Remko WKF70NEOcompact Manuel utilisateur
PDF
Descargar
Documento
Manuel d'utilisation et d'installation REMKO série WKF NEO-compact Thermopompes Smart Système air / eau pour le chauffage ou le refroidissement WKF NEO-compact 70, WKF NEO-compact 120, WKF NEO-compact 180 Instructions au spécialiste 0188-2019-08 Version 7, fr_FR Lire les instructions avant de commencer tous travaux ! Avant de mettre en service/d'utiliser cet appareil, lisez attentivement ce manuel d'installation ! R410A Ce mode d'emploi fait partie intégrante de l'appareil et doit toujours être conservé à proximité immédiate du lieu d'installation ou de l'appareil lui-même. Réfrigérant Sous réserve de modifications. Nous déclinons toute responsabilité en cas d'erreurs ou de fautes d'impression ! Traduction de l'original Table des matières 1 Consignes de sécurité et d'utilisation................................................................................................. 1.1 Consignes générales de sécurité.................................................................................................... 1.2 Identification des remarques........................................................................................................... 1.3 Qualifications du personnel............................................................................................................. 1.4 Dangers en cas de non-respect des consignes de sécurité........................................................... 1.5 Travail en toute sécurité.................................................................................................................. 1.6 Consignes de sécurité à l'attention de l'exploitant.......................................................................... 1.7 Consignes de sécurité à observer durant les travaux de montage, de maintenance et d'inspection.................................................................................................................................................. 1.8 Transformation arbitraire et et les changements............................................................................. 1.9 Utilisation conforme......................................................................................................................... 1.10 Garantie........................................................................................................................................ 1.11 Transport et emballage.................................................................................................................. 1.12 Protection de l‘environnement et recyclage.................................................................................. 5 5 5 5 5 6 6 6 6 6 7 7 7 2 Caractéristiques techniques................................................................................................................ 8 2.1 Caractéristiques des appareils........................................................................................................ 8 2.2 Données sur le produit.................................................................................................................. 10 2.3 Dimensions de l'appareil des modules externes........................................................................... 11 2.4 Dimensions de l'appareil des modules internes............................................................................ 11 2.5 Limites d'utilisation de la thermopompe en mode monovalent..................................................... 14 2.6 Caractéristiques de la pompe de chargement des modules internes........................................... 15 2.7 Niveau sonore total des modules externes................................................................................... 16 2.8 Caractéristiques............................................................................................................................ 19 3 Structure et fonctionnement.............................................................................................................. 28 3.1 Thermopompe en général............................................................................................................. 28 3.2 Équipement supplémentaire......................................................................................................... 34 4 Montage............................................................................................................................................... 4.1 Architecture du système WKF NEO 70......................................................................................... 4.2 Architecture du système WKF NEO 120....................................................................................... 4.3 Architecture du système WKF NEO 180....................................................................................... 4.4 Remarques générales pour le montage........................................................................................ 4.5 Installation, montage du module interne....................................................................................... 4.6 Installation, montage du module externe...................................................................................... 5 Raccordement hydraulique................................................................................................................ 44 6 Refroidissement pompe à chaleur.................................................................................................... 46 7 Protection contre la corrosion........................................................................................................... 48 8 Mode de chauffage d'urgence............................................................................................................ 50 9 Raccord de frigorigène....................................................................................................................... 51 9.1 Raccord des conduites de frigorigène........................................................................................... 51 9.2 Mise en service des techniques de refroidissement..................................................................... 52 10 Raccordement électrique................................................................................................................... 55 11 Avant la mise en service..................................................................................................................... 55 12 Mise en service.................................................................................................................................... 56 13 Entretien et maintenance................................................................................................................... 57 14 Mise hors service provisoire.............................................................................................................. 57 35 35 36 37 38 39 40 3 REMKO série WKF NEO-compact 15 Élimination des défauts et service après-vente............................................................................... 15.1 Dépannage général .................................................................................................................... 15.2 Messages sur le module externe................................................................................................ 15.3 Messages d'erreur du Smart-Control.......................................................................................... 58 58 59 61 16 Représentation de l'appareil et pièces de rechange........................................................................ 16.1 Représentation de l'appareil Module externe WKF NEO 70....................................................... 16.2 Pièces de rechange du module externe WKF NEO 70............................................................... 16.3 Représentation de l'appareil Module externe WKF NEO 120..................................................... 16.4 Pièces de rechange du module externe WKF NEO 120............................................................. 16.5 Représentation de l'appareil Module externe WKF NEO 180..................................................... 16.6 Pièces de rechange du module externe WKF NEO 180............................................................. 16.7 Représentation de l'appareil Modules internes WKF NEO compact........................................... 16.8 Pièces de rechange des modules internes WKF NEO compact 70/120/180.............................. 69 69 70 71 72 73 74 75 76 17 Terminologie générale........................................................................................................................ 78 18 Index..................................................................................................................................................... 80 4 1 Consignes de sécurité et d'utilisation 1.1 Consignes générales de sécurité Avant la première mise en service de l'appareil, veuillez attentivement lire le mode d'emploi. Ce dernier contient des conseils utiles, des remarques ainsi que des avertissements visant à éviter les dangers pour les personnes et les biens matériels. Le non-respect de ce manuel peut mettre en danger les personnes, l'environnement et l'installation et entraîner ainsi la perte de la garantie. Conservez ce mode d'emploi ainsi que la fiche de données du frigorigène à proximité de l'appareil. 1.2 Identification des remarques Cette section vous donne une vue d'ensemble de tous les aspects essentiels en matière de sécurité visant à garantir une protection optimale des personnes et un fonctionnement sûr et sans dysfonctionnements. Les instructions à suivre et les consignes de sécurité fournies dans ce manuel doivent être respectées afin d'éviter les accidents, les dommages corporels et les dommages matériels. Les indications qui figurent directement sur les appareils doivent impérativement être respectées et toujours être lisibles. Dans le présent manuel, les consignes de sécurité sont signalées par des symboles. Les consignes de sécurité sont précédées par des mots-clés qui expriment l'ampleur du danger. DANGER ! En cas de contact avec les composants sous tension, il y a danger de mort immédiate par électrocution. L'endommagement de l'isolation ou de certains composants peut être mortel. DANGER ! Cette combinaison de symboles et de mots-clés attire l'attention sur une situation dangereuse imminente qui provoque la mort ou de graves blessures lorsqu'elle n'est pas évitée. AVERTISSEMENT ! Cette combinaison de symboles et de mots-clés attire l'attention sur une situation potentiellement dangereuse qui peut provoquer la mort ou de graves blessures lorsqu'elle n'est pas évitée. PRECAUTION ! Cette combinaison de symboles et de mots-clés attire l'attention sur une situation potentiellement dangereuse qui peut provoquer des blessures ou qui peut provoquer des dommages matériels et environnementaux lorsqu'elle n'est pas évitée ou. REMARQUE ! Cette combinaison de symboles et de mots-clés attire l'attention sur une situation potentiellement dangereuse qui peut provoquer des dommages matériels et environnementaux lorsqu'elle n'est pas évitée. Ce symbole attire l'attention sur les conseils et recommandations utiles ainsi que sur les informations visant à garantir une exploitation efficace et sans dysfonctionnements. 1.3 Qualifications du personnel Le personnel chargé de la mise en service, de la commande, de l'inspection et du montage doit disposer de qualifications adéquates. 1.4 Dangers en cas de non-respect des consignes de sécurité Le non-respect des consignes de sécurité comporte des dangers pour les personnes ainsi que pour l'environnement et les appareils. Le non-respect des consignes de sécurité peut entraîner l'exclusion de demandes d'indemnisation. Dans certains cas, le non-respect peut engendrer les dangers suivants: 5 REMKO série WKF NEO-compact n Défaillance de fonctions essentielles des appareils. n Défaillance de méthodes prescrites pour la maintenance et l'entretien. n Mise en danger de personnes par des effets électriques et mécaniques. 1.5 Travail en toute sécurité Les consignes de sécurité, les consignes nationales en vigueur pour la prévention d'accidents ainsi que les consignes de travail, d'exploitation et de sécurité internes fournies dans le présent manuel d'emploi doivent être respectées. 1.6 Consignes de sécurité à l'attention de l'exploitant La sécurité de fonctionnement des appareils et composants est garantie uniquement sous réserve d'utilisation conforme et de montage intégral. n Seuls les techniciens spécialisés sont autorisés à procéder au montage, à l'installation et à la maintenance des appareils et composants. n Le cas échéant, il est interdit de démonter la protection contre les contacts accidentels (grille) des pièces mobiles durant l'exploitation de l'appareil. n Il est interdit d'exploiter les appareils et composants lorsqu'ils présentent des vices ou dommages visibles à l'œil nu. n Le contact avec certaines pièces ou composants des appareils peut provoquer des brûlures ou des blessures. n Les appareils et composants ne doivent jamais être exposés à des contraintes mécaniques, à des jets d'eau sous pression ou températures extrêmes. n Les espaces dans lesquels des fuites de réfrigérant peut suffisante pour charger et évent. Il y a sinon risque d'étouffement. n Tous les composants du carter et les ouvertures de l'appareil, telles que les ouvertures d'admission et d'évacuation de l'air, doivent être exempts de corps étrangers, de liquides et de gaz. n Les appareils doivent être contrôlés au moins une fois par an par un spécialiste. L'exploitant peut réaliser les contrôles visuels et les nettoyages après mise hors tension préalable. 1.7 Consignes de sécurité à observer durant les travaux de montage, de maintenance et d'inspection n Lors de l'installation, de la réparation, de la maintenance et du nettoyage des appareils, prendre les mesures qui s'imposent pour exclure tout danger émanant de l'appareil pour les personnes. n L'installation, le raccordement et l'exploitation des appareils et composants doivent être effectués dans le respect des conditions d'utilisation et d'exploitation conformément au manuel et satisfaire aux consignes régionales en vigueur. n Réglementations régionales et les lois et la Loi sur l'eau sont respectées. n L'alimentation électrique doit être adaptée aux spécifications des appareils. n Les appareils doivent uniquement être fixés sur les points prévus à cet effet en usine. Les appareils doivent uniquement être fixés ou installés sur les constructions et murs porteurs ou sur le sol. n Les appareils mobiles doivent être installés verticalement et de manière sûre sur des sols appropriés. Les appareils stationnaires doivent impérativement être fixés avant toute utilisation. n Les appareils et composants ne doivent en aucun cas être utilisés dans les zones présentant un danger d'endommagement accru. Les distances minimales doivent être observées. n Respectez une distance de sécurité suffisante entre les appareils et composants et les zones et atmosphères inflammables, explosives, combustibles, corrosives et poussiéreuses. n Dispositifs de sécurité ne doit pas être altéré ou contourné. 1.8 Transformation arbitraire et et les changements Il est interdit de transformer ou modifier les appareils et composants. De telles interventions pourraient être à l'origine de dysfonctionnements. Ne modifiez ou ne shuntez en aucun cas les dispositifs de sécurité. Les pièces de rechange d'origine et les accessoires agréés par le fabricant contribuent à la sécurité. L'utilisation de pièces étrangères peut annuler la responsabilité quant aux dommages consécutifs. 1.9 Utilisation conforme Les appareils sont conçus exclusivement et selon leur configuration et leur équipement pour une utilisation en tant qu'appareil de climatisation ou de chauffage du fluide de fonctionnement, l'air, au sein de pièces fermées. 6 Toute utilisation autre ou au-delà de celle évoquée est considérée comme non conforme. Le fabricant/ fournisseur ne saurait être tenu responsable des dommages en découlant. L'utilisateur assume alors l'intégralité des risques. L'utilisation conforme inclut également le respect des instructions de service et consignes d'installations ainsi que le respect des conditions de maintenance. Ne jamais dépasser les seuils définis dans les caractéristiques techniques. 1.10 Protection de l‘environnement et recyclage Mise au rebut de l‘emballage Pour le transport, tous les produits sont emballés soigneusement à l‘aide de matériaux écologiques. Contribuez à la réduction des déchets et à la préservation des matières premières en apportant les emballages usagés exclusivement aux points de collecte appropriés. Garantie Les éventuels droits de garantie ne sont valables qu'à condition que l'auteur de la commande ou son client renvoie à la société REMKO GmbH & Co. KG le « certificat de garantie » fourni avec l'appareil et dûment complété à une date proche de la vente et de la mise en service de l'appareil. Les conditions de la garantie sont définies dans les « Conditions générales de vente et de livraison ». En outre, seuls les partenaires contractuels sont autorisés à conclure des accords spéciaux. De ce fait, adressez-vous toujours d'abord à votre partenaire contractuel attitré. 1.11 1.12 Transport et emballage Les appareils sont livrés dans un emballage de transport robuste. Contrôlez les appareils dès la livraison et notez les éventuels dommages ou pièces manquantes sur le bon de livraison, puis informez le transporteur et votre partenaire contractuel. Aucune garantie ne sera octroyée pour des réclamations ultérieures. Mise au rebut des appareils et composants La fabrication des appareils et composants fait uniquement appel à des matériaux recyclables. Participez également à la protection de l‘environnement en ne jetant pas aux ordures les appareils ou composants (par exemple les batteries), mais en respectant les directives régionales en vigueur en matière de mise au rebut écologique. Veillez par exemple à apporter votre appareil à une entreprise spécialisée dans l‘élimination et le recyclage ou à un point de collecte communal agréé. AVERTISSEMENT ! Les sacs et emballages en plastique, etc. peuvent être dangereux pour les enfants! Par conséquent: - Ne pas laisser traîner l'emballage. - Laisser l'emballage hors de portée des enfants! 