Bosch Rexroth R911283268 Manuel utilisateur
PDF
Scarica
Documento
Manuel de programmation CN 17VRS Manuel utilisateur DOK-MTC200-NC**PRO*V17-ANW1-FR-P 2 8 3 2 6 8 A propos de cette documentation Titre Type de la documentation Document Classement interne Manuel de programmation CN 17VRS Manuel de programmation CN 17VRS Manuel utilisateur DOK-MTC200-NC**PRO*V17-ANW-FR-P • Classeur 1 / Registre 2 • Numéro identification: 109-0768-4194-00/05.97 Rôle de cette documentation Cette documentation sert de description du logiciel 005-17VRS. Dans les versions précédentes (Doc.-n° 109-0668-4183-xx) certaines fonctions décrites dans ce manuel n'existaient pas ou étaient limitées. Liste des modifications Protection Désignation des différentes éditions Date Remarque 109-0768-4194-00 05.97 Nouvelle édition version 17 INDRAMAT GmbH, 1997 La transmission et la reproduction de ce document, l’exploitation et la communication de son contenu sont interdits sauf autorisation écrite. Toute infraction donne lieu à des dommages et intérêts. Tous droits réservés en cas de délivrance d'un brevet ou de l'enregistrement d'un modèle d'utilité. (DIN 34-1) Obligation Editeur Tous droits de modification de ce document et de disponibilité du matériel réservés. INDRAMAT GmbH • Bgm.-Dr.-Nebel-Str. 2 • D-97816 Lohr am Main Téléphone 09352/40-0 • Tx 689421 • Télécopie 09352/40-4885 Abt. ENC (RL) DOK-MTC200-NC**PRO*V17-ANW-FR-P Manuel de programmation CN 17VRS Somaire I Sommaire 1 Généralités 1-1 1.1 Remarques........................................................................................................................................... 1-1 1.2 Organisation des programmes et des données ................................................................................... 1-2 2 Programmes CN 2-1 2.1 Organisation des listes de réglage....................................................................................................... 2-1 2.2 Structure du programme ...................................................................................................................... 2-2 Programme d’avance .................................................................................................................... 2-3 Programme de retrait .................................................................................................................... 2-3 2.3 Programmation spécifique au process................................................................................................. 2-4 2.4 Eléments d’un bloc............................................................................................................................... 2-5 Numéro de bloc............................................................................................................................. 2-5 Blocs optionnels ............................................................................................................................ 2-6 2.5 Mot CN ................................................................................................................................................. 2-6 Marque de saut ............................................................................................................................. 2-7 Remarque...................................................................................................................................... 2-8 Commentaire................................................................................................................................. 2-8 Commentaire dans le programme source..................................................................................... 2-9 2.6 Adresses disponibles ........................................................................................................................... 2-9 3 Instructions de déplacement, Programmation des cotes 3-1 3.1 Système de coordonnées .................................................................................................................... 3-1 3.2 Instruction de déplacement.................................................................................................................. 3-2 3.3 Données de dimension ........................................................................................................................ 3-3 Dimension absolue 'G90 ............................................................................................................... 3-3 Dimension incrémentale 'G91'....................................................................................................... 3-4 3.4 Points d’origine..................................................................................................................................... 3-5 3.5 Décalages d’origine.............................................................................................................................. 3-6 Décalages d’origine réglables 'G54 ... G59' .................................................................................. 3-8 Rotation du système de coordonnées avec un angle 'P'............................................................... 3-9 Banque de point d’origine 'O' ...................................................................................................... 3-10 Décalage d’origine absolu programmable 'G50' Décalage d’origine incrémental programmable 'G51' . 3-12 Point d’origine pièce programmable 'G52'................................................................................... 3-13 Annulation des décalages d’origine 'G53' ................................................................................... 3-14 Offset général réglable dans le tableau de point d’origine .......................................................... 3-14 Lecture et écriture de données DPO dans le programme CN 'OTD' .......................................... 3-14 3.6 Sélection du plan d’interpolation ........................................................................................................ 3-15 Sélection de plan 'G17’, 'G18’, 'G19’........................................................................................... 3-15 DOK-MTC200-NC**PRO*V17-ANW-FR-P II Sommaire Manuel de programmation CN 17VRS Sélection libre de plan 'G20'........................................................................................................ 3-16 3.7 Programmation au diamètre et au rayon 'G15' / 'G16' ....................................................................... 3-19 3.8 Unité de mesure................................................................................................................................. 3-20 Unité de mesure Inch 'G70'......................................................................................................... 3-20 Unité de mesure mm 'G71'.......................................................................................................... 3-21 3.9 Miroir des axes de coordonnées 'G72' / 'G73'.................................................................................... 3-22 3.10 Facteur d’échelle 'G78' / 'G79' ......................................................................................................... 3-24 3.11 Prise d’origine d’axe 'G74'................................................................................................................ 3-26 3.12 Déplacements contre butée fixe....................................................................................................... 3-26 Déplacements contre butée fixe 'G75'......................................................................................... 3-26 Suppression de toutes les précontraintes 'G76'.......................................................................... 3-28 3.13 Réaccostage et reprise d’usinage sur le contour............................................................................. 3-28 Réaccostage et reprise d’usinage en mode programme............................................................. 3-28 Réaccostage et reprise d’usinage à la position cible 'G77' ......................................................... 3-29 4 Blocs de déplacement 4-1 4.1 Axes ..................................................................................................................................................... 4-1 Axes linéaires principaux............................................................................................................... 4-1 Axes rotatifs principaux ................................................................................................................. 4-1 Axes linéaires et rotatifs auxiliaires ............................................................................................... 4-2 4.2 Conditions d’interpolation..................................................................................................................... 4-2 Interpolation à erreur de poursuite réduite'G06'............................................................................ 4-2 Interpolation avec erreur de poursuite 'G07' ................................................................................. 4-5 Vitesse de passage de bloc optimale 'G08'................................................................................... 4-7 Passage de bloc à vitesse réduite 'G09' ....................................................................................... 4-9 Arrêt précis 'G61'......................................................................................................................... 4-10 Changement bloc à la volée 'G62'............................................................................................... 4-12 Accélération programmable 'ACC' .............................................................................................. 4-13 4.3 Fonctions d’interpolation .................................................................................................................... 4-14 Interpolation linéaire, rapide 'G00'............................................................................................... 4-14 Interpolation linéaire, Avance 'G01'............................................................................................. 4-15 Interpolation circulaire 'G02' / 'G03'............................................................................................. 4-16 Interpolation hélicoïdale .............................................................................................................. 4-22 Filetage 'G33' .............................................................................................................................. 4-24 Enchaînement de blocs de filetage avec 'G33' ........................................................................... 4-28 Taraudage 'G63' / 'G64' .............................................................................................................. 4-30 Taraudage 'G65' – Broche comme axe maître............................................................................ 4-34 4.4 Avance ............................................................................................................................................... 4-36 Mot F ........................................................................................................................................... 4-36 Programmation en temps 'G93'................................................................................................... 4-37 Programmation de la vitesse 'G94'.............................................................................................. 4-38 Avance par tour 'G95'.................................................................................................................. 4-38 Temporisation 'G04' .................................................................................................................... 4-39 Rapport fondamental entre la vitesse de trajectoire programmée (F) et les vitesses des axes.. 4-40 4.5 Vitesse de rotation broche ................................................................................................................. 4-42 DOK-MTC200-NC**PRO*V17-ANW-FR-P Manuel de programmation CN 17VRS Somaire III Mot S pour l’introduction de la vitesse de rotation broche........................................................... 4-42 Sélection de la broche de référence 'SPF' .................................................................................. 4-43 Vitesse périphérique de meule constante (SUG) 'G66'............................................................... 4-44 Vitesse de coupe constante 'G96'............................................................................................... 4-45 Limitation de vitesse de rotation broche 'G92'............................................................................. 4-47 Vitesse de rotation broche en t/min 'G97'.................................................................................... 4-47 4.6 Programmation d’axe rotatif............................................................................................................... 4-47 Rayon d’application 'RX', 'RY', 'RZ'............................................................................................. 4-47 Programme CN - Commutation entre broche et axe C ............................................................... 4-49 Logique de déplacement pour un axe rotatif à mouvement continu............................................ 4-49 4.7 Transformations ................................................................................................................................. 4-51 Sélection d’usinage frontal ‘G31’................................................................................................. 4-51 Sélection de l’usinage sur corps de cylindre ‘G32’...................................................................... 4-54 Annulation des transformations 'G30'.......................................................................................... 4-56 Sélection de la broche de référence pour les transformations 'SPC'.......................................... 4-56 4.8 Synchronisation de broches............................................................................................................... 4-57 Application de synchronisation de broches principales............................................................... 4-57 Environnement fonctionnel de la synchronisation de broche...................................................... 4-57 Configurations admissibles ......................................................................................................... 4-57 Déroulement du procédé de synchronisation.............................................................................. 4-58 Programmation CN...................................................................................................................... 4-59 Données machine pour la synchronisation de broche ................................................................ 4-60 4.9 Axes entraînés et axes Gantry........................................................................................................... 4-61 Application des axes entraînés et des axes Gantry .................................................................... 4-61 Configurations admissibles ......................................................................................................... 4-61 Déroulement d’une procédure de synchronisation...................................................................... 4-62 Fonction auxiliaire pour l’exploitation synchrone......................................................................... 4-62 Programmation CN...................................................................................................................... 4-62 Données machine pour l’association d’axes synchrones............................................................ 4-63 5 Correction d’outil 5-1 5.1 Structure des données de correction d'outil......................................................................................... 5-1 5.2 Listes de réglages................................................................................................................................ 5-3 Rôle de la liste de réglages........................................................................................................... 5-3 Données de la liste de réglages.................................................................................................... 5-3 5.3 Liste d’outils ....................................................................................................................................... 5-11 Rôle de la liste d’outils................................................................................................................. 5-11 Données de la liste d’outils.......................................................................................................... 5-11 5.4 Correction de trajectoire d’outil .......................................................................................................... 5-25 Correction de trajectoire d’outil inactive ...................................................................................... 5-25 Correction de trajectoire d’outil active ......................................................................................... 5-26 Raccordement de contour........................................................................................................... 5-27 Mise en œuvre de la correction de trajectoire d’outil au début du contour.................................. 5-30 Annulation de la correction de trajectoire d’outil à la fin du contour............................................ 5-32 Changement de direction de correction ...................................................................................... 5-34 DOK-MTC200-NC**PRO*V17-ANW-FR-P IV Sommaire Manuel de programmation CN 17VRS 5.5 Sélection et annulation de la correction de trajectoire d’outil............................................................. 5-34 Annulation de la correction de trajectoire d’outil 'G40' ................................................................ 5-34 Correction de trajectoire à gauche 'G41'..................................................................................... 5-35 Correction de trajectoire à droite 'G42'........................................................................................ 5-35 Insertion d’un arc de cercle de transition 'G43' ........................................................................... 5-37 Insertion de chanfrein de transition 'G44'.................................................................................... 5-37 Vitesse d’avance du centre d’outil constante 'G98'..................................................................... 5-38 Vitesse d’avance constante sur le contour 'G99'......................................................................... 5-38 5.6 Correction de longueur d’outil ............................................................................................................ 5-39 Pas de correction de longueur 'G47' ........................................................................................... 5-40 Correction de longueur d’outil positive 'G48'............................................................................... 5-40 Correction de longueur d’outil négative 'G49'.............................................................................. 5-40 5.7 Accès aux données d’outils par le programme CN 'TLD'................................................................... 5-40 5.8 Correcteurs D..................................................................................................................................... 5-41 6 Fonctions auxiliaires (S, M, Q) 6-1 6.1 Généralités........................................................................................................................................... 6-1 6.2 Fonctions auxiliaires ‘M’....................................................................................................................... 6-1 Commandes de programme.......................................................................................................... 6-2 Commandes de broche................................................................................................................. 6-2 Indexage de broche....................................................................................................................... 6-3 Changement de rapport ................................................................................................................ 6-3 6.3 Mot S comme fonction auxiliaire .......................................................................................................... 6-4 6.4 Fonction Q............................................................................................................................................ 6-4 7 Evènements 7-1 7.1 Définition d'un évènement.................................................................................................................... 7-1 7.2 Modification d'évènementx................................................................................................................... 7-1 Mise à 1 d'évènement ‘SE’............................................................................................................ 7-1 Remise à 0 d'évènement ‘RE’ ....................................................................................................... 7-2 Attente jusqu'à mise à 1 d'évènement ‘WES’................................................................................ 7-2 Attente jusqu'à remise à 0 d'évènement ‘WER’ ............................................................................ 7-3 7.3 Sauts conditionnés par un évènement................................................................................................. 7-4 Saut sur évènement à 1 ‘BES’ ...................................................................................................... 7-4 Saut sur évènement à 0 ‘BER’ ...................................................................................................... 7-4 7.4 Gestion asynchrone d'évènements...................................................................................................... 7-5 Appel de sous-programme sur évènement à 1 ‘BEV’ ................................................................... 7-6 Saut de programme sur évènement à 1 ‘JEV’............................................................................... 7-6 Effacement de surveillance d'évènement ‘CEV’............................................................................ 7-7 Suspension de surveillance d'évènement ‘DEV’........................................................................... 7-7 Activation de surveillance d'évènement ‘EEV’............................................................................... 7-7 8 Instructions pour gestion d’outil 8-1 8.1 Mise en place des outils et des données d'outil................................................................................... 8-1 Présélection et appel d'outil ‘T’...................................................................................................... 8-1 DOK-MTC200-NC**PRO*V17-ANW-FR-P Manuel de programmation CN 17VRS Somaire V Sélection de la broche d'outil ‘SPT’............................................................................................... 8-2 Sélection d'arête de coupe ‘E’....................................................................................................... 8-2 8.2 Instructions de mouvements du magasin d'outil .................................................................................. 8-3 Prise d'origine du magasin d'outils ‘MRF’...................................................................................... 8-3 Retour du magasin d'outils en position de base ‘MHP’................................................................. 8-3 Mise en position d'un outil programmé ‘MTP’................................................................................ 8-4 Mise en position d'un emplacement programmé ‘MMP’................................................................ 8-5 Accès à un emplacement libre ‘MFP’............................................................................................ 8-6 Accès à l'emplacement précédent ‘MOP’...................................................................................... 8-6 Attente jusqu'à position atteinte ‘MRY’.......................................................................................... 8-7 Libération du magasin d'outils pour exploitation manuelle ‘MEN’ ................................................. 8-7 8.3 Instructions de changement d'outil....................................................................................................... 8-8 Exécution d'un changement d'outil complet ‘TCH’ ........................................................................ 8-8 Changement de l'outil du magasin dans la broche ‘TMS’ ............................................................. 8-8 Changement de l'outil de la broche dans le magasin ‘TSM’.......................................................... 8-9 Saut lorsque la broche est vide ‘BSE’ ........................................................................................... 8-9 Saut lorsque T0 a été programmé ‘BTE’....................................................................................... 8-9 9 Instructions de commande de process et de programme 9-1 9.1 Instructions de commande de process ................................................................................................ 9-1 Définition d’un process ‘DP’ .......................................................................................................... 9-2 Sélection de programme pour un process ‘SP’............................................................................. 9-2 Démarrage du programme retrait ‘RP’ .......................................................................................... 9-3 Démarrage programme d’avance ‘AP’ .......................................................................................... 9-3 Attente d’un process ‘WP’ ............................................................................................................. 9-3 Verrouillage de process ‘LP’.......................................................................................................... 9-4 Usinage terminé ‘POK’.................................................................................................................. 9-5 9.2 Transfert d’axes entre les process ‘FAX’, ‘GAX’ .................................................................................. 9-5 9.3 Instructions de commande de programme........................................................................................... 9-8 Fin de programme avec remise à 0 ‘RET’..................................................................................... 9-8 Saut avec stop ‘BST’..................................................................................................................... 9-8 Arrêt programmé ‘HLT’.................................................................................................................. 9-8 Saut inconditionnel ‘BRA’.............................................................................................................. 9-9 Saut dans un autre programme ‘JMP’........................................................................................... 9-9 9.4 Sous-programme ................................................................................................................................. 9-9 Technique de sous-programme .................................................................................................... 9-9 Structure d’un sous-programme.................................................................................................. 9-10 Emboîtement de sous-programme.............................................................................................. 9-10 Appel d’un programme CN en tant que sous-programme ‘JSR’................................................. 9-10 Appel de sous-programme ‘BSR’................................................................................................ 9-11 Retour d’un sous-programme ‘RTS’............................................................................................ 9-11 9.5 Vecteur de retrait................................................................................................................................ 9-12 Pose d’un vecteur de retrait ‘REV’ .............................................................................................. 9-12 9.6 Sauts conditionnels............................................................................................................................ 9-14 Saut quand broche vide ‘BSE’..................................................................................................... 9-14 DOK-MTC200-NC**PRO*V17-ANW-FR-P VI Sommaire Manuel de programmation CN 17VRS Saut quand T0 a été programmé ‘BTE’....................................................................................... 9-15 Saut si axes initialisés ‘BRF’........................................................................................................ 9-15 Saut sur événement à 1 ‘BES’ .................................................................................................... 9-15 Saut sur événement à 0 ‘BER’ .................................................................................................... 9-15 9.7 Sauts en fonction de résultats arithmétiques ..................................................................................... 9-16 Saut quand résultat égal à 0 ‘BEQ’ ............................................................................................. 9-16 Saut quand résultat différent de 0 ‘BNE’ ..................................................................................... 9-16 Saut quand résultat supérieur ou égal à 0 ‘BPL’......................................................................... 9-16 Saut quand résultat inférieur à 0 ‘BMI’ ........................................................................................ 9-16 10 Affectation de variables et fonctions mathématiques 10-1 10.1 Variables .......................................................................................................................................... 10-1 Affectation de variable................................................................................................................. 10-2 10.2 Unité d'angle pour les fonctions d'angle ‘RAD’, ‘DEG’..................................................................... 10-5 10.3 Expressions mathématiques............................................................................................................ 10-5 Opérandes................................................................................................................................... 10-6 Opérateurs .................................................................................................................................. 10-7 Parenthèses ................................................................................................................................ 10-7 Fonctions..................................................................................................................................... 10-7 11 Fonctions CN spéciales 11-1 11.1 Valeurs de position avec entraînements analogiques...................................................................... 11-1 Valeur de position sur front positif de l'entrée palpeur ‘PMP’...................................................... 11-1 Valeur de position sur front négatif de l'entrée palpeur ‘NMP’ .................................................... 11-1 11.2 Paramètres SERCOS APR.............................................................................................................. 11-1 Echange de données avec entraînements numériques ‘AXD’.................................................... 11-1 Couplage électronique d'axes et interpolateur de tableau .......................................................... 11-4 11.3 Lecture et écriture de données DPO par le programme CN ‘OTD’.................................................. 11-6 11.4 Accès aux données d'outil par le programme CN ‘TLD’................................................................... 11-8 11.5 Lecture et écriture des correcteurs D par le programme CN ‘DCD’............................................... 11-13 11.6 Lecture et écriture de données machine........................................................................................ 11-14 Utilisation des données machine............................................................................................... 11-14 Lecture et écriture d'éléments de données machine ‘MTD’ ...................................................... 11-15 11.7 Affectations possibles entre AXD, OTD, TLD, DCD, MTD .............................................................. 11-16 Emploi d'instructions AXD ......................................................................................................... 11-16 Emploi d'instructions OTD......................................................................................................... 11-17 Emploi d'instructions TLD.......................................................................................................... 11-17 Emploi d'instructions DCD......................................................................................................... 11-17 Emploi d'instructions MTD......................................................................................................... 11-18 Affectations entre instructions AXD, OTD, TLD, DCD et MTD.................................................. 11-18 12 Fonctions compilateur CN 12-1 12.1 Principes fondamentaux................................................................................................................... 12-1 12.2 12.2 Chanfreins et arrondis.............................................................................................................. 12-1 12.3 Technique de macro ........................................................................................................................ 12-3 DOK-MTC200-NC**PRO*V17-ANW-FR-P Manuel de programmation CN 17VRS Somaire VII Fonctions CN étendues avec la technique des macros .............................................................. 12-5 12.4 Fonction modale............................................................................................................................... 12-6 12.5 Fonction Look Ahead étendue ......................................................................................................... 12-9 12.6 Editeur graphique CN..................................................................................................................... 12-13 13 Méthode pour la programmation CN 13-1 13.1 Programmation CN optimale en temps............................................................................................ 13-1 14 Annexe 14-1 14.1 Tableau des groupes de code G...................................................................................................... 14-1 14.2 Tableau des groupes de fonctions M............................................................................................... 14-2 14.3 Aperçu rapide des fonctions............................................................................................................. 14-3 I. G00 à G20............................................................................................................................... 14-3 II. G30 à G49.............................................................................................................................. 14-4 III. G50 à G73............................................................................................................................. 14-5 IV. G74 à G99 ............................................................................................................................ 14-6 V. ACC à BTE ............................................................................................................................ 14-7 VI. CEV à MOP .......................................................................................................................... 14-8 VII. MRF à SE ............................................................................................................................ 14-9 VIII. SP à WP ........................................................................................................................... 14-10 14.4 Tableau des fonctions G ................................................................................................................ 14-11 I. G00 à G50............................................................................................................................. 14-11 II. G51 à G99............................................................................................................................ 14-12 14.5 En-tête de fichier............................................................................................................................ 14-13 15 Index DOK-MTC200-NC**PRO*V17-ANW-FR-P 15-1 VIII Sommaire Manuel de programmation CN 17VRS DOK-MTC200-NC**PRO*V17-ANW-FR-P Généralités 1-1 Manuel de programmation CN 17VRS 1 Généralités 1.1 Remarques Une CNC (Commande Numérique à Calculateur) est un ordinateur spécialement conçu pour la commande d'une machine-outil , d'un robot ou d'un poste de transfert. De même qu'un ordinateur personnel, la CNC dispose d'un système d'exploitation spécialement développé pour les applications numériques, incluant un logiciel appelé logiciel de commande. Le logiciel de commande traduit le programme CNC en un langage exploitable par la commande. Les caractéristiques relatives à une machine-outil à CN, à un robot ou à une installation transfert se trouvent dans le manuel du constructeur de la machine. Les caractéristiques du constructeur de machine prévalent sur celles de ce manuel de programmation. Les exemples de programmation sont conformes au format de programme DIN 66025/ISO Draft 6983/2 avec les extensions INDRAMAT. Toutes les données géométriques sont en unités métriques. Des associations entre la syntaxe CN et les autres fonctions non décrites dans ce manuel peuvent tourner sur la CN. Aucune réclamation sur ces associations ne sera cependant prise en compte dans le cas de nouvelles livraisons ou de service après-vente. INDRAMAT se réserve le droit de modification pour des raisons techniques d'extension de fonctionnalités. Ce manuel de programmation est valable pour des CNC avec: IHM à partir de la version : Logiciel d'exploitation à partir de la version: 05.17/VRS 03.17/VRS Remarque: Dans les champs ainsi repérés sont décrits des comportements particuliers de fonction dépendants du paramétrage. DOK-MTC200-NC**PRO*V17-ANW-FR-P 1-2 Généralités 1.2 Manuel de programmation CN 17VRS Organisation des programmes et des données Données de la CNC avec IHM sur un IBM PC et un SOT (terminal machine). MT-CNC données interface opérateur 99 paquet programmes CN 99 1 99 1 1 liste blocs paramètres données - SOT d'outils disque dur Interface 4 5 6 4 5 4 6 3 liste évenements CN 1 2 6 5 pour process 0 4 3 liste variables CN 1 2 pour process 0 6 3 3 liste liste d'outils 2 évenements CN 1 2 6 pour process 1 5 5 pour process 0 0 4 4 3 3 points liste 2 2 d'origine variables CN 1 1 pour process 0 pour process 0 5 blocs IMD 3 liste d'outils 2 pour process 1 0 points 3 2 d'origine pour process0 1 4 4 5 5 6 6 blocs IMD liaison série V24 19200 Baud liaison série V24 19200 Baud mémoire MT-CNC paramètres 20 .. .. 6 4 5 3 Axe 1 2 2 3 4 6 5 4 process 0 1 6 2 3 4 5 1 6 process 0 2 3 4 5 6 1 process 0 2 3 1 4 5 6 process 0 2 3 1 4 5 process 0 2 3 1 process 0 paramètres système paramètres axe paramètres process liste d'outils évenements CN variables CN programme pièce CN correcteurs D mémoire programme CN A points d'origine pour process 0 données pour process 0 1 1 2 2 3 3 4 4 5 5 mémoire programme CN B 6 6 points d'origine pour process 0 données pour process 0 liste de réglage liste de réglage programme CN Nr. 1 . . Nr. 99 programme CN Nr. 1 . . Nr. 99 1 1 2 2 3 3 4 4 5 5 6 6 Fig. 1-1: CNC Organisation des données Dans la version de base de la CNC on dispose d’environ 400 kBytes de mémoire de libre. La mémoire CNC est, comme représentée sur la figure 1, partagée en plusieurs zones. Ces zones sont rapidement décrites dans les paragraphes suivants. DOK-MTC200-NC**PRO*V17-ANW-FR-P Manuel de programmation CN 17VRS Généralités 1-3 La CNC est adaptée à chaque machine ou installation au moyen de paramètres. L‘IHM permet de traiter jusqu‘à 99 jeux de paramètres différents. Les paramètres sont partagés selon les groupes suivants: Paramètres système Les paramètres système déterminent le nombre de process et d'axes devant être traités par la CN ainsi que le type de gestion d'outil. Paramètres process Les paramètres. process déterminent les données caractéristiques du process telles que par exemple, le plan d'interpolation de base, le nombre de chiffres décimaux pour la programmation et l'affichage, la vitesse maximale de trajectoire... Paramètres d’axe Ce paramètre détermine à quel process l’axe est rattaché et fixe les valeurs limites de l’axe telles que vitesse maximale de l'axe, limites de déplacement… Vous trouverez une description détaillée des paramètres système, process et axe dans la "Description des paramètres„. Liste d’outils La liste d'outils d'un process contient les valeurs actuelles des données de tous les outils rattachés au process et présente ainsi le reflet du magasin d'outil de la station. L‘IHM permet de gérer jusqu'à 99 listes d'outils différentes. Les instructions CN pour la gestion d’outils sont décrites dans le chapitre 8. La description complète de toutes les données et fonctions en liaison avec les outils se trouve dans les descriptions "Gestion d'outils„ et "Gestion de données d'outils„. Evènements CN Les évènements CN sont des variables binaires accessibles par le programme CN. La description détaillée des événements et des fonctions y référant se trouve au chapitre 7. Variable CN Une variable CN représente une valeur numérique modifiable. Il y a au total 1792 variables CN disponibles (256 variables CN par process). Une description complète des possibilités sur les variables CN se trouve au chapitre 10 'Programmation de sous-programmes et de cycles'. Programmes de cycles CN La CNC dispose d'une plage mémoire réservée pour les cycles CN du constructeur de machine et d‘INDRAMAT. D'autres informations se trouvent dans la description 'Cycles CN'. Correcteurs D Les correcteurs D s’ajoutent au registre actif de données de géométrie d’outil . Leur action additive se fait sur les registres de géométrie L1, L2, L3 et R . Pour chacun des 7 process de la CNC on dispose de 99 correcteurs D. Chaque correcteur D dispose de registres L1, L2, L3 et R. L’attribution de valeurs aux registres de correcteur D se fait au moyen de l‘IHM de la CN ou par le SOT. Paquet programmes CN Un paquet programme CN contient toutes les listes de réglage nécessaires (valeurs de consigne d’outils) ainsi que les programmes CN pour tous les process d'usinage. L‘IHM permet de gérer jusqu‘à 99 paquets de programme CN. Le partage de la mémoire CN en deux zones A et B permet de gérer simultanément deux paquets programme. La sélection du paquet à exécuter se fait par l‘IHM ou par l‘AP. Devant l’exécution d'un paquet programme, un deuxième paquet programme peut être chargé en mémoire. Un paquet programme éventuellement déjà chargé est écrasé. DOK-MTC200-NC**PRO*V17-ANW-FR-P 1-4 Généralités Manuel de programmation CN 17VRS paquets programmes CN 1 ... 99 données pour process 0 1 2 3 4 5 6 liste de réglage (option) programme CN 1 programme CN 99 Fig. 1-2: Paquet programme CN Liste de réglage La liste de réglage contient, pour chaque numéro T utilisé dans le programme CN, un jeu de données d’outils définissant l'outil qui doit être utilisé ainsi que les caractéristiques qu'il doit posséder. Lorsque le constructeur de machine outil décide qu'aucune liste de réglage n'est nécessaire, le numéro T ainsi que le jeu de données correspondant sont consignés dans la liste d'outils. La liste de réglage doit cependant être remplie avant ou, au plus tard, lors de la création du programme. D'autres informations sur les listes d’outils se trouvent dans les descriptions "Gestion d'outils " et " Gestion de données d'outils". Pour chaque process, la CNC met à disposition jusqu'à 60 points d'origine (10 * (G54..G59)). Les points d'origine sont dans la mémoire CN A ou B du paquet de programmes actuellement actif. Les programmations de table de point d'origine sous l'IHM sont affectées à la mémoire de programme CN active. DOK-MTC200-NC**PRO*V17-ANW-FR-P Programmes CN 2-1 Manuel de programmation CN 17VRS 2 Programmes CN 2.1 Organisation des listes de réglage Pour chaque process utilisant des outils, on peut préparer une liste de réglages permettant l'affectation de n'importe quelle description d’outils ou numéro d’outil au numéro T utilisé par le programme CN. En outre, la liste de réglage contient les valeurs de consigne de l’outil. Les listes de réglage peuvent être organisées par station ou par programme. Organisation spécifique à la station Organisation spécifique au programme jusqu’à 7 listes de réglage (1 par process) possibles. jusqu’à 693 listes de réglages (7 process * 99 listes) possibles. paquet programme CN 1 process 0 PCN 1 process 1 LR PCN 1 PCN 99 process 6 LR PCN 1 LR PCN 99 PCN 99 Fig. 2-1: Listes de réglage en organisation spécifique à la station paquet programme 6 process 0 process 1 process 6 PCN 1 LR 1 PCN 1 LR 1 PCN 1 LR 1 PCN 2 LR 2 PCN 2 LR 2 PCN 2 LR 2 PCN 99 LR 99 PCN 99 LR 99 PCN 99 LR 99 Fig. 2-2: Listes de réglage en organisation spécifique au programme En organisation spécifique au programme les listes de réglage réduisent la zone mémoire pour le programme CN. Remarque: La détermination des listes de réglage spécifiques à la station ou au programme se fait par paramètre système ! Le constructeur de machine fixe dans le programme automate si la CN travaille avec ou sans liste de réglage Lors de la création du programme CN, la liste de réglage doit être remplie au plus tard avant la transmission du programme. Ce n'est que dans ce cas que les références au numéro T, dans le programme CN ont un sens. L'affectation définitive des outils chargés dans le magasin avec les numéros T utilisés dans le programme a lieu lors du lancement du programme (vérification optionnelle de l'équipement). DOK-MTC200-NC**PRO*V17-ANW1-FR-P 2-2 Programmes CN 2.2 Manuel de programmation CN 17VRS Structure du programme Le programme CN est composé d'un jeu d'instructions conformes à la norme DIN 66025 / ISO Draft 6983/2 complété par des extensions spécifiques INDRAMAT. L’IHM permet de gérer 99 paquets de programmes CN. Chaque paquet de programmes peut contenir jusqu'à 99 programmes CN pour chaque process. Ainsi un paquet de programmes peut contenir jusqu’à 693 programmes CN (7 process x 99 programmes CN).. mémoire programme CN B mémoire programme CN A programme CN 04 programme d'avance (Advance) mémoire cycle CN 9 programme de retour (Reverse) sous-programmes des programmes d'avance et de retour programme n° 99 programme n° 0 cycles utilisateur et sous-programmes sous-programmes et cycles du constructeur de machine et de INDRAMAT GmbH Fig. 2-3: Organisation du programme CN Un programme CN peut contenir indifféremment • Le programme d’avance ou • Le programme de retrait d’un usinage. Lorsqu’un sous-programme ou le programme de retrait n'est pas trouvé dans le programme CN actuel, la CN le recherche automatiquement dans le programme portant le numéro 99. Si le sous-programme ou le cycle n’y est pas trouvé, la CN le recherche dans le programme portant le numéro 0. Programme 99 Le programme 99 est adapté pour les modules de programme fréquemment utilisés tels que les cycles clients, le sous-programme de changement d'outil ou le Programme de retrait. Programme 0 Le programme 0 est réservé aux cycles d'usinage INDRAMAT ainsi qu'aux cycles du constructeur machine. Une description détaillée des cycles d'usinage INDRAMAT se trouve dans le manuel „Cycles CN„. Les programmes CN sont associés à leur process actuel : • le programme associé au process 0 (process maître) correspond au programme pièce, • les programmes CN associés aux process 1 à 6 correspondent aux programmes d’usinage • Lorsqu’une installation comporte plusieurs process, le programme pièce du process 0 assure la coordination des autres process. DOK-MTC200-NC**PRO*V17-ANW1-FR-P Programmes CN 2-3 Manuel de programmation CN 17VRS Programme d’avance Un programme d’avance est constitué d’une suite complète de blocs CN nécessaires à l'usinage d'une pièce. Il contient, outre les informations de trajectoire nécessaires à l'usinage, toutes les fonctions auxiliaires et les appels de sous-programmes et de cycles. Le programme d'avance se termine par un bloc comprenant l'instruction RET (fin de programme avec mise à 0). Exemple T4 BSR .M6 T8 MTP G00 G90 G54 X0 Y0 Z50 S5000 M03 G01 X46 Y144 Z2 Chargement d’outil SF D50 outil d’usinage suivant Mise à l’état de base Positionnement à distance de sécurité . . RET Programme de retrait Un programme de retrait est constitué d'une suite complète de blocs CN décrivant le déroulement d'un processus qui doit être exécuté pour la prise d'origine ou la mise dans un état de base d’une station, indépendamment de la complexité des mouvements de trajectoire nécessaires. En règle générale, un programme de retrait est programmé dans le programme 0 ou le programme 99, afin d’exécuter la prise d'origine ou la mise en état de base d'une station ou d'une machine en tant que sous-programme. Le programme de retrait commence par le bloc dans lequel le label HOME est programmé. D'autres points d’entrée dans le programme de retrait peuvent être définis dans le programme d'avance à l’aide la définition de vecteurs de retrait (voir chapitre 9 "Instructions de contrôle des process et des programmes). Avec une programmation de retrait adaptée et sans lacune, l’utilisateur a la possibilité, en cas de défaut ou de perturbation, ainsi que dans tous les cas d’arrêt d'urgence, de ramener les stations ou la machine dans une position de base et ce, sans danger ni risque de collision, quelle que soit de la complexité de la situation d'usinage. Exemple .HOME MRF D0 G40 G47 G53 G90 G74 Z0 F1000 G74 X0 Y0 F1000 RET Référence générale Prise d’origine du magasin d’outil Annulation des corrections D Annulation des corrections Prise d’origine axe Z Prise d’origine axe X et Y Remarque: La programmation d'un Programme de retrait n'est nécessaire que dans le cas où le constructeur de machine l’a fixée dans les paramètres process. DOK-MTC200-NC**PRO*V17-ANW1-FR-P 2-4 Programmes CN 2.3 Manuel de programmation CN 17VRS Programmation spécifique au process La CN est partagée en 7 process au maximum. Chaque process dispose d'un traitement de bloc propre qui combine les données du programme CN avec les données telles que point zéro, liste de réglage... Le nombre de process est déclaré dans les paramètres système. Lorsqu’il y a plus de 2 process, on utilise en général le process 0 pour la synchronisation des autres process. Exemple Application de plusieurs process sur un tour mono broche à deux chariots avec dispositif de fraisage • Process 0 Synchronisation des process 1 et 2. Coordonne si les autres process travaillent simultanément et de façon asynchrone ou synchrone • Process 1 Le process 1 contient les axes X et Z de la tête revolver supérieure. • Process 2 Le process 2 contient les axes X et Z de la tête revolver inférieure, la broche principale S1, l’axe C ainsi que la broche S2 comme broche d'outil. process 1 programme n° 10 X N0000 G90 G54 G18 N0001 G00 X20 Z0 . . . N00xx M030 Z process 1 process 0 programme n° 10 N0000.START N0001 DP1 DP2 N0002 SP1 10 N0003 SP2 10 N0004 AP1 AP2 C S2 process 2 process 2 programme n° 10 N0000 G90 G54 G18 N0001 G00 X20 Z0 . . . N00xx M030 Z X S2 Fig. 2-4: Tour mono broche à deux chariots pour fraisage tourné DOK-MTC200-NC**PRO*V17-ANW1-FR-P Programmes CN 2-5 Manuel de programmation CN 17VRS 2.4 Eléments d’un bloc Un bloc CN contient les données pour l'exécution d'un pas de travail. Un bloc CN est constitué d'un ou de plusieurs mots ainsi que d'instructions de contrôle CN. La longueur maximale d'un bloc CN est de 240 caractères, il peut-être partagé au maximum en quatre lignes. Un bloc CN comporte les éléments suivants : • Numéro de bloc, • Etiquette de saut, • Mots CN (Instructions CN) • Remarques • Commentaires dans le programme et • Commentaires dans le programme source. Structure d’un bloc CN : N0020 Ordre technique programme G54 G01 X50 Y60 Appel de correcteur Instructions de déplacement Instructions de géométrie N° de bloc F2000 S1500 Instructions de technologie M03 Fonction auxiliaire Mots CN (Instructions CN) Tous les éléments d'un bloc CN, excepté les attributions de fonction, doivent être séparés au minimum par un espace. ATTENTION La priorité d’exécution d’un bloc CN dans la mémoire CN est fixée comme indiqué ci-dessous : N° de bloc Etiqu. de saut Fonct. aux. avant mvt. Code G Variables Valeurs d’axe N1234 .END E M03 G01 @100=x X100 Y100 Paramètre Valeur F Valeur IPO S I0 J50 F1000 Fonct. aux. après mvt. S800 M03 Instructio Instruction Evène ns de s d’outils ments palettes Instruct Instructions contrôle ions proces programme s SEL 1 DP 1 MTP T6 SE 5 HLT Numéro de bloc Syntaxe N = 0..9 Chaque bloc CN commence par la lettre N suivie d’un nombre entier non signé de quatre chiffres représentant le numéro le bloc. La numérotation des blocs d'un programme CN commence toujours par 0000. La numérotation est automatiquement incrémentée par pas de 1 par l'interface utilisateur. Lors de l’insertion de blocs CN à partir de l’interface utilisateur, les numéros de tous les blocs suivants sont modifiés automatiquement. DOK-MTC200-NC**PRO*V17-ANW1-FR-P 2-6 Programmes CN Manuel de programmation CN 17VRS Blocs optionnels Sur une machine-outil à commande numérique, il doit être possible, de façon simple, de masquer des blocs CN afin de laisser exécuter ou de masquer de façon ciblée certaines fonctions telles que cycles de mesure, chargement et déchargement de pièces, et donc les blocs CN correspondant.. Les blocs du programme pièce ne devant pas être exécutés à chaque déroulement de programme sont repérés par la barre oblique / en début de bloc. Les blocs optionnels ne seront alors exécutés par la commande que lorsque l'utilisateur aura activé la fonction "Blocs optionnels„ sur le pupitre machine. Exemple N0100 G01 X20 F400 ;Coupure mesure additionnelle N0101 / G00 X300 M03 S6500 N0102 / G01 Z45 F100 N0103 / G00 X370 M05 N0104 / HLT Lors de l’exécution cyclique la CNC masque une série de blocs optionnels lorsque l'opérateur a activé la fonction bloc optionnel avant l’exécution du premier bloc de la séquence. Lorsque l'opérateur appuie sur la touche "Blocs optionnels„ lors de l'exécution d'une séquence de blocs optionnels, cela n'a pas de répercussion sur l'exécution. La CNC continue l’usinage sans en tenir compte. En exécution bloc à bloc la CNC vérifie au début de chaque bloc optionnel si la fonction de masquage est active ou non. Contrairement à l'exécution en continu, il est ainsi possible à l’opérateur de masquer certains blocs précis. Le caractère de bloc optionnel suspend la préparation des blocs. ATTENTION 2.5 Une exploitation en contournage n’est ainsi pas possible avec des blocs optionnels. Mot CN Un mot CN comporte les instructions de la norme DIN 66025 et les extensions spécifiques INDRAMAT. Le mot CN est partagé en : . • instructions géométriques • instructions de technologie • instructions de déplacement • fonctions auxiliaires • appel de correcteur • extensions Ø Position d’axe X__ Y__ Ø vitesse de broche, avance S__ F__ Ø Ø Ø rapide, interpolation circulaire G__ G__ arrosage, outil M__ T__ correcteur d’outil, point zéro G__ G__ sauts conditionnels, calculs Ø Un mot est composé d'une lettre d'adresse et d'une valeur numérique permettant de déclencher des mouvements machine et des fonctions auxiliaires Lettre d’adresse La lettre d’adresse est en général un caractère de texte. DOK-MTC200-NC**PRO*V17-ANW1-FR-P Programmes CN 2-7 Manuel de programmation CN 17VRS Valeur numérique La valeur numérique peut contenir un signe et un point décimal.. Le signe est placé entre la lettre d'adresse et la valeur numérique. Le signe + ne doit pas être programmé. structure d'un mot lettre adresse valeur numérique X 500 structure d'adresse étendue lettre adresse numéro S 1 espace valeur numérique 1000 Fig. 2-5: Structure d’un mot Exemple ; structure d’adresse étendue pour les axes X1- et Y1 G01 X1 50.45 Y1 35.456 F1000 position de filetage 1 Z10 Z en distance de sécurité ère M103 S1 1000 1 broche 1000 U/min Remarque: Il doit y avoir un espace entre l’adresse et la valeur numérique associée. La position du point décimal est en rapport avec la résolution possible : X0.00001 = X0.0001 = X0.001 = 0.01 µm 0.1 µm 1 µm etc. Avec des données décimales les zéros de tête et de queue peuvent être omis. L'introduction avec point décimal est possible avec les adresses suivantes : Adresses d’axe : I, J, K, P, S, F, contenu de @xxx Remarque: Le nombre maximum de chiffres après la virgule est défini dans les paramètres process. Marque de saut Syntaxe . = 0..9 , A..Z , a..z Une marque de saut renvoie à un label de saut dans un bloc cible. Une marque existe toujours en deux endroits: une fois dans le bloc où a lieu l’aiguillage et une fois dans le bloc cible du saut. Une marque de saut caractérise toujours un aiguillage dans le programme, indépendamment du fait que le saut soit conditionnel ou inconditionnel. L'adresse de saut (label cible) peut être dans le même programme CN. Lorsque l’adresse de saut n’est pas trouvée dans le programme, elle est recherchée dans le programme 99 ou dans le programme 0. Certaines marques de saut sont, de par leur nom, réservées aux cycles fixes de la Société INDRAMAT ou du constructeur de machine. ATTENTION DOK-MTC200-NC**PRO*V17-ANW1-FR-P 2-8 Programmes CN Manuel de programmation CN 17VRS La marque de saut commence par un point décimal suivi au minimum d’un et au maximum de six caractères imprimables. Il n’y a pas de différenciation entre les majuscules et les minuscules. Le caractère ‘*’ derrière le point décimal est réservé pour les cycles fixes INDRAMAT. Lorsqu’une marque de saut est programmée dans un bloc, elle doit se trouver comme premier élément derrière le numéro de bloc. Un ordre de saut avec une marque de saut appartient aux instructions de commande de programme et est exécuté avec la dernière priorité. Exemple G54 G90 G00 X0 Z0 G04 F5 BSR .ENDE RET .ENDE M05 G04 F1 RTS Remarque Syntaxe [ Texte ] Chaque bloc CN peut contenir une remarque qui est affichée, après l’exécution du bloc, dans le menu de diagnostic de l’interface utilisateur. La remarque reste affichée dans la ligne de diagnostic tant qu’elle n’est pas écrasée par une nouvelle remarque. Pour effacer une remarque dans la ligne de diagnostic, il faut programmer une remarque vide. La remarque est effacée de la ligne de diagnostic au lancement du programme. On ne peut programmer qu’une remarque par bloc. Une remarque est délimitée par deux crochets et doit avoir une longueur maximum de 48 caractères. On peut utiliser l’ensemble du jeu de caractères ASCII imprimables. La remarque peut être placée à n’importe quel endroit dans le bloc CN mais elle sera, dans tous les cas, traitée comme dernière fonction, à l’exception des commentaires. Exemple N1234 G01 G54, G90 [ Déplacer X à distance de sécurité ] F1000 N1235 X500 N1236 [ Déplacer Z à distance de sécurité ] G01 G51 G90 F1000 N1237 Z100 Commentaire Syntaxe ( Texte ) Un commentaire peut être inclus dans chaque bloc CN. Un commentaire est délimité par deux parenthèses et doit avoir une longueur maximum de 80 caractères. On peut utiliser l’ensemble du jeu de caractères ASCII imprimables. Le commentaire peut être placé à n’importe quel endroit dans le bloc CN. Il est transmis dans la mémoire de la CN et est inséré dans l’affichage du bloc courant.. Un bloc CN peut contenir au maximum un commentaire et une remarque. Exemple N1234 G00 (Déplacer X sur position de départ) X150 N1235 (Déplacer Z sur position de départ) G01 Z10 Restriction: Les remarques et commentaires ne doivent pas être programmés entre des fonctions G isolées. DOK-MTC200-NC**PRO*V17-ANW1-FR-P Programmes CN 2-9 Manuel de programmation CN 17VRS Commentaire dans le programme source Syntaxe ; Texte Chaque bloc CN peut contenir un commentaire dans le programme source. Ce commentaire est introduit par un point virgule. Tous les caractères après le point virgule sont interprétés comme commentaire. La notion de commentaire dans le programme source signifie que ce commentaire n’est disponible que dans le programme source et donc sur l’interface opérateur, mais n’est pas disponible dans la mémoire de la CN Cela présente l’avantage, par rapport à l’autre type de commentaire, de préserver de la place dans la mémoire de la commande. Un point virgule en début de bloc indique que l’ensemble du bloc est un commentaire, il n’y a pas de numéro de bloc. Exemple N0050 G01 X250 Y100 F1000 ; Appel du cycle de centrage N0051 BSR .*ZENBO 6. Position de perçage Restriction: Les commentaires dans le programme source ne doivent pas être programmés entre des mots CN isolés. 