HEIDENHAIN iTNC 530/340 490-04 CNC Control Manuel utilisateur
PDF
Télécharger
Document
Manuel d'utilisation Cycles palpeurs iTNC 530 Logiciel CN 340 490-04 340 491-04 340 492-04 340 493-04 340 494-04 Français (fr) 11/2007 Type de TNC, logiciel et fonctions Type de TNC, logiciel et fonctions Ce Manuel décrit les fonctions dont disposent les TNC à partir des numéros de logiciel CN suivants: Modèle de TNC N° de logiciel CN iTNC 530 340 490-04 iTNC 530 E 340 491-04 iTNC 530 340 492-04 iTNC 530 E 340 493-04 Poste de programmation iTNC 530 340 494-04 La lettre E désigne la version Export de la TNC. Les versions Export de la TNC sont soumises à la restriction suivante: Déplacements linéaires simultanés sur un nombre d'axes pouvant aller jusqu'à 4 A l'aide des paramètres machine, le constructeur peut adapter à sa machine l'ensemble des possibilités dont dispose la TNC. Ce Manuel décrit donc également des fonctions non disponibles sur chaque TNC. Les fonctions TNC qui ne sont pas disponibles sur toutes les machines sont, par exemple: Etalonnage d'outils à l'aide du TT Nous vous conseillons de prendre contact avec le constructeur de votre machine pour connaître l'étendue des fonctions de votre machine. De nombreux constructeurs de machines ainsi que HEIDENHAIN proposent des cours de programmation TNC. Il est conseillé de suivre de tels cours afin de se familiariser rapidement avec les fonctions de la TNC. Manuel d'utilisation: Toutes les fonctions TNC qui n'ont pas de rapport avec les palpeurs sont décrites dans le Manuel d'utilisation de l'iTNC 530. Si vous le désirez, adressez-vous à HEIDENHAIN pour recevoir ce Manuel d'utilisation iTNC 530. ID 533 190-xx Documentation utilisateur smarT.NC: Le mode de fonctionnement smarT.NC est décrit dans une brochure „Pilote“ séparée. Si nécessaire, adressez-vous à HEIDENHAIN pour recevoir ce Pilote. ID 533 191-xx. iTNC 530 HEIDENHAIN 3 Type de TNC, logiciel et fonctions Options de logiciel L'iTNC 530 dispose de diverses options de logiciel qui peuvent être activées par le constructeur de votre machine. Chaque option doit être activée séparément et comporte individuellement les fonctions suivantes: Option de logiciel 1 Interpolation du corps d'un cylindre (cycles 27, 28, 29 et 39) Avance en mm/min. avec axes rotatifs: M116 Inclinaison du plan d'usinage (cycles 19, fonction PLANE et softkey 3D ROT en mode de fonctionnement Manuel) Cercle sur 3 axes avec inclinaison du plan d'usinage Option de logiciel 2 Durée de traitement des séquences 0.5 ms au lieu de 3.6 ms Interpolation sur 5 axes Interpolation spline Usinage 3D: M114: Correction automatique de la géométrie de la machine lors de l’usinage avec axes inclinés M128: Conserver la position de la pointe de l'outil lors du positionnement des axes inclinés (TCPM) FUNTION TCPM: Conserver la position de la pointe de l'outil lors du positionnement des axes inclinés (TCPM) avec possibilité de réglage du mode d'action M144: Prise en compte de la cinématique de la machine pour les positions EFF/NOM en fin de séquence Autres paramètres Finition/ébauche et Tolérance pour axes rotatifs dans le cycle 32 (G62) Séquences LN (correction 3D) Option de logiciel DCM Collision Fonction de contrôle dynamique de zones définies par le constructeur de la machine pour éviter les collisions. Option de logiciel langues de dialogue supplémentaires Fonction destinée à activer les langues de dialogue slovène, slovaque, norvégien, letton, estonien, coréen. Option de logiciel DXF Converter Extraire des contours à partir de fichiers DXF (format R12). 4 Type de TNC, logiciel et fonctions Option de logiciel Configurations globales de programme Fonction de superposition de transformations de coordonnées en modes de fonctionnement Exécution de programme. Option de logiciel AFC Fonction d'asservissement adaptatif de l'avance pour optimiser les conditions d'usinage dans la production en série. Option de logiciel KinematicsOpt Cycles palpeurs pour contrôler et optimiser la précision de la machine. iTNC 530 HEIDENHAIN 5 Type de TNC, logiciel et fonctions Niveau de développement (fonctions de mise à jour „upgrade“) Parallèlement aux options de logiciel, d'importants nouveaux développements du logiciel TNC sont gérés par ce qu'on appelle les Feature Content Level (expression anglaise exprimant les niveaux de développement). Vous ne disposez pas des fonctions FCL lorsque votre TNC reçoit une mise à jour de logiciel. Lorsque vous recevez une nouvelle machine, vous recevez toutes les fonctions de mise à jour Upgrade sans surcoût. Dans ce Manuel, ces fonctions Upgrade sont signalées par l'expression FCL n; n précisant le numéro d'indice du niveau de développement. En achetant le code correspondant, vous pouvez activer les fonctions FCL. Pour cela, prenez contact avec le constructeur de votre machine ou avec HEIDENHAIN. 6 Fonctions FCL 4 Description Représentation graphique de la zone protégée avec contrôle anti-collision DCM actif Manuel d'utilisation Superposition de la manivelle (axes à l'arrêt) avec contrôle anti-collision DCM actif Manuel d'utilisation Rotation de base 3D (compensation de bridage) Manuel de la machine Fonctions FCL 3 Description Cycle palpeur pour palpage 3D Page 153 Cycles palpeurs pour l’initialisation automatique du centre d’une rainure/ d’un oblong Page 70 Réduction de l’avance lors de l’usinage de contours de poche lorsque l’outil est en position de pleine attaque Manuel d'utilisation Fonction PLANE: Introduction d'un angle d'axe Manuel d'utilisation Documentation utilisateur sous forme de système d’aide contextuelle Manuel d'utilisation smarT.NC: Programmer smarT.NC en parallèle à l'usinage Manuel d'utilisation smarT.NC: Contour de poche sur motifs de points Pilote smarT.NC Description smarT.NC: Aperçu de programmes de contours dans le gestionnaire de fichiers Pilote smarT.NC smarT.NC: Stratégie de positionnement lors d'opérations d'usinage de points Pilote smarT.NC Fonctions FCL 2 Description Graphisme filaire 3D Manuel d'utilisation Axe d'outil virtuel Manuel d'utilisation Gestion USB de périphériques-blocs (memory sticks, disques durs, lecteurs CD-ROM) Manuel d'utilisation Filtrage de contours créés sur un support externe Manuel d'utilisation Possibilité d'attribuer une profondeur séparée à chaque contour partiel pour la formule de contour Manuel d'utilisation Gestion dynamique d'adresses IP DHCP Manuel d'utilisation Cycle palpeur pour configuration globale de paramètres du palpeur Page 157 smarT.NC: Amorce de séquence avec graphisme Pilote smarT.NC smarT.NC: Transformations de coordonnées Pilote smarT.NC smarT.NC: Fonction PLANE Pilote smarT.NC Type de TNC, logiciel et fonctions Fonctions FCL 3 Lieu d'implantation prévu La TNC correspond à la classe A selon EN 55022. Elle est prévue principalement pour fonctionner en milieux industriels. iTNC 530 HEIDENHAIN 7 Type de TNC, logiciel et fonctions Nouvelles fonctions du logiciel 340 49x-02 Nouveau paramètre-machine pour définir la vitesse de positionnement (cf. „Palpeur à commutation, avance rapide pour déplacements de positionnement: MP6151” à la page 25) Nouveau paramètre-machine pour la prise en compte de la rotation de base en mode Manuel (cf. „Prendre en compte la rotation de base en mode Manuel: MP6166” à la page 24) Les cycles 420 à 431 destinés à l'étalonnage automatique des outils ont été complétés: Maintenant, le procès-verbal de mesure peut être affiché également à l'écran (cf. „Procès-verbal des résultats de la mesure” à la page 110) Création d'un nouveau cycle permettant l'initialisation globale des paramètres du palpeur (cf. „PALPAGE RAPIDE (cycle palpeur 441, DIN/ISO: G441, fonction FCL 2)” à la page 157) Nouvelles fonctions du logiciel 340 49x-03 Nouveau cycle d’initialisation d’un point de référence au centre d’une rainure (cf. „PREF CENTRE RAINURE (cycle palpeur 408, DIN/ISO: G408: Fonction FCL 3)” à la page 70) Nouveau cycle d’initialisation d’un point de référence au centre d’un oblong (cf. „PREF CENT. OBLONG (cycle palpeur 409, DIN/ISO: G409, fonction FCL 3)” à la page 73) Nouveau cycle de palpage 3D (cf. „MESURE 3D (cycle palpeur 4, fonction FCL 3)” à la page 153) Le cycle 401 permet désormais de compenser le désaxage d’une pièce grâce aussi à une rotation du plateau circulaire (cf. „ROTATION DE BASE avec deux trous (cycle palpeur 401, DIN/ISO: G401)” à la page 52) Le cycle 402 permet désormais de compenser le désaxage d’une pièce grâce aussi à une rotation du plateau circulaire (cf. „ROTATION DE BASE à partir de deux tenons (cycle palpeur 402, DIN/ISO: G402)” à la page 55) Pour les cycles d’initialisation du point de référence, les résultats de la mesure sont disponibles dans les paramètres Q15X (cf. „Résultats de la mesure dans les paramètres Q” à la page 69) 8 Type de TNC, logiciel et fonctions Nouvelles fonctions du logiciel 340 49x-04 Nouveau cycle de sauvegarde de la cinématique d'une machine (cf. „SAUVEGARDER CINEMATIQUE (cycle palpeur 450, DIN/ISO: G450, option)” à la page 162) Nouveau cycle de contrôle et d'optimisation de la cinématique d'une machine (cf. „MESURE CINEMATIQUE (cycle palpeur 451, DIN/ ISO: G451, option)” à la page 164) Cycle 412: Sélection possible du nombre de points de mesure dans le nouveau paramètre Q423 (cf. „POINT DE REFERENCE INTERIEUR CERCLE (cycle palpeur 412, DIN/ISO: G412)” à la page 82) Cycle 413: Sélection possible du nombre de points de mesure dans le nouveau paramètre Q423 (cf. „POINT DE REFERENCE EXTERIEUR CERCLE (cycle palpeur 413, DIN/ISO: G413)” à la page 86) Cycle 421: Sélection possible du nombre de points de mesure dans le nouveau paramètre Q423(cf. „MESURE TROU (cycle palpeur 421, DIN/ISO: G421)” à la page 119) Cycle 422: Sélection possible du nombre de points de mesure dans le nouveau paramètre Q423 (cf. „MESURE EXTERIEUR CERCLE (cycle palpeur 422, DIN/ISO: G422)” à la page 122) Cycle 3: Interdire l'affichage du message d'erreur si la tige de palpage est déjà déviée au début du cycle (cf. „MESURE (cycle palpeur 3)” à la page 151) iTNC 530 HEIDENHAIN 9 Fonctions modifiées par rapport aux versions antérieures 340 422-xx/ 340 423-xx Fonctions modifiées par rapport aux versions antérieures 340 422-xx/340 423-xx La gestion de plusieurs données d'étalonnage a été modifiée (cf. „Gérer plusieurs séquences de données d'étalonnage” à la page 34) 10 Table des matières 1 2 3 4 5 Introduction Cycles palpeurs en modes Manuel et Manivelle électronique Cycles palpeurs pour le contrôle automatique des pièces Cycles palpeurs pour la mesure automatique de la cinématique Cycles palpeurs pour l'étalonnage automatique des outils iTNC 530 HEIDENHAIN 11 1 Travail à l'aide des cycles palpeurs ..... 19 1.1 Généralités sur les cycles palpeurs ..... 20 Fonctionnement ..... 20 Cycles palpeurs en modes Manuel et Manivelle électronique ..... 21 Cycles palpeurs pour le mode automatique ..... 21 1.2 Avant que vous ne travailliez avec les cycles palpeurs! ..... 23 Course max. jusqu’au point de palpage: PM6130 ..... 23 Distance d'approche jusqu'au point de palpage: PM6140 ..... 23 Orienter le palpeur infrarouge dans le sens de palpage programmé: MP6165 ..... 23 Prendre en compte la rotation de base en mode Manuel: MP6166 ..... 24 Mesure multiple: PM6170 ..... 24 Zone de sécurité pour mesure multiple: PM6171 ..... 24 Palpeur à commutation, avance de palpage: PM6120 ..... 25 Palpeur à commutation, avance pour déplacements de positionnement: MP6150 ..... 25 Palpeur à commutation, avance rapide pour déplacements de positionnement: MP6151 ..... 25 KinematicsOpt, limite de tolérance pour le mode Optimisation: MP6600 ..... 25 KinematicsOpt, écart autorisé par rapport au rayon de la bille étalon: MP6601 ..... 25 Travail avec les cycles palpeurs ..... 26 HEIDENHAIN iTNC 530 13 2 Cycles palpeurs en modes Manuel et Manivelle électronique ..... 27 2.1 Introduction ..... 28 Vue d'ensemble ..... 28 Sélectionner le cycle palpeur ..... 28 Procès-verbal de mesure issu des cycles palpeurs ..... 29 Enregistrer les valeurs de mesure issues des cycles palpeurs dans un tableau de points zéro ..... 30 Enregistrer les valeurs de mesure issues des cycles palpeurs dans le tableau Preset ..... 31 2.2 Etalonnage du palpeur à commutation ..... 32 Introduction ..... 32 Etalonner la longueur effective ..... 32 Etalonner le rayon effectif et compenser le désaxage du palpeur ..... 33 Afficher les valeurs d'étalonnage ..... 34 Gérer plusieurs séquences de données d'étalonnage ..... 34 2.3 Compenser le désaxage de la pièce ..... 35 Introduction ..... 35 Calculer la rotation de base ..... 35 Enregistrer la rotation de base dans le tableau Preset ..... 36 Afficher la rotation de base ..... 36 Annuler la rotation de base ..... 36 2.4 Initialiser le point de référence avec palpeurs 3D ..... 37 Introduction ..... 37 Initialiser le point de référence sur un axe au choix ..... 37 Coin pris comme point de référence – Valider les points palpés pour la rotation de base ..... 38 Coin pris comme point de référence – Ne pas valider les points palpés pour la rotation de base ..... 38 Centre de cercle pris comme point de référence ..... 39 Axe central comme point de référence ..... 40 Initialiser des points de référence à partir de trous/tenons circulaires ..... 41 2.5 Etalonnage de pièces avec les palpeurs 3D ..... 42 Introduction ..... 42 Définir la coordonnée d’une position sur la pièce dégauchie ..... 42 Définir les coordonnées d’un coin dans le plan d’usinage ..... 42 Définir les cotes d’une pièce ..... 43 Définir l’angle compris entre l’axe de référence angulaire et une arête de la pièce ..... 44 2.6 Fonctions de palpage avec palpeurs mécaniques ou comparateurs ..... 45 Introduction ..... 45 14 3 Cycles palpeurs pour le contrôle automatique des pièces ..... 47 3.1 Enregistrer automatiquement le désaxage de la pièce ..... 48 Vue d'ensemble ..... 48 Particularités communes aux cycles palpeurs destinés à l'enregistrement du désaxage de la pièce ..... 49 ROTATION DE BASE (cycle palpeur 400, DIN/ISO: G400) ..... 50 ROTATION DE BASE avec deux trous (cycle palpeur 401, DIN/ISO: G401) ..... 52 ROTATION DE BASE à partir de deux tenons (cycle palpeur 402, DIN/ISO: G402) ..... 55 ROTATION DE BASE compensée avec axe rotatif (cycle palpeur 403, DIN/ISO: G403) ..... 58 INITIALISER LA ROTATION DE BASE (cycle palpeur 404, DIN/ISO: G404) ..... 61 Compenser le désaxage d'une pièce avec l'axe C (cycle palpeur 405, DIN/ISO: G405) ..... 62 3.2 Calcul automatique des points de référence ..... 66 Vue d'ensemble ..... 66 Caractéristiques communes à tous les cycles palpeurs pour l'initialisation du point de référence ..... 68 Résultats de la mesure dans les paramètres Q ..... 69 PREF CENTRE RAINURE (cycle palpeur 408, DIN/ISO: G408: Fonction FCL 3) ..... 70 PREF CENT. OBLONG (cycle palpeur 409, DIN/ISO: G409, fonction FCL 3) ..... 73 POINT DE REFERENCE INTERIEUR RECTANGLE (cycle palpeur 410, DIN/ISO: G410) ..... 76 POINT DE REFERENCE EXTERIEUR RECTANGLE (cycle palpeur 411, DIN/ISO: G411) ..... 79 POINT DE REFERENCE INTERIEUR CERCLE (cycle palpeur 412, DIN/ISO: G412) ..... 82 POINT DE REFERENCE EXTERIEUR CERCLE (cycle palpeur 413, DIN/ISO: G413) ..... 86 POINT DE REFERENCE EXTERIEUR COIN (cycle palpeur 414, DIN/ISO: G414) ..... 89 POINT DE REFERENCE INTERIEUR COIN (cycle palpeur 415, DIN/ISO: G415) ..... 92 POINT DE REFERENCE CENTRE CERCLE DE TROUS (cycle palpeur 416, DIN/ISO: G416) ..... 95 POINT DE REFERENCE DANS L'AXE DU PALPEUR (cycle palpeur 417, DIN/ISO: G417) ..... 98 POINT DE REFERENCE CENTRE de 4 TROUS (cycle palpeur 418, DIN/ISO: G418) ..... 100 PT DE REF SUR UN AXE (cycle palpeur 419, DIN/ISO: G419) ..... 103 HEIDENHAIN iTNC 530 15 3.3 Etalonnage automatique des pièces ..... 109 Vue d'ensemble ..... 109 Procès-verbal des résultats de la mesure ..... 110 Résultats de la mesure dans les paramètres Q ..... 112 Etat de la mesure ..... 112 Surveillance de tolérances ..... 112 Surveillance d'outil ..... 113 Système de référence pour les résultats de la mesure ..... 114 PLAN DE REFERENCE (cycle palpeur 0, DIN/ISO: G55) ..... 115 PLAN DE REFERENCE polaire (cycle palpeur 1) ..... 116 MESURE ANGLE (cycle palpeur 420, DIN/ISO: G420) ..... 117 MESURE TROU (cycle palpeur 421, DIN/ISO: G421) ..... 119 MESURE EXTERIEUR CERCLE (cycle palpeur 422, DIN/ISO: G422) ..... 122 MESURE INTERIEUR RECTANGLE (cycle palpeur 423, DIN/ISO: G423) ..... 125 MESURE EXTERIEUR RECTANGLE (cycle palpeur 424, DIN/ISO: G424) ..... 128 MESURE INTERIEUR RAINURE (cycle palpeur 425, DIN/ISO: G425) ..... 131 MESURE EXTERIEUR TRAVERSE (cycle palpeur 426, DIN/ISO: G426) ..... 133 MESURE COORDONNEE (cycle palpeur 427, DIN/ISO: G427) ..... 135 MESURE CERCLE DE TROUS (cycle palpeur 430, DIN/ISO: G430) ..... 138 MESURE PLAN (cycle palpeur 431, DIN/ISO: G431) ..... 141 3.4 Cycles spéciaux ..... 148 Vue d'ensemble ..... 148 ETALONNAGE TS (cycle palpeur 2) ..... 149 ETALONNAGE TS LONGUEUR (cycle palpeur 9) ..... 150 MESURE (cycle palpeur 3) ..... 151 MESURE 3D (cycle palpeur 4, fonction FCL 3) ..... 153 MESURE DU DESAXAGE (cycle palpeur 440, DIN/ISO: G440) ..... 155 PALPAGE RAPIDE (cycle palpeur 441, DIN/ISO: G441, fonction FCL 2) ..... 157 16 4 Cycles palpeurs pour la mesure automatique de la cinématique ..... 159 4.1 Mesure de cinématique avec les palpeurs TS (option KinematicsOpt) ..... 160 Principes ..... 160 Vue d'ensemble ..... 160 Conditions requises ..... 161 SAUVEGARDER CINEMATIQUE (cycle palpeur 450, DIN/ISO: G450, option) ..... 162 MESURE CINEMATIQUE (cycle palpeur 451, DIN/ISO: G451, option) ..... 164 HEIDENHAIN iTNC 530 17 5 Cycles palpeurs pour l'étalonnage automatique des outils ..... 175 5.1 Etalonnage d'outils avec le palpeur de table TT ..... 176 Vue d'ensemble ..... 176 Configurer les paramètres-machine ..... 176 Données d'introduction dans le tableau d'outils TOOL.T ..... 178 Afficher les résultats de la mesure ..... 179 5.2 Cycles disponibles ..... 180 Vue d'ensemble ..... 180 Différences entre les cycles 31 à 33 et 481 à 483 ..... 180 Etalonnage du TT (cycle palpeur 30 ou 480, DIN/ISO: G480) ..... 181 Etalonnage de la longueur d'outil (cycle palpeur 31 ou 481, DIN/ISO: G481) ..... 182 Etalonnage du rayon d'outil (cycle palpeur 32 ou 482, DIN/ISO: G482) ..... 184 Etalonnage complet de l'outil (cycle palpeur 33 ou 483, DIN/ISO: G483) ..... 186 18 Travail à l'aide des cycles palpeurs 1.1 Généralités sur les cycles palpeurs 1.1 Généralités sur les cycles palpeurs La TNC doit avoir été préparée par le constructeur de la machine pour l'utilisation de palpeurs 3D Lorsque vous voulez effectuer des mesures pendant l’exécution du programme, veillez à ce que les données d’outil (longueur, rayon, axe) puissent être exploitées soit à partir des données d’étalonnage, soit à partir de la dernière séquence TOOL CALL (sélection par PM7411). Fonctionnement Lorsque la TNC exécute un cycle palpeur, le palpeur 3D se déplace parallèlement à l'axe en direction de la pièce (y compris avec rotation de base activée et plan d'usinage incliné). Le constructeur de la machine définit l'avance de palpage dans un paramètre-machine (cf. „Avant que vous ne travailliez avec les cycles palpeurs“ plus loin dans ce chapitre). Lorsque la tige de palpage affleure la pièce, Z Y le palpeur 3D transmet un signal à la TNC qui mémorise les coordonnées de la position de palpage le palpeur 3D s'arrête et retourne en avance rapide à la position initiale de la procédure de palpage F F MAX X F Si la tige de palpage n'est pas déviée sur la course définie, la TNC délivre un message d'erreur (course: PM6130). 20 1 Travail à l'aide des cycles palpeurs 1.1 Généralités sur les cycles palpeurs Cycles palpeurs en modes Manuel et Manivelle électronique En mode Manuel et Manivelle électronique, la TNC dispose de cycles palpeurs vous permettant: d'étalonner le palpeur de compenser le désaxage de la pièce d'initialiser les points de référence Cycles palpeurs pour le mode automatique Outre les cycles palpeurs que vous utilisez en modes Manuel et manivelle électronique, la TNC dispose de nombreux cycles correspondant aux différentes applications en mode automatique: Etalonnage du palpeur à commutation (chapitre 3) Compensation du désaxage de la pièce (chapitre 3) Initialisation des points de référence (chapitre 3) Contrôle automatique de la pièce (chapitre 3) Etalonnage automatique des outils (chapitre 4) Vous programmez les cycles palpeurs en mode Mémorisation/édition de programme à l'aide de la touche TOUCH PROBE. Vous utilisez les cycles palpeurs de numéros à partir de 400 de la même manière que les nouveaux cycles d'usinage, paramètres Q comme paramètres de transfert. Les paramètres de même fonction que la TNC utilise dans différents cycles portent toujours le même numéro: Ainsi, par exemple, Q260 correspond toujours à la distance de sécurité, Q261 à la hauteur de mesure, etc. Pour simplifier la programmation, la TNC affiche un écran d'aide pendant la définition du cycle. L'écran d'aide affiche en surbrillance le paramètre que vous devez introduire (cf. fig. de droite). iTNC 530 HEIDENHAIN 21 1.1 Généralités sur les cycles palpeurs Définition du cycle palpeur en mode Mémorisation/édition Le menu de softkeys affiche – par groupes – toutes les fonctions de palpage disponibles Sélectionner le groupe de cycles de palpage, par exemple Initialisation du point de référence. Les cycles de digitalisation et les cycles destinés à l'étalonnage automatique d'outil ne sont disponibles que si votre machine a été préparée pour ces fonctions Exemple: Séquences CN 5 TCH PROBE 410 PT REF. INT. RECTAN Q321=+50 ;CENTRE 1ER AXE Q322=+50 ;CENTRE 2ÈME AXE Q323=60 ;1ER CÔTÉ Q324=20 ;2ÈME CÔTÉ Sélectionner le cycle, par exemple Initialisation du point de référence au centre de la poche. La TNC ouvre un dialogue et réclame toutes les données d’introduction requises; en même temps, la TNC affiche dans la moitié droite de l'écran un graphisme dans lequel le paramètre à introduire est en surbrillance Q261=-5 ;HAUTEUR DE MESURE Q320=0 ;DISTANCE D'APPROCHE Q260=+20 ;HAUTEUR DE SÉCURITÉ Q301=0 ;DÉPLAC. HAUT. SÉCU. Q305=10 ;NO DANS TABLEAU Introduisez tous les paramètres réclamés par la TNC et validez chaque introduction avec la touche ENT Q331=+0 ;POINT DE RÉFÉRENCE Q332=+0 ;POINT DE RÉFÉRENCE La TNC ferme le dialogue lorsque vous avez introduit toutes les données requises Q303=+1 ;TRANS. VAL. MESURE Q381=1 ;PALP. DS AXE PALPEUR Page Q382=+85 ;1ÈRE COO. DANS AXE PALP. Cycles d'enregistrement automatique et compensation du désaxage d'une pièce Page 48 Q383=+50 ;2ÈME COO. DANS AXE PALP. Q384=+0 ;3ÈME COO. DANS AXE PALP. Cycles d'initialisation automatique du point de référence Page 66 Q333=+0 ;POINT DE REFERENCE Cycles de contrôle automatique de la pièce Page 109 Cycles d'étalonnage, cycles spéciaux Page 148 Cycles d'étalonnage automatique d'outils (validés par le constructeur de la machine) Page 176 Groupe de cycles de mesure 22 Softkey 1 Travail à l'aide des cycles palpeurs 1.2 Avant que vous ne travailliez avec les cycles palpeurs! 1.2 Avant que vous ne travailliez avec les cycles palpeurs! Pour couvrir le plus grand nombre possible de types d'opérations de mesure, vous pouvez configurer par paramètres-machine le comportement de base de tous les cycles palpeurs: Course max. jusqu’au point de palpage: PM6130 Si la tige de palpage n'est pas déviée dans la course définie sous PM6130, la TNC délivre un message d'erreur. Distance d'approche jusqu'au point de palpage: PM6140 Z Y Dans PM6140, vous définissez la distance de pré-positionnement du palpeur par rapport au point de palpage défini – ou calculé par le cycle. Plus la valeur que vous introduisez est petite et plus vous devez définir avec précision les positions de palpage. Dans de nombreux cycles de palpage, vous pouvez définir une autre distance d'approche qui agit en plus du paramètre-machine 6140. X MP6130 Orienter le palpeur infrarouge dans le sens de palpage programmé: MP6165 Dans le but d'optimiser la précision de la mesure, configurez PM 6165 = 1: Avant chaque opération de palpage, vous pouvez ainsi orienter un palpeur infrarouge dans le sens programmé pour le palpage. De cette manière, la tige de palpage est toujours déviée dans la même direction. Si vous modifiez MP6165, vous devez alors réétalonner le palpeur. Z Y X MP6140 iTNC 530 HEIDENHAIN 23 1.2 Avant que vous ne travailliez avec les cycles palpeurs! Prendre en compte la rotation de base en mode Manuel: MP6166 Pour pouvoir augmenter aussi en mode de réglage la précision de la mesure lors du palpage de certaines positions données, vous pouvez paramétrer MP 6166 = 1 de manière à ce que la TNC prenne en compte pendant le palpage une rotation de base active et, si nécessaire, se déplace obliquement vers la pièce. La fonction de palpage oblique n'est pas active en mode Manuel pour les fonctions suivantes: Etalonnage de la longueur Etalonnage du rayon Calcul de la rotation de base Mesure multiple: PM6170 Pour optimiser la sécurité de la mesure, la TNC peut exécuter successivement trois fois la même opération de palpage. Si les valeurs de positions mesurées s'écartent trop les unes des autres, la TNC délivre un message d'erreur (valeur limite définie dans PM6171). Grâce à la mesure multiple, vous pouvez si nécessaire calculer des erreurs de mesure accidentelles (provoquées, par exemple, par des salissures). Si ces valeurs de mesure sont encore dans la zone de sécurité, la TNC mémorise la valeur moyenne obtenue à partir des positions enregistrées. Zone de sécurité pour mesure multiple: PM6171 Si vous exécutez une mesure multiple, définissez dans PM6171 la valeur par rapport à laquelle les valeurs de mesure peuvent varier entre elles. Si la différence entre les valeurs de mesure dépasse la valeur définie dans PM6171, la TNC délivre un message d'erreur. 24 1 Travail à l'aide des cycles palpeurs 1.2 Avant que vous ne travailliez avec les cycles palpeurs! Palpeur à commutation, avance de palpage: PM6120 Dans PM6120, vous définissez l'avance suivant laquelle la TNC doit palper la pièce. Palpeur à commutation, avance pour déplacements de positionnement: MP6150 Z Y Dans PM6150, vous définissez l'avance suivant laquelle la TNC doit prépositionner le palpeur ou le positionner entre des points de mesure. Palpeur à commutation, avance rapide pour déplacements de positionnement: MP6151 Dans MP6151, vous définissez si la TNC doit positionner le palpeur suivant l'avance définie dans MP6150 ou bien suivant l'avance rapide de la machine. X MP6120 MP6360 MP6150 MP6361 Valeur d'introduction = 0: Positionnement suivant l'avance définie dans MP6150 Valeur d'introduction = 1: Prépositionnement en avance rapide KinematicsOpt, limite de tolérance pour le mode Optimisation: MP6600 Dans MP6600, vous définissez la limite de tolérance à partir de laquelle la TNC doit afficher une remarque en mode Optimisation si les données de cinématique définies excèdent cette valeur limite. Configuration par défaut: 0.05. Plus la machine est grande et plus vous devez sélectionner des valeurs élevées Plage d'introduction: 0.001 à 0.999 KinematicsOpt, écart autorisé par rapport au rayon de la bille étalon: MP6601 Dans MP6601, vous définissez l'écart max. autorisé pour le rayon de la bille étalon mesuré automatiquement par les cycles par rapport au paramètre de cycle programmé. Plage d'introduction: 0.01 à 0.1 Pour les 5 points de palpage, la TNC calcule le rayon de la bille étalon deux fois sur chaque point de mesure. Si le rayon est supérieur à Q407 + MP6601, la commande délivre un message d'erreur en présupposant la présence de salissures. Si le rayon déterminé par la TNC est inférieur à 5 * (Q407 - MP6601), la TNC délivre également un message d'erreur. iTNC 530 HEIDENHAIN 25 1.2 Avant que vous ne travailliez avec les cycles palpeurs! Travail avec les cycles palpeurs Tous les cycles palpeurs sont actifs avec DEF. Par conséquent, la TNC exécute le cycle automatiquement lorsque la définition du cycle est exécutée dans le déroulement du programme. En début de cycle, veillez à ce que les valeurs de correction (longueur, rayon) soient activées soit à partir des données d'étalonnage, soit à partir de la dernière séquence TOOL CALL (sélection par PM7411, cf. Manuel d'utilisation de l'iTNC 530, „Paramètres utilisateur généraux“). Vous pouvez exécuter les cycles palpeurs 408 à 419 même si la rotation de base est activée. Toutefois, vous devez veiller à ce que l'angle de la rotation de base ne varie plus si, à l'issue du cycle de mesure, vous travaillez à partir du tableau de points zéro avec le cycle 7 Décalage point zéro. Les cycles palpeurs dont le numéro est supérieur à 400 permettent de positionner le palpeur suivant une logique de positionnement: Si la coordonnée actuelle du pôle sud de la tige de palpage est plus petite que la coordonnée de la hauteur de sécurité (définie dans le cycle), la TNC rétracte le palpeur tout d'abord dans l'axe du palpeur, jusqu'à la hauteur de sécurité, puis le positionne ensuite dans le plan d'usinage, sur le premier point de palpage. Si la coordonnée actuelle du pôle sud de la tige de palpage est plus grande que la coordonnée de la hauteur de sécurité, la TNC positionne le palpeur tout d'abord dans le plan d'usinage, sur le premier point de palpage, puis dans l'axe du palpeur, directement à la hauteur de mesure. 26 1 Travail à l'aide des cycles palpeurs Cycles palpeurs en modes Manuel et Manivelle électronique 2.1 Introduction 2.1 Introduction Vue d'ensemble En mode de fonctionnement Manuel, vous disposez des cycles palpeurs suivants: Fonction Softkey Page Etalonnage de la longueur effective Page 32 Etalonnage du rayon effectif Page 33 Calcul de la rotation de base à partir d'une droite Page 35 Initialisation du point de référence dans un axe au choix Page 37 Initialisation d'un coin comme point de référence Page 38 Initialisation du centre de cercle comme point de référence Page 39 Initialisation de l'axe central comme point de référence Page 40 Calcul de la rotation de base à partir de deux trous/tenons circulaires Page 41 Initialisation du point de référence à partir de quatre trous/tenons circulaires Page 41 Initialisation du centre de cercle à partir de trois trous/tenons Page 41 Sélectionner le cycle palpeur Sélectionner le mode Manuel ou Manivelle électronique Sélectionner les fonctions de palpage: Appuyer sur la softkey FONCTIONS PALPAGE. La TNC affiche d’autres softkeys: Cf. tableau ci-dessus 28 Sélectionner le cycle palpeur: par ex. appuyer sur la softkey PALPAGE ROT; la TNC affiche à l'écran le menu correspondant 2 Cycles palpeurs en modes Manuel et Manivelle électronique 2.1 Introduction Procès-verbal de mesure issu des cycles palpeurs La TNC doit avoir été préparée par le constructeur de la machine pour cette fonction. Consultez le manuel de la machine! Après avoir exécuté n'importe quel cycle palpeur, la TNC affiche la softkey IMPRIMER. Si vous appuyez sur cette softkey, la TNC établit le procès-verbal des valeurs actuelles du cycle palpeur actif. A l'aide de la fonction PRINT du menu de configuration de l'interface (cf. Manuel d'utilisation, „12 Fonctions MOD, Configuration de l'interface de données“), vous définissez si la TNC doit: imprimer les résultats de la mesure mémoriser les résultats de la mesure sur son disque dur mémoriser les résultats de la mesure sur un PC. Lorsque vous enregistrez les résultats de la mesure, la TNC créé le fichier ASCII %TCHPRNT.A. Si vous n'avez défini ni chemin d'accès, ni interface dans le menu de configuration d'interface, la TNC enregistre le fichier %TCHPRNT dans le répertoire principal TNC:\. Lorsque vous appuyez sur la softkey IMPRIMER, le fichier %TCHPRNT.A ne doit pas être sélectionné en mode Mémorisation/édition de programme. Sinon, la TNC délivre un message d'erreur. La TNC inscrit les valeurs de mesure uniquement dans le fichier %TCHPRNT.A. Si vous exécutez successivement plusieurs cycles palpeurs et désirez mémoriser les valeurs de la mesure, vous devez alors sauvegarder le contenu du fichier %TCHPRNT.A entre chaque cycle palpeur en le copiant ou le renommant. Le format et le contenu du fichier %TCHPRNT sont définis par le constructeur de votre machine. iTNC 530 HEIDENHAIN 29 2.1 Introduction Enregistrer les valeurs de mesure issues des cycles palpeurs dans un tableau de points zéro Cette fonction n'est active que si les tableaux de points zéro sont activés sur votre TNC (bit 3 dans le paramètremachine 7224.0 =0). Utilisez cette fonction si vous désirez enregistrer des valeurs de mesure dans le système de coordonnées pièce. Si vous voulez enregistrer les valeurs de mesure dans le système de coordonnées machine (coordonnées REF) utilisez la softkey ENTREE DS TABLEAU PRESET (cf. „Enregistrer les valeurs de mesure issues des cycles palpeurs dans le tableau Preset” à la page 31). Avec la softkey ENTREE DANS TAB. POINTS, la TNC peut enregistrer les valeurs de mesure dans un tableau de points zéro après l'exécution de n'importe quel cycle palpeur: Sachez que, lors d'un décalage actif du point zéro, la valeur palpée se réfère toujours au preset actif (ou au dernier point zéro initialisé en mode Manuel) bien que le décalage du point zéro soit compensé dans l'affichage de position. Exécuter une fonction de palpage au choix Inscrire les coordonnées désirées pour le point de référence dans les champs d'introduction proposés à cet effet (en fonction du cycle palpeur à exécuter) Introduire le numéro du point zéro dans le champ d'introduction Numéro dans tableau = Introduire le nom du tableau de points zéro (avec chemin d'accès complet) dans le champ d'introduction Tableau de points zéro Appuyer sur la softkey ENTREE DANS TAB. POINTS; la TNC enregistre le point zéro sous le numéro introduit dans le tableau de points zéro indiqué 30 2 Cycles palpeurs en modes Manuel et Manivelle électronique 2.1 Introduction Enregistrer les valeurs de mesure issues des cycles palpeurs dans le tableau Preset Utilisez cette fonction si vous désirez enregistrer des valeurs de mesure dans le système de coordonnées machine (coordonnées REF). Si vous voulez enregistrer les valeurs de mesure dans le système de coordonnées pièce (coordonnées REF) utilisez la softkey ENTREE DANS TAB. POINTS (cf. „Enregistrer les valeurs de mesure issues des cycles palpeurs dans un tableau de points zéro” à la page 30). Avec la softkey ENTREE DS TABLEAU PRESET, la TNC peut enregistrer les valeurs de mesure dans le tableau Preset après l'exécution de n'importe quel cycle palpeur. Les valeurs de mesure enregistrées se réfèrent alors au système de coordonnées machine (coordonnées REF). Le tableau Preset s'intitule PRESET.PR et est mémorisé dans le répertoire TNC:\. Sachez que, lors d'un décalage actif du point zéro, la valeur palpée se réfère toujours au preset actif (ou au dernier point zéro initialisé en mode Manuel) bien que le décalage du point zéro soit compensé dans l'affichage de position. Exécuter une fonction de palpage au choix Inscrire les coordonnées désirées pour le point de référence dans les champs d'introduction proposés à cet effet (en fonction du cycle palpeur à exécuter) Introduire le numéro de preset dans le champ d'introduction Numéro dans tableau: Appuyer sur la softkey ENTREE DS TABLEAU PRESET; la TNC enregistre le point zéro sous le numéro introduit dans le tableau Preset Lorsque vous remplacez le point de référence actif, la TNC affiche un message d’avertissement. Vous pouvez alors décider de remplacer (=touche ENT) ou non (=touche NO ENT) le point de référence. iTNC 530 HEIDENHAIN 31 2.2 Etalonnage du palpeur à commutation 2.2 Etalonnage du palpeur à commutation Introduction Vous devez étalonner le système de palpage lors: de la mise en route d'une rupture de la tige de palpage du changement de la tige de palpage d'une modification de l'avance de palpage d'irrégularités dues, par exemple, à une surchauffe de la machine Lors de l'étalonnage, la TNC calcule la longueur „effective“ de la tige de palpage ainsi que le rayon „effectif“ de la bille de palpage. Pour étalonner le palpeur 3D, fixez sur la table de la machine une bague de réglage de hauteur et de diamètre intérieur connus. Etalonner la longueur effective La longueur effective du palpeur se réfère toujours au point de référence de l'outil. En règle générale, le constructeur de la machine initialise le point de référence de l'outil sur le nez de la broche. Initialiser le point de référence dans l'axe de broche de manière à avoir pour la table de la machine: Z=0. Sélectionner la fonction d'étalonnage pour la longueur du palpeur: Appuyer sur la softkey FONCTIONS PALPAGE et ETAL L. La TNC affiche une fenêtre de menu comportant quatre champs d'introduction 32 Introduire l'axe d'outil (touche d'axe) Point de référence: Introduire la hauteur de la bague de réglage Les sous-menus Rayon effectif bille et Longueur effective ne requièrent pas d'introduction Déplacer le palpeur tout contre la surface de la bague de réglage Si nécessaire, modifier le sens du déplacement: Appuyer sur la softkey ou sur les touches fléchées Palper la surface: Appuyer sur la touche START externe Z Y 5 X 2 Cycles palpeurs en modes Manuel et Manivelle électronique 2.2 Etalonnage du palpeur à commutation Etalonner le rayon effectif et compenser le désaxage du palpeur Normalement, l'axe du palpeur n'est pas aligné exactement sur l'axe de broche. La fonction d'étalonnage enregistre le déport entre l'axe du palpeur et l'axe de broche et effectue la compensation. La routine d'étalonnage varie en fonction de la configuration du paramètre-machine 6165 (poursuite de broche active/inactive (cf. „Orienter le palpeur infrarouge dans le sens de palpage programmé: MP6165” à la page 23). Si la poursuite de broche est active, le processus d'étalonnage a lieu avec un seul start CN. Mais si la poursuite de broche est inactive, vous avez le choix d'étalonner ou non le désaxage. Lors de l'étalonnage du déport, la TNC fait pivoter le palpeur 3D de 180°. La rotation est déclenchée par une fonction auxiliaire définie par le constructeur de la machine dans le paramètre-machine 6160. Z Y X 10 Pour l'étalonnage manuel, procédez de la manière suivante: Positionner la bille de palpage en mode Manuel, dans l'alésage de la bague de réglage Sélectionner la fonction d'étalonnage du rayon de la bille de palpage et du désaxage du palpeur: Appuyer sur la softkey ETAL R Sélectionner l'axe d'outil. Introduire le rayon de la bague de réglage Palpage: Appuyer 4 fois sur la touche START externe. Le palpeur 3D palpe dans chaque direction une position de l'alésage et calcule le rayon effectif de la bille Si vous désirez maintenant quitter la fonction d'étalonnage, appuyez sur la softkey FIN La machine doit avoir été préparée par son constructeur pour pouvoir déterminer le désaxage de la bille de palpage. Consultez le manuel de la machine! Calculer le désaxage de la bille: Appuyer sur la softkey 180°. La TNC fait pivoter le palpeur de 180° Palpage: Appuyer 4 x sur la touche START externe. Le palpeur 3D palpe dans chaque direction une position de l'alésage et calcule le désaxage du palpeur. iTNC 530 HEIDENHAIN 33 2.2 Etalonnage du palpeur à commutation Afficher les valeurs d'étalonnage La TNC mémorise la longueur et le rayon effectifs ainsi que la valeur de désaxage du palpeur et les prendra en compte lors des utilisations ultérieures du palpeur 3D. Pour afficher les valeurs mémorisées, appuyez sur ETAL L et ETAL R. Si vous utilisez plusieurs palpeurs ou séquences de données d'étalonnage: Cf. „Gérer plusieurs séquences de données d'étalonnage”, page 34 Gérer plusieurs séquences de données d'étalonnage Si vous utilisez sur votre machine plusieurs palpeurs ou touches de palpage avec disposition en croix, vous devez éventuellement avoir recours à plusieurs séquences de données d'étalonnage. Pour pouvoir utiliser plusieurs séquences de données d'étalonnage, vous devez paramétrer le paramètre-machine MP 7411=1. La définition des données d'étalonnage est identique à la procédure employée lors de l'utilisation d'un seul palpeur, à ceci près que la TNC enregistre les données d'étalonnage dans le tableau d'outils lorsque vous quittez le menu d'étalonnage et validez avec la touche ENT l'écriture des données d'étalonnage dans le tableau. Le numéro d'outil actif définit la ligne du tableau d'outils dans lequel la TNC enregistre les données Sachez que le numéro d'outil correct est actif lorsque vous utilisez le palpeur et ce, que vous désiriez exécuter un cycle palpeur en mode Automatique ou en mode Manuel. 