Graco 3A7055L, SaniForce® Pompe à membrane à commande électrique 2150, 3000, 4000, Réparation / Pièces Manuel du propriétaire
PDF
Скачать
Документ
Réparation / Pièces SaniForce® Pompe à membrane à commande électrique 2150, 3000, 4000 3A7055L FR Pompes 2 po., 3 po. et 4 po. avec commande électrique pour des applications de transfert de fluide. Non homologuées pour une utilisation en atmosphères explosives ou dans des endroits (classés) dangereux. Pour plus d’informations, consultez la page Homologations. Pour un usage professionnel uniquement. Instructions de sécurité importantes Lisez tous les avertissements et instructions de ce manuel et de votre manuel d’utilisation avant d’utiliser l’équipement. Conservez ces instructions. Pour plus d'informations sur les pressions de service maximales, consulter les fiches Spécifications techniques. Consultez la page 10 pour les homologations. PROVEN QUALITY. LEADING TECHNOLOGY. Contents Manuels connexes ............................................. 2 Avertissements................................................... 3 Tableau des numéros de configuration pour les pompes 2150 FG .................................. 6 Tableau des numéros de configuration pour les pompes 2150, 3000 et 4000 HS ............. 8 Homologations ................................................... 10 Références de commande .................................. 11 Guide de dépannage .......................................... 12 Réparer ............................................................. 14 Procédure de décompression ....................... 14 Réparation du clapet anti-retour .................... 14 Réparation de membrane standard ............... 17 Réparation de membrane surmoulée............. 19 Réparation de la section centrale .................. 21 Installation des kits du compresseur .............. 26 Remplacement du compresseur.................... 27 Pièces ............................................................... 28 Kits et accessoires ....................................... 38 Spécifications techniques .................................... 39 Manuels connexes Numéro de manuel Titre 3A5132 Pompe à membrane à commande électrique SaniForce™ 2150, 3000, 4000, Fonctionnement 2 3A7055L Avertissements Avertissements Les avertissements présentés dans ce chapitre concernent à la mise en place, l’utilisation, la mise à la terre, la maintenance et la réparation de l’équipement. Le point d’exclamation indique un avertissement général tandis que les symboles de danger font référence aux risques spécifiques associés à la procédure en cours. Lorsque ces symboles apparaissent dans le texte du présent manuel ou sur des étiquettes d’avertissement, reportez-vous à ces Avertissements. Les symboles de danger et avertissements spécifiques au produit qui ne sont pas mentionnés dans cette section pourront, le cas échéant, apparaître dans le texte du présent manuel. DANGER RISQUE DE DÉCHARGE ÉLECTRIQUE GRAVE Il est possible d’alimenter cet équipement à plus de 240 V. Le contact avec cette tension provoque la mort ou de graves blessures. • Couper le courant au niveau de l’interrupteur principal avant de débrancher un câble et de procéder à une intervention d’entretien. • Cet équipement doit être mis à la terre. Raccorder uniquement à une source d’alimentation électrique mise à la terre. • Tout le câblage électrique doit être effectué par un électricien qualifié et être conforme avec l’ensemble des codes et des réglementations en vigueur localement. AVERTISSEMENT RISQUE D’INCENDIE ET D’EXPLOSION Les vapeurs inflammables, telles que les vapeurs de solvant, dans la zone de travail peuvent s’enflammer ou exploser. Le solvant s’écoulant dans l’équipement peut générer des étincelles d’électricité statique. Afin d’empêcher tout risque d’incendie ou d’explosion : • Utiliser l’équipement uniquement dans des locaux bien aérés. • Supprimer toutes les sources potentielles d’inflammation, telles que les veilleuses, cigarettes, lampes de poche et bâches plastiques (risque d’étincelles d’électricité statique). • Mettre à la terre tous les appareils présents dans la zone de travail. Voir les instructions de mise terre. à la terre • Veiller à ce que la zone de travail soit toujours exempte de débris, comme des solvants, des chiffons et de l’essence. • En présence de vapeurs inflammables, éviter de brancher (ou de débrancher) des cordons d’alimentation et d’allumer ou d’éteindre une lampe ou un interrupteur électrique. • Utiliser uniquement des conduites mises à la terre. • Arrêter immédiatement le fonctionnement en cas d’étincelles d’électricité statique ou de décharge électrique.. Ne pas l’utiliser tant que le problème n’a pas été identifié et corrigé. • La zone de travail doit être dotée d’un extincteur en état de marche dans la zone de travail. Il existe un risque d’accumulation d’électricité statique sur les pièces en plastique lors du nettoyage, susceptible de créer une décharge et d’enflammer des vapeurs inflammables. Pour prévenir tout risque d’incendie ou d’explosion : • Nettoyer les pièces en plastique uniquement dans une zone bien ventilée. • Ne pas les nettoyer avec un chiffon sec. 3A7055L 3 Avertissements AVERTISSEMENT RISQUES RELATIFS AUX ÉQUIPEMENTS SOUS PRESSION Du fluide s’échappant de l’équipement, ou provenant de fuites ou d’éléments endommagés, peut être projeté dans les yeux ou sur la peau et provoquer de graves blessures. • Exécuter la Procédure de décompression lors de l’arrêt de la pulvérisation/distribution et avant de nettoyer, de vérifier ou d’effectuer l’entretien de l’équipement. • Serrer tous les raccords de fluide avant de faire fonctionner l’équipement. • Vérifier quotidiennement les conduites de fluide, les tuyaux et les accouplements. Remplacer immédiatement les pièces usées ou endommagées. RISQUES LIÉS À UNE MAUVAISE UTILISATION DE L’ÉQUIPEMENT La mauvaise utilisation de l’équipement peut provoquer des blessures graves voire mortelles. • Ne pas utiliser l’unité en cas de fatigue ou sous l’emprise de médicaments, de drogue ou d’alcool. • Ne pas dépasser la pression de service ou la température maximales spécifiées pour le composant le plus sensible du système. Consulter le chapitre Spécifications techniques dans tous les manuels des équipements. • Utiliser des produits et des solvants compatibles avec les pièces de l’équipement en contact avec le produit. Consulter le chapitre Spécifications techniques dans tous les manuels des équipements. Lire les avertissements du fabricant de liquides et solvants. Pour plus d’informations sur le matériau, demander la fiche de données de sécurité (FDS) au distributeur ou au revendeur. • Éteindre tous les équipements et exécuter la procédure de décompression lorsque ces équipements ne sont pas utilisés. • Vérifier l'équipement quotidiennement. Réparer ou remplacer immédiatement toutes les pièces usées ou endommagées en utilisant uniquement des pièces d’origine. • Ne jamais altérer ou modifier l’équipement. Les modifications ou les altérations apportées risquent d’invalider les homologations et de créer des risques relatifs à la sécurité. • S’assurer que l’équipement est adapté et homologué pour l’environnement dans lequel il est utilisé. • Utiliser l’équipement uniquement aux fins auxquelles il est destiné. Pour plus d’informations, contactez votre distributeur. • Acheminer les conduites de fluide et les câbles à distance des zones de circulation, des bords coupants, des pièces en mouvement et des surfaces chaudes. • Éviter de tordre ou de plier excessivement les conduites de fluide. Ne pas les utiliser pour tirer l’équipement. • Tenir les enfants et les animaux à l’écart de la zone de travail. • Respecter toutes les consignes de sécurité en vigueur. RISQUES RELATIFS AUX PIÈCES EN ALUMINIUM SOUS PRESSION L'utilisation de fluides non compatibles avec l'aluminium peut provoquer une réaction chimique dangereuse et endommager l'équipement. Le non-respect de cet avertissement peut provoquer des blessures graves, voire mortelles, ou des dommages matériels. • Ne pas utiliser de trichloroéthane-1,1,1, de chlorure de méthylène ou d'autres solvants à base d'hydrocarbures halogénés, ni de fluides contenant de tels solvants. • Ne pas utiliser d'eau de Javel. • De nombreux autres fluides peuvent contenir des produits chimiques susceptibles de réagir avec l’aluminium. Vérifier la compatibilité des produits auprès du fournisseur du produit. 