2.6 Adresses disponibles Lettres d’adresse disponibles dans la CN : A réservé pour désignation d’axe P angle B réservé pour désignation d’axe Q fonction annexe C réservé pour désignation d’axe R rayon D correcteur S vitesse, position de broche E point de coupe T numéro d’outil F avance U réservé pour désignation d’axe G fonction G V réservé pour désignation d’axe H libre W réservé pour désignation d’axe I paramètre d’interpolation X réservé pour désignation d’axe J paramètre d’interpolation Y réservé pour désignation d’axe K paramètre d’interpolation Z réservé pour désignation d’axe L libre @ variable M fonction auxiliaire RX distance d’application en X N numéro de bloc RY distance d’application en Y O banque de points d’origine RZ distance d’application en Z Une structure d’adresse étendue est disponible pour les adresses suivantes : A(1..3) réservé pour désignation d’axe B(1..3) réservé pour désignation d’axe C(1..3) réservé pour désignation d’axe U(1..3) réservé pour désignation d’axe V(1..3) réservé pour désignation d’axe W(1..3) réservé pour désignation d’axe X(1..3) réservé pour désignation d’axe Y(1..3) réservé pour désignation d’axe Z(1..3) réservé pour désignation d’axe S(1..3) vitesse, position de broche Aucune distinction n’est faite dans la syntaxe CN entre majuscules et minuscules. Cela signifie que, pour programmer une position d’axe, on peut utiliser X400 ou x400. Pour des raisons de lisibilité, les instructions CN doivent, par principe être en majuscule. DOK-MTC200-NC**PRO*V17-ANW1-FR-P 2-10 Programmes CN Manuel de programmation CN 17VRS Pour les commentaires et les remarques, on peut utiliser le jeu ASCII complet. DOK-MTC200-NC**PRO*V17-ANW1-FR-P Manuel de programmation CN 17VRS Instructions de déplacement, Programmation des cotes 3-1 3 Instructions de déplacement, Programmation des cotes 3.1 Système de coordonnées Le système de coordonnées fixe la position d’un point ou d’un ensemble de points dans un plan ou dans l’espace relativement à 2 ou 3 axes CN. On utilise en général, en technique de commande numérique, un système de coordonnées cartésien direct orthogonal avec les axes X, Y et Z. Ce système se réfère aux axes principaux de la machine. Y Y B R C Z A X X Z Fig. 3-1: Système de coordonnées Tous les autres axes suivent ces trois axes principaux. A, B et C sont des axes rotatifs ou des articulations utilisant X, Y ou Z comme axe médian. L’axe A tourne autour de l’axe X, l’axe B autour de l’axe Y et C autour de Z. La direction positive de rotation correspond à une rotation à droite par rapport à l’axe. Sur une machine de fraisage, les axes principaux sont en général X, Y et Z, sur un tour les axes Z et X, sont définis en général Remarque: La désignation des axes peut être choisie librement par les paramètres d’axe! DOK-MTC200-NC**PRO*V17-ANW1-FR-P 3-2 Instructions de déplacement, Programmation des cotes 3.2 Manuel de programmation CN 17VRS Instruction de déplacement. Une instruction de déplacement ou de trajectoire occasionne le mouvement d'un axe. L'instruction de déplacement est composée de la lettre d'adresse de l'axe (par ex. X, Y ou Z), suivi du signe (+, -) correspondant à la direction et du chemin à parcourir : la valeur de coordonnée. Syntaxe Syntaxe: lettre adresse valeur de coordonnée Z 100.5 signe égal lettre adresse variable @120 = X lettre adresse valeur de coordonnée 245.65 espace X1 La valeur de coordonnée est composée : • du signe, • de 5 ou 6 chiffres avant la virgule, • du point décimal et • de 4 ou 5 chiffres après la virgule. • Lorsque aucun chiffre n'est programmé, la valeur de coordonnée est positive. Lorsque la valeur de coordonnée n'a pas de chiffres après le point décimal, celui-ci peut-être omis. Les zéros de tête et de queue peuvent être omis. Lorsque le point décimal est programmé, il doit y avoir au moins un chiffre derrière. Il ne doit pas y avoir, au total, plus de dix chiffres avant et après le point décimal. La plage maximale de programmation est de -214748.3648 à +214748.3647 avec 4 chiffres après le point décimal et de : -21474.83648 à +21474.83647 avec cinq chiffres après le point décimal. DOK-MTC200-NC**PRO*V17-ANW1-FR-P Manuel de programmation CN 17VRS 3.3 Instructions de déplacement, Programmation des cotes 3-3 Données de dimension Les instructions de déplacement des axes peuvent être introduites de deux façons : • données absolues (G90) ou • données incrémentales (G91). Dimension absolue ’G90 Lors de données de dimension absolue, toutes les informations de dimension font référence à un point zéro fixe. Lors du lancement du programme, l'état de base est G 90. Cet état reste actif tant qu'il n'est pas remplacé par G 91. Dans le programme CN, la programmation de G 90 n’est nécessaire que pour annuler G 91. Exemple Y 100 80 [P2] [P3] [P1] [P4] 60 40 20 20 40 60 80 100 120 140 X Fig. 3-2: Données de dimension absolue G00 G90 G54 X0 Y0 Z10 S1000 M03 G01 X50 Y50 F500 BSR .BOHR Y80 BSR .BOHR X100 BSR .BOHR Y50 BSR .BOHR M05 RET .BOHR G01 Z-10 F300 G04 F2 Z3 RTS DOK-MTC200-NC**PRO*V17-ANW1-FR-P Position de départ [P1] Appel du SP de perçage [P2] Appel du SP de perçage [P3] Appel du SP de perçage [P4] Appel du SP de perçage Arrêt broche Fin de programme Sous-programme (SP) de perçage Perçage à la profondeur Z Temporisation 2 secondes Outil à distance de sécurité Fin de sous-programme 3-4 Instructions de déplacement, Programmation des cotes Manuel de programmation CN 17VRS Dimension incrémentale 'G91' Les données de dimension incrémentale définissent toutes les données par rapport à la position du début du bloc (programmation relative). G 91 reste actif jusqu'à la fin du programme ou jusqu'à annulation par G 90 Exemple Y 100 80 [P2] [P3] [P1] [P4] 60 40 20 20 40 60 80 100 120 140 X Fig. 3-3: Données de dimension incrémentale G00 G90 G54 X0 Y0 Z3 S1000 M03 G01 G91 X50 Y50 F500 BSR .BOHR Y30 BSR .BOHR X50 BSR .BOHR Y-30 BSR .BOHR M05 RET .BOHR perçage Position de départ [P1] Appel du SP de perçage [P2] Appel du SP de perçage [P3] Appel du SP de perçage [P4] Appel du SP de perçage Arrêt broche Fin de programme Sous-programme (SP) G01 Z-13 F300 G04 F2 Z13 RTS Perçage à la profondeur Z Temporisation 2 secondes Outil à distance de sécurité Fin de sous-programme de DOK-MTC200-NC**PRO*V17-ANW1-FR-P Manuel de programmation CN 17VRS 3.4 Instructions de déplacement, Programmation des cotes 3-5 Points d’origine Sur chaque machine à commande numérique sont définis des points d'origine et différents points de référence par rapport auxquels les dimensions des pièces sont définies. Point d’origine machine Fehler! Textmarke nicht definiert. Le point d’origine machine est défini à l'origine du système de coordonnées machine et ne peut pas être déplacé. Représentation graphique du point d’origine machine Point de référence machine 0 Le point de référence machine est un point fixe dans la zone de travail de la machine. Il est utilisé, lors de la mise sous tension de la machine, pour fixer une position d'origine définie. Le point de référence machine est fixé par le constructeur machine pour chaque axe équipé d'un système de mesure incrémentale. Représentation graphique du point de référence machine 5 Remarque: Les mesures de référence sont fixées dans les paramètres machine. Point d’origine pièceFehler! Textmarke nicht definiert. Le point d'origine est l'origine du système de coordonnées de la pièce. Il est défini comme point d'origine programme par le programmateur pour fixer toutes les cotes de la pièce. La relation avec le point d'origine machine est déterminée lors du réglage de la machine, avec le décalage du point d'origine. Représentation graphique du point d’origine pièce : Exemple R Y table pièce W M DOK-MTC200-NC**PRO*V17-ANW1-FR-P X 3-6 Instructions de déplacement, Programmation des cotes Manuel de programmation CN 17VRS Fig. 3-4: Points d’origine – Machine de fraisage/perçage X R M W Z Fig. 3-5: Points d’origine - tour (usinage chariot avant) 3.5 Décalages d’origine Les décalages d'origine permettent le décalage de l'origine d’un axe de coordonnées d'une valeur définie par rapport au point zéro machine. La position du point zéro machine reste figée dans la CN et n'est pas modifiée par un décalage d'origine. Z Z' P Z Angle de rotation 'P' pour le plan actuel (G18) Y P X' X 'DPO' décalage de point d'origine Y X Fig. 3-6: Décalage d’origine Les décalages d’origine suivants sont disponibles dans la CN : • Décalage d’origine absolu programmable G50, • Décalage d’origine relatif programmable G51, • Décalage d’origine pièce programmable G52, • Décalage d’origine réglable G54 ... G59 et • Offset général réglable dans la table de point d’origine. On peut à l’aide des décalages d’origine G50, G51 et G54 ... G59 ainsi qu’avec le décalage d’origine pièce G52 fixer le point zéro des coordonnées de chaque axe à une position déterminée à l'intérieur ou à DOK-MTC200-NC**PRO*V17-ANW1-FR-P Manuel de programmation CN 17VRS Instructions de déplacement, Programmation des cotes 3-7 l’extérieur de la zone de déplacement. Il est ainsi possible d'exécuter un programme CN identique à différentes positions sur la machine. La position des points d'origine machine sur chaque axe est programmée dans les paramètres entraînement comme différence par rapport au point de référence. La valeur programmée dans les paramètres d'entraînement correspond à la valeur des coordonnées du point de référence dans le système de coordonnées machine. Annulation de tous les dégalages d'origine Origine pièce programmable Décalages d'origine réglables Introduction et modification par IHM modifié par O9 O8 programme CN G53 G52 O9 O8 O2 O1 O0 O2 O1 O0 G54 G59 G54 à G59 Offset général réglable dans la table des points d'origine Introduction par IHM W Décalage absolu d'origine programmable G50 Chargé par programme CN Annulation par sélection nouveau DPO ou par G53 Décalage incrémental d'origine programmable G51 Chargé par programme CN Annulation par sélection nouveau DPO ou par G53 Décalage d'origine total par rapport au point zéro machine Fig. 3-7: Somme des décalages d’origine La somme des décalages d'origine se compose des décalages d'origine réglables G54 ... G59 ou du point de référence pièce programmable G52 DOK-MTC200-NC**PRO*V17-ANW1-FR-P 3-8 Instructions de déplacement, Programmation des cotes Manuel de programmation CN 17VRS et des décalages d'origine programmables G50, G51 ainsi que des offsets de réglage dans la table des points de référence Les décalages d’origine programmables G50 et G51 sont inactifs lors de la programmation de G52, G53, G54 ... G59. ATTENTION Décalages d’origine réglables 'G54 ... G59' Les décalages d'origine réglables sont introduits au niveau de l'interface utilisateur dans la table et des points d’origine pour les axes disponibles. Les valeurs programmées correspondent à un décalage absolu par rapport au point de référence machine. La prise en compte a lieu après la programmation de G54 ... G59, dans le même bloc CN, lorsque l'axe concerné est programmé. G54 ... G59 sont suspendus par G53 ou G52 . • En fonction du réglage dans les paramètres process, les décalages d’origine réglable peuvent être l’état de base à la mise sous tension lors du lancement du programme CN. Exemple Y Y 100 80 80 [P2] 60 [P5] 40 60 20 [P1] 40 20 [P3] [P4] 20 40 60 80 100 120 X Programmation dans la table des décalages d'origine sous IHM avec G54: X52.1 Y48.8 20 40 60 80 100 120 X Fig. 3-8: Décalage d’origine réglable G54 G00 G90 G54 X0 Y0 Z10 S1000 M03 G01 X50 Y50 F1000 BSR .BOHR X70 Y60 BSR .BOHR X90 Y70 BSR .BOHR X110 Y80 BSR .BOHR M05 RET .BOHR perçage G01 Z-10 F300 Position de départ [P1] [P2] Appel du SP de perçage [P3] Appel du SP de perçage [P4] Appel du SP de perçage [P5] Appel du SP de perçage Arrêt broche AUS Fin de programme Sous-programme (SP) de Perçage à la profondeur Z DOK-MTC200-NC**PRO*V17-ANW1-FR-P Manuel de programmation CN 17VRS Instructions de déplacement, Programmation des cotes G04 F2 Z3 RTS 3-9 Temporisation 2 secondes Outil à distance de sécurité Fin de sous-programme Rotation du système de coordonnées avec un angle 'P' La rotation du système de coordonnées permet l'adaptation du système de coordonnées de la pièce à celui de la machine. L’angle de rotation P est associé aux décalages d'origine isolés G54 ... G59, G50, G51 et à l’offset programmable général. La rotation de coordonnées se fait toujours dans le plan sélectionné (par ex. G17). L’angle de rotation est programmé dans les décalages d'origine réglables G54 ... G59 et dans l’offset général par l'interface opérateur sous la désignation PHI dans le tableau de point d'origine. Avec les décalages d’origine programmables G50 et G51 l’angle de rotation est programmé sous l’adresse Pxxx. • Les conditions du décalage d'origine sont valables pour la somme de tous les angles de rotation actifs. • L’angle de rotation est, par principe, actif dans le bloc CN suivant. • Dans le système de commande, l’angle de rotation est calculé modulo 360° dans une plage de 0° à 360°. Cela signifie par exemple que la programmation d'un angle de rotation de 540° est interprétée comme un angle de 180°. • Aucune rotation de coordonnée ne peut être programmée dans le décalage programmable d'origine pièce G 52 • Exemple Y 80 Y [P3] X [P2] 60 40 20 P1 Programmation dans la table des décalages d'origine sous IHM avec G54: X52.1 Y40 PHI 45° 20 40 60 80 100 120 X Fig. 3-9 : Décalage d’origine réglable G 54 avec rotation de coordonnées G00 G90 G54 X0 Y0 Z10 S1000 M03 G01 X40 Y70 F800 BSR .BOHR X80 BSR .BOHR M05 RET .BOHR RTS DOK-MTC200-NC**PRO*V17-ANW1-FR-P Position de départ [P1] [P2] Appel du SP de perçage [P3] Appel du SP de perçage Arrêt broche AUS Sous-programme (SP) de perçage Fin de sous-programme 3-10 Instructions de déplacement, Programmation des cotes Manuel de programmation CN 17VRS Banque de point d’origine 'O' La CNC offre la possibilité d'adresser jusqu'à dix fois les décalages d'origine réglables G54 ... G59 avec des valeurs de coordonnées différentes. Le tableau des décalages d'origine peut être présent jusqu'à dix fois dans la CNC. La désignation de chaque tableau de décalage d’origine est la banque de point d'origine. Remarque: Le nombre de banques de points d’origine est fixé par le constructeur de machine dans les paramètres process ! Dans le programme CN, le critère de sélection est l’instruction O[0..9]qui, avec une donnée de 1 chiffre, adresse le numéro d’une banque de points d’origine parmi 10. . • L’état de base correspond à la banque de point d’origine 0. • Si on ne travaille qu’avec la banque de points d’origine 0 ou si cette banque doit être la première active dans le programme CN, elle ne doit pas être programmée séparément. • Si on doit changer de banque de points d’origine dans le programme CN, la fonction G53 est automatiquement active. • La sélection d’une banque de points d’origine reste modale jusqu’à la fin du programme. La sélection d’une banque de points d’origine est annulée par les instructions RET et BST. • L’instruction O doit être programmée dans un bloc CN séparé et doit être activée au moins un bloc CN avant la sélection d’un nouveau décalage d’origine. Décalages d'origine réglables Introduction et modification sous IHM Banque de PO O9 Banque de PO O9 Banque de PO O8 Banque de PO O7 Banque de PO O6 Banque de PO O5 Banque de PO O4 Banque de PO O3 Banque de PO O2 Banque de PO O1 Banque de PO O8 Banque de PO O7 Banque de PO O6 Banque de PO O5 Banque de PO O4 Banque de PO O3 Banque de PO O2 Banque de PO O1 Banque de PO O0 Banque de PO O0 G54 G59 Changement des banques de point d'origine pour introduction et modification des décalages d'origine sous IHM Fig. 3-10: Banque de point d’origine sur l’interface opérateur DOK-MTC200-NC**PRO*V17-ANW1-FR-P Manuel de programmation CN 17VRS Instructions de déplacement, Programmation des cotes 3-11 Exemple Y Y 100 80 60 80 Y 60 [P3] [P4] 100 40 [P2] [P5] 80 20 60 [P1] 40 20 Banque de points d'origine 0 Valeur G54: X17.5 Y46.5 40 20 40 60 80 100 X [P8] [P7] 20 [P6] 20 40 60 80 100 X Banque de points d'origine n° 1 Programmation de la table des décalages d'origine avec G54: X81.0 Y29.5 20 40 60 80 100 120 X Fig. 3-11: Appel de deux banques de points d’origine avec G54 [La banque d’origine n°.0 est active] G00 G90 G54 X0 Y0 Z10 S1000 M03 G01 X30 Y30 F1000 BSR .BOHR Y70 BSR .BOHR X70 BSR .BOHR Y30 BSR .BOHR [Activer banque n°1] O1 G00 G54 X0 Y0 G01 X40 Y40 F1000 BSR .BOHR X60 Y60 BSR .BOHR M05 RET .BOHR perçage G01 Z-10 F300 G04 F2 Z3 F1000 RTS DOK-MTC200-NC**PRO*V17-ANW1-FR-P Position de départ [P1] [P2] Appel du SP de perçage [P3] Appel du SP de perçage [P4] Appel du SP de perçage [P5] Appel du SP de perçage Position de départ [P6] [P7] Appel du SP de perçage [P8] Appel du SP de perçage Arrêt broche AUS Fin de programme Sous-programme (SP) Perçage à la profondeur Z Temporisation 2 secondes Outil à distance de sécurité Fin de sous-programme de 3-12 Instructions de déplacement, Programmation des cotes Manuel de programmation CN 17VRS Décalage d’origine absolu programmable 'G50' Décalage d’origine incrémental programmable 'G51' Les décalages d’origine programmable G50 et G51 décalent le point d’origine d’usinage • en absolu avec G50 . • en relatif avec G51 par rapport au dernier point d’origine pièce sélectionné. Les valeurs de décalage sont programmées sous les lettres adresse. On a en outre la possibilité d’effectuer une rotation du système de coordonnées d’usinage, en absolu avec G50 ou en relatif avec G51, d’un angle donné sous l’adresse P. • Les décalages d’origine programmables G50 et G51 sont actifs dans le bloc. Le décalage reste activé jusqu’à la prochaine modification du décalage d’origine ou du système de coordonnées. • Il ne faut programmer aucune autre fonction dans le bloc où est programmé un G50 ou un G51. Exemple X 80 X X 100 100 80 60 80 40 60 20 60 40 20 40 60 80 100 Z ZO 40 X2 P2 20 P3 P1 P4 P5 20 G54: Z18.0 X15.0 P0 20 20 40 40 60 60 80 100 80 Z 100 120 X Fig. 3-12: Décalage d’origine programmable G50 G00 G90 G54 X0 Z0 BSR .KONT G50 X2 BSR .KONT RET .KONT G01 X10 Z48 F750 X25 Z59 Z92 F1500 X11 Z100 F600 Z113 F1000 G00 X40 X0 RTS [P0] Appel du sous-programme de contournage Décalage d’origine de 2mm en X eme 2 appel du sous-programme de contournage Sous-programme de contournage [P1] [P2] [P3] [P4] [P5] Retour à la distance de sécurité Z0 [P0] Retour au programme principal DOK-MTC200-NC**PRO*V17-ANW1-FR-P Manuel de programmation CN 17VRS Instructions de déplacement, Programmation des cotes 3-13 Point d’origine pièce programmable 'G52' La fonction G52 permet de programmer sous une adresse d’axe un point d’origine pièce pour tous les axes disponibles. Lors de l'exécution de G52, les valeurs de coordonnées suivant le G52 sont attribuées aux positions actuelles. Cela correspond à la définition du point zéro pièce par rapport à la position actuelle. • Les axes qui ne sont pas programmés avec G52 travaillent en système de coordonnées machine. • La programmation de G52 provoque un G53. Tous les décalages d’origine actifs sont annulés. • Aucune autre fonction ne doit être programmée dans un bloc où se trouve G52. • On ne peut pas programmer de rotation de coordonnées P avec G52. Exemple Y 80 Y Y 100 60 100 80 60 P5 20 80 P5 P4 P2 P3 60 40 40 40 P4 P2 20 P3 P1 P1 20 40 60 80 100 X G52 X0 Y0 Table DPO X20 Y30 20 20 40 60 80 100 X G52 X-70 YO L'entrée dans la table des décalages de point d'origine serait, avec G52 : Y90 Y30 20 40 60 80 100 120 Fig. 3-13: Appel de G52 G90 G53 G00 X20 Y30 G52 X0 Y0 BSR .KONT G52 X-70 Y0 BSR .KONT RET .KONT G00 X0 Y0 G01 X40 Y20 F1000 X100 Y80 X40 Y20 G00 X0 Y0 RTS DOK-MTC200-NC**PRO*V17-ANW1-FR-P Appel de G52 Appel du sous-programme Appel de G52 Appel du sous-programme Sous-programme [P1] [P2] [P3] [P4] [P5] [P2] Retour au programme principal X 3-14 Instructions de déplacement, Programmation des cotes Manuel de programmation CN 17VRS Annulation des décalages d’origine 'G53' La programmation de G53 annule tous les décalages d'origine actifs. Cela provoque un passage du système de coordonnées pièce au système de coordonnées machine. • En fonction du réglage par paramètre process, G53 peut être l’état de base lors du lancement programme CN. • Lorsque G53 est programmé dans un bloc avec G91, l'affichage des positions se fait par rapport aux valeurs de mesure de la machine. • Lorsque l’annulation des décalages G53 est appelée alors que des correcteurs de trajectoire d’outil (G41, G42) sont actifs, cela force en interne un G40 (annulation des corrections de trajectoire d’outil). La correction de trajectoire d’outil sera de nouveau élaborée au prochain bloc de déplacement. Offset général réglable dans le tableau de point d’origine Grâce à l’offset général réglable de la table de point d’origine, la CNC offre la possibilité d'un décalage supplémentaire par rapport au décalage de point d'origine réglable et programmable. L’offset général réglable a une action additive aux décalages de point d'origine réglables ou programmables. Cela signifie que l’offset général réglable n'est actif que lorsqu’un décalage d'origine réglable ou programmable est activé. • G53 annule l’offset général réglable jusqu’au prochain appel d’un décalage d’origine. • Un angle de rotation peut être programmé sous l’adresse PHI dans le tableau des points d’origine. Sa valeur s’ajoute aux angles de rotations déjà actifs. • Conformément aux conditions ci-dessus, l’offset général ne peut pas être programmé seul. Lecture et écriture de données DPO dans le programme CN 'OTD' L’instruction OTD (Offset Table Data) permet, depuis le programme CN, la lecture et l’écriture des données des tableaux de décalage de point d'origine (DPO) et des décalages de points d'origine actif du programme CN. Syntaxe M P O V A OTD ([1/2], [0..6], [0..9], [0..9], [1..10]) Axe Décalage Banque d'origine Process Mémoire CN Une description détaillée de l'instruction OTD se trouve dans le chapitre „Lecture et écriture de données DPO dans le programme CN. DOK-MTC200-NC**PRO*V17-ANW1-FR-P Manuel de programmation CN 17VRS 3.6 Instructions de déplacement, Programmation des cotes 3-15 Sélection du plan d’interpolation La sélection du plan est une condition importante pour l'exécution correcte de toutes les instructions de déplacement d'un programme CN. Elle informe la commande du plan utilisé pour l'usinage afin que les valeurs de correction d'outils soient calculées correctement. Elle joue aussi un rôle en cas d’interpolation circulaire. Sélection de plan 'G17’, 'G18’, 'G19’ Les 3 axes de coordonnées X, Y et Z définissent les 3 plans XY, ZX et YZ. G17 G18 G19 Sélection du plan Sélection du plan Sélection du plan XY ZX YZ Les 3 axes principaux X, Y et Z, forment un système de coordonnées cartésien sur lequel s’appuient les plans XY, ZX et YZ. Le troisième axe est perpendiculaire au plan correspondant. Remarque: La signification des axes du système de coordonnées est définie par le constructeur de machine dans les paramètres d’axe. Les conditions de trajectoire G17, G18 ou G19 indiquent à la CN le plan d'usinage souhaité, l’axe de l'outil étant perpendiculaire au plan usinage. L’axe d’outil est figé par le type de machine, le plan d'usinage est ainsi déterminé. Ordonnée 2ème axe [Y] G18 Plan ZX G19 G17 Plan YZ Abscisse 1er axe [X] Plan XY Cote 3ème axe [Z] Fig. 3-14: Plans d’usinage Correction de longueur d’outil La correction de longueur d’outil a lieu dans la direction de l’axe d’outil. Elle se fait perpendiculairement au plan d’usinage. Correction de trajectoire d’outil La correction de trajectoire d’outil est toujours établie dans le plan d’usinage actif. Un changement de plan d’usinage entraîne la suspension de la correction de trajectoire d’outil. Après changement, la correction de trajectoire d’outil est appliquée dans le nouveau plan. Interpolation circulaire Les interpolations circulaires ne sont possibles que dans le plan d'usinage. Une interpolation hélicoïdale superpose à une interpolation circulaire dans le plan d'usinage un mouvement linéaire en direction de l'axe de l'outil. Remarque: Le plan de base est défini par le constructeur de machine dans les paramètres process. DOK-MTC200-NC**PRO*V17-ANW1-FR-P 3-16 Instructions de déplacement, Programmation des cotes Manuel de programmation CN 17VRS Une modification du plan d’usinage remplace le plan d’usinage précédent et reste modale. À la fin du programme ou sur un Control Reset le plan de base est sélectionné. Sélection libre de plan 'G20' La sélection libre de plan rend possible : • de choisir les axes définissant le système de coordonnées cartésien • de définir, dans ce système, le plan de travail ainsi que l’axe perpendiculaire. Fonctionalité des axes linéaires principaux Sig. axe X (1er axe lin. principal) Sig. axe Y (2ème axe lin. principal) Fonctionalité des axes secondaires Sig. axe Z (3ème axe lin. principal) G17 1er axe du 2ème axe du Axe perpenplan de travail plan de travail diculaire G18 2ème axe du Axe perpenplan de travail diculaire G19 Axe perpendiculaire G20 1er axe du 2ème axe du Axe perpenplan de travail plan de travail diculaire Sig. axe U (1er axe secondaire) Sig. axe V (2ème axe secondaire) Sig. axe W (3ème axe secondaire) Fonctionalité des axes rotatifs principaux Sig. axe A (1er axe rot. principal) Sig. axe B (2ème axe rot. principal) Sig. axe C (3ème axe rot. principal) Axe A Axe B Axe C 1er axe du plan de travail 1er axe du 2ème axe du plan de travail plan de travail Sélection libre de plan Axe X Axe Y Axe U Axe Z Axe V Axe W Fig. 3-15: Principe de fonctionnement de la sélection de plan (Exemple pour l’usinage d’un corps de cylindre avec G20 Z0 C0 X0) Programmation Syntaxe Conditions aux limites La sélection libre du plan se fait avec G20. L’utilisateur peut décrire la er e suite des axes qui assurent la fonction du 1 et du 2 axe du plan de travail et l’axe perpendiculaire au plan de travail. er e G20 [1 axe du plan] [2 axe du plan] {axe perpendiculaire} [ ]: paramètre obligatoire du plan de travail { }: paramètre optionnel • Un axe ne peut être programmé qu’une seule fois dans une instruction G20. • Les axes du magasin d’outil et les broches sont exclues. • L’utilisateur doit programmer 2 ou 3 axes avec G20. • Le plan de travail peut être défini par 2 axes circulaires. • Le 3 axe (axe perpendiculaire) doit être un axe linéaire. e • Lorsqu’un bloc CN contient l’instruction G20, aucun axe ne doit être programmé en dehors des axes de description. • Lorsque aucun axe n’est programmé comme axe perpendiculaire, la CN conserve l'axe actuel. • Chaque adresse d’axe doit contenir la valeur 0. • Les instructions G17... G20 forment un groupe (Groupe 2 de code G) • Une modification de sélection du plan de travail remplace le plan de travail précédent et reste modale. DOK-MTC200-NC**PRO*V17-ANW1-FR-P Manuel de programmation CN 17VRS Instructions de déplacement, Programmation des cotes 3-17 • Lors de la fin du programme (BST, RET, JMP, M02 et M30), sur un Control Reset et au passage en mode manuel, lorsque le JOG des axes entraîne un reset (définition par paramètre process), la CN choisit le système de coordonnées de base défini par paramètre (paramètre d’axe Cxx.053, Signification des axes) et sélectionner aussi le plan de travail correspondant (paramètre process Bxx.004 Sélection de plan). • Le constructeur de machine (pour des raisons de sécurité) doit associer aux axes concernés par l'instruction G20, les fonctionnalités d'axe nécessaires dans les paramètres de signification d’axe. Fonctions CN • L'affectation des paramètres d’interpolation I, J et K se fait en interpolation circulaire avec G20 actif de même façon qu’avec G17. Le paramètre d’interpolation (correspondant à l'axe perpendiculaire au plan de travail) ne doit pas être utilisé. . • La fonction de vitesse de coupe constante est propre à l'axe ayant la signification de l'axe X. Ce comportement particulier doit être pris en compte lors d'une sélection libre de plan, lorsque qu'un autre axe correspond à la désignation de l'axe X. • Les filetages (G33), taraudages (G63, G64 et G65) et les avances par tour (G95) sont des fonctions de l’axe linéaire principal. Tous les axes, à l’exception des axes circulaires, correspondants aux significations des axes X, Y ou Z peuvent les exécuter. • La CN traite toujours les corrections d’outils et les corrections D sur les axes ayant les significations X, Y et Z. • Lors du passage au plan libre avec G20, la CN abandonne la fonction vitesse de coupe constante (G96) et active la fonction vitesse de broche en t/min (G97). REMARQUE • En outre, lors de la sélection libre de plan, la CN active l’interpolation linéaire (G01 Description complémentaire DOK-MTC200-NC**PRO*V17-ANW1-FR-P D’autres informations sur la sélection libre de plan se trouvent dans la description „Sélection libre de plan et usinage sur corps de cylindre„ classeur 5. 3-18 Instructions de déplacement, Programmation des cotes Manuel de programmation CN 17VRS Exemple Un centre de tournage possède, à l’intérieur d’un process, les axes suivants (axes internes au centre tournage, process 0) : Désignation axe Signification axe X1 X chariot de tournage X2 W chariot de fraisage Y Y pour fraisage Z Z pour tournage et fraisage C C pour usinage sur corps de cylindre B B axe pivotant sur chariot de fraisage U U contre poupée S1 S1 broche principale S2 S2 broche d’outil pour fraisage X1 Remarque X2 B S2 Y Z U C/S1 Fig. 3-16: Position des axes dans le centre de tournage. Sélection et assignation des axes : Pour l’exécution des différentes phases d’usinage, les plans suivants sont sélectionnés durant l’exploitation machine : Code G Axes linéaires principaux Axes circulaires principaux Axes auxiliaires Plan de travail Axe. perpe ndicul aire Remarque Achsb. X Achsb. Y Achsb. Z Achsb. U Achsb. V Achsb. W Achsb. A Achsb. B Achsb. C G18 X1 Y Z U - X2 - B C Z X1 Y Tournage (= Sélection par défaut.) G20 X2=0 Y0 Z0 X2 Y Z U - X1 - B C X2 Y Z Fraisage (correspond à. G17 avec X2) G20 Z0 X2=0 Y0 Z X2 Y U - X1 - B C Z X2 Y Fraisage (correspond à. G18 avec X2) G20 Y0 Z0 X2=0 Y Z X2 U - X1 - B C YZ X2 Fraisage (correspond à. G19 avec X2) G20 Z0 C0 X2=0 G32 RI=80 Z C X2 U - X1 - B C CZ X2 Corps de cylindre DOK-MTC200-NC**PRO*V17-ANW1-FR-P Manuel de programmation CN 17VRS Instructions de déplacement, Programmation des cotes 3-19 Lors de la sélection du système de coordonnées pour l'usinage du corps de cylindre au moyen de ‘G20 Z0 C0 X2=0’, l'affectation de la signification des axes est la suivante : • A partir de l'affectation définie par les paramètres d'axe, l’axe Z reçoit la signification d’axe X et l’axe X1 la signification d'axe Z. • Dans un deuxième temps, l’axe C reçoit la signification d'axe Y et l'axe Y la signification d’axe C. • Dans un troisième temps la CN affecte à l'axe X2 la signification de d’axe Z et à l’axe X1 la signification d’axe W 3.7 Programmation au diamètre et au rayon 'G15' / 'G16' Les pièces usinées sur un tour présentent en général une section circulaire. La CNC offre la possibilité, lors de la programmation, de mesurer la pièce selon deux façons : • selon le diamètre et / ou • selon le rayon.. La signification des fonctions G est la suivante : G15 Programmation au rayon G16 Programmation au diamètre Remarque: L’état par défaut entre programmation au rayon ou au diamètre est fixé par le constructeur de machine dans les paramètres process. La programmation au diamètre se rapporte uniquement à l’axe X. Exemple avec programmation au diamètre ØX [P4] [P3] [P2] 50 [P1] 40 Z 100 Fig. 3-17: Exemple de programmation au diamètre ; Tour, G16 par défaut selon paramètre process G01 G90 X40 Z-8 F1000 [P1] Z-30 [P2] X50 Z-63 F500 [P3] Z-100 F1000 [P4] RET DOK-MTC200-NC**PRO*V17-ANW1-FR-P 3-20 Instructions de déplacement, Programmation des cotes Manuel de programmation CN 17VRS Les conditions suivantes sont valables pour la programmation au diamètre : • avec programmation absolue (G90), la valeur programmée est interprétée comme diamètre, les valeurs négatives (diamètre) sont autorisées. Avec un cercle, le centre et le point final sont programmés en diamètre. • avec programmation incrémentale (G91), on donne la différence de diamètre par rapport au point à atteindre. L’outil se déplace de la différence de chemin programmée, depuis l'ancien diamètre jusqu'à la nouvelle position. Dans le cas de programmation d'un cercle, le centre et le point d'arrivée sont introduits en tant que différence de diamètre par rapport au point de départ. • le pas de filetage, dans le cas d'un tournage de filetage plan est interprété au rayon. • les fonctions telles que vitesse de coupe constante et avance par tour dans la direction X ne sont pas modifiées par la programmation au diamètre. • lorsque des données de position pour un axe au diamètre sont lues dans une variable, elles correspondent à des valeurs de diamètre. • les décalages d'origine pour l'axe X sont programmés au rayon. • les corrections d’outil sur l'axe X sont interprétées au rayon. • avec programmation au diamètre, le signe de diamètre ∅. est affiché pour cet axe. 3.8 Unité de mesure Lors de la mise en service d'une machine outil, on définit une unité de programmation de base (mm ou inch). Afin de pouvoir usiner, sur cette machine, des pièces cotées avec une autre unité, il est possible de changer les unités de mesure pour les valeurs de coordonnées, de vitesse et de décalage programmables au moyen de fonction G.. Remarque: L’unité de programmation de base est fixée par le constructeur de machine dans les paramètres process. Unité de mesure Inch 'G70' Lorsque l’unité de base de programmation fixée dans les paramètres process, est le millimètre, les valeurs suivantes seront, après programmation de G70, interprétées comme données en inch (pouce) et converties en millimètres dans la CN : • Instructions de déplacement (valeur de coordonnées), par ex. X5.5 inch sera converti, en interne en X139.7 mm ; • Paramètres d’interpolation I, J et K et rayon R ; • Données de vitesse F et G95 F, par ex. F20 inch/min est converti, en interne en F508 mm/min ; • Décalages programmables G50, G51 et G52 ; • Instructions de déplacement (X=@050), paramètres d’interpolation (I=@051), données de vitesse (F=@052) et décalages programmables (G50 X=@053) programmés par variables. G70 reste actif jusqu’à la fin du programme ou jusqu’à annulation par G71. DOK-MTC200-NC**PRO*V17-ANW1-FR-P Manuel de programmation CN 17VRS Instructions de déplacement, Programmation des cotes 3-21 Unité de mesure mm 'G71' Lorsque l’unité de base de programmation fixée dans les paramètres process, est le pouce, les valeurs suivantes seront, après programmation de G71, interprétées comme données en millimètre et converties en inch par la CN. • Instructions de déplacement (valeur de coordonnées), par ex. X127 mm sera converti, en interne en X5 inch ; • Paramètres d’interpolation I, J et K et rayon R ; • Données de vitesse F et G95 F, par ex. F1500 mm/min est converti, en interne en F59.06 inch/min ; • Décalages programmables G50, G51 et G52 ; • Instructions de déplacement (X=@050), paramètres d’interpolation (I=@051), données de vitesse (F=@052) et décalages programmables (G50 X=@053) programmés par variables. G71 reste actif jusqu’à la fin du programme ou jusqu’à annulation par G70 Exemple ØX 76,2 [P4] [P3] 1/4 de cercle 1 inch +K +I [P2] 50,8 45 [P1] [P0] 20 5 50,8 76,2 90 100 Fig. 3-18: Programmation de base en mm et commutation en inch G70 G00 G90 G54 X45 Z100 G01 X50,8 Z90 F800 G70 Z3 F35 G02 X3 Z2 I3 K3 G71 G01 Z5 • RET DOK-MTC200-NC**PRO*V17-ANW1-FR-P [P0] [P1] Passage en inch [P2] [P3] Passage en mm [P4] Z 3-22 Instructions de déplacement, Programmation des cotes 3.9 Manuel de programmation CN 17VRS Miroir des axes de coordonnées 'G72' / 'G73' Syntaxe Miroir autour d’un axe La fonction miroir programmable permet la réflexion d'axes de coordonnées quelconques à l'intérieur d'un programme d'usinage. Lors de la réflexion d'un axe de coordonnées, le contour original est usiné avec la même taille, à la même distance de l'autre côté de l'axe miroir et inversé L'activation et la désactivation de la fonction miroir se programment par fonction G dans le programme pièce. La fonction miroir est activée par G73 et reste modale jusqu'à suppression par G72 ou automatiquement à la fin du programme (RET, M002 / M030) ou par instruction BST. G72 remet tous les axes miroir à l'état de base. G73 <désignation d’axe>-1 miroir actif G72 suppression fonction sur tous les axes Règles: • Les signes des coordonnées de l’axe réfléchi sont inversés. • Le sens de rotation d’une interpolation circulaire est inversé. (G02 → G03, G03 → G02) • La direction d’usinage de correction de trajectoire est inversée. (G41 → G42, G42 → G41) Miroir autour de 2 axes Règles: • Les signes des deux coordonnées réfléchies sont inversés. (X-Y, Z-X, Y-Z) • Le sens de rotation d’une interpolation circulaire reste inchangé. • La direction d’usinage de correction de trajectoire reste inchangée. Les décalages d'origine G54 ... G59, G52 et les offsets réglables ne sont pas réfléchis. Les décalages d'origine programmables G50 et G51 sont réfléchis lors d'une programmation après sélection de la fonction miroir. • Les fonctions G pour le miroir font partie du groupe G18. • L'activation du miroir n'entraîne pas de mouvement d’axe. La correction de trajectoire d’outil et la préparation de bloc sont interrompues lors de l'appel de la fonction miroir. Les longueurs d’outil ne sont pas réfléchies. • Lors de la réflexion des axes principaux, la pièce est toujours réfléchie. • L'affichage de position montre les coordonnées pièce correspondantes. DOK-MTC200-NC**PRO*V17-ANW1-FR-P Manuel de programmation CN 17VRS Instructions de déplacement, Programmation des cotes Exemple 3-23 Fonction miroir Y 70 60 50 40 30 20 10 -10 3 4 1 X 10 20 30 40 50 60 70 2 Fig. 3-19: Rapport lors de la réflexion d’un et de plusieurs axes de coordonnées Programme CN G00 G54 G90 X0 Y0 BSR .DREI G50 X50 G73 X-1 BSR .DREI G72 G50 X-20 Y40 G73 X-1 Y-1 BSR .DREI G72 G50 X-50 Y20 G73 Y-1 BSR .DREI G72 RET .DREI G90 G01 X30 Y30 F1000 X130 X30 Y90 Y30 G00 G54 X0 Y0 RTS DOK-MTC200-NC**PRO*V17-ANW1-FR-P Aucun axe réfléchi ÷ Réflexion axe X í Réflexion axes X- et Y ô Réflexion axe Y Sous-programme pour le triangle Point de départ du triangle Point d’arrivée = Point de départ 3-24 Instructions de déplacement, Programmation des cotes Manuel de programmation CN 17VRS 3.10 Facteur d’échelle 'G78' / 'G79' La fonction facteur d'échelle permet de modifier l’échelle des distances à parcourir de tous les axes d'une machine avec un facteur programmable. L'activation et la désactivation des fonctions d’échelle se programme par fonctions G dans le programme pièce. Le facteur d'échelle est activé par G79 et reste modal jusqu'à suppression par G78 ou automatiquement par la fin du programme (RET, M002/ M030) ou par l'instruction BST. G78 supprime la fonction d'échelle sur tous les axes. Syntaxe G79 <Désignation d’axes><facteur d’échelle> G78 d’échelle sur tous les axes activation EIN Suppression du facteur Les valeurs suivantes sont modifiées par le facteur d’échelle : • coordonnées d’axe • paramètres d’interpolation • rayon • décalages d’origine programmée G50 et G51 • pas de filetage • distance d’application Les décalages d’origine G54 ... G59, G52 et les offsets réglables ne sont pas modifiés. Les décalages d’origine programmables G50 et G51 sont mis à l’échelle lors de la programmation après sélection de la fonction facteur d’échelle. • Les fonctions G de la valeur d’échelle appartiennent au groupe de code G19. • Seules des valeurs positives sont autorisées pour le facteur d’échelle. • Pour la programmation de rayon de cercle avec R sous G02/G03 ou avec les rayons effectifs RX, RY et RZ seuls des facteurs d’échelle identiques dans le plan d’usinage sont autorisés. • La sélection d'un facteur d'échelle n’entraîne pas de mouvement d’axe. La correction de trajectoire d’outil et la préparation de blocs sont interrompus par la sélection d'un facteur d'échelle. Les longueurs d'outils ne sont pas affectées. • Lors d'une interpolation circulaire une erreur est générée lors d'utilisation de facteurs d'échelle différents. Il en est de même avec la programmation d'axe circulaire avec rayon effectif. • Sur l'affichage de position les valeurs de consigne affectées par le facteur d’échelle sont affichées. La valeur réelle et le reste à parcourir correspondent aux valeurs effectives des positions d’axe. • Facteur d’échelle > 1 la pièce originelle est agrandie. • Facteur d’échelle < 1 la pièce originelle est réduite. • Pour la définition des calculs internes l’image miroir est effectuée avant la mise à l’échelle DOK-MTC200-NC**PRO*V17-ANW1-FR-P Manuel de programmation CN 17VRS Instructions de déplacement, Programmation des cotes Exemple Facteur d’échelle Y 70 60 50 40 1 30 20 Premier mouvement après sélection de facteur d'échelle 10 -10 X 10 20 30 40 50 60 70 80 90 100 110 120 130 140 150 Y 80 70 60 50 40 30 20 10 2 X 10 20 30 40 50 100 Fig. 3-20: Exemple de programmation. Facteur d’échelle Programme CN DOK-MTC200-NC**PRO*V17-ANW1-FR-P G00 G54 G90 X0 Y0 BSR .DREI G50 X40 Y-70 G79 X0.5 Y0.5 BSR .DREI G78 G00 G54 G90 X0 Y0 RET .DREI G90 G01 X25 Y30 F1000 X100 X25 Y70 Y30 RTS Triangle sans facteur d’échelle Décalage d’origine Détermination du facteur d’échelle ô Triangle avec facteur d’échelle Suppression du facteur d’échelle Sous-programme pour le triangle Position de départ Position finale =position de départ 3-25 3-26 Instructions de déplacement, Programmation des cotes Manuel de programmation CN 17VRS 3.11 Prise d’origine d’axe 'G74' L’instruction de déplacement G74, prise d’origine axe, offre la possibilité dans le programme CN ou en mode IMD, d’envoyer un ou plusieurs axes à leur position d’origine. Syntaxe G74 <[Désignation d’axe][valeur de coordonnée=0]> <avance> Exemple G74 X0 Z0 F10000 G74 est actif dans le bloc. Lors d’une prise d’origine, chaque axe programmé se déplace à sa vitesse de prise d’origine définie dans les paramètres d’axe. Remarques sur la programmation de G74 • G74 désactive avec G40 les corrections de trajectoire et de longueur d’outil, sélectionne le point zéro machine (G53), passe en programmation de vitesse (G94) et en programmation absolue (G90). • Les valeurs de coordonnées des axes programmées dans un bloc avec G74 doivent avoir une valeur nulle • Lorsque plusieurs axes sont programmés dans un bloc avec G74, les déplacements des axes ne sont pas interpolés. • Une vitesse d'avance programmée dans un bloc avec G74 reste active pour d'autres types d’interpolation. Remarque: La mesure de référence et la vitesse de prise d’origine sont définies par le constructeur de machine dans les paramètres d’entraînements. 3.12 Déplacements contre butée fixe Le déplacement contre butée fixe permet de déplacer simultanément un ou plusieurs axes contre une butée mécanique, sans que cela n'entraîne un défaut d’asservissement. Les cas d'application possible sont, par exemple, de maintenir un axe sous contrainte contre une butée durant l'usinage ou de se servir de la position de l'axe contre la butée comme position de référence pour les usinages suivants. Déplacements contre butée fixe 'G75' L’instruction de déplacement G75 - Déplacements contre butée fixe – cause le déplacement de tous les axes programmés avec cette instruction dans la direction programmée sous la valeur de coordonnée. Syntaxe G75 <[ Désignation d’axe][valeur de coordonnée]> <avance > Exemple G75 X100 Z50 F500 G75 est actif dans le bloc. Les axes sont déplacés avec la vitesse programmée dans le bloc, dans la direction de la valeur de coordonnées programmée. Si, au cours de ce déplacement, une résistance mécanique, par exemple une butée mécanique, est rencontrée, le couple est limité par la valeur définie dans le paramètre d'axe "Couple réduit sur butée„. Cette limitation est proportionnelle au courant crête. La consigne n'augmente plus, le reste à parcourir est effacé et le couple de précontrainte est maintenu. DOK-MTC200-NC**PRO*V17-ANW1-FR-P Manuel de programmation CN 17VRS Remarque sur le déplacement contre butée Instructions de déplacement, Programmation des cotes 3-27 • Si aucune vitesse d'avance n'est programmée, la vitesse définie dans le paramètre d’axe "Vitesse maximale en déplacement contre butée„ est utilisée.. • Si la position finale programmée pour un axe est atteinte le message d'erreur : %XWpHHQGHKRUVGHOD]RQHGpILQLH est affiché. • Si, durant l'exploitation, la butée fait ressort et se déplace ou si le chariot est déplacé de sa position à cause d'une force antagoniste importante, la position de l'axe le suit. Si la position de départ ou la position finale du bloc est dépassée, le message d’erreur : %XWpHHQGHKRUVGHOD]RQHGpILQLH est affiché. • Dans un bloc avec G75, les données de mesure peuvent être programmées en absolu (G90) ou en relatif (G91). • Si plusieurs axes sont programmés dans un bloc avec G75, le déplacement des axes n’est pas interpolé. Remarque: Les paramètres "Couple réduit sur butée" et "Vitesse maximale en déplacement sur butée" sont définis par le constructeur de machine dans les paramètres d’axe. Exemple 0 100 170 Fig. 3-21: Déplacement contre butée G00 Z100 M3 S1250 G75 Z170 F200 • • G76 G01 Z100 F1000 G00 Z0 M5 RET DOK-MTC200-NC**PRO*V17-ANW1-FR-P Axe Z en position de départ Déplacement contre butée Suppression de la précontrainte d’axe Axe Z en position de départ Axe Z au point de référence 3-28 Instructions de déplacement, Programmation des cotes Manuel de programmation CN 17VRS Suppression de toutes les précontraintes 'G76' L'instruction de déplacement G76- - Suppression de toutes les contraintes d’axe - permet de supprimer les précontraintes de tous les axes en précontrainte. La valeur de partition réelle est prise comme valeur de consigne de position. Ainsi, la position de l'axe peut être prise comme position de référence pour les déplacements ultérieurs. Le reste à parcourir est ignoré. Syntaxe Remarque sur la programmation de G76 G76 • G76 est actif dans le bloc. • L'instruction G76 ne peut pas être programmée avec un axe. G76 supprime la précontrainte de tous les axes précontraints par G75 Déplacement sur butée -. • À la fin d’un programme par l'instruction RET, par un saut avec stop BST ou par intervention manuel avec control reset ou après une mise hors tension puissance, les précontraintes de tous les axes sont supprimées. 3.13 Réaccostage et reprise d’usinage sur le contour Les fonctions : • réaccostage et • reprise d’usinage au contour automatisent l’abord du contour après une interruption du programme. Après une interruption du programme au cours de laquelle l’utilisateur a dégagé manuellement l’outil du contour, par exemple pour vérifier et changer les plaquettes de coupe, la fonction réaccostage permet le retour au point d'interruption et la fonction reprise d'usinage, le retour au point de début de bloc. Les deux fonctions sont disponibles dans les modes manuel et programme. En mode manuel, la CN compense la différence de position entre la position à atteindre et la position actuelle, dans l'ordre dans lequel l'utilisateur a dégagé en JOG. En mode programme, les axes sont déplacés vers leur position à atteindre dans l'ordre dans lequel le constructeur de machine l’a défini dans un sous-programme CN. Réaccostage et reprise d’usinage en mode programme Généralement, l'opérateur n’utilise le réaccostage en manuel que pour amener les axes à proximité du contour. Lorsqu'il n'y a plus de risque de collision, il passe en mode programme automatique, semi-automatique ou déroulement en manuel et poursuit alors le réaccostage ou la reprise d'usinage par appui sur départ cycle. Avec le changement anticipé dans un mode programme, la coupe à vide d'un outil et ainsi la marque sur la pièce sont évités. Après réaccostage ou reprise d'usinage la CN poursuit l'exécution du programme sans nécessiter de nouveau départ cycle. DOK-MTC200-NC**PRO*V17-ANW1-FR-P Manuel de programmation CN 17VRS Instructions de déplacement, Programmation des cotes 3-29 X X Position de sortie Position de sortie Z Déplacement Z Déplacement Position finale du bloc Position finale du bloc Position de départ du bloc Position à atteindre = position d'interruption Fig. 3-22: Réaccostage en mode programme- Position à atteindre = Position de départ du bloc Position d'interruption Fig. 3-23: Reprise d’usinage en mode programme- Par appui sur le bouton "Réaccostage„ ou "Reprise d'usinage„ sur le pupitre machine, la fonction voulue est sélectionnée. Avec l’appui sur départ cycle, le réaccostage ou la reprise d'usinage est démarré et les axes sont déplacés dans un ordre programmé jusqu'à la position à atteindre. • L'enchaînement, suivi par les axes pour revenir au contour peut être donné par le constructeur de machine et s'adapter à chaque configuration machine. Cela est particulièrement nécessaire lorsque des axes rotatifs ou auxiliaires se trouvent près de la broche et des axes linéaires principaux. • Lorsque la CN a atteint le point cible, elle continue l'exécution programme sans départ cycle supplémentaire. Réaccostage et reprise d’usinage à la position cible 'G77' G77 force la CN à atteindre la position cible pour les axes programmés et, pour la broche, à reprendre l’état avant interruption. Avec G77, la CN compense pour les axes d'avance (signification d’axe X, Y, Z, U, V, W, A, B, C) le reste à parcourir entre la position à atteindre et la position actuelle, en exécutant une interpolation similaire à G00. Pour les axes, la position cible est la position à atteindre calculée, au début du réaccostage ou de la reprise d'usinage, en coordonnées machine. Syntaxe <[ Désignation d’axe][valeur de coordonnée=0]> <avance > Exemple Remarque sur la programmation de G77 G77 X0 Y0 Z0 F1000 • G77 est actif dans le bloc. • G77 S[x] 0 ([x]=1..3) force la CN à rétablir pour la broche, la dernière vitesse active ou à retourner à la position à atteindre programmée. Pour le retour à la position à atteindre la CN utilise, pour l’indexage de broche, la vitesse d'indexage définie par paramètre. Une valeur F ou S pour la vitesse d'indexage n'est pas nécessaire. • Avec des broches principales à possibilité d'axe circulaire, l’état lors de l'interruption (mode broche ou axe circulaire) doit être enregistré dans l’AP. Lors du réaccostage ou de la reprise d'usinage, la broche doit être remise dans l'état lors de l'interruption (broche ou axe circulaire). DOK-MTC200-NC**PRO*V17-ANW1-FR-P 3-30 Instructions de déplacement, Programmation des cotes Manuel de programmation CN 17VRS X Position de sortie Z Zone de déplacements autorisés pour le ré accostage Zone de déplacements autorisés pour la reprise d'usinage Position finale Position de départ Position d'interruption Fig. 3-24: Réaccostage ou reprise d’usinage du contour DOK-MTC200-NC**PRO*V17-ANW1-FR-P Manuel de programmation CN 17VRS 4 Blocs de déplacement 4.1 Axes Blocs de déplacement 4-1 Axes linéaires principaux Les axes linéaires principaux déterminent un système de coordonnées cartésien. Ils sont désignés par les significations d’axe: • 1 axe linéaire principal (symbole X) er • 2 axe linéaire principal (symbole Y) e • 3 axe linéaire principal (symbole Z). e La dénomination de l'axe (adresse de l'axe utilisé dans le programme CN) peut être choisie librement, mais la signification d'axe est fixée par la position de l'axe dans le système de coordonnées (voir fig. 4.1). Dans la CNC les axes sont associés de manière fixe à un process déterminé, mais peuvent cependant être transférés à un autre process (voir chap.11 „ Fonctions spéciales CN “). Un axe ne peut pas être utilisé simultanément par plusieurs process. Les interpolations circulaires et les corrections de rayon d'outil ne peuvent être exécutées que dans les plans d'usinage (G17, G18, G19, G20) définis par les axes linéaires principaux. Axes rotatifs principaux Les axes rotatifs principaux tournent autour des axes linéaires principaux. Les significations d’axe: • 1 axe rotatif principal (symbole A) er • 2 axe rotatif principal (symbole B) e • 3 axe rotatif principal (symbole C) e caractérisent ici, l’axe de coordonnées autour duquel l'axe rotatif correspondant tourne (voir 4.1). La dénomination de l'axe (adresse de l'axe) peut-être choisie librement, mais la signification d’axe est fixée par la position de l'axe dans le système de coordonnées. En programmation absolue (G90) la plage de déplacement et de ±360.000 degrés. En programmation absolue (G90) la position absolue programmée est atteinte par le chemin le plus court. En programmation incrémentale (G91) la plage de déplacement est de ±999999.9999 ou de ±99999.99999 degrés (en fonction de paramètres). Le signe donne le sens de déplacement. DOK-MTC200-NC**PRO*V17-ANW1-FR-P 4-2 Blocs de déplacement Manuel de programmation CN 17VRS Ordonnée 2ème axe [Y] [B] G18 Plan ZX G19 G17 Plan XY Abscisse Plan YZ [A] 1er axe [X] [C] Cote 3ème axe [Z] Fig. 4-1: Axes linéaires (X, Y, Z) et rotatifs (A, B, C) dans un système de coordonnées cartésien Axes linéaires et rotatifs auxiliaires Les axes linéaires et rotatifs auxiliaires peuvent prendre n’importe quelle position à l’intérieur de l’espace. • 1 axe auxiliaire (symbole U) er • 2 axe auxiliaire (symbole V) e • 3 axe auxiliaire (symbole W) e caractérisent ce type d’axe. Les significations d'axe U, V et W sont totalement équivalentes. Elles peuvent être choisies aussi bien pour des axes linéaires ou rotatifs ou pour des broches à capacité d’axe circulaire. Les axes auxiliaires acceptent des opérations de positionnement et des mouvements d’interpolation comme les autres axes et atteignent, comme eux, leur point d'arrivée au même instant. La vitesse de trajectoire (valeur F) donnée dans le programme CN, ne se rapporte cependant pas aux axes auxiliaires, mais aux axes principaux linéaires et rotatifs, dès lors qu'un de ces axes est programmé dans le bloc. 4.2 Conditions d’interpolation Interpolation à erreur de poursuite réduite'G06' La condition d’interpolation G06 active un algorithme à faible erreur de poursuite pour les mouvements d’axe. Tous les mouvements suivants se font quasiment sur la trajectoire. Les passages de bloc ne sont pas arrondis et se font sans interruption. Sur les angles du contour (rupture de trajectoire) la vitesse de trajectoire est presque réduite à zéro. L'algorithme de faible erreur de poursuite est réalisé avec une anticipation de vitesse dynamique. L’erreur de poursuite n’est due qu’à la limite de 2 ms de la fréquence d’interpolation. • Une exploitation quasiment sans erreur de poursuite n'est possible qu'avec des entraînements numériques INDRAMAT. Avec des entraînements analogiques G06 correspond à une exploitation à erreur de poursuite réduite. DOK-MTC200-NC**PRO*V17-ANW1-FR-P Blocs de déplacement 4-3 Manuel de programmation CN 17VRS • G06 reste modal après activation, jusqu’à annulation par G07 ou suppression automatique à la fin de programme ou par instruction BST. • Le facteur de gain KV peut, avec cette fonction, être augmenté jusqu’à la limite mécanique de la machine. Un facteur KV élevé assure une meilleure dynamique lors des mouvements d’axe. 404Kreis.fh7 Exemple D i amètre du c e rc le 1 6 0 mm Vite s s e d'us ina ge t= F1 0 0 0 , Fa c te ur Kv = 7 G0 6 , G0 8 Fo n ctio n o scillo sco p e Va le u r d e p o sitio n a xe Y [mm] Diffé re n ce p o sitio n : Va le u r n o m. d e p o s.: Fa cte u r d 'e xte n sio n : 1 6 9 3 .7 Numéro d'axe: 2 Typ e d 'a xe : Axe lin . d ig . Dé sig n a t. d 'a xe : Y Pro ce ssu s: MAHO Numéro d'axe: 1 Typ e d 'a xe : Axe lin . d ig . Dé sig n a t. d 'a xe : X Pro ce ssu s: MAHO Va le u r d e p o sitio n a xe X [mm] Fig. 4-2: Interpolation circulaire à faible erreur de poursuite à F8000 mm/min Dans le cercle représenté fig. 4-2, le contour réel a été multiplié par un facteur d’extension de 1693,7. Ci-dessous programme pièce pour l’oscillogramme du cercle (Fig. 4-2 à 4-5). T11 BSR .M6 changement d'outil SF D10 G00 G90 G54 G06 G08 X199 Y136 Z5 Position de départ S5000 M03 Mise en route broche G01 Z-5 F1000 Plongée fraise G41 X199 Y141 F8000 [ou F1000] Point de départ usinage cercle G03 X180 Y122 I199 J122 Cercle d'engagement G01 X180 Y100 Élément de transition G02 X180 Y100 I100 J100 Cercle entier ∅160 G01 X180 Y77 Élément de transition G03 X198 Y59 I198 J77 Cercle de dégagement G00 Z5 T0 BSR .M6 Outil à distance de Changement d'outil RET Fin de programme sécurité La fidélité au contour quasiment idéale a été obtenue côté CN, par la compensation d’erreur de poursuite. Il n'y a qu’au changement de quadrant que l’on peut observer un écart de position de 0.002 mm. L’écart de position au changement de quadrant peut être presque totalement compensé en programmant une compensation de couple de frottement (voir chap. 11 ‘Fonctions spéciales, Instructions AXD’). DOK-MTC200-NC**PRO*V17-ANW1-FR-P 4-4 Blocs de déplacement 404Kreis.fh7 Manuel de programmation CN 17VRS Vitesse d'usinage=F8000 KV-Faktor=7 G06, G08 Fonction oscilloscope Valeur de position axe Y [mm] Différence position: Valeur nom. de pos.: Facteur d'extension: 1693.7 Valeur de position axe X [mm] Coupe du cercle Exploitation au passage de quadrant Ecart de position Fig. 4-3: Interpolation circulaire à erreur de poursuite réduite, extrait 404Kreis.fh7 Ci-dessous, à titre de comparaison, cercle complet avec une vitesse de trajectoire de F1000 mm/min. D i ammè tre du c e rc le 1 6 0 mm Vite s s e d'us ina ge = F1 0 0 0 , Fa c te ur Kv =7 G0 6 , G0 8 Fo n ctio n o scillo sco p e Va le u r d e p o sitio n a xe Y [mm] Diffé re n ce p o sitio n : Va le u r n o m. d e p o s.: Fa cte u r d 'e xte n sio n : 2 2 7 9 .2 Numéro d'axe: 2 Typ e d 'a xe : Axe lin . d ig . Dé sig n a t. d 'a xe : Y Pro ce ssu s: MAHO Numéro d'axe: 1 Ty p e d ' a x e : A x e l i n . d i g . Dé sig n a t. d 'a xe : X Pro ce ssu s: MAHO Va le u r d e p o sitio n a xe X [mm] Fig. 4-4: Interpolation circulaire à erreur de poursuite réduite avec F1000 mm/min Ci-dessous mise en évidence de l’écart de position au passage de quadrant. DOK-MTC200-NC**PRO*V17-ANW1-FR-P Blocs de déplacement 4-5 404Kreis.fh7 Manuel de programmation CN 17VRS Vitesse d'usinage =F1000 mm/min KV-Faktor=7 G06, G08 Fonction oscilloscope Valeur de position axe Y [mm] Différence position: Valeur nom. de pos.: Facteur d'extension: 2279.2 Valeur de position axe X [mm] Coupe du cecle Exploitation au passage de quadrant Fig. 4-5: Interpolation circulaire extrait à F1000 mm/min à Ecart de position erreur de poursuite réduite, Interpolation avec erreur de poursuite ’G07’ L’instruction de déplacement ‘G07’ active l’algorithme de déplacement des axes avec erreur de poursuite. G07 est actif à la mise sous tension et reste actif jusqu’à la programmation de G06. A la fin de programme (RET) ou lors de l’instruction BST, G07 est automatiquement réactivé. Les passages de blocs qui ne sont pas tangentiels sont arrondis. 404Kreis.fh7 Exemple Diamètre de cercle 160 mm Vitesse d'usinage= F8000, Facteur Kv=7 G06, G08 Fonction oscilloscope Valeur de position axe Y [mm] Différence position: Valeur nom. de pos.: Facteur d'extension: 527.5 Numéro d'axe: 2 Type d'axe: Axe lin. dig. Désignat. d'axe: Y Processus: MAHO Numéro d'axe: 1 Ty p e d ' a x e : A x e l i n . d i g . Désignat. d'axe: X Processus: MAHO Valeur de position axe X [mm] Fig. 4-6: Interpolation circulaire à F 8000 mm/min et G07 Sur le cercle représenté (Fig. 4-6), le contour réel est multiplié par facteur d’extension de 527,5. Par opposition, le facteur en G06 était 1693,7, valeur trois fois supérieure pour interpréter les fluctuations l’écart de position. Ci-dessous programme pièce pour l’oscillogramme cercle (Fig 4-6 à 4-9). DOK-MTC200-NC**PRO*V17-ANW1-FR-P un de de du 4-6 Blocs de déplacement Manuel de programmation CN 17VRS T11 BSR .M6 Chgt. d’outil SF D10 G00 G90 G54 G07 G08 X199 Y136 Z5 Position de départ S5000 M03 Mise en route broche G01 Z-5 F1000 Plongée fraise G41 X199 Y141 F8000 [ou F1000] Point départ cercle G03 X180 Y122 I199 J122 Cercle d'engagement G01 X180 Y100 transition usinage Élément G02 X180 Y100 I100 J100 Cercle entier ∅160 G01 X180 Y77 Élément de transition G03 X198 Y59 I198 J77 Cercle de dégagement G00 Z5 Outil à sécurité T0 BSR .M6 Changement d'outil RET Fin de programme distance de de 404Kreis.fh7 Le diamètre du cercle programmé diminue en fonction de la vitesse programmée et du facteur de gain KV. Plus la vitesse est faible et plus le KV est important, meilleur est la tenue au contour programmé. Vitesse d'usinage =F8000 mm/min KV-Faktor=7 G06, G08 Fonction oscilloscope Valeur de position axe Y [mm] Différence position: Valeur nom. de pos.: Facteur d'extension: 527.5 Valeur de position axe X [mm] Coupe de cercle Exploitation du contour de cercle Ecart de position Fig. 4-7: Interpolation avec G07, extrait Ci-dessous, par comparaison, le même cercle avec une vitesse de trajectoire de F1000 mm/min. DOK-MTC200-NC**PRO*V17-ANW1-FR-P Blocs de déplacement 4-7 404Kreis.fh7 Manuel de programmation CN 17VRS Diamètre de cercle 160 mm Vi t e s s e d ' u s i n a g e = F 10 0 0 , K V- F a k t o r = 7 G 0 7, G 0 8 Fonction oscilloscope Va l e u r d e p o s i t i o n a x e Y [ m m ] D i ff é r e n c e p o s i t i o n : Va l e u r n o m . d e p o s . : Facteur d'extension: 1680.9 Numéro d'axe: 2 Ty p e d ' a x e : A x e l i n . d i g . Désignat. d'axe: Y Processus: MAHO Numéro d'axe: 1 Ty p e d ' a x e : A x e l i n . d i g . Désignat. d'axe: X Processus: MAHO Va l e u r d e p o s i t i o n a x e X [ m m ] Fig. 4-8: Interpolation circulaire à F1000 mm/min et G07 404Kreis.fh7 Ci-dessous, mise en évidence de l’écart de position au passage de quadrant. Vitesse d'usinage =F1000 mm/min KV-Faktor=7 G07, G08 Fonction oscilloscope Valeur de position axe Y [mm] Différence position: Valeur nom. de pos.: Facteur d'extension: 1680.9 Valeur de position axe X [mm] Coupe de cercle Exploitation au passage de quadrant Ecart de position Fig. 4-9: Interpolation circulaire avec G07, extrait à F1000 mm/min Vitesse de passage de bloc optimale ’G08’ Avec la condition d’interpolation G08, la vitesse de fin de bloc est adaptée de sorte que le passage au bloc CN suivant se fasse à vitesse maximale. La variation maximale de vitesse définie dans les paramètres d’axe est décisive. Lors de passage de blocs tangentiels à même vitesse de trajectoire, le passage de bloc se fait à vitesse constante. L’état de surface est régulier, la pièce n’est pas marquée par la fraise. • Lors d’un passage tangentiel avec G06 actif, par exemple passage d’une droite à un petit cercle, les axes freinent jusqu’à la vitesse de début du bloc suivant. • Lorsque G61, arrêt précis, est programmé avec G08, vitesse optimale de passage de bloc, G09, limitation de vitesse de passage de bloc est DOK-MTC200-NC**PRO*V17-ANW1-FR-P 4-8 Blocs de déplacement Manuel de programmation CN 17VRS automatiquement activée. G08 ne peut à nouveau être programmée qu’après annulation de G61. • La fonction G08 est active avec une atténuation d’avance de 1% à 100%. Avec des valeurs supérieures à 100% la vitesse est limitée à 100% lors des passages de bloc. • Les fonctions M suspendent l’exécution des blocs jusqu’à ce qu’elles soient acquittées. Dans les blocs avec fonction M, la fonction G08 n’a pas d ‘effet . • Après sélection, G08 reste modal jusqu’à annulation par G09, G61 ou fin de programme ou instruction BST. • Les blocs intermédiaires, dans lesquels aucun mouvement interpolé n’a lieu, entraînent une discontinuité de vitesse. Par exemple: l’insertion d’un bloc intermédiaire avec G01 F7000 appelle une discontinuité de vitesse. Remarque: La variation maximale de vitesse est fixée par le constructeur de machine dans les paramètres d’axe. Exemple 404Kreis.fh7 Dans le diagramme de vitesse (Fig. 4-10), on peut reconnaître le passage de bloc de la partie 1 à 2 de la pièce sans modification de vitesse . Lors du passage de bloc à la partie de la pièce 3, la vitesse est réduite à F7000 . Il y a un freinage optimal sans dépassement jusqu’à la vitesse de départ. 3 droites de X200 -- > X0 G06 und G08 Fonction oscilloscope Signal 1 + Signal 2 [(mm)/min * 10^3] Numéro d'axe: 1 Ty p e d ' a x e : A x e l i n . d i g . Désignat. d'axe: X Processus: MAHO Représentation somme de signaux: Signal 1 Signal 1: d( ( Signal 2: d( ( f( f( f( f( t t t t + Signal 2 ))/dt [(mm)/min] ) = position réelle ) ))/dt [(mm)/min] ) = écart de position ) Modification de vitesse entre la 2ème et 3ème partie de pièce de F8000 à F7000 Avance Fig. 4-10: Passage de blocs avec G08 et F8000. Exemple de programme pour les diagrammes de vitesse représentés dans les figures 4-10 et 4-11: G54 G90 G00 G06 G08 X200 Point de départ axe X G01 F8000 Vitesse d'avance X150 1 partie de pièce X50 2 ère ème partie de pièce ème partie de pièce, nouvelle valeur F X0 F7000 3 RET Fin de programme Dans le diagramme de vitesse suivant (Fig. 4-11) la modification de vitesse e e entre la 2 partie de pièce (F8000) et la 3 ( F7000) est agrandie avec une fonction loupe. Le passage de bloc avec vitesse optimale entre les deux parties de pièce est nettement visible. DOK-MTC200-NC**PRO*V17-ANW1-FR-P Blocs de déplacement 4-9 404Kreis.fh7 Manuel de programmation CN 17VRS G06 et G08 Passage de blocs de F8000 à F7000 Fonction oscilloscope Signal 1 + Signal 2 [(mm)/min * 10^3] Numéro d'axe: 1 Ty p e d ' a x e : A x e l i n . d i g . Désignat. d'axe: X Processus: MAHO R e p r é s e n ta t i o n s o m m e d e s i g n a u x : S i g n a l 1 Signal 1: d( ( Signal 2: d( ( f( f( f( f( t t t t + Signal 2 ) ) / dt [(mm)/min] ) = position réelle ) ) ) / dt [(mm)/min] ) = écart de position ) Modification de vitesse entre la 2ème et 3ème partie de pièce de F8000 à F7000 Av a n c e Fig. 4-11: Passage de bloc avec G08 de F8000 à F7000. Passage de bloc à vitesse réduite 'G09' Avec la condition d’interpolation G09, la vitesse de fin de bloc est adaptée de telle sorte que la variation maximale de vitesse définie dans les paramètres machine puisse être tenue. • La condition d’interpolation G09 permet de diminuer les écarts de position au passage de bloc. • L’usinage avec G09 nécessite plus de temps, et l’état de surface peut être détérioré par des marques dues à la fraise. • G09 est actif à la mise sous tension et reste mémorisé jusqu’à une annulation par G08. G09 est automatiquement sélectionné à la fin du programme (RET) ou par l’instruction BST. Remarque: La variation maximale de vitesse est fixée dans les paramètres d’axe par le constructeur de la machine. 404Kreis.fh7 Exemple 3 droites de X200 -- > X0 G06 et G09 Fonction oscilloscope Signal 1 + Signal 2 [(mm)/min * 10^3] Numéro d'axe: 1 Ty p e d ' a x e : A x e l i n . d i g . Désignat. d'axe: X Processus: MAHO Summensignalbildung: Signal 1 Signal 1: d( ( Signal 2: d( ( Avance f( f( f( f( t t t t + Signal 2 )/dt [(mm)/min] )) = Ist-Position ) ))/dt [(mm)/min] ) = Positions-Abweich. ) Fig. 4-12: Passage de bloc avec G09 à F8000 DOK-MTC200-NC**PRO*V17-ANW1-FR-P Modification de vitesse entre la 2ème et 3ème partie de pièce de F8000 à F7000 4-10 Blocs de déplacement Manuel de programmation CN 17VRS Le diagramme de vitesse (Fig. 4-12) montre de façon significative comment la vitesse de l’axe est pratiquement réduite à 0 entre les deux parties de la pièce. Le reste de vitesse, avec laquelle le bloc suivant est abordé, dérive du paramètre d’axe ‘’Variation maximale de vitesse“. Exemple de programme pour le diagramme de vitesse représenté fig. 412 et 4-13: G54 G90 G00 G06 G09 X200 Point de départ axe X G01 F8000 Vitesse d'avance X150 1ère partie de pièce X50 2 X0 F7000 3 RET Fin de programme ème partie de pièce ème partie de pièce, nouvelle valeur F 404Kreis.fh7 Dans le diagramme de vitesse suivant (Fig. 4-13) la modification de vitesse entre les deux parties 2 (F8000) et 3 (F7000) de la pièce est agrandie avec une fonction loupe. G06 et G09 Passage de bloc de F8000 à F7000 Fonction oscilloscope Signal 1 + Signal 2 [(mm)/min * 10^3] Numéro d'axe: 1 Ty p e d ' a x e : A x e l i n . d i g . Désignat. d'axe: X Processus: MAHO Summensignalbildung: Signal 1 Signal 1: d( ( Signal 2: d( ( Avance f( f( f( f( t t t t + Signal 2 ))/dt [(mm)/min] ) = Ist-Position ) ))/dt [(mm)/min] ) = Positions-Abweich. ) Modification de vitesse entre la 2ème et 3ème partie de pièce de F8000 à F7000 Fig. 4-13: Passage de bloc avec G09 de F8000 à F7000 Arrêt précis 'G61' Avec la condition d’interpolation G61, la position programmée est abordée à l’intérieur d’une limite prédéterminée d’arrêt précis. Cette limite d’arrêt précis est définie dans les paramètres d’axe par une fenêtre de position. Lorsque cette fenêtre de position est atteinte, l’enchaînement sur le bloc suivant est effectué et le mouvement d’axe suivant commence. • La programmation de G00 (Rapide) active automatiquement G61 (Arrêt précis). • La programmation de G61 annule la condition d’interpolation G08. G08 ne peut de nouveau être activé qu’après suppression de G61. • La sélection de G61 est recommandée pour l’usinage de contours à angle vif et les transitions non tangentielles. • Après sélection, G61 reste modal jusqu’à suspension par G62. G61 est supprimé automatiquement par la fin de programme ou l’instruction BST. Remarque: La taille de la fenêtre de positionnement est fixée dans les paramètres d’axe par le constructeur de machine. DOK-MTC200-NC**PRO*V17-ANW1-FR-P Blocs de déplacement 4-11 Manuel de programmation CN 17VRS 404Kreis.fh7 Exemple Testde contour: passage droite --> cercle non tangentiel , cercle --> cercle tangentiel Fonction oscilloscope Valeur de position axe Y [mm] Différence position: Valeur nom. de pos.: Facteur d'extension: 613.8 Avance F4000 G06, G61 KV = 7 Valeur de position axe X [mm] Passage droite --> cercle non tangentiel Passage cercle --> cercle tangentiel Ecart de position au passafe droite --> cercle Fig. 4-14: Diagramme de contour avec G61 Le diagramme de contour ci-dessus (Fig. 4-14) montre clairement, grâce à l’effet de G61, la tenue précise au contour lors des passages droite→ cercle et cercle→ cercle. Dans cet exemple la fenêtre de position est fixée à 0.010 mm dans les paramètres d’axes. L’écart de position dans la transition non tangentielle droite → cercle s’élève à 0.00249 mm. Si l’on diminuait la fenêtre de position dans les paramètres d’axe, la transition serait proportionnellement plus précise. Dans la transition tangentielle cercle → cercle, l’écart de position est inférieur à 0.001 mm. Programme pour l’exemple du diagramme des fig. 4-14 et 4-15: G00 G54 G90 G06 G08 X-100 Y-100 Point de départ G01 G61 X-50 Y-50 F4000 1 droite G02 X50 Y-50 I0 J-50 1 demi-cercle ère er ème G03 X100 Y-50 I75 J-50 2 RET demi-cercle Fin de programme 404Kreis.fh7 Le diagramme de vitesse suivant (Fig. 4-15) montre la diminution de vitesse jusqu’à l’atteinte de la fenêtre de position. Lorsque la fenêtre de position est atteinte, il y a enchaînement au bloc suivant et le mouvement d’axe suivant commence. D i a g r a m m e : pa s s a g e d r o i t e - - > c e r c l e n o n ta n g e n t i e l , c e r c l e - - > c e r c l e ta n g e n t i e l ( (Signal 1)2 + [(mm)/min * 10^3] Fonction oscilloscope ( S i g n a l 2) 2 ) Numéro d'axe: 1 Désignat. d'axe: X Numéro d'axe: 2 Désignat. d'axe: Y Av a n c e Summensignalbildung: ( Signal 1: d( ( Signal 2: d( ( f( f( f( f( t t t t (Signal 1)2 ) ) / dt [(mm)/min] ) = Ist-Position ) ) ) / dt [(mm)/min] ) = Ist-Position ) Passage droite --> cercle n o n ta n g e n t i e l Fig. 4-15: Diagramme de vitesse avec G61 DOK-MTC200-NC**PRO*V17-ANW1-FR-P + ( S i g n a l 2) 2 ) Av a n c e F 4 0 0 0 G06, G61 KV = 7 Passage cercle --> cercle ta n g e n t i e l 4-12 Blocs de déplacement Manuel de programmation CN 17VRS Changement bloc à la volée 'G62' Avec la condition d’interpolation G62, le passage au bloc suivant a lieu dès que les consignes de position délivrées par l’interpolation pour tous les axes du bloc ont atteint leur valeur finale programmée. Le système n’attend pas que les positions réelles aient aussi atteint leur position finale. L’erreur de poursuite éventuelle n'est pas annulée à la position finale. • La programmation de G00 (Rapide) suspend G62 (Changement de bloc à la volée). • Avec la programmation de G62, les arêtes de trajectoire et les transitions non tangentielles sont arrondies. • G62 est actif à la mise sous tension et reste actif jusqu’à annulation par G61. G62 est activé automatiquement à la fin du programme (RET) ou par l’instruction BST. • Le temps d’usinage est diminué par programmation avec G62 et G08. 404Kreis.fh7 Exemple Te s t c o n t o u r : pa s s a g e d r o i t e - - > c e r c l e n o n ta n g e n t i e l ; c e r c l e - - > c e r c l e ta n g e n t i e l Fonction oscilloscope Va l e u r d e p o s i t i o n a x e Y [mm] Différence position: Va l e u r n o m . d e p o s . : Facteur d'extension: 2444.6 Av a n c e : F4000 G06, G62 KV = 7 Va l e u r d e p o s i t i o n a x e X [mm] Passage droite --> cercle n o n ta n g e n t i e l Passage cercle --> cercle ta n g e n t i e l Ecart de position au pa s s a g e d r o i t e - - > cercle Fig. 4-16: Diagramme de contour avec G62 Le diagramme de contour ci-dessus montre clairement comment les transitions non tangentielles (droite → cercle) sont grignotées par l’action de G62. Le contour est parcouru à vitesse optimale (grâce à G08). Sur le contour même l’état de surface est identique à celui obtenu avec G61. Lors de la comparaison des diagrammes de contour des figures 4-14 (G61) et 4-16 (G62), il faut remarquer que le facteur d’allongement de l’écart de position est 4 fois supérieur dans la figure 4-16. Programme de l’exemple des diagrammes des fig. 4-16 et 4-17: G00 G54 G90 G06 G08 X-100 Y-100 Point de départ G01 G62 X-50 Y-50 F4000 1 droite G02 X50 Y-50 I0 J-50 1 demi-cercle G03 X100 Y-50 I75 J-50 RET ère er ème 2 demi-cercle Fin de programme Le diagramme de vitesse suivant (Fig. 4-17) montre la réduction de vitesse de trajectoire à cause du changement de direction lors de la transition non tangentielle droite → cercle. La transition tangentielle cercle → cercle s’effectue à vitesse de trajectoire constante grâce aux conditions G62 et G08. DOK-MTC200-NC**PRO*V17-ANW1-FR-P Blocs de déplacement 4-13 404Kreis.fh7 Manuel de programmation CN 17VRS Diagramme: passage droite --> cercle non tangentiel, cercle --> cercle tangentiel ( (Signal 1) 2 + [(mm)/min * 10^3] Fonction oscilloscope (Signal 2) 2 ) Numéro d'axe: 1 Désignat. d'axe: X Numéro d'axe: 2 Désignat. d'axe: Y Avance Summensignalbildung: ( Signal 1: d( ( Signal 2: d( ( f( f( f( f( t t t t (Signal 1) 2 + (Signal 2) 2 Avance F4000 G06, G62 KV = 7 ))/dt [(mm)/min] ) = Ist-Position ) ))/dt [(mm)/min] ) = Ist-Position ) Passage droite -- > cercle non tangentiel ) Passage cercle --> cercle tangentiel Fig. 4-17: Diagramme de vitesses avec G62 Accélération programmable 'ACC' La fonction ACC accélération programmable permet de limiter l’accélération à l’intérieur d’un programme CN. Cette fonction est, par exemple, utilisée lorsque les axes d’un porte pièce doivent être déplacés en fonction de la masse de la pièce. L’accélération programmée limite l’accélération maximale de trajectoire donnée dans les paramètres. Le facteur d’accélération est programmée en pour cent par rapport à l’accélération maximale de trajectoire définie en paramètre. Elle est active sur tous les axes programmés dans le bloc. • La plage de valeur du facteur d’accélération va de 1% à 100%. • Une valeur en dehors de cette plage conduit à un message d’erreur lors de l’exécution du programme. • Le facteur d’accélération peut aussi bien être programmé comme constante ou comme expression mathématique. Lors de la programmation avec une constante, on ne peut pas utiliser de valeur décimale. Lors de la programmation avec une expression mathématique, la valeur est automatiquement arrondie à une valeur entière. • Un facteur d’accélération programmé avec l’instruction ACC reste modal jusqu’à ce qu’il soit remplacé par une nouvelle valeur programmée ou remis automatiquement à 100% à la fin du programme ou par un BST. • Lorsque le paramètre ‘’accélération maximale de trajectoire’’ est programmé avec une très grande valeur n’ayant pas de rapport avec l’accélération maximale possible, l’instruction ACC peut être inefficace. Remarque: L’ accélération maximale de trajectoire est fixée dans les paramètres process par le constructeur de la machine. Exemple Syntaxe DOK-MTC200-NC**PRO*V17-ANW1-FR-P G01 ACC 50 X100 ACC avec constante G01 ACC=@10 X100 ACC avec variable G01 ACC=10*@10+30 X100 ACC avec expression mathématique 4-14 Blocs de déplacement Manuel de programmation CN 17VRS Programme CN G00 G54 G90 G61 G06 X200 Point de départ G01 X150 F8000 1 droite ACC 40 X50 2 ère ème droite facteur d’accélération 40% ème droite facteur d’accélération 15% ACC 15 X-50 3 RET Fin de programme 404Kreis.fh7 Dans le diagramme de vitesse représenté, le paramètre process pour l’accélération maximale de trajectoire était réglé à 500 mm/sec2. Les accélérations étaient donc de 200 mm/sec2 dans le bloc CN avec ACC 40 X50, et de 75 mm/sec2 dans le bloc avec ACC 15 X-50. D i agr a mme de v ite s s e : 3 droite s e n X a v e c a c c é lé ra tions diffé re n te s Fonction oscilloscope ( (Sig n a l 1 ) 2 + [(mm)/min * 1 0 ^3 ] (Sig n a l 2) 2 ) Numéro d'axe: 1 Ty p e d ' a x e : A x e l i n . d i g . Désignat. d'axe: X Processus: MAHO Avance Su mme n sig n a lb ild u n g : ( Sig n a l 1 : d ( ( Sig n a l 2 : d ( ( f( f( f( f( t t t t (Sig n a l 1 ) 2 + (Sig n a l 2) 2 ) ))/dt [(mm)/min ] ) = Ist-Po sitio n ) ))/dt [(mm)/min ] ) = Po sitio n s-Ab we ich . ) Fig. 4-18: Diagramme de vitesse pour l’accélération programmable. 