Bosch Rexroth FR323-3BR Manuel utilisateur
PDF
Descargar
Documento
Hägglunds VI Moteur hydraulique à pistons radiaux Manuel d’installation et de Remplace : maintenance FR 323-2h/2004 FR 323-3br/2011 Français Les données spécifiées dans ce document servent uniquement à décrire le produit. Aucune déclaration concernant une certaine condition ou disposition pour une certaine application ne peut différer de notre information. L’information fournie ne décharge pas l’utilisateur de l’obligation d’utiliser son propre jugement ou de faire des vérifications. Il faut se rappeler que nos produits sont sujets à un procédé naturel d’usure et de vieillissement. © Ce document, ainsi que les données, spécifications et autres informations qu’il contient, sont la propriété exclusive de Bosch Rexroth AG. Il ne peut pas être reproduit ou donné à des tiers sans consentement. Des changements dans l’équipement peuvent survenir. Nous nous réservons par conséquent le droit d’apporter des modifications dans le manuel que nous jugeons nécessaires, sans préavis ni obligations. Ce Manuel d’installation et de maintenance est valable pour les moteurs des séries 44, 64 et 84 fabriqués après le 1er janvier 1995. Pour les moteurs de production antérieure à cette date, prière de consulter votre représentant Bosch Rexroth le plus proche. La couverture montre un exemple de configuration. Le produit fourni peut donc différer de l’illustration. Les instructions d’utilisation d’origine ont été rédigées en anglais (EN 323-23br/2011). Table des matières 3/72 Table des matières 1 Généralités 4 1.1 Consignes de sécurité 4 1.2 Caractéristiques techniques des moteurs 5 1.3 Description de fonctionnement 6 2 Caractéristiques techniques 8 2.1 Pression de charge recommandée 2.2 Bruits émis par une installation complète 10 2.3 Choix du fluide hydraulique 10 3 Installation 13 3.1 8 Instructions de montage 13 3.1.1 Méthodes de levage courantes 14 3.1.2 Moteur – tambour de treuil – adaptateur d’arbre 16 3.1.3 Moteur – valves 18 3.1.4 Moteur – bras de réaction 19 3.1.5 Moteur – support avant 24 Montage des supports BB-46 et BB-85 sur la fondation 26 Montage du treuil sur la fondation 28 Ensemble de frein BA-43 et BA-63 29 Ensemble de freins BA-85 35 Cylindre de frein BCI-M pour ensembles de freins BA-43, BA-63 et BA-85 39 Drainage des cylindres de frein 41 Installation des ensembles de freins BA-43, BA-63 à simple effet et du cylindre de frein BCI-M 42 Installation des ensembles de freins BA-43, BA-63 à double effet et du cylindre de frein BCI-M 44 Installation de l’ensemble de freins BA-85 à simple + double effet 3.2 et du cylindre de frein BCI-M 46 Raccords d’huile 49 3.2.1 Raccords d’huile, moteur sans valve, séries 44 et 64 49 3.2.2 Raccords d’huile, série de moteurs 84 50 3.2.3 Raccords d’huile V46-C 52 3.2.4 Raccords d’huile V46-O 53 3.3 Inversion du sens de rotation 54 4 Manutention 56 4.1 Instructions pour le stockage 56 4.2 Avant la mise en service 57 4.3 Mise en service 57 4.4 Maintenance périodique 58 4.4.1 Nettoyage et entretien 62 4.5 Mise au rebut 62 5 Dépannage 63 6 Dessins 65 7 Déclaration de conformité 67 8 Notes 68 Hägglunds VI, FR 323-3br/2011, Manuel d’installation et de maintenance, Bosch Rexroth Mellansel AB 4/72 Généralités 1 Généralités 1.1 Consignes de sécurité Il est de la plus grande importance que les consignes de sécurité soient toujours respectées. Si vous êtes dans le doute, n’hésitez pas à demander conseil au bureau Hägglunds le plus proche. •• Symboles d’avertissement. Les symboles suivants apparaissent dans ce manuel pour indiquer la présence d’un danger potentiel qui peut ou pourrait causer des dommages corporels ou des dégâts matériels importants. Ils correspondent à trois niveaux de danger classifiés en fonction de la probabilité du danger ainsi que l’ampleur des dégâts. Symboles d’avertissement Signification DANGER Indique une situation dangereuse qui, si elle n’est pas évitée, peut causer de graves blessures voire la mort. AVERTISSEMENT Indique une situation dangereuse qui, si elle n’est pas évitée, peut causer de graves blessures voire la mort. PRUDENCE Indique une situation dangereuse qui, si elle n’est pas évitée, peut causer des blessures mineures ou modérées. NOTE Dommages matériels : Le produit ou l’environnement pourraient être endommagés. •• Domaines d’application. Toutes les applications, nouvelles ou reconstruites, doivent être surveillées et approuvées par le personnel de Hägglunds. •• Installation. Suivez attentivement les instructions fournies et soyez conscients des poids et efforts importants durant le levage. •• Avant la mise en service. Avant de mettre en service une installation nouvelle ou reconstruite, toutes les fonctions de sécurité et tous les accessoires devront avoir été testés et contrôlés. •• Entretien périodique. Notez les intervalles portés au tableau d’entretien (4.4) et maintenez un cahier de maintenance. •• Dépose. Suivez attentivement les instructions fournies et soyez conscients des poids et efforts importants durant le levage. Bosch Rexroth Mellansel AB, Manuel d’installation et de maintenance, Hägglunds VI, FR 323-3br/2011 Généralités 5/72 1.2 Caractéristiques techniques des moteurs Pleine cylindrée Type de moteur Volume Cylindrée réduite Couple Vitesse Vitesse Pression*** spécifique** nominale* max. max. Volume Couple Vitesse Vitesse spécifique** nominale* max. Rapport Vi Ts n n p Vi Ts n n 44-03300 3 325 53 100 200 320 1 662 26 100 200 1:2 44-04700 4 710 75 100 200 320 2 356 37 100 200 1:2 44-06800 6 790 108 90 170 320 3 393 54 90 170 1:2 44-09200 9 240 147 80 145 320 4 618 74 80 145 1:2 64-11100 11 080 176 70 120 320 5 542 88 70 120 1:2 64-13500 13 599 215 60 110 250 6 750 107 60 110 1:2 64-16300 16 340 260 50 100 250 8 171 130 50 100 1:2 84-14800 14 840 236 55 90 320 – – – – – 84-17900 17 961 286 55 85 320 – – – – – 84-21300 21 375 340 55 80 320 – – – – – 84-25100 25 090 399 55 75 320 – – – – – 84-38000 38 000 605 40 60 250 – – – – – 84-22300 22 300 355 55 55 320 11 150 177 60 85 1:2 1:2 84-33800 33 780 538 35 35 250 16 889 269 50 70 84-25100 25 090 399 40 55 250 8 362 133 45 75 1:3 84-38000 38 000 605 25 35 250 12 667 202 35 60 1:3 84-25100 25 090 399 40 55 250 16 724 266 45 75 2:3 * L iée à une pression de charge requise de 12 bars (175 psi) pour moteurs en mode de freinage. Considérations spécifiques concernant la pression de charge, le refroidissement et le choix du système hydraulique pour les vitesses supérieures aux nominales. ** Valeur théorique *** L es moteurs sont conçus selon les règles DNV. Pression de test 70 bars (1000 psi) au-dessus de la pression max. Une pression de test et de pointe de 70 bars (1000 psi) au-dessus de la pression maximale est admissible 10 000 fois. Quantité Cylindrée Couple spec. Vitesse Pression Symbole Vi = Ts = n = p = Métrique cm3/tr Nm/bar tr/min bar USA in3/rev lbf·ft/1000 psi tr/min psi Hägglunds VI, FR 323-3br/2011, Manuel d’installation et de maintenance, Bosch Rexroth Mellansel AB 6/72 Généralités Cylindrée totale Cylindrée de commutation Pression*** Couple Vitesse Vitesse spécifique** nominale* max. max. Vi Ts n n p 44-03300 203 2 695 100 200 44-04700 287 3 814 100 200 44-06800 414 5 492 90 44-09200 564 7 475 64-11100 676 8 971 Type de moteur Volume Couple Vitesse Vitesse spécifique** nominale* max. Vi Ts n n 4 650 101 1 347 100 200 1:2 4 650 144 1 907 100 200 1:2 170 4 650 207 2 746 90 170 1:2 80 145 4 650 282 3 738 80 145 1:2 70 120 4 650 338 4 485 70 120 1:2 Volume Rapport 64-13500 823 10 935 60 110 3 600 411 5 467 60 110 1:2 64-16300 997 13 227 50 100 3 600 499 6 613 50 100 1:2 84-14800 906 12 017 55 90 4 650 – – – – – 84-17900 1 096 14 546 55 85 4 650 – – – – – 84-21300 1 304 17 292 55 80 4 650 – – – – – 84-25100 1 531 20 306 55 75 4 650 – – – – – 84-38000 2 320 30 756 40 60 3 600 – – – – – 84-22300 1 361 18 048 55 55 4 650 680 9 024 60 85 1:2 84-33800 2 064 27 339 35 35 3 600 1 031 13 669 50 70 1:2 84-25100 1 531 20 306 40 55 3 600 510 6 769 45 75 1:3 84-38000 2 319 30 756 25 35 3 600 773 10 252 35 60 1:3 84-25100 1 531 20 306 40 55 3 600 1 021 13 537 45 75 2:3 84-38000 2 319 30 756 25 35 3 600 1 546 20 504 35 60 2:3 * L iée à une pression de charge requise de 12 bars (175 psi) pour moteurs en mode de freinage. Considérations spécifiques concernant la pression de charge, le refroidissement et le choix du système hydraulique pour les vitesses supérieures aux nominales. ** Valeur théorique *** L es moteurs sont conçus selon les règles DNV. Pression de test 70 bars (1000 psi) au-dessus de la pression max. Une pression de test et de pointe de 70 bars (1000 psi) au-dessus de la pression maximale est admissible 10 000 fois. Quantité Cylindrée Couple spec. Vitesse Pression Symbole Vi = Ts = n = p = Métrique cm3/tr Nm/bar tr/min bar USA in3/rev lbf·ft/1000 psi tr/min psi 1.3 Description de fonctionnement Les moteurs Hägglunds VI sont du type à pistons radiaux et carter tournant. Le carter est soutenu sur le bloc-cylindres fixe (5) par deux paliers principaux. Un nombre pair de pistons placés radialement (3), travaillent dans les alésages des cylindres dans le bloc-cylindres qui contient aussi les orifices d’entrée et de sortie (A et C). Chaque piston est accouplé par l’intermédiaire d’une tige de piston (2) à un tourillon de traverse (6) sur lequel quatre rouleaux à cames (7) sont montés. Les deux rouleaux intérieurs sont pressés contre la came (8) et les deux extérieurs travaillent au sein de leur plaque de guidage (1) respective. La came est ancrée dans le carter tournant. Le distributeur (4) dirige l’huile d’arrivée vers les pistons durant leur course de travail et retourne l’huile au réservoir d’huile. Le distributeur est raccordé au carter tournant par l’intermédiaire d’un accouplement de sécurité (9). Le moteur peut être accouplé à une machine commandée par l’intermédiaire de deux surfaces de montage sur le carter arrière du moteur. Bosch Rexroth Mellansel AB, Manuel d’installation et de maintenance, Hägglunds VI, FR 323-3br/2011 Généralités 7/72 La conception symétrique du moteur a permis de le construire comme un moteur à 2 vitesses. Cela signifie que deux différentes vitesses sont obtenues pour un débit donné. La méthode la plus simple pour changer de cylindrée est de connecter une valve spécifique, dite valve à 2 vitesses, directement à la bride de connexion sur le bloccylindres. La conception du moteur permet d’éviter les impulsions de pression dans le carter du moteur. Cela présente l’avantage que les impuretés ne sont pas aspirées dans le carter. 