4 3A7055L Avertissements AVERTISSEMENT RISQUE DE DILATATION THERMIQUE Les fluides soumis à la chaleur dans des espaces confinés, notamment les conduites, peuvent provoquer une montée rapide de la pression suite à une dilatation thermique. Une surpression peut briser l’équipement et causer de graves blessures. • Ouvrir une vanne pour relâcher du fluide dilaté lorsqu’il est en train de chauffer. • Remplacer régulièrement les conduites de façon proactive en fonction des conditions d’utilisation. RISQUES LIÉS AU SOLVANT DE NETTOYAGE DES PIÈCES EN PLASTIQUE De nombreux solvants peuvent dégrader les pièces en plastique et en provoquer la défaillance, ce qui pourrait entraîner des blessures graves ou des dommages matériels importants. • Utiliser uniquement des solvants compatibles pour nettoyer les pièces structurelles ou sous pression en plastique. • Voir Spécifications techniques des manuels des équipements pour connaître les matériaux de fabrication. Consulter le fabricant du solvant pour plus d'informations et pour des recommandations concernant la compatibilité. • Consulter le chapitre Spécifications techniques figurant dans le présent manuel d’instructions et dans les manuels d’instructions des autres équipements. Prendre connaissance des Fiches de Données de Sécurité (FDS) et des recommandations des fabricants de produits et de solvants. RISQUES RELATIFS AUX FLUIDES OU VAPEURS TOXIQUES Les fluides ou fumées toxiques peuvent provoquer des blessures graves, voire mortelles, en cas de projection dans les yeux ou sur la peau, ou en cas d’inhalation ou d’ingestion. • Consulter la fiche de données de sécurité (FDS) des fluides utilisés pour prendre connaissance des risques spécifiques. • Conserver les fluides dangereux dans des récipients homologués et les éliminer conformément à la réglementation en vigueur. RISQUES DE BRÛLURE Les surfaces de l’appareil et le produit chauffé peuvent devenir brûlants quand l’appareil est en service. Pour éviter des brûlures graves : • Ne pas toucher le fluide ni l’équipement lorsqu’ils sont brûlants. ÉQUIPEMENT DE PROTECTION INDIVIDUELLE Dans la zone de travail, porter un équipement de protection approprié afin de réduire le risque de blessures graves, notamment aux yeux, aux oreilles (perte auditive) ou par brûlure ou inhalation de fumées toxiques. Ces équipements de protection individuelle comprennent notamment : • Des lunettes de protection et une protection auditive. • Des masques respiratoires, des vêtements et des gants de protection recommandés par le fabricant de fluides et de solvants. 3A7055L 5 Tableau des numéros de configuration pour les pompes 2150 FG Tableau des numéros de configuration pour les pompes 2150 FG Rechercher le numéro de configuration de votre pompe sur sa plaquette d’identification. Utiliser le tableau suivant pour définir les composants de sa pompe. Lorsque vous recevez votre pompe, enregistrer le numéro de pièce à 9 caractères qui se trouve sur la caisse d’expédition (par ex. SP1B.0014) : _____________ Enregistrer également le numéro de configuration de la plaque d’identification de la pompe pour faciliter les commandes de pièces de rechange : _____________________________________ 2150FG--EA04AS13SSPTPTPT21 Exemple de numéro de configuration : 2150FG 2150 FG E A 04 A S13 Entr- Section Boîtier de Moteur Couvercles Modèle Section de en contact aîne- centrale vitesses et de fluide et ment pompe avec le compresseur collecteurs produit Pompe 2150 6 Section en contact avec Type d’entraînement le produit FG Qualité alimentaire E Électrique SS PT PT PT Membranes Joints de Sièges Billes ou collecteur clapets 21 Certification Moteur Matériau de la section Boîtier de vitesses et centrale compresseur A Moteur à induction 94 Pas de boîtier de vitesses ni de standard A Aluminium compresseur S Acier inoxydable 04 Rapport de C Moteur à induction transmission vitesse ATEX élevée 05 Rapport de trans- D Moteur à induction mission vitesse ininflammable élevée/Compresseur 120 V 06 Rapport de trans- G Pas de moteur mission vitesse élevée/Compresseur 240V 14 Rapport de transmission vitesse moyenne 15 Rapport de transmission vitesse moyenne/Compresseur 120 V 16 Rapport de transmission vitesse moyenne/Compresseur 240V 24 Rapport de transmission vitesse faible 25 Rapport de transmission vitesse faible/Compresseur 120 V 26 Rapport de transmission vitesse faible/Compresseur 240 V 3A7055L Tableau des numéros de configuration pour les pompes 2150 FG Couvercles de Matériau du fluide et collecteurs siège S13 Acier SS Acier ininoxydable, oxydTriClamp able 316 Acier S14 inoxydable, DIN 3A7055L Matériau des billes ou clapets CW Polychloroprène pesé Matériau des membranes PT PTFE/EPDM 2 pièces Joints de Certification collecteur pas de EP EPDM blanc certification PT PTFE SP PT SP Santoprene Santoprene/EPDM2 pièces PTFE 21 EN 10204 type 2.1 31 EN 10204 type 3.1 7 Tableau des numéros de configuration pour les pompes 2150, 3000 et 4000 HS Tableau des numéros de configuration pour les pompes 2150, 3000 et 4000 HS Rechercher le numéro de configuration de votre pompe sur sa plaquette d’identification. Utiliser le tableau suivant pour définir les composants de sa pompe. Lorsque vous recevez votre pompe, enregistrer le numéro de pièce à 9 caractères qui se trouve sur la caisse d’expédition (par ex. SP1B.0014) : _____________ Enregistrer également le numéro de configuration de la plaque d’identification de la pompe pour faciliter les commandes de pièces de rechange : _____________________________________ 2150HS--ES04ASSASSPTPSEP21 Exemple de numéro de configuration : 2150HS 2150 HS E S 04 A SSA Entr- Section Boîtier de Moteur Couvercles Modèle Section de en contact aîne- centrale vitesses et de fluide et ment pompe avec le compresseur collecteurs produit Pompe 2150 Section en contact avec Type d’entraînement le produit E ÉlecHS Haute qualité sanitaire trique 3000 3A Certifié 3A 4000 PH Secteur pharmaceutique 8 SS PT PS EP Membranes Joints de Sièges Billes ou collecteur clapets 21 Certification Moteur Matériau de la section Boîtier de vitesses et centrale compresseur A Moteur à induction S Acier inoxydable 94 Pas de boîtier de vitesses ni de standard compresseur 04 Rapport de C Moteur à induction transmission vitesse ATEX élevée 05 Rapport de trans- D Moteur à induction mission vitesse ininflammable élevée/Compresseur 120 V 06 Rapport de trans- G Pas de moteur mission vitesse élevée/Compresseur 240V 14 Rapport de transmission vitesse moyenne 15 Rapport de transmission vitesse moyenne/Compresseur 120 V 16 Rapport de transmission vitesse moyenne/Compresseur 240V 24 Rapport de transmission vitesse faible 25 Rapport de transmission vitesse faible/Compresseur 120 V 26 Rapport de transmission vitesse faible/Compresseur 240 V 3A7055L Tableau des numéros de configuration pour les pompes 2150, 3000 et 4000 HS Couvercles de Matériau du Matériau des billes fluide et collecteurs siège ou clapets — Battant, FL Battant en SSA Acier inoxydable, acier inclapet, acier Tri-Clamp oxydable inoxydable (HS/ 3-A/ 316 PH) SSB Acier SS Acier in- BN Buna-N inoxydable, oxydDIN, (HS/3able 316 A/PH) CW Polychloroprène pesé FK Fluoroélastomère FKM PT PTFE SP 3A7055L Matériau des membranes BN Buna-N Joints de Certification collecteur BN Buna-N 21 EN 10204 type 2.1 EO EPDM surmoulé EP EPDM FK Fluoroélastomère FKM PTFE/Santoprene 2 pièces Santoprene/EPDM2 pièces FK FKM PS SP 31 EN 10204 type 3.1 Santoprene 9 Homologations Homologations Homologations ✦ Les pompes avec code moteur C sont homologuées conformément à : ✚ Les pompes avec code moteur G sont homologuées conformément à : II 2 G Ex h d IIB T3 Gb II 2 G Ex h IIB T3 Gb ★ Les moteurs codés D sont homologués conformément à : Classe I, Div 1, Groupe D, T3B Classe II, Div 1, Groupes F & G, T3B Les matériaux de membrane codés EO, PT ou PS combinés avec des matériaux de contrôle codés FL ou PT sont conformes à : EC 1935/2004 Tous les modèles (sauf les codes 05, 15 et 25 du boîtier de vitesses et du compresseur ou le code de moteur D) sont homologués conformément à : Les matériaux de membrane codés EO, PT ou PS combinés avec des matériaux de contrôle codés FL ou PT sont conformes à : Classe VI Tous les matériaux en contact avec le produit sont conformes aux normes de la FDA et répondent au Code des règlements fédéraux (CFR). 10 3A7055L Références de commande Références de commande Pour trouver son distributeur le plus proche Visitez le site www.graco.com Pour configurer une nouvelle pompe Merci d’appeler votre distributeur. OU www.graco.com.. Rechercher le Sélecteur Sélecteur. Utiliser l’outil en ligne de sélection de pompe à membrane sur www.graco.com Pour commander des pièces de rechange Merci d’appeler votre distributeur. 3A7055L 11 Guide de dépannage Guide de dépannage • Suivre la Procédure de décompression, page 14 avant de vérifier ou d’effectuer un entretien sur l’appareil. • Passez en revue tous les problèmes possibles et leurs causes avant de procéder au démontage. Problème Cause Solution La pompe tourne mais ne s’amorce pas et/ou ne pompe. La pompe fonctionne trop rapidement, provoquant une cavitation avant l'amorçage. Ralentir le régulateur (variateur de fréquence (VFD)). Le corps central n’a pas de pression d’air ou la pression d’air est trop basse. Appliquer une pression d’air sur le corps central en fonction des conditions requises pour son application. La bille du clapet anti-retour est très usée ou bloquée dans son siège ou dans le collecteur. Remplacez la bille et le siège. La pression d’aspiration de la pompe Augmenter la pression d’aspiration. est insuffisante. Consulter le manuel d’utilisation. Le siège est très usé. Remplacez la bille et le siège. Obstruction de la sortie ou de l’entrée. Retirer ce qui fait obstruction. Les raccords d’entrée ou les collecteurs sont desserrés. Serrer. Les joints toriques du collecteur sont Remplacer les joints toriques. endommagés. Le corps central est extrêmement chaud. L’axe d’entraînement est cassé. Le remplacer. La pompe ne parvient pas à tenir la pression du fluide au calage. REMARQUE : Les clapets à battant ne sont pas étanches à 100 % au fluide. Les billes de clapet anti-retour, sièges ou joints toriques sont usés. Remplacer. Les vis du collecteur ou du couvercle Serrer. de produit sont desserrées. Le boulon de l’axe de membrane est Serrer. desserré Clapets à battant installés à l'envers. La pompe ne fonctionnera Le moteur ou le régulateur sont mal pas. câblés. installez la clapet à battant avec le côté texte face au siège. Câbler conformément au manuel. Le détecteur de fuites (si installé) s’est déclenché. Vérifier si la membrane est déchirée ou mal mise. Réparer ou remplacer. Le moteur est en marche mais la pompe ne tourne pas. L’accouplement à mâchoire entre le moteur et le boîtier de vitesses n’est pas connecté correctement. Vérifier la connexion. Le débit de la pompe est irrégulier. La conduite d’aspiration est bouchée. Vérifier ; nettoyer. Les clapets collent ou fuient. Nettoyer ou remplacer. Membrane (ou réserve) déchirée. Remplacer. La pompe émet des bruits La pompe fonctionne à proximité de inhabituels. ou à la pression de calage. 