34 2 Cycles palpeurs en modes Manuel et Manivelle électronique 2.3 Compenser le désaxage de la pièce 2.3 Compenser le désaxage de la pièce Introduction La TNC peut compenser mathématiquement un désaxage de la pièce au moyen d'une „rotation de base“. Pour cela, la TNC initialise l'angle de rotation à l'angle qu'une surface de la pièce doit former avec l'axe de référence angulaire du plan. Cf. figure de droite. Y Y Pour mesurer le désaxage de la pièce, sélectionner le sens de palpage de manière à ce qu'il soit toujours perpendiculaire à l'axe de référence angulaire. Dans le déroulement du programme et pour que la rotation de base soit calculée correctement, vous devez programmer les deux coordonnées du plan d'usinage dans la première séquence du déplacement. PA X A B X Vous pouvez aussi utiliser une rotation de base en combinaison avec la fonction PLANE. Dans ce cas, activez tout d'abord la rotation de base, puis la fonction PLANE. Lorsque vous modifiez la rotation de base, la TNC vous demande au moment de quitter le menu si vous désirez aussi enregistrer sur la ligne active du tableau Preset la rotation de base modifiée. Si oui, appuyez sur la touche ENT. La TNC peut aussi exécuter une compensation de bridage si votre machine est préparée à cet effet. Si nécessaire, prenez contact avec le constructeur de votre machine. Calculer la rotation de base Sélectionner la fonction de palpage: Appuyer sur la softkey PALPAGE ROT Positionner le palpeur à proximité du premier point de palpage Sélectionner le sens de palpage pour qu'il soit perpendiculaire à l'axe de référence angulaire: Sélectionner l'axe et le sens avec la softkey Palpage: Appuyer sur la touche START externe Positionner le palpeur à proximité du deuxième point de palpage Palpage: Appuyer sur la touche START externe. La TNC calcule la rotation de base et affiche l'angle à la suite du dialogue Angle de rotation = iTNC 530 HEIDENHAIN 35 2.3 Compenser le désaxage de la pièce Enregistrer la rotation de base dans le tableau Preset Après l'opération de palpage, introduire le numéro de Preset dans le champ Numéro dans tableau: dans lequel la TNC doit enregistrer la rotation active Appuyer sur la softkey ENTRÉE DS TABLEAU PRESET pour enregistrer la rotation de base dans le tableau Preset Afficher la rotation de base Lorsque vous sélectionnez à nouveau PALPAGE ROT, l'angle de la rotation de base apparaît dans l'affichage de l'angle de rotation. La TNC affiche également l'angle de rotation dans l'affichage d'état supplémentaire (INFOS POS.) L’affichage d’état fait apparaître un symbole pour la rotation de base lorsque la TNC déplace les axes de la machine conformément à la rotation de base. Annuler la rotation de base Sélectionner la fonction de palpage: Appuyer sur la softkey PALPAGE ROT Introduire l'angle de rotation „0“, valider avec la touche ENT Quitter la fonction de palpage: Appuyer sur la touche END 36 2 Cycles palpeurs en modes Manuel et Manivelle électronique 2.4 Initialiser le point de référence avec palpeurs 3D 2.4 Initialiser le point de référence avec palpeurs 3D Introduction La sélection des fonctions destinées à initialiser le point de référence sur la pièce serrée s’effectue avec les softkeys suivantes: Initialiser le point de référence dans un axe au choix avec PALPAGE POS Initialiser un coin comme point de référence avec PALPAGE P Initialiser le centre d'un cercle comme point de référence avec PALPAGE CC Axe central comme point de référence avec PALPAGE Sachez que, lors d'un décalage actif du point zéro, la valeur palpée se réfère toujours au preset actif (ou au dernier point zéro initialisé en mode Manuel) bien que le décalage du point zéro soit compensé dans l'affichage de position. Initialiser le point de référence sur un axe au choix Sélectionner la fonction de palpage: Appuyer sur la softkey PALPAGE POS Positionner le palpeur à proximité du point de palpage Sélectionner simultanément le sens de palpage et l'axe sur lequel doit être initialisé le point de référence, par ex. palpage de Z dans le sens Z–: Sélectionner par softkey Palpage: Appuyer sur la touche START externe Point de référence: Introduire la coordonnée nominale, valider avec la softkey INITIAL. POINT DE RÉFÉRENCE ou inscrire la valeur dans un tableau (cf. „Enregistrer les valeurs de mesure issues des cycles palpeurs dans un tableau de points zéro”, page 30 ou cf. „Enregistrer les valeurs de mesure issues des cycles palpeurs dans le tableau Preset”, page 31) Quitter la fonction de palpage: Appuyer sur la touche END iTNC 530 HEIDENHAIN Z Y X 37 2.4 Initialiser le point de référence avec palpeurs 3D Coin pris comme point de référence – Valider les points palpés pour la rotation de base Sélectionner la fonction de palpage: Appuyer sur la softkey PALPAGE P Points de palpage issus de la rotation de base ?: Appuyer sur la touche ENT pour valider les coordonnées des points de palpage Positionner le palpeur à proximité du premier point de palpage, sur l’arête de la pièce qui n’a pas été palpée pour la rotation de base Sélectionner le sens de palpage: Par softkey Palpage: Appuyer sur la touche START externe Positionner le palpeur à proximité du deuxième point de palpage, sur la même arête Palpage: Appuyer sur la touche START externe Point de référence: Introduire les deux coordonnées du point de référence dans la fenêtre du menu, valider avec la softkey INITIAL. POINT DE RÉFÉRENCE ou inscrire les valeurs dans un tableau (cf. „Enregistrer les valeurs de mesure issues des cycles palpeurs dans un tableau de points zéro”, page 30 ou cf. „Enregistrer les valeurs de mesure issues des cycles palpeurs dans le tableau Preset”, page 31) Quitter la fonction de palpage: Appuyer sur la touche END Y Y=? Y P P X=? X X Coin pris comme point de référence – Ne pas valider les points palpés pour la rotation de base Sélectionner la fonction de palpage: Appuyer sur la softkey PALPAGE P Points de palpage issus rotation de base ?: Répondre par la négative avec la touche NO ENT (question affichée seulement si vous avez déjà effectué une rotation de base) Palper deux fois chacune des deux arêtes de la pièce Point de référence: Introduire les coordonnées du point de référence, valider avec la softkey INITIAL. POINT DE RÉFÉRENCE ou inscrire les valeurs dans un tableau (cf. „Enregistrer les valeurs de mesure issues des cycles palpeurs dans un tableau de points zéro”, page 30 ou cf. „Enregistrer les valeurs de mesure issues des cycles palpeurs dans le tableau Preset”, page 31) Quitter la fonction de palpage: Appuyer sur la touche END 38 2 Cycles palpeurs en modes Manuel et Manivelle électronique Vous pouvez utiliser comme points de référence les centres de trous, poches/îlots circulaires, cylindres pleins, tenons, îlots circulaires, etc. Y Cercle interne: La TNC palpe automatiquement la paroi interne dans les quatre sens des axes de coordonnées. Y+ Pour des cercles discontinus (arcs de cercle), vous pouvez choisir librement le sens du palpage. X X+ Positionner la bille approximativement au centre du cercle Sélectionner la fonction de palpage: Appuyer sur la softkey PALPAGE CC Palpage: Appuyer quatre fois sur la touche START externe. Le palpeur palpe successivement 4 points de la paroi circulaire interne Si vous travaillez avec rotation à 180° dans les 2 sens (seulement sur machines avec orientation broche, dépend de PM6160), appuyer sur la softkey 180° puis palper à nouveau 4 points de la paroi circulaire interne Si vous désirez travailler sans rotation à 180° dans les deux sens: Appuyez sur la touche END Point de référence: Dans la fenêtre du menu, introduire les deux coordonnées du centre du cercle, valider avec la softkey INITIAL. POINT DE RÉFÉRENCE ou inscrire les valeurs dans un tableau (cf. „Enregistrer les valeurs de mesure issues des cycles palpeurs dans un tableau de points zéro”, page 30, ou cf. „Enregistrer les valeurs de mesure issues des cycles palpeurs dans le tableau Preset”, page 31) Y Quitter la fonction de palpage: Appuyer sur la touche END X Y Y X+ X Y+ X Cercle externe: Positionner la bille de palpage à proximité du premier point de palpage, à l’extérieur du cercle Sélectionner le sens de palpage: Appuyer sur la softkey correspondante Palpage: Appuyer sur la touche START externe Répéter la procédure de palpage pour les 3 autres points. Cf. figure en bas et à droite Point de référence: Introduire les coordonnées du point de référence, valider avec la softkey INITIAL. POINT DE RÉFÉRENCE ou inscrire les valeurs dans un tableau (cf. „Enregistrer les valeurs de mesure issues des cycles palpeurs dans un tableau de points zéro”, page 30 ou cf. „Enregistrer les valeurs de mesure issues des cycles palpeurs dans le tableau Preset”, page 31) Quitter la fonction de palpage: Appuyer sur la touche END A l'issue du palpage, la TNC affiche les coordonnées actuelles du centre du cercle ainsi que le rayon PR. iTNC 530 HEIDENHAIN 39 2.4 Initialiser le point de référence avec palpeurs 3D Centre de cercle pris comme point de référence 2.4 Initialiser le point de référence avec palpeurs 3D Axe central comme point de référence Sélectionner la fonction de palpage: Appuyer sur la softkey PALPAGE Positionner le palpeur à proximité du premier point de palpage Sélectionner le sens de palpage par softkey Palpage: Appuyer sur la touche START externe Positionner le palpeur à proximité du deuxième point de palpage Palpage: Appuyer sur la touche START externe Point de référence: Introduire la coordonnée du point de référence dans la fenêtre du menu, valider avec la softkey INITIAL. POINT DE RÉFÉRENCE ou inscrire la valeur dans un tableau (cf. „Enregistrer les valeurs de mesure issues des cycles palpeurs dans un tableau de points zéro”, page 30 ou cf. „Enregistrer les valeurs de mesure issues des cycles palpeurs dans le tableau Preset”, page 31) Y X X+ X Y Quitter la fonction de palpage: Appuyer sur la touche END X+ X X 40 2 Cycles palpeurs en modes Manuel et Manivelle électronique 2.4 Initialiser le point de référence avec palpeurs 3D Initialiser des points de référence à partir de trous/tenons circulaires Le second menu de softkeys contient des softkeys permettant d'utiliser des trous ou tenons circulaires pour initialiser le point de référence Définir si l'on doit palper des trous ou des tenons circulaires La configuration par défaut prévoit le palpage de trous. Sélectionner la fonction de palpage: Appuyer sur la softkey FONCTIONS PALPAGE, commuter à nouveau le menu de softkeys Salectionner la fonction de palpage, appuyer par exemple sur la softkey PALPAGE ROT L'opération consiste à palper des tenons circulaires: A définir par softkey L'opération consiste à palpeur des trous: A définir par softkey Palper les trous Pré-positionner le palpeur approximativement au centre du trou. L’action sur la touche START externe entraîne le palpage automatique de quatre points de la paroi du trou. Puis, la TNC déplace le palpeur jusqu’au trou suivant et répète la même procédure de palpage. Elle la répète jusqu'à ce que tous les trous aient été palpés pour déterminer le point de référence. Palper les tenons circulaires Positionner le palpeur à proximité du premier point de palpage sur le tenon circulaire. Avec la softkey, sélectionner le sens du palpage, exécuter le palpage à l'aide de la touche START externe. Répéter l'opération quatre fois en tout. Tableau récapitulatif Cycle Softkey Rotation de base à partir de 2 trous: La TNC calcule l'angle compris entre la ligne reliant les centres des trous et une position nominale (axe de référence angulaire) Point de référence à partir de 4 trous: La TNC calcule le point d'intersection des lignes reliant les deux premiers et les deux derniers trous palpés. Palpez en croix (comme sur la softkey) car sinon la TNC calcule un point de référence erroné. Centre de cercle à partir de 3 trous: La TNC calcule une trajectoire circulaire sur laquelle sont situés les 3 trous et détermine le centre de cercle de cette trajectoire circulaire. iTNC 530 HEIDENHAIN 41 2.5 Etalonnage de pièces avec les palpeurs 3D 2.5 Etalonnage de pièces avec les palpeurs 3D Introduction Vous pouvez aussi utiliser le palpeur en modes Manuel et Manivelle électronique pour exécuter des mesures simples sur la pièce. De nombreux cycles de palpage programmables sont disponibles pour les opérations de mesure complexes (cf. „Etalonnage automatique des pièces” à la page 109). Le palpeur 3D vous permet de calculer: les coordonnées d’une position et, à partir de là, les cotes et angles sur la pièce Définir la coordonnée d’une position sur la pièce dégauchie Sélectionner la fonction de palpage: Appuyer sur la softkey PALPAGE POS Positionner le palpeur à proximité du point de palpage Sélectionner simultanément le sens du palpage et l’axe auquel doit se référer la coordonnée: Sélectionner la softkey correspondante Lancer la procédure de palpage: Appuyer sur la touche START externe La TNC affiche comme point de référence la coordonnée du point de palpage. Définir les coordonnées d’un coin dans le plan d’usinage Calculer les coordonnées du coin: Cf. „Coin pris comme point de référence – Ne pas valider les points palpés pour la rotation de base”, page 38. La TNC affiche comme point de référence les coordonnées du coin ayant fait l'objet d'une opération de palpage. 42 2 Cycles palpeurs en modes Manuel et Manivelle électronique Sélectionner la fonction de palpage: Appuyer sur la softkey PALPAGE POS Positionner le palpeur à proximité du premier point de palpage A Sélectionner le sens de palpage par softkey Palpage: Appuyer sur la touche START externe Noter la valeur affichée comme point de référence (seulement si le point de référence initialisé précédemment reste actif) Point de référence: Introduire „0“ Quitter le dialogue: Appuyer sur la touche END Sélectionner à nouveau la fonction de palpage: Appuyer sur la softkey PALPAGE POS Positionner le palpeur à proximité du deuxième point de palpage B Sélectionner le sens du palpage par softkey: même axe, mais sens inverse de celui du premier palpage Palpage: Appuyer sur la touche START externe Z A Y X B l Dans l'affichage Point de référence, on trouve la distance entre les deux points situés sur l’axe de coordonnées. Réinitialiser l’affichage de position aux valeurs précédant la mesure linéaire Sélectionner la fonction de palpage: Appuyer sur la softkey PALPAGE POS Palper une nouvelle fois le premier point de palpage Initialiser le point de référence à la valeur notée précédemment Quitter le dialogue: Appuyer sur la touche END Mesurer un angle A l’aide d’un palpeur 3D, vous pouvez déterminer un angle dans le plan d’usinage. La mesure porte sur: l’angle compris entre l’axe de référence angulaire et une arête de la pièce ou l’angle compris entre deux arêtes L’angle mesuré est affiché sous forme d’une valeur de 90° max. iTNC 530 HEIDENHAIN 43 2.5 Etalonnage de pièces avec les palpeurs 3D Définir les cotes d’une pièce 2.5 Etalonnage de pièces avec les palpeurs 3D Définir l’angle compris entre l’axe de référence angulaire et une arête de la pièce Sélectionner la fonction de palpage: Appuyer sur la softkey PALPAGE ROT Angle de rotation: Noter l'angle de rotation affiché si vous désirez rétablir par la suite la rotation de base réalisée auparavant Exécuter la rotation de base avec le côté à comparer (cf. „Compenser le désaxage de la pièce” à la page 35) Avec la softkey PALPAGE ROT, afficher comme angle de rotation l'angle compris entre l'axe de référence angulaire et l'arête de la pièce Annuler la rotation de base ou rétablir la rotation de base d’origine Initialiser l'angle de rotation à la valeur notée précédemment Définir l’angle compris entre deux arêtes de la pièce Sélectionner la fonction de palpage: Appuyer sur la softkey PALPAGE ROT Angle de rotation: Noter l'angle de rotation affiché si vous désirez rétablir par la suite la rotation de base réalisée auparavant Exécuter la rotation de base pour le premier côté (cf. „Compenser le désaxage de la pièce” à la page 35) Palper également le deuxième côté, comme pour une rotation de base. Ne pas mettre 0 pour l'angle de rotation! Avec la softkey PALPAGE ROT, afficher comme angle de rotation l'angle PA compris entre les arêtes de la pièce Annuler la rotation de base ou rétablir la rotation de base d’origine: Initialiser l'angle de rotation à la valeur notée précédemment 44 PA Z L? Y a? 100 X a? 10 100 2 Cycles palpeurs en modes Manuel et Manivelle électronique 2.6 Fonctions de palpage avec palpeurs mécaniques ou comparateurs 2.6 Fonctions de palpage avec palpeurs mécaniques ou comparateurs Introduction Si vous ne disposez sur votre machine d'aucun palpeur 3D électronique, vous pouvez néanmoins utiliser toutes les fonctions de palpage manuelles décrites précédemment (exception: Fonctions d'étalonnage) à l'aide de palpeurs mécaniques ou par simple affleurement. Pour remplacer le signal électronique généré automatiquement par un palpeur 3D pendant la fonction de palpage, vous appuyez sur une touche pour déclencher manuellement le signal de commutation permettant de valider la position de palpage. Procédez de la manière suivante: Sélectionner par softkey la fonction de palpage désirée Placer le palpeur mécanique sur la première position que la TNC doit valider Valider la position: Appuyer sur la touche de validation de la position effective; la TNC enregistre la position actuelle Placer le palpeur mécanique sur la position suivante que la TNC doit valider Valider la position: Appuyer sur la touche de validation de la position effective; la TNC enregistre la position actuelle Le cas échéant, aborder les positions suivantes et les valider comme indiqué précédemment Point de référence: Dans la fenêtre du menu, introduire les coordonnées du nouveau point de référence, valider avec la softkey INIT. PT DE RÉF. ou inscrire les valeurs dans un tableau (cf. „Enregistrer les valeurs de mesure issues des cycles palpeurs dans un tableau de points zéro”, page 30, ou cf. „Enregistrer les valeurs de mesure issues des cycles palpeurs dans le tableau Preset”, page 31) Quitter la fonction de palpage: Appuyer sur la touche END iTNC 530 HEIDENHAIN 45 Cycles palpeurs pour le contrôle automatique des pièces iTNC 530 HEIDENHAIN 47 3.1 Enregistrer automatiquement le désaxage de la pièce 3.1 Enregistrer automatiquement le désaxage de la pièce Vue d'ensemble La TNC dispose de cinq cycles destinés à enregistrer et à compenser un désaxage de la pièce. En outre, vous pouvez annuler une rotation de base avec le cycle 404: Cycle Softkey Page 400 ROTATION DE BASE Enregistrement automatique à partir de 2 points, compensation avec la fonction Rotation de base Page 50 401 ROT 2 TROUS Enregistrement automatique à partir de 2 trous, compensation avec la fonction Rotation de base Page 52 402 ROT AVEC 2 TENONS Enregistrement automatique à partir de 2 tenons, compensation avec la fonction Rotation de base Page 55 403 ROT AVEC AXE ROTATIF Enregistrement automatique à partir de deux points, compensation par rotation du plateau circulaire Page 58 405 ROT AVEC AXE C Réglage automatique d'un déport angulaire entre le centre d'un trou et l'axe Y positif, compensation par rotation du plateau circulaire Page 62 404 INIT. ROTAT. DE BASE Initialisation de n'importe quelle rotation de base Page 61 48 3 Cycles palpeurs pour le contrôle automatique des pièces Pour les cycles 400, 401 et 402, vous pouvez définir avec le paramètre Q307 Configuration rotation de base si le résultat de la mesure doit être corrigé en fonction de la valeur d'un angle α connu (cf. fig. de droite). Ceci vous permet de mesurer la rotation de base sur n'importe quelle droite 1 de la pièce et d'établir la relation par rapport au sens 0° 2. 3.1 Enregistrer automatiquement le désaxage de la pièce Particularités communes aux cycles palpeurs destinés à l'enregistrement du désaxage de la pièce Y Þ 1 2 X iTNC 530 HEIDENHAIN 49 3.1 Enregistrer automatiquement le désaxage de la pièce ROTATION DE BASE (cycle palpeur 400, DIN/ISO: G400) Y Par la mesure de deux points qui doivent être situés sur une droite, le cycle palpeur 400 détermine le désaxage d'une pièce. Avec la fonction Rotation de base, la TNC compense la valeur mesurée (Cf. également „Compenser le désaxage de la pièce” à la page 35). 1 2 3 4 La TNC positionne le palpeur en avance rapide (valeur de PM6150 ou PM6361) et selon la logique de positionnement (cf. „Travail avec les cycles palpeurs” à la page 26) au point de palpage programmé 1. Ce faisant, la TNC décale le palpeur de la valeur de la distance d'approche, dans le sens opposé au sens de déplacement défini Le palpeur se déplace ensuite à la hauteur de mesure programmée et exécute la première opération de palpage suivant l'avance de palpage (PM6120 ou PM6360) Puis, le palpeur se déplace vers le point de palpage suivant 2 et exécute la deuxième opération de palpage La TNC rétracte le palpeur à la hauteur de sécurité et exécute la rotation de base calculée 2 1 X Remarques avant que vous ne programmiez Avant de définir le cycle, vous devez avoir programmé un appel d'outil pour définir l'axe du palpeur. La TNC annule une rotation de base active en début de cycle. 50 3 Cycles palpeurs pour le contrôle automatique des pièces 1er point mesure sur 1er axe Q263 (en absolu): Coordonnée du 1er point de palpage dans l'axe principal du plan d'usinage 1er point mesure sur 2ème axe Q264 (en absolu): Coordonnée du 1er point de palpage dans l'axe auxiliaire du plan d'usinage 2ème point mesure sur 1er axe Q265 (en absolu): Coordonnée du 2ème point de palpage dans l'axe principal du plan d'usinage 2ème point mesure sur 2ème axe Q266 (en absolu): Coordonnée du 2ème point de palpage dans l'axe auxiliaire du plan d'usinage Axe de mesure Q272: Axe du plan d'usinage sur lequel doit être effectuée la mesure: 1:Axe principal = axe de mesure 2:Axe auxiliaire = axe de mesure Sens déplacement 1 Q267: Sens de déplacement du palpeur en direction de la pièce: -1:Sens de déplacement négatif +1:Sens de déplacement positif Hauteur mesure dans axe palpage Q261 (en absolu): Coordonnée du centre de la bille (=point de contact) dans l'axe du palpeur sur lequel doit être effectuée la mesure Distance d'approche Q320 (en incrémental): Distance supplémentaire entre le point de mesure et la bille du palpeur. Q320 agit en complément de PM6140 Hauteur de sécurité Q260 (en absolu): Coordonnée dans l'axe du palpeur excluant toute collision entre le palpeur et la pièce (matériels de bridage) Déplacement haut. sécu. Q301: Définir comment le palpeur doit se déplacer entre les points de mesure: 0: Entre les points de mesure, à la hauteur de mesure 1: Entre les points de mesure, à la hauteur de sécurité Valeur config. rotation de base Q307 (en absolu): Introduire l'angle de la droite de référence si le désaxage à mesurer ne doit pas se référer à l'axe principal mais à une droite quelconque. Pour la rotation de base, la TNC calcule alors la différence entre la valeur mesurée et l'angle de la droite de référence Numéro Preset dans tableau Q305: Indiquer le numéro dans le tableau Preset sous lequel la TNC doit enregistrer la coordonnée rotation de base. Si l'on introduit Q305=0, la TNC enregistre la rotation de base calculée dans le menu ROT du mode de fonctionnement Manuel iTNC 530 HEIDENHAIN + Y Q267 + Q272=2 Q266 Q264 MP6140 + Q320 X Q263 Q265 Q272=1 Exemple: Séquences CN 5 TCH PROBE 400 ROTATION DE BASE Q263=+10 ;1ER POINT 1ER AXE Q264=+3,5 ;1ER POINT 2EME AXE Q265=+25 ;2EME POINT 1ER AXE Q266=+2 ;2EME POINT 2EME AXE Q272=2 ;AXE DE MESURE Q267=+1 ;SENS DEPLACEMENT Q261=-5 ;HAUTEUR DE MESURE Q320=0 ;DISTANCE D'APPROCHE Q260=+20 ;HAUTEUR DE SECURITE Q301=0 ;DEPLAC. HAUT. SECU. Q307=0 ;ROT. BASE CONFIGURÉE Q305=0 ;NO DANS TABLEAU 51 3.1 Enregistrer automatiquement le désaxage de la pièce 3.1 Enregistrer automatiquement le désaxage de la pièce ROTATION DE BASE avec deux trous (cycle palpeur 401, DIN/ISO: G401) Y Le cycle palpeur 401 enregistre les centres de deux trous. La TNC calcule ensuite l'angle formé par l'axe principal du plan d'usinage et la droite reliant les centres des trous. Avec la fonction Rotation de base, la TNC compense la valeur mesurée (Cf. également „Compenser le désaxage de la pièce” à la page 35). En alternative, vous pouvez aussi compenser le désaxage calculé par une rotation du plateau circulaire. 1 2 3 4 5 La TNC positionne le palpeur en avance rapide (valeur de PM6150 ou PM6361) et selon la logique de positionnement (cf. „Travail avec les cycles palpeurs” à la page 26) au centre programmé du premier trou 1 Le palpeur se déplace ensuite à la hauteur de mesure programmée et enregistre le centre du premier trou en palpant quatre fois Puis, la TNC rétracte le palpeur à la hauteur de sécurité et le positionne sur le centre programmé du second trou 2 La TNC déplace le palpeur à la hauteur de mesure programmée et enregistre le centre du deuxième trou en palpant quatre fois Pour terminer, la TNC rétracte le palpeur à la hauteur de sécurité et exécute la rotation de base calculée 2 1 X Remarques avant que vous ne programmiez Avant de définir le cycle, vous devez avoir programmé un appel d'outil pour définir l'axe du palpeur. La TNC annule une rotation de base active en début de cycle. Ce cycle palpeur n'est pas autorisé si la fonction Inclinaison du plan d'usinage est active. Si vous désirez compenser le désaxage au moyen d’une rotation du plateau circulaire, la TNC utilise alors automatiquement les axes rotatifs suivants: C avec axe d’outil Z B avec axe d’outil Y A avec axe d’outil X 52 3 Cycles palpeurs pour le contrôle automatique des pièces 1er trou: centre sur 1er axe Q268 (en absolu): Centre du 1er trou dans l'axe principal du plan d'usinage 1er trou: centre sur 2ème axe Q269 (en absolu): Centre du 1er trou dans l'axe auxiliaire du plan d'usinage 2ème trou: centre sur 1er axe Q270 (en absolu): Centre du 2ème trou dans l'axe principal du plan d'usinage 2ème trou: centre sur 2ème axe Q271 (en absolu): Centre du 2ème trou dans l'axe auxiliaire du plan d'usinage Hauteur mesure dans axe palpage Q261 (en absolu): Coordonnée du centre de la bille (=point de contact) dans l'axe du palpeur sur lequel doit être effectuée la mesure Hauteur de sécurité Q260 (en absolu): Coordonnée dans l'axe du palpeur excluant toute collision entre le palpeur et la pièce (matériels de bridage) Valeur config. rotation de base Q307 (en absolu): Introduire l'angle de la droite de référence si le désaxage à mesurer ne doit pas se référer à l'axe principal mais à une droite quelconque. Pour la rotation de base, la TNC calcule alors la différence entre la valeur mesurée et l'angle de la droite de référence 3.1 Enregistrer automatiquement le désaxage de la pièce Y Q271 Q269 Q268 Q270 X Z Q260 Q261 X iTNC 530 HEIDENHAIN 53 3.1 Enregistrer automatiquement le désaxage de la pièce 54 Numéro Preset dans tableau Q305: Indiquer le numéro dans le tableau Preset sous lequel la TNC doit enregistrer la coordonnée rotation de base. Si l'on introduit Q305=0, la TNC enregistre la rotation de base calculée dans le menu ROT du mode de fonctionnement Manuel. Ce paramètre est inopérant si le désaxage doit être compensé par une rotation du plateau circulaire (Q402=1). Dans ce cas, le désaxage n'est pas enregistré comme valeur angulaire Rotation base/alignement Q402: Définir si la TNC doit initialiser le désaxage calculé comme rotation de base ou bien effectuer l'alignement par une rotation du plateau circulaire: 0: Initialiser la rotation de base 1: Exécuter une rotation du plateau circulaire Si vous choisissez la rotation du plateau circulaire, la TNC n'enregistre pas le désaxage calculé, même si vous avez défini une ligne de tableau dans le paramètre Q305 Exemple: Séquences CN 5 TCH PROBE 401 ROT 2 TROUS Q268=-37 ;1ER CENTRE 1ER AXE Q269=+12 ;1ER CENTRE 2EME AXE Q270=+75 ;2EME CENTRE 1ER AXE Q271=+20 ;2EME CENTRE 2EME AXE Q261=-5 ;HAUTEUR DE MESURE Q260=+20 ;HAUTEUR DE SECURITE Q307=0 ;ROT. BASE CONFIGURÉE Q305=0 ;NO DANS TABLEAU Q402=0 ;ALIGNEMENT Q337=0 ;REMETTRE À ZÉRO Init. à zéro après réglage Q337: Définir si la TNC doit remettre à zéro l'affichage de l'axe rotatif après l'alignement: 0: Ne pas remettre à 0 l'affichage de l'axe rotatif après l'alignement 1: Remettre à 0 l'affichage de l'axe rotatif après l'alignement La TNC ne remet l'affichage à 0 que si vous avez défini Q402=1 3 Cycles palpeurs pour le contrôle automatique des pièces Le cycle palpeur 402 enregistre les centres de deux tenons. La TNC calcule ensuite l'angle formé par l'axe principal du plan d'usinage et la droite reliant les centres des tenons. Avec la fonction Rotation de base, la TNC compense la valeur mesurée (Cf. également „Compenser le désaxage de la pièce” à la page 35). En alternative, vous pouvez aussi compenser le désaxage calculé par une rotation du plateau circulaire. 1 2 3 4 5 La TNC positionne le palpeur en avance rapide (valeur de PM6150 ou MP6361) selon la logique de positionnement (cf. „Travail avec les cycles palpeurs” à la page 26) au point de palpage 1 du premier tenon Le palpeur se déplace ensuite à la hauteur de mesure 1 programmée et enregistre le centre du premier tenon en palpant quatre fois. Entre les points de palpage décalés de 90°, le palpeur se déplace sur un arc de cercle Puis, le palpeur retourne à la hauteur de sécurité et se positionne sur le point de palpage 5 du second tenon La TNC déplace le palpeur à la hauteur de mesure 2 programmée et enregistre le centre du deuxième tenon en palpant quatre fois Pour terminer, la TNC rétracte le palpeur à la hauteur de sécurité et exécute la rotation de base calculée 3.1 Enregistrer automatiquement le désaxage de la pièce ROTATION DE BASE à partir de deux tenons (cycle palpeur 402, DIN/ISO: G402) Y 5 1 X Remarques avant que vous ne programmiez Avant de définir le cycle, vous devez avoir programmé un appel d'outil pour définir l'axe du palpeur. La TNC annule une rotation de base active en début de cycle. Ce cycle palpeur n'est pas autorisé si la fonction Inclinaison du plan d'usinage est active. Si vous désirez compenser le désaxage au moyen d’une rotation du plateau circulaire, la TNC utilise alors automatiquement les axes rotatifs suivants: C avec axe d’outil Z B avec axe d’outil Y A avec axe d’outil X iTNC 530 HEIDENHAIN 55 3.1 Enregistrer automatiquement le désaxage de la pièce 1er tenon: Centre sur 1er axe (en absolu): Centre du 1er tenon dans l'axe principal du plan d'usinage 1er tenon: centre sur 2ème axe Q269 (en absolu): Centre du 1er tenon dans l'axe auxiliaire du plan d'usinage Diamètre tenon 1 Q313: diamètre approximatif du 1er tenon. Introduire de préférence une valeur trop grande Haut. mes. tenon 1 dans axe TS Q261 (en absolu): Coordonnée du centre de la bille (=point de contact) dans l'axe du palpeur sur lequel doit être effectuée la mesure du tenon 1 2ème tenon: centre sur 1er axe Q270 (en absolu): Centre du 2ème tenon dans l'axe principal du plan d'usinage 2ème tenon: centre sur 2ème axe Q271 (en absolu): Centre du 2ème tenon dans l'axe auxiliaire du plan d'usinage Diamètre tenon 2 Q314: Diamètre approximatif du 2ème tenon. Introduire de préférence une valeur trop grande Haut. mes. tenon 2 dans axe TS Q315 (en absolu): Coordonnée du centre de la bille (=point de contact) dans l'axe du palpeur sur lequel doit être effectuée la mesure du tenon 1 Distance d'approche Q320 (en incrémental): Distance supplémentaire entre le point de mesure et la bille du palpeur. Q320 agit en complément de PM6140 56 Y Q271 Q314 Q269 Q313 Q268 X Q270 Z Q261 Q315 MP6140 + Q320 Q260 X Hauteur de sécurité Q260 (en absolu): Coordonnée dans l'axe du palpeur excluant toute collision entre le palpeur et la pièce (matériels de bridage) 3 Cycles palpeurs pour le contrôle automatique des pièces Déplacement haut. sécu. Q301: Définir comment le palpeur doit se déplacer entre les points de mesure: 0: Entre les points de mesure, à la hauteur de mesure 1: Entre les points de mesure, à la hauteur de sécurité Exemple: Séquences CN 5 TCH PROBE 402 ROT 2 TENONS Q268=-37 ;1ER CENTRE 1ER AXE Valeur config. rotation de base Q307 (en absolu): Introduire l'angle de la droite de référence si le désaxage à mesurer ne doit pas se référer à l'axe principal mais à une droite quelconque. Pour la rotation de base, la TNC calcule alors la différence entre la valeur mesurée et l'angle de la droite de référence Q269=+12 ;1ER CENTRE 2EME AXE Q313=60 ;DIAMETRE TENON 1 Q261=-5 ;HAUT. MESURE TENON 1 Q270=+75 ;2EME CENTRE 1ER AXE Q271=+20 ;2EME CENTRE 2EME AXE Numéro Preset dans tableau Q305: Indiquer le numéro dans le tableau Preset sous lequel la TNC doit enregistrer la coordonnée rotation de base. Si l'on introduit Q305=0, la TNC enregistre la rotation de base calculée dans le menu ROT du mode de fonctionnement Manuel. Ce paramètre est inopérant si le désaxage doit être compensé par une rotation du plateau circulaire (Q402=1). Dans ce cas, le désaxage n'est pas enregistré comme valeur angulaire Q314=60 ;DIAMETRE TENON 2 Q315=-5 ;HAUT. MESURE TENON 2 Q320=0 ;DISTANCE D'APPROCHE Q260=+20 ;HAUTEUR DE SECURITE Q301=0 ;DEPLAC. HAUT. SECU. Q307=0 ;ROT. BASE CONFIGURÉE Q305=0 ;NO DANS TABLEAU Q402=0 ;ALIGNEMENT Q337=0 ;REMETTRE À ZÉRO Rotation base/alignement Q402: Définir si la TNC doit initialiser le désaxage calculé comme rotation de base ou bien effectuer l'alignement par une rotation du plateau circulaire: 0: Initialiser la rotation de base 1: Exécuter une rotation du plateau circulaire Si vous choisissez la rotation du plateau circulaire, la TNC n'enregistre pas le désaxage calculé, même si vous avez défini une ligne du tableau dans le paramètre Q305 3.1 Enregistrer automatiquement le désaxage de la pièce Init. à zéro après réglage Q337: Définir si la TNC doit remettre à zéro l'affichage de l'axe rotatif après l'alignement: 0: Ne pas remettre à 0 l'affichage de l'axe rotatif après l'alignement 1: Remettre à 0 l'affichage de l'axe rotatif après l'alignement La TNC ne remet l'affichage à 0 que si vous avez défini Q402=1 iTNC 530 HEIDENHAIN 57 3.1 Enregistrer automatiquement le désaxage de la pièce ROTATION DE BASE compensée avec axe rotatif (cycle palpeur 403, DIN/ISO: G403) Par la mesure de deux points situés sur une droite, le cycle palpeur 403 détermine le désaxage d'une pièce. La TNC compense le désaxage qu'elle a calculé pour la pièce au moyen d'une rotation de l'axe A, B ou C. La pièce peut être serrée n'importe où sur le plateau circulaire. Y Les combinaisons d'un axe de mesure (paramètre de cycle Q272) et d'un axe de compensation (paramètre de cycle Q312) citées cidessous sont autorisées. La fonction Inclinaison du plan d'usinage: Axe palpeur actif Axe de mesure Axe de compens. Z X (Q272=1) C (Q312=6) Z Y (Q272=2) C (Q312=6) Z Z (Q272=3) B (Q312=5) ou A (Q312=4) Y Z (Q272=1) B (Q312=5) Y X (Q272=2) C (Q312=5) Y Y (Q272=3) C (Q312=6) ou A (Q312=4) X Y (Q272=1) A (Q312=4) X Z (Q272=2) A (Q312=4) X X (Q272=3) B (Q312=5) ou C (Q312=6) 1 2 3 58 2 1 X La TNC positionne le palpeur en avance rapide (valeur de PM6150 ou PM6361) et selon la logique de positionnement (cf. „Travail avec les cycles palpeurs” à la page 26) au point de palpage programmé 1. Ce faisant, la TNC décale le palpeur de la valeur de la distance d'approche, dans le sens opposé au sens de déplacement défini Le palpeur se déplace ensuite à la hauteur de mesure programmée et exécute la première opération de palpage suivant l'avance de palpage (PM6120 ou PM6360) Puis, le palpeur se déplace vers le point de palpage suivant 2 et exécute la deuxième opération de palpage 3 Cycles palpeurs pour le contrôle automatique des pièces La TNC rétracte le palpeur à la hauteur de sécurité et positionne l'axe rotatif défini dans le cycle en fonction de la valeur calculée. En option, vous pouvez mettre à 0 l'affichage après le dégauchissage Remarques avant que vous ne programmiez Avant de définir le cycle, vous devez avoir programmé un appel d'outil pour définir l'axe du palpeur. N'utiliser le cycle 403 que si la fonction „Inclinaison du plan d'usinage“ est inactive. La TNC enregistre également dans le paramètre Q150 l'angle défini. 