Manuel d’utilisation 409-35001 29 JANV 2024 RÉV. D1 TRADUCTION DES INSTRUCTIONS D’ORIGINE Presses à connecteur CxP CBP-5T Mk II (2216056), CMP-5T Mk II (2216057), CMP-10T Mk II (2216058) and CSP-5T Mk II (2216055), Manuel d’utilisation et d’entretien PRÉCAUTIONS DE SÉCURITÉ - PRÉVENTION DES BLESSURES - À LIRE AVANT DE COMMENCER ! ................................................................................................ 3 1. INTRODUCTION .................................................................................................................. 5 2. SÉCURITÉ ............................................................................................................................ 5 Électricité ........................................................................................................................ 6 Protection des yeux et des oreilles ................................................................................ 6 Capots/protections de sécurité ....................................................................................... 7 Arrêt d’urgence de la machine (EMO)/ESTOP .............................................................. 7 Verrouillages d’arrêt d’urgence ...................................................................................... 7 Barrière immatérielle ...................................................................................................... 7 Système pneumatique ................................................................................................... 7 Particularités de la CMP ................................................................................................. 8 3. INSTALLATION ................................................................................................................... 9 INSTALLATION D’UNE CBP ......................................................................................... 9 INSTALLATION des CSP et CBP avec support 1-2216056-1/2 .................................. 11 INSTALLATION DE LA CMP ....................................................................................... 12 4. FIN DE VIE DE LA MACHINE ............................................................................................ 13 5. PRÉSENTATION DE LA PRESSE .................................................................................... 14 Objectif ......................................................................................................................... 14 Agencement ................................................................................................................. 15 Capacités ..................................................................................................................... 16 Accessoires en option .................................................................................................. 18 Configuration propre à la machine ............................................................................... 21 6. FONCTIONNEMENT (PRODUCTION) .............................................................................. 22 Démarrage ................................................................................................................... 22 Interface opérateur ....................................................................................................... 22 Mise sous tension ........................................................................................................ 23 Connexion .................................................................................................................... 23 Sélection de la carte ..................................................................................................... 25 Production de la carte .................................................................................................. 26 Boutons de l’écran Run ................................................................................................ 27 Affichage de la configuration de la carte ...................................................................... 28 Démarrer un pressage ................................................................................................. 28 User Signoff (validation de l’utilisateur) ...................................................................... 29 Modification de la séquence de pressage .................................................................. 29 Conditions d’erreur de profil liées à la carte, au connecteur, aux outils et aux programmes ........................................................................................... 29 Ce document contrôlé peut faire l’objet de modifications. Pour obtenir la dernière révision et la liste des services client par région, visitez notre site Web à TE Connectivity, TE connectivity (logo) et TE (logo) sont des marques commerciales. Les autres logos, produits et/ou noms d’entreprises peuvent être des l’adresse www.te.com. marques déposées de leurs propriétaires respectifs. © 2024 Groupe de sociétés TE Connectivity Tous droits réservés * Marque commerciale INFORMATIONS PRODUIT 1-800-522-6752 1 sur 94 409-35001 7. OUTILS ET GABARITS DE SUPPORT DE PRESSAGE .................................................. 30 Outils ............................................................................................................................ 30 Gabarits de support (Plateaux/ Gabarits de soutien) ................................................... 30 8. PROGRAMMATION ET SAISIE DES DONNÉES ............................................................. 31 L’éditeur d’outils ........................................................................................................... 31 L’éditeur de connecteurs .............................................................................................. 32 L’éditeur de profils ........................................................................................................ 34 Éditeur de conditions .................................................................................................... 44 Sequence Editor - Éditeur de séquences ..................................................................... 60 Optimisation SensiPress .............................................................................................. 65 9. écran de diagnostic .......................................................................................................... 70 Panneau de commande manuelle ............................................................................... 70 Onglet Inputs/Outputs (Entrées/Sorties) ...................................................................... 71 Panneau Load Cells (cellules de charge) .................................................................... 72 Panneau Calibration (étalonnage) ............................................................................... 72 10. UTILITAIRES DE DONNÉES ............................................................................................. 78 Message Viewer (visionneuse de messages) ............................................................ 78 Journaux machine ...................................................................................................... 80 11. CONFIGURATION DES UTILITAIRES .............................................................................. 81 Paramètres du système ............................................................................................. 81 Accès utilisateur ......................................................................................................... 84 Network Viewer - Visionneuse de réseau .................................................................. 86 Configuration Beckhoff ............................................................................................... 86 Beckhoff Remote Desktop - Bureau à distance ......................................................... 86 PPS Viewer - Visionneuse PPS ................................................................................. 87 12. MAINTENANCE PRÉVENTIVE ......................................................................................... 89 Accès à la tête de presse (CBP) ................................................................................ 89 Nettoyage ................................................................................................................... 89 Inspection ................................................................................................................... 89 Barrière immatérielle .................................................................................................. 89 Lubrification ................................................................................................................ 89 Couple de serrage critique de la visserie ................................................................... 90 Calendrier de maintenance périodique ...................................................................... 90 Ce document contrôlé peut faire l’objet de modifications. Pour obtenir la dernière révision et la liste des services par région, visitez être notredes site Web à TE Connectivity, TE connectivity (logo) et TE (logo) sont des marques commerciales. Les autres logos, produits et/ou nomsclient d’entreprises peuvent l’adresse www.te.com. marques déposées de leurs propriétaires respectifs. © 2024 Groupe de sociétés TE Connectivity Tous droits réservés * Marque commerciale INFORMATIONS PRODUIT 1-800-522-6752 2 sur 94 409-35001 PRÉCAUTIONS DE SÉCURITÉ - PRÉVENTION DES BLESSURES - À LIRE AVANT DE COMMENCER ! Les protections de sécurité sur cet équipement ont été conçues pour protéger les opérateurs et le personnel de maintenance contre la majorité des dangers liés à son utilisation. Cependant, certaines précautions de sécurité doivent être prises par l’opérateur et les techniciens de maintenance pour éviter les blessures et les dommages matériels. Pour de meilleurs résultats, l’équipement doit être utilisé dans un environnement sec et non poussiéreux. N’utilisez pas l’équipement dans un milieu gazeux ou dangereux. Respectez scrupuleusement les précautions de sécurité suivantes avant et pendant l’utilisation de l’équipement : Portez toujours des lunettes de protection homologuées lors de l’utilisation de l’équipement. Les pièces mobiles peuvent écraser et couper. Maintenez toujours les protections en place lors du fonctionnement normal de l’équipement. Pour éviter les risques d’électrocution, branchez systématiquement le câble éventuellement fourni par le client sur une prise avec mise à la terre. Avant toute opération de maintenance ou réparation sur l’équipement, assurez-vous de toujours débrancher en premier lieu la prise d’air et ensuite, le système d’échappement de la pression d’air. Faites preuve de prudence lorsque vous travaillez avec l’équipement. Risque d’électrocution. Ne mettez jamais les mains dans l’équipement installé. Ne portez jamais de vêtements amples ou de bijoux qui risqueraient de s’accrocher dans les pièces mobiles. Vérifiez si l’interrupteur principal est sur ON ou OFF. N’altérez jamais, ne modifiez jamais et n’utilisez jamais l’équipement d’une manière imprévue. Mettez l’équipement hors tension et débranchez l’alimentation électrique avant toute intervention de réparation ou de maintenance sur l’équipement. Vérifiez que les protections sont en place et correctement fixées à l’équipement. N’utilisez pas l’équipement en l’absence de protections. Ne fixez jamais la lumière vive destinée à éclairer la machine au risque de souffrir de lésions oculaires. Utilisez uniquement la machine pour son utilisation prévue, c’est-à-dire le pressage de connecteurs à des fils. N’utilisez en aucun cas la machine pour écraser des pièces. INFORMATIONS DE SÉCURITÉ IMPORTANTES REMARQUE Conservez toutes les étiquettes propres et lisibles et remplacez-les si nécessaire. DANGER RISQUE D’INCENDIE N’utilisez pas de solvants ou de liquides inflammables pour nettoyer la machine. Les solvants ou les liquides inflammables peuvent s’enflammer et provoquer des blessures graves ou des dommages matériels. RÉV. D1 Le non-respect de ces avertissements peut entraîner des blessures graves causées par des vapeurs nocives ou des brûlures par des débris volants. MISE EN GARDE Ne procédez à aucune opération d’entretien ou de maintenance non indiquée dans ce manuel, pour cause de risque de blessures ou d’endommagement de la machine. Le non-respect de ces précautions peut entraîner des blessures ou des dommages matériels. 3 sur 94 409-35001 CENTRE D’ASSISTANCE APPELEZ GRATUITEMENT LE 1-800-522-6752 (ÉTATS-UNIS ET PORTO RICO UNIQUEMENT) Le Centre d’assistance fournit un support technique en cas de besoin. En outre, des spécialistes après-vente sur site sont disponibles pour le réglage ou la réparation de l’équipement en cas de problèmes que votre personnel de maintenance n’est pas en mesure de corriger. INFORMATIONS REQUISES LORS DE TOUT CONTACT AVEC LE CENTRE D’ASSISTANCE Lors d’un contact avec le centre d’assistance pour une question relative à l’entretien ou à la réparation de l’équipement, il est souhaitable qu’une personne familiarisée avec l’appareil soit présente avec un exemplaire du manuel (schémas compris) pour recevoir les instructions. De cette manière, de nombreuses difficultés peuvent être évitées. Avant d’appeler le centre d’aide, préparez les informations suivantes : 1. Nom du client 7. Urgence de la demande 2. Adresse du client 8. Nature du problème 3. Personne à contacter (nom, titre, numéro de téléphone et poste) 9. Description du problème (pièces défectueuses...) 4. Personne appelant 10. Informations supplémentaires/commentaires pouvant être utiles 5. Numéro d’équipement (et numéro de série le cas échéant) 6. Référence du produit (et numéro de série le cas échéant) RÉV. D1 4 sur 94 409-35001 Figure 1 1. INTRODUCTION À la lecture de ce manuel, faites particulièrement attention aux notes indiquant un DANGER, une MISE EN GARDE ou une REMARQUE. DANGER Indique un danger imminent, susceptible de provoquer une blessure légère ou grave. MISE EN GARDE Indique une situation susceptible d’endommager un produit ou un équipement. REMARQUE Signale des informations particulières ou importantes. REMARQUE Les dimensions figurant dans ce manuel d’utilisation sont en unités métriques [les unités américaines usuelles figurent entre crochets]. Les schémas ne sont pas à l’échelle. Ce manuel contient les procédures d’installation, de sécurité, d’utilisation et de maintenance des presses CxP. Il concerne les modèles Connector Benchtop Press (CBP-5T Mk II), Connector Manual Presses (CBP-5T Mk II avec support 1-2216056-1/2), Connector Manual Press (CMP-5T Mk II et CMP-10T Mk II) et Connector Shuttle Press (CSP-5T Mk II). Les informations fournies s’appliquent à toutes les presses CxP, sauf indications contraires applicables à certains modèles. 2. SÉCURITÉ Les CxP sont conçues en conformité avec les dernières normes de sécurité de l’OSHA, de la NFPA-79 et de la CSA. En outre, toutes les machines sont conformes aux exigences CE actuelles. RÉV. D1 5 sur 94 409-35001 Électricité CBP/CSP Il est essentiel que la machine soit adéquatement reliée à la terre pour être utilisée en toute sécurité. Par conséquent, un conducteur de terre externe en cuivre d’une section de 2 mm2 minimum doit être raccordé au point de terre de la machine. Celui-ci se trouve sur le cadre droit et est étiqueté « PE ». N’oubliez pas l’existence des risques électriques signalés. L’interrupteur principal avec fonction de verrouillage est situé sur le côté droit de la machine et est clairement indiqué. CMP En raison des composants du filtre de ligne électrique, le courant de fuite est supérieur à 10 mA. Par conséquent, un boulon fileté est fixé au châssis de la machine et étiqueté avec un symbole de mise à la terre. Une ligne reliée à la terre supplémentaire et distincte doit être raccordée à ce point. La section du câble doit être d’au moins 10 mm2. L’interrupteur principal est situé sur le panneau arrière de la machine et est clairement indiqué. En position « ON », il est mécaniquement verrouillé pour empêcher l’ouverture de la porte d’accès. En position « OFF », l’interrupteur peut être verrouillé en insérant un cadenas dans l’un des trois emplacements de verrouillage (voir Figure 2). En plus du verrouillage mécanique, la porte est équipée d’une serrure à clé. Verrouillage/Étique tage Figure 2 Protection des yeux et des oreilles Des lunettes de protection doivent être portées à tout moment lors de l’utilisation et de l’entretien de cette machine. En cas de destruction d’un connecteur pendant l’opération de pressage, des pièces du connecteur pourraient être projetées en dehors de la machine. REMARQUE : le capteur laser ne nécessite pas de protection oculaire (voir Figure 3). Aucune protection auditive n’est requise. Le niveau de pression acoustique émis par le poste de travail ne dépasse pas les 70 dB(A). RÉV. D1 6 sur 94 409-35001 Figure 3 Capots/protections de sécurité Toutes les protections doivent être en place avant d’utiliser la presse. Cela inclut la tôle et les panneaux Lexan autour de la machine (voir Figure 4). Figure 4 Arrêt d’urgence de la machine (EMO)/ESTOP Le contrôleur de circuit d’arrêt d’urgence de la machine (EMO) surveille les verrouillages de sécurité (voir les informations de verrouillage ci-dessous) et l’ordinateur pour décider si le moteur peut être lancé et les mouvements autorisés en toute sécurité. Lorsque le circuit EMO est hors tension, le contrôleur asservi du moteur est désactivé et l’alimentation du moteur est coupée. Une fois tous les verrouillages de sécurité correctement réglés, le circuit EMO s’active sur demande depuis l’ordinateur. Toute interruption par verrouillage met le circuit EMO hors tension. REMARQUE : réinitialiser un verrouillage ne réactivera pas automatiquement le circuit EMO. Verrouillages d’arrêt d’urgence Les boutons d’arrêt d’urgence (Emergency Stops) sont situés aux angles inférieurs avant gauche et droit de la presse. Bien qu’ils soient clairement visibles, l’opérateur doit s’assurer de connaître leur position et d’être prêt à les utiliser en cas d’urgence. Appuyer sur l’un des interrupteurs met le circuit EMO hors tension et interrompt tout mouvement. Une fois enfoncé, l’interrupteur verrouille tout en l’état et doit être désactivé par rotation. Barrière immatérielle La barrière immatérielle (Light Curtain) est un dispositif secondaire de protection de l’opérateur. Lorsque la barrière immatérielle détecte un obstacle, le circuit EMO est mis hors tension et le mouvement est interrompu. La barrière se réinitialise automatiquement lorsqu’il n’y a plus d’obstacle (bien que le circuit EMO reste hors tension). Système pneumatique Un système pneumatique est fourni pour la table à air optionnelle, ce qui permet de faire flotter un gabarit de support de carte de circuit imprimé pour faciliter le positionnement sous la tête de la presse. Sur la CMP, le système pneumatique fournit également de l’air au coussin d’air qui fait flotter la tête pour un réglage côte à côte. Le système pneumatique ne nécessite aucune précaution particulière. RÉV. D1 7 sur 94 409-35001 Particularités de la CMP Les éléments de sécurité suivants ne concernent que les modèles CMP. Roulettes La CMP est montée sur quatre roulettes pivotantes. Les deux roulettes arrière sont verrouillables. En raison du poids de la machine, la déplacer nécessite deux personnes. Protections sismiques Il est possible de protéger l’équipement des mouvements sismiques indésirables en le boulonnant au sol. Nous décrivons ici deux façons de procéder parmi toutes celles qui existent. 1. Percez des trous à travers le tube inférieur du châssis sur les côtés droit et gauche de la machine. Fixez des boulons à œillets aux trous. Ancrez des boulons à œillets similaires au sol sous la machine. Fixez la machine au sol avec une chaîne ou un câble. 2. Fabriquez des cornières en acier à boulonner sur le tube inférieur du châssis à gauche et à droite de la machine. Ancrez les plaques d’angle au sol. REMARQUE Un kit de protections antisismiques est disponible sur demande auprès de TE. Construction du châssis et répartition du poids Le châssis est fabriqué en acier tubulaire soudé et supporte le très lourd poids du cadre de la presse. REMARQUE : illustration de la CMP-10T Mk II, la CMP-5T Mk II est similaire Figure 5 RÉV. D1 1 Plaques de cadre horizontales supérieures, point de levage de fourche préféré 2 Cadre inférieur, point de levage de fourche alternatif 8 sur 94 409-35001 3. INSTALLATION Cette section décrit les étapes d’installation et les prérequis pour les presses CBP, CSP et CMP. INSTALLATION D’UNE CBP Déballage La presse, le moniteur, les pieds réglables et les autres éléments séparés sont expédiés sur une seule et unique palette, qui est protégée sous un film rétractable. Retirez le film rétractable et déballez le moniteur et les autres éléments livrés. Enlevez la presse de la palette en dévissant les boulons de maintien situés sur les quatre pieds et en la soulevant à l’aide d’un chariot à fourche ou d’un palan. Placez les pieds du chariot à fourche sous un côté de la tête. Voir les flèches ci-dessous à la Figure 6. Les pieds du chariot à fourche doivent être enveloppés de plastique ou de bois afin de ne pas endommager les vitres arrière de la machine. REMARQUE Soulevez la machine depuis le bas de la structure. Gardez les fourches aussi larges que possible pour plus de stabilité. Montage initial 1. À l’aide des quatre pieds fournis (PN 2256177-1), installez les quatre niveleurs au bas de la presse et réglez les axes X/Y du plateau à l’aide d’un niveau à bulle. Figure 6 2. Installez le cordon d’alimentation à trois conducteurs fourni par le client en fonction de la tension et de la capacité de courant disponibles (200-240 VCA, monophasé, 6 A) à l’arrière de la CBP. 3. Menez le cordon d’alimentation à trois conducteurs fourni par le client à travers le serre-câble situé sur le côté de la presse. Connectez le conducteur de terre au bornage « PE » qui se trouve sur le côté du cadre de la presse. Raccordez les conducteurs de ligne aux bornes de l’interrupteur d’alimentation principal. 4. Le cas échéant, installez la tubulure d’air comprimé industrielle fournie par le client sur le raccord à ouverture rapide situé sur l’interrupteur à pédale de la Table à air en option. RÉV. D1 9 sur 94 409-35001 5. Si l’utilisation de la tête n’implique jamais son déplacement de gauche à droite, installez le moniteur sur le tiroir. Évitez de toucher la poignée pivotante (voir Figure 7 ci-dessous). Si l’utilisation de la tête prévue implique son déplacement, placez le moniteur sur le plateau de la table, à côté de la machine. De cette manière, la poignée pivotante peut être facilement atteinte et déplacée si nécessaire. Figure 7 6. Réinstallez le cordon d’alimentation du moniteur et le câble vidéo du moniteur. 7. Placez le clavier et la souris dans la cassette à clavier et connectez-les à l’ordinateur de l’interface utilisateur sur le panneau électrique. 8. Connectez le lecteur de codes-barres (s’il y en a un). 9. Retirez les supports de fixation de la tête de la presse, le cas échéant. 