Captage et traitement des aérosols de fluides de coupe
6
GUIDE PRATIQUE DE VENTILATION
L’Institut national de recherche et de sécurité (INRS)
Dans le domaine de la prévention des risques professionnels, l’INRS est un organisme scientifique et technique qui travaille, au plan institutionnel, avec la CNAMTS, les CRAM-CGSS et plus ponctuellement pour les services de l’État ainsi que pour tout autre organisme s’occupant de prévention des risques professionnels.
Il développe un ensemble de savoir-faire pluridisciplinaires qu’il met à la disposition de tous ceux qui, en entreprise, sont chargés de la prévention : chef d’entreprise, médecin du travail,
CHSCT, salariés. Face à la complexité des problèmes, l’Institut dispose de compétences scientifiques, techniques et médicales couvrant une très grande variété de disciplines, toutes au service de la maîtrise des risques professionnels.
Ainsi, l’INRS élabore et diffuse des documents intéressant l’hygiène et la sécurité du travail : publications (périodiques ou non), affiches, audiovisuels, site Internet… Les publications de l’INRS sont distribuées par les CRAM.
Pour les obtenir, adressez-vous au service prévention de la Caisse régionale ou de la Caisse générale de votre circonscription, dont l’adresse est mentionnée en fin de brochure.
L’INRS est une association sans but lucratif
(loi 1901) constituée sous l’égide de la CNAMTS et soumise au contrôle financier de l’État. Géré par un conseil d’administration constitué à parité d’un collège représentant les employeurs et d’un collège représentant les salariés, il est présidé alternativement par un représentant de chacun des deux collèges. Son financement est assuré en quasi-totalité par le Fonds national de prévention des accidents du travail et des maladies professionnelles.
Les Caisses régionales d’assurance maladie
(CRAM) et Caisses générales de sécurité sociale (CGSS)
Les Caisses régionales d’assurance maladie et les Caisses générales de sécurité sociale disposent, pour participer à la diminution des risques professionnels dans leur région, d’un service prévention composé d’ingénieursconseils et de contrôleurs de sécurité.
Spécifiquement formés aux disciplines de la prévention des risques professionnels et s’appuyant sur l’expérience quotidienne de l’entreprise, ils sont en mesure de conseiller et, sous certaines conditions, de soutenir les acteurs de l’entreprise (direction, médecin du travail, CHSCT, etc.) dans la mise en œuvre des démarches et outils de prévention les mieux adaptés à chaque situation.
Ils assurent la mise à disposition de tous les documents édités par l’INRS.
Toute représentation ou reproduction intégrale ou partielle faite sans le consentement de l’INRS, de l’auteur ou de ses ayants droit ou ayants cause, est illicite.
Il en est de même pour la traduction, l’adaptation ou la transformation, l’arrangement ou la reproduction, par un art ou un procédé quelconque (article L. 122-4 du code de la propriété intellectuelle).
La violation des droits d’auteur constitue une contrefaçon punie d’un emprisonnement de deux ans et d’une amende de 150 000 euros (article L. 335-2 et suivants du code de la propriété intellectuelle).
© INRS, 2005. Réalisation : [email protected]
GU I DE PRAT I QUE DE VENT I LAT I ON N°6
ED 972
Annule et remplace ED 680
6.Captageettraitement
desaérosolsdefluides decoupe
C
e guide concerne les opérations effectuées avec des fluides de coupe sous forme d’huiles minérales entières ou de fluides aqueux, notamment lors de l'enlèvement ou de la déformation des métaux. Il traite des risques as sociés à ces opérations et des moyens de les prévenir par une ventilation appropriée.
Il aborde les points suivants :
■
nature et évaluation des risques (additifs, effets sur la santé, valeurs limites d'exposition, métrologie des aérosols de fluides de coupe) ;
■
conception d'une installation de ventilation (captage localisé, ventilation générale, apport d'air de compensation, circuits de transport, traitement et rejet de l'air pollué) ;
■
contrôle et maintenance d'une installation de ventilation.
Une série de dos siers techniques, présentant des solutions précises aux problèmes pouvant être rencontrés sur les installations réelles, figure en fin de guide.
쐌 ventilation
쐌 captage
쐌 brouillard de fluide de coupe
C e document a été établi par un groupe de travail constitué sous l'égide de la Caisse nationale de l'assurance maladie et comprenant des spécialistes en ventilation et nuisances chimiques des Caisses régionales d'assurance maladie et de l'Institut national de recherche et de sécurité. Lors de son élaboration, les organismes professionnels suivants ont
été consultés : Centre technique des industries mécaniques (CETIM), Centre technique des industries aérauliques et thermiques (CETIAT), Union intersyndicale de matériel aéraulique, thermique et frigorifique (UNICLIMA), Centre technique de l'industrie du décolletage
(CT DEC).
L’ambition de ce guide est de servir de document de référence à l'usage des personnes et des entreprises concernées par la conception, la réalisation, l'utilisation et le contrôle des installations de captage et de traitement des aérosols dégagés dans les ateliers où sont mis en œuvre des fluides de coupe.
Ce document, se voulant avant tout un guide pratique, aborde essentiellement les points relatifs à la nature et à l'évaluation du risque dû aux fluides de coupe, à la conception des installations de captage et de ventilation et au traitement des polluants captés.
L'objectif final à atteindre est le maintien de la salubrité de l'air aux postes de travail et dans les ateliers, telle qu'elle est définie par les textes réglementaires ou par les normes et les règles de l'art.
Les critères de ventilation proposés constituent donc des moyens minimaux permettant d'atteindre les objectifs retenus dans la majorité des cas, sous réserve que l'ensemble des sources de pollution soit traité.
Ce guide, comme tous ceux qui sont publiés dans cette série, sera régulièrement réexaminé à la lumière des remarques éventuelles formulées par les utilisateurs et des résultats d'études nouvelles conduites sur ce thème.
1. Domaine d'application
Ce guide est applicable aux opérations d’enlèvement ou de déformation des métaux effectuées avec des fluides de coupe sous forme d'huiles entières ou de fluides aqueux.
2
Ceci concerne :
쐌 les machines travaillant par enlèvement de matière : tours à décolleter
(monobroche, multibroches), rectifieuses, fraiseuses, aléseuses, perceuses
(monobroche, multibroches), machines
à brocher, fileter, tarauder, tailler les engrenages… ;
쐌 les machines travaillant par déformation de matière : machines de frappe à froid, presses de découpage ou d’emboutissage, machines à rétreindre… ment d’hydrocarbures de synthèse (polyalkyl-benzènes) ;
쐌 les fluides aqueux dont on recherche surtout les qualités de refroidissement, parmi lesquels il est possible de distinguer :
■ les émulsions et micro-émulsions : ce sont des dispersions de gouttelettes d’huile plus ou moins fines (10 -3 à 2 μm de diamètre) stabilisées par un émulgateur ;
■ les solutions : tous les composés sont solubles dans l’eau ; on trouve
Dans les deux cas la concentration de matières actives dans l’eau varie de 2 à
10 %. fréquemment des produits de synthèse (polyglycols…).
N’entrent pas dans le champ d’application du présent guide, en raison de leurs aspects techniques très spécifiques :
쐌 les verreries mécaniques,
쐌 l’industrie textile (tissage en particulier),
쐌 les bains de traitement thermique
(trempe à l’huile),
쐌 les salles d’essai de moteurs,
쐌 l’usinage par électroérosion,
쐌 l’application d’huile de décoffrage,
쐌 les presses à injecter ou à mouler
(poteyage).
Les fluides de coupe, de formulation complexe, contiennent en général de nombreux additifs appartenant à des familles chimiques très diverses.
La liste des produits cités ci-dessous n’est pas exhautive.
Les additifs d’onctuosité
Ils améliorent l’efficacité et la lubrification (huiles grasses, esters d’origine naturelle ou synthétique…).
2. Nature des fluides et caractéristiques des polluants
On désigne par fluides de coupe des liquides qui, appliqués par arrosage sur la partie active d'un outil, facilitent l'opération d'usinage et contribuent à améliorer la durée de vie de l'outil ou la productivité de l'opération. Les deux effets principaux d'un fluide de coupe sont la lubrification et le refroidissement.
La norme NF ISO 6743-7 [1] donne une classification précise des fluides de coupe pour l'ensemble du travail des métaux.
Il existe deux grandes catégories de fluides de coupe [2], les huiles entières et les fluides aqueux.
En 2002, les ventes d’huiles de coupe entières étaient de 32 000 tonnes en
France, en baisse de 7,7 % par rapport à
2001. Celles de fluides aqueux concentrés étaient de 32 600 tonnes, en hausse de 1,4 % par rapport à 2001 [3].
2.1. Composition des fluides de coupe
Les additifs « extrême pression »
Ils facilitent la coupe dans les opérations sévères (composés organiques chlorés, soufrés ou phosphorés).
Actuellement, pour des considérations d’environnement, on cherche à remplacer les produits chlorés par d’autres additifs, notamment soufrés (sulfonates surbasés). Les paraffines chlorées à chaînes courtes sont interdites depuis le 6 janvier
2004 (directive 2002/45/CE).
Les additifs anti-usure
Ils limitent l’usure de l’outil de coupe dans les opérations moyennement sévères (phosphates d’aryles, alkyldithiophosphates de zinc…).
Les inhibiteurs de corrosion
Ils protègent le métal à usiner contre la corrosion (amines ou amides grasses, triéthanolamine, esters boriques…).
Les additifs dits « antibrouillards »
Ils visent à diminuer l’émission de brouillards d’huile par coalescence des particules les plus fines pour former des particules plus grosses, sédimentant plus facilement (exemple : polyisobutènes).
On distingue :
쐌 les huiles entières
à propriétés lubrifiantes prépondérantes, généralement à base d’huiles de pétrole, plus rare-
Les biocides (bactéricides et fongicides) et les biostatiques
Les biocides limitent la prolifération
Les chiffres entre crochets renvoient à la bibliographie.
Les termes marqués par * sont définis dans le glossaire à la fin du guide.
des micro-organismes (formaldéhyde, triazines).
Les biostatiques
Plus récents, ils confèrent aux fluides des propriétés de résistance améliorées.
Les parfums et colorants.
2.2. Caractéristiques des polluants
Les polluants émis lors de l'usinage peuvent être des composants de base du fluide, des produits de dégradation thermique et des particules solides en provenance des matériaux usinés ; ils sont émis sous forme de vapeurs et d’aérosols.
À la liste des additifs introduits volontairement dans la formulation d’un fluide de coupe, il faut ajouter les constituants dangereux qui accompagnent les produits de base pétroliers et ceux qui peuvent apparaître au cours du travail d’usinage ou de déformation.
Les hydrocarbures polycycliques aromatiques (HPA)
Le plus connu de ces composés est le benzo(a)pyrène classé cancérogène de catégorie 2* par la communauté européenne.
Ces substances peuvent être présentes en quantité importante dans les huiles entières lorsque le traitement en raffinerie est insuffisant (distillats non désaromatisés) ou lorsqu’il s’agit d’huiles régénérées sommairement. Lors de l'utilisation, un enrichissement progressif en
HPA peut se produire, lorsque les huiles sont soumises à des températures élevées.
Les nitrosamines
Elles peuvent se former dans les fluides aqueux ; parmi celle-ci, la N-nitrosodiéthanolamine est classée cancérogène de catégorie 2* par la communauté européenne.
Les métaux
Ils se présentent sous forme de particules ou solubilisés lors de l’usinage
(plomb dans le cas des aciers à décolleter ou cobalt dans le cas de la rectification des carbures frittés [4]).
Les impuretés
D’origines diverses, elles proviennent de la dégradation thermique ou chimique des composés organiques (produits d’oxydation des hydrocarbures, formaldéhyde…).
