Notice d'utilisation Transmetteur de température TCCxxx 80285272 / 00 02 / 2021 FR Contenu 1 Remarques préliminaires �������������������������������������������������������������������������������������3 1�1 Explication des symboles ������������������������������������������������������������������������������3 2 Consignes de sécurité �����������������������������������������������������������������������������������������3 3 Introduction rapide �����������������������������������������������������������������������������������������������4 4 Fonctionnement et caractéristiques ���������������������������������������������������������������������5 5 Fonction ���������������������������������������������������������������������������������������������������������������5 5�1 IO-Link �����������������������������������������������������������������������������������������������������������5 5�2 Signal de diagnostic ��������������������������������������������������������������������������������������6 5�3 Signal analogique ������������������������������������������������������������������������������������������6 5�4 Fonction de diagnostic �����������������������������������������������������������������������������������8 5�4�1 Fonction de contrôle de calibrage �������������������������������������������������������8 5�4�2 Messages de diagnostic �����������������������������������������������������������������������9 5�5 Mode de simulation �������������������������������������������������������������������������������������10 5�6 Transfert de données binaires (BLOB) �������������������������������������������������������� 11 6 Montage ������������������������������������������������������������������������������������������������������������� 11 6�1 Pour applications aseptiques selon 3-A������������������������������������������������������� 11 6�2 Pour applications aseptiques selon EHEDG �����������������������������������������������12 6�3 Appareils avec raccord process Clamp ������������������������������������������������������13 6�4 Appareils avec raccord process cône d'étanchéité G ½ ������������������������������14 6�4�1 Etanchéité affleurante et aseptique via un joint PEEK �����������������������14 6�4�2 Etanchéité affleurante via une zone d'étanchéité métal sur métal ����15 6�5 Appareils pour raccordement au process via une bague de serrage ���������15 7 Raccordement électrique �����������������������������������������������������������������������������������16 8 Eléments de service et d'indication �������������������������������������������������������������������17 9 Paramétrage ������������������������������������������������������������������������������������������������������17 9�1 Paramètres ��������������������������������������������������������������������������������������������������18 9�2 Fonctions d'analyse �������������������������������������������������������������������������������������18 10 Fonctionnement �����������������������������������������������������������������������������������������������19 11 Données techniques ����������������������������������������������������������������������������������������19 12 Correction de défauts ��������������������������������������������������������������������������������������19 2 13 Maintenance, réparation et élimination ������������������������������������������������������������21 14 Réglage usine ��������������������������������������������������������������������������������������������������21 1 Remarques préliminaires Données techniques, certificat usine, homologations, accessoires et plus d'informations sur www�ifm�com� 1.1 Explication des symboles ► > […] → Action à faire Retour d'information, résultat Désignation d'une touche, d'un bouton ou d'un affichage Référence Remarque importante Le non-respect peut aboutir à des dysfonctionnements ou perturbations� Information Remarque supplémentaire� FR 2 Consignes de sécurité • L'appareil décrit est un composant destiné à être intégré dans un système� - La sécurité du système est sous la responsabilité de l'installateur� - L'installateur