7 REMKO série WKF NEO-compact 2 Caractéristiques techniques 2.1 Caractéristiques des appareils WKF NEO 70 Série WKF NEO 120 WKF NEO 180 Fonction Chauffage ou refroidissement Système Séparation Air/eau Gestionnaire de thermopompes Smart-Control Ballon d'eau potable en émail Chauf. d’appoint électr./puissance nomin. Série 200 ou 300 litres kW 6,0 Chauffage d'eau potable (vanne d'inversion) Série Raccord de la chaudière fuel/gaz en option Limites d'utilisation du chauffage °C Température aller eau chaude, max. °C Puissance calorifique min. / max. kW -20 - +35 -20 - +45 55 1,2 - 6,0 2,5 - 12,5 3,1 - 17,7 Puissance calorifique / fréquence du compresseur / COP 1) avec A12/W35 kW/Hz/COP 6,00/56/5,10 10,96/61/4,82 16,02/56/5,33 avec A7/W35 kW/Hz/COP 5,46/54/4,62 9,86/61/4,44 14,02/56/4,53 avec A2/W35 kW/Hz/COP 4,61/65/3,50 6,95/60/3,64 9,32/56/3,53 avec A-7/W35 kW/Hz/COP 4,50/81/2,80 6,14/61/2,89 8,20/56/2,87 avec A-15/W35 kW/Hz/COP 4,70/88/2,50 4,82/61/2,39 6,36/56/2,40 avec A7/W45 kW/Hz/COP 5,00/56/3,60 10,15/58/3,67 12,27/58/3,46 avec A-7/W45 kW/Hz/COP 4,40/81/2,60 --- --- avec A7/W55 kW/Hz/COP 5,00/56/2,80 8,99/61/2,78 12,85/56/2,92 avec A-7/W55 kW/Hz/COP 4,70/81/1,70 4,63/61/1,79 6,99/56/1,94 avec A10/W35 kW/Hz/COP 5,80/54/4,92 11,2/61/4,74 15,9/56/4,83 Limites d'utilisation du refroidissement °C +10 - +46 Température aller min. refroidissement °C Puissance frigorifique min./max. kW +15 - +45 7 1,33 - 5,30 3,3 - 9,1 2,8 - 15,0 Puissance frigorifique / fréquence du compresseur / EER avec A35/W7 kW/Hz/EER 4,90/49/2,80 6,79/66/2,33 12,2/72/2,60 avec A35/W18 kW/Hz/EER 6,70/49/3,60 5,3/38/3,66 12,7/38/3,81 avec A27/W18 kW/Hz/EER 6,80/49/3,90 9,46/66/3,61 18,20/66/4,08 Frigorigène Quantité de rempliss. base module externe Quantité rempliss. en suppl.de frigorig. à partir de 5 m de longueur de tuyau simple 8 R410A2) kg 1,20 2,00 2,85 g/m 50 --- --- WKF NEO 70 Série Quantité rempliss. en suppl.de frigorig. à partir de 10 m de longueur de tuyau simple Raccords pour frigorigène g/m WKF NEO 180 --- 50 pouces (mm) 3/8" (9,52) / 5/8" (15,9) Longueur max. de la conduite de frigorigène m 30 Hauteur max. de la conduite de frigorigène m 20 Alimentation en tension WKF NEO 120 V/Hz 50 75 30 380-415/ 3~/50 220-240 / 50 Consommation électrique max. A 15,0 16,8 7,2 p. phase Consommation élect. nomin. avec A7/W35 A 5,19 10,44 5,02 p. phase Puissance absorbée nominale avec A7/W35 kW 1,18 2,22 3,09 Puissance absorbée nominale avec A2/W35 kW 1,32 1,91 2,64 Puissance absorbée max. kW 3,50 4,0 4,5 -- 0,99 0,97 0,95 A interne 16 20 3 x 16 A Débit volumique d’eau nominal (selon EN 14511, avec ∆t 5 K) m3/h 0,95 1,70 2,40 Perte de pression sur le condenseur au flux volumique nominal bar 0,095 Perte de pression externe kPa Débit volumique d'air max. module externe m3/h Pression de service max. de l'eau bar 3 Raccord. hydraul. aller/retour (à joint plat) pouces (mm) 1 1/4" (31,8) Niveau sonore selon les normes DIN EN 12102:2008-09 et ISO 9614-2 dB(A) 63,2 67,9 68,3 Niveau sonore LpA (module externe) 3) dB(A) 41,2 42,2 42,4 Son à composantes discrètes p. mod. ext. dB(A) 3 Dimensions du module interne 200 l (H/l/P) mm 1350/555/850 Dimensions du module interne 300 l (H/l/P) mm 14200/650/950 Dimensions du module externe (H/l/P) mm 640/880/310 Type de protection du module externe -- IP X4 Poids du module interne 200 l kg 131 133 135 Poids du module interne 300 l kg 154 156 158 Poids module externe kg 50 74 100 Facteur de puissance avec A7/W35 (cosφ) Protection côté client (module externe) 0,1 80 2650 4450 6200 998/940/330 1420/940/330 IP 24 1) COP = coefficient of performance (coefficient de performance) selon EN 14511, contrôle VDE 2) Contient du gaz à effet de serre conformément au protocole de Kyoto, GWP 1975 3) Distance 5 m, contrôle VDE, A7/W55/58 Hz, en cas d'élargissement de forme sphérique 9 REMKO série WKF NEO-compact 2.2 Données sur le produit Average condition 1) Série WKF NEO WKF NEO WKF NEO 70 120 180 Classe de rendement énergét. pour le chauffage 35°C/55°C A++ / A++ A+ / A+ A+ / A+ A A A Classe de rendement énergét. Eau chaude XL Puissance calorifique nominale P rated kW 5,0/6,0 10,0 14,0 Rendement énergét. du chauffage ambiant hs 35°C/55°C % 150 / 129 147/118 146/122 Contribution au rendement énergét. du chauffage ambiant de la REMKO Smart-Control % 4 4 4 Consommation énergét. annuelle QHE 35°C/55°C 4) Rendement éner. pour la préparation d'eau chaude hwH 2808/3705 5514/6610 7860/9098 % 103 102 107 Niveau sonore LWA (module externe) dB(A) 63,2 67,9 68,3 Niveau sonore LWA (module interne) dB(A) - - - Warmer condition 2) Série WKF NEO WKF NEO WKF NEO 70 120 180 Classe de rendement énergét. pour le chauffage 35°C/55°C A++ / A++ A++ / A+ A+++ / A+ + A A A Classe de rendement énergét. eau chaude XL Puissance calorifique nominale P rated kW 5,0/6,0 9,0 12,0 Rendement énergét. du chauffage ambiant hs 35°C/55°C % 174 / 157 165/123 180/143 Consommation énergét. annuelle QHE 35°C/55°C 4) 1389/1610 2968/3354 3803/5349 Colder condition 3) WKF NEO WKF NEO WKF NEO 70 120 180 Série Classe de rendement énergét. pour le chauffage 35°C/55°C Classe de rendement énergét. Eau chaude XL A+ / A+ A+ / A+ A+ / A+ A A A Puissance calorifique nominale P rated kW 6,0/8,0 12,0 18,0 Rendement énergét. du chauffage ambiant hs 35°C/55°C % 132 / 108 136/104 134/105 Consommation énergét. annuelle QHE 35°C/55°C 4) 4525/6889 8481/1228 13300/174 2 07 1) Average condition = période de temp. moyenne / 2) Warmer condition = période de temp. chaude 3) Colder condition = période de température froide 4) La valeur indiquée repose sur les résultats du contrôle de norme. La consommation réelle dépend de l'utilisation et de la localisation de l'appareil 10 2.3 Dimensions de l'appareil des modules externes A B D C E Fig. 1: Dimensions des modules externes WKF NEO compact 70/120/180 Dimensions en mm A B C D E WKF NEO 70 880 640 364 660 340 WKF NEO 120 940 1010 330 620 360 WKF NEO 180 940 1430 330 620 350 2.4 Dimensions de l'appareil des modules internes A B C Fig. 2: Dimensions des modules internes WKF NEO compact 70/120/180 Dimensions en mm A B C WKF NEO compact 200 l 1350 555 850 WKF NEO compact 300 l 1420 650 950 11 REMKO série WKF NEO-compact Agencement des embouts de tuyaux WKF NEO compact 70/120/180 - version 200 l 40 100 49,5 60 58 113 148 60 0 R1 12,5 92 R800 42 42 385 125 249,5 30 30 36 30 40 30 125 30 R282, 5 41 R2 502 522 Fig. 3: Agencement des embouts de tuyaux WKF NEO compact 70/120/180 - version 200 l (toutes les dimensions en mm) Désignations des raccords de tuyaux WKF NEO compact 70/120/180 - version 200 l 1 8 2 3 5 4 6 7 Fig. 4: Désignations des raccords de tuyaux WKF NEO compact 70/120/180 - version 200 l 1: 2: 3: 4: 5: 12 Eau chaude écrou-raccord 1" (joint plat) Circulation Eau froid écrou-raccord 1" (joint plat) Retour de chauffage 11/4" mâle Frigorigène - Conduite de liquide 3/8" 6 : Frigorigène - Conduite de gaz chaud 5/8" 7 : Aller de chauffage 11/4" mâle 8 : Passages de câbles Agencement des embouts de tuyaux WKF NEO compact 70/120/180 - version 300 l R2 622 R330 140 38,5 602 80 30 30 60 440 30 280,5 30 150 30 80 42 50 257 150 36 108 42 R700 148 16,5 0 R1 60 Fig. 5: Agencement des embouts de tuyaux WKF NEO compact 70/120/180 - version 300 l (toutes les dimensions en mm) Désignations des raccords de tuyaux WKF NEO compact 70/120/180 - version 300 l 1 8 2 5 4 3 6 7 Fig. 6: Désignations des raccords de tuyaux WKF NEO compact 70/120/180 - version 300 l 1: 2: 3: 4: 5: Circulation Eau chaude écrou-raccord 1" (joint plat) Eau froid écrou-raccord 1" (joint plat) Retour de chauffage 11/4" mâle Frigorigène - Conduite de liquide 3/8" 6 : Frigorigène - Conduite de gaz chaud 5/8" 7 : Aller de chauffage 11/4" mâle 8 : Passages de câbles 13 REMKO série WKF NEO-compact 2.5 Limites d'utilisation de la thermopompe en mode monovalent REMARQUE : la valeur de la température en bas dans les diagrammes se réfère à la température extérieure, celle à gauche, à la température aller d'eau de chauffage. Einsatzgrenzen WKF 120 60°C 35; 55 -10; 55 55°C Vorlauftemperatur [°C] 50°C B 45°C 40°C -20°C; 43°C 35°C 30°C 25°C 20°C -20°C; 22°C 15°C -30°C -20°C 35°C; 22°C -10°C 0°C 10°C A Außentemperatur [°C] 20°C 30°C 40°C Fig. 7: Limites d'utilisation et points de contrôle WKF NEO 70 A : Température extérieure [°C] / B : Temp. aller [°C] Température extérieure [°C] -20 Température aller [°C] 22 -20 -10 20 35 35 43 55 55 55 22 Einsatzgrenzen WKF 120 60°C 35; 55 -10; 55 55°C Vorlauftemperatur [°C] 50°C B 45°C 40°C -20°C; 43°C 35°C 30°C 25°C 20°C -20°C; 22°C 15°C -30°C -20°C 35°C; 22°C -10°C 0°C 10°C A Außentemperatur [°C] 20°C 30°C 40°C Fig. 8: Limites d'utilisation et points de contrôle WKF NEO 120 A : Température extérieure [°C] / B : Temp. aller [°C] Température extérieure [°C] -20 -20 -10 20 35 35 Température aller [°C] 22 43 55 55 55 22 14 60°C 35; 55 -10; 55 55°C Vorlauftemperatur [°C] 50°C B 45°C 40°C -20°C; 42°C 35°C 30°C 25°C 20°C -20°C; 22°C 15°C -30°C 35°C; 22°C -20°C -10°C 0°C 10°C 20°C 30°C 40°C A Außentemperatur [°C] Fig. 9: Limites d'utilisation et points de contrôle WKF NEO 180 A : Température extérieure [°C] / B : Temp. aller [°C] Température extérieure [°C] -20 -20 -10 20 35 35 Température aller [°C] 22 42 55 55 55 22 2.6 Caractéristiques de la pompe de chargement des modules internes 160 50 140 45 [W] 100 1 80 25 2 35 A 20 60 B 40 15 10 20 0 30 [l/min] 40 120 5 20 40 60 3 80 100 0 [%] Fig. 10: Pompe de recirculation Grundfoss UPML 25-105 180 PWM - Plage de puissance 1 : Puissance absorbée [W] 2 : Débit volumique [l/min] 3 : Demande [%] A : Caractéristique de débit volumique [l/mim] B : Caractéristique de puissance absorbée [W] Commande externe via l'entrée analogique Signal PWM. Les tolérances de chaque courbe sont conformes à EN 1151-1:2006 Puissance active absorbée [W] Consommation électrique [A] Disjoncteur-protecteur min. 7 0,07 résistant au courant de blocage max. 136 1,03 résistant au courant de blocage Niveau 15 REMKO série WKF NEO-compact 2.7 Niveau sonore total des modules externes Module externe WKF NEO 70 REMKO Wärmepumpe WP172 A7 / W 45 Typ: WKF85-AM Schallleistung LwA re 1pW A7 / W 45 A-Gesamt: 64,0 dB(A) 70,0 60,5 60,0 55,3 52,4 50,0 47,3 48,2 50,8 48,8 51,0 50,0 50,1 50,9 46,3 43,7 41,4 dB(A) 41,3 40,0 35,6 34,7 33,4 31,1 30,0 20,0 10,0 0,0 100 160 250 400 630 1000 1600 2500 4000 6300 Frequenz (Hz) Fig. 11: Niveau sonore total LP d'un module externe REMKO de type : WKF NEO 70 Fréquence moyenne [Hz] 25 31,50 40 50 63 80 100 125 160 LI [dBA] (25,6) (38,3) (30,8) (37,7) (35,1) (31,3) 38,2 39,1 39,7 LWo [dBA] (34,7) (47,4) (39,9) (46,9) (44,3) (40,4) 47,3 48,2 48,8 FPI [dB] -(14,7) -(8,2) -(8,8) -(5,2) -(3,5) 1(1,3) 0,6 2,0 4,7 Fréquence moyenne [Hz] 200 250 315 400 500 630 800 1000 1250 LI [dBA] 43,3 54,3 46,1 41,6 41,9 40,8 41,0 41,8 37,2 LWo [dBA] 52,4 60,5 55,3 50,8 51,0 50,0 50,1 50,9 46,3 FPI [dB] 6,3 4,0 7,4 10,0 10,9 12,8 12,0 11,1 13,0 Fréquence moyenne [Hz] 1600 2000 2500 3150 4000 5000 6300 8000 10000 LI [dBA] 34,6 21,9 32,1 32,3 26,5 25,6 24,3 (21,3) (24,1) LWo [dBA] 43,7 31,1 41,3 41,4 35,6 34,7 33,4 (30,4) (33,2) FPI [dB] 14,7 27,2 13,9 11,7 13,0 10,6 9,2 (7,7) (4,5) La détermination du niveau sonore correspond à la classe de précision 2. L'écart standard du niveau sonore A évalué ci-dessus est de 1,5 dB. LWo : Niveau sonore émis par le module externe FPI : Correcteurs liés à l'environnement LI : Intensité sonore 16 Module externe WKF NEO 120 REMKO Wärmepumpe WP171 80 62,7 70 dB(A) 50,0 60 55,7 54,9 54,3 55,9 54,6 57,4 57,1 59,0 54,3 50,5 49,9 A7 / W 55 A-Gesamt: 67,9 dB(A) NEUE GRAFIK ! 70,0 60,0 A7 / W 55 Typ: WKF120-AM Schallleistung LwA re 1pW dB 80,0 52,3 49,9 47,2 44,8 41,7 40,0 36,1 50 33,3 30,0 40 20,0 10,0 30 0,0 63 25 100 1 160 125 250 250 400 500 630 1000 1000 2000 1600 4000 2500 8000 4000 A L Hz 6300 Frequenz (Hz) Cursor: 2 Fig. 12: Niveau sonore total LP d'un module externe REMKO de type : WKF NEO 120 Fréquence moyenne [Hz] 25 31,50 40 50 63 80 100 125 160 LI [dBA] (27,6) (40,9) (38,3) (31,4) (45,3) (33,5) 40,0 44,4 40,6 LWo [dBA] (37,5) (50,8) (48,2) (41,3) (55,2) (43,4) 49,9 54,3 50,5 FPI [dB] -(14,3) -(8,3) -(8,5) -(6,6) -(3,6) -(2,0) -0,2 0,7 2,6 Fréquence moyenne [Hz] 200 250 315 400 500 630 800 1000 1250 LI [dBA] 45,0 52,8 45,8 46,0 44,7 47,5 47,2 49,1 44,4 LWo [dBA] 54,9 62,7 55,7 55,9 54,6 57,4 57,1 59,0 54,3 FPI [dB] 4,3 4,3 5,6 6,7 7,1 7,1 11,2 6,0 6,0 Fréquence moyenne [Hz] 1600 2000 2500 3150 4000 5000 6300 8000 10000 LI [dBA] 42,4 40,0 37,3 34,9 31,8 26,2 23,4 (21,6) (16,2) LWo [dBA] 52,3 49,9 47,2 44,8 41,7 36,1 33,3 (31,5) (26,1) FPI [dB] 5,7 5,5 5,5 5,4 5,1 6,0 6,3 (5,5) (5,3) La détermination du niveau sonore correspond à la classe de précision 2. L'écart standard du niveau sonore A évalué ci-dessus est de 1,5 dB. LWo : Niveau sonore émis par le module externe FPI : Correcteurs liés à l'environnement LI : Intensité sonore 17 REMKO série WKF NEO-compact Module externe WKF NEO 180 REMKO Wärmepumpe WP173 A7 / W 55 Typ: WKF180-AM Schallleistung LwA re 1pW A7 / W 55 80,0 A-Gesamt: 68,3 dB(A) 70,0 60,0 61,1 60,4 56,3 54,8 55,1 56,4 55,3 55,4 56,9 57,8 58,9 52,4 dB(A) 50,0 49,2 46,0 43,6 40,0 40,9 37,0 32,1 28,0 30,0 20,0 10,0 0,0 100 160 250 400 630 1000 1600 2500 4000 6300 Frequenz (Hz) Fig. 13: Niveau sonore total LP d'un module externe REMKO de type : WKF NEO 180 Fréquence moyenne [Hz] 25 31,50 40 50 63 80 100 125 160 LI [dBA] (31,4) (41,6) (32,8) (40,8) (37,3) (37,4) 49,8 45,8 50,5 LWo [dBA] (41,9) (52,1) (43,4) (51,3) (47,9) (47,9) 60,4 56,3 61,1 FPI [dB] -(11,6) -(9,2) -(7,7) -(5,4) -(3,2) -(2,0) 0,0 1,1 2,1 Fréquence moyenne [Hz] 200 250 315 400 500 630 800 1000 1250 LI [dBA] 44,3 44,6 45,8 44,8 44,9 46,4 47,2 48,4 41,9 LWo [dBA] 54,8 55,1 56,4 55,3 55,4 56,9 57,8 58,9 52,4 FPI [dB] 6,1 6,4 8,7 9,4 9,6 9,2 11,6 8,4 10,0 Fréquence moyenne [Hz] 1600 2000 2500 3150 4000 5000 6300 8000 10000 LI [dBA] 38,7 35,5 33,1 30,4 26,5 21,6 17,5 (18,1) (8,8) LWo [dBA] 49,2 46,0 43,6 40,9 37,0 32,1 28,0 (28,6) (19,3) FPI [dB] 11,4 13,9 13,2 13,0 13,5 14,7 15,2 (11,1) (14,8) La détermination du niveau sonore correspond à la classe de précision 2. L'écart standard du niveau sonore A évalué ci-dessus est de 1,5 dB. LWo : Niveau sonore émis par le module externe FPI : Correcteurs liés à l'environnement LI : Intensité sonore 18 2.8 Caractéristiques Puissance WKF NEO 70 calorifique à une température aller de 35 ℃ 15 n-max. 58 Hz 14 13 n-max. 73 Hz 12 11 [kW] 10 9 B 7 n-max. 88 Hz 8 54 Hz C n-max 6 5 4 3 n-min 2 1 0 -15 -14 -13 -12 -11 -10 -9 -8 -7 -6 -5 -4 -3 -2 -1 0 1 2 3 4 5 6 7 8 9 10 11 12 13 14 15 16 17 18 19 20 [°C] A Fig. 14: Puissance WKF NEO 70 calorifique à une température aller de 35 ℃ A : Température extérieure B : Puissance calorifique C : Fréquence nominale Puissance calorifique WKF NEO 70 à une température aller de 45 °C 15 14 n-max. 58 Hz 13 n-max. 73 Hz 12 11 [kW] 10 B n-max. 88 Hz 9 8 7 6 n-max 54 Hz C 5 4 3 n-min 2 1 0 -15 -14 -13 -12 -11 -10 -9 -8 -7 -6 -5 -4 -3 -2 -1 0 1 2 3 4 A 5 6 7 8 9 10 11 12 13 14 15 16 17 18 19 20 [°C] Fig. 15: Puissance calorifique WKF NEO 70 à une température aller de 45 °C A : Température extérieure B : Puissance calorifique C : Fréquence nominale 19 REMKO série WKF NEO-compact Puissance calorifique WKF NEO 70 à une température aller de 55 °C 15 14 n-max. 58 Hz 13 12 n-max. 73 Hz 11 [kW] 10 9 B 7 n-max. 88 Hz 8 6 n-max 5 54 Hz C 4 3 n-min 2 1 0 -15 -14 -13 -12 -11 -10 -9 -8 -7 -6 -5 -4 -3 -2 -1 0 1 2 3 4 5 A 6 7 8 9 10 11 12 13 14 15 16 17 18 19 20 [°C] Fig. 16: Puissance calorifique WKF NEO 70 à une température aller de 55 °C A : Température extérieure B : Puissance calorifique C : Fréquence nominale COP WKF NEO 70 à une température aller de 35 °C, 45 °C et 55 °C 6 5 D D COP [-] 4 D 3 35°C 45°C 55°C 2 1 0 -15 -14 -13 -12 -11 -10 -9 -8 -7 -6 -5 -4 -3 -2 -1 0 1 2 3 A 4 5 6 7 8 9 10 11 12 13 14 15 16 17 18 19 20 21 22 [°C] Fig. 17: COP WKF NEO 70 à une température aller de 35 °C, 45 °C et 55 °C A : Température extérieure 20 D : Température aller Puissance WKF NEO 120 calorifique à une température aller de 35 ℃ 15 n-max. 58 Hz 14 13 n-max. 73 Hz 12 11 [kW] 10 9 B 7 n-max. 88 Hz n-max 8 6 54 Hz C 5 4 3 n-min 2 1 0 -15 -14 -13 -12 -11 -10 -9 -8 -7 -6 -5 -4 -3 -2 -1 0 1 2 3 4 5 6 7 8 9 10 11 12 13 14 15 16 17 18 19 20 [°C] A Fig. 18: Puissance WKF NEO 120 calorifique à une température aller de 35 ℃ A : Température extérieure B : Puissance calorifique C : Fréquence nominale Puissance calorifique WKF NEO 120 à une température aller de 45 °C 15 14 n-max. 58 Hz 13 n-max. 73 Hz 12 11 [kW] 10 B n-max. 88 Hz 9 n-max 8 7 54 Hz C 6 5 4 3 n-min 2 1 0 -15 -14 -13 -12 -11 -10 -9 -8 -7 -6 -5 -4 -3 -2 -1 0 1 2 A 3 4 5 6 7 8 9 10 11 12 13 14 15 16 17 18 19 20 [°C] Fig. 19: Puissance calorifique WKF NEO 120 à une température aller de 45 °C A : Température extérieure B : Puissance calorifique C : Fréquence nominale 21 REMKO série WKF NEO-compact Puissance calorifique WKF NEO 120 à une température aller de 55 °C 15 14 n-max. 58 Hz 13 12 n-max. 73 Hz 11 [kW] 10 9 B 7 n-max. 88 Hz 8 n-max 6 54 Hz C 5 4 3 n-min 2 1 0 -15 -14 -13 -12 -11 -10 -9 -8 -7 -6 -5 -4 -3 -2 -1 0 1 2 3 A 4 5 6 7 8 9 10 11 12 13 14 15 16 17 18 19 20 [°C] Fig. 20: Puissance calorifique WKF NEO 120 à une température aller de 55 °C A : Température extérieure B : Puissance calorifique C : Fréquence nominale COP WKF NEO 120 à une température aller de 35 °C, 45 °C et 55 °C 6 45°C D 4 COP [-] 35°C D 5 D 55°C 3 2 1 0 -15 -14 -13 -12 -11 -10 -9 -8 -7 -6 -5 -4 -3 -2 -1 0 1 2 A 3 4 5 6 7 8 9 10 11 12 13 14 15 16 17 18 19 20 [°C] Fig. 21: COP WKF NEO 120 à une température aller de 35 °C, 45 °C et 55 °C A : Température extérieure 22 D : Température aller Puissance WKF NEO 180 calorifique à une température aller de 35 ℃ 20 n-max. 58 Hz 18 n-max. 73 Hz 16 [kW] 14 B n-max. 88 Hz n-max 12 C 10 8 6 4 n-min 2 0 -15 -14 -13 -12 -11 -10 -9 -8 -7 -6 -5 -4 -3 -2 -1 0 1 2 3 4 5 6 7 8 9 10 11 12 13 14 15 16 17 18 19 20 [°C] A Fig. 22: Puissance WKF NEO 180 calorifique à une température aller de 35 ℃ A : Température extérieure B : Puissance calorifique C : Fréquence