10. Mettez la presse sous tension en activant l’interrupteur principal. Le système va démarrer sur l’écran d’accueil. Le mot de passe par défaut de l’utilisateur par défaut (Administrator) est administrator. REMARQUE L’administrateur (client/propriétaire) doit modifier le mot de passe de connexion initiale pour protéger la machine des accès non autorisés. Étiquetage de l’équipement Le numéro de pièce de la machine, le numéro de série, la date de fabrication et les spécifications électriques figurent sur l’étiquette située sur le côté gauche de la machine, comme illustré à la Figure 8. Figure 8 Circuit d’alimentation électrique Le circuit d’alimentation électrique doit être sous 200-240 VCA, 50/60 Hz, monophasé. Alimentation pneumatique L’alimentation pneumatique doit être raccordée au port fourni dans l’interrupteur à pédale. L’air comprimé n’est utilisé que pour la table à air en option. La consommation d’air est minime. La pression de la table à air doit être réglée au minimum nécessaire pour faire « flotter » le gabarit de support de carte de circuit imprimé utilisé. RÉV. D1 10 sur 94 409-35001 INSTALLATION des CSP et CBP avec support 1-2216056-1/2 Figure 9 Déballage La presse, le moniteur, les pieds réglables, les roulettes et les autres éléments séparés sont expédiés sur une seule et unique palette, qui est protégée sous un film rétractable. Retirez le film rétractable et déballez le moniteur et les autres éléments livrés. Enlevez la presse de la palette en dévissant les boulons de maintien situés sur les quatre pieds et en la soulevant à l’aide d’un chariot à fourche ou d’un palan. Placez les pieds du chariot à fourche sous un côté de la tête. Voir les flèches ci-dessus à la Figure 9. Les pieds du chariot à fourche doivent être enveloppés de plastique ou de bois afin de ne pas endommager les vitres arrière de la machine. REMARQUE Soulevez la machine depuis le bas de la structure. Gardez les fourches aussi larges que possible pour plus de stabilité. Montage initial 1. À l’aide des quatre pieds fournis (PN 2256590-1), installez les quatre niveleurs au bas de la presse et réglez les axes X/Y du plateau à l’aide d’un niveau à bulle. 2. Installez les quatre roulettes fournies (PN 2256386-1) au bas du cadre. 3. Installez le cordon d’alimentation à trois conducteurs fourni par le client en fonction de la tension et de la capacité de courant disponibles (200-240 VCA, monophasé, 6 A) à l’arrière de la CSP. 4. Menez le cordon d’alimentation à trois conducteurs fourni par le client à travers le serre-câble situé sur le côté de la presse. Connectez le conducteur de terre au bornage « PE » qui se trouve sur le côté du cadre de la presse. Raccordez les conducteurs de ligne aux bornes de l’interrupteur d’alimentation principal. 5. Installez la tubulure d’air comprimé industrielle fournie par le client sur le raccord à ouverture rapide situé sur le panneau inférieur de la machine. La navette pneumatique nécessite de l’air à 80 PSI. 6. Installez le moniteur sur le tiroir. Réinstallez le cordon d’alimentation du moniteur et le câble vidéo du moniteur. 7. Placez le clavier et la souris dans la cassette à clavier et connectez-les à l’ordinateur de l’interface utilisateur sur le panneau électrique. 8. Connectez le lecteur de codes-barres (s’il y en a un). 9. NE RETIREZ PAS les éléments de fixation de la tête de la presse. 10. Mettez la presse sous tension en activant l’interrupteur principal. Le système va démarrer sur l’écran d’accueil. Le mot de passe par défaut de l’utilisateur par défaut (Administrator) est administrator. RÉV. D1 11 sur 94 409-35001 REMARQUE L’administrateur (client/propriétaire) doit modifier le mot de passe de connexion initiale pour protéger la machine des accès non autorisés. Étiquetage de l’équipement Le numéro de pièce de la machine, le numéro de série, la date de fabrication et les spécifications électriques figurent sur l’étiquette située sur le côté gauche de la machine, comme illustré à la Figure 10. Figure 10 Circuit d’alimentation électrique Le circuit d’alimentation électrique doit être sous 200-240 VCA, 50/60 Hz, monophasé. Alimentation pneumatique L’alimentation pneumatique doit être raccordée au port fourni sur la base de la machine. L’air comprimé est utilisé pour la navette pneumatique. La consommation d’air est minime. La pression de la navette pneumatique doit être réglée sur 80 PSI. INSTALLATION DE LA CMP Déballage/levage La presse, le moniteur, les pieds réglables et les autres éléments séparés sont expédiés sur une seule et unique palette et sont protégés par un film rétractable. Retirez le film rétractable et déballez le moniteur, l’ordinateur et les autres éléments livrés. Enlevez la presse de la palette en dévissant les boulons de maintien situés sur les quatre pieds et en la soulevant de quelques centimètres à l’aide d’un chariot à fourche. Utilisez des cales de bois « 2x4 » ou équivalent entre le dessous des plaques de cadre horizontales supérieures (voir Figure 5) et les lames du chariot élévateur. Il est également possible de soulever la machine en levant les traverses inférieures du cadre (voir Figure 5). Dans les deux cas, gardez les fourches aussi larges que possible pour plus de stabilité. Montage initial 1. À l’aide des quatre vis à tête creuse M8 x 12 (PN 6-1655316-7) fournies pour chaque roue, installez les quatre roulettes (2256047-1) au bas du cadre de la presse (2216143-7). 2. Installez le cordon d’alimentation à trois conducteurs fourni par le client en fonction de la tension et de la capacité de courant disponibles (200-240 VCA, monophasé, 10 A) en le faisant passer par le presse-étoupe à angle droit (situé sur le panneau gauche de la machine). À l’intérieur de la machine, RÉV. D1 12 sur 94 409-35001 faites passer le câble par le haut. Raccordez le fil de terre au bornage de terre sur le cadre de la machine. Raccordez les câbles de phase à l’interrupteur d’isolement principal (voir Figure 11). Figure 11 3. Installez la tubulure d’air comprimé industrielle fournie par le client sur le raccord à ouverture rapide situé en bas à l’arrière de la machine. Vérifiez que la pression de l’arrivée d’air comprimé soit d’au moins 552 kPa [80 psi] vers le régulateur d’air de la CMP. 4. Rattachez le bras articulé du moniteur (2216845-1) du côté de la machine que vous souhaitez. Fixez le moniteur au bras à l’aide des vis de montage fournies (3-18023-7). Rattachez le cordon d’alimentation du moniteur et le câble vidéo. 5. Réinstallez le lecteur de codes-barres (s’il y en a un). 6. Retirez les éléments de fixation de la tête de la presse (à gauche et à droite). 7. Fixez le clavier à l’ordinateur de l’interface utilisateur dans l’armoire de commande. 8. Fixez la souris, le clavier, l’écran tactile et les câbles USB externes à l’ordinateur de l’interface utilisateur dans l’armoire de commande. 9. Mettez la presse sous tension en activant l’interrupteur principal. Le système va démarrer sur l’écran d’accueil. Le mot de passe par défaut de l’utilisateur par défaut (Administrator) est administrator. REMARQUE L’administrateur (client/propriétaire) doit modifier le mot de passe de connexion initiale pour protéger la machine des accès non autorisés. Étiquetage de l’équipement Le numéro de pièce de la machine, le numéro de série, la date de fabrication et les spécifications électriques figurent sur l’étiquette située sur le côté gauche de la machine, comme illustré à la Figure 12. Figure 12 Circuit d’alimentation électrique Reportez-vous à l’étiquetage situé sur le côté gauche de la machine pour connaître les prérequis exacts, mais, en général, le circuit d’alimentation électrique doit répondre aux critères suivants : de 200 à 240 VCA, 50/60 Hz, monophasé, service à deux fils protection par un disjoncteur prévu pour au moins 10 000 IAC. Alimentation pneumatique L’alimentation pneumatique doit être raccordée au port situé dans le coin gauche inférieur de la presse. La pression doit être comprise entre 552 et 827 kPa [80-120 psi]. L’air comprimé n’est utilisé que pour le coussin d’air de positionnement de la tête et la table à air en option. La consommation d’air est minime. 4. FIN DE VIE DE LA MACHINE Toute machine mise hors service doit être retournée à TE Connectivity qui se chargera de sa bonne élimination. RÉV. D1 13 sur 94 409-35001 5. PRÉSENTATION DE LA PRESSE Cette section présente les presses CBP, CSP et CMP. Dans ce manuel, elles seront collectivement appelées les presses CxP. Leur objectif, leurs capacités, leurs options et leur agencement sont brièvement présentés. Objectif La presse électrique servocommandée CxP a été conçue à deux fins principales. Tout d’abord, pour répondre au besoin croissant en pressage de qualité contrôlée de connecteurs sur les circuits imprimés complexes contemporains. Plus la densité des connecteurs augmente, plus ils deviennent fragiles. Parallèlement, les cartes à circuits imprimés sont devenues plus complexes, sujettes à détériorations et coûteuses. Cette tendance va sans aucun doute se poursuivre et s’accélérer tandis que les circuits imprimés interconnectés poursuivront leur évolution de simples éléments passifs vers des systèmes toujours plus complexes dotés de dispositifs montés en surface et enterrés dans les couches internes. Ces dernières années, les ateliers de montage des cartes de fond de panier ont dû augmenter considérablement la sophistication de leurs procédés de fabrication. Il est devenu évident que les anciennes méthodes de montage rapide des connecteurs sur les cartes ne sont plus acceptables. De par ses fonctions de pressage asservies à commande électrique, la CxP contrôle avec précision la puissance et la vitesse de chaque cycle de pressage. Ce contrôle est étayé pour la première fois par un retour de la qualité sous la forme d’une analyse, d’un affichage et de rapports. Des données précieuses peuvent désormais être capturées et analysées pour améliorer l’ensemble du processus d’interconnexion. Le deuxième objectif consiste à améliorer l’efficacité du processus de pressage. Les techniques manuelles traditionnelles de pressage des connecteurs demandaient beaucoup de travail, n’étaient pas sûres et sont devenues inacceptables en termes d’ergonomie. Par conséquent, le rendement et la qualité dépendent de l’opérateur, ce qui produit inévitablement des résultats variables. La presse électrique asservie améliore le rendement tout en générant des résultats contrôlés par ordinateur plus cohérents avec un retour de données sur la qualité. Ainsi, le double objectif de cette presse répond simultanément aux besoins de l’atelier de montage et du client final. RÉV. D1 14 sur 94 409-35001 Agencement Dimensions CBP-5T Mk II Largeur Profondeur Hauteur 836 mm [32,9 po] 665 mm [26,2 po] 962 mm [37,9 po] CBP 5T Mk II avec support 1-2216056-1/2 836 mm [32,9 po] 665 mm [26,2 po] 1 775 mm [69,9 po] Figure 13 Dimensions Largeur Profondeur Hauteur CSP 5T Mk II 836 mm [32,9 po] 665 mm [26,2 po] 1 775 mm [69,9 po] Figure 14 RÉV. D1 15 sur 94 409-35001 Dimensions CMP-5T Mk II Largeur 1 205 mm [47,4 po]* Profondeur 1 176 mm [46,3 po]* Hauteur 1 752 mm [69,0 po] *sans le moniteur Figure 15 Dimensions CMP-10T Mk II Largeur 1 398 mm [55,0 po]* Profondeur 1 290 mm [50,8 po]* Hauteur 1 936 mm [76,2 po] *sans le moniteur Figure 16 Capacités Spécificités de la CBP La CBP fournit une force contrôlée allant jusqu’à 44 kN (10 000 lb) par l’intermédiaire d’une tête « flat rock » de 200 mm de long X 37 mm de large [7,87 po de long X 1,46 po de large]. Le débattement de l’axe Z est de 50 mm [1,97 po]. RÉV. D1 16 sur 94 409-35001 REMARQUE Un espace de pressage total de 160 mm [6,3 po] est disponible en installant un adaptateur de 50 mm [1,97 po] sur l’enclume. La position de rentrée normale génère un intervalle de 140 mm [5,51 po] entre la tête de la presse et le dessus de la table ; 90 mm [3,54 po] en position de sortie totale. L’adaptateur de 50 mm [1,97 po] ajuste les limites de l’intervalle à 90 mm [3,54 po] en position rentrée et à 40 mm [1,57 po] en position sortie. La position « haute » peut être programmée pour toute tolérance désirée au-dessus de l’outil pendant le pressage. Cela améliore l’efficacité en limitant le débattement par cycle. Il peut également être très pratique d’utiliser la tête de presse comme support d’outil dans les situations d’instabilité entre l’outil et le connecteur. De plus, la presse est équipée d’une tête de presse que l’on peut faire pivoter manuellement à 90° et d’une fonction de sustentation pneumatique du gabarit de support de carte sur le plateau. La taille limite des cartes de circuits imprimés est de 450 mm de large x 700 mm de long [17,72 po de large x 27,56 po de long]. La largeur d’ouverture de la structure est de 550 mm [21,65 po] et la tête de la presse peut être déplacée d’un côté à l’autre sur une glissoire pour accéder aux bords des grandes cartes. Spécificités de la CSP La CSP fournit une force contrôlée allant jusqu’à 44 kN (10 000 lb) par l’intermédiaire d’une tête « flat rock » de 200 mm de long X 37 mm de large [7,87 po de long X 1,46 po de large]. Le débattement de l’axe Z est de 50 mm [1,97 po]. REMARQUE Un espace de pressage total de 160 mm [6,3 po] est disponible en installant un adaptateur de 50 mm [1,97 po] sur l’enclume. La position de rentrée normale génère un intervalle de 140 mm [5,51 po] entre la tête de la presse et le dessus de la table ; 90 mm [3,54 po] en position de sortie totale. L’adaptateur de 50 mm [1,97 po] ajuste les limites de l’intervalle à 90 mm [3,54 po] en position rentrée et à 40 mm [1,57 po] en position sortie. La position « haute » peut être programmée pour toute tolérance désirée au-dessus de l’outil pendant le pressage. Cela améliore l’efficacité en limitant le débattement par cycle. Il peut également être très pratique d’utiliser la tête de presse comme support d’outil dans les situations d’instabilité entre l’outil et le connecteur. De plus, la presse est équipée d’une tête de presse que l’on peut faire pivoter manuellement à 90° et d’une fonction de sustentation pneumatique du gabarit de support de carte sur le plateau. La taille limite des cartes de circuits imprimés est de 450 mm de large x 700 mm de long [17,72 po de large x 27,56 po de long]. La largeur d’ouverture de la structure est de 550 mm [21,65 po] et la tête de la presse peut être déplacée d’un côté à l’autre sur une glissoire pour accéder aux bords des grandes cartes. Spécificités de la CMP La CMP fournit une force contrôlée allant jusqu’à 44 kN (5 tonnes/10 000 lb) pour la CMP-5T Mk II ou à 89 kN (10 tonnes/20 000 lb) pour la CMP-10T Mk II par l’intermédiaire d’une tête « flat rock » de 212 mm de long x 75 mm de large. Le débattement de l’axe Z est supérieur à 125 mm et la position « haute » peut être programmée pour toute tolérance désirée au-dessus de l’outil avant le pressage. Cela améliore l’efficacité en limitant le débattement par cycle. Il peut également être très pratique d’utiliser la tête de presse comme support d’outil dans les situations d’instabilité entre l’outil et le connecteur. La taille limite des cartes de circuits imprimés est de 610 mm de large x 915 mm de profondeur (CMP-5T Mk II) ou de 748,5 mm de large x 965,2 mm de profondeur (CMP-10T Mk II). La tête de la presse peut être déplacée d’un côté à l’autre pour accéder aux bords des grandes cartes. Contrôle précis du pressage Le programme de pressage est un simple tableau de types et de positions de connecteurs. Chaque cycle de pressage, appelé profil, est défini avec précision par l’utilisateur afin de contrôler la force, la vitesse et la distance pendant le pressage du connecteur. Cette technique d’une grande souplesse permet d’appliquer une gamme virtuellement illimitée d’options de pressage en réponse aux exigences des connecteurs actuels et futurs. Les données descriptives des connecteurs, les outils, les cartes et le profil de pressage sont stockés dans des bases de données modifiables en ligne ou hors ligne. RÉV. D1 17 sur 94 409-35001 Un grand nombre de fonctions et d’utilitaires sont fournis aux fins de maintenance. Cela comprend des vues d’écran de toutes les entrées de la machine et un accès au forçage de toutes les sorties. Il est possible pour l’utilisateur de définir les entrées/sorties par l’intermédiaire d’une connexion à l’arrière de la machine afin de contrôler la presse à distance en déclenchant et en étant averti de tous les événements. Le processus de pressage peut être contrôlé de l’une des cinq manières suivantes : 1. FORCE FIXE - Un connecteur peut, par exemple, être pressé selon une force prédéterminée de 5 kN [0,56 tonne/1 124 lb]. Il s’agit d’une technique couramment utilisée par les presses hydrauliques et pneumatiques. Il s’agit de la méthode la moins sophistiquée et la plus susceptible d’endommager la carte ou le connecteur. 2. FORCE FIXE PAR BROCHE – Un connecteur peut être pressé selon une force prédéterminée par broche, 150 N [33,7 lbf] par broche par exemple. Cette méthode est légèrement meilleure que la précédente parce qu’elle admet que la force appliquée doit être proportionnelle au nombre de broches à presser. Toutefois, elle ne peut pas compenser les écarts normaux de force par broche requise par différents connecteurs, dans différentes positions, sur différentes cartes. 3. PRESSAGE SELON LA HAUTEUR - Un connecteur peut être pressé selon une distance programmée en limite d’appui à la surface de la carte. Ceci est le procédé le plus modéré possible parce qu’il exerce uniquement la force suffisante pour presser les broches dans la carte. Aucune force de pressage excessive n’est exercée sur le plastique du connecteur ou la carte. Cette technique sophistiquée est rendue possible par le contrôle que permet l’utilisation d’une tête de presse électrique à servocommande et la rigidité de la structure de la presse. Pour une plus grande précision du pressage selon la hauteur, l’épaisseur de la carte doit être connue avec exactitude. Ceci est réalisable grâce à la sonde de mesure d’épaisseur et à la séquence fournies. 4. ÉCHANTILLON AVEC POURCENTAGE SUPÉRIEUR AUX LIMITES (PARS) – Un connecteur peut être pressé sous une force proportionnelle à la force antagoniste réelle détectée pendant le cycle de pressage. Cette fonction est appelée échantillon avec pourcentage supérieur aux limites ou PARS. Dans cette technique, la force antagoniste opposée par le connecteur pendant le pressage est échantillonnée et sa moyenne calculée sur une distance donnée avant la dépose sur la surface de la carte. Le pourcentage de force définitive supplémentaire assure le parfait appui du connecteur. Cette technique est la plus répandue parce qu’elle limite les contraintes subies par l’assemblage sans exiger une grande précision de mesure de l’épaisseur de la carte. 5. GRADIENT DE FORCE - Cette méthode surveille le taux d’évolution de la force par rapport à la distance. Elle est utilisée quand des connecteurs robustes doivent être posés sur la surface de la carte. D’une manière générale, la courbe de la force par rapport à la distance se redressera brusquement quand le connecteur entrera en contact avec la surface de la carte. Le déplacement du connecteur est arrêté afin d’augmenter rapidement la force. Un angle minimum de redressement est spécifié en termes de ΔForce sur ΔDistance, ce qui correspond à la force de pressage du connecteur contre la carte. Un outil de conversion est fourni pour ceux qui ont l’habitude d’utiliser l’ancienne méthode de programmation de gradient de force, qui se base sur l’échelle du graphique de production et l’angle de gradient du graphique. Mesure de l’épaisseur de la carte La mesure de l’épaisseur de la carte facilite la technique de pressage selon la hauteur en mesurant l’épaisseur réelle de la carte avant le lancement du cycle de pressage. Si l’épaisseur de la carte n’est pas mesurée, le programme utilise une épaisseur nominale dans des calculs de hauteurs. Accessoires en option Unité ACAL (étalonnage automatique) Il existe deux unités différentes : l’une pour les machines 5T et l’autre pour les 10T. Elles servent à réétalonner la machine, ce qui doit être fait chaque année. L’achat de cet accessoire permet à la société d’effectuer elle-même l’étalonnage de la machine. RÉV. D1 18 sur 94 409-35001 Lecteur de codes-barres L’option de lecteur de codes-barres permet de saisir rapidement les numéros de série des cartes à des fins de traçabilité. Les outils de pressage sont également identifiables par codes-barres en vue d’un contrôle efficace et précis. L’identification de l’outil peut être activée en ajoutant l’option Tool ID à la séquence de pressage. Rallonge d’enclume CBP MKII SensiPress Cette option SensiPress est spécifique à la machine CBP MKII. Le CBP avec support 1-2216056-1/2 n’est pas inclus. Trois numéros à tirets différents sont associés à la hauteur de la machine achetée. L’extension est plus grande que celle reçue à l’origine, de sorte à pouvoir rapprocher la tête du plateau si un produit plus petit doit être pressé. Rallonge en hauteur CMP L’option de rallonge en hauteur de la CMP permet de surélever la machine à une taille debout. Elle mesure 902 mm du haut de la table au sol, roulettes comprises (voir Figure 17). Cette machine doit être installée par un ingénieur de chantier. RÉV. D1 19 sur 94 409-35001 Figure 17 Kit de pièces de rechange CXP Chaque numéro de pièce de CXP peut être associé à un kit de pièces de rechange avec des pièces supplémentaires, telles que des barrières immatérielles ou des arrêts d’urgence. Ce kit est généralement acheté pour permettre une réparation immédiate en cas de panne. Navette manuelle ou pneumatique La navette pneumatique ne peut être utilisée que sur la machine CSP MKII, mais la navette manuelle peut être installée sur n’importe quelle machine après l’achatd’un autre plateau de table. Cette option est principalement d’ordre ergonomique. Grâce à elle, l’utilisateur n’a pas besoin d’aller loin sous la machine. RÉV. D1 20 sur 94 409-35001 Configuration propre à la machine L’écran principal est toujours affiché au démarrage ou lorsqu’aucun opérateur n’est connecté. Vous pouvez aussi appuyer sur logo TE en haut à gauche de l’écran pour afficher l’écran principal. Pour consulter la configuration de la machine, cliquez sur le menu déroulant « System » sur le côté gauche de la barre de navigation supérieure et sélectionnez About dans le menu. Les attributs de la machine sont illustrés à la Figure 18. Les utilisateurs disposant des droits d’accès d’administrateurs peuvent accéder à l’écran System Settings et sélectionner l’onglet Database Backup and Restore pour gérer les versions de la base de données. REMARQUE : écran About de la CMP – ceux des CBP et CSP sont similaires Figure 18 RÉV. D1 21 sur 94 409-35001 6. FONCTIONNEMENT (PRODUCTION) Démarrage Cette procédure de démarrage suppose que toutes les informations nécessaires ont été saisies dans les bases de données des outils (Tool Database), des connecteurs (Connector Database), des profils (Profile Database), des conditions (Condition Database) et des séquences (Sequence Database). Voir la section sur la programmation pour plus de renseignements sur la saisie des informations dans ces tableaux de bases de données. Les captures écrans utilisées dans les exemples ci-dessous proviennent d’une CBP. Ceux des CMP sont similaires. Interface opérateur Il est possible d’effectuer des sélections sur l’écran de l’ordinateur en le touchant avec le doigt ou en pointant et en faisant un clic gauche avec la souris. Les entrées alphanumériques peuvent être saisies à l’aide du clavier ou en touchant les boutons fournis à l’écran. Les données de certains champs de saisie de l’écran de production peuvent également être saisies à l’aide du lecteur de codes-barres en option. REMARQUE : le fonctionnement de l’écran tactile peut être perturbé par les gouttes d’humidité, qui devront alors être retirées. La navigation entre les principaux écrans fonctionnels s’effectue à l’aide de la barre d’outils opérateur située en bas de l’écran et des menus déroulants figurant dans la barre d’outils en haut de l’écran. La barre d’outils opérateur du bas de l’écran contient des boutons qui renvoient aux principaux écrans utilisés par l’opérateur pendant la production. Le menu déroulant System situé dans la barre d’outils supérieure contient des boutons qui renvoient aux écrans utilisés pour la configuration et la maintenance du système. Le menu déroulant Editors situé le long de la barre d’outils supérieure contient des boutons qui renvoient aux écrans utilisés pour la configuration des pièces et des séquences (voir Figure 19). Figure 19 Les écrans et boutons de fonctions spécifiques disponibles dépendent du niveau d’accès de l’utilisateur. Voir la section sur les accès utilisateur pour plus d’informations. Appuyez sur le bouton « Help » dans la barre d’outils supérieure pour afficher les informations du manuel d’utilisation. Durant la production, seule une barre d’outils est disponible au bas de l’écran. Les boutons de cette barre d’outils permettent l’accès aux fonctions disponibles durant le traitement des cartes. Les boutons de