du système est tenu d’effectuer une évaluation des risques et de rédiger, sur la base de cette dernière, une documentation conforme à toutes les exigences prescrites par la loi et par les normes et de la fournir à l'opérateur et à l'utilisateur du système� Cette documentation doit contenir toutes les informations et consignes de sécurité nécessaires à l'opérateur et à l'utilisateur et, le cas échéant, à tout personnel de service autorisé par l'installateur du système� • Lire ce document avant la mise en service du produit et le garder pendant le temps d'utilisation du produit� • Le produit doit être approprié pour les applications et les conditions environnantes concernées sans aucune restriction d'utilisation� • Utiliser le produit uniquement pour les applications pour lesquelles il a été prévu (→ Fonctionnement et caractéristiques). 3 • Utiliser le produit uniquement pour les fluides admissibles (→ Données techniques)� • Le non-respect des consignes ou des données techniques peut provoquer des dommages corporels et/ou matériels� • Le fabricant n'assume aucune responsabilité ni garantie pour les conséquences d'une mauvaise utilisation ou de modifications apportées au produit par l'utilisateur� • Le montage, le raccordement électrique, la mise en service, le fonctionnement et l'entretien du produit doivent être effectués par du personnel qualifié et autorisé par le responsable de l'installation� • Assurer une protection efficace des appareils et des câbles contre l'endommagement� 3 Introduction rapide L'appareil peut être utilisé sans paramétrage supplémentaire avec les réglages décrits dans le paragraphe → 14 Réglage usine� En cas de besoin, changement du réglage usine via l'interface IO-Link : ► Raccorder l'appareil au PC pour effectuer le paramétrage via l'interface IOLink� ► Régler l'unité de mesure standard� - [Uni]: °C ou °F ► Régler le signal analogique� - [OU2] : I = 4���20 mA ou Ineg = 20���4 mA ou OFF = sortie désactivée - [ASP] et [AEP] : mettre l'étendue de mesure à l'échelle� ► Configurer le signal analogique pour l'alarme� - [FOU2] : On = 21,5 mA ou OFF = 3,5 mA ► Régler la limite de contrôle de calibrage� - [ccL] : différence de la température à partir de laquelle l'appareil signale "avertissement"� ► Configurer la logique de commutation pour avertissement et alarme de la sortie de diagnostic� - [P-n] : PnP ou nPn 4 ► Activer / désactiver la LED sur l'appareil� - [LED] : On = LED allumée (vert, bleu, rouge) ou OFF = LED éteinte ou Notification = LED seulement pour avertissement et alarme ► Finir le paramétrage, installer (→ 6), raccorder (→ 8) et mettre en service l'appareil� 4 Fonctionnement et caractéristiques L'appareil mesure la température du fluide et transmet la valeur mesurée via un signal analogique et / ou TOR� L'appareil a une fonction de diagnostic intégrée et une fonction de contrôle de FR calibrage (→ 5.4.1)� Les messages de diagnostic sont fournis via un signal analogique et un signal de commutation ou comme signal de communication TOR via l'interface IO-Link� L'appareil a une LED qui indique des déviations du fonctionnement normal par un changement de couleur (→ 5.4.2)� 5 Fonction • L'appareil dispose d'une interface IO-Link� • L'appareil est conçu pour le fonctionnement 3 fils� Les signaux de sortie suivants sont disponibles : OUT1 (2 options) : - signal de diagnostic - signal IO-Link pour la mesure de température et le diagnostic OUT2 : - signal analogique pour la mesure de température et le diagnostic 5.1 IO-Link Cet appareil dispose d'une interface de communication IO-Link permettant l'accès direct aux données process et de diagnostic� De plus, le paramétrage de l'appareil est possible pendant le fonctionnement� L'utilisation de l'appareil via l'interface IO-Link nécessite un maître IO-Link� Pour une communication hors fonctionnement, il vous suffit d’un PC, d’un logiciel IO-Link approprié et d’un câble adaptateur IO-Link� 5 Les IODD nécessaires pour la configuration de l'appareil, les informations détaillées concernant la structure des données process, les informations de diagnostic et les adresses des