ne pas se produire chaque fois, mais si, lorsque cela se produit, c’est toujours au début du pilotage, cela pourrait être une EMI. Vérifiez les câbles de masse du système et pour AC200XT, vérifiez la connexion de la protection de torche sur le panneau arrière. 3. Si cela se produit par intermittence lors de la coupe ou de la marche au ralenti, cela pourrait être un câble plat intermittent. Ce code n’indique pas la section de l’onduleur, donc vous vous devez vérifier chaque câble plat pour s’assurer qu’il est correctement relié à chaque extrémité. Il est très improbable qu’un câble plat fonctionne par intermittence, mais si vous avez plus de 2 sections, essayez de débrancher une section à la fois et effectuez la découpe à un courant plus faible. Vérifiez si vous pouvez déceler celui qui cause le problème, et si c’est bien le cas, remplacer le câble plat en question. Les codes du groupe 3 ont trait au statut des contrôleurs des gaz et au protocole de communication Référez-vous aux codes de statut GCM 2010 à la fin de cette section sur les codes du groupe 3. 301 Défaut de communication du contrôle des gaz Pas de signal détecté sur le lien par fibre optique reliant le contrôle du gaz. Dans le cas de figure d’appareils additionnels autres que celui du COMMANDE DU GAZ (contrôle du gaz) branché au CANBUS, ce code indique que le COMMANDE DU GAZ rencontre des problèmes de communication, mais que les autres appareils CANBUS fonctionnent correctement. Nous ne disposons pas actuellement d’autres périphériques sur le bus CAN de sorte qu’il est plus probable que le code 501 serait ce qui est affiché. Dans tous les cas de figure, la procédure de dépannage est la même que pour l’erreur 501. Causes possibles : • La cause la plus probable est un câble ou un connecteur à fibre optique sale ou défectueux. • Câble vers GCM 2010, DMC ou DPC non connecté ou rompu. • Defective TABLEAU DE COMMANDE or bloc d’alimentation in the COMMANDE DU GAZ • CCM défectueux Dépannage : 1. Vérifiez que le câble de fibre optique est complètement connecté dans les deux prises. Nettoyez les extrémités de câble avec un chiffon doux et soufflez sur les prises avec de l’air. 2. Vérifiez les câbles de contrôle du gaz. Si un des câbles de contrôle des gaz n’est pas connecté, il n’y aura pas de communication puisqu’il n’y aura pas d’alimentation au contrôle. Cela peut se traduire comme un code 301 ou 501. De même, si le câble est rompu ou défectueux de sorte que le contrôle des gaz n’est pas activé, il peut avoir une alimentation, mais le cas du DMC ou du DPC, le voyant de défaillance clignotera erreur 101 tandis que le CCM détectera uniquement qu’il n’y a pas de communication et affichera 301 ou, éventuellement, 501. 302 Gas Communication de contrôles reply fault La communication a été établie, mais le contrôle des gaz n’a pas répondu à une requête du CCM dans les délais alloués. La cause probable est un problème de fibre optique (voir code 501), ou si le problème persiste, la cause pourrait être un circuit principal de COMMANDE DU GAZ (contrôle du gaz) défectueux. 303 Gas Défaut de pression Les erreurs de pression du gaz n’apparaissent lorsque vous essayez de démarrer la torche, pas pendant les écoulements de purge ou de paramétrage. Avec Auto-Cut 200 XT et Auto-Cut 300 XT (GCM 1000 XT), le capteur de pression de gaz est seulement sur le gaz au plasma et est en série avec le commutateur Run/Set. Un code 303 ici indique soit qu’il n’y a pas de gaz plasma ou que celui-ci est à très basse pression, moins de 50 PSI, ou que le commutateur RUN/SET (MARCHE/REGLAGE) est en position SET (REGLAGE). Pour démarrer avec le GCM2010 révision AG, nous mesurons la pression d’arrivée du gaz de plasma et du gaz de protection à l’entrée du collecteur de gaz. Si la pression est soit trop basse, soit trop élevée, il indique le code 303. Une A-84 ANNEXE 0-5264FR ULTRA-CUT 100 XT/200 XT/300 XT/400 XT révision antérieure ne devrait pas afficher le code 303. GCM2010 affichera quel gaz est responsable de l’erreur et sa pression actuelle. La pression à l’endroit où elle est mesurée devrait être de la plage de 100-135 PSI. Sauf pour le gaz de protection, si le sélecteur de gaz est à Pression, alors la pression minimum peut être de 85 PSI. Dans le contrôle de gaz GCM 2010, sur le circuit principal, on effectue la mesure entre les points de test TP1 (terre) et TP18 (protection) et TP19 (plasma) pour mesurer le débit sur les capteurs de pression. La tension doit être entre 2,6 V et 3,5 V pour 100 - 135 PSI. Avec le commutateur de protection fixé à basse pression limite est 2,1V. Quel que soit le gaz circulant, ces limites seront celles provoquant le défaut. N’oubliez pas que la pression peut s’abaisser au cours de l’opération, déclencher le code, puis retrouver leur niveau et afficher L303 lorsque vous effectuez la mesure. • Pour tester le capteur de pression défectueux ou une alimentation en gaz inadéquate avec trop de restriction. Pour le GCM 2010, placés l’interrupteur de mode en position SET Plasma and Shield (plasma et protection), positionnez les régulateurs mécaniques de pression en pression maximale et comparez les jauges mécaniques avec l’affichage de la pression. Si l’affichage de la pression ne correspond pas approximativement à la jauge, le capteur est probablement défectueux. Si la jauge et l’affichage de la pression montrent tous les deux une basse pression, l’approvisionnement du contrôle des gaz est trop limité. Le tuyau peut être trop long ou trop court. 304 Système de contrôle des gaz non prêt Ceci est le code normal lorsque la commande de gaz effectue une purge au démarrage ou lorsque le processus est chargé ou modifié, ou lorsque le système au plasma a été désactivé et est retourné sur « Activer ». Si c’est un GCM 2010, le sélecteur de mode pourrait ne pas être réglé au mode de FONCTIONNEMENT. Le code 304 combiné à 204 et à 402 lorsque l’activation plasma sur le contrôleur de gaz GCM 2010 est désactivée peut indiquer une défaillance dans le PCB E/S du CCM. En appuyant sur le commutateur pour revenir à Activé, la pompe ne redémarre pas si elle continue d’afficher 4-2, indiquant l’absence de liquide de refroidissement. Normalement, le code lors d’une désactivation doit être 101. Les circuits sur le PCB E/S détecte que l’activation plasma est désactivée et envoie un signal au microcontrôleur dans le CCM. Si une défaillance du CCM empêche l’envoi de ce signal au microcontrôleur, il ignore que le système est désactivé et il active ces trois autres codes. 305 Erreur de protocole de contrôle des gaz Erreur d’Application ou incompatibilité du microgiciel. Consultez l’usine pour obtenir les plus récentes mises à jour du microgiciel. Possible interférence électromagnétique de l’Arc Starter (démarreur de l’arc), inspectez la mise à la terre, l’isolation et les liaisons. 306 Non utilisé. Ceci est l’un des codes réservés des produits antérieurs. 307 Le système de contrôle des gaz renvoie une séquence de commande erronée. Incomptabilité du microgiciel. Consultez l’usine pour obtenir les plus récentes mises à jour du microgiciel. Possible interférence électromagnétique de l’Arc Starter (démarreur de l’arc), inspectez la mise à la terre, l’isolation et enfin, les liaisons. 308 Décalage entre le CCM et le type de contrôle des gaz. L’Auto-Cut XT CCM est conçu pour fonctionner avec le GCM 1000 (AC 300 XT) ou la commande de gaz intégré de l’AC XT 200. Essayer d’utiliser un contrôle automatique de gaz GCM 2010 ou DFC 3000 sur un arrêt automatique entraînera un code 308. De même, essayez d’utiliser un CCM provenant d’un Auto-Cut XT dans une alimentation d’Ultra-Cut XT entraînera également un code 308. 309 Anomalie de réponse des communications avec le système de contrôle des gaz. Le relais ne correspond pas aux critères requis. Possible incompatibilité du micrologiciel Consultez l’usine pour obtenir les plus récentes mises à jour du microgiciel. Possible interférence électromagnétique de l’Arc Starter (démarreur de l’arc), inspectez la mise à la terre, l’isolation et enfin, les liaisons. 310-313 0-5264FR Défaillances du module de gaz automatique DFC 3000. ANNEXE A-85 ULTRA-CUT 100 XT/200 XT/300 XT/400 XT Ces différents codes affichés sur l’alimentation indiquent simplement que l’un des modules Auto Gas (DPC pour les codes 310 ou 311; DMC pour les codes 312 et 313, soit l’un soit l’autre) a enregistré un défaut. Vous devez vous référer aux modules spécifiques clignotant un indicateur d’état LED rouge et les tableaux de codes d’état pour obtenir plus de renseignements. Codes d’état GCM 2010 GCM 2000 a une DEL sur le panneau fronda qui clignote différents codes. GCM 2010 a un panneau de DEL sur lequel s’affichent beaucoup des messages d’état. Néanmoins, quelques-uns ayant trait aux communications ne sont pas clairs. En cas d’une erreur de communication, celle-ci sera affichée, mais une fois le problème résolu, l’écran affiche la nature de l’erreur en affichant : ^E4 – Erreur de CANBUS de bas niveau dans laquelle le CCM n’a pas accusé réception d’un message du système de contrôle des gaz. ^E5 – Erreur de CANBUS de bas niveau dans laquelle le bus est éteint. ^E6 – La communication CANBUS (fibre optique) a expiré. Les codes du groupe 4 ont trait au système de refroidissement par liquide Description du système de refroidissement. System comprend un réservoir, une pompe, un ou plusieurs échangeurs de chaleur, un détecteur de débit, un détecteur de niveau et un capteur de débit sur certains modèles. Un filtre et divers raccords et tuyaux sont inclus. Du liquide de refroidissement frais est inséré dans le réservoir à partir d’une ouverture située sur le panneau avant de l’unité, où il y a également un indicateur visuel de niveau. Le liquide de refroidissement s’écoule vers l’admission de la pompe depuis le bas du réservoir, est pompé à travers une soupape de surpression ou de « dérivation », qui limite la pression MAZ à 150 PSI, ramenant l’écoulement excédentaire dans le réservoir. Le capteur de température du liquide de refroidissement, TS1, un capteur NTC linéaire, est monté sur la soupape de dérivation. À partir de la soupape de dérivation, dans la plupart des systèmes, le liquide de refroidissement est raccordé au raccord d’alimentation en liquide de refroidissement du panneau arrière où il va à la torche via le RAS 1000 XT, la télécommande arc démarreur. Les exceptions sont l’Ultra-Cut 400 XT qui dispose d’un échangeur de chaleur externe supplémentaire et le découpage automatique 200 XT qui a un arc interne démarreur. Pour l’Ultra-Cut 400 XT le il 400 XT échangeur de chaleur externe est placé entre le plasma et le bloc d’alimentation RAS 1000 XT avec le liquide de refroidissement d’alimentation passant par le radiateur de refroidissement supplémentaire. Dans le découpage automatique 200 XT liquide de refroidissement refroidi par de l’eau va à haute fréquence (HF), puis à la bobine flambeau sur le câble d’alimentation joint à la torche interne connexion de tablier. Pour le retour du liquide de refroidissement dans la plupart des systèmes le retour de la Torche va au RAS 1000 XT et sur le raccord de retour à l’arrière de l’alimentation. Dans le Ultra-Cut 400 XT le retour des AR1000XT traverse d’abord le il 400 XT puis au panneau arrière de l’alimentation. Pour le découpage automatique 200 XT le liquide de refroidissement revient de la torche à la torche à l’intérieur de l’unité de tablier. Liquide de refroidissement retournant de la torche est acheminée à travers le filtre du panneau arrière puis à travers le radiateur (échangeur de chaleur interne) et par l’intermédiaire de l’interrupteur de débit. Ultra-Cut modèles disposent également d’un capteur de débit en série avec le commutateur de débit qui peuvent détecter la présence de bulles dans le liquide de refroidissement. En quittant le radiateur, le liquide de refroidissement passe en bas convertisseur «plaque froide» ou dissipateur de chaleur refroidi par liquide. Il s’écoule à travers les onduleurs en série et retourne au réservoir. 