4.3 Fonctions d’interpolation Interpolation linéaire, rapide 'G00' Les valeurs coordonnées programmées avec G00 sont atteintes avec la vitesse de trajectoire maximale. Si plusieurs axes sont programmés sous cette adresse, le mouvement est interpolé G00. On peut programmer, avec G00, une vitesse d’avance sous l’adresse F. Si aucune avance n’est programmée dans le bloc le mouvement a lieu avec la vitesse maximale de trajectoire fixée dans les paramètres process. La vitesse de trajectoire est limitée à la vitesse maximale des axes fixée dans les paramètres d’axes, ce qui garantit dans tous les cas une interpolation linéaire. La valeur F programmée avec G00 reste active pour tous les déplacements et types d’interpolation suivants, jusqu’à remplacement par une nouvelle valeur de F. Le changement de bloc à la volée (G62) est suspendu par G00. Le passage au bloc suivant n’a lieu que lorsque tous les axes programmés se trouvent à l’intérieur de la fenêtre de position fixée dans les paramètres d’axes. Lorsque le passage de bloc à vitesse optimale est actif (G08), il est remplacé dans ce bloc, par le passage de bloc à vitesse limitée (G09). DOK-MTC200-NC**PRO*V17-ANW1-FR-P Blocs de déplacement 4-15 Manuel de programmation CN 17VRS Dès que G00 est remplacé par un autre type d’interpolation, G08 est réactivé automatiquement. G00 reste modal jusqu’à remplacement par une condition de déplacement du même groupe (G01, G02, G03). Exemple G00 G54 G90 X40 Y40 [P1] Rapide avec vitesse de trajectoiremaximale X120 Y60 F8000 [P2] Rapide avec mot F Y P2 60 P1 40 20 20 40 60 80 100 120 X 140 Fig. 4-19: Interpolation linéaire, rapide G00 Interpolation linéaire, Avance 'G01' Les axes programmés avec G01 sont déplacés en ligne droite dans le système de coordonnées actuel avec la vitesse d’avance courante. Les axes programmés démarrent simultanément et atteignent leur point programmé en même temps. Si une nouvelle avance F est programmée avec G01, la dernière valeur d’avance F active est remplacée. La valeur F programmée est une vitesse de trajectoire. De ce fait, lors de la programmation de plusieurs axes, la vitesse de chaque axe est inférieure à la vitesse de trajectoire programmée. Après mise sous tension de la commande, aucune vitesse F n’est active, une valeur de F doit donc être programmée avec G01. G01 est modal et reste actif jusqu’à ce qu’il soit remplacé par une condition de déplacement du même groupe (G00, G02, G03). Exemple Interpolation linéaire 2 axes Y [P4] 100 80 [P3] 100 [P4] 80 [P2] 60 60 40 40 20 20 [P1] [P1] 20 40 60 80 100 X Z Fig. 4-20: Interpolation linéaire G01 avec 2 axes DOK-MTC200-NC**PRO*V17-ANW1-FR-P X 10 0 -10 4-16 Blocs de déplacement Manuel de programmation CN 17VRS G00 G90 G54 G06 G08 Instructions de déplacement, conditions d'interpolation X0 Y0 Z10 S3000 M03 Position de départ, mise en route broche G01 X26.26 Y18 Z5 F2000 [P1] Position de départ usinage Z-5 Approche axe Z Y80 F1200 [P2] Interpolation linéaire, 1 axe X41 Y93.5 [P3] Interpolation linéaire, 2 axes X111 [P4] Interpolation linéaire, 1 axe G00 Z10 M05 Axe Z à distance de sécurité RET Exemple Interpolation linéaire sur 3 axes X Y [P3] [P2] [P3] 100 80 100 80 [P2] 60 60 [P1] 40 40 20 20 [P1] 20 40 60 80 100 X Z 10 0 -10 Fig. 4-21: Interpolation linéaire, G01 sur 3 axes G00 G90 G54 G06 G08 Instructions de déplacement, conditions d'interpolation X0 Y0 Z10 S3000 M03 Position de départ, mise en route broche G01 X40 Y25.5 Z5 F2000 [P1] Position de départ usinage Z-5 Approche axe Z X95.74 Y80 Z-10 F1200 [P2] Interpolation linéaire, 3 axes X100 Y100 Z10 F2000 [P3] Axe Z à distance de sécurité M05 Arrêt broche G00 X0 Y0 Retour au point de départ RET Fin de programme Interpolation circulaire ’G02’ / ’G03’ L’outil programmé avec les conditions de déplacement G02 ou G03 sera déplacé vers le point final programmé avec la vitesse active ou programmée (adresse F) sur une trajectoire circulaire. Les axes programmés démarrent simultanément et atteignent au même instant leur point final. Le déplacement circulaire a lieu: • dans le sens horaire avec G02 • dans le sens antihoraire avec G03 dans la direction du point final programmé (voir fig. 4-22). L’outil se déplace autour du centre programmé du cercle. En fonction de la sélection (G17, G18, G19, G20) un mouvement circulaire peut être effectué dans chaque plan. Le centre du cercle et le point d’arrivée doivent être dans le même plan d’usinage que le point de départ. DOK-MTC200-NC**PRO*V17-ANW1-FR-P Blocs de déplacement 4-17 Manuel de programmation CN 17VRS Ordonnée 2ème axe [Y] Plan ZX G18 GO2 GO2 GO3 G17 Plan XY Cote GO3 GO3 G19 GO2 Abscisse 1er axe [X] Plan YZ 3ème axe [Z] Fig. 4-22: Programmation d’un cercle en fonction du plan Le rayon et l’angle de départ de l’axe du cercle sont calculés en fonction du point de départ et du centre. Un rayon différent calculé à partir du centre et du point d’arrivée n’est pas pris en compte. Cela signifie que le point d’arrivée n’est pris en compte que pour le calcul de l’angle d’arrivée. Il s’ensuit qu’il peut arriver que le point d’arrivée programmée ne soit pas sur l’axe du cercle. Le point d’arrivée peut donc différer du point d’arrivée atteint. En programmation incrémentale (G91) les coordonnées du centre et du point d’arrivée font référence au point de départ; en programmation absolue (G90) elles font référence au point d’origine actuel. Les valeurs de coordonnées d’une lettre d’adresse non programmée (X, Y, Z, I, J, K) sont, en programmation absolue, affectées de la valeur correspondante du point de départ, et de la valeur 0 en programmation incrémentale. Pour la programmation d’un cercle entier, il suffit de programmer le centre car les coordonnées du point d’arrivée sont identiques à celles du point de départ. Le cercle ou l’arc de cercle est déterminé par les instructions d’axe et les paramètres d’interpolation programmés. Le point de départ du cercle est déterminé par le bloc précédent. Le point d’arrivée est fixé par les données des valeurs d’axe X, Y et Z dans le bloc avec G02/G03. Le centre du cercle est fixé par la donnée des paramètres d’interpolation I, J et K ou directement par le rayon R. . Paramètres d’interpolation I, J, K Des paramètres d’interpolation sont associés aux axes concernés par l’interpolation circulaire. Ils courent parallèlement aux axes, sont signés en fonction de leur direction, depuis le point d’origine, vers le centre du cercle. Selon DIN 66025 les paramètres d’interpolation I, J et K sont associés aux axes X, Y et Z. Si, aucune valeur de coordonnée n’est programmée avec les adresses I, J, K, la valeur du point de départ correspondant leur est attribuée en programmation absolue, la valeur 0 en programmation relative. En programmation G91, les paramètres d’interpolation définissent la distance entre le point de départ du cercle et le centre, et en G90 la distance entre le point d’origine actuel et le centre du cercle. DOK-MTC200-NC**PRO*V17-ANW1-FR-P 4-18 Blocs de déplacement Manuel de programmation CN 17VRS Y Point d'arrivée du cercle Point de départ du cercle -J (G91) Centre du cercle +I (G90) -I (G91) +J (G90) X Fig. 4-23: Interpolation circulaire et paramètres d’interpolation Exemple Cercle entier dans le plan X-Y avec G90 Y 100 80 I=60 60 40 KM [P1] J=60 20 20 40 60 80 100 120 140 X Fig. 4-24: Cercle entier avec G90 G00 G90 G54 G06 G08 Instructions de déplacement, conditions d'interpolation X0 Y0 Z10 S3000 M03 Position de départ, mise en route broche G01 X40 Y37.24 F2000 Point de départ cercle Z-10 F500 Approche axe Z G02 X40 Y37.24 I60 J60 Cercle entier sens horaire Alternative: G02 I60 J60 avec cercle entier, sans point d'arrivée G00 Z10 Axe Z à distance de sécurité M05 Arrêt broche X0 Y0 Retour au point de départ RET Fin de programme Exemple Cercle entier dans le plan X-Y avec G91 DOK-MTC200-NC**PRO*V17-ANW1-FR-P Blocs de déplacement 4-19 Manuel de programmation CN 17VRS Y I = 20 100 80 KM 60 J = 22.76 [P1] 40 20 20 40 60 80 100 120 140 X Fig. 4-25: Cercle entier avec G91 G00 G90 G54 G06 G08 Instructions de déplacement, conditions d'interpolation X0 Y0 Z10 S3000 M03 Position de départ, mise en route broche G91 G01 X40 Y37.24 F2000 Point de départ du cercle en relatif Z-20 F500 Approche axe Z G02 X0 Y0 I20 J22.76 Cercle entier sens horaire Alternative: G02 I20 J22.76 avec cercle entier, sans point d'arrivée G00 G90 Z10 Axe Z à distance de sécurité (G90) M05 Arrêt broche X0 Y0 Retour au point de départ RET Fin de programme Exemple Usinage sur tour dans le plan Z-X ØX 100 [P5] [P4] KM 80 +K +I 60 [P2] [P3] 40 [P1] 20 20 40 60 80 100 120 Fig. 4-26: Interpolation circulaire sur tour, en arrière de l’axe DOK-MTC200-NC**PRO*V17-ANW1-FR-P 140 Z 4-20 Blocs de déplacement Manuel de programmation CN 17VRS Exemple de programmation en absolu (G90) Instructions de déplacement, conditions d'interpolation G00 G90 G54 G06 G08 M03 S2000 Mise en route broche X34.5 Z136.5 [P1] Position de départ G01 X40 Z128.5 F500 [P2] Interpolation linéaire Z100 [P3] Point de départ du cercle G02 X80 Z60 I80 K100 [P4] Quart de cercle sens horaire G01 Z10 [P5] Point d'arrivée usinage G00 X100 Axe X à distance de sécurité M05 Arrêt broche RET Fin de programme Exemple de programmation en incrémental(G91) Instructions de déplacement, conditions d'interpolation G00 G90 G54 G06 G08 M03 S2000 Mise en route broche X34.5 Z136.5 [P1] Position de départ G01 G91 X5.5 Z-8 F500 [P2] Interpolation linéaire Z-28.5 [P3] Point de départ du cercle G02 X40 Z-40 I40 K0 [P4] Quart de cercle sens horaire G01 Z-50 [P5] Point d'arrivée usinage G90 G00 X100 Axe X à distance de sécurité M05 Arrêt broche RET Fin de programme Programmation avec rayon du cercle Afin de pouvoir utiliser directement les cotations de la pièce, il est possible de programmer la trajectoire circulaire en donnant directement le rayon dans le programme CN. Une trajectoire circulaire univoque est obtenue, par programmation sous G02 ou G03, uniquement à l’intérieur d’un demi-cercle (180°) (voir fig. 427). De ce fait, il est nécessaire d’indiquer si l’angle de déplacement doit être inférieur à 180°. Pour un demi-cercle supérieur à 180° la programmation du rayon doit être donnée avec un signe négatif. Syntaxe pour la programmation d’un cercle au rayon dans le plan G17 G02 G03 180° R+ ... pour angle de déplacement jusqu’à 180° X ... Y … Exemple R- ... pour angle de déplacement supérieur à Détermination de l’arc de cercle ØX 100 R = -30 80 [S] 60 [E] R = +30 40 20 20 40 60 80 100 120 140 Z Fig. 4-27: Programmation d’un cercle. Détermination du signe du rayon G01 X... Z... G02 X... Z... R±30 DOK-MTC200-NC**PRO*V17-ANW1-FR-P Blocs de déplacement 4-21 Manuel de programmation CN 17VRS Il est visible dans l’exemple représenté, qu’il y a deux possibilités pour le cercle programmé. Le choix du signe (R+30 ou R-30) détermine le cercle qui doit être parcouru. • Le sens de déplacement jusqu’au point d’arrivée est déterminé par G02 ou G03. • Pour un angle de déplacement de 0° ou de 360°, la programmation avec le rayon n’est pas autorisée. Les axes, restent à leur point de départ. • Lorsque le point d’arrivée est absent, les axes restent à leur point de départ. • Le rayon programmé est actif dans le plan d’usinage actuel (G17, G18, G19, G20). Exemple Programmation d’un cercle par le rayon dans le plan Z-X ØX 100 80 [P5] [P4] Centre du cercle R 60 [P3] 40 [P2] [P1] 20 20 40 60 80 100 120 140 Z Fig. 4-28: Programmation d’un cercle au rayon sur un tour, en arrière de l’axe Programme CN G00 G90 G54 G06 G08 d'interpolation DOK-MTC200-NC**PRO*V17-ANW1-FR-P Instructions de déplacement, conditions M03 S2000 Mise en route broche X34.5 Z136.5 [P1] Position de départ G01 X40 Z128.5 F500 [P2] Interpolation linéaire Z100 [P3] Point de départ du cercle G02 X80 Z60 R40 [P4] Quart de cercle sens horaire G01 Z10 [P5] Point d'arrivée usinage G00 X100 Axe X à distance de sécurité M05 Arrêt broche RET Fin de programme 4-22 Blocs de déplacement Manuel de programmation CN 17VRS Interpolation hélicoïdale L’interpolation hélicoïdale est une interpolation combinée linéaire-circulaire pour obtenir une trajectoire en forme d’hélice. Pour cela l’interpolation circulaire a lieu dans le plan choisi (G17, G18, G19, G20), l’interpolation linéaire simultanée a lieu sur le 3è axe perpendiculaire au plan de l’interpolation circulaire. Z -50 25 50 Y 50 X Fig. 4-29: Interpolation hélicoïdale Lors d’une interpolation hélicoïdale, un arc de cercle et une droite déterminée par son point d’arrivée dans une direction perpendiculaire sont programmés dans un bloc. Les mouvements d’axes sont coordonnés de telle sorte que l’outil décrive une ligne hélicoïdale à pas constant. On ne peut programmer, dans un bloc CN, qu’une révolution au maximum, ce qui correspond à un cercle complet. Plusieurs révolutions consécutives doivent être programmées avec un nombre correspondant de révolutions simples. La vitesse d’avance programmée (valeur F) correspond à la trajectoire d’outil effective. Toutes les autres conditions sont celles d’une interpolation circulaire. Exemple Interpolation hélicoïdale dans le plan X-Y avec G90 X Y 100 100 [P4] 80 80 60 60 40 [P1] [P2] 20 [P1] 20 40 KM I = 62.5 40 [P3] 20 J = 30 [P4] 60 80 100 X Z 10 0 -10 Fig. 4-30: Interpolation hélicoïdale avec G90 DOK-MTC200-NC**PRO*V17-ANW1-FR-P Blocs de déplacement 4-23 Manuel de programmation CN 17VRS Exemple de programmation absolue (G90) G00 G90 G54 G06 G08 Instructions de déplacement, conditions d'interpolation X0 Y0 Z10 S5000 M03 Position de départ, mise en route broche G01 X40 Y20 Z5 F2000 [P1] Axe Z à distance de sécurité Z-2.5 Axe Z à profondeur d'usinage X40 Y30 [P2] Point de départ de demi révolution G02 X85 Y30 I62.5 J30 Z-5 [P3] Hélice sens horaire G01 X85 Y10 [P4] Déplacement libre X et Y G00 Z5 Axe Z à distance de sécurité M05 Arrêt broche X0 Y0 Z10 Retour à position de départ RET Fin de programme Exemple Interpolation hélicoïdale dans le plan X-Y avec G91 I = 22.5 Y X 100 100 [P4] 80 80 60 60 [P1] 40 [P2] [P1] 20 [P3] 40 J=0 20 [P4] 20 40 60 80 100 X Z 10 0 -10 Fig. 4-31: Interpolation hélicoïdale avec G91 Exemple de programmation absolue (G91) DOK-MTC200-NC**PRO*V17-ANW1-FR-P G00 G90 G54 G06 G08 d'interpolation Instructions de déplacement, conditions X0 Y0 Z10 S5000 M03 Position de départ, Mise en route broche G91 G01 X40 Y20 Z-5 F2000 [P1] Axe Z à distance de sécurité Z-7.5 Axe Z à profondeur d'usinage Y10 [P2] Point de départ de demi révolution G02 X45 I22.5 J0 Z-2.5 [P3] Hélice sens horaire G01 Y-20 [P4] déplacement libre Y G00 Z10 Axe Z à distance de sécurité M05 Arrêt broche X-85 Y-10 Z5 Retour à position de départ RET Fin de programme 4-24 Blocs de déplacement Manuel de programmation CN 17VRS Filetage ’G33’ La fonction G33, filetage, permet de tailler: • des filetages longitudinaux à pas simples ou à pas multiples • des filetages plans • des filetages coniques à pas constant. Pas 1 filet Filetage longitudinal Fig. 4-32: filetages longitudinaux Syntaxe G33 <point d’arrivée[X,Y,Z]> <pas[I,J,K]> <angle de départ[P]> La longueur de filetage est obtenue par la différence entre le point de départ et le point d’arrivée programmé dans le bloc avec G33. Dans cette longueur, il faut tenir compte des courses d’engagement et de dégagement durant lesquelles l’axe accélère et freine. Les valeurs coordonnées peuvent être programmées en absolu (G90) ou en incrémental (G91). Le pas de filetage est donné sous les adresses. I, J et K . Un seul paramètre d’interpolation peut être programmé dans un bloc de filetage. Les paramètres d’interpolation I, J et K sont programmés comme valeur incrémentale, sans signe. Ils sont affectés aux axes X, Y et Z. L’angle de départ de filetage peut être programmé entre 0° et 360° sous l’adresse P. La programmation d’un angle de départ permet d’usiner des filetages multipas sans décaler le point de départ. Si aucune valeur n’est donnée sous l’adresse P, un angle de départ de 0° est utilisé . Le filetage à droite ou à gauche est obtenu par programmation du sens de rotation de la broche M03 ou M04. Lorsque l’on veut utiliser une autre broche pour le filetage avec G33, cette broche doit être activée avant le bloc G33 avec la commande ‘SPF <numéro de broche>’. A la mise sous tension, la première broche est toujours active. La broche doit être démarrée à la vitesse souhaitée avant ou dans le bloc avec G33. Pour le filetage avec G33, l’interpolation à erreur de poursuite réduite G06 doit être activée dans tous les cas, car cette fonction améliore l’état du filetage. G33 appartient au groupe des codes G actifs dans un bloc. A la fin du bloc, G33 n’est plus actif. Le filetage est effectué depuis le point de départ actuel jusqu’au point d’arrivée programmé. Des mouvements sur plusieurs axes sont possibles (filetage conique). • Jusqu’à 500 spires peuvent être effectuées dans chaque bloc de filetage. Si plus de 500 spires sont nécessaires, cela peut être obtenu au moyen d’enchaînement de filetages. • La vitesse de rotation de la broche doit être, durant le bloc de filetage, au maximum de 13500 t/min . La course d’engagement croît avec la vitesse de rotation et le pas du filet. DOK-MTC200-NC**PRO*V17-ANW1-FR-P Blocs de déplacement 4-25 Manuel de programmation CN 17VRS • La vitesse de coupe constante G96 est ignorée durant le filetage. La dernière vitesse de broche programmée sous G97 est utilisée. • Lorsque l’interpolation à faible erreur de poursuite G06 est utilisée en filetage, la vitesse de broche peut être modifiée avec l’atténuateur de broche durant la coupe, mais cela peut entraîner une perte de qualité. La vitesse d’avance est adaptée en conséquence. L’atténuateur d’avance est sans effet. • Lors d’un arrêt immédiat (arrêt d’urgence, stop en mode réglage) les vitesses de broche et d’avance sont diminuées de façon synchrone, et augmentées de façon synchrone après un nouveau départ. • Dans un filetage conique, le pas est donné par rapport à l’axe principal Lorsque le pas doit se rapporter à l’axe Z, il doit être programmé dans le paramètre d’interpolation K. S’il se rapporte à l’axe X, il doit être programmé dans le paramètre I. • Lors du tournage d’un filetage plan avec programmation au diamètre, le pas est interprété selon le rayon. • En fonction du réglage des paramètres, le plan peut être programmé avec 3 ou 4 chiffres avant la virgule et 5 ou 4 chiffres après la virgule. La fonction G33 n’est disponible qu’avec un présent (processeur d’axe). APR_3 REMARQUE Exemple Programme CN filetage longitudinal ØX 100 80 [P4] [P1] [P3] [P6] [P2] 60 40 [P5] 20 20 40 60 80 100 120 140 Z Fig. 4-33: Filetage longitudinal Pas du filetage: Profondeur du filet: DOK-MTC200-NC**PRO*V17-ANW1-FR-P 3 4 mm mm Profondeur de chaque passe: 2 mm 4-26 Blocs de déplacement Manuel de programmation CN 17VRS Programme CN G00 G54 G90 G06 G08 X80 Z130 S2000 M03 [P1] Conditions de départ ère G01 X45.5 F1500 [P2] Approche pour 1 coupe G33 Z30 K3 P180 [P3] 1ère passe de filetage G00 X80 [P4] Retrait Axe X Z130 [P1] Point de départ G01 X43.5 F1500 [P5] Approche pour 2ème coupe G33 Z30 K3 P180 [P6] 2ème passe de filetage G00 X80 [P4] Retrait Axe X M05 Arrêt broche RET Fin de programme Exemple Programme CN – filetage conique ØX 100 80 [P4] [P1] 105 mm Pas [P3] [P6] 60 17° 40 [P2] [P5] 10 mm 20 20 40 60 80 100 120 47.5 mm Z 140 Fig. 4-34: Filetage conique Pas du filetage: Profondeur du filet: 2.5 mm 3 mm Profondeur de chaque passe: 1.5 mm Programme CN G00 G54 G90 G06 G08 X100 Z130 S2000 M03 [P1] Conditions de départ G01 X39.89 F1500 [P2] Approche pour 1ère coupe G33 X71.99 Z25 K2.5 P90 [P3] 1 passe de filetage G00 X100 [P4] Retrait axe X Z130 [P1] Point de départ G01 X38.39 F1500 [P5] Approche ème pour 2 coupe G33 X70.49 Z25 K2.5 P90 [P6] 2 passe de filetage G00 X100 [P4] axe X M05 Arrêt broche RET Fin programme ère ème Retrait DOK-MTC200-NC**PRO*V17-ANW1-FR-P Blocs de déplacement 4-27 Manuel de programmation CN 17VRS Calcul l’axe: des points de début et de 3 3 ∗ ∗ 7$1 ° 3 ∗ 7$1 ° 3 3 ∗ ∗ 7$1 ° 3 ∗ 7$1 ° Exemple fin de filetage pour Programme CN – filetage plan ØX 100 80 [P6] [P3] [P4] 60 40 [P1] [P5] [P2] 20 20 40 60 80 100 120 Z 140 Fig. 4-35: Filetage plan Pas du filet: Profondeur du filet: 2 mm 3 mm Profondeur de chaque passe: 1.5 mm Programme CN: G00 G54 G90 G06 G08 X27.5 Z100 S2500 M03 [P1] Conditions de départ DOK-MTC200-NC**PRO*V17-ANW1-FR-P G01 Z78 F1500 [P2] Approche pour 1 coupe G33 X72.5 I2 P180 [P3] 1 passede filetage G00 Z100 [P4] Retrait axe Z X27.5 [P1] Point de départ G01 Z76.5 F1500 [P5] Approche pour 2 coupe ère ère ème ème G33 X72.5 I2 P180 [P6] 2 passe de filetage G00 Z100 [P4] Retrait axe Z M05 Arrêt broche RET Fin programme 4-28 Blocs de déplacement Manuel de programmation CN 17VRS Enchaînement de blocs de filetage avec 'G33' Il est possible, avec la fonction G33 - filetage – de programmer plusieurs blocs de filetage consécutifs avec des pas différents. Un enchaînement de filetage peut être composé de • filetages longitudinaux à pas simple ou pas multiple • filetages plans ou • filetages coniques dans n’importe quel ordre avec un pas constant pour chaque partie. Filetage longitudinal Pas 1er filet 2ème partie de pièce 1ère partie de pièce Fig. 4-36: Filetages longitudinaux avec deux parties à pas différents Syntaxe G33 <Point d’arrivée[X,Y,Z]> <Pas[I,J,K]> <Angle de départ[P]> G33 <Point d’arrivée[X,Y,Z]> <Pas[I,J,K]> <Angle de départ[P]> Les entraînements de filetage sont programmés comme blocs de filetage consécutifs. Entre chaque bloc de filetage est calculé, pour chaque axe, un chemin de transition pour les modifications de vitesse. La modification de vitesse est effectuée avec l’accélération maximale autorisée ce qui donne des paraboles de transition. • Avec les enchaînements de filetage, il faut que G08 (transition de bloc à vitesse optimale) soit actif. Afin d’obtenir la plus petite parabole de transition entre deux blocs de filetage, G06 (interpolation sans erreur de poursuite) doit être actif. • Entre et dans les blocs de filetage d’un enchaînement de filetages ne doivent être programmées aucunes fonctions entraînant une interruption de la préparation des blocs (par exemple: fonction auxiliaire, calcul). • Lorsque le mode bloc à bloc est actif, les blocs de filetage sont préparés séparément. Dans ce cas, une nouvelle distance d’engagement est nécessaire dans chaque bloc. L’enchaînement de filetage n’est donc, dans ce mode, pas possible. Toutes les autres conditions sont identiques à celle d’un filetage normal. DOK-MTC200-NC**PRO*V17-ANW1-FR-P Blocs de déplacement 4-29 Manuel de programmation CN 17VRS Exemple Programme CN – enchaînement de filetage ØX 100 80 [P6] 60 [P1] [P5] 40 [P4] [P9] [P10] 20 [P3] 3ème partie de pièce 20 40 [P2] [P7] 2ème partie [P8] 1ère partie de pièce de pièce 60 80 100 120 Z 140 Fig. 4-37: Enchaînement filetage Pas du filet: 1: 3 mm Profondeur du filet: 4 mm 2: 5 mm 3: 1 Profondeur de chaque passe: mm 2 mm Programme CN: G00 G54 G90 G06 G08 X60 Z135 S2000 M03 [P1] départ DOK-MTC200-NC**PRO*V17-ANW1-FR-P Conditions de G01 X23 F1500 [P2] Approche ère 1 coupe pour G33 Z90 K3 P180 [P3] 1 partie filetage / ère 1 passe G33 X38 Z50 K5 [P4] 2 partie filetage / ère 1 passe G33 Z10 K1 [P5] 3 partie filetage / ère 1 passe G00 X60 [P6] Retrait axe X Z135 [P1] Point de départ G01 X21 F1500 [P7] Approche ème 2 coupe G33 Z90 K3 P180 [P8] 1 partie filetage / ème 2 passe G33 X36 Z50 K5 [P9] 2 partie filetage / ème 2 passe G33 Z10 K1 [P10] 3 partie filetage ème 2 passe G00 X60 [P6] Retrait axe X M05 Arrêt broche RET Fin de programme ère ème ème pour ère ème ème 4-30 Blocs de déplacement Manuel de programmation CN 17VRS Taraudage ’G63’ / ’G64’ La fonction G63 permet d’effectuer des taraudages sans mandrin de compensation. Avec un taraudage sans compensation, la broche est pilotée non seulement en vitesse, comme pour un taraudage conventionnel, mais aussi en position. Le mouvement de la broche et les mouvements d’approche des axes programmés avec G63 sont interpolés linéairement. Une condition préalable au taraudage sans compensation est de disposer d’une broche capable de positionnement. La broche doit être entraînée directement (glissement) et le codeur de position doit se trouver directement sur la broche. La CNC dispose, pour le taraudage sans compensation, de deux instructions actives dans le bloc: • G63 - Arrêt broche en fin de tournage • G64 - Rotation de broche après la fin du filetage Les fonctions G63 et G64 ne se différencient que par la fin de mouvement. Syntaxe G63 <Point d’arrivée[X,Y,Z]> <Avance par tour de broche [F]> G64 <Point d’arrivée[X,Y,Z]> <Avance par tour de broche [F]> Il faut distinguer deux cas lors de l’établissement de l’accouplement avance / broche: • la broche est à l’arrêt (n=0) • la broche est déjà en rotation (n=S) Si la broche est à l’arrêt lors de l’établissement de l’accouplement avance / broche, l’accouplement peut être activé dès le début de la phase d’accélération conjointe, de telle sorte que la broche et l’axe d’avance accélèrent en interpolation. L’accélération choisie se détermine en fonction de l’axe le plus faible (broche principale en axe d’avance). Si la broche est déjà en rotation lors de l’établissement de l’accouplement, l’axe d’avance est accéléré jusqu’à la vitesse nécessaire avec son accélération maximale et le couplage est alors activé. La broche et les axes d’avance ne sont interpolés que dans la plage à vitesse constante. • Le taraudage à droite ou gauche est obtenu en donnant le sens de rotation broche M03 ou M04. • Si une autre broche doit être sélectionnée pour le taraudage avec G63 / G64, elle doit être activée avant le bloc de taraudage avec la commande SPF <numéros de broches>. A la mise sous tension, la première broche est toujours active. • Le taraudage devrait être exécuté avec la condition d’interpolation à faible erreur de poursuite G06. Lorsque G06 n’est pas actif lors du taraudage sans compensation, par exemple avec des axes analogiques, il faut que le même facteur de gain Kv soit réglé sur la broche et l’axe associé avec G63 / G64. • Les fonctions G08 (passage de bloc à vitesse optimale) et G61 (arrêt précis) sont sans effet lors du taraudage. • Une broche arrêtée à la fin du mouvement (G63) peut être redémarrée par une commande de broche M03 / M04 et programmation d’une vitesse de rotation (Valeur S). • Lorsque le taraud doit être ressorti du filet avec G64, la broche s’arrête, avec les entraînements numériques, un court instant à la fin du bloc, pour passer d’un asservissement de position à un asservissement de vitesse. DOK-MTC200-NC**PRO*V17-ANW1-FR-P Blocs de déplacement 4-31 Manuel de programmation CN 17VRS • Entre la commande G63 taraudage à la profondeur <X, Y ou Z> et la commande G63 / G64 retrait de l’axe de perçage, aucune commande autre que temporisation et fonction auxiliaire, ne doit être programmée. • Lorsque, avec des entraînements numériques, la broche est mise en route avant le bloc avec taraudage G63, elle s’arrête brièvement dans le bloc G63 pour passer de l’exploitation asservissement de vitesse à l’exploitation asservissement de position. • Le facteur d’accouplement avance par tour de broche doit être programmé dans un bloc avec G63 et G64 sous l’adresse F. • En fonction du paramétrage, le pas de taraudage peut être introduit avec 3 ou 4 chiffres avant la virgule et 5 ou 4 après la virgule. Exemple Programme CN – taraudage avec G63 Y X 100 100 [P3] [P4] 80 [P2] [P3] [P1] [P4] 80 60 60 [P1] 40 40 [P2] 20 20 20 40 60 80 100 X Z 10 -10 0 Fig. 4-38: taraudage avec G63 Programme CN avec G63: Broche à l'arrêt au début Broche arrêtée à la fin du mouvement DOK-MTC200-NC**PRO*V17-ANW1-FR-P du bloc avec G63 G00 G54 G90 G06 G08 X0 Y0 Z10 Instructions de déplacement conditions d'interpolation G01 X40 Y50 F2000 [P1] Position 1 filetage BSR .GEBO Appel SP taraudage Y80 [P2] Position 2 BSR .GEBO Appel SP X90 [P3] Position 3 BSR .GEBO Appel SP taraudage Y50 [P4 Position 4 BSR .GEBO Appel SP taraudage G00 X0 Y0 Retour au point de départ RET Fin de programme .GEBO Sous-Programme taraudage G63 Z-7.5 F2 S1000 M03 Taraudage à profondeur Z G63 Z10 F2 S750 M04 Retrait taraud RTS Fin sous-programme er ème filetage ème filetage ème filetage (SP) 4-32 Blocs de déplacement Manuel de programmation CN 17VRS Broche déjà en rotation au début Broche arrêtée à la fin du mouvement du bloc avec G63 G00 G54 G90 G06 G08 X0 Y0 Z10 Instructions de déplacement conditions d'interpolation G01 X40 Y50 F2000 M03 S1000 [P1] Position 1 mise en route broche BSR .GEBO Appel SP taraudage Y80 M03 S1000 [P2] Position 2 mise en route broche BSR .GEBO Appel SP taraudage X90 M03 S1000 [P3] Position 3 mise en route broche BSR .GEBO Appel SP taraudage Y50 M03 S1000 [P4] Position 4 mise en route broche BSR .GEBO Appel SP taraudage G00 X0 Y0 Retour au point de départ RET Fin de programme .GEBO Sous-Programme taraudage G63 Z-7.5 F2 Taraudage à profondeur Z G63 Z10 F2 S750 M04 Retrait taraud RTS Fin sous-programme Exemple er filetage, ème filetage, ème ème filetage, filetage, (SP) Programme CN – Taraudage avec G63 et G64 X Y 100 100 [P4] 80 [P2] 80 [P3] [P3] 60 60 [P2] [P1] [P4] 40 40 [P1] 20 20 20 40 60 80 100 X Z 10 0 -10 Fig. 4-39: Taraudage avec G63 et G64 DOK-MTC200-NC**PRO*V17-ANW1-FR-P Manuel de programmation CN 17VRS Blocs de déplacement 4-33 Programme CN avec G63 et G64: Broche à l'arrêt au début du bloc avec G63 Broche en rotation après la fin du mouvement G00 G54 G90 G06 G08 X0 Y0 Z10 Instructions de déplacement conditions d'interpolation G01 X40 Y50 F2000 [P1] Position 1 filetage BSR .GEBO Appel SP taraudage X55 Y80 [P2] Position 2 BSR .GEBO Appel SP taraudage X75 [P3] Position 3 BSR .GEBO Appel SP taraudage X90 Y50 [P4] Position 4 BSR .GEBO Appel SP taraudage M05 Arrêt broche G00 X0 Y0 Retour au point de départ RET Fin de programme .GEBO Sous-Programme taraudage G63 Z-7.5 F2 S1000 M03 Taraudage à profondeur Z G64 Z10 F2 S800 M04 Retrait taraud RTS Fin sous-programme er ème ème ème Broche déjà en rotation au début Broche en rotation après la fin du mouvement DOK-MTC200-NC**PRO*V17-ANW1-FR-P du filetage filetage filetage (SP) bloc avec G63 G00 G54 G90 G06 G08 X0 Y0 Z10 Instructions de déplacement conditions d'interpolation G01 X40 Y50 F2000 M03 S1000 [P1] Position 1 mise en route broche BSR .GEBO Appel SP taraudage X55 Y80 M03 S1000 [P2] Position 2 mise en route broche BSR .GEBO Appel SP taraudage X75 M03 S1000 [P3] Position 3 mise en route broche BSR .GEBO Appel SP taraudage X90 Y50 M03 S1000 [P4] Position 4 mise en route broche BSR .GEBO Appel SP taraudage M05 Arrêt broche G00 X0 Y0 Retour au point de départ RET Fin de programme .GEBO Sous-Programme taraudage G63 Z-7.5 F2 Taraudage à profondeur Z G64 Z10 F2 S800 M04 Retrait taraud RTS Fin sous-programme er filetage, ème filetage, ème ème filetage, filetage, (SP) 4-34 Blocs de déplacement Manuel de programmation CN 17VRS Taraudage ’G65’ – Broche comme axe maître La fonction G65 permet d’effectuer des filetages avec une broche principale sans interpolation avec asservissement de position. G65 exploite en outre les broches principales à entraînement indirect avec un codeur de position qui n’est pas monté directement sur la broche. Lors de taraudage avec G65 on utilisera généralement un mandrin de compensation. Le déplacement programmé avec G65 est dépendant de la position de la broche. A cause des temps morts imposés par le système, l’avance est toujours en retard sur la broche, ce qui, lors de l’inversion de sens de rotation, entraîne une contrainte double sur l’outil. Lors de taraudage sans compensation, il faut dans tous les cas préférer les fonctions G63 / G64. Syntaxe M05 Arrêt broche G65 <Avance par tour de broche[F]> Activation taraudage S500 M03 Vitesse et sens derotation broche Z-10 Taraudage à profondeur Z Z10 S800 M04 Détaraudage Comme condition préalable pour la fonction G65 - taraudage – la broche doit être capable de positionnement: • Lors de l’activation de G65 (taraudage) la broche doit au préalable être arrêtée avec MO5. • Après activation de G65, il n’est pas possible d’effectuer un déplacement en G00, une interpolation circulaire ou hélicoïdale avec G02 / G03 ou une prise d’origine G74. Les fonctions d’avance concernant le passage de bloc (G08, G09, G61, G62) sont supprimées. • Aucun déplacement d’axe ne doit être programmé dans un bloc avec G65. • La broche doit être démarrée après le bloc G65. Le sens de filetage (gauche ou droit) est donné par le sens de rotation broche M03 ou M04. La mise en route de la broche est déclenchée seulement par l’instruction de déplacement d’un axe principal. • Le facteur de couplage ‘’Avance par tour de broche’’ doit être programmé dans bloc avec G65 sous l’adresse F. • Le taraudage ne devrait être exécuté qu’avec la condition G06 interpolation à faible erreur de poursuite. • Avec des broches à entraînement direct et codeur monté sur la broche, la fonction G65 permet aussi d’exécuter des taraudages sans mandrin de compensation avec des vitesses moyennes • Lorsqu’une autre broche doit être choisie pour le taraudage avec G65, la broche doit être activée avec ‘SPF <numéro de broche>’ avant le bloc avec G65. A la mise sous tension, la première broche est toujours active. • G65 se superpose à G93 ou est activée par G94 ou G95 fonctions qui arrêtent automatiquement la broche. • En fonction du paramétrage, le pas du taraudage est donné avec 3 ou 4 chiffres avant la virgule et 5 ou 4 après la virgule. Seuls les axes linéaires principaux X, Y et Z peuvent être programmés lorsque G65 est actif. La programmation d’autres axes conduit à un message d’erreur. REMARQUE DOK-MTC200-NC**PRO*V17-ANW1-FR-P Blocs de déplacement 4-35 Manuel de programmation CN 17VRS Exemple Programme CN - Taraudage avec G65 X Y 100 100 [P4] 80 [P2] 80 [P3] [P3] 60 60 [P2] [P1] [P4] 40 40 [P1] 20 20 20 40 60 80 100 X Z 10 0 -10 Fig. 4-40: Taraudage avec G65 Programme CN avec G65: DOK-MTC200-NC**PRO*V17-ANW1-FR-P G00 G54 G90 G06 G08 X0 Y0 Z10 Instructions de déplacement conditions d'interpolation G01 X40 Y50 F2000 [P1] 1. Position de taraudage BSR .GEBO Appel SP taraudage X55 Y80 [P2] 2. Position de taraudage BSR .GEBO Appel SP taraudage X75 [P3] 3. Position de taraudage BSR .GEBO Appel SP taraudage X90 Y50 [P4] 4. Position de taraudage BSR .GEBO Appel SP taraudage M05 Arrêt broche G00 X0 Y0 Retour au point de départ RET Fin de programme .GEBO Sous-programme taraudage M05 Arrêt broche (SP) G65 F2 Activation taraudage S500 M03 Vitesse broche Z-7.5 Tarauder à profondeur Z Z10 S400 M04 Détaraudage G94 Annulation G65 RTS Fin de sous-programme et sens rotation 4-36 Blocs de déplacement 4.4 Manuel de programmation CN 17VRS Avance Mot F L’introduction d’une vitesse d’avance dans un programme CN se fait dans un mot d’avance composé de la lettre adresse F et d’une vitesse d’avance donnée par une constante ou une expression. La vitesse d’avance programmée fixe la vitesse d’usinage dans tous les modes d’interpolation. La vitesse d’avance est limitée de telle sorte que les valeurs limites fixées dans les paramètres ne soient pas dépassées. Lorsque le mot F est programmé en liaison avec une condition de déplacement, sa signification peut être modifiée. L’action correspondante est décrite dans les conditions de déplacement (G00, G04, G93, G95) correspondantes. Syntaxe F<Constante> Ø F1000 F<Expression> Ø F=@50 Lorsque le mot F est programmé comme vitesse d’avance, il sera utilisé comme consigne de vitesse d’usinage. Le mot F agit avec les codes G selon le tableau suivant: Signification Code G Action Format Programmation de vitesse G94 modal chiffres avant la virgule 6 5 chiffres après la virgule 1 2 Supprimé avec G95. La dernière valeur F programmée avec G94 est de nouveau active à l’appel du G94 suivant. Avance par tour G95 modal chiffres avant la virgule 4 3 chiffres après la virgule 4 5 Supprimé avec G94. La dernière valeur F programmée avec G95 est de nouveau active à l’appel du G95 suivant. G63, G64 dans le bloc 4 3 4 5 La valeur de F est de nouveau active avec un nouveau G63, G64. La valeur F de G94 n’est pas modifiée. G65 modal G04 dans le bloc 3 2 G93 dans le bloc 5 2 Temps en secondes Programmation en temps Remarque Conditions identiques à G95 ! Lorsque le mot F est seul dans un bloc, il est associé à la mémoire des conditions de déplacement du groupe d’avance actif. Lorsque le mot F est programmé avec l’une de ces conditions de déplacement, le mode d’avance est tout d’abord activé puis la valeur de F lui est associée. • Avec G94 (programmation de vitesse) l’unité de vitesse d’avance est le mm/min ou le inch/min. • Avec G63, G64, G65 (taraudage) et G95 (avance par tour), l’unité de vitesse d’avance est le mm/tour de broche ou inch/tour de broche. • Avec G04 (temporisation) et G93 (programmation en temps) le temps est donné en secondes sous l’adresse F. • La vitesse d’avance programmée peut être modifiée de 0% à 255% par l’atténuateur d’avance. La valeur 100 correspond à la vitesse programmée. Après une mise sous tension, un chargement d’un programme CN, une instruction BST ou RET ou un Control Reset, les valeurs d’avance sont remises à 0. Elles doivent être programmées au début d’un programme CN avant ou en même temps que la première instruction de déplacement. DOK-MTC200-NC**PRO*V17-ANW1-FR-P Blocs de déplacement 4-37 Manuel de programmation CN 17VRS Remarque: Les vitesse maximales de trajectoire ou d’axe sont fixées par le constructeur de machine dans les paramètres. Programmation en temps ’G93’ La fonction G93 - Programmation en temps – permet de fixer le temps d’usinage pour une distance de déplacement programmée. Le temps d’usinage est fixé dans le mot F. En fonction des valeurs limites la CN calcule la vitesse de trajectoire nécessaire pour le temps d’usinage donné. G93 F<temps en secondes> Syntaxe G93 est actif dans le bloc et doit être programmé avec un mot F. • G93 masque G94 ou G95 dans le bloc programmé. • La valeur F programmée avec G93 n’influence pas les valeurs F qui avaient été programmées avec G94 ou G95. • La valeur F programmée avec G93 peut être introduite avec cinq chiffres avant la virgule et deux après. Exemple Programme CN - avec G93 Y X [P4] 100 80 [P3] 100 [P4] 80 [P2] 60 60 40 40 20 20 20 [P1] [P1] 40 60 80 100 X Z 10 0 -10 Fig. 4-41: Interpolation linéaire, G01 avec 2 axes et programmation en temps DOK-MTC200-NC**PRO*V17-ANW1-FR-P G00 G90 G54 G06 G08 Instructions de déplacement conditions d'interpolation X0 Y0 Z10 S3000 M03 Position de départ, Mise route broche G93 G01 X26.26 Y18 Z5 F0.97 [P1] Position de départ, programmation en temps G93 Z-5 F0.3 Approche axe Z G93 Y80 F1.86 [P2] 1 axe Interpolation linéaire, G93 X41 Y93.5 F0.6 [P3] Interpolation 2 axes linéaire, G93 X111 F2.1 [P4] 1 axe linéaire, G00 Z10 M05 Axe Z à distance de sécurité RET Fin de programme Interpolation en 4-38 Blocs de déplacement Manuel de programmation CN 17VRS Programmation de la vitesse ’G94’ Avec la fonction G94 - Programmation en vitesse – le mot F programmé est interprété comme vitesse d’avance en mm/min ou inch/min. G94 est l’état de base à la mise sous tension de la CNC. Pour des axes linéaires, la valeur d’avance est programmée dans l’unité active (mm/inch). Pour des axes rotatifs, elle est programmée en divisions de la constante d’avance donnée dans les paramètres d’axes. • En fonction des réglages des paramètres process, G94 peut être l’état à la mise sous tension. G94 est modal et est suspendu par G95, G96 ou G65. • Après la mise sous tension, le chargement d’un programme CN, une instruction BST ou RET ou un Control Reset, G94 peut être en fonction du réglage des paramètres process, automatiquement sélectionné; les valeurs d’avance (valeur F) sont remises à zéro. • Les particularités pour les vitesses de trajectoire dépendant du rayon efficace pour les usinages en axes C sont décrites au chapitre 4.6 ‘Programmation d’un axe rotatif’, page 4-47 ‘Programmation d’axe rotatif’. Avance par tour ’G95’ Avec la fonction G95 - Avance par tour – le mot F programmé est interprété en ‘mm’ ou ‘inch’ par tour de broche. La vitesse de la trajectoire dépend de la valeur de la vitesse réelle de broche. Si aucun codeur de position n’est disponible pour la broche principale, la vitesse de la trajectoire dépend de la valeur de la consigne de vitesse de broche. Syntaxe G95 F<Avance par tour> G95 - Avance par tour – est modal et reste actif jusqu’à annulation par G94 ou G65 ou automatiquement à la fin du programme (RET) ou une instruction BST. G93 (Programmation en temps) masque G95. • A la mise sous tension, G95 se réfère toujours à la première broche. Si G95 doit se référer à une autre broche, celle-ci doit être sélectionnée avec la commande ‘SPF <inférieure à numéro de broche>’ avant le bloc G95. • En fonction du réglage des paramètres process, G95 peut être l’état de base. G95 (Avance par tour) est modal et reste actif jusqu’à annulation par G94 ou G65. G93 (Programmation en temps) masque G95. • Après la mise sous tension de la CN, le changement d’un programme CN, un BST, RET ou un Control Reset, G95 peut, en fonction du réglage des paramètres process, être activé; les valeurs d’avances (valeur F) sont remises à zéro. • La sélection de G96 active automatiquement G95. Si G95 n’avait jamais encore été activé, l’absence d’une valeur F génère un message d’erreur. • Lorsque G95 est actif, les mouvements d’axes qui avaient été commandés avec G01, G02 ou G03 ne peuvent être exécutés que si la broche est en rotation. • Les mouvements d’axes en rapide (G00) masquent G95 par G94 et seront effectués à la vitesse d’avance programmée en paramètres ou à la vitesse d’avance programmée dans le bloc avec G00. • Lorsque la broche est à l’arrêt ou avec S0, les mouvements d’axes programmés bloquent la suite de l’exécution du programme et entraînent un message d’erreur. DOK-MTC200-NC**PRO*V17-ANW1-FR-P Blocs de déplacement 4-39 Manuel de programmation CN 17VRS • Les valeur programmées F des fonctions G94 et G95 ne s’influencent pas. • Lorsque G95 est actif, l’atténuateur de broche influence la vitesse de rotation de broche et la vitesse d’avance. Temporisation ’G04’ La fonction G04 - Temporisation – permet de programmer dans un programme CN, un temps d’attente pour diverses fonctions telles que coupe libre, enclenchement de fonction machine etc. Syntaxe G04 F<Temps en seconde> G04 est actif dans le bloc et doit être programmé avec un mot F. Le mot F correspond alors à la durée de temporisation en secondes. • La durée maximale de temporisation est de 600 secondes (10 minutes), la résolution maximale est de 0.01 secondes. • La valeur F programmée avec G04 peut être introduite avec trois chiffres avant la virgule et deux après. • Dans un bloc où est programmée une temporisation ne peuvent être programmées que des fonctions M, S et Q. • La valeur F de temporisation programmée avec G04 n’influence pas les valeurs modales F présentes (avance). Exemple Programme CN avec G04 G00 G90 G54 G06 G08 Instructions de conditions d'interpolation X0 Y0 Z10 S3000 M03 Position de départ, Mise en route broche G04 F3.5 Temporisation 3.5 s. pour montée en vitesse broche G01 X26.26 Y18 Z5 F2000 Usinage • • RET DOK-MTC200-NC**PRO*V17-ANW1-FR-P Fin de programme déplacement 4-40 Blocs de déplacement Manuel de programmation CN 17VRS Rapport fondamental entre la vitesse de trajectoire programmée (F) et les vitesses des axes En interpolation, la CNC effectue le calcul de la vitesse de trajectoire selon: Formule de calcul de la vitesse de trajectoire )= ( ;& + <& + =& + $& ∗ 5 ; Exemple ) + (%& ∗ 5 ) + (&& ∗ 5 ) < = Vitesse de trajectoire lors d’un filetage Pas P Z = Vz C = VC VB = F Fig. 4-42: Vitesse de trajectoire en filetage Dans cet exemple la formule de calcul de vitesse de trajectoire est la suivante: ( ) = =& + && ∗ 5= ) En principe, deux possibilités de programmation de valeur F peuvent être considérées. Sans RZ La CNC interprète la valeur F comme vitesse dans la direction Z. Programme CN: G01 Z... C... F... Calcul: ) = =& = 3∗ Q: nw: P: Vitesse de rotation Pas du filetage DOK-MTC200-NC**PRO*V17-ANW1-FR-P Blocs de déplacement 4-41 Manuel de programmation CN 17VRS Effet: F = VZ C = VC VB Fig. 4-43: Vitesse d’avance (F) sans RZ L’axe C est ici interpolé simultanément. Avec RZ La CNC interprète la valeur F comme vitesse de trajectoire résultante. Programme CN: G01 Z... C... RZ... F... Calcul: ( ) = =& + && ∗ 5= PLW XQG ) =& = 3∗ Q: && ∗ 5= = π ∗ 5= ∗ Q: ⇒)= 3 + (π ∗ 5= ) ∗ Q: Effet: Z = VZ C = VC Fig. 4-44: Vitesse d'avance (F) avec RZ DOK-MTC200-NC**PRO*V17-ANW1-FR-P F = VB 4-42 Blocs de déplacement 4.5 Manuel de programmation CN 17VRS Vitesse de rotation broche Mot S pour l’introduction de la vitesse de rotation broche L’introduction de la vitesse de rotation broche dans un programme CN se fait avec le mot de vitesse composé de la lettre adresse S et d’une valeur de vitesse donnée comme constante ou par une expression. Le mot de vitesse peut être complété par un index de broche dans le cas où plusieurs broches sont disponibles. La vitesse de rotation est limitée de sorte que les valeurs entrées dans les paramètres ne soient pas dépassées. Lorsque G97 – vitesse de broche en tour/minute – est actif, le mot S est interprété comme vitesse de rotation broche. G97 est actif à la mise sous tension de la CNC. Le mode d’action du mot S en liaison avec les différentes fonctions de broches (G92, G96, G97, M19) est décrit dans les chapitres suivants. Syntaxe S<Constante> Ø S5000 S<Expression> Ø S=@55-100 S<Index> <Constante> Ø S2 3500 S<Index> <Expression> Ø S3=@150 avec structure étendue: La plage de valeurs de la vitesse de rotation de broche va de 0 à la valeur maximale programmée dans les paramètres de broche. La valeur S agit en relation avec les fonctions broche de la manière suivante: Signification Code G / M- Action Format Remarques Vitesse de rotation en t/min G97 avec M03/M04 Mx03 / Mx04 modal chiffres avant la virgule 5 chiffres après la virgule 2 Lorsque G97 est programmé après un G96,la dernière vitesse de rotation active est prise comme nouvelle consigne. (x = Index [1 ... 3]) M19 Mx19 dans la bloc 3 2 Indexage de broche en degrés. Vitesse de coupe constante G96 modal 5 2 Annulé par G97. Limitation de vitesse de broche G92 Actif seulemen t sous G96. modal jusqu’à G97. 5 2 Annulé par G97; Lors d’un nouveau G96, la dernière valeur de G92 est réactivée. Lorsque le mot S est seul dans le bloc, il est affecté à la mémoire de la dernière fonction de broche modale active. Lorsque le mot S est programmé avec une fonction broche dans un bloc, la fonction broche est tout d’abord activée et la valeur S est affectée à la mémoire correspondante. Il y a au maximum trois broches par process. L’index de broche est donc limité à la plage 1 à 3. Lorsqu’il y a plus d’une broche dans un process et que l’index est omis, la valeur de vitesse correspond à la première broche. Chaque broche a une mémoire propre pour les valeurs S. L’influence réciproque de valeur S est ainsi éliminée. DOK-MTC200-NC**PRO*V17-ANW1-FR-P Blocs de déplacement 4-43 Manuel de programmation CN 17VRS • La vitesse de rotation de broche programmée peut être modulée de 0% à 255% par l’atténuateur de broche. La valeur 100% correspond à la valeur S programmée. • La valeur S peut être introduite avec 5 chiffres avant la virgule et 2 après. • A la mise sous tension, au chargement d’un programme dans la CN, sur une instruction BST, RET ou sur un Control Reset les valeurs de vitesse de broche sont remises à zéro. • S’il y a plusieurs broches dans un process et que l’index de broche est omis, la valeur de vitesse programmée se rapporte à la première broche. • Le sens de rotation est fixé par les fonctions M03 –rotation à droite- et M04 – rotation à gauche-. S’il y a plusieurs broches dans un process, il faut programmer: • M103 / M104 pour la première broche, • M203 / M204 pour la deuxième broche • M303 / M304 pour la troisième broche Dans un bloc CN, chaque broche peut être appelée une fois. Exemple M103 S1 1500 M203 S2 2500 M303 S3 3500 Remarque: La vitesse maximale de rotation de broche est fixée dans les paramètres broche par le constructeur de machine. Sélection de la broche de référence 'SPF' Lorsqu’il y a plusieurs broches dans un process, il est nécessaire de pouvoir affecter certaines fonctions, telles que par exemple G96 (Vitesse de coupe constante), à une broche autre que la première. Syntaxe SPF <Numéro de broche> Les fonctions suivantes dépendent de la broche sélectionnée: • G33 Filetage • G63/G64 Taraudage • G65 Taraudage; broche comme axe maître • G95 Avance par tour • G96 Vitesse de coupe constante A la mise sous tension, la première broche est active. Lorsque l’une des fonctions ci-dessus doit être active pour une autre broche, celle-ci doit auparavant être sélectionnée comme broche de référence avec ‘SPF <Numéro de broche>’. • La sélection de la broche de référence doit avoir lieu au moins un bloc avant l’appel de la fonction. • SPF < Numéro de broche > reste actif de façon modale jusqu’à être remplacé par la sélection d’une autre broche ou jusqu’à la sélection automatique de la broche 1 à la fin du programme (RET) ou avec l’instruction BST. • La programmation de G97, vitesse de rotation en t/mn a une action sur toutes les broches disponibles dans le process. La broche de référence pour l’une des fonctions ci-dessus doit de nouveau être sélectionnée après la programmation d’un G97. • ‘SPF < Numéro de broche >’ ne peut être utilisé que pour une broche principale se trouvant en mode broche Une broche se trouvant en mode axe rotatif ne peut pas être sélectionnée comme broche de référence. DOK-MTC200-NC**PRO*V17-ANW1-FR-P 4-44 Blocs de déplacement Manuel de programmation CN 17VRS Exemple Programme CN - Filetage longitudinal avec la deuxième broche ØX 100 80 [P4] [P1] [P3] [P6] [P2] 60 40 [P5] 20 20 40 60 80 100 120 140 Z Fig. 4-45: Filetage longitudinal avec la deuxième broche Pas du filet: 3mm Profondeur du filet: 4mm Profondeur de chaque passe: Programme CN G00 G54 G90 G06 G08 X80 Z130 SPF 2 S2 2000 M203 G01 X45.5 F1500 G33 Z30 K3 P180 G00 X80 Z130 G01 X43.5 F1500 G33 Z30 K3 P180 G00 X80 M205 RET 2mm [P1] Conditions de départ Sélection broche de référence Mise en route broche 2 [P2] Approche pour 1ère coupe ère [P3] 1 passe de filetage [P4] Retrait axe X [P1] Point de départ ème [P5] Approche pour 2 coupe ème [P6] 2 passe de filetage [P4] Retrait axe X Arrêt broche 2 Fin de programme Vitesse périphérique de meule constante (SUG) 'G66' Avec G66 , la valeur programmée de S est interprétée comme vitesse périphérique de meule constante en m/s ou pieds/s. L’adaptation de la vitesse de rotation de broche en fonction du diamètre de la meule est automatique. Syntaxe G66 S<Vitesse périphérique de meule constante> G66 appartient au groupe de code G8 et peut être ainsi annulé par G96 ou G97. G66 se rapporte à la broche actuelle. A l’aide d’une instruction préalable SPF<Numéro de broche> G66 peut être sélectionné pour chaque broche. Conditions d’utilisation • Après sélection de SUG avec G66, toutes les vitesses de rotation pour la broche adressée sont interprétées en m/s ou pied/s. • La vitesse périphérique constante de meule reste active jusqu’à ce que le bloc de données d’outils de la broche correspondantes soit annulé ou jusqu’à ce que la broche en liaison avec le signal automate AxxCSPRST soit arrêté par un Control Reset. • Après sélection de SUG, la vitesse de rotation de broche nécessaire est calculée. DOK-MTC200-NC**PRO*V17-ANW1-FR-P Blocs de déplacement 4-45 Manuel de programmation CN 17VRS • Pour le calcul et la surveillance de la vitesse de rotation les éléments de données d’outils de la broche adressée sont utilisés. • Lors de la sélection de SUG avec G66, un bloc de données d’outils admissible (code d’outil 1, 2 et 3 [type de correcteur ≥ 3]) doit se trouver dans la broche correspondante. Sinon un message d’erreur est généré. • Lors de la sélection de SUG avec G66, les registres de longueur correspondante au diamètre de meule dans le bloc de données d’outils actif, doivent être > 0 sinon un message d’erreur est généré. • Le calcul de la vitesse de rotation est de nouveau effectué lorsque une nouvelle valeur S est programmée ou lorsque dans un autre bloc CN, il y a une modification dans le registre de géométrie correspondant du diamètre de meule. • Les éléments de données du correcteur D sont extraits de façon momentanée avant le calcul de la vitesse de rotation. • G96, G97, RET, BST, M30 annulent G66. Formule de calcul: 6 >PLQ S: SUG: dAKT: − @ = 68* G > P V @ ∗ $.7 > PP @ ∗π 6 >PLQ − @ = 68* G > IW V @ ∗ $.7 > LQFK @ ∗π Vitesse de rotation broche [t/min ] Vitesse périphérique de meule [m/s ou. feet/s] Diamètre meule [mm ou. inch] ATTENTION ⇒ Les éléments de données des données de base de l’outil ‘code d’outil et type de représentation’ nécessaire à la rectification ainsi que la sélection de SUG avec G66 ne sont actifs que si la donnée ‘technologie’ des paramètres systèmes est réglée sur rectification. Vitesse de coupe constante ’G96’ Avec la fonction G96 - Vitesse de coupe constante – la CN calcule la vitesse de rotation correspondant au diamètre de tournage actuel. G96 est une fonction typique des tours pour lesquels le tournage transversal représente les cas d’application les plus fréquents. L’axe d’approche pour G96 est déterminé par l’agencement d’axe G18 (ZX) typique pour un tour pour lequel l’axe X est l’axe d’approche. Lorsque G96 est actif, la vitesse de rotation de broche est inversement proportionnelle à la distance entre la pointe de l’outil et l’axe de tournage de telle sorte que cette vitesse croît lorsque la distance diminue. Syntaxe G96 S<Vitesse de coupe constante en m/min> Lorsque G00 est actif, la vitesse de broche est fixée à la valeur qu’elle doit avoir à la fin du bloc indépendamment de la position actuelle de X. G96 reste par la suite actif, mais l’association avec le mouvement d’avance est provisoirement suspendue. Le bloc est considéré comme terminé lorsque la broche a atteint sa consigne de vitesse et que les axes ont atteint leur position finale. La sélection de G96 active automatiquement G95. Si G95 n’avait auparavant pas encore été activé, l’absence de valeur F génère un message d’erreur. Pour des faibles valeurs de X entraînant une vitesse de rotation trop élevée, la vitesse de rotation de broche est limitée à la valeur du paramètre de vitesse maximale de broche. Lorsque G96 est actif, la valeur S est interprétée comme vitesse de coupe en m/mn. La vitesse de rotation de broche se calcule d’après: DOK-MTC200-NC**PRO*V17-ANW1-FR-P 4-46 Blocs de déplacement Manuel de programmation CN 17VRS 6= S: vc: r: YF ∗ U∗ 3, Vitesse de rotation broche [t/min ] Vitesse de coupe [m/min] Rayon effectif [mm], distance à l'axe de tournage • A la mise sous tension, G96 se rapporte toujours à la première broche. Si G96 doit se rapporter à une autre broche, celle-ci doit être sélectionnée par la commande ‘SPF <Numéro de broche>’ avant le bloc G96. • En fonction du réglage des paramètres process, G96 peut être l’état à la mise sous tension. G96 (Vitesse de coupe constante) reste modalement actif jusqu’à annulation par G97. • Après la mise sous tension de la CN, chargement d’un programme, instruction BST ou RET ou Control Reset, G96 peut en fonction du réglage des paramètres process, être automatiquement activé; les valeurs de vitesse de broche (valeur S) sont réactivées. • Lorsque, G96 étant actif, la valeur de S est modifiée, elle doit être programmée avec G96. • Lorsque G96 est actif, la vitesse maximale de rotation broche peut être limitée avec la commande ‘G92 S <Vitesse de rotation broche>’. • Lorsque G96 est actif, l’atténuateur de broche est limité à 100%. Une réduction de l’atténuateur de broche à une valeur inférieure à 100% a comme conséquence, une diminution de la vitesse de coupe. • Lorsque G96 est annulé par G97, la dernière vitesse de rotation broche active est prise comme nouvelle consigne de vitesse. Exemple Programme CN – Tournage transversal avec G96 ØX 100 80 [P5] [P2] [P1] 60 40 [P4] [P6] [P3] 20 20 40 60 80 100 120 140 Z Fig. 4-46: Tournage transversal Programme CN G00 G54 G90 G06 G08 X72.5 Z100 [P1] Conditions de départ S1 2500 M103 Mise en route broche G00 Z78 [P2] Approche pour 1ère coupe ère G96 X27.5 S1 400 [P3] 1 passe tournage transversal G00 Z100 [P4] Dégagement axe Z X72.5 [P1] Point de départ ème G00 Z76.5 [P5] Approche pour 2 coupe ème G96 X27.5 S1 400 [P6] 2 passe tournage transversal G00 Z100 [P4 Dégagement axe Z M105 Arrêt broche RET Fin de programme DOK-MTC200-NC**PRO*V17-ANW1-FR-P Manuel de programmation CN 17VRS Blocs de déplacement 4-47 Limitation de vitesse de rotation broche ’G92’ La fonction G92 permet, lorsque G96 est actif, de limiter la vitesse de rotation broche. Lorsque G96 est actif, la vitesse de coupe est maintenue constante. Cela peut, en tournage transversal, ou en tronçonnage jusqu’à l’axe de tournage, conduire, en théorie, à une vitesse de rotation infinie. Pour des raisons de technique d’usinage, il peut être nécessaire de limiter la vitesse de rotation à une valeur inférieure à la vitesse de rotation maximale fixée dans les paramètres. G92 fixe une limite supérieure à la vitesse de broche lorsque G96 est actif. Syntaxe G92 S<Valeur limite de vitesse de broche> G92 est actif dans le bloc. La valeur limite fixée pour la vitesse de broche reste modalement active jusqu’à nouvelle programmation d’un G92 avec nouvelle limite de vitesse ou annulation par programmation de G92 S0. • Une limitation de vitesse programmée avec G92 reste modalement active jusqu’à annulation par G92 S0 ou par une fin de programme (RET) ou une instruction BST. • La valeur limite de vitesse définie par G92 est annulée par la programmation de G97. Elle est de nouveau activée par la programmation d’un G96. • Dans un bloc CN où est programmé G92, il ne doit se trouver aucune autre fonction. Vitesse de rotation broche en t/min ’G97’ Avec la fonction G97 - vitesse de rotation en t/min – la valeur S programmée est interprétée en tour par minute. G97 est l’état à la mise sous tension et reste modalement actif jusqu’à annulation par G96. • En fonction des réglages des paramètres process, G97 peut être l’état à la mise sous tension. G97 – Vitesse de rotation en t/min – reste modal jusqu’à annulation par G96. • Après la mise sous tension de la CN, chargement d’un programme, instruction BST ou RET ou un Control Reset, G97 peut, en fonction du réglage des paramètres process, être automatiquement activé; les valeurs de vitesse de broche (Valeurs S) sont réactivées. • Lorsque G96 est annulé par G97, la dernière vitesse de broche active est prise comme consigne de vitesse. • La programmation de G97 est active sur toutes les broches du process. La sélection d’une broche de référence doit être de nouveau effectuée après programmation de G97. 4.6 Programmation d’axe rotatif Rayon d’application 'RX', 'RY', 'RZ' Avec toutes les conditions d’interpolation en G00 et G01, les composantes de vecteur local sont considérées comme constante durant un bloc CN. Les mouvements de translation et de rotation se font à vitesse constante Le calcul des projections de vitesse, de vitesse de coude et d’accélération de tous les axes concernés se fait comme précédemment, mais en tenant compte cependant de la rotation de l’axe principal. Pour les valeurs des distances à chaque axe principal, les distances effectives sont données avec les désignations RX, RY et RZ. La CNC tient compte des parties de trajectoires engendrées par la rotation de l’axe rotatif principal uniquement lorsque les distances d’application DOK-MTC200-NC**PRO*V17-ANW1-FR-P 4-48 Blocs de déplacement Manuel de programmation CN 17VRS correspondantes RX, RY et RZ des axes linéaires principaux concernés autour desquels la rotation s’effectue sont données. • Les distances d’application RX, RY et RZ donnent les distances relatives à chaque axe linéaire principal. Elles doivent être programmées sans signe dans le bloc. • Les distances d’application avec une valeur nulle ne sont programmées. • La programmation des distances d’application dans le programme CN est active dans le bloc et doit être programmée dans le bloc où elle est active. • La programmation des distances d’application dans un programme CN se fait dans n’importe quel ordre et sans relation avec les axes rotatifs. • L’introduction de données absurdes pour les distances d’application peut conduire à ce que les axes rotatifs principaux aient une composante de vitesse trop grande, trop faible ou nulle. En liaison avec un entraînement de broche KDA, il est impératif d’exécuter l’exploitation en axe C avec G06 – Interpolation à faible erreur de poursuite-. ATTENTION Exemple Programme CN – Rainure en spirale Axe C X Rayon applic. 50 mm RZ Y 70 mm 30 mm Fig. 4-47: Usinage d’une rainure en spirale sur la face frontale Programme CN G90 G06 G17 Plan d’usinage côté frontal XY, • • • G00 X-30 Y0 Z501 C90 G01 Z497 F500 [Usinage de la spirale] G01 G91 X-40 C-270 RZ50 F1200 Approche; positionnement l'axe C Engagement de la fraise de Rainure en spirale sur côté frontal • • RET Fin de programme DOK-MTC200-NC**PRO*V17-ANW1-FR-P Blocs de déplacement 4-49 Manuel de programmation CN 17VRS Programme CN - Commutation entre broche et axe C La commutation entre l’exploitation en axe C et en broche principale s’effectue, dans la syntaxe CN par programmation de l’axe C (Cxxx.xxx) ou de la broche principale (M03 Sxxxx). Lorsque, la broche principale étant active, l’axe C est programmé dans un bloc suivant, la CNC exécute le mécanisme de commutation avec l’aide de l’automate. La préparation et l’exécution du bloc sont suspendues jusqu’à la fin du process de commutation. Le même mécanisme a lieu lors de la commutation d’axe C à la broche principale. • Après la commutation de broche principale en axe C, tous les axes du process doivent être déplacés une fois en G90 (programmation absolue) avant de pouvoir être utilisé en G91 (programmation incrémentale). Commutation avec une broche principale à capacité d’axe circulaire M19 S0 Indexage broche G00 G54 G90 X100 Z200 M03 S1000 Etat de base, exploitation broche • Usinage G00 G17 G06 X100 Z250 C90 Etat de exploitation axe C base, • G01 G91 X-40 C-270 RZ50 F1200 Usinage • G00 G18 G54 G90 X120 Z200 M03 S1200 Etat de base, exploitation broche • RET Fin de programme Logique de déplacement pour un axe rotatif à mouvement continu Calcul modulo Le positionnement d’un axe rotatif à mouvement continu a lieu à l’aide de calcul modulo. Possibilités de positionnement: • Chemin le plus court G36 • Direction positive G37 • Direction négative G38 Le calcul modulo ne peut programmation absolue (G90). être effectué qu’en Il n’a pas d’action en programmation incrémentale (G91). REMARQUE Les instructions G36, G37 et G38 forment le groupe de code G ‘Logique de déplacement en axe circulaire’ (N°. 21). DOK-MTC200-NC**PRO*V17-ANW1-FR-P 4-50 Blocs de déplacement Chemin le plus court Manuel de programmation CN 17VRS Lors du calcul modulo ‘chemin le pus court’ G36, la position finale est atteinte par le chemin le plus court. position réelle = 20° G90 G36 : : position de G1 C-380 F1000 consigne = 380° : Fig. 4-48: Positionnement avec calcul modulo ‘Chemin le plus court’ (G36) • G36 est actif à la mise sous tension et peut être annulé par G37 ou G38. • A la fin de programme (BST, RET, JMP, M02, M30) l’état de base G36 est réactivé. Direction positive Lors du calcul modulo ‘Direction positive’ G37, la position finale est atteinte en direction positive. position réelle = 20° position de consigne = 380° G90 G37 : : G1 C-380 F1000 : Fig. 4-49: Positionnement avec calcul modulo ‘Direction positive’ (G37) • G37 peut être annulé par G36 ou G38. • A la fin de programme (BST, RET, JMP, M02, M30) l’état de base G36 est réactivé. Direction négative Lors du calcul modulo ‘Direction négative G38, la position finale est atteinte en direction négative. position réelle = 20° position de consigne = 380° G90 G38 : : G1 C-380 F1000 : Fig. 4-50: Positionnement avec calcul modulo ‘Direction négative (G38) • G38 peut être annulé par G36 ou G37. • A la fin de programme (BST, RET, JMP, M02, M30) l’état de base G36 est réactivé. Remarque: Le constructeur de machine peut modifier la présélection dans le paramètre process Bxx.056. DOK-MTC200-NC**PRO*V17-ANW1-FR-P Blocs de déplacement 4-51 Manuel de programmation CN 17VRS 4.7 Transformations Les transformations sont disponibles pour: • les usinages frontal • les usinages sur corps de cylindre. • Usinage sur corps de cylindre Usinage frontal Fig. 4-51: Usinage frontal et sur corps de cylindre Les instructions G30 (Annulation des transformations), G31 (transformation sur front) et G32 (transformation sur corps de cylindre) forment le groupe de code G ‘fonction de transformation’ (N°. 