CNC 800 M Nouvelles prestations (0204 fra) Version 2.1 (Juillet 1995) 1. P627(1). FACTEUR DIVISEUR DES SIGNAUX DES VOLANTS ÉLECTRONIQUES Le paramètre P627(1) s'utilise en même temps avec les paramètres P612(6), P626(6) et P627(6) qui indiquent le facteur multiplicateur des signaux du volant électronique de l'axe X, Y, Z respectivement. Le paramètre P627(1) indique si sont divisés ou non les signaux de tous les volants électroniques. P627(1)=0 P627(1)=1 Ne sont pas divisés. Les signaux de tous les volants sont divisés par 2. Exemples dans l'axe X pour que la CNC assume 100 impulsions/tour avec codeurs à 25, 50 et 100 impulsions/tour, il faut: Volant Fagor à 25 impulsions/tour:P612(6)=0 et P627(1)=0 25 x 4 / 1 = 100impulsions/tour. Volant Fagor à 50 impulsions/tour:P612(6)=1 et P627(1)=0 50 x 2 / 1 = 100impulsions/tour. Volant Fagor à 100 impulsions/tour: P612(6)=1 et P627(1)=1 100 x 2 / 2 = 100impulsions/tour. Version 2.4 (Juin 1996) 1. VOLANTS INFLUENCÉS PAR L’ARRÊT DES AVANCES On partait jusqu’à présent du principe que les volants réalisaient des fonctions de manivelles, raison pour laquelle ces derniers n’étaient pas influencées par l’Arrêt des Avances. Certaines applications exigent pourtant que les volants soient influencés par l’Arrêt des Avances. Le paramètre machine "P628(2)" indique si les volants sont influencés par l’Arrêt des Avances. P628(2) = 0 P628(2) = 1 2. Ne sont pas influencés par l’Arrêt des Avances. Sont influencés par l’Arrêt des Avances. CHANGEURS AUTOMATIQUES D’OUTILS Cette caractéristique permet à tout moment la conduite des changeurs d’outils. Jusqu’à présent, ce traitement avait uniquement lieu lorsqu’un programme (99996) était exécuté sous mode Automatique. Personnalisation: Le paramètre machine "P628(3)" indique si l’on dispose de Changeur Automatique d’Outils. P628(3) = 0 P628(3) = 1 On ne dispose pas de Changeur Automatique d’Outils. On dispose de Changeur Automatique d’Outils. Dans ces deux cas, la CNC tient compte des paramètres machine "P743" et "P745". P743 P745 Sous-routine standard à exécuter avant la fonction T Sous-routine standard à exécuter après la fonction T Les sous-routines associées à la fonction T doivent contenir la séquence de sélection d’outil et doivent être définies par le constructeur dans un des programmes spéciaux d’usager en code ISO: P99994 et P99996. Les deux sous-routines sont définies au moyen d’un nombre entier compris entre 0 et 89. Si elle est personnalisée avec la valeur 0, la CNC comprend qu’elle ne doit exécuter aucune sous-routine. -2- 2.1 MACHINE MUNIE DE CHANGEUR MANUEL D’OUTILS Le paramètre machine "P628(3)" doit être personnalisé avec la valeur "0" (on ne dispose pas de Changeur Automatique d’Outils). Fonctionnement de base sous mode Manuel ou Visualisateur Chaque fois qu’un nouvel outil est sélectionné, (T?? - START), la CNC agit de la manière suivante: 1.- Si le paramètre machine "P743" a été personnalisé avec une valeur autre que "0", la CNC exécute la sous-routine standard en question. 2.-. La CNC fait sortir le code BCD et assimile le nouvel outil 3.- Si le paramètre machine "P745" a été personnalisé avec une valeur autre que "0", la CNC exécute la sous-routine standard en question. Fonctionnement de base durant l’exécution d’une opération automatique Chaque fois que l’exécution d’une opération automatique exige un changement d’outil, (T01 étant active et le cycle demandant T02), la CNC agit de la manière suivante: 1.- Si le paramètre machine "P743" a été personnalisé avec une valeur autre que "0", la CNC exécute la sous-routine standard en question. 2.- Elle affiche le message "TOOL CHANGE" et arrête l’exécution du programme. 3.- Après que l’utilisateur a tapé sur la touche [Départ/Start], la CNC fait sortir le code BCD et assimile le nouvel outil 4.- Si le paramètre machine "P745" a été personnalisé avec une valeur autre que "0", la CNC exécute la sous-routine standard en question. 5.- La CNC poursuit l’exécution de l’opération automatique. Fonctionnement de base durant le programme ISO (99996) a) Un, ou les deux, paramètre(s) machine "P743" et "P745" ont été définis avec une valeur autre que "0". Chaque fois que l’exécution du programme ISO (99996) exige un changement d’outil, la CNC agit de la manière suivante: 1.- Si le paramètre machine "P743" a été personnalisé avec une valeur autre que "0", la CNC exécute la sous-routine standard en question. 2.- La CNC fait sortir le code BCD et assimile le nouvel outil. 3.- Si le paramètre machine "P745" a été personnalisé avec une valeur autre que "0", la CNC exécute la sous-routine standard en question. 4.- La CNC poursuit l’exécution du programme. b) Les deux paramètres machine "P743" et "P745" ont été définis avec la valeur "0". Chaque fois que l’exécution du programme ISO (99996) exige un changement d’outil, la CNC agit de la manière suivante: 1.-. La CNC fait sortir le code BCD de l’outil et l’assimile. 2.- Elle exécute la sous-routine standard N99, où: Elle affiche le message "TOOL CHANGE" et elle arrête l’exécution du programme (M00). 3.- Après que l’utilisateur a tapé sur la touche [Départ/Start], la CNC poursuit l’exécution du programme. -3- 2.2 MACHINE MUNIE DE CHANGEUR AUTOMATIQUE D’OUTILS Le paramètre machine "P628(3)" doit être personnalisé avec la valeur "1" (si l’on dispose de Changeur Automatique d’Outils). Fonctionnement de base sous mode Manuel ou Visualisateur Chaque fois qu’un nouvel outil est sélectionné, (T?? - START), la CNC agit de la manière suivante: 1.- Si le paramètre machine "P743" a été personnalisé avec une valeur autre que "0", la CNC exécute la sous-routine standard en question. 2.-. La CNC fait sortir le code BCD et assimile le nouvel outil. 3.- Si le paramètre machine "P745" a été personnalisé avec une valeur autre que "0", la CNC exécute la sous-routine standard en question. Fonctionnement de base durant l’exécution d’une opération automatique Chaque fois que l’exécution d’une opération automatique exige un changement d’outil, (T01 étant active et le cycle demandant T02), la CNC agit de la manière suivante: 1.- Si le paramètre machine "P743" a été personnalisé avec une valeur autre que "0", la CNC exécute la sous-routine standard en question. 2.- La CNC fait sortir le code BCD et assimile le nouvel outil. 3.- Si le paramètre machine "P745" a été personnalisé avec une valeur autre que "0", la CNC exécute la sous-routine standard en question. 4.- La CNC poursuit l’exécution de l’opération automatique. Fonctionnement de base durant le programme ISO (99996) a) Un, ou les deux, paramètre(s) machine "P743" et "P745" ont été définis avec une valeur autre que "0". Chaque fois que l’exécution du programme ISO (99996) exige un changement d’outil, la CNC agit de la manière suivante: 1.- Si le paramètre machine "P743" a été personnalisé avec une valeur autre que "0", la CNC exécute la sous-routine standard en question. 2.-. La CNC fait sortir le code BCD du nouvel outil et assimile le nouvel outil. 3.- Si le paramètre machine "P745" a été personnalisé avec une valeur autre que "0", la CNC exécute la sous-routine standard en question. 4.- La CNC poursuit l’exécution du programme. b) Les deux paramètres machine "P743" et "P745" ont été définis avec la valeur "0". Chaque fois que l’exécution du programme ISO (99996) exige un changement d’outil, la CNC agit de la manière suivante: 1.-. La CNC fait sortir le code BCD du nouvel outil et l’assimile. 2.- Elle exécute la sous-routine standard interne N99, où: Elle affiche le message "TOOL CHANGE" et elle arrête l’exécution du programme (M00). 3.- Après que l’utilisateur a tapé sur la touche [Départ/Start], la CNC poursuit l’exécution du programme. -4- 3. GESTION DE M19 (ORIENTATION DE LA BROCHE) Lorsque l’on dispose de Changeurs Automatiques d’Outil, il faut orienter la broche avant de procéder au changement. Cette caractéristique met en marche la fonction M19 afin de conduire l’orientation de la broche. Il est conseillé d’inclure la fonction M19 dans la sous-routine standard qui est exécutée avant la fonction T, à savoir, celle qui est définie par le paramètre machine P743. Conditions requises: Afin de pouvoir orienter la broche, il faut disposer d’un codeur de broche. Pour raccorder le codeur de broche il faut utiliser le connecteur "A5", le même qui est utilisé pour le raccordement du volant électronique associé à l’axe Z. Sur les machines disposant de volant associé à l’axe Z et si l’on désire utiliser cette caractéristique, on partagera le connecteur "A5" pour le raccordement du volant électronique associé à l’axe Z et pour le raccordement du codeur de broche. Précautions à prendre pour les machines disposant de volant associé à l’axe Z: . Il faudra échanger les mesures en question (volant et broche) . La CNC interprète la mesure du connecteur "A5" de la manière suivante: En mode "Orientation de la Broche" (M19) comme mesure de la broche. En mode "Broche en boucle ouverte" (M3, M4, M5) comme impulsions de Volant. . Si la broche passe du mode "Orientation de la Broche" au mode "Broche en boucle ouverte" et qu’on ne commute pas la mesure du connecteur "A5", la CNC interprétera les impulsions de la broche comme étant des impulsions du Volant. Personnalisation: Le paramètre machine "P800" indique si l’on dispose ou non de codeur de broche et si l’on dispose donc de la caractéristique "Orientation de la Broche". P800 = P800 <> 0 0 On ne dispose ni de codeur ni d’"Orientation de la Broche". Nombre d’impulsions du codeur de la Broche. En plus de disposer d’un codeur situé sur la broche (P800 autre que 0), il faut personnaliser les paramètres machine suivants: P609(2) P700 P601(7) P612(8) P619(6) P719 P717 P718 P716 Sens de comptage de la broche Vitesse de broche S lorsque l’on travaille en M19 Signe de la sortie S analogique associée à M19 Type d’impulsion de référence machine dans la BROCHE Arrêt orienté de la broche dans les deux sens (admet S négative) Signal analogique minimum de la broche avec M19 Fenêtre d’arrêt de la broche avec M19 Gain proportionnel K de la broche avec M19 Position d’arrêt de la broche lors de l’exécution de M19 sans S. Format de programmation La manière de programmer une Orientation de Broche est "M19 S4.3", où: M19 Indique qu’il s’agit d’un déplacement de broche en boucle fermée. S4.3 Indique la position sur laquelle on désire mettre en position la broche. La valeur en question sera exprimée en degrés et se référera au zéro machine. Format de Programmation en Mode Visualisateur Pour orienter la broche, il faut agir de la manière suivante: * Taper la séquence de touches [F] - [BEGIN] -[END] * La CNC affiche sur la partie inférieure le message "M" * Taper [1] - [9] - [S] - (valeur choisie) - [START] -5- Fonctionnement de base. L’exécution d’un bloc du type "M19 S4.3" se fait de la manière suivante: * La CNC indiquera à l’armoire électrique d’exécuter la fonction M19, ce transfert d’information se faisant comme n’importe quelle fonction auxiliaire "M". * Si la broche se trouvait en boucle ouverte (M3, M4), la CNC réduit la vitesse de la broche jusqu’à ce qu’elle arrive au-dessous de la vitesse indiquée par le paramètre "P700" et fait ensuite une recherche de zéro. * La CNC déplace la broche jusqu’au point indiqué (S4.3) et à la vitesse établie par le paramètre machine "P700". Si un bloc unique est exécuté avec un "M19", sans "S4.3", la CNC déplace la broche jusqu’à la position indiquée par le paramètre "P916". Si "P916=0", la Broche continue à tourner indéfiniment à la vitesse indiquée par M19. Le sens dans lequel se fait le positionnement est indiqué par le paramètre machine "P601(7); malgré ceci, le paramètre machine "P619(6)" permet de faire ce positionnement dans les deux sens. * La broche restera en boucle fermée jusqu’à ce que: - Une M3, M4, M5 soit exécutée Une S ???? soit exécutée Une REMISE À ZÉRO se produise La fonction M30 soit exécutée Se produise une erreur d’exécution quelconque Exemple: M3 S1000 M19 M19 S100 S1000 M19 S200 Broche en boucle ouverte, sens de rotation dans le sens horaire. Broche en boucle fermée, recherche de zéro et positionnement sur la coordonnée indiquée par le paramètre "P916". Positionnement à 100º Broche en boucle ouverte. Maintien du sens de rotation antérieur (M3). Broche en boucle fermée, recherche de zéro et positionnement à 200º. -6- Version 3.1 (Novembre 1997) 1. GÉNÉRATION D'UN PROGRAMME EN CODE ISO La CNC permet de générer, à partir d'une opération ou programme pièce, un programme en code ISO à bas niveau. Quand on veut disposer de cette prestation il faut personnaliser le paramètre machine "P630(1)=1". Le programme en code ISO généré par la CNC est toujours appelé 99996 et pourra être emmagasiné dans la CNC elle-même ou dans un ordinateur. Le programme 99996 est un programme spécial d'usager en code ISO, qui peut être: Généré à partir d'une opération ou programme pièce. Édité dans la CNC elle-même, avec l'option "Modes auxiliaires - Édition programme 99996" Être transmis à la CNC après avoir été élaboré dans un ordinateur. Génération du programme ISO en mémoire de la CNC (99996). Le CN800M dispose de 11 K de mémoire pour emmagasiner le programme 99996. Si le programme généré dépasse cette taille, la CNC affichera l'erreur correspondante. Pour générer le programme 99996 il faut suivre les pas suivants: * S'il s'agit d'une opération. Sélectionner ou définir l'opération désirée. * S'il s'agit d'un programme pièce. Sélectionner dans le dossier de programmes pièce le programme pièce et positionner le curseur sur la tête de celle-ci ("PIÈCE 01435". On devra voir la liste des opérations qui la composent). * Taper sur la séquence de touches [CALC] [7]. La CNC affichera la page de simulation graphique. * Taper sur la touche . La CNC commence la simulation et la génération du programme 99996. * Une fois finalisée la simulation, le programme 99996 emmagasiné en mémoire contiendra en code ISO tous les blocs qui ont été simulés. Génération du programme ISO (99996) dans un ordinateur Normalement, le programme 99996 généré à partir d'un programme pièce est supérieur à la mémoire disponible dans la CNC. Grâce à l'utilisation du DNC30 il est possible de générer ce programme (99996) dans la mémoire de l'ordinateur. Pour générer le programme 99996 dans un ordinateur il faut suivre les pas suivants: * Activer la communication DNC et exécuter le programme DNC30 dans l'ordinateur. * Sélectionner dans l'ordinateur l'option "Gestion de Programmes - Réception Digitalisée". * Dans la CNC sélectionner l'opération ou se positionner sur la tête du programme pièce ("PIÈCE 01435". On devra voir la liste des opérations qui la composent). * Taper sur la séquence de touches [CALC][8]. La CNC affichera la page de simulation graphique. * Taper sur la touche . La CNC commence la simulation et la génération du programme 99996. * Une fois finalisée la simulation, le programme 99996 qui a été généré dans l'ordinateur contiendra en code ISO tous les blocs qui ont été simulés dans la CNC. Ce programme peut être exécuté dans la CNC grâce à l'option "Exécution programme infini" du DNC30. Note: Pendant le processus de génération du programme ISO, il n'est pas appliqué de compensation pendant la simulation graphique qui se réalise. Cependant, dans le programme généré apparaissent les G41, G42 correspondants. -7- 2. DISPONIBILITÉ DU FILETAGE RIGIDE À partir de cette version il est possible d'effectuer des filetages typiques (avec compensateur) "P630(3)=0" ou des filetages rigides "P630(3)=1". Pour effectuer des filetages rigides, la CNC doit contrôler la broche, en vérifiant à chaque moment sa vitesse de rotation et en fournissant à l'armoire électrique le signal nécessaire pour que la broche tourne à la vitesse sélectionnée. Considérations générales: Le filetage rigide consiste en une interpolation entre la broche et l'axe Z. Il est recommandé que les temps d'accélération/décélération de la broche et de l'axe Z soient égaux. Les erreurs de poursuite de la broche et de l'axe Z doivent être proportionnelles. Par exemple, si le filetage est fait à F1000 mm/ min., S1000 t/mn (pas de filetage = 1 mm) et on obtient comme erreur poursuite Z=1 mm (observés) et S=360 degrés, on peut dire que les deux axes sont parfaitement synchronisés. Dans le but d'ajuster la réponse de la broche, accélération et décélération, dans chacune des gammes, on dispose d'un paramètre d'accélération/décélération pour chaque gamme de broche. Comme le gain de l'axe Z est différent pendant l'usinage et pendant le filetage rigide, la CNC dispose de 2 paramètres, un pour chaque cas. La sortie FILETAGE_ON (I97) est active chaque fois qu'un filetage rigide est effectué. Paramètres machine en rapport avec la broche: P800 P601(7) P609(2) P612(8) P719 Numéro d'impulsions du codeur de broche (0...9999) Signe de la sortie S analogique associée à M19 (0 ou 1) Sens de comptage de la broche (0 ou 1) Type d'impulsion de référence machine dans la broche (0 =Négatif, 1= Positif) Signal analogique minimum de la broche (0...255) P719=0 ==> 2,5 mV P719=10 ==>25.0mV (10 x 2.5) P719=1 ==> 2,5 mV P719=255 ==>637.5 mV (255 x 2.5) P717 Fenêtre d'arrêt de la broche. Numéro d'impulsions de comptage (0...255) La CNC applique internement aux signaux de mesure du codeur un facteur de multiplication x4. Ainsi, avec un codeur de 1000 impulsions par tour et P717= 100, la fenêtre d'arrêt sera: (360°/4000)x100= ±9° P718 Gain proportionnel K de la broche (0...255) Fixe le signal correspondant à 1 impulsion de comptage d'erreur de poursuite du codeur de la broche. Signal (mV.) = P718 x Erreur de Poursuite (impulsions) x 2,5 mV / 64 P751, P747, P748, P749 Durée rampe d'accélération/décélération de la broche en gamme 1,2,3,4 (0...255) Valeur 1=20 ms P746 Gain feed-forward de la broche en filetage rigide (0...255) P750 Gain proportionnel K1 de l'axe Z pendant le filetage rigide (0...255) P625(1) Le début du filet se trouve synchronisé avec Io de la broche (0=Non, 1=Oui) Entrées des systèmes de mesure: P630(4) = 0 Le connecteur A5 s'utilise pour la mesure de la broche et pour la mesure du volant associé à l'axe Z Les deux mesures doivent être commutées extérieurement. P630(4) = 1 Le connecteur A5 s'utilise seulement pour la mesure de la broche. Le connecteur A6 s'utilise pour la mesure du volant associé à l'axe X. Le connecteur A4 s'utilise pour la mesure du volant ou volants associés aux axes Y, Z. La sortie O46 du PLC indique l'axe que se déplace en tournant le volant branché au A4. Si O46=0 se déplace Y et si O46=1 se déplace Z. Programmation en code ISO Se programme à l'aide de la fonction G33 (filetage) en devant indiquer l'avance de l'axe et la vitesse de la broche. Exemples: G33 Z -10 F1000 S1000 M3 F1000 S1000 M3 G33 Z-10 Les fonctions G00, G01, G02 et G03 annulent la fonction G33. 3. VERSION DE SOFTWARE DANS LA CNC À partir de cette version, quand on accède à l'écran qu'affiche le cheksum de chacune des Eproms, [Modes Auxiliaires] [Modes Spéciaux] [8] La CNC affichera, le cheksum de chacune des Eprom et la Version de Software dont dispose la CNC. Par exemple: Version 3.1 4. PROTÈGE-ÉCRAN Quand on personnalise le paramètre machine “P626(7)=1” La fonction protège-écran agit de la façon suivante: Après chaque période de 5 minutes sans qu'aucune touche ne soit tapée, ou bien si la CNC n'a rien à actualiser sur l'écran, le signal vidéo est éliminé et l'écran s'éteint. En tapant sur n'importe quelle touche le vidéo réapparaît. -8- 5. FRAISAGE LINÉAIRE SEMI-AUTOMATIQUE Pour accéder à ce mode, sélectionner le fraisage linéaire automatique. et taper sur la touche pour accéder au mode semi- Cette opération ne pourra pas être mémorisée comme partie d'une pièce. Il faut définir l'angle (α) et la longueur (L) de la trajectoire. Déplacer la machine grâce aux volants jusqu'au point de départ voulu et taper sur la touche JOG correspondante (il suffit de taper dessus une fois, il n'est pas nécessaire de la maintenir appuyée). La machine se déplacera dans la direction indiquée et en maintenant l'angleα"" jusqu'à parcourir la distance "L" indiquée ou jusqu'à ce que la touche soit tapée. 6. FRAISAGE EN ARC SEMI-AUTOMATIQUE Pour accéder ce mode sélectionner le fraisage en arc automatique. et taper sur la touche pour accéder au mode semi- Cette opération ne pourra pas être mémorisée comme partie d'une pièce. Il faut définir le rayon d'arrondi (R). Le signe de cette donnée indique le sens de rotation (R+ et R-) Déplacer la machine au moyen des volants jusqu'au point de départ voulu et taper sur la touche JOG correspondante (il suffit de taper dessus une fois, il n'est pas nécessaire de la maintenir appuyée). La machine effectuera un arc de 90° dans le sens indiqué. 7. COMPENSATION CROISÉE En plus de compenser l'erreur de mesure causé par la inexactitude des vis utilisées dans chaque axe (erreur de vis), la CNC permet de compenser l'erreur de mesure produite par un axe dans un autre (compensation croisée). Un exemple typique de la compensation croisée est la compensation de flexion de bélier. Si l'on veut utiliser la compensation croisée il faut définir l'axe auquel s'applique la compensation croisée et l'axe qui en se déplaçant crée ces erreurs de mesure. Paramètres machine en rapport avec la compensation croisée: P623(1) P620(5) P620(4) P623(2), P623(3) La compensation croisée est appliquée à l'axe X (0=Non, 1=Oui) La compensation croisée est appliquée à l'axe Y (0=Non, 1=Oui) La compensation croisée est appliquée à l'axe Z (0=Non, 1=Oui) Axe qui se déplace à la compensation croisée AXE COMPENSÉ AXE À DÉPLACER P623 (1) P620(5) P620(4) Exemples: 8. P623(3) P623(2) X 1 0 0 X 0 1 Y 0 1 0 Y 1 0 Z 0 0 1 Z 1 1 Compenser Y par rapport au déplacement de Z P620 ( * * * 1 0 * * *) Compenser X par rapport au déplacement de Y P620 ( * * * 0 0 * * *) P623 ( * * * * * 0 0 0) P623 ( * * * * * 1 0 1) FONCTION M80 AVEC AXE Z VISUALISATEUR Cette prestation se trouve disponible quand l'axe Z est un axe Visualisateur "P617(4)=1". Chaque fois qu'il faut déplacer l'axe Z la CNC affiche le texte "Agir sur Z". En plus, à partir de cette version, elle exécute la fonction auxiliaire M80. Grâce à cette fonction on peut agir sur le dispositif hydraulique, mécanique, etc. qui contrôle l'axe Z. -9- 9. RÉGLEMENTATION DE SÉCURITÉ EN MACHINES La CNC dispose des prestations suivantes pour respecter la réglementation de sécurité sur machines. depuis le PLC Habilitation de la touche DEPART Cette prestation est disponible quand le paramètre "P630(5)=1" a été personnalisé. La sortie O25 du PLC indique si la touche DEPART est habilitée (=1) ou non (=0) Déplacements des axes affectés par l'Arrêt des Avances. (était déjà disponible) L'entrée d'Arrêt des Avances, pin 15 du connecteur I/O 1, doit se trouver normalement au niveau logique haut. Si pendant le déplacement des axes, l'entrée d'Arrêt des Avances se met au niveau logique bas, la CNC maintient la rotation de la broche et arrête l'avance des axes, en fournissant des signaux de valeur 0V et en maintenant les embrayages activés. Quand ce signal retourne au niveau logique haut, la CNC continuera avec le déplacement des axes. Avance des axes en mode manuel limitée depuis le PLC. Cette prestation est disponible quand le paramètre "P630(5)=1" a été personnalisé Chaque fois que la sortie O26 du PLC est activée, la CNC assume l'avance fixée dans le paramètre machine "P814" Volant géré depuis le PLC. Le paramètre "P628(2)" indique si le déplacement des axes avec volants est affecté par l'Arrêt des Avances (=1) ou non (=0) Le paramètre machine "P630(2)" indique si est appliqué le facteur correspondant à la position du commutateur (=0) ou si est appliqué le facteur indiqué par les sorties O44 et O45 du PLC (=1) 44 045 0 0 Prend en compte ce qui est indiqué par le commutateur 1 0 Équivalent à la position x1 du commutateur 0 1 Équivalent à la position x10 du commutateur 1 1 Équivalent à la position x100 du commutateur Contrôle de la broche depuis le PLC. Cette prestation est disponible quand le paramètre "P630(5)=1" a été personnalisé. La sortie O27 indique à la CNC qu'elle doit (O27=1) appliquer à la broche le signal fixé depuis le PLC. La valeur du signal est fixée dans le registre R156 et avec la marque M1956 est envoyée à la CNC. R156= 0000 1111 1111 1111 => + R156= 0000 0111 1111 1111 => + R156= 0000 0011 1111 1111 => + R156= 0000 0000 0000 0000 => + 10V. 5V. 2,5V. 0V. R156= 0001 1111 1111 1111 => R156= 0001 0111 1111 1111 => R156= 0001 0011 1111 1111 => R156= 0001 0000 0000 0000 => - De même, la sortie O43 du PLC, permet de contrôler la rotation de la broche. (Elle était déjà disponible) Normalement elle doit se trouver au niveau logique bas. Si elle est mise au niveau logique haut, la CNC arrête la rotation de la broche. Quand cette sortie retourne au niveau logique bas, la CNC récupère la rotation de la broche. Information au PLC de l'état de la recherche de référence machine I88 I100 I101 I102 Recherche de référence machine en processus Recherche de référence machine finalisée sur l'axe X Recherche de référence machine finalisée sur l'axe Y Recherche de référence machine finalisée sur l'axe Z - 10 - 10V. 5V. 2,5V. 0V. Information additionnelle de la CNC au PLC R120 La partie basse de ce registre indique le code de la touche tapée. Cette valeur se maintient pendant 200 millièmes de seconde, sauf si on tape une autre touche avant. Ce registre peut être annulé depuis le PLC, après avoir été géré. R121 bit 1 bit 2 bit 3 bit 4 bit 5 bit 6 bit 7 bit 8 bit 9 bit 10 bit 16 Indique que l'opération de Fraisage est sélectionnée (=1) Indique que l'opération de Positionnement est sélectionnée (=1) Indique que l'opération de Poche est sélectionnée (=1) Indique que l'opération de Moyeu est sélectionnée (=1) Indique que l'opération d'Ébauche d'arêtes est sélectionnée (=1) Indique que l'opération de Surfaçage est sélectionnée (=1) Indique que une des opérations d'usinage (Pointage, Perçage, etc.) est sélectionnée (=1) Indique que l'option Modes Auxiliaires est sélectionnée (=1) Indique que l'option Mesure d'outil est sélectionnée (=1) Indique que le mode de Simulation graphique est sélectionné (=1) Indique que le mode correspondant aux paramètres "Passe de finition, Avance de finition, Outil de finition et Distances de sécurité sur X et sur Z des cycles" est sélectionné (=1) - 11 - Version 3.3 (Mars 1998) 1. CNC MODULAIRE La CNC 800M modulaire est formée par les modules Unité Centrale, Moniteur et Clavier. Unité Centrale.Elle se trouve normalement dans l'armoire électrique et sa fixation s'effectue grâce à des orifices que le COUVERCLE SUPPORT possède à cet effet. Dimensions en mm. Couvercle Support Corps U.C 320 largueur x 265 hauteur Au moment de l'installation, il faut tenir compte que pour des manipulations futures à l'intérieur, il faudra disposer d'assez d'espace pour l'abattre. Quand on veut abattre l'Unité Centrale, il faut lâcher les 2 vis moletées situées dans la partie supérieure et procéder à l'abattement en soutenant le corps de celle-ci. Moniteur. Peut être situé dans n'importe quelle partie de la machine, il est pourtant conseillé de le situer à la hauteur des yeux de l'utilisateur. Moniteur 9" Ambre et 10" Couleur 1.2.3.4.5.6.7.- Contraste Brillant 2 fusibles rapides (F), un pour chaque ligne de réseau, de 3,15Amp./250V pour protection de l'entrée de réseau. Interrupteur de mise sous tension. Connecteur de raccordement à réseau, pour le raccorder à 220 V courant alternatif et terre. Borne pour le raccordement général de terres de la machine: métrique 6. Connecteur type SUB-D (mâle) avec 15 pins pour le raccordement avec l'Unité Centrale. - 12 - Moniteur 14" Couleur. X2 Connecteur type SUB-D (mâle) avec 15 pins pour le raccordement avec l'Unité Centrale. 1.- Borne pour le raccordement générale de terres de la machine: métrique 6. 2.- Connecteur de raccordement a réseau, pour le raccorder à 220 V. courant alternatif et terre. Habitacles Moniteur. Moniteur 9" et 11" Moniteur 14" A B C 25 mm 25 mm 25 mm E 25 mm 150 mm 100 mm 100 mm 100 mm 100 mm 50 mm Clavier. Peut être situé dans n'importe quelle partie de la machine Partie Postérieure 1.- Connecteur type SUB-D (femelle) avec 25 pins pour le raccordement avec l'Unité Centrale. 2.- Potentiomètre pour l'ajustage du volume du buzzer 3.- Buzzer - 13 - D Connecteur pour le raccordement de l'Unité Centrale avec le Moniteur. FAGOR AUTOMATION fournit le câble d'union nécessaire pour le raccordement, celui-ci étant formé d'un toron et de deux connecteurs, un mâle et un femelle, type SUB-D avec 15 pins. Les deux connecteurs ont un système d'enclenchement au moyen de deux vis UNC4.40. Le toron utilisé dispose de 6 paires de fils tressés 0.34mm² (6 x 2 x 0.34mm²), avec blindage global et couverture en mousse acrylique. Il dispose d'une impédance spécifique de 120 Ohms et il est permis une longueur maximum de 25m. Le blindage du toron est soudé dans les chapes métalliques qui recouvrent les deux connecteurs et aussi bien dans l'Unité Centrale comme dans le Moniteur ce blindage est uni par hardware au pin 1 du connecteur. PIN 1 2 3 4 5 6 7 8 9 10 11 12 13 14 15 Chape métallique SIGNAL GND H V I R G B Non raccordé Non raccordé H V I R G B Blindage Blindage Thermoadaptable Blindage extérieur soudé à chape métallique Chape métallique Connecteur pour le raccordement de l'Unité Centrale avec le Clavier. FAGOR AUTOMATION fournit le câble d'union nécessaire pour le raccordement, celui-ci étant formé d'un toron et de deux connecteurs mâle type SUB-D avec 25 pins, un dans chaque extrémité. Les deux connecteurs possèdent un système d'enclavement au moyen de 2 vis UNC4.40. Le toron utilisé dispose de 25 fils de 0.14mm² (25 x 0.14mm²), avec blindage global et couverture en mousse acrylique. Il est permis une longueur maximum de 25 m. Le blindage du toron est soudé dans les chapes métalliques qui recouvrent les deux connecteurs et aussi bien dans l'Unité Centrale comme dans le Clavier ce blindage est uni par hardware au pin 1 du connecteur. PIN 1 2 3 4 5 6 7 8 9 10 11 12 13 14 15 16 17 18 19 20 21 22 23 24 25 Chape métallique SIGNAL GND C9 C11 C13 C15 C1 C3 C5 C7 D1 D3 D5 D7 C8 C10 C12 C14 C0 C2 C4 C6 D0 D2 D4 D6 Blindage Blindage Thermoadaptable Blindage extérieur soudé à chape métallique Chape métallique - 14 - 2. PROGRAMMATION EN CODE ISO. NOUVELLE FONCTION F34 P1 = F34Le paramètre P1 prend le numéro de l'outil qui a provoqué l'appel à la routine associée aux outils. Il ne faut pas confondre avec la fonction F24 qui renvoie le numéro de l'outil avec lequel on est en train de travailler. 3. PROGRAMMATION EN CODE ISO. FILETAGE RIGIDE. Quand on effectue un filetage rigide dans le mode 800M, la CNC agit de la manière suivante: 1.- Elle crée internement la fonction M81 (commutation de mesures) 2.- Elle effectue le filetage rigide 3.- Elle crée internement la fonction M82 (récupère la mesure antérieure) Pour cela, quand on programme un filetage rigide en code ISO, il faut programmer la fonction M81 dans le bloc antérieur au bloc du filetage rigide et la fonction M82 dans le bloc postérieur. 4. CODEUR À 1000 IMPULSIONS COMME CODEUR À 1250 Cette performance permet à la CNC d'adapter la mesure du codeur à 1000 impulsions pour la traiter comme mesure à 1250 impulsions. P630(6) Adapte la mesure du codeur de l'axe X (0=Non, 1=Oui) P630(7) Adapte la mesure du codeur de l'axe Y (0=Non, 1=Oui) P630(8) Adapte la mesure du codeur de l'axe Z (0=Non, 1=Oui) Un cas typique: on dispose de moteurs avec codeur à 1000 impulsions et vis avec pas de 5 millimètres. Les calculs nécessaires pour définir la résolution de l'axe seront réalisés avec le nombre d'impulsions sélectionnées (1000 ou 1250) 5. PLCI. ENTRÉE I104 Quand le commutateur du panneau de commandes se trouve dans une des positions du volant (x1, x10, x100), l'entrée I104 est à "1" 6. PLCI. R120 ET TOUCHE A partir de cette version, bien que la touche est montré lorsqu'on tape dessus. soit désactivée par paramètre, P618(1), dans le registre R120 du PLCI son code Version 3,04 (Mars 2002) 1. ANNULER LE CORRECTEUR D’OUTIL Il est parfois utile de déplacer l’outil à une cote fixe mais sans compenser sa longueur. Dans ces cas il faut programmer «T.0», la CNC procède de la façon suivante: • Ne change pas d’outil (n’effectue aucun appel à la sous-routine associée). • Annule le correcteur associé (assume un correcteur d’une longueur 0 et d’un rayon 0). L’instruction «T.xx» peut être programmée à n’importe quel moment, même dans le programme P99996 ou la sous-routine associée. La CNC assume le nouveau correcteur «xx» indiqué. Si on programme «T.0» elle assume un correcteur d’une longueur 0 et d’un rayon 0. 2. FACTEUR DIVISEUR DES SIGNAUX DE MESURE Les paramètres P631(8), P631(7), P631(6), P631(5) et P631(4) s’utilisent en même temps que les paramètres P604(8), P604(7), P604(6), P604(5) et P616(8) qui indiquent le facteur multiplicateur des signaux de mesure des axes X, Y, C, W, V respectivement. Axe X Axe Y Axe Z Axe W Axe V P604(8) P604(7) P604(6) P604(5) P616(8) P631(8) P631(7) P631(6) P631(5) P631(4) Indiquent si les signaux de mesure se divisent (=1) ou non (=0). P631(8)=0, P631(7)=0, P631(6)=0, P631(5)=0 et P631(4)=0 P631(8)=1, P631(7)=1, P631(6)=1, P631(5)=1 et P631(4)=1 Ils ne se divisent pas Ils se divisent par 2. Exemple: Si l’on veut obtenir une résolution de 0,01 mm avec un codeur de signaux carrés placé sur l’axe X dont le pas de vis est de 5 mm. Nombre d’impulsions = pas de vis / (Facteur multiplication x Résolution) Avec P604(8)=0 et P631(8)=0 Facteur de multiplication x4 Nombre d’impulsions = 125 Avec P604(8)=1 et P631(8)=0 Facteur de multiplication x2 Nombre d’impulsions = 250 Avec P604(8)=0 et P631(8)=1 Facteur de multiplication x2 Nombre d’impulsions = 250 Avec P604(8)=1 et P631(8)=1 Facteur de multiplication x1 Nombre d’impulsions = 500 - 15 - 3. FACTEUR DE MESURE. La résolution de l’axe est fixée par le pas de vis et le nombre d’impulsions du codeur incorporé au moteur. Quelque fois, la résolution correspondant aux vis et codeurs disponibles ne coïncide pas avec aucune des résolutions que l’on peut fixer par paramètre machine (1, 2, 5, 10 microns ou dix millièmes de pouce). Exemple: Avec vis à pas de 6 mm et codeur de 2.500 impulsions/tour, on peut obtenir des résolutions de : Résolution = Pas de Vis / (Nombre d’impulsions du Codeur x Facteur de multiplication). Avec facteur de multiplication 1 Résolution 2,4 microns Avec facteur de multiplication 2 Résolution 1,2 microns Avec facteur de multiplication 4 Résolution 0,6 microns Pour résoudre ces cas, on dispose d’un nouveau paramètre machine par axe appelé Facteur de Mesure, qui permet d’adapter la résolution à la configuration disponible. P819 Facteur de mesure de l’axe X P820 Facteur de mesure de l’axe YP821 Facteur de mesure de l’axe Z Valeurs entre 0 et 65534, la valeur 0 indique que l’on ne désire pas cette performance. Pour calculer le «Facteur de Mesure», on doit utiliser la formule suivante : Facteur de Mesure = (Réduction x Pas de Vis / Nombre d’impulsions du Codeur) x 8.192 Exemples : Réduction 1 Pas de Vis 4.000 Codeur 2.500 Facteur de Mesure 13107,2 1 6.000 2.500 19.660,8 2 6.000 2.500 39.321,6 1 8.000 (microns) 2.500 (impulsions/tour) 26.214,4 Les paramètres machine n’admettent que des nombres entiers et parfois le «Facteur de Mesure possède une partie fractionnaire. Dans ce cas, on assigne la partie entière au paramètre machine et on utilise la table d’erreur de vis pour compenser la partie fractionnaire. Les valeurs à introduire dans la table se calculent avec la formule suivante : Cote de la vis = Erreur de vis (microns) x Partie entière du facteur de mesure / Partie fractionnaire du facteur de mesure Pour le cas: Réduction = 1Pas de vis = 6.000 Codeur = 2.500 Facteur de Mesure = 19.660,8Paramètre machine = 19660 Pour une erreur de vis de 20 micronsCote de la vis = 20 x 19.660 / 0.8 = 491.520 En continuant le calcul, on obtient la table suivante. Cote de la Vis Erreur de la Vis P0 = -1966.000 P1 = -0.080 P2 = -1474.500 P3 = -0.060 P4 = -983.000 P5 = -0.040 P6 = -491.500 P7 = -0.020 P8 = 0 P9 = 0 P10 = 491.500 P11 = 0.020 P12 = 983.000 P13 = 0.040 P14 = 1472.500 P15 = 0.060 P16 = 1966.000 P17 = 0.080 Headquarters (SPAIN): Fagor Automation S. Coop. Bº San Andrés s/n, Apdo. 144 E-20500 Arrasate - Mondragón Tel: +34-943-719200/039800 Fax: +34- 943-791712 +34-943-771118 (Service Dept.) www.fagorautomation.com E-mail: [email protected] - 16 - FAGOR - CNC 800M MANUEL D'UTILISATION Ref. 9701 (Fra) AU SUJET DE L’INFORMATION CONTENUE DANS LE PRESENT MANUEL Ce manuel s’adresse au conducteur de la machine. Il contient l’information nécessaire aux nouveaux usagers, en plus des sujets avancés qui s’adressent à tous ceux qui connaissent le CNC 800 M. Il ne sera pas nécessaire de lire intégralement ce manuel. Consultez la liste de Nouvelles Prestations et Modifications qui vous indiquera le chapitre ou section sur lequel se trouve expliqué le sujet que vous cherchez. Les chapitres 1, 2, 3, 4 et 5 indiquent le mode d’utilisation de la CNC. Le chapitre 6 "Travail avec des Programmes Pièce" indique le mode de création de pièces comprenant plusieurs Opérations Automatiques. Les Programmes Pièce sont sauvegardés dans la mémoire interne de la CNC et peuvent être envoyés vers un périphérique ou vers un ordinateur. Notes: L’information décrite dans le présent manuel peut être sujet à des variations provoquées par des modifications techniques. FAGOR AUTOMATION, S. Coop., se réserve le droit de modifier le contenu du manuel, n’étant pas tenue de notifier les variations. SOMMAIRE Section Page Tableau comparatif des modèles Fagor CNC 800 M ................................................. ix Nouvelles prestations et modifications ...................................................................... xiii INTRODUCTION Conditions de Sécurité .................................................................................................... 3 Conditions de Renvoi ..................................................................................................... 5 Documentation Fagor pour la CNC 800M ...................................................................... 6 Contenu du présent manuel ............................................................................................. 7 Chapitre 1 1.1 1.2 1.2.1 1.2.2 1.2.3 1.2.4 1.3 1.4 1.4.1 1.4.2 1.4.3 1.5 Description de la visualisation ................................................................................... 1 Description du clavier ................................................................................................ 3 Zone principale .......................................................................................................... 4 Zone de fonctions et d’opérations automatiques ....................................................... 5 Touches de fonction ................................................................................................... 6 Pupitre opérateur ........................................................................................................ 7 Unités d’affichage (mm/pouces) ................................................................................ 8 Systèmes de référence................................................................................................. 9 Recherche de l’origine ............................................................................................... 9 Présélection du zéro ................................................................................................... 10 Présélection des coordonnées .................................................................................... 10 Fonctionnement en mode incémental ........................................................................ 11 Chapitre 2 2.1 2.2 2.3 2.3.1 2.3.2 2.3.3 2.4. 2.4.1 2.4.2 2.5 2.5.1 2.5.2 2.5.3 2.5.4 2.5.5 2.6 CONCEPTS OPERATIONS DE BASE Fixation de la vitesse d’avance par axe ..................................................................... 1 Sélection des outils .................................................................................................... 2 Déplacement manuel des axes ................................................................................... 3 Déplacement manuel continu .................................................................................... 3 Déplacement manuel incrémental .............................................................................. 3 Déplacement manuel des axes par manivelle électronique ....................................... 4 Point de début (BEG) et de fin (END) ........................................................................ 6 Fixation des points BEGIN et END ............................................................................ 6 Positionnement sur les points BEGIN ou END .......................................................... 7 Contrôle de broche ..................................................................................................... 8 Fixation de la vitesse de broche ................................................................................. 8 Changement de plage de vitesses de broche .............................................................. 8 Rotation de broche dans le sens horaire ..................................................................... 9 Rotation de broche dans le sens anti-horaire ............................................................. 9 Arrêt de la broche ....................................................................................................... 9 Activation/désactivation des dispositifs externes ..................................................... 10 Section Page Chapitre 3 3.1 3.2 3.3 3.3.1 3.4 3.5 3.5.1 3.5.1.1 3.5.1.2 3.5.1.3 3.5.1.4 3.5.1.5 3.5.2 3.5.2.1 3.6 3.7 3.7.1 3.7.2 3.8 3.9 Millimètres < > pouces ............................................................................................... Compensation de longueur d’outil ............................................................................ Table d’outils ............................................................................................................. Modification des dimensions d’outil ......................................................................... Etalonnage des outils ................................................................................................. Exécution/simulation du programme 99996 ............................................................. Exécution du programme 99996 ................................................................................ Contrôle des outils ..................................................................................................... Modes d’exécution .................................................................................................... RAZ de la CNC .......................................................................................................... Affichage des blocs de programme ............................................................................ Modes d’affichage ...................................................................................................... Simulation du programme 99996 .............................................................................. Fonction zoom ........................................................................................................... Modes auxiliaires ....................................................................................................... Périphériques .............................................................................................................. Mode Périphérique ..................................................................................................... Communications DNC ............................................................................................... Blocage/déblocage .................................................................................................... Edition du programme 99996 .................................................................................... Chapitre 4 4.1 4.1.1 4.1.2 4.1.3 4.1.4 4.1.4.1 4.1.5 4.1.5.1 4.2 4.2.1 4.2.2 4.2.3 4.2.4 4.2.5 4.3 4.3.1 4.3.2 4.3.3 4.4 4.4.1 4.4.2 4.4.3 4.4.4 4.5 4.6 FONCTIONS AUXILIAIRES 1 1 2 3 4 5 5 6 7 7 7 8 10 11 12 13 13 14 15 16 OPERATIONS AUTOMATIQUES Généralités .................................................................................................................. Contrôle sur l’axe Z .................................................................................................... Fonctions auxiliaires “M” avant et après le cycle ..................................................... Conditions d’usinage ................................................................................................. Simulation .................................................................................................................. Fonction Zoom ........................................................................................................... Exécution ................................................................................................................... Contrôle de l’outil ...................................................................................................... Positionnement .......................................................................................................... Positionnement point à point ..................................................................................... Positionnement en ligne ............................................................................................ Positionnement en arc (trou de boulon) ..................................................................... Positionnement en rectangle ...................................................................................... Positionnement en grille ............................................................................................ Fraisage ...................................................................................................................... Fraisage linéaire ......................................................................................................... Fraisage courbe .......................................................................................................... Fraisage de profil ........................................................................................................ Poches ........................................................................................................................ Poche rectangulaire .................................................................................................... Poche circulaire .......................................................................................................... Moyeu rectangulaire .................................................................................................. Moyeu circulaire ........................................................................................................ Ebauche d’arêtes ........................................................................................................ Surfaçage .................................................................................................................... 2 2 3 4 5 6 7 8 9 10 11 12 13 14 15 16 17 18 23 24 27 29 32 34 37 Section Page Chapitre 5 5.1 5.1.1 5.2 5.2.1 5.3 5.3.1 5.4 5.4.1 5.5 5.5.1 Généralités .................................................................................................................. Fonctions auxiliaires “M” avant et après l'opération .................................................. Pointage ...................................................................................................................... Exemple de programmation ........................................................................................ Perçage ........................................................................................................................ Exemple de programmation ........................................................................................ Taraudage .................................................................................................................... Exemple de programmation ........................................................................................ Alésage ........................................................................................................................ Exemples de programmation....................................................................................... Chapitre 6 6.1 6.2 6.3 6.4 6.4.1 6.5 6.5.1 6.5.2 6.6 6.7 6.8 6.8.1 6.8.2 6.9 OPERATIONS D’USINAGE 2 3 4 5 6 7 8 9 10 11 FONCTIONNEMENT AVEC LES PROGRAMMES PIECE Accès à la table de programmes pièce ......................................................................... Sélection des programmes pièce ................................................................................. Edition des programmes pièce .................................................................................... Simulation de programmes pièce ................................................................................ Fonction Zoom ............................................................................................................ Exécution de programme pièce ................................................................................... Exécution d’une opération mémorisée au préalable dans un programme pièce ......... Contrôle de l’outil ....................................................................................................... Modification d’un programme pièce .......................................................................... Suppression d’un programme pièce ............................................................................ Périphériques ............................................................................................................... Mode périphérique ...................................................................................................... Communications DNC ................................................................................................ Blocage/déblocage ..................................................................................................... CODES D'ERREUR 1 2 3 4 5 6 7 8 9 10 11 11 12 13 TABLEAU COMPARATIF DES MODELES FAGOR CNC 800M MODELES CNC 800M DISPONIBLES CNC 800-MG CNC 800-MGI Contrôle d'axes X, Y l l Axe Z Visualisateur l l Axe Z Contrôlé l l Broche l l Outils 99 99 Compensation de rayon de l'outil l l Compensation de longueur de l'outil l l Manivelles Electroniques 3 3 Interface RS 232C l l Automate Intégré (PLCI) l Edition du programme en CODE ISO (P99996) l l Exécution du programme en CODE ISO (P99996) l l Représentation Graphique l l NOUVELLES PRESTATIONS ET MODIFICATIONS Date: Juillet 1995 PRESTATION Version logiciel: 2.1 et suivants MANUEL ET SECTION MODIFIEE Effacer la mémoire de tous les paramètres arithmétiques, en leur attribuant la valeur 0. Manuel Installation Manuel d'Utilisation Programmation en CODE ISO. Manuel Programmation Edition du programme 99996 dans la CNC Manuel Installation Manual d'Utilisation Section. 3.10 Section. 3.9 Lors de l'interruption de l'exécution restent opérantes les touches de broche, réfrigérant 01, 02, 03 et TOOL Manuel Installation Manuel d'Utilisation Manuel d'Utilisation Section. 3.5.1 Section. 3.5.1 Section. 6.5 Sous-programme associé à l'exécution d'outil (seulement en exécution du programme 99996) Manuel Installation Manuel Programmation Section. 4.3 Chapitre. 9. Date: Novembre 1995 PRESTATION Version logiciel: Section. 3.9 Section. 3.8 et 6.9 2.2 et suivants MANUEL ET SECTION MODIFIEE Sous-programmes à exécuter avant et après T (seulement en exécution du programme 99996) Manuel Installation Manuel Programmation Section. 4.3 Chapitre. 9. Fonctions "M" associées aux opérations automatiques Manuel d'Utilisation Section. 4.1.2 Fonctions "M" associées aux opérations d'usinage Manuel d'Utilisation Section. 5.1.1 INTRODUCTION Introduction - 1 CONDITIONS DE SÉCURITÉ Lisez les mesures de sécurité qui suivent, à l’objet d’éviter des lésions aux personnes et à prévenir des dommages à ce produit et aux produits qui y sont raccordés. L’appareil en pourra être réparé que par le personnel autorisé par Fagor Automation. Fagor Automation ne pourra en aucun cas être responsable de tout dommage physique ou matériel qui découlerait du non-respect de ces normes de bases de sécurité Précautions vis à vis de dommages à des personnes Avant d’allumer l’appareil, vérifiez que vous l’avez mis à la terre. En vue d’éviter des décharges électriques, vérifiez que vous avez procédé à la prise de terre. Ne pas travailler dans des ambiances humides. Pour éviter des décharges électriques, travaillez toujours dans des ambiances à humidité relative inférieure à 90% sans condensation à 45º C. Ne pas travailler dans des ambiances explosives Afin d’éviter des risques, des lésions ou des dommages, ne pas travailler dans des ambiances explosives. Précautions pour éviter l’endommagement du produit Ambiance de travail Cet appareil est préparé pour être utilisé dans des Ambiances Industrielles et respecte les directives et les normes en vigueur dans l’Union Européenne. Fagor Automation ne se responsabilise pas des dommages qu’il pourrait provoquer s’il est monté sous d’autres conditions (ambiances résidentielles ou domestiques). Installer l’appareil à l’endroit adéquat Il est recommandé d’installer la Commande Numérique, autant que possible, éloignée de liquides de refroidissement, de produits chimiques, de coups, etc., qui pourraient l’endommager. L’appareil respecte les directives européennes en ce qui concerne la compatibilité électromagnétique. Il est néanmoins conseillé de le tenir éloigné des sources de perturbation électromagnétique, telles que : - Les charges puissantes branchées au secteur sur lequel est raccordé l’équipement. - Les émetteurs-récepteurs portatifs proches (radiotéléphones, émetteurs radioamateurs), - Émetteurs-récepteurs de radio/télévision proches, - Appareils de soudure à l’arc proches, - Lignes de haute tensions proches, - Etc. Conditions de l’environnement La température ambiante qui doit exister au régime de fonctionnement doit être comprise entre +5ºC et +45ºC. La température ambiante qui doit exister au régime de non fonctionnement doit être comprise entre -25ºC et 70ºC. Introduction - 3 Protections de l’appareil Il incorpore 2 fusibles extérieurs rapides (F) de 3,15 Amp./ 250 V., pour la protection de l‘entrée de secteur. Toutes les entrées-sorties digitales sont protégées par 1 fusible extérieurs rapides (F) de 3,15 Amp./ 250 V contre l’éventuelle surtension de la source extérieure (plus de 33 Vcc.) et contre le branchement inversé de la source d’alimentation. Précautions à prendre durant les réparations Ne pas manipuler l’intérieur de l’appareil Seul le personnel autorisé par Fagor Automation peut manipuler l’intérieur de l’appareil. Ne pas manipuler les connecteurs lorsque l’appareil est branché au secteur Avant de manipuler les connecteurs (entrées/sorties, mesure, etc.), vérifiez que l’appareil est débranché du secteur. Symboles de sécurité Symboles pouvant apparaître sur le manuel Symbole ATTENTION. Il a un texte associé qui indique les actions ou les opérations pouvant provoquer des dommages aux personnes ou aux appareils. Symboles que peut présenter le produit Symbole ATTENTION. Il a un texte associé qui indique les actions ou les opérations pouvant provoquer des dommages aux personnes ou aux appareils. Symbole D’ÉLECTROCUTION. Il indique que le point en question peut être sous tension électrique. Symbole PROTECTION DE MASSES. Il indique que le point en question doit être branché au point central de mise à la terre de la machine afin de protéger les personnes et les appareils Introduction - 4 CONDITIONS DE RENVOI Si vous allez envoyer le CNC, emballez-les dans sa caisse en carton originale avec leur matériel d’emballage original. Si vous ne disposez pas du matériel d’emballage original, emballez-le de la façon suivante : 1.- Obtenez une caisse en carton dont les 3 dimensions internes auront au moins 15 cm (6 pouces) de plus que celles de l’appareil, Le carton utilisé pour la caisse doit avoir une résistance de 170 Kg (375 livres). 2.- Si vous avez l’intention de l’expédier à un bureau de Fagor Automation pour qu’il soit réparé, veuillez joindre une étiquette à l’appareil en indiquant le nom du propriétaire de l’appareil,, son adresse, le nom de la personne à contacter, le type d’appareil, le numéro de série, le symptôme et une description succincte de la panne. 3.- Enveloppez l’appareil avec un film de polyéthylène ou d’un matériau semblable afin de le protéger. Si vous allez expédier le moniteur, protégez tout particulièrement le verre de l’écran. 4.- Capitonnez l’appareil dans la caisse en carton, en la remplissant de mousse de polyuréthane de tous côtés. 5.- Scellez la caisse en carton avec du ruban d’emballage ou avec des agrafes industrielles. Introduction - 5 DOCUMENTATION FAGOR POUR LA CNC 800M Manuel CNC 800M OEM Il s’adresse au constructeur de la machine ou à la personne chargée de réaliser l’installation et la mise au point de la Commande Numérique. Le manuel d’installation se trouve à l’intérieur. Elle peut contenir occasionnellement un manuel ayant trait aux “Nouvelles Prestations” de logiciel récemment introduites. Manuel CNC 800M USER. Il s’adresse à l’usager final, c’est-à-dire, à la personne qui va travailler avec la Commande Numérique. Elle contient 2 manuels à l’intérieur : Le Manuel d’Utilisation qui décrit comment travailler avec la CNC. Le Manuel de Programmation, qui décrit comment élaborer un programme en code ISO. Elle peut contenir occasionnellement un manuel ayant trait aux “Nouvelles Prestations” de logiciel récemment introduites. Manuel DNC 25/30 Il s’adresse aux personnes qui vont utiliser l’option de logiciel de communication DNC. Manuel Protocole DNC Il s’adresse aux personne qui désirent réaliser leur propre communication de DNC, sans utiliser l’option de logiciel de communication DNC 25/30. Manuel PLCI Il doit être utilisé lorsque la CNC est munie d’Automate Intégré. Il s’adresse au constructeur de la machine ou à la personne qui se charge de réaliser l’installation et la mise au point de l’Automate Intégré. Manuel DNC-PLC Il s’adresse aux personnes qui vont utiliser l’option de logiciel de communication DNC-PLC. Manuel Floppy Disk Il s’adresse aux personnes qui utilisent le lecteur à disquettes de Fagor. Ce manuel indique comment ledit lecteur à disquettes doit être utilisé. Introduction - 6 CONTENU DU PRÉSENT MANUEL Le Manuel d’Utilisation se compose des parties suivantes : Index Tableau comparatif des modèles Fagor CNC 800M. Nouvelles Prestations et modifications. Introduction Résumé des conditions de sécurité. Conditions de Renvoi. Liste de Documents Fagor pour la CNC 800M. Contenu du présent Manuel. Chapitre 1 Sujets conceptuels Indique la distribution du clavier, du panneau de commandes et de l’information affichée sur le moniteur. Il explique les unités d’affichage et comment les modifier. Il indique les systèmes de référence qui doivent être définis. Comment rechercher le Zéro machine et une présélection de cotes. La manière de sélectionner le travail en cotes absolues ou incrémentales. Chapitre 2 Opérations de base. Il indique comment sélectionner la vitesse d’avance des axes. Comment déplacer la machine à la main ou au moyen du volant électronique. La manière de sélectionner le point de départ (BEGIN) et le point final (END). Comment déplacer l’outil sur le point BEGIN ou au point END. Contrôle de la broche. Sélection de la vitesse, changement de gamme, sens de rotation. Comment activer et désactiver les dispositifs externes. Chapitre 3 Fonctions auxiliaires Il indique comment sélectionner les unités de travail (mm / pouces). La façon de définir la table d’outils. Comment procéder à une mesure et à une inspection d’outil. Comment travailler avec les périphériques. Comment bloquer et débloquer la mémoire de programme. Comment éditer, exécuter et simuler le programme 99996. Chapitre 4 Opérations automatiques. Il indique comment sélectionner et programmer chaque opération automatique Le mode de travail en mode “Semi-Automatique “ et “Niveau Cycle”. Comment sélectionner les conditions d’usinage des opérations automatiques. Le mode d’exécution ou de simulation d’une opération automatique. Chapitre 5 Opérations d’usinage Il indique comment sélectionner chaque opération d’usinage. Comment associer une opération d’usinage à une opération automatique. La manière d’associer des fonctions auxiliaires “M” à l’opération d’usinage. Chapitre 6 Travail avec des pièces. Il indique comment avoir accès au directory de programmes pièce La manière de sélectionner un programme pièce, l’éditer, le simuler et l’exécuter. Comment exécuter une opération sauvegardée au préalable sur une pièce La manière de modifier un programme pièce Comment effacer un programme pièce La manière de travailler avec les périphériques. Comment bloquer et débloquer la mémoire de programme. Codes d’erreur. Introduction - 7 1. CONCEPTS A la mise sous tension de la CNC 800M, l’écran affiche le nom du modèle de CNC et le message suivant: ***GENERAL TEST*** Passed Frapper n’importe quelle touche pour accéder au mode de fonctionnement standard de la CNC. Si le TEST GENERAL a échoué, la CNC affichera les erreurs détectées, qui devront être corrigées avant la mise en service de la machine. 1.1 DESCRIPTION DE LA VISUALISATION La visualisation de ce modèle comprend les zones suivantes, ou fenêtres d’affichage: COMPTEUR 1. Cette fenêtre indique le mode de fonctionnement choisi: Visualisateur, Fraisage linéaire, Poche, etc... Elle indique également l’état de la CNC pendant l’exécution des opérations automatiques (en cours, interruption ou en position). Chapitre: 1 CONCEPTS Section: DESCRIPTION DE LA VISUALISATION Page 1 2. Fenêtre principale Cette fenêtre montre la position en cours de l’outil (coordonnées en X, Y et Z) et le numéro de l’outil sélectionné en cours. Quand une opération automatique est sélectionnée, cette fenêtre montre la position de l’axe sur une seule ligne. Le reste de la fenêtre sert à afficher une représentation graphique de l’opération automatique sélectionnée. 3. Cette fenêtre affiche les informations suivantes: * La vitesse d’avance de l’axe (F) en cours et le pourcentage de correction (%) en vigueur à ce moment. * La vitesse de broche (S) sélectionnée en cours (active) et le pourcentage de correction (%) en vigueur à ce moment. * Le sens de rotation de broche sélectionné en cours . * L’outil sélectionné en cours (T). 4. Cette partie indique les coordonnées du point de début BEGIN (BEG) et de fin (END). Quand une opération automatique est sélectionnée, cette fenêtre affiche les paramètres de définition de cette opération. 5. Fenêtre d’édition et d’affichage de messages CNC. Page Chapitre: 1 2 CONCEPTS Section: DESCRIPTION DE LA VISUALISATION 1.2 DESCRIPTION DU CLAVIER Avec ce clavier, il est possible de communiquer avec la CNC; il se compose des parties suivantes: 1. Touches de fonction 2. Pupitre opérateur 3. Zone pour fonctions et opérations automatiques 4. Zone principale Chapitre: 1 Section: Page CONCEPTS DESCRIPTION DU CLAVIER 3 1.2.1 ZONE PRINCIPALE Cette zone se compose des touches suivantes: Clavier numérique, avec les touches: ., -, 0, 1, 2, 3, 4, 5, 6, 7, 8, 9, permettant l’entrée d’entiers et de valeurs décimales, signés ou non. Permet d’affecter des valeurs aux paramètres de la machine. La frappe des touches vide l’écran. Pour repasser à l’affichage normal, frapper n’importe quelle touche. Si une erreur se produit dans la CNC pendant que l’écran est vide, il reprend son état normal. Après la frappe de cette touche, la valeur des coordonnées en X peut être fixée. Dès l’entrée de la valeur, valider par [ENTER]. Après la frappe de cette touche, la valeur des coordonnées en Y peut être fixée. Dès l’entrée de la valeur, valider par [ENTER]. Après la frappe de cette touche, la valeur des coordonnées en Z peut être fixée. Dès l’entrée de la valeur, valider par [ENTER]. La frappe de cette touche permet de fixer la vitesse d’avance de l’axe. Dès l’entrée de cette valeur, frapper pour la valider. La frappe de cette touche permet de fixer la vitesse de broche. Dès l’entrée de la valeur, valider par [ENTER]. La frappe de cette touche permet de définir le nouvel outil à sélectionner. Après la frappe, 2 choix sont possibles: * Frappe de pour permettre le choix du nouvel outil par la CNC. * Frappe de [ENTER] pour permettre à la CNC de charger cette valeur en mémoire sans sélectionner de nouvel outil. Cette option est utile pour l’édition d’opérations qui seront chargées en mémoire plus tard. La frappe de cette touche permet de sélectionner le numéro de programme pièce à éditer ou à exécuter. Ensuite, frapper [ENTER] pour valider le choix. Cette touche permet de valider les commandes CNC générées dans la fenêtre d’édition. Cette touche permet de récupérer les données entrées précédemment dans la mémoire de programmes pièce ou les tables CNC pour vérification ou modification. Avant de frapper cette touche, sélectionner les opérations ou la valeur à analyser au moyen des touches de curseur ou à flèche. Permet d’accéder au mode entrée de données pour toute opération automatique. Frapper une seconde fois pour sortir de ce mode. Supprime le dernier caractère introduit dans la fenêtre d’édition. Page Chapitre: 1 Section: 4 CONCEPTS DESCRIPTION DU CLAVIER 1.2.2 ZONE DE FONCTIONS ET D’OPERATIONS AUTOMATIQUES Cette zone se compose des touches suivantes: Permet de sélectionner les coordonnées du point de début (BEG) correspondant pour modification ultérieure ou commander le déplacement de la machine jusqu’à ce point. Permet de sélectionner les coordonnées du point de fin (END) correspondant pour modification ultérieure ou commander le déplacement de la machine jusqu’à ce point. Permet d’accéder au mode incrémental (INC). Quand le mode incrémental est sélectionné, la partie droite de la fenêtre principale affiche “INC”. Pour repasser au mode normal, frapper cette touche à nouveau. Permet de sélectionner le mode de fonctionnement pour exécution de l’opération automatique. Mode continu: l’opération sélectionnée est exécutée du début à la fin sans interruption. Mode passe par passe: l’opération sélectionnée est exécutée une passe à la fois. La touche doit être frappée avant chaque passe. Lorsque le mode passe par passe est sélectionné, la partie droite de l’écran affiche le symbole . Associe une opération d’usinage à l’opération automatique sélectionnée. Sélectionne l’opération automatique “Positionnement point à point” Sélectionne l’opération automatique “Positionnement en ligne” Sélectionne l’opération automatique “Positionnement en arc” (trou de boulon) Sélectionne l’opération automatique “Positionnement en rectangle” Sélectionne l’opération automatique “Positionnement en grille” Sélectionne l’opération automatique “Fraisage linéaire” Sélectionne l’opération automatique “Fraisage courbe” Sélectionne l’opération automatique “Fraisage de profil” Sélectionne l’opération automatique “Poche” Sélectionne l’opération automatique “Moyeu” (bossage) Sélectionne l’opération automatique “Ebauche d’arête” Sélectionne l’opération automatique “Surfaçage” Quand une opération automatique ou d’usinage a été sélectionnée, chaque frappe de cette touche affiche l’option suivante disponible. Chapitre: 1 Section: Page CONCEPTS DESCRIPTION DU CLAVIER 5 1.2.3 TOUCHES DE FONCTION Ces touches autorisent les fonctions suivantes: Accès au menu des fonctions auxiliaires disponibles avec cette CNC. Accès au mode simulation pour les opérations et les programmes. Accès au mode “Calculateur”. Cette option n’est pas disponible avec la version actuelle. Sélection des options précédentes et suivantes en réponse aux demandes du menu affiché et exécution de la recherche à la référence (zéro) machine. Déplacement d’un champ de données à un autre dans le mode introduction de données pour les opérations automatiques et d’usinage. Elles permettent également de sélectionner les données précédentes et suivantes dans les fonctions BEG et END. Mise en service et arrêt de l’arrosage. Activation et désactivation des sorties: O1, O2 et O3. Remise à zéro de la CNC afin qu’elle prenne les valeurs par défaut fixées par les paramètres de la machine. Cette touche doit également être frappée à chaque changement des paramètres machine afin que les nouveaux soient pris en compte par la CNC. Lorsqu’une opération automatique est en cours, elle doit d’abord être stoppée. La CNC demande confirmation de la commande, nécessaire avant de frapper cette touche à nouveau. Pour annuler la remise à zéro, frapper . Si la touche RESET (RAZ) est frappée pendant qu’une des opérations automatiques est sélectionnée, la CNC quitte ce mode et repasse au mode affichage. Page Chapitre: 1 Section: 6 CONCEPTS DESCRIPTION DU CLAVIER 1.2.4 PUPITRE OPERATEUR Le pupitre opérateur se compose des zones suivantes: 1. Clavier de commande des axes en continu. 2. Sélecteur, composé des éléments suivants: Permet de sélectionner le facteur de multiplication appliqué par la CNC aux impulsions provenant de la manivelle électronique (1, 10, 100). JOG Permet de sélectionner la distance de déplacement de l’axe (1, 10, 100, 1000 microns ou dix-millièmes de pouce) par la frappe de la touche correspondante. FEED Permet de faire varier l’avance programmée de 0 à 120%. 3. Clavier de commande de broche. Il permet de démarrer la broche dans le sens actif lors de l’arrêt ou de faire varier sa vitesse de rotation entre 50% et 120% de la vitesse programmée, par incréments de 5%. 4. Claviers pour [DEMARRAGE] ou [ARRET] des déplacements programmés, des opérations automatiques et des programmes pièce. Chapitre: 1 Section: Page CONCEPTS DESCRIPTION DU CLAVIER 7 1.3 UNITES D’AFFICHAGE (mm/pouces) La fenêtre principale de cette CNC affiche en permanence les coordonnées en X, Y et Z de la position de l’outil. Avec cette CNC, il est possible d’afficher la position des axes en mm ou en pouces. Pour changer de type d’unités d’affichage, frapper [AUX] et sélectionner les unités au moyen de l’option “MM/POUCE”. Chaque sélection permet de passer des mm aux pouces et vice-versa en montrant la position de l’outil dans les unités sélectionnées. Pour sortir du mode de fonctionnement des fonctions auxiliaires et repasser au mode affichage standard, frapper [AUX] ou [END]. Page Chapitre: 1 Section: 8 CONCEPTS UNITES D'AFFICHAGE 1.4 SYSTEMES DE REFERENCE Dans la machine équipée de cette CNC, le Zéro Machine doit être défini pour chaque axe. Ce point est défini par le constructeur comme origine du système de coordonnées (zéro pièce) de la machine. Il est également possible de définir un autre point d’origine pour la programmation des cotes de la pièce, ou Zéro Pièce. Ce nouveau point d’origine est laissé au choix de l’opérateur et les valeurs relatives aux positions indiquées par la CNC sont prises par rapport à ce point. Ne pas oublier que, pour sélectionner le Zéro Pièce, la CNC doit être en mode absolu. Si elle est en mode incrémental, le message “INC” s’affiche dans la partie droite de la fenêtre principale : frapper la touche . Le Zéro Pièce sélectionné est sauvegardé, même en cas de mise hors tension de la CNC; il n’est annulé que par la sélection d’un nouveau Zéro Pièce ou en cas de recherche du Zéro Machine. 1.4.1 RECHERCHE DE L’ORIGINE La recherche du Zéro Machine s’effectue sur un axe à la fois de la façon suivante: * Frapper la touche correspondant à l’axe dont on recherche l’origine [X], [Y], [Z], puis la touche flèche vers le haut. * La fenêtre d’édition demandera confirmation de la commande. Frapper la touche sur cet axe. pour ordonner à la CNC d’effectuer la recherche de l’origine Si vous ne désirez pas rechercher l’origine, frappez toute autre touche. Pour annuler la recherche en cours, frappez [CLEAR]. Pendant une recherche de l’origine, la CNC initialise les affichages de l’axe et annule le Zéro Pièce qui avait été sélectionné. Chapitre: 1 Section: Page CONCEPTS SYSTEMES DE REFERENCE 9 1.4.2 PRESELECTION DU ZERO Il est possible de présélectionner le Zéro Pièce désiré afin d’utiliser les coordonnées figurant sur les plans de la pièce sans avoir à modifier les divers points de la pièce. Pour présélectionner le Zéro Pièce, procéder comme suit: * La CNC doit être en mode absolu. Si elle est en mode incrémental, le message “INC” s’affiche dans la partie droite de la fenêtre principale; frapper la touche . * Frapper la touche correspondant à l’axe concerné par la présélection, soit [X], [Y], [Z], puis [ENTER]. La CNC demandera confirmation de la commande : frapper [ENTER] à nouveau. * Répéter cette opération pour les autres axes. Chaque fois que cette opération est exécutée, la CNC prend ce point comme la nouvelle origine des coordonnées. 1.4.3 PRESELECTION DES COORDONNEES Cette fonction permet de présélectionner les valeurs des coordonnées (position) désirées afin d’utiliser les coordonnées figurant sur les plans de la pièce sans avoir à modifier les divers points de la pièce. Ce type de présélection peut aussi être utilisé lorsqu’il est plus commode de travailler par rapport au zéro plutôt que par rapport à la valeur suivante comme habituellement. Pour présélectionner une valeur de coordonnées, procéder comme suit: * Frapper la touche correspondant à l’axe concerné par la présélection, soit [X], [Y], [Z]. * Introduire avec le clavier les valeurs de la position désirée pour ce point. * Frapper [ENTER]. La CNC demandera confirmation de la commande : frapper [ENTER] à nouveau. La CNC prend cette présélection comme nouvelle valeur de position (coordonnées) pour l’axe concerné. * Répéter cette opération pour les autres axes. A chaque présélection, la CNC prend en compte un nouveau Zéro Pièce, qui sera situé à une distance égale à la valeur présélectionnée par rapport au point présélectionné. Page Chapitre: 1 Section: 10 CONCEPTS SYSTEMES DE REFERENCE 1.5 FONCTIONNEMENT EN MODE INCREMENTAL Cette CNC permet de définir un Zéro Flottant ou un Zéro Incrémental en plus du Zéro Pièce décrit plus haut, afin d’utiliser les coordonnées par rapport à n’importe quel point de la pièce. Pour travailler en mode incrémental, les valeurs des coordonnées affichées par la CNC doivent être incrémentales; le message “INC” s’affiche dans la partie droite de la fenêtre principale. Si ce message n’apparaît pas, frapper . Attention: A chaque sélection du mode incrémental, la CNC prend comme Zéro Flottant le Zéro Pièce en cours actif. En conséquence, elle continuera à montrer les mêmes valeurs de position en X, Y et Z. Pour définir un autre Zéro Flottant, d’autres coordonnées ou un autre Zéro Pièce doivent être présélectionnés. A partir de cet instant, les coordonnées affichées par la CNC seront prises par rapport au nouveau Zéro Flottant défini. La CNC sauvegarde le Zéro Pièce présélectionné quand elle fonctionne en mode absolu et elle affichera la position en X, Y et Z par rapport à ce zéro lorsqu’elle repassera du mode incrémental au mode absolu. Chapitre: 1 CONCEPTS Section: FONCTIONNEMENT EN MODE INCREMENTAL Page 11 2. OPERATIONS DE BASE 2.1 FIXATION DE LA VITESSE D’AVANCE PAR AXE Cette CNC permet de fixer la vitesse d’avance (F) sur les axes aussi souvent que nécessaire afin d’assurer en permanence à la vitesse appropriée. De plus, le Pupitre Opérateur comporte un sélecteur à plusieurs positions permettant de modifier la vitesse d’avance pendant ces déplacements par l’application du pourcentage (%) de correction sélectionné à la vitesse d’avance définie dans chaque cas. Ce pourcentage de correction est indiqué par le Sélecteur de Correction de Vitesse d’avance (FEED); la plage de corrections est comprise entre 0 et 120% de la vitesse d’avance définie. Pour fixer la vitesse d’avance, procéder comme suit: * Frapper [F] * Introduire la valeur désirée par le clavier et frapper . Si les unités choisies sont en mm/mn, cette valeur doit être comprise entre 0 et 65535,000 mm/mn. Si les unités choisies sont en pouces/mn, cette valeur doit être comprise entre 0 et 25801.1811 pouces/mn. La CNC prend cette valeur en compte et l’affiche sur l’écran. Elle affiche également le pourcentage de correction de vitesse d’avance en cours sélectionné par le bouton FEED. Exemple: F120 100%. Attention: Quand la CNC affiche une valeur de “F0000”, elle applique la vitesse d’avance maximum définie par le paramètre machine correspondant à chaque axe. Chapitre: 2 OPERATIONS DE BASE Section: FIXATION DE LA VITESSE D’AVANCE PAR AXE Page 1 2.2 SELECTION DE L'OUTIL La CNC doit savoir en permanence quel est l’outil employé pour les opérations d’usinage. Pour ce faire, après la sélection du nouvel outil et l’opération de changement, frapper [TOOL] suivi de l’outil sélectionné, puis frapper . La CNC suppose toutes les valeurs de décalage correspondant au nouvel outil sélectionné. Ces valeurs (longueur et rayon d’outil) seront prises en compte par la CNC lorsqu’elle exécutera une opération ultérieure. Si un nouvel outil doit être sélectionné pendant l’exécution d’un cycle ou d’une pièce préprogrammée, la CNC procède de la façon suivante: * Elle interrompt l’exécution. * Elle exécute la fonction auxiliaire M05 pour stopper la broche. * Elle stoppe l’arrosage. * Elle affiche un message indiquant le numéro correspondant au nouvel outil à sélectionner. Dès la fin de l’opération de changement d’outil, frapper [ENTER]. La CNC rétablit l’arrosage, la broche reprend son mouvement de rotation dans le sens et à la vitesse précédents, puis elle reprend l’exécution de la pièce ou du cycle. Page 2 Chapitre: 2 Section: OPERATIONS DE BASE SELECTION DE L'OUTILE 2.3 DEPLACEMENT MANUEL DES AXES 2.3.1 DEPLACEMENT MANUEL CONTINU Cette option permet de déplacer chaque axe de la machine en manuel. Dès que la vitesse d’avance de l’axe a été présélectionnée et que la correction d’avance (0 à 120%) a été fixée par le sélecteur (FEED) du pupitre opérateur de la machine, frapper la touche JOG correspondant à l’axe concerné et à son sens de déplacement en manuel. Selon la valeur affectée au paramètre machine P12, ce déplacement s’effectue comme suit: * * Si P12 = Y, l’axe se déplace tant que la touche JOG est maintenue. Si P12 = N, les axes commencent à se déplacer lorsque la touche JOG est enfoncée et stoppent quand la touche ou la touche JOG d’un autre axe est actionnée. Dans ce cas, l’autre axe commence à se déplacer. Si la touche est actionnée pendant le déplacement manuel d’un axe, la CNC applique le pourcentage de correction indiqué ci-dessous: % sélectionné 0 2 4 10 20 30 40 50 60 70 80 90 100 110 120 % appliqué 0 102 104 110 120 130 140 150 160 170 180 190 200 200 200 Ce pourcentage reste en vigueur tant que cette touche est maintenue; dès son relâchement, le pourcentage de correction précédent (0 à 120%) est rétabli. 2.3.2 DEPLACEMENT MANUEL INCREMENTAL Cette option permet le déplacement manuel sur un axe donné et dans le sens défini sur une distance fixée par les positions en JOG du sélecteur FEED du pupitre opérateur. L’avance appliquée à ces déplacements en manuel est définie par le constructeur de la machine. Les positions disponibles avec ce sélecteur sont 1, 10, 100, 1000 et 10000, qui indiquent le nombre d’unités de déplacement. Ces unités sont celles utilisées dans le format d’affichage. Exemple: Position du sélecteur 1 10 100 1000 10000 Déplacement incrémental 0,001 mm 0,010 mm 0,100 mm 1,000 mm 10,000 mm ou ou ou ou ou 0,0001 pouce 0,0010 pouce 0,0100 pouce 0,1000 pouce 1,0000 pouce Après le choix de la position désirée pour le sélecteur, chaque frappe de la touche de déplacement en manuel déplacel’axe de la valeur indiquée dans le sens choisi. Chapitre: 2 OPERATIONS DE BASE Section: DEPLACEMENT MANUEL DES AXES Page 3 2.3.3 DEPLACEMENT MANUEL DES AXES PAR MANIVELLE ELECTRONIQUE Cette option permet de déplacer les axes de la machine en manuel au moyen de la manivelle électronique. Pour ce faire, sélectionner d’abord l’une des positions sur le sélecteur FEED du Pupitre Opérateur correspondant à la manivelle électronique Les positions disponibles sont 1, 10 et 100, qui indiquent le facteur de multiplication appliqué aux impulsions fournies par le volant électronique. C’est de cette manière et après avoir multiplié le facteur de multiplication par les impulsions fournies par le volant que l’on obtient le nombre d’unités que l’on veut déplacer l’axe. Les unités en question correspondent aux unités utilisées dans le format d’affichage. Exemple: Résolution de la manivelle: 250 lignes/tour. Position du sélecteur 1 10 100 Déplacement/tour 0,250 mm ou 0,0250 pouce 2,500 mm ou 0,2500 pouce 25,000 mm ou 2,5000 pouce Selon la valeur assignée au paramètre machine "P628(5)" dont il s’agisse, la CNC agit de la manière suivante dans le reste des positions du commutateur sélecteur du Panneau de Commande: P628(5) = 0 Les axes peuvent être déplacés au moyen du volant, tout comme si la position de volant «x1» était sélectionnée sur le sélecteur. P628(5) = 1 Les axes ne peuvent pas être déplacés au moyen du volant. Ce dernier est inactif. Si vous essayez de déplacer un axe à une vitesse supérieure à la vitesse d’avance définie par les paramètres machine "P110, P210 et P310", la CNC limitera ces valeurs en ignorant le reste des impulsions, ce qui évite toute erreur de poursuite. Page 4 Chapitre: 2 OPERATIONS DE BASE Section: DEPLACEMENT MANUEL DES AXES Machine à une manivelle électronique Dès que la position désirée du sélecteur a été choisie, frapper l’une des touches JOG correspondant à l’axe à déplacer en manuel. Cet axe apparaît en surbrillance sur l’écran. Si vous utilisez une manivelle FAGOR à touche de sélection d’axe, l’axe peut être sélectionné comme suit: * Frapper la touche située à l’arrière de la manivelle. La CNC sélectionne le 1er axe et l’affiche en surbrillance à l’écran. * Si cette touche est frappée à nouveau, la CNC sélectionne l’axe suivant et ainsi de suite en boucle (choix du premier axe après le dernier). * Si cette touche est maintenue plus de 2 secondes, la CNC annule la sélection de l’axe. La machine déplace l’axe sélectionné dès que la manivelle tourne dans un sens ou dans l’autre, selon le sens de rotation de la manivelle. Machine à deux ou trois manivelles La machine déplace chaque axe dès que la manivelle correspondante tourne selon la position du sélecteur sélectionnée et le sens de rotation. Chapitre: 2 OPERATIONS DE BASE Section: DEPLACEMENT MANUEL DES AXES Page 5 2.4 POINT DE DEBUT (BEG) ET DE FIN (END) Cette CNC permet de définir un point de début (BEG) et un point de fin (END) afin de faciliter les tâches d’usinage. Ces points peuvent être redéfinis aussi souvent que désiré et peuvent être utilisés pour définir les extrêmités de la pièce, les limites d’une zone à usiner donnée, etc... 2.4.1 FIXATION DES POINTS DE DEBUT (BEG) ET DE FIN (END) Frapper la touche [DATA] ou sur la touche correspondant au point à définir, soit [BEG] ou [END]. La CNC affichera la valeur en question en la mettant en relief. Les valeurs en X, Y et Z de ce point doivent être définies une par une et on doit suivre la démarche suivante: 1.- Taper sur la touche de l’axe que l’on veut définir [X] , [Y] , [Z] . La CNC affichera en mettant en relief la valeur du champ en question. 2.- Assigner au champ en question la valeur voulue. Il faut pour ce faire utiliser une des démarches suivantes: * Saisir par le clavier la cote correspondant au champ en question et taper sur la touche [ENTER] * Déplacer la machine au moyen des manivelles, du volant électronique ou au moyen des touches de JOG du panneau de commande jusqu’au point voulu et taper sur la touche [ENTER] . Cette option n’est pas disponible pour l’axe "Z". La CNC modifie la cote correspondant à l’axe sélectionné. Elle ne modifie pas les valeurs correspondant aux axes restants. 3.- La CNC affiche le champ suivant comme étant sélectionné. Pour pouvoir sélectionner un autre champ, il faut taper sur la touche de l’axe que l’on veut définir [X], [Y] [Z] ou bien utiliser les touches 4.- Répéter l’étape 2 afin de définir ce nouveau champ. 5.- Répéter les étapes 3 et 4 toutes les fois qu’il sera nécessaire. 6.- Pour abandonner le mode de sélection, il faut taper sur la touche [CLEAR] ou [DATA] Page 6 Chapitre: 2 Section: OPERATIONS DE BASE DEBUT et FIN 2.4.2 POSITIONNEMENT SUR LES POINTS “BEGIN” ou “”END” Pour amener l’outil jusqu’au point de début ou de fin, procéder comme suit: * Frapper [BEG] ou [END] pour amener l’outil jusqu’au point de début ou de fin respectivement. * Frapper . La CNC déplace l’axe Z en premier, puis les axes X et Y ensemble afin de positionner l’outil sur le point sélectionné. Ces déplacements s’effectuent à la vitesse d’avance programmée. Pour déplacer un seul axe, procéder comme suit: * Frapper [BEG] ou [END] pour amener l’outil jusqu’au point de début ou de fin respectivement. * Frapper la touche de l’axe correspondant, soit [X], [Y] ou [Z]. * Frapper . La CNC déplace l’outil automatiquement jusqu’au point sélectionné le long de cet axe à la vitesse d’avance programmée. Les autres axes restent immobiles. La sélection du champ suivant sera signalée si un autre déplacement doit être réalisé. Pour sélectionner un autre champ, frapper la touche de l’axe correspondant, soit [X], [Y] ou [Z], ou les touches . Chapitre: 2 OPERATIONS DE BASE Section: CONTROLE DE BROCHE Page 7 2.5 CONTROLE DE BROCHE 2.5.1 FIXATION DE LA VITESSE DE BROCHE Pour définir la vitesse de la broche, frapper [S]. Après l’entrée de la valeur désirée, frapper . Il est possible de définir une valeur entre S0 et S9999 tours/mn. Toutefois, la vitesse de rotation maximum est fixée par le constructeur et figure dans le manuel de la machine. La CNC appliquera cette valeur, même si l’opérateur définit une vitesse supérieure. Dès que la nouvelle vitesse a été définie, la CNC agit de la façon suivante: * Quand la broche est déjà en rotation, la CNC délivre la tension analogique correspondant à la nouvelle vitesse choisie. Si la vitesse en RPM (t/mn) choisie correspond à une autre gamme, la CNC génère un changement de gamme avant de délivrer la nouvelle tension analogique. * Si la broche est à l’arrêt, la CNC mémorise la valeur choisie afin de délivrer la tension analogique correspondante dès le démarrage de la broche. Si la nouvelle vitesse en RPM (t/mn) choisie correspond à une autre gamme, la CNC génère un changement de gamme. La vitesse de broche définie peut varier de 50 à 120% par pas de 5% au moyen des touches situées sur le pupitre opérateur. 2.5.2 CHANGEMENT DE PLAGE DE VITESSES DE BROCHE Avec cette CNC, la machine peut être équipée d’une boîte de vitesses permettant d’adapter les vitesses et les couples du moteur de broche aux diverses exigences de l’usinage. Quand la nouvelle vitesse de broche sélectionnée “S” implique un changement de gamme, la CNC intervient sur l’armoire électrique pour mettre ce changement en oeuvre sans intervention de l’opérateur. Page 8 Chapitre: 2 Section: OPERATIONS DE BASE CONTROLE DE BROCHE 2.5.3 ROTATION DE LA BROCHE DANS LE SENS HORAIRE Pour faire tourner la broche dans le sens horaire dès la définition de sa vitesse, frapper la touche . Quand la broche est en rotation, il est possible de sélectionner une nouvelle vitesse ou de changer la vitesse en cours par les touches suivantes: A chaque frappe de cette touche, la CNC augmente la vitesse de la broche de 5%, jusqu’au maximum de 120% de la vitesse programmée. Ne pas oublier que la vitesse maximum est limitée par la valeur affectée à la gamme sélectionnée en cours. A chaque frappe de cette touche, la CNC réduit la vitesse de la broche de 5%, le minimum étant de 50% de la vitesse programmée. 2.5.4 ROTATION DE LA BROCHE DANS LE SENS ANTI-HORAIRE Pour faire tourner la broche dans le sens anti-horaire dès la définition de sa vitesse, frapper . Quand la broche est en rotation, il est possible de sélectionner une nouvelle vitesse ou de changer la vitesse en cours par les touches suivantes: A chaque frappe de cette touche, la CNC augmente la vitesse de la broche de 5%, jusqu’au maximum de 120% de la vitesse programmée. Ne pas oublier que la vitesse maximum est limitée par la valeur affectée à la gamme sélectionnée en cours. A chaque frappe de cette touche, la CNC réduit la vitesse de la broche de 5%, le minimum étant de 50% de la vitesse programmée. 2.5.5 ARRET DE LA BROCHE Pour stopper la rotation de la broche, frapper . La CNC mémorise la vitesse “S” sélectionnée avant l’arrêt, et la broche reprend cette vitesse quand la touche ou est frappée. Chapitre: 2 OPERATIONS DE BASE Section: DISPOSITIFS EXTERNES Page 9 2.6 ACTIVATION/DESACTIVATION DES DISPOSITIFS EXTERNES Cette CNC permet d’activer et de désactiver 4 dispositifs externes, y compris l’arrosage. Les autres dispositifs dépendent du type de machine. Ces dispositifs peuvent être activés ou désactivés à tout moment, sauf indication contraire du constructeur de la machine. Les touches permettent d’exécuter ces opérations. Chaque frappe de ces touches change l’état (activé/désactivé) du dispositif correspondant. Page 10 Chapitre: 2 Section: OPERATIONS DE BASE DISPOSITIFS EXTERNES 3. FONCTIONS AUXILIAIRES Pour accéder à cette option, frapper [AUX] dès que la CNC est en mode DRO (visualisateur). La CNC affiche une liste d’options. Pour sélectionner une option, frapper la touche portant le numéro correspondant. L’opérateur peut accéder à toutes les options présentées, à l’exception de la dénommée “MODES AUXILIAIRES”. Quand cette option est sélectionnée, la CNC demande un code d’accès pour entrer dans les diverses tables et dans les modes disponibles pour le constructeur. Pour sortir d’une de ces options et repasser à l’affichage standard, frapper la touche [END]. 3.1 MILLIMETRES <—> POUCES Quand cette option est sélectionnée, la CNC fait passer les unités d’affichage de mm à pouces et vice-versa et affiche les nouvelles coordonnées en X, Y et Z dans les nouvelles unités. L’avance (F) de l’axe s’affiche également avec les nouvelles unités. Ne pas oublier que les valeurs mémorisées pour BEGIN (début) et END (fin) et que les données relatives à des opérations spéciales n’ont pas d’unités. En conséquence, les valeurs resteront inchangées lors du passage de mm à pouces et vice-versa. 3.2 COMPENSATION DE LONGUEUR D’OUTIL Lorsque cette option est sélectionnée, la CNC active ou annule la compensation de longueur d’outil. Lorsque la compensation de longueur d’outil n’est PAS appliquée, la CNC affiche la valeur de position (coordonnées) de la base de l’outil. Lorsque la compensation de longueur d’outil est appliquée, la CNC affiche soit la position de la pointe de l’outil, soit celle de la base de l’outil en fonction de l’état du paramètre machine P626(1). La partie droite de la fenêtre principale affiche le symbole compensation de longueur est active. Chapitre: 3 FONCTIONSAUXILIAIRES Section: chaque fois que la Page 1 3.3 TABLE D’OUTILS Quand cette option est sélectionnée, la CNC affiche les valeurs affectées à chaque correcteur, c’est-à-dire les dimensions de chaque outil devant être utilisé pour usiner les pièces. Dès que la table de correcteurs d’outil est sélectionnée, l’opérateur peut déplacer le curseur une ligne à la fois au moyen des touches à flèche vers le haut et le bas. Chaque correcteur d’outil se compose de plusieurs champs qui définissent les dimensions de l’outil. Ces champs sont les suivants: R Rayon de l’outil Le rayon est indiqué dans les unités en vigueur. La valeur maximum est : R 1.000,000 mm ou R 39,3700 pouces La CNC prendra cette valeur "R" en compte lors de l'application de la compensation de rayon d'outil. L Longueur de l’outil La longueur est indiquée dans les unités en vigueur. La valeur maximum est : L 1.000,000 mm ou L 39,3700 pouces La CNC prendra cette valeur "L" en compte lors de l'application de la compensation de longueur d'outil. I Usure du rayon de l’outil L’usure est indiquée dans les unités en vigueur. La valeur maximum est : I ± 32,766 mm ou I ± 1,2900 pouce La CNC ajoutera cette valeur au “R” nominal pour calculer le rayon réel (R + I). K Usure de la longueur de l’outil L’usure est indiquée dans les unités en vigueur. La valeur maximum est : K ± 32,766 mm ou K ± 1,2900 pouce La CNC ajoutera cette valeur au “L” nominal pour calculer la longueur réelle (L + K). Page 2 Chapitre: 3 FONCTIONSAUXILIAIRES Section: TABLE D’OUTILS 3.3.1 MODIFICATION DES DIMENSIONS D’OUTIL Pour initialiser une table en indiquant “0” dans tous les champs de chaque outil, frappez la séquence suivante: [F] [S] [P] [ENTER]. Cette CNC propose l’option “ETALONNAGE DE L’OUTIL” décrite plus loin. Lorsque les outils ont été calibrés, la CNC affecte à chaque correcteur d’outil les dimensions de l’outil correspondant. Pour modifier les valeurs de la table d’outils (valeurs “R”, “L”, “T” et “K”), sélectionner le correcteur correspondant au niveau de la CNC en frappant au clavier le numéro d’outil désiré avant de frapper [RECALL] (rappel). La zone d’édition affichera les valeurs en cours affectées à ce correcteur d’outil. Pour changer ces valeurs, amener le curseur sur la valeur en cours au moyen des touches à flèche vers le haut ou le bas. Les nouvelles valeurs doivent “écraser” les valeurs en cours. Dès que les nouvelles valeurs ont été introduites, frapper [ENTER] pour les charger en mémoire. Pour sortir de ce mode, déplacer le curseur vers la droite jusqu’à ce qu’il sorte de la zone éditée, puis frapper [END]. Chapitre: 3 FONCTIONSAUXILIAIRES Section: TABLE D’OUTILS Page 3 3.4 ETALONNAGE DES OUTILS Cette option permet d’étalonner les outils et de charger les dimensions des outils dans la table de correcteurs d’outils de la CNC. La CNC affiche un graphique dans l’angle inférieur droit du moniteur, qui sert de guide pour l’utilisateur pendant l’étalonnage en mettant en surbrillance les données à demander. La procédure d’étalonnage est la suivante: 1. La CNC demande la dimension en Z de la pièce (point de contact) à utiliser pour étalonner l’outil. Inscrire cette valeur et frapper [ENTER]. 