3
Les micro-organismes
Susceptibles de se développer dans les fluides aqueux, certains d'entre eux peuvent produire des toxines.
Les aérosols sont essentiellement dus à un phénomène mécanique localisé près du point d’impact entre le fluide et les pièces tournantes. Les microparticules formées sont dispersées dans l’atmosphère ; s’y ajoutent une partie des vapeurs qui recondensent ainsi que les fumées produites lors de l’usinage si les conditions sont particulièrement sévères : les températures à l’interface outil-copeau peuvent en effet dépasser
750° C. Il se forme alors des produits de distillation et de dégradation (craquage) suivis éventuellement de recombinaisons diverses (pyrosynthèse).
Le terme « brouillard d’huile », impropre pour les fluides aqueux, désignait à l’origine des aérosols émis lors d’usinages avec des huiles entières. En ce qui concerne les fluides aqueux, on admet, du moins pour les émulsions, que l’eau présente disparaît en partie par évaporation. L’aérosol résultant est mal connu mais serait peu différent de celui d’une huile entière.
Le spectre de répartition dimensionnelle des particules constituant l’aérosol est assez large. Les plus grosses gouttelettes peuvent sédimenter, les particules de faible diamètre (0,1 à environ 10 μm) forment dans l’air un aérosol stable.
3. Risques et nuisances
La dispersion des aérosols de fluides de coupe est à l’origine de plusieurs phénomènes.
Formation de films gras
Les plus grosses particules sédimentent sur les sols, les plans de travail et l’ensemble de la structure de l’atelier. Ce phénomène augmente la sensation générale de pollution par l’huile, et entraîne des risques de chutes par glissade sur les sols.
Formation dans l’atelier d’un brouillard bleuté
La couleur résulte de la diffusion de la lumière par les particules les plus fines, cela donne un effet visuel de pollution intense. Ce phénomène ne permet d’apprécier que de manière très subjective la concentration du brouillard, puisqu’il dépend de la taille des particules présentes.
Création d’odeurs d’huile « chaude » ou d’huile « brûlée »
Ces émanations proviennent de petites quantités de produits de décomposition thermique des hydrocarbures constituant l’huile minérale*.
Concernant les risques pour la santé, les fluides de coupe sont principalement
à l'origine de pathologies de la peau et des voies respiratoires [5, 6, 7].
3.1. Les pathologies cutanées
Ce sont les plus fréquemment observées. On distingue quatre catégories :
쐌
Les dermites d'irritation représentent une forte proportion des pathologies cutanées. Elles sont dues au pH relativement élevé de nombreux fluides de coupe aqueux et au caractère irritant de beaucoup des additifs utilisés. Elles peuvent être infectées par des bactéries ou des champignons.
쐌
Les dermites allergiques sont provoquées par certains des additifs utilisés
(en particulier de nombreux biocides) et par les métaux, sous forme de particules ou dissous (cobalt…), provenant des alliages usinés ou des outils. Nettement plus rares, elles sont souvent associées aux dermites d'irritation qui en favorisent l'apparition.
쐌
Les boutons d'huile « classiques », dus aux huiles entières, surviennent aujourd'hui plus rarement grâce à l'amélioration des conditions d'hygiène.
쐌
Les cancers de la peau et du scrotum sont causés par les HPA contenus dans les huiles minérales* insuffisamment raffinées (surtout observés pour des expositions anciennes, avant 1975).
Les coupures, érosions et frictions favorisent le passage des substances chimiques et les dermites irritatives et allergiques par rupture de la barrière épidermique.
3.2. Les affections respiratoires
쐌
Les pneumopathies, dues aux brouillards d'huiles minérales* ou synthétiques, peuvent se compliquer de fibroses ou de surinfections bronchiques.
쐌
Les pneumopathies d'irritation ou allergiques sont observées avec les huiles entières et les fluides aqueux. Elles peuvent être dues à certains des additifs et aux métaux sous forme de particules ou dissous (cobalt…) provenant des alliages usinés ou des outils.
쐌
Des pathologies respiratoires peuvent également avoir pour origine certains micro-organismes ayant colonisé des fluides aqueux.
3.3. Risques de cancers
Outres les cancers cutanés précédemment cités, des études épidémiologiques menées en particulier aux États-Unis dans l'industrie automobile montrent qu'il existe des arguments en faveur d'une relation entre les fluides de coupe et les localisations cancéreuses suivantes : larynx, pancréas, rectum et vessie.
Ces cancers seraient associés essentiellement aux huiles entières. Des arguments plus limités, incriminant les fluides aqueux, existent également concernant les cancers de l'œsophage et de l'estomac.
Des nitrosamines peuvent se former dans les fluides aqueux, certaines de ces molécules sont cancérogènes (voir
§ 2.2.).
3.4. Maladies professionnelles
Certaines pathologies cutanées ou respiratoires peuvent être reconnues comme maladies professionnelles, on trouve entre autres [8] :
쐌 les affections provoquées par les huiles minérales* ou synthétiques : tableau 36 (du régime général de la sécurité sociale) ;
쐌 les affections cutanées cancéreuses provoquées par les huiles minérales : tableau 36 bis ;
쐌 les affections provoquées par le formaldéhyde : tableau 43 ;
쐌 les affections provoquées par les amines aliphatiques ou alicycliques : tableaux 49 et 49 bis ;
쐌 les lésions eczématiformes de mécanisme allergique : tableau 65.
4. Évaluation des risques
L'appréciation des risques est un élément essentiel qui permet de décider des mesures de prévention à mettre en place.
La brochure ED 840 [9] propose une démarche pour l'évaluation des risques.
Différents outils techniques peuvent
être utilisés pour la réaliser.
4
4.1. Contrôle chimique et biologique des fluides de coupe
Plusieurs types de contrôles, différents pour les huiles entières et les fluides aqueux, peuvent être effectués sur les fluides de coupe.
4.1.1. Huiles entières, contrôles chimiques
Les teneurs en HPA des huiles entières neuves peuvent être contrôlées à partir de l’indice DMSO – UV [10] exigible auprès des fournisseurs. On considère que les huiles de coupe doivent présenter un indice DMSO – UV inférieur à 300
[11] (ce qui correspond à une teneur en benzo(a)pyrène inférieure à 30 μg/kg).
Pour les huiles en cours d’utilisation, la méthode DMSO – UV ne peut être employée. Si un vieillissement important de l’huile conduisant à un enrichissement en HPA est soupçonné, le contrôle de la teneur en benzo(a)pyrène comme traceur des HPA peut être réalisé. Cette teneur doit rester inférieure à 100 μg/kg [7].
4.1.2. Fluides aqueux, contrôles chimiques et biologiques
Pour une bonne efficacité des fluides aqueux, il est conseillé de surveiller différents paramètres en cours d'utilisation.
Certains d'entre eux ont également une importance pour la santé des salariés comme le pH, la concentration en produit actif et la teneur en micro-organismes.
Cette dernière peut facilement être
évaluée à l’aide de kits. La concentration maximale généralement admise pour le bon fonctionnement du fluide est de 10 6 bactéries par millilitre. Ne pas dépasser cette valeur contribue aussi à préserver la santé des salariés.
Le contrôle de la teneur en nitrites et en N-nitrosodiéthanolamine peut également être utile selon la composition du fluide et ses conditions d'utilisation.
L’absence de nitrites peut être contrôlée à l’aide de bandelettes réactives. En ce qui concerne la concentration en Nnitrosodiéthanolamine, l’INRS recommande de ne pas dépasser 1 mg/kg dans le fluide [7].
4.2. Valeurs limites et métrologie
4.2.1. Valeurs limites
Compte tenu de la complexité du problème et de la diversité des polluants mis en jeu, une approche globale sera privilégiée, plutôt qu'une recherche de polluants spécifiques.
Il n'existe pas de valeur limite française ou européenne pour les aérosols de fluides de coupe. La seule valeur limite actuellement disponible est celle de
0,5 mg/m 3 proposée par le NIOSH
(National Institute for Occupational
Safety and Health) pour la fraction inhalable de l'aérosol [12].
Pour les huiles minérales, l'ACGIH
(American Conference of Industrial
Hygienist) propose l'abaissement de la valeur limite concernant la fraction inhalable de l'aérosol de 5 à 0,2 mg/m 3 . Cette valeur, qui n’est pas spécifique des aérosols d'huile de coupe, n'est pas encore acceptée définitivement comme valeur limite par l'ACGIH.
Pour la suite du document on retiendra donc comme objectif , pour l'assainissement des ateliers utilisant des fluides de coupe (huiles entières et fluides aqueux), une concentration moyenne en aérosol de fluide dans l’air inhalé ne dépassant pas 0,5 mg/m 3 (fraction inhalable) .
Dans certains cas particuliers, il est nécessaire de considérer l'exposition à des polluants spécifiques en complément ou en remplacement de celle aux brouillards de fluides de coupe. Ainsi, lors de la rectification des carbures frittés, c'est l'exposition au cobalt qui doit
être prise en compte (il n'existe pas de valeur limite française ou européenne pour le cobalt et, aux États-Unis, l'ACGIH a fixé une valeur limite à 0,02 mg/m
3
).
Parmi les autres polluants qu'il est parfois nécessaire de prendre en compte, on peut citer le formaldéhyde (dans le cas où des biocides libérateurs de formaldéhyde sont utilisés) et le benzo(a)pyrène.
4.2.2. Métrologie
Différentes métrologies sont utilisables dans les ateliers d’usinage, mais il convient de faire un choix en fonction des objectifs retenus, et surtout des valeurs limites utilisables pour l’évaluation du risque.
Dans les années 1970-80, les huiles entières étaient prépondérantes. Les prélèvements étaient effectués sur filtres, généralement en ambiance à l’aide d’appareils de prélèvement à grand volume.
On obtenait, par extraction du filtre au solvant, la concentration en « matières extractibles » représentatives de l’aérosol d’huile entière ; il était aussi possible d’analyser les hydrocarbures polycycliques aromatiques (HPA), et notamment le benzo(a)pyrène (BaP), présents dans ces aérosols. Les résultats étaient alors comparés à une valeur limite de
1 mg/m 3 pour les huiles (valeur dite « de confort »), et de 150 ng/m 3 pour le BaP.
Cette méthode de prélèvement et d’analyse n’est cependant pas adaptée au cas des fluides d’usinage aqueux, compte tenu entre autres de la faible quantité d’huile présente dans l’air, conduisant à des concentrations en huile et en BaP toujours très inférieures aux limites indiquées ci-dessus.
Une approche différente a été proposée par le NIOSH. Elle consiste à effectuer une mesure de la concentration pondérale de l’aérosol et à la comparer à une valeur limite au-dessous de laquelle les problèmes respiratoires peuvent être considérés comme minimes. Dans un premier temps, le NIOSH avait suggéré de mesurer la fraction thoracique de l’aérosol, puisqu’il s’agit de la fraction pertinente dans le cas de problèmes respiratoires, et de la comparer à 0,4 mg/m 3 .
Cependant, les appareils de prélèvement correspondants étant peu répandus, une alternative a été proposée consistant à mesurer la fraction inhalable de l’aérosol et à la comparer à une valeur limite de
0,5 mg/m
3
, un peu plus élevée.
Lorsque l’on soupçonne la présence de particules solides (métalliques par exemple) et si la concentration mesurée dépasse 0,5 mg/m
3
, il est souhaitable de procéder à une analyse complémentaire permettant de n’évaluer que le fluide.
Ces méthodes de prélèvement et d’analyse sont décrites dans la fiche
« Métropol » n° 2 « Concentration pondérale sur filtre » [13] ainsi que dans la méthode NIOSH 5524 [14].
