80271020 / 00 11 / 2020 Notice d'utilisation Capteur de pression électronique PM16 PM17 FR Contenu 1 Remarques préliminaires�������������������������������������������������������������������������������������3 1.1 Symboles utilisés�������������������������������������������������������������������������������������������3 2 Consignes de sécurité�����������������������������������������������������������������������������������������4 3 Fonctionnement et caractéristiques���������������������������������������������������������������������4 3.1 Applications���������������������������������������������������������������������������������������������������5 4 Fonctions�������������������������������������������������������������������������������������������������������������5 4.1 IO-Link�����������������������������������������������������������������������������������������������������������6 4.1.1 Informations générales�������������������������������������������������������������������������6 4.1.2 Fonctions disponibles uniquement via la communication IO-Link��������6 4.1.3 Mise en service via IO-Link������������������������������������������������������������������6 4.1.4 Données process via IO-Link���������������������������������������������������������������6 4.2 Etat défini en cas de défaut���������������������������������������������������������������������������7 4.3 Modes de fonctionnement�����������������������������������������������������������������������������7 4.3.1 Fonctionnement 2 fils���������������������������������������������������������������������������7 4.3.2 Fonctionnement 3 fils���������������������������������������������������������������������������7 4.4 Sortie analogique�������������������������������������������������������������������������������������������7 5 Montage���������������������������������������������������������������������������������������������������������������9 5.1 Raccord G1A Aseptoflex Vario (PM17xx)����������������������������������������������������10 5.2 Pour applications aseptiques selon 3A�������������������������������������������������������� 11 5.3 Pour applications aseptiques selon EHEDG�����������������������������������������������12 5.4 Raccord cône d'étanchéité G1A (PM16xx)��������������������������������������������������12 5.5 Membrane d'échappement avec capuchon protecteur (pas PM1602)����������������������������������������������������������������������������������������������14 5.5.1 Fonctionnement de la membrane d'échappement�����������������������������14 5.5.2 Ajustage du couvercle du système de filtrage������������������������������������14 5.6 Couvercle du système de filtrage����������������������������������������������������������������15 6 Raccordement électrique�����������������������������������������������������������������������������������17 7 Paramétrage������������������������������������������������������������������������������������������������������18 7.1 Paramétrage via PC������������������������������������������������������������������������������������18 7.2 Paramétrage via le Memory Plug����������������������������������������������������������������18 7.3 Apprentissage de l'offset via le bouton d'apprentissage������������������������������19 7.3.1 Mise à l'échelle de la valeur analogique���������������������������������������������20 7.3.2 Régler l'unité par défaut de la mesure (option)����������������������������������20 2 7.4 Réglages utilisateur (option)������������������������������������������������������������������������20 7.4.1 Régler l'amortissement pour la sortie analogique������������������������������20 7.4.2 Régler l'amortissement pour le signal de commutation����������������������20 7.4.3 Calibrage du point zéro����������������������������������������������������������������������20 7.4.4 Liste des paramètres��������������������������������������������������������������������������21 