2. La CNC demande le numéro de l’outil (T) à étalonner. Inscrire le n° de l’outil et frapper [ENTER]. 3. Déplacer les axes en manuel au moyen des manivelles mécaniques ou électroniques, ou grâce aux touches JOG du pupitre opérateur jusqu’à ce que l’outil touche la pièce sur l’axe Z. Frapper [ENTER]. La CNC étalonne l’outil en longueur et met à jour le correcteur d’outil correspondant. La CNC demande si un nouvel outil doit être étalonné. Répéter les opérations 2 et 3 autant de fois que nécessaire. Frapper [END] pour quitter ce mode et repasser au mode d’affichage standard. Attention: Pendant l’étalonnage d’un outil, il est possible d’utiliser à tout moment les manivelles électroniques, les touches JOG et la broche du pupitre opérateur. Page 4 Chapitre: 3 FONCTIONSAUXILIAIRES Section: ETALONNAGEDESOUTILS 3.5 EXECUTION / SIMULATION DU PROGRAMME 99996 Le programme P99996 est un programme utilisateur spécial en code ISO. Il doit être édité (écrit) sur PC et envoyé à la CNC au moyen de l’option Périphériques. Quand l’option “Exécution du programme P99996” est activée, il est possible de l’exécuter ou de le simuler en frappant . 3.5.1 EXECUTION DU PROGRAMME P99996 Quand l’option “Exécution du programme P99996” est activée, la CNC affiche les informations suivantes: AUTOMATIQUE COMMANDE ACTUELLE RESTE La ligne supérieure affiche “AUTOMATIQUE”, le n° du programme (P99996) et le n° du premier bloc du programme ou celui du bloc en cours. L’écran affiche ensuite le contenu des premiers blocs du programme. Si le programme est en cours, le premier bloc de la liste est celui en cours d’exécution à cet instant. Les valeurs de position en X, Y et Z indiquent les valeurs programmées (COMMANDE), la position actuelle (ACTUELLE) et la distance restante (RESTE) avant que les axes n’atteignent la position “COMMANDE”. Le bas de l’écran affiche les conditions d’usinage sélectionnées en cours : l’avance F programmée, la correction de F en pourcentage, la vitesse de broche programmée S, la correction de S en pourcentage, l’outil programmé et les fonctions G et M actives. Pour exécuter le programme P99996, frapper partir du premier bloc. . L’exécution commence toujours à Si l’on désire interrompre l’exécution du programme, il faut frapper la touche L’exécution du programme s’arrête et les touches suivantes sont disponibles: Pour reprendre l’exécution du programme frapper la touche Chapitre: 3 FONCTIONSAUXILIAIRES . . Section: EXECUTION / SIMULATION P99996 Page 5 3.5.1.1 CONTROLE DES OUTILS Cette option permet d’interrompre l’exécution du programme P99996 et d’inspecter l’outil afin de vérifier son état et de le remplacer si nécessaire. Pour ce faire, procéder comme suit: a) Frapper pour interrompre le programme. b) Frapper [OUTIL]. A cet instant, la CNC exécute la fonction auxiliaire M05 pour stopper la broche et elle affiche sur l’écran: TOUCHES JOG DISPONIBLES OUT c) Amener l’outil à la position désirée au moyen des touches JOG. Dès que l’outil est “hors trajectoire”, la broche peut être démarrée et stoppée à nouveau par les touches correspondantes du pupitre opérateur. d) Dès la fin de l’inspection ou du changement de l’outil, frapper [END]. La CNC exécute une fonction M03 ou M04 pour démarrer la broche dans le sens en cours lors de l’interruption du programme. L’écran affiche alors: RETOUR AXES HORS POSITION “Axes hors position” signifie qu’ils ne se situent pas au même point que lorsque le programme a été interrompu. e) Déplacer les axes en manuel jusqu’à la position d’interruption du programme au moyen des touches JOG correspondantes. La CNC interdit le dépassement (surcourse) de cette position. Lorsque les axes sont en position, l’écran affiche: RETOUR AXES HORS POSITION AUCUN f) Frapper Page 6 pour reprendre l’exécution du programme P99996. Chapitre: 3 FONCTIONSAUXILIAIRES Section: EXECUTION / SIMULATION P99996 3.5.1.2 MODES D’EXECUTION Cette CNC permet d’exécuter le programme P99996 du début à la fin sans interruption ou en bloc à bloc par la frappe de . La ligne supérieure de l’écran affiche le mode de fonctionnement sélectionné, soit “Automatique”, soit “Bloc unique”. Pour changer de mode, frapper à nouveau. Dès que le mode d’exécution désiré est sélectionné, frapper gramme. pour exécuter le pro- 3.5.1.3 RAZ DE LA CNC Cette option permet d'initialiser la CNC , l'assignant toutes les conditions initiales définies par les paramètres machine. Quand vous quittez ce mode de fonctionnement, la CNC affiche le mode DRO (visualisateur). Pour pouvoir procéder à une REMISE A ZERO de la CNC, il faut interrompre l'exécution du programme et ensuite frapper la touche . La CNC demandera confirmation de cette fonction en affichant le message clignotant: “RESET?”. Pour poursuivre, frapper à nouveau; pour l’annuler, frapper la touche 3.5.1.4 AFFICHAGE DES BLOCS DE PROGRAMME Pour afficher les blocs situés avant et après ceux affichés à l’écran, frapper: Affiche les blocs précédents Affiche les blocs suivants Attention: Ne pas oublier que l’exécution de P99996 commence toujours au premier bloc du programme, quel que soit le bloc affiché à l’écran. Chapitre: 3 FONCTIONSAUXILIAIRES Section: EXECUTION / SIMULATION P99996 Page 7 3.5.1.5 MODES D’AFFICHAGE Quatre modes d’affichage sont disponibles; ils sont sélectionnés au moyen des touches suivantes: [0]STANDARD [1]POSITION ACTUELLE [2]ERREUR DE POURSUITE [3]PARAMETRES ARITHMETIQUES Mode d’affichage STANDARD Il s’agit du mode décrit précédemment. Lorsqu’on accède à l’option “Exécution du programme P99996”, la CNC sélectionne ce mode d’affichage. Mode d’affichage POSITION ACTUELLE AUTOMATIQUE POSITION ACTUELLE Mode d’affichage ERREUR DE POURSUITE AUTOMATIQUE ERREUR DE POURSUITE Page 8 Chapitre: 3 FONCTIONSAUXILIAIRES Section: EXECUTION / SIMULATION P99996 Mode d’affichage PARAMETRES ARITHMETIQUES AUTOMATIQUE COMMANDE ACTUELLE RESTE Ce mode présente un groupe de 8 paramètres arithmétiques. Pour visualiser les paramètres précédents et suivants, utiliser les touches ci-dessous: Affiche les paramètres précédents Affiche les paramètres suivants La valeur de chaque paramètre peut être exprimée dans l’un des formats suivants: P46 = -1724.9281 Notation décimale P47 = -.10842021 E-2 Notation scientifique “E-2” signifie 10-2 (1/100). En conséquence, les 2 types de notation pour le même paramètre ci-dessous ont la même valeur P46= -0.001234 P48= 1234.5678 P47= -0.1234 E-2 P48= 1.2345678 E3 Chapitre: 3 FONCTIONSAUXILIAIRES Section: EXECUTION / SIMULATION P99996 Page 9 3.5.2 SIMULATION DU PROGRAMME P99996 Cette CNC permet de vérifier le programme P9996 en effectuant une simulation avant de l’exécuter. Pour exécuter la simulation, frapper . La CNC affiche une représentation graphique. L’angle inférieur gauche de l’écran affiche le plan à représenter (XY, XZ ou YZ), ou XYZ tridimensionnel. Pour afficher un autre plan, frapper sa touche correspondante: [0]Plan XY [1]Plan XZ [2]Plan YZ [3]Plan tridimensionnel XYZ Cette CNC peut afficher les graphiques sur un maximum de 3 plans. Elle n’affiche donc que les plans sélectionnés. Pour sélectionner d’autres plans, procéder comme suit: Frapper non. : la CNC demande si chacun des plans possibles doit être sélectionné ou Pour sélectionner le plan, frapper [Y]; sinon, frapper [ENTER]. Dès que les plans ont été définis, la zone d’affichage doit être délimitée en indiquant les coordonnées XYZ du centre de l’écran et la largeur de la zone d’affichage. Après l’entrée de chaque valeur, frapper [ENTER]. Centre Largeur Pour vérifier la pièce, frapper correspondante. . Cette opération lance la simulation graphique Pendant la simulation, il est possible d’accéder à un autre plan (touches 0, 1, 2 et 3) mais il est impossible de les définir. Pour définir d’autres plans ou modifier la zone d’affichage, la simulation du programme doit être interrompue en frappant . Frapper [CLEAR] pour vider l’écran et [END] pour quitter le mode simulation. Page 10 Chapitre: 3 FONCTIONSAUXILIAIRES Section: EXECUTION / SIMULATION P99996 3.5.2.1 FONCTION ZOOM Cette fonction permet d’agrandir ou de réduire la totalité ou une partie du graphique. Pour ce faire, il est nécessaire d’interrompre la simulation du programme ou d’attendre sa fin. Dès que le plan du dessin à agrandir ou à réduire a été sélectionné, frapper [Z]. L’écran affiche un rectangle sur le dessin d’origine. Ce rectangle est la fenêtre de zoom, qui représente la nouvelle zone d’affichage pour la partie à agrandir ou à réduire. Pour changer les dimensions du rectangle, utiliser les touches suivantes: Réduit la taille du rectangle (zoom avant) Augmente la taille du rectangle (zoom arrière) Utiliser pour déplacer la fenêtre de zoom. Pour définir la zone sélectionnée avec la fenêtre de zoom comme nouvelle zone d’affichage, frapper [ENTER]. Pour voir la zone sélectionnée agrandie ou réduite tout en conservant les valeurs de la zone d’affichage précédente, frapper . La zone contenue dans la fenêtre de zoom remplit maintenant la totalité de l’écran. Pour revenir à la zone d’affichage précédente (avant le zoom) frapper [END]. Pour utiliser à nouveau le zoom, il suffit de frapper [Z] et de procéder comme indiqué plus haut. Pour quitter la fonction ZOOM et revenir à la représentation graphique, frapper [END]. Chapitre: 3 FONCTIONSAUXILIAIRES Section: EXECUTION / SIMULATION P99996 Page 11 3.6 MODES AUXILIAIRES Lorsque cette option est sélectionnée, la CNC affiche le menu suivant: 1 - MODES SPECIAUX 2 - PERIPHERIQUES 3 - BLOCAGE / DEBLOCAGE Si on sélectionne l’option "Modes Spéciaux", la CNC demandera le code d’accès du fabriquant, qui se trouve dans le manuel d’Installation. Après avoir accédé à l’un de ces mode et travaillé avec lui, frapper [END] pour sortir. A ce moment, la CNC affiche à nouveau ce menu. Frapper [END] à nouveau pour repasser au mode d’affichage standard. Page 12 Chapitre: 3 FONCTIONSAUXILIAIRES Section: MODESAUXILIAIRES 3.7 PERIPHERIQUES Cette CNC permet de communiquer avec l’unité de disquettes FAGOR, un périphérique général ou un ordinateur afin de transférer des programmes entre eux. Ces communications peuvent être gérées depuis la CNC en “Mode périphérique” ou depuis l’ordinateur au moyen du protocole DNC de FAGOR; dans ce dernier cas, le mode de fonctionnement de la CNC n’a aucune importance. 3.7.1 MODE PERIPHERIQUE Dans ce mode, la CNC peut communiquer avec l’unité de disquettes FAGOR, un périphérique général ou un ordinateur disposant d’un programme de communications standard du commerce. Pour accéder à ce mode, frapper la touche [AUX] et après avoir sélectionné “Modes auxiliaires” frapper la touche correspondant à “PERIPHERIQUES”. Dès que l’option est sélectionnée, l’angle supérieur gauche de la CNC affiche le menu suivant: 0 - ENTREE DE L’UNITE DE DISQUETTES (Fagor) 1 - SORTIE SUR UNITE DE DISQUETTES (Fagor) 2 - ENTREE DE PERIPHERIQUE (générale) 3 - SORTIE SUR PERIPHERIQUE (générale) 4 - REPERTOIRE DE L’UNITE DE DISQUETTES (Fagor) 5 - EFFACER PROGRAMME UNITE DE DISQUETTES (Fagor) 6 - DNC ON/OFF Pour utiliser l’une de ces options, le mode DNC doit être inactif. Sinon (l’angle supérieur droit de l’écran affiche DNC), frapper [6] (DNC ON/OFF) pour le désactiver (l’indication DNC disparaît). Les options 0, 1, 2 et 3, permettent de transférer les paramètres machine, la table de fonctions M décodées et la table de compensation d’erreur de vis vers un périphérique. L’angle inférieur droit de l’écran de la CNC affichera un répertoire contenant jusqu’à 7 programmes pièce de la CNC. Pour exécuter le transfert, frapper le n° désiré quand la CNC demande le n° du programme à transférer et frapper [ENTER]. Les numéros de programme qu'il est possible de sélectionner sont les suivants: P00000 à P99990 P99994 et P99996 P99997 P99998 P99999 Correspond aux programmes pièce Programme utilisateur spécial en code ISO. Pour utilisation interne; ne peut PAS être déplacé. Utilisé pour associer des textes à des messages PLCI. Paramètres machine et tables. Attention: Les programmes pièce ne peuvent pas être édités au niveau du périphérique ou de l’ordinateur. Le moniteur affichera le message “RECEPTION” ou “EMISSION” pendant le transfert du programme et le message “PROGRAMME N° P23256 (par exemple) REÇU” ou “ENVOYE” à la fin de la transmission. Chapitre: 3 FONCTIONSAUXILIAIRES Section: PERIPHERIQUES Page 13 Quand la transmission est défectueuse, “Erreur de transmission” s’affiche et, quand la CNC ne reconnait pas les données reçues (format différent), elle émet le message “Données incorrectes reçues”. Lors de toute transmission de données, la mémoire de la CNC doit être déverrouillée; sinon, la CNC repasse au menu du mode périphérique. En cas de transmission depuis un périphérique autre qu’une unité de disquettes FAGOR, on tiendra compte des éléments suivants: * Le programme doit commencer par un caractère “NUL” (00 en ASCII) suivi de “%” “n° du programme” (par exemple, %23256) et un caractère “LINE FEED” (LF) de changement de ligne. Les espaces, la touche retour chariot et le signe “+” sont ignorés Le programme doit se terminer par 20 caractères “NULS” (00 en ASCII), un caractère “ESCAPE” ou un caractère “EOT”. Frapper [CL] pour annuler la transmission. La CNC émet le message: PROCESSUS INTERROMPU. * * * REPERTOIRE DE L’UNITE DE DISQUETTES Cette option affiche les programmes chargés sur le disque introduit dans l’unité de disquettes FAGOR et le nombre de caractères (taille) de chacun d’eux. Elle indique également le nombre de caractères libres disponibles (espace mémoire libre) sur la bande. EFFACER PROGRAMME UNITE DE DISQUETTES Cette option permet d’effacer un programme se trouvant dans l’unité de disquettes FAGOR. La CNC demande le n° du programme à effacer. Après avoir entré le n° désiré, frapper [ENTER]. Dès que le programme est effacé, la CNC affiche le message “PROGRAMME N°: P______ EFFACE”. Elle indique aussi le nombre de caractères libres sur la disquette (espace mémoire disponible). 3.7.2 COMMUNICATIONS DNC Pour utiliser cette fonction, les communications DNC doivent être actives (l’angle supérieur droit de l’écran affiche DNC). Pour ce faire, les paramètres correspondants [P605(5,6,7,8); P606(8)] doivent être définis en conséquence et l’option [6] du mode “Périphériques” doit être sélectionnée si elle n’était pas active. Dès que cette option est active et au moyen du logiciel d’application FAGOR DNC fourni, il est possible d’exécuter sur demande les opérations suivantes depuis l’ordinateur: . . . . Obtention du répertoire de programmes pièce CNC Transfert de programmes pièce et de tables de/vers la CNC. Effacement de programmes pièce au niveau de la CNC. Un certain contrôle à distance de la machine. Attention: Tout mode de fonctionnement peut être sélectionné depuis la CNC. Page 14 Chapitre: 3 FONCTIONSAUXILIAIRES Section: PERIPHERIQUES 3.8 BLOCAGE/DEBLOCAGE Cette option permet de bloquer/débloquer la mémoire de programmes pièce. Pour pouvoir sélectionner cette option, frapper la touche [AUX] et après avoir sélectionné "Modes Auxiliaires", frapper la touche correspondant à "BLOCAGE / DEBLOCAGE". Les codes utilisés dans ce cas sont: [BEG] 0000 [ENTER] Déblocage de la mémoire de programmes pièce [BEG] 1111 [ENTER] Blocage de la mémoire de programmes pièce [P] F100 [ENTER] Efface le contenu de tous les paramètres arithmétiques (données des opérations automatiques). Il leur assigne la valeur 0. Chapitre: 3 FONCTIONSAUXILIAIRES Section: BLOCAGE/DEBLOCAGE Page 15 3.9 EDITION DU PROGRAMME 99996 Le programme 99996 est un programme spécial d’usager en code ISO. Il peut être édité dans ce mode de travail ou bien être transmis à la CNC après avoir été élaboré dans un ordinateur. Pour pouvoir sélectionner cette option, taper sur la touche [AUX] et taper sur la touche correspondant à "ÉDITEUR PROGRAMME 99996".. La CNC accède à la page d’édition du programme 99996. Si le programme est déjà édité, la CNC affiche un groupe de blocs de programme. Pour voir les blocs précédents et suivants, il faut utiliser les touches Pour pouvoir éditer un nouveau bloc, il faut suivre la démarche suivante: 1.- Si le numéro de bloc n’est pas le voulu, il faut l’effacer au moyen de la touche [CL] et introduire le nouveau numéro. 2.- Introduire toutes les données du nouveau bloc et taper sur la touche [ENTER] . Le format de programmation à utiliser est expliqué dans le manuel de programmation. Les touches suivantes du panneau peuvent être utilisées: [X], [Y], [Z], [T], [F], [S], [P]. Néanmoins, étant donné que certaines touches de fonction (G, M, I, K) manquent, l’édition aidée a été installée. Il faut pour cela taper sur la touche [AUX] . La CNC, après avoir analysé syntactiquement la partie de bloc qui a été éditée, affichera une par une toutes les fonctions qui peuvent être éditées à ce moment. Pour effacer des caractères un par un, il faut utiliser la touche [CL] . Pour pouvoir modifier un bloc qui est déjà édité , il faut suivre la démarche suivante: 1.- Si le numéro de bloc affiché sur la partie inférieure de l’écran n’est pas le voulu, il faut l’effacer au moyen de la touche [CL] et introduire le nouveau numéro. 2.- Tapez sur la touche [RECALL] . La CNC affichera sur la partie inférieure, zone d’édition, le contenu du bloc en question. 3.- Pour pouvoir modifier le bloc, il faut utiliser une des méthodes suivantes: a) Utiliser la touche [CL] pour effacer des caractères un par un et l’éditer tel qu’il a été précédemment indiqué. b) Utiliser les touches pour se situer sur la partie que l’on veut modifier et utiliser la touche [CL] pour effacer des caractères ou taper sur la touche [INC/ABS] pour insérer des données. Page 16 Chapitre: 3 FONCTIONSAUXILIAIRES Section: EDITION DU PROGRAMME 99996 Lorsque l’on est dans le mode de saisissement des données, les caractères postérieurs au curseur sont affiché en mode clignotant. Il n’est pas possible d’utiliser le mode d’édition aidée, touche [AUX]. Saisir toutes les données voulues et taper sur la touche [INC/ABS] . Si le nouveau bloc est syntactiquement correct, la CNC le réaffichera normalement, mais s’il n’est pas syntactiquement correct, il continuera à l’afficher en mode clignotant et il faudra le corriger. 4.- Une fois le bloc modifié, taper sur la touche [ENTER] . La CNC l’assumera en changeant le précédent. Pour pouvoir effacer le contenu d’un bloc, il faut suivre la démarche suivante: 1.- Si le numéro de bloc affiché sur la partie inférieure de l’écran n’est pas le voulu, il faut l’effacer au moyen de la touche [CL] et introduire le nouveau numéro. 2.- Taper sur la touche [DATA] . La CNC l’effacera de la mémoire. Chapitre: 3 FONCTIONSAUXILIAIRES Section: EDITION DU PROGRAMME 99996 Page 17 4. OPERATIONS AUTOMATIQUES Cette CNC comporte un ensemble de touches permettant d’accéder à chacune de ses opérations automatiques. Les opérations de base sélectionnées par la frappe de leur touche correspondante sont les suivantes: Sélectionne “Positionnement point à point” Sélectionne “Positionnement en ligne” “Positionnement en arc” (type diamètre de perçage) “Positionnement en rectangle” “Positionnement en grille” “Fraisage linéaire” “Fraisage courbe” “Fraisage de profil” “Poche” “Moyeu” (bossage) “Ebauche d’arête” “Surfaçage” Chaque fois que l’une de ces opérations est sélectionnée, la CNC affiche: * Dans la fenêtre principale, une représentation graphique de l’opération automatique sélectionnée. * Au bas de l’écran, les données correspondant à l’opération automatique sélectionnée. Chapitre: 4 OPERATIONSAUTOMATIQUES Section: Page 1 4.1 GENERALITES Dès que l’opération désirée a été sélectionnée, frapper [DATA] pour accéder au mode introduction de données. La CNC met en surbrillance la première donnée sur le graphique ainsi que dans la zone d’édition de données. Pour affecter la valeur désirée à cette donnée, frapper cette valeur, puis [ENTER]. La CNC prend en compte la nouvelle valeur et met la donnée suivante en surbrillance. Pour sélectionner une autre donnée, frapper les touches . Dès que toutes les données ont été définies, frapper [DATA] pour sortir du mode introduction de données. Une opération d’usinage peut être associée aux opérations de positionnement automatique. L’opération d’usinage s’effectuera à chaque point de positionnement. Pour savoir comment définir et associer une opération d’usinage, voir le chapitre “Opérations d’usinage”. Il est ensuite possible de: * * * Vérifier l’opération en frappant [SIMUL]. Exécuter l’opération en frappant . Mémoriser l’opération en tant que section d’un programme pièce. Pour quitter l’opération automatique, frapper [END]. La CNC mémorisera toutes les données définies et les affichera à nouveau dès que cette opération sera sélectionnée. 4.1.1 CONTROLE SUR L’AXE Z La donnée “ZSAF” (coordonnée de sécurité en Z) doit être définie pour toutes les opérations automatiques. Avant d’effectuer l’usinage correspondant à l’opération automatique, la CNC déplace l’outil jusqu’à la position de sécurité définie “ZSAF”. Quand l’axe Z est un axe DRO (visualisateur) (non contrôlé par la CNC) et se situe endessous des coordonnées de “ZSAF”, la CNC affiche un message demandant à l’opérateur de déplacer l’axe Z jusqu’à ce point de sécurité. Pour reprendre l’exécution, frapper la touche . Si l’opération comporte plusieurs fonctions d’usinage, la CNC positionne l’outil sur le point “ZSAF” avant d’exécuter chaque fonction. Page 2 Chapitre: 4 OPERATIONSAUTOMATIQUES Section: GENERALITES 4.1.2 FONCTIONS AUXILIAIRES "M" AVANT ET APRES LE CYCLE Il est possible d’associer à chaque cycle l’exécution de deux fonctions auxiliaires "M". L’une d’elles sera exécutée avant le cycle et l’autre, après l’exécution de celui-ci. Les écrans d’aide de chaque cycle affichent, à droite des données de définition du cycle, les 2 fonctions auxiliaires "M" sélectionnées dans chaque cycle. La "M" située sur la partie supérieure indique la fonction auxiliaire "M" qui est exécutée avant le cycle et la "M" située sur la partie inférieure indique la fonction auxiliaire «M» qui est exécutée après le cycle. Si l’une d’elles affiche la valeur "M--", cela veut dire qu’il n’y a aucune fonction auxiliaire "M" associée. Pour pouvoir sélectionner la fonction auxiliaire «M» que l’on désire exécuter avant le cycle, il faut agir de la manière suivante: Taper la séquence de touches [F] [BEGIN] Introduire le numéro de la fonction voulue Taper sur touche [ENTER] Pour pouvoir sélectionner la fonction auxiliaire "M" que l’on désire exécuter après le cycle, il faut agir de la manière suivante: Taper la séquence de touches [F] [END] Introduire le numéro de la fonction voulue Taper sur touche [ENTER] Pour pouvoir effacer une des fonctions auxiliaires "M" qui sont sélectionnées, il faut agir de la manière suivante: Taper la séquence de touches [F] [BEGIN] ou [F] [END] Taper sur touche [ENTER] La CNC affichera la valeur "M--" Attention: Lorsqu’une opération automatique est mémorisée, la CNC sauvegarde les deux fonctions auxiliaires "M" sélectionnées, avec les données et autres paramètres définissant l’opération automatique. De cette manière, chaque fois qu’une pièce mémorisée au préalable est exécutée, la CNC exécutera chacune des opérations automatiques sous les conditions d’usinage qui furent établies pour elle. A la mise sous tension ou après une REMISE A ZERO, la CNC initialise tous les cycles (non ceux qui sont mémorisés), en assignant aux deux champs la valeur "M--" (il n’y a aucune fonction auxiliaire "M" associée). Chapitre: 4 Section: Page OPERATIONSAUTOMATIQUES GENERALITES 3 4.1.3 CONDITIONS D’USINAGE La CNC affiche les informations suivantes: F Avance de l’axe sélectionné en cours. % Pourcentage de correction en cours appliqué à l’avance “F”. S Vitesse de broche définie pour l’opération d’usinage Pour définir la vitesse de broche, deux méthodes sont disponibles: * Frapper [S], introduire la valeur désirée et frapper [ENTER]. La CNC suppose que cette valeur doit être appliquée lors de l’exécution suivante de l’opération automatique en cours d’édition. Elle ne change donc pas la vitesse de broche actuelle. * Frapper [S], introduire la valeur désirée et frapper . La CNC remplace la vitesse de broche actuelle par celle qui vient d’être définie. Elle prend également la nouvelle valeur comme vitesse de broche à appliquer lors de l’exécution suivante de l’opération automatique en cours d’édition. % Pourcentage actuel de correction de vitesse de broche. Sens de rotation de broche pour l’usinage Pour changer le sens de rotation, frapper [3]. La CNC affiche le nouveau sens de rotation mais ne change PAS le sens de rotation actuel de la broche. T Outil à utiliser pour l’usinage. Pour sélectionner l’outil d’usinage, frapper [T] et, après avoir introduit le n° de l’outil désiré, frapper [ENTER]. La CNC prend ce nouveau numéro d’outil comme étant celui à utiliser avec l’opération automatique en cours d’édition. En conséquence, elle conserve le numéro de l’outil actuel affiché dans la fenêtre principale. Attention: Quand une opération automatique est chargée en mémoire, la CNC mémorise toutes ces conditions d’usinage sauf le pourcentage de correction, avec les données et les paramètres définissant l’opération automatique. De cette façon, chaque fois qu’une pièce programmée précédemment sera exécutée, la CNC réalisera chacune des opérations automatiques avec les conditions d’usinage définies pour cette pièce. Page 4 Chapitre: 4 OPERATIONSAUTOMATIQUES Section: GENERALITES 4.1.4 SIMULATION Cette CNC permet de vérifier une opération automatique en effectuant une simulation avant de l’exécuter. Pour exécuter la simulation, frapper . La CNC affiche une représentation graphique. L’angle inférieur gauche de l’écran affiche le plan à représenter (XY, XZ ou YZ), ou XYZ tridimensionnel. Pour afficher un autre plan, frapper sa touche correspondante: [0]Plan XY [1]Plan XZ [2]Plan YZ [3]Plan tridimensionnel XYZ Cette CNC peut afficher les graphiques sur un maximum de 3 plans. Elle n’affiche donc que les plans sélectionnés. Pour sélectionner d’autres plans, procéder comme suit: Frapper ou non. : la CNC demande si chacun des plans possibles doit être sélectionné Pour sélectionner le plan, frapper [Y]; sinon, frapper [ENTER]. Dès que les plans ont été définis, la zone d’affichage doit être délimitée en indiquant les coordonnées XYZ du centre de l’écran et la largeur de la zone d’affichage. Après l’entrée de chaque valeur, frapper [ENTER]. Centre Largeur Pour vérifier la pièce, frapper correspondante. . Cette opération lance la simulation graphique Pendant la simulation, il est possible d’accéder à un autre plan (touches 0, 1, 2 et 3) mais il est impossible de les définir. Pour définir d’autres plans ou modifier la zone d’affichage, la simulation du programme doit être interrompue en frappant . Frapper [CLEAR] pour vider l’écran et [END] pour quitter le mode simulation. Chapitre: 4 Section: Page OPERATIONSAUTOMATIQUES GENERALITES 5 4.1.4.1 FONCTION ZOOM Cette fonction permet d’agrandir ou de réduire la totalité ou une partie du graphique. Pour ce faire, il est nécessaire d’interrompre la simulation du programme ou d’attendre sa fin. Dès que le plan du dessin à agrandir ou à réduire a été sélectionné, frapper [Z]. L’écran affiche un rectangle sur le dessin d’origine. Ce rectangle est la fenêtre de zoom, qui représente la nouvelle zone d’affichage pour la partie à agrandir ou à réduire. Pour changer les dimensions du rectangle, utiliser les touches suivantes: Réduit la taille du rectangle (zoom avant) Augmente la taille du rectangle (zoom arrière) Utiliser pour déplacer la fenêtre de zoom. Pour définir la zone sélectionnée avec la fenêtre de zoom comme nouvelle zone d’affichage, frapper [ENTER]. Pour voir la zone sélectionnée agrandie ou réduite tout en conservant les valeurs de la zone d’affichage précédente, frapper . La zone contenue dans la fenêtre de zoom remplit maintenant la totalité de l’écran. Pour revenir à la zone d’affichage précédente (avant le zoom) frapper [END]. Pour utiliser à nouveau le zoom, il suffit de frapper [Z] et de procéder comme indiqué plus haut. Pour quitter la fonction ZOOM et revenir à la représentation graphique, frapper [END]. Page 6 Chapitre: 4 OPERATIONSAUTOMATIQUES Section: GENERALITES 4.1.5 EXECUTION Cette CNC permet d’exécuter une opération automatique du début à la fin ou en pas à pas (bloc à bloc) grâce à la touche . Chaque fois que le mode “bloc à bloc” est sélectionné, la partie droite de l’écran affiche le symbole . Pour annuler la sélection de ce mode et revenir au mode exécution en continu, frapper Dès que le mode désiré a été sélectionné, frapper . . La CNC prend en compte les valeurs d’usinage F, S et T ainsi que le sens de rotation de broche choisis et elle exécute l’opération automatique de la façon suivante: 1. Si l’opération a été programmée avec un nouvel outil, la CNC demande la sélection de cet outil. Dès que l’outil a été changé, frapper pour reprendre l’exécution de l’opération. 2. La CNC démarre la broche à la vitesse et selon le sens de rotation sélectionnés. 3. L’outil se positionne sur le point de sécurité “ZSAF” pré-établi. 4. La CNC exécute l’opération automatique de fraisage. 5. L’outil retourne à la position de sécurité “ZSAF”. 6. La CNC stoppe la broche. Si nécessaire, il est possible d’inspecter et de changer un outil pendant l’exécution d’une opération automatique. Chapitre: 4 OPERATIONSAUTOMATIQUES Section: GENERALITES Page 7 4.1.5.1 CONTROLE DES OUTILS Cette option permet d’interrompre l’exécution de l’opération automatique et d’inspecter l’outil afin de vérifier son état et de le remplacer si nécessaire. Pour ce faire, procéder comme suit: a) Frapper pour interrompre le programme. b) Frapper [TOOL] A cet instant, la CNC exécute la fonction auxiliaire M05 pour stopper la broche et elle affiche sur l’écran: TOUCHES JOG DISPONIBLES OUT c) Amener l’outil à la position désirée au moyen des touches JOG. Dès que l’outil est “hors trajectoire”, la broche peut être démarrée et stoppée à nouveau par les touches correspondantes du pupitre opérateur. d) Dès la fin de l’inspection ou du changement de l’outil, frapper [END]. La CNC exécute une fonction M03 ou M04 pour démarrer la broche dans le sens en cours lors de l’interruption du programme. L’écran affiche alors: RETOUR AXES HORS POSITION “Axes hors position” signifie qu’ils ne se situent pas au même point que lorsque le programme a été interrompu. e) Déplacer les axes en manuel jusqu’à la position d’interruption du programme au moyen des touches JOG correspondantes. La CNC interdit le dépassement (surcourse) de cette position. Lorsque les axes sont en position, l’écran affiche: RETOUR AXES HORS POSITION AUCUN f) Page 8 Frapper pour reprendre l’exécution de l’opération automatique. Chapitre: 4 OPERATIONSAUTOMATIQUES Section: GENERALITES 4.2 POSITIONNEMENT Les divers types de positionnement automatique offerts par cette CNC facilitent la définition des points où des opérations d’usinage spécifiques seront exécutées. Les choix de positionnement disponibles sont les suivants: * Positionnement point à point. Il doit être utilisé lorsque les points sont situés au hasard (selon aucun modèle défini) à la surface de la pièce. * Positionnement en ligne. * Positionnement en arc (type diamètre de perçage). * Positionnement en rectangle. * Positionnement en grille. Tous les mouvements de positionnement s’effectuent en rapide. Quand l’axe Z est contrôlé par la CNC (n’est pas un axe DRO), il est possible d’associer une opération automatique d’usinage aux types de positionnement comme décrit plus loin dans le chapitre intitulé “Opérations d’usinage”. Ces opérations sont les suivantes: Perçage Taraudage Alésage Pointage De cette façon, il est possible de tarauder des trous suivant une droite, de percer des trous suivant un arc (ou un diamètre de perçage), etc... Si aucune opération d’usinage n’est associée au positionnement, la CNC demande à l’opérateur d’agir sur l’axe Z après chaque déplacement de positionnement. Ensuite, chaque choix de positionnement possible est décrit, ainsi que les données nécessaires pour le définir. Chapitre: 4 Section: Page OPERATIONS AUTOMATIQUES POSITIONNEMENT 9 4.2.1 POSITIONNEMENT POINT A POINT Cette option est sélectionnée au moyen de la touche . Il est possible de définir jusqu’à 8 points en affectant les valeurs de leurs coordonnées en X et Y. Ces valeurs peuvent être introduites: * en déplaçant les axes en manuel jusqu’au point désiré au moyen des manivelles mécaniques ou électroniques, ou des touches JOG du pupitre opérateur et en frappant [ENTER]. * ou en les introduisant au moyen du clavier et en frappant [ENTER]. Si moins de 8 points sont utilisés, les valeurs des coordonnées pour le premier point inutilisé doivent être identiques à celles du dernier point utilisé. Exemple: X1 X2 X3 X4 X5 X6 X7 X8 10.278 Y1 18.345 Y2 27.789 Y3 27.789 Y4 00.000 Y5 00.000 Y6 00.000 Y7 00.000 Y8 Z SAF 10.000 Page 10 12.876 23.456 90.122 90.122 00.000 00.000 00.000 00.000 1er point 2ème point Dernier point Point de sécurité en Z Chapitre: 4 OPERATIONS AUTOMATIQUES Section: POSITIONNEMENT POINT A POINT 4.2.2 POSITIONNEMENT EN LIGNE Cette option est sélectionnée au moyen de la touche . Le premier point “X1 Y1” doit toujours être défini. Ceci peut être effectué de la façon suivante: * en déplaçant les axes en manuel jusqu’au point désiré au moyen des manivelles mécaniques ou électroniques, ou des touches JOG du pupitre opérateur et en frappant [ENTER]. * ou au moyen du clavier et en frappant [ENTER]. La trajectoire doit être définie par une des méthodes suivantes: 1. Définir la longueur “L” et l’angle “A” de la trajectoire. Dans ce cas, définir le nombre de points (N) ou le pas entre deux points consécutifs (I). 2. Définir le dernier point “Xn Yn” en positionnant la machine sur ce point et en frappant [ENTER] ou en l’introduisant au moyen du clavier et en frappant [ENTER]. Dans ce cas, définir “L0” et le nombre de points (N) ou le pas entre deux points consécutifs (I). 3. Définir les valeurs “N”, “I” et “A” (nombre de points, pas entre points et angle de la trajectoire respectivement). Dans ce cas, définir: “L0”, “Xn = X1” et “Yn = Y1” Exemple de programmation: Les formats suivants peuvent être utilisés: X1=0 X1=0 Y1=0 Y1=0 L=60 L=60 X1=0 X1=0 Y1=0 Y1=0 Xn=51.961 Xn=51.961 Yn=30 Yn=30 Xn=0 Yn=0 L=0 X1=0 Y1=0 Chapitre: 4 OPERATIONS AUTOMATIQUES A=30 A=30 N=4 I=20 L=0 L=0 N=4 Section: POSITIONNEMENTENLIGNE N=4 I=20 I=20 A=30 Page 11 4.2.3 POSITIONNEMENT EN ARC Cette option est sélectionnée au moyen de la touche . Le centre de l’arc “Xc Yc” doit toujours être défini. Ceci peut être effectué de la façon suivante: * en déplaçant les axes en manuel jusqu’au point désiré au moyen des manivelles mécaniques ou électroniques, ou des touches JOG du pupitre opérateur et en frappant [ENTER]. * ou au moyen du clavier et en frappant [ENTER]. Le premier point peut être défini par une des méthodes suivantes: 1. Définir le rayon “R” et l’angle “A” du premier point. L’angle “A” du premier point est pris par rapport l’axe X et sa valeur est indiquée en degrés (avec ou sans signe). La valeur est négative ou positive selon que le déplacement se fait dans le sens horaire ou anti-horaire respectivement. 2. Définir le premier point “X1 Y1” en positionnant la machine sur ce point ou en introduisant ses coordonnées au moyen du clavier et en frappant [ENTER]. Dans ce cas, définir “R0”. Le nombre de points (N) et le déplacement angulaire entre points consécutifs (B) doivent toujours être définis. Le déplacement angulaire “B” est donné en degrés (valeur signée ou non) et il indique le sens des pas. Ce sens est horaire pour B négatif et anti-horaire pour B positif. Pour réaliser un cercle complet, programmer B0. Les déplacements de positionnement s’effectueront dans le sens anti-horaire. Page 12 Chapitre: 4 OPERATIONS AUTOMATIQUES Section: POSITIONNEMENTENARC 4.2.4 POSITIONNEMENT EN RECTANGLE Cette option est sélectionnée au moyen de la touche . Le premier point “X1 Y1” doit toujours être défini. Ceci peut être effectué de la façon suivante: * en déplaçant les axes en manuel jusqu’au point désiré au moyen des manivelles mécaniques ou électroniques, ou des touches JOG du pupitre opérateur et en frappant [ENTER]. * ou au moyen du clavier et en frappant [ENTER]. Les données suivantes doivent également être définies: “A”Angle du trajet de l’abcisse par rapport à l’axe X. “B”Angle du trajet de l’ordonnée par rapport au trajet de l’abcisse. Pour que les 2 trajets soient parallèles aux axes X et Y, définir A=0 et B=90. Pour décrire les trajets en X et en Y, les options suivantes sont disponibles: 1. Définition de la longueur du trajet, “LX” “LY” et du nombre de points sur ce trajet, soit “NX” “NY”. 2. Définition de la longueur du trajet, “LX” “LY” et du déplacement entre points consécutifs “IX” “IY”. 3. Définition des pas entre points “IX” “IY” et du nombre de points du trajet “NX” “NY”. Chapitre: 4 OPERATIONS AUTOMATIQUES Section: POSITIONNEMENTEN RECTANGLE Page 13 4.2.5 POSITIONNEMENT EN GRILLE Cette option est sélectionnée au moyen de la touche . Le premier point “X1 Y1” doit toujours être défini. Ceci peut être effectué de la façon suivante: * en déplaçant les axes en manuel jusqu’au point désiré au moyen des manivelles mécaniques ou électroniques, ou des touches JOG du pupitre opérateur et en frappant [ENTER]. * ou au moyen du clavier et en frappant [ENTER]. Les données suivantes doivent également être définies: “A”Angle du trajet de l’abcisse par rapport à l’axe X. “B”Angle du trajet de l’ordonnée par rapport au trajet de l’abcisse. Pour que les 2 trajets soient parallèles aux axes X et Y, définir A=0 et B=90. Pour décrire les trajets en X et en Y, les options suivantes sont disponibles: 1. Définition de la longueur du trajet, “LX” “LY” et du nombre de points sur ce trajet, soit “NX” “NY”. 2. Définition de la longueur du trajet, “LX” “LY” et du déplacement entre points consécutifs “IX” “IY”. 3. Définition des pas entre points “IX” “IY” et du nombre de points du trajet “NX” “NY”. Page 14 Chapitre: 4 OPERATIONS AUTOMATIQUES Section: POSITIONNEMENTENGRILLE 4.3 FRAISAGE Les opérations de fraisage disponibles sont: * Fraisage linéaire * Fraisage courbe * Fraisage de profil Avant le fraisage, l’axe Z se déplace jusqu’au point “ZSAF”. Si l’axe Z est un axe DRO (visualisateur) (non contrôlé par la CNC), le message correspondant s’affiche. Ensuite, l’outil se positionne à la profondeur d’usinage programmée “Z”. La CNC autorise la fixation du pourcentage de correction de l’avance pour ce déplacement. Le fraisage s’effectue à l’avance F sélectionnée. Quand l’opération de fraisage est achevée, l’axe Z passe au point “ZSAF”. Si l’axe Z est un axe DRO (visualisateur) (non contrôlé par la CNC), le message correspondant s’affiche. Les diverses opérations de fraisage disponibles sont décrites plus loin. Chapitre: 4 Section: Page OPERATIONS AUTOMATIQUES FRAISAGE 15 4.3.1 FRAISAGE LINEAIRE Cette option est sélectionnée au moyen de la touche . Le premier point “X1 Y1” doit toujours être défini. Ceci peut être effectué de la façon suivante: * en déplaçant les axes en manuel jusqu’au point désiré au moyen des manivelles mécaniques ou électroniques, ou des touches JOG du pupitre opérateur et en frappant [ENTER]. * ou au moyen du clavier et en frappant [ENTER]. La trajectoire doit être définie par une des méthodes suivantes: 1. Définir la longueur “L” et l’angle “A” de la trajectoire. 2. Définir le dernier point “X2 Y2” (soit en déplacant la machine, soit en introduisant les coordonnées au moyen du clavier). Dans ce cas, définir: “L0”. L’opération de fraisage peut être effectuée avec ou sans compensation de rayon d’outil. Pour faire un choix, frapper [T] et sélectionner l’une des options ci-dessous au moyen des touches . a) Pas de compensation de rayon d’outil. b) Avec compensation de rayon d’outil à gauche. La pièce reste à la droite de l’outil. c) Avec compensation de rayon d’outil à droite. La pièce reste à la gauche de l’outil. Pour fixer la profondeur de fraisage, indiquer la valeur “Z” (en déplaçant la machine ou en introduisant la valeur au moyen du clavier) et le pourcentage de correction d’avance à appliquer. Page 16 Chapitre: 4 OPERATIONS AUTOMATIQUES Section: FRAISAGELINEAIRE 4.3.2 FRAISAGE COURBE Cette option est sélectionnée au moyen de la touche . Le premier point “X1 Y1” et le dernier “X2 Y2” doivent toujours être définis. Ceci peut être effectué de la façon suivante: * en déplaçant les axes en manuel jusqu’au point désiré au moyen des manivelles mécaniques ou électroniques, ou des touches JOG du pupitre opérateur et en frappant [ENTER]. * ou au moyen du clavier et en frappant [ENTER]. La trajectoire doit être définie en indiquant le rayon “R” et le sens du déplacement “P”. Après la frappe de [P], frapper la touche correspondante [1], [2], [3] ou [4]. L’opération de fraisage peut être effectuée avec ou sans compensation de rayon d’outil. Pour faire un choix, frapper [T] et sélectionner l’une des options ci-dessous au moyen des touches a) Pas de compensation de rayon d’outil. b) Avec compensation de rayon d’outil à gauche. La pièce reste à la droite de l’outil. c) Avec compensation de rayon d’outil à droite. La pièce reste à la gauche de l’outil. Pour fixer la profondeur de fraisage, indiquer la valeur “Z” (en déplaçant la machine ou en introduisant la valeur au moyen du clavier) et le pourcentage de correction d’avance à appliquer. Chapitre: 4 Section: Page OPERATIONS AUTOMATIQUES FRAISAGECOURBE 17 4.3.3 FRAISAGE DE PROFIL Cette option est sélectionnée au moyen de la touche . Les données suivantes doivent être définies: * * * * Point de départ “BEG” Premier point sur le profil “X1 Y1” Les sections droites ou courbes constituant le profil (7 maximum). Le point de sortie ou “END”. Point de départ “BEG” Le point de départ “BEG” et la profondeur de fraisage “Z” doivent toujours être définis. * Le point de départ peut appartenir au profil ou se situer à l’extérieur. * Pour définir la profondeur de fraisage, indiquer la valeur “Z” (en déplaçant la machine ou en l’introduisant par le clavier) et le pourcentage de correction d’avance à appliquer. Compensation de rayon d'outil L’opération de fraisage peut être effectuée avec ou sans compensation de rayon d’outil. Pour faire un choix, frapper [T] et sélectionner l’une des options ci-dessous au moyen des touches a) Pas de compensation de rayon d’outil. b) Avec compensation de rayon d’outil à gauche. La pièce reste à la droite de l’outil. c) Avec compensation de rayon d’outil à droite. La pièce reste à la gauche de l’outil. Page 18 Chapitre: 4 OPERATIONS AUTOMATIQUES Section: FRAISAGEDEPROFIL Premier point du profil “X1 Y1” Le premier point “X1 Y1” doit toujours être défini. Ceci peut être obtenu en déplaçant les axes en manuel et en frappant [ENTER] ou en introduisant les coordonnées par le clavier et en frappant [ENTER]. Pour obtenir un meilleur fini, il est possible d’utiliser l’entrée tangentielle. Pour ce faire, définir sa valeur “r”. Les sections droites ou courbes constituant le profil (7 au maximum) Sur un profil, il est possible de définir jusqu’à 7 sections. Pour définir le type de section, frapper les touches suivantes: Section droite. Elle est signalée par l’indicateur: . Section courbe. Elle est signalée par l’indicateur: . Les sections indéfinies sont signalées par l’indicateur . Quand la CNC rencontre un indicateur , elle suppose qu’il n’y a plus de sections. Elle considère donc la section précédente comme étant la dernière du profil. Pour annuler ou supprimer une section déjà définie, frapper maintenant repérée par l’indicateur . . La section est Section droite Sur une section droite, l’indicateur être définis. et le point d’arrivée XY de la section doivent Le congé entre cette section et la suivante doit également être défini. Définir “r” pour les relier par un rayon et, pour chanfreiner le joint, définir la distance “C” par rapport au joint (point XY). Chapitre: 4 Section: Page OPERATIONS AUTOMATIQUES FRAISAGEDEPROFIL 19 Section courbe Sur une section courbe, l’indicateur de déplacement doivent être définis. , le point d’arrivée XY, le rayon “R” et le sens Pour définir le sens du déplacement, frapper [P] suivi de la touche correspondante: [1], [2], [3] ou [4]. Quand la section à définir est tangente à la précédente, R doit être à “0” (R=0). La transition entre cette section et la suivante doit également être définie en fixant la valeur “r” lorsqu’elles sont réunies par un congé. Point de sortie ou “END” Dès que les sections définies ont été exécutées, l’outil se positionne sur le point de sortie “END”. Ce point “END” doit toujours être défini. Pour ce faire, on peut soit déplacer les axes jusqu’à ce point et frapper [ENTER] soit introduire les valeurs de ses coordonnées et frapper [ENTER]. Pour obtenir un meilleur fini, il est possible d’utiliser la sortie tangentiellee. Pour ce faire, définir son rayon “r” sur la dernière section du profil. Page 20 Chapitre: 4 OPERATIONS AUTOMATIQUES Section: FRAISAGEDEPROFIL Exemples de programmation Point de départ “BEG” ZSAF=2 BEG X=70 Z=-10 Y=20 %F(Z)=50 Premier point du profil “X1Y1” X1 =80 r =3 Y1 =20 Profil X2 =80 r =5 C =0 Y2 =0 X3 =50 r =5 C =0 Y3 =0 X4 =20 R =15 r =5 Y4 =0 P =4 X5 =0 R =20 r =5 Y5 =20 P =3 X6 =0 r =10 C =0 Y6 =45 X7 =80 r =0 C =10 Y7 =45 X8 =80 r =3 Y8 =20 Point de sortie “END” END X=70 Y= 20 Chapitre: 4 OPERATIONS AUTOMATIQUES Section: FRAISAGEDEPROFIL Page 21 Point de départ “BEG” ZSAF X=2 BEG X=0 Z=-10 Y=-10 %F(Z)=50 Premier point du profil “X1Y1” X1 =0 r =3 Y1 =0 Profil X2 =67.57 r =0 C =0 X4 =23 R =0 r =0 X6 = r = C = P Y2 =18.27 X3 =69.73 R =0 r =0 Y4 =-28.45 =3 X5 =0 R =0 r =3 Y3 =-1.37 P=1 P Y5 =0 =1 Y6 = Point de sortie “END” END Page 22 X=0 Y= -10 Chapitre: 4 OPERATIONS AUTOMATIQUES Section: FRAISAGEDEPROFIL 4.4 POCHES Deux touches permettent de sélectionner le type de poche. La touche pour une poche intérieure. La touche pour un moyeu ou bossage. Comme cette CNC permet d’exécuter 2 poches intérieures et 2 moyeux, utiliser la touche pour sélectionner le type désiré. Les types de poche disponibles sont les suivants: 1. Poche rectangulaire 2. Moyeu rectangulaire (bossage rectangulaire) 3. Poche circulaire 4. Moyeu circulaire (bossage circulaire) Avant d’exécuter la poche, l’axe Z se déplace jusqu’à la position de sécurité “ZSAF”. Si l’axe Z est un axe DRO (visualisateur) (non contrôlé par la CNC), et s’il est situé avant cette position de sécurité, le message correspondant est émis. Ensuite, chacune des poches possibles est décrite avec les données nécessaires pour la définir. Chapitre: 4 Section: Page OPERATIONS AUTOMATIQUES POCHES 23 4.4.1 POCHE RECTANGULAIRE Les données suivantes doivent être définies: “X1 Y1” Indique l’angle de la poche. Il peut être défini: * en déplaçant les axes en manuel jusqu’au point désiré au moyen des manivelles mécaniques ou électroniques, ou des touches JOG du pupitre opérateur et en frappant [ENTER]. * ou en introduisant ses coordonnées au moyen du clavier et en frappant [ENTER]. “L” Définit la longueur de la poche. Le signe indique le sens de l’usinage. “H” Définit la largeur de la poche. “r”,”C” Définit les angles de la poche. Pour une poche à angles arrondis, introdure “C0” et affecter la valeur du congé à “r”. Page 24 Chapitre: 4 OPERATIONS AUTOMATIQUES Section: POCHERECTANGULAIRE Pour une poche à angles chanfreinés, introduire “r0” et affecter à “C” la distance du chanfrein par rapport à l’angle théorique. En cas d’exécution d’une poche standard sans angles arrondis ou chanfreinés, programmer “r0” et “C0”. “G” Définit la phase de balayage dans le plan XY. La totalité de la poche est fraisée par phases identiques, qui seront égales ou inférieures aux phases programmées. Si une valeur “0” est programmée, la CNC prendra une valeur par défaut égale à 0,75 fois le diamètre de l’outil. “E” Définit la passe de finition. Si “0” est introduit, aucune passe de finition n’est exécutée. “%F” Indique le pourcentage d’avance utilisé pour la passe de finition. Si ce pourcentage est fixé à “0”, l’avance utilisée pour la passe de finition sera identique à celle utilisée pour les passes d’ébauchage. “A” Angle de la poche par rapport à l’axe X. “Z” Définit la coordonnée Z supérieure de la poche. “P” Définit la profondeur de la poche. “I” Définit la passe de fraisage. La CNC exécute des passes identiques pour la totalité de la poche, qui seront égales ou inférieures aux passes programmées. “%F(Z)” Indique le pourcentage d’avance utilisé pour l’axe Z (plongée). Si la valeur choisie est “0”, l’avance de l’axe Z est égale à l’avance programmée. Chapitre: 4 Section: Page OPERATIONS AUTOMATIQUES POCHERECTANGULAIRE 25 Opération de base: 1. Déplacement de l’outil jusqu’à la position de sécurité “ZSAF”. 