En pratique on pourra utiliser :
쐌 en prélèvement individuel ou d’ambiance, un capteur type « cassette fermée », correspondant à celui décrit dans la norme NF X 43-257 [15] ;
쐌 en prélèvement d’ambiance, un capteur de la fraction inhalable de l’aérosol type CATHIA (ou à défaut un capteur de la fraction totale de l’aérosol, comme celui décrit dans la norme NF X 43-261
[16]), couplé à un appareil de prélèvement à fort débit.
Cette approche a des limites certaines :
쐌 il s’agit d’une mesure globale, donc assez sommaire ;
쐌 dans le cas de prélèvements individuels, le faible débit de l’appareil de prélèvement peut conduire à une incertitude importante sur la concentration, ce qui impose des prélèvements de longue durée, au moins six heures en pratique ;
5
쐌 elle n’est pas pertinente si l’on soupçonne la présence de polluants atmosphériques particuliers, gazeux ou sous forme de liquides volatils.
Mais elle présente aussi plusieurs avantages :
쐌 elle est réalisable avec tout appareil permettant de capter sur filtre la fraction inhalable de l’aérosol ; il est donc possible de réaliser des prélèvements individuels ou des prélèvements d’ambiance ;
쐌 l’exploitation des prélèvements par gravimétrie est relativement simple, ce qui permet de multiplier les prélèvements dans un même atelier ;
쐌 elle permet une bonne estimation de la qualité de l’air des locaux.
5. Prévention
Les mesures de prévention, collectives ou individuelles, sont déjà pour l’essentiel connues et restent valables même si les produits évoluent constamment. Elles s’appliquent, pour la plupart, aux deux types de fluides que l'on rencontre simultanément dans beaucoup d'ateliers.
Dans tous les cas, il est pertinent de choisir, en priorité, les fluides de coupe les moins dangereux pour la santé, comme les huiles minérales* raffinées
(tant pour la formulation de base que pour le conditionnement des additifs). Il peut également être utile d'employer des fluides contenant des additifs destinés à limiter la formation des aérosols.
L’utilisation des procédés produisant peu d'aérosols, comme les techniques de microlubrification ou d'usinage à sec en tenant compte de l’émission de poussières, permet d’éviter l’arrosage des pièces ; sinon les débits d'arrosage doivent être limités au strict nécessaire. Une
étude allemande [17] sur la microlubrification montre que, lors d’essais d’usinage sur différents matériaux avec des lubrifiants du marché, les émissions d’aérosols sont faibles. Toutefois, les lubrifiants de très faible viscosité (3 mm 2 /min à
40° C) sont à éviter car ils entraînent de fortes émissions d’aérosols et de vapeurs.
Le capotage des machines et le captage des aérosols à la source, complétés le cas
échéant par une ventilation générale efficace, permettent de réduire l'exposition des salariés (voir § 6. et 7.).
Le suivi des fluides s’avère indispensable (voir § 4.1.) afin d’assurer le maintien de leur qualité dans le temps. La lutte contre les micro-organismes peut nécessiter des ajouts de biocides. Il est important de respecter les préconisations des fournisseurs, une concentration trop faible pouvant entraîner la sélection de micro-organismes résistants au biocide, alors qu'une forte concentration favorisera l'apparition d'irritations et d'allergies chez les opérateurs. De plus, il convient de nettoyer les cuves avant tout changement de fluide contaminé pour prévenir le développement rapide des micro-organismes dans le nouveau fluide. Alterner deux types de biocides permet d’éviter l’apparition de résistances des microorganismes. L’utilisation de biocides concentrés nécessite des précautions particulières en se référant à leurs fiches de données de sécurité.
Les équipements de protection individuelle permettent d'éviter les contacts avec les fluides de coupe, on utilise :
쐌 des gants de protection pour manutentionner les pièces couvertes de fluide ; la matière recommandée aussi bien pour les fluides aqueux que pour les huiles entières est le nitrile [18] ; les gants en caoutchouc naturel (latex) sont
à éviter à cause de leur mauvaise résistance aux huiles et des risques d’allergies qu’ils entraînent ;
쐌 des vêtements de travail couvrant les bras, à changer périodiquement et rapidement lorsqu’ils sont souillés ;
쐌 si nécessaire des tabliers de protection.
Il est recommandé de respecter des mesures d'hygiène :
쐌 se laver les mains, notamment avant le repas et les pauses, en proscrivant les solvants et les détergents trop alcalins ainsi que ceux chargés en particules abrasives ;
쐌 se doucher en fin de poste.
Certaines mesures de prévention, concernant le choix et l’utilisation des fluides de coupe aqueux sont spécifiques. Il est nécessaire :
쐌 de préférer les constituants les moins agressifs possible (bactériostatiques plutôt que bactéricides, émulgateurs non ioniques... ) ;
쐌 d'éviter les additifs précurseurs de nitrosamines (nitrites, éthanolamines, mais prendre garde aussi aux biocides nitrés ou aux nitrates de l'eau de dilution) et les biocides générateurs de formaldéhyde ;
쐌 de prendre des formulations à pH modéré (9 - 9,2) ;
쐌 de respecter les concentrations de fluide dans l'eau préconisées par le formulateur.
Pour le problème plus spécifique des métaux dissous (usinage de carbures métalliques en particulier), on recommande l’utilisation des fluides spécifiques adaptés à ce type de travail : fluides qui ne dissolvent pas le cobalt (absence d'amines complexantes dans la formulation) et dont l'efficacité a pu être démontrée sur le terrain [4].
6. Rappel des principes généraux de ventilation
L’objectif de la mise en place d'une ventilation dans les ateliers est d'abaisser la concentration en aérosols de fluides de coupe aux postes de travail à un niveau inférieur à 0,5 mg.m
-3 (voir § 4.2.1.).
Pour atteindre ce résultat, il faut que les différentes sources de pollution soient connues et correctement traitées. Deux techniques de ventilation peuvent être mises en œuvre, séparément ou conjointement.
6.1. La ventilation par aspiration locale
Cette solution consiste à capter les polluants au plus près de leur point d'émission, avant qu'ils ne pénètrent dans la zone d'évolution des travailleurs et ne soient disséminés dans toute l'atmosphère de l'atelier. Elle se compose de dispositifs de captage localisé et d'introduction d'air de compensation. Elle doit être retenue en priorité.
6.2. La ventilation générale
Cette technique consiste, grâce à un apport d'air neuf en quantité suffisante, à diluer les polluants émis afin que leur concentration dans l'ambiance ne dépasse pas 0,5 mg.m
-3
. Les travailleurs doivent être suffisamment éloignés des sources de pollution pour ne pas être soumis aux fortes concentrations existant au voisinage immédiat de celles-ci.
La ventilation générale peut être assurée par une ventilation naturelle ou mécanique selon que les introductions et les extractions sont ou non maîtrisées par des moyens mécaniques.
Cependant, cette méthode, en tant que technique principale, n’est à retenir que lorsqu’il est impossible de mettre en
œuvre la ventilation par aspiration locale. Par contre, une ventilation géné-
6
rale complémentaire est souvent nécessaire pour éliminer les polluants résiduels non captés à la source par les aspirations locales. Le guide de ventilation n° 0 [19] traite de manière plus approfondie des principes généraux de ventilation.
7. Conception d'une installation de ventilation
Une installation correctement conçue doit comprendre les fonctions suivantes
[20, 21, 22] :
쐌 captage localisé ;
쐌 ventilation générale pour diluer et
évacuer les polluants non captés à la source ;
쐌 compensation de l’air extrait par les dispositifs de captage ;
쐌 transport de l'air pollué ;
쐌 traitement de l'air pollué (épuration, rejet à l'extérieur, recyclage partiel
éventuel).
7.1. Captage localisé
On distingue deux types de dispositif, le captage enveloppant et le captage inducteur.
Pour des raisons d’efficacité, il convient de privilégier le captage enveloppant chaque fois que cela est techniquement possible.
7.1.1. Captage enveloppant
(tableau I)
Ce dispositif est conçu de telle sorte que la source de pollution soit totalement enfermée et qu'aucune dispersion des polluants à l'extérieur du dispositif ne soit possible.
Sa réalisation est souvent aisée puisque de nombreuses machines sont équipées de capots destinés à limiter, d'une part les risques d'éjection des pièces ou des outils, d'autre part les projections d'huile sur les opérateurs, le sol ou les murs.
Le captage peut être obtenu par encoffrement total de la machine ou uniquement par encoffrement de la partie génératrice de brouillards d'huile (tête d'usinage par exemple).
Le dispositif de captage doit de plus
être conçu pour éviter :
쐌 une dispersion des brouillards dans l'atelier au moment de l'ouverture du capot ;
쐌 un mauvais fonctionnement de l'épurateur à cause d'une concentration excessive d’aérosols de fluides de coupe dans l'air à épurer.
Deux solutions sont possibles.
Dépression importante dans le capot, faible débit d'air, balayage préalable du capot avant son ouverture
Une dépression de l'ordre de 20 à 50 Pa
(environ 2 à 5 mm de colonne d'eau) est obtenue par une bonne étanchéité du capot
(photo 1)
.
Cette dépression induit des vitesses d'air au niveau des fuites de l'ordre de 3 à
6 m.s
-1 [23].
À l'arrêt de la machine, le capot doit
être entrouvert pendant un certain temps avant d'être ouvert totalement, afin de permettre un balayage de l'enceinte par de l'air propre. Cette méthode est particulièrement indiquée en cas de projections d'huile sous forte pression.
Types de matériels
Capot sans ouverture avec dépression importante
TABLEAU I
C
ARACTÉRISTIQUES DES DIFFÉRENTS CAPTAGES ENVELOPPANTS
Dépression
à l’intérieur du capot par rapport à l’atelier
(Pa)
Vitesse d’air dans les ouvertures ou aux fuites
(m.s
-1 )
Vitesse d’air de balayage dans le capot
(m.s
-1 )
20 à 50
≈ 3 à 6
Négligeable Faible débit d’air
Pas de balayage du capot (photo 1)
≈ 0,2 à 0,5
Observations
Ouverture du capot en deux temps :
1) partielle temporisée pour permettre le balayage des polluants ;
2) totale ensuite
Dépression et vitesse de balayage bien maîtrisées
Débit d’air important balayage du capot (air neuf)
20 à 50
≈ 3 à 6
Capot avec ouverture
Dimensions des ouvertures bien définies et faibles devant celles du capot
So/Sc < 0,2
(photo 2)
-
≈ 2 à 3
Dimensions des ouvertures mal définies et non négligeables devant celles du capot
So/Sc > 0,2
(photo 3)
-
≈ 0,5 à 1
Les mesures de pression dans le capot sont faites avec la machine arrêtée pour éviter les projections.
Les mesures de vitesses sont faites avec la machine en fonctionnement.
S
S o c
: Section des ouvertures dans le capot.
: Section du capot perpendiculaire à l'écoulement de l'air.
≈ 0,2 à 0,5
≈ 0,2 à 0,5
7
Photo 1. Dispositif de captage enveloppant sur tour à décolleter.
Photo 2. Dispositif de captage fermé avec ouverture de section faible.
Dispositif d'épuration avant rejet dans l'atmosphère
Ventilation mécanique
L'air de l'atelier n'est aspiré que lors de l'ouverture de l'écran coulissant p u é
Δp = 20
à 50 Pa
Enceinte fermée
Prise d'air
à température extérieure
Photo 3. Rectifieuse avec capteur.
Singularité permettant d'obtenir la dépression souhaitée dans l'enceinte
Figure 1. Capotage enveloppant avec amenée d’air neuf à l’intérieur du capot.