17). Sélection d’usinage frontal ‘G31’ Avec la fonction G31 – sélection d’usinage frontal - la CNC commute sur un système de coordonnées cartésien fictif. Les axes linéaires fictifs définis prennent part à l’interpolation à la place des axes réels principaux. La vitesse de trajectoire, lors de fonction de transformation est programmée, comme en fraisage, sous l’adresse F, en tant que vitesse relative entre outil et pièce. La vitesse de trajectoire est réduite de telle sorte que la vitesse de rotation maximale de l’axe circulaire ne soit pas dépassée. Cela est particulièrement vrai pour les mouvements à proximité de centre. Syntaxe Conditions d’utilisations G31 • La CNC supporte la fonction transformation dans le plan XY (G17). Les axes réels participant à la transformation doivent avoir les significations d’axe X et C. • L’axe réel Y (si disponible) devient un axe auxiliaire avec la signification d’axe V. Lors de l’annulation de la transformation, la CNC rétablit le contexte d’origine. • Lors de la sélection de la transformation (G31), les décalages d’origines sont annulés(G53), les corrections de trajectoire et de longueur d’outil sont désactivées (G40, G47). La CNC passe en programmation au rayon (G15). • Lors de l’accès à la transformation l’axe X doit être en cote positive. • Après commutation dans la transformation, les décalages d’origine des axes fictifs sont, selon sélection, activés. Les décalages d’origine des axes réels associés des axes fictifs sont inefficaces. • Après des commutations dans la transformation, les cotes peuvent être programmées directement en absolu (G90) ou en incrémental (G91). • Une entrée de programme par survol de bloc est possible durant la fonction de transformation ; la transformation (G31) et les conditions de DOK-MTC200-NC**PRO*V17-ANW1-FR-P 4-52 Blocs de déplacement Manuel de programmation CN 17VRS base associées (G54, G48 etc.) doivent être fixées avant le départ cycle en IMD. • Les axes fictifs ne peuvent pas être transférés à un autre process (FAX, GAX). • La broche de référence pour la programmation d’avance en taraudage (G63, G64, G65) doit être enclenchée à l’aide d’instruction automate. • A la mise sous tension, la transformation se rapporte toujours à la première broche. Si elle doit se rapporter à une autre broche, celle-ci doit être sélectionnée avec 'SPC <Numéro de broche>' avant l’appel de la transformation. • Durant la transformation, les axes réels principaux associés aux axes fictifs ne doivent pas être programmés. • G31 - Transformation – reste modalement actif jusqu’à annulation par G30 ou G32, ou par une fin de programme (RET) ou par un BST. Remarque: Lors de l’activation de la transformation, la CNC utilise pour les 2 axes fictifs formant le plan actuel de travail, des désignations d’axes 1 et 2 différentes de celles fixées en paramètres machine. Les désignations d’axe des axes fictifs sont fixées par le constructeur machine dans les paramètres d’axe ! La fonction de transformation est une option nécessitant une structure Hardware spéciale. REMARQUE Tous les axes participant à la transformation doivent être sur une même carte APR. Durant la transformation, les axes réels principaux associés aux axes fictifs ne doivent pas être programmés. Pour une fonction de transformation sur une machine ayant un axe Y réel, il ne doit pas y avoir d’axe avec la signification d’axe V dans le process correspondant. ATTENTION Lors de l’activation de la fonction de transformation, la CNC force automatiquement une exploitation en axe circulaire. Lors de l’activation et de l’annulation de l’usinage frontal, la CN annule tous les décalages d’origine et force G53. Lorsque, durant l’usinage frontal, la programmation au diamètre (G16) est sélectionnée, la CN interprète toutes les valeurs de position de l’axe fictif avec la désignation d’axe X comme valeur au diamètre. Description détaillée Des informations complémentaires sur l’usinage frontal se trouvent dans la description ‘’Fonction de transformation’’ classeur 5. DOK-MTC200-NC**PRO*V17-ANW1-FR-P Blocs de déplacement 4-53 Manuel de programmation CN 17VRS Exemple Programme CN – Usinage frontal X1 [P1] [P8] 50 40 30 20 10 [P2] Y1 70 70 [P7] 50 40 30 20 10 [P5] [P6] [P4] [P5] Fig. 4-52: Usinage frontal avec transformation Programme CN T12 M6 ;Changement ;outil entraîné d'outil M89 ;Couplage outil entraîné S2 3500 M203 ;Mise en route ;outil entraîné G00 G17 G54 G48 Z100 DOK-MTC200-NC**PRO*V17-ANW1-FR-P X140 C0 ;Etat de base ;commutation pour G31 ;Enclenchement transformation G54 G90 G06 G08 G48 ; Etat de base G00 G42 G94 X1 60 Y1 20 ;[P1] Point de départ usinage G01 Z-0.5 F500 ;Approche axe Z X1 20 Y1 60 F400 ;[P2] 1. Droite X1 -20 ;[P3] 2. Droite X1 -50 Y1 30 ;[P4] 3. Droite G02 X1 -50 Y1 -30 I-50 J0 ;[P5] Demi-cercle sens horaire G01 X1 -20 Y1 -60 ;[P6] 4. Droite X1 20 ;[P7] 5. Droite X1 60 Y1 -20 ;[P8] 6. Droite Y1 20 ;[P1] 7. Droite G00 Z10 ;Axe Z à distance de sécurité G30 ;Annulation transformation G54 G48 G00 X140 ; Etat de base Z200 ;Retrait axe Z M90 ;Découplage outil entraîné M30 ;Fin de programme la 4-54 Blocs de déplacement Manuel de programmation CN 17VRS Sélection de l’usinage sur corps de cylindre ‘G32’ Avec l’usinage sur corps de cylindre G32, la CN engendre des droites et des cercles sur un corps de cylindre conformément aux blocs G00, G01, G02 et G03 du programme CN. Les droites et les cercles sur un corps de cylindre se programment dans un plan obtenu par déroulement du cylindre et formé d’un axe linéaire et d’un axe rotatif. C [mm] Y G20 Z0 C0 X0 G32 RI 60 X B A Z RI C O Z [mm] X [mm] Fig. 4-53: Usinage sur corps de cylindre Programmation Syntaxe Le programmateur peut programmer l’axe rotatif utilisé pour l’usinage sur corps de cylindre, comme un axe linéaire en [mm] ou en [inch]. G32 RI=w ou G32 RI w w: Valeur du rayon d’application Rayon d’application • L’introduction du rayon d’application RI est indispensable. • La programmation d’un rayon d’application RI ≤ 0 n’est pas autorisée. • Le rayon d’application RI ne doit pas être modifié lorsque l’usinage sur corps de cylindre est actif (une annulation avec G30 est au préalable nécessaire). • Lorsque 2 axes circulaires forment le plan d’usinage, la CN tient compte du rayon d’application RI sur les 2 axes. • La rayon d’application RI est modal. La CN retient le rayon d’application jusqu’à annulation de l’usinage sur corps de cylindre. Sélection du plan On effectue, en général, une sélection de plan libre G20 avant l’appel de l’usinage sur corps de cylindre. G20 ... Condition d’utilisation • Durant l’usinage sur corps de cylindre, l’axe circulaire participant reçoit la fonctionnalité d’un axe linéaire principal. Les fonctions telles que, par exemple correction de trajectoire de rayon d’outil et les décalages d’origine y compris la rotation de coordonnée peuvent être utilisées même durant l’usinage sur corps de cylindre. • Durant l’usinage sur corps de cylindre, la CN surveille les limites de l’axe circulaire (limite de déplacements) comme durant une exploitation normale. • Les axes rotatifs sont, durant l’usinage sur corps de cylindre, programmés en [mm] ou [inch]. • Lors de l’activation de l’usinage sur corps de cylindre, la CN passe automatiquement en programmation au rayon (G15). • Lors de l'annulation, la CN réactive la programmation au rayon (G15) ou au diamètre (G16) en fonction du réglage des paramètres process. • G32 - Transformation – reste modal jusqu’à annulation par G30 ou G31 ou annulation automatique à la fin du programme (BST, RET, JMP, M02, M03). DOK-MTC200-NC**PRO*V17-ANW1-FR-P Blocs de déplacement 4-55 Manuel de programmation CN 17VRS Avant l’activation de l’usinage sur cylindre il doit y avoir au moins un axe rotatif définissant le plan de travail actif. Cela est possible avec G20 – Sélection libre du plan de REMARQUE travail. ⇒ Lors de l’activation et de l’annulation de l'usinage sur corps de cylindre la CN désactive tous les décalages d’origine et valide G53. ⇒ Lorsque la programmation du diamètre (G16) est appelée et lorsque l'usinage sur corps de cylindre est actif, la CN interprète toutes les valeurs de position avec la signification d’axe X, comme données au diamètre. ATTENTION Description complémentaire Des informations complémentaires sur l'usinage sur corps de cylindre se trouvent dans la description ‘Sélection libre de plan et usinage sur corps de cylindre’ classeur 5. Exemple Programme CN – Usinage sur corps de cylindre Y 70 50 0 -50 -150 -100 -50 0 X Fig. 4-54: Usinage sur corps de cylindre avec transformation Programme CN DOK-MTC200-NC**PRO*V17-ANW1-FR-P : Fraisage du contour ‘caractère 1’ N0008 G55 G15 G94 G97 G6 G8 S2 3000 M203 N0009 G0 C0 N0010 G20 Z0 C0 X0 Sélection libre de plan N0011 G32 RI 36.5 Activation usinage sur corps de cylindre N0012 G55 G48 Z1-36.15 N0013 Y1 25 Z1-36.15 N0014 X38 N0015 G1 X36 F150 N0016 G42 Y1 25 Z1-42 F297 N0017 Y1 50 Z1-42 N0018 G2 Y1 54.2426 Z1-30.7574 I-35 J50 N0019 G1 Y1 34.2426 Z1-10.7574 N0020 G2 Y1 25.7574 Z1-19.2426 I-15 J30 N0021 G1 Y1 36.5147 Z1-30 N0022 Y1 5 Z1-30 N0023 G2 Y1 5 Z1-42 I-36 J5 N0024 G1 Y1 25 Z1-42 N0025 G0 X38 N0026 G30 Annulation usinage sur corps de cylindre : 4-56 Blocs de déplacement Manuel de programmation CN 17VRS Annulation des transformations ’G30’ Avec la fonction G30 - annulation des transformations – la CN annule la transformation active (G31, G32). L’annulation des transformations (G30) annule également les décalages d’origine (G53), la correction de trajectoire et de longueur d’outil (G40, G47). G30 est l’état à la mise sous tension et est modal. G30 est annulé par G31 ou G32. Après chargement d’un programme CN, après un BST, RET ou Control Reset, G30 est automatiquement sélectionné. Annulation de la transformation d’usinage frontal G31 Le système de coordonnées cartésien fictif est annulé et le système défini par les paramètres process est activé. Les axes fictifs sont annulés et ne doivent plus être programmés. Le plan précédant, défini en paramètres process, est pris comme plan actuel d’usinage, la CNC commute sur la programmation pièce (rayon/diamètre) définie dans les paramètres process. Après annulation de la transformation, on peut programmer directement en absolu (G90) ou en incrémental (G91). Les axes fictifs ne doivent plus être programmés. ATTENTION Annulation de l'usinage sur corps de cylindre G32 Les décalages d’origine pour les axes réels sont préparés. Les décalages d’origine des axes fictifs associés aux axes réels principaux sont inactifs. Lors de l’annulation, la CN rétablit la programmation au rayon (G15) ou au diamètre (G16). ⇒ La CN désactive les décalages d’origine et active G53. ATTENTION Sélection de la broche de référence pour les transformations 'SPC' Lorsqu’il y a, dans un process, plusieurs broches susceptibles d’être utilisées pour une transformation, il est nécessaire de sélectionner la broche qui sera utilisée. Syntaxe SPC <Numéro de broche> A la mise sous tension, la première broche est toujours active. Si la transformation doit avoir lieu avec une autre broche, celle-ci doit être sélectionnée avant l’appel de la transformation G31 ou G32, avec l’instruction ‘SPC <Numéro de broche>’ La sélection de la broche de référence doit avoir lieu en mode d’exploitation broche principale. Une sélection durant l’exploitation en axe C n’est pas possible. ‘SPC <Numéro de broche>’ reste modal jusqu’à sélection d’une autre broche ou re-sélection automatique de la première broche par la fin de programme (RET) ou un BST. DOK-MTC200-NC**PRO*V17-ANW1-FR-P Blocs de déplacement 4-57 Manuel de programmation CN 17VRS 4.8 Synchronisation de broches Application de synchronisation de broches principales La synchronisation de broches est principalement utilisée sur les tours pour le transfert et le tronçonnage de pièces pour l'usinage d'arbre, le tournage et le tournage en faux ronds. Environnement fonctionnel de la synchronisation de broche Dans la CNC on peut synchroniser jusqu’à trois broches dans un même process. Une broche est utilisée comme broche maîtresse pendant que les 2 autres sont utilisées comme broches synchrones. La CNC déplace toujours les broches maîtresse et synchrone en synchronisation angulaire absolue. L’exemple ci-dessous explique la relation de synchronisme angulaire entre une broche maîtresse et un broche synchronisée. Position angulaire des broches Remarque brochesynchrone Les 2 broches se trouvent dans une position quelconque. synchronisation brochemaîtresse Après événement de synchronisation brochemaîtresse brochesynchrone La broche synchrone effectue un déplacement pour réaliser le décalage angulaire (= 90°) programmé (rapport d’entraînement = 1). Après une rotation brochemaîtresse brochesynchrone La broche synchrone a tourné de 90° avec la broche maîtresse. brochemaîtresse brochesynchrone La broche a tourné de 45° par rapport à la broche maîtresse. Avant la de 90° Après modification de l’offset de position de 45° L’exploitation en synchronisation angulaire absolue offre l’avantage d’avoir à tout instant un décalage angulaire réglable et défini entre les broches maîtresses et synchrone. Configurations admissibles Ci-dessous sont présentes les règles décrivant les configurations admissibles pour la synchronisation de broches principales. Si une de ces règles est omise au début ou durant la synchronisation, la CN interrompt l’usinage et génère un message d’erreur. • Une synchronisation de broches principales ne peut avoir qu’une seule broche maîtresse. • Toutes les broches participant à une synchronisation doivent appartenir à un même process. • Dès qu’une broche d’un autre process doit participer à une synchronisation, elle doit être transférée au process concerné au moyen de la commande de transfert d’axe. DOK-MTC200-NC**PRO*V17-ANW1-FR-P 4-58 Blocs de déplacement Manuel de programmation CN 17VRS • Toutes les broches participant à une même synchronisation doivent se trouver sur une même carte APR. • Dans chaque groupe de synchronisation on peut avoir au maximum deux broches synchrones d’une broche maîtresse. • A l’intérieur de la broche SERCOS, la broche maître doit avoir un numéro d’entraînement inférieur à la broche synchrone. • Une broche ne doit pas être simultanément maître et synchrone. Seuls des entraînements de broche numérique à interface SERCOS et des entraînements d’axe DDS 2.2. avec fonction de broche et interface SERCOS peuvent participer à une synchronisation de broche principale. REMARQUE Déroulement du procédé de synchronisation Activation de la synchronisation de broche principale La synchronisation de broche principale se fait en exploitation programme dans le programme CN au moyen d’une fonction auxiliaire. En mode manuel, la synchronisation peut être effectuée par une touche de pupitre machine ou par une autre touche. Un signal d’interface entre l’automate et la CN rend possible la synchronisation de broches principales dans tous les modes d’exploitation. Avant le lancement de la synchronisation, il faut encore indiquer, depuis l’interface opérateur, le programme CN ou automate: • la broche maître associée à la synchronisation, • le rapport de réduction entre les broches maîtres et synchrones, • le sens de rotation des broches synchrones, • le décalage angulaire et l’offset de position entre les deux broches • les limites de tolérance pour la surveillance des différences de position les broches maîtres et synchrones. Fonction auxiliaires pour la sélection et l’annulation de synchronisation de broches A partir de la version 5.15.xx, les fonctions Q9000 à Q9999 sont des fonctions spécifiques réservées à INDRAMAT. Les fonctions Q9700 à Q9764 sont prévues pour la synchronisation de broches principales. L’affectation des fonctions auxiliaires pour la synchronisation de broche principale (SBP) se fait comme suit: 9 réservé pour INDRAMAT 7 réservé pour SBP Numéro de process x = 0...6 Fonction Remarque Q 9 7 x 0 Arrêt association de synchronisation 1 et 2 Q 9 7 x 1 Mise en marche association synchronisation 1 Q 9 7 x 2 Mise en marche association synchronisation 2 Q 9 7 x 3 Arrêt association synchronisation 1 Q 9 7 x 4 Arrêt association synchronisation 2 Processus de synchronisation Si les broches sont en rotation à des vitesses différentes lors de la synchronisation (Arrêt = vitesse nulle), la broche synchrone accélère ou freine avec une accélération maximale jusqu’à atteindre la vitesse de synchronisation. Dès que la vitesse de synchronisation est atteinte, la CN passe en asservissement de position et entraîne la broche synchrone en moins d’un tour, et selon le chemin le plus court à la position prescrite. SI les broches maîtres et synchrones se trouvent à l’arrêt, la broche synchrone prend sa position de consigne en tenant compte du rapport de réduction et du décalage angulaire et de l’offset de position programmé. DOK-MTC200-NC**PRO*V17-ANW1-FR-P Manuel de programmation CN 17VRS Blocs de déplacement 4-59 La CN commute toutes les broches participant à la synchronisation en asservissement de position. Si des fonctions telles que M03, M04 ou G95 sont actives lors de l’enclenchement de la synchronisation, la CN poursuit, pour ces broches, la mise en asservissement de position. Ce procédé de commutation n’a pas d’influence négative sur l’état de surface de la pièce. Arrêt de la synchronisation La synchronisation de broche peut être arrêtée, indépendamment du mode d’exploitation, par remise à zéro du signal d’interface d’enclenchement. Toutes les broches participant à la synchronisation conservent alors leur vitesse de rotation. Si les broches doivent être arrêtées après l’annulation de la synchronisation, il faut programmer M05 ou M19. A l’arrêt de la synchronisation, la CN commute les broches participantes en asservissement de vitesse, dès lors qu’à cet instant une fonction nécessitant l’asservissement de vitesse est active. Programmation CN Les broches participant à une synchronisation ne doivent pas être programmées durant la phase de synchronisation. Dans le cas contraire, la CN interrompt l’usinage et génère un message d’erreur. De ce fait, durant l’exploitation en synchronisation, les broches maîtres et synchrones ne doivent pas être utilisées en mode axe rotatif ou effectuer de changement de rapport de gamme. Dans le cas contraire, la CN interrompt l’usinage et génère un message d’erreur. • Le mode de synchronisation reste actif en fin de programme (BST, RET, M02 et M30), après un Control Reset ou en JOG manuel, tant que l’automate n’annule pas la synchronisation. • Durant la synchronisation, la broche maître doit être la broche de référence. Les fonctions G33 (filetage), G95 (avance par tour) et G96 (vitesse de corps constante) font référence uniquement à la broche maître durant la synchronisation. De ce fait, la broche maître doit être déclarée broche de référence avant l’enclenchement de la synchronisation. • Durant la synchronisation, l’utilisateur ne doit pas transférer les broches participant à la synchronisation entre des process. L’utilisation d’une commande de transfert d’axe de broche participant à une synchronisation entraîne l’interruption du programme et la génération d’un message d’erreur. Les broches participant à une synchronisation et appartenant à un autre process, doivent être transférées dans le process concerné avant l’enclenchement de la synchronisation et ne doivent être rendues au process initial qu’après arrêt de la synchronisation. Les broches effectuant du taraudage G63, G64 ou G65 ne doivent être ni broche maître, ni synchrone. REMARQUE DOK-MTC200-NC**PRO*V17-ANW1-FR-P 4-60 Blocs de déplacement Manuel de programmation CN 17VRS Données machine pour la synchronisation de broche Les données machine pour la synchronisation de broche resservent une page avec la désignation de la synchronisation. A l’intérieur de cette page, on trouve pour chaque process la structure de données suivantes: N°. Désignation Plage de valeur Description 001 Mise en synchronisation broche 1 ok 0/1 0: 1: Mise en synchronisation non ok Mise en synchronisation ok 002 Mise en synchronisation broche 2 ok 0/1 0: 1: Mise en synchronisation non ok Mise en synchronisation ok 003 Signification d’axe broche maître 0, 10, 11, 12 0: 10: 11: 12: Pas de broche maître disponible; Broche S1; Broche S2; Broche S3 004 Signification d'axe broche synchrone 1 0, 10, 11, 12 0: 10: 11: 12: Pas de broche synchrone disponible; Broche S1; Broche S2; Broche S3 005 Décalage angulaire broche synchrone.1 0.0000°-359.9999° Décalage angulaire entre broche maître et broche synchrone.1. 006 Offset de position broche synchrone 1 0.0000°-359.9999° Offset de position entre broche maître et broche synchrone 1. 007 Nombre de tours broche maître i_LS/SS1 1 - 65536 Le rapport de réduction se calcule par nombre de tours broche maître / nombre de tours broche synchrone. 008 Nombre de tours broche synchrone 1 i_LS/SS1 1 - 65536 Le rapport de réduction se calcule par nombre de tours broche maître / nombre de tours broche synchrone. 009 Sens de rotation broche synchrone 1 0/1 010 Fenêtre mise en synchronisme broche synchrone 1 0.0000°-359.9999° Fenêtre de mise en synchronisme pour le signal d'interface AxxSSS1OK 011 Limite erreur broche synch.1 0.0000°-359.9999° Limite erreur pour le signal d'interface AxxSSS1ER 012 Signification d'axe broche synchrone.2 0, 10, 11, 12 0: Pas de broche synchrone disponible; 10: Broche S1; 11: Broche S2; 12: Broche S3 013 Décalage angulaire broche synchrone 2 0.0000°-359.9999° Décalage angulaire entre broche maître et broche synchrone 2. 014 Offset de position broche synchrone 2 0.0000°-359.9999° Offset de position entre broche maître et broche synchrone 2. 015 Nombre de tours broche maître i_LS/SS2 1 - 65536 Le rapport de réduction se calcule par nombre de tours broche maître / nombre de tours broche synchrone. 016 Nombre de tours broche synchrone 2 i_LS/SS2 1 - 65536 Le rapport de réduction se calcule par nombre de tours broche maître / nombre de tours broche synchrone. 017 Sens de rotation broche synchrone 2 0/1 018 Fenêtre mise en synchronisme broche synchrone 2 0.0000°-359.9999° Fenêtre de mise en synchronisme pour le signal d'interface AxxSSS2OK 019 Limite erreur broche synch. 2 0.0000°-359.9999° Limite erreur pour le signal d'interface AxxSSS2ER 0: 1: 0: 1: Même sens de rotation Sens de rotation inverse Même sens de rotation Sens de rotation inverse Chaque élément de données peut être modifié à tout instant par l’automate via l’interface opérateur ou par le programme CN dès lors que la broche maître ou synchrone correspondant n’est pas active. Si l’utilisateur accède par l’automate ou l’IHM aux données d’une broche participant à une synchronisation, il reçoit un message d’erreur. Si l’opérateur tente cette opération à partir du programme CN à l’aide d’une instruction MTD, il y a DOK-MTC200-NC**PRO*V17-ANW1-FR-P Manuel de programmation CN 17VRS Blocs de déplacement 4-61 émission d’un message d’erreur et la CN interrompt l’usinage. Les exceptions sont le décalage angulaire et l’offset de position des broches synchrones 1 et 2. Ces données peuvent être modifiées par l’opérateur à chaque instant, depuis l’automate via l’IHM ou depuis le programme CN. 4.9 Axes entraînés et axes Gantry Application des axes entraînés et des axes Gantry Les fonctions axes entraînés et axes Gantry –appelés par la suite exploitation synchrone- rendent possible d’exploiter jusqu’à quatre axes de façon synchrone. Chaque axe d’avance peut être déclaré comme axe maître et jusqu’à 3 axes suiveurs synchrones peuvent y être associés. L’axe maître et les suiveurs forment une association d’axes synchrones. Ceux-ci peuvent être, indépendamment du mode d’exploitation, enclenchés et déclenchés ou maintenus durant l’exploitation machine, y compris la prise d’origine. A l’état inactif, ils peuvent être reconfigurés par l’automate, la CN ou par l’interface opérateur. On peut avoir au total, jusqu’à quatre associations d’axes synchrones simultanément actives par process. Durant l’exploitation synchrone, tous les axes suiveurs d’une association exécutent le même déplacement que l’axe maître en tenant compte de leur propre rapport de réduction et sens de rotation. Configurations admissibles Les règles suivantes décrivent les configurations admissibles pour une exploitation synchrone. Si ces règles sont outrepassées, la CN suspend l’usinage et génère un message d’erreur. • Chaque association d’axe synchrone doit avoir un axe maître et au moins un axe suiveur. • Une association d’axes synchrones ne peut avoir au minimum qu ‘un seul axe maître. • Chaque association d’axes synchrones peut avoir, outre l’axe maître, au maximum trois axes suiveurs. • Tous les axes d’une association doivent appartenir à un même process. • Dès qu’un axe d’un autre process doit faire partie, comme axe maître ou comme axe suiveur, d’une association d’axes synchrones, il doit être transféré dans le process concerné par la commande de transfert d’axe. • Tous les axes d’une association doivent se trouver sur la même carte APR. • Dans la boucle SERCOS, l’axe maître doit avoir une adresse inférieure à celle des axes suiveurs. • Un axe ne peut pas être simultanément maître et suiveur. • Tous les axes d’une association doivent au même type d’axe (linéaire, rotatif à mouvements sans fin ou rotatif à mouvements limités). • Les axes de magasins d’outil peuvent participer comme axe maître ou suiveur à une association d’axes synchrones • Lorsque des axes rotatifs forment une association, ils doivent avoir la même division par tour. • Les axes maîtres ou suiveurs d’une association ne peuvent être utilisés dans une autre association active, ni comme maître, ni comme axe synchrone. DOK-MTC200-NC**PRO*V17-ANW1-FR-P 4-62 Blocs de déplacement Manuel de programmation CN 17VRS Déroulement d’une procédure de synchronisation Une association d’axes synchrones peut être activée durant le déroulement du programme CN au moyen d’une fonction auxiliaire. En mode manuel l’utilisateur peut activer une exploitation synchrone par une touche du pupitre machine ou par une touche quelconque. Un signal d’interface entre l’automate et la CN permet l’enclenchement du mode synchrone dans n’importe quel mode d’exploitation. Il faut veiller à ce que, avant l’enclenchement de l’exploitation synchrone, les axes maîtres et suiveurs aient atteint leur position finale et que les données machine correspondantes soient entièrement complétées. Indépendamment du mode d’exploitation, l’utilisation synchrone peut être annulée par remise à zéro du signal d’interface. Tous les axes de l’association gardent, après annulation, leur position. Fonction auxiliaire pour l’exploitation synchrone A partir de la version 5.15.xx les fonctions Q9000 à Q9999 sont réservées à INDRAMAT. Les fonctions Q9800 à Q9868 sont réservées à l’exploitation synchrone. L’utilisation de ces fonctions est décrite cidessous: 9 réservé pour INDRAMAT 8 réservé pour mode synchrone. Numéro process x = 0...6 Fonction Remarques Q 9 8 x 0 Association axes synch. 1 - 4 OFF Q 9 8 x 1 Association axes synchr. 1 ON Q 9 8 x 2 Association axes synchr. 2 ON Q 9 8 x 3 Association axes synchr. 3 ON Q 9 8 x 4 Association axes synchr. 4 ON Q 9 8 x 5 Association axes synchr. 1 OFF Q 9 8 x 6 Association axes synchr. 2 OFF Q 9 8 x 7 Association axes synchr. 3 OFF Q 9 8 x 8 Association axes synchr. 4 OFF Programmation CN Durant l’exploitation synchrone, l’utilisateur ne doit programmer que l’axe maître d’une association. Les axes suiveurs ne doivent pas être programmés. Si l’utilisateur le tente, par exemple en effectuant une image miroir ou un facteur d’échelle sur un axe suiveur, la CN interrompt le programme et génère un message d’erreur. La CN ne prend en compte les décalages d’origine et les corrections d’outil (y compris le correcteur D) que pour l’axe maître. Durant le mode synchrone, les axes suiveurs reçoivent exclusivement la consigne de l’axe maître en tenant compte de leur propre rapport de réduction et de leur sens de rotation. • L’association d’axes synchrones reste active à la fin du programme (BST, RET, M02 et M30), lors d’un Control Reset ainsi qu’en déplacement en JOG, tant que l’automate ne désactive pas la synchronisation. • Durant le déroulement de la synchronisation, l’utilisateur ne doit pas transférer les axes participant entre 2 process. L’utilisation d’une commande de transfert d’axe sur un axe participant entraîne l’interruption du programme et la génération d’un message d’erreur. Les axes participant à une synchronisation et appartenant à un autre DOK-MTC200-NC**PRO*V17-ANW1-FR-P Blocs de déplacement 4-63 Manuel de programmation CN 17VRS process doivent être transférés au process avant l’activation de l’association d’axes synchrones et ne doivent être re-transférés à leur process d’origine qu’après la désactivation. • Le déplacement contre butée (G75) n’est pas autorisé en mode de synchronisation. • Lorsqu’une transformation est active (G31) et (G32), les axes participant à la transformation (axes avec signification d’axe X et C) ne doivent pas faire partie d’une association d’axes synchrones active. Données machine pour l’association d’axes synchrones Les données machine pour les axes entraînés et les axes Gantry utilisent une page avec la désignation ‘’axes entraînés et axes Gantry’’. A l’intérieur de cette page la structure de données suivante existe pour chaque process et chaque association d’axes synchrones: N°. Désignation Plage de valeur Description 001 L’association d’axes est enclenchée 0/1 0: 1: Association d'axes synchrones non enclenchée Association d'axes synchrones enclenchée 002 Signification d'axe de l'axe maître 0-9 0: 1 - 9: Aucun axe maître disponible Signification d'axe X - C 003 Signification d'axe de l'axe suiveur 1 0-9 0: 1 - 9: Aucun axe suiveur disponible Signification d'axe X - C 004 Nombre de. tours axe maître i_LA/FA1 1 - 65536 Le rapport de réduction se calcule par nombre de tours axe maître / nombre de tours axe suiveur. 005 Nombre de. tours axe suiveur 1i_LA/FA1 1 - 65536 Le rapport de réduction se calcule par nombre de tours axe maître / nombre de tours axe suiveur. 006 Sens de rotation axe suiveur 1 0/1 0: 1: 007 Axe suiveur 1 = axe Gantry 0/1 Cet élément de donnée n'est actuellement pas exploité. 008 Signification d'axe de l'axe suiveur 2 0 -9 0: 1 - 9: 009 Nombre de. tours axe maître i_LA/FA2 1 - 65536 Le rapport de réduction se calcule par nombre de tours axe maître / nombre de tours axe suiveur. 010 Nombre de. tours axe suiveur 2i_LA/FA2 1 - 65536 Le rapport de réduction se calcule par nombre de tours axe maître / nombre de tours axe suiveur. 011 Sens de rotation axe suiveur 2 0/1 0: 1: 012 Axe suiveur 2 = axe Gantry 0/1 Cet élément de donnée n'est actuellement pas exploité. 013 Signification d'axe de l'axe suiveur 3 0-9 0: 1 - 9: 014 Nombre de. tours axe maître i_LA/FA3 1 - 65536 Le rapport de réduction se calcule par nombre de tours axe maître / nombre de tours axe suiveur. 015 Nombre de. tours axe suiveur 3i_LA/FA3 1 - 65536 Le rapport de réduction se calcule par nombre de tours axe maître / nombre de tours axe suiveur. 016 Sens de rotation axe suiveur 3 0/1 0: 1: 017 Axe suiveur 3 = axe Gantry 0/1 Cet élément de donnée n'est actuellement pas exploité. Même sens de rotation Sens de rotation opposé Aucun axe suiveur disponible Signification d'axe X - C Même sens de rotation Sens de rotation opposé Aucun axe suiveur disponible Signification d'axe X - C Même sens de rotation Sens de rotation opposé Chaque élément de données peut être reconfiguré par l’automate via le pupitre utilisateur ou par le programme CN dès lors que l’association d’axe n’est pas active. Dès que l’utilisateur accède, par l’automate ou l’interface opérateur, à des données d’une association d’axes synchrones active, il obtient un message d’erreur. Si l’utilisateur tente de le faire dans le programme CN avec une instruction MTD, la CN interrompt l’usinage et génère un message d’erreur. DOK-MTC200-NC**PRO*V17-ANW1-FR-P 4-64 Blocs de déplacement Manuel de programmation CN 17VRS DOK-MTC200-NC**PRO*V17-ANW1-FR-P Correction d’outil 5-1 Manuel de programmation CN 17VRS 5 Correction d’outil 5.1 Structure des données de correction d'outil La gestion d’outils a besoin des listes de réglage spécifique des données théoriques et réelles d’outil pour l’exécution de la vérification automatique de l’équipement. Avec vérification automatique de l'équipement Prozeß 0 4 3 2 1 5 6 Process 0 Paquet programmes CN 4 3 2 1 5 6 Process 0 Liste de réglage optionnelle (données théoriques) 4 3 2 1 5 6 Process 6 Process 5 Process 4 Process 3 Process 2 Process 1 Process 0 Magasin d'outil Liste du magasin (valeurs actuelles) Mode de travail avec organisation le listes de réglage spécifiques Fig. 5-1: Principe de travail avec vérification automatique de l’équipement Sans vérification automatique de l'équipement Process 0 1 2 3 5 4 6 Paquet programmes CN Process 0 Liste de magasin (valeurs réelles) 1 2 3 4 5 6 Process 6 Process 5 Process 4 Process 3 Process 2 Process 1 Process 0 Magasin d'outil Mode de travail sans utilisation de la liste de réglage Fig. 5-2: Principe de travail sans vérification automatique de l’équipement DOK-MTC200-NC**PRO*V17-ANW1-FR-P 5-2 Correction d’outil Manuel de programmation CN 17VRS La comparaison ci-dessous entre liste de réglages et liste d’outils donne un aperçu de leur utilisation. Liste de réglages Liste d’outils Tâche Rassemblement des données de consigne pour tous les outils utilisés lors de l'usinage. Préparation et mémorisation des données actuelles de tous les outils disponibles dans le magasin. Contenu Données de base de l'outil: Ø Caractérisation de l'outil Données de base de l'outil: Ø Caractérisation de l'outil Ø Emplacement Ø Unité Ø Données utilisateur (Option) Données de coupe: Ø Caractérisation du point de coupe Ø Valeurs limites de géométrie (Option) Données de coupe: Ø Caractérisation du point de coupe Ø Temps d'utilisation (Option) Ø Données géométriques (Option) Ø Données utilisateur (Option) Identification Chaque outil est identifié d'après son numéro et sa désignation (ID). Chaque outil est identifié d'après son emplacement et sa désignation (ID).. Modification (depuis PC, SOT, SPS- ou programme CN) Les listes de réglage ne peuvent pas être modifiées à l'intérieur de la CN. Les données des listes d'outils peuvent être modifiées au sein de la CN même durant l'usinage. Modification par la CN La CN ne fait aucune modification. La CN actualise le temps d'utilisation ainsi que l'état d'usure à un instant donné. Organisation générale Les listes de réglages font toujours partie d'un paquet de programmes CN. Les listes d'outils sont gérées indépendamment les unes des autres et des autres données. Organisation sur l'interface opérateur Listes de réglages spécifiques à une station: Il peut y avoir une liste de réglages pour chaque process (station) à l'intérieur d'un paquet programmes . Chaque process peut gérer jusqu'à 99 listes d'outils. Listes de réglages spécifiques à un programme: Il peut y avoir une liste de réglages pour chaque programme à l'intérieur d'un paquet programmes. Chargement dans la commande Les listes de réglages disponibles dans un paquet de programmes sont chargées en même temps que les programmes CN. Les listes d'outils sont chargées indépendamment les unes des autres et des autres données. Activation Les listes de réglages sont chargées, en fonction da la mémoire sélectionnée, dans la mémoire A ou B en même temps que le paquet de programmes. Pour chaque process disposant d'un magasin d'outils, une liste d’outils préparée est chargée dans la CN. Archivage La sauvegarde a lieu automatiquement avec le paquet de programmes. Les listes d'outils sont sauvegardées séparément. DOK-MTC200-NC**PRO*V17-ANW1-FR-P Manuel de programmation CN 17VRS 5.2 Correction d’outil 5-3 Listes de réglages Rôle de la liste de réglages La présence de tous les outils nécessaires à l’usinage ainsi que la possibilité de les employer pour exécuter l’usinage est définie par la liste de réglages. Elle garantit en outre la vérification automatique de l’équipement. Pour chaque process équipé d’un magasin d’outils et devant exécuter un usinage au moyen d’outils, une liste de réglages doit être établie au moment de la création du programme CN (voir aussi description de l’interface utilisateur ‚Gestion des données d’outils‘). La liste de réglages n’est indispensable que lorsque le constructeur machine l’a déterminé dans le programme automate. Données de la liste de réglages Une liste de réglages est composée de la somme de tous les outils nécessaires. Pour chaque outil utilisé dans un programme CN, il doit y avoir une entrée dans la liste de réglages correspondant. Chaque entrée d’outils est composée de: • Données de base de l’outil • Données de coupe Il y a autant de données de coupe qu’il y a de points de coupe dans les données de base. Les plages de valeurs autorisées pour chaque donnée de la liste de réglages ainsi que les unités possibles sont représentées dans le tableau suivant. DOK-MTC200-NC**PRO*V17-ANW1-FR-P 5-4 Correction d’outil Manuel de programmation CN 17VRS DESIGNATION Données de base Caractérisation d'outil Adresse index ID (désignation outil) Magasin Place Numéro d'outil Numéro duplo Type de correcteur Nombre de coupes Etat outil Données d'emplacement Demi places libres Ancien emplacement Magasin prochain outil Place prochain outil Magasin outil précédent Place outil précédent Unités Unité de temps Unité de longueur Données de technologie Code d'outil Type de représentation Données utilisateur Données utilisateur 1 . . . Données utilisateur 9 Commentaire Données de coupe Caractérisation de coupe Position de coupe Etat de coupe Données de temps Temps restant Seuil d'alerte Durée max. d'utilisation Durée d'utilisation acteulle Données géométriques Longueur L1 Longueur L2 Longueur L3 Rayon R Usure L1 Usure L2 Usure L3 Usure R Offset L1 Offset L2 Offset L3 Offset R Valeurs limites de géométie L1_min L1_max L2_min L2_max L3_min L3_max R_min R_max Facteurs d'usure Facteur d'usure L1 PLAGE DE VALEURS TYPE DE DONNEES UNITE ELEMENT DE DONNEE OPTION EL WL X X X X X X X X X (par outil) Mot double (32 bits) hexadécimal (lecture seule) jusqu'à 28 caractères libres 0 - 2 (0: Magasin/Revolver, 1: broche, 2: changeur) 0 - 999 1 - 9999999 1 - 999 1-4 1-9 0/1 (32 bits d'état) STRING28 DINT INT USINT USINT - 01 02 03 04 05 06 07 08 09 - X X X 0-4 1 - 999 0 - 2 (0: Magasin/Revolver, 1: broche, 2: changeur) 1 - 999 0 - 2 (0: Magasin/Revolver, 1: broche, 2: changeur) 1 -999 USINT INT INT INT INT INT - 10 11 12 13 14 15 X X 0/1 (0: min, 1: cycles) 0/1 (0: mm, 1: inch) USINT USINT - 16 17 X X USINT INT - 18 19 REAL quelconque 20 X X . . . REAL . . . quelconque . . . 28 . . . X . . . X 1- 9 0 - 999 -38 +38 +/- 1.2 ∗ 10 - +/- 3.4 ∗ 10 et 0 (entrée temp. par IHM: comme pour données géométriques) . . . -38 +38 +/- 1.2 ∗ 10 - +/- 3.4 ∗ 10 et 0 (entrée temp. par IHM: comme pour données géométriques) jusqu'à 5 x 76 caractères quelconques (par coupe) - X X X X X X 0-8 0/1 (16 bits d’état) USINT WORD 0.0 - 100.00 0.1 - 100.00 0 - 9999999 (0: Enregistrement du temps désactivée) 0 - 9999.999 REAL REAL REAL REAL % % min ou cycles min ou cycles 03 04 05 06 -9999.9999 - +9999.9999 ou -999.99999 - +999.99999 -9999.9999 - +9999.9999 ou -999.99999 - +999.99999 -9999.9999 - +9999.9999 ou -999.99999 - +999.99999 -9999.9999 - +9999.9999 ou -999.99999 - +999.99999 -9999.9999 - +9999.9999 ou -999.99999 - +999.99999 -9999.9999 - +9999.9999 ou -999.99999 - +999.99999 -9999.9999 - +9999.9999 ou -999.99999 - +999.99999 -9999.9999 - +9999.9999 ou -999.99999 - +999.99999 -9999.9999 - +9999.9999 ou -999.99999 - +999.99999 -9999.9999 - +9999.9999 ou -999.99999 - +999.99999 -9999.9999 - +9999.9999 ou -999.99999 - +999.99999 -9999.9999 - +9999.9999 ou -999.99999 - +999.99999 DINT DINT DINT DINT DINT DINT DINT DINT DINT DINT DINT DINT mm ou inch mm ou inch mm ou inch mm ou inch mm ou inch mm ou inch mm ou inch mm ou inch mm ou inch mm ou inch mm ou inch mm ou inch 07 08 09 10 11 12 13 14 15 16 17 18 X X X X X X X X -9999.9999 - +9999.9999 ou -999.99999 - +999.99999 -9999.9999 - +9999.9999 ou -999.99999 - +999.99999 -9999.9999 - +9999.9999 ou -999.99999 - +999.99999 -9999.9999 - +9999.9999 ou -999.99999 - +999.99999 -9999.9999 - +9999.9999 ou -999.99999 - +999.99999 -9999.9999 - +9999.9999 ou -999.99999 - +999.99999 -9999.9999 - +9999.9999 ou -999.99999 - +999.99999 -9999.9999 - +9999.9999 ou -999.99999 - +999.99999 DINT DINT DINT DINT DINT DINT DINT DINT mm ou inch mm ou inch mm ou inch mm ou inch mm ou inch mm ou inch mm ou inch mm ou inch 19 20 21 22 23 24 25 26 X X X X X X X X -9999.9999 - +9999.9999 ou -999.99999 - +999.99999 DINT 27 X X -9999.9999 - +9999.9999 ou -999.99999 - +999.99999 DINT 28 X X Facteur d'usure L2 -9999.9999 - +9999.9999 ou -999.99999 - +999.99999 DINT 29 X X Facteur d'usure L3 -9999.9999 - +9999.9999 ou -999.99999 - +999.99999 DINT mm ou inch/ min ou cycles mm ou inch/ min ou cycles mm ou inch/ min ou cycles mm ou inch/ min ou cycles 30 X X X 01 02 - X X X X X X X X X X X X X X X X X X X X X X X X X X X X X X Facteur d'usure R Légende EL: = Donnée spécifique à la liste de réglages WL: = Donnée spécifique à la liste d’outils DOK-MTC200-NC**PRO*V17-ANW1-FR-P Correction d’outil 5-5 Manuel de programmation CN 17VRS Caractérisation de l'outil Désignation de l’outil (ID) La désignation d’outil composée d’une chaîne comportant jusqu’à 28 caractères quelconques, aussi appelée ID , sert à distinguer clairement les outils utilisés. A l’intérieur du système de commande, elle est affichée sur l’IHM et sur les SOTs (Station Operator Terminal). Tous les outils utilisés doivent être clairement décrits afin d’être identifiés sans équivoque par la désignation d’outil. Les outils pouvant être remplacés par un autre (outils frères) sont rangés sous la même désignation d’outil. La différentiation entre ces outils se fait au moyen du numéro duplo supplémentaire. La large description d’outil permet de conserver chaque système de désignation d'outil spécifique au niveau de la CN. Numéro d’outil A l’intérieur d’un programme CN on peut accéder à un outil ou à un emplacement d’outil à l’aide du mot T celui-ci est composé de la lettre adresse T suivie d’un numéro d’outil (jusqu’à 7 chiffres) ou d’un numéro d’emplacement (jusqu’à 3 chiffres). La programmation d’un numéro d’outil force le gestionnaire d’outil à déterminer la place actuelle de l’outil d’après le numéro et la description d’outil contenus dans la liste de réglages ainsi qu’avec l’aide de la désignation et de l’emplacement d’outil contenus dans la liste d’outils. L’accès à un outil depuis le programme CN est possible avec l’association entre le numéro d’outil (tel qu’il est utilisé dans le programme) et l’outil (désignation d’outil spécifique à l’exploitation), association contenue dans la liste de réglages. Type de correcteur Le type de correcteur détermine le nombre et la position des correcteurs d’un outil (voir aussi Fig. 5-3). Correcteur de type 1 (outil de perçage) Correcteur de type 2 (outil de fraisage) Correcteur de type 3 (outil de tournage) Correcteur de type 4 (outil d'équerre) Un outil avec correcteur de type 1 ne possède qu'une correction de longueur (L3) qui est toujours perpendiculaire au plan d'usinage. Un outil avec correcteur de type 2 possède outre la correction de longueur (L3) perpendiculaire au plan d'usinage, une correction de rayon (R) dans le plan d'usinage. Un outil avec correcteur de type 3 possède 2 corrections de longueur (L1, L2) ainsi qu'une correction de rayon (R) dans le plan d'usinage. Les outils de ce type peuvent avoir une correction de longueur (L1, L2, L3) dans les directions des 3 axes principaux (X, Y, Z), ainsi qu'une correction de rayon (R) dans le plan d'usinage. La longueur L3 est toujours perpendiculaire au plan de travail, les longueurs L1 et L2, sont toujours dans le plan d'usinage. Le type de correcteur de l’outil en mémoire doit correspondre au type demandé par la liste de réglages afin de pouvoir être utilisé pour l’usinage envisagé. Lorsque la lettre N est introduite comme type de correcteur, l’IHM affiche pour les données L1, L2, L3 et R les valeurs de coupe correspondant aux paramètres système. Lors de la vérification de l’équipement, seules les valeurs limites de géométrie correspondant au type de correcteur seront extraites de la liste de réglages. DOK-MTC200-NC**PRO*V17-ANW1-FR-P Mode d'action des correcteurs 1. Correcteur: Y Y L3 X X R X Y X Z L1 1 Correction de longueur perpendiculaire au plan d'usinagee X R L3 Z R X Z L1 L3 R X L2 Z 0-8 longueur 1 Outil d'équerre longueur 1/2 Y L3 L1 L2 L1 rayon Z R 2 Correction de longueur dans le plan d'usinage X L2 Y L2 L1 L2 Z Y Outil de tournage Y R L2 L1 0 rayon R 4 Correcteur: L3 Z Y Correction de rayon dans le plan d'usinage Correction de rayon dans le plan d'usinage R 0 Outil de fraisage L3 L3 2 Correction de longueur dans le plan d'usinage 4 Z longueur 3 R 3 Correcteur X Y Y Z 3 L3 Position de coupe X rayon 0-8 Manuel de programmation CN 17VRS DOK-MTC200-NC**PRO*V17-ANW1-FR-P )LJ'pWHUPLQDWLRQGXW\SHGHFRUUHFWHXU Correction de rayon dans le plan d'usinage X Z 2 Correcteur: 1 Correction de longueur perpendiculaire au plan d'usinage Outil de perçage Y L3 Z 2 Exemple G 19 longueur 3 1 Correction de longueur perpendiculaire au plan d'usinage G 18 longueur 2 1 G 17 longueur 3 Type Correcteurs effectifs 5-6 Correction d’outil Détermination des types de correcteurs Manuel de programmation CN 17VRS Nombre d'arêtes de coupe Correction d’outil 5-7 A chaque outil peuvent être associés au maximum jusqu’à 9 blocs de données de coupe, indépendamment du fait que l’outil dispose d’autant d’arêtes de coupe ou non. Afin d’éviter la perte inutile de place mémoire, le nombre maximum de coupes peut être réduit au moyen des paramètres système correspondant, jusqu’à une coupe par outil. Le nombre de coupes demandées par la liste de réglages doit être rempli par l’outil correspondant afin qu’il puisse être utilisé pour l’usinage. La programmation de la lettre N comme nombre de coupes entraîne, dans la liste de réglages, l’affichage sur l’IHM, d’autant de points de coupe qu’il a été défini dans le paramètre système ‘’nombre maximale de coupes’’. Lors de la vérification de l’équipement, seuls les blocs de données de couple disponibles dans la liste d’outils seront utilisés par la liste de réglages. Unités Unités de temps Les unités de temps disponibles sont: • les minutes [min] ou • les cycles [zykl]. Toutes les données de temps d’utilisation de l’outil ou de l’outil frère (à l’exception du temps restant et de la limite d’alerte exprimés en pour cent) sont élaborées et mises à jour dans l’unité de temps sélectionnée. A partir de la version 4.14, l’élément de données d’unité de temps n’est plus disponible que dans la liste d’outils. Il n’est plus disponible dans la liste de réglages. Unités de longueur Toutes les données géométriques d’un outil peuvent être programmées: • en millimètre [mm] ou • en pouce [inch]. L’unité de longueur de la liste de réglages ne doit pas forcément correspondre à celle de la liste d’outils; en effet, lors du chargement dans la commande, toutes les données géométriques sont converties dans l’unité de base du programme valide pour le process. Données utilisateur de la liste de réglages Commentaires Chaque entrée de la liste de réglages peut être accompagnée d’un commentaire d’une longueur max. de 5 x 76 caractères, dès lors que cela a été sélectionné dans les paramètres système. Le commentaire permet d’enregistrer des informations diverses pour chaque groupe d’outil frère, comme par exemple des consignes d’assemblage. Remarque: Le commentaire n’est disponible que sur le PC. Reconnaissance de coupe Position du point de coupe DOK-MTC200-NC**PRO*V17-ANW1-FR-P La position du point de coupe permet de mesurer les outils avec types de correcteur 3 (outils de tournage) et 4 (outils d’équerre) par rapport à la position théorique P , sans qu’il apparaisse des imprécisions lors des usinages ultérieurs. 5 1 4 S S S P P P L2 Position du point de coupe: P S 6 P P=S S 8 0 Y(G17) Y(G18) Y(G19) P P P S S S 2 3 7 Y(G17) Y(G18) Y(G19) L1 5 4 1 S S S P P P P L2 S 0 Y(G17) Y(G18) Y(G19) 8 P P=S S 6 P P P S S S 3 2 7 Y(G17) Y(G18) Y(G19) L1 5-8 Correction d’outil Manuel de programmation CN 17VRS Fig. 5-4: Positions possibles du point de coupe DOK-MTC200-NC**PRO*V17-ANW1-FR-P Manuel de programmation CN 17VRS Correction d’outil 5-9 Données de temps d’utilisation Durée maximale d’utilisation La durée maximale d’utilisation est la durée d’usinage en: • minutes ou • cycles durant laquelle un outil, neuf au départ, peut enlever du copeau, pour une association outil / matière donnée, jusqu’à usure totale. • L’introduction de la valeur 0 pour la durée maximale d’utilisation, désactive la mise à jour de la durée d’utilisation pour un outil donné. A partir de la version 4.14, l’élément durée maximale d’utilisation n’est plus disponible que dans la liste d’outils; elle n’est plus affichée dans la liste de réglages. Durée d’utilisation actuelle La durée d’utilisation actuelle donne la durée d’usinage pendant laquelle l’outil correspondant a été en contact avec la pièce à usiner. La durée d’utilisation actuelle permet, avec l’utilisation du programme CN ou automate spécifiques à l’utilisateur, d’effectuer certaines vérifications; il est ainsi possible de vérifier que les données d’utilisation actuelles de tous les outils actuellement dans le magasin ont une durée suffisante pour effectuer une fabrication. Valeurs limites de géométrie Les valeurs limites de géométrie permettent de vérifier que les outils disponibles dans le magasin peuvent être utilisés pour un usinage donné. La vérification selon laquelle la longueur ou le rayon d’un outil permet l’exécution d’un usinage a lieu durant la vérification automatique de l’équipement lors du départ cycle d’un programme. Elle évite ainsi les temps morts durant l’usinage. Outre l’assurance et la disponibilité de l’outil, l’introduction judicieuse de valeur limite de géométrie permet d’éviter les collisions lors de l’écriture du programme. • La correction d’outil ne tient aucun compte des valeurs limites de géométrie de la liste de réglages. Longueurs maximales et minimales • Les longueurs maximales: L1_max, L2_max et L3_max ainsi que • les longueurs minimales: L1_min, L2_min et L3_min donnent les limites des longueurs correspondantes pour lesquelles un usinage donné peut encore être effectué. Rayon maximum et minimum • Le rayon maximum: R_max et • le rayon minimum: R_min donnent les limites du rayon de l’outil pour lesquelles un usinage prévu peut encore être effectué. Facteurs d’usure Les facteurs d’usure permettent de compenser les modifications de longueur ou de rayon dues à l’usure. A partir de la version 4.14, l’élément facteur d’usure n’est plus disponible que dans la liste d’outils; il ne peut donc plus être affiché dans la liste de réglages. DOK-MTC200-NC**PRO*V17-ANW1-FR-P 5-10 Correction d’outil Facteurs d’usure de longueur (L1, L2 et L3) Manuel de programmation CN 17VRS La compensation d’usure de longueur est activée lorsque la correction de longueur est enclenchée avec G48 ou G49. La valeur de compensation pour la correction d’usure de longueur de l’outil est calculée par le gestionnaire d’outil à partir de la durée d’usinage de l’outil multipliée par le facteur d’usure de longueur. Si le facteur d’usure de longueur est programmé en ‘mm / min’ ou ‘inch / min’, le gestionnaire d’outil prend en compte, comme durée d’usinage, tous les temps au cours desquels ont eu lieu des mouvements de travail (tous les mouvements exceptés ceux avec G00) alors que l’outil était actif. Si le facteur d’usure de longueur est programmé en 'mm/ cycle' ou en 'inch/ cycle' , le gestionnaire d’outil prend un cycle comme durée d’usinage. Le gestionnaire d’outil actualise la durée d’usinage et la valeur de compensation automatiquement: • lors du passage à un autre point de coupe, • lors du rappel d’un point de coupe, • lorsque l’outil est remis dans le magasin (registre outil = magasin), • lorsque l’outil est basculé depuis sa position d’usinage (registre = revolver), • lors de la désélection de l’outil avec TO (registre outil = revolver ou pas de registre outil sélectionné). Facteur d’usure de rayon (R) La compensation d’usure de rayon est activée lorsque la correction de trajectoire d’outil est enclenchée avec G41 ou G42. La valeur de compensation pour la correction d’usure de rayon est calculée par le gestionnaire d’outil à partir de la durée d’usinage de l’outil multipliée par le facteur d’usure de rayon. Si le facteur d’usure de rayon est programmé en ‘mm/min’ ou ‘inch/min’, le gestionnaire d’outil prend compte, comme durée d’usinage, tous les temps au cours desquels ont eu lieu des mouvements de travail (tous les mouvements exceptés ceux avec G00) alors que l’outil était actif. Si le facteur d’usure de rayon est programmé en 'mm/ cycle' ou en 'inch/ cycle' , le gestionnaire d’outil prend un cycle comme durée d’usinage. Le gestionnaire d’outil actualise la durée d’usinage et la valeur de compensation automatiquement: • lors du passage à un autre point de coupe, • lors du rappel d’un point de coupe, • lorsque l’outil est remis dans le magasin (registre outil = magasin), • lorsque l’outil est basculé depuis sa position d’usinage (registre = revolver), • lors de la désélection de l’outil avec TO (registre outil = revolver ou pas de registre outil sélectionné). DOK-MTC200-NC**PRO*V17-ANW1-FR-P Manuel de programmation CN 17VRS 5.3 Correction d’outil 5-11 Liste d’outils Rôle de la liste d’outils Les listes d’outils servent exclusivement à la préparation et à l’archivage de données d’outil. Ces données peuvent être crées, modifiées et numérisées au moyen de l’IHM sur PC durant un usinage. L’opérateur est ainsi en état de préparer l’équipement du magasin d’outil pour les usinages suivants. Le temps nécessaire pour garnir le magasin est ainsi réduit au minimum. L’utilisateur change dans la CN la liste d’outils déjà préparée et garnit le magasin conformément à la liste d’outils. Dès qu’un usinage a commencé, la liste d’outils encore disponible sur le PC perd sa signification et seule la liste d’outils contenue dans la CN reflète l’état actuel d’un outil du magasin. Outre les données de base, la liste d’outils contient toutes les données nécessaires à la coupe (reconnaissance de point de coupe, géométrie, données d’utilisation ainsi que données définies par l’utilisateur) de tous les outils répertoriés. • Les modifications concernant l'équipement actuel d'outils, telles que l'adjonction, la suppression ou le changement d'un outil, ou les modifications de données d'outil doivent être apportées directement dans les données d'outils actuelles. Données de la liste d’outils Une liste d’outils est composée de toutes les données des outils disponibles dans le magasin. Le tableau suivant décrit les plages de valeurs et des unités possibles pour chaque données de la liste. DOK-MTC200-NC**PRO*V17-ANW1-FR-P 5-12 Correction d’outil Manuel de programmation CN 17VRS DESIGNATION Données de base Caractérisation d'outil Adresse index ID (désignation outil) Magasin Place Numéro d'outil Numéro duplo Type de correcteur Nombre de coupes Etat outil Données d'emplacement Demi places libres Ancien emplacement Magasin prochain outil Place prochain outil Magasin outil précédent Place outil précédent Unités Unité de temps Unité de longueur Données de technologie Code d'outil Type de représentation Données utilisateur Données utilisateur 1 . . . Données utilisateur 9 Commentaire Données de coupe Caractérisation de coupe Position de coupe Etat de coupe Données de temps Temps restant Seuil d'alerte Durée max. d'utilisation Durée d'utilisation acteulle Données géométriques Longueur L1 Longueur L2 Longueur L3 Rayon R Usure L1 Usure L2 Usure L3 Usure R Offset L1 Offset L2 Offset L3 Offset R Valeurs limites de géométie L1_min L1_max L2_min L2_max L3_min L3_max R_min R_max Facteurs d'usure Facteur d'usure L1 PLAGE DE VALEURS TYPE DE DONNEES UNITE ELEMENT DE DONNEE OPTION EL WL X X X X X X X X X (par outil) Mot double (32 bits) hexadécimal (lecture seule) jusqu'à 28 caractères libres 0 - 2 (0: Magasin/Revolver, 1: broche, 2: changeur) 0 - 999 1 - 9999999 1 - 999 1-4 1-9 0/1 (32 bits d'état) STRING28 DINT INT USINT USINT - 01 02 03 04 05 06 07 08 09 - X X X 0-4 1 - 999 0 - 2 (0: Magasin/Revolver, 1: broche, 2: changeur) 1 - 999 0 - 2 (0: Magasin/Revolver, 1: broche, 2: changeur) 1 -999 USINT INT INT INT INT INT - 10 11 12 13 14 15 X X 0/1 (0: min, 1: cycles) 0/1 (0: mm, 1: inch) USINT USINT - 16 17 X X USINT INT - 18 19 REAL quelconque 20 X X . . . REAL . . . quelconque . . . 28 . . . X . . . X 1- 9 0 - 999 -38 X X X X +38 +/- 1.2 ∗ 10 - +/- 3.4 ∗ 10 et 0 (entrée temp. par IHM: comme pour données géométriques) . . . -38 +38 +/- 1.2 ∗ 10 - +/- 3.4 ∗ 10 et 0 (entrée temp. par IHM: comme pour données géométriques) jusqu'à 5 x 76 caractères quelconques (par coupe) - X X 0-8 0/1 (16 bits d'état) USINT WORD 0.0 - 100.00 0.1 - 100.00 REAL REAL REAL REAL % % min ou cycles min ou cycles 03 04 05 06 -9999.9999 - +9999.9999 ou -999.99999 - +999.99999 -9999.9999 - +9999.9999 ou -999.99999 - +999.99999 -9999.9999 - +9999.9999 ou -999.99999 - +999.99999 -9999.9999 - +9999.9999 ou -999.99999 - +999.99999 -9999.9999 - +9999.9999 ou -999.99999 - +999.99999 -9999.9999 - +9999.9999 ou -999.99999 - +999.99999 -9999.9999 - +9999.9999 ou -999.99999 - +999.99999 -9999.9999 - +9999.9999 ou -999.99999 - +999.99999 -9999.9999 - +9999.9999 ou -999.99999 - +999.99999 -9999.9999 - +9999.9999 ou -999.99999 - +999.99999 -9999.9999 - +9999.9999 ou -999.99999 - +999.99999 -9999.9999 - +9999.9999 ou -999.99999 - +999.99999 DINT DINT DINT DINT DINT DINT DINT DINT DINT DINT DINT DINT mm ou inch mm ou inch mm ou inch mm ou inch mm ou inch mm ou inch mm ou inch mm ou inch mm ou inch mm ou inch mm ou inch mm ou inch 07 08 09 10 11 12 13 14 15 16 17 18 X X X X X X X X -9999.9999 - +9999.9999 ou -999.99999 - +999.99999 -9999.9999 - +9999.9999 ou -999.99999 - +999.99999 -9999.9999 - +9999.9999 ou -999.99999 - +999.99999 -9999.9999 - +9999.9999 ou -999.99999 - +999.99999 -9999.9999 - +9999.9999 ou -999.99999 - +999.99999 -9999.9999 - +9999.9999 ou -999.99999 - +999.99999 -9999.9999 - +9999.9999 ou -999.99999 - +999.99999 -9999.9999 - +9999.9999 ou -999.99999 - +999.99999 DINT DINT DINT DINT DINT DINT DINT DINT mm ou inch mm ou inch mm ou inch mm ou inch mm ou inch mm ou inch mm ou inch mm ou inch 19 20 21 22 23 24 25 26 X X X X X X X X -9999.9999 - +9999.9999 ou -999.99999 - +999.99999 DINT 27 X X Facteur d'usure L2 -9999.9999 - +9999.9999 ou -999.99999 - +999.99999 DINT 28 X X Facteur d'usure L3 -9999.9999 - +9999.9999 ou -999.99999 - +999.99999 DINT 29 X X Facteur d'usure R Données utilisateur Données utilisateur 1 -9999.9999 - +9999.9999 ou -999.99999 - +999.99999 DINT mm ou inch/ min ou cycles mm ou inch/ min ou cycles mm ou inch/ min ou cycles mm ou inch/ min ou cycles 30 X X REAL quelconque 31 X X . . . REAL . . . quelconque . . . 35 . . . X . . . X DINT . . . DINT quelconque . . . quelconque 36 . . . 40 X . . . X X . . . X . . . Données utilisateur 5 Données utilisateur 6 . . . Données utilisateur 10 0 - 9999999 (0: gestion de temps d'utilisation désactivée) 0 - 9999.999 -38 X 01 02 X X X X X X X X X X X X X X X X X X X X X X X X X X X X X X +38 +/- 1.2 ∗ 10 - +/- 3.4 ∗ 10 et 0 (entrée temp. par IHM: comme pour données géométriques) . . . -38 +38 +/- 1.2 ∗ 10 - +/- 3.4 ∗ 10 et 0 (entrée temp. par IHM: comme pour données géométriques) -9999.9999 - +9999.9999 ou -999.99999 - +999.99999 . . . -9999.9999 - +9999.9999 ou -999.99999 - +999.99999 Légende - EL: = Donnée spécifique à la liste de réglages WL: = Donnée spécifique à la liste d’outils DOK-MTC200-NC**PRO*V17-ANW1-FR-P Manuel de programmation CN 17VRS Correction d’outil 5-13 Caractérisation de l'outil Désignation d’outil (ID) La désignation d’outil composée d’une chaîne comportant jusqu’à 28 caractères quelconques, aussi appelée ID , sert à distinguer clairement les outils utilisés. A l’intérieur du système de commande, elle est affichée sur l’IHM et sur les SOTs (Station Operator Terminal). Tous les outils utilisés doivent être clairement décrits afin d’être identifiés sans équivoque par la désignation d’outil. Les outils pouvant être remplacés par un autre (outils frères) sont rangés sous la même désignation d’outil. La différentiation entre ces outils se fait au moyen du numéro duplo supplémentaire. La large description d’outil permet de conserver chaque système de désignation d'outil spécifique au niveau de la CN. Magasin La donnée magasin n’apparaît pas directement dans la liste d’outils car cette liste ne traite, outre le magasin d’outil propre (Magasin = 0) que la broche (Magasin = 1). Les broches sont, à l’intérieur de la liste d’outils, caractérisées par un numéro de place précédé de la lettre S. Place La donnée place fixe l’emplacement de l’outil à l’intérieur du magasin, ou la broche d’outil dans le cas d’une broche, où se trouve l’outil. A l’aide de la liste d’outils, toutes les places d’un magasin et toutes les broches disponibles peuvent être préparées quant à leur données techniques. ATTENTION Numéro d'outil A l’intérieur d’un programme CN on peut accéder à un outil ou à un emplacement d’outil à l’aide du mot T celui-ci est composé de la lettre adresse T suivie d’un numéro d’outil (jusqu’à 7 chiffres) ou d’un numéro d’emplacement (jusqu’à 3 chiffres). La programmation d’un numéro d’outil force le gestionnaire d’outil à déterminer la place actuelle de l’outil d’après le numéro et la description d’outil contenus dans la liste de réglages ainsi qu’avec l’aide de la désignation et de l’emplacement d’outil contenus dans la liste d’outils. REMARQUE Numéro duplo Après le chargement d’une liste d’outils dans la CN, il faut vérifier la concordance de l’équipement effectivement disponible dans le magasin avec la listes d’outils. Une concordance erronée peut entraîner un endommagement de la pièce ou de la machine. A partir de la version 4.14, l’élément numéro d’outil est disponible dans la liste de réglages et dans la liste d’outils. Si la vérification automatique de l’équipement est active, les numéros d’outils de la liste de réglages ont priorité et remplacent une éventuelle affectation dans la liste d’outils. Le numéro duplo sert: • à une identification univoque des outils frères (outils avec une même désignation et un même numéro T) et • à la détermination de l’ordre de remplacement des outils frères pour l’usinage. Les outils frères sont utilisés en fonction de leur numéro duplo, un outil avec un numéro duplo faible sera utilisé avant un outil avec un numéro plus élevé, dès lors qu’il n’est pas usé ou verrouillé. Le programme CN accède aux outils frères avec le même numéro T. Le passage à un outil frère est déclenché par la CN seulement lors d’un nouvel appel avec le même numéro T, lorsque l’outil actuel (outil avec même numéro et même désignation et numéro duplo inférieur) est usé ou verrouillé. DOK-MTC200-NC**PRO*V17-ANW1-FR-P 5-14 Correction d’outil Manuel de programmation CN 17VRS Type de correcteur Le type de correcteur détermine le nombre et la position des correcteurs d’un outil (voir aussi Fig. 5-5). Correcteur de type 1 (outil de perçage) Correcteur de type 2 (outil de fraisage) Correcteur de type 3 (outil de tournage) Correcteur de type 4 (outil d'équerre) Un outil avec correcteur de type 1 ne possède qu'une correction de longueur (L3) qui est toujours perpendiculaire au plan d'usinage. Un outil avec correcteur de type 2 possède outre la correction de longueur (L3) perpendiculaire au plan d'usinage, une correction de rayon (R) dans le plan d'usinage. Un outil avec correcteur de type 3 possède 2 corrections de longueur (L1, L2) ainsi qu'une correction de rayon (R) dans le plan d'usinage. Les outils de ce type peuvent avoir une correction de longueur (L1, L2, L3) dans les directions des 3 axes principaux (X, Y, Z), ainsi qu'une correction de rayon (R) dans le plan d'usinage. La longueur L3 est toujours perpendiculaire au plan de travail, les longueurs L1 et L2, sont toujours dans le plan d'usinage. Le type de correcteur de l’outil en mémoire doit correspondre au type demandé par la liste de réglages afin de pouvoir être utilisé pour l’usinage envisagé. DOK-MTC200-NC**PRO*V17-ANW1-FR-P Mode d'action des correcteurs 1. Correcteur: Y Y L3 X R X X Y Z L1 X R L3 Z R L3 L1 L2 L1 X Z L1 L3 R X L2 Z longueur 1 Outil d'équerre longueur 1/2 Y R 2 Correction de longueur dans le plan d'usinage rayon Z Y L2 X L2 0-8 X rayon 0-8 Correction d’outil 5-15 1 Correction de longueur perpendiculaire au plan d'usinagee L1 L2 Z Y 0 Outil de tournage Y R X 0 rayon L2 4 Correcteur: L3 Z L1 Position de coupe Outil de fraisage R R Correction de rayon dans le plan d'usinage Correction de rayon dans le plan d'usinage R Y 2 Correction de longueur dans le plan d'usinage 4 Z L3 L3 3 Correcteur X Y Y Z 3 L3 longueur 3 Fig. 5-5: Détermination du type de correcteur Correction de rayon dans le plan d'usinage X Z 2 Correcteur: 1 Correction de longueur perpendiculaire au plan d'usinage Outil de perçage Y L3 Z 2 Exemple G 19 longueur 3 1 Correction de longueur perpendiculaire au plan d'usinage G 18 longueur 2 1 G 17 longueur 3 Type Correcteurs effectifs Manuel de programmation CN 17VRS DOK-MTC200-NC**PRO*V17-ANW1-FR-P Détermination des types de correcteurs 5-16 Correction d’outil Manuel de programmation CN 17VRS Nombre de points de coupe A chaque outil peuvent être associés au maximum jusqu’à 9 blocs de données de coupe, indépendamment du fait que l’outil dispose d’autant d’arêtes de coupe ou non. Afin d’éviter la perte inutile de place mémoire, le nombre maximum de coupes peut être réduit au moyen des paramètres système correspondants, jusqu’à une coupe par outil. Le nombre de coupes demandées par la liste de réglages doit être rempli par l’outil correspondant afin qu’il puisse être utilisé pour l’usinage. Etat de l’outil Les bits d’état de l’outil donnent des renseignements sur l’état de chaque emplacement ainsi que sur l’état de l’outil, dès qu’il y a un outil dans cet emplacement. Le tableau montre les bits d’état de la liste d’outils. Groupe Bit d'état Symbole Remarque Verrouillage emplacement Place verrouillée L en préparation Réservation emplacement Occupation emplacement Etat d’usure Demi-place supérieure verrouillée pour outil à emplacement fixe codé en préparation Demi-place inférieure verrouillée pour outil à emplacement fixe codé en préparation Demi-place supérieure réservée en préparation Demi-place inférieure réservée en préparation Demi-place supérieure occupée en préparation Demi-place inférieure occupée en préparation Place occupée Valeur mise à jour automatiquement Outil usé d Valeur non modifi. Limite d'alerte atteinte w Valeur non modifi. Reconnaissance Outil d'usinage p Valeur non modifi. outil frère Outil de remplacement s Valeur non modifi. Codage emplacement fixe Outil à emplacement fixe codé C en préparation Etat outil Outil verrouillé L Valeur modifiable Etat outil utilisateur 1 Etat outil utilisateur 1 quelconque Valeur modifiable Etat outil utilisateur 2 Etat outil utilisateur 2 quelconque Valeur modifiable Etat outil utilisateur 3 Etat outil utilisateur 3 quelconque Valeur modifiable Etat outil utilisateur 4 Etat outil utilisateur 4 quelconque Valeur modifiable Etat outil utilisateur 5 Etat outil utilisateur 5 quelconque Valeur modifiable Etat outil utilisateur 6 Etat outil utilisateur 6 quelconque Valeur modifiable Etat outil utilisateur 7 Etat outil utilisateur 7 quelconque Valeur modifiable Etat outil utilisateur 8 Etat outil utilisateur 8 quelconque Valeur modifiable A l’intérieur de la liste d’outils, l’utilisateur peut, au moyen du bit d’état ‘verrouillage d’outil’ verrouiller ou déverrouiller des outils. Il est en outre possible d’associer aux données de base de chaque outil jusqu’à 8 bits d’état spécifiques à l’utilisateur, bits qui peuvent être présentés à l’intérieur de la liste d’outils. Les bits d’état spécifiques usuels tels que: • outil usé (d), • limite d’alerte atteinte (w), • outil d’usinage (p) et • outil de remplacement (s) ne peuvent pas être modifiés dans la liste d’outils. Seuls les bits d’état ‘Outil usé’ et ‘Limite d’alerte atteinte’ peuvent être remis à zéro au moyen de la fonction Reset (voir description IHM ‘Gestion d’outil’). DOK-MTC200-NC**PRO*V17-ANW1-FR-P Manuel de programmation CN 17VRS Correction d’outil 5-17 Données d’emplacements Demi-place libre Les outils larges sont marqués par la donnée demi-place libre: 0: il s’agit d’un outil de largeur normale ne recouvrant aucune place en dehors de sa place propre 1: l’outil recouvre à droite et à gauche de son emplacement propre encore une demi-place 2: l’outil recouvre à droite et à gauche de son emplacement propre encore deux demi-places 3: l’outil recouvre à droite et à gauche de son emplacement propre encore trois demi-places 4: l’outil recouvre à droite et à gauche de son emplacement propre encore quatre demi-places. Sur l’IHM du PC et du SOT, les demi-places recouvertes sont visualisées avec des traits obliques. Ancienne place L’élément ancienne place n’est pas représenté dans la listes d’outils. Il est cependant intégré au jeu de données afin d’assurer une place fixe pour les outils à place fixe codée se trouvant dans la broche. Unités Unités de temps Les unités de temps disponibles sont: • les minutes [min] ou • les cycles [zykl]. Toutes les données de temps d’utilisation de l’outil ou de l’outil frère (à l’exception du temps restant et de la limite d’alerte exprimés en pour cent) sont élaborées et mises à jour dans l’unité de temps sélectionnée. A partir de la version 4.14, l’élément de données d’unité de temps n’est plus disponible que dans la liste d’outils. Il n’est plus disponible dans la liste de réglages. Unités de longueur Les unités de temps disponibles sont: • les minutes [min] ou • les cycles [zykl]. L’unité de longueur de la liste de réglages ne doit pas forcément correspondre à celle de la liste d’outils; en effet, lors du chargement dans la commande, toutes les données géométriques sont converties dans l’unité de base du programme valide pour le process. Données d’outils utilisateur Données utilisateur 1 - 9 Les données d’utilisateur 1 - 9 dans les données de base d’outils permettent d’associer des données utilisateur quelconques à un outil. Par introduction de la description voulue dans les paramètres système, les données utilisateur sont extraites des blocs de données actifs et affichées dans la liste d’outils actuelle (voir aussi 'Description des paramètres'). Les données utilisateur, comme les autres données, peuvent être préparées dans la liste d’outils. Des exemples typiques de données utilisateur sont: • Masse d’outil (influence la vitesse de changement d’outil) • Vitesse de rotation maximale de l’outil • Dimensions maximales de l’outil (pour test de collision). DOK-MTC200-NC**PRO*V17-ANW1-FR-P 5-18 Correction d’outil Manuel de programmation CN 17VRS Y(G17) Y(G18) Y(G19) La position du point de coupe permet de mesurer les outils avec types de correcteur 3 (outils de tournage) et 4 (outils d’équerre) par rapport à la position théorique P , sans qu’il apparaisse des imprécisions lors des usinages ultérieurs. S S 8 L2 S Y(G17) Y(G18) Y(G19) P P 4 S P S P P 6 S P P=S S P 1 S S P 5 4 S P L2 Position du point de coupe: S S 0 P 8 Y(G17) Y(G18) Y(G19) P P S 3 2 7 L1 Y(G17) Y(G18) Y(G19) 5 1 S P S P=S P 6 0 P P S 2 3 7 L1 Caractérisation du point de coupe Fig. 5-6: Position possible du point de coupe DOK-MTC200-NC**PRO*V17-ANW1-FR-P Correction d’outil 5-19 Manuel de programmation CN 17VRS Etat de l’arête de coupe Les bits d’état donnent des renseignements sur l’état de l’arête respective. Le tableau suivant montre les bits d’état de coupe. Groupe Bits d'état Symbole Remarque Etat d’usure Arête de coupe usée d Valeur non modifiable Limite d'alerte atteinte w Valeur non modifiable Bit d'état utilisateur 1 Bit d'état utilisateur 1 quelconque Valeur modifiable Bit d'état utilisateur 2 Bit d'état utilisateur 2 quelconque Valeur modifiable Bit d'état utilisateur 3 Bit d'état utilisateur 3 quelconque Valeur modifiable Bit d'état utilisateur 4 Bit d'état utilisateur 4 quelconque Valeur modifiable A chaque coupe peuvent être associés jusqu’à quatre bits d’état utilisateur qui peuvent être préétablis dans la liste d’outils. Les deux bits d’état: • Arête de coupe usée (d) et • Limite d’alerte atteinte (w) ne peuvent pas être directement modifiés dans la liste d’outils. Ils peuvent être remis à zéro par la fonction Reset (voir description IHM ‘Gestion d’outils’). Données de temps d’utilisation Temps d’utilisation restant en pour cent Le temps d’utilisation restant en pour cent donne l’état d’usure d’un outil en pour cent, indépendamment de l’association outil / matériaux et des données de technologie. Temps dutilisation restant [%] = Temps dutilisation restant [min] ou [zykl] •100 [%] Durée maximale dutilisation [min] ou [zykl] Un outil neuf ou affûté a un temps d’utilisation restant de 100%, et un outil usé un temps de 0%. Le gestionnaire d’outils gère et surveille l’état d’usure de l’outil d’après le temps d’utilisation restant, indépendamment de l’association outil / pièce de l’usinage en cours. L’actualisation du temps d’utilisation restant a lieu: • lors de la vérification automatique de l’équipement, • lors du passage à une autre arête de coupe, • lors du rappel de l’arête de coupe, • lorsque l’outil est remis en magasin ou • lorsque l’outil est basculé de sa position d’usinage (magasin = revolver) • lors de la désélection d’un outil avec T0 (emplacement = revolver ou pas d’emplacement). Le calcul du temps d’utilisation restant se fait d’après: WHPSVG XWLOUHVW SRXUFHQWDSUqV WHPSVG XWLOUHVW SRXUFHQWDYDQW GXUpHG XWLOLVDWLRQ>PLQ@RX>F\FOHV@ ∗ GXUpHPD[G XWLOLVDWLRQ>PLQ@RX>F\FOHV@ A chaque actualisation, le gestionnaire d’outil vérifie le temps d’utilisation restant et positionne le signal d’interface 'PxxSMGTWO' vers l’automate lorsque le temps restant d’un outil pour lequel il n’y a pas d’outil frère disponible est dépassé. Limite d’alerte en pour cent DOK-MTC200-NC**PRO*V17-ANW1-FR-P La limite d’alerte en pour cent indique à partir de quel pourcentage de temps restant le gestionnaire d’outil affiche l’état de limite atteinte. A chaque actualisation, le gestionnaire d’outil vérifie le temps restant et positionne le signal d’interface 'PxxSMGWRN' vers l’automate lorsque le temps 5-20 Correction d’outil Manuel de programmation CN 17VRS d’utilisation d’un outil, pour lequel aucun outil frère n’est disponible, atteint la limite d’alerte. Durée maximale d’utilisation La durée maximale d’utilisation est la durée d’usinage en: • minutes ou • cycles durant laquelle un outil, depuis l’affûtage jusqu’à l’usure totale, peut enlever du copeau en tenant compte des conditions de coupe pour une association outil / matériaux donnée. L’introduction d’une valeur 0 comme durée maximale d’utilisation désactive l’actualisation du temps d’utilisation de l’outil concerné. REMARQUE Remarque: A partir de la version 4.14, la durée maximale d’utilisation n’est plus disponible que dans la liste d’outils et ne peut plus être affichée dans la liste de réglages. Données géométriques Lorsque la correction correspondante est activée, les dimensions d’un outil sont automatiquement compensés à l’aide des données géométriques. Les données géométriques se répartissent selon: Géométrie Usure Offset Longueur L1 Usure L1 Offset L1 Longueur L2 Usure L2 Offset L2 Longueur L3 Usure L3 Offset L3 Rayon R Usure R Offset R Les registres d’usure et d’offset peuvent être choisis comme option à l’aide des paramètres système. Les registres de géométrie servent de mémoires indépendantes du programme à l’aide desquelles les dimensions des outils peuvent être compensées. La CNC utilise le registre d’usure pour compenser l’usure dans le temps de l’outil, à l’aide des facteurs d’usure. Pour cela, elle calcule à des instants précis, l’usure correspondante et ajoute cette valeur à la valeur déjà présente dans le registre d’usure. Dès que les facteurs d’usure ne sont pas sélectionnés dans les paramètres système, ou que le bloc de données est à zéro, les registres d’usure sont exclusivement à la disposition de l’utilisateur. Les registres d’usure sont influencés par la fonction Reset. Outre le rechargement à 100 % du temps restant d’utilisation, la fonction Reset efface les registres d’usure de tous les outils. Les registres d’offset ne sont pas influencés par la CNC. Ils peuvent donc être utilisés comme mémoire pour des décalages additionnels, par exemple pour la compensation des dimensions d’un dispositif d’adaptation. DOK-MTC200-NC**PRO*V17-ANW1-FR-P Correction d’outil 5-21 Manuel de programmation CN 17VRS Correcteurs de longueur (L1, L2, L3) Les longueurs L1, L2, L3 d’un outil se calculent comme suit: Correction de longueur L1 = Longueur L1 + Usure L1 + Offset L1 Correction de longueur L2 = Longueur L2 + Usure L2 + Offset L2 Correction de longueur L3 = Longueur L3 + Usure L3 + Offset L3 Longueur L3: Usure L3: Offset L3: + + 210.000 0.030 0.015 = Correction de longueur L3: 209.985 L3_min = 200 mm Correction de longueur L3 = 209.985 L3_max = 230 mm Fig. 5-7: Correction de longueur L3 sur un foret. Seules les données géométriques correspondant au type de correcteur choisi sont affichées sur l’IHM du PC ou du SOT et calculées par la CN. Correcteur de rayon (R) La correction de Rayon R d’un outil se calcule selon: Correction de Rayon R = Rayon R + Usure R + Offset R + + Rayon R: Usure R: Offset R: 15.000 -0.002 -0.150 = correction de rayon R: 14.848 R_min =14.8mm Correction de rayon = 14.848mm R_max =14.9mm Fig. 5-8: Correction de rayon R sur une fraise de dégrossissage DOK-MTC200-NC**PRO*V17-ANW1-FR-P 5-22 Correction d’outil Manuel de programmation CN 17VRS Exemples mesure d’outil Z R L1 P S X Valeurs de corrections déterminées: Type de correc. Position coupe Longueur L1 Usure L1 L2 Offset L1 Longueur L2 3 3 +38.322 0 0 +197.827 Usure L2 0 Offset L2 0 Rayon R 3.2 Usure R 0 Offset R 0 Fig. 5-9: Exemple pour la mesure d'un outil de perçage DOK-MTC200-NC**PRO*V17-ANW1-FR-P Correction d’outil 5-23 Manuel de programmation CN 17VRS Z Valeurs de correction déterminées: 1) Sans prise en compte du rayon Type de correct. 