7.5 Fonctions de diagnostic�������������������������������������������������������������������������������21 7.5.1 Lecture des valeurs min. et max. pour la pression du système����������21 8 Fonctionnement�������������������������������������������������������������������������������������������������22 9 Correction de défauts����������������������������������������������������������������������������������������22 10 Données techniques et schéma d'encombrement�������������������������������������������23 11 Entretien, réparation et élimination������������������������������������������������������������������23 12 Réglage usine��������������������������������������������������������������������������������������������������23 1 Remarques préliminaires 1.1 Symboles utilisés ► > […] → Action à faire Retour d'information, résultat Désignation d'une touche, d'un bouton ou d'un affichage Référence Remarque importante Le non-respect peut aboutir à des dysfonctionnements ou perturbations. Information Remarque supplémentaire 3 FR 2 Consignes de sécurité • L'appareil décrit est un composant destiné à être intégré dans un système. - La sécurité du système est sous la responsabilité de l'installateur. - L'installateur du système est tenu d’effectuer une évaluation des risques et de rédiger, sur la base de cette dernière, une documentation conforme à toutes les exigences prescrites par la loi et par les normes et de la fournir à l'opérateur et à l'utilisateur du système. Cette documentation doit contenir toutes les informations et consignes de sécurité nécessaires à l'opérateur et à l'utilisateur et, le cas échéant, à tout personnel de service autorisé par l'installateur du système. • Lire ce document avant la mise en service du produit et le garder pendant le temps d'utilisation du produit. • Le produit doit être approprié pour les applications et les conditions environnantes concernées sans aucune restriction d'utilisation. • Utiliser le produit uniquement pour les applications pour lesquelles il a été prévu (→ Fonctionnement et caractéristiques). • Utiliser le produit uniquement pour les fluides admissibles (→ Données techniques). • Le non-respect des consignes ou des données techniques peut provoquer des dommages corporels et/ou matériels. • Le fabricant n'assume aucune responsabilité ni garantie pour les conséquences d'une mauvaise utilisation ou de modifications apportées au produit par l'utilisateur. • Le montage, le raccordement électrique, la mise en service, le fonctionnement et l'entretien du produit doivent être effectués par du personnel qualifié et autorisé par le responsable de l'installation. • Assurer une protection efficace des appareils et des câbles contre l'endommagement. 3 Fonctionnement et caractéristiques L'appareil mesure et surveille la pression du système de machines et d'installations. 2 sorties sont disponibles : - OUT1 : valeur de pression mesurée via IO-Link. Plus d'informations → 4.1 et → 7. - OUT2 : signal de commutation proportionnel à la pression 4...20 mA 4 3.1 Applications Type de pression : pression relative Informations concernant la tenue en pression et la pression d‘éclatement → fiche technique L'utilisation n'est pas possible dans des installations qui doivent satisfaire aux critères du point E1.2 / 63-03 de la norme 3A, n° 63-03. L'emploi des appareils dans des applications gaz avec des pressions > 25 bar est seulement admissible si on renonce à l'utilisation de joints d'étanchéité en élastomère pour l'adaptation du capteur ou si on utilise le joint métallique. Prendre des mesures appropriées afin d'éviter que les pics de pression statiques et dynamiques ne dépassent la tenue en pression indiquée. La pression d'éclatement indiquée ne doit pas être dépassée. Même si la pression d'éclatement n'est dépassée que brièvement, l'appareil peut être détruit. INFORMATION IMPORTANTE : risque de blessures ! Les appareils sont résistants au