fonctions disponibles dépendent du niveau d’accès de l’utilisateur (voirFigure 20). Figure 20 RÉV. D1 22 sur 94 409-35001 Mise sous tension L’interrupteur principal est situé sur le côté (pour la CBP) ou à l’arrière (pour la CMP) de la machine. Placez l’interrupteur en position « OFF » pour couper l’alimentation électrique L’interrupteur peut être bloqué dans cette position pour des raisons de sécurité. Placez-le en position « ON » pour démarrer la machine. Connexion L’écran d’accueil principal apparaît au lancement du programme. L’utilisateur doit se connecter à l’écran Operator avant de pouvoir naviguer sur d’autres écrans. Sélectionnez le bouton Operator (voir Figure 21 à gauche) dans la barre d’outils inférieure ou l’icône Operator (voir Figure 21 à droite) sur le côté droit de la barre d’outils supérieure pour afficher l’écran Operator. Toute tentative de navigation vers un autre écran avant la connexion redirigera automatiquement l’utilisateur vers l’écran Operator. Une fois connecté, l’utilisateur est automatiquement redirigé vers l’écran auquel il essayait précédemment d’accéder (voir Figure 22). Figure 21 Figure 22 REMARQUE Sélectionnez votre nom dans la liste déroulante d’utilisateurs. Si votre nom n’apparaît pas dans la liste, vous devez consulter l’ADMINISTRATEUR du système pour qu’il l’ajoute. RÉV. D1 23 sur 94 409-35001 Figure 23 Sélectionnez le champ de saisie du mot de passe et saisissez votre mot de passe à l’aide d’un clavier physique ou du clavier virtuel. Appuyez sur « Login » pour valider les informations d’identification d’utilisateur et terminer le processus de connexion (voir Figure 24). RÉV. D1 24 sur 94 409-35001 Figure 24 Sélection de la carte Appuyez sur le bouton « Select Sequence » dans la barre d’outils inférieure (voir Figure 25). Figure 25 Sélectionnez maintenant la séquence dans la liste présentée. Utilisez la barre de défilement à droite de la liste pour consulter la liste complète des séquences. Tous les programmes disponibles sont classés par ordre alphabétique. Sélectionnez le bouton « Load Sequence » pour charger la séquence sélectionnée. Une fois la séquence chargée avec succès, l’utilisateur est automatiquement redirigé vers l’écran Production. Sélectionnez le bouton « Delete Sequence » (voir Figure 26) pour supprimer définitivement une séquence de la base de données. Une boîte de dialogue s’ouvre et invite l’utilisateur à confirmer qu’il souhaite toujours supprimer la séquence sélectionnée. Sélectionnez le bouton « Delete » dans la boîte de dialogue de confirmation pour terminer la suppression de la séquence. Figure 26 RÉV. D1 25 sur 94 409-35001 Production de la carte Cliquez sur le bouton « Production » pour passer en mode d’exécution de production (voir Figure 27). Si l’axe de la machine n’a pas encore été remis en position initiale, des messages à l’écran vous guideront à travers les étapes pour effectuer cette action. Après avoir appuyé sur le bouton « Run » à l’écran, la barrière immatérielle doit rester en place jusqu’au retour à la position initiale. Figure 27 Le premier écran affiché lors de l’accès au mode Run dépend de la séquence chargée pour la carte actuelle. Reportez-vous à la section sur le démarrage du pressage pour les détails demandés avant de produire une carte. L’écran d’exécution vous montrera une représentation de la carte basée sur les données figurant en haut à gauche et, en haut à droite, un graphique vide concernant les données de force et de distance de pressage, ainsi qu’un bouton « action » multi-objets contenant des messages et des informations textuelles sur le statut en bas à gauche, des informations sur la séquence de pressage en cours et le connecteur en bas à droite, avec une barre d’outils de boutons en bas. Voir la section de programmation ci-dessous pour plus de détails sur la configuration des séquences de carte et la création de connecteurs et d’outils dans la base de données. Figure 28 RÉV. D1 26 sur 94 409-35001 Boutons de l’écran Run Les boutons disponibles dépendent du niveau d’accès de l’utilisateur connecté. Voici, de gauche à droite, l’objet de chaque bouton : Z Up : Utilisé pour complètement remonter l’axe Z. Après avoir appuyé sur ce bouton, la presse se déplacera jusqu’à sa position de dégagement si la barrière immatérielle fonctionne et si la presse n’est pas soumise à une force excessive. Fonction Goto : Utilisé pour accéder aléatoirement à un connecteur de la carte. Sélectionnez le connecteur souhaité en touchant l’image du connecteur sur la représentation de la carte à gauche de l’écran, ou en faisant un clic-gauche dessus. Le connecteur sélectionné apparaît en rouge. Offsets : Utilisé pour modifier la hauteur de pressage. Cette fenêtre permet de modifier un décalage stocké pour le type de connecteur actuel de la carte. Connector Offset est particulièrement utile pour compenser les nombreuses variétés des lots de produits rencontrées lors du pressage en hauteur. Le décalage indiqué lorsque ce bouton est utilisé s’appliquera au prochain connecteur qui sera pressé dans la séquence actuelle. Lors de la modification d’un décalage, vérifiez le nom du connecteur dans le panneau d’information en bas à droite de l’écran pour éviter des résultats inattendus. Le bouton Offset n’est pas disponible pour tous les utilisateurs, cela dépend du niveau d’accès. Connector offset doit uniquement être utilisé pour compenser la variation normale du lot de produits et non les erreurs dans les données sur l’outil/le connecteur/la hauteur de l’appareil ou les définitions de profil incorrectes (voir Figure 29). Reset Part Viewer Zoom : Utilisé pour réinitialiser le réglage de zoom sur le panneau de visionneuse de pièces. Cela réinitialise le réglage du zoom de sorte à afficher le graphique complet de la carte. Figure 29 « New Board » - Utilisé pour réinitialiser le pointeur de séquence sur le premier connecteur. Le résultat est le même qu’en touchant ou en appuyant sur le connecteur #1 (si le connecteur est la première étape de la séquence). « Exit » - Utilisé pour revenir à l’écran principal tel qu’affiché au démarrage. On s’en sert généralement à la fin d’un cycle de pressage. Une nouvelle carte peut ensuite être sélectionnée depuis l’écran principal ou l’utilisateur peut se déconnecter. Pour empêcher tout accès non autorisé, veuillez vous déconnecter avant de vous éloigner de la machine. RÉV. D1 27 sur 94 409-35001 Affichage de la configuration de la carte Le dessin de configuration de la carte montre l’emplacement des connecteurs les uns par rapport aux autres et aux bords de la carte. Il permet de vérifier qu’il n’y a pas d’erreur flagrante avant de lancer un nouveau programme pour la première fois. Il mettra par exemple en évidence tout connecteur situé hors de la carte, les interférences entre les emplacements de plusieurs connecteurs ou l’inadéquation des angles de connecteurs avec l’agencement de la carte actuelle (voir Figure 30). Figure 30 Le dessin s’affiche dès que le premier connecteur à presser est en rouge. Il s’agira du premier connecteur de la séquence. Les connecteurs sont représentés par des rectangles. Le numéro, le nom et le message du connecteur sont également affichés en fonction du paramétrage de la séquence. Pour lire en détail toutes les informations, zoomez en double cliquant sur le dessin avec le bouton gauche de la souris (ou tapez deux fois sur l’écran tactile). Démarrer un pressage Chaque séquence individuelle est démarrée en appuyant sur « Run Sequence » lorsque vous y êtes invité. Toutes les étapes de séquence antérieures à la première étape de pressage seront exécutées avant que l’opérateur ne soit invité à utiliser le bouton pour démarrer l’opération de pressage. Il est possible qu’une combinaison de toutes ou d’une partie des diverses conditions forme une séquence avant le pressage. Les informations requises peuvent être saisies à partir du clavier, saisies via l’écran tactile ou, si l’opération est une opération de lecture de codes-barres, scannées à l’aide du lecteur de codes-barres en option. Connector Substitution : cette fonction permet de sélectionner des connecteurs interchangeables, généralement de différents fabricants, pendant l’exécution. Si un connecteur de la carte actuellement sélectionnée a une alternative et que cette fonction a été cochée dans l’éditeur de séquence (voir Connecteur et éditeurs de séquence pour la programmation de cette fonction), vous serez invité à faire une sélection. PCB Verify : cette fonction nécessite la vérification du « type » ou du « modèle » de la carte en cours d’exécution. Idéalement, la carte sera pourvue d’un code-barres comportant ces informations, mais il est aussi possible de les saisir. Cette fonction s’active en ajoutant une condition « PCB Verify » à la séquence. PCB Serial Number : cette fonction nécessite le numéro de série de chaque carte. La lecture du code-barres est la méthode la plus pratique à utiliser, mais le numéro de série peut également être saisi à partir du clavier ou de l’écran tactile. Pour les options des données, reportez-vous à la section Éditeur de séquence de presse. Cette fonction s’active en ajoutant une condition « PCB Serial Number » à la séquence (voir Figure 31). RÉV. D1 28 sur 94 409-35001 Figure 31 Verify Tool ID : cette fonction nécessite de vérifier l’identification de l’outil avant de pouvoir continuer le pressage. Il s’agit d’une confirmation de qualité qui réduit le risque d’inadéquation entre ce que la presse attend et ce que fait l’opérateur. L’identifiant peut être saisi ou scanné. Cette fonction s’active en ajoutant une condition « Verify Tool ID » à la séquence. User Signoff (validation de l’utilisateur) Si cette fonction est activée, la presse s’arrêtera une fois la première carte terminée et ne poursuivra pas son exécution tant qu’une validation n’aura pas été effectuée. Cette fonction s’active en ajoutant une condition « User Sign Off » à la séquence de pressage. Modification de la séquence de pressage Le prochain connecteur à presser peut être modifié après la fin ou l’interruption d’un cycle. À l’aide du pointeur de la souris ou d’un doigt sur l’écran tactile, sélectionnez le prochain connecteur à presser. La séquence se poursuit à partir du nouveau point et passe automatiquement au connecteur ou à la condition suivants de la séquence du programme. Si le programme de la carte spécifie le mode non séquentiel (Non-Sequential) (reportez-vous à la section Éditeur de séquence de presse), la presse restera sur la position actuelle du connecteur (ou sur la mesure de l’épaisseur de la carte) jusqu’à ce qu’un autre connecteur soit sélectionné. Ce mode est principalement utilisé pour les activités de réparation des cartes imprimées. Conditions d’erreur de profil liées à la carte, au connecteur, aux outils et aux programmes Certaines des conditions d’erreur de profil les plus courantes rencontrées pendant le pressage sont détaillées ci-dessous. Les conditions d’erreur générées par le programme Profile sont définies par l’utilisateur, leur libellé peut donc varier. Le programmeur de profil peut également définir d’autres messages d’erreur. Premature Contact : il s’agit probablement de l’erreur de profil la plus courante rencontrée pendant un fonctionnement normal. Elle se produit lorsque la tête de la presse entre en contact avec l’outil plus tôt que prévu. La force de contact et les seuils de position sont définis dans le profil du connecteur. Voici quelques causes possibles : le connecteur a bougé et se trouve trop haut l’outil de pressage est levé sur le connecteur en raison d’une broche pliée le connecteur est soulevé au-dessus de la carte de circuit imprimé par une broche pliée qui empêche le connecteur sous la tête n’est pas celui attendu (la carte de circuit imprimé est dans la mauvaise certaines broches de pénétrer dans les trous il y a une erreur dans le fichier Press Profile (*.prs) de sorte que la tête entre en contact avec l’outil plus position) la carte ou l’épaisseur de gabarit de support indiquées dans le fichier Press Data (*.pdf) sont incorrectes la hauteur d’outil indiquée dans la base de données de l’outil est incorrecte la hauteur d’approche du connecteur indiquée dans la base de données du connecteur est incorrecte tôt que prévu Lorsque cette condition apparaît, la tête de la presse se soulève jusqu’à la position de dégagement de la carte et affiche un message. Une inspection minutieuse révèle généralement le problème. Si l’erreur est générée lors de la première exécution d’un nouveau programme, il s’agit probablement d’une erreur de dimension dans l’un RÉV. D1 29 sur 94 409-35001 des fichiers de données. Dans certains cas, il est possible d’essayer à nouveau, par exemple lorsque le connecteur non pressé a bougé et que la tête a corrigé l’inclinaison en touchant l’outil. Il faut être prudent lors de la nouvelle tentative, car si une broche est tordue, elle risque de se courber davantage et de s’enfoncer à plat sur le fond du connecteur. Un profil correctement défini détectera cette condition et générera une erreur appropriée, mais le connecteur peut être endommagé au point de ne plus être réparable. Missing Connector : cette erreur est générée lorsqu’il manque un connecteur. Si aucun connecteur ne manque, il y a probablement une erreur dans les dimensions du profil ou de l’outil/du connecteur/du circuit imprimé/de l’appareil, et le programmateur doit la corriger. Cela peut également se produire si le réglage Machine Zero est incorrect en raison d’une condition nécessitant une réparation de la presse. Excess Force : cette erreur s’affiche lorsque la force requise pour mettre en place le connecteur dépasse la limite programmée. Il se peut qu’il y ait un problème avec le connecteur (broches surdimensionnées/courbées) ou la carte de circuit imprimé (trous sous-dimensionnés) causant une résistance trop importante avant que le connecteur n’atteigne sa hauteur finale. Le support, la carte de circuit imprimé, l’outil et/ou le connecteur peuvent être trop épais, entraînant un contact plus intense que prévu entre le connecteur et la carte de circuit imprimé. Il peut y avoir un problème avec les définitions de force ou de hauteur dans le programme Profile. En plus du message d’erreur de profil défini par l’utilisateur, un message d’erreur de profil « Excess Force » s’affiche chaque fois que la force maximale par broche (MaxFPP) spécifiée dans la base de données des connecteurs est dépassée, même lorsqu’une autre force (comme PARS) et/ou une force d’action sont spécifiées sur la ligne de profil. Insufficient Force : cette erreur peut être causée par une interférence broche contre trou trop légère. Cela peut également être dû à un gabarit de support trop fin, à des problèmes d’épaisseur du connecteur, à des dimensions incorrectes entrées dans l’outil ou la base de données du connecteur, ou à des erreurs de programme Profil. Le programmeur doit être consulté pour corriger le problème. Diagnostics : les menus « Cursors » et « Graph Options » situés sous le graphique de production peuvent être utilisés pour activer ou désactiver diverses options de graphique de diagnostic et curseurs. Ces données peuvent être utiles pour comprendre le chemin pris par le profil lors du pressage. Data Collection : des données détaillées sont collectées pour chaque pressage et consignées dans le journal de la machine. « Export Production Graph » : ce bouton se trouve sous le menu « Graph Options » et peut être utilisé pour enregistrer le graphique Force vs. Distance affiché en pdf sur un appareil externe. 7. OUTILS ET GABARITS DE SUPPORT DE PRESSAGE Cette section définit les exigences générales applicables aux outils de pressage et aux gabarits de support (plateaux) des connecteurs qui seront utilisés lors du pressage. Dans la plupart des cas, les outils d’insertion et les gabarits de support utilisés lors des autres opérations de pressage manuel peuvent être utilisés dans cette presse. Outils Les directives ci-dessous doivent être respectées pour garantir des performances optimales. Width : peut être toute largeur supportant adéquatement la force de pressage Height : il existe une tolérance de 130 mm entre la table et la tête de pressage en position haute maximale (moins si une entretoise d’enclume est utilisée sur la carte de circuit imprimé). L’outil, le gabarit de soutien, le connecteur et la carte doivent être inférieurs à cette mesure. Length : jusqu’à 250 mm (pour demeurer dans les limites de capture de la tête « flat rock »), combinaison d’outils simple ou multiple. Gabarits de support (Plateaux/ Gabarits de soutien) Le gabarit support, parfois appelé plateau, doit être constitué d’une matière normalement dure. Pour des résultats optimaux, sa planéité ne doit pas varier de plus de 0,10 mm. La plupart des gabarits en service sur les autres presses sont adéquats, mais leur planéité est fréquemment médiocre. Le pressage en hauteur sera problématique si le gabarit n’est pas plat. RÉV. D1 30 sur 94 409-35001 8. PROGRAMMATION ET SAISIE DES DONNÉES La presse est un outil hautement polyvalent grâce à ses fonctions de programmation simples et flexibles. Cinq bases de données guident la presse via des séquences d’opérations particulières. Les variables stockées comprennent les informations physiques des outils de pressage, les informations des profils de pressage, les informations physiques sur les connecteurs, les opérations de séquence sans pressage (appelées « conditions ») et les informations sur les cartes et le gabarit de soutien. Une fois stockées, les informations sont disponibles pour être utilisées par les programmes actuels et futurs. L’accès aux éditeurs est normalement limité aux utilisateurs de niveaux supérieurs à « opérateur ». Les éditeurs sont accessibles depuis le menu déroulant Editors. Pour ouvrir un écran d’éditeur, sélectionnez l’élément approprié dans le menu déroulant Editors. L’éditeur d’outils Figure 32 Objectif L’éditeur d’outils est utilisé pour visualiser et modifier la base de données des outils, un fichier sqlite. Il contient toutes les informations nécessaires sur les outils de pressage mécaniques utilisés pendant le processus de pressage. L’éditeur est accessible depuis le menu déroulant Editors. Les champs suivants sont maintenus dans la base de données et sauvegardés à l’aide du bouton « Save ». Rubriques « Tool Type » : le nom que vous choisissez peut comporter jusqu’à 30 caractères, avec espaces, et sera désormais utilisé pour désigner cet outil. Pour saisir un nouveau type d’outil, sélectionnez « New ». Vous pouvez également sélectionner « Copy » pour copier l’outil actuellement affiché. Vous devez saisir un nouveau nom. Sélectionnez « Delete » pour supprimer l’outil actuellement affiché. Sélectionnez « Save » pour enregistrer l’outil actuellement affiché. « Tool ID » : il s’agit du numéro unique utilisé pour identifier l’outil. Il peut être gravé et/ou codé à l’aide d’un code-barres. Il est pratique d’utiliser un lecteur de codes-barres pour confirmer le type d’outil au moment de l’exécution. RÉV. D1 31 sur 94 409-35001 REMARQUE SEULS les doublons interchangeables peuvent avoir le même identifiant. Dans ce cas, il n’y a qu’une seule entrée dans la base de données. « Dimensions » Tool Height : les informations relatives à la hauteur de l’outil sont nécessaires pour confirmer la hauteur pressée du connecteur. Saisissez la hauteur de l’outil entre la surface supérieure et le plan de pressage sur le connecteur, ainsi que le montre le schéma. Tool Clearance : les informations sur la tolérance de l’outil sont nécessaires pour calculer l’espace à laisser entre l’enclume et l’outil lorsque l’enclume de la presse se déplace à la hauteur de dégagement avant le pressage. Tool Width : cette entrée est utilisée à des fins de traçabilité et ne sert à aucune partie de l’opération de pressage. Tool Length : cette entrée est utilisée à des fins de traçabilité et ne sert à aucune partie de l’opération de pressage. « Comments » Vous pouvez saisir des commentaires, par ex. une courte description de l’application de l’outil. L’éditeur de connecteurs Figure 33 Objectif Connector Editor (voir Figure 33) est utilisé pour afficher et modifier la base de données des connecteurs, qui est un fichier sqlite. L’éditeur est accessible depuis le menu déroulant Editors. Toutes les modifications sont enregistrées lorsque l’on appuie sur le bouton « Save ». RÉV. D1 32 sur 94 409-35001 Rubriques « Connector Name » : le nom que vous choisissez peut comporter jusqu’à 30 caractères, avec espaces, et sera désormais utilisé pour désigner ce connecteur. Pour saisir un nouveau type de connecteur, sélectionnez « New ». Vous pouvez également sélectionner « Copy » pour copier le connecteur actuellement affiché. Vous devez saisir un nouveau nom. Sélectionnez « Delete » pour supprimer le connecteur actuellement affiché. Sélectionnez « Save » pour enregistrer le connecteur dans la base de données. Le bouton « Import » peut être utilisé pour importer un ancien fichier de connecteur dans la base de données des connecteurs. « Tool » : il s’agit du type ou du nom de l’outil à utiliser pour presser le connecteur. Il est prélevé dans les listes de la base de données de l’outil depuis le menu déroulant. L’outil doit être saisi dans la base de données des outils avant de pouvoir terminer la saisie des données du connecteur. « Number of Pins » : il s’agit du nombre de broches sur le connecteur. Il est utilisé pour calculer la force lors de l’utilisation de la force max. ou min. par broche dans le profil. Il est également utilisé pour calculer et dessiner la courbe de la force par broche sur l’écran d’exécution. « Profil » : il s’agit du nom du fichier de profils à utiliser en relation avec le connecteur. Il est prélevé dans les listes de la base de données des profils depuis le menu déroulant. Le profil doit être complété avant de pouvoir générer la base de données des connecteurs. Onglet « Dimensions » Primary Dimensions (dimensions principales) : Height : il s’agit de la mesure de la distance entre le haut du connecteur et la surface d’appui du connecteur. En soustrayant « Unseated Top » de « Height », vous obtiendrez la distance restante réelle restante pour presser le connecteur à sa position finale. Length : cette dimension est utilisée uniquement à des fins de traçabilité et de rendu de l’image du connecteur sur l’écran Production. Width : cette dimension est utilisée uniquement à des fins de traçabilité et de rendu de l’image du connecteur sur l’écran Production. Secondary Dimensions (dimensions secondaires) : Base Thickness : il s’agit de l’épaisseur du connecteur entre le fond intérieur (surface d’appui) et le fond extérieur, comme indiqué. Ce paramètre permet de calculer la position que la tête doit atteindre pour positionner le connecteur à la hauteur adéquate. Unseated Top : il s’agit de la mesure de la distance entre la surface supérieure du connecteur et la surface supérieure de la carte de circuit imprimé. Seated Height : il s’agit de la distance souhaitée entre la surface de la carte et le bas du connecteur après le pressage. Elle est généralement nulle, mais peut être réglée au-dessus de la surface de la carte pour les applications de pressage en hauteur. « Force » ● Min Force / Pin : il s’agit de la force minimale acceptable par broche. Elle est référencée dans le profil de pressage. ● Max Force / Pin : il s’agit de la force maximale acceptable par broche. Elle est référencée dans le profil de pressage. ● User Force / Pin : il s’agit de la force définie par l’utilisateur pour chaque broche. Elle est référencée dans le profil de pressage. ● Other Force : il s’agit d’un décalage total (pas par broche) de force fixe défini par un utilisateur qui peut être utilisé pour compenser l’utilisation d’un moule de pressage à ressort. Cette force est soustraite des mesures de force avant qu’elles ne soient comparées aux limites de force du profil de la presse et représentées graphiquement. RÉV. D1 33 sur 94 409-35001 Volet Force Gradient : Force Gradient surveille le taux d’évolution de la force par rapport à la distance. D’une manière générale, la courbe de la force par rapport à la distance se redressera brusquement quand le connecteur