STEMMER IMAGING CapaCam Manuel utilisateur
Vous trouverez ci-dessous de brèves informations sur CapaCam Système de contrôle de surface. Ce système de contrôle de surface détecte les pores, les retassures et les défauts sur des pièces moulées complexes. Il permet le contrôle exhaustif de la qualité, en intégrant le contrôle au processus de production. Se distinguant grâce à ses temps de contrôle très réduits et une résolution élevée, ce système est par ailleurs configuré pour l'inspection d'une multitude de types de pièces.
PDF
Télécharger
Document
> Contrôle de qualité DOMAINE D'APPLICATION > INDUSTRIE AUTOMOBILE > Contrôle de surface à grande vitesse pour pièces moulées complexes Le système de contrôle CapaCam, de l’Institut Fraunhofer IIS pour circuits intégrés, situé à Erlangen, détecte les pores, les retassures et les défauts sur des pièces moulées de formes complexes. Un tel système vérifie, chaque jour, plusieurs milliers de carters de convertisseurs, de Daimler AG. La forte pression, exercée sur les coûts dans le secteur de l’industrie automobile et de ses fournisseurs, ainsi que la contrainte de qualité «zéro défaut», poussent de plus en plus les fabricants à se doter de systèmes de contrôle optique automatisés, intégrés aux lignes de fabrication. C’est particulièrement vrai dans le domaine de la production et de l’usinage de pièces moulées en fonte, entrant dans la composition de nombreuses pièces montées sur les véhicules, comme les transmissions, les moteurs ou les châssis. L’institut Fraunhofer IIS, situé à Erlangen, travaille depuis de nombreuses années dans le domaine du traitement industriel de l’image. Ses chercheurs, du département «Traitement de l’image et technique médicale», ont développé le système CapaCam, dédié au contrôle des surfaces de pièces moulées. Cette solution, entièrement automatisée, permet d’inspecter toutes sortes de surfaces et d’alésages de pièces et, par conséquent, de réaliser un contrôle exhaustif de la qualité, en intégrant le contrôle au processus de production. Se distinguant, grâce à ses temps de contrôle très réduits et une résolution élevée, ce système est par ailleurs configuré pour l’inspection d’une multitude de types de pièces. En outre, sa fiabilité Photo 1: Inspection optique du carter de convertisseur d’une transmission automatique est maximale, même si les surfaces sont « difficiles » en raison de leur géométrie ou de leurs caractéristiques. Depuis plusieurs mois, le système CapaCam est utilisé chez Daimler AG, plus précisément à l’usine de Hedelfingen, en Allemagne, pour vérifier quotidiennement plusieurs milliers de pièces, fabriquées par des équipes travaillant en trois huit. La majeure partie des composants du système de traitement d’image a été fournie par STEMMER IMAGING. > Des tâches de contrôle indispensables Parmi les objets-types à contrôler, on trouve les carters de convertisseurs, comme ceux montés dans les transmissions automatiques pour véhicules de tourisme (photo 1). Le composant est fabriqué selon le procédé de moulage sous pression de l’aluminium, puis usiné par enlèvement de copeaux, enfin ébavuré par jet d’eau à haute pression et séché. Son bon fonctionnement dépend de la qualité de la surface usinée, dont l’importance est capitale puisqu’elle assure une fonction d’étanchéité. «Les défauts, les plus fréquemment rencontrés sur les pièces moulées, sont les pores et les retassures, soit de petites cavités dans imaging is our passion le matériau coulé, susceptibles d’apparaître lors du fraisage d’une surface», explique Klaus Spinnler. Le responsable du groupe «Traitement industriel de l’image», de l’institut Fraunhofer IIS, explique la formation de ces défauts et leurs conséquences éventuelles: «Ils proviennent de bulles, se formant inévitablement pendant le processus de moulage, qui peuvent entraîner l’apparition de défauts sur la surface. De plus, les surfaces peuvent être endommagées lors du maniement des pièces et par l’usure d’outillages, arrivés en fin de vie. Montés sur un véhicule, les composants, présentant ce genre de défauts, engendreront de coûteux dysfonctionnements». > Contrôle de qualité > Des géométries diverses Pour que le système de contrôle fonctionne parfaitement bien, il est indispensable d’obtenir d’excellentes données d’images des surfaces à contrôler. A cet effet, le système CapaCam a été doté de capteurs disposés en fonction des différentes dimensions, géométries et caractéristiques des surfaces, et possède également les éclairages spéciaux nécessaires, le cas échéant. Ainsi, la pièce figurant sur la photo n°1 comporte-t-elle, par exemple, deux surfaces d’environ 3 cm x 3 cm, captées par des caméras industrielles FireWire d’un prix abordable. Un éclairage indirect à LED assure une illumination optimale de la surface. «Les surfaces planes de plus grandes