ESAB m2™ Plasma Smart Plasmarc™ 200 Cutting System Manuel utilisateur
PDF
Herunterladen
Dokument
Système de coupage Smart Plasmarc ™ 200 Manuel d’utilisation (FR) 0558012541 02/2015 Smart Plasmarc 200 TM ASSUREZ-VOUS QUE CETTE INFORMATION EST DISTRIBUÉE À L'OPÉRATEUR. VOUS POUVEZ OBTENIR DES COPIES SUPPLÉMENTAIRES CHEZ VOTRE FOURNISSEUR. aTTENTION Les INSTRUCTIONS suivantes sont destinées aux opérateurs qualifiés seulement. Si vous n’avez pas une connaissance approfondie des principes de fonctionnement et des règles de sécurité pour le soudage à l’arc et l’équipement de coupage, nous vous suggérons de lire notre brochure « Precautions and Safe Practices for Arc Welding, Cutting and Gouging, » Formulaire 52-529. Ne permettez PAS aux personnes non qualifiées d’installer, d’opérer ou de faire l’entretien de cet équipement. Ne tentez PAS d’installer ou d’opérer cet équipement avant de lire et de bien comprendre ces instructions. Si vous ne comprenez pas bien les instructions, communiquez avec votre fournisseur pour plus de renseignements. Assurez-vous de lire les Règles de Sécurité avant d’installer ou d’opérer cet équipement. RESPONSABILITÉS DE L'UTILISATEUR Cet équipement opérera conformément à la description contenue dans ce manuel, les étiquettes d’accompagnement et/ou les feuillets d’information si l’équipement est installé, opéré, entretenu et réparé selon les instructions fournies. Vous devez faire une vérification périodique de l’équipement. Ne jamais utiliser un équipement qui ne fonctionne pas bien ou n’est pas bien entretenu. Les pièces qui sont brisées, usées, déformées ou contaminées doivent être remplacées immédiatement. Dans le cas où une réparation ou un remplacement est nécessaire, il est recommandé par le fabricant de faire une demande de conseil de service écrite ou par téléphone chez le Distributeur Autorisé de votre équipement. Cet équipement ou ses pièces ne doivent pas être modifiés sans permission préalable écrite par le fabricant. L’utilisateur de l’équipement sera le seul responsable de toute défaillance résultant d’une utilisation incorrecte, un entretien fautif, des dommages, une réparation incorrecte ou une modification par une personne autre que le fabricant ou un centre de service désigné par le fabricant. ASSUREZ-VOUS DE LIRE ET DE COMPRENDRE LE MANUEL D'UTILISATION AVANT D'INSTALLER OU D'OPÉRER L'UNITÉ. PROTÉGEZ-VOUS ET LES AUTRES ! 3 Smart Plasmarc 200 Page intentionnellement laissée en blanc 4 TM Smart Plasmarc 200 TM Table des matières SÉCURITÉ Précautions de sécurité . . . . . . . . . . . . . . . . . . . . . . . . . . . . . . . . . . . . . . . . . . . . . . . . . . . . . . . . . . . . . . . . . . . . . . . . . . 11 DESCRIPTION Généralités . . . . . . . . . . . . . . . . . . . . . . . . . . . . . . . . . . . . . . . . . . . . . . . . . . . . . . . . . . . . . . . . . . . . . . . . . . . . . . . . . . . . . 15 m2 Smart Plasmarc 200 System Interconnect Diagram . . . . . . . . . . . . . . . . . . . . . . . . . . . . . . . . . . . . . . . . . . . . . 16 Commandes d’ensembles . . . . . . . . . . . . . . . . . . . . . . . . . . . . . . . . . . . . . . . . . . . . . . . . . . . . . . . . . . . . . . . . . . . . . . . . . . . . 17 Câbles et tuyaux . . . . . . . . . . . . . . . . . . . . . . . . . . . . . . . . . . . . . . . . . . . . . . . . . . . . . . . . . . . . . . . . . . . . . . . . . . . . . . . . . 18 Console Plasma . . . . . . . . . . . . . . . . . . . . . . . . . . . . . . . . . . . . . . . . . . . . . . . . . . . . . . . . . . . . . . . . . . . . . . . . . . . . . . . . . 20 Caractéristiques . . . . . . . . . . . . . . . . . . . . . . . . . . . . . . . . . . . . . . . . . . . . . . . . . . . . . . . . . . . . . . . . . . . . . . . . . . . . . . . . . . . . . 20 Caractéristiques techniques . . . . . . . . . . . . . . . . . . . . . . . . . . . . . . . . . . . . . . . . . . . . . . . . . . . . . . . . . . . . . . . . . . . . . . . . . . 20 Dimensions . . . . . . . . . . . . . . . . . . . . . . . . . . . . . . . . . . . . . . . . . . . . . . . . . . . . . . . . . . . . . . . . . . . . . . . . . . . . . . . . . . . . . . . . . 21 Commande interface (IC) . . . . . . . . . . . . . . . . . . . . . . . . . . . . . . . . . . . . . . . . . . . . . . . . . . . . . . . . . . . . . . . . . . . . . . . . . . . . 21 Régulateur de gaz combinés (CGC-2) . . . . . . . . . . . . . . . . . . . . . . . . . . . . . . . . . . . . . . . . . . . . . . . . . . . . . . . . . . . . . . 23 Connexions . . . . . . . . . . . . . . . . . . . . . . . . . . . . . . . . . . . . . . . . . . . . . . . . . . . . . . . . . . . . . . . . . . . . . . . . . . . . . . . . . . . . . . . . . 23 Spécifications . . . . . . . . . . . . . . . . . . . . . . . . . . . . . . . . . . . . . . . . . . . . . . . . . . . . . . . . . . . . . . . . . . . . . . . . . . . . . . . . . . . . . . . 24 Dimensions . . . . . . . . . . . . . . . . . . . . . . . . . . . . . . . . . . . . . . . . . . . . . . . . . . . . . . . . . . . . . . . . . . . . . . . . . . . . . . . . . . . . . . . . . 24 Démarreur à arc à distance-2 (RAS) . . . . . . . . . . . . . . . . . . . . . . . . . . . . . . . . . . . . . . . . . . . . . . . . . . . . . . . . . . . . . . . 28 Spécifications . . . . . . . . . . . . . . . . . . . . . . . . . . . . . . . . . . . . . . . . . . . . . . . . . . . . . . . . . . . . . . . . . . . . . . . . . . . . . . . . . . . . . . . 28 Dimensions . . . . . . . . . . . . . . . . . . . . . . . . . . . . . . . . . . . . . . . . . . . . . . . . . . . . . . . . . . . . . . . . . . . . . . . . . . . . . . . . . . . . . . . . . 28 Connexions . . . . . . . . . . . . . . . . . . . . . . . . . . . . . . . . . . . . . . . . . . . . . . . . . . . . . . . . . . . . . . . . . . . . . . . . . . . . . . . . . . . . . . . . . 29 Dimensions de fixation . . . . . . . . . . . . . . . . . . . . . . . . . . . . . . . . . . . . . . . . . . . . . . . . . . . . . . . . . . . . . . . . . . . . . . . . . . . . . . 31 Torche de coupage mécanisée Plasmarc PT-36 . . . . . . . . . . . . . . . . . . . . . . . . . . . . . . . . . . . . . . . . . . . . . . . . . . . . . 32 Options d’ensembles disponibles . . . . . . . . . . . . . . . . . . . . . . . . . . . . . . . . . . . . . . . . . . . . . . . . . . . . . . . . . . . . . . . . . . . . 32 Spécifications . . . . . . . . . . . . . . . . . . . . . . . . . . . . . . . . . . . . . . . . . . . . . . . . . . . . . . . . . . . . . . . . . . . . . . . . . . . . . . . . . . . . . . . 32 Dimensions . . . . . . . . . . . . . . . . . . . . . . . . . . . . . . . . . . . . . . . . . . . . . . . . . . . . . . . . . . . . . . . . . . . . . . . . . . . . . . . . . . . . . . . . . 33 Régulateurs recommandés . . . . . . . . . . . . . . . . . . . . . . . . . . . . . . . . . . . . . . . . . . . . . . . . . . . . . . . . . . . . . . . . . . . . . . . . . . . 33 Liquide de refroidissement . . . . . . . . . . . . . . . . . . . . . . . . . . . . . . . . . . . . . . . . . . . . . . . . . . . . . . . . . . . . . . . . . . . . . . . . . . . 33 INSTALLATION Installation . . . . . . . . . . . . . . . . . . . . . . . . . . . . . . . . . . . . . . . . . . . . . . . . . . . . . . . . . . . . . . . . . . . . . . . . . . . . . . . . . . . . . 37 Généralités . . . . . . . . . . . . . . . . . . . . . . . . . . . . . . . . . . . . . . . . . . . . . . . . . . . . . . . . . . . . . . . . . . . . . . . . . . . . . . . . . . . . . . . . . . 37 Déballage . . . . . . . . . . . . . . . . . . . . . . . . . . . . . . . . . . . . . . . . . . . . . . . . . . . . . . . . . . . . . . . . . . . . . . . . . . . . . . . . . . . . . . . . . . . 37 À vérifier dès réception . . . . . . . . . . . . . . . . . . . . . . . . . . . . . . . . . . . . . . . . . . . . . . . . . . . . . . . . . . . . . . . . . . . . . . . . . . . . . . 37 Avant installation . . . . . . . . . . . . . . . . . . . . . . . . . . . . . . . . . . . . . . . . . . . . . . . . . . . . . . . . . . . . . . . . . . . . . . . . . . . . . . . . . . . . 37 Mise à la terre . . . . . . . . . . . . . . . . . . . . . . . . . . . . . . . . . . . . . . . . . . . . . . . . . . . . . . . . . . . . . . . . . . . . . . . . . . . . . . . . . . . 38 Introduction . . . . . . . . . . . . . . . . . . . . . . . . . . . . . . . . . . . . . . . . . . . . . . . . . . . . . . . . . . . . . . . . . . . . . . . . . . . . . . . . . . . . . . . . . 38 Éléments d’un système de mise à la terre . . . . . . . . . . . . . . . . . . . . . . . . . . . . . . . . . . . . . . . . . . . . . . . . . . . . . . . . . . . . . 41 Tige de mise à la terre . . . . . . . . . . . . . . . . . . . . . . . . . . . . . . . . . . . . . . . . . . . . . . . . . . . . . . . . . . . . . . . . . . . . . . . . . . . . . . . 46 Schéma de mise à la terre de la machine . . . . . . . . . . . . . . . . . . . . . . . . . . . . . . . . . . . . . . . . . . . . . . . . . . . . . . . . . . . . . . 49 5 Smart Plasmarc 200 TM Placement de la Console Plasma . . . . . . . . . . . . . . . . . . . . . . . . . . . . . . . . . . . . . . . . . . . . . . . . . . . . . . . . . . . . . . . . . . 50 Branchement de l’alimentation d’entrée . . . . . . . . . . . . . . . . . . . . . . . . . . . . . . . . . . . . . . . . . . . . . . . . . . . . . . . . . . . . . . 51 Conducteurs d’entrée . . . . . . . . . . . . . . . . . . . . . . . . . . . . . . . . . . . . . . . . . . . . . . . . . . . . . . . . . . . . . . . . . . . . . . . . . . . . . . . . 52 Procédure de connexion de refroidissement . . . . . . . . . . . . . . . . . . . . . . . . . . . . . . . . . . . . . . . . . . . . . . . . . . . . . . . . . . 57 Connexions de sortie . . . . . . . . . . . . . . . . . . . . . . . . . . . . . . . . . . . . . . . . . . . . . . . . . . . . . . . . . . . . . . . . . . . . . . . . . . . . . . . . 59 Connexions des composants individuels . . . . . . . . . . . . . . . . . . . . . . . . . . . . . . . . . . . . . . . . . . . . . . . . . . . . . . . . . . . . . 62 Placement du Régulateur de gaz combinés (CGC-2) . . . . . . . . . . . . . . . . . . . . . . . . . . . . . . . . . . . . . . . . . . . . . . . . 66 Connexions de CGC-2 à RAS . . . . . . . . . . . . . . . . . . . . . . . . . . . . . . . . . . . . . . . . . . . . . . . . . . . . . . . . . . . . . . . . . . . . . . . . . . 67 Placement de la boîte RAS . . . . . . . . . . . . . . . . . . . . . . . . . . . . . . . . . . . . . . . . . . . . . . . . . . . . . . . . . . . . . . . . . . . . . . . 68 Connexions sur la boîte RAS - Montage à distance sur la machine . . . . . . . . . . . . . . . . . . . . . . . . . . . . . . . . . . . . . . 68 Connexions sur la boîte RAS - Montage local sur la Console Plasma . . . . . . . . . . . . . . . . . . . . . . . . . . . . . . . . . . . . 70 Connexions de la torche . . . . . . . . . . . . . . . . . . . . . . . . . . . . . . . . . . . . . . . . . . . . . . . . . . . . . . . . . . . . . . . . . . . . . . . . . 71 Connexion de la torche au système au plasma . . . . . . . . . . . . . . . . . . . . . . . . . . . . . . . . . . . . . . . . . . . . . . . . . . . . . . . . 71 Montage de la torche sur la machine . . . . . . . . . . . . . . . . . . . . . . . . . . . . . . . . . . . . . . . . . . . . . . . . . . . . . . . . . . . . . . . . 72 Préparation à la coupe . . . . . . . . . . . . . . . . . . . . . . . . . . . . . . . . . . . . . . . . . . . . . . . . . . . . . . . . . . . . . . . . . . . . . . . . . . . . . . . 73 FONCTIONNEMENT Fonctionnement . . . . . . . . . . . . . . . . . . . . . . . . . . . . . . . . . . . . . . . . . . . . . . . . . . . . . . . . . . . . . . . . . . . . . . . . . . . . . . . . 81 Commande interface . . . . . . . . . . . . . . . . . . . . . . . . . . . . . . . . . . . . . . . . . . . . . . . . . . . . . . . . . . . . . . . . . . . . . . . . . . . . 83 Écrans d’affichage . . . . . . . . . . . . . . . . . . . . . . . . . . . . . . . . . . . . . . . . . . . . . . . . . . . . . . . . . . . . . . . . . . . . . . . . . . . . . . . . . . . 84 Séquence de fonctionnement . . . . . . . . . . . . . . . . . . . . . . . . . . . . . . . . . . . . . . . . . . . . . . . . . . . . . . . . . . . . . . . . . . . . . . . . 85 E/S numériques . . . . . . . . . . . . . . . . . . . . . . . . . . . . . . . . . . . . . . . . . . . . . . . . . . . . . . . . . . . . . . . . . . . . . . . . . . . . . . . . . . . . . 91 Description du câblage d’interface . . . . . . . . . . . . . . . . . . . . . . . . . . . . . . . . . . . . . . . . . . . . . . . . . . . . . . . . . . . . . . . . . . . 92 DONNÉES DE COUPE Données de coupe . . . . . . . . . . . . . . . . . . . . . . . . . . . . . . . . . . . . . . . . . . . . . . . . . . . . . . . . . . . . . . . . . . . . . . . . . . . . . . . 97 Les données de coupe ont été recueillies à l’aide des matériaux suivants : . . . . . . . . . . . . . . . . . . . . . . . . . . . . . . 99 Production - acier carbone . . . . . . . . . . . . . . . . . . . . . . . . . . . . . . . . . . . . . . . . . . . . . . . . . . . . . . . . . . . . . . . . . . . . . . . . . . 101 Production - aluminium . . . . . . . . . . . . . . . . . . . . . . . . . . . . . . . . . . . . . . . . . . . . . . . . . . . . . . . . . . . . . . . . . . . . . . . . . . . . . 111 Production - acier inoxydable . . . . . . . . . . . . . . . . . . . . . . . . . . . . . . . . . . . . . . . . . . . . . . . . . . . . . . . . . . . . . . . . . . . . . . . 123 6 Smart Plasmarc 200 TM MAINTENANCE / TROUBLESHOOTING Maintenance . . . . . . . . . . . . . . . . . . . . . . . . . . . . . . . . . . . . . . . . . . . . . . . . . . . . . . . . . . . . . . . . . . . . . . . . . . . . . . . . . . . 137 General . . . . . . . . . . . . . . . . . . . . . . . . . . . . . . . . . . . . . . . . . . . . . . . . . . . . . . . . . . . . . . . . . . . . . . . . . . . . . . . . . . . . . . . . . . . . 137 Cleaning . . . . . . . . . . . . . . . . . . . . . . . . . . . . . . . . . . . . . . . . . . . . . . . . . . . . . . . . . . . . . . . . . . . . . . . . . . . . . . . . . . . . . . . . . . . 137 Troubleshooting . . . . . . . . . . . . . . . . . . . . . . . . . . . . . . . . . . . . . . . . . . . . . . . . . . . . . . . . . . . . . . . . . . . . . . . . . . . . . . . 142 Troubleshooting Guide . . . . . . . . . . . . . . . . . . . . . . . . . . . . . . . . . . . . . . . . . . . . . . . . . . . . . . . . . . . . . . . . . . . . . . . . . . . . . 142 Fault Isolation . . . . . . . . . . . . . . . . . . . . . . . . . . . . . . . . . . . . . . . . . . . . . . . . . . . . . . . . . . . . . . . . . . . . . . . . . . . . . . . . . . . . . . 143 IC Maintenance/Troubleshooting . . . . . . . . . . . . . . . . . . . . . . . . . . . . . . . . . . . . . . . . . . . . . . . . . . . . . . . . . . . . . . . . 144 Error Messages on the IC Display . . . . . . . . . . . . . . . . . . . . . . . . . . . . . . . . . . . . . . . . . . . . . . . . . . . . . . . . . . . . . . . . . . . . 145 Module Errors . . . . . . . . . . . . . . . . . . . . . . . . . . . . . . . . . . . . . . . . . . . . . . . . . . . . . . . . . . . . . . . . . . . . . . . . . . . . . . . . . . . . . . 147 Process Errors . . . . . . . . . . . . . . . . . . . . . . . . . . . . . . . . . . . . . . . . . . . . . . . . . . . . . . . . . . . . . . . . . . . . . . . . . . . . . . . . . . . . . . 148 CAN PS Errors . . . . . . . . . . . . . . . . . . . . . . . . . . . . . . . . . . . . . . . . . . . . . . . . . . . . . . . . . . . . . . . . . . . . . . . . . . . . . . . . . . . . . . 149 Torch Maintenance/Troubleshooting . . . . . . . . . . . . . . . . . . . . . . . . . . . . . . . . . . . . . . . . . . . . . . . . . . . . . . . . . . . . 151 Torch Front End Disassembly . . . . . . . . . . . . . . . . . . . . . . . . . . . . . . . . . . . . . . . . . . . . . . . . . . . . . . . . . . . . . . . . . . . . . . . . 151 Torch Front End Assembly . . . . . . . . . . . . . . . . . . . . . . . . . . . . . . . . . . . . . . . . . . . . . . . . . . . . . . . . . . . . . . . . . . . . . . . . . . 154 Torch Front End Assembly using the Speedloader (optional) . . . . . . . . . . . . . . . . . . . . . . . . . . . . . . . . . . . . . . . . . . 155 Torch Body Maintenance . . . . . . . . . . . . . . . . . . . . . . . . . . . . . . . . . . . . . . . . . . . . . . . . . . . . . . . . . . . . . . . . . . . . . . . . . . 156 Torch Body Removal and Replacement . . . . . . . . . . . . . . . . . . . . . . . . . . . . . . . . . . . . . . . . . . . . . . . . . . . . . . . . . . . . . . 157 Reduced Consumable Life . . . . . . . . . . . . . . . . . . . . . . . . . . . . . . . . . . . . . . . . . . . . . . . . . . . . . . . . . . . . . . . . . . . . . . . . . 159 Checking for Coolant Leaks . . . . . . . . . . . . . . . . . . . . . . . . . . . . . . . . . . . . . . . . . . . . . . . . . . . . . . . . . . . . . . . . . . . . . . . . . 160 REPLACEMENT PARTS Replacement Parts . . . . . . . . . . . . . . . . . . . . . . . . . . . . . . . . . . . . . . . . . . . . . . . . . . . . . . . . . . . . . . . . . . . . . . . . . . . . . 163 General . . . . . . . . . . . . . . . . . . . . . . . . . . . . . . . . . . . . . . . . . . . . . . . . . . . . . . . . . . . . . . . . . . . . . . . . . . . . . . . . . . . . . . . . . . . . 163 Ordering . . . . . . . . . . . . . . . . . . . . . . . . . . . . . . . . . . . . . . . . . . . . . . . . . . . . . . . . . . . . . . . . . . . . . . . . . . . . . . . . . . . . . . . . . . . 163 7 Smart Plasmarc 200 8 TM SÉCURITÉ SAFETY Page intentionnellement laissée en blanc 10 SAFETY Précautions de sécurité Les utilisateurs du matériel de soudage et de coupage plasma ESAB ont la responsabilité ultime d'assurer que toute personne qui opère ou qui se trouve dans l'aire de travail observe les précautions de sécurité pertinentes. Les précautions de sécurité doivent répondre aux exigences applicables à ce type de matériel de soudage ou de coupage plasma. Les recommandations suivantes doivent être observées en plus des règles standard qui s'appliquent au lieu de travail. Tous les travaux doivent être effectués par un personnel qualifié possédant de bonnes connaissances par rapport au fonctionnement du matériel de soudage et de coupage plasma. Un fontionnement incorrect du matériel peut produire des situations dangereuses qui peuvent causer des blessures à l'opérateur ou des dommages au matériel. 1. Toute personne travaillant avec le matériel de soudage ou de coupage plasma doit connaître : - son fonctionnement; - l'emplacement des interrupteurs d'arrêt d'urgence; - sa fonction; - les précautions de sécurité pertinentes; - les procédures de soudage et/ou de coupage plasma. 2. L'opérateur doit assurer que : - seules les personnes autorisées à travailler sur l'équipement se trouvent dans l'aire de travail lors de la mise en marche de l'équipement; - toutes les personnes dans l'aire de travail sont protégées lorsque l'arc est amorcé. 3. Le lieu de travail doit être : - aménagé convenablement pour acquérir le matériel en toute sécurité; - libre de courants d'air. 4. Équipement de sécurité personnelle - Vous devez toujours utiliser un équipement de sécurité convenable tels que les lunettes de protection, les vêtement ininflammables et des gants de protection. - Vous ne devez jamais porter de vêtements amples, tels que foulards, bracelets, bagues, etc., qui pourraient se prendre dans l'appareil ou causer des brûlures. 5. Précautions générales : - Assurez-vous que le câble de retour est bien branché. - La réparation d'un équipement de haute tension doit être effectuée par un électricien qualifié seulement. - Un équipement d'extinction d'incendie approprié doit être à proximité de l'appareil et l'emplacement doit être clairement indiqué. - Vous ne devez jamais procéder à la lubrification ou l'entretien du matériel lorsque l'appareil est en marche. Classe de boîtier Le code IP indique la classe du boîtier, à savoir le niveau de protection offert contre toute pénétration par des objets solides ou de l’eau. La protection est fournie contre le contact d’un doigt, la pénétration d’objets solides d’une taille supérieure à 12 mm et contre l’eau pulvérisée jusqu’à 60 degrés de la verticale. L’équipement marqué IP21S peut être stocké mais ne doit pas être utilisé à l’extérieur quand il pleut à moins d’être sous abri. ATTENTION Si l’équipement est placé sur une surface inclinée de plus de 15°, il y a danger de basculement et en conséquence, des blessures personnelles et/ou des dommages importants à l’équipement. Inclinaison maximum autorisée 15° 11 SAFETY AVERTISSEMENT LE SOUDAGE ET LE COUPAGE À L'ARC PEUVENT CAUSER DES BLESSURES À L'OPÉRATEUR OU LES AUTRES PERSONNES SE TROUVANT DANS L'AIRE DE TRAVAIL. ASSUREZ-VOUS DE PRENDRE TOUTES LES PRÉCAUTIONS NÉCESSAIRES LORS D'UNE OPÉRATION DE SOUDAGE OU DE COUPAGE. DEMANDEZ À VOTRE EMPLOYEUR UNE COPIE DES MESURES DE SÉCURITÉ QUI DOIVENT ÊTRE ÉLABORÉES À PARTIR DES DONNÉES DES RISQUE DU FABRICANT. CHOC ÉLECTRIQUE - peut être mortel. - Assurez-vous que l'unité de soudage ou de coupage plasma est installée et mise à la terre conformément aux normes applicables. - Ne touchez pas aux pièces électriques sous tension ou les électrodes si vos mains ne sont pas bien protégées ou si vos gants ou vos vêtements sont humides. - Assurez-vous que votre corps est bien isolé de la mise à la terre et de la pièce à traiter. - Assurez-vous que votre position de travail est sécure. VAPEURS ET GAZ - peuvent être danereux pour la santé. - Gardez votre tête éloignée des vapeurs. - Utilisez un système de ventilation et/ou d'extraction à l'arc pour évacuer les vapeurs et les gaz de votre zone respiratoire. RAYONS DE L'ARC - peuvent endommager la vue ou brûler la peau. - Protégez vos yeux et votre corps. Utilisez un écran de soudage/coupage plasma convenable équipé de lentilles teintées et portez des vêtements de protection. - Protégez les personnes se trouvant dans l'aire de travail à l'aide d'un écran ou d'un rideau protecteur convenable. RISQUE D'INCENDIE - Les étincelles (projections) peuvent causer un incendie. Assurez-vous qu'il n'y a pas de matériel inflammable à proximité de l'appareil. BRUIT - un bruit excessif peut endommager la capacité auditive. - Protégez vos oreilles. Utilisez des protecteurs d'oreilles ou un autre type de protection auditive. - Avertissez les personnes se trouvant dans l'aire de travail de ce risque. FONCTIONNEMENT DÉFECTUEUX - Dans le cas d'un fonctionnement défectueux demandez l'aide d'une personne qualifiée. ASSUREZ-VOUS DE LIRE ET DE COMPRENDRE LE MANUEL D'UTILISATION AVANT D'INSTALLER OU D'OPÉRER L'UNITÉ. PROTÉGEZ-VOUS ET LES AUTRES ! ATTENTION Ce produit est uniquement destiné à la découpe du plasma. Toute autre utilisation peut entraîner des blessures ou endommager l’équipement. ATTENTION Pour éviter toute blessure personnelle et/ou endommagement à l’équipement, soulever à l’aide de la méthode et des points d’attache indiqués ici. 12 DESCRIPTION description Page intentionnellement laissée en blanc 14 description AVERTISSEMENT L’utilisation de torches non conçues pour être utilisées avec cette console pourrait créer un RISQUE DE CHOC ÉLECTRIQUE. Généralités Le Système de coupage m2 Smart Plasmarc TM 200 peut être assemblé comme l’indique le schéma de câblage et est prêt à couper après avoir été connecté à une alimentation d’entrée et une source d’air comprimé. Le système utilise la torche PT-36 de qualité industrielle pour fournir une puissance de coupage pour couper des matériaux allant jusqu’à 2,00” (50 mm). Consulter les pages suivantes pour les descriptions de ensembles disponibles ainsi que les spécifications de performance. Le schéma d’interconnexion montre les configurations disponibles sur le Système de coupage m2 Smart Plasmarc TM 200. Une variété de configurations est disponible pour répondre aux exigences des clients. Le présent manuel à pour but de fournir à l’opérateur toutes les informations requises pour installer et exploiter l’ensemble de coupage. Du matériel de référence technique est également fourni pour faciliter le dépannage de l’ensemble de coupage. Kit de démarrage m2 200A PT-36 ............................................................................ réf. 0558012329 Quantité Réf. Description 1 0558002533 DÉFLECTEUR 4 TROUS x 0,032" PT-36 1 0558001625 DÉFLECTEUR 8 TROUS x 0,047" PT-36 5 0558012000 ÉLECTRODE AIR TL, Standard PT-36 5 0558012318 ÉLECTRODE O2 TL, Standard PT-36 5 0558011619 BUSE XR 1,9 mm (0,073") PT-36 5 0558010722 BUSE XR 2,2 mm (0,085") PT-36 5 0004470031 DIFFUSEUR 24 FENTES 5 0558009551 ÉCRAN XR 5,1 mm (0,200") PT-36 5 0004485648 JOINT TORIQUE 1,614 DI x 0,070 NBR 5 0004470034 JOINT TORIQUE 1,114 DI x 0,070 CR 10 0558010084 JOINT TORIQUE 0,864 DI x 0,070 FKM 15 THREE ALIMENTATION PHASE ÉLECTRIQUE INPUT TRIPHASÉE POWER { Plasma Console Console Plasma w/ avec IC commande Interfaceinterface ControlIC ALIMENTATION POWER DONNÉES DATA To Vers Work la table Table de travail Travail Work LIQUIDE LIQUID GAZ GAS To Vers CNC CNC // contrôle External externe Control Câble d’alimentation Power Cable CâbleArc arc pilote Pilot Cable Électrode Electrode Arc pilote Pilot Arc En option Optional Fourni parSupplied le client Customer Tuyau de retour de réfrigérant Coolant Return Hose RAS Remote Démarreur à arc Arcà distance Starter-2 RAS-2 CAN CAN on all standard packages. (Brackets supplied with Plasma Console) Combined Régulateur de gaz combinés Gas Control CGC-2 CGC-2 TM Gaz de protection Shield Gas Gaz plasma Plasma Gas Câble de diviseur tension Voltage DividerdeCable PT-36 Torche Torch PT-36 IC - Interface Control [Commande interface] IC - Interface Control RAS - Remote Arc Starter RAS [Démarreur arcStarter-2 à distance] - 2 - RemoteàArc CGC - 2 - Combined Gas Control deControl gaz combinés] CGC-2 - [Régulateur Combined Gas To Vers contrôle Auto de hauteur Height automatique Control (le cas (Iféchéant) Equipped) Alimentation/liquide de refroidissement, Arc pilote (buse), Terre Power/Coolant , Pilot Arc (Nozzle) , Ground Gaz de protection Shield Gas Gaz plasma Plasma Gas Note: Starterà is Remarque : LeArc démarreur arcmounted est monté surto l’arrière dePlasma la Console Plasma rear of Console sur tous les ensembles standard. Activation PS Enable PS Pilot Arc Arc pilote PS Control Commande PS TuyauCoolant d’alimentation de Hose réfrigérant Supply Câble commande RAS RASdeControl Cable Place Ferrite Core (supplied w/ Plasma Console) on CAN cable at Plasma Console end J1 RAS J1 (RAS) CAN1 1 CAN Interconnect Schéma de Diagram câblage TM m2 Smart Plasmarc 200 System Système m2 Smart Diagram Plasmarc 200 m2 Smart Plasmarc 200 System Interconnect Analog Interface analogique Interface 1 1 1 1 1 2 8,5' 26' 8,5' 1 1 1 6 - 8,5' 26' 8,5' 1 1 1 6 8,5' 26' 8,5' 1 1 1 6 1 1 1 1 1 2 - 8,5' 26' 8,5' 1 1 1 6 1 1 1 1 2 1 0558012536 0558012535 0558012534 m2-200 Pkg m2-200 Pkg m2-200 Pkg 575 V 400 V CE 400 V CE PT-36 25' PT-36 15m PT-36 7.6m 1 1 1 1 1 1 1 1 1 1 1 1 1 1 1 1 1 2 0558012537 m2-200 Pkg 575 V PT-36 50' 1 1 1 1 - 8,5' 26' 8,5' 1 1 1 6 1 1 1 1 1 2 - 0558012533 m2-200 Pkg 380 V CCC PT-36 15m 1 1 1 1 - 8,5' 26' 8,5' 1 1 1 6 1 1 1 1 2 1 0558012532 m2-200 Pkg 380 V CCC PT-36 7.6m 1 1 1 1 - 8,5' 26' 8,5' 1 1 1 6 1 1 1 1 1 2 - 0558012531 m2-200 Pkg 230/460 V PT-36 50' 1 1 1 1 - 8,5' 26' 8,5' 1 1 1 6 1 1 1 1 2 1 0558012530 m2-200 Pkg 230/460 V PT-36 25' 1 1 1 1 - Console Plasma m2 200 A 230/460 V Console Plasma m2 200 A EPP-202 380 V CCC Console Plasma m2 200 A 400 V CE Console Plasma m2 200 A 575 V Démarreur à arc à distance-2 (RAS) Régulateur de gaz combinés (CGC-2) Kit, raccords-adaptateurs d'entrée (CGC-2), CGA Kit, raccords-adaptateurs d'entrée (CGC-2), BSPP « G » 0558012390 0558012391 0558012392 0558012393 0558011591 0558012394 0558012478 0558012479 0558101089 0558012525 0558012526 0558012527 0558012329 0558004297 73010004 0558012396 0558011840 0558008471 0558008478 0558012480 0558008330 0558008331 0558012507 Câble, Arc pilote (soudage n° 8) Câble, Terre 8 awg (sans bague 1/4), 0,6 m Câble, Terre 8 awg (bague n° 10 - bague 1/4), 7,6 m Câble, Terre 8 awg (bague n° 10 - bague 1/4), 15 m Kit de démarrage m2 200A PT-36 Torche plasma à liquide de refroidissement 25 % PG Câble, Alimentation et travail (soudage 1/0) PT-36 15 m Câble, Commande RAS (14PX-14S), 2,9 m Câble, Alimentation CGC-2 et CAN M12 (8P-8P), 8 m Câble, Alimentation CGC-2 et CAN M12 (8P-8P), 15 m Câble, CNC E/S DB37 (37P-libre), 15 m Câble, Activation Console (2P-libre), 10 m Câble, Activation Console (2P-libre), 15 m Tuyau, alimentation/retour du liquide de refroidissement, 2,6 m 0558008307 PT-36 7,6 m Description Réf. Les options des ensembles de Système de coupage m2 Smart Plasmarc TM 200 sont disponibles auprès du concessionnaire ESAB. Consulter le tableau ci-dessous pour connaître le contenu des ensembles et/ou la section Pièces de rechange pour connaître les références des composants. Commandes d’ensembles description Câbles et tuyaux Câble Désignation Commande RAS-2 (14PX-14S) Réf. ESAB 2,9 m (9,5) 0558011840 7,6 m (25) 0558011631 10 m (33) 0558011632 15 m (50) 0558011633 20 m (66) 0558011634 23 m (75) 0558011635 25 m (82) 0558011636 30 m (100) 0558011637 Longueurs disponibles m (pieds) Réf. ESAB 8 m (26) 0558008471 9 m (30) 0558008472 10 m (33) 0558008473 11 m (36) 0558008474 12 m (39) 0558008475 13 m (43) 0558008476 14 m (46) 0558008477 15 m (50) 0558008478 20 m (66) 0558008479 25 m (82) 0558008809 30 m (100) 0558008481 36 m (118) 0558008480 40 m (131) 0558008482 45 m (150) 0558008483 Câble Désignation Longueurs disponibles m (pieds) Réf. ESAB CNC E/S DB37 (37P-libre) 15 m (50) 0558012480 Câble Désignation Alimentation CGC-2 et CAN M12 (8P-8P) 18 Longueurs disponibles m (pieds) description Câble Désignation Activation Console (2P-libre) Câble Désignation Diviseur de tension (VDR) M8 (3P-libre) Longueurs disponibles m (pieds) Réf. ESAB 5 m (16 ) 0558008329 10 m (33 ) 0558008330 15 m (50 ) 0558008331 20 m (66 ) 0558008807 25 m (82 ) 0558008808 30 m (100 ) 0558009763 Longueurs disponibles m (pieds) Réf. ESAB 1,5 m (5 ) 0560946753 3 m (10 ) 0560946754 5 m (16 ) 0560946755 10 m (33 ) 0560946756 20 m (66 ) 0560946757 Câble Désignation Longueurs disponibles m (pieds) Réf. ESAB Puissance de sortie (câble de soudage 1/0) p/pied 73010004 Arc pilote (câble de soudage n° 8) p/pied 0558101089 Terre (8 Awg vert/jaune) p/pied 0560945427 Tuyau Désignation Longueurs disponibles m (pieds) Réf. ESAB *2,6 m (8,5 ) 0558012507 5 m (16 ) 0558005246 Alimentation / retour de liquide de refroidissement EPDM 5/8” noir Mâle gauche 5/8-18 et femelle droite 5/8-18 (*EPDM 3/8” noir) 10 m (33 ) 0558005563 15 m (50 ) 0558005564 20 m (66 ) 0558005565 25 m (82 ) 0558006629 30 m (100 ) 0558005247 19 description Console Plasma La Console Plasma m2 est conçue pour le coupage plasma mécanisé. Il est utilisé avec d’autres produits ESAB tels que la torche PT36, RAS-2 et CGC-2 pour fournir un ensemble de coupage complet. Caractéristiques • • • • • • • • • Commandes RAS-2 et CGC-2 Interface d’opérateur LCD facile à utiliser Plage de courant de 25 à 200 ampères pour le coupage Refroidissement par air forcé Transistors bipolaires à grille isolée (IGBT) refroidis par liquide Circulateur de refroidissement interne Alimentation c.c. à semi-conducteur À protection thermique Cycle de service à 100 % Caractéristiques techniques Référence Sortie (cycle de service à 100 %) m2 Plasma Console, 200A, 575 V, 60 Hz, 0558012393 30 A à 200 A Puissance Tension en circuit ouvert m2 Plasma Console, 200A, 400 V CE, 50 Hz, 0558012392 160 V c.c. Plage de courant c.c. (coupage) 32 kW 360 V c.c. 342/360 V c.c. 360 V c.c. 366 V c.c. Tension (triphasé) 200/230/460 V 380/400 V 400 V 575 V Courant (triphasé) 115/96/50 A RMS 60/57 A RMS 57 A RMS 43 A RMS 60 Hz 50 Hz 50 Hz 60 Hz kVA 39,5 kVA 39,5 kVA 39,5 kVA 39,5 kVA Puissance 35,5 kW 35,5 kW 35,5 kW 35,5 kW 90% 90% 90% 90% 150/125/70 A 80/75 A 75 A 60 A 427 426 434 492 Facteur de puissance Fusible d’entrée (recommandé) Poids (kg) 20 m2 Plasma Console, 200A, 380 CCC, 50 Hz, 0558012391 Tension Fréquence Entrée m2 Plasma Console, 200A, 230/460 V, 60 Hz, 0558012390 description Dimensions 603,25 mm 1200 mm 1035 mm Commande interface (IC) La commande interface [Interface Control] (IC) fournit le contrôle du processus de plasma y compris le contrôle de courant et de gaz. Elle sert également d’interface entre le client CNC et la Console Plasma. En même temps, elle sert de hub pour communication CAN. 21 description Carte directe CNC Réf. 0558038419 La carte directe CNC est la carte de contrôle et d’interface à l’intérieur de l’IC. Elle fournit le contrôle de processus, l’interface au client CNC, la configuration du système, l’interface du panneau, etc. Cette illustration est une esquisse de cette carte CNC. Elle montre les principaux composants et les principaux connecteurs sur la carte. Le tableau ci-dessous indique les fonctions de ces connexions. Port Fonction Port X1 Contrôle CNC, DB37 X2 RS232 X3 CAN1 et entrée 24 V CC XP1 Port de programmation 1 X4 CAN2 XP2 Port de programmation 2 X6 E/S de secours X7 Réservé V12 IC, processeur principal X8 Contrôle auxiliaire, DB25 V13 EEProm, Enregistrer données pour configuration du système, historique des erreurs, etc. X9 Communication ASIOB1 V41 IC pour ASIOB1 S2, S3 J1 22 Fonction Interrupteurs ID, par défaut S2=1, S3=4 description Régulateur de gaz combinés (CGC-2) Réf. 0558012394 Le Combined Gas Control [Régulateur de gaz combinés] règle la sortie du gaz plasma [plasma gas] (PG) et contrôle le débit du gaz de protection [shield gas] (SG). Il est alimenté par du 24 volts CC à partir de la Console Plasma et reçoit des commandes via le CAN-bus directement de l’IC. Il comporte 2 entrées de gaz (1 gaz plasma, 1 gaz de protection) et 2 sorties de gaz (SG, PG). Les deux kits de raccords d’adaptateur sont disponibles pour s’adapter sur des connexions de tuyaux standard métriques ou CGA. La sortie de gaz du CGC-2 est surveillée et réalimentée par le CAN-bus vers l’IC pour autodiagnostic. Les raccords et adaptateurs de gaz sont listés dans les tableaux suivants. Connexions Il y a un câble connecté au CGC-2 pour alimentation et communication CAN. Il y a 2 entrées de gaz : PG (N2/Air/ O2) et SG (N2/Air). Les raccords de gaz sont listés ci-dessous. Remarque : Le châssis doit être connecté à la terre de la machine. Remarque : Adaptateurs d’entrée métriques Adaptateurs d’entrée CGA Raccord Référence ESAB Plasma N2/Air/O2 G-1/4” mâle droit x G-1/4” mâle droit 0558010163 Protection N2/Air G-1/4” mâle droit x G-1/4” mâle droit 0558010163 Air G-1/4” mâle droit x « B » mâle droit air/eau 0558010165 N2 G-1/4” mâle droit x « B » mâle droit gaz inerte 0558010166 O2 G-1/4” mâle droit x « B » mâle droit oxygène 0558010167 Air G-1/4” mâle droit x « B » mâle droit air/eau 0558010165 N2 G-1/4” mâle droit x « B » mâle droit gaz inerte 0558010166 SG 1/4” NPT x 5/8»-18 mâle gauche 10Z30 PG 1/4” NPT x “A” mâle droit oxygène 0558012518 Plasma Protection Outputs Réf. Kit ESAB 0558012478 Gaz Réf. Kit ESAB 0558012479 La torche PT-36 est expédiée avec des longueurs de tuyau qui ne permettront pas de monter le CGC-2 à plus de deux mètres (6,6 pieds) de la torche. S’assurer que l’acheminement des tuyaux standard leur permettra de se plier et de se connecter correctement avant de monter de manière permanente le CGC-2. 23 description Spécifications Poids : 2,7 kg Entrée d’alimentation : 24 V c.a./c.c. Dimensions REMARQUE : Le câble CAN doit être acheminé séparé des fils de la torche. A 127,0 mm C F H G J 142,8 mm 142,8 mm 152,4 mm 127,0 mm 24 description Vers CNC / contrôle externe Démarreur à arc à distance-2 (RAS) Console Plasma TERRE CAN 1/CAN Gaz fournis par le client Gaz plasma Gaz de protection A J Gaz plasma Régulateur G de gaz H Gaz de protection combinés C CGC-2 F Torche PT-36 Désignation de localisation des composants (Voir illustrations des composants) Vers contrôle de hauteur automatique (le cas échéant) Désignations de localisation des composants du régulateur de gaz combinés REMARQUE : Consulter la section Câbles et tuyaux pour les longueurs disponibles et les références. 25 description Schéma de débit CGC-2 Filtre Entrée de Gaz plasma gaz plasma vers la torche Filtre Orifice Entrée de Gaz de protection gaz de protection vers la torche Chaque gaz a une condition requise de débit et de pression maximum comme indiqué dans le tableau ci-dessous : Gaz Protection N2/Air/O2 N2/Air Rideau d’air Air Plasma 26 Pression 125 psi (8,6 bar), 255 SCFH (7,2 SCMH) 125 psi (8,6 bar), 250 SCFH (7,1 SCMH) 80 psi (5,5 bar), 1200 SCFH (34,0 SCMH) Gaz et pression Débit maximum du gaz - CFH (CMH) avec la torche PT-36 Pureté du gaz Air (85 psi / 5,9 bar) Procédé 269 (7,6) Propre, sec, sans huile Filtré à 25 microns Nitrogène (125 psi / 8,6 bar) 385 (10,9) 99,99%, filtré à 25 microns Oxygène (125 psi / 8,6 bar) 66 (1,9) 99,5%, filtré à 25 microns 2- analogique 1- Entrée Terre Sortie PWM2 Alimentation de vanne 24 V CC Sortie PWM1 Alimentation de vanne 24 V CC analogique 1+ Entrée OV CC COMMUN Alimentation de détecteur 24 V CC 2+ Entrée analogique OV CC COMMUN Entrée analogique +24 V CC +24 V CC CAN Terre GRIS ROSE BLEU ROUGE 5* 7* 8* 4* 6* VERT JAUNE 3* BLANC MARRON CC COMMUN 8* 1* +24 V CC 2* CAN Terre 6* CAN Bas CAN Haut CAN Terre CAN Bas CAN Haut 7* 4* 5* Sortie CAN Haut Sortie CAN Bas 3* CAN Terre 1* 2* Entrée CAN Bas Entrée CAN Haut +24 V CC S2=2 +24 V CC S1= STATION Remarque : Inspecter le kit de fils pour une information détaillée sur le câblage et les connecteurs Vanne de gaz de protection Vanne de démarrage/ coupure de gaz Transmetteur de pression Transmetteur de pression Alimentation de détecteur 24 V CC description Schéma électrique CGC-2 27 description Démarreur à arc à distance-2 (RAS) Réf. 0558011591 Le Remote Arc Starter-2 est couramment appelé la boîte RAS. La boîte RAS sert d’interface entre la torche au plasma et la Console Plasma permettant de produire un arc de plasma stable. La boîte RAS fournit également un feedback de tension au système de levage de la torche au plasma. Cette tension est utilisée pour régler la hauteur de la torche pendant la coupe tout en maintenant la hauteur appropriée de la torche au-dessus de la pièce à travailler. Dans la boîte RAS se trouve une carte circuit imprimé de diviseur de haute fréquence/tension qui fournit une ionisation d’arc pilote et des fonctions de diviseur de tension pour régler la hauteur de la torche. Les connexions du liquide de refroidissement et les connexions d’alimentation de torche se font au sein de la boîte RAS et fournissent une interface entre la Console Plasma, le circulateur du liquide de refroidissement et la torche. Spécifications Dimensions : 8,75” (222,3 mm) hauteur x 7,50” (190,5 mm) largeur x 17,00” (431,8 mm) profondeur Poids : 12,9 kg Dimensions 222,3 mm 431,8 mm 190,5 mm 28 description Connexions Remarque : Le châssis doit être connecté à la terre de la machine. A G, H D C F E Lettre Description A Connexion du diviseur de tension à 3 broches au système de levage C Connexion de la Console Plasma Amphenol à 14 broches D Activation Console Plasma E Entrée du liquide de refroidissement - Écoulement vers la torche F Retour du liquide de refroidissement - Retour d'écoulement vers le circulateur du liquide de refroidissement à partir de la torche G, H Raccords de réducteur de tension I Connexion d'enveloppe de torche J Connexion à la terre de machine J I 29 description Vers CNC / contrôle externe Désignation de localisation des composants (Voir illustrations des composants) Activation PS D A Câble de commande RAS Câble d’alimentation Console Plasma Câble arc pilote C Démarreur à arc G à distance-2 (RAS) H I Tuyau d’alimentation de réfrigérant E Tuyau de retour de réfrigérant J F Gaz fournis par le client Câble de diviseur de tension Alimentation/liquide de refroidissement, Arc pilote (buse), Terre TERRE Régulateur de gaz combinés CGC-2 Torche PT-36 Vers contrôle de hauteur automatique (le cas échéant) Désignations de localisation des composants de la boîte Remote Arc Starter-2 [Démarreur à arc à distance] REMARQUE : Consulter la section Câbles et tuyaux pour les longueurs disponibles et les références. 30 description Dimensions de fixation La boîte comporte quatre trous de fixation filetés M6 x 1 indiqués dans le modèle ci-dessous. MISE EN GARDE Si les fixations sont filetées dans la boîte du dessous, la longueur des fixations ne doit pas les laisser s’étendre à plus de 0,25” au-delà du chant des filets femelles internes. Si les fixations sont trop longues, elles peuvent interférer avec les composants à l’intérieur de la boîte. 127,00 mm 2,54 mm 69,85 mm 349,25 mm Dimensions de plaque de fixation de la boîte RAS Réf. 0558008461 469,9 mm 444,5 mm 222,3 mm 82,6 mm 190,5 mm 165,1 mm 31 description Torche de coupage mécanisée Plasmarc PT-36 La torche de coupage mécanisée Plasmarc PT-36 est une torche plasma à arc assemblée en usine pour fournir une concentricité des composants de torche et une précision de découpe constante. Pour cette raison, le corps de la torche ne peut être reconstruit sur site. Seul le devant de la torche comporte des pièces remplaçables. Cette section a pour objet de fournir à l’opérateur une information préliminaire sur la torche de coupage mécanisée Plasmarc PT-36. Le matériel de référence technique est également fourni dans les sections relatives à l’Installation, au Fonctionnement et à la Maintenance de ce manuel. Options d’ensembles disponibles Options d’ensemble PT-36 disponibles auprès du concessionnaire ESAB. Voir la section Pièces de rechange pour les références d’ensembles et/ou de composants. Spécifications Type : Torche de coupage mécanisée Plasmarc refroidie par eau, à deux gaz Courant nominal : 1 000 A à 100 % de facteur de charge Diamètre de fixation : 2" (50,8 mm) Longueur de torche sans fils : 16,7" (42 cm) Tension nominale IEC 60974-7 : crête de 500 volts Tension de sortie (valeur maximale de tension HAUTE FRÉQUENCE) : 8 000 V CA Débit minimum du liquide de refroidissement : 1,3 gallon/min (5,9 l/min) Pression minimale du liquide de refroidissement au niveau de l'entrée : 175 psig (12,1 bar) Pression maximale du liquide de refroidissement au niveau de l'entrée : 200 psig (13,8 bar) Valeur nominale minimale acceptable du recirculateur du liquide de refroidissement : 4 450 BTU/HR (1,3 kW) à température élevée du liquide de refroidissement - Ambiante = 45 °F (25 °C) et 1,6 gallon US/min (6 l/min) Pressions de gaz maximales sécuritaires aux entrées de la torche : 125 psig (8,6 bar) Verrouillages de sécurité : Cette torche est prévue pour être utilisée avec les systèmes et les contrôles de coupage Plasmarc ESAB employant un fluxostat sur la ligne de retour du liquide de refroidissement à partir de la torche. Le retrait de la coupelle de retenue de la buse pour entretenir la torche interrompt la voie de retour du liquide de refroidissement. 32 description Dimensions 191,5 mm 50,8 mm 231,9 mm 156,7 mm 266,7 mm Longueur de manchon Régulateurs recommandés Service des bouteilles de gaz liquide : O2 : R-76-150-540LC .................................................................................................................................. Réf. 19777 N2 : R-76-150-580LC ................................................................................................................................... Réf. 19977 Service des bouteilles à haute pression : O2 : R-77-150-540 ............................................................................................................................ Réf. 0558010676 Ar & N2 : R-77-150-580.................................................................................................................. Réf. 0558010682 H2 & CH4 : R-77-150-350 .............................................................................................................. Réf. 0558010680 Air industriel : R-77-150-590 .............................................................................................. Réf. 0558010684 Service des stations/pipelines : O2 : R-76-150-024 ............................................................................................................................ Réf. 0558010654 Ar & N2 : R-76-150-034.................................................................................................................. Réf. 0558010658 Air, H2, & CH4 : R-6703 .............................................................................................................................. Réf. 22236 Liquide de refroidissement Torche plasma à liquide de refroidissement 25 % PG .......................................Réf. 0558004297 Torche plasma à liquide de refroidissement 50 % EG .......................................Réf. 0560950312 33 description Kit de Speedloader Série XR PT-36 .........................................................................Réf. 0558006628 Consulter la section sur la torche pour les instructions d’utilisation pour le Kit de Speedloader Série XR PT-36. 3 2 4 5 6 Élément Qté Réf. Description 1 1 0558006164 SPEEDLOADER PORTABLE (Inclut éléments 2 à 8) 2 1 0558006436 SPEEDLOADER D'APPAREILS 3 1 0558006435 POIGNÉE DE SPEEDLOADER 4 1 61340094 VIS SKT HEX 1/4-20 x 3,00 5 1 64302996 RONDELLE FREIN 1/4'' 6 1 995565 TROU DE FICHE DE 0,750 DIA 7 3 0558005916 SPEEDLOADER DE RETENUE DE BUSE 8 1 0558005917 SPEEDLOADER PRÉASSEMBLAGE D'OUTIL 9 1 0558006624 COUPELLE DE RETENUE DE BUSE XR-SPEEDLOADER PT-36 10 10 0558006625 ESPACEUR XR-SPEEDLOADER PT-36 11 10 0558006626 RETENUE XR-SPEEDLOADER PT-36 12 2 0004485648 JOINT TORIQUE 1,614 DI x 0,070 NBR Éléments 9-12 non illustrés. Pour les éléments 7 et 8, consulter la section « Ensemble de devant de torche à l’aide du Speedloader (en option) ». 34 INSTALLATION installation Page intentionnellement laissée en blanc 36 installation Installation Généralités AVERTISSEMENT LE NON-respect des instructions peut causer des dégâts matériels et des blessures graves, voire mortelles. respecter ces instructions pour éviter les blessures et les dégâts. respecter les codes de sécurité et électriques EN VIGUEUR. Déballage • • • Inspecter le produit dès réception pour vérifier qu’il n’a pas été endommagé durant le transport. Retirer toutes les pièces de la boîte d’expédition sans oublier les pièces détachées pouvant s’y trouver. Inspecter les évents pour détecter les obstructions. À vérifier dès réception 1. Vérifier que tous les composants du système de la commande ont bien été reçus. 2. Inspecter les composants du système pour tout dommage matériel qui aurait pu se produire pendant l’expédition. En présence de dommages, prière de contacter le fournisseur avec la référence du modèle et le numéro de série de la plaque signalétique. Avant installation AVERTISSEMENT L’installation et l’entretien des systèmes d’électricité et de plomberie doivent se conformer aux codes nationaux et locaux de l’électricité et de la plomberie. L’installation doit être effectuée uniquement par un personnel qualifié et licencié. Consulter les autorités locales pour toute question de réglementation. Localiser les principaux composants sur la droite avant de procéder à toute connexion électrique, de gaz et d’interface. Consulter les schémas d’interconnexion du système pour l’emplacement des principaux composants. Mettre tous les principaux composants à la terre à un point. Pour prévenir toute fuite, s’assurer de bien serrer toutes les connexions de gaz et d’eau à un couple spécifique. 