Balayage minimal de l'intérieur du capot par de l'air propre
Ce balayage a pour effet de limiter les concentrations en brouillards d'huile et de les ramener à des valeurs acceptables
à l’entrée des épurateurs. Une vitesse de balayage de l'ordre de 0,2 à 0,5 m.s
-1
être considérée comme acceptable. peut
Une méthode consiste à mettre en place des capots ayant des ouvertures
conçues volontairement et qui assurent un écoulement préférentiel de l'air.
Lorsque les dimensions des ouvertures sont bien définies et faibles par rapport à celles du capot
(photo 2)
, les vitesses d'air dans les ouvertures doivent être de l'ordre de 2 à 3 m.s
-1 . Par contre, lorsque les dimensions des ouvertures sont mal définies et non négligeables par rapport
à celles du capot
(photo 3)
, les vitesses d'air dans les ouvertures doivent être de l'ordre de 0,5 à 1 m.s
-1
[24].
Une autre méthode consiste à amener de l'air neuf provenant de l'extérieur du local à l'intérieur du capot qui est totalement fermé
(fig. 1)
. Elle permet de maîtriser la dépression (20 à 50 Pa) et la vitesse de balayage à l'intérieur du capot et ainsi d'envisager des économies d'énergie substantielles car l'air extrait pour évacuer les polluants n'est pas pris dans l'atelier, sauf durant le temps où le capot est ouvert (récupération de pièces par exemple).
Remarques
Les dispositifs peu encombrants, dits « bras de récupération », permettent de réduire considérablement l'ouverture laissée dans le capotage, d'où une diminution très appréciable de la quantité de brouillard d'huile émis dans l'atelier. En outre, ils suppriment l'intervention manuelle de l'opérateur près des organes mécaniques en mouvement, le contact répété des mains avec les pièces souillées par le fluide de coupe et la détérioration des pièces fragiles.
Il existe aussi des robots de positionnement et de récupération des pièces. Ces appareils nécessitent en général l’utilisation d’air comprimé pour extraire la pièce et évacuer les copeaux, ce qui génère une pollution importante alors que le capot est ouvert.
8
7.1.2. Captage inducteur
Cette technique est à employer uniquement lorsque l'utilisation du captage enveloppant s'avère impossible ou difficile.
Contrairement au captage enveloppant, la source d'émission de polluants est à l'extérieur du dispositif de captage.
Celui-ci doit induire des vitesses d'air suffisantes dans la zone d'émission des polluants pour les entraîner à l'intérieur du réseau d'aspiration
(photo 4)
.
Lors de la conception d'un tel dispositif, il y a lieu :
쐌 de prévoir de le placer au plus près du point d'émission, en utilisant au mieux les mouvements naturels de l'air, tout en prenant en compte les turbulences provoquées par les pièces en mouvement ;
쐌 de calculer ses dimensions ;
쐌 de déterminer la vitesse de captage
à mettre en œuvre ;
쐌 de calculer le débit d'aspiration nécessaire pour assurer cette vitesse de captage.
Les vitesses de captage au point d'émission doivent tenir compte des conditions de travail, des différents facteurs de génération des brouillards (pression d'huile, vitesse de rotation des outils…) et de l'implantation du dispositif par rapport au point d'émission.
Le
tableau II
indique des ordres de grandeur des vitesses de captage à mettre en œuvre aux points d'émission de polluants selon l'implantation du dispositif de captage et selon la façon dont le fluide de coupe est amené à proximité des pièces.
La
figure 2
donne les relations permettant de calculer le débit d'air nécessaire à créer pour assurer une vitesse de captage
« v » à une distance « x » d'un dispositif selon la forme de celui-ci.
Remarques
- La mise au point d'un dispositif de captage inducteur est délicate et son efficacité peut chuter considérablement pour un dimensionnement ou une implantation incorrects ;
- la mise en place d'écrans permet souvent d'améliorer l'efficacité de tels dispositifs en limitant la zone de captage et les effets perturbateurs des courants d’air.
7.2. Ventilation générale
La ventilation générale a essentiellement pour fonction de diluer puis d’extraire les polluants résiduels. Elle ne peut
Photo 4. Dispositif de captage inducteur.
TABLEAU II
C
ARACTÉRISTIQUES DES DISPOSITIFS DE CAPTAGE INDUCTEURS
Fluide amené sous faible pression
(jet large) [24]
Fluide amené sous forte pression
(jet étroit) [20]
Captage au-dessus de la source de pollution
Disposition à retenir lorsque les courants de convection sont non négligeables
v > 0,5m.s
-1 v > 2,5 m.s
-1 en aucun cas remplacer les techniques de captage localisé. Pour concevoir un système de ventilation générale, il faut déterminer le nombre, la position et le débit des dispositifs d’extraction et d’introduction d’air ; ces éléments doivent
être le résultat d’une étude prenant en compte les données suivantes :
쐌 le nombre, la répartition, la position et le débit d’émission des sources de polluant ;
쐌 la dynamique éventuelle des émissions (vitesse d’émission, effet ascensionnel des gaz chauds…) ;
쐌 la toxicité des polluants, les valeurs limites ;
쐌 la présence de sources thermiques.
Ces données sont souvent difficiles à obtenir et l’étude de conception est en général complexe à mener. Elle peut s’ap-
Captage sur le côté de la source de pollution
(photo 4)
v > 0,75 m.s
-1 v > 2,5 m.s
-1 puyer sur des moyens d’investigation conséquents comme les techniques de simulation par la ventilation prévisionnelle. L’INRS, des Centres de mesures physiques des Caisses régionales d’assurance maladie et certains bureaux d’étude spécialisés disposent de telles techniques [25, 26, 27].
Plusieurs principes de base doivent
être respectés :
쐌 les dispositifs d’extraction et d’introduction mécaniques sont à privilégier ;
쐌 l’air introduit doit être pris à l’extérieur de l’atelier dans une zone non polluée en évitant toute interférence avec les rejets d’air pollué ;
쐌 les débits d’air extrait (en tenant compte des captages localisés) et introduit doivent être équilibrés ;
9
Bouches d'aspiration (
L b
≤ 5 ou circulaire)
X
Bouche isolée sans collerette :
Q = (
10 X
2
+ A)V
V
X
V
Bouche isolée avec collerette :
Q =
0,75(10 X
2
+ A)V
X
Bouche sans collerette reposant sur un plan :
Q = (
5 X
2
+ A)V
V
X
V
Bouche avec collerette reposant sur un plan :
Q =
0,75(5 X
2
+ A)V
Pour X assez grand
Q =
3,14 X
2
V
Fentes d'aspiration (
L b
> 5) Formules valables si X > 0,4 b
X
V
Fente isolée sans colerette
Q =
3,7L X V
V
X
Fente isolée avec colerette
Q =
2,8L X V
V
X
Fente sans colerette appuyée sur un plan :
Q =
2,8L X V
L
V
X
Fente aspirant dans un volume limité par deux plans :
Q =
1,6L X V
0,4H
V
H
Hotte en dôme :
•
4 côtés ouverts
Q =
1,4PHV
•
2 côtés ouverts b et L
Q = (b + L)HV
Q = débit d'aspiration (m
3
.s-1)
L = longueur de la bouche ou de la fente (m) b = largeur de la bouche ou de la fente (m)
A = Lb = section de la bouche ou de la fente (m
2
)
P = périmètre de la source (m)
V = vitesse de l'air à la distance X (m.s-1)
Figure 2. Relations entre le débit d’aspiration et les vitesses d’air induites devant un dispositif de captage inducteur (d’après [18]).
쐌 la ventilation doit être compatible avec les mouvements naturels de l’air et des polluants (notamment les mouvements ascensionnels dus aux sources chaudes) ;
쐌 les courants d’air, qui peuvent provoquer une diminution des efficacités des captages, doivent être évités ;
쐌 la présence de zones mal ventilées
(accumulation possible de polluants) doit être évitée ;
쐌 les vitesses et températures d’air dans l’atelier doivent permettre d’assurer le confort thermique des opérateurs
[28].
Pratiquement, une solution satisfaisante consiste à introduire l'air neuf en partie basse ou mi-basse (environ 3 m du sol) en plusieurs endroits et à extraire l'air pollué en partie haute de l'atelier
(ventilation par déplacement d'air). Hors saison de chauffage, l’air neuf, légèrement sous-tempéré, va s'écouler dans les zones de travail, se réchauffer, puis entraîner dans un flux ascendant les polluants. Ce type d'installation participe à l'assainissement de l'air ambiant et permet d'améliorer les conditions de travail.
Toutefois, dans des locaux sans apports thermiques internes élevés, où l’air neuf est chauffé en hiver, cette solution ne peut convenir que si l’air neuf est insufflé vers le bas, par des diffuseurs placés à une hauteur comprise entre 2 et
3,50 m et dimensionnés de telle sorte que les vitesses résiduelles soient de l'ordre de 0,25 m/s dans la zone d’évolution des travailleurs. Dans tous les cas, il est nécessaire d'asservir le fonctionnement des extracteurs à l'introduction d'air neuf pendant les phases de travail.
7.3. Apport d'air de compensation
L'air extrait par les dispositifs d'aspiration locale ou de ventilation générale est compensé par des apports d'air provenant de l'extérieur.
Plutôt que de laisser l'air pénétrer de façon incontrôlée dans les locaux, il est nécessaire de prévoir, en même temps que les dispositifs d'extraction, des dispositifs d'apport d'air de compensation, de façon à :
쐌
éliminer les courants d'air à grande vitesse provenant des ouvertures
(portes, fenêtres, fissures…) qui peuvent provoquer une diminution de l'efficacité de captage ou un inconfort thermique pour le personnel ;
쐌
éviter que l'air provenant de zones
10
« polluées » ne soit entraîné vers des zones « propres » ;
쐌
éliminer les zones où peuvent s'accumuler les polluants.
L'introduction de l'air de compensation peut être naturelle ou mécanique.
Chaque fois que cela est possible, il est préférable de choisir l'introduction mécanique car elle permet :
쐌 de contrôler la pression à l'intérieur du local par rapport à l'extérieur ; en général, l'introduction se fait à un débit égal au débit total extrait par tous les dispositifs d'extraction, auquel on ajoute les débits d'air nécessaires aux appareils de chauffage par combustion ;
쐌 de distribuer l'air en des endroits judicieusement choisis de l'atelier, de façon à contrôler les écoulements, assurer la répartition la plus homogène possible et ne pas perturber le bon fonctionnement des dispositifs de captage inducteurs.
L'air de compensation doit être pris à l'extérieur des ateliers dans une zone non polluée en évitant toute interférence avec les rejets d'air pollué de l'atelier.
Afin d'assurer un certain confort thermique aux travailleurs, l'air neuf doit être réchauffé pendant les périodes froides de l'année. Les systèmes de chauffage nécessitent d’être installés et maintenus de façon à ce qu’ils n'accumulent pas de dépôts d’huile en provenance de l’atelier, de tels dépôts pouvant être à l’origine d’incendies.
L'efficacité globale de la ventilation d'un atelier dépend notamment de l'implantation des extractions locales et générales, et des introductions d'air neuf
(fig. 3)
.
Les avantages et les inconvénients des introductions et des extractions mécaniques ou naturelles sont développés dans le guide pratique de ventilation n° 0
[19]. La fiche pratique ED 86 [29] traite
également de la compensation de l’air d’une installation de ventilation. ments à angle droit, de réductions ou d'augmentations de section non progressives [19] ;
쐌 de limiter l'emploi des conduits flexibles annelés et de les remplacer par des conduits rigides, de préférence circulaires (la perte de charge d'un flexible peut atteindre cinq fois celle d'un conduit rigide de même longueur et même diamètre).