paramètres ainsi que toutes les informations nécessaires concernant le matériel et le logiciel IO-Link sont disponibles sur www� ifm�com� L'interface IO-Link offre les fonctions suivantes : • Paramétrage à distance de l'appareil� • Transmission des valeurs process résistante aux parasites et sans perte de valeurs mesurées� • Transmission du paramétrage lors du remplacement d'un appareil ou à d'autres appareils du même type� • Lecture simultanée des deux valeurs de température (élément de mesure et élément de référence), de la sortie de diagnostic (fonction de contrôle de calibrage) et de l'état de l'appareil� • Sauvegarde sans papier des paramétrages, des valeurs process et des informations de diagnostic� 5.2 Signal de diagnostic La sortie de diagnostic est uniquement utilisée pour la mise à disposition des avertissements et des alarmes (→ Fiche technique pour le courant nominal maximal de la sortie de commutation)� La sortie de commutation est fermée en fonctionnement normal (normalement fermé)� Si l'appareil détecte un cas de diagnostic, la sortie s'ouvre� La logique de commutation (PnP / nPn) et la limite de contrôle de calibrage (ccL) à partir de laquelle la sortie commute sont réglables� Les messages de diagnostic sont définis et ne peuvent pas être changés (→ 12)� 5.3 Signal analogique L'appareil convertit la valeur de température mesurée en un signal analogique proportionnel à la température� De plus, la sortie analogique est utilisée pour le diagnostic (→ 5.4 Fonction de diagnostic)� La transmission de la valeur de température mesurée est interrompue pour des alarmes et un signal analogique selon Namur NE43 de 3,5 mA (FOU2 = OFF) ou 6 21,5 mA (FOU2 = On) est fourni� Le signal analogique continue à être utilisé pour des avertissements� Selon le paramétrage (→ 9), le signal analogique est dans l'étendue de mesure : 4���20 mA avec réglage [OU2] = I ou 20���4 mA avec réglage [OU2] = Ineg� L'étendue de mesure peut être mise à l'échelle : • [ASP] définit à quelle valeur de température mesurée le signal analogique est de 4 mA (OU2 = I) ou de 20 mA (OU2 = Ineg)� • [AEP] définit à quelle valeur de température mesurée le signal analogique est de 20 mA (OU2 = I) ou de 4 mA (OU2 = Ineg)� FR Distance minimale entre [ASP] et [AEP] = 5 K� Si la valeur de température mesurée est en dehors de l'étendue de mesure mise à l'échelle, le signal analogique est d'abord entre 20...20,5 mA ou 3,8...4 mA (→ Fig� 1)� Si la valeur de température mesurée continue à augmenter ou à chuter le signal analogique passe à la valeur de 3,5 mA ou 21,5 mA� I [mA] 1 FOU2 = On 21�5 20�5 20 4 3�8 FOU2 = OFF 3�5 2 -60 -25 -10 150 160 200 cr�UL MAW ASP AEP MEW cr�OL T [°C] Figure 1 : Caractéristique de sortie analogique avec réglage usine 1 Réglage [OU2] = I 2 Réglage [OU2] = Ineg MAW = valeur initiale de l'étendue de mesure, MEW = valeur finale de l'étendue de mesure, ASP = valeur minimum de la sortie analogique, AEP = valeur maximum de la sortie analogique, cr�UL = zone de détection non atteinte, cr�OL = zone de détection dépassée 7 5.4 Fonction de diagnostic L'appareil contrôle en continue la mesure de la température (→ 5.4.1 Fonction de contrôle de calibrage) et détecte d'autres événements sur l'appareil� En cas de déviation du fonctionnement normal un message de diagnostic est fourni (→ 5.4.2)� 5.4.1 Fonction de contrôle de calibrage En mesurant avec deux éléments différents et thermiquement couplés, l'appareil détecte automatiquement une différence de température pendant la mesure de la température� La valeur process est mesurée par l'élément de mesure et fournie via la sortie analogique� La valeur de référence est utilisée pour comparer et vérifier la valeur process� Si la différence de température entre la valeur process et la valeur de référence dépasse la valeur réglée comme limite de contrôle de calibrage [ccL] un avertissement est déclenché : la LED passe à bleu et la sortie de diagnostic s'ouvre� T [°K] 1 CCL 2 t Figure 2 : Fonction de contrôle de calibrage Exemple : L'élément de mesure (1) mesure 61,05 °C, l'élément de référence (2) mesure 60 °C� En cas de réglage ccL = 1 K