Thermal Dynamics Auto-Cut 200 XT Mode d'emploi
Vous trouverez ci-dessous de brèves informations sur Auto-Cut 200 XT. Ce générateur de coupage à l'arc plasma est conçu pour des opérations de coupage performantes. Il offre un courant de sortie maximal de 200A et est compatible avec divers gaz comme l'air comprimé, l'oxygène et l'azote. Adapté à la coupe de l'acier doux, de l'acier inoxydable et de l'aluminium, il assure une qualité de coupe élevée avec des applications de gaz spécifiques.
PDF
Télécharger
Document
200 AUTO-CUT XT ™ AUTO-CUT 200 XT GENERATEUR DE COUPAGE À L’ARC PLASMA Manuel d’instructions Rév. AC Date : 28 Sept. 2013 Manuel #0-5284FR Caractéristiques opératoires : 200 3 400 NOUS SOMMES HEUREUX DE VOUS COMPTER PARMI NOS CLIENTS ! Félicitations pour votre nouveau produit Victor Thermal Dynamics. Nous sommes fiers de vous compter au nombre de nos clients et ferons tout notre possible pour vous fournir un service et une fiabilité sans égal dans notre secteur. Ce produit bénéficie d'une garantie étendue et d’un réseau de service après-vente mondial. Pour trouver un distributeur ou un service après-vente local, veuillez appeler le numéro suivant 1-800-426-1888 ou vous rendre sur notre site web : www. thermal-dynamics.com. Le présent manuel d’instructions a été rédigé pour vous fournir des informations sur les conditions de fonctionnement et d’exploitation du produit Victor Thermal Dynamics que vous avez acheté. Parce que nous attachons une importance toute particulière à l'exploitation sécurisée du produit et à la satisfaction que vous en retirerez, nous vous demandons de bien vouloir prendre le temps de lire l’intégralité de ce manuel, notamment les « consignes de sécurité », afin d’éviter les risques potentiels qui pourraient surgir lors de l’utilisation du produit. VOUS ETES EN BONNE COMPAGNIE ! La marque de choix des entrepreneurs et des constructeurs dans le monde entier. Victor Thermal Dynamics est une marque internationale de produits de coupage manuel et automatique à l’arc plasma de Victor Technologies Inc. Nous nous démarquons de nos concurrents grâce à la fiabilité de nos produits qui se sont hissés au premier rang du marché et ont fait leurs preuves au fil des ans. L’innovation technique, des prix concurrentiels, des délais de livraison hors pair, un niveau supérieur de service après-vente et d'assistance technique, ainsi que l'expérience appréciable de nos équipes de vente et de marketing, font l’objet de notre fierté. Mais par dessus tout, nous nous engageons à mettre au point des produits de pointe sur le plan technologique afin d’assurer un environnement de travail plus sûr dans le secteur du soudage. ! MISE EN GARDE Merci de lire et de bien comprendre l’intégralité de ce manuel ainsi que les procédures de sécurité sur le lieu de travail avant d'installer, d'exploiter et de réparer ce produit. Si les informations contenues dans ce manuel reflètent le discernement du fabricant, celui-ci décline toute responsabilité quant à son utilisation. Générateur de coupage à l’arc plasma, Auto-Cut® 200 XT™ Manuel d’instructions n° 0-5284FR Publié par : Victor Technologies 82 Benning Street West Lebanon, New Hampshire, USA 03784 (603) 298-5711 www.thermal-dynamics.com © Copyright 2013 par Victor Technologies Tous droits réservés. Il est interdit de reproduire cet ouvrage, intégralement ou partiellement, sans l’autorisation écrite de l’éditeur. L’éditeur décline par la présente toute responsabilité à l’égard de tiers en cas de perte ou de dommages provoqués par une quelconque erreur ou une quelconque ommission dans ce manuel, que lesdites erreurs soient le résultat d’une négligence, d'un accident ou de toute autre cause. Date de publication : 17 avril 2013 Date de révision : 28 Sept. 2013 Noter les renseignements suivants aux fins de la garantie : Lieu d’achat : __________________________________________ Date d’achat :___________________________________________ N° de série du générateur :_________________________________ N° de série de la torche :___________________________________ LA TABLE DES MATIÈRES CHAPITRE 1 : INFORMATIONS GÉNÉRALES........................................................................1-1 1.01 1.02 1.03 1.04 1.05 Remarque, Attention et Avertissement........................................................1-1 Precautions De Securite Importantes..........................................................1-1 Documents De Reference...........................................................................1-2 Déclaration de conformité............................................................................1-3 Déclaration de garantie................................................................................1-4 CHAPITRE 2 : CARACTÉRISTIQUES.....................................................................................2-1 2.01 2.02 2.03 2.04 2.05 2.06 2.07 2.08 2.09 2.10 Description générale du système................................................................2-1 Générateur à l’arc plasma...........................................................................2-1 Torche de coupage à l’arc plasma...............................................................2-1 Schéma des composants du système.........................................................2-1 Spécifications du bloc d’alimentation et Installations électriques................2-2 Dimensions du générateur...........................................................................2-3 Fonctions du panneau arrière du générateur..............................................2-4 Caractéristiques du gaz...............................................................................2-5 Applications du gaz......................................................................................2-5 XTTM-301 Spécifications de la torche ..........................................................2-6 CHAPITRE 3 : INSTALLATION................................................................................................3-1 3.01 3.02 3.03 3.04 3.05 3.06 3.07 3.08 3.09 3.10 3.11 3.12 3.13 3.14 3.15 Conditions d’installation...............................................................................3-1 Identification des câbles..............................................................................3-2 Identification des câbles..............................................................................3-2 Levage du générateur..................................................................................3-3 Connexions électriques primaires................................................................3-4 Connexions de masse.................................................................................3-6 Connexion du câble de retour......................................................................3-8 Connexion des conduits d’alimentation en gaz...........................................3-9 Connexion du câble CNC..........................................................................3-10 Raccordements de contrôle de la hauteur.................................................3-11 Connexion des fils de la torche dans le démarreur de l’arc.......................3-12 Installation et connexion de la tête de la torche.........................................3-14 Installation des consommables de la torche..............................................3-15 Diviseur de tension (« V-D ») pour contrôler la hauteur de torche iHC.....3-18 Remplissage du système de refroidissement............................................3-20 CHAPITRE 4 : FONCTIONNEMENT.......................................................................................4-1 4.01 4.02 4.03 4.04 4.05 4.06 4.07 Panneau de commande du générateur.......................................................4-1 Fonctionnalités du pupitre de commande....................................................4-2 Configuration du fonctionnement.................................................................4-4 Fonctionnement du système........................................................................4-6 Sélection du gaz..........................................................................................4-8 Codes de fonctionnement du générateur....................................................4-9 Qualité de découpe....................................................................................4-15 LA TABLE DES MATIÈRES CHAPITRE 5 : ENTRETIEN.....................................................................................................5-1 5.01 5.02 5.03 5.04 5.05 Entretien général.........................................................................................5-1 Procédure de nettoyage du filtre du liquide de refroidissement...................5-1 Procédure de remplacement du liquide de refroidissement........................5-2 Fonctionnement du démarreur de l’arc........................................................5-3 Réglage de l’éclateur du démarreur de l’arc................................................5-4 CHAPITRE 6 : ÉLÉMENTS ET PIÈCES DE RECHANGE.......................................................6-1 6.01 6.02 6.03 6.04 6.05 6.06 6.07 6.08 6.09 6.10 Générateur de rechange..............................................................................6-1 Fils et Câbles...............................................................................................6-2 Pièces de rechange externes pour le générateur .......................................6-3 Pièces de rechange d’alimentation électrique - Côté inférieur droit.............6-4 Pièces de rechange d’alimentation électrique - Côté supérieur droit..........6-5 Pièces de rechange de l’alimentation - Partie inférieure gauche.................6-6 Pièces de rechange de l’alimentation - Partie supérieure gauche...............6-7 Pièces de rechange d’alimentation électrique - Panneau arrière................6-8 Pièces de rechange du bloc d’alimentation - Partie avant...........................6-9 Tuyau d’alimentation du gaz recommandé................................................6-10 CHAPITRE 7 : ENTRETIEN DE LA TORCHE.........................................................................7-1 7.01 7.02 7.03 7.04 Enlèvement des consommables..................................................................7-1 Lubrification du joint torique.........................................................................7-2 Usure des pièces.........................................................................................7-2 Installation des consommables de la torche................................................7-3 ANNEXE 1 : Module de commande CNC............................................................................... A-1 Raccordements de commande du PCB................................................................... A-1 Fonctions du CNC.................................................................................................... A-2 ANNEXE 2 : Conception du circuit de l’unité centrale du CCM............................................. A-10 ANNEXE 3 : Conception du circuit E/S du CCM................................................................... A-12 ANNEXE 4 : Conception du PCB du pilote........................................................................... A-14 ANNEXE 5 : Conception du circuit Relais et Interface.......................................................... A-16 ANNEXE 6 : Conception du PCB de l’écran d’affichage....................................................... A-18 ANNEXE 7 : Conception du PCB du Système Bias.............................................................. A-20 ANNEXE 8 : Conception du circuit de l’onduleur principal bas............................................. A-22 ANNEXE 9 : Conception du circuit de l’onduleur principal haut............................................ A-24 ANNEXE 10 : Conception du circuit Contrôle et Pannes...................................................... A-26 ANNEXE 11 : Conception du circuit du Système Cap Bias bas............................................ A-28 LA TABLE DES MATIÈRES ANNEXE 12 : Conception du circuit du Système Cap Bias haut........................................... A-29 ANNEXE 13 : Conception du circuit du suppresseur............................................................ A-30 ANNEXE 14 : Pg schématique 1 du système....................................................................... A-32 ANNEXE 15 : Pg schématique 2 du système....................................................................... A-34 ANNEXE 16 : HISTORIQUE DE PUBLICATION.................................................................. A-36 Auto-cut 200 XT CHAPITRE 1 : INFORMATIONS GÉNÉRALES 1.01 Remarque, Attention et Avertissement Dans ce manuel, les mots “remarque,” “attention,” et “avertissement” sont utilisés pour mettre en relief des informations à caractère important. Ces mises en relief sont classifiées comme suit : FUMÉE et GAZ La fumée et les gaz produits par le procédé de jet de plasma peuvent présenter des risques et des dangers de santé. • Eloignez toute fumée et gaz de votre zone de respiration. Gardez votre tête hors de la plume de fumée provenant du chalumeau. • Utilisez un appareil respiratoire à alimentation en air si l’aération fournie ne permet pas d’éliminer la fumée et les gaz. • Les sortes de gaz et de fumée provenant de l’arc de plasma dépendent du genre de métal utilisé, des revêtements se trouvant sur le métal et des différents procédés. Vous devez prendre soin lorsque vous coupez ou soudez tout métal pouvant contenir un ou plusieurs des éléments suivants : REMARQUE Toute opération, procédure ou renseignement général sur lequel il importe d’insister davantage ou qui contribue à l’efficacité de fonctionnement du système. antimoinecadmiummercure argentchromenickel arseniccobaltplomb baryumcuivresélénium béryllium manganèse vanadium ATTENTION Toute procédure pouvant résulter l’endommagement du matériel en cas de non-respect de la procédure en question. ! AVERTISSEMENT Toute procédure pouvant provoquer des blessures de l’opérateur ou des autres personnes se trouvant dans la zone de travail en cas de non-respect de la procédure en question. 1.02 Precautions De Securite Importantes • Lisez toujours les fiches de données sur la sécurité des matières (sigle américain “MSDS”); celles-ci devraient être fournies avec le matériel que vous utilisez. Les MSDS contiennent des renseignements quant à la quantité et la nature de la fumée et des gaz pouvant poser des dangers de santé. • Pour des informations sur la manière de tester la fumée et les gaz de votre lieu de travail, consultez l’article 1 et les documents cités à la page 5. • Utilisez un équipement spécial tel que des tables de coupe à débit d’eau ou à courant descendant pour capter la fumée et les gaz. • N’utilisez pas le chalumeau au jet de plasma dans une zone où se trouvent des matières ou des gaz combustibles ou explosifs. • Le phosgène, un gaz toxique, est généré par la fumée provenant des solvants et des produits de nettoyage chlorés. Eliminez toute source de telle fumée. • Ce produit, dans le procéder de soudage et de coupe, produit de la fumée ou des gaz pouvant contenir des éléments reconnu dans L’état de la Californie, qui peuvent causer des défauts de naissance et le cancer. AVERTISSEMENTS L’OPÉRATION ET LA MAINTENANCE DU MATÉRIEL DE SOUDAGE À L’ARC AU JET DE PLASMA PEUVENT PRÉSENTER DES RISQUES ET DES DANGERS DE SANTÉ. Coupant à l’arc au jet de plasma produit de l’énergie électrique haute tension et des émissions magnétique qui peuvent interférer la fonction propre d’un “pacemaker” cardiaque, les appareils auditif, ou autre matériel de santé electronique. Ceux qui travail près d’une application à l’arc au jet de plasma devrait consulter leur membre professionel de médication et le manufacturier de matériel de santé pour déterminer s’il existe des risques de santé. Il faut communiquer aux opérateurs et au personnel TOUS les dangers possibles. Afin d’éviter les blessures possibles, lisez, comprenez et suivez tous les avertissements, toutes les précautions de sécurité et toutes les consignes avant d’utiliser le matériel. Composez le + 603-298-5711 ou votre distributeur local si vous avez des questions. Manual 0-5284 CHOC ELECTRIQUE Les chocs électriques peuvent blesser ou même tuer. Le procédé au jet de plasma requiert et produit de l’énergie électrique haute tension. Cette énergie électrique peut produire des chocs graves, voire mortels, pour l’opérateur et les autres personnes sur le lieu de travail. • Ne touchez jamais une pièce “sous tension” ou “vive”; portez des gants et des vêtements secs. Isolez-vous de la pièce de travail ou des autres parties du circuit de soudage. • Réparez ou remplacez toute pièce usée ou endommagée. • Prenez des soins particuliers lorsque la zone de travail est humide ou moite. • Montez et maintenez le matériel conformément au Code électrique national des Etats-Unis. (Voir la page 5, article 9.) • Débranchez l’alimentation électrique avant tout travail d’entretien ou de réparation. • Lisez et respectez toutes les consignes du Manuel de consignes. 1-1 GENERAL INFORMATION Auto-cut 200 XT INCENDIE ET EXPLOSION BRUIT Les incendies et les explosions peuvent résulter des scories chaudes, des étincelles ou de l’arc de plasma. Le procédé à l’arc de plasma produit du métal, des étincelles, des scories chaudes pouvant mettre le feu aux matières combustibles ou provoquer l’explosion de fumées inflammables. Le bruit peut provoquer une perte permanente de l’ouïe. Les procédés de soudage à l’arc de plasma peuvent provoquer des niveaux sonores supérieurs aux limites normalement acceptables. Vous dú4ez vous protéger les oreilles contre les bruits forts afin d’éviter une perte permanente de l’ouïe. • Soyez certain qu’aucune matière combustible ou inflammable ne se trouve sur le lieu de travail. Protégez toute telle matière qu’il est impossible de retirer de la zone de travail. • Pour protéger votre ouïe contre les bruits forts, portez des tampons protecteurs et/ou des protections auriculaires. Protégez également les autres personnes se trouvant sur le lieu de travail. • Procurez une bonne aération de toutes les fumées inflammables ou explosives. • Il faut mesurer les niveaux sonores afin d’assurer que les décibels (le bruit) ne dépassent pas les niveaux sûrs. • Ne coupez pas et ne soudez pas les conteneurs ayant pu renfermer des matières combustibles. • Pour des renseignements sur la manière de tester le bruit, consultez l’article 1, page 5. • Prévoyez une veille d’incendie lors de tout travail dans une zone présentant des dangers d’incendie. • Le gas hydrogène peut se former ou s’accumuler sous les pièces de travail en aluminium lorsqu’elles sont coupées sous l’eau ou sur une table d’eau. NE PAS couper les alliages en aluminium sous l’eau ou sur une table d’eau à moins que le gas hydrogène peut s’échapper ou se dissiper. Le gas hydrogène accumulé explosera si enflammé. ! MENT PLOMB AVERTISSE- AVERTISSEMENT : Ce produit contient des produits chimiques, notamment du plomb, reconnus par l'État de Californie comme pouvant causer des malformations congénitales et d'autres troubles de la reproduction. Se laver les mains après toute manipulation. RAYONS D’ARC DE PLASMA 1.03 Documents De Reference Les rayons provenant de l’arc de plasma peuvent blesser vos yeux et brûler votre peau. Le procédé à l’arc de plasma produit une lumière infra-rouge et des rayons ultra-violets très forts. Ces rayons d’arc nuiront à vos yeux et brûleront votre peau si vous ne vous protégez pas correctement. • Consultez les normes suivantes ou les révisions les plus récentes ayant été faites à celles-ci pour de plus amples renseignements : 1. OSHA, NORMES DE SÉCURITÉ DU TRAVAIL ET DE PROTECTION DE LA SANTÉ, 29CFR 1910, disponible auprès du Superintendent of Documents, U.S. Government Printing Office, Washington, D.C. 20402 Pour protéger vos yeux, portez toujours un casque ou un écran de soudeur. Portez toujours des lunettes de sécurité munies de parois latérales ou des lunettes de protection ou une autre sorte de protection oculaire. 