Les sections des conduits doivent être calculées pour obtenir des vitesses de transport de l'ordre de 7 à 12 m.s
-l afin de limiter l’entraînement de fluide dans le groupe de filtration. Il est conseillé de respecter certaines précautions pour limiter le dépôt d'huile sur les parois : brides de raccordement entre conduits bien ajustées, prévision d’une légère pente et de dispositifs de purge pour collecter les huiles déposées sur les parois, possibilité de démontage facile pour un nettoyage périodique. Des vitesses de transfert supérieures peuvent toutefois
être nécessaires lorsque les brouillards contiennent des proportions significatives de particules solides (abrasifs par exemple).
L'équilibrage du réseau gagne à être assuré par conception ; il peut être complété par l'implantation de registres de réglage nécessitant l’utilisation d’un outil pour toute modification du réglage.
Il est recommandé de prévoir des orifices (brides, prises de pression, points de mesure) pour permettre les contrôles périodiques.
7.5. Traitement de l'air pollué après captage
Quels que soient les dispositifs de captage et de transport des polluants mis en
œuvre, il convient d'assurer le traitement de l'air pollué ainsi que son rejet à l’extérieur ou son recyclage partiel. Deux procédés peuvent être utilisés.
Le rejet à l'extérieur du local
Il s’accompagne de l'épuration de l'air dans un souci de respect de l’environnement. Ce procédé doit être retenu en priorité.
Le recyclage partiel
Il consiste à réintroduire dans le local une partie de l'air capté après l'avoir
épuré
(encadré 1)
.
Le guide de ventilation n° 1 [23] précise les conditions dans lesquelles le recyclage partiel peut être pratiqué. Dans le cas particulier des aérosols de fluides de a) b)
7.4. Circuits de transport
Pour le bon fonctionnement des dispositifs de captage localisé et pour diminuer la puissance absorbée par les ventilateurs, il est important de limiter les pertes de charge des circuits de transport.
Pour réduire ces pertes, il convient :
쐌 de limiter l'utilisation de coudes à faible rayon de courbure, de raccordec) d)
Figure 3. Principes de dispositifs d’apport d’air de compensation.
a) Diffusion d’air au plafond. b) Diffusion à basse vitesse en partie basse.
c) Diffusion à basse vitesse en partie mi-basse. d) Tourelle d’introduction.
11
coupe, ces conditions ne sont pas totalement remplies (traces de constituants non déterminés). Toutefois, le recyclage partiel de l'air peut être retenu dans la mesure où il satisfait aux recommandations du présent guide (concentration en aérosols de fluides coupe ne dépassant pas 0,5 mg.m
-3 ) et aux conditions suivantes :
쐌 l'installation doit toujours autoriser un rejet direct à l'extérieur du local par un système « by-pass » (en période tempérée et dans tous les cas où l'épurateur n'assure plus correctement sa fonction) ;
쐌 le recyclage ne doit être mis en
œuvre que durant la saison froide (en effet, il ne se justifie que pour des raisons d'économies d'énergie) ;
쐌 l'introduction contrôlée d'une quantité minimale d'air neuf est tenu d’être assurée ;
쐌 un système de surveillance permanent doit permettre de déceler une défaillance de l'appareil d'épuration ;
쐌 des contrôles périodiques de l'efficacité d'épuration doivent être réalisés.
Il est important que la concentration à l’aval de l’épurateur n’excède pas le cinquième de la valeur limite recommandée
[30] fixée à 0,5 mg.m
-3
, soit 0,1 mg.m
-3
.
En pratique cette valeur d’efficacité ne peut être atteinte qu’en équipant les
épurateurs d’une filtration terminale à très haute efficacité, de type H12 ou plus
(cf. classification selon NF EN 1822-1
[31]).
L'avis du service prévention de la
Caisse régionale d'assurance maladie peut être utilement sollicité à ce sujet.
7.5.1. Principaux procédés d'épuration de l'air
L'épuration de l'air pollué, consiste à abaisser la concentration en gouttelettes dispersées. Plusieurs principes peuvent
être exploités à cette fin dans les appareils d'épuration. Ils sont regroupés sous les termes génériques d'épurateurs ou de séparateurs puisqu'ils permettent de séparer effectivement deux phases en présence : une phase continue, constituée par l'air contenant éventuellement quelques polluants gazeux, et une phase dispersée constituée par l’aérosol (microgouttelettes d’huile et particules solides produites par le travail des métaux ou provenant de l’atelier).
On distingue généralement quatre grandes familles de séparateurs, d'importance inégale selon leurs caractéristiques et leur diffusion commerciale
(tableau III)
.
E
NCADRÉ
1
Le recyclage
Le recyclage de l’air a pour objectif de réaliser des économies d’énergie pour le chauffage
(ou la climatisation) de l’atelier.
La prévention des maladies professionnelles conduit à déconseiller le recyclage, en effet :
■ en ce qui concerne les brouillards d’huile, l’épuration de l’air ne permet pas de garantir une parfaite salubrité de l’atmosphère de l’atelier :
■ l’efficacité vis-à-vis des brouillards produits à partir de fluides aqueux est mal connue;
■ les médias filtrants voient leur efficacité diminuer légèrement lorsqu’ils se chargent en liquide (voir § 7.5.3) ;
■ il subsiste des incertitudes sur les risques à long terme liés à l’inhalation d’aérosols de fluides de coupe, notamment pour les risques cancérogènes (voir § 3.).
Les systèmes de recyclage installés sur les machines et rejetant directement dans l’atelier sans
passer par une installation centralisée sont formellement déconseillés, en effet :
■
■ ils ne permettent pas de rejeter l’air à l’extérieur en dehors des périodes de chauffage ; pour rester efficaces, ils doivent faire l’objet d’une maintenance régulière qui peut être difficile à suivre et coûteuse lorsque les machines sont nombreuses ;
■ en cas de dysfonctionnement (le Code du travail, art. 232-5-8, prévoit que les installations de recyclage doivent comporter un système de surveillance permettant de déceler les défauts des dispositifs d’épuration), la seule solution pour ne pas recycler de l’air pollué dans l’atelier est l’arrêt de la machine ;
■ actuellement, les seuls dispositifs permettant de mettre en évidence une défaillance du système d’épuration sont ceux basés sur la détection d’une variation brutale de la perte de charge sur l’étage de filtration terminal. Ceux-ci ne permettent pas de mettre en évidence une dégradation progressive de l’efficacité du média filtrant ou la présence de microfuites. Les systèmes de surveillance de la concentration en particules à l’aval de l’épurateur, basés par exemple sur la détection de la charge électrique portée par l’aérosol, donnent des résultats satisfaisants notamment avec les dépoussiéreurs pour poussières de bois, mais ils ne sont pas applicables aux brouillards d’huile ; aujourd’hui, le suivi continu de la concentration en polluants de l’air recyclé n’est techniquement pas réalisable et ne peut être utilisé comme système de surveillance imposé par la réglementation.
Prix
TABLEAU III
C
ARACTÉRISTIQUES DES DIFFÉRENTS PRINCIPES DE SÉPARATION
Technique
Avantage
Inconvénient
Efficacité
Perte de charge
Maintenance
Tricot métallique
Maintenance réduite
Efficacité faible (préfiltre)
Faible si d < 3 à 5 µm
Faible et constante
Faible : se limite au nettoyage
Faible
Ces principes de séparation peuvent se rencontrer seuls, mais sont le plus souvent sous forme combinée : par exemple, un étage électrostatique associé à un filtre terminal ou encore, une pré-séparation centrifuge suivie de un à plusieurs médias filtrants. Généralement un pré-
Séparateur centrifuge
Maintenance réduite
Perte de charge élevée
Faible
à moyenne
Élevée et constante
Réduite
Élevé
Média filtrant
Diversité
Encrassement rapide
Faible
à très élevée
Faible
à élevée selon colmatage
Fréquente : remplacement
Faible à élevé filtre constitué d’un tricot métallique permet de protéger les éléments filtrants vis-
à-vis des déchets métalliques susceptibles d’être transportés par le flux d’air.
Ces tricots n’assurent pas vraiment de fonction de filtration compte tenu de leur très faible efficacité.
Séparateur
électrostatique
Efficacité
élevée
Prix élevé
Élevée
Faible et constante
Faible : se limite au nettoyage
Élevé
12
Séparateurs centrifuges
Ces appareils sont généralement constitués d'un ou plusieurs tambours, pourvus de lamelles et de guides, comportant parfois un média filtrant et lancé en rotation à grande vitesse. L'air pollué est aspiré au niveau des tambours où les gouttelettes d'huile sont précipitées puis
éliminées vers la périphérie sous l'effet de la force centrifuge développée lors de la rotation.
Les guides assurent l'élimination de l'huile qui est ensuite collectée par gravité. En complément, des dispositifs de pré-séparation sont également proposés dont le principe consiste à créer des zones de turbulences favorisant le dépôt de l’aérosol d’huile.
Les séparateurs centrifuges ne permettent pas d’atteindre de très hauts niveaux d’efficacité et doivent être réservés à la pré-séparation.
Séparateurs à médias filtrants
Ces appareils comportent un ou plusieurs médias filtrants capables d'arrêter les particules par la juxtaposition de plusieurs effets : effet tamis, inertie, interception, diffusion, effet électrostatique.
La coalescence des particules s'effectue sur le média et l'huile ainsi collectée est généralement éliminée partiellement par gravité. La phase liquide retenue diminue généralement l'efficacité de filtration des plus fines particules. Ces dispositifs permettent d’atteindre des degrés d’efficacité très élevés (filtration terminale à très haute efficacité de type
HEPA).
Séparateurs électrostatiques
Des électrodes soumises à un potentiel
élevé de plusieurs milliers de volts permettent d'ioniser localement l'air. Les gouttelettes amenées dans cet espace sont alors chargées par les ions présents et, sous l'effet du champ, migrent vers des électrodes collectrices où elles se déposent. L'huile est ensuite éliminée régulièrement par gravité. Ces systèmes permettent d’obtenir des niveaux d’efficacité élevés.
Ce type de séparateur ne doit pas être utilisé pour des brouillards de produits inflammables à basse température (température d’ébullition < 200° C, point d'éclair < 90° C).
D’autre part, du fait de la dispersion dans l'air d'un produit combustible, il est recommandé que la concentration du brouillard dans l'épurateur ne dépasse pas la valeur seuil de 1 g.m
-3 (environ
10 % de la limite inférieure d'explosivité d'un brouillard).
7.5.2. Caractéristiques et efficacité des épurateurs
Les séparateurs de brouillards d'huile sont essentiellement conçus pour arrêter les gouttelettes et non les vapeurs d'huile.
Dans un souci de simplification, les concentrations d'huile utilisées dans les paragraphes suivants ne concerneront que l'huile dispersée sous forme d'aérosols. Des travaux récents ont néanmoins mis en évidence des problèmes d’évaporation partielle de l’huile arrêtée par les séparateurs à médias filtrants [32].
Débit nominal
Le débit nominal désigne le débit de fonctionnement d'un appareil placé dans les conditions normales d'utilisation prévues par le constructeur. Ce débit est généralement exprimé en m 3 .h
-1 d'air traité. Les constructeurs indiquent parfois une plage de débit utilisable.
Perte de charge
La perte de charge (exprimée en daPa ou en mm de colonne d'eau) mesure la résistance opposée par l'épurateur à l'écoulement de l'air pollué. La perte de charge nominale est relative au débit nominal ; elle augmente généralement avec le temps pour les appareils à médias filtrants.
Efficacité
L'efficacité (notée
η) est le rapport de la quantité d'aérosol collectée par le séparateur pendant une unité de temps à la quantité parvenant à l'épurateur pendant le même temps. Si le débit d’air aval égale le débit amont, l’efficacité est alors donnée par :
η = 1 - –––
C
E
Avec C
S et C
E les concentrations de l'aérosol respectivement à l'entrée et à la sortie de l'épurateur.