401 Niveau de refroidissement faible Le réservoir de liquide de refroidissement dispose d’un commutateur de niveau de type flotteur (réservoir sec) normalement ouvert, LS1. Lorsque le niveau du liquide de refroidissement dans le réservoir est inférieure à environ ½ du plein, ce défaut signalera de la nécessité d’ajouter du liquide. Il n’empêchera pas le processus pendant une coupure, mais plutôt de montrer les 405 défaut comme un avertissement. Dès que la coupe s’arrête, aucune autre ne peut commencer tant que le problème n’est pas résolu. Causes possibles : • Faible quantité de liquide de refroidissement • Le Level Switch (interrupteur de niveau) (interrupteur de niveau) est défectueux, débranché ou installé à l’envers. • Carte relais défectueuse ou J7 débranché. A-86 ANNEXE 0-5264FR ULTRA-CUT 100 XT/200 XT/300 XT/400 XT • CCM défectueux. Dépannage : 1. Vérifiez à l’œil que le flotteur du niveau de liquide est sous le liquide de refroidissement, sinon rajoutez du liquide de refroidissement dans le réservoir. 2. Vérifiez J7 sur la carte de relais. a. S’il est correctement connecté, enlevez J7 et vérifiez la continuité entre les broches 2 et 4 (broches 2 et 3 sur J71 sur le commutateur lui-même). b. En l’absence de continuité à J71 sur le commutateur, si celui-ci est toujours ouvert, remplacez le commutateur. 3. S’il y a une continuité à J7, reconnectez-le et mesurez la tension à la broche 9 du câble plat à 40 broches (carte de relais J4 à CCM J23). En général TP1 est soit sur la carte de relais soit sur la carte E/S. a. La broche 9 doit être élevée, entre +10 et +15 V. Dans le cas contraire, la carte de relais est défectueuse ou le câble plat est court-circuité. b. Pour tester le câble-ruban, enlevez les deux extrémités, J4 sur la carte relais et J23 sur la carte E / S et effectuez la mesure de la broche 9 du câble-ruban aux broches 8 et 10 du câble. Les deux doivent être ouvertes. Dans le cas contraire, remplacer le câble plat. Dans le cas contraire, il s’agit de la carte Relay (relais). 4. Si la broche 9 de câble plat à 40 broches était élevée à l’étape 3.a, le CCM est défectueux. 402 Faible débit du liquide de refroidissement L’interrupteur de débit FS1 est monté en série avec le radiateur où il mesure le flux de retour de la torche. L’interrupteur de débit sert à deux points, le premier est de s’assurer d’un écoulement adéquat pour les besoins de refroidissement; le deuxième, de s’assurer que les consommables de la torche soient en place afin que la sortie négative de l’alimentation ne soit pas exposée. Cette fonction est appelée « Pièces en place » ou PIP. La sortie ne peut pas être activée si les pièces ne sont pas en place. L’interrupteur de débit normalement ouvert nécessite 0,7 GPM (2,65 litre / min.) +/- environ 10 % pour se fermer. Le PAK 200i utilise un réglage différent du commutateur de débit, fixé à 0,9565 litre/min. Lorsque le système est mis en marche et activé et ne parvient pas à obtenir un débit de liquide de refroidissement après 4 minutes, le code 404 sera réglé. Obtenir un code 402 signifie qu’il y avait initialement un débit suffisant, mais que quelque chose a entraîné une réduction du débit. Vous trouverez ici une liste d’événements qui peuvent se produire lors de la découpe et entraîner une diminution de l’écoulement. Pour d’autres causes, comme la défaillance de composantes, reportez-vous au code 404. Causes possibles pour un écoulement faible : • Filtre de liquide de refroidissement bouché. • Joint torique défectueux dans le clapet antiretour de la torche XT. • Réglage incorrect ou panne de la soupape de dérivation de la pompe externe. Communiquez avec l’usine pour des instructions. • Pompe défectueuse. • Alimentation en liquide de refroidissement ou tuyau de retour tordu ou pincé, ce qui réduit l’écoulement. Si l’écoulement de liquide de refroidissement n’est pas bas, mais que le code est toujours présent, les causes possibles sont les suivantes : • Interrupteur de débit déconnecté ou défectueux. • Circuit relais. • CCM. Dépannage : 1. Veuillez noter si la défaillance est un « E », ce qui signifie que le niveau est actuellement bas ou un « L », ce qui signifie que le niveau a été bas, mais qu’il ne l’est plus. Un débit qui reste bas pourrait indiquer une composante défectueuse ou un blocage, comme un filtre bouché ou un tuyau pincé. Cela veut également dire que vous devriez pouvoir mesurer l’écoulement pour déterminer s’il est très faible, ou bien si le capteur a un problème. 0-5264FR ANNEXE A-87 ULTRA-CUT 100 XT/200 XT/300 XT/400 XT 2. Tout d’abord, réenclenchez l’alimentation. Si l’écoulement continue d’être bas ou si un composant est défectueux, le code devrait passer à 404. Allez à cette section pour de plus amples renseignements sur le dépannage. 3. Si après avoir réenclenché l’alimentation, il n’y a pas de code, continuez le coupage pour voir si le problème se reproduit. Prenez note lorsque cela se produit, par exemple si c’est avec la torche à une extrémité de la table, les fils pourraient-ils y être coincés? En tout cas, allez à la section du code 404 pour obtenir plus de renseignements. 403 Liquide de refroidissement surchauffé. TS1 est un capteur de résistance linéaire de coefficient de température négatif (NTC) fixé au raccord en laiton à la sortie de la soupape de dérivation. Ici, nous déterminons que le liquide de refroidissement apporté à la torche est inférieur à la température nécessaire, qui est actuellement de 75 degrés Celcius (167 degrés Fahrenheit). Le radiateur est sur le côté inférieur droit de l’unité. Le ventilateur se trouve derrière l’échangeur de chaleur externe et souffle à travers le radiateur. Les ventilateurs fonctionnent pendant la coupe et pendant 4 minutes après la dernière coupe, puis l’arrêt. Sauf pour AC 200 XT, pour lequel les ventilateurs sont en marche dès que l’appareil est alimenté. Le ventilateur de l’échangeur de chaleur externe, HE400, est commandé par Thermostat de sorte qu’il ne se met en marche que lorsque le fluide de refroidissement est supérieure à 60°C. Il s’éteindra lorsque les autres ventilateurs s’éteignent. Raisons possibles pouvant expliquer la surchauffe du liquide de refroidissement; Ventilateur(s) de liquide de refroidissement défectueux ou ventilateur défectueux contrôle le relai MC2. • Ailettes du radiateur obstruées par la saleté. • Cycle de travail dépassé (température ambiante supérieure à 40 degrés Celcius et fonctionnement à un cycle de travail élevé). • Faire fonctionner avec un objet placé à proximité de la sortie d’air (côté droit de l’unité) ou sur les ouvertures d’arrivée du panneau avant. • Faire fonctionner pour une durée prolongée avec le panneau inférieur droit enlevé. • Carte de relais défectueuse. • CCM défectueux. Dépannage : 1. Vérifiez que de l’air sort de l’unité. N’oubliez pas que, sauf pour l’AC 200 XT, les ventilateurs ne fonctionnent que lorsque le signal CNC START est déclenché et pour 4 minutes après la découpe; vous pourriez donc avoir besoin de redéclencher le signal de démarrage pour relancer le fonctionnement pendant 4 minutes. Le démarrage des ventilateurs peut être forcé en omettant TP2 sur la carte E/S du CCM vers TP1 (masse). a. Si vous utilisez un échangeur de chaleur externe HE400XT, en option pour 300 A, standard pour 400 A, vérifiez qu’il en sort de l’air. Veuillez noter que le ventilateur HE400XT, contrôlé par un interrupteur thermique dans le HE400XT, ne fonctionne que si le liquide de refroidissement dépasse les 60°C et que les ventilateurs internes fonctionnent. Avec 100 et 200A, s’il dispose de 2 ventilateurs, assurez-vous que les deux ventilateurs fonctionnent en vérifiant l’air en haut et en bas de l’ouverture. Les fans sont difficiles à voir, vous pourriez peut-être utiliser un miroir d’inspection. Assurez-vous de ne pas mettre le miroir ou vos mains dans les lames. 2. Les ventilateurs sont alimentés en 230 Vca. L’alimentation de 230Vca du(des) ventilateur(s) est commutée par le relais de commande de MC2 (sauf pour l’AC XT 200, où le(s) ventilateur(s) est (sont) alimenté(s) directement par le transformateur T1 à J13). A-88 ANNEXE 0-5264FR ULTRA-CUT 100 XT/200 XT/300 XT/400 XT E/S du CCM J4-19 +24 1 K4 D24 2 4 5 Contrôle BIAS de ventilateur MC2B J8 24 VAC 3 R MC2A (65A) Circuit relais à J70-3 1 2 TP1 3 TP2 J13 4 230 VAC à partir deT1 Pour tester le cavalier du relais du ventilateur TP2 à TP1. 1 2 3 4 5 6 7 8 9 10 11 12 13 14 15 16 (64A) (161) SA3 MC2 (69) (70) J72 1 2 3 BK C4 VENT1 BN BL R (69) (70) Commande de ventilateur J73 1 2 3 (70) à J70-2 Masse Suppresseur d’arc (160) Art # 12311FR 3. Vérifiez qu’il y a 230 Vca à chacun des connecteurs de ventilateur, J72 et J7It peuvent aussi être mesurés au niveau du connecteur J70 sur le panneau arrière pour le ventilateur HE400XT. a. Si les ventilateurs n’obtiennent pas 230 Vca, vérifiez s’il y a 24 Vca sur la bobine de MC2. Si tel est le cas et que les contacts de relais ne sont pas fermés, le relai est défectueux. Veuillez noter que la bobine est rectifiée, et que vous n’avez donc pas besoin de mesurer la continuité de la bobine. b. S’il n’y a pas 24 Vca sur la bobine MC2, vérifiez que la DEL D24 sur la carte de relais est ALLUMEE. Si elle est allumée, la carte de relais devrait fournir les 24 Vca. Dans le cas contraire, la carte de relais doit être défectueuse. c. Si D24 n’est pas allumée, mesurez sur la carte E/S du CCM entre TP2 et le commun à TP1. Il doit être faible, quasiment zéro volts. Dans le cas contraire, le CCM est probablement défectueux. Cavalier TP2 (carte I/O) à TP1. Si les ventilateurs démarrent maintenant, remplacez le CCM. d. Si contourner TP2 pour TP1 ne fait pas s’allumer les ventilateurs, alors la carte de relais ou la broche 19 du câble plat à 40 broches sont défectueuses. 404 Système de refroidissement pas prêt Lorsqu’une tension est appliquée au système avec Activation plasma externe valide et Alimentation au plasma activé (interrupteur sur 2010 ou TSC 3000), en supposant qu’il existe suffisamment de liquide de refroidissement dans le réservoir, après quelques tests initiaux prenant environ 15-20 secondes (voir la section 4 du mode d’emploi pour plus de détails de la séquence de démarrage), la pompe démarre. Le coulant sera pompé dans l’ensemble du système. Le débit est mesuré par l’interrupteur de débit FS1 placé sur le parcours de retour du liquide de refroidissement de la torche, juste avant le radiateur (voir le diagramme de tuyauterie). Si le débit n’atteint pas au moins 0,75 gal/min (2,8 l/ min) en 4 minutes, l’erreur 404 s’affiche. La raison des quatre minutes est qu’un nouveau système sec, surtout un avec de longs fils de torche, prend un certain temps avant que le fils, les tuyaux, le radiateur et les plaques thermiques soient pleines de liquide de refroidissement. Il se peut qu’il faille ajouter du liquide de refroidissement. Sur un système ayant déjà fonctionné auparavant, il ne faut que quelques secondes pour établir un écoulement correct. Dans tous les cas, la pompe fonctionnera pendant 4 minutes avant d’afficher l’erreur 404. Déterminez tout d’abord sir le moteur de pompe est en marche et, si oui, si le liquide de refroidissement s’écoule. Avec le panneau latéral inférieur droit enlevé, touchez la pompe et sentez la vibration pour savoir si le moteur fonctionne. Observez les tubes transparents de liquide de refroidissement pour vous assurer qu’ils soient bien remplis de liquide de refroidissement. Il existe deux raccords de tuyau à l’arrière du réservoir. Le panneau supérieur est le retour du liquide de refroidissement. Retirez le couvercle de remplissage du réservoir. Vous devriez voir un courant de liquide de refroidissement assez fort à partir de ce raccord. La fixation inférieure provient de la vanne de dérivation de pompe. Si la pompe fonctionne, il pourrait s’échapper du liquide de refroidissement de cette buse