nominale Puissance calorifique WKF NEO 180 à une température aller de 45 °C 20 n-max. 58 Hz 18 n-max. 73 Hz 16 [kW] 14 B n-max. 88 Hz 12 n-max 10 C 8 6 4 n-min 2 0 -15 -14 -13 -12 -11 -10 -9 -8 -7 -6 -5 -4 -3 -2 -1 0 1 2 A 3 4 5 6 7 8 9 10 11 12 13 14 15 16 17 18 19 20 [°C] Fig. 23: Puissance calorifique WKF NEO 180 à une température aller de 45 °C A : Température extérieure B : Puissance calorifique C : Fréquence nominale 23 REMKO série WKF NEO-compact Puissance calorifique WKF NEO 180 à une température aller de 55 °C 20 18 n-max. 58 Hz 16 n-max. 73 Hz [kW] 14 B 12 n-max. 88 Hz n-max C 10 8 6 4 2 0 n-min -15 -14 -13 -12 -11 -10 -9 -8 -7 -6 -5 -4 -3 -2 -1 0 1 2 3 A 4 5 6 7 8 9 10 11 12 13 14 15 16 17 18 19 20 [°C] Fig. 24: Puissance calorifique WKF NEO 180 à une température aller de 55 °C A : Température extérieure B : Puissance calorifique C : Fréquence nominale COP WKF NEO 180 à une température aller de 35 °C, 45 °C et 55 °C 6 5 COP [-] 4 D 35°C D 45°C D 55°C 3 2 1 0 -15 -14 -13 -12 -11 -10 -9 -8 -7 -6 -5 -4 -3 -2 -1 0 1 2 A 3 4 5 6 7 8 9 10 11 12 13 14 15 16 17 18 19 20 [°C] Fig. 25: COP WKF NEO 180 à une température aller de 35 °C, 45 °C et 55 °C A : Température extérieure 24 D : Température aller Pertes de chauffage et de refroidissement Selon la longueur de la conduite de frigorigène et la différence de hauteur entre les modules interne et externe, des pertes de puissance calorifique ou frigorifique peuvent survenir. Les diagrammes suivants permettent de les calculer. Pertes de puissance calorifique avec WKF NEO 70 +30 m 30 25 95% 92% 95% 92% [m] 20 15 0m A 10 5 0 100% 97% -5 -10 -15 -20 -25 -30 0 -30 m 99% 95% 5 10 15 20 25 30 95% 35 40 92% 45 50 B [m] Fig. 26: Pertes de puissance calorifique avec WKF NEO 70 A : Différence de hauteur B : Longueur de la conduite de frigorigène Pertes de puissance frigorifique avec WKF NEO 70 +30 m 30 25 90% 87% 90% 87% [m] 20 15 0m A 10 5 0 100% 95% -5 -10 -15 -20 -30 m 98% -25 -30 0 95% 5 10 15 20 25 30 90% 35 40 87% 45 50 B [m] Fig. 27: Pertes de puissance frigorifique avec WKF NEO 70 A : Différence de hauteur B : Longueur de la conduite de frigorigène 25 REMKO série WKF NEO-compact Pertes de puissance calorifique avec WKF NEO 120 [m] +30 m 0m A -30 m 30 25 20 15 10 5 0 -5 -10 -15 -20 -25 -30 100% 95% 90% 86% 95% 0 5 10 15 20 25 30 35 40 45 50 B [m] Fig. 28: Pertes de puissance calorifique avec WKF NEO 120 A : Différence de hauteur B : Longueur de la conduite de frigorigène Pertes de puissance frigorifique avec WKF NEO 120 [m] +30 m 0m -30 m A 30 25 20 15 10 5 0 -5 -10 -15 -20 -25 -30 100% 98% 95% 92% 89% 95% 0 5 10 15 20 25 30 35 40 45 50 B [m] Fig. 29: Pertes de puissance frigorifique avec WKF NEO 120 A : Différence de hauteur 26 B : Longueur de la conduite de frigorigène Pertes de puissance calorifique avec WKF NEO 180 [m] +30 m 0m A -30 m 30 25 20 15 10 5 0 -5 -10 -15 -20 -25 -30 100% 0 5 10 85% 90% 15 20 25 30 35 40 80% 45 50 55 60 65 70 75 B [m] Fig. 30: Pertes de puissance calorifique avec WKF NEO 180 A : Différence de hauteur B : Longueur de la conduite de frigorigène Pertes de puissance frigorifique avec WKF NEO 180 [m] +30 m 0m -30 m A 30 25 20 15 10 5 0 -5 -10 -15 -20 -25 -30 100% 0 5 10 86% 90% 15 20 25 30 35 40 83% 45 50 55 80% 60 65 70 75 B [m] Fig. 31: Pertes de puissance frigorifique avec WKF NEO 180 A : Différence de hauteur B : Longueur de la conduite de frigorigène 27 REMKO série WKF NEO-compact 3 Structure et fonctionnement 3.1 Thermopompe en général Arguments en faveur des thermopompes inverter de REMKO n n n n n n n Des coûts de chauffage plus faibles que ceux du fuel ou du gaz. Les thermopompes contribuent à préserver l'environnement. Émissions de CO2 plus faibles que celles des chauffages au fuel ou au gaz. Tous les modèles chauffent et refroidissent. Le module externe a un faible niveau sonore. Modèle fractionnable pour une grande flexibilité d'installation. Coûts de maintenance quasiment inexistants. La chaleur est obtenue à 75%* gratuitement à partir de l'air 75% * énergie solairegratuite de l'air 25% * énergie motriceélectrique Chauffage Fig. 32: Chaleur gratuite * Ce rapport peut varier en fonction des températures extérieures et des conditions de fonctionnement. Chauffage économique et respectant l'environnement La combustion de supports fossiles pour produire de l'énergie a des conséquences lourdes pour l'environnement. Une forte proportion d'énergie issue d'éléments fossiles pose également un problème dû aux réserves limitées en pétrole et en gaz et aux coûts en hausse en résultant. Beaucoup considèrent aujourd'hui le chauffage avec un regard économique et respectant l'environnement. Ces deux aspects sont pris en compte par l'utilisation des techniques de thermopompes. Cette technique utilise l'énergie présente en permanence dans l'air, 28 l'eau et la terre et la transforme en chaleur en absorbant l'énergie électrique. 1 kWh d'électricité suffit cependant pour générer 4 kWh de chaleur. Le reste est mis à disposition gracieusement par l'environnement. Source de chaleur Les thermopompes à saumure tirent l'énergie du sol. Le système peut être composé de serpentins de tuyaux posés à une profondeur de 1 m environ ou par forage. L'inconvénient est le grand besoin de surface pour les serpentins de tuyaux ou le coût élevé du forage. Un refroidissement durable du sol est également envisageable. Le circuit de refroidissement est constitué d'un évaporateur, d'un compresseur, d'un condenseur et d'un détendeur. Le frigorigène s'évapore à basse pression dans l'évaporateur à lamelles, ce également à des températures de source de chaleur peu élevées, en absorbant l'énergie ambiante. Le frigorigène est porté, dans le compresseur, à une pression plus élevé et donc un niveau de température plus élevé, par de l'énergie électrique et par compression. Puis le gaz très chaud du frigorigène est conduit dans le condenseur, un échangeur thermique à plaques. Le gaz très chaud se condense ici en donnant de la chaleur au système de chauffage. Le frigorigène liquide est alors détendu par un organe d'étranglement, le détendeur, et ainsi refroidi. Le frigorigène retourne alors dans l'évaporateur fermant le circuit. Les thermopompes à eau ont besoin de deux puits pour la production de chaleur à partir des eaux souterraines, un puits d'aspiration et un puits absorbant. Le raccordement à cette source n'est pas possible partout, est onéreux et soumis à autorisation. La régulation est assurée par le Smart-Control un fonctionnement autonome en plus des fonctions de sécurité. Un filtre intégré, une vanne d’inversion à 3 voies intégrée et un ballon d’eau sanitaire en émail d’une capacité de 200 / 300 l au choix font partie du circuit d’eau dans le module interne. Fonctionnement de la thermopompe Les accessoires suivants sont disponibles, consoles murales et de sol, bac à condensat, chauffage de bac à condensat, vanne d'inversion à 3 voies, vanne de surtension et sonde supplémentaire. Trois sources de chaleur importantes peuvent fournir de l'énergie aux thermopompes. Ce sont l'air, la terre et les eaux souterraines. Les thermopompes à air présentent l'avantage d'utiliser une source à présence illimité partout et pouvant être raccordée gratuitement. Leur inconvénient est que l'air extérieur est le plus froid lorsque les besoins en chauffage sont les plus forts. Une thermopompe est un appareil qui absorbe, vie un support, la chaleur ambiante à faible température et la transporte là où elle peut être utilisée à des buts de chauffage. Les thermopompes travaillent suivant le même principe que les réfrigérateurs. La différence est que sur les thermopompes, la chaleur, donc le « déchet » du réfrigérateur, est le produit recherché. B A 1 2 C 4 D 3 Fig. 33: Schéma fonctionnel du chauffage dans le cas d'une thermopompe inverter A : Zone extérieure / B: Zone intérieure C : Module externe de la thermopompe D : Module interne de la thermopompe 1 : Compression / 2: Évaporation 3 : Détente / 4: Condensation 29 REMKO série WKF NEO-compact Mode de fonctionnement de la thermopompe Les thermopompes fonctionnent dans plusieurs modes de fonctionnement. Monovalent La thermopompe est, tout au long de l'année, l'unique source de chaleur des bâtiments. Ce mode de fonctionnement est particulièrement adapté aux installations de chauffage à températures de préchauffage basses et est particulièrement utilisé en combinaison avec des thermopompes saumure/eau ou eau/eau. Mono-énergétique La thermopompe est équipée d'un chauffage électrique pour couvrir les charges de pointe. La thermopompe couvre la majeure partie des besoins en puissance calorifique. Le chauffage électrique d'appoint ne s'allume que quelques jours par an, lors de températures extérieures très basses et soutient la thermopompe. Bivalent alternatif La thermopompe fournit la totalité de la chaleur de chauffage jusqu'à une température extérieure définie. Lorsque la température extérieure descend en dessous de cette valeur définie, un deuxième générateur de chaleur s'allume pendant que la thermopompe s'arrête. Nous faisons ici une différence entre le fonctionnement alternatif avec un chauffage au fuel ou au gaz et un fonctionnement régénératif à l'énergie solaire ou au bois. Ce mode de fonctionnement est possible pour tous les systèmes de répartition du chauffage. Dimensionnement Il est nécessaire, pour configurer et dimensionner une installation de chauffage, de calculer exactement la charge de chauffe du bâtiment, suivant EN 12831. On peut également déterminer le besoin en chaleur en fonction de l'année de construction et du type du bâtiment. Le tableau Ä à la page 31 indique la charge de chauffe spécifique de certains types de bâtiments. Si on la multiplie par la surface à chauffer, on obtient le rendement nécessaire de l'installation de chauffage. Lors d'un calcul exact, il faut définir différents éléments. Le besoin en chaleur transmise, le besoin en chaleur ventilée et un supplément pour la production d'eau sanitaire donnent la somme de puissance calorifique devant être préparée par l'installation de chauffage. Pour déterminer le besoin en chaleur transmise, on prend les surfaces de sol, de murs extérieurs, de fenêtres, de portes et de toiture. On doit également prendre en compte les matériaux de construction utilisés, donnant différents coefficients de 30 passage de chaleur (la valeur U). On doit également avoir la température ambiante et la température extérieure normalisée, la température moyenne extérieure la plus basse, de l'année. L'équation de détermination du besoin en chaleur transmise est Q=A x U x (tR-tA), il doit être calculé individuellement pour toutes les surfaces de fermeture de pièces. Le besoin en chaleur ventilée prend en compte la fréquence d'échange de la température ambiante chauffée contre la température extérieure plus froide. On prend, en plus de la température ambiante et de la température extérieure normalisée, le volume ambiant V, le taux de renouvellement d'air n et la capacité de chaleur spécifique c de l'air. L'équation est la suivante : Q=V x n x c (tRtA) Le supplément pour la préparation d'eau sanitaire est, selon la norme VDI 2067, par personne de : 0,2 kW. Exemple Nous avons pris comme exemple une maison avec une surface habitable de 150 m² et un besoin en chaleur d'env. 80 W/m². Cinq personnes habitent dans cette maison. La charge de chauffe est de 11,5 kW. Avec un supplément en eau potable de 0,2 kW/personne, on obtient une puissance calorifique à atteindre de 12,5 kW. En fonction du support énergétique, il faut encore ajouter un supplément pour prendre en compte des éventuels temps de blocage. Le dimensionnement et la détermination du point de bivalence de la thermopompe sont calculés d'après le diagramme de puissance calorifique de la thermopompe en fonction des températures de préchauffage (35 °C pour un chauffage par le sol dans l'exemple). On marque tout d'abord la charge de chauffe à la température extérieure normalisée (température la plus basse de l'année en fonction de la région) et la limite de chauffe. Le besoin en chaleur en fonction de la température extérieure est saisi de manière simplifiée dans le diagramme de puissance calorifique (Voir la Fig. 34) en tant que ligne de liaison droite entre la charge de chauffe et le début de la chauffe. L'intersection de la droite avec la courbe de puissance calorifique nominale est marquée sur l'axe X et on y lit la température du point de bivalence (d'env. -3 °C dans l'exemple). Le rendement minimal du 2e générateur de chaleur est la différence entre la charge de chauffe et la puissance calorifique maximale de la thermopompe pendant ces jours (dans l'exemple, la puissance nécessaire pour couvrir la charge de pointe est d'env. 3 kW). Type de bâtiment Puissance calorifique spécifique en W/m2 Maison à énergie passive 10 Maison basse énergie de 2002 40 Suivant le décret d'isolation thermique de 1995 60 Construction neuve depuis 1984 80 Construction ancienne avant 1977 partiellement rénovée 100 Construction ancienne avant 1977 non rénovée 200 Rendement de chauffe à une température de démarrage de 35°C 20 Rendement de chauffe [kW] 18 16 14 Rendement minimal 2. Générateur de chaleur Charge de chauffe suivant DIN EN 12831 n.max Évaluation de la fréquence 57 Hz 12 10 8 6 4 2 0 n-min Charge de chauffe -15 -14 -13 -12 -11 -10 -9 -8 -7 -6 -5 -4 -3 -2 -1 Température extérieure normalisée Charge de chauffe plus besoin en eau chaude et ajout temps de blocage 0 Point de bivalence 1 2 3 4 5 6 7 8 9 10 11 12 13 14 15 16 17 18 19 20 Température extérieure [°C] Limite de chauffe pour les bâtiments anciens suivant VDI 4650 Fig. 34: Diagramme de puissance calorifique de la thermopompe WKF NEO 180 Propriétés de la thermopompe inverter de REMKO Source de chaleur air extérieur Une thermopompe air/eau tire de l'énergie de la source de chaleur air extérieur et la restitue au système de chauffage. Elle présente les avantages suivants par rapport aux thermopompe saumure/eau et eau/eau : n et partout. L'air est disponible partout et de manière illimitée. Aucun puits n'est nécessaire, par exemple. n Pas de travaux d'enfouissement. Pas besoin de grandes surfaces pour les collecteurs terriens. n Bon marché. Pas de forage onéreux. n Un bon rapport qualité-prix et une installation simple. n Particulièrement adaptées pour les maisons basse énergie et de faibles températures aller. 31 REMKO série WKF NEO-compact n Idéales en fonctionnement bivalent pour économiser de l'énergie. n Fonctionnement élevé grâce à la technologie Inverter. Appareil de fractionnement La thermopompe inverter de Remko est un appareil dit de fractionnement. Ce qui signifie qu'il se compose d'un module externe et d'un module interne reliés entre eux par des tuyaux en cuivre conduisant le froid. On ne pose donc pas de conduites d'eau de l'intérieur vers l'extérieur, dont il faudrait assurer la protection contre le gel. Le module externe se compose uniquement d'un compresseur, d'un évaporateur et d'un détendeur. L'unité extérieure est donc nettement plus petite. Le module interne comporte le condenseur du circuit et les raccordements au réseau de chauffage. (aucune puissance). La thermopompe se met en marche lorsqu'une température définie n'est pas atteinte et s'éteint lorsque cette température est atteinte. Ce type de régulation de puissance est très insuffisant. La régulation de pression du modèle de thermopompe inverter REMKO s'adapte au besoin réel. Un convertisseur de fréquence est intégré au système électronique, il permet de modifier la vitesse de rotation du compresseur et du ventilateur en fonction des besoins. En pleine charge, le compresseur fonctionne à une vitesse de rotation plus élevée qu'en charge partielle. La vitesse de rotation plus faible prolonge la durée de vie des composants, améliore les caractéristiques de rendement et génère moins de bruits. Une vitesse de rotation plus faible signifie également une consommation moindre en énergie (courant) et des temps de fonctionnement plus longs. Ce qui signifie : Pendant la période de chauffage, les thermopompes inverter fonctionnent presque sans interruption. Ceci avec la meilleur efficacité possible. Technologie Inverter REMKO Température Le condenseur de la thermopompe est équipé au besoin d'une régulation de vitesse de rotation. La régulation de rendement des thermopompes conventionnelles ne possède que deux états, « MARCHE » (pleine puissance) et « ARRÊT » Système conventionnel Inverter Des variations de températures minimales permettent de faire des économies d'énergie Temps 1/3 Au démarrage, l'inverter n'a besoin que d'1/3 du temps nécessaire aux systèmes conventionnels Fig. 35: Technologie Inverter moderne 32 En refroidissement dynamique, le rendement de refroidissement est transmis sur l'air ambiant. Ceci est effectué à l'aide de convecteurs de ventilation guidés par l'eau. On attend ici des températures de démarrage inférieures au point de rosée, pour transmettre un plus fort refroidissement et déshumidifier l'air ambiant. Grâce à la technologie inverter innovante, cette thermopompe sera presque toujours en fonctionnement en période de chauffage, en adaptant son rendement de chauffage à vos besoins actuels et ne s'arrêtera que lorsque vous n'aurez réellement plus besoin de chaleur. (il en va de même à l'inverse pour la réfrigération) En refroidissement calme, la chaleur est captée par les surfaces de sol, murs ou plafond refroidies. Les tuyaux d'eau transforment les éléments en échangeurs thermiques efficaces. Les températures de frigorigène doivent alors être inférieures au point de rosée pour éviter la formation de condensat. Il est donc nécessaire de surveiller le point de rosée. Dégel par inversion de circuit Lors de températures inférieures à +5°C, l'humidité de l'air gèle sur l'évaporateur (module externe) et une couche de glace peut se former et diminuer le passage de chaleur de l'air sur le frigorigène et le flux d'air. Cette glace doit être éliminée. Le circuit de frigorigène est inversé à l'aide d'un distributeur 4 voies, de manière à ce que le gaz chaud du compresseur passe dans l'évaporateur d'origine et fasse fondre la glace. La mise en œuvre du processus de dégel ne se fait pas à un moment défini, mais en fonction des besoins afin d'économiser de l'énergie. Nous recommandons un refroidissement dynamique à convecteurs soufflants pour atteindre une meilleure puissance frigorifique et déshumidifier les pièces lors de journées orageuses. Les appareils correspondants de la série KWD, KWK et WLT-S figurent sur notre page Internet : « www.remko.de ». Aucune surveillance du point de rosée n'est alors nécessaire. La zone de confort de l'image indique clairement les températures et l'humidité ressenties comme confortables par l'homme. Il est important d'atteindre cette zone lors de la chauffe ou de la climatisation de bâtiments. Mode Refroidissement humidité relative en % L'inversion de circuit permet également de refroidir. En refroidissement, les composants du circuit de refroidissement sont utilisés pour générer de l'eau froide permettant d'extraire la chaleur d'un bâtiment. Ceci peut se faire en refroidissement dynamique ou en refroidissement calme. peu confortable humide confortable encore confortable peu confortable sec 10 12 14 16 18 20 22 24 26 28 30 Température de l'air ambiant en °C Fig. 36: Zone de confort 33 REMKO série WKF NEO-compact 3.2 Équipement supplémentaire Le module interne est en outre doté d’un ballon d'eau potable en émail de 200 ou 300 l. Un chauffage d'appoint électrique de 6 kW est déjà installé. Cette série est donc l'appareil idéal lorsque la thermopompe est prévue en tant que générateur de chaleur unique (fonctionnement mono-énergétique). Un fonctionnement monoénergétique par REMKO Smart-Serv ou bivalent par REMKO Smart-BVT est également réalisable. Installer tous les raccords en haut sur l'appareil. La société REMKO GmbH & Co. KG confirme par la présente que le produit livré est conforme à la liste positive UBA. 34 4 Montage 4.1 Architecture du système WKF NEO 70 1b 1a 3 1c 4 1d 1 B A 2a 2b 2 2c Fig. 37: Architecture du système WKF NEO 70 A: B: 1: 1a : 1b : 1c : Zone extérieure Zone intérieure Module interne Aller de chauffage (11/4" mâle) Retour de chauffage (11/4" mâle) Câble d’alimentation secteur du module interne, 230V /1~/ 50Hz, 10A (par ex. 3 x 1,5 mm2) 1d : Câble d'alimentation secteur du chauffage d’appoint électrique (par ex. 5 x 1,5 mm2) 2 : Module externe 2a : Ventilateur 2b : Câble d’alimentation secteur du module externe, 230V /1~/ 50Hz, 16A (par ex. 3 x 2,5 mm2) 2c : Bac à condensat du module externe (l’évacuation doit être protégée du gel !) 