1er point mesure sur 1er axe Q263 (en absolu): Coordonnée du 1er point de palpage dans l'axe principal du plan d'usinage 1er point mesure sur 2ème axe Q264 (en absolu): Coordonnée du 1er point de palpage dans l'axe auxiliaire du plan d'usinage 2ème point mesure sur 1er axe Q265 (en absolu): Coordonnée du 2ème point de palpage dans l'axe principal du plan d'usinage 2ème point mesure sur 2ème axe Q266 (en absolu): Coordonnée du 2ème point de palpage dans l'axe auxiliaire du plan d'usinage Axe de mesure Q272: Axe sur lequel doit être effectuée la mesure: 1: Axe principal = axe de mesure 2: Axe auxiliaire = axe de mesure 3: Axe palpeur = axe de mesure Sens déplacement 1 Q267: Sens de déplacement du palpeur en direction de la pièce: -1: Sens de déplacement négatif +1: Sens de déplacement positif Hauteur mesure dans axe palpage Q261 (en absolu): Coordonnée du centre de la bille (=point de contact) dans l'axe du palpeur sur lequel doit être effectuée la mesure Distance d'approche Q320 (en incrémental): Distance supplémentaire entre le point de mesure et la bille du palpeur. Q320 agit en complément de PM6140 Hauteur de sécurité Q260 (en absolu): Coordonnée dans l'axe du palpeur excluant toute collision entre le palpeur et la pièce (matériels de bridage) iTNC 530 HEIDENHAIN + Y + Q272=2 A B C Q266 Q264 Q267 MP6140 + Q320 X Q263 Q265 Q272=1 Z Q260 Q261 X 59 3.1 Enregistrer automatiquement le désaxage de la pièce 4 3.1 Enregistrer automatiquement le désaxage de la pièce 60 Déplacement haut. sécu. Q301: Définir comment le palpeur doit se déplacer entre les points de mesure: 0: Entre les points de mesure, à la hauteur de mesure 1: Entre les points de mesure, à la hauteur de sécurité Exemple: Séquences CN 5 TCH PROBE 403 ROT SUR AXE C Q263=+0 ;1ER POINT 1ER AXE Axe pour déplacement de compensation Q312: Définir avec quel axe rotatif la TNC doit compenser le désaxage mesuré: 4: Compenser le désaxage avec l'axe rotatif A 5: Compenser le désaxage avec l'axe rotatif B 6: Compenser le désaxage avec l'axe rotatif C Q264=+0 ;1ER POINT 2EME AXE Q265=+20 ;2EME POINT 1ER AXE Q266=+30 ;2EME POINT 2EME AXE Q272=1 ;AXE DE MESURE Init. à zéro après réglage Q337: Définir si la TNC doit remettre à zéro l'affichage de l'axe rotatif après l'alignement: 0: Ne pas remettre à 0 l'affichage de l'axe rotatif après l'alignement 1:Remettre à 0 l'affichage de l'axe rotatif après l'alignement Q267=-1 ;SENS DÉPLACEMENT Q261=-5 ;HAUTEUR DE MESURE Q320=0 ;DISTANCE D'APPROCHE Q260=+20 ;HAUTEUR DE SÉCURITÉ Q301=0 ;DEPLAC. HAUT. SECU. Q312=6 ;AXE DE COMPENSATION Q337=0 ;REMETTRE À ZÉRO Q305=1 ;NO DANS TABLEAU Q303=+1 ;TRANS. VAL. MESURE Q380=+90 ;ANGLE DE RÉFÉRENCE Numéro dans tableau Q305: Indiquer le numéro dans le tableau Preset/tableau de points zéro sous lequel la TNC doit remettre à zéro l'axe rotatif. N'agit que si Q337 = 1 Transfert val. mesure (0,1) Q303: Définir si la rotation de base calculée doit être enregistrée dans le tableau de points zéro ou dans le tableau Preset: 0: Inscrire la rotation de base calculée comme décalage de point zéro dans le tableau de points zéro actif. Le système de référence est le système de coordonnées pièce actif 1: Inscrire la rotation de base calculée dans le tableau Preset. Le système de référence est le système de coordonnées machine (coordonnées REF) Angle de réf. ? (0=axe principal) Q380: Angle sur lequel la TNC doit orienter la droite palpée. N'agit que si l'axe rotatif sélectionné est C (Q312 = 6) 3 Cycles palpeurs pour le contrôle automatique des pièces 3.1 Enregistrer automatiquement le désaxage de la pièce INITIALISER LA ROTATION DE BASE (cycle palpeur 404, DIN/ISO: G404) Pendant l'exécution du programme, vous pouvez initialiser automatiquement n'importe quelle rotation de base à l'aide du cycle palpeur 404. Ce cycle est préconisé si vous désirez annuler une rotation de base qui a déjà été exécutée. Exemple: Séquences CN 5 TCH PROBE 404 ROTATION DE BASE Q307=+0 ;ROT. BASE CONFIGURÉE Valeur config. rotation de base: Valeur angulaire sur laquelle doit être initialisée la rotation de base iTNC 530 HEIDENHAIN 61 3.1 Enregistrer automatiquement le désaxage de la pièce Compenser le désaxage d'une pièce avec l'axe C (cycle palpeur 405, DIN/ISO: G405) Le cycle palpeur 405 vous permet de déterminer Y le désaxage angulaire entre l'axe Y positif du système de coordonnées actif et la ligne médiane d'un trou ou le désaxage angulaire entre la position nominale et la position effective d'un centre de trou 2 3 La TNC compense le désaxage angulaire calculé de la pièce par une rotation de l'axe C. La pièce peut être serrée n'importe où sur le plateau circulaire mais la coordonnée Y du trou doit toujours être positive. Si vous mesurez le désaxage angulaire du trou avec l'axe Y du palpeur (position horizontale du trou), il peut s'avérer nécessaire d'exécuter plusieurs fois le cycle car une imprécision d'environ 1% du désaxage résulte de la stratégie de la mesure 1 2 3 4 5 62 La TNC positionne le palpeur en avance rapide (valeur de PM6150 ou PM6361) et selon la logique de positionnement (cf. „Travail avec les cycles palpeurs” à la page 26) au point de palpage 1. La TNC calcule les points de palpage à partir des données contenues dans le cycle et de la distance d'approche programmée dans PM6140 Le palpeur se déplace ensuite à la hauteur de mesure programmée et exécute la première opération de palpage suivant l'avance de palpage (PM6120 ou PM6360). La TNC détermine automatiquement le sens du palpage en fonction de l'angle initial programmé Le palpeur se déplace ensuite en suivant une trajectoire circulaire, soit à la hauteur de mesure, soit à la hauteur de sécurité, jusqu'au point de palpage suivant 2 et exécute à cet endroit la deuxième opération de palpage La TNC positionne le palpeur au point de palpage 3 puis au point de palpage 4, y exécute la troisième ou quatrième opération de palpage et positionne le palpeur au centre du trou calculé La TNC rétracte ensuite le palpeur à la hauteur de sécurité et règle la pièce par rotation du plateau circulaire. Pour cela, la TNC fait pivoter le plateau circulaire de manière à ce que le centre du trou soit situé après compensation – aussi bien avec axe vertical ou horizontal du palpeur – dans le sens positif de l'axe Y ou à la position nominale du centre du trou. Le désaxage angulaire mesuré est disponible également dans le paramètre Q150 1 4 X Y X 3 Cycles palpeurs pour le contrôle automatique des pièces 3.1 Enregistrer automatiquement le désaxage de la pièce Remarques avant que vous ne programmiez Pour éviter toute collision entre le palpeur et la pièce, introduisez le diamètre nominal de la poche (trou) de manière à ce qu'il soit de préférence trop petit. Si les dimensions de la poche et la distance d'approche ne permettent pas d'effectuer un pré-positionnement à proximité des points de palpage, la TNC palpe toujours en partant du centre de la poche. Dans ce cas, le palpeur ne se déplace pas à la hauteur de sécurité entre les quatre points de mesure. Avant de définir le cycle, vous devez avoir programmé un appel d'outil pour définir l'axe du palpeur. Centre 1er axe Q321 (en absolu): Centre du trou dans l'axe principal du plan d'usinage Centre 2ème axe Q322 (en absolu): Centre du trou dans l'axe auxiliaire du plan d'usinage. Si vous programmez Q322 = 0, la TNC aligne le centre du trou sur l'axe Y positif; si vous programmez Q322 différent de 0, la TNC aligne le centre du trou sur la position nominale (angle résultant du centre du trou) Diamètre nominal Q262: Diamètre approximatif de la poche circulaire (trou). Introduire de préférence une valeur trop petite Angle initial Q325 (en absolu): Angle compris entre l'axe principal du plan d'usinage et le premier point de palpage Y Q247 Q325 Q322 Q321 Q262 X Incrément angulaire Q247 (en incrémental): Angle compris entre deux points de mesure; le signe de l'incrément angulaire détermine le sens de rotation (= sens horaire) pour le déplacement du palpeur vers le point de mesure suivant. Si vous désirez étalonner des arcs de cercle, programmez un incrément angulaire inférieur à 90° Plus l'incrément angulaire programmé est petit et plus le centre de cercle calculé par la TNC sera imprécis. Valeur d'introduction min.: 5°. iTNC 530 HEIDENHAIN 63 3.1 Enregistrer automatiquement le désaxage de la pièce 64 Hauteur mesure dans axe palpage Q261 (en absolu): Coordonnée du centre de la bille (=point de contact) dans l'axe du palpeur sur lequel doit être effectuée la mesure Z Distance d'approche Q320 (en incrémental): Distance supplémentaire entre le point de mesure et la bille du palpeur. Q320 agit en complément de PM6140 Hauteur de sécurité Q260 (en absolu): Coordonnée dans l'axe du palpeur excluant toute collision entre le palpeur et la pièce (matériels de bridage) Déplacement haut. sécu. Q301: Définir comment le palpeur doit se déplacer entre les points de mesure: 0: Entre les points de mesure, à la hauteur de mesure 1: Entre les points de mesure, à la hauteur de sécurité Init. à zéro après réglage Q337: Déterminer si la TNC doit remettre l'affichage de l'axe C à zéro ou si elle doit inscrire le désaxage angulaire dans la colonne C du tableau de points zéro: 0: Remettre à 0 l'affichage de l'axe C >0:Inscrire le désaxage angulaire avec son signe dans le tableau de points zéro. Numéro de ligne = valeur de Q337. Si un décalage C est déjà inscrit dans le tableau de points zéro, la TNC additionne le désaxage angulaire mesuré en tenant compte de son signe Q260 Q261 MP6140 + Q320 X Exemple: Séquences CN 5 TCH PROBE 405 ROT AVEC AXE C Q321=+50 ;CENTRE 1ER AXE Q322=+50 ;CENTRE 2ÈME AXE Q262=10 ;DIAMÈTRE NOMINAL Q325=+0 ;ANGLE INITIAL Q247=90 ;INCRÉMENT ANGULAIRE Q261=-5 ;HAUTEUR DE MESURE Q320=0 ;DISTANCE D'APPROCHE Q260=+20 ;HAUTEUR DE SÉCURITÉ Q301=0 ;DÉPLAC. HAUT. SÉCU. Q337=0 ;REMETTRE À ZÉRO 3 Cycles palpeurs pour le contrôle automatique des pièces 3.1 Enregistrer automatiquement le désaxage de la pièce Exemple: Déterminer la rotation de base à l'aide de deux trous Y Y 35 15 25 80 X Z 0 BEGIN PGM CYC401 MM 1 TOOL CALL 0 Z 2 TCH PROBE 401 ROT 2 TROUS Q268=+25 ;1ER CENTRE 1ER AXE Centre du 1er trou: Coordonnée X Q269=+15 ;1ER CENTRE 2ÈME AXE Centre du 1er trou: Coordonnée Y Q270=+80 ;2ÈME CENTRE 1ER AXE Centre du 2ème trou: Coordonnée X Q271=+35 ;2ÈME CENTRE 2ÈME AXE Centre du 2ème trou: Coordonnée Y Q261=-5 ;HAUTEUR DE MESURE Coordonnée dans l'axe du palpeur où s'effectue la mesure Q260=+20 ;HAUTEUR DE SÉCURITÉ Hauteur où l'axe palpeur peut se déplacer sans risque de collision Q307=+0 ;ROT. BASE CONFIGURÉE Angle de la droite de référence Q402=1 ;ALIGNEMENT Compenser le désaxage par rotation du plateau circulaire Q337=1 ;REMETTRE À ZÉRO Après l'alignement, remettre l'affichage à zéro 3 CALL PGM 35K47 Appeler le programme d'usinage 4 END PGM CYC401 MM iTNC 530 HEIDENHAIN 65 3.2 Calcul automatique des points de référence 3.2 Calcul automatique des points de référence Vue d'ensemble La TNC propose douze cycles vous permettant de calculer automatiquement les points de référence et de les traiter de la manière suivante: Initialiser directement les valeurs calculées comme valeurs d'affichage Inscrire les valeurs calculées dans le tableau Preset Inscrire les valeurs calculées dans un tableau de points zéro Cycle Softkey Page 408 PTREF CENTRE RAINURE Mesurer l'intérieur d’une rainure, initialiser le centre de la rainure comme point de référence Page 70 409 PTREF CENT. OBLONG Mesurer l'extérieur d’un oblong, initialiser le centre de l'oblong comme point de référence Page 73 410 PT REF. INT. RECTAN Mesure interne de la longueur et de la largeur d'un rectangle; initialiser le centre comme point de référence Page 76 411 PT REF. EXT. RECTAN Mesure externe de la longueur et de la largeur d'un rectangle; initialiser le centre comme point de référence Page 79 412 PT REF. INT. CERCLE Mesure interne de 4 points au choix du cercle; initialiser le centre comme point de référence Page 82 413 PT REF. EXT. CERCLE Mesure externe de 4 points au choix du cercle; initialiser le centre comme point de référence Page 86 414 PT REF. EXT. COIN Mesure externe de 2 droites; initialiser leur point d'intersection comme point de référence Page 89 415 PT REF. INT. COIN Mesure interne de 2 droites; initialiser leur point d'intersection comme point de référence Page 92 66 3 Cycles palpeurs pour le contrôle automatique des pièces Softkey Page 416 PT REF CENTRE C.TROUS (2ème niveau de softkeys) Mesure de 3 trous au choix sur cercle de trous; initialiser le centre du cercle de trous comme point de référence Page 95 417 PT REF DANS AXE PALP (2ème niveau de softkeys) Mesure d'une position au choix dans l'axe du palpeur et initialisation comme point de référence Page 98 418 PT REF AVEC 4 TROUS (2ème niveau de softkeys) Mesure de 2 fois 2 trous en croix; initialiser le point d'intersection des deux droites comme point de référence Page 100 419 PT DE REF SUR UN AXE (2ème niveau de softkeys) Mesure d'une position au choix sur un axe à sélectionner librement et initialisation comme point de référence Page 103 iTNC 530 HEIDENHAIN 3.2 Calcul automatique des points de référence Cycle 67 3.2 Calcul automatique des points de référence Caractéristiques communes à tous les cycles palpeurs pour l'initialisation du point de référence Vous pouvez exécuter les cycles palpeurs 408 à 419 même si la rotation de base est activée (rotation de base ou cycle 10). Point de référence et axe du palpeur La TNC initialise le point de référence dans le plan d'usinage en fonction de l'axe du palpeur défini dans votre programme de mesure: Axe palpeur actif Initialisation point de réf. en Z ou W X et Y Y ou V Z et X X ou U Y et Z 68 3 Cycles palpeurs pour le contrôle automatique des pièces 3.2 Calcul automatique des points de référence Enregistrer le point de référence calculé Pour tous les cycles permettant l'initialisation du point de référence, vous pouvez définir avec les paramètres d'introduction Q303 et Q305 la manière dont la TNC doit enregistrer le point de référence calculé: Q305 = 0, Q303 = valeur au choix: La TNC initialise l'affichage du point de référence calculé. Le nouveau point de référence est aussitôt activé Q305 différent de 0, Q303 = -1 Cette combinaison ne peut exister que si vous importez des programmes contenant les cycles 410 à 418 ayant été créés sur une TNC 4xx vous importez des programmes contenant les cycles 410 à 418 ayant été créés avec une version de logiciel antérieure de l'iTNC 530 vous avez défini le cycle en intégrant le paramètre Q303 pour le transfert des valeurs de mesure Dans de tels cas, la TNC délivre un message d'erreur car le processus complet en liaison avec les tableaux de points zéro (coordonnées REF) a été modifié et vous devez définir avec le paramètre Q303 un transfert de valeurs de mesure. Q305 différent de 0, Q303 = 0 La TNC enregistre dans le tableau de points zéro actif le point de référence calculé. Le système de référence est le système de coordonnées pièce actif. La valeur du paramètre Q305 détermine le numéro de point zéro. Activer le point zéro dans le programme CN avec le cycle 7 Q305 différent de 0, Q303 = 1 La TNC enregistre dans le tableau Preset le point de référence calculé. Le système de référence est le système de coordonnées machine (coordonnées REF). La valeur du paramètre Q305 détermine le numéro de Preset. Activer le Preset dans le programme CN avec le cycle 247 Résultats de la mesure dans les paramètres Q Les résultats de la mesure du cycle palpeur concerné sont mémorisés par la TNC dans les paramètres Q150 à Q160 à effet global. Vous pouvez utiliser ultérieurement ces paramètres dans votre programme. Tenez compte du tableau des paramètres de résultat contenu dans chaque définition de cycle. iTNC 530 HEIDENHAIN 69 3.2 Calcul automatique des points de référence PREF CENTRE RAINURE (cycle palpeur 408, DIN/ISO: G408: Fonction FCL 3) Le cycle palpeur 408 calcule le centre d'une rainure et initialise ce centre comme point de référence. Si vous le désirez, la TNC peut aussi inscrire le centre dans un tableau de points zéro ou de Preset. 1 La TNC positionne le palpeur en avance rapide (valeur de PM6150 ou PM6361) et selon la logique de positionnement (cf. „Travail avec les cycles palpeurs” à la page 26) au point de palpage 1. La TNC calcule les points de palpage à partir des données contenues dans le cycle et de la distance d'approche programmée dans PM6140 Le palpeur se déplace ensuite à la hauteur de mesure programmée et exécute la première opération de palpage suivant l'avance de palpage (PM6120 ou PM6360) Puis, le palpeur se déplace soit paraxialement à la hauteur de mesure, soit linéairement à la hauteur de sécurité, jusqu'au point de palpage suivant 2 et exécute à cet endroit la deuxième opération de palpage Pour terminer, la TNC rétracte le palpeur à la hauteur de sécurité et traite le point de référence calculé en fonction des paramètres de cycle Q303 et Q305 (cf. „Enregistrer le point de référence calculé” à la page 69) et enregistre les valeurs effectives dans les paramètres Q indiqués ci-après Ensuite, si on le désire, la TNC calcule aussi, dans une opération de palpage séparée, le point de référence dans l'axe du palpeur 2 3 4 5 Numéro paramètre Signification Q166 Valeur effective pour la largeur de rainure mesurée Q157 Valeur effective de la position de l'axe médian Y 1 2 X Remarques avant que vous ne programmiez Pour éviter toute collision entre le palpeur et la pièce, introduisez la largeur de la rainure de manière à ce qu'elle soit de préférence trop petite. Si la largeur de la rainure et la distance d'approche ne permettent pas d'effectuer un prépositionnement à proximité des points de palpage, la TNC palpe toujours en partant du centre de la rainure. Dans ce cas, le palpeur ne se déplace pas à la hauteur de sécurité entre les deux points de mesure. Avant de définir le cycle, vous devez avoir programmé un appel d'outil pour définir l'axe du palpeur. 70 3 Cycles palpeurs pour le contrôle automatique des pièces Centre 2ème axe Q322 (en absolu): Centre de la rainure dans l'axe auxiliaire du plan d'usinage Largeur de la rainure Q311 (en incrémental): Largeur de la rainure indépendamment de la position dans le plan d'usinage Axe de mesure (1=1er axe/2=2ème axe) Q272: Axe sur lequel doit être effectuée la mesure: 1: Axe principal = axe de mesure 2: Axe auxiliaire = axe de mesure Hauteur mesure dans l'axe du palpeur Q261 (en absolu): Coordonnée du centre de la bille (=point de contact) dans l'axe du palpeur sur lequel doit être effectuée la mesure Distance d'approche Q320 (en incrémental): Distance supplémentaire entre le point de mesure et la bille du palpeur. Q320 agit en complément de PM6140 Hauteur de sécurité Q260 (en absolu): Coordonnée dans l'axe du palpeur excluant toute collision entre le palpeur et la pièce (matériels de bridage) Déplacement haut. sécu. Q301: Définir comment le palpeur doit se déplacer entre les points de mesure: 0: Entre les points de mesure, à la hauteur de mesure 1: Entre les points de mesure, à la hauteur de sécurité Numéro dans tableau Q305: Indiquer le numéro dans le tableau de points zéro/tableau Preset sous lequel la TNC doit mémoriser les coordonnées du centre de la rainure. Si vous introduisez Q305=0, la TNC initialise automatiquement le nouveau point de référence sur le centre de la rainure Y 3.2 Calcul automatique des points de référence Centre 1er axe Q321 (en absolu): Centre de la rainure dans l'axe principal du plan d'usinage MP6140 + Q320 Q311 Q322 X Q321 Z Q260 Q261 X Nouveau pt de réf. Q405 (en absolu): Coordonnée dans l'axe de mesure à laquelle la TNC doit initialiser le centre de la rainure. Configuration par défaut = 0 iTNC 530 HEIDENHAIN 71 3.2 Calcul automatique des points de référence 72 Transfert val. mesure (0,1) Q303: Définir si le point de référence défini doit être enregistré dans le tableau de points zéro ou dans le tableau Preset: 0: Inscrire dans le tableau de points zéro actif le point de référence calculé. Le système de référence est le système de coordonnées pièce actif 1: Inscrire dans le tableau Preset le point de référence calculé. Le système de référence est le système de coordonnées machine (coordonnées REF) Exemple: Séquences CN 5 TCH PROBE 408 PTREF CENTRE RAINURE Q321=+50 ;CENTRE 1ER AXE Q322=+50 ;CENTRE 2ÈME AXE Q311=25 ;LARGEUR RAINURE Q272=1 ;AXE DE MESURE Palpage dans axe palpeur Q381: Définir si la TNC doit également initialiser le point de référence dans l'axe du palpeur: 0: Ne pas initialiser le point de référence dans l'axe du palpeur 1: Initialiser le point de référence dans l'axe du palpeur Q261=-5 ;HAUTEUR DE MESURE Q320=0 ;DISTANCE D'APPROCHE Q260=+20 ;HAUTEUR DE SÉCURITÉ Q301=0 ;DÉPLAC. HAUT. SÉCU. Q305=10 ;NO DANS TABLEAU Palp. axe palp.: Coord. 1er axe Q382 (en absolu): Coordonnée du point de palpage dans l'axe principal du plan d'usinage à laquelle le point de référence doit être initialisé dans l'axe du palpeur. N'agit que si Q381 = 1 Q405=+0 ;POINT DE RÉFÉRENCE Q303=+1 ;TRANS. VAL. MESURE Q381=1 ;PALP. DS AXE PALPEUR Q382=+85 ;1ÈRE COO. DANS AXE PALP. Palp. axe palp.: Coord. 2ème axe Q383 (en absolu): Coordonnée du point de palpage dans l'axe auxiliaire du plan d'usinage à laquelle le point de référence doit être initialisé dans l'axe du palpeur. N'agit que si Q381 = 1 Q383=+50 ;2ÈME COO. DANS AXE PALP. Q384=+0 ;3ÈME COO. DANS AXE PALP. Q333=+1 ;POINT DE RÉFÉRENCE Palp. axe palp.: Coord. 3ème axe Q384 (en absolu): Coordonnée du point de palpage dans l'axe auxiliaire du l'axe du palpeur à laquelle le point de référence doit être initialisé dans l'axe du palpeur. N'agit que si Q381 = 1 Nouveau pt de réf. sur axe palpeur Q333 (en absolu): Coordonnée dans l'axe du palpeur à laquelle la TNC doit initialiser le point de référence. Configuration par défaut = 0 3 Cycles palpeurs pour le contrôle automatique des pièces Le cycle palpeur 409 calcule le centre d'un oblong et initialise ce centre comme point de référence. Si vous le désirez, la TNC peut aussi inscrire le centre dans un tableau de points zéro ou de Preset. 1 2 3 4 5 La TNC positionne le palpeur en avance rapide (valeur de PM6150 ou PM6361) et selon la logique de positionnement (cf. „Travail avec les cycles palpeurs” à la page 26) au point de palpage 1. La TNC calcule les points de palpage à partir des données contenues dans le cycle et de la distance d'approche programmée dans PM6140 Le palpeur se déplace ensuite à la hauteur de mesure programmée et exécute la première opération de palpage suivant l'avance de palpage (PM6120 ou PM6360) Puis, le palpeur se déplace à la hauteur de sécurité vers le point de palpage suivant 2 et exécute la deuxième opération de palpage Pour terminer, la TNC rétracte le palpeur à la hauteur de sécurité et traite le point de référence calculé en fonction des paramètres de cycle Q303 et Q305 (cf. „Enregistrer le point de référence calculé” à la page 69) et enregistre les valeurs effectives dans les paramètres Q indiqués ci-après Ensuite, si on le désire, la TNC calcule aussi, dans une opération de palpage séparée, le point de référence dans l'axe du palpeur Numéro paramètre Signification Q166 Valeur effective largeur oblong mesurée Q157 Valeur effective de la position de l'axe médian 3.2 Calcul automatique des points de référence PREF CENT. OBLONG (cycle palpeur 409, DIN/ISO: G409, fonction FCL 3) Y 2 1 X Remarques avant que vous ne programmiez Pour éviter toute collision entre le palpeur et la pièce, introduisez la largeur de l’oblong de manière à ce qu'elle soit de préférence trop grande. Avant de définir le cycle, vous devez avoir programmé un appel d'outil pour définir l'axe du palpeur. iTNC 530 HEIDENHAIN 73 Centre 1er axe Q321 (en absolu): centre de l'oblong dans l'axe principal du plan d'usinage Centre 2ème axe Q322 (en absolu): centre de l'oblong dans l'axe auxiliaire du plan d'usinage Largeur oblong Q311 (en incrémental): Largeur de l'oblong indépendamment de la position dans le plan d'usinage Axe de mesure (1=1er axe/2=2ème axe) Q272: Axe sur lequel doit être effectuée la mesure: 1: Axe principal = axe de mesure 2: Axe auxiliaire = axe de mesure Hauteur mesure dans l'axe du palpeur Q261 (en absolu): Coordonnée du centre de la bille (=point de contact) dans l'axe du palpeur sur lequel doit être effectuée la mesure Distance d'approche Q320 (en incrémental): Distance supplémentaire entre le point de mesure et la bille du palpeur. Q320 agit en complément de PM6140 Hauteur de sécurité Q260 (en absolu): Coordonnée dans l'axe du palpeur excluant toute collision entre le palpeur et la pièce (matériels de bridage) Numéro dans tableau Q305: Indiquer le numéro dans le tableau de points zéro/tableau Preset sous lequel la TNC doit mémoriser les coordonnées du centre de l'oblong. Si vous introduisez Q305=0, la TNC initialise automatiquement le nouveau point de référence sur le centre de la rainure 74 Nouveau pt de réf. Q405 (en absolu): Coordonnée dans l'axe de mesure à laquelle la TNC doit initialiser le centre de l'oblong. Configuration par défaut = 0 MP6140 + Q320 Y Q311 3.2 Calcul automatique des points de référence Q322 X Q321 Z Q260 Q261 X 3 Cycles palpeurs pour le contrôle automatique des pièces Transfert val. mesure (0,1) Q303: Définir si le point de référence défini doit être enregistré dans le tableau de points zéro ou dans le tableau Preset: 0: Inscrire dans le tableau de points zéro actif le point de référence calculé. Le système de référence est le système de coordonnées pièce actif 1: Inscrire dans le tableau Preset le point de référence calculé. Le système de référence est le système de coordonnées machine (coordonnées REF) Exemple: Séquences CN 5 TCH PROBE 409 PTREF CENT. OBLONG Q321=+50 ;CENTRE 1ER AXE Q322=+50 ;CENTRE 2ÈME AXE Q311=25 ;LARGEUR OBLONG Q272=1 ;AXE DE MESURE Palpage dans axe palpeur Q381: Définir si la TNC doit également initialiser le point de référence dans l'axe du palpeur: 0: Ne pas initialiser le point de référence dans l'axe du palpeur 1: Initialiser le point de référence dans l'axe du palpeur Q261=-5 ;HAUTEUR DE MESURE Q320=0 ;DISTANCE D'APPROCHE Q260=+20 ;HAUTEUR DE SÉCURITÉ Q305=10 ;NO DANS TABLEAU Q405=+0 ;POINT DE RÉFÉRENCE Palp. axe palp.: Coord. 1er axe Q382 (en absolu): Coordonnée du point de palpage dans l'axe principal du plan d'usinage à laquelle le point de référence doit être initialisé dans l'axe du palpeur. N'agit que si Q381 = 1 Q303=+1 ;TRANS. VAL. MESURE Q381=1 ;PALP. DS AXE PALPEUR Q382=+85 ;1ÈRE COO. DANS AXE PALP. Q383=+50 ;2ÈME COO. DANS AXE PALP. Palp. axe palp.: Coord. 2ème axe Q383 (en absolu): Coordonnée du point de palpage dans l'axe auxiliaire du plan d'usinage à laquelle le point de référence doit être initialisé dans l'axe du palpeur. N'agit que si Q381 = 1 Q384=+0 ;3ÈME COO. DANS AXE PALP. Q333=+1 ;POINT DE RÉFÉRENCE Palp. axe palp.: Coord. 3ème axe Q384 (en absolu): Coordonnée du point de palpage dans l'axe auxiliaire du l'axe du palpeur à laquelle le point de référence doit être initialisé dans l'axe du palpeur. N'agit que si Q381 = 1 Nouveau pt de réf. sur axe palpeur Q333 (en absolu): Coordonnée dans l'axe du palpeur à laquelle la TNC doit initialiser le point de référence. Configuration par défaut = 0 iTNC 530 HEIDENHAIN 75 3.2 Calcul automatique des points de référence 3.2 Calcul automatique des points de référence POINT DE REFERENCE INTERIEUR RECTANGLE (cycle palpeur 410, DIN/ISO: G410) Le cycle palpeur 410 calcule le centre d'une poche rectangulaire et initialise ce centre comme point de référence. Si vous le désirez, la TNC peut aussi inscrire le centre dans un tableau de points zéro ou de Preset. 1 La TNC positionne le palpeur en avance rapide (valeur de PM6150 ou PM6361) et selon la logique de positionnement (cf. „Travail avec les cycles palpeurs” à la page 26) au point de palpage 1. La TNC calcule les points de palpage à partir des données contenues dans le cycle et de la distance d'approche programmée dans PM6140 Le palpeur se déplace ensuite à la hauteur de mesure programmée et exécute la première opération de palpage suivant l'avance de palpage (PM6120 ou PM6360) Puis, le palpeur se déplace soit paraxialement à la hauteur de mesure, soit linéairement à la hauteur de sécurité, jusqu'au point de palpage suivant 2 et exécute à cet endroit la deuxième opération de palpage La TNC positionne le palpeur au point de palpage 3 puis au point de palpage 4, y exécute la troisième ou la quatrième opération de palpage Pour terminer, la TNC rétracte le palpeur à la hauteur de sécurité et traite le point de référence calculé en fonction des paramètres de cycle Q303 et Q305 (cf. „Enregistrer le point de référence calculé” à la page 69). Ensuite, si on le désire, la TNC calcule aussi, dans une opération de palpage séparée, le point de référence dans l'axe du palpeur et enregistre les valeurs effectives dans les paramètres Q suivants 2 3 4 5 6 Numéro paramètre Signification Q151 Valeur effective centre axe principal Q152 Valeur effective centre axe auxiliaire Q154 Valeur effective côté axe principal Q155 Valeur effective côté axe auxiliaire Y 4 3 1 2 X Remarques avant que vous ne programmiez Pour éviter toute collision entre le palpeur et la pièce, introduisez le 1er et le 2ème côté de la poche de manière à ce qu'il soit de préférence trop petit. Si les dimensions de la poche et la distance d'approche ne permettent pas d'effectuer un pré-positionnement à proximité des points de palpage, la TNC palpe toujours en partant du centre de la poche. Dans ce cas, le palpeur ne se déplace pas à la hauteur de sécurité entre les quatre points de mesure. Avant de définir le cycle, vous devez avoir programmé un appel d'outil pour définir l'axe du palpeur. 76 3 Cycles palpeurs pour le contrôle automatique des pièces Centre 2ème axe Q322 (en absolu): Centre de la poche dans l'axe auxiliaire du plan d'usinage 1er côté Q323 (en incrémental): Longueur de la poche parallèle à l'axe principal du plan d'usinage 2ème côté Q324 (en incrémental): Longueur de la poche parallèle à l'axe auxiliaire du plan d'usinage Distance d'approche Q320 (en incrémental): Distance supplémentaire entre le point de mesure et la bille du palpeur. Q320 agit en complément de PM6140 Hauteur de sécurité Q260 (en absolu): Coordonnée dans l'axe du palpeur excluant toute collision entre le palpeur et la pièce (matériels de bridage) Q323 Q322 MP6140 + Q320 Hauteur mesure dans axe palpage Q261 (en absolu): Coordonnée du centre de la bille (=point de contact) dans l'axe du palpeur sur lequel doit être effectuée la mesure Y Nouveau pt de réf. axe principal Q331 (en absolu): Coordonnée dans l'axe principal à laquelle la TNC doit initialiser le centre de la poche calculé. Configuration par défaut = 0 Nouveau pt de réf. axe auxiliaire Q332 (en absolu): Coordonnée dans l'axe auxiliaire à laquelle la TNC doit initialiser le centre de la poche calculé. Configuration par défaut = 0 iTNC 530 HEIDENHAIN X Q321 Z Déplacement haut. sécu. Q301: Définir comment le palpeur doit se déplacer entre les points de mesure: 0: Entre les points de mesure, à la hauteur de mesure 1: Entre les points de mesure, à la hauteur de sécurité Numéro point zéro dans tableau Q305: Indiquer le numéro dans le tableau de points zéro/tableau Preset sous lequel la TNC doit mémoriser les coordonnées du centre de la poche. Si vous introduisez Q305=0, la TNC initialise automatiquement le nouveau point de référence au centre de la poche 3.2 Calcul automatique des points de référence Centre 1er axe Q321 (en absolu): Centre de la poche dans l'axe principal du plan d'usinage Q324 Q260 Q261 X 77 3.2 Calcul automatique des points de référence 78 Transfert val. mesure (0,1) Q303: Définir si le point de référence défini doit être enregistré dans le tableau de points zéro ou dans le tableau Preset: -1: Ne pas utiliser! Sera inscrit par la TNC si d'anciens programmes sont importés (cf. „Enregistrer le point de référence calculé” à la page 69) 0: Inscrire dans le tableau de points zéro actif le point de référence calculé. Le système de référence est le système de coordonnées pièce actif 1: Inscrire dans le tableau Preset le point de référence calculé. Le système de référence est le système de coordonnées machine (coordonnées REF) Exemple: Séquences CN 5 TCH PROBE 410 PT REF. INT. RECTAN Q321=+50 ;CENTRE 1ER AXE Q322=+50 ;CENTRE 2ÈME AXE Q323=60 ;1ER CÔTÉ Q324=20 ;2ÈME CÔTÉ Q261=-5 ;HAUTEUR DE MESURE Q320=0 ;DISTANCE D'APPROCHE Palpage dans axe palpeur Q381: Définir si la TNC doit également initialiser le point de référence dans l'axe du palpeur: 0: Ne pas initialiser le point de référence dans l'axe du palpeur 1: Initialiser le point de référence dans l'axe du palpeur Q260=+20 ;HAUTEUR DE SÉCURITÉ Q301=0 ;DÉPLAC. HAUT. SÉCU. Q305=10 ;NO DANS TABLEAU Q331=+0 ;POINT DE RÉFÉRENCE Q332=+0 ;POINT DE RÉFÉRENCE Palp. axe palp.: Coord. 1er axe Q382 (en absolu): Coordonnée du point de palpage dans l'axe principal du plan d'usinage à laquelle le point de référence doit être initialisé dans l'axe du palpeur. N'agit que si Q381 = 1 Q303=+1 ;TRANS. VAL. MESURE Palp. axe palp.: Coord. 2ème axe Q383 (en absolu): Coordonnée du point de palpage dans l'axe auxiliaire du plan d'usinage à laquelle le point de référence doit être initialisé dans l'axe du palpeur. N'agit que si Q381 = 1 Palp. axe palp.: Coord. 3ème axe Q384 (en absolu): Coordonnée du point de palpage dans l'axe auxiliaire du l'axe du palpeur à laquelle le point de référence doit être initialisé dans l'axe du palpeur. N'agit que si Q381 = 1 Nouveau pt de réf. sur axe palpeur Q333 (en absolu): Coordonnée dans l'axe du palpeur à laquelle la TNC doit initialiser le point de référence. Configuration par défaut = 0 Q381=1 ;PALP. DS AXE PALPEUR Q382=+85 ;1ÈRE COO. DANS AXE PALP. Q383=+50 ;2ÈME COO. DANS AXE PALP. Q384=+0 ;3ÈME COO. DANS AXE PALP. Q333=+1 ;POINT DE RÉFÉRENCE 3 Cycles palpeurs pour le contrôle automatique des pièces Y Le cycle palpeur 411 calcule le centre d'un tenon rectangulaire et initialise ce centre comme point de référence. Si vous le désirez, la TNC peut aussi inscrire le centre dans un tableau de points zéro ou de Preset. 1 2 3 4 5 6 La TNC positionne le palpeur en avance rapide (valeur de PM6150 ou PM6361) et selon la logique de positionnement (cf. „Travail avec les cycles palpeurs” à la page 26) au point de palpage 1. La TNC calcule les points de palpage à partir des données contenues dans le cycle et de la distance d'approche programmée dans PM6140 Le palpeur se déplace ensuite à la hauteur de mesure programmée et exécute la première opération de palpage suivant l'avance de palpage (PM6120 ou PM6360) Puis, le palpeur se déplace soit paraxialement à la hauteur de mesure, soit linéairement à la hauteur de sécurité, jusqu'au point de palpage suivant 2 et exécute à cet endroit la deuxième opération de palpage La TNC positionne le palpeur au point de palpage 3 puis au point de palpage 4, y exécute la troisième ou la quatrième opération de palpage Pour terminer, la TNC rétracte le palpeur à la hauteur de sécurité et traite le point de référence calculé en fonction des paramètres de cycle Q303 et Q305 (cf. „Enregistrer le point de référence calculé” à la page 69). Ensuite, si on le désire, la TNC calcule aussi, dans une opération de palpage séparée, le point de référence dans l'axe du palpeur et enregistre les valeurs effectives dans les paramètres Q suivants Numéro paramètre Signification Q151 Valeur effective centre axe principal Q152 Valeur effective centre axe auxiliaire Q154 Valeur effective côté axe principal Q155 Valeur effective côté axe auxiliaire 3.2 Calcul automatique des points de référence POINT DE REFERENCE EXTERIEUR RECTANGLE (cycle palpeur 411, DIN/ISO: G411) 4 3 1 2 X Remarques avant que vous ne programmiez Pour éviter toute collision entre le palpeur et la pièce, introduisez le 1er et le 2ème côté du tenon de manière à ce qu'il soit de préférence trop grand. Avant de définir le cycle, vous devez avoir programmé un appel d'outil pour définir l'axe du palpeur. iTNC 530 HEIDENHAIN 79 Centre 1er axe Q321 (en absolu): Centre du tenon dans l'axe principal du plan d'usinage Centre 2ème axe Q322 (en absolu): Centre du tenon dans l'axe auxiliaire du plan d'usinage Longueur 1er côté Q323 (en incrémental): longueur du tenon parallèle à l'axe principal du plan d'usinage Longueur 2ème côté Q324 (en incrémental): longueur du tenon parallèle à l'axe auxiliaire du plan d'usinage Hauteur mesure dans axe palpage Q261 (en absolu): Coordonnée du centre de la bille (=point de contact) dans l'axe du palpeur sur lequel doit être effectuée la mesure Distance d'approche Q320 (en incrémental): Distance supplémentaire entre le point de mesure et la bille du palpeur. Q320 agit en complément de PM6140 Hauteur de sécurité Q260 (en absolu): Coordonnée dans l'axe du palpeur excluant toute collision entre le palpeur et la pièce (matériels de bridage) 80 Y MP6140 + Q320 Q323 Q324 3.2 Calcul automatique des points de référence Q322 X Q321 Z Déplacement haut. sécu. Q301: Définir comment le palpeur doit se déplacer entre les points de mesure: 0: Entre les points de mesure, à la hauteur de mesure 1: Entre les points de mesure, à la hauteur de sécurité Numéro point zéro dans tableau Q305: Indiquer le numéro dans le tableau de points zéro/tableau Preset sous lequel la TNC doit mémoriser les coordonnées du centre du tenon. Si vous introduisez Q305=0, la TNC initialise automatiquement le nouveau point de référence au centre du tenon Nouveau pt de réf. axe principal Q331 (en absolu): Coordonnée dans l'axe principal à laquelle la TNC doit initialiser le centre du tenon calculé. Configuration par défaut = 0 Nouveau pt de réf. axe auxiliaire Q332 (en absolu): Coordonnée dans l'axe auxiliaire à laquelle la TNC doit initialiser le centre du tenon calculé. Configuration par défaut = 0 Q260 Q261 X 3 Cycles palpeurs pour le contrôle automatique des pièces Transfert val. mesure (0,1) Q303: Définir si le point de référence défini doit être enregistré dans le tableau de points zéro ou dans le tableau Preset: -1: Ne pas utiliser! Sera inscrit par la TNC si d'anciens programmes sont importés (cf. „Enregistrer le point de référence calculé” à la page 69) 0: Inscrire dans le tableau de points zéro actif le point de référence calculé. Le système de référence est le système de coordonnées pièce actif 1: Inscrire dans le tableau Preset le point de référence calculé. Le système de référence est le système de coordonnées machine (coordonnées REF) Exemple: Séquences CN 5 TCH PROBE 411 PT REF. EXT. RECTAN Q321=+50 ;CENTRE 1ER AXE Q322=+50 ;CENTRE 2ÈME AXE Q323=60 ;1ER CÔTÉ Q324=20 ;2ÈME CÔTÉ Q261=-5 ;HAUTEUR DE MESURE Q320=0 ;DISTANCE D'APPROCHE Palpage dans axe palpeur Q381: Définir si la TNC doit également initialiser le point de référence dans l'axe du palpeur: 0: Ne pas initialiser le point de référence dans l'axe du palpeur 1: Initialiser le point de référence dans l'axe du palpeur Q260=+20 ;HAUTEUR DE SÉCURITÉ Q301=0 ;DÉPLAC. HAUT. SÉCU. Q305=0 ;NO DANS TABLEAU Q331=+0 ;POINT DE RÉFÉRENCE Q332=+0 ;POINT DE RÉFÉRENCE Palp. axe palp.: Coord. 