37 installation Mise à la terre Introduction La mise à la terre de la machine, qui peut être grandement simplifiée si elle est préparée à l’avance, est une partie importante du processus d’installation. La partie la plus difficile du processus de mise à la terre est de concevoir et d’installer une tige de mise à la terre à faible impédance. Néanmoins, plus la tige de mise à la terre est bonne, moins il y a de chances d’avoir des problèmes d’interférence électromagnétique une fois l’installation terminée. La majorité des codes nationaux de l’électricité traitent la mise à la terre à des fins de prévention et de protection contre les courts-circuits ; ils ne traitent pas de la protection de l’équipement ni de la réduction des bruits des interférences électromagnétiques. Par conséquent, ce manuel présente des exigences plus rigoureuses pour la mise à la terre de machine. AVERTISSEMENT Risque de choc électrique. Une mise à la terre inappropriée peut provoquer des blessures graves voire la mort. Une mise à terre inappropriée peut endommager les composants électriques de la machine. La machine doit être correctement mise à la terre avant d’être mise en service. La table de coupe doit être connectée à la tige de mise à la terre de la machine. 38 installation Aperçu de la mise à la terre Un système de mise à la terre comporte trois parties : • • • Un symbole courant utilisé pour identifier une terre de châssis sur les schémas. Mise à la terre des composants ou « châssis » Mise à la terre Mise à la terre de protection La mise à la terre des composants connecte toutes les pièces à un seul composant, comme le châssis de la machine, qui est alors connecté à un point commun connu comme le point étoile. Cela fournit une voie pour l’interférence électromagnétique (EMI) du boîtier à la mise à la terre. Une mise à la terre fournit une interférence électromagnétique (EMI) pour retourner à sa source. La terre de protection (PE) [masse] offre une voie sûre pour le courant de défaut. Sans un système correctement mis à la terre, une voie non intentionnelle par le biais de personnes ou d’équipement sensible peut exister entraînant des blessures graves, la mort et/ou une défaillance prématurée de l’équipement. Un symbole courant utilisé pour identifier une mise à la terre sur les schémas. Cette section se concentre sur les machines disposant d’un système de coupage à plasma. Les machines ayant des capacités de coupage au plasma sont particulièrement prédisposées aux problèmes d’interférences électromagnétiques et utilisent souvent des tensions et des courants dangereux. Toutes les machines doivent avoir des composants électriques mis à la terre et attachés à une mise à la terre, quel que soit le type de processus (coupe de formes, marquage ou autre préparation de matériel). Un symbole courant utilisé pour identifier une mise à la terre de protection (PE). 39 installation Plan d’ensemble de base Le plan d’ensemble électrique est semblable pour les grandes et les petites machines. La terre du châssis 44 , le fil électrique positif du plasma 66 et les câbles de masse de rails 77 sont attachés à un point commun 88 sur la table de coupe. On appelle cette connexion commune un point étoile (voir l’illustration ci-dessous). Un câble 33 se connecte au point étoile sur la tige de mise à la terre 11 . La taille des câbles de masse dépend de la sortie de courant maximum de la Console Plasma plasma 5 . La spécification des tailles de câbles sera traitée plus loin dans ce manuel. Les normes ou directives de certains pays requièrent une tige de mise à la terre séparée 99 pour la Console Plasma. Consulter les schémas de la machine pour plus d’informations. 8 Remarque : L’entrée électrique triphasée2 à la Console Plasma plasma doit inclure une masse électrique. 40 Cette illustration démontre plusieurs câbles de masse fixés à un seul boulon pour créer un point étoile 88 . L’emplacement du point étoile sur la table de coupage variera. installation Éléments d’un système de mise à la terre Le système de mise à la terre comporte cinq composants principaux : • • • • • voie de retour de courant plasma terre de sécurité du système plasma terre électrique d’alimentation terre de châssis de machine de coupage terre de sécurité du système à rails. S’assurer de prendre les dispositions nécessaires pendant l’installation pour chacun de ces éléments afin de créer un système de mise à la terre complet. Voie de retour de courant plasma Le câble de masse de la voie de retour est l’élément le plus important du système de mise à la terre. Il complète la voie pour le courant plasma. Des connexions électriques solides, à faible impédance et bien entretenues sont essentielles. Le courant de coupage au plasma est généré par la Console Plasma plasma 11 . Un câble de soudage transporte le courant de la connexion négative (-) 22 dans la Console Plasma plasma via la chaîne de câble d’axe x 33 vers la torche. Le courant effectue alors un arc 4 sur la pièce à travailler sur la table de coupage. La voie du courant doit être fermée de sorte que le courant puisse facilement revenir à sa source. Ceci se fait en connectant la table de coupage à la connexion positive (+) 55 sur la Console Plasma plasma. Si le câble de masse de la voie de retour n’est pas connecté, le système au plasma ne fonctionnera pas. Il sera impossible d’établir l’arc entre la torche et la pièce à travailler. Si le câble est connecté mais que les connexions ont une résistance très élevée, il limitera le courant de l’arc et provoquera de dangereux niveaux de tension entre les composants du système. 1 3 2 4 5 41 installation Le seul moyen de s’assurer que tous les composants se trouvent au même niveau de tension (même potentiel) et ainsi éliminent la possibilité de chocs, est de s’assurer que toutes les interconnexions ont un bon contact électrique. Pour avoir un bon contact électrique, il faut que les connexions soient faites avec un contact de métal nu à métal, que les connexions soient très serrées et soient protégées de la rouille et de la corrosion. Utiliser une meule ou une brosse métallique pour nettoyer la totalité de la peinture, de la rouille et de la saleté de la surface lors de la connexion des cosses de câble sur toute surface métallique. Utiliser un composé à joints électriques entre les cosses de câble et les surfaces métalliques pour prévenir toute rouille et toute corrosion futures. Utiliser des boulons, écrous et rondelles les plus grands possibles, et serrer à fond. Utiliser des rondelles de sécurité pour garantir que les connexions restent bien serrées. Terre de sécurité du système au plasma La terre de sécurité du système au plasma (ou tige de mise à la terre) sert à plusieurs fins importantes. Elle fournit : • • • • 42 Une tension de châssis pour la sécurité du personnel en assurant qu’il n’existe pas de différences de potentiel entre les composants du système et ceux du bâtiment. Une référence de signal stable pour tous les signaux électriques numériques et analogiques sur la machine de coupage. Permet de contrôler l’interférence électromagnétique (ou EMI). Fournit une voie de décharge pour les courts-circuits et les pointes de haute tension, tels que ceux causés par des coups de foudre. installation Il existe un grand nombre d’idées fausses sur la tige de mise à la terre ainsi que sur son rôle dans la réduction de l’interférence électromagnétique. En théorie, la tige de mise à la terre est présente pour éliminer les différences de potentiel éventuelles entre l’équipement et les structures du bâtiment. Néanmoins, beaucoup de gens pensent que la tige de mise à la terre permet à tous les bruits de radiofréquence 1 d’être absorbés et de disparaître dans la terre. L’expérience a démontré qu’une bonne tige de mise à la terre éliminera les problèmes de bruit de radiofréquence. Fausse idée sur les tiges de mise à la terre. 1 43 installation En réalité, la tige de mise à la terre fournit une voie à faible impédance par laquelle les courants de bruit 11 peuvent retourner à leur source 22 . Réalité sur les tiges de mise à la terre. 2 44 1 installation Terre de sécurité du système de rails La terre de sécurité du système de rails garantit que tout le rail se trouve sur le potentiel de terre, éliminant ainsi tout risque de choc possible et en offrant une masse de secours pour la terre de châssis de la machine en cas de court-circuit du courant plasma. Tous les quatre coins du système de rails doivent être connectés à la table de coupage. 45 installation Tige de mise à la terre Le meilleur moyen de s’assurer que la connexion de mise à la terre est optimisée est de faire appel aux services d’un professionnel. Il existe un certain nombre de sociétés d’ingénierie qui se spécialisent dans la conception et l’installation des systèmes de mise à la terre. Toutefois, si cette option ne peut être utilisée, on peut faire un certain nombre de choses pour s’assurer que la connexion de mise à la terre est bonne : Tige de mise à la terre Il est possible d’optimiser la tige de mise à la terre de deux manières : longueur et diamètre. Plus la tige de mise à la terre est longue, plus la connexion est bonne. Il en est de même pour le diamètre : plus le diamètre est grand, plus la connexion est bonne. Néanmoins, si la résistance au sol est très faible, une tige de mise à la terre plus longue que 3 m [10 pieds] ne fait pas de différence significative. Étant donné que la résistivité du sol est rarement aussi bonne qu’elle pourrait l’être, une tige de mise à la terre standard devrait être de 25 mm [1 pouce] de diamètre et de 6 m [20 pieds] de longueur. Résistivité du sol La résistivité du sol peut être modifiée de deux façons : en modifiant la teneur en substances minérales, la teneur en humidité, ou les deux. La solution idéale pour une résistivité de sol médiocre est d’excaver la zone immédiate et de la remplir avec des additifs de sol conditionnés. Dans des zones extrêmement sèches, la teneur en humidité peut être améliorée en installant un système de goutte à goutte qui hydrate en continu le sol entourant la tige de mise à la terre. Une manière rudimentaire d’affecter l’hydratation et la teneur du sol est d’utiliser de l’eau salée ou du sel gemme pour conditionner le sol environnant. 46 installation Masse électrique d’alimentation des services publics La terre électrique d’alimentation des services publics doit accompagner toutes les alimentations triphasées et monophasées. Cette masse électrique fournit la référence appropriée pour toute l’alimentation entrante. Ne pas fournir cette masse constitue une violation de la majorité des codes d’électricité et un grave risque de sécurité. En fonction de l’aménagement de l’alimentation triphasée (soit un « Delta » soit un « Y »), la tension ligne-terre peut être égale ou inférieure à la tension ligne-ligne. Il y a un problème à chaque fois que la tension ligneterre est supérieure à toute tension ligne-ligne individuelle (différence de potentiel). Contacter la société locale de services publics en cas de doute sur la masse électrique de l’alimentation triphasée. S’assurer que l’entrepreneur en électricité installe correctement le fil de masse électrique avec toutes les alimentations triphasées et monophasées. La masse électrique doit être connectée à la borne appropriée de la Console Plasma plasma. Dimensionner le fil conformément aux codes locaux de l’électricité. 3 2 1 1 Masse électrique d’alimentation des services publics 2 Alimentation électrique triphasée 3 Console Plasma plasma 47 installation Tiges multiples de mise à la terre Il existe un certain nombre de raisons pour lesquelles il ne faut pas utiliser des tiges multiples de mise à la terre. Tandis que l’installation de plusieurs tiges peut améliorer une terre de sécurité ou une terre d’éclairs, elle n’offre aucun avantage pour la réduction d’interférence électromagnétique, et peut causer plus de problèmes qu’il n’en vaut la peine. Le problème avec des tiges multiples de mise à la terre est que chaque tige utilise une « sphère d’interférence électromagnétique d’interfaçage » 1 de terre, ayant un rayon de 1,1 fois la longueur de la tige. Un chevauchement des ces sphères d’interférence électromagnétique 22 entraîne une perte de l’efficacité de la mise à la terre proportionnelle au montant du chevauchement. Des points de masse multiples peuvent également créer des voies « furtives » indétectables pour les courants de bruit de radiofréquence, causant en fait plus d’interférence ! Au lieu d’envisager des tiges multiples de mise à la terre, prendre des mesures pour rendre une seule tige de mise à la terre une connexion de terre aussi bonne que possible. 1.1 l l 1 2 Éviter d’utiliser des tiges multiples de mise à la terre dans la mesure du possible. Néanmoins, si on a tout essayé pour amoindrir les interférences électroniques du système, des tiges multiples de mise à la terre sont une option. 2.5 l 48 Ce système doit être installé par un professionnel et la distance entre les tiges doit excéder 2,5 fois la longueur des tiges. installation Schéma de mise à la terre de la machine 2 1 3 4 8 10 5 (+) 9 1 Boîtier de commande principal 2 Boîtiers de composants 3 Mise à la terre principale en étoile 7 • • 5 Table de coupage • • 6 Mise à la terre en étoile du système (sur la table) • 4 Rails 7 Tige de mise à la terre 8 Console Plasma plasma 9 Mise à la terre de la Console Plasma plasma (obligatoire selon les normes EU) 10 Mise à la terre du système électrique • 6 Tous les boîtiers électriques boulonnés au châssis de la machine. Châssis de la machine mis à la terre au point étoile sur la table de coupage. Rails mis à la terre sur la table de coupage. Mise à la terre par plasma au point étoile sur la table de coupage. Tige de mise à la terre connectée au point étoile sur la table de coupage. Une tige de mise à la terre séparée est requise pour la Console Plasma plasma par certaines réglementations et directives. Consulter les réglementations locales pour déterminer si cette tige de mise à la terre additionnelle est requise. 49 installation Placement de la Console Plasma • • • • • Un dégagement d’un mètre à l’avant et à l’arrière doit être assuré pour la circulation de l’air de refroidissement. Prévoir un espace suffisant pour le retrait du panneau supérieur et des panneaux latéraux pour l’entretien, le nettoyage et l’inspection. Placer la Console Plasma relativement près d’une alimentation électrique à fusible adaptée. La zone sous la Console Plasma doit être dégagée pour la circulation de l’air de refroidissement. L’environnement doit être relativement exempt de poussières, de fumées et de chaleur excessive. Ces facteurs affecteraient l’efficacité du refroidissement. AVERTISSEMENT 50 La poussière et les débris conducteurs dans la Console Plasma peuvent causer des coups d’arc. L’équipement pourrait être endommagé. Un court-circuit électrique pourrait se produit s’il est permis à la poussière de s’accumuler dans la source d’alimentation. Consulter la section Entretien. installation Branchement de l’alimentation d’entrée AVERTISSEMENT LES CHOCS électriques peuvent causer la mort ! assurer une protection maximum contre les chocs électriques. avant de procéder à tout branchement dans la machine, ouvrir le sectionneur mural pour couper l’alimentation. Alimentation principale Une alimentation d’entrée triphasée doit être fournie par l’intermédiaire d’un sectionneur mural contenant des fusibles ou des disjoncteurs conformément à la règlementation en vigueur. Dimensions des conducteurs d’entrée et des fusibles d’alimentation secteur recommandées : Exigences d’alimentation à la charge nominale Conducteurs d’entrée et de terre en cuivre Fusible d’alimentation secteur temporisé Volts Ampères calibre américain / mm2 Ampères 200 115 2/0 AWG 150 230 96 1 AWG 125 380 CCC 60 2 25 mm 80 400 CE 57 25 mm2 75 460 50 4 AWG 70 575 43 4 AWG 60 La charge nominale est la sortie de 200 A à 160 V. Dimensions selon le code électrique national américain pour des conducteurs en cuivre approuvés pour 90 °C à une température ambiante de 40 °C. Pas plus de trois conducteurs dans un conduit ou un câble. Les codes en vigueur doivent être respectés s’ils spécifient des dimensions différentes de celles indiquées ci-dessus. Pour estimer le courant d’entrée pour diverses conditions de sortie, utiliser la formule ci-dessous. Courant d’entrée = AVIS (V arc) x (I arc) x 0,73 (V ligne) Une ligne électrique dédiée peut être requise. L’unité plasma est équipée d’une compensation de tension secteur ; une ligne électrique dédiée peut néanmoins être nécessaire pour éviter les mauvaises performances dues à un circuit surchargé. 51 installation Conducteurs d’entrée • • • Fournis par le client Peuvent être des conducteurs en cuivre recouverts de caoutchouc épais (trois pour l’alimentation et un pour la terre) ou d’un conduit massif ou flexible. Dimensionnés conformément au tableau. AVERTISSEMENT une mauvaise mise à la masse peut entraîner des blessures graves, voire mortelles. le châssis doit être connecté à une masse électrique approuvée. le fil de terre ne doit pas être connecté à une borne primaire. Procédure de connexion d’entrée 1. 2. 3. 4. 5. 6. 7. Retirer le petit panneau arrière de l’unité plasma. Acheminer les câbles par l’ouverture d’accès dans le panneau arrière. Attacher les câbles avec un protecteur de cordon au niveau de l’ouverture. Brancher le fil de terre au plot du châssis. Brancher les fils d’alimentation aux bornes primaires. Brancher les conducteurs d’entrée au disjoncteur mural (secteur). Avant de mettre sous tension, replacer le panneau arrière. Bornes primaires Ouverture d’accès du câble d’entrée d’alimentation (panneau arrière) Masse du châssis 52 installation Configuration de tension d’entrée et de changement 200/230/460 VAC Modèles - livrée par l’usine, ce modèle de EPP-202 est configuré pour la tension la plus élevée connectable. Si vous utilisez d’autres tensions d’entrée, les liens sur le bornier (TB) à l’intérieur de l’unité doivent être repositionnés pour la tension d’entrée. Voir les illustrations ci-dessous pour les configurations de tension d’entrée. Pour y accéder, retirer le panneau supérieur ou le panneau de droite. Fil de raccordement Fil de raccordement REMARQUE : (200) & (400) IL FAUT CHANGER LA CONNEXION SECONDAIRE AU NIVEAU DU TRANSFORMATEUR PRINCIPAL ET REPOSITIONNER LES CAVALIERS À FILS SUR LA PLAQUE À BORNES SITUÉE SUR LE CÔTÉ OPPOSÉ DE L’UNITÉ VOIR LE MANUEL REMARQUE : (200) & (400) IL FAUT CHANGER LA CONNEXION SECONDAIRE AU NIVEAU DU TRANSFORMATEUR PRINCIPAL ET REPOSITIONNER LES CAVALIERS À FILS SUR LA PLAQUE À BORNES SITUÉE SUR LE CÔTÉ OPPOSÉ DE L’UNITÉ VOIR LE MANUEL BORNIER ENTRÉE MODÈLES 230/460 VCA BORNIER ENTRÉE MODÈLES 230/460 VCA Configuration 230 VCA Configuration 460 VCA L’unité est également configurable pour un service d’entrée de 200/400 VCA mais les connexions secondaires du transformateur principal doivent être déplacées sur les 3 bobines de transformateur et les fils de raccordement sur le TB2 doivent être repositionnés. Un panneau de service amovible est situé au-dessus des connexions du transformateur pour améliorer l’accès. 53 installation 1 1 2 3 4 5 6 2 3 4 5 6 7 TB2 7 8 9 10 11 12 8 9 10 11 12 Positions des cavaliers pour du 230/460 VCA REMARQUE : Les fils du TB2 connectés sur du 230/460 doivent être reconnectés sur du 200/400. 1 2 3 4 5 6 7 8 9 10 11 12 1 2 3 4 5 6 7 8 9 10 11 12 TB2 Positions des cavaliers pour du 200/400 VCA 1 2 3 4 5 6 7 8 9 10 11 12 REMARQUE : 1 2 3 Prise 200/400 4 5 6 7 8 9 10 11 12 Les fils connectés sur la prise du transformateur principal 230/460 doivent être reconnectés à la prise du transformateur principal 200/400 sur les 3 bobines. S’assurer de remettre en place les couvercles isolants en vinyle sur les connexions. Prise 230/460 Fil de raccordement Fil de raccordement REMARQUE : (200) & (400) IL FAUT CHANGER LA CONNEXION SECONDAIRE AU NIVEAU DU TRANSFORMATEUR PRINCIPAL ET REPOSITIONNER LES CAVALIERS À FILS SUR LA PLAQUE À BORNES SITUÉE SUR LE CÔTÉ OPPOSÉ DE L’UNITÉ VOIR LE MANUEL 54 REMARQUE : (200) & (400) IL FAUT CHANGER LA CONNEXION SECONDAIRE AU NIVEAU DU TRANSFORMATEUR PRINCIPAL ET REPOSITIONNER LES CAVALIERS À FILS SUR LA PLAQUE À BORNES SITUÉE SUR LE CÔTÉ OPPOSÉ DE L’UNITÉ VOIR LE MANUEL BORNIER ENTRÉE MODÈLES 230/460 VCA BORNIER ENTRÉE MODÈLES 230/460 VCA Configuration 200 VCA Configuration 400 VCA installation 380 VAC et 400 VAC Modèles - livrée par l’usine, ces modèles de EPP-202 sont configurés pour la tension d’entrée unique figurant sur la plaque signalétique. Si vous utilisez d’autres tensions d’entrée, il est possible de configurer ces unités soit pour 380 VAC ou 400 VAC entrée. Il ya trois étapes à suivre lors de cette conversion: 1. Reconfigurer le robinet de tension sur le transformateur de commande (T2) pour la tension d’entrée correcte: Déplacer cette connexion bancaire à: 400 VAC - H5 380 VAC - H4 460 VAC - (est représentée) 55 installation 1 2 3 4 5 6 7 8 9 10 11 12 1 2 3 4 5 6 7 8 9 10 11 12 2 3 4 5 6 7 8 9 10 11 12 380 VAC et 400 VAC modèles (suite) 2. Reconfigurer TB2 bornier pour la bonne tension. 1 TB2 Positions des cavaliers pour 400 VAC 1 2 3 4 5 6 7 8 9 10 11 12 TB2 Positions des cavaliers pour 380 VAC Prise 380 1 2 3 4 5 6 7 8 9 10 11 12 1 2 3 4 5 6 7 8 9 10 11 12 REMARQUE: Fils connectés sur la principale prise de transformateur doivent être reconnectées à 400 ou 380 principales prises de transformateur sur les 3 bobines. Veillez à remplacer revêtement de vinyle isolant sur des connexions. Panneau d’accès Prise 400 3. Reconfigurer les prises secondaires sur les trois principales bobines de transformateur. Un panneau de service amovible est situé au-dessus les connexions du transformateur pour améliorer l’accès. 575 modèles ACC - ce modèle ne est pas configurable à tout autre tension d’entrée. 56 installation Procédure de connexion de refroidissement MISE EN GARDE Ne pas laisser la pompe tourner avec le réservoir de refroidissement vide pour ne pas endommager la pompe de façon permanente. MISE EN GARDE Ne pas brancher les tuyaux à une électrovanne qui peut être fermée lorsque la pompe fonctionne. Ceci pourrait endommager la pompe. 1. Ouvrir le panneau d’accès sur l’avant inférieur de la Console Plasma en retirant (4) vis M6. 2. Acheminer les tuyaux de refroidissement par les ouvertures en bas de la Console Plasma, juste derrière le panneau avant. 3. Brancher les tuyaux aux bornes désignées montées dans la Console Plasma. 4. Fermer le panneau d’accès avant. Panneau d’accès avant ouvert Panneau d’accès avant fermé Retirer les quatre vis M6 pour ouvrir le panneau d’accès Connexions de refroidissement Pour faciliter la connexion, acheminer les câbles/tuyaux par ces 2 trous d’accès. Une fois la torche branchée, remplir le réservoir de liquide de refroidissement pour torche spécialement formulé (environ 15 litres). Ne pas utiliser de solutions antigel, tel que pour une automobile, car les additifs endommageraient la pompe et la torche. La référence ESAB n° 0558004297 est recommandée pour des températures allant jusqu’à -11 °C. La référence ESAB n° 156F05 est recommandée pour les températures de -11 °C à -36 °C. Après avoir rempli le réservoir, mettre l’appareil sous tension et laisser la pompe tourner avec le réservoir ouvert pour purger l’air du radiateur, des tuyaux et de la torche. Vérifier de nouveau le niveau de liquide de refroidissement pour s’assurer que le réservoir est rempli. Remettre le bouchon du réservoir en place une fois la purge terminée et après avoir vérifié le niveau de liquide de refroidissement. Vérifier qu’il n’y a pas de fuites. 