12 Ajuster la pression d’air ou réduire la vitesse de la pompe. 3A7055L Guide de dépannage Problème Cause La consommation d’air Un raccord est desserré. est plus élevée que prévu. Solution Serrer. Inspecter le produit d’étanchéité pour filetage. Joints toriques ou joint d’axe desserrés ou endommagés. Remplacer. Membrane (ou réserve) déchirée. Remplacer. La conduite d’aspiration est desserrée. Serrer. Membrane (ou réserve) déchirée. Remplacer. Collecteurs desserrés, sièges ou joints toriques endommagés. Resserrer les boulons de collecteur, remplacer les sièges ou les joints toriques. Un boulon de l’axe de la membrane est desserré. Serrer. La pompe laisse échapper le liquide à l'extérieur par les joints. Desserrer les vis du collecteur ou les vis du couvercle de produit. Serrer. Le régulateur est défaillant ou s’arrête. Un DDFT s’est déclenché. Retirer le régulateur du circuit du DDFT. L’alimentation électrique est faible. Déterminer et corriger la source du problème électrique. Les limites opérationnelles sont dépassées. Voir le graphique des performances, veiller à ce que la pompe fonctionne dans sa plage de fonctionnement continu. Présence de bulles d’air dans le produit. Les joints toriques du collecteur sont Remplacer les joints toriques. usés. La variateur de fréquence Entrée clapet anti-retour signale une panne de bouchée/mal mise en place régénération excessive Boulon de membrane cassé du moteur Enlever les saletés/l’installer correctement Remplacer le boulon REMARQUE : En cas de problème avec le variateur de fréquence (VFD), voir le manuel du variateur de fréquence utilisé. 3A7055L 13 Réparer Réparer REMARQUE : Lors du remontage des composants de la section fluide, assemblez d’abord sans serrer pour assurer un alignement acceptable. Une fois que tous les composants sont en place, serrez tous les colliers. Procédure de décompression Suivre la procédure de décompression chaque fois que ce symbole s'affiche. anti--retour Démontage du clapet anti 1. Appliquer la Procédure de décompression, page 14. Débranchez l’alimentation du moteur. Débranchez toutes les conduites de fluide et les conduites d’air. 2. Retirez les colliers (31) maintenant le collecteur de sortie (3) sur les couvercles de fluide (2), puis retirez le collecteur de sortie. 3. Retirez les ensembles de clapets anti-retour à bille : a. Sur le modèle 2150FG, retirez les sièges (6), les billes (7) et les joints toriques (8). b. Sur le modèle 2150HS, retirer les arrêts de billes (28), les billes (7) et les joints (8a). Cet équipement reste sous pression tant que la pression n’a pas été relâchée manuellement. Pour éviter de sérieuses blessures provoquées par du fluide sous pression, comme des injections éclaboussures, suivez la Procédure de décompression lorsque vous arrêtez la pulvérisation et avant un nettoyage, une vérification ou un entretien de l'équipement. 1. Arrêtez la pompe et coupez l’alimentation du système. 2. Fermez la vanne d’air principale (J) pour couper l’air à la pompe. 3. Ouvrez la vanne de vidange de produit (L) pour relâcher la pression du fluide. Tenez un récipient prêt à récupérer le produit vidangé. 4. Sur le boîtier pneumatique, fermez l’orifice d’entrée d’air (E) de la pompe. anti--retour Réparation du clapet anti 4. Répétez ces opérations pour le collecteur d'entrée. 5. Pour poursuivre le démontage de la membrane, voir Démontage des membranes standard, page 17. anti--retour à bille Remontage du clapet anti 1. Nettoyer toutes les pièces et vérifier leur état d’usure ou d’endommagement. Remplacer des pièces si nécessaire. 2. Remonter en ordre inverse, en suivant toutes les remarques de l’illustration. Placez le collecteur d'entrée en premier. Veiller à ce que les clapets anti-retour à bille et les collecteurs soient montés exactement comme illustré. Si elles sont présentes sur les couvercles de fluide (2), les flèches (A) doivent pointer vers le collecteur de sortie (3). Pour les couvercles de fluide sans flèches, l’ouverture la plus grande dans le couvercle de fluide doit être fixée au collecteur de sortie. Outils nécessaires • Extracteur de joint torique NOTE : Des kits sont disponibles pour de nouveaux sièges et billes de clapet anti-retour en diverses matières. Des kits de joints toriques sont également disponibles. NOTE : Pour que les billes de clapet anti-retour soient bien placées dans leur siège, toujours remplacer les sièges lorsque l’on remplace les billes. De même, les joints toriques doivent être remplacés à chaque dépose du collecteur. 14 3A7055L Réparer 1 2 3A7055L La flèche (A) doit être tournée vers le collecteur de sortie. La surface d'appui arrondie doit être orientée vers la bille (7). Le large chanfrein du diamètre extérieur doit être orienté vers le joint torique. 15 Réparer anti--retour à battant Démontage du clapet anti anti--retour à battant Remontage du clapet anti 1. Appliquez la Procédure de décompression, page 14. Débranchez l’alimentation du moteur. Débranchez toutes les conduites de fluide et les conduites d’air. 1. Nettoyer toutes les pièces et vérifier leur état d’usure ou d’endommagement. Remplacer des pièces si nécessaire. 2. Retirez les colliers (31) maintenant le collecteur de sortie (3) sur les couvercles de fluide, puis retirez le collecteur de sortie. 3. Retirez les battants (7a) et les joints (8a). 4. Répétez les étapes pour retirer le collecteur d’entrée (4). Retirez les battants (7a) et les joints (8a). 2. Remonter le tout dans l’ordre inverse du démontage. Placer d’abord le collecteur d’entrée. Veiller à ce que les clapets à battant et les collecteurs soient montés exactement comme illustré. REMARQUE: installez la clapet à battant (7a) avec le côté texte face au siège. 5. Pour poursuivre le démontage de la membrane, voir Démontage des membranes standard, page 17. 16 3A7055L Réparer Réparation de membrane standard b. Tournez l’axe d’entraînement pour déplacer le piston entièrement de l’autre côté. Répétez l’étape 4a. Outils nécessaires 5. Pour poursuivre le démontage de la section centrale, voir Démontage de la partie centrale, page 21. • Clé dynamométrique • Clé hexagonale 10 mm • Clé plate de 28 mm • Extracteur de joint torique Démontage des membranes standard REMARQUE : Les kits de membrane sont disponibles dans une gamme de matériaux et de styles. Voir la section Pièces. 1. Appliquer la Procédure de décompression, page 14. Débranchez l’alimentation du moteur. Débranchez toutes les conduites de fluide et les conduites d’air. 2. Déposez les collecteurs et démontez les clapets anti-retour à bille comme indiqué dans Réparation du clapet anti-retour, page 14. 3. Retirez les colliers (30) des couvercles de fluide, puis retirez les couvercles de fluide de la pompe. 4. Pour retirer les membranes, le piston doit être déplacé entièrement d’un côté. Si la pompe n’est pas attachée au boîtier de vitesses, tournez l’axe à la main pour déplacer le piston. Si la pompe est toujours attachée au boîtier de vitesses, desserrez les vis et déposez le couvercle du ventilateur. Tournez le ventilateur à la main pour déplacer le piston vers un côté. CONSEIL : Le couvercle d’air contient 2 trous (H), un à 9 heures et l’autre à 3 heures. Utilisez la goupille (131) introduite dans un de ces trous (H) comme support pour la clé lorsque vous déposez ou mettez les boulons de la membrane. a. Tenez la tige de piston exposée avec une clé de 28 mm, côté méplats. Utilisez une autre clé (clé hexagonale de 10 mm) sur le boulon d’axe (13) pour l’enlever. Retirez ensuite toutes les pièces de l’ensemble membrane. 3A7055L 17 Réparer Remontage des membranes standard AVIS 5. Appliquez du frein-filet de force moyenne (bleu) sur les filetages du boulon. Après le remontage, laissez sécher le frein-filet pendant 12 heures, ou la durée préconisée par le fabricant, avant de faire fonctionner la pompe. Des boulons d’axe de membrane desserrés pourraient endommager la pompe. 