1er axe Q382 (en absolu): Coordonnée du point de palpage dans l'axe principal du plan d'usinage à laquelle le point de référence doit être initialisé dans l'axe du palpeur. N'agit que si Q381 =1 Q303=+1 ;TRANS. VAL. MESURE Palp. axe palp.: Coord. 2ème axe Q383 (en absolu): Coordonnée du point de palpage dans l'axe auxiliaire du plan d'usinage à laquelle le point de référence doit être initialisé dans l'axe du palpeur. N'agit que si Q381 =1 Palp. axe palp.: Coord. 3ème axe Q384 (en absolu): Coordonnée du point de palpage dans l'axe auxiliaire du l'axe du palpeur à laquelle le point de référence doit être initialisé dans l'axe du palpeur. N'agit que si Q381 = 1 Nouveau pt de réf. sur axe palpeur Q333 (en absolu): Coordonnée dans l'axe du palpeur à laquelle la TNC doit initialiser le point de référence. Configuration par défaut = 0 iTNC 530 HEIDENHAIN Q381=1 ;PALP. DS AXE PALPEUR Q382=+85 ;1ÈRE COO. DANS AXE PALP. Q383=+50 ;2ÈME COO. DANS AXE PALP. Q384=+0 ;3ÈME COO. DANS AXE PALP. Q333=+1 ;POINT DE RÉFÉRENCE 81 3.2 Calcul automatique des points de référence 3.2 Calcul automatique des points de référence POINT DE REFERENCE INTERIEUR CERCLE (cycle palpeur 412, DIN/ISO: G412) Le cycle palpeur 412 calcule le centre d'une poche circulaire (trou) et initialise ce centre comme point de référence. Si vous le désirez, la TNC peut aussi inscrire le centre dans un tableau de points zéro ou de Preset. 1 La TNC positionne le palpeur en avance rapide (valeur de PM6150 ou PM6361) et selon la logique de positionnement (cf. „Travail avec les cycles palpeurs” à la page 26) au point de palpage 1. La TNC calcule les points de palpage à partir des données contenues dans le cycle et de la distance d'approche programmée dans PM6140 Le palpeur se déplace ensuite à la hauteur de mesure programmée et exécute la première opération de palpage suivant l'avance de palpage (PM6120 ou PM6360). La TNC détermine automatiquement le sens du palpage en fonction de l'angle initial programmé Le palpeur se déplace ensuite en suivant une trajectoire circulaire, soit à la hauteur de mesure, soit à la hauteur de sécurité, jusqu'au point de palpage suivant 2 et exécute à cet endroit la deuxième opération de palpage La TNC positionne le palpeur au point de palpage 3 puis au point de palpage 4, y exécute la troisième ou la quatrième opération de palpage Pour terminer, la TNC rétracte le palpeur à la hauteur de sécurité et traite le point de référence calculé en fonction des paramètres de cycle Q303 et Q305 (cf. „Enregistrer le point de référence calculé” à la page 69) et enregistre les valeurs effectives dans les paramètres Q indiqués ci-après Ensuite, si on le désire, la TNC calcule aussi, dans une opération de palpage séparée, le point de référence dans l'axe du palpeur 2 3 4 5 6 Numéro paramètre Signification Q151 Valeur effective centre axe principal Q152 Valeur effective centre axe auxiliaire Q153 Valeur effective diamètre 82 Y 2 3 1 4 X 3 Cycles palpeurs pour le contrôle automatique des pièces 3.2 Calcul automatique des points de référence Remarques avant que vous ne programmiez Pour éviter toute collision entre le palpeur et la pièce, introduisez le diamètre nominal de la poche (trou) de manière à ce qu'il soit de préférence trop petit. Si les dimensions de la poche et la distance d'approche ne permettent pas d'effectuer un pré-positionnement à proximité des points de palpage, la TNC palpe toujours en partant du centre de la poche. Dans ce cas, le palpeur ne se déplace pas à la hauteur de sécurité entre les quatre points de mesure. Avant de définir le cycle, vous devez avoir programmé un appel d'outil pour définir l'axe du palpeur. Centre 1er axe Q321 (en absolu): Centre de la poche dans l'axe principal du plan d'usinage Centre 2ème axe Q322 (en absolu): Centre de la poche dans l'axe auxiliaire du plan d'usinage Si vous programmez Q322 = 0, la TNC aligne le centre du trou sur l'axe Y positif; si vous programmez Q322 différent de 0, la TNC aligne le centre du trou sur la position nominale Diamètre nominal Q262: Diamètre approximatif de la poche circulaire (trou). Introduire de préférence une valeur trop petite Angle initial Q325 (en absolu): Angle compris entre l'axe principal du plan d'usinage et le premier point de palpage Incrément angulaire Q247 (en incrémental): Angle compris entre deux points de mesure; le signe de l'incrément angulaire détermine le sens de rotation (= sens horaire) pour le déplacement du palpeur vers le point de mesure suivant. Si vous désirez étalonner des arcs de cercle, programmez un incrément angulaire inférieur à 90° Plus l'incrément angulaire programmé est petit et plus le point de référence calculé par la TNC sera imprécis. Valeur d'introduction min.: 5°. Hauteur mesure dans axe palpage Q261 (en absolu): Coordonnée du centre de la bille (=point de contact) dans l'axe du palpeur sur lequel doit être effectuée la mesure Distance d'approche Q320 (en incrémental): Distance supplémentaire entre le point de mesure et la bille du palpeur. Q320 agit en complément de PM6140 Hauteur de sécurité Q260 (en absolu): Coordonnée dans l'axe du palpeur excluant toute collision entre le palpeur et la pièce (matériels de bridage) iTNC 530 HEIDENHAIN Y Q247 Q325 Q322 Q321 Q262 X Z Q260 Q261 MP6140 + Q320 X 83 3.2 Calcul automatique des points de référence 84 Déplacement haut. sécu. Q301: Définir comment le palpeur doit se déplacer entre les points de mesure: 0: Entre les points de mesure, à la hauteur de mesure 1: Entre les points de mesure, à la hauteur de sécurité Numéro point zéro dans tableau Q305: Indiquer le numéro dans le tableau de points zéro/tableau Preset sous lequel la TNC doit mémoriser les coordonnées du centre de la poche. Si vous introduisez Q305=0, la TNC initialise automatiquement le nouveau point de référence au centre de la poche 3 Cycles palpeurs pour le contrôle automatique des pièces Nouveau pt de réf. axe principal Q331 (en absolu): Coordonnée dans l'axe principal à laquelle la TNC doit initialiser le centre de la poche calculé. Configuration par défaut = 0 Exemple: Séquences CN 5 TCH PROBE 412 PT REF. INT. CERCLE Q321=+50 ;CENTRE 1ER AXE Nouveau pt de réf. axe auxiliaire Q332 (en absolu): Coordonnée dans l'axe auxiliaire à laquelle la TNC doit initialiser le centre de la poche calculé. Configuration par défaut = 0 Q322=+50 ;CENTRE 2ÈME AXE Q262=75 ;DIAMÈTRE NOMINAL Q325=+0 ;ANGLE INITIAL Transfert val. mesure (0,1) Q303: Définir si le point de référence défini doit être enregistré dans le tableau de points zéro ou dans le tableau Preset: -1: Ne pas utiliser! Sera inscrit par la TNC si d'anciens programmes sont importés (cf. „Enregistrer le point de référence calculé” à la page 69) 0: Inscrire dans le tableau de points zéro actif le point de référence calculé. Le système de référence est le système de coordonnées pièce actif 1: Inscrire dans le tableau Preset le point de référence calculé. Le système de référence est le système de coordonnées machine (coordonnées REF) Q247=+60 ;INCRÉMENT ANGULAIRE Q261=-5 ;HAUTEUR DE MESURE Q320=0 ;DISTANCE D'APPROCHE Q260=+20 ;HAUTEUR DE SÉCURITÉ Q301=0 ;DÉPLAC. HAUT. SÉCU. Q305=12 ;NO DANS TABLEAU Q331=+0 ;POINT DE RÉFÉRENCE Q332=+0 ;POINT DE RÉFÉRENCE Q303=+1 ;TRANS. VAL. MESURE Q381=1 ;PALP. DS AXE PALPEUR Q382=+85 ;1ÈRE COO. DANS AXE PALP. Q383=+50 ;2ÈME COO. DANS AXE PALP. Q384=+0 ;3ÈME COO. DANS AXE PALP. Q333=+1 ;POINT DE RÉFÉRENCE Q423=4 ;NB POINTS DE MESURE Palpage dans axe palpeur Q381: Définir si la TNC doit également initialiser le point de référence dans l'axe du palpeur: 0: Ne pas initialiser le point de référence dans l'axe du palpeur 1: Initialiser le point de référence dans l'axe du palpeur Palp. axe palp.: Coord. 1er axe Q382 (en absolu): Coordonnée du point de palpage dans l'axe principal du plan d'usinage à laquelle le point de référence doit être initialisé dans l'axe du palpeur. N'agit que si Q381 =1 Palp. axe palp.: Coord. 2ème axe Q383 (en absolu): Coordonnée du point de palpage dans l'axe auxiliaire du plan d'usinage à laquelle le point de référence doit être initialisé dans l'axe du palpeur. N'agit que si Q381 =1 Palp. axe palp.: Coord. 3ème axe Q384 (en absolu): Coordonnée du point de palpage dans l'axe auxiliaire du l'axe du palpeur à laquelle le point de référence doit être initialisé dans l'axe du palpeur. N'agit que si Q381 = 1 Nouveau pt de réf. sur axe palpeur Q333 (en absolu): Coordonnée dans l'axe du palpeur à laquelle la TNC doit initialiser le point de référence. Configuration par défaut = 0 Nombre de points de mesure (4/3) Q423: Définir si la TNC doit mesurer le trou avec 4 ou 3 points de mesure: 4: Utiliser 4 points de mesure (configuration par défaut) 3: Utiliser 3 points de mesure iTNC 530 HEIDENHAIN 85 3.2 Calcul automatique des points de référence 3.2 Calcul automatique des points de référence POINT DE REFERENCE EXTERIEUR CERCLE (cycle palpeur 413, DIN/ISO: G413) Le cycle palpeur 413 calcule le centre d'un tenon circulaire et initialise ce centre comme point de référence. Si vous le désirez, la TNC peut aussi inscrire le centre dans un tableau de points zéro ou de Preset. 1 La TNC positionne le palpeur en avance rapide (valeur de PM6150 ou PM6361) et selon la logique de positionnement (cf. „Travail avec les cycles palpeurs” à la page 26) au point de palpage 1. La TNC calcule les points de palpage à partir des données contenues dans le cycle et de la distance d'approche programmée dans PM6140 Le palpeur se déplace ensuite à la hauteur de mesure programmée et exécute la première opération de palpage suivant l'avance de palpage (PM6120 ou PM6360). La TNC détermine automatiquement le sens du palpage en fonction de l'angle initial programmé Le palpeur se déplace ensuite en suivant une trajectoire circulaire, soit à la hauteur de mesure, soit à la hauteur de sécurité, jusqu'au point de palpage suivant 2 et exécute à cet endroit la deuxième opération de palpage La TNC positionne le palpeur au point de palpage 3 puis au point de palpage 4, y exécute la troisième ou la quatrième opération de palpage Pour terminer, la TNC rétracte le palpeur à la hauteur de sécurité et traite le point de référence calculé en fonction des paramètres de cycle Q303 et Q305 (cf. „Enregistrer le point de référence calculé” à la page 69) et enregistre les valeurs effectives dans les paramètres Q indiqués ci-après Ensuite, si on le désire, la TNC calcule aussi, dans une opération de palpage séparée, le point de référence dans l'axe du palpeur 2 3 4 5 6 Numéro paramètre Signification Q151 Valeur effective centre axe principal Q152 Valeur effective centre axe auxiliaire Q153 Valeur effective diamètre Y 2 3 1 4 X Remarques avant que vous ne programmiez Pour éviter toute collision entre le palpeur et la pièce, introduisez le diamètre nominal de la poche (trou) de manière à ce qu'il soit de préférence trop grand. Avant de définir le cycle, vous devez avoir programmé un appel d'outil pour définir l'axe du palpeur. 86 3 Cycles palpeurs pour le contrôle automatique des pièces Centre 2ème axe Q322 (en absolu): Centre du tenon dans l'axe auxiliaire du plan d'usinage. Si vous programmez Q322 = 0, la TNC aligne le centre du trou sur l'axe Y positif; si vous programmez Q322 différent de 0, la TNC aligne le centre du trou sur la position nominale Diamètre nominal Q262: Diamètre approximatif du tenon. Introduire de préférence une valeur trop grande Angle initial Q325 (en absolu): Angle compris entre l'axe principal du plan d'usinage et le premier point de palpage Incrément angulaire Q247 (en incrémental): Angle compris entre deux points de mesure; le signe de l'incrément angulaire détermine le sens de rotation (= sens horaire) pour le déplacement du palpeur vers le point de mesure suivant. Si vous désirez étalonner des arcs de cercle, programmez un incrément angulaire inférieur à 90° Plus l'incrément angulaire programmé est petit et plus le point de référence calculé par la TNC sera imprécis. Valeur d'introduction min.: 5°. Hauteur mesure dans axe palpage Q261 (en absolu): Coordonnée du centre de la bille (=point de contact) dans l'axe du palpeur sur lequel doit être effectuée la mesure Distance d'approche Q320 (en incrémental): Distance supplémentaire entre le point de mesure et la bille du palpeur. Q320 agit en complément de PM6140 Hauteur de sécurité Q260 (en absolu): Coordonnée dans l'axe du palpeur excluant toute collision entre le palpeur et la pièce (matériels de bridage) Déplacement haut. sécu. Q301: Définir comment le palpeur doit se déplacer entre les points de mesure: 0: Entre les points de mesure, à la hauteur de mesure 1: Entre les points de mesure, à la hauteur de sécurité Numéro point zéro dans tableau Q305: Indiquer le numéro dans le tableau de points zéro/tableau Preset sous lequel la TNC doit mémoriser les coordonnées du centre du tenon. Si vous introduisez Q305=0, la TNC initialise automatiquement le nouveau point de référence au centre du tenon iTNC 530 HEIDENHAIN 3.2 Calcul automatique des points de référence Centre 1er axe Q321 (en absolu): Centre du tenon dans l'axe principal du plan d'usinage Y Q247 Q325 Q322 Q321 Q262 X Z Q260 Q261 MP6140 + Q320 X 87 3.2 Calcul automatique des points de référence 88 Nouveau pt de réf. axe principal Q331 (en absolu): Coordonnée dans l'axe principal à laquelle la TNC doit initialiser le centre du tenon calculé. Configuration par défaut = 0 Exemple: Séquences CN 5 TCH PROBE 413 PT REF. EXT. CERCLE Q321=+50 ;CENTRE 1ER AXE Nouveau pt de réf. axe auxiliaire Q332 (en absolu): Coordonnée dans l'axe auxiliaire à laquelle la TNC doit initialiser le centre du tenon calculé. Configuration par défaut = 0 Q322=+50 ;CENTRE 2ÈME AXE Q262=75 ;DIAMÈTRE NOMINAL Q325=+0 ;ANGLE INITIAL Transfert val. mesure (0,1) Q303: Définir si le point de référence défini doit être enregistré dans le tableau de points zéro ou dans le tableau Preset: -1: Ne pas utiliser! Sera inscrit par la TNC si d'anciens programmes sont importés (cf. „Enregistrer le point de référence calculé” à la page 69) 0: Inscrire dans le tableau de points zéro actif le point de référence calculé. Le système de référence est le système de coordonnées pièce actif 1: Inscrire dans le tableau Preset le point de référence calculé. Le système de référence est le système de coordonnées machine (coordonnées REF) Q247=+60 ;INCRÉMENT ANGULAIRE Q261=-5 ;HAUTEUR DE MESURE Q320=0 ;DISTANCE D'APPROCHE Q260=+20 ;HAUTEUR DE SÉCURITÉ Q301=0 ;DÉPLAC. HAUT. SÉCU. Q305=15 ;NO DANS TABLEAU Q331=+0 ;POINT DE RÉFÉRENCE Q332=+0 ;POINT DE RÉFÉRENCE Q303=+1 ;TRANS. VAL. MESURE Q381=1 ;PALP. DS AXE PALPEUR Q382=+85 ;1ÈRE COO. DANS AXE PALP. Q383=+50 ;2ÈME COO. DANS AXE PALP. Q384=+0 ;3ÈME COO. DANS AXE PALP. Q333=+1 ;POINT DE RÉFÉRENCE Q423=4 ;NB POINTS DE MESURE Palpage dans axe palpeur Q381: Définir si la TNC doit également initialiser le point de référence dans l'axe du palpeur: 0: Ne pas initialiser le point de référence dans l'axe du palpeur 1: Initialiser le point de référence dans l'axe du palpeur Palp. axe palp.: Coord. 1er axe Q382 (en absolu): Coordonnée du point de palpage dans l'axe principal du plan d'usinage à laquelle le point de référence doit être initialisé dans l'axe du palpeur. N'agit que si Q381 = 1 Palp. axe palp.: Coord. 2ème axe Q383 (en absolu): Coordonnée du point de palpage dans l'axe auxiliaire du plan d'usinage à laquelle le point de référence doit être initialisé dans l'axe du palpeur. N'agit que si Q381 = 1 Palp. axe palp.: Coord. 3ème axe Q384 (en absolu): Coordonnée du point de palpage dans l'axe auxiliaire du l'axe du palpeur à laquelle le point de référence doit être initialisé dans l'axe du palpeur. N'agit que si Q381 = 1 Nouveau pt de réf. sur axe palpeur Q333 (en absolu): Coordonnée dans l'axe du palpeur à laquelle la TNC doit initialiser le point de référence. Configuration par défaut = 0 Nombre de points de mesure (4/3) Q423: Définir si la TNC doit mesurer le tenon avec 4 ou 3 points de mesure: 4: Utiliser 4 points de mesure (configuration par défaut) 3: Utiliser 3 points de mesure 3 Cycles palpeurs pour le contrôle automatique des pièces Le cycle palpeur 414 détermine le point d'intersection de deux droites et l'initialise comme point de référence. Si vous le désirez, la TNC peut aussi inscrire le point d'intersection dans un tableau de points zéro ou de Preset. 1 2 Y La TNC positionne le palpeur en avance rapide (valeur de PM6150 ou PM6361) et selon la logique de positionnement (cf. „Travail avec les cycles palpeurs” à la page 26) au point de palpage 1 (cf. fig. en haut et à droite). Ce faisant, la TNC décale le palpeur de la valeur de la distance d'approche, dans le sens opposé au sens de déplacement concerné Le palpeur se déplace ensuite à la hauteur de mesure programmée et exécute la première opération de palpage suivant l'avance de palpage (PM6120 ou PM6360). La TNC détermine automatiquement le sens du palpage en fonction du 3ème point de mesure programmé 4 3 2 1 X La TNC mesure toujours la première droite dans le sens de l'axe auxiliaire du plan d'usinage. Y Y 3 4 5 6 Puis, le palpeur se déplace vers le point de palpage suivant 2 et exécute la deuxième opération de palpage La TNC positionne le palpeur au point de palpage 3 puis au point de palpage 4, y exécute la troisième ou la quatrième opération de palpage Pour terminer, la TNC rétracte le palpeur à la hauteur de sécurité et traite le point de référence calculé en fonction des paramètres de cycle Q303 et Q305 (cf. „Enregistrer le point de référence calculé” à la page 69) et enregistre les coordonnées du coin calculé dans les paramètres Q indiqués ci-après Ensuite, si on le désire, la TNC calcule aussi, dans une opération de palpage séparée, le point de référence dans l'axe du palpeur 3 Y A B 1 2 2 1 X Y C 3 3 X Numéro paramètre Signification Q151 Valeur effective du coin dans l'axe principal Q152 Valeur effective du coin dans l'axe auxiliaire 2 1 1 2 3 X D X Remarques avant que vous ne programmiez Par la position des points de mesure 1 et 3, vous définissez le coin sur lequel la TNC initialise le point de référence (cf. fig. de droite, au centre et tableau ci-après). Avant de définir le cycle, vous devez avoir programmé un appel d'outil pour définir l'axe du palpeur. iTNC 530 HEIDENHAIN 89 3.2 Calcul automatique des points de référence POINT DE REFERENCE EXTERIEUR COIN (cycle palpeur 414, DIN/ISO: G414) Coordonnée X Coordonnée Y A Point 1 supérieur point 3 Point 1 inférieur point 3 B Point 1 inférieur point 3 Point 1 inférieur point 3 C Point 1 inférieur point 3 Point 1 supérieur point 3 D Point 1 supérieur point 3 Point 1 supérieur point 3 Y 1er point mesure sur 2ème axe Q264 (en absolu): Coordonnée du 1er point de palpage dans l'axe auxiliaire du plan d'usinage Distance 1er axe Q326 (en incrémental): Distance entre le 1er et le 2ème point de mesure dans l'axe principal du plan d'usinage Q296 Q297 Q264 MP6140 + Q320 3ème point mesure sur 1er axe Q296 (en absolu): Coordonnée du 3ème point de palpage dans l'axe principal du plan d'usinage Q326 3ème point mesure sur 2ème axe Q297 (en absolu): Coordonnée du 3ème point de palpage dans l'axe auxiliaire du plan d'usinage Distance 2ème axe Q327 (en incrémental): Distance entre le 3ème et le 4ème point de mesure dans l'axe auxiliaire du plan d'usinage 90 1er point mesure sur 1er axe Q263 (en absolu): Coordonnée du 1er point de palpage dans l'axe principal du plan d'usinage Q327 3.2 Calcul automatique des points de référence Coin Hauteur mesure dans axe palpage Q261 (en absolu): Coordonnée du centre de la bille (=point de contact) dans l'axe du palpeur sur lequel doit être effectuée la mesure Distance d'approche Q320 (en incrémental): Distance supplémentaire entre le point de mesure et la bille du palpeur. Q320 agit en complément de PM6140 Hauteur de sécurité Q260 (en absolu): Coordonnée dans l'axe du palpeur excluant toute collision entre le palpeur et la pièce (matériels de bridage) Déplacement haut. sécu. Q301: Définir comment le palpeur doit se déplacer entre les points de mesure: 0: Entre les points de mesure, à la hauteur de mesure 1: Entre les points de mesure, à la hauteur de sécurité Exécuter rotation de base Q304: Définir si la TNC doit compenser le désaxage de la pièce par une rotation de base: 0: Ne pas exécuter de rotation de base 1: Exécuter une rotation de base Q263 X Y Q260 Q261 X 3 Cycles palpeurs pour le contrôle automatique des pièces Numéro point zéro dans tableau Q305: Indiquer le numéro dans le tableau de points zéro/tableau Preset sous lequel la TNC doit mémoriser les coordonnées du coin. Si vous introduisez Q305=0, la TNC initialise automatiquement le nouveau point de référence sur le coin Nouveau pt de réf. axe principal Q331 (en absolu): Coordonnée dans l'axe principal à laquelle la TNC doit initialiser le coin calculé. Configuration par défaut = 0 Nouveau pt de réf. axe auxiliaire Q332 (en absolu): Coordonnée dans l'axe auxiliaire à laquelle la TNC doit initialiser le coin calculé. Configuration par défaut = 0 Transfert val. mesure (0,1) Q303: Définir si le point de référence défini doit être enregistré dans le tableau de points zéro ou dans le tableau Preset: -1: Ne pas utiliser! Sera inscrit par la TNC si d'anciens programmes sont importés (cf. „Enregistrer le point de référence calculé” à la page 69) 0: Inscrire dans le tableau de points zéro actif le point de référence calculé. Le système de référence est le système de coordonnées pièce actif 1: Inscrire dans le tableau Preset le point de référence calculé. Le système de référence est le système de coordonnées machine (coordonnées REF) Palpage dans axe palpeur Q381: Définir si la TNC doit également initialiser le point de référence dans l'axe du palpeur: 0: Ne pas initialiser le point de référence dans l'axe du palpeur 1: Initialiser le point de référence dans l'axe du palpeur Palp. axe palp.: Coord. 1er axe Q382 (en absolu): Coordonnée du point de palpage dans l'axe principal du plan d'usinage à laquelle le point de référence doit être initialisé dans l'axe du palpeur. N'agit que si Q381 = 1 Palp. axe palp.: Coord. 2ème axe Q383 (en absolu): Coordonnée du point de palpage dans l'axe auxiliaire du plan d'usinage à laquelle le point de référence doit être initialisé dans l'axe du palpeur. N'agit que si Q381 = 1 Palp. axe palp.: Coord. 3ème axe Q384 (en absolu): Coordonnée du point de palpage dans l'axe auxiliaire du l'axe du palpeur à laquelle le point de référence doit être initialisé dans l'axe du palpeur. N'agit que si Q381 = 1 Nouveau pt de réf. sur axe palpeur Q333 (en absolu): Coordonnée dans l'axe du palpeur à laquelle la TNC doit initialiser le point de référence. Configuration par défaut = 0 iTNC 530 HEIDENHAIN Exemple: Séquences CN 5 TCH PROBE 414 PT REF. INT. COIN Q263=+37 ;1ER POINT 1ER AXE Q264=+7 ;1ER POINT 2ÈME AXE Q326=50 ;DISTANCE 1ER AXE Q296=+95 ;3ÈME POINT 1ER AXE Q297=+25 ;3ÈME POINT 2ÈME AXE Q327=45 ;DISTANCE 2ÈME AXE Q261=-5 ;HAUTEUR DE MESURE Q320=0 ;DISTANCE D'APPROCHE Q260=+20 ;HAUTEUR DE SÉCURITÉ Q301=0 ;DÉPLAC. HAUT. SÉCU. Q304=0 ;ROTATION DE BASE Q305=7 ;NO DANS TABLEAU Q331=+0 ;POINT DE RÉFÉRENCE Q332=+0 ;POINT DE RÉFÉRENCE Q303=+1 ;TRANS. VAL. MESURE Q381=1 ;PALP. DS AXE PALPEUR Q382=+85 ;1ÈRE COO. DANS AXE PALP. Q383=+50 ;2ÈME COO. DANS AXE PALP. Q384=+0 ;3ÈME COO. DANS AXE PALP. Q333=+1 ;POINT DE RÉFÉRENCE 91 3.2 Calcul automatique des points de référence 3.2 Calcul automatique des points de référence POINT DE REFERENCE INTERIEUR COIN (cycle palpeur 415, DIN/ISO: G415) Le cycle palpeur 415 détermine le point d'intersection de deux droites et l'initialise comme point de référence. Si vous le désirez, la TNC peut aussi inscrire le point d'intersection dans un tableau de points zéro ou de Preset. 1 La TNC positionne le palpeur en avance rapide (valeur de PM6150 ou PM6361) et selon la logique de positionnement (cf. „Travail avec les cycles palpeurs” à la page 26) au point de palpage 1 (cf. fig. en haut et à droite) que vous définissez dans le cycle. Ce faisant, la TNC décale le palpeur de la valeur de la distance d'approche, dans le sens opposé au sens de déplacement concerné Le palpeur se déplace ensuite à la hauteur de mesure programmée et exécute la première opération de palpage suivant l'avance de palpage (PM6120 ou PM6360). Le sens de palpage résulte du numéro du coin 2 Y 4 3 1 2 X La TNC mesure toujours la première droite dans le sens de l'axe auxiliaire du plan d'usinage. 3 Puis, le palpeur se déplace vers le point de palpage suivant 2 et exécute la deuxième opération de palpage La TNC positionne le palpeur au point de palpage 3 puis au point de palpage 4, y exécute la troisième ou la quatrième opération de palpage Pour terminer, la TNC rétracte le palpeur à la hauteur de sécurité et traite le point de référence calculé en fonction des paramètres de cycle Q303 et Q305 (cf. „Enregistrer le point de référence calculé” à la page 69) et enregistre les coordonnées du coin calculé dans les paramètres Q indiqués ci-après Ensuite, si on le désire, la TNC calcule aussi, dans une opération de palpage séparée, le point de référence dans l'axe du palpeur 4 5 6 Numéro paramètre Signification Q151 Valeur effective du coin dans l'axe principal Q152 Valeur effective du coin dans l'axe auxiliaire Remarques avant que vous ne programmiez Avant de définir le cycle, vous devez avoir programmé un appel d'outil pour définir l'axe du palpeur. 92 3 Cycles palpeurs pour le contrôle automatique des pièces Distance 1er axe Q326 (en incrémental): Distance entre le 1er et le 2ème point de mesure dans l'axe principal du plan d'usinage Distance 2ème axe Q327 (en incrémental): Distance entre le 3ème et le 4ème point de mesure dans l'axe auxiliaire du plan d'usinage Coin Q308: Numéro du coin sur lequel la TNC doit initialiser le point de référence Hauteur mesure dans axe palpage Q261 (en absolu): Coordonnée du centre de la bille (=point de contact) dans l'axe du palpeur sur lequel doit être effectuée la mesure Distance d'approche Q320 (en incrémental): Distance supplémentaire entre le point de mesure et la bille du palpeur. Q320 agit en complément de PM6140 Hauteur de sécurité Q260 (en absolu): Coordonnée dans l'axe du palpeur excluant toute collision entre le palpeur et la pièce (matériels de bridage) Déplacement haut. sécu. Q301: Définir comment le palpeur doit se déplacer entre les points de mesure: 0: Entre les points de mesure, à la hauteur de mesure 1: Entre les points de mesure, à la hauteur de sécurité MP6140 + Q320 Y 1er point mesure sur 2ème axe Q264 (en absolu): Coordonnée du 1er point de palpage dans l'axe auxiliaire du plan d'usinage 3.2 Calcul automatique des points de référence 1er point mesure sur 1er axe Q263 (en absolu): Coordonnée du 1er point de palpage dans l'axe principal du plan d'usinage Q327 Q308=4 Q308=3 Q308=1 Q308=2 Q264 Q326 X Q263 Z Q260 Q261 X Exécuter rotation de base Q304: Définir si la TNC doit compenser le désaxage de la pièce par une rotation de base: 0: Ne pas exécuter de rotation de base 1: Exécuter une rotation de base iTNC 530 HEIDENHAIN 93 3.2 Calcul automatique des points de référence 94 Numéro point zéro dans tableau Q305: Indiquer le numéro dans le tableau de points zéro/tableau Preset sous lequel la TNC doit mémoriser les coordonnées du coin. Si vous introduisez Q305=0, la TNC initialise automatiquement le nouveau point de référence sur le coin Nouveau pt de réf. axe principal Q331 (en absolu): Coordonnée dans l'axe principal à laquelle la TNC doit initialiser le coin calculé. Configuration par défaut = 0 Nouveau pt de réf. axe auxiliaire Q332 (en absolu): Coordonnée dans l'axe auxiliaire à laquelle la TNC doit initialiser le coin calculé. Configuration par défaut = 0 Transfert val. mesure (0,1) Q303: Définir si le point de référence défini doit être enregistré dans le tableau de points zéro ou dans le tableau Preset: -1: Ne pas utiliser! Sera inscrit par la TNC si d'anciens programmes sont importés (cf. „Enregistrer le point de référence calculé” à la page 69) 0: Inscrire dans le tableau de points zéro actif le point de référence calculé. Le système de référence est le système de coordonnées pièce actif 1: Inscrire dans le tableau Preset le point de référence calculé. Le système de référence est le système de coordonnées machine (coordonnées REF) Palpage dans axe palpeur Q381: Définir si la TNC doit également initialiser le point de référence dans l'axe du palpeur: 0: Ne pas initialiser le point de référence dans l'axe du palpeur 1: Initialiser le point de référence dans l'axe du palpeur Palp. axe palp.: Coord. 1er axe Q382 (en absolu): Coordonnée du point de palpage dans l'axe principal du plan d'usinage à laquelle le point de référence doit être initialisé dans l'axe du palpeur. N'agit que si Q381 = 1 Palp. axe palp.: Coord. 2ème axe Q383 (en absolu): Coordonnée du point de palpage dans l'axe auxiliaire du plan d'usinage à laquelle le point de référence doit être initialisé dans l'axe du palpeur. N'agit que si Q381 = 1 Palp. axe palp.: Coord. 3ème axe Q384 (en absolu): Coordonnée du point de palpage dans l'axe auxiliaire du l'axe du palpeur à laquelle le point de référence doit être initialisé dans l'axe du palpeur. N'agit que si Q381 = 1 Nouveau pt de réf. sur axe palpeur Q333 (en absolu): Coordonnée dans l'axe du palpeur à laquelle la TNC doit initialiser le point de référence. Configuration par défaut = 0 Exemple: Séquences CN 5 TCH PROBE 415 PT REF. EXT. COIN Q263=+37 ;1ER POINT 1ER AXE Q264=+7 ;1ER POINT 2ÈME AXE Q326=50 ;DISTANCE 1ER AXE Q296=+95 ;3ÈME POINT 1ER AXE Q297=+25 ;3ÈME POINT 2ÈME AXE Q327=45 ;DISTANCE 2ÈME AXE Q261=-5 ;HAUTEUR DE MESURE Q320=0 ;DISTANCE D'APPROCHE Q260=+20 ;HAUTEUR DE SÉCURITÉ Q301=0 ;DÉPLAC. HAUT. SÉCU. Q304=0 ;ROTATION DE BASE Q305=7 ;NO DANS TABLEAU Q331=+0 ;POINT DE RÉFÉRENCE Q332=+0 ;POINT DE RÉFÉRENCE Q303=+1 ;TRANS. VAL. MESURE Q381=1 ;PALP. DS AXE PALPEUR Q382=+85 ;1ÈRE COO. DANS AXE PALP. Q383=+50 ;2ÈME COO. DANS AXE PALP. Q384=+0 ;3ÈME COO. DANS AXE PALP. Q333=+1 ;POINT DE RÉFÉRENCE 3 Cycles palpeurs pour le contrôle automatique des pièces 3.2 Calcul automatique des points de référence POINT DE REFERENCE CENTRE CERCLE DE TROUS (cycle palpeur 416, DIN/ISO: G416) Le cycle palpeur 416 calcule le centre d'un cercle de trous en mesurant trois trous et initialise ce centre comme point de référence. Si vous le désirez, la TNC peut aussi inscrire le centre dans un tableau de points zéro ou de Preset. 1 2 3 4 5 6 7 8 La TNC positionne le palpeur en avance rapide (valeur de PM6150 ou PM6361) et selon la logique de positionnement (cf. „Travail avec les cycles palpeurs” à la page 26) au centre programmé du premier trou 1 Le palpeur se déplace ensuite à la hauteur de mesure programmée et enregistre le centre du premier trou en palpant quatre fois Puis, la TNC rétracte le palpeur à la hauteur de sécurité et le positionne sur le centre programmé du second trou 2 La TNC déplace le palpeur à la hauteur de mesure programmée et enregistre le centre du deuxième trou en palpant quatre fois Puis, la TNC rétracte le palpeur à la hauteur de sécurité et le positionne sur le centre programmé du troisième trou 3 La TNC déplace le palpeur à la hauteur de mesure programmée et enregistre le centre du troisième trou en palpant quatre fois Pour terminer, la TNC rétracte le palpeur à la hauteur de sécurité et traite le point de référence calculé en fonction des paramètres de cycle Q303 et Q305 (cf. „Enregistrer le point de référence calculé” à la page 69) et enregistre les valeurs effectives dans les paramètres Q indiqués ci-après Ensuite, si on le désire, la TNC calcule aussi, dans une opération de palpage séparée, le point de référence dans l'axe du palpeur Numéro paramètre Signification Q151 Valeur effective centre axe principal Q152 Valeur effective centre axe auxiliaire Q153 Valeur effective diamètre cercle de trous Y 1 2 3 X Remarques avant que vous ne programmiez Avant de définir le cycle, vous devez avoir programmé un appel d'outil pour définir l'axe du palpeur. iTNC 530 HEIDENHAIN 95 Centre 1er axe Q273 (en absolu): Centre du cercle de trous (valeur nominale) dans l'axe principal du plan d'usinage Centre 2ème axe Q274 (en absolu): Centre du cercle de trous (valeur nominale) dans l'axe auxiliaire du plan d'usinage Diamètre nominal Q262: Introduire le diamètre approximatif du cercle de trous. Plus le diamètre du trou est petit et plus vous devez introduire un diamètre nominal précis Angle 1er trou Q291 (en absolu): Angle en coordonnées polaires du 1er centre de trou dans le plan d'usinage Y Q291 Q292 3.2 Calcul automatique des points de référence 96 Q274 62 Q2 Q293 Q273 Angle 2ème trou Q292 (en absolu): Angle en coordonnées polaires du 2ème centre de trou dans le plan d'usinage Angle 3ème trou Q293 (en absolu): Angle en coordonnées polaires du 3ème centre de trou dans le plan d'usinage Hauteur mesure dans axe palpage Q261 (en absolu): Coordonnée du centre de la bille (=point de contact) dans l'axe du palpeur sur lequel doit être effectuée la mesure Hauteur de sécurité Q260 (en absolu): Coordonnée dans l'axe du palpeur excluant toute collision entre le palpeur et la pièce (matériels de bridage) Numéro point zéro dans tableau Q305: Indiquer le numéro dans le tableau de points zéro/tableau Preset sous lequel la TNC doit mémoriser les coordonnées du cercle de trous. Si vous introduisez Q305=0, la TNC initialise automatiquement le nouveau point de référence au centre du cercle de trous Nouveau pt de réf. axe principal Q331 (en absolu): Coordonnée dans l'axe principal à laquelle la TNC doit initialiser le centre calculé pour le cercle de trous. Configuration par défaut = 0 Nouveau pt de réf. axe auxiliaire Q332 (en absolu): Coordonnée dans l'axe auxiliaire à laquelle la TNC doit initialiser le centre calculé pour le cercle de trous. Configuration par défaut = 0 X Y X 3 Cycles palpeurs pour le contrôle automatique des pièces Transfert val. mesure (0,1) Q303: Définir si le point de référence défini doit être enregistré dans le tableau de points zéro ou dans le tableau Preset: -1: Ne pas utiliser! Sera inscrit par la TNC si d'anciens programmes sont importés (cf. „Enregistrer le point de référence calculé” à la page 69) 0: Inscrire dans le tableau de points zéro actif le point de référence calculé. Le système de référence est le système de coordonnées pièce actif 1: Inscrire dans le tableau Preset le point de référence calculé. Le système de référence est le système de coordonnées machine (coordonnées REF) Exemple: Séquences CN 5 TCH PROBE 416 PT REF. CENTRE C. TROUS Q273=+50 ;CENTRE 1ER AXE Q274=+50 ;CENTRE 2EME AXE Q262=90 ;DIAMÈTRE NOMINAL Q291=+34 ;ANGLE 1ER TROU Q292=+70 ;ANGLE 2EME TROU Q293=+210 ;ANGLE 3ÈME TROU Palpage dans axe palpeur Q381: Définir si la TNC doit également initialiser le point de référence dans l'axe du palpeur: 0: Ne pas initialiser le point de référence dans l'axe du palpeur 1: Initialiser le point de référence dans l'axe du palpeur Q261=-5 ;HAUTEUR DE MESURE Q260=+20 ;HAUTEUR DE SÉCURITÉ Q305=12 ;NO DANS TABLEAU Q331=+0 ;POINT DE RÉFÉRENCE Q332=+0 ;POINT DE RÉFÉRENCE Palp. axe palp.: Coord. 1er axe Q382 (en absolu): Coordonnée du point de palpage dans l'axe principal du plan d'usinage à laquelle le point de référence doit être initialisé dans l'axe du palpeur. N'agit que si Q381 = 1 Q303=+1 ;TRANS. VAL. MESURE Q381=1 ;PALP. DS AXE PALPEUR Q382=+85 ;1ÈRE COO. DANS AXE PALP. Q383=+50 ;2ÈME COO. DANS AXE PALP. Palp. axe palp.: Coord. 2ème axe Q383 (en absolu): Coordonnée du point de palpage dans l'axe auxiliaire du plan d'usinage à laquelle le point de référence doit être initialisé dans l'axe du palpeur. N'agit que si Q381 = 1 Q384=+0 ;3ÈME COO. DANS AXE PALP. Q333=+1 ;POINT DE RÉFÉRENCE Palp. axe palp.: Coord. 