2. Déplacement jusqu’au centre de la poche. 3. Premier mouvement de plongée à %F(Z) de l’avance sélectionnée actuelle “F”. 4. Fraisage de la surface de la poche à l’avance sélectionnée actuelle “F”. La passe de finition sera exécutée à %F de l’avance sélectionnée actuelle “F”. Pour obtenir un fini satisfaisant des faces de la poche, la CNC applique une entrée et une sortie tangentielles lors de la dernière passe. 5. Positionnement de l’outil au centre de la poche et retrait jusqu’à 1 mm au-délà de la surface usinée. 6. Passes de fraisage suivantes jusqu’à ce que la profondeur totale de la poche soit atteinte après exécution des opérations 3, 4 et 5. 7. Retrait jusqu’à la position de sécurité “ZSAF”. Page 26 Chapitre: 4 OPERATIONS AUTOMATIQUES Section: POCHERECTANGULAIRE 4.4.2 POCHE CIRCULAIRE Les données suivantes doivent être définies: “Xc Yc” Indique le centre de la poche. Il peut être défini: * en déplaçant les axes en manuel jusqu’au point désiré au moyen des manivelles mécaniques ou électroniques, ou des touches JOG du pupitre opérateur et en frappant [ENTER]. * ou en introduisant ses coordonnées au moyen du clavier et en frappant [ENTER]. “R” Définit le rayon de la poche. Le signe indique le sens de l’usinage. “G” Définit la phase de balayage dans le plan XY. La totalité de la poche est fraisée par phases identiques, qui seront égales ou inférieures aux phases programmées. Si une valeur “0” est programmée, la CNC prendra une valeur par défaut égale à 0,75 fois le diamètre de l’outil. “E” Définit la passe de finition. Si “0” est introduit, aucune passe de finition n’est exécutée. Chapitre: 4 Section: Page OPERATIONS AUTOMATIQUES POCHECIRCULAIRE 27 “%F” Indique le pourcentage d’avance utilisé pour la passe de finition. Si ce pourcentage est fixé à “0”, l’avance utilisée pour la passe de finition sera identique à celle utilisée pour les passes d’ébauchage. “Z” Définit la coordonnée Z supérieure de la poche. “P” Définit la profondeur de la poche. “I” Définit la passe de fraisage. La CNC exécute des passes identiques pour la totalité de la poche, qui seront égales ou inférieures aux passes programmées. “%F(Z)” Indique le pourcentage d’avance utilisé pour l’axe Z (plongée). Si la valeur choisie est “0”, l’avance de l’axe Z est égale à l'avance programmée. Opération de base: 1. Déplacement de l’outil jusqu’à la position de sécurité “ZSAF”. 2. Déplacement jusqu’au centre de la poche. 3. Premier mouvement de plongée à %F(Z) de l’avance sélectionnée actuelle “F”. 4. Fraisage de la surface de la poche à l’avance sélectionnée actuelle “F”. La passe de finition sera exécutée à %F de l’avance sélectionnée actuelle “F”. Pour obtenir un fini satisfaisant des faces de la poche, la CNC applique une entrée et une sortie tangentielles lors de la dernière passe. 5. Positionnement de l’outil au centre de la poche et retrait jusqu’à 1 mm au-délà de la surface usinée. 6. Passes de fraisage suivantes jusqu’à ce que la profondeur totale de la poche soit atteinte après exécution des opérations 3, 4 et 5. 7. Retrait jusqu’à la position de sécurité “ZSAF”. Page 28 Chapitre: 4 OPERATIONS AUTOMATIQUES Section: POCHECIRCULAIRE 4.4.3 MOYEU RECTANGULAIRE Les données suivantes doivent être définies: “X1 Y1” Indique l’angle de la poche. Il peut être défini: * en déplaçant les axes en manuel jusqu’au point désiré au moyen des manivelles mécaniques ou électroniques, ou des touches JOG du pupitre opérateur et en frappant [ENTER]. * ou en introduisant ses coordonnées au moyen du clavier et en frappant [ENTER]. “L” Définit la longueur de la poche. Le signe indique le sens de l’usinage. “H” Définit la largeur de la poche. “r”,”C” Définit les angles de la poche. Pour une poche à angles arrondis, introdure “C0” et affecter la valeur du congé à “r”. Chapitre: 4 Section: Page OPERATIONS AUTOMATIQUES MOYEURECTANGULAIRE 29 Pour une poche à angles chanfreinés, introduire “r0” et affecter à “C” la distance du chanfrein par rapport à l’angle théorique. En cas d’exécution d’une poche standard sans angles arrondis ou chanfreinés, programmer “r0” et “C0”. “G” Définit la phase de balayage dans le plan XY. La totalité de la poche est fraisée par phases identiques, qui seront égales ou inférieures aux phases programmées. Si une valeur “0” est programmée, la CNC prendra une valeur par défaut égale à 0,75 fois le diamètre de l’outil. “Q” Définit l’excès de matière à enlever en X et en Y. “E” Définit la passe de finition. Si “0” est introduit, aucune passe de finition n’est exécutée. “%F” Indique le pourcentage d’avance utilisé pour la passe de finition. Si ce pourcentage est fixé à “0”, l’avance utilisée pour la passe de finition sera identique à celle utilisée pour les passes d’ébauchage. “A” Angle de la poche par rapport à l’axe X. “Z” Définit la coordonnée Z supérieure de la poche. “P” Définit la profondeur de la poche. “I” Définit la passe de fraisage. La CNC exécute des passes identiques pour la totalité de la poche, qui seront égales ou inférieures aux passes programmées. “%F(Z)” Indique le pourcentage d’avance utilisé pour l’axe Z (plongée). Si la valeur choisie est “0”, l’avance de l’axe Z est égale à l’avance programmée. Page 30 Chapitre: 4 OPERATIONS AUTOMATIQUES Section: MOYEURECTANGULAIRE Opération de base: 1. Déplacement de l’outil jusqu’à la position de sécurité “ZSAF”. 2. Premier mouvement de plongée à %F(Z) de l’avance sélectionnée actuelle “F”. 3. Fraisage de la surface extérieure de la poche à l’avance sélectionnée actuelle “F”. La passe de finition sera exécutée à %F de l’avance sélectionnée actuelle “F”. Pour obtenir un fini satisfaisant des faces de la poche, la CNC applique une entrée et une sortie tangentielles lors de la dernière passe. 4. Positionnement de l’outil au centre de la poche et retrait jusqu’à 1 mm au-délà de la surface usinée. 5. Passes de fraisage suivantes jusqu’à ce que la profondeur totale de la poche soit atteinte après exécution des opérations 2, 3 et 4. 6. Retrait jusqu’à la position de sécurité “ZSAF”. Chapitre: 4 Section: Page OPERATIONS AUTOMATIQUES MOYEURECTANGULAIRE 31 4.4.4 MOYEU CIRCULAIRE Les données suivantes doivent être définies: “Xc Yc” Indique le centre de la poche. Il peut être défini: * en déplaçant les axes en manuel jusqu’au point désiré au moyen des manivelles mécaniques ou électroniques, ou des touches JOG du pupitre opérateur et en frappant [ENTER]. * ou en introduisant ses coordonnées au moyen du clavier et en frappant [ENTER]. “R” Définit le rayon de la poche. Le signe indique le sens de l’usinage. “G” Définit la phase de balayage dans le plan XY. La totalité de la poche est fraisée par phases identiques, qui seront égales ou inférieures aux phases programmées. Si une valeur “0” est programmée, la CNC prendra une valeur par défaut égale à 0,75 fois le diamètre de l’outil. “Q” Page 32 Définit l’excès de matière à enlever en X et en Y. Chapitre: 4 OPERATIONS AUTOMATIQUES Section: MOYEUCIRCULAIRE “E” Définit la passe de finition. Si “0” est introduit, aucune passe de finition n’est exécutée. “%F” Indique le pourcentage d’avance utilisé pour la passe de finition. Si ce pourcentage est fixé à “0”, l’avance utilisée pour la passe de finition sera identique à celle utilisée pour les passes d’ébauchage. “Z” Définit la coordonnée Z supérieure de la poche. “P” Définit la profondeur de la poche. “I” Définit la passe de fraisage. La CNC exécute des passes identiques pour la totalité de la poche, qui seront égales ou inférieures aux passes programmées. “%F (Z)”Indique le pourcentage d’avance utilisé pour l’axe Z (plongée). Si la valeur choisie est “0”, l’avance de l’axe Z est égale à l’avance programmée. Opération de base: 1. Déplacement de l’outil jusqu’à la position de sécurité “ZSAF”. 2. Premier mouvement de plongée à %F(Z) de l’avance sélectionnée actuelle “F”. 3. Fraisage de la surface extérieure de la poche à l’avance sélectionnée actuelle “F”. La passe de finition sera exécutée à %F de l’avance sélectionnée actuelle “F”. Pour obtenir un fini satisfaisant des faces de la poche, la CNC applique une entrée et une sortie tangentielles lors de la dernière passe. 4. Positionnement de l’outil au point de début de la poche et retrait jusqu’à 1 mm au-délà de la surface usinée. 5. Passes de fraisage extérieur suivantes jusqu’à ce que la profondeur totale de la poche soit atteinte après exécution des opérations 2, 3 et 4. 6. Retrait jusqu’à la position de sécurité “ZSAF”. Chapitre: 4 Section: Page OPERATIONS AUTOMATIQUES MOYEUCIRCULAIRE 33 4.5 EBAUCHE D’ARETES Cette CNC permet l’ébauchage d’arêtes carrées, rondes ou chanfreinées comme montré cidessous: Pour sélectionner cette option, frapper la touche . Les données suivantes doivent être définies: Sens de l'usinage Pour pouvoir changer le sens de l'usinage, il faut frapper la touche [T] et ensuite la touche ou “X1 Y1” Indique les coordonnées intérieures de l’angle. Il peut être défini: * en déplaçant les axes en manuel jusqu’au point désiré au moyen des manivelles mécaniques ou électroniques, ou des touches JOG du pupitre opérateur et en frappant [ENTER]. * ou en introduisant ses coordonnées au moyen du clavier et en frappant [ENTER]. Page 34 Chapitre: 4 OPERATIONS AUTOMATIQUES Section: EBAUCHED’ARETES “L”,”H” Définit la longueur de la poche en X et en Y respectivement. Selon l’arête à usiner, le signe sera positif ou négatif comme montré ci-dessous. “r”,”C” Définit le type d’arête à usiner Pour une arête arrondie, définir “C0” et affecter la valeur du congé à “r”. Pour une arête chanfreinée, définir “r0” et affecter à “C” la distance entre le chanfrein et l’arête théorique. Dans le cas de l’exécution d’une arête aigüe classique, frapper “r0” et “C0”. Les valeurs assignées à "r" et "C" doivent ètre inférieures à celles qui ont été assignées aux paramètres "L" et "H". “G” Définit la phase de balayage dans le plan XY. La totalité de l’arête est fraisée par phases identiques, qui seront égales ou inférieures aux phases programmées. Si une valeur “0” est programmée, la CNC prendra une valeur par défaut égale à 0,75 fois le diamètre de l’outil. “E” Définit la passe de finition. Si “0” est introduit, aucune passe de finition n’est exécutée. “%F” Indique le pourcentage d’avance utilisé pour la passe de finition. Si ce pourcentage est fixé à “0”, l’avance utilisée pour la passe de finition sera identique à celle utilisée pour les passes d’ébauchage. “A” Angle de la poche par rapport à l’axe X. “Z” Définit la coordonnée Z supérieure de la poche. Chapitre: 4 Section: Page OPERATIONS AUTOMATIQUES EBAUCHED’ARETES 35 “P” Définit la profondeur de la poche. “I” Définit la passe de fraisage. La CNC exécute des passes identiques pour la totalité de la poche, qui seront égales ou inférieures aux passes programmées. “%F(Z)” Indique le pourcentage d’avance utilisé pour l’axe Z (plongée). Si la valeur choisie est “0”, l’avance de l’axe Z est égale à l’avance programmée. Opération de base: 1. Déplacement de l’outil jusqu’à la position de sécurité “ZSAF”. 2. Déplacement jusqu’à l’extérieur de l’arête. 3. Premier déplacement de plongée à %F(Z) de l’avance sélectionnée actuelle “F”. 4. Fraisage de l’arête à l’avance sélectionnée actuelle “F”. La passe de finition sera exécutée à %F de l’avance sélectionnée actuelle “F”. 5. Passes de fraisage suivantes jusqu’à ce que la profondeur totale soit atteinte. 6. Retrait jusqu’à la position de sécurité “ZSAF”. Page 36 Chapitre: 4 OPERATIONS AUTOMATIQUES Section: EBAUCHED’ARETES 4.6 SURFAÇAGE Cette option est activée par la frappe de la touche . Comme cette CNC permet 4 types différents de surfaçage, le choix du type s’effectue par la frappe de la touche . Les types de surfaçage disponibles sont les suivants: Bidirectionnel en X Unidirectionnel en X Bidirectionnel en Y Chapitre: 4 Section: Page OPERATIONS AUTOMATIQUES SURFAÇAGE 37 Unidirectionnel en Y Les données suivantes doivent être définies dès que le type de surfaçage a été sélectionné: “X1 Y1” Indique l’arête de la surface à fraiser. Elle peut être définie: * en déplaçant les axes en manuel jusqu’au point désiré au moyen des manivelles mécaniques ou électroniques, ou des touches JOG du pupitre opérateur et en frappant [ENTER]. * ou en introduisant ses coordonnées au moyen du clavier et en frappant [ENTER]. “L”,”H” Définit la longueur et la largeur de la surface à fraiser. En surfaçage unidirectionnel, le signe de ces paramètres indique le sens de l’usinage. Page 38 Chapitre: 4 OPERATIONS AUTOMATIQUES Section: SURFAÇAGE “G” Définit le balayage entre deux passes consécutives. La totalité de la surface est fraisée par phases identiques, qui seront égales ou inférieures aux phases programmées. Si une valeur “0” est programmée, la CNC prendra une valeur par défaut égale à 0,75 fois le diamètre de l’outil. “E” Définit la valeur du dépassement de course de l’outil par rapport à chaque côté de la pièce afin d’obtenir un fini parfait sur les arêtes. “ZSAF” Définit la coordonnée de sécurité en Z. “Z” Définit la hauteur du plan à surfacer. “P” Définit la profondeur de fraisage. “I” Définit la passe de fraisage. La CNC exécute des passes identiques pour la totalité de la poche, qui seront égales ou inférieures aux passes programmées. Opération de base: 1. Déplacement de l’outil jusqu’à la position de sécurité “ZSAF”. 2. Déplacement jusqu’à un point situé à une distance “E” par rapport à l’arête, X1 Y1. 3. Premier mouvement de plongée et fraisage de la surface à l’avance sélectionnée actuelle “F”. Pour obtenir un fini parfait aux arêtes, l’outil effectue un dépassement de course sur une distance “E” de chaque côté. 4. Déplacement de l’outil jusqu’au point situé à une distance “E” de l’arête, X1 Y1, et retrait jusqu’à 1 mm par rapport à la surface usinée. 5. Passes de fraisage suivantes jusqu’à ce que la profondeur programmée soit atteinte après exécution des opérations 3 et 4. 6. Retrait jusqu’à la position de sécurité “ZSAF”. Chapitre: 4 Section: Page OPERATIONS AUTOMATIQUES SURFAÇAGE 39 5. OPERATIONS D’USINAGE Cette CNC permet d’effectuer les opérations d’usinage suivantes: * * * * Pointage Perçage Taraudage Alésage Chacune de ces opérations peut être exécutée lorsque la CNC est en mode DRO ou peut être associée à toute opération de positionnement automatique. Quand la CNC fonctionne en mode DRO, les axes doivent être déplacés jusqu’au point où l’usinage sera effectué. Procéder comme suit: * Frapper pour accéder aux opérations d’usinage. * Frapper ou d’usinage désirée. * Définir correctement toutes les données correspondant à l’opération sélectionnée. * Frapper autant de fois que nécessaire pour sélectionner l’opération pour lancer l’usinage. Procéder comme suit pour associer une opération d’usinage à une opération de positionnement: * Sélectionner et définir l’opération de positionnement automatique (point à point, en ligne, en arc, en rectangle ou en grille). * Frapper * Frapper ou d’usinage désirée. * Définir correctement toutes les données correspondant à l’opération sélectionnée. * La CNC associe l’opération d’usinage au positionnement automatique de façon qu’il soit possible de définir “Positionnement en ligne + Perçage”, “Positionnement en arc + Alésage", etc. pour accéder aux opérations d’usinage. autant de fois que nécessaire pour sélectionner l’opération Les conditions d’usinage doivent être définies dans l’opération automatique. Chapitre: 5 OPERATIONSD’USINAGE Section: Page 1 Chaque fois qu’une opération d’usinage est sélectionnée, la CNC affiche: * Une représentation graphique de l’opération automatique sélectionnée dans la zone de visualisation principale. * Les données correspondant à l’opération sélectionnée au bas de l’écran. 5.1 GENERALITES Dès que l’opération d’usinage a été sélectionnée, frapper l’une des touches suivantes: Permet de quitter l’opération d’usinage et de repasser à l’opération de positionnement automatique. Aucun usinage n’est associé au positionnement. Permet la prise en compte des données d’usinage par la CNC et le retour à l’opération de positionnement automatique. L’opération d’usinage est associée à l’opération de positionnement. Permet d’accéder au mode entrée de données. La CNC met en surbrillance les premières données sur le graphique et dans la zone d’édition de données. Introduire la valeur désirée pour les données et frapper [ENTER]. La CNC prend la nouvelle valeur en compte et met en surbrillance la donnée suivante. Pour sélectionner une autre donnée, il suffit d’actionner les touches . Dès que toutes les données ont été définies, frapper [DATA] pour sortir du mode entrée de données. La CNC enregistre les données d’usinage et retourne à l’opération de positionnement automatique. L’opération d’usinage est associée à l’opération de positionnement Page 2 Chapitre: 5 OPERATIONSD’USINAGE Section: GENERALITES 5.1.1 FONCTIONS "M" AVANT ET APRES L 'OPERATION Il est possible d’associer à chaque opération d'usinage l’exécution de deux fonctions auxiliaires "M". L’une d’elles sera exécutée avant l'opération et l’autre, après l’exécution de celle-ci. Les écrans d’aide de chaque opération affichent, à droite des données de définition les 2 fonctions auxiliaires "M" sélectionnées dans chaque opération. La "M" située sur la partie supérieure indique la fonction auxiliaire "M" qui est exécutée avant ll'opération et la "M" située sur la partie inférieure indique la fonction auxiliaire «M» qui est exécutée après l'opération. Si l’une d’elles affiche la valeur "M--", cela veut dire qu’il n’y a aucune fonction auxiliaire "M" associée. Pour pouvoir sélectionner la fonction auxiliaire «M» que l’on désire exécuter avant l'opération, il faut agir de la manière suivante: Taper la séquence de touches [F] [BEGIN] Introduire le numéro de la fonction voulue Taper sur touche [ENTER] Pour pouvoir sélectionner la fonction auxiliaire "M" que l’on désire exécuter après l'opération, il faut agir de la manière suivante: Taper la séquence de touches [F] [END] Introduire le numéro de la fonction voulue Taper sur touche [ENTER] Pour pouvoir effacer une des fonctions auxiliaires "M" qui sont sélectionnées, il faut agir de la manière suivante: Taper la séquence de touches [F] [BEGIN] ou [F] [END] Taper sur touche [ENTER] La CNC affichera la valeur "M--" Attention: Lorsqu’une opération automatique est mémorisée, la CNC sauvegarde les deux fonctions auxiliaires "M" sélectionnées, avec les données et autres paramètres définissant l’opération automatique. De cette manière, chaque fois qu’une pièce mémorisée au préalable est exécutée, la CNC exécutera chacune des opérations automatiques sous les conditions d’usinage qui furent établies pour elle. A la mise sous tension ou après une REMISE A ZERO, la CNC initialise toutes les opérations (mais non celles qui sont mémorisées), en assignant aux deux champs la valeur "M--" (il n’y a aucune fonction auxiliaire "M" associée). Chapitre: 5 OPERATIONSD’USINAGE Section: GENERALITES Page 3 5.2 POINTAGE Pour définir la distance de pénétration du foret à centrer dans la pièce, on utilisera l’une des méthodes suivantes: * Définition de la profondeur de pointage (P) * Définition de l’angle “A” du foret et du diamètre ( ) du point à réaliser. Dans les deux cas, les données suivantes doivent être définies: “Z” Point (coordonnées) où l’usinage sera effectué. “K” Temporisation (en secondes) entre le pointage et le retrait de l’outil. Opération de base: 1. Pointage selon l’avance “F” et les données définies. 2. Temporisation si “K” a été programmé. 3. Retrait en rapide jusqu’à la position de sécurité “ZSAF”. Page 4 Chapitre: 5 OPERATIONSD’USINAGE Section: POINTAGE 5.2.1 EXEMPLE DE PROGRAMMATION Définition du “Positionnement en ligne” X1 = 20 L = 50 N =6 ZSAF = 1 Y1 = 10 A = 25 Définition du “Pointage” Z =0 P = 1,5 K=0 Chapitre: 5 OPERATIONSD’USINAGE Section: POINTAGE Page 5 5.3 PERÇAGE Les données suivantes doivent être définies: “Z” Point (coordonnées) où l’usinage doit être effectué. “P” Profondeur de perçage “I” Passe de perçage “K” Temporisation (en secondes) entre la fin du perçage et le retrait de l’outil. Opération de base: 1. Premier déplacement de perçage jusqu’à “Z-I” à la vitesse d’avance “F”. 2. Retrait en rapide jusqu’en Z. 3. Approche en rapide jusqu’à 1 mm de la plongée précédente. 4. Nouveau déplacement de perçage (plongée) sur une distance “I” à la vitesse d’avance “F”. 5. Répétition des opérations 2, 3, 4 jusqu’à ce que la profondeur programmée totale soit atteinte. 6. Temporisation si “K” a été programmé. 7. Retrait en rapide jusqu’à la position de sécurité “ZSAF”. Page 6 Chapitre: 5 OPERATIONSD’USINAGE Section: PERÇAGE 5.3.1 EXEMPLE DE PROGRAMMATION Définition du “Positionnement en ligne” X1 = 20 L = 50 N =6 ZSAF = 1 Y1 = 10 A = 25 Définition du “Perçage” Z P I K =0 = 12 =5 =1 Chapitre: 5 Section: Page OPERATIONSD’USINAGE PERÇAGE 7 5.4 TARAUDAGE Les données suivantes doivent être définies: “Z” Point (coordonnées) où l’usinage doit être effectué. “P” Profondeur de taraudage “K” Temporisation (en secondes) en fond de trou. Opération de base: 1. Taraudage sur la distance totale à 100% de la vitesse d’avance sélectionnée “F” (aucune correction n’est possible). 2. Si “K” n’a pas été programmé, la broche change de sens de rotation. Si “K” a été programmé, les opérations sont les suivantes: * Arrêt de la broche * Attente pendant une durée “K” (temporisation) * Inversion du sens de rotation de la broche 3. Retrait jusqu’à la position de sécurité “ZSAF” à la vitesse d’avance programmée “F”. 4. Si “K” n’a pas été programmé, le sens de rotation de la broche s’inverse à nouveau; la broche repasse donc au sens de rotation initial. Si “K” a été programmé, les opérations sont les suivantes: * Arrêt de la broche * Attente pendant une durée “K” (temporisation) * Inversion du sens de rotation de la broche, qui repasse donc au sens de rotation initial. Page 8 Chapitre: 5 OPERATIONSD’USINAGE Section: TARAUDAGE 5.4.1 EXEMPLE DE PROGRAMMATION Définition du “Positionnement en ligne” X1 = 20 L = 50 N =6 ZSAF = 1 Y1 = 10 A = 25 Définition du “Perçage” Z =0 P = 12 K =1 Chapitre: 5 Section: Page OPERATIONSD’USINAGE TARAUDAGE 9 5.5 ALESAGE Les données suivantes doivent être définies: “Z” Point (coordonnées) où l’usinage sera effectué. “P” Profondeur d’alésage. “K” Temporisation (en secondes) en fond de trou. Opération de base: 1. Pointage selon l’avance “F” et les données définies. 2. Temporisation si “K” a été programmé. 3. Retrait en rapide jusqu’à la position de sécurité “ZSAF” à la vitesse d’avance programmée “F”. Page 10 Chapitre: 5 OPERATIONSD’USINAGE Section: ALESAGE 5.5.1 EXEMPLES DE PROGRAMMATION Exemple de perçage pour alésage “Positionnement sur diamètre de perçage” (sur un arc) Xc = 70 R = 40 N =8 ZSAF = 1 Yc = 20 A = -15 B = 30 Définition du perçage Z =0 P = 12 K =1 Exemple d’alésage “Positionnement en grille” X1 = 20 A =0 LX = 90 LY = 40 ZSAF = 1 Y1 = 10 B = 90 NX = 4 NY = 3 Définition de l’alésage Z =0 P = 12 K =1 Chapitre: 5 OPERATIONSD’USINAGE Section: ALESAGE Page 11 6. FONCTIONNEMENT AVEC LES PROGRAMMES PIECE La CNC 800M permet de mémoriser jusqu’à 7 programmes pièce. Chacun de ces programmes peut comporter jusqu’à 20 opérations de base. Chacune de ces opérations aura été éditée par l’opérateur dans le mode “AUTOMATIQUE” (CYCLE) et dans les conditions décrites dans le chapitre sur les “OPERATIONS AUTOMATIQUES”. 6.1 ACCES A LA TABLE DE PROGRAMMES PIECE Pour accéder à cette table, frapper [RECALL]. La partie supérieure droite de l’écran affiche un répertoire de 7 programmes pièce maximum sur les 10 pouvant être mémorisés; ils sont numérotés avec 5 chiffres maximum, entre “000000” et”99995". Pour afficher la suite, frapper les touches . Les tirets signalent l’absence de programme pièce. Les symboles figurant à la droite du numéro de pièce correspondant ont les significations suivantes: PIECE 01435 [*] 47632 [*] 32540 [*] ----- [ ] ----- [ ] ----- [ ] ----- [ ] SORTIE [*] Signale que le programme pièce a déjà été édité et contient des données. [ ] Signale que le programme pièce ne contient pas de données. Pour affecter un numéro à la pièce désirée, procéder comme suit: . Positionner le curseur sur la pièce au moyen des touches ; la sélection est déroulante. . Frapper [P]. La ligne sélectionnée apparaît en vidéo inverse et le numéro “00000” clignote. . Frapper les chiffres du numéro à affecter, puis [ENTER]. Si le numéro continue à clignoter après la frappe de cette touche, c’est que ce numéro a déjà été affecté à une autre pièce. . Si [CLEAR] est frappé, la ligne sélectionnée revient à son numéro précédent, si elle en comportait un. Pour sortir de la table de programmes pièce, positionner le curseur sur “SORTIE” et frapper [ENTER]. Chapitre: 6 FONCTIONNEMENTAVECLES PROGRAMMESPIECE Section: ACCES A LA TABLE DE PROGRAMMESPIECE Page 1 6.2 SELECTION DES PROGRAMMES PIECE Pour analyser le contenu d’un programme pièce afin de l’éditer ou de le modifier, il doit être sélectionné dans la table de programmes pièce avant de frapper [RECALL]. Chaque pièce peut comporter jusqu’à 20 opérations de base. La partie supérieure droite de l’écran affiche un ensemble de 7 opérations. Chaque fois que l’on accède à un programme pièce, le curseur apparaît sur le premier emplacement libre. PIECE 01346 1 -POCH.RECT 2 -POCH.CIRC 3 -P.ARC+PER 4 -MOY.CIRC. 5? 6? 7? SORTIE Les emplacements libres sont indiqués par le caractère “?”, alors que les emplacements occupés signalent le type d’opération qui a été édité à ces emplacements. Bien que les profils soient traités comme des opérations uniques, ils occupent deux emplacements. Chacune de ces opérations aura été éditée au préalable par l’opérateur dans le mode “AUTOMATIQUE” (CYCLE) et dans les conditions décrites dans le chapitre traitant des “OPERATIONS AUTOMATIQUES”. Pour sélectionner l’une de ces opérations, positionner le curseur sur celle-ci au moyen des touches . Pour sortir de l’option programmes pièce, positionner le curseur sur “SORTIE” et frapper [ENTER]. Pour revenir au répertoire de programmes pièce (menu précédent), frapper la touche à flèche vers le haut jusqu’à ce que le curseur se positionne sur “PIECE 01346”, puis frapper la touche une seconde fois. Page 2 Chapitre: 6 FONCTIONNEMENTAVECLES PROGRAMMESPIECE Section: SELECTIONDES PROGRAMMESPIECE 6.3 EDITION DES PROGRAMMES PIECE Un programme pièce comporte plusieurs opérations. Pour l’éditer, il est donc nécessaire d’éditer ses différentes opérations. Chaque opération est éditée comme toute opération normale dans les conditions décrites dans la section “OPERATIONS AUTOMATIQUES”. Dès qu’elle a été définie, l’opération peut être simulée ou exécutée afin de vérifier qu’elle se déroule correctement. Pour mémoriser l’opération en tant que programme pièce, placer le curseur sur le numéro de l’opération qui doit lui être affectée et frapper [ENTER]. La CNC demande confirmation de la commande. Deux cas sont possibles: * Le numéro de l’opération sélectionnée était libre Dès que la commande de chargement en mémoire est confirmée, la CNC incorpore la nouvelle opération à l’emplacement indiqué et la liste des opérations est mise à jour. * Le numéro de l’opération sélectionnée était occupé Quand la CNC demande confirmation de cette commande, elle demande si l’opérateur désire effectuer une opération: Replace par la frappe de [ENTER]. La nouvelle opération occupera l’emplacement sélectionné et la précédente disparaîtra. Les autres opérations conservent leur emplacement d’origine. Insert par la frappe de [1]. La nouvelle opération occupera l’emplacement sélectionné; celle qui occupait cet emplacement ainsi que les suivantes (y compris les emplacements libres) reculent d’un emplacement. Si l’emplacement n° 20 est déjà occupé, la CNC affiche un message indiquant que cette commande ne peut pas être exécutée. Ignore (ne rien faire) par la frappe de [CLEAR]. Attention: Quand plusieurs opérations d’un programme pièce sont éditées, il est recommandé de commencer par l’opération “1” et d’utiliser les emplacements consécutifs. Quand un programme pièce est exécuté, la CNC commence toujours par l’opération “1” et termine l’exécution quand elle rencontre un emplacement libre, même si le programme comporte d’autres opérations. Chaque opération du programme pièce est mise en mémoire avec toutes les données éditées avec elle, y compris les conditions d’usinage: F, S, T, sens de rotation de broche, etc... Chapitre: 6 FONCTIONNEMENTAVECLES PROGRAMMESPIECE Section: EDITIONDESPROGRAMMES PIECE Page 3 6.4 SIMULATION DES PROGRAMMES PIECE Cette CNC permet de vérifier un programme pièce en effectuant une simulation avant de l’exécuter. Quand une simulation est effectuée, la CNC commence toujours par l’opération “1” et stoppe quand elle rencontre un emplacement libre, même si la pièce comporte d’autres opérations. PIECE 01346 1 -POCH.RECT 2 -POCH.CIRC 3 -P.ARC+PER 4 -MOY.CIRC. 5? 6? 7? SORTIE Pour exécuter la simulation, placer le curseur sur le numéro de la pièce (PART 01346) et frapper . La CNC affiche une représentation graphique. L’angle inférieur gauche de l’écran affiche le plan à représenter (XY, XZ ou YZ), ou XYZ tridimensionnel. Pour afficher un autre plan, frapper sa touche correspondante: [0] [1] [2] [3] Plan XY Plan XZ Plan YZ Plan tridimensionnel XYZ Cette CNC peut afficher les graphiques sur un maximum de 3 plans. Elle n’affiche donc que les plans sélectionnés. Pour sélectionner d’autres plans, procéder comme suit: Frapper ou non. : la CNC demande si chacun des plans possibles doit être sélectionné Pour sélectionner le plan, frapper [Y]; sinon, frapper [ENTER]. Dès que les plans ont été définis, la zone d’affichage doit être délimitée en indiquant les coordonnées XYZ du centre de l’écran et la largeur de la zone d’affichage. Après l’entrée de chaque valeur, frapper [ENTER]. Centre Largeur Page 4 Chapitre: 6 FONCTIONNEMENTAVECLES PROGRAMMESPIECE Section: SIMULATIONDES PROGRAMMESPIECE Pour vérifier la pièce, frapper correspondante. . Cette opération lance la simulation graphique Pendant la simulation, il est possible d’accéder à un autre plan (touches 0, 1, 2 et 3) mais il est impossible de les définir. Pour définir d’autres plans ou modifier la zone d’affichage, la simulation du programme doit être interrompue en frappant . Frapper [CLEAR] pour vider l’écran et [END] pour quitter le mode simulation. 6.4.1 FONCTION ZOOM Cette fonction permet d’agrandir ou de réduire la totalité ou une partie du graphique. Pour ce faire, il est nécessaire d’interrompre la simulation du programme ou d’attendre sa fin. Dès que le plan du dessin à agrandir ou à réduire a été sélectionné, frapper [Z]. L’écran affiche un rectangle sur le dessin d’origine. Ce rectangle est la fenêtre de zoom, qui représente la nouvelle zone d’affichage pour la partie à agrandir ou à réduire. Pour changer les dimensions du rectangle, utiliser les touches suivantes: Réduit la taille du rectangle (zoom avant) Augmente la taille du rectangle (zoom arrière) Utiliser pour déplacer la fenêtre de zoom. Pour définir la zone sélectionnée avec la fenêtre de zoom comme nouvelle zone d’affichage, frapper [ENTER]. Pour voir la zone sélectionnée agrandie ou réduite tout en conservant les valeurs de la zone d’affichage précédente, frapper . La zone contenue dans la fenêtre de zoom remplit maintenant la totalité de l’écran. Pour revenir à la zone d’affichage précédente (avant le zoom) frapper [END]. Pour utiliser à nouveau le zoom, il suffit de frapper [Z] et de procéder comme indiqué plus haut. Pour quitter la fonction ZOOM et revenir à la représentation graphique, frapper [END]. Chapitre: 6 FONCTIONNEMENTAVECLES PROGRAMMESPIECE Section: SIMULATIONDES PROGRAMMESPIECE Page 5 6.5 EXECUTION DU PROGRAMME PIECE Quand la CNC exécute un programme pièce, elle commence toujours par l’opération “1” et stoppe quand elle rencontre un emplacement libre, même si la pièce comporte d’autres opérations. PIECE 01346 1 -POCH.RECT 2 -POCH.CIRC 3 -P.ARC+PER 4 -MOY.CIRC. 5? 6? 7? SORTIE Pour exécuter un programme pièce, il doit être sélectionné en plaçant le curseur sur l’en-tête de la pièce (PART 01346) avant la frappe de . Dès que le programme pièce est sélectionné, il exécute une opération après l’autre en commençant par la première. Chaque fois que la CNC sélectionne une opération, elle la met en surbrillance et fait une copie dans la zone d’édition (au bas de l’écran), qui affiche l’opération sélectionnée avec tous ses paramètres. Dès la fin de l’opération, l’outil se met en position de sécurité “ZSAF”. Son déplacement jusqu’au premier point de l’opération suivante s’effectue sur une droite conservant la coordonnée “ZSAF”. Avant d’exécuter chaque opération, la CNC prend en compte les conditions d’usinage F, S, T définies pour l’opération. A la fin de chaque opération, l’outil repasse à la position de sécurité “ZSAF” de cette opération. Si l’opération suivante exige un changement d’outil, la CNC déplace l’outil jusqu’à la coordonnée Z au début du programme (où il se trouvait avant la frappe de ), stop-pe la broche et affiche le message de changement d’outil. Avant de démarrer l’opération suivante, l’outil se positionne sur le point “ZSAF” de cette opération. L’exécution du programme pièce cesse quand la CNC rencontre un emplacement libre, même si d’autres opérations sont définies dans des blocs suivants. L’outil repasse à la coordonnée en Z où l’exécution du programme pièce a commencé (où il se trouvait lors de la frappe de ). Si l'on désire interrompre l'exécution du programme, il faut frapper la touche L'exécution du programme s'arrête et les touches suivantes sont disponibles: Pour reprendre l'exécution du programme frapper la touche . . Attention: Ne pas oublier que la CNC exécute toujours les opérations définies dans la zone d’édition au bas de l’écran. En conséquence, le curseur doit être positionné sur l’en-tête de la pièce (PART 01346) avant la frappe de . Si, lors de la frappe de , le curseur est positionné sur une opération automatique, la CNC n’exécute que cette opération. Page 6 Chapitre: 6 FONCTIONNEMENTAVECLES PROGRAMMESPIECE Section: EXECUTIONDUPROGRAMME PIECE 6.5.1 EXECUTION D’UNE OPERATION MEMORISEE PREALABLE DANS UN PROGRAMME PIECE AU Pour exécuter une opération mémorisée au préalable dans un programme pièce, sélectionner le programme pièce, positionner le curseur sur l’opération désirée et frapper [RECALL]. La CNC rappelle toutes les valeurs qui avaient été mémorisées avec l’opération et les affiche au bas de l’écran. * Données spécifiques à l’opération. * Conditions d’usinage: F, S, T, sens de rotation de broche, etc... Ensuite, frapper pour exécuter l’opération sélectionnée. Il est possible de modifier toute donnée avant de frapper Chapitre: 6 FONCTIONNEMENTAVECLES PROGRAMMESPIECE en cas de besoin. Section: EXECUTIONDUPROGRAMME PIECE Page 7 6.5.2 CONTROLE DE L’OUTIL Cette option permet d’interrompre l’exécution d’un programme pièce et d’inspecter l’outil afin de vérifier son état et de le remplacer si nécessaire. Pour ce faire, procéder comme suit: a) Frapper pour interrompre le programme. b) Frapper [TOOL] A cet instant, la CNC exécute la fonction auxiliaire M05 pour stopper la broche et elle affiche sur l’écran: TOUCHES JOG DISPONIBLES OUT c) Amener l’outil à la position désirée au moyen des touches JOG. Dès que l’outil est “hors trajectoire”, la broche peut être démarrée et stoppée à nouveau par les touches correspondantes du pupitre opérateur. d) Dès la fin de l’inspection ou du changement de l’outil, frapper [END]. La CNC exécute une fonction M03 ou M04 pour démarrer la broche dans le sens en cours lors de l’interruption du programme. L’écran affiche alors: RETOUR AXES HORS POSITION “Axes hors position” signifie qu’ils ne se situent pas au même point que lorsque le programme a été interrompu. e) Déplacer les axes en manuel jusqu’à la position d’interruption du programme au moyen des touches JOG correspondantes. La CNC interdit le dépassement (surcourse) de cette position. Lorsque les axes sont en position, l’écran affiche: RETOUR AXES HORS POSITION AUCUN f) Page 8 Frapper pour reprendre l’exécution du programme pièce. Chapitre: 6 FONCTIONNEMENTAVECLES PROGRAMMESPIECE Section: EXECUTIONDUPROGRAMME PIECE 6.6 MODIFICATION D’UN PROGRAMME PIECE Pour modifier une opération, sélectionner le programme pièce correspondant, positionner le curseur sur l’opération désirée et frapper [RECALL]. La CNC rappelle toutes les valeurs qui avaient été mémorisées avec cette opération et les affiche au bas de l’écran. A partir de ce moment, l’opération peut être modifiée comme toute opération normale et dans les conditions décrites à la section “OPERATIONS AUTOMATIQUES”. Dès que toutes les modifications ont été effectuées, il est possible de simuler ou d’exécuter l’opération pour vérifier qu’elle s’exécute correctement, avant de la mémoriser. Dès que [ENTER] a été frappé, la CNC demande confirmation de la commande. Frapper [ENTER] à nouveau pour confirmer (option remplacer). Pour supprimer une opération, sélectionner le programme pièce correspondant, positionner le curseur sur l’opération désirée et frapper [CLEAR]. La CNC demandera confirmation de la commande. Quand elle supprime une opération, la CNC comprime le programme pièce et remonte toutes les opérations suivantes d’un emplacement. Pour insérer une nouvelle opération, procéder comme pour l’édition d’un programme pièce. Dès que l’opération a été définie, positionner le curseur sur le numéro de l’opération qui doit être affectée au programme et frapper [ENTER] pour la charger en mémoire. La CNC demande confirmation de la commande. Frapper [1] pour insérer cette nouvelle opération ou [ENTER] pour remettre en place l’opération en cours (ancienne). Pour copier une opération existante dans un autre emplacement, amener le curseur sur l’opération à copier et frapper [RECALL]. La CNC rappelle toutes les valeurs qui avaient été mémorisées avec cette opération et les affiche au bas de l’écran. Ensuite, sélectionner le numéro de l’opération où la copie doit s’effectuer et frapper [ENTER]. La CNC demandera confirmation de la commande. Chapitre: 6 FONCTIONNEMENTAVECLES PROGRAMMESPIECE Section: MODIFICATIOND’UN PROGRAMMEPIECE Page 9 6.7 SUPPRESSION D’UN PROGRAMME PIECE Pour supprimer un programme pièce, choisir l’une des méthodes suivantes: Sélectionner le programme pièce désiré dans le répertoire de programmes et frapper [CLEAR] ou sélectionner le programme pièce désiré, positionner le curseur sur son en-tête (PIECE 01435) et frapper [CLEAR]. Dans les deux cas, la CNC demandera confirmation de la commande. PIECE 01435 [*] 47632 [*] 32540 [*] ----- [ ] ----- [ ] ----- [ ] ----- [ ] SORTIE Page 10 PIECE 01345 1 -POCH.RECT 2 -POCH.CIRC 3 -P.ARC+PER 4 -MOY.CIRC. 5? 6? 7? SORTIE Chapitre: 6 FONCTIONNEMENTAVECLES PROGRAMMESPIECE Section: SUPPRESSION D’UN PROGRAMMEPIECE 6.8 PERIPHERIQUES Cette CNC permet de communiquer avec l’unité de disquettes FAGOR, un périphérique général ou un ordinateur afin de transférer des programmes entre eux. Ces communications peuvent être gérées depuis la CNC en “Mode périphérique” ou depuis l’ordinateur au moyen du protocole DNC de FAGOR; dans ce dernier cas, le mode de fonctionnement de la CNC n’a aucune importance. 6.8.1 MODE PERIPHERIQUE Dans ce mode, la CNC peut communiquer avec l’unité de disquettes FAGOR, un périphérique général ou un ordinateur disposant d’un programme de communications standard du commerce. Pour accéder à ce mode, frapper la touche [AUX] et après avoir sélectionné "Modes auxiliaires" frapper la touche correspondant à "PERIPHERIQUES". Dès que l’option est sélectionnée, l’angle supérieur gauche de la CNC affiche le menu suivant: 0123456- ENTREE DE L’UNITE DE DISQUETTES (Fagor) SORTIE SUR UNITE DE DISQUETTES (Fagor) ENTREE DE PERIPHERIQUE (générale) SORTIE SUR PERIPHERIQUE (générale) REPERTOIRE DE L’UNITE DE DISQUETTES (Fagor) EFFACER PROGRAMME UNITE DE DISQUETTES (Fagor) DCN ON/OFF Pour utiliser l’une de ces options, le mode DNC doit être inactif. Sinon (l’angle supérieur droit de l’écran affiche DNC), frapper [6] (DNC ON/OFF) pour le désactiver (l’indication DNC disparaît). Les options 0, 1, 2 et 3, permettent de transférer les paramètres machine, la table de fonctions M décodées et la table de compensation d’erreur de vis vers un périphérique. L’angle inférieur droit de l’écran de la CNC affichera un répertoire contenant jusqu’à 7 programmes pièce de la CNC. Pour exécuter le transfert, frapper le n° désiré quand la CNC demande le n° du programme à transférer et frapper [ENTER]. P00000 à P99990 P99994 et P99996 P99997 P99998 P99999 Correspond aux programmes pièce Programme utilisateur spécial en code ISO. Pour utilisation interne; ne peut PAS être déplacé. Utilisé pour associer des textes à des messages PLCI. Paramètres machine et tables. Attention: Les programmes pièce (P00000-P99994) ne peuvent pas être édités au niveau du périphérique ou de l’ordinateur. Le moniteur affichera le message “RECEPTION” ou “EMISSION” pendant le transfert du programme et le message “PROGRAMME N° P23256 (par exemple) RECU” ou “ENVOYE” à la fin de la transmission. Chapitre: 6 FONCTIONNEMENTAVECLES PROGRAMMESPIECE Section: PERIPHERIQUES Page 11 Quand la transmission est défectueuse, “Erreur de transmission” s’affiche et, quand la CNC ne reconnait pas les données reçues (format différent), elle émet le message “Données incorrectes reçues”. Lors de toute transmission de données, la mémoire de la CNC doit être déverrouillée; sinon, la CNC repasse au menu du mode périphérique. En cas de transmission depuis un périphérique autre qu’une unité de disquettes FAGOR, on tiendra compte des éléments suivants: * * * * Le programme doit commencer par un caractère “NUL” (00 en ASCII) suivi de “%” “n° du programme” (par exemple, %23256) et un caractère “LINE FEED” (LF). Les espaces, la touche retour chariot et le signe “+” sont ignorés Le programme doit se terminer par 20 caractères “NULS” (00 en ASCII), un caractère “ESCAPE” ou un caractère “EOT”. Frapper [CL] pour annuler la transmission. La CNC émet le message: "PROCESSUS INTERROMPU". REPERTOIRE DE L’UNITE DE DISQUETTES Cette option affiche les programmes chargés sur le disque introduit dans l’unité de disquettes FAGOR et le nombre de caractères (taille) de chacun d’eux. Elle indique également le nombre de caractères libres disponibles (espace mémoire libre) sur la bande. EFFACER PROGRAMME UNITE DE DISQUETTES Cette option permet d’effacer un programme se trouvant dans l’unité de disquettes FAGOR. La CNC demande le n° du programme à effacer. Après avoir entré le n° désiré, frapper [ENTER]. Dès que le programme est effacé, la CNC affiche le message “PROGRAMME N°: P______ EFFACE”. Elle indique aussi le nombre de caractères libres sur la disquette (espace mémoire disponible). 