2. Norme ANSI Z49.1, LA SÉCURITÉ DES OPÉRATIONS DE COUPE ET DE SOUDAGE, disponible auprès de la Société Américaine de Soudage (American Welding Society), 550 N.W. LeJeune Rd., Miami, FL 33126 • Portez des gants de soudeur et un vêtement protecteur approprié pour protéger votre peau contre les étincelles et les rayons de l’arc. • Maintenez votre casque et vos lunettes de protection en bon état. Remplacez toute lentille sale ou comportant fissure ou rognure. • Protégez les autres personnes se trouvant sur la zone de travail contre les rayons de l’arc en fournissant des cabines ou des écrans de protection. • 4. Norme ANSI Z87.1, PRATIQUES SURES POUR LA PROTECTION DES YEUX ET DU VISAGE AU TRAVAIL ET DANS LES ECOLES, disponible de l’Institut Américain des Normes Nationales (American National Standards Institute), 1430 Broadway, New York, NY 10018 Utilisez la nuance de lentille qui est suggèrée dans le recommendation qui suivent ANSI/ASC Z49.1 : Courant Arc Nuance Minimum Protective Numéro Nuance Suggerée Numéro Moins de 300* 8 9 300 - 400* 9 12 400 - 800* 10 14 5. Norme ANSI Z41.1, NORMES POUR LES CHAUSSURES PROTECTRICES, disponible auprès de l’American National Standards Institute, 1430 Broadway, New York, NY 10018 6. Norme ANSI Z49.2, PRÉVENTION DES INCENDIES LORS DE L’EMPLOI DE PROCÉDÉS DE COUPE ET DE SOUDAGE, disponible auprès de l’American National Standards Institute, 1430 Broadway, New York, NY 10018 * Ces valeurs s’appliquent ou l’arc actuel est observé clairement. L’experience a démontrer que les filtres moins foncés peuvent être utilisés quand l’arc est caché par moiceau de travail. GENERAL INFORMATION 3. NIOSH, LA SÉCURITÉ ET LA SANTÉ LORS DES OPÉRATIONS DE COUPE ET DE SOUDAGE À L’ARC ET AU GAZ, disponible auprès du Superintendent of Documents, U.S. Government Printing Office, Washington, D.C. 20402 7. Norme A6.0 de l’Association Américaine du Soudage (AWS), LE SOUDAGE ET LA COUPE DE CONTENEURS AYANT RENFERMÉ DES PRODUITS COMBUSTIBLES, disponible auprès de la American Welding Society, 550 N.W. LeJeune Rd., Miami, FL 33126 1-2 Manual 0-5284 Auto-cut 200 XT 8. Norme 51 de l’Association Américaine pour la Protection contre les Incendies (NFPA), LES SYSTEMES À GAZ AVEC ALIMENTATION EN OXYGENE POUR LE SOUDAGE, LA COUPE ET LES PROCÉDÉS ASSOCIÉS, disponible auprès de la National Fire Protection Association, Batterymarch Park, Quincy, MA 02269 9. Norme 70 de la NFPA, CODE ELECTRIQUE NATIONAL, disponible auprès de la National Fire Protection Association, Batterymarch Park, Quincy, MA 02269 10. Norme 51B de la NFPA, LES PROCÉDÉS DE COUPE ET DE SOUDAGE, disponible auprès de la National Fire Protection Association, Batterymarch Park, Quincy, MA 02269 11. Brochure GCA P-1, LA MANIPULATION SANS RISQUE DES GAZ COMPRIMÉS EN CYLINDRES, disponible auprès de l’Association des Gaz Comprimés (Compressed Gas Association), 1235 Jefferson Davis Highway, Suite 501, Arlington, VA 22202 12. Norme CSA W117.2, CODE DE SÉCURITÉ POUR LE SOUDAGE ET LA COUPE, disponible auprès de l’Association des Normes Canadiennes, Standards Sales, 178 Rexdale Boulevard, Rexdale, Ontario, Canada, M9W 1R3 13. Livret NWSA, BIBLIOGRAPHIE SUR LA SÉCURITÉ DU SOUDAGE, disponible auprès de l’Association Nationale de Fournitures de Soudage (National Welding Supply Association), 1900 Arch Street, Philadelphia, PA 19103 14. Norme AWSF4.1 de l’Association Américaine de Soudage, RECOMMANDATIONS DE PRATIQUES SURES POUR LA PRÉPARATION À LA COUPE ET AU SOUDAGE DE CONTENEURS ET TUYAUX AYANT RENFERMÉ DES PRODUITS DANGEREUX , disponible auprès de la American Welding Society, 550 N.W. LeJeune Rd., Miami, FL 33126 15. Norme ANSI Z88.2, PRATIQUES DE PROTECTION RESPIRATOIRE, disponible auprès de l’American National Standards Institute, 1430 Broadway, New York, NY 10018 1.04 Déclaration de conformité Fabricant : Adresse : Victor Thermal Dynamics 82 Benning Street West Lebanon, New Hampshire 03784 USA L'équipement décrit dans ce manuel est conforme à tous les aspects applicables et les règlements de la "Directive Basse tension" (2006/95 EC) et à la législation nationale pour la mise en application de cette directive. L'équipement décrit dans ce manuel est conforme à tous les aspects applicables et les règlements de la "Directive EMC" (Directive de la Commission Européenne 2004/108/EC) et à la législation nationale pour la mise en application de cette directive. Les numéros de série, la description des composants, les pièces de fabrication utilisées et la date de fabrication sont uniques pour chaque appareil. Normes et caractéristiques techniques nationales Le produit a été conçu et fabriqué conformément à un certain nombre de normes et de caractéristiques techniques. Celles-ci comprennent : * Norme CSA (Canadian Standards Association) CAN/CSA E60974-1 : 2011/12/01 pour l'équipement de soudure à l'arc. * UL Étalonnage UL (Underwriters Laboratory) 94VO Test d'inflammabilité pour tous les circuits imprimés utilisés. * Norme CENELEC EN 60974-10 :2007 EMC Product pour l'équipement de soudure à l'arc. * ISO/IEC 60974-1 : 2012 (BS 638-PT10) (EN 60 974-1) (EN50192) (EN50078) applicable à l'équipement de découpe au plasma et aux accessoires associés. * Pour les environnements à risque accru d'électrochocs, les appareils électriques portant la marque 'S' sont conformes à la norme EN50192 utilisés en association avec des torches à main à pointes de découpe exposées, si elles sont équipées de guides d'écartement convenablement installés. * Dans le cadre du procédé de conception et de fabrication général, un contrôle complet portant sur la conception du produit est effectué à l’usine. Le but est de garantir la sécurité du produit, lorsqu’il est utilisé conformément aux instructions de ce guide et aux normes industrielles connexes, et qu’il fonctionne selon les spécifications. Des essais rigoureux sont inclus dans le procédé de fabrication afin de s’assurer que le produit fabriqué respecte les caractéristiques conceptuelles ou y est supérieur. Victor Thermal Dynamics fabrique des produits depuis plus de 30 ans et continue de viser l’excellence dans ce domaine de production. Représentant du fabricant : Manual 0-5284 Steve Ward Operations Director Victor Technologies Europe Europa Building Chorley N Industrial Park Chorley, Lancashire, England PR6 7BX 1-3 GENERAL INFORMATION Auto-cut 200 XT 1.05 Déclaration de garantie GARANTIE LIMITEE : Thermal Dynamics® Corporation (dénommée ci-après « Thermal ») garantit que ses produits sont exempts de défauts de matière et de vices de fabrication. En cas de constat de non-conformité à ladite garantie survenue au cours de la période de validité des produits Thermal énoncée ci-dessous, Thermal s'engage, après notification de celle-ci et preuves à l’appui que le produit a bien été entreposé, installé, exploité et entretenu conformément aux spécifications, instructions, recommandations de Thermal et aux procédures sanctionnées par la pratique industrielle, et non sujets à une mauvaise utilisation, réparation, négligence, altération ou accident, à corriger lesdits défauts en réparant ou en remplaçant, sur décision exclusive de Thermal, tout composant ou partie du produit que Thermal jugera défectueux. CETTE GARANTIE EST EXCLUSIVE ET REMPLACE TOUTE GARANTIE DE QUALITE MARCHANDE OU DE BON FONCTIONNEMENT POUR UNE UTILISATION PARTICULIERE. LIMITATION DE RESPONSABILITE : Thermal ne sera en aucun cas responsable des dommages particuliers ou indirects tels que, mais non limités à : endommagement ou perte des biens achetés ou remplacés ou réclamations de la part des clients du distributeur (dénommé ci-après « Acheteur ») en cas d’interruption du service. Les voies de recours de l’Acheteur énoncées ci-après sont exclusives et la responsabilité de Thermal en ce qui concerne un contrat quelconque, ou tout acte y afférent, y compris l’exécution ou la violation dudit contrat, ou découlant de la fabrication, vente, livraison, revente ou utilisation des biens couverts ou fournis par Thermal, qu’il s'agisse d'une conséquence du contrat, d’une négligence, d’un acte dommageable ou des clauses d’une garantie quelconque ou autre, ne devront pas, sauf disposition expresse contraire, dépasser le prix des biens sur lequel se fonde la responsabilité. L’UTILISATION DE PIECES DE RECHANGE OU D’ACCESSOIRES SUSCEPTIBLES DE COMPROMETTRE LA SECURITE OU LES PRESTATIONS DE L’UN DES PRODUITS THERMAL ENTRAINERA LA DECHEANCE DE LA PRESENTE GARANTIE. LA PRESENTE GARANTIE EST NULLE ET NON AVENUE SI LE PRODUIT EST VENDU PAR DES PERSONNES NON HABILITEES A LE FAIRE. La validité de la garantie limitée pour ce produit devrait être : un maximum de trois (3) ans à compter de la date de vente par un distributeur agréé et un maximum de deux (2) ans à compter de la date de vente par ce distributeur à l’acheteur, et avec des limites ultérieures sur cette période de deux (2) ans (voir tableau ci-dessous). Pièces Main d’oeuvre Auto-Cut XT™ et Ultra-Cut XT™ Blocs d'alimentation et composants 2 Ans 1 An 1 An 1 An 90 Jours 90 Jours Torche et Conduites Torche XTTM / XTTM-301 (hors consommables) Réparation/pièces de rechange Les demandes de réparation ou de remplacement sous garantie doivent être envoyées par un centre de réparation Thermal Dynamics® agréé dans les trente (30) jours de la réparation. Aucun frais de transport ne sera payé dans le cadre de cette garantie. Les frais de transport pour envoyer les produits à un centre de réparation agréé seront à la charge du client. Tous les produits renvoyés le seront aux risques et aux frais du client. Cette garantie remplace toute autre garantie Thermal précédente. Effective 23 Octobre 2012 GENERAL INFORMATION 1-4 Manual 0-5284 AUTO-CUT 200 XT CHAPITRE 2 : CARACTÉRISTIQUES 2.01 Description générale du système Un système Auto-Cut 200 XT™ de coupage à l’arc plasma de Plasma comprend : • Un bloc d’alimentation • Un chalumeau coupeur à arc plasma à usage général avec des tuyaux de liaison • Un kit de pièces détachées pour la torche Les composants sont raccordés lors de l’installation. 2.02 Générateur à l’arc plasma Le générateur fournit le courant nécessaire pour les opérations de coupage. Le générateur supervise également les performances du système et il refroidit et fait circuler le liquide de refroidissement pour la torche et les câbles. 2.03 Torche de coupage à l’arc plasma La torche fourni le courant contrôlé à la pièce par l’intermédiaire de l’arc principal, ce qui permet de couper le métal. 2.04 Schéma des composants du système G: Incendiez le fil réglé, protégé - Alimentation du liquide w/ Négatif - Retour du liquide - Retour de l’arc pilote - Gaz plasmagène - Gaz de protection Auto-Cut XT Générateur CNC Câble CNC P Tube plongeur Puissance principale Câble de masse Torche F1 Câble de mise à la terre O Pièce Art # A-11687FC_AB Manuel n° 0-5284FR 2-1 SPECIFICATIONS AUTO-CUT 200 XT 2.05 Spécifications du bloc d’alimentation et Installations électriques Spécifications du système Auto-Cut 200 XT™ OCV max (U0) 425 VCC Courant de sortie max 200 A Tension de sortie 60 - 170 VCC Caractéristique du facteur de marche 100% à 200A à 200V (40 kW) Plage de fonctionnement De 14°F à 122°F (de -10°C à + 50°C) Facteur de puissance 0.94 à 200 ADC Output Refroidissement Air forcé (Classe F) et liquide de refroidissement Générateur Auto-Cut 200 XTMD Entrée Puissance absorbée Intensité Tailles conseillées (Voir Remarque) Tension Fréquence Triphasée Triphasée Fusible (A) Fil (AWG) Fil (mm2) (Volts) (Hz) (kVA) (A) Triphasée Triphasée Triphasée 400 50/60 41 60 100 #6 16 * La taille suggérée pour les câbles est basée sur le code national d’électricité américain NFPA 70 édition 2011, publiée par la National Fire Prevention Association. Les listes sont issues du tableau 400.5(A)(2) pour les cordons souples de certains types étalonnés pour 75°C à température ambiante atteignant jusqu’à 30°C. Utiliser des câbles à faible cote de température ou des types différents d’isolation peut exiger des tailles de câblage plus grandes. Réduire la valeur nominale des températures ambiantes plus élevées. Il s’agit uniquement de suggestions. Référez-vous toujours à vos législations locales et nationales qui s’appliquent à votre région pour la détermination finale du bon type et de la bonne taille de câblage ATTENTION La taille des fusibles et des câble ssont uniquement à titre de référence. L’installation doit se faire conformément aux codes nationaux et locaux pour le type et la méthode de câble utilisé. SPECIFICATIONS 2-2 Manuel n° 0-5284FR AUTO-CUT 200 XT 2.06 Dimensions du générateur 47.77 inch 1213 mm 35.97 inch 914 mm 27.6 inch 701 mm 490 lb / 222 kg Art # A-11460_AB Manuel n° 0-5284FR 2-3 SPECIFICATIONS AUTO-CUT 200 XT 2.07 Fonctions du panneau arrière du générateur Disjoncteurs Clients ports en option Port gaz plasma Connecteur CNC C.C.M. USER INPUT Port de gaz de protection HEIGHT CONTROL J15 - CNC AIR / O2 PLASMA Port optionnel brouillard d'eau N2 / H35 PLASMA CB2 - 5A 120 VAC CB3 - 5A 24 VAC Torche mène le port Torch mène borne de terre CB4 - 5A 120 VAC F1 - 8A SB 230 VAC F2 - 8A SB 230 VAC Travailler port de câble Deux filtre à air de l'étape Fusibles Filtre du liquide de refroidissement Borne de terre de puissance d'entrée à l'intérieur Art # A-11470FEU SPECIFICATIONS 2-4 Manuel n° 0-5284FR AUTO-CUT 200 XT 2.08 Caractéristiques du gaz Le client fournira tous les gaz et les régulateurs de pression. Les gaz doivent être de haute qualité. Les régulateurs de pression doivent être à double étage et installés à moins de 3 mètres de la console du gaz. Générateur Auto-Cut 200 XT™ : caractéristiques de qualité, débits et pressions du gaz Gaz Qualité Pression minimale Flow O2 (Oxygène) 99.5% Pureté (Liquide recommandé) 120 psi 8.3 bar / 827 kPa 200 scfh (5700 l/h) N2 (Azote) 99.5% Pureté (Liquide recommandé) <1000 ppm O2, <32 ppm H2O) 120 psi 8.3 bar / 827 kPa 300 scfh (8496 l/h) Air comprimé Propre, sec, Exempt d’huile (Consultez remarque 1) 90 psi 6.2 bar / 621 kPa 400 scfh (11327 l/h) H35 (ArgonHydrogène) H35 = 35% Hydrogène, 65% Argon 99.995% Pureté (gaz recommandé) 120 psi 8.3 bar / 827 kPa 200 scfh (5664 l/h) For systems with optional H2O water mist H2O (Eau) Consultez remarque 2 50 psi (3.5 bar) 10 gph (38 lph) REMARQUE 1 : La source d’air doit être correctement filtrée afin d’éliminer toute trace d’huile ou de graisse. La contamination d’huile ou de graisse provenant de l’air comprimé ou en bouteille peut provoquer des incendies quand elle s’accompagne de la présence d’oxygène. Pour le filtrage, un filtre coalescent capable de filtrer jusqu’à 0,01 microns devrait être placé le plus près possible des orifices de gaz sur le module de commande du gaz. REMARQUE 2 : L’eau du robinet n’a pas besoin d’être déionisée mais dans les systèmes à l’eau avec un contenu minéral extrêmement élevé, il est recommandé d’utiliser un adoucisseur d’eau. L’eau du robinet présentant des niveaux élevés de particules doit être filtrée. 2.09 Applications du gaz MATÉRIAU Operation 55A CUT 100A CUT ACIER DOUX Plasma Shield Air Air O2 Air Air Air O2 Air Air Air O2 Air 200A CUT Manuel n° 0-5284FR ACIER INOXYDABLE Aluminium Plasma Shield Plasma Shield Air Air Air Air Air Air Air Air N2 H 2O N2 H 2O H35 N2 H35 N2 Air Air Air Air N2 H 2O N2 H 2O H35 N2 H35 N2 2-5 SPECIFICATIONS AUTO-CUT 200 XT 2.10 XTTM-301 Spécifications de la torche A. Dimensions de la torche Art # A-11538FC Capuchon 19" 482.7 mm 2.25" 57.15 mm XT-301 100 ampérages de base Tube plongeur 2.0" 50.8 mm 15.5" 393.8 mm 6.3" 160.1 mm 2.4" 61 mm 3.98" 101.1 mm 2.7" 69.6 mm 1.6" 40. mm 1.49" 37.8 mm SPECIFICATIONS 2-6 Manuel n° 0-5284FR AUTO-CUT 200 XT B. Longueur de câblage de la torche Montage de la tuyauterie de la torche Longueurs Pieds Mètres 10 3.05 15 4.6 25 7.6 50 15.2 75 22.8 100 30.4 C. Pièces de la torche (pièces génériques montrées) Distributeur du gaz plasmagène Distributeur du gaz de protection Art # A-04741 Coiffe de protection Tuyère Jupe Electrode Cartouche D. Pièces - en - place (PIP) La torche est conçue pour être utilisée avec un générateur qui détecte le débit de retour du liquide de refroidissement pour confirmer que les pièces de la torche sont en place. Si le débit de retour du liquide de refroidissement vers le générateur est absent ou insuffisant le générateur ne fournira pas de courant à la torche. Les fuites de liquide de refroidissement au niveau de la torche indiquent également que des pièces de la torche sont mancantes ou mal installées. E. Type de refroidissement Un mélange de flux de gaz à travers la torche et de liquide de refroidissement. Manuel n° 0-5284FR 2-7 SPECIFICATIONS AUTO-CUT 200 XT F. Données de torche F. XT TM -301 (avec le bloc d’alimentation Auto-Cut 200 XT™) Caractéristiques nominales du chalumeau XT TM -301 (utilisée avec le bloc d’alimentation Auto-Cut 200 XT™) Température ambiante 104° F 40° C Facteur de marche 100% à 200 A Intensité maximale 200 A Tension (Vpeak) 500V Tension d’amorçage d’arc 10kV Courant Jusqu’à 200 A, DC, Polarité directe (Voir Remarque) Caractéristiques du gaz pour le chalumeau 301 XTTM-301 SPECIFICATIONS Gaz à plasma Air comprimé, Oxygène, Azote, H35, F5 Gaz d’écran : Air comprimé, Azote, Eau Pression de fonctionnement 120 psi ± 10 psi 8.3 bar ± 0.7 bar Pression maximale en entrée 135 psi / 9.3 bar Débit de gaz 10 - 450 scfh Bloc d’alimentation utilisé avec : Auto-Cut 200 2-8 Manuel n° 0-5284FR AUTO-CUT 200 XT CHAPITRE 3 : INSTALLATION 3.01 Conditions d’installation Alimentation électrique Le réseau d’alimentation électrique, le système d’alimentation en gaz et en eau doivent respecter les normes de sécurité locales. Du personnel qualifié contrôlera cette conformité. Auto-Cut 200 XT™Power Supply Entrée Puissance absorbée Intensité Tailles conseillées (Voir Remarque) Tension Fréquence Triphasée Triphasée Fusible (A) Fil (AWG) Fil (mm2) (Volts) (Hz) (kVA) (A) Triphasée Triphasée Triphasée 400 50/60 41 #6 16 60 100 REMARQUE * La taille suggérée pour les câbles est basée sur le code national d’électricité américain NFPA 70 édition 2011, publiée par la National Fire Prevention Association. Les listes sont issues du tableau 400.5(A) (2) pour les cordons souples de certains types étalonnés pour 75°C à température ambiante atteignant jusqu’à 30°C. Utiliser des câbles à faible cote de température ou des types différents d’isolation peut exiger des tailles de câblage plus grandes. Réduire la valeur nominale des températures ambiantes plus élevées. Il s’agit uniquement de suggestions. Référez-vous toujours à vos législations locales et nationales qui s’appliquent à votre région pour la détermination finale du bon type et de la bonne taille de câblage ATTENTION Les sections des fils et des fusibles sont données à titre de référence uniquement. L’installation doit être conforme aux codes locaux et nationaux en ce qui concerne le type et la méthode de câblage utilisés. Alimentation en gaz Le client doit fournir tous les gaz et les régulateurs de pression. Les gaz doivent être de haute qualité. Les régulateurs de pression doivent être à double étage et être installés le plus près possible de la console de gaz. Le gaz contaminé peut provoquer un ou plusieurs des problèmes suivants : • Une vitesse de coupe réduite • Une mauvaise qualité de coupe • Une mauvaise précision de coupe • Une durée de vie réduite des consommables • La contamination d’huile ou de graisse provenant de l’air comprimé ou en bouteille peut provoquer des incendies quand elle est accompagnée d’oxygène. Manuel n° 0-5284FR 3-1 INSTALLATION AUTO-CUT 200 XT Caractéristiques du système de refroidissement Le liquide de refroidissement doit être ajouté au système lors de l’installation. La quantité requise varie en fonction de la longueur des câbles de la torche. Thermal Dynamics recommande d’utiliser ses liquides de refroidissement 7-3580 et 7-3581 (pour les basses températures). Capacités du liquide de refroidissement Numéro de la catégorie et mélange Mélange Protège jusqu’à 7-3580 ‘Extra-CoolTM’ 25 / 75 10° F / -12° C 7-3581 ‘Ultra-CoolTM’ 50 / 50 27° F / -33° C 7-3582 ‘Extreme CoolTM’ Concentré* -65° F / -51° C * Pour être mélangé avec D Cool -I TM 7-3583 3.02 Identification des câbles Cf. § 3.05 et 3.06 pour les connexions de raccordement à la terre et les câbles de raccordement à la terre. G: Incendiez le fil réglé, protégé - Alimentation du liquide w/ Négatif - Retour du liquide - Retour de l’arc pilote - Gaz plasmagène - Gaz de protection Auto-Cut XT Générateur CNC Câble CNC P Tube plongeur Puissance principale Câble de masse Torche F1 Câble de mise à la terre O Pièce Art # A-11687FC_AB 3.03 Identification des câbles F1 Câble de masse, de l’amorce de l’arc à distance à la mise à la terre 1/0 vert / jaune (50 mm2) Câble de la torche blindé G O Câble 1/0 (50 mm2) Câble de mise à la terre P Câble CNC (fil 14) Art # A-11688FC INSTALLATION 3-2 Manuel n° 0-5284FR AUTO-CUT 200 XT 3.04 Levage du générateur MISE EN GARDE Ne pas toucher les composants électriques sous tension. Débrancher les conducteurs de courant de la ligne d’alimentation hors tension avant de déplacer l’appareil. TOUTE CHUTE DE MATERIEL peut entraîner des lésions corporelles graves et endommager le matériel. Utiliser les quatre oeillets de levage lors de l’utilisation de sangles pour soulever le générateur. Utiliser un chariot élévateur, une grue ou un treuil pour soulever l’appareil de la palette d’expédition comme cela est montré. Maintenir le générateur stable et à la verticale. Ne pas le soulever plus que nécessaire pour dégager la palette d’expédition. S’assurer que tous les panneaux et les vis soient bien fixés avant d’effectuer le levage. Art # A-11503 Placer le générateur sur une surface solide et plane. L’installateur peut attacher le générateur au sol ou à une fixation de soutien avec un élément passant à travers les pièces horizontales des pieds du générateur. Manuel n° 0-5284FR 3-3 INSTALLATION AUTO-CUT 200 XT 3.05 Connexions électriques primaires Le câble d’alimentation primaire et un anneau du guide-câble doivent être fournis par l’utilisateur final et connectés au bloc d’alimentation. Veuillez-vous référer aux codes locaux et nationaux d’électricité pour en savoir plus sur le câble recommandé et les tailles de fusible. Raccorder les câbles de l’alimentation et de masse du système 1. Enlever le couvercle de l’alimentation en entrée à droite du filtre à liquide de refroidissement à l’arrière de l’alimentation électrique. Pour ce faire, enlever les deux vis puis soulever le couvercle et l’enlever. 2. Couper soigneusement la gaine extérieur du câble de l’alimentation principale pour dénuder les différents fils.Réduire l’isolation sur les différents fils. Orienter le câble vers le haut à travers le port d’alimentation en entrée en bas du panneau. 