entrera en contact avec la surface de la carte. Un angle minimum de redressement est spécifié, il correspond à la force de pressage du connecteur contre la carte. Cette pente est saisie à l’aide d’unΔ Force/un Δ Distance (la variation de la force divisée par la variation de la distance). Δ Force : saisissez la variation de la force en numérateur de la pente que vous souhaitez surveiller pour terminer le cycle de pressage. La valeur saisie est utilisée en conjonction avec le Δ Distance lorsque Force Grad de Connector Database est sélectionné dans Profile Editor. Δ Distance : saisissez la variation de la distance en dénominateur de la pente que vous souhaitez surveiller pour terminer le cycle de pressage. La valeur saisie est utilisée en conjonction avec le Δ Force lorsque Force Grad de Connector Database est sélectionné dans Profile Editor. Legacy Force Gradient : les utilisateurs habitués à utiliser la méthode de gradient de force implémentée sur les anciennes machines peuvent utiliser l’outil de conversion situé dans le volet « Force Gradient » pour déterminer automatiquement le Δ de Force et le Δ de Distance en saisissant la valeur de l’ancienne échelle de graphique et l’ancienne valeur d’angle. Les valeurs Δ Force et Δ Distance sont automatiquement calculées et mises à jour lorsque les champs « Angle » ou « Scale » sont modifiés. « PARS » : un connecteur peut être pressé sous une force proportionnelle à la force antagoniste réelle détectée pendant le cycle de pressage. Ce profil est contrôlé par la hauteur du connecteur au début et à la fin et par le pourcentage de force appliqué sur ce qui est détecté à la fin du cycle. La valeur en pourcentage saisie ici est utilisée lorsque PARS from Connector Databse est sélectionné dans Profile Editor. « Comments » : ce champ recueille les commentaires utiles L’éditeur de profils Objectif Profile Editor (Figure 34, Figure 35et Figure 36) est utilisé pour afficher et modifier les profils de pressage. Un profil de pressage contient les informations utilisées pour contrôler la vitesse, la force et la hauteur du processus de pressage. Il constitue le cœur de la séquence de commande et permet à l’utilisateur de définir exactement la façon dont un connecteur est pressé sur la carte de circuit imprimé. L’éditeur propose de saisir jusqu’à 20 étapes, numérotées à gauche de l’écran, pour un profil donné. Les profils sont stockés dans une base de données sqlite avec un nom spécifié par l’utilisateur. L’éditeur de profil est accessible dans le menu déroulant Editors. RÉV. D1 34 sur 94 409-35001 Figure 34 Figure 35 RÉV. D1 35 sur 94 409-35001 Figure 36 Explication Le processus d’insertion commence à la ligne 1 et se poursuit à partir de là. Chaque ligne peut être de l’un des trois types suivants : « Move to Height or Force », « Delay » et « Retract ». Le type « Move to Height or Force » est le type d’étape le plus couramment utilisé. Ce type d’étape comporte une condition « Height » et une condition « Force ». Au fur et à mesure que la tête de presse descend, le programme surveille ces conditions en continu et réagit à celle qui survient en premier. La condition Height est vérifiée en premier, de sorte qu’elle est prioritaire dans le cas où les deux se produisent simultanément. Le type d’étape « Delay » peut être utilisé pour retarder le profil de pressage d’une durée spécifiée en millisecondes avant de poursuivre avec le reste du profil. Le type d’étape « Retract » peut être utilisé pour relever la tête de la presse à une distance spécifiée avant de poursuivre avec le reste du profil. Chaque condition (« Height », « Force », « Delay » ou « Retract ») correspond à une « action », qui poursuit le processus de pressage à une autre étape ou génère une erreur. Ces événements et actions sont utilisés pour : ● détecter et annoncer un contact inattendu ● détecter une force anormalement haute ou basse générée pendant le pressage ● détecter une condition de connecteur manquante ● presser à/vérifier la bonne hauteur d’appui ● represser un connecteur qui a déjà été partiellement pressé ● faire une pause d’une durée déterminée avant de continuer ● rétracter légèrement la tête pour relâcher momentanément la force avant de continuer Il existe quatre méthodes de pressage de base et chacune nécessite un profil spécifique. FORCE FIXE PAR BROCHE – Un connecteur peut être pressé selon une force proportionnelle au nombre de broches, par exemple 30 livres par broche. Cette méthode est légèrement meilleure que la méthode de pressage la plus simple selon une force totale fixe et unique parce qu’elle admet que la force appliquée doit être proportionnelle au nombre de broches à presser. Toutefois, elle ne peut pas compenser les écarts normaux de force par broche requise par différents connecteurs, dans différentes positions, sur différentes cartes. RÉV. D1 36 sur 94 409-35001 ÉCHANTILLON AVEC POURCENTAGE SUPÉRIEUR AUX LIMITES (PARS) – Un connecteur peut être pressé sous une force d’appui proportionnelle à la force antagoniste réelle de la broche détectée pendant le cycle de pressage. Cette fonction s’appelle le « Pourcentage au-dessus de la plage de l’échantillon », ou PARS. Dans cette technique, la force antagoniste opposée par la broche du connecteur pendant le pressage est échantillonnée et sa moyenne calculée sur une distance donnée avant la dépose sur la surface de la carte. La force finale exercée sur le connecteur est limitée à un pourcentage au-dessus de la plage de l’échantillon programmé par l’utilisateur. Ce pourcentage ajouté complète la parfaite assise du connecteur sur la carte. Cette technique est la plus répandue parce qu’elle limite les contraintes subies par l’assemblage sans exiger une mesure de l’épaisseur de la carte précise et ajuste automatiquement les petites variations d’épaisseur du connecteur et de la carte. PRESSAGE SELON LA HAUTEUR - Un connecteur peut être pressé selon une distance programmée en limite d’appui à la surface de la carte. Ceci est le procédé le plus modéré possible parce qu’il exerce uniquement la force suffisante pour presser les broches dans les trous plats de la carte. Aucune force de pressage excessive n’est exercée sur le plastique du connecteur ou la carte. Cette technique sophistiquée est rendue possible par le contrôle que permet l’utilisation d’une tête de presse électrique à servocommande et la rigidité de la structure de la presse. Pour une plus grande précision du pressage selon la hauteur, l’épaisseur de la carte doit être connue avec exactitude. Ceci est réalisable grâce à la sonde de mesure d’épaisseur et à la séquence fournies. GRADIENT DE FORCE - Cette méthode surveille le taux d’évolution de la force par rapport à la distance. Elle est utilisée quand des connecteurs robustes doivent être posés sur la surface de la carte. D’une manière générale, la courbe de la force à la distance se redressera brusquement quand le connecteur entrera en contact avec la surface de la carte. Le déplacement du connecteur est arrêté afin d’augmenter rapidement la force. Un angle minimum de redressement est spécifié, il correspond à la force de pressage du connecteur contre la carte. Veuillez noter que l’angle de redressement est calculé en utilisant le rapport de la variation de la force (ΔForce) sur la variation de la distance (ΔDistance) spécifié par l’utilisateur dans le profil ou dans la partie connecteur. Un profil « standard » associé à chacune des techniques ci-dessus est fourni avec la presse. Chaque profil utilise des variables dont les valeurs proviennent des bases de données des connecteurs et des outils plutôt que des nombres discrets. Puisque chaque connecteur exige la même procédure de base, un profil avec variables sera utilisable pour un grand nombre de connecteurs différents. Les profils standard sont nommés « standard_force_CDB », « standard_pars_CDB », « standard_HGT » et « standard_FG_CDB ». L’exemple #1 ci-dessous utilise le profil « standard_pars ». Onglets de navigation « Profile Step Sequence » : cet onglet affiche le profil sous la forme d’une liste étape par étape. Le nom et les détails de chaque étape sont affichés en lecture seule. Le bouton « Add Step » peut être utilisé pour créer une nouvelle étape à ajouter au profil. La nouvelle étape s’ouvrira dans l’onglet « Profile Step Editor ». Le bouton « Edit Step » (icône du crayon) se trouve à la droite de chaque étape. Ce bouton ouvrira l’étape correspondante dans l’onglet « Profile Step Editor » pour modification. Le bouton « Delete Step » (icône de poubelle) supprimera l’étape correspondante (l’utilisateur sera invité à vérifier l’opération avant de supprimer l’étape). « Profile Step Editor » : cet onglet montre une étape unique en mode d’édition, permettant à l’utilisateur de personnaliser tous les aspects de l’étape de profil à l’aide des différentes entrées répertoriées cidessous. « Legacy Profile Viewer » : cet onglet affiche l’ensemble du profil dans une vue identique à la mise en page de l’ancien éditeur de profil press fit. RÉV. D1 37 sur 94 409-35001 Rubriques « Step Name » : cette entrée sert à définir ou à décrire l’objectif de cette étape. « Step Number » : cette entrée est utilisée pour spécifier l’emplacement séquentiel de l’étape dans le profil. « Speed (mm/s or in/s) » : il s’agit de la vitesse cible de l’étape actuelle du processus. La vitesse commence à « Run Speed » et change linéairement jusqu’à la vitesse indiquée à l’étape 1. Lorsque la hauteur de l’étape 1 est atteinte, la vitesse augmente jusqu’à la vitesse donnée à la prochaine étape traitée. Il s’agit généralement de l’étape 2, sauf si une action « Goto Step » a été programmée (voir Figure 37). La plage de vitesses typique est de 8 mm [0,315 po]/seconde pendant l’approche, puis de 1 mm/seconde lors du pressage. Il pourrait être nécessaire de procéder à quelques tests pour optimiser le procédé. Certains connecteurs sont plus fragiles que d’autres et nécessitent des vitesses lentes, tandis que d’autres peuvent être pressés rapidement. Figure 37 « Step Type » : est utilisé pour spécifier si l’étape sera de type « Move to Height or Force », « Delay » ou « Retract ». Figure 38 « Height Dimension » : est utilisé pour définir l’emplacement suivant de pressage de l’outil sur la carte. Ce champ spécifie si une dimension de l’empilement de connecteurs doit être référencée (« Unseated Tool Top », « Seated Height ») ou si l’utilisateur doit spécifier une hauteur fixe à l’aide du champ de saisie « Custom Height » (voir Figure 39). Figure 39 « Offset » : est utilisé en conjonction avec « Height Dimension » pour définir l’emplacement suivant de pressage de l’outil sur la carte. Une valeur de décalage positive ou négative peut être saisie pour ajuster la hauteur à atteindre, afin qu’elle soit légèrement au-dessus ou en dessous de la hauteur « Height Dimension » sélectionnée. (Remarque : ce champ n’est pas utilisé lorsque « Custom Height » est sélectionné). La tête de la presse descend jusqu’à la hauteur définie par ces champs à une vitesse qui augmente linéairement par rapport à la hauteur et à la vitesse de l’étape précédente. RÉV. D1 38 sur 94 409-35001 La hauteur initiale (avant l’étape 1) est définie par la hauteur d’empilement de la carte, du gabarit de support, du connecteur, de l’outil et de la tolérance de l’outil. Les dimensions « Height Dimensions » disponibles sont indiquées ici. Une hauteur numérique positive fixe peut également être saisie. Cela spécifie une hauteur de l’outil au-dessus du plateau de la table de la presse, indépendamment de l’épaisseur de la carte de circuit imprimé, du connecteur ou du gabarit de support. « Height Action » : définit l’action à effectuer lorsque la hauteur de cette étape est atteinte, comme illustré à la Figure 40. Les actions sont sélectionnées dans le menu déroulant. Les actions disponibles sont : Next Step : permet de passer à l’étape suivante ci-dessous. GoTo : aiguille le processus vers sa poursuite à l’étape spécifiée. Le numéro d’étape est saisi dans le champ numérique. Complete : indique que le processus de pressage est terminé. La tête s’arrête immédiatement et monte à la hauteur suivante de dégagement de l’outil. Un message d’achèvement peut être saisi par l’utilisateur dans le champ adjacent. Error : il s’agit de messages d’erreur définis par l’utilisateur. Si la hauteur est atteinte et que l’action est une erreur, le processus de pressage est immédiatement interrompu et le message d’erreur s’affiche à l’écran. L’opérateur doit valider le message d’erreur pour continuer. Figure 40 « Force Measurement » : définit la force qui déclenchera l’action de force. Le menu déroulant propose de choisir entre onze variables. Il est possible de saisir une force réelle (en livres) dans un champ numérique à l’aide de l’option « Custom Force » (voir Figure 41). Figure 41 PARS : il s’agit d’une fin de cycle de pressage dynamique basée sur les forces réelles générées pendant le processus de pressage. PARS signifie échantillon avec pourcentage supérieur aux limites. Cette condition de force utilise un algorithme spécial qui calcule la force moyenne générée lors du pressage du connecteur sur la carte de circuit imprimé. Les cases « Start » et « Distance » au milieu de l’écran définissent les limites pour la moyenne. Ainsi, au lieu de presser selon une force spécifique, la force réelle requise est calculée dynamiquement pour chaque cycle et la fin est basée sur cette force. Le pourcentage est une force avec excès exprimée en pourcentage de la moyenne calculée, qui est ajoutée à la moyenne pour s’assurer que le connecteur est bien en place. RÉV. D1 39 sur 94 409-35001 Par exemple : 0,40 mm (0,016 po) est indiqué pour « Start Height » et 0,20 mm (0,008 po) pour « Distance ». La force PARS est invoquée dans la colonne « Force (N) », ligne 4, où 25 % a été saisi. Lors du pressage du connecteur, les mesures de force comprises entre 0,40 mm et 0,20 mm [0,016 po et 0,008 po] au-dessus de la carte sont prises dans la moyenne. La tête continue de presser jusqu’à ce que la force générée soit supérieure de 25 % à cette moyenne. Notez que si la force dépasse 125 % de la moyenne avant que la ligne PARS (ligne 4 dans cet exemple) soit atteinte, la presse s’arrêtera à la valeur de pourcentage supérieure atteinte lorsque la ligne 4 est atteinte. La fonction « FPPL » signifie que la presse s’arrêtera toujours en cas d’erreur si la valeur Max FPP (spécifiée dans Connector Editor) est dépassée avant que la valeur PARS spécifiée ne soit atteinte. PARS from Connector Databse : la situation est identique à celle ci-dessus, sauf que les valeurs de pourcentage, de hauteur de départ et de distance sont obtenues à partir des saisies de la base de données des connecteurs pour ce type de connecteur. Auto PARS : cette condition de force localise la région PARS située sous la hauteur « Start Height » saisie et sous la « Distance » saisie dont la force moyenne est la plus petite et en effectue une analyse PARS en fonction du pourcentage PARS saisi. Il s’agit en fait d’une analyse PARS « roulante » qui utilise ce qui est théoriquement la meilleure région PARS en dessous de la hauteur « Start Height » saisie. Auto PARS from Connector Database : la situation est identique à celle ci-dessus, sauf que les valeurs de pourcentage, de hauteur de départ et de distance sont obtenues à partir des saisies de la base de données des connecteurs pour ce type de connecteur. Force Gradient : cette technique surveille le taux d’évolution de la force par rapport à la distance. Elle est utilisée quand des connecteurs robustes doivent être fermement installés. D’une manière générale, la courbe de la force par rapport à la distance se redressera brusquement quand le composant entrera en contact avec la surface d’appui. Le déplacement du composant est arrêté afin d’augmenter rapidement la force. Un angle minimum de redressement est spécifié, il correspond à la force de pressage du composant. L’angle de redressement est calculé en utilisant le rapport du Δde la Force sur le Δ de la distance spécifiés par l’utilisateur. Force Gradient from Connector Database : la situation est identique à celle ci-dessus, sauf que les valeurs de pourcentage sont obtenues à partir des saisies de la base de données des connecteurs pour ce type de connecteur. Min Force/Pin * Number of Pins : cette force est calculée en multipliant le nombre de broches dans le connecteur pressé par la force minimale requise par broche. Le nombre de broches et la force minimale par broche sont des entrées de la base de données des connecteurs. Cette fonction peut être utilisée pour garantir la génération d’une force minimale pendant le processus de pressage. Max Force/Pin * Number of Pins : cette force est calculée en multipliant le nombre de broches dans le connecteur pressé par la force maximale permise par broche. Le nombre de broches et la force maximale par broche sont des entrées de la base de données des connecteurs. Cette fonction peut être utilisée pour prévenir la génération d’une force excessive pendant le processus de pressage. User Force/Pin * Number of Pins : cette variable est fournie pour pouvoir définir avec flexibilité une variable d’événement de force autre que Max and Min force per pin. Son utilisation est laissée à la discrétion du programmeur. Par exemple, lors du pressage selon la force, il peut être utile de terminer par « User Force/Pin * Number of Pins » plutôt que par « Max Force/Pin * Number of Pins ». La variable « Max Force/Pin * Number of Pins » sera toujours utilisée pour générer une erreur si la force autorisée est dépassée. User Force/Pin * Number of Pins * : la situation est identique à celle ci-dessus, sauf qu’un multiplicateur personnalisé spécifique à l’étape peut être ajouté pour ajuster la valeur calculée. Custom Force : ceci permet à l’utilisateur de spécifier une valeur de force totale personnalisée et fixe qui déclenchera l’action de force. « Force Action » : définit l’action à effectuer lorsque la force prévue à cette étape est atteinte. Les actions sont sélectionnées dans le menu déroulant. Les actions liées à la force sont les mêmes que les actions liées à la hauteur (voir Figure 42). RÉV. D1 40 sur 94 409-35001 Figure 42 « Delay » : précise en millisecondes un délai d’attente pendant lequel le profil attendra avant de poursuivre l’action « Delay Action ». Delay Action : définit l’action à effectuer une fois que le délai d’attente prévu à cette étape a été respecté. Les actions sont sélectionnées dans le menu déroulant. Les actions liées à un délai d’attente sont les mêmes que les actions liées à la hauteur. « Retract » : spécifie une distance à laquelle la tête de la presse se rétractera (ou se déplacera vers le haut) avant de poursuivre l’action « Retract Action ». Retract Action : définit l’action à effectuer une fois que le mouvement de rétraction prévu à cette étape a été exécuté. Les actions sont sélectionnées dans le menu déroulant. Les actions liées à une rétraction sont les mêmes que les actions liées à la hauteur. Boutons d’action Principaux boutons de l’éditeur de profils : « New » : appuyez pour créer un nouveau profil. Le profil ne sera pas enregistré dans la base de données tant que le bouton « Save » n’aura pas été actionné. « Save » : appuyez sur ce bouton pour valider et enregistrer le profil actuel dans la base de données. Une tentative de validation et d’enregistrement de l’étape en cours d’édition aura aussi lieu si elle n’a pas été validée. Pour enregistrer le profil sous un autre nom, appuyez sur « Copy » pour dupliquer le profil actuel et sur « Save » pour l’enregistrer sous un autre nom. « Copy » : appuyez pour créer un duplicata du profil actuel. Le nouveau duplicata ne sera pas enregistré dans la base de données tant que le bouton « Save » n’aura pas été actionné. « Delete » : appuyez pour supprimer le profil actuel de la base de données des profils. L’utilisateur sera invité à confirmer qu’il souhaite supprimer le profil avant exécution. « Cancel » : appuyez sur ce bouton pour annuler toute modification non enregistrée du profil actuel. « Import » : appuyez sur ce bouton pour importer un ancien fichier de profil vers la base de données des profils. Boutons de l’éditeur d’étapes de profils : « Add Step » : appuyez pour créer une nouvelle étape vide. Remarque : l’étape ne sera pas ajoutée au profil tant qu’elle n’aura pas été validée à l’aide du bouton « Validate Step ». « Delete Step » : appuyez pour supprimer l’étape en cours. Remarque : l’utilisateur sera invité à confirmer qu’il souhaite supprimer l’étape avant exécution « Save Step » : appuyez sur ce bouton pour confirmer que tous les champs d’étape requis ont des entrées valides et ajouter ou mettre à jour l’étape actuelle dans le profil. La nouvelle étape ne sera pas ajoutée au profil tant qu’elle n’aura pas été validée. Les modifications ou mises à jour d’une étape existante ne seront pas ajoutées au profil tant qu’elles n’auront pas été validées. « Cancel Changes » : rejetez une nouvelle étape non validée ou rejetez les modifications d’une étape existante non validée. RÉV. D1 41 sur 94 409-35001 Exemple : Pressage avec PARS (FigureFigure 43) Figure 43 La capture d’écran de la Figure 43 est un profil de pressage PARS typique. Le libellé à l’extrémité gauche de chaque ligne indique l’action que la ligne exécutera. En général, le pressage PARS est la méthode à privilégier, car elle empêche toute force de pressage excessive tout en pressant néanmoins le connecteur dans la surface de la carte. Les connecteurs fragiles qui ne peuvent pas supporter de force excessive doivent être pressés en hauteur comme dans l’exemple ci-dessous. 1. Déplacez la tête de la hauteur de dégagement de l’outil (comme indiqué dans la base de données des outils) vers le bas, à 0,75 mm [0,030 po] au-dessus du haut sans appui de l’outil. La vitesse va accélérer linéairement depuis la vitesse de pressage « Run Speed » à 7 mm [0,276 po] par seconde. Lorsque la hauteur est atteinte, la séquence passe à l’étape suivante. Si plus de 250 Newtons [899 ozf] sont détectés avant que la hauteur ne soit atteinte, l’opération est interrompue et affiche l’erreur #1, généralement « Premature contact detected » (contact prématuré). 2. Continuez à descendre jusqu’à ce que le connecteur se trouve à 1,0 mm au-dessus de sa hauteur d’appui. La vitesse est réduite à 5 mm/seconde. Cette ligne teste si un connecteur est effectivement détecté. Si c’est le cas, comme indiqué par la détection d’une force équivalant à au moins la force minimale par broche (MinFPP), le processus passe à la ligne suivante. Si ce n’est pas le cas, le processus passe à la ligne 5 pour essayer de presser à nouveau un connecteur précédemment pressé (pression complète ou partielle). 3. Pressez jusqu’à ce que le connecteur se trouve à 0,25 mm de la hauteur d’appui souhaitée. Lorsque cette position est atteinte, le connecteur se trouve à une tolérance de hauteur d’appui généralement acceptée. Les 0,25 mm peuvent être ajustés en fonction des circonstances spécifiques. Si la force dépasse la force maximale par broche (MaxFPP) avant que la hauteur ne soit atteinte, un message d’erreur s’affiche. 4. L’exécution de cette étape pressera théoriquement le connecteur à l’excès, mais le processus sera effectivement terminé dès lors que la force atteindra la région PARS moyenne + un pourcentage additionnel spécifié dans la base de données des connecteurs. La hauteur donnée fournit un emplacement qui ne sera pas atteint parce que les conditions de force seront satisfaites en premier. Si l’emplacement est atteint avant que la force PARS soit atteinte, alors il est très probable qu’une erreur se soit introduite dans les paramètres utilisés pour calculer la relation de distance entre le connecteur, l’outil et la surface de la carte. Si ceci se produit, contrôlez la hauteur de l’outil, l’épaisseur de la base du connecteur, l’épaisseur du gabarit de soutien et l’épaisseur de la carte. Notez qu’une ligne PARS surveille également la donnée MaxFPP. Si la valeur MaxFPP est dépassée avant d’atteindre la force PARS, le pressage s’arrêtera avec une erreur « excess force ». La vitesse ralentira linéairement à 2 mm/seconde depuis la hauteur cible. RÉV. D1 42 sur 94 409-35001 5. Cette étape n’est atteinte que par l’action liée à la hauteur « GO TO » à partir de l’étape 2. Elle teste si un connecteur n’a pas atteint la donnée MinFPP à la hauteur appropriée, en vérifiant si une force de 250 Newtons a été détectée dans les 0,1 mm sous la hauteur minimale MinFPP depuis l’étape 2. La vitesse ralentira linéairement à 2 mm/seconde depuis la hauteur cible. Figure 44 6. En cas de non-détection d’une force de 250 Newtons, même sous la hauteur d’appui la plus basse, cette étape vérifie s’il manque un connecteur. Dès que ce niveau de force est détecté, le processus passe à la ligne suivante. 