57 installation Réglage de la pression d’alimentation La pression d’alimentation est contrôlée par la vanne de détente montée près de la pompe dans le réservoir. Tourner la vis de réglage de la pression dans le sens horaire pour augmenter la pression sur le ressort et la pression d’alimentation. La tourner dans le sens antihoraire pour réduire la pression sur le ressort et réduire la pression d’alimentation. La pression est ajustée en usine pour fournir environ 12 bar à 5,7 l/min. Ceci est un réglage approprié pour le PT-36 sur un système M3. Normalement, aucun autre réglage n’est requis. La vanne de détente envoie du liquide de refroidissement dérivé par la plaque refroidie de l’IGBT et le ramène dans le réservoir. En conséquence, une ligne d’’avacuation fermée ne devrait pas endommager la pompe. La pompe est munie d’une vanne de détente intégrée. Cette vanne est réglée par le fabricant pour s’ouvrir complètement à 15,5 bar. Son unique rôle est de protéger la pompe si la vanne de détente externe se ferme. Cette vanne de détente ne doit pas être réglée sur site. Vis de réglage de la pression Unité de Console Plasma vue de dessus sans panneau supérieur 58 installation Connexions de sortie AVERTISSEMENT LES CHOCS électriques peuvent causer la mort ! tension et courant dangereux ! pour tous les travaux autour d’une source d’alimentation plasma avec couvercles retirés : • DÉBRANCHER LA SOURCE D’ALIMENTATION AU NIVEAU DU DISJONCTEUR MURAL (SECTEUR). • UNE PERSONNE QUALIFIÉE DOIT VÉRIFIER LES BARRES DU BUS DE SORTIE (POSITIVE ET NÉGATIVE) À L’AIDE D’UN VOLTMÈTRE. Câbles de sortie Choisir les câbles de sortie pour le coupage plasma sur la base d’un câble en cuivre isolé de 600 V et de 4/0 AWG pour 400 ampères de courant de sortie. Remarque : Les câbles de soudage isolés de 100 V ne sont pas suffisants. Ne pas les utiliser. AVERTISSEMENT ne pas mettre l’unité plasma en marche lorsque les couvercles sont retirés. les composants haute tension sont exposés, augmentant le risque de chocs électriques. les composants internes peuvent être endommagés car les ventilateurs de refroidissement perdent leur efficacité. 59 installation Procédure de connexion de sortie 1. Ouvrir le panneau d’accès en bas sur la partie avant de la Console Plasma en retirant quatre vis M6. 2. Acheminer les câbles de sortie par les ouvertures en bas de la Console Plasma, juste derrière le panneau avant. 3. Brancher les câbles aux bornes désignées montées à l’intérieur de la Console Plasma en utilisant des serre-fils répertoriés UL. 4. Fermer le panneau d’accès avant. Panneau d’accès avant ouvert Panneau d’accès avant fermé Retirer les quatre vis M6 pour ouvrir le panneau d’accès Pour faciliter la connexion, acheminer les câbles/ tuyaux par ces 3 trous d’accès. L’unité plasma n’est pas munie d’un interrupteur marche/arrêt. L’alimentation principale est commandée par le disjoncteur mural (secteur). 60 installation Connecteurs de câbles d’interface Connexion du câble CAN Ceci est le connecteur du bus de communication CAN. Le câble venant de ce connecteur est attaché au CGC-2. J1 (RAS) Ceci est un connecteur pour interfacer avec l’unité Remote Arc Starter-2 (RAS). Le câble venant de ce connecteur transporte des signaux tels que : Haute fréquence ON. Interface analogique (connecteur à 37 broches) Ceci est la connexion utilisée pour interfacer avec un CNC externe. Interface analogique CAN J1 (RAS) Panneau de connecteurs de câbles d’interface (partie inférieure du panneau avant) 61 installation Connexions des composants individuels Câble CAN Câble Désignation Longueurs disponibles m (pieds) Réf. ESAB Alimentation CGC-2 et CAN M12 (8P-8P) 8 m (26) 9 m (30) 10 m (33) 11 m (36) 12 m (39) 13 m (43) 14 m (46) 15 m (50) 20 m (66) 25 m (82) 30 m (100) 36 m (118) 40 m (131) 45 m (150) 0558008471 0558008472 0558008473 0558008474 0558008475 0558008476 0558008477 0558008478 0558008479 0558008809 0558008481 0558008480 0558008482 0558008483 REMARQUE : Le câble CAN doit être acheminé séparé des fils de la torche. Panneau de connecteurs de câbles d’interface (partie inférieure du panneau avant) Devant CGC 62 installation Câble d’interface J1 (RAS) Câble Désignation Commande RAS-2 (14PX-14S) Longueurs disponibles m (pieds) Réf. ESAB 2,9 m (9,5) 0558011840 7,6 m (25) 0558011631 10 m (33) 0558011632 15 m (50) 0558011633 20 m (66) 0558011634 23 m (75) 0558011635 25 m (82) 0558011636 30 m (100) 0558011637 Panneau de connecteurs de câbles d’interface (partie inférieure du panneau avant) Devant RAS 63 installation Interface analogique (connecteur à 37 broches) Câble Désignation CNC E/S DB37 (37P-libre) Longueurs disponibles m (pieds) 15 m (50) Réf. ESAB 0558012480 Panneau de connecteurs de câbles d’interface (partie inférieure du panneau avant) Vers CNC / contrôle externe 64 installation Noyau de ferrite (p / n 952157) Le noyau de ferrite est utilisé pour supprimer le bruit dans le câble de communication CAN. Cet article est emballé dans un sac en tissu, à l’intérieur du panneau avant en bas, avec une attache de câble utilisé pour fixer la ferrite en place. CAN câble de communication Le noyau de ferrite doit être monté comme indiqué sur le câble de communication CAN. Fixez le collier de serrage sous ferrite pour assurer ferrite en place. noyau de ferrite serre-câble 65 installation Placement du Régulateur de gaz combinés (CGC-2) Le CGC règle le gaz plasma et le gaz de protection. Pour une performance optimale, il doit toujours être placé à moins de 2 mètres (6 pieds) du corps de la torche. En fonction du matériau à couper, le client doit sélectionner et connecter les gaz d’entrée appropriés. Des filtres en ligne sont intégrés dans les raccords d’entrée. S’assurer que tous les gaz d’entrée répondent aux exigences de pression et de débit. REMARQUE : Le câble CAN doit être acheminé séparé des fils de la torche. Gaz Protection N2/Air/O2 N2/Air Rideau d’air Air Plasma Pression 125 psi (8,6 bar), 255 SCFH (7,2 SCMH) 125 psi (8,6 bar), 250 SCFH (7,1 SCMH) 80 psi (5,5 bar), 1200 SCFH (34,0 SCMH) Débit maximum du gaz - CFH (CMH) avec la torche PT-36 Pureté du gaz Air (85 psi / 5,9 bar) Procédé 269 (7,6) Propre, sec, sans huile Filtré à 25 microns Nitrogène (125 psi / 8,6 bar) 385 (10,9) 99,99%, filtré à 25 microns Oxygène (125 psi / 8,6 bar) 66 (1,9) 99,5%, filtré à 25 microns Adaptateurs d’entrée métriques Adaptateurs d’entrée CGA Référence ESAB Plasma N2/Air/O2 G-1/4” mâle droit x G-1/4” mâle droit 0558010163 Protection N2/Air G-1/4” mâle droit x G-1/4” mâle droit 0558010163 Air G-1/4” mâle droit x « B » mâle droit air/eau 0558010165 N2 G-1/4” mâle droit x « B » mâle droit gaz inerte 0558010166 O2 G-1/4” mâle droit x « B » mâle droit oxygène 0558010167 Air G-1/4” mâle droit x « B » mâle droit air/eau 0558010165 N2 G-1/4” mâle droit x « B » mâle droit gaz inerte 0558010166 SG 1/4” NPT x 5/8»-18 mâle gauche 10Z30 PG 1/4” NPT x “A” mâle droit oxygène 0558012518 Plasma Protection Outputs 66 Raccord Réf. Kit ESAB 0558012478 Gaz Réf. Kit ESAB 0558012479 Gaz et pression installation Connexions de CGC-2 à RAS Le CGC-2 et la boîte RAS doivent être mis à la terre ensemble à l’aide du fil de connexion de mise à la terre fourni. 67 installation Placement de la boîte RAS La boîte RAS peut être montée dans 2 configurations différentes : - Montage à distance sur la machine - Montage local sur la Console Plasma Connexions sur la boîte RAS - Montage à distance sur la machine Avec cette configuration de montage, la boîte RAS peut être montée sur la machine à un point permettant un bon fonctionnement des connexions. Les connexions sont les suivantes : AVERTISSEMENT Le couvercle est mis à la terre à la boîte Remote Arc Starter-2 intérieurement avec un fil de mise à la terre court. Retirer soigneusement le couvercle pour éviter d’endommager le fil ou de desserrer le fil de mise à la terre. 1. Retirer ou déverrouiller les vis du couvercle et soulever le couvercle de la boîte pour exposer les composants internes. 2. Les câbles d’alimentation passent par les raccords de réducteur de tension. 3. Dénuder l’isolation du câble de 1/0 (53,5 mm2), approximativement 38 mm. 4. Insérer le câble de 1/0 (53,5 mm2) dans le trou de la barre/du bloc omnibus jusqu’à ce que le cuivre s’étende jusqu’au bord de la barre/du bloc omnibus. Le câble arc pilote entre par le raccord de réducteur de tension vers le Diviseur de tension (VDR) Liquide de refroidissement IN (entrée) vers Activation Console Plasma vers Console Plasma Liquide de refroidissement OUT (sortie) Raccords de réducteur de tension Les câbles de source d’alimentation entrent par les raccords de réducteur de tension Remarque : Le châssis doit être connecté à la terre de la machine. 68 installation Barre/bloc omnibus Isolation Nomex Connexion VDR Vis de blocage Connexion pour câble arc pilote 5. Serrer la ou les vis de blocage sur le câble. 6. Sur le câble VDR (fourni par le client), l’extrémité comportant le connecteur doit être connecté à la boîte RAS à sa prise correspondante qui est étiquetée « Voltage Divider » [Diviseur de tension] . Câble Désignation Diviseur de tension (VDR) M8 (3P-libre) Longueurs disponibles m (pieds) Réf. ESAB 1,5 m (5 ) 0560946753 3 m (10 ) 0560946754 5 m (16 ) 0560946755 10 m (33 ) 0560946756 20 m (66 ) 0560946757 Câble VDR (avec extrémité libre) L’extrémité libre du câble VDR sera connectée au dispositif de levage. Bien qu’il s’agisse d’un câble à trois conducteurs, seuls deux des fils sont utilisés, MARRON (VDR - ) et BLEU (WORK). Le fil noir est un fil de réserve qui doit être terminé et bouché à l’intérieur du dispositif de levage. La broche correspondante au niveau de la boîte RAS est terminée en usine. La boîte RAS ne doit pas être modifiée. Il est impératif que le fil BLEU soit connecté à la terre. Le fil MARRON est la sortie VDR(-). Intensité N° requis de câbles 1/0 Jusqu’à 200 A 1 MARRON (VDR-) BLEU (TRAVAIL) Câble VDR NOIR (RÉSERVE) Dispositif de levage fourni par le client La masse dans le dispositif de levage est requise pour référence 69 installation AVERTISSEMENT LES CHOCS électriques peuvent causer la mort ! tension et courant dangereux ! pour tous les travaux autour d’une source d’alimentation plasma avec couvercles retirés : • DÉBRANCHER LA SOURCE D’ALIMENTATION AU NIVEAU DU DISJONCTEUR MURAL (SECTEUR). • UNE PERSONNE QUALIFIÉE DOIT VÉRIFIER LES BARRES DU BUS DE SORTIE (POSITIVE ET NÉGATIVE) À L’AIDE D’UN VOLTMÈTRE. Connexions sur la boîte RAS - Montage local sur la Console Plasma Avec cette configuration de montage, toutes les connexions sont les mêmes qu’avec le montage à distance sur la machine. La boîte RAS peut être montée sur l’arrière de la Console Plasma comme il l’est indiqué à l’aide des supports fournis. Lors de l’utilisation de la boîte RAS à cet emplacement, s’assurer que le fil de mise à la terre est installé avant toute opération. Attacher le fil de mise à la terre ici, cette masse doit également être connectée au CGC-2 Acheminer le fil à travers la bague dans le panneau arrière de la source d’alimentation 70 Ouvrir couvercle Attacher le fil de mise à la terre ici à la cosse fournie installation Connexions de la torche Connexion de la torche au système au plasma DANGER LES CHOCS électriques peuvent causer la mort! • Déconnecter la Console Plasma primaire avant d’effectuer tout réglage. • Déconnecter la source primaire avant de procéder à toute maintenance sur les composants du système. • Ne pas toucher les pièces avant de la torche (buse, coupelle de retenue, etc.) sans couper l’alimentation primaire. La torche PT-36 possède deux câbles d’alimentation refroidis par eau qui doivent être connectés à la sortie négative de la boîte RAS à partir de la Console Plasma. Le raccord droit 7/16-20 est sur le câble fournissant le liquide de refroidissement à la torche. Le raccord gauche 7/16-20 est sur le câble retournant le liquide de refroidissement à la torche. Le câble arc pilote est également connecté à la boîte RAS. Ces câbles ont un fil vert/jaune qui doit être connecté à une borne de masse comme il l’est indiqué. Connexion de l’arc pilote Borne de masse Fil de mise à la terre de châssis vert/jaune Câble arc pilote Connexions du câble d’alimentation/ liquide de refroidissement Tuyau SG Câble d’alimentation / Liquide de refroidissement Tuyau PG 71 installation Montage de la torche sur la machine DANGER Serrer le corps de la torche risque d’entraîner l’écoulement d’un courant dangereux dans le châssis de la machine. Monter la torche sur la gaine isolée ici • • • • • • Ne pas monter sur le corps de torche en acier inoxydable. Le corps de torche est isolé électriquement, toutefois, le courant de démarrage haute fréquence peut effectuer un arc pour trouver une masse. Un serrage à proximité du corps de la torche peut entraîner une formation d’arc entre le corps et la machine. Lorsque cette formation d’arc a lieu, le corps de la torche peut nécessiter une pièce de rechange non couvert par la garantie. Les composants de la machine risquent d’être endommagés. Serrer uniquement sur la gaine de torche isolée (directement au-dessus de l’étiquette) à pas moins de 1,25» (31,75 mm) de l’extrémité torche de la gaine. NE PAS monter sur le corps de torche en acier ici 72 installation Préparation à la coupe • Sélectionner une condition appropriée des Cut Data [Données de coupe] (Fichier SDP) et installer les pièces avant de la torche (buse, électrode, etc.) Voir les Données de coupe pour identifier les pièces et les paramètres. • Positionner la torche sur le matériau à l’emplacement de démarrage souhaité. • Voir la section Console Plasma pour les paramètres appropriés. • Voir les sections Description et Installation pour les procédures de contrôle de gaz et de mise en marche. Découpe de miroirs Lors de la découpe de miroirs, un déflecteur de gaz à tourbillon inverse et un diffuseur inverse sont requis. Ces pièces inverses feront « tournoyer » le gaz dans le sens opposé, inversant ainsi le « bon » côté de la coupe. Dispositif de retenue d’écran Déflecteur inverse 4 x .032 Réf. 0558002534 Déflecteur inverse 8 x .047 Réf. 0558002530 Diffuseur inverse Réf. 0004470115 Écran Dispositif de retenue de buse Diffuseur Buse Électrode Déflecteur 0558002530 Support Qualité de la coupe Les causes affectant la qualité de la coupe sont interdépendantes. Le changement d’une variable affecte toutes les autres. Il peut être difficile de déterminer une solution. Le guide suivant offre des solutions possibles pour les différents résultats de coupe indésirables. Pour commencer, sélectionner la condition la plus prédominante : • • • • • Angle de coupe, négatif ou positif Planéité de la coupe Fini de surface Laitiers Précision dimensionnelle En général, les paramètres de coupe recommandés donneront une qualité de coupe optimale ; de temps à autre, les conditions peuvent varier suffisamment pour que de légers réglages soient nécessaires. Dans ce cas : • Effectuer de petits ajustements cumulatifs lors des corrections. • Ajuster la tension de l’arc en incréments de 5 volts, à la hausse ou à la baisse selon les besoins. • Ajuster la vitesse de coupe à 5 % ou moins selon les besoins jusqu’à amélioration des conditions. 73 installation MISE EN GARDE Avant de tenter TOUTE correction, vérifier les variables de coupe avec les paramètres recommandés d’usine/les références des pièces d’usure listés dans les Données de coupe. Angle de coupe Angle de coupe négatif La dimension du dessus est supérieure à celle du dessous. • • • • • Mauvais alignement de la torche Matériau courbé ou gauchi Consommables usagés ou endommagés Entretoise basse (tension d’arc) Vitesse de coupe basse (taux de déplacement de la machine) Baisse Pièce Pièce Angle de coupe positif La dimension du dessus est inférieure à celle du dessous. • • • • • • Mauvais alignement de la torche Matériau courbé ou gauchi Consommables usagés ou endommagés Entretoise haute (tension d’arc) Vitesse de coupe rapide Courant haut ou bas. (Voir Données de coupe pour le niveau de courant recommandé pour les buses spécifiques). Pièce Baisse 74 Pièce installation Planéité de la coupe Dessus et dessous arrondis. Condition se produit généralement lorsque le matériau est d’une épaisseur maximale de 0,25» (6,4 mm). • Haut courant pour épaisseur de matériau quelconque. (Voir les Données de coupe pour les paramètres appropriés). Baisse Pièce Dégagement de bord supérieur • Entretoise basse (tension d’arc) Baisse Pièce 75 installation Fini de surface Rugosité induite par processus La face coupée est toujours rugueuse. Peut ou non être confinée à un axe. • • Vue du dessus Face coupée Mélange de gaz de protection incorrect (Voir Données de coupe). Consommables usagés ou endommagés. Rugosité induite par machine Rugosité induite par machine Peut être difficile à distinguer de la rugosité induite par processus. Souvent confinée à un seul axe. La rugosité est inconsistante. • • Rails, roues et/ou support/pignon d’entraînement sales. Ajustement de roues de chariot. ou Rugosité induite par processus Face coupée Lignes de décalage Laitiers Les laitiers sont un sous-produit du processus de coupe. Il s’agit du matériau indésirable qui reste attaché à la pièce. Dans la majorité des cas, les laitiers peuvent être réduits ou éliminés avec une configuration de paramètres de torche et de coupe appropriés. Consulter la section Données de coupe. Laitiers à haute vitesse Matériau soudé ou roulement sur la surface inférieure le long d’une saignée. Difficile à retirer. Peut nécessiter meulage ou écaillage. Lignes de décalage en forme de « S ». • • Roulement Vue latérale Entretoise haute (tension d’arc). Vitesse de coupe rapide. Lignes de décalage Face coupée Laitiers à faible vitesse Forment comme des globules sur le bas le long de la saignée. Se retirent facilement. • Globules Vitesse de coupe faible. Vue latérale 76 installation MISE EN GARDE Dans la majorité des cas, la vitesse de coupe et la tension d’arc recommandées donneront une performance de coupe optimale. De petits ajustements cumulatifs peuvent être nécessaires en raison de la qualité du matériau, de la température du matériau et de l’alliage spécifique. L’opérateur ne doit pas oublier que toutes les variables de coupe sont interdépendantes. Modifier un paramètre affecte tous les autres et la qualité de la coupe pourrait se détériorer. Toujours commencer avec les paramètres recommandés. Laitiers supérieurs Apparaissent comme des projections sur le dessus du matériau. En général, se retirent facilement. • • Vitesse de coupe rapide Entretoise haute (tension d’arc). Vue latérale Éclaboussures Laitiers intermittents Apparaissent sur le dessus ou le dessous, le long de la saignée. Non continus. Peuvent apparaître comme toute sorte de laitiers. • Consommables usagés possibles Autres facteurs affectant les laitiers : • • • Face coupée Température du matériau Calamine ou rouille importante Alliages à teneur élevée en carbone MISE EN GARDE Avant de tenter TOUTE correction, vérifier les variables de coupe avec les paramètres recommandés d’usine/les références des pièces d’usure listés dans les Données de coupe. Précision dimensionnelle Généralement, l’utilisation de la vitesse la plus lente possible (dans des niveaux approuvés) optimisera la précision des pièces. Sélectionner des consommables pour permettre une tension d’arc inférieure et une vitesse de coupe plus lente. La vitesse de coupe et la tension d’arc recommandées donneront une performance de coupe optimale. AVIS De petits ajustements cumulatifs peuvent être nécessaires en raison de la qualité du matériau, de la température du matériau et de l’alliage spécifique. L’opérateur ne doit pas oublier que toutes les variables de coupe sont interdépendantes. Modifier un paramètre affecte tous les autres et la qualité de la coupe pourrait se détériorer. Toujours commencer avec les paramètres recommandés. Avant de tenter TOUTE correction, vérifier les variables de coupe avec les paramètres recommandés d’usine/les références des pièces d’usure listés dans la section Données de coupe et/ou dans le manuel. 77 installation Passages d’écoulement dans la torche Sortie Eau et Alimentation Arc pilote Entrée de gaz plasma Entrée Eau (L.H.) 78 Entrée de gaz de protection FONCTIONNEMENT Fonctionnement Page intentionnellement laissée en blanc 80 Fonctionnement Fonctionnement Panneau avant A - Voyant alimentation Cet indicateur s’allume lorsque l’alimentation d’entrée est appliquée à la Console Plasma. B - Voyant d’erreur Cet indicateur s’allume à chaque fois qu’il y a une erreur. Il peut rester allumé en permanence ou clignoter avec des intervalles 50 % ON/OFF en fonction du type d’erreur. Si l’erreur est une défaillance thermique, l’indicateur restera allumé [ON] en permanence. Pour les autres types d’erreur, il clignotera. L’information réelle d’erreur/de panne s’affiche sur l’écran du panneau avant. C - Affichage Interface Control (IC) [Commande interface] Il s’agit de l’interface d’opérateur primaire pour configurer le système au plasma. D - Roue codeuse d’Interface Control (IC) [Commande interface] Utilisée pour naviguer la commande interface. A B C D 81 82 24 V c.a. 120 V c.a. PS 24 V c.c. COMMUN 120 V c.a. SOUS TENSION 120 V c.a. NEUTRE 24 V c.c. PSCAN CAN PS CAN CAN ANALOG INTERFACE INTERFACE ANALOGIQUE SÉLECTION DU TYPE DE TORCHE PS 24 V c.c. COMMUN 120 V c.a. NEUTRE HF ACTIVÉ / VANNE D’INVERSION MODE MARQUAGE ACTIVÉ 120 V c.a. SOUS TENSION 14 câble conducteur CARTE HF/VDR Boîtier RAS ACTIVATION PS DB37 Cable to Customer CNC Câble DB37 à CNC client COMMUNICATION CAN CAN COMMUNICATION ACTIVATION PS B A 5 câble conducteur CONNEXION ACTIVATION PS CNC/système de commande de processus Fonctionnement m2 Smart Plasmarc J1 (RAS) - Schéma de l’interface Fonctionnement Commande interface La commande interface (IC) est utilisée pour interfacer la commande de processus ESAB m2 avec le CNC client à l’aide d’une E/S numérique. Les pages suivantes décrivent le fonctionnement de l’IC. Affichage Interface Control (IC) [Commande interface] Roue codeuse d’Interface Control (IC) [Commande interface] 83 Fonctionnement Écrans d’affichage Lors de la mise sous tension, l’écran IC affiche l’information suivante pendant 3 secondes : Écran de démarrage Écran de menu supérieur Numéro d’écran Écran de configuration Écran principal Écran du journal d’erreurs Écran de diagnostic Écran information système 84 Fonctionnement Écran principal Nom Écran Arrière Numéro d’écran Sélection de paramètres. Provient de la base de données à l’intérieur de l’EEPROM, avec une largeur de 20 caractères. Sélectionner en faisant défiler. Si le cercle est rempli, les paramètres ne sont pas les paramètres par défaut. Paramètres des gaz. Peuvent être modifiés mais, quand modifiés, remplir le champ « Custom Parameter » [Paramètre personnalisé]. Restaure les valeurs par défaut pour les paramètres. État du système complet : • READY [PRÊT] - prêt à fonctionner • PREFLOW [PRÉ-ÉCOULEMENT] - Pré-écoulement du plasma et du gaz de protection • START [DÉMARRAGE] - Démarrage de la torche • RUN [FONCTIONNEMENT] - Couper avec la torche • STOP [ARRÊT] - Arrêter la séquence de coupe • FAULT [ERREUR] - Erreur dans le système • WARN [AVERTISSEMENT] - Niveau du liquide de refroidissement est bas État de module : • Vide - Module absent de l’omnibus CAN • Continu - Module sur l’omnibus CAN et prêt • Clignotant - Erreur de module Séquence de fonctionnement 1. 2. 3. 4. Allumer les gaz d’entrée pour l’unité CGC-2. Vérifier que les pièces d’usure dans la torche PT-36 correspondent à la condition de coupe requise. Mettre la Console Plasma en marche [ON]. Aller à l’Écran principal (sélectionner fichier) et régler le fichier pour correspondre aux données de coupe requises. 5. S’il n’y a pas d’erreurs sur le CNC, envoyer un signal de démarrage au système m2 Smart Plasmarc. 