2 plaques supplémentaires sont incluses à l’entrée du câble. En jeter une ou les deux permet de changer la taille d’ouverture pour admettre de plus gros câbles / manchons. USER INPUT HEIGHT CONTROL J15 - CNC AIR / O2 PLASMA N2 / H35 PLASMA CB2 - 5A 120 VAC CB3 - 5A 24 VAC CB4 - 5A 120 VAC F1 - 8A SB 230 VAC F2 - 8A SB 230 VAC Alimentation Art # A-11949FEU INSTALLATION 3-4 Manuel n° 0-5284FR AUTO-CUT 200 XT 3. Placer l’extrémité dénudée des fils triphasés sur le bornier L1, L2 et L3. Raccorder les différents câbles comme cela est montré. 4. Raccorder le cordon de masse du câble d’alimentation au bornier de mise à la terre. Système Auto-Cut XT CE Machine de découpe / passerelle Torche CNC Device Auto-Cut Power Supply Table de découpe Câble de masse 1/0 fourni par le client Câble de mise à la terre 1/0 Câble de masse 1/0 (F1) Piquet de terre Masse ‘étoilée’ Idéal 0 - 10 ft (0 - 3 m) Maximum 20 ft (6 m) Manuel n° 0-5284FR 3-5 Art # A-11950FEU INSTALLATION AUTO-CUT 200 XT 3.06 Connexions de masse A. Interférence électromagnétique (EMI) L’amorçage de l’arc pilote génère une certaine quantité d’interférence électromagnétique (EMI), couramment appelée bruit RF. Ce bruit RF peut interférer avec d’autres équipements électroniques tels que les contrôleurs de la CNC, les télécommandes, les contrôleurs de hauteur, etc. Pour réduire au minimum l’interférence RF, suivre ces procédures de mises à la terre lors de l’installation de systèmes mécanisés : B. Mise à la terre 1. La disposition de mise à la terre préférée est la mise à la terre en un point unique ou « étoilée ». Le point unique, habituellement sur la table de découpe, est raccordé avec un fil AWG 1/0 (Européen 50 mm2) ou plus grand à une bonne masse (mesurant moins de 3 ohm ; une masse idéale mesure 1 ohm ou moins). Se reporter au paragraphe ‘C’, Création d’une masse. Le piquet de terre doit être le plus près possible de la table de découpe, de préférence à moins de 10 ft (3,0 m) mais pas à plus de 20 ft (6,1 m) de la table de découpe. REMARQUE Tous les fils de garde doivent être les plus courts possible. Les longs fils possèdent une plus grande résistance visà-vis des fréquences RF. Un fil d’un diamètre inférieur possède une résistance majeure vis-à-vis des fréquences RF, il vaut donc mieux utiliser un fil de diamètre plus élevé. 2. La mise à la terre pour les composants montés sur la table de découpe (contrôleurs de la CNC, contrôleurs de hauteur, télécommandes au plasma, etc.) devrait respecter les recommandations du fabricant pour la section du fil, le type et les emplacements du point de connexion. Pour les composants Thermal Dynamics (à l’exception de l’amorce d’arc à distance et du module de commande du gaz), il est recommandé d’utiliser un minimum de câble AWG 10 (européen 6 mm2) ou une tresse en cuivre plate avec une section supérieure ou égale au câble AWG 10 raccordé au châssis de la table de découpe. L’amorce d’arc à distance utilise un fil de garde 1/0 et le module de commande du gaz devrait utiliser un câble AWG 4 minimum. Le point de connexion doit être en métal nu ; la rouille et la peinture portent à de mauvaises connexions. Pour tous les composants, des fils plus grands que le minimum recommandé peuvent être utilisés et peuvent améliorer la protection sonore. 3. Le châssis de la machine de découpe est alors raccordé au point « étoilé » au moyen d’un câble AWG 1/0 (européen 50 mm2) ou plus grand. 4. Le câble du générateur au plasma (voir REMARQUE) est raccordé à la table de découpe au niveau de la mise à la terre « étoilée » en un point unique. REMARQUE Ne pas raccorder le câble de mise à la terre directement au piquet de terre. 5. S’assurer que le câble de mise à la terre et les câbles de masse soient raccordés correctement. Le câble de mise à la terre doit avoir un raccordement solide à la table de découpe. Les raccordements de mise à la terre et de masse doivent être exempts de rouille, saleté, graisse, huile et peinture. Si cela s’avère nécessaire, affiler ou sabler jusqu’à ce qu’on atteigne le métal nu. Utiliser des rondelles d’arrêt pour que les raccordements soient serrés. Il est également recommandé d’utiliser une pâte à joint électrique pour prévenir la corrosion. 6. Le châssis du générateur au plasma est raccordé à la masse du système de distribution du courant selon les prescriptions des codes électriques. Si l’alimentation au plasma est proche de la table de découpe (voir REMARQUE), il n’est normalement pas nécessaire d’avoir un deuxième piquet de terre. En fait, il pourrait être néfaste car il peut porter à une boucle de masse qui provoque des interférences. Quand le générateur au plasma est loin du piquet de terre et qu’il y a des interférences, il peut être utile d’installer un deuxième piquet de terre à côté du générateur au plasma. Le châssis du générateur au plasma devrait alors être raccordé à ce piquet de terre. REMARQUE Il est recommandé que l’alimentation électrique du plasma soit entre 20 - 30 ft (6,1 – 9,1 m) de la table de découpe, si possible. INSTALLATION 3-6 Manuel n° 0-5284FR AUTO-CUT 200 XT 7. Le câble de commande du plasma devrait être blindé avec une protection raccordée uniquement à l’extrémité de la machine de découpe. Si l’on raccorde la protection aux deux extrémités, cela permettra la création d’une boucle de masse qui peut provoquer plus d’interférences que quand il n’y a aucune protection. C. Création d’une masse 1. Pour créer une masse solide, à faible résistance, faire passer un piquet de terre en cuivre d’un diamètre supérieur ou égal à 1/2 in (12 mm) sur au moins 6 – 8 ft (1,8 – 2,4 m) dans la terre afin que le piquet soit au contact du terrain sur la plupart de sa longueur. Selon l’emplacement, une plus grande profondeur peut être requise pour obtenir une masse à faible résistance (voir REMARQUE). Les piquets de terre, habituellement d’une longueur de 10 ft (3,0 m), peuvent être soudés entre eux pour obtenir de plus grandes longueurs. Localiser le piquet le plus près possible de la table de travail. Installer un fil de garde, supérieur ou égal à AWG 1/0 (européen 50 mm2), entre le piquet de terre et le point de masse étoilé sur la table de découpe. REMARQUE Un piquet de terre installé correctement devrait avoir une résistance inférieure ou égale à trois ohms. Pour vérifier la bonne mise à la terre, consulter le diagramme suivant. Idéalement, la lecture au niveau du multimètre doit être de 3 V C.A. pour le conduit 115 V C.A., ou de 1,5 V C.A. pour le conduit 230 V C.A. ATTENTION Retirer tous les autres raccordements du piquet de mise à la terre pendant ce test. Ce test considère qu’un neutre de source 115 ou 230 V C.A. est raccordé à la masse utilitaire. Piquet de terre avec les autres raccordements enlevés MISE EN GARDE Mise à la terre NEUTRE Faire extrêmement attention. Ce test se fait sous tension CHAUD Sur ligne CA 115 V : 3 VCA = 3 Ohm 1 VCA = 1 Ohm Ampoule incandescente 100 W* VAC SONDE CHAUDE SONDE NEUTRE * Peut remplacer une ampoule avec une résistance de 100 W. Utiliser 100 ohm pour 115 VCA Utiliser 500 ohm pour 230 VCA. Sur ligne CA 230 V : 1,5 VCA = 3 Ohm 0,5 VCA = 1 Ohm Art # A-07252FEU Test de mise à la terre MISE EN GARDE Il y a une tension élevée dangereuse lorsque le bloc d’alimentation est connecté à une entrée de puissance. Éviter de connecter une puissance d’entrée ou de mettre en marche le bloc d’alimentation, à moins que le couvercle des raccordements ne soit bien fixé. 2. L’augmentation de la longueur du piquet de terre supérieure à 20 - 30 ft (6,1 - 9,1 m) n’augmente généralement pas l’efficacité du piquet de terre. Un piquet possédant un diamètre supérieur qui dispose d’une surface plus grande peut aider. Parfois il peut être utile de maintenir le sol humide autour du piquet de terre en faisant couler en continu une faible quantité d’eau. L’ajout de sel dans le sol en le plongeant dans de l’eau salée peut également réduire sa résistance. Vous pouvez également essayer un piquet de terre chimique. Quand on utilise ces méthodes, il est nécessaire de contrôler périodiquement la résistance de masse pour s’assurer que la masse est encore bonne. Manuel n° 0-5284FR 3-7 INSTALLATION AUTO-CUT 200 XT D. Routage des câbles de la torche 1. Afin de réduire au minimum l’interférence RF, positionner les câbles de la torche le plus loin possible des composants de la CNC, des moteurs d’entraînement, des câbles de commande ou des lignes d’alimentation principales. Si les câbles doivent passer par dessus les câbles de la torche, le faire avec un angle. Ne pas faire passer les câbles de commande de l’arc plasma ou les autres câbles de commande en parallèle avec les câbles de la torche dans les voies de puissance. 2. Maintenir les câbles de la torche propres. La saleté et les particules métalliques soutirent l’énergie ce qui provoque un démarrage difficile et augmente les probabilités d’interférence RF. 3.07 Connexion du câble de retour 1. 1. Se référer à l’illustration ci-dessous. Passer l’extrémité du câble de retour à travers le serre-câbles derrière le panneau arrière du bloc d’alimentation, ensuite à travers l’ouverture inférieure de la cloison du panneau. 2. Se référer à l’illustration ci-dessous. Connecter le fil au boulon dans le premier trou de la barre omnibus tel qu’indiqué. Bien serrer. Ne trop serrez pas. MISE EN GARDE S’assurer que l’élément de fixation du fil a les bonnes dimensions. Une longueur excessive pourrait causer des dommages si l’élément touche les autres pièces du système. Art # A11951 INSTALLATION 3-8 Manuel n° 0-5284FR AUTO-CUT 200 XT 3.08 Connexion des conduits d’alimentation en gaz 1. Connecter les conduits d’alimentation en gaz aux ports d’entrée appropriés tel qu’indiqué ci-dessous. La première vue montre l’utilisation d’usine par défaut pour l’air comprimé. Tous les autres gaz doivent utiliser la seconde vue, en passant par le filtre à air à deux niveaux. REMARQUE Lorsque vous utilisez l’air comprimé, le raccordement doit être effectué à travers le filtre à air à deux niveaux situé au centre du panneau arrière. Ne pas utiliser le filtre à air à deux niveaux pour les autres gaz. Par défaut de l'usine air/air, à l'aide d'air comprimé de l'atelier Tous les gaz, sauf l'air Gaz plasma port Gaz plasma port USER INPUT USER INPUT Gaz de protection port Gaz de protection port HEIGHT CONTROL HEIGHT CONTROL J15 - CNC AIR / O2 PLASMA Option brouillard d'eau port Chalumeau conduit port N2 / H35 PLASMA CB2 - 5A 120 VAC CB3 - 5A 24 VAC CB4 - 5A 120 VAC F1 - 8A SB 230 VAC Chalumeau conduit borne de masse F2 - 8A SB 230 VAC IN OUT J15 - CNC AIR / O2 PLASMA Option brouillard d'eau port N2 / H35 PLASMA CB2 - 5A 120 VAC CB3 - 5A 24 VAC Chalumeau conduit port CB4 - 5A 120 VAC F1 - 8A SB 230 VAC Chalumeau conduit borne de masse F2 - 8A SB 230 VAC Travaux port câble Travaux port câble Boutique d'entrée d'air Art # A-11952FEU Manuel n° 0-5284FR Art # A-11953FEU 3-9 INSTALLATION AUTO-CUT 200 XT 3.09 Connexion du câble CNC 1. Connecter une extrémité du câble CNC à la prise du bloc d’alimentation marquée « CNC ». 2. Raccorder l’autre extrémité du câble CNC à la CNC. 3. La protection du câble CNC doit être fixée à la terre. USER INPUT HEIGHT CONTROL à CNC J15 - CNC AIR / O2 PLASMA N2 / H35 PLASMA CB2 - 5A 120 VAC CB3 - 5A 24 VAC CB4 - 5A 120 VAC F1 - 8A SB 230 VAC F2 - 8A SB 230 VAC Art # A-11527FC_AB INSTALLATION 3-10 Manuel n° 0-5284FR AUTO-CUT 200 XT 3.10 Raccordements de contrôle de la hauteur La plaque à bornes a une connexion de tension d’arc (-) à la borne de la TORCHE vers la sortie négative du générateur, une connexion de tension d’arc (+) vers la borne de TRAVAIL de la sortie positive du générateur. Elles servent pour un contrôle de la hauteur qui requiert la connexion à la tension d’arc non-divisée complète. La plaque à bornes présente également les valeurs 120 VCA (120,0) et 24 VCA (24, 0). Noter que les deux 0 ne sont pas communs. L’appel de courant admissible est de 100 mA à 120 VCA et 1 A à 24 VCA. Art # A-11900 TB4 1 2 24 VCA à1A 3 4 5 6 7 120 VCA Travail à 100 mA Astuce les tensions (Pilote) Tension d’arc (Torche) Art # A-11954FEU Il y a également un trou ajouté sur le panneau arrière au-dessus du réceptacle pour le câblage du client. On le préfèrera à celui situé dans le CCM pour le câblage du client ajouté (et le réducteur de tension) pour les raccordements aux commandes de hauteur, etc. Manuel n° 0-5284FR 3-11 INSTALLATION AUTO-CUT 200 XT 3.11 Connexion des fils de la torche dans le démarreur de l’arc 1. Enlever le couvercle supérieur. 2. Passer les fils de la torche et du liquide de refroidissement à travers le port des fils de la torche situé à l’arrière du module. S’assurer que la gaine extérieure des fils coulisse dans le port. ATTENTION Utiliser les gants de protection lors de la manipulation des fils. Éviter de plier ou de nouer les fils. 3. Dans le module, glisser le serre-fils au-dessus des fils et le fixer uniquement lorsque tous les fils sont connectés. 4. Connecter les fils dans le module tel qu’illustré. Les fils du liquide de refroidissement et les connecteurs ont des codes de couleur ; le rouge pour le retour du liquide de refroidissement et le vert pour l’alimentation en liquide de refroidissement. Les raccordements du gaz de protection et du gaz plasmagène disposent d’un filetage à gauche et à droite et ne sont pas interchangeables. Câblage de la torche : Alimentation et retour en liquide de refroidissement Gaz plasmagène Gaz de protection Blindage des conducteurs extérieurs 1 Collier * (Type de serrage peut varier) 2 3 Art # A-11528FEU INSTALLATION 3-12 Manuel n° 0-5284FR AUTO-CUT 200 XT Raccord de l’alimentation en liquide de refroidissement (avec une étiquette verte) Raccordement du gaz plasmagène Raccordement du gaz de protection Raccord du retour du liquide de refroidissement (avec une étiquette rouge) Art # A-11529FEU Câblage de la torche 5. Plier l’extrémité des fils externes de la gaine de protection palmée à l’arrière et au-dessus de l’anneau de connexion dans le module. Pousser le serre-fils sur la gaine et visser le serre-fils ainsi que la gaine à l’anneau de connexion. 6. Réinstaller le couvercle du (des) face(s) latérale(s). 4 Bride Art # A-11530FC Manuel n° 0-5284FR 3-13 INSTALLATION AUTO-CUT 200 XT 3.12 Installation et connexion de la tête de la torche Procédure d’installation de la torche : 1. Installer le bloc de montage de la torche sur la table de découpe (portique). Serrer le bloc. 2. Laisser l’embout sur les fils de la torche. Enlever et séparer les embouts de protection du tube de montage. 3. Installer le joint torique dans la rainure de l’extrémité supérieure du tube de montage. Faire glisser le tube de montage de la torche sur les fils assez loin pour exposer les raccords des extrémités des fils. 4. Connecter la tête de la torche aux fils de la torche. Suivre la procédure suivante. Éviter que les fils ne se tordent. Capuchon Montré pour illustrer l'ordre d'assemblage seulement; les pièces doivent rester fermés hermétiquement. Joint torique Papier isolant Câblage du plasma Câble de l’arc pilote Câblage de la torche Connecteur du câblage du plasma Tube plongeur Joint torique 1 2 Retour du liquide de refroidissement Clapet de non-retour et Connecteur Détail du tube plongeur Trous filetés Trous de vidange Connecteur du gaz de protection (’secondaire’) Papier isolant Connecteur d’alimentation du liquide Art # A-06258FEU 5. Glisser le tube de positionnement sur la tête de la torche. Immobiliser la tête de la torche. Tourner le tube de positionnement sur la tête de la torche. Renvoyer les fils au besoin pour assurer un bon ajustement dans le tube de montage. Éviter que les fils de la torche ne se tordent. INSTALLATION 3-14 Manuel n° 0-5284FR AUTO-CUT 200 XT ATTENTION S’assurer que le câblage ne s’entortille pas à l’intérieur du tube plongeur. Le câblage doit se présenter comme sur le schéma d’installation. 6. L’extrémité inférieure du tube de montage comprend quatre trous filetés. Installer une vis de réglage Allen du kit matériel dans l’un des trous filetés pour sécuriser l’assemblage de la tête de la torche sur le tube de montage. 7. Visser le tube de positionnement dans le bloc de montage. Glisser l’embout des fils dans le tube de positionnement de la torche. S’assurer que l’embout rejoint le joint torique dans la partie supérieure du tube de positionnement. 8. Installer la coupelle protectrice et l’ensemble de cartouche (y compris les consommables) sur la tête de la torche. 3.13 Installation des consommables de la torche 1. Se référer aux tableaux de vitesse de la torche pour sélectionner les pièces indiquées pour l’application. L’application détermine les pièces de la torche à utiliser. Se référer aux tableaux de vitesse pour connaitre les pièces de la torche indiquées à installer dans une application sélectionnée. ATTENTION Éviter d’interchanger les pièces. S’assurer que l’extrémité et l’électrode dans la torche correspondent aux gaz de protection et plasmagènes utilisés pour l’application. 2. Installer les consommables comme suit afin de garantir un fonctionnement correct. Ces étapes aideront à garantir que les pièces soient placées correctement. REMARQUE Pour les consommables de 200 ampères, lors du remplacement de la retenue pour protecteur ou de la coupelle protectrice, assembler premièrement ces deux pièces avant le montage des autres consommables. B A 1 - Assembler « A » 200 A uniquement. 2 - Assembler « B ». 3 - Assembler « B .sur « C ». he uc rto Ca de tro ec El D ga istri z p bu las teu m rd ag u èn e Tu yè re Jupe C pr oiffe ot d ec e tio n Dispositif de retenue D ga istri z d bu e p teu ro r d te u ct io n Art # A-08303FEU C 4 - Assembler « A » sur le bloc « B-C ». 3. Empiler les consommables ensemble. 4. Insérer la pile des consommables dans la cartouche. S’assurer que l’embout du grand joint torique de la torche entre complètement dans la cartouche. Si l’une des pièces du joint torique dépasse de la cartouche, cela signifie qu’elle n’est pas bien fixée. Manuel n° 0-5284FR 3-15 INSTALLATION AUTO-CUT 200 XT 2: Appuyer la cartouche contre les pièces empilées 1: Empiler les pièces Electrode Distributeur du gaz plasmagène Joint torique supérieur sur la tuyère Aucun vide entre les pièces Tuyère Distributeur du gaz de protection La cartouche couvre le joint torique supérieur sur la tuyère de la torche Coiffe de protection 3: Enfiler la jupe sur la cartouche 4: Contrôler que la jupe dépasse Jupe Bouclier cap La coiffe de protection dépasse de 0.063-0.083" (1.6 - 2.1 mm) Art # A-04873FC 5. Utiliser l’outil de retrait pour tenir l’ensemble de cartouche tout en tournant la coupelle protectrice dans l’ensemble de cartouche. Lorsque ce groupe est entièrement assemblé, le protecteur doit dépasser la partie supérieure de la coupelle protectrice de 0,063” à 0,083” (1,6-2,1 mm). Si cette saillie n’apparaît pas, alors la coupelle protectrice n’est pas bien serrée sur l’ensemble de cartouche. Outil pour la cartouche Cartouche montée Art # A-04344FEU Jupe Installation de la coupelle protectrice sur la cartouche INSTALLATION 3-16 Manuel n° 0-5284FR AUTO-CUT 200 XT 6. Enlever l’outil de retrait de la cartouche. Ajuster l’ensemble de cartouche sur la tête de la torche. La cartouche doit coller sur le grand joint torique au niveau du corps de la torche tel qu’indiqué. Si la cartouche ne colle pas sur le joint torique, alors elle n’est pas bien serrée. ATTENTION Éviter de forcer la cartouche si elle n’est pas entièrement serrée. Enlever la cartouche et nettoyer délicatement les fils du corps de la tête de la torche à l’aide d’une brosse métallique. Appliquer le lubrifiant compatible à l’oxygène (fourni avec la torche) sur les fils. Corps de la torche Cartouche montée Art # A-03893FEU Installation de la cartouche sur le corps de torche 7. Confirmer le bon assemblage des pièces tel qu’illustré. Corps de torche Joint torique du corps de torche Saillie de 0.063 - 0.083" (1,6 – 2,1 mm) Art # A-07202FEU Installation de la cartouche sur le corps de torche 8. Faire glisser la borne du capteur ohmique sur la jupe si l’on utilise la détection de la hauteur de la torche ohmique. REMARQUE La détection de la hauteur ohmique n’est pas recommandée avec une feuille d’étanchéité. L’eau sur la plaque interfère électriquement avec le circuit de détection ohmique. Borne du capteur ohmique A-03393 9. Raccorder le câblage de l’altimètre à la borne du capteur ohmique si l’on utilise la détection de la hauteur de la torche ohmique. Manuel n° 0-5284FR 3-17 INSTALLATION AUTO-CUT 200 XT 3.14 Diviseur de tension (« V-D ») pour contrôler la hauteur de torche iHC Pour obtenir les meilleures performances de découpe au plasma, il est nécessaire de maintenir une hauteur (distance de dégagement) constante au-dessus du métal pendant la coupe. Les tables de découpe utilisent un contrôle de la hauteur de torche (THC), également appelé contrôle sur l’axe Z, et la plupart d’entre elles se basent sur une rétroaction de la tension d’arc pour ajuster la hauteur. Plusieurs de ces dispositifs de contrôle, y compris l’iHC (contrôle de hauteur interne), qui fait partie du contrôleur CNC Victor Technologies XT, sont munis d’un circuit imprimé diviseur de tension (« carte V-D », pour « Voltage-Divider » en anglais) qui doit être installé à l’intérieur de l’alimentation du plasma pour abaisser la tension d’arc et qui sera utilisé par les circuits de commande. Un espace est prévu pour le montage de la carte V-D, sur la partie supérieure d’un panneau vertical interne situé près de l’arrière de l’alimentation. Des trous pré-percés permettent le montage de la carte V-D iHT, ou d’un autre circuit fréquemment utilisé de commande de hauteur. CAUTION Si vous utilisez une autre carte, qui ne s’aligne pas avec les trous existants, retirez le panneau avant d’en percer d’autres. Si ce n’est pas possible, toutes les précautions doivent être prises pour empêcher la limaille de se déposer à l’intérieur de l’alimentation. Installation de la carte V-D. 1. Localisez la carte V-D qui devrait être avec l’iCNC. 2. À l’intérieur de l’alimentation, localisez et retirez les 2 vis et le panneau de la plaque de montage. 