6.8.2 COMMUNICATIONS DNC Pour utiliser cette fonction, les communications DNC doivent être actives (l’angle supérieur droit de l’écran affiche DNC). Pour ce faire, les paramètres correspondants doivent être définis en conséquence par le constructeur et l’option [6] du mode “Périphériques” doit être sélectionnée si elle n’était pas active. Dès que l’option est active et au moyen du logiciel d’application FAGORDNC fourni, il est possible d’exécuter sur demande les opérations suivantes depuis l’ordinateur: . . . . Obtention du répertoire de programmes pièce CNC Transfert de programmes pièce et de tables de/vers la CNC. Effacement de programmes pièce au niveau de la CNC. Un certain contrôle à distance de la machine. Attention: Tout mode de fonctionnement peut être sélectionné depuis la CNC. Page 12 Chapitre: 6 FONCTIONNEMENTAVECLES PROGRAMMESPIECE Section: PERIPHERIQUES 6.9 BLOCAGE/DEBLOCAGE Cette option permet de bloquer/débloquer la mémoire de programmes pièce. Pour pouvoir sélectionner cette option, frapper la touche [AUX] et après avoir sélectionné "Modes Auxiliaires", frapper la touche correspondant à "BLOCAGE/DEBLOCAGE" Les codes utilisés dans ce cas sont: [BEG] 0000 [ENTER] Déblocage de la mémoire de programmes pièce [BEG] 1111 [ENTER] Blocage de la mémoire de programmes pièce [P] F100 [ENTER] Efface le contenu de tous les paramètres arithmétiques (données des opérations automatiques). Il leur assigne la valeur 0. Chapitre: 6 FONCTIONNEMENTAVECLES PROGRAMMESPIECE Section: BLOCAGE/DEBLOCAGE Page 13 CODES D'ERREUR 001 Cette erreur apparaît dans les cas suivants: * Quand le premier caractère du bloc à exécuter n’est pas”N”. * Lorsque, pendant une édition en ARRIERE-PLAN, le programme en cours appelle un sous-programme situé dans le programme en cours d’édition ou dans un programme ultérieur. L’ordre de chargement des programmes pièce en mémoire apparaît dans le répertoire de programmes pièce. Si, pendant l’exécution d’un programme, un nouveau programme est édité, il sera placé à la fin de la liste. 002 Trop de chiffres lors de la définition d’une fonction en général. 003 Cette erreur apparaît dans les cas suivants: * Quand une valeur négative a été affectée à une fonction qui n’accepte pas le signe “-”. * Quand une valeur incorrecte a été affectée à une opération automatique: - Positionnement en ligne - Positionnement en arc - Positionnement en rectangle ou en grille - Poche rectangulaire - Poche circulaire - Ebauche d’arêtes - Surfaçage Si Si Si Si Si Si Si Si Si Si Si Si Si Si Si Si Si 004 Inutilisé actuellement. 005 Bloc de paramètres programmé de façon incorrecte. 006 Affectation de plus de 10 paramètres à un bloc. 007 Division par zéro. 008 Racine carrée d’un nombre négatif. 009 Valeur du paramètre trop grande 010 M41, M42, M43 ou M44 a été programmé. 011 Plus de 7 fonctions “M” dans un bloc. 012 Cette erreur apparaît dans les cas suivants: L=0, Xn=X1, Yn=Y1, I=0 L=0, Xn=X1, Yn=Y1, N=0 I=0, N=0 I>0, fraction L/I N=0 R=0, Xc=X1, Yc=Y1 LX=0, IX=0 ou LY=0, IY=0 LX=0, NX=0 ou LY=0, NY=0 LX>0, IX=0, NX<2 ou LY>0, IY=0, NY<2 LX>0, IX>0, fraction LX/IX LY>0, IY>0, fraction LY/IY L=0 ou H=0 r>(L/2) ou r>(H/2) Rayon d’outil > R L=0 ou H=0 r>L ou r>H L=0 ou H=0 > La fonction G50 est programmée de façon incorrecte. > Les valeurs des dimensions d’outils sont trop élevées. > Les valeurs de décalage du zéro (G53/G59) sont trop élevées. 013 Inutilisé actuellement. 014 Un bloc incorrect par lui-même ou par rapport à l’historique du programme jusqu’à présent a été programmé. 015 Les fonctions G20, G21, G22, G23, G24, G25, G26, G27, G28, G29, G30, G31, G32, G50, G52, G53, G54, G55, G56, G57, G58, G59, G72, G73, G74, G92 et G93 doivent être programmées seules dans un bloc. 016 Le sous-programme ou bloc appelé n’existe pas, ou le bloc cherché par la fonction spéciale F17 n’existe pas. 017 Valeur du pas du filet négative ou trop élevée. 018 Erreur dans des blocs où les points sont définis par angle-angle ou angle-coordonnée. 019 Cette erreur apparaît dans les cas suivants: > Après la définition de G20, G21, G22 ou G23, le numéro du sous-programme auquel les fonctions renvoient est manquant. > Le caractère “N” n’a pas été programmé après la fonction G25, G26, G27 ou G29. > Trop de niveaux d’imbrication. 020 Les axes de l’interpolation circulaire ne sont pas programmés correctement. 021 Pas de bloc à l’adresse définie par le paramètre affecté à F18, F19, F20, F21, F22. 022 Un axe est répété lors de la programmation de G74. 023 K n’a pas été programmé après G04. 024 Inutilisé actuellement. 025 Erreur de définition de bloc ou d’appel de sous-programme ou lors de la définition de sauts conditionnels ou inconditionnels. 026 Cette erreur apparaît dans les cas suivants: > Débordement de mémoire. > Espace libre sur bande ou en mémoire CNC insuffisant pour mémoriser le programme pièce. 027 I/J/K n’a pas été défini pour une interpolation circulaire ou un filet. 028 Tentative de sélection d’un correcteur d’outil sur la table d’outils d’un outil externe qui n’existe pas (le nombre d’outils est défini par le paramètre machine). 029 Valeur trop élevée affectée à une fonction. Cette erreur est souvent émise si une valeur est programmée en mm/mn (pouces/mn), en cas de passage aux valeurs en mm/tour (pouce/tour) sans changement des valeurs de F. 030 La fonction G programmée n’existe pas. 031 La valeur du rayon d’outil est trop élevée. 032 La valeur du rayon d’outil est trop élevée. 033 Un déplacement sur 8388 mm ou 330,26 pouces a été programmé. Exemple: Soit X-5000 la position de l’axe X: si un déplacement au point X5000 est demandé, la CNC émettra l’erreur 33 lors de la programmation du bloc N10 X5000 puisque le déplacement programmé sera égal à 5000 - (-5000) = 10000 mm. Pour effectuer ce déplacement sans émission de cette erreur, l’opération doit se dérouler en 2 phases comme suit: N10 X0 N10 X5000 déplacement de 5000 mm déplacement de 5000 mm 034 Valeur de S ou F trop élevée 035 Informations sur l’arrondi aux angles, le chanfreinage ou la compensation insuffisantes. 036 Répétition de sous-programme. 037 La fonction M19 a été programmée de façon incorrecte. 038 La fonction G72 ou G73 a été programmée de façon incorrecte. Ne pas oublier que si G72 n’est appliqué que sur un seul axe, cet axe doit être positionné sur le zéro pièce (valeur 0) au moment de l’application du facteur d’échelle. 039 Cette erreur apparaît dans les cas suivants: > Plus de 15 niveaux d’imbrication lors de l’appel de sous-programmes. > Programmation d’un bloc contenant un saut sur lui-même. Exemple: N120 G25 N120. 040 L’arc programmé ne passe pas par le point de fin défini (tolérance de 0,01 mm) ou aucun arc ne passe par les points définis par G08 ou G09. 041 Cette erreur est émise en cas de programmation d’une entrée tangentielle dans les conditions suivantes: > Pas de place pour exécuter une entrée tangentielle. Un débattement égal au double du rayon congé ou plus est nécessaire. > Si l’entrée tangentielle doit être appliquée à un arc (G02, G03), elle doit être définie dans un bloc linéaire. 042 Cette erreur est émise en cas de programmation d’une sortie tangentielle dans les conditions suivantes: > Pas de place pour exécuter une sortie tangentielle. Un débattement égal au double du rayon congé ou plus est nécessaire. > Si la sortie tangentielle doit être appliquée à un arc (G02, G03), elle doit être définie dans un bloc linéaire. 043 Définition incorrecte des coordonnées polaires d’origine (G93). 044 Inutilisé actuellement. 045 Programmation incorrecte de la fonction G36, G37, G38 ou G39. 046 Définition incorrecte des coordonnées polaires. 047 Un déplacement nul a été programmé pendant une compensation de rayon ou un congé aux angles. 048 Inutilisé actuellement. 049 Programmation de chanfrein incorrecte dans une opération de poche rectangulaire ou d’ébauche d’arête de telle sorte que: * L’outil est incapable d’effectuer l’usinage car le chanfrein est trop petit. * Le chanfrein d’une aussi grande taille ne peut pas être usiné avec ces valeurs de paramètre L, H et E. 050 Les fonctions M06, M22, M23, M24, M25 doivent être programmées seules dans un bloc. 051 * Un changement d’outil ne peut pas être effectué si l’outil n’est pas en position de changement. 052 * L’outil demandé ne se trouve pas dans le magasin. 053 Inutilisé actuellement. 054 Pas de ruban dans le lecteur de cassette ou la porte du lecteur est ouverte. 055 Erreur de parité lors de la lecture ou de l’enregistrement d’une cassette. 056 Inutilisé actuellement. 057 Ruban protégé en écriture. 058 Transport de ruban “paresseux” 059 Erreur de communications entre la CNC et le lecteur de cassettes. 060 Erreur matériel interne de la CNC. Consulter les Services Techniques Après-Vente. 061 Erreur de batterie. Le contenu de la mémoire sera sauvegardé 10 jours au-délà du jour de l’apparition de l’erreur (avec la CNC à l’arrêt). L’ensemble du module batterie situé sur la face arrière doit être changé. Consulter les Services Techniques Après-Vente. Attention: En raison du risque d’explosion ou de combustion, ne pas essayer de recharger la batterie, ne pas l’exposer à des températures supérieures à 100° et ne pas mettre les câbles de batterie en court-circuit. 064 * Une entrée externe d’urgence (broche 14 du connecteur d’E/S 1) est activée. 065 Inutilisé actuellement. 066 * Dépassement de limite de course en X Cette erreur est émise quand la machine dépasse la limite fixée ou si un bloc forçant la machine à dépasser ces limites a été programmé. 067 * Dépassement de limite de course en Y Cette erreur est émise quand la machine dépasse la limite fixée ou si un bloc forçant la machine à dépasser ces limites a été programmé. 068 * Dépassement de limite de course en Z Cette erreur est émise quand la machine dépasse la limite fixée ou si un bloc forçant la machine à dépasser ces limites a été programmé. 069 Inutilisé actuellement. 070 ** Erreur de poursuite en X 071 ** Erreur de poursuite en Y 072 ** Erreur de poursuite en Z 073 Inutilisé actuellement. 074 ** Valeur de vitesse de broche excessive 075 ** Erreur de réinjection sur le connecteur A1. 076 ** Erreur de réinjection sur le connecteur A2. 077 ** Erreur de réinjection sur le connecteur A3. 078 ** Erreur de réinjection sur le connecteur A4. 079 ** Erreur de réinjection sur le connecteur A5. 080 Cette erreur s’est produite lors de l’utilisation d’un outil plus petit que la passe d’usinage “G” en usinage de poche rectangulaire/circulaire ou d’ébauche d’arête. 081 Cette erreur est émise quand le rayon de l’outil est supérieur à “(L/H2)-E” ou “(H/2)-E”. 082 ** Erreur de parité dans les paramètres généraux. 083 Cette erreur est émise en cas de programmation de “r>0” ou “C>0” en usinage de poche rectangulaire/circulaire ou d’ébauche d’arête. 084 Cette erreur est émise si un rayon d’outil supérieur à “R-E” est programmé dans une poche circulaire. 085 Cette erreur est émise si un outil de rayon nul (correcteur d’outil) est utilisé après avoir programmé “G=0” (passe d’usinage) en usinage de poche rectangulaire/circulaire ou d’ébauche d’arête. 086 Cette erreur est émise quand une valeur incorrecte est affectée à une opération automatique ou à une opération d’usinage: - Poche rectangulaire ................... Si Poche circulaire......................... Si Ebauche d’arêtes ....................... Si Surfaçage ................................... Si Pointage .................................... Si Perçage ...................................... Si Taraudage ................................. Si Alésage ...................................... Si P=0 P=0 P=0 P=0 P=0, P=0 P=0 P=0 ou ou ou ou I=0 I=0 I=0 I=0 =0 ou I=0 087 ** Erreur matériel interne de la CNC. Consulter les Services Techniques Après-Vente. 088 ** Erreur matériel interne de la CNC. Consulter les Services Techniques Après-Vente. 089 * Tous les axes ne sont pas revenus au zéro. Cette erreur apparaît quand une recherche du zéro sur tous les axes est obligatoire après la mise sous tension. Cette obligation est définie par un paramètre machine. 090 ** Erreur matériel interne de la CNC. Consulter les Services Techniques Après-Vente. 091 ** Erreur matériel interne de la CNC. Consulter les Services Techniques Après-Vente. 092 ** Erreur matériel interne de la CNC. Consulter les Services Techniques Après-Vente. 093 ** Erreur matériel interne de la CNC. Consulter les Services Techniques Après-Vente. 094 Erreur de parité dans la table d’outils ou la table de correcteurs d’outils G53-G59. 095 Cette erreur est émise quand le rayon de l’outil est supérieur au rayon congé “r” en usinage de poche rectangulaire ou en ébauche d’arêtes. 096 ** Erreur de parité dans les paramètres d’axe Z. 097 ** Erreur de parité dans les paramètres d’axe Y. 098 ** Erreur de parité dans les paramètres d’axe X. 099 ** Erreur de parité dans la table M. 100 ** Erreur matériel interne de la CNC. Consulter les Services Techniques Après-Vente. 101 ** Erreur matériel interne de la CNC. Consulter les Services Techniques Après-Vente. 105 Cette erreur est émise dans les cas suivants: > Un commentaire a plus de 43 caractères. > Un programme a été défini avec plus de 5 caractères. > Un numéro de bloc comporte plus de 4 caractères. > Apparition de caractères bizarres en mémoire. 106 ** Température limite interne dépassée. 107 Inutilisé actuellement. 108 ** Erreur dans les paramètres de compensation d’erreur de pas de vis sur l’axe Z. 109 ** Erreur dans les paramètres de compensation d’erreur de pas de vis sur l’axe Y. 110 ** Erreur dans les paramètres de compensation d’erreur de pas de vis sur l’axe X. 111 112 Inutilisé actuellement. Inutilisé actuellement. 113 Inutilisé actuellement. 114 Inutilisé actuellement. 115 * Erreur de chien de garde dans le module périodique. Cette erreur apparaît quand le temps d’exécution du module périodique dépasse 5 millisecondes. 116 * Erreur de chien de garde dans le module principal. Cette erreur apparaît quand le temps d’exécution du module principal est supérieur à la moitié du temps indiqué dans le paramètre machine “P279”. 117 * Les informations CNC internes demandées par l’activation des repères M1901 à M1949 ne sont pas disponibles. 118 * Tentative de modification d’une variable interne CNC indisponible au moyen des repères M1950 à M1964. 119 Erreur lors de l’écriture de paramètres machine, de la table de fonctions M décodées et des tables de compensation d’erreur de vis dans la mémoire EEPROM. Cette erreur peut apparaître lorsque, après verrouillage des paramètres machine, de la table de fonctions M décodées et des tables de compensation d’erreur de vis, l’opérateur tente de sauvegarder ces informations dans la mémoire EEPROM. 120 Erreur de somme de contrôle lors de la récupération (rétablissement) des paramètres machine, de la table de fonctions M décodées et des tables de compensation d’erreur de vis dans la mémoire EEPROM. Elles stoppent l’avance des axes et la rotation de la broche en annulant les signaux de validation ainsi que les sorties analogiques de la CNC. Attention: Les ERREURS signalées par “*” agissent de la façon suivante: - Elles stoppent l’avance des axes et la rotation de la broche en annulant les signaux de validation ainsi que les sorties analogiques de la CNC. - Elles interrompent l’exécution du programme pièce de la CNC s’il était en cours d’exécution. Les ERREURS signalées par “**” agissent non seulement comme celles repérées par “*”, mais activent en plus la SORTIE D’URGENCE INTERNE. FAGOR - CNC 800M MANUEL DE PROGRAMMATION Ref. 9701 (Fra) AU SUJET DE L’INFORMATION CONTENUE DANS LE PRESENT MANUEL Le présent manuel doit être utilisé lorsque l’on désirera élaborer un programme en code ISO. La CNC peut sauvegarder 2 programmes d’usager en code ISO: P99994 P99996 Programme spécial de sous-programmes d’usager en code ISO Programme pièce d’usager en code ISO Les deux programmes peuvent être élaborés sur un ordinateur pour être postérieurement envoyés à la CNC. La section Périphériques du Manuel d’Utilisation explique comment la transmission d’information entre la CNC et l’ordinateur doit être menée. Vous pourrez éditer ou modifier le programme P99996 à partir de la CNC elle-même, mais vous ne pourrez pas accéder au programme P99994. Le programme P99994 doit en effet être élaboré sur un ordinateur ou un périphérique. Le présent manuel décrit toute l’information concernant le code ISO que la CNC 800M utilise. Notes: L’information décrite dans le présent manuel peut être sujet à des variations provoquées par des modifications techniques. FAGOR AUTOMATION, S. Coop., se réserve le droit de modifier le contenu du manuel, n’étant pas tenue de notifier les variations. SOMMAIRE Section Page Tableau comparatif des modèles Fagor CNC 800 M ............................................ ix Nouvelles prestations et modifications ................................................................... xiii INTRODUCTION Conditions de Sécurité .................................................................................................... 3 Conditions de Renvoi ..................................................................................................... 5 Documentation Fagor pour la CNC 800M ...................................................................... 6 Contenu du présent manuel ............................................................................................. 7 Chapitre 1 1.1 1.2 1.2.1 1.3 1.4 1.4.1 Structure d'un programme dans la CNC .................................................................. 1 Numéro de bloc .......................................................................................................... 2 Blocs conditionnels ................................................................................................... 2 Bloc de programme .................................................................................................... 3 Fonctions préparatoires (G) ....................................................................................... 4 Table des fonctions G utilisées dans la CNC ......................................................... 4 Chapitre 2 2.1 2.2 2.3 2.4 2.4.1 2.4.2 2.4.3 2.4.4 2.4.5 PROGRAMMATION DES COORDONNEES Sélection de plans (G17, G18, G19) ........................................................................ 1 Unités de mesures. Millimètres (G71) ou pouces (G70) ....................................... 2 Programmation absolue (G90), programmation incrémentale (G91) ................... 3 Programmation des coordonnées .............................................................................. 4 Coordonnées cartésiennes ......................................................................................... 4 Coordonnées polaires ................................................................................................ 5 Coordonnés cylindriques .......................................................................................... 8 Deux angles (A1, A2) ................................................................................................ 9 Angle et une coordonnée cartésienne ..................................................................... 10 Chapitre 3 3.1 3.2 3.3 3.4 3.5 CONSTRUCTION D'UN PROGRAMME SYSTEMES DE REFERENCE Recherche de référence machine (G74) ................................................................... 1 Présélection des valeurs des coordonnées (G92) ................................................... 2 Présélection d'origine polaire (G93) ........................................................................ 3 Transfers d'origne (G53...G59) .................................................................................. 5 Mémorisation et prélèvement du point zéro du programme (G31-G32) ............. 7 Section Page Chapitre 4 4.1 4.1.1 4.2 4.3 4.3.1 4.4 Programmation de l'avance (F) ................................................................................. 1 FEED-RATE programmable (G49) ........................................................................... 2 Vitesse de rotation de la broche (S) ........................................................................ 3 Programmation de l'outil (T) .................................................................................... 4 Chargement des dimensions d'outil sur la table (G50) ......................................... 5 Fonctions auxiliaires (M) .......................................................................................... 6 Chapitre 5 5.1 5.2 5.3 5.4 5.5 5.5.1 5.5.2 5.5.3 5.6 5.7 5.8 5.9 5.10 5.11 FONCTIONS PREPARATOIRES ADDITIONNELLES Temporisation (G04) .................................................................................................. 1 Image miroir (G10, G11, G12, G13) ........................................................................ 2 Affichage du code d'erreur (G30) ............................................................................. 4 Sauts/Appels inconditionnels (G25) ........................................................................ 5 Facteur d'échelle (G72) ............................................................................................. 7 Facteur d'échelle affectant tous les axes ................................................................. 7 Facteur d'échelle appliqué à un seul axe ................................................................ 8 Rotation de la figure (G73) ...................................................................................... 9 Traitement de bloc unique. Activation (G47) Annulation (G48) ........................ 10 Chapitre 7 7.1 7.1.1 7.1.2 7.1.3 7.1.4 7.2 CONTROLE DE TRAJECTOIRE Arête arrondie (G05) .................................................................................................. 1 Arête vive (G07) ......................................................................................................... 1 Positionnement rapide (G00) .................................................................................... 2 Interpolation linéaire (G01) ...................................................................................... 3 Interpolation circulaire (G02, G03) ......................................................................... 4 Interpolation circulaire avec programmation du rayon de l'arc ........................... 8 Interpolation circulaire avec programmation du centre de l'arc en coordonnées absolues (G06) ............................................................................... 9 Interpolation hélicoïdale ........................................................................................... 10 Trajectoire circulaire tangente à la trajectoire précédente (G08) ........................ 12 Interpolation circulaire programmée à l'aide de trois points (G09) .................... 13 Entrée tangentielle (G37) .......................................................................................... 14 Sortie tangentielle (G38) ........................................................................................... 15 Contrôle de l'arrondie des angles (G36) ................................................................. 16 Chanfrein (G39) .......................................................................................................... 17 Chapitre 6 6.1 6.2 6.3 6.4 6.5 6.5.1 6.5.2 6.6 6.7 FONCTIONS COMPLEMENTAIRES COMPENSATION D'OUTIL Compensation de rayon d'outil (G40,. G41, G42) ................................................. 1 Sélection et initialisation de la compensation de rayon d'outil (G41, G42) ..... 2 Fonctionnement avec une compensation de rayon d'outil (G41, G42) .............. 6 Annulation de la compensation de rayon (G40) .................................................... 9 Exemples d'usinage avec comppensation de rayon ............................................... 11 Compensation de la longueur de l'outil (G43, G44) ............................................. 14 Section Page Chapitre 8 8.1 8.2 8.3 8.4 8.5 8.6 8.7 8.8 8.9 8.10 8.11 8.12 8.13 8.14 8.15 Positionnement point à point (G67 N0 et P202=K0) ............................................ 2 Positionnement en ligne (G67 N0 et P202=K1) ................................................... 3 Positionnement en rectangle (G67 N0 et P202=K2) ............................................. 4 Positionnement en grille (G67 N0 et P202=K3) .................................................... 5 Positionnement en arc (G67 N0 et P202=K4) ........................................................ 6 Poche rectangulaire d'usinage intérieur (G67 N1 et P202=K0) ........................... 7 Poche circulaire d'usinage intérieur (G67 N1 et P202=K1) ................................. 9 Moyeu (Bossage) rectangulaire (G67 N2 et P202=K0) ......................................... 11 Moyeu (Bossage) circulaire (G67 N2 et P202=K1) ............................................... 13 Surfaçage (G67 N3) .................................................................................................... 15 Ebauche d'arêtes (G67 N4) ........................................................................................ 18 Perçage (G67 N6) ....................................................................................................... 20 Taraudage (G67 N7) ................................................................................................... 22 Alésage (G67 N8) ....................................................................................................... 24 Pointage (G67 N9) ..................................................................................................... 26 Chapitre 9 9.1 9.2 9.3 9.4 9.5 9.6 9.7 SOUS-PROGRAMMES Programme spécial de sous-programmes d'usager P99994 ................................... 1 Identification d'un sous-programme standard (G22) .............................................. 2 Appel d'un sous-programme standard (G20) ........................................................... 2 Identification d'un sous programme paramétrique (G23) ...................................... 3 Appel d'un sous-programme paramétrique (G21) ................................................... 3 Exemples de programmation .................................................................................... 4 Niveaux d'emboîtement (d'imbrication) .................................................................. 8 Chapitre 10 10.1 10.2 10.3 10.4 10.5 CYCLES FIXES D'USINAGE PROGRAMMATION PARAMETRIQUE Attributions ................................................................................................................. 2 Opérateurs "F1" à "F16" ............................................................................................ 3 Opérateurs "F17" à "F29" .......................................................................................... 5 Opérateurs binaires "F30" à "F33" ........................................................................... 7 Fonctions de saut conditionnel (G26, G27, G28, G29) ........................................ 8 CODES D'ERREUR TABLEAU COMPARATIF DES MODELES FAGOR CNC 800M MODELES CNC 800M DISPONIBLES CNC 800-MG CNC 800-MGI Contrôle d'axes X, Y l l Axe Z Visualisateur l l Axe Z Contrôlé l l Broche l l Outils 99 99 Compensation de rayon de l'outil l l Compensation de longueur de l'outil l l Manivelles Electroniques 3 3 Interface RS 232C l l Automate Intégré (PLCI) l Edition du programme en CODE ISO (P99996) l l Exécution du programme en CODE ISO (P99996) l l Représentation Graphique l l NOUVELLES PRESTATIONS ET MODIFICATIONS Date: Juillet 1995 PRESTATION Version logiciel: 2.1 et suivants MANUEL ET SECTION MODIFIEE Effacer la mémoire de tous les paramètres arithmétiques, en leur attribuant la valeur 0. Manuel Installation Manuel d'Utilisation Programmation en CODE ISO. Manuel Programmation Edition du programme 99996 dans la CNC Manuel Installation Manual d'Utilisation Section. 3.10 Section. 3.9 Lors de l'interruption de l'exécution restent opérantes les touches de broche, réfrigérant 01, 02, 03 et TOOL Manuel Installation Manuel d'Utilisation Manuel d'Utilisation Section. 3.5.1 Section. 3.5.1 Section. 6.5 Sous-programme associé à l'exécution d'outil (seulement en exécution du programme 99996) Manuel Installation Manuel Programmation Section. 4.3 Chapitre. 9. Date: Novembre 1995 PRESTATION Version logiciel: Section. 3.9 Section. 3.8 et 6.9 2.2 et suivants MANUEL ET SECTION MODIFIEE Sous-programmes à exécuter avant et après T (seulement en exécution du programme 99996) Manuel Installation Manuel Programmation Section. 4.3 Chapitre. 9. Fonctions "M" associées aux opérations automatiques Manuel d'Utilisation Section. 4.1.2 Fonctions "M" associées aux opérations d'usinage Manuel d'Utilisation Section. 5.1.1 INTRODUCTION Introduction - 1 CONDITIONS DE SÉCURITÉ Lisez les mesures de sécurité qui suivent, à l’objet d’éviter des lésions aux personnes et à prévenir des dommages à ce produit et aux produits qui y sont raccordés. L’appareil en pourra être réparé que par le personnel autorisé par Fagor Automation. Fagor Automation ne pourra en aucun cas être responsable de tout dommage physique ou matériel qui découlerait du non-respect de ces normes de bases de sécurité Précautions vis à vis de dommages à des personnes Avant d’allumer l’appareil, vérifiez que vous l’avez mis à la terre. En vue d’éviter des décharges électriques, vérifiez que vous avez procédé à la prise de terre. Ne pas travailler dans des ambiances humides. Pour éviter des décharges électriques, travaillez toujours dans des ambiances à humidité relative inférieure à 90% sans condensation à 45º C. Ne pas travailler dans des ambiances explosives Afin d’éviter des risques, des lésions ou des dommages, ne pas travailler dans des ambiances explosives. Précautions pour éviter l’endommagement du produit Ambiance de travail Cet appareil est préparé pour être utilisé dans des Ambiances Industrielles et respecte les directives et les normes en vigueur dans l’Union Européenne. Fagor Automation ne se responsabilise pas des dommages qu’il pourrait provoquer s’il est monté sous d’autres conditions (ambiances résidentielles ou domestiques). Installer l’appareil à l’endroit adéquat Il est recommandé d’installer la Commande Numérique, autant que possible, éloignée de liquides de refroidissement, de produits chimiques, de coups, etc., qui pourraient l’endommager. L’appareil respecte les directives européennes en ce qui concerne la compatibilité électromagnétique. Il est néanmoins conseillé de le tenir éloigné des sources de perturbation électromagnétique, telles que : - Les charges puissantes branchées au secteur sur lequel est raccordé l’équipement. - Les émetteurs-récepteurs portatifs proches (radiotéléphones, émetteurs radioamateurs), - Émetteurs-récepteurs de radio/télévision proches, - Appareils de soudure à l’arc proches, - Lignes de haute tensions proches, - Etc. Conditions de l’environnement La température ambiante qui doit exister au régime de fonctionnement doit être comprise entre +5ºC et +45ºC. La température ambiante qui doit exister au régime de non fonctionnement doit être comprise entre -25ºC et 70ºC. Introduction - 3 Protections de l’appareil Il incorpore 2 fusibles extérieurs rapides (F) de 3,15 Amp./ 250 V., pour la protection de l‘entrée de secteur. Toutes les entrées-sorties digitales sont protégées par 1 fusible extérieurs rapides (F) de 3,15 Amp./ 250 V contre l’éventuelle surtension de la source extérieure (plus de 33 Vcc.) et contre le branchement inversé de la source d’alimentation. Précautions à prendre durant les réparations Ne pas manipuler l’intérieur de l’appareil Seul le personnel autorisé par Fagor Automation peut manipuler l’intérieur de l’appareil. Ne pas manipuler les connecteurs lorsque l’appareil est branché au secteur Avant de manipuler les connecteurs (entrées/sorties, mesure, etc.), vérifiez que l’appareil est débranché du secteur. Symboles de sécurité Symboles pouvant apparaître sur le manuel Symbole ATTENTION. Il a un texte associé qui indique les actions ou les opérations pouvant provoquer des dommages aux personnes ou aux appareils. Symboles que peut présenter le produit Symbole ATTENTION. Il a un texte associé qui indique les actions ou les opérations pouvant provoquer des dommages aux personnes ou aux appareils. Symbole D’ÉLECTROCUTION. Il indique que le point en question peut être sous tension électrique. Symbole PROTECTION DE MASSES. Il indique que le point en question doit être branché au point central de mise à la terre de la machine afin de protéger les personnes et les appareils Introduction - 4 CONDITIONS DE RENVOI Si vous allez envoyer le CNC, emballez-les dans sa caisse en carton originale avec leur matériel d’emballage original. Si vous ne disposez pas du matériel d’emballage original, emballez-le de la façon suivante : 1.- Obtenez une caisse en carton dont les 3 dimensions internes auront au moins 15 cm (6 pouces) de plus que celles de l’appareil, Le carton utilisé pour la caisse doit avoir une résistance de 170 Kg (375 livres). 2.- Si vous avez l’intention de l’expédier à un bureau de Fagor Automation pour qu’il soit réparé, veuillez joindre une étiquette à l’appareil en indiquant le nom du propriétaire de l’appareil,, son adresse, le nom de la personne à contacter, le type d’appareil, le numéro de série, le symptôme et une description succincte de la panne. 3.- Enveloppez l’appareil avec un film de polyéthylène ou d’un matériau semblable afin de le protéger. Si vous allez expédier le moniteur, protégez tout particulièrement le verre de l’écran. 4.- Capitonnez l’appareil dans la caisse en carton, en la remplissant de mousse de polyuréthane de tous côtés. 5.- Scellez la caisse en carton avec du ruban d’emballage ou avec des agrafes industrielles. Introduction - 5 DOCUMENTATION FAGOR POUR LA CNC 800M Manuel CNC 800M OEM Il s’adresse au constructeur de la machine ou à la personne chargée de réaliser l’installation et la mise au point de la Commande Numérique. Le manuel d’installation se trouve à l’intérieur. Elle peut contenir occasionnellement un manuel ayant trait aux “Nouvelles Prestations” de logiciel récemment introduites. Manuel CNC 800M USER. Il s’adresse à l’usager final, c’est-à-dire, à la personne qui va travailler avec la Commande Numérique. Elle contient 2 manuels à l’intérieur : Le Manuel d’Utilisation qui décrit comment travailler avec la CNC. Le Manuel de Programmation, qui décrit comment élaborer un programme en code ISO. Elle peut contenir occasionnellement un manuel ayant trait aux “Nouvelles Prestations” de logiciel récemment introduites. Manuel DNC 25/30 Il s’adresse aux personnes qui vont utiliser l’option de logiciel de communication DNC. Manuel Protocole DNC Il s’adresse aux personne qui désirent réaliser leur propre communication de DNC, sans utiliser l’option de logiciel de communication DNC 25/30. Manuel PLCI Il doit être utilisé lorsque la CNC est munie d’Automate Intégré. Il s’adresse au constructeur de la machine ou à la personne qui se charge de réaliser l’installation et la mise au point de l’Automate Intégré. Manuel DNC-PLC Il s’adresse aux personnes qui vont utiliser l’option de logiciel de communication DNC-PLC. Manuel Floppy Disk Il s’adresse aux personnes qui utilisent le lecteur à disquettes de Fagor. Ce manuel indique comment ledit lecteur à disquettes doit être utilisé. Introduction - 6 CONTENU DU PRÉSENT MANUEL Le Manuel de Programmation se compose des parties suivantes : Index Tableau comparatif des modèles Fagor CNC 800M. Nouvelles Prestations et modifications. Introduction Résumé des conditions de sécurité. Conditions de Renvoi. Liste de Documents Fagor pour la CNC 800M. Contenu du présent Manuel. Chapitre 1 Construction d’un programme. Il indique la structure que doit avoir le programme pièce et tous les blocs qui le forment. Il montre toutes les fonctions préparatoires G qui sont disponibles. Chapitre 2 Programmation de cotes. Il montre la manière de sélectionner les plans de travail, les unités de travail, le type de programmation (absolu / incrémental). Il explique les systèmes de coordonnées pour la programmation de cotes (cartésiennes, polaires, cylindriques au moyen de deux angles, au moyen d’angle et de coordonnée cartésienne). Chapitre 3 Systèmes de référence. Il indique comment programmer la recherche de référence machine, la présélection de cotes, les transferts d’origine et la présélection du zéro polaire. Il indique comment garder et comment récupérer l’origine des coordonnées. Chapitre 4 Fonctions complémentaires. Il montre la manière de programmer les fonctions préparatoires d’avance et de vitesse. Il indique la manière de programmer la vitesse de rotation de la broche. Il montre comment il faut programmer l’outil et comment modifier les valeurs de la table à partir du programme d’usager. Il indique comment programmer les fonctions auxiliaires “M”. Chapitre 5 Contrôle de la trajectoire. Il indique comment programmer le travail en arête vive et en arête arrondie. Il montre comment programmer le positionnement rapide, l’interpolation linéaire et l’interpolation circulaire. Il indique comment programmer les entrées et les sorties tangentielles et l’arrondissement et le chanfreinage des arêtes. Chapitre 6 Fonctions préparatoires supplémentaires. Il montre comment programmer une temporisation. Il indique comment appliquer les fonctions image de miroir Il indique comment afficher le code d’erreur. Il expose comment travailler avec des sauts et des appels inconditionnels Il indique comment appliquer le facteur d’échelle. Il expose comment appliquer la rotation de coordonnées Il expose comment programmer le traitement de bloc unique. Chapitre 7 Compensation d’outils. Il montre comment programmer la compensation de rayon et de longueur d’outil. Chapitre 8 Cycles fixes d’usinage. Il affiche comment programmer les différents cycles fixes d’usinage. Introduction - 7 Chapitre 9 Sous-routines. Programme spécifique de sous-routines d’usager P99994 Il indique comment identifier une sous-routine standard et paramétrique. Il indique comment programmer un appel à une sous-routine standard ou paramétrique Il affiche les niveaux d’emboîtement des sous-routines Chapitre 10 Programmation paramétrique Il montre comment il faut faire la programmation paramétrique (assignations, opérateurs, fonctions de saut, etc.). Codes d’erreur. Introduction - 8 1. CONSTRUCTION D’UN PROGRAMME Un programme de contrôle numérique est formé par un ensemble de blocs ou instructions. Ces blocs ou instructions sont formées par des mots composés de lettres majuscules et de format numérique. Le format numérique dont dispose la CNC comporte: - les signes - les chiffres . +0 1 2 3 4 5 6 7 8 9 La programmation admet l’omission du format numérique si celui-ci a la valeur zéro, ou du signe si ce dernier est positif. Le format numérique d’un mot peut être substitué par un paramètre arithmétique dans la programmation. Plus tard, lors de l’exécution de base, le contrôle substituera le paramètre arithmétique par sa valeur, par exemple: Si XP3 a été programmé, la CNC substituera P3 par sa valeur numérique lors de l’exécution, obtenant des résultats tels que X20, X20.567, X-0.003, etc. 1.1 STRUCTURE D’UN PROGRAMME DANS LA CNC Tous les blocs composant le programme auront la structure suivante: Numéro de bloc + Bloc de programme Chapitre: 1 CONSTRUCTIOND’UNPROGRAMME Section: Page 1 1.2 NUMERO DE BLOC Le numéro de bloc sert à identifier chacun des blocs qui forment un programme. Il sera représenté par la lettre N suivie d’un maximum de 4 chiffres (0-9999). Les blocs de programme devront être numériquement ordonnés. Il est vivement conseillé de ne pas assigner des numéros corrélatifs aux blocs afin de pouvoir intercaler de nouveaux blocs en cas de besoin. Attention: Tout au long du présent manuel, le format “N4” sera énuméré pour faire mention du numéro de bloc, en indiquant qu’il faut le définir au moyen de la lettre N suivie d’un maximum de 4 chiffres (les décimales ne sont pas admises). 1.2.1 BLOCS CONDITIONNELS Il y a deux types de blocs conditionnels: a) BLOC CONDITIONNEL STANDARD N4 Si dans un numéro de bloc N4 (0-9999) un point décimal (.) est écrit juste à côté du numéro de bloc, celui-ci est considéré comme étant un bloc conditionnel normal. Cela signifie que la CNC n’exécutera ce bloc que si le signal correspondant (entrée validant les blocs conditionnels) est activé. Durant l’exécution d’un programme la CNC lit 4 blocs en avance. Ainsi le signal extérieur devra être activé au moins avant l’exécution du cinquième bloc antérieur au bloc conditionnel afin que ce dernier soit exécuté. b) BLOC CONDITIONNEL SPÉCIAL N4. Si après le numéro de bloc N4 (0-9999) deux points décimaux sont écrits (..) le bloc est caractérisé comme un bloc conditionnel spécial. La CNC n’exécutera ce bloc que si le signal correspondant (entrée validant les blocs conditionnels) est activé. Dans ce cas, pour exécuter le bloc conditionnel, il suffit d’activer le signal extérieur (entrée validant les blocs conditionnels) au moment de l’exécution du bloc précédant le bloc conditionnel spécial. Le bloc conditionnel spécial N4..,annule la compensation de rayon de l’outil G41 ou G42. Page Chapitre: 1 Section: 2 CONSTRUCTIOND’UNPROGRAMME NUMERODEBLOC 1.3 BLOC DE PROGRAMME Il sera écrit avec des commandes en langage ISO, spécialement conçu pour contrôler le déplacement des axes, car il fournit des informations et des conditions de déplacement, ainsi que des indications sur l’avance. Chaque bloc de programmation peut disposer des fonctions suivantes: G X, Y, Z F S T M Fonctions préparatoires Coordonnées des axes Vitesse d’avance Vitesse de rotation de la broche Numéro d’outil Fonctions auxiliaires Il faut maintenir cet ordre dans chaque bloc, bien qu’il ne soit pas nécessaire que chaque bloc possède toutes les informations. Selon les unités de travail sélectionnées (mm ou pouces) il faut utiliser le format de programmation suivant: Format en millimètres: N4 G2 X+/-4.3 Y+/-4.3 Z+/-4.3 F5.4 S4 T2.2 M2 Format en pouces: N4 G2 X+/-3.4 Y+/-3.4 Z+/-3.4 F4.5 S4 T2.2 M2 Format en paramétriques: N4 GP?? XP?? YP?? ZP?? FP?? SP?? TP??.P?? MP?? Tout au long du présent manuel les formats suivants seront énumérés: “N4” Pour indiquer le numéro de bloc, en indiquant qu’il doit être défini par la lettre N suivie d’un maximum de 4 chiffres (N0 à N9999). “G2” Pour indiquer une fonction préparatoire, en indiquant qu’elle doit être définie par la lettre G suivie d’un maximum de 2 chiffres (G00 à G99). +/- 4.3 Derrière la lettre qu’elle accompagne (X, Y, Z), il peut être écrit un chiffre positif ou négatif avec un maximum de 4 chiffres devant le point décimal et un maximum de 3 derrière. +/- 3.4 Derrière la lettre qu’elle accompagne (X, Y, Z), il peut être écrit un chiffre positif ou négatif avec un maximum de 3 chiffres devant le point décimal et un maximum de 4 derrière. “F5.4” Avance des axes en mm./min. Il faut définir, au moyen de la lettre F suivie d’un chiffre positif, avec un maximum de 5 chiffres devant le point décimal et un maximum de 4 derrière. “F4.5” Avance des axes en pouces./min. Il faut définir, au moyen de la lettre F suivie d’un chiffre positif, avec un maximum de 4 chiffres devant le point décimal et un maximum de 5 derrière. “S4” Pour indiquer la vitesse de la broche, en indiquant qu’elle doit être définie au moyen de la lettre S, suivie d’un maximum de 4 chiffres (S0 à S9999). T2.2 Pour indiquer l’outil de travail, en indiquant qu’il doit être défini au moyen de la lettre T, et qu’elle peut disposer d’un maximum de 2 chiffres devant le point décimal et d’un maximum de 2 chiffres derrière. “M2” Pour indiquer les fonctions auxiliaires, en indiquant qu’elle doit être définie au moyen de la lettre M, suivie d’un maximum de 2 chiffres (M0 à M99). Chapitre: 1 CONSTRUCTIOND’UNPROGRAMME Section: Page BLOCDEPROGRAMME 3 1.4 FONCTIONS PREPARATOIRES (G) Les fonctions préparatoires sont programmées à l’aide de la lettre G suivie de 2 chiffres (G2). Elles sont toujours programmées au début du bloc et sont utilisées pour déterminer la géométrie et l’état de fonctionnement de la CNC. 1.4.1 TABLE DES FONCTIONS G UTILISEES DANS LA CNC Fonction G00 G01 G02 G03 G04 G05 M * * * * * G06 G07 G08 G09 G10 G11 G12 G13 G17 G18 G19 G20 G21 G22 G23 G24 G25 G26 G27 G28 G29 G30 G31 G32 G36 G37 G38 G39 * * * * * * * * D Signification * Positionnement rapide Interpolation linéaire Interpolation circulaire, arc de sens horaire Interpolation circulaire, arc de sens anti-horaire Temporisation * Angle arrondi Interpolation circulaire avec programmation du centre de l’arc en coordonnées absolues * Angle vif Trajectoire circulaire tangente à la trajectoire précédente Trajectoire circulaire programmée par 3 points * Annulation de l’image miroir Image miroir sur l’axe X. Image miroir sur l’axe Y. Image miroir sur l’axe Z * Sélection du plan XY Sélection du plan XZ Sélection du plan YZ Appel de sous-programme standard Appel de sous-programme paramétrique Définition de sous-programme standard Définition de sous-programme paramétrique Fin de sous-programme Saut/appel inconditionnel Saut/appel conditionnel si = 0 Saut/appel conditionnel si différent de zéro Saut/appel conditionnel si inférieur Saut/appel conditionnel si supérieur Erreur visualisée définie par K Mémorisation du point zéro actuel du programme Prélèvement du point zéro mémorisé par G31 Arrondi contrôlé des angles Approche tangentielle Dégagement tangentiel Chanfrein (Modal) Page Chapitre: 1 4 CONSTRUCTIOND’UNPROGRAMME Section 5.3 5.4 5.5 5.5 6.1 5.1 5.5.2 5.2 5.6 5.7 6.2 6.2 6.2 6.2 2.1 2.1 2.1 9.3 9.5 9.2 9.4 9. 