3ème axe Q384 (en absolu): Coordonnée du point de palpage dans l'axe auxiliaire du l'axe du palpeur à laquelle le point de référence doit être initialisé dans l'axe du palpeur. N'agit que si Q381 = 1 Nouveau pt de réf. sur axe palpeur Q333 (en absolu): Coordonnée dans l'axe du palpeur à laquelle la TNC doit initialiser le point de référence. Configuration par défaut = 0 iTNC 530 HEIDENHAIN 97 3.2 Calcul automatique des points de référence Le cycle palpeur 417 mesure une coordonnée au choix dans l'axe du palpeur et l'initialise comme point de référence. Si vous le désirez, la TNC peut aussi inscrire la coordonnée mesurée dans un tableau de points zéro ou dans le tableau Preset. 1 La TNC positionne le palpeur en avance rapide (valeur de PM6150 ou PM6361) et selon la logique de positionnement (cf. „Travail avec les cycles palpeurs” à la page 26) au point de palpage programmé 1. Ce faisant, la TNC décale le palpeur de la valeur de la distance d'approche, dans le sens positif de l'axe du palpeur Puis, le palpeur se déplace dans l'axe du palpeur jusqu'à la coordonnée programmée pour le point de palpage 1 et enregistre la position effective en palpant simplement Pour terminer, la TNC rétracte le palpeur à la hauteur de sécurité et traite le point de référence calculé en fonction des paramètres de cycle Q303 et Q305 (cf. „Enregistrer le point de référence calculé” à la page 69) et enregistre la valeur effective dans le paramètre Q indiqué ci-après 2 3 Numéro paramètre Signification Q160 Valeur effective du point mesuré Avant de définir le cycle, vous devez avoir programmé un appel d'outil pour définir l'axe du palpeur. La TNC initialise ensuite le point de référence sur cet axe. 98 1 Q264 X Q263 Z Remarques avant que vous ne programmiez Y MP6140 + Q320 3.2 Calcul automatique des points de référence POINT DE REFERENCE DANS L'AXE DU PALPEUR (cycle palpeur 417, DIN/ISO: G417) 1er point mesure sur 1er axe Q263 (en absolu): Coordonnée du 1er point de palpage dans l'axe principal du plan d'usinage Q294 1 Q260 X 1er point mesure sur 2ème axe Q264 (en absolu): Coordonnée du 1er point de palpage dans l'axe auxiliaire du plan d'usinage 1er point mesure sur 3ème axe Q294 (en absolu): Coordonnée du 1er point de palpage dans l'axe du palpeur Distance d'approche Q320 (en incrémental): Distance supplémentaire entre le point de mesure et la bille du palpeur. Q320 agit en complément de PM6140 Hauteur de sécurité Q260 (en absolu): Coordonnée dans l'axe du palpeur excluant toute collision entre le palpeur et la pièce (matériels de bridage) 3 Cycles palpeurs pour le contrôle automatique des pièces Numéro point zéro dans tableau Q305: Indiquer le numéro dans le tableau de points zéro/tableau Preset sous lequel la TNC doit mémoriser la coordonnée. Si vous introduisez Q305=0, la TNC initialise automatiquement l'affichage de manière à ce que le nouveau point de référence soit situé sur la surface palpée Exemple: Séquences CN 5 TCH PROBE 417 PT REF. DANS AXE TS Q263=+25 ;1ER POINT 1ER AXE Q264=+25 ;1ER POINT 2EME AXE Q294=+25 ;1ER POINT 2EME AXE Nouveau pt de réf. sur axe palpeur Q333 (en absolu): Coordonnée dans l'axe du palpeur à laquelle la TNC doit initialiser le point de référence. Configuration par défaut = 0 Q320=0 ;DISTANCE D'APPROCHE Q260=+50 ;HAUTEUR DE SÉCURITÉ Q305=0 ;NO DANS TABLEAU Transfert val. mesure (0,1) Q303: Définir si le point de référence défini doit être enregistré dans le tableau de points zéro ou dans le tableau Preset: -1: Ne pas utiliser! Sera inscrit par la TNC si d'anciens programmes sont importés (cf. „Enregistrer le point de référence calculé” à la page 69) 0: Inscrire dans le tableau de points zéro actif le point de référence calculé. Le système de référence est le système de coordonnées pièce actif 1: Inscrire dans le tableau Preset le point de référence calculé. Le système de référence est le système de coordonnées machine (coordonnées REF) Q333=+0 ;POINT DE RÉFÉRENCE Q303=+1 ;TRANS. VAL. MESURE iTNC 530 HEIDENHAIN 3.2 Calcul automatique des points de référence 99 3.2 Calcul automatique des points de référence POINT DE REFERENCE CENTRE de 4 TROUS (cycle palpeur 418, DIN/ISO: G418) Le cycle palpeur 418 calcule le point d'intersection des lignes reliant deux fois deux centres de trous et l'initialise comme point de référence. Si vous le désirez, la TNC peut aussi inscrire le point d'intersection dans un tableau de points zéro ou de Preset. 1 2 3 4 5 6 7 La TNC positionne le palpeur en avance rapide (valeur de PM6150 ou PM6361) et selon la logique de positionnement (cf. „Travail avec les cycles palpeurs” à la page 26) au centre du premier trou 1 Le palpeur se déplace ensuite à la hauteur de mesure programmée et enregistre le centre du premier trou en palpant quatre fois Puis, la TNC rétracte le palpeur à la hauteur de sécurité et le positionne sur le centre programmé du second trou 2 La TNC déplace le palpeur à la hauteur de mesure programmée et enregistre le centre du deuxième trou en palpant quatre fois La TNC répète les procédures 3 et 4 pour les trous 3 et 4 Pour terminer, la TNC rétracte le palpeur à la hauteur de sécurité et traite le point de référence calculé en fonction des paramètres de cycle Q303 et Q305 (cf. „Enregistrer le point de référence calculé” à la page 69). La TNC calcule le point de référence comme étant le point d'intersection des deux lignes reliant les centres des trous 1/3 et 2/4 et enregistre les valeurs effectives dans les paramètres Q ci-après Ensuite, si on le désire, la TNC calcule aussi, dans une opération de palpage séparée, le point de référence dans l'axe du palpeur Numéro paramètre Signification Q151 Valeur effective du point d'intersection avec l'axe principal Q152 Valeur effective du point d'intersection avec l'axe auxiliaire Y 4 3 1 2 X Remarques avant que vous ne programmiez Avant de définir le cycle, vous devez avoir programmé un appel d'outil pour définir l'axe du palpeur. 100 3 Cycles palpeurs pour le contrôle automatique des pièces 1er centre sur 1er axe Q268 (en absolu): Centre du 1er trou dans l'axe principal du plan d'usinage 1er centre sur 2ème axe Q269 (en absolu): Centre du 1er trou dans l'axe auxiliaire du plan d'usinage 2ème centre sur 1er axe Q270 (en absolu): Centre du 2ème trou dans l'axe principal du plan d'usinage 2ème centre sur 2ème axe Q271 (en absolu): Centre du 2ème trou dans l'axe auxiliaire du plan d'usinage 32ème centre sur 1er axe Q316 (en absolu): Centre du 3ème trou dans l'axe principal du plan d'usinage 3ème centre sur 2ème axe Q317 (en absolu): Centre du 3ème trou dans l'axe auxiliaire du plan d'usinage 4ème centre sur 1er axe Q318 (en absolu): Centre du 4ème trou dans l'axe principal du plan d'usinage 4ème centre sur 2ème axe Q319 (en absolu): Centre du 4ème trou dans l'axe auxiliaire du plan d'usinage Hauteur mesure dans axe palpage Q261 (en absolu): Coordonnée du centre de la bille (=point de contact) dans l'axe du palpeur sur lequel doit être effectuée la mesure Hauteur de sécurité Q260 (en absolu): Coordonnée dans l'axe du palpeur excluant toute collision entre le palpeur et la pièce (matériels de bridage) Y Q318 Q316 Q319 Q317 Q269 Q271 Q268 Q270 X Z Q260 Q261 X iTNC 530 HEIDENHAIN 101 3.2 Calcul automatique des points de référence 3.2 Calcul automatique des points de référence 102 Numéro point zéro dans tableau Q305: Indiquer le numéro dans le tableau de points zéro/tableau Preset sous lequel la TNC doit mémoriser le point d'intersection des lignes. Si vous introduisez Q305=0, la TNC initialise automatiquement l'affichage de manière à ce que le nouveau point de référence soit situé à l'intersection des lignes Exemple: Séquences CN 5 TCH PROBE 418 PT REF. AVEC 4 TROUS Q268=+20 ;1ER CENTRE 1ER AXE Q269=+25 ;1ER CENTRE 2EME AXE Q270=+150 ;2EME CENTRE 1ER AXE Nouveau pt de réf. axe principal Q331 (en absolu): Coordonnée dans l'axe principal à laquelle la TNC doit initialiser le point d'intersection des lignes reliant les centres des trous. Configuration par défaut = 0 Q271=+25 ;2EME CENTRE 2EME AXE Q316=+150 ;3EME CENTRE 1ER AXE Q317=+85 ;3EME CENTRE 2EME AXE Nouveau pt de réf. axe auxiliaire Q332 (en absolu): Coordonnée dans l'axe auxiliaire à laquelle la TNC doit initialiser le point d'intersection des lignes reliant les centres des trous. Configuration par défaut = 0 Q318=+22 ;4EME CENTRE 1ER AXE Q319=+80 ;4EME CENTRE 2EME AXE Transfert val. mesure (0,1) Q303: Définir si le point de référence défini doit être enregistré dans le tableau de points zéro ou dans le tableau Preset: -1: Ne pas utiliser! Sera inscrit par la TNC si d'anciens programmes sont importés (cf. „Enregistrer le point de référence calculé” à la page 69) 0: Inscrire dans le tableau de points zéro actif le point de référence calculé. Le système de référence est le système de coordonnées pièce actif 1: Inscrire dans le tableau Preset le point de référence calculé. Le système de référence est le système de coordonnées machine (coordonnées REF) Palpage dans axe palpeur Q381: Définir si la TNC doit également initialiser le point de référence dans l'axe du palpeur: 0: Ne pas initialiser le point de référence dans l'axe du palpeur 1: Initialiser le point de référence dans l'axe du palpeur Palp. axe palp.: Coord. 1er axe Q382 (en absolu): Coordonnée du point de palpage dans l'axe principal du plan d'usinage à laquelle le point de référence doit être initialisé dans l'axe du palpeur. N'agit que si Q381 = 1 Palp. axe palp.: Coord. 2ème axe Q383 (en absolu): Coordonnée du point de palpage dans l'axe auxiliaire du plan d'usinage à laquelle le point de référence doit être initialisé dans l'axe du palpeur. N'agit que si Q381 = 1 Palp. axe palp.: Coord. 3ème axe Q384 (en absolu): Coordonnée du point de palpage dans l'axe auxiliaire du l'axe du palpeur à laquelle le point de référence doit être initialisé dans l'axe du palpeur. N'agit que si Q381 = 1 Nouveau pt de réf. sur axe palpeur Q333 (en absolu): Coordonnée dans l'axe du palpeur à laquelle la TNC doit initialiser le point de référence. Configuration par défaut = 0 Q261=-5 ;HAUTEUR DE MESURE Q260=+10 ;HAUTEUR DE SÉCURITÉ Q305=12 ;NO DANS TABLEAU Q331=+0 ;POINT DE RÉFÉRENCE Q332=+0 ;POINT DE RÉFÉRENCE Q303=+1 ;TRANS. VAL. MESURE Q381=1 ;PALP. DS AXE PALPEUR Q382=+85 ;1ÈRE COO. DANS AXE PALP. Q383=+50 ;2ÈME COO. DANS AXE PALP. Q384=+0 ;3ÈME COO. DANS AXE PALP. Q333=+0 ;POINT DE RÉFÉRENCE 3 Cycles palpeurs pour le contrôle automatique des pièces Le cycle palpeur 419 mesure une coordonnée au choix sur un axe pouvant être sélectionné et l'initialise comme point de référence. Si vous le désirez, la TNC peut aussi inscrire la coordonnée mesurée dans un tableau de points zéro ou dans le tableau Preset. 1 2 3 La TNC positionne le palpeur en avance rapide (valeur de PM6150 ou PM6361) et selon la logique de positionnement (cf. „Travail avec les cycles palpeurs” à la page 26) au point de palpage programmé 1. Ce faisant, la TNC décale le palpeur de la valeur de la distance d'approche, dans le sens opposé au sens de palpage programmé Pour terminer, le palpeur se déplace à la hauteur de mesure programmée et enregistre la position effective en par simple palpage Pour terminer, la TNC rétracte le palpeur à la hauteur de sécurité et traite le point de référence calculé en fonction des paramètres de cycle Q303 et Q305 (cf. „Enregistrer le point de référence calculé” à la page 69). Remarques avant que vous ne programmiez Avant de définir le cycle, vous devez avoir programmé un appel d'outil pour définir l'axe du palpeur. MP6140 + Q320 Y Q267 + + Q272=2 Q264 1 X Q272=1 Q263 + Z Q272=3 Q267 1er point mesure sur 1er axe Q263 (en absolu): Coordonnée du 1er point de palpage dans l'axe principal du plan d'usinage 1er point mesure sur 2ème axe Q264 (en absolu): Coordonnée du 1er point de palpage dans l'axe auxiliaire du plan d'usinage Hauteur mesure dans axe palpage Q261 (en absolu): Coordonnée du centre de la bille (=point de contact) dans l'axe du palpeur sur lequel doit être effectuée la mesure Distance d'approche Q320 (en incrémental): Distance supplémentaire entre le point de mesure et la bille du palpeur. Q320 agit en complément de PM6140 Hauteur de sécurité Q260 (en absolu): Coordonnée dans l'axe du palpeur excluant toute collision entre le palpeur et la pièce (matériels de bridage) iTNC 530 HEIDENHAIN Q261 1 Q260 X Q272=1 103 3.2 Calcul automatique des points de référence PT DE REF SUR UN AXE (cycle palpeur 419, DIN/ISO: G419) 3.2 Calcul automatique des points de référence Axe de mesure (1...3: 1=axe principal) Q272: Axe sur lequel doit être effectuée la mesure: 1: Axe principal = axe de mesure 2: Axe auxiliaire = axe de mesure 3: Axe palpeur = axe de mesure Axe palpeur actif: Q272 = 3 Affectation des axes Axe principal associé: Q272 = 1 Axe auxiliaire associé: Q272 = 2 Exemple: Séquences CN 5 TCH PROBE 419 PT DE REF. SUR UN AXE Q263=+25 ;1ER POINT 1ER AXE Q264=+25 ;1ER POINT 2EME AXE Q261=+25 ;HAUTEUR DE MESURE Q320=0 ;DISTANCE D'APPROCHE Q260=+50 ;HAUTEUR DE SÉCURITÉ Q272=+1 ;AXE DE MESURE Z X Y Y Z X Q267=+1 ;SENS DÉPLACEMENT X Y Z Q305=0 ;NO DANS TABLEAU Q333=+0 ;POINT DE RÉFÉRENCE Q303=+1 ;TRANS. VAL. MESURE 104 Sens déplacement Q267: Sens de déplacement du palpeur en direction de la pièce: -1: Sens de déplacement négatif +1: Sens de déplacement positif Numéro point zéro dans tableau Q305: Indiquer le numéro dans le tableau de points zéro/tableau Preset sous lequel la TNC doit mémoriser la coordonnée. Si vous introduisez Q305=0, la TNC initialise automatiquement l'affichage de manière à ce que le nouveau point de référence soit situé sur la surface palpée Nouveau pt de réf. Q333 (en absolu): Coordonnée à laquelle la TNC doit initialiser le point de référence. Configuration par défaut = 0 Transfert val. mesure (0,1) Q303: Définir si le point de référence défini doit être enregistré dans le tableau de points zéro ou dans le tableau Preset: -1: Ne pas utiliser! Cf. „Enregistrer le point de référence calculé”, page 69 0: Inscrire dans le tableau de points zéro actif le point de référence calculé. Le système de référence est le système de coordonnées pièce actif 1: Inscrire dans le tableau Preset le point de référence calculé. Le système de référence est le système de coordonnées machine (coordonnées REF) 3 Cycles palpeurs pour le contrôle automatique des pièces Y Y 30 25 25 X 25 Z 0 BEGIN PGM CYC413 MM 1 TOOL CALL 0 Z iTNC 530 HEIDENHAIN Appeler l'outil 0 pour définir de l'axe du palpeur 105 3.2 Calcul automatique des points de référence Exemple: Initialiser le point de référence centre de l'arc de cercle et arête supérieure de la pièce 3.2 Calcul automatique des points de référence 2 TCH PROBE 413 PT REF EXT. CERCLE Q321=+25 ;CENTRE 1ER AXE Centre du cercle: Coordonnée X Q322=+25 ;CENTRE 2ÈME AXE Centre du cercle: Coordonnée Y Q262=30 ;DIAMÈTRE NOMINAL Diamètre du cercle Q325=+90 ;ANGLE INITIAL Angle en coordonnées polaires pour 1er point de palpage Q247=+45 ;INCRÉMENT ANGULAIRE Incrément angulaire pour calculer les points de palpage 2 à 4 Q261=-5 ;HAUTEUR DE MESURE Coordonnée dans l'axe du palpeur où s'effectue la mesure Q320=2 ;DISTANCE D'APPROCHE Distance d'approche en complément de PM6140 Q260=+10 ;HAUTEUR DE SÉCURITÉ Hauteur où l'axe palpeur peut se déplacer sans risque de collision Q301=0 ;DÉPLAC. HAUT. SÉCU. Entre les points de mesure, ne pas aller à hauteur de sécurité Q305=0 ;NO DANS TABLEAU Initialiser l'affichage Q331=+0 ;POINT DE RÉFÉRENCE Initialiser à 0 l'affichage sur X Q332=+10 ;POINT DE RÉFÉRENCE Initialiser à 10 l'affichage sur Y Q303=+0 ;TRANS. VAL. MESURE Sans fonction car l'affichage doit être initialisé Q381=1 ;PALP. DS AXE PALPEUR Initialiser également le point de référence dans l'axe du palpeur Q382=+25 ;1ÈRE COO. DANS AXE PALP. Point de palpage coordonnée X Q383=+25 ;2ÈME COO. DANS AXE PALP. Point de palpage coordonnée Y Q384=+25 ;3ÈME COO. DANS AXE PALP. Point de palpage coordonnée Z Q333=+0 ;POINT DE RÉFÉRENCE Initialiser à 0 l'affichage sur Z 3 CALL PGM 35K47 Appeler le programme d'usinage 4 END PGM CYC413 MM 106 3 Cycles palpeurs pour le contrôle automatique des pièces Le centre du cercle de trous mesuré doit être inscrit dans un tableau Preset pour pouvoir être utilisé ultérieurement. Y Y 1 35 2 50 3 35 X 20 Z 0 BEGIN PGM CYC416 MM Appeler l'outil 0 pour définir de l'axe du palpeur 1 TOOL CALL 0 Z 2 TCH PROBE 417 PT REF. DANS AXE TS Définition cycle pour initialiser le point de réf. dans l'axe du palpeur Q263=+7.5 ;1ER POINT 1ER AXE Point de palpage: Coordonnée X Q264=+7,5 ;1ER POINT 2ÈME AXE Point de palpage: Coordonnée Y Q294=+25 ;1ER POINT 3ÈME AXE Point de palpage: Coordonnée Z Q320=0 ;DISTANCE D'APPROCHE Distance d'approche en complément de PM6140 Q260=+50 ;HAUTEUR DE SÉCURITÉ Hauteur où l'axe palpeur peut se déplacer sans risque de collision Q305=1 ;NO DANS TABLEAU Inscrire la coordonnée Z sur la ligne 1 Q333=+0 ;POINT DE RÉFÉRENCE Initialiser l'axe palpeur à 0 Q303=+1 ;TRANS. VAL. MESURE Enregistrer dans le tableau PRESET.PR le point de référence calculé par rapport au système de coordonnées machine (système REF) iTNC 530 HEIDENHAIN 107 3.2 Calcul automatique des points de référence Exemple: Initialiser le point de référence arête supérieure de la pièce et centre du cercle de trous 3.2 Calcul automatique des points de référence 3 TCH PROBE 416 PT REF. CENTRE C. TROUS Q273=+35 ;CENTRE 1ER AXE Centre du cercle de trous: Coordonnée X Q274=+35 ;CENTRE 2ÈME AXE Centre du cercle de trous: Coordonnée Y Q262=50 ;DIAMÈTRE NOMINAL Diamètre du cercle de trous Q291=+90 ;ANGLE 1ER TROU Angle en coordonnées polaires pour 1er centre de trou 1 Q292=+180 ;ANGLE 2ÈME TROU Angle en coordonnées polaires pour 2ème centre de trou 2 Q293=+270 ;ANGLE 3ÈME TROU Angle en coordonnées polaires pour 3ème centre de trou 3 Q261=+15 ;HAUTEUR DE MESURE Coordonnée dans l'axe du palpeur où s'effectue la mesure Q260=+10 ;HAUTEUR DE SÉCURITÉ Hauteur où l'axe palpeur peut se déplacer sans risque de collision Q305=1 ;NO DANS TABLEAU Inscrire centre du cercle de trous (X et Y) sur la ligne 1 Q331=+0 ;POINT DE RÉFÉRENCE Q332=+0 ;POINT DE RÉFÉRENCE Q303=+1 ;TRANS. VAL. MESURE Enregistrer dans le tableau PRESET.PR le point de référence calculé par rapport au système de coordonnées machine (système REF) Q381=0 ;PALP. DS AXE PALPEUR Ne pas initialiser de point de référence dans l'axe du palpeur Q382=+0 ;1ÈRE COO. DANS AXE PALP. Sans fonction Q383=+0 ;2ÈME COO. DANS AXE PALP. Sans fonction Q384=+0 ;3ÈME COO. DANS AXE PALP. Sans fonction Q333=+0 ;POINT DE RÉFÉRENCE Sans fonction 4 CYCL DEF 247 INIT. PT DE RÉF. Q339=1 Activer nouveau Preset avec le cycle 247 ;NUMÉRO POINT DE RÉF. 6 CALL PGM 35KLZ Appeler le programme d'usinage 7 END PGM CYC416 MM 108 3 Cycles palpeurs pour le contrôle automatique des pièces 3.3 Etalonnage automatique des pièces 3.3 Etalonnage automatique des pièces Vue d'ensemble La TNC dispose de douze cycles destinés à l'étalonnage automatique de pièces: Cycle Softkey Page 0 PLAN DE REFERENCE Mesure de coordonnée dans un axe sélectionnable Page 115 1 PLAN DE REF POLAIRE Mesure d'un point, sens de palpage avec angle Page 116 420 MESURE ANGLE Mesure d'un angle dans le plan d'usinage Page 117 421 MESURE TROU Mesure de la position et du diamètre d'un trou Page 119 422 MESURE EXT. CERCLE Mesure de la position et du diamètre d'un tenon circulaire Page 122 423 MESURE INT. RECTANG. Mesure de la position, longueur et largeur d'une poche rectangulaire Page 125 424 MESURE EXT. RECTANG. Mesure de la position, longueur et largeur d'un tenon rectangulaire Page 128 425 MESURE INT. RAINURE (2ème niveau de softkeys) Mesure interne de la largeur d'une rainure Page 131 426 MESURE EXT. TRAVERSE (2ème niveau de softkeys) Mesure externe d'une traverse Page 133 427 MESURE COORDONNEE (2ème niveau de softkeys) Mesure d'une coordonnée au choix dans un axe au choix Page 135 430 MESURE CERCLE TROUS (2ème niveau de softkeys) Mesure de la position et du diamètre d'un cercle de trous Page 138 431 MESURE PLAN (2ème niveau de softkeys) Mesure d'angle des axes A et B d'un plan Page 141 iTNC 530 HEIDENHAIN 109 3.3 Etalonnage automatique des pièces Procès-verbal des résultats de la mesure Pour tous les cycles (sauf les cycles 0 et 1) destinés à l'étalonnage automatique des pièces, vous pouvez faire établir un procès-verbal de mesure par la TNC. Dans le cycle de palpage utilisé, vous pouvez définir si la TNC doit enregistrer le procès-verbal de mesure dans un fichier restituer à l'écran le procès-verbal de mesure et interrompre le déroulement du programme ne pas générer de procès-verbal de mesure Si vous désirez enregistrer le procès-verbal de mesure dans un fichier, la TNC mémorise en standard les données sous la forme d'un fichier ASCII à l'intérieur du répertoire dans lequel vous exécutez le programme de mesure. En alternative, le procès-verbal de mesure peut être aussi restitué directement sur une imprimante ou mémorisé sur un PC via l'interface de données. Pour cela, réglez la fonction Print (menu de configuration de l'interface) sur RS232\ (cf. également Manuel d'utilisation, „Fonctions MOD, Configuration de l'interface“). Toutes les valeurs de mesure contenues dans le fichier du procès-verbal de mesure se réfèrent au point zéro qui était actif au moment de l'exécution du cycle concerné. Le système de coordonnées peut en outre faire l'objet d'un pivotement dans le plan ou d'une inclinaison avec 3D ROT. Dans ces cas de figure, la TNC convertit les résultats de la mesure dans le système de coordonnées actif. Utilisez le logiciel de transfert de données TNCremo de HEIDENHAIN pour restituer le procès-verbal de mesure via l'interface de données. 110 3 Cycles palpeurs pour le contrôle automatique des pièces 3.3 Etalonnage automatique des pièces Exemple: Fichier procès-verbal pour cycle palpeur 421: Procès-verbal mesure cycle 421 Mesure trou Date: 30-06-2005 Heure: 6:55:04 Programme de mesure: TNC:\GEH35712\CHECK1.H Valeurs nominales:Centre axe principal: 50.0000 Centre axe auxiliaire: 65.0000 Diamètre: 12.0000 Valeurs limites allouées:Cote max. centre axe principal: 50.1000 Cote min. centre axe principal: 49.9000 Cote max. centre axe auxiliaire: 65.1000 Cote min. centre axe auxiliaire: 64.9000 Cote max. trou: 12.0450 Cote min. trou: 12.0000 Valeurs effectives: Centre axe principal: 50.0810 Centre axe auxiliaire: 64.9530 Diamètre: 12.0259 Ecarts: Centre axe principal: 0.0810 Centre axe auxiliaire: -0.0470 Diamètre: 0.0259 Autres résulats de mesure: Hauteur de mesure: -5.0000 Fin procès-verbal de mesure iTNC 530 HEIDENHAIN 111 3.3 Etalonnage automatique des pièces Résultats de la mesure dans les paramètres Q Les résultats de la mesure du cycle palpeur concerné sont mémorisés par la TNC dans les paramètres Q150 à Q160 à effet global. Les écarts par rapport à la valeur nominale sont mémorisés dans les paramètres Q161 à Q166. Tenez compte du tableau des paramètres de résultat contenu dans chaque définition de cycle. Lors de la définition du cycle, la TNC affiche en outre dans l'écran d'aide du cycle concerné les paramètres de résultat (cf. fig. en haut et à droite). Le paramètre de résultat en surbrillance correspond au paramètre d'introduction concerné. Etat de la mesure Avec certains cycles, vous pouvez interroger l'état de la mesure avec les paramètres Q à effet global Q180 à Q182: Etat de la mesure Val. paramètre Valeurs de mesure dans la tolérance Q180 = 1 Retouche nécessaire Q181 = 1 Pièce à rebuter Q182 = 1 La TNC active les marqueurs de réusinage ou de rebut dès que l'une des valeurs de mesure est située hors tolérance. Pour déterminer le résultat de la mesure hors tolérance, consultez également le procèsverbal de mesure ou vérifiez les résultats de la mesure concernés (Q150 à Q160) par rapport à leurs valeurs limites. Avec le cycle 427, la TNC définit (par défaut) que vous mesurez une cote externe (tenon). En choisissant la cote max. et la cote min. en liaison avec le sens du palpage, vous pouvez toutefois rectifier la nature de la mesure. La TNC active également les marqueurs d'état même si vous n'avez pas introduit de tolérances ou de cotes max./ min.. Surveillance de tolérances Pour la plupart des cycles permettant le contrôle des pièces, vous pouvez faire exécuter par la TNC une surveillance de tolérances. Pour cela, lors de la définition du cycle, vous devez définir les valeurs limites nécessaires. Si vous ne désirez pas exécuter de surveillance de tolérances, introduisez 0 pour ce paramètre (= valeur par défaut) 112 3 Cycles palpeurs pour le contrôle automatique des pièces 3.3 Etalonnage automatique des pièces Surveillance d'outil Avec certains cycles permettant le contrôle des pièces, vous pouvez faire exécuter par la TNC une surveillance d'outil. Dans ce cas, la TNC vérifie si le rayon d'outil doit être corrigé en fonction des écarts de la valeur nominale (valeurs dans Q16x) l'écart par rapport à la valeur nominale (valeurs dans Q16x) est supérieur à la tolérance de rupture de l'outil Correction de l'outil Cette fonction n'est réalisable que si: le tableau d'outils est actif vous activez la surveillance d'outil dans le cycle: Pour Q330, introduire une valeur différente de 0 ou un nom d'outil. Vous introduisez le nom de l'outil par softkey. Remarque: La TNC n'affiche plus le guillement de droite. Si vous exécutez plusieurs mesures de correction, la TNC additionne l'écart mesuré à la valeur déjà mémorisée dans le tableau d'outils. La TNC corrige toujours le rayon d'outil dans la colonne DR du tableau d'outils, même si l'écart mesuré est situé hors tolérance. Pour savoir si vous devez réusiner, consultez le paramètre Q181 dans votre programme CN (Q181=1: réusinage). Pour le cycle 427, il convient en outre de noter que: si un axe du plan d'usinage actif a été défini comme axe de mesure (Q272 = 1 ou 2), la TNC exécute une correction du rayon d'outil tel que décrit précédemment. Le sens de la correction est calculé par la TNC à l'aide du sens de déplacement défini (Q267) si l'axe du palpeur a été sélectionné comme axe de mesure (Q272 = 3), la TNC exécute une correction d'outil linéaire iTNC 530 HEIDENHAIN 113 3.3 Etalonnage automatique des pièces Surveillance de rupture d'outil Cette fonction n'est réalisable que si: le tableau d'outils est actif vous activez la surveillance d'outil dans le cycle (Q330 différent de 0) vous avez introduit dans le tableau, pour le numéro d'outil programmé, une tolérance de rupture RBREAK supérieure à 0 (cf. également Manuel d'utilisation, chap. 5.2 „Données d'outils“) La TNC délivre un message d'erreur et stoppe l'exécution du programme lorsque l'écart mesuré est supérieur à la tolérance de rupture de l'outil. Elle verrouille simultanément l'outil dans le tableau d'outils (colonne TL = L). Système de référence pour les résultats de la mesure La TNC délivre tous les résultats de la mesure dans les paramètres de résultat ainsi que dans le fichier de procès-verbal en système de coordonnées actif – et le cas échéant, décalé ou/et pivoté/incliné. 114 3 Cycles palpeurs pour le contrôle automatique des pièces 3.3 Etalonnage automatique des pièces PLAN DE REFERENCE (cycle palpeur 0, DIN/ISO: G55) 1 2 3 En suivant une trajectoire 3D, le palpeur aborde en avance rapide (valeur de PM6150 ou PM6361) le pré-positionnement programmé dans le cycle 1 Le palpeur exécute ensuite l'opération de palpage suivant l'avance de palpage (PM6120 ou PM6360). Le sens du palpage est à définir dans le cycle Lorsque la TNC a enregistré la position, elle rétracte le palpeur au point initial de l'opération de palpage et enregistre la coordonnée mesurée dans un paramètre Q. Par ailleurs, la TNC enregistre dans les paramètres Q115 à Q119 les coordonnées de la position où se trouve le palpeur au moment du signal de commutation. Pour les valeurs de ces paramètres, la TNC ne tient pas compte de la longueur et du rayon de la tige de palpage Z 1 X Remarques avant que vous ne programmiez Pré-positionner le palpeur de manière à éviter toute collision à l'approche du pré-positionnement programmé. N° paramètre pour résultat: Introduire le numéro du paramètre Q auquel doit être affectée la valeur de coordonnée Axe de palpage/sens de palpage: Introduire l'axe de palpage avec la touche de sélection d'axe ou à partir du clavier ASCII, ainsi que le signe du sens du déplacement. Valider avec la touche ENT Positions à atteindre: Introduire toutes les coordonnées de pré-positionnement du palpeur à l'aide des touches de sélection des axes ou à partir du clavier ASCII Terminer l'introduction: Appuyer sur la touche ENT iTNC 530 HEIDENHAIN Exemple: Séquences CN 67 TCH PROBE 0.0 PLAN DE RÉFÉRENCE Q5 X68 TCH PROBE 0.1 X+5 Y+0 Z-5 115 3.3 Etalonnage automatique des pièces PLAN DE REFERENCE polaire (cycle palpeur 1) Le cycle palpeur 1 détermine une position au choix sur la pièce, dans n'importe quel sens de palpage 1 2 3 En suivant une trajectoire 3D, le palpeur aborde en avance rapide (valeur de PM6150 ou PM6361) le pré-positionnement programmé dans le cycle 1 Le palpeur exécute ensuite l'opération de palpage suivant l'avance de palpage (PM6120 ou PM6360). Lors de l'opération de palpage, la TNC déplace le palpeur simultanément sur 2 axes (en fonction de l'angle de palpage). Il convient de définir le sens de palpage avec l'angle polaire dans le cycle Lorsque la TNC a enregistré la position, le palpeur retourne au point initial de l'opération de palpage. La TNC enregistre dans les paramètres Q115 à Q119 les coordonnées de la position où se trouve le palpeur au moment du signal de commutation. Y 1 X Remarques avant que vous ne programmiez Pré-positionner le palpeur de manière à éviter toute collision à l'approche du pré-positionnement programmé. 116 Axe de palpage: Introduire l'axe de palpage avec la touche de sélection d'axe ou à partir du clavier ASCII. Valider avec la touche ENT Angle de palpage: Angle se référant à l'axe de palpage sur lequel le palpeur doit se déplacer Positions à atteindre: Introduire toutes les coordonnées de pré-positionnement du palpeur à l'aide des touches de sélection des axes ou à partir du clavier ASCII Terminer l'introduction: Appuyer sur la touche ENT Exemple: Séquences CN 67 TCH PROBE 1.0 PLAN DE RÉFÉRENCE POLAIRE 68 TCH PROBE 1.1 X ANGLE: +30 69 TCH PROBE 1.2 X+5 Y+0 Z-5 3 Cycles palpeurs pour le contrôle automatique des pièces Le cycle palpeur 420 détermine l'angle formé par n'importe quelle droite et l'axe principal du plan d'usinage. 1 2 3 4 Y La TNC positionne le palpeur en avance rapide (valeur de PM6150 ou PM6361) et selon la logique de positionnement (cf. „Travail avec les cycles palpeurs” à la page 26) au point de palpage programmé 1. Ce faisant, la TNC décale le palpeur de la valeur de la distance d'approche, dans le sens opposé au sens de déplacement défini Le palpeur se déplace ensuite à la hauteur de mesure programmée et exécute la première opération de palpage suivant l'avance de palpage (PM6120 ou PM6360) Puis, le palpeur se déplace vers le point de palpage suivant 2 et exécute la deuxième opération de palpage La TNC rétracte le palpeur à la hauteur de sécurité et mémorise l'angle calculé dans le paramètre Q suivant: Numéro paramètre Signification Q150 Angle mesuré se référant à l'axe principal du plan d'usinage 2 1 X + Y Remarques avant que vous ne programmiez 1er point mesure sur 1er axe Q263 (en absolu): Coordonnée du 1er point de palpage dans l'axe principal du plan d'usinage 1er point mesure sur 2ème axe Q264 (en absolu): Coordonnée du 1er point de palpage dans l'axe auxiliaire du plan d'usinage 2ème point mesure sur 1er axe Q265 (en absolu): Coordonnée du 2ème point de palpage dans l'axe principal du plan d'usinage 2ème point mesure sur 2ème axe Q266 (en absolu): Coordonnée du 2ème point de palpage dans l'axe auxiliaire du plan d'usinage Axe de mesure Q272: Axe sur lequel doit être effectuée la mesure: 1: Axe principal = axe de mesure 2: Axe auxiliaire = axe de mesure 3: Axe du palpeur = axe de mesure + Q272=2 Avant de définir le cycle, vous devez avoir programmé un appel d'outil pour définir l'axe du palpeur. Q267 Q266 Q264 MP6140 + Q320 X Q263 Q265 Q272=1 Si l'axe du palpeur = axe de mesure: Sélectionner Q263 égal à Q265 si l'angle doit être mesuré en direction de l'axe A; sélectionner Q263 différent de Q265 si l'angle doit être mesuré en direction de l'axe B. iTNC 530 HEIDENHAIN 117 3.3 Etalonnage automatique des pièces MESURE ANGLE (cycle palpeur 420, DIN/ISO: G420) 3.3 Etalonnage automatique des pièces Sens déplacement 1 Q267: Sens de déplacement du palpeur en direction de la pièce: -1: Sens de déplacement négatif +1: Sens de déplacement positif Hauteur mesure dans axe palpage Q261 (en absolu): Coordonnée du centre de la bille (=point de contact) dans l'axe du palpeur sur lequel doit être effectuée la mesure Distance d'approche Q320 (en incrémental): Distance supplémentaire entre le point de mesure et la bille du palpeur. Q320 agit en complément de PM6140 Hauteur de sécurité Q260 (en absolu): Coordonnée dans l'axe du palpeur excluant toute collision entre le palpeur et la pièce (matériels de bridage) Déplacement haut. sécu. Q301: Définir comment le palpeur doit se déplacer entre les points de mesure: 0: Entre les points de mesure, à la hauteur de mesure 1: Entre les points de mesure, à la hauteur de sécurité 118 Procès-verb. mes. Q281: Définir si la TNC doit ou non établir le procès-verbal de mesure: 0: Ne pas établir de procès-verbal de mesure 1: Etablir un procès-verbal de mesure: La TNC mémorise en configuration par défaut le fichier de procès-verbal TCHPR420.TXT dans le répertoire où se trouve également votre programme de mesure 2: Interrompre le déroulement du programme et afficher le procès-verbal de mesure à l'écran de la TNC. Poursuivre le programme avec Start CN Exemple: Séquences CN 5 TCH PROBE 420 MESURE ANGLE Q263=+10 ;1ER POINT 1ER AXE Q264=+10 ;1ER POINT 2ÈME AXE Q265=+15 ;2ÈME POINT 1ER AXE Q266=+95 ;2ÈME POINT 2ÈME AXE Q272=1 ;AXE DE MESURE Q267=-1 ;SENS DÉPLACEMENT Q261=-5 ;HAUTEUR DE MESURE Q320=0 ;DISTANCE D'APPROCHE Q260=+10 ;HAUTEUR DE SÉCURITÉ Q301=1 ;DÉPLAC. HAUT. SÉCU. Q281=1 ;PROCÈS-VERBAL MESURE 3 Cycles palpeurs pour le contrôle automatique des pièces 3.3 Etalonnage automatique des pièces MESURE TROU (cycle palpeur 421, DIN/ISO: G421) Le cycle palpeur 421 détermine le centre et le diamètre d'un trou (poche circulaire). Si vous définissez les tolérances correspondantes dans le cycle, la TNC compare les valeurs effectives aux valeurs nominales et mémorise les écarts dans les paramètres-système. 1 2 3 4 5 La TNC positionne le palpeur en avance rapide (valeur de PM6150 ou PM6361) et selon la logique de positionnement (cf. „Travail avec les cycles palpeurs” à la page 26) au point de palpage 1. La TNC calcule les points de palpage à partir des données contenues dans le cycle et de la distance d'approche programmée dans PM6140 Le palpeur se déplace ensuite à la hauteur de mesure programmée et exécute la première opération de palpage suivant l'avance de palpage (PM6120 ou PM6360). La TNC détermine automatiquement le sens du palpage en fonction de l'angle initial programmé Le palpeur se déplace ensuite en suivant une trajectoire circulaire, soit à la hauteur de mesure, soit à la hauteur de sécurité, jusqu'au point de palpage suivant 2 et exécute à cet endroit la deuxième opération de palpage La TNC positionne le palpeur au point de palpage 3 puis au point de palpage 4, y exécute la troisième ou la quatrième opération de palpage La TNC rétracte ensuite le palpeur à la hauteur de sécurité et mémorise les valeurs effectives ainsi que les écarts dans les paramètres Q suivants: Numéro paramètre Signification Q151 Valeur effective centre axe principal Q152 Valeur effective centre axe auxiliaire Q153 Valeur effective diamètre Q161 Ecart centre axe principal Q162 Ecart centre axe auxiliaire Q163 Ecart de diamètre Y 2 3 4 1 X Remarques avant que vous ne programmiez Avant de définir le cycle, vous devez avoir programmé un appel d'outil pour définir l'axe du palpeur. iTNC 530 HEIDENHAIN 119 Centre 2ème axe Q274 (en absolu): Centre du trou dans l'axe auxiliaire du plan d'usinage Diamètre nominal Q262: Introduire le diamètre du trou Angle initial Q325 (en absolu): Angle compris entre l'axe principal du plan d'usinage et le premier point de palpage Incrément angulaire Q247 (en incrémental): Angle compris entre deux points de mesure; le signe de l'incrément angulaire détermine le sens de rotation (- = sens horaire). Si vous désirez étalonner des arcs de cercle, programmez un incrément angulaire inférieur à 90° Q247 Plus l'incrément angulaire programmé est petit et plus la cote du trou calculée par la TNC sera imprécise. Valeur d'introduction min.: 5°. 