1. Plaque de guidage 5. Bloc-cylindres 4. Distributeur A = Orifice A 9. Accouplement de sécurité C = Orifice C 3. Piston 2. Tige de piston 7. Rouleau à cames 6. Tourillon de traverse 8. Came Fig. 1: Le moteur VI Hägglunds Hägglunds VI, FR 323-3br/2011, Manuel d’installation et de maintenance, Bosch Rexroth Mellansel AB 8/72 Caractéristiques techniques 2 Caractéristiques techniques 2.1 Pression de charge recommandée Le moteur doit être connecté au système hydraulique de sorte à recevoir une pression de charge suffisante au point de connexion de la basse pression. Cela s’applique pour toutes les installations. AVERTISSEMENT En cas de fonctionnement avec une charge menante, la pression de charge doit être définie en fonction du diagramme ci-dessous pour toutes les conditions de fonctionnement. Deux alternatives de service du moteur doivent être considérées : 1. L e diagramme concerne les moteurs utilisés dans une configuration de demicylindrée (« gamme haute vitesse ») ou qui travaillent comme unité de freinage (durant le freinage hydrostatique). 2. P our les moteurs travaillant uniquement en mode entraînement, la pression de charge est de 30 % des valeurs selon le diagramme mais doit être de minimum 2 bars/29 psi. Les séries 44, 64 et 84 : Pression max. du carter : 3 bars/43,5 psi (pour 1 % du temps d’exploitation équitablement réparti, pointes de pression de maximum 5 secondes jusqu’à 8 bars/116 psi sont admissibles). La pression maximum admissible dans le carter à l’arrêt est de 8 bars (116 psi). Pour les moteurs montés avec des joints en caoutchouc silicone, ces pressions doivent être réduites de 50 %. Bosch Rexroth Mellansel AB, Manuel d’installation et de maintenance, Hägglunds VI, FR 323-3br/2011 Caractéristiques techniques pc bar 16 pc psi 44-06800 S’applique pour une pression de carter de 1 bar/14,5 psi Avec une pression de carter accrue, la pression de charge doit être augmentée en conséquence. 14 12 9/72 64-16300 64-13500 64-11100 200 44-09200 44-04700 150 10 8 100 6 4 50 2 0 0 10 20 30 40 50 60 70 80 90 100 n r/min Fig. 2: Pression de charge pc bar 14 pc psi S’applique pour une pression du carter de 1 bar (14,5 psi). Avec une pression 12 de carter accrue, la pression de charge doit être augmentée en 10 conséquence. 200 84-38000 84-14800 84-17900 84-21300 84-25100 8 100 6 4 2 0 0 10 20 30 50 40 rpm Fig. 3: Concerne moteurs des types A et B sans valve à 2 vitesses pc bar 14 12 10 pc psi 200 S’applique pour une pression du carter de 1 bar (14,5 psi). Avec une pression de carter accrue, la pression de charge doit être augmentée en conséquence. 84-38000 84-22300 8 100 6 4 2 0 0 10 20 30 40 50 60 rpm tr/ min Fig. 4: Concerne moteurs des types A et B avec valve à 2 vitesses Hägglunds VI, FR 323-3br/2011, Manuel d’installation et de maintenance, Bosch Rexroth Mellansel AB 10/72 Caractéristiques techniques 2.2 Bruits émis par une installation complète Bruits de fond Groupe motopompe Bruits de tuyauterie Moteur hydraulique Bruit provenant de l´unité entraînée Bruit de l´embase et de la construction Remarque : Bruits de fond Normalement, les bruits de fond ne peuvent pas être influencés mais ils sont habituellement connus ou faciles à mesurer. Unité de pompe L’unité de pompe est une source connue de bruits. Bruits des tuyauteries Les tuyauteries sont probablement la source majeure d’émission de bruits résultants d’erreurs d’installations : toutes les fixations de tuyaux doivent être de type antivibratoires, ancrées dans un plafond, mur ou sol en béton. Il faut éviter d’ancrer ces éléments dans des structures métalliques non rigides ou celles susceptibles de créer des résonances. Moteur hydraulique Le moteur hydraulique est une source connue de bruits. (Tableaux des données acoustiques – voir sous-section 4.9 dans le Engineering Manual). Unité commandée L’unité commandée est (pour nous) une source inconnue en ce qui concerne les bruits mais des informations devraient être disponibles auprès du constructeur. Avant de procéder à l’ancrage du bras de réaction d’un moteur hydraulique dans la fondation de l’enveloppe d’une machine commandée, il est extrêmement important d’étudier la construction de la fondation/enveloppe. Cela pourrait être le majeur facteur à considérer compte tenu que de nombreuses structures peuvent créer des résonances avec, comme résultats, de sérieux problèmes de bruits. 2.3 Choix du fluide hydraulique Les moteurs hydrauliques Hägglunds sont principalement conçus pour fonctionner avec des huiles hydrauliques à base de pétrole. L’huile hydraulique peut être choisie de concert avec le fournisseur d’huile auprès de votre agence de ventes locale, en tenant compte de ce qui suit : Bosch Rexroth Mellansel AB, Manuel d’installation et de maintenance, Hägglunds VI, FR 323-3br/2011 Caractéristiques techniques 11/72 Généralités L’huile doit satisfaire aux exigences selon FZG 90, étape de test 11, de la norme IP 334 (DIN 51354). L’huile doit également contenir des inhibiteurs pour prévenir l’oxydation, la corrosion et la formation de mousse. En ce qui concerne les huiles minérales, leur viscosité dépend beaucoup de la température. Ainsi, le choix de l’huile doit tenir compte de la température de service prévue ou déterminée dans le système, et non de la température dans le réservoir hydraulique. Les températures élevées dans le système réduisent nettement la durée de vie de service des joints en caoutchouc ; elles aboutissent également en une viscosité moindre ce qui, à son tour, se traduit par une mauvaise lubrification. La teneur en eau doit être inférieure à 0,1 %. Dans les applications industrielles, la teneur en eau doit être inférieure à 0,05 %. Viscosité recommandée à la température de service 40-150 cSt/187-720 SSU. Limites de température La température normale de service doit être inférieure à +50 °C (122 °F) Joints nitrile (moteurs std) Joints Viton -35 °C à +70 °C -20 °C à +100 °C Joints nitrile (moteurs std) Joints Viton -31 °F à +158 °F -4 °F à +212 °F Limites de viscosité Indice de viscosité =100 recommandé =150* pour exploitation avec grandes différences de température Min. admissible en expl. constante Min. admissible en expl. intermittente Maximum admissible 40 cSt/187 SSU 20 cSt/98 SSU** 10000 cSt/48000 SSU *P our nombre de fluides hydrauliques avec additifs VI, la viscosité peut être temporairement ou constamment réduite. ** U ne faible viscosité entraîne une durée de vie réduite pour les moteurs et une réduction de la puissance maxi admissible pour « Hägglunds VI ». Fluides ininflammables Exploitation avec fluides ininflammables Les fluides suivants ont été testés pour les moteurs Hägglunds : (ISO/DP 6071) Fluide HFA : Huile (3-5 %) en émulsion aqueuse HFB : Émulsion invertie 40-45 % eau dans huile Approuvé Joints Peinture interne Non – – Oui Nitrile (moteur std) Non peint* * À spécifier dans la commande. Hägglunds VI, FR 323-3br/2011, Manuel d’installation et de maintenance, Bosch Rexroth Mellansel AB 12/72 Caractéristiques techniques Fluide Approuvé Joints Oui Nitrile (moteur std) Non peint* HFD:R – Ester phosphorique Oui Viton Non peint* HFD:S – Hydrocarbures chlorés Oui Viton Non peint* HFD:T – Mélange de ceux ci-dessus Oui Viton Non peint* HFD:U – Autres compositions Oui Viton Non peint* HFC : Eau – Éthylène glycol Peinture interne HFD fluides synthétiques * À spécifier dans la commande. IMPORTANT ! Un nouveau calcul des données de pression et de la durée de vie de service doit être fait si des fluides ininflammables sont utilisés. Pour ces types de fluides, il faut toujours contacter Hägglunds ou son représentant agréé pour approbation. Fluides acceptables du point de vue environnemental Approuvé Joints Peinture intérieure Végétal */** Fluide HTG Oui Nitrile (moteur std) – Synthétique**/Esters HE Oui Nitrile (moteur std) – Fluide * Les fluides végétaux assurent une excellente lubrification et de faibles variations de la viscosité aux différentes températures. Il est nécessaire de contrôler ces fluides tous les 3 mois et, pour assurer une bonne durée de service du fluide, la température doit être inférieure à +45 °C (113 °F). ** Les fluides acceptables sur le plan environnemental assurent la même durée de vie pour les moteurs que les huiles minérales. Filtration L’huile d’un circuit hydraulique doit toujours être filtrée, tout comme l’huile de votre fournisseur lorsque l’on fait l’appoint dans le circuit. Plus on investit financièrement dans l’amélioration de la filtration d’un circuit hydraulique, plus sa durée de vie sera prolongée. Il est important, pour obtenir la durée de vie indiquée, d’observer nos recommandations concernant la pollution. Lors de la sélection du filtre, il est important de tenir compte du volume des particules pouvant être absorbées par le filtre tout en gardant un fonctionnement satisfaisant. Pour cette raison, nous préconisons la mise en place d’un filtre équipé d’un indicateur de colmatage déclenchant un signal lorsqu’il est nécessaire de remplacer la cartouche de filtre. Recommandations pour la filtration Avant la mise en service, s’assurer que le circuit a fait l’objet d’un nettoyage complet. •• 1. Généralement, le niveau de contamination dans nos moteurs ne doit pas excéder ISO 4406 19/15 (NAS 10). •• 2. Pour les applications industrielles lourdes, le niveau de contamination ne doit pas excéder ISO 4406:1999 18/16/13 (NAS 1638, classe 7). •• 3. Lors du remplissage du réservoir et du carter du moteur, nous préconisons l’utilisation d’un filtre d’un degré de filtration de β10=75. Bosch Rexroth Mellansel AB, Manuel d’installation et de maintenance, Hägglunds VI, FR 323-3br/2011 Installation 13/72 Explication du « DEGRÉ DE FILTRATION » Degré de filtration ß10=75 signifie ce qui suit : •• β10 signifie que les particules de taille ≥10µm seront éliminées par filtration. •• =75 désigne le degré de filtration de la taille des particules susmentionnées. On définit le degré de filtration comme étant le nombre de particules contenues dans l’huile avant la filtration, par rapport au nombre de particules contenues dans l’huile après la filtration. •• Par exemple : Degré de filtration β10=75. •• Avant la filtration, l’huile contient un nombre N de particules de taille ≥10μm et après passage dans le filtre, l’huile contient un nombre de ≥10μm. •• Ceci signifie qu’un (=98,6 %). N N particules de taille 75 N = 74·N nombre de particules a été éliminé par filtration 75 75 3 Installation 3.1 Instructions de montage Pour assurer un fonctionnement correct du moteur, il est important de procéder avec la plus grande précaution lors de son installation. Tout composant connecté au moteur et qui ne répond pas aux exigences stipulées dans les instructions qui suivent, peut causer des contraintes qui affectent la durée de vie de service du moteur. Pour chaque série de moteurs, les charges axiales et radiales ressortent des caractéristiques techniques dans le Manuel d’ingénierie. Le moteur est normalement rempli d’huile jusqu’à l`arbre. Si le réservoir d’huile est placé au-dessus de la pointe de l’arbre, le niveau