6. Tenez la tige de piston avec une clé de 28 mm, côté méplats. Vissez l’écrou sur l’axe et serrez-le au couple de 135 N•m (100 pi-lb). CONSEIL : Si vous réparez également la section centrale ou faites un entretien dessus (axe d’entraînement, piston, etc.), suivez Réparation de la section centrale, page 21 avant de remettre les membranes. 1. Nettoyez toutes les pièces et vérifiez leur état d'usure ou de détérioration. Remplacez des pièces si nécessaire. Veillez à ce que la section centrale soit propre et sèche. 2. Nettoyez soigneusement ou remplacez le boulon de la membrane (13). Installez le joint torique (34). 3. Montez la plaque côté fluide (9), la membrane (11), la membrane de réserve (12, si elle est présente), et la plaque de membrane côté air (10) sur le boulon exactement comme indiqué. 7. Tournez l’axe d’entraînement pour déplacer le piston entièrement d’un côté. Voir les instructions de l’étape 4 de Démontage des membranes standard, page 17. 8. Répétez l’opération pour l’autre ensemble membrane. 9. Attachez les couvercles de produit. La flèche sur chaque couvercle de fluide doit pointer vers le collecteur de sortie. 10. Remontez les clapets anti-retour et les collecteurs. Voir Remontage du clapet anti-retour à bille, page 14. 11. Remettez le couvercle du ventilateur de refroidissement du moteur et la goupille (131) à leur emplacement d’origine. 4. Nettoyez les filetages femelles de la tige de piston avec une brosse métallique trempée dans un solvant pour enlever toute trace résiduelle de frein-filet. Appliquez une couche primaire pour frein-filet et laissez sécher. 1 Le côté arrondi fait face à la membrane. 2 Appliquer un adhésif frein-filet de force moyenne (bleu) sur les filetages. 3 4 Les repères CÔTÉ AIR de la membrane doivent être orientés vers le logement central. Si la vis se desserre ou est remplacée, appliquer un frein-filet permanent (rouge) sur les filetages côté membrane. Appliquer un adhésif frein-filet de force moyenne (bleu) sur les filetages du côté de l’axe. 5 Serrer au couple de 135 N•m (100 pi-lb) à maximum 100 tr/min. 6 Appliquer une couche primaire sur les filetages femelles. Laissez sécher. 18 PS,, PT PT,, ou SP SP)) Modèles 2 pièces (PS 3A7055L Réparer Réparation de membrane surmoulée b. Tournez l’axe d’entraînement pour déplacer le piston entièrement de l’autre côté. Répétez l’étape 4a. Outils nécessaires 5. Pour poursuivre le désassemblage, voir Démontage de la partie centrale, page 21. • Clé plate de 28 mm Démontage des membranes surmoulées REMARQUE : Les kits de membrane sont disponibles dans une gamme de matériaux et de styles. Voir la section Pièces. 1. Appliquer la Procédure de décompression, page 14. Débranchez l’alimentation du moteur. Débranchez toutes les conduites de fluide et les conduites d’air. 2. Déposez les collecteurs et démontez les clapets anti-retour à bille comme indiqué dans Réparation du clapet anti-retour, page 14. 3. Retirez les clamps (30) des couvercles de fluide, puis retirez les couvercles de fluide de la pompe. 4. Pour retirer les membranes, le piston doit être déplacé entièrement d’un côté. Si la pompe n’est pas attachée au boîtier de vitesses, tournez l’axe à la main pour déplacer le piston. Si la pompe est toujours attachée au boîtier de vitesses, desserrez les vis et déposez le couvercle du ventilateur. Tournez le ventilateur à la main pour déplacer le piston vers un côté. CONSEIL : Le couvercle d’air contient 2 trous (H), un à 9 heures et l’autre à 3 heures. Utilisez la goupille (131) introduite dans un de ces trous (H) comme support pour la clé lorsque vous déposez ou mettez les boulons de la membrane. a. Tenez la tige de piston exposée avec une clé de 28 mm, côté méplats. Saisissez bien la membrane autour du bord extérieur et tournez-la dans le sens antihoraire. 3A7055L 19 Réparer Remontage des membranes surmoulées AVIS Après le remontage, laissez sécher le frein-filet pendant 12 heures, ou la durée préconisée par le fabricant, avant de faire fonctionner la pompe. Des boulons d’axe de membrane desserrés pourraient endommager la pompe. CONSEIL : Si vous réparez également la section centrale ou faites un entretien dessus (axe d’entraînement, piston, etc.), suivez Réparation de la section centrale, page 21 avant de remettre les membranes. 1. Nettoyez toutes les pièces et vérifiez leur état d'usure ou de détérioration. Remplacez des pièces si nécessaire. Veillez à ce que la section centrale soit propre et sèche. 2. Nettoyez soigneusement ou remplacez le boulon de la membrane (13). Installez le joint torique (34). 3. Montez la plaque côté fluide (9), la membrane (11), la membrane de réserve (12, si elle est présente), et la plaque de membrane côté air (10) sur le boulon exactement comme indiqué. 1 Le côté arrondi fait face à la membrane. 2 Appliquez un adhésif frein-filet de force moyenne (bleu) sur les filetages. 3 Appliquez une couche primaire sur les filetages femelles. Laissez sécher. 20 4. Nettoyez les filetages femelles de la tige de piston avec une brosse métallique trempée dans un solvant pour enlever toute trace résiduelle de frein-filet. Appliquez une couche primaire pour frein-filet et laissez sécher. 5. Appliquez du frein-filet de force moyenne (bleu) sur les filetages du boulon. 6. Tenez la tige de piston avec une clé de 28 mm, côté méplats. Vissez l’écrou sur l’axe et serrez-le au couple de 135 N•m (100 pi-lb). 7. Tournez l’axe d’entraînement pour déplacer le piston entièrement d’un côté. Voir les instructions de l’étape 4 de Démontage des membranes surmoulées, page 19. 8. Répétez l’opération pour l’autre ensemble membrane. 9. Attachez les couvercles de fluide. 10. Remontez les clapets anti-retour et les collecteurs. Voir Remontage du clapet anti-retour à bille, page 14. 11. Remettez le couvercle du ventilateur de refroidissement du moteur et la goupille (131) à leur emplacement d’origine. EO)) à 1 pièce Modèle (EO 3A7055L Réparer Réparation de la section centrale Démontage de la partie centrale Reportez-vous aux illustrations de la page 18. 1. Appliquer la Procédure de décompression, page 14. Débranchez toutes les conduites de fluide et les conduites d’air. 2. Déposez les collecteurs et les pièces du clapet anti-retour comme indiqué au chapitre Démontage du clapet anti-retour, page 14. 3. Déposez les couvercles de produit et les membranes comme indiqué à le chapitre Démontage des membranes standard, page 17. ASTUCE : Attachez le support du boîtier de vitesses (15) sur l’établi. Laissez la pompe raccordée au moteur. 4. Utilisez une clé hexagonale de 10 mm pour déposer les 4 boulons (117). Sortez la pompe hors du logement d’alignement (116). ASTUCE : Il peut s’avérer nécessaire de tapoter sur la pompe avec un maillet en caoutchouc pour dégager l’accouplement. 5. Utilisez une clé hexagonale 5/16 pour déposer le bouchon (124). Utilisez une clé à douilles de 30 mm pour enlever le boulon de roulement (106) et le joint torique (108) de la partie supérieure. 6. Tournez l’ensemble de l’axe (112) de sorte que sa rainure soit vers le haut, alignée avec les repères d’alignement. 3A7055L 7. Utilisez un boulon 3/4–16 pour faire sortir l’ensemble d’axe d’entraînement (112). Le boulon du coussinet (106) peut également être utilisé, à condition de retirer au préalable le coussinet (107). Veillez à ce que la rainure de l’axe d’entraînement reste alignée sur les repères dans la section centrale. REMARQUE : Enlevez le boulon après avoir dégagé l’axe d’entraînement. AVIS Un alignement correct est essentiel. Ne pas appliquer un couple supérieur à environ 1,1 N•m (10 po-lb). Un couple excessif pourrait détériorer le filetage du boîtier. En cas de résistance, vérifier l’alignement ou contacter votre distributeur. 8. Il se peut que l’accouplement de l’axe (113) sorte en même temps que l’ensemble d’axe d’entraînement. Sinon, l’enlever du boîtier de vitesses (118). 9. Enlever la cartouche d’étanchéité (110), le joint torique (109) et le joint radial (111) de l’ensemble de l’axe d’entraînement. 10. Glisser l’ensemble de piston (102) hors de la partie centrale. 11. N’enlever le corps d’alignement (116) que si c’est nécessaire. Utilisez une clé hexagonale de 10 mm pour déposer les 4 boulons (120). Tirer le logement d’alignement hors du boîtier de vitesses (118). 12. Sauf détérioration, laisser le manchon de raccordement (114) du boîtier de vitesses attaché sur l’axe du boîtier de vitesses (118). S’il faut quand même l’enlever, il faut utiliser un extracteur de palier. 21 Réparer Remontage de la partie centrale 1. Nettoyez et séchez le boîtier central (101), le centre du piston (102) et l’axe d’entraînement (112). 2. Vérifier si les paliers du piston et du corps central ne sont pas trop usés et les remplacer si nécessaire. Graisser le piston comme indiqué et l’installer dans le corps central avec la rainure sur le dessus, alignée sur les repères d’alignement dans le corps central. 3. Mettre le joint torique (108) à sa place et appliquer de l’adhésif frein-filet de force moyenne (bleu) sur le boulon (106) du joint à soufflet et le visser dans le corps central. Veiller à ce que le joint à soufflet (107) se trouve dans la rainure du piston, comme montré sur la figure. Veiller à ce que le piston se déplace librement. Serrer le boulon au couple de 20-34 N•m (15-25 pi-lb). 5. Mettre le joint torique (109*) sur le corps central (101). 