3 : Conduite de commande blindée (par ex. 2 x 1 mm2) 4 : Conduites de frigorigène 3/8" et 5/8“ 35 REMKO série WKF NEO-compact 4.2 Architecture du système WKF NEO 120 1a 1b 3 1c 4 1d 1 B A 2a 2b 2 2c Fig. 38: Architecture du système WKF NEO 120 A: B: 1: 1a : 1b : 1c : Zone extérieure Zone intérieure Module interne Aller de chauffage (11/4" mâle) Retour de chauffage (11/4" mâle) Câble d’alimentation secteur du module interne, 230V /1~/ 50Hz, 10A (par ex. 3 x 1,5 mm2) 1d : Câble d'alimentation secteur du chauffage d’appoint électrique (par ex. 5 x 1,5 mm2) 2 : Module externe 36 2a : Ventilateur 2b : Câble d’alimentation secteur du module externe, 230V /1~/ 50Hz, 20A (par ex. 3 x 2,5 mm2) 2c : Bac à condensat du module externe (l’évacuation doit être protégée du gel !) 3 : Conduite de commande blindée (par ex. 2 x 1 mm2) 4 : Conduites de frigorigène 3/8" et 5/8“ 4.3 Architecture du système WKF NEO 180 1a 1b 4 1c 5 1d 1 B A 2a 2a 2 2b 2c Fig. 39: Architecture du système WKF NEO 180 A: B: 1: 1a : 1b : 1c : Zone extérieure Zone intérieure Module interne Aller de chauffage (11/4" mâle) Retour de chauffage (11/4" mâle) Câble d’alimentation secteur du module interne, 230V /1~/ 50Hz, 10A (par ex. 3 x 1,5 mm2) 1d : Câble d'alimentation secteur du chauffage d’appoint électrique (par ex. 5 x 1,5 mm2) 2 : Module externe 2a : Ventilateur 2b : Câble d’alimentation secteur du module externe = 400V/3~/50Hz, 3 x 16A (par ex. 5 x 1,5 mm2) 2c : Bac à condensat du module externe (l’évacuation doit être protégée du gel !) 3 : Conduite de commande blindée (par ex. 2 x 1 mm2) 4 : Conduites de frigorigène 3/8" et 5/8“ 37 REMKO série WKF NEO-compact Les modules externe et interne sont à raccorder aux conduites de frigorigène de dimensions (diamètre extérieur) 3/8“ (=9,52 mm) et 5/8“ (=15,88 mm). Poser, entre les modules, une conduite de commande à 2 brins au minimum. Les modules interne et externe ont besoin chacun d'une alimentation en tension séparée. AVERTISSEMENT ! Toutes les conduites électriques doivent être dimensionnées et posées conformément aux prescriptions de la VDE. REMARQUE ! Les conduites ouvertes de frigorigène doivent être protégées par des capuchons, ou des bandes adhésives, de manière à prévenir l'infiltration d'humidité et de saleté. Les conduites de frigorigène ne doivent être en aucun cas pliées ou écrasées ! Les conduites de frigorigène sont à raccourcir exclusivement à l'aide d'outils de coupe de tuyaux adaptés (ne pas utiliser de scie à cadre ou similaire)! DANGER ! 4.4 Remarques générales pour le montage n Observer impérativement cette notice pour l'installation du système complet. n Amenez l'appareil dans son emballage d'origine aussi près que possible du lieu de montage, afin d'éviter les avaries de transport. n Vérifiez que l'appareil ne comporte pas de dommages visibles liés au transport. Déclarez immédiatement tout dommage à votre partenaire de contrat et à la société de transport. n Sélectionnez des endroits de montage adaptés en fonction du niveau sonore de fonctionnement et des voies d'installation. n N'ouvrez les vannes d'arrêt des conduites de frigorigène qu'après la mise en service. n Les modules externes ne sont pas conçus pour une installation fixe permanente. Respectez pour ce faire les tableaux dans le paragraphe « Appoint de frigorigène » dans Ä Chapitre 9.2 « Mise en service des techniques de refroidissement » à la page 52 n Réalisez tous les branchements électriques conformément aux dispositions DIN et VDE en vigueur. n Fixez toujours les câbles électriques correctement dans les bornes correspondantes. Une mauvaise fixation peut être source d'incendie. n Veillez à ne pas faire passer les tuyaux d'apport de frigorigène, ni les tuyaux d'eau par les chambres ou les pièces à vivre. Toutes les installations électriques doivent impérativement être réalisées par des entreprises spécialisées ! Perçage mural n Il est nécessaire de percer une ouverture murale d'au moins 70 mm de diamètre et 10 mm d'inclinaison de l'intérieur vers l'extérieur. n Nous vous conseillons de capitonner l'intérieur du perçage ou, par exemple, de l'habiller avec un tuyau PVC afin de protéger les conduites contre les éventuels endommagements (voir figure). n Une fois le montage terminé, rebouchez le perçage, en respectant la protection calorifuge, à l'aide d'un mastic adéquat. 2 1 4 3 Fig. 40: Perçage mural DANGER ! Seuls les techniciens spécialisés agréés sont habilités à raccorder les tuyaux de frigorigène et à manipuler le frigorigène (catégorie de compétences I). 38 1 : Conduite d’injection / 2 : Conduite de commande 3 : Alimentation / 4 : Conduite d'aspiration Distances minimales des modules internes Nous recommandons l'utilisation d'un presseétoupe REMKO pour mettre en place une entrée de tuyau/câble étanche et pour éviter les dommages. 500 4.5 Installation, montage du module interne n Placez le module interne sur un sol stable et plat. n La portance du sol doit être adaptée au poids du module interne. n Orientez correctement le module interne à l'aide des pieds de réglage réglables en hauteur. n Montez le module interne de manière à ce qu'il y ait suffisamment de place de tous côtés pour effectuer les travaux de montage et d'entretien. Vous devez également laisser assez de place au-dessus du module pour le montage des tuyaux et du groupe de sécurité. 300 300 500 Fig. 42: Distances minimales des modules internes Fig. 41: Pose au sol AVERTISSEMENT ! Utilisez exclusivement du matériel de fixation adapté à l'application. 39 REMKO série WKF NEO-compact 4.6 Installation, montage du module externe Lieu de pose du module externe n Ne fixez l'appareil qu'à des éléments de construction ou des murs pouvant le supporter. Attention, le module ne peut être installé qu'à la verticale. Le lieu d'installation doit être bien ventilé. n Afin de minimiser le développement sonore, nous vous conseillons un montage sur des consoles de sol à amortisseurs et le respect d'une bonne distance avec les murs réfléchissant les sons. n Respectez, pour l'installation, les distances minimales indiquées en page suivante. Ces distances minimales permettent de garantir une admission et une évacuation sans gêne de l'air. L’air sortant ne doit pas être réaspiré. Observez à cet effet les données de puissance des modules externes. Vous devez de plus vous assurer qu'il y a suffisamment de place pour le montage, l'entretien et les réparations. n Si vous placez le module externe à un emplacement très venté, vous devez le protéger du vent et des moyens de stabilisation supplémentaires sont recommandés. Cela peut être réalisé par exemple avec des câbles métalliques ou d’autres constructions (Voir la Fig. 43). Vérifiez les limites d'enneigement (Voir la Fig. 44). n Placez le module externe systématiquement sur amortisseurs. Les amortisseurs empêchent la transmission des vibrations vers le sol ou les maçonneries. n Le bac de condensat chauffant assure l'écoulement du condensat du bac. Vous devez assurer un écoulement de ce condensat à l’abri du gel (graviers, drainage). Respectez la loi sur l’approvisionnement en eau. n Si vous ne disposez pas de suffisamment d'espace sous l'appareil pour les conduites de frigorigène, vous pouvez enlever les encoches pré-embouties sous la tôle d'habillage latérale et guider les conduites par ces ouvertures. n Veillez, lors de l'installation, à la hauteur d'enneigement attendue et prévoyez un espace d'env. 20 cm permettant, toute l'année, l'aspiration et la soufflerie de l'air extérieur (Voir la Fig. 44). n Placez, si possible, en accord avec l'exploitant, le module externe, de manière à ce que le « bruit de fonctionnement ne gêne pas », et non seulement en fonction du « chemin le plus court ». Car : La technique Splitt permet de nombreuses possibilités de pose, à efficacité presque égale. 40 1 Fig. 43: Protection contre le vent 1 : Vent REMARQUE ! Sélectionnez le lieu d'implantation du module externe de manière à ce que les sons en émanant ne gênent ni les habitants, ni les utilisateurs de l'installation. Suivez les indications de la TA (directive technique de protection contre le bruit) ainsi que le tableau des dessins de niveau sonore en fonction de la distance. 20 cm 1 Fig. 44: Protection contre la neige 1 : Neige Lieu d'émission Niveau d'évaluation de la bruyance TA le jour en dB(A) la nuit en dB(A) Zones industrielles 70 70 Zones d'activités 65 50 Centres, villages et milieux mixtes 60 45 Zones d'habitation et petits lotissements 55 40 Zones d'habitation pures 50 35 Lieux de cure, hôpitaux et centres de soins 45 35 Les pointes d'émissions sonores ponctuelles ne doivent pas excéder les limites de son, le jour de plus de 30 dB(A), et la nuit de plus de 20 dB(A). Définition de la zone de danger AVERTISSEMENT ! L'accès à l'appareil est réservé aux seules personnes autorisées et qualifiées. Les personnes non autorisées ne peuvent pas approcher des zones de danger. Celles-ci doivent être signalées par des panneaux/barrières. n La zone de danger extérieure renferme l'appareil et prévoit au moins 2 m autour de son boîtier. n La zone de danger extérieure peut varier sur site en fonction de l'installation. Il revient à l'entreprise spécialisée qui se charge de l'installation d'en décider. n La zone de danger intérieure se trouve à l'intérieur de la machine et n'est accessible qu'à l'aide d'un outil adapté. L'accès est interdit à toute personne non autorisée ! 41 REMKO série WKF NEO-compact Distances minimales des modules externes >= 1500 6 >= 250 >= 600 >= 300 >= 1500 >= 1500 >= 250 5 >= 250 4 >= 250 3 2 1 >= 2000 >= 600 Fig. 45: Distances minimales en cas d'installation du module externe en mm 1 : Devant un mur, évacuation d'air vers l'avant, blocage de flux à l'arrière 2 : Devant un mur, évacuation d'air en direction du mur, blocage de flux à l'avant 3 : Entre deux murs, évacuation d'air en direction du mur, côtés libres : blocage de flux à l'avant et à l'arrière 4 : Dans une niche, évacuation d'air vers l'avant, blocage de flux à l'arrière et vers les deux côtés 3 >= 250 2 >= 1500 1 5 : Devant un mur abrité, évacuation d'air vers l'avant, blocage de flux à l'arrière et vers le haut 6 : Devant un mur abrité, évacuation d'air en direction du mur, blocage de flux à l'arrière et vers le haut a : WKF NEO 70 >= 150 mm WKF NEO 120/WKF NEO 180 >= 200 mm >= 300 >= 600 >= 600 >= 600 >= 600 >= 1500 >= 600 >= 3000 >= 3000 >= 250 >= 600 >= 1500 >= 250 4 Fig. 46: Distances minimales en cas d'installation de plusieurs modules externes en mm 1 : Devant un mur, évacuation d'air en direction du mur, blocage de flux à l'avant 2 : Dans une niche, évacuation d'air vers l'avant, blocage de flux à l'arrière et vers les deux côtés 3 : Entre deux murs, évacuation d'air en direction du mur et de l'autre appareil, côtés libres : blocage de flux à l'avant et à l'arrière 42 4 : Entre deux murs, évacuation d'air en direction du mur, côtés des appareils extérieurs libres : blocage de flux à l'avant, à l'arrière et pour les appareils intérieurs sur les côtés a : WKF NEO 70 >= 150 mm WKF NEO 120/WKF NEO 180 >= 200 mm Raccord pour condensat et dérivation sécurisée B E 5 B 5 8 7 A 1 D 1 3 F 10 C Fig. 48: Dimensions des fondations de bande (vue du dessus) 1 2 Pour les désignations 1, 3, 5, 7, 8 et 10, consultez la légende des Voir la Fig. 47 3 4 5 6 5 Dimensions des fondations de bande (toutes les mesures en mm) 7 WKF NEO 120 8 9 9 11 10 11 Fig. 47: Conduite de condensat, évacuation de condensat et fondations de bande (coupe) 1: 2: 3: Module externe Longeron Cuve collectrice du condensat, avec chauffage de carter 4 : Console de sol BK 660/1000 5 : Fondations de bande armées H x l x P = 300 x 200 x 800 mm 6 : Couche de graviers pour l'évacuation 7 : Canal d'évacuation d'eau 8 : Tuyau de protection pour les conduites de frigorigène et pour les conduites de raccordement électrique (résistance thermique jusqu'à 80 °C min.) 9 : Limite du gel 10 : Tuyau de drainage 11 : Sol Dim. WKF NEO 70 WKF NEO 180 A 800/1000 800/1000 B 200 200 C 660 620 D 340 E 400 420 F 100 100 1) WKF NEO 120 2) WKF NEO 180 360 1) 350 2) Raccord pour condensat La température descendant en dessous du point de rosée au niveau du condenseur à lamelles, du condensat se forme en mode Chauffage. Il est recommandé d'installer une cuve à condensat sous l'appareil pour évacuer le condensat. REMARQUE ! Avec le séparateur d'huile REMKO OA2, les conduites de frigorigène doivent être insérées par l'arrière, sur le côté, ou par l'avant dans le boîtier. WKF NEO compact 70/120/180 43 REMKO série WKF NEO-compact n La conduite de condensat doit être posée par le client avec une inclinaison min. de 2 %. Au besoin, prévoyez une isolation hermétique à la diffusion de vapeur. n En cas de fonctionnement de l'appareil lorsque la température extérieure est inférieure à 4 °C, veillez à ce que la conduite de condensat soit protégée contre le gel. De la même manière, le revêtement inférieur du carter et le collecteur de condensat doivent être protégés du gel afin de garantir un écoulement permanent du condensat. Si nécessaire, prévoyez un chauffage auxiliaire pour les tuyaux. n Une fois le montage terminé, vérifiez que le condensat s'écoule sans entrave et que l'étanchéité soit garantie en permanence. Évacuation sécurisée en présence de fuites Le séparateur d'huile REMKO OA 2.2 répond aux exigences présentées ci-dessous des consignes et législations régionales. REMARQUE ! Les consignes et législations régionales relatives à la protection de l'environnement, par ex. la loi allemande sur le régime des eaux (WHG), peuvent prévoir la prise de mesures adéquates afin de prévenir les évacuations incontrôlées en présence de fuites en garantissant une élimination sûre de l'huile de machines frigorifiques ou de fluides présentant un danger potentiel. REMARQUE ! En cas de raccordement d'un écoulement externe au niveau du séparateur d'huile, celui-ci doit être protégé du gel. 5 Raccordement hydraulique Chaque installation doit avoir une configuration séparée en fonction du volume nominal (voir caractéristiques techniques). n Un accumulateur peut être utilisé en tant que répartiteur hydraulique pour le désaccouplement hydraulique des circuits de chauffage. Un découplage hydraulique est nécessaire quand : - différentes températures d'aller doivent être réalisées, par ex. chauffage au sol / radiateurs - la chute de pression du système de répartition du chauffage est supérieure à 80 kPa – en cas d’utilisation d’autres générateurs de chaleur comme par ex. chaudière de combustibles solides, solaire ou systèmes bivalents. n Un calcul du réseau de tuyauterie doit être effectué avant l'installation. Après l'installation de la thermopompe, vous devez effectuer une compensation hydraulique des circuits de chauffage. n Protégez les chauffages au sol contre de trop fortes températures d'entrée. n La section des raccordements d'entrée et de sortie ne doit pas être réduite avant le raccordement à un accumulateur. n Prévoir des vannes et des robinets de purge aux endroits appropriés. n Rincez tout le réseau de tuyauterie avant de le raccorder à la thermopompe. n Posez un ou plusieurs vases d'expansion pour le système hydraulique. n Adaptez la pression de l'installation au système hydraulique et contrôlez la pression à l'arrêt de la thermopompe. Adaptez également la pré-pression à la hauteur de transport définie. n Le groupe de sécurité fourni est composé d'un manomètre, d'un aérateur et d'une soupape de sécurité. Il est monté sur le module interne, au raccord de tuyau prévu à cet effet. 