ESAB Precision Plasmarc System with Electronic Flow Control Guide d'installation
PDF
Télécharger
Document
F-15-662 December, 2001 French Manuel d’Installation, Opération et Entretien pour le SYSTÈME de PRÉCISION PLASMARC avec Régulation du Débit Électronique CUTTING SYSTEMS 411 s. Ebenezer Road Florence, SC 29501-0545 L’équipement décrit dans ce manuel est potentiellement dangereux. Soyez prudent pendant l’installation, l’opération et l’entretien de cet équipement. L’acheteur est le seul responsable de la sécurité pendant l’utilisation de la machine et de tous les produits reliés. Il doit se conformer aux règles du OSHA et à tout autre standard officiel. ESAB Cutting Systems n’a aucune responsabilité relative aux blessures personnelles ou aux autres dommages résultant de l’utilisation des produits fabriqués et vendus par ESAB. Référez-vous aux termes et conditions standards de ESAB pour une déclaration spécifique des responsabilités et des limitations connexes. La satisfaction totale du client est prioritaire pour ESAB Cutting Systems. Nous recherchons continuellement continuellement des méthodes pour améliorer nos produits, services et documentation. En conséquence, nous procédons aux améliorations et/ou modifications tels que requis. ESAB s’efforce à maintenir la documentation à jour. Nous ne pouvons pas vous garantir que la documentation reçue comprend les plus récentes modifications. Par conséquent, les renseignements contenus dans ce document sont sujets aux changements sans préavis. Ce manuel est ESAB Pièce Numéro F15662 (Avril,01) indiquée relative à l’ajout des numéros de pièce pour les câbles dans la section 2 Nouvelle Date (December,01) Le chapiter du pièces de recharge été modifié Ce manuel est pour usage de l’acheteur et facilite son utilisation de la machine à découpage. Ceci n’est pas un contrat et n’est nullement une obligation de la part de ESAB Cutting Systems. © ESAB Cutting Systems, 2001 Imprimé au États-Unis Précision Plasma Régulation du Débit Électronique Table des Matières Page Section 1 Sécurité 1.1 Introduction....................................................................................... 1 1.2 Sécurité : Notations et Symboles....................................................... 1 1.3 Renseignement Généraux de Sécurité ............................................... 2 1.4 Précautions relatives à l’Installation .................................................... 4 1.5 Mise à la Terre Électrique .................................................................. 4 1.6 Utilisation de la Machine à Découpage au Plasma.............................. 5 1.7 Précautions relatives à l’entretien....................................................... 11 1.8 Références relatives à la Sécurité ...................................................... 12 Section 2 Description 2.1 Général ............................................................................................. 1 2.2 Objectif ............................................................................................. 1 2.3 Options d’Ensemble Disponibles ....................................................... 1-2 2.4 Spécifications Techniques 2.4.1 Système de Précision au Plasma .............................................. 2-3 2.4.2 Gaz au Plasma.......................................................................... 4 2.4.3 Gaz de Démarrage ................................................................... 4 2.4.4 Gaz Secondaire ........................................................................ 4 2.4.5 Torche PT-24 ........................................................................... 4 Section 3 Installation 3.1 Général ............................................................................................. 1 3.2 Équipement Requis ........................................................................... 1 3.3 Emplacement.................................................................................... 1 3.4 Connexions de l’Entrée Électrique Primaire ........................................ 2 3.5 Lignes d’Interconnexion..................................................................... 4 Précision Plasmarc Schéma d’Interconnexion des Composants......... 7 3.6 Assemblage de la Torche .................................................................. 10 3.7 Refroidisseur de la Torche ................................................................. 11 3.8 Inspection des Lignes à Gaz et de Refroidissement ........................... 12 3.9 Remplacement de l’EPROM dans le Contrôleur de Logique Programmable (PLC) de la Source (bloc) d’Alimentation.................... 12 i Précision Plasma Régulation du Débit Électronique Table des Matières Section 4 Opération 4.1 Commandes de la Source (bloc) d’Alimentation 4.1.1 Interrupteur d’Alimentation Principal ........................................... 1 4.1.2 Interrupteur de l’Arc Pilote.......................................................... 1 4.1.3 Lumières Indicatrices de Défauts................................................ 2 4.1.4 Appareil de Mesure.................................................................... 2 4.1.5 Interrupteur de Régulation du Courant........................................ 3 4.2 Qualité de la Coupe 4.2.1 Introduction ............................................................................... 3 4.2.2 Angle de la Coupe ..................................................................... 4 4.2.3 Planéité de la Coupe.................................................................. 5 4.2.4 État de Finition de la Surface...................................................... 6 4.2.5 Scories ...................................................................................... 7 4.2.6 Précision Dimensionnelle............................................................ 9 4.3 Le Choix de Gaz Influence la Qualité de la Coupe 4.3.1 Introduction ............................................................................... 10 4.3.2 Aluminium.................................................................................. 10 4.3.3 Acier au Carbone....................................................................... 11 4.3.4 Acier Inoxydable ........................................................................ 12 4.4 Données de Procédé 4.4.1 Introduction ............................................................................... 15 4.4.2 Caractéristiques de Réglage des Données de Procédé............... 16 Données de Marquage au Plasma ..................................... 4.4.3 Relation de la Largeur de la Saignée relative aux Ampères et l’Épaisseur du Matériel ......................................................................... 56 4.4.3.1 Aluminium - Valeurs des Saignées...................................... 78 4.4.3.2 Acier au Carbone - Valeurs des Saignées........................... 80 4.4.3.3 Acier Inoxydable - Valeurs des Saignées O2/N2/O2 .............. 83 4.4.3.4 Acier Inoxydable - Valeurs des Saignées Air/Air/CH4 ........... 84 4.4.3.5 Acier Inoxydable - Valeurs des Saignées N2/N2/CH4 ............ 85 4.4.3.6 Acier Inoxydable - Valeurs des Saignées N2/N2 ................... 86 4.4.3.7 Acier Inoxydable - Valeurs des Saignées Air/Air .................. 88 ii 78 Précision Plasma Régulation du Débit Électronique Table des Matières Section 5 Entretien 5.1 Général ............................................................................................. 1 5.2 Inspection et Nettoyage..................................................................... 1 5.3 PT-24 Description de la Torche ......................................................... 2 5.4 Entretien de la Torche ....................................................................... 5 5.5 PT-24 Démontage et Inspection de Consommables .......................... 7 5.6 PT-24 Ré-assemblage de l’Embout de la Torche ............................... 9 Section 6 Troubleshooting 6.1 General Safety .................................................................................. 1 6.2 Programmable Logic Controller (PLC) ............................................... 1 6.2.1 PLC LED Introduction............................................................... 2 6.2.2 PLC LED Functions .................................................................. 2 6.3 Troubleshooting Guide 6.3.1 Reduced Consumable Life ........................................................ 3 6.3.2 Poor Cut Quality........................................................................ 4 6.3.3 No Pilot Arc............................................................................... 4 6.3.4 No Arc Transfer......................................................................... 4 6.3.5 No Preflow ................................................................................ 4 6.3.6 Torch Fails to Fire ...................................................................... 4 6.3.7 Nozzle Life Extremely Short ....................................................... 5 6.3.8 Short Electrode Life ................................................................... 5 6.3.9 Short Electrode AND Nozzle Life ............................................... 5 6.4 Flow Control Schematic .................................................................... 6 6.5 Gas Flow Schematic ......................................................................... 7 6.6 Junction Box Wiring Diagram............................................................. 8 6.7 Junction Box Schematic..................................................................... 9 6.8 Precision Plasma Power Module Wiring Diagram ............................... 10-11 6.9 Power Module Schematic.................................................................. 12 6.10 Power Source Wiring Diagrams ....................................................... 13-17 6-11 Power Source Schematic................................................................ 18-19 iii Précision Plasma Régulation du Débit Électronique Table des Matières 6.12 Technical Guide to Using/Understanding the Operation of the EFC ... 20 6.12.1 Precision Process Timers ......................................................... 21 6.12.2 Process Timer Values .............................................................. 22 6.12.3 Process Window Key Functions ............................................... 23 6.12.4 Proportional Valve Analog Values for PARAM.CUT and DEF.TEC . 24 6.12.5 Process Gas Selection Requirements....................................... 25 6.12.6 EFC Process Gas Flow Chart ................................................... 26 6.12.7 Station On, Flush/Pressurize Cycle Timers................................ 6.12.8 Solenoid/Proportional Valve Requirements and Gas Error Monitoring Carbon Steel PG-O2, SG-O2 .................................................... 27 Carbon Steel PG-O2, SG-N2/O2 ............................................... 30 Carbon Steel PG-O2, Sg-O2 .................................................... 32 Stainless Steel PG-N2, SG-N2 ................................................. 34 Stainless Steel PG-N2, SG-N2/CH4 ........................................... 36 Stainless Steel PG-Air, SG-Air................................................. 38 Stainless Steel PG-Air, SG-Air/CH4 .......................................... 40 Aluminum PG-N2, SG- N2 ........................................................ 42 Aluminum PG-N2, SG-N2/CH4 .................................................. 44 Marking PG-Argon, SG-Air...................................................... 46 28 Section 7 Replacement Parts 7.1 General.............................................................................................. 1 7.2 Ordering ............................................................................................ 2 7.3 Plasmarc Power Source – Exterior Components ................................ 3 7.4 Plasmarc Power Source – Internal Components ................................. 8 7.5 Power Source Module ....................................................................... 18 7.6 EFC Junction Box .............................................................................. 26 7.7 Electronic Flow Control Box ............................................................... 7.8 PT-24 Torch Assembly EFC Series A/M ............................................ 32 36 7.9 T Gas Shut-off Valve Assembly - Series A/M Torch ............................ 38 7.10 PT-24 Torch Assembly – Version 1 .................................................. 40 7.11 Solenoid Assembly - EFC Torch – Version 1..................................... 42 Information Technique/Client Couverture Arrière du Manuel iv SECTION 1 SÉCURITÉ 1.1 Introduction Le procédé de découpage des métaux avec un équipement au plasma fournit un outil précieux et souple à l’industrie. Les machines de découpage ESAB sont conçues pour offrir un bon rendement et une utilisation sécuritaire. Pour atteindre une pleine utilité de la machine une attention particulière aux procédures d’opération, aux précautions et aux règles de sécurité est nécessaire. Toute personne, qu’elle soit impliquée dans l’opération, le service ou en tant qu’observateur, doit se conformer aux précautions établies et aux règles de sécurité. La négligence de certaines précautions peut entraîner des blessures corporelles sérieuses ou des dommages graves à l’équipement. Les précautions suivantes ne sont que des directives générales qui doivent être appliquées avec l’utilisation d’une machine à découpage. Des précautions plus détaillées relatives à la machine de base et aux accessoires se trouvent dans la littérature d’instruction. Pour des renseignements plus approfondis sur la sécurité concernant les appareils de découpage et de soudage, procurez-vous et consultez les publications listées dans les Références Recommandées. 1.2 Sécurité : Notations et Symboles ! ! DANGER ! AVERTISSEMENT ! ATTENTION ATTENTION AVIS Les mots et symboles qui suivent sont utilisés régulièrement dans ce manuel. Ils indiquent des niveaux variés de règles de sécurité requises. ALERTE ou ATTENTION. Votre sécurité est impliquée ou une défaillance potentielle de l’équipement existe. Utilisé avec d’autres symboles et renseignements. Utilisé pour porter une attention aux dangers immédiats qui risquent de causer des blessures corporelles graves ou la perte de vie. Utilisé pour porter une attention aux dangers potentiels qui risquent de causer des blessures corporelles ou la perte de vie. Utilisé pour porter une attention aux dangers qui risquent de causer des blessures corporelles mineures ou d’endommager l’équipement. Utilisé pour porter une attention aux dangers mineurs a l’équipement. Utilisé pour porter une attention aux renseignements importants concernant l’installation, l’utilisation ou l’entretien de la machine non reliés directement aux risques de sécurité. Précision Plasma avec Régulation du Débit Électronique – 1-1 SECTION 1 SÉCURITÉ 1.3 Renseignements Généraux de Sécurité ! AVERTISSEMENT ! AVERTISSEMENT Machine démarre automatiquement. Cet équipement se déplace en diverses directions et à des vitesses variantes. • Machinerie Machinerie en mouvement peut écraser. • Confiez toujours l’utilisation ou l’entretien de l’équipement au personnel qualifié. • Gardez tout le personnel, les matériaux et l’équipement nonnon-impliqués dans le procédé de la production dans un rayon sécuritaire à l’écart d du u système. • Gardez les supports pour l’équipement et les rails libres de débris ou obstructions, par exemple des outils ou des vêtements. • Séparez l’entière zone de travail par une clôture pour empêcher le personnel d’approcher la région environnant l’équipement. l’équipement. • Affichez des enseignes d’AVERTISSEMENT appropriées à l’entrée de chaque zone de travail. • Suivez la méthode de verrouillage avant de procéder à l’entretien. Tout défaut de suivre les instructions d’utilisation risque d’entraîner des blessures sérieuses ou la mort. Lisez et comprenez ce manuel d’utilisateur d’utilisateur avant d’opérer cette machine. 1-2 • Lisez la procédure entière avant d’opérer ou de procéder à un entretien du système. • Portez une attention particulière aux avertissements de danger. Ils communiquent des informations essentielles concernant la sécurité sécurité personnelle et/ou un dommage possible à l’équipement. • Toutes les précautions de sécurité relatives à l’équipement électrique et aux procédés d’utilisation doivent être strictement observées par toutes personnes ayant une responsabilité ou accès au systèm système. e. • Lisez toutes les publications de sécurité disponible par votre compagnie. Précision Plasma avec Régulation du Débit Électronique – SECTION 1 SÉCURITÉ ! AVERTISSEMENT Tout défaut de suivre les instructions d’avertissement de sécurité sur les étiquettes risque d’entraîner des blessures sérieuses ou la mort. Lisez et comprenez toutes les étiquettes d’avertissement de sécurité sur la machine. Référezmanuel nuel d’utilisateur pour des Référez-vous au ma renseignements de sécurité supplémentaires. 1. 4 Précautions relatives à l’Installation ! AVERTISSEMENT Tout équipement installé incorrectement risque d’entraîner une blessure ou la mort. Suivez Suivez ces directives pour l’installation de la machine: Ne connectez pas de cylindre directement à l’entrée de la machine. Un régulateur de cylindre approprié doit être installé sur un cylindre de gaz pour réduire la pression en une pression d’alimentation raisonnable à l’entrée. Le régulateur de la machine est ensuite utilisé pour obtenir la pression requise par la torche. Contactez votre représentant de ESAB avant l’installation. Il pourrait vous suggérer de plus amples précautions concernant l’installation l’installation de la tuyauterie et le levage de la machine etc. pour vous assurer une sécurité maximale. Évitez toutes modifications à la machine ou ajouts d’appareil avant de consulter un représentant qualifié de ESAB. Observez les exigences de dégagement autour de la machine pour obtenir une utilisation efficace et une sécurité personnelle. Précision Plasma avec Régulation du Débit Électronique – 1-3 SECTION 1 SÉCURITÉ 1.5 Mise à la Terre Électrique Une mise à la terre électrique est essentielle pour une utilisation efficace de la machine et la SÉCURITÉ. Référez-vous à la section d’installation de ce manuel pour des instructions détaillées concernant la mise à la terre. ! AVERTISSEMENT Risque de Choc Électrique. Une mise à la terre incorrecte peut causer des blessures sérieuses ou la mort. La machine doit être mise mise à la terre correctement avant de mettre en service. ! AVERTISSEMENT 1-4 Une mise à la terre incorrecte peut endommager la machine et les composants électriques. • La machine doit être mise à la terre correctement avant de mettre en service. • La table de découpage doit être mise à la terre correctement et reliée à un bon piquet de prise de terre. Précision Plasma avec Régulation du Débit Électronique – SECTION 1 SÉCURITÉ 1.6 Utilisation de la Machine à Découpage au Plasma ! AVERTISSEMENT ! AVERTISSEMENT Risques de projection de débris et de bruit extrêmement élevé. • Éclaboussement chaud peut brûler et blesser les yeux. AssurezAssurez-vous de porter des lunettes pour protéger vos yeux contre les brûlures et les projections de débris générées pendant l’utilisation. • Les laitiers de coupe écaillés peuvent être être chauds et projetés à des distances considérables. Les personnes se trouvant à proximité doivent également porter des lunettes de sécurité. • L’arc au plasma produit un bruit élevé qui peut Assurez--vous de portez endommager l’ouïe. Assurez une protection auditive efficace pendant les procédés de découpage auau-dessus de l’eau. Risque de brûlure. Le métal chaud peut brûler. • Ne touchez pas à la plaquette de métal ni aux autres pièces immédiatement après le découpage. Permettez a au u métal un temps de refroidissement ou trempeztrempez-le dans l’eau. • Ne touchez pas à la torche au plasma immédiatement après le découpage. Permettez à la torche un temps de refroidissement. Précision Plasma avec Régulation du Débit Électronique – 1-5 SECTION 1 SÉCURITÉ ! AVERTISSEMENT ! AVERTISSEMENT Danger : haute tension. Choc électrique peut vous tuer. • Ne touchez PAS à la torche au plasma, la table de découpage ou les liaisons par câble durant le procédé de découpage au plasma. • Coupez toujours l’alimentation électrique de la machine avant de toucher ou de procéder à l’entretien de la torche au plasma. • Coupez toujours l’alimentation électrique de la machine avant d’ouvrir ou de procéder à l’entretien de la plomberie ou de la boîte de régulation du débit. • Ne touchez pas aux pièces électriques sous tension. • Gardez tous les panneaux et couvercles en place quand la machine est branchée à la source d’énergie. • IsolezIsolez-vous adéquatement de la pièce à tailler et de la mise à la terre électrique : portez des gants, chaussures et vêtements isolants. • Gardez vos gants, chaussures, vêtements, vêtements, l’espace de travail et l’équipement au sec en tout temps. Risque de pincement. Les coulisses verticales mobiles peuvent écraser ou pincer. Gardez vos mains éloignées de la torche et de la l’utilisation. on. coulisse pendant l’utilisati 1-6 Précision Plasma avec Régulation du Débit Électronique – SECTION 1 ! SÉCURITÉ AVERTISSEMENT Risque de vapeurs. Les vapeurs et les gaz générés par le procédé de découpage au plasma peuvent poser un risque sérieux à votre santé. ! AVERTISSEMENT • Ne respirez PAS les vapeurs. • N’utilisez pas la torche au plasma sans avoir correctement mis en marche le système d’évacuation de vapeur. • Appropriez une ventilation additionnelle pour évacuer les vapeurs si nécessaire. • Utilisez un respirateur approuvé si la ventilation n’est pas adéquate. Risque de rayonnement. Les rayons provenant de l’arc peuvent blesser les yeux et brûler la peau. • AssurezAssurez-vous de porter une protection adéquate pour les yeux et le corps. • Portez des lunettes de sécurité fumées ou des lunettes à écrans latéraux. Référez Référezéférez-vous au tableau suivant pour les teintes des lentilles recommandées pour le découpage au plasma: Courant dans l’arc Lentilles Jusqu'à 100 A Teinte No. 8 100Teinte No. 10 100-200 A 200200-400 A Teinte No. 12 Plus de 400 Teinte No. 14 400 A • Remplacez vos lunettes dès que les lentilles sont marquées ou brisées. • Avertissez les personnes se trouvant à proximité de la machine de ne pas regarder l’arc directement sans avoir une protection adéquate couvrant les yeux. • Préparez l’aire de découpage pour réduire les réflexions et la transmission des lumières ultraviolettes. • Peinturez les murs et autres surfaces avec des teintes foncées pour réduire les réflexions. • Installez des écrans protecteurs ou des rideaux pour réduire réduire les transmissions ultraviolettes. Précision Plasma avec Régulation du Débit Électronique – 1-7 SECTION 1 SÉCURITÉ ! AVERTISSEMENT La Rupture d’un Cylindre de Gaz peut Tuer. Les cylindres de gaz traumatisés peuvent éclater et produire une libération dangereuse des gaz. 1-8 • Évitez la manipulation brutale des cylindres. • Gardez les valves des cylindres cylindres fermées lorsqu’ils ne sont pas utilisés. • Maintenez les conduits et les accessoires en bon état. • Sécurisez toujours les cylindres dans une position verticale retenus par des chaînes ou des attaches à un objet convenable et stable ne faisant pas partie d’un circuit électrique. • Trouvez un emplacement pour les cylindres éloigné de la chaleur, les étincelles et les flammes. Ne frottez jamais l’arc contre un cylindre. • RéférezRéférez-vous à CGA Standard PP-1, « Precautions for Safe Handling of Compressed Gases Gases in Cylinders », disponible du « Compressed Gas Association ». Précision Plasma avec Régulation du Débit Électronique – SECTION 1 SÉCURITÉ ! AVERTISSEMENT Risque d’étincelle. La chaleur, les éclaboussements et les étincelles peuvent causer des feux et des brûlures. • N’exécutez jam jamais ais de découpage près des matériaux combustibles. • N’exécutez jamais le découpage d’un contenant ayant servi pour d’autres combustibles. • Ne gardez pas de combustibles sur votre personne (e.g. briquet au butane). • L’arc pilote peut occasionner des brûlures. Gardez la buse de la torche éloignée de votre corps et de toutes autres personnes pendant l’activation du procédé au plasma. • AssurezAssurez-vous d’une protection adéquate pour les yeux et le corps entier. • AssurezAssurez-vous de porter des gants à crispins, chaussures res de sécurité et un casque de des chaussu sécurité. • AssurezAssurez-vous de porter des vêtements ininflammables couvrant toutes les parties du corps exposées. • AssurezAssurez-vous de porter des pantalons sans rebords pour prévenir l’entrée des étincelles et des laitiers. Précision Plasma avec Régulation du Débit Électronique – 1-9 SECTION 1 SÉCURITÉ ATTENTION LE DÉCOUPAGE AU-DESSUS DE L’EAU PEUT ENTRAÎNER UN RENDEMENT MÉDIOCRE. La PT-24 est conçue pour les procédés de découpage au sec. Le découpage auau-dessus de l’eau peut entraîner les résultats suivants : • une durée de vie consommable réduite • dégradation de la qualité qualité de la coupe Le découpage auau-dessus de l’eau peut entraîner un rendement de découpage médiocre. Une vapeur d’eau est créée par le contact des matériaux échauffés ou les étincelles avec un liquide et peut entraîner un amorçage à l’arc à l’intérieur de la torche. Pendant le procédé de découpage sur une table à eau, réduisez le niveau d’eau pour permettre le maximum d’espace libre entre l’eau et le matériel. ! AVERTISSEMENT Risque d’explosion. Certains alliages aluminiumaluminium-lithium liquide (Al(Al-Li) peuvent provoquer des explosions lorsque le découpage au plasma est effectué auau-dessus de l’eau. N’exécutez pas de découpage au plasma pour les alliages AlAl-Li suivant avec l’eau: Alithlite (Alcoa) Alithally (Alcoa) 2090 Alliage (Alcoa) X8090A (Alcoa) X8092 (Alcoa) 1-10 X8192 (Alcoa) Navalite (US Navy) Navy) Lockalite (Lockheed) Kalite (Kaiser) 8091 (Alcan) • Ces alliages doivent être coupés au sec seulement et sur une table sèche. • N’exécutez PAS de découpage au sec auaudessus de l’eau. • Contactez votre fournisseur fournisseur d’aluminium pour des renseignements de sécurité additionnels par rapport aux risques associés à ces alliages. Précision Plasma avec Régulation du Débit Électronique – SECTION 1 SÉCURITÉ 1.7 Précautions relatives à l’entretien ATTENTION Établissez et adhérezadhérez-vous à un entretien préventif. Un programme programme composé peut être établi à partir des plans recommandés dans la littérature d’instruction. Ne laissez jamais des appareils d’essais ou des petits outils sur la machine. L’équipement (ou la machine) peut subir des dommages électriques ou mécaniques mécaniques graves. ! ATTENTION Prenez toutes les précautions nécessaires en sondant les circuits avec un oscilloscope ou un voltmètre. Les circuits intégrés sont susceptibles à des dommages dus à la surtension. Mettez toujours la machine hors hors tension avant l’utilisation des sondes d’essai pour prévenir les courtcourt-circuits accidentels des composants. Avant d’alimenter la machine assurezassurez-vous que toutes les plaquettes de circuit imprimé sont bien fixées dans leurs supports, tous les câbles son sontt bien branchés, toutes les armoires sont fermées à clef, et tous les dispositifs de protection et les couvercles sont remis en place. Ne JAMAIS branché ou débranché une plaquette à circuit imprimé pendant que la machine est alimentée. Une surcharge inst instantanée antanée de tension électrique ou de courant peut endommager les composants électriques. Précision Plasma avec Régulation du Débit Électronique – 1-11 SECTION 1 SÉCURITÉ 1.8 Références Relatives à la Sécurité Les publications recommandées ci-dessous ont une renommée nationale concernant la sécurité des opérations de soudage et de découpage. Ces publications sont préparées dans le but de protéger les personnes contre les blessures ou les maladies et de protéger l’équipement contre les dommages matériels provenant des méthodes opératoires dangereuses. Bien que quelques publications ne soient pas spécifiquement établies pour ce type d’appareil de découpage industriel, les principes de sécurité sont les mêmes. 