aussi. Si ces buses sont inférieures au niveau de liquide de refroidissement, vous pourriez devoir vidanger une certaine partie du liquide de refroidissement pour le voir. Si un puissant flux quitte la buse de dérivation (inférieure), mais rien de la buse supérieure, il y a probablement un blocage quelconque. Raisons pour les défauts 404 (le liquide de refroidissement ne coule pas) : 0-5264FR ANNEXE A-89 ULTRA-CUT 100 XT/200 XT/300 XT/400 XT • Dans les nouvelles installations, le liquide de refroidissement n’a pas encore complètement circulé dans les conduits. Ajouter plus de liquide de refroidissement si nécessaire et réenclencher l’alimentation pour redémarrer la pompe et une minuterie de 4 minutes. • Les faisceaux d’alimentation et de retour du liquide de refroidissement sont inversés, vérifiez la soupape dans le retour de liquide de refroidissement de torche empêche l’inversion de débit. • Pièces de la torche enlevés ou mal installés, de sorte que le clapet antiretour de la torche coupe le débit. • Tube de liquide de refroidissement de la torche endommagé ou extension de tube (si nécessaire) manquant. • Pas d’alimentation sur le moteur de la pompe. • Panne pompe/moteur. • Soupape de dérivation défectueuse ou mal ajustée. Tuyau de liquide de refroidissement endommagé Le tuyau de liquide de refroidissement est muni d’un clapet antiretour à son extrémité supérieure. Lorsque la cartouche de consommables n’est pas installé, le tube de fluide de refroidissement à ressort est en extension complète, fermant le clapet anti-retour empêchant les fuites de liquide de refroidissement. Lorsque les consommables sont en place, ils poussent le tube vers l’intérieur, ouvrant le clapet anti-retour, ce qui permet la circulation du liquide de refroidissement. Le tube de fluide de refroidissement comporte des doigts sur l’extrémité pour communiquer avec l’intérieur de l’électrode et permettre au liquide de réfrigération de circuler à travers les ouvertures entre les doigts. Les doigts peuvent être repliés ou brisés si des mesures raisonnables ne sont pas prises lorsque la cartouche n’est pas en place. Si les doigts sont tordus ou cassés, cela raccourcit le tuyau, de sorte que les consommables pourraient ne pas pousser le tuyau suffisamment pour ouvrir la valve de vérification, et il n’y aura pas d’écoulement de liquide de refroidissement. L’ensemble du tube du fluide de refroidissement peut être remplacé séparément de la tête de la torche. Certains consommables utilisent une extension pour le tube de liquide de refroidissement. Une extension manquante ne permettra pas de vérifier la soupape à ouvrir. Clapet anti-retour interne Doigts Rallonge du tuyau de liquide de refroidissement Art # 12312FR Pas d’alimentation sur le Pump Motor (moteur de la pompe). Le moteur de la pompe est sous une alimentation de 230 VAC contrôlée par le relais de commande de MC3. Pendant les 4 minutes qui suivent l’allumage, avant que le code d’erreur 404 ne s’affiche, vérifiez qu’il y a 230 Vca aux broches 1 à 3 du connecteur de moteur J16. a. Si le moteur de pompe n’obtient pas 230 Vca, vérifiez s’il y a for 24 Vca sur la bobine de MC3. Si tel est le cas et que les contacts de relais ne sont pas fermés, le relai est défectueux. Veuillez noter que la bobine est rectifiée, et que vous n’avez donc pas besoin de mesurer la continuité de la bobine. b. S’il n’y a pas 24 Vca sur la bobine MC3, vérifiez que la DEL D27 sur la carte de relais est ALLUMEE. Si elle est allumée, la carte de relais devrait fournir les 24 Vca. Dans le cas contraire, la carte de relais pourrait être défectueuse. Mesurez s’il y a bien 24 VCA de tension sur J9-6 à J9-12 sur la carte Relay (relais). S’il y a 24 Vca et que la DEL D27 est allumée, la carte de relais ou le faisceau de fils sont défectueux. c. Si D27 n’est pas allumée, mesurez sur la carte E/S du CCM entre TP3 et le commun à TP1. Il doit être faible, quasiment zéro volts. Dans le cas contraire, le CCM est probablement défectueux. Cavalier TP3 (carte I/O) à TP1. Si la pompe s’allume maintenant, remplacez le CCM. d. Si contourner TP3 pour TP1 ne fait pas s’allumer les ventilateurs, alors la carte de relais ou la broche 13 du câble plat à 40 broches sont défectueuses. A-90 ANNEXE 0-5264FR ULTRA-CUT 100 XT/200 XT/300 XT/400 XT TP3 1 4 J13 2 230 V c.a. du T1 3 E/S du CCM À relais de pompe d'essai jump TP3 à TP1. TP1 MC3A (66) (65B) Circuit relais J4-13 J8 24 VAC +24 1 D27 K5 2 4 5 3 Contrôle de la pompe de liquide de refroidissement 1 2 3 4 5 6 7 8 9 10 11 12 13 14 15 16 (64B) (162) SA4 MC3B Masse (67) J16 M1 1 2 3 Torche pompe de liquide de refroidissement MC3 Contrôle de la pompe de liquide de refroidissement Suppresseur d’arc (163) Art # 12313FR Le liquide de refroidissement s’écoule, mais le débit est inférieur au minimum requis : Testez et réglez la soupape de la pompe/de la dérivation : Cet essai mesure la « hauteur à débit nul » ou la pression de débit bouchée sur le raccord d’alimentation en liquide de refroidissement du panneau arrière. Effectuez ce test uniquement une fois le système de refroidissement complètement amorcé, c’est-à-dire après que le liquide de refroidissement a bien circulé à travers tout le système, et qu’il ne contient quasiment plus de bulles. Il faut un manomètre avec un raccord #6 JIC. La jauge doit pouvoir afficher au moins 173 PSI. Retirez le tuyau d’alimentation en liquide de refroidissement et rebranchez la jauge de pression à sa place. Pour Auto-Cut 200 XT, connectez la jauge à la place du tuyau d’alimentation en liquide de refroidissement sur la cloison de connexion de torche. Ceci est un raccord JIC #5. REMARQUE ! N’alignez pas la jauge pas et n’essayez pas de pincer le tuyau pour bloquer l’écoulement. Il est très difficile de bloquer totalement l’écoulement, et si ce n’est pas le cas, le contournement (by-pass) ne sera pas configuré correctement. Allumez l’appareil. Vous aurez 4 minutes pour effectuer le test et le réglage avant que le système ne s’arrête en indiquant une panne de circulation du liquide de refroidissement. Si cela se produit, vous pouvez éteindre et rallumer l’appareil pour bénéficier de 4 minutes supplémentaires. 1. La pression sur la jauge devrait être proche de 173 (170 - 175) PSI. Si c’est le cas, la pompe et la dérivation sont OK. 2. Si la pression est inférieure à 173 PSI, ajustez la vis de la soupape de dérivation dans le sens des aiguilles d’une montre pour augmenter la pression. Si vous pouvez changer la pression avec la vis de soupape de dérivation, mais ne pouvez pas atteindre 173 PSI, il est probable que la pompe soit usée ou endommagée. Si la pression ne change pas avec la vis de la soupape de dérivation, il est probable que la dérivation est défectueuse. 3. Si la pression est supérieure à 173 PSI, réduisez la pression en ajustant la vis de la soupape de dérivation dans le sens inverse des aiguilles d’une montre. Test de l’écoulement du liquide de refroidissement : En plus du test de pression ou à la place de celui-ci si vous n’avez pas de jauge, déterminez si le débit revenant de la torche (débit qui traverse FS1) est supérieur au débit minimum nécessaire. Avec l’appareil éteint, enlevez le tuyau de retour de l’arrière de l’alimentation. Placez-le dans un récipient dont vous connaissez le volume. Allumez l’appareil et faites tourner la pompe pendant 30 secondes exactement. Il doit pomper au moins 1,4 l. Utilisez un grand bac, dans le cas où le débit est plus abondant et déborde. Si le débit est inférieur à 2,84 l/min (0,95 l/min pour le Pak200i) : 0-5264FR ANNEXE A-91 ULTRA-CUT 100 XT/200 XT/300 XT/400 XT • Cherchez tout élément pouvant provoquer une obstruction, comme des plis, un élément qui pince les tuyaux de refroidissement ou les fils de la torche. • D’autres possibilités sont la vanne de contournement (by-pass) qui n’a pas bien été réglée (quelqu’un pourrait avoir touché à la vis de réglage), voir la partie concernent le test/réglage de la pression ci-dessus. • La pompe est usée (peut être le cas d’une unité plus ancienne). L’écoulement du liquide de refroidissement est correct, mais le système ne le détecte pas en raison de composantes défectueuses : • Interrupteur de débit FS1 défectueux ou déconnecté. • Carte relais. • CCM. Interrupteur de débit FS1 déconnecté – FS1 est fourni avec un fil d’environ 1 pi. et un connecteur qui se connecte à un faisceau de 3 fils. Cela pourrait être déconnecté à l’une des extrémités, J74 ou J5 sur la carte de relais. FS1 défectueux – l’interrupteur de débit, qui est normalement ouvert et se ferme lorsque le débit qui le traverse dépasse 0,75 gal/min, pourrait être ouvert. L’endroit le plus facile pour mesurer l’interrupteur est au connecteur de faisceau J5 qui se connecte à la carte du pilote. En supposant que vous avez auparavant déterminé que le débit est insuffisant, déconnectez J5 de la carte du pilote, démarrez l’unité pour que le liquide de refroidissement s’écoule et mesurez la continuité entre les 2 broches de J5. • S’il n’y a pas de continuité, soit le commutateur est ouvert soit le faisceau entre J5 et J74 à FS1 est ouvert. • S’il y a une continuité entre les broches de J5 et un débit de liquide de refroidissement suffisant, alors soit la carte de relais soit le CCM sont défectueux. 405 Alarme de basse niveau du liquide de refroidissement Si le niveau de liquide de refroidissement devient faible pendant la coupe, il n’est pas nécessaire d’arrêter immédiatement la coupe, puisqu’il y a encore suffisamment de liquide de refroidissement pour continuer, et le code E405 s’affiche comme mise en garde. Une fois que la découpe s’arrête, si le liquide de refroidissement est toujours bas, l’écran affiche E401 et empêche de commencer une nouvelle découpe. Reportez-vous à la section du code 401 pour effectuer le dépannage. 406 Alarme de bas débit de liquide de refroidissement Ce code est un avertissement, il n’empêche pas la coupe, mais cela persiste la cause doit être examinée. Les modèles Ultra-Cut XT, en plus d’un interrupteur de débit du liquide de refroidissement, sont munis d’un capteur de débit de turbine FL1, désigné dans le schéma de plomberie sous le nom de « détecteur de bulles», avec une sortie d’impulsion qui mesure avec précision le débit de liquide de refroidissement et en outre est capable de détecter la présence de bulles de gaz dans le liquide de refroidissement. Il a été prouvé que des bulles de gaz des joints non étanches dans la torche ou les raccords de tuyaux réduisaient la durée de vie des consommables. Ce code est un avertissement, il n’empêche pas la coupe, mais cela persiste la cause doit être examinée. 407 Surchauffe du liquide de refroidissement en raison d’une température ambiante élevée Tel que décrit à la section sur les codes 259-264, le CCM mesure la température ambiante au moyen du capteur TS2 et, comme les onduleurs, si le liquide de refroidissement est surchauffé, nous vérifier d’abord la température ambiante et si celle-ci est supérieure à 40 oC, nous attribuons la cause de la surchauffe du liquide de refroidissement à la température ambiante élevée et, bien sûr, la solution est de réduire la température ambiante ou le cycle de travail. L’autre possibilité est que le circuit de mesure de la température ambiante est défectueux et que le liquide de refroidissement est en surchauffe. Dans ce cas de figure, reportez-vous à la section correspondante au code 403 pour trouver la cause de la surchauffe du liquide de refroidissement ainsi qu’à la section correspondante aux codes 259-264 pour déterminer la cause du problème avec le circuit TS2. Groupe 5 renvoie aux erreurs de communication de BUSCAN (fibre optique) 501 Le CANBUS ne reconnaît pas la défaillance. Le CCM communique avec les commandes de gaz (à l’exception de GCM 1000 XT) sur un câble à fibre optique à l’aide du bus CAN. Le CCM est à la recherche d’un signal provenant de la commande de gaz (GCM 2010 ou DMC) sur la liai- A-92 ANNEXE 0-5264FR ULTRA-CUT 100 XT/200 XT/300 XT/400 XT son en fibre optique. Aucun signal n’a été détecté. La communication avec le DPC dont le relais est assuré par le DMC définit un code différent, 301, en cas de problème. Causes possibles : • Le contrôle est gaz est GCM 1000 XT (Auto-Cut 300XT), qui n’a pas de fibre optique, avec un problème d’ID de base. • Problème de CANBUS / fibre optique sur le GCM 2010 ou le DMC (portion du DFC 3000). • Le câble de commande au DMC ou GCM 2010 est défectueux. • Fusible du PCB principal du contrôle des gaz (DMC ou GCM 2010) grillé ou défectueux. • Fusible du PCB d’alimentation du DMC grillé ou défectueux. • CCM défectueux. Dépannage : 1. GCM 1000XT (aussi appelé contrôle des gaz de base) n’utilise pas la communication CANBUS (fibre optique). Un cavalier dans le connecteur de commande du gaz J56 broches 8 et 9, donne le signal « Basic ID », indiquant au CCM de ne pas attendre de CANBUS. Si le circuit est ouvert quelque part, dans le câble de contrôle des gaz, les broches de connecteur, la connexion du connecteur GCM du panneau arrière, J55, au CCM (J26), le CCM s’attendra à voir une connexion CANBUS et signalera cette erreur, car il n’y a pas de CANBUS connecté. 