2 1 Fig. 49: Groupe de sécurité 1 : manomètre 2 : Aérateur automatique 3 : Vanne de sécurité 44 3 n Vérifiez le filtre lors de chaque entretien de l'installation. n Le module interne est doté d'une purge manuelle pour la purge de la thermopompe. n Vous devez isoler toutes les surfaces métalliques apparentes. n Le refroidissement via les circuits de chauffage nécessite une isolation étanche à la diffusion de vapeur de toute la tuyauterie. n Sécurisez tous les circuits de chauffage, y compris le raccordement pour la préparation d'eau sanitaire, de l'eau en circulation à l'aide de clapets anti-retour. n Rincez soigneusement l'installation avant sa mise en service. Vous devez également vérifier l'étanchéité et purger soigneusement le module interne et l'installation complète, plusieurs fois selon la norme DIN. Vous trouverez le schéma actuel des liaisons hydrauliques sur Internet, sur www.remko.de Schéma hydraulique Fonctions : Chauffage et eau chaude incl. barrette chauffée de secours Smart-Serv. Ce schéma hydraulique sert uniquement de référence, le système hydraulique côté client doit être planifié et installé par l'installateur ! 1 2 3 D E C A B Fig. 50: Exemple de schéma hydraulique A: B: C: D: Module externe Module interne Smart-Control Touch Sonde d'extérieur E: 1: 2: 3: Température ambiante / capteur d’humidité Eau froide Eau chaude Circuit non mixte 45 REMKO série WKF NEO-compact La thermopompe WKF NEO compact est idéale pour une utilisation dans les nouvelles constructions lorsque la thermopompe est le seul générateur de chaleur. En cas d'urgence, un chauffage supplémentaire électrique (version monoénergétique) peut être activé sur la Smart Control. Le ballon d'eau potable REMKO est un ballon d'eau potable en émail. La vanne d'inversion à 3 voies est commutée par la commande intelligente Smart-Control pour la préparation WW et est également intégrée au module interne. La pompe primaire très efficace peut être utilisée comme pompe à circuit de chauffe et la vitesse de rotation est régulée sur demande. La perte de pression côté client est de 80 kPa max. Si les pertes de pression côté client sont supérieures, un ballon séparé, par ex. REMKO KPS 300 doit être utilisé comme répartiteur hydraulique. Un groupe de pompes de circuit de chauffe non mixte de type HGU et deux groupes de pompes de circuit de chauffe mixtes de type HGM de REMKO sont disponibles. De plus, les raccords pour l'eau chaude, l'alimentation en eau froide et la circulation sont branchés en haut sur le module interne. Les conditions de base suivantes doivent être remplies pour que la thermopompe puisse charger de manière efficace et sans panne le système de chauffage (sans ballon tampon) avec de l'eau de chauffage : n Le système de chauffage doit fonctionner avec une température d’entrée (ex. Chauffage au sol uniquement) n La chute de pression du système de chauffage ne doit pas dépasser 80 kPa. n Un débit volumique d’eau min. de 20 l/min doit être garanti. Si cela n’est pas possible, une vanne doit être installée à un endroit approprié (dernier répartiteur du circuit de chauffe). n Les sections de raccordement des conduites de la thermopompe jusqu’aux répartiteurs du circuit de chauffe ne doivent pas être réduites n Le volume d’eau min. en cas de refroidissement actif doit être observé. Réglage du point de rosée par la télécommande à câble Smart Control 6 Refroidissement pompe à chaleur Description de l'installation de refroidissement Refroidissement par mixte circuit de chauffage (circuit de chauffage en surface) Le refroidissement avec la thermopompe de série WKF est possible grâce au mixte circuit de chauffage. Le raccordement hydraulique est identique au raccordement en tant que circuit hydraulique. En cas d'utilisation du circuit pour le chauffage ou le refroidissement, celui-ci est raccordé comme le représente le schéma hydraulique à la page et . Les capteurs S12 et S11 enregistrent les températures d'entrée et de retour, quand un chauffage/ refroidissement tampon est utilisé. Si la fonction de refroidissement doit être effectuée avec la thermopompe série WKF, la télécommande à câble Smart Control doit être montée dans la pièce de référence sélectionnée (par ex. salon). Il est recommandé de la monter au mur. Dans ce cas, assurez-vous que l'air ambiant peut circuler librement autour de la télécommande. La télécommande capte la température et l'humidité ambiante. Cela lui permet de déterminer le point de rosée par calcul et de commander de manière correspondante la température de l'eau de refroidissement avec un écart de sécurité suffisant de sorte à ce que le point de rosée sur la surface supérieure de la surface de la pièce activée ainsi que sur la tuyauterie non encastrée soit atteint. Refroidissement par un circuit de refroidissement distinct Si, pour le refroidissement du système, un circuit de refroidissement distinct est utilisé en plus des circuits de chauffage, une vanne d'inversion (A14) actionnée avec 230 V doit être montée à cet effet dans la conduite d'entrée. Celle-ci est posée sur la A14 du régulateur. En mode de refroidissement, la vanne sous tension fonctionne dans le circuit de refroidissement AB/A. Si le mode de refroidissement ne fonctionne pas, la vanne hors tension se situe dans le circuit de chauffage AB/B. La température de l'eau dans la tuyauterie est maintenue au-dessus de la température de point de rosée déterminée par calcul grâce au régulateur pour éviter la condensation dans la tuyauterie non encastrée ainsi que dans celle posée sous un revêtement en crépi. Il est recommandé de monter un contrôleur de point de rosée à 230 V avec les capteurs de temp. de tuyaux correspondants sur les conduites d'entrée en dehors de la thermopompe. L'emplacement doit être choisi de sorte à ce qu'il soit monté à l'en- 46 droit permettant le moins que le point de rosée ne soit pas atteint. Le contrôleur de point de rosée doit être câblé de sorte à couper le raccordement dans l'alimentation du blocage EVU vers le régulateur (entrée S16) afin de désactiver la TP. Refroidissement sans télécommande à câble montée dans la pièce En l'absence d'installation d'une télécommande supplément. en dehors de la thermopompe dans la pièce, la régulation de la temp. d'entrée minimale est effectuée par la température extérieure moins 6 K. Il est alors impératif d'installer un contrôleur de point de rosée à 230 V supplémentaire avec des capteurs de température de tuyaux correspondants sur les conduites d'entrée en dehors de la thermopompe. L'emplacement doit être choisi de sorte à ce qu'il soit monté à l'endroit permettant le moins que le point de rosée ne soit pas atteint. Le contrôleur de point de rosée doit être câblé de sorte à couper le raccordement dans l'alimentation du blocage EVU vers le régulateur (entrée S16) afin de désactiver la thermopompe. Refroidissement par un ballon tampon parallèle en tant que limite de système Si le système est utilisé avec un ballon tampon parallèle servant de limite de système vers le circuit utilisateur, il n'est pas nécessaire de monter une télécommande dans le salon lorsque la régulation du circuit de refroidissement utilisé fonctionne à l'aide d'un régulateur externe. Refroidissement par une valeur fixe En l'absence d'installation de télécommande supplémentaire dans la pièce, le refroidissement peut être effectué par une valeur fixe supérieure au point de rosée. Exemple: Temp. min. de départ pas moins de +16 °C REMARQUE ! Volume d'eau minimal Si le volume d'eau/de l'installation côté construction dans le circuit de refroidiss. est inférieur à 5 L/kW de la puissance frigorifique, l'utilisation d'un ballon tampon supplémentaire est recommandée pour l'augmentation du volume. Celuici peut être utilisé en tant qu'accumulateur en série dans le retour ou en tant qu'aiguillage hydraulique. Le ballon tampon de la série KPS peut pour cela être livré par REMKO. 47 REMKO série WKF NEO-compact 7 Protection contre la corrosion Lorsque les matériaux métalliques d'une installation de chauffage viennent à corroder, c'est toujours un souci lié à l'oxygène. L'acidité et la teneur en sel jouent également un rôle très important. Le défi : Lorsqu'un installateur souhaite garantir à son client une installation de chauffage à eau chaude sans risque d'oxydation - et sans utiliser de produits chimiques - il doit veiller aux points suivants : n pose correcte du système par le constructeur/planificateur de l'installation et n En fonction des matériaux installés : Remplissage de l'installation de chauffage en eau adoucie ou en eau DI désalinisée, contrôle du pH après 8 à 12 semaines. Pour les types d’installations énumérés ci-après, la directive VDI 2035 est applicable. Pour ces installations, en cas de dépassement des valeurs recommandées pour l’eau de remplissage, d’appoint et de circulation, un traitement de l’eau est nécessaire. Champ d’application de la directive VDI 2035 : n Installations de chauffage d’eau potable selon DIN 4753 (feuillet 1 uniquement) n Installations de chauffage d’eau chaude sanitaire selon DIN EN 12828 à l’intérieur d’un bâtiment jusqu’à une température de départ de 100°C n Installations approvisionnant des complexes immobiliers et dont le volume d’eau d’appoint cumulé sur la durée de vie ne dépasse pas le double du volume de remplissage Vous trouverez, au tableau suivant, les exigences de la norme VDI 2035, feuille 1, en termes de dureté. Dureté totale [°dH] en fonction du volume spécifique de l'installation Puissance totale de chauffe- en kW <20 l/kW ³20 l/kW et <50 l/kW ³50 l/kW jusqu'à 50 kW £16,8 °dH £11,2 °dH £0,11 °dH Le tableau suivant indique la teneur en oxygène autorisée en fonction de la teneur en sel. Valeurs indicatives pour l'eau de chauffage selon la norme VDI 2035, feuille 2 Capacité de conduction électrique à 25°C Teneur en oxygène pauvre en sel salée μS/cm < 100 100-1500 mg/l < 0,1 < 0,02 pH à 25°C 8,2 - 10,0 *) *) Pour l'aluminium et les alliages d'aluminium, la plage pH est limitée : Le pH à 25°C est de 8,2-8,5 (9,0 maximum pour les alliages d'aluminium) Le traitement de l'eau par des produits chimiques n'est pas nécessaire Le traitement de l'eau par des produits chimiques doit se limiter à des cas exceptionnels. La norme VDI 2035, feuille 2 exige explicitement au point 8.4.1 la justification et la documentation au journal de l'installation de toutes les mesures de traitement de l'eau. Ceci est justifié: n Une mauvaise utilisation de produits chimiques provoque fréquemment la non activation des élastomères n des bouchages et dépôts dus à la boue 48 n des défauts des joints de glissement des pompes et n enfin la formation de pellicules biologiques pouvant causer une corrosion d'origine microbienne et détériorer la transmission de la chaleur. Des concentrations d'oxygène de 0,5 mg/l sont acceptables dans des eaux à faible teneur en sel et un pH correct. REMARQUE ! Les pompes à chaleur et équipements de l’entreprise REMKO ne doivent être remplis et utilisés qu’avec de l’eau totalement déminéralisée. De plus, nous vous recommandons l’utilisation de notre produit de protection intégrale pour chaudière. Pour les installations utilisées à des fins de refroidissement, utilisez du glycol avec notre produit de protection intégrale. Lors de chaque visite d’entretien, et au minimum une fois par an, une vérification de l’eau de l’installation doit être effectuée. Sont exclus de la garantie tous les dommages résultant d’un non-respect des consignes. Vous trouverez ci-après un modèle de compterendu de remplissage. Remplissage de l’installation de chauffage avec de l’eau totalement déminéralisée Remplissage initial 2e année 3e année 4e année Remplie le Sous réserve de modifications techniques et d’erreurs. Volume de l’installation [litres] Valeur °dH Valeur pH Conductivité [µS/cm] Agent de conditionnement (nom et quantité) Teneur en molybdène [mg/l] Signature Votre chauffagiste : DI 2035 Directive V ne mesure u r e u t c e ff E par an ! de contrôle Fig. 51: Compte-rendu de remplissage d’eau totalement déminéralisée 49 REMKO série WKF NEO-compact Fluides véhiculés des pompes 8 Pompe Grundfos La pompe est adaptée pour la recirculation des fluides suivants : n Fluides purs, liquides, non agressifs et non explosifs sans composés solides ou à longues fibres n Liquides de refroidissement sans huile minérale n Eau déminéralisée La viscosité cinématique de l’eau est de ϑ=1 mm2/s (1 cSt) pour 20 °C. Lorsque vous utilisez la pompe pour transporter des liquides avec une autre viscosité, le débit de la pompe est réduit. Exemple : Un mélange eau-glycol avec une teneur en glycol de 50 % possède à 20 °C une viscosité d’env. 10 mm2/s (10 cSt). Le débit est alors réduit d’env. 15 %. Aucun additif pouvant altérer le fonctionnement de la pompe ne doit être ajouté dans l’eau. Lors de la conception de la pompe, la viscosité du fluide véhiculé doit être considérée. Pompe Wilo La pompe peut être utilisée pour transporter les mélanges eau-glycol avec un pourcentage de glycol max. de 50 %. Exemple pour un mélange eau-glycol : Viscosité maximale autorisée : entre 10 et 50 cSt. Cela correspond à un mélange eau-éthylène glycol avec un pourcentage de glycol d’env. 50 % à -10 °C. La pompe est régulée à l’aide d'une fonction de limitation de débit qui la protège contre la surchauffe. Le transport de mélanges de glycol a une influence sur la courbe caractéristique MAX, parce que le débit est réduit en fonction de la teneur en glycol et de la température du fluide. Pour que l’effet du glycol perdure, les températures au-dessus de la température nominale indiquée pour le fluide doivent être évitées. En général, la durée de fonctionnement avec des températures de fluides élevées doit être minimisée. Avant d’ajouter le mélange de glycol, l’installation doit absolument être nettoyée et rincée. Pour éviter la corrosion ou les précipités, le mélange de glycol doit être vérifié régulièrement et remplacé si nécessaire. Si le mélange de glycol doit être davantage dilué, les instructions du fabricant de glycol doivent être observées. 50 Mode de chauffage d'urgence En cas de panne du module externe, vous pouvez démarrer le mode de chauffage d'urgence comme suit : 1. Appuyez sur le logo REMKO dans le coin supérieur droit de l’écran pour accéder au niveau « Experts ». À l’aide des touches « + » et « - », entrez le mot de passe « 0321 » et confirmez la saisie en cliquant sur le champ « OK » dans le coin inférieur droit. 2. Au niveau expert de l’option de menu « Réglages – Réglages de base - Configuration du système », la thermopompe doit être désactivée. Après avoir arrêté la thermopompe, le chauffage d’appoint est activé. 3. Il n’est pas nécessaire d’effectuer un réglage manuel de la valeur de consigne sur l’élément de chauffage électrique. 4. Le Smart Control applique le réglage de chauffage complet et le raccordement de l'élément de chauffe. Pour désactiver à nouveau le mode chauffage d’urgence, réactiver la thermopompe dans le niveau expert. 9 Raccord de frigorigène 9.1 Raccord des conduites de frigorigène n Raccordez le module externe et le module interne à deux tuyaux en cuivre (tuyaux en cuivre de qualité réfrigérateur) de dimensions 3/8" = 9,5 mm et 5/8" = 15,88 mm (accessoires REMKO). n Veillez, lors du cintrage des conduites de frigorigène à l'angle de cintrage afin d'éviter de les plier. Ne cintrez jamais deux fois le même endroit de tuyau pour éviter toute porosité ou formation de fissure. n Veillez à une fixation adaptée et à une bonne isolation lors de la pose des conduites de frigorigène. n Les tuyaux de cuivre utilisés pour les raccordements des modules doivent être dotés de bords relevés. Attention à la forme des bords relevés et à des écrous-raccords adaptés (fournis) (Voir la Fig. 52 à Voir la Fig. 54). 1 Fig. 53: Sertissage de la conduite de frigorigène 1 : Dudgeonnière 1 2 Fig. 52: Ébavurage de la conduite de frigorigène 1 : Conduite de frigorigène 2 : Outil à ébavurer Fig. 54: Bord relevé de forme adéquate Diamètre extérieur du tuyau de cuivre Dimensions d’élargissement ø A 3/8" = 9,5 mm 12,4 - 12,8 mm 5/8" = 15,88 21,9 - 22,3 mm 51 REMKO série WKF NEO-compact Raccordement à l'appareil n Le cache du module externe doit également être démonté. Enlevez, si nécessaire, les passages estampés. n Les bouchons de protection montés en usine doivent être enlevés. Les écrous-raccords peuvent être réutilisés pour le montage ultérieur. Assurez-vous que l'écrou-raccord se trouve sur le tuyau avant de relever les bords des tuyaux. n Raccordez tout d'abord les conduites de frigorigène à la main aux raccords de l'appareil pour assurer leur bonne position. Puis fixez les raccords vissés à l'aide d'une clé à fourche adaptée. Utilisez une clé pour les maintenir l’un contre l’autre (Voir la Fig. 55). REMARQUE ! Utilisez uniquement des outils homologués pour une utilisation dans le domaine frigorifique (p.ex. : Pince à cintrer, guillotines, outil à ébavurer et dudgeonnière) les tuyaux de frigorigène ne doivent pas être sciés. REMARQUE ! Évitez impérativement, lors de tous les travaux, l'introduction de saleté, copeaux, eau, etc. dans les tuyaux de frigorigène ! 1 Les modules externes sont fournis avec des écrous-raccords à bords relevés. 9.2 Mise en service des techniques de refroidissement Contrôle de l'étanchéité Une fois tous les branchements effectués, la station-manomètre est connectée comme suit aux différents raccords pour vannes Schrader (selon équipement) : 2 Fig. 55: Serrage des raccords vissés 1 : Serrage avec la première clé plate 2 : Maintien avec la deuxième clé plate Dimensions du tuyau Couple de serrage 3/8" = 9,5 mm 32 - 40 Nm 5/8" = 15,88 65 - 75 Nm n Les conduites de frigorigène installées incluant les raccords relevés doivent être dotées d’un matériau isolant approprié. n Vous n'avez aucune mesure à prendre pour le retour d'huile de l'huile du compresseur. 