1-12 • “Precautions and Safe Practices in Welding and Cutting with Oxygen-Fuel Gas Equipment,” Form 2035. ESAB Cutting Systems. • “Precautions and Safe Practices for Electric Welding and Cutting,” Form 52-529. ESAB Cutting Systems. • “Safety in Welding and Cutting” - ANSI Z 49.1, American Welding Society, 2501 NW 7th Street, Miami, Florida, 33125. • “Recommended Safe Practices for Shielded Gases for Welding and Plasma Arc Cutting” AWS C5.10-94, American Welding Society. • “Recommended Practices for Plasma Arc Welding” - AWS C5.1, American Welding Society. • “Recommended Practices for Arc Cutting” AWS C5.2, American Welding Society. • “Safe Practices” - AWS SP, American Welding Society. • “Standard for Fire Protection in Use of Cutting and Welding Procedures” - NFPA 51B, National Fire Protection Association, 60 Batterymarch Street, Boston, Massachusetts, 02110. • “Standard for Installation and Operation of Oxygen - Fuel Gas Systems for Welding and Cutting” - NFPA 51, National Fire Protection Association. Précision Plasma avec Régulation du Débit Électronique – SECTION 1 SÉCURITÉ • “Safety Precautions for Oxygen, Nitrogen, Argon, Helium, Carbon Dioxide, Hydrogen, and Acetylene,” Form 3499. ESAB Cutting Systems. Obtainable through your ESAB representative or local distributor. • "Design and Installation of Oxygen Piping Systems," Form 5110. ESAB Cutting Systems. • “Precautions for Safe Handling of Compressed Gases in Cylinders”, CGA Standard P-1, Compressed Gas Association. De la littérature applicable aux règles de sécurité concernant le soudage et le découpage avec des matériaux gazeux est aussi disponible au Compressed Gas Association, Inc 500 Fifth Ave., New York, NY 10036. Précision Plasma avec Régulation du Débit Électronique – 1-13 SECTION 1 SÉCURITÉ Cette page est en blanc intentionnellement. 1-14 Précision Plasma avec Régulation du Débit Électronique – SECTION 2 DESCRIPTION 2.1 Général Le Système de Précision Plasmarc comprend quatre composants distincts. La source (bloc) d’alimentation, la boîte de jonction, la boîte de régulation du débit et la torche PT-24. La source (bloc) d’alimentation fournit le courant et le refroidissement à la torche PT-24 par l’entremise de la boîte de jonction. 2.2 Objectif Le but de ce manuel est de fournir à l’utilisateur toutes les informations requises pour installer et opérer le Système de Précision Plasmarc. Des matériaux de référence technique sont aussi inclus pour aider dans le dépannage de l’ensemble de découpage. 2.3 Options d’Ensemble Disponibles Les options d’ensembles Précision Plasmarc sont disponibles par l’entremise de votre détaillant ESAB Précision Plasmarc – Source (bloc) d’Alimentation ( 200/230/380/415/460/575) 3P/N 37358 phase 50/60 Hz (requis) - Version CE Boîte de Régulation du Débit Électronique (requise) Boîte de Jonction (requise) Torche PT-24 Débit Électronique - Séries A/M (1 unité requise) Faisceau d’Alimentation (une longueur requise) Faisceau de Ligne à Gaz (une longueur requise) Câble Standard Conducteur de Régulation – Console du Débit à la Boîte de Jonction (une longueur requise) Câble souple (recommandé pour les applications relatives à la voie d’alimentation ) 4.5 pi. (1.4 m) 12 pi. (4.4 m) 17 pi. (5.2 m) 12 pi. (3.6 m) 25 pi. (7.6 m) 40 pi. (12.2 m) 60 pi. (18 m) 80 pi. (24.4 m) 100 pi. (30 m) 10 pi. (3 m) 20 pi. (6 m) 30 pi. (9 m) 60 pi. (18 m) 100 pi. (30 m) 10 pi. (3 m) 20 pi. (6 m) 30 pi. (9 m) 60 pi. (18 m) 100 pi. (30 m) 10 pi. (3 m) 20 pi. (6 m) 30 pi. (9 m) 40 pi. (12 m) 60 pi. (18 m) 100 pi. (30 m) Précision Plasma avec Régulation du Débit Électronique – P/N 22406 P/N 22407 P/N 0558001463 P/N 0558001877 P/N 0558001464 P/N 22428 P/N 21905 P/N 22504 P/N 21906 P/N 22505 P/N 21907 P/N 37533 P/N 37534 P/N 37535 P/N 37536 P/N 37537 P/N 21917 P/N 21918 P/N 21919 P/N 21920 P/N 21921 P/N 56997111 P/N 56997112 P/N 56997113 P/N 0560986745 P/N 56997114 P/N 56997115 2-1 SECTION 2 DESCRIPTION Conducteur de Régulation – Source d’Alimentation à la Machine de Découpage E/S 30 pi. (9.1 m ) P/N 57002248 50 pi. (15.2 m) P/N 57002249 75 pi. (22.8 m ) P/N 57002250 100 pi. (30.5 m) P/N 57002251 160 pi. (48.8 m) P/N 57002252 Câble d’Alimentation à Haute Fréquence – Source (bloc) d’Alimentation à la Boîte de Jonction – ou- Source (bloc) d’Alimentation à la Machine de Découpage E/S, selon la configuration 3 pi. (.9 m) P/N 57000419 50 pi. (15.2 m) P/N 57000420 75 pi. (22.8 m) P/N 57000421 100 pi. (30.5 m) P/N 57000422 125 pi. (38.1 m) P/N 57000423 150 pi. (45.7 m) P/N 57000424 175 pi. (53.3 m) P/N 57000425 200 pi. (61 m) P/N 57000426 Refroidisseur pour la Torche (contenants d’un gallon (3.8 L). Quatre gallons P/N 156F05 (15 L) requis) NOTES: • Conducteur de Régulation reliant la source d’alimentation au CNC du client est fourni selon la commande du client. • Le client doit fournir l’alimentation en gaz, les boyaux, les câbles de masse et les câbles d’entrée primaires. • Voir les Données de Procédé pour une liste des pièces consommables de la torche. 2.4 Précision Plasma : Spécifications Techniques 2.4.1 Système de Précision au Plasma 2-2 Tension Électrique - Entrée 200/230/380/415/460/575 V 3 phase 50/60 Hz Courant d’Entrée 65/60/50/40/30/25 A par phase Facteur d’Alimentation 0.95 Portée du Courant d’Entrée 15-100 A dc Tension Électrique du Conducteur de Sortie 120 V dc Cycle de Service 100% Tension Électrique du Circuit Ouvert 315 V dc Précision Plasma avec Régulation du Débit Électronique – SECTION 2 DESCRIPTION BOÎTE DE JONCTION SOURCE (BLOC) D’ALIMENTATION 6.75" (171mm) P IL O T A RC C ON T RO L 10.62" (270mm) P O WR E 19.75" (502mm) C URE N T RECISION PLASMA RC POIDS = 26.5 lbs.(12 kg) 44" (1118mm) BOÎTE DE RÉGULATION DU DÉBIT ÉLECTRONIQUE 42" (1067mm) 22" (559mm) 14.5" (1118mm) POIDS = 560 lbs. (254 kg) ME T H N 2 O2 O 2 H 3- 5 N2 A IR N2 A IR S H IE D L GAS S H IE D L GAS P A L S MA GA S P A L S MA G A S N O .1 N O .2 N O .1 N O .2 N IT R G OE N N IT R G OE N OX Y GE N M E T HAN E N IT R G OE N OX Y GE N 12.25" (311mm) H Y R DOG E N A IR A IR AR O GN 12" (305mm) POIDS = 51 lbs. (23 kg) Précision Plasma avec Régulation du Débit Électronique – 2-3 SECTION 2 DESCRIPTION 2.4.2 Gaz au Plasma : Spécifications Techniques Type O2, N2, Air Pression 125 psig (8.6 bars) 100 cfh (47 l/min) max. (varie selon l’application) O2-99.995% N2-99.995% Air-propre, sec et sans huiles Oxygène: R-76-150-540LC (P/N 19777) Gaz inerte: R-76-150-580LC (P/N 19977) Oxygène: R-77-150-540 (P/N 998337 Hydrogène/Méthane:R-77-150-350 (P/N 998342) Nitrogène: R-77-150-580 (P/N 998344) Air Industriel: R-77150=590 (P/N 998348) Débit Pureté Requise* Recommandé : Mano-détendeurs de Service pour Cylindres Liquides Recommandé : Mano-détendeurs 2Phases pour Cylindres Recommandé : Mano-détendeurs de Station ou de Canalisation - Débit Élevé - Série Lourde Recommandé : Mano-détendeurs de Station ou de Canalisation de Haute Capacité Oxygène: R-76-150-024 (P/N 19151) R-6703 (P/N 22236) 25 microns avec cuvette protectrice (P/N 56998133)) Filtre à Gaz Requis 2.4.3 Gaz de Démarrage : Spécifications Techniques Type N2, Air Pression 125 psig (8.6 bar) 60 cfh (28 l/min) max (varie selon l’application) 99.995% Débit Pureté Minimum Requise 2.4.4 Gaz Secondaire : Spécifications Techniques Type Pression Débit Pureté Minimum Requise N2, O2, H-35, Méthane, Air 100 psi (6.6 bar) H-35, Méthane; 125 psi (8.6 bar) N2, O2, Air 60 cfh (28 l/min) max (varie selon l’application) 99.995% 2.4.5 Torche Pt-24 : Spécifications Techniques 2-4 Type Refroidi à l’eau, Gaz Double Valeur Nominale 100 A @ 100 % cycle de service Dimensions Voir Options d’Ensemble (2.3) Précision Plasma avec Régulation du Débit Électronique – SECTION 3 INSTALLATION 3.1 Général AVIS 3.2 Équipement Requis Une installation effectuée correctement du Système de Précision Plasmarc peut contribuer à une utilisation efficace et sans problèmes. Il est fortement suggéré d’étudier chaque étape dans cette section et de suivre les instructions soigneusement. • • • • 3.3 Emplacement • • • ! ATTENTION Alimentation en Gaz et Boyaux. L’Alimentation en gaz peut provenir d’une source en vrac ou d’une banque de cylindres distributeurs et réglés à une alimentation de 25 psi (8.6 bar) au Régulateur du Débit (le débit du gaz). Câble de Masse. Un câble AWG No. 4 est recommandé pour la connexion de la pièce ouvrée à la source d’alimentation. Câble d’Entrée Primaire. Filtres à gaz de 25 microns (ou plus) sont requis sur le côté de l’alimentation pour un fonctionnement efficace du EFC. Une ventilation est nécessaire pour fournir un refroidissement adéquat à la source (bloc) d’alimentation. Efforcez-vous de garder la saleté, la poussière et l’exposition aux sources de chaleur au minimum. Prévoyez un minimum de deux pieds d’espace libre autour de la source (bloc) d’alimentation pour une circulation d’air adéquate. Ne Restreignez pas la Circulation d’Air Une restriction de l’entrée d’air par l’entremise de tout genre de filtre placé sur ou autour de la source (bloc) d’alimentation peut entraîner une annulation de la garantie. Précision Plasma avec Régulation du Débit Électronique - 3-1 SECTION 3 INSTALLATION 3.4 Connexions de l’Entrée Électrique Primaire ! DANGER Le Choc Électrique Peut Tuer! Assurez-vous d’une protection maximale contre le choc électrique. Avant de procéder aux connexions dans la machine, ouvrez l’interrupteur d’isolement de ligne (mur) et débranchez le câble d’alimentation. ! AVERTISSEMENT Configuration de l’Alimentation d’Entrée La machine doit être configurée correctement pour votre alimentation d’entrée. La machine est configurée chez le manufacturier pour une entrée de 575 V, 60 Hz. Ne connectez PAS de source d’alimentation réglée pour une autre tension électrique à moins d’une reconfiguration de la machine. L’équipement subira des dommages. Connexion de l’Alimentation d’Entrée au Mur Un interrupteur d’isolement de ligne (mur) contenant des fusibles ou un disjoncteur doit être disponible sur le panneau de distribution d’alimentation principal. Connectez le câble d’entrée de la source d’alimentation directement à l’interrupteur d’isolement ou procurez-vous une fiche et une prise appropriés chez votre détaillant en électricité. (Voir le tableau qui suit pour les recommandations relatives aux conducteurs d’entrée et aux fusibles) Grandeurs Recommandées pour Conducteurs d’Ent d’Entrée rée et Fusibles de Ligne Entrée & Calibres des conducteur de fusibles/ phase, terre, Phase Ampères ampères 2 cu/awg/mm 3 70 No. 4 25 100 3 60 No. 6 16 80 3 50 No. 8 10 80 3 40 No. 10 6 60 3 30 No. 10 6 50 3 25 No. 10 6 40 Exigences d’Entrée Volts 208 230 380 415 460 575 3-2 Précision Plasma avec Régulation du Débit Électronique - SECTION 3 INSTALLATION La procédure suivante explique les étapes d’installation nécessaires pour la connexion de l’alimentation électrique primaire à la source (bloc) d’alimentation. 1. Enlevez le panneau du côté droit. 2. Assurez-vous que le câble de l’entrée d’alimentation est débranché de toute source électrique. Connexion de Mise à la Terre TB2 Câble de l’Alimentation 3. Acheminez le câble de l’alimentation d’entrée à d’Entrée travers le réducteur de tension situé prés du (Fourni par le Client) panneau arrière. K1 200 230 380 415 460 575 Contacteur Principal PHASE 2 PHASE 3 200 230 380 415 460 575 PHASE 1 200 230 380 415 460 575 TB1 200 230 380 415 460 575 Bloc de Raccordement - 7 Positions AutoTransformateur Régulation par le Manufacturier à 575 volts ! ATTENTION 4. Tirez le câble d’alimentation d’entrée à travers le réducteur de tension pour permettre aux fils une longueur suffisante pour la connexion au contacteur principal. Resserrez le réducteur de tension pour assurer que le câble de l’alimentation d’entrée est sécurisé. 5. Connectez le fil de terre du câble d’alimentation d’entrée à la borne de mise à la terre présente sur la base de la source d’alimentation. 6. Connectez les trois conducteurs de courant du câble d’alimentation d’entrée aux terminaux situés sur le dessus du contacteur principal. Serrez chaque vis pour sécuriser les conducteurs. 7. Connectez les câbles de liaison d’alimentation dans le bas du contacteur principal à la tension électrique d’entrée appropriée selon les indications sur l’autotransformateur. L’unité est réglée par le manufacturier à 575 V (démontrée à la gauche). Connexion des liaisons d’alimentation d’entrée AssurezAssurez-vous que chaque câble de liaison d’alimentation est connecté à la tension d’entrée appropriée sur l’autotransformateur. Câblage réglé par le Manufacturier à 575 volts 8. Connectez le fil de liaison au connecteur ayant la tension d’entrée appropriée située sur le bloc de raccordement à sept positions. TB2 Précision Plasma avec Régulation du Débit Électronique - 3-3 SECTION 3 INSTALLATION 3.5 Lignes d’Interconnexion Noir Rouge -Orange Jaune Bleu 1. Tous les branchements d’interconnexion fournis sont numérotés ou codés par couleur à chaque extrémité avec les numéros/couleurs correspondants indiqués sur l’armoire. Plaquette de Support Faisceau de Ligne à Gaz Installation du Faisceau de Ligne à Gaz 3-4 2. Connectez les quatre lignes dans le Faisceau de Ligne à Gaz à la Boîte de Régulation du Débit et la Boîte de Jonction. Les lignes et les connexions son codées par couleur. De plus, les espacements entre les ouvertures sur la plaquette de support sont asymétrique pour prévenir une mauvaise connexion. L’ordre des couleurs doit être: bleu, jaune, rouge/orange, noir. Précision Plasma avec Régulation du Débit Électronique - SECTION 3 INSTALLATION Connexion de la Source d’Alimentation et du EFC à la Boîte de Jonction Faisceau de la Source d’Alimentation Source d’Alimentation Connexion Négative 3. Connectez les lignes d’alimentation et de refroidissement (venant du Faisceau Connexion d’Alimentation) de la source d’alimentation à la Boyau #7 boîte de jonction. Le faisceau d’alimentation (de la Source d’Alimentation) comprend des lignes de refroidissement #6 et # 7 (avec connecteurs 5/8-18 L.H.), un câble d’alimentation (#3 AWG) et un câble jaune pour l’arc pilote (#16 AWG). Les deux lignes de refroidissement sont marquées d’un 6 ou d’un 7 sur le connecteur pour assister à l’identification. Connexion Arc Pilote Connexion Boyau #6 (à la Source d’Alimentation) Connexions Faisceau Connexion de Ligne à Gaz du Conducteur de Régulation du EFC Précision Plasma avec Régulation du Débit Électronique - 3-5 de la Torche SECTION 3 INSTALLATION Connexions Boyau/Câble d’Alimentation de la Torche 4. Connectez les conducteurs et les boyaux du Faisceau de la Torche à la Boîte de Jonction. (voir le schéma du Bloc d’Interconnexion) Boîte de Jonction à la Torche Faisceau de la Torche 3-6 Connexion de l’Arc Pilote de la Torche Précision Plasma avec Régulation du Débit Électronique - SECTION 3 INSTALLATION Précision Plasmarc - Schéma d’Interconnexion des Composants 1 2 3 4 5 ASIOB N2 O2 CH4 Air Ar 7 6 8 9 10 11 12 13 15 14 1 2 3 4 5 6 7 8 9 10 11 12 13 14 25 micron - Filtres EFC Conducteur de Régulation EFC/Boîte de Jonction CNC Haute Fréquence 120VAC Faisceau ligne á gaz Haute Fréquence 120VAC Faisceau d’Alimentation Boîte de Jonction Torche Table de Découpage Câble de Masse Câble d’Alimentation Primaire Piquet de Prise de Terre 15 Conducteur de Régulation Source d’Alimentation au CNC Précision Plasma avec Régulation du Débit Électronique - 3-7 SECTION 3 ! INSTALLATION Une Contamination de la Ligne à Gaz Entraînera des Dommages aux Valves Proportionnelles. ATTENTION Purgez les Lignes à Gaz Avant de connecter les lignes d’alimentation de gaz au Régulateur Régulateur du Débit Électronique purgez toutes les lignes complètement. Des résidus provenant de la fabrication du boyau peuvent boucher/endommager les valves proportionnelles dans votre EFC. 5. Purgez les lignes à gaz entre l’alimentation et le EFC avant de procéder à la connexion. Les valves proportionnelles dans le EFC sont très sensibles à la poussière et toute particule étrangère. 1/4 NPT 6. Connectez les lignes d’alimentation de Gaz au Régulateur du Débit Électronique. Installez des filtres à Gaz de 25 microns dans toutes les lignes d’alimentation entre les sources de gaz et le EFC. 25 micron – Filtre à Gaz 25µFiltres N2 3-8 O2 CH4 Air Ar Précision Plasma avec Régulation du Débit Électronique - SECTION 3 INSTALLATION Enlevez le Panneau de Service Pilot Arc Work Torch Pilot Arc 7. Enlevez le panneau arrière de la console et attachez l’arc pilote, la torche et le câble de masse. Work Torch Source d’Alimentation Conducteur de Régulation CNC 600 A Fusible Commun Conducteur de Régulation du Débit Étiquette de classement Étiquette de série 8 . Connectez le conducteur de régulation entre la console et le Régulateur du Débit Électronique. Connectez les lignes de refroidissement provenant du Faisceau d’Alimentation. Refroidisseur entrant de la Torche – Connexion # 6 Refroidisseur sortant à la Torche – Connexion # CONDUCTEUR DE RÉGULATION Précision Plasma avec Régulation du Débit Électronique - 3-9 SECTION 3 INSTALLATION 3.6 Assemblage de la Torche ATTENTION Ne Pas Couvrir le Trou d’Évent. Pendant l’assemblage, ne couvrez pas le petit trou d’évent situé sur le côté du manchon. Dans le cas d’un bris dans le branchement ce trou per permet met au liquide de refroidissement de s’égoutter de l’intérieur du manchon. Options d’Assemblage de la Torche. Collet 1.812" (46mm) Diamètre Manchon 2.0" (51mm) Diamètre • Normalement la torche est assemblée par le manchon de 2.0 pouces de diamètre (51mm). Ne pas couvrir le trou d’évent. • Pour un assemblage alternatif personnalisé, la torche peut être assemblée par le collet de 1.812" de diamètre (46 mm) illustré. Ce collet isolé et son épaulement sont usinés en relation avec le filet du dispositif de retenue de la buse situé sur le corps de la torche. • Utilisez seulement les surfaces d’assemblage spécifiées. Trou d’Évent 3-10 Précision Plasma avec Régulation du Débit Électronique - SECTION 3 INSTALLATION 3.7 Refroidisseur de la Torche PILOT ARC L CONTRO POWER T CURREN RECISION PLASMARC Bouchon du Réservoir de Refroidissement ! ATTENTION • Enlevez le bouchon couvrant le réservoir de liquide de refroidissement sur le devant de la console et remplissez ce réservoir avec 4 gallons (15 litres) de liquide de refroidissement, P/N 156F05 (un gallon). • Ne remplissez pas au-dessus du niveau maximum. • Réinstallez le bouchon. L’Emploi d’un Antigel Commercial Entraînera un Mauvais Fonctionnement de la Torche Utilisez un Refroidisseur Spécialement Conçu pour la Torche! P/N156F05 N’utilisez PAS de l’eau courante ou de l’antigel commercial pour le refroidissement de la torche en raison de la conductivité électrique élevée. Un refroidisseur conçu spécialement pour la torche est REQUIS. Ce refroidisseur protège aussi de la congélation à – 34° C. Si l’unité est mise en fonction sans refroidisseur la pompe de refroidissement subira des dommages permanents. 3.8 Inspection des Lignes à Gaz et de Refroidissement Pour compléter l’installation, il est nécessaire d’inspecter les connexions assemblées en chantier pour la possibilité de fuite. • Pour les lignes à gaz, utilisez une solution savonneuse standard. Mettez le système sous pression à partir du régulateur (fichier SDP) • Refroidisseur- surveillez les connexions pour toute trace d’humidité. Précision Plasma avec Régulation du Débit Électronique - 3-11 SECTION 3 INSTALLATION 3.9 Remplacement de l’EPROM dans le Contrôleur de Logique Programmable (PLC) de la Source (Bloc) d’Alimentation Le Système de Précision Plasmarc peut être configuré pour une régulation du débit manuelle (Série “A”) à l’expédition. Dans ce cas, le EPROM dans le Contrôleur de Logique Programmable doit être remplacé par un EPROM EFC expédié avec la source (bloc) d’alimentation. ! ATTENTION Les Composants du Système Peuvent Subir des Dommages si le Mauvais EPROM est Utilisé. La Série “ A” et les EPROM EFC sont programmés avec des logiciels différents. Le EPROM EFC ne reconnaît pas les entrées pour les interrupteurs de pression du gaz de transformation et n’inclut pas le purgeur de gaz de transformation requis pour la Série “ A” . ! ATTENTION La Manipulation sans Précautions Peut Endommager les Composants Électroniques. Manipulez les composants électroniques avec soins. • N’échappez pas les composants électroniques • Ne pliez pas les tiges • Ne touchez pas aux composants de circuit – manipulez sur les bords si possible ! ATTENTION Les Composants Électroniques peuvent Subir des Dommages Provenant d’une Décharge Électro-Statique (ESD) Les pièces du Circuit Intégré sont susceptibles aux surtensions. Il est possible que les dommages ne soient pas visibles immédiatement mais ils apparaîtront sous forme de défaillance prématurée. Le EPROM EFC est expédié dans un sac antistatique. Entreposez le EPROM dans ce sac. Portez une talonnière anti-statique protectrice lorsque vous manipulez des composants électroniques sensibles. 3-12 Précision Plasma avec Régulation du Débit Électronique - SECTION 3 ! INSTALLATION Le Choc Électrique Peut Tuer! AVERTISSEMENT Débranchez le câble d’alimentation (au mur) de la source (bloc) d’alimentation avant de faire des connexions ou des ajustements à l’intérieur de la source (bloc) d’alimentation. 1. Assurez-vous que la Source (bloc) d’Alimentation Plasmarc est débranchée de la source d’électricité. PILOT ARC CONTROL POWER CURRENT RC N PLASMA RECISIO 2. Exposez le PLC en enlevant le panneau du côté gauche de la Source (bloc) d’Alimentation Plasmarc. Panneau de gauche 3. Ouvrez le couvercle du EPROM sur le PLC pour exposer le EPROM. PLC Emplacement du EPROM EFC à l’expédition Précision Plasma avec Régulation du Débit Électronique - 3-13 SECTION 3 INSTALLATION ATTENTION L’Utilisation d’un Outil d’Extraction pour le EPROM Peut Endommager le Connecteur L’enlèvement forcé d’un EPROM encastré dans le PLC peut causer un bris du connecteur/EPROM. Un Connecteur d’EPROM Spécial à Zéro Force est utilisé pour éliminer le besoin d’outil. EPROM Levier Sécurisé 4. Retirez le EPROM du connecteur. CECI NE NÉCESSITE PAS L’UTILISATION D’UN OUTIL D’EXTRACTION. Relâchez le levier sécurisant le EPROM en place et sortez le EPROM Série “A” de son connecteur. 5. Enlevez le EPROM EFC de son emballage. 6. Alignez soigneusement les tiges du EPROM EFC avec les trous du connecteur et insérez-le. 7. Sécurisez le EPROM en replaçant le levier tout en tenant le EPROM en place. 8. Replacez le couvercle du EPROM et le panneau du côté gauche de la Source (bloc) d’Alimentation. EPPESA= Série “A” EPROM, régulation du débit manuelle P/N 99513607 EPROM Levier Relâché 3-14 EPPSEFC= EFC EPROM, régulation du débit électronique P/N 99513608 Précision Plasma avec Régulation du Débit Électronique - SECTION 4 OPÉRATION 4.1 Commandes de la Source (bloc) d’Alimentation 4.1.1 Interrupteur d’Alimentation Principal LOW DO NOT SWITCH WHILE CUTTING Interrupteur d’Alimentation Principal Contrôle l’entrée d’alimentation au ventilateur, refroidisseur d’eau et la carte PC. Lumière indicatrice de couleur ambre à la gauche de l’interrupteur. EMERGENCY STOP 4.1.2 Interrupteur de l’Arc Pilote EMERGENCY STOP Interrupteur de l’Arc Pilote Cet interrupteur est utilisé pour choisir la mise en service, soit haute ou basse, de l’Arc Pilote selon les conditions de découpage. Voir les Données de Procédé pour de plus amples renseignements sur les conditions nécessitant une mise en service haute ou basse. POWER ON OFF ATTENTION L’Ajustement de l’Arc Pilote Pendant Utilisation Peut Endommager la Torche. N’ajustez jamais l’interrupteur de l’arc pilote pendant l’utilisation. Ajustez avant la mise en service de la torche. Précision Plasma avec Régulation du Débit Électronique - 4-1 SECTION 4 OPÉRATION 4.1.3 Lumières Indicatrices de Défauts Lumières Indicatrices de Défauts • • • • • • • 4.1.4 Appareil de Mesure 4-2 Coolant flow - indique que le débit du refroidisseur est bas. Quand la machine est alimentée, la lumière indiquera brièvement un défaut et elle s’éteindra. Plasma Gas Pressure - indique que la pression du Gaz au Plasma est basse. La torche ne fera pas de feu. Non utilisé pour le EFC. Start Gas Pressure -indique que la pression du gaz de démarrage est basse. La torche ne fera pas de feu. Non utilisé pour le EFC. P/S Temp - indique que la température est trop haute dans l’inverseur de la source d’alimentation. L’alimentation sera interrompue. P/S Fault - indique un défaut dans le régulateur de plasma PCB dans l’inverseur de la source d’alimentation. L’alimentation sera interrompue. Over-Under Voltage - indique que la tension d’entrée est plus haute/basse que les tolérances de la console PCU. Celle-ci sera verrouillée jusqu'à ce que l’alimentation soit recyclée par l’interrupteur principal. Emergency Stop - indique la situation de l’enclenchement CNC. La source d’alimentation ne fonctionnera pas.. • Cutting Current Meter (A) – affiche le courant du découpage actuel en ampères. • Cutting Voltage Meter (V) – affiche le courant du découpage actuel. Précision Plasma avec Régulation du Débit Électronique - SECTION 4 OPÉRATION 4.1.5 Interrupteur de Régulation du Courant Interrupteur Panneau/Distant de Régulation • • • Panel Position – courant de sortie est réglé par le cadran (current) de courant. Output Current Dial – règle le courant de découpage quand le réglage doit être fait à partir de la console (panneau avant). Cadran indique 0 à 99.9 A. 70.0 A illustré. Remote Position – courant de sortie est réglé par le CNC (remote pot) avec un signal analogue dc 010 Vdc = 0-100 Adc 4.2 Qualité de la Coupe 4.2.1 Introduction Les causes affectant la qualité de la coupe sont interdépendantes. Le changement d’une variable affecte les autres. La solution peut être difficile à trouver. Le guide suivant offre des solutions possibles pour des différents résultats de découpage non désirables. Pour débuter choisissez l’état proéminent. § 4.2.2 Angle de la coupe, négatif ou positif § 4.2.3 Coupe non plate, arrondie ou en sillon § 4.2.4 Rugosité de Surface § 4.2.5 Scories Les paramètres de découpage recommandés donnent ordinairement une qualité de coupe optimale mais parfois, avec la variation des conditions des petits ajustements sont requis. Si c’est le cas : • • • AVIS Faites des ajustements graduels en exécutant toutes corrections. Ajustez la Tension de l’Arc en ascendant ou descendant de 5 volts à la fois, au besoin. Ajustez la vitesse de découpage de 5% ou moins jusqu’a amélioration des conditions. Avant de procéder à TOUTES corrections, vérifiez les variables de découpage auprès des réglages/ numéros des pièces consommables du manufacturier énumérés dans les Données de Procédé. Précision Plasma avec Régulation du Débit Électronique - 4-3 SECTION 4 OPÉRATION 4.2.2 Angle de la Coupe Angle de Coupe Négatif La dimension du haut est supérieure à celle du bas. Pièce • Défaut d’alignement de la Torche • Matériel tordu ou gauchi • Pièces consommables lasses ou endommagées • Écart trop bas (tension de l’arc) • Vitesse de découpage trop lente (vitesse de mouvement de la machine) Chute Pièce Angle de Coupe Positif La dimension du haut est inférieure à celle du bas. Pièce • Défaut d’alignement de la Torche • Matériel tordu ou gauchi • Pièces consommables lasses ou endommagées • Écart trop haut (tension de l’arc) • Vitesse de découpage trop haute • Chute 4-4 Pièce Courant trop haut ou trop bas. (Voir les Données de Procédé pour le niveau de courant recommandé pour les buses spécifiques). Précision Plasma avec Régulation du Débit Électronique - SECTION 4 OPÉRATION 4.2.3 Planéité de la Coupe Le haut et le bas sont arrondis Condition qui se produit ordinairement quand l’épaisseur du matériel est de .25” (6,4mm) ou moins • Chute Courant trop haut pour une épaisseur donnée du matériel (Voir les Données de Procédé pour les réglages appropriés). Pièce Sillon sur l’arête supérieure • Chute Écart trop bas (Tension de l’Arc) Pièce Précision Plasma avec Régulation du Débit Électronique - 4-5 SECTION 4 OPÉRATION 4.2.4 État de Finition de la Surface Rugosité provoquée par le Procédé La face de coupe est invariablement rugueuse. Peut (mais pas en tous les cas) se limiter à un axe. • Vue de dessus • Un mélange de Gaz Protecteur incorrect (Voir les Données de Procédé) Consommables usés ou endommagés Face de la coupe Rugosité provoquée par la Machine M Il peut être difficile de distinguer entre la rugosité provoquée par la Machine et la rugosité provoquée par le Procédé. Se limite souvent à un axe. La rugosité est inconsistante. ou Rugosité provoquée par la Machine Rugosité provoquée par le Procédé 4-6 • • Rails, roues et/ou crémaillère d’entraînement sont sales. (Référez-vous à la Section Entretien dans le manuel d’utilisateur). Ajustement des roues du Chariot Précision Plasma avec Régulation du Débit Électronique - SECTION 4 OPÉRATION 4.2.5 Scories Les scories sont des sous-produits du procédé de découpage. Ce sont les matériaux indésirables laissés sur les pièces suivant le procédé. Dans la plupart des cas, les scories peuvent être réduites ou éliminées par le paramétrage approprié de la torche et du découpage. Référez-vous aux Données de Procédé. Lignes de Traînée Face de la coupe Scories de Haute Vitesse Matériel de soudure ou renversement sur la surface inférieure le long de la saignée. Difficile à enlever. Ceci peut exiger un meulage ou un écaillage. Lignes de Renversement traînée en forme de “S”. • Écart trop élevé (tension de l’arc) • Vitesse de découpage trop rapide Vue de côté Lignes de Traînée Face de la coupe Globules Scories de Basse Vitesse Des globules se forment sur la surface inférieure le long de la saignée. S’enlèvent facilement. • Vitesse de découpage trop lente Vue de côté Précision Plasma avec Régulation du Débit Électronique - 4-7 SECTION 4 Vue de côté OPÉRATION Éclaboussures Scories Supérieures Des éclaboussures apparaissent sur la surface supérieure du matériel. S’enlèvent facilement dans la plupart des cas. Face de la coupe • Vitesse de découpage trop rapide • Écart trop élevé (tension de l’arc). Scories Intermittentes Elles apparaissent sur la surface inférieure ou supérieure le long de la saignée. Scories non-continuent et variantes. • Consommables possiblement usés Autres Facteurs Affectant les Scories; • • • 4-8 Température du matériel Battitures denses ou rouille Alliages au carbone élevés Précision Plasma avec Régulation du Débit Électronique - SECTION 4 OPÉRATION 4.2.6 Précision Dimensionnelle Généralement l’utilisation des plus basses vitesses possibles (a l’intérieur des niveaux approuvés) saura optimiser la précision des pièces. Choisissez les consommables permettant une tension de l’arc plus basse et une vitesse de découpage plus lente. AVIS Une performance de découpage optimale sera obtenue dans la plupart des cas en utilisant les vitesses de découpage et les tensions de l’arc recommandées. Des petits ajustements graduels peuvent être nécessaires dû à la qualité du matériel, la température du matériel et l’alliage spécifié. L’utilisateur doit se souvenir que toutes les variables sont interdépendantes. Un changement dans les réglages aura un effet sur les autres et la qualité de la coupe pourrait détériorer. Nous vous suggérons de toujours commencer avec les réglages recommandés. AVIS Avant de procéder à TOUTES corrections, vérifiez les variables de découpage avec les recommandations du manufacturier relatives aux réglages/numéros des pièces consommables énumérés dans les Données de Procédé. Précision Plasma avec Régulation du Débit Électronique - 4-9 SECTION 4 OPÉRATION 4.3 Le choix de Gaz Influence la Qualité de la Coupe 4.3.1 Introduction Tous les gaz ne sont pas convenables à toutes les situations. Certains gaz utilisés sont plus propices pour le découpage d’un matériel spécifique et selon l’épaisseur. Les informations suivantes expliquent pourquoi certains gaz sont choisis et leurs influence sur là pièce finie. D’autres influences telles que la tension de l’arc et la pression/débit des gaz sont abordées dans les Données de Procédé. Référez-vous aux Données de Procédé de Découpage dans cette section pour les réglages recommandés relatives au débit/pression. AVIS 4.3.2 Aluminium Épaisseur du Épaisseurs entre .062" à .625" (1,6 mm à 15,9 mm) Matériel: Qualités des Coupes: • • Face de coupe lisse Pratiquement pas de scories Gaz au Plasma: Nitrogène Gaz Protecteur: Nitrogène/Méthane Le mélange de gaz protecteur est très important. Entre 2 et 3 parties de Discussion: nitrogène, à 1 partie méthane est la proportion désirée. La proportion incorrecte résultera en des scories denses. 