vide. FR 4 Fonctions • La pression du système est détectée au moyen d'un principe de mesure céramique-capacitive. Les signaux mesurés sont évalués par l'électronique. • L'appareil convertit la pression du système en un signal de sortie analogique (4...20 mA). • L'appareil dispose d'une interface IO-Link qui permet de fournir d'autres valeurs : - OUT1 : valeur de pression mesurée via IO-Link. • Valeur de pression mesurée (sortie cyclique) • Température de l'appareil (sortie acyclique) • Valeurs diagnostiquées - OUT2 : signal de commutation proportionnel à la pression 4...20 mA 5 4.1 IO-Link 4.1.1 Informations générales Cet appareil dispose d'une interface de communication IO-Link. Son fonctionnement nécessite l’utilisation d’un maître IO-Link. L'interface IO-Link permet l'accès direct aux données de process et de diagnostic et offre la possibilité de paramétrer l'appareil pendant le fonctionnement. De plus, la communication est possible via un raccordement point-à-point avec un câble adaptateur USB. Les IODD nécessaires pour la configuration de l'appareil, les informations détaillées concernant la structure des données process, les informations de diagnostic et les adresses des paramètres ainsi que toutes les informations nécessaires concernant le matériel et le logiciel IO-Link sont disponibles sur www.ifm.com. 4.1.2 Fonctions disponibles uniquement via la communication IO-Link • Température de l'appareil : la température interne du capteur peut être lue via la voie IO-Link acyclique. • Etiquette électronique spécifique application : texte à définir librement, affecté à l'appareil. • Function Tag : texte à définir librement, décrit la fonction de l'appareil dans l'installation. • Location Tag : texte à définir librement, décrit le lieu de montage dans l'installation. Vous trouverez des informations détaillées dans le fichier PDF "IO Device Description" spécifique à l'appareil sur www.ifm.com. 4.1.3 Mise en service via IO-Link Les paramètres de l'appareil peuvent être réglés via IO-Link : • Le paramétrage s'effectue via l'interface IO-Link (→ 4.1 et → 7). • Tous les réglages peuvent également être effectués avant l'installation de l'appareil. 4.1.4 Données process via IO-Link Toutes les données process sont disponibles via IO-Link : • L'appareil est conçu pour une communication entièrement bidirectionnelle. • Les options suivantes sont disponibles : 6 - Indication à distance : lecture et affichage de la pression actuelle du système. - Réglage à distance : lecture et modification du paramétrage actuel via le paramétrage IO-Link (→ 4.1). 4.2 Etat défini en cas de défaut • Si un défaut de l'appareil est détecté, la sortie analogique passe à un état défini ( = 21,5 mA). En cas de signalisation de défauts ( = 21,5 mA) ► Lire le paramètre via IO-Link ou consulter le fabricant 4.3 Modes de fonctionnement Le mode de fonctionnement est déterminé par le raccordement (→ 6 Raccordement électrique) et détecté automatiquement par l'appareil. 4.3.1 Fonctionnement 2 fils OUT2 (broche 2) FR Signal de commutation proportionnel à la pression 4...20 mA 4.3.2 Fonctionnement 3 fils OUT1 (broche 4) OUT2 (broche 2) Communication par IO-Link Signal de commutation proportionnel à la pression 4...20 mA 4.4 Sortie analogique L'appareil fournit un signal analogique qui est proportionnel à la pression. Dans l'étendue de mesure le signal analogique est à 4...20 mA. L'étendue de mesure peut être mise à l'échelle : • [ASP2] détermine à quelle valeur mesurée le signal de sortie est 4 mA. • [AEP2] détermine à quelle valeur mesurée le signal de sortie est 20 mA. Distance minimale entre [ASP2] et [AEP2] = 20 % de la valeur finale de l'étendue de mesure (MEW). Si la valeur mesurée est hors de l'étendue de mesure ou dans le cas d'une erreur interne, le signal de courant indiqué dans la figure 1 est fourni. 