On distingue efficacité totale (par rapport à la totalité de l’aérosol) et efficacité fractionnelle, définie pour une gamme de diamètres de particules. On parle d’efficacité totale en masse ou en nombre selon que les concentrations sont exprimées en masse ou en nombre.
L’efficacité fractionnelle est indépendante de l’unité dans laquelle est exprimée la concentration. En pratique, il est possible de mesurer l'efficacité fractionnelle sur un intervalle de diamètre, à l'aide par exemple d'un compteur optique.
L’efficacité totale dépend de la répartition granulométrique de l’aérosol, à la différence de l’efficacité fractionnelle, et il est important de noter qu’une efficacité totale en masse élevée n'est pas incompatible avec une efficacité faible pour de fines particules.
7.5.3. Performances des séparateurs industriels
Des travaux ont été effectués [33, 34,
35] afin d’évaluer en laboratoire et sur site, les performances d’épurateurs soumis à des brouillards d'huile entière. Ces essais ont mis en évidence la grande disparité des performances des séparateurs.
L’étude a également montré que l’efficacité des séparateurs à médias filtrants tendait à diminuer au cours du temps. Ce comportement particulier des filtres vis-
à-vis des aérosols liquides (type brouillard d'huile) est différent de celui généralement observé pour des dépoussiéreurs à médias colmatés par des particules solides. Des études récentes effectuées par l’INRS [36] le confirme.
Les mesures sur site attestent les résultats de laboratoire et mettent en avant deux éléments importants :
쐌
Le premier est l'existence d'une concentration d'huile en phase vapeur, nettement plus élevée que lors des essais de laboratoire, qu’aucun des séparateurs testés n’est capable d’éliminer. Ce phénomène est même renforcé par le fait qu'une partie de l'huile retenue sur les médias filtrants est susceptible de s'évaporer [32].
쐌
Le deuxième concerne la granulométrie des brouillards d'huile analysés.
Les auteurs confirment la présence de particules submicroniques, généralement très mal séparées par les séparateurs dynamiques (centrifuges sans filtration terminale). La répartition granulométrique du brouillard d'huile influence donc le rendement de séparation total. La sensibilité des autres systèmes (média filtrant, électrostatique) vis-à-vis de la taille des particules est moindre.
De plus, il a été montré que, par suite d'un montage inadapté ou d'une absence d’entretien, de mauvais rendements peuvent être observés avec des séparateurs en principe performants. La baisse du rendement des séparateurs à médias filtrants en fonction du temps a été confirmée en entreprise.
Les performances des épurateurs de brouillards d’huile peuvent être testées à partir de la méthode d’essai normalisée
13
(NF X 44-060) [37, 38] applicable aux séparateurs de débit inférieur à
5 000 m 3 .h
-1 . Cette méthode n’est en principe prévue que pour les brouillards d’huile entière.
7.5.4. Rejet de l'air épuré
à l'extérieur
Le rejet de l'air épuré à l'extérieur nécessite une étude de la configuration générale du bâtiment et de son environnement, de manière à éviter toute réintroduction intempestive des polluants résiduels [30].
Les arrêtés du 30 juin 1997 et du 2 février 1998 réglementent les émissions de polluants par les installations industrielles. Les brouillards d’huile ne sont pas explicitement pris en compte par cette réglementation. Concernant le travail mécanique des métaux et alliages, la rubrique 2560 de l’arrêté type du 30 juin
1997 semble être la plus adaptée de la réglementation sur les installations classées pour la protection de l’environnement. Les installations correspondant à cette rubrique sont soumises à autorisation si « la puissance installée de l’ensemble des machines fixes, concourrant au fonctionnement de l’installation » est supérieure ou égale à 500 kW. Les installations dont la puissance est comprise entre 50 et 500 kW sont soumises à déclaration. Aucune disposition concernant les rejets des installations de puissance inférieure à 50 kW n’est prévue.
Les valeurs limites de rejet en poussières prévues diffèrent selon les installations.
Installation soumise à autorisation :
C = 100 mg.m
-3 , si D ≤ 1 kg/h
(arrêté du 2 février 1998)
C = 40 mg.m
-3
, si D > 1 kg/h
C désigne la valeur limite de la concentration pondérale de l’aérosol contenu dans l’effluent et D le débit massique horaire maximal autorisé par arrêté préfectoral.
Les rejets doivent être évacués par l’intermédiaire de cheminées équipées d’un point de prélèvement d’échantillon. Un contrôle annuel des paramètres C et D doit être effectué par un organisme choisi en accord avec l’inspection des installations classées. L’arrêté préfectoral d’autorisation peut fixer des dispositions plus sévères que celles prescrites dans l’arrêté du 2 février 1998.
Installation soumise à déclaration
(arrêté du 30 juin 1997) :
C = 150 mg.Nm
-3 .
Le point de rejet doit dépasser d’au moins 3 m les bâtiments situés dans un rayon de 15 m. Le contrôle de C doit être effectué au moins tous les 3 ans par un organisme agréé par le ministère chargé de l’environnement.
8. Contrôles et maintenance d’une installation de ventilation
Pour maintenir son efficacité dans le temps, une installation de ventilation doit être correctement réceptionnée, puis maintenue régulièrement et faire l'objet de contrôles périodiques.
8.1. Dossier d’installation
Le dossier d'installation, défini par l’arrêté du 8 octobre 1987 du ministère chargé du travail, est à établir par le chef d'établissement dans un délai d'un mois après la première mise en service d'une installation de ventilation nouvelle ou ayant fait l'objet de modifications notables.
Il comprend :
쐌 une notice d’instruction établie et remise par le maître d’ouvrage, celle-ci comprend des valeurs de référence qui caractérisent l'installation par ses paramètres initiaux ;
쐌 les consignes d'utilisation qui constituent un guide pratique pour la conduite et le suivi de l'installation ; elles doivent comporter trois parties :
■ les dispositions prises pour la ventilation (les paramètres principaux de l'installation),
■ les éléments pour la conduite,
■ l'entretien ;
쐌 un recueil des résultats des contrôles périodiques.
Pour plus d’informations sur le dossier d’installation, il est possible de se reporter à l’Aide-mémoire juridique sur l’aération et l’assainissement des locaux de travail [39].
8.2. Réception de l'installation
Au plus tard un mois après sa mise en service, l'installation doit être caractérisée par des valeurs de référence qui seront déterminées dans les conditions nominales de fonctionnement. Ces valeurs de référence constituent les valeurs réputées satisfaisantes pour le bon fonctionnement de l'installation.
Elles servent de base à l'entretien de l'installation et aux contrôles de son efficacité.
Pour les installations existantes, le dossier de valeurs de référence peut être constitué à partir des résultats des premiers contrôles périodiques.
Remarque
Des orifices (brides, prises de pression, points de mesure) doivent être prévus pour permettre les mesures dans les conduits lors de la réception puis des contrôles périodiques.
8.2.1. Installations avec rejet direct
à l'extérieur
Le descriptif de l'installation et les valeurs de référence doivent comporter les éléments suivants :
쐌 caractéristiques détaillées des éléments constituant l'installation (nombre de dispositifs de captage, caractéristiques du ou des ventilateurs, type et caractéristiques de l'introduction d'air...) ;
쐌 débits, pressions statiques ou vitesses d'air pour chaque dispositif de captage, débit dans les conduits pour les dispositifs enveloppants et inducteurs ou, à défaut, vitesses d'air dans les ouvertures pour les dispositifs enveloppants ;
쐌 efficacité minimale de chaque dispositif de captage ;
쐌 débit global d'air extrait ;
쐌 caractéristiques des systèmes de surveillance ;
쐌 consignes en cas de panne ou de dysfonctionnement.
8.2.2. Installations avec système de recyclage partiel
En complément des données nécessaires pour les installations avec rejet direct à l’extérieur, les installations avec système de recyclage partiel devront être caractérisées par les éléments suivants :
쐌 débit global d'air neuf introduit ;
쐌 débit de recyclage ;
쐌 efficacité minimale des systèmes d'épuration (ces valeurs peuvent être fournies par le constructeur à partir des essais normalisés réalisés sur son matériel, cf. § 7.5.3.) ;
쐌 concentrations en brouillards d'huile : dans le conduit de recyclage en aval de l'épurateur, et en ambiance, à poste fixe, en des points représentatifs de la pollution de l'atelier ;
14
쐌 caractéristiques des systèmes de surveillance du recyclage et moyens de contrôle.
9. Prévention des risques d’incendie
8.3. Opérations de maintenance
La fréquence des opérations de maintenance (nettoyage des capteurs, purge des conduits, changement des filtres des
épurateurs, nettoyage des plaques ou des
électrodes... ) doit être définie par le chef d'entreprise de façon à ce que la concentration moyenne ambiante en brouillards d'huile reste inférieure en permanence à
0,5 mg.m
-3
.
Les travaux réalisés et leur date d'exécution sont obligatoirement consignés dans le dossier de maintenance qui doit de plus indiquer la conduite à tenir en cas de panne ou de dysfonctionnement
(par exemple, passer au rejet à l'extérieur en cas de panne des épurateurs).
Des départs de feu sont possibles à l’intérieur du capotage des machines utilisant des huiles entières comme fluide de coupe. Le feu est susceptible de se propager par les conduits de ventilation, ce qui peut avoir des conséquences importantes pour les installations et faire courir des risques graves aux personnes.
Parmi les moyens de prévention des risques d’incendie on peut retenir :
Les systèmes d’extinction automatique par gaz carbonique
Compte tenu des risques (en particulier d’asphyxie) pour les personnes, il est recommandé que ceux-ci soient conformes aux règles APSAD de la
Fédération française des sociétés d’assurance dommage).
Les systèmes d’extinction automatique par brouillard d’eau avec propulsion par de l’azote
Il faut prendre en compte qu’un nouveau départ de feu est possible après l’arrêt du système d’extinction.
8.4. Contrôles périodiques
Ces contrôles, réalisés par un technicien qualifié appartenant ou non à l'entreprise, sont obligatoires. Pour les installations de ventilation avec rejet à l'extérieur, les contrôles périodiques suivants doivent être réalisés tous les ans :
쐌 mesure du débit global d'air extrait par l'installation ;
쐌 mesure des pressions statiques ou des vitesses d'air dans les conduits ou, à défaut, mesure des vitesses d’air dans les ouvertures ;
쐌 examen visuel de l'état de tous les
éléments de l'installation.
Pour les installations de ventilation avec recyclage partiel, il est nécessaire, en plus, d'effectuer tous les six mois :
쐌 des mesures de la concentration en brouillards d'huile dans le conduit de recyclage en aval de l'épurateur ;
쐌 un contrôle des systèmes de surveillance.
Tous ces contrôles permettent de s'assurer que l'on ne s'éloigne pas des valeurs de référence. Ils doivent être consignés sur le dossier de maintenance.
10. Dossiers techniques
Ce chapitre présente quelques réalisations industrielles dans lesquelles des mesures ont été effectuées en vue de déterminer les niveaux de pollution en fluides de coupe. Ces réalisations doivent
être considérées non comme exemplaires, mais comme représentatives des situations actuellement rencontrées dans les activités étudiées.
La plupart de ces dossiers permettent néanmoins de confirmer qu'il est possible d'assainir efficacement l'atmosphère des ateliers et de maintenir une concentration en brouillards d'huile inférieure à la valeur de 0,5 mg.m
-3 conisée dans ce guide.
d'air pré-
Les dossiers techniques présentent :
쐌 le type d'activité et les caractéristiques de l'atelier étudié ;
쐌 les caractéristiques aérauliques des dispositifs de captage et de ventilation ;
쐌 les résultats des prélèvements d'atmosphère effectués dans différentes configurations de ventilation afin d'apprécier l'efficacité globale de l'installation ; les concentrations en brouillards d'huile sont exprimées en mg.m
-3 d'air.