2. DFC3000. Si le contrôle des gaz n’a pas d’alimentation, il ne pourra pas communiquer. Vérifiez l’alimentation aux cartes de contrôle du gaz. a. Lors de l’utilisation de gaz Auto (DFC3000) avec DMC et DPC, s’il n’y a pas de courant alimentant la carte principale DMC, le témoin lumineux vert sur le panneau avant DMC ne sera pas éclairé. La carte principale reçoit plusieurs tensions de sa carte d’alimentation séparée. Pour la communication, +5 Vcc sont nécessaires. Il existe une LED verte, D17 (la première à gauche de la rangée de LED.) qui s’allume lorsque la carte principale a une alimentation de + 5V. b. La carte d’alimentation DMC comporte plusieurs LED bleues qui s’allument lorsque la carte est sous tension. Si aucune d’entre-elles n’est allumée, vérifiez que le câble de contrôle est connecté ou le disjoncteur du circuit, CB2, sur le panneau arrière de l’alimentation plasma pourrait être ouvert, dans quel cas il y a probablement un court-circuit quelque part. c. L’alimentation DMC qui fournit plusieurs tensions pourrait rater une ou plusieurs tensions, mais ont encore quelques LED bleues allumées. Vérifiez les tensions. 3. GCM 2010. 4. Les erreurs de communication CANBUS / fibre optique peuvent être difficiles à résoudre, en particulier lorsqu’elles sont intermittentes. Voir « Test the Fiber » (tester la fibre) ci-dessous. Things to look for are: a. Les connecteurs ne sont pas verrouillés en place à l’une ou l’autre extrémité de la fibre. b. La fibre est endommagée ou abruptement courbée. Cela ne devrait pas être le cas si la fibre est à l’intérieur de la gaine de protection et si le tuyau est bien en place dans le dispositif de décharge de traction, mais ceci n’est pas toujours le cas. c. Saleté aux extrémités de la fibre ou dans le récepteur/émetteur où la fibre est connectée. Soufflez doucement de l’air sec et propre tout comme pour le nettoyage des lentilles d’un appareil photo. d. Interférence électrique excessive. Même si la fibre est insensible aux interférences EM, ellepeut déranger les circuits aux extrémités. Vérifiez que toutes les connexions à la terre sont effectuées conformément au manuel, et qu’elles sont propres et bien serrées. Vérifiez la résistance de la tige de masse (tous les fils en étant déconnectés). Il peut avoir augmenté à cause d’un air plus sec. Voir les instructions dans le manuel d’installation du plasma. e. Récepteur/émetteur ou autres circuits défectueux sur le CCM ou la carte mère du contrôle des gaz. Dans le cas contraire, remplacez soit la carte principale de COMMANDE DU GAZ (contrôle du gaz), soit le CCM, ou les deux. Tests des émetteurs/récepteurs Le couple émetteur/récepteur sur la carte et le câble de fibre ressemble à ceci : 0-5264FR ANNEXE A-93 ULTRA-CUT 100 XT/200 XT/300 XT/400 XT Art # 12314 Testez la fibre : Veuillez noter que la fibre va du noir à une extrémité au bleu à l’autre extrémité. Placez une source de lumière intense d’un côté et la lumière devrait briller de l’autre côté. Cela vous indique que la lumière est en train de passer, mais ne prouve pas qu’elle est assez forte. Le CCM est le maître de communication. Il transmet puis attend une réponse du COMMANDE DU GAZ Module (Module de contrôle du gaz (GCM). Le GCM n’émet pas tout seul, mais uniquement en réponse à une demande du CCM. L’extrémité noire du câble de fibre est insérée dans l’émetteur qui est le boîtier gris sur la carte. L’autre extrémité de la fibre d’émission est bleue et entre dans le récepteur avec le boîtier noir. Quelques secondes après la mise en marche, lorsque la pompe a démarré, le CCM essayera de transmettre en continu pendant quelque temps. Vous pouvez débrancher la fibre du CCM et devriez voir la LED rouge de l’émetteur allumé sur le clignotement de la carte CCM. Il peut s’interrompre après un certain temps, donc, redémarrez la machine avant de décider qu’il s’agisse bien d’une panne. En l’absence de lumière, vérifiez une des autres paires de transmetteur/ émetteur. Si aucune d’elle ne clignote, le problème réside dans le CCM. Si au moins un transmetteur clignote, rebranchez la fibre optique sur ce transmetteur puis sur l’extrémité du contrôle des gaz de la fibre optique (déconnectée), vous devriez voir la lumière rouge sortant de l’extrémité bleue. L’émetteur de commande de gaz n’émet pas, sauf en réponse à une demande du CCM de sorte que vous ne verrez aucune lumière de l’émetteur de GCM avec le câble débranché. Néanmoins, si vous tournez le connecteur de 90 degrés et que vous insérez l’extrémité bleue dans le récepteur (boîtier noir), en laissant l’émetteur ouvert, le GCM devrait recevoir les demandes du CCM et faire clignoter son transmetteur (boîtier gris) en réponse. Dans le cas contraire, le problème réside vraisemblablement dans le fait que la carte de GCM en supposant que celle-ci est alimentée. Il est toujours possible, même si vous voyez une lumière rouge briller à l’extrémité GCM de la fibre, qu’il y ait de la poussière dans le transmetteur, le récepteur, ou sur les extrémités de la fibre, ou bien que la fibre soit endommagée, ce qui expliquerait que, bien qu’elle soit visible, la lumière reste trop faible pour la carte GCM. Si toutes les autres solutions ont échoué, remplacez le câble optique et les deux PCB de CCM et de GCM. 502 CANBUS arrêté en raison d’un nombre excessif d’erreurs. Voir le code 501 pour dépanner les défauts de CANBUS. 503 Avertissement d’erreur de données CANBUS. Ceci est un Avertissement, qui n’arrête pas le système, mais indique que le système va sans doute s’arrêter bientôt (code 502). Dépannage identique à celui du 501. 504 Réservé pour une utilisation future. Ne devrait pas apparaître; si tel est le cas, cela pourrait être dû à l’EMI. Communiquez avec le service à la clientèle. Les codes du groupe 6 ont trait au CCM et aux mises à jour du programme. Une exception est le code 619 qui est un défaut de l’interrupteur FS1 d’écoulement du liquide de refroidissement. 601-611 Diverses défaillances internes de la carte UC du CCM. Pour la plupart de ces défaillances, essayez de réenclencher l’alimentation, mais si le problème réapparaît, la seule chose à faire est de remplacer le CCM. Exceptions are: 1. 603 Un des codes réservés d’une version antérieure du produit. Inutilisé, il ne devrait, donc, jamais se produire; si tel est le cas, communiquez avec le service à la clientèle. 2. 607 Il pourrait se produire une surchauffe du processeur si la température de l’air ambiant dans la zone du CCM est trop élevée. Essayez d’ouvrir le panneau latéral en haut à droite, vous aurez peut-être à souffler un peu d’air pour le refroidir. Si cela n’aide pas ou si la température ambiante est trop élevée au départ, remplacez le CCM. A-94 ANNEXE 0-5264FR ULTRA-CUT 100 XT/200 XT/300 XT/400 XT 3. L’erreur de code 611 a diverses causes dont la plupart exigent le remplacement du CCM. Néanmoins, une cause possible est que le cavalier de programmation sur la carte CPU (sous le PCB de suppression statique) a été laissé en position PROG. Ceci est un réglage d’usine utilisé lors de la programmation initiale et ne doit jamais se trouver dans le champ. Il n’est PAS utilisé pour les mises à jour du code d’Application. Cependant, si quelqu’un le déplace, cela entraînera un code 611. 612 Erreur d’alimentation du port USB. Alimentations du port USB + 5V pour alimenter certains périphériques USB tels que le lecteur flash (clé USB, carte mémoire) utilisé pour les mises à jour du programme. Une clé USB est le seul dispositif utilisé sur ce port USB. Ce défaut indique peu ou pas de sur le port. Cela pourrait être dû à un lecteur flash ou tout autre dispositif court-circuité qui tire trop de courant dépassant les limites de l’alimentation USB. Essayez un autre lecteur flash ou si vous êtes certain que celui-ci est normal (cela fonctionne avec un ordinateur), alors remplacez le CCM. 613 Erreur de création du fichier journal USB Lors de la mise à jour des programmes du CCM, du DMC et du DPC à partir d’un lecteur USB, un fichier journal appelé CCM_LOG.TXT est créé sur le lecteur et contient les résultats de la mise à jour, y compris tout problème qui pourrait être survenu. Si ce fichier journal ne peut pas être créé, le code d’erreur 613 s’affiche. Cela peut être un problème lié au lecteur flash ayant trop d’autres fichiers ou un problème lié à son format qui peut ne pas être compatible avec le CCM. 1. Essayez de mettre les fichiers de mise à jour sur un autre lecteur flash, de préférence vide. 2. Ou bien sauvegardez tous les fichiers de la clé usb dans un autre dossier sur votre ordinateur, puis effacez tous les fichiers sur la clé usb. Maintenant, copiez sur la clé usb uniquement les fichiers nécessaires pour les mises à jour du programme. 3. Si les étapes ci-dessus ne fonctionnent pas, assurez-vous de toujours avoir des copies des fichiers et formatez votre lecteur USB, ce qui supprime tout ce qui s’y trouve. Maintenant, chargez uniquement les fichiers nécessaires pour la mise à jour du programme. 614 Aucun fichier USF Le fichier VTCCMFW.USF est requis sur le lecteur éclair avec les fichiers du programme lors d’une mise à jour du programme. S’il n’est ni manquant ni corrompu, b614 s’affichera. Le « b » indique que le défaut est généré par le programme du chargeur de démarrage plutôt que le code du programme d’Application normal. Veuillez noter que chaque nouvelle version des fichiers du programme est accompagnée d’un nouveau fichier VTCCMFW.USF. Même si le nom est le même, il exige la nouvelle version de ce fichier, qui est fournie avec le code d’Application. 1. Installez le bon fichier VTCCMFW.USF sur la clé usb. 2. Si vous avez déjà la version correcte de VTCCMFW.USF, le lecteur USB pourrait être la source du problème. Suivez les instructions du code 613. 615-617 Aucun fichier d’actualisation trouvé pour le CCM, le DPC ou le DMC Les fichiers du programme pour le CCM, le DMC et le DPC peuvent être mis à jour en utilisant le port USB de l’alimentation en plasma. Le GCM2010 est mis à jour par d’autres moyens. Pour une unité avec GCM 2010, le CCM peut toujours être mis à jour au moyen du port USB. Les fichiers de mise à jour du programme sont au format Cx_x_0.S (CCM) ; Mx_x_0.S (DMC) et Px_x_0.S (DPC). Si le Bootloader détecte 3 dispositifs, CCM, DMC et DPC, sur le CANBUS, mais que le lecteur USB n’a pas les trois fichiers de mise à jour, il mettra à jour ceux qu’il a, mais affichera un code indiquant qu’un ou plusieurs sont manquants (615 pour CCM; 616 pour DMC; 617 pour DPC). Essayez un autre lecteur flash ou si vous êtes certain que celui-ci est normal (cela fonctionne avec un ordinateur), alors remplacez le CCM. Les codes du groupe 7 se rapportent au module 1Torch en option Schéma simplifié de l’alimentation : Pour plus de détails et pour le dépannage, reportez-vous au schéma 042X1366 du module et des connexions de la XT 1Torch. 