il y aurait un avertissement� 8 Si un avertissement est déclenché, la LED reste bleue même si la différence de température tombe en dessous de la valeur ccL� Démarche à suivre : Vérifier si le capteur doit être utilisé ou remplacé, sinon procéder comme suit : ► Augmenter la valeur ccL jusqu'à ce que la LED s'allume de nouveau en vert� > La sortie de diagnostic se ferme� > Le changement ccL est mémorisé (→ 5.6)� En cas de défaillance de l'élément de référence la fonction de contrôle de calibrage échoue et la LED passe à bleu� Plage de réglage ccL → Données techniques. Du fait des tolérances de production, une différence de température de max� 0,1 K peut aussi se produire avec de nouveaux éléments de mesure et de référence� Cela n'affecte pas la fonction de contrôle de calibrage� Pour assurer que la fonction de contrôle de calibrage ne détecte qu'une différence de température des éléments de mesure et de référence une temporisation interne de 10 minutes a été réglée� 5.4.2 Messages de diagnostic Les messages de diagnostic sont fournis comme suit : • Signal LED : La LED indique tous les avertissements et alarmes par un changement de couleur (bleu = avertissement ; rouge = alarme)� • Signal de diagnostic: La sortie de diagnostic fournit tous les avertissements et alarmes par un signal de commutation� • Signal analogique : La sortie analogique ne fournit que des alarmes�En cas d'alarme le signal analogique passe à 3,5 mA ou 21,5 mA� • IO-Link : Lorsque l'interface IO-Link est utilisée tous les messages de diagnostic sont affichés via un logiciel raccordé ou transmis au système de commande supérieur�En plus, un bit de diagnostic qui correspond au comportement de la sortie de commutation physique est fourni� Liste de tous les messages de diagnostic qui peuvent être lus via IO-Link → IO Device Description (IODD) sur www.ifm.com. 9 FR Diagnostic LED • Déviation de température entre Mode de l'élément de mesure et l'élément fonctionnement de référence ≤ limite de contrôle verte normal de calibrage (ccL) • Aucun défaut • Déviation de température entre l'élément de mesure et l'élément Avertissement de référence > limite de contrôle bleue de calibrage (ccL) • Défaillance élément de référence • Défaillance élément de mesure ou défaillance des deux éléments Alarme rouge de mesure et de référence D'autres défauts → 12 Sortie de diagnostic Sortie analogique 4���20 mA1) 4���20 mA1) 21,5 mA2) Tableau 1: Fonction de diagnostic 1) pour [OU2] = Ineg: 20���4 mA 2) pour [FOU2] = OFF: 3,5 mA Des avertissements sont fournis avec une temporisation de 10 minutes� Des alarmes sont fournies tout de suite� 5.5 Mode de simulation Cette fonction permet de simuler le mode de fonctionnement normal et la fonction de diagnostic (avertissement et alarme) avec des paramètres sélectionnés librement� ► Régler la durée souhaitée de la simulation avec [S�Tim]� ► Régler la valeur de simulation ou le défaut pour l'élément de mesure avec [TEMP]� ► Régler la valeur de simulation ou le défaut pour l'élément de référence avec [REF_[TEMP]� ► Remonter les valeurs à l'appareil� ► Cliquer sur [Start simulation]� > La simulation prend le temps réglé sous [S�Tim]� ► Cliquer sur [Stop simulation] pour abandonner la simulation� 10 • Un avertissement simulé du contrôle de calibrage (LED bleue) est fourni avec une temporisation de 30 secondes� • Une alarme simulée (LED rouge) est fournie sans temporisation� • Pendant la simulation le logiciel de paramétrage indique [S�On] = On� 5.6 Transfert de données binaires (BLOB) L'appareil mémorise les 20 derniers événements et les 20 derniers avertissements du contrôle de calibrage dans une mémoire FIFO� • Dans [Event log] tous les événements y compris les heures de fonctionnement et les numéros d'événement sont mémorisés (Events→ 12 ; tableau)� FR • Dans [Calibration check alarm log] tous les avertissements du contrôle de calibrage y compris les heures de fonctionnement, la valeur mesurée, la valeur de différence de température, la valeur ccL réglée et l'état d'événement sont mémorisés� 6 Montage ► S'assurer avant le montage et le démontage de l'appareil que l'installation