7. Cette ligne vérifie que le connecteur est pressé dans la tolérance de hauteur généralement acceptée et que la force maximale par broche n’est pas dépassée. 8. Cette ligne indique une destination inférieure à la hauteur d’appui nominale et se termine par la force maximale par broche multipliée par le nombre de broches. Cette variable peut également être « user force per pin » au lieu de MaxFPP, si une force de repressage inférieure doit être utilisée. L’appui final d’un repressage se fait généralement selon une force cible, car il n’est pas possible de connaître la position initiale d’un repressage. La complétion PARS ne peut pas être utilisée pour un repressage, car il n’y a souvent pas de région de force de « pénétration de broche » à échantillonner lorsque le connecteur a déjà été partiellement pressé. Bien que la complétion par Force Gradient puisse être utilisée avec des connecteurs et des circuits imprimés très rigides (après avoir atteint une hauteur d’appui et une force minimales), la plupart des repressages de connecteurs utilisent la fonction MaxFPP. RÉV. D1 43 sur 94 409-35001 Éditeur de conditions Objectif Condition Editor (voir Figure 45) est utilisé pour saisir et enregistrer des actions de séquence sans pressage appelées Conditions dans la base de données. Une condition est une série d’une ou plusieurs étapes contenant des actions de la machine organisées dans un format logique si/alors/sinon (When/Then/Else). Les conditions sont utilisées avec les connecteurs pour créer la séquence de pressage. Les conditions sont enregistrées dans une base de données sqlite. Lors de la génération d’une nouvelle condition ou de l’utilisation d’une condition selon un modèle, il peut parfois être pratique d’ouvrir une condition existante et d’en faire une copie (« Copy ») pour dupliquer la condition et d’utiliser « Save » pour enregistrer la condition sous un nouveau nom. Condition Editor est accessible à l’aide du menu déroulant « Editors ». Figure 45 Explication Chaque étape de condition se compose généralement de trois parties : une opération « When » (si), une opération « Then » (alors) et une opération « Else » (sinon). L’opération « When » fonctionne comme l’entrée d’étape, qui détermine si ce seront les opérations de sortie « Then » ou « Else » qui seront exécutées. Si le résultat de l’opération « When » est oui, l’opération de sortie « Then » est exécutée. Si le résultat de l’opération « When » est non ou si l’opération expire, l’opération de sortie « Else » est exécutée. Vous pouvez voir un exemple facile ci-dessous. Opération When : Si l’entrée digitale DI1 est égale à 1 dans une plage de 1 000 ms, Opération Then : Alors réglez la sortie numérique DO1 sur 0. Opération Else : Sinon, affichez le message « Entrée non activée ! » RÉV. D1 44 sur 94 409-35001 Dans l’exemple ci-dessus, l’étape de condition vérifie en permanence l’entrée numérique DI1 pour voir si elle a été activée (opération « When »). Si l’entrée est activée avant le délai d’une seconde, l’opération « When » détermine la valeur « true » (oui) et la sortie numérique DO1 est désactivée (l’opération « Then » est exécutée). Si l’entrée numérique DI1 n’est pas activée avant le délai d’une seconde, l’opération « Else » est exécutée et une boîte de dialogue s’affiche pour informer l’utilisateur que l’entrée n’a pas été activée. En plus des opérations effectuées par chaque étape de condition, les opérations de sortie « Then » et « Else » ont également une action de complétion qui leur est associée et qui définit la poursuite de la condition après la fin de l’étape. Les actions de complétion disponibles sont « Complete », « Error », « Next Step » et « Goto Step n ». Complete : après avoir exécuté l’opération « Then » ou « Else », la condition se termine avec succès et l’étape suivante de la séquence de pressage s’exécute. Error : après avoir exécuté l’opération « Then » ou « Else », la condition se termine avec succès et interrompt la séquence de pressage. La première étape de la séquence de pressage sera chargée et exécutée. Next Step : (uniquement disponible pour les conditions à plusieurs étapes) après avoir exécuté l’opération « Then » ou « Else », l’étape suivante de la condition s’exécute. Goto Step n : (uniquement disponible pour les conditions à plusieurs étapes) après avoir exécuté l’opération « Then » ou « Else », l’étape n de la condition s’exécute. Rubriques « Condition Name » : le nom que vous choisissez peut comporter jusqu’à 30 caractères, avec espaces, et sera désormais utilisé pour désigner cette condition. Pour saisir un nouveau type de condition, sélectionnez « New ». Vous pouvez également sélectionner « Copy » pour copier la condition actuellement affichée. Vous devez saisir un nouveau nom. Sélectionnez « Delete » pour supprimer la condition actuellement affichée. Sélectionnez « Save » pour enregistrer la condition dans la base de données. « Multi-Step Condition » : cochez cette case si cette condition doit comporter plusieurs étapes. Décochez cette case s’il s’agit d’une condition à une seule étape. « Execute Once Per Batch » : cochez cette case pour que cette condition ne soit exécutée que lors de la première exécution de la séquence de pressage pour le lot en cours. Recharger la séquence de pressage démarrera un nouveau lot. Onglet When/Then/Else Editor : cet onglet contient tous les boutons et champs de saisie nécessaires pour créer une étape de condition. Appuyez sur le bouton « Add Step » pour créer une nouvelle étape de condition à plusieurs étapes. Appuyer sur le bouton « Delete Step » pour supprimer l’étape actuellement sélectionnée d’une condition à plusieurs étapes. Appuyez sur le bouton « Save Step » pour enregistrer toutes les modifications apportées à l’étape en cours d’une condition à plusieurs étapes (les modifications ne seront PAS enregistrées dans la base de données). Appuyez sur le bouton « Cancel Changes » pour annuler toutes les modifications d’une étape qui a été éditée. « Step Name » : le nom de l’étape est utilisé pour décrire et identifier l’étape de condition actuelle. « Use Condition Name » : (conditions à une étape uniquement) en cochant cette case, le nom de l’étape (« Step Name ») est automatiquement défini de sorte à être identique au nom de la condition (« Condition Name »). « Step Number » : (conditions à plusieurs étapes uniquement) cette entrée est utilisée pour spécifier l’emplacement séquentiel de l’étape dans la condition. Case « When » : les entrées de cette case définissent et décrivent le fonctionnement de l’opération d’entrée « When » de l’étape de condition actuelle. RÉV. D1 45 sur 94 409-35001 « Input Type » : ce menu déroulant permet de sélectionner le type d’opération d’entrée à effectuer pour cette étape de condition. Les types d’entrée disponibles sont « Step Start », « Message Response », « Clearance Move », « Measure Board », « Digital Input », « COM Port », «Move Shuttle » et « PPS Tool ». Step Start : ce type d’entrée est utilisé pour que l’opération « When » donne toujours pour résultat « true » (oui). L’étape passera directement à l’exécution de l’opération « Then », et l’opération « Else » sera masquée dans la fenêtre de l’éditeur. Ce type d’entrée est utile lorsque l’utilisateur a besoin d’une étape de condition qui exécute toujours une opération de sortie unique avant de poursuivre. Message Response : ce type d’entrée est utilisé pour afficher un message à l’écran via une boîte de dialogue ou le bouton d’action de production. Ce type d’entrée peut également solliciter une réponse de l’utilisateur qui appuiera sur un bouton et exécuter l’opération « Then » ou « Else » en fonction de la réponse de l’utilisateur. Ce type d’entrée est utile pour fournir des mises à jour d’état, interroger l’utilisateur et exiger la validation d’un utilisateur disposant de droits d’accès élevés. « Message Editor » : ce bouton ouvre la fenêtre « When » de Message Editor (voir Figure 46utilisée pour personnaliser l’affichage du message. Pour conserver les modifications apportées dans cette fenêtre, cliquez sur « OK ». Pour annuler toute modification effectuée dans cette fenêtre, cliquez sur « Cancel ». Last Press Result : ce type d’entrée évalue le résultat du dernier pressage de connecteur. « Result Mode » : ce menu déroulant permet de sélectionner la partie du résultat de pressage à évaluer. Chaque résultat de pressage contient un état (« Status »), un « Code » et un « Message » qui peuvent être évalués. « Status » : ce menu déroulant s’affiche lorsque le mode de résultat « Status » est sélectionné. L’état du résultat du pressage peut être « Complete » ou « Error ». C’est la façon la plus élémentaire d’évaluer le résultat du pressage. « Code » : ce champ de saisie s’affiche lorsque le mode de résultat « Code » est sélectionné. Le code de résultat du pressage est un nombre à trois chiffres qui indique si le pressage a été effectué avec succès ou s’il y a eu une erreur et indique l’étape de profil de pressage terminé. Les pressages terminés avec succès auront un code qui va de 151 à 200. Les pressages qui ont rencontré une erreur auront un code supérieur à 200 ou inférieur à 151. Le code peut être utilisé pour évaluer le pressage afin d’obtenir un résultat complet ou erroné généré par une étape spécifique. « Message » : ce champ de saisie s’affiche lorsque le mode de résultat « Message » est sélectionné. Le message de résultat du pressage est le texte saisi dans le champ « Message » d’une étape de profil de pressage avec une action « Complete » ou « Error ». Le message peut être utilisé pour évaluer le pressage afin d’obtenir un résultat complet ou erroné généré par une étape spécifique ou un groupe d’étapes spécifiques aux messages identiques. Figure 46 RÉV. D1 46 sur 94 409-35001 « Type de message » : ce menu déroulant permet de sélectionner le type de message à afficher. Les types de messages disponibles sont : Acknowledge : ce type de message affiche une boîte de dialogue avec un seul bouton « OK » permettant à l’utilisateur d’accepter le message. Query : ce type de message affiche une boîte de dialogue avec un bouton « Yes » (Oui) et un bouton « No » (Non) qui permettent à l’utilisateur de répondre à une question. Accept : ce type de message affiche une boîte de dialogue avec un bouton « OK » et un bouton « Cancel » (Annuler) permettant à l’utilisateur d’accepter ce qui est proposé dans l’invite de message ou d’annuler. Action Button : ce type de message affiche un message au bouton d’action de production et à la case du statut du bouton d’action. Ce type est utile pour inviter l’utilisateur à lancer l’étape suivante de la séquence de pressage. User Sign Off : ce type de message affiche une boîte de dialogue avec un formulaire de connexion utilisateur. Un utilisateur avec le niveau d’accès requis doit sélectionner son nom d’utilisateur et saisir son mot de passe pour valider l’opération ou l’action en cours. Text Entry : ce type de message affiche une boîte de dialogue avec un champ de saisie. Le texte saisi dans le champ peut être analysé et évalué de la même manière que les types d’entrée COM Port. Pour plus d’explications sur les options d’analyse de texte, reportez-vous à la section « Paramètres de données » sous le type d’entrée « COM Port » (pages 44 et 45). Ce type de message peut être utilisé pour les données de traçabilité (comme un numéro de série) lorsqu’aucun lecteur de codes-barres n’est disponible. « Message Class » : ce menu déroulant permet de sélectionner la couleur du message (indisponible pour les messages de type « User Sign Off », qui utilisent par défaut la classe « Info »). Info : message bleu Error : message rouge Warning : message jaune/doré Success : message vert « Message Title » : ce champ de saisie spécifie le texte qui s’affiche sur l’en-tête de la boîte de dialogue (indisponible pour les messages de type « Action Button », remplacé par le champ « Button Prompt »). « Message Text » : ce champ de saisie spécifie le texte affiché dans le corps du message principal de la boîte de dialogue (indisponible pour les messages de type « Action Button », remplacé par le champ « Status Text »). « Required Access Level » : (types de message de validation par un utilisateur uniquement) ce menu déroulant permet de sélectionner le niveau d’accès minimum qu’un utilisateur doit avoir pour valider avec succès un User Sign Off. Les niveaux d’accès sont répertoriés du plus haut niveau d’accès au plus bas. « Button Prompt » : (types de message de bouton d’action uniquement) ce champ de saisie sert à spécifier le texte affiché dans la zone principale du bouton d’action. « Status Text » : (types de message du bouton d’action uniquement) ce champ de saisie sert à spécifier le texte affiché dans la zone d’état sous le bouton d’action. « When Response = »/« When User Sign Off Is » : ce menu déroulant permet de sélectionner la réponse au message qui fait que l’opération « When » (si) apporte pour réponse « true » (oui). Les options de ce menu déroulant varieront en fonction du type de message « Message Type » sélectionné. Certains types de messages n’auront qu’une seule option disponible. RÉV. D1 47 sur 94 409-35001 Preview : ce bouton permet d’ouvrir un aperçu du message en fonction des paramètres sélectionnés dans « Message Editor ». Clearance Move : ce type d’entrée est utilisé pour se déplacer à la hauteur de dégagement de l’outil de pressage de connecteur actuellement chargé indépendamment du pressage actuellement chargé (lorsqu’une étape de pressage est exécutée, la presse se déplace vers le dégagement de l’outil ou invite l’utilisateur à passer au dégagement de l’outil par défaut). « Speed » : ce champ de saisie indique la vitesse à laquelle la presse se déplace jusqu’au dégagement. Measure Board : ce type d’entrée est utilisé pour mesurer automatiquement l’épaisseur de la carte pressée à l’aide de la tête de presse. Cette mesure de la carte remplacera l’épaisseur de la carte programmée dans l’éditeur de séquence. « Measure Board Settings » : ce bouton ouvre la fenêtre Meaure Board Settings (voir Figure 47) où les paramètres de mesure de la carte peuvent être saisis. Sélectionnez « OK » pour enregistrer les paramètres saisis et « Cancel » pour annuler les modifications apportées aux paramètres. Figure 47 « Speed » : ce champ de saisie sert à spécifier la vitesse de mouvement de la tête de la presse pendant la mesure de la carte. « Probe Height » : ce champ de saisie sert à spécifier la hauteur de la sonde de mesure utilisée pour mesurer l’épaisseur de la carte. « Measurement Force » : ce champ de saisie spécifie la force que la presse appliquera à la sonde de mesure pendant la mesure de la carte. Digital Input : ce type d’entrée est utilisé pour lire l’état de l’une des entrées numériques de la machine. « Number » : ce menu déroulant permet de sélectionner le canal d’entrée numérique (Digital Input) à lire. Toutes les entrées disponibles seront répertoriées dans le menu déroulant. « Input State » : ce menu déroulant sélectionne l’état d’entrée recherché par l’opération « When ». Si cet état d’entrée est trouvé, l’opération « When » est considérée « true ». L’état de l’entrée peut être « 1 » (activé) ou « 0 » (désactivé). RÉV. D1 48 sur 94 409-35001 COM Port : ce type d’entrée est utilisé pour lire les données d’entrée des dispositifs de port COM série USB connectés à la machine. Il est généralement utilisé pour lire et agir sur les données des lecteurs de codes-barres. « COM Port Settings » : ce bouton ouvre la fenêtre « When » de COM Port Settings (voir Figure 48) où les paramètres de communication du périphérique du port COM peuvent être saisis. Sélectionnez « OK » pour enregistrer les paramètres saisis et « Cancel » pour annuler les modifications apportées aux paramètres. Figure 48 « Port Number » : ce menu déroulant permet de sélectionner le périphérique de port COM à lire. Seuls les ports COM disponibles seront répertoriés. « Baud Rate » : ce champ de saisie spécifie le débit de bauds en kbps à utiliser lors de la communication avec le périphérique de port COM. « Data Bits » : ce champ de saisie indique le nombre de bits de données contenus dans chaque trame de message reçue du périphérique de port COM. « Stop Bits » : ce menu déroulant permet de sélectionner le nombre de bits d’arrêt utilisés dans chaque trame de message reçue du périphérique de port COM. « Parity » : ce menu déroulant permet de sélectionner le type de parité utilisé dans chaque trame de message reçue du périphérique de port COM. « Flow Control » : ce menu déroulant permet de sélectionner le type de flux de contrôle éventuellement utilisé dans chaque trame de message reçue du périphérique de port COM. RÉV. D1 49 sur 94 409-35001 « Use Serial Trigger » : en cochant cette case, une commande de déclenchement en série sera envoyée à l’appareil avant d’essayer de lire les données à partir du port COM. Cette fonction est utilisée pour les scanners et les autres appareils qui n’envoient pas de données sans être déclenchés ou interrogés. Dans ce cas, l’opération de lecture se déroule comme suit : envoi de la commande « On » lecture des données depuis l’appareil envoi de la commande « Off » « Trigger On Command » : (uniquement utilisé lorsque l’option « Use Serial Trigger » est activée) ce champ de saisie spécifie la séquence de caractères qui sera envoyée au périphérique du port COM pour déclencher ou interroger l’appareil et lancer l’envoi des données. « Trigger Off Command » : (uniquement utilisé lorsque l’option « Use Serial Trigger » est activée) ce champ de saisie spécifie la séquence de caractères qui sera envoyée au périphérique du port COM pour stopper l’envoi des données après leur lecture. « Data Settings » : ce bouton ouvre la fenêtre « When » de COM Port Settings (voir Figure 49) où les paramètres de lecture et d’analyse des données du périphérique du port COM peuvent être saisis. Sélectionnez « OK » pour enregistrer les paramètres saisis et « Cancel » pour annuler les modifications apportées aux paramètres. Figure 49 « Maximum Data Length » : ce champ de saisie indique le nombre maximal de caractères pouvant être lus sur l’appareil. « Minimum Data Length » : ce champ de saisie indique le nombre minimal de caractères devant être lus depuis l’appareil pour un scan réussi. RÉV. D1 50 sur 94 409-35001 « Parse substring starting at character number » : ce champ de saisie sert à indiquer où commencer l’analyse des caractères dans les données lues. Il peut être utile dans les cas où l’utilisateur ne veut analyser qu’une partie des données totales lues à partir de l’appareil. Par exemple, si un « 3 » est saisi dans ce champ et que la chaîne de données « SN123456 » est lue à partir de l’appareil, le premier caractère analysé est « 1 ». « Number of characters to parse » : ce champ de saisie sert à indiquer combien de caractères des données lues doivent être analysés, en commençant par le numéro de caractère spécifié dans le champ « Parse substring starting at character number ». Il peut être utile dans les cas où l’utilisateur ne veut analyser qu’une partie des données totales lues à partir de l’appareil. La somme du nombre de caractères à analyser et le numéro du caractère par lequel commencer ne peut pas dépasser la longueur minimale des données. Par exemple, si un « 4 » est saisi dans ce champ, qu’il faut commencer par le caractère numéro « 3 » et que la chaîne de données « SN123456 » est lue à partir de l’appareil, la chaîne de caractères analysée est « 1234 ». « Data Received »/« Data Received Matches Substring » : ce bouton permet de sélectionner comment l’opération « When » évaluera une situation comme « true ». Si l’option « Data Received » est sélectionnée, l’opération « When » évalue une situation comme « true » à chaque fois que des données sont reçues, indépendamment de ce qu’elles contiennent. Si « Data Received Matches Substring » est sélectionné, l’opération « When » n’évaluera une situation comme « true » que si la sous-chaîne analysée à partir des données reçues correspond à la sous-chaîne saisie dans le champ de saisie « When parsed substring matchs ». Cette option est utile dans les cas où la séquence de pressage doit vérifier un numéro d’identification d’outil spécifique ou le numéro de pièce ou de modèle d’une carte ou d’un connecteur. « When parse substring matches » : (visible uniquement lorsque « Data Received Matches Substring » est sélectionné) ce champ de saisie spécifie la sous-chaîne que l’opération « When » comparera à la sous-chaîne analysée lue à partir du périphérique du port COM. « User Prompt Message Text » : ce champ de saisie spécifie le texte à afficher dans la boîte de dialogue de message qui apparaît en attendant la lecture des données du périphérique du port COM. « Enable Keyboard Entry » : cocher cette case permet à l’utilisateur de saisir des données à l’aide du clavier affiché sur l’écran comme alternative à la lecture de données à partir du port COM. Lorsque cette option est activée, la condition utilisera les données reçues ou saisies en premier. Move Shuttle : (uniquement disponible si la navette est activée) ce type d’entrée est utilisé pour déplacer la navette vers une position désignée indépendamment de l’opération de pressage du connecteur. Lorsque la navette est activée pour un pressage de connecteur dans l’éditeur de séquence, la navette passe de la position de pressage à la position de chargement dans le cadre de l’opération de pressage. « Shuttle Position » : ce menu déroulant permet de sélectionner la position vers laquelle la navette sera déplacée par la condition. Les positions disponibles seront basées sur le type de navette sélectionné dans Machine Configuration. PPS Tool : (uniquement disponible si PPS Tool est activé) ce type d’entrée est utilisé pour envoyer une commande à PPS Tool et agir selon sa réponse, indépendamment de l’opération de pressage du connecteur. Si « PPS » est activé pour un connecteur dans l’éditeur de séquence, les vérifications standard de l’outil PPS sont effectuées dans le cadre de l’opération de pressage. « Command » : ce menu déroulant permet de sélectionner la commande à envoyer à PPS Tool. Les commandes disponibles seront basées sur le type d’outil PPS (certaines commandes pourraient être indisponibles lors de l’utilisation d’anciens outils PPS). RÉV. D1 51 sur 94 409-35001 « Command Settings » : ce bouton ouvre la fenêtre « When » de PPS Settings (voir Figure 50). Cette fenêtre est utilisée pour définir comment l’opération « When » doit évaluer comme « true » et quelles données de commande envoyer pour paramétrer(« Set ») les commandes PPS. Les options de paramétrage varient en fonction de la commande sélectionnée. Les commandes PPS « Set » entraîneront toujours l’évaluation de l’opération « When » comme « true » si une réponse valide est reçue et qu’aucune erreur ne se produit. Figure 50 « Valid Response Received »/« Response Data Meets Condition » : (utilisée uniquement pour les commandes PPS de type « Get ») cette fonction permet de sélectionner quand l’opération « When » doit être évaluée comme « true ». Si l’option « Valid Response Received » est sélectionnée, l’opération « When » se finit sur « true » tant qu’aucune erreur de communication ne se produit avec l’outil PPS, indépendamment des données reçues de l’outil. Si « Response Data Meets Condition » est sélectionné, l’opération « When » est évaluée comme « true » si les données reçues en retour de l’outil PPS correspondent à certains critères spécifiés par l’utilisateur. « When Pass/Fail Status = » : (disponible uniquement