4-10 Précision Plasma avec Régulation du Débit Électronique - SECTION 4 OPÉRATION Référez-vous aux Données de Procédé de Découpage dans le manuel PT24 pour les réglages recommandés relatives au débit/pression. AVIS 4.3.3 Acier au Carbone Épaisseur du 26 GA (.018") à 10 GA (.135") (0,5 mm à 3,4 mm) Matériel: Qualités des Coupes: • • Face de coupe lisse Pratiquement pas de scories Gaz au Plasma: Oxygène Gaz Gaz Protecteur: Oxygène/Nitrogène Discussion: Gaz protecteur est normalement le nitrogène. Une petite quantité d’oxygène mélangée avec du nitrogène peut efficacement réduire la formation de scories sur un matériel mince de 26 GA à 10 GA d’acier au carbone. Par ailleurs, un gaz protecteur d’oxygène seulement peut entraîner des résultats acceptables pour les matériaux plus minces. Épaisseur du .125" à .75" (3,2 mm à 19,1 mm) Matériel: Qualités des Coupes: • • Face de coupe lisse Pratiquement pas de scories Gaz au Plasma: Oxygène Gaz Protecteur: Nitrogène Discussion: Le découpage de l’acier au carbone avec de l’oxygène résultera en une réaction exothermique. Cette réaction chimique cause le brûlement du carbone dans le matériel semblable au découpage oxygène-gaz. Ceci, en plus de l’énergie électrique, utilise des niveaux d’ampérage moins élevés sans perdre la vitesse de découpage. Précision Plasma avec Régulation du Débit Électronique - 4-11 SECTION 4 OPÉRATION Référez-vous aux Données de Procédé de Découpage dans le manuel PT24 pour les réglages recommandés relatives au débit/pression. AVIS 4.3.4 Acier Inoxydable Épaisseur du Matériel: 22 GA (.028") à 16 GA (.062") (0,7 mm à 1,6 mm) Qualités des Coupes: • • • Angle de coupe positif Excellente performance relative aux scories Surface de coupe brillante. Gaz au Plasma: Nitrogène Gaz Protecteur: Nitrogène/Méthane Les vitesses de découpage élevées entraînent un angle positif de la face de Discussion: coupe. Utilisez une buse de 70 ampères à 50 ampères pour permettre la sortie d’une quantité plus élevée de gaz par la buse. Épaisseur du Matériel: 26 GA (.018") à 16 GA (.062") (0,5 mm à 1,6 mm) Qualités des Coupes: • • • Face de coupe foncée Pratiquement pas de scories Équerrage amélioré de la coupe Gaz au Plasma: Oxygène Gaz Protecteur: Oxygène/Nitrogène Discussion: Une coupe plus équerre dans les matériaux minces est produite par un ampérage de découpage plus bas et une vitesse moindre. L’oxygène entraîne une tension de l’arc plus basse, améliorant l’équerrage de la coupe. La buse “B” est utilisé à 30 ampères. Épaisseur du Matériel: .125" à .625" (3,2 mm à 15,9 mm) Qualités des Coupes: • • • Bord de la coupe est foncé Bonne performance relative aux scories Bon angle de la coupe Gaz au Plasma: Air Gaz Protecteur: Air Discussion: 4-12 Quand ils sont identiques, les gaz au plasma et protecteur se mélangent. Ceci produit un effet d’augmentation de la pression et du débit des gaz de découpage. Cette augmentation de pression et du débit influence directement l’équerrage de la coupe. Précision Plasma avec Régulation du Débit Électronique - SECTION 4 OPÉRATION Référez-vous aux Données de Procédé de Découpage pour les réglages recommandés relatives au débit/pression. AVIS Acier Inoxydable Épaisseur du Matériel: .125" à .625" (3,2 mm à 15,9 mm) Qualités des Coupes: • • • • Bord de la coupe a une apparence mate Couleur gris pâle Finition beaucoup plus lisse Possibilité d’une légère augmentation dans l’angle de la coupe Gaz au Plasma: Air Gaz Protecteur: Air/Méthane Discussion: Épaisseur du Matériel: Qualités des Coupes: Trop de méthane dans le mélange de gaz protecteur peut entraîner une augmentation de la formation de scories. Une proportion de 4:1 air au méthane est recommandée. Possibilité d’une légère augmentation dans les angles de coupe dû au fait que le méthane est un gaz combustible. .125" to .625" (3,2 mm to 15,9 mm) • • • Face de la coupe foncée semblable à l’air Excellente performance relative aux scories Bon angle de la coupe Gaz au Plasma: Nitrogène Gaz Protecteur: Nitrogène Discussion: Avec un mélange de gaz au plasma et protecteur le volume/pression du gaz protecteur peut avoir un effet négatif sur l’équerrage de la coupe. Un volume de gaz protecteur élevé produit un angle négatif à la coupe. Un volume plus bas produit un angle positif. Épaisseur du Matériel: .187" to .625" (4,7 mm to 15,9 mm) Qualités des Coupes: Coupes: • • • Face de la coupe brillante Formation d’un bec dans le bas La formation de scories peut être considérable et difficile à enlever. Gaz au Plasma: Nitrogène Gaz Protecteur:: Nitrogène/Méthane Discussion: Les taux de débit/pression peuvent affecter l’angle de la coupe dû au fait que le méthane est un gaz combustible. Un débit/pression élevé résultera en un angle de coupe négatif, un débit/pression bas résultera en un angle de coupe positif. La proportion de nitrogène au méthane est 10 parties à 14 parties N2/ 1 partie CH4. La formation de bec sur la face de coupe inférieure est sévère donc le mélange du gaz protecteur nitrogène/méthane ne convient pas pour certaines applications des pièces finies. Précision Plasma avec Régulation du Débit Électronique - 4-13 SECTION 4 OPÉRATION Cette page est en blanc intentionnellement. 4-14 Précision Plasma avec Régulation du Débit Électronique - SECTION 4 OPÉRATION 4.4 Données de Procédé 4.4.1 Introduction L’information qui suit est un résultat d’un grand nombre d’heures d’essais et doit être observée en tant que guide général pour l’installation et l’utilisation du Système de Précision Plasmarc PT-24. Dans la plupart des cas ces réglages produiront des coupes de qualité. Les données comprennent les valeurs pour: • le découpage de l’aluminium, le carbone et l’acier inoxydable • tension de l’arc (écart) • vitesse de découpage • courant (ampères) • taux des débits de gaz pour toutes combinaisons de gaz au plasma/protecteur Les fichiers SDP contiennent des données identiques. (Voir le manuel de contrôle pour de plus amples renseignements sur les fichiers SDP.) Vous trouverez également de l’information relative aux numéros des pièces consommables pour le courant en utilisation. Précision Plasma avec Régulation du Débit Électronique - 4-15 SECTION 4 OPÉRATION 4.4.2 Données de Procédé Matériel: Ampères: Aluminium 30 Gaz au Plasma: Nitrogène @ 125 PSI / 8.6 Bar Gaz Protecteur: Nitrogène @ 125 PSI / 8.6 Bar Gaz Protecteur Mélange : Méthane @ 100 PSI / 6.9 Bar PT-24 Torche Corps de la Torche P/N 21758 Chicane à Eau P/N 21725 AnneauAnneau-O P/N 638797 AnneauAnneau-O P/N 86W62 AnneauAnneau-O P/N 950714 AnneauAnneau-O P/N 98W18 Électrode P/N 21539 ! Chicane à Turbulence P/N 21536 (3 trous) ! Buse P/N 21541, "B" Reteneur/Diffuseur de la Buse P/N 22007 Isolateur de la Cuvette Protectrice Protectrice P/N 22010 Protecteur Isolant Reteneur /Anneau/Anneau-O P/N 21712 AnneauAnneau-O - Reteneur Réf. P/N996528 Cuvette protectrice/ Reteneur P/N 22531 ! Chicane et Buse sont les seules pièces remplaçables dans l’extrémité avant de la torche qui peuvent varier selon l’ampérage 4-16 Précision Plasma avec Régulation du Débit Électronique - SECTION 4 OPÉRATION 30 Ampères Aluminium Données de Procédé PG SG1 SG2 N2 N2 CH4 PO 0.062 0.075 0.090 0.125 0.187 0.250 MM 1,6 1,9 2,3 3,2 4,7 6,4 0 0 0 0 0 0 Épaisseur du Matériel Délai de Perçage (SEC.) Paramètres d’Installation (voir notes) Gaz Plasma - Démarrage 1 40 40 40 40 40 40 55 55 55 55 55 55 SG1-Démarrage 45 45 45 45 45 45 SG1- Découpage 20 20 20 20 20 20 SG2- Débit/Coupe 10 10 10 10 10 10 150 152 153 158 170 189 IPM 150 135 105 78 30 25 MM/MIN 3810 3429 2667 1981 762 635 Gaz Plasma - Découpage 1 Gaz Protecteur (Relevé de Débit) Relevé de Débit Tension de l’Arc (écart) Vitesse de Déplacement Notes: 1. Arc Pilote –BAS. 2. Gaz de découpage et ALT se mélangent dans Régulation du Débit. 3. Flotteur – Centre de la Boule Précision Plasma avec Régulation du Débit Électronique - 4-17 SECTION 4 OPÉRATION Matériel: Ampères: Aluminium 55 Gaz au Plasma: Nitrogène @ 125 PSI / 8.6 Bar Gaz Protecteur: Nitrogène @ 125 PSI / 8.6 Bar Gaz Protecteur Mélange: Méthane @ 100 PSI / 6.9 Bar PT-24 Torche Corps de la Torche Torche P/N 21758 Chicane à Eau P/N 21725 AnneauAnneau-O P/N 638797 AnneauAnneau-O P/N 86W62 AnneauAnneau-O P/N 950714 AnneauAnneau-O P/N 98W18 Électrode P/N 21539 ! Chicane à Turbulence P/N 21692 (4 trous) ! Buse P/N 21542, "C" Reteneur/Diffuseur de la Buse P/N 22007 Isolateur de la Cuvette Protectrice P/N 22010 Protecteur Isolant Reteneur /Anneau/Anneau-O P/N 21712 AnneauAnneau-O - Reteneur (Réf. P/N 996528) Cuvette protectrice/ Reteneur P/N 22531 ! Chicane et Buse sont les seules pièces remplaçables dans l’extrémité avant de la torche qui peuvent varier selon l’ampérage 4-18 Précision Plasma avec Régulation du Débit Électronique - SECTION 4 OPÉRATION 55 Ampères Aluminium Données de Procédé PG SG1 SG2 N2 N2 CH4 PO 0.062 0.125 0.187 0.250 MM 1,6 3,2 4,7 6,4 0 0 0 0 Épaisseur du Matériel Délai de Perçage (SEC.) Paramètres d’Installation (voir notes) Gaz Plasma - Démarrage 1 45 45 45 45 75 75 75 85 SG1-Démarrage 55 55 55 55 SG1- Découpage 20 20 20 20 SG2- Débit Coupe 10 10 10 10 136 139 152 168 IPM 170 130 78 46 MM/MIN 4318 3302 1981 1168 Gaz Plasma - Découpage 1 Gaz Protecteur (Relevé de Débit) Relevé de Débit Tension de l’Arc (écart) Vitesse de Déplacement Notes: 1. Arc Pilote – HAUT. 2. Gaz de découpage et ALT se mélangent dans Régulation du Débit. 3. Flotteur – Centre de la Boule Précision Plasma avec Régulation du Débit Électronique - 4-19 SECTION 4 OPÉRATION Matériel: Ampères: Aluminium 70 Gaz au Plasma: Nitrogène @ 125 PSI / 8.6 Bar Gaz Protecteur: Nitrogène @ 125 PSI / 8.6 Bar Gaz Protecteur Mélange: Méthane @ 100 PSI / 6.9 Bar PT-24 Torche Corps de la Torche P/N 21758 Chicane à Eau P/N 21725 AnneauAnneau-O P/N 638797 AnneauAnneau-O P/N 86W62 AnneauAnneau-O P/N 9 950714 50714 AnneauAnneau-O P/N 98W18 Électrode P/N 21539 ! Chicane à Turbulence P/N 21692 (4 trous) ! Buse P/N 21543, "D" Reteneur/Diffuseur de la Buse P/N 22007 Isolateur de la Cuvette Protectrice P/N 22010 Protecteur Isolant Reteneur /Anneau/Anneau-O P/N 21712 AnneauAnneau-O - Reteneur (Réf. P/N 996528) Cuvette protectrice/ Reteneur P/N 22531 ! Chicane et Buse sont les seules pièces remplaçables dans l’extrémité avant de la torche qui peuvent varier selon l’ampérage 4-20 Précision Plasma avec Régulation du Débit Électronique - SECTION 4 OPÉRATION 70 Ampères Aluminium Données de Procédé PG SG1 SG2 N2 N2 CH4 PO 0.187 0.250 0.375 0.500 MM 4,7 6,4 9,5 12,7 0 0 0.1 0.2 Épaisseur du Matériel Délai de Perçage (SEC.) Paramètres d’Installation (voir notes) Gaz Plasma - Démarrage 1 65 65 65 65 50 50 100 100 SG1-Démarrage 45 45 45 45 SG1- Découpage 20 20 20 20 SG2- Débit/Coupe 10 10 10 10 150 157 168 182 80 65 55 30 2032 1651 1397 762 Gaz Plasma - Découpage 1 Gaz Protecteur (Relevé de Débit) Relevé de Débit Tension de l’Arc (écart) Vitesse de Déplacement IPM MM/MIN Notes: 1. Arc Pilote – HAUT. 2. Gaz de découpage et ALT se mélangent dans Régulation du Débit. 3. Flotteur – Centre de la Boule Précision Plasma avec Régulation du Débit Électronique - 4-21 SECTION 4 OPÉRATION Matériel: Ampères: Aluminium 100 Gaz au Plasma: Nitrogène @ 125 PSI / 8.6 Bar Gaz Protecteur: Nitrogène @ 125 PSI / 8.6 Bar Gaz Protecteur Mélange: Méthane @ 100 PSI / 6.9 Bar PT-24 Torche Corps de la Torche P/N 21758 Chicane à Eau P/N 21725 AnneauAnneau-O P/N 638797 AnneauAnneau-O P/N 86W62 AnneauAnneau-O P/N 950714 AnneauAnneau-O P/N 98W18 Électrode P/N 21539 ! Chicane à Turbulence P/N 21692 (4 trous) ! Buse Buse P/N 21923, "E" Reteneur/Diffuseur de la Buse P/N 22007 Isolateur de la Cuvette Protectrice P/N 22010 Protecteur Isolant Reteneur /Anneau/Anneau-O P/N 21712 AnneauAnneau-O - Reteneur (Réf. P/N 996528) Cuvette protectrice/ Reteneur P/N 22531 ! Chicane et Buse sont les seules pièces remplaçables dans l’extrémité avant de la torche qui peuvent varier selon l’ampérage 4-22 Précision Plasma avec Régulation du Débit Électronique - SECTION 4 OPÉRATION 100 Ampères Aluminium Données de Procédé PG SG1 SG2 N2 N2 N2 PO 0.250 0.375 0.500 0.625 MM 6,4 9,5 12,7 15,9 0 0 0.1 0.1 Épaisseur du Matériel Délai de Perçage (SEC.) Paramètres d’Installation (voir notes) Gaz Plasma - Démarrage 1 80 80 80 80 100 100 100 100 SG1-Démarrage 60 60 60 60 SG1- Découpage 31 31 31 31 SG2- Débit/Coupe 10 10 10 10 155 160 166 174 65 80 65 50 2413 2032 1778 1270 Gaz Plasma - Découpage 1 Gaz Protecteur (Relevé de Débit) Relevé de Débit Tension de l’Arc (écart) Vitesse de Déplacement IPM MM/MIN Notes: 1. Arc Pilote – HAUT. 2. Gaz de découpage et ALT se mélangent dans Régulation du Débit. 3. Flotteur – Centre de la Boule Précision Plasma avec Régulation du Débit Électronique - 4-23 SECTION 4 OPÉRATION Matériel: Ampères: Acier au Carbone 16 Gaz au Plasma: Oxygène @ 125 PSI / 8.6 Bar Gaz Protecteur: Nitrogène @ 125 PSI / 8.6 Bar Gaz Protecteur Mélange: Oxygène @ 125 PSI / 8.6 Bar PT-24 Torche Corps de la Torche P/N 21758 Chicane à Eau P/N 21725 AnneauAnneau-O P/N 638797 AnneauAnneau-O P/N 86W62 AnneauAnneau-O P/N 950714 AnneauAnneau-O P/N 98W18 Électrode P/N 21539 ! Chicane à Turbulence P/N 21852 (2 trous) ! Buse P/N 21540, "A" Reteneur/Diffuseur de la Buse P/N 22007 Isolateur de la Cuvette Protectrice P/N 22010 Protecteur Isolant Reteneur /Anneau/Anneau-O P/N 21712 AnneauAnneau-O - Reteneur (Réf. P/N 996528) Cuvette protectr protectrice/ ice/ Reteneur P/N 22531 ! Chicane et Buse sont les seules pièces remplaçables dans l’extrémité avant de la torche qui peuvent varier selon l’ampérage 4-24 Précision Plasma avec Régulation du Débit Électronique - SECTION 4 OPÉRATION 16 Ampères Acier au Carbone Données de Procédé PG SG1 SG2 O2 N2 O2 PO 20GA 18GA 16GA 14GA 12GA 10GA MM 0,9 1,2 1,6 2,0 2,7 3,4 0 0 0 0.1 0.5 0.1 Épaisseur du Matériel Délai de Perçage (SEC.) Paramètres d’Installation (voir notes) Gaz Plasma - Démarrage 1 20 20 20 20 20 20 11 11 11 11 11 11 SG1-Démarrage 20 20 20 20 20 20 SG1- Découpage 0 0 0 0 0 0 SG2- Débit/Coupe 6 6 6 6 6 6 103 105 115 118 116 117 IPM 100 85 80 60 50 36 MM/MIN 2540 2159 2032 1524 1270 914 Gaz Plasma - Découpage 1 Gaz Protecteur (Relevé de Débit) Relevé de Débit Tension de l’Arc (écart) Vitesse de Déplacement Notes: 1. Arc Pilote – BAS. 2. Gaz de découpage et ALT se mélangent dans Régulation du Débit. 3. Flotteur – Centre de la Boule Précision Plasma avec Régulation du Débit Électronique - 4-25 SECTION 4 OPÉRATION Matériel: Ampères: Acier au Carbone 35 Gaz au Plasma: Oxygène @ 125 PSI / 8.6 Bar Gaz Protecteur: Nitrogène @ 125 PSI / 8.6 Bar Gaz Protecteur Mélange: Oxygène @ 125 PSI / 8.6 Bar PT-24 Torche Corps de la Torche P/N 21758 Chicane à Eau P/N 21725 AnneauAnneau-O P/N 638797 AnneauAnneau-O P/N 86W62 AnneauAnneau-O P/N 950714 AnneauAnneau-O P/N 98W18 Électrode Électrode P/N 21539 ! Chicane à Turbulence P/N 21536 (3 trous) ! Buse P/N 21541, "B" Reteneur/Diffuseur de la Buse P/N 22007 Isolateur de la Cuvette Protectrice P/N 22010 Protecteur Isolant Reteneur /Anneau /Anneaunneau-O P/N 21712 AnneauAnneau-O - Reteneur (Réf. P/N 996528) Cuvette protectrice/ Reteneur P/N 22531 ! Chicane et Buse sont les seules pièces remplaçables dans l’extrémité avant de la torche qui peuvent varier selon l’ampérage 4-26 Précision Plasma avec Régulation du Débit Électronique - SECTION 4 OPÉRATION 35 Ampères Acier au Carbone Données de Procédé PG SG1 SG2 O2 N2 O2 PO 14GA 0.125 0.135 0.187 0.250 MM 1,9 3,2 3,4 4,7 6,4 0 0 0 0 0 Épaisseur du Matériel Délai de Perçage (SEC.) Paramètres d’Installation (voir notes) Gaz Plasma - Démarrage 1 38 38 38 38 38 15 15 15 15 15 SG1-Démarrage 50 50 50 50 50 SG1- Découpage 0 0 0 0 0 SG2- Débit/Coupe 6 6 6 6 6 113 119 120 122 124 80 55 52 40 30 3032 1397 1320 1016 762 Gaz Plasma - Découpage 1 Gaz Protecteur (Relevé de Débit) Relevé de Débit Tension de l’Arc (écart) Vitesse de Déplacement IPM MM/MIN Notes: 1. Arc Pilote – HAUT. 2. Gaz de découpage et ALT se mélangent dans Régulation du Débit. 3. Flotteur – Centre de la Boule Précision Plasma avec Régulation du Débit Électronique - 4-27 SECTION 4 OPÉRATION Matériel: Ampères: Acier au Carbone 45 Gaz au Plasma: Oxygène @ 125 PSI / 8.6 Bar Gaz Protecteur: Nitrogène @ 125 PSI / 8.6 Bar Gaz Protecteur Mélange: Oxygène @ 125 PSI / 8.6 Bar PT-24 Torche Corps de la Torche P/N 21758 Chicane à Eau P/N 21725 AnneauAnneau-O P/N 638797 AnneauAnneau-O P/N 86W62 AnneauAnneau-O P/N 950714 AnneauAnneau-O P/N 98W18 Électrode P/N 21539 ! Chicane à Turbulence P/N 21692 (4 trous) ! Buse P/N 21542, "C" Reteneur/Diffuseur de la Buse P/N 22007 Isolateur de la Cuvette Protectrice P/N 22010 Protecteur Isolant Reteneur /Anneau/Anneau-O P/N 21712 AnneauAnneau-O - Reteneur (Réf. P/N 996528) Cuvette protectrice/ Reteneur P/N 22531 ! Chicane et Buse sont les seules pièces remplaçables dans l’extrémité avant de la torche qui peuvent varier selon l’ampérage 4-28 Précision Plasma avec Régulation du Débit Électronique - SECTION 4 OPÉRATION 45 Ampères Acier au Carbone Données de Procédé PG SG1 SG2 O2 N2 O2 PO 0.125 0.135 0.187 0.250 0.375 MM 3,2 3,4 4,7 6,4 9,5 Délai de Perçage (SEC.) 0.3 0.3 0.3 0.3 0.4 Épaisseur du Matériel Paramètres d’Installation (voir notes) Gaz Plasma - Démarrage 1 50 50 50 50 50 20 20 20 20 20 SG1-Démarrage 50 50 50 50 50 SG1- Découpage 16 16 16 16 10 SG2- Débit/Coupe 0 0 0 0 0 108 111 114 121 124 60 50 45 35 20 1524 1270 1143 889 508 Gaz Plasma - Découpage 1 Gaz Protecteur (Relevé de Débit) Relevé de Débit Tension de l’Arc (écart) Vitesse de Déplacement IPM MM/MIN Notes: 1. Arc Pilote – HAUT. 2. Gaz de découpage et ALT se mélangent dans Régulation du Débit. 3. Flotteur – Centre de la Boule Précision Plasma avec Régulation du Débit Électronique - 4-29 SECTION 4 OPÉRATION Matériel: Ampères: Acier au Carbone 70 Gaz au Plasma: Oxygène @ 125 PSI / 8.6 Bar Gaz Protecteur: Nitrogène @ 125 PSI / 8.6 Bar Gaz Protecteur Mélange: Oxygène @ 125 PSI / 8.6 Bar PT-24 Torche Corps de la Torche P/N 21758 Chicane Chicane à Eau P/N 21725 AnneauAnneau-O P/N 638797 AnneauAnneau-O P/N 86W62 AnneauAnneau-O P/N 950714 AnneauAnneau-O P/N 98W18 Électrode P/N 21539 ! Chicane à Turbulence P/N 21692 (4 trous) ! Buse P/N 21543, "D" Reteneur/Diffuseur Reteneur/Diffuseur de la Buse P/N 22007 Isolateur de la Cuvette Protectrice P/N 22010 Protecteur Isolant Reteneur /Anneau/Anneau-O P/N 21712 AnneauAnneau-O - Reteneur (Réf. P/N 996528) Cuvette protectrice/ Reteneur ! Chicane et Buse sont les seules pièces remplaçables dans l’extrémité avant de la torche qui peuvent varier selon l’ampérage 4-30 Précision Plasma avec Régulation du Débit Électronique - SECTION 4 OPÉRATION 70 Ampères Acier au Carbone Données de Procédé PG SG1 SG2 O2 N2 O2 PO 0.187 0.250 0.312 0.375 0.500 0.625 MM 4,7 6,4 7,9 9,5 12,7 12,9 0 0 0 0.1 0.2 0.5 Épaisseur du Matériel Délai de Perçage (SEC.) Paramètres d’Installation (voir notes) Gaz Plasma - Démarrage 1 60 60 60 60 60 25 25 25 25 25 25 SG1-Démarrage 60 60 60 60 60 60 SG1- Découpage 33 33 33 33 20 20 SG2- Débit/Coupe 0 0 0 0 0 0 108 110 114 113 135 140 IPM 110 100 70 60 30 25 MM/MIN 2794 2413 1778 1524 762 635 Gaz Plasma - Découpage 1 Gaz Protecteur (Relevé de Débit) Relevé de Débit Tension de l’Arc (écart) Vitesse de Déplacement Notes: 1. Arc Pilote – HAUT. 2. Gaz de découpage et ALT se mélangent dans Régulation du Débit. 3. Flotteur – Centre de la Boule Précision Plasma avec Régulation du Débit Électronique - 4-31 SECTION 4 OPÉRATION Matériel: Ampères: Acier au Carbone 100 Gaz au Plasma: Oxygène @ 125 PSI / 8.6 Bar Gaz Protecteur: Nitrogène @ 125 PSI / 8.6 Bar Gaz Protecteur Mélange: Oxygène @ 125 PSI / 8.6 Bar PT-24 Torche Corps de la Torche P/N 21758 Chicane à Eau P/N 21725 AnneauAnneau-O P/N 638797 AnneauAnneau-O P/N 86W62 AnneauAnneau-O P/N 950714 AnneauAnneau-O P/N 98W18 Électrode P/N 21539 ! Chicane à Turbulence P/N 21692 (4 trous) ! Buse P/N 21923, "E" Reteneur/Diffuseur de la Buse P/N 22007 Isolateur de la Cuvette Protectrice P/N 22010 Protecteur Isolant Reteneur /Anneau/Anneau-O P/N 21712 AnneauAnneau-O - Reteneur (Réf. P/N 996528) Cuvette protectrice/ Reteneur P/N 22531 ! Chicane et Buse sont les seules pièces remplaçables dans l’extrémité avant de la torche qui peuvent varier selon l’ampérage 4-32 Précision Plasma avec Régulation du Débit Électronique - SECTION 4 OPÉRATION 100 Ampères Acier au Carbone Données de Procédé PG SG1 SG2 O2 N2 O2 PO 0.312 0.375 0.500 0.625 0.750 MM 7,9 9,5 12,9 15,9 19,1 0 0 0.1 0.1 0.1 Épaisseur du Matériel Délai de Perçage (SEC.) Paramètres d’Installation (voir notes) Gaz Plasma - Démarrage 1 80 80 80 80 80 30 30 30 30 30 SG1-Démarrage 60 60 60 60 60 SG1- Découpage 30 30 30 30 30 SG2- Débit/Coupe 0 0 0 0 0 115 120 132 137 143 90 80 50 30 25 2290 2030 1270 760 630 Gaz Plasma - Découpage 1 Gaz Protecteur (Relevé de Débit) Relevé de Débit Tension de l’Arc (écart) Vitesse de Déplacement IPM MM/MIN Notes: 1. Arc Pilote – HAUT. 2. Gaz de découpage et ALT se mélangent dans Régulation du Débit. 3. Flotteur – Centre de la Boule Précision Plasma avec Régulation du Débit Électronique - 4-33 SECTION 4 OPÉRATION Matériel: Ampères: Acier Inoxydable 30 Gaz au Plasma: Oxygène @ 125 PSI / 8.6 Bar Gaz Protecteur: Nitrogène @ 125 PSI / 8.6 Bar Gaz Protecteur Mélange: Oxygène @ 125 PSI / 8.6 Bar PT-24 Torche Corps de la Torche P/N 21758 Chicane à Eau P/N 21725 AnneauAnneau-O P/N 638797 AnneauAnneau-O P/N 86W62 AnneauAnneau-O P/N 950714 AnneauAnneau-O P/N 98W18 Électrode P/N 21539 ! Chicane à Turbulence P/N 21536 (3 trous) ! Buse P/N 21541, "B" Reteneur/Diffuseur de la Buse P/N 22007 Isolateur de la Cuvette Protectrice P/N P/N 22010 Protecteur Isolant Reteneur /Anneau/Anneau-O P/N 21712 AnneauAnneau-O - Reteneur (Réf. P/N 996528) Cuvette protectrice/ Reteneur P/N 22531 ! Chicane et Buse sont les seules pièces remplaçables dans l’extrémité avant de la torche qui peuvent varier selon l’ampérage 4-34 Précision Plasma avec Régulation du Débit Électronique - SECTION 4 OPÉRATION 30 Ampères Acier Inoxydable Données de Procédé PG SG1 SG2 O2 N2 O2 PO 26GA 24GA 22GA 18GA 16GA MM 0,4 0,6 0,7 1,2 1,6 0 0 0 0 0 Épaisseur du Matériel Délai de Perçage (SEC.) Paramètres d’Installation (voir notes) Gaz Plasma - Démarrage 1 45 45 45 45 45 18 18 18 18 18 SG1-Démarrage 40 40 40 40 40 SG1- Découpage 20 20 20 20 20 SG2- Débit/Coupe 5 5 5 5 5 105 105 107 109 111 IPM 250 200 190 140 100 MM/MIN 6350 5080 4826 3556 2540 Gaz Plasma - Découpage 1 Gaz Protecteur (Relevé de Débit) Relevé de Débit Tension de l’Arc (écart) Vitesse de Déplacement Notes: 1. Arc Pilote – BAS. 2. Gaz de découpage et ALT se mélangent dans Régulation du Débit. 3. Flotteur – Centre de la Boule Précision Plasma avec Régulation du Débit Électronique - 4-35 SECTION 4 OPÉRATION Matériel: Ampères: Acier Inoxydable 50 Gaz au Plasma: Air @ 125 PSI / 8.6 Bar Gaz Protecteur: Air @ 125 PSI / 8.6 Bar Gaz Protecteur Mélange: Air @ 125 PSI / 8.6 Bar PT-24 Torche Corps de la Torche P/N 21758 Chicane Chicane à Eau P/N 21725 AnneauAnneau-O P/N 638797 AnneauAnneau-O P/N 86W62 AnneauAnneau-O P/N 950714 AnneauAnneau-O P/N 98W18 Électrode P/N 21539 ! Chicane à Turbulence P/N 21692 (4 trous) ! Buse P/N 21542, "C" Reteneur/Diffuseur Reteneur/Diffuseur de la Buse P/N 22007 Isolateur de la Cuvette Protectrice P/N 22010 Protecteur Isolant Reteneur /Anneau/Anneau-O P/N 21712 AnneauAnneau-O - Reteneur (Réf. P/N 996528) Cuvette protectrice/ Reteneur P/N 22531 ! Chicane et Buse sont les seules pièces remplaçables dans l’extrémité avant de la torche qui peuvent varier selon l’ampérage 4-36 Précision Plasma avec Régulation du Débit Électronique - SECTION 4 OPÉRATION 50 Ampères Acier Inoxydable Données de Procédé PG SG1 SG2 Air Air Air PO 0.125 0.187 0.250 0.375 MM 3,2 4,7 6,4 9,5 0 0 01 0.2 Épaisseur du Matériel Délai de Perçage (SEC.) Paramètres d’Installation (voir notes) Gaz Plasma - Démarrage 1 60 60 60 60 95 95 95 95 SG1-Démarrage 45 45 45 45 SG1- Découpage 35 35 35 35 SG2- Débit/Coupe 0 0 0 0 134 140 145 155 90 60 40 18 2286 1524 1016 457 Gaz Plasma - Découpage 1 Gaz Protecteur (Relevé de Débit) Relevé de Débit Tension de l’Arc (écart) Vitesse de Déplacement IPM MM/MIN Notes: 1. Arc Pilote – HAUT. 2. Gaz de découpage et ALT se mélangent dans Régulation du Débit. 3. Flotteur – Centre de la Boule Précision Plasma avec Régulation du Débit Électronique - 4-37 SECTION 4 OPÉRATION Matériel: Ampères: Acier Inoxydable 70 Gaz au Plasma: Air @ 125 PSI / 8.6 Bar Gaz Protecteur: Air @ 125 PSI / 8.6 Bar Gaz Protecteur Mélange: Air @ 125 PSI / 8.6 Bar PT-24 Torche Corps de la Torche P/N 21758 Chicane à Eau P/N 21725 AnneauAnneau-O P/N 638797 AnneauAnneau-O P/N 86W62 AnneauAnneau-O P/N 950714 AnneauAnneau-O P/N 98W18 Électrode P/N 21539 ! Chicane à Turbulence P/N 21692 (4 trous) ! Buse P/N 21543, "D" Reteneur/Diffuseur de la Buse P/N 22007 Isolateur de la Cuvette Protectrice P/N 22010 Protecteur Isolant Reteneur /Anneau/Anneau-O P/N 21712 AnneauAnneau-O - Reteneur (Réf. P/N 996528) Cuvette protectrice/ Reteneur Reteneur P/N 22531 ! Chicane et Buse sont les seules pièces remplaçables dans l’extrémité avant de la torche qui peuvent varier selon l’ampérage 4-38 Précision Plasma avec Régulation du Débit Électronique - SECTION 4 OPÉRATION 70 Ampères Acier Inoxydable Données de Procédé PG SG1 SG2 Air Air Air PO 0.187 0.250 0.375 0.500 MM 4,7 6,4 9,5 12,7 Délai de Perçage (SEC.) 0.3 0.4 0.5 0.6 Épaisseur du Matériel Paramètres d’Installation (voir notes) Gaz Plasma - Démarrage 1 70 70 70 70 95 95 95 95 SG1-Démarrage 60 60 60 60 SG1- Découpage 40 40 40 40 SG2- Débit/Coupe 0 0 0 0 131 152 158 162 IPM 100 50 28 20 MM/MIN 2540 1270 711 609 Gaz Plasma - Découpage 1 Gaz Protecteur (Relevé de Débit) Relevé de Débit Tension de l’Arc (écart) Vitesse de Déplacement Notes: 1. Arc Pilote – HAUT. 2. Gaz de découpage et ALT se mélangent dans Régulation du Débit. 