52 bleu = grande vanne = pression d'aspiration Une fois le branchement effectué, il convient de procéder au contrôle de l'étanchéité au moyen d'azote sec. Pour contrôler l'étanchéité, les différents raccords sont vaporisés au moyen d'un produit détecteur de fuite en aérosol. Lorsque des bulles apparaissent, cela signifie que le raccord n'est pas correct. Serrez alors plus fermement le raccord vissé ou recommencez le sertissage si nécessaire. Évacuation Une fois le contrôle de l'étanchéité réussi, la surpression est évacuée des conduites de frigorigène et une pompe à vide est mise en service avec une pression partielle finale absolue minimale de 10 mbar afin de créer un espace exempt d'air dans les conduites. De plus, cette mesure permet d'évacuer l'humidité des conduites. REMARQUE ! Un vide absolu d'au moins 10 mbar doit impérativement être généré! La durée nécessaire pour la génération du vide varie en fonction du volume des conduites de l'unité intérieure et de la longueur des conduites de condensat. La procédure dure toutefois au moins 60 minutes. Une fois le système entièrement exempt de gaz étrangers et d'humidité, les vannes de la station-manomètre sont fermées et celles de l'unité extérieure sont ouvertes comme décrit au chapitre « Mise en service ». Mise en service n Contrôle de la température de la surface de la conduite d'aspiration et détermination de la surchauffe de l'évaporateur. Pour mesurer la température, maintenez le thermomètre sur la conduite d'aspiration et soustrayez de la température mesurée la température d'ébullition qui s'affiche sur le manomètre. n Consignez les températures relevées dans le protocole de mise en service. Test fonctionnel du mode Chauffage 1. Retirez les capuchons des vannes. 2. Entamez la mise en service en ouvrant brièvement les vannes d'arrêt de l'unité extérieure jusqu'à ce que le manomètre affiche une pression d'env. 2 bar. 3. Contrôlez l'étanchéité de tous les raccords à l'aide d'un détecteur de fuites en aérosol et d'appareils de recherche de fuites adaptés. Si aucune fuite n'est détectée, ouvrez les vannes d'arrêt en les faisant tourner à l'aide d'une clé six pans dans le sens inverse des aiguilles d'une montre jusqu'à la butée. En cas de constatation de fuites, aspirez le frigorigène et rétablissez le raccord défectueux. Il est impératif de recréer le vide et de procéder à un nouveau séchage ! 4. Activez l'interrupteur principal ou le fusible. 5. Programmez la Smart Control. 6. Activez le mode Chauffage REMARQUE ! Seul un personnel formé à cet effet peut effectuer et documenter en conséquence la mise en service. Pour mettre en service l'ensemble du dispositif, respectez les modes d'emploi des unités intérieure et extérieure. Une fois tous les composants branchés et contrôlés, l'installation peut être mise en service. Afin de s'assurer que l'installation fonctionne correctement, réalisez un contrôle fonctionnel avant de la transmettre à l'exploitant. Cette mesure permet de détecter les éventuelles irrégularités survenant lors du fonctionnement de l'appareil. Ce contrôle dépend de l'unité intérieure montée. Le mode d'emploi de l'unité intérieure à mettre en service contient les procédures à suivre. En raison de l'activation temporisée, le compresseur ne démarre que quelques minutes plus tard. 7. Durant la marche d'essai, contrôlez le fonctionnement et le paramétrage corrects de tous les dispositifs de réglage, de commande et de sécurité. 8. Mesurez toutes les valeurs spécifiques aux applications frigorifiques, consignez-les dans le protocole de mise en service. 9. Retirez le manomètre. Contrôle fonctionnel et marche d'essai Contrôle des points suivants : n Étanchéité des conduites de frigorigène. n Marche régulière du compresseur et du ventilateur. n Distribution d'eau chaude dans le module interne et distribution d'air froid dans le module externe en mode Chauffage. n Contrôle fonctionnel de l'unité intérieure et de toutes les séquences de programmation. Mesures finales n Réglez la température de consigne à la valeur souhaitée par le biais de la Smart Control. n Remontez toutes les pièces préalablement démontées. n Initiez l'exploitant à l'utilisation de l'installation. 53 REMKO série WKF NEO-compact REMARQUE ! Contrôlez l'étanchéité des vannes d'arrêt et capuchons après chaque intervention sur le circuit frigorifique. Le cas échéant, utilisez des joints adaptés. Longueur simple de tuyaux Quantité de remplissage supplémentaire WKF NEO 70 de 5 à max. 30 m par circuit 50 g/m Quantité de remplissage supplémentaire Appoint de frigorigène Longueur simple de tuyaux DANGER ! Seuls les techniciens spécialisés agréés sont habilités à raccorder les tuyaux de frigorigène et à manipuler le frigorigène (catégorie de compétences I). WKF NEO 120 WKF NEO 180 Jusqu'à 10 m 0 g/m 0 g/m de 10 à max. 50 m par circuit 50 g/m --- de 10 à max. 75 m par circuit --- 50 g/m DANGER ! Le frigorigène utilisé doit être sous forme liquide! Exemples Quantité de remplissage supplémentaire PRECAUTION ! Toutes les autres séries Danger de blessures émanant du frigorigène! Les frigorigènes dégraissent au contact de la peau et provoquent des gelures. 5m 0g 0g Donc: 10 m 250 g 0g - Durant tous les travaux avec des frigorigènes, porter des gants de protection résistants aux produits chimiques. 15 m 500 g 250 g 20 m 750 g 500 g - Pour la protection des yeux, porter des lunettes de protection. 25 m 1000 g 750 g REMARQUE ! REMARQUE ! La quantité de remplissage de frigorigène doit être vérifiée en fonction de la surchauffe. n Le module externe est prérempli avec du frigorigène pour une longueur de tuyau max. (voir tableaux ci-après). n Si la longueur de la tuyauterie excède la longueur de tuyau max., vous devez effectuer un appoint supplémentaire par longueur supplémentaire de mètre de tuyaux (longueur simple) (voir les tableaux ci-après). Longueur simple de tuyaux Jusqu'à 5 m 54 WKF NEO 70 Longueur simple de tuyaux Quantité de remplissage supplémentaire WKF NEO 70 0 g/m La fuite de frigorigène contribue au changement climatique. En cas de fuite, les frigorigènes à faible potentiel d‘effet de serre contribuent moins au réchauffement planétaire que ceux dont le potentiel est élevé. Cet appareil contient un frigorigène à potentiel d‘effet de serre de 1975. Ainsi, une fuite d‘1 kg de ce frigorigène aurait des effets 1975 fois plus importants sur le réchauffement planétaire qu‘1 kg de CO2 sur 100 ans. Ne procédez à aucune tâche sur le circuit de refroidissement ou ne désassemblez pas l‘appareil - ayez toujours recours à du personnel spécialisé. 10 Raccordement électrique Information important Vous trouverez des informations sur les raccords électriques des modules interne et externe, sur l'affectation des bornes du module E/S, ainsi que les schémas électriques dans le mode d'emploi « Raccordement électrique » REMARQUE ! Pour un bloc existant de la pompe à chaleur par les entreprises d'approvision. en énergie (circ. des services publics) a la S16 de contrôleur Smart-Control de contact de commande va utiliser. 11 Avant la mise en service Respectez strictement les points suivants avant la mise en service : n L'installation de chauffage est remplie d’eau déminéralisée selon VDI 2035. Nous recommandons l’ajout de la protection totale du chauffage REMKO (voir chapitre "Protection contre la corrosion" ). n Une température d’eau ou du système de min. 20 °C doit être garantie dans le circuit de retour (ex. au moyen de la barrette chauffée/du mode de chauffage d'urgence). n L’ensemble du réseau de chauffage est rincé, nettoyé et purgé (réglage hydraulique incl.). n Les quantités de remplissage de frigorigène doivent être augmentées si nécessaire ! Pour WKF >10 m environ 50 g/m (quantité pour la conduite totale simple des deux appareils). n Les conduites de frigorigène doivent être posées sans coude dans le tuyau de protection. Le tuyau de protection est sec et fermé correctement et de manière étanche à l’eau pour empêcher toute infiltration d’eau. n La thermopompe n’est pas activée si une température extérieure inférieure à 10 °C est mesurée sur la sonde d'extérieur et si la température d’admission d’eau (retour) est inférieure à 15 °C. REMARQUE ! En cas de non-respect des points ci-dessus, aucune mise en service ne doit avoir lieu. Les dommages qui en résultent sont alors exclus de la garantie ! 55 REMKO série WKF NEO-compact 12 Mise en service Aperçu des éléments de commande Écran tactile et consignes pour la mise en service La Smart Control gère la commande et le pilotage de toute l'installation de chauffage. La commande de la Smart-Control se fait sur écran tactile. n L'installation est pré-installée en usine. Les paramètres de livraison sont chargés après une réinitialisation de la Smart-Control. n Effectuez un contrôle visuel approfondi avant la mise en service. n Mettez sous tension. n Ensuite, les données pré-installées sont chargées et les paramètres peuvent être réglés à l'aide de l'assistant à la mise en service ou dans la configuration du système. Vous trouverez les informations correspondantes dans les modes d’emploi séparés de la Smart Control. REMARQUE ! Avant la mise en service l'ensemble du système et le réservoir d'eau chaude doit être rempli ! 1 2 3 4 Fig. 56: Éléments de commande de la Smart Control Touch 1: 2: 3: 4: Vue d´ensem de base (accès rapide) Informations (accès rapide) Réglages (accès rapide) Messages (avertissements, consignes et erreurs) Fonction de l’écran La régulation du REMKO Smart-Control Touch est un module de commande avec écran tactile. La commande est intuitive et facile à comprendre grâce à l'affichage en texte clair dans l’interface utilisateur du régulateur. Pour ajuster et modifier les paramètres, aucune touche n'est nécessaire ; il faut toucher le surface du régulateur aux endroits correspondants. L’installation d'autres fonctions comme KNX ou Smart-Web est possible en installant d’autres logiciels supplémentaires disponibles dans les accessoires. 56 13 Entretien et maintenance Des travaux d'entretien et de maintenance réguliers garantissent un fonctionnement impeccable de l'installation de thermopompe et contribuent à augmenter sa durée de vie. Entretien n Éliminez toutes les saletés, végétations ou autres dépôts venus s'accumuler sur les unités intérieure et extérieure. n Nettoyez l'appareil en utilisant un chiffon humide. N'utilisez pas de produits à récurer, de nettoyants agressifs ou d'agents contenant des solvants. Evitez également d'utiliser un jet d'eau puissant. n Nettoyez au moins une fois par an les lamelles de l'unité extérieure. Maintenance n Nous vous conseillons de souscrire un contrat de maintenance à intervalle d'un an avec une société spécialisée compétente pour le contrôle d'étanchéité légal. 14 Mise hors service provisoire Lorsque l'installation de chauffage est inutilisée pendant une longue période (des vacances, p.ex.), elle ne doit cependant pas être mise hors tension ! n Pendant une mise hors service provisoire, l'installation doit être mise en mode « Disposition ». n Vous pouvez programmer des temps de chauffage pendant la durée de votre absence. n Avant d'interrompre la mise hors service, vous devez remettre l'installation dans le mode de fonctionnement précédent. n Le changement de mode de fonctionnement est décrit au chapitre correspondant du manuel de la Smart Control. REMARQUE ! En mode de fonctionnement « Disposition », la pompe à chaleur est en mode veille. Seule la fonction de protection contre le gel de toute l'installation est activée. REMARQUE ! Si l'équivalent en CO2 est supérieur à ce qui est spécifié ci-dessous, le circuit de réfrigération doit être vérifié pour les fuites. > 5 t 1 x par an > 50 t 2 x par an > 500 t 4 x par an Une thermopompe doit être, d'une manière générale, entretenue tous les ans. C'est pourquoi nous vous conseillons la signature d'un contrat de maintenance incluant le contrôle d'étanchéité. 57 REMKO série WKF NEO-compact 15 15.1 Élimination des défauts et service après-vente Dépannage général L'appareil a été conçu selon des méthodes de fabrication de pointe et a été soumis à plusieurs reprises à des contrôles fonctionnels. Toutefois, si des défauts devaient survenir, vérifiez l'appareil en vous référant à la liste suivante. Une fois tous les contrôles fonctionnels réalisés, si votre appareil présente toujours des dysfonctionnements, contactez le revendeur spécialisé le plus proche. Dysfonctionnement Causes possibles Solution La thermopompe ne démarre pas ou se coupe automatiquement Panne de courant, sous-tension Contrôlez la tension, le cas échéant, patientez jusqu'au rétablissement Défaut au niveau du fusible secteur Interrupteur principal désactivé Echangez le fusible secteur, allumez l'interrupteur principal Le câble d'alimentation est endommagé Confiez la réparation à une entreprise spécialisée Temps de blocage EVU Attendez la fin du temps de blocage EVU et le redémarrage de la thermopompe, si besoin Limites de température dépassées ou non atteintes Observez les plages de température Température de consigne dépassée mauvais mode de fonctionnement La température de consigne doit être supérieure à la température du générateur de chaleur, vérifiez le mode de fonctionnement Eteignez le module extérieur, rebranchez les bornes correctement à l'aide du schéma électrique. Remettez le module extérieur sous tension. Vérifiez également le bon raccordement des câbles de protection Pompe du circuit de chauffe ne s'arrête pas Mauvais raccordement de la pompe Vérifiez le raccordement de la pompe, au niveau spécialisé "Circuit de chauffe" Les pompes du circuit de chauffe ne se mettent pas en marche Mauvais mode de fonctionnement Vérifiez le mode de fonctionnement Fusible de la platine de commande défectueux au boîtier électrique du module intérieur Echanger le fusible côté gauche de la platine de commande Mauvais programme de chauffage Vérifiez le programme de chauffage. Nous vous recommandons, en période froide, le mode de fonctionnement "Chauffage" Mauvais écart de température, c'est à dire que la température extérieure est supérieure à la température ambiante Observez les plages de température Faute module extérieure Contacter le service client Rouge voyant de contrôle 58 15.2 Messages sur le module externe Affichage des erreurs du module externe 1 1 A B 1 : Écran d'affichage / A: WKF NEO 70 Écran d'affichage Affichage à DEL rouge vert E101 - E102 B : WKF NEO 120 et WKF NEO 180 jaune Platine Connecteur - - IM CN31 Erreur de communic. entre le module inter. et le module externe ou versions de platines incorrectes - - - IM CN31 Interruption de la communication entre IM et AM E162 - - - IM Erreur EEPROM E177 l (+) m AM Module ext. a reçu un signal d'arrêt d'urgence E201 l Z m AM CN31 Erreur de communic. entre le module inter. et le module externe ou versions de platines incorrectes E202 l l ou m m AM CN31 Interruption de la communication entre IM et AM E203 l l Z AM CN39 Erreur de communication entre la platine principale et la platine inverter E221 l Z m AM CN43 1,2 Erreur de la sonde de température extérieure E231 l Z m AM CN43 3,4 Erreur de la sonde de l'évaporateur E251 l Z m AM CN43 3,4 Erreur de la sonde de température du gaz chaud E320 l Z m AM CN43 7,8 1. Erreur sonde OLP (protect. contre surcharges) E403 l Z m AM Protection contre le gel du compresseur (uniquement pour le mode de refroidissement) E404 l Z m AM Protection contre les surcharges du compresseur (mode normal) E407 l Z m AM CN34 E416 l Z m AM CN43 E419 l Z m AM CN81 Pin Signification E237 Coupure due au pressostat haute pression 5,6 Protection contre la surchauffe du compresseur (mode normal) Défaut de la vanne d'expansion élec. Défaut d'erreur de phase. Au moins un conducteur extérieur manque (uniquement WKF NEO 180) ou EEPROM incorrect sur la platine principale (uniquement WKF NEO 120) E425 l Z m AM E440 l Z m AM CN43 1,2 Mode chauffage impos.; temp. extérieure > 35 °C E441 l Z m AM CN43 1,2 Mode de refroidis. impos. ; temp. extér. < +10 °C 59 REMKO série WKF NEO-compact Écran d'affichage Affichage à DEL jaune Platine Connecteur rouge vert E443 l Z m AM CN42 E458 m m l AM Erreur de démarrage de compresseur, surintensité ou erreur de ventilateur BLDC E461 m Z m AM La consommation électrique du compresseur n’est pas plausible (trop basse) E462 l Z m AM La consommation électrique du compresseur n’est pas plausible (trop élevée) E463 l Z m AM E464 Z m m AM Consom. électr. IPM trop élevée sur la platine inverter ou version logicielle de la platine principale E465 m l Z AM Consommation électr. compresseur trop élevée E466 Z l m AM Défaut d'alimentation en tension CA/CC E467 l m l AM Défaut d'erreur de phase. Un conducteur extérieur est manquant sur le compresseur E468 l Z Z AM Défaut du capteur de consommation électrique de la platine principale/platine inverter E469 l Z m AM Défaut du capteur de tension CC (platine inverter) E470 l Z m AM Défaut d'EEPROM (erreur de lecture) E471 l Z m AM La version EEPROM de la platine principale ne convient pas à l’inverter E472 AM Vérifier la tension d’entrée CA E473 AM Compresseur bloqué CN43 Pin Signification Erreur de fuite de gaz (avant le fonctionnement), basse pression sur capteur HD 7,8 Protection contre la surchauffe (OLP) du compresseur déclenchée (supérieure à 115 °C) E474 Z Z m AM Défaut d'IPM (module IGBT) E475 m m l AM Défaut du ventilateur BLDC 2 E484 l Z l AM Défaut de surcharge PFC (platine inverter) E485 l Z m AM Défaut de puissance absorbée totale E500 Z Z m AM Défaut de surchauffe de la platine inverter E554 l Z m AM Défaut de quantité de frigorigène E556 m m Z AM La version EEPROM de la platine principale et la version Com-Kit ne correspondent pas E901 l Z m IM CN41 1,2 Défaut du capteur de retour E902 l Z m IM CN41 5,6 Défaut du capteur d'entrée l Z m IM CN41 3,4 Défaut du capteur de conduite de liquide E904 E906 E912 EA l = allumé/Z = clignotant/m = éteint/IM = Module interne/AM = Module externe 60 15.3 Messages d'erreur du Smart-Control Messages d'exploitation, avertissements et affichage des erreurs sur le Smart-Control Messages d'exploitation ID Description Dés. ID6000 Temp. max. du ballon 1 atteinte La température au niveau de l'un des capteurs du ballon 1 est supérieure à la température de ballon maximale autorisée ID6001 Demande en eau chaude Besoin actif de charger le ballon ID6002 Thermopompe Démarrage du compresseur Thermopompe - Démarrage du compresseur ID6003 Blocage de la manœuvre (I/O2) La thermopompe a été bloquée pour réduire les commutations du compresseur ID6005 Pompe interne - Délai d'entrée La pompe interne fonctionne à vitesse réduite pendant le délai d'entrée de la pompe ID6006 Blocage de la manœuvre La thermopompe a été bloquée pour réduire les commutations du compresseur ID6007 Temps d'attente min. La thermopompe est bloquée en raison d'un temps d'attente minimal. ID6008 Signal de blocage ID6009 Signal blocage (E/S 2) La thermopompe est bloquée par un signal de blocage ID6010 Thermopompe Démarrage du compresseur (E/S 2) Thermopompe - Démarrage du compresseur ID6012 Débit volumique min. (I/O 