7 1 [mA] 5 21,5 20,5 20 4 3,8 2 3 4 UL P MAW -1,25 0 ASP AEP MEW OL 100 103,13 [% MEW] Fig. 1 : caractéristique de sortie analogique selon Namur 1 Signal analogique 2 Valeur mesurée 3 Etendue de mesure 4 Etendue de mesure mise à l'échelle 5 Signalisation de défauts 21.5 mA (→ 9 Correction de défauts) P : pression MAW :valeur initiale de l'étendue de mesure pour une étendue de mesure non mise à l'échelle MEW :valeur finale de l'étendue de mesure pour une étendue de mesure non mise à l'échelle ASP : valeur minimum de la sortie analogique si l'étendue de mesure est mise à l'échelle AEP valeur maximum de la sortie analogique si l'étendue de mesure est mise à l'échelle UL : plage d'affichage non atteinte OL : plage d'affichage dépassée 8 5 Montage ► S'assurer avant le montage et le démontage de l'appareil que l'installation est hors pression et qu'il n'y a pas de fluide dans le tuyau. ► Tenir compte des dangers dus aux températures de l'installation et du fluide. ► En cas de montage encastré du capteur, utiliser une clé 0 œil ouverte ou une douille 6 pans avec le bon contour intérieur. ► Lors du montage du capteur, n’exercer aucun effet de levier axial avec l'outil (1) sur le couvercle orientable du système de filtrage (2) (→ Fig. 1). ► En cas de montage à l'aide d'une douille 6 pans (3), s'assurer que la hauteur intérieure libre de l'outil est de 30 mm minimum (→ Fig. 2). Aligner le couvercle orientable du système de filtrage sur le méplat de la clé. 2 ≥ 30mm 1 FR ► Insérer l'appareil dans un raccord process. ► Serrer fermement. Couple de serrage recommandé : Raccord process Couple de serrage en Nm G1A Aseptoflex Vario 35 Cône d'étanchéité G1A 20 En fonction de la version de joint d'étanchéité, de la pression appliquée et de la lubrification ! La fonction d'apprentissage permet un calibrage du point zéro de la valeur de mesure (→ 7.3 Apprentissage de l‘offset via le bouton d‘apprentissage) 9 5.1 Raccord G1A Aseptoflex Vario (PM17xx) ► Insérer l'appareil avec adaptateur process dans le raccord process et serrer à l'aide d'une clé de serrage. Informations sur des raccords disponibles sur www.ifm.com. ► Lire la notice de l'adaptateur utilisé. ► Utiliser une pâte lubrifiante qui est appropriée et homologuée pour l'application. L'appareil peut être adapté à différents raccords process. Il y a les possibilités suivantes : Montage par adaptateur avec joint d’étanchéité (conformité aseptique) Références E332xx / E333xx. ► Utiliser des adaptateurs process avec orifice de fuite pour satisfaire aux exigences d'hygiène. Les adaptateurs sont livrés avec un joint torique EPDM (référence E30054). D'autres joints sont disponibles comme accessoires : • joint torique FKM (référence E30123). • joint d’étanchéité PEEK (référence E30124). Le joint d'étanchéité PEEK a une stabilité à long terme et ne nécessite aucune maintenance. ► En cas de remplacement du joint d’étanchéité PEEK ou d'utilisation d'un joint torique au lieu d'un joint d’étanchéité PEEK l'adaptateur process doit également être remplacé par un nouvel adaptateur équivalent. 2 Montage par raccord à souder avec joint d’étanchéité (conformité aseptique) ► Pour satisfaire aux exigences d'hygiène utiliser un adaptateur process avec orifice de fuite. ► S'assurer que l'adaptateur process ne se déforme pas lors du soudage. Utiliser le bouchon de soudage E30452. ► Même en cas d'un traitement de surface ultérieur, le chanfrein d'étanchéité ne doit aucunement être affecté.(→ Instructions dans la notice d'utilisation de l'adaptateur). Les adaptateurs sont livrés avec un joint torique EPDM (référence E30054). Un autre joint d’étanchéité est disponible comme accessoire : • joint torique FKM (référence E30123). 1 10 Montage par raccord process avec joint d'étanchéité métal sur métal Références E337xx / E338xx L'effet d'étanchéité stable à long terme, sans maintenance, d'une zone d'étanchéité métal sur métal est seulement garanti si l'appareil n'est monté qu'une seule fois. ► Pour chaque nouveau montage faisant suite à un démontage, un nouvel adaptateur doit être utilisé. 