3. Installez les entretoises de la carte V-D et la carte elle-même, en provenance de l’iCNC du XT, puis revissez le panneau avec les 2 vis de fixation, ce qui sécurise la carte V-D. Si vous utilisez une autre carte V-D, suivez les instructions fournies pour l’installer à ce même endroit. Jeu pour V-D carte Ouverture du borne du capteur ohmique installé V-D Board carte Art # A-12079FR Raccordement du V-D carte La carte V-D est illustrée avec le faisceau de câbles en option pour le contrôleur iHC Câble de contrôle. La carte iHC peut être livrée avec un faisceau de câbles et le connecteur correspondant (voir image précédente), qui doivent être installés dans le trou du panneau arrière portant la mention « Height Control » (contrôle de la hauteur). Le connecteur se branche sur un câble de l’iHC. Si vous utilisez une autre carte V-D pour le contrôle de la hauteur, vous pouvez installer un serre-câbles dans ce trou. Reportez-vous à l’annexe pour le schéma de câblage. INSTALLATION 3-18 Manuel n° 0-5284FR AUTO-CUT 200 XT Ouverture du borne du capteur ohmique J55 - GCM USER INPUT J15 - CNC HEIGHT CONTROL Raccordement du V-D carte J54 - TSC /COMM J59 - RAS CB2 - 5A 120 VAC CB3 - 5A 24 VAC J70 - HE CB4 - 5A 120 VAC F1 - 8A SB 230 VAC F2 - 8A SB 230 VAC Art # A-12080FR Connexions de tension d’arc. Le XT plasma présente un bornier TB4, sur le côté droit à l’avant du module CCM pour les connexions à Arc-V (Torch) [torche], Tip V (Pilot) [pilote] et Arc V + (Work) [travail]. Au cas où la carte V-D nécessite une alimentation séparée, des bornes à 24 VCA et 120 VCA sont disponibles sur le bornier TB4. Reportez-vous au schéma de câblage en annexe pour plus d’informations. TB4 1 2 24 VCA à1A 3 4 5 6 7 120 VCA Travail à 100 mA Astuce les tensions (Pilote) Tension d’arc (Torche) Art # A-11954FEU Câble « Ohmique » ou de buse. Certains contrôles de hauteur, y compris l’iHC, détectent la plaque en utilisant une mesure de contact électrique ou de résistance, c’est-à-dire « ohmique », le contact entre l’extrémité conductrice de la torche et le métal ou « plaque » étant coupé. Un fil métallique, généralement un câble unique hautement flexible capable de résister à la chaleur d’arc réfléchie, relie la carte V-D à la buse de la torche. La torche XT comprend une pince à ressort métallique qui se glisse dans une rainure de la buse permettant d’enlever facilement les pièces à changer. Le fil ohmique peut être connecté à cette pince par une borne femelle de ¼ po (6,35 mm) à pression. Une quantité importante d’énergie à haute fréquence (HF), provoquant des interférences électromagnétiques (EMI), peut être transmise par ce fil, en raison de son couplage serré avec la torche. C’est la raison pour laquelle la carte V-D est placée loin du CCM et à proximité du panneau arrière, où le fil ohmique n’a pas besoin de passer à proximité d’autres appareils électroniques sensibles. Il est particulièrement recommandé de ne pas faire passer le fil ohmique à proximité du module CCM ou le long des câbles de la torche. Reportez-vous à l’annexe pour le schéma de câblage. Noyaux de ferrite. Il est recommandé d’enrouler le fil de détection ohmique autour d’un noyau de ferrite en faisant plusieurs tours, au minimum 3 et de préférence davantage, pour atténuer l’énergie transférée à la carte V-D et à l’alimentation du plasma. Le noyau de ferrite doit être placé sur le fil à l’endroit où il entre dans l’alimentation du plasma. Un deuxième noyau de ferrite ajouté à environ 2 m (plusieurs pieds) de la torche permettra de réduire davantage les interférences dans le fil, qui peuvent être transmises à d’autres câbles/fils et provoquer des interférences ailleurs. Reportez-vous à l’annexe pour le schéma de câblage. Manuel n° 0-5284FR 3-19 INSTALLATION AUTO-CUT 200 XT 3.15 Remplissage du système de refroidissement 1. Remplir le réservoir du liquide de refroidissement au niveau indiqué avec le liquide de refroidissement Thermal Dynamics. Le niveau du liquide de refroidissement est visible à travers le réservoir translucide du liquide de refroidissement. La quantité du liquide de refroidissement requis dépend de la longueur des fils de la torche. 2. Remplacer le couvercle du réservoir. Capacités du liquide de refroidissement Numéro de la catégorie et mélange Mélange Protège jusqu’à 7-3580 ‘Extra-CoolTM’ 25 / 75 10° F / -12° C 7-3581 ‘Ultra-CoolTM’ 50 / 50 27° F / -33° C 7-3582 ‘Extreme CoolTM’ Concentré* -65° F / -51° C * Pour être mélangé avec D-I CoolTM 7-3583 Réservoir du liquide de refroidissement Plage de remplissage Art # A-11463FEU 3. Quand l’ensemble du système a été installé, contrôler que le liquide de refroidissement a été pompé à travers le système comme suit (voir REMARQUE) : REMARQUE Le système consommera une grande quantité de liquide de refroidissement après sa première mise en marche. a. Mettre le commutateur MARCHE / ARRÊT sur MARCHE. Le bloc d’alimentation commence à envoyer le liquide de refroidissement à travers le système. b. Au bout de 4 minutes, le système pourrait s’arrêter si les fils ne sont pas remplis du liquide de refroidissement. c. Mettre le commutateur MARCHE / ARRÊT sur ARRÊT. Remplir le réservoir du liquide de refroidissement au besoin. d. Au bout de 10 secondes, mettre une fois de plus le commutateur MARCHE / ARRÊT sur MARCHE. e. Répéter les étapes « b » à « d » jusqu’à ce que le système ne s’éteigne plus. En fonction de la longueur des fils de la torche, cette séquence peut devoir être répétée trois à cinq fois. f. Une fois que le système est opérationnel, laisser la pompe fonctionner pendant dix minutes pour bien évacuer l’air contenu dans les conduits du liquide de refroidissement avant d’utiliser le système. 4. Remplir à nouveau le réservoir et réinstaller le couvercle de remplissage. REMARQUE Le circuit interne du bloc d’alimentation va générer le message : « liquide de refroidissement bas », si le niveau est très bas. INSTALLATION 3-20 Manuel n° 0-5284FR AUTO-CUT 200 XT CHAPITRE 4 : FONCTIONNEMENT 4.01 Panneau de commande du générateur Témoin d’alimentation CA A/ Témoin de gaz Témoin de température Témoin de fonctionnement Témoin d’alimentation CC A/ Art # A-11467FEU Témoin d’alimentation CA Il indique que l’alimentation CA est fournie aux inverseurs quand l’interrupteur Marche/Arrêt est sur la position Marche. Quand l’interrupteur est d’abord mis sur Marche, le témoin reste éteint jusqu’à ce que le cycle d’irruption soit terminé et que la tension correcte soit confirmée. Témoin de température : Il est normalement éteint. Le témoin s’allume quand les capteurs de la température interne détectent des températures supérieures aux limites normales. Laisser l’équipement refroidir avant de poursuivre les opérations. Témoin de gaz : Clignote au démarrage de la purge des gaz / amorçage de la pompe, puis reste fixe quand le gaz s’écoule. Indique la pression de gaz suffisante pour le fonctionnement. Témoin d’alimentation CC : Indique que le générateur produit une tension CC de sortie. A/ Témoin de fonctionnement : Montre la version du code CCM au démarrage, suivie du réglage de contrôle d’intensité électrique et du statut du système. Cf. section 4.05 et Code de statut pour plus de détails. Lampe d’alimentation électrique C.A. du panneau arrière Indique que l’appareil est sous tension C.A. Manuel n° 0-5284FR 4-1 FONCTIONNEMENT AUTO-CUT 200 XT 4.02 Fonctionnalités du pupitre de commande Système standard PLASMA SHIELD Art # A-11468FEU RUN SET A Jauge de pression de gaz plasma PLASMA SHIELD Le bouton de commande de pression de gaz plasma Jauge de pression de gaz bouclier Le bouton de commande de pression de gaz Bouclier RUN Exécuter / set sélecteur SET A Ampérage / sélecteur de courant Mise en marche / Réglage du sélecteur : Utiliser la touche Régler pour ajuster les pressions et les débits de gaz plasmagène et de protection. Une fois les pressions et débits ajustés, appuyer sur la touche Mise en marche pour démarrer le fonctionnement de votre appareil. Boutons de commande de la pression du gaz plasmagène et de protection : Régler les pressions du gaz plasmagène et de protection. Tourner les boutons pour définir les niveaux souhaités. Jauges de pression du gaz plasmagène et de protection : Afficher les pressions de gaz plasmagène et de protection. Sélecteur d’ampérage : Réglage en continu de 5 à 200 A. Visible ici : A/ Sélecteur du type de gaz plasmagène (panneau arrière) : Sélectionne la tension de fonctionnement appropriée pour Air & O2 ou N2 & H35. Utiliser également le paramètre N2/H35 pour F5. FONCTIONNEMENT 4-2 Manuel n° 0-5284FR AUTO-CUT 200 XT Système optionnel avec brouillard d’eau (H2O) PLASMA SHIELD H20 MIST RUN SET SHIELD GAS Art # A-11468FEU H20 MIST A Jauge de pression de gaz plasma PLASMA SHIELD Jauge de pression de gaz bouclier Bouclier pression de gaz bouton de commande Plasma pression de gaz bouton de commande H20 MIST RUN Exécuter / set sélecteur SET SHIELD GAS H20 MIST A ampérage / courant sélecteur sélecteur bouclier Eau Mist (bouclier) débitmètre et le bouton de commande Mise en marche / Réglage du sélecteur : Utiliser la touche Régler pour ajuster les pressions et les débits de gaz plasmagène et de protection. Une fois les pressions et débits ajustés, appuyer sur la touche Mise en marche pour démarrer le fonctionnement de votre appareil. Boutons de commande de la pression du gaz plasmagène et de protection : Régler les pressions du gaz plasmagène et de protection. Tourner les boutons pour définir les niveaux souhaités. Jauges de pression du gaz plasmagène et de protection : Afficher les pressions de gaz plasmagène et de protection. Sélecteur de bouclier : Sélectionne le liquide, le gaz de protection ou le brouillard d’eau H2O (Eau). Bouton de commande du débitmètre pour brouillard d’eau (H2O) : Sélecteur de bouclier : Sélectionne le liquide, le gaz de protection ou le brouillard d’eau (Eau). Débitmètre pour brouillard d’eau et bouton de commande : Contrôle le débit du brouillard d’eau. A/ Sélecteur d’ampérage : Réglage en continu de 5 à 200 A. Visible ici : Sélecteur du type de gaz plasmagène (panneau arrière) : Sélectionne la tension de fonctionnement appropriée pour Air & O2 ou N2 & H35. Utiliser également le paramètre N2/H35 pour F5. Manuel n° 0-5284FR 4-3 FONCTIONNEMENT AUTO-CUT 200 XT 4.03 Configuration du fonctionnement Suivre cette procédure de configuration à chaque exploitation du système : MISE EN GARDE Couper l’alimentation principale à la source avant de monter ou de démonter l’alimentation électrique, les pièces de la torche, la torche et les assemblages de câbles ou avant d’ajouter le liquide de refroidissement. A. Inspection du niveau du liquide de refroidissement Vérifier le niveau du liquide de refroidissement contenu dans le réservoir à l’avant de l’appareil. Si le niveau du réservoir est inférieur aux 3/4, ajouter le liquide de refroidissement. B. Sélection des pièces de la torche Vérifier l’état de la torche pour un montage approprié. Installer les pièces de la torche qui conviennent, conformément à la section Torche du manuel. C. Alimentation d’entrée Vérifier la source d’alimentation pour une tension d’entrée appropriée. Fermer l’interrupteur principal ou brancher l’appareil pour connecter l’alimentation principale au système. D. Connexion du câble de masse S’assurer que la pièce ou la table de coupe soit solidement et convenablement connectée au câble de masse. La zone de branchement doit être exempte de peinture et de rouille. E. Branchement de la torche Vérifier que la torche est branchée comme correctement. F. Alimentations en gaz Connecter les gaz plasmagènes et de protection souhaités. S’assurer que les sources de gaz sont conformes aux exigences. Vérifier les branchements et ouvrir l’alimentation en gaz. Définir le commutateur de sélection de gaz, situé sur le panneau arrière, sur le gaz plasmagène utilisé approprié. Avec l’option de brouillard d’eau : Sélectionner le gaz de protection souhaité comme suit : 1. Pour l’utilisation du gaz de protection, définir le commutateur de sélection du bouclier sur la touche GAZ. 2. Pour l’utilisation du brouillard d’eau, définir le commutateur de sélection du mode bouclier sur la touche BROUILLARD D’EAU ‘H2O. Connecter l’eau au branchement d’eau sur le panneau arrière2. REMARQUE Utiliser l’eau de distribution uniquement pour le gaz de protection. Si la pression d’eau de distribution est supérieure à 100 psi (6,9 bars), alors installer un régulateur de pression d’eau (Catalogue No. 8-6118) entre la source d’eau et l’alimentation. H. Purge de gaz plasmagène Définir le commutateur MARCHE / ARRÊT de l’alimentation sur la position MARCHE. Une purge automatique du gaz permettra d’éliminer toute condensation accumulée dans la torche et les câbles lorsque le système est à l’arrêt. Une fois la purge terminée, si la fonction MISE EN MARCHE / RÉGLAGE est sur la position RÉGLAGE, alors le gaz s’écoule. I. Sélection de l’ampérage Sélectionner l’ampérage de sortie du courant souhaité. FONCTIONNEMENT 4-4 Manuel n° 0-5284FR AUTO-CUT 200 XT J. Réglages de pression et de débit 1. Se référer au manuel de la torche pour les détails sur la pression et le débit selon le matériel à couper. Régler la touche MISE EN MARCHE / RÉGLAGE sur la position RÉGLAGE. (Le gaz s’écoulera à travers la torche). Régler les pressions et les débits de gaz comme suit : 2. Réglage de pression du gaz plasmagène : a. Tirer le bouton situé sur le bouton de commande de la pression du gaz plasmagène. b. Tourner le bouton pour ajuster la pression du gaz. c. Appuyer sur le bouton de retour pour verrouiller le réglage de la pression. 3. Réglage de la pression de gaz de protection : Pour bouclier à gaz : a. Définir la touche de sélection du mode Bouclier sur la position GAZ b. Appuyer sur le bouton de commande de pression du gaz de protection. c. Tourner le bouton pour ajuster la pression du gaz. d. Appuyer sur le bouton de retour pour verrouiller le réglage de la pression. Pour le brouillard d’eau H2 : a. Régler la touche de sélection du mode Bouclier sur la position Brouillard d’eau H2O b. Appuyer sur le bouton de commande de brouillard d’eau pour régler la pression. REMARQUE À moins que l’installation ne comporte un matériel de sélection de gaz compris entre les approvisionnements en gaz et le pupitre de commande, la commutation entre les gaz nécessite la déconnexion de conduit(s) d’alimentation en gaz à partir du panneau arrière du pupitre de commande et la connexion des gaz d’entrée appropriés. L’entrée d’eau peut rester connectée en permanence car le commutateur de sélection du bouclier désactive et active la fonction d’écoulement de l’eau pour le brouillard d’eau H2O. Manuel n° 0-5284FR 4-5 FONCTIONNEMENT AUTO-CUT 200 XT 4.04 Fonctionnement du système Ce chapitre contient des informations sur le fonctionnement qui sont spécifiques à l’alimentation électrique. MISE EN GARDE Passer en revue les précautions de sécurité de la section 1. Si le cordon d’alimentation électrique comporte une prise ou n’est pas connecté de façon permanente sur l’alimentation électrique, s’assurer que la sortie est déconnectée au moment du branchement. Déconnecter l’alimentation électrique primaire à la source avant d’assembler ou de désassembler l’alimentation électrique, des pièces de la torche, ou des montages de la torche et de ses fils, ou d’ajouter du liquide de refroidissement. Il ne suffit pas de positionner l’interrupteur Marche/Arrêt de l’appareil sur Arrêt quand les opérations de découpe sont terminées. Ouvrir toujours l’interrupteur de déconnexion de l’alimentation électrique cinq minutes après la fin de la dernière découpe. Avant de faire démarrer le système, déterminer le procédé à utiliser. Le procédé est déterminé par le type et l’épaisseur du métal à découper. Sélectionner et installer les consommables nécessaires, connecter les gaz nécessaires au système. 1. Raccorder le système à la source de courant principale. Un indicateur s’allume sur le panneau arrière quand l’appareil est sous tension C.A. 2. Mettre l’interrupteur MARCHE / ARRET sur MARCHE (haut). Les ventilateurs se mettent en marche. Le système passe par la séquence de démarrage”. • Pendant environ 10 secondes, les décimales de l’affichage à 4 chiffres clignotent de droite à gauche. • Ensuite, les 4 indicateurs LED rectangulaires éclairent tous les secteurs comme un test. • Ensuite, pendant environ 6 secondes, l’écran affiche la lettre “C” (code) suivie de la version du code CCM. Exemple “C1.2.0”. Pendant ce temps, divers tests de tension en entrée sont effectués. Si une panne est détectée, son code s’affiche et la séquence de démarrage s’arrête. Les pannes s’affichent par “E” ou “L”. • La pompe de refroidissement se met alors en marche et l’indicateur de gaz clignote tandis que les gaz de coupe sont purgés pendant 20 secondes. L’écran affiche au même moment le réglage de la commande en cours. Exemple : “200” • Une fois le débit du liquide de refroidissement détecté, généralement 5 secondes après le démarrage de la pompe, le contacteur d’entrée W1 se ferme et l’indicateur C.A clignote. POWER I ON OFF O OFF O OFF O OFF Art # A-11461 FONCTIONNEMENT 4-6 Manuel n° 0-5284FR AUTO-CUT 200 XT 3. Réglage des pressions de gaz a. Régler la fonction MISE EN MARCHE / RÉGLAGE en mode RÉGLAGE. b. Ajuster les régulateurs de pression de gaz plasmagène et de protection à une pression appropriée ou à un débit approprié pour l’utilisation de l’option Brouillard d’eau H2O. (se référer au manuel de carte de coupe pour la pression / le débit appropriés.) c. Redéfinir la fonction MISE EN MARCHE / RÉGLAGE en mode MARCHE. 4. Réglage du courant de coupe. a. Ajuster le bouton de commande de courant au courant de sortie requis sur l’afficheur à 4 chiffres. 5. Prêt à couper. a. Protéger vos yeux et vos oreilles. b. Placer la torche à une distance de transfert appropriée au-dessus de la pièce. 6. Appuyer sur DÉMARRER. • Lorsque l’indicateur de gaz clignote, le pré-écoulement de gaz commence. • Lors du pré-écoulement de gaz, l’alimentation est mise en marche. La lampe DC s’allume. 7. L’arc pilote • À la fin du pré-écoulement, l’inflammation se produit (feux pour démarreur d’arc) et l’arc pilote est fixé. 8. Transfert • Si la torche est correctement positionnée, l’arc pilote la transfert presque immédiatement au service et elle devient un arc de coupe (transféré). • Le niveau du courant augmente rapidement jusqu’au niveau fixé par la commande de courant et l’arc passe à travers le métal. • La fonction ‘OK pour déplacer’ devient active et la torche se déplace pour effectuer la coupe. 9. Fin de la coupe. • Lorsque le signal DÉMARRER est désactivé, le courant baisse et ne passe plus. • Les gaz continuent de s’écouler pendant la période post-écoulement sélectionnée, puis s’arrêtent. • La pompe se met en marche pendant 4 minutes, puis s’arrête. 10. Pour effectuer une coupe supplémentaire, répéter les étapes 5-9. Une fois la première coupe achevée, il est possible de démarrer une deuxième. 11. Arrêt du système. a. Régler le commutateur MARCHE / ARRÊT, situé sur le panneau avant de l’appareil, sur ARRÊT. MISE EN GARDE! L’alimentation C.A. traverse encore l’appareil. • Le système de ventilation et la pompe, ainsi que tous les indicateurs, arrêtent de fonctionner. • L’écran peut afficher un code d’erreur pendant un moment : c’est une étape normale de l’arrêt d’alimentation et cela n’indique pas une panne. b. Activer (désactiver) l’alimentation principale. L’appareil perd alors toute son énergie. • L’indicateur C.A du panneau arrière s’arrête. Manuel n° 0-5284FR 4-7 FONCTIONNEMENT AUTO-CUT 200 XT Suggestions opérationnelles 1. Attendre quatre minutes avant de régler l’interrupteur Marche/Arrêt sur Arrêt après utilisation. Cela permet aux ventilateur de refroidissement de fonctionner afin de dissiper la valeur de l’alimentation électrique. 2. Pour maximiser la durée de vie des pièces, ne pas faire fonctionner l’arc pilote plus longtemps que nécessaire. 3. Faire attention en manipulant le câblage de la torche et le protéger de tout dommage. 4. Si vous utilisez de l’eau comme écran, notez les points suivants : • Utiliser de l’eau du robinet potable de bonne qualité pour contribuer à empêcher tout colmatage par des particules dans la plomberie de l’écran du système. • Une contamination par des particules et un colmatage peuvent réduire la durée de vie des consommables et faire tomber prématurément la torche en panne. • Un filtre à particules de type cartouche peut aider à optimiser les performances de découpe. 