0-5264FR ANNEXE A-95 ULTRA-CUT 100 XT/200 XT/300 XT/400 XT (219A) À Barre de bus de sortie négative #49 W5 10 AWG (223A) L4 T4 L3 T3 L2 T2 L1 T1 10 AWG(219B) (223B) (219C) + (223C) 12 AWG(224B) PCB de relais J85 Embout 1TORCH (220B) W4-A (52B-1) (220C) W4-B (220D) (52B-2) J87 1 2 Embout (52A-1) (52A-2) J40 1 2 3 4 5 Pièce Torche automatique À partir de INV 1A + Art # A-12787FR 2 1 (220A) J84 Circuit imprimé du pilote J41 Q2 Pièce J86 J11 FGA30N120FTD ATC 1TORCH MODULE ONDULEUR Fonctionnement de la 1Torch et de ses circuits de verrouillage. La 1Torch peut être utilisée dès que la séquence de démarrage de l’alimentation se termine. Il n’est pas nécessaire de télécharger un processus d’automatisation. La 1Torch peut être utilisée pendant le téléchargement et la purge d’un processus d’automatisation. La 1Torch ne peut pas être utilisée lorsque la torche automatisée est en prégaz, en pilote/ coupe ou en post-écoulement. Cette dernière doit être inactive et n’effectuer aucun processus de découpe avant l’utilisation de la 1Torch. Condition des circuits avant d’appuyer sur la gâchette de la 1Torch : 1. Lorsque la torche automatisée fonctionne ou est en prégaz, en pilote/coupe ou en post-écoulement, le K200 (module 1Torch) est ouvert pour empêcher le signal de la gâchette de la 1Torch (démarrage) de passer à la carte de relais. 2. Lorsque la torche automatisée est inactive, le K200 est sous tension, prêt à communiquer le signal du commutateur d’amorçage de la 1Torch. 3. Initialement, le K201 et le W5 et ne sont pas activés. Le W4, ajouté à l’alimentation XT lorsque l’option 1Torch est installée, est mis sous tension, par les contacts « NC aux » sur le W5. Le W4 connecte la pointe de la torche automatisée au pilote chaque fois que la 1Torch n’est pas activée. Lorsque l’utilisateur appuie sur la gâchette de la 1Torch, un circuit de verrouillage détermine d’abord si les consommables de la 1Torch sont en place, et un contact bien établi est nécessaire pour démarrer le pilote. 1. Une tension de -15 V (J85-3) est appliquée à l’électrode de la 1Torch au moyen des contacts K201 NC, et revient de la pointe au J85-1, où la mesure est prise par l’U13A sur la carte de relais. Le signal « /Pressure OK 1Torch » sur la broche 6 du câble plat à 40 broches (entre les circuits de relais et d’E/S, J4 et J23) est utilisé à la fois pour le verrouillage et pour confirmer la pression du gaz. Lorsque ce signal s’abaisse lors du test de la continuité des pièces, il indique que la 1Torch peut être mise sous tension sans problème. Une DEL D35, appelée T-E CONTACT, s’allume pour indiquer que ce test est satisfait. Un défaut de continuité générera le code de panne 702. 2. Une fois qu’il est confirmé les consommables sont en place, K201 et W5 sont mis sous tension et le contact auxiliaire normalement fermé de W5 (W5 AUX) le relais de mise hors tension W4, lequel isole la pointe de la torche automa- A-96 ANNEXE 0-5264FR ULTRA-CUT 100 XT/200 XT/300 XT/400 XT tisée de la pointe de la 1Torch. Si pour une raison quelconque K201 n’est pas mis sous tension, ou si le manostat PS2 ferme le circuit, cela générera le code de panne 703. 3. À ce point, le solénoïde du gaz de la 1Torch est allumé et le gaz doit sortir, ce qui entraîne le retrait de la cartouche d’amorçage de la 1Torch, qui s’éloigne de la pointe. Simultanément, l’onduleur est sous tension pour produire une tension en circuit ouvert. Si la cartouche d’amorçage est séparée de la pointe, l’alimentation XT détecte une tension en circuit ouvert entre la pointe et l’électrode. S’il n’y a pas assez de pression, au moins 2,4 bar, le code de panne de pression, 704, sera généré. Si la pression est supérieure à 2,4 bar, mais que la cartouche ne se sépare pas, alors le code de panne de la cartouche d’amorçage, 705, sera généré. 4. En supposant qu’il existe une pression de gaz suffisante (qui devrait être de 4,83 à 5,86 bar) et que la cartouche d’amorçage fonctionne correctement, le gaz est alors coupé, les parties se réunissent et le courant pilote les traverse, le gaz est rétabli et les parties se séparent, entraînant la formation d’un arc qui est propulsé hors de la pointe par l’écoulement de gaz. Mesures au cours du verrouillage pendant le fonctionnement de la torche XT automatisée : 1. Qu’une 1Torch soit ou non branchée sur l’ATC, une tension de -15 V est appliquée par l’intermédiaire de K201 au circuit de l’électrode de la 1Torch (borne négative de l’ATC), comme expliqué précédemment. Si un des trois contacts négatifs de W5, qui devrait être ouvert, est fermé (soudé ou coincé), le -15 V sera mesuré par U13B, produisant le signal « Contactor Fault 1Torch » (panne de contacteur 1Torch). Si aucune panne de contacteur n’est détectée, la torche automatisée peut être mise sous tension. 2. Si une 1Torch est branchée et que ses parties sont en place et créent un contact, le circuit de la pointe sera également sous tension à -15 V, et si le contact du pilote W5 (pointe) est fermé (soudé ou coincé), U13D détectera le -15 V et signalera « Contactor Fault 1Torch » (panne de contacteur 1Torch). « Contactor Fault 1Torch » (panne de contacteur 1Torch) génère le code de panne 701. Si aucune panne de contacteur n’est détectée, la torche automatisée peut être mise sous tension. Une DEL verte sur la carte de relais, D40, s’allume lorsque le circuit est dans un état satisfaisant, sans condition de panne. Dépannage du module 1Torch. En premier lieu, lisez les Descriptions ci-dessus. Ce guide suppose que vous disposez d’une copie du schéma 42X1366 du module et des connexions de la XT 1Torch. Le module 1Torch est fixé sur le panneau avant du XT par des vis compatibles avec les tournevis Torx T25 ou à tête creuse de 8 mm. Si la procédure vous oblige à le déposer, les fils sont suffisamment longs pour permettre d’écarter le module assez loin du panneau pour enlever également le capot. Pour travailler sur le module, il faudra le poser sur un support. Retrait et ouverture du module 1Torch. Si le dépannage ou la réparation nécessite d’accéder à l’intérieur du module 1Torch, voici ce qu’il faut faire. Commencez par retirer les panneaux latéraux de droite et vérifiez que le connecteur J86 à l’arrière du module est branché. Il y a 6 vis dans le panneau avant du module : 4 l’attachent au panneau et 2 maintiennent le couvercle ; retirez-les toutes. Retirez le module du panneau avant jusqu’à ce que vous puissiez accéder aux vis du capot : 2 de chaque côté et 2 à l’arrière. Le faisceau et les câbles restent connectés. L’arrière du capot est à encoches, de sorte qu’il suffit de desserrer les vis. Vous aurez besoin de soutenir le module en le faisant. Aucun code de panne affiché. Certains problèmes peuvent ne générer aucun code de panne, par exemple : 1. L’absence de réponse à la gâchette de la 1Torch. Pour que la gâchette de la 1Torch fonctionne, la torche automatisée doit être inactive, pas en prégaz, pas en post-écoulement, etc. Lorsque la torche automatisée XT est inactive, le K200 dans le module 1Torch devrait être sous tension et mettre la gâchette de la torche en connexion avec la carte de relais et le CCM. Sur le circuit E/S CCM, localisez le D70, la DEL d’amorçage de la 1Torch, juste à gauche du J28. Ce voyant doit s’allumer lorsque la gâchette de la 1Torch est pressée. S’il ne s’allume pas, vérifiez que la coupelle protectrice et les consommables sont en place. Vérifiez que le connecteur ATC de la 1Torch est bien en place. a. Si le D70 est éteint, commencez par retirer J11 de la carte de relais. Mesurez que la résistance entre les broches 2 et 3 du connecteur de faisceau J11 se situe entre 400 et 800 ohms (n’utilisez pas la plage de mesure pour diodes du voltmètre). Si la résistance mesurée indique que les broches sont entièrement déconnectées ou au contraire en court-circuit, le problème est alors dans le module 1Torch. b. Si la résistance entre les broches 2 et 3 du J11 est correcte, rebranchez le J11 et mesurez la tension entre J11-2 et TB1 sur la carte de relais. Elle devrait être de 24 V CC. Mesurez ensuite sur la J11-3. Cette tension devrait être 0-5264FR ANNEXE A-97 ULTRA-CUT 100 XT/200 XT/300 XT/400 XT faible, inférieure à 2 volts. Si elle n’est pas faible, mais à 24 V CC, alors K200 n’est pas activé et le problème se situe peut-être dans la carte de relais ou le CCM. c. Mesurez la tension de la broche 5 sur le câble plat à 40 broches (J23/J4) ; si elle est élevée, à environ 15 V CC, il se peut que le CCM soit défectueux, et ne détecte pas que la torche automatisée est inactive. Si la tension sur la broche 5 est faible, inférieure à 2 V CC et que celle de J11-3 n’était pas faible, alors la carte de relais est défectueuse. 2. Contacteur W5 hors tension. Ce problème générera un code de panne 102, défaillance du pilote, après quelques secondes, parce que si W5 n’est pas sous tension, l’alimentation ne sera pas reliée à la 1Torch et il n’y aura donc pas de pilote. a. Vérifiez que la tension entre J11-1 et J11-12 est à 24 V CA. Si c’est le cas, vous devrez ouvrir le module 1Torch pour continuer l’analyse. b. S’il n’y a pas de tension à 24 V CA, vérifiez que le disjoncteur CB3, sur le panneau arrière, ne s’est pas déclenché. Ensuite, mesurez le signal « /Contactor Enable 1Torch » (activation du contacteur 1Torch) sur la broche 20 du câble plat à 40 broches (J23/J4). Cette tension devrait être faible, inférieure à 2 V CC. Si elle l’est, la carte de relais est défectueuse. Si la tension de la broche 20 n’est pas faible, le CCM est probablement la cause du problème. 3. Le contacteur W4 ne se fermera pas lorsque le système est en mode inactif ou automatisé. Cela permettra d’éviter d’établir le pilote de la torche XT, et génère le code 102 après une tentative de démarrage du pilote qui dépasse 15 secondes. Contournez le W4 pour voir si cela permet de démarrer le pilote de la XT. Débranchez le J41 (le connecteur à 2 broches entre W4 et le circuit pilote) du circuit pilote. Retirez le connecteur J41 (J87) dont les fils 52A-1 et 52A-2 se connectent au J87 de l’autre côté du W4, et branchez-le sur le J41 du circuit pilote. Cela remet l’appareil dans l’état où il était avant l’installation de la 1Torch en option. Si le pilote fonctionne désormais, c’est qu’il y avait un problème avec le W4. La torche XT automatisée peut être utilisée en contournant le W4. Dépannage du W4. 1. La bobine du W4 présente une résistance de 10 à 15 ohms à la température ambiante, typiquement entre 12 et 13 ohms. Retirez un fil nº 210 ou 210A de la bobine avant de mesurer la résistance. Si la bobine du W4 est rompue ou en court-circuit, remplacez-la. 2. Le W4 est alimenté par 24 V CA. Sur la carte de relais J11, mesurez la tension entre les broches 10 (fil 210A sur la bobine du W4) et 12. Cette tension devrait être de 24 V CA. Si ce n’est pas le cas, vérifiez que le disjoncteur CB3 sur le panneau arrière ne s’est pas déclenché. a. Coupez l’alimentation et retirez J11 de la carte de relais. Mesurez la résistance entre le connecteur de faisceau J11 et l’autre côté de la bobine du W4 (fil 210). Ces deux points devraient être connectés, avec une tension proche de zéro ohm. Sinon, le contact auxiliaire du W5 (W5 AUX), normalement fermé, peut être ouvert. Il va falloir ouvrir le module 1Torch. Reportez-vous à la section Retrait et ouverture du module 1Torch près du début de cette section-ci. b. Déterminez si W5 est coincé d’une manière qui maintient ouvert le contact AUX SW. Trouvez le contacteur ; c’est un contacteur noir de grande taille. Au milieu du couvercle, vous verrez une ouverture rectangulaire avec une languette en plastique légèrement en retrait à l’intérieur. Elle devrait se déplacer vers le bas et remonter librement quand vous appuyez dessus et que vous la relâchez. Si ce n’est pas le cas, remplacez le contacteur. Le contact AUX se trouve sur le côté du contacteur vers l’arrière du boîtier. Déterminez s’il est correctement fixé au contacteur. Il devrait être enclenché. S’il est défectueux et ne peut pas être réparé, il faudra remplacer le contacteur complet. 