4 Montage sur flasque G1 / manchon fileté G1 L'étanchéité du process est assurée par un joint d’étanchéité extérieur sur le capteur. FR ► La zone d'étanchéité sur le flasque / manchon doit être à plat par rapport au filet intérieur et avoir un état de surface d'au moins Rz = 6,3. 3 5.2 Pour applications aseptiques selon 3A Pour des appareils avec homologation 3A il s'applique : ► N'utiliser que des adaptateurs avec homologation 3A pour le raccord process. ► L'appareil ne doit pas être installé au point le plus bas du tuyau ou de la cuve (→ position 5) pour assurer l'écoulement du fluide de la zone autour des éléments de mesure et de référence. 11 5.3 Pour applications aseptiques selon EHEDG Si le capteur est correctement installé, il est approprié pour le NEP (nettoyage en place). ► Prendre en compte les limites d'utilisation (résistance à la température et résistance du matériau) selon la fiche technique. ► S'assurer d'une intégration du capteur dans l'installation selon EHEDG : ► Utiliser une installation auto-vidant. ► Utiliser uniquement des adaptateurs process homologués EHEDG ayant des joints d'étanchéité spéciaux exigés par la norme EHEDG. Le joint d'étanchéité de l'interface du système ne doit pas être en contact avec le point d'étanchéité du capteur. ► En cas de composants présents dans la cuve, ils doivent être installés de manière affleurante et permettre l'accès d'un jet de nettoyage direct. S'assurer que toutes les zones en contact avec la matière soient bien nettoyées. ► Installer les orifices de fuite de manière bien visible et orientés vers le bas en cas de conduites verticales. ► Pour éviter des zones mortes respecter les dimensions : L < (D). 1 L D 1: orifice de fuite 5.4 Raccord cône d'étanchéité G1A (PM16xx) Informations sur des raccords disponibles sur www.ifm.com. ► Lire la notice de l'adaptateur utilisé. Une étanchéité stable à long terme et ainsi sans entretien et sans fentes du joint métallique est seulement garantie si l'appareil n'est monté qu'une seule fois. 12 L'appareil peut être adapté à différents raccords process.Il y a les possibilités suivantes : 1 Montage par adaptateur autoserrant Référence E3360x Informations sur des raccords disponibles sur www.ifm.com. ► Lire la notice de l'adaptateur utilisé. ► Utiliser une pâte lubrifiante qui est appropriée et homologuée pour l'application. ► Couple de serrage recommandé 35 Nm. FR Le raccord E33602 est fourni avec un joint torique EPDM (réf. E30438) et un joint torique FKM (réf. E30437). 2 Montage par raccord à souder Référence E30013 raccord à souder : métal sur métal Référence E30072 raccord à souder : avec joint d’étanchéité Informations sur des raccords disponibles sur www.ifm.com. ► Lire la notice de l'adaptateur utilisé. ► S'assurer que l'adaptateur process ne se déforme pas lors du soudage. ► Utiliser une pâte lubrifiante qui est appropriée et homologuée pour l'application. Le raccord E30072 est fourni avec un joint torique EPDM (réf. E30438) et un joint torique FKM (réf. E30437). 3 Montage par adaptateur G 1 sur G ½ Référence E30116 Informations sur des raccords disponibles sur www.ifm.com. ► Lire la notice de l'adaptateur utilisé. ► Utiliser une pâte lubrifiante qui est appropriée et homologuée pour l'application. ► Couple de serrage recommandé 20 Nm. 13 5.5 M embrane d'échappement avec capuchon protecteur (pas PM1602) 5.5.1 Fonctionnement de la membrane d'échappement La membrane d'échappement assure la mesure de la pression relative car des changements de pression barométriques et dus à la température par rapport à l'environnement sont compensés dans la cellule de mesure. La membrane d'échappement est protégée par un capuchon vissé disposant d’orifices sur tout le pourtour. Respecter le suivant pour un bon fonctionnement de la membrane : ► Rincer des souillures et des produits de nettoyage immédiatement avec une projection de beaucoup d'eau peu calcaire. Si le capteur est dans une phase de refroidissement liée au process : ► Ne pas exposer la membrane à des liquides : > Pour éviter toute dépression dans le système de mesure, une valeur mesurée faiblement erronée ainsi que toute charge supplémentaire pour la membrane. 