4.05 Sélection du gaz A. Gaz plasmagènes 1. Plasma à l’air • Le plus souvent utilisé sur les matériaux ferreux ou à base de carbone pour une bonne qualité avec des vitesses de coupe plus rapides. • Le plasma à l’air est normalement utilisé avec un rideau d’air. • Il est recommandé de n’utiliser que de l’air propre et sec avec le gaz plasmagène. Toute présence d’huile ou d’humidité dans l’air réduira considérablement la durée de vie des pièces de la torche. • Fournit des résultats satisfaisants sur les matériaux non-ferreux et une soudabilité réduite sur les matériaux ferreux. 2. Plasma à l’argon/azote (H35) • Recommendé pour une utilisation sur l’acier inoxydable d’une épaisseur de 3/4 in (19 mm) et plus. Recommandé sur les matériaux non-ferreux d’une épaisseur de 1/2 inch (12 mm) et plus. Le Ar/H2 n’est normalement pas utilisé sur les matériaux non-ferreux plus fins car des gaz moins coûteux peuvent obtenir une qualité de coupe similaire. • Mauvaise qualité de coupe sur les matériaux ferreux. • Fournit des vitesses de coupe plus rapide et une qualité de coupe élevée sur les matériaux plus épais pour compenser les coûts supérieurs. • Un mélange de 65% d’argon et de 35% d’azote devrait être utilisé. 3. Plasma à l’oxygène (O2) • L’oxygène est recommandé pour le coupage des matériaux ferreux. • Fournit des vitesses de coupe plus rapides. • Fournit des finitions très lisses et réduit au minimum les dépôts de nitrure sur la surface de découpe (les dépôts de nitrure peuvent provoquer des problèmes lors de la production de soudures de grande qualité s’ils ne sont pas enlevés). 4. Plasma à l’azote (N2) • Fournit une meilleure qualité de coupe sur les matériaux non-ferreux comme l’acier inoxydable et l’aluminium. • Peut être utilisé à la place du plasma à l’air avec un rideau d’air de protection. • De l’azote avec un bon degré de soudage devrait être utilisé. FONCTIONNEMENT 4-8 Manuel n° 0-5284FR AUTO-CUT 200 XT B. Gaz de protection 1. Rideau d’air comprimé • Un rideau d’air est normalement utilisé quand on opère avec du plasma à l’air. • Améliore la qualité de coupe sur certains matériaux ferreux. • Economique - frais d’exploitation réduits. 2. Protection avec de l’azote (N2) • La protection avec de l’azote est utilisée avec le plasma à l’Ar/H2 (H35). • Fournit des finitions lisses sur les matériaux non-ferreux. • Peut réduire la fumée quand il est utilisé avec le plasma à l’Ar/H2. 3. Rideau d’eau • Normalement utilisé avec l’azote. • Fournit une surface de coupe très lisse. • Réduit la fumée et la chaleur au niveau de la pièce à usiner. • Efficace en cas d’utilisation avec N2 jusqu’à 2» (50 mm) maximum d’épaisseur de matériau. • L’eau du robinet permet un coût réduit. 4.06 Codes de fonctionnement du générateur Lors du démarrage et durant le fonctionnement, la circuiterie de commande du générateur effectue différents tests. Si la circuiterie détecte une situation nécessitant l’attention de l’opérateur, le statut qui s’affiche sur le panneau avant affiche un code de 3 chiffres précédé par la lettre «E» (erreur active) ou la lettre «L» (erreur récente ou loquet) signifiant qu’une erreur est survenue lors du processus mais n’est pas active. Certaines conditions peuvent être actives indéfiniment tandis que d’autres sont momentanées. Le générateur verrouille les conditions momentanées ; certaines conditions momentanées peuvent couper le système. Le témoin peut montrer des conditions multiples en séquence ; il est important de reconnaître toutes les conditions possibles qui peuvent être affichées. REMARQUE Il n’existe pas 500 codes. Code de fonctionnement CCM Groupe 1 Procédé plasma Code Remède / Commentaire Message Activation plasma éteinte ; Mise hors service externe activée ou bretelle manquante CCM TB1-1 & 2 ; 40 câbles ruban de circuit du relais PCB au code CCM déconnecté ou défectueux ; 101 Plasma désactivé 102 L’arc pilote n’a pas démarré dans les 15 secondes. Les consommables de la torche sont-ils Échec de l’allumage usés ? S’assurer que les paramètres de contrôle du courant correspondent aux consommables ; pression Plasma trop élevée ; Amorce d’arc défectueuse ; PCB Pilot défectueux ; du pilote onduleur 1A défectueux. 103 Pilote perdu Le pilote est parti après démarrage. Les consommables de la torche sont-ils usés ? S’assurer que le réglage du contrôle de courant corresponde aux consommables ; pression Plasma trop élevée ; 104 Transfert perdu L’arc a été transféré au système pendant plus de 50 ms, puis sorti lors du démarrage. L’arc a perdu le contact avec le système, désactiver l’arête, sur le trou, etc. cales d’écartement trop élevées ; s’assurer que le réglage de contrôle du courant corresponde aux consommables ; mauvaise pression de gaz 105 Non utilisé Réservé pour le produit de legs Manuel n° 0-5284FR 4-9 FONCTIONNEMENT AUTO-CUT 200 XT 106 Expiration de délai pilote, pas de transfert Le transfert du pilote à l’arc de découpe doit se faire sous 0,085 s (SW8-1 OFF) ou sous 3 s (SW8-1 ON). Cales d’écartement trop élevées ou nulles dans la pièce sous la torche ; réglage de contrôle de courant trop bas pour les consommables, ce qui entraîne : Un courant pilote trop faible pour les consommables ; une pression de gaz erronée. 107 Non utilisé Réservé pour le produit de legs 108 Mauvaise tension entre la pointe et l’électrode. Tension pointe très proche de la tension de l’électrode. Commutateur de gaz du panneau arrière réglé sur le mauvais gaz, consommables pièces de la torche usés, mauvais consommables installées causant un court circuit à l’extrémité de l’électrode, pression trop faible, fuite dans le tuyau du plasma de la torche, courant de contrôle réglé très haut pour les consommables, pilote PCB défectueux, corps de la torche court-circuité. 109 Non utilisé Réservé pour le produit de legs 110 Non utilisé Réservé pour le produit de legs Code de fonctionnement CCM Groupe 2 -- Alimentation électrique du plasma Code Message Remède / Commentaire 201 Phase C.A. manquante Fusible mural disjoncté ; fusible de l’appareil F1 ou F2 ou du panneau arrière disjoncté ; mauvaise connexion du câble d’alimentation ; système Bias PCB défectueux. 202 Non utilisé Réservé pour le produit de legs 203 Non utilisé Réservé pour le produit de legs 204 Non utilisé Réservé pour le produit de legs 205 Sortie DC faible Inférieure à 60 V c. c. ; court-circuit du fil négatif vers la pièce d’usinage ou la terre ; onduleur défectueux (court-circuit en sortie) ; tension CCM (J24) déconnectée ou fil rompu ; CCM défectueux. 206 Non utilisé Réservé pour le produit de legs 207 Intensité supérieure à 8 A dans le fil d’usinage avant l’allumage ou le transfert du pilote. Intensité inattendue Court-circuit du fil négatif à la terre ou au châssis de l’allumage de l’arc ; fil d’usinage de dans le fil d’usinage l’ampèremètre HCT1 défectueux ; relais PCB défectueux. 208 Intensité inattendue Intensité supérieure à 6 A dans le circuit du pilote avant allumage. Consommables faux ou dans le circuit du décalés, provoquant un court-circuit à l’extrémité de l’électrode, câble pilote court-circuité au pilote négatif dans le tube de la torche, relais PCB défectueux, possibilité de court-circuiter la torche. 209 Non utilisé Réservé pour le produit de legs 210 Courant de sortie très élevé Le courant du câble de masse détecté dépasse le réglage du processus de 20%. Possible signal erroné causé par le capteur du courant de masse HCT1 ou le relais PCB défectueux, CCM défectueux. 211 Courant de sortie très faible Le courant de fonctionnement détecté est inférieur au processus de réglage de 20%. Possible signal erroné causé par le capteur du courant de masse HCT1 ou le relais PCB défectueux, possible défectuosité de la commande PCB (court-circuit IGBT), 212 Intensité basse en sortie de l’onduleur 1A Intensité de travail du plasma basse pendant la découpe et attribuée à une intensité basse en sortie de la section A du module onduleur 1 ; sortie de l’onduleur déconnectée ; possibilité de câble ruban défectueux ; si le problème persiste, remplacer le module onduleur 1. 213 Intensité basse en sortie de l’onduleur 1B Intensité de travail du plasma basse pendant la découpe et attribuée à une intensité basse en sortie de la section B du module onduleur 1 ; sortie de l’onduleur déconnectée ; possibilité de câble ruban défectueux ; si le problème persiste, remplacer le module onduleur 1. 214 Intensité basse en sortie de l’onduleur 2A Intensité de travail du plasma basse pendant la découpe et attribuée à une intensité basse en sortie de la section A du module onduleur 2 ; sortie de l’onduleur déconnectée ; possibilité de câble ruban défectueux ; si le problème persiste, remplacer le module onduleur 2. 215 Non utilisé Réservé pour d’autres modèles avec les sections d’onduleurs supplémentaires. 216 Non utilisé Réservé pour d’autres modèles avec les sections d’onduleurs supplémentaires. 217 Non utilisé Réservé pour d’autres modèles avec les sections d’onduleurs supplémentaires. FONCTIONNEMENT 4-10 Manuel n° 0-5284FR AUTO-CUT 200 XT 218 Intensité haute en sortie de l’onduleur 1A Intensité de travail du plasma haute pendant la découpe et attribuée à une intensité haute en sortie de la section A du module onduleur 1 ; si le problème persiste, remplacer le module onduleur 1. 219 Intensité haute en sortie de l’onduleur 1B Intensité de travail du plasma haute pendant la découpe et attribuée à une intensité haute en sortie de la section B du module onduleur 1 ; si le problème persiste, remplacer le module onduleur 1. 220 Intensité haute en sortie de l’onduleur 2A Intensité de travail du plasma haute pendant la découpe et attribuée à une intensité haute en sortie de la section A du module onduleur 2 ; si le problème persiste, remplacer le module onduleur 2. 221 Non utilisé Réservé pour d’autres modèles avec les sections d’onduleurs supplémentaires. 222 Non utilisé Réservé pour d’autres modèles avec les sections d’onduleurs supplémentaires. 223 Non utilisé Réservé pour d’autres modèles avec les sections d’onduleurs supplémentaires. 224 Onduleur 1 introuvable Le module 1 de l’onduleur section A nécessite le pilotage, le câble plat CCM 1A au module 1 de l’onduleur section A est endommagé ou déconnecté 225 Révision incompatible de l’onduleur 1A Révision de l’onduleur non supportée ; câble ruban CCM J31 au module onduleur 1 section A endommagé ; version du code CCM incompatible avec la révision ou le modèle de l’onduleur 226 Révision incompatible de l’onduleur 1B Révision de l’onduleur non supportée ; câble ruban CCM J32 au module onduleur 1 section B endommagé ; version du code CCM incompatible avec la révision ou le modèle de l’onduleur 227 Révision incompatible de l’onduleur 2A Révision de l’onduleur non supportée ; câble ruban CCM J33 au module onduleur 2 section A endommagé ; version du code CCM incompatible avec la révision ou le modèle de l’onduleur 228 Non utilisé Réservé pour d’autres modèles avec les sections d’onduleurs supplémentaires. 229 Non utilisé Réservé pour d’autres modèles avec les sections d’onduleurs supplémentaires. 230 Non utilisé Réservé pour d’autres modèles avec les sections d’onduleurs supplémentaires. 231 Mauvais appariement de l’onduleur 1A V C.A. Tension nominale CA de l’onduleur incompatible avec la tension nominale du bloc d’alimentation ; câble-ruban CCM J31 du Module 1 Section A de l’onduleur endommagé ou desserré ; mauvaise tension du Module 1 de l’onduleur installé ; module d’onduleur défectueux 232 Mauvais appariement de l’onduleur 1B V C.A. Tension nominale CA de l’onduleur incompatible avec la tension nominale du bloc d’alimentation ; câble-ruban CCM J32 du Module 1 Section B de l’onduleur endommagé ou desserré ; mauvaise tension du Module 1 de l’onduleur installé ; module d’onduleur défectueux 233 Mauvais appariement de l’onduleur 2A V C.A. Tension nominale CA de l’onduleur incompatible avec la tension nominale du bloc d’alimentation ; câble-ruban CCM J33 du Module 2 Section A de l’onduleur endommagé ou desserré ; mauvaise tension du Module 2 de l’onduleur installé ; module d’onduleur défectueux 234 Non utilisé Réservé pour d’autres modèles avec les sections d’onduleurs supplémentaires. 235 Non utilisé Réservé pour d’autres modèles avec les sections d’onduleurs supplémentaires. 236 Non utilisé Réservé pour d’autres modèles avec les sections d’onduleurs supplémentaires. 237 Pas assez d’onduleurs trouvés Il faut au moins deux sections d’onduleurs pour fonctionner ; câble ruban CCM à la section d’onduleur endommagé ou déconnecté 238 BIAS V C.A. Invalide Sélection de tension CA non valide ; raccordement défectueux ou desserré au J61 de l’alimentation de la polarisation du système 239 Tension C.A. haute La tension détectée sur le système Bias PCB est supérieure à la tension d’étalonnage de l’alimentation électrique ; connexion de sélection de tension J61 de l’alimentation du système Bias endommagée ou déconnectée ; système Bias PCB défectueux ; CCM défectueux 240 Tension C.A. basse La tension détectée sur le système Bias PCB est inférieure à la tension d’étalonnage de l’alimentation électrique ; connexion de sélection de tension J61 de l’alimentation du système Bias endommagée ou déconnectée ; système Bias PCB défectueux ; CCM défectueux 241 Erreur de tension d’entrée de l’onduleur 1A Défaut de tension en entrée d’onduleur ; tension hors limites ou phase manquante à l’entrée C.A. du module onduleur 1 section A ; mauvaise qualité de l’alimentation C.A. ; contact W1 défectueux ; connexion détachée ou ouverte entre les bornes d’entrée et le contact W1 ou entre le contact et l’entrée de la section d’onduleur ; module onduleur défectueux Manuel n° 0-5284FR 4-11 FONCTIONNEMENT AUTO-CUT 200 XT 242 Erreur de tension d’entrée de l’onduleur 1B Défaut de tension en entrée d’onduleur ; tension hors limites ou phase manquante à l’entrée C.A. du module onduleur 1 section B ; mauvaise qualité de l’alimentation C.A. ; contact W1 défectueux ; connexion détachée ou ouverte entre les bornes d’entrée et le contact W1 ou entre le contact et l’entrée de la section d’onduleur ; module onduleur défectueux 243 Erreur de tension d’entrée de l’onduleur 2A Défaut de tension en entrée d’onduleur ; tension hors limites ou phase manquante à l’entrée C.A. du module onduleur 2 section A ; mauvaise qualité de l’alimentation C.A. ; contact W1 défectueux ; connexion détachée ou ouverte entre les bornes d’entrée et le contact W1 ou entre le contact et l’entrée de la section d’onduleur ; module onduleur défectueux 244 Non utilisé Réservé pour d’autres modèles avec les sections d’onduleurs supplémentaires. 245 Non utilisé Réservé pour d’autres modèles avec les sections d’onduleurs supplémentaires. 246 Non utilisé Réservé pour d’autres modèles avec les sections d’onduleurs supplémentaires. 247 Circuit de l’onduleur Le module onduleur 1 section A a détecté un défaut dans le circuit ; module onduleur 1 1A défectueux endommagé 248 Circuit de l’onduleur Le module onduleur 1 section B a détecté un défaut dans le circuit ; module onduleur 1 1B défectueux endommagé 249 Circuit de l’onduleur Le module onduleur 2 section A a détecté un défaut dans le circuit ; module onduleur 2 2A défectueux endommagé 250 Non utilisé Réservé pour d’autres modèles avec les sections d’onduleurs supplémentaires. 251 Non utilisé Réservé pour d’autres modèles avec les sections d’onduleurs supplémentaires. 252 Non utilisé Réservé pour d’autres modèles avec les sections d’onduleurs supplémentaires. 253 Température exces- Le module 1 d’onduleur section A a détecté une erreur de température excédentaire, vérifier le sive de l’onduleur flux d’air limité, radiateur obstrué, ventilateur défectueux, si le problème persiste, remplacer le 1A module d’onduleur. 254 Température exces- Le module 1 d’onduleur section B a détecté une erreur de température excédentaire, vérifier le sive de l’onduleur flux d’air limité, radiateur obstrué, ventilateur défectueux, si le problème persiste, remplacer le 1B module d’onduleur. 255 Température exces- Le module 2 d’onduleur section A a détecté une erreur de température excédentaire, vérifier le sive de l’onduleur flux d’air limité, radiateur obstrué, ventilateur défectueux, si le problème persiste, remplacer le 2A module d’onduleur. 256 Non utilisé Réservé pour d’autres modèles avec les sections d’onduleurs supplémentaires. 257 Non utilisé Réservé pour d’autres modèles avec les sections d’onduleurs supplémentaires. 258 Non utilisé Réservé pour d’autres modèles avec les sections d’onduleurs supplémentaires. 259 Température ambiante excessive pour l’onduleur 1A La température du circuit de l’onduleur est excessive, probablement parce que la température ambiante est supérieure à 40°C ; réduire l’alimentation électrique du cycle de découpe ; réduire la température ambiante ; ajouter un refroidisseur auxiliaire. 260 Température ambiante excessive pour l’onduleur 1B La température du circuit de l’onduleur est excessive, probablement parce que la température ambiante est supérieure à 40°C ; réduire l’alimentation électrique du cycle de découpe ; réduire la température ambiante ; ajouter un refroidisseur auxiliaire. 261 Température ambiante excessive pour l’onduleur 2A La température du circuit de l’onduleur est excessive, probablement parce que la température ambiante est supérieure à 40°C ; réduire l’alimentation électrique du cycle de découpe ; réduire la température ambiante ; ajouter un refroidisseur auxiliaire. 262 Non utilisé Réservé pour d’autres modèles avec les sections d’onduleurs supplémentaires. 263 Non utilisé Réservé pour d’autres modèles avec les sections d’onduleurs supplémentaires. 264 Non utilisé Réservé pour d’autres modèles avec les sections d’onduleurs supplémentaires. 265 Onduleur 1A Pas La section d’onduleur peut ne pas avoir d’alimentation électrique en entrée. Le contacteur d’alimentation élec- n’est pas fermé ; contacteur défectueux ou CB4 déclenché ; l’entrée de la section de l’onduleur trique en entrée n’est pas connectée ; onduleur défectueux. 266 Onduleur 1B Pas La section d’onduleur peut ne pas avoir d’alimentation électrique en entrée. Le contacteur d’alimentation élec- n’est pas fermé ; contacteur défectueux ou CB4 déclenché ; l’entrée de la section de l’onduleur trique en entrée n’est pas connectée ; onduleur défectueux. FONCTIONNEMENT 4-12 Manuel n° 0-5284FR AUTO-CUT 200 XT 267 Onduleur 2A Pas La section d’onduleur peut ne pas avoir d’alimentation électrique en entrée. Le contacteur d’alimentation élec- n’est pas fermé ; contacteur défectueux ou CB4 déclenché ; l’entrée de la section de l’onduleur trique en entrée n’est pas connectée ; onduleur défectueux. 268 Non utilisé Réservé pour d’autres modèles avec les sections d’onduleurs supplémentaires. 269 Non utilisé Réservé pour d’autres modèles avec les sections d’onduleurs supplémentaires. 270 Non utilisé Réservé pour d’autres modèles avec les sections d’onduleurs supplémentaires. 271 Erreur de lecture de CCM a trouvé des valeurs ID incohérentes pendant la lecture. Ruban du CCM à une section ID de l’onduleur d’onduleur endommagé ou déconnecté ; mauvais routage du câble ruban. Code de fonctionnement CCM Groupe 3 -- Statut & Protocole du contrôleur de gaz Code Message 301 Non utilisé 302 Réservé Remède / Commentaire Réservé pour d’autres modèles. Aucune information disponible ; Contactez le service de client 303 Pression d’alimentation en gaz hors limites. 304 Purge du contrôle des Cela est normal après la mise sous tension ou la remise en service après désactivation du gaz plasma. 305 Non utilisé Réservé pour d’autres modèles. 306 Non utilisé Réservé à une utilisation ultérieure 307 Non utilisé Réservé pour d’autres modèles. 308 Mauvais appariement dans le contrôle des gaz Mauvais CCM, doit être de type Auto-Cut. 309 Non utilisé Réservé pour d’autres modèles. 310 Non utilisé Réservé pour d’autres modèles. 311 Non utilisé Réservé pour d’autres modèles. 312 Non utilisé Réservé pour d’autres modèles. 313 Non utilisé Réservé pour d’autres modèles. Autocut est en mode SET ou la pression du gaz plasmagène est trop faible ; le capteur de pression de gaz est défectueux (PS1). Code de fonctionnement CCM Groupe 4 -- Système de refroidissement de la torche Code Message Remède / Commentaire 401 Bas niveau de liquide de Vérifier le niveau de liquide de refroidissement ; en rajouter si nécessaire. refroidissement 402 Le débit de liquide de refroidissement tel que mesuré par le débitmètre FS1 est inférieur à Faible débit du liquide de 0,7 gpm (2,65 l/min) ; filtre bouché ; restriction dans la tuyauterie ou la tête de la torche refroidissement ; mauvais type de consommables ; tube de refroidissement ou vanne de contrôle de la torche rompu ou défectueux ; pompe ou soupape de dérivation. 403 La température d’alimentation en liquide de refroidissement a dépassé 75°C (167°F). Surchauffe du liquide de Fonctionne avec chaque panneau latéral inférieur desserré ou enlevé ; le ventilateur du refroidissement liquide de refroidissement est en panne ; les ailettes du radiateur sont encrassées. Manuel n° 0-5284FR 4-13 FONCTIONNEMENT AUTO-CUT 200 XT 404 Système de refroidissement pas prêt. Un débit de liquide de refroidissement de 0,7 gpm (2,65 l/min) tel que mesuré par le débitmètre FS1 n’a pas été obtenu pendant l’amorçage, jusqu’à 4 minutes. Une nouvelle installation peut exiger un/des cycle(s) d’amorçage supplémentaire(s) pour remplir les tuyaux avec du liquide de refroidissement ; puissance de cycle nécessaire pour redémarrer l’amorçage ; inversion des tuyaux de liquide de refroidissement ou de tuyaux de la torche ; filtre du liquide de refroidissement bouché ; restriction dans les fils de la torche ou la tête ; consommables inappropriés ; tube du liquide de refroidissement de la torche / condensateur de blocage cassé ou défectueux, pompe ou clapet de dérivation défectueux. 