de l’huile augmentera d’autant. Il est recommandé d’agencer le drainage de sorte que le moteur soit complètement rempli d’huile, surtout lorsqu’il s’agit de petites vitesses. La purge du moteur peut être réalisée à l’aide du bouchon BSP 1 1/4" sur le couvercle de l’extrémité avant. Le moteur doit toujours être connecté de manière qu’une pression suffisante soit obtenue à la connexion basse pression. Cela est particulièrement important lorsqu’il s’agit de grandes vitesses et inversions rapides. L’orifice de drain « D » doit être raccordé directement (non étranglé) au réservoir pour éviter le dépassement de la pression de carter maximum admissible. Le diamètre intérieur recommandé pour la ligne de drain est de 18 mm ou 3/4" pour les séries 44 et 64 et de 28 mm ou 1" pour la série 84. Les séries 44, 64 et 84 Pression max. du carter : 3 bars/43,5 psi (pour 1 % du temps d’exploitation équitablement réparti, pointes de pression de maximum 5 secondes jusqu’à 8 bars/116 psi sont admissibles). La pression maximum admissible dans le carter à l’arrêt est de 8 bars (116 psi). Pour les moteurs montés avec des joints en caoutchouc silicone, ces pressions doivent être réduites de 50 %. Hägglunds VI, FR 323-3br/2011, Manuel d’installation et de maintenance, Bosch Rexroth Mellansel AB 14/72 Installation Sur le moteur, il y a une flèche qui indique le sens de rotation. Lorsque l’huile est fournie vers l’orifice « A », le moteur tourne dans ce sens. Le sens de rotation est également indiqué sur la plaque d’identité (voir exemple sur la figure ci-dessous). IMPORTANT ! Avec de longues lignes de drain et un balayage à travers le moteur, des calculs particulièrement minutieux doivent être faits pour déterminer les dimensions de ces lignes. HIGH TORQUE HYDRAULIC MOTOR TYPE MK -64 -16300 -AO -RN -XXXX INDIVID. NO. TORQUE DISPLACEMENT Rotation à droite 3 cm /r MAX. PRESSURE Nm/bar (vue du côté des connexions * l’huile du moteur) de 3.1.1 Méthodes de levage courantes Levage du moteur Fig. 5: Bosch Rexroth Mellansel AB, Manuel d’installation et de maintenance, Hägglunds VI, FR 323-3br/2011 Installation 15/72 Boulons de levage acier Points de levage sur le couvercle moteur séries 44, 64 3 x M16 série 84 3 x M20 Max 30° Fig. 6: AVERTISSEMENT Prévoir des élingues de levage avec une bonne marge de sécurité par rapport au poids total de l’objet soulevé. Série moteurs Moteur Moteur + BB + BA +BCI kg lb kg lb 520 1 150 808 1 785 64 750 1 653 1 038 2 288 84 1 550 3 417 2 356 5 198 44 Levage du bras de réaction Fig. 7: TAC 1250-B Hägglunds VI, FR 323-3br/2011, Manuel d’installation et de maintenance, Bosch Rexroth Mellansel AB 16/72 Installation Fig. 8: TAC 1000-K DANGER Avant toute opération de levage, vérifier où se situe le centre de gravité. Ne jamais séjourner sous un moteur suspendu ni sous le bras de réaction. Poids Bras de réaction kg lb TAC 1000-K 69 152 TAC 1250-B 120 265 3.1.2 Moteur – tambour de treuil – adaptateur d’arbre Montage du tambour de treuil ou de l’adaptateur d’arbre Nettoyer soigneusement les surfaces de montage avant l’assemblage. (Ceci est un joint à friction). Serrer les boulons au couple correct. Tous les boulons seront lubrifiés à l’huile, voir plus loin. Les écarts d’excentricité et axiaux des surfaces de montage sur les équipements associés, tels que l’arbre et les tambours de treuil, doivent être de maximum 0,15 mm (0,006 in) pour les flasques intérieurs et extérieurs. Bosch Rexroth Mellansel AB, Manuel d’installation et de maintenance, Hägglunds VI, FR 323-3br/2011 Installation 17/72 Séries 44 et 64 M16 ou 5/8 UNC M20 ou 3/4 UNC Moteur Arbre adaptateur 24 trous Ø 22 mm (0,87 in) Tambour de treuil 24 trous Ø 18 mm (0,71 in) Fig. 9: Couple de serrage pour boulons d’assemblage, classe min. 12.9* (ISO 898/1) : Couple M16 = 340 Nm (250 lbf·ft) Couple 5/8 UNC = 320 Nm (236 lbf·ft) Couple M20 = 700 Nm (516 lbf·ft) Couple 3/4 UNC = 600 Nm (443 lbf·ft) * La classe 12.9 est requise pour la charge maxi admissible sur le moteur. Pour une charge moindre, d’autres boulons peuvent être utilisés. Série 84 M20 M24 Arbre adaptateur Moteur 24 trous Ø 28 mm (1,10 in) Tambour de treuil 24 trous Ø 22 mm (0,87 in) Fig. 10: Couple de serrage pour boulons d’assemblage, classe min. 12.9* (ISO 898/1) : Couple M20 = 700 Nm (516 lbf·ft) Couple M24 = 1200 Nm (885 lbf·ft) * La classe 12.9 est requise pour la charge maxi admissible sur le moteur. Pour une charge moindre, d’autres boulons peuvent être utilisés. Hägglunds VI, FR 323-3br/2011, Manuel d’installation et de maintenance, Bosch Rexroth Mellansel AB 18/72 Installation 3.1.3 Moteur – valves Montage de la valve V 46-O sur les moteurs des séries 44 et 64 NOTE ! Avant de monter la valve, contrôler que le moteur est monté dans son support avec « D2 » sur la surface de montage du moteur orienté vers le bas, voir Fig. 12. Moteur Couvercle 1 2 Valve Fig. 11: 1: 4 pces 5/8 UNC x 165 mm (6.5 in). Classe 8.8 (ISO 898/1). Couple de serrage 200 Nm (150 lbf·ft). 2: 2 pces 5/8 UNC x 178 mm (7 in). Classe 8.8 (ISO 898/1). Couple de serrage 200 Nm (150 lbf·ft). A D2 Surface de montage moteur A Bouchon 2 vitesses Fig. 12: •• Déposer le couvercle de la surface de montage du moteur. •• Déposer tous les bouchons de la surface de montage du moteur. •• Monter le bouchon BSTP 3/4" (inclus dans le kit de montage) au fond du trou pour l’orifice « A », voir Fig. 12. •• Positionner les joints toriques correctement sur la surface de montage de la valve. Utiliser de la graisse pour maintenir les joints en place. •• Monter la valve contre le moteur avec les orifices dans leur position correspondante. Bosch Rexroth Mellansel AB, Manuel d’installation et de maintenance, Hägglunds VI, FR 323-3br/2011 Installation 19/72 Montage de la valve V 46-C sur les moteurs des séries 44 et 64 NOTE ! Avant de monter la valve, contrôler que le moteur est monté dans son support avec « D2 » sur la surface de montage du moteur orienté vers le haut, voir Fig. 14. •• Déposer le couvercle de la surface de montage du moteur. •• Déposer tous les bouchons de la surface de montage du moteur. •• Monter le bouchon BSTP 3/4" (inclus dans le kit de montage) au fond du trou pour l’orifice « A », voir Fig. 14. •• Positionner les joints toriques correctement sur la surface de montage de la valve. Utiliser de la graisse pour maintenir les joints en place. •• Monter la valve contre le moteur avec les orifices dans leur position correspondante. Moteur Couvercle Valve Fig. 13: Bouchon 2 vitesses Surface de montage moteur Fig. 14: 3.1.4 Moteur – bras de réaction Montage du bras de réaction sur les moteurs des séries 44 et 64 •• Déposer le couvercle de la surface de montage du moteur. •• Installer le bras de réaction sur le bloc-cylindres comme le montre la figure. La connexion « D2 » sur le moteur doit être tournée vers le haut. Hägglunds VI, FR 323-3br/2011, Manuel d’installation et de maintenance, Bosch Rexroth Mellansel AB 20/72 Installation Pour TAC 1000-K, lubrifier le moyeu et les clavettes du bloc-cylindres avec de l’huile. Positionner les clavettes correctement et les introduire en place. Attention ! Ne pas introduire les clavettes trop loin. Il y a risque d’endommager la bague d’usure sur le bloc-cylindres. Une bague d’usure déformée peut causer une fuite d’huile. •• Reposer le couvercle. PRUDENCE Ne pas souder, percer, meuler ni entreprendre d’autres travaux sur le bras de réaction sans l’autorisation de Hägglunds. Arbre sur machine commandée Accouplement d’arbre Moteur Bras de réaction, TAC 1000-K Fig. 15: 1. 2. 3. 4. 5. Fig. 16: Bras de réaction TAC 1000-K Bosch Rexroth Mellansel AB, Manuel d’installation et de maintenance, Hägglunds VI, FR 323-3br/2011 Bague d’usure Clavette Bloc-cylindres Couvercle Bras de réaction Installation 21/72 Montage du bras de réaction sur les moteurs de la série 84 •• Monter le bras de réaction sur la flasque de montage du moteur. La connexion « D1 » orientée vers le haut. •• Lubrifier les vis avec de l’huile et les serrer au couple de serrage prescrit : M24 – 1200 Nm (885 lbf·ft) 1" UNC – 1400 Nm (1033 lbf·ft) Attention ! Pour les vis, voir marquage sur le couvercle arrière du moteur. Une encoche = filetage métrique Deux encoches = filetage UNC 1 3 2 1. Bras de réaction 2. Flasque de montage du moteur 3. 24 vis MC6S 24 x 65, classe 12.9 (ISO 898/1), ou 24 vis UC6S 1" UNC x 64 (2 1/2"), classe de puissance 12.9 (ISO 898/1) Fig. 17: Bras de réaction TAC 1250-B Montage des attaches Les attaches pour TAC 1000-K et TAC 1250-B doivent être soudées aux support. Voir Fig. 18 et 19. Pour les attaches rigides, il suffit de souder une des surfaces d’assemblage. Exigences qualité : Classe de soudage K1 selon HS 2020 2015, EN 25 817:1992. Classe de soudage Sv2 selon les normes de soudage de construction bâtiment StBk-N2. Classe de soudage AK selon DIN 8562. ASME Code Chaudière Section VIII. BS 1500:1 et BS 1515:1. NOTE ! Il est fort recommandé d’utiliser des attaches pivotantes Hägglunds VI, FR 323-3br/2011, Manuel d’installation et de maintenance, Bosch Rexroth Mellansel AB Installation Jeu 22/72 Jeu Acier : SS 2134-01 DIN St E39 BS 4360 Nuance 50 C Jeu total : TAC 1000-K 0,42-0,73 (0,017-0,029) TAC 1250-B 0,45-0,80 (0,018-0,032) Position alternative À protéger contre la corrosion après soudure. Fig. 18: Montage de l’attache rigide Montage du bras de réaction sur les moteurs de la série 84 L’attache pivotante sera montée et ajustée selon les Fig. 19 et 20. Contrôle Contrôler que l’extrémité libre du bras de réaction peut se déplacer au point d’attache dans les directions et tolérances prescrites aux Fig. 18 et 19. Pour la lubrification du bras de réaction, voir 4.4. « Maintenance périodique ». x = ± 2 mm (0,079) désalignement d’installation. x ± 15 mm (0,59) déplacement en utilisation. ±25° Position alternative Acier : EN 10113S355N DIN St E39 BS 4360 Nuance 50 C x 10 À protéger contre la corrosion après soudure. Fig. 19: Montage de l’attache pivotante Bosch Rexroth Mellansel AB, Manuel d’installation et de maintenance, Hägglunds VI, FR 323-3br/2011 Installation 23/72 Fig. 20: Montage du bras de réaction sur attache pivotante ZONE DANGEREUSE En cas de défaillance dans l’installation du bras de réaction Fig. 21: Dépose du bras de réaction sur les moteurs des séries 44 et 64 Utiliser un extracteur approprié pour retirer le bras de réaction. Les trous de l’extracteur ressortent de la figure ci-dessous. Note ! Si le bras de réaction est difficile à retirer, on peut réchauffer son moyeu prudemment. TAC 1000-K 2 trous M16 x 40 mm (1,6 in) Fig. 22: Trous d’extracteur sur TAC 1000-K DANGER S’assurer que la fondation peut supporter les forces exercées par le bras de réaction. AVERTISSEMENT Avant de démarrer le moteur, contrôler que le carter tournant du moteur ne risque pas de causer des endommagements. Hägglunds