120 Y Q274±Q280 Q325 Q273±Q279 Q275 MP6140 + Q320 Q262 Centre 1er axe Q273 (en absolu): Centre du trou dans l'axe principal du plan d'usinage Q276 3.3 Etalonnage automatique des pièces X Z Hauteur mesure dans axe palpage Q261 (en absolu): Coordonnée du centre de la bille (=point de contact) dans l'axe du palpeur sur lequel doit être effectuée la mesure Distance d'approche Q320 (en incrémental): Distance supplémentaire entre le point de mesure et la bille du palpeur. Q320 agit en complément de PM6140 Hauteur de sécurité Q260 (en absolu): Coordonnée dans l'axe du palpeur excluant toute collision entre le palpeur et la pièce (matériels de bridage) Déplacement haut. sécu. Q301: Définir comment le palpeur doit se déplacer entre les points de mesure: 0: Entre les points de mesure, à la hauteur de mesure 1: Entre les points de mesure, à la hauteur de sécurité Cote max. du trou Q275: Diamètre max. autorisé pour le trou (poche circulaire) Cote min. du trou Q276: Diamètre min. autorisé pour le trou (poche circulaire) Tolérance centre 1er axe Q279: Ecart de position autorisé dans l'axe principal du plan d'usinage Tolérance centre 2ème axe Q280: Ecart de position autorisé dans l'axe auxiliaire du plan d'usinage Q260 Q261 X 3 Cycles palpeurs pour le contrôle automatique des pièces Procès-verb. mes. Q281: Définir si la TNC doit ou non établir le procès-verbal de mesure: 0: Ne pas établir de procès-verbal de mesure 1: Etablir un procès-verbal de mesure: La TNC mémorise en configuration par défaut le fichier de procès-verbal TCHPR421.TXT dans le répertoire où se trouve également votre programme de mesure 2: Interrompre le déroulement du programme et afficher le procès-verbal de mesure à l'écran de la TNC. Poursuivre le programme avec Start CN Arrêt PGM si tolérance dépassée Q309: Définir si la TNC doit ou non interrompre l'exécution du programme et délivrer un message d'erreur en cas de dépassement des tolérances: 0: ne pas interrompre l'exécution du programme, ne pas délivrer de message d'erreur 1: interrompre l'exécution du programme, délivrer un message d'erreur Numéro d'outil pour surveillance Q330: Définir si la TNC doit exécuter une surveillance de l'outil (cf. „Surveillance d'outil” à la page 113) 0: Surveillance inactive >0: Numéro d'outil dans le tableau d'outils TOOL.T Nombre de points de mesure (4/3) Q423: Définir si la TNC doit mesurer le tenon avec 4 ou 3 points de mesure: 4: Utiliser 4 points de mesure (configuration par défaut) 3: Utiliser 3 points de mesure iTNC 530 HEIDENHAIN Exemple: Séquences CN 3.3 Etalonnage automatique des pièces 5 TCH PROBE 421 MESURE TROU Q273=+50 ;CENTRE 1ER AXE Q274=+50 ;CENTRE 2ÈME AXE Q262=75 ;DIAMÈTRE NOMINAL Q325=+0 ;ANGLE INITIAL Q247=+60 ;INCRÉMENT ANGULAIRE Q261=-5 ;HAUTEUR DE MESURE Q320=0 ;DISTANCE D'APPROCHE Q260=+20 ;HAUTEUR DE SÉCURITÉ Q301=1 ;DÉPLAC. HAUT. SÉCU. Q275=75,12 ;COTE MAX. Q276=74,95 ;COTE MIN. Q279=0,1 ;TOLÉRANCE 1ER CENTRE Q280=0,1 ;TOLÉRANCE 2ND CENTRE Q281=1 ;PROCÈS-VERBAL MESURE Q309=0 ;ARRÊT PGM SI ERREUR Q330=0 ;NUMÉRO D'OUTIL Q423=4 ;NB POINTS DE MESURE 121 3.3 Etalonnage automatique des pièces MESURE EXTERIEUR CERCLE (cycle palpeur 422, DIN/ISO: G422) Le cycle palpeur 422 détermine le centre et le diamètre d'un tenon circulaire. Si vous définissez les tolérances correspondantes dans le cycle, la TNC compare les valeurs effectives aux valeurs nominales et mémorise les écarts dans les paramètres-système. 1 2 3 4 5 La TNC positionne le palpeur en avance rapide (valeur de PM6150 ou PM6361) et selon la logique de positionnement (cf. „Travail avec les cycles palpeurs” à la page 26) au point de palpage 1. La TNC calcule les points de palpage à partir des données contenues dans le cycle et de la distance d'approche programmée dans PM6140 Le palpeur se déplace ensuite à la hauteur de mesure programmée et exécute la première opération de palpage suivant l'avance de palpage (PM6120 ou PM6360). La TNC détermine automatiquement le sens du palpage en fonction de l'angle initial programmé Le palpeur se déplace ensuite en suivant une trajectoire circulaire, soit à la hauteur de mesure, soit à la hauteur de sécurité, jusqu'au point de palpage suivant 2 et exécute à cet endroit la deuxième opération de palpage La TNC positionne le palpeur au point de palpage 3 puis au point de palpage 4, y exécute la troisième ou la quatrième opération de palpage La TNC rétracte ensuite le palpeur à la hauteur de sécurité et mémorise les valeurs effectives ainsi que les écarts dans les paramètres Q suivants: Numéro paramètre Signification Q151 Valeur effective centre axe principal Q152 Valeur effective centre axe auxiliaire Q153 Valeur effective diamètre Q161 Ecart centre axe principal Q162 Ecart centre axe auxiliaire Q163 Ecart de diamètre Y 2 3 1 4 X Remarques avant que vous ne programmiez Avant de définir le cycle, vous devez avoir programmé un appel d'outil pour définir l'axe du palpeur. 122 3 Cycles palpeurs pour le contrôle automatique des pièces Diamètre nominal Q262: Introduire le diamètre du tenon Angle initial Q325 (en absolu): Angle compris entre l'axe principal du plan d'usinage et le premier point de palpage Incrément angulaire Q247 (en incrémental): Angle compris entre deux points de mesure; le signe de l'incrément angulaire détermine le sens de rotation (= sens horaire). Si vous désirez étalonner des arcs de cercle, programmez un incrément angulaire inférieur à 90° Plus l'incrément angulaire programmé est petit et plus la cote du tenon calculée par la TNC sera imprécise. Valeur d'introduction min.: 5°. Hauteur mesure dans axe palpage Q261 (en absolu): Coordonnée du centre de la bille (=point de contact) dans l'axe du palpeur sur lequel doit être effectuée la mesure Distance d'approche Q320 (en incrémental): Distance supplémentaire entre le point de mesure et la bille du palpeur. Q320 agit en complément de PM6140 Hauteur de sécurité Q260 (en absolu): Coordonnée dans l'axe du palpeur excluant toute collision entre le palpeur et la pièce (matériels de bridage) Déplacement haut. sécu. Q301: Définir comment le palpeur doit se déplacer entre les points de mesure: 0: Entre les points de mesure, à la hauteur de mesure 1: Entre les points de mesure, à la hauteur de sécurité Cote max. du tenon Q277: Diamètre max. autorisé pour le tenon Cote min. du tenon Q278: Diamètre min. autorisé pour le tenon Tolérance centre 1er axe Q279: Ecart de position autorisé dans l'axe principal du plan d'usinage Tolérance centre 2ème axe Q280: Ecart de position autorisé dans l'axe auxiliaire du plan d'usinage iTNC 530 HEIDENHAIN Y Q247 Q325 Q274±Q280 MP6140 + Q320 Q273±Q279 X Z Q261 Q260 X 123 3.3 Etalonnage automatique des pièces Centre 2ème axe Q274 (en absolu): Centre du tenon dans l'axe auxiliaire du plan d'usinage Q277 Q262 Centre 1er axe Q273 (en absolu): Centre du tenon dans l'axe principal du plan d'usinage Q278 3.3 Etalonnage automatique des pièces 124 Procès-verb. mes. Q281: Définir si la TNC doit ou non établir le procès-verbal de mesure: 0: Ne pas établir de procès-verbal de mesure 1: Etablir un procès-verbal de mesure: La TNC mémorise en configuration par défaut le fichier de procès-verbal TCHPR422.TXT dans le répertoire où se trouve également votre programme de mesure 2: Interrompre le déroulement du programme et afficher le procès-verbal de mesure à l'écran de la TNC. Poursuivre le programme avec Start CN Arrêt PGM si tolérance dépassée Q309: Définir si la TNC doit ou non interrompre l'exécution du programme et délivrer un message d'erreur en cas de dépassement des tolérances: 0: ne pas interrompre l'exécution du programme, ne pas délivrer de message d'erreur 1: interrompre l'exécution du programme, délivrer un message d'erreur Numéro d'outil pour surveillance Q330: Définir si la TNC doit exécuter une surveillance de l'outil (cf. „Surveillance d'outil” à la page 113): 0: Surveillance inactive >0: Numéro d'outil dans le tableau d'outils TOOL.T Nombre de points de mesure (4/3) Q423: Définir si la TNC doit mesurer le tenon avec 4 ou 3 points de mesure: 4: Utiliser 4 points de mesure (configuration par défaut) 3: Utiliser 3 points de mesure Exemple: Séquences CN 5 TCH PROBE 422 MESURE EXT. CERCLE Q273=+50 ;CENTRE 1ER AXE Q274=+50 ;CENTRE 2ÈME AXE Q262=75 ;DIAMÈTRE NOMINAL Q325=+90 ;ANGLE INITIAL Q247=+30 ;INCRÉMENT ANGULAIRE Q261=-5 ;HAUTEUR DE MESURE Q320=0 ;DISTANCE D'APPROCHE Q260=+10 ;HAUTEUR DE SÉCURITÉ Q301=0 ;DÉPLAC. HAUT. SÉCU. Q275=35.15 ;COTE MAX. Q276=34.9 ;COTE MIN. Q279=0.05 ;TOLÉRANCE 1ER CENTRE Q280=0.05 ;TOLÉRANCE 2ND CENTRE Q281=1 ;PROCÈS-VERBAL MESURE Q309=0 ;ARRÊT PGM SI ERREUR Q330=0 ;NUMÉRO D'OUTIL Q423=4 ;NB POINTS DE MESURE 3 Cycles palpeurs pour le contrôle automatique des pièces 3.3 Etalonnage automatique des pièces MESURE INTERIEUR RECTANGLE (cycle palpeur 423, DIN/ISO: G423) Le cycle palpeur 423 détermine le centre, la longueur et la largeur d'une poche rectangulaire. Si vous définissez les tolérances dans le cycle, la TNC compare les valeurs effectives aux valeurs nominales et mémorise les écarts dans les paramètres-système. 1 2 3 4 5 La TNC positionne le palpeur en avance rapide (valeur de PM6150 ou PM6361) et selon la logique de positionnement (cf. „Travail avec les cycles palpeurs” à la page 26) au point de palpage 1. La TNC calcule les points de palpage à partir des données contenues dans le cycle et de la distance d'approche programmée dans PM6140 Le palpeur se déplace ensuite à la hauteur de mesure programmée et exécute la première opération de palpage suivant l'avance de palpage (PM6120 ou PM6360) Puis, le palpeur se déplace soit paraxialement à la hauteur de mesure, soit linéairement à la hauteur de sécurité, jusqu'au point de palpage suivant 2 et exécute à cet endroit la deuxième opération de palpage La TNC positionne le palpeur au point de palpage 3 puis au point de palpage 4, y exécute la troisième ou la quatrième opération de palpage La TNC rétracte ensuite le palpeur à la hauteur de sécurité et mémorise les valeurs effectives ainsi que les écarts dans les paramètres Q suivants: Numéro paramètre Signification Q151 Valeur effective centre axe principal Q152 Valeur effective centre axe auxiliaire Q154 Valeur effective côté axe principal Q155 Valeur effective côté axe auxiliaire Q161 Ecart centre axe principal Q162 Ecart centre axe auxiliaire Q164 Ecart côté axe principal Q165 Ecart côté axe auxiliaire Y 4 3 1 2 X Remarques avant que vous ne programmiez Avant de définir le cycle, vous devez avoir programmé un appel d'outil pour définir l'axe du palpeur. Si les dimensions de la poche et la distance d'approche ne permettent pas d'effectuer un pré-positionnement à proximité des points de palpage, la TNC palpe toujours en partant du centre de la poche. Dans ce cas, le palpeur ne se déplace pas à la hauteur de sécurité entre les quatre points de mesure. iTNC 530 HEIDENHAIN 125 Centre 2ème axe Q274 (en absolu): Centre de la poche dans l'axe auxiliaire du plan d'usinage Longueur 1er côté Q282: Longueur de la poche parallèle à l'axe principal du plan d'usinage Longueur 2ème côté Q283: Longueur de la poche parallèle à l'axe principal du plan d'usinage Hauteur mesure dans axe palpage Q261 (en absolu): Coordonnée du centre de la bille (=point de contact) dans l'axe du palpeur sur lequel doit être effectuée la mesure Distance d'approche Q320 (en incrémental): Distance supplémentaire entre le point de mesure et la bille du palpeur. Q320 agit en complément de PM6140 Hauteur de sécurité Q260 (en absolu): Coordonnée dans l'axe du palpeur excluant toute collision entre le palpeur et la pièce (matériels de bridage) 126 Centre 1er axe Q273 (en absolu): Centre de la poche dans l'axe principal du plan d'usinage Y Q284 Q282 Q285 Q287 Q283 Q286 3.3 Etalonnage automatique des pièces Q274±Q280 Z Déplacement haut. sécu. Q301: Définir comment le palpeur doit se déplacer entre les points de mesure: 0: Entre les points de mesure, à la hauteur de mesure 1: Entre les points de mesure, à la hauteur de sécurité Cote max. 1er côté Q284: Longueur max. autorisée pour la poche Cote min. 1er côté Q285: Longueur min. autorisée pour la poche Cote max. 2ème côté Q286: Largeur max. autorisée pour la poche Cote min. 2ème côté Q287: Largeur min. autorisée pour la poche Tolérance centre 1er axe Q279: Ecart de position autorisé dans l'axe principal du plan d'usinage Tolérance centre 2ème axe Q280: Ecart de position autorisé dans l'axe auxiliaire du plan d'usinage X Q273±Q279 Q260 Q261 MP6140 + Q320 X 3 Cycles palpeurs pour le contrôle automatique des pièces Procès-verb. mes. Q281: Définir si la TNC doit ou non établir le procès-verbal de mesure: 0: Ne pas établir de procès-verbal de mesure 1: Etablir un procès-verbal de mesure: La TNC mémorise en configuration par défaut le fichier de procès-verbal TCHPR423.TXT dans le répertoire où se trouve également votre programme de mesure 2: Interrompre le déroulement du programme et afficher le procès-verbal de mesure à l'écran de la TNC. Poursuivre le programme avec Start CN Arrêt PGM si tolérance dépassée Q309: Définir si la TNC doit ou non interrompre l'exécution du programme et délivrer un message d'erreur en cas de dépassement des tolérances: 0: ne pas interrompre l'exécution du programme, ne pas délivrer de message d'erreur 1: interrompre l'exécution du programme, délivrer un message d'erreur Numéro d'outil pour surveillance Q330: Définir si la TNC doit exécuter une surveillance de l'outil (cf. „Surveillance d'outil” à la page 113) 0: Surveillance inactive >0: Numéro d'outil dans le tableau d'outils TOOL.T iTNC 530 HEIDENHAIN Exemple: Séquences CN 3.3 Etalonnage automatique des pièces 5 TCH PROBE 423 MESURE INT. RECTANG. Q273=+50 ;CENTRE 1ER AXE Q274=+50 ;CENTRE 2ÈME AXE Q282=80 ;1ER CÔTÉ Q283=60 ;2ÈME CÔTÉ Q261=-5 ;HAUTEUR DE MESURE Q320=0 ;DISTANCE D'APPROCHE Q260=+10 ;HAUTEUR DE SÉCURITÉ Q301=1 ;DÉPLAC. HAUT. SÉCU. Q284=0 ;COTE MAX. 1ER CÔTÉ Q285=0 ;COTE MIN. 1ER CÔTÉ Q286=0 ;COTE MAX. 2ÈME CÔTÉ Q287=0 ;COTE MIN. 2ÈME CÔTÉ Q279=0 ;TOLÉRANCE 1ER CENTRE Q280=0 ;TOLÉRANCE 2ND CENTRE Q281=1 ;PROCÈS-VERBAL MESURE Q309=0 ;ARRÊT PGM SI ERREUR Q330=0 ;NUMÉRO D'OUTIL 127 3.3 Etalonnage automatique des pièces MESURE EXTERIEUR RECTANGLE (cycle palpeur 424, DIN/ISO: G424) Le cycle palpeur 424 détermine le centre ainsi que la longueur et la largeur d'un tenon rectangulaire. Si vous définissez les tolérances correspondantes dans le cycle, la TNC compare les valeurs effectives aux valeurs nominales et mémorise les écarts dans les paramètressystème. 1 2 3 4 5 La TNC positionne le palpeur en avance rapide (valeur de PM6150 ou PM6361) et selon la logique de positionnement (cf. „Travail avec les cycles palpeurs” à la page 26) au point de palpage 1. La TNC calcule les points de palpage à partir des données contenues dans le cycle et de la distance d'approche programmée dans PM6140 Le palpeur se déplace ensuite à la hauteur de mesure programmée et exécute la première opération de palpage suivant l'avance de palpage (PM6120 ou PM6360) Puis, le palpeur se déplace soit paraxialement à la hauteur de mesure, soit linéairement à la hauteur de sécurité, jusqu'au point de palpage suivant 2 et exécute à cet endroit la deuxième opération de palpage La TNC positionne le palpeur au point de palpage 3 puis au point de palpage 4, et y exécute la troisième ou la quatrième opération de palpage La TNC rétracte ensuite le palpeur à la hauteur de sécurité et mémorise les valeurs effectives ainsi que les écarts dans les paramètres Q suivants: Numéro paramètre Signification Q151 Valeur effective centre axe principal Q152 Valeur effective centre axe auxiliaire Q154 Valeur effective côté axe principal Q155 Valeur effective côté axe auxiliaire Q161 Ecart centre axe principal Q162 Ecart centre axe auxiliaire Q164 Ecart côté axe principal Q165 Ecart côté axe auxiliaire Y 4 3 1 2 X Remarques avant que vous ne programmiez Avant de définir le cycle, vous devez avoir programmé un appel d'outil pour définir l'axe du palpeur. 128 3 Cycles palpeurs pour le contrôle automatique des pièces Centre 2ème axe Q274 (en absolu): Centre du tenon dans l'axe auxiliaire du plan d'usinage Longueur 1er côté Q282: Longueur du tenon parallèle à l'axe principal du plan d'usinage Longueur 2ème côté Q283: Longueur du tenon parallèle à l'axe auxiliaire du plan d'usinage Hauteur mesure dans axe palpage Q261 (en absolu): Coordonnée du centre de la bille (=point de contact) dans l'axe du palpeur sur lequel doit être effectuée la mesure Distance d'approche Q320 (en incrémental): Distance supplémentaire entre le point de mesure et la bille du palpeur. Q320 agit en complément de PM6140 Hauteur de sécurité Q260 (en absolu): Coordonnée dans l'axe du palpeur excluant toute collision entre le palpeur et la pièce (matériels de bridage) Y Q284 Q282 Q285 Q274±Q280 Z Déplacement haut. sécu. Q301: Définir comment le palpeur doit se déplacer entre les points de mesure: 0: Entre les points de mesure, à la hauteur de mesure 1: Entre les points de mesure, à la hauteur de sécurité Cote max. 1er côté Q284: Longueur max. autorisée pour le tenon Cote min. 1er côté Q285: Longueur min. autorisée pour le tenon Cote max. 2ème côté Q286: Largeur max. autorisée pour le tenon Cote min. 2ème côté Q287: Largeur min. autorisée pour le tenon Tolérance centre 1er axe Q279: Ecart de position autorisé dans l'axe principal du plan d'usinage Tolérance centre 2ème axe Q280: Ecart de position autorisé dans l'axe auxiliaire du plan d'usinage iTNC 530 HEIDENHAIN X Q273±Q279 Q260 Q261 MP6140 + Q320 X 129 3.3 Etalonnage automatique des pièces Centre 1er axe Q273 (en absolu): Centre du tenon dans l'axe principal du plan d'usinage Q287 Q283 Q286 3.3 Etalonnage automatique des pièces 130 Procès-verb. mes. Q281: Définir si la TNC doit ou non établir le procès-verbal de mesure: 0: Ne pas établir de procès-verbal de mesure 1: Etablir un procès-verbal de mesure: La TNC mémorise en configuration par défaut le fichier de procès-verbal TCHPR424.TXT dans le répertoire où se trouve également votre programme de mesure 2: Interrompre le déroulement du programme et afficher le procès-verbal de mesure à l'écran de la TNC. Poursuivre le programme avec Start CN Arrêt PGM si tolérance dépassée Q309: Définir si la TNC doit ou non interrompre l'exécution du programme et délivrer un message d'erreur en cas de dépassement des tolérances: 0: ne pas interrompre l'exécution du programme, ne pas délivrer de message d'erreur 1: interrompre l'exécution du programme, délivrer un message d'erreur Numéro d'outil pour surveillance Q330: Définir si la TNC doit exécuter une surveillance de l'outil (cf. „Surveillance d'outil” à la page 113): 0: Surveillance inactive >0: Numéro d'outil dans le tableau d'outils TOOL.T Exemple: Séquences CN 5 TCH PROBE 424 MESURE EXT. RECTANG. Q273=+50 ;CENTRE 1ER AXE Q274=+50 ;CENTRE 2ÈME AXE Q282=75 ;1ER CÔTÉ Q283=35 ;2ÈME CÔTÉ Q261=-5 ;HAUTEUR DE MESURE Q320=0 ;DISTANCE D'APPROCHE Q260=+20 ;HAUTEUR DE SÉCURITÉ Q301=0 ;DÉPLAC. HAUT. SÉCU. Q284=75.1 ;COTE MAX. 1ER CÔTÉ Q285=74.9 ;COTE MIN. 1ER CÔTÉ Q286=35 ;COTE MAX. 2ÈME CÔTÉ Q287=34.95 ;COTE MIN. 2ÈME CÔTÉ Q279=0,1 ;TOLÉRANCE 1ER CENTRE Q280=0,1 ;TOLÉRANCE 2ND CENTRE Q281=1 ;PROCÈS-VERBAL MESURE Q309=0 ;ARRÊT PGM SI ERREUR Q330=0 ;NUMÉRO D'OUTIL 3 Cycles palpeurs pour le contrôle automatique des pièces 3.3 Etalonnage automatique des pièces MESURE INTERIEUR RAINURE (cycle palpeur 425, DIN/ISO: G425) Le cycle palpeur 425 détermine la position et la largeur d'une rainure (poche). Si vous définissez les tolérances correspondantes dans le cycle, la TNC compare la valeur effective à la valeur nominale et mémorise l'écart dans un paramètre-système. 1 2 3 4 La TNC positionne le palpeur en avance rapide (valeur de PM6150 ou PM6361) et selon la logique de positionnement (cf. „Travail avec les cycles palpeurs” à la page 26) au point de palpage 1. La TNC calcule les points de palpage à partir des données contenues dans le cycle et de la distance d'approche programmée dans PM6140 Le palpeur se déplace ensuite à la hauteur de mesure programmée et exécute la première opération de palpage suivant l'avance de palpage (PM6120 ou PM6360). 1er palpage toujours dans le sens positif de l'axe programmé Si vous introduisez un décalage pour la deuxième mesure, la TNC déplace le palpeur paraxialement par rapport au point de palpage suivant 2 et exécute à cet endroit la deuxième opération de palpage. Si vous n'introduisez pas de décalage, la TNC mesure directement la largeur dans le sens opposé La TNC rétracte ensuite le palpeur à la hauteur de sécurité et mémorise les valeurs effectives ainsi que l'écart dans les paramètres Q suivants: Numéro paramètre Signification Q156 Valeur effective longueur mesurée Q157 Valeur effective de la position de l'axe médian Q166 Ecart de la longueur mesurée Y 2 1 X Remarques avant que vous ne programmiez Avant de définir le cycle, vous devez avoir programmé un appel d'outil pour définir l'axe du palpeur. iTNC 530 HEIDENHAIN 131 3.3 Etalonnage automatique des pièces Point initial 2ème axe Q329 (en absolu): Point initial de l'opération de palpage dans l'axe auxiliaire du plan d'usinage Décalage pour 2ème mesure Q310 (en incrémental): Valeur pour le décalage du palpeur avant qu'il effectue la 2ème mesure. Si vous introduisez 0, la TNC ne décale pas le palpeur Axe de mesure Q272: Axe du plan d'usinage sur lequel doit être effectuée la mesure: 1:Axe principal = axe de mesure 2:Axe auxiliaire = axe de mesure Hauteur mesure dans axe palpage Q261 (en absolu): Coordonnée du centre de la bille (=point de contact) dans l'axe du palpeur sur lequel doit être effectuée la mesure Hauteur de sécurité Q260 (en absolu): Coordonnée dans l'axe du palpeur excluant toute collision entre le palpeur et la pièce (matériels de bridage) Longueur nominale Q311: (en incrémental): Valeur nominale de la longueur à mesurer Cote max. Q288: Longueur max. autorisée Cote min. Q289: Longueur min. autorisée Procès-verb. mes. Q281: Définir si la TNC doit ou non établir le procès-verbal de mesure: 0: Ne pas établir de procès-verbal de mesure 1: Etablir un procès-verbal de mesure: La TNC mémorise en configuration par défaut le fichier de procès-verbal TCHPR425.TXT dans le répertoire où se trouve également votre programme de mesure 2: Interrompre le déroulement du programme et afficher le procès-verbal de mesure à l'écran de la TNC. Poursuivre le programme avec Start CN 132 Point initial 1er axe Q328 (en absolu): Point initial de l'opération de palpage dans l'axe principal du plan d'usinage Q288 Q311 Q289 Y Q272=2 Q310 Q329 X Q272=1 Q328 Z Q260 Q261 X Exemple: Séquences CN 5 TCH PRONE 425 MESURE INT. RAINURE Q328=+75 ;PT INITIAL 1ER AXE Arrêt PGM si tolérance dépassée Q309: Définir si la TNC doit ou non interrompre l'exécution du programme et délivrer un message d'erreur en cas de dépassement des tolérances: 0: ne pas interrompre l'exécution du programme, ne pas délivrer de message d'erreur 1: interrompre l'exécution du programme, délivrer un message d'erreur Q329=-12.5 ;PT INITIAL 2EME AXE Q310=+0 ;DECALAGE 2EME MESURE Q272=1 ;AXE DE MESURE Q261=-5 ;HAUTEUR DE MESURE Q260=+10 ;HAUTEUR DE SECURITE Q311=25 ;LONGUEUR NOMINALE Numéro d'outil pour surveillance Q330: Définir si la TNC doit exécuter une surveillance de l'outil (cf. „Surveillance d'outil” à la page 113): 0: Surveillance inactive >0: Numéro d'outil dans le tableau d'outils TOOL.T Q288=25.05 ;COTE MAX. Q289=25 ;COTE MIN. Q281=1 ;PROCES-VERBAL MESURE Q309=0 ;ARRET PGM SI ERREUR Q330=0 ;NUMERO D'OUTIL 3 Cycles palpeurs pour le contrôle automatique des pièces 3.3 Etalonnage automatique des pièces MESURE EXTERIEUR TRAVERSE (cycle palpeur 426, DIN/ISO: G426) Le cycle palpeur 426 détermine la position et la largeur d'une traverse. Si vous définissez les tolérances correspondantes dans le cycle, la TNC compare la valeur effective à la valeur nominale et mémorise l'écart dans un paramètre-système. 1 2 3 4 Y La TNC positionne le palpeur en avance rapide (valeur de PM6150 ou PM6361) et selon la logique de positionnement (cf. „Travail avec les cycles palpeurs” à la page 26) au point de palpage 1. La TNC calcule les points de palpage à partir des données contenues dans le cycle et de la distance d'approche programmée dans PM6140 Le palpeur se déplace ensuite à la hauteur de mesure programmée et exécute la première opération de palpage suivant l'avance de palpage (PM6120 ou PM6360). 1er palpage toujours dans le sens négatif de l'axe programmé Puis, le palpeur se déplace à la hauteur de sécurité vers le point de palpage suivant et exécute la deuxième opération de palpage La TNC rétracte ensuite le palpeur à la hauteur de sécurité et mémorise les valeurs effectives ainsi que l'écart dans les paramètres Q suivants: Numéro paramètre Signification Q156 Valeur effective longueur mesurée Q157 Valeur effective de la position de l'axe médian Q166 Ecart de la longueur mesurée 1 2 X Remarques avant que vous ne programmiez Avant de définir le cycle, vous devez avoir programmé un appel d'outil pour définir l'axe du palpeur. 1er point mesure sur 1er axe Q263 (en absolu): Coordonnée du 1er point de palpage dans l'axe principal du plan d'usinage 1er point mesure sur 2ème axe Q264 (en absolu): Coordonnée du 1er point de palpage dans l'axe auxiliaire du plan d'usinage 2ème point mesure sur 1er axe Q265 (en absolu): Coordonnée du 2ème point de palpage dans l'axe principal du plan d'usinage 2ème point mesure sur 2ème axe Q266 (en absolu): Coordonnée du 2ème point de palpage dans l'axe auxiliaire du plan d'usinage Q288 Q311 Q289 Y Q272=2 Q264 Q266 MP6140 + Q320 Q265 iTNC 530 HEIDENHAIN Q263 X Q272=1 133 3.3 Etalonnage automatique des pièces Distance d'approche Q320 (en incrémental): Distance supplémentaire entre le point de mesure et la bille du palpeur. Q320 agit en complément de PM6140 Hauteur de sécurité Q260 (en absolu): Coordonnée dans l'axe du palpeur excluant toute collision entre le palpeur et la pièce (matériels de bridage) Longueur nominale Q311: (en incrémental): Valeur nominale de la longueur à mesurer Cote max. Q288: Longueur max. autorisée Cote min. Q289: Longueur min. autorisée Procès-verb. mes. Q281: Définir si la TNC doit ou non établir le procès-verbal de mesure: 0: Ne pas établir de procès-verbal de mesure 1: Etablir un procès-verbal de mesure: La TNC mémorise en configuration par défaut le fichier de procès-verbal TCHPR426.TXT dans le répertoire où se trouve également votre programme de mesure 2: Interrompre le déroulement du programme et afficher le procès-verbal de mesure à l'écran de la TNC. Poursuivre le programme avec Start CN Z Hauteur mesure dans axe palpage Q261 (en absolu): Coordonnée du centre de la bille (=point de contact) dans l'axe du palpeur sur lequel doit être effectuée la mesure 134 Axe de mesure Q272: Axe du plan d'usinage sur lequel doit être effectuée la mesure: 1:Axe principal = axe de mesure 2:Axe auxiliaire = axe de mesure Q260 Q261 X Exemple: Séquences CN 5 TCH PROBE 426 MESURE EXT. TRAVERSE Arrêt PGM si tolérance dépassée Q309: Définir si la TNC doit ou non interrompre l'exécution du programme et délivrer un message d'erreur en cas de dépassement des tolérances: 0: ne pas interrompre l'exécution du programme, ne pas délivrer de message d'erreur 1: interrompre l'exécution du programme, délivrer un message d'erreur Numéro d'outil pour surveillance Q330: Définir si la TNC doit exécuter une surveillance de l'outil (cf. „Surveillance d'outil” à la page 113) 0: Surveillance inactive >0: Numéro d'outil dans le tableau d'outils TOOL.T Q263=+50 ;1ER POINT 1ER AXE Q264=+25 ;1ER POINT 2EME AXE Q265=+50 ;2EME POINT 1ER AXE Q266=+85 ;2EME POINT 2EME AXE Q272=2 ;AXE DE MESURE Q261=-5 ;HAUTEUR DE MESURE Q320=0 ;DISTANCE D'APPROCHE Q260=+20 ;HAUTEUR DE SECURITE Q311=45 ;LONGUEUR NOMINALE Q288=45 ;COTE MAX. Q289=44.95 ;COTE MIN. Q281=1 ;PROCES-VERBAL MESURE Q309=0 ;ARRET PGM SI ERREUR Q330=0 ;NUMERO D'OUTIL 3 Cycles palpeurs pour le contrôle automatique des pièces 3.3 Etalonnage automatique des pièces MESURE COORDONNEE (cycle palpeur 427, DIN/ISO: G427) Le cycle palpeur 427 détermine une coordonnée dans un axe sélectionnable et mémorise la valeur dans un paramètre-système. Si vous définissez les tolérances correspondantes dans le cycle, la TNC compare les valeurs effectives aux valeurs nominales et mémorise l'écart dans des paramètres-système. 1 2 3 La TNC positionne le palpeur en avance rapide (valeur de PM6150 ou PM6361) et selon la logique de positionnement (cf. „Travail avec les cycles palpeurs” à la page 26) au point de palpage 1. Ce faisant, la TNC décale le palpeur de la valeur de la distance d'approche, dans le sens opposé au sens de déplacement défini La TNC positionne ensuite le palpeur dans le plan d'usinage, sur le point de palpage programmé 1 et enregistre à cet endroit la valeur effective dans l'axe sélectionné La TNC rétracte ensuite le palpeur à la hauteur de sécurité et mémorise la coordonnée calculée dans le paramètre Q suivant: Numéro paramètre Signification Q160 Coordonnée mesurée Z 1 X Remarques avant que vous ne programmiez Avant de définir le cycle, vous devez avoir programmé un appel d'outil pour définir l'axe du palpeur. iTNC 530 HEIDENHAIN 135 3.3 Etalonnage automatique des pièces 1er point mesure sur 1er axe Q263 (en absolu): Coordonnée du 1er point de palpage dans l'axe principal du plan d'usinage MP6140 + Q320 Y + + Q272=2 1er point mesure sur 2ème axe Q264 (en absolu): Coordonnée du 1er point de palpage dans l'axe auxiliaire du plan d'usinage Q267 Hauteur mesure dans axe palpage Q261 (en absolu): Coordonnée du centre de la bille (=point de contact) dans l'axe du palpeur sur lequel doit être effectuée la mesure Q264 Distance d'approche Q320 (en incrémental): Distance supplémentaire entre le point de mesure et la bille du palpeur. Q320 agit en complément de PM6140 Axe de mesure (1..3: 1=axe principal) Q272: Axe sur lequel doit être effectuée la mesure: 1:Axe principal = axe de mesure 2:Axe auxiliaire = axe de mesure 3: Axe du palpeur = axe de mesure Sens déplacement 1 Q267: Sens de déplacement du palpeur en direction de la pièce: -1: Sens de déplacement négatif +1: Sens de déplacement positif Hauteur de sécurité Q260 (en absolu): Coordonnée dans l'axe du palpeur excluant toute collision entre le palpeur et la pièce (matériels de bridage) X Q272=1 Q263 Z + Q272=3 Q267 Q261 Q260 X Q272=1 136 3 Cycles palpeurs pour le contrôle automatique des pièces Procès-verb. mes. Q281: Définir si la TNC doit ou non établir le procès-verbal de mesure: 0: Ne pas établir de procès-verbal de mesure 1: Etablir un procès-verbal de mesure: La TNC mémorise en configuration par défaut le fichier de procès-verbal TCHPR427.TXT dans le répertoire où se trouve également votre programme de mesure 2: Interrompre le déroulement du programme et afficher le procès-verbal de mesure à l'écran de la TNC. Poursuivre le programme avec Start CN Exemple: Séquences CN 5 TCH PROBE 427 MESURE COORDONNEE Q263=+35 ;1ER POINT 1ER AXE Q264=+45 ;1ER POINT 2EME AXE Q261=+5 ;HAUTEUR DE MESURE Q320=0 ;DISTANCE D'APPROCHE Q272=3 ;AXE DE MESURE Cote max. Q288: Valeur de mesure max. autorisée Q267=-1 ;SENS DEPLACEMENT Cote min. Q289: Valeur de mesure min. autorisée Q260=+20 ;HAUTEUR DE SECURITE Arrêt PGM si tolérance dépassée Q309: Définir si la TNC doit ou non interrompre l'exécution du programme et délivrer un message d'erreur en cas de dépassement des tolérances: 0: ne pas interrompre l'exécution du programme, ne pas délivrer de message d'erreur 1: interrompre l'exécution du programme, délivrer un message d'erreur Q281=1 ;PROCES-VERBAL MESURE Q288=5.1 ;COTE MAX. Q289=4.95 ;COTE MIN. Q309=0 ;ARRET PGM SI ERREUR Q330=0 ;NUMERO D'OUTIL 3.3 Etalonnage automatique des pièces Numéro d'outil pour surveillance Q330: Définir si la TNC doit exécuter une surveillance de l'outil (cf. „Surveillance d'outil” à la page 113): 0: Surveillance inactive >0: Numéro d'outil dans le tableau d'outils TOOL.T iTNC 530 HEIDENHAIN 137 3.3 Etalonnage automatique des pièces MESURE CERCLE DE TROUS (cycle palpeur 430, DIN/ISO: G430) Le cycle palpeur 430 détermine le centre et le diamètre d'un cercle de trous grâce à la mesure de trois trous. Si vous définissez les tolérances correspondantes dans le cycle, la TNC compare la valeur effective à la valeur nominale et mémorise l'écart dans un paramètre-système. 1 2 3 4 5 6 7 La TNC positionne le palpeur en avance rapide (valeur de PM6150 ou PM6361) et selon la logique de positionnement (cf. „Travail avec les cycles palpeurs” à la page 26) au centre programmé du premier trou 1 Le palpeur se déplace ensuite à la hauteur de mesure programmée et enregistre le centre du premier trou en palpant quatre fois Puis, la TNC rétracte le palpeur à la hauteur de sécurité et le positionne sur le centre programmé du second trou 2 La TNC déplace le palpeur à la hauteur de mesure programmée et enregistre le centre du deuxième trou en palpant quatre fois Puis, la TNC rétracte le palpeur à la hauteur de sécurité et le positionne sur le centre programmé du troisième trou 3 La TNC déplace le palpeur à la hauteur de mesure programmée et enregistre le centre du troisième trou en palpant quatre fois La TNC rétracte ensuite le palpeur à la hauteur de sécurité et mémorise les valeurs effectives ainsi que les écarts dans les paramètres Q suivants: Numéro paramètre Signification Q151 Valeur effective centre axe principal Q152 Valeur effective centre axe auxiliaire Q153 Valeur effective diamètre cercle de trous Q161 Ecart centre axe principal Q162 Ecart centre axe auxiliaire Q163 Ecart diamètre cercle de trous Y 1 2 3 X Remarques avant que vous ne programmiez Avant de définir le cycle, vous devez avoir programmé un appel d'outil pour définir l'axe du palpeur. 138 3 Cycles palpeurs pour le contrôle automatique des pièces Diamètre nominal Q262: Introduire le diamètre du cercle de trous Angle 1er trou Q291 (en absolu): Angle en coordonnées polaires du 1er centre de trou dans le plan d'usinage Angle 2ème trou Q292 (en absolu): Angle en coordonnées polaires du 2ème centre de trou dans le plan d'usinage Angle 3ème trou Q293 (en absolu): Angle en coordonnées polaires du 3ème centre de trou dans le plan d'usinage Hauteur mesure dans axe palpage Q261 (en absolu): Coordonnée du centre de la bille (=point de contact) dans l'axe du palpeur sur lequel doit être effectuée la mesure Hauteur de sécurité Q260 (en absolu): Coordonnée dans l'axe du palpeur excluant toute collision entre le palpeur et la pièce (matériels de bridage) Cote max. Q288: Diamètre max. autorisé pour le cercle de trous Cote min. Q289: Diamètre min. autorisé pour le cercle de trous Tolérance centre 1er axe Q279: Ecart de position autorisé dans l'axe principal du plan d'usinage Tolérance centre 2ème axe Q280: Ecart de position autorisé dans l'axe auxiliaire du plan d'usinage iTNC 530 HEIDENHAIN Q274±Q280 Q291 Q293 Q273±Q279 X Z Q260 Q261 X 139 3.3 Etalonnage automatique des pièces Y Q288 Centre 2ème axe Q274 (en absolu): Centre du cercle de trous (valeur nominale) dans l'axe auxiliaire du plan d'usinage Q262 Q289 Centre 1er axe Q273 (en absolu): Centre du cercle de trous (valeur nominale) dans l'axe principal du plan d'usinage Q292 3.3 Etalonnage automatique des pièces Procès-verb. mes. Q281: Définir si la TNC doit ou non établir le procès-verbal de mesure: 0: Ne pas établir de procès-verbal de mesure 1: Etablir un procès-verbal de mesure: La TNC mémorise en configuration par défaut le fichier de procès-verbal TCHPR430.TXT dans le répertoire où se trouve également votre programme de mesure 2: Interrompre le déroulement du programme et afficher le procès-verbal de mesure à l'écran de la TNC. Poursuivre le programme avec Start CN Arrêt PGM si tolérance dépassée Q309: Définir si la TNC doit ou non interrompre l'exécution du programme et délivrer un message d'erreur en cas de dépassement des tolérances: 0: ne pas interrompre l'exécution du programme, ne pas délivrer de message d'erreur 1: interrompre l'exécution du programme, délivrer un message d'erreur Numéro d'outil pour surveillance Q330: Définir si la TNC doit exécuter une surveillance de rupture de l'outil (cf. „Surveillance d'outil” à la page 113): 0: Surveillance inactive >0: Numéro d'outil dans le tableau d'outils TOOL.T Exemple: Séquences CN 5 TCH PROBE 430 MESURE CERCLE TROUS Q273=+50 ;CENTRE 1ER AXE Q274=+50 ;CENTRE 2EME AXE Q262=80 ;DIAMETRE NOMINAL Q291=+0 ;ANGLE 1ER TROU Q292=+90 ;ANGLE 2EME TROU Q293=+180 ;ANGLE 3EME TROU Q261=-5 ;HAUTEUR DE MESURE Q260=+10 ;HAUTEUR DE SECURITE Q288=80.1 ;COTE MAX. Q289=79.9 ;COTE MIN. Q279=0.15 ;TOLERANCE 1ER CENTRE Q280=0.15 ;TOLERANCE 2ND CENTRE Q281=1 ;PROCES-VERBAL MESURE Q309=0 ;ARRET PGM SI ERREUR Q330=0 ;NUMERO D'OUTIL Attention: ici, seule la surveillance de rupture est active; pas de correction automatique d'outil. 140 3 Cycles palpeurs pour le contrôle automatique des pièces Le cycle palpeur 431 détermine l'angle d'un plan grâce à la mesure de trois points et mémorise les valeurs dans les paramètres-système. 1 2 3 4 La TNC positionne le palpeur en avance rapide (valeur de PM6150 ou PM6361) et selon la logique de positionnement (cf. „Travail avec les cycles palpeurs” à la page 26) au point de palpage programmé 1 où celui-ci mesure le premier point du plan. Ce faisant, la TNC décale le palpeur de la valeur de la distance d'approche, dans le sens opposé au sens de palpage Le palpeur est ensuite rétracté à la hauteur de sécurité, puis positionné dans le plan d'usinage, sur le point de palpage 2 où il mesure la valeur effective du deuxième point du plan Le palpeur est ensuite rétracté à la hauteur de sécurité, puis positionné dans le plan d'usinage, sur le point de palpage 3 où il mesure la valeur effective du troisième point du plan La TNC rétracte ensuite le palpeur à la hauteur de sécurité et mémorise les valeurs angulaires calculées dans les paramètres Q suivants: Numéro paramètre Signification Q158 Angle de l'axe de projection A Q159 Angle de l'axe de projection B Q170 Angle dans l'espace A Q171 Angle dans l'espace B Q172 Angle dans l'espace C Q173 Valeur de mesure dans l'axe du palpeur iTNC 530 HEIDENHAIN +Y Z Y +X 3 B 2 X 1 A 141 3.3 Etalonnage automatique des pièces MESURE PLAN (cycle palpeur 431, DIN/ISO: G431) 3.3 Etalonnage automatique des pièces Remarques avant que vous ne programmiez Avant de définir le cycle, vous devez avoir programmé un appel d'outil pour définir l'axe du palpeur. Pour que la TNC puisse calculer les valeurs angulaires, les trois points de mesure ne doivent pas être situés sur une droite. Les angles dans l'espace utilisés avec la fonction d'inclinaison du plan d'usinage sont enregistrés dans les paramètres Q170 - Q172. Les deux premiers points de mesure servent à définir la direction de l'axe principal pour l'inclinaison du plan d'usinage. Le troisième point de mesure est défini dans le sens de l'axe d'outil. Définir le troisième point de mesure dans le sens positif de l’axe Y pour que l'axe d'outil soit situé correctement dans le système de coordonnées sens horaire (cf. figure). Si vous exécutez le cycle avec inclinaison du plan d'usinage, l'angle dans l'espace mesuré se réfère au système de coordonnées incliné. Dans ce cas, continuer à traiter avec PLANE RELATIV les angles dans l'espace calculés. 