6. Attendre l’entrée numérique ARC ON du système et régler Activer mouvement sur le CNC pour continuer à couper avec la machine. 7. Pour toute erreur sur l’affichage, consulter la section Dépannage de ce manuel. 85 Fonctionnement Écran de configuration Consulter l’Écran principal Le temps de pré-écoulement est le temps total pour le pré-écoulement avant de tenter de démarrer l’arc. Il ne peut pas être inférieur au temps de pré-écoulement minimum pour les fils de torche. « Standard » affiche les unités en PSI/CFH. « Metric » affiche les unités en BAR/CMH. Filtre la sélection de paramètres pour les options sélectées. Désactiver les erreurs du système. Sauvegarde les paramètres sur l’EEPROM. Recharge les paramètres de l’EEPROM. Enregistrer écran Recharger écran Confirme l’enregistrement de configuration de l’EEPROM Annule l’enregistrement 86 Annule le rechargement Confirme le rechargement de configuration de l’EEPROM Fonctionnement Écran Setup-> Error Disable [Configuration -> Désactiver erreur] Désactive les erreurs de pression de sortie du gaz plasma trop haute et trop basse. Désactive les erreurs d’écoulement de sortie du gaz de protection trop haut et trop bas. Désactive les erreurs de sortie de courant trop haute et trop basse. Désactive l’erreur de perte d’arc. Modification d’un paramètre sur l’affichage Uniquement disponible lorsque la communication est réglée sur Néant ou que l’interrupteur Local/À distance est réglé sur Local. 1. 2. 3. 4. Utiliser la roue codeuse pour défiler vers le paramètre. Appuyer sur la roue. Faire tourner la roue pour modifier la valeur. Appuyer sur la roue à nouveau pour verrouiller la valeur. Écran Setup-> Parameter Filter [Configuration -> Filtres de paramètres] Options de sélection de matériaux disponibles : MS, ALL Options de sélection de gaz plasma : N2, O2, Air 87 Fonctionnement Accès à l’écran du journal d’erreurs Écran du journal d’erreurs Consulter l’Écran principal Dernière erreur - consulter la section Maintenance/ Dépannage PROC - voir section Erreurs de processus IC - voir section Erreurs IC GC ou PS - voir section Erreurs de module Efface l’écran du journal d’erreurs Consulter l’Écran principal Écran d’erreurs Type de module Nombre de mises en marche depuis le dernier redémarrage Code d’erreur Détails d’erreur 88 Fonctionnement Accès à l’écran de diagnostics Écran de diagnostic Démarrage du plasma à partir du CNC Maintenir le signal à partir du CNC Test gaz à partir du CNC Signal Arc activé au CNC Signal erreur au CNC Sortie du rideau d’air Diagnostics de Console Plasma Diagnostics de contrôle de gaz Écran Diagnostics - > Plasma Console [Diagnostics -> Console Plasma] Démarrage plasma vers carte de contrôle Arc activé à partir de la carte de contrôle Niveau du liquide de refroidissement à partir de la carte de contrôle Écoulement du liquide de refroidissement Courant de sortie Courant d’arc pilote Courant de démarrage Courant de coupe Courant d’arrêt Temps d’augmentation de courant Temps de réduction de courant 89 Fonctionnement Écran Diagnostics - > Plasma Console [Diagnostics -> Console Plasma] Consulter l’Écran principal Pression de gaz plasma commandée Pression de sortie de gaz plasma Écoulement de gaz de protection commandé Écoulement de gaz de protection Consulter l’Écran principal Accès à l’écran information système Écran information système Version du micrologiciel sur la Commande Interface. Version du micrologiciel sur la Console Plasma. Version du jeu de données de paramètres. Version du micrologiciel sur le PCUP. Version du PLC local sur le contrôle de gaz. 90 Fonctionnement E/S numériques Entrées numériques Les entrées numériques ne peuvent être activées qu’avec du 24 V CC. Toute autre tension risque d’endommager la carte ou d’entraîner des résultats imprévisibles. La meilleure méthode est d’envoyer de 24 V CC à partir du connecteur DB37 sur l’entrée, via un relais ou une puce d’isolateur optique. Nom du signal Démarrage du plasma Test de gaz Maintenir Description Démarre le processus de plasma Démarre le processus de plasma sans allumer la torche Empêche le système de démarrer la Console Plasma Sorties numériques Les sorties numériques ne doivent être que de 24 V CC avec une exigence de courant inférieur à 80 milli-ampères. Nom du signal Arc activé Erreur de système Description Ce signal est élevé lorsque l'arc est activé L'IC a détecté un problème qui nécessite l'arrêt du processus. Consulter le journal d'erreurs pour obtenir le jeu exact d'erreurs. 91 Fonctionnement Description du câblage d’interface Câblage d’interface Connecteur DB37 Ce câble doit être un câble à paires torsadées sur un blindage global attaché à la coque sur les deux extrémités du câble. Il comporte un connecteur mâle DB37 sur une extrémité et une coupe à ras sur l’autre extrémité. N° BROCHE Couleur de fil Nom du signal 4 VERT Sortie numérique 1 (-) Émetteur d'activation de mouvement 5 VERT/BLANC Sortie numérique 2 (-) Émetteur d'erreurs de système 6 ORANGE/BLANC Sortie numérique 3 (-) Émetteur de rideau d'air 7 NOIR/BLANC Sortie numérique 4 (-) Émetteur de sortie de réserve 12 GRIS/BLANC Entrée numérique 1 Maintien d'allumage 13 ROUGE/BLANC Entrée numérique 2 Test de gaz 15 GRIS Entrée numérique 4 Démarrage de cycle 17 ROUGE 24 V CC Alimentation 24 V CC 18 NOIR TERRE *23 ORANGE Sortie numérique 1 (+) tresse de blindage PE Fonction Terre Collecteur de sorties numériques Mise à la terre potentiel * Tous les collecteurs de sorties numériques sont combinés ensemble. Recommandée DB-37 E / S Connexions au contrôleur de la clientèle 92 Fonctionnement Exemples de câblage de sorties numériques Les sorties numériques ne doivent être que de 24 V CC avec une exigence de courant inférieur à 80 milli-ampères. Pour ce faire, il existe deux bonnes méthodes. Il y a une petite baisse de tension sur l’isolateur optique dans le hub de commande interface, il est donc recommandé d’utiliser une tension d’au moins 12 V CC pour protéger contre le bruit généré par le circuit de démarrage du système au plasma. Méthode 1 : Utilisation de 24 V CC pour entraîner un circuit d’entrées numériques sur l’entrée du CNC. 24 24VV DO+ 1 SN SN DO- 1 R1 R2 10K 1M 5V 5V R3 2.74K Méthode 2 : Utilisation de 24 V CC pour entraîner une bobine de relais et utilisation du contact sur la bobine de la façon le CNC en a besoin. 24 24VV V SN DO+ 1 R2 K 1M 5V R3 2.74K SN DO1 A coil BOBINE B External CNC Serial Digital I/O External Power 230V/3A w/ Height Control Water Injection External CNC Serial RAS BOX w/o Height Control 120V/3A or Injection Water 93 CAN PS Fonctionnement Page intentionnellement laissée en blanc 94 DONNÉES DE COUPE Données de coupe Page intentionnellement laissée en blanc 96 Données de coupe Données de coupe Utiliser les pages suivantes pour les paramètres de coupe initiale. Les divers matériaux et conditions peuvent exiger d’effectuer certains réglages pour obtenir les résultats souhaités. DANGER Risque d’explosion d’hydrogène ! Lire ce qui suit avant de tenter de couper avec une table à eau. Un risque est présent lorsqu’une table à eau est utilisée pour le coupage à l’arc plasma. De graves explosions peuvent avoir lieu suite à une accumulation d’hydrogène sous la plaque en cours de coupe. Des milliers de dollars de dégâts matériels peuvent être causés par ces explosions. Des blessures graves, voire mortelles, peuvent être causées par de telles explosions. La meilleure information disponible indique l’existence de trois sources d’hydrogène possibles dans les tables à eau : 1. Réaction au métal liquide La majeure partie de l’hydrogène est libérée suite à la réaction rapide du métal liquide de la saignée dans l’eau formant des oxydes métalliques. Cette réaction explique pourquoi les métaux réactifs présentant une plus grande affinité avec l’oxygène, tels que l’aluminium et le magnésium, libèrent des volumes supérieurs d’hydrogène durant la coupe que ceux libérés par le fer ou l’acier. La majeure partie de cet hydrogène atteint immédiatement la surface, mais une certaine quantité s’attache aux petites particules métalliques. Ces particules se déposent au fond de la table à eau et des bulles d’hydrogène remontent graduellement à la surface. 2. Réaction chimique lente L’hydrogène peut aussi résulter de réactions chimiques plus lentes de particules métalliques froides avec l’eau, des métaux non similaires ou des produits chimiques présents dans l’eau. Des bulles d’hydrogène remontent graduellement à la surface. 3. Gaz plasma L’hydrogène peut provenir du gaz plasma. À des courants supérieurs à 750 A, H-35 est utilisé comme gaz de coupe. Ce gaz contient 35 % d’hydrogène par volume et un total de 125 pieds cubes/heure d’hydrogène sera libéré. Indépendamment de la source, le gaz d’hydrogène peut être recueilli dans des poches formées par la plaque en cours de coupe et des lamelles sur la table, ou des poches provenant d’une plaque gauchie. Il peut aussi y avoir une accumulation d’hydrogène sous le plateau de scories ou même dans le réservoir d’air, ci ceux-ci font partie de la conception de la table. L’hydrogène, en présence d’oxygène ou d’air, peut être allumé par l’arc plasma ou l’étincelle d’une source quelconque. 4. Suivre ces pratiques pour réduire la formation et l’accumulation d’hydrogène : A. Nettoyer fréquemment les scories (particulièrement les particules fines) du fond de la table. Remplir de nouveau la table avec de l’eau propre. B. Ne pas laisser les plaques sur la table jusqu’au lendemain ou tout un weekend. C. Si une table d’eau a été inutilisée pour plusieurs heures, la faire vibrer d’une certaine façon avant de poser la première plaque en position. Ceci permet à l’hydrogène accumulé dans le rejet d’être libéré et de se dissiper avant d’être confiné par une plaque sur la table. Ceci peut être accompli en posant la première plaque sur la table avec une légère secousse puis en relevant la plaque pour permettre à l’hydrogène de s’échapper avant qu’elle soit finalement posée pour la coupe. D. Pour une coupe au-dessus de l’eau, installer des ventilateurs pour faire circuler l’air entre la plaque et la surface de l’eau. E. Pour la coupe sous l’eau, agiter l’eau sous la plaque pour éviter l’accumulation d’hydrogène. Ceci peut être accompli en aérant l’eau à l’aide d’air comprimé. F. Si possible, modifier le niveau de l’eau entre les coupes pour dissiper l’hydrogène accumulé. G. Maintenir le pH de l’eau neutre (proche de 7). Ceci permet de réduire la réaction chimique entre l’eau et les métaux. 97 Données de coupe AVERTISSEMENT Risque d’explosion dû aux alliages aluminium-lithium de couple plasma ! Des alliages aluminium-lithium (Al-Li) sont utilisés dans l’industrie aérospatiale en raison des économies de poids de 10 % par rapport aux alliages d’aluminium conventionnels. Il a été rapporté que les alliages Al-Li liquides peuvent causer des explosions lorsqu’ils entrent en contact avec l’eau. En conséquence, la coupe plasma de ces alliages ne doit pas être tentée en présence d’eau. Ces alliages doivent uniquement être coupés à sec sur une table sèche. Alcoa a déterminé que la coupe sèche sur une table sèche est sécuritaire et donne de bons résultats. NE PAS couper à sec au-dessus d’eau. NE PAS couper avec injection d’eau.. Voici certains des alliages Al-Li actuellement disponibles : Alithlite (Alcoa) X8192 (Alcoa) Alithally (Alcoa) Navalite (Navy américaine) 2090 Alloy (Alcoa) Lockalite (Lockheed) X8090A (Alcoa) Kalite (Kaiser) X8092 (Alcoa) 8091 (Alcan) Pour plus de détails et d’informations sur l’utilisation en toute sécurité de ces alliages, contacter le fournisseur d’aluminium. AVERTISSEMENT L’huile et la graisse peuvent brûler violemment ! • Ne jamais utiliser d’huile ou de graisse sur cette torche. • Manipuler la torche avec des mains propres uniquement sur une surface propre. • Utiliser un lubrifiant silicone uniquement quand il l’est indiqué. • L’huile et la graisse s’enflamment facilement et brûlent violemment en présence d’oxygène sous pression. AVERTISSEMENT Risque d’explosion d’hydrogène. Ne pas couper sous l’eau avec H-35 ! Une accumulation dangereuse d’hydrogène est possible dans l’eau. L’hydrogène est un gaz extrêmement explosif. Réduire le niveau d’eau à 4 pouces minimum sous la pièce à travailler. Faire vibrer la plaque, brasser l’air et l’eau fréquemment pour prévenir toute accumulation d’hydrogène. AVERTISSEMENT Risque d’étincelles. La chaleur, les projections et les étincelles causent des incendies et des brûlures. • Ne pas couper à proximité d’un matériau combustible. • Ne pas couper de conteneurs ayant contenu des combustibles. • Ne pas avoir de combustible sur soi (par ex. un briquet au butane). • L’arc pilote peut provoquer des brûlures. Conserver la buse de la torche à l’écart de soi et d’autrui lors de l’activation du processus au plasma. • Porter une protection des yeux et du corps appropriée. • Porter des gants à crispins, des chaussures et un casque de sécurité. • Porter des vêtements ignifuges couvrant entièrement le corps. • Porter un pantalon sans revers pour prévenir l’entrée d’étincelles et de scories. 98 Données de coupe Débit maximum du gaz avec la torche PT-36 Débit maximum du gaz - CFH (CMH) avec la torche PT-36 Pureté du gaz Air (85 psi / 5,9 bar) Procédé 269 (7,6) Filtré à 25 microns Qualité DIN ISO 8573-1 Taille des particules 0,1µm Classe 1 Température +3SDgrC Classe 4 Nitrogène (125 psi / 8,6 bar) 385 (10,9) 99,99%, filtré à 25 microns Oxygène (125 psi / 8,6 bar) 66 (1,9) 99,5%, filtré à 25 microns Gaz et pression Les données de coupe ont été recueillies à l’aide des matériaux suivants : Aluminium: 6061,Al-Mg1SiCu,AlMg1SiCu,3.3211 Acier carbone: AISI 1008, ASTM A572 Gr.50, ASTM A36 Acier inoxydable: 304, 1.4301 CrNi DIN 17440 X5CrNi18-10 DIN EN 10088 ***Pour obtenir des résultats optimaux, il faudra peut-être ajuster les paramètres de coupe publiés pour les matériaux ayant des compositions et propriétés différentes.*** 99 Données de coupe Références de consommables et de pièces d’usureElectrode PT-36 Holders Part No Description 0558003924 Réf. 0558003924 Part No 0558005457 0558002533 Réf. 0558001625 0558005457 0558002533 0558001625 Part No 0558005459 0558012000 Réf. 0558003928 0558005459 0558012318 0558012000 0558003928 Part No 0558006010 0558006014 Réf. 0558006018 0558006010 0558006020 0558006014 0558006023 0558006018 0558006023 Part No 0558011619 Réf. 0558010722 0558011619 0558010722 Part No Réf. 0004470045 0004470045 0558009715 0558009715 0558009550 0558009550 0558006624 0558006624 Part No Réf. 0004470030 0004470030 0004470031 0004470031 Part Réf.No 0558006130 0558006130 0558006141 0558006141 0558006166 Réf.No Part 0558009551 0558009551 Réf. Part No 0004470046 0004470046 0558009548 0558009548 ELECTRODE HOLDER PT-36 Porte-électrodes Description PORTE-ÉLECTRODES PT-36 Baffles Description BAFFLE 4 HOLE x .022" PT-36 Déflecteurs BAFFLE 4 HOLE x .032" PT-36 Description BAFFLE 8 HOLE x .047" PT-36 DÉFLECTEUR 4 TROUS x 0,022" PT-36 DÉFLECTEUR 4 TROUS x 0,032" PT-36 DÉFLECTEUR 8 TROUS x 0,047" PT-36 Electrodes Description ELECTRODE O2/N2, Low Current PT-36 Électrodes ELECTRODE O2 TL, Standard PT-36 Description ELECTRODE N2/H35, PT-36 ÉLECTRODE O2/N2, FaibleStandard courant PT-36 ÉLECTRODE O2 / AIR T076 PT-36 ÉLECTRODE O2 TL, Standard PT-36 Standard Nozzles ÉLECTRODE N2/H35, Standard PT-36 Description NOZZLE 1.0mm (.040") PT-36 Buses standard (.055") PT-36 NOZZLE 1.4mm Description NOZZLE 1.8mm (.070") PT-36 BUSE 1,0 mm (0,040") PT-36PT-36 (.080") NOZZLE 2.0mm BUSE 1,4 mm (0,055") PT-36PT-36 (.090") NOZZLE 2.3mm BUSE 1,8 mm (0,070") PT-36 BUSE 2,3 mm (0,090") PT-36 XR Series Nozzles Description Buses Série XR PT-36 NOZZLE XR 1.9mm (.073")Description (.085") NOZZLE XR 2.2mm BUSE XR 1,9 mm (0,073") PT-36 PT-36 BUSE XR 2,2 mm (0,085") PT-36 Nozzle Retaining Cups Description Coupelles de retenue de buse NOZZLE RETAINING CUP Description PT-36 COUPELLERETAINING DE RETENUE DE BUSE NOZZLE CUP w/PT-36 BRASS CAP PT-36 COUPELLERETAINING DE RETENUE DE BUSE PT-36 avec CAPUCHON EN LAITON NOZZLE CUP XR PT-36 COUPELLERETAINING DE RETENUE DE BUSE XR PT-36 NOZZLE CUP XR-SPEEDLOADER PT-36 COUPELLE DE RETENUE DE BUSE XR-SPEEDLOADER PT-36 Diffusers Diffuseurs DIFFUSER 16-HOLE DIFFUSEUR 16 TROUS DIFFUSER 24-SLOT Description Description DIFFUSEUR 24 FENTES Standard Shields Écrans standard Description Description (.120") PT-36 SHIELD 3.0mm ÉCRAN 3,0 mm (0,120") PT-36 (.160") PT-36 SHIELD 4.1mm ÉCRAN 4,1 mm (0,160") PT-36 ÉCRAN 6,6 mm (0,259") PT-36 Écrans Série XR XR Series Shields Description Description ÉCRAN XRXR 5,1mm (0,200") PT-36PT-36 (.200") SHIELD 5.1mm Dispositifs de retenue d’écran Shield Retainers Description Description DISPOSITIF DE RETENUE D’ÉCRAN PT-36 SHIELD RETAINER PT-36 DISPOSITIF DE RETENUE D’ÉCRAN XR PT-36 SHIELD RETAINER XR PT-36 Outils Réf. Part No 0558003918 0558007105 0558003918 0004470049 0558007105 0004470049 100 Tools Description Description PORTE-ÉLECTRODES D'OUTIL PT-36 TOURNE-ÉCROU 7/16" (Outil à électrodes) TOOL ELECTRODE HOLDER PT-36 CLÉ HEXAGONALE 0,109" (Electrode Tool) NUT DRIVER 7/16" WRENCH HEX KEY 0.109" Version 1.0, 28.08.2014 330 305 295 270 160 100 75 60 0.036 0.048 0.060 0.080 0.125 0.160 0.200 0.250 1 PicNo 345 0.030 Gaz de protection – 2 355 -- Gaz de protection – 1 0.024 AIR Gaz de découpe Vitesse (po/ min) AIR Gaz d’amorçage Épaisseur (po) AIR Courant (Ampères) 0.055 0.055 0.045 0.045 0.040 0.040 0.040 0.040 0.040 0.040 Dispositif de retenue d’écran 155 150 150 145 140 140 140 140 140 140 0.160 0.160 0.160 0.160 0.160 0.200 0.200 0.200 0.200 0.200 0.160 0.160 0.160 0.160 0.160 0.120 0.120 0.120 0.120 0.120 0.200 0.164 0.150 0.130 0.120 0.120 0.120 0.120 0.120 0.120 Hauteur Hauteur Hauteur Tension de de initiale d’arc perçage découp (po) (po) (po) 45 Matériaux Largeur de saignée (po/ min) S-01 Acier carbone Sélectionner fichier Production 0.1 0.1 0.1 0.1 0.1 0.1 0.1 0.1 0.0 0.0 Retard au perçage (s) Écran 0.5 0.5 0.5 0.5 0.5 0.5 0.5 0.5 0.5 0.5 Retard du CAH (s) 50 50 50 50 50 50 50 50 50 50 Amorçage (psi) 65 65 65 65 65 65 65 65 65 65 100 100 100 100 100 100 100 100 100 100 Découpe Amorçage/ (psi) Découpe (cfh) Gaz de protection SG Diffuseur Gaz plasma PG Dispositif de retenue de buse Buse Électrode Déflecteur Support Production - acier carbone 101 102 -- Gaz de protection – 2 7750 7490 6860 4060 2540 1910 1520 1 1.2 1.5 2 3 4 5 6 1 PicNo 8760 8380 0.8 9020 AIR Gaz de protection – 1 0.5 AIR Gaz de découpe Vitesse (mm/ min) AIR Gaz d’amorçage Épaisseur (mm) 45 Courant (Ampères) 1.4 1.4 1.1 1.1 1.0 1.0 1.0 1.0 1.0 1.0 Dispositif de retenue d’écran 155 150 150 145 140 140 140 140 140 140 4 4 4 4 4 5 5 5 5 5 4 4 4 4 4 3 3 3 3 3 5.1 4.2 3.8 3.3 3.0 3.0 3.0 3.0 3.0 3.0 Hauteur Hauteur Hauteur Tension de de initiale d’arc perçage découp (mm) (mm) (mm) Acier carbone Matériaux Largeur de saignée (mm/ min) S-01 Sélectionner fichier Production 0.1 0.1 0.1 0.1 0.1 0.1 0.1 0.1 0.0 0.0 Retard au perçage (s) Écran 0.5 0.5 0.5 0.5 0.5 0.5 0.5 0.5 0.5 0.5 Retard du CAH (s) 3.45 3.45 3.45 3.45 3.45 3.45 3.45 3.45 3.45 3.45 Amorçage (bar) Gaz de protection SG Diffuseur 4.48 4.48 4.48 4.48 4.48 4.48 4.48 4.48 4.48 4.48 2.83 2.83 2.83 2.83 2.83 2.83 2.83 2.83 2.83 2.83 Découpe Amorçage/ (bar) Découpe (cmh) Gaz plasma PG Dispositif de retenue de buse Buse Électrode Déflecteur Support Production - acier carbone Version 1.0, 28.08.2014 Version 1.0, 28.08.2014 130 AIR AIR AIR -- Matériaux Courant (Ampères) Gaz d’amorçage Gaz de découpe Gaz de protection – 1 Gaz de protection – 2 Dispositif de retenue d’écran Écran 180 150 105 80 60 40 16 12 0.188 0.250 0.375 0.500 0.625 0.750 1.000 1.250 56 PicNo 0.075 220 0.134 0.150 0.150 0.125 0.110 0.080 0.080 0.075 0.070 Vitesse (po/ min) Épaisseur (po) Largeur de saignée (po/ min) 219 208 197 190 182 180 168 167 165 0.160 0.160 0.160 0.160 0.160 0.160 0.160 0.160 0.160 0.500 0.500 0.375 0.360 0.280 0.290 0.175 0.175 0.160 0.500 0.400 0.375 0.360 0.280 0.290 0.175 0.175 0.150 Hauteur Hauteur Hauteur Tension de de initiale d’arc perçage découp (po) (po) (po) 1.5 1.5 1.0 0.8 0.5 0.4 0.3 0.2 0.1 Retard au perçage (s) 0.5 0.5 0.5 0.5 0.5 0.5 0.5 0.5 0.5 25 25 25 25 25 25 25 25 25 Amorçage (psi) 60 60 60 60 60 60 60 60 60 130 130 130 130 130 130 130 130 130 Découpe Amorçage/ (psi) Découpe (cfh) Gaz de protection SG Diffuseur Gaz plasma PG Dispositif de retenue de buse Retard du CAH (s) Remarque : Perçage non recommandé sur des épaisseurs supérieures à 1,00 pouce S-02 Acier carbone Sélectionner fichier Production Buse Électrode Déflecteur Support Production - acier carbone 103 104 Acier carbone 130 AIR AIR AIR -- Matériaux Courant (Ampères) Gaz d’amorçage Gaz de découpe Gaz de protection – 1 Gaz de protection – 2 Dispositif de retenue d’écran Écran Dispositif de retenue de buse 5590 4570 3810 2670 2030 1520 1020 410 300 3 5 6 10 12 16 20 25 32 56 PicNo Vitesse (mm/ min) Épaisseur (mm) 3.8 3.8 3.2 2.8 2.0 2.0 1.9 1.9 1.8 Largeur de saignée (mm/ min) 219 208 197 190 182 180 168 167 165 4 4 4 4 4 4 4 4 4 13 13 10 9 7 7 4 4 4 12.7 10.2 9.5 9.1 7.1 7.4 4.4 4.4 3.8 Hauteur Hauteur Hauteur Tension de de initiale d’arc perçage découp (mm) (mm) (mm) 1.5 1.5 1.0 0.8 0.5 0.4 0.3 0.2 0.1 Retard au perçage (s) 0.5 0.5 0.5 0.5 0.5 0.5 0.5 0.5 0.5 Retard du CAH (s) 1.72 1.72 1.72 1.72 1.72 1.72 1.72 1.72 1.72 Amorçage (bar) Gaz de protection SG Diffuseur 4.13 4.13 4.13 4.13 4.13 4.13 4.13 4.13 4.13 3.68 3.68 3.68 3.68 3.68 3.68 3.68 3.68 3.68 Découpe Amorçage/ (bar) Découpe (cmh) Gaz plasma PG Remarque : Perçage non recommandé sur des épaisseurs supérieures à 25 mm S-02 Sélectionner fichier Production Buse Électrode Déflecteur Support Production - acier carbone Version 1.0, 28.08.2014 Version 1.0, 28.08.2014 130 O2 O2 AIR -- Matériaux Courant (Ampères) Gaz d’amorçage Gaz de découpe Gaz de protection – 1 Gaz de protection – 2 Dispositif de retenue d’écran Écran Dispositif de retenue de buse Diffuseur 110 80 60 55 20 15 12 10 0.375 0.500 0.625 0.750 1.000 1.250 1.375 1.500 59 PicNo 129 0.315 0.180 0.180 0.180 0.160 0.110 0.080 0.080 0.080 0.080 0.080 0.080 217 150 0.160 240 0.125 0.250 0.080 Vitesse (po/ min) Épaisseur (po) Largeur de saignée (po/ min) 180 177 175 172 144 146 145 135 131 127 127 127 0.160 0.160 0.160 0.160 0.160 0.160 0.160 0.160 0.160 0.160 0.160 0.160 0.500 0.500 0.500 0.500 0.375 0.312 0.240 0.188 0.160 0.160 0.160 0.160 0.380 0.380 0.340 0.380 0.214 0.255 0.240 0.170 0.140 0.100 0.090 0.080 Hauteur Hauteur Hauteur Tension de de initiale d’arc perçage découp (po) (po) (po) 1.5 1.5 1.5 1.5 1.0 0.6 0.6 0.6 0.5 0.5 0.3 0.3 Retard au perçage (s) 1.0 1.0 1.0 1.0 0.2 0.2 0.2 0.2 0.2 0.2 0.2 0.2 Retard du CAH (s) 18 18 18 18 18 18 18 18 18 18 18 18 Amorçage (psi) Gaz de protection SG 50 50 50 50 50 50 50 50 50 50 50 50 110 110 110 110 110 110 110 110 110 110 110 110 Découpe Amorçage/ (psi) Découpe (cfh) Gaz plasma PG Remarque : Perçage non recommandé sur des épaisseurs supérieures à 1,00 pouce S-11 Acier carbone Sélectionner fichier Production Buse Électrode Déflecteur Support Production - acier carbone 105 106 Acier carbone 130 O2 O2 AIR -- Matériaux Courant (Ampères) Gaz d’amorçage Gaz de découpe Gaz de protection – 1 Gaz de protection – 2 Dispositif de retenue d’écran Écran Dispositif de retenue de buse Diffuseur 59 PicNo 250 38 1400 20 300 1520 16 35 2030 12 510 2790 10 380 3280 8 32 3810 6 25 5510 4780 4 6100 3 5 Vitesse (mm/ min) Épaisseur (mm) 4.6 4.6 4.6 4.1 2.8 2.0 2.0 2.0 2.0 2.0 2.0 2.0 2.0 Largeur de saignée (mm/ min) 180 177 175 172 144 146 145 135 131 127 127 127 127 4 4 4 4 4 4 4 4 4 4 4 4 4 13 13 13 13 10 8 6 5 4 4 4 4 4 9.7 9.7 8.6 9.7 5.4 6.5 6.1 4.3 3.5 2.5 2.3 2.2 2.0 Hauteur Hauteur Hauteur Tension de de initiale d’arc perçage découp (mm) (mm) (mm) 1.5 1.5 1.5 1.5 1.0 0.6 0.6 0.6 0.5 0.5 0.3 0.3 0.3 Retard au