VI, FR 323-3br/2011, Manuel d’installation et de maintenance, Bosch Rexroth Mellansel AB 24/72 Installation 3.1.5 Moteur – support avant Tambour de treuil Support arrière Moteur Couvercle Support avant Fig. 23: Montage du support avant sur les moteurs des séries 44 et 64 •• Déposer le couvercle. •• Placer le moteur dans le support. La connexion « D2 » sera orientée vers le haut *. •• Lubrifier le moyeu et les clavettes du bloc-cylindres avec de l’huile. Positionner les clavettes correctement et les introduire en place. •• Reposer le couvercle. Note ! Ne pas introduire les clavettes trop loin. Il y a risque d’endommager la bague d’usure sur le bloc-cylindres. Une bague d’usure déformée peut causer une fuite d’huile. Voir 3.1.4 « Moteur – bras de réaction, montage du bras de réaction sur les moteurs des séries 44 et 64 ». * Si la valve V46-O est utilisée, la connexion « D2 » du moteur doit être orienté vers les bas. Montage du support avant sur les moteurs de la série 84 •• Placer le moteur dans le support. La connexion « D1 » du moteur sera orientée vers le haut. Lubrifier les vis avec de l’huile et les monter. Couple de serrage : M24 – 1200 Nm (885 lbf·ft) Note ! Pour les vis, voir marquage sur le couvercle arrière du moteur. Une encoche = filetage métrique Deux encoches = filetage UNC Voir 3.1.4 « Moteur – bras de réaction, montage du bras de réaction sur les moteurs de la série 84 ». Bosch Rexroth Mellansel AB, Manuel d’installation et de maintenance, Hägglunds VI, FR 323-3br/2011 Installation 25/72 D2 A B D1 C Fig. 24: Fig. 25: DANGER Ne jamais séjourner sous le moteur durant le démontage. AVERTISSEMENT S’assurer toujours que l’équipement de levage est suffisamment puissant pour supporter le poids du moteur. Hägglunds VI, FR 323-3br/2011, Manuel d’installation et de maintenance, Bosch Rexroth Mellansel AB 26/72 Installation Montage des supports BB-46 et BB-85 sur la fondation Vis Filetage Classe de puissance (ISO 898/1) Couple de serrage Nm/lbf·ft BB-46 M24 10,9 BB-85 M24 10,9 Support Vis Filetage Classe de puissance (ISO 898/1) Couple de serrage Nm/lbf·ft 960/710 1" UNC 10,9 1100/810 960/710 1" UNC 10,9 1100/810 Poids Exigences planéité contre fondation (zone support uniquement) kg lb 0,5 (0,0197) 150 330 0,5 (0,0197) 496 1094 Coordonnées de perçage A±1,5 (A±0,059) B±0,4 (B±0,016) * * ** ** 460±0,3 (18,11±0,012) 840±1 (33,07±0,039) 8 x 28 (1,10) Voir 1) note 1 ** ** * * 50±0,5 (1,97±0,020) 75 ±0,5 (2,95 ±0,020) 70 ±0,5 (2,76 ±0,020) C±2 (C±0,079) Fig. 26: BB-46 Série moteurs Dimensions A mm pouce B mm pouce C mm pouce 44 257 10,1 43 1,69 74 2,91 64 264 10,3 48 1,88 81 3,19 Note ! Seuls les trous repérés (*) sont nécessaires pour montage de support sans ensemble de frein. ** Longueur des vis pour les bandes de frein des moteurs 64: 90 (3,5), moteurs 44 : 130 (5,0). Bosch Rexroth Mellansel AB, Manuel d’installation et de maintenance, Hägglunds VI, FR 323-3br/2011 Installation 27/72 480±0,5 (18,898±0,020) 43±0,6 (1,693±0,024) 1100±1 (43,31±0,039) 800±1 (31,50±0,039) 11 x Ø28 (1,10) 411,5±2 (16,201±0,079) 347±0,5 (13,661±0,020) 245±0,5 (9,646±0,020) 135±0,5 (5,315±0,020) Fig. 27: BB-85 Fig. 28: Erreur maximum de parallélisme entre les deux supports Hägglunds VI, FR 323-3br/2011, Manuel d’installation et de maintenance, Bosch Rexroth Mellansel AB 28/72 Installation Montage du treuil sur la fondation Méthode no 1 •• Un cadre séparé usiné après la soudure à une tolérance de parallélisme de : 0,2 100 •• Le cadre peut être soudé ou boulonné sur la fondation. Fig. 29: Méthode no 2 •• Usiner les surfaces des éléments du cadre contre les supports à une planéité de 0,5 mm (0,020 in). •• Souder les éléments du cadre à la fondation à l’aide d’un outil d’alignement (si nécessaire, utilisez le treuil à cet effet). •• Après la soudure, déposez l’outil d’alignement et poser une couche d’épaisseur 1 à 2 mm (0,04-0,08 in) de Devcon B-compound entre les supports et les éléments du cadre. Assembler le treuil sans serrer les vis. Laisser le Devcon-B compound durcir selon la spécification du produit. •• Serrer les vis, voir le couple de serrage pour chaque support. Fig. 30: Bosch Rexroth Mellansel AB, Manuel d’installation et de maintenance, Hägglunds VI, FR 323-3br/2011 Installation 29/72 Méthode no 3 •• Usiner les surfaces des éléments du cadre contre les supports à une planéité de 0,5 mm (0,020 in). •• Souder les éléments du cadre à la fondation à l’aide d’un outil d’alignement (si nécessaire, utilisez le treuil à cet effet). •• Après la soudure, déposer l’outil d’alignement et placer une règle sur les deux éléments du cadre et utiliser un palpeur pour contrôler l’épaisseur des rondelles de réglages sur chaque position de vis. •• Placer des rondelles de réglage aux positions de vis et assembler le treuil. Couple de serrage : voir le couple de serrage pour chaque support. Fig. 31: Ensemble de frein BA-43 et BA-63 Couple de freinage dans le sens de la force de freinage* avec coefficient de frottement μ = 0,35 après la période de rodage. Ensemble de frein Simple effet Double effet Nm lbf·ft Nm lbf·ft BA-43 76 000 56 000 55 000 40 500 BA-63 90 000 66 300 65 000 47 900 *S i le frein est utilisé à l’opposé de son sens d’action prévu, on peut s’attendre à environ 20 % de sa capacité de freinage. AVERTISSEMENT De l’huile sur les garnitures du frein réduit le couple de freinage. Sens de la force de freinage Charge Charge Sens horaire Sens antihoraire Double effet Fig. 32: Hägglunds VI, FR 323-3br/2011, Manuel d’installation et de maintenance, Bosch Rexroth Mellansel AB 30/72 Installation Dimensions BA-43 et BA-63, simple effet Points de lubrification Fig. 33: Vis d’ajustage du frein Trous de tirage 2 pces M16 Fig. 34: Série moteurs A B mm pouce mm 44 871 34,29 906 35,67 64 915 36,02 950 37,40 Bosch Rexroth Mellansel AB, Manuel d’installation et de maintenance, Hägglunds VI, FR 323-3br/2011 pouce Installation 31/72 Dimensions BA-43 et BA-63, double effet Fig. 35: Vis d’ajustage du frein Trous de tirage 2 pces M16 Points de lubrification Fig. 36: Série moteurs A mm pouce B mm pouce 44 871 34,29 906 35,67 64 915 36,02 950 37,40 Hägglunds VI, FR 323-3br/2011, Manuel d’installation et de maintenance, Bosch Rexroth Mellansel AB 32/72 Installation Remplacement de la bande de frein La garniture du frein est usée et l’ensemble de la bande de frein doit être remplacée lorsque la cote, bande plus garniture, est celle représentée à la figure 37. Min 13 mm (0,51 in) Min 15 mm (0,59 in) Fig. 37: Réglage des freins BA-43 et BA-63 FK = Cote de réglage Sans couple de freinage FK min = 103 mm (4,06 in) FK max = 117 mm (4,61 in) Sans charge La position correcte de l’indicateur après réglage Avec couple de freinage voir le Manuel I&M Avec charge Avertissement ! FK doit toujours être supérieure à 60 mm (2,37 in) Zone blanche Zone verte Fig. 38: Simple effet, plaque 1 Bosch Rexroth Mellansel AB, Manuel d’installation et de maintenance, Hägglunds VI, FR 323-3br/2011 Installation 33/72 AVERTISSEMENT Les garnitures devant être rodées, la cote FK doit être de 127 mm (5,0 in) avec des garnitures nouvellement installées. Contrôler la cote après 10 opérations de freinage et la régler à 117 mm (4,61 in). Réglage du frein - Sans couple de freinage FK min = 103 mm (4,06 in) FK max = 117 mm (4,61 in) Réglez A égale à B Zone blanche Zone verte Zone rouge Sans couple de freinage Régler lorsque l’indicateur passe au rouge. Voir « Réglage du frein sans couple de freinage ». Avec couple de freinage Échelle non applicable. Fig. 39: Double effet, plaque 2 Réglage des freins BA-43 et BA-63 Simple effet Réglage du frein sans couple de freinage. 1. Déposer les dispositifs de verrouillage des vis de réglage. 2. T endre les bandes à l’aide des vis de réglage avec la pression appliquée au cylindre de frein. Contrôler à l’aide de l’indicateur rouge, que les bandes sont équitablement réglées. Voir plaque 1. Drainer le cylindre de frein et contrôler la cote FK. Ajuster jusqu’à ce qu’elle soit de 117 mm (4,61 in). Les indicateurs de l’échelle, plaque 2, doivent être dans la zone verte. 3. Remonter les dispositifs de verrouillage des vis de réglage. Hägglunds VI, FR 323-3br/2011, Manuel d’installation et de maintenance, Bosch Rexroth Mellansel AB 34/72 Installation e t lag en ég m er ste td ju in éa Po er td in Po Réglage des freins avec couple de freinage La valeur du couple de freinage doit être utilisée pour le contrôle du réglage. Relever à partir du diagramme si un réglage s’impose. Pour la procédure de réglage, voir « Réglage du frein sans couple de freinage ». Exemple : Avec BA-63, une force de câble F de 100 000 N et un tambour de treuil de rayon r = 0,5 m, le couple de freinage est Mb = 50 000 Nm. Le frein doit être réglé si la cote FK est inférieure à 77 mm (3,03 in). Ajuster FK à 91 mm (3,58 in). Voir le diagramme pour BA-63. td in Po e in Po t en m te us aj ré ge la g ré e td Bosch Rexroth Mellansel AB, Manuel d’installation et de maintenance, Hägglunds VI, FR 323-3br/2011 Installation 35/72 AVERTISSEMENT Le contrôle du réglage des freins avec couple de freinage doit être fait uniquement lorsque les freins ne peuvent pas être libérés de leur couple de freinage. Double effet Réglage du frein sans couple de freinage. 1. Déposer les dispositifs de verrouillage des vis de réglage. 2. T endre les bandes à l’aide des vis de réglage avec la pression appliquée au cylindre de frein. Contrôler à l’aide des échelles, que les bandes sont équitablement réglées. Voir plaque 1. Drainer le cylindre de frein et contrôler la cote FK. Ajuster jusqu’à ce qu’elle soit de 117 mm (4,61 in). Les indicateurs de l’échelle, plaque 2, doivent être dans la zone verte. 3. Remonter les dispositifs de verrouillage des vis de réglage. Réglage du frein avec couple de freinage. Non possible. Ensemble de freins BA-85 Couple de freinage dans le sens de la force de freinage* avec coefficient de frottement μ = 0,35 après la période de rodage. Ensemble de frein Simple effet BA-85 Double effet Nm lbf·ft Nm lbf·ft 195 000 143 800 120 000 85 000 * S i le frein est utilisé à l’opposé de son sens d’action prévu, on peut s’attendre à environ 20 % de sa capacité de freinage. Sens de la force de freinage Charge Charge Sens horaire Sens antihoraire Double effet Fig. 40: AVERTISSEMENT De l’huile sur les garnitures du frein réduit le couple de freinage. Hägglunds VI, FR 323-3br/2011, Manuel d’installation et de maintenance, Bosch Rexroth Mellansel AB 36/72 Installation Dimensions du BA-85 à simple et double effet. 