A
telier d’affûtage
L’entreprise est une PMI (32 salariés) spécialisée dans l'affûtage par rectification et la création d'outils spéciaux en matériaux durs tels que l'acier rapide, les aciers au cobalt et au tungstène, la céramique et le diamant. Les outils affûtés sont utilisés dans de nombreux domaines industriels (aéronautique, automobile, secteur ferroviaire…).
Un parc de 36 machines est implanté dans l'atelier de rectification et d'affûtage de matériaux durs.
Environ 1 à 2 tonnes de carbures métalliques sont consommées par mois sous la forme de :
쐌
10 % de S36T contenant 76,5 % de carbure de tungstène (WC), 4 % de carbure de titane (TiC), 7,5 % de carbure de tantale niobium (Ta (Nb) C) et
12 % de cobalt (Co)
쐌
90 % de TSM 30 contenant 90 % de carbure de tungstène (WC) et 10 % de cobalt (Co)
Le fluide de coupe aqueux est dilué
à 3 % dans l’eau ; il est régénéré en continu.
Réalisations
À l'occasion du transfert de ses activités et suite à l'apparition de deux maladies cutanées liées aux fluides de coupe, l’entreprise a recherché des solutions pour réduire ces risques.
En parallèle à un captage des polluants aux postes de travail, l'entreprise a mis en place un système centralisé d'épuration des fluides par effet centrifuge.
Toutes les machines, sauf une, sont
équipées de captages inducteurs, semi-enveloppants ou enveloppants.
Les caractéristiques de l’installation de ventilation sont présentées dans le
tableau IV
.
L'air neuf entre naturellement par les ouvertures de l’atelier et l'air capté est filtré puis rejeté à l'extérieur. Le groupe de filtration a été placé à l'extérieur des locaux de travail afin de limiter les nuisances sonores dues au ventilateur.
Pour leur épuration, les fluides de
e d’outils en carbure de tungstène
coupe sont pompés, dans chaque bac de récupération placé sous les machines à affûter, avant d’être traités dans un système central de centrifugation où les particules métalliques sont séparées. Cette installation est placée dans un local extérieur à l'atelier.
Résultats des mesures
Le débit d'air extrait sur le réseau centralisé est de 36 000 m 3 /h.
Les vitesses de transport dans les conduits varient de 7 à 30 m/s et les vitesses près du point d'émission des polluants de 0,5 à 5 m/s.
Les tests réalisés au tube fumigène montrent que les efficacités de captage de toutes les machines sont correctes.
Quatre prélèvements d'ambiance sur trois périodes différentes (de mars
2000 à février 2002) ont été réalisés sur une période de 300 minutes.
Les moyennes des quatre prélèvements pour chaque période sont données dans le
tableau V
.
Bilan
Les résultats d'analyse indiquent que les niveaux de pollution aux poussières inhalables et aux métaux ont fortement diminué et sont très inférieurs aux valeurs de référence.
La mise en place simultanée du système de captage des particules de métaux durs et des aérosols de fluides de coupe, d’une part, et d’autre part, du système d'épuration des fluides a permis de réduire de façon notable :
쐌 les émissions de brouillards de fluide de coupe dans l'atelier ;
TABLEAU IV
Date Poussières inhalables
(mg/m 3 )
Cobalt
(mg/m 3 )
Tungstène
(mg/m 3 )
Valeurs recommandées
Prélèvements Mars 2000
Juin 2000
Février 2002
0,5
0,58
0,32
0,15
0,02*
0,007
0,02
< 0,001
5
0,04
0,09
< 0,003
* Valeur limite de l’ACGIH.
Mars 2000 : état initial • Juin 2000 : déménagement dans de nouveaux locaux • Février 2002 : fonctionnement définitif de la ventilation et de l'épuration de l'huile.
TABLEAU V
C
ARACTÉRISTIQUES DE L
'
INSTALLATION DE VENTILATION
Nombre de machines :
à équiper fonctionnant simultanément
36
30
Capotages
Type de gaine
Diamètre des prises d’air
Puissance du ventilateur
Débit nominal
Dépression
Vitesse de rotation du ventilateur
Niveau sonore de l’installation
Recyclage
Type de filtration
Visualisation de la saturation du système d’épuration inducteurs, semi-enveloppants et enveloppants galvanisée
130 mm
30 kW
36 000 m 3 /h (1 000 m 3 /h par machine)
3 000 Pa
1 110 tr/min
70 dB(A) by-pass manuel été/hiver
■
3 étages : décantation
■ filtration métallique
■ filtre à poches
+ 1 filtre à très haute efficacité
(pour le recyclage) détecteur de pression avec coupure de l’aspiration en cas de colmatage des filtres
D
OSSIER
T
ECHNIQUE
1
Photo 5. Vue générale de l’installation avec en premier plan le réseau d’alimentation et de récupération des fluides de coupe.
쐌 l'exposition des salariés aux poussières des métaux durs ;
쐌 les risques de dermites, en améliorant la qualité bactériologique du fluide de coupe ;
쐌 les manutentions de fluides de lubrification et des résidus d'affûtage ;
쐌 les risques de glissade ;
쐌 les odeurs nauséabondes aux postes de travail.
Photo 6. Tronçonneuse capotée
15
16
A
ffûtage de lames pour la menuiserie
Installation de ventilation sur des machines réputées difficiles à capoter.
L’activité principale de cette entreprise est d’affûter des lames pour des menuiseries.
L’atelier d’une surface de 430 m 2 dispose de trois zones de travail : une zone d’affûtage sous fluides aqueux (affûtage à l’humide), une autre d’affûtage à sec et, dans un local à part, une dernière d’affûtage à sec sur des scies à ruban. La zone d’affûtage des lames sous fluides aqueux s’étend à peu près sur la moitié de l’atelier.
11 machines d’affûtage travaillent sous fluides de coupe : 10 sous fluide aqueux dilué à 3 % environ et une sous huile entière. Deux détalonneuses usinent des lames au carbure.
Réalisations
L’entreprise a profité de son agrandissement et de sa restructuration pour traiter l’acoustique et pour installer deux réseaux de captages des polluants : l’un pour les machines travaillant à l’humide et l’autre pour celles travaillant à sec.
Suivant les types de machines et les types de travaux effectués sous fluides de coupe, des capotages complets
(photo 7)
ou des capteurs localisés
(photo 8)
ont été installés. Les capotages disposent tous de parties coulissantes ou relevables pour permettre l’introduction manuelle des pièces et le réglage des machines avant l’affûtage.
Photo 7. Affûteuse avec capotage complet.
D
OSSIER
T
ECHNIQUE
2
métalliques. Les huiles collectées sur ces filtres sont récupérées en partie basse du groupe.
La compensation de l’air est assurée par des entrées d’air statiques situées à proximité d’aérothermes.
Résultats des mesures
Photo 8. Rectifieuse avec capteur mobile.
La participation des opérateurs a été nécessaire pour définir au mieux les dimensions et les accès à maintenir pour chacun des capotages.
Capotages et capteurs sont reliés au réseau d’extraction centralisé ; pour les capteurs des rectifieuses, des canalisations souples annelées ont été choisies afin de permettre le déplacement du capteur avec le chariot d’affûtage.
Un groupe de filtration, situé en dehors de l’atelier, rejette l’intégralité de l’air épuré à l’extérieur. La filtration est assurée par deux étages de tricots
Le débit d’air global extrait sur ce réseau est de 9000 m 3 /h. Les débits d’air unitaires varient de 400 à 1400 m
3
/h suivant les machines, que ce soit pour les affûteuses ou les rectifieuses.
Les vitesses d’air de transport dans les conduits varient de 12 à 16 m/s selon les machines.
Les résultats des prélèvements d’atmosphères sont donnés dans le
tableau VI
.
Cette réalisation assure un assainissement correct de l’air de cet atelier : que ce soit pour les brouillards de fluides de coupe ou pour les particules de cobalt, les valeurs restent très inférieures aux valeurs limites.
La qualité de l’air ainsi obtenue dans l’atelier permet, de plus, d’éviter l’encrassement du traitement acoustique installé sous toiture et de maintenir ses performances dans le temps.
Polluants
Cobalt
Fluides de coupe
TABLEAU VI
Valeurs recommandées
0,02 mg/m 3
0,5 mg/m 3
Concentration en mg/m 3 d’air
ambiant près des machines : < 0,002 individuel : 0,006 à 0,008 ambiant entre les machines : 0,02 à 0,05
E
Zone d'affûtage
à sec
A
A p
A
A
Bureau
D p
D
R
R p
R
R p
R
Affûtage des lames de scies
à ruban
GF
Rejet extérieur
Légendes
A affûteuse
D détalonneuse
R rectifieuse
GF groupe de filtration
E entrée de l'air de compensation p point de prélèvement pour les mesures de concentrations atmosphériques
E
Schéma de l’atelier d’affûtage, avec l’implantation du réseau de captage des fluides de coupe.
A
telier de rectification
Diminution des niveaux d’exposition aux aérosols suite à l’optimisation des systèmes de captage.
L’établissement fabrique des outils coupants en carbure de tungstène, des outils pneumatiques portatifs, des fraises et autres instruments dentaires.
L’atelier est occupé par une cinquantaine de machines d’usinage dont 5 rectifieuses. Toutes les machines sont reliées à un réseau centralisé de captage des polluants.
sentés dans le
tableau VI
, mettent en
évidence l’amélioration significative apportée par le nouveau système de captage.
Capotage initial
Capotage ajouté à l’arrière de la machine
La machine présentée dans ce dossier est une rectifieuse de type « centerless ». L’usinage des pièces est effectué par passage entre deux meules tournant à vitesse élevée.
Les produits fabriqués sont des forets en acier et carbure de tungstène. Le fluide de coupe utilisé est de l’eau sans additif.
Des prélèvements effectués en 2000 ont montré que le poste sur la rectifieuse type « centerless » était celui qui présentait les expositions les plus importantes au cobalt.
Réalisations
Le capotage de la machine et le système de ventilation en place ont été optimisés suite à des interventions et des prélèvements d’atmosphère successifs.
Chronologie des aménagements effectués sur la machine :
■ 2000 : Optimisation du capotage de l’outil et à l’arrière de la machine
(photos 9 et 10) .
■
2002 : Optimisation du protecteur en plastique transparent placé devant l’outil en rotation
(photo 11) .
■ 2003 : Ajout d’un système de captage des polluants au plus près de la source d’aérosols. Il est relié à un ventilateur indépendant pouvant assurer un débit maximum de 1 250 m
3
/h.
(photo 9) .
Photo 10. Capotage arrière de la machine.
Capteur inducteur
D
OSSIER
T
ECHNIQUE
3
Photo 9. Capotage à l’avant de la machine.
Protecteur plastique transparent
Photo 11. Protecteur en plastique transparent.
Résultats des mesures
Les résultats des prélèvements de cobalt effectués avant et après la modification du système de captage, pré-
Photo 12. Capteur inducteur ajouté.
Photo 13. Vue d’ensemble de la machine.
Nature du prélèvement
Cobalt
14/12/00
0,207
TLV-TWA (ACGIH) du cobalt = 0,020 mg/m 3 .
TABLEAU VI
C moy. mg/m 3
12/06/02
C moy. mg/m 3
0,039
23/10/03
C moy. mg/m 3
< 0,002
17
18
A
telier de décolletage
Installation de captage d’aérosols de fluides de coupe avec recyclage partiel.
Les dispositifs de ventilation ont
été installés lors du déménagement de l’entreprise dans des locaux neufs.