3. Flotteur – Centre de la Boule Précision Plasma avec Régulation du Débit Électronique - 4-39 SECTION 4 OPÉRATION Matériel: Ampères: Acier Inoxydable 100 Gaz au Plasma: Air @ 125 PSI / 8.6 Bar Gaz Protecteur: Air @ 125 PSI / 8.6 Bar Gaz Protecteur Mélange: Air @ 125 PSI / 8.6 Bar PT-24 Torche Corps de la Torche P/N 21758 Chicane à Eau P/N 21725 AnneauAnneau-O P/N 638797 AnneauAnneau-O P/N 86W62 AnneauAnneau-O P/N 950714 AnneauAnneau-O P/N 98W18 Électrode P/N 21539 ! Chicane à Turbulence P/N 21692 (4 trous) ! Buse P/N 21923, "E" Reteneur/Diffuseur de la Buse P/N 22007 Isolateur de la Cuvette Protectrice P/N 22010 Protecteur Isolant Reteneur /Anneau/Anneau-O P/N 21712 AnneauAnneau-O - Reteneur (Réf. P/N 996528) Cuvette protectrice/ Reteneur P/N 22531 ! Chicane et Buse sont les seules pièces remplaçables dans l’extrémité avant de la torche qui peuvent varier selon l’ampérage 4-40 Précision Plasma avec Régulation du Débit Électronique - SECTION 4 OPÉRATION 100 Ampères Acier Inoxydable Données de Procédé PG Épaisseur du Matériel SG1 SG2 Air Air Air PO 0.250 0.375 0.500 0.625 MM 6,4 9,5 12,7 15,9 Délai de Perçage (SEC.) 0.3 0.4 0.5 0.6 Paramètres d’Installation (voir notes) Gaz Plasma - Démarrage 1 80 80 80 80 65 65 65 70 SG1-Démarrage 60 60 60 60 SG1- Découpage 35 35 35 40 SG2- Débit/Coupe 0 0 0 0 129 135 142 150 80 60 35 25 2030 1520 889 635 Gaz Plasma - Découpage 1 Gaz Protecteur (Relevé de Débit) Relevé de Débit Tension de l’Arc (écart) Vitesse de Déplacement IPM MM/MIN Notes: 1. Arc Pilote – HAUT. 2. Gaz de découpage et ALT se mélangent dans Régulation du Débit. 3. Flotteur – Centre de la Boule Précision Plasma avec Régulation du Débit Électronique - 4-41 SECTION 4 OPÉRATION Matériel: Ampères: Acier Inoxydable 70 Gaz au Plasma: Air @ 125 PSI / 8.6 Bar Gaz Protecteur: Air @ 125 PSI / 8.6 Bar Gaz Protecteur Mélange: Méthane @ 100 PSI / 6.9 Bar PT-24 Torche Corps de la Torche P/N 21758 Chicane à Eau P/N 21725 AnneauAnneau-O P/N 638797 AnneauAnneau-O P/N 86W62 AnneauAnneau-O P/N 950714 AnneauAnneau-O P/N 98W18 Électrode P/N 21539 ! Chicane à Turbulence P/N 21692 (4 trous) ! Buse P/N 21543, "D" Reteneur/Diffuseur de la Buse P/N 22007 Isolateur de la Cuvette Protectrice P/N 22010 Protecteur Isolant Reteneur /Anneau/Anneau-O P/N 21712 AnneauAnneau-O - Reteneur (Réf. P/N 996528) Cuvette protectrice/ Reteneur P/N 22531 ! Chicane et Buse sont les seules pièces remplaçables dans l’extrémité avant de la torche qui peuvent varier selon l’ampérage 4-42 Précision Plasma avec Régulation du Débit Électronique - SECTION 4 OPÉRATION 70 Ampères Acier Inoxydable Données de Procédé PG SG1 SG2 Air Air CH4 PO 0.125 0.187 0.250 0.387 0.500 MM 3,2 4,7 6,4 9,5 12,7 Délai de Perçage (SEC.) 0.2 0.3 0.4 0.5 0.6 Épaisseur du Matériel Paramètres d’Installation (voir notes) Gaz Plasma - Démarrage 1 70 70 70 70 70 100 100 100 100 100 SG1-Démarrage 60 60 60 60 60 SG1- Découpage 40 40 40 40 40 SG2- Débit/Coupe 10 10 10 10 10 131 146 154 166 175 IPM 120 80 50 30 24 MM/MIN 3048 2032 1270 762 609 Gaz Plasma - Découpage 1 Gaz Protecteur (Relevé de Débit) Relevé de Débit Tension de l’Arc (écart) Vitesse de Déplacement Notes: 1. Arc Pilote – HAUT. 2. Gaz de découpage et ALT se mélangent dans Régulation du Débit. 3. Flotteur – Centre de la Boule Précision Plasma avec Régulation du Débit Électronique - 4-43 SECTION 4 OPÉRATION Matériel: Ampères: Acier Inoxydable 100 Gaz au Plasma: Air @ 125 PSI / 8.6 Bar Gaz Protecteur: Air @ 125 PSI / 8.6 Bar Gaz Protecteur Mélange: Méthane @ 100 PSI / 6.9 Bar PT-24 Torche Corps de la Torche P/N 21 21758 758 Chicane à Eau P/N 21725 AnneauAnneau-O P/N 638797 AnneauAnneau-O P/N 86W62 AnneauAnneau-O P/N 950714 AnneauAnneau-O P/N 98W18 Électrode P/N 21539 ! Chicane à Turbulence P/N 21692 (4 trous) ! Buse P/N 21923, "E" Reteneur/Diffuseur de la Buse P/N 22007 Isolateur de la Cuvette Protectrice P/N 22010 Protecteur Isolant Reteneur /Anneau/Anneau-O P/N 21712 AnneauAnneau-O - Reteneur (Réf. P/N 996528) Cuvette protectrice/ Reteneur P/N 22531 ! Chicane et Buse sont les seules pièces remplaçables dans l’extrémité avant de la torche qui peuvent varier selon l’ampérage 4-44 Précision Plasma avec Régulation du Débit Électronique - SECTION 4 OPÉRATION 100 Ampères Acier Inoxydable Données de Procédé PG SG1 SG2 Air Air CH4 PO 0.250 0.375 0.500 0.625 MM 6,4 9,5 12,7 15,9 Délai de Perçage (SEC.) 0.3 0.4 0.5 0.6 Épaisseur du Matériel Paramètres d’Installation (voir notes) Gaz Plasma - Démarrage 1 80 80 80 80 100 100 100 100 SG1-Démarrage 60 60 60 60 SG1- Découpage 40 40 40 40 SG2- Débit/Coupe 7 10 10 10 140 150 159 170 80 60 35 25 2030 1524 889 635 Gaz Plasma - Découpage 1 Gaz Protecteur (Relevé de Débit) Relevé de Débit Tension de l’Arc (écart) Vitesse de Déplacement IPM MM/MIN Notes: 1. Arc Pilote – HAUT. 2. Gaz de découpage et ALT se mélangent dans Régulation du Débit. 3. Flotteur – Centre de la Boule Précision Plasma avec Régulation du Débit Électronique - 4-45 SECTION 4 OPÉRATION Matériel: Ampères: Acier Inoxydable 50 Gaz au Plasma: Nitrogène @ 125 PSI / 8.6 Bar Gaz Protecteur: Nitrogène @ 125 PSI / 8.6 Bar Gaz Protecteur Mélange: PT-24 Torche Corps de la Torche P/N 21758 Chicane à Eau P/N 21725 AnneauAnneau-O P/N 638797 AnneauAnneau-O P/N 86W62 AnneauAnneau-O P/N 950714 AnneauAnneau-O P/N 98W18 Électrode P/N 21539 ! Chicane à Turbulence P/N 21692 (4 trous) ! Buse P/N 21542, "C" Reteneur/Diffuseur de la Buse P/N 22007 Isolateur de la Cuvette Protectrice P/N 22010 Protecteur Isolant Reteneur /Anneau/Anneau-O P/N 21712 AnneauAnneau-O - Reteneur (Réf. P/N 996528) Cuvette prot protectrice/ ectrice/ Reteneur P/N 22531 ! Chicane et Buse sont les seules pièces remplaçables dans l’extrémité avant de la torche qui peuvent varier selon l’ampérage 4-46 Précision Plasma avec Régulation du Débit Électronique - SECTION 4 OPÉRATION 50 Ampères Acier Inoxydable Données de Procédé PG SG1 N2 N2 PO 0.125 0.187 0.250 0.375 MM 3,2 4,7 6,4 9,5 0 0 0.1 0.2 Épaisseur du Matériel Délai de Perçage (SEC.) SG2 Paramètres d’Installation (voir notes) Gaz Plasma - Démarrage 1 60 60 60 60 85 85 85 85 SG1-Démarrage 45 45 45 45 SG1- Découpage 35 35 35 35 SG2- Débit/Coupe 0 0 0 0 128 133 144 155 90 60 40 22 2286 1524 1016 558 Gaz Plasma - Découpage 1 Gaz Protecteur (Relevé de Débit) Relevé de Débit Tension de l’Arc (écart) Vitesse de Déplacement IPM MM/MIN Notes: 1. Arc Pilote – HAUT. 2. Gaz de découpage et ALT se mélangent dans Régulation du Débit. 3. Flotteur – Centre de la Boule Précision Plasma avec Régulation du Débit Électronique - 4-47 SECTION 4 OPÉRATION Matériel: Ampères: Acier Inoxydable 70 Gaz au Plasma: Nitrogène @ 125 PSI / 8.6 Bar Gaz Protecteur: Nitrogène @ 125 PSI / 8.6 Bar Gaz Protecteur Mélange: PT-24 Torche Corps de la Torche P/N 21758 Chicane à Eau P/N 21725 AnneauAnneau-O P/N 638797 AnneauAnneau-O P/N 86W62 AnneauAnneau-O P/N 950714 AnneauAnneau-O P/N 98W18 Électrode P/N 21539 ! Chicane à Turbulence P/N 21692 (4 trous) ! Buse P/N 21543, "D" Reteneur/Diffuseur de la Buse P/N 22007 Isolateur de la Cuvette Protectrice P/N 22010 Protecteur Isolant Reteneur /Anneau/Anneau-O P/N 21712 AnneauAnneau-O - Reteneur (Réf. P/N 996528) Cuvette protectrice/ Reteneur Reteneur P/N 22531 ! Chicane et Buse sont les seules pièces remplaçables dans l’extrémité avant de la torche qui peuvent varier selon l’ampérage 4-48 Précision Plasma avec Régulation du Débit Électronique - SECTION 4 OPÉRATION 70 Ampères Acier Inoxydable Données de Procédé PG SG1 N2 N2 PO 0.187 0.250 0.375 0.500 MM 4,7 6,4 9,5 12,7 Délai de Perçage (SEC.) 0.3 0.4 0.5 0.6 Épaisseur du Matériel SG2 Paramètres d’Installation (voir notes) Gaz Plasma - Démarrage 1 70 70 70 70 95 95 95 95 SG1-Démarrage 60 60 60 60 SG1- Découpage 40 40 40 40 SG2- Débit/Coupe 0 0 0 0 132 150 154 159 75 50 28 24 1905 1270 711 609 Gaz Plasma - Découpage 1 Gaz Protecteur (Relevé de Débit) Relevé de Débit Tension de l’Arc (écart) Vitesse de Déplacement IPM MM/MIN Notes: 1. Arc Pilote – HAUT. 2. Gaz de découpage et ALT se mélangent dans Régulation du Débit. 3. Flotteur – Centre de la Boule Précision Plasma avec Régulation du Débit Électronique - 4-49 SECTION 4 OPÉRATION Matériel: Ampères: Acier Inoxydable 100 Gaz au Plasma: Nitrogène @ 125 PSI / 8.6 Bar Gaz Protecteur: Nitrogène @ 125 PSI / 8.6 Bar Gaz Protecteur Mélange: PT-24 Torche Corps de la Torche P/N 21758 Chicane à Eau P/N 21725 AnneauAnneau-O P/N 638797 AnneauAnneau-O P/N 86W62 AnneauAnneau-O P/N 950714 AnneauAnneau-O P/N 98W18 Électrode P/N 21539 ! Chicane à Turbulence P/N 21692 (4 trous) ! Buse P/N 21923, "E" Reteneur/Diffuseur de la Buse P/N 22007 Isolateur de la Cuvette Protectrice P/N 22010 Protecteur Isolant Reteneur /Anneau/Anneau-O P/N 21712 AnneauAnneau-O - Reteneur (Réf. P/N 996528) Cuvette protectrice/ Reteneur Reteneur P/N 22531 ! Chicane et Buse sont les seules pièces remplaçables dans l’extrémité avant de la torche qui peuvent varier selon l’ampérage 4-50 Précision Plasma avec Régulation du Débit Électronique - SECTION 4 OPÉRATION 100 Ampères Acier Inoxdable Données de Procédé PG SG1 N2 N2 PO 0.250 0.375 0.500 0.625 MM 6,4 9,5 12,7 15,9 Délai de Perçage (SEC.) 0.3 0.4 0.5 0.6 Épaisseur du Matériel SG2 Paramètres d’Installation (voir notes) Gaz Plasma - Démarrage 1 80 80 80 80 95 95 95 95 SG1-Démarrage 60 60 60 60 SG1- Découpage 50 35 35 35 SG2- Débit/Coupe 0 0 0 0 135 145 153 157 80 60 35 25 2032 1520 889 635 Gaz Plasma - Découpage 1 Gaz Protecteur (Relevé de Débit) Relevé de Débit Tension de l’Arc (écart) Vitesse de Déplacement IPM MM/MIN Notes: 1. Arc Pilote – HAUT. 2. Gaz de découpage et ALT se mélangent dans Régulation du Débit. 3. Flotteur – Centre de la Boule Précision Plasma avec Régulation du Débit Électronique - 4-51 SECTION 4 OPÉRATION Matériel: Ampères: Acier Inoxydable 70 Gaz au Plasma: Nitrogène @ 125 PSI / 8.6 Bar Gaz Protecteur: Nitrogène @ 125 PSI / 8.6 Bar Gaz Protecteur Mélange: Méthane @ 100 PSI / 6.9 Bar PT-24 Torche Corps de la Torche P/N 21758 Chicane à Eau P/N 21725 AnneauAnneau-O P/N 638797 AnneauAnneau-O P/N 86W62 AnneauAnneau-O P/N 950714 AnneauAnneau-O P/N 98W18 Électrode P/N 21539 ! Chicane à Turbulence P/N 21692 (4 trous) ! Buse P/N 21543, "D" Reteneur/Diffuseur de la Buse P/N 22007 Isolateur de la Cuvette Protectrice P/N 22010 Protecteur Isolant Reteneur /Anneau/Anneau-O P/N 21712 AnneauAnneau-O - Reteneur (Réf. P/N 996528) Cuvette protectrice/ protectrice/ Reteneur P/N 22531 ! Chicane et Buse sont les seules pièces remplaçables dans l’extrémité avant de la torche qui peuvent varier selon l’ampérage 4-52 Précision Plasma avec Régulation du Débit Électronique - SECTION 4 OPÉRATION 70 Ampères Acier Inoxydable Données de Procédé PG SG1 SG2 N2 N2 CH4 PO 0.187 0.250 0.375 0.500 MM 4,7 6,4 9,5 12,7 Délai de Perçage (SEC.) 0.3 0.4 0.5 0.6 Épaisseur du Matériel Paramètres d’Installation (voir notes) Gaz Plasma - Démarrage 1 75 75 75 75 85 85 85 85 SG1-Démarrage 60 60 60 60 SG1- Découpage 43 43 43 43 SG2- Débit/Coupe 5 5 5 5 136 150 159 162 75 50 28 24 1905 1270 711 609 Gaz Plasma - Découpage 1 Gaz Protecteur (Relevé de Débit) Relevé de Débit Tension de l’Arc (écart) Vitesse de Déplacement IPM MM/MIN Notes: 1. Arc Pilote – HAUT. 2. Gaz de découpage et ALT se mélangent dans Régulation du Débit. 3. Flotteur – Centre de la Boule Précision Plasma avec Régulation du Débit Électronique - 4-53 SECTION 4 OPÉRATION Matériel: Ampères: Acier Inoxydable 100 Gaz au Plasma: Nitrogène @ 125 PSI / 8.6 Bar Gaz Protecteur: Nitrogène @ 125 PSI / 8.6 Bar Gaz Protecteur Mélange: Méthane @ 100 PSI / 6.9 Bar PT-24 Torche Corps de la Torche P/N 21758 Chicane à Eau P/N 21725 AnneauAnneau-O P/N 638797 AnneauAnneau-O P/N 86W62 AnneauAnneau-O P/N 950714 AnneauAnneau-O P/N 98W18 Électrode P/N 21539 !Chicane à Turbulence P/N 21692 (4 trous) !Buse P/N 21923, "E" Reteneur/Diffuseur de la Buse P/N 22007 Isolateur de la Cuvette Protectrice P/N 22010 Protecteur Isolant Reteneur /Anneau/Anneau-O P/N 21712 AnneauAnneau-O - Reteneur (Réf. P/N 996528) Cuvette protectrice/ Reteneur Reteneur P/N 22531 ! Chicane et Buse sont les seules pièces remplaçables dans l’extrémité avant de la torche qui peuvent varier selon l’ampérage 4-54 Précision Plasma avec Régulation du Débit Électronique - SECTION 4 OPÉRATION 100 Ampères Acier Inoxydable Données de Procédé PG SG1 SG2 N2 N2 CH4 PO 0.250 0.375 0.500 0.625 MM 6,4 9,5 12,7 5,9 Délai de Perçage (SEC.) 0.3 0.4 0.5 0.6 Épaisseur du Matériel Paramètres d’Installation (voir notes) Gaz Plasma - Démarrage 1 80 80 80 80 95 95 95 95 SG1-Démarrage 50 70 60 42 SG1- Découpage 45 45 45 42 SG2- Débit/Coupe 5 5 5 7 138 150 162 170 80 60 35 25 2032 1524 889 635 Gaz Plasma - Découpage 1 Gaz Protecteur (Relevé de Débit) Relevé de Débit Tension de l’Arc (écart) Vitesse de Déplacement IPM MM/MIN Notes: 1. Arc Pilote – HAUT. 2. Gaz de découpage et ALT se mélangent dans Régulation du Débit. 3. Flotteur – Centre de la Boule Précision Plasma avec Régulation du Débit Électronique - 4-55 SECTION 4 OPÉRATION Marquage au Plasma - Buse “ B” Ampères: 10 Gaz au Plasma: Argon @ 125 PSI / 8.6 Bar Gaz Protecteur: Air @ 125 PSI/ 8.6 Bar PT-24 Torche Corps de la Torche P/N 21758 Chicane à Eau P/N 21725 AnneauAnneau-O P/N 638797 AnneauAnneau-O P/N 86W62 AnneauAnneau-O P/N 950714 AnneauAnneau-O P/N 98W18 Électrode P/N 21539 !Chicane à Turbulence P/N 21536 (3 Trous) !Buse P/N 21541 “B” Reteneur/Diffuseur Reteneur/Diffuseur de la Buse P/N 22007 Isolateur de la Cuvette Protectrice P/N 22010 Protecteur Isolant Reteneur /Anneau/Anneau-O P/N 21712 AnneauAnneau-O - Reteneur (Réf. P/N 996528) Cuvette protectrice/ Reteneur P/N 22531 ! Chicane et Buse sont les seules pièces remplaçables dans l’extrémité avant de la torche qui peuvent varier selon l’ampérage 4-56 Précision Plasma avec Régulation du Débit Électronique - SECTION 4 OPÉRATION Marquage au Plasma Buse “ B” 10 Ampères Données de Procédé Paramètres d’Installation (voir notes) Gaz Plasma - Démarrage 1 Gaz Plasma - Découpage 1 Gaz Protecteur (Relevé de Débit) 35 35 SG1-Démarrage 35 SG1- Découpage 35 SG2- Débit/Coupe 0 Relevé de Débit Tension de l’Arc (écart) 77 Vitesse de Déplacement IPM 200 MM/MIN 5080 Notes: 1. Arc Pilote – HAUT. 2. Gaz de découpage et ALT se mélangent dans Régulation du Débit. 3. Flotteur – Centre de la Boule Précision Plasma avec Régulation du Débit Électronique - 4-57 SECTION 4 OPÉRATION Marquage au Plasma - Buse “ B” Ampères: 15 Gaz au Plasma: Argon @ 125 PSI / 8.6 Bar Gaz Protecteur: Air @ 125 PSI/ 8.6 Bar PT-24 Torche Corps de la Torche P/N 21758 21758 Chicane à Eau P/N 21725 AnneauAnneau-O P/N 638797 AnneauAnneau-O P/N 86W62 AnneauAnneau-O P/N 950714 AnneauAnneau-O P/N 98W18 Électrode P/N 21539 !Chicane à Turbulence P/N 21536 3 trous !Buse P/N 21541 “B” Reteneur/Diffuseur Reteneur/Diffuseur de la Buse P/N 22007 Isolateur de la Cuvette Protectrice P/N 22010 Protecteur Isolant Reteneur /Anneau/Anneau-O P/N 21712 AnneauAnneau-O - Reteneur (Réf. P/N 996528) Cuvette protectrice/ Reteneur P/N 22531 ! Chicane et Buse sont les seules pièces remplaçables dans l’extrémité avant de la torche qui peuvent varier selon l’ampérage 4-58 Précision Plasma avec Régulation du Débit Électronique - SECTION 4 OPÉRATION Marquage au Plasma Buse “ B” 15 Ampères Données de Procédé Paramètres d’Installation (voir notes) Gaz Plasma - Démarrage 1 Gaz Plasma - Découpage 1 Gaz Protecteur (Relevé de Débit) 35 35 SG1-Démarrage 35 SG1- Découpage 35 SG2- Débit/Coupe 0 Relevé de Débit Tension de l’Arc (écart) 77 Vitesse de Déplacement IPM 300 MM/MIN 7620 Notes: 1. Arc Pilote – HAUT. 2. Gaz de découpage et ALT se mélangent dans Régulation du Débit. 3. Flotteur – Centre de la Boule Précision Plasma avec Régulation du Débit Électronique - 4-59 SECTION 4 OPÉRATION Marquage au Plasma - Buse “ C” Ampères: 10 Gaz au Plasma: Argon @ 125 PSI / 8.6 Bar Gaz Protecteur: Air @ 125 PSI/ 8.6 Bar PT-24 Torche Corps de la Torche P/N 21758 Chicane à Eau P/N 21725 AnneauAnneau-O P/N 638797 AnneauAnneau-O P/N 86W62 AnneauAnneau-O P/N 950714 AnneauAnneau-O P/N 98W18 Électrode P/N 21539 !Chicane à Turbulence P/N 21692 (4 trous) !Buse P/N 21542 “C” Reteneur/Diffuseur Reteneur/Diffuseur de la Buse P/N 22007 Isolateur de la Cuvette Protectrice P/N 22010 Protecteur Isolant Reteneur /Anneau/Anneau-O P/N 21712 AnneauAnneau-O - Reteneur (Réf. P/N 996528) Cuvette protectrice/ Reteneur P/N 22531 ! Chicane et Buse sont les seules pièces remplaçables dans l’extrémité avant de la torche qui peuvent varier selon l’ampérage 4-60 Précision Plasma avec Régulation du Débit Électronique - SECTION 4 OPÉRATION Marquage au Plasma Buse “ C” 10 Ampères Données de Procédé Paramètres d’Installation (voir notes) Gaz Plasma - Démarrage 1 Gaz Plasma - Découpage 1 Gaz Protecteur (Relevé de Débit) 62 62 SG1-Démarrage 37 SG1- Découpage 37 SG2- Débit/Coupe 0 Relevé de Débit Tension de l’Arc (écart) 77 Vitesse de Déplacement IPM 100 MM/MIN 2540 Notes: 1. Arc Pilote – HAUT. 2. Gaz de découpage et ALT se mélangent dans Régulation du Débit. 3. Flotteur – Centre de la Boule Précision Plasma avec Régulation du Débit Électronique - 4-61 SECTION 4 OPÉRATION Marquage au Plasma - Buse “ C” Ampères: 15 Gaz au Plasma: Argon @ 125 PSI / 8.6 Bar Gaz Protecteur: Air @ 125 PSI/ 8.6 Bar PT-24 Torche Corps de la Torche P/N 21758 Chicane Chicane à Eau P/N 21725 AnneauAnneau-O P/N 638797 AnneauAnneau-O P/N 86W62 AnneauAnneau-O P/N 950714 AnneauAnneau-O P/N 98W18 Électrode P/N 21539 !Chicane à Turbulence P/N 21692 (4 trous) !Buse P/N 21542 “C” Reteneur/Diffuseur Reteneur/Diffuseur de la Buse P/N 22007 Isolateur de la Cuvette Protectrice P/N 22010 Protecteur Isolant Reteneur /Anneau/Anneau-O P/N 21712 AnneauAnneau-O - Reteneur (Réf. P/N 996528) Cuvette protectrice/ Reteneur P/N 22531 ! Chicane et Buse sont les seules pièces remplaçables dans l’extrémité avant de la torche qui peuvent varier selon l’ampérage 4-62 Précision Plasma avec Régulation du Débit Électronique - SECTION 4 OPÉRATION Marquage au Plasma Buse “ C” 15 Ampères Données de Procédé Paramètres d’Installation (voir notes) Gaz Plasma - Démarrage 1 Gaz Plasma - Découpage 1 Gaz Protecteur (Relevé de Débit) 62 62 SG1-Démarrage 35 SG1- Découpage 35 SG2- Débit/Coupe 0 Relevé de Débit Tension de l’Arc (écart) 77 Vitesse de Déplacement IPM 200 MM/MIN 5080 Notes: 1. Arc Pilote – HAUT. 2. Gaz de découpage et ALT se mélangent dans Régulation du Débit. 3. Flotteur – Centre de la Boule Précision Plasma avec Régulation du Débit Électronique - 4-63 SECTION 4 OPÉRATION Marquage au Plasma - Buse “ D” Ampères: 10 Gaz au Plasma: Argon @ 125 PSI / 8.6 Bar Gaz Protecteur: Air @ 125 PSI/ 8.6 Bar PT-24 Torche Corps de la Torche P/N 21758 Chicane Chicane à Eau P/N 21725 AnneauAnneau-O P/N 638797 AnneauAnneau-O P/N 86W62 AnneauAnneau-O P/N 950714 AnneauAnneau-O P/N 98W18 Électrode P/N 21539 !Chicane à Turbulence P/N 21692 (4 trous) !Buse P/N 21543 “D” Reteneur/Diffuseur Reteneur/Diffuseur de la Buse P/N 22007 Isolateur de la Cuvette Protectrice P/N 22010 Protecteur Isolant Reteneur /Anneau/Anneau-O P/N 21712 AnneauAnneau-O - Reteneur (Réf. P/N 996528) Cuvette protectrice/ Reteneur P/N 22531 ! Chicane et Buse sont les seules pièces remplaçables dans l’extrémité avant de la torche qui peuvent varier selon l’ampérage 4-64 Précision Plasma avec Régulation du Débit Électronique - SECTION 4 OPÉRATION Marquage au Plasma Buse “ D” 10 Ampères Données de Procédé Paramètres d’Installation (voir notes) Gaz Plasma - Démarrage 1 Gaz Plasma - Découpage 1 Gaz Protecteur (Relevé de Débit) 77 77 SG1-Démarrage 100 SG1- Découpage 100 SG2- Débit/Coupe 0 Relevé de Débit Tension de l’Arc (écart) 77 Vitesse de Déplacement IPM 100 MM/MIN 2540 Notes: 1. Arc Pilote – HAUT. 2. Gaz de découpage et ALT se mélangent dans Régulation du Débit. 3. Flotteur – Centre de la Boule Précision Plasma avec Régulation du Débit Électronique - 4-65 SECTION 4 OPÉRATION Marquage au Plasma - Buse “ D” Ampères: 15 Gaz au Plasma: Argon @ 125 PSI / 8.6 Bar Gaz Protecteur: Air @ 125 PSI/ 8.6 Bar PT-24 Torche Corps de la Torche P/N 21758 Chicane à Eau P/N 21725 AnneauAnneau-O P/N 638797 AnneauAnneau-O P/N 86W62 AnneauAnneau-O P/N 950714 AnneauAnneau-O P/N 98W18 Électrode P/N 21539 !Chicane à Turbulence P/N 21692 (4 trous) !Buse P/N 21923, "E" Reteneur/Diffuseur Reteneur/Diffuseur de la Buse P/N 22007 Isolateur de la Cuvette Protectrice P/N 22010 Protecteur Isolant Reteneur /Anneau/Anneau-O P/N 21712 AnneauAnneau-O - Reteneur (Réf. P/N 996528) Cuvette protectrice/ Reteneur P/N 22531 ! Chicane et Buse sont les seules pièces remplaçables dans l’extrémité avant de la torche qui peuvent varier selon l’ampérage 4-66 Précision Plasma avec Régulation du Débit Électronique - SECTION 4 OPÉRATION Marquage au Plasma Buse “ D” 15 Ampères Données de Procédé Paramètres d’Installation (voir notes) Gaz Plasma - Démarrage 1 Gaz Plasma - Découpage 1 Gaz Protecteur (Relevé de Débit) 62 62 SG1-Démarrage 37 SG1- Découpage 37 SG2- Débit/Coupe 0 Relevé de Débit Tension de l’Arc (écart) 77 Vitesse de Déplacement IPM 300 MM/MIN 7620 Notes: 1. Arc Pilote – HAUT. 2. Gaz de découpage et ALT se mélangent dans Régulation du Débit. 3. Flotteur – Centre de la Boule Précision Plasma avec Régulation du Débit Électronique - 4-67 SECTION 4 OPÉRATION Marquage au Plasma - Buse “ D” Ampères: 20 Gaz au Plasma: Argon @ 125 PSI / 8.6 Bar Gaz Protecteur: Air @ 125 PSI/ 8.6 Bar PT-24 Torche Corps de la Torche P/N 21758 Chicane à Eau P/N 21725 AnneauAnneau-O P/N 638797 AnneauAnneau-O P/N 86W62 AnneauAnneau-O P/N 950714 AnneauAnneau-O P/N 98W18 Électrode P/N 21539 !Chicane à Turbulence P/N 21692 (4 trous) !Buse P/N 21543 “D” Reteneur/Diffuseur Reteneur/Diffuseur de la Buse P/N 22007 Isolateur de la Cuvette Protectrice P/N 22010 Protecteur Isolant Reteneur /Anneau/Anneau-O P/N 21712 AnneauAnneau-O - Reteneur (Réf. P/N 996528) Cuvette protectrice/ Reteneur P/N 22531 ! Chicane et Buse sont les seules pièces remplaçables dans l’extrémité avant de la torche qui peuvent varier selon l’ampérage 4-68 Précision Plasma avec Régulation du Débit Électronique - SECTION 4 OPÉRATION Marquage au Plasma Buse “ D” 20 Ampères Données de Procédé Paramètres d’Installation (voir notes) Gaz Plasma - Démarrage 1 Gaz Plasma - Découpage 1 Gaz Protecteur (Relevé de Débit) 77 77 SG1-Démarrage 100 SG1- Découpage 100 SG2- Débit/Coupe 0 Relevé de Débit Tension de l’Arc (écart) 77 Vitesse de Déplacement IPM 200 MM/MIN 5080 Notes: 1. Arc Pilote – HAUT. 2. Gaz de découpage et ALT se mélangent dans Régulation du Débit. 3. Flotteur – Centre de la Boule Précision Plasma avec Régulation du Débit Électronique - 4-69 SECTION 4 OPÉRATION Marquage au Plasma - Buse “ D” Ampères: 30 Gaz au Plasma: Argon @ 125 PSI / 8.6 Bar Gaz Protecteur: Air @ 125 PSI/ 8.6 Bar PT-24 Torche Corps de la Torche P/N 21758 Chicane à Eau P/N 21725 AnneauAnneau-O P/N 638797 AnneauAnneau-O P/N 86W62 AnneauAnneau-O P/N 950714 AnneauAnneau-O P/N 98W18 Électrode P/N 21539 !Chicane à Turbulence P/N 21692 (4 trous) !Buse P/N 21543 “D” Reteneur/Diffuseur de la Buse P/N 22007 Isolateur de la Cuvette Protectrice P/N 22010 Protecteur Isolant Reteneur /Anneau/Anneau-O P/N 21712 AnneauAnneau-O - Reteneur (Réf. P/N 996528) Cuvette protectrice/ Reteneur P/N 22531 ! Chicane et Buse sont les seules pièces remplaçables dans l’extrémité avant de la torche qui peuvent varier selon l’ampérage 4-70 Précision Plasma avec Régulation du Débit Électronique - SECTION 4 OPÉRATION Marquage au Plasma Buse “ D” 30 Ampères Données de Procédé Paramètres d’Installation (voir notes) Gaz Plasma - Démarrage 1 Gaz Plasma - Découpage 1 Gaz Protecteur (Relevé de Débit) 77 77 SG1-Démarrage 100 SG1- Découpage 100 SG2- Débit/Coupe 0 Relevé de Débit Tension de l’Arc (écart) 77 Vitesse de Déplacement IPM MM/MIN 500 12700 Notes: 1. Arc Pilote – HAUT. 2. Gaz de découpage et ALT se mélangent dans Régulation du Débit. 3. Flotteur – Centre de la Boule Précision Plasma avec Régulation du Débit Électronique - 4-71 SECTION 4 OPÉRATION Marquage au Plasma - Buse “ E” Ampères: 10 Gaz au Plasma: Argon @ 125 PSI / 8.6 Bar Gaz Protecteur: Air @ 125 PSI/ 8.6 Bar PT-24 Torche Corps de la Torche Torche P/N 21758 Chicane à Eau P/N 21725 AnneauAnneau-O P/N 638797 AnneauAnneau-O P/N 86W62 AnneauAnneau-O P/N 950714 AnneauAnneau-O P/N 98W18 Électrode P/N 21539 !Chicane à Turbulence P/N 21692 (4 trous) !Buse P/N 21923, "E" Reteneur/Diffuseur de la Buse P/N 22007 Isolateur de la Cuvette Protectrice P/N 22010 Protecteur Isolant Reteneur /Anneau/Anneau-O P/N 21712 AnneauAnneau-O - Reteneur (Réf. P/N 996528) Cuvette protectrice/ Reteneur P/N 22531 ! Chicane et Buse sont les seules pièces remplaçables dans l’extrémité avant de la torche qui peuvent varier selon l’ampérage 4-72 Précision Plasma avec Régulation du Débit Électronique - SECTION 4 OPÉRATION Marquage au Plasma Buse “ E” 10 Ampères Données de Procédé Paramètres d’Installation (voir notes) Gaz Plasma - Démarrage 1 Gaz Plasma - Découpage 1 Gaz Protecteur (Relevé de Débit) 85 85 SG1-Démarrage 100 SG1- Découpage 100 SG2- Débit/Coupe 0 Relevé de Débit Tension de l’Arc (écart) 77 Vitesse de Déplacement IPM 100 MM/MIN 2540 Notes: 1. Arc Pilote – HAUT. 2. Gaz de découpage et ALT se mélangent dans Régulation du Débit. 3. Flotteur – Centre de la Boule Précision Plasma avec Régulation du Débit Électronique - 4-73 SECTION 4 OPÉRATION Marquage au Plasma - Buse “ E” Ampères: 20 Gaz au Plasma: Argon @ 125 PSI / 8.6 Bar Gaz Protecteur: Air @ 125 PSI/ 8.6 Bar PT-24 Torche Corps de lla a Torche P/N 21758 Chicane à Eau P/N 21725 AnneauAnneau-O P/N 638797 AnneauAnneau-O P/N 86W62 AnneauAnneau-O P/N 950714 AnneauAnneau-O P/N 98W18 Électrode P/N 21539 !Chicane à Turbulence P/N 21692 (4 trous) !Buse P/N 21923, "E" Reteneur/Diffuseur de la Buse P/N 22007 Isolateur de la Cuvette Protectrice P/N 22010 Protecteur Isolant Reteneur /Anneau/Anneau-O P/N 21712 AnneauAnneau-O - Reteneur (Réf. P/N 996528) Cuvette protectrice/ Reteneur P/N 22531 ! Chicane et Buse sont les seules pièces remplaçables dans l’extrémité avant de la torche qui peuvent varier selon l’ampérage 4-74 Précision Plasma avec Régulation du Débit Électronique - SECTION 4 OPÉRATION Marquage au Plasma Buse “ E” 20 Ampères Données de Procédé Paramètres d’Installation (voir notes) Gaz Plasma - Démarrage 1 Gaz Plasma - Découpage 1 Gaz Protecteur (Relevé de Débit) 85 85 SG1-Démarrage 100 SG1- Découpage 100 SG2- Débit/Coupe 0 Relevé de Débit Tension de l’Arc (écart) 77 Vitesse de Déplacement IPM 300 MM/MIN 7620 Notes: 1. Arc Pilote – HAUT. 2. Gaz de découpage et ALT se mélangent dans Régulation du Débit. 3. Flotteur – Centre de la Boule Précision Plasma avec Régulation du Débit Électronique - 4-75 SECTION 4 OPÉRATION Marquage au Plasma - Buse “ E” Ampères: 30 Gaz au Plasma: Argon @ 125 PSI / 8.6 Bar Gaz Protecteur: Air @ 125 PSI/ 8.6 Bar PT-24 Torche Corps Corps de la Torche P/N 21758 Chicane à Eau P/N 21725 AnneauAnneau-O P/N 638797 AnneauAnneau-O P/N 86W62 AnneauAnneau-O P/N 950714 AnneauAnneau-O P/N 98W18 Électrode P/N 21539 !Chicane à Turbulence P/N 21692 (4 trous) !Buse P/N 21923, "E" Reteneur/Diffuseur de la Buse P/N 22007 Isolateur de la Cuvette Protectrice P/N 22010 Protecteur Isolant Reteneur /Anneau/Anneau-O P/N 21712 AnneauAnneau-O - Reteneur (Réf. P/N 996528) Cuvette protectrice/ Reteneur P/N 2 22531 2531 ! Chicane et Buse sont les seules pièces remplaçables dans l’extrémité avant de la torche qui peuvent varier selon l’ampérage 4-76 Précision Plasma avec Régulation du Débit Électronique - SECTION 4 OPÉRATION Marquage au Plasma Buse “ E” 30 Ampères Données de Procédé Paramètres d’Installation (voir notes) Gaz Plasma - Démarrage 1 Gaz Plasma - Découpage 1 Gaz Protecteur (Relevé de Débit) 85 85 SG1-Démarrage 100 SG1- Découpage 100 SG2- Débit/Coupe 0 Relevé de Débit Tension de l’Arc (écart) 77 Vitesse de Déplacement IPM MM/MIN 500 12700 Notes: 1. Arc Pilote – HAUT. 2. Gaz de découpage et ALT se mélangent dans Régulation du Débit. 