405 Alarme de bas niveau du liquide de refroidissement Un bas niveau de liquide de refroidissement n’interrompra pas la découpe. Ajouter du liquide de refroidissement si nécessaire. 406 Non utilisé Réservé pour d’autres modèles. 407 Surchauffe du liquide de refroidissement, température ambiante excessive La température ambiante supérieure à 40 °C entraîne une surchauffe du liquide de refroidissement. Réduire le cycle de service de coupe ; réduire la température ambiante ; ajouter un refroidisseur séparé. REMARQUE Il n’existe pas 500 codes. Code de fonctionnement CCM Groupe 6 -- CCM Code Message Remède / Commentaire 601 Erreur de tension analogique CCM défectueux, remplacez. 602 Erreur ADC ou DAC CCM défectueux, remplacez. 603 Réservé Aucune information disponible ; Contactez le service de client 604 Erreur de mémoire 605 Défaut de mémoire du CCM défectueux, remplacez. programme 606 Bas niveau +5V Logic 607 Température excessive Réduire la température ambiante ; CCM défectueux ; le remplacer du processeur 608 Alimentation 5 V faible pour communication CCM défectueux, remplacez. RS 485/422. 609 Erreur matérielle d’actualisation du logiciel CCM défectueux ; remplacez 610 Erreur de protocole d’actualisation du logiciel CCM défectueux ; remplacez 611 Défaut du contrôleur USB CCM défectueux ; remplacez 612 Défaut d’alimentation USB Retirer le périphérique USB défectueux ; CCM défectueux 613 Défaut de création de log USB Impossible de créer un fichier de connexion sur le lecteur USB Flash ; dernière tentative d’actualisation du logiciel ; utiliser un autre lecteur USB Flash ou reformater FONCTIONNEMENT CCM défectueux, remplacez. CCM défectueux, remplacez. 4-14 Manuel n° 0-5284FR AUTO-CUT 200 XT Fichier VTCCMFW.USF manquant dans le lecteur Flash ; ajouter des fichiers adéquats au lecteur Flash pour actualiser le logiciel ; utiliser un autre lecteur USB Flash ou reformater 614 Pas de fichier USF 615 Pas de fichier d’actua- Logiciel CCM spécifié dans VTCCMFW.USF introuvable ; ajouter les fichiers adéquats au lisation CCM lecteur Flash pour actualiser le logiciel 616 Défaut d’actualisation DPC Une panne est survenue en essayant d’actualiser le logiciel DPC ; ajouter les fichiers adéquats au lecteur USB Flash pour actualiser le logiciel ; reportez-vous à CCM_LOG.TXT sur le lecteur Flash pour plus de détails 617 Défaut d’actualisation DMC Une panne est survenue en essayant d’actualiser le logiciel DMC ; ajouter les fichiers adéquats au lecteur USB Flash pour actualiser le logiciel ; reportez-vous à CCM_LOG.TXT sur le lecteur Flash pour plus de détails 618 Défaut d’étalonnage ADC Étalonnage trop large de l’ADC ; si la panne persiste, le CCM est défectueux ; 619 Panne de débitmètre Le débitmètre rapporte un débit de liquide de refroidissement quand la pompe est coupée ; 620 Erreur mémoire ROM Le stockage de mémoire ROM a été corrompu et écrasé ; si la panne persiste, le CCM est défectueux. 4.07 Qualité de découpe Les exigences de qualité de découpe diffèrent en fonction de l’application. En l’occurrence, l’accumulation de nitrures et l’angle de biseau peuvent être des facteurs majeurs quand la surface doit être soudée après découpe. Une découpe sans mattes est importante quand on désire une bonne qualité de la finition de découpe pour éviter une opération de nettoyage secondaire. La qualité de la découpe varie selon les matériaux et leur épaisseur. Largeur de saignée Angle de coupe du flanc gauche Angle du chanfrein de la surface de coupe Perles sur le bord supérieur Angle de coupe du flanc droit Arrondi de l’arête supérieure Formation d’écume A-00512FC Rayures de la surface de la coupe A-00007FC Surface de découpe L’état (lisse ou rugueux) de la face de découpe. Angle de biseau 4. Définir le bouton MISE EN MARCHE / RÉGLAGE sur la position MARCHE. Définir le bouton MISE EN MARCHE / RÉGLAGE sur la position MARCHE. L’angle entre la surface de découpe et un plan perpendiculaire à la surface de la plaque. Une découpe parfaitement perpendiculaire donnera un angle de biseau de 0°C. Arrondi de l’angle supérieur Arrondi sur le bord supérieur d’une découpe dû à l’usure par le contact initial de l’arc à plasma sur la pièce d’usinage. Accumulation de matte et éclaboussure supérieure La matte est du matériau fondu qui n’est pas expulsé de la zone de découpe et qui se resolidifie sur la plaque. Les éclaboussures supérieures sont de la matte qui s’accumule sur la surface supérieure de la pièce d’usinage. Un excès de matte peut nécessiter des opérations de nettoyage secondaire après découpe. Manuel n° 0-5284FR 4-15 FONCTIONNEMENT AUTO-CUT 200 XT Largeur de coupe La largeur du matériau enlevé pendant la découpe. Accumulation de nitrures Des dépôts de nitrure qui peuvent rester sur l’angle de découpe d’un acier au carbone quand de l’azote est présent dans le jet de gaz du plasma. Des accumulations de nitrures peuvent poser des problèmes si l’acier doit être soudé après découpe. Direction de découpe Le jet de gaz plasma tourbillonne en sortant de la torche en maintenant une colonne de gaz régulière. Cet effet de tourbillon a pour effet qu’un côté de la découpe est plus carré que l’autre. Vu suivant la direction de déplacement, le côté droit de la découpe est plus carré que le gauche. Angle de coupe du flanc gauche Dans le sens des aiguilles d'une montre Angle de coupe du flanc droit Chute Dans le sens contraire des aiguilles d'une montre Chute Objet A-00512FC Art # A-04182FC Effet de tourbillonnement sur les caractéristiques des côtés de découpe Pour faire une coupe carrée le long du diamètre interne d’un cercle, la torche doit se déplacer dans le sens inverse des aiguilles d’une montre le long du cercle. Pour maintenir l’angle carré le long du diamètre externe d’une découpe, la torche doit se déplacer dans le sens des aiguilles d’une montre. Découpe sous l’eau Il n’est pas recommandé d’effectuer des découpes à l’eau, que ce soit sous l’eau ou avec de l’eau en contact avec la plaque ou avec un système d’amortissement à eau. Si vous utilisez un système de découpe à eau, le niveau d’eau doit être d’un minimum de 4 pouces (10 cm) au-dessus du fond de la plaque. Ne pas suivre cette recommandation peut entraîner une mauvaise qualité de découpe et une réduction de la durée de vie des pièces. Capteur ohmique de hauteur La détection de la hauteur ohmique n’est pas recommandée avec une feuille d’étanchéité. L’eau sur la plaque interfère électriquement avec le circuit de détection ohmique. FONCTIONNEMENT 4-16 Manuel n° 0-5284FR AUTO-CUT 200 XT CHAPITRE 5 : ENTRETIEN 5.01 Entretien général Effectuez périodiquement les contrôles suivants afin de garantir des performances correctes du système. Planning d’entretien du générateur Chaque jour Contrôler le niveau du liquide de refroidissement, en ajouter le cas échéant. Contrôler les raccordements des tuyaux du gaz et les pressions. Vérifier le ventilateur de refroidissement, le nettoyer si besoin est. Chaque mois Contrôler le ventilateur de refroidissement et le radiateur ; les nettoyer le cas échéant Contrôler les tuyaux du gaz pour vérifier qu’ils ne présentent pas de fissures, de fuites ou d’abrasion. Remplacer si besoin est. Contrôler tous les raccordements électriques pour vérifier qu’ils ne présentent pas de fissures ou d’abrasion. Remplacer si besoin est. Nettoyer le filtre à eau (en cas de pulvérisation d’H2O) Tous les 6 mois Remplacer le filtre du liquide de refroidissement. Nettoyer le réservoir du liquide de refroidissement. Evacuer tout dépôt de poussière présent à l’intérieur du générateur. 5.02 Procédure de nettoyage du filtre du liquide de refroidissement Le nettoyage périodique du filtre du liquide de refroidissement garantit l’efficacité maximale du débit de liquide de refroidissement. Un mauvais débit du liquide de refroidissement provoque un refroidissement inefficace des pièces de la torche, ce qui porte à une usure plus rapide des consommables. Nettoyer le filtre du liquide de refroidissement comme suit : 1. Débrancher le système de l’alimentation principale. 2. Dévisser et enlever la cuve du filtre à la main. Grande cartouche filtrante située à l’arrière de l’alimentation. Veiller à conserver le joint torique. 3. Inspectez et remplacez le filtre si nécessaire. Remettre la cuve en la serrant à la main. Veiller à ce que le joint torique soit en place. 4. Allumer le système et contrôler s’il y a des fuites. Manuel n° 0-5284FR 5-1 ENTRETIEN AUTO-CUT 200 XT 5.03 Procédure de remplacement du liquide de refroidissement Remplacer le liquide de refroidissement comme suit : 1. Débrancher le système de l’alimentation principale. 2. Enlever le panneau latéral inférieur droit. 3. Repérez l’accouplement dans la ligne de refroidissement qui part du fond du réservoir de liquide de refroidissement, n°1 dans l’illustration suivante. Déconnectez la ligne de refroidissement au niveau de ce raccordement et drainez le liquide de refroidissement dans un réservoir jetable de taille suffisante. Rappelez-vous que vous drainerez plus que le contenu du réservoir de liquide de refroidissement. 4. Lorsque le liquide de refroidissement est en cors de drainage, débranchez le couplage du tuyau gris n°2 dans l’illustration ci-dessous. Laissez s’écouler le liquide de refroidissement en excès, puis appliquez un maximum de 5 psi pour purger les lignes. ATTENTION Appliquer plus de 5 psi de pression d’air peut entraîner des dommages à l’appareillage. Faites particulièrement attention quand vous effectuez ce travail. 2 1 Art # A11689 5. Rebranchez ces deux raccordements puis enlevez le boîtier à filtre du réservoir à l’arrière de l’alimentation électrique. Déversez le reliquat du liquide de refroidissement dans le réservoir et remettez le boîtier à filtre en place. REMARQUE S’il vous faut encore remplacer le liquide de refroidissement restant dans les conduites, débranchez-les de l’alimentation électrique et drainez-les manuellement. 6. Remplissez le réservoir de liquide de refroidissement jusqu’au niveau indiqué ; vérifiez qu’il n’y a pas de fuites. 7. Allumez l’appareillage, laissez-le fonctionnement quelques minutes et vérifiez le niveau de liquide de refroidissement ; remettez-en si nécessaire. Pour cette tâche, se référer à la Section 3 :14 Remplissage du système de refroidissement, de la procédure. ENTRETIEN 5-2 Manuel n° 0-5284FR AUTO-CUT 200 XT 5.04 Fonctionnement du démarreur de l’arc Carte de fonctionnement du démarreur de l’arc Symptôme Indice Check Solution Le liquide de refroidissement est devenu conducteur Utiliser un conductimètre Purger le système, remplacer le liquide de refroidissement. Le fil de retour du pilote n’est pas connecté Inspection visuelle Brancher le câble. L’éclateur est réglé de trop près. Vérifier avec la jauge d’épaisseur Le cap de haute-fréquence (C4) Pas d’allumage du est peut être ouvert pilote : Ferrites endommagées ou Étincelle dans manquantes le démarreur de l’arc sans aucun Faire un court-circuit dans la allumage bobine d’induction (L1) Régler à 0,063” ±0,002” Utiliser un capacimètre Reconnecter ou remplacer. Inspection visuelle Remplacer. Inspection visuelle Enlever le court-circuit ; augmenter les écarts de la bobine. Couvercles d’éclateur de bus(C1, C2, C3) endommagés ou défectueux Capacimètre Remplacer. L’alimentation négative n’est pas correctement connectée Inspection visuelle Raccordez. L’éclateur est réglé trop haut Vérifier avec la jauge d’épaisseur Régler à 0,063” ±0,002” Transformateur défectueux Mesure de la résistance Remplacer. Vérifier la tension d’entrée au filtre EMI Procéder aux raccordements ; remplacer les fils couplés. Inspection visuelle Raccordez. Pas d’allumage du pilote : Pas d’alimentation de 120 v Aucune étincelle dans le démarreur Raccord inexistant ou desserré de l’arc au niveau de l’éclateur Filtre EMI défectueux Mesure de tension/ de résistance Remplacer. Mauvaise(s) fixation(s) Inspection visuelle Resserrer les fixations. Inspection visuelle Remplacer une bobine HF. Inspection visuelle Remplacer le(s) conduit(s) du liquide de refroidissement. Pas ou pas assez de refroidissement : Dégât aux joints brasés (L1) Liquide de Conduit(s) du liquide de refroidissement des refroidissement endommagé(s) fuites ou percé(s). Assortir les couleurs des Les tuyaux d’alimentation et de Inspection visuelle des connexions de liquide de Pas ou pas assez retour ont été intervertis connexions codées par couleurs refroidissementà celles des de refroidissement : connexions de l’allumage de l’arc. Pas d’écoulement de liquide de Desserrer légèrement les pièces Blocage dans la bobine oules refroidissement de raccord et vérifier le débit du Système de vidange. tuyaux d’arrivée / retour. liquide de refroidissement Comportement erratique du système (Interférence électromagnétique) Le bouclier du conduit de la torche n’est pas relié ou lâche. Câble de mise à la terre F1 non connecté. Inspection visuelle du joint de fixation du démarreur de l’arc Reconnecter / resserrer les connecteurs. Raccordement à la terre manquant ou mal connecté Inspection visuelle du fil de mise à la terre au démarreur de l’arc Faire ou resserrer les raccords pour une meilleure mise à la terre. Couvercle C5 non connecté, Inspection visuelle / condensateur ouvert ou desserré de mesure Manuel n° 0-5284FR 5-3 Remplacer le circuit. ENTRETIEN AUTO-CUT 200 XT 5.05 Réglage de l’éclateur du démarreur de l’arc 1. Arrêt du système d’entrée. Enlever le couvercle de la console supérieure. 2. Régler l’éclateur comme illustré. Réinstaller le couvercle supérieur. 0.063" ± 0.002" 1.6 ± 0.05 mm Art # A-11464 ENTRETIEN 5-4 Manuel n° 0-5284FR AUTO-CUT 200 XT CHAPITRE 6 : ÉLÉMENTS ET PIÈCES DE RECHANGE 6.01 Générateur de rechange Unité complète / Composant Numéros des catalogues Numéro du catalogue Générateur Auto-Cut 200 XT™, 400V C.A. +10 -15% CE Manuel n° 0-5284FR 6-1 3-9112-4 Liste des pièces détachées AUTO-CUT 200 XT 6.02 Fils et Câbles Se référer à la section 3.05 pour le raccord des mises à la terre et les câbles de mise à la terre. G: Incendiez le fil réglé, protégé - Alimentation du liquide w/ Négatif - Retour du liquide - Retour de l’arc pilote - Gaz plasmagène - Gaz de protection Auto-Cut XT Générateur CNC Câble CNC P Tube plongeur Puissance principale Câble de masse Torche F1 Câble de mise à la terre O Pièce Art # A-11687FC_AB Numéros des catalogues des fils ; bloc d’alimentation Auto-Cut 200 XT, Torche XT-301 Longueur de fils Touche Description F1 Câble de mise à la terre, Alimentation à la terre G Montage de la tuyauterie de la torche O Câble de mise à la terre P Câble de commande, CNC pour l’alimentation 10 ft 15 ft 3.05 m 4.5 m 25 ft 35 ft 50 ft 75 ft 100 ft 125 ft 7.6 m 10.6 m 15.2 m 22.8 m 30.5 m 38.1 m 9-4924 9-4925 9-4926 9-4927 9-4928 9-4929 4-3044 4-3045 4-3046 4-3047 4-3048 9-9300 9-9301 9-9302 9-9303 9-9304 9-9305 9-9306 9-9307 9-8312 9-8313 9-8315 9-8316 9-8317 REMARQUE Le kit de fils fournis comprend un câble de retour pilote, un câble négatif, des tuyaux d’arrivée et de retour du liquide de refroidissement et un câble de commande. F1 1/0 vert / jaune (50 mm2) Câble de la torche blindé G O Câble de masse, de l’amorce de l’arc à distance à la mise à la terre Câble 1/0 (50 mm2) Câble de mise à la terre P Câble CNC (fil 14) Art # A-11688FC Liste des pièces détachées 6-2 Manuel n° 0-5284FR AUTO-CUT 200 XT 6.03 Pièces de rechange externes pour le générateur N°comp. Qté Description Numéro du catalogue 1 1 Panneau supérieur d’alimentation 9-7300 2 1 Alimentation supérieure des parties droite et gauche 9-7301 3 1 Alimentation inférieure de la partie droite 9-7302 4 1 Alimentation inférieure de la partie gauche 9-7304 5 1 Couvercle de l’alimentation d’entrée 9-7346 1 2 2 4 5 3 Art # A-11947 Manuel n° 0-5284FR 6-3 Liste des pièces détachées AUTO-CUT 200 XT 6.04 Pièces de rechange d’alimentation électrique - Côté inférieur droit N°comp. Qté Description Ref. Des. Numéro du catalogue 1 1 Réservoir du liquide de refroidissement, Couvercle 8-5124 2 1 Réservoir du liquide de refroidissement 9-7306 3 1 Capteur, Niveau du liquide de refroidissement 9-7307 4 1 Pompe, Liquide de refroidissement, Montage 9-7309 5 1 Moteur, Pompe 9-8166 6 1 Ventilateur d’échangeur de chaleur (2 par unité) 7 1 Radiateur 8 1 Écoulement, Interrupteur FAN1,2 9-7312 9-7311 FS1 9-7310 (placé derrière les ventilateurs de refroidissement) 1 2 3 4 Art # A-011572 5 6 Liste des pièces détachées 7 6-4 Manuel n° 0-5284FR AUTO-CUT 200 XT 6.05 Pièces de rechange d’alimentation électrique - Côté supérieur droit N°comp. Qté Description Ref. Des. Numéro du catalogue 1 1 Relais de commande du moteur de la pompe MC3 9-7314 2 1 Relais de commande d’appel de courant K1 9-7337 3 1 Relais d’appel de courant MC1 9-7336 4 1 Transformateur auxiliaire T1 9-7315 5 1 Circuit imprimé de l’écran d’affichage 6 1 Coupe-circuit Marche/Arrêt 7 1 Alimentation de polarisation 9-9253 8 1 Circuit imprimé Relais et Interface 9-9251 9 1 Montage CCM PCB 9-7324 9-9252 CB1 9-7316 7 6 8 5 4 3 2 1 9 Art # A-11567_AB Manuel n° 0-5284FR 6-5 Liste des pièces détachées AUTO-CUT 200 XT 6.06 Pièces de rechange de l’alimentation - Partie inférieure gauche N°comp. Qté Description Ref. Des. Numéro du catalogue 1 1 Grille d’arrêt CA PCB 9-9254 2 1 PCB pilote AC-200XT 9-9255 3 1 Onduleur demi-pont 9-7319 4 1 Onduleur complet 9-7317 5 1 Contacteur principal 6 1 Filtre EMI PCB (2 au total) W1 9-7318 9-9264 1 2 3 6 4 5 Art # A-11946 Liste des pièces détachées 6-6 Manuel n° 0-5284FR AUTO-CUT 200 XT 6.07 Pièces de rechange de l’alimentation - Partie supérieure gauche N°comp. 1 Qté 1 Description Solénoïde à gaz Ref. Des. Numéro du catalogue SOL 1, 2, 3 9-6319 (2 nécessitent 3 avec l’option de pulvérisation d’eau) 2 1 Filtre à eau complet (en option. Nécessite un 3ème solénoïde à gaz) 8-3460 3 1 PCB, RAS1000 RF Capsule de carte électronique 9-9423 4 1 Montage de la bobine HF, démarreur de l’arc 9-4959 5 1 Pressostat PS1 9-6318 3 2 5 4 1 Art # A-11569_AB Manuel n° 0-5284FR 6-7 Liste des pièces détachées AUTO-CUT 200 XT 6.08 Pièces de rechange d’alimentation électrique - Panneau arrière N°comp. Qté Description Numéro du catalogue 1 1 Montage du filtre à liquide de refroidissement. 9-7320 2 1 Filtre à liquide de refroidissement 9-7322 3 1 Fonction de sélection de gaz 9-3325 4 1 Filtre à air complet AC200-XT - Élément de la première partie du filtre uniquement - Élément de la deuxième partie du filtre uniquement 9-7527 9-1021 9-1022 1 USER INPUT HEIGHT CONTROL 3 J15 - CNC AIR / O2 PLASMA 2 N2 / H35 PLASMA CB2 - 5A 120 VAC CB3 - 5A 24 VAC CB4 - 5A 120 VAC F1 - 8A SB 230 VAC 4 F2 - 8A SB 230 VAC 5 Art # A-11948 Liste des pièces détachées 6-8 Manuel n° 0-5284FR AUTO-CUT 200 XT 6.09 Pièces de rechange du bloc d’alimentation - Partie avant N°comp. Qté Description Numéro du catalogue 1 1 Manomètre 8-6800 2 1 Régulateur de gaz 9-9509 3 1 Mise en marche / Réglage du sélecteur 9-3427 4 1 Potentiomètre 9-2685 5 1 Débitmètre, H2O 9-7762 6 1 Écran de protection du sélecteur de gaz Les commandes optionnelles avec un brouillard d'eau Les contrôles standard PLASMA 9-3426 SHIELD PLASMA SHIELD H20 MIST RUN RUN SET SHIELD GAS H20 MIST SET A A PLASMA PLASMA SHIELD 1 1 SHIELD 1 1 2 2 2 H20 MIST RUN RUN 3 SET SHIELD GAS H20 MIST 5 SET 3 A 4 A 6 Manuel n° 0-5284FR 6-9 Art # A-11571FEU Liste des pièces détachées AUTO-CUT 200 XT 6.10 Tuyau d’alimentation du gaz recommandé N°comp. 1 Qté Description Numéro du catalogue Tuyau Synflex gris 3/8” Pas de raccords inclus. Numéro du catalogue par pied 9-3616 Liste des pièces détachées 6-10 Manuel n° 0-5284FR AUTO-CUT 200 XT CHAPITRE 7 : ENTRETIEN DE LA TORCHE 7.01 Enlèvement des consommables 1. Utiliser l’outil de retrait pour tenir immobile l’ensemble formé de la jupe et de la cartouche. Tourner la jupe pour l’enlever de la cartouche. Outil pour la cartouche Cartouche montée Art # A-04344FEU Jupe 2. Utiliser l’outil de retrait pour tenir immobile l’ensemble formé de la jupe et de la cartouche. Tourner la jupe pour l’enlever de la cartouche. Outil pour la cartouche Cartouche Art # A-04345FEU Manuel n° 0-5284FR 7-1 RELATIVES À LA TORCHE AUTO-CUT 200 XT 7.02 Lubrification du joint torique Lubrifier les trois joints toriques sur la cartouche et les trois joints toriques sur le corps de la torche périodiquement avec le lubrifiant pour joint torique fourni. Enlever le circlip de la cartouche et faire glisser la bague de serrage vers le bas pour accéder au joint torique en dessous de la bague de serrage. Joints toriques Joint torique interne (n° cat. 8-0545) Emplacement (sous la bague de serrage) Corps de torche N° cat. 9-9041 Joint torique, n° cat. 8-0544 Joint torique, n° cat. 8-0540 N° cat. 8-0539 N° cat. 8-3487 N° cat. 8-0530 Cartouche Circlip Art # A-04066FEU Art # A-04071FEU ATTENTION N’utiliser que du lubrifiant pour joint torique Thermal Dynamics n° 9-4893 (Christo Lube MCG-129) avec cette pièce de la torche. L’utilisation d’autres lubrifiants peut provoquer des dégâts irréparables à la torche. 