6. Appliquer du lubrifiant antigrippant sur les bords de contact de l’axe d’entraînement, comme montré sur la figure, page 18. 7. Centrer le piston dans le logement et installer l’axe d’entraînement (112) dans le logement central (101), rainure orientée vers le haut. 8. Recherchez des traces d’usure au niveau du manchon de raccordement (113) de l’axe ; remplacez-le si nécessaire. Procédez à l'installation sur l’axe d’entraînement. 9. S’il a été enlevé, mettre le corps d’alignement sur le corps central. Appliquer du frein-filet de force moyenne (bleu) et installer les vis du boîtier (117). Serrer à un couple de 15-18 N•m (130-160 po-lb). 10. S’il a été enlevé, mettre le manchon de raccordement (114) du boîtier de vitesses sur l’axe du boîtier de vitesses (118). Utiliser un boulon M12 x 30 et une grande rondelle introduite dans le trou dans l’axe pour pousser le manchon de raccordement jusqu’à ce qu’il soit à sa place. Le manchon de raccordement est bien mis quand il est à ras de l’extrémité de l’axe. 11. Veiller à ce que le manchon de raccordement (114) du boîtier de vitesses soit correctement aligné. Tourner à la main si nécessaire. Raccorder la pompe à l’ensemble du boîtier de vitesses en introduisant les manchons. 4. Veiller à ce que la surface d’étanchéité de l’axe d’entraînement (112) soit propre. Installer la cartouche d’étanchéité (110) et le joint radial (111) sur l’axe d’entraînement. Les lèvres du joint radial (111) doivent être face à IN vers le centre. Vérifier si la lèvre du joint n’est pas endommagée. Remplacez-les le cas échéant. 22 12. Appliquer du frein-filet de force moyenne (bleu) et introduire les vis (120) du boîtier de vitesses. Serrer à un couple de 15-18 N•m (130-160 po-lb). 13. S’assurer que le joint torique (127) est sur le bouchon (124). Placer le bouchon et serrer à 20-34 N•m (15-25 pi-lb). 14. Voir Remontage des membranes standard, page 18 et Remontage du clapet antiretour à bille, page 14. 3A7055L Réparer 1 Appliquer un adhésif frein-filet de force moyenne (bleu) sur les filetages. 2 Serrer à un couple de 20-34 N•m (15-25 pi-lb). 3 Les lèvres doivent être face à IN vers le centre. 4 Appliquer une couche épaisse de lubrifiant anti-grippant sur les surfaces radiales de l’ensemble d’axe d’entraînement. 5 Montez l’ensemble d'axe d’entraînement avec la rainure orientée vers le haut. 6 Serrer les vis dans un ordre entrecroisé, 5 tours à la fois, pour introduire uniformément le manchon de raccordement. Serrer à un couple de 15-18 N•m (130-160 po-lb). 7 Appliquer du lubrifiant sur la surface de contact intérieure. 3A7055L 23 Réparer Déconnexion du moteur et du boîtier de vitesses Pour prévenir les blessures à la suite d’un incendie, d’une explosion ou d’une décharge électrique, tout le câblage électrique doit être effectué par un électricien qualifié et répondre à tous les règlements et réglementations locaux en vigueur. REMARQUE : Normalement, le moteur reste connecté au boîtier de vitesses. Débrancher le moteur seulement si l’on pense que le moteur ou le boîtier de vitesses doit être remplacé. ASTUCE : Attacher le support du boîtier de vitesses (15) sur l’établi. Commencer à l’étape 1 pour les moteurs ATEX ou antidéflagrants.. Les moteurs à courant alternatif 24 standard (04A, 05A ou 06A) forment une pièce avec le boîtier de vitesses ; il faut donc commencer par l’étape 4. REMARQUE : Utiliser un palan et une élingue pour que le moteur ne pèse plus sur le boîtier de vitesses lorsque vous l’enlevez. 1. Arrêter la pompe et couper le courant. 2. Utiliser une clé à douille de 3/4 po. pour déposer les 4 vis (122). 3. Sortir le moteur (121) du boîtier de vitesses (118) en le tirant tout droit. 4. Utiliser une clé à douille de 19 mm (3/4 po.) pour déposer les 4 boulons (17) et écrous (18, si présents). Extraire le boîtier de vitesses de son support en le soulevant. NOTE: Si l’on a un moteur à courant alternatif avec un boîtier de vitesses, soulever l’ensemble hors du support. 3A7055L Réparer Réparation du capteur de fuites REMARQUE : il existe un ancien modèle du capteur de fuites. Si votre capteur de fuites contient un contre-écrou, se reporter au manuel 3A5133A pour obtenir les instructions de réparation. f. Le capteur de fuites peut être remplacé ou remis à sa place. Lorsque le capteur de fuites est correctement positionné, les deux flèches imprimées sur deux des surfaces plates de la tête hexagonale du capteur sont verticales et pointent vers le bas. Test du capteur de fuites Il est possible de procéder à la vérification de continuité du capteur de fuites pour assurer son bon fonctionnement. Si la vérification de continuité indique que le capteur de fuites ne fonctionne pas, un kit de remplacement, de modèle 25B435, peut être commandé séparément. Exercez une pression d’air sur la pompe et utilisez une solution savonneuse autour de la douille pour assurer un scellement hermétique. En cas d’apparition de bulles, effectuez à nouveau les étapes ci-dessus relatives à la décompression et au retrait de la douille de la pompe. Appliquez une nouvelle pâte d’étanchéité pour joints filetés sur la douille et installez-la dans la pompe afin que le capteur de fuites soit correctement positionné. Répétez cette étape pour vérifier l’absence de fuite d’air autour de la douille. 3. Retirez et remplacez le capteur de fuites dans la pompe : a. prenez note des emplacements où sont raccordés les fils du capteur de fuites dans le variateur de fréquence ou dans un autre appareil de surveillance, puis débranchez les fils du capteur de fuites. 1. Appliquer la Procédure de décompression, page 14. Mettez le moteur hors tension. b. Retirez le capteur de fuites et la douille du corps central de la pompe. 2. Pour tester le capteur de fuites sans retirer la pompe : c. a. prenez note des emplacements où sont raccordés les fils du capteur de fuites dans le variateur de fréquence ou dans un autre appareil de surveillance, puis débranchez les fils du capteur de fuites. b. L’utilisation d’un ohmmètre relié au capteur de fuites entraîne la vérification de conductivité du capteur de fuites. La continuité est confirmée lorsque l’ohmmètre indique 0 à 5 ohms. c. Desserrez la douille du capteur de fuites d’un demi-tour (la flèche du capteur de fuites pointe vers le haut). d. L’utilisation d’un ohmmètre relié au capteur de fuites entraîne la vérification de conductivité du capteur de fuites. Un circuit ouvert doit être indiqué. La position de fonctionnement normal est indiquée par une ligne de flottaison sombre. Une ligne de flottaison plus claire indique la position de fonctionnement en circuit ouvert. e. Si les résultats de la vérification de continuité indiquent que le capteur de fuites ne fonctionne pas correctement, passez à l’étape 3. Dans le cas contraire, serrez la douille dans sa position d’origine pour que les flèches situées sur le capteur de fuites pointent vers le bas. Attachez les fils retirés du capteur de fuites à l’endroit où ils étaient déconnectés du variateur de fréquence ou de tout autre dispositif de contrôle. 3A7055L Appliquez un adhésif ou une pâte à filetage sur les filets de la douille et serrez fermement avec vos doigts dans la pompe. d. Pour vous assurer d’obtenir un joint étanche à l’eau, appliquez le freinfilet Assure™ 425 de Loctite® fourni avec le kit de capteur de fuites sur les filets du capteur de fuites et vissez le capteur de fuites dans la douille. e. Vérifiez que le capteur de fuites est correctement orienté dans la pompe pour que les flèches imprimées sur la tête hexagonale du capteur de fuites soient verticales et qu’elles pointent vers le bas. Serrer davantage la douille et le capteur de fuites peut être nécessaire pour obtenir un positionnement correct. f. L’utilisation d’un ohmmètre relié au capteur de fuites entraîne la vérification de conductivité du capteur de fuites. La continuité est confirmée lorsque l’ohmmètre indique 0 à 5 ohms. Raccordez les fils du capteur de fuites au variateur de fréquence ou à un autre appareil de surveillance. g. Exercez une pression d’air sur la pompe et utilisez une solution savonneuse autour de la douille pour assurer un scellement hermétique. En cas d’apparition de bulles, effectuez à nouveau les étapes ci-dessus relatives à la décompression et au retrait de la douille de la pompe. Appliquez une nouvelle pâte d’étanchéité pour joints filetés sur la douille et installez-la dans la pompe afin que le capteur de fuites soit correctement positionné. Répétez cette étape pour vérifier l’absence de fuite d’air autour de la douille. 25 Réparer Installation des kits du compresseur Installation des kits de compresseur pour les pompes HS Pour prévenir les blessures à la suite d’un incendie, d’une explosion ou d’une décharge électrique, tout le câblage électrique doit être effectué par un électricien qualifié et répondre à tous les règlements et réglementations locaux en vigueur. Installation des kits de compresseur pour les pompes FG Suivez cette procédure pour installer votre kit de compresseur pour les pompes de qualité alimentaire Voir Kits et accessoires, page 38 pour connaître les options du kit de compresseur. 1. Appliquer la Procédure de décompression, page 14. 