701 Panne du contacteur d’isolation (W5). Ce code indique qu’un ou plusieurs des contacts du W5 sont fermés quand ils ne devraient pas être. Cela se produit soit parce que le W5 est sous tension à un moment où il ne devrait pas l’être en raison d’un circuit imprimé défectueux, soit parce qu’un ou plusieurs contacts sont physiquement coincés. 1. Pointe de la 1Torch en contact avec la pièce ou la terre a. Si la pointe standard de la 1Torch est en contact avec la pièce ou la terre au moment de la mise sous tension, la pompe ne démarrera pas et n’amorcera pas le système de refroidissement. Si pendant l’amorçage, la pointe A-98 ANNEXE 0-5264FR ULTRA-CUT 100 XT/200 XT/300 XT/400 XT contacts travail ou la masse La pompe s’arrête. Dans les deux cas, un code de panne E701 s’affiche ; dans ce cas, il ne s’agit pas d’une panne du W5, mais d’un artefact du circuit qui vérifie le fonctionnement du W5. b. Une fois l’amorçage terminé, un contact entre la pointe et la pièce n’arrêtera pas la pompe, mais affichera un code E701. c. Coupe glissante avec la 1Torch. Pour optimiser l’utilisation des consommables, la coupe glissante doit utiliser le capuchon spécial pour coupe glissante ou le guide d’écartement de la coupelle protectrice, qui ne permettent pas à la pointe de contacter la pièce, préviennent les codes de panne 701 et permettent d’effectuer la coupe à pleine intensité de 100 A. Avec la pointe d’écartement standard, s’il se produit un contact avec la pièce, le courant est réduit à 40 A pour éviter d’endommager la pointe. Vous pouvez effectuer la coupe glissante de cette manière, Avec une intensité réduite, mais la durée de vie de la pointe peut en souffrir. Avec la pointe standard, en raison du code 701, vous devez déclencher la 1Torch avec la pointe au-dessus de la pièce pour démarrer le prégaz. Ensuite, la pointe peut être mise en contact avec la pièce pour effectuer la coupe à intensité réduite. 2. Contacteur W5 hors tension ou coincé. a. La DEL de la carte de relais, D40, devrait rester allumée lorsque le W5 fonctionne correctement. S’il est éteint, retirez J84 de la carte de relais. Si le D40 est toujours éteint, la carte de relais est défectueuse. b. Si D40 s’allume lorsque J84 est enlevé, mais que vous obtenez toujours un code de panne 701, mesurez la tension entre la broche 20 du câble plat à 40 broches (qui relie J23 du CCM à J4 du relais) et TP1 sur le CCM ou la carte de relais. Si la tension sur la broche 20 est faible, inférieure à 2 V CC, alors le CCM est probablement défectueux. Si la tension sur la broche 20 est trop élevée alors que J84 a été ôté, alors la carte de relais est défectueuse. 3. W5 est sous tension. Avant de démonter le module 1Torch pour inspecter le W5, examinez la carte de relais pour voir si la DEL verte, D26, juste au-dessus de K3, est allumée. Cela indiquerait que la carte de relais, ou peut-être le CCM, met le W5 sous tension quand il ne devrait pas l’être. Vous pouvez également tester si le 24 V CA provenant de la carte de relais atteint J11-1 et J11-12. a. Sur le câble plat à 40 broches (de J23 du CCM à J4 du relais), si la tension de la broche 20 est faible, inférieure à 2 V, par rapport à TP1 sur le CCM ou la carte de relais, alors le CCM met W5 sous tension. Remplacez le CCM. b. Si la tension de la broche 20 est élevée, environ 15 V CC, mais que D26 est allumé, la carte de relais est défectueuse. 4. Contacteur W5 hors tension ou coincé. Il va falloir ouvrir le module pour l’inspecter, et probablement remplacer W5. Coupez complètement l’alimentation de l’appareil avant de le démonter. a. Trouvez le contacteur ; c’est un contacteur noir de grande taille. Au milieu du couvercle, vous verrez une ouverture rectangulaire avec une languette en plastique légèrement en retrait à l’intérieur. Elle devrait se déplacer vers le bas et remonter librement quand vous appuyez dessus et que vous la relâchez. Si ce n’est pas le cas, remplacez le contacteur. Retirez le couvercle du contacteur et les 2 vis, et inspectez les contacts. Ils ne doivent pas être excessivement brûlés et devraient se déplacer librement. Si ce n’est pas le cas, remplacez le contacteur. 702 Panne de contact au démarrage due aux consommables. Comme expliqué ci-dessus, la carte de relais applique une tension de -15 V CC à l’électrode et s’attend à voir cette tension sur la pointe, ce qui garantit que l’électrode, la cartouche d’amorçage et la pointe sont en place et en contact électrique. 1. La cause la plus fréquente de cette panne est l’établissement d’un arc et l’apparition de piqûres sur la surface de la cartouche d’amorçage et sur la pointe. Celles-ci peuvent être nettoyées, ou remplacées si elles sont en trop mauvais état. N’utilisez pas de papier de verre, car des particules abrasives peuvent entrer dans la cartouche d’amorçage. 2. Sur la carte de relais, la DEL verte D35, devrait s’allumer lorsque les composants sont en contact. a. Si D35 est allumé, vérifiez si la tension entre la broche 11 du câble plat à 40 broches et le TP1 de la carte de relais est faible, inférieure à 2 V CC. Si c’est le cas, alors le CCM ou le câble plat à 40 broches est défectueux. b. Si D35 est éteint, enlevez J85 de la carte de relais et vérifiez si la broche 3 de la tête J85 du PCB est sous tension de l’ordre de -12-15 V CC. Si cette tension n’est pas présente, la carte de relais est défectueuse. Si la tension est présente, remettez le J85 et mesurez de nouveau la broche 3. Si la tension a maintenant disparu, alors il y a un court-circuit dans le module ou les fils. 0-5264FR ANNEXE A-99 ULTRA-CUT 100 XT/200 XT/300 XT/400 XT c. En supposant que la tension est correcte au niveau du J85-3, mesurez-la au J85-1. Elle devrait être négative et dépasser les 5 V. Dans ce cas, la carte de relais est défectueuse. 3. Problème à l’intérieur du module 1Torch. Reportez-vous à la section Retrait et ouverture du module 1Torch près du début de cette section-ci pour les instructions d’ouverture du module. a. Trouvez le contacteur W5. Avec le système sous tension et inactif, mesurez la tension de T2, T3 ou T4 sur le terminal principal de W5. Mettez le fil négatif du voltmètre en contact avec TP1, soit sur la carte de relais du XT, soit sur les circuits du CCM. La tension devrait être négative et dépasser les 5 V CC, normalement entre -12 et -15 V CC. Si cette tension n’est pas présente à cet endroit-là, prenez une mesure pour la détecter sur K201-5. Si elle n’est toujours pas présente, il se peut que le faisceau de câbles entre J85 et J86 ou le fil de J86 à K201 soient défectueux. b. Confirmez que K201 n’est pas alimenté en mesurant la tension autour de sa bobine, de la broche 7 à la broche 8. Elle devrait être nulle, mais si elle est à 24 V, la carte de relais est défectueuse. c. 703 Si la tension était correcte à K201-5, mesurez-la entre TP1 et K201-1. Si elle y est nulle, le contact NC de K201 est ouvert ou la diode D201 est ouverte. D202 se situe dans le fil 223/223D sous la gaine thermorétractable. Panne du circuit de détection. 1. Lorsque la gâchette de la 1Torch est pressée, les circuits vérifient que les pièces consommables sont en place (expliqué dans la section du code 702). Lorsque les consommables sont en place et que K201 n’est pas sous tension, le signal « /Pressure OK 1Torch » (pression de la 1Torch correcte) sur la carte de relais sera bas. Dès que K201 est mis sous tension, la pointe à -15 V CC n’est plus connectée à J85-1 et D35 s’éteint. Étant donné que le solénoïde de gaz SOL4 n’a pas encore été mis sous tension, le signal « /Pressure OK 1Torch » (pression de la 1Torch correcte) se relèvera. Cela permet de vérifier que K201 fonctionne et que le manostat PS2 est normalement ouvert. Si l’un des deux ne fonctionne pas correctement, cela génère le code de panne 703. Tout cela se passe très rapidement, de sorte qu’il est presque impossible de le mesurer avec un voltmètre et qu’il faudra effectuer une analyse par élimination. a. Retirez le connecteur à 3 broches J85 de la carte de relais. Appuyez sur la gâchette de la 1Torch. Vous devriez voir s’afficher le code de panne 702. Si au contraire, vous obtenez le code 703, la PS2 est fermée, en court-circuit. C’est une défaillance peu probable. b. Si vous obtenez toujours le code 703 avec J85 enlevé, vous devrez déterminer si la carte de relais essaie sans succès de mettre K201 sous tension, ou si la carte elle-même est défectueuse. Rebranchez J85. En réponse à la panne, même si la carte de relais met K201 sous tension, il le remettra immédiatement hors tension. Si la tension est appliquée correctement, votre voltmètre devrait détecter une brève impulsion de tension, ou tout simplement clignoter. i. Mesurez la tension entre TP1 (le commun) sur la carte de relais et J11-9. Chaque fois que vous appuyez sur la gâchette de la torche, le voltmètre devrait tressaillir. Si c’est le cas, vous devrez ouvrir le module 1Torch pour continuer l’analyse à l’intérieur. Reportez-vous à la section Retrait et ouverture du module 1Torch près du début de cette section-ci pour les instructions d’ouverture du module. S’il n’y a aucun signe de tension à J11-9, la carte de relais peut être défectueuse, mais nous devons d’abord vérifier que la bobine K201 ou le D202 ne sont pas court-circuités. ii. Coupez l’alimentation. Retirez J11 de la carte de relais. Mesurez que la résistance entre les broches 8 et 9 du connecteur de faisceau J11 se situe entre 400 et 800 ohms. N’utilisez pas la plage de mesure pour diodes du voltmètre. Si la résistance est inférieure à 400 ohms, inversez vos fils, il se peut que vous ayez mesuré la diode D202. Si vous mesurez un court-circuit, c.-à-d. une résistance très inférieure à 400 ohms, cela peut être la raison pour laquelle vous n’observez aucun transitoire sur le voltmètre. iii. Une tension qui indique un court-circuit ou un circuit ouvert va nécessiter l’ouverture du module 1Torch pour en déterminer la cause. Reportez-vous à la section Retrait et ouverture du module 1Torch près du début de cette section-ci pour les instructions d’ouverture du module. Dans le cas d’un court-circuit, il faut déterminer si le D202 est défectueux ou si la bobine du relais est court-circuitée ou ouverte. K201 est le relais vers l’avant du module ; K200 est celui à l’arrière. 704 Défaut de pression La pression normale de fonctionnement de la 1Torch est de 4,83 à 5,86 bar. Néanmoins, la pression minimale pour le manostat est de 2,4 bar. Lorsque la gâchette de la 1Torch est pressée, que les tests indiquent que les consommables sont en place (702) et que le circuit de détection fonctionne (703), alors le solénoïde de gaz SOL4 est allumé. Si la A-100 ANNEXE 0-5264FR ULTRA-CUT 100 XT/200 XT/300 XT/400 XT pression d’entrée du gaz est supérieure à 2,4 bar, le manostat SW PS1 doit se fermer. Une pression d’entrée inférieure à 2,4 bar ou un régulateur de gaz qui n’est pas réglé au-dessus de 2,4 bar entraîneront un code de panne 704. 1. Assurez-vous qu’une alimentation en air capable de délivrer de 4,83 à 5,86 bar est connectée au raccord d’entrée du module 1Torch. Si la ligne d’air est munie d’un filtre en option, vérifiez qu’il n’est pas obstrué. 2. Appuyez sur la gâchette de la torche pendant quelques instants pour démarrer le prégaz. Tournez le régulateur du module 1Torch dans le sens des aiguilles d’une montre pour augmenter la pression à un minimum de 4,83 bar (jusqu’à 5,86 bar pour de longs fils). 