2) Dégivrage de la thermopompe ID6020 Pompe interne - Délai de post-fonctionnement La pompe interne fonctionne à vitesse réduite pendant le délai de post-fonctionnement ID6022 Temps d’attente min. (I/O2) La thermopompe est bloquée en raison d'un temps d'attente minimal. ID6103 Demande de chauffage de la thermopompe Demande de chauffage de la thermopompe ID6104 Demande de refroidissement de la thermopompe Demande de refroidissement de la thermopompe ID6105 Dégivrage de la thermopompe Dégivrage de la thermopompe ID6107 Mode de veille actif Mode de veille actif ID6108 Temporisation aléatoire après panne de courant Temporisation aléatoire après panne de courant (jusqu'à 200 secondes après rétablissement de la tension) - L'objectif de la température aléatoire est d'éviter une charge de réseau si de nombreux consommateurs sont activés simultanément ID6109 Temp. ext. Limites d'utilisation de la thermopompe Temp. ext. Limites d'utilisation de la thermopompe - La thermopompe est bloquée en raison d'un non-respect de la plage d'utilisation S16 Détails La thermopompe est bloquée par un signal de blocage 61 REMKO série WKF NEO-compact ID Description Dés. Détails ID6111 Température bivalente de la thermopompe Température bivalente de la thermopompe - La thermopompe est bloquée car la température bivalente n'est pas atteinte ID6113 Chauffage solaire Chauffage solaire - Les générateurs de chaleur sont bloqués ID6115 Faible différence de pression La différence de pression est trop faible pour démarrer le compresseur ID6116 Temps de dégivrage maximal Temps de dégivrage maximal Erreur ID Description ID7050 Protection antigel ID7103 Séquence de phases incorrecte Dés. Détails La protection anti-gel de l'échangeur de chaleur de la thermopompe a été déclenchée sous l'effet d'une température aller trop faible. Une fois la cause de l'erreur résolue, l’erreur doit être réinitialisée sous (Experts/Paramètres/Thermopompe/ Paramètres de base) et au besoin l’unité extérieure doit être mise hors tension. µPC Séquence de phases incorrecte (champ tournant). Veuillez vérifier la séquence de phases (le champ tournant) de l’alimentation en tension. La protection anti-gel de l'échangeur de chaleur de la thermopompe a été déclenchée sous l'effet d'une température retour trop faible. Une fois la cause de l'erreur résolue, l’erreur doit être réinitialisée sous (Experts/Paramètres/Thermopompe/ Paramètres de base) et au besoin l’unité extérieure doit être mise hors tension. ID7108 Protection antigel ID7150 Erreur du moteur EEV µPC Erreur du moteur EEV. Veuillez contacter un technicien de service agréé ID7200 Contact ouvert - Ballon 1 Sonde inférieure S02 Contact ouvert - Ballon 1 Sonde inférieure ID7201 Court-circuit - Ballon 1 Sonde inférieure S02 Court-circuit - Ballon 1 Sonde inférieure ID7202 Contact ouvert - Ballon 1 Sonde du milieu S09 Contact ouvert - Ballon 1 Sonde du milieu ID7203 Court-circuit - Ballon 1 Sonde du milieu S09 Court-circuit - Ballon 1 Sonde du milieu ID7204 Contact ouvert - Ballon 1 Sonde supérieure S08 Contact ouvert - Ballon 1 Sonde supérieure ID7205 Court-circuit - Ballon 1 Sonde supérieure S08 Court-circuit - Ballon 1 Sonde supérieure ID7206 Contact ouvert - Sonde d'extérieur S10 Contact ouvert - Sonde d'extérieur ID7207 Court-circuit Sonde d’extérieur S10 Court-circuit - Sonde d'extérieur ID7208 Contact ouvert - Sonde de frigorigène S07 Contact ouvert - Sonde de frigorigène 62 ID Description Dés. Détails ID7209 Court-circuit - Sonde de frigorigène S07 Court-circuit - Sonde de frigorigène ID7210 Contact ouvert - Sonde de temp. de circulation S05 Contact ouvert - Sonde de température de circulation d'eau potable ID7211 Court-circuit - Sonde de temp. de circulation S05 Court-circuit - Sonde de température de circulation d'eau potable ID7212 Contact ouvert - Sonde de temp. aller S13 Contact ouvert - Sonde de temp. aller ID7213 Contact de court-circuit - Sonde de temp. aller S13 Contact de court-circuit - Sonde de temp. aller ID7214 Temp. min. du frigorigène S07 La température minimale du frigorigène n’est pas atteinte. Protection anti-gel de l'échangeur de chaleur. ID7215 Temp. min. du frigorigène (I/O2) S07.2 ID7218 Contact ouvert Collecteur 1 Sonde S01 Contact ouvert - Collecteur 1 Sonde ID7219 Court-circuit Collecteur 1 Sonde S01 Court-circuit - Collecteur 1 Sonde ID7228 Contact ouvert - Sonde de temp. aller S13.2 Contact ouvert - Sonde de temp. aller ID7229 Contact de court-circuit - Sonde de temp. aller S13.2 Contact de court-circuit - Sonde de temp. aller La température minimale du frigorigène (I/O2) n’est pas atteinte. Protection anti-gel de l'échangeur de chaleur. La protection antigel de l'échangeur thermique de la thermopompe a été déclenchée sous l'effet d'une température aller inférieure à 5 °C. Une fois la cause de l'erreur résolue, le régulateur doit être redémarré afin de réinitialiser l'erreur ID7231 Protec. antigel (E/S 2) ID7236 Contact ouvert - Sonde de temp. aller du circuit de chauffe mixte S12 Contact ouvert - Sonde de température aller du circuit mixte ID7237 Court-circuit - Sonde de temp. aller du circuit de chauffe mixte S12 Court-circuit - Sonde de température aller du circuit mixte ID7238 Contact ouvert - Sonde de temp. retour du circuit de chauffe mixte S11 Contact ouvert - Sonde de température retour du circuit mixte ID7239 Court-circuit - Sonde de temp. retour du circuit de chauffe mixte S11 Court-circuit - Sonde de température retour du circuit mixte ID7240 Connexion à l'interface KNX KNX Connexion perdue à l’interface KNX IP ID7241 Différence de temp. négative µPC Une différence de température n'est pas plausible lorsque le générateur de chaleur est actif. ID7245 Tunnel occupé KNX Le tunnel présentant l’adresse physique définie dans le régulateur (PA du SMT) est déjà occupé par un autre appareil KNXnet/IP (par exemple : PC ETS) ou n’est pas disponible sur l’interface. ID7246 Basse pression µPC Le compresseur est bloqué en raison d'un défaut de basse pression. 63 REMKO série WKF NEO-compact ID Description Dés. Détails ID7247 Appareil hors ligne µPC Appareil hors ligne - Veuillez vérifier la liaison de données entre la platine du régulateur et l'inverter ID7248 L’interface n’est pas prise en charge KNX Le protocole KNXnet/IP Tunneling n’est pas pris en charge par l’interface KNX détectée. ID7249 Interface incorrecte détectée KNX L’adresse physique de l’interface KNXnet/IP détectée ne correspond pas à la configuration du régulateur SMT. ID7250 Débit volumique min. (I/O 2) Le débit volumique minimal de la thermopompe n'a pas été atteint pendant un dégivrage ou en mode de refroidissement. Une fois la cause de l'erreur résolue, le régulateur doit être redémarré afin de réinitialiser l'erreur ID7251 Débit volumique min. Le débit volumique minimal de la thermopompe n'a pas été atteint pendant un dégivrage ou en mode de refroidissement. Une fois la cause de l'erreur résolue, les modules interne et externe doivent être redémarrés afin de réinitialiser l'erreur ID7252 Message d'erreur de la thermopompe ID7253 Message d'erreur de la thermopompe 2 ID7254 Erreur générale de l'inverter µPC Erreur générale de l'inverter - Veuillez contacter un technicien de service agréé ID7255 Erreur EEPROM µPC Erreur EEPROM. Veuillez contacter un technicien de service agréé ID7256 Erreur Envelope µPC Erreur Envelope - Le compresseur fonctionne hors de la courbe programmée. Veuillez contacter un technicien de service agréé ID7257 Surcharge de l'aérateur µPC Le compresseur est bloqué par une surcharge de l'aérateur ID7258 Température maximale du gaz chaud µPC Température maximale du gaz chaud - Le compresseur se bloque lorsque la température maximale du gaz chaud est atteinte ID7259 Défaut de haute pression µPC Défaut de haute pression. Si cette erreur se répète souvent, veuillez contacter un technicien de service agréé ID7260 Défaut de haute pression du transducteur µPC Le compresseur est bloqué en raison d'un défaut de haute pression ID7262 Erreur capteur de température extérieure µPC Erreur capteur de température extérieure. Veuillez vérifier le capteur de température extérieure de la platine de l'inverter et son branchement ID7264 Erreur du capteur de température d’entrée µPC Erreur du capteur de température d'entrée. Veuillez vérifier le capteur de température d’entrée de la platine de l'inverter et son branchement ID7267 Erreur du capteur de température de sortie µPC Erreur du capteur de température de sortie. Veuillez vérifier le capteur de température de sortie de la platine de l'inverter et son branchement ID7269 Erreur du capteur de température de gaz chaud µPC Erreur du capteur de température de gaz chaud. Veuillez vérifier le capteur de température de gaz chaud de la platine de l'inverter et son branchement. ID7270 Erreur du capteur de température de gaz d’aspiration µPC Erreur du capteur de température de gaz d’aspiration. Veuillez vérifier le capteur de température de gaz d’aspiration de la platine de l'inverter et son branchement. 64 S20 Message d'erreur de la thermopompe S20.2 Message d'erreur de la thermopompe 2 ID Description Dés. Détails ID7271 Erreur du capteur de haute pression µPC Erreur du capteur de haute pression. Veuillez vérifier le capteur de haute pression de la platine de l'inverter et son branchement. ID7272 Erreur du capteur de basse pression µPC Erreur du capteur de basse pression. Veuillez vérifier le capteur de basse pression de la platine de l'inverter et son branchement. ID7273 Code d'erreur WKF E101 Erreur de communication entre Com-Kit et le module extérieur. F1/F2 tordu ou rupture de câble ID7274 Code d'erreur WKF E177 Le compresseur a été arrêté par un signal d'arrêt d'urgence. Une fois la cause de l'erreur résolue, les modules interne et externe doivent être redémarrés afin de réinitialiser l'erreur ID7275 Code d'erreur WKF E221 Court-circuit ou contact ouvert - Sonde de température de l'air ambiant Platine principale du module externe CN43 broches 1&2 ID7276 Redémarrage nécessaire En raison d'un changement de système (réglage/résistance de codage), un redémarrage du régulateur est nécessaire - déconnexion de l'alimentation en tension pendant env. 10 secondes ID7278 Faible surchauffe Le compresseur est bloqué par une surchauffe trop faible. ID7283 Contact ouvert - Sonde de temp. retour interne S15 Contact ouvert - Sonde de température retour interne ID7284 Court-circuit - Sonde de température retour interne S15 Court-circuit - Sonde de température retour interne ID7285 Faible température du gaz d'aspiration µPC Le compresseur est bloqué par une température de gaz d'aspiration trop faible ID7286 Erreur de codage Rc En raison de la résistance de codage au niveau de la borne Rc, aucune identification d'appareil unique n'a pu être affectée ID7287 Faible température d'évaporation µPC Le compresseur est bloqué en raison d'une température d'évaporation trop faible ID7288 Température d'évaporation élevée µPC Le compresseur est bloqué en raison d'une température d'évaporation trop élevée ID7289 Température de condensation élevée µPC Le compresseur est bloqué en raison d'une température de condensation trop élevée ID7290 Code d'erreur WKF E102 Erreur de communication entre Com-Kit et le module extérieur. F1/F2 tordu ou rupture de câble ID7291 Code d'erreur WKF E201 Erreur de communication entre Com-Kit et le module externe L'établissement de la liaison a échoué ou le platine ne présente pas la bonne version ID7292 Code d'erreur WKF E231 Court-circuit ou contact ouvert - Sonde de température de l'évaporateur Platine principale du module externe CN43 broches 3&4 ID7293 Code d'erreur WKF E251 Court-circuit ou contact ouvert - Sonde de température du gaz chaud Platine principale du module externe CN43 broches 5&6 ID7294 Code d'erreur WKF E320 Court-circuit ou contact ouvert - Sonde de protection contre les surcharges (OLP) Platine principale du module externe CN43 broches 7&8 ID7295 Code d'erreur WKF E416 Le compresseur a été arrêté par le dispositif de protection contre les surchauffes 65 REMKO série WKF NEO-compact ID Description Dés. Détails ID7296 Contact ouvert - Temp. retour du 2e circuit de chauffe mixte S14 Contact ouvert - Temp. retour du 2e circuit mixte ID7297 Court-circuit - Temp. retour du 2e circuit de chauffe mixte S14 Court-circuit - Temp. retour du 2e circuit mixte ID7298 Contact ouvert - Temp. aller du 3e circuit de chauffe mixte S12.2 Contact ouvert - Temp. aller du 3e circuit mixte ID7299 Court-circuit - Temp. aller du 3e circuit de chauffe mixte S12.2 Court-circuit - Temp. Aller du 3e circuit mixte ID7300 Contact ouvert - Temp. retour du 3e circuit de chauffe mixte S11.2 Contact ouvert - Temp. retour du 3e circuit mixte ID7301 Court-circuit - Temp. retour du 3e circuit de chauffe mixte S11.2 Court-circuit - Temp. retour du 3e circuit mixte ID7302 Contact ouvert - Temp. aller du 4e circuit de chauffe mixte S06.2 Contact ouvert - Temp. aller du 4e circuit mixte ID7303 Court-circuit - Temp. aller du 4e circuit de chauffe mixte S06.2 Court-circuit - Temp. aller du 4e circuit mixte ID7304 Contact ouvert - Temp. retour du 3e circuit de chauffe mixte S14.2 Contact ouvert - Temp. retour du 4e circuit mixte ID7305 Court-circuit - Temp. retour du 4e circuit de chauffe mixte S14.2 Court-circuit - Temp. retour du 4e circuit mixte ID7306 Contact ouvert - Sonde de frigorigène (E/S 2) S07.2 Contact ouvert - Sonde de frigorigène (E/S 2) ID7307 Court-circuit - Sonde de S07.2 Court-circuit - Sonde de frigorigène (E/S 2) frigorigène (E/S 2) ID7308 Code d'erreur WKF E464 Surintensité au niveau du module d'inverter IPM (module de transistor IGBT). Vérifier la version du logiciel de la platine principale ID7309 Code d'erreur WKF E425 Défaut erreur de phase, un conducteur extérieur est manquant au niveau du convertisseur de fréquence (uniquement possible sur WKF NEO 180 - vérifier la version du logiciel de la platine principale) ID7310 Code d'erreur WKF E203 Erreur de communication entre la platine principale (affichage à 7 segments) et la platine d'inverter ID7311 Code d'erreur WKF E466 Sous-tension ou surtension au niveau du circuit intermédiaire de tension continue du convertisseur de fréquence. ID7312 Code d'erreur WKF E469 Défaut du capteur de tension au niveau du circuit intermédiaire de tension continue du convertisseur de fréquence - au besoin, remplacer la platine de l'inverter 66 ID Description Dés. Détails ID7313 Code d'erreur WKF E458 Courant élevé non plausible au niveau du capteur de courant ou défaut au niveau du moteur BLDC de l'aérateur 1. ID7314 Code d'erreur WKF E475 Défaut du moteur BLDC de l'aérateur 2 ID7315 Code d'erreur WKF E461 Courant faible non plausible au niveau du capteur de courant de la platine de l'inverter au démarrage du compresseur (peut être dû à un endommagement du compresseur) ID7316 Code d'erreur WKF E467 Conducteur extérieur (phase) manquant au niveau du compresseur ID7317 Code d'erreur WKF E462 Erreur de surintensité (côté primaire) - Alimentation en tension/ vérifier le fusible de la platine EMI ID7318 Code d'erreur WKF E463 Température excessive du compresseur (OLP). Valeur de la sonde supérieure à 115 °C (inférieure à 12,7 kohm). Peut être provoqué par le serrage de la vanne d'expansion ID7319 Code d'erreur WKF E554 Défaut de quantité de frigorigène/perte de frigorigène ID7320 Code d'erreur WKF E556 Les indications de puissance de la platine Com-Kit (IM) et de la platine principale (AM) ne concordent pas - Vérifier les versions des platines. ID7328 Contact ouvert - Temp. aller du 2e circuit de chauffe mixte S06 Contact ouvert – Temp. Aller du 2e circuit mixte ID7329 Court-circuit - Temp. aller du 2e circuit de chauffe mixte S06 Court-circuit – Temp. Aller du 2e circuit mixt µPC La protection anti-gel de l'échangeur de chaleur de la thermopompe a été déclenchée sous l'effet d'une température aller trop faible. Une fois la cause de l'erreur résolue, le régulateur doit être redémarré afin de réinitialiser l'erreur. ID7332 Protection antigel ID7333 Différence de temp. négative Une différence de température n'est pas plausible lorsque le générateur de chaleur est actif ID7334 Signal comm. La communication entre l'unité de commande SMT 1 et l'unité de puissance SMT 1 E/S a été interrompue. Avertissements ID Description ID8100 Température du système trop faible La température du système est trop faible pour permettre le démarrage de la thermopompe. ID8102 Écart de température dans le circuit solaire La température du collecteur est au moins 60 K supérieure à la température du ballon Température du collecteur la nuit La nuit, une température de collecteur d'au moins 45 °C est survenue Débit volumique de consigne La valeur actuelle n'atteint pas le débit volumique de consigne ID8103 ID8105 Dés. Détails 67 REMKO série WKF NEO-compact ID Description ID8107 Statut du compresseur ID8108 Erreur de démarrage du compresseur µPC Erreur de démarrage du compresseur ID8109 Erreur de la sonde EVD EVO µPC Erreur de la sonde EVD EVO ID8110 Pilote hors ligne µPC Pilote hors ligne ID8132 Protection anti-gel active La protection anti-gel est active pour l'instant - Vérifiez le mode de climat ambiant réglé ID8138 Temp. de consigne du ballon d'eau chaude La température de consigne du ballon d'eau chaude a baissé en raison de basses températures extérieures ID8139 Plage d'utilisation inférieure (chauffage) La plage d'utilisation garantie de l'unité extérieure en mode de chauffage n'est pas atteinte pour l'instant ID8140 Plage d'utilisation supérieure (chauffage) La plage d'utilisation garantie de l'unité extérieure en mode de chauffage est dépassée pour l'instant ID8141 Plage d'utilisation inférieure (refroidissement) La plage d'utilisation garantie de l'unité extérieure en mode de refroidissement n'est pas atteinte pour l'instant ID8142 Plage d'utilisation supérieure (refroidissement) La plage d'utilisation garantie de l'unité extérieure en mode de refroidissement est dépassée pour l'instant ID8144 Débit volumique de consigne (E/S 2) La valeur actuelle n'atteint pas le débit volumique de consigne ID8223 Erreur de carte SD (hôte) Erreur de carte SD (hôte) : La carte SD n'est pas insérée correctement ou une erreur est survenue ID8224 Erreur de carte SD Erreur de carte SD (CP) : La carte SD n'est pas insérée ou une erreur est survenue ID8225 Surveillance du point de rosée Le contrôle du point de rosée a été activé. Cependant, aucun ControlPanel (avec sonde d'humidité et de température) n'a été associé au circuit de refroidissement afin de calculer le point de rosée ID8226 Température aller min. pas atteinte Température aller min. (ou point de rosée) pas atteinte Demande de refroidissement supprimée ID8227 Fonction d'hygiène : Valeur de consigne pas atteinte La fonction d'hygiène a été interrompue, le temps de fonctionnement maximal ayant été atteint avant que la température de consigne n'ait été atteinte ID8229 2. générateur de chaleur actif Une température de retour insuffisante pendant un dégivrage a activé le 2e générateur de chaleur 68 Dés. Détails Le mode de sécurité est activé étant donné que le compresseur est actif sans avoir été sollicité CP 16 16.1 Représentation de l'appareil et pièces de rechange Représentation de l'appareil Module externe WKF NEO 70 10 12 7 14 2 5 4b 3 16 4a 20 9 8 1 15 13 10 11 18 19 17 Fig. 57: Vue éclatée du module extérieur WKF NEO 70 69 REMKO série WKF NEO-compact 16.2 Pièces de rechange du module externe WKF NEO 70 N° Désignation 1 Compresseur 2 Échangeur thermique à lamelles 3 Vanne d'inversion à 4 voies 4 Vannes d'arrêt 5 Ailette du ventilateur 6 Plaque de recouvrement 7 Tôle latérale, gauche 8 Grille de protection du ventilateur 9 Tôle frontale 10 Cache écran 11 Tôle latérale, droite 12 Grille, arrière 13 Plaque de montage de vanne 14 Moteur de ventilateur 15 Capteur ensemble évaporateur / compresseur gaz chaud / température extérieure 16 Détendeur électronique 17 Plaque principale avec écran 18 Platine inverter 19 F1/F2 Filtre 20 Étrangleur WKF NEO 70 Sur demande en indiquant le numéro de série Pour les commandes de pièces de rechange, précisez la référence mais également le numéro de l'appareil et le type d'appareil (voir la plaque signalétique) ! 