450 ± 3 (17,7 ± 0,12) 550 ± 3 (21,6 ± 0,12) Fig. 41: Vis de réglage du frein 20 trous Ø 28 espacés de 15° Points de lubrification Fig. 42: Remplacement de la bande de frein La garniture du frein est usée et l’ensemble de la bande de frein doit être remplacé lorsque la cote, bande plus garniture, est celle représentée à la figure 43. Bosch Rexroth Mellansel AB, Manuel d’installation et de maintenance, Hägglunds VI, FR 323-3br/2011 Installation 37/72 Min. 15 mm (0,59 in) Fig. 43: AVERTISSEMENT Les bandes devant être rodées, la cote FK doit être de 117 mm (4,61 in) avec des bandes neuves. Contrôler la cote après 10 opérations de freinage et la régler à 107 mm (4,21 in). Réglage du frein BA-85 Sans couple de freinage FK min = 93 mm (3,67 in) FK max = 107 mm (4,22 in) Sans charge m Avec charge FK Avec couple de freinage voir le Manuel I&M Définition FK valable pour les deux cylindres Avertissement ! FK doit toujours être supérieure à 60 mm (2,37 in) UT VALID WITHO Zone blanche Zone verte G IN AK BR Zone rouge TO R Q UE Fig. 44: Double effet, plaque 2 Hägglunds VI, FR 323-3br/2011, Manuel d’installation et de maintenance, Bosch Rexroth Mellansel AB 38/72 Installation Sans couple de freinage Régler lorsque l’indicateur passe au rouge. Voir « Réglage du frein sans couple de freinage ». Avec couple de freinage Échelle non applicable. Pour le réglage des freins avec application du couple, voir ci-dessous. Réglage du frein sans couple de freinage 1. Déposer les dispositifs de verrouillage des vis de réglage. 2. T endre les bandes à l’aide des vis de réglage avec la pression appliquée au cylindre de frein. Drainer le cylindre de frein et contrôler la cote FK. Ajuster jusqu’à ce qu’elle soit de 107 mm (4,21 in). Les indicateurs de l’échelle, plaque 2, doivent être dans la zone verte. 3. Remonter les dispositifs de verrouillage des vis de réglage. BA-85 Po i nt Po i nt de de ré g la ge ré aj u st em en t Réglage des freins avec couple de freinage AVERTISSEMENT Le contrôle du réglage des freins avec couple de freinage doit être fait uniquement lorsque les freins ne peuvent pas être libérés de leur couple de freinage. La valeur du couple de freinage doit être utilisée pour le contrôle du réglage. Relever à partir du diagramme si un réglage s’impose. Pour la procédure de réglage, voir « Réglage du frein sans couple de freinage ». Exemple : Avec BA-85, une force de câble F de 100 000 N et un tambour de treuil de rayon r = 0,5 m, le couple de freinage est Mb = 50 000 Nm. Le frein doit être réglé si la cote FK est inférieure à 84 mm (3,03 in). Ajuster FK à 98 mm (3,86 in). Bosch Rexroth Mellansel AB, Manuel d’installation et de maintenance, Hägglunds VI, FR 323-3br/2011 Installation 39/72 Cylindre de frein BCI-M pour ensembles de freins BA-43, BA-63 et BA-85 Type de cylindre de frein Commence à ouvrir à pression à l’orifice « A » Complètement ouvert à pression à l’orifice « A » Pression max. admissible Orifice « A » Orifice « B » Cylindrée Poids bar psi bar psi bar psi bar psi cm3 in3 kg lb BCI M-1X-XXX 4 58 8 115 320 4 600 320 4 600 1300 79,3 68 150 BCI M-30-XXX 16 230 26 380 320 4 600 320 4 600 350 21,4 70 154 Fonctionnement haute pression BCI M-10 – XXX (sans balayage) « D » vers réservoir Obturé Fig. 45: BCI M-11 – XXX (avec balayage) « D » vers réservoir Étrangleur Ø 1 mm (0,04 in) Fig. 46: À ∆p 2 bars (29 psi), le débit de balayage est de 0,9 lit/min À ∆p 5 bars (72 psi), le débit de balayage est de 1,4 lit/min À ∆p 10 bars (145 psi), le débit de balayage est de 2,0 lit/min À ∆p 15 bars (217 psi), le débit de balayage est de 2,4 lit/min Hägglunds VI, FR 323-3br/2011, Manuel d’installation et de maintenance, Bosch Rexroth Mellansel AB 40/72 Installation Fonctionnement haute pression BCI M-30 – XXX (sans balayage) « D » obturé Bouchon déposé Fig. 47: Note ! En variante, l’orifice « D » peut être utilisé comme orifice principal mais dans ce cas, l’orifice « A » doit être obturé. Pour assurer une bonne aération, choisissez la connexion au point le plus haut comme orifice principal. Dépose du bouchon Clé six pans Fig. 48: DANGER Ne pas démonter le cylindre de frein sans outils spéciaux. Bosch Rexroth Mellansel AB, Manuel d’installation et de maintenance, Hägglunds VI, FR 323-3br/2011 Installation 41/72 Drainage des cylindres de frein Le diagramme ci-dessous montre comment le couple de freinage Mmax. pour différents cylindres de frein baisse proportionnellement à la contre-pression dans la ligne de drainage du cylindre. Exemple : L’équipement de freins à double effet, BA-63, est équipé d’un cylindre de frein désigné BCI-M-1X et a un couple de freinage de (Mmax.) 65 000 Nm / 47 900 lbf·ft quand le cylindre de frein n’est pas sous pression et μ = 0,35. Supposons que la contre-pression dans la ligne de drainage du cylindre de frein est de 1,5 bar/75 psi. Le diagramme représente alors le couple de freinage réel (Mact.) qui correspond à 60 % seulement du Mmax.. % 100 50 150 250 200 300 350 psi 100 50 BC I-M -1X I-M BC -30 0 0 1,5 5 10 15 20 bar Contre-pression dans la ligne de drainage du cylindre de frein. AVERTISSEMENT Si le frein est utilisé dans un environnement froid, comme frein d’urgence, il doit être balayé. AVERTISSEMENT Les moteurs dotés de freins spéciaux peuvent avoir différents modes de travail. Veuillez contrôler le code de commande pour votre frein. Hägglunds VI, FR 323-3br/2011, Manuel d’installation et de maintenance, Bosch Rexroth Mellansel AB 42/72 Installation Installation des ensembles de freins BA-43, BA-63 à simple effet et du cylindre de frein BCI-M Note ! IMPORTANT ! Sens de montage avec le verrouillage du palier articulé contre la rondelle et l’écrou. Note ! Pour BA-43, des entretoises (11) sont à monter entre le support et les bandes de frein. Fig. 49: L’illustration montre le sens horaire de la force de freinage 1. Monter les coussinets (32) sur le support (910 ou 911) avec l’arbre excentrique (16 ou 17) comme outil. Graisser les coussinets avec Texaco Multifak EP2 ou graisse équivalente, sans additifs solides. Remplir de graisse aussi l’espace entre les coussinets. 2. Monter l’arbre arrière (56), l’entretoise (57) et le circlips (58). Graisser l’arbre avant le montage : Voir point 1 ci-dessus. 3. Positionner le manchon (55) sur l’arbre arrière. Monter le support arrière du cylindre de frein (925), la rondelle (54) et l’écrou (27). 4. Presser le coussinet (34) dans le levier (41 ou 42). Note ! S’assurer que les trous de lubrification coïncident. Introduire le graisseur (35) et le chapeau de protection (70). 5. Graisser l’arbre excentrique (16 ou 17) – voir point 1 – et l’introduire en place. Monter la clavette (31), le levier (41 ou 42), la rondelle (28) et l’écrou (27). 6. Monter la tige de piston du cylindre de frein sur le levier (41 ou 42). Assembler la vis (36) et l’écrou (33). 7. Monter la tête de bielle (29), la rondelle (28) et l’écrou (27). Introduire le graisseur (26) et le chapeau de protection (70). 8. Monter le moteur, voir 3.1.5 « Moteur – support avant sur les moteurs des séries 44 et 64 ». Bosch Rexroth Mellansel AB, Manuel d’installation et de maintenance, Hägglunds VI, FR 323-3br/2011 Installation 43/72 9. Monter les bandes de frein inférieures (6 ou 8). Lubrifier les paliers selon point 1. Assembler les rondelles (25) et les vis (A). Si les vis ne peuvent pas être serrées avec une clé dynamométrique, serrer jusqu’à ce que les rondelles (25) soient plates. 10. Monter les bandes de frein supérieures (5 ou 7). Monter vis (12), rondelle (13), pointe (15) et écrous (14). Lubrifier les vis avant le montage – voir point 1. Note ! Les bandes de frein doivent être mobiles par rapport à la tête de bielle. Il ne faut donc pas serrer les vis au point de comprimer la tête de bielle (29). 11. Monter les bandes avec vis de réglage (10), entretoises (9 et 2) et écrous (1). Avant le montage, graisser les vis de réglage (10) avec du Molycote G ou produit équivalent. 12. Fixer l’échelle (46), plaque support (47) et entretoises (48) avec les vis (45). 13. Fixer par rivets la plaque de réglage de frein (64) et la plaque du sens de force de freinage (917). 14. Avant la mise en marche, régler l’ensemble de freins. Voir le réglage de frein pour BA-43 et BA-63 à simple effet. 15. Mettre en place contre-écrous (4) et vis (3). 16. Contrôler que l’ensemble de freins est installé de sorte que le bon sens de la force de freinage soit obtenu et que les plaques (60 et 917) correspondent à l’ensemble de freins installé. Vis (A) Classe (ISO 898/1) Couple de serrage* Nm lbf·ft M24 10,9 960 710 1" UNC 10,9 1 100 810 *Lubrifier avec de l’huile Hägglunds VI, FR 323-3br/2011, Manuel d’installation et de maintenance, Bosch Rexroth Mellansel AB 44/72 Installation Installation des ensembles de freins BA-43, BA-63 à double effet et du cylindre de frein BCI-M Note ! IMPORTANT ! Sens de montage avec le verrouillage du palier articulé contre la rondelle et l’écrou. Goujon prisonnier (53) Emplacement alternatif pour 60 et 63 Goujon prisonnier (52) Montage du bars (51) Note ! Pour BA-43, des entretoises (11) sont à monter entre le support et les bandes de frein. Fig. 50: 1. Monter les coussinets (32) sur le support (912 ou 913) avec l’arbre excentrique (18 ou 20 et 19 ou 21) comme outils. Graisser les coussinets avec Texaco Multifak EP2 ou graisse équivalente, sans additifs solides. Remplir de graisse aussi l’espace entre les coussinets. 2. Graisser et monter les arbres excentriques (18 ou 20 et 19 ou 21). Voir point 1 ci-dessus. 3. Presser les coussinets (34 et 38) dans les leviers (39 et 40). Note ! S’assurer que les trous de lubrification sur le levier (39) coïncident. Introduire le graisseur (35) et le chapeau de protection (70). 4. Monter les clavettes (31) et monter les leviers (39 et 40) sur l’arbre excentrique. Monter rondelles (28) et écrous (27). 5. Monter la tige de piston du cylindre de frein (925) sur le levier (39). Monter le boulon de fixation (36) et l’écrou (33). 6. Aligner le support du cylindre de frein contre le levier de frein arrière (40). Monter le boulon de fixation (37), la rondelle (59) et l’écrou (14). Note ! Ne pas serrer l’écrou au point d’empêcher le cylindre de frein et le levier de se déplacer librement l’un par rapport à l’autre. Bosch Rexroth Mellansel AB, Manuel d’installation et de maintenance, Hägglunds VI, FR 323-3br/2011 Installation 45/72 7. Monter les têtes de bielle (29), les rondelles (28) et les écrous (27). Introduire les graisseurs (26) et le chapeau de protection (70). 8. Monter le moteur, voir 3.1.5 « Moteur – support avant sur les moteurs des séries 44 et 64 ». 9. Monter les bandes de frein inférieures (6 ou 8). Lubrifier les paliers selon point 1. Assembler les rondelles (25) et les vis (A). Si les vis ne peuvent pas être serrées avec une clé dynamométrique, serrer jusqu’à ce que les rondelles (25) soient plates. 10. Monter les bandes de frein supérieures (5 ou 7). Graisser et monter les vis (12). Voir point 1. Monter aussi rondelles (13) et écrous (14). Note ! Les bandes de frein doivent être mobiles par rapport aux têtes de bielle. Il ne faut donc pas serrer les vis au point de comprimer les têtes de bielle (29). 