2. Arrêtez la pompe et débranchez l’alimentation de l’unité. Suivez cette procédure pour installer votre kit de compresseur pour les pompes de haute qualité sanitaire Voir Kits et accessoires, page 38 pour connaître les options du kit de compresseur. 1. Appliquer la Procédure de décompression, page 14. 2. Arrêtez la pompe et débranchez l’alimentation de l’unité. 3. Vous trouverez l’illustration de votre modèle de pompe sur le site Pièces, page 28, qui vous servira de référence pour l’installation de votre kit de compresseur. 4. Fixez le couvercle (42) au compresseur (16) à l’aide des boulons (43). REMARQUE : Veillez à aligner la fente du couvercle (42) avec le moteur du compresseur à l’intérieur du compresseur (16). 3. Vous trouverez l’illustration de votre modèle de pompe sur le site Pièces, page 28, qui vous servira de référence pour l’installation de votre kit de compresseur. 5. Appliquez de la Loctite haute résistance à l’extrémité des vis (40), puis fixez-les dans les écrous filetés du compresseur (16) de manière à ce que 4,13 cm des vis dépassent de l’écrou. Laissez la Loctite durcir selon les instructions du fabricant. 4. Fixez le support du tuyau montant (35) au boîtier du compresseur (16) à l’aide des boulons (35a). 6. Alignez le moteur de la pompe (121) sur la base de montage (39). REMARQUE : Veillez à aligner la fente du support du tuyau montant (35) avec le moteur du compresseur à l’intérieur du boîtier du compresseur (16). 5. Fixez le moteur de la pompe (121) au boîtier du compresseur (16) à l’aide des boulons (17). Utilisez de la Loctite à résistance moyenne® pour fixer les boulons et serrez-les à 27 N•m. 6. Consultez le manuel de fonctionnement de la pompe pour connaître les instructions de câblage. 26 REMARQUE : Utilisez des sangles de levage pour supporter le poids de la pompe. 7. Positionnez l’ensemble du compresseur (16) sous la base de montage (39). Fixez le compresseur à la base à l’aide des vis (40) et des écrous (18). Utilisez de la Loctite de force moyenne pour fixer les écrous et serrez-les à 27 N•m. 8. Couvrez la partie exposée des vis filetées (40) avec des capuchons (41). 9. Consultez le manuel de fonctionnement de la pompe pour connaître les instructions de câblage. 3A7055L Réparer Remplacement du compresseur Pour prévenir les blessures à la suite d’un incendie, d’une explosion ou d’une décharge électrique, tout le câblage électrique doit être effectué par un électricien qualifié et répondre à tous les règlements et réglementations locaux en vigueur. 1. Appliquer la Procédure de décompression, page 14. 2. Mettre la pompe hors tension. 3. Retirer les 8 boulons qui maintiennent la pompe sur la surface de fixation. 4. Incliner la pompe sur le côté pour pouvoir accéder au boîtier de compresseur. 5. Démonter le support (35) du tuyau montant. 6. Retirer la conduite d’air (A1) du compresseur. Débrancher les fils de compresseur du bornier (L1, L2 et terre). Enlevez les quatre boulons et retirez avec précaution le compresseur. 7. Utiliser les quatre boulons pour installer le compresseur neuf. Raccorder la conduite d’air de A1 à A1, comme illustré. 8. Branchez les fils du nouveau compresseur au bornier, comme dans l'illustration. 9. Remplacer le support du tuyau montant. 10. Rattacher la pompe sur son support de fixation. Fixez-le à l'aide des 8 boulons. 11. Rétablissez l’alimentation électrique de la pompe. A L2 L1 3A7055L 27 Pièces Pièces 2150FG Pompe 28 3A7055L Pièces anti--retour 2150HS Pompe à clapet anti à bille 3A7055L 29 Pièces Pompe à battant 3000HS 30 3A7055L Pièces Pompe à battant 4000HS 3A7055L 31 Pièces Référence simplifiée pour Pièces/Kits Utilisez ce tableau comme référence simplifiée pour les pièces/kits. Consultez les pages mentionnées dans le tableau pour obtenir la description complète du contenu des kits. Description Réf. Pièce Kit — — — — — — MODULE, entraînement; 1 Qté. 1 Réf. Pièce 10 Voir page 30. 2 2a 2b 3 4 CAPOT, fluide ; acier inox. 2 277264 — — — 2150FG — — — 25E575 2150HS, 3A — — — 25P042 2150PH — — — 25E576 COUVERCLE, fluide, gauche, 3000HS — — — 25N998 COUVERCLE, fluide, gauche, 4000HS — — — 25E577 COUVERCLE, fluide, droite, 3000HS — — — 25N999 COUVERCLE, fluide, droite, 4000HS COLLECTEUR, sortie; acier inoxydable 277270 — — — 2150FG Bride 24U153 — — — 2150FG DIN — — — 25E578 — — — 25P053 2150HS, Tri-clamp 3A — — — 25E579 — — — 25P025 Tri-Clamp battant 3000HS 6 7 8a 9 32 1 — — — — — — MEMBRANE, réserve, 1 13 — — — 25B443 15 — — — 25B421 1 1 16 — — — 25B431 — — — 25B432 1 kit 18 4 4 Santoprene 30 15B491 26C569 Fluoroélastomère FKM 15H834 26C244 Polychloroprène pesé 4000HS 4 1 JOINT D’ÉTANCHÉITÉ, sanitaire, ensemble de 4 ; voir page 37 189299 — — — PLAQUE, côté fluide ; acier 2 inoxydable, n’est pas utilisé avec les membranes EO EQ1475 25B421 25E586 21 � 112361 26C242 1 120 volts 240 volts EQ1519 25B421 17a — — — 25E586 2 16a, 40, 41, 42 et 43 si nécessaire 17 1 28 JOINT TORIQUE, — — — 15H831 PTFE — — — 15H829 EPDM 1 BOULON, axe ; n’est pas 2 utilisé avec les membranes EO 1 SUPPORT, boîtier de vitesses, pour les modèles 2150FG sans compresseur; inclut 4 de chacune des réf. 17 et 18 1 COMPRESSEUR, ensemble; inclut les réf. COMPRESSEUR 24Y544 — — — 120 volts 24Y545 — — — 240 volts Tri-Clamp 2150PH CLAPET ANTI-RETOUR, battant, lot de 4 3000HS 2 inclus avec la réf. 11 si nécessaire 16a PTFE — — — 25E582 — — — 25P086 8 12 112359 26C241 7a Qté. 25B445 — — — 2150FG — — — 25E583 tous les autres modèles, paquets de 2 — — — — — — MEMBRANE, kit; Voir 1 Tri-Clamp battant 4000HS Tri-Clamp battant 3000HS — — — 25P024 Tri-Clamp battant 4000HS 15H826 — — — SIÈGES BILLES, les kits sont des paquets de 4 15B492 26C243 Buna-N Description PLAQUE, côté air page 32. Tri-Clamp 2150PH COLLECTEUR, entrée; acier inoxydable 277269 — — — 2150FG Bride 24U152 — — — 2150FG DIN — — — 25E580 2150HS, Tri-clamp 3A — — — 25P052 — — — 25E581 11 Kit 1 4 BOULON, tête cyl. à six pans creux, M8–1,25 x 32 mm Kit VIS, boîtier de vitesses, 1 pour tous les modèles sauf 2150FG, inclut 4 de chaque réf. 17a, 18 4 ÉCROU 1 ÉTIQUETTE, sécurité 188621 — — — 2150FG — — — 25P457 tous les autres modèles — — — 25E584 BUTÉE, bille, paquet de 4 COLLIER, sanitaire, membrane 15H513 — — — 2150FG 15G323 — — — 2150HS/3-A/PH, 3000HS 25P107 — — — 4000HS 30a 26C033 — — — POIGNÉE, en T 31 COLLIER, sanitaire — — — 15D475 2150 tous les modèles 1 2 2 4 510490 — — — 3000HS 16D245 — — — 4000HS 32 � 198382 ÉTIQUETTE, sécurité, multilingue, 2150FG uniquement 1 3A7055L Pièces Description JOINT TORIQUE, pour boulon d’axe de membrane ; Pas utilisé avec membranes EO 25B426 SUPPORT, tuyau montant ; utilisé pour les modèles 2150FG avec compresseur, comprend la réf. 35a 25B426 BOULON, boîtier du compresseur d’air, M8 x 1,25, 20 mm — — — COUVERCLE, boîtier du compresseur d’air, bas, 2150HS/3A/PH, 3000HS, 4000HS 25E384 COMMANDE, air, avec support 25E585 EMBASE, montage Réf. Pièce Kit 34 — — — 25B443 35 ——— 35a — — — 35b 17Z195 38 ——— 39 ——— 39a — — — 25E585 39b — — — 25E585 39c — — — 25E585 3A7055L Qté. 2 1 10 1 Description Réf. Pièce Kit 39d — — — 25E585 RONDELLE 40 — — — — — — VIS, réglage, 1/2 X 2,25, lot de 4 41 — — — — — — CAPUCHON, écrou 3/4", rigide 42 — — — — — — COUVERCLE, plaque du boîtier de compresseur, Qté. 8 1 1 1 inclus avec la réf. 16 43 — — — — — — BOULON, tête hex., M8 x 10 1,25 x 20 mm, inclus avec la réf. 16 — — — Non vendu séparément. 1 1 RENFORT, montage 2 VIS, à bride 4 CONTRE-ÉCROU 4 � Des étiquettes, des plaques et des fiches d’avertissement de rechange sont mises à disposition gratuitement. 33 Pièces Section centrale Exemple de numéro de configuration Modèle Matériau de de la pompe partie en contact avec le produit 2150 FG 34 Entr- Matériau aîne- de la ment section centrale Boîtier de Moteur vitesses et moteur E 04 A A Couvercles de fluide et collecteurs Sièges Billes Membranes Joints de collecteur Certification S13 SS PT PT 21 PT 3A7055L Pièces Réf. 101 Pièce Désignation Qté CORPS, central, ensemble ; 1 25B415 25B416 Axx) Aluminium (Axx Axx Sxx) Acier inoxydable (Sxx Sxx ; joint 102 103 25B400 ——— 104 25B442 1 PISTON, ensemble JOINT TORIQUE, couvercle 2 d’air ; fourni avec la réf. 104 COUVERCLE D’AIR, fourni 2 Réf. 118a Pièce ——— Désignation MANCHON DE RACCORDEMENT ; fourni 118b ——— CLÉ ; fournie avec la réf. fourni avec les bouchons torique également inclus 105 ——— 120 121 25B401 avec les réf. 103, 105 BOULON, couvercle d’air ; 16 25B402 1 25B403 fourni avec la réf. 104 106 BOULON, roulements ; fourni avec les réf. 107 et 108 25B419 pour boîtier central en aluminium ROULEMENTS, galet de came. Fourni avec la réf. 107 ——— 108 ——— JOINT TORIQUE, taille 019, 1 fluoroélastomère ; fourni 109† ——— 110† 111† 112 ——— ——— JOINT TORIQUE, taille 153, 1 Buna-N 1 CARTOUCHE, étanchéité 1 JOINT, radial 1 AXE, entraînement, ensemble ; joint torique 25B414 25B413 114 17S683 avec la réf. 106 MANCHON DE RACCORDEMENT, axe MANCHON DE RACCORDEMENT, boîtier de vitesses ; comprend le CORPS, alignement, ensemble ; fourni avec 117 24Y534 125 127 ——— ——— 130 131 ——— ——— 132 135 136 ——— 137 25B435 1 1 189930 ——— avec la réf. 118 1 118 VIS, tête cyl. à six pans creux, M8 x 20 mm MOTEUR 4 1 moteur à engrenages vitesse faible moteur à engrenages vitesse moyenne moteur à engrenages vitesse élevée ATEX vitesse faible ATEX vitesse moyenne ATEX vitesse élevée ignifuge vitesse faible ignifuge vitesse moyenne ignifuge vitesse élevée VIS, d’assemblage, 1/2–13 x 4 38,1 mm (1,5 po.) 1 BOUCHON, accès avant inclut la réf. 127 VIS, mise à la terre, M5 x 0,8 1 1 JOINT TORIQUE fourni avec la réf. 124 COUDE, 1/8–27 npt 1 GOUPILLE, d’arrêt, 4,8 mm 1 (5/16 po.) x 31,75 mm (1-1/4 po.) 1 BOUCHON ; 1/8-27 npt 1 ÉTIQUETTE, attention DOUILLE fournie avec la réf. 137 1 Détecteur de fuites inclut la réf. 136 les vis (réf. 25B417 25B418 ——— 124 106 matériel de montage 116 122 25B406 25B405 25B404 25B409 25B408 25B407 ——— 1 (réf. 109), cartouche (réf. 110) et joint (réf. 111) inclus 113 ——— Qté 1 Axx) Aluminium (Axx Axx Sxx) Acier inoxydable (Sxx Sxx 4 VIS, tête creuse, M8 x 50 mm ; fournie avec la réf. — — — Non vendu séparément. † Inclus dans le Kit de réparation de joint d’axe 25B420. 