5.5.2 Ajustage du couvercle du système de filtrage Le couvercle du système de filtrage est librement orientable sur l'axe du capteur et donc adaptable aux conditions environnantes. En cas d'installation verticale du capteur, la condensation échappe par les orifices du capuchon protecteur à cause de la force de gravité. En cas d'installation horizontale du capteur ou de position de montage comparable, le couvercle protecteur du système de filtrage doit être orienté vers une des deux faces latérales afin de réaliser une position verticale de la membrane GORE. Ceci assure un drainage optimisé de fluides. Pour garantir une fonction optimale de l'élément de compensation de pression, le couvercle du système de filtrage doit être orienté comme dans la fig. 1. 14 2 1 3 ► Orientation idéale (1) :couvercle du système de filtrage en position horizontale. La membrane d'échappement (2) dans le couvercle du système de filtrage est en position verticale. ► Inclinaison maximale : 30° (3) FR Fig. 1 : orientation 5.6 Couvercle du système de filtrage Remplacer le couvercle du système de filtrage : 1 Changement du couvercle du système de filtrage y compris la membrane GORE (E30142) 2 Le couvercle du système de filtrage peut être remplacé par un capot fermé (E30148) Améliorer l’effet de protection du couvercle du système de filtrage : 3 Le couvercle du système de filtrage peut être remplacé par un capot avec raccord qui sera muni d'un tube de ventilation dont l’extrémité se terminera dans une zone protégée et sèche (E30139). 4 Kit d'accessoires (E30467) avec membrane de remplacement (GORE) intégrée, pour les applications avec un haut degré de souillure et / ou en cas de haute contrainte climatique. Fonction : (→ notice de montage E30467) ► Eviter toute souillure et toute humidité pendant le remplacement ► Nettoyer le filetage tout en douceur et sans laisser de résidus ► Ne pas endommager la surface adhésive du capteur ► Prendre en compte l'orientation du couvercle du système de filtrage (→ notices de montage E30139 / 30467) 15 1 2 3 4 * Dans le cas d'utilisation du capot fermé, la compensation de pression de ( ) la cellule de mesure n'est plus garantie. Ecarts de mesure à cause de : • fluctuations de la pression atmosphérique • fluctuations de la pression à l'intérieur de l'appareil en cas de changements de température (Δ 10 K ≤ 30 mbar). 16 6 Raccordement électrique L'appareil doit être raccordé par un électricien qualifié. Les règlements nationaux et internationaux relatifs à l'installation de matériel électrique doivent être respectés. Alimentation en tension selon EN 50178, TBTS, TBTP. ► Mettre l'installation hors tension. ► Raccorder l'appareil comme suit : Couleurs des fils conducteurs 1 BN brun 2 WH blanc 3 BU bleu 4 BK noir 2 1 3 4 Fonctionnement 2 fils 1 BN L+ 2 WH OUT2 FR Fonctionnement 3 fils 1 BN 2 WH 4 BK 3 BU L+ OUT2 OUT1 L OUT1 : communication via IO-Link OUT2 : sortie analogique Couleurs selon DIN EN 60947-5-2 Exemple de raccordement (2 fils) 1 x analogique (3 fils) 1 x analogique 1 BN 1 BN L+ 2 WH 2 WH L 3 BU (3 fils) 1 x analogique / 1 x IO-Link 1 BN L+ 2 WH 4 BK 3 BU L L (3 fils) 1 x IO-Link 1 BN 4 BK 3 BU IO-Link L+ L+ IO-Link L 17 Test CEM selon EN 61000-4-5 ondes de choc : 0,5kV 7 Paramétrage L'appareil peut être paramétré via IO-Link. ► Préparer le matériel et le logiciel IO-Link pour l'opération de paramétrage. ► Raccorder l'appareil par ex. à l'interface IO-Link (→ 7.1) ou au Memory Plug programmé (→ 7.2). ► Procéder au paramétrage. ► Mettre l'appareil en service. Les paramètres peuvent être réglés avant le montage et la mise en service ou pendant le fonctionnement. Apporter des modifications aux paramètres pendant l'opération peut affecter le mode de fonctionnement de l'installation ! ► S'assurer qu'il n'y aura pas de mauvais fonctionnement dans l'installation. 