7.03 Usure des pièces Remplacer le distributeur de gaz s’il est carbonisé ou fissuré. Remplacer le distributeur de gaz si la bride est endommagée. Remplacer la tuyère et/ou l’électrode si elles sont usées. Tuyère en bon état Tuyère usagée Electrode en bon état Electrode usagée Art # A-04861FC RELATIVES À LA TORCHE 7-2 Manuel n° 0-5284FR AUTO-CUT 200 XT 7.04 Installation des consommables de la torche 1. Installer les consommables comme suit : MISES EN GARDE Ne pas placer de consommables dans la cartouche quand celle-ci est fixée au corps de la torche. Faire en sorte qu’aucun matériau étranger ne pénètre dans les consommables et la cartouche. Manipuler soigneusement toutes les pièces afin d’éviter de les endommager car cela pourrait affecter les performances de la torche. Art # A-03887FR REMARQUE Pour les consommables de 200 ampères, lors du remplacement de la retenue pour protecteur ou de la coupelle protectrice, assembler premièrement ces deux pièces avant le montage des autres consommables. B A 1 - Assembler « A » 200 A uniquement. 2 - Assembler « B ». Manuel n° 0-5284FR 3 - Assembler « B .sur « C ». 7-3 he uc rto Ca de tro ec El D ga istri z p bu las teu m rd ag u èn e Tu yè re Jupe C pr oiffe ot d ec e tio n Dispositif de retenue D ga istri z d bu e p teu ro r d te u ct io n Art # A-08303FEU C 4 - Assembler « A » sur le bloc « B-C ». RELATIVES À LA TORCHE AUTO-CUT 200 XT 2: Appuyer la cartouche contre les pièces empilées 1: Empiler les pièces Electrode Distributeur du gaz plasmagène Joint torique supérieur sur la tuyère Tuyère Aucun vide entre les pièces Distributeur du gaz de protection La cartouche couvre le joint torique supérieur sur la tuyère de la torche Coiffe de protection 3: Enfiler la jupe sur la cartouche 4: Contrôler que la jupe dépasse Jupe Bouclier cap La coiffe de protection dépasse de 0.063-0.083" (1.6 - 2.1 mm) Art # A-04873FC 2. Enlever l’outil de retrait de la cartouche et monter la cartouche assemblée sur le corps de torche. ATTENTION La cartouche doit couvrir le joint torique sur le corps de torche. Ne pas forcer sur la cartouche si elle ne se serre pas entièrement. Enlever la cartouche et nettoyer délicatement les filets sur le corps de torche avec une brosse métallique. Appliquer un lubrifiant compatible avec l’oxygène (fourni avec la torche) sur les filets. RELATIVES À LA TORCHE 7-4 Manuel n° 0-5284FR AUTO-CUT 200 XT Corps de torche Joint torique du corps de torche Saillie de 0.063 - 0.083" (1,6 – 2,1 mm) Art # A-07202FEU Installation de la cartouche sur le corps de torche Borne du capteur ohmique A-03393 Installation de la cartouche sur le corps de torche 3. Faire glisser la borne du capteur ohmique sur la jupe si l’on utilise la détection de la hauteur de la torche ohmique. REMARQUE La détection de la hauteur ohmique n’est pas recommandée avec une feuille d’étanchéité. L’eau sur la plaque interfère électriquement avec le circuit de détection ohmique. 4. Raccorder le câblage de l’altimètre à la borne du capteur ohmique. Manuel n° 0-5284FR 7-5 RELATIVES À LA TORCHE AUTO-CUT 200 XT E. Dépannage en cas de fuite du liquide de refroidissement Ne jamais faire fonctionner le système s’il y a des fuites de liquide de refroidissement provenant de la torche. Un écoulement stable indique que les pièces de la torche sont endommagées ou mal installées. Si l’on utilise le système dans ces conditions, on risque d’endommager le corps de torche. Se reporter au tableau suivant pour avoir des instructions en cas de fuite du liquide de refroidissement provenant du corps de torche. La torche fuit Les consommables de la torche sont-ils montés ? Non Fuite provenant de l’alimentation ou du retour du liquide de refroidissement ? Commander le kit de rechange du tube du liquide de refroidissement Alimentation Oui Les pièces sontelles neuves ou utilisées ? Commander le kit du clapet de non-retour du liquide de refroidissement 9-4846 Retour Les pièces sont probablement usagées. Consulter le tableau pour connaître la durée de vie moyenne. Usagé Il se peut que la torche soit endommagée. Voir la page pour déterminer si le corps a été endommagé. Neuf Les pièces sontelles entièrement montées dans la torche ? Oui La torche est-elle endommagée ? Enlever et lubrifier tous les joints toriques sur le corps de torche, la cartouche de consommables et les consommables. Remonter la torche. Fuit-elle encore ? Non Vous n’êtes pas sûr ? Ja Oui Démonter entièrement et remonter la torche correctement. Consulter le manuel d’installation. Intensité du courant 30 50 70 100 Electrodes de la torche Remplacer la cartouche des consomambles et la jupe. La torche fuit-elle encore ? Oui Remplacer le corps de torche Gaz plasmagène O2 Air O2 Air O2 Air O2 H35 Profondeur d’usure recommandée pour le remplacement Pouce 0.04 0.04 0.04 0.08 0.04 0.08 0.04 0.08 mm 1 2 1 2 1 2 1 2 Art # A-04704FR RELATIVES À LA TORCHE 7-6 Manuel n° 0-5284FR AUTO-CUT 200 XT ANNEXE 1 : Module de commande CNC Raccordements de commande du PCB TB1 (LV) Déplacement autorisé 2 12 élevé +10V 10K 11 Commande du courant analogique 10 essuie-glace / entrée faible(-) Volts de l’arc divisé Sortie Entrée démarrage/arrêt 9 (+) 8 (-) 7 (+) 6 (-) 5 Arrêt (NC) 4 (LV) Déplacement autorisé 2 3 (+) 2 (-) 1 CNC enable plasma TB2 Déplacement autorisé (+) 12 SW6 11 DC 10 9 8 Sortie de l’arc pilote activée (Contacts) Flux préliminaire activée Retenir le démarrage 7 6 5 (+) 4 (-) 3 (+) 2 Art # A-11512FEU (-) 1 TB3 Rechange # 2 sorties contacts normalement ouverts 12 Rechange #2 sorties contacts normalement fermés 10 Rechange #1 sorties contacts normalement fermés 8 23X5560_AB Métal déployé Manuel n° 0-5284FR Réduction du courant d'angle Marquage plasma à distance 11 9 7 (-) 6 (+) 5 (-) 4 + 3 (-) 2 (+) 1 A-1 ANNEXE AUTO-CUT 200 XT Fonctions du CNC. Les circuits E/S CNC fournissent au moins 1000 V d’isolation galvanique de l’alimentation électrique du plasma. Lors de l’isolation des circuits CNC du bloc d’alimentation, un bon nombre de signaux retourne sur le J15 et le TB1, et deux sont communs l’un vers l’autre. Les broches 1, 4, 5 et 10 du J15 et TB1-1, 5, 7, 9, et TB2-1 & 3 sont toutes communes. Les broches J15 12 et TB2-10 sont également connectées aux autres quand l’interrupteur SW6 (sélection ‘OK to Move’) est réglé sur Tension. Connecteur J15 de la CNC du panneau arrière : Circuit 14 (A CPC) à distance standard : Terre du châssis (pour le blindage de câble SC-11) 1 Démarrage / Arrêt 1 Ok to Move (contacts or voltage ) 1 Volts de l’arc divisé (rapport pouvant être 1 3 (+); 4 (-) 12(-); 14 (+) 2 sélectionné 50 :1; 40 :1; 30 :1; 16.6 :1, 25 :1) 5 (-); 6 (+) Activation du pré-écoulement (PreFlow ON) 7 (+); 9 (-) Réduction d’intensité de coin (Corner Current Reduction) 10 (+); 11 (-) Circuit Comm isolé (pour SC-11) 8 Terre du châssis 13 Il y a également des duplications sur TB1, TB2 & TB3 : utiliser l’un ou l’autre mais pas deux ensemble. Des fonctions supplémentaires sont uniquement disponibles sur le TB1, le TB2 et le TB3. 1 Le SW6 sur le CCM E / S PCB, sélectionner ‘OK pour déplacer’ pour la fermeture de contact isolé ou les volts CC (15-18 V) à <100 mA. Lors du réglage pour les contacts, le circuit ‘OK pour déplacer’ est réglé à une valeur nominale de 120 V C.A. / 28 V c. c. @ 1A. 2 Raccordements internes à la CNC. TB1, TB2 et TB3 sur le module du CCM. Les raccordements sont fournis sur les plaques à bornes TB1, TB2 et TB3 du module du CCM y compris la plupart des fonctions du panneau arrière plus certaines fonctions supplémentaires. Tous ces signaux sont isolés du générateur à plasma mais les signaux marqués (comm.) et (-) sont communs à chacun. Les utilisateurs sont censés installer leur propre câble CNC sur ces raccordements. Le trou d’expulsion est fourni dans le panneau arrière du module du CCM. L’utilisateur doit fournir le réducteur de tension pour le câble installé par l’utilisateur. TB1 FonctionConnexion Activation/Désactivation CNC TB1-2 (+), TB1-1(-)(comm.) ‘OK to Move’ 2 Contacts TB1-3 & TB1-12 seulement, étalonné 1A @ 28 V C.A./ c. c. Stop verrouillé (NC) 4 TB1-4 (+) & TB1-5 (-) (comm.) utilisé avec Start verrouillé Start/Stop Ret 4 TB1-6 (+), TB1-5 (-) (comm.) ou Start verrouillé (NO) 4 TB1-6 (+), TB1-5 (-) (comm.) utilisé avec Stop verrouillé Tension d’arc divisé TB1-8 (+), TB1-7 (-) comm. Contrôle d’intensité analogique à distance TB1-9 Analogique Comm. (-) ou 10K CC Pot bas TB1-10 Analogique en (+) ou CC contact de potentiomètre (Pot Wiper) TB1-11 10K CC Pot Hi (+10V @ 1 mA. Alimentation) ANNEXE A-2 Manuel n° 0-5284FR AUTO-CUT 200 XT TB2 FonctionConnexion Retenir le démarrage TB2-2 (+),TB2-1 (-) (comm. ) Activation du pré-écoulement (PreFlow ON) TB2-4 (+), TB2-3 (-) (comm.) Pilote sur Marche (contacts) TB2-6, TB2-8 de valeur nominale 1A @ 120 V C.A. ou 28 V c. c. ‘OK to Move’ (contacts ou DC Volts)5 TB2-12 (+), TB2-10 (-) TB3 FonctionConnexion Repère plasma TB3-2(+), TB3-1(-) (comm.) Réduction d’intensité de coin (Corner Current Reduction) TB-4(+), TB3-3(-)(comm.) Découpe de métal déployé TB3-6(+), TB3-5(-)(comm.) Contact NO de rechange TB3-7, TB3-8 Contact NC de rechange TB3-9, TB3-10 Contact NO de rechange TB3-11, TB3-12 Manuel n° 0-5284FR A-3 ANNEXE AUTO-CUT 200 XT Description de l’entrée/de la sortie de la CNC Toutes les entrées exceptées les commandes de courant analogique (contact ou fermeture SW) Activer / Désactiver CNC (entrée) — Nécessite un raccordement fermé à valeur nominale de 10 mA. @ 20V c. c. pour le fonctionnement de l’appareil. La bretelle installée en usine entre le TB1-1&2 doit être retirée lors du raccordement du circuit Activer / Désactiver fourni par l’utilisateur. 4 Démarrage / Arrêt (entrée)—Interrupteur (momentané ou soutenu) à valeur nominale de 35 mA. @ 20 V c. c. Configuration Démarrage / Arrêt du circuit. Les fonctions Démarrage / Arrêt momentané (Verrouillage) sont uniquement disponibles pour le TB1. SOUTENU DÉBUT / FIN DÉBUT / FIN MOMENTANÉ FIN DÉBUT / FIN TB1-4 TB1-5 TB1-5 TB1-6 DÉBUT TB1-6 Sortie de la tension d’arc divisée — Le signal de la tension d’arc est isolé du générateur à plasma, néanmoins (-) est courant avec d’autres signaux de la CNC isolés. Le niveau du signal de la tension d’arc divisée maximum dépend du rapport de division des délais de la tension d’arc effective, néanmoins il ne peut dépasser 12 V environ. 2Entrée de commande du courant analogique — Peut utiliser un potentiomètre à distance de 10K ohm ou un signal analogique de 0-10V c. c. Utiliser l’ensemble d’entrée SW 11 de la commande du courant analogique pour baisser la position sur le PCB E / S (la plus grande des 2 cartes CCM) et sur le PCB de l’UC (petite carte). Mettre le SW8-2 en marche (vers le haut). Régler le potentiomètre de la commande à distance du courant ou le signal analogique au courant de coupe (ou de marquage) désiré. Le système calcule le niveau correct du pilote, le démarrage de l’arc et les niveaux d’augmentation et de baisse sur le réglage du niveau de coupe. Le réglage du courant de coupe ou de marquage s’affiche sur le panneau avant lors de l’utilisation de l’entrée de la commande à distance du courant analogique. L’écran présente la lettre « A » suivie de la valeur du courant définie. S’il existe un message d’erreur ou un statut, l’écran alterne entre la présentation de la valeur du courant et le message d’erreur ou le statut. Pour éviter le raccordement à un module d’isolation séparé, l’entrée de la commande à distance du courant analogique comprend une isolation du bloc d’alimentation en plasma. Cependant, l’entrée inférieure est commune avec les autres entrées CNC isolées. La mise à l’échelle de l’entrée de la commande du courant analogique est 0 V = 0 A, 10 V. = sortie maximum et elle est linéaire au milieu. Néanmoins la sortie minimale est de 5 A. L’utilisateur est responsable pour la configuration de la tension analogique correcte afin de maintenir une sortie d’au moins 5 A. Entrée retenir le démarrage —Normalement ouvert, fermé pour retenir le démarrage. La valeur nominale du circuit est de 10 mA. @ 20V c. c. Retarde l’allumage du pilote, le flux préliminaire du gaz continue. Utilisé pour la synchronisation des démarrages lorsque plusieurs blocs d’alimentation en plasma se trouvent sur la même table de découpe. L’utilisateur fournit le circuit pour conserver les entrées ‘Retenir le démarrage’ actives jusqu’à ce que toutes les torches trouvent leur hauteur. Preflow On (input)— Normalement ouverte, fermée pour lancer le flux préliminaire avant le signal de DÉMARRAGE normal. La valeur nominale du circuit est de 10 mA. @ 20V c. c. Les commandes de la hauteur des torches (THC) émettent normalement le signal de Démarrage pour l’alimentation en plasma lorsque la hauteur de la torche a été trouvée. Ensuite, le plasma prend 1-2 secondes (ou plus) pour effectuer le flux préliminaire avant l’allumage du pilote. Certaines commandes de la hauteur de torche (THC) disposent d’une sortie leur permettant de commencer le flux préliminaire plus tôt, pendant la recherche des hauteurs, permettant ainsi de gagner 1 ou 2 secondes sur chaque coupe. ANNEXE A-4 Manuel n° 0-5284FR AUTO-CUT 200 XT Sortie de l’arc pilote activée – Les contacts du relais ont une valeur nominale de 1 A à 120 VCA / 28 VCC Les contacts se ferment quand l’arc pilote est activé. Ils peuvent être câblés en parallèle avec les contacts Déplacement autorisé afin de démarrer le mouvement de la machine quand l’arc pilote est établi. Utilisé lors du démarrage sur les trous. Le démarrage sur les trous requiert la configuration du SW8-1 activé (haut) sur le PCB de l’UC pour un temps prolongé de l’arc pilote. L’utilisation d’un temps prolongé de l’arc pilote pour démarrer sur les trous ou pour le coupage sur les trous réduira la durée de vie des pièces. Sortie Déplacement autorisé — Active quand l’arc de coupage est établi, l’arc est transféré. Utilisé pour dire à la table de découpe de démarrer le mouvement X-Y. Les contacts du relais ont une valeur nominale de 1 A à 120 VCA ou 28 VCC quand le SW6 est configuré pour les contacts. Quand le SW6 est configuré pour le VCC, la sortie fournit 15-18 V.CC à 100 mA. Il peut être câble en parallèle avec l’arc pilote activé pour démarrer le mouvement de la machine de découpe dès que l’arc pilote est établi. Un deuxième parallèle ‘Ok pour se déplacer’ (OK2) est disponible sur le TB1-3 & 12. Il est exclusivement réservé aux contacts et possède une tension nominale de 28 V c. c. Sélection à distance du marquage au plasma (entrée)--- Le marquage au plasma n’est pas disponible avec l’Auto-cut. Réduction du courant à l’angle (entrée)--- Lorsque cette entrée est activée, normalement à partir de l’angle du contrôleur de la table ou d’un signal d’inhibition de commande de la hauteur, montrant la réduction de la vitesse de coupe pour passer un angle ou un petit rayon, le courant actuel est réduit à une valeur fixe à un niveau prédéterminé pour une meilleure coupe à une vitesse inférieure. Métal déployé coupé (entrée)---En général, le bloc d’alimentation au plasma est optimal pour la découpe par perforage, une grande hauteur de perforage au-dessus du métal à découper, un temps pilote court, etc. L’activation de cette entrée permet d’ajuster le bloc d’alimentation au plasma pour optimiser ses paramètres de coupe du métal déployé, perforé, et pour un fonctionnement le long des bords etc. Parmi les autres changements, l’on peut citer une égalisation de la hauteur de transfert avec la hauteur de coupe. En plus de l’activation, l’interrupteur SW1-1 de l’entrée CCM du métal déployé coupé doit être mis en marche automatiquement, il faut redémarrer le pilote et régler SW8-1 sur une temps pilote plus long. Contacts de rechange --- Ils ne sont pas actifs mais sont réservés pour un usage ultérieur. Manuel n° 0-5284FR A-5 ANNEXE AUTO-CUT 200 XT Circuit CNC simplifié Auto-Cut XT CCM Simpli fied CNC & Gas Control TB1 OK2 (contact) +10V (CC Pot Hi) CC Pot Wiper CC Pot Low Div Arc V (+) Div Arc V (-) /Start - Stop (+) /Start - Stop (-) Stop Mom NC OK2 (contact) / CNC Enable (+) / CNC Enable (-) 12 11 10 9 8 7 6 5 4 3 2 1 OK TO MOVE SELECT 18 VDC or Contacts SW6A +18VDC DC VOLTS CONTACTS OK SW6B TB2 OK to MOVE (+) 12 + 5 - 6 5 3 4 VOLTAGE DIVIDER 7 Preflow ON (+) Preflow ON (-) Hold Start (+) Hold Start (-) 4 2 PILOT is ON B 3 8 PILOT is ON 11 10 9 8 7 6 5 4 3 2 1 1 OK to MOVE (-) ALL SW OFF f or SW12A ( 1) ON = SW12B ( 2) ON = SW12C ( 3) ON = SW12D ( 4) ON = SW12D SW12C Spare #1b NO / Cut ExpandedMetal (-) / Cut ExpandedMetal (+) / Corner Current Reduction (-) / Corner Current Reduction (+) / Plasma Marking (-) / Plasma Marking (+) 12 11 10 9 8 7 6 5 4 3 2 1 SW12A Spare #2 NC SW12B TB3 Spare #2 NO 50: 16. 30: 40: 25: 1 ( def aul t ) 7: 1 ( SC- 11) 1 1 1 PSR Art # A-11578 ANNEXE A-6 Manuel n° 0-5284FR AUTO-CUT 200 XT (124) PS1 PLASMA (51 PSI) GAS ON (131) (104) SW 1 RUN / SET (128) AC 24V-GCM2 (B8) (123) (121) (124) (131) (129) (125) (123) J26 (126) +10V 1 2 3 4 5 6 7 8 9 10 11 12 13 14 15 16 17 18 (130) CURRENT CONTROL SW 2 (130) GAS (127) GND / CNC Plasma Enable (+) / CNC Plasma Enable (-) (130) R? 10K 2 (125) (126) (127) SOL1 (142) AC 24V Ret-GCM2 (B8) 3 PLAS_ENABLE SW PLAS_ EN_SW_RET / GAS PRESS OK / BASIC ID (130) 1 ENABLE 1 2 3 4 5 6 7 8 9 10 11 12 13 14 15 16 (165) PLASMA H2O (164) SOL3 (133) (134) (137) (139) (138) (143) SOL2 H2O Mist SHIELD (111) (111) H2O Mist Option (140) (141) (136) (135) Installing H2O Mist Option -----------------------------------------------------------------Remove #130 from Shield SOL, connect #165 in it's place. Connect #111 with other #111 on Shield SOL. Connect #130 from SW2 with other #130 on SW1. J21 GND GND 1 2 3 4 5 6 7 8 9 10 11 12 13 14 15 16 17 18 19 20 SPARE #1 1 2 3 4 5 6 7 8 9 10 11 12 13 14 (133) (134) (135) (136) (137) (138) (139) (140) (141) (142) (143) J15-1 to chassis used for SC-11 cable shield 3- / CNC Start (+) 4- / CNC Start (-) 5- Divided Arc V (-) 6- Divided Arc V (+) 7- / Preflow ON (+) 8- COMM Ref (1K Ohm) 9- / Preflow ON (-) 10- Corner Current Reduction (+) 11- Corner Current Reduction (-) 12- OK to Move (-) 14- OK to Move (+) J15-CNC J15-13 connects SC-11 chassis to PS chassis. Chassis The COMM Ref at pin 8 is also for the SC-11 J22 Art # A-11578 Manuel n° 0-5284FR A-7 ANNEXE AUTO-CUT 200 XT Connexions CNC Machine de découpe Câble CNC Générateur J15 * DÉMARRAGE/ARRÊT (1) 1 * ( 2) 2 NC (3) 3 .......... (4) 4 ( 5) 5 (6) 6 .......... Arc divisé V (+) ( 7) 7 .......... Flux préliminaire activé (+) Source, 16 VDC, 10 ma. ... Arc divisé V (-) 8 { 9 .......... Flux préliminaire activé (-) (10) 10 .......... Réduction du courant d'angle (+) (11) 11 ... Réduction du courant d'angle (-) (12) 12 Commencez mouvement (Déplacement autorisé) Déplacement autorisé Contact DCV (-) relais ou DC (1 A à DCV (+) 120 VCA ( 15 - 18 VCC ou 28 VCC) jusqu’à 100 mA) 13 * (14) (+) Coin (9) 14 Coiffe SW6 ** * Art # A-11502FEU ANNEXE Alimentation GND n'est pas utilisé pour le câble CNC Ne pas connecter le fil n ° 1 à rien. ** Câble fil de drain blindage doit être relié à la terre à la machine à découper. A-8 Manuel n° 0-5284FR AUTO-CUT 200 XT Page volontairement laissée vierge. Manuel n° 0-5284FR A-9 ANNEXE AUTO-CUT 200 XT ANNEXE 2 : Conception du circuit de l’unité centrale du CCM = Test Point = Test Point Art # A-11675 ANNEXE A-10 Manuel n° 0-5284FR AUTO-CUT 200 XT Circuit de l’unité centrale du CCM Points de test TP1 MISE À LA TERRE TP2 ISO +5.0V TP3 +24V TP4 +3.3V TP5 ISO MISE À LA TERRE TP6 +5.0V TP7 DEMANDE TOTALE 3,3 V = 400 A TP9 /WR TP10 /RD TP11 CAPTEUR DE TEMPÉRATURE DE L’UNITÉ CENTRALE TP12 +3.3VA TP13 -15VD C.A. TP14 PC2 TP15 +15VD C.A. TP16 CLKO TP18 OSC_CLOCK Référence LED D2 Rouge RXD D3 Rouge TXD D4 Rouge Sortie Fibre 2 D7 Rouge Sortie Fibre 1 D11 Vert Usage futur D17 Vert Usage futur Manuel n° 0-5284FR A-11 ANNEXE AUTO-CUT 200 XT ANNEXE 3 : Conception du circuit E/S du CCM = Test Point 19 Art # A-11676 WORK CURRENT = Test Point ANNEXE A-12 Manuel n° 0-5284FR AUTO-CUT 200 XT Circuit E/S du CCM E/S Connecteurs J Points de test J21 BASIC CNC TP1 MISE À LA TERRE J22 EXTENDED CNC TP2 /VENTILATEURS DE REFROIDISSEMENT ON J23 PANNEAU INTERFACE RELAIS J24 TENSION ARC / POINTE TP3 /POMPE DE LA TORCHE ON J25 TEST TP4 Faible débit du liquide de refroidissement (SW) J26 RÉSERVOIR DE GAZ TP5 SIGNAL DU DÉBIT DU LIQUIDE DE REFROIDISSEMENT (PULSATION) J28 VERS L’UNITÉ CENTRALE (CPU) J29 VERS L’UNITÉ CENTRALE (CPU) TP6 +15V ISOLÉ TP7 -15V ISOLÉ TP8 +18V ISOLÉ TP9 CONTRÔLE D’INTENSITÉ ANALOGIQUE 0-3.3V TP10 MISE À LA TERRE ISOLÉ TP11 /PILOTE ACTIVÉ TP12 +5V c. c. TP13 -15V c. c. TP14 +15V c. c. TP15 24 V c. c. TP18 +5V ISOLÉ TP19 INTENSITÉ DE TRAVAIL Référence LED D2 Vert ACTIVATION PLASMA D3 Vert E-STOP_PS D4 Vert GAZ ON D6 Vert DÉMARRAGE DU CNC D8 Vert RETENIR LE DÉMARRAGE D12 Vert PRÉ-ÉCOULEMENT ON D13 Vert CSD D18 Vert REPÈRE D20 Vert RECHANGE1 D25 Vert MÉTAL DÉPLOYÉ D33 Vert OK TO MOVE D37 Vert PSR D41 Vert RECHANGE SORTIE POUR LE TERRAIN 2 D43 Vert RECHANGE SORTIE POUR LE TERRAIN 1 Manuel n° 0-5284FR A-13 ANNEXE AUTO-CUT 200 XT ANNEXE 4 : Conception du PCB du pilote = Test Point = Test Point Art # A-11677 ANNEXE A-14 Manuel n° 0-5284FR AUTO-CUT 200 XT Points de test du PCB du pilote TP1 MISE À LA TERRE TP2 PORTAIL DU PILOTE TP3 +5V TP4 TIP Référence LED D2 Vert PILOTE ACTIVÉ D11 Vert +5V Manuel n° 0-5284FR A-15 ANNEXE AUTO-CUT 200 XT ANNEXE 5 : Conception du circuit Relais et Interface = Test Point = Test Point Art # A-11678 ANNEXE A-16 Manuel n° 0-5284FR AUTO-CUT 200 XT Points de test du circuit Relais et Interface TP1 MISE À LA TERRE TP2 -15V TP3 +5V