142 3 Cycles palpeurs pour le contrôle automatique des pièces 1er point mesure sur 1er axe Q263 (en absolu): Coordonnée du 1er point de palpage dans l'axe principal du plan d'usinage 1er point mesure sur 2ème axe Q264 (en absolu): Coordonnée du 1er point de palpage dans l'axe auxiliaire du plan d'usinage 1er point mesure sur 3ème axe Q294 (en absolu): Coordonnée du 1er point de palpage dans l'axe du palpeur 2ème point mesure sur 1er axe Q265 (en absolu): Coordonnée du 2ème point de palpage dans l'axe principal du plan d'usinage 2ème point mesure sur 2ème axe Q266 (en absolu): Coordonnée du 2ème point de palpage dans l'axe auxiliaire du plan d'usinage 2ème point de mesure 3ème axe Q295 (en absolu): Coordonnée du 2ème point de palpage dans l'axe du palpeur 3ème point mesure sur 1er axe Q296 (en absolu): Coordonnée du 3ème point de palpage dans l'axe principal du plan d'usinage 3ème point mesure sur 2ème axe Q297 (en absolu): Coordonnée du 3ème point de palpage dans l'axe auxiliaire du plan d'usinage 3ème point de mesure sur 3ème axe Q298 (en absolu): Coordonnée du 3ème point de palpage dans l'axe du palpeur Distance d'approche Q320 (en incrémental): Distance supplémentaire entre le point de mesure et la bille du palpeur. Q320 agit en complément de PM6140 Hauteur de sécurité Q260 (en absolu): Coordonnée dans l'axe du palpeur excluant toute collision entre le palpeur et la pièce (matériels de bridage) Procès-verb. mes. Q281: Définir si la TNC doit ou non établir le procès-verbal de mesure: 0: Ne pas établir de procès-verbal de mesure 1: Etablir un procès-verbal de mesure: La TNC mémorise en configuration par défaut le fichier de procès-verbal TCHPR431.TXT dans le répertoire où se trouve également votre programme de mesure 2: Interrompre le déroulement du programme et afficher le procès-verbal de mesure à l'écran de la TNC. Poursuivre le programme avec Start CN iTNC 530 HEIDENHAIN Y Q266 Q297 Q264 Q263 Q265 X Q296 Z Q260 MP6140 + Q320 Q295 Q298 Q294 X Exemple: Séquences CN 5 TCH PROBE 431 MESURE PLAN Q263=+20 ;1ER POINT 1ER AXE Q264=+20 ;1ER POINT 2EME AXE Q294=-10 ;1ER POINT 3EME AXE Q265=+50 ;2EME POINT 1ER AXE Q266=+80 ;2EME POINT 2EME AXE Q295=+0 ;2EME POINT 3EME AXE Q296=+90 ;3EME POINT 1ER AXE Q297=+35 ;3EME POINT 2EME AXE Q298=+12 ;3EME POINT 3EME AXE Q320=0 ;DISTANCE D'APPROCHE Q260=+5 ;HAUTEUR DE SECURITE Q281=1 ;PROCES-VERBAL MESURE 143 3.3 Etalonnage automatique des pièces Déroulement du programme: - Ebauche du tenon rectangulaire avec surépaisseur 0,5 Y Y 80 - Mesure du tenon rectangulaire - Finition du tenon rectangulaire en tenant compte des valeurs de mesure 50 60 3.3 Etalonnage automatique des pièces Exemple: Mesure d'un tenon rectangulaire et retouche 50 X 10 Z 0 BEGIN PGM BEAMS MM 1 TOOL CALL 0 Z Appel d'outil, préparation 2 L Z+100 R0 FMAX Dégager l'outil 3 FN 0: Q1 = +81 Longueur de la poche en X (cote d'ébauche) 4 FN 0: Q2 = +61 Longueur de la poche en Y (cote d'ébauche) 5 CALL LBL 1 Appeler le sous-programme pour l'usinage 6 L Z+100 R0 FMAX Dégager l'outil, changer l'outil 7 TOOL CALL 99 Z Appeler le palpeur 8 TCH PROBE 424 MESURE EXT. RECTANG. Mesurer le rectangle fraisé 144 Q273=+50 ;CENTRE 1ER AXE Q274=+50 ;CENTRE 2ÈME AXE Q282=80 ;1ER CÔTÉ Longueur nominale en X (cote définitive) Q283=60 ;2ÈME CÔTÉ Longueur nominale en Y (cote définitive) Q261=-5 ;HAUTEUR DE MESURE Q320=0 ;DISTANCE D'APPROCHE Q260=+30 ;HAUTEUR DE SÉCURITÉ Q301=0 ;DÉPLAC. HAUT. SÉCU. Q284=0 ;COTE MAX. 1ER CÔTÉ Q285=0 ;COTE MIN. 1ER CÔTÉ Q286=0 ;COTE MAX. 2ÈME CÔTÉ Valeurs d'introduction pour contrôle de tolérance non nécessaire 3 Cycles palpeurs pour le contrôle automatique des pièces ;COTE MIN. 2ÈME CÔTÉ Q279=0 ;TOLÉRANCE 1ER CENTRE Q280=0 ;TOLÉRANCE 2ND CENTRE Q281=0 ;PROCÈS-VERBAL MESURE Ne pas éditer de procès-verbal de mesure Q309=0 ;ARRÊT PGM SI ERREUR Ne pas délivrer de message d'erreur Q330=0 ;NUMÉRO D'OUTIL Pas de surveillance de l'outil 9 FN 2: Q1 = +Q1 - +Q164 Calcul longueur en X à partir de l'écart mesuré 10 FN 2: Q2 = +Q2 - +Q165 Calcul longueur en Y à partir de l'écart mesuré 11 L Z+100 R0 FMA Dégager le palpeur, changement d'outil 12 TOOL CALL 1 Z S5000 Appel d'outil pour la finition 13 CALL LBL 1 Appeler le sous-programme pour l'usinage 14 L Z+100 R0 FMAX M2 Dégager l'outil, fin du programme 15 LBL 1 Sous-programme avec cycle usinage tenon rectangulaire 3.3 Etalonnage automatique des pièces Q287=0 16 CYCL DEF 213 FINITION TENON Q200=20 ;DISTANCE D'APPROCHE Q201=-10 ;PROFONDEUR Q206=150 ;AVANCE PLONGEE EN PROF. Q202=5 ;PROFONDEUR DE PASSE Q207=500 ;AVANCE FRAISAGE Q203=+10 ;COORD. SURFACE PIECE Q204=20 ;SAUT DE BRIDE Q216=+50 ;CENTRE 1ER AXE Q217=+50 ;CENTRE 2EME AXE Q218=80 ;1ER COTE Longueur en X variable pour ébauche et finition Q219=Q2 ;2EME COTE Longueur en Y variable pour ébauche et finition Q220=0 ;RAYON D'ANGLE Q221=0 ;SUREPAISSEUR 1ER AXE 17 CYCL CALL M3 Appel du cycle 18 LBL 0 Fin du sous-programme 19 END PGM BEAMS MM iTNC 530 HEIDENHAIN 145 Y Y 90 40 70 3.3 Etalonnage automatique des pièces Exemple: Etalonnage d'une poche rectangulaire, procès-verbal de mesure 50 X -20 -15 Z 0 BEGIN PGM BSMESU MM 1 TOOL CALL 1 Z Appel d'outil pour le palpeur 2 L Z+100 R0 FMA Dégager le palpeur 3 TCH PROBE 423 MESURE INT. RECTANG. 146 Q273=+50 ;CENTRE 1ER AXE Q274=+40 ;CENTRE 2EME AXE Q282=90 ;1ER COTE Longueur nominale en X Q283=70 ;2EME COTE Longueur nominale en Y Q261=-5 ;HAUTEUR DE MESURE Q320=0 ;DISTANCE D'APPROCHE Q260=+20 ;HAUTEUR DE SECURITE Q301=0 ;DEPLAC. HAUT. SECU. Q284=90.15 ;COTE MAX. 1ER COTE Cote max. en X Q285=89.95 ;COTE MIN. 1ER COTE Cote min. en X Q286=70.1 ;COTE MAX. 2EME COTE Cote max. en Y Q287=69.9 ;COTE MIN. 2EME COTE Cote min. en Y Q279=0.15 ;TOLERANCE 1ER CENTRE Ecart de position autorisé en X Q280=0.1 ;TOLERANCE 2ND CENTRE Ecart de position autorisé en Y Q281=1 ;PROCES-VERBAL MESURE Délivrer le procès-verbal de mesure Q309=0 ;ARRET PGM SI ERREUR Ne pas afficher de message d'erreur si tolérance dépassée Q330=0 ;NUMERO D'OUTIL Pas de surveillance de l'outil 3 Cycles palpeurs pour le contrôle automatique des pièces 3.3 Etalonnage automatique des pièces 4 L Z+100 R0 FMAX M2 Dégager l'outil, fin du programme 5 END PGM BSMESU MM iTNC 530 HEIDENHAIN 147 3.4 Cycles spéciaux 3.4 Cycles spéciaux Vue d'ensemble La TNC dispose de six cycles destinés aux applications spéciales suivantes: Cycle Softkey Page 2 ETALONNAGE TS: Etalonnage de rayon du palpeur à commutation Page 149 9 PALPEUR ETAL. LONG. Etalonnage de longueur du palpeur à commutation Page 150 3 MESURE Cycle de mesure pour création de cycles constructeurs Page 151 4 MESURE 3D Cycle de mesure pour palpage 3D destiné à l’élaboration de cycles constructeurs Page 153 440 MESURE DU DESAXAGE Page 155 441 PALPAGE RAPIDE Page 157 148 3 Cycles palpeurs pour le contrôle automatique des pièces 3.4 Cycles spéciaux ETALONNAGE TS (cycle palpeur 2) Le cycle palpeur 2 permet d'étalonner automatiquement un palpeur à commutation sur une bague d'étalonnage ou un tenon d'étalonnage. Avant l'étalonnage, vous devez définir dans les paramètres-machine 6180.0 à 6180.2 le centre de la pièce d'étalonnage dans la zone de travail de la machine (coordonnées REF). Si vous travaillez sur plusieurs zones de déplacement, pour chacune des zones vous pouvez mémoriser une séquence de coordonnées pour le centre de la pièce d'étalonnage (PM6181.1 à 6181.2 et MP6182.1 à 6182.2.). 1 2 3 4 Le palpeur se déplace en avance rapide (valeur de PM6150) à la hauteur de sécurité (seulement si la position actuelle est située endessous de la hauteur de sécurité) Puis, la TNC positionne le palpeur dans le plan d'usinage, au centre de la bague d'étalonnage (étalonnage interne) ou à proximité du premier point de palpage (étalonnage externe) Le palpeur se déplace ensuite à la profondeur de mesure (paramètres-machine 618x.2 et 6185.x) et palpe successivement la bague d'étalonnage en X+, Y+, X- et Y Pour terminer, la TNC rétracte le palpeur à la hauteur de sécurité et inscrit le rayon actif de la bille de palpage dans les données d'étalonnage Hauteur de sécurité (en absolu): Coordonnée dans l'axe du palpeur excluant toute collision entre le palpeur et la pièce d'étalonnage (matériels de bridage) Rayon bague étalon: Rayon de la pièce de calibrage Etalon. interne =0/externe=1: Définir si la TNC doit réaliser un étalonnage interne ou externe: 0: Etalonnage interne 1: Etalonnage externe iTNC 530 HEIDENHAIN Exemple: Séquences CN 5 TCH PROBE 2.0 ETALONNAGE TS 6 TCH PROBE 2.1 HAUT.: +50 R +25.003 TYPE MESURE: 0 149 3.4 Cycles spéciaux ETALONNAGE TS LONGUEUR (cycle palpeur 9) Le cycle palpeur 9 permet d'étalonner automatiquement la longueur d'un palpeur à commutation sur un point que vous devez définir. 1 2 3 Prépositionner le palpeur de manière à ce que la coordonnée définie dans le cycle puisse être abordée sans risque de collision dans l'axe du palpeur La TNC déplace le palpeur dans le sens de l'axe d'outil négatif jusqu'à ce qu'un signal de commutation soit délivré Pour terminer, la TNC rétracte à nouveau le palpeur au point initial de l'opération de palpage et inscrit la longueur effective du palpeur dans les données d'étalonnage 150 Exemple: Séquences CN Coordonnée point de référence (en absolu): Coordonnée exacte du point à palper Système de réf.? (0=EFF/1=REF): Définir le système de coordonnées auquel le point de référence programmé doit se référer: 0: Le point de référence programmé se réfère au système de coordonnées pièce actif (système EFF) 1: Le point de référence programmé se réfère au système de coordonnées machine actif (système REF) 5 L X-235 Y+356 R0 FMAX 6 TCH PROBE 9.0 PALPEUR ETAL. LONG. 7 TCH PROBE 9.1 POINT DE RÉFÉRENCE +50 SYSTÈME DE RÉFÉRENCE 0 3 Cycles palpeurs pour le contrôle automatique des pièces 3.4 Cycles spéciaux MESURE (cycle palpeur 3) Le mode de fonctionnement exact du cycle palpeur 3 est défini par le constructeur de votre machine ou par un fabricant de logiciels utilisant le cycle 3 à l'intérieur de cycles palpeurs spéciaux. Le cycle palpeur 3 détermine une position au choix sur la pièce et quelque soit le sens du palpage. Contrairement aux autres cycles de mesure, le cycle 3 vous permet d'introduire directement la course de mesure DIST ainsi que l'avance de mesure F. Même le retrait après l'enregistrement de la valeur de mesure s'effectue en fonction d'une valeur MB que vous pouvez programmer. 1 2 3 Selon l'avance programmée, le palpeur se déplace de la position actuelle, dans le sens de palpage défini. Le sens de palpage doit être défini dans le cycle avec angle polaire Lorsque la TNC a enregistré la position, le palpeur s'arrête. La TNC mémorise les coordonnées X, Y et Z du centre de la bille de palpage dans trois paramètres qui se suivent. La TNC n'exécute ni correction linéaire ni correction de rayon. Vous définissez le numéro du premier paramètre de résultat dans le cycle Pour terminer et dans le sens inverse du sens de palpage, la TNC rétracte le palpeur de la valeur que vous avez définie dans le paramètre MB Remarques avant que vous ne programmiez Les paramètres-machine 6130 (course max. jusqu'au point de palpage) et 6120 (avance de palpage) qui agissent dans d'autres cycles n'ont pas d'effet dans le cycle palpeur 3. A noter que la TNC décrit toujours 4 paramètres Q successifs. Si la TNC n'a pas pu calculer un point de palpage valide, le programme est alors exécuté sans message d'erreur. Dans ce cas, la TNC attribue la valeur -1 au 4ème paramètre de résultat; vous pouvez ainsi vous-même traiter les erreurs de manière adéquate. La TNC rétracte le palpeur au maximum de la longueur de la course de retrait MB mais sans aller au delà du point initial de la mesure. Ainsi, aucune collision ne peut donc se produire lors du retrait. Avec la fonction FN17: SYSWRITE ID 990 NR 6 vous pouvez définir si le cycle doit agir sur l'entrée palpeur X12 ou X13. iTNC 530 HEIDENHAIN 151 3.4 Cycles spéciaux 152 N° de paramètre pour résultat: Introduire le numéro du paramètre Q auquel doit être affectée la valeur de la première coordonnée (X) calculée. Les valeurs Y et Z sont dans les paramètres Q situés directement après Axe de palpage: Introduire l'axe dans le sens duquel doit s'effectuer le palpage; valider avec la touche ENT Angle de palpage: Angle se référant à l'axe de palpage défini et sur lequel le palpeur doit se déplacer; valider avec la touche ENT Exemple: Séquences CN 4 TCH PROBE 3.0 MESURE 5 TCH PROBE 3.1 Q1 6 TCH PROBE 3.2 X ANGLE: +15 7 TCH PROBE 3.3 DIST +10 F100 MB1 SYSTÈME DE RÉFÉRENCE: 0 8 TCH PROBE 3.4 ERRORMODE1 Course de mesure max.: Introduire le déplacement correspondant à la distance que doit parcourir le palpeur à partir du point initial; valider avec la touche ENT. Avance de mesure: Introduire l'avance de mesure en mm/min. Course de retrait max.: Course de déplacement dans le sens opposé au sens du palpage après déviation de la tige de palpage. La TNC rétracte le palpeur au maximum jusqu'au point initial pour éviter toute collision SYSTÈME DE RÉF. (0=EFF/1=REF): Définir si le résultat de la mesure doit être enregistré dans le système de coordonnées actuel (EFF; peut donc être décalé ou pivoté) ou bien par référence au système de coordonnées machine (REF) Mode erreur (0=OFF/1=ON): Définir si la TNC doit délivrer (0) ou ne pas délivrer (1) un message d'erreur en début de cycle lorsque la tige de palpage est déviée. Si le mode 1 a été sélectionné, la TNC enregistre la valeur 2.0 dans le 4ème paramètre de résultat et continue à exécuter le cycle Terminer l'introduction: Appuyer sur la touche ENT 3 Cycles palpeurs pour le contrôle automatique des pièces 3.4 Cycles spéciaux MESURE 3D (cycle palpeur 4, fonction FCL 3) Le cycle palpeur 4 détermine une position au choix sur la pièce dans un sens de palpage défini par vecteur. Contrairement aux autres cycles de mesure, le cycle 4 vous permet d'introduire directement la course de mesure ainsi que l'avance de mesure. Même le retrait après l'enregistrement de la valeur de mesure s'effectue en fonction d'une valeur que vous avez programmée. 1 2 3 Selon l'avance programmée, le palpeur se déplace de la position actuelle, dans le sens de palpage défini. Le sens de palpage est à définir dans le cycle au moyen d’un vecteur (valeurs Delta en X, Y et Z) Lorsque la TNC a enregistré la position, le palpeur s'arrête. La TNC mémorise les coordonnées X, Y et Z du centre de la bille de palpage dans trois paramètres qui se suivent. Vous définissez le numéro du premier paramètre dans le cycle Pour terminer et dans le sens inverse du sens de palpage, la TNC rétracte le palpeur de la valeur que vous avez définie dans le paramètre MB Remarques avant que vous ne programmiez La TNC rétracte le palpeur au maximum de la longueur de la course de retrait MB mais sans aller au delà du point initial de la mesure. Ainsi, aucune collision ne peut donc se produire lors du retrait. A noter que la TNC décrit toujours 4 paramètres Q successifs. Si la TNC n'a pas pu calculer un point de palpage valable, la valeur -1 est attribuée au 4ème paramètre de résultat. Avec la fonction FN17: SYSWRITE ID 990 NR 6 vous pouvez définir si le cycle doit agir sur l'entrée palpeur X12 ou X13. iTNC 530 HEIDENHAIN 153 3.4 Cycles spéciaux 154 N° de paramètre pour résultat: Introduire le numéro du paramètre Q auquel doit être affectée la valeur de la première coordonnée (X) Course de mesure relative en X: Composante X du vecteur de sens dans le sens où le palpeur doit se déplacer Course de mesure relative en Y: Composante Y du vecteur de sens dans le sens où le palpeur doit se déplacer Course de mesure relative en Z: Composante Z du vecteur de sens dans le sens où le palpeur doit se déplacer Course de mesure max.: Introduire la course que doit parcourir le palpeur du point initial en longeant le vecteur de sens Avance de mesure: Introduire l'avance de mesure en mm/min. Course de retrait max.: Course de déplacement dans le sens opposé au sens du palpage après déviation de la tige de palpage SYSTÈME DE RÉF. (0=EFF/1=REF): Définir si le résultat de la mesure doit être enregistré dans le système de coordonnées actuel (EFF; peut donc être décalé ou pivoté) ou bien par référence au système de coordonnées machine (REF) Exemple: Séquences CN 5 TCH PROBE 4.0 MESURE 3D 6 TCH PROBE 4.1 Q1 7 TCH PROBE 4.2 IX-0.5 IY-1 IZ-1 8 TCH PROBE 4.3 DIST +45 F100 MB50 SYSTÈME DE RÉFÉRENCE:0 3 Cycles palpeurs pour le contrôle automatique des pièces 3.4 Cycles spéciaux MESURE DU DESAXAGE (cycle palpeur 440, DIN/ISO: G440) Le cycle palpeur 440 vous permet de calculer les dérives d'axes de votre machine. Pour cela, il convient d'utiliser un outil d'étalonnage cylindrique ayant été mesuré avec précision à l'aide du TT 130. Conditions requises: Avant d'exécuter pour la première fois le cycle 440, vous devez auparavant étalonner le TT au moyen du cycle 30. Les données de l'outil d'étalonnage doivent être inscrites dans le tableau d'outils TOOL.T. Avant d'exécuter le cycle, vous devez activer l'outil d'étalonnage avec TOOL CALL. Le palpeur de table TT doit être raccordé sur l'entrée palpeur X13 de l'unité logique et être en état de fonctionnement (paramètre-machine 65xx). 1 2 3 4 5 La TNC positionne l'outil d'étalonnage en avance rapide (valeur de PM6550) et selon la logique de positionnement (cf. chap. 1.2) à proximité du TT La TNC exécute tout d'abord une mesure dans l'axe du palpeur. Pour cela, l'outil d'étalonnage est décalé en fonction de la valeur que vous avez définie dans la colonne TT:R-OFFS du tableau d'outils TOOL.T (en standard: rayon d'outil). La mesure dans l'axe du palpeur est toujours réalisée La TNC exécute ensuite la mesure dans le plan d'usinage. Vous définissez dans le paramètre Q364 l'axe du plan d'usinage ainsi que le sens en fonction desquels doit être effectué le palpage Lorsque vous effectuez un étalonnage, la TNC en mémorise les données de manière interne. Lorsque vous effectuez une mesure, la TNC compare les valeurs de mesure aux données d'étalonnage et inscrit les écarts dans les paramètres Q suivants: Numéro paramètre Signification Q185 Ecart par rapport à la valeur d'étalonnage en X Q186 Ecart par rapport à la valeur d'étalonnage en Y Q187 Ecart par rapport à la valeur d'étalonnage en Z Vous pouvez utiliser directement les écarts pour exécuter la compensation au moyen d'un décalage incrémental du point zéro (cycle 7). Pour terminer, l'outil d'étalonnage retourne à la hauteur de sécurité iTNC 530 HEIDENHAIN 155 3.4 Cycles spéciaux Remarques avant que vous ne programmiez Avant d'exécuter une opération de mesure, vous devez avoir étalonné la pièce au moins une fois; sinon la TNC délivre un message d'erreur. Si vous travaillez avec plusieurs zones de déplacement, vous devez étalonner pour chaque zone de déplacement. Lors de chaque exécution du cycle 440, la TNC désactive les paramètres de résultat Q185 à Q187. Si vous désirez définir une valeur limite pour le déplacement d'axe sur les axes de la machine, inscrivez dans ce cas cette valeur limite souhaitée dans le tableau d'outil TOOL.T et dans les colonnes LTOL (pour l'axe de broche) et RTOL (pour le plan d'usinage). Lorsque les valeurs limites sont franchies, la TNC délivre à l'issue d'une mesure de contrôle un message correspondant. A la fin du cycle, la TNC rétablit l'état de la broche qui était actif avant le cycle (M3/M4). Opération: 0=étalon., 1=mesure?: Définir si vous désirez effectuer une opération d'étalonnage ou une mesure de contrôle: 0: Etalonnage 1: Mesure Sens de palpage: Définir le(s) sens de palpage dans le plan d'usinage: 0: Mesure seulement dans le sens positif de l'axe principal 1: Mesure seulement dans le sens positif de l'axe auxiliaire 2: Mesure seulement dans le sens négatif de l'axe principal 3: Mesure seulement dans le sens négatif de l'axe auxiliaire 4: Mesure dans le sens positif de l'axe principal et positif de l'axe auxiliaire 5: Mesure dans le sens positif de l'axe principal et négatif de l'axe auxiliaire 6: Mesure dans le sens négatif de l'axe principal et positif de l'axe auxiliaire 7: Mesure dans le sens négatif de l'axe principal et négatif de l'axe auxiliaire Exemple: Séquences CN 5 TCH PROBE 440 MESURE DU DESAXAGE Q363=1 ;TYPE MESURE Q364=0 ;SENS DE PALPAGE Q320=2 ;DISTANCE D'APPROCHE Q260=+50 ;HAUTEUR DE SECURITE Le sens de palpage lors de l'étalonnage/de la mesure doit coïncider. Sinon la TNC fournit des valeurs erronées. 156 Distance d'approche (en incrémental): Distance supplémentaire entre le point de mesure et le disque de palpage. Q320 agit en complément de PM6540 Hauteur de sécurité (en absolu): Coordonnée dans l'axe du palpeur excluant toute collision entre le palpeur et la pièce (matériels de bridage) (se réfère au point de référence actif) 3 Cycles palpeurs pour le contrôle automatique des pièces 3.4 Cycles spéciaux PALPAGE RAPIDE (cycle palpeur 441, DIN/ISO: G441, fonction FCL 2) Le cycle de palpage 441 vous permet de configurer divers paramètres du palpeur (l'avance de positionnement, par exemple) et ce, de manière globale pour tous les cycles de palpage utilisés par la suite. Ceci facilite l'optimisation du programme et raccourcit du même coup les durées globales d'usinage. Remarques avant que vous ne programmiez Le cycle 441 n'exécute aucun déplacement de la machine et sert seulement à configurer divers paramètres de palpage. END PGM, M02, M30 annulent les configurations globales du cycle 441. Vous ne pouvez activer la poursuite d'angle automatique (paramètre de cycle Q399) que si vous avez configuré le paramètre-machine 6165=1. La modification du paramètre-machine 6165 ne nécessite aucun réétalonnage du palpeur. Avance positionnement Q396: Définir l'avance avec laquelle vous désirez exécuter les déplacements de positionnement du palpeur Avance positionnement=FMAX (0/1) Q397: Définir si vous désirez utiliser FMAX (avance rapide machine) pour les déplacements de positionnement du palpeur: 0: Déplacement avec l'avance de Q396 1: Déplacement avec XFMAX Poursuite angle Q399: Définir si la TNC doit orienter le palpeur avant chaque opération de palpage: 0: Ne pas orienter 1: Exécuter une orientation de la broche avant chaque opération de palpage pour augmenter la précision Interruption automatique Q400: Définir si la TNC doit interrompre le déroulement du programme après un cycle de mesure pour l'étalonnage automatique d'outil et afficher à l'écran les résultats de la mesure: 0: Par principe, ne pas interrompre le déroulement du programme, y compris si vous avez choisi dans le cycle de palpage concerné d'afficher à l'écran les résultats de la mesure 1: Par principe, interrompre le déroulement du programme et afficher à l'écran les résultats de la mesure. On peut poursuivre le déroulement du programme en appuyant sur la touche Start CN iTNC 530 HEIDENHAIN Exemple: Séquences CN 5 TCH PROBE 441 PALPAGE RAPIDE Q396=3000 ;AVANCE POSITIONNEMENT Q397=0 ;SELECTION AVANCE Q399=1 ;POURSUITE ANGLE Q400=1 ;INTERRUPTION 157 Cycles palpeurs pour la mesure automatique de la cinématique iTNC 530 HEIDENHAIN 159 4.1 Mesure de cinématique avec les palpeurs TS (option KinematicsOpt) 4.1 Mesure de cinématique avec les palpeurs TS (option KinematicsOpt) Principes Les exigences en matière de précision ne cessent de croître, en particulier pour l'usinage 5 axes. Les pièces complexes doivent pouvoir être produites dans une précision capable d'être reproduite, y compris sur de longues périodes. Pour l'usinage sur plusieurs axes, la source des imprécisions provient - entre autres - des écarts entre le modèle cinématique enregistré sur la commande numérique (cf. figure de droite 1) et les conditions cinématiques réellement présentes sur la machine (cf. figure de droite 2). Lors du positionnement des axes rotatifs, ces écarts induisent un défaut sur la pièce (cf. figure de droite 3). Il est donc nécessaire de se procurer la possibilité d'harmoniser au mieux le modèle et la réalité. 3 1 2 La nouvelle fonction KinematicsOpt de la TNC est un élément important destiné à faire face réellement à ces exigences complexes: Un cycle pour palpeur 3D étalonne de manière entièrement automatique les axes rotatifs présents sur la machine; peu importe que les axes rotatifs soient sous la forme d’un axe de plateau ou de tête. Une bille étalon est fixée à un endroit quelconque de la table de la machine et mesurée à la finesse que vous avez définie. Lors de la définition du cycle, il vous suffit d'introduire séparément pour chaque axe rotatif la plage que vous voulez mesurer. A partir des valeurs mesurées, la TNC détermine la précision statique d'inclinaison. Le logiciel minimise les erreurs de positionnement résultant des déplacements d'inclinaison et, à la fin de la mesure, enregistre automatiquement la géométrie de la machine dans les constantes-machine correspondantes du tableau de cinématique. Vue d'ensemble La TNC propose des cycles vous permettant de sauvegarder, restaurer, contrôler et optimiser automatiquement la cinématique de votre machine: Cycle Softkey Page 450 SAUVEGARDER CINEMATIQUE: Sauvegarde et restauration automatique de cinématiques Page 162 451 MESURE CINEMATIQUE: Contrôle et optimisation automatique de la cinématique de la machine Page 164 160 4 Cycles palpeurs pour la mesure automatique de la cinématique 4.1 Mesure de cinématique avec les palpeurs TS (option KinematicsOpt) Conditions requises Pour pouvoir utiliser KinematicsOpt, les conditions suivantes doivent être remplies: Les options de logiciel 48 (KinematicsOpt) et 8 (option de logiciel 1) ainsi que les fonctions FCL3 doivent être activées Le palpeur 3D utilisé pour l'étalonnage doit être calibré Une bille étalon (diamètre connu avec précision) suffisamment rigide doit être fixée à n'importe quel endroit de la table de la machine. Les billes étalon peuvent être approvisionnées auprès de divers constructeurs de matériels de mesure La description de la cinématique de la machine doit être définie intégralement et correctement. Les cotes de transformation doivent être inscrites avec une précision d'environ 1 mm Tous les axes rotatifs doivent être des axes CN; KinematicsOpt ne gère pas la mesure d'axes réglables manuellement La machine doit être étalonnée géométriquement et intégralement (opération réalisée par le constructeur de la machine lors de sa mise en route) Dans le paramètre-machine MP6600, il faut définir la limite de tolérance à partir de laquelle la TNC doit afficher une remarque en mode Optimisation si les données de cinématique définies excèdent cette valeur limite (cf. „KinematicsOpt, limite de tolérance pour le mode Optimisation: MP6600” à la page 25) Dans le paramètre-machine MP6601, il faut définir l'écart max. autorisé pour le rayon de la bille étalon mesuré automatiquement par les cycles par rapport au paramètre de cycle programmé (cf. „KinematicsOpt, écart autorisé par rapport au rayon de la bille étalon: MP6601” à la page 25) iTNC 530 HEIDENHAIN 161 4.1 Mesure de cinématique avec les palpeurs TS (option KinematicsOpt) SAUVEGARDER CINEMATIQUE (cycle palpeur 450, DIN/ISO: G450, option) Le cycle palpeur 450 vous permet de sauvegarder la cinématique active de la machine ou de restaurer une cinématique de machine qui avait déjà été sauvegardée. On dispose de 10 mémoires (numéros 0 à 9). Remarques avant que vous ne programmiez Avant de réaliser l'optimisation d'une cinématique, nous vous conseillons de sauvegarder systématiquement la cinématique active. Avantage: Si le résultat ne correspond pas à votre attente ou si des erreurs se produisent lors de l'optimisation (une coupure de courant, par exemple), vous pouvez alors restaurer les anciennes données. Mode Sauvegarder: Systématiquement, la TNC mémorise toujours en même temps le dernier code introduit sous MOD (on peut définir librement le code). Par la suite, pour ne pouvez écraser cette mémoire qu'à condition d'introduire ce code. Si vous avez sauvegardé une cinématique sans code, la TNC écrase cette mémoire lors de l'opération suivante de sauvegarde et ce, sans message d'interrogation! Mode Créer: La TNC ne peut restaurer les données sauvegardées que dans une description de cinématique identique. Mode Créer: N'oubliez pas qu'une modification de la cinématique a toujours pour conséquence une modification de la valeur Preset. Si nécéssaire, la valeur Preset. 162 Mode: 0=Sauvegarder/1=Créer? Q410: Définir si vous désirez sauvegarder ou restaurer une cinématique: 0: Sauvegarder la cinématique active 1: Restaurer la cinématique enregistrée précédemment Mémoire (0…9) Q409: Numéro de la mémoire dans laquelle vous désirez sauvegarder toute la cinématique ou bien numéro de la mémoire à partir de laquelle vous voulez restaurer la cinématique mémorisée Exemple: Séquences CN 5 TCH PROBE 450 SAUVEG. CINEMATIQUE Q410=0 ;MODE Q409=1 ;MÉMOIRE 4 Cycles palpeurs pour la mesure automatique de la cinématique 4.1 Mesure de cinématique avec les palpeurs TS (option KinematicsOpt) Fonction procès-verbal Après avoir exécuté le cycle 450, la TNC génère un procès-verbal contenant les données suivantes: Date et heure auxquelles le procès-verbal a été établi Chemin d'accès au programme CN à partir duquel le cycle a été exécuté Mode utilisé (0=sauvegarder/1=créer) Numéro de la mémoire (0 à 9) Numéro de ligne de la cinématique dans le tableau de cinématique Code (dans le mesure où vous avez introduit un code juste avant l'exécution du cycle 450) iTNC 530 HEIDENHAIN 163 4.1 Mesure de cinématique avec les palpeurs TS (option KinematicsOpt) MESURE CINEMATIQUE (cycle palpeur 451, DIN/ISO: G451, option) Le cycle palpeur 451 vous permet de contrôler et, si nécessaire, optimiser la cinématique de votre machine. A l'aide d'un palpeur 3D TS, vous mesurez une bille étalon (au choix) que vous fixez sur la table de la machine. La TNC détermine la précision statique d'inclinaison. Le logiciel minimise les erreurs spatiales résultant des déplacements d'inclinaison et, à la fin de la mesure, enregistre automatiquement la géométrie de la machine dans les constantes-machine correspondantes du tableau de cinématique. 1 2 3 4 5 Brider la bille étalon; assurer une liberté suffisante pour éliminer tout risque de collision En mode de fonctionnement Manuel, initialiser le point de référence au centre de la bille Positionner manuellement le palpeur dans l'axe du palpeur au dessus de la bille étalon et dans le plan d'usinage, au centre de la bille Sélectionner le mode de fonctionnement Exécution de programme et démarrer le programme de calibrage La TNC mesure automatiquement et successivement tous les axes rotatifs avec la finesse que vous avez définie 164 4 Cycles palpeurs pour la mesure automatique de la cinématique 4.1 Mesure de cinématique avec les palpeurs TS (option KinematicsOpt) Sens du positionnement Le sens du positionnement de l'axe rotatif à mesurer résulte de l'angle initial et de l'angle final que vous avez définis dans le cycle. Choisir l'angle initial et l'angle final de manière à ne pas avoir à mesurer deux fois la même position. Ainsi, par exemple, avec un angle initial de 0° et un angle final de 360°, la TNC délivre un message d'erreur. Le double enregistrement de points de mesure (par exemple, position de mesure +90° et -270°) n'est pas judicieux mais n'entraîne pourtant pas l'apparition d'un message d'erreur dans la mesure où cela peut donner lieu à des positions de mesure différentes. Exemple: Angle initial = -270°, angle final = +90° La position angulaire sera identique mais cela peut donner lieu à différentes positions de mesure: Angle initial = +90° Angle final = -270° Nombre de points de mesure = 4 Incrément angulaire qui en résulte = (-270 - +90) / (4-1) = -120° Point de mesure 1= +90° Point de mesure 2= -30° Point de mesure 3= -150° Point de mesure 4= -270° iTNC 530 HEIDENHAIN 165 4.1 Mesure de cinématique avec les palpeurs TS (option KinematicsOpt) Machines avec axes à denture Hirth Pour réaliser le positionnement, l'axe doit sortir du crantage Hirth. Par conséquent, prévoyer une distance d'approche suffisante pour éviter toutes collisions entre le palpeur et la bille étalon. Dans le même temps, veiller à ce qu'il y ait suffisamment de place pour aborder la distance d'approche (fins de course de logiciel). Définir une hauteur de retrait Q408 supérieure à 0 si l'option de logiciel 9 (M128, FUNCTION TCPM) n'est pas disponible. Lorsque vous choissiez le point initial et le point final, veillez à ce que chaque incrément angulaire s'intègre bien dans le crantage Hirth. Pour les axes Hirth, la TNC vérifie en début de cycle si l'incrément angulaire défini convient au crantage Hirth. Si tel n'est pas le cas, la TNC délivre un message d'erreur et ferme le cycle. Les positions sont calculées à partir de l'angle initial, de l'angle final et du nombre de mesures pour l'axe concerné. Exemple de calcul des positions de mesure pour un axe A: Angle initial Q411 = -30 Angle final Q412 = +90 Nombre de points de mesure Q414 = 4 Incrément angulaire calculé = ( Q412 - Q411 ) / ( Q414 -1 ) Incrément angulaire calculé = ( 90 - -30 ) / ( 4 - 1 ) = 120 / 3 = 40 Position de mesure 1 = Q411 + 0 * incrément angulaire = -30° Position de mesure 2 = Q411 + 1 * incrément angulaire = +10° Position de mesure 3 = Q411 + 1 * incrément angulaire = +50° Position de mesure 4 = Q411 + 1 * incrément angulaire = +90° 166 4 Cycles palpeurs pour la mesure automatique de la cinématique 4.1 Mesure de cinématique avec les palpeurs TS (option KinematicsOpt) Choix du nombre de points de mesure Pour gagner du temps, vous pouvez procéder à une optimisation grossière avec un petit nombre de points de mesure (1-2). Vous exécuter ensuite une optimisation précise avec un nombre moyen de points de mesure (valeur préconisée = 4). Un nombre plus important de points de mesure n'apporte généralement pas de meilleurs résultats. De manière idéale, il est conseillé de répartir les points de mesure régulièrement sur toute la plage d'inclinaison de l'axe. Nous conseillerions donc de mesurer un axe ayant une plage d'inclinaison de 0-360° avec 3 points de mesure situés à 90°, 180° et 270°. Si vous désirez mesurer la précision correspondante, vous pouvez alors indiquer un nombre plus élevé de points de mesure en mode Contrôler. Vous ne devez pas mesurer un axe rotatif sur 0° ou 360°. Ces positions ne fournissent pas de données de mesure pertinentes! Choix de la position de la bille étalon sur la table de la machine En principe, vous pouvez installer la bille étalon à n'importe quel endroit accessible sur la table de la machine. Vous pouvez aussi fixer la bille étalon sur des matériels de bridage ou des pièces (par exemple avec attache magnétique). Les facteurs suivants peuvent avoir une incidence sur le résultat de la mesure: Machine équipée d'un plateau circulaire/d'une table pivotante: Brider la bille étalon aussi loin que possible du centre de rotation Machines avec très grandes courses: Brider la bille étalon aussi près que possible de la future position d'usinage iTNC 530 HEIDENHAIN 167 4.1 Mesure de cinématique avec les palpeurs TS (option KinematicsOpt) Remarques relative à la la précision Les erreurs de géométrie et de positionnement de la machine influent sur les valeurs de mesure et, par conséquent, sur l'optimisation d'un axe rotatif. Une erreur résiduelle que l'on ne peut pas éliminer sera toujours présente. S'il n'y avait pas d'erreurs de géométrie et de positionnement, on pourrait reproduire avec précision les valeurs déterminées par le cycle à n'importe quel point de la machine et à un moment précis. Plus les erreurs de géométrie et de positionnement sont importantes et plus les résultats de la mesure connaissent une dispersion si vous installez la bille étalon à différentes positions du système de coordonnées de la machine. La dispersion qu'indique la TNC dans le procès-verbal est une valeur pour définir la précision des déplacements statiques d'inclinaison d'une machine. Lorsque l'on observe la précision, on doit néanmoins tenir compte aussi du rayon du cercle de mesure et du nombre et de la position des points de mesure. La dispersion ne peut pas être définie avec un seul point de mesure; la dispersion obtenue correspond dans ce cas à l'erreur spatiale du point de mesure. Si plusieurs axes rotatifs se déplacent simultanément, leurs erreurs se superposent et, dans le cas le plus défavorable, elles s'additionnent. Si votre machine est équipée d'une broche asservie, nous vous conseillons d'activer la poursuite angulaire au moyen du paramètre-machine MP6165. Ceci vous permet généralement d'améliorer les précisions des mesures réalisées avec un palpeur 3D. Désactiver si nécessaire le serrage des axes rotatifs pendant la durée de la mesure; car sinon, les résultats de la mesure pourraient être faussés. Consultez le manuel de votre machine. En mode Optimisation, la TNC précise une évaluation dans le procèsverbal. Le chiffre d'évaluation est une valeur d'influence des translations corrigées sur le résultat de la mesure. Plus le chiffre d'évaluation est élevé et meilleure est l'optimisation réalisée par la TNC. Le chiffre d'évaluation de chaque axe rotatif ne doit pas être inférieur à une valeur de 2. Il faut viser des valeurs supérieures ou égales à 4. Si les chiffres d'évaluation sont trop faibles, agrandissez la plage de mesure de l'axe rotatif ou augmentez le nombre de points de mesure. Si cette mesure n'apporte aucune amélioration du chiffre d'évaluation, cela peut provenir d'une description de cinématique erronée. Si nécessaire, prenez contact avec le service après-vente. 