7.1 Paramétrage via PC Pour le paramétrage il faut un logiciel compatible avec IO-Link (par ex. LINERECORDER DEVICE). Pour le raccordement de l'appareil via l'interface USB d'un ordinateur, des interfaces IO-Link d'ifm sont disponibles → www.ifm.com. ► Préparer l'ordinateur, le logiciel et l'interface. ► Raccorder l'appareil à l'interface IO-Link. ► Suivre le menu du logiciel IO-Link. ► Procéder au paramétrage. ► Mettre l'appareil en service. Paramètres réglables (→ 7.4.4). 7.2 Paramétrage via le Memory Plug Des paramètres peuvent être écrits sur / enregistrés par l'appareil via un Memory Plug (module de mémoire ifm) → www.ifm.com. 18 Afin que des données en provenance du Memory Plug puissent être écrites sur le capteur, celui-ci doit avoir les réglages usine. Si un réglage des paramètres du capteur a été effectué, le Memory Plug mémorise ce paramétrage qui peut ensuite être transféré à des capteurs de même type. ► Ecrire les paramètres appropriés dans le Memory Plug (par ex. via un PC ou en provenance d'un capteur de même type). ► Raccorder le Memory Plug entre le capteur et le connecteur femelle. > Capteur avec les réglages usine : lors de la mise sous tension, les paramètres FR sont transmis du Memory Plug au capteur. > Capteur avec réglages modifiés : lors de la mise sous tension, le Memory Plug mémorise le paramétrage du capteur. ► Enlever le Memory Plug. ► Mettre l'appareil en service. Paramètres réglables (→ 7.4.4). Plus d'informations sur le Memory Plug sont disponibles dans la documentation technique sur → www.ifm.com. 7.3 Apprentissage de l'offset via le bouton d'apprentissage Un bouton d'apprentissage externe (E30425) permet d'effectuer un calibrage du point zéro (Calibration offset). La valeur mesurée actuelle est adoptée comme point zéro interne si cette valeur mesurée se trouve dans une plage de +/- 3% de la valeur finale de l'étendue de mesure. Raccordement voir fiche technique E30425 Si un bouton d'apprentissage est raccordé, aucune communication IO-Link n'est possible ► Intégrer le bouton d'apprentissage entre le capteur installé et le connecteur. ► Maintenir la pression du système à zéro de façon constante (plage paramétrable = +/- 3% de l'échelle de mesure). ► Appuyer sur le bouton pendant > 2 ... < 10 s. > Lors de la mise sous tension, la LED dans le bouton clignote à 2 Hz et effectue le paramétrage du point zéro (Calibration offset). > Lors d’un défaut, la LED clignote à 8 Hz. 19 7.3.1 Mise à l'échelle de la valeur analogique ► Sélectionner [ASP2] et régler la valeur correspondante au 4 mA. ► Sélectionner [AEP2] et régler la valeur correspondante au 20 mA. Distance minimale entre ASP2 et AEP2 = 20 % de l'échelle de mesure (facteur d'échelle 5). [ASP2] [AEP2] 7.3.2 Régler l'unité par défaut de la mesure (option) ► S électionner [uni.P] et régler l'unité de mesure :[bAr] / [mbar] / [MPA] / [kPA] / [PSI] / [mWS] / [inH2O] Les unités à sélectionner dépendent de l'appareil correspondant. [uni] 7.4 Réglages utilisateur (option) 7.4.1 Régler l'amortissement pour la sortie analogique ► S électionner [dAA] et régler la constante d'amortissement en secondes (temps réglable 10...90 %). Plage de réglage : 0,000...4,000 s. L'amortissement [dAA] influence seulement la sortie analogique / signal analogique. [dAA] 7.4.2 Régler l'amortissement pour le signal de commutation ► S électionner [dAP] et régler la constante d'amortissement en secondes (valeur t : 63 %). Plage de réglage : 0,000...4,000 s. L'amortissement [dAP] influence le flux de données process (communication IO-Link). [dAP] 7.4.3 Calibrage du point zéro ► Sélectionner [cof] La valeur mesurée interne (la valeur de travail du capteur) est décalée par rapport à la valeur mesurée réelle. • Plage d'apprentissage : - 3...