6.4 10.6 10.6 10.6 10.6 6.3 3.5 3.5 5.10 5.8 5.9 5.11 Section: FONCTIONS PREPARATOIRES (G) Fonction G40 G41 G42 G43 G44 G47 G48 G49 G50 G53/G59 G67 N0 P202=K0 G67 N0 P202=K1 G67 N0 P202=K2 G67 N0 P202=K3 G67 N0 P202=K4 G67 N1 P202=K0 G67 N1 P202=K1 G67 N2 P202=K0 G67 N2 P202=K1 G67 N3 G67 N4 G67 N6 G67 N7 G67 N8 G67 N9 G70 G71 G72 G73 G74 G90 G91 G92 G93 M * * * * * * * * * * * * * * * D Signification * Annulation de la compensation de rayon Compensation de rayon, outil à gauche Compensation de rayon, outil à droite Compensation de longueur * Annulation de la compensation de longueur Traitement d’un seul bloc * Annulation de traitement de bloc seul FEED RATE programmable Chargement des dimensions de l'outil dans la table Décalages du zéro Cycle fixe de positionnement point à point Cycle fixe de positionnement en ligne Cycle fixe de positionnement en rectangle Cycle fixe de positionnement en grille Cycle fixe de positionnement en arc Cycle fixe pour poche rectangulaire Cycle fixe pour poche circulaire Cycle fixe pour moyeu (bossage) rectangulaire Cycle fixe pour moyeu (bossage) circulaire Cycle fixe de surfaçage Cycle fixe d'ébauche d'arête Cycle fixe de perçage Cycle fixe de taraudage Cycle fixe d'alésage Cycle fixe de pointage Programmation en pouces Programmation en métrique Facteur d’Echelle Rotation de la Figure Recherche automatique du zéro de référence * Programmation des coordonnées en absolu Programmation des coordonnées en incrémental Présélection des coordonnées Présélection de l’origine polaire Section 7.1.3 7.1.1 7.1.1 7.2 7.2 6.7 6.7 4.1.1 4.3.1 3.4 8.1 8.2 8.3 8.4 8.5 8.6 8.7 8.8 8.9 8.10 8.11 8.12 8.13 8.14 8.15 2.2 2.2 6.5 6.6 3.1 2.3 2.3 3.2 3.3 Le “M” veut dire MODALE, c’est-à-dire, qu’une fois la fonction G programmée, elle reste active, tant qu’une autre G incompatible ne soit programmée ou que soit exécutée M02, M30, URGENCE ou RESET ou que la CNC ne soit éteinte et rallumée. La lettre “D” veut dire PAR DÉFAUT, c’est-à-dire, qu’elles seront assumées par la CNC, à la misse sous tension, après que M02, M30 auront été exécutées ou après un ARRET D'URGENCE ou une REMISE A ZERO. Le paramètre machine “P613(5)” indique si la CNC assume la fonction G05 ou G07. Dans un même bloc, il est possible de programmer toutes les fonctions G que l’on voudra et dans n’importe quel ordre, sauf G20, G21, G22, G23, G24, G25, G26, G27, G28, G29, G30, G31, G32, G50, G51, G53/G59, G72, G74 et G92, qui doivent être seules dans le bloc, du fait qu’elles sont spéciales. Si dans un même bloc, des fonctions G incompatibles sont programmées, la CNC assume la dernière qui ait été programmée. Chapitre: 1 CONSTRUCTIOND’UNPROGRAMME Section: FONCTIONS PREPARATOIRES (G) Page 5 2. PROGRAMMATION DES COORDONNEES 2.1 SELECTION DE PLANS (G17, G18, G19) G17: Sélection du plan XY. G18: Sélection du plan XZ. G19: Sélection du plan YZ. La sélection de plan doit être correctement effectuée lors de la programmation des interpolations circulaires, des arrondis d’angle, des approches et des dégagements tangentiels, des chanfreins, des cycles fixes et des compensations de longueur ou de rayon de fraise. La CNC applique la compensation de rayon aux deux axes du plan sélectionné et la compensation de longueur à l’axe perpendiculaire au plan. Les fonctions G17, G18 et G19 sont modales et incompatibles les unes avec les autres. La CNC assume la fonction G17 à la mise sous tension, après l’exécution d’un code M02/M30, après un ARRÊT D’URGENCE et après une REMISE A ZERO. Chapitre: 2 PROGRAMMATIONDESCOORDONNÉES Section: SELECTION DE PLANS (G17, G18, G19) Page 1 2.2 UNITES DE MESURES. MILLIMETRES (G71) OU POUCES (G70) La CNC dispose du paramètre machine “P13” pour définir les unités de mesure de la CNC. Ces unités de mesures peuvent être néanmoins altérées tout au long du programme, les fonctions suivantes étant disponibles à cet effet: G70 G71 Programmation en pouces Programmation en millimètres Selon que l’on ait programmé G70 ou G71, la CNC assume le système d’unités en question pour tous les blocs programmés ensuite. Les fonctions G70/G71 sont modales et incompatibles entre elles. A la mise sous tension, après M02, M30, ARRÊT D’URGENCE et après une REMISE A ZERO, la CNC assume le système d’unités défini par le paramètre machine P13. Page Chapitre: 2 2 PROGRAMMATIONDESCOORDONNÉES Section: MILLIMÈTRES (G71) OU POUCES (G70) 2.3 PROGRAMMATION ABSOLUE (G90), PROGRAMMATION INCRÉMENTALE (G91) La programmation des coordonnées d’un point peut s’effectuer en coordonnées absolues G90 ou en coordonnées incrémentales G91. En mode G90, les coordonnées du point programmé se rapportent à un point dont les coordonnées sont par rapport à l’origine. En mode G91, les coordonnées du point programmé se rapportent à un point sur le chemin prévu. Les valeurs programmées identifient la distance tout au long de l’axe concerné. Après une mise sous tension de la CNC, M02, M30, ARRÊT D’URGENCE et après REMISE À ZÉRO, la CNC se trouve dans le mode G90. Les fonctions G90/G91 sont modales et incompatibles entre elles. Exemple de programmation: Point de départ (P0) X20 Y10 Programmation absolue G90 N20 G90 X50 Y40 N30 Y10 N40 X20 P0 ==> P1 P1==> P2 P2==> P0 Programmation incrémentale G91 N20 G91 X30 Y30 N30 Y-30 N40 X-30 Chapitre: 2 PROGRAMMATIONDESCOORDONNÉES Section: ABSOLUE (G90), INCREMENTALE(G91) P0 ==> P1 P1==> P2 P2==> P0 Page 3 2.4 PROGRAMMATION DES COORDONNEES Un point peut être programmé dans la CNC en utilisant différentes méthodes: - 2.4.1 Coordonnées cartésiennes Coordonnées polaires Coordonnées cylindriques Deux angles Un angle et une coordonnée cartésienne COORDONNEES CARTESIENNES Le format des valeurs des coordonnées des axes est: En mm En pouces X+/-4.3, Y+/-4.3, Z+/-4.3 X+/-3.4, Y+/-3.4, Z+/-3.4 Les valeurs des coordonnées programmées seront en absolu ou en incrémental selon que G90 ou G91 est programmé. Il n’est pas indispensable d’écrire le signe plus (+) dans le cas des valeurs de coordonnées positives. Les zéros de tête et de queue peuvent être omis. Exemple de programmation, le point initial étant (X0, Y0). Valeurs N10 N20 N30 de coordonnés en absolu: G90 G01 X150.5 Y200 X300 X0 Y0 Valeurs N10 N20 N30 de coordonnés en incrémental: G91 G01 X150.5 Y200 X149,5 X-300 Y-200 Page Chapitre: 2 4 PROGRAMMATIONDESCOORDONNÉES Section: COORDONNEES CARTESIENNES 2.4.2 COORDONNEES POLAIRES Seulement deux axes simultanés peuvent être programmés en coordonnées polaires. Ces deux déplacements doivent se trouver dans le même plan d’interpolation. Si des mouvements dans l’espace sont désirés (3 axes) ils doivent être programmés en coordonnées cartésiennes ou cylindriques. Le format pour identifier un point particulier en coordonnées polaires est: En mm: En pouces: R+/-4.3 R+/-3.4 A+/-3.3 A+/-3.3 R est la valeur du rayon et A la valeur de l’angle (A toujours en degrés) par rapport au centre polaire. Les valeurs de R et de A seront programmées en G90 (absolu) ou G91 (incrémental) en fonction du mode sélectionné. Quand une interpolation circulaire est programmée (G02, G03), les valeurs de l’angle A+/-3.3 et les coordonnées du centre par rapport au point de départ de l’arc doivent être programmées. Si le centre de l’arc est le point de l’origine polaire, il suffit de programmer l’angle sans avoir besoin de programmer les coordonnées du centre par rapport au point initial. Attention: Après une mise sous tension, M02, M30, ARRÊT D’URGENCE et après une REMISE À ZÉRO, la CNC prend X0 et Y0 comme origine polaire. A chaque fois qu’il y a un changement de plan principal dans l’exécution d’un programme, l’origine polaire prendra les coordonnées d'origine de ce plan. Quand G18 est programmé, l’origine polaire prend le point X0 Z0 et quand G19 est programmé, l’origine polaire prend le point Y0 Z0. Quand une interpolation circulaire G02, G03 est programmée, la CNC prend le centre de l’arc comme nouvelle origine polaire. Avec la fonction G93, tous les points de ce plan peuvent être présélectionnés comme origine polaire. Chapitre: 2 Section: Page PROGRAMMATIONDESCOORDONNÉES COORDONNEES POLAIRES 5 SENS ET SIGNES DES ANGLES Plan XY Plan XZ P605(4)=0 Plan XZ P605(4)=1 Plan YZ Page Chapitre: 2 Section: 6 PROGRAMMATIONDESCOORDONNÉES COORDONNEES POLAIRES Exemple: L’outil démarre du point X0, Y0 N0 N5 N10 N15 N20 N25 N30 N35 N40 N45 N50 N55 N60 N65 N70 N75 G93 G01 G02 G01 G02 G01 G03 G01 G02 G01 G03 G01 G02 G01 G02 G01 I20 J20 G90 R5 A180 F150 A75 G91 R5 A-15 R10 A15 R10 A-50 R-10 A15 R-10 A-15 R-5 G90 A180 X0 Y0 Chapitre: 2 Section: Page PROGRAMMATIONDESCOORDONNÉES COORDONNEES POLAIRES 7 2.4.3 COORDONNEES CYLINDRIQUES Un point dans l’espace peut être défini par des valeurs de coordonnées cartésiennes sur les trois axes X, Y, Z, ou bien par une valeur de coordonnées cylindriques. Le format utilisé pour définir un point dans ce système, avec G17 sélectionné (Plan XY), est N10 G01 R...A...Z.... R et A définissent la projection du point sur le plan principal en coordonnées polaires et Z définit la valeur de la coordonnée Z á ce point. Les formats pour G18 (Plan XZ): N10 G01 R... A... Y... Les formats pour G19 (Plan YZ): N10 G01 R... A... X... Page Chapitre: 2 8 PROGRAMMATIONDESCOORDONNÉES Section: COORDONNEES CYLINDRIQUES 2.4.4 DEUX ANGLES (A1, A2) Un point intermédiaire d’une trajectoire peut être défini par: A1 A2 XY (YZ ou XZ). A1 est l’angle de sortie du point de départ de la trajectoire (P0). A2 est l’angle de sortie du point intermédiaire (P1). XY, (YZ ou XZ) sont les coordonnées du point final P2. La CNC calcule automatiquement les coordonnées de P1. Exemple: Point de départ: X0 Y0 N10 X20 Y10 N20 A45 A30 N30 X70 Y50 (Coordonnées de P0) (Angles de sortie de P0 et P1) (Coordonnées de P2) Chapitre: 2 Section: Page PROGRAMMATIONDESCOORDONNÉES DEUX ANGLES (A1, A2) 9 2.4.5 ANGLE ET UNE COORDONNEE CARTESIENNE Il est aussi possible de définir un point au moyen de l’angle de sortie de la trajectoire sur le point précédent et une coordonnée cartésienne du point que l’on désire définir. Exemple de programmation, supposant que le point de départ est: P0 (X10 Y20) N10 N20 N30 N40 N50 A45 X30 ; (Point P1) A90 Y60 ; (Point P2) A-45 X50 ; (Point P3) A-135 Y20 ; (Point P4) A180 X10 ; (Point P0) Dans la définition de points d’une trajectoire au moyen de deux angles ou d’un angle et d’une coordonnée, il est possible d’intercaler des arrondis, des chanfreins, des entrées et des sorties tangentielles. TRAJECTOIRE COMPENSÉE TRAJECTOIRE PROGRAMMÉE Point de départ X0 Y0 et rayon de l’outil T1 = 5 mm. N100 N110 N120 N130 N140 N150 N160 N170 N180 N190 T1.1 G37 G39 X50 G36 G39 G36 G38 G40 M30 R10 R5 Y60 R7 R10 R10 R10 X0 G41 X20 Y20 A90 A0 A-45 X70 A45 A-90 X100 Y20 X20 Y0 Page Chapitre: 2 10 PROGRAMMATIONDESCOORDONNÉES Section: ANGLEETCOORDONNEE CARTESIENNE 3. SYSTEMES DE REFERENCE 3.1 RECHERCHE DE REFERENCE MACHINE (G74) Lorsque G74 est programmé dans un bloc, la CNC déplace les axes au point zéro de référence. Deux cas peuvent se présenter: a) Référence pour tous les axes. Si G74 est programmé seul dans un bloc, la CNC déplace d’abord l’axe qui est perpendiculaire au plan programmé. C’est-à-dire: Celui-ci sera l’axe Z si la fonction G17 est active. L’axe Y, si c’est G18, l’axe X, si c’est G19. Les déplacements sur les autres axes du plan vont suivre. b) Référence pour un axe ou deux dans un ordre déterminé. Si la recherche du zéro de référence dans un seul axe est désirée, la programmation de G74 s’effectue dans l’ordre de déplacement désiré. Si la recherche du zéro de référence dans un ordre différent au précédent est désirée, on doit programmer G74 et après les axes en ordre chronologique. Aucune autre fonction ne peut être programmée dans un bloc contenant G74. Dans les deux cas, a) et b), lorsque les axes ont atteint le point de référence, les distances entre ce point et le dernier point zéro programmé de la pièce sont visualisées. Chapitre: 3 SYSTEMESDEREFERENCE Section: RECHERCHEDEREFERENCE MACHINE(G74) Page 1 3.2 PRESELECTION DES VALEURS DES COORDONNEES (G92) La fonction G92 peut être utilisée pour modifier les valeurs des registres de position des axes de la CNC, dans le but de décaler les coordonnées de l'origine programmée. Lorsque la fonction G92 est programmée, il n'y a aucun déplacement sur les axes. La CNC accepte les valeurs programmées après un code G92 comme étant les nouvelles valeurs de coordonnées des axes. Format du bloc: N4 G92 X Y Z Exemple de programmation, le point initial étant (X0, Y0). Sans utiliser la fonction G92: N10 G00 G90 X100 Y100 N20 X400 Si G92 est utilisé, le programme devient: N10 G92 X500 Y500 L'origine des coordonnées (X0, Y0) est décalée au point X500, Y500. N20 G00 G90 X600 Y600 N30 X900 Aucune autre fonction ne peut être programmée dans un bloc contenant G92. La présélection des valeurs de coordonnées par G92 se fait toujours par rapport à la position théorique dans laquelle les axes se trouvent. Page Chapitre: 3 2 SYSTEMESDEREFERENCE Section: PRESELECTIONDES COORDONNEES (G92) 3.3 PRESELECTION D’ORIGINE POLAIRE (G93) Il est possible, au moyen de la fonction G93, de présélectionner n’importe quel point du plan comme origine de coordonnées polaires. Il y a deux façons de présélectionner une origine de coordonnées polaires: a) En définissant les coordonnées de l’origine polaire. Format N4 G93 I+/-4.3 J+/-4.3 en mm N4 G93 I+/-3.4 J+/-3.4 en pouces N Numéro de bloc G93 Code de présélection d’origine polaire I Valeur de l’abscisse de l’origine des coordonnées polaires, toujours en valeur absolue, c’est-à-dire, la valeur de X (plans XY et XZ) ou la valeur de Y (plan YZ). J Valeur de l’abcisse de l’origine des coordonnées polaires, toujours en valeur absolue, c’est-à-dire, la valeur de Y (plan XY) ou la valeur de (plans XZ et YZ). Si l’on programme de cette manière la présélection d’origine polaire, la CNC n’admet aucune autre information dans le même bloc. b) En assumant le point actuel comme nouvelle origine polaire. Si dans un bloc quelconque l’on programme en plus G93, celle-ci impliquera qu’avant que le mouvement que le bloc implique se fasse, l’origine polaire deviendra le point sur lequel se trouvera la machine à ce moment-là. Attention: Lorsque l’on programme une interpolation circulaire avec G02, G03, la CNC assume le centre de l’arc comme nouvelle origine polaire. Lorsqu’il change de plan principal, la CNC assume comme origine polaire l’origine de coordonnées cartésiennes de ce plan. Avec G17, il assume X0 Y0; avec G18, il assume X0 Z0; avec G19, il assume Y0 Z0. Après une mise sous tension, M02, M30, ARRÊT D’URGENCE et après REMISE À ZÉRO, la CNC prend X0 et Y0 comme origine polaire. Deux exemples de programmation sont ci-après indiqués. Chapitre: 3 SYSTEMESDEREFERENCE Section: PRESELECTIOND’ORIGINE POLAIRE (G93) Page 3 Exemple de programmation, le point initial étant (X0, Y0): ORIGINE POLAIRE N0 G93 I200 J0 Il définit le point X200 Y0 comme nouvelle origine polaire. Déplacement en G01 jusqu’au point X200 Y150 N5 G01 R150 A90 F500 Exemple de programmation, le point initial étant (X0, Y0): P1 P2 ORIGINE POLAIRE N0 G93 G01 R200 A135 F500 Il définit le point X0 Y0 comme nouvelle origine polaire et déplacement en G01 jusqu’au point P1 N5 R100 A90 Déplacement en G01 jusqu’au point P2 Page Chapitre: 3 4 SYSTEMESDEREFERENCE Section: PRESELECTIOND’ORIGINE POLAIRE (G93) 3.4 TRANSFERTS D’ORIGINE (G53...G59) 7 transferts du point zéro peuvent être sélectionnés indépendamment par les fonctions G53,G54,G55,G56,G57,G58 et G59. Les valeurs de ces transferts sont stockées dans la mémoire de la CNC à la suite de la table des fiches d’outils et sont référencées par rapport au point zéro machine. Pour accéder à la table des tranferts d’origine G53-G59, il faut taper la séquence de touches suivantes Une fois dans la table, il est possible d’effacer tous les transferts d’origine: il faut pour cela taper la séquence de touches suivantes Les fonctions G53-G59 doivent être utilisées pour le chargement d’un transfert d’origine sur la table ou pour appliquer un transfert d’origine se trouvant sur la table au programme en cours. Chargement d’un transfert d’origine sur la table. Chargement absolu de valeurs. Il permet de charger dans la direction de la table indiquée (G53-G59) les valeurs définies par X, Y, Z. Format: N4 G53-G59 X+/-4.3 Y+/-4.3 Z+/-4.3 en mm, N4 G53-G59 X+/-3.4 Y+/-3.4 Z+/-3.4 en pouces. N G X Y Z Numéro du bloc. Code de transfert (G53-G59) Valeur en X du transfert par rapport au point zéro-machine. Valeur en Y du transfert par rapport au point zéro-machine. Valeur en Z du décalage par rapport au point zéro-machine. Chargement incrémental de valeurs. Il permet d’incrémenter les valeurs existantes dans la direction de la table indiquée (G53-G59), dans la quantité définie en I, J, K. Format: N G I J K N4 G53-G59 I+/-4.3 J+/-4.3 K+/-4.3 en mm, N4 G53-G59 I+/-3.4 J+/-3.4 K+/-3.4 en pouces. Número de bloc Code du transfer du zéro (G53-G59). Quantité à additionner ou à soustraire à la valeur de X mémorisée dans la table Quantité à additionner ou à soustraire à la valeur de Y mémorisée dans la table Quantité à additionner ou à soustraire à la valeur de Z mémorisée dans la table Pour appliquer un transfer de zéro, mémorisé dans la table, dans programme en cours: Format: le N4 G53-G59 Ce format est utilisé pour déclancher un transfer de zéro dans le programme en cours. La valeur du transfer est donnée par les valeurs mémorisées dans la table des transfers de zéro (G53-G59). Chapitre: 3 SYSTEMESDEREFERENCE Section: TRANSFERTSD’ORIGINE (G53...G59) Page 5 Exemple de programmation, en supposant que le point de départ, X0, Y0, coïncide avec le zéro machine: N1 N2 N3 G53 X0 Y0 ................................... Charge le transfert d’origine G53 sur la table G54 X-40 Y-40 ............................. Charge le transfert d’origine G54 sur la table G55 X-30 Y10 .............................. Charge le transfert d’origine G55 sur la table N10 G0 G90 X70 Y20 N20 G1 Y35 F200 N30 X60 N40 G03 X60 Y20 I0 J-7,5 N50 G01 X70 Y20 N60 G54 ................................................ Applique le transfert d’origine G54 N70 G25 N10.50.1 N80 G55 ................................................ Applique le transfert d’origine G55 N90 G25 N10.50.1 N100 G53 ............................................. Applique le transfert d’origine G53. Récupère celui qui se trouvait auparavant. N110 X0 Y0 N120 M30 Page Chapitre: 3 6 SYSTEMESDEREFERENCE Section: TRANSFERTS D’ORIGINE (G53G59) 3.5 MEMORISATION ET PRELEVEMENT DU POINT ZERO DU PROGRAMME (G31-G32) G31 : Mémorisation du point zéro actuel du programme. G32 : Prélèvement du point zéro mémorisé par G31. Avec la fonction G31 on peut à tout moment mémoriser l'origine des coordonées du programme actuel et prélever ultérieurement par G32. Cette caractéristique est prévue pour simplifier le fonctionnement avec des programmes à plusieurs points zéro et permet référer une partie du programme à une origine determinée, sauvegarder cette origine avec G31, faire un changement avec G92 ou G53-G59, référer la continuation du programme par rapport au nouveau origine et prélèver ultérieurement avec G32. Aucune autre fonction ne peut être programmée dans un bloc contenant G31 ou G32. Le format est: N4 G31 N4 G32 Mémorisation du point zéro actuel du programme Prélèvement du point zéro mémorisé par G31 Exemple de programmation, en supposant que l’outil se trouve sur le point X0 Y0 Z5: N10 N20 N30 N40 G00 G20 X60 G20 G90 X-50 Y50 ................. Déplacement au centre de l’usinage 1 N1.1 ..................................... Exécute l’usinage de base (sous-routine N1) Y110 .................................... Déplacement au centre de l’usinage 2 N1.1 ..................................... Exécute l’usinage de base (sous-routine N1) N50 X35 Y-90 .................................... Déplacement au centre de l’usinage 3 N60 G20 N1.1 ..................................... Exécute l’usinage de base (sous-routine N1) N70 M30 .............................................. Fin du programme Chapitre: 3 SYSTEMESDEREFERENCE Section: MEMORISATION/PRELEV. DU POINT ZERO (G31-G32) Page 7 N100 G22 N1 ....................................... Usinage de base (définition sous-routine N1) N110 G31 ............................................... Mémoriser l’origine de coordonnées actuelle N120 G92 X0 YO N130 G1 Z-20 F350 N140 X— Y— N—N—N—N—N—N200 G0 Z5 N210 G32 ............................................... Récupérer l’origine de coordonnées sauvegardée N220 G24 ............................................... Fin de l’usinage de base, fin du sousprogramme. Page Chapitre: 3 8 SYSTEMESDEREFERENCE Section: MEMORISATION/PRELEV. DU POINT ZERO (G31-G32) 4. FONCTIONS COMPLEMENTAIRES 4.1 PROGRAMMATION DE L'AVANCE (F) La vitesse d'avance des axes est programmée au moyen de la lettre "F" et sa valeur change selon que le système utilisé dans la programmation soit en mm. ou en pouces. Programmation en millimètres : Format Unité de programmation F 5.4 F1= 1mm/min Valeur minimale Valeur maximale F0.0001 (0.0001 mm/min) F65535.000 (63535 mm/min) Programmation en pouces : Lorsque l'on travaille en pouces, nous conseillons de personnaliser le paramètre machine P615(6) à la valeur "1", afin que les unités de programmation soient en pouces/minute. P615(6) = 0 Format de programmation F1=0,1"/min. Pour compatibilité avec des versions très anciennes. Lorsque le format n'admettait pas de décimales. P615(6) = 1 Format de programmation F1=1"/min. P615(6) Format Unité de programmation Valeur minimale Valeur maximale P615(6)=0 F 5.4 F1= 0,1 pouce/min F0.001 (0,0001 pouce/min) F25801.1810 (2580,1181 pouce/min) P615(6)=1 F 5.4 F1= 1 pouce/min F0.0001 (0,0001 pouce/min) F25801.1810 (25801,1810 pouce/min) L’avance réelle maximale d’usinage peut être limitée à una valeur inférieure (voir manuel d’instruction de la machine). L’avance maximale d’usinage peut être programmée en utilisant le code F0. Exemple: Sur une machine ayant une possibilité d’avance maximale d’usinage programmable de 10.000 mm/mn, il n’y a pas de différence entre la programmation de F0 ou F10.000. L’avance programmée F est effective lors des opérations d’interpolation linéaire (G01) ou d’interpolation circulaire (G02/G03). Si la fonction F n’est pas programmée, la CNC déclarera active l’avance F0. Lors des opérations de positionnement (G00), la machine se déplace en rapide sans tenir compte du code F programmé. Chapitre: 4 FONCTIONSCOMPLEMENTAIRES Section: PROGRAMMATIONDE L'AVANCE (F) Page 1 L’avance rapide est fixée pour chaque axe pendant le réglage final de la machine, la valeur maximale possible étant 65,535 mm/mn (voir manuel d’instruction de la machine). L’avance programmée peut être modulée entre 0 et 120 % ou entre 0 et 100 % suivant le paramètre machine P606(2), au moyen d’un sélecteur situé sur le tableau de commandes. Lorsque la fonction G47 est active l’action de ce sélecteur est inhibée et les avances s’effectuent à 100% de F programmé. 4.1.1 FEED-RATE PROGRAMMABLE (G49) La fonction G49 sert à indiquer le % de la vitesse d’avance F qui est désirée dans chaque programme. La fonction G49 étant activée, le sélecteur de M.F.O. n’est plus opérationnel. Le format de programmation est : G49 K (1/120) Lors de la programmation, le % de l’avance F désiré doit suivre G49 K. Une valeur entière comprise entre 1 et 120 peut être programmée. La fonction G49 est modale, c’est-à-dire, une fois programmé le % celui-ci reste actif jusqu’à ce qu’un autre soit programmé ou jusqu’à ce que la fonction soit annulée. Pour cela, programmer: G49 K ou G49 seulement. L’exécution de M02, M30, REMISE A ZERO, ARRET D'URGENCE annule aussi la fonction G49. La fonction G49 K doit être programmée toute seule dans le bloc. Page Chapitre: 4 2 FONCTIONSCOMPLEMENTAIRES Section: PROGRAMMATIONDE L'AVANCE (F) 4.2 VITESSE DE ROTATION DE LA BROCHE (S) La vitesse de broche est programmée directement en tours/mn à l’aide du code S4. N’importe quelle valeur entre S0 et S9999 peut être programmée, c’est-à-dire entre 0 et 9999 tours/mn. Cette valeur est limitée par la vitesse maximale de la machine et est fixée par un paramètre machine. Le livre d’instruction de la machine doit être consulté dans chaque cas particulier. Les commandes situées sur le tableau de commandes peuvent être utilisées pour faire varier de 50 à 120% la vitesse de broche programmée. Lors de l’exécution du taraudage ou lorsque la fonction G47 est activée la vitesse de tour S programmée est verrouillée à 100%. Chapitre: 4 FONCTIONSCOMPLEMENTAIRES Section: VITESSE DE ROTATION DE LA BROCHE (S) Page 3 4.3 PROGRAMMATION DE L’OUTIL (T) La CNC dispose d’une table de 100 outils (00-99) pour compensation de rayon et longueur d’outil. L’outil à utiliser est programmé au moyen du code T2.2 Les deux chiffres à gauche du point décimal indiquent le numéro d’outil que l’on désire sélectionner. Les deux chiffres à droite du point décimal indiquent le numéro de correcteur d’outil que l’on désire utiliser. Un maximum de 100 outils T0 à T99 sont disponibles, ainsi que 100 correcteurs Txx0 à Txx99 La fonction T peut être programmée des façons suivantes: T2.2 La CNC sélectionne l’outil indiqué et tient compte des valeurs indiquées par le correcteur sélectionné. T2 La CNC sélectionne l’outil indiqué et prend les valeurs indiquées par le correcteur du même numéro. Programmer T3 équivaut à programmer T3.3. T.2 La CNC ne change pas d’outil et tient compte des valeurs indiquées par le nouveau correcteur sélectionné. Lorsque l’on programme G41 ou G42, la CNC applique comme valeur de compensation de rayon la somme des valeurs R+I sauvegardées en mémoire, à l’adresse T (00-99) programmée. Si l’on programme G43, la CNC applique comme valeur de compensation de longueur la somme des valeurs L+K sauvegardées en mémoire, à l’adresse T (0099) programmée. Si aucune T n’a été programmée, la CNC applique les valeurs de l’adresse 00.00. Les valeurs suivantes sont sauvegardées dans chaque adresse de la table: R L I K Rayon de l’outil +/-1000,000 mm(+/-39,3699 pouces) Longueur de l’outil +/-1000,000 mm(+/-39,3699 pouces) Correction du rayon de l’outil +/-32,766 mm (+/-1,2900 pouces) Correction de la longueur de l’outil +/-32,766 mm (+/-1,2900 pouces) Attention: Si le constructeur de la machine a associé une routine quelconque à la fonction T, il ne faut rien programmer après la fonction T. Dans le cas contraire, la CNC affichera l’erreur correspondante. Si le changement d’outil n’a aucune routine associée avant d’être sélectionnée (constructeur), la CNC fait ressortir le code du nouvel outil, affiche le message “TOOL CHANGE” et arrête l’exécution du programme. Page Chapitre: 4 4 FONCTIONSCOMPLEMENTAIRES Section: PROGRAMMATIONDEL’OUTIL (T) 4.3.1 CHARGEMENT DES DIMENSIONS D’OUTIL SUR LA TABLE (G50) Il est possible d’introduire les dimensions des différents outils sur la table au moyen de la fonction G50. Deux cas peuvent se présenter: a) Chargement de toutes les dimensions d’un outil Elle permet de charger la table d’outils sans besoin de les introduire manuellement. Format en mm: Format en pouces: N4 G50 T2 R+/-4.3 L+/-4.3 I+/-2.3 K+/-2.3. N4 G50 T2 R+/-2.4 L+/-2.4 I+/-1.4 K+/-1.4. Les valeurs définies par R, L, I, K sont chargées à l’adresse de la table indiquée par T2. N4 G50 T R I L K Numéro du bloc Code de chargement des dimensions. Adresse de la table d'outils. (T00-T99) Rayon de l'outil. Correction d’usure du rayon de l'outil. Longueur de l'outil. Correction d’usure de la longueur de l'outil. Les valeurs de R, L, I, K remplacent les valeurs précédemment mémorisées à l’adresse spécifiée par T2. Si R et L sont seulement programmées, ils sont remplacées par les nouvelles valeurs programmées et les valeurs de correction I, et K sont mis à zéro. b) Modification incrémentale des valeurs I K Elle permet de corriger les usures d’outil au fur et à mesure qu’elles se produiront. Format en mm: Format en pouces: N4 G50 T2 I+/-2.3 K+/-2.3. N4 G50 T2 I+/-1.4 K+/-1.4. Les valeurs I, K de l’adresse de la table indiquée par T2 sont modifiées. N4 G50 T I K Numéro du bloc Code de chargement des dimensions. Adresse de la table d'outils. (T00-T99) Valeur à ajouter ou à soustraire de la valeur de I précédemment mémorisée. Valeur à ajouter ou à soustraire de la valeur de K précédemment mémorisée. Attention: Aucune autre information ne peut être programmée dans un bloc contenant un code G50. La valeur de compensation du rayon sera R+I. La valeur de compensation de longueur sera L+K. Chapitre: 4 FONCTIONSCOMPLEMENTAIRES Section: CHARGEMENTDES DIMENSIONS D’OUTIL (G50) Page 5 4.4 FONCTIONS AUXILIAIRES (M) Les fonctions auxiliaires sont programmées par le code M2. 96 fonctions auxiliaires différentes (M00-M99) peuvent être programmées à l’exception de M41, M42, M43 et M44 affectées à S. Les fonctions auxiliaires sont envoyées vers l’interface en code binaire (M00/ M254) ou en BCD (M00/M99) selon la valeur asignée au paramétre machine P617(8). La CNC a aussi 15 sorties décodées pour les fonctions auxiliaires. Ces sorties seront affectées aux fonctions désirées pendant la mise en service de la machine. Les fonctions auxiliaires qui ne sont pas affectées à une sortie décodée sont toujours exécutées au début du bloc dans lequel elles sont programmées. Lorsqu’une sortie décodée est affectée à une fonction auxiliaire, il faut aussi préciser si cette fonction doit être exécutée au début ou à la fin du bloc dans lequel elle est programmée. Il est possible de programmer jusqu’à un maximum de 7 fonctions auxiliaires dans le même bloc. Lorsque c’est le cas, la CNC les traite dans l’ordre dans lequel elles ont été programmées. Certaines fonctions auxiliaires ont une affectation interne dans la CNC. M00. ARRET DU PROGRAMME Lorsque la CNC lit le code M00 dans un bloc, elle arrête l’exécution du programme. Il faut appuyer sur Départ Cycle pour reprendre son déroulement. Il est recommandé de personnaliser cette fonction dans le tableau des fonctions M décodées de façon qu’elle soit exécutée à la fin du bloc dans lequel elle est programmée (voir Manuel d’Installation et de Mise en Service). M01. ARRET CONDITIONNEL DU PROGRAMME Identique à la fonction M00, excepté que la CNC ne la prend en compte que si l’entrée “Arrêt Optionnel” est activée. M02. FIN DE PROGRAMME Ce code indique la fin du programme et effectue une remise à zéro générale de la CNC (retour à l’état initial). Cette fonction agit aussi comme la fonction M05. Comme dans le cas d’un M00, cette fonction doit être personnalisée de façon qu’elle soit exécutée à la fin du bloc dans lequel elle est programmée. Page Chapitre: 4 6 FONCTIONSCOMPLEMENTAIRES Section: FONCTIONSAUXILIAIRES(M) M30. FIN DE PROGRAMME ET RETOUR AU DEBUT Cette fonction est identique à M02. Elle effectue en plus le retour au premier bloc du programme. Elle agit aussi comme la fonction M05. Si le paramètre P609(3)=0, lorsqu’on effectue une RAZ, la CNC affiche le code M30. M03. ROTATION SENS HORAIRE DE LA BROCHE Il est recommandé de personnaliser cette fonction de façon qu’elle soit exécutée au début du bloc dans lequel elle est programmée. M04. ROTATION SENS ANTI-HORAIRE DE LA BROCHE Il est recommandé de personnaliser cette fonction de façon qu’elle soit exécutée au début du bloc dans lequel elle est programmée. M05. ARRÊT DE BROCHE Il est recommandé de personnaliser cette fonction de façon qu’elle soit exécutée à la fin du bloc dans lequel elle est programmée. M10, M11. ASSOCIÉES AU DISPOSITIF EXTERNE 01 M12, M13. ASSOCIÉES AU DISPOSITIF EXTERNE 02 M14, M15. ASSOCIÉES AU DISPOSITIF EXTERNE 03 Codes associés aux touches correspondant aux dispositifs externes “O1”, “O2” et “O3”. Les codes M10, M12 et M14 indiquent activation et les codes M11, M13 et M15, désactivation du dispositif externe correspondant. Chapitre: 4 FONCTIONSCOMPLEMENTAIRES Section: FONCTIONSAUXILIAIRES(M) Page 7 5. CONTROLE DE TRAJECTOIRE 5.1 ARETE ARRONDIE (G05) Lors du fonctionnement en G05, la CNC commence à exécuter le bloc suivant du programme dès que les axes commencent leur décélération à la fin du bloc précédent. En d’autres mots, les déplacements programmés dans le bloc suivant sont exécutés avant que les axes de la machine aient atteint leur position exacte programmée dans le bloc précédent. Exemple de programmation, le point initial étant X50, Y30. N100 G91 G01 G05 Y70 F100 N110 X90 Comme illustré dans l’exemple, les angles seraient arrondis. La différence entre les profils théoriques et réels est en fonction de l’avance. Plus l’avance est grande, plus la différence entre les profils théoriques et réels est importante. La fonction G05 est modale et incompatible avec G07 La fonction G05 peut être programmée comme G5. 5.2 ARETE VIVE (G07) Lors du fonctionnement en G07, la CNC n’exécute le bloc suivant que lorsque les axes ont réellement atteint la position programmée dans le bloc précédent. Exemple de programmation, le point initial étant X50, Y30. N100 G91 G01 G07 Y70 F100 N110 X90 Les profils théoriques et réels sont confondus. La fonction G07 est modale et incompatible avec G05. La fonction G07 peut être programmée par G7. Après la mise sous tension et après M02, M30, ARRÊT D’URGENCE et REMISE A ZERO, la CNC retient la fonction G07 ou G05 selon la valeur attribué au paramètre machine P613(5), c’est-à-dire, avec P613(5)=0 retient G07 et avec P613(5)=1 retient G05. Chapitre: 5 CONTROLEDETRAJECTOIRE Section: ARETEARRONDIE(G05) ARETEVIVE(G07) Page 1 5.3 POSITIONNEMENT RAPIDE (G00) Les déplacements programmés à la suite d’une fonction G00 sont effectués à l’avance rapide introduite dans les paramètres lors de la mise en conditions initiales. Lorsque deux ou trois axes se déplacent simultanément, la trajectoire résultante est une ligne droite entre le point de départ et le point final. L’avance sera déterminée par l’axe le plus lent. Quand G00 est programmé, la dernière vitesse F n’est pas annulée. Cela signifie que quand G01, G02 ou G03 est programmé à nouveau, la vitesse F mentionnée est retrouvée. Le paramètre P4 peut être utilisé pour activer le sélecteur de correction manuel des avances entre 0% et 100% ou fixe à 100%. Le code G00 est modal et incompatible avec G01, G02, G03 et G33. La fonction G00 peut se programmer avec G, ou G0. A la mise sous tension de la CNC, après l’exécution M02/M30 ou après un ARRÊT D’URGENCE, ou une REMISE A ZERO, la CNC se trouve en mode G00. Page Chapitre: 5 2 CONTROLEDETRAJECTOIRE Section: POSITIONNEMENTRAPIDE (G00) 5.4 INTERPOLATION LINEAIRE (G01) Les déplacements programmés à la suite d’une fonction préparatoire G01 sont effectués suivant une pente (ligne droite) à l’avance F programmée. Lorsque 2 ou 3 axes se déplacent simultanément, la trajectoire résultante est une ligne droite (pente) entre le point initial et le point final. L’avance de l’outil le long de sa trajectoire est celle programmée sous la lettre F. La CNC calcule l’avance de chaque axe de façon que l’avance le long de la trajectoire résultante soit celle de la fonction F programmée. Exemple de programmation, le point initial étant X150 Y150. N100 G90 G01 X650 Y400 F150 Le sélecteur (M.F.O) situé sur la face avant de la CNC peut être utilisé pour moduler l’avance F programmée entre 0% et 120% ou entre 0% et 100% suivant le paramètre P606(2). Si au cours d’un déplacement en G01, une touche JOG d’avance rapide est activée, ce déplacement sera exécuté un double de l’avance programmée si le paramètre P606(2) est à zéro (0). La même chose peut se produire si l’entrée extérieure START est activée et que le paramètre P609(7) est à (1). La fonction G01 est modale et incompatible avec G00, G02 et G03. La fonction G01 peut être programmée par G1 uniquement. A la mise sous tension de la CNC, après l’exécution M02/M30 ou après un ARRÊT D’URGENCE, ou une REMISE A ZERO, la CNC se trouve en mode G00. Chapitre: 5 CONTROLEDETRAJECTOIRE Section: INTERPOLATIONLINEAIRE (G01) Page 3 5.5 INTERPOLATION CIRCULAIRE (G02, G03) G02: Interpolation circulaire dans le sens horaire. G03: Interpolation circulaire dans le sens anti-horaire. Les déplacements programmés à la suite de G02/G03 sont effectués suivant des trajectoires circulaires à l’avance F programmée. Les définitions de sens horaire (G02) et de sens anti-horaire (G03) ont été fixés selon le système de coordonnées ci-dessous. Ce système de coordonnées se rapporte au mouvement de l’outil au-dessus de la pièce. Le sens de G02 et G03, dans le plan XZ, peut être inversé en modifiant le paramètre machine P605(4). Si on change le sens des axes, le sens de G02 et G03 est inversé. Les fonctions G02/G03 sont modales et incompatibles entre elles, et aussi avec G00, G01 et G33. Les fonctions G74 et les cycles fixes annulent G02, G03. Les fonctions G02/G03 peuvent être programmées comme G2/G3. Page Chapitre: 5 4 CONTROLEDETRAJECTOIRE Section: INTERPOLATIONCIRCULAIRE (G02, G03) Le format d’un bloc pour programmer une interpolation circulaire en coordonnées cartésiennes est le suivant: Plan XY G17 G02 (G03) X+/-4.3 Y+/-4.3 I+/-4.3 J+/-4.3 F5.4 Plan XZ G18 G02 (G03) X+/-4.3 Z+/-4.3 I+/-4.3 K+/-4.3 F5.4 Plan YZ G19 G02 (G03) Y+/-4.3 Z+/-4.3 J+/-4.3 K+/-4.3 F5.4 Soit: X Y Z I J K Coordonnée X du point final de l’arc Coordonnée Y du point final de l’arc Coordonnée Z du point final de l’arc Distance depuis le point de départ au centre, selon l’axe X Distance depuis le point de départ au centre, selon l’axe Y Distance depuis le point de départ au centre, selon l’axe Z Les paramètres I, J. K doivent toujours être définis, malgré qu’ils aient la valeur 0. Le format de bloc pour programmer une interpolation circulaire en coordonnées polaires est le suivant: Plan XY Plan XZ Plan YZ Soit: A I J K G17 G02 (G03) A+/-3.3 I+/-4.3 J +/-4.3 F5.4 G18 G02 (G03) A+/-3.3 I+/-4.3 K+/-4.3 F5.4 G19 G02 (G03) A+/-3.3 J+/-4.3 K+/-4.3 F5.4 Angle par rapport au centre polaire du point final de l’arc Distance depuis le point de départ au centre, selon l’axe X Distance depuis le point de départ au centre, selon l’axe Y Distance depuis le point de départ au centre, selon l’axe Z Les paramètres I, J. K doivent toujours être définis, malgré qu’ils aient la valeur 0. Lorsqu’une interpolation circulaire G02, G03 est programmée en coordonnées polaires, la CNC assume que le centre de l’arc est la nouvelle origine polaire. Le sélecteur (M.F.O) situé sur la face avant de la CNC peut être utilisé pour moduler l’avance F programmée entre 0% et 120% ou entre 0% et 100% suivant le paramètre P606(2). Si au cours d’un déplacement en G02/G03, une touche JOG d’avance rapide est activée, ce déplacement sera exécuté un double de l’avance programmée si le paramètre P606(2) est à zéro (0). La même chose peut se produire si l’entrée extérieure START est activée et que le paramètre P609(7) est à (1). Chapitre: 5 CONTROLEDETRAJECTOIRE Section: INTERPOLATIONCIRCULAIRE (G02, G03) Page 5 Exemple 1: COORDONNEES CARTESIENNES G17 G02 G91 X26 Y26 I18 J8 G17 G02 G91 X26 Y-26 I8 J-18 COORDONNEES POLAIRES G17 G02 G91 A-138 I18 J8 G17 G02 G91 A-138 I8 J-18 Exemple 2: Coordonnées cartésiennes: N5 G90 G17 G03 X110 Y90 I0 J50 F150 N10 X160 Y40 I50 J0 Page Chapitre: 5 6 CONTROLEDETRAJECTOIRE Section: INTERPOLATIONCIRCULAIRE (G02, G03) Coordonnées polaires: N5 G90 G17 G03 A0 I0 J50 F150 N10 A-90 I50 J0 ou N5 G91 G17 G03 A90 I0 J50 F150 N10 A90 I50 J0 ou N5 N10 N15 N20 G93 I60 J90 G90 G17 G03 A0 F150 G93 I160 J90 A-90 ou N5 N10 N15 N20 G93 I60 J90 G91 G17 G03 A90 F150 G93 I160 J90 A90 Exemple 3: Programmation d’un cercle entier dans un seul bloc. Point de départ supposé X170 Y80 Coordonnées cartésiennes: N5 G90 G17 G02 X170 Y80 I-50 J0 F150 Coordonnées polaires: N5 G90 G17 G02 A360 I-50 J0 F150 ou N5 G93 I120 J80 (Définition du centre polaire) N10 G17 G02 A360 Chapitre: 5 Section: INTERPOLATIONCIRCULAIRE (G02, G03) CONTROLEDETRAJECTOIRE Page 7 5.5.1 INTERPOLATION CIRCULAIRE AVEC PROGRAMMATION DU RAYON DE L’ARC (G02, G03) Format en mm: plan XY: plan XZ: plan YZ: G17 G02 (G03) X+/-4.3 Y+/-4.3 R+/-4.3 F5.4 G18 G02 (G03) X+/-4.3 Z+/-4.3 R+/-4.3 F5.4 G19 G02 (G03) Y+/-4.3 Z+/-4.3 R+/-4.3 F5.4 Format en pouces: plan XY: plan XZ: plan YZ: G17 G02 (G03) X+/-3.4 Y+/-3.4 R+/-4.3 F4.5 G18 G02 (G03) X+/-3.4 Z+/-3.4 R+/-4.3 F4.5 G19 G02 (G03) Y+/-3.4 Z+/-3.4 R+/-4.3 F4.5 Soit: G02(G03) X Y Z R F la fonction qui définit le sens de l’interpolation circulaire coordonnée X du point final de l’arc coordonnée Y du point final de l’arc coordonnée Z du point final de l’arc rayon de l’arc vitesse d’avance Ceci signifie qu’un arc peut être programmé en spécifiant les coordonnées de son point d’arrivée plus le rayon. Les coordonnées (I, J, K) du centre ne sont pas nécessaires. Si l’arc est inférieur à 180 degrés, le rayon sera programmé avec un signe positif et s’il est supérieur à 180 degrés, le signe sera négatif. Si P0 est le point de départ et P1 le point d’arrivée de l’arc, il y a 4 possibilités d’arcs pour une même valeur donnée au rayon. En combinant le sens (G02/G03) et le signe du rayon l’arc désiré est identifié. Ainsi, le format de programmation des arcs du schéma sera le suivant: Arc Arc Arc Arc 1 2 3 4 G02 G02 G03 G03 X X X X Y Y Y Y R R R R + + - Attention: Si un cercle complet est programmé avec la programmation du rayon, la CNC affichera l’erreur 47, étant donné qu’il existe des solutions infinies. Page Chapitre: 5 8 CONTROLEDETRAJECTOIRE Section: INTERPOLATIONCIRCULAIRE (G02, G03) 5.5.2 INTERPOLATION CIRCULAIRE AVEC PROGRAMMATION DU CENTRE DE L’ARC EN COORDONNÉES ABSOLUES (G06) Si la fonction G06 est ajoutée dans un bloc d’interpolation circulaire, il est possible de programmer les valeurs de coordonnée du centre de l’arc (I,J,K) en coordonnées absolues ; c’est-à-dire, par rapport au point zéro d’origine et non pas au point initial de l'arc. La fonction G06 n’est pas modale. Elle doit être programmée chaque fois qu’il est désiré de programmer les valeurs de coordonnée du centre de l’arc en coordonnées absolues. Exemple de programmation, le point de départ étant X60 Y40: Interpolation circulaire avec programmation du rayon. N5 G90 G17 G03 X110 Y90 R50 F150 N10 X160 Y40 R50 Interpolation circulaire avec programmation du centre en coordonnées absolues. N5 G90 G17 G06 G03 X110 Y90 I60 J90 F150 N10 G06 X160 Y40 I160 J90 Chapitre: 5 CONTROLEDETRAJECTOIRE Section: INTERPOLATIONCIRCULAIRE (G02, G03) Page 9 5.5.3 INTERPOLATION HELICOIDALE Une interpolation hélicoïdale est définie par une interpolation circulaire dans le plan principal plus un déplacement linéaire synchronisé sur l'autre axe. Une telle interpolation se programme comme suit: Coordonnées cartésiennes Plan XY G02 (G03) X+/-4.3 Y+/-4.3 I+/-4.3 J+/-4.3 Z+/-4.3 K4.3 F5.4 Plan XZ G02 (G03) X+/-4.3 Z+/-4.3 I+/-4.3 K+/-4.3 Y+/-4.3 J4.3 F5.4 Plan YZ G02 (G03) Y+/-4.3 Z+/-4.3 J+/-4.3 K+/-4.3 X+/-4.3 I4.3 F5.4 Sur le plan XY: XY Coordonnées du point d’arrivée de l’arc IJ Coordonnées du centre par rapport au point de départ de l’arc. Z Coordonnée du point d’arrivée en Z. K Angle d’élévation suivant l’axe Z. Coordonnées polaires Plan XY G02 (G03) A+/-3.3 I+/-4.3 J+/-4.3 Z+/-4.3 K4.3 F5.4 Plan XZ G02 (G03) A+/-3.3 I+/-4.3 K+/-4.3 Y+/-4.3 J4.3 F5.4 Plan YZ G02 (G03) A+/-3.3 J+/-4.3 K+/-4.3 X+/-4.3 I4.3 F5.4 Exemple: Point de départ X0, Y0, Z0: Coordonnées cartésiennes N10 G03 X0 Y0 I15 J0 Z50 K5 F150 Coordonnées polaires N10 G03 A180 I15 J0 Z50 K5 F150 Attention: Quand le programme est exécuté en mode de fonctionnement CYCLE À VIDE (4), les déplacements de la machine ne sont pas réels. Le chemin de l’outil en interpolation hélicoïdale ne sera pas affiché sur la représentation graphique ni en fonction ZOOM si cette dernière est utilisée. Page Chapitre: 5 10 CONTROLEDETRAJECTOIRE Section: INTERPOLATION HÉLICOÏDALE Dans une interpolation hélicoïdale, le déplacement circulaire finit lorsque la position finale sur l’axe perpendiculaire au plan principal est atteinte (Z dans le plan XY). A partir de ce point jusqu’au point final programmé, les axes du plan principal vont se déplacer d’une façon non contrôlée et avec une avance équivalente à celle de l’axe perpendiculaire au plan principal, jusqu’au point final programmé. Exemple: Point de départ X0 Y0 Z0: N10 G03 X0 Y0 I15 J0 Z35 K10 F250 Attention: Lorsqu’une interpolation circulaire (hélicoïdale) avec G02/G03, la CNC assume que le centre de l'arc est la nouvelle origine polaire. Chapitre: 5 CONTROLEDETRAJECTOIRE Section: INTERPOLATION HÉLICOÏDALE Page 11 5.6 TRAJECTOIRE CIRCULAIRE TANGENTE A LA TRAJECTOIRE PRECEDENTE (G08) La commande G08 permet de programmer une trajectoire circulaire tangente à la trajectoire précédente. Les coordonnées du centre (I, J, K) ne sont pas nécessaires. Le format du bloc en coordonnées cartésiennes (plan XY) est le suivant: N4 G08 X+/-4.3 Y+/-4.3 en mm. N4 G08 X+/-3.4 Y+/-3.4 en pouces. N4 G08 X Y Numéro du bloc Code définissant que l’interpolation circulaire doit être tangente à la trajectoire précédente. Coordonnée en X du point d’arrivée de l’arc. Coordonnée en Y du point d’arrivée de l’arc. Le format du bloc en coordonnées polaires est le suivant: N4 G08 R+/-4.3 A+/-4.3 en mm. N4 G08 R+/-3.4 A+/-3.4 en pouces. N4 G08 R A Numéro du bloc Code définissant que l’interpolation circulaire doit être tangente à la trajectoire précédente. Rayon (par rapport à l’origine polaire) du point final de l’arc. Angle (par rapport à l’origine polaire) du point final de l’arc. Exemple: Le point de départ étant X0 Y40, la programmation de la trajectoire suivante est décrite ci-dessous: - Ligne droite - Arc tangent à la ligne précédente. - Arc tangent à l’arc précédent. N0 N5 G90 G01 G08 X90 X70 F100 Y60 N10 G08 X110 Y60 Etant donné que les arcs sont tangents, il n'est pas nécessaire de programmer les coordonnées (I, J). Sans G08, la programmation sera: N100 G90 G01 N105 G03 X90 N110 G02 X110 X70 F100 Y60 I0 J20 Y60 I10 J0 La fonction G8 n’est pas modale, seulement remplace G02 et G03 dans le bloc dans lequel elle est programmée. Elle est employée lorsque l’exécution d’un arc tangent à la trajectoire précédente est désirée. La trajectoire précédente peut être une ligne droite ou un arc. Attention: Une circonférence ne peut pas être exécutée avec la fonction G08 car il existe d’infinies solutions. La CNC affichera le code erreur 47. Page Chapitre: 5 12 CONTROLEDETRAJECTOIRE Section: CIRCULAIRETANGENTEALA PRECEDENTE(G08) 5.7 INTERPOLATION CIRCULAIRE PROGRAMMEE A L’AIDE DE TROIS POINTS (G09) Avec la fonction G09 on peut établir une trajectoire circulaire (arc), en programmant le point d'arrivée et un point intermédiaire (le point initial de l'arc est le point de départ du mouvement) En d’autres mots, un point intermédiaire est programmé au lieu de programmer les coordonnées du centre. Le format du programmation du bloc en coordonnées cartésiennes sur le plan XY est le suivant: N4 G09 X+/-4.3 Y+/-4.3 I+/-4.3 J+/-4.3 N4 G09 X Y I J Numéro du bloc Code définissant la trajectoire circulaire en trois points. Coordonnée en X du point d’arrivée de l’arc. Coordonnée en Y du point d’arrivée de l’arc. Coordonnée en X du point intermédiaire de l’arc. Coordonnée en Y du point intermédiaire de l’arc. Le format du programmation du bloc en coordonnées polaires sur le plan XY est le suivant: N4 G09 R+/-4.3 A+/-4.3 I+/-4.3 J+/-4.3 où, N4 G09 R A I J Numéro du bloc Code définissant la trajectoire circulaire en trois points. Rayon (par rapport à l’origine polaire) du point final de l’arc. Angle (par rapport à l’origine polaire) du point final de l’arc. Coordonnée en X du point intermédiaire Coordonnée en Y du point intermédiaire. Le point intermédiaire doit toujours être programmé en coordonnées cartésiennes. Exemple: Point initial X-50 Y0 N10 G09 X35 Y20 I-15 J25 G09 n’est pas modal. Il n’est pas nécessaire de programmer le sens de déplacement G02, G03 lors de la programmation de G09. La fonction G09 seulement remplace les codes G02 et G03 dans le bloc dans lequel elle est programmée. Attention: Une circonférence complète ne peut pas être effectuée par la fonction G09. Il faut trois points différents pour définir un arc avec cette fonction. Dans ce cas l’erreur 40 sera affichée. Chapitre: 5 CONTROLEDETRAJECTOIRE Section: CIRCULAIREAL’AIDEDE TROIS POINTS (G09) Page 13 5.8 ENTREE TANGENTIELLE (G37) Au moyen de la fonction préparatoire G37, il est possible d’enlacer tangentiellement deux trajectoires sans avoir à calculer les points d’intersection. La fonction G37 n’est pas modale, c’est-à-dire, qu’elle devra être programmée chaque fois que l’on voudra enlacer tangentiellement deux trajectoires. Ces trajectoires pourront être droite-droite, ou bien droite-courbe. Il faudra programmer le rayon de l’arc d’entrée, R4.3 en mm ou R3.4 en pouces, après G37. La valeur du rayon devra toujours être positive. La programmation en question devra se trouver dans le bloc qui