116 118 BOÎTIER DE VITESSES ; 1 fourni avec les réf. 118a, 118b et 122 25B410 25B411 vitesse faible vitesse moyenne 25B412 vitesse élevée 3A7055L 35 Pièces Membranes Exemple de numéro de configuration Modèle Matériau de de la pompe partie en contact avec le produit 2150 FG Entr- Matériau aîne- de la ment section centrale Boîtier de Moteur vitesses et moteur Couvercles de fluide et collecteurs Sièges Billes Membranes Joints de Certificacollecteur tion E 04 S13 SS PT PT PT A Kits de membranes à boulon traversant Pour 2150FG PT 25B451 SP 25B452 Pour tous les modèles HS, 3A, PH BN 253223 FK 25P268 PS 25P266 SP 25B452 A 21 Kit de membrane surmoulée Pour tous les modèles HS, 3A, PH EO 25P270 Les kits contiennent : • 2 membranes (11) avec vis de réglage (13) Les kits contiennent : • 2 membranes (11) • 2 pièces d’appui (12), le cas échéant • 1 paquet d’adhésif anaérobie • 2 joints toriques 36 3A7055L Pièces Kits de joints sanitaires Les descriptions des kits apparaissent dans l'ordre suivant : Modèle de pompe, matériau Taille Réf. Matériau 2150 25R602 Buna-N 25P063 EPDM 26A892 FKM 26A915 Collage PTFE/EPDM* reporter à Tableau des numéros de configuration pour les pompes 2150 FG, page 6 , et Tableau des numéros de configuration pour les pompes 2150, 3000 et 4000 HS, page 8 pour définir les composants. 25R603 Buna-N Kits de réparation de la section fluide 25P064 EPDM Kit Description 26A893 FKM 25R698 2150HS-PH --,BN.BN.BN 26A916 Collage PTFE/EPDM* 25R699 2150HS-PH --,CW,EO,EP 25R605 Buna-N 25R707 2150HS-PH --,CW,FK,FK 25P066 EPDM 25R709 2150HS-PH --,EP,EO,EP 26A895 FKM 2 2150HS-PH --,FK,FK,FK 26A918 Collage PTFE/EPDM* 25R713 2150HS-PH --,PT,EO,EP 25R715 2150HS-PH --,PT,PS,EP 25R720 3250HS FL,--,BN.BN 25R721 3250HS FL,--,EO,EP 25R722 3250HS FL,--,FK,FK 25R724 3250HS FL,--,PS,EP 25R727 4150HS FL,--,BN,BN 25R728 4150HS FL,--,EO,EP 25R729 4150HS FL,--,FK,FK 25R731 4150HS FL,--,PS,EP 25T463 2150E HS-PH --,CW,SP,EP 25T464 2150E HS-PH --,EP,SP,EP 25T465 2150E HS-PH --,PT,SP,EP 25T466 2150E HS-PH --,SP,SP,EP 25T468 3000E HS FL,--,SP,EP 25T470 4000E HS FL,--,SP,EP 3000 4000 * Option PTFE/EPDM proposée uniquement en remplacement. des sièges, matériau de la bille, matériau de la membrane, matériau du joint d’étanchéité. Pae exemple, 2150HS-PH --,CW,EO,EP. Se Les kits contiennent : • 4 billes ou clapets à battant (7 ou 7a) • 2 membranes (11) • 2 pièces d’appui de membrane (12) le cas échéant • 4 joints d’étanchéité (8a) • 1 paquet d'adhésif anaérobie, le cas échéant • 2 joints toriques (34), (pour toutes les membranes, sauf EO) 3A7055L 37 Pièces Kits et accessoires Le kit d’outil 25B434 de réparation de la section centrale comprend les outils nécessaires pour retirer les roulements de la section centrale. Le kit extracteur de roulements 17J718 comprend un ensemble d’extracteurs de roulements interchangeable. Double entrée et double sortie Pour passer à une double entrée ou sortie, les pièces suivantes sont nécessaires : Entrée double : Réf. Pièce/kit Description Qté. 45 25P084 SIÈGE, battant, SP3F 2 25P085 SIÈGE, battant, SP4F 2 25P065 JOINT, EPDM, SP3R 2 25P067 JOINT, EPDM, SP4F 2 15D475 CLAMP, battant SP3F 2 510490 CLAMP, battant SP4F 2 25P082 CHAMBRE, battant, SP3F 2 25P083 CHAMBRE, battant, SP4F 2 25P065 JOINT, EPDM, SP3R 2 25P067 JOINT, EPDM, SP4F 2 15D475 CLAMP, battant SP3F 2 510490 CLAMP, battant SP4F 2 47 48 Double sortie : 46 47 48 38 3A7055L Spécifications techniques Spécifications techniques Pompe électrique à double membrane SaniForce Système impérial (E.U.) Système métrique 2150 100 psi 0,69 Mpa, 6,9 bar 3000HS, 4000HS 60 psi 0,41 Mpa, 4,1 bar 2150 20 à 100 psi 0,14 à 0,69 MPa, 1,4 à 6,9 bars 3000HS, 4000HS 20 à 60 psi 0,14 à 0,41 MPa, 1,4 à 4,1 bars Pression de service maximale du fluide Plage des pressions d’air de service Dimension de l’entrée d’air 3/8 po. npt(f) Hauteur d’aspiration maximale (réduite si les clapets ne se sont pas correctement assis en raison d’un dommage, d’un blocage ou de la vitesse extrême de pompage) 2150 (à 20 Hz) Pompe amorcée : 30 pi. Pompe amorcée : 9,1 m Pompe non amorcée : Pompe non amorcée : 4,3 m 14 pi. 3000HS, 4000HS Mouillée : 30 pi. Mouillée : 9,1 m. Sèche : 4.5 pi. Sèche : 1.4 m Taille maximale des matières solides pompables 2150FG, billes 2 po. 0,25 po 6,3 mm 2150HS/3A/PH 0,5 po 12,7 mm 3000HS, 3 po. battant 2,5 po 62,5 mm 4000HS, 4 po. battant 3,8 po. 96,5 mm 32° F 0° C 2150 0,6 gallon 2,3 litres 3000HS, 4000HS 0,4 gallon 1,5 litre 2150 100 gpm 378 lpm 3000HS 56 gpm 212 lpm 4000HS 52 gpm 197 lpm Température minimale de l’air ambiant pour le fonctionnement et le stockage. REMARQUE : L’exposition à des températures extrêmement basses peut endommager les pièces en plastique. Déplacement du fluide par cycle (débit libre) Débit libre maximal (marche continue) 60 Hz/160 cpm Vitesse de pompage maximale (marche continue) Dimensions de l’entrée et de la sortie de fluide 2150FG, acier inoxydable Raccord sanitaire 2,5 po. ou 65 mm DIN 11851 2150HS, 3A, PH Raccord sanitaire 2 po. ou 50 mm DIN 11851 3000HS, acier inoxydable Raccord sanitaire 3 po. ou 80 mm DIN 11851 4000HS, acier inoxydable Raccord sanitaire 4 po. ou 100 mm DIN 11851 100 Moteur électrique AC, norme CE (04A, 05A (Non CE), 06A) Puissance Nombre de pôles du moteur Vitesse Couple constant Rapport de transmission 7.5 HP 5,5 kW 4 pôles 1800 tr/min (60 Hz) ou 1500 tr/min (50 Hz) 6:1 11,25 Tension 230 V triphasé / 460 V triphasé Ampérage maximal en charge 19,5 A (230 V) / 9,75 A (460 V) Classification IE IE3 AC, norme CE (14A, 15A (Non CE), 16A) 3A7055L 39 Spécifications techniques Puissance 5.0 HP Nombre de pôles du moteur Vitesse 3,7 kW 4 pôles 1800 tr/min (60 Hz) ou 1500 tr/min (50 Hz) 6:1 Couple constant Rapport de transmission 16.46 Tension 230 V triphasé / 460 V triphasé Ampérage maximal en charge 13,0 A (230 V) / 6,5 A (460 V) AC, norme CE (04A, 05A, 06A) Puissance 3.0 HP Nombre de pôles du moteur Vitesse 2,2 kW 4 pôles 1800 tr/min (60 Hz) ou 1500 tr/min (50 Hz) 6:1 Couple constant Rapport de transmission 26.77 Tension 230 V triphasé / 460 V triphasé Ampérage maximal en charge 7,68 A (230 V) / 3,84 A (460 V) IE3 Classification IE AC, ATEX (04C) Puissance 7.5 HP Nombre de pôles du moteur Vitesse 5,5 kW 4 pôles 1800 tr/min (60 Hz) ou 1500 tr/min (50 Hz) 6:1 Couple constant Rapport de transmission 11.88 Tension 240V triphasé / 415V triphasé Ampérage maximal en charge 20 A (230 V) / 11,5 A (460 V) AC, ATEX (14C) Puissance 5.0 HP Nombre de pôles du moteur Vitesse 4,0 kW 4 pôles 1800 tr/min (60 Hz) ou 1500 tr/min (50 Hz) 6:1 Couple constant Rapport de transmission 16.46 Tension 240V triphasé / 415V triphasé Ampérage maximal en charge 14,7 A (230 V) / 8,5 A (460 V) AC, ATEX (24C) Puissance 3.0 HP Nombre de pôles du moteur Vitesse 2,2 kW 4 pôles 1800 tr/min (60 Hz) ou 1500 tr/min (50 Hz) 6:1 Couple constant Rapport de transmission 26.77 Tension 240V triphasé / 415V triphasé Ampérage maximal en charge 8,5 A (230 V) / 5,0 A (460 V) AC, antidéflagrant (04D) Puissance Nombre de pôles du moteur Vitesse Couple constant Rapport de transmission 40 7.5 HP 5,5 kW 4 pôles 1800 tr/min (60 Hz) ou 1500 tr/min (50 Hz) 6:1 11.88 Tension 230 V triphasé / 460 V triphasé Ampérage maximal en charge 20,0 A (230 V) / 10,0 A (460 V) 3A7055L Spécifications techniques AC, antidéflagrant (14D) Puissance 5.0 HP Nombre de pôles du moteur Vitesse 3,7 kW 4 pôles 1800 tr/min (60 Hz) ou 1500 tr/min (50 Hz) 6:1 Couple constant Rapport de transmission 16.46 Tension 230 V triphasé / 460 V triphasé Ampérage maximal en charge 13,0 A (230 V) / 6,5 A (460 V) AC, antidéflagrant (24D) Puissance 3.0 HP Nombre de pôles du moteur Vitesse 2,2 kW 4 pôles 1800 tr/min (60 Hz) ou 1500 tr/min (50 Hz) 6:1 Couple constant Rapport de transmission 26.77 Tension 230 V triphasé / 460 V triphasé Ampérage maximal en charge 8 A (230 V) / 4 A (460 V) Détecteur de fuites Classification des contacts : État Tension Fermé(e) normalement Courant Puissance 0,28 A max à 120 V CA 0,14 A max à 240 V CA 0,28 A max à 24 V CC 0,07 A max à 120 V CC 30 W max Température ambiante -20° à 40°C (-4° à 104°F) 240 V max (CA/CC) Classification Ex : Classification : « appareil simple » conformément à UL/EN/CEI 60079-11, art. 5.7 Classe I, Groupe D, Classe II, Groupe F&G, Code de temp T3B Paramètres II 2 G Ex ib IIC T3 Ui = 24 V Ii = 280 mA Pi = 1,3 W