1 Position coupe 0 Longueur L3 162.13 Usure L3 0 Offset L3 0 L3 2) Avec prise en compte du rayon Type de correct. 2 Position coupe 0 Longueur L3 162.13 Usure L3 0 Offset L3 0 Rayon R 8 Usure R 0 Offset R 0 R Fig. 5-10: Exemple pour la mesure d’un outil de tournage Facteurs d’usure Les facteurs d’usure permettent de compenser les modifications de longueur et de rayon dues à l’usure. A partir de la version 4.14 , les facteurs d’usure ne sont plus disponibles que dans la liste d’outils et ne peuvent plus être affichés dans la liste de réglages. Facteurs d’usure de longueur (L1, L2 et L3) La compensation d’usure de longueur est activée lorsque la correction de longueur d’outil est enclenchée avec G48 ou G49. Le gestionnaire d’outil calcule la valeur de compensation de longueur par la durée d’usinage de l’outil multipliée par le facteur d’usure de longueur. Si le facteur d’usure de longueur est exprimé en mm/ min ou inch/ min, le gestionnaire d’outil prend comme durée d’usinage tous les temps durant lesquels ont lieu des mouvements (excepté les mouvements en G00) où l’outil est actif. Si le facteur d’usure est exprimé en mm/ cycles ou inch/ cycles le gestionnaire d’outil prend comme temps, un cycle pour le calcul de la compensation de longueur. Le gestionnaire d’outil actualise la donnée d’usinage et donc les valeurs de compensation d’usure de longueur: • lors du passage à une autre arête de coupe, DOK-MTC200-NC**PRO*V17-ANW1-FR-P 5-24 Correction d’outil Manuel de programmation CN 17VRS • lors du réappel de la coupe, • lors du retour de l’outil au magasin (emplacement outil = magasin), • lorsque la position d’usinage de l’outil est basculée (emplacement outil = revolver) • lors de l’annulation de l’outil avec T0 (emplacement outil = revolver ou pas d’emplacement). Facteur d’usure de rayon (R) La compensation d’usure de rayon est activée lorsque la correction de longueur d’outil est enclenchée avec G41 ou G42. Le gestionnaire d’outil calcule la valeur de compensation de rayon par la durée d’usinage de l’outil multipliée par le facteur d’usure de rayon. Si le facteur d’usure de rayon est exprimé en mm/ min ou inch/ min, le gestionnaire d’outil prend comme durée d’usinage tous les temps durant lesquels ont lieu des mouvements (excepté les mouvements en G00) où l’outil est actif. Si le facteur d’usure est exprimé en mm/ cycles ou inch/ cycles le gestionnaire d’outil prend comme temps, un cycle pour le calcul de la compensation de rayon. Le gestionnaire d’outil actualise la donnée d’usinage et donc les valeurs de compensation d’usure de rayon: • lors du passage à une autre arête de coupe, • lors du réappel de la coupe, • lors du retour de l’outil au magasin (emplacement outil = magasin), • lorsque la position d’usinage de l’outil est basculée (emplacement outil = revolver) • lors de l’annulation de l’outil avec T0 (emplacement outil = revolver ou pas d’emplacement). Données de coupe utilisateur Donnée de coupe utilisateur 1-5 Les données utilisateurs 1 - 5 permettent d’associer à chaque coupe des informations quelconques spécifiques à l’utilisateur. Avec l’introduction de la désignation voulue dans les paramètres système, les données utilisateur de chaque jeu de coupe sont prises en compte et affichées dans la liste d’outils et la liste d’outils actuelle (voir aussi 'Description des paramètres'). Les données utilisateur peuvent être préparées dans la liste d’outils comme les autres données. Des applications typiques des données utilisateurs de coupe sont: • vitesse de coupe, • avance par dent, • vitesse de rotation broche, • avance d’usinage, • mémoire intermédiaire de correction de dimension, • valeur moyenne et • valeur pratique. Données utilisateur 6 – 10 Les données de coupe utilisateur 6 - 10 permettent au constructeur de machine de définir des éléments supplémentaires dans les blocs de données outil par introduction de la qualification correspondante. Dans les données de coupe utilisateur 6 - 10 (de type DINT avec valeur sur 32 bits sans exposants) on peut stocker des nombres avec jusqu’à 8 chiffres significatifs. DOK-MTC200-NC**PRO*V17-ANW1-FR-P Correction d’outil 5-25 Manuel de programmation CN 17VRS 5.4 Correction de trajectoire d’outil Correction de trajectoire d’outil inactive Sans correction de trajectoire de rayon d’outil, le point de coupe théorique P est le point de référence pour la CN. Le point de coupe théorique P se déplace toujours sur le contour programmé. Dans le cas de déplacements non parallèles aux axes, cela entraîne des défauts de justesse. Z X PB PB P S B P BB PB S S R S S Position du point de coupe 3 : contour obtenu : trajectoire du point de coupe théorique 'P' (contour programmé) : trajectoire du centre de plaquette 'S' P S B pointe d'outil théorique centre de plaquette point de contact effectif Fig. 5-11: Apparition de défauts de justesse lors de l’usinage sans correction de trajectoire d’outil Sur le dessin, la surface hachurée ne sera pas usinée car la CN se réfère au point de coupe théorique P. Lorsque la correction de trajectoire de rayon d’outil est activée, la CNC déplace automatiquement le point réel de contact B sur le contour programmé. Le contour obtenu cadre alors avec le contour programmé. DOK-MTC200-NC**PRO*V17-ANW1-FR-P 5-26 Correction d’outil Manuel de programmation CN 17VRS Correction de trajectoire d’outil active Lorsque la correction de trajectoire d’outil est enclenchée (G41/ G42), la CNC calcule automatiquement la correction de longueur active dans le plan de travail par rapport au point de coupe milieu S, pour laquelle elle ajoute ou soustrait le rayon par rapport au point de coupe théorique. Z X PB PB PB P S B PB R S S S S : contour obtenu (contour programmé) : trajectoire de la pointe théorique d'outil 'P' : trajectoire du centre de plaquette 'S' P S B pointe d'outil théorique centre de plaquette point de contact effectif Fig. 5-12: Usinage sans défaut avec correction de trajectoire de rayon d’outil. Lorsque la correction de trajectoire d’outil est active, le point de coupe milieu de l’outil se déplace sur une trajectoire parallèle au contour programmé, décalée de la valeur du rayon d’outil. DOK-MTC200-NC**PRO*V17-ANW1-FR-P Correction d’outil 5-27 Manuel de programmation CN 17VRS Raccordement de contour Angles intérieurs Dans les angles intérieurs le point de passage de bloc corrigé s’obtient par le point d’intersection des contours parallèles. R R S' S' S S R R S S' S' R S S' S point de coupe théorique centre de plaquette point de contact effectif Fig. 5-13: Angles intérieurs Angles extérieurs Afin de ne pas être endommagés, les angles extérieurs doivent être contournés par le centre de l’outil. Deux méthodes sont proposées pour cela: 1. Insertion d’un arc de cercle comme élément de transition avec l’instruction CN G43 et 2. Insertion d’un chanfrein comme élément de transition avec l’instruction CN G44. • L’insertion d’un chanfrein n’est possible que pour une transition droite ↔ droite. Un chanfrein sera inséré comme élément de transition lorsque l’angle entre les deux droites est supérieur à 90°. Lorsque l’angle est inférieur à 90°, un point de transition est calculé à l’intersection des contours parallèles. DOK-MTC200-NC**PRO*V17-ANW1-FR-P 5-28 Correction d’outil Manuel de programmation CN 17VRS R S2 ' S2 ' R S S1 ' S1 ' R R S2 ' S R S S1 ' S2 ' S2 ' S S1 ' S1 ' rayon d'outil point de transition de bloc programmé point de transition de bloc corrigé 1 point de transition de bloc corrigé 2 Fig. 5-14: Elément de transition par arc de cercle avec G43 angle de raccordement supérieur à 90° S R R S2 ' S1 ' ß S angle de raccordement inférieur ou égal à 90° S' S R R ß S S' S1 ' S2 ' = rayon d'outil = angle de raccordement = transition de blocs programmée = transition de blocs corrigée pour ß<90° = transition de blocs corrigée1 pour ß>90° = transition de blocs corrigée 2 pour ß>90° Fig. 5-15: Elément de transition par chanfrein et point de transition corrigé Aussi bien lors de l’insertion d’un arc de cercle que d’un chanfrein, un bloc de transition supplémentaire est généré automatiquement par la CN; il doit être considéré comme bloc CN propre et doit, en mode bloc à bloc, être aussi démarré séparément. DOK-MTC200-NC**PRO*V17-ANW1-FR-P Correction d’outil 5-29 Manuel de programmation CN 17VRS Lors du calcul prévisionnel de la trajectoire corrigée du centre d’outil, seul l’angle de transition à l’élément de contour du bloc de déplacement est pris en compte et non la longueur de l’élément du contour. Les cas représentés ATTENTION dans la fig. 5-16 ne sont pas reconnus. S' S' S' S' S' S' S' S' Fig. 5-16: Conditions limites lors d’éléments de contour Les éléments de contour représentés par des droites peuvent évidemment être remplacés par des arcs de cercles. Des surcoupes éventuelles avec un élément autre que l’élément du contour suivant ne sont pas pris en compte . Lors d’arcs de cercles concaves (fig. 5-17), le cas représenté est reconnu et l’exécution du programme est arrêtée avec un message d’erreur. S' Fig. 5-17: Elément d’arc de cercle concave DOK-MTC200-NC**PRO*V17-ANW1-FR-P 5-30 Correction d’outil Manuel de programmation CN 17VRS Le cas d’arc de cercle concave représenté dans la figure suivante entraîne un endommagement du contour. S' Fig. 5-18: Arc de cercle concave, plusieurs éléments de contour Du fait qu’au maximum quatre blocs CN sont préparés à l’avance, l’un des trois blocs suivants doit être un bloc de mouvement qui, au minimum, contient la modification d’un axe de coordonnées appartenant au plan d’usinage. Autrement, le déplacement sur le contour est considéré comme terminé et la prochaine transition au contour n’est pas calculée. La préparation de bloc est interrompue par des calculs dans le programme CN, ce qui entraîne la fin d’un contour. De ce fait, un contour ne peut pas être programmé avec des variables. Mise en œuvre de la correction de trajectoire d’outil au début du contour Dans le cas de correction de trajectoire d’outil, le point de départ corrigé du contour [P1] se trouve sur la perpendiculaire au contour programmé au point de départ [P0] dans la direction de mouvement. [P1] R [P0] [P0] [P1] R R [P0] R [P0] [P1] [P1] rayon d'outil point de départ programmé du contour point de départ corrigé du contour DOK-MTC200-NC**PRO*V17-ANW1-FR-P Correction d’outil 5-31 Manuel de programmation CN 17VRS Fig. 5-19: Point de départ en correction de trajectoire d’outils La mise en œuvre de la correction de trajectoire d’outil nécessite un mouvement supplémentaire dans le plan d’usinage, mouvement qui doit être un mouvement linéaire. mouvement linéaire exécuté [Ps] [P1] mouvement linéaire programmé R [Ps] [P0] [P1] R [P0] rayon d'outil point de départ de la correction de trajectoire d'outil point de départ programmé du contour point de départ corrigé du contour Fig. 5-20: Mise en œuvre de la correction de trajectoire d’outil La tentative de commencer la correction de trajectoire d’outil avec un mouvement circulaire entraîne le message d’erreur: &RUUHFWLRQ GH WUDMHFWRLUH FRPPHQFpH VXU XQ FHUFOH et l’interruption du programme CN. Afin d’éviter de blesser l’entrée au contour, le point de départ de la correction de trajectoire d’outil doit être choisi de telle sorte que l’outil doit être entièrement dans le quadrant opposé à l’angle de trajectoire. [P1] R [Ps] R [Ps] [P0] [P1] [P0] rayon d'outil point de départ de la correction de trajectoire d'outil point de départ programmé du contour point de départ corrigé du contour Fig. 5-21: Engagement au contour dans la correction de trajectoire d’outil Dans un contour fermé, si le point de départ de la correction de trajectoire est dans un angle intérieur, cela entraîne une blessure à la fin du contour (voir fig. 5-22). DOK-MTC200-NC**PRO*V17-ANW1-FR-P 5-32 Correction d’outil Manuel de programmation CN 17VRS [P2] [P3] endommagement du contour [Ps1] R [P6] [P1],[P7] [P5] [P4] R [P0] [P1] rayon d'outil point de départ programmé du contour point de départ corrigé du contour Fig. 5-22: Correction de trajectoire d’outil sur un contour fermé. Annulation de la correction de trajectoire d’outil à la fin du contour Dans le cas de correction de trajectoire d’outil le point d’arrivée corrigé du contour [Pe1] se trouve sur la perpendiculaire au contour programmé au point d’arrivée [Pe0] dans la direction de mouvement. [Pe1] R [Pe0] [Pe0] R [Pe1] [Pe0] R R [Pe0] [Pe1] [Pe1] rayon d'outil point d'arrivée programmé du contour point d'arrivée corrigé du contour Fig. 5-23: Point d’arrivée avec correction de trajectoire d’outil L’annulation de la correction de trajectoire d’outil nécessite un mouvement supplémentaire dans le plan d’usinage, mouvement qui doit être un mouvement linéaire (voir fig. 5-24). DOK-MTC200-NC**PRO*V17-ANW1-FR-P Correction d’outil 5-33 Manuel de programmation CN 17VRS mouvement linéaire exécuté [Pee] [Pe1] mouvement linéaire programmé [Pe0] R [Pee] [Pe0] [Pe1] rayon d'outil point d'arrivée de la correction de trajectoire d'outil point d'arrivée programmé du contour point d'arrivée corrigé du contour Fig. 5-24: Annulation de la correction de trajectoire d’outil L’annulation de correction de trajectoire d’outil sur un arc de cercle n’entraîne pas de message d’erreur mais entraîne une erreur de contour imprévisible. Afin d’éviter de blesser la sortie du contour, le point final de la correction de trajectoire d’outil doit être choisi de telle sorte que l’outil entier se trouve dans le quadrant opposé à l’angle de trajectoire. [Pee] [Pe1] R R [Pee] [Pe0] [Pe1] [Pe0] rayon d'outil point d'arrivée de la correction de trajectoire d'outil point d'arrivée programmé du contour point d'arrivée corrigé du contour Fig. 5-25: Fin de contour avec correction de trajectoire d’outil Dans un contour fermé, si le point d’arrivée de la correction de trajectoire se trouve dans un angle intérieur, cela entraîne une blessure au début du contour (voir fig. 5-26). [P2] Endommagement du contour [P3] [Pe7] R [P6] [P1],[P7] [P5] [P4] R [P7] [Pe7] rayon d'outil point d'arrivée programmé du contour point d'arrivée corrigé du contour Fig. 5-26: Correction de trajectoire d’outil dur un contour fermé DOK-MTC200-NC**PRO*V17-ANW1-FR-P 5-34 Correction d’outil Manuel de programmation CN 17VRS Changement de direction de correction Le changement de direction de trajectoire agit comme annulation suivie du rappel inversé de la correction. [Ps0] Mouvement linéaire exécuté R [Ps1] [Pe0] Mouvement linéaire programmé R [Pe1] R [Pe0] [Pe1] [Ps0] [Ps1] rayon d'outil point d'arrivée programmé du premier contour point d'arrivée corrigé du premier contour point de départ programmé du deuxième contour point de départ corrigé du deuxième contour Fig. 5-27: Inversion de la direction de correction L’inversion de la direction de correction de trajectoire d’outil nécessite un mouvement linéaire supplémentaire dans le plan d’usinage. La tentative d’inversion de correction de trajectoire d’outil sur un mouvement circulaire entraîne le message d’erreur: &RUUHFWLRQGHWUDMHFWRLUHFRPPHQFpHVXUXQ ATTENTION FHUFOH et l’interruption du programme CN. Les corrections décrites dans les chapitres 'Mise en œuvre de la correction de trajectoire d’outil au début du contour', page et ‘Annulation de la correction de trajectoire d’outil à la fin du contour’, page 5-32 sont valables quant au danger de blessure à l’entrée et à la sortie du contour. 5.5 Sélection et annulation de la correction de trajectoire d’outil Annulation de la correction de trajectoire d’outil 'G40' La fonction G40 annule une correction de trajectoire d’outil activée. Lorsque la correction est annulée, le centre d’outil se déplace sur la trajectoire programmée. Lorsqu’une correction de trajectoire d’outil active (G41 ou G42) est annulée, le mouvement suivant doit être un mouvement linéaire dans le plan d’usinage pour lequel les valeurs d’axe des deux axes principaux doivent être programmées dans le bloc afin de pouvoir annuler la correction de trajectoire. • G40 est l’état à la mise sous tension et est modal. G40 est annulé par G41 ou G42. • Après une mise sous tension, chargement d’un programme dans la CN, après un BST, RET ou un contrôle Reset, G40 est automatiquement activé. DOK-MTC200-NC**PRO*V17-ANW1-FR-P Correction d’outil 5-35 Manuel de programmation CN 17VRS Correction de trajectoire à gauche 'G41' Avec la fonction G41, la correction de trajectoire d’outil est activée à gauche du contour. Lorsque la correction d’outil à gauche du contour est active, le centre d’outil se déplace sur une trajectoire parallèle au contour programmé, à gauche dans le sens de déplacement et décalé du contour de la valeur du rayon d’outil. Lorsque G41 est programmé alors que G40 ou G42 était actif, le mouvement suivant doit être une droite dans le plan d’usinage. Les valeurs des deux axes principaux doivent être programmées dans le bloc afin de pouvoir établir ou inverser la correction de trajectoire. • G41 reste modal jusqu’à annulation par G40 ou G42 ou automatiquement par une fin de programme (RET) ou une instruction BST. • Lorsque la correction de trajectoire d’outil est active on ne peut avoir au maximum que deux blocs sans mouvement programmés dans le plan actuel d’usinage. S’il y a plus de deux blocs CN sans mouvement programmé, la correction de trajectoire est annulée par G40. ATTENTION La tentative d’établir la correction de trajectoire sur un arc de cercle entraîne un message d’erreur: &RUUHFWLRQGHWUDMHFWRLUHFRPPHQFpHVXU XQFHUFOH et l’interruption du programme CN. Correction de trajectoire à droite 'G42' Avec la fonction G42, la correction de trajectoire d’outil est activée à droite du contour. Lorsque la correction d’outil à droite du contour est active, le centre d’outil se déplace sur une trajectoire parallèle au contour programmé, à droite dans le sens de déplacement et décalé du contour de la valeur du rayon d’outil. Lorsque G42 est programmé alors que G40 ou G41 était actif, le mouvement suivant doit être une droite dans le plan d’usinage. Les valeurs des deux axes principaux doivent être programmées dans le bloc afin de pouvoir établir ou inverser la correction de trajectoire. • G42 reste modal jusqu’à annulation par G40 ou G41 ou automatiquement par une fin de programme (RET) ou une instruction BST. • Lorsque la correction de trajectoire d’outil est active on ne peut avoir au maximum que deux blocs sans mouvement programmés dans le plan actuel d’usinage. S’il y a plus de deux blocs CN sans mouvement programmé, la correction de trajectoire est annulée par G40. ATTENTION DOK-MTC200-NC**PRO*V17-ANW1-FR-P La tentative d’établir la correction de trajectoire sur un arc de cercle entraîne un message d’erreur: &RUUHFWLRQGHWUDMHFWRLUHFRPPHQFpHVXU XQFHUFOH et l’interruption du programme CN. 5-36 Correction d’outil Manuel de programmation CN 17VRS Exemple Programme CN – Correction de trajectoire d'outil avec G42 Y 100 80 60 40 20 20 40 60 80 100 120 140 160 180 X Fig. 5-28: Correction de trajectoire à droite (G42) Programme CN avec G42 (CHANGEMENT D'OUTIL: IDENT=SF D5) T4 BSR .M6 G00 G54 G06 G08 X115 Y99.5 Z5 Instruction de déplacement conditions d'interpolation G01 Z2 F1000 S2000 M03 1. Position de départ Z-10 F1200 Engagement fraise G42 X117.5 Y99.5 F1500 Etablissement de la correctionde trajectoire d'outil G02 X98 Y80 I98 J99.5 Accès au contour avec ¼ de cercle ère G01 X45 Y80 Usinage 1 partie de pièce er G03 X40 Y75 I45 J75 Usinage 1 quart de cercle ème G01 X40 Y25 Usinage 2 partie de pièce ème G03 X45 Y20 I45 J25 Usinage 2 quart de cercle ème G01 X135 Y20 Usinage 3 partie de pièce ème G03 X140 Y25 I135 J25 Usinage 3 quart de cercle ème G01 X140 Y75 Usinage 4 partie de pièce ème G03 X135 Y80 I135 J75 Usinage 4 quart de cercle ème G01 X90 Y80 Usinage 5 partie de pièce G02 X73.5 Y96.5 I90 J96.5 Dégagement du contour avec ¼ de cercle G01 X73.5 Y99.5 Position finale hors du contour G00 Z2 Axe Z à distance de sécurité G40 X68 Y49.5 Position de départ contour intérieur G01 Z-10 F1000 Engagement fraise G42 X65.5 Y49.5 F1500 Etablissement de la correctionde trajectoire d'outil X65.5 Y50.5 Mouvement linéaire G02 X90 Y75 I90 J50,5 Accès au contour avec ¼ de cercle ère G01 X130 Y75 Usinage 1 partie de pièce er G02 X135 Y70 I130 J70 Usinage 1 quart de cercle ème G01 X135 Y30 Usinage 2 partie de pièce ème G02 X130 Y25 I130 J30 Usinage 2 quart de cercle ème G01 X50 Y25 Usinage 3 partie de pièce ème G02 X45 Y30 I50 J30 Usinage 3 quart de cercle ème G01 X45 Y70 Usinage 4 partie de pièce ème G02 X50 Y75 I50 J70 Usinage 4 quart de cercle ème G01 X98 Y75 Usinage 5 partie de pièce G02 X119.5 Y53.5 I98 J53.5 Dégagement du contour avec ¼ de cercle G01 X119.5 Y49.5 Position finale contour intérieur G00 Z2 Axe Z à distance de sécurité (CHANGEMENT D'OUTIL: Dépôt dernier outil) T0 BSR .M6 RET Fin de programme DOK-MTC200-NC**PRO*V17-ANW1-FR-P Correction d’outil 5-37 Manuel de programmation CN 17VRS Insertion d’un arc de cercle de transition 'G43' Lorsque la correction de trajectoire d’outil est active (G41 ou G42) G43 va, sur les angles saillants, insérer un élément de transition en arc de cercle. Les angles saillants doivent, pour ne pas être endommagés, être contournés par le centre d’outil. Un arc de cercle devrait toujours être inséré comme élément de transition cercle ↔ droite ou cercle ↔ cercle. • G43 est l’état de base et reste modal jusqu’à annulation par G44. • L’activation de G43 n’est possible que sous G41 ou G42. Lorsque la correction de trajectoire d’outil est désactivée, (G40) G43 n’a aucune action. A la fin du programme (RET) ou sur une instruction BST, G43 est automatiquement activé. • Lorsqu’un élément de transition en arc de cercle est inséré par G43, la CN génère automatiquement un bloc de transition supplémentaire qui est un bloc CN propre. Il doit être démarré séparément en mode bloc à bloc. • Les conditions pour l’insertion d’éléments de transition sont décrites au chapitre `Raccordement de contour` 5-26. R S2 ' S S2 ' R S1 ' S1 ' R S S1 ' S2 ' rayon d'outil point de raccordement programmé point de raccordement corrigé 1 point de raccordement corrigé 2 Fig. 5-29: Insertion d’éléments de transition en arc de cercle Insertion de chanfrein de transition ’G44’ Lorsque la correction de trajectoire d’outil est active (G41 ou G42), G44 va, dans le cas d’angles XEtérieurs supérieurs à 90°, insérer un chanfrein comme élément de transition. Pour des angles XEtérieurs inférieurs ou égaux à 90° , le point de transition corrigé est le point d’intersection des contours parallèles. • Un chanfrein comme élément de transition n’est utilisé que lors de transition entre deux droites. Pour toutes les autres transitions, un arc de cercle est inséré même quand G44 est actif. • Après sélection, G44 reste actif jusqu’à annulation par G43 ou automatiquement par une fin de programme (RET) ou une instruction BST. L’activation de G44 n’est possible que sous G41 ou G42. Lorsque la correction de trajectoire d’outil est désactivée (G40), G44 n’a aucune action. • Lorsqu’un élément de transition en chanfrein est inséré avec G44, la CN génère automatiquement un bloc de transition supplémentaire qui est un bloc CN propre. En mode bloc à bloc, il doit être démarré séparément. • Les conditions pour l’insertion d’éléments de transition sont décrites au chapitre `Raccordement de contour` page 5-26. DOK-MTC200-NC**PRO*V17-ANW1-FR-P 5-38 Correction d’outil Manuel de programmation CN 17VRS Angle de raccordement supérieur à 90° S R S S1 ' S2 ' R R S2 ' S1 ' = rayon d'outil = point de raccordement programmé = point de raccordement corrigé 1 = point de raccordement corrigé 2 Angle de raccordement inférieur ou égal à 90° S' S R S S' R = rayon d'outil = point de raccordement programmé = point de raccordement corrigé Fig. 5-30: Insertion d’un chanfrein de transition Vitesse d’avance du centre d’outil constante 'G98' Lorsque la correction de trajectoire d’outil est active (G41 ou G42) G98 n’entraîne, sur les arcs de cercle, aucune correction de vitesse de trajectoire. La vitesse de trajectoire programmée se rapporte ainsi au centre de l’outil et non sur le contour. Sur des arcs de cercle convexes (cercle extérieur) cela entraîne une réduction de la vitesse de trajectoire sur le contour, sur des arcs de cercles concaves (cercles intérieurs) cela entraîne une augmentation. • G98 est l’état de base et reste modal jusqu’à annulation par G99. L’activation de G98 n’est possible que sous G41 ou G42. Lorsque la correction de trajectoire d’outil est désactivée (G40) G98 n’aucune action. A la fin de programme (RET) ou sur une instruction BST, G98 est automatiquement activé. Vitesse d’avance constante sur le contour 'G99' Lorsque la correction de trajectoire est constante (G41 ou G42), G99 entraîne sur les arcs de cercles, une correction de la vitesse de trajectoire. La vitesse de trajectoire sur le contour correspond alors à la vitesse programmée. Sur des arcs de cercle convexes (cercle extérieur) cela entraîne une augmentation de la vitesse de trajectoire du centre d’outil, sur des arcs de cercle concaves (cercle extérieur) une diminution. • G99 reste modal après activation jusqu’à annulation par G98 ou automatiquement à la fin du programme (RET) ou sur une instruction BST. L’activation de G99 n’est possible que sous G41 ou G42. Lorsque la correction de trajectoire d’outils est désactivée (G40) G99 n’a aucune action. DOK-MTC200-NC**PRO*V17-ANW1-FR-P Correction d’outil 5-39 Manuel de programmation CN 17VRS 5.6 Correction de longueur d’outil Lors de mouvements de direction de l’axe de l’outil et correction de longueur d’outil inactive, toutes les données de position se réfèrent à la position du nez de broche. Z+ valeur Z programmée Fig. 5-31: Correction de longueur d’outil inactive Lors de mouvements en direction de l’axe de l’outil et correction de longueur d’outil active, la longueur d’outil effective programmée dans la liste du magasin est calculée automatiquement par la CN; ainsi les données de position se réfèrent à la pointe de l’outil. Lors de l’appel ou de l’annulation de correction de longueur d’outil, un mouvement en direction de l’axe de l’outil est nécessaire ; le point final sera abordé de telle sorte que, lors de l’annulation, le nez de broche arrive à la position programmée. La direction de l’axe de l’outil est la direction principale perpendiculaire au plan de travail. Un changement du plan d’usinage (G17, G18, G19) suppose la modification de la position de l’axe de l’outil. L’annulation (G47) et la sélection (G48) de correction de longueur devrait se faire dans le programme de changement d’outil. longueur d'outil Z+ valeur Z programmée Fig. 5-32: Correction de longueur d’outil DOK-MTC200-NC**PRO*V17-ANW1-FR-P 5-40 Correction d’outil Manuel de programmation CN 17VRS Pas de correction de longueur ’G47’ La fonction G47 annule une correction de longueur d’outil sélectionné. Lors de mouvements en direction de l’axe d’outil, toutes les données de position se réfèrent à la position du nez de broche. Lorsque G47 annule une correction de longueur d’outil (G48 ou G49), il doit y avoir un mouvement programmé en direction de l’axe d’outil. Les mouvements sans rapport avec l’enlèvement de copeau comme par exemple un changement d’outil, se font en général sans correction de longueur. • En fonction du réglage des paramètres process, G47 peut être l’état de base. G47 reste modal jusqu’à annulation par G48 ou G49. • Après mise sous tension, chargement d’un programme, un BST, RET ou un control Reset G47 peut, en fonction du réglage des paramètres process, être réactivé. Correction de longueur d’outil positive 'G48' Lors de l’activation de la correction de longueur d’outil avec G48, la CN compense les longueurs des outils définis dans la liste du magasin dans la direction d’axe positive, dès le prochain mouvement en direction de l’axe concerné. • En fonction du réglage des paramètres process, G47 peut être l’état de base. G48 reste modal jusqu’à annulation par G47 ou G49. • Après mise sous tension, chargement d’un programme, un BST, RET ou un control Reset G47 peut, en fonction du réglage des paramètres process, être réactivé. Correction de longueur d’outil négative 'G49' Lors de l’activation de la correction de longueur d’outil avec G49, la CN compense les longueurs des outils définies dans la liste du magasin dans la direction d’axe négative, dès le prochain mouvement en direction de l’axe concerné. • G49 reste modal jusqu’à annulation par G47 ou G48 ou automatiquement à la fin d’un programme (RET) ou d’une instruction BST. 5.7 Accès aux données d’outils par le programme CN 'TLD' L’instruction TLD (Tool-Data) permet au programme CN de lire, et avec certaines restrictions d’écrire les données d’outils. Syntaxe P A S/T L/D E D S TLD([0..6],[0], [0..2] ,[1..999],[0..9],[1..35],[1..32]) TLD([0..6],[1],[1..9999999],[1..999],[0..9],[1..35],[1..32]) Etat Elément de donnée Arête de coupe N° emplacement/duplo Stockage [0..2] /noméro d'outil Adressage Process Toutes les données disponibles dans la liste d’outils peuvent être lues. Chaque élément de donnée est adressé par se désignation. Une description détaillée des instructions TLD se trouve dans le chapitre ‘Fonctions spéciales CN’. DOK-MTC200-NC**PRO*V17-ANW1-FR-P Correction d’outil 5-41 Manuel de programmation CN 17VRS Plage de valeur et signification des paramètres Désignation Sym Plage de valeur Signification Process P 0..6 Numéro process. Adressage A 0 Emplacement S 0..2 Place L S=0: S=1: S=2: N° outil (T-Nr.) T 1..9999999 Numéro d'outil N° duplo D 1..999 Numéro duplo Coupe E 0..9 Elément de donnée D E=0: E=1..9: 3..26 1..35 E=0: Accès données de base outil E=1..9: Accès données de coupe Etat S E=0: E=1..9: 1..32 1..16 E=0: Accès aux bits d'état outil E=1..9: Accès aux bits d'état de coupe 5.8 1 0: Adressage par emplacement et place 1: Adressage par n° d'outil et n° duplo S=0: Magasin/revolver S=1: Broche S=2: Changeur 1..999 1..4 1..4 S=0: Place mag./revolver S=1: N° outil-broche S=2: N° changeur E=0: Données de base outil E=1..9: Données de coupe Correcteurs D Les correcteurs D s’ajoutent aux registres de données géométriques d’outil. Les correcteurs D ont une action additionnelle sur les registres géométriques L1, L2, L3 et R. Il y a 99 correcteurs D disponibles pour chacun des 7 process de la CN. L’affectation de valeur des correcteurs D peut se faire par l’IHM ou par le SOT. Syntaxe D0 Ø Annulation correcteur D D<D N° de correcteur [1..99]> Ø Sélection d’un correcteur D Les correcteurs D agissent comme les données géométriques du gestionnaire d'outil. Ils peuvent être utilisés lorsque le gestionnaire d’outil est disponible, comme par exemple le registre de décalage de point de référence d’outil. Si aucun gestionnaire d’outil n’est disponible dans un process CN , l’utilisation de correcteur D peut le remplacer pour des applications simples. Les correcteurs D agissent comme les correcteurs de type 4 du gestionnaire d’outil. Une position d’arrêt de coupe ne peut pas être définie dans les correcteurs D. DOK-MTC200-NC**PRO*V17-ANW1-FR-P 5-42 Correction d’outil Manuel de programmation CN 17VRS Modes d’action des correcteurs D G17 G18 Y G19 Y Y R L2 L3 L1 R L3 L1 L1 X L2 X L2 X L3 R Z Z Z Fig. 5-33: Mode d’action des correcteurs D dans les différents plans d’usinage Les registres de géométrie L1, L2 et L3 ne sont appelés que lorsque la correction de longueur d’outil est active (G48/G49) . Le registre de géométrie n’est appelé que lorsque la correction de trajectoire d’outil est active (G41/ G42). Lorsque le gestionnaire d’outil est actif avec un outil sélectionné, et les correcteurs D actifs, les longueurs et les rayons d’outil se calculent selon: Correction de longueur L1 = Longueur L1 + Usure L1 + Offset L1 + L1 du correctur D Correction de longueur L2 = Longueur L2 + Usure L2 + Offset L2 + L2 du correctur D Correction de longueur L3 = Longueur L3 + Usure L3 + Offset L3 + L3 du correctur D Correction de rayon R = Rayon R + Usure R + Offset R + R du correctur D Utilisation des correcteurs D 70.4 mm L1 du correcteur D 10 34.6 mm L3 du correcteur D 10 Valeurs de correcteur: valeur de géométrie d'outil type de correcteur position d'arête de coupe longueur L3 usure L3 offset L3 1 0 241 0 0 correcteur D 10 longueur L1 longueur L2 longueur L3 rayon 70.4 0 34.6 0 241 mm correction de lonfgueur L3 Fig. 5-34: Définition du point de référence outil à l’aide des correcteurs D DOK-MTC200-NC**PRO*V17-ANW1-FR-P Manuel de programmation CN 17VRS Correction d’outil 5-43 • Les registres de géométrie L1, L2, L3 et R du correcteur D sélectionné ne sont actifs que lorsque la correction de longueur (G48/G49) ou de trajectoire d’outil (G41/G42) est enclenchée. • A la mise sous tension, D0 est activé et il n’y a pas de compensation par correcteur D. • Un correcteur D programmé est modal. Il est annulé par D0. Après chargement d’un programme, un BST, RET ou control Reset, D0 est activé. • Lorsque, un correcteur D étant actif, la correction de longueur ou de rayon est désactivée, le correcteur D sera de nouveau actif lors de la prochaine sélection de correction de longueur et/ ou de rayon. • Les registres de géométrie L1, L2 et L3 agissent, en fonction du plan d’usinage sélectionné, dans la direction des trois axes principaux (X, Y, Z). La longueur L3 agit toujours perpendiculairement au plan d’usinage, L1 et L2 toujours dans le plan d’usinage. Remarque: Les correcteurs D ne sont disponibles dans un process CN que si le constructeur de machine l’a décidé ainsi dans les paramètres process. Les valeurs maximales d’entrée pour les registres de géométrie L1, L2, L3 et R sont fixées dans les paramètres process. DOK-MTC200-NC**PRO*V17-ANW1-FR-P 5-44 Correction d’outil Manuel de programmation CN 17VRS DOK-MTC200-NC**PRO*V17-ANW1-FR-P Fonctions auxiliaires (S, M, Q) 6-1 Manuel de programmation CN 17VRS 6 Fonctions auxiliaires (S, M, Q) 6.1 Généralités Les fonctions de commutation et fonctions auxiliaires sont transmises à l'automate; celui-ci les exécute et, finalement, les acquitte. De ce fait, les fonctions de commutation nécessaires au programme automate doivent être définies. • L'exécution des blocs est suspendue jusqu'à ce qu'une fonction auxiliaire transmise à l'automate soit acquittée. La programmation d'une fonction auxiliaire non définie dans l'automate bloque donc le déroulement du REMARQUE programme. • La programmation de fonction de commutation et de fonction auxiliaire suspend l'exécution du programme. Des fonctions telles que G08 (transition de bloc à vitesse optimale) sont, de ce fait interrompues. • Le traitement des fonctions de commutation et des fonctions auxiliaires dans le bloc s'effectue dans l'ordre S, M, Q. 6.2 Fonctions auxiliaires ‘M’ Les fonctions M sont des instructions avec lesquelles des fonctions d'enclenchement prédominantes de la machine ou de la commande sont programmées (par ex. mise en route ou arrêt broche, arrosage, changement de rapport de boîte …). Une fonction auxiliaire est programmée sous la lettre adresse M suivie d'un code jusqu'à 3 chiffres. Le code des fonctions auxiliaires est fixé en partie par la norme DIN 66025 volume 2, en partie par le constructeur de la machine. Répartition des fonctions M en groupe de fonction 1 2 2 3 4 5 5 6 7 8 8 9 10 11 11 12 13 14 15 16 Commandes de programme Commandes de broche Commandes de broche Commandes de broche Commandes de broche Arrosage et lubrification Arrosage et lubrification Arrosage et lubrification Arrosage et lubrification Serrage et desserrage Serrage et desserrage Serrage et desserrage Serrage et desserrage Changement de gamme Changement de gamme Changement de gamme Changement de gamme Atténuateur de broche Atténuateur d'avance Fonctions M actives dans le bloc ainsi que toutes les fonctions M définies par le constructeur de machine DOK-MTC200-NC**PRO*V17-ANW1-FR-P Broche 1 Broche 1 Broche 2 Broche 3 Broche 1 Broche 1 Broche 2 Broche 3 Broche 1 Broche 1 Broche 2 Broche 3 Broche 1 Broche 1 Broche 2 Broche 3 M000, M001, M002, M030 M003, M004, M005, M013, M014 M103, M104, M105, M113, M114 M203, M204, M205, M213, M214 M303, M304, M305, M313, M314 M007, M008, M009 M107, M108, M109 M207, M208, M209 M307, M308, M309 M010, M011 M110, M111 M210, M211 M310, M311 M040, .., M045 M140, .., M145 M240, .., M245 M340, .., M345 M046, M047 M048, M049 M019, M119, M219, M319 Mxxx 6-2 Fonctions auxiliaires (S, M, Q) Manuel de programmation CN 17VRS Toutes les fonctions M, exceptées les commandes de broche Mx03, Mx04, Mx05, Mx13, Mx14, les commandes de programme Mx00, Mx01, Mx02, Mx30 et la fonction M active dans le bloc M019, sont librement disponibles pour le constructeur de machine, car elles ne déclenchent aucune fonction interne à la CN (x = 1...3). • A l'intérieur d'un bloc on ne peut programmer qu'une seule fonction M d'un même groupe. • Les fonctions M000 à 399 peuvent être programmées sur la CNC. • Dans un bloc CN, on peut programmer au maximum 4 fonctions M. • Les fonctions M d'un même groupe s'annulent mutuellement. Remarque: Lorsque plus d'un rapport de gamme est défini dans les paramètres d'axe, les fonctions M de changement de rapport ne sont plus librement disponibles. Commandes de programme Arrêt programmé (inconditionnel) M000 M000 permet de définir une interruption de programme, par ex. pour le contrôle d'un outil. Après vérification, le programme peut être relancé par appui sur la touche départ cycle. M000, comme l'instruction HLT entraîne un arrêt du programme dans tous les modes de programme de la CN. Par opposition à l'instruction HLT, la CN transmet, à la fin du mouvement, la fonction auxiliaire M000 à l'automate. Arrêt conditionnel M001 M001 produit le même effet que M000 lorsque le signal d'interface 'Arrêt conditionnel' (PxxCM01) est mis à 1 par le pupitre machine. La CN exploite le signal d'interface . 'Arrêt conditionnel' après acquittement de la fonction auxiliaire. Fin de programme M002 / M030 M002 / M030 produisent le même effet que l'instruction RET. En outre, la CN transmet la fonction auxiliaire programmée à l'automate. Les deux fonctions signalent à l'automate la fin du programme avec réinitialisation en début de programme. La CN reprend son état de base. Après exécution de M002 ou de M030, tous les niveaux de sous programmes et les vecteurs de retraits sont effacés, la CN se trouve dans l'état de base dans le programme principal. Commandes de broche Avec les commandes de broche M003, M004, M005, M013, M014 les broches sont mises en route ou arrêtées. Le premier chiffre de la fonction M sert d'index de broche. L'index de broche 0 (M003) correspond à la première broche, l'index de broche 2 (M203) correspond à la deuxième broche. • Les commandes de broche Mx03, Mx04, Mx13 et Mx14 peuvent être programmées dans un bloc avec des mouvements d'axes, mais elles ne seront transmises à l'automate qu'à la fin des mouvements. Mx03 Rotation broche sens horaire Mx04 Rotation broche sens antihoraire Mx05 Arrêt broche Mise en route de la broche avec rotation en sens horaire. Mise en route de la broche avec rotation en sens antihoraire. Arrêt de la broche et arrêt arrosage / lubrification. Mx13 Rotation broche sens horaire et mise en route arrosage Mise en route de la broche avec rotation en sens horaire et enclenchement de la fonction arrosage lorsque la fonction de commutation nécessaire est définie dans le programme automate. Mx14 Rotation broche sens antihoraire et mise en route arrosage Mise en route de la broche avec rotation en sens antihoraire et enclenchement de la fonction arrosage lorsque la fonction de commutation nécessaire est définie dans le programme automate. DOK-MTC200-NC**PRO*V17-ANW1-FR-P Manuel de programmation CN 17VRS Fonctions auxiliaires (S, M, Q) 6-3 Indexage de broche La fonction M19 S... permet d’orienter la broche principale. La programmation de l’angle d’indexage se fait sous l’adresse S en degré. L'indexage de la broche est possible aussi bien à l'arrêt qu'en rotation. • Lorsque l'automate a acquitté la fonction Mx19, la CN considère le bloc comme terminé lorsque la broche a atteint sa position finale. • La programmation de Mx19 sans mot S entraîne un message d'erreur lors de l'exécution du programme. • La fonction M19 n'est possible qu'avec des broches à capacité de positionnement. Syntaxe M19 S<Constante> Ø M19 S180 M19 S=<Expression> Ø M19 S=@070 M<Index de broche>19 S< Index de broche ><constante>Ø M219 S2 90 M< Index de broche >19 S< Index de broche >=<Expression>Ø M319 S3=@060 Changement de rapport Lorsque le nombre de rapport pour une broche, défini dans les paramètres d'axe, est supérieur à un, les groupes de fonction M 11 – 13 sont réservés à des fonctions internes à la CN. Fonctions M pour le changement de rapport et groupes de fonction correspondant: 11 Changement de gamme broche 1 Mx40, .., Mx44 (x=0 ou 1) 12 Changement de gamme broche 2 M240, .., M244 13 Changement de gamme broche 3 M340, .., M344 Signification des fonctions M: Mx40 changement de gamme automatique broche X er Mx41 1 rapport broche x ème Mx42 2 rapport broche x ème Mx43 3 rapport broche x ème Mx44 4 rapport broche x • Le changement de gamme automatique (Mx40) dépend des paramètres d'axe fixés par le constructeur machine. • S'il n'y a qu'un seul rapport de gamme fixe, les fonctions M peuvent être utilisées à d'autres fins. DOK-MTC200-NC**PRO*V17-ANW1-FR-P 6-4 Fonctions auxiliaires (S, M, Q) 6.3 Manuel de programmation CN 17VRS Mot S comme fonction auxiliaire Lorsqu'un process est défini sans broche (paramètres process), le mot S a la signification d'une fonction auxiliaire. Pour cela, une lettre adresse supplémentaire est disponible pour les fonctions auxiliaires définies par l'utilisateur dans le programme automate. La fonction S peut être programmée avec une constante entière non signée jusqu'à quatre chiffres. La plage de valeur va de 0 à 999. Syntaxe S<Constante> Ø S1234 A la place d'une constante, on peut aussi utiliser une expression. S=<Expression> 6.4 Ø S=@123+@124 Fonction Q La lettre adresse Q suivie d'une constante entière non signée jusqu'à 4 chiffres permet d'appeler une fonction auxiliaire définie par l'utilisateur dans le programme automate. La plage de valeurs va de 0 à 9999. Syntaxe Q<Constante> Ø Q1234 Les fonctions Q9000 à Q9999 sont réservées à des fonctions spécifiques INDRAMAT. DOK-MTC200-NC**PRO*V17-ANW1-FR-P Manuel de programmation CN 17VRS 7 Evènements 7.1 Définition d'un évènement Evènements 7-1 Les évènements sont des variables binaires utilisables par la CN et qui, comme les marqueurs du programme automate, peuvent représenter un état quelconque défini par le programmeur. Les évènements peuvent être positionnés et remis à zéro par le programme CN ou par l'automate. Il est possible d'effectuer une synchronisation de process par attente d'un état défini d'un évènement. Il y a au total 224 évènements disponibles dans la CN. A chaque process sont affectés 32 évènements locaux. Au moyen de l'adressage avec le numéro de process, les 224 évènements peuvent être utilisés dans un process, que le process soit défini ou non. L'identification d'un évènement se fait par son appartenance à un process (numéro de process) et le numéro d'évènement. Si le numéro de process n'est pas indiqué, la déclaration correspond au process où l'évènement est programmé. A l'aide d'évènements, des aiguillages de programme peuvent être effectués sous interruption. Cette possibilité est décrite au chapitre 7.4 'Gestion asynchrone d'évènements' page 7-4. • Si le caractère '*' est utilisé à la place du numéro d'évènement, tous les évènements du process sont adressés. • Le programme automate peut aussi agir sur les évènements. Se reporter aux instructions du constructeur de machine qui peut avoir utilisé différents évènements dans un but de synchronisation. • L'état des évènements est mémorisé lors de la mise hors tension. Avant d'être utilisés dans le programme, les évènements doivent être positionnés dans un état défini. • Les évènements 0 à 7 sont réservés pour les branchements de programme sous interruption et doivent en général être laissé libres pour cet usage. • Divers évènements sont utilisés dans les cycles standards INDRAMAT. Leur numéro se trouve dans la description correspondante. • Dans un bloc CN, il peut y avoir au maximum quatre instructions de modifications d'évènement et un saut sous contrôle d'évènement. 7.2 Modification d'évènementx Mise à 1 d'évènement ‘SE’ Syntaxe Avec l’instruction SE - Mise à 1 d'évènement – l'évènement défini par le paramètre de l'instruction est mis à 1. Si l'évènement était déjà à 1, l'instruction n'a pas d'action. L'évènement reste à 1 jusqu'à effacement par instruction RE – Remise à 0 d' évènement -. SE <N° de process[0..6]>:<N° d' évènement[0..31]> Ø SE 1:15 SE <Numéro d'évènement[0..31]> Ø SE 9 • Si le caractère '*' est utilisé à la place du numéro d'évènement, tous les évènements du process sont adressés. • Le programme automate peut aussi agir sur les évènements. Se reporter aux instructions du constructeur de machine qui peut avoir utilisé différents évènements dans un but de synchronisation. DOK-MTC200-NC**PRO*V17-ANW1-FR-P 7-2 Evènements Manuel de programmation CN 17VRS • Bien qu'il soit possible de mettre à 1 les évènements d'un autre process, il est recommandé de ne modifier les évènements que dans leur process et de les interroger dans les autres process. Remise à 0 d'évènement ‘RE’ Avec l’instruction RE - Mise à 0 d'évènement – l'évènement défini par le paramètre de l'instruction est mis à 0. Si l'évènement était déjà à 0, l'instruction n'a pas d'action. L'évènement reste à 0 jusqu'à mise à 1 par instruction SE – Mise à 1 d' évènement -. Syntaxe RE <N° de process[0..6]>:<N° d'évènement[0..31]> Ø RE 1:15 RE <Numéro d'évènement[0..31]> Ø RE 9 • Si le caractère '*' est utilisé à la place du numéro d'évènement, tous les évènements du process sont adressés. • Le programme automate peut aussi agir sur les évènements. Se reporter aux instructions du constructeur de machine qui peut avoir utilisé différents évènements dans un but de synchronisation. • Bien qu'il soit possible de mettre à 0 les évènements d'un autre process, il est recommandé de ne modifier les évènements que dans leur process et de les interroger dans les autres process. Attente jusqu'à mise à 1 d'évènement ‘WES’ Avec l’instruction WES - Attente jusqu'à mise à 1 d'évènement - , le déroulement du programme du process où est programmée l'instruction WES, est suspendu jusqu'à ce que l'évènement concerné soit mis à 1. Si l'évènement était déjà à 1, le programme se continue sans interruption. Syntaxe WES <N° de process[0..6]>:<N° d'évènement[0..31]> Ø WES <Numéro d'évènement[0..31]> Ø WES 1:15 WES 9 • Si le caractère '*' est utilisé à la place du numéro d'évènement, le système attend jusqu'à ce qu'au moins un évènement du process soit à 1. • Le programme automate peut aussi agir sur les évènements. Se reporter aux instructions du constructeur de machine qui peut avoir utilisé différents évènements dans un but de synchronisation. • Comme un process attendant un évènement ne peut pas lui même mettre cet évènement à 1, l'attente ne doit se faire que sur un évènement modifié dans un autre process. • L'instruction WES ne devrait pas être programmée dans une partie de programme où la correction de trajectoire d'outil est active. Si cela ne peut être évité, utiliser des transitions de blocs linéaires. DOK-MTC200-NC**PRO*V17-ANW1-FR-P Evènements 7-3 Manuel de programmation CN 17VRS Attente jusqu'à remise à 0 d'évènement ‘WER’ Avec l’instruction WER - Attente jusqu'à remise à 0 d'évènement - , le déroulement du programme du process où est programmée l'instruction WES, est suspendu jusqu'à ce que l'évènement concerné soit remis à 01. Si l'évènement était déjà à 0, le programme se continu sans interruption. Syntaxe WER <N° process[0..6]>:<N° d'évènement[0..31]> WER <Numéro d'évènement[0..31]> Ø Ø WER 1:15 WER 9 • Si le caractère '*' est utilisé à la place du numéro d'évènement, le système attend jusqu'à ce qu'au moins un évènement du process soit à 0. • Le programme automate peut aussi agir sur les évènements. Se reporter aux instructions du constructeur de machine qui peut avoir utilisé différents évènements dans un but de synchronisation. • Comme un process attendant un évènement ne peut pas lui même mettre cet évènement à 0, l'attente ne doit se faire que sur un évènement modifié dans un autre process. • L'instruction WER ne devrait pas être programmée dans une partie de programme où la correction de trajectoire d'outil est active. Si cela ne peut être évité, utiliser des transitions de blocs linéaires. Exemple Programme CN - Modification d'évènement Au début des deux programmes pièce, tous les évènements de chaque process sont remis à 0. le programme du process 2 se suspend dans la ème ligne jusqu'à ce que le programme du process 1 positionne 3 ème l'évènement 1 dans la 6 ligne. Programme pièce process 1 RE 1:* DOK-MTC200-NC**PRO*V17-ANW1-FR-P ;Remise à 0 de tous les évènement du process 1 Programme pièce process 2 RE 2:* ; Remise à 0 de tous les évènement du process 2 T1 BSR .M6 ;Changement d'outil T1 ; Changement d'outil M03 S150 ;Mise en route broche WES 1:1 ;Attente évènement 1 du process 1 G04 F15 ;Temporisation M03 S150 ; Mise en route broche M05 ; Arrêt broche G04 F15 ; Temporisation SE 1:1 ;Mise à 1 d'évènement 1 dans process 1 M05 ; Arrêt broche RET ;Fin de programme RET ; Fin de programme 7-4 Evènements 7.3 Manuel de programmation CN 17VRS Sauts conditionnés par un évènement Saut sur évènement à 1 ‘BES’ Avec l’instruction BES -Saut sur évènement à 1 – le programme se continue à l'adresse donnée si l'évènement concerné est à 1. Syntaxe Ø Ø BES <Adresse de saut> <N° process[0..6]>:<N° d'évènement[0..31]> BES <Adresse de saut> <Numéro d'évènement[0..31]> BES .LABEL 1:15 BES .LABEL 9 • Si le caractère '*' est utilisé à la place du numéro d'évènement, le saut est effectué si au moins un évènement du process est à 1. • Le programme automate peut aussi agir sur les évènements. Se reporter aux instructions du constructeur de machine qui peut avoir utilisé différents évènements dans un but de synchronisation. Saut sur évènement à 0 ‘BER’ Avec l’instruction BER -Saut sur évènement à 1 – le programme se continue à l'adresse donnée si l'évènement concerné est à 0 Syntaxe BER <Adresse de saut> <N° process[0..6]>:<N° d'évènement[0..31]> Ø BER .LABEL 1:15 BER <Adresse de saut> <Numéro d'évènement[0..31]> Ø BER .LABEL 9 • • Si le caractère '*' est utilisé à la place du numéro d'évènement, le saut est effectué si tous les évènements du process est à 0. Le programme automate peut aussi agir sur les évènements. Se reporter aux instructions du constructeur de machine qui peut avoir utilisé différents évènements dans un but de synchronisation. Exemple Programme CN - Sauts conditionnés par un évènement Au début des deux programmes pièce, tous les évènements de chaque process sont remis à 0. Si l'évènement 15 du process 1 est mis à 1 avant que le process 2 n'atteigne la ligne 3, le process 2 continue son déroulement à l'adresse de saut WARTEN à la ligne 7. Autrement, il continue son programme ligne 4.. Programme pièce process 1 RE 1:* ; Remise à 0 de tous les évènement du process 1 T1 BSR .M6 ; Changement d'outil Programme pièce process 2 ; Remise à 0 de tous les évènement du process 2 T1 ; Changement d'outil RE 2:* SE 1:15 ;Mise à 1 d'évènement 15 du process 1 BES .WARTEN 1:15 M03 S150 ; Mise en route broche M03 S150 ;Saut au label WARTEN si l'évènement 15 du process 1 est à 1 ; Mise en route G04 F15 M05 RET ;Temporisation ;Arrêt broche ;Fin de programme G04 F15 M05 RET ; Temporisation ; Arrêt broche ; Fin de programme broche DOK-MTC200-NC**PRO*V17-ANW1-FR-P Manuel de programmation CN 17VRS 7.4 Evènements 7-5 Gestion asynchrone d'évènements Avec l’aide d'évènements, la CNC offre la possibilité de modifier le programme CN à tout moment. Comme les évènements peuvent être modifiés par l'automate ou les autres process, il est possible d'influencer le déroulement du programme en fonction du niveau de certains signaux. L'influence du déroulement d'un programme CN consiste en l'interruption du bloc CN actif, y compris les mouvements actuels des axes, et l'appel d'un sous-programme, à la fin duquel le bloc interrompu est repris, ou le programme continue à un autre endroit. La gestion asynchrone d'évènements permet, par exemple, le palpage sur une position (fin de course), des cycles de mesure (palpeur de mesure) ou des opérations d'emboîtement (capteur d'effort). D'autres conditions nécessitant l'interruption d'un mouvement ou une modification du déroulement du programme peuvent être envisagées. Le temps de réaction par la CN sur un évènement extérieur est de 50 millisecondes. Les évènements 0 à 7 de chaque process sont réservés au déroutement de programme sous interruption. Une condition réalisée est représentée par le premier état de l'évènement correspondant. La priorité des évènements croît avec leur numéro. L'évènement 1 a une priorité supérieure à celle de l'évènement 0. L'évènement 7 a la plus haute priorité. Cela permet la réaction sur un évènement externe alors que le traitement d'un évènement précédent de priorité plus faible n'est pas encore terminé. La première action pour la gestion d'un évènement externe consiste en l'arrêt le plus rapide possible de tous les axes du process. Les broches ne sont pas arrêtées lors d'un appel d'évènement. La position d'arrêt est ensuite calculée dans le système de coordonnées programmé afin de servir de position de départ pour le prochain mouvement. Puis les blocs de déplacement préparés sont effacés et le traitement des blocs recommence à partir du point du programme qui a été défini comme départ de la gestion d'évènement. Le départ de la gestion d'évènement est caractérisé par un label de saut qui a été programmé en même temps que l'évènement. • La surveillance d'évènement et la réaction correspondante n'a lieu que lors du déroulement en avant du programme. Toutes les surveillances d'évènement sont désactivées à la fin du programme, lors du jog d'un axe ou lors de la réinitialisation du programme par un control Reset. • Les instructions d'évènement sont traitées à la fin du bloc. Dans un bloc CN il ne peut y avoir au maximum qu'une seule instruction pour la gestion asynchrone d'évènements. • Le programme automate peut aussi agir sur les évènements. Se reporter aux instructions du constructeur de machine qui peut avoir utilisé différents évènements dans un but de synchronisation. DOK-MTC200-NC**PRO*V17-ANW1-FR-P 7-6 Evènements Manuel de programmation CN 17VRS Appel de sous-programme sur évènement à 1 ‘BEV’ Avec l’instruction BEV - Appel de sous-programme sur évènement à 1 (Branch on Event) – la surveillance de l'évènement indiqué dans le paramètre de l'instruction est activée. Lorsque l'évènement prend la valeur 1, le sous-programme dont l'adresse est dans l'instruction BEV est appelé. Le changement d'état d'un évènement avec une priorité plus faible ou de l'évènement déclenché est ignoré jusqu'à la fin du sous-programme. Des interruptions de sous-programme par des évènements à priorité supérieure sont encore possibles. Syntaxe BEV <Adresse de saut> <N° d'évènement[0..7]> Ø BEV .LABEL 4 Après retour du sous-programme, la préparation de blocs est reprise au début du bloc CN interrompu, de telle sorte que ce bloc est entièrement réexécuté; cela garantit que toutes les fonctions du bloc interrompu sont exécutées. En programmation relative et en programmation incrémentale avec variables (@01=@01+3), cela peut conduire à des résultats inattendus. • La partie de programme traitée comme sous-programme doit se terminer par une instruction de retour de sous-programme (RTS), la surveillance de l'évènement déclenché ainsi que celle des évènements de priorité inférieure est alors réactivée. • La répétition d'affectation d'une adresse de saut à un évènement avec l'instruction BEV écrase l'affectation précédente ainsi qu'un autre embranchement éventuel défini par une instruction JEV (Saut de programme sur évènement à 1). • Le programme automate peut aussi agir sur les évènements. Se reporter aux instructions du constructeur de machine qui peut avoir utilisé différents évènements dans un but de synchronisation. Saut de programme sur évènement à 1 ‘JEV’ Avec l’instruction JEV - Saut de programme sur évènement à 1 (Jump on Event) – la surveillance de l'évènement indiqué dans le paramètre de l'instruction est activée. Lorsque l'évènement prend la valeur 1, le programme se branche à l'adresse indiquée dans l'instruction JEV. Le changement d'état d'un évènement avec une priorité plus faible ou de l'évènement déclenché est ignoré jusqu'à la fin du sous-programme. Des interruptions de sous-programme par des évènements à priorité supérieure sont encore possibles. Syntaxe JEV <Adresse de saut> <N° d'évènement[0..7]> Ø JEV .LABEL 4 • Après interruption réussie par déclenchement de l'évènement, le programme se continue à l'adresse définie et ne peut plus revenir, comme avec l'instruction BEV, revenir au bloc de programme interrompu.. • La répétition d'affectation d'une adresse de saut à un évènement avec l'instruction JEV écrase l'affectation précédente ainsi qu'un autre embranchement éventuel défini par une instruction BEV (Appel de sous-programme sur évènement à 1). • Le programme automate peut aussi agir sur les évènements. Se reporter aux instructions du constructeur de machine qui peut avoir utilisé différents évènements dans un but de synchronisation. DOK-MTC200-NC**PRO*V17-ANW1-FR-P Evènements 7-7 Manuel de programmation CN 17VRS Effacement de surveillance d'évènement ‘CEV’ Avec l’instruction CEV - Effacement de surveillance d'évènement – une surveillance d'évènement activée par une instruction BEV ou JEV peut être désactivée. La surveillance d'évènement est désactivée pour l'évènement défini par le paramètre de l'instruction. Syntaxe Ø CEV <Numéro d'évènement[0..7]> CEV 5 Suspension de surveillance d'évènement ‘DEV’ Avec l’instruction DEV - Suspension de surveillance d'évènement - une surveillance d'évènement activée par une instruction BEV ou JEV peut être suspendue durant une partie de programme précise jusqu'à réactivation par une instruction EEV (Activation de surveillance d'évènement). La surveillance d'évènement est suspendue pour tous les évènements. Syntaxe DEV Activation de surveillance d'évènement ‘EEV’ Avec l’instruction EEV - Activation de surveillance d'évènement – la surveillance d'évènement suspendue par DEV est réactivée. La surveillance d'évènement est activée pour tous les évènements. Syntaxe EEV Exemple Programme CN - Gestion asynchrone d'évènements Une pièce pré usinée comporte deux types. Sur le premier type, des trous sont percés, comme représenté sur la fig. 7.1, ces trous doivent être taraudés. Le nombre de trous peut varier entre 1 et 5, mais leur position est fixée. Chaque position de perçage est fixée par un décalage d'origine (G54..G58). Sur le deuxième type, sans perçage, il n'y a qu'un usinage normal à effectuer. Un palpeur fixé sur l'axe Z teste la présence des trous. Le palpeur est raccordé à une entrée automate. Lorsque cette entrée est à 0, l'automate met à 1 l'évènement 6 du process 0. Y 100 80 Bloc CN : G01 X97.5 F700 sur évènémént actif BEV .GEWB 0:6 60 40 20 20 40 60 80 100 Fig. 7-1: Taraudage en fonction d’un évènement DOK-MTC200-NC**PRO*V17-ANW1-FR-P X 7-8 Evènements Programme CN Manuel de programmation CN 17VRS ; Usinage normal CEV T1 BSR .M6 G00 G90 G54 G06 G08 X0 Y0 Z10 S3000 M03 • • • T0 BSR .M6 @50=0 O1 M52 G00 G90 G59 G06 G08 X32.5 Y65 G01 Z2 F500 M54 BEV .GEWB 6 G01 X97.5 F700 M55 M53 O0 RET .GEWB DEV M55 M53 @51=X-OTD(,,,,1) @52=Y-OTD(,,,,2) @53=Z-OTD(,,,,3) T15 BSR .M6 G90 G=54+@50 G06 G08 G01 X40 Y65 Z10 F2000 M03 S1000 G63 Z-7.5 F2 G63 Z10 F2 S1200 M04 T0 BSR .M6 @50=@50+1 M52 G00 G90 G59 G06 G08 X=@51+5 Y=@52 Z=@53 M54 EEV RTS Désactivation de la surveillance d'évènement Changement d'outil: outil 1 Instructions de déplacement conditions d'interpolation Position de départ d'usinage Usinage Initialisation des variables du décalage d'origine ème Sélection 2 banque de points d’origine Sortie palpeur Position de base, DPO pour palpeur Position de départ Axe Z sur palpage, activation palpeur Activation surveillance d'évènement Test perçage Désactivation et rentrée palpeur ère Sélection 1 banque de points d’origine Suspension surveillance evts. Désactivation et rentrée palpeur Repère position actuelle Sélection outil taraudage Le DPO fixe les positions de perçage! Position de taraudage Taraudage à profondeur Z Détaraudage DPO pour trou suivant Sortie palpeur Position de base, DPO pour palpeur Retour à position d'interruption Axe X +5 mm comme distance de sécurité Activation palpeur Activation surveillance evts. Retour position d'interruption DOK-MTC200-NC**PRO*V17-ANW1-FR-P Instructions pour gestion d’outil 8-1 Manuel de programmation CN 17VRS 8 Instructions pour gestion d’outil 8.1 Mise en place des outils et des données d'outil La mise en place des outils et des données d'outil se différencie fondamentalement, entre magasin et revolver, par le fait que, d'une part, dans un magasin, un transfert d'outil physique et logique entre broche et magasin (le cas échéant avec un changeur) est nécessaire, et que, d'autre part, avec la plupart des magasins, une présélection d'outil et donc une rotation en temps masqué du magasin peut être effectuée. Avec l'emploi d'un magasin, on fait principalement la différence entre l'outil préparé et l'outil actif dans une broche. Une présélection d'outil forcée par le programme CN amène l'outil présélectionné dans une positon de changement prédéterminée. Jusqu'au