+ 3 % de l'échelle de mesure [cof] Un nouveau réglage à zéro est effectué par la commande "Apprentissage de COF".[cof] est remis par la commande "Remise de COF". 20 7.4.4 Liste des paramètres Paramètres Fonctions Valeur minimum de la sortie analogique ASP2 Valeur mesurée à laquelle 4 mA sont fournis. Valeur maximum de la sortie analogique AEP2 Valeur mesurée à laquelle 20 mA sont fournis. Ecart minimum entre ASP et AEP = 20 % de l'échelle de mesure. Unité de mesure standard pour la pression du système (affichage) : [bAr] / [mbar] / [MPA] / [kPA] / [PSI] / [mWS] / [inH2O] uni Les unités à sélectionner dépendent de l'appareil correspondant. coF dAA dAP Lo Hi Calibrage du point zéro (Calibration offset) La valeur mesurée interne (la valeur de travail du capteur) est décalée par rapport à la valeur mesurée réelle. • Plage d'apprentissage : - 3...+ 3 % de l'échelle de mesure. Amortissement pour la sortie analogique Les pics de pression de courte durée ou de haute fréquence peuvent être filtrés. Amortissement de la valeur process (ne concerne que l'évaluation IO-Link). Mémoire valeur minimum pour la pression du système (non influencée par l'amortissement réglé) Mémoire valeur maximum pour la pression du système (non influencée par l'amortissement réglé) 7.5 Fonctions de diagnostic 7.5.1 Lecture des valeurs min. et max. pour la pression du système ► Sélectionner [Hi] ou [Lo] pour afficher la valeur process mesurée la plus basse ou la plus élevée : - [Hi] = Valeur maximum de la pression du système - [Lo] = Valeur minimum de la pression du système [Hi] [Lo] La mémoire peut être remise à zéro. 21 FR 8 Fonctionnement Après la mise sous tension et la temporisation de démarrage d'env. 0,5 s, l'appareil se trouve en mode RUN (= mode de fonctionnement normal). Il exécute ses fonctions de mesure et d'évaluation et génère des signaux de sortie selon les paramètres réglés. 9 Correction de défauts L'appareil dispose de possibilités étendues pour l'autodiagnostic.Il se surveille automatiquement pendant le fonctionnement. Des avertissements et des défauts sont signalisés via IO-Link. En cas de défaillance d'une des valeurs process, les autres valeurs process continuent à être disponibles. Des fonctionnalités étendues sont disponibles via IO-Link : → description des interfaces IODD sur www.ifm.com. Consulter l'IODD pour les codes de défaut IO-Link Comportement Correction de défauts de la sortie Type Description Défaut Appareil défectueux / mauvais fonctionnement 21,5 mA Remplacer l'appareil. Défaut Tension d'alimentation trop basse Inactive Vérifier la tension d'alimentation Défaut Paramétrage en dehors de la plage valable 21,5 mA Répéter le paramétrage Défaut Erreur lors de la mesure de pression 21,5 mA Vérifier la mesure de pression. Remplacer l'appareil. Avertissement Gamme de pression dépassée (>= 105 %MEW*) OU Vérifier la gamme de pression. Avertissement Gamme de pression non atteinte (>= -5 %MAW*) OU Vérifier la gamme de pression. *MEW = valeur finale de l'étendue de mesure, **MAW = valeur initiale de l'étendue de mesure En cas d'avertissement, le signal analogique se comporte selon les paramètres [OU]. 22 10 Données techniques et schéma d'encombrement Données techniques et schéma d'encombrement sur www.ifm.com. 11 Entretien, réparation et élimination ► L'appareil ne peut pas être réparé. ► S'assurer d'une élimination écologique de l'appareil après son usage selon les règlements nationaux en vigueur. ► En cas de retour, s’assurer que l'appareil est exempt d'impuretés, en particulier de substances dangereuses et toxiques. 12 Réglage usine ASP2 AEP2 uni.P uni cof dAA dAP MEW *= Réglage usine 0% MEW* 100% MEW* bar / mbar °C 0,0 0,1 0,06 FR Réglage utilisateur Valeur finale de l'étendue de mesure La valeur de réglage représente le pourcentage indiqué de la valeur finale de l'étendue de mesure du capteur correspondant, en bar/mbar. Plus d'informations sur www.ifm.com 23 ">
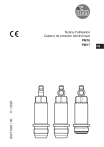
公開リンクが更新されました
あなたのチャットの公開リンクが更新されました。