est hors pression et qu'il n'y a pas de fluide dans le tuyau� ► Tenir compte des dangers dus aux températures de l'installation et du fluide� 6.1 Pour applications aseptiques selon 3-A ► S'assurer d'une intégration du capteur dans l'installation selon 3-A� ► Utiliser uniquement des raccords avec homologation 3-A et marqués avec le symbole 3-A (→ Accessoires sur www.ifm.com). Le raccord process doit être muni d'un orifice de fuite� Ceci est assuré en cas d'utilisation des raccords avec homologation 3-A� ► Installer les orifices de fuite de manière bien visible et orientés vers le bas en cas de conduites verticales� ► Observer les réglementations pour le nettoyage et la maintenance en cas d'utilisation selon 3-A� L'utilisation n'est pas possible dans des installations qui doivent satisfaire aux critères du point E1�2 / 63-03 de la norme 3-A, 63-03� 11 1 2 3 Pour des appareils avec homologation 3-A il s'applique : ► N'utiliser que des adaptateurs avec homologation 3-A pour le raccord process� ► L'appareil ne doit pas être installé au point le plus bas du tuyau ou de la cuve (→ position 5) pour assurer l'écoulement du fluide de la zone autour des éléments de mesure et de référence� 4 5 6.2 Pour applications aseptiques selon EHEDG Si le capteur est correctement installé, il est approprié pour le NEP (nettoyage en place)� ► Prendre en compte les limites d'utilisation (résistance à la température et résistance de la matière) selon la fiche technique� ► S'assurer d'une intégration du capteur dans l'installation selon EHEDG� ► Utiliser une installation auto-vidant� ► Utiliser uniquement des adaptateurs process homologués EHEDG ayant des joints d'étanchéité spéciaux exigés par la norme EHEDG� Le joint d'étanchéité de l'interface du système ne doit pas être en contact avec le point d'étanchéité du capteur� ► En cas de composants présents dans la cuve, ils doivent être installés de manière affleurante et permettre l'accès d'un jet de nettoyage direct� S'assurer que toutes les zones en contact avec la matière soient bien nettoyées� ► Installer les orifices de fuite de manière bien visible et orientés vers le bas en cas de conduites verticales� ► Pour éviter des zones mortes respecter les dimensions selon la fig� 1 : L < (D - d)� 12 TCC8xx / TCC9xx TCC5xx 2 3 1 L 4 FR 5 L 3 Ø d = 6 mm d = 6 mm ØD D Fig� 1 : Dimensions de montage si utilisé selon EHEDG 1: étanchéité spéciaux exigés par la norme EHEDG 2: joint d’étanchéité côté capteur 3: adaptateur 4: orifice de fuite 5: joint PEEK 6.3 Appareils avec raccord process Clamp Les appareils monoblocs de type TCC8xx avec Clamp 1,5" et de type TCC9xx avec Clamp 2" sont les plus faciles à utiliser pour l'installation aseptique� ► Suivre les instructions de montage : → 6.1 Pour applications aseptiques selon 3-A → 6.2 Pour applications aseptiques selon EHEDG 13 6.4 Appareils avec raccord process cône d'étanchéité G ½ Les appareils de type TCC5xx peuvent être adaptés aux raccords process standards via deux versions d'étanchéité� Pour les deux versions d'étanchéité, il est recommandé : ► Utiliser seulement des accessoires d'ifm electronic� Le bon fonctionnement n'est pas assuré en cas d'utilisation de composants d'autres fabricants� ► Lire la notice de l'adaptateur utilisé� Le joint d'étanchéité côté capteur (fig� 1 → 6.2) peut compenser des profondeurs de vissage et des tolérances variables� Il évite la pénétration de fluides autour du filetage� Le joint d'étanchéité côté capteur ne peut pas absorber à lui seul la pression du système� 6.4.1 Etanchéité affleurante et aseptique via un joint PEEK ► Utiliser le joint PEEK fourni� - Le joint PEEK est approprié pour l'utilisation dans des installations aseptiques selon EHEDG et 3-A� - Le joint PEEK a une stabilité à long terme et ne nécessite aucune maintenance� - En cas de montage répété, vérifier le joint PEEK et le remplacer, si nécessaire� - Le joint PEEK est conçu pour les adaptateurs ifm avec une butée mécanique vers le fluide� ► Utiliser des adaptateurs avec orifices de fuite� ► Visser le capteur dans l'adaptateur� Couple de serrage recommandé 20 Nm� ► Suivre les instructions