3. Flotteur – Centre de la Boule Précision Plasma avec Régulation du Débit Électronique - 4-77 SECTION 4 OPÉRATION 4.4.3.1 Aluminium – Valeurs des Saignées N2/N2/CH4 Aluninium N /N /CH 30 Ampères 2 2 4 Épaisseur du Matériel (mm) 1.905 2.286 3.175 4.750 6.350 0.140 3.556 0.120 3.048 2.540 0.100 2.210 0.080 0.087 1.524 0.060 0.040 1.270 1.270 1.270 0.050 0.050 2.032 1.651 1.524 0.065 0.060 0.050 Saignée (mm) Saignée (pouces) 1.575 1.016 0.508 0.020 0.000 0.000 0.062 0.075 0.090 0.125 0.187 0.250 Épaisseur du Matériel (pouces) Aluminium N2/N2/CH4 50 Ampères Épaisseur du Matériel (mm) 3.175 4.775 6.350 0.140 3.556 0.120 3.048 2.362 0.100 2.032 0.080 1.651 1.524 0.060 0.060 0.093 2.032 0.080 1.524 0.065 0.040 1.016 0.020 0.508 0.000 0.000 0.062 0.125 0.188 Épaisseur du Matériel (pouces) 4-78 2.540 Précision Plasma avec Régulation du Débit Électronique - 0.250 Saignée (mm) Saignée (pouces) 1.575 SECTION 4 OPÉRATION Aluminium N2/N2/CH4 70 Ampères Épaisseur du Matériel (mm) 6.350 9.525 12.700 0.190 4.826 0.170 4.318 0.150 3.810 0.130 3.048 3.302 2.845 0.110 0.090 2.540 0.112 0.100 2.540 0.120 0.100 2.794 Saignée (mm) Saignée (pouces) 4.750 2.286 1.778 0.070 1.270 0.050 0.187 0.250 0.375 0.500 Épaisseur du Matériel (pouces) Aluminium N2/N2/CH4 100 Ampères Épaisseur du Matériel (mm) 9.525 12.700 15.875 0.190 4.826 0.170 4.318 0.150 3.810 3.302 3.302 0.130 2.921 0.110 0.090 2.667 2.540 0.100 0.130 2.794 0.115 0.105 Saignée (mm) Saignée (pouces) 6.350 2.286 1.778 0.070 1.270 0.050 0.250 0.375 0.500 0.625 Épaisseur du Matériel (pouces) Précision Plasma avec Régulation du Débit Électronique - 4-79 SECTION 4 OPÉRATION 4.4.3.2 Acier au Carbone – Valeurs des Saignées O2/N2/O2 Acier au Carbone O2/N2/O2 16 Ampères Épaisseur du Matériel (mm) 3.404 0.140 3.556 0.120 3.048 0.100 2.540 0.080 2.032 1.473 0.060 1.118 0.040 1.524 0.058 Saignée (mm) Saignée (pouces) 1.219 1.016 0.044 0.508 0.020 0.000 0.000 0.048 0.134 Épaisseur du Matériel (pouces) Acier au Carbone O2/N2/O2 35 Ampères Épaisseur du Matériel (mm) 3.175 6.350 0.140 3.556 0.120 3.048 0.100 2.540 0.080 2.032 1.499 0.060 1.168 0.040 0.046 1.524 1.321 0.059 0.052 1.016 0.508 0.020 0.000 0.000 0.060 0.125 0.250 Épaisseur du Matériel (pouces) 4-80 Précision Plasma avec Régulation du Débit Électronique - Saignée (mm) Saignée (pouces) 1.524 SECTION 4 OPÉRATION Acier au Carbone O2/N2/O2 45 Ampères Épaisseur du Matériel (mm) 6.350 9.525 0.140 3.556 0.120 3.048 2.413 0.100 0.095 1.930 0.080 1.626 0.060 2.540 2.032 0.076 1.524 0.064 0.040 1.016 0.020 0.508 Saignée (mm) Saignée (pouces) 3.175 0.000 0.000 0.125 0.250 0.375 Épaisseur du Matériel (Pouces) Acier au Carbone O2/N2/O2 70 Ampères Épaisseur du Matériel (mm) 3.429 6.350 9.525 12.700 0.140 3.556 0.120 3.048 2.540 2.032 0.080 1.778 1.575 0.060 0.100 2.032 0.080 0.070 1.524 0.062 0.040 1.016 0.020 0.508 Saignée (mm) Saignée (pouces) 2.540 0.100 0.000 0.000 0.135 0.250 0.375 0.500 Épaisseur du Matériel (pouces) Précision Plasma avec Régulation du Débit Électronique - 4-81 SECTION 4 OPÉRATION Acier au Carbone O2/N2/O2 100 Ampères Épaisseur du Matériel (mm) 9.525 12.700 19.050 3.556 0.140 3.048 3.048 0.120 0.120 2.540 2.337 0.100 0.080 0.092 2.032 0.060 1.524 0.040 1.016 0.020 0.508 0.000 0.000 0.375 0.500 0.750 Épaisseur du Matériel (pouces) 4-82 Précision Plasma avec Régulation du Débit Électronique - Saignée (mm) Saignée (puces) 2.540 0.100 SECTION 4 OPÉRATION 4.4.3.3 Acier Inoxydable – Valeurs des Saignées O2/N2/O2 Acier Inoxydable O2/N2/O2 30 Ampères Épaisseur du Matériel (mm) 0.584 0.726 1.207 1.588 0.140 3.556 0.120 3.048 0.100 2.540 0.080 2.032 0.060 1.524 1.143 0.040 0.889 0.889 0.035 0.035 0.889 0.035 0.889 0.045 Saignée (mm) Saignée (pouces) 0.457 1.016 0.035 0.508 0.020 0.000 0.000 26GA 24GA 22GA 18GA 16GA Épaisseur du Matériel (pouces) Précision Plasma avec Régulation du Débit Électronique - 4-83 SECTION 4 OPÉRATION 4.4.3.4 Acier Inoxydable – Valeurs des Saignées Air/Air/CH4 Acier Inoxydable Air/Air/CH4 70 Ampères Épaisseur du Matériel (mm) 3.175 4.775 6.350 9.525 12.700 3.556 0.140 2.921 0.120 0.115 2.032 0.080 0.060 2.540 2.286 1.778 0.100 0.090 2.032 0.080 0.070 1.524 0.040 1.016 0.020 0.508 Saignée (mm) Saignée (pouces) 2.540 0.100 3.048 0.000 0.000 0.125 0.188 0.250 0.375 0.500 Épaisseur du Matériel (pouces) Acier Inoxydable Air/Air/CH4 100 Ampères Épaisseur du Matériel (mm) 9.525 12.700 15.875 0.190 4.826 0.170 4.318 0.150 3.556 0.130 3.048 0.140 0.120 0.110 2.286 3.302 2.794 2.540 0.090 3.810 0.100 2.286 0.090 1.778 0.070 1.270 0.050 0.250 0.375 0.500 Épaisseur du Matériel (pouces) 4-84 Précision Plasma avec Régulation du Débit Électronique - 0.625 Saignée (mm) Saignée (pouces) 6.350 SECTION 4 OPÉRATION 4.4.3.5 Acier Inoxydable – Valeurs des Saignées N2/N2/CH4 Acier Inoxydable N2/N2/CH4 70 Ampères Épaisseur du Matériel (mm) 4.750 6.350 9.525 12.700 3.556 0.140 2.921 Saignée (pouces) 2.667 2.413 0.100 2.032 3.048 0.115 2.540 0.105 0.095 2.032 0.080 0.080 0.060 1.524 0.040 1.016 0.020 0.508 Saignée (mm) 0.120 0.000 0.000 0.187 0.250 0.375 0.500 Épaisseur du Matériel (pouces) Acier Inoxydable N2/N2/CH4 100 Ampères Épaisseur du Matériel (mm) 6.350 9.525 12.700 15.875 0.190 4.826 0.170 4.318 3.810 3.302 0.150 3.302 0.130 0.130 2.794 0.110 0.090 2.540 2.794 0.110 0.100 Saignée (mm) Saignée (pouces) 3.810 0.150 2.286 1.778 0.070 1.270 0.050 0.250 0.375 0.500 0.625 Épaisseur du Matériel (pouces) Précision Plasma avec Régulation du Débit Électronique - 4-85 SECTION 4 OPÉRATION 4.4.3.6 Acier Inoxydable – Valeurs des Saignées N2/N2 Acier Inoxydable N2/N2 50 Ampères Épaisseur du Matériel (mm) 4.750 6.350 9.525 0.140 3.556 0.120 3.048 0.100 2.540 2.032 0.080 2.032 1.778 1.524 0.060 0.060 0.080 1.651 0.065 0.070 1.524 0.040 1.016 0.020 0.508 Saignée (mm) Saignée (pouces) 3.175 0.000 0.000 0.125 0.187 0.250 0.375 Épaisseur du Matériel (pouces) Acier Inoxydable N2/N2 70 Ampères Épaisseur du Matériel (mm) 4.750 6.350 9.525 12.700 0.140 3.556 0.120 3.048 0.080 0.060 2.286 1.778 0.090 2.286 2.540 0.100 0.090 2.032 0.070 1.524 0.040 1.016 0.020 0.508 0.000 0.000 0.187 0.250 0.375 Épaisseur du Matériel (pouces) 4-86 Précision Plasma avec Régulation du Débit Électronique - 0.500 Saignée (mm) Saignée (pouces) 2.540 0.100 SECTION 4 OPÉRATION Acier Inoxydable N2/N2 100 Ampères Épaisseur du Matériel (mm) 9.525 12.700 15.875 0.190 4.826 0.170 4.318 0.150 3.556 0.130 3.048 2.794 0.110 0.090 2.540 0.140 0.120 3.810 3.302 2.794 0.110 0.100 Saignée (mm) Saignée (pouces) 6.350 2.286 1.778 0.070 1.270 0.050 0.250 0.375 0.500 0.625 Épaisseur du Matériel (pouces) Précision Plasma avec Régulation du Débit Électronique - 4-87 SECTION 4 OPÉRATION 4.4.3.7 Acier Inoxydable – Valeurs des Saignées Air/Air Acier Inoxydable Air/Air 50 Ampères Épaisseur du Matériel (mm) 4.750 6.350 9.525 0.140 3.556 0.120 3.048 2.413 0.100 2.032 2.540 0.095 2.032 0.080 1.524 0.060 0.060 1.651 0.080 1.524 0.065 0.040 1.016 0.020 0.508 Saignée (mm) Saignée (pouces) 3.175 0.000 0.000 0.125 0.187 0.250 0.375 Épaisseur du Matériel (pouces) Acier Inoxydable Air/Air 70 Ampères Épaisseur du Matériel (mm) 4.750 6.350 9.525 12.700 3.556 0.140 2.921 0.110 0.100 0.080 2.921 2.794 0.115 0.115 2.540 1.905 2.032 0.075 0.060 1.524 0.040 1.016 0.020 0.508 0.000 0.000 0.187 0.250 0.375 Épaisseur du Matériel (pouces) 4-88 3.048 Précision Plasma avec Régulation du Débit Électronique - 0.500 Saignée (mm) Saignée (pouces) 0.120 SECTION 4 OPÉRATION Acier Inoxydable Air/Air 100 Ampères Ampères Épaisseur du Matériel (mm) 6.350 9.525 12.700 15.875 4.826 Saignée (pouces) 0.170 4.064 0.150 3.556 3.302 0.130 2.921 0.110 0.160 0.140 4.318 3.810 3.302 0.130 2.794 0.115 0.090 2.286 0.070 1.778 Saignée (mm) 0.190 1.270 0.050 0.250 0.375 0.500 0.625 Épaisseur du Matériel (pouces) Précision Plasma avec Régulation du Débit Électronique - 4-89 SECTION 4 OPÉRATION Cette page est en blanc intentionnellement. 4-90 Précision Plasma avec Régulation du Débit Électronique - SECTION 5 ENTRETIEN 5.1 Général Dans le cas d’un rendement non conforme de l’équipement, arrêtez les travaux immédiatement et examinez la cause. Le travail d’entretien doit être fait par un personnel qualifié. Ne permettez pas aux personnes non qualifiées d’exécuter les tâches d’inspection, de nettoyage ou de réparation. Utilisez seulement des pièces de remplacement recommandées. ! AVERTISSEMENT Le Choc Électrique Peut Tuer! Avant de procéder à l’inspection ou à une réparation à l’intérieur d’un composant du Système Précision Plasma, ouvrez l’interrupteur mural ou le disjoncteur mural. 5.2 Inspection et Nettoyage Il est recommandé de faire une inspection et un nettoyage du Système de Précision Plasmarc régulièrement pour assurer une sécurité optimale et un rendement efficace. Considérez les points suivants pendant l’inspection et le nettoyage : Emplacement du filtre de la pompe • Vérifiez le câble de masse allant au connecteur de la pièce ouvrée. • Vérifiez la sécurité de la mise à la terre de la pièce ouvrée et du châssis de la source d’alimentation. • Vérifiez l’écran de chaleur sur la torche. Si l’écran est endommagé remplacez-le. • Vérifiez l’électrode et la buse de découpage de la torche pour l’usure quotidienne. • Assurez-vous que les câbles et les tuyaux ne sont pas endommagés ou pliés. • Assurez-vous que les prises, les accessoires et les connexions de mise à la terre soient bien sécurisés. • Vérifiez périodiquement le filtre à tamis dans la pompe de refroidissement située à l’intérieur de la Source (bloc) d’alimentation et purgez selon le besoin. Précision Plasma avec Régulation du Débit Électronique – 5-1 SECTION 5 ENTRETIEN ! AVERTISSEMENT Risque de Projection de Débris. Les projections de débris peuvent entraîner des blessures sérieuses aux yeux. Assurez-vous de porter une protection adéquate sur les yeux pendant le nettoyage à l’air comprimé. ATTENTION Évitez les Dommages Potentiels à l’Équipement Il peut avoir une accumulation d’eau et/ou d’huile dans les lignes d’air comprimé. Assurez-vous de bien diriger le premier jet d’air à l’écart de l’équipement pour éviter des dommages à la boîte de jonction ou à la boîte de régulation du débit. • Après le débranchement de toute source d’alimentation d’entrée et avec une protection adéquate pour les yeux et le visage, soufflez dans l’intérieur de la source (bloc) d’alimentation, régulateur du débit et la boîte de jonction en utilisant de l’air comprimé propre/sec. • Occasionnellement, purgez toute l’eau du filtre situé au-dessous du régulateur du filtre d’air. • Assemblage. La torche peut être assemblée par le manchon de 2" (51 mm) dia. ou par la surface usinée de 1.812" (46 mm) dia (illustrée). Cette surface isolée et son épaulement sont usinés en relation avec le filet du dispositif de retenue de la buse sur le corps de la torche. Ils sont maintenus concentrique à la buse de découpage à l’intérieur d’une lecture d’indicateur totale de 0.010" (0.25 mm) ou le trou de la buse est à l’intérieur de 0.005" (0.127 mm) de n’importe quel point sur le 1.812" (46 mm) dia. Pendant l’assemblage ne couvrez pas le trou d’évent sur le côté du manchon. Ce trou sert à prévenir une accumulation de liquide de refroidissement à l’intérieur du manchon en cas de fuites. • Lignes de Service. Lignes de 4.5 pi. (1.4m), 12 pi. (3.7m), 17pi. (5.2m) et 20 pi. (6.1m) sont blindées et se branchent à la boîte de jonction par une connexion de mise à la terre à friction. 5.3 Pt-24 Description de la Torche Collet 46 mm Diamètre Manchon 51 mm Diamètre Trou d’Évent 5-2 Précision Plasma avec Régulation du Débit Électronique – SECTION 5 ENTRETIEN • Gaz de Découpage et de Démarrage au Plasma. Ces gaz entrent dans la torche par les connections abritant les valves de retenue à l’intérieur du corps de la torche. Ces valves, agissant conjointement avec les valves solénoïdes, contrôlent la commutation directionnelle des gaz de démarrage et de découpage. Argon O2 125 psi N2 125 psi H35 100 psi CH4 100 psi Air Industriel Alimentation en Gaz - entrant Ar AIR-1 O2-1 N2-1 PS1 AIR-2 N2-2 METH Interrupteur de Pression Air Industriel O2-2 SCHÉMA DES DÉBITS DE GAZ N2-3 O2 N2 METH Air Valve Solénoïde Ar Interrupteur de Pression PS5 PS4 PS2 PS3 Valve Sentronic Débitmètre Valve de retenue VALVE 4 6-BAR SENTRONIC VALVE 3 6-BAR SENTRONIC VALVE 2 9-BAR SENTRONIC VALVE 1 9-BAR SENTRONIC Valve de retenue Tableau d'Interface Valve Solénoïde Bidirectionnelle SG2 NOIR SG1 ORG PG2 JAU PG1 BLEU Raccord Rapide pour Gaz EFC Boîte-J SG2 SG1 PG2 PG1 Torche PT-24 Assemblage du Manifold Électronique Note: L’air de l’atelier ne doit pas être utilisé pour remplacer l’air industriel. Précision Plasma avec Régulation du Débit Électronique – 5-3 SECTION 5 ENTRETIEN • 2 1 3 Gaz protecteur. Le pré-débit/post-débit du gaz protecteur et le gaz protecteur de découpage entrent dans la torche par une seule connexion. Ces gaz passent par: § le corps de la torche, § le diffuseur du gaz protecteur, § • l’orifice dans le couvercle protecteur entourant le jet de plasma. Lignes d’Alimentation et de l’Arc Pilote. Le refroidisseur entre dans la torche (IN) par le câble d’alimentation (-). Le refroidisseur sort (OUT) de la torche par la ligne de l’arc pilote (+). Refroidissement d’eau. 4 1. Le refroidisseur entre dans la torche par le câble d’alimentation (-), 2. circule à travers le corps de la torche et l’électrode, 5 3. traverse à la section de la buse (+) du corps de la torche par des tubes de raccordement diélectrique, 4. il fait un retour à travers le corps de la torche et circule entre le reteneur de la buse et la buse, 5. et enfin il retourne à travers le corps de la torche vers la boîte de jonction via le câble de l’arc pilote. 6 10 7 9 8 1 Tube de Raccordement 2 Refroidisseu Refroidisseur entre via le Câ Câble d’ d’Alimentation 3 Refroidisseur sort via le Câ Câble de l’l’Arc Pilote 4 Corps de l’l’Électrode 5 Corps de l’l’Arc Pilote 6 Chicane à Turbulence 7 Électrode 8 Buse 9 Reteneur de la Buse 10 Chicane à Eau 5-4 Précision Plasma avec Régulation du Débit Électronique – SECTION 5 ENTRETIEN 5.4 Entretien de la Torche ! AVERTISSEMENT Le Choc Électrique Peut Tuer! Avant de procéder à l’entretien de la torche: • Réglez l’interrupteur d’alimentation sur la console à la position arrêt (OFF). • Déconnectez l’alimentation d’entrée primaire. AnneauxAnneaux-O dans le Corps de la Torche Anneau-O P/N 950714 • À chaque jour avant l’utilisation, vérifiez les anneaux-O dans le corps de la torche. Remplacez les anneaux endommagés ou usés. • Appliquez une couche de silicone (graisse) mince sur les anneaux-O avant d’assembler la torche. N’utilisez pas le Krytox. • L’anneau-O, P/N 638797, à l’intérieur du corps de la torche scellant la buse est très critique. Anneau-O P/N 86W62 Anneau-O P/N 638797 § Le dommage ou l’usure n’est pas facilement identifiable à cause de son emplacement, § Nous vous suggérons de remplacer cet anneauO sur une base quotidienne. § Prenez soin de ne pas érafler ou endommager la surface de la torche. § Un cure-dents en bois sert bien pour enlever les anneaux-O. § L’anneau-O peut être remplacé sans enlever la chicane à eau P/N 21725; par contre si la chicane est enlevée, utilisez toujours une clé hexagonale 3/16" (5 mm) ou un tournevis à douille. Évent du Manchon de la Torche • Des fuites d’eau, de l’humidité ou du refroidisseur dégouttant du trou d’évent indiquent des dommages à la ligne de service. • Pour remplacer les lignes de service utilisez toujours deux clés pour éviter de tordre les tubes de métal. Trou d’Évent Précision Plasma avec Régulation du Débit Électronique – 5-5 SECTION 5 ENTRETIEN Manchon P/N 822568 ATTENTION Corps de la Valve de Retenue P/N 821739 Boule P/N 821740 Manchon de la Torche • Le manchon de la torche P/N 822568 est fileté dans le corps de la torche. • Si le manchon est trop serré pour enlever à la main utilisez une grosse clé ajustable sur les parties plats de la torche ou serrez les parties plats dans un étau. Une fois le corps sécurisé utilisez les deux mains pour le libérer. Sinon, utilisez une clé à sangle. • Avant de remplacer le manchon, vérifiez toujours les connexions des lignes de service pour des fuites. La performance de découpage sera affectée si les valves de retenue de la Torche sont endommagées ou non-conformes. • Prenez soin de ne pas endommager le siège de la valve de retenue, la boule et le ressort durant la manipulation. • N’installez pas de substituts substituts pour les ressorts et les boules. Si les pièces se perdent ou elles sont endommagées, remplacezremplacez-les toujours par des pièces de remplacement du manufacturier. • L’utilisation des valves de retenue nonnon-autorisées ou endommagées aura un effet sur les réglages réglages de pression et causera un démarrage/perçage médiocre. Ressort P/N 821741 ATTENTION 5-6 Les Accessoires Attachés Incorrectement Peuvent Entraîner des Fuites et une Performance Médiocre. • Gardez les filetages et les sièges propres pendant l’assemblage des valves valves de retenue. • Dans le cas d’une contamination des valves de retenue par des corps étrangers, démontez et nettoyez ou remplacez. Précision Plasma avec Régulation du Débit Électronique – SECTION 5 ENTRETIEN 5.5 PT-24 Démontage et Inspection des Consommables ! AVERTISSEMENT Le Choc Électrique Peut Tuer! • Mettez l’interrupteur d’alimentation de la console à la position arrêt (OFF). • Déconnectez l’alimentation d’entrée primaire. Si le reteneur/diffuseur de la buse est difficile à enlever, la console peut être dans la position marche (ON). PT-24 Extrémité Avant NOTE: Si la console est en marche, la pompe sera en fonction et la pression du refroidisseur derrière le reteneur empêchera la libération de la buse. Vérifiez la console avant d’enlever l’écrou. Il est à noter qu’une petite quantité de refroidisseur est perdue à chaque fois qu’un consommable est remplacé. Ceci est normal et vous devez éventuellement remplacer le refroidisseur. Vérifiez le refroidisseur avant chaque utilisation. 1. Dévissez la cuvette protectrice/reteneur. Examinez autour de l’orifice pour des dommages. Remplacez le bord de l’orifice s’il est fêlé ou endommagé. Un orifice déformé ne produira pas des coupes droites. Isolateur de la Cuvette Protectrice Protecteur Isolant Reteneur Cuvette Protectrice/ Reteneur 2. Dévissez et enlevez le protecteur isolant reteneur 3. L’isolateur de la cuvette protectrice est pris entre la cuvette et le reteneur/diffuseur de la buse. Il peut demeurer attaché au reteneur de la buse à cause de l’espace restreint entre ces deux pièces. Précision Plasma avec Régulation du Débit Électronique – 5-7 SECTION 5 ENTRETIEN Buse Reteneur de la Buse Aucun dommage à l’air de contact 4. Dévissez le reteneur/diffuseur de la buse. Examinez pour des dommages, spécifiquement à l’endroit où le reteneur prend contact avec la buse. La surface entre le reteneur et la buse crée un joint étanche de métal contre métal pour le refroidisseur. Un dommage à cette surface d’étanchéité causera une fuite et entraînera un découpage médiocre. Remplacez si nécessaire, mais ne tentez pas de faire des réparations. Vérifiez les petits passages de gaz pour des obstructions. Dégagez ces obstructions à l’aide d’un jet d’air. Buse 5. Utilisez l’outil fourni pour enlever la buse. Placez la fente autour de la rainure de la buse et libérez-le en tirant. Outil pour l’Électrode et la Buse P/N 21765 5-8 Précision Plasma avec Régulation du Débit Électronique – SECTION 5 ENTRETIEN Électrode 6. Enlevez la chicane à turbulence de la buse. Si la chicane demeure dans la torche, elle sera libérée en enlevant l’électrode. Vérifiez les petits passages de gaz dans la chicane à turbulence pour des obstructions et dégagez ces obstructions à l’aide d’un jet d’air. Si les obstructions ne peuvent être dégagées, remplacez la chicane. N’insérez RIEN dans les trous quand vous tentez un dégagement. Une déformation de ces trous entraînera une performance de découpage médiocre. Chicane à Turbulence Buse 7. Utilisez l’outil de l’électrode et de la buse fourni pour dévisser l’électrode. (P/N 21765). Précision Plasma avec Régulation du Débit Électronique – 5-9 SECTION 5 ENTRETIEN 5.6 PT-24 Ré-assemblage de l’Embout de la Torche 1. Électrode Appliquez une couche de silicone (graisse) mince sur l’anneau-O, seulement assez pour produire une surface brillante. Filetez l’électrode en place et sécurisez avec l’outil fourni. NE SERREZ PAS TROP. Reteneur de la Buse Buse Petite Quantité de Krytox 2. Buse & Chicane à Turbulence Placez la chicane à turbulence dans la buse en mettant le bout rayé de la chicane à l’intérieur de la buse. Après un assemblage conforme, le petit embout sphérique de la buse forme un joint étanche de métal à métal pour le refroidisseur avec le reteneur de la buse. Appliquez une petite quantité de Krytox (un composé anti-saisissant) sur le diamètre inférieur du reteneur de la buse (voir l’illustration). Cette graisse empêche les éraillures/saisies possibles entre la buse et le reteneur. Elle facilite l’établissement d’un joint étanche. Ne mettez pas de Krytox sur la buse. 3. Reteneur/Diffuseur de la Buse Filetez le reteneur de la buse sur la torche and serrez à la main. Joint d’Eau 5-10 Précision Plasma avec Régulation du Débit Électronique – SECTION 5 ENTRETIEN 4. Isolateur de la Cuvette Protectrice Pressez l’isolateur de la cuvette protectrice sur le reteneur de la buse. Ce composant est à ajustement forcé et peut Isolateur de la demeurer assemblé pendant le démontage. Cuvette Protectrice Cuvette Protectrice Reteneur de la Buse 5. Protecteur Isolant Reteneur Appliquez une couche de silicone (graisse) mince sur l’anneau-O et filetez le protecteur isolant reteneur sur la cuvette protectrice. Serrez à la main. AVIS N’attachez pas l’Isolateur au corps de la torche en premier lieu. Si l’isolateur est fileté sur le corps de la torche en premier lieu les gaz protecteurs ne circuleront pas correctement. Tout d’abord, filetez l’isolateur sur la cuvette protectrice et ensuite raccordez raccordez les deux pièces sur le corps de la torche. 6. Cuvette Protectrice et Reteneur Vissez cet assemblage (Isolateur/Cuvette protectrice et Reteneur) sur la torche et serrez à la main. ATTENTION Inspection et Lubrification de l’Anneau-O • Examinez les AnneauxAnneaux-O souvent pour des fêlures et l’usure. Des anneauxanneaux-O endommagés ou usés auront un effet sur la qualité de démarrage et du découpage. • En appliquant une couche de silicone (graisse) mince sur les anneauxanneaux-O de l’embout de la torche pendant l’assemblage d’entretien, le démontage ultérieur sera plus facile. • N’utilisez pas de Krytox sur les anneauxanneaux-O. Krytox est un lubrifiant antianti-saisissant et se dissipera avec le temps. Démontage sera difficile. Précision Plasma avec Régulation du Débit Électronique – 5-11 SECTION 5 ENTRETIEN Cette page est en blanc intentionnellement. 5-12 Précision Plasma avec Régulation du Débit Électronique – SECTION 6 TROUBLESHOOTING 6.1 General Safety ! WARNING Electric Shock Can Kill! ! WARNING High Voltages Can Be Stored In Capacitors. Externally disconnect all primary power to the machine before servicing. Open the line (wall) disconnect switch or circuit breaker before attempting inspection or work inside the power source. Even when power is disconnected or unit is de-energized, capacitors can store high voltages. Assure power supply capacitors are grounded prior to performing maintenance. 6.2 Programmable Logic Controller (PLC) • Located in the Precision Plasma Power Source. • Capable of providing predefined outputs depending on state of the inputs. The precise conditions are programmed and permanently stored in the PLC. • Visible through the plexiglas window on the left side panel of the power source. • Provides predefined outputs in response to input signals from external devices. • The signal exchange between the PLC and external devices are both time dependent and condition dependent. If a required signal is not received in the proper sequence, the PLC will discontinue the process and generate a fault signal to the CNC. Precision Plasma with Electronic Flow Control - 6-1 SECTION 6 TROUBLESHOOTING 6.2.1 PLC LEDs (Light Emmiting Diode) OUTPUT Highly reliable indicators. It is not likely that one will "burn out". However, if the technician is not confident that the LEDs are working, the presence of a signal can be confirmed by using a meter and taking a measurement on the appropriate pin. Refer to the schematic and wiring diagrams. 1 CH 0 1 2 3 4 5 6 7 8 9 10 11 • This exchange of signals can be confirmed by observing the LEDs on the top of the PLC while troubleshooting. These indications are useful in isolating a system failure to the most likely device. • The LEDs are divided into two groups; POWER RUN ALARM ERROR INPUT 0 CH § Input (0-15) light when the corresponding signal is detected by the PLC. § Output (0-11) light when the PLC issues a signal to an external device. 0 1 2 3 4 5 6 7 8 9 10 11 12 13 14 15 6.2.2 PLC LED Functions INPUT 6-2 OUTPUT LED Function LED Function 0 Start/Stop 0 Not Used 1 Not Used 1 Hi-Frequency 2 Arc-On 2 Pilot Arc Relay 3 Not Used 3 Power Source 4 Not Used 4 Not Used 5 Fault 5 Fault Output 6 Not Used 6 Not Used 7 Not Used 7 Not Used 8 Not Used 8 Not Used 9 Not Used 9 Not Used 10 Not Used 10 Not Used 11 Not Used 11 Not Used 12 Not Used 13 Not Used 14 Not Used 15 Not Used Precision Plasma with Electronic Flow Control - SECTION 6 TROUBLESHOOTING 6.3 Troubleshooting Guide 6.3.1 Reduced Consumable Life Cutting Up Skeletons Cutting skeletons (discarded material left after all pieces have been removed from a plate) to facilitate their removal from the table can adversely affect electrode life by: • Causing the torch to run off the work. • Continuous Pilot Arc edge starts • Greatly increasing the frequency of starts. This is mainly a problem for O2 cutting and can be alleviated by choosing a path with a minimum number of starts. • Increase likelihood that the plate will spring up against the nozzle causing a double arc. This can be mitigated by careful operator attention and by increasing standoff and reducing cutting speeds. If possible, use a gas torch for skeleton cutting. Height Control Problems • • Torch diving is usually caused by a change in arc voltage when an automatic height control is in use. Usually the voltage change is the result of plate falling away from the arc. These problems can effectively be eliminated by disabling the height control and extinguishing the arc earlier when finishing the cut on a falling plate. Diving can also be caused by a faulty height control. Piercing Standoff Too Low Increase pierce standoff Starting on edges with Position torch more carefully or start on adjacent continuous pilot arc scrap material. Work Flipping The nozzle may be damaged if the torch hits a flipped up part. Catching on Pierce Spatter Increase standoff or start with longer lead-in Pierce not complete before starting Increase initial delay time. Precision Plasma with Electronic Flow Control - 6-3 SECTION 6 TROUBLESHOOTING See Cut Quality In Section 4 6.3.2 Poor Cut Quality 6.3.3 No Pilot Arc Contaminated Electrode Clean or replace electrode Insufficient spark gap setting Set spark gap to 0.040” (1.016 mm) in plumbing box. Pilot Arc Contactor (PAC) Replace contactor malfunctioning 6.3.4 No Arc Transfer Cutting current Raise cutting current (see Process Data) setting too low. Torch too high Lower torch standoff (see Process Data) above workpiece Work lead not Ensure work lead is firmly connected to workpiece connect to cutting table or cutting table N2 or O2 check valve in torch body may be stuck open See maintenance section for check valve repair. 