Ci = 2,4 pF Li = 1,00 µH Caractéristiques sonores Puissance sonore (mesurée selon la norme ISO-9614–2) à une pression du liquide de 90 psi et 80 cpm à une pression du liquide de 2 bars (0,2 MPa, 60 psi) et 160 c/min (débit max.) Pression sonore [testée à 1 m de l’équipement] à une pression du liquide de 90 psi et 80 cpm à une pression du liquide de 2 bars (0,2 MPa, 60 psi) et 160 c/min (débit max.) Pièces en contact avec le produit 84 dBa 92 dBa 74 dBa 82 dBa Les pièces en contact avec le produit comprennent le(s) matériau(x) sélectionné(s) pour les options de sièges, de billes et de membrane, plus le matériau de construction de la pompe : Aluminium, polypropylène, acier inoxydable, polypropylène conducteur ou PVDF Pièces sans contact avec le produit Les pièces sans contact avec le produit sont en aluminium, en acier au carbone revêtu, en PTFE, en acier inoxydable, en polypropylène 3A7055L 41 Matériau de la pompe Moteur/Boîtier de vitesses AC standard Modèle 2150FG 2150HS/3A/PH 3000HS 4000HS Section centrale 04A AC ATEX 14A 24A 04C Pas de moteur à engrenages AC ininflammable 14C 24C 04D 14D 24D 94G lb kg lb kg lb kg lb kg lb kg lb kg lb kg lb kg lb kg lb kg Aluminium 360 163 328 149 308 139 475 215 351 159 325 147 517 234 427 194 418 190 217 98 Acier inoxydable 442 200 410 186 390 177 557 253 433 196 407 185 599 271 509 231 500 227 299 136 Aluminium 358 162 326 148 306 139 473 215 349 158 323 146 515 234 425 193 416 189 215 98 Acier inoxydable 440 200 408 185 388 176 555 252 431 195 405 184 597 271 507 230 498 226 297 135 Aluminium 365 166 333 151 313 142 480 218 356 161 330 150 522 237 432 196 423 192 222 101 Acier inoxydable 447 203 415 188 395 179 562 255 438 199 412 187 604 274 514 233 505 229 304 138 Aluminium 407 185 375 170 355 161 522 237 398 180 372 169 564 256 474 215 465 211 264 120 Acier inoxydable 489 222 457 207 437 198 604 274 480 218 454 206 646 293 556 252 547 248 346 157 Spécifications techniques 42 Poids de la pompe 3A7055L California Proposition 65 Mécanisme d’entraînement à fréquence variable (2 cv) Modèle CV/kW Plage de tension d’entrée Tension nominale de sortie † 17K696 3,0/2,2 170–264 V CA 208–240 V CA, triphasé 17K697 3,0/2,2 340–528 V CA 400–480 V CA, triphasé 25B446 5,0/4,0 170–264 V CA 208–240 V CA, triphasé 25B447 5,0/4,0 340–528 V CA 400–480 V CA, triphasé 25B448 7,5/5,5 170–264 V CA 208–240 V CA, triphasé 25B449 7,5/5,5 340–528 V CA 400–480 V CA, triphasé † La tension de sortie dépend de la tension d’entrée. Composant/Modèle Système impérial (É--U) (É Système métrique 28 lb 13 kg Compresseur Plage de température de fluide AVIS Les limites de température sont fonction uniquement de l’effort mécanique. Certains produits chimiques vont davantage réduire la plage des températures de produit. Restez dans la plage de température de la pièce en contact avec le produit la plus restreinte. Le fonctionnement à une température de produit trop élevée ou trop basse pour les composants de pompe utilisée peut endommager l’équipement. Plage de températures du fluide de la pompe en acier inoxydable Matériau de membrane/bille/siège Fahrenheit Celsius Clapets à billes en polychloroprène (CW) 14° à 176°F -10° à 80°C Clapets à billes en PTFE ou membrane PTFE/EPDM à deux pièces (PT) -40° à 220°F -40° à 104°C Clapets à billes en Buna–N (BN) 10° à 180°F -12° à 82°C Clapets à billes en fluoroélastomère FKM (FK)* -40° à 275°F -40° à 135°C Membrane en PTFE/Santoprene 2 pièces (PS) 40° à 180°F 4° à 82°C Clapets à billes en Santoprene ou membrane à deux pièces (SP) -40° à 180°F -40° à 82°C Membrane surmoulée en EPDM (EO) -40° à 250°F -40° à 121°C * La température maximale indiquée est fondée sur la norme ATEX pour la classe de température T3. California Proposition 65 RÉSIDENTS DE CALIFORNIE AVERTISSEMENT: Cancer et effet nocif sur la reproduction — www.P65warnings.ca.gov. 3A7055L 43 Graco Garantie standard Graco garantit que tout l'équipement mentionné dans le présent document, fabriqué par Graco et portant son nom est exempt de défaut de matériel et de fabrication à la date de la vente à l'acheteur et utilisateur initial. Sauf garantie spéciale, élargie ou limitée publiée par Graco, Graco réparera ou remplacera, pendant une période de douze mois à compter de la date de vente, toute pièce de l’équipement que Graco juge défectueuse. Cette garantie s’applique uniquement si le matériel est installé, utilisé et entretenu conformément aux recommandations écrites de Graco. Cette garantie ne couvre pas et Graco ne sera pas tenue responsable de l’usure et de la détérioration générales, ou de tout autre dysfonctionnement, des dégâts ou des traces d’usure causés par une mauvaise installation, une mauvaise utilisation, l’abrasion, la corrosion, une maintenance inappropriée ou incorrecte, la négligence, un accident, une modification ou un remplacement par des pièces ou des composants qui ne sont pas de la marque Graco. Graco ne serait être tenue responsable en cas de dysfonctionnement, dommage ou usure dus à l'incompatibilité de l'équipement de Graco avec des structures, accessoires, équipements ou matériaux non fournis par Graco ou encore dus à un défaut de conception, de fabrication, d'installation, de fonctionnement ou d'entretien de structures, d'accessoires, d'équipements ou de matériaux non fournis par Graco. Cette garantie est conditionnée par l’envoi en port payé du matériel objet de la réclamation à un distributeur Graco agréé pour vérification du défaut signalé. Si le défaut est confirmé, Graco réparera ou remplacera gratuitement toutes les pièces défectueuses. L’équipement sera retourné à l’acheteur d’origine en port payé. Si l’examen de l’équipement ne révèle aucun vice de matériau ou de fabrication, les réparations seront effectuées à un coût raisonnable pouvant inclure le coût des pièces, de la main-d’œuvre et du transport. CETTE GARANTIE EST UNE GARANTIE EXCLUSIVE QUI REMPLACE TOUTE AUTRE GARANTIE, EXPRESSE OU IMPLICITE, COMPRENANT, MAIS SANS S’Y LIMITER, UNE GARANTIE MARCHANDE OU UNE GARANTIE DE FINALITÉ PARTICULIÈRE. La seule obligation de Graco et la seule voie de recours de l’acheteur pour toute violation de la garantie seront tels que définis ci-dessus. L’acheteur convient qu’aucun autre recours (pour dommages indirects ou consécutifs de manque à gagner, perte de marché, dommages corporels ou matériels ou tout autre dommage indirect ou consécutif, la liste n’ayant aucun caractère exhaustif) ne sera possible. Toute action pour violation de la garantie doit être intentée dans les deux (2) ans à compter de la date de vente. GRACO NE GARANTIT PAS ET REFUSE TOUTE GARANTIE RELATIVE À LA QUALITÉ MARCHANDE ET À UNE FINALITÉ PARTICULIÈRE EN RAPPORT AVEC LES ACCESSOIRES, ÉQUIPEMENTS, MATÉRIAUX GRACO. Ces articles vendus, mais non fabriqués OU COMPOSANTS VENDUS MAIS NON FABRIQUÉS PAR GRACO par Graco (tels que les moteurs électriques, commutateurs, flexibles, etc.) sont couverts par la garantie, s'il en existe une, de leur fabricant. Graco fournira à l'acheteur une assistance raisonnable pour toute réclamation faisant appel à ces garanties. Graco ne sera en aucun cas tenue responsable des dommages indirects, accessoires, particuliers ou consécutifs résultant de la fourniture par Graco de l’équipement en vertu des présentes ou de la fourniture, de la performance, ou de l’utilisation de produits ou d’autres biens vendus au titre des présentes, que ce soit en raison d’une violation contractuelle, d’une violation de la garantie, d’une négligence de Graco, ou autre. POUR LES CLIENTS DE GRACO CANADA The Parties acknowledge that they have required that the present document, as well as all documents, notices and legal proceedings entered into, given or instituted pursuant hereto or relating directly or indirectly hereto, be drawn up in English. Les parties reconnaissent avoir convenu que la rédaction du présent document sera en anglais, ainsi que tous les documents, avis et procédures judiciaires exécutés, donnés ou intentés, à la suite de ou en rapport, directement ou indirectement, avec les procédures concernées. Graco Informations Pour connaître les dernières informations concernant les produits Graco, consulter le site www.graco.com. Pour connaître les informations relatives aux brevets, consulter la page www.gracocom/patents. Pour commander, contactez votre distributeur Graco ou téléphonez pour trouver votre distributeur le plus proche. Téléphone : +1 612 623 6921 ou appel gratuit : +1 800 328 0211 Fax : 612-378-3505 Tous les textes et illustrations contenus dans ce document reflètent les dernières informations disponibles concernant le produit au moment de la publication. Graco se réserve le droit de procéder à tout moment, sans préavis, à des modifications. Traduction des instructions originales. This manual contains French. MM 3A5133 GracoSiège social : Minneapolis Bureaux à l’étranger : Belgique, Chine, Japon, Corée GRACO INC. ET FILIALES • P.O. BOX 1441 • MINNEAPOLIS MN 55440-1441 • ÉTATS-UNIS Copyright 2017, Graco Inc. Tous les sites de fabrication de Graco sont certifiés ISO 9001. www.graco.com Révision L, janvier 2021 ">
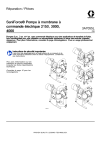
Публичная ссылка обновлена
Публичная ссылка на ваш чат обновлена.