c. c. TP4 +12V TP5 +24V TP6 +15V TP7 +5V c. c. Référence LED D2 Vert 1 GAZ DE LA TORCHE ON D7 Vert PILOTE ACTIVÉ D11 Vert COURANT DU PILOTE DÉTECTÉ D12 Vert COURANT D’USINAGE DÉTECTÉ D22 Vert CONTACTEURS ON D23 Vert RF ON D24 Vert VENTILATEURS ON D25 Vert ACTIVATION PLASMA D26 Vert 1 TORCHE ON D27 Vert LIQUIDE DE REFROIDISSEMENT DE LA TORCHE ON Manuel n° 0-5284FR A-17 ANNEXE AUTO-CUT 200 XT ANNEXE 6 : Conception du PCB de l’écran d’affichage = Test Point = Test Point Art # A-11679 ANNEXE A-18 Manuel n° 0-5284FR AUTO-CUT 200 XT Points de test du PCB de l’écran d’affichage TP1 MISE À LA TERRE TP2 +5V c. c.TP3 TP3 +24 V c. c. Manuel n° 0-5284FR A-19 ANNEXE AUTO-CUT 200 XT ANNEXE 7 : Conception du PCB du Système Bias = Test Point = Test Point Art # A-11680 ANNEXE A-20 Manuel n° 0-5284FR AUTO-CUT 200 XT Points de test du PCB du Système Bias TP1 MISE À LA TERRE TP2 24 V c. c. TP3 ENTRÉE DC POSITIVE TP4 VCC1 TP5 VCC2 TP6 PORTAIL TP7 MISE À LA TERRE PRIMAIRE TP8 +12V PRIMAIRE TP9 P_ISOL_MISE À LA TERRE TP10 CAPTEUR DC POSITIF Référence LED D3 Rouge PHASE MANQUANTE D4 Rouge C.A. V HAUT D14 Rouge C.A. V BAS D15 Vert V C.A._IDA D26 Vert +12V PRIMAIRE D27 Vert V C.A._IDB D30 Vert 24 V c. c. D44 Vert TRANSFORMATEUR ON Manuel n° 0-5284FR A-21 ANNEXE AUTO-CUT 200 XT ANNEXE 8 : Conception du circuit de l’onduleur principal bas ANNEXE Art # A11681 = Test Point = Test Point A-22 Manuel n° 0-5284FR AUTO-CUT 200 XT Points de test du circuit de l’onduleur principal bas TP1 MISE À LA TERRE TP2 PORTAIL 2A TP3 PORTAIL 1A TP4 PORTAIL 3A TP5 PORTAIL 4A TP6 PORTAIL 2B TP7 PORTAIL 1B TP8 PORTAIL 4B TP9 PORTAIL 3B TP10 +12VP TP11 +12V c. c. TP12 THERMISTOR CÔTÉ A TP13 THERMISTOR CÔTÉ B TP14 +5V c. c. TP15 P MISE À LA TERRE Référence LED D3 Rouge DÉSÉQUILIBRE D4 Vert Manuel n° 0-5284FR PRÊT A-23 ANNEXE AUTO-CUT 200 XT ANNEXE 9 : Conception du circuit de l’onduleur principal haut ANNEXE Art # A11682 = Test Point = Test Point A-24 Manuel n° 0-5284FR AUTO-CUT 200 XT Points de test du circuit de l’onduleur principal haut TP1 MISE À LA TERRE TP2 PORTAIL 2A TP3 PORTAIL 1A TP4 PORTAIL 3A TP5 PORTAIL 4A TP6 PORTAIL 2B TP7 PORTAIL 1B TP8 PORTAIL 4B TP9 PORTAIL 3B TP10 +12VP TP11 +12V c. c. TP12 THERMISTOR CÔTÉ A TP13 THERMISTOR CÔTÉ B TP14 +5V c. c. TP15 P MISE À LA TERRE Référence LED D3 Rouge DÉSÉQUILIBRE D4 Vert Manuel n° 0-5284FR PRÊT A-25 ANNEXE AUTO-CUT 200 XT ANNEXE 10 : Conception du circuit Contrôle et Pannes = Test Point = Test Point /230V Art # A11683 ANNEXE A-26 Manuel n° 0-5284FR AUTO-CUT 200 XT Points de test du circuit Contrôle et Pannes TP1 MISE À LA TERRE TP22 +12V c. c. TP23 +5V c. c. TP24 PORTAIL 1+ TP25 A_OUT1 TP26 B_OUT1 TP27 PORTAIL 1- TP28 I_SNS1 TP29 PORTAIL 2+ TP30 I_DMD1 0,5 V - 6,7 V TP31 PORTAIL 2- TP32 -12V c. c. TP33 DÉMARRAGE 2 TP34 SHDN TP35 ACTIVATION TP36 PRÊT IN TP37 PRÊT OUT Référence LED D1 Rouge INV FLT D14 Rouge TEMPÉRATURE EXCESSIVE D24 Vert D32 Rouge PRI OC Manuel n° 0-5284FR PWM ON A-27 ANNEXE AUTO-CUT 200 XT ANNEXE 11 : Conception du circuit du Système Cap Bias bas Art # A-11685 ANNEXE A-28 Manuel n° 0-5284FR AUTO-CUT 200 XT ANNEXE 12 : Conception du circuit du Système Cap Bias haut Art # A-11686 Manuel n° 0-5284FR A-29 ANNEXE AUTO-CUT 200 XT ANNEXE 13 : Conception du circuit du suppresseur Art # A-11684 ANNEXE A-30 Manuel n° 0-5284FR AUTO-CUT 200 XT Page volontairement laissée vierge. Manuel n° 0-5284FR A-31 ANNEXE AUTO-CUT 200 XT ANNEXE 14 : Pg schématique 1 du système 1 2 3 5 4 INVERTER 1/2 MODULE (IM) #2 (top) A J105A L6 1 2 (7) IM #2 Section A (lower) AC INPUT J104A 1 2 (8) (1) 1 2 IN1 (2) EMI FILTER PCB 2 1 IN2 1 2 019x502000 OUT2 INVERTER MODULE (IM) #`1 (bottom) 2 1 GND2B IN3 W1A OUT3 J105B L5 (7) B 1 2 (8) J103B W1C 1 2 (9) 019x502700 Toriod Core (1) 1 2 IN1 (2) EMI FILTER PCB J105A L4 1 2 1 IN3 D6, GREEN, -12V D11, GREEN, +12VP D13, GREEN, +12V IM #1 Section A (lower) AC INPUT J104A 1 2 (8) OUT2 (22) 2 1 GND2B CONTROL PCB LEDS D1, RED, INV FLT D14, RED, OVER TEMP D24, GREEN, PWM ON D32, RED, PRI OC 1 2 (7) (21) 2 1 IN2 (3) IM #1 Section B (upper) MAIN PCB LEDS D3, RED, CAP IMBALANCE D4, GREEN, READY CAP BIAS PCB LEDS (20) 2 1 OUT1 1 2 AC INPUT 1 2 J104B W1B CHASSIS GND L1 1 2 Toriod Core 2 1 1 2 (3) J103A (9) OUT1 J103A (9) 1 2 OUT3 C L3 1 Earth 1 CHASSIS GND (1) CHASSIS GND 380-415 VAC INPUT (Customer supplied power cord must pass through ferrite core assembly.) (2) (3) 019x502000 Component Locations (not including PCB components) AC SUPPRESSION PANEL AC INDICATOR PCB (10) 1 J50 1 2 3 4 5 6 7 8 9 10 11 12 13 14 2 3 4 C1-3 Capacitor, 1900 pf, 15Kv. (Sht 1, A10) CB1 Circuit Breaker /ON/OFF SW, 15A 480V (Sht 1, D1) CB2-4 Circuit Breaker, 5A, 250V (Sht 2, B3) F1, 2 Fuse, 8A, 500V, S.B. (Sht 1, E1) FAN1, 2 Fan, Heat Exchanger , 230 VAC (Sht 2, D2) FS1 Flow SW, 1.0 GPM (3.8 lpm), N.O. (Sht 2, A2) HCT1 Current Sensor, Hall Effect 200A, Work Lead (Sht 1, D9) K1 Relay, 24VAC, Inrush Control (Sht 2, B9) L2 Inductor, HF, 400A, Water Cooled (Sht 1, A10) L3-6 Toriod Core Common Mode Ind (Sht1 B9, B&C3) LS1 Level Switch, Coolant Tank (Sht 2, A3) LT1, LT2 Indicator, Neon, 250V, AC Volts Present (Sht 1, C3) M1 Motor, Pump, ½ hp 230VAC, 50/60 Hz, 1Ph (Sht 2, C2) MC1 Relay, 120 VAC, Inrush, Coil (Sht 2, B9), Contact (Sht2, A1) MC3 Relay, 120 VAC, Pump Motor Control (Coil at Sht 2, A7) (Contacts at Sht 2, C2) PS1 Pressure Switch, Plasma Gas, N.O. , 51 PSI (Sht 2, C9) Current Control 10K (sht 2, D9) R1 R2 Inrush, 4.7 ohm 30W (Sht2, A1) SA1, 2 Snubber, Contactor & Relay coil (Sht 2, A7) SG1 Spark Gap (Sht 1, A9) SOL1 Solenoid, Plasma Gas, 24 VAC (Sht 2, D9) SOL2 Solenoid, Shield Gas, 24 VAC (Sht 2, D9) SOL3 Solenoid, H2O Mist (water shield), 24 VAC (Sht 2, D10) SW1 Switch, RUN / SET, DPDT (Sht 2, D10) SW2 Switch, Shield Mode, SPDT (Sht 2, D10) SW3 Switch, Gas Mode, SPST, rear panel (Sht 2, B2) T1 Aux Transformer (Sht 2, B2) T2 Transformer, HV, 120/6000V (Sht 1, A9) TB4 Terminal Block (Sht 1, C9) TS1 Temperature Sensor, NTC, Coolant Return (Sht 2, A5) TS2 Temperature Sensor, NTC, Ambient (Sht 2, A5) W1 Contactor , Input (Coil at Sht 2, A8) (Contacts at Sht 1, B2) (11) LT1 J51 INTERNAL AC INDICATOR 1 2 3 4 GND (12) (13) LT2 J52 019X504000 AC LINE CHASSIS GND LT1 & LT2 INPUT POWER NEON INDICATORS Rear Panel & Internal (21) (20) (22) (26) (27A&B) D CB1 ON / OFF (28) WORK (+) (20) 1 (21) L2 (22) Toriod Core 18 AWG wire both in and out of CB1 to J60 F2 F1 8A, 250V, SB 8A, 250V, SB E AC INPUT (85A) (86B) (27B) (85B) LEDS D3, RED, MISSING PHASE D4, RED, AC V HIGH D14, RED, AC V LOW D26, GREEN, +12V PRI D30, GREEN, 24VDC D44, GREEN, T1 ON +24VDC 019X501900 1 TEST POINTS TP1 SECONDARY GND TP2 24VDC TP3 DC INPUT POSITIVE TP4 VCC1 TP5 VCC2 TP6 GATE TP7 PRIMARY GND TP8 +12V PRIMARY TP9 P ISOL GND 2 +V 3 4 5 6 7 8 9 10 GND 11 480V-ID 400V-ID 208-230V-ID COM (27A) SYSTEM BIAS SUPPLY 1 2 3 4 5 6 7 8 9 10 11 12 13 14 15 16 17 18 J63 1 2 3 4 5 6 7 8 9 10 11 12 J60 12 13 14 J62 J61 4 3 2 1 (86A) VOLTAGE SELECTION F J63 = Mini-Fit Jr goes to J12 on T1 primary 400 VAC -- Single 18 AWG in pins 1 & 12 480 VAC -- Single 18 AWG in pins 1 & 12 230 VAC -- 18 AWG wires in pins 1, 6, 7, 12 TO AUX TRANSFORMER (44A) TO J12 T1 PRIMARY (Sht 2, A1) (43A) Art # A-11944 1 ANNEXE 2 (48) Wire #48 from J61-1 to: J61-2 for 208-230 VAC J61-3 for 400 VAC J61-4 for 480 VAC 3 24 VDC 24 VDC MISSING PHASE a MISSING PHASE b AC V HIGH a AC V HIGH b AC V LOW a 24 VDC_RET 24 VDC_RET AC V LOW b VAC_IDA a / VAC_IDA b VAC_IDB a / VAC_IDB b To J27 on CCM I/O PCB (Sht 2, E3) 230V 400V 480V ERR /VAC_IDAb 0 1 0 1 /VAC_IDBb 0 0 1 1 Measure relative to TP1 (24VDC_RET) "0" = 10-12V "1" = 24V 4 A-32 (29) (30) (31) (32) (33) (34) (35) (36) (37) (38) (39) (40) (41) (42) 5 Manuel n° 0-5284FR AUTO-CUT 200 XT 6 7 8 9 TO CCM CPU PCB J33 (Sht 2, C3) C1 T2 6.5K 1W (99) AC 120V (Sht 2, A8) SG1 C2 0.062" (98) AC 120V_RET (Sht 2, A8) 10 6.5K 1W (49) L2 (49) J100 -- 30 CKT RIBBON J102A 5 4 3 2 1 ELECTRODE (-) WORK (+) L3 (49C) (51C) (49) PILOT BOARD LED'S D2 PILOT ENABLE D11 +5V OUTPUT TO CCM CPU PCB J32 (Sht 2, B3) J100 -- 30 CKT RIBBON A C3 120 / 6000 VAC Toriod Core HF COIL_WC NEG CGND TEST POINTS TP1 GND TP2 PILOT GATE TP3 +5V PLT (52) CHASSIS GND J102B (49) (51B) B J43 OUTPUT ELECTRODE TO CCM CPU PCB J31 (Sht 2, B3) 1 WORK (+) (49B) 5 4 3 2 1 1 ELECTRODE (-) PILOT PCB TORCH J44 J100 -- 30 CKT RIBBON 1 J102A ELECTRODE (-) WORK (+) (49A) 5 4 3 2 1 INVERTER J41 J40 (50) OUTPUT PILOT (52) 2 1 5 4 3 2 1 1 TIP SHIELD 019X501600 WORK (Sht 2, D3) (-) TB4 (49) 7 (51) ARC VOLTS (55) (60) AC 120V- TB4-4 (Sht 2, B8) (61) AC 120V- Ret- TB4-3 (Sht 2, B8) (62) AC 24V-TB4-2 (Sht 2, B8) (63) AC 24V- Ret -TB4-1 (Sht 2, B8) HCT1 (51A) 3 Tip 120 VAC @ 100 ma. WORK Work 1 2 1 (+) 24 VAC @ 1A 4 3 1 Ready Ready_RTN INVERTER_FLT INVERTER_FLT_RTN OVERTEMP_FLT OVERTEMP_FLT_RTN SPARE SPARE_RTN VAC_SELA 1VAC_SELB 1OUT_COM (+5V) IS_IDA IS_IDB IS_IDC ENABLE ENABLE_RTN START2 START2_RTN 215 OHM TO COMM SYNC SYNC/ 215 OHM TO COMM NC COMM DEMAND + DEMANDCOMM CURRENT+ CURRENTCOMM (+) WORK 4 Hall Effect Sensor TO J1 on RELAY PCB (Sht 2, A5) (56) (57) (58) (59) 4 3 2 D J16 1 1 2 3 4 5 6 7 8 9 10 11 12 13 14 15 16 17 18 19 20 21 22 23 24 25 26 27 28 29 30 5 (51) 2 RIBBON CABLE 30 ckt. CCM (J31-33) - INVERTER (J100) (Sht 2, C4) (Sht 1, A6, B6) ARC VOLTS (TORCH) 6 C Electrode TIP VOLTS (51) To J24 on I-O PCB 1 2 3 4 5 6 7 8 10 ckt Ribbon (Sht 2, A6) (53) J45 (55) TO J3 on RELAY PCB (53) J42 CHASSIS GND TO I/O BOARD TO RELAY BOARD 1 2 3 4 5 6 7 8 9 10 (51A) +15 VDC -15 VDC SIG (+) COMMON RIBBON CABLE 40 ckt CCM (J23 (Sht 2, C7)) - RELAY PCB (J4 (Sht 2, B7)) 1 COMMON 21 /PLASMA ENABLE RELAY 2 /1TORCH START * 22 COMMON RIBBON CABLE 16 ckt 3 NA 23 PILOT CURRENT SIGCCM ( J37 (Sht 2, C8)) 4 /1TORCH GAS SOL ON * 24 NC DISPLAY PCB (J17 (Sht 2, C9)) 5 /MAIN TORCH IDLE * 25 PILOT CURRENT SIG+ 6 /1TORCH PRESS OK * 1,3,5,7 24 VDC 26 COMMON 7 FLOW SENSOR (pulses) 2,4,6,8 COMMON 27 WORK CURRENT SIG8 LOW COOLANT FLOW 9,10 NC 28 WORK CURRENT SIG+ 9 COOLANT LEVEL OK 11-16 SERIAL DATA 29 NC 10 COMMON 30 AMBIENT TEMP 11 NA RIBBON CABLE 10 ckt 31 COOLANT TEMP 12 /PLASMA ENABLE-HMI RELAY PCB (J3 (Sht 2, A6)) 32 COMMON 13 /COOLANT PUMP ON PILOT PCB (J42 (Sht 1, C8)) 33 -15 VDC 14 COMMON 34 COMMON 1,2 24 VAC 15 /PILOT ENABLE 35 24 VDC 3,4,7,10 COMMON 16 /RAS ON 36 COMMON 5 PILOT ENABLE + 17 /CONTACTORS ON 37 24 VDC 6 PILOT ENABLE – 18 COMMON 38 COMMON 8 PILOT CURRENT SIG – 19 /COOLANT FANS ON 39 24 VDC 9 PILOT CURRENT SIG + 20 /1TORCH CONTACTOR ON * 40 COMMON * Used with 1 Torch Option E Art # A-11944 Revision Rev By Date 00 Initial Design DAT 4/18/2012 01 Added MC3 Pump Control DAT 8/31/2012 02 Added R1, K1, MC1 inrush DAT 1/16/2013 Revision Rev By Date Victor Technologies Headquarters 16052 Swingley Ridge Road, Suite 300 St Louis, Missouri 63017 USA F Date Printed 4/8/2013 Drawn Date The information contained herein is proprietary to Victor Technologies. Not for release, reproduction or distribution without written consent. Size Sheet Title Drawing Number SCHEMATIC Auto-Cut XT 200A CE 380-415 VAC 6 Manuel n° 0-5284FR 7 8 A-33 9 DAT C Date Revised 3/8/2013 04/18/2012 1 of 2 042X1350 10 ANNEXE AUTO-CUT 200 XT ANNEXE 15 : Pg schématique 2 du système 1 3 4 Mini-Fit Jr (166) N2, H35, OTHER Gas Selection T1 460V 1 2 3 4 (167) 1 5 2 6 3 7 4 8 J12 24V RET 24V B 400V (79) BLUE 6 RED 5 3 RED 2 (78) CB2 5 A (76) (74) (75) CB3 5 A (73) (71) (72) 1 CB4 5 A J14 120V-1 RET 120V_1 J9 J16 (66) 1 2 3 Harness from Pilot PCB J45 (Sht 1, C8) TIP VOLTS FAN1 1 2 3 WORK 230 VAC J72 (65C) (64C) J73 J34 - 30 CKT RIBBON J32 - 30 CKT RIBBON J34 - 30 CKT RIBBON J33- 30 CKT RIBBON J34 - 30 CKT RIBBON CCM CPU PCB (53) 1 2 3 4 5 6 7 8 (55) FAN2 1 2 3 J24 CHASSIS GND Harness from System Bias PCB (Sht 1, E4) 24 VDC 24 VDC MISSING PHASE a MISSING PHASE b AC V HIGH a AC V HIGH b AC V LOW a 24 VDC_RET 24 VDC_RET AC V LOW b VAC_IDA a / VAC_IDA b VAC_IDB a / VAC_IDB b E (29) (30) (31) (32) (33) (34) (35) (36) (37) (38) (39) (40) (41) (42) 1 2 3 4 5 6 7 8 9 10 400V 1 0 480V 0 1 J28 30 CKT PIN HEADER I / O PCB LEDS ---------------------------------------------D2 CNC PLASMA ENABLE D3 E-STOP_PS D4 GAS ON (Auto-cut, PAK) D6 CNC START D8 HOLD START D12 PREFLOW ON D13 CSD (corner current reduction) D18 MARK D20 SPARE D25 EXP METAL D33 OK_CNC D37 PSR D41 SPARE OUT 2 D43 SPARE OUT 1 I / O PCB TEST POINTS ------------------------------------TP1 PCB COMMON TP2 COOLANT FANS ON TP3 PUMP ON TP4 LOW FLOW (SW) TP5 FLOW SIGNAL (pulse, Ultracut only) TP6 +15VDC_ISO (ref to TP10) TP7 -15VDC_ISO (ref to TP10) TP8 +16-18 VDC_ISO (ref to TP10) TP9 ANALOG CURRENT SIGNAL (remote & Autocut only) TP10 ISOLATED VOLTAGE COMMON TP11 1 TORCH CONTACTOR ON TP12 +5 VDC TP13 -15 VDC TP14 +15 VDC TP15 +24 VDC TP18 +5 VDC_ISO (ref to TP10) 11 12 13 14 J27 . 230V J62-12 (/VAC_IDAb) 0 J62-14 (/VAC_IDBb) 0 019X501100 CCM I-O PCB (51) D J15 N/C (67) (65A) (64A) 019X501700 J28 30 CKT RECEPTACLE - BOTTOM ENTRY Torch Coolant Pump ARC VOLTS MC3B TEMP SENSOR 1 TORCH INTERFACE N/C M1 CHASSIS GND (64B) TP1, GND TP2, -15V TP3, +5VDC TP4, +12V TP5, +24V TP6 +15V N/C To J100 of IM #2A (Sht 1, A6) 1 2 3 (64) (64B) (65) (65B) 4 Mini-Fit MC3A J2 D2, GREEN, 1TORCH GAS ON D7, GREEN, PILOT ENABLED D11, GREEN, PILOT CURRENT D12, GREEN, WORK CURRENT D22, GREEN, CONTACTORS ON D23, GREEN, RF ON D24, GREEN, FANS ON D25, GREEN, PLASMA ENABLED D26, GREEN, 1TORCH ON D27, GREEN, COOLANT ON J31 - 30 CKT RIBBON To J100 of IM #1B (Sht 1, B6) J13 J1 RELAY & INTERFACE PCB To J100 of IM #1A (Sht 1, B6) 0V C SIGNAL 12 11 10 9 8 7 6 5 4 3 2 1 (77) 4 BLUE YELLOW 120V_2 220V +5VDC J6 YELLOW 120V_2 RET J7 (94) (95) COOLANT FLOW SWLEVEL SENSORS WORK CURRENT SENSOR AIR / O2 TS1 (93) (92) 1 J5 SW3 1 2 3 4 5 6 7 8 COMMON SIG (+) -15 VDC +15 VDC 0.7 GPM 8 7 6 5 4 3 2 1 (87) (83) COOLANT FS1 BIAS TRANSFORMER 4.7 30W (84) 1 2 2 1 R2 J74 2 MC1A COOLANT TS2 (59) (58) (57) (56) COOLANT LEVEL AMBIENT 3 (44A) (43A) (90) (89) 2 4 LS1 From J63 (Sht 1, F2) A 5 TO HCT1 (Work) (Sht 1, D7) 4 J71 6 5 4 3 2 1 3 2 14 13 12 11 10 9 8 7 6 5 4 3 2 1 1 J12 = Mini-Fit Jr 400 VAC -- Single 18 AWG in pins 1 & 4 480 VAC -- Single 18 AWG in pins 1 & 8 230 VAC -- 18 AWG wires in pins 1,5,2,6 ERR 1 1 I / O PCB DIP SW --------------------------------------------SW6 OK TO MOVE (CONTACTS, VOLTS) SW11 ANALOG CC SOURCE SW12 DIVIDED ARC VOLTAGE (50:1, 16.7:1, 30:1, 40:1, 25:1) 19X501200 Measured relative to TP1 (24VDC_RET) "0" = 10-12V "1" = 24V F Art # A-11945 1 ANNEXE 2 3 4 A-34 5 Manuel n° 0-5284FR AUTO-CUT 200 XT 6 7 (163) (162) / PILOT ENABLE / PILOT ENABLE RET SA2 10 SA1 A ARC_SUPPRESSOR AC 120V_RET (Sht 1, A8) AC 120V (Sht 1, A8) 24 VDC 18 17 16 15 14 13 12 11 10 9 8 7 6 5 4 3 2 1 120 VAC_RET 24 VAC 120 VAC HMI/GCM J4 -- 40 CKT RIBBON CABLE 3 B INRUSH AC 24V- Ret -TB4-1 (Sht 1, C9) (61) AC 120V- Ret- TB4-3 (Sht 1, C9) (61) J17 RxTx+ Rx+ Tx- Display PCB 1 2 3 4 5 6 J30 2 WIRE J37 019X501800 16 CKT RIBBON C (124) 1 2 3 4 5 6 7 8 9 10 11 12 13 14 15 16 ENABLE PLAS_ENABLE SW PLAS_ EN_SW_RET / GAS PRESS OK / BASIC ID TB1 OK2 (contact) +10V (CC Pot Hi) CC Pot Wiper CC Pot Low Div Arc V (+) Div Arc V (-) /Start - Stop (+) /Start - Stop (-) Stop Mom NC OK2 (contact) / CNC Enable (+) / CNC Enable (-) 12 11 10 9 8 7 6 5 4 3 2 1 / CNC Plasma Enable (+) / CNC Plasma Enable (-) TB2 OK to MOVE (+) OK to MOVE (-) PILOT is ON PILOT is ON Preflow ON (+) Preflow ON (-) Hold Start (+) Hold Start (-) (131) (104) 12 11 10 9 8 7 6 5 4 3 2 1 OK +10V 1 2 3 4 5 6 7 8 9 10 11 12 13 14 15 16 17 18 SW 1 AC 24V-GCM2 (B8) (129) (123) (125) (126) (127) RUN / SET (128) (123) (121) (124) J26 GND PLASMA (51 PSI) PS1 (130) RUN SET (131) (125) (126) (127) R1 10K (130) (130) 2 GAS ON J23- 40 ckt ribbon cable CPU PCB TEST POINTS -------------------------------------------TP1 GND (PCB common) TP2 +5V_ISO (REF TP5) TP3 +24 VDC TP4 +3.3V TP5 GND_ISO TP6 +5.0 V TP7 TOTAL DEMAND (3.3V = 400A) TP9 /WR TP10 /RD TP11 CPU TEMP SENSE TP12 +3.3VA TP13 -15VDAC TP14 PC2 TP15 +15VDAC TP16 CLKO TP18 OSC_CLOCK 5 (63) J20 J29 30 CKT RECEPTACLE - BOTTOM ENTRY CPU PCB LEDs ---------------------------D2 RXD (red) D3 TXD (red) D4 CAN BUS (slave) D7 CAN BUS (MAIN) D11 5 VDC POWER D17 STATUS CODE D18 INITIALIZING / PROGRAMMING (red) 4 AC 24V Ret-GCM2 (D9) (63) GND GND 1 2 3 4 5 6 7 8 9 10 11 12 J19 J29 30 CKT PIN HEADER (107) 2 AC 120V- TB4-4 (Sht 1, C9) (111) 4 WIRE NORMAL PROGRAM J18 K1 AC 24V-TB4-2 (Sht 1, C9) 1 2 3 4 1 2 3 4 5 6 7 8 9 PROG USB IC (62) 1 J10 J39 1 2 3 4 5 6 AC 24V-GCM2 (D9) (60) USB PORT 1 2 3 4 5 6 7 8 9 10 11 12 120VAC (104) (62) CURRENT CONTROL SW 2 (130) GAS SOL1 (142) (165) PLASMA AC 24V Ret-GCM2 (B8) (133) (164) SOL3 SOL2 (134) (137) (139) (138) (143) D H2O 3 GND RS 232 D-SUB SERIAL PROG PORT MC1 (60) CONTROL OUTPUTS 1 J8 120 VAC Ret 120 VAC to RAS 16 15 14 13 12 11 10 9 8 7 6 5 4 3 2 1 2 1 (98) (99) PILOT PCB J38 9 W1 Input Contactor (97) (96) ARC_SUPPRESSOR 4 3 5 6 7 8 9 10 PILOT A SIG Vin+ PILOT A SIG Vin- 10 CKT RIBBON J3 8 MC3 Pump Motor Control TO PILOT PCB J42 (Sht 1, C7) H2O Mist SHIELD (111) (111) H2O Mist Option (140) (141) (136) (135) Installing H2O Mist Option -----------------------------------------------------------------Remove #130 from Shield SOL, connect #165 in it's place. Connect #111 with other #111 on Shield SOL. Connect #130 from SW2 with other #130 on SW1. J21 GND CPU PCB DIP SW TB3 --------------------------------------------12 Spare #2 NO SW1 AUTO PILOT RESTART 11 10 SW3 PREFLOW TIME Spare #2 NC 9 SW4 POSTFLOW TIME 8 Spare #1b NO SW5 FUNCTION 7 / Cut Expanded Metal (-) 6 SW8 SYSTEM CONTROL / Cut Expanded Metal (+) 5 (pilot time, etc.) / Corner Current Reduction (-) 4 / Corner Current Reduction (+) 3 SW9 RESERVED (future) / Plasma Marking (-) 2 SW10 ADDRESS (default = 0) / Plasma Marking (+) 1 SW13 UNIT TYPE (AC / UC) SW14 LINE TERMINATION (serial comm.) GND PSR SPARE #1 1 2 3 4 5 6 7 8 9 10 11 12 13 14 15 16 17 18 19 20 1 2 3 4 5 6 7 8 9 10 11 12 13 14 (133) (134) (135) (136) (137) (138) (139) (140) (141) (142) (143) J15-1 to chassis used for SC-11 cable shield 3- / CNC Start (+) 4- / CNC Start (-) 5- Divided Arc V (-) 6- Divided Arc V (+) 7- / Preflow ON (+) 8- COMM Ref (1K Ohm) 9- / Preflow ON (-) 10- / Corner Current Reduction (+) 11- / Corner Current Reduction (-) 12- OK to Move (-) E 14- OK to Move (+) J15-CNC CHASSIS GND J15-13 connects SC-11 chassis to PS chassis. J22 The COMM Ref at pin 8 is also for the SC-11 Art # A-11945 Revision Rev 00 INITIAL By DAT Date Revision Rev By Date Victor Technologies Headquarters 4/18/2012 01 Added MC3 Pump Control DAT 8/31/2012 02 Added R1, K1, MC1 inrush DAT 1/16/2013 16052 Swingley Ridge Road, Suite 300 St Louis, Missouri 63017 USA F Date Printed 4/8/2013 Drawn Date Revised 3/8/2013 Date The information contained herein is proprietary to Victor Technologies. Not for release, reproduction or distribution without written consent. Size Sheet Title Drawing Number SCHEMATIC Auto-cut XT 200A CE 380-415 VAC 6 Manuel n° 0-5284FR 7 8 A-35 9 DAT C 04/18/2012 2 of 2 042X1350 10 ANNEXE AUTO-CUT 200 XT ANNEXE 16 : HISTORIQUE DE PUBLICATION Date de la couverture 17 avril 2013 2 juillet 2013 AA AB 28 sept. 2013 AC ANNEXE Rév Modification(s) Première édition. Section 3 mise à jour avec des informations sur l’installation de carte V-D pour le contrôle de la hauteur selon ECOB2488 Section 3 mise à jour avec des informations sur l’installation de carte V-D pour le contrôle de la hauteur selon ECOB2488 A-36 Manuel n° 0-5284FR THE AMERICAS Denton, TX USA U.S. Customer Care Ph : 1-800-426-1888 (tollfree) Fax : 1-800-535-0557 (tollfree) International Customer Care Ph : 1-940-381-1212 Fax : 1-940-483-8178 Miami, FL USA Sales Office, Latin America Ph : 1-954-727-8371 Fax : 1-954-727-8376 Oakville, Ontario, Canada Canada Customer Care Ph : 1-905-827-4515 Fax : 1-800-588-1714 (tollfree) EUROPE Chorley, United Kingdom Customer Care Ph : +44 1257-261755 Fax : +44 1257-224800 Milan, Italy Customer Care Ph : +39 0236546801 Fax : +39 0236546840 ASIA/PACIFIC Cikarang, Indonesia Customer Care Ph : 6221-8990-6095 Fax : 6221-8990-6096 Rawang, Malaysia Customer Care Ph : +603 6092-2988 Fax : +603 6092-1085 Melbourne, Australia Australia Customer Care Ph : 1300-654-674 (tollfree) Ph : 61-3-9474-7400 Fax : 61-3-9474-7391 International Ph : 61-3-9474-7508 Fax : 61-3-9474-7488 Shanghai, China Sales Office Ph : +86 21-64072626 Fax : +86 21-64483032 Singapore Sales Office Ph : +65 6832-8066 Fax : +65 6763-5812 TECHNOLOGIES ™ I n n o vati o n t o S h ap e t h e W o r l d ™ U.S. Customer Care : 800-426-1888 / fax 800-535-0557 • Canada Customer Care : 905-827-4515 / International Customer Care : 940-381-1212 / fax 940-483-8178 © 2012 Victor Technologies International, Inc. victortechnologies.com fax 800-588-1714 Printed in U.S.A. ">
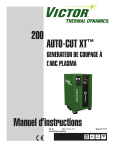
Lien public mis à jour
Le lien public vers votre chat a été mis à jour.
Caractéristiques clés
- Courant de sortie maximal de 200 A
- Compatible avec divers gaz plasmagènes (Air, O2, N2, H35)
- Conçu pour la coupe manuelle et automatisée
- Refroidissement par air forcé et liquide de refroidissement
- Fonctionne avec différentes tensions d'entrée triphasées
Questions fréquemment posées
Le Auto-Cut 200 XT™ est compatible avec l'air comprimé, l'oxygène, l'azote et H35 comme gaz plasmagène, et avec l'air comprimé, l'azote et l'eau comme gaz de protection.
Le générateur Auto-Cut 200 XT™ a une plage de fonctionnement de 14 ° F à 122 ° F (de -10°C à + 50°C).
La tension de sortie du Auto-Cut 200 XT™ est de 60 - 170 VCC.