moment du transfert d'outil qui, éventuellement peut être déclenché par le programme CN, les données de cet outil ne sont pas prises en compte. Ce n'est qu'avec la commande de transfert que le gestionnaire d'outil met les données correspondantes à disposition pour la suite de l'usinage. En ère outre l'outil présélectionné devient l'outil actif et la 1 arête de coupe devient l'arête active. Durant l'usinage les données de correction et de temps d'utilisation du point de coupe actif servent à la correction de longueur et de rayon d'outil ainsi qu'à l'évaluation des temps d'utilisation. Dans un revolver, l'outil appelé en position de travail devient l'outil actif. La présélection d'outil forcée par le programme CN amène l'outil présélectionné en positon de travail. Simultanément le gestionnaire d'outil met les données correspondantes à disposition pour la suite de l'usinage. ère La 1 arête de coupe devient l'arête active. Durant l'usinage les données de correction et de temps d'utilisation du point de coupe actif servent à la correction de longueur et de rayon d'outil ainsi qu'à l'évaluation des temps d'utilisation. Présélection et appel d'outil ‘T’ La valeur associée à la lettre adresse T par une constante ou une expression mathématique donne le numéro d'outil ou de place. Cette valeur doit être un nombre entier compris entre 0 et 9999999. Syntaxe T<Constante> Ø T1234 T=<Expression> Ø T=@50 Dans le cas d'un magasin, le mot T avec les instructions CN MTP et MMP (voir chapitre ‘Instructions de mouvement du magasin d'outils', page 8-2) entraîne exclusivement le positionnement du magasin. La mise en place des données correspondantes n'a lieu qu'avec le transfert d'outil suivant sur instruction CN TCH et TMS (voir chapitre ‘Instructions de changement d'outil, page 8-7). Lorsqu'un revolver est utilisé, le mot T avec les instructions CN MTP et MMP fait que l'outil correspondant est amené en position d'usinage et que les données d'outil correspondantes sont activées. L'appel de T0 avec la commande de mouvement MTP fait qu'un emplacement libre du magasin est amené en position de changement d'outil. L'annulation des données d'outil correspondantes a lieu avec le prochain appel de transfert. Avec un revolver, l'appel de T0 avec MTP n'entraîne pas de mouvement, les données d'outil correspondantes sont seulement annulées. DOK-MTC200-NC**PRO*V17-ANW1-FR-P 8-2 Instructions pour gestion d’outil Manuel de programmation CN 17VRS Sélection de la broche d'outil ‘SPT’ Lorsque, dans un process, plusieurs broches sont disponibles, il peut être nécessaire que certaines fonctions comme par exemple la sélection de l'arête de coupe E, se rapportent à une autre broche que la première. Syntaxe SPT <Numéro de broche[1..4]> A la mise sous tension, la première broche est toujours active. Si l'arête de coupe doit se référer à une broche autre que la première, la broche d'outil doit auparavant être sélectionnée avec 'SPT <Numéro de broche>'. • La sélection de la broche d'outil doit avoir lieu au moins un bloc CN avant l'appel de la fonction. • SPT <Numéro de broche> reste modal jusqu'à effacement par une ère autre broche ou sélection automatique de la 1 broche à la fin du programme (RET) ou par un BST. • La surveillance de temps d'utilisation, les facteurs d'usure, les corrections de trajectoire et de longueur d'outil sont valables pour l'outil de la broche sélectionnée. Sélection d'arête de coupe ‘E’ Le chiffre (1 - 9) directement associé à la lettre adresse E sélectionne l'arête de coupe. Syntaxe E<Constante[1..9]> Ø E1 E=<Expression> Ø E=@20 L'appel de l'arête de coupe entraîne en interne la mise à disposition des correcteurs et données de temps d'utilisation correspondants qui seront utilisés par le gestionnaire d'outil pour la suite de l'usinage. Chaque transfert d'outil dans la broche entraîne, outre la mise à disposition des données d'outil, la sélection de l'arête 1 comme arête active. De même, chaque appel d'outil avec un revolver, entraîne, outre la mise à disposition des données d'outil, la sélection de l'arête 1 comme arête active. Comme dans la majorité des cas la première arête est utilisée pour l'usinage, une sélection séparée d'arête de coupe n'est pas nécessaire. DOK-MTC200-NC**PRO*V17-ANW1-FR-P Manuel de programmation CN 17VRS 8.2 Instructions pour gestion d’outil 8-3 Instructions de mouvements du magasin d’outil Tous les mouvements du magasin d'outil se font de manière asynchrone par rapport aux autres mouvements des axes CN. Les commandes de mouvement de la CN démarrent les mouvements du magasin, mais n'attendent pas que ceux soient terminés. Entre temps, la CN peut continuer l'usinage. Une commande permet de savoir si le mouvement démarré auparavant est terminé. le déroulement du programme CN est alors arrêté et synchronisé avec le magasin d'outil. Prise d'origine du magasin d'outils ‘MRF’ L’instruction MRF démarre le retour à la position d'origine de l'axe du magasin d'outil. Syntaxe MRF Cette instruction est comparable u G74 pour un axe CN d'un process. Après mise sous tension de la CN, la référence du magasin d'outil doit être établie avant qu'il ne puisse être déplacé à une position donnée. L'instruction MRF doit donc être programmée dans le programme de retour d'un process, indépendamment du type de l'axe et du magasin. Avant l'exécution de l'instruction MRF, il faut s'assurer que le mouvement du magasin d'outil n'empêche pas la prise d'origine d'autres axes CN. Retour du magasin d'outils en position de base ‘MHP’ L’instruction MHP force le magasin d'outils à retourner à sa position de base. Le gestionnaire d'outils fait en sorte que, indépendamment du type d'axe et de magasin, l'emplacement 1 est amené sur la marque de référence. Syntaxe MHP(<Direction[0..2]>) Ø MHP(1) MHP(<Variable>) Ø MHP(@120) Direction = 0: Direction quelconque Direction = 1: Direction positive Direction = 2: Direction négative Le sens de déplacement vers la position de base peut optionnellement être indiqué. Si aucun sens n'est indiqué le déplacement se fait par le chemin le plus court. Avec le retour sur la position de bas, le gestionnaire d'outils transmet à l'automate, dans le cas d'un magasin piloté par l'automate, l'emplacement 1 sur lequel l'automate doit faire le retour à la position de base. La CN n'attend pas que le magasin ait atteint la position de base, mais continue l'exécution du programme CN en parallèle. Si cela n'est pas souhaité, le déroulement du programme CN peut être suspendu jusqu'à la fin du mouvement du magasin à l'aide de l'instruction MRY (Attente jusqu'à position atteinte). Remarque: La position de base de l'axe outil piloté par la CN est définie par le constructeur machine dans les paramètres d'axe! DOK-MTC200-NC**PRO*V17-ANW1-FR-P 8-4 Instructions pour gestion d’outil Manuel de programmation CN 17VRS Mise en position d'un outil programmé ‘MTP’ L’instruction MTP démarre un mouvement du magasin d'outils pour amener l'outil sélectionné pat le mot T du programme CN à la position indiquée (position de changement, de chargement ou d'usinage). Syntaxe MTP MTP(<Position[1..4]>) Ø MTP(3) MTP(<Position[1..4]>,<Direction[0..2]>) Ø MTP(1,2) MTP(<Variable>,<Variable>) Ø MTP(@110,@90) Position = 1: Position = 2: Position = 3: Position = 4: Amener l'outil sélectionné en position 1 Amener l'outil sélectionné en position 2 Amener l'outil sélectionné en position 3 Amener l'outil sélectionné en position 4 Direction = 0: Direction quelconque Direction = 1: Direction positive Direction = 2: Direction négative La position à laquelle l'outil sélectionné doit être amené ainsi que le sens de déplacement sont optionnels. Si aucun sens ni aucune direction ne sont indiqués, le gestionnaire d'outils choisit le chemin le plus court et la position 1. Si plusieurs outils ont la même désignation et le même numéro T –outils appelés outils frères -, l'outil avec le statut outil d'usinage est automatiquement sélectionné par le gestionnaire d'outils. Sur des machines disposant d'un magasin d'outils et sur lesquelles le pré positionnement peut être effectué durant l'usinage, l'instruction MTP est souvent utilisée pour la rotation du magasin. MTP est alors, en général, programmée avec la présélection d'outil T… immédiatement après le chargement de l'outil précédemment nécessaire dans le programme CN. Ainsi, l'outil suivant est déjà amené en position de changement pendant le déroulement de l'usinage. Cette instruction est principalement utilisée avec des changeurs d'outils à double préhenseurs, lorsque l'outil utilisé jusqu'à présent doit être déposé dans l'emplacement d'où est pris le nouvel outil. • L'instruction T0 MTP amène, comme MFP, le prochain emplacement libre à la position donnée. • La CN n'attend pas que le magasin ait terminé le mouvement, mais continue l'exécution du programme CN en parallèle. Si cela n'est pas souhaité, le déroulement du programme CN peut être suspendu jusqu'à la fin du mouvement du magasin à l'aide de l'instruction MRY (Attente jusqu'à position atteinte). DOK-MTC200-NC**PRO*V17-ANW1-FR-P Instructions pour gestion d’outil 8-5 Manuel de programmation CN 17VRS Mise en position d'un emplacement programmé ‘MMP’ L’instruction MMP démarre un mouvement du magasin d'outils pour amener l'emplacement sélectionné pat le mot T du programme CN à la position indiquée (position de changement, de chargement ou d'usinage). Syntaxe MMP MMP(<Position[1..4]>) Ø MMP(2) MMP(<Position[1..4]>,<Direction[0..2]>) Ø MMP(3,1) MMP(<Variable>,<Variable>) Ø MMP(@56,@55) Position = 1: Position = 2: Position = 3: Position = 4: Amener l'emplacement sélectionné en position 1 Amener l'emplacement sélectionné en position 2 Amener l'emplacement sélectionné en position 3 Amener l'emplacement sélectionné en position 4 Direction = 0: Direction quelconque Direction = 1: Direction positive Direction = 2: Direction négative La position à laquelle l'emplacement sélectionné doit être amené ainsi que le sens de déplacement sont optionnels. Si aucun sens ni aucune direction ne sont indiqués, le gestionnaire d'outils choisit le chemin le plus court et la position 1. L'instruction MMP est en général utilisée pour le tri ou l'échange d'outils en passant par une position intermédiaire.. • L'instruction MMP se rapporte, avec le mot T exclusivement à l'emplacement et non à l'outil. De ce fait, lors de l'appel d'un outil à emplacement fixe avec MMP durant l'usinage, seul un outil frère sera éventuellement pris en compte lorsque cela est explicité dans le programme CN à l'aide du mot T et de l'emplacement correspondant. • La CN n'attend pas que le magasin ait terminé le mouvement, mais continue l'exécution du programme CN en parallèle. Si cela n'est pas souhaité, le déroulement du programme CN peut être suspendu jusqu'à la fin du mouvement du magasin à l'aide de l'instruction MRY (Attente jusqu'à position atteinte). DOK-MTC200-NC**PRO*V17-ANW1-FR-P 8-6 Instructions pour gestion d’outil Manuel de programmation CN 17VRS Accès à un emplacement libre ‘MFP’ L’instruction MFP démarre un mouvement du magasin d'outils amenant le prochain emplacement libre à la position donnée. Syntaxe MFP MFP(<Position[1..4]>) Ø MFP(1) MFP(<Position[1..4]>,<Direction[0..2]>) Ø MFP(3,1) MFP(<Variable>,<Variable>) Ø MFP(@56,@55) Position = 1: Position = 2: Position = 3: Position = 4: Amener le prochain emplacement libre en position 1 Amener le prochain emplacement libre en position 2 Amener le prochain emplacement libre en position 3 Amener le prochain emplacement libre en position 4 Direction = 0: Direction quelconque Direction = 1: Direction positive Direction = 2: Direction négative La position à laquelle l'emplacement libre doit être amené ainsi que le sens de déplacement sont optionnels. Si aucun sens ni aucune direction ne sont indiqués, le gestionnaire d'outils choisit le chemin le plus court et la position 1. Cette instruction est utilisée pour ranger l'outil se trouvant dans la broche ou dans le changeur dans le prochain emplacement libre du magasin. Ceci est particulièrement nécessaire dans le cas de changement d'outil sans préhenseur ou avec préhenseur à un seul bras, lorsqu'il faut d'abord déposer l'ancien outil avant de prendre le nouveau. • La CN n'attend pas que le magasin ait terminé le mouvement, mais continue l'exécution du programme CN en parallèle. Si cela n'est pas souhaité, le déroulement du programme CN peut être suspendu jusqu'à la fin du mouvement du magasin à l'aide de l'instruction MRY (Attente jusqu'à position atteinte). Accès à l'emplacement précédent ‘MOP’ L’instruction MOP démarre un mouvement du magasin d'outils qui amène l'ancien emplacement de l'outil actuellement dans la broche à la position donnée. Syntaxe MOP MOP(<Position[1..4]>) Ø MOP(2) MOP(<Position[1..4]>,<Direction[0..2]>,<Broche>) Ø MOP(2,1,2) MOP(<Variable>,<Variable>,<Variable>) Ø MOP(@56,@55,@54) Position = 1: Position = 2: Position = 3: Position = 4: Direction = 0: Direction = 1: Direction = 2: Broche = 1: Broche = 2: Broche = 3: Amener l’ancien emplacement en position 1 Amener l’ancien emplacement en position 2 Amener l’ancien emplacement en position 3 Amener l’ancien emplacement en position 4 Direction quelconque Direction positive Direction négative Ancien emplacement de l'outil dans la broche 1 Ancien emplacement de l'outil dans la broche 2 Ancien emplacement de l'outil dans la broche 3 DOK-MTC200-NC**PRO*V17-ANW1-FR-P Manuel de programmation CN 17VRS Instructions pour gestion d’outil 8-7 La programmation de la position, du sens de déplacement et de la broche sont optionnelles. Si aucune position, aucune direction et aucune broche ne sont indiquées, le gestionnaire d'outils choisit l'ancien emplacement de l'outil situé dans la broche 1 et l'emmène par le chemin le plus court à la position 1. La conséquence de l'utilisation de cette instruction est que tous les outils se retrouvent à leur place initiale après l'usinage. L'agencement du magasin d'outils est maintenu. Cela peut être souhaité par exemple lorsque des outils larges doivent toujours être entreposés dans le même emplacement. La CN n'attend pas que le magasin ait terminé le mouvement, mais continue l'exécution du programme CN en parallèle. Si cela n'est pas souhaité, le déroulement du programme CN peut être suspendu jusqu'à la fin du mouvement du magasin à l'aide de l'instruction MRY (Attente jusqu'à position atteinte). Attente jusqu'à position atteinte ‘MRY’ L’instruction MRY entraîne la suspension de l'exécution du programme CN lorsque la dernière instruction de déplacement du magasin d'outils n'est pas encore terminée. Syntaxe MRY Ce n'est que lorsque la position programmée est atteinte que le programme CN continue. Cela permet de synchroniser l'axe du magasin d'outils avec le programme d'usinage. Libération du magasin d'outils pour exploitation manuelle ‘MEN’ A l’aide de l’instruction MEN, un magasin d'outils peut être déplacé en manuel, par exemple pour changer un outil durant la production, durant l'exploitation en automatique (mode d'exploitation automatique). Syntaxe MEN Outre l'instruction MEN, la condition pour une exploitation manuelle du magasin est que l'automate sélectionne le mode manuel pour le déplacement du magasin. Après la commutation du magasin en manuel avec l'instruction MEN, la CN continue l'exploitation du programme de ce process jusqu'à la prochaine instruction de mouvement de magasin ou de changement d'outil. Elle délivre alors le message d'état suivant: ¶/D VWDWLRQ DWWHQG OD ILQ GH O H[pFXWLRQ GH O LQVWUXFWLRQGXPDJDVLQ¶ Lors du passage du magasin en mode programme le message est effacé et les instructions en attente sont exécutées. • Chaque instruction de mouvement de magasin ou de changement d'outil dans le programme CN (en général dans un sous-programme de changement d'outil), nécessite la restauration du magasin. • Si une autre instruction de mouvement de magasin ou de changement d'outil suit le bloc où MEN a été programmé, et est lue avant la commutation en manuel, le magasin ne pourra pas être déplacé en manuel durant le déroulement du programme, jusqu'à une prochaine instruction MEN, BST, RET ou un control Reset. DOK-MTC200-NC**PRO*V17-ANW1-FR-P 8-8 Instructions pour gestion d’outil 8.3 Manuel de programmation CN 17VRS Instructions de changement d’outil Les instructions de changement d'outil ne doivent être utilisées que sur une machine équipée d'un magasin lorsque des outils doivent être échangés entre la broche et le magasin (éventuellement à l'aide d'un changeur). Exécution d'un changement d'outil complet ‘TCH’ L’instruction TCH engage un changement d’outil entre la broche et l'emplacement magasin se trouvant dans la position programmée. Syntaxe TCH TCH(<Position[1..4]>) Ø TCH(1) TCH(<Position[1..4]>,<Broche[1..3]>) Ø TCH(2,1) TCH(<Variable>,<Variable>) Ø TCH(@70,@71) Position = 1: Position = 2: Position = 3: Position = 4: Amener l’emplacement choisi en position 1 Amener l’emplacement choisi en position 2 Amener l’emplacement choisi en position 3 Amener l’emplacement choisi en position 4 Broche = 1: Broche = 2: Broche = 3: Changement d’outil en broche 1 Changement d’outil en broche 2 Changement d’outil en broche 3 Durant l'opération de changement d'outil pilotée par l'automate, la CNC suspend le déroulement du programme. La programmation de la position et de la broche sont optionnelles. Si aucune position ni aucune broche ne sont indiquées, le gestionnaire d'outils choisit la position 1 et la broche 1. • Le magasin doit être déjà positionné à l'emplacement correspondant avant l'appel de TCH. • TCH est utilisé principalement avec un préhenseur à deux bras. Changement de l'outil du magasin dans la broche ‘TMS’ L’instruction TMS engage un transfert d’outil entre l’emplacement du magasin se trouvant à la position définie et la broche. Syntaxe TMS TMS(<Position[1..4]>) Ø TMS(3) TMS(<Position[1..4]>,<Broche[1..3]>) Ø TMS(2,2) TMS(<Variable>,<Variable>) Ø TMS(@80,@81) Position = 1: Position = 2: Position = 3: Position = 4: Amener l’emplacement choisi en position 1 Amener l’emplacement choisi en position 2 Amener l’emplacement choisi en position 3 Amener l’emplacement choisi en position 4 Broche = 1: Broche = 2: Broche = 3: Changement d’outil en broche 1 Changement d’outil en broche 2 Changement d’outil en broche 3 Durant l'opération de changement d'outil pilotée par l'automate, la CNC suspend le déroulement du programme. La programmation de la position et de la broche sont optionnelles. Si aucune position ni aucune broche ne sont indiquées, le gestionnaire d'outils choisit la position 1 et la broche 1. DOK-MTC200-NC**PRO*V17-ANW1-FR-P Instructions pour gestion d’outil 8-9 Manuel de programmation CN 17VRS • Avant l'appel de TMS, l'emplacement du magasin doit être à la position programmée avec l'outil à charger et aucun outil ne doit se trouver dans la broche. • Cette instruction est nécessaire pour un changeur à un seul bras ou sans préhenseur et lorsque l'opération de changement doit se décomposer en une séquence de prise et une séquence de dépose. Changement de l'outil de la broche dans le magasin ‘TSM’ L’instruction TSM engage un transfert d’outil entre la broche et l'emplacement du magasin se trouvant à la position définie. Syntaxe TSM TSM(<Position[1..4]>) Ø TSM(4) TSM(<Position[1..4]>,<Broche[1..3]>) Ø TSM(4,2) TSM(<Variable>,<Variable>) Ø TSM(@90,@91) Position = 1: Position = 2: Position = 3: Position = 4: Amener l’emplacement choisi en position 1 Amener l’emplacement choisi en position 2 Amener l’emplacement choisi en position 3 Amener l’emplacement choisi en position 4 Broche = 1: Broche = 2: Broche = 3: Changement d’outil depuis broche 1 Changement d’outil depuis broche 2 Changement d’outil depuis broche 3 Durant l'opération de changement d'outil pilotée par l'automate, la CNC suspend le déroulement du programme. La programmation de la position et de la broche sont optionnelles. Si aucune position ni aucune broche ne sont indiquées, le gestionnaire d'outils choisit la position 1 et la broche 1. • Avant l'appel de TSM, il doit y avoir un outil dans la broche et le magasin doit être à la position programmée avec un emplacement libre. • Cette instruction est nécessaire pour un changeur à un seul bras ou sans préhenseur et lorsque l'opération de changement doit se décomposer en une séquence de prise et une séquence de dépose. Saut lorsque la broche est vide ‘BSE’ L’instruction BSE permet de déterminer si la broche est sans outil. Syntaxe BSE <Adresse de saut> Ø BSE .SPLE S'il n'y a pas d'outil dans la broche, le programme est dérouté à l'adresse indiquée dans le paramètre de l'instruction. Saut lorsque T0 a été programmé ‘BTE’ L’instruction BTE permet de déterminer si T0 a été programmé en dernier, donc s'il faut extraire l'outil de la broche sans en prendre un nouveau. Syntaxe BTE <Adresse de saut> Ø BTE .PRT0 Si T0 a été programmé, le programme est dérouté à l'adresse indiquée dans le paramètre de l'instruction. DOK-MTC200-NC**PRO*V17-ANW1-FR-P 8-10 Instructions pour gestion d’outil Manuel de programmation CN 17VRS L’emplacement du magasin est il libre ‘TPE’ L’instruction TPE teste si l’emplacement actuellement en position 1 est libre. Syntaxe TPE Si l’emplacement correspondant est libre, le gestionnaire d’outil enchaîne le programme. Autrement, le programme est arrêté et un message d’erreur est généré. Cette instruction permet d’éviter une collision lors du dépôt d’un outil, lorsqu’elle est utilisée, avant l’exécution du mouvement, dans la séquence de dépôt du sous-programme de changement d’outil. • L’instruction TPE se réfère toujours à l’emplacement se trouvant en position 1. La broche est elle libre ‘TSE’ L’instruction TSE teste si il y a actuellement un outil dans la broche 1. Syntaxe TSE Si la broche est libre, le gestionnaire d’outil enchaîne le programme. Si un outil se trouve actuellement dans la broche, le gestionnaire d’outil interrompt le déroulement du programme et génère un message d’erreur. Cette instruction permet d’éviter une collision lors de la prise d’un outil, lorsqu’elle est utilisée, avant l’exécution du mouvement, dans la séquence de prise d’outil du sous-programme de changement d’outil. L’instruction TSE se réfère toujours à la broche 1. DOK-MTC200-NC**PRO*V17-ANW1-FR-P Manuel de programmation CN 17VRS Instructions de commande de process et de programme 9 Instructions de commande de process et de programme 9.1 Instructions de commande de process 9-1 Du fait de la structure multi-process de la CNC, il est nécessaire de coordonner chaque process. Lorsque plus de 2 process sont disponibles dans la CNC on utilise, en général, le process 0 pour la coordination des programmes. Le process avec le numéro 0 prend en charge la fonction de gestion pour la coordination de tous les process participant à l’usinage. Les instructions de commande de process sont transmises à l’interface CN automate. MT-CNC (station de tête) Process 0 Process 1 Process 2 Process 3 Process 4 Process 5 Process 6 mécanisme externe 8 mécanisme externe 9 mécanisme externe 10 mécanisme externe 11 mécanisme externe 13 mécanisme externe 14 mécanisme externe 15 mécanisme externe 16 mécanisme externe 18 mécanisme externe 19 mécanisme externe 20 mécanisme externe 21 mécanisme externe 23 mécanisme externe 24 mécanisme externe 25 mécanisme externe 26 mécanisme externe 28 mécanisme externe 29 mécanisme externe 30 mécanisme externe 31 MT-CNC Station 1 mécanisme externe 7 MT-CNC Station 2 mécanisme externe 12 MT-CNC Station 3 mécanisme externe 17 MT-CNC Station 4 mécanisme externe 22 MT-CNC Station 5 mécanisme externe 27 Fig. 9-1: Process et mécanisme externes de la CNC Outre le process maître, la CNC peut piloter 6 autres process et 25 mécanismes externes. DOK-MTC200-NC**PRO*V17-ANW1-FR-P 9-2 Instructions de commande de process et de programme Manuel de programmation CN 17VRS Un process maître (process 0) doit toujours être présent. Il doit s’occuper de la synchronisation des process présents et des mécanismes externes. Si l’installation est composée d’une seule station, les tâches de coordination et les axes sont directement attachés au process maître. Remarque: Le nombre et le partage des process et des mécanismes externes sont fixés par le constructeur machine dans les paramètres système! Définition d’un process ‘DP’ L’instruction DP indique à l’automate avec un signal interne, que le process sera nécessaire durant l’exécution du programme CN. L’automate utilise ces signaux spécifiques à l’initialisation du process. Syntaxe DP <Process> Ø DP 2 DP <Variable> Process[0..6] process internes Process[7..31] mécanismes externes Toutes les autres commandes de process ne seront acceptées que lorsque le process correspondant aura été défini avec l’instruction DP. • A l’intérieur d’un bloc CN l’instruction DP peut être utilisée plusieurs fois. Dans un bloc CN on peut définir plusieurs process. • La définition d’un process avec DP est de nouveau annulée à la fin de programme. Sélection de programme pour un process ‘SP’ L’instruction SP sélectionne, pour le process donné le programme à l’aide de son numéro dans le paquet programme CN actif. Le numéro de programme est le numéro indiqué dans le répertoire programme du process concerné. Syntaxe SP <Process> <Numéro programme>Ø SP 3 25 SP <Variable> <Variable> Process[0..6] process internes Process[7..31] mécanismes externes Numéro programme[1..99] Numéro de programme dans le paquet programme actif Lorsqu’un process est encore actif, il est possible de déjà choisir le numéro de programme pour le travail suivant. L’activation du programme sélectionné n’a lieu qu’au prochain départ cycle. • A l’intérieur d’un bloc CN l’instruction SP ne peut être utilisée qu’une seule fois. DOK-MTC200-NC**PRO*V17-ANW1-FR-P Manuel de programmation CN 17VRS Instructions de commande de process et de programme 9-3 Démarrage du programme retrait ‘RP’ L’instruction RP démarre le sous-programme adressé par le vecteur de retrait dans le process donné. Un programme d’avance éventuellement actif est interrompu et le vecteur de retrait actif, à cet instant, détermine l’adresse de saut dans le programme de retour. Syntaxe RP <Process> Ø RP 4 RP <Variable> Process[0..6] process internes Process[7..31] mécanismes externes • Le sous-programme adressé par le vecteur de retrait doit se trouver dans le programme dans lequel le vecteur de retrait est programmé. • A l’intérieur d’un bloc CN, l’instruction RP peut être utilisée plusieurs fois. Dans un bloc CN, plusieurs programmes de retour peuvent être démarrés simultanément. Démarrage programme d’avance ‘AP’ L’instruction AP démarre, dans un process non actif le programme d’avance donné. Si le process était déjà actif, le traitement de bloc du process, dans lequel AP est programmé, est suspendu jusqu’à ce que le process démarré soit entièrement terminé. Finalement le process donné est démarré, et le traitement des blocs du process suspendu reprend. Syntaxe AP <Process> Ø AP 1 AP <Variable> Process[0..6] process internes Process[7..31] mécanismes externes • A l’intérieur d’un bloc CN, l’instruction AP peut être utilisée plusieurs fois. Dans un bloc CN, plusieurs programmes d’avance peuvent être démarrés simultanément. Attente d’un process ‘WP’ Le traitement des bloc du programme appelant reste bloqué dans le bloc où est programmé WP jusqu’à ce que le process sélectionné par l’instruction soit entièrement terminé. Syntaxe WP <Process> Ø WP 5 WP <Variable> Process[0..6] process internes Process[7..31] mécanismes externes Si le process sélectionné par l’instruction est déjà terminé le traitement de bloc du programme appelant se poursuit. • L’instruction WP peut être programmée plusieurs fois dans un bloc CN. • L’instruction WP ne devrait pas être programmée dans une partie de programme dans laquelle la correction de trajectoire d’outil est active. Si cela ne peut être évité, ne le faire qu’entre des transitions de droites. DOK-MTC200-NC**PRO*V17-ANW1-FR-P 9-4 Instructions de commande de process et de programme Manuel de programmation CN 17VRS Verrouillage de process ‘LP’ L’instruction LP définit quel process doit être dans un état déterminé afin que le programme pièce puisse être exécuté. Cet état doit rester constant jusqu’à ce que le programme pièce soit terminé. Syntaxe Ø LP <Process> LP 4 LP <Variable> Process[0..6] process internes Process[7..31] mécanismes externes Cette instruction permet par exemple de définir qu’une station non utilisée pour un usinage doit être mise hors service ou doit rester à une position déterminée pour ne pas mettre en danger l’usinage en cours. • Les stations verrouillées par LP ne peuvent pas non plus être utilisées en manuel, même si elle ne participent pas à l’usinage. • L’instruction de commande de process LP est annulée à la fin du programme par RET ou BST ou par un control Reset. Exemple Programme CN – Instructions de commande de process Programme de gestion .START DP 1 DP 2 SP 1 15 SP 2 15 AP 1 AP 2 WP1 WP 2 Si, dans un process, aucun vecteur de retour n’est programmé, un saut au label .HOME est effectué dans ce process. SP 1 16 SP 2 16 AP 1 AP 2 WP1 WP 2 BST .START .HOME DP 1 DP 2 SP 1 15 SP 2 15 RP 1 RP 2 WP1 WP 2 BST .START FIN DE PROGRAMME Label de saut pour BST .START Définition des process 1 & 2 Sélection programme, programme 15 process 1 Sélection programme, programme 15 process 2 Démarrage programme d'avance process 1 & 2 Attente jusqu'à ce que les deux process aient terminé leur travail Sélection programme, programme 16 process 1 Sélection programme, programme 16 process 2 Démarrage programme d'avance process 1 & 2 Attente jusqu'à ce que les deux process aient terminé leur travail Saut avec stop au label .START Label de saut pour programme .HOME Définition des process 1 & 2 Sélection programme, programme 15 process 1 Sélection programme, programme 15 process 2 Démarrage programme de retour process 1 & 2 Attente jusqu'à ce que les deux process aient terminé leur travail Saut avec stop au label .START Programme pièce 15 process 1 G00 G90 G54 G06 G08 G00 Y0 Z50 M03 S1500 G01 X50 Y100 F1000 . M05 RET ;Instructions de déplacement ;Pos. de départ ;Mise en route broche ;Usinage 1ère position ;Arrêt broche ;Fin programme Programme pièce 16 process 1 G00 G90 G54 G06 G08 X0 Y0 Z30 M03 S1500 G01 X90 Y150 F1200 . Process 0 programme-numéro 15 ;Instructions de déplacement ;Pos. de départ ;Mise en route broche ;Usinage 1ère position Programme pièce 15 process 2 G18 G90 G54 G06 G08 G00 X0 Z0 Y70 M03 S1500 G01 X50 Z40 F1500 . M05 RET ;Instructions de déplacement ;Pos. de départ ;Mise en route broche ;Usinage 1ère position ;Arrêt broche ;Fin programme Programme pièce 16 process 2 G18 G90 G54 G06 G08 G00 X0 Z0 Y55 M03 S1500 G01 X10 Z110 F2000 . ;Instructions de déplacement ;Pos. de départ ;Mise en route broche ;Usinage 1ère position DOK-MTC200-NC**PRO*V17-ANW1-FR-P Manuel de programmation CN 17VRS M05 RET Instructions de commande de process et de programme ;Arrêt broche ;Fin programme M05 RET 9-5 ;Arrêt broche ;Fin programme Usinage terminé ‘POK’ Avec la programmation de l’instruction POK (Part OK.) le programmeur peut déterminer, dans le programme d’usinage, quand l’usinage est totalement terminé. L’exécution du POK entraîne la délivrance d’un signal (spécifique au process) à l’automate. Syntaxe POK Lorsque l’instruction POK est programmée dans le process 0, le signal automate ne sera mis à 1 que lorsque tous les process définis par DP (y compris les mécanismes externes) auront exécuté l’instruction POK. • Les signaux de l’instruction POK sont remis à 0 à la fin de programme (RET ou BST) ainsi que sur un control Reset. 9.2 Transfert d’axes entre les process ‘FAX’, ‘GAX’ Certaines applications nécessitent de suspendre la distribution fixe des axes entre les process et de partager les axes entre plusieurs groupements d’interpolation (process). Chaque axe est affecté à un process maître, et peut être en outre affecté à trois process esclaves au maximum. La désignation et la signification d’axes dans le système de coordonnées est identique dans tous les process où l’axe peut être libéré. Il est en outre possible de solliciter différents axes avec la même désignation depuis plusieurs process. Syntaxe Libération de l’axe <désignation d’axe> par le process dans lequel l’axe se trouve: FAX (<Désignation d'axe>) Ø FAX (Y) Sollicitation de l’axe <désignation d’axe> par le process défini par le paramètre de l’instruction: GAX (<Process>:<Désignation d'axe>) (1:Y) Ø GAX • Dans la déclaration de process de l’instruction GAX, il faut toujours indiquer le process père. Lorsque l’axe est demandé au process père au moyen de GAX, celui-ci peut s’en départir. Un transfert d’axe n’a lieu que lorsque l’axe est libéré par le process où il se trouve et est sollicité par un autre process. Le process qui demande l’axe (GAX), doit attendre jusqu’à ce que l’autre process le libère. De même le process qui libère un axe attend jusqu’à ce qu’un autre process le sollicite. Un état apatride ne peut ainsi pas exister. Les axes commutables sont affichés dans l’affichage de position de tous les process auxquels ils peuvent appartenir. Lorsqu’un axe commutable se trouve dans un process qui est affiché, le jeu complet de données de l’axe est affiché. Lorsque cet axe est associé à cet instant à un autre process, les données de position et de vitesse sont masquées. • Tous les axes de la CNC, à l’exception des axes de magasin et de revolver, peuvent transférer entre process. • Le transfert d’axe d’un transfert à un autre ne s’effectue que lors d’un transfert de bloc. Le traitement de bloc est suspendu et ne reprendra que lorsqu’il est sûr que la valeur d’atténuateur est active sur les axes dans le nouveau process. • Les axes rotatifs et linéaires ne peuvent être transférés entre process qu’à l’arrêt. DOK-MTC200-NC**PRO*V17-ANW1-FR-P 9-6 Instructions de commande de process et de programme Manuel de programmation CN 17VRS • Les broches peuvent être transférées avec une vitesse de rotation définie, entre process. Les modes d’avance dépendant de la broche, comme par exemple avance par tour, sont cependant annulés lors du transfert de la broche. • Même après transfert d’un axe dans un process esclave, l’axe reste affecté au process maître. Les erreurs d’axe et leur diagnostic correspondant seront affichés dans le process maître. • A la fin d’un programme RET ou BST ou sur control Reset , ainsi que lors de déplacement en JOG en mode manuel, tous les axes appartenant à un autre process maître sont libérés, et tous les axes se trouvant dans un autre process sont sollicités par leur process père. Remarque: Le constructeur de machine détermine dans les paramètres d’axe entre quels process un axe peut être échangé. Exemple Programme CN – Transfert d'axe Un centre d’usinage équipé de 2 tables et partagé en 3 process CN. Afin que les deux pièces usinées sur les deux tables soient identiques on veut utiliser les mêmes programmes CN. Le décalage de l’axe X est obtenu par réécriture du décalage de point d’origine. Les process sont partagés de la façon suivante: − Le process 0 est le process d’usinage avec les trois axes principaux X, Y et Z ainsi que la broche principale S. L’appui sur départ cycle démarre simultanément les process 0, 1 et 2. − Le process 1 gère le plateau (axe B) de la partie droite et, en fonction des demandes, libère l’axe B ou le reprend. La programmation d’évènements permet de synchroniser les process. − Le process 2 gère le plateau (axe B) de la partie gauche et, en fonction des demandes, libère l’axe B ou le reprend. La programmation d’évènements permet de synchroniser les process. Les initialisations nécessaires et le programme de retour correspondant ne sont pas représentés dans le programme CN. Lors de l’interruption du programme, différents mécanismes et initialisations seraient nécessaires pour assurer un état déterminé. Z Y B B X Fig. 9-2: Transfert d’axe sur un centre d’usinage à 2 tables DOK-MTC200-NC**PRO*V17-ANW1-FR-P Manuel de programmation CN 17VRS Instructions de commande de process et de programme Process 1 – Axe B droit Process 2 - Axe B gauche .BEARB .BEARB FAX (B) WES 9 B Label pour boucle de saut Libération axe B Attente jusqu'à axe FAX (B) WES 9 B en P0 RE 9 GAX (B) Reprise axe Blorsque libéré dans programme usinage BER .BEARB 10 Boucler jusqu'à fin usinage en P0 RE 10 RET 9-7 Label pour boucle de saut Libération axe B Attente jusqu'à axe en P0 RE 9 GAX (B) Reprise axe Blorsque libéré dans programme usinage BER .BEARB 10 Boucler jusqu'à fin usinage en P0 RE 10 RET Process 0 - Usinage RE 1:10 RE 2:10 T1 BSR .M6 [Partie droite] GAX (1:B) SE 1:9 WER 1:9 BSR .BET1 [Partie gauche] GAX (2:B) SE 2:9 WER 2:9 BSR .BET1 T2 BSR .M6 [Partie droite] GAX (1:B) SE 1:9 WER 1:9 BSR .BET2 [Partie gauche] GAX (2:B) SE 2:9 WER 2:9 BSR .BET2 ì ì SE 1:10 SE 2:10 T0 BSR .M6 RET .BET1 G00 G54 G90 X0 Y0 Z100 B0 M03 S1000 Remise à 0 évènements pour boucle dans process 1 & 1 er Changement 1 outil Prendre axe B au process 1 Le process 1 est arrêté à partir dece bloc Attente jusqu'à process 1 synchrone Usinage partie droite Prendre axe B au process 2 Le process 2 est arrêté à partir de ce bloc Attente jusqu'à process 2 synchrone Usinage partie gauche er Changement 1 outil Prendre axe B au process 1 Le process 1 est arrêté à partir de ce bloc Attente jusqu'à process 1 synchrone Usinage partie droite Prendre axe B au process 2 Le process 2 est arrêté à partir de ce bloc Attente jusqu'à process 2 synchrone Usinage partie gauche Terminer boucle de saut dans process 1 & 2. Fin de programme er Programme d'usinage 1 outil Instructions de déplacement, conditions d'usinage ì ;Usinage ì M05 FAX (B) RTS .BET2 ì DOK-MTC200-NC**PRO*V17-ANW1-FR-P Libération axe B Fin SP usinage 1 ème Programme d'usinage 2 outil 9-8 Instructions de commande de process et de programme RTS 9.3 Manuel de programmation CN 17VRS Fin SP usinage 2 Instructions de commande de programme Fin de programme avec remise à 0 ‘RET’ L’instruction RET caractérise la fin d’un programme CN. L’instruction RET agit de la même façon que M002/M030, sans que la fonction auxiliaire ne soit transmise à l’automate. L’exécution de l’instruction RET déroute le programme sélectionné sur le premier bloc, positionne les conditions de déplacement de l’état de base et attend un signal de départ cycle. Après exécution de l’instruction RET le vecteur de retrait pointe sur le label de saut HOME. Syntaxe RET Après exécution de l’instruction RET, tous les niveaux de sousprogramme et leurs vecteurs de retour sont effacés, et la CN se trouve à l’état de base dans le programme principal. • L’instruction RET est par sa fonction similaire aux fonctions M002/M030 de DIN 66025. Saut avec stop ‘BST’ L’instruction de saut BST déroute le programme sur le label défini dans le paramètre de l’instruction, positionne les conditions de déplacement de l’état de base et attend un départ cycle. Après un BST, le vecteur de retrait pointe sur le label de saut HOME. Syntaxe BST <Adresse de saut> Ø BST .HALT Après un BST tous les niveaux de sous-programme et leurs vecteurs de retour sont effacés, et la CN se trouve à l’état de base dans le programme principal. • BST ne peut pas être utilisé à l’intérieur d’un sous-programme. Un saut à l’extérieur du sous-programme entraîne un message d’erreur. Arrêt programmé ‘HLT’ L’instruction HLT interrompt le déroulement du programme et attend un départ cycle. Cette instruction agit comme la fonction M000 sans qu’une fonction auxiliaire ne soit transmise à l’automate. Syntaxe HLT Lorsqu’une remarque doit être émise avec une instruction HLT, il faut veiller à ce que la remarque soit programmée dans un bloc avant l’instruction HLT. La raison en est que, dans l’ordre d’exécution des instructions CN, l’instruction HLT est exécutée avant l’émission d’une remarque (voir chapitre ‘Éléments d’un bloc CN). DOK-MTC200-NC**PRO*V17-ANW1-FR-P Manuel de programmation CN 17VRS Instructions de commande de process et de programme 9-9 Saut inconditionnel ‘BRA’ L’instruction de saut BRA déroule le programme à l’adresse de saut définie dans le paramètre de l’instruction Le programme continue son déroulement à partir de là. Syntaxe Ø BRA <Adresse de saut> BRA .WEITER Saut dans un autre programme ‘JMP’ L’instruction de saut JMP force un branchement dans le programme donné par le paramètre de l’instruction et continue le déroulement du programme à partir du premier bloc Syntaxe JMP <Numéro programme[1..99]> Ø JMP 50 JMP <Variable> Ø JMP @100 Le saut peut être effectué dans n’importe quel programme du paquet de programmes actifs. Les vecteurs de retrait ne sont pas modifiés par un saut dans un autre programme. 9.4 Sous-programme Technique de sous-programme Lors de l’usinage d’une pièce, il peut arriver qu’une partie d’usinage soit répétée plusieurs fois. Ce processus d’usinage peut être programmé comme sous-programme afin d’exécuter plusieurs fois les mêmes séquences d’usinage. Ce sous-programme peut être appelé à partir de différents points du programme d’usinage comme un module fonctionnel fermé. Les sous-programmes sont organisés dans la CNC selon le schéma suivant: Mémoire programme CN Mémoire programme CN A Programmes CN [1..98] Programe d'avance (advance) Mémoire cycles CN programme de retrait (Reverse) sous-programmes des programmes d'avance et de retrait Programme n° 99 Programme n° 0 sous-programmes et paquet programme CN cycles spécifiques sous-programmes et cycles du constructeur et INDRAMAT Fig. 9-3: Organisation de programme dans la CNC Les sous-programmes spécifiques à un programme CN sont programmés dans le programme CN actuel. Les sous-programmes spécifiques à un paquet de programmes sont programmés dans le programme 99. Ils peuvent être appelés à partir de n’importe quel programme CN du paquet. Les sous-programmes paramétrables et les cycles d’usinage sont programmés dans le mémoire des cycles CN. Ces programmes peuvent être appelés à partir de n’importe quelle mémoire CN, process et paquet programme. DOK-MTC200-NC**PRO*V17-ANW1-FR-P 9-10 Instructions de commande de process et de programme Manuel de programmation CN 17VRS Structure d’un sous-programme Un sous-programme est constitué: • d’un début de sous-programme, • des blocs CN du sous-programme • d’une fin de sous-programme .LABEL Début de sous-programme Blocs CN Blocs CN du sous-programme RTS Fin de sous-programme Fig. 9-4: Structure de sous-programme La syntaxe du label d’entrée commence par un point décimal suivi au minimum de 6 caractères imprimables. Il n’y a pas de différence entre les majuscules et les minuscules. Le caractère ‘∗’ derrière le point décimal est réservé pour les cycles fixes INDRAMAT. Emboîtement de sous-programme Un sous-programme peut être appelé non seulement depuis un programme pièce, mais aussi depuis un autre sous-programme. Dans la CNC il y a 10 niveaux d’appel de sous-programme. Cela signifie qu’il peut y avoir au maximum 9 emboîtements de sous-programme. Niveaux d'appel de programmes: 1 2 3 .UP1 .UP2 4 5 6 7 8 9 10 .UP6 .UP7 .UP8 9 emboîtements pogramme CN appel BSR .UP1 BSR .UP2 BSR .UP3 RTS RTS .UP3 BSR .UP4 .UP4 BSR .UP5 RTS RTS .UP5 BSR .UP6 RTS BSR .UP7 BSR .UP8 RTS RTS .UP9 BSR .UP9 RTS RTS Fig. 9-5: Emboîtement de sous-programme Appel d’un programme CN en tant que sous-programme ‘JSR’ L’instruction JSR déroute l’exécution sur le programme dont le numéro est indiqué dans le paramètre de l’instruction. L’exécution reprend au bloc 1 de ce programme. La différence par rapport à l’instruction JMP est que, après exécution de l’instruction RTS le programme retourne au programme appelant. Cela permet d’utiliser un programme CN complet en tant que sous-programme. Syntaxe JSR <Numéro programme[1..99]> Ø JSR 15 JSR <Variable> Ø JSR @25 N’importe quel programme du paquet de programmes actif peut être appelé. Les vecteurs de retrait ne sont pas modifiés par un saut dans un autre programme CN. DOK-MTC200-NC**PRO*V17-ANW1-FR-P Manuel de programmation CN 17VRS Instructions de commande de process et de programme 9-11 Appel de sous-programme ‘BSR’ L’instruction BSR déroute le programme à l’adresse de saut indiquée dans le paramètre de l’instruction. Le programme continue son déroulement à partir de ce point. Syntaxe Ø BSR <Adresse de saut> BSR .UP1 Après retour d’un sous-programme appelé par l’instruction BSR le programme appelant est repris à l’instruction suivante. Retour d’un sous-programme ‘RTS’ L’instruction RTS caractérise la fin d’un sous-programme Après exécution de l’instruction RTS, le système retourne au programme appelant et le déroulement reprend à l’instruction suivant BSR ou JSR. Syntaxe RTS • Si aucun appel de sous-programme (BSR, JSR) n’avait eu lieu avant le retour de sous-programme, il y a arrêt du programme et génération d’un message d’erreur. . BSR .UP1 . . BSR .UP1 . . BSR .UP1 . . RET .UP1 . . RTS Fig. 9-6: Appel de sous-programme DOK-MTC200-NC**PRO*V17-ANW1-FR-P 9-12 Instructions de commande de process et de programme 9.5 Manuel de programmation CN 17VRS Vecteur de retrait La CNC offre la possibilité, en fonction d’états définis du programme se reportant à des positions déterminées de la machine, de définir des marqueurs pour un programme de retrait. Dans ce programme de retrait sera programmée la façon dont les axes se retireront de leur position propre pour retrouver un état bien défini. Les marqueurs pour le programme de retrait sont caractérisés par un label de saut et sont désignés comme vecteurs de retour. Après mise sous tension le label de saut .HOME est défini, comme vecteur de retrait de base. Il doit faire partie de chaque programme CN ou être disponible dans le programme 99 ou dans la mémoire des cycles et marque le début du programme de retour de base. Après chaque fin de programme par RET ou BST et chaque remise de la CN à l’état de base, le vecteur de retrait pointe sur le label de saut .HOME et tous les vecteurs de retrait des sous-programmes sont effacés. Pose d’un vecteur de retrait ‘REV’ Le bloc CN avec l’adresse de saut définie par le paramètre de l’instruction REV est défini comme le premier bloc CN du programme de retour. Cela signifie qu’un programme de retour commencera à ce bloc. Syntaxe REV <Adresse de saut> Ø REV .HOLE1 Des vecteurs de retrait peuvent également être définis à l’intérieur de sousprogrammes, avec la même structure d’emboîtement dans les programmes de retrait que dans le programme d’avance. Les programmes de retrait des sous-programmes doivent également être terminés avec l’instruction RTS. • Lorsque l’on quitte un sous-programme, les vecteurs de retrait définis dans le sous-programme sont automatiquement effacés. • Un vecteur de retrait programmé dans un bloc CN n’est actif qu’à la fin du bloc. • La marque de saut programmée avec REV doit se trouver dans le même programme CN que l’instruction REV. L’instruction REV ne trouve pas la marque de saut dans le programme global 99 ou dans la mémoire de cycles. Exemple .HOME MRF D0 G40 G47 G53 G90 G74 Z0 F1000 G74 X0 Y0 F1500 T0 BSR .M6 MRY RET Programme CN – Programme d'origine général Vecteur de retrait de base Prise d'origine magasin d'outils Annulation des correcteurs D Détermination de l'état de base Prise d'origine axe Z Prise d'origine axes X & Y Dépose outil de broche dans magasin Attente de magasin en position Fin de programme DOK-MTC200-NC**PRO*V17-ANW1-FR-P Manuel de programmation CN 17VRS Instructions de commande de process et de programme 9-13 Lors d’un control Reset, tous les vecteurs de retrait (REV) sont effacés. le programme de retrait pointe sur le vecteur de retrait de base .HOME. Les blocs CN définis par les vecteurs de retrait (REV) ne ATTENTION seront plus exécutés. Seuls les blocs du vecteur de retrait de base .HOME seront pris en compte. Exemple ; Programme de changement d'outil N0000 .M6 ; Engager nouvel outil? N0001 .M6_TOL @0:00=TLD(,0,1,1,0,5,) N0002 @0:00=@0:00-T BEQ .M6_T0 ; Positionnement du magasin N0003 BTE .M6_BAC N0004 MTP N0005 BRA .M6_TCH N0006 .M6_BAC MFP T0 programmé ? Accès à emplacement programmé Accès à emplacement libre ; Changement d'outil N0007 .M6_TCH G40 G47 G53 G90 M9 N0008 SE 0:15 N0009 G0 Z392 M19 S90 MRY REV .RM6_2 N0010 Q1 N0011 Q2 N0012 TMS N0013 Q7 N0014 Q3 N0015 Q8 N0016 Q6 N0017 Q5 N0018 RE 0:12 Lire n° outil. broche1 L'outil est il nécessaire ? REV .RM6_3 REV .RM6_4 REV .RM6_5 REV .RM6_6 REV .RM6_7 REV .RM6_8 REV .RM6_9 REV .RM6_10 Annulation correction outil, décalages origine, programmation absolue Axe A et broche en position changement Fermeture changeur Libération outil Sortie changeur Rotation changeur Entrée changeur Serrage broche Ouverture changeur Transfert: G1 -> broche, G0 -> Mag. N0019 TSM REV .RM6_12 N0020 RE 0:15 N0021 BTE .M6_T0 T0 programmé ? N0022 G48 [ ] RTS ;Pas de changement d'outil nécessaire (outil déjà dans la broche) ou ;T0 programmé N0023 .M6_T0 N0024 [ ] RTS ; DOK-MTC200-NC**PRO*V17-ANW1-FR-P 9-14 Instructions de commande de process et de programme Manuel de programmation CN 17VRS ; Vecteurs de retour du programme de changement d’outil N0025 .RM6_6 Q3 Rotation inverse bras N0026 .RM6_5 Q8 Déplacement changeur N0027 .RM6_4 SE 0:12 Transfert G1 -> mag. G0 -> broche N0028 TSM N0029 .RM6_3 Q6 Fermeture disp. serrage N0030 .RM6_2 Q5 Ouverture pince N0031 RTS N0032 .RM6_7 Q8 Déplacement changeur N0033 .RM6_8 Q6 Fermeture disp. serrage N0034 .RM6_9 Q5 Ouverture pince N0035 .RM6_10 RE 0:12 N0036 TSM N0037 .RM6_12 BTE .M6_T0 N0038 G48 [ ] RTS N0039 RTS Avec une programmation de vecteur de retrait adaptée, les erreurs pouvant arriver durant l’exécution du programme sont prises en compte. Par exemple, si un défaut survient lors de l ‘exécution d’une fonction Q, la machine est remise dans une position non critique avec les vecteurs de retrait. Lors de l’effacement des vecteurs de retrait par un control Reset, cela n’est plus possible • Mesure à prendre Dans de telles situations, l’effacement des vecteurs de retrait par le control Reset doit être empêché. Cela est possible avec un événement (ici événement 0 :15) et son utilisation dans le programme automate. (&WUO5HVHW æ 6 æ Tant que l’événement est à 1(durant l’exécution des fonctions Q), aucun control Reset n’est possible. Un control Reset ne sera autorisé qu’après remise à 0 de l’événement. Remarque: Si dans une situation exceptionnelle, un control Reset devait être possible alors que l’événement est à 1, l’événement peut être manuellement remis à 0 par l’IHM. De cette façon, le constructeur de machine peut faire la différence entre utilisateurs autorisés et non-autorisés. Lors du changement d’outil, il faut veiller à l’actualisation du gestionnaire d’outil . 9.6 Sauts conditionnels Les sauts conditionnels ne sont effectués que lorsque la condition correspondante est remplie. Sinon, le déroulement du programme se continue au bloc suivant. Saut quand broche vide ‘BSE’ L’instruction de saut BSE permet de déterminer si la broche est vide. Syntaxe BSE <Adresse de saut> Ø BSE .SPLE Si la broche est vide, le programme se continue à l’adresse indiquée dans le paramètre de l’instruction. DOK-MTC200-NC**PRO*V17-ANW1-FR-P Manuel de programmation CN 17VRS Instructions de commande de process et de programme 9-15 Saut quand T0 a été programmé ‘BTE’ L’instruction de saut BTE permet de déterminer si T0 a été programmé en dernier, donc s’il faut extraire un outil de la broche sans en insérer un nouveau. Syntaxe Ø BTE <Adresse de saut> BTE .PRT0 Lorsque T0 a été programmé, le programme se continue à l’adresse indiquée dans le paramètre de l’instruction. Saut si axes initialisés ‘BRF’ L’instruction de saut BRF permet de déterminer si les axes du process sont référencés. Syntaxe Ø BRF <Adresse de saut> BRF .NORE Lorsque les axes ont été initialisés, le programme se continue à l’adresse indiquée dans le paramètre de l’instruction. Saut sur événement à 1 ‘BES’ Avec l’instruction de saut BES, le programme continue à l’adresse indiquée dans le paramètre de l’instruction si l’événement défini est à 1. Syntaxe BES <Adresse de saut> < N° process [0..6]>:< N° évènement [0..31]> BES <Adresse de saut> < N° évènement [0..31]> Ø Ø BES .LABEL 1:15 BES .LABEL 9 • Si le caractère ‘*’ est programmé à la place du numéro d’événement, le saut est effectué si au moins un événement du process concerné est à 1. • Le programme automate peut aussi agir sur les évènements. Se reporter aux instructions du constructeur de machine qui peut avoir utilisé différents évènements dans un but de synchronisation. Saut sur événement à 0 ‘BER’ Avec l’instruction de saut BER, le programme continue à l’adresse indiquée dans le paramètre de l’instruction si l’événement défini est à 0. Syntaxe BER <Adresse de saut> <N° process[0..6]>:<N° évènement[0..31]> Ø BER .LABEL 1:15 BER <Adresse de saut> < N° évènement [0..31]> Ø BER .LABEL 9 • Si le caractère ‘*’ est programmé à la place du numéro d’événement, le saut est effectué si tous les événements du process concerné sont à 0. • Le programme automate peut aussi agir sur les évènements. Se reporter aux instructions du constructeur de machine qui peut avoir utilisé différents évènements dans un but de synchronisation. DOK-MTC200-NC**PRO*V17-ANW1-FR-P 9-16 Instructions de commande de process et de programme 9.7 Manuel de programmation CN 17VRS Sauts en fonction de résultats arithmétiques Les sauts en fonction de résultats arithmétiques se rapportent au résultat de la dernière opération mathématique exécutée. Saut quand résultat égal à 0 ‘BEQ’ Avec l’instruction de saut BEQ, le programme continue à l’adresse indiquée dans le paramètre de l’instruction si le résultat de la dernière opération mathématique était nul. Syntaxe BEQ <Adresse de saut> Ø BEQ .ZERO Saut quand résultat différent de 0 ‘BNE’ Avec l’instruction de saut BNE, le programme continue à l’adresse indiquée dans le paramètre de l’instruction si le résultat de la dernière opération mathématique était différent de 0. Syntaxe BNE <Adresse de saut> Ø BNE .NZERO Saut quand résultat supérieur ou égal à 0 ‘BPL’ Avec l’instruction de saut BPL, le programme continue à l’adresse indiquée dans le paramètre de l’instruction si le résultat de la dernière opération mathématique était supérieur ou égal à 0 Syntaxe Ø BPL <Adresse de saut> BPL .GZERO Saut quand résultat inférieur à 0 ‘BMI’ Avec l’instruction de saut BMI, le programme continue à l’adresse indiquée dans le paramètre de l’instruction si le résultat de la dernière opération mathématique était inférieur à 0. Syntaxe Ø BMI <Adresse de saut> BMI .LZERO Tableau récapitulatif @10=A-B @10=B-A A = B BEQ BEQ A <> B BNE BNE A < B BMI --- A <= B --- BPL A > B --- BMI A >= B BPL --- DOK-MTC200-NC**PRO*V17-ANW1-FR-P Manuel de programmation CN 17VRS Instructions de commande de process et de programme 9-17 Exemple Programme CN @51=0 .NEXT @51=@51+1 @100=MTD(250,0,1,@51) @100=@100-25 BEQ .BREAK @100=@51-10 BMI .NEXT [aucun élément des données machine n'a la valeur 25] M00 BRA .EXIT .BREAK [un élément des données machine a la valeur 25] M00 .EXIT M30 DOK-MTC200-NC**PRO*V17-ANW1-FR-P Construction de boucles Initialisation de la variable de boucle Marque de début de boucle Incrémentation de la variable de boucle Lecture de la variable de donnée machine Page=250, LV1=0, LV2=1, Elément=@51 Quitter la boucle quand la variable de donnée machine = 25 Test de variable de boucle, condition de bouclage remplie Délivrer information arrêt programmé acquittement automate Saut à fin de programme Marque de sortie de boucle Délivrer information arrêt programmé acquittement automate Marque de fin de programme Fin de programme acquittée par automate 9-18 Instructions de commande de process et de programme Manuel de programmation CN 17VRS DOK-MTC200-NC**PRO*V17-ANW1-FR-P Manuel de programmation CN 17VRS 10 Affectation de variables et fonctions mathématiques 10-1 Affectation de variables et fonctions mathématiques Variables Dans un programme CN, les variables remplacent des valeurs numériques. Une valeur peut être attribuée à une variable par le programme CN, le programme automate ou par l'IHM. De même, la valeur d'une variable peut être lue de façon identique.. Les variables sont caractérisées par: • l'adresse @, • la donnée optionnelle du numéro de process suivie de deux points • un numéro à trois chiffres maximum. Il y a 256 variables (0 à 255) de disponibles pour chaque process. Il y a au total 1792 variables de disponibles dans la CN, et elles peuvent être utilisées indépendamment du nombre de process définis. Syntaxe @<Numéro de process[0..6]>:<Numéro de variable[0..255]> Ø @1:100 Lorsque le numéro du process n'est pas programmé, la variable se réfère au process dans lequel elle est programmée. Syntaxe pour l'affectation à une variable @< Numéro process [0..6]>:< Numéro de variable [0..255]>=<Expression mathématique> @1:100=5*100 La représentation interne d'une variable est en format 'réel double'. La plage de valeur pour l'introduction va de -1.0E300 à +1.0E300. Au maximum, 15 chiffres peuvent être introduits ou affichés. Syntaxe pour la représentation des données .123456789123456 123456789123456 15E+20 90E-10 Lorsqu'une variable doit être affectée avec un nombre négatif, la variable doit être mise entre parenthèses. Syntaxe pour le contenu négatif d'une variable X=-(@100) @120=-(@119) -(@57)=@58 @130=X Indépendamment du mode d'affichage (système de coordonnées pièce ou machine), la lecture de valeurs d'axe se fait toujours en coordonnées machine.. ATTENTION DOK-MTC200-NC**PRO*V17-ANW1-FR-P 10-2 Affectation de variables et fonctions mathématiques Manuel de programmation CN 17VRS Affectation de variable Les valeurs des adresses suivantes peuvent être affectées aux variables de la CNC, de même, les valeurs des adresses CNC suivantes peuvent être lues dans des variables: Valeur de coordonnées des axes disponibles Lors de la lecture de valeurs de coordonnées, les coordonnées machine sont lues. Adresses valides: X, Y, Z, A, B, C, U, V, W X[1..3], Y[1..3], Z[1..3], A[1..3], B[1..3], C[1..3], U[1..3], V[1..3], W[1..3] @100=X X1=@101 Paramètres d'interpolation Adresses valides: J=@102 variable. Rayon Seule l'avance actuelle peut être lue (@xxx=F); cependant toutes les valeurs de F peuvent être écrites, par ex. G04 F=@99 pour une temporisation. @104=F F=@105 Facteur d'accélération Lire l'avance actuelle dans une variable. Valeur F par contenu d'une variable. Seul l'angle de rotation P de rotation de coordonnées peut être lu L'angle de départ P d'un filetage ne peut pas être lu. Adresse valide: P G33 Z30 K3 P=@109 Angle de départ d'un filetage par contenu d'une variable. Adresse valide: ACC T Transfert du numéro d'outil actuel dans une variable. Appel d'outil par contenu d'une variable. Adresse valide: @114=E E=@115 Distance d'application Facteur d'accélération par contenu d'une variable. Adresse valide: @112=T T=@113 Numéro d'arête de coupe S S[1..3] Lire la vitesse de rotation broche actuelle dans une variable. Vitesse de rotation broche par contenu d'une variable. ACC=@111 Numéro d'outil F Adresse valide: @106=S S1=@107 Angle R Programmation du rayon par le contenu de la variable. Adresse valide: Vitesse de rotation broche I, J, K Lecture de la coordonnée Y du centre du cercle dans la Adresse valide : R=@103 Avance Transfert de la valeur de position de l'axe X dans la variable. Axe X1 à la position contenue dans la variable. E Transfert du numéro d'arête de coupe actuelle dans une variable. Sélection du numéro d'arête de coupe par contenu d'une variable. Les distances d'application RX, RY et RZ ne peuvent pas être lues. Adresses valides: RX=@116 RX, RY, RZ Distance d'application à l'axe X par contenu d'une variable. DOK-MTC200-NC**PRO*V17-ANW1-FR-P Manuel de programmation CN 17VRS Banque de points d’origine Fonction auxiliaire Affectation de variables et fonctions mathématiques Adresse valide: 10-3 O O=@116 Sélection d'une banque par contenu d'une variable. @117=O Lecture du numéro de banque actuelle. La fonction auxiliaire actuelle Q ne peut pas être lue. Adresse valide: Q Q=@117 Correcteur D Délivrance d'une fonction auxiliaire par contenu d'une variable. Le correcteur actuel D ne peut pas être lu. Adresse valide: D=@122 Fonctions G Fonction G D Sélection d'un correcteur D par contenu d'une variable Adresses valides en lecture: Adresses valides en écriture: Groupe code G G(<Groupe code G[1..19]>) G = Expression action Signification G00, G01, G02, G03 1 modale Fonctions d’interpolation G17, G18, G19, G20 2 modale Sélection de plan G40, G41, G42 3 modale Correction de trajectoire d'outil G52 bis G59 4 modale Décalages d'origine G15, G16 5 modale Programmation au rayon / diamètre. G90, G91 6 modale Données de cotes G65, G94, G95 7 modale Programmation d'avance G96, G97 8 modale Programmation de vitesse de rotation broche G70, G71 9 modale Unités de mesure G43, G44 10 modale Eléments de transition G61, G62 11 modale Changement de bloc G98, G99 12 modale Vitesse KB/MB G47, G48, G49 13 modale Correction de longueur d'outil G08, G09 14 modale Vitesse de transition de blocs G06, G07 15 modale Erreur de poursuite avec / sans G04 G33 G50, G51 G63, G64 G74 G75, G76 G77 G92 G93 16 16 16 16 16 16 16 16 16 bloc bloc bloc bloc bloc bloc bloc bloc bloc Temporisation Filetage Décalage d'origine programmé Taraudage Prise d'origine Déplacement sur butée Dégagement et réaccostage Limitation de vitesse de rotation broche Programmation en temps G30, G31,G32 17 modale Transformations G72, G73 18 modale Miroir G78, G79 19 modale Facteur d'échelle G36, G37, G38 21 modale Logique de déplacement axes circulaires Les fonctions G valides dans un bloc ne peuvent être lues que dans le bloc où elles sont programmées. Sinon, lors de la lecture d'une fonction G valide dans un bloc, la valeur 1 est obtenue. @118=G(4) Transfert de la fonction G actuelle du groupe 4 dans la variable. G=@119 Ecriture d'une fonction G par contenu d'une variable. DOK-MTC200-NC**PRO*V17-ANW1-FR-P 10-4 Affectation de variables et fonctions mathématiques Fonctions M Les fonctions M programmables sont réparties en 16 groupes de fonction. Adresses valides en lecture: Adresses valides en écriture: Fonction M Manuel de programmation CN 17VRS Groupe fonction M M(<Groupe de fonction[1..16]>) M = Expression Action Signification M000, M001, M002, M030 1 modale Commandes de contrôle programme M3, M4, M5, M13, M14 2 modale Commandes de broche S M103, M104, M105, M113, M114 2 modale Commandes de broche 1 M203, M204, M205, M213, M214 3 modale Commandes de broche 2 M303, M304, M305, M313, M314 4 modale Commandes de broche 3 M007, M008, M009 5 modale Arrosage S M107, M108, M109 5 modale Arrosage S1 M207, M208, M209 6 modale Arrosage S2 M307, M308, M309 7 modale Arrosage S3 M010, M011 8 modale Serrage & desserrage S M110, M111 8 modale Serrage & desserrage S1 M210, M211 9 modale Serrage & desserrage S2 M310, M311 10 modale Serrage & desserrage S3 M040, ..., M045 11 modale Changement de rapport S M140, ..., M145 11 modale Changement de rapport S1 M240, ..., M245 12 modale Changement de rapport S2 M340, ..., M345 13 modale Changement de rapport S3 M046, M047 14 modale Atténuateur de broche M048, M049 15 modale Atténuateur d'avance M019, ..., M319, Mxxx 16 bloc Indexage de broche & fonctions machines spécifiques constructeur Les fonctions M valides dans un bloc ne peuvent être lues que dans le bloc où elles sont programmées. Sinon, lors de la lecture d'une fonction M valide dans un bloc, la valeur 1 est obtenue. @120=M(13) M=@121 Transfert de la fonction G actuelle du groupe 4 dans la variable Ecriture d'une fonction M par contenu d'une variable DOK-MTC200-NC**PRO*V17-ANW1-FR-P Manuel de programmation CN 17VRS Affectation de variables et fonctions mathématiques 10-5 Unité d'angle pour les fonctions d'angle ‘RAD’, ‘DEG’ Les arguments des fonctions d’angle SIN, COS, TAN et les résultats des fonctions inverses ASIN, ACOS, ATAN peuvent être introduits et calculés aussi bien en radian qu'en degré. Syntaxe RAD DEG • L'unité RAD est l'état de base et est modale jusqu'à remplacement par l'unité DEG. A la fin du programme (RET ou BST) l'unité RAD est automatiquement sélectionnée. Expressions mathématiques L'affectation d'une expression est introduite par le signe égal et se termine par un espace ou une fin de ligne. • A l'intérieur d'une expression, un espace est interprété comme fin de l'expression et entraîne son interruption. Les caractères suivants conduiront généralement à une erreur de syntaxe. Le calcul d'une expression suspend le traitement de bloc, c'est à dire que l'interprétation des blocs suivants n'aura lieu que lorsque l'expression aura été entièrement calculée. Il s'ensuit que les mouvements de déplacement s'arrêteront à leur point final et que les mesures de lissage de passage de bloc (G06, G08) sont inefficaces. Les expressions sont composées de: • opérandes, • opérateurs, • parenthèses et • fonctions. Exemple Expressions @100=X+SQRT(2)*SQRT(X*X+Z*Z) F=0.1*PI*800 @101=TAN© @102=SQRT(@100)+F @103=@105+@106/@107-50 DOK-MTC200-NC**PRO*V17-ANW1-FR-P 10-6 Affectation de variables et fonctions mathématiques Manuel de programmation CN 17VRS Opérandes Les opérandes peuvent être: • des constantes, • des constantes système, • des variables, • des lettres adresse et • des fonctions. Constantes Les constantes en virgule flottante éléments suivants: peuvent être composées des • signe de la mantisse, • jusqu'à 6 chiffres, • point décimal avec, derrière jusqu'à 6 chiffres, • marque d'exposant E, • signe de l'exposant et • jusqu'à 2 chiffres pour l'exposant. La condition pour la représentation interne en virgule flottante est la présence d'un point décimal ou de la marque d'exposant. Exemple constantes en virgule flottante -0. +123456. 1E0 -123456E+1 0.1E-00 +100.000E12 Une valeur décimale sans point décimal ou sans exposant sera interprétée comme constante entière. Les constantes entières sont composées d'un signe optionnel et de jusqu'à 6 chiffres. Exemple constantes entières -0 1 +1234567890 Constantes système Le nombre ‘PI’ (3.14159265...) ainsi que le facteur de conversion inch/millimètres ‘KI’ (25.4) sont disponibles comme constantes système. Du fait de leur haute précision interne, ces constantes doivent être utilisées. DOK-MTC200-NC**PRO*V17-ANW1-FR-P Manuel de programmation CN 17VRS Affectation de variables et fonctions mathématiques 10-7 Opérateurs Les opérateurs disponibles sont les symboles usuels pour les opérations mathématiques de base: + Addition − Soustraction ∗ Multiplication / Division % Reste de division entière (Modulo) • La division par 0 conduit à une erreur. • Les opérations d'ordre supérieur sont réalisées par des fonctions. Parenthèses Pour l'emboîtement d'expressions ainsi que pour contourner l'ordre de préséance des opérateurs, des parties d'expressions peuvent être mises entre parenthèses. Le nombre de niveau de parenthèses n'est pas limité. Fonctions Les fonctions mathématiques suivantes sont disponibles dans la CNC: ABS valeur absolue INT partie entière SQRT racine carrée SIN sinus COS cosinus TAN tangente ASIN arc sinus ACOS arc cosinus ATAN arc tangente E^ puissance base e 10^ puissance base 10 2^ puissance base 2 LN logarithmes népériens e LG logarithmes décimaux 10 LD logarithmes sur base 2 TIME temps en seconde Les opérandes des fonctions mathématiques sont entre parenthèses. Les opérandes des fonctions peuvent également être des expressions, les fonctions peuvent être emboîtées. Valeur absolue – ABS La fonction ABS donne la valeur positive de l'opérande. x < 0: ABS(x) =-x x = 0: ABS(x) = 0 x > 0: ABS(x) = x Exemple ABS(-1.23) DOK-MTC200-NC**PRO*V17-ANW1-FR-P Ø 1.23 10-8 Affectation de variables et fonctions mathématiques Partie entière - INT Manuel de programmation CN 17VRS La fonction INT donne la partie entière inférieure de l'opérande . Exemple INT(1.99) INT(1.01) INT(-2.99) INT(-2.01) Racine carrée - SQRT Ø Ø Ø Ø 1 1 -2 -2 La fonction SQRT donne la racine carrée de l'opérande. Exemple SQRT(2) 1.4142.. Ø La fonction SQRT n'accepte pas d'opérande négatif. Sinus - SIN L'opérande de la fonction SIN est interprété en fonction de l'unité angulaire choisie (RAD, DEG). -1 × SIN(x) Ø +1 Plage de valeur: Exemple Cosinus - COS RAD SIN(PI/6) Ø 0.5 DEG SIN(30) Ø 0.5 L'opérande de la fonction COS est interprété en fonction de l'unité angulaire choisie (RAD, DEG). Plage de valeur: -1 × COS(x) Ø +1 Exemple Tangente – TAN RAD COS(PI/6) Ø 0.866.. DEG COS(30) Ø 0.866.. L'opérande de la fonction COS est interprété en fonction de l'unité angulaire choisie (RAD, DEG). Exemple RAD TAN(PI/4) Ø 1 DEG TAN(45) Ø 1 La fonction tangente n'est pas définie pour π/2 et -π/. Arc sinus – ASIN L'opérande de la fonction ASIN doit être compris entre –1 et +1. Avec l'unité angulaire radian, on a: Plage de valeur: -π/2 × ASIN(x) × +π/2 Exemple ASIN(0.5) Ø 0.523.. (π/6) Avec l'unité angulaire degré, on a: Plage de valeur: -180 × ASIN(x) × +180 Exemple ASIN(0.5) Ø 30 DOK-MTC200-NC**PRO*V17-ANW1-FR-P Manuel de programmation CN 17VRS Arc cosinus – ACOS Affectation de variables et fonctions mathématiques 10-9 L'opérande de la fonction ASIN doit être compris entre –1 et +1. Avec l'unité angulaire radian, on a Plage de valeur: -π/2 × ACOS(x) × +π/2 Exemple ACOS(0.5) Ø 1.047.. (π/3) Avec l'unité angulaire degré, on a: Plage de valeur: -180 × ACOS(x) × +180 Exemple ACOS(0.5) Arc tangente - Ø 60 Avec l'unité angulaire radian, on a: Plage de valeur: -π/2 × ATAN(x) × +π/2 Exemple ATAN(-1) Ø -0.785.. (-π/4) Avec l'unité angulaire degré, on a: Plage de valeur: -180 × ATAN(x) × +180 Exemple ATAN(-1) Puissance base e - E^ 0.082... Ø 1000 Ø 256 Exemple 2^(8) Logarithmes népériens - LN Ø Exemple 10^(3) Puissance base 2 - 2^ -45 Exemple E^(-2.5) Puissance base 10 - 10^ Ø L'opérande de la fonction LN doit être positif. Exemple LN(10) Logarithmes décimaux - LG Ø 2.302... L'opérande de la fonction LG doit être positif . Exemple LG(100) Logarithmes en base 2 - LD Ø 2 L'opérande de la fonction LD doit être positif. Exemple LD(8) Temps en seconde - TIME DOK-MTC200-NC**PRO*V17-ANW1-FR-P Ø 3 La fonction TIME délivre un temps sans référence, en secondes, avec une précision de 2 millisecondes. Ce temps peut être utilisé pour évaluer une différence de temps. 