de montage : → 6.1 Pour applications aseptiques selon 3-A → 6.2 Pour applications aseptiques selon EHEDG 14 6.4.2 Etanchéité affleurante via une zone d'étanchéité métal sur métal L'effet d'étanchéité stable à long terme, sans maintenance, d'une zone d'étanchéité métal sur métal est seulement garanti si l'appareil n'est monté qu'une seule fois� ► Ne pas utiliser le joint PEEK fourni� ► Visser le capteur dans l'adaptateur� Couple de serrage recommandé 20 Nm� 6.5 Appareils pour raccordement au process via une bague de serrage Les appareils de type TCC2xx sont montés dans le tuyau ou la cuve en tant que sondes rigides via un adaptateur à bague de serrage� Exemples de montage : FR Fig� 2 : Installation directe (par ex� avec adaptateur E30407) Fig� 3 : Installation avec tube protecteur (par ex� avec adaptateur E37421) 15 7 Raccordement électrique L'appareil doit être raccordé par un électricien qualifié� Alimentation en tension selon EN 50178, TBTS, TBTP� L'appareil est seulement conçu pour le fonctionnement 3 fils� ► Mettre l'installation hors tension� ► Raccorder l'appareil comme suit : Broche 4 (OUT1) 2 (OUT2) 1 BN 2 WH 4 BK 3 BU L+ OUT2 OUT1 L Couleurs selon DIN EN 60947-5-2 BK : noir BN : brun BU : bleu WH : blanc • signal de diagnostic • signal IO-Link pour la mesure de température et le diagnostic • signal analogique pour la mesure de température et le diagnostic Exemples de circuits : 1 1 x commutation positive / 1 x analogique 1 BN 2 WH L+ 3 4 BK 2 WH 3 BU 16 L 1 x IO-Link / 1 x analogique 1 BN 1 x commutation négative / 1 x analogique 1 BN 4 BK L+ 2 WH 4 BK 3 BU 2 L+ IO-Link L 3 BU L 8 Eléments de service et d'indication 1 • Sur le côté face du capteur se trouve une LED qui s'allume en vert en fonctionnement normal� • Si l'appareil détecte une déviation trop grande entre les deux éléments de mesure et de référence la LED passe à bleu (→ 5.4.1 Fonction de contrôle de calibrage)� • En cas de détection d'une alarme FR la LED s'allume en rouge� • En cas de court-circuit la LED clignote en rouge� • En cas d'utilisation de la commande pour l'identification du capteur dans l'installation la LED clignote en vert� 1: LED (verte, bleue, rouge) 9 Paramétrage Les paramètres peuvent être réglés avant le montage et la mise en service de l'appareil ou pendant le fonctionnement via l'interface IO-Link� En cas de changement du paramétrage pendant le fonctionnement, la fonction de l'installation peut être affectée� ► S'assurer du bon fonctionnement de l'installation� Pendant le paramétrage l'appareil reste fonctionnel� Il continue à exécuter ses fonctions de surveillance avec le paramètre précédent jusqu'à ce que le paramétrage soit validé� ► Raccorder l'appareil à un logiciel de paramétrage via un matériel approprié� ► Régler les paramètres ou utiliser la fonction d'analyse� 17 9.1 Paramètres Paramètre Explication ou2 Configuration du signal analogique : I = 4���20 mA ou Ineg = 20���4 mA ou OFF = sortie désactivée P-n Logique de commutation de la sortie de diagnostic : PnP ou nPn� ASP2 Valeur minimum de la sortie analogique pour la valeur de température mesurée AEP2 Valeur maximum de la sortie analogique pour la valeur de température mesurée FOU2 Signal analogique en cas d'alarme : On = 21,5 mA ; OFF = 3,5 mA ccL Limite de contrôle de calibrage = déviation de température entre la valeur process et la valeur de référence à partir de laquelle l'appareil fournit un avertissement� uni Réglage de l'unité de mesure standard : °C ou °F Mode LED Allumer et éteindre la LED sur l'appareil : On = LED toujours allumée Off = LED toujours éteinte Notification = LED allumée seulement en cas d'avertissement ou d'alarme Rétablir les réglages usine Rétablir les réglages usine� Il est utile de noter vos réglages avant d'exécuter la fonction (→ 14 Réglage usine)� 9.2 Fonctions d'analyse Affichages / commandes Explication Champs de texte libre pour informations sur l'appareil - Application - Fonction - Localisation - Date d'installation Affichages de diagnostic - Hi = valeur de température mesurée maximale - Lo = valeur de température mesurée minimale Clignotement active / désactivé (Flash On / Flash Off) 18 Identification facile de l'appareil sur le terrain par un clignotement de la LED Affichages / commandes Explication Reset - [Hi] and [Lo] memory - [Hi] memory - [Lo] memory Remise à zéro de la valeur de température mesurée maximale et/ou minimale Simulation Simulation de la mesure de température (éléments de mesure et de référence) et du diagnostic hors fonctionnement → 5.5 Mode de simulation� Protocoles (entrées journal) - Etat d'appareil - Etat d'appareil détaillé - Event history - Heures de fonctionnement depuis la première mise en service - Mémoire de l'historique des heures de fonctionnement (taux d'échantillonnage 1 s) - Température interne - Erreur de paramétrage Transmission de données binaires (fonction BLOB) Commande pour mémoriser un fichier de protocole de tous les avertissements du contrôle de calibrage ou de tous les événements → 5.6� 10 Fonctionnement Après la mise sous tension, l'appareil se trouve en mode RUN avec un retard à la disponibilité de 6 s (= mode de fonctionnement normal)� Il exécute ses fonctions de mesure et d'évaluation et fournit des signaux de sortie selon les paramètres réglés� 11 Données techniques Données techniques sur www�ifm�com� 12 Correction de défauts L'appareil dispose de possibilités étendues pour l'autodiagnostic� Il se surveille automatiquement pendant le fonctionnement (→ 5.4 Fonction de diagnostic)� Les messages de diagnostic sont indiqués par LED (LED bleue = avertissement ; LED rouge = alarme)� De plus, ces messages sont disponibles via IO-Link� 19 FR ► Raccorder l'appareil à un PC et lire via l'interface IO-Link� ► Prendre des mesures pour rétablir le fonctionnement normal� Diagnostic LED Démarche à suivre Avertissement de contrôle de 0x8CAE calibrage (36014) (différence de température entre les deux éléments de mesure et de référence supérieure à ccL) bleue ► Vérifier l'appareil, le cas échéant adapter ccL ► Remplacer l'appareil Défaillance élément de référence 0x5010 (20496) bleue ► Prévoir le remplacement de l'appareil Défaillance élément de mesure 0x5010 (20496) rouge ► Remplacer l'appareil Défaut du matériel sur l'appareil 0x5000 (20480) rouge ► Remplacer l'appareil Erreur de paramétrage 0x6320 (25376) rouge ► Vérifier la validité des valeurs de paramètres réglées (→ Fiche technique) Court-circuit 0x7710 (30480) clignote en rouge ► Vérifier l'installation Etendue de mesure largement dépassée (valeur process supérieure à cr�OL ou inférieure à cr�UL → 5.3, fig� 1) 0x8C20 (35872) rouge ► Vérifier la plage de température PV Overrun (valeur process supérieure à MEW → 5.3, fig� 1) 0x8C10 (34576) aucun effet* ► Vérifier la plage de température PV Underrun (valeur process inférieure à MAW → 5.3, fig� 1) 0x8C30 (34608) aucun effet* ► Vérifier la plage de température Température interne de l'appareil dépassée (> 125 °C / > 257 °F) 0x4210 (16912) aucun effet* ► Eliminer la cause de la chaleur Simulation active 0x8C01 (35841) aucun effet** ► Terminer le mode de simulation Fonction de clignotement pour localiser le capteur active 0x8CDB (36059) clignote en vert ► Terminer la fonction de clignotement avec la commande Flash-Off 20 Event * La couleur LED dépend de l'état de fonctionnement actuel� ** La couleur LED dépend de l'état de fonctionnement simulé� MAW = valeur initiale de l'étendue de mesure MEW = valeur finale de l'étendue de mesure 13 Maintenance, réparation et élimination En cas de fonctionnement correct, il n'est pas nécessaire de prendre des mesures relatives à la maintenance et la réparation� L'appareil ne doit être réparé que par le fabricant� ► S'assurer d'une élimination écologique de l'appareil après son usage selon les règlements nationaux en vigueur� FR ► Définir des intervalles de vérification du calibrage adaptés aux exigences du process� 14 Réglage usine Paramètre Réglage usine OU2 I ASP -10 °C AEP 150 °C ccL 1K FOU2 On P-n PnP Uni °C LED On Mode de simulation Réglage utilisateur Valeur process : 20 °C Valeur de référence : 20 °C S�Tim : 3 min 21 ">
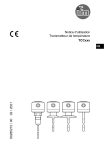
Lien public mis à jour
Le lien public vers votre chat a été mis à jour.