6.3.5 No Preflow No start signal Check input 0 LED on PLC. Should be lit. This verifies a start command has been given Emergency stop signal open Check for continuity between TB3-18 and TB3-19 Shorted, closed or jumpered out Check cooling water LED on front panel. Should be Cooling Water Flow Switch lit. No Cooling Water Check reservoir. Add coolant until full. 6.3.6 Torch Fails To Fire Start Gas Lower start gas flow Cooling water Flow Pump pressure too low. Should be 115 psi. (7.9 bar) Faulty cooling water flow switch Replace CWFS switch (CWFS) Obstruction in torch Coolant flow through torch should be greater than limiting cooling water flow 0.5 gal/min (1.5 l/min) 6-4 Precision Plasma with Electronic Flow Control - SECTION 6 TROUBLESHOOTING 6.3.7 Nozzle Life Extremely Short Pilot Arc H/L switch Refer to Process Data in wrong position Nozzle arcing inside bore Nitrogen quality too low. Requires 99.995 % purity Start gas flow too low Check Process Data cutting parameters 6.3.8 Short Electrode Life Insufficient cooling Check pump for 115/130 psi (7.9/9.0 bar)output pressure Start gas quality Gas quality needs to be 99.995 % purity minimum Cut gas quality Oxygen gas needs to be 99.8 % purity 6.3.9 Short Electrode And Nozzle Life Water leak on torch frontfront-end Follow torch leak procedure Precision Plasma with Electronic Flow Control - 6-5 SECTION 6 TROUBLESHOOTING 1 2 2 PLASMA GAS 2 SHIELD GAS 1 3 3 SHIELD GAS 1 4 SHIELD GAS 2 COMMON P4 SHIELD GAS 2 5 PLASMA GAS 1 PLASMA GAS 2 4 PLASMA GAS 1 1 6.4 Flow Control Schematic 5 6 7 A. C. COMMON 8 CHASSIS P5 COMMON 120 vac (11 ne) 6 4 7 1 2 3 8 9 9 10 10 4 amp 7 8 5 6 FUSED 24vac TO CNC 24vac COMMON VALVE 1 SHIELD (SH) 1 CHASSIS GROUND VALVE 1 GND (GN) 2 24 vdc GROUND 3 VALVE 1 SET PT. VALVE 1 SET PT. (SP) 4 VALVE 1 + 24 VDC VALVE 2 SET PT. (SP) 5 VALVE 2 SET PT. VALVE 2 +24V (PR) 6 VALVE 1 +24 VALVE (PR) VALVE 2 +24 VDC } PLASMA GAS 1 VALVE 2 SHIELD (SH) VALVE 2 GND (GN) } PLASMA GAS 2 } SHIELD GAS 1 } SHIELD GAS 2 VALVE 3 SHIELD (SH) P1 VALVE 3 GND VALVE 3 SET PT. 8 VALVE 3 +24 VDC 9 VALVE 4 SET PT. 10 VALVE 4 +24 VDC 1 PRES. SW. 15 V. SOURCE (SR1) 2 PRES. SW 24 V. SOURCE (SR2) 3 VALVE 3 +24 V (PR) 7 VALVE 3 SET PT. (SP) PS5 (SHIELD GAS 2) VALVE 4 SHIELD (SH) VALVE 4 GND (GN) VALVE 4 SET PT. (SP) VALVE 4 +24V (PR) { { { { { PS5 JP1 (SHIELD GAS 2) PS5 PS4 JP2 (SHIELD GAS 1) 4 PS4 5 PS3 6 PS2 (PLASMA GAS 1) 7 PS1 PS1 (PROCESS AIR) SELECTOR VALVE COMMON 1 METHANE 2 H-35 NOT USED 3 N2-3 4 N2-2 5 N2-1 RC1 8 1 METH 2 H-35 3 SOLENOID METH H.F 120 V FROM POWER SUPPLY H.F. 120 V TO J-BOX JP5 PS1 10 PS2 (PROCESS AIR) PS3 (PLASMA GAS 2) P2 JP4 PS2 (PLASMA GAS 1) PS4 (SHIELD GAS 1) H.F. 120 V FROM POWER SUPPLY H.F. 120 V TO J-BOX JP3 (PLASMA GAS 2) 9 PS3 1 amp N-3 RC2 4 5 SOLENOID H-35 1 amp RC3 6 N-2 7 SOLENOID N-3 1 amp RC4 8 N-1 9 N-1 10 O-2 11 O-2 12 O-1 13 SOLENOID N-2 1 amp RC5 SOLENOID 1 amp P3 RC6 6 7 O2-1 8 AIR-2 9 AIR-1 10 SOLENOID O2-2 ARGON 1 amp 15 AIR-2 16 AIR-1 17 AIR-1 18 AR 19 RC7 14 SOLENOID O-1 AIR-2 1 amp RC8 SOLENOID 1 amp RC9 SOLENOID 1 amp RC10 20 SOLENOID 1 amp TB1 6-6 Precision Plasma with Electronic Flow Control - SECTION 6 TROUBLESHOOTING AIR-1 Process Air 125 psi Argon 125 psi O2 125 psi N2 125 psi H35 100 psi CH4 100 psi 6.5 Gas Flow Schematic Ar O2-1 N2-1 PS1 AIR-2 N2-2 METH O2-2 N2-3 METH N2 O2 Air Solenoid Valve Ar Pressure Switch PS5 PS4 PS3 PS2 Sentronic Valve Flow Meter Check Valve Interface Board VALVE 4 6-BAR SENTRONIC VALVE 3 6-BAR SENTRONIC VALVE 2 9-BAR SENTRONIC VALVE 1 9-BAR SENTRONIC Check Valve 2 Way Solenoid Valve SG2 BLK SG1 ORG PG2 YEL PG1 BLU Gas Quick Coupling EFC Junction Box Electronic Manifold Assembly PT-24 Torch Precision Plasma with Electronic Flow Control - 6-7 SECTION 6 TROUBLESHOOTING 6.6 Junction Box Wiring Diagram T1-X1 RED PILOT ARC BLU 1 2 GND1 GRN 3 PCB1 J1-M GRY J1 J1 PILOTARC J1-A GRN PCB1-3 GRN PCB1-2 BLU J2 J1 SPLICE J2-5 J2-6 J2-7 J2-8 WHT WHT WHT WHT J1-C WHT DENOTES IN-LINE SPLICE DENOTES SELF LEAD A B C D E F G H I J K L M N GRN GND1 BLU J2-2 WHT SPLICE YEL J2-1 BLK J2-3 ORN J2-4 GRY T3-H1 BLK T3-H2 Precision Plasma with Electronic Flow Control - 1 2 3 4 5 6 7 8 9 YEL BLU BLK ORN WHT WHT WHT WHT --- J1-F J1-B J1-J J1-L SPLICE SPLICE SPLICE SPLICE --- J2 C2 2 X2 GND1 6-8 C1 SG1-1 RED X3 1 SG1-2 BLU T1 X1 1 PCB1-1 RED C1-1 BLU BLU SG1-1 RED X2 2 X1 X2 T1-X2 BLU SG1-2 BLU T3 X3 T3-X1 RED T3-X2 BLU T1-X1 RED H1 H2 T2 SG1 X1 C1-2 BLU J1-N BLK SECTION 6 TROUBLESHOOTING 6.7 Junction Box Schematic J1 A B C D E TO FLOW CONTROL J2 YEL J2 PLASMA-1 SOLENOID COMMON GND1 PLASMA-2 F G H J K L M N I SHIELD GAS 1 SHIELD GAS 2 H2 T3 6 5 3 3 1 4 9 2 PG-2 PG-1 4 ORG BLK SG-1 SG-2 MANIFOLD EFC A/M X2 2 H1 2 5 6 7 8 1 BLU SG1 1 X1 2 C1 .002 uf 10KV C2 2500pf 15KV 1 NEG X1 X2 PCB1 1 2 X3 T1 X1 NEG X2 3 CABLE CONNECTIONS TO CONSOLE X3 T2 TORCH CONNECTIONS GND1 PILOT ARC PILOT ARC WORK SCHEMATIC DIAGRAM Precision Plasma with Electronic Flow Control - 6-9 SECTION 6 TROUBLESHOOTING 6.8 Power Module Wiring Diagram Page 1 6-10 Precision Plasma with Electronic Flow Control - SECTION 6 TROUBLESHOOTING Power Module Wiring DiagramPage 2 Precision Plasma with Electronic Flow Control - 6-11 SECTION 6 TROUBLESHOOTING 6.9 Power Module Schematic – CE Version 6-12 Precision Plasma with Electronic Flow Control - SECTION 6 TROUBLESHOOTING 6.10 Precision Plasma Power Source Wiring Diagrams Part 1 PCB1 P1 1 2 3 4 5 6 7 8 9 10 11 12 13 14 15 16 17 18 P4-14(BRN) P4-13(RED) PCB1 P1-6(BLK) PCB1 P1-5(BLK) PLC1 P2-11(WHT) PLC1 P2-12(ORN) PLC1 P2-13(GRY) PLC1 P2-14(YEL) PCB1 P1-12(BLK) PCB1 P1-11(BLK) MOD1 P1-5 (BLK) MOD1 P1-6 (RED) MOD1 P1-2 (BLU) MOD1 P1-1 (VIO) PCB1 P1-18(BLK) PCB1 P1-17(BLK) P2 1 P4-10(VIO) 2 P4-9(VIO) 3 4 P4-8(ORN) 5 P4-7(ORN) 6 7 8 P3-3(GRY) 9 P3-4(RED) 10 P3-5(GRY) 11 P4-4(BRN) 12 P4-3(BRN) 13 P4-2(BLU) 14 P4-1(BLU) 15 P3-1(YEL) 16 P3-2(YEL) 1 2 3 4 5 6 7 8 9 10 11 12 13 14 15 16 17 18 P3 P4-11(GRY) P4-12(BLU) MOD1 P1-3(ORN) MOD1 P1-4(WHT) PCB-TB P1-6(YEL) MOD1 P1-7(BLU) 1 2 3 4 5 6 7 8 9 10 11 12 13 14 15 16 17 18 P4 PLC1 P1-1(BRN) PLC1 P1-2(GRY) MOD1 P3-1(RED) MOD1 P3-2(YEL) P5 1 PLC1 P1-5 (BLK) 2 PLC1 P1-6 (VIO) P7 1 PLC1 P2-5(BLK) 2 3 TB6-5(RED) P9 1 MOD1 P1-14(RED) 2 3 MOD1 P1-15(BLK) 1 2 3 4 5 P10 S3-5(VIO) S3-2(RED) P3-7(BLK) P3-6(WHT) P3-8(WHT) PLC1 P1-3(YEL) PLC1 P1-8(ORN) PLC1 P1-3(YEL) PLC1 P1-4(WHT) MOD1 P3-7(RED) MOD1 P3-8(BLK) MOD1 P3-9(VIO) MOD1 P3-10(YEL) MOD1 P3-3(BLU) MOD1 P3-4(ORN) J1 2 1 3 MOD1 P1-9 (ORN) S3-4 (BLU) VIEW OF R2 S3-1 (BRN) 1 P1 18 4 P5 1 H2 H1 S2-5 (BLK) PLC-COMM6 (BLU) F PLC-0109 (GRY) G K5-A (BLK) J PLC-0110 (WHT) K K6-A (YEL) L PLC-0111 (BRN) M PLC-0101 (VIO) N PLC1 J2-9 (GRY) S K2-L3(BLU) T U 18 3 P7 1 PLC1 J2-4 (ORN) D R L1 P2 1 PCB4 PLC-0108 (YEL) C P 16 4 P9 1 B H SEE VIEW OF R2 R2-3(BLU) 4 5 6 1,3 S3 R2-2(BRN) 1 2 3 2 PCB1 P10-2(RED) R2 TB6-7(ORN) GND2 (GRN) E PCB1 P10-1(VIO) TB6-8(GRY) MOD1 P1-7(BLU) A V P3 J2 1 18 1 J1-A (GRN) K1-L2 (BLU) F4-1 (YEL) * 12 S1 3 4 56 K1-L1 (BRN) 14 25 36 S2 P4 M1-GND (GRN) GND2 MOD1 TB2-1 (RED) T3-H1 (RED) P10 1 5 L1-H2 (BLK) BLK S2 A TB3-20 (BLU) B TB3-21 (GRY) C TB3-13 (ORN) D TB3-23 (BLK) E TB3-18 (VIO) F TB3-19 (YEL) G TB3-4 (WHT) H TB3-14 (BRN) I TB3-3 (ORN) J TB3-12 (VIO) K TB3-22 (WHT) L TB3-11 (RED) M TB3-2 (GRY) N TB3-1 (BRN) K2-L3 (BLU) J2 CB1-1 (BLK) TB2-3 (RED) M2-4 SPLICE (WHT) CB2-1 (BLK) M1-2 (WHT) MOD1 TB2-2(GRY) 3 J1 * TB2-1(BLU) 6 2 R1-2 (BLK) S1-2(YEL) 4 5 1 R7-2 (ORN) 12 F4 12 CB2 12 CB1 MOD1 TB2-1(BLK)* 1 * GND2 (GRN) GND M1 2 CB1-1 (WHT) * NC RED * FS1C BLK * ORN NO * J4-14(BRN) J4-13(RED) Precision Plasma with Electronic Flow Control - 6-13 SECTION 6 TROUBLESHOOTING Wiring Diagram – Precision Plasma Power Source Part 2 B T2-BH2 BR1-C C C T2-CH2 S1-5 (BRN) H1 H3 H2 T2-AH2 MOVB T2-BH2 MOVC MOV T2-CH2 F4-2(BLU) T3-H2(BLK) T3-H3(GRY) CB2-1(RED) T3-H4(YEL) T3-H5(BRN) T3-H6(ORN) T3-H7(VIO) T3-H1(GRY) (YEL) T3-H3(GRY) (BLK) H7 B S1-1 (BLU) A MOD1 TOP H6 H5 H4 T2-AH2 BR1-B J3-2(YEL) X7 J4-2(BLU) X8 J4-1(BLU) BR1 (VIO) LINE LOAD A A Detail for CE units only T1 (ORN) (BRN) BR1-A X6 X1 J4-10(VIO) X2 J4-9(VIO) X3 J4-4(BRN) X4 J4-3(BRN) X5 J3-1(YEL) J3-4(BLK) J3-5(GRY) X16 X15 J3-8(WHT) J3-3(GRY) X14 X12 X13 J4-8(ORN) X9 X10 X11 J4-7(ORN) J3-6(WHT) J3-7(RED) Note: PLC1 (connection) refers to an area located on an enclosure that housed the former Programmable Logic Controller. This plasma power supply is CNC (cutting machine) controlled and does not use a PLC. J4-11(GRY) TB2 SEE DETAIL L1 CB2 - 2 WHT J4 - 6 WHT ZD3 M2 - 1 (SPLICE) RED J4 - 5 BLK M2 - 4 (SPLICE) RED T3 - H1 RED T1 T1 MOV1 AH2 K4 SEE T3 DETAIL B 1 4 3 6 5 BH2 M2 J4-12(BLU) T3 TB1 MOD1 BR1-A K4 2 T2 L3 B K1 SEE DETAIL T3 A L2 ZD1 A MOD1 BR1-B SEE DETAIL MOD1 BR1-C CH2 1 2 3 4 5 6 7 8 9 10 11 12 13 14 15 16 17 18 MOV2 MOV3 BLK BLK BLK T2 SPLICE M2 1 3 2 GRN 6 MOD1 TB2-1(RED) WHT (INTERNAL) RED (INTERNAL) TB2-4 (YEL) CB2-2 (WHT) BRN (INTERNAL) TB2-5 (BRN) 4 H4 H1 S1-6 (RED) T1-H1 (RED) H5 T3 TB2-6 (ORN) SPLICE TB2-7 (VIO) H6 H2 H7 H3 TB2-2 (BLK) TB2-3 (GRY) T1-H3 (GRY) 6-14 Precision Plasma with Electronic Flow Control - TB2 1 2 3 4 5 6 7 BLK SECTION 6 TROUBLESHOOTING Wiring Diagram – Precision Plasma Power Source Part 3 MOD1 TB2 CB1-2(GRY) M1-1(BLK) 2 1 S1-6(RED) M2-1 SPLICE (RED) MOD1 MOD1 P4 1 TB3-7(RED) 2 TB3-8(YEL) 3 TB3-9(BLU) 4 TB3-10(ORN) 5 TB3-11(RED) 6 TB3-12(VIO) 7 F3-1(RED) 8 TB3-16(BLK) 9 TB3-18(VIO) MOD1 P4-7 (RED) 1 2 TB3-15 (RED) F3 TB4 SEE DETAIL TB2 TB3 TB3 1 PA P4 1 2 3 WORK 10 4 5 10 TB3-19(YEL) TORCH 6 7 J3 8 1 T1-X5(YEL) 2 T1-X6(YEL) 9 3 T1-X14(GRY) 10 4 T1-X15(BLK) 5 T1-X16(GRY) 6 T1-X11(WHT) 1 13 7 T1-X12(RED) J4 14 8 T1-X13(WHT) J3 11 1 12 8 15 16 1 T1-X8(BLU) 2 T1-X7(BLU) 3 T1-X4(BRN) 4 18 19 20 21 T1-X3(BRN) 22 5 23 6 7 T1-X10(ORN) 8 T1-X9(ORN) 9 T1-X2(VIO) 10 T1-X1VIO) 11 K1-A(GRY) 12 K1-B(BLU) 13 FS1-NO(RED) 14 FS1-C(BRN) 15 16 16 17 J4 24 PLC-0000 (BRN) J2-N (BRN) PLC(-24VDC) (GRY) J2-M (GRY) J2-I(ORN) PLC-COMM 2 (ORN) J2-G(WHT) PLC-0100 (WHT) PLC1 J1-5 (BLK) PLC1 J1-6 (VIO) MOD1 P4-1(RED) MOD1 P4-2(YEL) MOD1 P4-3(BLU) MOD1 P4-4(ORN) MOD1 P4-5(RED) J2-L(RED) MOD1 P4-6(VIO) J2-J(VIO) PCB2 P1-2(ORN) J2-C(ORN) PCB2 P1-3(BRN) J2-H(BRN) F3-2 (RED) MOD1 P4-8(BLK) MOD1 P4-9(VIO) J2-E(VIO) MOD1 P4-10(YEL) J2-F (YEL) K8-9 (BLU) J2-A (BLU) K8-6 (GRY) J2-B(GRY) K7-B (WHT) J2-K(WHT) K7-A (BLK) J2-D(BLK) REAR VIEW WITH REAR PANEL REMOVED Precision Plasma with Electronic Flow Control - 6-15 SECTION 6 TROUBLESHOOTING Wiring Diagram – Precision Plasma Power Source Part 4 PLC1 MODULE PLC TB4-1(VIO) L2 PLC1 J2-1(BLK) PLC-COMM1(BLK) TB3-4 (WHT) TB3-3 (ORN) J1-M (VIO) PLC1 J2-7 (BLU) PLC-COMM4 (BLU) PLC1 J2-10(RED) PLC-COMM3 (BLU) PLC1 J1-1(BRN) PLC1 J1-2(GRY) K3-A (VIO) K4-A (WHT) K8-A (ORN) 0100 COMM 2 0101 COMM 3 0102 COMM 4 0103 COMM 5 0104 0105 0106 0107 COMM 6 TB5 PCB2-PA(YEL) PCB2 K2-T1 (YEL) PA PLC1 J2-5(RED) MOD1 SH1-2(BLK) PCB2 P1-1 (RED) 0108 0109 0110 0111 COMM 7 WORK PCB2 P1-6 (BLK) MOD1 TB3-1(BLK) TORCH VIEW F-F J1 L1 J2 1 PLC-0103(BRN) 1 PLC-L2(BLK) 2 PLC-COMM5(GRY) 2 TB4-1 (VIO) 3 TB4-1(VIO) 3 PLC-COMM7(BLU) 4 PLC-0002(WHT) 4 J1-C(ORN) 5 TB3-5 (BLK) 5 TB5-WORK(RED) 6 TB3-6 (VIO) 6 7 7 8 9 PLC-COMM3 (BLU) 8 PLC-0006(ORN) 9 10 J1-N(GRY) 10 PLC-0102(RED) 11 K3-6(WHT) 12 K3-9(ORN) 13 K4-9(GRY) PLC-COMM 7 (BLU) J1-D(BLU) J1-B (YEL) J1-F (GRY) J1-J (WHT) J1-L (BRN) PLC1 J2-3(BLU) PLC-COMM 6 (BLU) 14 K4-6(YEL) 15 TB4-2(BRN) 16 TB5-PA(YEL) 0000 0001 HS COMM 0002 0003 0004 0006 COMM 1 +24VDC -24VDC PCB2 - P1 P1-1 P1-2 TB5-WORK(RED) TB3-13(ORN) P1-3 TB3-14(BRN) P1-6 TB5-TORCH(BLK) VIEW E-E TB3-1 (BRN) K7-4 (BLU) PLC-(+24VDC) (VIO) PLC1 J1-4(WHT) K5-9 (YEL) K6-9 (RED) PLC1 J1-8(ORN) PLC-L2(BLK) PLC-HS COMM (VIO) TB3-2 (GRY) K7-6 (GRY) E J1 L1 L2 0100 COMM 2 0101 COMM 3 0102 COMM 4 0103 COMM 5 0104 0105 0106 0107 COMM 6 0108 0109 0110 0111 COMM 7 PCB2 2 2 BLU BLU 1 BLU K8 1 1 1 36 4 7 A 9B R7 R10 R9 R8 J2 F 1 1 +24VDC -24VDC TB5 2 2 0006 0007 BLU 2 0000 0001 HS COMM 0002 0003 0004 BLU PLC S2-3 (BLK) S2-6 (ORN) F COMM 1 MOD1 SH1-1 (GRY) E K6 K7 1 36 4 7 A 9B 1 63 4 7 9 AB K5 K4 1 3 1 36 4 7 A 9B 4 6 7 A 9B K3 1 36 4 7 A 9B TB4 PLC1 J2-2(VIO) R1 PLC1 J2-15(BRN) K3-B(BRN) PLC-L1(VIO) K5-6(VIO) K4-B(BRN) 1 TB4 K5-B(BRN) PLC1 J1-3(VIO) K6-B(BRN) K8-B (BRN) K4 K3 1 3 4 6 7 9 A B 1 3 4 6 7 9 A B 1 3 4 6 7 9 A B Precision Plasma with Electronic Flow Control - PLC1 J2-11(WHT) K5 1 3 4 6 7 9 A B TB4-2(BRN) K6 TB4-2(BRN) PLC1 J2-13(GRY) PLC1 J2-14(YEL) PLC-0104 (VIO) J1-K (YEL) TB3-22 (WHT) ZD3 PLC-(-24VDC) (GRY) TB3-23 (BLK) PLC-0001 (BLU) TB4-2(BRN) TB3-20 (BLU) TB3-21 (GRY) PLC-0106 (ORN) 1 3 4 6 7 9 A B TB4-2(BRN) PLC-0003 (YEL) TB4-1(VIO) PLC-0105 (WHT) K7 1 3 4 6 7 9 A B TB4-2(BRN) PLC-0004 (RED) TB4-1(VIO) J1-G (BLK) K8 PLC1 J2-12(ORN) T2 6-16 2 K6-6(VIO) SECTION 6 TROUBLESHOOTING Wiring Diagram – Precision Plasma Power Source Part 5 MOD1 P3 P1 P2 SH1 1 PCB1 P4-3(RED) 1 1 PCB1 P1-16(VIO) 1 R10-1 (GRY) 2 PCB1 P4-4(YEL) 2 2 PCB1 P1-15(BLU) 2 TB5-WORK(BLK) 3 PCB1 P4-15(BLU) 3 3 PCB1 P3-12(ORN) 4 PCB1 P4-16(ORN) 4 4 PCB1 P3-13(WHT) 5 TB6-6(BRN) 5 5 PCB1 P1-13(BLK) 6 TB6-8(GRY) 6 6 PCB1 P1-14(RED) 7 PCB1 P4-11(RED) 7 7 PCB1 P3-18(BLU) 8 PCB1 P4-12(BLK) 8 9 PCB1 P4-13(VIO) 8 PCB-TB P1-1(YEL) 10 PCB1 P4-14(YEL) 9 R2-1(ORN) NOT USED S3-4(BLU) 10 11 12 13 14 PCB1 P9-1(RED) 15 PCB1 P9-3(BLK) 16 R3 PCB1 P7-3(RED) MOD1-TB3-1 (RED) 1 2 3 4 5 6 7 8 MOD1 P3-6(GRY) S3-6(GRY) S3-3(ORN) R5 R6 MOD1 P3-5(BRN) C2-2 (WHT) TB5-PA (YEL) C2-1 (YEL) TB6 R4 MOD1 WHT T1 T2 T3 P1 8 P1 1 K2 ZD2 A L1 L2 L3 B 1 P3 1 K2-L3 (BLU) 16 L1-H1 (BLU) PLC1 P2-10 (RED) SEE DETAIL S2-2 (BLU) 1 2 3 4 5 6 7 8 C1-1 (BLU) TB6 PLC1 P2-9 (VIO) WHT P3 1 PCB1 P2-15(YEL) 2 PCB1 P2-16(YEL) 3 PCB1 P2-8(GRY) 4 PCB1 P2-9(RED) 5 PCB1 P2-10(GRY) 6 PCB1 P10-4(WHT) 7 PCB1 P10-3(BLK) 8 PCB1 P10-5(WHT) P4 1 PCB1 P2-14(BLU) 16 2 PCB1 P2-13(BLU) 3 PCB1 P2-12(BRN) 4 PCB1 P2-11(BRN) PCB1 P4-1(BRN) 2 PCB1 P4-2(GRY) 3 PCB1 P4-7(YEL) 1 P4-10(VIO) PLC1 P2-7 (VIO) 2 P4-9(VIO) 1 4 PCB1 P4-10(WHT) 3 P4-2(BLU) 5 PCB1 P5-1 (BLK) 4 P4-1(BLU) 6 PCB1 P5-2(VIO) PLC1 P2-15(BLU) 7 5 8 6 9 7 10 8 9 PCB1 P7-1(BLK) PLC1 P2-1 (VIO) 2 R11 1 2 SH1 K2-T1(YEL) K2-T3(WHT) R14-1 (GRY) TB6-2(RED) TB5-TORCH(BLK) 1 D1 8 R15-2 (RED) 1 PLC MOD P3 PLC1 P2-9 (VIO) PCB1 P4-9(YEL) PCB1 P4-8(ORN) R13 P2 P1 1 C1 16 PLC1 MODULE 1 R12 C2 10 P2 1 P2 TB3 8 1 P4 PLC1 P2-4(BLU) MOD1 TB3-1 (RED) 2 2 R15 1 PLC1 P2-3(BLU) D1(-) GRY R14 1 PLC1 P2-2 (VIO) 5 K2-A (VIO) 6 10 K2-B(RED) 11 PCB1 P1-7(WHT) 12 PCB1 P1-8(ORN) 13 PCB1 P1-9(GRY) 7 PCB1 P2-5(ORN) 8 PCB1 P2-4(ORN) 9 PCB1 P2-2(VIO) 10 PCB1 P2-1(VIO) PLC1 P2-2(VIO) 14 PCB1 P1-10(YEL) 15 PLC1 P2-4(BLU) PLC1 P2-1(VIO) 16 FRONT VIEW WITH FRONT PANEL REMOVED Precision Plasma with Electronic Flow Control - 11 PCB1 P3-1(GRY) 12 PCB1 P3-2(BLU) 13 PCB1 P1-3(RED) 14 PCB1 P1-2(BRN) 15 16 6-17 SECTION 6 TROUBLESHOOTING 6.11 Schematic- Precision Plasma Power Source Part 1 PLC1 PLC MODULE #1 1 P2 J2 2 1 2 H2 H1 H1 200V 1 15A 120VAC 11 P3-1 12 P3-2 13 P1-3 14 15 16 J4 P4 P1-2 TB2 1 F4 2 12VAC NC 2 3 LED8 5 2 1 M1 PLASMA GAS P1-10 LED9 LED6 CB1 3A 460V 415V 380V MOV2 230V ØB L2 T2 200V 18 17 16 15 14 13 415V 380V 230V 200V 10 9 8 7 T2 P1-12 T1 575V 460V 415V 6 380V 230V 200V 6 5 4 3 2 1 CH2 6 A K6 B 15 16 17 18 19 20 9 6 P4-10 P5-1 4 P5-2 6 K6 21 B 22 5 23 24 25 P1-17 26 CH1 BH5 BH4 BH3 27 28 29 30 P4-14 P4-13 P4-12 P4-11 P10-1 P10-2 P4-16 P4-15 P4-4 P4-3 BH6 PCB TRIM POT 838193 31 32 33 34 P3-18(-) P3-17(+) 1 BH2 6 P9-3 P9-1 P1-14 P1-13 P3-13 P3-12 P1-15 P1-16 BH1 35 AH6 36 AH5 AH4 J2 37 NOT USED ON PRECISION PLASMA CONSOLE 1 2 3 4 5 6 7 8 38 P1 1 2 3 4 AH3 AH2 AH1 TB1 A B C TB2-2 TB2-1 BR1-A BR1-B BR1-C FN1 6-18 B P1-18 AH8 610V K5 P1-11 CH3 AH7 L1 6 A MOV1 ØA B 7 9 10 1 2 3 8 P4-1 P4-2 P4-7 P4-8 P4-9 CH4 610V 11 K4 9 P1 J1 CH5 BH8 12 B 6 A CH6 BH7 460V K3 9 13 2 MOV3 575V 6 A V1 VOLTMETER AUTO XFMR 575V 610V 9 12 9 CH8 5 11 A CH7 L3 T3 11 14 P1-9 B 4 ØC 6 P1-8 START GAS 120VAC K1 5 P7-3 12 1 A P7-1 P1-7 AM1 AMMETER ZD1,180V 10 14 LED3 S1 1 8 10 C 6 FNT PNL ON/OFF 7 8 13 + NO FS1 9 P1-6 H3 H2 230V 2 LED5 P1-5 3 LED2 P6 H3 380V 24VAC 7 + H4 LED7 - 4 H4 24VAC LED4 - 415V 24VAC 4 5 TB4-2 6 9 LED1 + H5 18VAC 18VAC P8 H6 H5 460V 18VAC 18VAC PCB1 ISOLATION AMPLIFIER AND FAULT SIGNAL PCB 38103 P10-5 P10-3 P10-4 P2-10 P2-9 P2-8 P2-16 P2-15 P2-14 P2-13 P2-12 P2-11 P2-7 P2-6 P2-5 P2-4 P2-2 P2-1 + H6 575V 6 5 2 H7 8 7 6 5 4 3 2 1 - T3 H7 J3 P3 X13 X12 X11 X16 X15 X14 X6 X5 X8 1 X7 2 X4 3 X3 4 5 6 X10 7 X9 8 X2 9 X1 10 - 7A CB2 2 T1 1 7 1 TB4-1 3 4 15 PUMP MOTOR M2 1 4 3 Precision Plasma with Electronic Flow Control - MOD1 POWER MODULE #1 5 6 7 8 9 10 11 12 13 14 15 16 SECTION 6 TROUBLESHOOTING Schematic- Precision Plasma Power Source Part 2 1 2 3 4 5 J1 6 A 7 B C 8 D 9 10 TO FLOW CONTROL BOX J1 E L1 1 1 L2 2 2 3 3 4 4 5 5 6 6 7 0100 7 8 Comm 2 0006 8 9 0101 0007 9 10 Comm 3 10 11 PLC 11 0102 12 Comm 4 12 13 0103 13 14 Comm 5 14 START GAS 15 0104 15 PLASMA GAS 16 0105 16 17 0106 17 COMM 1 18 18 0107 19 Comm 6 19 START GAS ON, NITROGEN 20 0108 20 CUT GAS ON, OXYGEN 21 0109 21 FULL SHIELD 22 0110 22 REGULATED SHIELD +24VDC 23 23 0111 COMMON -24VDC 24 24 Comm 7 0000 0001 HS COMM 0002 0003 0004 11 12 13 14 ZD3 180 VAC A K7 B 4 6 F G H J K L M N P R S T U V J2 TB3 120VAC RELAY 1 N 2 M 3 I G 4 15 5 16 17 18 6 START SIGNAL FROM CNC TO P.S., 120VAC 8 9 20 10 21 START SIGNAL FROM CNC TO P.S., 24VAC L 11 PLC1 PLC MODULE #1 22 23 1 F3 2 12 J +10VDC REMOTE CURRENT SETTING FROM CNC TO P.S. 13 C VOLTAGE DIVIDER, (+) 14 H VOLTAGE DIVIDER, (-) 18 E 19 F EMERGENCY STOP FROM CNC TO P.S. RELAY/CONTACTOR NORMALLY CLOSED OPEN IN CASE OF EMERGENCY 20 A 21 B 22 K 23 D 15 1A 24 ARC ON SIGNAL FROM P.S. TO CNC, RELAY CLOSING ARC ON SIGNAL FROM P.S. TO CNC, TRANSISTOR 7 19 START SIGNAL FROM CNC TO P.S., RELAY CLOSING 16 25 17 31 B K2 L1 T1 L2 T2 L3 T3 TB6-5 R6 39K 2W 120VAC RELAY R3 4.99K 36 2 5 37 38 1 2 3 4 5 6 7 8 9 10 R5 39K 2W FRONT PNL CURRENT SETTING LOCAL/REMOTE DPDT S3 P4 10 9 8 7 FRONT PNL PILOT ARC SELECTOR S2 6 5 HI 4 H2 L1 3 2 C1 20uf 400V P3 FAULT SIGNAL FROM P.S. TO CNC RELAY CLOSING, DRY CONTACT 120VAC PREFLOW SIGNAL FROM CNC TO P.S. 24 TB6-2 H1 4 6 1 10K 8W CURRENT SETTING POT R2 10K MIN MAX 1 3 2 R4 4.99K 35 3 R11 20uf 400V TB6-8 TB6-6 TB6-7 32 33 34 C2 TB6-4 D1 LO R1 R7 20 OHM 300W R8 20 OHM 300W 20 OHM 300W R9 1 R7 10K OHM 8W R7 10K OHM 8W R14 20 OHM 50W 20 OHM 300W P1-2 R10 3.1 OHM 300W TOJUNCTION BOXJ1 A TOCUTTINGMACHINECNC CONNECTORCHASSISGNDSUPPLIED BYCUTTINGMACHINEGROUP ZD2 180 VAC WORK P1-1 START UP PCB2 P1-3 838131 P1-6 26 27 28 29 30 PA PILOT ARC TORCH 6 5 MOD1 POWER MODULE #1 4 R15 20 OHM 50W 3 2 1 SH1-2 SH1-1 TB3-1 Precision Plasma with Electronic Flow Control - 6-19 SECTION 6 TROUBLESHOOTING 6.12 Technical Guide To Using And Understanding The Operation Of The Electronic Flow Control Introduction The following information is a guide for troubleshooting The Precision Plasma Electronic Flow Control. Knowledge of machine and control operation is required. 6-20 Precision Plasma with Electronic Flow Control - SECTION 6 TROUBLESHOOTING 6.12.1 Precision Process Timers Timer Description Plasma Preflow Time The minimum interval of time between the receipt of a plasma process start signal and the issuance of the signal to turn the plasma power supply on. Plasma process start gas flows are in effect during this time. Line Purge Time The interval of time allowed to purge the plasma process gas lines. Plasma process purge/fill gas flows are in effect during this time. Plasma Firing Time The maximum interval of time allowed for receipt of an arcon signal from the issuance of the signal to turn the plasma power supply on. Plasma process start gas flows are in effect during this time. Plasma Pierce Time The interval of time allowed for piercing the work piece after receipt of the arc-on signal. Plasma process cut gas flows are in effect during this time. (Torch stationary, AHC disabled, machine stationary). Plasma AHC Delay The interval of time allowed after expiration of the PLASMA PIERCE TIME timer before enabling AHC. Plasma process cut gas flows are in effect during this time. (Torch stationary, AHC disabled, machine moving). Plasma Arc Delay The interval of time for filtering the arc-on signal to allow the signal to assume a stable mode / condition. Plasma process cut gas flows are in effect during this time. Master Up The interval of time allowed to raise the plasma torch after receipt of a plasma process off signal. Plasma process start gas flows are in effect during this time. Analog Channel Disable The interval of time allowed before enabling the plasma process idle flow analog values. Plasma process start gas flow analog values are in effect during this time. Line Fill Time The interval of time allowed to fill the plasma process gas lines. Plasma process purge/fill gas flows are in effect during this time. Plasma Postflow The interval of time allowed for plasma process gases to flow after expiration of the MASTER UP timer. Plasma process start gas flows are in effect during this time. Line Vent Time The interval of time allowed to vent the plasma process gas lines. Plasma process idle gas flows are in effect during this time. Flow Control Vent Time The interval of time allowed to vent the flow control gas lines. Plasma process purge/fill gas flows are in effect during this time. Precision Plasma with Electronic Flow Control - 6-21 SECTION 6 TROUBLESHOOTING 6.12.2 Process Timer Values For Vision Cutting Record File PARAM.CUT Vision Interpretation Data File DEF.TEC V (Hidden Flag) DEF .TEC Qx (Upper Editing Limit) Wx (Preset Value) Ux (Lower Editing Limit) PARAM.CUT V = Hidden Flag Enabled TIMERS Plasma Preflow Time 0.6 0.5 50.0 V Line Purge Time 1.0 1.0 50.0 V Plasma Firing Time 6.0 4.0 6.0 V Plasma Pierce Time 0.0 0.0 50.0 Plasma Ahc Delay 0.0 0.0 50.0 Plasma Arc Delay 0.3 0.0 0.5 Master Up 2.0 0.0 50.0 600.0 600.0 600.0 V Line Fill Time 5.0 5.0 50.0 V Plasma Postflow 5.0 5.0 50.0 V Line Vent Time / Flow Control Vent Time 2.0 2.0 50.0 V Analog Channel Disable 6-22 Precision Plasma with Electronic Flow Control - V SECTION 6 TROUBLESHOOTING 6.12.3 Process Window Key Functions Key Function Description • Plasma AHC Allow Icon • • • (F2 PushPush-Button) • Plasma AHC Icon • • (F3 PushPush-Button) Icon permits the machine operator to allow or disallow plasma AHC. Icon does not turn plasma AHC on. Plasma AHC is allowed if the icon is highlighted (darkened). Plasma AHC is not allowed if the icon is not highlighted. Icon permits machine operator to manually turn plasma AHC on or off. Icon also permits the operator to perform a plasma IHS cycle if the plasma process is not active. The plasma AHC allow icon must be highlighted highlighted. Plasma Start Parameter Test Icon • Icon permits the machine operator to manually test/adjust the plasma process start parameters with the exception of the plasma gas 2 start flow. • Icon permits the machine operator to manually test/adjust the plasma gas 2 start flow. The plasma start parameter test icon must be highlighted. highlighted (F4 PushPush-Button) Plasma Gas 2 Test Icon • (F5 PushPush-Button) Plasma Cut Parameter Test Icon • • Icon permits the machine operator to manually test/adjust the plasma process cut parameters. The plasma plasma start parameter test icon must be highlighted. highlighted (F6 PushPush-Button) Plasma Start Icon • • Icon permits the machine operator to manually start or stop the plasma process. The plasma start parameter test icon must not be highlighted. highlighted (F6 PushPush-Button) Precision Plasma with Electronic Flow Control - 6-23 SECTION 6 TROUBLESHOOTING 6.12.4 Proportional Valve Analog Flow Values For Param.Cut And Def.Tec Analog Flow Values Jx (Upper Channel Limit) Ix (Lower Limit) mit) Channel Li Xx (Lower Parameter Limit) Yy (Upper Parameter Limit) V (Hidden Flag) DEF.TEC Qx (Upper Editing Limit) Ux (Lower Editing Limit) Wx (Preset Value) PARAM.CUT V = Hidden Flag Enabled Plasma Gas 1 Start Flow Analog Out 0.0 0.0 100.0 0.0 100.0 0.0 255.0 Plasma Gas 1 Cut Flow Analog Out 0.0 0.0 100.0 0.0 100.0 0.0 255.0 Plasma Gas 2 Start Flow Analog Out 0.0 0.0 100.0 0.0 100.0 0.0 255.0 Plasma Gas 2 Cut Flow Analog Out 0.0 0.0 100.0 0.0 100.0 0.0 255.0 Shield Gas 1 Start Flow Analog Out 0.0 0.0 100.0 0.0 100.0 0.0 255.0 Shield Gas 1 Cut Flow Analog Out 0.0 0.0 100.0 0.0 100.0 0.0 255.0 Shield Gas 2 Start Flow Analog Out 0.0 0.0 100.0 0.0 100.0 0.0 255.0 Shield Gas 2 Cut Flow Analog Out 0.0 0.0 100.0 0.0 100.0 0.0 255.0 Plasma Gas 1 Soft Flow Analog Out 10.0 10.0 10.0 V 0.0 100.0 0.0 255.0 Plasma Gas 1 Purge/Fill/Vent Flow Analog Out 100.0 100.0 100.0 V 0.0 100.0 0.0 255.0 Plasma Gas 1 Idle Flow Analog Out 0.0 0.0 0.0 V 0.0 100.0 0.0 255.0 Plasma Gas 2 Soft Flow Analog Out 10.0 10.0 10.0 V 0.0 100.0 0.0 255.0 Plasma Gas 2 Purge/Fill/Vent Flow Analog Out 100.0 100.0 100.0 V 0.0 100.0 0.0 255.0 Plasma Gas 2 Idle Flow Analog Out 0.0 0.0 0.0 V 0.0 100.0 0.0 255.0 Shield Gas 1 Soft Flow Analog Out 10.0 10.0 10.0 V 0.0 100.0 0.0 255.0 Shield Gas 1 Purge/Fill/Vent Flow Analog Out 100.0 100.0 100.0 V 0.0 100.0 0.0 255.0 Shield Gas 1 Idle Flow Analog Out 0.0 0.0 0.0 V 0.0 100.0 0.0 255.0 Shield Gas 2 Soft Flow Analog Out 10.0 10.0 10.0 V 0.0 100.0 0.0 255.0 Shield Gas 2 Purge/Fill/Vent Flow Analog Out 100.0 100.0 100.0 V 0.0 100.0 0.0 255.0 Shield Gas 2 Idle Flow Analog Out 0.0 0.0 0.0 V 0.0 100.0 0.0 255.0 6-24 Precision Plasma with Electronic Flow Control - SECTION 6 TROUBLESHOOTING 6.12.5 Process Gas Selection Requirements • Plasma process gas selection is accomplished with activation of the appropriate SDP file. • The correct CUTTING RECORD FLAG must be in each SDP file. • Selection is keyed to the value in the CUTTING RECORD FLAG. • Please refer to the ATAS description of the cutting package for a detailed explanation of The cutting record flag. Material Type Plasma Gas Shield Gas Abbreviation Cutting Record Flag Carbon steel O2 N2 CS1-O2-N2 M1000000000000000 Carbon steel O2 N2 with O2 mix CS2-O2-N2/O2 M0100000000000000 Carbon steel O2 O2 CS3-O2-O2 M0000000000010000 Stainless steel N2 N2 SS1-N2-N2 M0010000000000000 Stainless steel N2 N2 with CH4 mix SS2-N2-N2/CH4 M0001000000000000 Stainless steel Air Air SS4-Air-Air M0000010000000000 Stainless steel Air Air with CH4 mix SS5-Air-Air/CH4 M0000001000000000 Aluminum N2 N2 Al1-N2-N2 M0000000010000000 Aluminum N2 N2 with CH4 mix Al2-N2-N2/CH4 M0000000001000000 Plasma marking Argon Air PM1-Argon-Air M0000000000100000 Precision Plasma with Electronic Flow Control - 6-25 SECTION 6 TROUBLESHOOTING 6.12.6 EFC Process Gas Flow Chart 1 Vision Shift/Start Numbers Line vent Flow control vent 2 Idle (Station off) 13 # correspond to columns on solenoid/ proportional valve requirement charts and gas error monitoring charts 9 no Station on? Test (start) yes Section 6.7.7 for details Line Purge 6 Process start. Station on Flush/ Pressure cycle Plasma stop? 3 Station on? Error condition? yes no no yes 5 no Plasma stop no 7 yes yes Plasma test (start O2)? Plasma test? 10 Error condition? yes yes 8 Station on? yes yes Station on? no Plasma start? Test (start O2) yes no yes no no no Process Postflow New SDP file selected? no Plasma test? yes no Analog disable timing? no yes New SDP file selected? Plasma test cut? yes no no 12 Idle (Station On) Station on? no no Plasma test (start O2)? no Station on? yes yes yes New SDP file selected? no Plasma test? yes no Plasma start? no yes 6-26 Precision Plasma with Electronic Flow Control - Plasma test cut? no yes yes New SDP file selected? no Plasma test? no no New SDP file selected? no yes yes Station on? yes yes yes yes Plasma test cut? Station on? yes Plasma test? no Arc established ? yes Process cut no no no yes yes Station on? ready New SDP files selected? 