11. Monter les bandes avec vis de réglage (10), entretoises (9 et 2) et écrous (1). Avant le montage, graisser les vis de réglage (10) avec du Molycote G ou produit équivalent. 12. Fixer l’échelle (46), plaque support (47) et entretoises (48) avec les vis (45). 13. Fixer par rivets la plaque de réglage de frein (62) et la plaque du sens de force de freinage (917). 14. Percer et obturer des trous M8 dans les tourillons sur les rubans de frein selon figure. Monter les goujons prisonniers (52 et 53), écrous (50), bras (51) et écrous (50). Monter les vis (49) et écrous (27). 15. Avant la mise en marche, régler l’ensemble de freins. Voir le réglage de frein pour BA-43 et BA-63 à double effet. 16. Mettre en place contre-écrous (4) et vis (3). 17. Contrôler que l’ensemble de freins est installé de sorte que le bon sens de la force de freinage double effet soit obtenu et que les plaques (60 et 917) correspondent à l’ensemble de freins installé. Vis (A) Classe (ISO 898/1) Couple de serrage* Nm lbf·ft M24 10,9 960 710 1" UNC 10,9 1 100 810 *Lubrifier avec de l’huile Hägglunds VI, FR 323-3br/2011, Manuel d’installation et de maintenance, Bosch Rexroth Mellansel AB 46/72 Installation Installation de l’ensemble de freins BA-85 à simple + double effet et du cylindre de frein BCI-M Note ! IMPORTANT ! Sens de montage avec le verrouillage du palier articulé contre la rondelle et l’écrou. Fig. 51: L’illustration représente le sens de freinage à double effet 1. Graisser les coussinets (1) avec Texaco Multifak EP2 ou graisse équivalente sans additifs solides et les monter sur le support (910). 2. Graisser l’arbre excentrique – voir point 1. Monter les coussinets (2) et les arbres excentriques (3 ou 50 et 4 ou 51). 3. Presser les coussinets (5) dans les leviers (6). Note ! S’assurer que les trous de lubrification coïncident. Introduire le graisseur (7). 4. Monter les leviers (6) et les clavettes (8). Voir fig. 1, 2 ou 3 pour l’emplacement des clavettes des sens de freinage respectifs. Monter les vis de verrouillage (9). 5. Monter les bagues de verrouillage (10) sur les arbres excentriques. Introduire les graisseurs (7). 6. Monter les goujons prisonniers (13), rondelles élastiques (15) et vis (16). Couple de serrage : 750 Nm (553 lbf·ft). Note ! Les encoches pour tendeur sur le goujon prisonnier (13) doivent être montées au niveau de l’axe du cylindre de frein. Bosch Rexroth Mellansel AB, Manuel d’installation et de maintenance, Hägglunds VI, FR 323-3br/2011 Installation 47/72 7. Graisser les goujons prisonniers (13) selon point 1 et monter le cylindre de frein (925) par dessus. Monter rondelles (17) et écrous (18). Couple de serrage : 100 Nm (73 lbf·ft). Note ! Après le serrage des écrous (18), s’assurer que les cylindres de frein sont mobiles sur les goujons prisonniers (13). Positionner les extrémités de la tige de piston sur les leviers (6). Monter les boulons de fixation (19) et les écrous (18). Couple de serrage : 40 Nm (29 lbf·ft). 8. Monter les têtes de bielle (20) sur les arbres excentriques. 9. Monter le moteur, voir 3.1.5. 10. Monter les bandes de frein (25). Lubrifier le trou des extrémités des bandes de frein avec du Molycote G. 11. Lubrifier les arbres (24) avec du Molycote G. Monter les autres extrémités des bandes de frein avec arbres (24) et rondelles (23). Verrouiller avec des bagues de verrouillage (22). Voir fig. 1, 2 ou 3 pour l’emplacement des arbres pour les sens de freinage respectifs. 25 23 22 24 Fig. 52: 12. Monter les bandes de frein (26). Monter les vis (33) et écrous (35). Lubrifier les vis avant le montage – voir point 1. Note ! Les bandes de frein doivent être mobiles par rapport aux têtes de bielle. Il ne faut donc pas serrer les vis au point de comprimer les têtes de bielle. Monter les bandes avec vis de réglage (36), entretoises (37) et écrous (39). Avant le montage, graisser les vis de réglage (36) avec du Molycote G ou produit équivalent. 13. Fixer par rivets la plaque de réglage de frein (46) et la plaque du sens de force de freinage (911), selon l’ensemble de freins installé. 14. Fixer les échelles (27), plaques support (28), vis (30) et écrous (31). 15. Avant la mise en marche, régler l’ensemble de freins. Voir le réglage de frein pour BA-85. 16. Mettre en place contre-écrous (40 et 42) et vis (41). 17. Contrôler que l’ensemble de freins est installé de sorte que le bon sens de la force de freinage soit obtenu et que les plaques (45 et 911) correspondent à l’ensemble de freins installé. Hägglunds VI, FR 323-3br/2011, Manuel d’installation et de maintenance, Bosch Rexroth Mellansel AB 48/72 Installation Clavette (8) Fig. 53: Sens horaire (Frein droit) Clavette (8) Fig. 54: Sens antihoraire (Frein gauche) Clavette (8) Fig. 55: Double effet Bosch Rexroth Mellansel AB, Manuel d’installation et de maintenance, Hägglunds VI, FR 323-3br/2011 Installation 49/72 3.2 Raccords d’huile 3.2.1 Raccords d’huile, moteur sans valve, séries 44 et 64 D 2 A D1 B C Séries de moteurs 44 & 64 : Ø 195 mm (7,677 in) Fig. 56: Double effet Orifice Description Dimensions Remarque : A Raccord principal BSP 1 1/4" Si A est utilisé comme entrée, le moteur tourne dans le sens de la flèche B Raccord principal BSP 1 1/4" Normalement obturé. C Raccord principal BSP 1 1/4" Si C est utilisé comme entrée, le moteur tourne dans le sens opposé de la flèche D1 Raccord de drain BSP 3/4 D2 Raccord de balayage BSP 3/4 Raccords de drain D1 et D2 uniquement D2 Raccords principaux A, B et C Utilisé pour le balayage du carter moteur uniquement D2 Fig. 57: Double effet Hägglunds VI, FR 323-3br/2011, Manuel d’installation et de maintenance, Bosch Rexroth Mellansel AB 50/72 Installation PRUDENCE Contrôler le sens de rotation 3.2.2 Raccords d’huile, série de moteurs 84 Moteur sans valve à deux vitesses Moteur avec valve à deux vitesses 135±1 (5,315±0,04) Y C 15° A UNC ¾ D2 90° 135±1 (5,315±0,04) D1 X 165±1 165±1 (6,496±0,04)(6,496±0,04) Fig. 58: Orifice Description Dimensions Remarque : A* Raccord principal SAE 2" Si A est utilisé comme entrée, le moteur tourne dans le sens de la flèche C* Raccord principal SAE 2" Si C est utilisé comme entrée, le moteur tourne dans le sens opposé de la flèche D1 Raccord de drain BSP 1" D2 Raccord de balayage BSP 1" Utilisé pour le balayage du carter moteur Y** Raccord de pression pilote BSP 3/4 Cylindrée 57,9 cm3 (5,35 in3), valve 2 positions Cylindrée 90,5 cm3 (5,52 in3), valve 3 positions Donne la demi-cylindrée X** Raccord de pression pilote BSP 3/4 Seulement avec valve à 3 positions, cylindrée 32,6 cm3 (1,99 in3) Donne la cylindrée totale * Bride SAE J518 C, code 62 414 bars (6000 psi). ** La pression pilote requise aux raccords Y et X pour assurer une commutation rapide et sûre est de 8 bars (116 psi). La pression pilote maximum admissible aux Y et X est de 50 bars (725 psi). Les valves antichocs incorporées sont réglées à 350 bars (5100 psi) pour les moteurs 84-22300. Pour les moteurs 84-25100, 84-33800 et 38000, le réglage est de 300 bars (4320 psi). Bosch Rexroth Mellansel AB, Manuel d’installation et de maintenance, Hägglunds VI, FR 323-3br/2011 Installation 51/72 Fig. 59: Raccords principaux A et C Fig. 60: Raccords de drain D1 et D2 Fig. 61: Raccords de pression pilote X et Y PRUDENCE Contrôler le sens de rotation Hägglunds VI, FR 323-3br/2011, Manuel d’installation et de maintenance, Bosch Rexroth Mellansel AB 52/72 Installation 3.2.3 Raccords d’huile V46-C SD Cm D SA D2 D1 P D2 C M1 P M2 Am Cm Fig. 62: Orifice Description Dimensions Remarque : P* Raccord principal 1 1/2" Si P est utilisé comme entrée, le moteur tourne dans le sens de la flèche C* Raccord principal 1 1/2" Si C est utilisé comme entrée, le moteur tourne dans le sens opposé de la flèche D Raccord de drain BSP 3/4" M1 Raccord de pression de charge BSP 3/4" M2 Raccord de pression de charge BSP 3/4" Obturé. Utilisé comme point additionnel de charge SD Raccord de pression pilote BSP 1/2" Obturé SA Raccord de pression pilote BSP 1/2" 12 bars (170 psi). 6 bars (85 psi) pour valve fonctionnant à débit nul P Raccord de prise de pression BSP 1/2" Am, Cm Raccord de prise de pression BSP 3/4" Cm Raccord de prise de pression BSP 1/2" D2 Raccord de balayage ext. BSP 3/4" Note : Non marqué sur la valve * Bride SAE J518 C, code 62, 414 bars (6000 psi). Bosch Rexroth Mellansel AB, Manuel d’installation et de maintenance, Hägglunds VI, FR 323-3br/2011 Installation 53/72 3.2.4 Raccords d’huile V46-O M2 Am P Br Cm C D2 P D2 D1 D Cm SD SA Fig. 63: Orifice Description Dimensions P* Raccord principal 1 1/2" Remarque : C* Raccord principal 1 1/2" D Raccord de drain BSP 3/4" M2 Raccord de pression de charge BSP 3/8" SD Raccord de pression pilote BSP 1/2" Raccord de commutation cylindrée SA Raccord de pression pilote BSP 1/2" Raccord pilote externe pour valve d’équilibrage P, Cm Raccord de prise de pression BSP 1/2" A, Cm Raccord de prise de pression BSP 3/4" Br Raccord ligne de frein BSP 3/8" D2 Raccord de balayage ext. BSP 3/4" Note : Non marqué sur la valve * Bride SAE J518 C, code 62, 414 bars (6000 psi). Hägglunds VI, FR 323-3br/2011, Manuel d’installation et de maintenance, Bosch Rexroth Mellansel AB 54/72 Installation 3.3 Inversion du sens de rotation Il y a deux méthodes pour changer le sens de rotation du moteur : 1. L’alimentation d’huile est déplacée du raccord « A » (P) au raccord « C ». Le moteur tourne ensuite dans le sens inverse. 