perçage (s) 1.0 1.0 1.0 1.0 0.2 0.2 0.2 0.2 0.2 0.2 0.2 0.2 0.2 Retard du CAH (s) 1.24 1.24 1.24 1.24 1.24 1.24 1.24 1.24 1.24 1.24 1.24 1.24 1.24 Amorçage (bar) Gaz de protection SG 3.45 3.45 3.45 3.45 3.45 3.45 3.45 3.45 3.45 3.45 3.45 3.45 3.45 3.11 3.11 3.11 3.11 3.11 3.11 3.11 3.11 3.11 3.11 3.11 3.11 3.11 Découpe Amorçage/ (bar) Découpe (cmh) Gaz plasma PG Remarque : Perçage non recommandé sur des épaisseurs supérieures à 25 mm S-11 Sélectionner fichier Production Buse Électrode Déflecteur Support Production - acier carbone Version 1.0, 28.08.2014 Version 1.0, 28.08.2014 200 AIR AIR AIR -- Matériaux Courant (Ampères) Gaz d’amorçage Gaz de découpe Gaz de protection – 1 Gaz de protection – 2 Dispositif de retenue d’écran Écran Dispositif de retenue de buse Diffuseur 0.190 0.215 140 105 85 65 35 25 22 20 12 8 0.375 0.500 0.625 0.750 1.000 1.250 1.375 1.500 1.750 2.000 58 PicNo 0.110 190 0.250 0.250 0.190 0.180 0.135 0.130 0.120 0.115 0.090 Vitesse (po/ min) Épaisseur (po) Largeur de saignée (po/ min) 232 230 218 198 195 188 182 181 170 164 155 0.160 0.160 0.160 0.160 0.160 0.160 0.160 0.160 0.160 0.160 0.160 0.629 0.625 0.625 0.625 0.625 0.500 0.375 0.312 0.250 0.188 0.160 0.629 0.580 0.530 0.400 0.380 0.330 0.250 0.207 0.207 0.170 0.100 Hauteur Hauteur Hauteur Tension de de initiale d’arc perçage découp (po) (po) (po) 1.5 1.0 1.0 1.0 1.0 1.0 0.5 0.3 0.3 0.3 0.3 Retard au perçage (s) 0.5 0.5 0.5 0.5 0.5 0.5 0.5 0.5 0.5 0.5 0.5 Retard du CAH (s) 25 25 25 25 25 25 25 25 25 25 25 Amorçage (psi) Gaz de protection SG 60 60 60 60 60 60 60 60 60 60 60 130 130 130 130 130 130 130 130 130 130 130 Découpe Amorçage/ (psi) Découpe (cfh) Gaz plasma PG Remarque : Perçage non recommandé sur des épaisseurs supérieures à 1,25 pouce S-03 Acier carbone Sélectionner fichier Production Buse Électrode Déflecteur Support Production - acier carbone 107 108 Acier carbone 200 AIR AIR AIR -- Matériaux Courant (Ampères) Gaz d’amorçage Gaz de découpe Gaz de protection – 1 Gaz de protection – 2 Dispositif de retenue d’écran Écran Dispositif de retenue de buse Diffuseur 5.5 3560 2670 2160 1650 890 640 560 510 300 200 10 12 16 20 25 32 35 38 45 50 58 PicNo 4.8 4830 6 6.4 4.8 4.6 3.4 3.3 3.0 2.9 2.8 2.3 Vitesse (mm/ min) Épaisseur (mm) Largeur de saignée (mm/ min) 232 230 218 198 195 188 182 181 170 164 155 4 4 4 4 4 4 4 4 4 4 4 16 16 16 16 16 13 10 8 6 5 4 16.0 14.7 13.5 10.2 9.7 8.4 6.4 5.3 5.3 4.3 2.5 Hauteur Hauteur Hauteur Tension de de initiale d’arc perçage découp (mm) (mm) (mm) 1.5 1.0 1.0 1.0 1.0 1.0 0.5 0.3 0.3 0.3 0.3 Retard au perçage (s) 0.5 0.5 0.5 0.5 0.5 0.5 0.5 0.5 0.5 0.5 0.5 Retard du CAH (s) 1.72 1.72 1.72 1.72 1.72 1.72 1.72 1.72 1.72 1.72 1.72 Amorçage (bar) Gaz de protection SG 4.13 4.13 4.13 4.13 4.13 4.13 4.13 4.13 4.13 4.13 4.13 3.68 3.68 3.68 3.68 3.68 3.68 3.68 3.68 3.68 3.68 3.68 Découpe Amorçage/ (bar) Découpe (cmh) Gaz plasma PG Remarque : Perçage non recommandé sur des épaisseurs supérieures à 32 mm S-03 Sélectionner fichier Production Buse Électrode Déflecteur Support Production - acier carbone Version 1.0, 28.08.2014 Version 1.0, 28.08.2014 200 O2 O2 AIR -- Matériaux Courant (Ampères) Gaz d’amorçage Gaz de découpe Gaz de protection – 1 Gaz de protection – 2 Dispositif de retenue d’écran Écran Dispositif de retenue de buse Diffuseur 50 1.000 60 PicNo 11 65 0.875 2.000 80 0.750 17 100 0.625 1.750 0.147 120 0.500 38 140 0.375 25 174 0.313 1.250 210 0.250 1.500 0.128 275 0.188 0.225 0.209 0.180 0.126 0.125 0.117 0.109 0.109 0.099 0.089 0.081 Vitesse (po/ min) Épaisseur (po) Largeur de saignée (po/ min) 187 173 170 160 158 152 145 144 143 138 139 140 130 0.230 0.230 0.230 0.230 0.230 0.230 0.230 0.230 0.230 0.230 0.230 0.230 0.230 0.625 0.625 0.625 0.625 0.500 0.438 0.375 0.312 0.250 0.230 0.230 0.230 0.230 0.449 0.291 0.319 0.282 0.250 0.208 0.165 0.134 0.104 0.090 0.090 0.090 0.064 Hauteur Hauteur Hauteur Tension de de initiale d’arc perçage découp (po) (po) (po) 1.5 1.3 1.3 1.3 1.0 0.8 0.7 0.5 0.4 0.4 0.3 0.3 0.3 Retard au perçage (s) 0.1 0.1 0.1 0.1 0.1 0.1 0.1 0.3 0.5 0.5 0.5 0.5 0.5 Retard du CAH (s) 18 18 18 18 18 18 18 18 18 18 18 18 18 Amorçage (psi) Gaz de protection SG 60 60 60 60 60 60 60 60 60 60 60 60 60 200 200 200 200 200 200 200 200 200 200 200 200 200 Découpe Amorçage/ (psi) Découpe (cfh) Gaz plasma PG Remarque : Perçage non recommandé sur des épaisseurs supérieures à 1,25 pouce S-12 Acier carbone Sélectionner fichier Production Buse Électrode Déflecteur Support Production - acier carbone 109 110 Acier carbone 200 O2 O2 AIR -- Matériaux Courant (Ampères) Gaz d’amorçage Gaz de découpe Gaz de protection – 1 Gaz de protection – 2 Dispositif de retenue d’écran Écran Dispositif de retenue de buse Diffuseur 280 50 60 PicNo 430 1270 25 45 3.7 1650 22 970 2030 20 640 2533 16 32 3050 12 38 3.3 3560 10 5.7 5.3 4.6 3.2 3.2 3.0 2.8 2.8 2.5 2.3 5330 4420 2.1 8 6990 5 6 Vitesse (mm/ min) Épaisseur (mm) Largeur de saignée (mm/ min) 187 173 170 160 158 152 145 144 143 138 139 140 130 6 6 6 6 6 6 6 6 6 6 6 6 6 16 16 16 16 13 11 10 8 6 6 6 6 6 11.4 7.4 8.1 7.2 6.4 5.3 4.2 3.4 2.6 2.3 2.3 2.3 1.6 Hauteur Hauteur Hauteur Tension de de initiale d’arc perçage découp (mm) (mm) (mm) 1.5 1.3 1.3 1.3 1.0 0.8 0.7 0.5 0.4 0.4 0.3 0.3 0.3 Retard au perçage (s) 0.1 0.1 0.1 0.1 0.1 0.1 0.1 0.3 0.5 0.5 0.5 0.5 0.5 Retard du CAH (s) 1.24 1.24 1.24 1.24 1.24 1.24 1.24 1.24 1.24 1.24 1.24 1.24 1.24 Amorçage (bar) Gaz de protection SG 4.13 4.13 4.13 4.13 4.13 4.13 4.13 4.13 4.13 4.13 4.13 4.13 4.13 5.66 5.66 5.66 5.66 5.66 5.66 5.66 5.66 5.66 5.66 5.66 5.66 5.66 Découpe Amorçage/ (bar) Découpe (cmh) Gaz plasma PG Remarque : Perçage non recommandé sur des épaisseurs supérieures à 32 mm S-12 Sélectionner fichier Production Buse Électrode Déflecteur Support Production - acier carbone Version 1.0, 28.08.2014 Version 1.0, 28.08.2014 85 75 0.200 0.250 7 PicNo 120 0.160 Gaz de protection – 2 160 -- Gaz de protection – 1 0.125 N2 Gaz de découpe Vitesse (po/ min) N2 Gaz d’amorçage Épaisseur (po) N2 Courant (Ampères) 0.060 0.050 0.050 0.050 Dispositif de retenue d’écran 188 180 176 172 0.160 0.160 0.160 0.160 0.250 0.166 0.160 0.160 0.250 0.166 0.160 0.156 Hauteur Hauteur Hauteur Tension de de initiale d’arc perçage découp (po) (po) (po) 50 Matériaux Largeur de saignée (po/ min) S-16 Aluminium Sélectionner fichier Production 0.2 0.2 0.2 0.2 Retard au perçage (s) Écran 0.8 0.8 0.8 0.8 Retard du CAH (s) 25 25 25 25 Amorçage (psi) 80 80 80 80 150 150 150 150 Découpe Amorçage/ (psi) Découpe (cfh) Gaz de protection SG Diffuseur Gaz plasma PG Dispositif de retenue de buse Buse Électrode Déflecteur Support Production - aluminium 111 112 3050 2160 1900 4 5 6 7 PicNo 4060 3 -- Gaz de protection – 2 4750 N2 Gaz de protection – 1 2 N2 Gaz de découpe Vitesse (mm/ min) N2 Gaz d’amorçage Épaisseur (mm) 50 Courant (Ampères) 1.5 1.3 1.3 1.3 1.3 Dispositif de retenue d’écran 188 180 176 172 168 4 4 4 4 4 6 4 4 4 4 6.4 4.2 4.1 4.0 3.8 Hauteur Hauteur Hauteur Tension de de initiale d’arc perçage découp (mm) (mm) (mm) Aluminium Matériaux Largeur de saignée (mm/ min) S-16 Sélectionner fichier Production 0.2 0.2 0.2 0.2 0.2 Retard au perçage (s) Écran 0.8 0.8 0.8 0.8 0.8 Retard du CAH (s) 1.72 1.72 1.72 1.72 1.72 Amorçage (bar) Gaz de protection SG Diffuseur 5.51 5.51 5.51 5.51 5.51 4.25 4.25 4.25 4.25 4.25 Découpe Amorçage/ (bar) Découpe (cmh) Gaz plasma PG Dispositif de retenue de buse Buse Électrode Déflecteur Support Production - aluminium Version 1.0, 28.08.2014 Version 1.0, 28.08.2014 AIR AIR AIR -- Courant (Ampères) Gaz d’amorçage Gaz de découpe Gaz de protection – 1 Gaz de protection – 2 70 0.250 1 PicNo 80 0.200 0.045 0.045 0.045 0.045 110 100 0.125 130 0.080 0.160 0.045 Vitesse (po/ min) Épaisseur (po) Dispositif de retenue d’écran 160 160 160 160 160 0.160 0.160 0.160 0.160 0.160 0.160 0.160 0.160 0.160 0.160 0.120 0.120 0.120 0.120 0.120 Hauteur Hauteur Hauteur Tension de de initiale d’arc perçage découp (po) (po) (po) 55 Matériaux Largeur de saignée (po/ min) S-07 Aluminium Sélectionner fichier Production 0.1 0.1 0.1 0.1 0.1 Retard au perçage (s) Écran 0.5 0.5 0.5 0.5 0.5 Retard du CAH (s) 50 50 50 50 50 Amorçage (psi) 60 60 60 60 60 100 100 100 100 100 Découpe Amorçage/ (psi) Découpe (cfh) Gaz de protection SG Diffuseur Gaz plasma PG Dispositif de retenue de buse Buse Électrode Déflecteur Support Production - aluminium 113 114 2030 1780 5 6 1 PicNo 2790 2540 3 4 3300 2 -- Gaz de protection – 2 Vitesse (mm/ min) AIR Gaz de protection – 1 Épaisseur (mm) AIR 1.1 1.1 1.1 1.1 1.1 Largeur de saignée (mm/ min) AIR Dispositif de retenue d’écran 160 160 160 160 160 4 4 4 4 4 4 4 4 4 4 3.0 3.0 3.0 3.0 3.0 Hauteur Hauteur Hauteur Tension de de initiale d’arc perçage découp (mm) (mm) (mm) 55 Courant (Ampères) Gaz d’amorçage Aluminium Matériaux Gaz de découpe S-07 Sélectionner fichier Production 0.1 0.1 0.1 0.1 0.1 Retard au perçage (s) Écran 0.5 0.5 0.5 0.5 0.5 Retard du CAH (s) 3.45 3.45 3.45 3.45 3.45 Amorçage (bar) Gaz de protection SG Diffuseur 4.13 4.13 4.13 4.13 4.13 2.83 2.83 2.83 2.83 2.83 Découpe Amorçage/ (bar) Découpe (cmh) Gaz plasma PG Dispositif de retenue de buse Buse Électrode Déflecteur Support Production - aluminium Version 1.0, 28.08.2014 Version 1.0, 28.08.2014 50 0.500 8 PicNo 75 0.375 Gaz de protection – 2 80 -- Gaz de protection – 1 0.250 N2 Gaz de découpe Vitesse (po/ min) N2 Gaz d’amorçage Épaisseur (po) N2 Courant (Ampères) 0.045 0.065 0.065 Dispositif de retenue d’écran 160 155 153 0.160 0.160 0.160 0.250 0.188 0.160 0.190 0.180 0.160 Hauteur Hauteur Hauteur Tension de de initiale d’arc perçage découp (po) (po) (po) 100 Matériaux Largeur de saignée (po/ min) S-17 Aluminium Sélectionner fichier Production 0.7 0.7 0.7 Retard au perçage (s) Écran 0.8 0.8 0.5 Retard du CAH (s) 20 20 20 Amorçage (psi) 40 40 40 150 150 150 Découpe Amorçage/ (psi) Découpe (cfh) Gaz de protection SG Diffuseur Gaz plasma PG Dispositif de retenue de buse Buse Électrode Déflecteur Support Production - aluminium 115 116 100 N2 N2 N2 -- Courant (Ampères) Gaz d’amorçage Gaz de découpe Gaz de protection – 1 Gaz de protection – 2 1970 1900 1270 8 10 12 8 PicNo 1.7 2030 6 1.1 1.7 1.7 Vitesse (mm/ min) Épaisseur (mm) Dispositif de retenue d’écran 160 155 154 153 4 4 4 4 6 5 4 4 4.8 4.6 4.3 4.1 Hauteur Hauteur Hauteur Tension de de initiale d’arc perçage découp (mm) (mm) (mm) Aluminium Matériaux Largeur de saignée (mm/ min) S-17 Sélectionner fichier Production 0.6 0.6 0.6 0.6 Retard au perçage (s) Écran 0.8 0.8 0.7 0.5 Retard du CAH (s) 1.38 1.38 1.38 1.38 Amorçage (bar) Gaz de protection SG Diffuseur 2.76 2.76 2.76 2.76 4.25 4.25 4.25 4.25 Découpe Amorçage/ (bar) Découpe (cmh) Gaz plasma PG Dispositif de retenue de buse Buse Électrode Déflecteur Support Production - aluminium Version 1.0, 28.08.2014 Version 1.0, 28.08.2014 AIR AIR AIR -- Gaz d’amorçage Gaz de découpe Gaz de protection – 1 Gaz de protection – 2 90 80 70 50 40 30 0.313 0.375 0.500 0.625 0.750 1.000 56 PicNo 0.095 100 0.250 0.105 0.100 0.095 0.095 0.095 0.095 Vitesse (po/ min) Épaisseur (po) Dispositif de retenue d’écran 207 193 193 182 180 178 175 0.160 0.160 0.160 0.160 0.160 0.160 0.160 0.750 0.500 0.500 0.375 0.375 0.375 0.195 0.349 0.300 0.300 0.245 0.220 0.205 0.195 Hauteur Hauteur Hauteur Tension de de initiale d’arc perçage découp (po) (po) (po) 130 Largeur de saignée (po/ min) Aluminium Matériaux S-08 Courant (Ampères) Sélectionner fichier Production 1.5 0.7 0.7 0.7 0.7 0.7 0.7 Retard au perçage (s) Écran 0.5 0.5 0.5 0.5 0.5 0.5 0.5 Retard du CAH (s) 30 30 30 30 30 30 30 Amorçage (psi) 60 60 60 60 60 60 60 130 130 130 130 130 130 130 Découpe Amorçage/ (psi) Découpe (cfh) Gaz de protection SG Diffuseur Gaz plasma PG Dispositif de retenue de buse Buse Électrode Déflecteur Support Production - aluminium 117 118 130 AIR AIR AIR -- Courant (Ampères) Gaz d’amorçage Gaz de découpe Gaz de protection – 1 Gaz de protection – 2 2290 2030 1778 1270 1020 760 8 10 12 16 20 25 56 PicNo 2.4 2540 6 2.7 2.5 2.4 2.4 2.4 2.4 Vitesse (mm/ min) Épaisseur (mm) Dispositif de retenue d’écran 207 193 193 182 180 178 175 4 4 4 4 4 4 4 20 13 13 10 10 10 5 8.9 7.6 7.6 6.2 5.6 5.2 5 Hauteur Hauteur Hauteur Tension de de initiale d’arc perçage découp (mm) (mm) (mm) Aluminium Matériaux Largeur de saignée (mm/ min) S-08 Sélectionner fichier Production 1.5 0.7 0.7 0.7 0.7 0.7 0.7 Retard au perçage (s) Écran 0.5 0.5 0.5 0.5 0.5 0.5 0.5 Retard du CAH (s) 2.06 2.06 2.06 2.06 2.06 2.06 2.06 Amorçage (bar) Gaz de protection SG Diffuseur 4.14 4.14 4.14 4.14 4.14 4.14 4.14 3.68 3.68 3.68 3.68 3.68 3.68 3.68 Découpe Amorçage/ (bar) Découpe (cmh) Gaz plasma PG Dispositif de retenue de buse Buse Électrode Déflecteur Support Production - aluminium Version 1.0, 28.08.2014 Version 1.0, 28.08.2014 AIR AIR AIR -- Gaz d’amorçage Gaz de découpe Gaz de protection – 1 Gaz de protection – 2 110 85 70 60 40 30 0.375 0.500 0.625 0.750 1.000 1.250 23 PicNo 0.130 125 0.250 0.157 0.140 0.140 0.140 0.130 0.110 Vitesse (po/ min) Épaisseur (po) Dispositif de retenue d’écran 192 189 182 170 167 165 155 0.160 0.160 0.160 0.160 0.160 0.160 0.160 0.625 0.500 0.375 0.375 0.250 0.250 0.187 0.375 0.375 0.375 0.375 0.250 0.250 0.187 Hauteur Hauteur Hauteur Tension de de initiale d’arc perçage découp (po) (po) (po) 200 Largeur de saignée (po/ min) Aluminium Matériaux S-09 Courant (Ampères) Sélectionner fichier Production 1.1 0.7 0.5 0.5 0.5 0.5 0.5 Retard au perçage (s) Écran 0.7 0.6 0.5 0.6 0.3 0.3 0.4 Retard du CAH (s) 30 30 30 30 30 30 30 Amorçage (psi) 44 44 44 44 44 44 44 201 201 201 201 201 201 201 Découpe Amorçage/ (psi) Découpe (cfh) Gaz de protection SG Diffuseur Gaz plasma PG Dispositif de retenue de buse Buse Électrode Déflecteur Support Production - aluminium 119 120 200 AIR AIR AIR -- Courant (Ampères) Gaz d’amorçage Gaz de découpe Gaz de protection – 1 Gaz de protection – 2 2980 2790 2160 1880 1780 1520 1020 830 760 8 10 12 15 16 20 25 30 32 23 PicNo 3.1 3180 6 4.0 3.9 3.6 3.6 3.6 3.5 3.3 3.3 2.8 Vitesse (mm/ min) Épaisseur (mm) Dispositif de retenue d’écran 192 191 189 182 170 169 167 165 160 155 4 4 4 4 4 4 4 4 4 4 16 15 13 10 10 9 6 6 6 5 9.5 9.5 9.5 9.5 9.5 8.7 6.4 6.4 5.6 4.7 Hauteur Hauteur Hauteur Tension de de initiale d’arc perçage découp (mm) (mm) (mm) Aluminium Matériaux Largeur de saignée (mm/ min) S-09 Sélectionner fichier Production 1.1 1.0 0.7 0.5 0.5 0.5 0.5 0.5 0.5 0.4 Retard au perçage (s) Écran 0.7 0.7 0.6 0.5 0.6 0.5 0.3 0.3 0.3 0.4 Retard du CAH (s) 2.00 2.00 2.00 2.00 2.00 2.00 2.00 2.00 2.00 2.00 Amorçage (bar) Gaz de protection SG Diffuseur 3.03 3.03 3.03 3.03 3.03 3.03 3.03 3.03 3.03 3.03 5.69 5.69 5.69 5.69 5.69 5.69 5.69 5.69 5.69 5.69 Découpe Amorçage/ (bar) Découpe (cmh) Gaz plasma PG Dispositif de retenue de buse Buse Électrode Déflecteur Support Production - aluminium Version 1.0, 28.08.2014 Version 1.0, 28.08.2014 85 62 40 27 20 17 15 0.500 0.625 0.750 1.000 1.250 1.375 1.500 9 PicNo 105 0.375 Gaz de protection – 2 125 -- Gaz de protection – 1 0.250 N2 Gaz de découpe Vitesse (po/ min) N2 Gaz d’amorçage Épaisseur (po) N2 Courant (Ampères) 0.180 0.180 0.157 0.120 0.110 0.102 0.095 0.100 0.100 Dispositif de retenue d’écran 195 193 192 192 180 170 162 145 140 0.160 0.160 0.160 0.160 0.160 0.160 0.160 0.160 0.160 0.750 0.688 0.625 0.500 0.375 0.312 0.250 0.188 0.160 0.380 0.380 0.375 0.271 0.330 0.274 0.218 0.120 0.115 Hauteur Hauteur Hauteur Tension de de initiale d’arc perçage découp (po) (po) (po) 200 Matériaux Largeur de saignée (po/ min) S-18 Aluminium Sélectionner fichier Production 1.1 1.1 1.1 0.7 0.5 0.5 0.5 0.5 0.5 Retard au perçage (s) Écran 0.6 1.1 1.1 0.9 0.6 0.6 0.6 0.6 0.6 Retard du CAH (s) 10 10 10 10 10 10 10 10 10 Amorçage (psi) 46 46 46 46 46 46 46 46 46 150 150 150 150 150 150 150 150 150 Découpe Amorçage/ (psi) Découpe (cfh) Gaz de protection SG Diffuseur Gaz plasma PG Dispositif de retenue de buse Buse Électrode Déflecteur Support Production - aluminium 121 122 200 N2 N2 N2 -- Courant (Ampères) Gaz d’amorçage Gaz de découpe Gaz de protection – 1 Gaz de protection – 2 2910 2670 2160 1730 1570 1020 690 560 510 430 380 8 10 12 15 16 20 25 30 32 35 38 9 PicNo 2.5 3180 6 4.6 4.6 4.0 3.7 3.0 2.8 2.6 2.5 2.4 2.5 2.5 Vitesse (mm/ min) Épaisseur (mm) Dispositif de retenue d’écran 195 193 192 192 192 180 170 168 162 145 143 140 4 4 4 4 4 4 4 4 4 4 4 4 19 17 16 15 13 10 8 8 6 5 4 4 9.7 9.7 9.5 8.8 6.9 8.4 7.0 6.6 5.5 3.0 3.0 2.9 Hauteur Hauteur Hauteur Tension de de initiale d’arc perçage découp (mm) (mm) (mm) Aluminium Matériaux Largeur de saignée (mm/ min) S-18 Sélectionner fichier Production 1.1 1.1 1.1 1.0 0.7 0.5 0.5 0.5 0.5 0.5 0.5 0.4 Retard au perçage (s) Écran 0.6 1.1 1.1 1.0 0.9 0.6 0.6 0.6 0.6 0.6 0.6 0.6 Retard du CAH (s) 0.69 0.69 0.69 0.69 0.69 0.69 0.69 0.69 0.69 0.69 0.69 0.69 Amorçage (bar) Gaz de protection SG Diffuseur 3.17 3.17 3.17 3.17 3.17 3.17 3.17 3.17 3.17 3.17 3.17 3.17 4.25 4.25 4.25 4.25 4.25 4.25 4.25 4.25 4.25 4.25 4.25 4.25 Découpe Amorçage/ (bar) Découpe (cmh) Gaz plasma PG Dispositif de retenue de buse Buse Électrode Déflecteur Support Production - aluminium Version 1.0, 28.08.2014 Version 1.0, 28.08.2014 AIR AIR AIR -- Gaz d’amorçage Gaz de découpe Gaz de protection – 1 Gaz de protection – 2 105 75 50 45 0.125 0.160 0.200 0.250 1 PicNo 0.045 150 0.080 0.045 0.045 0.045 0.045 Vitesse (po/ min) Épaisseur (po) Dispositif de retenue d’écran 150 150 147 143 140 0.160 0.160 0.160 0.160 0.160 0.160 0.160 0.160 0.160 0.160 0.120 0.120 0.120 0.120 0.120 Hauteur Hauteur Hauteur Tension de de initiale d’arc perçage découp (po) (po) (po) 55 Largeur de saignée (po/ min) Acier inoxydable Matériaux S-04 Courant (Ampères) Sélectionner fichier Production 0.1 0.1 0.1 0.1 0.1 Retard au perçage (s) Écran 0.5 0.5 0.5 0.5 0.5 Retard du CAH (s) 50 50 50 50 50 Amorçage (psi) 60 60 60 60 60 100 100 100 100 100 Découpe Amorçage/ (psi) Découpe (cfh) Gaz de protection SG Diffuseur Gaz plasma PG Dispositif de retenue de buse Buse Électrode Déflecteur Support Production - acier inoxydable 123 124 -- Gaz de protection – 2 1900 1270 1140 4 5 6 1 PicNo 3810 2670 2 3 4650 AIR Gaz de protection – 1 1 AIR Gaz de découpe Vitesse (mm/ min) AIR Gaz d’amorçage Épaisseur (mm) 55 Courant (Ampères) 1.1 1.1 1.1 1.1 1.1 1.1 Dispositif de retenue d’écran 150 150 147 143 140 137 4 4 4 4 4 4 4 4 4 4 4 4 3.0 3.0 3.0 3.0 3.0 3.0 Hauteur Hauteur Hauteur Tension de de initiale d’arc perçage découp (mm) (mm) (mm) Acier inoxydable Matériaux Largeur de saignée (mm/ min) S-04 Sélectionner fichier Production 0.1 0.1 0.1 0.1 0.1 0.1 Retard au perçage (s) Écran 0.5 0.5 0.5 0.5 0.5 0.5 Retard du CAH (s) 3.45 3.45 3.45 3.45 3.45 3.45 Amorçage (bar) Gaz de protection SG Diffuseur 4.13 4.13 4.13 4.13 4.13 4.13 2.83 2.83 2.83 2.83 2.83 2.83 Découpe Amorçage/ (bar) Découpe (cmh) Gaz plasma PG Dispositif de retenue de buse Buse Électrode Déflecteur Support Production - acier inoxydable Version 1.0, 28.08.2014 Version 1.0, 28.08.2014 150 105 75 50 0.080 0.125 0.160 0.200 16 PicNo 275 -- Gaz de protection – 2 0.040 N2 Gaz de protection – 1 Vitesse (po/ min) N2 Gaz de découpe Épaisseur (po) N2 Gaz d’amorçage 0.050 0.050 0.050 0.050 .040 Dispositif de retenue d’écran 150 148 146 140 140 0.160 0.160 0.160 0.160 0.160 0.160 0.160 0.160 0.160 0.160 0.120 0.120 0.110 0.080 0.080 Hauteur Hauteur Hauteur Tension de de initiale d’arc perçage découp (po) (po) (po) 70 Largeur de saignée (po/ min) Acier inoxydable Matériaux S-13 Courant (Ampères) Sélectionner fichier Production 0.1 0.1 0.1 0.1 0.1 Retard au perçage (s) Écran 0.4 0.4 0.4 0.1 0.1 Retard du CAH (s) 25 25 25 25 25 Amorçage (psi) 50 50 50 50 50 250 250 250 250 250 Découpe Amorçage/ (psi) Découpe (cfh) Gaz de protection SG Diffuseur Gaz plasma PG Dispositif de retenue de buse Buse Électrode Déflecteur Support Production - acier inoxydable 125 126 3300 2540 1780 3 4 5 16 PicNo 6100 2 -- Gaz de protection – 2 6980 N2 Gaz de protection – 1 1 N2 Gaz de découpe Vitesse (mm/ min) N2 Gaz d’amorçage Épaisseur (mm) 70 Courant (Ampères) 1.3 1.3 1.3 1.3 1.0 Dispositif de retenue d’écran 150 148 146 140 140 4 4 4 4 4 4 4 4 4 4 3.0 3.0 2.8 2.0 2.0 Hauteur Hauteur Hauteur Tension de de initiale d’arc perçage découp (mm) (mm) (mm) Acier inoxydable Matériaux Largeur de saignée (mm/ min) S-13 Sélectionner fichier Production 0.1 0.1 0.1 0.1 0.1 Retard au perçage (s) Écran 0.4 0.4 0.4 0.2 0.1 Retard du CAH (s) 1.72 1.72 1.72 1.72 1.72 Amorçage (bar) Gaz de protection SG Diffuseur 3.45 3.45 3.45 3.45 3.45 7.08 7.08 7.08 7.08 7.08 Découpe Amorçage/ (bar) Découpe (cmh) Gaz plasma PG Dispositif de retenue de buse Buse Électrode Déflecteur Support Production - acier inoxydable Version 1.0, 28.08.2014 Version 1.0, 28.08.2014 100 70 50 30 20 0.250 0.375 0.500 0.625 0.750 56 PicNo 110 -- Gaz de protection – 2 0.188 AIR Gaz de protection – 1 Vitesse (po/ min) AIR Gaz de découpe Épaisseur (po) AIR Gaz d’amorçage 0.135 0.110 0.095 0.085 0.085 0.085 Dispositif de retenue d’écran 200 190 186 175 170 170 0.160 0.160 0.160 0.160 0.160 0.160 0.600 0.400 0.400 0.400 0.400 0.400 0.400 0.330 0.290 0.230 0.200 0.200 Hauteur Hauteur Hauteur Tension de de initiale d’arc perçage découp (po) (po) (po) 130 Largeur de saignée (po/ min) Acier inoxydable Matériaux S-05 Courant (Ampères) Sélectionner fichier Production 1.0 0.6 0.6 0.4 0.4 0.4 Retard au perçage (s) Écran 0.5 0.5 0.5 0.5 0.5 0.5 Retard du CAH (s) 30 30 30 30 30 30 Amorçage (psi) 60 60 60 60 60 60 200 200 200 200 200 200 Découpe Amorçage/ (psi) Découpe (cfh) Gaz de protection SG Diffuseur Gaz plasma PG Dispositif de retenue de buse Buse Électrode Déflecteur Support Production - acier inoxydable 127 128 130 AIR AIR AIR -- Courant (Ampères) Gaz d’amorçage Gaz de découpe Gaz de protection – 1 Gaz de protection – 2 2540 1780 1270 760 500 6 10 12 16 20 56 PicNo 2.2 2795 5 3.4 2.8 2.4 2.2 2.2 Vitesse (mm/ min) Épaisseur (mm) Dispositif de retenue d’écran 200 190 186 175 170 170 4 4 4 4 4 4 10 10 10 10 10 10 10 8 7 6 5 5 Hauteur Hauteur Hauteur Tension de de initiale d’arc perçage découp (mm) (mm) (mm) Acier inoxydable Matériaux Largeur de saignée (mm/ min) S-05 Sélectionner fichier Production 1.0 0.6 0.6 0.4 0.4 0.4 Retard au perçage (s) Écran 0.5 0.5 0.5 0.5 0.5 0.5 Retard du CAH (s) 2.07 2.07 2.07 2.07 2.07 2.07 Amorçage (bar) Gaz de protection SG Diffuseur 4.14 4.14 4.14 4.14 4.14 4.14 5.67 5.67 5.67 5.67 5.67 5.67 Découpe Amorçage/ (bar) Découpe (cmh) Gaz plasma PG Dispositif de retenue de buse Buse Électrode Déflecteur Support Production - acier inoxydable Version 1.0, 28.08.2014 Version 1.0, 28.08.2014 30 27 25 0.500 0.625 0.750 8 PicNo 45 0.375 Gaz de protection – 2 85 -- Gaz de protection – 1 0.250 N2 Gaz de découpe Vitesse (po/ min) N2 Gaz d’amorçage Épaisseur (po) N2 Courant (Ampères) 0.110 0.105 0.105 0.105 0.090 Dispositif de retenue d’écran 180 170 165 155 150 0.160 0.160 0.160 0.160 0.160 0.500 0.500 0.190 0.190 0.190 0.300 0.200 0.125 0.120 0.090 Hauteur Hauteur Hauteur Tension de de initiale d’arc perçage découp (po) (po) (po) 130 Matériaux Largeur de saignée (po/ min) S-14 Acier inoxydable Sélectionner fichier Production 0.9 0.7 0.6 0.5 0.3 Retard au perçage (s) Écran 0.3 0.3 0.3 0.3 0.3 Retard du CAH (s) 15 15 15 15 15 Amorçage (psi) 55 55 55 55 55 150 150 150 150 150 Découpe Amorçage/ (psi) Découpe (cfh) Gaz de protection SG Diffuseur Gaz plasma PG Dispositif de retenue de buse Buse Électrode Déflecteur Support Production - acier inoxydable 129 130 130 N2 N2 N2 -- Courant (Ampères) Gaz d’amorçage Gaz de découpe Gaz de protection – 1 Gaz de protection – 2 1630 1140 760 690 640 8 10 12 16 20 8 PicNo 2.5 2160 6 2.8 2.7 2.7 2.7 2.3 Vitesse (mm/ min) Épaisseur (mm) Dispositif de retenue d’écran 180 170 160 155 153 150 4 4 4 4 4 4 13 11 5 5 5 5 7.6 5.1 3.2 3.0 2.7 2.3 Hauteur Hauteur Hauteur Tension de de initiale d’arc perçage