3. Si aucune pression n’est mesurée sur le manomètre, le solénoïde peut être défectueux ou la carte de relais peut ne pas l’allumer. a. En premier lieu, déterminez si la DEL D2, « GAZ DE LA TORCHE ON » (gaz de la torche actif ), sur la carte de relais s’allume lorsque vous appuyez sur le commutateur de la torche. Sinon, il y a un problème sur la carte de relais ou le CCM. Si D2 s’allume, passez à l’étape 3c. b. Sur le câble plat à 40 broches qui relie le CCM et la carte de relais (J23-J4), mesurez la tension entre la broche 4 et le TP1. Cette tension devrait être faible, inférieure à 2 volts, lorsque vous appuyez sur la gâchette de la 1Torch. Si ce n’est pas le cas, alors le CCM (ou le câble plat) est défectueux. Si la tension de la broche 4 est faible ou descend quand la gâchette est enfoncée, mais que D2 ne s’allume pas sur la carte de relais, la carte de relais est défectueuse. c. Si D2 s’allume sur la carte de relais lorsque le commutateur de la torche est enfoncé, il faut déterminer si la carte de relais alimente le solénoïde. En premier lieu, branchez le voltmètre pour mesurer 24 V CA entre les broches 13 et 14 sur le J11 de la carte de relais. Appuyez sur la gâchette de la 1Torch. S’il n’y a aucune tension, la carte de relais peut être défectueuse. d. S’il aucune tension de 24 V CA n’est apparue, débranchez J11 et mesurez la résistance entre les broches 13 et 14 du connecteur de faisceau J11. Elle devrait être d’environ 21 ohms. C’est la résistance du solénoïde. Si elle est infinie ou nettement moindre, cela indique que la bobine peut être en court-circuit et qu’il faudra remplacer l’ensemble solénoïde. Le circuit RC amortisseur, SA201, ne fait PAS partie de l’ensemble solénoïde, par conséquent gardez-le, vous en aurez besoin sur le nouveau solénoïde. Reportez-vous à la section Retrait et ouverture du module 1Torch près du début de cette section-ci pour les instructions d’ouverture du module. 705 Panne de la cartouche d’amorçage. Comme expliqué dans la section Fonctionnement de la 1Torch et de ses circuits de verrouillage, pendant le prégaz la pression du gaz devrait provoquer la séparation de la cartouche d’amorçage et de la pointe. Après un léger retard laissant le temps de cette séparation, l’onduleur est activé pour fournir la tension en circuit ouvert qui est mesurée et doit être supérieure à 200 volts. Si la cartouche ne bouge pas et ne se sépare pas de la pointe, ou que quelque chose d’autre entraîne un court-circuit entre la pointe et l’électrode, cela générera un code 705. En outre, comme ce test utilise l’alimentation de l’onduleur, si ce dernier ne produit pas une tension circuit ouvert, la tension mesurée sera faible et le code de panne 705 sera produit. 1. Si le voyant CC clignote momentanément sur le panneau avant de l’appareil chaque fois que vous appuyez sur la gâchette de la 1Torch, c’est un bon signe que l’onduleur fonctionne correctement. Essayez également d’utiliser la torche automatisée XT, si elle fonctionne, l’onduleur est bon. 2. Le problème le plus probable est le blocage de la cartouche d’amorçage. Démontez les consommables pour voir si la cartouche se déplace librement. Essayez avec une nouvelle cartouche et une nouvelle pointe. Ceci complète les Informations de dépannage avancé. 0-5264FR ANNEXE A-101 ULTRA-CUT 100 XT/200 XT/300 XT/400 XT ANNEXE 31 : SL100 INTERCONNECTION 1 2 3 4 5 Interconnection to XT Power Supply (Simplified) A J4 B 1 2 3 4 5 6 7 8 9 10 11 12 13 14 15 16 17 18 19 20 21 22 23 24 25 26 27 28 29 30 31 32 33 34 35 36 37 38 39 40 L4 500uH L4 500uH / Start 1 Torch / Gas Sol ON 1 Torch / Main torch Idle 1 Torch / Press OK 1 Torch R9 100.0 L4 Contactor Fault 1Torch 500uH 24 VDC (-) C5 0.1uF 50V 24 VDC (-) 24 VDC (+) 24 VAC 1 Torch Contactor ON D? 24 VDC (+) GBU404 / Contactor Enable 1 Torch 24 VAC Ret 5 1 2 3 4 5 6 7 8 9 10 11 12 13 14 (201) (202) (203) (204) (205) (206) (207) (208) (209) (210A) (212) (213) (214) J11 K3 (Existing) 4 24 VAC 1 3 / Contactor Enable 1 Torch 2 CONTACTOR CONTROL 1-TOR 5 K8 4 1 / Gas Sol ON 1 Torch 1 Torch Gas ON 3 2 R? 1K Gas SOL Control WORK D35 D35 ON = 1 Torch consumables present and in contact. OK to enable 1 Torch -15 MICROSMD005F 1 C 8 GREEN D38 T-E CONTACT EARTH 3 2 1 MRA4007 (215) (216) J85 4 1 Harness connector to Relay PCB TIP R? 10K +24 VDC ELECTRODE R? 10K Relay PCB (simplified) 24 VAC I/O PCB +15 VDC - 2 + 3 -4.8 VDC 255K U13A LM293 255K U13B 2 U13C D40 14 GREEN D41 - 8 + 9 -4.8 VDC 4 5 -4.8 VDC 255K LM339 1 2 3 4 5 255K U13D LM339 1 TORCH CONTACTOR OK + 13 D40 ON = W5 open, OK to enable automation. - 10 + 11 (219) NEG (220) PILOT J84 -4.8 VDC 255K LM339 255K D PILOT PCB Q2 J41 J41 1 2 2 1 TIP FGA30N120FTD E W4-A (220C) (52B-1) W4-B ( 220D ) (52B-2) J87 1 2 J41 (J87) 2 1 (52A-1) Automation Torch ( 52A -2) W4 Added to XT Supply for 1 Torch Option J40 1 2 3 4 5 WORK From INV 1A + INVERTER F Art # A-12792_AB 1 A-102 2 3 ANNEXE 4 5 0-5264FR ULTRA-CUT 100 XT/200 XT/300 XT/400 XT 6 7 8 9 10 Optional 1 Torch Module A XT 1 TORCH MODULE +24VDC 1N4007 7 2 6 4 1 3 (222) (204) (209) B D201 (208) 24 VDC coil 8 1N4007 K201 1A 24 VAC Ret TIP 6 2 Energized with W5 Isolates test ckt. when W5 closed SA200 W5 AUX (201) 1TORCH SL100 w/ 100A Consumables * W5 (219B) (222) (224) 10 AWG L4 T4 L3 T3 (224A) (223D) (219) (220) (219C) ATC CONNECTOR (212A) D202 1N4007 1A 1000V To NEG OUTPUT BUSS BAR #49 C PIP SWITCH (221) W5 TIP (212) ELECTRODE Snubber (210) (224A) 4 5 3 (216) ELECTRODE (224) W4, energized whenever 1 Torch cutting is NOT enabled, is de-energized when 1 Torch is enabled (W5 energized) to isolate the automation tip from the 1 Torch tip when cutting with 1 Torch. (223) 1 (210) (215) W4 (221) (205) (214) (210A) K200 1A 35 PSI (213) (219) (220) Relay under control of CCM isolates torch Start wires (for noise) when Automation cutting. 8 PS2 (207) (206) 24 VAC Ret 24 VAC Ret 24 VAC ELECTRODE TIP J86 Snubber D200 5 (212) (213) (214) (215) (216) (202) (203) / Main Torch Idle / 1 Torch START /1 Torch START Ret (Common) / 1 Torch Press OK Ret (Common) / 1 Torch Press OK 24 VDC (-) 24 VDC (+) 7 (219) (220) 1 Torch Contactor ON (24VAC) SOL4 (212) (213) (214) (215) (216) (201) (202) (203) (204) (205) (206) (207) (208) (209) (210) SA201 1 2 3 4 5 6 7 8 9 10 11 12 13 14 15 16 17 18 19 20 Snubber (201) (202) (203) (204) (205) (206) (207) (208) (209) (210) (225) 1 2 3 4 5 6 7 8 - (223A) 10 AWG TORCH SWITCH 1 2 3 4 5 6 7 8 (223B) + (223C) (219A) 14 AWG L2 T2 L1 T1 12 AWG (220A) (224B) D WORK (220B) 1 Torch Module Component Locations D200 D201 D202 K200 K201 SA200 SA201 PS2 SOL4 W4 W5 Diode, 1A, 1kv (A9) Diode, 1A, 1kv (B9) Diode, 1A, 1kv (C9) Relay, DPDT, 24VDC coil (B9) Relay, DPDT, 24VDC coil (B9) RC Snubber, (C8) RC Snubber, (B8) Pressure SW, 35 PSI, N. O (B8) Solenoid, 24VAC (B8) Contactor, Pilot Isolation, 40A 2P, 24VAC coil (6B, E3) Contactor, 1 Torch Isolation, 40A 4P, 24 VAC coil (8D, 8C) E Art # A-12792_AB Rev AA Revision ECO-B2687 By DAT Date Revision Rev By Date Thermal Dynamics Corporation 10/20/2014 2800 Airport Rd. Denton, Texas 76207 USA F Date Printed Date Revised 11/20/2014 12/16/2014 Drawn Date The information contained herein is proprietary to Thermal Dynamics. Not for release, reproduction or distribution without written consent. Title 0-5264FR 7 8 ANNEXE C Sheet 1 of 1 Drawing Number SCHEMATIC XT 1 Torch Module & Interconnections 6 5/29/2014 D Tatham Size 9 042X1366 10 A-103 ULTRA-CUT 100 XT/200 XT/300 XT/400 XT ANNEXE 32 : HE 400 XT CONNECTION 1 2 3 4 5 6 A A Groupe motoventilateur B B R 1 2 3 4 5 6 7 (2) (3) Ventilateur1 C4 J72 (6) 1 2 3 (6A) J71 BN G/Y BL R TS1 GND BK GND 130F C C Art # A-12793_AB Revision Rev AA By ECO-B2687 DAT Date Thermal Dynamics Corporation 8/20/2014 2800 Airport Rd. Denton, Texas 76207 USA D Date Printed Date Revised 11/25/2014 12/16/2014 Drawn Date Size Title Drawing Number SCHEMATIC A-104 2 3 4 ANNEXE A Sheet 1 of 1 042X1667 HE400XT 1 8/20/2014 DAT The information contained herein is proprietary to Thermal Dynamics. Not for release, reproduction or distribution without written consent. D 5 6 0-5264FR ULTRA-CUT 100 XT/200 XT/300 XT/400 XT ANNEXE 33 : SL100 Torch en option Préparation en vue de l’exploitation REMARQUE ! Le coupage plasma automatisée et manuelle ne peut pas être exécutée en même temps. Le 1torche est ignoré lors de l’automatisation de déclenchement est en cours de coupe, et Xt signal de démarrage est ignorée lors de la découpe. Les opérateurs doivent attendre postflow est terminée avant de couper avec la torche de rechange Au début de chaque séance de soudage : AVERTISSEMENT Couper l’alimentation primaire du bloc d’alimentation avant de monter ou de démonter le bloc d’alimentation, les composants de la torche ou la torche et son câblage. Raccordement de la torche Au besoin, raccorder la torche au bloc d’alimentation. Raccorder uniquement le modèle de torche manuelle SL100 de Thermal Dynamics à ce bloc d’alimentation. La longueur maximum du câble de torche est de 100 pi / 30,5 m, y compris avec les rallonges. 1. Aligner l’ATC connecteur mâle (sur la torche câble) avec le connecteur femelle. Insérer le connecteur mâle dans le réceptacle femelle. Exercer une légère pression pour insérer les connecteurs. 2. Fixer solidement le raccord en tournant l’écrou autofreiné dans le sens horaire jusqu’à ce qu’il s’enclenche. NE PAS utiliser l’écrou autofreiné pour rapprocher les extrémités de la connexion. Ne pas utiliser d’outils pour fixer solidement le raccord. 2 Art # A-12761 Raccordement de la torche au bloc d’alimentation 0-5264FR ANNEXE A-105 ULTRA-CUT 100 XT/200 XT/300 XT/400 XT Coupe glissante avec la 1Torch. Pour optimiser l’utilisation des consommables, la coupe glissante doit utiliser le capuchon spécial pour coupe glissante ou le guide d’écartement de la coupelle protectrice, qui ne permettent pas à la pointe de contacter la pièce permettent d’effectuer la coupe à pleine intensité de 100 A. Avec la pointe d’écartement standard 100 A, s’il se produit un contact avec la pièce, le courant est réduit à 40 A pour éviter d’endommager la pointe. Vous pouvez effectuer la coupe glissante de cette manière, Avec une intensité réduite, mais la durée de vie de la pointe peut en souffrir. Avec la pointe standard, en raison du code 701, vous devez déclencher la 1Torch avec la pointe au-dessus de la pièce pour démarrer le prégaz. Ensuite, la pointe peut être mise en contact avec la pièce pour effectuer la coupe à intensité réduite. Pièces en place (PIP) La torche est dotée d’un circuit pièces en place (PIP). Une fois correctement installé, le bouclier ferme un interrupteur. La torche ne pourra pas fonctionner si l’interrupteur est ouvert. Interrupteur de la torche vers ATC Interrupteur PIP Bouclier Art # A-12758FR Schéma de circuit des pièces en place pour la torche manuelle Pré-écoulement Après le déclenchement de la flamme est tirée, l’air circulera pendant 2 secondes. Cela permet à la contamination possible d’être éliminé de la torche avant de l’arc est établi. Après soudage Après le flambeau déclencheur libéré de l’arc s’arrêtera et l’air s’écoule pendant 20 secondes. Cela permet à l’opérateur de passer en toute sécurité modes aux Alimentation XT qui ne permettra pas à la la découpe automatisée pour se produire. Arc pilote Lorsque la torche quitte la pièce l arc pilote redémarre instantanément, et l’arc de découpe redémarre instantanément lorsque l arc pilote contacts la pièce. Foldback fonctionnalité L’unité passera automatiquement la coupure de courant jusqu’à 45 ampères si la pointe touche la plaque exposée lors de la coupe. Ces travaux amélioreront considérablement astuce de la durée de vie des pièces. Connexion de l’alimentation en air à l’appareil La torche SL100 a besoin d’une alimentation en air séparée de celle de l’alimentation XT. La connexion est la même pour l’air comprimé ou les cylindres haute pression. S’il faut installer un filtre facultatif sur la conduite d’air, consulter les deux sous-sections suivantes. 