dimensions, jusqu’à 40 cm x 40 cm, sont saisies par le système CapaCam au moyen d’un numériseur à caméra linéaire, spécialement conçu à cette fin», poursuit Spinnler. «Monté sur un chariot linéaire, il ne lui faut pas plus de quelques secondes pour se placer au-dessus du composant.» La caméra linéaire, commandée par un déclencheur local, est connectée à une échelle graduée en verre, située dans le chariot linéaire, ce qui permet de saisir une image numérique haute résolution, cadrée avec exactitude. Un éclairage linéaire, issu de LED d’une grande longévité, assure une illumination adaptée sur toute la ligne captée par la caméra. Outre des surfaces planes, de tels composants comportent souvent aussi des alésages, par exemple pour les raccordements aux con- Photos 2: Vue d’ensemble du système d’inspection doté de deux stations de contrôle duites de lubrifiant, qui doivent être vérifiés afin d’en détecter toute porosité. Selon la profondeur de l’alésage, il est nécessaire d’utiliser des optiques grand-angle. «Nous avons aussi choisi ce procédé dans la dernière application du système pour un alésage de 15 mm de diamètre», explique Spinnler. Selon lui, dans les cas où l’alésage est trop profond pour permettre un contrôle exhaustif, il est possible d’utiliser des endoscopes, munis d’optiques panoramiques. Ainsi, la profondeur de l’alésage n’est-elle pas un obstacle pour un contrôle rapide de la surface interne. La technologie PanCam de l’institut Fraunhofer IIS, reposant sur un traitement mathématique de l’image panoramique, est déjà utilisée dans l’industrie depuis des années ; elle est compatible avec le système CapaCam. > Un endoscope aux capacités accrues Lorsque les alésages sont larges, la technique actuelle de l’endoscopie atteint toutefois ses propres limites. C’est pourquoi, les chercheurs de l’institut Fraunhofer ont développé une tête de caméra spéciale, ressemblant à un périscope pour les alésages de grande taille. «Celle-ci est dotée d’une caméra linéaire, d’une source de lumière à LED, développée par l’institut Fraunhofer IIS, selon les exigences du client, et d’une optique à vision latérale pour saisir toute la surface d’un alésage de 150 mm de diamètre, situé dans le carter de convertisseur. En tournant sur lui-même à 360°, ce périscope, extrêmement sensible, saisit entièrement le pourtour des alésages et détecte infailliblement les défauts, même si les alésages sont larges», dit Spinnler. Selon la pièce et le contrôle à réaliser, le système CapaCam peut être équipé de divers modules de capteurs et adapté pour satisfaire à chaque exigence. Le cadre logiciel, sur lequel est basé le système, permet de contrôler par chevauchement plusieurs pièces, chacune étant placée sur un poste de contrôle à part, un procédé également mis en œuvre dans l’installation réalisée chez Daimler (photo 2). Le w w w. st e m m e r- i mag i n g .c o m cœur du logiciel d’application est composé d’algorithmes puissants, développés par l’institut Fraunhofer IIS, et dédiés à l’inspection des surfaces. Afin de respecter les cadences de production imposées par le client, l’architecture de l’application est extensible et permet des configurations différentes, allant de l’ordinateur isolé jusqu’au traitement, réalisé en parallèle, dans diverses grappes d’ordinateurs. Une jonction extensible, d’un ou plusieurs ordinateurs industriels, assure alors une analyse rapide de toutes les données d’image saisies, afin de trier les pièces automatiquement. Dans le cas du contrôle des carters de convertisseurs, chez Daimler, il s’agit de deux machines à processeurs double cœur, dotées au total de quatre unités centrales Pentium avec 3,6 GHz. Ainsi, des exigences élevées du client, telles que la réduction de moitié du temps de contrôle, peuvent être satisfaites en doublant le nombre d’ordinateurs. La simple modification d’un fichier de configuration permet à une installation de fonctionner avec 8 processeurs, par exemple. L’intégration à la ligne de fabrication est réalisée, en souplesse, via un bus industriel standardisé. > Contrôle de qualité > Adaptation automatique de la zone de contrôle Les zones de contrôle à évaluer peuvent être définies, de façon interactive, dans le programme de configuration du logiciel CapaCam, dans les limites liées aux divers angles de vision des caméras. Ainsi, la personne en charge de la qualité choisit librement les surfaces à inspecter dans le détail. Selon Spinnler, malgré des qualités de surface hétérogènes pouvant aussi comporter des traces d’usinage et d’eau, le logiciel détecte les défauts importants avec fiabilité. De nombreuses années d’expériences ont permis d’optimiser et d’améliorer continuellement les performances des algorithmes du logiciel CapaCam. Spinnler mentionne une autre particularité du nouveau logiciel CapaCam: «Il permet l’adaptation automatique de