70 16.3 Représentation de l'appareil Module externe WKF NEO 120 6 12 18 19 11 2 14 17 5 3 7 16 13 4 1 8 15 20 9 10 Fig. 58: Vue éclatée du module extérieur WKF NEO 120 Nous nous réservons le droit d’apporter des modifications de cotes et de construction susceptibles de servir au progrès technique. 71 REMKO série WKF NEO-compact 16.4 Pièces de rechange du module externe WKF NEO 120 N° Désignation 1 Compresseur 2 Échangeur thermique à lamelles 3 Vanne d'inversion à 4 voies 4 Vannes d'arrêt 5 Ailette du ventilateur 6 Plaque de recouvrement 7 Tôle latérale, avant gauche 8 Grille, avant 9 Tôle latérale, avant droite 10 Coin de montage, avant droite 11 Tôle latérale, arrière droite 12 Grille, arrière 13 Coin de montage, arrière droite 14 Moteur de ventilateur 15 Jeu de capteurs de l'évaporateur/ capteurs du compresseur 15 Jeu de capteurs de gaz chaud/ capteurs de température extérieure 16 Détendeur électronique 17 Plaque principale avec écran 18 Platine inverter 19 Platine EMI 20 Fond de l’appareil / bac à condensat WKF NEO 120 Sur demande en indiquant le numéro de série Pièces de rechange sans illustration Étrangleur Sur demande en indiquant le numéro de série Pour les commandes de pièces de rechange, précisez la référence mais également le numéro de l'appareil et le type d'appareil (voir la plaque signalétique) ! 72 16.5 Représentation de l'appareil Module externe WKF NEO 180 6 12 2 16 20 18 19 11 14 3 5 7 4 8 17 1 13 21 10 9 15 Fig. 59: Vue éclatée du module extérieur WKF NEO 180 Nous nous réservons le droit d'apporter des modifications de cotes et de construction susceptibles de servir au progrès technique 73 REMKO série WKF NEO-compact 16.6 Pièces de rechange du module externe WKF NEO 180 N° Désignation 1 Compresseur 2 Échangeur thermique à lamelles 3 Vanne d'inversion à 4 voies 4 Vannes d'arrêt 5 Ailette du ventilateur 6 Plaque de recouvrement 7 Tôle latérale, avant gauche 8 Grille, avant 9 Tôle latérale, avant droite 10 Coin de montage, avant droite 11 Tôle latérale, arrière droite 12 Grille, arrière 13 Coin de montage, arrière droite 14 Moteur de ventilateur 15 Jeu de capteurs de l'évaporateur/ capteurs du compresseur 15 Jeu de capteurs de gaz chaud/ capteurs de température extérieure 16 Étrangleur 17 Détendeur électronique 18 Plaque principale avec écran 19 Platine inverter 20 Platine EMI 21 Fond de l’appareil / bac à condensat WKF NEO 180 Sur demande en indiquant le numéro de série Pour les commandes de pièces de rechange, précisez la référence mais également le numéro de l'appareil et le type d'appareil (voir la plaque signalétique) ! 74 16.7 Représentation de l'appareil Modules internes WKF NEO compact 12 2a 2b 6 11 15a 15 15b 13 16a 16b 3 7 8 9 10 1a 1b 14 4 17 5 18 Fig. 60: Vue éclatée du module interne WKF NEO compact Nous nous réservons le droit d’apporter des modifications de cotes et de construction susceptibles de servir au progrès technique. 75 REMKO série WKF NEO-compact 16.8 Pièces de rechange des modules internes WKF NEO compact 70/120/180 N° Désignation 1a Tôle frontale / capot - variante 200 l 1b Tôle frontale / capot - variante 300 l 2a Capot - variante 200 l 2b Capot - variante 300 l 3 Smart-Control Touch, installé 4 Échangeur thermique à plaques 5 Filtre 1" 6 Module SMT E/S 7 Relais Smart-Serv 6 kW 8 Transformateur de platine Comkit 9 Platine de commande Comkit 10 Chauffage d’appoint STB 11 Débitmètre 12 Servomoteur - vanne 3 voies 13 Corps de vanne 3 voies 14 Chauffage d’appoint 6 kW (Smart-Serv) 15 Vanne de dérivation complète 16a Ballon d’eau potable 200 l 16b Ballon d’eau potable 300 l 17 Pompe de recirculation Grundfos UPML 18 Robinet KFE 1/2" 76 WKF NEO compact 70/120/180 Sur demande en indiquant le numéro de série Pièces de rechange sans illustration Désignation WKF NEO compact 70/120/180 Conduite d'eau froide en acier inoxydable Conduite d'eau chaude en acier inoxydable Module électrique complet Vanne de sécurité 1/2" Anode-tige Anode-chaîne Carte SD module I/O (logiciel actuel sans Smart-Count et sans Smart-Web) *) Sur demande en indiquant le numéro de série Carte SD Smart-Control Touch (logiciel actuel sans Smart-Count et sans Smart-Web) *) Résistance de codage Capteur Pt1000 (S08) Capteur Pt1000 (S13) Capteur Pt1000 (S15) *) En cas de remplacement de la carte SD, remplacez toujours les deux cartes et commander 2 cartes en conséquence. Composants du kit d'accessoires (non illustrés) Désignation WKF NEO compact Kit complet d'accessoires Sonde à immerger Robinet à boisseau sphérique 1“, rouge Robinet à boisseau sphérique 1“, bleu Sur demande en indiquant le numéro de série Groupe de sécurité Sonde d'extérieur Pour les commandes de pièces de rechange, précisez la référence mais également le numéro de l'appareil et le type d'appareil (voir la plaque signalétique) ! 77 REMKO série WKF NEO-compact 17 Terminologie générale Appareil monobloc Forme de construction pour laquelle tous les composants de technique frigorifique sont montés dans un boîtier.Aucune opération de technique frigorifique ne doit être effectuée. Arrêt EVU Votre distributeur d'énergie (EVU) vous propose des tarifs spéciaux pour l'utilisation de pompes à chaleur. Lorsque la coupure des entreprises d'alimentation uniquement sur la barrière est en condition de contact que d'une source de chaleur (pompe à chaleur) est bloqué. Être éteint au fonctionnement monoénergétique, l'alimentation de l'élément de chauffage électrique avec. Ballon tampon Nous recommandons systématiquement l'utilisation d"un ballon tampon d'eau pour augmenter le temps de fonctionnement de la thermopompe lors de faibles besoins en chaleur. Sur les thermopompes air/eau, l'utilisation d'un ballon tampon est nécessaire pour compenser les temps de blocage. Condenseur Echangeur thermique d'une installation de froid qui restitue l'énergie calorifique à l'environnement (par exemple au réseau de chauffage) par condensation d'un fluide de travail. Contrôle d'étanchéité Conformément au décret sur les produits chimiques et la couche d'ozone (EU-VO 2037/2000) ainsi que le décret sur le gaz F (EU-VO 842/2006), tous les exploitants d'installation de froid et de climatisation ont l'obligation d'empêcher toute émanation de frigorigène. Ils doivent, de plus, effectuer une maintenance, ou une révision, annuelle ainsi qu'un contrôle d'étanchéité des installations de froid avec un volume de remplissage de frigorigène supérieur à 3kg. Dégivrage Lors de températures extérieures inférieures à 5°C, de la glace peut se former sur l'évaporateur des thermopompes air/eau. Son élimination est nommée dégivrage et est effectuée soit par intervalle, soit au besoin, par apport de chaleur. Les thermopompes air/eau à inversion de circuit sont caractérisées par un dégivrage correspondant au besoin, rapide et efficient en énergie. Besoins annuels Évaporateur Les besoins annuels correspondent au besoin (p.ex. énergie électrique) nécessaire pour couvrir une utilisation définie (p.ex. énergie de chauffage). Les besoins annuels contiennent également l'énergie des entraînements auxiliaires. Les besoins annuels sont calculés en fonction de la Directive VDI 4650. Echangeur thermique d'une installation de froid qui absorbe l'énergie calorifique de l'environnement par évaporation d'un fluide de travail (par exemple l'air extérieur), à faible température. Calcul du besoin en chaleur Un bon dimensionnement est indispensable pour augmenter l'efficience des thermopompes. La détermination du besoin en chaleur répond à des normes spécifiques au pays. Vous trouverez le besoin en chaleur d'un bâtiment dans le tableau W/m² puis multiplié par la surface habitable à chauffer. Le résultat donne le besoin global en chauffage qui contient également le besoin en transmission et en ventilation de chaleur. Compresseur Agrégat de transport et de compression de gaz. La compression fait augmenter la pression et la température du fluide de manière significative. 78 Frigorigène Le fluide de travail d'une installation de froid, p.ex. une thermopompe, est appelé frigorigène. Le frigorigène est un fluide utilisé pour la transmission de chaleur dans une installation de froid et absorbant, à basse température et basse pression, la chaleur par modification de l'état de l'agrégat Lors de fortes températures et de haute pression, c'est de la chaleur qui est émise par une nouvelle modification de l'état de l'agrégat. Fonctionnement bivalent La thermopompe fournit la totalité de la chaleur de chauffage jusqu'à une température extérieure définie (p.ex. 0°C). Lorsque la température descend en-dessous de cette valeur, la thermopompe s'arrête et le deuxième générateur d'énergie, comme une chaudière, p.ex., prend le relais du chauffage. Fonctionnement mono-énergétique Performances annuelles La thermopompe couvre la majeure partie des besoins en chauffage. Pendant quelques jours, lors de températures extérieures très basses, une résistance électrique complète la thermopompe. Le dimensionnement de la thermopompe est généralement effectué, en ce qui concerne les thermopompes air/eau, sur une température limite (également appelée point de bivalence) d'env. -5°C. Relation entre la quantité de chaleur émise par l'installation de thermopompe et l'énergie électrique apportée dans l'année correspond aux performances annuelles. Elles ne doivent pas être confondues avec les performances. Les performances annuelles correspondent à la valeur inversée des besoins annuels. Fonctionnement monovalent Dans ce mode de fonctionnement, la thermopompe couvre les besoins en chaleur du bâtiment pendant toute l'année. Ce sont en général les thermopompes saumure/eau ou eau/eau qui sont utilisées pour ce mode de fonctionnement. Réglementations et directives Seuls des spécialistes qualifiés sont habilités à poser, installer et mettre en service les thermopompes. Ils doivent, pour ce faire, respecter différentes normes et décrets. Rendement de froid Installation de pompe à chaleur Une installation de pompe à chaleur se compose d'une pompe à chaleur et d'une installation de source de chaleur. Sur les pompes à chaleur saumure/eau et eau/eau, l'installation de source de chaleur doit être raccordée séparément. Inverter Régulation de puissance qui adapte la vitesse de rotation du moteur du compresseur et du ventilateur de l'évaporateur au besoin en chauffage. Flux de chaleur absorbé dans l'évaporateur de l'environnement (air, eau ou terre). Source de chaleur Moyen duquel de la chaleur est absorbée par la thermopompe, donc terre, air et eau. Support de chaleur Moyen liquide ou gazeux (p.ex. eau, saumure ou air) transportant la chaleur. Niveau sonore Température limite / point de bivalence Le niveau sonore est une caractéristique comparable de rendement acoustique d'une machine, par exemple, d'une thermopompe. Le niveau d'immiscion d'écho peut être mesuré à des distances définies et dans un environnement sonore. La norme prévoit le niveau sonore comme une caractéristique de bruyance. Température extérieure à laquelle le 2ème générateur d'énergie est démarré lors d'un fonctionnement bivalent. Performances La relation momentanée entre le rendement de chaleur émis par la thermopompe et l'électricité absorbée sont appelées performances, elles sont mesurée en laboratoire dans des conditions cadres normalisées, conformément à la norme EN 255 / EN 14511. Une performance de 4 signifie que la chaleur disponible est 4 fois supérieure à la charge électrique utilisée. Vanne d'expansion Composant de la thermopompe destiné à baisser la température de liquéfaction sur la pression d'évaporation. La vanne d'expansions régule également la quantité de frigorigène injecté en fonction de la charge de l'évaporateur. 79 REMKO série WKF NEO-compact 18 Index A P Appoint de frigorigène . . . . . . . . . . . . . . . . . . . . 54 Architecture du système . . . . . . . . . . . . 35, 36, 37 Average condition . . . . . . . . . . . . . . . . . . . . . . . 10 Pompe de chargement, Caractéristiques . . . . . 15 Pompe de chargement, Disjoncteur-protecteur 15 Protection de l‘environnement . . . . . . . . . . . . . . . 7 B R Besoin en chaleur transmise . . . . . . . . . . . . . . . 30 Besoin en chaleur ventilée . . . . . . . . . . . . . . . . 30 Raccord pour condensat et dérivation sécurisée . . . . . . . . . . . . . . . . . . . . . . . . . . . . . . . . . 43 Recherche des erreurs Messages du Smart-Control . . . . . . . . . . . . . 61 Messages sur le module externe . . . . . . . . . 59 Recyclage . . . . . . . . . . . . . . . . . . . . . . . . . . . . . . 7 Refroidissement dynamique . . . . . . . . . . . . . . . 33 refroidissement pompe à chaleur . . . . . . . . . . . 46 Refroidissement statique . . . . . . . . . . . . . . . . . . 33 C Chauffage Chauffage économique . . . . . . . . . . . . . . . . 28 Chauffage respectant l'environnement . . . . . 28 Coefficient de passage de chaleur . . . . . . . . . . 30 Coefficient de performance . . . . . . . . . . . . . . . . . 9 Colder condition . . . . . . . . . . . . . . . . . . . . . . . . 10 Commande de pièces de rechange . . . . 70, 72, 74 Contrôle de l'étanchéité . . . . . . . . . . . . . . . . . . . 52 COP . . . . . . . . . . . . . . . . . . . . . . . . . . . . . . . . . . 9 S Fonction de l’écran . . . . . . . . . . . . . . . . . . . . . . 56 Sécurité Consignes de sécurité à l'attention de l'exploitant . . . . . . . . . . . . . . . . . . . . . . . . . . . . . . 6 Consignes de sécurité à observer durant les travaux de inspection . . . . . . . . . . . . . . . . 6 Consignes de sécurité à observer durant les travaux de maintenance . . . . . . . . . . . . . . 6 Consignes de sécurité à observer durant les travaux de montage . . . . . . . . . . . . . . . . . 6 Consignes générales . . . . . . . . . . . . . . . . . . . 5 Dangers en cas de non-respect des consignes de sécurité . . . . . . . . . . . . . . . . . . . . . . . 5 Identification des remarques . . . . . . . . . . . . . 5 Qualifications du personnel . . . . . . . . . . . . . . 5 Transformation arbitraire et fabrication de pièces de rechange . . . . . . . . . . . . . . . . . . . . 6 Travail en toute sécurité . . . . . . . . . . . . . . . . . 6 Sorties de tuyau du module interne, dimensions . . . . . . . . . . . . . . . . . . . . . . . . . . . . . . 12, 13 G T Garantie . . . . . . . . . . . . . . . . . . . . . . . . . . . . . . . 7 Gaz à effet de serre conformément au protocole de Kyoto . . . . . . . . . . . . . . . . . . . . . . . . . . . 9 Taux de renouvellement d'air . . . . . . . . . . . . . . . Thermopompe Dimensionnement . . . . . . . . . . . . . . . . . . . . Exemple . . . . . . . . . . . . . . . . . . . . . . . . . . . . Fonctionnement de la thermopompe . . . . . . Modes de fonctionnement . . . . . . . . . . . . . . Propriétés de la thermopompe inverter . . . . D Dépannage dépannage général . . . . . . . . . . . . . . . . . . . 58 Diagramme de puissance calorifique . . . . . . . . . 31 Distances minimales des modules externes . . . 42 E Éléments de commande, aperçu . . . . . . . . . . . . 56 Embouts de tuyaux sur le module interne, agencement . . . . . . . . . . . . . . . . . . . . . . . . 12, 13 Évacuation . . . . . . . . . . . . . . . . . . . . . . . . . . . . 52 Évacuation sécurisée en présence de fuites . . . 44 F I Intensité sonore . . . . . . . . . . . . . . . . . . . 16, 17, 18 M Mise au rebut de l‘emballage . . . . . . . . . . . . . . . 7 Mise au rebut des appareils . . . . . . . . . . . . . . . . 7 Mode Refroidissement . . . . . . . . . . . . . . . . . . . 33 Montage Module externe . . . . . . . . . . . . . . . . . . . . . . 40 Semelle filante . . . . . . . . . . . . . . . . . . . . . . . 43 N Niveau sonore total . . . . . . . . . . . . . . . . 16, 17, 18 80 30 30 30 29 30 31 U Utilisation conforme . . . . . . . . . . . . . . . . . . . . . . . 6 W Warmer condition . . . . . . . . . . . . . . . . . . . . . . . 10 81 REMKO série WKF NEO-compact 82 REMKO SYSTÈMES DE QUALITÉ REMKO GmbH & Co. KG Klima- und Wärmetechnik Téléphone +49 (0) 5232 606-0 Télécopieur +49 (0) 5232 606-260 Hotline Allemagne +49 (0) 52 32 606-0 Im Seelenkamp 12 32791 Lage Courriel Internet Hotline International +49 (0) 5232 606-130 [email protected] www.remko.de Sous réserve de modifications techniques, informations non contractuelles ! Climat | Chaleur | Nouvelles énergies ">
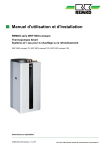
Enlace público actualizado
El enlace público a tu chat ha sido actualizado.