10-10 Affectation de variables et fonctions mathématiques Manuel de programmation CN 17VRS Exemple @50=TIME • • • @60=TIME-@50 temps actuel différence de temps La fonction TIME n'a pas d'opérande. La génération de temps démarre avec la mise sous tension de la CN et dure environ 50 jours. Exemple Programme CN – Programmation de sous-programmes Y @ 100=90 100 80 R=5 @ 102=5 60 @ 101=50 40 20 20 40 60 80 100 120 140 160 180 X Fig. 10-1: Rectangle comme sous-programme Programme CN T4 BSR .M6 G00 G54 G06 G08 X160 Y80 Z10 G01 Z-10 F1000 G42 X135 Y80 F1500 Changement d'outil Position de départ Déplacement axe Z Etablissement de la correction de trajectoire d’outil @100=90 @101=50 @102=5 @103=1200 BSR .RE1 G90 G00 Z10 Préparation des variables Appel de sousprogramme Axe Z à distance de sécurité G40 G01 X160 Y110 Annulation de la correction de trajectoire d’outil T0 BSR .M6 RET Dépose outil Fin de programme .RE1 G01 G91 F=@103 Sous-programme rectangle X=-(@100) G03 X=-(@102) Y=-(@102) J=-(@102) G01 Y=-(@101) G03 X=@102 Y=-(@102) I=@102 G01 X=@100 G03 X=@102 Y=@102 J=@102 G01 Y=@101 G03 X=-(@102) Y=@102 I=-(@102) G01 X=-(@101/50) Y=@101/10 RTS Programmation incrémentale, valeur d'avance ère 1 droite en X er 1 ¼ de cercle ème 2 droite en Y ème 2 ¼ de cercle ème 2 droite en X ème 3 ¼ de cercle ème 2 droite en Y ème 4 ¼ de cercle Déplacement X Déplacement Y Fin sous-programme DOK-MTC200-NC**PRO*V17-ANW1-FR-P Fonctions CN spéciales 11-1 Manuel de programmation CN 17VRS 11 Fonctions CN spéciales 11.1 Valeurs de position avec entraînements analogiques Les fonctions PMP et NMP délivrent la valeur de position de l'axe indiqué par la lettre adresse, lors d'un front positif ou négatif sur l'entrée de palpage. Valeur de position sur front positif de l'entrée palpeur ‘PMP’ L’instruction PMP délivre la valeur de position de l'axe indiqué par la lettre adresse, lors d'un front positif sur l'entrée palpeur. Syntaxe PMP(<Désignation d'axe>) Ø @50=PMP(X) Remarque: L’instruction PMP – valeur de position sur front positif de l'entrée palpeur- n'est disponible qu'avec les entraînements analogiques. Valeur de position sur front négatif de l'entrée palpeur ‘NMP’ L’instruction NMP délivre la valeur de position de l'axe indiqué par la lettre adresse, lors d'un front négatif sur l'entrée palpeur. Syntaxe NMP(<Désignation d'axe >) Ø @51=NMP(Y) Remarque: L’instruction NMP – valeur de position sur front négatif de l'entrée palpeur- n'est disponible qu'avec les entraînements analogiques. 11.2 Paramètres SERCOS APR Echange de données avec entraînements numériques ‘AXD’ Avec l’instruction AXD, les données d'entraînement d'un entraînement numérique raccordé à la CNC par une interface SERCOS peuvent être lues ou écrites par le programme CN. La donnée d'entraînement à lire ou à écrire est adressée par l'adresse de donnée du paramètre de l'instruction. Adresse de donnée <Désignation d'axe>:<N° identification SERCOS > Les désignations d'axe autorisées correspondent aux lettres X; Y, Z, U, V, W, A, B, C, et S avec extension d'adresse optionnelle [1..3. Une condition nécessaire est que ces axes soient paramétrés et raccordés par l'interface SERCOS. Numéro d'identification SERCOS <Lettre de groupe>-<N° du jeu de paramètres>-<N° du bloc de données> La lettre de groupe permet de faire la différence entre: • données standards (S), définies par le groupe de travail SERCOS et • données produit (P), déterminées par le constructeur de l'entraînement. Le signe moins (-) sert à séparer les différents paramètres. Le numéro du jeu de paramètres adresse le jeu de paramètres souhaité. Il peut prendre une valeur comprise entre 0 et 7. Les données d'entraînements sont adressées avec le numéro de bloc de données. Le numéro de bloc de données prend une valeur comprise entre 0 (0000) et 4095. DOK-MTC200-NC**PRO*V17-ANW1-FR-P 11-2 Fonctions CN spéciales Manuel de programmation CN 17VRS La signification des paramètres SERCOS (lettre de groupe S) et leur fonction sont précisées dans la description 'Interface SERCOS' du groupe de travail SERCOS. La signification des paramètres SERCOS (lettre de groupe P) et leur fonction sont précisées dans la description de l'entraînement à interface SERCOS. • La lecture ou l'écriture de données d'entraînement avec l'instruction AXD doit être programmée seule dans un bloc CN. • La lecture ou l'écriture de données d'entraînement avec l'instruction AXD a lieu seulement à la fin du bloc, c'est à dire que l'affectation d'une valeur d'entraînement dans une variable ne peut pas être utilisée dans le même bloc pour la décision d'un saut conditionnel. • Le traitement de bloc est interrompu par la lecture ou l'écriture de données d'entraînement avec l'instruction AXD, de telle sorte qu'une éventuelle correction de trajectoire d'outil (G41, G42) est considérée comme terminée et une transition de blocs à vitesse optimale (G08) n'est plus possible. • Une valeur d'entraînement lue ne peut être que affectée à une variable et non à une lettre adresse. L'expression affectée ne doit être composée que de l'instruction AXD. Aucun autre opérateur ou opérande n'est autorisé. • Lors de l'écriture d'une donnée d'entraînement avec l'instruction AXD, l'expression d'affectation peut avoir une forme quelconque ou être une constante. Les paramètres modifiés avec l'instruction AXD sont valides, avec leur nouvelle valeur, dans tous les modes d'exploitation. Un jeu de paramètres fonctionnel standard doit être sauvegardé sur le disque dur de l'IHM de la REMARQUE CNC. Exemple Programme CN – instruction AXD La validation de la compensation de couple de frottement permet de compenser l'écart de position lors de la transition de quadrant dans un cercle. Dans cet exemple, le facteur de gain est aussi augmenté de 4 à 7. Programme CN T11 BSR .M6 G00 G90 G54 G06 G08 X199 Y136 Z5 S5000 M03 @50=AXD(X:S-0-0104) @51=AXD(Y:S-0-0104) AXD(X:S-0-0104)=7*1000 AXD(Y:S-0-0104)=7*1000 AXD(X:S-0-0155)=70 AXD(Y:S-0-0155)=110 G01 Z-5 F1000 G41 X199 Y141 F8000 G03 X180 Y122 I199 J122 G01 X180 Y100 G02 X180 Y100 I100 J100 G01 X180 Y77 G03 X198 Y59 I198 J77 G00 Z5 AXD(X:S-0-0104)=@50 AXD(Y:S-0-0104)=@51 AXD(X:S-0-0155)=0 Changement d’outil SF D10 Position de départ Mise en route broche Lecture du facteur de gain actuel de l'axe X Lecture du facteur de gain actuel de l'axe Y Nouveau facteur de gain sur X Nouveau facteur de gain sur Y Compensation de couple de frottement sur X Compensation de couple de frottement sur Y Engagement fraise Point de départ usinage cercle Cercle d'engagement Elément de transition Cercle complet ∅ 160 Elément de transition Cercle de dégagement Fraise à distance de sécurité Ancien facteur de gain sur X Ancien facteur de gain sur Y Suppression compensation de couple de frottement sur X DOK-MTC200-NC**PRO*V17-ANW1-FR-P Fonctions CN spéciales 11-3 Manuel de programmation CN 17VRS AXD(Y:S-0-0155)=0 Suppression compensation de couple de frottement sur Y Changement d’outil Fin de programme 404Kreis.fh7 T0 BSR .M6 RET Fonction oscilloscope Va l e u r d e p o s i t i o n a x e Y [ m m ] Différence position: Va l e u r n o m . d e p o s . : Facteur d'extension: 1693.7 Numéro d'axe: 2 Ty p e d ' a x e : A x e l i n . d i g . Désignat. d'axe: Y Processus: MAHO Numéro d'axe: 1 Ty p e d ' a x e : A x e l i n . d i g . Désignat. d'axe: X Processus: MAHO Kreisdurchmesser 160 mm Va l e u r d e p o s i t i o n a x e X [ m m ] 404Kreis.fh7 404Kreis.fh7 Fig. 11-1: Compensation de couple de frottement au passage de quadrant Fonction oscilloscope Va l e u r d e p o s i t i o n a x e Y [mm] Différence position: Va l e u r n o m . d e p o s . : Facteur d'extension: 1693.7 Va l e u r d e p o s i t i o n a x e X [mm] Fig. 11-2: Extrait de cercle pour évaluation d'écart de position DOK-MTC200-NC**PRO*V17-ANW1-FR-P 11-4 Fonctions CN spéciales Manuel de programmation CN 17VRS Couplage électronique d'axes et interpolateur de tableau Le couplage électronique d'axe autorise des couplages supplémentaires entre les axes. On peut, pour l'axe de référence, avoir accès à: • la position de consigne, • la position réelle 1 ou • la position réelle 2 (codeur additionnel). • En fonction du mode de calcul, cette valeur peut être multipliée par un facteur ou être additionnée avec un offset pris dans un tableau et transmise comme valeur de consigne à l'axe à influencer. Exemple Axe oblique X X a Z (Z) Formules de calcul: X' = X + X * [{1-sin(a)} / sin(a)] Z' = Z X * cot(a) 1-sin(a) sin(a) X X -cot(a) Z Z Fig. 11-3: Axe oblique DOK-MTC200-NC**PRO*V17-ANW1-FR-P Fonctions CN spéciales 11-5 Manuel de programmation CN 17VRS Activation de la transformation dans le programme de référence .HOME ... BRF .HOME_1 G74 Z0 G74 X0 G1 Z0 F5000 Prise d’origine Retour point zéro machine G1 X0 F5000 AXD(X:P-7-3608)=(limite déplacement X+)*10000 AXD(X:P-7-3609)=( limite déplacement X- )*10000 AXD(X:P-7-3613)=2 AXD(X:P-7-3616)=(1-sin(α)/sin(α))*10000 AXD(X:P-7-3619)=2 AXD(X:P-7-3620)=Numéro d'axe de l'axe X AXD(X:P-7-3621)=1 AXD(Z:P-7-3608)=( limite déplacement Z+)*10000 AXD(Z:P-7-3609)=( limite déplacement Z- )*10000 AXD(Z:P-7-3613)=2 AXD(Z:P-7-3616)=(-cot(α))*10000 AXD(Z:P-7-3619)=2 AXD(Z:P-7-3620)= Numéro d'axe de l'axe X AXD(Z:P-7-3621)=1 Charger limite de déplacements X-Achse axe X Activation offset de position Tableau de facteurs en 0.0001 Multiplication N° d'axe de l'axe oblique Activation transformation X Charger limite de déplacements Z-Achse axe Z Activation offset de position Tableau de facteurs en 0.0001 Multiplication N° d'axe de l'axe oblique Activation transformation Z .HOME_1 ... Annulation de la transformation • La ligne d'instruction AXD(<Désignation d'axe>:P-7-3621)=0 annule la transformation pour l'axe sélectionné. • Lors de la mise hors puis sous tension de la commande, la transformation est annulée. Lors de l'annulation de la transformation avec l'instruction AXD, les axes se déplacent avec leur vitesse maximale vers leur position réellement programmée. ATTENTION La correction de position avec la formule de calcul n'est plus prise en compte. ⇒ L'annulation de la transformation avec l'instruction AXD ne doit se faire que dans un état sûr de la machine. Axe virtuel DOK-MTC200-NC**PRO*V17-ANW1-FR-P A partir de la version 5.17 la fonctionnalité d'axe virtuel est en outre disponible. 11-6 Fonctions CN spéciales Manuel de programmation CN 17VRS 11.3 Lecture et écriture de données DPO par le programme CN ‘OTD’ L’instruction OTD (Offset Table Data) permet au programme CN de lire ou d'écrire des données du tableau de décalage de points d'origine. Syntaxe M P O V A OTD ([1/2], [0..6], [0..9], [0..9], [1..10]) Axe Décalage Banque d'origine Process Mémoire CN Désignation Symb. Plage de valeur Signification Mémoire CN M 1/2 1: Mémoire CN A ou 2: Mémoire CN B Si le paramètre n'est pas indiqué, la mémoire CN actuelle est adressée. Process P 0..6 Si aucun process n'est indiqué, le process actuel est adressé. Banque de points d'origine O 0..9 Si ce paramètre n'est pas indiqué, la banque de point d'origine actuelle est adressée. Décalage V 0..9 0= décalage actif 1= décalage de la valeur de G50/G51 2= décalage de la valeur de G52 3= offset général 4= valeur G54 5= valeur G55 6= valeur G56 7= valeur G57 8= valeur G58 9= valeur G59 Si ce paramètre n'est pas indiqué, le décalage actuel est adressé. Axe A 1..10 1= valeur de l'axe X 2= valeur de l'axe Y 3= valeur de l'axe Z 4= valeur de l'axe U 5= valeur de l'axe V 6= valeur de l'axe W 7= valeur de l'axe A 8= valeur de l'axe B 9= valeur de l'axe C 10= valeur de l'angle de rotation Le paramètre d'axe doit être indiqué. La lettre d'axe se réfère à la signification d'axe DOK-MTC200-NC**PRO*V17-ANW1-FR-P Fonctions CN spéciales 11-7 Manuel de programmation CN 17VRS Conditions générales pour l'instruction OTD • Une variable peut aussi être utilisée à la place de la constante. • Une expression mathématique ne peut pas être utilisée a la place d'une constante ou d'une variable. • Les paramètres optionnels peuvent être omis. • Les virgules séparant les paramètres doivent toujours être introduites. Les valeurs de décalage des points d'origine pour G50/G51 et la valeur de décalage d'origine active ne peuvent pas être modifiées par l'instruction OTD. Exemple DPO Programme CN – Lecture de données @100=OTD(,,,,1) Lecture de la valeur de décalage active sur l'axe X • X=OTD(1,0,2,4,1) • @80=G(4) @80=@80-50 • @100=OTD(,,,@080,1) Déplacement de l'axe x à la position donnée par le tableau de DPO de la ème mémoire CN A du G54 de la 2 banque de points d’origine pour le process 0 Lecture fonction G de décalage d'origine Préparation valeur pour instruction OTD Lecture de la valeur de décalage active de l'axe X pour l'entrée DPO correspondant à la fonction G active (G52..G59) Exemple DPO Programme CN – Ecriture de données OTD(,,,4,1)=SQRT(X*X+Y*Y) Attribution du résultat du calcul à l'entrée pour l'axe X pour le décalage correspondant à G54 de la banque de DPO active de la mémoire CN actuelle pour le process actif. • OTD(,,,4,1)=@100+OTD(,,,,1) Calcul de la nouvelle valeur pour le décalage de l'axe X pour G54 à partir du contenu de la variable 100 et du décalage actif de l'axe X. Lors de la lecture des données de décalage de point d'origine, il s'agit de données relatives aux coordonnées machine. ATTENTION DOK-MTC200-NC**PRO*V17-ANW1-FR-P 11-8 Fonctions CN spéciales Manuel de programmation CN 17VRS 11.4 Accès aux données d'outil par le programme CN ‘TLD’ L’instruction TLD (Tool-Data) permet au programme CN de lire et, dans une certaine mesure, de modifier les données d'outil. Syntaxe P A TLD([0..6],[0], S/T [0..2] L/D E D S ,[1..999],[0..9],[1..35],[1..32]) TLD([0..6],[1],[1..9999999],[1..999],[0..9],[1..35],[1..32]) Etat Elément de donnée Arête de coupe N° emplacement/duplo Stockage [0..2] /noméro d'outil Adressage Process Toutes les données disponibles dans la liste d'outil peuvent être lues. Chaque élément de données est adressé par un repère. Les repères de chaque élément de données sont représentés dans le tableau – Données de la liste d'outil pour l'instruction TLD -. Plage de valeur et signification des paramètres Désignation Sym Plage de valeur Signification Process P 0..6 Numéro de process Adressage A 0 Stockage S 0..3 Emplacement L S=0: S=1: S=2: S=3: N° outil (T-Nr.) T 1..9999999 Numéro outil N° duplo D 1..999 Numéro duplo Arête de coupe E 0..9 Elément de donnée D E=0: E=1..9: 3..28 1..35 E=0: Accès aux données de base outil E=1..9: Accès données arête de coupe Etat S E=0: E=1..9: 1..32 1..16 E=0: Accès aux bits état outil E=1..9: Accès aux bits état de coupe 1 0: Adressage par stockage et place 1: Adressage par n° outil et duplo S=0: Magasin/Revolver S=1: Broche S=2: Changeur S=3: Position 1..999 1..4 1..4 1..4 S=0: Place mag./Revo.. S=1: N° de broche S=2: N) changeur S=3: N) position E=0: Données de base outil E=1..9: Données d'arête de coupe DOK-MTC200-NC**PRO*V17-ANW1-FR-P Fonctions CN spéciales 11-9 Manuel de programmation CN 17VRS 'RQQpHVGHODOLVWHG RXWLOSRXU O LQVWUXFWLRQ7/' DESIGNATION Données de base Caractérisation d'outil Adresse index ID (désignation outil) Magasin Place Numéro d'outil Numéro duplo Type de correcteur Nombre de coupes Etat outil Données d'emplacement Demi places libres Ancien emplacement Magasin prochain outil Place prochain outil Magasin outil précédent Place outil précédent Unités Unité de temps Unité de longueur Données de technologie Code d'outil Type de représentation Données utilisateur Données utilisateur 1 . . . Données utilisateur 9 Commentaire Données de coupe Caractérisation de coupe Position de coupe Etat de coupe Données de temps Temps restant Seuil d'alerte Durée max. d'utilisation PLAGE DE VALEURS TYPE DE DONNEES UNITE ELEMENT DE DONNEE OPTION EL WL X X X X X X X X X (par outil) Mot double (32 bits) hexadécimal (lecture seule) jusqu'à 28 caractères libres 0 - 2 (0: Magasin/Revolver, 1: broche, 2: changeur) 0 - 999 1 - 9999999 1 - 999 1-4 1-9 0/1 (32 bits d'état) STRING28 DINT INT USINT USINT - 01 02 03 04 05 06 07 08 09 X X X 0-4 1 - 999 0 - 2 (0: Magasin/Revolver, 1: broche, 2: changeur) 1 - 999 0 - 2 (0: Magasin/Revolver, 1: broche, 2: changeur) 1 -999 USINT INT INT INT INT INT - 10 11 12 13 14 15 X X 0/1 (0: min, 1: cycles) 0/1 (0: mm, 1: inch) USINT USINT - 16 17 X X USINT INT - 18 19 REAL quelconque 20 X X . . . REAL . . . quelconque . . . 28 . . . X . . . X 1- 9 0 - 999 -38 X X X X +38 +/- 1.2 ∗ 10 - +/- 3.4 ∗ 10 et 0 (entrée temp. par IHM: comme pour données géométriques) . . . -38 +38 +/- 1.2 ∗ 10 - +/- 3.4 ∗ 10 et 0 (entrée temp. par IHM: comme pour données géométriques) jusqu'à 5 x 76 caractères quelconques (par coupe) - X X 0-8 0/1 (16 bits d'état) USINT WORD 0.0 - 100.00 0.1 - 100.00 REAL REAL REAL REAL % % min ou cycles min ou cycles 03 04 05 06 -9999.9999 - +9999.9999 ou -999.99999 - +999.99999 -9999.9999 - +9999.9999 ou -999.99999 - +999.99999 -9999.9999 - +9999.9999 ou -999.99999 - +999.99999 -9999.9999 - +9999.9999 ou -999.99999 - +999.99999 -9999.9999 - +9999.9999 ou -999.99999 - +999.99999 -9999.9999 - +9999.9999 ou -999.99999 - +999.99999 -9999.9999 - +9999.9999 ou -999.99999 - +999.99999 -9999.9999 - +9999.9999 ou -999.99999 - +999.99999 -9999.9999 - +9999.9999 ou -999.99999 - +999.99999 -9999.9999 - +9999.9999 ou -999.99999 - +999.99999 -9999.9999 - +9999.9999 ou -999.99999 - +999.99999 -9999.9999 - +9999.9999 ou -999.99999 - +999.99999 DINT DINT DINT DINT DINT DINT DINT DINT DINT DINT DINT DINT mm ou inch mm ou inch mm ou inch mm ou inch mm ou inch mm ou inch mm ou inch mm ou inch mm ou inch mm ou inch mm ou inch mm ou inch 07 08 09 10 11 12 13 14 15 16 17 18 X X X X X X X X -9999.9999 - +9999.9999 ou -999.99999 - +999.99999 -9999.9999 - +9999.9999 ou -999.99999 - +999.99999 -9999.9999 - +9999.9999 ou -999.99999 - +999.99999 -9999.9999 - +9999.9999 ou -999.99999 - +999.99999 -9999.9999 - +9999.9999 ou -999.99999 - +999.99999 -9999.9999 - +9999.9999 ou -999.99999 - +999.99999 -9999.9999 - +9999.9999 ou -999.99999 - +999.99999 -9999.9999 - +9999.9999 ou -999.99999 - +999.99999 DINT DINT DINT DINT DINT DINT DINT DINT mm ou inch mm ou inch mm ou inch mm ou inch mm ou inch mm ou inch mm ou inch mm ou inch 19 20 21 22 23 24 25 26 X X X X X X X X -9999.9999 - +9999.9999 ou -999.99999 - +999.99999 DINT mm ou inch/ min ou cycles 27 X X Facteur d'usure L2 -9999.9999 - +9999.9999 ou -999.99999 - +999.99999 DINT mm ou inch/ min ou cycles 28 X X Facteur d'usure L3 -9999.9999 - +9999.9999 ou -999.99999 - +999.99999 DINT mm ou inch/ min ou cycles 29 X X Facteur d'usure R Données utilisateur Données utilisateur 1 -9999.9999 - +9999.9999 ou -999.99999 - +999.99999 DINT mm ou inch/ min ou cycles 30 X X Durée d'utilisation actuelle Données géométriques Longueur L1 Longueur L2 Longueur L3 Rayon R Usure L1 Usure L2 Usure L3 Usure R Offset L1 Offset L2 Offset L3 Offset R Valeurs limites de géométrie L1_min L1_max L2_min L2_max L3_min L3_max R_min R_max Facteurs d'usure Facteur d'usure L1 . . . Données utilisateur 5 Données utilisateur 6 . . . Données utilisateur 10 0 - 9999999 (0: gestion de temps d'utilisation désactivée) 0 - 9999.999 -38 DOK-MTC200-NC**PRO*V17-ANW1-FR-P X X X X X X X X X X X X X X X X X X X X X X X X X X X X X X X +38 +/- 1.2 ∗ 10 - +/- 3.4 ∗ 10 et 0 (entrée temp. par IHM: comme pour données géométriques) . . . -38 +38 +/- 1.2 ∗ 10 - +/- 3.4 ∗ 10 et 0 (entrée temp. par IHM: comme pour données géométriques) -9999.9999 - +9999.9999 ou -999.99999 - +999.99999 . . . -9999.9999 - +9999.9999 ou -999.99999 - +999.99999 Légende 01 02 - REAL quelconque 31 X X . . . REAL . . . quelconque . . . 35 . . . X . . . X DINT . . . DINT quelconque . . . quelconque 36 . . . 40 X . . . X X . . . X EL: = Donnée spécifique à la liste de réglage WL: = Donnée spécifique à la liste d'outil 11-10 Fonctions CN spéciales Manuel de programmation CN 17VRS %LWVG pWDWG RXWLOSRXU O LQVWUXFWLRQ7/' Désignation du groupe Information du groupe Présence Outil absent/ outil présent Outil non utilisé/ outil utilisé Type correcteur erroné/ Type correcteur correct Défaut type de correcteur Défaut n° de point de coupe Défaut arête de coupe Symbole Accès en écriture Art Bit ! WZM EL 1 ? WZM EL 2 t WZM EL 3 N° point de coupe erroné/ N° point de coupe correct e WZM EL Arête(s) de coupe erronée(s)/ Arête(s) de coupe correcte(s) f WZM EL Val. Remarque 1 0 1 0 1 0 Outil absent 4 1 0 Le numéro de point de coupe ne correspond pas à la demande 5 1 0 Les données de point de coupe ne correspondent pas à la demande 1 ANP/BED: par ex. emplacement endommagé WZM: outil engagé Verrouillée pour outil CEF se trouvant dans broche ou pince Verrouillée pour outil CEF se trouvant dans broche ou pince Par ex. pour transfert d'outil Outil non nécessaire à l'usinage Le type de correcteur ne correspond pas à la demande Réservé pour extensions éventuelles ! (Bit 6 - 8) ANP/BED PL 9 WZM WZM PL 10 WZM PL 11 Réservation de place emplacement non verrouillé Demi place sup. pour outil codé verrouillée/libre Demi place inf. pour outil codé verrouillée/libre Demi place sup. réservée/ non réservée ANP PL 12 ANP PL 13 Occupation d’emplacement Demi place inf. réservée/ non réservée Demi place sup. recouverte / non recouverte WZM PL 14 Demi place inf. recouverte / non recouverte Emplacement utilisé/ libre Outil usé/ outil non usé Limite d'alerte atteinte/ limite d'alerte non atteinte Outil d’usinage/ pas d’outil d’usinage Outil de remplacement/ pas d'outil de remplacement WZM PL 15 WZM PL 16 d WZM WZ 17 w WZM WZ 18 p WZM WZ 19 s WZM WZ 20 Outil à code emplacement fixe pas d'outil à code d'emplacement fixe. C ANP/BED WZ 21 Outil verrouillé/ non verrouillé L ANP/BED WZ 22 Verrouillage d’emplacement Etat d’usure Outil frère Codage emplacement fixe Etat d’outil Emplacement verrouillé/ B 0 1 0 1 0 1 0 1 0 1 0 Par ex. pour transfert d'outil 1 0 1 0 1 0 1 0 1 0 1 0 1 0 La demi place inférieure est recouverte par un outil Un outil se trouve à cet emplacement L'outil ne peut plus être utilisé (changer l'outil) Le temps d'utilisation touche à sa fin (changer l'outil) Il y a un outil d’usinage pour chaque groupe d'outil frère L'outil de remplacement est encore disponible, pas en usinage L'outil reste toujours au même emplacement dans le magasin 1 0 Par utilisateur ou programme. Par ex. outil cassé La demi place supérieure est recouverte par un outil Réservé pour extensions éventuelles ! (Bit 23 - 24) Etat outil utilisateur 1 Bit d'état outil utilisateur 1 quelcon que ANP/BED WZ 25 1 0 Signification quelconque Bit d'état outil utilisateur 8 quelcon que ANP/BED WZ 32 1 0 Signification quelconque . . . Etat outil utilisateur 8 Légende: WZM: ANP: BED: EL: PL: WZ: = Gestionnaire d’outil = Programme spécifique utilisateur de l'automate ou de la CNC = Utilisateur = Bit d'état spécifique à la liste de réglage = Bit d'état spécifique à l'emplacement = Bit d'état spécifique à l'outil DOK-MTC200-NC**PRO*V17-ANW1-FR-P Fonctions CN spéciales 11-11 Manuel de programmation CN 17VRS Bits d'état de point de coupe pour l'instruction TLD: Symbole Accès en écriture Position de coupe erronée / correcte o WZM EL 1 1 0 L1 erronée L1 erronée/correcte 1 WZM EL 2 1 0 L2 erronée L2 erronée/correcte 2 WZM EL 3 1 0 L3 erronée L3 erronée/correcte 3 WZM EL 4 1 0 R erroné R erroné/correcte r WZM EL 5 1 0 Désignation du groupe Information du groupe Position de coupe erronée Type Bit Valeur Réservé pour extensions éventuelles ! (Bit 6 - 8) Etat d’usure Arête de coupe usée/ non usée d WZM WZ 9 1 0 Limite d'alerte atteinte/ non atteinte w WZM WZ 10 1 0 Réservé pour extensions éventuelles ! (Bit 11 - 12) Bit d'état de coupe utilisateur 1 Bit d'état de coupe utilisateur 1 quelcon que ANP/BE D WZ 13 1 0 Bit d'état de coupe utilisateur 4 quelcon que ANP/BE D WZ 16 1 0 . . . Bit d'état de coupe utilisateur 4 Légende: Conditions générales pour l'instruction TLD WZM: BED: WZ: = Gestionnaire d’outil = Utilisateur = Bit d'état spécifique à l'outil EL: PL: ANP: = Bit d'état spécifique à la liste de réglage = Bit d'état spécifique à l'emplacement = Spécifique programme automate ou CNC • Une variable peut être utilisée à la place de la constante. • Une expression mathématique ne peut pas être utilisée a la place d'une constante ou d'une variable. • Les paramètres optionnels peuvent être omis. • Les virgules séparant les paramètres doivent toujours être introduites. Paramètres optionnels pour l'instruction TLD DOK-MTC200-NC**PRO*V17-ANW1-FR-P • Dès que le process [0..6] n'est pas indiqué, le process actuel est utilisé. • Lorsque l'adressage de paramètre [0/1] n'est pas indiqué, la CNC force la valeur 0 et interprète les deux paramètres suivants comme stockage et emplacement. • Lorsque le numéro duplo [1..999] n'est pas indiqué, la CNC force le numéro duplo de l'outil primaire correspondant. • Lorsque l'arête de coupe [0..9] n'est pas indiquée, la CNC force la valeur 0 et accède ainsi aux données de base de l'outil. • Le paramètre d'état [1..32] n'est indiqué que lors d'accès à un bit d'état d'outil ou de point de coupe. 11-12 Fonctions CN spéciales Manuel de programmation CN 17VRS Vérifications générales pour l'instruction TLD La validité des valeurs programmées des paramètres ne peut être vérifiée que lors de l'exécution de l'instruction, donc au moment de l'exécution du programme CN. Si l'un des paramètres est erroné ou invalide, la CNC fait un arrêt immédiat et délivre le message d'erreur: 3DUDPqWUH>1GXSDUDPqWUHHUURQp@HUURQp ORUVGHO LQVWUXFWLRQG DFFqVDX[GRQQpHV Vérifications lors de l'écriture avec l'instruction TLD • Les éléments spécifiques à la liste de réglage ne peuvent pas être écrits. • Les bits d'état d'outil et de point de coupe qui sont associés au gestionnaire d'outil ne doivent pas être écrits. • Les éléments de données de numéro d'emplacement, de stockage et d'outil ne peuvent pas être écrits. • Lorsqu'une de ces conditions n'est pas vérifiée, la CNC fait un arrêt immédiat et délivre le message d'erreur: $FFqVQRQDXWRULVpjXQpOpPHQWGHGRQQpH Exemple Programme CN – Lecture avec une instruction TLD Le numéro de l'outil se trouvant dans la broche 2 doit être affecté à une variable @55=TLD(,0,1,2,0,5,) Elément de donnée=5 : Numéro d'outil Point de coupe=0 : Données de base outil Place=2 : Broche 2 Stockage=1 : Broche Adressage=0 : Adressage par stockage et place Process : process actuel Exemple Programme CN – Ecriture avec une instruction TLD Le dernier outil utilisé doit être verrouillé. @55=T Mémorisation du numéro d'outil actuel dans une variable TLD(3,1,@55,,0,9,22)=1 Bit état outil=22 : Verrouillage outil Elément de donnée=9 : Bit d'état outil Point de coupe=0 : Données de base outil N° duplo : Numéro duplo de l'outil primaire correspondant N° d'outil=@55 : Numéro d'outil par variable 55 Adressage=1 : Adressage par outil et numéro duplo Process=3 : Process 3 DOK-MTC200-NC**PRO*V17-ANW1-FR-P Fonctions CN spéciales 11-13 Manuel de programmation CN 17VRS 11.5 Lecture et écriture des correcteurs D par le programme CN ‘DCD’ L'instruction DCD permet au programme CN de lire et d'écrire les correcteurs D. Syntaxe P S W DCD([0..6],[1..99],[1..4]) Valeur Stockage Process Désignation Symb. Plage de valeur Signification Process P 0..6 Si aucun process n'est indiqué, le process actuel est adressé. Mémoire S 1..99 Si aucun paramètre n'est indiqué, la mémoire actuelle est adressée. Valeur W 1..4 1= 2= 3= 4= Conditions générales pour l'instruction DCD Valeur pour correction de longueur L1 Valeur pour correction de longueur L2 Valeur pour correction de longueur L3 Valeur pour correction de rayon R • Une variable peut être utilisée à la place de la constante. • Une expression mathématique ne peut pas être utilisée a la place d'une constante ou d'une variable. • Les paramètres optionnels peuvent être omis. • Les virgules séparant les paramètres doivent toujours être introduites. • Vérifications durant l'accès Les valeurs des paramètres doivent être à l'intérieur des plages autorisées. La validité des valeurs programmées n'est vérifiée que lors de l'exécution du programme CN. Si l'une des valeurs des paramètres est erronée, la CNC fait un arrêt immédiat et délivre un message d'erreur. Exemple DOK-MTC200-NC**PRO*V17-ANW1-FR-P @102=DCD(,3,4) La variable 102 reçoit la valeur de correction de rayon R de la mémoire D numéro 3. DCD(1,2,1)=Z-10 la valeur ‘Z-10’ est introduite dans la ème correction de longueur L1 de la 2 mémoire D du process 1. DCD(,,3)=DCD(,,3)+1 La valeur L3 du correcteur D actif du process actif est incrémentée de 1. 11-14 Fonctions CN spéciales Manuel de programmation CN 17VRS 11.6 Lecture et écriture de données machine Utilisation des données machine Tâche Les données machines modifiables servent: • de paramètres machine modifiables (données machine de la commande) pour des fonctions de commande particulières comme par exemple registres de réglages, axes entraînés et axes Gantry ou synchronisation de broches principales, • de données protégées (données machine OEM) comme par exemple pour la gestion d'options machine ou la mémorisation de données de mesure, • de mémoire de travail dans laquelle le constructeur de machines range des données structurées (données machine OEM), par exemple pour la réalisation de gestion de palettes ou la mémorisation de positions d'axe, • au travail de grandes quantités de données (données machine utilisateur) , par exemple pour la mémorisation de données géométriques et de tolérance pour l'usinage de pièces. Structures de données nécessaires Le nombre prépondérant de données dont la CN, le constructeur de machine et l'utilisateur ont besoin peut être représenté sous forme: • d'une structure, • d'un champ à une ou deux dimensions ou • d'un champ à une ou deux dimensions sur une structure. Données machine modifiables Données machine commande Données machine OEM Page: 001-099 Page: 001: désignation de page Page: 100-199 Page: 100: désignation de page Index 1 I n d e x 2 Données machine utilisateur Page: 200-299 Page: 200: désignation de page Index 1 Limit 1 Limit 2 Limit 3 Limit 4 Limit 1 Limit 2 Limit 3 Limit 4 Limit 1 Limit 2 Limit 3 Limit 4 Limit 1 Limit 2 Limit 3 Limit 4 Limit 1 Limit 2 Limit 3 Limit 4 Limit 1 Limit 2 Limit 3 Limit 4 Limit 1 Limit 2 Limit 3 Limit 4 Limit 1 Limit 2 Limit 3 Limit 4 Limit 1 Limit 2 Limit 3 Limit 4 Limit 1 Limit 2 Limit 3 Limit 4 Limit 1 Limit 2 Limit 3 Limit 4 Limit 1 Limit 2 Limit 3 Limit 4 Limit 1 Limit 2 Limit 3 Limit 4 Limit 1 Limit 2 Limit 3 Limit 4 Limit 1 Limit 2 Limit 3 Limit 4 Limit 1 Limit 2 Limit 3 Limit 4 I n d e x 2 Index 1 Herst 1 Herst 2 Herst 3 Herst 4 Herst 1 Herst 2 Herst 3 Herst 4 Herst 1 Herst 2 Herst 3 Herst 4 Herst 1 Herst 2 Herst 3 Herst 4 Herst 1 Herst 2 Herst 3 Herst 4 Herst 1 Herst 2 Herst 3 Herst 4 Herst 1 Herst 2 Herst 3 Herst 4 Herst 1 Herst 2 Herst 3 Herst 4 Herst 1 Herst 2 Herst 3 Herst 4 Herst 1 Herst 2 Herst 3 Herst 4 Herst 1 Herst 2 Herst 3 Herst 4 Herst 1 Herst 2 Herst 3 Herst 4 Herst 1 Herst 2 Herst 3 Herst 4 Herst 1 Herst 2 Herst 3 Herst 4 Herst 1 Herst 2 Herst 3 Herst 4 Herst 1 Herst 2 Herst 3 Herst 4 I n d e x 2 Anw. 1 Anw. 2 Anw. 3 Anw. 4 Anw. 1 Anw. 2 Anw. 3 Anw. 4 Anw. 1 Anw. 2 Anw. 3 Anw. 4 Anw. 1 Anw. 2 Anw. 3 Anw. 4 Anw. 1 Anw. 2 Anw. 3 Anw. 4 Anw. 1 Anw. 2 Anw. 3 Anw. 4 Anw. 1 Anw. 2 Anw. 3 Anw. 4 Anw. 1 Anw. 2 Anw. 3 Anw. 4 Anw. 1 Anw. 2 Anw. 3 Anw. 4 Anw. 1 Anw. 2 Anw. 3 Anw. 4 Anw. 1 Anw. 2 Anw. 3 Anw. 4 Anw. 1 Anw. 2 Anw. 3 Anw. 4 Anw. 1 Anw. 2 Anw. 3 Anw. 4 Anw. 1 Anw. 2 Anw. 3 Anw. 4 Anw. 1 Anw. 2 Anw. 3 Anw. 4 Anw. 1 Anw. 2 Anw. 3 Anw. 4 Fig. 11-4: Principe de constitution des données machine DOK-MTC200-NC**PRO*V17-ANW1-FR-P Fonctions CN spéciales 11-15 Manuel de programmation CN 17VRS Lecture et écriture d'éléments de données machine ‘MTD’ L’instruction MTD (Machine Table Data) permet au programme CN de lire et, dès lors que l'écriture est autorisée, d'écrire des éléments de données machine. Instruction MTD Syntaxe PG L1 L2 EL MTD([1..299],[-1000..+1000],[-1000..+1000],[1..1000]) Elément n° Index 2 Index 1 N° page Désignation Symb. Plage de valeur Signification Numéro de page PG 1..299 001 .. 099 Pages des données machine de la commande 100 .. 199 Pages des données machine OEM 200 .. 299 Pages des données machine utilisateur Variable courante 1 L1 Val. min. ..val. max. Val. min.: Val. max.: Variable courante 2 L2 Val. min. ..val. max. Val. min.: Val. max.: Elément N° EL 1.. val. max. Val. max. ≤ 1000 Conditions générales pour l'instruction MTD 1 valeur de la définition de la structure ( ≥ -1000) ème 2 valeur de la définition de la structure ( ≤ +1000) (valeur supérieure – valeur inférieure ≤ 1000) ère 1 valeur de la définition de la structure ( ≥ -1000) ème 2 valeur de la définition de la structure ( ≤ +1000) (valeur supérieure – valeur inférieure ≤ 1000) ère • Les différents numéros doivent être séparés par des virgules. • Une variable peut aussi être utilisée à la place de la constante. • Une expression mathématique ne peut pas être utilisée à la place d'une constante ou d'une variable. • Tous les paramètres ci-dessus doivent toujours être présents. Vérifications durant l'accès Les valeurs des paramètres doivent être à l'intérieur des limites indiquées. La CN ne vérifie leur validité qu'au moment de l'exécution. Si un paramètre est en dehors de sa plage de valeur, la CN interrompt le déroulement du programme et délivre un message d'erreur. La CN réagit de la même façon lorsque l'utilisateur tente d'écrire dans un élément de donnée protégé. Lorsqu'un utilisateur affecte une valeur en dehors de la plage autorisée à un élément de données, la CN la limite automatiquement, sans message d'erreur, à la plus petite ou à la plus grande valeur de l'élément de données. Description complémentaire Des informations complémentaires sur les fonctions et la manipulation de données machine se trouvent dans la description 'Données machine' classeur 1. DOK-MTC200-NC**PRO*V17-ANW1-FR-P 11-16 Fonctions CN spéciales Manuel de programmation CN 17VRS Exemple @100=MTD(250,1,2,4) X=MTD(260,1,,5) @50=MTD(270,,3,6) @120=MTD(280,1,1,4)+4 MTD(250,1,2,4)=@100 MTD(260,1,,5)=X MTD(270,,3,6)=@110+@120 Lecture de l'élément de données machine Page=250, L1=1, L2=2, EL=4 Déplacement axe X à la position contenue dans l'élément de données machine. L2 n'est pas présent. L1 est de type PROCESS. Les éléments du process actuel sont lus. Une introduction spéciale du process est aussi possible. Utilisation dans un calcul. Ecriture d'un élément de donnée machine Ecriture de la valeur actuelle de X dans un élément de donnée machine. Affectation avec calcul. A l'intérieur d'un bloc CN, un nombre quelconque d'éléments peut être lu avec l'instruction MTD, mais un seul peut être écrit (voir chapitre suivant 'Affectations possibles entre AXD, TLD, OTD, DCD, MTD’) REMARQUE 11.7 Affectations possibles entre AXD, OTD, TLD, DCD, MTD Quelques restrictions doivent être prises en compte lors de l'utilisation des instructions AXD, OTD, TLD, DCD et MTD. Emploi d’instructions AXD Exemples d’affectations possibles AXD(X:P-7-3616)=@100 AXD(X:P-7-3616)=@100+@110+@120 @100=AXD(X:P-7-3616) Exemples d’affectations interdites @100=AXD(X:P-7-3616) @110=AXD(X:P-7-3616) @100=(AXD(X:P-7-3616)+@110)+@120 AXD(X:P-7-3616)=1000 AXD(X:P-7-3616)=1 AXD(X:P-7-3616)=AXD(X:P-7-3616) ATTENTION Il ne peut y avoir qu'une seule instruction AXD par bloc CN Pro. Plusieurs affections AXD par ligne ne sont pas autorisées. Des instructions AXD entre parenthèses ne sont pas autorisées. DOK-MTC200-NC**PRO*V17-ANW1-FR-P Manuel de programmation CN 17VRS Fonctions CN spéciales 11-17 Emploi d’instructions OTD Exemples d’affectations possibles @100=OTD(,,,4,1) OTD(,,,4,1)=@110 OTD(,,,4,1)=@100+@110+@120 @100=OTD(,,,4,1)+OTD(,,,4,1) @100=OTD(,,,4,1)+OTD(,,,4,1)+OTD(,,,4,1) @100=OTD(,,,4,1) @110=OTD(,,,4,1) @120=OTD(,,,4,1) OTD(,,,4,1)=OTD(,,,5,1) OTD(,,,4,1)=OTD(,,,5,1)+OTD(,,,5,1) Exemples d’affectations interdites OTD(,,,4,1)=@100 OTD(,,,5,1)=@110 OTD(,,,6,1)=@120 @100=(OTD(,,,4,1)+@110)+@120 A l'intérieur d'un bloc CN, un nombre quelconque d'éléments du tableau de décalages d'origine peut être lu avec l'instruction OTD, mais un seul peut être écrit. Des instructions OTD entre parenthèses ne sont pas autorisées. ATTENTION Emploi d’instructions TLD Exemples d’affectations possibles @100=TLD(,1,1,,0,6,) TLD(,1,1,,0,6,)=5 TLD(,1,1,,0,6,)=3+1+2 @100=TLD(,1,1,,0,6,)+TLD(,1,1,,0,5,) @100=TLD(,1,1,,0,6,)+TLD(,1,1,,0,5,)+TLD(,1,1,,0,6,) TLD(,1,1,,0,6,)=TLD(,1,1,,0,5,) TLD(,1,1,,0,6,)=TLD(,1,1,,0,6,)+TLD(,1,1,,0,5,) Exemples d’affectations interdites @100=TLD(,1,1,,0,5,) @110=TLD(,1,1,,0,6,) @120=TLD(,1,1,,0,6,) TLD(,1,1,,0,5,)=1 TLD(,1,1,,0,6,)=1 TLD(,1,1,,0,6,)=1 @100=(TLD(,1,1,,0,5,)+@110)+@120 VORSICHT A l'intérieur d'un bloc CN, plusieurs éléments de données machine peuvent être lus avec l'instruction TLD, mais un seul peut être écrit. Contrairement aux instructions OTD et MTD, il ne peut y avoir qu'une seule affectation par bloc CN (même en lecture). Des instructions TLD entre parenthèses ne sont pas autorisées. Emploi d’instructions DCD Exemples d’affectations possibles @100=DCD(,,1) DCD(,,1)=@110 DCD(,,1)=@100+@110+@120 @100=DCD(,,1)+DCD(,,1) @100=DCD(,,1)+DCD(,,1)+DCD(,,1) @100=DCD(,,1) @110=DCD(,,1) @120=DCD(,,1) DCD(,,1)=DCD(,,1) DCD(,,1)=DCD(,,1)+DCD(,,1) Exemples d’affectations interdites DCD(,,1)=@100 DCD(,,2)=@110 DCD(,,3)=@120 @100=(DCD(,,1)+@110)+@120 DOK-MTC200-NC**PRO*V17-ANW1-FR-P 11-18 Fonctions CN spéciales Manuel de programmation CN 17VRS A l'intérieur d'un bloc CN, un nombre quelconque de correcteurs D peut être lu avec l'instruction DCD, mais un seul peut être écrit. Des instructions DCD entre parenthèses ne sont pas autorisées. ATTENTION Emploi d’instructions MTD Exemples d’affectations possibles @100=MTD(110,1,1,1) MTD(110,1,1,1)=@110 MTD(110,1,1,1)=@100+@110+@120 @100=MTD(110,1,1,1)+MTD(110,1,1,1) @100=MTD(110,1,1,1)+MTD(110,1,1,1)+MTD(110,1,1,1) @100=MTD(110,1,1,1) @110=MTD(110,1,1,1) @120=MTD(110,1,1,1) MTD(110,1,1,1)=MTD(110,1,1,2) MTD(110,1,1,1)=MTD(110,1,1,2)+MTD(110,1,1,3) Exemples d’affectations interdites MTD(110,1,1,1)=@100 MTD(110,1,1,2)=@110 MTD(110,1,1,3)=@120 @100=(MTD(110,1,1,1)+@110)+@120 A l'intérieur d'un bloc CN, un nombre quelconque d'éléments de données machine peut être lu avec l'instruction MTD, mais un seul peut être écrit. Des instructions OTD entre parenthèses ne sont pas ATTENTION autorisées. Affectations entre instructions AXD, OTD, TLD, DCD et MTD Exemples d’affectations possibles AXD(X:P-7-3616)=MTD(110,1,1,1)+MTD(110,1,1,1) AXD(X:P-7-3616)=OTD(,,,4,1)+OTD(,,,4,1) AXD(X:P-7-3616)=TLD(,1,1,,0,6,)+TLD(,1,1,,0,6,) AXD (X:P-7-3616)=DCD(,,1)+DCD(,,1) Exemples d’affectations interdites MTD(110,1,1,1)=AXD(X:P-7-3616) TLD(,1,1,,0,6,)=AXD(X:P-7-3616) OTD(,,,4,1)=AXD(X:P-7-3616) DCD(,,1)=AXD(X:P-7-3616) Lors de l'affectation entre les instructions AXD, OTD, TLD, DCD et MTD, les limitations de chaque instruction doivent être observées. REMARQUE DOK-MTC200-NC**PRO*V17-ANW1-FR-P Fonctions compilateur CN 12-1 Manuel de programmation CN 17VRS 12 Fonctions compilateur CN 12.1 Principes fondamentaux Le compilateur CN incorporé dans l'IHM à partir de la version logicielle 5.17 permet l'interprétation de programmes CN. Compilateur CN Les fonctions: • chanfreins et arrondi, • fonction Look Ahead étendue, • éditeur graphique CN (pour programmation de contour et d'usinage), • Technique de macro et • fonction modale sont réalisées avec l'utilisation de cette possibilité. 12.2 12.2 Chanfreins et arrondis Les instructions: • CF (insertion de chanfrein) et • RD (insertion d'arrondi) permettent l'insertion de chanfreins et d'arrondis. Chanfreins et arrondis CF.. ou CF=... ;insertion de chanfrein (camfer) RD.. ou RD=... ;insertion d’arrondi (round) Syntaxe • Entre un contour de droite et de cercle, il est possible d'insérer un contour linéaire (chanfrein) ou circulaire (arrondi) supplémentaire. Explications RD RD RD RD CF CF CF CF CF C F CF CF Fig. 12-1: Insertion de chanfreins et d'arrondis entre des contours linéaires et circulaires DOK-MTC200-NC**PRO*V17-ANW1-FR-P 12-2 Fonctions compilateur CN Manuel de programmation CN 17VRS • Avec la programmation d’une instruction RD, un arc de cercle de rayon RD est inséré entre les instructions de déplacement précédente et suivante. • L'instruction CF entraîne que, sur les deux trajectoires, la longueur CF du chanfrein est retirée à partir du point d'intersection des deux trajectoires. Les points obtenus sont reliés par un élément de droite (G1). • La valeur après CF caractérise la largeur du chanfrein, celle après RD le rayon de l'arrondi. • L'instruction CF ou RD peut être introduite entre deux blocs de déplacement à la fin du premier. Le chanfrein ou l'arrondi voulu est inséré à la fin du bloc dans lequel l'instruction est programmée. L'instruction CF ou RD peut aussi être programmée dans un bloc propre entre les deux blocs de déplacement. • Les chanfreins et arrondis sont toujours réalisés dans le plan actif. Exemple Fig. 12-2: Insertion d’arrondi Continuité des blocs de déplacement • Les chanfreins et arrondis ne doivent être insérés qu'entre des blocs de déplacement continu. Entre deux blocs de déplacement devant être reliés par un chanfrein ou un arrondi peuvent se trouver, au maximum vingt blocs ne comprenant pas de mouvement. • Le bloc de déplacement précédent ainsi que le bloc de déplacement suivant doit contenir un mouvement linéaire ou circulaire. • La commande d'insertion de chanfrein ou d'arrondi doit se trouver soit dans le premier bloc de déplacement, soit après, mais avant le deuxième bloc de déplacement. Si le compilateur trouve la commande d'insertion de chanfrein ou d'arrondi dans le deuxième bloc de déplacement, il insère un chanfrein ou un arrondi entre le deuxième bloc et le bloc de déplacement suivant. • Si l'instruction d'insertion se trouve dans un bloc propre, le bloc précédent doit impérativement comprendre le premier bloc de déplacement linéaire ou circulaire. • Les déplacements ne se trouvant pas dans le plan d'usinage actif ne peuvent pas être reliés par un chanfrein ou un arrondi. DOK-MTC200-NC**PRO*V17-ANW1-FR-P Manuel de programmation CN 17VRS Commandes interdites Fonctions compilateur CN 12-3 Les chanfreins et arrondis ne peuvent pas être insérés entre deux blocs de déplacement lorsque l'une des fonctions suivantes est sélectionnée ou annulée: • Programmation au rayon / au diamètre (G15, G16), • Changement de plan (G17, G18, G19 und G20), • Fonctions de transformation (G30, G31, G32), • Décalage et rotation d'origine (G50 bis G59), • Unité de mesure inch/mm (G70, G71), • Fonction miroir (G72, G73), • Prise d'origine d'axe (G74), • Déplacement contre butée fixe / Suppression des contraintes d'axe (G75, G76), • Dégagement et ré accostage (G77), • Facteur d'échelle (G78, G79), • Programmation absolue / incrémentale (G90, G91), • Instructions de saut ou d'aiguillage de programme (BEQ, BER, BES, BEV, BMI, BNE, BPL, BRA, BRF, BSR, BST, BTE, JVE JMP, JSR) ainsi que • Label de saut. Pas de variables Dans les blocs CN entre lesquels un chanfrein ou un arrondi doit être inséré, les points d'arrivée ne doivent pas être définis par une variable. Remarque: Entre les deux blocs de déplacement, il doit être géométriquement possible d'insérer un chanfrein ou un arrondi. Dans le cas contraire, le compilateur réduit le chanfrein ou l'arrondi à une valeur possible (le cas échéant à 0, sans message d'erreur!). 12.3 Technique de macro Macro Syntaxe On entend par macro, la réunion de plusieurs instructions isolées qui sont, en général souvent programmées plusieurs fois, en une instruction globale avec une désignation propre. DEFINE ... AS ... Explications Des instructions qui, par exemple pour des raisons de sécurité, doivent toujours être programmées dans un ordre déterminé, peuvent être ainsi regroupées. Les codes G DIN (tels que cycles de perçage G80 à G89) ou les fonctions auxiliaires DIN (exemple M6) peuvent aussi être représentées. De plus le déroulement de fonctions, sur lesquelles l'automate n'a pas accès, comme par exemple la commande de broche durant l'exploitation programme, peut être piloté par la CN au moyen d'une simple commande. Macros globales / locales A côté des macros locales que l'utilisateur peut définir et utiliser à l'intérieur d'un programme CN, le constructeur de machine peut déposer des macros globales dans le menu Options CN (sous le point de menu Programmation CN). Par opposition aux macros locales, leurs définitions sont valables dans tous les programmes CN et en IMD avec l'IHM graphique. DOK-MTC200-NC**PRO*V17-ANW1-FR-P 12-4 Fonctions compilateur CN Exemple Manuel de programmation CN 17VRS Changement d’outil N0035 DEFINE M860 AS M86 M3 S10 Découplage lorsque la broche tourne lentement N0036 DEFINE M6 AS BSR .WZW Image de la fonction DIN de changement d'outil M6 N0037 DEFINE QUICK AS G01 F15000 déplacement rapide à 15 m/min N0038 DEFINE ANPOS_X AS MTD (112, 1, 8, 1) Pos. de recul X pour chgt. d'outil N0039 DEFINE ANPOS_Y AS MTD (112, 1, 8, 2) Pos. de recul Y pour chgt. d'outil N0040 DEFINE ANPOS_Z AS MTD (112, 1, 8, 3) Pos. de recul Z pour chgt. d'outil ; N0041 QUICK X = ANPOS_X Y = ANPOS_Y M860 Approche rapide en X et Y et découplage N0042 Z = ANPOS_Z M6 Approche rapide en Z et changement d'outil : Calcul de correction d'outil : N0086 DEFINE L3_KORR AS TLD ( , 1, @101, , 1, 13, ) Usure d'outil N0087 DEFINE D_SOLL AS MTD (114, 2, 0, 1) Diamètre réel d'outil N0088 DEFINE D_IST AS MTD (114, 2, 0, 2) Diamètre théorique d'outil ; N0089 L3_KORR = (D_SOLL - D_IST) /2 Calcul de l'usure d'outil : Remarques: • Le nom d'une macro peut avoir jusqu'à 20 caractères de long. • Les instructions appartenant à une macro globale peuvent comporter jusqu'à 156 caractères (en deux lignes de 78 caractères). • Avec des macros locales, le compilateur interprète toutes les instructions CN suivant le mot clé AS comme une suite d'instructions à mettre en jeu à la place du nom de la macro. • Un emboîtement de macros n'est pas possible: dans une suite d'instructions définissant une macro, il ne doit pas y avoir d'appel de macro. Exemple: DEFINE M860 AS M86 M3 S10 • L'utilisateur peut, avec l'IHM graphique en IMD, définir des macros globales, ce qui n'est pas possible avec l'IHM texte ou avec un SOT. • Les mots clé ne doivent pas être redéfinis par des macros. Utiliser la technique des macros avec précaution car le langage de programmation s'en trouve fortement modifié. ATTENTION DOK-MTC200-NC**PRO*V17-ANW1-FR-P Fonctions compilateur CN 12-5 Manuel de programmation CN 17VRS Fonctions CN étendues avec la technique des macros A l’aide de la technique de macros, le constructeur de machine peut définir ses propres fonctions CN, fonctions qui peuvent être appelées par l'utilisateur dans le programme CN. Sous le menu 'Programmation CN' (point de menu 'Options CN'), des macros globales peuvent être construites. Elles sont valables dans tous les programmes CN, ainsi qu'en mode IMD. D'autres informations se trouvent dans la description 'Compilateur CN'. Positions prédéfinies Le constructeur de machine a la possibilité de programmer, dans la table de macros, plusieurs positions fixes, telles que positions de référence, position de changement d'outil, positions de chargement et de déchargement, etc. Il peut donner à ces positions une abréviation qui sera utilisée ultérieurement dans le programme CN. Exemple Table de macros: DEFINE P_WSW AS X... Y... broche Y Z magasin outil : position de changement pièce X Fig. 12-3: Déplacement vers une position prédéfinie : G00 P_WSW : Remarque: Des blocs CN complets ou des appels de sousprogramme peuvent être programmés dans la table de macros; ils pourront être exécutés à l'aide du mot clé. Le constructeur de machine peut ainsi définir des blocs de déplacement spéciaux dépendants de l'installation et qui pourront être activés par l'utilisateur à l'aide du mot clé. Mouvements de retrait avec position intermédiaire Lors du déplacement vers la position d'origine ou une position de changement d'outil, il est souvent nécessaire de déplacer d'abord l'outil hors de la zone d'usinage afin de pouvoir exécuter un mouvement de retrait sûr. Les deux mouvements peuvent être rassemblés en une instruction avec l'utilisation de la technique de macro. Exemple Table de macros: DOK-MTC200-NC**PRO*V17-ANW1-FR-P DEFINE RETURN AS G0 BSR .P_RT 12-6 Fonctions compilateur CN Manuel de programmation CN 17VRS X Position intermédiaire ( 80 / 50 ) Position de retrait ( 80 / 75 ) Z Fig. 12-4: Mouvement de retrait avec position intermédiaire : RETURN X80 Z50 ;Programmation intermédiaire de la position : M30 Le sous-programme suivant est programmé dans la mémoire des cycles: .P_RT G0 X80 Z75 RTS ;Cycle de déplacement à la position de retrait Remarque: D'autres instructions DEFINE et d'autres sousprogrammes peuvent être définis. Il est ainsi possible d'accéder à des positions fixes via une position intermédiaire. Des déroulements complets peuvent être programmés dans les sous-programmes. Les sous-programmes et les macros sont définis par le constructeur machine. L'utilisateur n'a besoin que de programmer l'instruction RETURN dans le programme CN. 12.4 Fonction modale Fonction modale Syntaxe Explications La fonction modale MODF_ON(STRI) permet à l'utilisateur de n'écrire qu'une seule fois des expressions répétitives. MODF_ON(STRI) ;Activation fonction modale (modal function on) MODF_OFF ;Annulation fonction modale (modal function off) • La chaîne de caractères STRI définie entre parenthèses avec la fonction modale peut contenir jusqu'à 80 caractères. • Elle est insérée dans tous les blocs suivants avec des mouvements d'axe. • L'annulation de la fonction modale se fait avec l'utilisation du mot clé MODF_OFF. DOK-MTC200-NC**PRO*V17-ANW1-FR-P Fonctions compilateur CN 12-7 Manuel de programmation CN 17VRS Remarques: • Dans les blocs CN dans lesquels l'utilisateur écrit une fonction modale à l'aide de l'instruction MODF_ON, cette instruction est aussitôt exécutée. • L'instruction MODF_OFF annule, dans le bloc où elle est programmée, la fonction modale. • Il faut remarquer que la fonction modale, telle que par exemple MODF_ON(RD 2), n'a aucune action sur les blocs sans mouvement d'axe. Cela est aussi valable pour les contours issus de l'éditeur graphique et appelés comme fonction dans le programme CN. Exemples 1) Perçage de trous Y N15 N14 N13 200 N12 100 N9 N10 N11 X N8 100 200 300 400 Fig. 12-5: Exemple: perçage de trous ; N0000 T6 M6 N0001 G54 G0 X-10 Y-10 Z50 S3500 M3 ; ;************ G83 – Perçage de trous profonds avec débourrage*********** ; N0002 @171=-20.0 Profondeur (abs.) N0003 @172=6.0 Profondeur de passe (incr.) N0004 @173=2.0 Distance de sécurité (abs.) N0005 @174=0.5 Distance de réglage (incr.) N0006 @175=0.0 Temporisation N0007 @176=250.0 Avance ;*************************************************************************** ; N0008 X100 Y100 Z10 MODF_ON (BSR .*G83) N0009 X200 N0010 X300 N0011 X400 N0012 Y200 N0013 X300 N0014 X200 N0015 X100 N0016 MODF_OFF N0017 T0 M6 N0018 G0 G53 X570 Y490 N0019 M30 DOK-MTC200-NC**PRO*V17-ANW1-FR-P 12-8 Fonctions compilateur CN Manuel de programmation CN 17VRS 2) Chanfreins et arrondis modaux X 180 160 140 RD RD RD RD RD RD 120 RD CF RD 100 CF 80 CF CF 60 CF CF 40 CF CF 20 CF 40 80 120 160 200 240 280 320 360 400 Z 440 Fig. 12-6: Exemple: chanfreins et arrondis modaux N0000 (Description de pièce : escaliers) N0001 T3 BSR .M6 (Outil de dégrossissage) N0002 G18 G54 G16 G90 G71 N0003 M69 N0004 G92 S2000 N0005 [Tournage du contour C1 en une passe] N0006 G0 G18 G54 G16 G95 G97 G9 G7 Z444 S2000 M3 M9 N0007 X0 N0008 G1 G42 Z440 F.3 N0009 X20 MODF_ON (CF2.0) N0010 Z400 N0011 X40 N0012 Z360 N0013 X60 N0014 Z320 N0015 X80 N0016 Z280 N0017 X100 N0018 Z160 MODF_ON (RD2.5) N0019 X120 N0020 Z120 N0021 X140 N0022 Z80 N0023 X160 N0024 Z40 N0025 X180 N0026 Z0 MODF_OFF N0027 G0 G40 X182 Z1 N0028 X184 N0029 Z450 N0030 M5 N0031 M70 N0032 M62 N0033 G53 G90 G47 M5 N0034 M30 [ ] DOK-MTC200-NC**PRO*V17-ANW1-FR-P Fonctions compilateur CN 12-9 Manuel de programmation CN 17VRS 12.5 Fonction Look Ahead étendue Fonction Look Ahead étendue La fonction Look Ahead étendue optimise le profil de vitesse des mouvements de trajectoires programmées durant le processus de compilation ou le déchargement de programme. Pour cela elle introduit, sans modifier le contour programmé, des blocs intermédiaires nécessaires pour obtenir un profil de vitesse de trajectoire plus régulier. Utilisation de la fonction Look Ahead étendue L'utilisation de la fonction Look Ahead étendue est toujours très intéressante lorsque un programme CN, composé de blocs CN très courts, doit être exécuté et n'atteint pas la prévision interne. Lors de passage de blocs non tangentiels, la CN réduit toujours la vitesse à 0 lors de transitions effectuées avec G06 et G08. Il y a de ce fait, souvent un freinage continu sur plusieurs blocs pour obtenir un arrêt au dernier bloc. Du fait que la fonction Look Ahead interne à la CNC ne reconnaît en général, dans le cas de blocs CN très courts, la fin d'un bloc de polygones ou d'éléments de transitions non tangentiels que trop tard, la CN ne commence le processus de freinage que trop tard et interrompt le déroulement du programme durant le freinage avec le message d'erreur: ‘'LVWDQFHGHIUHLQDJHWURSFRXUWH’. L'utilisation de la fonction Look Ahead étendue permet au compilateur d'adapter le profil de vitesse d'une séquence de programme déterminée du programme à la vitesse maximale et à la capacité de freinage des axes. Pour cela, le compilateur découpe, dans les phases d'accélération et de freinage, les blocs CN en parties de bloc avec des vitesses F différentes. Syntaxe LA_ON LA_OFF Variables globales DOK-MTC200-NC**PRO*V17-ANW1-FR-P ;activation fonction Look Ahead étendue (Look Ahead-Funktion, on) ;annulation fonction Look Ahead étendue (Look Ahead-Funktion, off) Des variables globales, que l'utilisateur n'a, en général, pas à modifier, ont été introduites pour le passage de paramètres à la fonction Look Ahead étendue. On peut accéder à une partie d'entre elles dans le menu Options CN ( sous le point Programmation CN). METB ;Plus petit temps d'exécution d'un bloc CN Explication: Donne le plus petit temps d'exécution d'un bloc CN à l'intérieur d'un chemin polygonal à optimiser. Il doit être choisi supérieur ou égal au temps de cycle de bloc. VFBT ;Facteur de vitesse pour transition de bloc Explication: Il permet d'influencer la modification de vitesse au passage de blocs non tangentiels. BBTRC ;Buffer de blocs pour la correction de rayon d’outil Explication: Donne le nombre de blocs CN que la fonction Look Ahead étendue doit prendre en compte à l'avance lors du calcul et de la vérification de correction de trajectoire de rayon d'outil. 12-10 Fonctions compilateur CN Manuel de programmation CN 17VRS TL_RADIUS ;Prédétermination rayon d'outil Explication: Les instructions TL_RADIUS[T-Nr., E-Nr.] permettent de définir les rayons d'outil nécessaires à la fonction Look Ahead étendue au début du programme. Dès lors qu'aucun n° T ou E n'est défini, le compilateur commence par le n° T ou E actuel. Exemple: : N0005 TL_RADIUS[1234567,1]=24.995 N0006 TL_RADIUS[923,3]=20.31 N0007 TL_RADIUS[9,9]=29.89 : Lorsque la correction d'outil de la fonction Look Ahead étendue est utilisée (TRC <> 0), le rayon d'outil prédéfini donné par le champ TL_RADIUS[T-Nr., E-Nr.] doit aussi être disponible lors de l'usinage. ATTENTION TRC ;Correction de trajectoire de rayon d’outil Explication: TRC=0: La fonction Look Ahead étendue n'exécute pas de correction de trajectoire de rayon d'outil. TRC=1: La fonction Look Ahead étendue exécute une correction de trajectoire de rayon d'outil avec le rayon d'outil donné par TL_RADIUS à gauche de la trajectoire. TRC=2: La fonction Look Ahead étendue exécute une correction de trajectoire de rayon d'outil avec le rayon d'outil donné par TL_RADIUS à droite de la trajectoire. ADTRC ;Segment d'approche pour établissement de la correction de trajectoire Explication: ADTRC = 0 La fonction Look Ahead étendue ne prend en compte aucun segment d'approche ou de retrait pour l'établissement de la correction de trajectoire de rayon d'outil. ADTRC 0 La fonction Look Ahead étendue insère avant le premier élément du polygone (premier bloc de mouvement après LA_ON) et après le dernier élément (dernier bloc de déplacement avant LA_OFF) un segment de droite avec abord tangentiel et de longueur donnée dans l'instruction, lorsque la correction de trajectoire de rayon d'outil est activée avec TRC=1 ou TRC=2. Continuité des blocs de trajectoire A l'intérieur de la séquence de programme à optimiser, il ne doit y avoir que des blocs CN contenants des mouvements G1, G2 et G3, des instructions d'événement (SE, RE), des informations de vitesse (F), des limitations d'accélération (ACC_EFF) et des sorties de fonction auxiliaire rapide (MQxxx, QQxxxx et Sxxxxx.xx lorsque S est paramétré comme fonction auxiliaire rapide). Pas de variables Dans les blocs CN dont le profil de vitesse doit être traité par la fonction Look Ahead étendue, les positions finales ne doivent pas être données par des variables. DOK-MTC200-NC**PRO*V17-ANW1-FR-P Fonctions compilateur CN 12-11 Manuel de programmation CN 17VRS Gestion d’outils Les changements d’outil, y compris les appels T correspondants et la sélection d'arête de coupe, doivent être exécutés avant l'activation ou après l'annulation de la fonction Look Ahead étendue. Correction d'accélération en pour cent Dans certaines séquences de programme déterminées par exemple sous l'influence du poids de la pièce ou de l'outil il peut être nécessaire de réduire l'accélération résultante sur la trajectoire. Avec ACC_EFF ;modification de l'accélération effective de trajectoire l'accélération résultante sur la trajectoire peut être modifiée. La plage de valeur du facteur d'accélération va de 1% à 200% Remarque: Au contraire de l'instruction ACC, l'instruction ACC_EFF ne limite pas l'accélération maximale de trajectoire donnée par les paramètres process, mais modifie l'accélération réelle conformément à la valeur programmée. Vitesses spécifiques aux axes A côté de la vitesse de trajectoire, des vitesses d'axe spécifiques peuvent aussi être programmées sous l'adresse F pendant l'exécution de la fonction Look Ahead étendue. Pour programmer une vitesse d'axe il faut introduire la désignation d'axe sans espace après la lettre F. Syntaxe: F<Désignation d'axe>=<Vitesse de l'axe en mm/min> Exemple: : N0045 G01 X 2034 Z1 421 FZ1=4500 ;Vitesse d’axe spécifique à Z1 : Remarque: Lorsque l'utilisateur programme plusieurs vitesses à l'intérieur d'un bloc CN ce bloc ainsi que les suivants sont exécutés avec la dernière vitesse programmée jusqu'à la prochaine instruction de vitesse. Accès aux données actuelles dans la commande L'instruction d'accès aux données actuelles ACD_COMP[...] permet l'accès aux données actuelles de la commande au moment de la compilation (pour l'instant uniquement aux variables CN!). Exemple Lecture du rayon d'outil au moment de la compilation Un programme de dressage actualise le diamètre de meule dans la variable CN @1:120 à chaque dressage de meule. Au moment de la compilation cette valeur est prise comme rayon d'outil. TL_RADIUS[1,1] = ACD_COMP[@1:120]-0,2; Récupération du rayon d'outil depuis la variable @1:120 et soustraction de 0,2 mm. Exemple Rectification d'une broche Un chemin polygonal prédéterminé doit être parcouru en balayage avant et arrière avec la plus grande vitesse possible. Pour cela le profil de vitesse de la trajectoire programmée doit être optimisé à l'aide de la fonction Look Ahead étendue. DOK-MTC200-NC**PRO*V17-ANW1-FR-P 12-12 Fonctions compilateur CN Manuel de programmation CN 17VRS Y X Fig. 12-7: Profil de vitesse d'une trajectoire polygonale à optimiser lors de la rectification d'une broche ;Rectification d’une broche dans le plan X-Y ;Rayon de meule: 2.50000 ;Nom du fichier: TP1 ; N0000 (Désignation de pièce : TP1) N0001 T2 BSR .M6 [MEULE D5] Activation outil N0002 TL_RADIUS [ ] = ACD_COMP[@200] Lecture rayon actuel pour compilateur N0003 G0 G17 G40 G54 G71 G48 G8 G6 G98 X-0.19306 Y3.49431 S1 3000 M3 Création de l'état de sortie N0004 @101=200 Compteur de passe pour nombre de balayages = 200 N0005 .PEN @100=@101-0 BEQ .ENDPEN Fin de balayage ? N0006 F4000 Charger vitesse de trajectoire ; N0007 TRC=1 Correction de rayon à gauche du contour N0008 ADTRC=1 N0009 ACC_EFF=90 N0010 LA_ON ; N0011 G1 X0.8 Y1.2 : : N0030 LA_OFF : ; N0051 @101=@101-1 BRA .PEN N0052 .ENDPEN BSR .ABRICH N0053 RTS ; Segment pour établismt. correction rayon outil Modif. accélération effective de trajectoire Activation fonction Look Ahead étendue Chemin polygonal Annul. fonction Look Ahead étendue Décrémenter compteur de prise de passe Appel cycle dressage N0054 PROGRAMMENDE Remarques: • Lors de l'utilisation de l'instruction LA_ON, il faut programmer LA_OFF dans le vecteur de retrait. • Les modifications de vitesse, dues à la rotation du contour, des axes participant au mouvement ne sont pas prises en compte par le compilateur. Description complémentaire Des informations complémentaires sur les fonctions du compilateur CN se trouvent dans la description Compilateur CN classeur 5. DOK-MTC200-NC**PRO*V17-ANW1-FR-P Fonctions compilateur CN 12-13 Manuel de programmation CN 17VRS 12.6 Editeur graphique CN Fonction L'éditeur graphique CN représente un moyen d'aide très précis pour la réalisation de programme pièce. Il offre à l'utilisateur un moyen simple de définir des éléments géométriques graphiques et de préparer leur usinage. A la fin du dialogue de travail, l'utilisateur peut choisir de définir les données nécessaires à l'usinage sous forme de blocs CN ou d'appel de fonctions avec leurs paramètres correspondants. Syntaxe Les instructions générées par l'éditeur graphique CN consistent en: • WINDOW_01 (..., ..., . . .) ;Définition de la taille de la fenêtre pour travaux de tournage • WINDOW_02 (..., ..., . . .) ; Définition de la taille de la fenêtre pour travaux de fraisage • CONT (..., ..., . . .) ;Définition du contour de départ ou du contour fini : : END_CONT • FORM_20 (..., ..., . . .) ;Tournage de rainures • FORM_50 (..., ..., . . .) ;Fraisage de trous oblongs droits • FORM_51 (..., ..., . . .) ; Fraisage de trous oblongs ronds • FORM_52 (..., ..., . . .) ;Fraisage de cercle • FORM_53 (..., ..., . . .) ;Fraisage d'angle • FORM_54 (..., ..., . . .) ;Fraisage de texte droit • FORM_55 (..., ..., . . .) ;Fraisage de texte rond • FORM_56 (..., ..., . . .) ;Fraisage de rectangle • FORM_57 (..., ..., . . .) ;Fraisage de milieu de rectangle • CYCLE_10 (..., ..., . . .) ;Dressage de contour • CYCLE_11 (..., ..., . . .) ;Tournage • CYCLE_12 (..., ..., . . .) ;Tournage finition • CYCLE_40 (..., ..., . . .) ;Fraisage de contour ATTENTION Description complémentaire DOK-MTC200-NC**PRO*V17-ANW1-FR-P Les données d'outil introduites durant la création du programme d'usinage: • position du point de coupe, • rayon d'outil, • angle de dépouille et • angle d'incidence doivent être présentes lors de l'usinage. Des informations complémentaires sur les fonctions du compilateur CN se trouvent dans la description Compilateur CN classeur 5. 12-14 Fonctions compilateur CN Manuel de programmation CN 17VRS DOK-MTC200-NC**PRO*V17-ANW1-FR-P Manuel de programmation CN 17VRS 13 Méthode pour la programmation CN 13-1 Méthode pour la programmation CN 13.1 Programmation CN optimale en temps Les règles ci-dessous garantissent que la puissance de la CN sera utilisée au mieu. Remarque: Tout ce qui peut, du point de vue de la syntaxe, peut être programmé dans un bloc, devrait, si cela ne va pas à l'encontre de la logique de déroulement, être programmé dans un bloc Que peut-on programmer dans un même bloc ? • Label de saut (par ex. .HOME) • Conditions de déplacement (une condition de chacun des 16 groupes) ∈ {RAD,DEG} • Unité d'angle • Affectation d'une valeur à une variable (plusieurs fois) (par ex. @12=3) • Affectation d'une valeur à une donnée d'entraînement (par ex. AXD(X:S-0-0405)=3) • Donnée de cote (une donnée pour chaque axe) {X,Y,Z,U,V,W,A,B,C} • Paramètres d'interpolation I • Paramètres d'interpolation J • Paramètres d'interpolation K • Mot F ∈ {S,S1,S2,S3} • Mot S • Mot P • Banque de points d'origine (O-Wort) • Accélération de trajectoire en pour cent (ACC) • Fonctions auxiliaires M (une pour chacun des 16 groupes) • Fonctions auxiliaires Q (Q-Wort) • Numéro d'outil (T-Wort) • Numéro de point de coupe (E-Wort) • Instruction d'outil • Mise à 1 d'évènement (SE) • Mise à 0 d'évènement (RE) • Attente de mise à 1 d'évènement (WES) • Attente de mise à 0 d'évènement (WER) • Définition de process • Sélection de programme pour process (SP) • Démarrage programme de retrait (RP) (plusieurs fois) • Démarrage programme d'avance (AP) (plusieurs fois) • Attente de process (WP) (plusieurs fois) • Verrouillage de process • Mise à 1 état terminé • Instructions de commande de programme • Remarques • Commentaires DOK-MTC200-NC**PRO*V17-ANW1-FR-P (DP) (plusieurs fois) (LP) (plusieurs fois) (POK) 13-2 Méthode pour la programmation CN Manuel de programmation CN 17VRS Exemple Programme CN N0000 G00 N0001 S5000 N0002 M03 N0003 F10000 N0004 X100 Y50 Optimisation de temps, la broche démarre après les mouvements: N0000 G00 X100 Y50 F10000 S5000 M03 Optimisation de temps, la broche démarre avant les mouvements: N0000 M03 S5000 N0001 G00 X100 Y50 F10000 /HVSULRULWpVG H[pFXWLRQG XQEORF&1VRQWGpFULWHVVLGHVVRXV Numéro de bloc Label de saut N1234 .ENDE Fon. aux. avant mouvmt. M03 Codes G Variables Valeurs Paramètres d'axe IPO- Valeur F Valeur S Fon. aux. après mouvmt Instr. de palette Instr. d'outil G01 @100= x X100 Y100 F1000 S800 M03 SEL 1 MTP T6 I0 J50 Evène ments Instr. de proces Instr. de cmde progr. SE 5 DP 1 HLT • Même lorsque toutes les instructions CN données ci-dessus peuvent être programmées dans un bloc, la longueur maximale du bloc est limitée à 240 caractères. • Dans un bloc ne peuvent être programmées au maximum que 4 fonctions auxiliaires (S, M, Q). Remarque: Evitez la répétition de fonctions déjà actives. Faites attention aux états modaux à la mise sous tension. Exemple Programme CN N0000 G07 G09 G40 G43 G47 G53 G62 G90 G94 RAD Etat de base N0001 G00 G90 S5000 M03 F10000 X100 Y50 N0002 G00 G90 F10000 X200 Y50 N0003 G01 G90 F10000 Y100 Optimisé: N0000 G00 X100 Y50 F10000 S5000 M03 N0001 X200 N0002 G01 Y100 Remarque: Calculez les constantes lors de l'écriture du programme et affectez les sans signe égal. Exemple Programme CN N0000 DEG X=100 Y=20+100*SIN(30) Optimisé: N0000 X100 Y70 Remarque: Evitez les instructions qui interrompent la préparation des blocs! DOK-MTC200-NC**PRO*V17-ANW1-FR-P Manuel de programmation CN 17VRS ,QVWUXFWLRQVTXLLQWHUURPSHQWOD SUpSDUDWLRQGHVEORFV Méthode pour la programmation CN 13-3 • Conditions de déplacement ∈ {G33, G50 ... G59, G63, G64, G65, G74, G75, G95, G96} und • Annulation des conditions de déplacement avec G93, G94 et G97 • Affectation de valeurs aux variables, données de palette et données d'entraînement • Fonctions auxiliaires (S, M et Q) • Numéro d'outil (T) • Instructions d'outil • Attentes d'évènements (WES,WER) • Instructions de commande de process • Instructions de commande de programme ∈ {BST, BES, BER , JMP, RET, BTE, BSE, BRF, HLT, JEV, BEV, CEV, JSR} Les instructions de commande: RTS, BRA, BSR, REV, BEQ, BNE, BPL, BMI, EEV und DEV n'arrêtent pas la préparation de bloc. Remarque: Utilisez le gestionnaire d'outil comme process parallèle pour une programmation optimale! Exemple Programme CN pour changeur d'outil à double préhenseur N0000 T1 MTP N0001 TCH N0005 BSR .BEARB2 Positionnement magasin sur outil 1 Echange outil entre broche et emplacement magasin Usinage 1 Positionnement magasin sur outil 2 Echange outil entre broche et emplacement magasin Usinage 2 Optimisé: N0000 T1 MTP Positionnement magasin sur outil 1 N0002 BSR .BEARB1 N0003 T2 MTP N0004 TCH N0001 TCH N0002 T2 MTP N0003 BSR .BEARB1 N0004 TCH N0005 BSR .BEARB2 Echange outil entre broche et emplacement magasin Positionnement magasin sur outil 2 (en parallèle) Usinage 1 Echange outil entre broche et emplacement magasin Usinage 2 Le positionnement du magasin dans le bloc 2 se fait de façon asynchrone par rapport à l'exécution du programme, cela signifie que l'exécution du programme se continue de façon ininterrompue. L'instruction TCH attend automatiquement que le positionnement du magasin soit terminé. Données de temps de la CNC Données de temps avec entraînements numériques •7HPSVGHF\FOHGHEORF PV •,QWHUSRODWLRQILQH •7HPSVGHFKJWGHEORF PV •7HPSVGHF\FOHG DVVHUYLVVHPHQW PV •7HPSVGHF\FOHG LQWHUSRODWLRQPV •7HPSVGHF\FOHG DVVHUYLVVHPHQWPV DOK-MTC200-NC**PRO*V17-ANW1-FR-P PV 13-4 Méthode pour la programmation CN Manuel de programmation CN 17VRS DOK-MTC200-NC**PRO*V17-ANW1-FR-P Annexe 14-1 Manuel de programmation CN 17VRS 14 Annexe Tableau des groupes de code G Fonction G Groupe de code G Action Signification G00, G01, G02, G03 1 modale Fonctions d’interpolation G17, G18, G19, G20 2 modale Sélection de plan G40, G41, G42 3 modale Correction de trajectoire d'outils G52 bis G59 4 modale Décalages d'origine G15, G16 5 modale Programmation rayon / diamètre. G90, G91 6 modale Données de cotes G65, G94, G95 7 modale Programmation d'avance G96, G97 8 modale Programmation de vitesse de rotation broche G70, G71 9 modale Unités de mesure G43, G44 10 modale Eléments de transition G61, G62 11 modale Changement de bloc G98, G99 12 modale Vitesse KB/MB G47, G48, G49 13 modale Correction de longueur d'outils G08, G09 14 modale Vitesse de transition de blocs G06, G07 15 modale Erreur de poursuite avec / sans G04 G33 G50, G51 G63, G64 G74 G75, G76 G77 G92 G93 16 16 16 16 16 16 16 16 16 bloc bloc bloc bloc bloc bloc bloc bloc bloc Temporisation Filetage Décalage d'origine programmable Taraudage Prise d'origine Déplacement sur butée Dégagement et ré accostage Limitation de vitesse de broche Programmation en temps G30, G31,G32 17 modale Transformation G72, G73 18 modale Miroir G78, G79 19 modale Echelle G36, G37, G38 21 modale Logique d'accès axe rotatif Les fonctions G valides dans un bloc ne peuvent être lues que dans le bloc où elles sont programmées, sinon la lecture donne comme résultat la valeur 1. DOK-MTC200-NC**PRO*V17-ANW1-FR-P 14-2 Annexe Manuel de programmation CN 17VRS Tableau des groupes de fonctions M Fonction M Groupe de fonction M action Signification M000, M001, M002, M030 1 modale Commandes de pilotage de programme M3, M4, M5, M13, M14 2 modale Commandes de broche S M103, M104, M105, M113, M114 2 modale Commandes de broche , broche 1 M203, M204, M205, M213, M214 3 modale Commandes de broche , broche 2 M303, M304, M305, M313, M314 4 modale Commandes de broche , broche 3 M007, M008, M009 5 modale Arrosage S M107, M108, M109 5 modale Arrosage S1 M207, M208, M209 6 modale Arrosage S2 M307, M308, M309 7 modale Arrosage S3 M010, M011 8 modale Serrage / desserrage S M110, M111 8 modale Serrage / desserrage S1 M210, M211 9 modale Serrage / desserrage S2 M310, M311 10 modale Serrage / desserrage S3 M040, ..., M045 11 modale Changement de rapport S M140, ..., M145 11 modale Changement de rapport S1 M240, ..., M245 12 modale Changement de rapport S2 M340, ..., M345 13 modale Changement de rapport S3 M046, M047 14 modale Atténuateur de broche M048, M049 15 modale Atténuateur d'avance M019, ..., M319, Mxxx 16 dans le bloc Indexage de broche et fonctions spécifiques constructeur machine Les fonctions M valides dans un bloc ne peuvent être lues que dans le bloc où elles sont programmées, sinon la lecture donne comme résultat la valeur 1 DOK-MTC200-NC**PRO*V17-ANW1-FR-P Annexe 14-3 Manuel de programmation CN 17VRS $SHUoXUDSLGHGHVIRQFWLRQV I. G00 à G20 Fonction Groupe G G00 1 Signification Description Page Interpolation linéaire rapide Syntaxe: G00 ; Les valeurs de coordonnées programmées sont atteintes avec la vitesse maximale. 