1. Connecter le module du filtre à son port d’admission. L’illustration montre des raccordements types à titre illustratif. REMARQUE ! Pour une parfaite étanchéité, appliquer une pâte d’étanchéité pour raccords filetés selon les instructions du fabricant. Ne pas utiliser de ruban adhésif Téflon en tant que mastic à filetage, dans la mesure où de fines particules de l’adhésif peuvent se détacher et obstruer les minuscules passages d’air dans la torche. A-106 ANNEXE 0-5264FR ULTRA-CUT 100 XT/200 XT/300 XT/400 XT Port d'admission Raccord 1/4 NPT ou ISO-R à 1/4 po (6 mm) Pince de serrage Conduite d'alimentation en gaz Art # A-12759FR Connexion de la conduite d’air à l’orifice d’admission Vérifier la qualité de l’air L’air doit être exempt d’huile et d’humidité. Pour tester la qualité de l’air : 1. Tirez déclencher pendant un court instant pour lancer le débit d’air/gaz. 2. Placer une lentille de filtre à soudage devant la torche et ouvrir l’admission d’air. Ne pas amorcer d’arc! Toute trace d’huile ou d’humidité sera visible sur la lentille. Contrôle pression d’air + Le contrôle de pression est utilisée pour régler la pression de l’air. Tirez déclencher pendant un court instant pour lancer le débit d’air/gaz. Pour régler la pression Tirez la molette et appuyer pour verrouiller. 1. S’assurer que le circuit d’air comprimé correspond bien aux caractéristiques. Pression d’entrée: 90 psi min. - 120 psi max. (6.2 bars min - 8.3 bars max.). Débit d’entrée : 6,7 CFM (189 lpm). 2. Vérifier les branchements et allumer l’alimentation en air. 3. Pour couper, ajuster la pression d’air de sortie de 70 - 85 psi / 4,8 - 5,9 bars. Consulter le tableau de réglage de pression de détails. Gas Réglage de la pression du gazs 0-5264FR Longueur des fils SL100 (Torche manuelle) Jusqu’à 25 pi (7,6 m) 70 psi 4.8 bar ANNEXE A-107 ULTRA-CUT 100 XT/200 XT/300 XT/400 XT Chaque 25 pi (7,6 m) supplémentaire Ajouter 5 psi 0.4 bar installation d’un filtre monoétagé en option On recommande l’utilisation d’un jeu de filtres supplémentaire en option pour améliorer la filtration de l’air comprimé et maintenir l’humidité et les débris hors de la torche. 1. Fixez le Single - Stade flexible de filtre à l’orifice d’admission. 2. Fixer le module du filtre à son tuyau. 3. Connecter le module du filtre à son tuyau. L’illustration montre des raccordements types à titre illustratif. REMARQUE ! Pour une parfaite étanchéité, appliquer une pâte d’étanchéité pour raccords filetés selon les instructions du fabricant. Ne pas utiliser de ruban adhésif Téflon en tant que mastic à filetage, dans la mesure où de fines particules de l’adhésif peuvent se détacher et obstruer les minuscules passages d’air dans la torche. Connecter de la manière suivante : Port d'admission Regulator/Filter Assembly Pince de serrage Conduite d'alimentation en gaz Raccord 1/4 NPT à 1/4 po (6 mm) Art # A-12760FR Filtre à air à un étage Pièce jointe A-108 ANNEXE 0-5264FR ULTRA-CUT 100 XT/200 XT/300 XT/400 XT Pièces de rechange 2 3 1 4 5 6 Art # A-12762FR Description 9-7379 9-6319 9-1044 0-5264FR BOM ID qté 1 1 2 1 3 1 Nom Contacteur Assemblage du solénoïde Pressostat ANNEXE Description 8-6800 9-9509 9-7380 BOM ID qté 4 1 5 1 6 2 Nom Manomètre Régulateur Relais A-109 ULTRA-CUT 100 XT/200 XT/300 XT/400 XT Qty Description Catalogue # 1 Kit pour filtre monoétagé (comprend filtre & tuyau) 1 Corps de filtre de rechange 1 Tuyau de filtre de rechange (non illustré) 2 Élément filtrant de rechange 7-7507 9-7740 9-7742 9-7741 Boîtier Elément filtrant (n° cat. 9-7741) Ressort Joint torique (n° cat. 9-7743) Filtre assemblé Couvercle Raccord cannelé Art # A-02476 Remplacement En une seule étape Facultatif D’Élément filtrant Ces instructions s’appliquent aux alimentations d’énergie où le filtre en une seule étape facultatif a été installé. Lorsque l’élément de filtre est complètement saturée Il ne sera pas capable de fournir la pression requise pour le module SL100/lampe torche. L’élément filtrant peut être enlevé de son logement, être séché, et réutilisé. Accordez 24 heures pour l’élément sec. Référez-vous à la section 6, liste des pièces, pour le nombre de catalogue d’élément filtrant de rechange. 1. Coupez l’alimentation électrique de l’alimentation d’énergie. 2. Air et système coupés de purge en bas avant de démonter l’élément filtrant de changement de filtre. 3. Débrancher le tuyau d’alimentation du gaz. 4. .Tourner le couvercle du filtre dans le sens antihoraire avant de le déposer. L’élément filtrant est plac à l’intérieur du logement. 5. Déposer l’élément filtrant du boîtier et le mettre de côté pour le faire sécher. 6. Chiffon à l’intérieur de du logement propre, puis isolant le côté ouvert d’élément filtrant de rechange d’abord. 7. Remettre le boîtier sur le couvercle. 8. Rattachez l’offre de gaz. REMARQUE ! Si l’unité fuit entre le carter et le couvercle, inspecter le joint torique de coupures ou d’autres dommages. A-110 ANNEXE 0-5264FR ULTRA-CUT 100 XT/200 XT/300 XT/400 XT Página intencionalmente en blanco. 0-5264FR ANNEXE A-111 ULTRA-CUT 100 XT/200 XT/300 XT/400 XT ANNEXE 34 : HISTORIQUE DE PUBLICATION Date de la couverture Rév Modification(s) 29 avril 2013 AA Première édition 21 mai 2013 AB Actualisation avec les nouvelles informations RAS 1000 XT selon ECOB2428 2 juillet 2013 AC Section 3 mise à jour avec des informations sur l’installation de carte V-D pour le contrôle de la hauteur selon ECOB2488 Mise à jour de l’annonce beaucoup d’articles, le texte et l’art dans tout le manuel. Ajouté le dépannage avancé et la plomberie des diagrammes pour l’annexe par ECOB2552. Ajouter Sect 3 Testeur de terre à faible coût du texte. Mis à jour l’art et de la secte 6/catégorie # s. Annexe Tableau des codes couleurs CNC. Fan art mis à jour par l’ÉCO-B2554. Mise à jour Sect 3/6 IL400XT art et texte par ECO-B2663. Dans le Appdx, ajouté à la torche 1SL100 et schémas du système, mis à jour le code couleur des câbles CNC art, mis à jour tous les schémas du système et mis à jour les informations de dépannage avancé. Dans la section 6, partie du système mises à jour de câble flexible et numéros de cartes et de références. L’article 3 mise à jour de l’art de câble tous par ECOB2694. Retour à l’image de marque Changement la dynamique thermique. Lisez-moi d’ajouter des pages. Nouvelle section de la sécurité, de nouvelles icônes de sécurité dans l’ensemble. Il-400 Mise à jour de la section d’art 3. Ajouter une note pour un art terre-11875. Ajouter flambeau hebdomadaire. maint. Remarque La section 5. Mise à jour de l’art du panneau arrière pour montrer qu’il-400 connexion A-11842. Ajouter la pompe et le moteur des numéros dans la section 6 et de mettre à jour les numéros de téléphone et le couvercle arrière et l’intérieur de la couverture avant. ECOB2712. Modifier l’ordre des TOC et DOC, de l’eau ajoutée Spec Section 2,09 p. 2-6& 2-7, correction d’orthographe de l’article 4, corrigée du bouchon du réservoir de liquide de refroidissement numéro de catalogue à partir de 8-5124 à 8-5142 p. 6-8, mis à jour un art-04066 p. 7-2 (joint torique p/n a changé à partir de 9-3027 à 8-0524), corrigée du texte d’activation/de désactivation de CNC p. A-10, mis à jour le texte de dépannage avancé p. A-86, Déclaration de garantie supplémentaire à l’intérieur de la page arrière. VCR-01534 Torche corrigée entraîner p/n de l’article 6 AC300 XT, a fait changer à DPC-3000 Module de commande des pièces de remplacement pour les manuels avec DFC 3000 groupe 4, Corrigé le texte en annexe Dépannage avancé. Retiré de la sécurité canadienne en français à partir de la version anglaise du texte de l’article 1. 16 janvier 2014 AD 30 mai, 2014 AE 2 octobre, 2014 AF 30 janvier 2015 AG 27 mai 2015 AH 14 janvier, 2016 AJ 5 janvier, 2017 A-112 AK ANNEXE 0-5264FR DÉCLARATION DE GARANTIE GARANTIE LIMITÉE : Thermal Dynamics® Corporation (dénommée ci-après « Thermal ») garantit que ses produits sont exempts de défauts de matière et de vices de fabrication. En cas de constat de non-conformité à ladite garantie survenue au cours de la période de validité des produits Thermal énoncée ci-dessous, Thermal s'engage, après notification de celle-ci et preuves à l’appui que le produit a bien été entreposé, installé, exploité et entretenu conformément aux spécifications, instructions, recommandations de Thermal et aux procédures sanctionnées par la pratique industrielle, et non sujets à une mauvaise utilisation, réparation, négligence, altération ou accident, à corriger lesdits défauts en réparant ou en remplaçant, sur décision exclusive de Thermal, tout composant ou partie du produit que Thermal jugera défectueux. CETTE GARANTIE EST EXCLUSIVE ET REMPLACE TOUT AUTRE GARANTIE DE QUALITÉ MARCHANDE OU DE BON FONCTIONNEMENT POUR UNE UTILISATION PARTICULIÈRE. LIMITATION DE RESPONSABILITÉ : Thermal ne sera en aucun cas responsable des dommages particuliers ou indirects comme, mais non limités à : endommagement ou perte des biens achetés ou remplacés, ou réclamations de la part du client des distributeurs (dénommés ci-après « Acheteur ») en cas d’interruption de service. Les voies de recours de l’Acheteur énoncée ciaprès sont exclusives et la responsabilité de Thermal en ce qui concerne un contrat quelconque, ou tout acte y afférent, y compris l’exécution ou la violation dudit contrat, ou découlant de la fabrication, vente, livraison, revente ou utilisation des biens couverts ou fournis par Thermal, qu’il s’agisse d’une conséquence du contrat, d’une négligence, d’un acte dommageable ou des clauses d’une garantie quelconque ou autre, ne devront pas, sauf disposition expresse contraire, dépasser le prix des biens sur lequel se fonde la responsabilité. L’UTILISATION DES PIÈCES DE RECHANGE OU D’ACCESSOIRES SUSCEPTIBLES DE COMPROMETTRE LA SÉCURITÉ OU LES PRESTATIONS DE L’UN DES PRODUITS THERMAL ENTRAÎNE LA DÉCHÉANCE DE LA PRÉSENTE GARANTIE. LA PRÉSENTE GARANTIE EST INVALIDE SI LE PRODUIT EST VENDU PAR DES PERSONNES NON AGRÉES. La validité de la garantie limitée pour ce produit devrait être : un maximum de trois (3) ans à compter de la date de vente par un distributeur agréé et un maximum de deux (2) ans à compter de la date de vente par ce distributeur à l’acheteur, et avec des limites ultérieures sur cette période de deux (2) ans (voir tableau ci-dessous). Pièces Main d’oeuvre Ultra-Cut XT™ et Auto-Cut XT™ Blocs d'alimentation et composants 2 Ans 1 An 1 An 1 An 90 Jours 90 Jours Torche et Conduites XTTM / XTTM-301 Torche (Hors consommables) Réparation/pièces de rechange Les demandes de réparation ou de remplacement sous garantie doivent être envoyées par un centre de réparation Thermal Dynamics® agréé dans les trente (30) jours de la réparation. Aucun frais de transport ne sera payé dans le cadre de cette garantie. Les frais de transport pour envoyer les produits à un centre de réparation agréé seront à la charge du client. Tous les produits renvoyés le seront aux risques et aux frais du client. Cette garantie remplace toute autre garantie Thermal précédente. Effective October 23, 2012 THE AMERICAS Denton, TX USA U.S. Customer Care Ph: 1-800-279-2628 (tollfree) Fax: 1-800-535-0557 (tollfree) International Customer Care Ph: 1-940-381-1212 Fax: 1-940-483-8178 Oakville, Ontario, Canada Canada Customer Care Ph: 1-905-827-4515 Fax: 1-800-588-1714 (tollfree) EUROPE Chorley, United Kingdom Customer Care Ph: +44 1257-261755 Fax: +44 1257-224800 Milan, Italy Customer Care Ph: +39 0236546801 Fax: +39 0236546840 ASIA/PACIFIC Cikarang, Indonesia Customer Care Ph: 6221-8990-6095 Fax: 6221-8990-6096 Rawang, Malaysia Customer Care Ph: +603 6092-2988 Fax: +603 6092-1085 Melbourne, Australia Australia Customer Care Ph: 1300-654-674 (tollfree) Ph: 61-3-9474-7400 Fax: 61-3-9474-7391 International Ph: 61-3-9474-7508 Fax: 61-3-9474-7488 Shanghai, China Sales Office Ph: +86 21-64072626 Fax: +86 21-64483032 Singapore Sales Office Ph: +65 6832-8066 Fax: +65 6763-5812 Service à la clientèle aux États-Unis : 866-279-2628 / fax 800-535-0557 • Service à la clientèle au Canada : 905-827-4515 / Service à la clientèle international : 940-381-1212 / fax 940-483-8178 © 2015, 2016 Thermal Dynamics Corp. thermal-dynamics.com fax 800-588-1714 ">
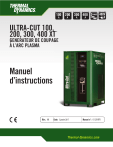
Public link updated
The public link to your chat has been updated.