pour la commande « Get Pass Fail » lorsque « Response Data Meets Condition » est sélectionné) ce menu déroulant permet de sélectionner le type de réponse de réussite/d’échec PPS qui doit entraîner l’évaluation de la condition « When » comme « true ». « Pass data for pins that are... » : (disponible uniquement pour les commandes « Get Pin States » et « Get Pin Mask » lorsque « Valid Response Received » est sélectionné) ce menu déroulant permet de sélectionner si les données des broches pressées ou non pressées doivent être transmises à l’opération « Then » de la condition. RÉV. D1 52 sur 94 409-35001 Pin State Selector : (uniquement disponible pour la commande « Set Pin Mask », et pour les commandes « Get Pin States » et « Get Pin Mask » lorsque « Response Data Meets Condition » est sélectionné) cet onglet permet à l’utilisateur de spécifier le type de données de broches que l’opération « When » cherchera à évaluer comme « true » (pour les commandes « Get »), ou le type de broches inclus dans le masque de broches actuel (pour la commande « Set Pin Mask »). Pin Checkboxes : chaque case à cocher représente une broche dans l’outil PPS. La sélection d’une case ajoutera la broche à la liste des broches évaluées ou envoyées par l’opération « When ». Pour les commandes « Get », les broches qui ne sont pas incluses dans le masque de broches actuel ne peuvent pas être sélectionnées. Select Pin Range : les boutons « Select Pins » et « Deselect Pins » peuvent être utilisés conjointement avec les champs de saisie « Range Start » et « Range End » pour sélectionner ou désélectionner rapidement un grand nombre de cases de broches. Tous les numéros de broche entre « Range Start » et « Range End » seront sélectionnés ou désélectionnés à l’aide du bouton correspondant. Pour les commandes « Get », les broches qui ne sont pas incluses dans le masque de broches actuel ne peuvent pas être sélectionnées. « When selected pins are… » : (disponible uniquement pour les commandes « Get Pin States » et « Get Pin Mask » lorsque « Response Data Meets Condition » est sélectionné) ce menu déroulant permet de sélectionner si l’opération « When » évalue les broches sélectionnées selon le fait qu’elles aient été pressées ou non. « When active mask number = » : (disponible uniquement pour la commande « Get Active Mask » lorsque « Response Data Meets Condition » est sélectionné) ce menu déroulant permet de sélectionner la réponse relative au numéro de masque actif qui doit entraîner l’évaluation de la condition « When » comme « true ». « When Serial Number = » : (disponible uniquement pour la commande « Get Serial Number » lorsque « Response Data Meets Condition » est sélectionné) ce champ de saisie permet de spécifier la réponse relative au numéro de série qui doit entraîner l’évaluation de la condition « When » comme « true ». « When Boilerplate = » : (disponible uniquement pour la commande « Get Boilerplate Number » lorsque « Response Data Meets Condition » est sélectionné) ce champ de saisie permet de spécifier la réponse relative à l’expression standard qui doit entraîner l’évaluation de la condition « When » comme « true ». « When Page Count = » : (disponible uniquement pour la commande « Get Page Count » lorsque « Response Data Meets Condition » est sélectionné) ce champ de saisie permet de spécifier la réponse relative au nombre de pages qui doit entraîner l’évaluation de la condition « When » comme « true ». « When Pin Logic = » : (disponible uniquement pour la commande « Get Pin Logic » lorsque « Response Data Meets Condition » est sélectionné) ce menu déroulant permet de sélectionner le type de réponse logique relative aux broches qui doit entraîner l’évaluation de la condition « When » comme « true ». « Set Pin Logic to » : (uniquement disponible pour la commande « Set Pin Logic ») ce menu déroulant permet de sélectionner le type de logique relatif aux broches que l’outil PPS utilisera. « Set Active Mask to » : (uniquement disponible pour la commande « Set Active Mask ») ce menu déroulant permet de sélectionner le masque actif que l’outil PPS doit utiliser. Bouton d’icône d’horloge : ce bouton ouvre la fenêtre « When » de Time Settings (voir Figure 51). Si aucun paramètre n’est saisi dans cette fenêtre, les valeurs « Timeout » et « Polling Interval » par défaut seront utilisées en fonction du type d’entrée (« Input Type ») sélectionné. « Timeout » : ce champ de saisie permet d’indiquer, en millisecondes, le délai pendant lequel l’opération « When » pourra évaluer une valeur comme « true » avant qu’elle soit évaluée comme RÉV. D1 53 sur 94 409-35001 « false » et que l’opération « Else » soit exécutée. La valeur 0 fera attendre l’opération « When » indéfiniment. « Polling Interval » : ce champ de saisie spécifie, en millisecondes, la fréquence à laquelle l’opération « When » évaluera l’opération comme potentiellement « true ». Cette valeur doit être inférieure ou égale à la valeur « Timeout ». Par exemple, si l’opération « When » vérifie si une entrée numérique a été activée et si la valeur « Polling Interval » est de « 20 », l’entrée numérique sera vérifiée une fois toutes les 20 millisecondes pour déterminer si l’entrée a été activée et si l’opération doit être évaluée comme « true ». Figure 51 Cases « Then » et « Else » : les entrées de ces cases définissent et décrivent les opérations de sortie « Then » et « Else » de l’étape de condition actuelle. L’opération « Then » se produit si l’opération « When » est évaluée comme « true ». L’opération « Else » se produit si l’opération « When » est évaluée comme « false » ou expire. « Output Type » : ce menu déroulant permet de sélectionner le type d’opération de sortie à effectuer pour cette opération d’étape de condition. Les types de sortie disponibles sont « Step Complete », « Message », « Clearance Move », « Digital Output », « COM Port », « Move Shuttle » et « PPS Tool ». Step Complete : ce type de sortie est utilisé pour terminer immédiatement l’opération de sortie conformément à la complétion de l’« Action » sélectionnée, sans effectuer de tâches supplémentaires. Ceci est utile pour les conditions qui effectuent une simple vérification lors de l’opération « When » ou pour les conditions à plusieurs étapes qui vérifient plusieurs entrées. Message : ce type de sortie est utilisé pour afficher un message à l’écran via une boîte de dialogue ou le bouton d’action de production, ou pour effacer ou fermer des messages existants à l’écran. Ce type de sortie est utile pour fournir des mises à jour d’état ou effacer d’anciens messages. « Message Editor » : ce bouton ouvre la fenêtre « When » de Message Editor utilisée pour personnaliser l’affichage du message. Pour conserver les modifications apportées dans cette fenêtre, cliquez sur « OK ». Pour annuler toute modification effectuée dans cette fenêtre, cliquez sur « Cancel ». « Type de message » : ce menu déroulant permet de sélectionner le type de message à afficher. Les types de messages disponibles sont : Acknowledge : ce type de message affiche une boîte de dialogue avec un seul bouton « OK » permettant à l’utilisateur d’accepter le message. RÉV. D1 54 sur 94 409-35001 Disabled Action Button : ce type de message désactive le bouton d’action et affiche un message au bouton d’action de production et à la case d’état du bouton d’action. Ce type est utile pour afficher l’opération de la machine en cours tout en empêchant l’utilisateur d’interrompre l’opération en appuyant sur le bouton d’action. L’utilisateur peut toujours quitter l’écran ou interagir avec celui-ci d’une autre manière. Info : ce type de message affiche une boîte de dialogue de message sans bouton. Cette boîte de message verrouille l’écran jusqu’à ce qu’une étape de condition ultérieure ferme le message. Ce type de message est utile pour empêcher complètement l’utilisateur d’interagir avec la machine jusqu’à la fin de certaines opérations. Close Messages : ce type de message ferme toutes les boîtes de dialogue de message ouvertes à l’écran. Clear Action Button : ce type de message supprime tous les messages personnalisés (les messages affichés à l’aide d’une « Condition ») du bouton d’action de production et de la case d’état du bouton. « Message Class » : ce menu déroulant permet de sélectionner la couleur du message (indisponible pour les messages de type « User Sign Off », qui utilisent par défaut la classe « Info »). Info : message bleu Error : message rouge Warning : message jaune/doré Success : message vert « Message Title » : (uniquement disponible pour les messages de type « Acknowledge » et « Info ») ce champ de saisie spécifie le texte qui s’affiche dans la partie en-tête de la boîte de dialogue. « Message Text » : (uniquement disponible pour les messages de type « Acknowledge » et « Info ») ce champ de saisie spécifie le texte affiché dans le corps du message principal de la boîte de dialogue. La variable « ${data} » peut être utilisée dans le texte du message pour afficher toutes les données de résultat transmises à partir de l’opération « When » (si activée). « Button Prompt » : (types de message Disabled Action Button uniquement) ce champ de saisie sert à spécifier le texte affiché dans la zone principale du bouton d’action. « Status Text » : (types de message Disabled Action Button uniquement) ce champ de saisie sert à spécifier le texte affiché dans la zone d’état sous le bouton d’action. «Display data passed from “When” result using ${data} variable » : cette case à cocher permet d’afficher les données de résultat de l’opération « When » dans le texte du message à l’aide de la variable « ${data} » (non disponible pour « Close message » ou « Clear Action Button »). Preview : ce bouton permet d’ouvrir un aperçu du message en fonction des paramètres sélectionnés dans « Message Editor ». Clearance Move : ce type de sortie est utilisé pour se déplacer à la hauteur de dégagement de l’outil de pressage de connecteur actuellement chargé, indépendamment du pressage actuellement chargé (lorsqu’une étape de pressage est exécutée, la presse se déplace vers le dégagement de l’outil ou invite l’utilisateur à passer au dégagement de l’outil par défaut). « Speed » : ce champ de saisie indique la vitesse à laquelle la presse se déplace jusqu’au dégagement. Digital Output : ce type de sortie est utilisé pour lire l’état de l’une des sorties numériques de la machine. RÉV. D1 55 sur 94 409-35001 « Number » : ce menu déroulant permet de sélectionner le canal de sortie numérique (Digital Output) à lire. Toutes les sorties disponibles seront répertoriées dans le menu déroulant. « Output State » : ce menu déroulant permet de sélectionner l’état de sortie fixé par l’opération « Then/Else ». L’état de sortie peut être « 1 » (activé) ou « 0 » (désactivé). COM Port : ce type de sortie est utilisé pour lire les données de sortie des dispositifs de port COM série USB connectés à la machine. « COM Port Settings » : ce bouton ouvre la fenêtre « Then/Else » de COM Port Settings où les paramètres de communication du périphérique du port COM peuvent être saisis. Sélectionnez « OK » pour enregistrer les paramètres saisis et « Cancel » pour annuler les modifications apportées aux paramètres. « Port Number » : ce menu déroulant permet de sélectionner le périphérique de port COM auquel envoyer les données. Seuls les ports COM disponibles seront répertoriés. « Baud Rate » : ce champ de saisie spécifie le débit de bauds en kbps à utiliser lors de la communication avec le périphérique de port COM. « Data Bits » : ce champ de saisie indique le nombre de bits de données contenus dans chaque trame de message envoyée au périphérique de port COM. « Stop Bits » : ce menu déroulant permet de sélectionner le nombre de bits d’arrêt utilisés dans chaque trame de message envoyée au périphérique de port COM. « Parity » : ce menu déroulant permet de sélectionner le type de parité utilisé dans chaque trame de message envoyée au périphérique de port COM. « Flow Control » : ce menu déroulant permet de sélectionner le type de flux de contrôle éventuellement utilisé dans chaque trame de message envoyée au périphérique de port COM. « Data Settings » : ce bouton ouvre la fenêtre « Then/Else » de COM Data Settings où les paramètres d’envoi des données au périphérique du port COM peuvent être saisis. Sélectionnez « OK » pour enregistrer les paramètres saisis et « Cancel » pour annuler les modifications apportées aux paramètres. « Message Data » : ce champ de saisie sert à spécifier la chaîne de caractères de données qui sera envoyée au périphérique du port COM. Move Shuttle : (uniquement disponible si la navette est activée) ce type de sortie est utilisé pour déplacer la navette vers une position désignée indépendamment de l’opération de pressage du connecteur. Lorsque la navette est activée pour un pressage de connecteur dans l’éditeur de séquence, la navette passe de la position de pressage à la position de chargement dans le cadre de l’opération de pressage. « Shuttle Position » : ce menu déroulant permet de sélectionner la position vers laquelle la navette sera déplacée par la condition. Les positions disponibles seront basées sur le type de navette sélectionné dans Machine Configuration. PPS Tool : (uniquement disponible si PPS Tool est activé) ce type de sortie est utilisé pour envoyer une commande à PPS Tool, indépendamment de l’opération de pressage du connecteur. Si « PPS » est activé pour un connecteur dans l’éditeur de séquence, les vérifications standard de l’outil PPS sont effectuées dans le cadre de l’opération de pressage. « Command » : ce menu déroulant permet de sélectionner la commande à envoyer à PPS Tool. Les commandes disponibles seront basées sur le type d’outil PPS (certaines commandes pourraient être indisponibles lors de l’utilisation d’anciens outils PPS). « Command Settings » : (uniquement disponible pour les commandes « Set ») ce bouton ouvre la fenêtre « Then/Else » de PPS Settings. Cette fenêtre est utilisée pour définir quelles données de commande envoyer aux commandes « Set » PPS. Les options de paramétrage varient en fonction de la commande sélectionnée. RÉV. D1 56 sur 94 409-35001 Pin State Selector : (uniquement disponible pour la commande « Set Pin Mask ») cet onglet permet à l’utilisateur de spécifier les broches à inclure dans le masque de broches actuel. Pin Checkboxes : chaque case à cocher représente une broche dans l’outil PPS. La sélection d’une case ajoutera la broche à la liste des broches envoyées à PPS Tool. Select Pin Range : les boutons « Select Pins » et « Deselect Pins » peuvent être utilisés conjointement avec les champs de saisie « Range Start » et « Range End » pour sélectionner ou désélectionner rapidement un grand nombre de cases de broches. Tous les numéros de broche entre « Range Start » et « Range End » seront sélectionnés ou désélectionnés à l’aide du bouton correspondant. « Set Pin Logic to » : (uniquement disponible pour la commande « Set Pin Logic ») ce menu déroulant permet de sélectionner le type de logique relatif aux broches que l’outil PPS utilisera. « Set Active Mask to » : (uniquement disponible pour la commande « Set Active Mask ») ce menu déroulant permet de sélectionner le masque actif que l’outil PPS doit utiliser. Bouton d’icône d’horloge : ce bouton ouvre la fenêtre « Then/Else » de Time Settings. Si aucun paramètre n’est saisi dans cette fenêtre, les valeurs « Duration » par défaut seront utilisées en fonction du type de sortie (« Output Type ») sélectionné. « Duration » : ce champ de saisie indique, en millisecondes, le temps pendant lequel l’opération exécutera l’opération de sortie. L’utilisation la plus courante de cette fonction est l’impulsion ou le réglage d’une sortie digitale sur un état donné pendant une durée limitée. Une valeur de « 0 » correspond à une durée indéterminée. « Then »/« Else » Complete Action : ce menu déroulant permet de sélectionner la façon dont l’opération de sortie se terminera après avoir effectué sa tâche (voir Figure 52). Il y a quatre possibilités de complétion d’« Actions ». Complete : après avoir exécuté l’opération « Then » ou « Else », la condition se termine avec succès et l’étape suivante de la séquence de pressage s’exécute. Error : après avoir exécuté l’opération « Then » ou « Else », la condition se termine avec succès et interrompt la séquence de pressage. La première étape de la séquence de pressage sera chargée et exécutée. Next Step : (uniquement disponible pour les conditions à plusieurs étapes) après avoir exécuté l’opération « Then » ou « Else », l’étape suivante de la condition s’exécute. Goto Step n : (uniquement disponible pour les conditions à plusieurs étapes) après avoir exécuté l’opération « Then » ou « Else », l’étape n de la condition s’exécute. Figure 52 RÉV. D1 57 sur 94 409-35001 Onglet JavaScript Viewer : (masqué pour la plupart des utilisateurs) cet onglet contient une fenêtre de texte en lecture seule qui peut être utilisée pour afficher le script généré par les étapes de condition spécifiées dans l’onglet « When/Then/Else Editor ». Il est surtout utile pour le débogage avancé et l’analyse d’une condition. Exemples Measure Board Thickness : cette condition met en œuvre une fonction de pressage de carte couramment utilisée qui mesure l’épaisseur de la carte de circuit imprimé à l’aide d’une sonde de mesure. Les conditions de modèle standard ne peuvent pas être modifiées (voir Figure 53), mais elles peuvent au besoin être copiées, modifiées et enregistrées sous un autre nom. Figure 53 Une modification courante de la condition « Measure Board Thickness » consiste à activer ou désactiver l’option « Execute Once Per Batch » (voir Figure 54) en fonction de la fréquence à laquelle l’épaisseur de la carte doit être mesurée pour l’application de l’utilisateur. Si l’option est désactivée, toutes les cartes pressées seront mesurées. Si l’option est activée, seule la première carte pressée du lot sera mesurée. Recharger la séquence de pressage démarrera un nouveau lot. Figure 54 Une autre modification courante de la condition « Measure Board Thickness » est l’ajustement de la mesure « Probe Height » à la bonne hauteur en fonction de la sonde de mesure utilisée (voir Figure 55). La hauteur de la sonde peut être ajustée en appuyant sur le bouton « Measure Board Settings » dans la case d’opération « When » et en saisissant une nouvelle valeur dans la fenêtre de paramètres. Figure 55 RÉV. D1 58 sur 94 409-35001 PCB Verify : la condition PCB Verify nécessite que l’opérateur scanne ou saisisse le numéro de pièce ou de modèle de la carte pour vérification avant de presser la carte. Cette condition de modèle standard et d’autres qui impliquent un lecteur de codes-barres doivent souvent être modifiées pour s’adapter au lecteur spécifique. Le numéro de modèle par rapport auquel la carte de circuit imprimé sera vérifiée doit également être personnalisé. Pour modifier la condition de vérification PCB Verify standard, copiez la condition, renommez-la et enregistrez-la sous un nouveau nom. Ouvrez la fenêtre « COM Port Settings » en appuyant sur le bouton correspondant dans la case de l’opération « When » (voir Figure 56). Sélectionnez le numéro de port (« Port Number ») approprié (voir Figure 57) pour le lecteur de codes-barres utilisé (la liste des dispositifs de port COM disponibles peut être actualisée sur l’écran des paramètres du système). Modifiez au besoin les autres paramètres du port COM pour pouvoir travailler avec le lecteur de codesbarres. Figure 56 Figure 57 Saisissez le numéro de modèle personnalisé à vérifier en ouvrant la fenêtre « COM Data Settings » à l’aide du bouton correspondant de la case de l’opération « When » (voir Figure 56). Modifiez les champs des paramètres de données selon le numéro de modèle analysé (voir Figure 58). Figure 58 RÉV. D1 59 sur 94 409-35001 Supposons par exemple que le format des numéros de modèle scannés est « PCB_XXXXX_MODEL » et que le bon numéro de modèle de carte est « 45612 ». Cela signifie que la bonne chaîne du numéro de modèle sera « PCB_45612_MODEL ». La partie de la chaîne du numéro de modèle qui doit être analysée commence au caractère numéro 5, il faut donc saisir « 5 » dans le champ « Parse substring starting at character number ». Comme le numéro de modèle comporte 5 chiffres, « 5 » est également saisi dans le champ « Number of characters to parse ». Comme au moins 9 chiffres sont nécessaires pour lire le numéro complet du modèle, « 9 » sera saisi dans le champ « Minimum Data Length ». Enfin, « 45612 » est saisi dans le champ « When parse substring matches field », car il s’agit de la sous-chaîne exacte du numéro de modèle qui doit être vérifié (voir Figure 59). Figure 59 Sequence Editor - Éditeur de séquences Objectif Sequence Editor (Figures 52, 53 et 54) est utilisé pour saisir et stocker les données relatives à la carte (y compris ses caractéristiques physiques et l’emplacement des connecteurs) et à la séquence de pressage. Tous les connecteurs et conditions à utiliser concernant la carte en cours de programmation doivent être définis dans la base de données des connecteurs ou des conditions avant de pouvoir générer le fichier des données de pressage. La séquence est enregistrée dans une base de données sqlite. Lors de la génération d’un nouveau programme de pressage, il peut parfois être pratique d’ouvrir un fichier de pressage existant et d’en faire une copie (« Copy ») pour dupliquer la séquence et d’utiliser « Save » pour enregistrer la séquence sous un nouveau nom. Rubriques REMARQUE Les rubriques décrites ne concernent pas tous les types de presse. RÉV. D1 60 sur 94 409-35001 « Revision » : il s’agit du niveau de révision de la carte à presser ou de la révision du programme Press Sequence. Cette fonction est uniquement utilisée comme référence dans le fichier. Onglet Board Dimensions (dimensions de la carte) « Board Width » : il s’agit de la dimension de la carte dans le sens de l’axe X (de gauche à droite) telle que normalement positionnée dans la machine. Il ne s’agit pas obligatoirement du plus court côté de la carte. Pour les presses positionnées manuellement, cette dimension est uniquement utilisée pour dessiner la carte. « Board Length » : il s’agit de la dimension de la carte dans le sens de l’axe Y (du devant vers l’arrière) telle que normalement positionnée dans la machine. Il ne s’agit pas obligatoirement du plus long côté de la carte. Pour les presses positionnées manuellement, cette dimension est uniquement utilisée pour dessiner la carte. « Board Thickness » : il s’agit de l’épaisseur nominale de la carte qui est utilisée pour calculer la hauteur de pressage du connecteur. Si l’option de mesure de l’épaisseur de la carte est sélectionnée, l’épaisseur mesurée sera utilisée à la place. Figure 60 RÉV. D1 61 sur 94 409-35001 « Part Viewer Mode » : le mode de visionneuse de pièces détermine le type d’affichage de la carte qui apparaît pendant l’exécution. La visionneuse de pièces est également affichée dans l’éditeur de séquence, à côté du champ de saisie des dimensions de la carte. ● Picture : cette option utilise une photo d’appareil numérique ou un scan de photo pour montrer la carte qui est en cours de pressage. Les informations de position et d’angle du connecteur saisies dans l’onglet Sequence sont utilisées pour générer des superpositions d’images de connecteur sur l’image de la carte. ● Data : cette option crée une image à partir des données d’angle X et Y, et des données de connecteur à afficher pendant l’exécution. Les informations de connecteur sont saisies dans l’onglet Sequence. La séquence de pressage du mode séquentiel suit l’ordre des connecteurs de l’onglet Sequence. ● None : aucune image de la carte de circuit imprimé n’est affichée à l’écran en mode Run. Au lieu de cela, une liste des connecteurs de la carte de circuits imprimés s’affiche avec leurs outils associés. Au lieu d’utiliser la fonction d’exécution « Goto », cliquez sur la liste pour choisir le prochain connecteur à presser. Cette option peut être utile pour les opérations de réparation de la carte de circuit imprimé. « Comments » : il s’agit d’une description générale de la carte à presser. Cette fonction est uniquement utilisée comme