2. La position du distributeur change par rapport à la came (carter moteur). Ce changement est obtenu en déplaçant le distributeur à une autre encoche de clavette. Ces encoches de clavette existent sur les distributeurs des moteurs sauf pour les 84-14800, 84-25100 et 84-38000, qui n’ont qu’une seule encoche sur le distributeur. Contrôler qu’il s’adapte à la même profondeur qu’avant la dépose. Le distributeur doit être positionné de sorte que le « R » estampé pour rotation à droite ou le « L » pour rotation à gauche, s’aligne avec le « O » sur la came sous le bouchon dans le couvercle d’extrémité avant. Voir la fig. ci-dessous pour les respectives séries de moteurs. Pour un réglage plus précis du distributeur, voir les instructions spécifiques d’entretien. Sur les moteurs des séries 44 et 64, le distributeur est tourné de 90°. Pour les types 84-25100, 84-14800 et 84-38000, le distributeur est tourné de 180° et de 67,5° pour les types 84-22300 et 84-33800 Quand on change la rotation par cette méthode, il faut l’annoter sur la plaque construction et inverser la flèche sur le couvercle de l’extrémité avant. IMPORTANT ! Lors du remplissage et de la dépose du distributeur, faites attention pour ne pas causer d’endommagements. Vérifier qu’il s’insère à la même profondeur qu’avant sa dépose. PRUDENCE Contrôler le sens de rotation M10 Tous les moteurs Distributeur Fig. 64: Bosch Rexroth Mellansel AB, Manuel d’installation et de maintenance, Hägglunds VI, FR 323-3br/2011 Installation Couvercle d’extrémité arrière Accouplement de sécurité 55/72 Distributeur Bouchon Distributeur Bloc-cylindres Couvercle d’extrémité avant 4 goupilles de Ø 6 x 14 mm (Ø0,236 x 0,551 in) Fig. 65: Séries 44 et 64 Couvercle d’extrémité arrière Accouplement de sécurité Distributeur Bouchon Distributeur Bloc-cylindres Couvercle d’extrémité avant 4 goupilles de Ø 8 x 19 mm (Ø0,315 x 0,709 in) Fig. 66: Types 84-38000, 84-25100 et 84-14800 Couvercle d’extrémité arrière Accouplement de sécurité Distributeur Bouchon Distributeur L R Bloc-cylindres Couvercle d’extrémité avant 4 goupilles de Ø 6 x 14 mm (Ø0,236 x 0,551 in) Fig. 67: Types 84-22300 et 84-33800 Hägglunds VI, FR 323-3br/2011, Manuel d’installation et de maintenance, Bosch Rexroth Mellansel AB 56/72 Manutention 4 Manutention 4.1 Instructions pour le stockage A la livraison, le moteur est protégé à l’intérieur par un film d’huile et à l’extérieur par un film anticorrosion. Cette protection est suffisante pour le stockage dans un local fermé pour une période de 12 mois. IMPORTANT ! La protection antirouille doit être complétée après le transport et la manutention. Si le moteur doit être stocké pour plus de 3 mois dans un local non chauffé et 12 mois dans un local chauffé, il faut le remplir d’huile et le positionner avec le bloccylindres tourné vers le haut. Voir 2.3 « Choix du fluide hydraulique ». Remplir le moteur avec de l’huile filtrée en procédant dans l’ordre suivant : « 1 », « D1 », « C » et « A ». Soyez très prudent pour qu’aucune impureté ne pénètre dans le moteur avec l’huile. Obturer les raccords pour protéger leurs filetages et pour empêcher la pénétration d’impuretés. Contrôler que tous les bouchons sont correctement serrés. Les moteurs tenus en stock doivent être tournés de quelques tours à des intervalles réguliers (une fois par mois) afin de conserver le film d’huile sur toutes les pièces internes du moteur. Quantité d’huile requise pour les différents types de moteurs : 1 D1 A C Fig. 68: Séries Volume Litres US gallon 44 35 9,2 64 40 10,6 84 80 21,1 Bosch Rexroth Mellansel AB, Manuel d’installation et de maintenance, Hägglunds VI, FR 323-3br/2011 Manutention 57/72 4.2 Avant la mise en service Remplir le moteur avec de l’huile filtrée en procédant dans l’ordre suivant : « 1 », « D1 », « C » et « A ». Les points suivants doivent être vérifiés, en fonction du type de moteur, avant la mise en service : 1. Contrôler que le moteur est raccordé pour le sens de rotation correct. (voir 3.2 « Raccords d’huile » et 3.3 « Inversion du sens de rotation »). 2. Choisir le type de fluide hydraulique qui correspond aux recommandations d’huile (voir 2.3 « Choix de fluide hydraulique »). 3. Remplir le logement du moteur de fluide hydraulique au moins jusqu’au niveau de (voir 3.1 « Instructions de montage »). PRUDENCE 4. Contrôler la ligne de drainage pour rechercher les étranglements éventuels pouvant causer une surpression dans le carter du moteur (voir 3.1 « Instructions de montage »). 5. Contrôler que le moteur est protégé contre les surcharges (voir 1.2 « Caractéristiques techniques des moteurs »). 6. Contrôler que la pression de charge correspond au diagramme de la pression de charge (voir 2.1 « Pression recommandée »). 4.3 Mise en service Durant la période de mise en service, l’installation hydraulique doit être contrôlée régulièrement et soigneusement à des intervalles fréquents. La pression de service et celle de charge doivent être contrôlées et correspondre aux valeurs calculées. Les séries 44, 64 et 84 •• La pression dans la ligne de drainage, mesurée au moteur, doit être inférieure à 3 bars/43,5 psi (pour 1 % de la durée d’opération équitablement répartie, pointes de pression de maximum 5 secondes jusqu’à 8 bars /116 psi sont admissibles). •• Pour les moteurs avec joints en caoutchouc silicone, ces valeurs sont à réduire de 50 %. •• Ces limitations des pressions sont importantes pour la durée de vie de service du moteur. •• Dans le cas de fuites, réparer et effectuer ensuite les contrôles. •• Contrôler les lignes, raccords, brides, boulons etc. Serrez-les si besoin. •• Contrôler les autres points possibles de fuites et remplacer toute pièce défectueuse. •• Vidanger immédiatement le fluide hydraulique contaminé. •• Contrôler que les pièces en mouvement ne risquent pas de causer d’endommagements. Balayage du carter du moteur Pour éviter une température élevée dans le carter du moteur, il faut éliminer la chaleur par refroidissement, comme une température élevée donne une viscosité moindre avec résultat une durée de vie de service réduite. Une faible viscosité donne également une puissance de sortie admissible réduite du moteur. Hägglunds VI, FR 323-3br/2011, Manuel d’installation et de maintenance, Bosch Rexroth Mellansel AB 58/72 Manutention Pour un service constant dans les applications avec température ambiante de +20 °C (+68 °F), le carter du moteur doit être balayé lorsque la puissance de sortie dépasse les valeurs suivantes : Puissance max. sans balayage VI séries 44 et 64 120 kW 161 CV VI série 84 140 kW 188 CV Pour le calcul du balayage requis, veuillez contacter votre représentant Hägglunds. 4.4 Maintenance périodique Au bout d’un certain temps de service du système hydraulique, ce dernier doit faire l’objet d’une maintenance et d’une inspection à des intervalles réguliers, en fonction de l’équipement et du type d’exploitation. Cette maintenance périodique concerne les points suivants : •• Contrôler le système hydraulique du point de vue des fuites. Serrer les boulons, remplacer les joints et garnitures défectueux et, si nécessaire, nettoyer le système. •• Inspecter et nettoyer tous les filtres à air, à huile et magnétiques. Remplacer les cartouches de filtres, inspecter et, si nécessaire, laver réservoir, pompe, filtre etc. •• Réparer ou remplacer les pièces usées ou endommagées. •• Contrôler la pression et la température du fluide hydraulique et effectuer les autres contrôles de routine. Au besoin, ajuster les valves etc. •• Contrôler que le fluide hydraulique n’a pas vieilli. •• S’assurer qu’aucune impureté n’a pénétrée dans le système en cours de l’inspection. Si le moteur hydraulique d’un système est maintenu propre, les fuites et défectuosités peuvent être détectées plus tôt. Nous recommandons de tenir un journal de bord et d’effectuer les inspections programmées à des intervalles déterminés. Les contrôles et mesures sont à effectuer comme suit : Moteur Si le moteur n’est pas utilisé pendant une période prolongé, d’un mois environ, il doit être protégé de la corrosion interne. Plusieurs méthodes sont possibles : 1. Mélanger l’agent antirouille avec le fluide hydraulique. Utilisez par ex. 5 % Rust Veto Concentrate (fabricant : E.F. Houghton & Co., Philadelphia, USA). Cet additif peut être utilisé constamment et devrait protéger pendant un an. (Au bout de cette période, il faut faire tourner le moteur). 2. Sans additif, il faut faire tourner le moteur de quelques tours à des intervalles réguliers en démarrant le système hydraulique. 3. Dans l’impossibilité de faire tourner le moteur, obturer tous les raccords. Ouvrir le bouchon BSP 1 1/4" sur le couvercle d’extrémité avant et remplir le moteur d’huile (voir fig. à la page suivante). Bosch Rexroth Mellansel AB, Manuel d’installation et de maintenance, Hägglunds VI, FR 323-3br/2011 Manutention 59/72 Filtres Le premier entretien doit avoir lieu au bout de 1 mois ou 100 heures de service. Ensuite, les contrôles seront effectués tous les 6 mois ou toutes les 500 heures de service. Huiles L’huile perd sa viscosité au bout d’un certain temps, ce qui réduit son effet de lubrification. Une température et pression élevées réduisent toujours la durée de vie de l’huile. •• Au bout de 6 mois ou 4000 heures de service, (l’événement qui intervient le premier), il faut analyser l’huile. •• Nettoyer le réservoir d’huile hydraulique tous les ans. •• Vidanger l’huile dès que cela s’impose. •• Contrôler que le réservoir est propre à chaque vidange. Bouchon BSP 1 1/4" Fig. 69: Bras de réaction Si le bras de réaction de conception pivotante est exposé à une ambiance corrosive, il doit être lubrifié une fois par mois. Hägglunds VI, FR 323-3br/2011, Manuel d’installation et de maintenance, Bosch Rexroth Mellansel AB 60/72 Manutention PRUDENCE Ne pas souder, percer, poncer, meuler ou effectuer d´autres travaux similaires sur le bras de réaction sans l’accord de Hägglunds. Fig. 70: TAC 1250-B Équipement de frein Si l’équipement de frein est exposé à une ambiance corrosive : Sur le pont d’un navire, il doit être lubrifié une fois par mois. AVERTISSEMENT Contrôler que les garnitures de frein sont exemptes d’huile et d’impuretés ! Bosch Rexroth Mellansel AB, Manuel d’installation et de maintenance, Hägglunds VI, FR 323-3br/2011 Manutention 61/72 Fig. 71: TAC 1000-K Tableau d’entretien Série Après 1 mois ou Après 3 mois ou 100 heures 500 heures Tous les 6 mois Tous les douze mois Filtre à huile R R R – Huile – – C – Équipement de frein C* C C – Bras de réaction C* – C – R = Remplacement C = Contrôle * Si exposé à une ambiance corrosive, l’équipement doit être lubrifié une fois par mois. Hägglunds VI, FR 323-3br/2011, Manuel d’installation et de maintenance, Bosch Rexroth Mellansel AB 62/72 Manutention 4.4.1 Nettoyage et entretien PRUDENCE Les détergents agressifs peuvent endommager les joints sur le moteur hydraulique et accélérer leur vieillissement. ▶▶ • Ne jamais utiliser de solvants ou de détergents agressifs. ▶▶ • En cas de doute, vérifier la compatibilité du détergent avec le type d’étanchéité ▶▶ (Nitrile ou Viton) spécifié dans le moteur hydraulique. PRUDENCE L’utilisation d’un nettoyeur haute pression peut endommager le capteur de vitesse et les joints du moteur hydraulique. ▶▶ • Ne pas diriger le nettoyeur haute pression sur des composants sensibles, par ex. l’étanchéité de l’arbre, les joints en général, les connexions électriques et le capteur de vitesse. ▶▶ Pour le nettoyage et l’entretien du moteur hydraulique, respecter les consignes suivantes : ▶▶ • Boucher toutes les ouvertures avec des capuchons de protection/des dispositifs appropriés. ▶▶ • Vérifier si tous les bouchons et leurs joints sont correctement insérés pour assurer que l’humidité ne peut pas pénétrer dans le moteur hydraulique pendant le nettoyage. ▶▶ • Utiliser uniquement de l’eau et, si nécessaire, un détergent doux, pour nettoyer le moteur hydraulique. ▶▶ • Enlever les saletés grossières sur l’extérieur de la machine et maintenir propres les composants sensibles et importants, comme les capteurs et les blocs distributeurs. 