4-14 Syntaxe: G01 Valeur F ; Les axes programmés démarrent et atteignent leur position finale en même temps. 4-15 * modale G01 1 Interpolation linéaire avance * modale G02 1 Interpolation circulaire sens horaire * modale G03 1 Interpolation circulaire sens anti-horaire * modale G04 16 temporisation * bloc G06 G07 15 15 Interpolation à faible erreur de poursuite Syntaxe: G02 <Point final> <Paramètres d'interpolation [I,J,K]> ou <Rayon [R]> ; Un mouvement circulaire est effectué dans le plan sélectionné (G17, G18 G19). Syntaxe: G03 <Point final> <Paramètres d'interpolation [I,J,K]> ou <Rayon [R]> ; Un mouvement circulaire est effectué dans le plan sélectionné (G17, G18 G19). Syntaxe: G04 F<Temps en secondes> ; La durée maximale est de 600 secondes. 4-16 4-16 4-39 * modale Syntaxe: G06 ; Algorithme à faible erreur de poursuite pour tous les mouvements d'axe. Les passages de blocs ne sont pas arrondis. Interpolation avec erreur de poursuite Syntaxe: G07 ; Algorithme à erreur de poursuite pour tous les mouvements d'axe. Les passages de blocs non tangentiels sont arrondis. 4-5 Syntaxe: G08 ; La vitesse des blocs est adaptée de sorte que le passage au bloc suivant se fait à vitesse maximale. 4-7 Syntaxe: G09 ; Avec G09, les écarts de position lors du passage de bloc sont minimums. 4-9 4-2 * Etat de base , *modale G08 14 Passage de blocs à vitesse optimale * modale G09 14 Passage de blocs à vitesse limitée * Etat de base, * modale G15 5 Programmation au rayon * modale G16 5 Programmation au diamètre * modale G17 2 Sélection de plan XY * modale G18 2 Sélection de plan ZX * modale G19 2 Sélection de plan YZ * modale G20 2 Sélection libre de plan * modale DOK-MTC200-NC**PRO*V17-ANW1-FR-P Syntaxe: G15 ; L'état de base à la mise sous tension pour la programmation au rayon ou au diamètre est fixé par le constructeur de machines dans les paramètres process. Syntaxe: G16 ; L'état de base à la mise sous tension pour la programmation au rayon ou au diamètre est fixé par le constructeur de machines dans les paramètres process. 3-19 3-19 Syntaxe: G17 ; Le plan de base à la mise sous tension est fixé par le constructeur de machines dans les paramètres process. 3-15 Syntaxe: G18 ; Le plan de base à la mise sous tension est fixé par le constructeur de machines dans les paramètres process. 3-15 Syntaxe: G19 ; Le plan de base à la mise sous tension est fixé par le constructeur de machines dans les paramètres process. 3-15 er ème Syntaxe: G20 [1 axe du plan] [2 axe du plan] {axe perpendiculaire} ; Lors de la sélection de plan libre avec G20, la CN désactive la vitesse de coupe constante (G96) et active la fonction vitesse de broche en t/mn (G97). Elle sélectionne aussi l'interpolation linéaire. 3-15 14-4 Annexe Manuel de programmation CN 17VRS II. G30 à G49 Fonction Groupe G G30 17 Signification Description Page Annulation des transformations Syntaxe: G30 ; G30 annule une transformation active. Les axes fictifs ne doivent plus être programmés. 4-56 Syntaxe: G31 ; La CN active le plan G17 et les axes réels correspondant deviennent axes fictifs. 4-51 * Etat de base * modale G31 17 Sélection de l'usinage frontal * modale G32 Sélection de l'usinage sur corps de cylindre * modale G33 16 Filetage * bloc G36 21 Logique de déplacement pour axe rotatif sans fin * modale G37 21 Logique de déplacement pour axe rotatif sans fin * modale G38 G40 21 3 Logique de déplacement pour axe rotatif sans fin Syntaxe: G32 RI w ou G32 RI=w ; La CN engendre des droites et des cercles sur un corps de cylindre. Avant la sélection de l'usinage sur corps de cylindre, il doit y avoir au minimum un axe rotatif développant de plan de travail.. Syntaxe: G33 <Point final> <Pas> <Angle de départ> ; G33 exécute un filetage longitudinal, plan ou conique à pas constant, simple ou multiple. Syntaxe: G36 ; Positionnement avec calcul modulo 'Chemin le plus court'. Le calcul modulo ne peut se faire qu'en programmation absolue (G90). Syntaxe: G37 ; Positionnement avec calcul modulo 'Direction positive'. Le calcul modulo ne peut se faire qu'en programmation absolue (G90). 4-54 4-24 4-49 4-51 * modale Syntaxe: G38 ; Positionnement avec calcul modulo 'Direction négative. Le calcul modulo ne peut se faire qu'en programmation absolue (G90). Annulation de correction de trajectoire d'outils Syntaxe: G40 ; Si une correction de trajectoire d'outils est annulée, le mouvement suivant doit être une droite dans le plan d'usinage. 5-34 Syntaxe: G41 ; Si G41 est programmé alors que G40 ou G42 était actif, le mouvement suivant doit être une droite dans le plan d'usinage. 5-35 Syntaxe: G42 ; Si G42 est programmé alors que G40 ou G41 était actif, le mouvement suivant doit être une droite dans le plan d'usinage. 5-35 Syntaxe: G43 ; Lorsque G41 ou G42 est actif, un arc de cercle est inséré comme élément de transition sur les angles saillants. 5-37 Syntaxe: G44 ; Lorsque G41 ou G42 est actif, un chanfrein est inséré comme élément de transition sur les angles supérieurs à 90°. 5-37 Syntaxe: G47 ; lors de déplacements en direction de l'axe d'outil, toutes les données de position font référence au nez de broche. 5-40 Syntaxe: G48 ; La longueur d'outil programmée est compensée dans le sens positif en direction de l'axe principal. 5-40 Syntaxe: G49 ; La longueur d'outil programmée est compensée dans le sens négatif en direction de l'axe principal. 5-40 4-51 * Etat de base, * modale G41 3 Correction de trajectoire d'outils à gauche * modale G42 3 Correction de trajectoire d'outils à droite * modale G43 10 Arc de cercle comme élément de transition * Etat de base, * modale G44 10 Chanfrein comme élément de transition * modale G47 13 Annulation correction longueur d'outil * Etat de base , *modale G48 13 Correction longueur d'outil positive * modale G49 13 Correction longueur d'outil négative * modale DOK-MTC200-NC**PRO*V17-ANW1-FR-P Annexe 14-5 Manuel de programmation CN 17VRS III. G50 à G73 Fonction Groupe G G50 16 Description Signification Décalage absolu d'origine programmable Page Syntaxe: G50 <Axe> ; Décalage absolu du point d'origine d'usinage de la valeur de l'axe programmé sous G50. 3-12 Syntaxe: G51 <Axe> ; Décalage relatif du point d'origine d'usinage de la valeur de l'axe programmé sous G51. 3-12 Syntaxe: G52 <Axe> ; Une origine pièce est programmée avec la valeur programmée sous l'adresse d'axe. Tous les DPO sont annulés. 3-13 Syntaxe: G53 ; Passage du système de coordonnées pièce au système de coordonnées machine. 3-14 Syntaxe: G54-G59 ; Les décalages sont programmés sous l'IHM G54..G59 sont annulés pas G52 ou G53. 3-8 Syntaxe: G61 ; La position à atteindre est accostée à l'intérieur d'une limite de précision déterminée. 4-10 4-12 modale Syntaxe: G62 ; Avec la programmation de G62 les discontinuités de trajectoire et les transitions non tangentielles sont arrondies. Taraudage sans mandrin compensateur Syntaxe: G63 <Point d'arrivée> <Avance par tour de broche[F]> ; Avec G63, la broche est arrêtée à la fin du mouvement. 4-30 Syntaxe: G64 <Point d'arrivée> <Avance par tour de broche[F]> ; Avec G64, la broche reste en rotation à la fin du mouvement. 4-30 Syntaxe: G65 <Avance par tour de broche[F]> ; G65 permet le taraudage avec des broches sans capacité d'interpolation. 4-34 Syntaxe: G66 S <Vitesse périphérique de meule constante> ; La valeur de S programmée avec G66 est interprétée en m/s ou pied/s. 4-44 Syntaxe: G70 ; L'unité de programmation de base est fixée par le constructeur de machine dans les paramètres process. 3-20 3-21 * modale Syntaxe: G71 ; L'unité de programmation de base est fixée par le constructeur de machine dans les paramètres process. Annulation de la fonction miroir Syntaxe: G72 ; La fonction miroir de tous les axes est annulée. * bloc G51 16 Décalage relatif d'origine programmable * bloc G52 4 Décalage d'origine pièce programmable * modale G53 4 Annulation des décalages d'origine * Etat de base , *modale G54 G59 4 Décalages d'origine réglables * modale G61 11 Arrêt précis * modale G62 G63 11 16 Changement de bloc au vol * * bloc G64 16 Taraudage sans mandrin compensateur * bloc G65 7 Taraudage avec broche comme axe maître * modale G66 8 Vitesse périphérique de meule constante (SUG) * modale G70 9 Unité de mesure Inch * modale G71 G72 9 18 Unité de mesure millimètre 3-22 * Etat de base , * modale G73 18 Sélection de la fonction miroir * modale DOK-MTC200-NC**PRO*V17-ANW1-FR-P Syntaxe: G73 <Désignation d'axe>-1 ; Les coordonnées de l'axe programmé sous la désignation d'axe sont inversées. 3-22 14-6 Annexe Manuel de programmation CN 17VRS IV. G74 à G99 Fonction Groupe G G74 16 Signification Description Page Prise d’origine axe Syntaxe: G74 <Désignation d'axe> <Valeur de coordonnée> <Avance> ; G74 active G40, G47,G53, G90, G94 3-26 Syntaxe: G75 <Désignation d'axe> <Valeur de coordonnée> <Avance> ; G75 est possible avec G90 ou G91 3-26 Annulation de toutes les précontraintes d'axe * bloc Syntaxe: G76 ; G76 annule les précontraintes de tous les axes déplacés contre butée avec G75. 3-28 Retrait et ré accostage * bloc Syntaxe: G77 <Désignation d'axe> <Valeur de coordonnée[0)> ; Les valeurs de coordonnées d'origine (Vitesse de rotation de broche) sont rétablies. Annulation de la fonction d'échelle Syntaxe: G78 ; Le facteur d'échelle de tous les axes est annulé. * bloc G75 16 Déplacement contre butée * bloc G76 G77 G78 16 16 19 3-29 3-24 * Etat de base , * modale G79 G90 19 6 Activation de la fonction d'échelle * modale Syntaxe: G79 <Désignation d'axe> <Facteur d'échelle> ; Les cotes de déplacements des axes concernés sont diminuées ou agrandies. Programmation absolue Syntaxe: G90 ; Toutes les données de cotes se rapportent à une origine fixe. 3-24 3-3 * Etat de base , * modale G91 6 Programmation relative Syntaxe: G91 ; Toutes les données de cotes suivantes se réfèrent à la position de départ du bloc. 3-4 4-47 * bloc Syntaxe: G92 S<Valeur limite de vitesse de rotation de broche> ; La valeur limite fixée reste modale. Programmation en temps Syntaxe: G93 F<Temps en secondes> ; G93 masque G94 ou G95 dans le bloc. * modale G92 G93 16 16 Limitation de vitesse de broche 4-37 * bloc G94 7 Programmation en vitesse Syntaxe: G94 ; La valeur de F programmée est interprétée comme avance en mm/min. G94 est annulé par G95 ou G65. 4-38 Syntaxe: G95 F<Avance par tour> ; La valeur de F programmée est interprétée comme mm ou inch par tour de broche. 4-38 4-44 * modale Syntaxe: G96 S<Vitesse de coupe constante en m/min> ; La CNC calcule la vitesse de broche adaptée en fonction du diamètre actuel. Vitesse de rotation broche en t/min Syntaxe: G97 ; Avec la programmation de G97 la valeur S est interprétée en t/min. 4-47 Syntaxe: G98 ; Lorsque G41 ou G42 est actif, il n'y a pas de correction de vitesse de trajectoire sur les arcs de cercle. 5-38 Syntaxe: G99 ; Lorsque G41 ou G42 est actif, la vitesse de trajectoire sur les arcs de cercle est corrigée. 5-38 * Etat de base , *modale G95 7 Avance par tour * modale G96 G97 8 8 Vitesse de coupe constante * Etat de base , * modale G98 12 Vitesse du centre d'outil constante * Etat de base , * modale G99 12 Vitesse de contour constante * modale DOK-MTC200-NC**PRO*V17-ANW1-FR-P Annexe 14-7 Manuel de programmation CN 17VRS V. ACC à BTE Fonction ACC AP AXD BEQ BER BES BEV BMI BNE BPL BRA BRF BSE Groupe G Signification Description Page Accélération programmable 4-13 * modale Syntaxe: ACC <Constante> ; L'accélération des axes programmés dans le bloc avec ACC est limitée en pour cent à la valeur donnée. Démarrage programme d'avance Syntaxe: AP <Process> ; Le programme sélectionné par SP pour le process donné est démarré. 9-3 Echange de données avec entraînement numérique Syntaxe : AXD(<Désignation d'axe>: <N° identification SERCOS >) ; Lecture et écriture de données entraînement par l'interface SERCOS. Saut sur résultat nul Syntaxe: BEQ <Adresse de saut> ; Si le dernier résultat était égal à zéro, le programme est dérouté à l'adresse indiquée. Saut sur remise à 0 d'évènement Syntaxe: BER <Adresse de saut> <Numéro de process>: <Numéro d'évènement> ; Sur remise à 0 d'événement, le programme est dérouté à l'adresse indiquée. Saut sur mise à 1 d'évènement Syntaxe: BES <Adresse de saut> <Numéro de process>: <Numéro d'évènement> ; Sur mise à 1 d'événement, le programme est dérouté à l'adresse indiquée. Appel de sousprogramme sur événement à 1 (Interruption) Syntaxe: BEV <Adresse de saut>: <Numéro d'évènement> ; L' instruction BEV active la surveillance d'événement. Si l'évènement prend la valeur 1, le sous-programme est exécuté. 7-6 Saut sur résultat négatif Syntaxe: BMI <Adresse de saut> ; Si le dernier résultat était inférieur à zéro, le programme est dérouté à l'adresse indiquée. 9-16 Saut sur résultat différent de 0 Syntaxe: BNE <Adresse de saut> ; Si le dernier résultat était différent de zéro, le programme est dérouté à l'adresse indiquée 9-16 Saut sur résultat supérieur ou égal à0 Syntaxe: BPL <Adresse de saut> ; Si le dernier résultat était supérieur ou égal à zéro, le programme est dérouté à l'adresse indiquée. 9-16 Saut inconditionnel Syntaxe: BRA <Adresse de saut> ; Le programme est dérouté à l'adresse indiquée. Saut sur axes initialisés Syntaxe: BRF <Adresse de saut> ; Si les axes sont initialisés, le programme est dérouté à l'adresse indiquée. Saut si broche vide Syntaxe: BSE <Adresse de saut> Ø BSE .SPLE ; L'instruction BSE permet de déterminer si la broche est 11-1 9-16 9-15 9-15 9-9 9-15 8-9 vide. BSR BST BTE Appel de sous programme Syntaxe: BSR <Adresse de saut> ; Le programme se continue à l'adresse indiquée dans le paramètre de l'instruction.. 9-11 Saut avec arrêt Syntaxe: BST <Adresse de saut> ; Le programme est dérouté à l'adresse indiquée et les conditions de base sont activées. 9-8 Syntaxe: BTE <Adresse de saut> ; Le programme est dérouté à l'adresse indiquée si T0 a été programmé. 9-15 Saut si T0 a été programmé DOK-MTC200-NC**PRO*V17-ANW1-FR-P 14-8 Annexe Manuel de programmation CN 17VRS VI. CEV à MOP Fonction Groupe G Signification Description Page Effacement de la surveillance d'évènement (Interruption) Syntaxe: CEV: <Numéro d'évènement> ; Une surveillance d'événement activée (BEV, JEV) est effacée 7-7 Sélection d'une correction D Syntaxe: D<D-Korrektur Nummer[0..99]> ; D 1..99 Sélection d'un décalage additif de géométrie d'outil si G48/G49 ou G41/G42 sont actifs. D0 Annulation du décalage. 5-41 Unité angulaire degré Syntaxe: DEG ; Arguments et fonctions inverses des fonctions angulaires SIN, COS, TAN, et ASIN, ACOS, ATAN en degré. 10-5 Masquage de surveillance d'évènements (Interruption) Syntaxe: DEV ; Une surveillance d'événement activée (BEV, JEV) est masquée. 7-7 Définition de process Syntaxe: DP <Process> ; L'automate est informé que le process est nécessaire à l'exécution du programme. 9-2 Sélection d'arête de coupe Syntaxe: E<Constante> ; L'arête de coupe définie par la constante devient arête active. 8-2 Activation de la surveillance d'évènement Syntaxe: EEV ; Une surveillance d'événement masquée (BEV, JEV) est réactivée. 7-7 FAX, GAX Transfert d'axe entre process Syntaxe: FAX (<Désignation d'axe>) ,GAX (<Process>: <Désignation d'axe>) ; FAX libère l'axe; GAX sollicite l'axe. 9-5 HLT Arrêt programmé Syntaxe: HLT ; Le déroulement programme est interrompu, un nouveau départ cycle est attendu. 9-8 Déroutement programme sur événement à 1 (Interruption) Syntaxe: JEV <Adresse de saut> <Numéro d'évènement> ; L'instruction JEV active la surveillance d'événement. Si l'événement prend l'état 1, le programme se continue à l'adresse indiquée. 7-6 Saut dans un autre programme CN Syntaxe: JMP <Numéro de programme> ; Le déroulement du programme se continue dans le programme indiqué. 9-9 Appel d'un programme CN comme sousprogramme Syntaxe: JSR <Numéro de programme> ; Le programme indiqué est exécuté comme sous programme. 9-10 LP Verrouillage de process Syntaxe: LP <Process> ; Le process concerné est mis dans un état défini. 9-4 MEN Libération magasin pour exploitation manuelle Syntaxe: MEN ; A l'aide de l'instruction MEN, le magasin peut être déplacé en manuel durant l'exploitation en automatique. 8-7 Déplacement sur emplacement libre Syntaxe: MFP(<Position>,<Direction>) { (.,.) optionnel} ; L'axe de magasin d'outil est déplacé vers le premier emplacement libre. 8-6 Déplacement magasin sur position de base Syntaxe: MHP(<Direction>) { (.) optionnel} ; L'axe de magasin d'outil est déplacé vers la position de base (Place 1). 8-3 Déplacement emplacement programmé en position Syntaxe: MMP(<Position>,<Direction>) { (.,.) optionnel} ; L'axe de magasin d'outil est déplacé sur l'emplacement adressé par le mot T. 8-5 Déplacement vers position d'origine Syntaxe: MOP(<Position>,<Direction>, <Broche>) { (.,., ) optionnel} ; L'axe de magasin d'outil est déplacé sur l'emplacement d'où l'outil a été pris. 8-6 CEV D *modale DEG DEV DP E *modale EEV JEV JMP JSR MFP MHP MMP MOP DOK-MTC200-NC**PRO*V17-ANW1-FR-P Annexe 14-9 Manuel de programmation CN 17VRS VII. MRF à SE Fonction MRF MRY MTD MTP NMP O OTD P PMP POK RAD RE RET REV RP RTS SE Groupe G Signification Description Page Prise d’origine magasin d’outil Syntaxe: MRF ; L'axe de magasin d'outil est envoyé en position d'origine. 8-3 Attente jusqu'à position atteinte Syntaxe: MRY ; Le déroulement du programme est suspendu jusqu'à ce que le magasin d'outil soit en position. Lecture et écriture d'éléments de donnée machine Syntaxe: MTD([N° de page],[Index1], [Index 2], [N0 élément.) ; Un nombre quelconque d'éléments de donnée machine peut être lu dans un bloc CN. Un seul peut être écrit. Déplacement outil en position Syntaxe: MTP(<Position>,<Direction>) { (.,.) optionnel } ; L'outil magasin est déplacé à la position donnée. Valeur de pos. sur front négatif entrée palpeur Syntaxe: NMP(<Désignation d'axe>) ; La fonction NMP n'est disponible que sur les entraînements analogiques. 11-1 Sélection de banque de PO pour G54..G59 Syntaxe: O <Numéro de banque de point d'origine> ; En fonction du réglage des paramètres, une banque de point d'origine de 0 à 9 peut être sélectionnée. 3-10 Lecture et écriture de données DPO Syntaxe: OTD([Mémoire CN],[Process],[Banque DPO], [Décalage],[Axe]) Rotation de coordonnées uniquement avec G50, G51, G54 .. G59 Syntaxe: G50-G51 P<Angle> ; La rotation de coordonnées est toujours active dans le plan actuel et est activée dans le bloc suivant. 3-6 Valeur de pos. sur front positif entrée palpeur Syntaxe PMP(<Désignation d'axe>) ; La fonction PMP n'est disponible que sur les entraînements analogiques. 11-1 Usinage terminé Syntaxe: POK ; L'instruction POK permet de déterminer que l'usinage est terminé. 9-5 Unité angulaire radian Syntaxe: RAD ; Arguments et fonctions inverses des fonctions angulaires SIN, COS, TAN, et ASIN, ACOS, ATAN en radian. 10-5 Remise à 0 d'évènement Syntaxe: RE <Numéro de process>: <Numéro d'évènement> ; L'événement défini est remis à 0 et reste à 0 jusqu'à mise à 1 par instruction SE. Fin de programme avec remise à 0 Syntaxe: RET ; Il y a saut au premier bloc et l'état de base est réinitialisé. Chargement de vecteur de retrait Syntaxe: REV <Adresse de saut> ; L'adresse de saut donnée est définie comme première adresse de programme de retrait. 9-12 Démarrage programme de retrait Syntaxe: RP <Process> ; Pour le process donné, le programme adressé par le vecteur de retrait est démarré. 9-3 Retour de sousprogramme Syntaxe: RTS ; Il y a retour au programme appelant, le déroulement programme se continue au bloc suivant. 9-11 Mise à 1 d'évènement Syntaxe: SE <Numéro de process>: <Numéro d'évènement> ; L'événement défini est mis à 1 et reste à 1 jusqu'à remise à 0 par instruction RE. DOK-MTC200-NC**PRO*V17-ANW1-FR-P 8-7 11-14 8-4 11-6 7-2 9-8 7-1 14-10 Annexe Manuel de programmation CN 17VRS VIII. SP à WP Fonction SP SPC Groupe G Signification Description Page Sélection de programme pour un process Syntaxe: DP <Process> <Numéro de programme> ; Le programme donné est sélectionné pour le process donné. 9-2 Sélection broche de référence pour la transformation* Syntaxe: SPC <Numéro de broche> ; SPC sélectionne la broche de référence pour la transformation. La sélection de broche doit se faire avant l'appel de la transformation. modale SPF Syntaxe: SPF <Numéro de broche> ; SPF sélectionne la broche de référence pour G33, G63/G64, G65, G95 und G96. 4-43 8-2 * modale Syntaxe: SPT <Numéro de broche> ; SPT sélectionne la broche d'outil pour la sélection d'arête de coupe E. Sélection et appel d'outil Syntaxe: T<Constante> ; Le numéro ou l'emplacement d'outil donné est sélectionné. 8-1 Exécution changement d'outil complet Syntaxe: TCH(<Position>,<Broche>) { (.,.) optionnel } ; Changement d'outil complet entre broche et magasin. 8-8 Accès aux données d'outil par le programme Syntaxe: TLD([Process],[Adresse],[Stock /Numéro d'outil], [Numéro place/duplo],[Arête de coupe], [Elément de donnée],[Etat]) Changement d’outil du magasin dans la broche Syntaxe: TMS(<Position>,<Brochel>) { (.,.) optionnel } ; Echange d’outil entre magasin et broche. 8-8 Changement d’outil de la broche dans le magasin Syntaxe: TSM(<Position>,<Broche>) { (.,.) optionnel } ; Echange d’outil entre broche et magasin. 8-9 Attente jusqu'à remise à 0 d'évènement Syntaxe: WER <Numéro de process>: <Numéro d'évènement> ; Le déroulement programme est interrompu jusqu'à ce que l'événement soit remis à 0. Attente jusqu'à mise à 1 d'évènement Syntaxe: WES <Numéro de process>: <Numéro d'évènement> ; Le déroulement programme est interrompu jusqu'à ce que l'événement soit mis à 1. Attente de process Syntaxe: WP <Process> ; Le déroulement programme est interrompu jusqu'à ce que le process soit terminé. Sélection broche de référence * modale SPT T TCH TLD TMS TSM WER WES WP 4-56 Sélection de broche d'outil 11-8 7-3 7-2 9-3 DOK-MTC200-NC**PRO*V17-ANW1-FR-P Annexe 14-11 Manuel de programmation CN 17VRS Tableau des fonctions G Légende * P S Etat de base L'état de base peut être défini par paramètre process Actif dans le bloc I. G00 à G50 Fonction G Signification Syntaxe Page G00 P Interpolation linéaire en rapide G00 4-14 G01 P Interpolation linéaire G01 4-15 G02 Interpolation circulaire sens horaire G02 <Point d'arrivée> <Paramètres d'interpolation [I,J,K]> ou <Rayon[R]> 4-16 G03 Interpolation circulaire sens anti-horaire G03 <Point d'arrivée> <Paramètres d'interpolation [I,J,K]> ou <Rayon[R]> 4-16 Temporisation G04 F<Temps en secondes.> 4-39 Interpolation à faible erreur de poursuite G06 4-2 Interpolation avec erreur de poursuite G07 4-5 Passage de bloc à vitesse optimale G08 4-7 G04 S G06 G07 * G08 G09 * Passage de bloc à vitesse limitée G09 4-9 G15 P Programmation au rayon G15 3-19 G16 P Programmation au diamètre G16 3-19 G17 P Sélection de plan XY G17 3-15 G18 P Sélection de plan ZX G18 3-15 G19 P Sélection de plan YZ G19 3-15 er ème Sélection de plan libre G20 [1 axe du plan] [2 {Axe perpendiculaire} Annulation de transformation G30 4-56 G31 Sélection d'usinage frontal G31 4-51 G32 Sélection d'usinage sur corps de cylindre G32 RI w ou G32 RI=w 4-54 G20 G30 * axe du plan] 3-15 G33 S Filetage G33 <Point d'arrivée> <Pas> <Angle de départ> 4-24 G36 P Logique de déplacement axe circulaire G36 (Chemin le plus court) 4-49 G37 P Logique de déplacement axe circulaire G37 (Direction positive) 4-51 G38 P Logique de déplacement axe circulaire G38 (Direction négative) 4-51 G40 * Annulation correction de trajectoire d’outil G40 5-34 G41 Correction de trajectoire d'outil à gauche G41 5-35 G42 Correction de trajectoire d'outil à droite G42 5-35 G43 Insertion arc de cercle de transition G43 5-37 G44 Insertion chanfrein de transition G44 5-37 G47 P Pas de correction de longueur d'outil G47 5-40 G48 P Correction de longueur d'outil positive G48 5-40 Correction de longueur d'outil négative G49 5-40 Décalage absolu programmable de point d'origine G50 <Désignation d'axe(en)> <Valeur de coordonnées> 3-12 G49 G50 S DOK-MTC200-NC**PRO*V17-ANW1-FR-P 14-12 Annexe Manuel de programmation CN 17VRS II. G51 à G99 Fonction G G51 S G52 Signification Syntaxe Page Décalage relatif programmable de point d'origine G51 <Désignation d'axe(en)> <Valeur de coordonnées> 3-12 Origine pièce programmable G52 <Désignation d'axe(en)> <Valeur de coordonnées> 3-13 G53 P Annulation décalages d'origine G53 3-14 G54 P Décalage d'origine réglable 1 G54 3-8 G55 P Décalage d'origine réglable 2 G55 3-8 G56 P Décalage d'origine réglable 3 G56 3-8 G57 P Décalage d'origine réglable 4 G57 3-8 G58 P Décalage d'origine réglable 5 G58 3-8 G59 P Décalage d'origine réglable 6 G59 3-8 Arrêt précis G61 4-10 G61 G62 * Changement de bloc au vol G62 4-12 G63 S Taraudage sans mandrin de compensation G63 <Point d'arrivée> <Avance par tour de broche[F]> 4-30 G64 S Taraudage sans mandrin de compensation G64 <Point d'arrivée> <Avance par tour de broche[F]> 4-30 G65 Taraudage, broche = axe maître G65 <Avance par tour de broche[F]> 4-34 G66 Vitesse périphérique de meule constante (SUG) G66 S <Vitesse périphérique de meule constante> 4-44 G70 P Unité de mesure Inch G70 3-20 G71 P Unité de mesure millimètre G71 3-21 G72 * Annulation fonction miroir G72 3-22 Sélection fonction miroir G73 <Désignation d'axe>-1 3-22 G73 G74 S Prise d’origine axe G74 <Désignation d'axe> <Valeur de coordonnées> <Avance> 3-26 G75 S Déplacement contre butée G75 <Désignation d'axe> <Valeur de coordonnées> <Avance> 3-26 G76 S Annulation précontraintes axe G76 3-28 G77 S Retrait et ré accostage G77 <Désignation d'axe> < Valeur de coordonnées [0]> 3-29 G78 * Annulation fonction facteur d'échelle G78 3-24 Sélection fonction facteur d'échelle G79 <Désignation d'axe> <Facteur d'échelle> 3-24 Programmation absolue G90 3-3 Programmation relative G91 3-4 G79 G90 * G91 G92 S Limitation vitesse de broche G92 S<Valeur limite de vitesse de rotation> 4-47 G93 S Programmation en temps G93 F<Temps en secondes> 4-37 G94 P Programmation de vitesse G94 4-38 G95 P Avance par tour G95 F<Avance par tour> 4-38 G96 P Vitesse de coupe constante G96 S<Vitesse de coupe constante en m/min> 4-44 G97 P Vitesse de rotation broche en t/min G97 4-47 G98 * Vitesse de centre d’outil constante G98 5-38 Vitesse au contour constante G99 5-38 G99 DOK-MTC200-NC**PRO*V17-ANW1-FR-P Annexe 14-13 Manuel de programmation CN 17VRS En-tête de fichier Il est possible d'utiliser un éditeur de texte externe à la place de celui disponible dans l'IHM. Importation de données Les programmes CN créés de cette façon doivent posséder un entête afin de pouvoir être lus, au moyen de la fonction 'Importation de données' dans le répertoire programme correspondant. L'entête est composé de la façon suivante: Exemple: %NPG:0:01:1:001 !01.00 #Jeu de paramètre 1 1670127.04.9719:05:04 $Texte de commentaire ... $ Texte de commentaire... $ Texte de commentaire... $ Texte de commentaire... *Progr. Nr. 1 %NPG Les lignes de l'entête ont la signification suivante: Code Signification Plage de valeur %NPG Identifie le fichier comme programme CN - :0 N° d'appareil 0 - 15 :01 N° de paquet CN 01 - 99 :1 N° de process 0-6 :001 N° de répertoire 001 - 099 !01.00 Version - # Jeu de paramètre 1 Jeu de paramètre sous lequel le programme a été créé - $Texte de commentaire ... 4 lignes de commentaire max. 78 caractères par ligne *Progr. Nr. 1 Descripteur de programme max. 32 caractères %NPG Marque la fin de l'entête - Fig. 14-Fehler! Unbekanntes Schalterargument.: Entête d'un fichier programme Entête minimale Lors de l'exportation d'un programme CN sur un support de données externe un entête complèt est généré. Lors de l'importation, seul un entête minimum est nécessaire. Il est composé des chaînes de caractères suivantes: %NPG:0:00:0:000 !01.00 # $ *Descripteur %NPG Si, après importation, un descripteur de programme doit apparaître dans le répertoire de programmes, il doit être introduit avec '*'. Lors de l'importation d'un programme CN, l'entête est, à l'exception du descripteur DOK-MTC200-NC**PRO*V17-ANW1-FR-P 14-14 Annexe Manuel de programmation CN 17VRS et des lignes de commentaires, écrasé avec les valeurs actuelles de numéro d'appareil, de paquet CN, de process, de répertoire et avec le jeu de paramètres actifs.. Numéros de blocs CN Dans le point 2 du menu principal 'Traitement du programme CN' de l'IHM, différentes options peuvent être déterminées. Vis à vis des fonctions Import/Export de données, on peut définir, à cet endroit, si les numéros de blocs CN doivent être émis ou non. En tenant compte de ce fait, il y a quatre combinaisons possibles déterminant si le programme créé à l'extérieur doit contenir les numéros de bloc ou non: Nr. Fichier à importer Emettre les numéros des blocs CN 1 avec numéros de bloc oui 2 sans numéro de bloc oui 3 avec numéros de bloc non 4 sans numéro de bloc non Fig. 14-Fehler! Unbekanntes Schalterargument.: Emission de numéros de blocs CN Seules les combinaisons 1 et 4 débouchent sur un programme CN importé correct. Si le fichier importé contient des numéros de blocs, l'option pour l'émission des numéros de blocs CN doit être sur OUI. Dans le cas contraire, elle doit être sur NON. DOK-MTC200-NC**PRO*V17-ANW1-FR-P Manuel de programmation CN 17VRS Index 15-1 ,QGH[ ‘ ‘DEG’ ‘RAD’ 10-5 10-5 A ABS ACC Accélération programmable 'ACC' Accès aux données d’outils par le programme CN 'TLD' Accès aux données d'outil par le programme CN ‘TLD’ Bits d'état de point de coupe Conditions générales Ecriture avec une instruction TLD Lecture avec une instruction TLD Paramètres optionnels Plage de valeur Signification Vérifications générales Vérifications lors de l'écriture 10-7 4-13 4-13 5-40 11-8 11-11 11-11 11-12 11-12 11-11 11-8 11-8 11-12 11-12 Accès aux données d'outil par le programme CN 'TLD' Signification 5-41 Accès aux données d'outil par le programme CN 'TLD' Plage de valeurs ACOS Adresse S Adresses disponibles structure d'adresse étendue Affectation de variables et fonctions mathématiques Affectations possibles entre AXD, OTD, TLD, DCD, MTD Affectations entre instructions AXD, OTD, TLD, DCD et MTD Affectations interdites Affectations possibles Emploi d’instructions AXD Affectations interdites Affectations possibles Emploi d’instructions DCD Affectations interdites Affectations possibles Emploi d’instructions MTD Affectations interdites Affectations possibles Emploi d’instructions OTD Affectations interdites Affectations possibles Emploi d’instructions TLD Affectations interdites Affectations possibles Angle de rotation Annulation des transformations 'G30' Arrêt précis 'G61' Arrondi ASIN ATAN Avance Avance par tour 'G95' Avances par tour (G95) Axes Axes entraînés et axes Gantry Axes linéaires et rotatifs auxiliaires Axes linéaires principaux DOK-MTC200-NC**PRO*V17-ANW1-FR-P 5-41 10-9 6-3 2-9 2-9 10-1 11-16 11-18 11-18 11-18 11-16 11-16 11-16 11-17 11-17 11-17 11-18 11-18 11-18 11-17 11-17 11-17 11-17 11-17 11-17 Voir Décalages d’origine 4-56 4-10 12-1 10-8 10-9 4-36 4-38 3-17 4-1 4-61 4-2 4-1 15-2 Index Manuel de programmation CN 17VRS Axes rotatifs principaux 4-1 B Blocs de déplacement Blocs optionnels 4-1 Voir Eléments d’un bloc CN C Centre de tournage Sélection et assignation des axes 3-18 Chanfrein Chanfreins et arrondis 12-1 12-1 Commandes interdites Continuité des blocs de déplacement Insertion d'arrondi Insertion de chanfrein Pas de variables 12-3 12-2 12-1 12-1 12-3 Changement bloc à la volée 'G62' Commandes de broche ‘M003’, ‘M004’, ‘M005’, ‘M013’,‘ M014’ Commentaire Commentaire dans le programme source Compilateur CN Conditions d’interpolation Correcteurs D Mode d’action des correcteurs D dans les différents plans d’usinage Utilisation Correction de longueur d’outil 4-12 6-2 Voir Mot CN Voir Mot CN 12-1 4-2 1-3, 5-41 5-42 5-42 5-39 Correction de longueur active Correction de longueur inactive Correction de longueur négatice 'G49' Correction de longueur positive 'G48' Pas de correction de longueur 'G47' 5-39 5-39 5-40 5-40 5-40 Correction de trajectoire d’outil 5-25 Annulation de la correction de trajectoire d’outils à la fin du contour Changement de direction de correction Correction de trajectoire d'outil active Correction de trajectoire d'outil inactive Mise en œuvre de la correction de trajectoire d’outils au début du contour Raccordement de contour Angles extérieurs Angles intérieurs Correction d’outil COS 5-32 5-34 5-26 5-25 5-30 5-27 5-27 5-27 5-1 10-8 D Décalages d’origine 3-6 Annulation des décalages d’origine'G53' Banque de point d'origine 'O' Décalage d’origine absolu programmable ‘G50’ Décalage d’origine incrémental programmable 'G51' Lecture et écriture de données DPO dans le programme CN 'OTD' Offset général réglable dans le tableau de point d’origine Point d’origine pièce programmable ‘G52’ Rotation de coordonnées avec angle 'P' 3-14 3-10 3-12 3-12 3-14 3-14 3-13 3-9 Décalages d'origine Décalage d’origine réglable ‘G54 ... G59’ Somme des décalages d'origine 3-8 3-8 Déplacements contre butée fixe 3-26 Déplacements contre butée fixe G75 Suppression de toutes les précontraintes G76 Dimension absolue ’G90 Dimension incrémentale 'G91' Données de dimension Données en pouce 3-26 3-28 3-3 3-4 3-3 3-20 DOK-MTC200-NC**PRO*V17-ANW1-FR-P Manuel de programmation CN 17VRS Index 15-3 E Editeur graphique CN 12-1, 12-13 Fonction Syntaxe 12-13 12-13 Eléments d’un bloc CN 2-5 Blocs optionnels Numéros de bloc 2-6 2-5 Enchaînement de blocs de filetage avec 'G33' Enchaînement de filetage En-tête de fichier Entête minimale Evènements 4-28 4-28 14-13 14-13 7-1 Gestion asynchrone d'évènements Activation de surveillance d'évènement ‘EEV’ Appel de sous-programme sur évènement à 1 ‘BEV’ Effacement de surveillance d'évènement ‘CEV’ Saut de programme sur évènement à 1 ‘JEV’ Suspension de surveillance d'évènement ‘DEV’ Modification d'évènements Attente jusqu'à mise à 1 d'évènement ‘WES’ Attente jusqu'à remise à 0 d'évènement ‘WER’ Mise à 1 d'évènement Remise à 0 d'évènement ‘RE’ Sauts conditionnés par un évènement Saut sur évènement à 0 ‘BER’ Saut sur évènement à 1 ‘BES’ 7-5 7-7 7-6 7-7 7-6 7-7 7-2 7-3 7-1 7-2 7-4 7-4 7-4 Evènements CN Expressions mathématiques 1-3 10-5 Fonctions Arc cosinus -ACOS Arc sinus -ASIN Arc tangente -ATAN Cosinus -COS Logarithmes décimaux - LG Logarithmes en base 2 - LD Logarithmes népériens - LN Partie entière - INT Puissance base 10 - 10^ Puissance base 2 - 2^ Puissance base e - E^ Racine carrée -SQRT Sinus -SIN Tangente -TAN Temps en secondes - TIME Valeur absolue - ABS Opérandes OpérandesConstantes OpérandesConstantes en virgule flottante OpérandesConstantes entières OpérandesConstantes système Opérateurs Addition Division / Multiplication ∗ Reste de division entière (modulo)% Soustraction Parenthèses 10-7 10-9 10-8 10-9 10-8 10-9 10-9 10-9 10-8 10-9 10-9 10-9 10-8 10-8 10-8 10-9 10-7 10-6 10-6 10-6 10-6 10-6 10-7 10-7 10-7 10-7 10-7 10-7 10-7 F F 4-36 Facteur d’échelle 'G78' / 'G79' Filetage 'G33' Fonction Look Ahead étendue 3-24 4-24 12-1, 12-9 ACC_EFF modification de l'accélération effective de trajectoire Accès aux données actuelles ADTRC Segment d'approche pour établissement de la correction de trajectoire BBTRC Buffer de blocs pour la correction de rayon d'outil DOK-MTC200-NC**PRO*V17-ANW1-FR-P 12-11 12-11 12-10 12-9 15-4 Index Manuel de programmation CN 17VRS Continuité des blocs de trajectoire Correction d'accélération en pourcent Gestion d'outils Lecture du rayon d'outil au moment de la compilation METB plus petit temps d'exécution d'un bloc CN Pas de variables Possibilités d'utilisation Rectification d'une broche TL_RADIUS Prédétermination rayon d'outil TRC Correction de trajectoire de rayon d'outil Variables globales VFBT Facteur de vitesse pour transition de bloc Vitesse spécifiques aux axes Fonction M Fonction modale 12-10 12-11 12-11 12-11 12-9 12-10 12-9 12-11 12-10 12-10 12-9 12-9 12-11 6-1 12-1, 12-6 Chanfreins et arrondis Perçage de trous 12-8 12-7 Fonction Q Fonctions Fonctions auxiliaires ‘M’ 6-4 14-3 6-1 Changement de rapport Commandes de broche Arrêt broche Mx05 Rotation broche sens antihoraire et mise en route arrosage Mx14 Rotation broche sens antihoraire Mx04 Rotation broche sens horaire et mise en route arrosage Mx13 Rotation broche sens horaire Mx03 Commandes de programme Arrêt programmé (inconditionnel) ‘M000’ Arrêt programmé conditionnel ‘M001’ Fin de programme ‘M002/M030’ Indexage de broche Fonctions compilateur CN Fonctions d’interpolation Fonctions d'angle SIN, COS, TAN Fonctions G 6-3 6-2 6-2 6-2 6-2 6-2 6-2 6-2 6-2 6-3 12-1 4-14 10-5 14-11 G G 91 G00 G01 G02 G03 G04 G06 G08 G09 G15 Programmation au rayon G16 Programmation au diamètre G17 Sélection du plan XY G18 Sélection du plan ZX G19 Sélection du plan YZ G20 G30 G31 G32 G33 G36 G37 G38 G40 G41 G42 G43 G44 G47 3-4 4-14 4-15 4-16 4-16 4-39 4-2 4-7 4-9 3-19 3-19 3-15 3-15 3-15 3-16 4-56 4-51 4-54 4-24, 4-28 4-49 4-49 4-49 5-34 5-35 5-35 5-37 5-37 5-40 DOK-MTC200-NC**PRO*V17-ANW1-FR-P Manuel de programmation CN 17VRS G48 G49 G50 absolu G51 incrémental G52 G53 G54 ... G59 G61 G62 G63 G65 G66 G70 G72 suppression fonction sur tous les axes G73 – Activation miroir G74 G75 G76 G77 G78 – Désactivation facteur d’échelle sur tous les axes G79 – Activation facteur d’échelle G92 G93 G94 G95 G96 G97 G98 G99 Index 15-5 5-40 5-40 3-12 3-12 3-13 3-14 3-8 4-10 4-12 4-30 4-34 4-44 3-20 3-22 3-22 3-26 3-26 3-28 3-29 3-24 3-24 4-47 4-37 4-38 4-38 4-43, 4-45 4-47 5-38 5-38 I ID 5-5, 5-13 Instruction ACC_EFF Instruction ACD_COMP[...] Instruction ADTRC Instruction AP Instruction AXD Instruction BBTRC Instruction BER Instruction BES Instruction BEV Instruction BSE Instruction BSR Instruction BTE Instruction CEV Instruction CF Instruction de déplacement adresse d’axe valeur de coordonnée Instruction de saut BEQ Instruction de saut BER Instruction de saut BES Instruction de saut BMI Instruction de saut BNE Instruction de saut BPL Instruction de saut BRA Instruction de saut BRF Instruction de saut BSE Instruction de saut BST Instruction de saut BTE Instruction de saut JMP Instruction DEV Instruction DP DOK-MTC200-NC**PRO*V17-ANW1-FR-P 12-11 12-11 12-10 9-3 11-1, 11-16 12-9 7-4 7-4 7-6 8-9 9-11 8-9 7-7 12-2 3-2 3-2 3-2 9-16 9-15 9-15 9-16 9-16 9-16 9-9 9-15 9-14 9-8 9-15 9-9 7-7 9-2 15-6 Index Manuel de programmation CN 17VRS Instruction EEV Instruction GAX Instruction HLT Instruction JEV Instruction JSR Instruction LP Instruction MEN Instruction METB Instruction MFP Instruction MHP Instruction MMP Instruction MOP Instruction MRF Instruction MRY Instruction MTD Instruction MTP Instruction NMP Instruction O Instruction OTD Instruction PMP Instruction POK Instruction RD Instruction RE Instruction RET Instruction REV Instruction RP Instruction RTS Instruction SE Instruction SP Instruction TCH Instruction TL_RADIUS Instruction TLD Instruction TMS Instruction TRC Instruction TSM Instruction VFBT Instruction WER Instruction WES Instruction WP Instructions de changement d’outil 7-7 9-5 9-8 7-6 9-10 9-4 8-7 12-9 8-6 8-3 8-5 8-6 8-3 8-7 11-15, 11-18 8-4 11-1 3-10 3-14, 11-6, 11-17 11-1 9-5 12-2 7-2 9-8 9-12 9-3 9-11 7-1 9-2 8-8 12-10 5-40, 11-8, 11-17 8-8 12-10 8-9 12-9 7-3 7-2 9-3 8-8 Changement de l'outil de la broche dans le magasin ‘TSM’ Changement de l'outil du magasin dans la broche ‘TMS’ Exécution d'un changement d'outil complet ‘TCH’ Saut lorsque la broche est vide ‘BSE’ Saut lorsque T0 a été programmé ‘BTE’ 8-9 8-8 8-8 8-9 8-9 Instructions de commande de programme Arrêt programmé ‘HLT’ Fin de programme avec remise à 0 ‘RET’ Saut avec stop ‘BST’ Saut dans un autre programme ‘JMP’ Saut inconditionnel ‘BRA’ 9-8 9-8 9-8 9-9 9-9 Instructions de commande de process 9-1 Attente d’un process ‘WP’ Définition d’un process ‘DP’ Démarrage du programme retrait ‘RP’ Démarrage programme d’avance ‘AP’ Sélection de programme pour un process ‘SP’ Usinage terminé ‘POK’ Verrouillage de process ‘LP’ 9-3 9-2 9-3 9-3 9-2 9-5 9-4 Instructions de commande de programme Instructions de mouvements du magasin d’outil 9-8 8-3 Accès à l'emplacement précédent ‘MOP’ Accès à un emplacement libre ‘MFP’ Attente jusqu'à position atteinte ‘MRY’ Libération du magasin d'outils pour exploitation manuelle ‘MEN’ Mise en position d'un emplacement programmé 'MMP' Mise en position d'un outil programmé 'MTP' 8-6 8-6 8-7 8-7 8-5 8-4 DOK-MTC200-NC**PRO*V17-ANW1-FR-P Manuel de programmation CN 17VRS Prise d’origine du magasin d’outil ’MRF’ Retour du magasin d’outils en position de base ’MHP’ Instructions pour gestion d’outil INT Interpolation à erreur de poursuite réduite'G06' Interpolation avec erreur de poursuite 'G07' Interpolation circulaire 'G02' / 'G03' Interpolation hélicoïdale Interpolation linéaire, Avance 'G01' Interpolation linéaire, rapide 'G00' Index 15-7 8-3 8-3 8-1 10-8 4-2 4-5 4-16 4-22 4-15 4-14 L LA_OFF LA_ON Lecture et écriture de données DPO par le programme CN ‘OTD’ Conditions générales Ecriture de données DPO Lecture de données DPO Lecture et écriture de données machine Lecture et écriture d'éléments de données machine ‘MTD’ Conditions générales pour l'instruction MTD Vérifications durant l'accès Utilisation des données machine Structure de données nécessaire Lecture et écriture des correcteurs D par le programme CN ‘DCD’ Lettre adresse ACC D 10-3 E 10-2 F 10-2 G 10-3 M 10-4 O 10-3 P 10-2 Q 10-3 R 10-2 S, S[1..3] T 10-2 Lettre adresse E Lettre adresse M Lettre adresse Q Lettre adresse T Lettre d’adresse Lettres adresse I,J,K RX, RY, RZ X, Y, Z, A, B, C, U, V, W Lettres d’adresse disponibles Limitation de vitesse de rotation broche 'G92' Liste d’outils Données de la liste d’outils Unités Unités de temps Liste d’outils Données de la liste d’outils Caractérisation de l'outil Désignation d'outil (ID) Etat de l'outil Magasin Nombre de points de coupe Numéro d'outil Numéro duplo Place Type de correcteur Caractérisation du point de coupe Etat de l'arête de coupe Données de coupe utilisateur DOK-MTC200-NC**PRO*V17-ANW1-FR-P 12-9 12-9 11-6 11-7 11-7 11-7 11-14 11-15 11-15 11-15 11-14 11-14 11-13 10-2 10-2 8-2 6-1 6-4 5-5, 5-13, 8-1 2-6 10-2 10-2 10-2 2-9 4-47 5-17 1-3, 5-11 5-11 5-13 5-13 5-16 5-13 5-16 5-13 5-13 5-13 5-14 5-18 5-19 5-24 15-8 Index Manuel de programmation CN 17VRS Données de coupe utilisateur 1..5 Données de coupe utilisateur 6..10 Données de temps d'utilisation Durée maximale d'utilisation Limite d'alerte Temps d'utilisation restant Données d'emplacement Ancienne place Demi place libre Données d'outil utilisateur Données utilisateur 1..9 Données géométriques Correcteur de rayon (R) Correcteurs de longueur (L1, L2, L3) Registres de géométrie Registres d'offset Registres d'usure Facteurs d'usure Facteur d'usure de rayon (R) Facteurs d'usure de longueur (L1, L2, L3) Unités Unités de longueur Rôle de la liste d’outils Liste de réglage Liste de réglages 5-24 5-24 5-19 5-20 5-19 5-19 5-17 5-17 5-17 5-17 5-17 5-20 5-21 5-21 5-20 5-20 5-20 5-23 5-24 5-23 5-17 5-17 5-11 1-4 Données de la liste de réglages Commentaires Désignation de l’outil (ID) Données de temps d'utilisation Durée d'utilisation actuelle Durée maximale d'utilisation Facteur d'usure Facteurs d'usure Facteurs d'usure de longueur (L1, L2 et L3) Facteurs d'usure de rayon (R) Nombre d'arêtes de coupe Numéro d’outil Reconnaissance de coupe Position du point de coupe Type de correcteur Unités Unités de longueur Unités de temps Valeurs limites de géométrie Longueurs maximales Longueurs minimales Rayon maximum Rayon minimum 5-7 5-5 5-9 5-9 5-9 5-9 5-10 5-10 5-7 5-5 5-7 5-7 5-5 5-7 5-7 5-7 5-9 5-9 5-9 5-9 5-9 Liste de réglages Données de la liste de réglages Caractérisation de l’outil Rôle 5-3 5-5 5-3 Listes de réglages 5-3 M M000 M001 M002/M03 M19S... Marque de saut Miroir des axes de coordonnées Miroir des axes de coordonnées ‘G72’ / 'G73 Miroir d’un axe ' Miroir sur deux axes 3-22 3-22 Mise à 1 d'évènement ‘SE’ Mise en place des outils et des données d'outil Présélection et appel d'outil 'T' Sélection d'arête de coupe 'E' 6-2 6-2 6-2 6-3 Voir Mot CN 3-22 7-1 8-1 8-1 8-2 DOK-MTC200-NC**PRO*V17-ANW1-FR-P Index 15-9 Manuel de programmation CN 17VRS Sélection de la broche d'outil 8-2 MODF_OFF MODF_OFF- Annulation fonction modale MODF_ON MODF_ON(STRI)- Activation fonction modale Mot CN 12-6 12-6 12-6 12-6 2-6 Commentaire Commentaire dans le programme source Marque de saut Remarque 2-8 2-9 2-7 2-8 Mot F Mot S Mot S comme fonction auxiliaire Mx03 Mx04 Mx05 Mx13 Mx14 Mx40 Mx41 Mx42 Mx43 Mx44 4-36 6-4 6-4 6-2 6-2 6-2 6-2 6-2 6-3 6-3 6-3 6-3 6-3 N Numéro de broche Numéros de bloc 4-43, 4-56 Voir Eléments d’un bloc CN O O[0..9] Organisation de la liste de réglage organisation spécifique au programme Organisation des listes de réglage Organisation spécifique à la station 3-10 2-1 2-1 2-1 P P 3-9 Paquet programmes CN Paramètres d’axe Paramètres d’interpolation I, J, K Paramètres process Paramètres SERCOS APR Couplage électronique d'axes et interpolateur de tableau Activation de transformation Annulation de transformation Axe oblique Axe virtuel Echange de données avec entraînements numériques ‘AXD’ Adresse de données Lettre de groupe Munéro de bloc de données Numéro d'identification SERCOS Nunéro du jeu de paramètres Paramètres système Passage de bloc à vitesse réduite 'G09' PHI Point d’origine Point de référence machine Points d’origine Prise d’origine d’axe 'G74' Programmation au diamètre 'G16' Programmation au rayon 'G15' Programmation avec rayon du cercle DOK-MTC200-NC**PRO*V17-ANW1-FR-P 1-3 1-3 4-17 1-3 11-1 11-4 11-5 11-5 11-4 11-5 11-1 11-1 11-1 11-1 11-1 11-1 1-3 4-9 3-9 3-5 3-5 3-26 3-19 3-19 4-20 15-10 Index Manuel de programmation CN 17VRS Programmation CN Programmation CN optimale en temps 13-1 13-1 Instructions qui interrompent la préparation des blocs Priorités Programmation d’axe rotatif Programmation de la vitesse 'G94' Programmation en temps 'G93' Programmation spécifique au process Programme 99 Programme CN - Commutation entre broche et axe C Programmes CN 13-3 13-2 4-38, 4-47 4-38 4-37 2-4 2-2 4-49 2-1 R Rayon d’application 'RX', 'RY', 'RZ' Réaccostage et reprise d’usinage sur le contour Réaccostage en mode programme Réaccostage et reprise d’usinage sur la position finale ‘G77’ 4-47 3-28 3-28 3-29 Voir Mot CN 4-47 4-47 4-47 Remarque RX RY RZ S S 4-42 Sauts conditionnels 9-14 Saut quand broche vide ‘BSE’ Saut quand T0 a été programmé ‘BTE’ Saut si axes initialisés ‘BRF’ Saut sur événement à 0 ‘BER’ Saut sur événement à 1 ‘BES’ 9-14 9-15 9-15 9-15 9-15 Sauts en fonction de résultats arithmétiques Saut quand résultat différent de 0 ‘BNE’ Saut quand résultat égal à 0 ‘BEQ’ Saut quand résultat inférieur à 0 ‘BMI’ Saut quand résultat supérieur ou égal à 0 ‘BPL’ Sélection d’usinage frontal ‘G31’ Sélection de l’usinage sur corps de cylindre ‘G32’ Sélection de la broche de référence 'SPF' Sélection de plan 'G17’, 'G18’, 'G19’ Correction de longueur d’outil Sélection de plan 'G17’, 'G18’, 'G19’ Correction de trajectoire d’outil Interpolation circulaire Sélection libre de plan 'G20’ Correcteurs d’outils et correcteurs D Filetage (G33) Programmation circulaire Taraudage (G63, G64 et G65) Vitesse de coupe constante 9-16 9-16 9-16 9-16 9-16 4-51 4-54 4-43 3-15 3-15 3-15 3-15 3-16 3-17 3-17 3-17 3-17 3-17 Sélection du plan d’interpolation Sélection et annulation de la correction de trajectoire d’outil Annulation de la correction de trajectoire d’outil ’G40’ Correction de trajectoire à droite 'G42' Correction de trajectoire à gauche 'G41' Insertion d'un arc de cercle de transition 'G43' Insertion d'un chanfrein de transition 'G44' Vitesse d'avance constante sur le contour 'G99' Vitesse d'avance du centre d'outil constante 'G98' Signal d’interface 'PxxSMGTWO' Signal d’interface 'PxxSMGWRN' SIN Sous-programme 3-15 5-34 5-35 5-35 5-37 5-37 5-38 5-38 5-19 5-19 10-8 9-9 Appel d’un programme CN en tant que sous-programme ‘JSR’ Appel de sous-programme ‘BSR’ Emboîtement de sous-programme 9-10 9-11 9-10 DOK-MTC200-NC**PRO*V17-ANW1-FR-P Index 15-11 Manuel de programmation CN 17VRS Retour d’un sous-programme ‘RTS’ Structure d’un sous-programme 9-11 9-10 SPT <Numéro de broche> SQRT Structure d’un mot Structure des données 8-2 10-8 2-7 Principe de travail avec vérification automatique de l’équipement Principe de travail sans vérification automatique de l’équipement Structure des données de correction d'outil Structure des données d'outil 5-1 5-1 5-1 Liste d’outils Liste de réglages 5-2 5-2 Structure programme 2-2 Programme 0 Programme 99 Programme d’avance Programme de retrait 2-2 2-2 2-3 2-3 Synchronisation de broches Système de coordonnées Système de coordonnées cartésiennes 4-57 3-1 Voir Système de coordonnées T Tableau des groupes de code G Tableau des groupes de fonctions M TAN Taraudage 'G63' / 'G64' Taraudage 'G65' – Broche comme axe maître Technique de macro Fonctions CN étendues Macro Macros globales Macros locales Technique de sous-programme Temporisation ’G04’ TIME Transfert d’axes entre les process ‘FAX’, ‘GAX’ Libération d’axe - FAX Sollicitation de l’axe - GAX Transformations 14-1 14-2 10-8 4-30 4-34 12-1 12-5 12-3 12-3 12-3 9-9 4-39 10-9 9-5 9-5 9-5 4-51 U Unité d'angle pour les fonctions d'angle et ‘DEG’ Unité de mesure Inch ‘G70’ Unité de mesure mm ‘G71’ 10-5 3-20 3-20 3-21 V Valeur de position sur front négatif de l'entrée palpeur ‘NMP’ Valeur de position sur front positif de l'entrée palpeur ‘PMP’ Valeur numérique Valeurs de position avec entraînements analogiques Variable CN Variables Affectation Affectation de variable Angle Angle de départ P Angle de rotation P Avance Banque de points d'origine Correcteur D Distance d'application Facteur d'accélération Fonction auxiliaire DOK-MTC200-NC**PRO*V17-ANW1-FR-P 11-1 11-1 2-7 11-1 1-3 10-1 10-1 10-2 10-2 10-2 10-2 10-3 10-3 10-2 10-2 10-3 12 Index Manuel de programmation CN 17VRS Fonction G Fonction M Numéro d'arête de coupe Numéro d'outil Paramètres d'interpolation Rayon Valeurs de coordonnées des axes disponibles Vitesse de rotation broche Affectation d'une variable Contenu négatif Représentation Variables binaires Vecteur de retrait 10-3 10-4 10-2 10-2 10-2 10-2 10-2 10-2 10-2 10-1 10-1 7-1 9-12 Pose d'un vecteur de retrait ‘REV’ Effacement par control Reset Pose d'un vecteur de retrait ‘REV’ Pose d'un vecteur de retrait 'REV' Programme d'origine général 9-14 9-12 9-12 Vitesse de coupe constante ’G96’ Vitesse de passage de bloc optimale ’G08’ Vitesse de rotation broche Vitesse de rotation broche en t/min ’G97’ Vitesse périphérique de meule constante (SUG) 'G66' 4-45 4-7 4-42 4-47 4-44 DOK-MTC200-NC**PRO*V17-ANW1-FR-P Manuel de programmation CN 17VRS /LVWHGHVILJXUHV Fig. 1-1: CNC Organisation des données 1-2 Fig. 1-2: Paquet programme CN 1-4 Fig. 2-1: Listes de réglage en organisation spécifique à la station 2-1 Fig. 2-2: Listes de réglage en organisation spécifique au programme 2-1 Fig. 2-3: Organisation du programme CN 2-2 Fig. 2-4: Tour mono broche à deux chariots pour fraisage tourné 2-4 Fig. 2-5: Structure d’un mot 2-7 Fig. 3-1: Système de coordonnées 3-1 Fig. 3-2: Données de dimension absolue 3-3 Fig. 3-3: Données de dimension incrémentale3-4 Fig. 3-4: Points d’origine – Machine de fraisage/perçage 3-6 Fig. 3-5: Points d’origine - tour (usinage chariot avant) 3-6 Fig. 3-6: Décalage d’origine 3-6 Fig. 3-7: Somme des décalages d’origine 3-7 Fig. 3-8: Décalage d’origine réglable G54 3-8 Fig. 3-9 : Décalage d’origine réglable G 54 avec rotation de coordonnées 3-9 Fig. 3-10: Banque de point d’origine sur l’interface opérateur 3-10 Fig. 3-11: Appel de deux banques de points d’origine avec G54 3-11 Fig. 3-12: Décalage d’origine programmable G50 3-12 Fig. 3-13: Appel de G52 3-13 Fig. 3-14: Plans d’usinage 3-15 Fig. 3-15: Principe de fonctionnement de la sélection de plan (Exemple pour l’usinage d’un corps de cylindre avec G20 Z0 C0 X0) 3-16 Fig. 3-16: Position des axes dans le centre de tournage. 3-18 Fig. 3-17: Exemple de programmation au diamètre 3-19 Fig. 3-18: Programmation de base en mm et commutation en inch G70 3-21 Fig. 3-19: Rapport lors de la réflexion d’un et de plusieurs axes de coordonnées 3-23 Fig. 3-20: Exemple de programmation. Facteur d’échelle 3-25 Fig. 3-21: Déplacement contre butée 3-27 Fig. 3-22: Réaccostage en mode programmeFig. 3-23: Reprise d’usinage en mode programme3-29 Fig. 3-24: Réaccostage ou reprise d’usinage du contour 3-30 Fig. 4-1: Axes linéaires (X, Y, Z) et rotatifs (A, B, C) dans un système de coordonnées cartésien 4-2 Fig. 4-2: Interpolation circulaire à faible erreur de poursuite à F8000 mm/min 4-3 Fig. 4-3: Interpolation circulaire à erreur de poursuite réduite, extrait 4-4 Fig. 4-4: Interpolation circulaire à erreur de poursuite réduite avec F1000 mm/min4-4 Fig. 4-5: Interpolation circulaire à erreur de poursuite réduite, extrait à F1000 mm/min 4-5 Fig. 4-6: Interpolation circulaire à F 8000 mm/min et G07 4-5 Fig. 4-7: Interpolation avec G07, extrait 4-6 Fig. 4-8: Interpolation circulaire à F1000 mm/min et G07 4-7 Fig. 4-9: Interpolation circulaire avec G07, extrait à F1000 mm/min 4-7 Fig. 4-10: Passage de blocs avec G08 et F8000. 4-8 Fig. 4-11: Passage de bloc avec G08 de F8000 à F7000. 4-9 Fig. 4-12: Passage de bloc avec G09 à F80004-9 Fig. 4-13: Passage de bloc avec G09 de F8000 à F7000 4-10 DOK-MTC200-NC**PRO*V17-ANW1-FR-P Liste des figures 16-1 Fig. 4-14: Diagramme de contour avec G614-11 Fig. 4-15: Diagramme de vitesse avec G614-11 Fig. 4-16: Diagramme de contour avec G624-12 Fig. 4-17: Diagramme de vitesses avec G624-13 Fig. 4-18: Diagramme de vitesse pour l’accélération programmable. 4-14 Fig. 4-19: Interpolation linéaire, rapide G004-15 Fig. 4-20: Interpolation linéaire G01 avec 2 axes 4-15 Fig. 4-21: Interpolation linéaire, G01 sur 3 axes4-16 Fig. 4-22: Programmation d’un cercle en fonction du plan 4-17 Fig. 4-23: Interpolation circulaire et paramètres d’interpolation 4-18 Fig. 4-24: Cercle entier avec G90 4-18 Fig. 4-25: Cercle entier avec G91 4-19 Fig. 4-26: Interpolation circulaire sur tour, en arrière de l’axe 4-19 Fig. 4-27: Programmation d’un cercle. Détermination du signe du rayon 4-20 Fig. 4-28: Programmation d’un cercle au rayon sur un tour, en arrière de l’axe 4-21 Fig. 4-29: Interpolation hélicoïdale 4-22 Fig. 4-30: Interpolation hélicoïdale avec G904-22 Fig. 4-31: Interpolation hélicoïdale avec G914-23 Fig. 4-32: filetages longitudinaux 4-24 Fig. 4-33: Filetage longitudinal 4-25 Fig. 4-34: Filetage conique 4-26 Fig. 4-35: Filetage plan 4-27 Fig. 4-36: Filetages longitudinaux avec deux parties à pas différents 4-28 Fig. 4-37: Enchaînement filetage 4-29 Fig. 4-38: taraudage avec G63 4-31 Fig. 4-39: Taraudage avec G63 et G64 4-32 Fig. 4-40: Taraudage avec G65 4-35 Fig. 4-41: Interpolation linéaire, G01 avec 2 axes et programmation en temps 4-37 Fig. 4-42: Vitesse de trajectoire en filetage 4-40 Fig. 4-43: Vitesse d'avance (F) sans RZ 4-41 Fig. 4-44: Vitesse d'avance (F) avec RZ 4-41 Fig. 4-45: Filetage longitudinal avec la deuxième broche 4-44 Fig. 4-46: Tournage transversal 4-46 Fig. 4-47: Usinage d'une rainure en spirale sur la face frontale 4-48 Fig. 4-48: Positionnement avec calcul modulo ‘Chemin le plus court’ (G36) 4-50 Fig. 4-49: Positionnement avec calcul modulo ‘Direction positive’ (G37) 4-50 Fig. 4-50: Positionnement avec calcul modulo ‘Direction négative (G38) 4-50 Fig. 4-51: Usinage frontal et sur corps de cylindre 4-51 Fig. 4-52: Usinage frontal avec transformation4-53 Fig. 4-53: Usinage sur corps de cylindre 4-54 Fig. 4-54: Usinage sur corps de cylindre avec transformation 4-55 Fig. 5-1: Principe de travail avec vérification automatique de l’équipement 5-1 Fig. 5-2: Principe de travail sans vérification automatique de l’équipement 5-1 Fig. 5-3: Détermination du type de correcteur5-6 Fig. 5-4: Positions possibles du point de coupe5-8 Fig. 5-5: Détermination du type de correcteur5-15 Fig. 5-6: Position possible du point de coupe5-18 Fig. 5-7: Correction de longueur L3 sur un foret. 5-21 Fig. 5-8: Correction de rayon R sur une fraise de dégrossissage 5-21 Fig. 5-9: Exemple pour la mesure d'un outil de perçage 5-22 Fig. 5-10: Exemple pour la mesure d'un outil de tournage 5-23 Fig. 5-11: Apparition de défauts de justesse lors de l’usinage sans correction de trajectoire d’outil 5-25 Fig. 5-12: Usinage sans défaut avec correction de trajectoire de rayon d’outil. 5-26 Fig. 5-13: Angles intérieurs 5-27 16-2 Liste des figures Manuel de programmation CN 17VRS Fig. 5-14: Elément de transition par arc de cercle avec G43 5-28 Fig. 5-15: Elément de transition par chanfrein et point de transition corrigé 5-28 Fig. 5-16: Conditions limites lors d’éléments de contour 5-29 Fig. 5-17: Elément d’arc de cercle concave5-29 Fig. 5-18: Arc de cercle concave, plusieurs éléments de contour 5-30 Fig. 5-19: Point de départ en correction de trajectoire d’outils 5-31 Fig. 5-20: Mise en œuvre de la correction de trajectoire d’outil 5-31 Fig. 5-21: Engagement au contour dans la correction de trajectoire d’outil 5-31 Fig. 5-22: Correction de trajectoire d’outil sur un contour fermé. 5-32 Fig. 5-23: Point d’arrivée avec correction de trajectoire d’outil 5-32 Fig. 5-24: Annulation de la correction de trajectoire d’outil 5-33 Fig. 5-25: Fin de contour avec correction de trajectoire d’outil 5-33 Fig. 5-26: Correction de trajectoire d’outil dur un contour fermé 5-33 Fig. 5-27: Inversion de la direction de correction 5-34 Fig. 5-28: Correction de trajectoire à droite (G42) 5-36 Fig. 5-29: Insertion d’éléments de transition en arc de cercle 5-37 Fig. 5-30: Insertion d’un chanfrein de transition5-38 Fig. 5-31: Correction de longueur d’outil inactive 5-39 Fig. 5-32: Correction de longueur d’outil 5-39 Fig. 5-33: Mode d’action des correcteurs D dans les différents plans d’usinage 5-42 Fig. 5-34: Définition du point de référence outil à l’aide des correcteurs D 5-42 Fig. 7-1: Taraudage en fonction d'un évènement 7-7 Fig. 9-1: Process et mécanisme externes de la CNC 9-1 Fig. 9-2: Transfert d’axe sur un centre d’usinage à 2 tables 9-6 Fig. 9-3: Organisation de programme dans la CNC 9-9 Fig. 9-4: Structure de sous-programme 9-10 Fig. 9-5: Emboîtement de sous-programme 9-10 Fig. 9-6: Appel de sous-programme 9-11 Fig. 10-1: Rectangle comme sous-programme10-10 Fig. 11-1: Compensation de couple de frottement au passage de quadrant 11-3 Fig. 11-2: Extrait de cercle pour évaluation d'écart de position 11-3 Fig. 11-3: Axe oblique 11-4 Fig. 11-4: Principe de constitution des données machine 11-14 Fig. 12-1: Insertion de chanfreins et d'arrondis entre des contours linéaires et circulaires 12-1 Fig. 12-2: Insertion d'arrondi 12-2 Fig. 12-3: Déplacement vers une position prédéfinie 12-5 Fig. 12-4: Mouvement de retrait avec position intermédiaire 12-6 Fig. 12-5: Exemple: perçage de trous 12-7 Fig. 12-6: Exemple: chanfreins et arrondis modaux 12-8 Fig. 12-7: Profil de vitesse d'une trajectoire polygonale à optimiser lors de la rectification d'une broche 12-12 DOK-MTC200-NC**PRO*V17-ANW1-FR-P Manuel de programmation CN 17VRS Liste des représentations Liste des représentations Allemagne Région centre Région est Région ouest Région nord INDRAMAT GmbH D-97816 Lohr am Main Bgm.-Dr.-Nebel-Str. 2 INDRAMAT GmbH D-09120 Chemnitz Beckerstraße 31 INDRAMAT GmbH D-40849 Ratingen Hansastraße 25 INDRAMAT GmbH D-22085 Hamburg Fährhausstraße 11 Telefon: 09352/40-0 Telefax: 09352/40-4885 Telefon: 0371/3555-0 Telefax: 0371/3555-230 Telefon: 02102/4318-0 Telefax: 02102/41315 Telefon: 040/227126-16 Telefax: 040/227126-15 Région sud Région sud ouest INDRAMAT Service-Hotline INDRAMAT GmbH D-80339 München Ridlerstraße 75 INDRAMAT GmbH D-71229 Leonberg Böblinger Straße 25 INDRAMAT GmbH Telefon: D-0172/660 040 6 Telefon: 089/540138-30 Telefax: 089/540138-10 Telefon: 07152/972-6 Telefax: 07152/972-727 -ouTelefon: D-0171/333 882 6 Représentations en Allemagne Europe Autriche Autriche Belgique Danemark G.L.Rexroth Ges.m.b.H. Geschäftsbereich INDRAMAT A-1140 Wien Hägelingasse 3 G.L.Rexroth Ges.m.b.H. Geschäftsbereich INDRAMAT A-4061 Pasching Randlstraße 14 Mannesmann Rexroth N.V.-S.A. Geschäftsbereich INDRAMAT B-1740 Ternat Industrielaan 8 BEC Elektronik AS DK-8900 Randers Zinkvej 6 Telefon: 1/9852540-400 Telefax:1/9852540-93 Telefon: 07229/64401-36 Telefax: 07229/64401-80 Telefon: 02/5823180 Telefax: 02/5824310 Angleterre Finlande France France Mannesmann Rexroth Ltd. INDRAMAT Division Cirencester, Glos GL7 1YG 4 Esland Place, Love Lane Rexroth Mecman OY SF-01720 Vantaa Riihimiehentie 3 Rexroth - Sigma S.A. Division INDRAMAT F-92632 Gennevilliers Cedex Parc des Barbanniers 4, Place du Village Rexroth - Sigma S.A. Division INDRAMAT F-69634 Venissieux - Cx 91, Bd 1 Joliot Curie Telefon: 01285/658671 Telefax: 01285/654991 Telefon: 0/848511 Telefax: 0/846387 Telefon: 1/41475430 Telefax: 1/47946941 Telefon: 086/447866 Telefax: 086/447160 Telefon: 4/78785256 Telefax: 4/78785231 France Italie Italie Pays Bas Rexroth - Sigma S.A. Division INDRAMAT F-31100 Toulouse 270, Avenue de lardenne Rexroth S.p.A. Divisione INDRAMAT I-20063 Cernusco S/N.MI Via G. Di Vittoria, 1 Rexroth S.p.A. Divisione INDRAMAT Via Borgomanero, 11 I-10145 Torino Hydraudyne Hydrauliek B.V. Kruisbroeksestraat 1a P.O. Box 32 NL-5280 AA Boxtel Telefon: 5/61499519 Telefax: 5/61310041 Telefon: 02/92365-270 Telefax: 02/92108069 Telefon: 011/7712230 Telefax: 011/7710190 Telefon: 04116/51951 Telefax: 04116/51483 Espagne Espagne Suède Suisse Rexroth S.A. Centro Industrial Santiago Obradors s/n E-08130 Santa Perpetua de Mogoda (Barcelona) Goimendi S.A. División Indramat Jolastokieta (Herrera) Apartado 11 37 San Sebastion, 20017 AB Rexroth Mecman INDRAMAT Division Varuvägen 7 S-125 81 Stockholm Rexroth SA Département INDRAMAT Chemin de l`Ecole 6 CH-1036 Sullens Telefon: 03/718 68 51 Telex: 591 81 Telefax: 03/718 98 62 Telefon: 043/40 01 63 Telex: 361 72 Telefax: 043/39 93 95 Telefon: 08/727 92 00 Telefax: 08/64 73 277 Telefon: 021/731 43 77 Telefax: 021/731 46 78 Suisse Russie Rexroth AG Geeschäftsbereich INDRAMAT Gewerbestraße 3 CH-8500 Frauenfeld Tschudnenko E.B. Arsenia 22 153000 Ivanovo Rußland Telefon: 052/720 21 00 Telefax: 052/720 21 11 Telefon: 093/22 39 633 Représentations en Europe sauf Allemagne DOK-MTC200-NC**PRO*V17-ANW1-FR-P Liste des représentations Manuel de programmation CN 17VRS Hors d’europe Argentine Argentine Australie Brésil Mannesmann Rexroth S.A.I.C. Division INDRAMAT Acassusso 48 41/7 1605 Munro (Buenos Aires) Argentina Nakase Asesoramiento Tecnico Diaz Velez 2929 1636 Olivos (Provincia de Buenos Aires) Argentina Argentina Australian Industrial Machenery Services Pty. Ltd. Unit 3/45 Horne ST Campbellfield VIC 2061 Australia Mannesmann Rexroth Automação Ltda. Divisão INDRAMAT Rua Georg Rexroth, 609 Vila Padre Anchieta BR-09.951-250 Diadema-SP Caixa Postal 377 BR-09.901-970 Diadema-SP Telefon: 01/756 01 40 01/756 02 40 Telex: 262 66 rexro ar Telefax: 01/756 01 36 Telefon: 03/93 59 0228 Telefax: 03/93 59 02886 Telefon 01/790 52 30 Telefon: 011/745 90 65 011/745 90 70 Telefax: 011/745 90 50 Canada Chine Chine Chine Basic Technologies Corporation Burlington Division 3426 Mainway Drive Burlington, Ontario Canada L7M 1A8 Rexroth (China) Ldt. Shanghai Office Room 206 Shanghai Intern. Trade Centre 2200 Yanan Xi Lu Shanghai 200335 P.R. China Rexroth (China) Ldt. Shanghai Parts & Service Centre 199 Wu Cao Road, Hua Cao Minhang District Shanghai 201 103 P.R. China Rexroth (China) Ldt. 1430 China World Trade Centre 1, Jianguomenwai Avenue Beijing 100004 P.R. China Telefon: 905/335-55 11 Telefax: 905/335-41 84 Telefon: 021/627 55 333 Telefax: 021/627 55 666 Telefon: 021/622 00 058 Telefax: 021/622 00 068 Telefon: 010/50 50 380 Telefax: 010/50 50 379 Chine Honkong Inde Japon Rexroth (China) Ldt. A-5F., 123 Lian Shan Street Sha He Kou District Dalian 116 023 P.R. China Rexroth (China) Ldt. 19 Cheung Shun Street 1st Floor, Cheung Sha Wan, Kowloon, Honkong Mannesmann Rexroth (India) Ltd. INDRAMAT Division Plot. 96, Phase III Peenya Industrial Area Bangalore - 560058 Rexroth Co., Ltd. INDRAMAT Division I.R. Building Nakamachidai 4-26-44 Tsuzuki-ku, Yokohama 226 Japan Telefon: 0411/46 78 930 Telefax: 0411/46 78 932 Telefon: 741 13 51/-54 und 741 14 30 Telex: 3346 17 GL REX HX Telefax: 786 40 19 786 07 33 Telefon: 80/839 21 01 80/839 73 74 Telex: 845 5028 RexB Telefax: 80/839 43 45 Telefon: 045/942-72 10 Telefax: 045/942-03 41 Corée Corée Mexique Rexroth-Seki Co Ltd. 1500-12 Da-Dae-Dong Saha-Gu, Pusan, 604-050 Seo Chang Corporation Ltd. Room 903, Jeail Building 44-35 Yoido-Dong Youngdeungpo-Ku Seoul, Korea Motorización y Diseño de Controles, S.A. de C.V. Av. Dr. Gustavo Baz No. 288 Col. Parque Industrial la Ioma Apartado Postal No. 318 54060 Tlalnepantla Estado de Mexico Telefon: 051/264 90 01 Telefax: 051/264 90 10 Telefon: 02/780-82 07 ~9 Telefax: 02/784-54 08 Telefon: 5/397 86 44 Telefax: 5/398 98 88 USA USA Rexroth Corporation INDRAMAT Division 5150 Prairie Stone Parkway Hoffman Estates, Illinois 60192 Rexroth Corporation INDRAMAT Division 2110 Austin Avenue Rochester Hills, Michigan 48309 Telefon: 847/645-36 00 Telefax: 857/645-62 01 Telefon: 810/853-82 90 Telefax: 810/853-82 90 Représentation hors d'Europe DOK-MTC200-NC**PRO*V17-ANW1-FR-P Manuel de programmation CN 17VRS Notes DOK-MTC200-NC**PRO*V17-ANW1-FR-P Liste des figures 16-1 ">
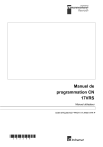
Link pubblico aggiornato
Il link pubblico alla tua chat è stato aggiornato.