référence dans le fichier. « Connector Drag Enabled/Disabled » : placez ce bouton sur « Enabled » pour permettre à l’utilisateur de glisser-déposer les connecteurs dans la visionneuse de pièces afin de définir leur emplacement x et y sur la carte. Pour éviter toute modification accidentelle des emplacements des connecteurs, placez ensuite le bouton sur « Disabled ». Onglet Settings (Paramètres) « Fixture Thickness » : il s’agit de l’épaisseur du gabarit de support ou du « plateau » qui soutient la carte. Elle doit être mesurée avec précision pour un pressage exact. « Fixture ID » : cette fonction est destinée à vérifier que le gabarit (plateau de support) utilisé avec la carte de circuit imprimé est le bon. Saisir du texte dans ce champ ne modifie en rien le fonctionnement de la séquence de pressage, mais peut être utile pour la traçabilité et l’identification des séquences de pressage des systèmes MES. La vérification de l’ID du gabarit de support peut être ajoutée à la séquence de pressage à l’aide de la condition « Verify Fixture ID » dans la base de données des conditions. La configuration initiale de cette condition doit être effectuée par le personnel d’après-vente de TE. « Prompt for Connector Substitution » : cette case à cocher permet de sélectionner les connecteurs de substitution pendant l’exécution. Par exemple, le fabricant « A » peut être la source principale d’un connecteur donné, mais « B » est également approuvé comme connecteur interchangeable pour cette carte. Si cette case est cochée, l’opérateur se verra proposer une sélection d’alternatives possibles pour le connecteur pendant l’exécution. Leur sélection fera que l’outil et le profil sélectionnés serviront au pressage de ce connecteur. Il est donc possible de presser un connecteur alternatif qui demande un outil et un profil différents du connecteur principal. Les alternatives sont associées les unes aux autres par des « codes de substitution » définis dans la base de données des connecteurs. Les connecteurs associés sont saisis individuellement dans la base de données, mais sont « liés » par un code de substitution commun. Voir l’éditeur de connecteurs pour plus de détails sur la saisie des codes de substitution de connecteurs. « Connector Name as Label » : lorsque cette fonction est cochée, le nom de chaque connecteur (d’après la base de données des connecteurs) s’affiche avec le numéro de connecteur sur chaque connecteur sur le schéma de production de la carte. Cette option prévaut sur l’option « Use Connector Message as Label ». RÉV. D1 62 sur 94 409-35001 « Use Connector Message as Label » : lorsque cette fonction est cochée, le texte saisi dans le champ de chaque position de connecteur sera affiché avec le numéro de séquence sur chaque connecteur sur le schéma de production de la carte. Figure 61 « Start Sequence Automatic » : lorsque cette fonction est cochée, la séquence de pressage démarre automatiquement quand vous accédez à l’écran « Production ». Cette fonction est surtout utilisée pour la plupart des séquences de pressage à plusieurs connecteurs afin de supprimer l’actionnement par bouton nécessaire pour démarrer chaque séquence de pressage de carte. Onglet Press Sequence (séquence de pressage) Pressing Order - Le mode choisi détermine si la séquence de pressage suit l’ordre des connecteurs saisis ou est déterminée par l’opérateur au moment de l’exécution. ● Sequential : la séquence de pressage suit l’ordre des connecteurs de Press Sequence. ● Non-Sequential : l’opérateur doit sélectionner le prochain connecteur à presser lors de l’exécution. En mode Digital Picture ou Data Image, cela se fait avec la fonction d’exécution « GoTo ». Lorsque le mode Image est défini sur « None », l’opérateur choisit le type de connecteur à utiliser dans une liste. La presse pressera le même connecteur jusqu’à ce que l’opérateur en choisisse un autre. Ce mode est souvent utilisé pour les activités de réparation des cartes. Figure 62 RÉV. D1 63 sur 94 409-35001 « Add Connector » : appuyez sur ce bouton pour ajouter un connecteur à la liste actuelle des étapes de la séquence de pressage. « Add Condition » : appuyez sur ce bouton pour ajouter une condition à la liste actuelle des étapes de la séquence de pressage. Step Editing Controls - Contrôles d’édition des étapes : Bouton Save Step (icône de coche) : appuyez sur ce bouton pour enregistrer l’étape dans la séquence de pressage après avoir ajouté ou modifié un connecteur ou une condition. Bouton Cancel Step (icône X) : appuyez sur ce bouton pour annuler toute modification apportée au connecteur actuel ou à l’étape de condition. Si c’est une nouvelle étape, elle sera supprimée de la séquence de pressage. Bouton Preview (icône d’œil) : appuyez sur ce bouton pour afficher une synthèse du connecteur ou de la condition actuellement sélectionnés pour l’étape. Bouton Delete (icône de corbeille) : appuyez sur ce bouton pour supprimer un connecteur ou une étape de condition de la séquence de pressage. Bouton Move Step Up (icône de flèche vers le haut) : appuyez sur ce bouton pour échanger une étape avec l’étape qui la précède dans la séquence de pressage. Bouton Move Step Down (icône de flèche vers le bas) : appuyez sur ce bouton pour échanger une étape avec l’étape qui la suit dans la séquence de pressage. Bouton Edit Step (icône de crayon) : appuyez sur ce bouton pour modifier un connecteur ou une étape de condition de la séquence de pressage. « Connector » : le connecteur à presser est sélectionné dans la base de données des connecteurs à l’aide du menu déroulant. Tous les connecteurs à utiliser sur la carte doivent être définis dans la base de données des connecteurs avant de pouvoir générer le fichier des données de pressage. La séquence de pressage suit l’ordre des connecteurs qui y sont saisis, il faut donc réfléchir à la façon d’optimiser les mouvements. Pour minimiser les changements d’outils, les connecteurs d’un même type devraient être pressés avant de passer au suivant. « Message » : commentaire défini par l’utilisateur pour référence ultérieure et rappel. Il peut être utilisé comme texte d’invites de l’utilisateur pour chaque connecteur et/ou superposé sur l’image d’exécution de la carte pour identifier chaque connecteur. « X, Y » : ces entrées définissent la position du connecteur par rapport au coin inférieur gauche de la carte. Chaque paire de coordonnées définit l’emplacement du centre géométrique de la zone d’engagement de l’outil de pressage. Il s’agit généralement du centroïde du connecteur, mais ce n’est pas toujours le cas. Ces entrées sont uniquement utilisées pour dessiner la carte et pour les données de traçabilité. « Angle » : définit l’angle du connecteur par rapport à la carte montée sur la machine. Sélectionnez l’angle approprié dans le menu déroulant. Les angles sont définis avec zéro degré vers la droite. La position positive à 90 degrés est de ¼ de tour dans le sens inverse des aiguilles d’une montre, vu du dessus. Le « pointeur » du connecteur pour les angles est l’extrémité polarisée, si définie. Cette dimension est uniquement utilisée pour dessiner la carte et les données de traçabilité. « Use PPS » : la sélection de cette option (si disponible) active l’outil PPS pour l’étape du connecteur. « Start Press automatically » : la sélection de cette option lance automatiquement l’opération de pressage pour cette étape de connecteur lorsque la séquence de pressage l’atteint. Cette option est généralement sélectionnée pour les séquences de navette automatisée à connecteur unique, pour éviter que le lancement du cycle de pressage par bouton ne cause un retard. « Use Shuttle » : la sélection de cette option (si disponible) active automatiquement la navette pour l’étape du connecteur. RÉV. D1 64 sur 94 409-35001 « Condition » : la condition à exécuter est sélectionnée dans la base de données des conditions à l’aide du menu déroulant. Toutes les conditions à utiliser dans la séquence de pressage doivent être définies dans la base de données des conditions avant de pouvoir générer la séquence de pressage. Optimisation SensiPress Introduction À mesure que l’industrie se tourne vers des connecteurs à haute performance plus denses en broches et avec des queues de broche plus petites, il devient de plus en plus complexe de détecter les broches tordues au début du cycle de pressage. Les capacités de mesure à haute sensibilité de la technologie SensiPress permettent aux presses TE Connector de mesurer plus précisément la force de pressage et d’arrêter le cycle de positionnement en cas de détection de contact précoce avec l’outil, ce qui peut indiquer qu’une ou plusieurs broches sont pliées ou mal alignées. TE Connectivity a amélioré la détection des broches tordues dans les applications d’insertion des connecteurs par force, en réduisant le bruit mécanique, en augmentant ainsi la précision, en réduisant les mises au rebut et en simplifiant le dépannage et la maintenance. Fonctionnement La machine fonctionne en suivant un profil (une série d’étapes) et en analysant les données de force et de position pour déterminer l’action à entreprendre après chaque étape. Chaque étape précise une force et une hauteur cibles. Lors du déplacement à la hauteur cible, la force est contrôlée. Si la valeur de force cible est atteinte avant que la hauteur cible ne soit atteinte, l’action de force est déclenchée. Si la hauteur est atteinte, l’action de hauteur est déclenchée. Les anomalies du processus sont détectées par une étape du profil qui recherche une force donnée dans une plage de hauteur spécifique. La détection d’une broche tordue fonctionne de la même manière. Les broches tordues (ou les connecteurs mal pré-installés) sont détectées en recherchant une valeur de force faible dans une plage de hauteur située juste au-dessus de l’endroit où l’enclume entre normalement en contact avec l’outil et commence à augmenter la force. Aucune analyse nouvelle ou spéciale n’est associée à SensiPress. L’ajout de SensiPress a amélioré la détection des erreurs en permettant l’utilisation d’une force beaucoup plus faible (elle était auparavant de 50 à 100 livres et est désormais de 2 à 5 livres). Cela permet de détecter un nombre croissant de broches tordues ou écrasées. Détection d’une erreur de broche tordue Les machines détectent une erreur lorsqu’une force est détectée dans la zone de détection de contact précoce (« Early Contact Detection Zone »). Grâce à la technologie SensiPress, nous sommes désormais en mesure de détecter les forces de contact précoces dans les 2 à 5 lbf (voir Figure 63). Figure 63 Si la broche est trop pliée, elle ne générera pas de force dans la zone de détection de contact précoce et ne sera donc pas détectée comme une erreur. Dans ce cas, la différence globale de force se situera bien dans la variation normale du processus de pressage. Par conséquent, elle sera indétectable avec une analyse de force classique, indépendamment de sa sensibilité ou de sa précision (voir Figure 64). RÉV. D1 65 sur 94 409-35001 Figure 64 Configuration du profil (voir Figure 65) 1. Ajoutez la ligne 1 au profil de connecteur actuel. Pour cette ligne, la force peut aller de 25 à 50 livres. 2. Assurez-vous que la valeur Line 1 Unseated Tool Top +.xxxx est supérieure d’au moins 0,0500 à la hauteur Tool Clearance (dans Tool Editor). 3. Réglez la ligne 2 de manière à ce qu’elle puisse détecter une broche tordue très près du haut de l’outil sans appui. Utilisez les données de pressage bien réalisées pour régler cette valeur. 4. Les lignes 1 et 2 déterminent la zone « Early Contact Detection Zone ».1 - 0,035 nous donne une plage de 0,065 pouce dans laquelle nous recherchons une force de contact précoce de 5 livres (comme spécifié à la ligne 2) La force de la ligne 2 peut être réglée pour détecter une broche tordue. La CMP 5T peut utiliser un réglage de force de détection précoce de seulement 1 lbf. Cependant, il est recommandé de commencer par 5 livres et de diminuer si nécessaire. Figure 65 RÉV. D1 66 sur 94 409-35001 Pas de broche tordue (voir Figure 66) Figure 66 Ajustez les dimensions « Unseated top Tool + x.xxx » des lignes 1 et 2 si nécessaire pour régler la zone de contact précoce sur la force par défaut juste avant le début de la courbe. Quelques pressages d’essai sans broches pliées peuvent être nécessaires pour régler correctement le profil. Pressage de broche tordue Figure 67 Optimisation du profil Pour des performances optimales : RÉV. D1 Il peut être nécessaire de personnaliser un profil pour chaque connecteur ou famille de connecteurs. La vitesse ne doit pas être modifiée entre les étapes 1 et 2. L’inertie de l’enclume peut induire une force sur les cellules de charge pendant l’accélération, ce qui pourrait déclencher une erreur de contact précoce erronée. La vitesse peut influencer les performances. En général, les vitesses plus lentes permettent d’obtenir de meilleures performances. 67 sur 94 409-35001 Autres facteurs Comme la détection de broche tordue dépend de la recherche d’une force très faible dans une plage de hauteur étroite, tout ce qui peut avoir un impact sur la hauteur totale de la pile aura une influence sur la fiabilité et la fonctionnalité. Par conséquent, les clients devront éliminer autant que possible les sources de variation. Figure 68 Planéité des cartes et des gabarits de support Toute courbure de la carte de circuit imprimé ou du gabarit de support affecte la hauteur à laquelle la force de pressage commence. Les courbures et les variations de courbures compliqueront la recherche des broches tordues. Cela peut entraîner à la fois des faux positifs et des faux négatifs. En augmentant la force de détection ou la hauteur de détection H2, on limitera la capacité à détecter les broches tordues. Figure 69 RÉV. D1 68 sur 94 409-35001 Tolérance sur l’épaisseur de la carte Pour des performances optimales, les variations d’épaisseur de la carte doivent être minimales. Si elles sont trop importantes, les performances seront incohérentes. Si des variations excessives de l’épaisseur de la carte peuvent se produire, utilisez l’option Measure Board Thickness dans l’éditeur de données de pressage pour vérifier l’épaisseur de la carte. Figure 70 Association d’outil et de gabarit de support Il n’est pas recommandé d’utiliser des outils d’appui et des gabarits de support de manière interchangeable. Si le client a plusieurs exemplaires d’un même outil ou d’un même gabarit de support, il est recommandé de dédier une combinaison d’outillage à une machine spécifique et de régler le profil sur cette machine pour qu’il corresponde à l’outillage. Une autre option consiste à appliquer un identifiant unique à chaque outil et gabarit, puis à utiliser les champs d’identification de l’outil et du gabarit dans le logiciel pour vérifier que le bon outillage est utilisé. Il faut alors créer des programmes pour chaque combinaison potentielle d’outils. Bien entendu, cela pourrait devenir compliqué s’il existe de nombreux exemplaires du même outillage. Si aucune de ces options ne fonctionne, l’alternative consiste à ajuster le profil pour qu’il tolère mieux les variations, ce qui le rendra moins susceptible de détecter des broches tordues. Figure 71 RÉV. D1 69 sur 94 409-35001 9. ÉCRAN DE DIAGNOSTIC Le logiciel de pressage fournit des utilitaires de maintenance sur l’écran Diagnostics comme décrit ci-dessous. L’écran Diagnostics se trouve dans le menu déroulant System. Panneau de commande manuelle Le panneau de commande manuelle (voir Figure 72) est utilisé à des fins de configuration, de maintenance et de dépannage du servomoteur. Le panneau de gauche présente les commandes de manettes pour faire fonctionner manuellement l’axe asservi. Le bouton Power permet d’allumer ou d’éteindre l’amplificateur via les circuits de sécurité. Le bouton Home lance une séquence pour initialiser la position du moteur. Le champ Speed permet de régler la vitesse du mouvement asservi du mode Diagnostic en saisissant un nombre dans la case. Les boutons fléchés haut et bas permettent de déplacer la tête vers le haut ou vers le bas. Le champ d’incrément définit l’augmentation de distance par laquelle la tête de la presse se déplacera à chaque actionnement des boutons de déplacement manuel vers le haut ou vers le bas. Appuyez sur le bouton « Goto Position » pour déplacer la tête de la presse vers la position spécifiée dans le champ de saisie « Position ». La barre de progression à droite indique la position actuelle de la tête de la presse par rapport aux limites supérieure et inférieure de la presse. La partie inférieure du panneau de gauche affiche la force totale de la machine et les forces individuelles des cellules de charge en unités de force, ainsi qu’un graphique à barres. Le curseur Max Force situé sous le graphique à barres de mesure de la force définit la limite de force souhaitée pour le fonctionnement des manettes. Le champ de saisie Max Force permet de saisir une limite de force maximale précise. Lorsque la force totale s’approche de cette limite, les graphiques à barres de force deviennent jaunes. Lorsque la limite est dépassée, les graphiques à barres deviennent rouges et tout autre mouvement vers le bas est empêché. Il convient de faire preuve de prudence en cas de fonctionnement à proximité de la limite de force souhaitée. Les autres mouvements descendants doivent être effectués par très petites étapes et/ou à des vitesses très lentes. Une descente rapide avec une charge rigide peut générer des forces bien supérieures à la limite définie avant que le mouvement ne puisse être arrêté. Figure 72 RÉV. D1 70 sur 94 409-35001 Onglet Inputs/Outputs (Entrées/Sorties) L’onglet Inputs/Outputs est fourni à des fins de diagnostic et est affiché dans la moitié droite de l’écran de diagnostic. Le sous-panneau « Inputs » (voir Figure 72indique l’état de toutes les entrées numériques standard disponibles qui ne concernent pas la sécurité. Une icône d’indicateur vert avec une coche signale une condition « activée » pour l’entrée donnée et une case à cocher rouge vide signale une condition « désactivée ». Les états Home Swith et Limit Switch sont également affichés sur ce panneau, de la même manière que les autres entrées indiquées. Le sous-panneau « Outputs » (voir Figure 73indique l’état de toutes les sorties numériques standard de la machine. Cliquez sur une icône de sortie pour activer/désactiver la sortie correspondante. Une icône verte avec une coche indique que la sortie est actuellement à l’état « activé », tandis qu’une case à cocher rouge vide indique que la sortie est actuellement à l’état « désactivé ». Figure 73 Les positions disponibles pour la navette sont indiquées sur la première ligne du panneau « Shuttle » (voir Figure 74). La sélection d’une position de navette déplacera la navette vers cette position, à condition que les conditions de sécurité et d’alimentation requises soient remplies. Les états Tool ID Switches sont également affichés sur ce panneau, de la même manière que les autres entrées indiquées sur le sous-panneau « Inputs ». Remarque : le sous-panneau Shuttle n’est visible que sur les machines CSP. Figure 74 RÉV. D1 71 sur 94 409-35001 Panneau Load Cells (cellules de charge) Le panneau « Load Celles » (voir Figure 75) contient deux graphiques à barres qui montrent les mesures de force individuelles de chaque cellule de charge. Cet écran contient également le bouton « Tare Load Cells », qui peut être utilisé pour remettre à zéro les cellules de charge. Appuyez sur le bouton « Tare Load Cells » si la machine lit une valeur de force en l’absence de charge. Les valeurs « Load Cell Tare Values » sont affichées sous le bouton «Tare Load Cells ». Ces valeurs indiquent le décalage actuel par rapport à la mesure de la force brute utilisée pour définir correctement le point zéro de chaque cellule de charge. Figure 75 Panneau Calibration (étalonnage) Le panneau Calibration permet d’accéder aux fonctions d’étalonnage de la hauteur (voir Figure 76) et à la fonction d’étalonnage automatique des cellules de charge (force) (voir Figure 77), ainsi que d’afficher des informations sur le dernier étalonnage effectué (voir Figure 79). REMARQUE TE Connectivity propose également un service d’étalonnage des cellules de charge. Les fonctions d’étalonnage de la hauteur se trouvent sous le sous-panneau « Height » du panneau Calibration. Figure 76 RÉV. D1 72 sur 94 409-35001 Figure 77 RÉV. D1 73 sur 94 409-35001 Figure 78 Figure 79 RÉV. D1 74 sur 94 409-35001 Figure 80 Le bouton « Get Limits » lance une séquence pour trouver les positions de contacteur de fin de course et régler les limites de mouvement supérieure et inférieure à une distance appropriée des positions du contacteur. Le bouton « Calibrate Height » permet d’exécuter une séquence de mouvement qui exercera la force spécifiée dans le champ de saisie « Block Force » sur un bloc d’espacement de hauteur pour étalonner la position de l’axe par rapport à la surface de la table de la machine. Avant l’étalonnage, la hauteur du bloc d’espacement doit être saisie dans le champ de saisie « Block Height » et la force d’étalonnage de la hauteur doit être saisie dans le champ de saisie « Force Block ». La vitesse à laquelle l’axe doit descendre pour effectuer le calibrage doit être saisie dans le champ « Calibration Speed ». Le zéro de l’axe Z est défini comme la position où la surface de pressage de la tête est en contact avec la table et chargée de la force spécifiée dans le champ de saisie « Block Force ». La charge est appliquée pour s’assurer que tout dégagement est éliminé des différents composants de la tête, comme les vis sphériques et la tête, pour éliminer les espaces d’air. Étant donné que la tête ne peut pas se déplacer jusqu’à ce point, un bloc d’espacement doit être placé entre la tête et la table pour régler la position zéro. Un outil est fourni à cette fin avec la presse. Ce même outil est également utilisé pour mesurer l’épaisseur de la carte de circuit imprimé. La hauteur de cet outil doit être saisie dans le champ de saisie « Block Height » avant l’étalonnage de la hauteur. Pour régler ou vérifier la position zéro de l’axe Z, placez le bloc d’espacement sur la table, centré sous l’enclume de la tête. La tête doit être positionnée au centre de la machine. Il est recommandé de définir le champ « Calibration Speed » sur moins de 1 mm/s. À ce stade, appuyez sur « Calibrate Height ». AVERTISSEMENT En raison de la grande rigidité de la machine, la force peut s’accumuler très rapidement et entraîner un dépassement important de la force si l’axe Z se déplace à une vitesse supérieure à la vitesse minimale. Réduisez toujours la vitesse lorsque vous vous approchez d’un objet tel que l’outil de sonde d’épaisseur. Utilisez le mode progressif à 0,10 mm ou 0,02 mm lorsque vous appuyez manuellement sur la manette. RÉV. D1 75 sur 94 409-35001 Les fonctions d’étalonnage de la force se trouvent sous le sous-panneau « Force » du panneau Calibration. Pour effectuer un étalonnage forcé, vous devez être connecté en tant qu’administrateur TE. Avant de procéder à l’étalonnage forcé, l’unité ACAL doit être connectée à la connexion USB-RT de la machine et l’affichage numérique doit être connecté à la cellule de charge ACAL et mis sous tension. Placez l’unité ACAL sous l’enclume et centrez-la avec l’outil de centrage ayant pour référence 2216917-1 (voir Figure 81). Figure 81 Retirez l’outil de centrage, puis abaissez manuellement l’enclume juste au-dessus de la cellule de charge. Le bouton « Calibrate » ouvre la fenêtre du formulaire de certificat d’étalonnage. L’utilisateur doit remplir tous les champs de ce formulaire avant l’étalonnage (voir Figure 82 à Figure 85 Appuyez sur le bouton « Begin Calibration » pour démarrer la séquence de mouvement d’étalonnage de la force. Une fois l’étalonnage terminé, le certificat d’étalonnage s’ouvre et le graphique d’étalonnage est rempli avec la date de l’étalonnage de la position de force. Pour rouvrir le certificat d’étalonnage, appuyez sur le bouton « View Calibration Certificate » (voir Figure 77 et Figure 78). RÉV. D1 76 sur 94 409-35001 Figure 82 Figure 83 RÉV. D1 77 sur 94 409-35001 Figure 84 Figure 85 10. UTILITAIRES DE DONNÉES Message Viewer (visionneuse de messages) L’écran « Message Viewer » (Figure 86se trouve sous le menu déroulant System. La visionneuse de messages permet à l’utilisateur d’afficher l’historique des 1 000 derniers messages envoyés entre l’interface homme-machine (IHM) et la partie middleware du logiciel. La plupart des utilisateurs n’auront pas besoin d’utiliser cet écran régulièrement. Cet écran est surtout utilisé par le personnel de TE à des fins de dépannage. Les messages de cet écran donnent un historique détaillé des opérations de la machine. La partie inférieure de l’écran affiche l’historique des messages. La case à cocher « Suppress Ping/Pong » peut être utilisée pour filtrer les messages ping/pong, qui sont uniquement utilisés pour vérifier que la connexion entre l’IHM et le middleware existe toujours. La case à cocher « Suppress RX » peut être sélectionnée pour filtrer les messages reçus par l’IHM, et la case à cocher « Suppress TX » peut être sélectionnée pour filtrer les messages transmis de l’IHM au middleware. Le bouton de pause (icône « Pause ») peut être enfoncé pour mettre en pause le flux de messages ajoutés à l’historique des messages. Vous pouvez aussi appuyer sur le bouton pause pour inverser l’ordre de tri des messages, passer directement au dernier message ou au premier. Appuyez sur le bouton de lecture (icône « Play ») pour reprendre l’envoi des messages dans l’historique des messages. RÉV. D1 78 sur 94 409-35001 La zone de texte en haut de l’écran « Message Viewer » peut être utilisée pour envoyer des messages personnalisés au middleware à partir de l’IHM à des fins de diagnostic. Elle peut être utilisée pour revoir une série d’actions effectuées par l’utilisateur. Utilisez le bouton « Send Message » pour envoyer un message au middleware après avoir saisi un message valide dans la zone de texte. Le bouton « Export Message History » permet d’exporter les 1 000 derniers messages de l’historique des messages sous forme de fichier texte vers une clé USB branchée sur le port USB de l’ordinateur de l’IHM, sur le côté de la machine. Figure 86 RÉV. D1 79 sur 94 409-35001 Journaux machine L’écran « Log Viewer » (voir Figure 87se trouve sous le menu déroulant System. L’écran « Log Viewer » permet de visualiser les différents fichiers de journaux liés au fonctionnement de la machine. Le champ de saisie de texte « Search » peut être utilisé pour faire une recherche par nom dans la liste des journaux (« Log Files »). Il est possible de visualiser la totalité d’un journal ou de n’en charger qu’une partie. Pour charger un fichier journal complet, sélectionnez le fichier journal souhaité dans la liste des fichiers, laissez les champs de saisie « Begin » et « End » vides, puis appuyez sur « Get Log ». Pour obtenir une partie d’un fichier journal, saisissez l’index de caractère numérique à partir duquel commencer à consulter le fichier dans le champ de saisie « Begin » et l’index du caractère de fin dans le champ « End ». Par exemple, la saisie d’un début de « 500 » et d’une fin de « 750 » affichera les caractères 501 à 750 du fichier journal (index des caractères 500 à 749). Figure 87 Le menu déroulant « Directory » permet de sélectionner le répertoire à partir duquel les fichiers journaux sont récupérés. Le répertoire « Logs » contient les fichiers journaux standard de la presse et de la machine. Le répertoire « MachineData » contient les fichiers journaux d’étalonnage. Appuyez sur le bouton « Export Selected Log » pour enregistrer le fichier journal sélectionné sur un dispositif de stockage externe. Appuyez sur le bouton « Export All Logs In Directory » pour enregistrer tous les fichiers journaux du répertoire sélectionné sur un périphérique de stockage externe. Une version étendue des journaux de séquence peut être créée et exportée à l’aide des boutons « Export Expanded Logs By Sequence » et « Export All Expanded Sequence Logs ». Le journal de séquence étendu contient les données du journal de pressage de toutes les presses de connecteur correspondantes dans la séquence jointe à la fin du journal de séquence. Les journaux étendus de tous les journaux de séquences disponibles peuvent être exportés à l’aide du bouton « Export All Expanded Sequence Logs ». Pour exporter les journaux étendus pour une seule séquence particulière, appuyez sur le bouton « xport Expanded Logs By Sequence » et saisissez le nom de la séquence dans la zone de saisie de texte qui s’affiche. Le journal d’erreurs est automatiquement joint à chaque message d’erreur affiché pendant toute fonction de la machine. Cela inclut son horodatage et sa description. L’examen des journaux permet d’évaluer le fonctionnement de la machine à un niveau détaillé. RÉV. D1 80 sur 94 409-35001 11. CONFIGURATION DES UTILITAIRES Paramètres du système L’écran « System Settings » est accessible via le menu déroulant System et sert à régler la configuration de la machine et divers autres paramètres, comme décrit ci-dessous. Paramètres de localisation Distance Units : paramètre l’IHM de façon à ce qu’elle affiche la distance en millimètres ou en pouces. Force Units : paramètre l’IHM de façon à ce qu’elle affiche la force en Newtons ou en livres. Temperature Units : paramètre l’IHM de façon à ce qu’elle affiche la température en degrés Fahrenheit ou Celsius. Decimal Format : définit si l’IHM affiche le séparateur de décimales sous la forme d’un point ou d’une virgule. Language : définit la langue dans laquelle l’IHM affiche le texte. Keyboard Layout : définit la disposition du clavier à l’écran. Date and Time Settings : règle la date et l’heure du système de la machine, ainsi que le format d’affichage des dates. Locale : définit le format d’affichage des dates sur l’IHM. Time Zone : définit le fuseau horaire à utiliser pour la date et l’heure du système d’IHM. Use Time Server : cochez cette option pour intégrer un serveur de temps réseau à utiliser pour la date et l’heure du système IHM. Figure 88 RÉV. D1 81 sur 94 409-35001 Configuration de la machine L’onglet Machine Configuration (voir Figure 89) contient divers paramètres utilisés pour définir certains aspects du mouvement de la machine et dispose d’options pour activer ou désactiver certaines fonctionnalités de la machine. Après la mise à jour de la configuration de la machine, le bouton « Save Machine Configuration » doit être utilisé pour enregistrer la configuration actuelle dans la base de données de la machine. La plupart des options de configuration de la machine ne peuvent être modifiées que par le personnel de TE. Quelques options de configuration de la machine peuvent être modifiées par un utilisateur qui ne fait pas partie du personnel de TE. L’option de configuration de la machine « MES Enabled » est utilisée pour configurer les paramètres de connexion MES pour la connexion à un serveur MQTT. Une fois la configuration enregistrée, ces paramètres peuvent être testés à l’aide des boutons « Connect To MQTT Server » et « Disconnect MQTT ». L’option de configuration « Spacebar Action Enabled » de la machine permet à la barre d’espace du clavier de l’équipement de déclencher le bouton « Action Button » sur l’écran « Production ». Cette fonction permet à l’utilisateur d’initier un pressage de connecteur à l’aide du clavier de l’équipement au lieu de l’écran tactile. Le bouton « Refresh COM Ports » peut être utilisé pour mettre à jour la liste des ports COM actuellement disponibles si un nouveau périphérique a été connecté à la machine. Les plans d’entrée et de sortie définis par l’utilisateur peuvent également être définis à l’aide des onglets « Input Map » et « Output Map ». Entrez un texte descriptif pour le canal d’entrée ou de sortie approprié et cliquez sur « Save Machine Configuration » pour enregistrer le plan dans la base de données de la machine. Les noms d’entrée ou de sortie du plan s’affichent lorsque ces entrées ou sorties apparaissent à l’écran « Machine Diagnostics ». L’onglet « Machine State Map » peut être utilisé pour attribuer une sortie numérique qui s’activera, se désactivera ou clignotera en fonction de l’état actuel de la machine. Il peut être utilisé lors de la connexion d’une colonne témoin à une machine. Si l’utilisateur a acheté une licence ACAL, le bouton « Import ACAL License » est utilisé pour ajouter la licence achetée à la machine et déverrouiller la fonction d’étalonnage de la force pour les utilisateurs qui ne sont pas des administrateurs TE. Figure 89 RÉV. D1 82 sur 94 409-35001 Sauvegarde et restauration des bases de données L’onglet Database Backup and Restore (voir Figure 90) contient des boutons permettant de gérer les bases de données des utilisateurs et des machines. Pour sauvegarder la base de données utilisateur, utilisez le navigateur de fichiers de la base de données utilisateur de sauvegarde pour sélectionner un emplacement de fichier dans lequel enregistrer la sauvegarde de la base de données, puis appuyez sur le bouton « Backup User Database ». Pour restaurer la base de données utilisateur à partir d’une sauvegarde antérieure, utilisez le navigateur de fichiers de restauration de la base de données utilisateur pour sélectionner la base de données à partir de laquelle effectuer la restauration et appuyez sur le bouton « Restore User Database ». Pour restaurer les paramètres d’usine de la base de données utilisateur, appuyez sur le bouton « Restore User Database to Factory State ». La base de données utilisateur contient tous les éléments (outils, profils, connecteurs, conditions et séquences) et les données utilisateur. La base de données de la machine contient des informations pertinentes pour la configuration de la machine et ne peut être réinitialisée, sauvegardée ou restaurée que par le personnel de TE. Le bouton « Update Machine Software » sert à installer les mises à jour du logiciel de la machine. Pour installer une mise à jour logicielle, copiez le fichier de mise à jour (au format « PressFitMachineUpdateaaaa-mmjj.zip ») dans le dossier racine d’une clé USB. Ne décompressez pas le fichier de mise à jour. Branchez la clé USB dans le port USB de l’IHM, sur le côté de la machine. Appuyez sur le bouton « Update Machine Software » et sélectionnez le fichier .zip de mise à jour dans le navigateur de fichiers. La machine installera automatiquement la mise à jour et redémarrera chaque composant logiciel. Le processus de mise à jour prendra environ cinq minutes. Le bouton «Compress and Transfer Log and Machine Data Files » exportera un fichier.zip contenant tous les fichiers journaux et de données machine de la machine vers une clé USB. Ce processus peut prendre jusqu’à une heure. Figure 90 Network Settings - Paramètres réseau L’onglet Network Settings contient les paramètres de configuration des interfaces de réseau sur l’ordinateur de l’IHM. Ces paramètres permettent de configurer la machine pour qu’elle se connecte à un réseau externe ou à un serveur MES. L’ordinateur de l’IHM dispose de deux interfaces de réseau. L’une de ces interfaces est utilisée pour communiquer avec l’API Beckhoff de la machine et ne doit pas être modifiée. Cette interface est généralement configurée avec 192.168.0.1 pour adresse IP. L’autre interface de réseau dispose d’un point de connexion sur le côté de la machine et peut être utilisée pour se connecter à un système MES ou à un autre réseau externe. Le bouton « Set Network Configuration » permet d’enregistrer les paramètres réseau actuels sur l’ordinateur de l’IHM de la machine. RÉV. D1 83 sur 94 409-35001 Accès utilisateur L’accès des utilisateurs aux différentes fonctions de la machine est contrôlé par des comptes utilisateurs individuels protégés par mot de passe. Pour créer un nouvel utilisateur, une personne disposant des droits d’accès administrateur doit se connecter et utiliser le bouton « Add Operator » sur l’écran « Operator » (Opérateur). Les limites d’accès du nouvel utilisateur seront en fonction du type d’opérateur (« Operator Type ») sélectionné lors de la création de l’utilisateur. Seuls les administrateurs peuvent modifier les autorisations d’un compte d’utilisateur existant. Toutefois, un administrateur ne peut pas modifier ses propres droits d’accès, seul un autre administrateur peut le faire. Tous les utilisateurs peuvent modifier leurs propres mots de passe. Figure 91 RÉV. D1 84 sur 94 409-35001 Saisissez le nom de l’opérateur, le mot de passe et sélectionnez le type d’opérateur dans le menu déroulant pour définir les écrans et les fonctions auxquels l’utilisateur aura accès. Les types d’opérateurs et les niveaux d’accès disponibles sont (par ordre hiérarchique) : « Administrator », « Maintenance », « Techninician », « Inspector », « Operator » et « Restricted Operator » (voir Figure 92). Figure 92 RÉV. D1 85 sur 94 409-35001 Network Viewer - Visionneuse de réseau L’écran Network Viewer (voir Figure 93affiche des informations sur la connexion entre l’ordinateur de l’IHM (interface homme-machine) et le reste du logiciel de la machine. Vous pouvez également consulter ici des informations sur les connexions des machines MES. Figure 93 Configuration Beckhoff L’écran Beckhoff Configuration affiche des informations sur le contrôleur d’API Beckhoff utilisé dans la machine. Cet écran est surtout utilisé par le personnel de TE à des fins de dépannage. Beckhoff Remote Desktop - Bureau à distance L’écran Beckhoff Remote Desktop est utilisé pour lancer l’utilitaire de bureau à distance qui permet d’accéder à l’ordinateur d’API Beckhoff. Cet écran est uniquement utilisé pour accéder au logiciel utilitaire du lecteur de codes-barres et aux autres logiciels de dispositif tiers à des fins de configuration et de maintenance. Cliquez sur le bouton « Launch Remote Desktop » (Figure 94) pour lancer la visionneuse de bureau à distance et accéder à l’ordinateur d’API Beckhoff. Figure 94 RÉV. D1 86 sur 94 409-35001 PPS Viewer - Visionneuse PPS L’écran PPS Viewer permet d’accéder à toutes les commandes de l’outil PPS disponibles pour la configuration et le dépannage. L’écran PPS Viewer ne sera disponible que si PPS est activé pour la machine. L’onglet « Basic Commands » (voir Figure 95) permet d’accéder aux commandes PPS les plus couramment utilisées. Ces commandes sont utilisées pour afficher les états des broches et configurer le ou les masques de broches pour l’outil. Figure 95 RÉV. D1 87 sur 94 409-35001 Les commandes « Advanced Commands » (voir Figure 96) permettent d’accéder aux commandes pour afficher des informations sur l’outil PPS et sur la configuration de l’outil. Figure 96 L’onglet « Setup Commands » (voir Figure 97) permet d’accéder aux commandes de configuration de l’outil PPS ou de la carte de circuit imprimé de l’outil PPS. La plupart des commandes de cet onglet sont uniquement accessibles au personnel de TE. Figure 97 RÉV. D1 88 sur 94 409-35001 12. MAINTENANCE PRÉVENTIVE La presse a été conçue pour minimiser la maintenance dans toute la mesure du possible. Les procédures de maintenance préventive suivantes doivent être exécutées selon la périodicité donnée ci-dessous. TE propose un service annuel d’inspection, de réglage et d’étalonnage. DANGER Toujours éteindre l’interrupteur principal et débrancher le cordon électrique de la source d’alimentation avant toute intervention de maintenance. Accès à la tête de presse (CBP) Pour accéder à la tête de la presse CBP à des fins d’inspection ou de maintenance, ouvrez la porte avant ou arrière du capot supérieur. Actionner le verrou pour ouvrir le capot avant ou arrière. Pour accéder à la tête de la presse CMP, retirez le panneau avant. Nettoyage Toutes les surfaces doivent être maintenues propres et exemptes de dépôts de poussière. Essuyez toutes les surfaces planes exposées avec un chiffon doux. Si cela est autorisé, utilisez de l’air comprimé basse pression pour procéder à un soufflage de haut en bas des différentes portions de la tête de presse et de la structure. Inspection Procédez à un contrôle d’aspect de la tête de presse. Le capot supérieur en tôle ou le panneau de couverture frontal doivent être enlevés une fois par an afin de procéder à une inspection approfondie Reportez-vous à la section 12.1 pour consulter la procédure de retrait du capot. Chaque fois que le capot supérieur en tôle est retiré (CBP) ou que l’armoire électrique arrière est ouverte (CMP), la protection principale contre les surtensions doit être vérifiée. La protection contre les surtensions est située à l’extrême gauche du rail DIN du panneau. Lorsque la machine est sous tension, vérifiez que la LED verte de protection contre les surtensions est allumée. Si ce n’est pas le cas, il est probable que la machine ait été exposée à une surtension extrême ou à plusieurs surtensions importantes, telles que celles générées par la foudre à proximité des lignes électriques alimentant l’installation. Si la LED n’est pas allumée, la machine continue de fonctionner, mais n’est plus protégée contre les événements potentiellement destructeurs de la ligne électrique. Remplacez la protection contre les surtensions pour restaurer la protection. Barrière immatérielle La barrière immatérielle est le principal dispositif de protection de l’opérateur. Lorsque la barrière immatérielle détecte un obstacle, le circuit EMO est mis hors tension et le mouvement est interrompu. Pour garantir un fonctionnement sûr, la barrière immatérielle nécessite des contrôles périodiques. Reportez-vous au manuel d’utilisation de la barrière immatérielle pour obtenir des instructions sur la réalisation du test périodique à l’aide du témoin détecteur fourni pour un fonctionnement correct et sûr. Lubrification Utilisez une huile légère pour machines ou de l’huile moteur 30W non détergente pour lubrifier les zones suivantes de la machine : Tiges de l’axe Z Avec l’axe Z en position basse, appliquez une petite quantité d’huile sur les tiges au-dessus de chaque palier de guidage linéaire. Graissez les paliers de guidage linéaire via les graisseurs. Vérin à vis de l’axe Z Avec l’axe Z en position basse, appliquez une petite quantité d’huile sur le vérin à vis et essuyez avec un chiffon. Il ne doit rester qu’une fine couche d’huile. Graissez le mécanisme via les graisseurs de l’écrou. RÉV. D1 89 sur 94 409-35001 Couple de serrage critique de la visserie REMARQUE Cette procédure nécessite d’ôter le capot supérieur en tôle de la CBP (voir la section 12.1 pour les détails de la procédure). La visserie de la tête de pressage doit faire l’objet d’un contrôle de couple de serrage. Le logement de roulement de l’axe Z est un bloc d’une épaisseur de 50 mm [1,97 po] monté sur deux plaques verticales avec 6 boulons à tête creuse M10 x 1,5. Serrez les boulons à un couple de 90 Nm [66,4 lb/pi]. Calendrier de maintenance périodique Figure 98 fournit un calendrier de maintenance préventive des machines. ÉLÉMENT Soufflage de la machine TOUS LES JOURS TOUTES LES SEMAINES TOUS LES TRIMESTRES TOUS LES ANS ● ● Essuyage de la machine Inspection des fils et flexibles ● Huiler selon procédure ci-dessus ● Serrage des vis de la tête ● Purger le séparateur d’humidité ● Étalonner les cellules de charge de l’axe Z ● Inspecter le vérin à vis ● Figure 98 RÉV. D1 90 sur 94 409-35001 ANNEXE A – PIÈCES DE RECHANGE Liste des pièces de rechange CBP NUMÉRO DE PIÈCE TE 2216929-2 DESCRIPTIF KIT, PIÈCES DE RECHANGE CXP RÉVISION B REMARQUES : ● Identifiez le kit conformément à la spécification TE 115-67-12 (numéro de pièce, lettre de révision et pays d’origine) ● Le kit 2216929-2 est utilisé avec toutes les configurations de CBP de niveau supérieur (voir schéma 2216056) Liste des pièces détachées du CBP avec support NUMÉRO DE PIÈCE TE 2216929-1 DESCRIPTIF KIT, PIÈCES DE RECHANGE CXP RÉVISION B REMARQUES : ● Identifiez le kit conformément à la spécification TE 115-67-12 (numéro de pièce, lettre de révision et pays d’origine) ● Le kit 2216172-1 est utilisé avec toutes les configurations de CBP de niveau supérieur (voir le schéma 1-2216056-1/2) Liste des pièces de rechange CSP NUMÉRO DE PIÈCE TE 2216929-1 DESCRIPTIF KIT, PIÈCES DE RECHANGE CXP RÉVISION B REMARQUES : ● Identifiez le kit conformément à la spécification TE 115-67-12 (numéro de pièce, lettre de révision et pays d’origine) ● Le kit 2216929-1 est utilisé avec toutes les configurations de CSP de niveau supérieur (voir schéma 2216055) Liste des pièces de rechange CMP CMP-5T NUMÉRO DE PIÈCE TE 2216259-1 DESCRIPTIF KIT, PIÈCES DE RECHANGE CMP-5T RÉVISION A REMARQUES : ● Identifiez le kit conformément à la spécification TE 115-67-12 (numéro de pièce, lettre de révision et pays d’origine) CMP-10T NUMÉRO DE PIÈCE TE 2216260-1 DESCRIPTIF KIT, PIÈCES DE RECHANGE CMP-10T RÉVISION A REMARQUES : ● Identifiez le kit conformément à la spécification TE 115-67-12 (numéro de pièce, lettre de révision et pays d’origine) RÉV. D1 91 sur 94 409-35001 ANNEXE B – CARACTÉRISTIQUES ET SPÉCIFICATIONS Caractéristiques Calcul, affichage, journal et impression SPC Écran tactile Schémas et photographies de la configuration en ligne Connexion et déconnexion de l’opérateur avec protection par mot de passe Plusieurs niveaux d’opérateur pour limiter l’accès aux fonctions Journal d’erreurs avec date, heure et informations sur l’opérateur enregistrées sur le disque Maintenance et configuration des utilitaires logiciels Affichage graphique de la carte utilisée Graphiques force vs distance affichés à l’écran Profil de pressage contrôlé par logiciel avec détection des erreurs et messages définis par l’utilisateur Pressage électrique asservi (axe Z) Grande rigidité : 2 grandes tiges de guidage axe Z avec paliers de guidage linéaires Force de pressage Mesure de l’épaisseur des cartes et pressage selon la hauteur Pressage par PARS et Gradient de Force Détection de connecteur manquant Propre et silencieuse Économie d’énergie Conformité CE Spécificités CBP-5T Mk II Force : 44 kN [5 tonnes] Sensibilité de force : 50 N [12 lbf] Débattement de l’axe Z : >50 mm [2 po] Vitesse de l’axe Z : jusqu’à 8 mm [0,31 po]/sec Alimentation électrique : 200-240 VCA, monophasé, 6 A Dimensions : Pour machine de table standard : 766 mm de largeur x 612 mm de profondeur x 960 mm de hauteur (31 po de largeur X 25 po de profondeur X 38 po de hauteur) Pour CBP-5T avec support (1-2216056-1/2) : 766 mm de largeur x 612 mm de profondeur x 1 775 mm de hauteur (31 po de largeur X 25 po de profondeur X 69,6 po de hauteur) Poids : Pour machine de table standard : Environ 180 kg (400 lb) Pour CBP-5T avec support (1-2216056-1/2) : Environ 270 kg (600 lb) CSP-5T Mk II Force : 44 kN [5 tonnes] Sensibilité de force : 50 N [12 lbf] Débattement de l’axe Z : >50 mm [2 po] Vitesse de l’axe Z : jusqu’à 8 mm [0,31 po]/sec Alimentation électrique : 200-240 VCA, monophasé, 6 A Dimensions : 766 mm de largeur x 612 mm de profondeur x 960 mm de hauteur (31 po de largeur X 25 po de profondeur X 38 po de hauteur) Poids : Environ 180 kg (400 lb) RÉV. D1 92 sur 94 409-35001 CMP-5T Mk II Force : 53 kN [6 tonnes] Sensibilité de force : 80 N [18 lbf] Débattement de l’axe Z : >130 mm [5 po] Vitesse de l’axe Z : jusqu’à 30 mm [1,2 po]/sec Alimentation électrique : 200-240 VCA, monophasé, 10 A Dimensions : 1 270 mm de largeur x 915 mm de profondeur x 1 780 mm de hauteur [50 po de largeur X Poids : Environ 680 kg (1 500 lb) 36 po de profondeur X 70 po de hauteur) CMP-10T Mk II Force : 106 kN [12 tonnes] Sensibilité de force : 100 N [23 lbf] Débattement de l’axe Z : >130 mm [5 po] Vitesse de l’axe Z : jusqu’à 19 mm [0,75 po]/sec Alimentation électrique : 200-240 VCA, monophasé, 10 A Dimensions : 766 mm de largeur x 612 mm de profondeur x 960 mm de hauteur (31 po de largeur X Poids : Environ 1 130 kg (2 500 lb) 25 po de profondeur X 38 po de hauteur) Options Lecteur de codes-barres Unité ACAL Outils PPS (CSP 5T Mk II uniquement) Mises à jour Pour savoir comment obtenir la dernière version du système d’exploitation CxP, composez le (888) 782-3349 ou visitez notre site Web à l’adresse www.tooling.te.com. RÉV. D1 93 sur 94 409-35001 ANNEXE C – SCHÉMA ÉLECTRIQUE/MÉCANIQUE CBP-5T, CMP-5T ET CMP-10T NUMÉRO TE DWG 2216706 DESCRIPTIF SCHÉMA ÉLECTRIQUE RÉVISION B NUMÉRO TE DWG 2216052 DESCRIPTIF SCHÉMA ÉLECTRIQUE RÉVISION B CSP-5T RÉV. D1 94 sur 94 ">
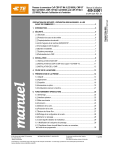
公開リンクが更新されました
あなたのチャットの公開リンクが更新されました。