4 Station on? Test (cut) yes yes no Line fill Station on? yes no no 11 no yes no SECTION 6 TROUBLESHOOTING SOLENOID VALVES Plasma Gas 1 Supply Solenoid Valve N2-2 Plasma Gas 1 Supply Solenoid Valve AirAir-2 Finish 16 Milliseconds 0.5 Seconds 1.0 Second 0.5 Seconds 1.5 Seconds 2.0 Seconds Start 16 Milliseconds 6.12.7..Station On, Flush/Pressurize Cycle PG-N2,O2 SG-N2 X = OPEN / ENABLED, BLANK = CLOSED / DISABLED, ANALOG VALUE = 0 - 10 VDC X X X X X X X X X X X X X X X X X X X X X X X Plasma Gas 1 Supply Solenoid Valve Argon Plasma Gas 2 Supply Solenoid Valve O2-2 Shield Gas 1 Supply Solenoid Valve O2-1 Shield Gas 1 Supply Solenoid Valve N2-1 Shield Gas 1 Supply Solenoid Valve AirAir-1 Shield Gas 2 Supply Solenoid Valve N2-3 Shield Gas 2 Supply Solenoid Valve Ch4 Plasma Gas 1 Torch Solenoid Valve Plasma Gas 2 Torch Solenoid Valve Shield Gas 1 Torch Solenoid Valve Shield Gas 2 Torch Solenoid Valve X X X X X X X X X X X Analog Flow Values Plasma Gas 1 Start Flow Analog Out Plasma Gas 1 Cut Flow Analog Out Plasma Gas 2 Start Flow Analog Out Plasma Gas 2 Cut Flow Analog Out Shield Gas 1 Start Flow Analog Out Shield Gas 1 Cut Flow Analog Out Shield Gas 2 Start Flow Analog Out Shield Gas 2 Cut Flow Analog Out Plasma Gas 1 Soft Flow Analog Out X Plasma Gas 1 Purge/Fill/Vent Flow Analog Out X X X X X X X X X X X X X X X X X X X Plasma Gas 1 Idle Flow Analog Out Plasma Gas 2 Soft Flow Analog Out X Plasma Gas 2 Purge/Fill/Vent Flow Analog Out Plasma Gas 2 Idle Flow Analog Out Shield Gas 1 Soft Flow Analog Out X Shield Gas 1 Purge/Fill/Vent Flow Analog Out Shield Gas 1 Idle Flow Analog Out Shield Gas 2 Soft Flow Analog Out X Shield Gas 2 Purge/Fill/Vent Flow Analog Out Shield Gas 2 Idle Flow Analog Out Precision Plasma with Electronic Flow Control - 6-27 SECTION 6 TROUBLESHOOTING 12 13 Idle (Station Off) 11 Test (Cut) Test (Start) (O2) Test (Start) Process Post Flow Process Cut Process Start Ready Line Fill Line Purge Flow Control Vent Lin Line e Vent ➊ ➋ ➌ ➍ ➎ ➏ ➐ ➑ ➒ ➓ Idle (Station On) 6.12.8 Solenoid And Proportional Valve Requirements Carbon Steel PG-O2, SG-N2 X = Open / Enabled, Blank = Closed Closed / Disabled, Analog Value = 0 - 10 Vdc SOLENOID VALVES X Plasma Gas 1 Supply Solenoid Valve N2-2 X X X X X X X X X X X X X X X X X X X X X X X X X X X X X X X Plasma Gas 1 Supply Solenoid Valve AirAir-2 Plasma Gas 1 Supply Solenoid Valve Argon Plasma Gas 2 Supply Solenoid Valve O2-2 Shield Gas 1 Supply Solenoid Valve O2-1 X Shield Gas 1 Supply Solenoid Valve N2-1 Shield Gas 1 Supply Solenoid Valve AirAir-1 X Shield Gas 2 Supply Solenoid Valve N2-3 Shield Gas 2 Supply Solenoid Valve Ch4 Plasma Gas 1 Torch Solenoid Valve X X Plasma Gas 2 Torch Solenoid Valve X X X Shield Gas 1 Torch Solenoid Valve X X X Shield Gas 2 Torch Solenoid Valve X X X X X X X X X X X X X X X X X X X X Analog Flow Values Plasma Gas 1 Start Flow Analog Out Plasma Gas 1 Cut Flow Analog Out Plasma Gas 2 Start Flow Analog Out X X X Plasma Gas 2 Cut Flow Analog Out X Shield Gas 1 Start Flow Analog Out X X X Shield Gas 1 Cut Flow Analog Out X X X Shield Gas 2 Start Flow Analog Out Shield Gas 2 Cut Flow Analog Out Plasma Gas 1 Soft Flow Analog Out X Plasma Gas 1 Purge/Fill/Vent Flow Analog Out X X X Plasma Gas 1 Idle Flow Analog Out X X X X X X X X Plasma Gas 2 Soft Flow Analog Out X Plasma Gas 2 Purge/Fill/Vent Flow Analog Out X X Plasma Gas 2 Idle Flow Analog Out Shield Gas 1 Soft Flow Analog Out X Shield Gas 1 Purge/Fill/Vent Flow Analog Out X X X Shield Gas 1 Idle Flow Analog Out Shield Gas 2 Soft Flow Analog Out X Shield Gas 2 Purge/Fill/Vent Flow Analog Out Shield Gas 2 Idle Flow Analog Out 6-28 X X Precision Plasma with Electronic Flow Control - SECTION 6 TROUBLESHOOTING 6.12.9 Gas Error Monitoring Carbon Steel PG-O2, SG-N2 Plasma Gas 2 Pressure Switch O O Shield Gas 1 Pressure Switch O Shield Gas 2 Pressure Switch O 13 Idle (Station Off) 12 Idle (Station On) Test (Cut) Test (Start) (O2) (Start) t) Test (Star Process Post Flow Process Cut Process Start Ready 11 X = Monitored For Pressure Present, O = Monitored For Absence Of Pressure X X Process Gas Pressure Switches Plasma Gas 1 Pressure Switch Line Fill Line Purge Flow Control Vent Line Vent ➊ ➋ ➌ ➍ ➎ ➏ ➐ ➑ ➒ ➓ X X X X 1 Vision Shift/Start Numbers Line vent Flow control vent 2 Idle (Station off) 13 # correspond to columns on solenoid/ proportional valve requirement charts and gas error monitoring charts 9 no Station on? Test (start) yes Section 6.7.7 for details Line Purge 6 Process start. Station on Flush/ Pressure cycle Plasma stop? 3 Station on? Error condition? yes yes no 4 Station on? no no yes ready 5 no Plasma stop 7 yes New SDP file selected? no Plasma test? no yes yes Plasma test (start O2)? Plasma test cut? no yes New SDP file selected? Plasma test? 10 yes no Error condition? no no yes no yes yes no yes 8 Station on? no Process Postflow Station on? New SDP file selected? no Plasma test? yes no Analog disable timing? no Test (start O2) yes yes no Plasma start? yes yes yes no no Station on? Station on? yes yes no Plasma test? Plasma test cut? Arc established ? yes Process cut New SDP files selected? yes no yes Station on? Test (cut) no yes no Line fill Station on? yes yes no no 11 no yes New SDP file selected? Plasma test cut? yes no no 12 Idle (Station On) Station on? no no Plasma test (start O2)? yes no Station on? yes yes yes New SDP file selected? no Plasma test? yes no Plasma start? no yes Precision Plasma with Electronic Flow Control - 6-29 SECTION 6 TROUBLESHOOTING 12 13 Idle (Station Off) 11 Test (Cut) Test (Start) (O2) Test (Start) Process Post Flow Process Cut Process Start Ready Line Fill Line Purge Flo Flow w Control Vent Line Vent ➊ ➋ ➌ ➍ ➎ ➏ ➐ ➑ ➒ ➓ Idle (Station On) 6.12.10 Solenoid And Proportional Valve Requirements Carbon Steel PG-O2, SG-N2/O2 X = Open / Enabled, Blank = Closed / Disabled, Disabled, Analog Value = 0 - 10 Vdc SOLENOID VALVES X X X X X X X X X X Plasma Gas 2 Supply Solenoid Valve O2-2 X X X X X X X X X Shield Gas 1 Supply Solenoid Valve O2-1 X X X X X X X X X X X X X X X X X X X X X X X X X Plasma Gas 1 Supply Solenoid Valve N2-2 Plasma Gas 1 Supply Solenoid Valve AirAir-2 Plasma Gas 1 Supply Solenoid Valve Argon X Shield Gas 1 Supply Solenoid Valve N2-1 Shield Gas 1 Supply Solenoid Valve AirAir-1 Shield Gas 2 Supply Solenoid Valve N2-3 Shield Gas 2 Supply Solenoid Valve Ch4 Plasma Gas 1 Torch Solenoid Valve X X Plasma Gas 2 Torch Solenoid Valve X X Shield Gas 1 Torch Solenoid Valve X X Shield Gas 2 Torch Solenoid Valve X X X X X X X X X X X X X X X X X X X X X X X Analog Flow Values Plasma Gas 1 Start Flow Analog Out Plasma Gas 1 Cut Flow Analog Out Plasma Gas 2 Start Flow Analog Out X X X Plasma Gas 2 Cut Flow Analog Out X Shield Gas 1 Start Flow Analog Out Shield Gas 1 Cut Flow Analog Out X X Shield Gas 2 Start Flow Analog Out X X X X X Shield Gas 2 Cut Flow Analog Out X X X X Plasma Gas 1 Soft Flow Analog Out X Plasma Gas 1 Purge/Fill/Vent Flow Analog Out X X X Plasma Gas 1 Idle Flow Analog Out X X X X X X X X Plasma Gas 2 Soft Flow Analog Out X Plasma Gas 2 Purge/Fill/Vent Flow Analog Out X X Plasma Gas 2 Idle Flow Analog Out Shield Gas 1 Soft Flow Analog Out X Shield Gas 1 Purge/Fill/Vent Flow Analog Out X X X Shield Gas 1 Idle Flow Analog Out Shield Gas 2 Soft Flow Analog Out X Shield Gas 2 Purge/Fill/Vent Flow Analog Out Shield Gas 2 Idle Flow Analog Out 6-30 X X X Precision Plasma with Electronic Flow Control - SECTION 6 TROUBLESHOOTING 6.12.11 Gas Error Monitoring Carbon Steel PG-O2, SG-N2/O2 Plasma Gas 2 Pressure Switch O O Shield Gas 1 Pressure Switch Shield Gas 2 Pressure Switch 13 Idle (Station Off) 12 Idle (Station On) Test (Cut) Test (Start) (O2) Test (Start) Process Post Flow Process Cut Process Start 11 X = Monitored For Pressure Present, O = Monitored For Absence Of Pressure X X Process Gas Pressure Switches Plasma Gas 1 Pressure Switch Ready Line Fill Line Purge Line Vent Flow Control Vent ➊ ➋ ➌ ➍ ➎ ➏ ➐ ➑ ➒ ➓ X X O X X O X X 1 Vision Shift/Start Numbers Line vent Flow control vent 2 Idle (Station off) 13 # correspond to columns on solenoid/ proportional valve requirement charts and gas error monitoring charts 9 no Station on? Test (start) yes Section 6.7.7 for details Line Purge 6 Process start. Station on Flush/ Pressure cycle Plasma stop? 3 no Error condition? yes yes no 4 Station on? no no yes ready 5 no Plasma stop yes yes 7 New SDP file selected? no Plasma test? no yes no no Station on? yes Plasma test? Plasma test cut? yes Plasma test (start O2)? Plasma test cut? no yes Plasma test? 10 yes no New SDP file selected? Error condition? no no yes no yes yes no yes 8 Station on? no Process Postflow Station on? New SDP file selected? no Plasma test? yes no Analog disable timing? no Test (start O2) yes yes no Plasma start? yes no Station on? yes yes no Arc established ? yes Process cut New SDP files selected? yes yes Station on? Test (cut) no yes no Line fill Station on? yes yes no Station on? 11 no yes New SDP file selected? Plasma test cut? yes no no 12 Idle (Station On) Station on? no no Plasma test (start O2)? yes no Station on? yes yes yes New SDP file selected? no Plasma test? yes no Plasma start? no yes Precision Plasma with Electronic Flow Control - 6-31 SECTION 6 TROUBLESHOOTING 11 12 13 Idle (Station On) Idle (Station Off) Test (Start) (O2) Test (Start) Process Post Flow Process Cut Process Start Ready Line Fill Line Purge Flow Control Vent Line Vent ➊ ➋ ➌ ➍ ➎ ➏ ➐ ➑ ➒ ➓ Test (Cut) 6.12.12 Solenoid And Proportional Valve Requirements Carbon Steel PG-O2, SG-O2 X = Open / Enabled, Blank = Closed / Disabled,, Analog Value = 0 - 10 Vdc SOLENOID VALVES X X X X X X X X X X Plasma Gas 2 Supply Solenoid Valve O2-2 X X X X X X X X X Shield Gas 1 Supply Solenoid Valve O2-1 X X X X X X X X X X X X X X X X X X X X X X X X X Plasma Gas 1 Supply Solenoid Valve N2-2 Plasma Gas 1 Supply Solenoid Valve AirAir-2 Plasma Gas 1 Supply Solenoid Valve Argon X Shield Gas 1 Supply Solenoid Valve N2-1 Shield Gas 1 Supply Solenoid Valve AirAir-1 Shield Gas 2 Supply Solenoid Valve N2-3 Shield Gas 2 Supply Solenoid Valve Ch4 Plasma Gas 1 Torch Solenoid Valve X X Plasma Gas 2 Torch Solenoid Valve X X Shield Gas 1 Torch Solenoid Valve X X Shield Gas 2 Torch Solenoid Valve X X X X X X X X X X X X X X X X Analog Flow Values Plasma Gas 1 Start Flow Analog Out X X X X X Plasma Gas 1 Cut Flow Analog Out Plasma Gas 2 Start Flow Analog Out X X X Plasma Gas 2 Cut Flow Analog Out X Shield Gas 1 Start Flow Analog Out Shield Gas 1 Cut Flow Analog Out X X Shield Gas 2 Start Flow Analog Out X X X X X Shield Gas 2 Cut Flow Analog Out X X X X Plasma Gas 1 Soft Flow Analog Out X Plasma Gas 1 Purge/Fill/Vent Flow Analog Out X X X Plasma Gas 1 Idle Flow Analog Out X X X X X X X X Plasma Gas 2 Soft Flow Analog Out X Plasma Gas 2 Purge/Fill/Vent Flow Analog Out X X Plasma Gas 2 Idle Flow Analog Out Shield Gas 1 Soft Flow Analog Out X Shield Gas 1 Purge/Fill/Vent Flow Analog Out X X X Shield Gas 1 Idle Flow Analog Out Shield Gas 2 Soft Flow Analog Out X Shield Gas 2 Purge/Fill/Vent Flow Analog Out Shield Gas 2 Idle Flow Analog Out 6-32 X X X Precision Plasma with Electronic Flow Control - TROUBLESHOOTING Plasma Gas 2 Pressure Switch O O Shield Gas 1 Pressure Switch Shield Gas 2 Pressure Switch 13 Idle (Station Off) 12 Idle (Station On) Test (Start) (O2) Test (Start) Process Flow w Post Flo Process Cut Process Start 11 X = Monitored For Pressure Present, O = Monitored For Absence Of Pressure X X Process Gas Pressure Switches Plasma Gas 1 Pressure Switch Ready Line Fill Line Purge Flow Control Vent ➊ ➋ ➌ ➍ ➎ ➏ ➐ ➑ ➒ ➓ Line Vent 6.12.13 Gas Error Monitoring Carbon Steel PG-O2, SG- O2 Test (Cut) SECTION 6 X X O X X O X X 1 Vision Shift/Start Numbers Line vent Flow control vent 2 Idle (Station off) 13 # correspond to columns on solenoid/ proportional valve requirement charts and gas error monitoring charts 9 no Station on? Test (start) yes Section 6.7.7 for details Line Purge 6 Process start. Station on Flush/ Pressure cycle Plasma stop? 3 no Error condition? yes yes no 4 Station on? no no yes ready 5 no Plasma stop yes yes 7 New SDP file selected? no Plasma test? no yes no no Station on? yes Plasma test? Plasma test cut? yes Plasma test (start O2)? Plasma test cut? no yes Plasma test? 10 yes no New SDP file selected? Error condition? no no yes no yes yes no yes 8 Station on? no Process Postflow Station on? New SDP file selected? no Plasma test? yes no Analog disable timing? no Test (start O2) yes yes no Plasma start? yes no Station on? yes yes no Arc established ? yes Process cut New SDP files selected? yes yes Station on? Test (cut) no yes no Line fill Station on? yes yes no Station on? 11 no yes New SDP file selected? Plasma test cut? yes no no 12 Idle (Station On) Station on? no no Plasma test (start O2)? yes no Station on? yes yes yes New SDP file selected? no Plasma test? yes no Plasma start? no yes Precision Plasma with Electronic Flow Control - 6-33 Test (Start) Process Post Flow Process Cut Process Start Ready Line Fill Line Purge Flow Control Vent Line Vent ➊ ➋ ➌ ➍ ➎ ➏ ➐ ➑ ➒ 11 12 13 Idle (Station Off) 6.12.14 Solenoid And Proportional Valve Requirements Stainless Steel PG-N2, SG-N2 Idle (Station On) TROUBLESHOOTING Test (Cut) SECTION 6 X = OPEN / ENABLED, BLANK = CLOSED / DISABLED, ANALOG VALUE = 0 - 10 VDC Solenoid Valves Plasma Gas 1 Supply Solenoid Valve N2-2 X X X X X X X X X X X X X X X X X X Plasma Gas 1 Supply Solenoid Valve AirAir-2 Plasma Gas 1 Supply Solenoid Valve Argon Plasma Gas 2 Supply Solenoid Valve O2-2 Shield Gas 1 Supply Solenoid Valve O2-1 Shield Gas 1 Supply Solenoid Valve N2N2-1 Shield Gas 1 Supply Solenoid Valve AirAir-1 Shield Gas 2 Supply Solenoid Valve N2-3 X Shield Gas 2 Supply Solenoid Valve CH4 Plasma Gas 1 Torch Solenoid Valve X X X X X X X X X Plasma Gas 2 Torch Solenoid Valve X X Shield Gas 1 Torch Solenoid Valve X X X X X X X X X Shield Gas 2 Torch Solenoid Valve X X X X X Analog Flow Values Plasma Gas 1 Start Flow Analog Out X X Plasma Gas 1 Cut Flow Analog Out X X Plasma Gas 2 Start Flow Analog Out Plasma Gas 2 Cut Flow Analog Out Shield Gas 1 Start Flow Analog Out X Shield Gas 1 Cut Flow Analog Out X X X X X Shield Gas 2 Start Flow Analog Out Shield Gas 2 Cut Flow Analog Out Plasma Gas 1 Soft Flow Analog Out Plasma Gas 1 Purge/Fill/Vent Flow Analog Out Plasma Gas 1 Idle Flow Analog Out X X X X X X X X X X X X Plasma Gas 2 Soft Flow Analog Out Plasma Gas 2 Purge/Fill/Vent Flow Analog Out Plasma Gas 2 Idle Flow Analog Out X X Shield Gas 1 Soft Flow Analog Out Shield Gas 1 Purge/Fill/Vent Flow Analog Out Shield Gas 1 Idle Flow Analog Out X X X X Shield Gas 2 Soft Flow Analog Out Shield Gas 2 Purge/Fill/Vent Flow Analog Out Shield Gas 2 Idle Flow Analog Out 6-34 X X X Precision Plasma with Electronic Flow Control - 12 13 Idle (Station Off) Test (Start) Process Post Flow Process Cut Process Start Ready 11 X = Monitored For Pressure Present, O = Monitored For Absence Of Pressure X X Process Gas Pressure Switches Plasma Gas 1 Pressure Switch Line Fill Line Purge Flow Control Vent ➊ ➋ ➌ ➍ ➎ ➏ ➐ ➑ ➒ Line Vent 6.12.15 Gas Error Monitoring Stainless Steel PG-N2, SG-N2 Idle (Station On) TROUBLESHOOTING Test (Cut) SECTION 6 Plasma Gas 2 Pressure Switch O O Shield Gas 1 Pressure Switch O X X Shield Gas 2 Pressure Switch O X X 1 Vision Shift/Start Numbers Line vent Flow control vent 2 Idle (Station off) 13 # correspond to columns on solenoid/ proportional valve requirement charts and gas error monitoring charts 9 no Station on? Test (start) yes Section 6.7.7 for details Line Purge 6 Process start. Station on Flush/ Pressure cycle Plasma stop? 3 no Error condition? yes yes no 4 Station on? no no yes ready 5 no Plasma stop yes yes no New SDP file selected? no Plasma test? no yes no 7 Station on? yes Plasma test? Plasma test cut? yes Plasma test (start O2)? Plasma test cut? no yes Plasma test? 10 yes no New SDP file selected? Error condition? no no yes no yes yes no yes 8 Station on? no Process Postflow Station on? New SDP file selected? no Plasma test? yes no Analog disable timing? no Test (start O2) yes yes no Plasma start? yes no Station on? yes yes no Arc established ? yes Process cut New SDP files selected? yes yes Station on? Test (cut) no yes no Line fill Station on? yes yes no Station on? 11 no yes New SDP file selected? Plasma test cut? yes no no 12 Idle (Station On) Station on? no no Plasma test (start O2)? yes no Station on? yes yes yes New SDP file selected? no Plasma test? yes no Plasma start? no yes Precision Plasma with Electronic Flow Control - 6-35 SECTION 6 TROUBLESHOOTING SOLENOID VALVES 11 12 13 Idle (Station On) Idle (Station Off) Test (S (Start) tart) Process Post Flow Process Cut Process Start Ready Line Fill Line Purge Flow Control Vent Line Vent ➊ ➋ ➌ ➍ ➎ ➏ ➐ ➑ ➒ Test (Cut) 6.12.16 Solenoid And Proportional Valve Requirements Stainless Steel PG-N2, SG-N2/CH4 X = Open / Enabled, Blank = Closed / Disabled, Analog Value = 0 - 10 Vdc X X X X X X X X X Plasma Gas 1 Supply Solenoid Valve N2-2 Plasma Gas 1 Supply Solenoid Valve AirAir-2 Plasma Gas 1 Supply Solenoid Valve Argon Plasma Gas 2 Supply Solenoid Valve O2-2 Shield Gas 1 Supply Solenoid Valve O2-1 Shield Gas 1 Supply Solenoid Valve N2-1 X X X X X X X X X X X X X X X X X Shield Gas 1 Supply Solenoid Valve AirAir-1 Shield Gas 2 Supply Solenoid Valve N2-3 X Shield Gas 2 Supply Solenoid Valve CH4 Plasma Gas 1 Torch Solenoid Valve X X X X X X X X X Plasma Gas 2 Torch Solenoid Valve X X Shield Gas 1 Torch Solenoid Valve X X X X X X X X X Shield Gas 2 Torch Solenoid Valve X X X X X X Analog Flow Values Plasma Gas 1 Start Flow Analog Out X X Plasma Gas 1 Cut Flow Analog Out X X X X Plasma Gas 2 Start Flow Analog Out Plasma Gas 2 Cut Flow Analog Out Shield Gas 1 Start Flow Analog Out X X Shield Gas 1 Cut Flow Analog Out X X X X Shield Gas 2 Start Flow Analog Out Shield Gas 2 Cut Flow Analog Out X X X X X Plasma Gas 1 Soft Flow Analog Out Plasma Gas 1 Purge/Fill/Vent Flow Analog Out Plasma Gas 1 Idle Flow Analog Out X X X X X X X X X X X X Plasma Gas 2 Soft Flow Analog Out Plasma Gas 2 Purge/Fill/Vent Flow Analog Out Plasma Gas 2 Idle Flow Analog Out X X Shield Gas 1 Soft Flow Analog Out Shield Gas 1 Purge/Fill/Vent Flow Analog Out Shield Gas 1 Idle Flow Analog Out X X X X Shield Gas 2 Soft Flow Analog Out Shield Gas 2 Purge/Fill/Vent Flow Analog Out Shield Gas 2 Idle Flow Analog Out 6-36 X X X X Precision Plasma with Electronic Flow Control - SECTION 6 TROUBLESHOOTING 12 13 Idle (Station On) Idle (Station) Off) Test (Start) Process Post Flow Process Cut Process Start Ready Plasma Gas 2 Pressure Switch O O Shield Gas 1 Pressure Switch O X X O X X Shield Gas 2 Pressure Switch 11 X = Monitored For Pressure Present, O = Monitored Monitored For Absence Of Pressure X X Process Gas Pressure Switches Plasma Gas 1 Pressure Switch Line Fill Line Purge Flow Control Vent Line Vent ➊ ➋ ➌ ➍ ➎ ➏ ➐ ➑ ➒ Test (Cut) 6.12.17 Gas Error Monitoring Stainless Steel PG-N2, SG-N2/CH4 1 Vision Shift/Start Numbers Line vent Flow control vent 2 Idle (Station off) 13 # correspond to columns on solenoid/ proportional valve requirement charts and gas error monitoring charts 9 no Station on? Test (start) yes Section 6.7.7 for details Line Purge 6 Process start. Station on Flush/ Pressure cycle Plasma stop? 3 Station on? Error condition? yes yes no 4 Station on? no no yes ready 5 no Plasma stop no yes New SDP file selected? no Plasma test? no yes yes Plasma test (start O2)? Plasma test cut? no yes Plasma test? 10 yes no New SDP file selected? Error condition? no no yes no yes yes no yes 8 Station on? no Process Postflow Station on? New SDP file selected? no Plasma test? yes no Analog disable timing? no Test (start O2) yes yes no Plasma start? yes yes yes no 7 Station on? Station on? yes yes no Plasma test? Plasma test cut? Arc established ? yes Process cut New SDP files selected? yes no yes Station on? Test (cut) no yes no Line fill Station on? yes yes no no 11 no yes New SDP file selected? Plasma test cut? yes no no 12 Idle (Station On) Station on? no no Plasma test (start O2)? yes no Station on? yes yes yes New SDP file selected? no Plasma test? yes no Plasma start? no yes Precision Plasma with Electronic Flow Control - 6-37 SECTION 6 TROUBLESHOOTING Solenoid Solenoid Valves 11 12 13 Idle (Station On) Idle (Station Off) Test (Start) Process Post Flow Process Cut Process Start Ready Line Fill Line Purge Flow Control Vent Line Vent ➊ ➋ ➌ ➍ ➎ ➏ ➐ ➑ ➒ Test (Cut) 6.12.18 Solenoid And Proportional Valve Requirements Stainless Steel PG-Air, SG-Air X = Open / Enabled, Blank = Closed / Disabled, Analog Value = 0 - 10 Vdc X Plasma Gas 1 Supply Solenoid Valve N2-2 Plasma Gas 1 Supply Solenoid Valve AirAir-2 X X X X X X X X X X X X X X X X Plasma Gas 1 Supply Solenoid Valve Argon Plasma Gas 2 Supply Solenoid Valve O2-2 Shield Gas 1 Supply Solenoid Valve O2-1 Shield Gas 1 Supply Solenoid Valve N2-1 X Shield Gas 1 Supply Solenoid Valve AirAir-1 Shield Gas 2 Supply Solenoid Valve N2-3 X Shield Gas 2 Supply Solenoid Valve Ch4 Plasma Gas 1 Torch Solenoid Valve X X X X X X X X X Plasma Gas 2 Torch Solenoid Valve X X Shield Gas 1 Torch Solenoid Valve X X X X X X X X X Shield Gas 2 Torch Solenoid Valve X X X X X Analog Flow Values Plasma Gas 1 Start Flow Analog Out X X Plasma Gas 1 Cut Flow Analog Out X X Plasma Gas 2 Start Flow Analog Out Plasma Gas 2 Cut Flow Analog Out Shield Gas 1 Start Flow Analog Out X Shield Gas 1 Cut Flow Analog Out X X X X X Shield Gas 2 Start Flow Analog Out Shield Gas 2 Cut Flow Analog Out Plasma Gas 1 Soft Flow Analog Out Plasma Gas 1 Purge/Fill/Vent Flow Analog Out Plasma Gas 1 Idle Flow Analog Out X X X X X X X X X X X X Plasma Gas 2 Soft Flow Analog Out Plasma Gas 2 Purge/Fill/Vent Flow Analog Out Plasma Gas 2 Idle Flow Analog Out X X Shield Gas 1 Soft Flow Analog Out Shield Gas 1 Purge/Fill/Vent Flow Analog Out Shield Gas 1 Idle Flow Analog Out X X X X Shield Gas 2 Soft Flow Analog Out Shield Gas 2 Purge/Fill/Vent Flow Analog Out Shield Gas 2 Idle Flow Analog Out 6-38 X X X Precision Plasma with Electronic Flow Control - Plasma Gas 2 Pressure Switch O O Shield Gas 1 Pressure Switch O Shield Gas 2 Pressure Switch O 12 13 Idle (Station) Off) Test (Start) Process Post Flow Process Cut Process Start Ready 11 X = Monitored For Pressure Present, O = Monitored For Absence Of Pressure X X Process Gas Pressure Switches Plasma Gas 1 Pressure Switch Line Fill Line Purge Flow Control Vent ➊ ➋ ➌ ➍ ➎ ➏ ➐ ➑ ➒ Line Vent 6.12.19 Gas Error Monitoring Stainless Steel PG-Air, SG-Air Idle (Station On) TROUBLESHOOTING Test (Cut) SECTION 6 X X 1 Vision Shift/Start Numbers Line vent Flow control vent 2 Idle (Station off) 13 # correspond to columns on solenoid/ proportional valve requirement charts and gas error monitoring charts 9 no Station on? Test (start) yes Section 6.7.7 for details Line Purge 6 Process start. Station on Flush/ Pressure cycle Plasma stop? 3 Station on? Error condition? yes yes no 4 Station on? no no yes ready 5 no Plasma stop no yes New SDP file selected? no Plasma test? no yes yes Plasma test (start O2)? Plasma test cut? no yes Plasma test? 10 yes no New SDP file selected? Error condition? no no yes no yes yes no yes 8 Station on? no Process Postflow Station on? New SDP file selected? no Plasma test? yes no Analog disable timing? no Test (start O2) yes yes no Plasma start? yes yes yes no 7 Station on? Station on? yes yes no Plasma test? Plasma test cut? Arc established ? yes Process cut New SDP files selected? yes no yes Station on? Test (cut) no yes no Line fill Station on? yes yes no no 11 no yes New SDP file selected? Plasma test cut? yes no no 12 Idle (Station On) Station on? no no Plasma test (start O2)? yes no Station on? yes yes yes New SDP file selected? no Plasma test? yes no Plasma start? no yes Precision Plasma with Electronic Flow Control - 6-39 Solenoid Valves Test (Start) Process Post Flow Process Cut Process Start Ready Line Fill Purge e Line Purg Flow Control Vent Line Vent ➊ ➋ ➌ ➍ ➎ ➏ ➐ ➑ ➒ 11 12 13 Idle (Station Off) 6.12.20 Solenoid And Proportional Valve Requirements Stainless Steel PG-Air, SG-Air/CH4 Idle (Station On) TROUBLESHOOTING Test (Cut) SECTION 6 X = Open / Enabled, Blank = Closed / Disabled, Analog Value = 0 - 10 Vdc X Plasma Gas 1 Supply Solenoid Valve N2-2 Plasma Gas 1 Supply Solenoid Valve AirAir-2 X X X X X X X X X X X X X X X X X X X X X X X X X X X X X X X X Plasma Gas 1 Supply Solenoid Valve Argon Plasma Gas 2 Supply Solenoid Valve O2-2 Shield Gas 1 Supply Solenoid Valve O2-1 Shield Gas 1 Supply Solenoid Valve N2-1 X Shield Gas 1 Supply Solenoid Valve AirAir-1 Shield Gas 2 Supply Solenoid Valve N2-3 X Shield Gas 2 Supply Solenoid Valve Ch4 Plasma Gas 1 Torch Solenoid Valve X X X X X X X X X Plasma Gas 2 Torch Solenoid Valve X X Shield Gas 1 Torch Solenoid Valve X X X X X X X X X Shield Gas 2 Torch Solenoid Valve X X X X X X Analog Flow Values Plasma Gas 1 Start Flow Analog Out X X Plasma Gas 1 Cut Flow Analog Out X X X X Plasma Gas 2 Start Flow Analog Out Plasma Gas 2 Cut Flow Analog Out Shield Gas 1 Start Flow Analog Out X X Shield Gas 1 Cut Flow Analog Out X X X X Shield Gas 2 Start Flow Analog Out Shield Gas 2 Cut Flow Analog Out X X X X X Plasma Gas 1 Soft Flow Analog Out Plasma Gas 1 Purge/Fill/Vent Flow Analog Out Plasma Gas 1 Idle Flow Analog Out X X X X X X X X X X X X Plasma Gas 2 Soft Flow Analog Out Plasma Gas 2 Purge/Fill/Vent Flow Analog Out Plasma Gas 2 Idle Flow Analog Out X X Shield Gas 1 Soft Flow Analog Out Shield Gas 1 Purge/Fill/Vent Flow Analog Out Shield Gas 1 Idle Flow Analog Out X X X X Shield Gas 2 Soft Flow Analog Out Shield Gas 2 Purge/Fill/Vent Flow Analog Out Shield Gas 2 Idle Flow Analog Out 6-40 X X X X Precision Plasma with Electronic Flow Control - Process Gas Pressure Switches Plasma Gas 1 Pressure Switch 11 12 13 Idle (Station) Off) Test (Start) Process Post Flow Process Cut Process Start Ready Line Fill Line Purge Flow Control Vent ➊ ➋ ➌ ➍ ➎ ➏ ➐ ➑ ➒ Line Vent 6.12.21 Gas Error Monitoring Stainless Steel PG-Air, SG-Air/CH4 Idle (Station On) TROUBLESHOOTING Test (Cut) SECTION 6 X = Monitored For Pressure Present, O = Monitored For Absence Of Pressure X X Plasma Gas 2 Pressure Switch O O Shield Gas 1 Pressure Switch O X X Shield Gas 2 Pressure Switch O X X 1 Vision Shift/Start Numbers Line vent Flow control vent 2 Idle (Station off) 13 # correspond to columns on solenoid/ proportional valve requirement charts and gas error monitoring charts 9 no Station on? Test (start) yes Section 6.7.7 for details Line Purge 6 Process start. Station on Flush/ Pressure cycle Plasma stop? 3 no Error condition? yes yes no 4 Station on? no no yes ready 5 no Plasma stop yes yes no New SDP file selected? no Plasma test? no yes no 7 Station on? yes Plasma test? Plasma test cut? yes Plasma test (start O2)? Plasma test cut? no yes Plasma test? 10 yes no New SDP file selected? Error condition? no no yes no yes yes no yes 8 Station on? no Process Postflow Station on? New SDP file selected? no Plasma test? yes no Analog disable timing? no Test (start O2) yes yes no Plasma start? yes no Station on? yes yes no Arc established ? yes Process cut New SDP files selected? yes yes Station on? Test (cut) no yes no Line fill Station on? yes yes no Station on? 11 no yes New SDP file selected? Plasma test cut? yes no no 12 Idle (Station On) Station on? no no Plasma test (start O2)? yes no Station on? yes yes yes New SDP file selected? no Plasma test? yes no Plasma start? no yes Precision Plasma with Electronic Flow Control - 6-41 Solenoid Valves Test (Start) Process Post Flow Process Cut Process Start Ready Line Fill Line Purge Flow Control Vent Line Vent ➊ ➋ ➌ ➍ ➎ ➏ ➐ ➑ ➒ 11 12 13 Idle (Station Off) 6.12.22 Solenoid And Proportional Valve Requirements Aluminum PG-N2, SG-N2 Idle (Station On) TROUBLESHOOTING Test (C (Cut) ut) SECTION 6 X = Open / Enabled, Blank = Closed / Disabled, Analog Value = 0 - 10 Vdc X X X X X X X X X Plasma Gas 1 Supply Solenoid Valve N2-2 Plasma Gas 1 Supply Solenoid Valve AirAir-2 Plasma Gas 1 Supply Solenoid Valve Argon Plasma Gas 2 Supply Solenoid Valve O2-2 Shield Gas 1 Supply Solenoid Valve O2-1 Shield Gas 1 Supply Solenoid Valve N2-1 X X X X X X X X X Shield Gas 1 Supply Solenoid Valve AirAir-1 Shield Gas 2 Supply Solenoid Valve N2-3 X Shield Gas 2 Supply Solenoid Valve Ch4 Plasma Gas 1 Torch Solenoid Valve X X X X X X X X X Plasma Gas 2 Torch Solenoid Valve X X Shield Gas 1 Torch Solenoid Valve X X X X X X X X X Shield Gas 2 Torch Solenoid Valve X X X X X Analog Flow Values Plasma Gas 1 Start Flow Analog Out X X Plasma Gas 1 Cut Flow Analog Out X X Plasma Gas 2 Start Flow Analog Out Plasma Gas 2 Cut Flow Analog Out Shield Gas 1 Start Flow Analog Out X Shield Gas 1 Cut Flow Analog Out X X X X X Shield Gas 2 Start Flow Analog Out Shield Gas 2 Cut Flow Analog Out Plasma Gas 1 Soft Flow Analog Out Plasma Gas 1 Purge/Fill/Vent Flow Analog Out Plasma Gas 1 Idle Flow Analog Out X X X X Plasma Gas 2 Soft Flow Analog Out X Plasma Gas 2 Purge/Fill/Vent Flow Analog Out X Plasma Gas 2 Idle Flow Analog Out X X X X X X X X X Shield Gas 1 Soft Flow Analog Out Shield Gas 1 Purge/Fill/Vent Flow Analog Out Shield Gas 1 Idle Flow Analog Out X X X X Shield Gas 2 Soft Flow Analog Out Shield Gas 2 Purge/Fill/Vent Flow Analog Out Shield Gas 2 Idle Flow Analog Out 6-42 X X X Precision Plasma with Electronic Flow Control - Process Gas Pressure Switches Plasma Gas 1 Pressure Switch Plasma Gas 2 Pressure Switch O O Shield Gas 1 Pressure Switch O Shield Gas 2 Pressure Switch 11 12 13 Idle (Station) Off) Test (Start) Process Post Flow Process Cut Process Start Ready Filll Line Fil Line Purge Flow Control Vent ➊ ➋ ➌ ➍ ➎ ➏ ➐ ➑ ➒ Line Vent 6.12.23 Gas Error Monitoring Aluminum PG-N2, SG-N2 Idle (Station On) TROUBLESHOOTING Test (Cut) SECTION 6 X = Monitored For Pressure Present, O = Monitored For Absence Of Pressure X X X X O 1 Vision Shift/Start Numbers Line vent Flow control vent 2 Idle (Station off) 13 # correspond to columns on solenoid/ proportional valve requirement charts and gas error monitoring charts 9 no Station on? Test (start) yes Section 6.7.7 for details Line Purge 6 Process start. Station on Flush/ Pressure cycle Plasma stop? 3 Station on? Error condition? yes yes no 4 Station on? no no yes ready 5 Plasma stop yes yes 7 New SDP file selected? no Plasma test? no yes no no Station on? yes Plasma test? Plasma test cut? yes Plasma test (start O2)? Plasma test cut? no yes Plasma test? 10 yes no New SDP file selected? Error condition? no no yes no yes yes no yes 8 Station on? no Process Postflow Station on? New SDP file selected? no Plasma test? yes no Analog disable timing? no Test (start O2) yes yes no Plasma start? yes no Station on? yes yes no Arc established ? yes Process cut no New SDP files selected? yes yes Station on? Test (cut) no yes no Line fill Station on? yes yes no no 11 no yes New SDP file selected? Plasma test cut? yes no no 12 Idle (Station On) Station on? no no Plasma test (start O2)? yes no Station on? yes yes yes New SDP file selected? no Plasma test? yes no Plasma start? no yes Precision Plasma with Electronic Flow Control - 6-43 SECTION 6 TROUBLESHOOTING Solenoid Valves 11 12 13 Idle (Station On) Idle (Station Off) Test (Start) Process Post Flow Process Cut Process Start Ready Line Fill Line Purge Flow Control Vent Line Vent ➊ ➋ ➌ ➍ ➎ ➏ ➐ ➑ ➒ Test (Cut) 6.12.24 Solenoid And Proportional Valve Requirements Aluminum PG-N2, SG-N2/CH4 X = Open / Enabled, Blank = C Closed losed / Disabled, Analog Value = 0 - 10 Vdc X X X X X X X X X Plasma Gas 1 Supply Solenoid Valve N2-2 Plasma Gas 1 Supply Solenoid Valve