4.5 Mise au rebut Lorsque le système ou un composant en particulier est usé, il doit être mis au rebut d’une manière respectueuse de l’environnement. De manière générale, les déchets doivent en premier lieu être réutilisés ou recyclés, suivi par leur élimination sans danger. Toute négligence en matière de mise au rebut du système, de ses composantes et de l’huile, peut conduire à la pollution de l’environnement. Veuillez par conséquent observer ce qui suit : •• Mettre au rebut les produits ou/et les composants en conformité avec les réglementations nationales dans votre pays et/ou les spécifications internes à votre entreprise. •• Mettre l’huile au rebut conformément à la fiche de données de sécurité du matériel applicable. Bosch Rexroth Mellansel AB, Manuel d’installation et de maintenance, Hägglunds VI, FR 323-3br/2011 Dépannage 63/72 5 Dépannage Symptôme Cause probable Action corrective Panne mécanique dans le système. Contrôler la pression système. Si la pression est montée à la valeur réglée sur la valve, décharger le moteur. Le moteur ne fournit pas un couple suffisant à cause d’une trop basse pression différentielle aux bornes du moteur, comparé à la charge. Contrôler le niveau de pression dans le système et corriger les réglages de la valve de décharge si besoin. Le réglage du distributeur a été modifié. Démonter le raccord de sécurité et le distributeur. Si les demisraccords se sont déplacés l’un par rapport à l’autre, remettez-les en position correcte à l’aide du trou d’indication (Ø 3 mm /0,118 in). Ensuite, monter de nouvelles goupilles : CP 6 x 14 mm (0,236 x 0,551 in) pour les séries 44 et 64. CP 8 x 19 mm (0,315 x 0,709 in) pour la série 84 en perçant sur le même rayon que les goupilles d’origine. Le moteur ne reçoit pas assez ou pas du tout d’huile. Contrôler le système hydraulique. Contrôler le moteur pour toute fuite externe (Raccord « D »). Raccords d’huile transférés. Raccords inversés. Distributeur mal monté. Déposer le distributeur et l’accouplement de sécurité et remonter pour une rotation correcte. Variations de pression ou de débit dans le système hydraulique. Contrôler le système hydraulique ou la transmission mécanique. Les réglages du distributeur ont été changés. Démonter le raccord de sécurité et le distributeur. Si les demisraccords se sont déplacés l’un par rapport à l’autre, remettez-les en position correcte à l’aide du trou d’indication (Ø 3 mm /0,118 in). Ensuite, monter de nouvelles goupilles : CP 6 x 14 mm (0,236 x 0,551 in) pour les séries 44 et 64. CP 8 x 19 mm (0,315 x 0,709 in) pour la série 84 en perçant sur le même rayon que les goupilles d’origine. Le moteur tournes à une pression de charge trop basse. Régler au niveau correct. Voir 2.1 « Pression de charge recommandée ». Les réglages du distributeur ont été changés. Démonter le raccord de sécurité et le distributeur. Si les demisraccords se sont déplacés l’un par rapport à l’autre, remettez-les en position correcte à l’aide du trou d’indication (Ø 3 mm /0,118 in). Ensuite, monter de nouvelles goupilles : CP 6 x 14 mm (0,236 x 0,551 in) pour les séries 44 et 64. CP 8 x 19 mm (0,315 x 0,709 in) pour la série 84 en perçant sur le même rayon que les goupilles d’origine. Panne interne au moteur. Si possible, contrôler l’huile de drain. Placer un aimant dans le flux d’huile et examiner tout matériau qui s’y attache. Des particules d’acier indiquent des dommages. Observer que de fines particules de l’acier fondu sont constamment rejetées et n’indiquent donc pas nécessairement une panne interne. La bague d’étanchéité dans l’extrémité avant est usée. Remplacer la bague. Le moteur ne marche pas Le moteur tourne dans le mauvais sens Le moteur tourne irrégulièrement Bruits dans le moteur. Fuites d’huile externes du moteur Hägglunds VI, FR 323-3br/2011, Manuel d’installation et de maintenance, Bosch Rexroth Mellansel AB 64/72 Dépannage Moteur hydraulique avec valve 2 vitesses, V46-C Panne Le moteur ne travaille que sur une vitesse Impossible de faire tourner le moteur en vitesse simple ou double (valve à 2 vitesses ou de type trois positions). Cause probable Action Bouchon 2 vitesses non monté. Monter le bouchon 2 vitesses au fond du raccord « A » dans le moteur. Valve à 2 vitesses de type à 2 positions montée - pression pilote trop basse. Pression pilote appropriée: Voir 3.2.5 pour la valve V46-C. Le piston de la valve est coincé en position vitesse unique à cause d’impuretés dans l’huile. Démonter le piston et retirer les impuretés. Pression pilote trop basse. Pression pilote requise : Voir 3.2.5 pour la valve V46-C. Le piston de la valve est coincé en position 0 à cause d’impuretés. Démonter le piston et retirer les impuretés. Moteur hydraulique avec valve d’équilibrage V46-O Panne Cause probable Action Le moteur ne tourne que dans un sens Le piston de la valve est coincé dans la position déchargée. Démonter le piston et retirer les impuretés. Le moteur ne fournit pas de pression de retour. Le piston de la valve est coincé dans la position entièrement ouverte. Démonter le piston et retirer les impuretés. Moteur hydraulique avec frein à bande Panne Cause probable Action Le frein est mal réglé. Régler le frein. Voir les instructions pour le réglage du frein au 3.1.5 « Moteur – support avant ». Le cylindre du frein n’est pas drainé comme prescrit, une contre-pression excessive dans la conduite de drainage. Éliminer la cause de la pression. Pour la pression d’ouverture requise, voir la section portant sur le drainage du cylindre de frein au 3.1.5 « Moteur – support avant ». Le frein à bande et la surface du frein sont sales ou graisseux. Démonter la bande de frein et polir la surface de la garniture avec du papier émeri. Nettoyer la surface de freinage sur le moteur. Si besoin, remplacer la bande de frein complète. Le moteur cogne au ralenti Le frein est trop tendu. La bande du frein est appliquée malgré l’ouverture du frein. Soulager la tension. Voir la section portant sur le drainage du cylindre de frein au 3.1.5 « Moteur – support avant ». Le frein ne s’ouvre pas Pression insuffisante pour l’ouverture du frein. Pour la pression d’ouverture requise, voir la section portant sur le drainage du cylindre de frein au 3.1.5 « Moteur – support avant ». Fuite d’huile du cylindre de frein Joints ou piston endommagés. Remplacer les joints/les pistons. IMPORTANT / PRUDENCE ! Le ressort dans le cylindre de frein est tendu. Couple de freinage insuffisant Bosch Rexroth Mellansel AB, Manuel d’installation et de maintenance, Hägglunds VI, FR 323-3br/2011 Dessins 65/72 6 Dessins Bloc-cylindres Palier principal arrière Accouplement de sécurité Couvercle Distributeur Couvercle d’extrémité arrière Plaque de guidage Palier principal avant Piston et tige de piston Tourillon de traverse Came Galet de roulement Couvercle d’extrémité avant Fig. 72: Série 44 Bloc-cylindres Couvercle Accouplement de sécurité Distributeur Palier principal arrière Couvercle d’extrémité arrière Plaque de guidage Palier principal avant Couvercle d’extrémité avant Piston et tige de piston Galet de roulement Tourillon de traverse Came Fig. 73: Série 64 Hägglunds VI, FR 323-3br/2011, Manuel d’installation et de maintenance, Bosch Rexroth Mellansel AB 66/72 Dessins Bloc-cylindres Couvercle Accouplement de sécurité Distributeur Palier principal arrière Couvercle d’extrémité arrière Plaque de guidage Palier principal avant Piston et tige de piston Rouleau à cames Tourillon de traverse Came Couvercle d’extrémité avant Fig. 74: Série 84 Bosch Rexroth Mellansel AB, Manuel d’installation et de maintenance, Hägglunds VI, FR 323-3br/2011 Déclaration de conformité 67/72 7 Déclaration de conformité Exemple de Déclaration de conformité délivrée par Hägglunds Drives AB Declaration of Incorporation of partly completed machinery As defined by the EC Machinery Directive 2006/42/EC, Appendix II B The manufacturer Hägglunds Drives AB hereby declares that the partly completed machinery Name: Function: Model: Type: Trade name: Viking Hydraulic motor Viking Viking Viking satisfies the following essential requirements of Machinery Directive 2006/42/EC in accordance with the chapter numbers in Appendix I: General principle no. 1. 1.1.3 1.1.5 1.3.1 1.3.2 1.3.3 1.3.4 1.3.6 1.3.7 1.5.3 1.5.5 1.5.6 1.5.8 1.5.13 1.6.1 1.6.3 1.7.2 1.7.3 1.7.4 1.5.4 The requirements are fulfilled provided that the data in the product documentation (fitting instructions, operating instructions, project management and configuration documents) are implemented by the product user. The requirements of Appendix I to Machinery Directive 2006/42/EC not mentioned here are not applied and have no relevance for the product. It is also declared that the special technical documents for this partly completed machinery have been compiled in accordance with Appendix VII, Part B. These are transferred on request to the market surveillance body in paper-based/electronic format. Conformity with the provisions of further EU Directives, Standards or Specifications: SS-EN 982 SS-EN ISO 12100-1 SS-EN ISO 12100-2 The partly completed machinery may only be put into operation when it has been established that the machine into which the partly completed machinery is to be incorporated conforms to the provisions of EC Machinery Directive 2006/42/EC, where relevant according to this directive. The individual below is authorized to compile the relevant technical files: Name: Address: Björn Leidelöf Hägglunds Drives AB, S-890 42 Mellansel Mellansel, 2009-12-29 We reserve the right to make changes to the content of the Declaration of Incorporation. Current issue on request. La déclaration de conformité ci-dessus est disponible sur demande pour les fournitures de Hägglunds Drives AB. Cette déclaration existe aussi traduite en d’autres langues. Hägglunds VI, FR 323-3br/2011, Manuel d’installation et de maintenance, Bosch Rexroth Mellansel AB 68/72 Dessins NOTES Bosch Rexroth Mellansel AB, Manuel d’installation et de maintenance, Hägglunds VI, FR 323-3br/2011 Dessins 69/72 NOTES Hägglunds VI, FR 323-3br/2011, Manuel d’installation et de maintenance, Bosch Rexroth Mellansel AB 70/72 Dessins NOTES Bosch Rexroth Mellansel AB, Manuel d’installation et de maintenance, Hägglunds VI, FR 323-3br/2011 Dessins 71/72 NOTES Hägglunds VI, FR 323-3br/2011, Manuel d’installation et de maintenance, Bosch Rexroth Mellansel AB Bosch Rexroth Mellansel AB SE-895 80 Mellansel Suède Tél. +46 (0) 660 870 00 Fax +46 (0) 660 871 60 [email protected] www.boschrexroth.com/hagglunds Vous trouverez votre contact local à l’adresse : www.boschrexroth.com/adresses Nous nous réservons le droit d’effectuer à tout moment des modifications sans préavis Imprimé en Suède FR 323-3br/2011 ">
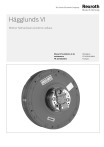
Enlace público actualizado
El enlace público a tu chat ha sido actualizado.