découp (mm) (mm) (mm) Acier inoxydable Matériaux Largeur de saignée (mm/ min) S-14 Sélectionner fichier Production 0.9 0.7 0.6 0.5 0.4 0.3 Retard au perçage (s) Écran 0.3 0.3 0.3 0.3 0.3 0.3 Retard du CAH (s) 1.03 1.03 1.03 1.03 1.03 1.03 Amorçage (bar) Gaz de protection SG Diffuseur 3.79 3.79 3.79 3.79 3.79 3.79 4.25 4.25 4.25 4.25 4.25 4.25 Découpe Amorçage/ (bar) Découpe (cmh) Gaz plasma PG Dispositif de retenue de buse Buse Électrode Déflecteur Support Production - acier inoxydable Version 1.0, 28.08.2014 Version 1.0, 28.08.2014 200 AIR AIR AIR -- Gaz d’amorçage Gaz de découpe Gaz de protection – 1 Gaz de protection – 2 Dispositif de retenue d’écran Écran Dispositif de retenue de buse Diffuseur 20 1.250 58 PicNo 8 40 1.000 2.000 60 0.750 12 85 0.625 10 120 0.500 1.750 170 0.375 1.500 210 190 0.313 240 0.188 0.250 Vitesse (po/ min) Épaisseur (po) 0.200 0.174 0.160 0.160 0.125 0.110 0.097 0.080 0.080 0.090 0.080 0.080 Largeur de saignée (po/ min) 223 210 207 205 185 175 166 165 163 160 158 155 0.160 0.160 0.160 0.160 0.160 0.160 0.160 0.160 0.160 0.160 0.160 0.160 0.625 0.625 0.625 0.625 0.500 0.375 0.375 0.375 0.375 0.250 0.250 0.160 0.600 0.450 0.400 0.400 0.250 0.225 0.200 0.180 0.180 0.170 0.150 0.150 Hauteur Hauteur Hauteur Tension de de initiale d’arc perçage découp (po) (po) (po) 1.5 1.5 1.5 1.5 1.0 0.5 0.5 0.5 0.5 0.5 0.2 0.2 Retard au perçage (s) 0.5 0.5 0.5 0.5 0.5 0.5 0.5 0.5 0.5 0.5 0.5 0.5 Retard du CAH (s) 30 30 30 30 30 30 30 30 30 30 30 30 Amorçage (psi) Gaz de protection SG 60 60 60 60 60 60 60 60 60 60 60 60 200 200 200 200 200 200 200 200 200 200 200 200 Découpe Amorçage/ (psi) Découpe (cfh) Gaz plasma PG Remarque : Perçage non recommandé sur des épaisseurs supérieures à 1,25 pouce Acier inoxydable Matériaux S-06 Courant (Ampères) Sélectionner fichier Production Buse Électrode Déflecteur Support Production - acier inoxydable 131 132 Acier inoxydable 200 AIR AIR AIR -- Matériaux Courant (Ampères) Gaz d’amorçage Gaz de découpe Gaz de protection – 1 Gaz de protection – 2 Dispositif de retenue d’écran Écran Dispositif de retenue de buse Diffuseur 4320 3050 2160 1525 1020 510 305 250 200 10 12 16 20 25 32 38 45 50 58 PicNo 5335 4830 6 6100 5 8 Vitesse (mm/ min) Épaisseur (mm) 5 4.4 4 4 3.2 2.8 2.5 2 2 2 2 2 Largeur de saignée (mm/ min) 223 210 207 205 185 175 166 165 163 160 158 155 4 4 4 4 4 4 4 4 4 4 4 4 16 16 16 16 13 10 10 10 10 6 6 4 15 11 10 10 6 5.5 5 4.6 4.6 4.3 3.8 3.8 Hauteur Hauteur Hauteur Tension de de initiale d’arc perçage découp (mm) (mm) (mm) 1.5 1.5 1.5 1.5 1.0 0.5 0.5 0.5 0.5 0.5 0.2 0.2 Retard au perçage (s) 0.5 0.5 0.5 0.5 0.5 0.5 0.5 0.5 0.5 0.5 0.5 0.5 Retard du CAH (s) 2.07 2.07 2.07 2.07 2.07 2.07 2.07 2.07 2.07 2.07 2.07 2.07 Amorçage (bar) Gaz de protection SG 4.14 4.14 4.14 4.14 4.14 4.14 4.14 4.14 4.14 4.14 4.14 4.14 5.66 5.66 5.66 5.66 5.66 5.66 5.66 5.66 5.66 5.66 5.66 5.66 Découpe Amorçage/ (bar) Découpe (cmh) Gaz plasma PG Remarque : Perçage non recommandé sur des épaisseurs supérieures à 32 mm S-06 Sélectionner fichier Production Buse Électrode Déflecteur Support Production - acier inoxydable Version 1.0, 28.08.2014 Version 1.0, 28.08.2014 80 65 50 30 0.500 0.625 0.750 1.000 10 PicNo 120 0.375 Gaz de protection – 2 165 -- Gaz de protection – 1 0.250 N2 Gaz de découpe Vitesse (po/ min) N2 Gaz d’amorçage Épaisseur (po) N2 Courant (Ampères) 0.120 0.115 0.115 0.093 0.093 0.085 Dispositif de retenue d’écran 175 164 158 148 145 135 0.160 0.160 0.160 0.160 0.160 0.160 0.580 0.460 0.400 0.340 0.245 0.160 0.580 0.460 0.400 0.340 0.245 0.150 Hauteur Hauteur Hauteur Tension de de initiale d’arc perçage découp (po) (po) (po) 200 Matériaux Largeur de saignée (po/ min) S-15 Acier inoxydable Sélectionner fichier Production 1.6 1.4 0.7 0.6 0.6 0.5 Retard au perçage (s) Écran 0.3 0.3 0.3 0.3 0.3 0.3 Retard du CAH (s) 15 15 15 15 15 15 Amorçage (psi) 30 30 30 30 30 150 150 150 150 150 Découpe Amorçage/ (psi) Découpe (cfh) 30 150 Gaz de protection SG Diffuseur Gaz plasma PG Dispositif de retenue de buse Buse Électrode Déflecteur Support Production - acier inoxydable 133 134 200 N2 N2 N2 -- Courant (Ampères) Gaz d’amorçage Gaz de découpe Gaz de protection – 1 Gaz de protection – 2 3070 2030 1780 1330 1190 890 760 8 10 12 15 16 20 25 10 PicNo 2.3 4190 6 3.0 2.9 2.9 2.9 2.8 2.4 2.2 Vitesse (mm/ min) Épaisseur (mm) Dispositif de retenue d’écran 175 164 158 157 153 145 140 135 4 4 4 4 4 4 4 4 19 18 18 16 9 6 6 6 14.7 11.7 10.2 9.8 8.6 6.2 5.1 3.8 Hauteur Hauteur Hauteur Tension de de initiale d’arc perçage découp (mm) (mm) (mm) Acier inoxydable Matériaux Largeur de saignée (mm/ min) S-15 Sélectionner fichier Production 1.6 1.4 .7 .7 .5 .5 .5 .5 Retard au perçage (s) Écran 0.3 0.3 0.3 0.3 0.3 0.3 0.3 0.3 Retard du CAH (s) 1.03 1.03 1.03 1.03 1.03 1.03 1.03 1.03 Amorçage (bar) Gaz de protection SG Diffuseur 2.07 2.07 2.07 2.07 2.07 2.07 2.07 2.07 4.25 4.25 4.25 4.25 4.25 4.25 4.25 4.25 Découpe Amorçage/ (bar) Découpe (cmh) Gaz plasma PG Dispositif de retenue de buse Buse Électrode Déflecteur Support Production - acier inoxydable Version 1.0, 28.08.2014 MAINTENANCE / TROUBLESHOOTING Maintenance/Troubleshooting This page intentionally left blank. 136 Maintenance/Troubleshooting Maintenance General WARNING WARNING Electric Shock Can Kill! Shut off power at the line (wall) disconnect before attempting any maintenance. Eye Hazard When Using Compressed Air To Clean. • • CAUTION Wear approved eye protection with side shields when cleaning the Plasma Console. Use only low pressure air. Maintenance On This Equipment Should Only Be Performed By Trained Personnel. Cleaning Regularly scheduled cleaning of the Plasma Console is required to help keep the unit running trouble free. The frequency of cleaning depends on environment and use. 1. Turn power off at wall disconnect. 2. Remove side panels. 3. Use low pressure compressed dry air, remove dust from all air passages and components. Pay particular attention to heat sinks in the front of the unit. Dust insulates, reducing heat dissipation. Be sure to wear eye protection. CAUTION Air restrictions may cause plasma unit heat to over heat. Thermal Switches may be activated causing interruption of function. Do not use air filters on this unit. Keep air passages clear of dust and other obstructions. WARNING Electric Shock Hazard! Be sure to replace any covers removed during cleaning before turning power back on. 137 Maintenance/Troubleshooting Plasma Console Block Diagram WARNING Main Fan Dangerous Voltages and Current! Electric Shock Can Kill! Before operation, ensure installation and grounding procedures have been followed. Do not operate this equipment with covers removed. 200/230/380/ 400/460/575V 3 ~ Input Input Fuses (F1, F2) Main Contactor Soft Start Relay Main Transformer 3 x 2 Ohm 300 Watt Resistors 3~ Rectifier IGBT Driver Board 1 x 6000uf 450V Capacitors 2 x 400 Amp IGBT’s Inductor Output 138 1 ~ T2 Control Transformer Main Control Board Hall Sensors Fuse F3 CAN Pump IC (Interface Control) Relay Block Maintenance/Troubleshooting Plasma Console Coolant Flow Diagram As soon as the Plasma Console is supplied with input power, the coolant pump motor turns ON. Coolant pumps out to the torch and returns back to the coolant tank through the radiators, filter, flow sensor, and IGBTs cold plate respectively. The pump has an internal adjustable bypass valve set to 225 psi (15.5 bar). There is also an external adjustable regulator, set to 175 psi (12 bar), to bypass the coolant flow if pressure exceeds 175 psi (12 bar). The coolant flow diagram is as shown in the figure below. GAUGE IGBT COLD PLATE FLOW SENSOR (FS1) LEVEL SENSOR (LS1) 139 Maintenance/Troubleshooting Turbine Flow Sensor Features : Small and compact dimension Easy connection, 1/2” BSP thread High reliability and durability Installation flexibility : vertical or horizontal Wide rated voltage : 2.4 to 26 VDC Hall effect sensor, digital output Electrical : Supply voltage : 2.4 – 26 V DC Supply current : typical 3.0 mA, maximum 6.0 mA. Output mode : open collector Output rise time : typical 1.0μsecond. maximum 10μsecond. Output falling time : typical 0. 3μsecond. maximum 1.5μsecond. Wire connection : Termianl 1 (Red) : Vdd Terminal 2 (Brown) : Vout Terminal 3 (Black) : Gnd Application : Mounting Method : Horizontal to Vertical Range of Flow Rate : 1.5 – 25 L/min. Maximum working pressure : 1MPa Fluid : Cold / Warm Water Fluid temperature : 0 ~ 80o C Environment temperature : -20 ~ 80o C Body Materials : PPS with 40% glass fiber Inside turbine holder : Acetal copolymer (POM) Turbine : plastic magnet Turbine stick : ceramic 140 NOM CURRENT: FLOAT SG: MAX PRESSURE: LEADS: Maintenance/Troubleshooting Level Switch Level switch is used to tell if the level of coolant in the tank drops below certain level. When the level of the coolant drops belowPROPRIETARY level switch position in the tank, control board reads the switch open signal, an error signal is AND CONFIDENTIAL sent THE to INFORMATION CNC/Process controller by the Plasma Console through CAN communication. CONTAINED IN THIS DRAWING IS THE SOLE PROPERTY 411 S. Ebenez (8)0558011991 OF ESAB WELDING & CUTTING. ANY REPRODUCTION IN PART OR AS A WHOLE WITHOUT THE WRITTEN PERMISSION OF ESAB WELDING & CUTTING IS PROHIBITED. VENDOR: MADISON COMPANY VENDOR P/N: Florence, SC DESCRIPTION: PLASTIC SIDE-MOUNTED SWITCH M8790 STEM: POLYPROPYLENE FLOAT: POLYPROPYLENE MAX TEMP: 105C NOM CURRENT: 30VA SPST SWITCH FLOAT SG: 0.60 MAX PRESSURE: 100PSIG LEADS: 22GA, 24INCHES Coolant Filter A filter is used to prevent the foreign particles entering the Plasma Console through coolant and damaging the equipment. NAME DIMENSIONS ARE IN INCHES TOLERANCES: DRAWN MEA FRACTIONAL .03 CHECKED PMD ANGULAR: MACH .1 BEND .5 ENG APPR. TWO PLACE DECIMAL .015 MEA THREE PLACE DECIMAL .005 MATERIAL DATE PA6900-11-16 10/20/11 11/14/12 11/14/12 11/15/12 SWITCH LEVEL BULKHEAD COMMENTS: FINISH REVISIONS PTION 30VA SPST SWITCH 0.60 100PSIG 22GA, 24INCHES DATE APPROVED DO NOT SCALE DRAWING SIZE (8)0558011991 A DWG. NO. SCALE:1:5 WEIGHT: REV. -+ SHEET 1 OF 1 141 Maintenance/Troubleshooting Troubleshooting WARNING Electric Shock Can Kill! Do not permit untrained persons to inspect or repair this equipment. Electrical work must be performed by an experienced electrician. CAUTION Stop work immediately if Plasma Console does not work properly. Have only trained personnel investigate the cause. Use only recommended replacement parts. Check the problem against the symptoms in the following troubleshooting guide. The remedy may be quite simple. If the cause cannot be quickly located, shut off the input power, open up the unit, and perform simple visual inspection of all the components and wiring. Check for secure terminal connections, loose or burned wiring or components, bulged or leaking capacitors, or any other sign of damage or discoloration. The cause of control malfunctions can be found by referring to the sequence of operations, electrical schematics and checking the various components. A volt-ohmmeter will be necessary for some of these checks. Troubleshooting Guide When the input power is applied to m2 Smart Plasmarc system, pump motor should turn ON immediately, the power light on the front panel will be ON and fault light will be OFF (if there are no errors/faults) indicating normal operation. Check the following: 1. If pump motor doesn’t turn ON, fuse(F3) might be bad or check for a bad connection to pump motor. 2. If POWER light doesn’t turn ON or main contactor and main fan doesn’t turn ON, then it could be caused by blown fuses F1 or F2. 3. If the FAULT light is ON, then check the CNC/Process Controller display screen for the type of error message from Plasma Console. Fault Light, Main Contactor and Main Fan status for different errors/faults: Type of Fault Fault Light Status Fault Light Frequency K1 and Main Fan Status Thermal or Ambient ON Continuous ON Servo Fault TOGGLE 50% duty cycle with a period of 1 second OFF All other Faults TOGGLE 50% duty cycle with a period of 2 seconds OFF When fault light is in either one of the above-mentioned states, check the Interface Control screen for the description of the error and further details in this section. 142 Maintenance/Troubleshooting Fault Isolation Fan Not Working Problem Fan does not turn ON Possible Cause Action This is normal when unit is in idle mode for more than 5 minutes. None Broken or disconnected wire in fan motor circuit. Repair wire. Faulty fan(s) Replace fans Relay failed to close Check relay connection and/or replace relay. Torch Will Not Fire Problem Possible Cause Action Communication between plasma unit Check communication cable. and CNC or process controller is lost. Main Arc Transfers to the work with a short “pop”, placing only a small dimple in the workpiece. CNC or Process Controller removes the start signal when the main arc transfers to the work. Make sure CNC or Process Controller is sending start signal correctly. Remote current values are not present. Check if correct current values are sent down the CAN Bus. Current value is too low. Increase current value. Open connection between the Plasma Repair connection. Console positive output and the work. Arc does not start. There is no arc at the torch. Open circuit voltage is OK. Pilot current and/or start current should be increased for better starts when using consumables for 100A or higher (Refer to process data included in torch manuals). Increase pilot current. (Refer to process data included in torch manuals). Fault light is ON. Check Help Codes table. Faulty PCB1 (control board). Replace PCB1 (control board). 143 Maintenance/Troubleshooting IC Maintenance/Troubleshooting Digital Input Problems Problem Resolution The wrong input on the screen is changing when the CNC turns on an input to the IC Make sure the inputs are wired to the proper input on the IC. No input on the screen is changing when the CNC turns on an input to the IC Make sure the CNC is only sending the 24 VDC from DB37 connector back to the IC as the input when turning the input on. Digital Output Problems Problem The IC shows the output turning on but there is no voltage on the output’s emitter side. Resolution Check for voltage on the collector side. If there is a DC voltage there greater than 10 volts, then call service. Gas Problems Problem The CNC turns on a gas test and no gas comes out of the torch. 144 Resolution Make sure the plasma gas box and shield gas box have power (green LED on the same side as the cable connections is lit). Maintenance/Troubleshooting Error Messages on the IC Display Error Log Screen Last received error always shown at top. Clear all errors on screen. This screen displays a log of the last 13 errors received by the IC. By moving the cursor to the error and pressing the hand wheel, more details of the error are displayed. Error Screen Module Type Number of starts since last reboot Error code Error details 145 Maintenance/Troubleshooting Error Screen Type of Error Number of starts since IC boot up Plasma Console error code Error details Error Screen Type of Error Number of starts since IC boot up Error ID Command value for error Actual value when error occurred Error details 146 Maintenance/Troubleshooting Module Errors ID Problem Solution 9 The checksum of the station constants do not match the station constants. This error will normally correct itself. If it continues, replace the module/board. B The watchdog telegram has not been received in 400 ms. 1. Check for all the dip switches on the IC board are toward the display. 2. Check for SW1 on the control board in the Plasma Console is set to "Closed" 3. Check for the CAN cable is properly connected to the module. 4. Check for coiling of the CAN cable near power leads. 1E The CAN send buffer has overflowed. 1F The CAN receive buffer has overflowed. 23 The checksum of the calibration data is wrong. Replace the gas control module. 53 The checksum of the local PLC on the gas control is wrong. Replace the gas control module. 60 The output to the valve on channel 1 is drawing too much current. 1. Check for a short on the output of the channel. 2. Replace the valve. 61 The output to the valve on channel 2 is drawing too much current. 1. Check for a short on the output of the channel. 2. Replace the valve. 62 The output to the valve on channel 3 is drawing too much current. 1. Check for a short on the output of the channel. 2. Replace the valve. 63 The output to the valve on channel 4 is drawing too much current. 1. Check for a short on the output of the channel. 2. Replace the valve. 64 The module's telegram counters do not match the interface control's telegram counters. 1. Check for all the dip switches on the IC board are toward the display. 2. Check for SW1 on the control board in the Plasma Console is set to "Closed" 3. Check for the CAN cable is properly connected to the module. 4. Check for coiling of the CAN cable near power leads. 65 The module has reset itself. 147 Maintenance/Troubleshooting Process Errors ID Problem Solution 1 The shield gas output flow is higher than expected. 1. Check that the correct consumables are installed in the torch. 2. Check for a leak in the shield output gas line from the gas control. 3. Check the flow reading while the start signal is low. If there is more than XX CFH (X.X CMH), replace the shield gas pressure sensor. 2 The shield gas output flow is lower than expected. 1. Check that the correct consumables are installed in the torch. 2. Check for a clog in the shield output gas line from the gas control. 3. Check that there is power to the pressure sensor. 4. Check for a loose or misplaced wire from the pressure sensor. 3 The gas control is not properly communicating on the CAN bus. 1. Check for all the switches on SW1 of the IC board are toward the display. 2. Check for SW1 on the control board in the Plasma Console is set to "Closed" 3. Check for the CAN cable is properly connected to the module. 4. Check for power to the module. 4 The plasma gas output pressure is higher than expected. 1. Check that the correct consumables are installed in the torch. 2. Check for a clog in the plasma output gas line from the gas control. 3. Check the pressure reading while the start signal is low. If there is more than X PSI (X.X BAR), replace the plasma gas pressure sensor. 5 The plasma gas output pressure is lower than expected. 1. Check that the correct consumables are installed in the torch. 2. Check for a leak in the plasma output gas line from the gas control. 3. Check that there is power to the pressure sensor. 4. Check for a loose or misplaced wire from the pressure sensor. 6 The current output of the Plasma Console is higher than expected. 7 The current output of the Plasma Console is lower than expected. 8 The arc was lost before plasma start signal was removed. 1. Pierce height is too high during start. 2. No plate under torch during cutting. 3. Pierce time is too long. 9 Coolant flow is lower than 1.0 GPM. 1. Check the coolant level in the coolant tank. 2. Check for a clog in the filter. 3. Check for a clog in the flow sensor. 4. Check for a kink in the coolant lines. 5. Check for power to the flow sensor. A The Plasma Console has thrown an error. Check the CAN PS error code for more details. B The control board is not properly communicating on the CAN bus. 1. Check for all the switches on SW1 of the IC board are toward the display. 2. Check for SW1 on the control board in the Plasma Console is set to "Closed" 3. Check for the CAN cable is properly connected to the control board. 4. Check for power to the control board. C The system failed to start. 1. Check that the torch is close enough to the work piece. 2. Check that the work piece and work leads from the Plasma Console are connected electrically (< 10 Ohms). D Coolant level is below the recommended level for operation. 1. Refill the coolant tank with coolant. 2. Replace the coolant level sensor. E The cycle start was present during boot up. 1. Check the start signal to the interface control while the Plasma Console is off. If there is voltage on the input, find and fix the wiring error. 2. Check the start signal to the interface control while the Plasma Console is on. If there is voltage on the input while the output of the CNC is off, check the interface control wiring for a short to the input. 3. Replace the interface control. F The plasma gas pressure sensor was reading a pressure when there was no command. 1. Check the input pressure to the plasma gas. 2. Check the wiring for the plasma gas pressure sensor. 3. Replace the plasma gas pressure sensor. 10 The shield gas pressure sensor was reading a flow when there was no command. 1. Check the input pressure to the shield gas. 2. Check the wiring for the shield gas pressure sensor. 3. Replace the shield gas pressure sensor. 148 Maintenance/Troubleshooting CAN PS Errors Error code Problem 01 Supply Line Voltage exceeded or dropped below + / - 15% of rated input when machine is in Idle mode 1. Check the input voltage to the machine with a voltage meter. 2. Check the input power cable for correct size and resistance. 3. Check the Main Transformer (T1) voltage tapping connections. 4. Check the input fuses in the PS. 5. Check the input line fuses in the disconnect box. 6. Check the multi-color ribbon cable between J12 on PCB1 and J2 and PCB2. 02 Supply Line Voltage exceeded or dropped below + or - 20% of rated input while cutting 1. Check the input line voltages to the machine with a voltage meter. 2. Check the input power cable for correct size and resistance. 3. Check the Main Transformer (T1) voltage tapping connections. 4. Check the input fuses in the PS. 5. Check the input line fuses in the disconnect box. 6. Check the multi-color ribbon cable between J12 on PCB1 and J2 and PCB2. 7. Notify your power company of the line stiffness issues. 03 Control Transformer not supplying proper voltage to control board or the +24 and +/-15 volt bias supplies are not balanced 1. Check the input voltage taps on the control transformer. 2. Check the control transformer output voltages on TB3, if the voltages read within +/-15% of the specified value then replace the control board else replace control transformer. 04 There is a thermal fault inside the Plasma Console. Fix any coolant flow errors before investigating this error. 1. Wait 10 minutes for the unit to cool. If the thermal fault clears on its own then check for the ambient temperature being above 40C or dirt in the radiators. 2. Check if main fan is functioning and it is pulling air through the Plasma Console. 3. Shut off the Plasma Console and allow the machine to cool. 4. Check the diode bridge for an open thermal switch. If the switch is still open after certain time then replace the switch. 5. Check the IGBT module for an open thermal switch. If the switch is still open after certain time then replace the switch. 05 CYCLE START signal is high while the power source is booting up. 1. Check the start signal to the Plasma Console while the Plasma Console is OFF. If there is voltage on the input, find and fix the wiring error. 2. Check the start signal to the Plasma Console while the Plasma Console is ON. If there is voltage on the input while CNC is OFF, check the Plasma Console control wiring for a short to the input. 06 Failed to fire/ ignition did not take place within 4 seconds after HF is turned ON. 1. Check the distance from the work piece matches the recommended ignition height. 2. Check the electrical connection from the work piece to the work connection on the Plasma Console. 3. Check the HF relay inside the Plasma Console. 4. Check the 115VAC voltage on the control transformer. 