la zone de contrôle, dans les limites configurables, à la forme de la pièce moulée. La surface maximale de la zone à contrôler est garantie, sans déclenchement de fausses alarmes gênantes par des contours d’objets de taille variable.» La nomenclature de pores, employée, renferme les prescriptions de qualité, relatives aux pièces moulées courantes dans l’industrie automobile et sert à l’évaluation de l’importance des défauts détectés en tenant compte de paramètres tels que les écarts au bord entre les pores, les écarts au bord des surfaces à traiter et également les règles spéciales pour pores particuliers. En s’appuyant sur des modèles livrés avec le logiciel, l’opérateur peut en outre définir ses propres catégories de pores et les affecter aux zones de contrôle. Grâce à cette souplesse offerte par le système CapaCam, l’opérateur peut simultanément assurer une parfaite qualité et traiter un débit de pièces élevé. CapaCam gère les variantes de pièces via une banque de données de paramètres, dont la taille dépend uniquement de la capacité de l’ordinateur. Les paramètres de contrôle, pour chaque type de pièce, y sont sauvegardés et gérés. Grâce à l’emploi de modèles, l’opérateur peut saisir rapidement et sûrement de nouveaux types de pièces. Une préparation automatique de l’installation, lors du changement de type permet d’éviter les temps d’arrêt et diminue les coûts de main d’œuvre. La fiabilité du fonctionnement du système CapaCam en matière de traitement d’image est, selon les cas, assurée par: 4 caméras avec liaison via interface FireWire 2 caméras linéaires reliées aux ordinateurs via carte d’acquisition CameraLink Divers objectifs compacts 3 éclairages à LED standard 3 autres éclairages spéciaux à LED, développés par l’institut Fraunhofer IIS, selon les exigences du client. «Lors de la configuration et de l’optimisation de situations de prises de vues difficiles, le soutien, que STEMMER IMAGING nous a apporté sous forme de nombreuses positions d’essai, s’est révélé très précieux pour résoudre la tâche et choisir les composants les mieux adaptés», résume Spinnler. Un problème, souvent sous-estimé, est le câblage adapté aux environnements industriels pour caméras dotées d’interfaces numériques. «Là aussi, nous avons pu relever des défis et satisfaire les clients, quand il s’agissait de respecter des longueurs de transmission limitées ou de recourir à des câbles mobiles dans le numériseur; STEMMER IMAGING a mis à notre disposition les accessoires adaptés, tels des répéteurs ou des câbles adaptés aux chemins d’entraînement.» ” notre partenaire fraunhofer iis L’institut Fraunhofer IIS pour circuits intégrés (www.iis.fraunhofer.de), dont le siège social se trouve à Erlangen, et disposant d’autres sites à Nuremberg, Fürth et Dresde, est le plus grand institut de la société Fraunhofer. Spécialisé dans la recherche et le développement en Sciences Appliquées, il travaille pour des entreprises industrielles et des services publics. L’institut développe des systèmes et des appareils microélectroniques, ainsi que les circuits intégrés et les logiciels correspondants nécessaires. Les chercheurs travaillent, entre autres, dans les domaines de la microélectronique, des techniques cinématographique et médicale et du traitement d’image, appliqué aux techniques de contrôle optique et de contrôle par radiographie, destinées à l’automation dans la construction mécanique et la construction d’équipements. Ce sont des domaines, dans lesquels le codage de signaux audio et vidéo et leur standardisation internationale jouent un rôle primordial. L’institut Fraunhofer IIS a développé, entre autres, le procédé de codage audio mondialement connu, mp3. w w w. ste m m e r- i mag i ng .co m • i mag i n g i s o u r pas s i o n a l l e magn e r oyau m e - u n i france suisse Téléphone: +49 89 80902-0 [email protected] Téléphone: +44 1252 780000 [email protected] Téléphone: +33 1 45069560 [email protected] Téléphone: +41 55 4159090 [email protected] PP-IIS1-01/2009 ∙ Sous réserve de modifications techniques et d‘erreurs. > Soutien précieux ">
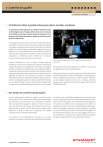
Lien public mis à jour
Le lien public vers votre chat a été mis à jour.
Caractéristiques clés
- Détection de pores, retassures et défauts sur pièces moulées complexes
- Contrôle de surface à grande vitesse
- Adapté à l'industrie automobile
- Intégration aux lignes de fabrication
- Inspection automatisée des surfaces et alésages
- Adaptation automatique de la zone de contrôle
Questions fréquemment posées
Le système CapaCam détecte les pores, les retassures et les défauts de surface sur les pièces moulées.
Le système CapaCam est principalement utilisé dans l'industrie automobile.
Oui, le système CapaCam est intégré aux lignes de fabrication pour un contrôle qualité continu.
Daimler AG utilise le système CapaCam.