incorpore le déplacement dont on désire modifier la trajectoire. Le déplacement devra être rectiligne (G00 ou G01). Si G37 R4.3 est programmé dans un bloc incorporant un déplacement circulaire (G02 ou G03), la CNC affichera l’erreur du type 41. Exemple: N0 G90 G01 X40 F100 N5 G02 X60 Y10 I20 J0 Si on veut que l’entrée de l’outil à la pièce à usiner soit tangentielle à la trajectoire (voir le croquis), en décrivant un rayon de 5 mm, il faudra programmer: N0 G90 G01 G37 R5 X40 F100 N5 G02 X60 Y10 I20 J0 Tel que l’on peut le voir sur le croquis, la CNC modifie la trajectoire du bloc N0 de sorte que l’outil commence à usiner avec une entrée tangentielle à la pièce. Page Chapitre: 5 14 CONTROLEDETRAJECTOIRE Section: ENTREETANGENTIELLE(G37) 5.9 SORTIE TANGENTIELLE (G38) Au moyen de la fonction préparatoire G38, il est possible d’enlacer tangentiellement deux trajectoires sans avoir à calculer les points d’intersection. La fonction G38 n’est pas modale, c’est-à-dire, qu’elle devra être programmée chaque fois que l’on voudra enlacer tangentiellement deux trajectoires. Ces trajectoires pourront être droite-droite, ou bien courbe-droite. Il faudra programmer le rayon de l’arc d’entrée, R4.3 en mm ou R3.4 en pouces, après G38. La valeur du rayon devra toujours être positive. Pour pouvoir programmer dans un bloc G38, il faut que la trajectoire soit rectiligne (G00 ou G01). Si la trajectoire suivante est circulaire (G02 ou G03), la CNC affichera l’erreur du type 42. Exemple: N0 G90 G01 X40 F100 N5 G02 X80 Y30 I20 J0 N10 G00 X120 Si on veut qu’à la fin de l’usinage, la sortie de l’outil soit tangentielle, avec par exemple un rayon de 5 mm, il faudra programmer: N0 G90 G01 X40 F100 N5 G90 G02 G38 R5 X80 Y30 I20 J0 N10 G00 X120 Chapitre: 5 CONTROLEDETRAJECTOIRE Section: SORTIETANGENTIELLE(G38) Page 15 5.10 CONTROLE DE L’ARRONDI DES ANGLES (G36) La fonction G36 arrondit les angles de la valeur du rayon programmé, sans qu’il y ait besoin de calculer les coordonnées du centre et les points de départ et d’arrivée de l’arc. G36 n’est pas modal. Il doit être programmé à chaque fois qu’un angle doit être arrondi. Il doit être programmé dans le même bloc que le déplacement dont la fin doit être arrondie. Le rayon de l’arc à effectuer doit toujours être positif (R4.3 en mm), (R3.4 en pouces). Exemple 1: Point de départ X20 Y20 N50 G90 G01 G36 R5 X35 Y60 F100 N60 X50 Y0 Exemple 2: Point de départ X20 Y20 N50 G90 G03 G36 R5 X50 Y50 I0 J30 F100 N60 G01 X50 Y0 Page Chapitre: 5 16 CONTROLEDETRAJECTOIRE Section: CONTROLEDEL’ARRONDI DES ANGLES (G36) 5.11 CHANFREIN (G39) La fonction G39 effectue un chanfrein entre deux usinages linéaires sans qu’il soit nécessaire de calculer les coordonnées des deux intersections. G39 n’est pas modal. Il doit être programmé à chaque fois qu’un chanfrein est nécessaire dans le même bloc que le déplacement qui doit se terminer par un chanfrein. Le mot R4.3 en mm. ou R3.4 en pouces doit être utilisé pour programmer la distance entre le point final programmé et le point où le chanfrein doit commencer. La valeur de R doit toujours être positive. Exemple: Point de départ X20 Y20 N0 G90 G01 G39 R15 X35 Y60 F100 N10 X50 Y0 Chapitre: 5 Section: Page CONTROLEDETRAJECTOIRE CHANFREIN (G39) 17 6. FONCTIONS PREPARATOIRES ADDITIONNELLES 6.1 TEMPORISATION (G04) La fonction G04 s’utilise pour programmer une temporisation. La valeur de la temporisation est programmée par le mot K. Exemple: G04 K0.05 G04 K2.5 Temporisation de 0,05 secondes Temporisation de 2,5 secondes Si K est programmé directement, sa valeur doit être entre 0,00 et 99,99. Cependant, si la temporisation K se trouve dans un paramètre (K P3) les limites pourront être comprises entre 0,00 et 655,35 secondes. La temporisation est exécutée au début du bloc dans lequel elle est programmée. La fonction G04 peut se programmer comme G4. Chapitre: 6 Section: Page FONCTIONSPREPARATOIRESADDITIONNELLES TEMPORISATION (G04) 1 6.2 IMAGE MIROIR (G10, G11, G12, G13) G10 G11 G12 G13 : Annulation de l’image miroir. : Image miroir sur l’axe X. : Image miroir sur l’axe Y. : Image miroir sur l’axe Z. Lorsque la CNC fonctionne avec les codes G11, G12 ou G13 actifs, elle exécute les déplacements programmés sur les axes, X, Y et Z en inversant les signes. Les fonctions G11, G12 et G13 sont modales, c’est-à-dire qu’une fois programmées elles restent actives jusqu’à ce qu’un code G10 soit programmé. Les fonctions G11, G12 et G13 peuvent être toutes programmées dans le même bloc, car elles ne sont pas incompatibles. Exemple: a) N5 N10 N12 N15 N20 N25 N30 G91 G01 X30 Y30 F100 Y60 X20 Y-20 X40 G02 X0 Y-40 I0 J-20 G01 X-60 X-30 Y-30 b) N35 G11 N40 G25 N5.30 c) N45 G10 G12 N50 G25 N5.30 Page Chapitre: 6 2 FONCTIONSPREPARATOIRESADDITIONNELLES Section: IMAGE MIROIR G11, G12, G13 G10, d) N55 G11 G12 N60 G25 N5.30 N65 M30 Exemple 2: N10 N20 N30 N40 N50 N60 N70 N80 X— Y— ‘ ‘ ‘ ‘ ‘ ‘ ‘ ‘ G11 G12 G25 N10.60 M30 Si l’image miroir est programmée alors que G73 (rotation de la figure) est actif, la CNC va d’abord appliquer l’image miroir puis la rotation. A la mise sous tension, après l’exécution d’un code M02/M30, après un ARRET D’URGENCE et après REMISE A ZERO la CNC assume la fonction G10 . Chapitre: 6 FONCTIONSPREPARATOIRESADDITIONNELLES Section: IMAGE MIROIR G11, G12, G13 Page G10, 3 6.3 AFFICHAGE DU CODE D’ERREUR (G30) Sitôt la CNC lit un bloc portant le code G30, elle arrête le programme en cours et affiche le numéro d’erreur indiqué. Format de programmation: N4 G30 K2 N4 Numéro de bloc G30 Code indiquant la programmation d’une erreur K2(0-99) Code d’erreur programmé. Il est aussi possible de programmer le numéro d’erreur au moyen d’un paramètre arithmétique, valeur comprise entre P0 et P255. Par exemple: N4 G30 KP123 Ce code combiné avec les codes G26, G27, G28 et G29 permet d’arrêter le programme et de détecter de possibles erreurs de mesure, etc. Dans un bloc dans lequel G30 soit programmé, il n’est pas possible de programmer d’information supplémentaire. Attention: Si l’on désire que le commentaire propre aux codes d’erreur de la CNC ne soit pas affiché, le numéro de code après G30 devra être supérieur à ceux que la CNC utilise. Il faut aussi rappeler que l’usager peut écrire des commentaires sur le programme qui seront affichés lors de l’exécution du bloc correspondant. Page Chapitre: 6 4 FONCTIONSPREPARATOIRESADDITIONNELLES Section: AFFICHAGEDUCODE D’ERREUR(G30) 6.4 SAUTS/APPELS INCONDITIONNELS (G25) La fonction G25 peut être utilisée pour effectuer un saut à un bloc hors séquence du programme en cours. Aucune information supplémentaire ne peut être programmé dans un bloc contenant G25. Il existe deux formats de programmation possibles: Format a) N4 G25 N4 N4 G25 N4 Numéro du bloc Code pour les sauts non conditionnels Numéro du bloc où le saut doit aboutir Lorsque la CNC lit ce bloc elle effectue un saut au bloc indiqué et le programme se poursuit. Exemple : N0 N5 N10 N15 N20 N50 G00 X100 Z50 G25 N50 X50 Z70 G01 X20 Lorsque le bloc 10 est lu, la CNC effectue un saut au bloc 50 et ensuite exécute le programme jusqu’à la fin. Format b) N4 G25 N4.4.2 N4 G25 N4.4.2 Numéro de bloc Code de saut non conditionnel Nombre de répétitions Numéro du dernier bloc à exécuter Numéro du bloc auquel le saut doit aboutir Lorsque la CNC lit un tel bloc elle effectue un saut au bloc indiqué par le chiffre compris entre N et le premier point décimal. Ensuite elle exécute la section du programme comprise entre ce bloc et celui identifié entre les deux points décimaux et ceci autant de fois qu’il est indiqué par le dernier chiffre. Ce dernier chiffre peut avoir une valeur comprise entre 0 et 99. Cependant, il peut prendre une valeur entre 0 et 255 si se programme avec un paramètre. Si seulement N4.4 est programmé, la CNC assume N4.4.1. Lorsque l’exécution de cette section est terminée, la CNC retourne au bloc qui suit celui dans lequel G25 N4.4.2. était programmé. Chapitre: 6 FONCTIONSPREPARATOIRESADDITIONNELLES Section: SAUTS/APPELS INCONDITIONNELS (G25) Page 5 Exemple: N0 N5 N10 N15 N20 N25 N30 G00 Z20 G01 G00 X0 G25 M30 X10 X50 M3 Z0 N0.20.8 Lorsque le bloc N25 est atteint, la CNC effectue un saut au bloc 0 et exécute 8 fois la section N0-N20. Ensuite elle retourne au bloc N30. Les fonctions G26, G27, G28, G29 et G30 correspondant aux sauts/appels conditionels seront décrites au chapitre correspondant de ce manuel: PROGRAMMATION PARAMETRIQUE, UTILISATION DES PARAMETRES. Page Chapitre: 6 6 FONCTIONSPREPARATOIRESADDITIONNELLES Section: SAUTS/APPELS INCONDITIONNELS (G25) 6.5 FACTEUR D’ECHELLE (G72) Le code G72 permet d’usiner à l’aide d’un même programme des pièces de forme identique mais de taille différente. G72 doit être programmé seul dans un bloc. Il y a deux cas possibles de programmation. 6.5.1 FACTEUR D’ECHELLE AFFECTANT TOUS LES AXES Format de programmation: N4 G72 K2.4 N4 G72 K2.4 Numéro de bloc Code de mise à l’échelle Valeur du facteur d’échelle Valeur Min. K0.0001 (multiplié par 0,0001) Valeur Max. K100 (multiplié par 100) Les compensations de rayon et de longueur d’outil sont compatibles avec ce mode de mise à l’échelle. Toutes les valeurs de coordonnées programmées après G72 seront multipliées par K, jusqu'à nouvelle définition du facteur d'échelle G72 ou jusqu'à son annulation. Le facteur d'échelle programmé est annulé en programmant K1, ou par M02, M30, ARRET D’URGENCE ou REMISE A ZERO. Exemple de programmation: Le point de départ est X-30 Y30 N10 G0 G90 X-19 Y0 N20 G01 X0 Y10 F150 N30 G02 X0 Y-10 I0 J-10 N40 G01 X-19 Y0 N45 G31 ............................................... (Garde point zéro d’origine) N50 G92 X-79 Y-30 ........................... (Changement du point zéro du programme) N60 G72 K2 ....................................... (Applique un facteur d’échelle 2) N70 G25 N10.40.1 N80 G72 K1 ....................................... (Annule le facteur d’échelle) N85 G32 ............................................... (Prélèvement du point zéro) N90 G0 X-30 Y10 ............................... (Retour au point d’origine) N100 M30 .............................................. (Fin du programme) Chapitre: 6 Section: Page FONCTIONSPREPARATOIRESADDITIONNELLES FACTEURD’ECHELLE(G72) 7 6.5.2 FACTEUR D’ECHELLE APPLIQUE A UN SEUL AXE Le format de programmation est le suivant: N4 G72 X,Y,Z 2.4 N4 G72 X,Y,Z 2.4 Numéro du bloc Fonction qui définit le facteur d’échelle Axes affectés par le facteur d’échelle Facteur d’échelle Valeur Min. 0,0001 Valeur Max. 15,9999 La coordonnée de l’axe affecté par le facteur d’échelle doit être à l'origine (valeur zéro) lorsque ce facteur est annulé ou activé. Lorsque le programme est affecté par un facteur d’échelle concernant un seul axe, il n’est pas possible de modifier le système de référence des axes par une fonction G92, G53/G59 ou G32. Si on applique une compensation de rayon à l’axe auquel on applique le facteur d’échelle, cette compensation sera elle aussi affectée par le facteur d’échelle. Si dans le même programme, deux méthodes de facteur d’échelle sont utilisées, la CNC appliquera à l’axe affecté par les deux un facteur d’échelle égal à la multiplication de les deux facteurs d'échelle programmés. Quand un programme est contrôlé en mode graphique et dispose de quelque bloc, avec le facteur d’échelle appliqué à un axe seulement, les coordonnées affichées et le graphique représentent les valeurs programmées sans la application du facteur d'échelle. Afin d’annuler le facteur d’échelle appliqué à un axe, il suffit d’appliquer un autre facteur d’échelle de valeur 1 à l’axe correspondant. On peut aussi l’annuler en exécutant M02 ou M30, lors de l’exécution d’une REMISE A ZERO, après un ARRET D'URGENCE ou lorsqu’une valeur de facteur d’échelle sur un autre axe est définie. Page Chapitre: 6 8 FONCTIONSPREPARATOIRESADDITIONNELLES Section: FACTEURD’ECHELLE APPLIQUE À UN SEUL AXE 6.6 ROTATION DE LA FIGURE (G73) La fonction G73 permet la rotation des coordonnées des axes autour du point zéro du programme dans le plan principal. Format de rotation de la figure: N4 G73 A+/-3.3 N4 G73 A+/-3.3 Numéro du bloc Code de rotation de la figure Angle de rotation Valeur Min. 0,000 degré Valeur Max. 360,000 degrés G73 est relatif, c’est-à-dire, que les différentes valeurs de A seront additionnées. La fonction G73 doit être programmée seule dans un bloc. La rotation de la figure est annulée par G17, G18, G19, G73 (sans valeur), un code M02, M30, un ARRÊT D’URGENCE, ou REMISE A ZERO. Un point ne peut pas être défini par un angle et une coordonnée cartésienne en coordonnées absolues (G90), tant que la fonction giratoire G73 est active. Exemple: Le point de départ est X0 Y0 N10 N20 N30 N40 N50 N60 N70 G01 X21 Y0 F300 G02 A0 I5 J0 G03 A0 I5 J0 A180 I-10 J0 G73 A45 G25 N10.50.7 M30 Section: ROTATION DE LA FIGURE (G73) FONCTIONSPREPARATOIRESADDITIONNELLES Chapitre: 6 Page 9 6.7 TRAITEMENT DE BLOC UNIQUE ACTIVATION (G47) ET ANNULATION (G48) La CNC considère comme “Bloc Unique” le groupe de blocs se trouvant entre les fonctions G47 et G48. Après l’exécution de la fonction G47, la CNC exécute tous les blocs venant ensuite jusqu’à ce qu’il exécute un bloc contenant la fonction G48. Lorsque le programme P99996 est exécuté en mode “Bloc à Bloc”, la CNC exécute, en cycle continu, la fonction G47 et tous les blocs venant ensuite, et s’arrête lorsqu’il exécute un bloc contenant la fonction G48. Si on appuie sur la touche durant l’exécution d’un “Bloc unique”, en mode Automatique ou Bloc à Bloc, la CNC continue l’exécution jusqu’à l’exécution de la fonction G48, moment où l’exécution s’arrête. La fonction G47 étant active, le sélecteur M.F.O. et les touches de variation de la vitesse de rotation de la broche seront mis hors de service, le programme s’exécutant alors au 100% de la F et la S programmées. Les fonctions G47 et G48 sont modales et incompatibles entre elles. Lorsqu’on allume la CNC, après avoir exécuté M02/M30, après un ARRET D'URGENCE ou après une REMISE A ZERO, la CNC assume le code G48. Page Chapitre: 6 10 FONCTIONSPREPARATOIRESADDITIONNELLES Section: BLOCUNIQUE (G47, G48) 7. COMPENSATION D'OUTIL 7.1 COMPENSATION DE RAYON D'OUTIL (G40, G41, G42) En fraisage normal, la trajectoire de l’outil doit être calculée et définie en tenant compte de son rayon, pour obtenir les cotes désirées sur la pièce usinée. La compensation de rayon d'outil permet de programmer directement le profil de la pièce sans prendre en compte les dimensions de l’outil. La CNC calcule automatiquement la trajectoire à suivre par l’outil basée sur le profil de la pièce et la valeur du rayon de l'outil mémorisée dans le tableau des outils. Il existe trois fonctions préparatoires pour la compensation du rayon d'outil. G40: Annulation de la compensation du rayon d'outil. G41: Compensation de rayon, outil à gauche. G42: Compensation de rayon, outil à droite. G41: L'outil se trouve à gauche de la pièce, vue dans le sens du déplacement. G42: L'outil se trouve à droite de la pièce, vue dans le sens du déplacement. La CNC a un tableau pouvant aller jusqu’à 100 paires de valeurs pour la compensation de rayon d'outil. R identifie le rayon de l’outil. La CNC va ajouter (ou soustraire) la valeur de I à la valeur de R. Les valeurs maximales de compensation sont: R ±1000 mm ou ±39,3699 pouces I ±32,766 mm ou ±1,2900 pouces Les valeurs de compensation doivent être mémorisées dans le tableau des outils avant de commencer l’usinage ou au début du programme à l’aide de G50. Dès que le plan dans lequel la compensation doit être appliquée, a été déterminé par les codes G17, G18, G19, il devient possible d’activer la compensation par le code G41 ou G42. Les valeurs de compensation sont prélevées dans le tableau des outils par le code Txx.xx (Txx.00-Txx.99). Les fonctions G41 et G42 sont modales. Elles sont annulées par G40, G74, M02 et M30, par L’ARRET D’URGENCE et REMISE A ZERO. Chapitre: 7 COMPENSATIOND'OUTIL Section: COMPENSATIONDERAYON G40, G41, G42 Page 1 7.1.1 SELECTION ET INITIALISATION DE LA COMPENSATION DE RAYON D'OUTIL (G41, G42) Une fois que G17, G18 ou G19 a été programmée pour sélectionner le plan dans lequel la compensation doit être appliquée, le code G41 ou G42 doit être utilisé pour initialiser cette compensation. G41: L’outil reste à gauche de la pièce vu dans le sens de l’usinage. G42: L’outil reste à droite de la pièce vu dans le sens de l’usinage. La fonction Txx.xx (Txx.00-Txx.49) doit être programmée dans le même bloc que G41 ou G42 ou dans un bloc précédent. Cette fonction Txx.xx sélectionne dans le tableau des outils, la valeur de la correction à appliquer. Si aucun outil n’est sélectionné, la CNC assume la valeur T00.00. La sélection de la compensation de rayon d'outil (G41/G42) ne peut s’effectuer que lorsque G00 ou G01 (déplacement linéaire) est actif. Si le premier appel de compensation est effectué lorsque G02/G03 est actif, la CNC affiche le message d’erreur 40. Les figures des pages suivantes illustrent de nombreux cas d’initialisation de compensation de rayon d'outil. Page Chapitre: 7 2 COMPENSATIOND'OUTIL Section: SELECTIONETINITIALISATION (G41, G42) TRAJECTOIRE DE PENTE A PENTE T.C.= Trajectoire compensée T.P.= Trajectoire programmée T.C. T.P. T.C. T.P. T.C. T.P. (Trajectoire programméeen deux blocs) T.C. T.P. T.C. T.P. T.C. T.P. Chapitre: 7 COMPENSATIOND'OUTIL Section: SELECTIONETINITIALISATION (G41, G42) Page 3 TRAJECTOIRE DE PENTE A ARC T.C.= Trajectoire compensée T.P.= Trajectoire programmée T.C. T.P. T.C. T.P. T.C. T.P. T.C. T.P. T.C. T.P. T.C. T.P. Page Chapitre: 7 4 COMPENSATIOND'OUTIL Section: SELECTIONETINITIALISATION (G41, G42) Cas spéciaux à considérer: a) Si la compensation est programmée dans un bloc où il n’y a pas de déplacement, l’initialisation de la compensation est différente du cas précédemment illustré (comparer avec l’exemple de trajectoire de pente à pente). N0 G91 G41 G01 T00.00 N5 Y-100 N10 X+100 b) Si la compensation est introduite avec la programmation d’un déplacement zéro: N0 G91 G01 X100 Y100 N5 G41 X0 T00.00 N10 Y-100 Chapitre: 7 COMPENSATIOND'OUTIL Section: SELECTIONETINITIALISATION (G41, G42) Page 5 7.1.2 FONCTIONNEMENT AVEC UNE COMPENSATION DE RAYON D'OUTIL (G41, G42) Les figures ci-dessous illustrent de nombreuses trajectoires suivies par un outil lorsque la compensation de rayon est active. Page Chapitre: 7 6 COMPENSATIOND'OUTIL Section: COMPENSATIONDERAYON D'OUTIL (G41, G42) Chapitre: 7 COMPENSATIOND'OUTIL Section: COMPENSATIONDERAYON D'OUTIL (G41, G42) Page 7 Lorsque la CNC fonctionne avec une compensation de rayon, elle lit quatre blocs à l’avance de façon à anticiper le calcul de la trajectoire à suivre. Cependant, il y a des cas particuliers où il faut prendre des précautions. Par exemple: Trois blocs sans déplacement, entre des blocs de déplacement, dans le plan de compensation. N0 N5 N10 N15 N20 N25 N30 G01 G91 G17 G41 X50 Y50 F100 T1.1 Y100 X200 Z100 M07 Z200 Y-100 Le code d’erreur 35 sera visualisé au point 1. Les blocs contenant G20, G21, G22, G23, G24, G25, G26, G27, G28, G29 ne vont pas générer l’erreur 35, car ils ne vont pas être considerés comme blocs sans déplacement. Page Chapitre: 7 8 COMPENSATIOND'OUTIL Section: COMPENSATIONDERAYON D'OUTIL (G41, G42) 7.1.3 ANNULATION DE LA COMPENSATION DE RAYON (G40) La fonction G40 annule la compensation de rayon. Cependant, elle ne peut être programmée que dans un bloc contenant un déplacement linéaire (G00,G01). Si G40 est programmé dans un bloc contenant G02 ou G03, la CNC va afficher le message d’erreur 40. Les figures suivantes illustrent de nombreux cas d’annulation de la compensation. TRAJECTOIRE DE PENTE A ARC Chapitre: 7 COMPENSATIOND'OUTIL Section: ANNULATIONDELA COMPENSATIONDERAYON Page 9 TRAJECTOIRE DE PENTE A PENTE Trajectoire compensée Trajectoire programmée T.C T.P T.C T.P T.C T.P T.C T.P Trajectoire programmée en deux blocs T.C T.P T.C T.P T.C T.P Page Chapitre: 7 10 COMPENSATIOND'OUTIL Section: ANNULATIONDELA COMPENSATIONDERAYON 7.1.4 EXEMPLES D’USINAGE AVEC COMPENSATION DE RAYON Exemple 1 Trajectoire compensée Trajectoire programmée (profil de la pièce) Rayon de l'outil : Numéro de l'outil: 10 mm T1.1 Il est pris comme hypothèse qu’il n’y a pas de déplacement sur l’axe Z. N0 N5 N10 N15 N20 N25 N30 N35 G92 G90 G41 Y70 X90 Y30 X40 G40 X0 Y0 G17 S100 G01 X40 ZO T1.1 M03 Y30 F125 G00 X0 Y0 M30 Chapitre: 7 COMPENSATIOND'OUTIL Section: COMPENSATIONDERAYON (EXEMPLES) Page 11 Exemple 2 Trajectoire compensée Trajectoire programmée (profil de la pièce) Rayon de l'outil: Numéro de l'outil: 10 mm T1.1 Il est pris comme hypothèse qu’il n’y a pas de déplacement sur l’axe Z. N0 N5 N10 N15 N20 N25 N30 N35 N40 N45 N50 N55 G92 X0 Y0 Z0 G90 G17 G01 F150 S100 T1.1 M03 G42 X30 Y30 X50 Y60 X80 X100 Y40 X140 X120 Y70 X30 Y30 G40 G00 X0 Y0 M30 Page Chapitre: 7 12 COMPENSATIOND'OUTIL Section: COMPENSATIONDERAYON (EXEMPLES) Exemple 3 Trajectoire compensée Trajectoire programmée (profil de la pièce) Rayon de l'outil: Numéro de l'outil: 10 mm T1.1 Il est pris comme hypothèse qu’il n’y a pas de déplacement sur l’axe Z. N0 N5 N10 N15 N20 N25 N30 N35 N40 N45 N50 N55 G92 G90 G42 X50 X70 G03 G02 G01 X55 G02 G01 G40 X0 Y0 Z0 G01 G17 F150 S100 T1.1 M03 X20 Y20 Y30 X85 Y45 I0 J15 X100 Y60 I15 J0 Y70 X25 Y70 I-15 J0 X20 Y20 G00 X0 Y0 M05 M30 Chapitre: 7 COMPENSATIOND'OUTIL Section: COMPENSATIONDERAYON (EXEMPLES) Page 13 7.2 COMPENSATION DE LA LONGUEUR DE L’OUTIL (G43, G44) La compensation de la longueur de l’outil permet de corriger les différences entre l’outil programmé et l’outil utilisé. Comme précédemment indiqué dans la section concernant la compensation de rayon d'outil, la CNC a la possibilité de mémoriser les dimensions, rayon et longueurs de 100 outils (Txx.00-txx99). L identifie la longueur de l’outil et K l’usure de l’outil. La CNC va ajouter (ou soustraire) la valeur de K à la valeur de L. Les valeurs maximales de compensation de longueur sont: L+/-1000mm ou 39,3699 pouces. K+/-32,766mm ou 1,2900 pouces. Les codes d’appel de la compensation de longueur sont: G43: G44: Compensation de longueur. Annulation de la compensation de longueur. Lorsque G43 est programmé, la CNC corrige la longueur suivant la valeur sélectionnée dans le tableau des outils (Txx.00-Txx.99). La compensation de longueur est appliquée à l’axe perpendiculaire au plan principal. G17: G18: G19: Compensation de longueur sur l’axe Z. Compensation de longueur sur l’axe Y. Compensation de longueur sur l’axe X. La fonction G43 est modale (maintenue). Elle est annulée par G44, G74, M02, M30, un ARRET D’URGENCE et REMISE A ZERO. La compensation de longueur peut être utilisée en conjonction avec les cycles fixes. Cependant, elle doit être appliquée avant le début du cycle. Page Chapitre: 7 14 COMPENSATIOND'OUTIL Section: COMPENSATIONDELA LONGUEUR (G43, G44) Exemple de compensation de longueur Reportons nous à la figure ci-dessus et prenons comme hypothèse que l’outil utilisé est plus court de 4 mm que l’outil programmé Le numéro de l’outil est T1.1 (la valeur enregistrée dans le tableau des outils est L-4). N0 N5 N10 N15 N20 N25 N30 N35 N40 N45 G92 G91 G43 G01 G00 X40 G01 G00 G90 M30 X0 G00 Z-25 G07 Z12 Y0 Z0 G05 X50 Y35 S500 M03 T1.1 Z-12 F100 Z-17 G05 G44 Z42 M05 G07 X0 Y0 Chapitre: 7 COMPENSATIOND'OUTIL Section: COMPENSATIONDELA LONGUEUR (G43, G44) Page 15 8. CYCLES FIXES D’USINAGE La CNC dispose des cycles fixes d’usinage suivants. G67 G67 G67 G67 G67 G67 G67 G67 G67 G67 G67 G67 G67 G67 G67 N0et P202=K0 N0 et P202=K1 N0 et P202=K2 N0 et P202=K3 N0 et P202=K4 N1 et P202=K0 N1 et P202=K1 N2 et P202=K0 N2 et P202=K1 N3 N4 N6 N7 N8 N9 Cycle fixe de positionnement point à point Cycle fixe de positionnement en ligne Cycle fixe de positionnement en rectangle Cycle fixe de positionnement en grille Cycle fixe de positionnement en arc Cycle fixe de poche rectangulaire d’usinage intérieur Cycle fixe de poche circulaire d’usinage intérieur Cycle fixe pour moyeu (bossage) rectangulaire Cycle fixe pour moyeu (bossage) circulaire Cycle fixe de surfaçage Cycle fixe d’ébauche d’arêtes Cycle fixe de perçage Cycle fixe de taraudage Cycle fixe d’alésage Cycle fixe de pointage Paramètres en rapport avec les cycles fixes: Les cycles fixes peuvent altérer le contenu des paramètres P0 à P99. Les paramètres P200 à P209 sont réservés à la CNC, certains d’entre eux possèdent, tel qu’indiqué ci-après, un sens spécifique. La CNC actualise, lors de la mise sous tension , après UNE REMISE A ZERO et chaque fois que l’on abandonne le mode d’exécution du programme P99996, les paramètres arithmétiques suivants: P200 P201 P209 L’axe Z est personnalisé comme axe contrôlé (0) ou comme visualisateur (1) Unités de travail (0=mm, 1=pouces) Des interpolations avec l’axe Z sont permises (0) ou ne sont pas permises (1) Lorsque les cycles fixes sont programmés, si la valeur d’un paramètre quelconque est une constante, il faut taper sur la touche K après le symbole =. Par exemple: P0 = K25 ... Chapitre: 8 CYCLESFIXESD’USINAGE Section: Page 1 8.1 POSITIONNEMENT POINT A POINT (G67 N0 et P202=K0) Paramètres de base de définition du cycle: P106 P110, P112, P114, P116, P118, P120, P122, P124, P111 P113 P115 P117 P119 P121 P123 P125 Position de sécurité en Z Valeur des coordonnées X, Valeur des coordonnées X, Valeur des coordonnées X, Valeur des coordonnées X, Valeur des coordonnées X, Valeur des coordonnées X, Valeur des coordonnées X, Valeur des coordonnées X, Y Y Y Y Y Y Y Y du du du du du du du du 1er point 2ème point 3ème point 4ème point 5ème point 6ème point 7ème point 8ème point Paramètres en rapport avec l’avance (F): P205 Valeur à la vitesse d'avance (F) qui est sélectionnée. Il est conseillé de définir ce paramètre chaque fois que l’on sélectionnera une nouvelle avance, lorsque l’on travaille avec des cycles fixes. Exemple de sélection d’une avance F100: P205=K100 Assigne au paramètre P205 la valeur de l’avance désirée (100) FP205 Sélectionne l’avance par P205. Exemple de programmation: N10 P205=K100 ............................................. Définition de l’avance de l’usinage N20 FP205 N30 P106=K1 ................................................. Paramètres de positionnement en ligne P110=K10 P111=K10 ........................... Valeur de la coordonnée du 1er point P112=K60 P113=K15 ........................... Valeur de la coordonnée du 2ème point P114=K25 P115=K30 ........................... Valeur de la coordonnée du 3ème point P116=K25 P117=K30 ........................... Il n’y a plus de points N40 P202=K0 ................................................. Indicatif du type de positionnement point à point N50 G67 N0 .................................................... Appel du cycle fixe N60 M30 .......................................................... Fin du programme Page Chapitre: 8 2 CYCLESFIXESD’USINAGE Section: POSITIONNEMENT POINT A POINT 8.2 POSITIONNEMENT EN LIGNE (G67 N0 et P202=K1) Paramètres de base de définition du cycle: P106 P110, P111 Position de sécurité en Z Valeur des coordonnées X, Y du point de départ (X1, Y1). Il faut toujours définir Valeur des coordonnées en X, Y du point final (Xn, Yn). Longueur(L) Pas entre points (I) Nombre de points (N) Angle de la trajectoire (A) P112, P113 P130 P131 P132 P133 Pour définir la trajectoire, il faut utiliser une des façons suivantes: Définition des données (L, A, N) .................. Paramètres P130, P133, P132. Définition des données (L, A, I) .................... Paramètres P130, P133, P131. Définition des données (Xn, Yn, L=0, N) .... Paramètres P112, P113, P130=K0, P132 Définition des données (Xn, Yn, L=0, I)) .... Paramètres P112, P113, P130=K0, P131 Définition des données (I, N, A) ................... Paramètres P131, P132, P133. Dans ce dernier cas, il faut définir (L=0, Xn=X1, Yn=Y1) Paramètres en rapport avec l’avance (F): P205 Valeur à la vitesse d'avance (F) qui est sélectionnée. Il est conseillé de définir ce paramètre chaque fois que l’on sélectionnera une nouvelle avance, lorsque l’on travaille avec des cycles fixes. Exemple de sélection d’une avance F100: P205=K100 Assigne au paramètre P205 la valeur de l’avance désirée (100) FP205 Sélectionne l’avance par P205. Exemple de définition: Les formats suivants peuvent être utilisés: P110=K P110=K P110=K P110=K P110=K P111=K P111=K P111=K P111=K P111=K P130=K60 P130=K60 P112=K51.961 P112=K51.961 P112=K P113=K Chapitre: 8 CYCLESFIXESD’USINAGE P133=K30 P133=K30 P113=K30 P113=K30 P130=K P132=K4 P131=K20 P130=K P132=K4 P130=K P131=K20 P131=K20 P132=K4 P133=K30 Section: POSITIONNEMENTENLIGNE Page 3 8.3 POSITIONNEMENT EN RECTANGLE (G67 N0 et P202=K2) Paramètres de base de définition du cycle: P106 Position de sécurité en Z P110, P111 Valeur des coordonnées X, Y du point de départ (X1, Y1). Il faut toujours définir P130 Longueur en X (Lx) P131 Pas entre points en X (Ix) P132 Nombre de points en X (Nx) P134 Longueur en Y (Ly) P135 Pas entre points en Y (Iy) P136 Nombre de points en Y (Ny) P133 Angle de la trajectoire (A). Il faut toujours définir P137 Angle entre les trajectoires (B) Il faut toujours définir Si on désire que les deux déplacements soient parallèles aux axes X et Y, il faut définir: P133=K0........... P137=K90 ......... A=0 B=90 Pour définir la trajectoire, il faut utiliser une des façons suivantes: Définition des données (L, N) .............. Paramètres P130, P132 et P134, P136 Définition des données (L, I) ............... Paramètres P130, P131 et P134, P135 Définition des données (I, N) ............... Paramètres P131, P132 et P135, P136 Paramètres en rapport avec l’avance (F): P205 Valeur à la vitesse d'avance (F) qui est sélectionnée. Il est conseillé de définir ce paramètre chaque fois que l’on sélectionnera une nouvelle avance, lorsque l’on travaille avec des cycles fixes. Exemple de sélection d’une avance F100: P205=K100 Assigne au paramètre P205 la valeur de l’avance désirée (100) FP205 Sélectionne l’avance par P205. Page Chapitre: 8 4 CYCLESFIXESD’USINAGE Section: POSITIONNEMENTEN RECTANGLE 8.4 POSITIONNEMENT EN GRILLE (G67 N0 et P202=K3) Paramètres de base de définition du cycle: P106 Position de sécurité en Z P110, P111 Valeur des coordonnées X, Y du point de départ (X1, Y1). Il faut toujours définir. P130 Longueur en X (Lx) P131 Pas entre points en X (Ix) P132 Nombre de points en X (Nx) P134 Longueur en Y (Ly) P135 Pas entre points en Y (Iy) P136 Nombre de points en Y (Ny) P133 Angle de la trajectoire (A). Il faut toujours définir P137 Angle entre les trajectoires (B) Il faut toujours définir Si on désire que les deux déplacements soient parallèles aux axes X et Y, il faut définir: P133=K0........... P137=K90 ......... A=0 B=90 Pour définir la trajectoire, il faut utiliser une des façons suivantes: Définition des données (L, N) .............. Paramètres P130, P132 et P134, P136 Définition des données (L, I) ............... Paramètres P130, P131 et P134, P135 Définition des données (I, N) ............... Paramètres P131, P132 et P135, P136 Paramètres en rapport avec l’avance (F): P205 Valeur à la vitesse d'avance (F) qui est sélectionnée. Il est conseillé de définir ce paramètre chaque fois que l’on sélectionnera une nouvelle avance, lorsque l’on travaille avec des cycles fixes. Exemple de sélection d’une avance F100: P205=K100 Assigne au paramètre P205 la valeur de l’avance désirée (100) FP205 Sélectionne l’avance par P205. Chapitre: 8 CYCLESFIXESD’USINAGE Section: POSITIONNEMENTENGRILLE Page 5 8.5 POSITIONNEMENT EN ARC (G67 N0 et P202=K4) Paramètres de base de définition du cycle: P106 Position de sécurité en Z P110, P111 Valeur des coordonnées X, Y du point de départ (X1, Y1). P138, P139 Valeur des coordonnées X, Y du centre (Xc, Yc). Il faut toujours définir. P141 Rayon de l’arc (R) P140 Angle du premier point (A) P132 Nombre de points (N). Il faut toujours définir P142 Pas angulaire entre points (B). Il faut toujours définir Le pas angulaire “B” est défini en degrés et indique le sens du déplacement. Dans le sens des aiguilles d’une montre avec B négatif et en sens contraire avec B positif. Lorsque l’on veut parcourir toute la circonférence, il faut programmer B0. Le parcours se fait en sens contraire des aiguilles d’une montre. Pour définir le point initial, il faut utiliser une des formes suivantes: Définition des données (R, A) ................. Paramètres P141, P140 Définition des données (X1, Y1, R=0) ... Paramètres P110, P111, P141=K0 Paramètres en rapport avec l’avance (F): P205 Valeur à la vitesse d'avance (F) qui est sélectionnée. Il est conseillé de définir ce paramètre chaque fois que l’on sélectionnera une nouvelle avance, lorsque l’on travaille avec des cycles fixes. Exemple de sélection d’une avance F100: P205=K100 Assigne au paramètre P205 la valeur de l’avance désirée (100) FP205 Sélectionne l’avance par P205. Page Chapitre: 8 Section: 6 CYCLESFIXESD’USINAGE POSITIONNEMENTENARC 8.6 POCHE RECTANGULAIRE D’USINAGE INTERIEUR (G67 N1 et P202=K0) Z SEC Paramètres de base de définition du cycle: P106 P110, P111 P146 Position de sécurité en Z Valeur des coordonnées X, Y du point de départ (angle X1, Y1) Longueur de la poche (L). Le signe indique le sens de l’usinage P147 P150 P151 Largeur de la poche (H) Rayon d’arrondi (r) Chanfrein (C) Lorsque l’on désire une poche avec des angles arrondis, il faut définir “C0” et il faut assigner au paramètre “r” le rayon d’arrondi désiré. Si l’on désire une poche à angles chanfreinés, il faut définir “r0” et le paramètre “C” indique à quelle distance de l’angle théorique se fait le chanfrein. Lorsque l’on désire faire une poche normale, sans arrondis ni chanfreins, il faut alors programmer “r0” et “C0”. P148 Passe d’usinage (G). Si elle est programmée avec la valeur 0, on prend comme valeur 0.75 du diamètre de l’outil. Chapitre: 8 CYCLESFIXESD’USINAGE Section: POCHERECTANGULAIRE D’USINAGEINTÉRIEUR Page 7 P149 Passe de finition (E). Si elle est programmée avec valeur 0, la passe de finition n’est pas exécutée. P198 % d’avance F qui est utilisé comme avance de finition (%F). Si la valeur 0 lui est assignée la passe de finition se fait avec la même avance qui a été utilisée lors de l’ébauche de la pièce. P133 Angle de la poche (A) Paramètres en rapport avec l’axe Z: Ces paramètres doivent être définis lorsque l’axe Z est personnalisé comme axe contrôlé. Paramètre machine “P617(4)=0”. P107 P108 P109 P199 Coordonnée à laquelle on désire réaliser la poche (Z) Profondeur de la poche (P) Pas de plongée (I) % de l’avance F qui est utilisé lors de la plongée de l’axe Z (%F Z). Si on lui assigne la valeur 0, la plongée se fait à l’avance sélectionnée. Paramètres en rapport avec l’avance (F): P205 Valeur à la vitesse d'avance (F) qui est sélectionnée. Il est conseillé de définir ce paramètre chaque fois que l’on sélectionnera une nouvelle avance, lorsque l’on travaille avec des cycles fixes. Exemple de sélection d’une avance F100: P205=K100 Assigne au paramètre P205 la valeur de l’avance désirée (100) FP205 Sélectionne l’avance par P205. Page Chapitre: 8 8 CYCLESFIXESD’USINAGE Section: POCHERECTANGULAIRE D’USINAGEINTÉRIEUR 8.7 POCHE CIRCULAIRE D’USINAGE INTERIEUR (G67 N1 et P202=K1) Z SEC Paramètres de base de définition du cycle: P106 Position de sécurité en Z P110, P111 Valeur des coordonnées X, Y du centre de la poche (Xc, Yc) P141 Rayon de la poche (R). Le signe indique le sens de l’usinage. P148 Passe d’usinage (G). Si elle est programmée avec valeur 0, on prend comme valeur 0,75 du diamètre de l’outil P149 Passe de finition (E). Si elle est programmée avec valeur 0, la passe de finition n’est pas exécutée P198 % d’avance F qui est utilisé comme avance de finition (%F). Si la valeur 0 lui est assignée la passe de finition se fait avec la même avance qui a été utilisée lors de l’ébauche de la pièce Paramètres en rapport avec l’axe Z: Ces paramètres doivent être définis lorsque l’axe Z est personnalisé comme axe contrôlé. Paramètre machine “P617(4)=0”. P107 P108 P109 P199 Coordonnée à laquelle on désire réaliser la poche (Z) Profondeur de la poche (P) Passe de fraisage (I) % de l’avance F qui est utilisé lors de la plongée de l’axe Z (%F Z). Si on lui assigne la valeur 0, la plongée se fait à l’avance sélectionnée. Chapitre: 8 CYCLESFIXESD’USINAGE Section: POCHECIRCULAIRE D’USINAGEINTÉRIEUR Page 9 Paramètres en rapport avec l’avance (F): P205 Valeur à la vitesse d'avance (F) qui est sélectionnée. Il est conseillé de définir ce paramètre chaque fois que l’on sélectionnera une nouvelle avance, lorsque l’on travaille avec des cycles fixes. Exemple de sélection d’une avance F100: P205=K100 Assigne au paramètre P205 la valeur de l’avance désirée (100) FP205 Sélectionne l’avance par P205. Page Chapitre: 8 10 CYCLESFIXESD’USINAGE Section: POCHECIRCULAIRE D’USINAGEINTÉRIEUR 8.8 MOYEU (BOSSAGE) RECTANGULAIRE (G67 N2 et P202=K0) Z SEC Paramètres de base de définition du cycle: P106 P110, P111 P146 Position de sécurité en Z Valeur des coordonnées X, Y du point de départ (angle X1, Y1) Longueur de la poche (L). Le signe indique le sens de l’usinage P147 P150 P151 Largeur de la poche (H) Rayon d’arrondi (r) Chanfrein (C) Lorsque l’on désire une poche avec des angles arrondis, il faut définir “C0” et il faut assigner au paramètre “r” le rayon d’arrondi désiré. Si l’on désire une poche à angles chanfreinés, il faut définir “r0” et le paramètre “C” indique à quelle distance de l’angle théorique se fait le chanfrein. Lorsque l’on désire faire une poche normale, sans arrondis ni chanfreins, il faut alors programmer “r0” et “C0”. P148 Passe d’usinage (G). Si elle est programmée avec la valeur 0, on prend comme valeur 0.75 du diamètre de l’outil. Chapitre: 8 CYCLESFIXESD’USINAGE Section: MOYEU(BOSSAGE) RECTANGULAIRE Page 11 P152 Tolérance de matière, tant en X comme en Y, que l’on désire éliminer (Q) P149 Passe de finition (E). Si elle est programmée avec valeur 0, la passe de finition n’est pas exécutée. P198 % d’avance F qui est utilisé comme avance de finition (%F). Si la valeur 0 lui est assignée la passe de finition se fait avec la même avance qui a été utilisée lors de l’ébauche de la pièce. P133 Angle de la poche (A) Paramètres en rapport avec l’axe Z: Ces paramètres doivent être définis lorsque l’axe Z est personnalisé comme axe contrôlé. Paramètre machine “P617(4)=0”. P107 P108 P109 P199 Coordonnée à laquelle on désire réaliser la poche (Z) Profondeur de la poche (P) Passe de fraisage (I) % de l’avance F qui est utilisé lors de la plongée de l’axe Z (%F Z). Si on lui assigne la valeur 0, la plongée se fait à l’avance sélectionnée. Paramètres en rapport avec l’avance (F): P205 Valeur à la vitesse d'avance (F) qui est sélectionnée. Il est conseillé de définir ce paramètre chaque fois que l’on sélectionnera une nouvelle avance, lorsque l’on travaille avec des cycles fixes. Exemple de sélection d’une avance F100: P205=K100 Assigne au paramètre P205 la valeur de l’avance désirée (100) FP205 Sélectionne l’avance par P205. Page Chapitre: 8 12 CYCLESFIXESD’USINAGE Section: MOYEU(BOSSAGE) RECTANGULAIRE 8.9 MOYEU (BOSSAGE) CIRCULAIRE (G67 N2 et P202=K1) Z SEC Paramètres de base de définition du cycle: P106 Position de sécurité en Z P110, P111 Valeur des coordonnées X, Y du centre de la poche (Xc, Yc) P141 Rayon de la poche (R). Le signe indique le sens de l’usinage. P148 Passe d’usinage (G). Si elle est programmée avec valeur 0, on prend comme valeur 0,75 du diamètre de l’outil P152 Tolérance de matière, tant en X comme en Y, que l’on désire éliminer (Q) P149 Passe de finition (E). Si elle est programmée avec valeur 0, la passe de finition n’est pas exécutée P198 % d’avance F qui est utilisé comme avance de finition (%F). Si la valeur 0 lui est assignée la passe de finition se fait avec la même avance qui a été utilisée lors de l’ébauche de la pièce Paramètres en rapport avec l’axe Z: Ces paramètres doivent être définis lorsque l’axe Z est personnalisé comme axe contrôlé. Paramètre machine “P617(4)=0”. P107 P108 Coordonnée à laquelle on désire réaliser la poche (Z) Profondeur de la poche (P) Chapitre: 8 CYCLESFIXESD’USINAGE Section: MOYEU(BOSSAGE) CIRCULAIRE Page 13 P109 P199 Passe de fraisage (I) % de l’avance F qui est utilisé lors de la plongée de l’axe Z (%F Z). Si on lui assigne la valeur 0, la plongée se fait à l’avance sélectionnée. Paramètres en rapport avec l’avance (F): P205 Valeur à la vitesse d'avance (F) qui est sélectionnée. Il est conseillé de définir ce paramètre chaque fois que l’on sélectionnera une nouvelle avance, lorsque l’on travaille avec des cycles fixes. Exemple de sélection d’une avance F100: P205=K100 Assigne au paramètre P205 la valeur de l’avance désirée (100) FP205 Sélectionne l’avance par P205. Page Chapitre: 8 14 CYCLESFIXESD’USINAGE Section: MOYEU(BOSSAGE) CIRCULAIRE 8.10 SURFAÇAGE (G67 N3) La CNC dispose de 4 types de surfaçage. Pour un sélectionner un, il faut utiliser le paramètre arithmétique P202. Les types de surfaçage dont on dispose sont les suivants: P202=K0 Surfaçage Bidirectionnel en X Z SEC P202=K1 Surfaçage Bidirectionnel en Y Z SEC P202=K2 Surfaçage Unidirectionnel en X Z SEC Chapitre: 8 Section: Page CYCLESFIXESD’USINAGE SURFAÇAGE 15 P202=K3 Surfaçage Unidirectionnel en Y Z SEC Paramètres de base de définition du cycle: P106 Position de sécurité en Z P202 Type de surfaçage P110, P111 Valeur des coordonnées X, Y du point de départ (angle X1, Y1) P146 Longueur de la surface à fraiser(L). Dans les surfaçages unidirectionnels, le signe indique le sens de l’usinage P147 Largeur de la surface à fraiser(H). Dans les surfaçages unidirectionnels, le signe indique le sens de l’usinage P148 Pas entre deux passes successives (G). S’il est programmé avec la valeur 0, on prend comme valeur 0,75 du diamètre de l’outil P152 Il définit la quantité que l’outil sort sur chacun des côtés de la pièce afin d’obtenir une bonne finition sur ses angles (E) Page Chapitre: 8 Section: 16 CYCLESFIXESD’USINAGE SURFAÇAGE Paramètres en rapport avec l’axe Z: Ces paramètres doivent être définis lorsque l’axe Z est personnalisé comme axe contrôlé. Paramètre machine “P617(4)=0”. P107 P108 P109 P199 Coordonnée à laquelle on désire réaliser le surfaçage (Z) Profondeur du surfaçage (P) Passe de fraisage (I) % de l’avance F qui est utilisé lors de la plongée de l’axe Z (%F Z). Si on lui assigne la valeur 0, la plongée se fait à l’avance sélectionnée. Paramètres en rapport avec l’avance (F): P205 Valeur à la vitesse d'avance (F) qui est sélectionnée. Il est conseillé de définir ce paramètre chaque fois que l’on sélectionnera une nouvelle avance, lorsque l’on travaille avec des cycles fixes. Exemple de sélection d’une avance F100: P205=K100 Assigne au paramètre P205 la valeur de l’avance désirée (100) FP205 Sélectionne l’avance par P205. Chapitre: 8 Section: Page CYCLESFIXESD’USINAGE SURFAÇAGE 17 8.11 EBAUCHE D’ARETES (G67 N4) La CNC permet d’ébaucher des arêtes vives, arrondies ou chanfreinées, tel que l’indique le croquis suivant: Paramètres de base de définition du cycle: Z SEC P154 Sens d’usinage P154=0 P154=1 P106 Position de sécurité en Z P110, P111 Valeur des coordonnées X, Y du point intérieur de l’angle (X1, Y1) P146 , P147 Longueurs selon l’axe X et l’axe Y respectivement (L, H) Selon que soit l’angle que l’on désirera usiner, ces paramètres auront un signe positif ou négatif. Page Chapitre: 8 Section: 18 CYCLESFIXESD’USINAGE EBAUCHED’ARETES P150 P151 Rayon d’arrondi (r) Chanfrein (C) Lorsque l’on désire un angle arrondi, il faut définir C0 et il faut assigner au paramètre r le rayon d’arrondi désiré Si l’on désire un angle chanfreiné, il faut définir r0 et le paramètre C indique à quelle distance de l’angle théorique se fait le chanfrein Lorsque l’on désire faire une arête vive, sans arrondis ni chanfreins, il faut alors programmer r0 et C0 P148 Passe d’usinage (G). Si elle est programmée avec valeur 0, on prend comme valeur 0,75 du diamètre de l’outil P149 Passe de finition (E). Si elle est programmée avec valeur 0, la passe de finition n’est pas exécutée P198 % d’avance F qui est utilisé comme avance de finition (%F). Si la valeur 0 lui est assignée la passe de finition se fait avec la même avance qui a été utilisée lors de l’ébauche de la pièce P133 Angle que forme l’angle avec l’axe X (A) Paramètres en rapport avec l’axe Z: Ces paramètres doivent être définis lorsque l’axe Z est personnalisé comme axe contrôlé. Paramètre machine “P617(4)=0”. P107 P108 P109 P199 Coordonnée à laquelle on désire réaliser la poche (Z) Profondeur de la poche (P) Passe de fraisage (I) % de l’avance F qui est utilisé lors de la plongée de l’axe Z (%F Z). Si on lui assigne la valeur 0, la plongée se fait à l’avance sélectionnée. Paramètres en rapport avec l’avance (F): P205 Valeur à la vitesse d'avance (F) qui est sélectionnée. Il est conseillé de définir ce paramètre chaque fois que l’on sélectionnera une nouvelle avance, lorsque l’on travaille avec des cycles fixes. Exemple de sélection d’une avance F100: P205=K100 Assigne au paramètre P205 la valeur de l’avance désirée (100) FP205 Sélectionne l’avance par P205. Chapitre: 8 Section: Page CYCLESFIXESD’USINAGE EBAUCHED’ARETES 19 8.12 PERÇAGE (G67 N6) Paramètres de base de définition du cycle: P107 P108 P109 P143 Coordonnée à laquelle on désire réaliser l’usinage (Z) Profondeur du perçage (P) Passe de perçage (I) Temporisation, en secondes, après le perçage, jusqu’au moment où commence le retour (K) Paramètres en rapport avec l’avance (F): P205 Valeur à la vitesse d'avance (F) qui est sélectionnée. Il est conseillé de définir ce paramètre chaque fois que l’on sélectionnera une nouvelle avance, lorsque l’on travaille avec des cycles fixes. Exemple de sélection d’une avance F100: P205=K100 Assigne au paramètre P205 la valeur de l’avance désirée (100) FP205 Sélectionne l’avance par P205. Exemple de programmation de perçage N10 P205=K100 ............................................. Définition de l’avance de l’usinage N20 FP205 N30 G01 X107 Y78 ....................................... Déplacement au point à percer N40 P107=K0 P108=K12 P109=K5 ............ Paramètres de perçage P143=K1 N50 G67 N6 .................................................... Appel du cycle de perçage N60 M30 .......................................................... Fin du programme Page Chapitre: 8 Section: 20 CYCLESFIXESD’USINAGE PERÇAGE Associer Opération de perçage à Cycle fixe de Positionnement Lorsque l’on désire associer l’opération de perçage à un cycle fixe de positionnement, il faut: 1. 2. 3. 4. 5. Définir les paramètres de base de définition de l’opération de perçage Définir les paramètres de base du cycle fixe de positionnement Mettre l’indicatif d’opération de perçage. P203=K1 Mettre l’indicatif du type de positionnement. P202=K* Faire un appel au cycle fixe de positionnement. G67 N0 (Il ne faut pas faire d’appel au cycle fixe de perçage. G67 N6) Exemples de perçage en ligne: N10 P205=K100 ............................................. Définition de l’avance de l’usinage N20 FP205 N30 P107=K0 P108=K12 P109=K5 ............ Paramètres de perçage P143=K1 N40 P106=K1 P110=K20 P111=K10 .......... Paramètres de positionnement en ligne P130=K50 P133=K25 P132=K6 N50 P203=K1 ................................................. Indicatif d’opération de perçage P202=K1 ................................................. Indicatif du type de positionnement en ligne N60 G67 N0 .................................................... Appel du cycle de positionnement en ligne N70 M30 .......................................................... Fin du programme Chapitre: 8 Section: Page CYCLESFIXESD’USINAGE PERÇAGE 21 8.13 TARAUDAGE (G67 N7) Paramètres de base de définition du cycle: P107 P108 P143 Coordonnée à laquelle on désire réaliser l’usinage (Z) Profondeur du taraudage (P) Temporisation, en secondes, après le taraudage, jusqu’au moment où commence le retour (K) Paramètres en rapport avec l’avance (F): P205 Valeur à la vitesse d'avance (F) qui est sélectionnée. Il est conseillé de définir ce paramètre chaque fois que l’on sélectionnera une nouvelle avance, lorsque l’on travaille avec des cycles fixes. Exemple de sélection d’une avance F100: P205=K100 Assigne au paramètre P205 la valeur de l’avance désirée (100) FP205 Sélectionne l’avance par P205. Exemple de programmation de taraudage N10 P205=K100 ............................................. Définition de l’avance de l’usinage N20 FP205 N30 G01 X107 Y78 ....................................... Déplacement au point à fileter N40 P107=K0 P108=K12 P143=K1 ............ Paramètres de taraudage N50 G67 N7 .................................................... Appel du cycle de taraudage N60 M30 .......................................................... Fin du programme Page Chapitre: 8 Section: 22 CYCLESFIXESD’USINAGE TARAUDAGE Associer Opération de taraudage à Cycle fixe de Positionnement Lorsque l’on désire associer l’opération de taraudage à un cycle fixe de positionnement, il faut: 1. 2. 3. 4. 5. Définir les paramètres de base de définition de l’opération de taraudage. Définir les paramètres de base du cycle fixe de positionnement Mettre l’indicatif d’opération de taraudage P203=K2 Mettre l’indicatif du type de positionnement. P202=K* Faire un appel au cycle fixe de positionnement. G67 N0 (Il ne faut pas faire d’appel au cycle fixe de taraudage. G67 N7) Exemples de taraudage en ligne: N10 P205=K100 ............................................. Définition de l’avance de l’usinage N20 FP205 N30 P107=K0 P108=K12 P143=K1 ............ Paramètres de taraudage N40 P106=K1 P110=K20 P111=K10 .......... Paramètres de positionnement en ligne P130=K50 P133=K25 P132=K6 N50 P203=K2 ................................................. Indicatif d’opération de perçage P205=K1 ................................................. Indicatif du type de positionnement en ligne N60 G67 N0 .................................................... Appel du cycle de positionnement en ligne N70 M30 .......................................................... Fin du programme Chapitre: 8 Section: Page CYCLESFIXESD’USINAGE TARAUDAGE 23 8.14 ALESAGE (G67 N8) Paramètres de base de définition du cycle: P107 P108 P143 Coordonnée à laquelle on désire réaliser l’usinage (Z) Profondeur de l’alésage (P) Temporisation, en secondes, après l’usinage, jusqu’au moment où commence le retour (K) Paramètres en rapport avec l’avance (F): P205 Valeur à la vitesse d'avance (F) qui est sélectionnée. Il est conseillé de définir ce paramètre chaque fois que l’on sélectionnera une nouvelle avance, lorsque l’on travaille avec des cycles fixes. Exemple de sélection d’une avance F100: P205=K100 Assigne au paramètre P205 la valeur de l’avance désirée (100) FP205 Sélectionne l’avance par P205. Exemple de taraudage N10 P205=K100 ............................................. Définition de l’avance de l’usinage N20 FP205 N30 G01 X107 Y78 ....................................... Déplacement au point à aléser N40 P107=K0 P108=K12 P143=K1 ............ Paramètres d’alésage N50 G67 N8 .................................................... Appel du cycle d’alésage N60 M30 .......................................................... Fin du programme Page Chapitre: 8 Section: 24 CYCLESFIXESD’USINAGE ALESAGE Associer Opération d’alésage à Cycle fixe de Positionnement Lorsque l’on désire associer l’opération d'alésage à un cycle fixe de positionnement, il faut: 1. 2. 3. 4. 5. Définir les paramètres de base de définition de l’opération d'alésage Définir les paramètres de base du cycle fixe de positionnement Mettre l’indicatif d’opération d'alésage. P203=K3 Mettre l’indicatif du type de positionnement. P202=K* Faire un appel au cycle fixe de positionnement. G67 N0 (Il ne faut pas faire d’appel au cycle fixe d'alésage G67 N8) Exemples d’alésage en arc: N10 P205=K100 ............................................. Définition de l’avance de l’usinage N20 FP205 N30 P107=K0 P108=K12 P143=K1 ............ Paramètres d'alésage N40 P106=K1 P138=K70 P139=K20 .......... Paramètres de positionnement en arc P141=K40 P140=K-15 P142=K30 P132=K8 N50 P203=K3 ................................................. Indicatif d’opération d'alésage P202=K4 ................................................. Indicatif du type de positionnement en arc N60 G67 N0 .................................................... Appel du cycle de positionnement en arc N70 M30 .......................................................... Fin du programme Chapitre: 8 CYCLESFIXESD’USINAGE Section: ALESAGE Page 25 8.15 POINTAGE (G67 N9) Paramètres de base de définition du cycle: P107 P108 P144 P145 P143 Coordonnée à laquelle on désire réaliser l’usinage (Z) Profondeur de pointage (P) Diamètre du pointage (F) Angle du foret (A) Temporisation, en secondes, après le pointage, jusqu’au moment où commence le retour (K) Pour définir la distance de penétration du foret à centrer dans la pièce, il faut utiliser une des deux formes suivantes: Définir la profondeur du pointage (P) .......... Paramètre P108 Définir P=0, angle du foret (A) et diamètre du pointage (F) .............. Paramètres P108=K, P144, P145 Paramètres en rapport avec l’avance (F): P205 Valeur à la vitesse d'avance (F) qui est sélectionnée. Il est conseillé de définir ce paramètre chaque fois que l’on sélectionnera une nouvelle avance, lorsque l’on travaille avec des cycles fixes. Exemple de sélection d’une avance F100: P205=K100 Assigne au paramètre P205 la valeur de l’avance désirée (100) FP205 Sélectionne l’avance par P205. Exemple de pointage N10 P205=K100 ............................................. Définition de l’avance de l’usinage N20 FP205 N30 G01 X107 Y78 ....................................... Déplacement au point à usiner N40 P107=K0 P108=K1.5 P143=K0 ........... Paramètres de pointage N50 G67 N9 .................................................... Appel du cycle de pointage N60 M30 .......................................................... Fin du programme Page Chapitre: 8 Section: 26 CYCLESFIXESD’USINAGE POINTAGE Associer Opération de pointage à Cycle fixe de Positionnement Lorsque l’on désire associer l’opération de pointage à un cycle fixe de positionnement, il faut: 1. 2. 3. 4. 5. Définir les paramètres de base de définition de l’opération de pointage Définir les paramètres de base du cycle fixe de positionnement Mettre l’indicatif d’opération de pointage. P203=K4 Mettre l’indicatif du type de positionnement. P202=K* Faire un appel au cycle fixe de positionnement. G67 N0 (Il ne faut pas faire d’appel au cycle fixe de pointage G67 N9) Exemples de pointage en grille: N10 P205=K100 ............................................. Définition de l’avance de l’usinage N20 FP205 N30 P107=K0 P108=K1.5 P143=K0 ........... Paramètres de pointage N40 P106=K1 P110=K20 P111=K10 .......... Paramètres de positionnement en grille P130=K90 P132=K4 P134=K40 P136=K3 P133=K0 P137=K90 N50 P203=K4 ................................................. Indicatif d’opération de pointage P202=K3 ................................................. Indicatif du type de positionnement en grille N60 G67 N0 .................................................... Appel du cycle de positionnement en grille N70 M30 .......................................................... Fin de programme Chapitre: 8 Section: Page CYCLESFIXESD’USINAGE POINTAGE 27 9. SOUS-PROGRAMMES Un sous-programme est une partie du programme qui a été spécifiquement identifiée et peut être appelée pour son exécution à partir de n’importe quelle position du programme. Un sous-programme peut être appelé plusieurs fois depuis différentes positions du programme ou depuis des programmes différents. Un simple appel peut être utilisé pour demander son exécution jusqu’à un maximum de 255 fois. Un sous-programme peut être inséré dans un programme d’usager P99996 ou bien être sauvegardé dans le programme spécial de sous-programmes d’usager P99994. Les sous-programmes standards et paramétriques sont pratiquement identiques. La seule différence entre eux est que dans le cas des sous-programmes paramétriques, il est possible de définir jusqu’à 15 paramètres dans le bloc d’appel (G21 N2.2). Dans les sous-programmes standards, les paramètres ne peuvent pas être définis dans le bloc d’appel. Le nombre maximal de paramètres d’un sous-programme (standard ou paramétrique) est de 255 (P0-P254). 9.1 PROGRAMME SPÉCIAL DE SOUS-PROGRAMMES D’USAGER P99994 Le programme P99994 doit être élaboré dans un ordinateur pour être ensuite envoyé à la CNC. Il ne peut être modifié depuis la CNC. Il doit s’agir d’un programme contenant uniquement les sous-programmes d’usager élaborés en code ISO. Si pendant l’exécution du programme P99996 on fait appel à un sous-programme, la CNC recherchera le sous-programme en question dans le programme P99996 et dans le programme spécial de sous-programmes P99994. Il est conseillé de l’utiliser lorsque l’on travaille avec plusieurs programmes d’usager P99996. Si on élabore ainsi le programme P99994 avec toutes les sous-programmes habituellement utilisés, il ne sera pas nécessaire de les répéter dans chaque programme P99996. Il est conseillé de sauvegarder tous les sous-programmes associés à l’outil, paramètres machine “P743” et “P745”, dans le programme P99994. Chapitre: 9 SOUS-PROGRAMMES Section: Page 1 9.2 IDENTIFICATION D’UN SOUS-PROGRAMME STANDARD (G22) Un sous-programme standard (non paramétrique) commence toujours par un bloc qui contient la fonction G22. La structure d’un bloc d’ouverture d’un sous-programme est: N4 G22 N2 N4 G22 N2 Numéro du bloc Indique le début d’un sous-programme Identifie le sous-programme (Peut être un nombre compris entre N0 et N99) Ce bloc ne peut pas contenir d’information supplémentaire. Le bloc d’ouverture du sous-programme est suivi des blocs composant ce sousprogramme. Un sous-programme standard peut contenir des blocs paramétriques. Un sous-programme doit toujours se terminer par un bloc de la forme N4 G24. La fonction G24 indique fin du sous-programme. Ce bloc ne peut pas contenir d’information supplémentaire. Exemple de programmation: N0 N10 N15 N20 G22 N25 X20 P0=P0 F1 P1 G24 Attention: Les sous-programmes N91 à N99 ne peuvent être définis, car la CNC les utilise. Deux sous-programmes, ayant le même numéro d’identification mais appartenant à différents programmes, ne peuvent pas être présents en même temps dans la mémoire de la CNC. Cependant, un sous-programme standard et un sous-programme paramétrique peuvent être identifiés par le même numéro. 9.3 APPEL D’UN SOUS-PROGRAMME STANDARD (G20) Un sous-programme standard peut être appelé à partir de n’importe quel programme ou à partir d’autres sous-programmes (standard ou paramétrique). L’appel d’un sousprogramme se fait à l’aide de la fonction G20. La structure d’un bloc d’appel est: N4 G20 N2.2 N4 G20 N2.2 Numéro du bloc Appel de sous-programme Les deux figures situées à gauche du point décimal identifient le numéro du sous-programme appelé (00-99). Les deux figures situées à droite du point décimal indiquent le nombre de fois que le sous-programme doit être exécuté (00-99). Il est aussi possible de programmer le nombre de fois au moyen d’un paramètre arithmétique, valeur comprise entre P0 et P255. Par exemple: N4 G20 N10.P123 Si on ne programme pas le nombre de fois que l’on désire répéter le sous-programme, la CNC l’exécute une seule fois. Aucune information supplémentaire ne peut être programmée dans le bloc d’appel d’un sous-programme standard. Page Chapitre: 9 2 SOUS-PROGRAMMES Section: SOUS-PROGRAMME STANDARD (G20, G22) 9.4 IDENTIFICATION D'UN SOUS-PROGRAMME PARAMETRIQUE (G23) Un sous-programme paramétrique commence toujours par la fonction G23. La structure du premier bloc d'un sous-programme paramétrique est: N4 G23 N2 N4 Numéro du bloc. G23 Indique le début d'un sous-programme paramétrique. N2 Identifie le sous-programme paramétrique (peut être un nombre compris entre N0 et N99). Ce bloc ne peut pas contenir d’information supplémentaire. Après le bloc de début de sous-programme, on programme les blocs que l’on désire. Entre les blocs programmés dans un sous-programme paramétrique il peut y avoir des blocs paramétriques. Un sous-programme doit toujours s’achever par un bloc de la forme: N4 G24. La fonction G24 indique fin de sous-programme. On ne peut programmer aucune autre information dans ce bloc. Attention: Les sous-programmes N91 à N99 ne peuvent être définis, car la CNC les utilise. Deux sous-programmes paramétriques, ayant le même numéro d'identification mais appartenant à différents programmes, ne peuvent pas être présents en même temps dans la mémoire de la CNC. Cependant, un sous-programme standart et un sous-programme paramétrique peuvent être identifiés par le même numéro. 9.5 APPEL D’UN SOUS-PROGRAMME PARAMETRIQUE (G21) Un sous-programme paramétrique peut être appelé à partir d’un programme principal ou à partir d’un autre sous-programme (standard ou paramétrique). L’appel d’un sous-programme paramétrique se fait par la fonction G21. La structure du bloc appelé est : N4 G21 N2.2 P3=K+/-5.5 P3=K+/-5.5 N4 Numéro du bloc G21 Appel de sous-programme paramétrique. N2.2 Les deux figures situées à gauche du point décimal identifient le numéro du sous-programme paramétrique appelé (00-99). Les deux figures situées à droite du point décimal indiquent le nombre de fois que le sous-programme paramétrique doit etre répété (00-99). Il est aussi possible de programmer le nombre de fois au moyen d’un paramètre arithmétique, valeur comprise entre P0 et P255. Par exemple: N4 G21 N10.P123 Si on ne programme pas le nombre de fois que l’on désire répéter le sousprogramme paramétrique, la CNC l’exécute une seule fois. P3 K Valeur du paramètre arithmétique (P00-P254). Valeur de paramètre arithmétique. Attention: Lorsque l’exécution du sous-programme paramétrique (G24) s’achève, les valeurs des paramètres assignés dans le bloc d’appel sont récupérées, bien que l’on leur ait assigné des valeurs différentes tout au long du sous-programme. Chapitre: 9 SOUS-PROGRAMMES Section: SOUS-PROGRAMME PARAMETRIQUE (G21, G23) Page 3 9.6 EXEMPLES DE PROGRAMMATION Exemple 1. Utilisation d'un sous-programme standard sans paramètres. Cet exemple illustre le perçage de 4 trous de 15 mm de profondeur. N0 G90 G00 X35 Y35 M03 N5 G22 N1 .......................................... Définition du sous-programme standard N10 Z-32 N15 G01 Z-50 F100 N20 G04 K1.0 N25 G00 Z0 N30 G24 ................................................ Fin du sous-programme N35 X60 N40 G20 N1.1 ...................................... Appel de sous-programme N1 N45 X80 Y30 N50 G20 N1.1 ...................................... Appel de sous-programme N1 N55 X100 N60 G20 N1.1 ...................................... Appel de sous-programme N1 N65 X0 Y0 M05 N70 M30 ................................................ Fin du programme Page Chapitre: 9 4 SOUS-PROGRAMMES Section: EXEMPLESDE PROGRAMMATION Exemple 2. Utilisation d'un sous-programme standard avec des paramètres. N10 P0=K48 P1=K24 N20 G1 X40 Y32 F0 N30 G22 N10 ...................................... Définition du sous-programme standard N40 G91 XP0 F500 N50 YP1 N60 X-P0 N70 Y-P1 N80 G24 ............................................... Fin du sous-programme N90 G90 X-6 Y72 N100 P0=K24 P1=K16 N110 G20 N10.1 .................................. Appel d'un sous-programme standard N120 G01 G90 X0 Y0 F0 N130 M30 .............................................. Fin du programme Chapitre: 9 SOUS-PROGRAMMES Section: EXEMPLESDE PROGRAMMATION Page 5 Exemple 3. Utilisation de sous-programmes paramétriques avec des paramètres Il s’agit de réaliser les usinages représentés sur le croquis, en utilisant le même sous-programme paramétrique. On suppose que l’outil se déplace sur la cote Z10, au-dessus de la surface de la pièce et que la profondeur de l’usinage est de Z-10. N0 G90 G00 X20 Y20 N10 G01 Z-10 F100 N15 G21 N1.1 P0=K20 N20 G90 G00 Z10 N25 X60 Y20 N30 G01 Z-10 N35 G21 N1.1 P0=K30 N40 G90 G00 Z10 N45 X110 Y120 N50 G01 Z-10 N55 G21 N1.1 P0=K10 N60 G90 G00 Z10 N65 X0 Y0 M05 N70 M30 N100 N105 N110 N115 N120 N145 Z10 S1500 M03 P1=K30 P2=K-20 P3=K-10 P4=K-20 ........ Pièce 1 P1=K10 P2=K-30 P3=K20 P4=K-30 .......... Pièce 2 P1=K30 P2=K-10 P3=K0 P4=K-30 ............ Pièce 3 G23 N1 .......................... Définition du sous-programme G01 G91 YP0 F100 XP1 XP2 YP3 XP4 G24 .................................. Fin du sous-programme Page Chapitre: 9 6 SOUS-PROGRAMMES Section: EXEMPLESDE PROGRAMMATION Exemple 4. Utilisation d'un sous-programme paramétrique sans paramètres Point de départ X0 Y0 N10 G90 G01 X40 Y30 F0 N20 G23 N8 ......................................... Définition du sous-programme paramétrique N30 G01 G91 X50 F500 N40 Y30 N50 X-10 N60 G03 X-30 Y0 I-15 J0 N70 G01 X-10 N80 Y-30 N90 G24 ................................................ Fin du sous-programme N100 G01 G90 X0 Y0 F0 N110 X-70 Y50 N120 G21 N8.1 .................................... Appel d'un sous-programme N130 G01 G90 X0 Y0 F0 N140 M30 .............................................. Fin du programme Une fois que la CNC ait lu le bloc 120 elle exécutera le sous-programme (N8) qui est défini entre les blocs 30 et 80. Chapitre: 9 SOUS-PROGRAMMES Section: EXEMPLESDE PROGRAMMATION Page 7 9.7 NIVEAUX D’EMBOITEMENT (D'IMBRICATION) Un sous-programme peut être appelé à partir d’un programme principal ou à partir d’un autre sous-programme (standard ou paramétrique). A partir de ce sousprogramme il est encore possible d’appeler un autre sous-programme et ainsi de suite jusqu’à un maximum de 15 niveaux d’emboîtement. Chaque niveau de sousprogramme peut être répété 255 fois. Diagramme d'appels des sous-programmes Programme principal Sous-programme 1 Page Chapitre: 9 8 SOUS-PROGRAMMES Sous-programme 2 Sous-programme 3 Section: NIVEAUXD’EMBOITEMENT (D'IMBRICATION) 10. PROGRAMMATION PARAMETRIQUE La CNC a 255 paramètres (P0-P254) qui permettent d’effectuer les opérations suivantes: programmation de blocs paramétriques, nombreuses opérations mathématiques, sauts à l’intérieur d’un programme. Les blocs paramétriques peuvent être écrits n’importe où dans le programme. Les différentes opérations possibles entre paramètres sont les suivantes: F1 F2 F3 F4 F5 F6 F7 F8 F9 F10 F11 F12 F13 F14 F15 F16 F17 F18 F19 F20 F21 F22 F23 F24 F25 F26 F27 F28 F29 F30 F31 F32 F33 Addition Soustraction Multiplication Division Racine carrée Racine carrée de l’addition des carrés A2 +B 2 Sinus Cosinus Tangente Tangente de l’arc Comparaison Partie entière Partie entière plus un Partie entière moins un Valeur absolue Complément Adresse de mémoire du bloc indiqué Coordonnée X du bloc dont on indique l’adresse Coordonnée Y du bloc dont on indique l’adresse Coordonnée Z du bloc dont on indique l’adresse Sans fonction Adresse de mémoire du bloc précédant celui qui est indiqué Numéro de correcteur d’outils avec lequel on est en train d’opérer Valeur R du correcteur indiqué Valeur L du correcteur indiqué Valeur I du correcteur indiqué Valeur K du correcteur indiqué Sans fonction Numéro de l’outil sélectionné Fonction logique AND Fonction logique OR Fonction logique XOR Fonction logique NOR Chapitre: 10 PROGRAMMATIONPARAMETRIQUE Section: Page 1 10.1 ATTRIBUTIONS Il est possible d’assigner n’importe quelle valeur à n’importe quel paramètre. a) N4 P1 = P2 Indique que P1 prend la valeur de P2, et P2 conserve sa valeur. b) N4 P1 = K1,5 P1 prend la valeur 1,5 La lettre K identifie une constante. Les constantes peuvent avoir des valeurs comprises entre +/-99999,9999. c) N4 P1 = H (Valeur en HEXADECIMAL) P1 prend la valeur en HEXADÉCIMAL indiqué après H. Possibles valeurs de H: 0/FFFFFFFF. d) N4 P1 = X P1 prend la valeur théorique de la position actuelle de l’axe X. e) N4 P1 = Y P1 prend la valeur théorique de la position actuelle de l’axe Y. f) N4 P1 = Z P1 prend la valeur théorique de la position actuelle de l’axe Z. g) N4 P1 = T La CNC est munie d’une horloge interne qui mesure le temps d’exécution. Cette fonction assigne au paramètre P1 la valeur qu’a l’horloge en question à ce moment-là. La valeur est exprimée en centièmes de secondes. Pour pouvoir connaître le temps d’exécution de certaines pièces ou de certaines opérations, il faut inclure des blocs de ce type au début et à la fin de la zone que l’on désire mesurer et ensuite faire une soustraction des valeurs obtenues. h) N4 P1 = 0X P1 prend la valeur théorique de l’axe X par rapport à la position zéro machine de la CNC. i) N4 P1 = 0Y P1 prend la valeur théorique de l’axe Y par rapport à la position zéro machine de la CNC. j) N4 P1 = 0Z P1 prend la valeur théorique de l’axe Z par rapport à la position zéro machine de la CNC. Page Chapitre: 10 2 PROGRAMMATIONPARAMETRIQUE Section: ATTRIBUTIONS 10.2 OPERATEURS “F1” à “F16” F1 Somme Exemple: N4 P1 = P2 F1 P3 P1 prend la valeur de la somme de P2 et de P3 , c’est-à-dire que P1 = P2 + P3. On peut aussi programmer, N4 P1 = P2 F1 K2 c’est-à-dire que P1 = P2 + 2. La lettre K indique une constante. Lorsque le même paramètre apparaît comme terme de l’addition et comme résultat, c’est-à-dire, N4 P1 = P1 F1 K2, il indique qu’à partir d’ici, P1 = P1 + 2. F2 Soustraction N4 P10 = P2 F2 P3 ............... P10 = P2 - P3 N4 P10 = P2 F2 K3 .............. P10 = P2 - 3 N4 P10 = P10 F2 K1 ............ P10 = P10 - 1 F3 Multiplication N4 P17 = P2 F3 P30 ............. P17 = P2 x P30 N4 P17 = P2 F3 K ................ P17 = P2 x 4 N4 P17 = P17 F3 K8 ............ P17 = P17x 8 F4 Division N4 P8 = P7 F4 P35 ............... P8 = P7 : P35 N4 P8 = P2 F4 K5 ................ P8 = P2 : 5 N4 P8 = P8 F4 K2 ................ P8 = P8 : 2 F5 Racine carrée N4 P15 = F5 P23 .................. P15 = P23 N4 P14 = F5 K9 .................... P14 = 9 N4 P18 = F5 P18 .................. P18 = P18 F6 Racine carrée de la somme des carrés N4 P60 = P2 F6 P3 ............. P60 = P2 2 + P3 2 N4 P50 = P40 F6 K5 ............ P50 = P40 2 + 52 N4 P1 = P1 F6 K4 ............... P1 = P1 2 + 42 F7 Sinus N4 P1 = F7 K5 ...................... P1 = Sin 5 degrés N4 P1 = F7 P2 ....................... P1 = Sin P2 L’angle a été programmé en degrés (P2 doit être programmé en degrés). F8 Cosinus N4 P1 = F8 P2 ....................... P1 = Cosinus P2 N4 P1 = F8 K75 .................... P1 = Cosinus 75 degrés Chapitre: 10 PROGRAMMATIONPARAMETRIQUE Section: OPERATEURS "F1" à "F16" Page 3 F9 Tangente N4 P1 = F9 P2 ........................ P1 = Tg P2 N5 P1 = F9 K30 ..................... P1 = Tg 30 degrés F10 Tangente de l’arc N4 P1 = F10 P2 ...................... P1 = Arc. Tg P2 (résultat en degrés) N4 P1 = F10 K0,5 .................. P1 = Arc. Tg 0,5 F11 Comparaison Cette opération compare différents paramètres ou un paramètre et une constante, et active l'indicateur (flag) de sauts conditionnels. Son application sera décrite dans la Section Sauts Conditionnels G26, G27, G28, G29. N4 P1 = F11 P2 Si P1 = P2, l'indicateur de saut "si zéro" sera activé. Si P1 est égal ou plus grand que P2, l'indicateur de saut si plus grand ou égal sera activé. Si P1 est plus petit que P2, l'indicateur de saut si plus petit sera activé. N4 P1 = F11 K6 peut aussi être programmé. F12 Partie entière N4 P1 = F12 P2 ...................... P1 prend la valeur entière de P2. N4 P1 = F12 K5,4 .................. P1 = 5 F13 Partie entière plus un N4 P1 = F13 P2 ...................... P1 prend la valeur entière de P2 plus 1. N4 P1 = F13 K5,4 .................. P1 = 5 + 1 = 6 F14 Partie entière moins un N4 P1 = F14 P27 ................... P1 prend la valeur entière de P27 moins un. N4 P5 = F14 K5,4 .................. P5 = 5 - 1 = 4 F15 Valeur absolue N4 P1 = F15 P2 ...................... P1 prend pour valeur la valeur absolue de P2 N4 P1 = F15 K-8 ................... P1 = 8 F16 Complément N4 P7 = F16 P20 ................ P7 prend la valeur complémentaire de P20, c’est à-dire, P7 = - P20 N4 P7 = F16 K10 ................ P7 = -10 Page Chapitre: 10 4 PROGRAMMATIONPARAMETRIQUE Section: OPERATEURS "F1" à "F16" 10.3 OPÉRATEURS “F17” à “F29” Elles n’affectent pas l'indicateur de saut conditionnel. F17 N4 P1 = F17 P2 P1 prend la valeur de l’adresse mémoire dans laquelle se trouve le bloc P2. Exemple: N4 P1 = F17 K12. P1 prend la valeur de l’adresse mémoire dans laquelle se trouve le bloc N12. F18 N4 P1 = F18 P2 P1 prend la valeur de la coordonnée X du bloc situé en P2. F18 n’accepte pas une constante comme opérande. Exemple: P1 = F18 K2 n’est pas possible. F19 N4 P1 = F19 P2 P1 prend la valeur de la coordonnée Y du bloc situé en P2. F19 n’accepte pas une constante comme opérande. Exemple : P1 = F19 K3 n’est pas possible. F20 N4 P1 = F20 P2 P1 prend la valeur de la coordonnée Z du bloc situé en P2. F20 n’accepte pas une constante comme opérande. Exemple: P1 = F20 K5 n'est pas possible. F21 Sans fonction F22 N4 P1 = F22 P2 P1 prend la valeur de l'adresse mémoire dans le bloc précédent à celui défini par P2. F22 n’accepte pas une constante comme opérande. Exemple : P1 = F22 K4 n'est pas possible. F23 N4 P1 = F23 Le paramètre P1 prend le numéro de correcteur d’outil avec lequel on est en train d’opérer à ce moment-là. F24 Cette fonction peut être programmée de deux façons différentes: N4 P9=F24 K2 Le paramètre P9 prend de la table des correcteurs la valeur de R correspondant au correcteur indiqué (correcteur 2). N4 P8=F24 P12 Le paramètre P8 prend de la table des correcteurs la valeur de R correspondant au correcteur indiqué par le paramètre P12. Chapitre: 10 PROGRAMMATIONPARAMETRIQUE Section: OPÉRATEURS “F17” à “F29” Page 5 F25 Cette fonction peut être programmée de deux façons différentes: N4 P15=F25 K16 Le paramètre P15 prend de la table des correcteurs la valeur de L correspondant au correcteur indiqué (correcteur 16). N4 P13=F25 P34 Le paramètre P13 prend de la table des correcteurs la valeur de L correspondant au correcteur indiqué par le paramètre P34. F26 Cette fonction peut être programmée de deux façons différentes: N4 P6=F26 K32 Le paramètre P6 prend de la table des correcteurs la valeur de I correspondant au correcteur indiqué (correcteur 32). N4 P14=F26 P15 Le paramètre P14 prend de la table des correcteurs la valeur de I correspondant au correcteur indiqué par le paramètre P15. F27 Cette fonction peut être programmée de deux façons différentes: N4 P90=F27 K13 Le paramètre P90 prend de la table des correcteurs la valeur de K correspondant au correcteur indiqué (correcteur 13). N4 P28=F27 P5 F28 Sans fonction. F29 N4 P1 = F29 Le paramètre P28 prend de la table des correcteurs la valeur de K correspondant au correcteur indiqué par le paramètre P5. Le paramètre P1 prend le numéro d’outil avec lequel on est en train d’opérer à ce moment-là. Dans un même bloc, on peut introduire toutes les assignations et toutes les opérations que l’on voudra, toutefois qu’elles ne modifient pas un nombre de paramètres supérieur à 15. Page Chapitre: 10 6 PROGRAMMATIONPARAMETRIQUE Section: OPÉRATEURS “F17” à “F29” 10.4 OPERATEURS BINAIRES “F30” à “F33” Les opérations binaires dont on dispose sont: F30 F31 F32 F33 Fonction Fonction Fonction Fonction logique logique logique logique AND OR XOR NOR Elles activent aussi les indicateurs internes (FLAGS) selon la valeur du résultat pour leur traitement ultérieur en SAUTS/APPELS CONDITIONNELS (G26, G27, G28, G29) Les opérations binaires peuvent s’appliquer entre: Paramètres Paramètres et constantes Constantes P1 = P2 F30 P3 P11 = P25 F31 H(8) P19 = K2 F32 K5 La valeur de la constante H doit être en code hexadécimal, entière, positive, ne pas dépasser 8 caractères (entre 0 et FFFFFFFF) et elle ne peut pas appartenir au premier opérande. F30 Fonction logique AND Exemple: N4 P1 = P2 F30 P3 Valeur de P2 A5C631F F31 Valeur de P3 C883D Valeur de P1 C001D Fonction logique OR Exemple: N4 P11 = P25 F31 H35 AF9 D01 Valeur de P25 48BE6 F32 Valeur de H 35AF9D01 Valeur de P11 35AF9FE7 Fonction logique XOR Exemple: N4 P19 = P72 F32 H91 C6EF Valeur de P72 AB456 F33 Valeur de H 91C6EF Valeur de P19 9B72B9 Fonction logique NOR Exemple: N4 P154 = F33 P88 P154 prend la valeur de P88 en complément à 1 Valeur de P88 4A52D63F Chapitre: 10 PROGRAMMATIONPARAMETRIQUE Valeur de P154 B5AD29C0 Section: OPERATEURS BINAIRES “F30” à “F33” Page 7 10.5 FONCTIONS DE SAUT CONDITIONNEL (G26, G27, G28, G29) Ces fonctions sont similaires à la fonction G25 (saut inconditionnel) qui est expliquée au chapitre “Fonctions Préparatoires Additionnelles” du présent manuel. Les fonctions G26, G27, G28, G29, avant de faire le saut de bloc ou d’exécuter la partie de programme indiquée, vérifient que la condition requise s’est produite. G26 Saut si zéro. Exige que la condition de “Zéro” soit présente. G27 Saut si autre que zéro. Exige que la condition de “Zéro” ne soit pas présente. G28 Saut si plus petit que zéro. Exige que la condition de “Plus petit” soit présente. G29 Saut si égal ou plus grand que zéro. Exige que la condition de “Plus petit” ne soit pas présente. La condition de “Zéro”, appelée aussi égalité, est activée dans les cas suivants: * Lorsque le résultat d’une opération est égal à zéro. Exemple: N001 P1 = P3 F2 K5 La condition zéro est présente si P3 = 5 * Si dans une comparaison, les deux termes sont égaux. Exemple: N002 P1 F11 K8 La condition zéro est présente si P1 = 8 La condition de “Plus petit”, appelées aussi négative, est activée dans les cas suivants: * Lorsque le résultat d’une opération est plus petit que zéro.(négatif) Exemple: N001 P1 = P3 F2 K5 La condition zéro est présente si P3 est plus petit que 5. * Si dans une comparaison, le premier terme est plus petit que le second. Exemple: N002 P1 F11 K8 La condition zéro est présente si P1 est plus petit que 8 Attention: Les assignations et les fonctions non paramétriques n’altèrent pas l’état des indicateurs de condition. Exemple de programmation: N060 N065 N070 N071 N072 N073 P2 F11 K22 G01 X10 Y20 G26 N100 G28 N200 G29 N300 Dans le bloc N060 une comparaison est faite. Les blocs N65 et N70 n’altèrent pas l’état des indicateurs de condition. Ainsi, Si P2 vaut 22, le programme se poursuivra dans le bloc N100 Si P2 vaut moins que 22, le programme se poursuivra dans le bloc N200 Si P2 vaut plus que 22, le programme se poursuivra dans le bloc N300 Page Chapitre: 10 8 PROGRAMMATIONPARAMETRIQUE Section: FONCTIONS DE SAUT (G26, G27, G28, G29) Il faut faire attention lors de la programmation des fonctions G26 et G29. Si dans l’exemple précédent on avait programmé: N071 N072 N073 G28 N200 G29 N300 G26 N100 Le programme n’exécuterait pas le bloc N073. Avec P2 plus petit que 22, le bloc se poursuit dans N200 et avec P2 égal ou plus grand que 22, il se poursuit dans le bloc N300. Exemple de programmations en paramétriques pour le calcul de coordonnées des différents points qui composent une cardioïde dont la formule est R=B |cos A/2| Soit le point de départ X0 Y0 et P0 P1 P2 P3 P4 P5 = = = = = = N10 N20 N30 N40 N50 N60 N70 N80 N90 A (angle) B A/2 cos A/2 |cos A/2| R = B |cos A/2| G93 G01 F500 P0=K0 P1=K30 ............................................................ A=0, B=30 P2=P0 F4 K2 P3=F8 P2 P4=F15 P3 P5=P1 F3 P4 R = B |cos A/2| G01 G05 R P5 A P0 ................................................... Bloc de déplacement P0=P0 F1 K5 ............................................................... Incrément angulaire de 5º P0=F11 K365 ............................................................... Si A=365° Fin G27 N30 ....................................................................... Sinon, nouveau calcul X0 Y0 M30 Chapitre: 10 PROGRAMMATIONPARAMETRIQUE Section: FONCTIONS DE SAUT (G26, G27, G28, G29) Page 9 CODES D'ERREUR 001 Cette erreur apparaît dans les cas suivants: * Quand le premier caractère du bloc à exécuter n’est pas”N”. * Lorsque, pendant une édition en ARRIERE-PLAN, le programme en cours appelle un sous-programme situé dans le programme en cours d’édition ou dans un programme ultérieur. L’ordre de chargement des programmes pièce en mémoire apparaît dans le répertoire de programmes pièce. Si, pendant l’exécution d’un programme, un nouveau programme est édité, il sera placé à la fin de la liste. 002 Trop de chiffres lors de la définition d’une fonction en général. 003 Cette erreur apparaît dans les cas suivants: * Quand une valeur négative a été affectée à une fonction qui n’accepte pas le signe “-”. * Quand une valeur incorrecte a été affectée à une opération automatique: - Positionnement en ligne - Positionnement en arc - Positionnement en rectangle ou en grille - Poche rectangulaire - Poche circulaire - Ebauche d’arêtes - Surfaçage Si Si Si Si Si Si Si Si Si Si Si Si Si Si Si Si Si 004 Inutilisé actuellement. 005 Bloc de paramètres programmé de façon incorrecte. 006 Affectation de plus de 10 paramètres à un bloc. 007 Division par zéro. 008 Racine carrée d’un nombre négatif. 009 Valeur du paramètre trop grande 010 M41, M42, M43 ou M44 a été programmé. 011 Plus de 7 fonctions “M” dans un bloc. 012 Cette erreur apparaît dans les cas suivants: L=0, Xn=X1, Yn=Y1, I=0 L=0, Xn=X1, Yn=Y1, N=0 I=0, N=0 I>0, fraction L/I N=0 R=0, Xc=X1, Yc=Y1 LX=0, IX=0 ou LY=0, IY=0 LX=0, NX=0 ou LY=0, NY=0 LX>0, IX=0, NX<2 ou LY>0, IY=0, NY<2 LX>0, IX>0, fraction LX/IX LY>0, IY>0, fraction LY/IY L=0 ou H=0 r>(L/2) ou r>(H/2) Rayon d’outil > R L=0 ou H=0 r>L ou r>H L=0 ou H=0 > La fonction G50 est programmée de façon incorrecte. > Les valeurs des dimensions d’outils sont trop élevées. > Les valeurs de décalage du zéro (G53/G59) sont trop élevées. 013 Inutilisé actuellement. 014 Un bloc incorrect par lui-même ou par rapport à l’historique du programme jusqu’à présent a été programmé. 015 Les fonctions G20, G21, G22, G23, G24, G25, G26, G27, G28, G29, G30, G31, G32, G50, G52, G53, G54, G55, G56, G57, G58, G59, G72, G73, G74, G92 et G93 doivent être programmées seules dans un bloc. 016 Le sous-programme ou bloc appelé n’existe pas, ou le bloc cherché par la fonction spéciale F17 n’existe pas. 017 Valeur du pas du filet négative ou trop élevée. 018 Erreur dans des blocs où les points sont définis par angle-angle ou angle-coordonnée. 019 Cette erreur apparaît dans les cas suivants: > Après la définition de G20, G21, G22 ou G23, le numéro du sous-programme auquel les fonctions renvoient est manquant. > Le caractère “N” n’a pas été programmé après la fonction G25, G26, G27 ou G29. > Trop de niveaux d’imbrication. 020 Les axes de l’interpolation circulaire ne sont pas programmés correctement. 021 Pas de bloc à l’adresse définie par le paramètre affecté à F18, F19, F20, F21, F22. 022 Un axe est répété lors de la programmation de G74. 023 K n’a pas été programmé après G04. 024 Inutilisé actuellement. 025 Erreur de définition de bloc ou d’appel de sous-programme ou lors de la définition de sauts conditionnels ou inconditionnels. 026 Cette erreur apparaît dans les cas suivants: > Débordement de mémoire. > Espace libre sur bande ou en mémoire CNC insuffisant pour mémoriser le programme pièce. 027 I/J/K n’a pas été défini pour une interpolation circulaire ou un filet. 028 Tentative de sélection d’un correcteur d’outil sur la table d’outils d’un outil externe qui n’existe pas (le nombre d’outils est défini par le paramètre machine). 029 Valeur trop élevée affectée à une fonction. Cette erreur est souvent émise si une valeur est programmée en mm/mn (pouces/mn), en cas de passage aux valeurs en mm/tour (pouce/tour) sans changement des valeurs de F. 030 La fonction G programmée n’existe pas. 031 La valeur du rayon d’outil est trop élevée. 032 La valeur du rayon d’outil est trop élevée. 033 Un déplacement sur 8388 mm ou 330,26 pouces a été programmé. Exemple: Soit X-5000 la position de l’axe X: si un déplacement au point X5000 est demandé, la CNC émettra l’erreur 33 lors de la programmation du bloc N10 X5000 puisque le déplacement programmé sera égal à 5000 - (-5000) = 10000 mm. Pour effectuer ce déplacement sans émission de cette erreur, l’opération doit se dérouler en 2 phases comme suit: N10 X0 N10 X5000 déplacement de 5000 mm déplacement de 5000 mm 034 Valeur de S ou F trop élevée 035 Informations sur l’arrondi aux angles, le chanfreinage ou la compensation insuffisantes. 036 Répétition de sous-programme. 037 La fonction M19 a été programmée de façon incorrecte. 038 La fonction G72 ou G73 a été programmée de façon incorrecte. Ne pas oublier que si G72 n’est appliqué que sur un seul axe, cet axe doit être positionné sur le zéro pièce (valeur 0) au moment de l’application du facteur d’échelle. 039 Cette erreur apparaît dans les cas suivants: > Plus de 15 niveaux d’imbrication lors de l’appel de sous-programmes. > Programmation d’un bloc contenant un saut sur lui-même. Exemple: N120 G25 N120. 040 L’arc programmé ne passe pas par le point de fin défini (tolérance de 0,01 mm) ou aucun arc ne passe par les points définis par G08 ou G09. 041 Cette erreur est émise en cas de programmation d’une entrée tangentielle dans les conditions suivantes: > Pas de place pour exécuter une entrée tangentielle. Un débattement égal au double du rayon congé ou plus est nécessaire. > Si l’entrée tangentielle doit être appliquée à un arc (G02, G03), elle doit être définie dans un bloc linéaire. 042 Cette erreur est émise en cas de programmation d’une sortie tangentielle dans les conditions suivantes: > Pas de place pour exécuter une sortie tangentielle. Un débattement égal au double du rayon congé ou plus est nécessaire. > Si la sortie tangentielle doit être appliquée à un arc (G02, G03), elle doit être définie dans un bloc linéaire. 043 Définition incorrecte des coordonnées polaires d’origine (G93). 044 Inutilisé actuellement. 045 Programmation incorrecte de la fonction G36, G37, G38 ou G39. 046 Définition incorrecte des coordonnées polaires. 047 Un déplacement nul a été programmé pendant une compensation de rayon ou un congé aux angles. 048 Inutilisé actuellement. 049 Programmation de chanfrein incorrecte dans une opération de poche rectangulaire ou d’ébauche d’arête de telle sorte que: * L’outil est incapable d’effectuer l’usinage car le chanfrein est trop petit. * Le chanfrein d’une aussi grande taille ne peut pas être usiné avec ces valeurs de paramètre L, H et E. 050 Les fonctions M06, M22, M23, M24, M25 doivent être programmées seules dans un bloc. 051 * Un changement d’outil ne peut pas être effectué si l’outil n’est pas en position de changement. 052 * L’outil demandé ne se trouve pas dans le magasin. 053 Inutilisé actuellement. 054 Pas de ruban dans le lecteur de cassette ou la porte du lecteur est ouverte. 055 Erreur de parité lors de la lecture ou de l’enregistrement d’une cassette. 056 Inutilisé actuellement. 057 Ruban protégé en écriture. 058 Transport de ruban “paresseux” 059 Erreur de communications entre la CNC et le lecteur de cassettes. 060 Erreur matériel interne de la CNC. Consulter les Services Techniques Après-Vente. 061 Erreur de batterie. Le contenu de la mémoire sera sauvegardé 10 jours au-délà du jour de l’apparition de l’erreur (avec la CNC à l’arrêt). L’ensemble du module batterie situé sur la face arrière doit être changé. Consulter les Services Techniques Après-Vente. Attention: En raison du risque d’explosion ou de combustion, ne pas essayer de recharger la batterie, ne pas l’exposer à des températures supérieures à 100° et ne pas mettre les câbles de batterie en court-circuit. 064 * Une entrée externe d’urgence (broche 14 du connecteur d’E/S 1) est activée. 065 Inutilisé actuellement. 066 * Dépassement de limite de course en X Cette erreur est émise quand la machine dépasse la limite fixée ou si un bloc forçant la machine à dépasser ces limites a été programmé. 067 * Dépassement de limite de course en Y Cette erreur est émise quand la machine dépasse la limite fixée ou si un bloc forçant la machine à dépasser ces limites a été programmé. 068 * Dépassement de limite de course en Z Cette erreur est émise quand la machine dépasse la limite fixée ou si un bloc forçant la machine à dépasser ces limites a été programmé. 069 Inutilisé actuellement. 070 ** Erreur de poursuite en X 071 ** Erreur de poursuite en Y 072 ** Erreur de poursuite en Z 073 Inutilisé actuellement. 074 ** Valeur de vitesse de broche excessive 075 ** Erreur de réinjection sur le connecteur A1. 076 ** Erreur de réinjection sur le connecteur A2. 077 ** Erreur de réinjection sur le connecteur A3. 078 ** Erreur de réinjection sur le connecteur A4. 079 ** Erreur de réinjection sur le connecteur A5. 080 Cette erreur s’est produite lors de l’utilisation d’un outil plus petit que la passe d’usinage “G” en usinage de poche rectangulaire/circulaire ou d’ébauche d’arête. 081 Cette erreur est émise quand le rayon de l’outil est supérieur à “(L/H2)-E” ou “(H/2)-E”. 082 ** Erreur de parité dans les paramètres généraux. 083 Cette erreur est émise en cas de programmation de “r>0” ou “C>0” en usinage de poche rectangulaire/circulaire ou d’ébauche d’arête. 084 Cette erreur est émise si un rayon d’outil supérieur à “R-E” est programmé dans une poche circulaire. 085 Cette erreur est émise si un outil de rayon nul (correcteur d’outil) est utilisé après avoir programmé “G=0” (passe d’usinage) en usinage de poche rectangulaire/circulaire ou d’ébauche d’arête. 086 Cette erreur est émise quand une valeur incorrecte est affectée à une opération automatique ou à une opération d’usinage: - Poche rectangulaire ................... Si Poche circulaire......................... Si Ebauche d’arêtes ....................... Si Surfaçage ................................... Si Pointage .................................... Si Perçage ...................................... Si Taraudage ................................. Si Alésage ...................................... Si P=0 P=0 P=0 P=0 P=0, P=0 P=0 P=0 ou ou ou ou I=0 I=0 I=0 I=0 =0 ou I=0 087 ** Erreur matériel interne de la CNC. Consulter les Services Techniques Après-Vente. 088 ** Erreur matériel interne de la CNC. Consulter les Services Techniques Après-Vente. 089 * Tous les axes ne sont pas revenus au zéro. Cette erreur apparaît quand une recherche du zéro sur tous les axes est obligatoire après la mise sous tension. Cette obligation est définie par un paramètre machine. 090 ** Erreur matériel interne de la CNC. Consulter les Services Techniques Après-Vente. 091 ** Erreur matériel interne de la CNC. Consulter les Services Techniques Après-Vente. 092 ** Erreur matériel interne de la CNC. Consulter les Services Techniques Après-Vente. 093 ** Erreur matériel interne de la CNC. Consulter les Services Techniques Après-Vente. 094 Erreur de parité dans la table d’outils ou la table de correcteurs d’outils G53-G59. 095 Cette erreur est émise quand le rayon de l’outil est supérieur au rayon congé “r” en usinage de poche rectangulaire ou en ébauche d’arêtes. 096 ** Erreur de parité dans les paramètres d’axe Z. 097 ** Erreur de parité dans les paramètres d’axe Y. 098 ** Erreur de parité dans les paramètres d’axe X. 099 ** Erreur de parité dans la table M. 100 ** Erreur matériel interne de la CNC. Consulter les Services Techniques Après-Vente. 101 ** Erreur matériel interne de la CNC. Consulter les Services Techniques Après-Vente. 105 Cette erreur est émise dans les cas suivants: > Un commentaire a plus de 43 caractères. > Un programme a été défini avec plus de 5 caractères. > Un numéro de bloc comporte plus de 4 caractères. > Apparition de caractères bizarres en mémoire. 106 ** Température limite interne dépassée. 107 Inutilisé actuellement. 108 ** Erreur dans les paramètres de compensation d’erreur de pas de vis sur l’axe Z. 109 ** Erreur dans les paramètres de compensation d’erreur de pas de vis sur l’axe Y. 110 ** Erreur dans les paramètres de compensation d’erreur de pas de vis sur l’axe X. 111 112 Inutilisé actuellement. Inutilisé actuellement. 113 Inutilisé actuellement. 114 Inutilisé actuellement. 115 * Erreur de chien de garde dans le module périodique. Cette erreur apparaît quand le temps d’exécution du module périodique dépasse 5 millisecondes. 116 * Erreur de chien de garde dans le module principal. Cette erreur apparaît quand le temps d’exécution du module principal est supérieur à la moitié du temps indiqué dans le paramètre machine “P279”. 117 * Les informations CNC internes demandées par l’activation des repères M1901 à M1949 ne sont pas disponibles. 118 * Tentative de modification d’une variable interne CNC indisponible au moyen des repères M1950 à M1964. 119 Erreur lors de l’écriture de paramètres machine, de la table de fonctions M décodées et des tables de compensation d’erreur de vis dans la mémoire EEPROM. Cette erreur peut apparaître lorsque, après verrouillage des paramètres machine, de la table de fonctions M décodées et des tables de compensation d’erreur de vis, l’opérateur tente de sauvegarder ces informations dans la mémoire EEPROM. 120 Erreur de somme de contrôle lors de la récupération (rétablissement) des paramètres machine, de la table de fonctions M décodées et des tables de compensation d’erreur de vis dans la mémoire EEPROM. Elles stoppent l’avance des axes et la rotation de la broche en annulant les signaux de validation ainsi que les sorties analogiques de la CNC. Attention: Les ERREURS signalées par “*” agissent de la façon suivante: - Elles stoppent l’avance des axes et la rotation de la broche en annulant les signaux de validation ainsi que les sorties analogiques de la CNC. - Elles interrompent l’exécution du programme pièce de la CNC s’il était en cours d’exécution. Les ERREURS signalées par “**” agissent non seulement comme celles repérées par “*”, mais activent en plus la SORTIE D’URGENCE INTERNE. ">
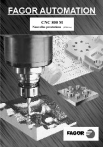
Публичная ссылка обновлена
Публичная ссылка на ваш чат обновлена.