168 4 Cycles palpeurs pour la mesure automatique de la cinématique 4.1 Mesure de cinématique avec les palpeurs TS (option KinematicsOpt) Remarques relatives aux différentes méthodes de calibrage Optimisation grossière lors de la mise en route après l'introduction de valeurs approximatives Nombre de points de mesure entre 1 et 2 Incrément angulaire des axes rotatifs: Environ 90° Optimisation fine sur toute la course de déplacement Nombre de points de mesure entre 3 et 6 L'angle initial et l'angle final doivent autant que possible couvrir une grande course de déplacement des axes rotatifs Positionnez la bille étalon sur la table de la machine de manière à obtenir pour les axes rotatifs de la table un grand rayon du cercle de mesure ou bien de manière à ce que la mesure ait lieu pour les axes rotatifs de la tête à une position représentative (par exemple, au centre de la course de déplacement) Optimisation d'une position spéciale de l'axe rotatif Nombre de points de mesure entre 2 et 3 Les mesures sont effectuées autour de l'angle de l'axe rotatif où l'usinage doit avoir lieu par la suite Positionnez la bille étalon sur la table de la machine de manière à ce que le calibrage ait lieu au même endroit que celui de l'usinage Vérifier la précision de la machine Nombre de points de mesure entre 4 et 8 L'angle initial et l'angle final doivent autant que possible couvrir une grande course de déplacement des axes rotatifs Déterminer le jeu de l'axe rotatif lors du contrôle Nombre de points de mesure entre 8 et 12 L'angle initial et l'angle final doivent autant que possible couvrir une grande course de déplacement des axes rotatifs iTNC 530 HEIDENHAIN 169 4.1 Mesure de cinématique avec les palpeurs TS (option KinematicsOpt) Jeu Par jeu, on entend un mouvement léger (généré lors d'un changement de sens) entre le capteur rotatif (système de mesure angulaire) et la table. Si les axes rotatifs ont du jeu en dehors de la chaîne d'asservissement, ils peuvent générer d'importantes erreurs lors de l'inclinaison. Le cycle active automatiquement la compensation interne de jeu pour les axes rotatifs numériques sans entrée de mesure de position séparée. En mode Contrôler, la TNC parcourt deux cycles de mesure pour chaque axe afin de pouvoir atteindre les positions de mesure dans les deux sens. Dans le procès-verbal, la TNC délivre la moyenne arithmétique des valeurs absolues du jeu mesuré pour l'axe rotatif. Si le rayon du cercle de mesure est < 100 mm, la TNC ne calcule pas le jeu pour des raisons de précision. Plus le rayon du cercle de mesure est grand et plus la TNC peut déterminer de manière précise le jeu de l'axe rotatif. 170 4 Cycles palpeurs pour la mesure automatique de la cinématique 4.1 Mesure de cinématique avec les palpeurs TS (option KinematicsOpt) Définir le cycle Remarques avant que vous ne programmiez Veiller à ce que toutes les fonctions d'inclinaison du plan d'usinage aient été réinitialisées. M128 ou FUNCTION TCPM ne doivent pas être activées. Choisir la position de la bille étalon sur la table de la machine de manière à ce que l'opération de mesure puisse être exécutée sans risque de collision. Avant la définition du cycle, vous devez initialiser le point de référence au centre de la bille étalon et l'activer. Comme avance de positionnement pour aborder la hauteur de palpage dans l'axe du palpeur, la TNC utilise la valeur la plus faible du paramètre de cycle Q253 et du paramètre-machine MP6150. La TNC exécute systématiquement les déplacements des axes rotatifs avec l'avance de positionnement Q253; la surveillance du palpeur est inactive. En mode Optimisation, si les données de cinématique calculées sont supérieures à la valeur limite autorisée (MP6600), la TNC délivre un message d'avertissement. Vous devez alors valider les valeurs calculées avec Marche CN. N'oubliez pas qu'une modification de la cinématique a toujours pour conséquence une modification de la valeur Preset. Après une optimisation, réinitialiser la valeur Preset. Dans une première opération de palpage, la TNC détermine tout d'abord le rayon de la bille étalon. Si le rayon déterminé pour la bille est différent du rayon programmé, et ce d'une valeur supérieure à celle que vous avez définie dans le paramètre-machine MP6601, la TNC délivre un message d'erreur et ferme la mesure. Si vous interrompez le cycle pendant la mesure, les données de cinématique risquent de ne plus être conformes à leur état d'origine. Avant d'effectuer une optimisation, sauvegardez la cinématique active avec le cycle 450 pour pouvoir restaurer la dernière cinématique active en cas d'erreur. Programmation en pouces: La TNC délivre systématiquement en mm les résultats des mesures et les données du procès-verbal. iTNC 530 HEIDENHAIN 171 4.1 Mesure de cinématique avec les palpeurs TS (option KinematicsOpt) 172 Mode (0=Contrôler/1=Mesurer) Q406: Définir si la TNC doit vérifier la cinématique ou l'optimiser: 0: Vérifier la cinématique active de la machine. La TNC mesure la cinématique sur les axes rotatifs que vous avez définis mais n'apporte pas de modifications à la cinématique active. Elle affiche les résultats des mesures dans un procès-verbal de mesure 1: Optimiser la cinématique active de la machine. La TNC mesure la cinématique sur les axes rotatifs que vous avez définis et optimise la cinématique active Exemple: Programme de calibrage 4 TOOL CALL “PALPEUR“ Z 5 TCH PROBE 450 SAUVEG. CINEMATIQUE Q410=0 ;MODE Q409=5 ;MÉMOIRE 6 TCH PROBE 451 MESURE CINÉMATIQUE Q406=1 ;MODE Rayon bille calibr. exact Q407: Introduire le rayon exact de la bille étalon utilisée Q407=14.9996 ;RAYON DE LA BILLE Q320=0 ;DISTANCE D'APPROCHE Distance d'approche Q320 (en incrémental): Distance supplémentaire entre le point de mesure et la bille du palpeur. Q320 agit en complément de PM6140 Q408=0 ;HAUTEUR RETRAIT Q253=750 ;AVANCE PRÉ-POSIT. Hauteur de retrait Q408 (en absolu): Q380=0 ;ANGLE DE RÉFÉRENCE Introduction 0: Ne pas aborder la hauteur de retrait; la TNC aborde la position de mesure suivante sur l'axe à mesurer. Non autorisé pour les axes Hirth! La TNC aborde la première position de mesure dans l'ordre A, puis B, puis C Introduction >0: Hauteur de retrait dans le système de coordonnées pièce non incliné à laquelle la TNC positionne l'axe de broche avant d'effectuer un positionnement d'axe rotatif. La TNC positionne en outre le palpeur au point zéro, dans le plan d'usinage. Dans ce mode, la surveillance du palpeur est inactive; définir la vitesse de positionnement dans le paramètre Q253 Q411=-90 ;ANGLE INITIAL AXE A Q412=+90 ;ANGLE FINAL AXE A Q413=0 ;ANGLE REGL. AXE A Q414=2 ;POINTS DE MESURE AXE A Q415=-90 ;ANGLE INITIAL AXE B Q416=+90 ;ANGLE FINAL AXE B Q417=0 ;ANGLE REGL. AXE B Q418=2 ;POINTS DE MESURE AXE B Q419=-90 ;ANGLE INITIAL AXE C Q420=+90 ;ANGLE FINAL AXE C Q421=0 ;ANGLE REGL. AXE C Q422=2 ;POINTS DE MESURE AXE C Avance de pré-positionnement Q253: Vitesse de déplacement de l'outil lors du positionnement, en mm/min. Angle de référence Q380 (en absolu): Angle de référence (rotation de base) pour enregistrer les points de mesure dans le système de coordonnées pièce actif. La définition d'un angle de référence peut accroître considérablement la plage de mesure d'un axe 4 Cycles palpeurs pour la mesure automatique de la cinématique Angle initial axe A Q411 (en absolu): Angle initial sur l'axe A sur lequel doit avoir lieu la première mesure Angle final axe A Q412 (en absolu): Angle final sur l'axe A sur lequel doit avoir lieu la dernière mesure Angle de réglage axe A Q413: Angle de réglage de l'axe A dans lequel doivent être mesurés les autres axes rotatifs Nb points de mesure axe A Q414: Nombre de palpages que la TNC doit exécuter pour mesurer l'axe A Angle initial axe B Q415 (en absolu): Angle initial sur l'axe B sur lequel doit avoir lieu la première mesure Angle final axe B Q416 (en absolu): Angle final sur l'axe B sur lequel doit avoir lieu la dernière mesure Angle de réglage axe B Q417: Angle de réglage de l'axe B dans lequel doivent être mesurés les autres axes rotatifs Nb points de mesure axe B Q418: Nombre de palpages que la TNC doit exécuter pour mesurer l'axe B Angle initial axe C Q419 (en absolu): Angle initial sur l'axe C sur lequel doit avoir lieu la première mesure Angle final axe C Q420 (en absolu): Angle final sur l'axe C sur lequel doit avoir lieu la dernière mesure Angle de réglage axe C Q421: Angle de réglage de l'axe C dans lequel doivent être mesurés les autres axes rotatifs Nb points de mesure axe C Q422: Nombre de palpages que la TNC doit exécuter pour mesurer l'axe C iTNC 530 HEIDENHAIN 4.1 Mesure de cinématique avec les palpeurs TS (option KinematicsOpt) 173 4.1 Mesure de cinématique avec les palpeurs TS (option KinematicsOpt) Fonction procès-verbal Après avoir exécuté le cycle 451, la TNC génère un procès-verbal contenant les données suivantes: Date et heure auxquelles le procès-verbal a été établi Chemin d'accès au programme CN à partir duquel le cycle a été exécuté Mode utilisé (0=Contrôler/1=Optimiser) Numéro de la cinématique active Rayon de la bille étalon introduit Pour chaque axe rotatif mesuré: Angle initial Angle final Nombre de points de mesure Angle de réglage Rayon du cercle de mesure Jeu moyen Dispersion mesurée Dispersion optimisée Valeurs de correction Evaluations 174 4 Cycles palpeurs pour la mesure automatique de la cinématique Cycles palpeurs pour l'étalonnage automatique des outils 5.1 Etalonnage d'outils avec le palpeur de table TT 5.1 Etalonnage d'outils avec le palpeur de table TT Vue d'ensemble La machine et la TNC doivent avoir été préparées par le constructeur de la machine pour la mise en œuvre du palpeur TT. Il est possible que tous les cycles ou fonctions décrits ici ne soient pas disponibles sur votre machine. Consultez le manuel de votre machine. Grâce au palpeur de table et aux cycles d'étalonnage d'outils de la TNC, vous pouvez effectuer automatiquement l'étalonnage de vos outils: Les valeurs de correction pour la longueur et le rayon sont stockées dans la mémoire centrale d'outils TOOL.T et converties automatiquement à la fin du cycle de palpage. Modes d'étalonnage disponibles: Etalonnage d'outil avec outil à l'arrêt Etalonnage d'outil avec outil en rotation Etalonnage dent par dent Configurer les paramètres-machine Pour l'étalonnage avec broche à l'arrêt, la TNC utilise l'avance de palpage de MP6520. Pour l'étalonnage avec outil en rotation, la TNC calcule automatiquement la vitesse de rotation et l'avance de palpage. La vitesse de rotation broche est calculée de la manière suivante: n = MP6570 / (r • 0,0063) avec n MP6570 r Vitesse de rotation [tours/min.] Vitesse max. de déplacement sur le pourtour [m/min.] Rayon d'outil actif [mm] L'avance de palpage résulte de: v = tolérance de mesure • n avec v Tolérance de mesure n 176 Avance de palpage [mm/min.] Tolérance de mesure [mm], dépend de MP6507 Vitesse de rotation [t/min.] 5 Cycles palpeurs pour l'étalonnage automatique des outils 5.1 Etalonnage d'outils avec le palpeur de table TT MP6507 vous permet de configurer l'avance de palpage: MP6507=0: La tolérance de mesure reste constante – indépendamment du rayon d'outil. Si l'on utilise de très gros outils, l'avance de palpage évolue néanmoins vers zéro. Plus sont réduites la vitesse de déplacement sur le pourtour (MP6570) et la tolérance admissible (MP6510) sélectionnées et plus cet effet peut être constaté. MP6507=1: La tolérance de mesure est modifiée si le rayon d'outil augmente. Ceci permet de s'assurer qu'il existe encore une avance de palpage suffisante, y compris si l'on utilise des outils avec rayons d'outils importants. La TNC modifie la tolérance selon le tableau suivant: Rayon d'outil Tolérance de mesure jusqu’à 30 mm MP6510 30 à 60 mm 2 • MP6510 60 à 90 mm 3 • MP6510 90 à 120 mm 4 • MP6510 MP6507=2: L'avance de palpage reste constante; toutefois, l'erreur de mesure croît de manière linéaire lorsque le rayon d'outil augmente: Tolérance de mesure = (r • MP6510)/ 5 mm) avec r MP6510 Rayon d'outil actif [mm] Erreur de mesure max. admissible iTNC 530 HEIDENHAIN 177 5.1 Etalonnage d'outils avec le palpeur de table TT Données d'introduction dans le tableau d'outils TOOL.T Abrév. Données d'introduction Dialogue CUT Nombre de dents de l'outil (20 dents max.) Nombre de dents? LTOL Ecart admissible par rapport à la longueur d'outil L pour la détection d'usure. Si la valeur introduite est dépassée, la TNC bloque l'outil (état L). Plage d'introduction: 0 à 0,9999 mm Tolérance d'usure: Longueur? RTOL Ecart admissible par rapport au rayon d'outil R pour la détection d'usure. Si la valeur introduite est dépassée, la TNC bloque l'outil (état L). Plage d'introduction: 0 à 0,9999 mm Tolérance d'usure: Rayon? DIRECT. Sens de coupe de l'outil pour l'étalonnage avec outil en rotation Sens rotation palpage (M3 = –)? TT:R-OFFS Etalonnage de la longueur: Déport de l'outil entre le centre de la tige et le centre de l'outil. Valeur par défaut: Rayon d'outil R (touche NO ENT génère R) Déport outil: Rayon? TT:L-OFFS Etalonnage du rayon: Déport supplémentaire de l'outil pour MP6530 entre l'arête supérieure de la tige de palpage et l'arête inférieure de l'outil. Valeur par défaut: 0 Déport outil: Longueur? LBREAK Ecart admissible par rapport à la longueur d'outil L pour la détection de rupture. Si la valeur introduite est dépassée, la TNC bloque l'outil (état L). Plage d'introduction: 0 à 0,9999 mm Tolérance de rupture: Longueur? RBREAK Ecart admissible par rapport au rayon d'outil R pour la détection de rupture. Si la valeur introduite est dépassée, la TNC bloque l'outil (état L). Plage d'introduction: 0 à 0,9999 mm Tolérance de rupture: Rayon? Exemple de données à introduire pour types d'outils courants Type d'outil CUT TT:R-OFFS Foret – (sans fonction) 0 (aucun désaxage nécessaire car la pointe du foret doit être étalonnée) Fraise cylindrique de diamètre < 19 mm 4 (4 dents) 0 (aucun désaxage nécessaire car le diamètre de l'outil est inférieur au diamètre du disque du TT) 0 (aucun désaxage supplémentaire nécessaire lors de l'étalonnage du rayon. Utilisation du désaxage de MP6530) Fraise cylindrique de diamètre > 19 mm 4 (4 dents) 0 (désaxage nécessaire car le diamètre de l'outil est supérieur au diamètre du disque du TT) 0 (aucun désaxage supplémentaire nécessaire lors de l'étalonnage du rayon. Utilisation du désaxage de MP6530) Fraise à bout hémisphérique 4 (4 dents) 0 (aucun désaxage nécessaire car le pôle sud de la bille doit être étalonné) 5 (toujours définir le rayon d'outil comme désaxage pour que le diamètre ne soit pas étalonné dans le rayon) 178 TT:L-OFFS 5 Cycles palpeurs pour l'étalonnage automatique des outils 5.1 Etalonnage d'outils avec le palpeur de table TT Afficher les résultats de la mesure En modes de fonctionnement Machine, vous pouvez faire apparaître les résultats de l'étalonnage d'outil dans l'affichage d'état supplémentaire. La TNC affiche alors le programme à gauche et les résultats de la mesure à droite. Les valeurs de mesure qui dépassent la tolérance d'usure sont signalées par un astérisque „*“– et celles qui dépassent la tolérance de rupture, par un „B“. iTNC 530 HEIDENHAIN 179 5.2 Cycles disponibles 5.2 Cycles disponibles Vue d'ensemble Programmez les cycles d'étalonnage d'outil en mode Mémorisation/ édition de programme à l'aide de la touche TOUCH PROBE. Vous disposez des cycles suivants: Ancien format Cycle Nouveau format Etalonnage du TT Etalonnage de la longueur d'outil Etalonnage du rayon d'outil Etalonnage de la longueur et du rayon d'outil Les cycles d'étalonnage ne fonctionnent que si la mémoire centrale d'outils TOOL.T est active. Avant de travailler avec les cycles d'étalonnage, vous devez introduire dans la mémoire centrale d'outils toutes les données nécessaires à l'étalonnage et appeler l'outil à étalonner avec TOOL CALL. Vous pouvez étalonner les outils avec inclinaison du plan d'usinage. Différences entre les cycles 31 à 33 et 481 à 483 L'ensemble des fonctions ainsi que le déroulement du cycle sont identiques. Seules différences entre les cycles 31 à 33 et 481 à 483: Les cycles 481 à 483 sont également disponibles en DIN/ISO en tant que cycles G481 à G483 Pour l'état de la mesure, les nouveaux cycles utilisent le paramètre fixe Q199 au lieu d'un paramètre librement sélectionnable 180 5 Cycles palpeurs pour l'étalonnage automatique des outils 5.2 Cycles disponibles Etalonnage du TT (cycle palpeur 30 ou 480, DIN/ISO: G480) Le processus du cycle d'étalonnage dépend du paramètre-machine 6500. Consultez le manuel de votre machine. Avant d'effectuer l'étalonnage, vous devez introduire dans le tableau d'outils TOOL.T le rayon et la longueur exacts de l'outil d'étalonnage. Il convient de définir dans les paramètres-machine 6580.0 à 6580.2 la position du TT à l'intérieur de la zone de travail de la machine. Si vous modifiez l'un des paramètres-machine 6580.0 à 6580.2, vous devez effectuer un nouvel étalonnage. Vous étalonnez le TT avec le cycle de mesure TCH PROBE 30 ou TCH PROBE 480 (cf. également „Différences entre les cycles 31 à 33 et 481 à 483” à la page 180). L'opération d'étalonnage est automatique. La TNC calcule également de manière automatique le désaxage de l'outil d'étalonnage. Pour cela, elle fait pivoter la broche de 180° à la moitié du cycle d'étalonnage. Utilisez comme outil d'étalonnage une pièce parfaitement cylindrique, par exemple une tige cylindrique. Les valeurs d'étalonnage ainsi obtenues sont stockées dans la TNC et prises en compte automatiquement par elle lors des étalonnages d'outils ultérieurs. Hauteur de sécurité: Introduire la position dans l'axe de broche à l'intérieur de laquelle aucune collision ne peut se produire avec les pièces ou matériels de bridage. La hauteur de sécurité se réfère au point de référence pièce actif. Si vous avez introduit une hauteur de sécurité si petite que la pointe de l'outil puisse être en deçà de l'arête supérieure de l'assiette, la TNC positionne automatiquement l'outil d'étalonnage au-dessus de l'assiette (zone de sécurité dans MP6540) Exemple: Séquences CN de l'ancien format 6 TOOL CALL 1 Z 7 TCH PROBE 30.0 ÉTALONNAGE TT 8 TCH PROBE 30.1 HAUT: +90 Exemple: Séquences CN dans le nouveau format 6 TOOL CALL 1 Z 7 TCH PROBE 480 ÉTALONNAGE TT Q260=+100 iTNC 530 HEIDENHAIN ;HAUTEUR DE SECURITE 181 5.2 Cycles disponibles Etalonnage de la longueur d'outil (cycle palpeur 31 ou 481, DIN/ISO: G481) Avant d'étalonner des outils pour la première fois, vous devez introduire dans le tableau d'outils TOOL.T le rayon et la longueur approximatifs, le nombre de dents ainsi que la direction de la dent de l'outil concerné. Vous programmez l'étalonnage de la longueur d'outil à l'aide du cycle de mesure TCH PROBE 31 ou TCH PROBE 480 (cf. également „Différences entre les cycles 31 à 33 et 481 à 483” à la page 180). En introduisant un paramètre, vous pouvez déterminer la longueur d'outil de trois manières différentes: Si le diamètre de l'outil est supérieur au diamètre de la surface de mesure du TT, étalonnez avec outil en rotation Si le diamètre de l'outil est inférieur au diamètre de la surface de mesure du TT ou si vous calculez la longueur de forets ou de fraises à bout hémisphérique, étalonnez avec outil à l'arrêt Si le diamètre de l'outil est supérieur au diamètre de la surface de mesure du TT, effectuez l'étalonnage dent par dent avec outil à l'arrêt Déroulement de l'„étalonnage avec outil en rotation“ Pour déterminer la dent la plus longue, l'outil à étalonner est décalé au centre du système de palpage et déplacé en rotation sur la surface de mesure du TT. Pour déterminer la dent la plus longue, l'outil à étalonner est décalé au centre du système de palpage et déplacé en rotation sur la surface de mesure du TT. Programmez le décalage dans le tableau d’outils sous Décalage d'outil: Rayon (TT: R-OFFS). Déroulement de l'„étalonnage avec outil à l'arrêt“ (pour foret, par exemple) L'outil à étalonner est déplacé au centre, au dessus de la surface de mesure. Il se déplace ensuite avec broche à l'arrêt sur la surface de mesure du TT. Pour terminer, il se déplace avec broche à l’arrêt sur la surface de mesure du TT. Pour ce type de mesure, introduisez „0“ pour le décalage d'outil: Rayon (TT: R-OFFS) dans le tableau d'outils. 182 5 Cycles palpeurs pour l'étalonnage automatique des outils 5.2 Cycles disponibles Déroulement de l'„étalonnage dent par dent“ La TNC pré-positionne l'outil à étalonner sur le côté de la tête de palpage. La surface frontale de l'outil se situe à une valeur définie dans MP6530, au-dessous de l'arête supérieure de la tête de palpage. La surface frontale de l’outil se situe à une valeur définie dans MP6530, au-dessous de l’arête supérieure de la tête de palpage. Dans le tableau d'outils, vous pouvez définir un autre décalage sous Décalage d'outil: Longueur (TT: L-OFFS). La TNC palpe ensuite radialement avec outil en rotation pour déterminer l'angle initial destiné à l'étalonnage dent par dent. Pour terminer, on étalonne la longueur de toutes les dents en modifiant l'orientation de la broche. Pour ce type de mesure, programmez ETALONNAGE DENTS dans le cycle TCH PROBE 31 = 1. Vous pouvez exécuter l'étalonnage dent par dent sur les outils qui peuvent comporter jusqu'à 20 dents. Définition du cycle Mesure outil=0 / contrôle=1: Définir si vous désirez étalonner l'outil pour la première fois ou contrôler un outil déjà étalonné. Pour un premier étalonnage, la TNC écrase la longueur d'outil L dans la mémoire centrale d'outils TOOL.T et initialise la valeur Delta DL à 0. Si vous contrôlez un outil, la longueur mesurée est comparée à la longueur d'outil L dans TOOL.T. La TNC calcule l'écart en tenant compte du signe et l'inscrit comme valeur Delta DL dans TOOL.T. Cet écart est également disponible dans le paramètre Q115. Si la valeur Delta est supérieure à la tolérance d'usure ou à la tolérance de rupture admissibles pour la longueur d'outil, la TNC bloque l'outil (état L dans TOOL.T) N° paramètre pour résultat?: numéro de paramètre sous lequel la TNC mémorise l'état de la mesure: 0,0: outil dans les tolérances 1,0: Outil usé (LTOL dépassée) 2,0: Outil cassé (LBREAK dépassée). Si vous ne désirez pas continuer à traiter le résultat de la mesure dans le programme, valider la question de dialogue avec la touche NO ENT Hauteur de sécurité: Introduire la position dans l'axe de broche à l'intérieur de laquelle aucune collision ne peut se produire avec les pièces ou matériels de bridage. La hauteur de sécurité se réfère au point de référence pièce actif. Si vous avez introduit une hauteur de sécurité si petite que la pointe de l'outil puisse être en deçà de l'arête supérieure de l'assiette, la TNC positionne automatiquement l'outil au-dessus de l'assiette (zone de sécurité dans MP6540) Exemple: Premier étalonnage avec outil en rotation; ancien format 6 TOOL CALL 12 Z 7 TCH PROBE 31.0 LONGUEUR D'OUTIL 8 TCH PROBE 31.1 CONTROLE: 0 9 TCH PROBE 31.2 HAUT: +120 10 TCH PROBE 31.3 ETALONNAGE DENTS: 0 Exemple: Contrôle avec étalonnage dent par dent, mémorisation de l'état dans Q5; ancien format 6 TOOL CALL 12 Z 7 TCH PROBE 31.0 LONGUEUR D'OUTIL 8 TCH PROBE 31.1 CONTROLE: 1 Q5 9 TCH PROBE 31.2 HAUT: +120 10 TCH PROBE 31.3 ETALONNAGE DENTS: 1 Exemple: Séquences CN; nouveau format 6 TOOL CALL 12 Z 7 TCH PROBE 481 LONGUEUR D'OUTIL Q340=1 ;CONTRÔLE Q260=+100 ;HAUTEUR DE SÉCURITÉ Q341=1 ;ETALONNAGE DENTS Etalonnage dents 0=Non / 1=Oui: Définir s'il faut effectuer un étalonnage dent par dent (étalonnage possible de 20 dents max.) iTNC 530 HEIDENHAIN 183 5.2 Cycles disponibles Etalonnage du rayon d'outil (cycle palpeur 32 ou 482, DIN/ISO: G482) Avant d'étalonner des outils pour la première fois, vous devez introduire dans le tableau d'outils TOOL.T le rayon et la longueur approximatifs, le nombre de dents ainsi que la direction de la dent de l'outil concerné. Vous programmez l'étalonnage du rayon d'outil à l'aide du cycle de mesure TCH PROBE 32 ou TCH PROBE 482 (cf. également „Différences entre les cycles 31 à 33 et 481 à 483” à la page 180). En introduisant un paramètre, vous pouvez déterminer le rayon d'outil de deux manières différentes: Etalonnage avec outil en rotation Etalonnage avec outil en rotation suivi d'un étalonnage dent par dent Les outils de forme cylindrique avec surface diamant peuvent être étalonnés avec broche à l'arrêt. Pour cela, vous devez définir le nombre de dents CUT = 0 dans le tableau d'outils et harmoniser le paramètre machine 6500. Consultez le manuel de votre machine. Processus de la mesure La TNC pré-positionne l'outil à étalonner sur le côté de la tête de palpage. La surface frontale de la fraise se situe à une valeur définie dans MP6530, au-dessous de l'arête supérieure de la tête de palpage. La TNC palpe ensuite radialement avec outil en rotation. Si vous désirez réaliser en plus un étalonnage dent par dent, mesurez les rayons de toutes les dents au moyen de l'orientation broche. 184 5 Cycles palpeurs pour l'étalonnage automatique des outils N° paramètre pour résultat?: numéro de paramètre sous lequel la TNC mémorise l'état de la mesure: 0,0: outil dans les tolérances 1,0: outil usé (RTOL dépassée) 2,0: Outil cassé (RBREAK dépassée). Si vous ne désirez pas continuer à traiter le résultat de la mesure dans le programme, valider la question de dialogue avec la touche NO ENT Hauteur de sécurité: Introduire la position dans l'axe de broche à l'intérieur de laquelle aucune collision ne peut se produire avec les pièces ou matériels de bridage. La hauteur de sécurité se réfère au point de référence pièce actif. Si vous avez introduit une hauteur de sécurité si petite que la pointe de l'outil puisse être en deçà de l'arête supérieure de l'assiette, la TNC positionne automatiquement l'outil au-dessus de l'assiette (zone de sécurité dans MP6540) Exemple: Premier étalonnage avec outil en rotation; ancien format 6 TOOL CALL 12 Z 7 TCH PROBE 32.0 RAYON D'OUTIL 8 TCH PROBE 32.1 CONTROLE: 0 9 TCH PROBE 32.2 HAUT: +120 10 TCH PROBE 32.3 ETALONNAGE DENTS: 0 Exemple: Contrôle avec étalonnage dent par dent, mémorisation de l'état dans Q5; ancien format 6 TOOL CALL 12 Z 7 TCH PROBE 32.0 RAYON D'OUTIL 8 TCH PROBE 32.1 CONTROLE: 1 Q5 9 TCH PROBE 32.2 HAUT: +120 10 TCH PROBE 32.3 ETALONNAGE DENTS: 1 Exemple: Séquences CN; nouveau format 6 TOOL CALL 12 Z 7 TCH PROBE 482 RAYON D'OUTIL Q340=1 ;CONTRÔLE Q260=+100 ;HAUTEUR DE SÉCURITÉ Q341=1 ;ETALONNAGE DENTS Etalonnage dents 0=Non / 1=Oui: Définir s'il faut en plus effectuer ou non un étalonnage dent par dent (étalonnage possible de 20 dents max.) iTNC 530 HEIDENHAIN 185 5.2 Cycles disponibles Définition du cycle Mesure outil=0 / contrôle=1: Définir si vous désirez étalonner l'outil pour la première fois ou contrôler un outil déjà étalonné. Pour un premier étalonnage, la TNC écrase le rayon d'outil R dans la mémoire centrale d'outils TOOL.T et met pour la valeur Delta DR = 0. Si vous contrôlez un outil, le rayon mesuré est comparé au rayon d'outil dans TOOL.T. La TNC calcule l'écart en tenant compte du signe et l'inscrit comme valeur Delta DR dans TOOL.T. Cet écart est également disponible dans le paramètre Q116. Si la valeur Delta est supérieure à la tolérance d’usure ou à la tolérance de rupture admissibles pour le rayon d’outil, la TNC bloque l’outil (état L dans TOOL.T). 5.2 Cycles disponibles Etalonnage complet de l'outil (cycle palpeur 33 ou 483, DIN/ISO: G483) Avant d'étalonner des outils pour la première fois, vous devez introduire dans le tableau d'outils TOOL.T le rayon et la longueur approximatifs, le nombre de dents ainsi que la direction de la dent de l'outil concerné. Pour étalonner l'outil en totalité, (longueur et rayon), programmez le cycle TCH PROBE 33 ou TCH PROBE 482 (cf. également „Différences entre les cycles 31 à 33 et 481 à 483” à la page 180). Le cycle convient particulièrement au premier étalonnage d'outils; il représente en effet un gain de temps considérable par rapport à l'étalonnage dent par dent de la longueur et du rayon. Avec les paramètres d'introduction, vous pouvez étalonner l'outil de deux manières différentes: Etalonnage avec outil en rotation Etalonnage avec outil en rotation suivi d'un étalonnage dent par dent Les outils de forme cylindrique avec surface diamant peuvent être étalonnés avec broche à l'arrêt. Pour cela, vous devez définir le nombre de dents CUT = 0 dans le tableau d'outils et harmoniser le paramètre machine 6500. Consultez le manuel de votre machine. Processus de la mesure La TNC étalonne l'outil suivant une procédure programmée et définie. Le rayon d'outil est tout d'abord étalonné; vient ensuite la longueur d'outil. Le processus de la mesure correspond aux phases des cycles 31 et 32. 186 5 Cycles palpeurs pour l'étalonnage automatique des outils N° paramètre pour résultat?: numéro de paramètre sous lequel la TNC mémorise l'état de la mesure: 0,0: outil dans les tolérances 1,0: outil usé (LTOL ou/et RTOL dépassée) 2,0: outil cassé (LBREAK ou/et RBREAK dépassée). Si vous ne désirez pas continuer à traiter le résultat de la mesure dans le programme, valider la question de dialogue avec la touche NO ENT Hauteur de sécurité: Introduire la position dans l'axe de broche à l'intérieur de laquelle aucune collision ne peut se produire avec les pièces ou matériels de bridage. La hauteur de sécurité se réfère au point de référence pièce actif. Si vous avez introduit une hauteur de sécurité si petite que la pointe de l'outil puisse être en deçà de l'arête supérieure de l'assiette, la TNC positionne automatiquement l'outil au-dessus de l'assiette (zone de sécurité dans MP6540) Exemple: Premier étalonnage avec outil en rotation; ancien format 6 TOOL CALL 12 Z 7 TCH PROBE 33.0 MESURE D'OUTIL 8 TCH PROBE 33.1 CONTROLE: 0 9 TCH PROBE 33.2 HAUT: +120 10 TCH PROBE 33.3 ETALONNAGE DENTS: 0 Exemple: Contrôle avec étalonnage dent par dent, mémorisation de l'état dans Q5; ancien format 6 TOOL CALL 12 Z 7 TCH PROBE 33.0 MESURE D'OUTIL 8 TCH PROBE 33.1 CONTROLE: 1 Q5 9 TCH PROBE 33.2 HAUT: +120 10 TCH PROBE 33.3 ETALONNAGE DENTS: 1 Exemple: Séquences CN; nouveau format 6 TOOL CALL 12 Z 7 TCH PROBE 483 MESURE D'OUTIL Q340=1 ;CONTRÔLE Q260=+100 ;HAUTEUR DE SÉCURITÉ Q341=1 ;ETALONNAGE DENTS Etalonnage dents 0=Non / 1=Oui: Définir s'il faut en plus effectuer ou non un étalonnage dent par dent (étalonnage possible de 20 dents max.) iTNC 530 HEIDENHAIN 187 5.2 Cycles disponibles Définition du cycle Mesure outil=0 / contrôle=1: Définir si vous désirez étalonner l'outil pour la première fois ou contrôler un outil déjà étalonné. Pour un premier étalonnage, la TNC écrase le rayon d'outil R et la longueur d'outil L dans la mémoire centrale d'outils TOOL.T et initialise les valeurs Delta DR et DL à 0. Si vous contrôlez un outil, les données d'outil mesurées sont comparées aux données d'outil correspondantes dans TOOL.T. La TNC calcule les écarts en tenant compte du signe et les inscrit comme valeurs Delta DR et DL dans TOOL.T. Ces écarts sont également disponibles dans les paramètres Q115 et Q116. Si l'une des valeurs Delta est supérieure à la tolérance d'usure ou à la tolérance de rupture admissibles, la TNC bloque l'outil (état L dans TOOL.T). F P Angle d'un plan, mesurer ... 141 Avance de palpage ... 25 Fonction FCL ... 6 Niveau de développement ... 6 Point de réf., initialisation automatique ... 66 Centre d'un cercle de trous ... 95 Centre de 4 trous ... 100 Centre oblong ... 73 Centre poche circulaire (trou) ... 82 Centre poche rectangulaire ... 76 Centre rainure ... 70 Centre tenon circulaire ... 86 Centre tenon rectangulaire ... 79 dans l'axe du palpeur ... 98 dans un axe au choix ... 103 Extérieur coin ... 89 intérieur coin ... 92 Point de référence Enregistrer dans tableau de points zéro ... 69 Enregistrer dans tableau Preset ... 69 Point de référence, initialisation manuelle à partir de trous/tenons ... 41 Axe central comme point de référence ... 40 Centre de cercle comme point de référence ... 39 Coin comme point de référence ... 38 dans un axe au choix ... 37 Procès-verbal des résultats de la mesure ... 110 P R K C Cercle de trous, mesurer ... 138 Cercle, mesurer l'extérieur ... 122 Cercle, mesurer l'intérieur ... 119 Compensation du désaxage de la pièce Configurations globales ... 157 Contrôle de l'outil ... 113 Correction d'outil ... 113 Cycles de palpage Mode Manuel ... 28 pour le mode automatique ... 22 D Désaxage pièce, compenser à partir d'un axe rotatif ... 58, 62 à partir de deux tenons circulaires ... 41, 55 à partir de deux trous ... 41, 52 Par mesure de deux points d'une droite ... 35, 50 Dilatation thermique, mesurer ... 155, 157 E Etalonnage automatique d'outils ... 178 Etalonnage automatique d'outils, cf. Etalonnage d'outil Etalonnage d'outils ... 178 Afficher les résultats de la mesure ... 179 Etalonnage complet ... 186 Etalonnage du TT ... 181 Longueur d'outil ... 182 Paramètres-machine ... 176 Rayon d'outil ... 184 Vue d'ensemble ... 180 Etalonnage d'une poche rectangulaire ... 128 Etalonnage des outils Etalonnage des pièces ... 109 Etalonner les pièces ... 42 Etat de la mesure ... 112 HEIDENHAIN iTNC 530 KinematicsOpt ... 160 L Logique de positionnement ... 26 M Mesure d'une coordonnée donnée ... 135 Mesure de cinématique ... 160 Chois de la position de mesure ... 167 Choix du nombre de points de mesure ... 167 Conditions requises ... 161 Denture Hirth ... 166 Fonction procès-verbal ... 163, 174 Jeu ... 170 Mesurer cinématique ... 164 Méthodes de calibrage ... 169 Précision ... 168 Sauvegarder cinématique ... 162 Mesure multiple ... 24 Mesurer cinématique ... 164 Mesurer l'angle d'un plan ... 141 Mesurer un angle ... 117 N Palpage rapide ... 157 Palpeurs 3D ... 20 Etalonnage à commutation ... 32, 149, 150 Gestion de différentes données d'étalonnage ... 34 Paramètres de résultat ... 69, 112 Paramètres-machine pour palpeur 3D ... 23 Rainure, mesurer l'extérieur ... 133 Rainure, mesurer l'intérieur ... 131 Rainure, mesurer la largeur ... 131 Résultats de la mesure dans les paramètres Q ... 69, 112 Rotation de base Enregistrer en mode Manuel ... 35 Enregistrer pendant le déroulement du programme ... 48 Initialisation directe ... 61 189 Index A Index S Surveillance de tolérances ... 112 T Tableau de points zéro Valider les résultats du palpage ... 30 Tableau Preset ... 69 Valider les résultats du palpage ... 31 Tenon rectangulaire, étalonner ... 125 Traverse, mesurer l'extérieur ... 133 Trou, étalonner ... 119 U Utiliser les fonctions de palpage avec palpeurs mécaniques ou comparateurs à cadran ... 45 V Valeurs de palpage dans tableau de points zéro, enregistrer ... 30 Valeurs de palpage dans tableau Preset, enregistrer ... 31 Z Zone de sécurité ... 24 190 Cycles palpeurs Numéro cycle Désignation du cycle Actif DEF 0 Plan de référence Page 115 1 Point de référence polaire Page 116 2 Etalonnage TS rayon Page 149 3 Mesure Page 151 4 Mesure 3D Page 153 9 Etalonnage TS longueur Page 150 30 Etalonnage du TT Page 181 31 Etalonnage/contrôle de la longueur d'outil Page 182 32 Etalonnage/contrôle du rayon d'outil Page 184 33 Etalonnage/contrôle de la longueur et du rayon d'outil Page 186 400 Rotation de base à partir de deux points Page 50 401 Rotation de base à partir de deux trous Page 52 402 Rotation de base à partir de deux tenons Page 55 403 Compenser le désaxage avec l'axe rotatif Page 58 404 Initialiser la rotation de base Page 61 405 Compenser un désaxage avec l'axe C Page 62 408 Initialiser le point de référence au centre d'une rainure (fonction FCL 3) Page 70 409 Initialiser le point de référence au centre d'un oblong (fonction FCL 3) Page 73 410 Initialiser point de référence intérieur rectangle Page 76 411 Initialiser point de référence extérieur rectangle Page 79 412 Initialiser point de référence intérieur cercle (trou) Page 82 413 Initialiser point de référence extérieur cercle (tenon) Page 86 414 Initialiser point de référence extérieur coin Page 89 415 Initialiser point de référence intérieur coin Page 92 416 Initialiser point de référence centre cercle de trous Page 95 417 Initialiser point de référence dans l'axe du palpeur Page 98 iTNC 530 HEIDENHAIN Actif CALL Page 191 Tableau récapitulatif Tableau récapitulatif Tableau récapitulatif Numéro cycle Désignation du cycle Actif DEF 418 Initialiser point de référence au centre de 4 trous Page 100 419 Initialiser point de référence sur un axe à sélectionner librement Page 103 420 Mesurer la pièce, angle Page 117 421 Mesurer la pièce, intérieur d'un cercle (trou) Page 119 422 Mesurer la pièce, extérieur d'un cercle (tenon) Page 122 423 Mesurer la pièce, intérieur d'un rectangle Page 125 424 Mesurer la pièce, extérieur d'un rectangle Page 128 425 Mesurer la pièce, intérieur d'une rainure Page 131 426 Mesurer la pièce, extérieur d'une rainure Page 133 427 Mesurer la pièce, un axe à sélectionner librement Page 135 430 Mesurer la pièce, cercle de trous Page 138 431 Mesurer la pièce, plan Page 141 440 Mesurer le désaxage Page 155 441 Palpage rapide: Configuration globale des paramètres du palpeur (fonction FCL 2) Page 157 450 Sauvegarder la cinématique (option) Page 162 451 Mesurer la cinématique (option) Page 164 480 Etalonnage du TT Page 181 481 Etalonnage/contrôle de la longueur d'outil Page 182 482 Etalonnage/contrôle du rayon d'outil Page 184 483 Etalonnage/contrôle de la longueur et du rayon d'outil Page 186 192 Actif CALL Page DR. JOHANNES HEIDENHAIN GmbH Dr.-Johannes-Heidenhain-Straße 5 83301 Traunreut, Germany { +49 (86 69) 31-0 | +49 (86 69) 50 61 E-Mail: [email protected] Technical support | +49 (86 69) 32-10 00 Measuring systems { +49 (86 69) 31-31 04 E-Mail: [email protected] TNC support { +49 (86 69) 31-31 01 E-Mail: [email protected] NC programming { +49 (86 69) 31-31 03 E-Mail: [email protected] PLC programming { +49 (86 69) 31-31 02 E-Mail: [email protected] Lathe controls { +49 (86 69) 31-31 05 E-Mail: [email protected] www.heidenhain.de Les palpeurs 3D de HEIDENHAIN vous aident à réduire les temps morts: Par exemple • • • • Dégauchissage des pièces Initialisation des points de référence Etalonnage des pièces Digitalisation de formes 3D avec les palpeurs de pièces TS 220 avec câble TS 640 avec transmission infra-rouge • Etalonnage d‘outils • Surveillance de l‘usure • Enregistrement de rupture d‘outil avec le palpeur d‘outils TT 140 Ve 02 533 189-32 · SW04 · 1 · 10/2007 · F&W · Printed in Germany · Sous réserve de modifications ">
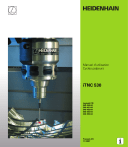
Lien public mis à jour
Le lien public vers votre chat a été mis à jour.