AirAir-2 Plasma Gas 1 Supply Solenoid Valve Argon Plasma Gas 2 Supply Solenoid Valve O2-2 Shield Gas 1 Supply Solenoid Valve O2-1 Shield Gas 1 Supply Solenoid Valve N2-1 X X X X X X X X X X X X X X X X X Shield Gas 1 Supply Solenoid Valve AirAir-1 Shield Gas 2 Supply Solenoid Valve N2-3 X Shield Gas 2 Supply Solenoid Valve Ch4 Plasma Gas 1 Torch Solenoid Valve X X X X X X X X X Plasma Gas 2 Torch Solenoid Valve X X Shield Gas 1 Torch Solenoid Valve X X X X X X X X X Shield Gas 2 Torch Solenoid Valve X X X X X X Analog Flow Values Plasma Gas 1 Start Flow Analog Out X X Plasma Gas 1 Cut Flow Analog Out X X X X Plasma Gas 2 Start Flow Analog Out Plasma Gas 2 Cut Flow Analog Out Shield Gas 1 Start Flow Analog Out X X Shield Gas 1 Cut Flow Analog Out X X X X Shield Gas 2 Start Flow Analog Out Shield Gas 2 Cut Flow Analog Out X X X X X Plasma Gas 1 Soft Flow Analog Out Plasma Gas 1 Purge/Fill/Vent Flow Analog Out Plasma Gas 1 Idle Flow Analog Out X X X X X X X X X X X X Plasma Gas 2 Soft Flow Analog Out Plasma Gas 2 Purge/Fill/Vent Flow Analog Out Plasma Gas 2 Idle Flow Analog Out X X Shield Gas 1 Soft Flow Analog Out Shield Gas 1 Purge/Fill/Vent Flow Analog Out Shield Gas 1 Idle Flow Analog Out X X X X Shield Gas 2 Soft Flow Analog Out Shield Gas 2 Purge/Fill/Vent Flow Analog Out Shield Gas 2 Idle Flow Analog Out 6-44 X X X X Precision Plasma with Electronic Flow Control - SECTION 6 TROUBLESHOOTING Process Gas Pressure Switches Plasma Gas 1 Pressure Switch 11 12 13 Idle (Station On) Idle (Station) Off) Test (Start) Process Post Flow Process Cut Process Start Ready Line Fill Line Purge Flow Control Vent Line Vent ➊ ➋ ➌ ➍ ➎ ➏ ➐ ➑ ➒ Test (Cut) 6.12.25 Gas Error Monitoring Aluminum PG-N2, SG-N2/CH4 X = Monitored For Pressure Present, O = Monitored For Absence Of Pressure X X Plasma Gas 2 Pressure Switch O O Shield Gas 1 Pressure Switch O X X Shield Gas 2 Pressure Switch O X X 1 Vision Shift/Start Numbers Line vent Flow control vent 2 Idle (Station off) 13 # correspond to columns on solenoid/ proportional valve requirement charts and gas error monitoring charts 9 no Station on? Test (start) yes Section 6.7.7 for details Line Purge 6 Process start. Station on Flush/ Pressure cycle Plasma stop? 3 no Error condition? yes yes no 4 Station on? no no yes ready 5 no Plasma stop yes yes no New SDP file selected? no Plasma test? no yes no 7 Station on? yes Plasma test? Plasma test cut? yes Plasma test (start O2)? Plasma test cut? no yes Plasma test? 10 yes no New SDP file selected? Error condition? no no yes no yes yes no yes 8 Station on? no Process Postflow Station on? New SDP file selected? no Plasma test? yes no Analog disable timing? no Test (start O2) yes yes no Plasma start? yes no Station on? yes yes no Arc established ? yes Process cut New SDP files selected? yes yes Station on? Test (cut) no yes no Line fill Station on? yes yes no Station on? 11 no yes New SDP file selected? Plasma test cut? yes no no 12 Idle (Station On) Station on? no no Plasma test (start O2)? yes no Station on? yes yes yes New SDP file selected? no Plasma test? yes no Plasma start? no yes Precision Plasma with Electronic Flow Control - 6-45 SECTION 6 TROUBLESHOOTING Solenoid Valves 11 12 13 Idle (Station On) Idle (Station Off) Test (Start) Process Post Flow Process Cut Process Start Ready Line Fill Line Purge Flow Control Vent Line Vent ➊ ➋ ➌ ➍ ➎ ➏ ➐ ➑ ➒ Test (Cut) 6.12.26 Solenoid And Proportional Valve Requirements Marking PG-Argon, SG-Air X = Open / Enabled, Blank = Closed / Disabled, Analog Value = 0 - 10 Vdc X Plasma Gas 1 Supply Solenoid Valve N2-2 Plasma Gas 1 Supply Solenoid Valve AirAir-2 Plasma Gas 1 Supply Solenoid Valve Argon X X X X X X X X X X X X X X X X Plasma Gas 2 Supply Solenoid Valve O2-2 Shield Gas 1 Supply Solenoid Valve O2-1 Shield Gas 1 Supply Solenoid Valve N2-1 X Shield Gas 1 Supply Solenoid Valve AirAir-1 Shield Gas 2 Supply Solenoid Valve N2-3 X Shield Gas 2 Supply Solenoid Valve Ch4 Plasma Gas 1 Torch Solenoid Valve X X X X X X X X X Plasma Gas 2 Torch Solenoid Valve X X Shield Gas 1 Torch Solenoid Valve X X X X X X X X X Shield Gas 2 Torch Solenoid Valve X X X X X Analog Flow Values Plasma Gas 1 Start Flow Analog Out X X Plasma Gas 1 Cut Flow Analog Out X X Plasma Gas 2 Start Flow Analog Out Plasma Gas 2 Cut Flow Analog Out Shield Gas 1 Start Flow Analog Out X Shield Gas 1 Cut Flow Analog Out X X X X X Shield Gas 2 Start Flow Analog Out Shield Gas 2 Cut Flow Analog Out Plasma Gas 1 Soft Flow Analog Out Plasma Gas 1 Purge/Fill/Vent Flow Analog Out Plasma Gas 1 Idle Flow Analog Out X X X X X X X X X X X X Plasma Gas 2 Soft Flow Analog Out Plasma Gas 2 Purge/Fill/Vent Flow Analog Out Plasma Gas 2 Idle Flow Analog Out X X Shield Gas 1 Soft Flow Analog Out Shield Gas 1 Purge/Fill/Vent Flow Analog Out Shield Gas 1 Idle Flow Analog Out X X X X Shield Gas 2 Soft Flow Analog Out Shield Gas 2 Purge/Fill/Vent Flow Analog Out Shield Gas 2 Idle Flow Analog Out 6-46 X X X Precision Plasma with Electronic Flow Control - SECTION 6 TROUBLESHOOTING Process Gas Pressure Switches Plasma Gas 1 Pressure Switch Plasma Gas 2 Pressure Switch O O Shield Gas 1 Pressure Switch O Shield Gas 2 Pressure Switch O 11 12 13 Idle (Station On) Idle (Station) Off) Test (Start) Process Post Flow Process Cut Process Start Ready Line Fill Line Purge Flow Control Vent Lin Line e Vent ➊ ➋ ➌ ➍ ➎ ➏ ➐ ➑ ➒ Test (Cut) Gas Error Monitoring --Marking PG-Argon, SG-Air X = Monitored For Pressure Present, O = Monitored For Absence Of Pressure X X X X 1 Vision Shift/Start Numbers Line vent Flow control vent 2 Idle (Station off) 13 # correspond to columns on solenoid/ proportional valve requirement charts and gas error monitoring charts 9 no Station on? Test (start) yes Section 6.7.7 for details Line Purge 6 Process start. Station on Flush/ Pressure cycle Plasma stop? 3 no Error condition? yes yes no 4 Station on? no no yes ready 5 no Plasma stop no yes New SDP file selected? no Plasma test? no yes yes Plasma test (start O2)? Plasma test cut? no yes Plasma test? 10 yes no New SDP file selected? Error condition? no no yes no yes yes no yes 8 Station on? no Process Postflow Station on? New SDP file selected? no Plasma test? yes no Analog disable timing? no Test (start O2) yes yes no Plasma start? yes yes yes no 7 Station on? Station on? yes yes no Plasma test? Plasma test cut? Arc established ? yes Process cut New SDP files selected? yes no yes Station on? Test (cut) no yes no Line fill Station on? yes yes no Station on? 11 no yes New SDP file selected? Plasma test cut? yes no no 12 Idle (Station On) Station on? no no Plasma test (start O2)? yes no Station on? yes yes yes New SDP file selected? no Plasma test? yes no Plasma start? no yes Precision Plasma with Electronic Flow Control - 6-47 SECTION 6 TROUBLESHOOTING This page intentionally left blank. 6-48 Precision Plasma with Electronic Flow Control - SECTION 7 REPLACEMENT PARTS 7.1 General Always provide the serial number of the unit on which the parts will be used. The serial number is stamped on the unit nameplate. 7.2 Ordering To ensure proper operation, it is recommended that only genuine ESAB parts and products be used with this equipment. The use of non-ESAB parts may void your warranty. Replacement parts may be ordered from your ESAB Distributor or from: ESAB Welding and Cutting Products ATTN: Customer Service Department PO Box 100545 Ebenezer Road Florence, SC USA 29501-0545 Phone (843) 664-4405 (800) ESAB-123 (372-3123) ESAB Cutting Systems - Canada 6010 Tomken Road Mississauga, Ontario, Canada L5T 1X9 Phone (905) 670-0220 Fax (905) 670-4879 ESAB-HANCOCK GmbH Robert-Bosch-Strasse 20 Postfach 1128 D-61184 Karben Phone 011-49-6039-400 Fax 011-49-6039-403-02 http://www.esab.de Be sure to indicate any special shipping instructions when ordering replacement parts. Refer to the Communications Guide located on the last page of this manual for a list of customer service phone numbers. Precision Plasma with Electronic Flow Control - 7-1 SECTION 7 REPLACEMENT PARTS 7.3 Plasmarc Power Source-Exterior Components 1 3 2 6 8 4 5 7 7-2 Precision Plasma with Electronic Flow Control - SECTION 7 REPLACEMENT PARTS Item Number 1 Part Number Symbol (Elec-Ay) Description 2 A-995227 Label Warning-Exposed High Volt 3 B-2091514 Label Warning 4 A-34941 5 A-13734588 Logo ESAB Clear 6 C-35924YL Panel Right Side 7 D-35923YL Panel Left Side 8 61328087 Screw, HMH ¼-20 X .50 L Cover-Top D-35925YL Lens Clear Precision Plasma with Electronic Flow Control - 7-3 SECTION 7 REPLACEMENT PARTS 6 5 4 3 2 1 7 8 9 11 10 See "TEE" Detail Page 7-12 7-4 Precision Plasma with Electronic Flow Control - SECTION 7 REPLACEMENT PARTS Item Number 1 Part Number A-672508 Symbol (Elec-Ay) S1 Description Switch Toggle 2PST 2 Pos 15A 2 A-634518 S2,3 Switch Toggle DPDT 2 Pos 15A 3 A-951061 AM1,VM1 Meter LED 5VDC 4 A-951061 AM1,VM1 Meter LED 5VDC 5 A-634518 S2,3 6 A-2234589 R2 7 B-954751 8 D-32286GY 9 A-598481 Gauge 200 PSI 10 C-952182 Spout Remote Filler w/Cap 11 C-36346GY Switch Toggle DPDT 2 Pos 15A POT 10K 10 Turn Overlay Precision Plasma Panel Front BRKT, Remote Filler Precision Plasma with Electronic Flow Control - 7-5 SECTION 7 REPLACEMENT PARTS 1 11 2 10 3 9 13 4 CE 12 5 8 6 7 7-6 Precision Plasma with Electronic Flow Control - SECTION 7 REPLACEMENT PARTS Item Number 1 Part Number Symbol (Elec-Ay) Description 2 952209 3 97W63 4 23610197 5 950874 CB2 6 952137 F4 7 32202GY 8 58V75 Adaptor B/A-W F ¼ NPTM BKHD 9 954599 Label Rating Precision Plasma 10 950829 11 950937 Strain Relief 12 13730763 Plate, Serial 13 954565 Door Access Rear 35928GY J2 Conn Box Recpt 19 FS SH 3 Strain Relief Plug Hole .875 Dia. .125 CT Nyl BK Circuit Breaker 7 AMP Fuse 7A 500 VAC Fast Acting Panel Rear CB1 Circuit Breaker 3 AMP Label “CE” logo (CE version only) Precision Plasma with Electronic Flow Control - 7-7 SECTION 7 REPLACEMENT PARTS 7.4 Plasmarc Power Source-Internal Components 18 17 Reference: PCB1 Isolation Amp Reference: Meter LED AM1,VM1 4 3 5 3 6 7 8 15 2 16 10 1 12 13 11 7-8 Precision Plasma with Electronic Flow Control - 14 SECTION 7 REPLACEMENT PARTS Item Number 1 Part Number Symbol (Elec-Ay) 2 A-950487 TB4 3 D-38103 A-950096 A-952053 A-952034 A952030 A-952032 A-952205 PCB1 PCB1 P9,7 Description Base, Precision Plasma D-35920GY PCB1 P10 PCB1 P1,3,4 PCB1 P2 PCB1 P5 Term Block 2 pos PCB Isolation AMP Housing Contact, Crimp 3 pin Standoff #6-32 X .88 L Plug 5 Pos Plug 18 Pos Plug 16 Pos Receptacle P/C 4 Pos Box PLC 4 D-37345GY 5 A-951209 PLC 6 C-38131 PCB2 Board, PC Startup 7 A-950760 K3-6,8 Relay Enclosed DPDT 24VAC 8 17300020 R1,7,8,9 10 A-13735308 K7 11 A952012 12 C-35682 13 B-952179 Tank, Water 14 A-952013 Caster Swivel 15 A-639533 Bushing, Snap .88 I.D. X 1.09 MH X .45 L 16 17300931 Resistor, 300W 3.1ohm 10% 17 A-952095 Spacer, LED 18 71200732 Adhesive, SIRBR Clr PLC Controller Resistor 300W 20ohm 10% Relay Enclose DPDT 120VAC 20A Caster Fixed T2 XFMR Auto Precision Plasma with Electronic Flow Control - 7-9 SECTION 7 REPLACEMENT PARTS 4 3 16 2 1 8 12 9 1 5 6 10 7 11 13 7 14 15 7-10 Precision Plasma with Electronic Flow Control - SECTION 7 REPLACEMENT PARTS Item Number 1 Part Number 952026 Symbol (Elec-Ay) TB2 Description 2 673502 K1 3 672002GY 4 2062334 5 36417GY 6 951215 7 951347 8 13735308 9 0558002158 10 33550 11 37805 12 32203GY Bracket, Auto XFMR 13 182W82 Elbow 90 DEG. ¼ NPT 14 10Z30 Adaptor, B/A-W M ¼ NPTM 15 950179 Tee, Pipe Branch ¼ Brs 16 37360 Terminal Block Contactor 3 Pole 75A Shroud, Fan M1 Motor, Fan Shroud, Fan M2 Motor, Carb 1/3 Hp Pump, Carb w/Strainer K4 Relay Enclose DPDT 120VAC 20A Kit, Wire Primary Bracket, Motor T3 MOD1(CE) Auto XFMR Module, Power – CE Version Precision Plasma with Electronic Flow Control - 7-11 SECTION 7 REPLACEMENT PARTS 5 6 8 9 4 1 7 9 8 2 2 3 7 9 3 12 13 11 “TEE” Detail 10 X5 7-12 Precision Plasma with Electronic Flow Control - 7 SECTION 7 REPLACEMENT PARTS Item Number 1 Part Number Symbol (Elec-Ay) Description 2 A-950001 3 C-21124 Valve, Check Assy 4 B-36539 Hose, Assy Flowswitch To Core 5 90858009 TBG, Nylobrade 3/8 I.D X .625 O.D. 6 B-36418 Hose Assy Tank Bottom- Pump Inlet 7 A-58V75 Adaptor, B/A-W F ¼ NPTM BKHD 8 A-182W82 9 A-10Z30 Adaptor, B/A-W M ¼ NPTM 10 A-994471 Clamp, Hose W/D .50 Dia X 1.06 SS 11 A-952179 Tank, Water 12 C-952182 Spout, Remote Filler w/Cap 13 A-952181 Tee, Plastic Pipe Hose, Assy Pump Outlet- Torch out B-36538 FS1 Switch, Flow .25 GPM SPSTB Elbow 90 Deg. ¼ NPT Precision Plasma with Electronic Flow Control - 7-13 SECTION 7 REPLACEMENT PARTS 10 6 5 4 3 7 2 9 7 1 8 7-14 Precision Plasma with Electronic Flow Control - SECTION 7 REPLACEMENT PARTS Item Number 1 Part Number Symbol (Elec-Ay) Description C-13735961 Heat Exchanger 2 A-950823 Bushing, Snap 3 A-950167 Grommet, Rub 1.12 I.D. X 1.50 O.D. X .06 W 4 A-995103 TB3 Terminal Block 24 POS 15A 5 A-36919 TB5 Board, Terminal Output 6 A-96W10 Holder, Fuse 7 A-92W57 Grommet, Rub .63 I.D. X .88 O.D. X .06 W 8 A-639533 Bushing, Snap .88 I.D. X 1.09 MH X .45 L 9 D-35930GY BRKT, Heat Exchanger 10 A-2234891 Plug, 10 Pos Precision Plasma with Electronic Flow Control - 7-15 SECTION 7 REPLACEMENT PARTS 6 13 5 7 8 4 9 3 10 2 11 1 12 7-16 Precision Plasma with Electronic Flow Control - SECTION 7 REPLACEMENT PARTS Item Number 1 Part Number Symbol (Elec-Ay) Description 2 17750020 3 C-36527GY 4 A-951161 C1,2 Cap, Metpoly 20uf 400VDC 5 A-673458 K2 Contactor, Pilot Arc 3P 40A 6 A-2234521 P4,MOD1 P1,PLC1 P2 Plug, 16 Pos 7 A-2234891 MOD1 P3, 4, PLC1 P1 Plug, 10 Pos 8 A-2234518 J3 9 A-2234521 P1,PLC1 P2 Plug, 16 Pos 10 A-2234519 J4, PLC1 J2 Receptacle, 16 Pos 11 A-635686 TB6 Terminal Strip, 8 Pos 12 A-647065L1 13 C-38193 Bushing, Snap A-950823 R11,12 Res 20 ohm 50W Cover, Terminal Board Receptacle, 8 Pos Choke Signal #Ch12 PCB-TB Printed Circuit Board Trim Pot Precision Plasma with Electronic Flow Control - 7-17 SECTION 7 REPLACEMENT PARTS 7.5 Power Source Power Module 4 3 2 5 6 1 7 7-18 Precision Plasma with Electronic Flow Control - SECTION 7 REPLACEMENT PARTS Item Number 1 Part Number Symbol (Elec-Ay) 35914GY Base Power Module 2 37102 Bracket, PCB KYDEX 3 35799 Wire Kit, Power Module 4 951339 951340 5 37101GY 6 951981 7 35700 PCB1 P1, 5 PCB1 P2, 6 Description Plug, Female 12 Position Plug, Female 14 Position Deck, Power Module Heat Sink L1 Inductor, Power Factor Precision Plasma with Electronic Flow Control - 7-19 SECTION 7 REPLACEMENT PARTS A 9 CE only 2 3 4 1 10 CE only 5 A 6 8 7 Section A-A 7-20 Precision Plasma with Electronic Flow Control - SECTION 7 REPLACEMENT PARTS Item Number 1 Part Number 2234877 Symbol (Elec-Ay) J3,4 Description 2 951182 M1 Fan, Axial 3 950487 TB2 Terminal Strip 2 Position 4 950823 5 35700 L1 Inductor, Power Factor 6 17280215 R2 Resistor 1.5K OHM 100W 7 35680 L2 Inductor Assembly Output 8 35681 T3 Transformer Assembly, Main 9 952160 FN5 Filter Inductor, Single Phase – CE Version only 10 952612 FN1 Filter EM1 – CE Version only Block Terminal 10 Position Bushing, Snap Precision Plasma with Electronic Flow Control - 7-21 SECTION 7 REPLACEMENT PARTS 3 4 5 2 1 6 7 7-22 Precision Plasma with Electronic Flow Control - SECTION 7 REPLACEMENT PARTS Item Number 1 Part Number 2234518 Symbol (Elec-Ay) J2 Description 2 38047 SH1 3 2234519 J1 4 35917GY 5 951981 6 2234877 J3, 4 Block Terminal, 10 Position 7 674156 TB3 Adaptor Block Terminal, 8 Position Shunt, Feedback Block Terminal, 16 Position Baffle Heatsink Heatsink Precision Plasma with Electronic Flow Control - 7-23 SECTION 7 REPLACEMENT PARTS CE units only 12 13 10 14 11 10 28 8 9 7 6 15 5 28 CE units only 16 4 17 3 18 19 2 20 1 19 21 22 7-24 21 23 24 21 25 26 27 Precision Plasma with Electronic Flow Control - SECTION 7 REPLACEMENT PARTS Item Number 1 Part Number 2 951978 952611 951192 951833 3 35794 4 951979 951196 SCR1 SCR 90A Pad Thermal SCR Module 5 951980 Q1,2 IGBT 300A 600V 6 17750020 951194 R4,5 Resistor 20OHM 50W NI Pad Thermal Power Resistor 50W 7 647345 8 17250005 R1 9 951940 C6,7 Capacitor 1uf 600VDC 10 951983 C4,5 Capacitor 3300 uf 11 35793 Busbar IGBT (-)/Capacitor 12 950823 Bushing Snap .687 13 35792 Busbar IGBT (+)/Capacitor 14 35844 Nomex Insulator 15 951191 951980 35940 Symbol (Elec-Ay) T1 BR1 Description Transformer Control Bridge Diode 3PH 130A Bridge Diode 3 PH Pad Thermal Bridge Pad Termal IGBT 1200V Busbar Input Bridge Bushing Snap 1.31 I.D. X 1.5 MH .44 L Q1,2 Resistor 5OHM 50W Pad Thermal IGBT 1200V IGBT 300A 600V 16 35799 Wire Kit Module 17 35918 Busbar Shunt 18 639533 R6,7,8,9 19 17721020 D1,2 20 951185 Module Diode 100A 600V 21 647345 Bushing Snap 1.31 I.D. X 1.5 MH .44 L 22 36873 23 952255 24 36872 T2 25 32958 TS1,2 26 950711 27 REF REF C1 C3 28 952157 FN2,3 C8,9 Bushing Snap .875 I.D. X 1.093 MH Resistor 20 OHM 25W NI Busbar Capacitor/IGBT Capacitor Film 40uf 400VDC Busbar Capacitor Transformer, Current Switch Thermal 194 Deg. F. Wire Kit Wire Kit Filter - CE Version only Precision Plasma with Electronic Flow Control - 7-25 SECTION 7 REPLACEMENT PARTS 7.6 Precision Plasma Junction Box Replacement Parts 2 A 1 2 REF 8 7 3 6 5 4 A 7-26 Precision Plasma with Electronic Flow Control - Section A-A SECTION 7 REPLACEMENT PARTS Item Number 1 Part Number Symbol (Elec-Ay) Description 2 674969 PCB1 PCB Assembly Filter 3 37250 T2,3 XFMR H.F. Auto 4 2062119 J2 Conn ( Pos 5 37391 BKHD A/A-W*F B/A-W*F 6 37392 BKHD A/A-W*F B/A-W*F 7 950256 C1 Cap Mica .002uf 10 KwV 8 677905 SG1 Spark Gap Assy Wire Kit, Junction Box Precision Plasma 37515 Precision Plasma with Electronic Flow Control - 7-27 SECTION 7 REPLACEMENT PARTS 4 B 2 1 C C B 5 3 6 Section B-B 7-28 Precision Plasma with Electronic Flow Control - 7 8 Section C-C SECTION 7 Item Number REPLACEMENT PARTS Part Number Symbol (Elec-Ay) J1 Description Conn Box Recpt 14 MP Shell 20 1 6271128 2 37522 Base Kydex J Box 3 37523 Cover Kydex J Box 4 Ref 5 Ref Torch Cable Conn Reference 6 Ref Torch Conn NEG Reference 7 Ref Pilot Arc Torch Reference 8 Ref PCB1 J2 Precision Plasma with Electronic Flow Control - 7-29 SECTION 7 REPLACEMENT PARTS 1 2 4 5 7-30 Precision Plasma with Electronic Flow Control - 3 SECTION 7 REPLACEMENT PARTS Item Number 1 Part Number Symbol (Elec-Ay) Description 954075 Name Plate 2 37361 Torch Conn Shield 951188 Locknut, Conduit 2NPT 3 954509 Label Warning High Volt Symbol 4 952928 Coupling, Quick Disconn F 14 Hose 5 950518 Grommet RBR 2.12 I.D. X 2.50 O.D. X .06W Precision Plasma with Electronic Flow Control - 7-31 SECTION 7 REPLACEMENT PARTS 7.7 Electronic Flow Control Box ➀ P/N 952920 1 3 2 TB1 N-1 AIR1 AR PS1 PR SP V1 SH GN ASSY. 000-005-0007 RC8 RC7 SH GN PR PS2 PS3 PS4 PS5 V2 SP SR2 SR1 SR2 SR1 SR2 RC10 1 P1 SR2 SR1 SR2 SR1 GN SP PR SP SH V3 V4 SH JP1 GN PR JP2 6 JP3 7 JP4 4 JP5 SR1 RC9 1 P2 AIR2 O-1 RC4 RC5 O-2 RC6 1 P3 N-2 1 N-3 P4 H35 METH RC1 RC2 1 RC3 P5 ➂ P/N 952921 5 ➅ P/N 952922 ➁ P/N 952868 Process Air Argon Air Air N2 Air-2 Air-1 Argon Oxygen Nitrogen Argon Argon O2 Air O2 N2 O2-2 N2-3 N2-2 O2-1 N2-1 Oxygen Nitrogen H-35 Methane Meth H-35 N2 H-35 H-35 ➆ P/N 953914 7-32 Methane Methane ➃ P/N 952913 Precision Plasma with Electronic Flow Control - ➄ P/N 952915 SECTION 7 REPLACEMENT PARTS Item Number 1 Part Number Symbol (Elec-Ay) Description 952920 Switch, Pressure 50 PSI Non-Adj 2 952686 PCB Prec Flow Control Interface Board 3 952921 Valve Sol 2-Way 02 4 952913 Manifold Assembly Complete Prec Flow 5 952915 XMFR Control 115/230V 50/60 HZ 6 952922 Lamp Pilot 28V Green 7 952914 Manifold Assembly w/Check Valves ONLY Precision Plasma with Electronic Flow Control - 7-33 SECTION 7 REPLACEMENT PARTS Plasma Gas 1 Plasma Gas 2 6 Shield Gas 1 7 Shield Gas 2 Vent 1 Vent 2 Vent 3 Valve 1 Valve 2 Valve 3 Vent 4 Valve 4 1 5 4 2 3 6 7 ➁➂➃➄ P/Ns 952919,952918, 952916, 952917 7-34 Precision Plasma with Electronic Flow Control - SECTION 7 REPLACEMENT PARTS Item Number 1 Part Number Symbol (Elec-Ay) Description Purchase Locally 2 952916 Valve, Analog 0-6 Bar 0-10 VDC Valve4 SG2 3 952917 Valve, Analog 0-6 Bar 0-10 VDC Valve3 SG1 4 952918 Valve, Analog 0-9 Bar 0-10 VDC Valve2 PG2 5 952919 Valve, Analog 0-9 Bar 0-10 VDC Valve 1 PG1 6 639571 Flow Meter Tube ONLY SG2 ¼-33-G-5 PG2, SG1, 7 0558002392 Flow Meter Tube ONLY ¼ -15-G-5 PG1 Fuse, Glass Body, Slow Acting 3AG 4A Precision Plasma with Electronic Flow Control - 7-35 SECTION 7 REPLACEMENT PARTS 7.8 PT-24 Torch Assembly EFC Series A/M P/N 0558001462 Notes: 1* = Plasma 2 in Yellow 2* = Plasma 2 Out Yellow 3* = Plasma 1 in Blue 4* = Plasma 1 Out Blue 5* = Shield 2 In Black 6* = Shield 2 Out Black 7* = Shield 1 In Orange/Red 8* = Shield 1 Out Orange/Red 20 18 7* 6* 13 5* 4* 3* 16 2* 1* 10 14 19 6 9 8 11 2 7 12 4 3 5 1 5/8 - 18 L.H. (Ref) 21 3/8 - 24 L.H. (Ref) 22 23 24 25 7-36 Precision Plasma with Electronic Flow Control - Not Shown SECTION 7 Item Number 1 2 3 4 5 6 7 8 9 10 11 12 13 14 15 16 17 18 19 20 21 22 23 24 25 REPLACEMENT PARTS Part Number Description 21758 22568 22381 22380 22382 See Process Data See Process Data 22007 22010 21712 21539 22531 0558001336 22375 21765 0558001447 77500101 2234133 996565 0558001470 0558001875 0558001471 21739 21740 21741 37609 Body & Tube Assembly PT-24 Torch Sleeve, Torch PT-24 Gas Line Start Blue Gas Line Cut Yellow Gas Line Shield Orange/Red Swirl Baffle (See Process Data) Nozzle (see Process Data) Retainer/Diffuser Insulator Shield Cup Insulator Shield Retainer Electrode Cup Shield w/Retainer T Gas Shutoff VLV Assembly EFC Protector Gortiflex Sensor 7LG Tool Electrode & Nozzle (NOT Shown) Quick Disconnect 90 Deg. Elbow 1.18 L LUB Grease DOW DC-111 (NOT Shown) Clamp, Worm Drive Clamp, Hose PT-24 Cable Bundle Assembly 4.5 Ft. PT-24 Cable Bundle Assembly 12 Ft. PT-24 Cable Bundle Assembly 17 Ft. Check Valve Body Ball Spring PTPT-24 StartStart-up Kit (Quantity of each) Nozzle “A”(2); Nozzle “B”(2); Nozzle “C”(2); Nozzle “D”(2); Nozzle “E”(2); Swirl Baffle 15A(1); Swirl Baffle 30A(1); Swirl Baffle 50/70A(1); Lubricant(1); Electrode and Nozzle Tool(1); Shield Insulator Cup(1); O-ring 1.239 x 0.07(1); O-ring 0.614 X 0.07(1), O-ring 1.498 X 0.07(1); Electrode(5) 56996213 Torch Spare Parts Kit (Quantity of each) 21536, 21539 21541, 21542 21543, 21692 21693, 21725 21765, 21923 22007, 22101 22531, 86W62 638797, 950714 Swirl Baffle(2), Oxy Electrode(5) Nozzle “B”(5), Nozzle “ C”(5) Nozzle “D”(5), Swirl Baffle 50/70A(2) Retainer Shield Cup(1), Water Baffle(1) Electrode and Nozzle Tool(1), Nozzle “ E”(3) Retainer diffuser Nozzle(1), Shield Insulator Cup(3) Shield(6), O-ring 1.239 x 0.07(3) O-ring 0.614 X 0.07(3), O-ring 1.498 X 0.07(3) Precision Plasma with Electronic Flow Control - 7-37 SECTION 7 REPLACEMENT PARTS 7.9 T Gas Shut-off Valve Assembly EFC Series A/M 3 2 1 2 3 4 5 6 Plasma 1 & 2 Common Shield 1 & 2 Common Shield 1 Shield 2 Plasma 2 Plasma 1 1 7-38 Precision Plasma with Electronic Flow Control - SECTION 7 REPLACEMENT PARTS Item Number 1 Part Number Symbol (Elec-Ay) Description 0558001502 Flange 2 952921 2 Way Solenoid Valves 3 593985 O-Ring Precision Plasma with Electronic Flow Control - 7-39 SECTION 7 REPLACEMENT PARTS 7.10 PT-24 Torch EFC Version 1 16 18 14 10 13 19 6 9 8 11 7 12 Detail Torch Front End 2 4 3 5 25 15 26 17 21 20 22 1 23 24 7-40 Precision Plasma with Electronic Flow Control - Not Shown SECTION 7 Item Number 1 2 3 4 5 6 7 8 9 10 11 12 13 14 15 16 17 18 19 20 21 22 23 24 25 26 REPLACEMENT PARTS Part Number 21758 22568 22381 22380 22382 See Process Data See Process Data 22007 22010 21712 21539 22531 22422 22375 21765 951168 77500101 2234133 996565 0558001470 0558001875 0558001471 22378 22427 22389 21739 21740 21741 37609 Description Body & Tube Assembly PTPT-24 Torch Sleeve, Torch PTPT-24 Gas Line Start Blue Gas Line Cut Yellow Gas Line Shield Orange/Red Swirl Baffle (See Process Data) Nozzle (see Process Data) Retainer/Diffuser Insulator Shield Cup Insulator Insulator Shield Retainer Electrode Cup Shield w/Retainer Solenoid Assembly Electronic Flow Control V1 Protector Gortiflex Sensor 7LG Tool Electrode & Nozzle (NOT Shown) Clamp, BandBand-it LUB Grease DOW DCDC-111 (NOT Shown) Clamp, Worm Drive Clamp, Hose PTPT-24 Cable Bundle Bundle Assembly 4.5 Ft. “ “ “ “ 12 Ft. “ “ “ “ 17 Ft. Cable, Solenoid 4 ft. Cable, Solenoid 12 ft. Cable, Solenoid 17 ft. Check Valve Body Ball Spring PTPT-24 StartStart-up Kit Nozzle “A”; Nozzle “B”; Nozzle “C”; Nozzle “D”; Nozzle “E”; Swirl Baffle 15A; Swirl Baffle 30A; Swirl Baffle 50/70A; Lubricant; Electrode and Nozzle Tool; Shield Insulator Cup; O-rings; Electrode 56996213 Torch Spare Parts Kit (Quantity of each) 21536, 21539 21541, 21542 21543, 21692 21693, 21725 21765, 21923 22007, 22101 22531, 86W62 638797, 950714 Swirl Baffle(2), Oxy Electrode(5) Nozzle “B”(5), Nozzle “ C”(5) Nozzle “D”(5), Swirl Baffle 50/70A(2) Retainer Shield Cup(1), Water Baffle(1) Electrode and Nozzle Tool(1), Nozzle “ E”(3) Retainer diffuser Nozzle(1), Shield Insulator Cup(3) Shield(6), O-ring 1.239 x 0.07(3) O-ring 0.614 X 0.07(3), O-ring 1.498 X 0.07(3) Precision Plasma with Electronic Flow Control - 7-41 SECTION 7 REPLACEMENT PARTS 7.11 Solenoid Assembly Torch, Electronic Flow Control Version 1 4 1 2 8 6 6 3 7 8 7 10 5 9 COM/COM COM/COM Shield 2 Shield 1 Plasma 2 Plasma 1 9 5 7-42 Precision Plasma with Electronic Flow Control - SECTION 7 REPLACEMENT PARTS Item Number 1 Part Number Symbol (Elec-Ay) Description 22422 Solenoid Assembly Electronic Flow Version 1 2 596985 O-Ring, 1.42 X .103 NEOP 70A 3 952931 Plug Block 6 Pos 4 22421 Bracket, Solenoid EFC 5 952703 Solenoid, 2 Way 6 22367 Quick Disconnect Connector, Yellow 7 952697 Solenoid, 3 Way 8 22366 Quick Disconnect Connector, Blue 9 22365 Quick Disconnect Connector, Orange/Red 10 22364 Quick Disconnect Connector, Silver Precision Plasma with Electronic Flow Control - 7-43 SECTION 7 REPLACEMENT PARTS 7.12 Interface Cables/Hoses 1 ASIOB 2 3 N2 4 O2 5 CNC 6 7 Cutting Table 8 7-44 10 9 Precision Plasma with Electronic Flow Control - CH4 Air Ar SECTION 7 REPLACEMENT PARTS Item Number Part Number 1 Reference 2 21917 21918 21919 21920 21921 56997111 56997112 56997113 0560986745 59667114 56997115 3 Reference High Freq, Console to EFC 37533 37534 37535 37536 37537 57000419 57000420 57000421 57000422 57000423 57000424 57000425 57000426 22428 21905 22504 21906 22505 21907 10 ft. (3 m), Gas Line Bundle 20 ft. (6 m), Gas Line Bundle 30 ft. (9 m), Gas Line Bundle 60 ft. (18 m), Gas Line Bundle 100 ft. (30 m), Gas Line Bundle 3ft (.9 m), High Freq Cable, EFC/Junction Box 50 ft. (15.2 m), High Freq Cable, EFC/Junction Box 75 ft. (23 m), High Freq Cable, EFC/Junction Box 100 ft. (30 m), High Freq Cable, EFC/Junction Box 125 ft. (38 m), High Freq Cable, EFC/Junction Box 150 ft. (46 m), High Freq Cable, EFC/Junction Box 175 ft. (53 m), High Freq Cable, EFC/Junction Box 200 ft. (61 m), High Freq Cable, EFC/Junction Box 12 ft. (3.6 m), Power Bundle 25 ft. (7.6 m), Power Bundle 40 ft. (12 m), Power Bundle 60 ft. (18 m), Power Bundle 80 ft. (24 m), Power Bundle 100 ft. (30 m), Power Bundle 7 Reference Work Lead (positive) 8 Reference Earth Ground Cable 9 57002248 57002249 57002250 57002251 57002252 30 ft. (9 m), Control Lead, Console / Machine I/O 50 ft. (15 m), Control Lead, Console / Machine I/O 75 ft. (23 m), Control Lead, Console / Machine I/O 100 ft. (30.5 m), Control Lead, Console / Machine I/O 160 ft. (49 m), Control Lead, Console / Machine I/O 10 Reference Primary Power from Wall Disconnect 4 5 6 Description CNC Interface Cables, 12/c and 18/c flex, see machine schematic 10 ft. (3 m), Control Lead EFC/Junction Box, Standard Cable 20 ft. (6 m), Control Lead EFC/Junction Box, Standard Cable 30 ft. (9 m), Control Lead EFC/Junction Box, Standard Cable 60 ft. (18 m), Control Lead EFC/Junction Box, Standard Cable 100 ft. (30 m), Control Lead EFC/Junction Box, Standard Cable 10 ft. (3 m), Control Lead EFC/Junction Box, Flex Cable 20 ft. (6 m), Control Lead EFC/Junction Box, Flex Cable 30 ft. (9 m), Control Lead EFC/Junction Box, Flex Cable 40 ft. (12 m), Control Lead EFC/Junction Box, Flex Cable 60 ft. (18 m), Control Lead EFC/Junction Box, Flex Cable 100 ft. (30 m), Control Lead EFC/Junction Box, Flex Cable Precision Plasma with Electronic Flow Control - 7-45 SECTION 7 REPLACEMENT PARTS Notes: 7-46 Precision Plasma with Electronic Flow Control - See back of Title Page for revision list. Customer // Technical Support (843) 664-4405 (800) ESAB-123 (372-2123) ESAB Welding and Cutting Products PO BOX 100545 Ebenezer Road Florence, SC 29501-0545 http://www.esab.com ESAB Cutting Systems – Canada 6010 Tomken Road Mississauga, Ontario Canada L5T 1X9 Phone: (905) 670-0220 Fax: (905) 670-4879 ESAB Cutting Systems GMBH Robert-Bosch-Strasse 20 Postfach 1128 D-61184 Karben 1 Germany Phone 011-49-6039-400 Fax 011-49-6039-403-02 http://www.esab.de Printed in U.S.A ">
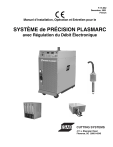
Lien public mis à jour
Le lien public vers votre chat a été mis à jour.