5. Check the consumables. 08 Torch error/Electrode current was present before the PWM was enabled. 1. Check the jumper inside the RAS box between pins L and J on the 14-pin Amphenol connector. 2. Check for short between electrode and nozzle. 3. Check the IGBT gate pulse voltage connection on the driver board. 4. Check for shorted IGBT. 5. Check for shorted diode (D9). 09 Arc voltage is greater than 40V in Idle mode. 1. Check for shorted IGBT. 2. Check for shorted diode (D9). 3. Check the arc voltage feedback connection on the driver board from the Electrode (-) terminal. 4. Check IGBT gate pulse voltage connection on the driver board. 11 Output current is greater than the minimum idle current. 1. Check for shorted IGBT. 2. Check for shorted diode (D9). 3. Check the IGBT gate pulse voltage connection on the driver board. If there is positive voltage then replace the driver board. 4. Check the hall sensors and their connections to the control board. 5. Replace the control board. 12 A phase of the input power is missing. 1. Check the fuses in the disconnect box for bad fuse. 2. Check the main contactor contacts for any damage. 3. Verify the input to the Plasma Console is providing all 3 phases. 13 Open circuit voltage did not reach 280 volts within 200 msec. 1. Check for short between the electrode and nozzle. 2. Check for short between the electrode cable and a connection to the work output of the Plasma Console. 3. Check for an open IGBT. 4. Check the IGBT gate pulse voltage connection on the driver board. 5. Check the multi-color ribbon connection from J12 on PCB1 to J2 on PCB2. 14 Ambient temperature exceeded 75° C in control enclosure. 1. Check the temperature inside the control panel, if it reads below 55C and still the error is present then replace the control board. 2. Cool the area around the Plasma Console to below 40C. This is the upper limit of the rated operating range for the Plasma Console. 15 Bus voltage failed to reach 200 VDC with in 500 ms. 1. Check for faulty input fuse. 2. Check for shorted bus filter capacitor. 3. Check the bus charger contactor (K2) contacts and coil for any damage. 4. Check the bus-charger contactor relay (RB1-1) for failure. 5. Check bus charger resistors connections. 6. Check the ribbon cable connection between J6 and Relay Module (RB1). 7. Check the multi-color ribbon cable connection between J12 on PCB1 to J2 on PCB2. 8. Check the 24VAC supply on the control transformer. Solution 149 Maintenance/Troubleshooting 18 Output voltage fell below 70 volts during cutting or below 40 volts during marking. 1. Check for short in the torch cable. 2. Check cutting or marking height is too low. 3. Check for short between electrode and nozzle. 4. Check for short between Work (+) and Electrode (-) terminals on the Plasma Console. 5. Check for coiled or looped up electrode or work cables. 20 Output or Arc voltage detected before START signal issued 1. Check for a shorted IGBT. 2. Check the gate pulse voltage to IGBT from driver board. If there is a positive voltage during idle, replace the driver board. 3. Check the IGBT gate pulse voltage connections and make sure they are as per schematics. 4. Check the arc voltage feedback connections on the driver board. 5. Check for shorted diode (D9). 6. Check the multi-color ribbon cable connection between J12 on PCB1 and J2 on PCB2. 21 Main contactor failed to engage or disengage. 1. Check the input fuses inside the disconnect box. 2. Check the main contactor (K1) contacts. 3. Check the main transformer auxiliary windings connection on TB2 for 115VAC. 4. Check the relay RB1-2 on the relay module RB1. 5. Check the ribbon cable connection between J6 and relay module RB1. 22 Work current is greater than Electrode current plus threshold limit during cutting. 1. Check the feedback from the hall sensors. 2. Check the connection from hall sensors to the control board. 3. Replace the control board. 23 The Plasma Console enable signal is missing. 1. Check the Plasma Console enable signal is present. This should be a dry contact output from the CNC. 2. Check for the Plasma Console enable signal going to J1 connector on PCB1. 3. Check the enable signal contacts on K4 relay. 4. Check control transformer 24VAC voltage on TB3 powering K4 and K5. 5. Replace the control board. 24 There was an SPI communication error between the main and servo micro on control board. 1. Shut off the Plasma Console for at least 5 minutes. If the error clears, check the grounding of the machine and the Plasma Console. 2. Replace the control board. 25 The EEPROM on the control has failed. 1. Shut off the Plasma Console for at least 5 minutes. If the error clears, check the grounding of the machine and the Plasma Console. 2. Replace the control board. 27 The servo and supervisor on the control board of the Plasma Console has firmware version mismatch. Replace the control board. 28 Jumper in the RAS box is missing. 1. Check the jumper inside the RAS box between pins L and J on the 14-pin Amphenol connector. 2. Check for damaged control cable. 3. Replace the control board. 30 The servo on the control board has fault. 1. Check for bad hall sensor. 2. Check for diode (D9) connection on the IGBT module bus bars. 3. Shut off the Plasma Console for at least 5 minutes. If the error clears, check the grounding of the machine and the Plasma Console. 4. Replace the control board. 31 Coolant flow is below 0.45GPM. 1. Check the coolant level. 2. Check for a clogged filter. 3. Check for leaks in the coolant return line. 4. Check the bypass regulator for bypassing too much coolant. 5. Check input power to the pump. 6. Check for proper pump function by looking for flow into the tank. If there is no flow and the motor in running, replace the pump head. 7. Check the connection of the flow sensor to the control board. 8. Check for the SW6 position set properly according the flow sensor either turbine flow or rotor flow sensor. 9. Replace the control board. 32 Coolant flow is above 2.4GPM. 1. Check the connection of the flow sensor to the control board. 2. Check for the SW6 position set properly according the flow sensor either turbine flow or rotor flow sensor. 3. Replace the control board. 33 There was a watchdog error on the CAN bus. 1. Check the CAN connection between the interface control and the Plasma Console’s control board. 2. Check the input power to the interface control. 3. Check for all the dip switches on the IC board are toward the display. 4. Check for SW5 on the control board in the Plasma Console is set to “CLOSE”. 5. Check for coiling of the CAN cable near power leads. 34 Ignition/Arc lost in dwell state immediately after it attached to the plate. 1. Check that the piercing distance of the torch is at the recommended level. 2. Check that the ignition distance of the torch is at the recommended level. 3. Check the consumables. 35 The station constant’s CRC received from the controller did not match the calculated CRC. This will normally correct itself, if not replace the control board. 39 Hall Sensor Connector is removed or jumper is missing. 1. Check the hall sensor feedback connector for proper wiring. 150 Maintenance/Troubleshooting Torch Maintenance/Troubleshooting Torch Front End Disassembly Wear on torch parts is a normal occurrence to plasma cutting. Starting a plasma arc is an erosive process to both the electrode and nozzle. Regularly scheduled inspection and replacement of PT-36 parts must take place to maintain cut quality and consistent part size. DANGER Hot Torch Will Burn Skin! Allow torch to cool before servicing. 1. Remove the Shield Cup Retainer. NOTE: If the shield cup retainer is difficult to remove, try to screw the nozzle retaining cup tighter to relieve pressure on the shield cup retainer. 2. Inspect mating metal surface of shield cup and shield cup retainer for nicks or dirt that might prevent these two parts from forming a metal to metal seal. Look for pitting or signs of arcing inside the shield cup. Look for melting of the shield tip. Replace if damaged. 3. Inspect diffuser for debris and clean as necessary. Wear on the top notches does occur, effecting gas volume. Replace this part every other shield replacement. Heat from cutting many small parts in a concentrated area or when cutting material greater than 0.75" (19.1mm) may require more frequent replacement. CAUTION Incorrect assembly of the diffuser in the shield will prevent the torch from working properly. Diffuser notches must be mounted away from the shield as illustrated. Diffuser Shield Cup Torch Body Nozzle Electrode Nozzle Retaining Cup Shield Cup Retainer 151 Maintenance/Troubleshooting 4. Unscrew nozzle retainer and pull nozzle straight out of torch body. Inspect insulator portion of the nozzle retainer for cracks or chipping. Replace if damaged. Inspect nozzle for: • • • • • melting or excessive current transfer. gouges from internal arcing. nicks or deep scratches on the O-ring seating surfaces . O-ring cuts, nicks, or wear. Remove hafnium particles (from the nozzle) with steel wool. Replace if any damage is found. NOTE: Discoloration of internal surfaces and small black starting marks are normal and do not effect cutting performance. If the holder was tightened sufficiently, the electrode may unscrew without being attached to the electrode holder. When installing the electrode, use only sufficient force to adequately secure the electrode. 5. Remove electrode using electrode removal tool. 6. Disassemble electrode from electrode holder. Insert flats on the holder into a 5/16" wrench. Using the electrode tool, rotate electrode counter-clockwise to remove. Replace electrode if center insert is pitted more than 3/32” (2.4mm). Torch Body Electrode Removal Tool Electrode Replace electrode if center insert is pitted more than 3/32” (2.4mm) 152 Maintenance/Troubleshooting 7. Remove electrode holder from torch body. Hex on the end of the electrode holder removal tool will engage in a hex in the holder. Removal Tool Gas Baffle Electrode Holder Assembly Electrode NOTE: The electrode holder is manufactured in two pieces. Do not disassemble. If the holder is damaged, replace the electrode holder assembly. 8. Disassemble electrode holder and gas baffle. Carefully remove O-ring from electrode holder and slide baffle from holder. Inspect nozzle seating surface (front edge) for chips. Look for cracks or plugged holes. Do not attempt to clear holes. Replace baffle if damaged. NOTE: Check all O-rings for nicks or other damage that might prevent O-ring from forming a gas/water tight seal. Gas Baffle Electrode Holder Assembly O-ring NOTE: Discoloration of these surfaces with use is normal. It is caused by galvanic corrosion. 153 Maintenance/Troubleshooting Torch Front End Assembly Over-tightened parts will be difficult to disassemble and may damage torch. Do not over tighten parts during reassembly. Threaded parts are designed to work properly when hand-tightened, approximately 40 to 60 inch/pounds. CAUTION • • • • Reverse order of disassembly. Apply a very thin coat of silicone grease to O-rings before assembling mating parts. This facilitates easy future assembly and disassembly for service. Installing the electrode requires only moderate tightening. If the electrode holder is made tighter than the electrode, it is possible to change worn electrodes without removing the electrode holder. Turn on the coolant circulator and purge the gases through the torch. NOTE: When assembling, place the nozzle inside the nozzle retaining cup and thread the nozzle retaining cup/nozzle combination on the torch body. This will help align the nozzle with the assembly. The shield cup and shield cup retainer should be installed only after installing the nozzle retaining cup and nozzle. Otherwise the parts will not seat properly and leaks may occur. Diffuser Nozzle Nozzle Retaining Cup Shield Cup Shield Cup Retainer 154 Electrode Torch body Maintenance/Troubleshooting Torch Front End Assembly using the Speedloader (optional) Use of a speedloader, p/n 0558006164, will ease assembly of the torch front end parts. step 1. To use the speedloader, first insert the nozzle into the nozzle retaining cup. Nozzle Nozzle Retaining Cup step 2. Screw the speedloader into the nozzle retaining cup to secure the nozzle. Preassembly tool step 3. Secure retaining nut on nozzle with preassembly tool, p/n 0558005917 included with the speedloader. step 4. Remove the speedloader. It is very important to remove the speedloader to ensure proper seating of the remaining parts. Retaining nut p/n 0558005916 step 5. Insert the diffuser into the shield cup. Shield Cup Diffuser Shield cup retainer step 6. Insert the nozzle retaining cup assembly into the shield cup retainer. Nozzle retaining cup assembly Shield cup retainer assembly step 7. Screw shield cup retainer assembly onto nozzle retaining cup assembly. 155 Maintenance/Troubleshooting Torch Body Maintenance • • • Inspect O-rings daily and replace if damaged or worn. Apply a thin coat of silicone grease to O-rings before assembling torch. This facilitates easy future assembly and disassembly for service. O-ring [1.61" (41mm) I.D. x .07" (1.8mm) BUNA-70A] p/n 996528. WARNING Electric Shock Can Kill! Before performing torch maintenance: • • Turn power switch of the Plasma Console console to the OFF position. Disconnect primary input power. O-Ring locations • • • Keep electrical contract ring contact points free of grease and dirt. Inspect ring when changing nozzle. Clean with cotton swab dipped in isopropyl alcohol. Contact Ring Points Contact Ring Contact Ring Screw Contact Ring Points 156 Maintenance/Troubleshooting Torch Body Removal and Replacement WARNING Electric Shock Can Kill! Before performing torch maintenance: • • Turn power switch of the Plasma Console console to the OFF position . Disconnect primary input power. 1. Loosen the worm gear hose clamp so that the torch sleeving can be freed and pulled back up the cable bundle. Approximately 7” (177.8mm) should be far enough. Unscrew the torch sleeve and slide it back until the pilot arc connection is exposed. Handle Torch Body 2. Disconnect the power cables which are threaded onto the shorter stems at the back of the torch. Note that one of these connections is left-handed. Unscrew the gas hoses from the torch head assembly by using a 7/16" (11.1mm) and a 1/2" (12.7mm) wrench. Removal of the gas hoses is easier if the power cables are removed first. 1/2" HEX Power Cable & Water Return Connections 1/2" HEX Shield Gas Connection 7/16" HEX Plasma Gas Connection 157 Maintenance/Troubleshooting 3. Unwrap the electrical tape at the back of the gray plastic insulator over the pilot arc connection. Slide the insulator back and undo the knife connectors. Pilot Arc Cable PA Insulator Electrical Tape (shown removed) Knife-splice connection 4. To install the new torch head assembly - Connect the pilot arc cable and the main power cable by reversing the steps taken to disconnect them. Be sure the gas and water fittings are tight enough to prevent leaks, but do not use any kind of sealant on them. If the knife connection seems loose, tighten the connection by pressing on the parts with needle-nosed pliers after they are assembled. Secure the gray pilot arc insulator with 10 turns of electrical tape. New Torch Head Assembly 5. Slide the handle forward and thread it firmly onto the torch body. 158 Maintenance/Troubleshooting Reduced Consumable Life 1. Cutting Up Skeletons Cutting skeletons (discarded material left after all pieces have been removed from a plate). Their removal from the table can adversely affect electrode life by: • • • Causing the torch to run off the work. Greatly increasing the start frequency. This is mainly a problem for O2 cutting and can be alleviated by choosing a path with a minimum number of starts. Increasing likelihood that the plate will spring up against the nozzle causing a double arc. This can be mitigated by careful operator attention and by increasing standoff and reducing cutting speeds. If possible, use an OXWELD torch for skeleton cutting or operate the PT-36 at a high standoff. 2. Height Control Problems • Torch crashing is usually caused by a change in arc voltage when an automatic height control is used. The voltage change is usually the result of plate falling away from the arc. Disabling the height control and extinguishing the arc earlier when finishing the cut on a falling plate can effectively eliminate these problems. • Torch crashing can also occur at the start if travel delay is excessive. This is more likely to occur with thin material. Reduce delay or disable the height control. • Torch crashing can also be caused by a faulty height control. 3. Piercing Standoff Too Low Increase pierce standoff 4. Starting on edges with continuous pilot arc Position torch more carefully or start on adjacent scrap material. 5. Work Flipping The nozzle may be damaged if the torch hits a flipped up part. 6. Catching on Pierce Spatter Increase standoff or start with longer lead-in. 7. Pierce not complete before starting Increase initial delay time. 8. Coolant flow rate low, Plasma gas flow rate high, Current set too high Correct settings 9. Coolant leaks in torch Repair leaks 159 Maintenance/Troubleshooting Checking for Coolant Leaks Coolant leaks can originate from seals on the electrode, electrode holder, nozzle, and torch body. Leaks could also originate from a crack in the insulating material of the torch or nozzle retaining cup or from a power cable. To check for leaks from any source remove the shield cup, clean off the torch, purge it, and place it over a clean dry plate. With the gases off, run the water cooler for several minutes and watch for leaks. Turn on the plasma gas and watch for any mist from the nozzle exit. If there isn’t any, turn off the plasma gas, turn on the shield gas, and watch for any mist from the shield gas passages in the nozzle retaining cup. If a leak appears to be coming from the nozzle orifice, remove and inspect the o-rings on the nozzle, electrode, and electrode holder. Check the sealing surfaces on the electrode holder and stainless steel torch liner. If you suspect that a leak is coming from the electrode itself, you can install a 100 to 200 amp 2-piece nozzle base without a nozzle tip. After purging, run the water cooler with the gas off and observe the end of the electrode. If water is seen to collect there, make sure it is not running down the side of the electrode from a leak at an o-ring seal. WARNING 160 If it is necessary to supply power to the Plasma Console to run the water cooler, it is possible to have high voltages at the torch with no arc present. Never touch the torch with the Plasma Console energized. REPLACEMENT PARTS Replacement Parts This page intentionally left blank. 162 Replacement Parts Replacement Parts General Always provide the serial number of the unit on which the parts will be used. The serial number is stamped on the unit nameplate. m2 Smart Plasmarc Information m2 Plasma Console, 200A, 230/460V, 60Hz, 0558012390 m2 Plasma Console, 200A, 380 CCC, 50Hz, 0558012391 m2 Plasma Console, 200A, 400V CE, 50Hz, 0558012392 m2 Plasma Console, 200A, 575V, 60Hz, 0558012393 Ordering To ensure proper operation, it is recommended that only genuine ESAB parts and products be used with this equipment. The use of non-ESAB parts may void your warranty. Replacement parts may be ordered from your ESAB Distributor. Be sure to indicate any special shipping instructions when ordering replacement parts. Refer to the Communications Guide located on the back page of this manual for a list of customer service phone numbers. NOTE: Schematics and Wiring Diagrams on 279.4 mm x 431.8 mm (11” x 17”) paper are included inside the back cover of this manual. Items listed in the assembly drawing Bill of Materials (included in the back of this publication) that do not have a part number shown are not available from ESAB as a replaceable item and cannot be ordered. Descriptions are shown for reference only. Please use local retail hardware outlets as a source for these items. 163 Replacement Parts This page intentionally left blank. 164 REVISION HISTORY ESAB subsidiaries and representative offices Europe AUSTRIA ESAB Ges.m.b.H Vienna--Liesing Tel: +43 1 888 25 11 Fax: +43 1 888 25 11 85 BELGIUM S.A. ESAB N.V. Brussels Tel: +32 2 745 11 00 Fax: +32 2 745 11 28 THE CZECH REPUBLIC ESAB VAMBERK s.r.o. Prague Tel: +420 2 819 40 885 Fax: +420 2 819 40 120 DENMARK Aktieselskabet ESAB Copenhagen--Valby Tel: +45 36 30 01 11 Fax: +45 36 30 40 03 FINLAND ESAB Oy Helsinki Tel: +358 9 547 761 Fax: +358 9 547 77 71 FRANCE ESAB France S.A. Cergy Pontoise Tel: +33 1 30 75 55 00 Fax: +33 1 30 75 55 24 GERMANY ESAB GmbH Solingen Tel: +49 212 298 0 Fax: +49 212 298 218 GREAT BRITAIN ESAB Group (UK) Ltd Waltham Cross Tel: +44 1992 76 85 15 Fax: +44 1992 71 58 03 ESAB Automation Ltd Andover Tel: +44 1264 33 22 33 Fax: +44 1264 33 20 74 HUNGARY ESAB Kft Budapest Tel: +36 1 20 44 182 Fax: +36 1 20 44 186 ITALY ESAB Saldatura S.p.A. Mesero (Mi) Tel: +39 02 97 96 81 Fax: +39 02 97 28 91 81 THE NETHERLANDS ESAB Nederland B.V. Utrecht Tel: +31 30 2485 377 Fax: +31 30 2485 260 NORWAY AS ESAB Larvik Tel: +47 33 12 10 00 Fax: +47 33 11 52 03 POLAND ESAB Sp.zo.o. Katowice Tel: +48 32 351 11 00 Fax: +48 32 351 11 20 PORTUGAL ESAB Lda Lisbon Tel: +351 8 310 960 Fax: +351 1 859 1277 SLOVAKIA ESAB Slovakia s.r.o. Bratislava Tel: +421 7 44 88 24 26 Fax: +421 7 44 88 87 41 SPAIN ESAB Ibérica S.A. Alcalá de Henares (MADRID) Tel: +34 91 878 3600 Fax: +34 91 802 3461 SWEDEN ESAB Sverige AB Gothenburg Tel: +46 31 50 95 00 Fax: +46 31 50 92 22 ESAB International AB Gothenburg Tel: +46 31 50 90 00 Fax: +46 31 50 93 60 SWITZERLAND ESAB AG Dietikon Tel: +41 1 741 25 25 Fax: +41 1 740 30 55 North and South America ARGENTINA CONARCO Buenos Aires Tel: +54 11 4 753 4039 Fax: +54 11 4 753 6313 Asia/Pacific CHINA Shanghai ESAB A/P Shanghai Tel: +86 21 5308 9922 Fax: +86 21 6566 6622 INDIA ESAB India Ltd Calcutta Tel: +91 33 478 45 17 Fax: +91 33 468 18 80 INDONESIA P.T. ESABindo Pratama Jakarta Tel: +62 21 460 0188 Fax: +62 21 461 2929 JAPAN ESAB Japan Tokyo Tel: +81 3 5296 7371 Fax: +81 3 5296 8080 MALAYSIA ESAB (Malaysia) Snd Bhd Shah Alam Selangor Tel: +60 3 5511 3615 Fax: +60 3 5512 3552 SINGAPORE ESAB Asia/Pacific Pte Ltd Singapore Tel: +65 6861 43 22 Fax: +65 6861 31 95 Representative offices BULGARIA ESAB Representative Office Sofia Tel/Fax: +359 2 974 42 88 EGYPT ESAB Egypt Dokki--Cairo Tel: +20 2 390 96 69 Fax: +20 2 393 32 13 ROMANIA ESAB Representative Office Bucharest Tel/Fax: +40 1 322 36 74 RUSSIA-- CIS ESAB Representative Office Moscow Tel: +7 095 937 98 20 Fax: +7 095 937 95 80 ESAB Representative Office St Petersburg Tel: +7 812 325 43 62 Fax: +7 812 325 66 85 Distributors For addresses and phone numbers to our distributors in other countries, please visit our home page www.esab.com SOUTH KOREA ESAB SeAH Corporation Kyungnam Tel: +82 55 269 8170 Fax: +82 55 289 8864 UNITED ARAB EMIRATES ESAB Middle East FZE Dubai Tel: +971 4 887 21 11 Fax: +971 4 887 22 63 BRAZIL ESAB S.A. Contagem--MG Tel: +55 31 2191 4333 Fax: +55 31 2191 4440 CANADA ESAB Group Canada Inc. Missisauga, Ontario Tel: +1 905 670 02 20 Fax: +1 905 670 48 79 MEXICO ESAB Mexico S.A. Monterrey Tel: +52 8 350 5959 Fax: +52 8 350 7554 USA ESAB Welding & Cutting Products Florence, SC Tel: +1 843 669 44 11 Fax: +1 843 664 57 48 ESAB AB SE-- 695 81 LAXÅ SWEDEN Phone +46 584 81 000 www.esab.com 041227 ">
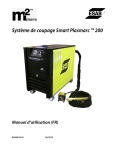
Öffentlicher Link aktualisiert
Der öffentliche Link zu Ihrem Chat wurde aktualisiert.