EPU
L’atelier de décolletage est composé de trois secteurs (voir schéma de l’installation) :
■ un secteur décolletage composé de
15 tours à décolleter monobroche traditionnels fonctionnant avec des huiles entières ; ces machines ont été équipées, lors de la réalisation du réseau de captage, de capots mobiles enveloppants la partie usinage ;
■ un secteur de décolletage composé de 17 tours à commande numérique fonctionnant avec un fluide aqueux ; ces machines sont équipées d’origine de capots relativement étanches ;
■ un secteur reprise qui n’est pas encore raccordé complètement au réseau d’aspiration.
Réalisations
Chaque secteur de décolletage possède son propre réseau de captage et d’épuration.
La vitesse d’air dans les réseaux est comprise entre 6 et 12 m/s. Des dispositifs permettent de récupérer les condensats en parties basses des réseaux.
Une partie de l’air capté (60 % environ) est recyclée après épuration pendant la saison hivernale. L’air neuf, nécessaire à la compensation du débit d’air extrait (40 % du débit de l’air capté), est pris à l’extérieur de l’atelier et introduit dans le local après réchauffage.
Chaque réseau de ventilation est
équipé d’un by-pass permettant le
Décolletage traditionnel
Décolletage
à commande numérique
EPU
Schéma d’installation des secteurs de décolletage.
rejet à l’extérieur en dehors des périodes de chauffage ou en cas de dysfonctionnement du système d’épuration.
Les systèmes de filtration, installés sur chaque réseau, comportent :
Avant le by-pass :
■
■
■
■ cité,
■
1 filtre à chicanes,
2 étages de tricots métalliques, cité.
1 média filtrant moyenne effica-
Après le by-pass, et donc utilisé seulement en cas de recyclage :
1 filtre à poches moyenne effica-
1 filtre très haute efficacité (H12) polyèdres (fibres de verre).
conduit de recyclage du réseau de fluides aqueux et de 0,105 mg/m 3 dans le conduit de recyclage des huiles entières. Ces résultats respectent les préconisations de la note technique du 5 novembre 1990 [30] qui précise que
«des concentrations dans les conduits de recyclage inférieures au 1/5 des valeurs limites de moyenne d’exposition devraient permettre de traiter de façon satisfaisante un grand nombre de situations». On peut remarquer que, même avec une filtration de très haute efficacité, les concentrations en aérosols (huile entière) dans le conduit de recyclage sont proches de la limite de cette recommandation.
Résultats des mesures
Les prélèvements d’aérosols de fluides d’usinage ont été réalisés conformément à la méthode NIOSH décrite dans ce document.
Les résultats des prélèvements ambiants font état de concentrations comprises entre 0,07 et 0,17 mg/m
3
, valeurs inférieures ou égales au tiers de la valeur recommandée de 0,5 mg/m
3
.
Les prélèvements isocinétiques, réalisés dans les conduits de recyclage, montrent des concentrations de fluides d’usinage de 0,013 mg/m
3 dans le
Photo 15. Capotage amovible d’un tour à décolleter.
Réseau décolletage traditionnel
Réseau décolletage commande numérique
TABLEAU VII
Nombre de machines
15
17
Débit par machine
600 m 3 /h
530 m
3
/h
Débit global
9 000 m 3 /h
9 000 m
3
/h
Photo 14. Tour à décolleter.
D
OSSIER
T
ECHNIQUE
4
19
A
mélioration du captage et de la ventilation générale sur une chaîne d'usinage existante
D
OSSIER
T
ECHNIQUE
5
L'entreprise produit des pompes
à huile de directions assistées pour l'industrie automobile avec un effectif de 425 salariés.
L'essentiel de la production est réalisé sur une chaîne comprenant 25 stations d'usinage. Celles-ci ne peuvent pas être complètement capotées.
L'usinage est effectué sous fluide aqueux.
Le mauvais assainissement de l'air de l'atelier posait aux opérateurs de multiples difficultés, notamment une trop forte présence de brouillards d'huiles et des sols glissants.
Réalisations
Plusieurs faiblesses ont été diagnostiquées :
■ captage localisé sur machines insuffisant,
■ filtres électrostatiques ne donnant pas satisfaction,
■ ventilation générale se limitant à des systèmes d'ouverture statique en partie haute de la zone et compensation de l’air extrait par de l'air neuf, filtré et chauffé, soufflé à forte vitesse et de haut en bas (buses à induction) dans l'atelier, et rabattant l’air pollué vers le bas
(photo 16)
.
En 2002, il a été décidé d'améliorer l'installation afin d'obtenir une meilleure qualité de l'air.
La priorité était de capter le maximum de polluants directement sur les centres d'usinage. Cependant, compte tenu de leur conception, un capotage
Dépôts d’huile
Buse à induction rabattant les brouillards
Photo 16. Amenée de l’air neuf avant travaux.
total n'était pas possible, d'où la nécessité de disposer d'une ventilation générale efficace pour diluer et évacuer les polluants non captés à la source.
Le captage a été amélioré par la conception de nouveaux capteurs.
Sur chaque îlot de captage, en pré-filtration, les filtres électrostatiques ont
été remplacés par 20 filtres à chocs.
Leur emploi évite l'encrassement des réseaux de gaines et réduit le risque d'incendie. L'air est ensuite filtré une deuxième fois par des filtres en média plissé, avant le rejet à l'extérieur, via trois réseaux d'extraction
(photo 17)
.
Le débit d'air total extrait est de
37 000 m 3 /h .
En partie haute, deux tourelles d’extraction de 8 000 m 3 /h chacune ont été installées à côté des extracteurs statiques qui ont été conservés
(photo 18)
.
Pour assurer la compensation, un débit d'air neuf de 60 000 m 3 /h filtré et réchauffé en hiver est introduit à environ 3 m du sol. L'air est diffusé à faible vitesse par des diffuseurs à déplacement d'air thermo-orientables. Le principe est de diffuser l’air à faible vitesse horizontalement, lorsque la température de l’air soufflé est fraîche, et vers le bas lorsque la température de cet air est plus chaude
(photo 19)
.
Résultats des mesures
Cette réalisation montre que la ventilation générale n’est, à elle seule, pas suffisante pour atteindre l’objectif de
0,5 mg/m 3 , il est indispensable de capoter les machines.
Captage localisé
Photo 17.
Extracteur statique conservé
Ancien réseau d’amenée d’air neuf en partie haute mis hors service
Tourelle d’extraction
Photo 18.
La modification du système de ventilation a entraîné une nette amélioration des conditions de travail des opérateurs :
■
■ moins de brouillards dans l'atelier, moins d'odeurs.
Des prélèvements ont été réalisés après achèvement des travaux. Les prélèvements d’ambiance sont à la limite de la valeur recommandée et certains prélèvements individuels se situent au-dessus, ce qui représente cependant une amélioration certaine.
Compte tenu de l'ancienneté de la chaîne, pour descendre nettement en deçà de 0,5 mg/m 3 , certaines sources polluantes connues devront être mieux enveloppées.
Photo 19.
Première filtration
à chocs
Amenée d’air neuf
à faible vitesse en partie mi-basse
Amenée d’air neuf
à faible vitesse en partie mi-basse
C
entre d’usinage de pièces pour l’automobile
Machines entièrement capotées.
D
OSSIER
T
ECHNIQUE
6
Cet atelier produit des pièces de climatiseurs pour l’automobile, en acier ou en aluminium.
Les centres d’usinage sont répartis en
6 lignes de 4 machines sur une surface d’environ 500 m 2 située à peu près au centre d’un atelier de plus de 3 000 m
2
.
Ces machines travaillent toutes avec un fluide aqueux contenant 7 % d’huile environ. L’alimentation et la récupération des pièces usinées se font manuellement.
L’entreprise a souhaité dès le départ garantir un assainissement correct de l’air de cet atelier.
Réalisations
L’ensemble des centres d’usinage est raccordé à un système de captage des
émissions d’aérosols de fluides de coupe. L’installation de ventilation est composée de la manière suivante
(schéma et photo 20)
:
■ tion ; deux réseaux distincts d’extrac-
■ chaque réseau est raccordé à trois rangées de quatre machines, soit 12 machines par réseau ;
■ un capotage complémentaire a été installé sur toute la partie supérieure de chacun des centres d’usinage ; l’élément remarquable de cette réalisation réside dans le fait que ces capots peuvent s’ouvrir complètement sur leur
Photo 20. Vue générale d’un réseau de captage avec, en premier plan, le groupe de filtration. Un conduit d’arrivée d’air de compensation est
également visible.
GF
Rejet extérieur
Silencieux
GF
Entrée d'air neuf
Rejet extérieur
Silencieux c.u.
c.u.
c.u.
p c.u.
c.u.
c.u.
c.u.
c.u.
c.u.
p c.u.
c.u.
c.u.
c.u.
c.u.
c.u.
p c.u.
1
c.u.
2
c.u.
3
c.u.
4
c.u.
5
c.u.
6
Légendes
c.u.
쑱 centre d'usinage p
쑱
GF
쑱 groupe de filtration point de prélèvement pour les mesures de concentrations atmosphériques
Schéma des réseaux de captage des brouillards de fluides de coupe.
c.u.
c.u.
c.u.
dessus pour faciliter les opérations de maintenance
(photo 21)
;
■ chaque réseau dispose d’un groupe de filtration qui rejette l’air
épuré à l’extérieur du bâtiment ;
■ ces groupes de filtration sont situés dans l’atelier et disposent chacun d’un silencieux acoustique (destiné à diminuer le bruit pour le voisinage) ;
■ la filtration est assurée par trois
étages de filtres en tricots métalliques ; les huiles collectées sur les filtres sont récupérées en partie basse du groupe ;
■ la compensation de l’air est assurée par un réseau d’introduction maîtrisé en tout air neuf et disposant d’un système de réchauffage de l’air pour les périodes froides.
Résultats des mesures
Les vitesses d’air de transport dans les conduits varient de 8 à 12 m/s suivant les conduits des réseaux.
Les centres d’usinage sont en dépression très suffisante : des émissions de fumigène dans les plans d’ouverture frontaux des machines, notamment lorsque les opérateurs récupèrent les pièces usinées, montrent un rapide entraînement des fumées dans l’enceinte des machines.
Les résultats des prélèvements d’atmosphères sont répertoriés dans le
tableau VIII
.
Le débit d’air extrait par réseau est de
7200 m 3 /h.
Les débits d’air unitaires sont d’environ 600 m 3 /h par centre d’usinage.
Photo 21. Capotage supérieur ouvrant sur un centre d’usinage.
TABLEAU VIII
Polluant
Valeur recommandée (mg/m
3
)
Concentration en mg/m 3 d’air ambiant entre les machines
1. Avant la mise en place de captage
2. 6 mois après fluides de coupe
0,5
0,1 à 0,4
0,08
A
telier d’usinage
L’atelier d’usinage est occupé par 7 machines numériques (2 scies et 5 tours). Les matières usinées sont principalement : l’aluminium, le tantale, le titane, le chrome et des métaux précieux. Le fluide de coupe utilisé est une
émulsion à 5 % d’huile dans l’eau.
Le chauffage et le rafraîchissement de l’atmosphère sont effectués par une pompe à chaleur dont le rendement est de l’ordre de 3 pour la production du froid et supérieur à 3 pour la production de chaleur.
Réalisations
Les machines numériques de l’atelier sont reliées à un réseau d’extraction centralisé pour le captage des aérosols de fluides de coupe. Il n’y a pas de recyclage de l’air.
Le capotage permet d’assurer une protection mécanique (copeaux, projection d’huile…) et d’optimiser le débit de ventilation.
Le captage des polluants est effectué
à l’opposé du point d’émission (face opposée au mandrin). Un déflecteur est placé à quelques centimètres devant l’orifice du capteur pour éviter que le fluide de coupe soit aspiré en quantité importante.
L’air de compensation : il est introduit par des bouches libres ; l’air neuf est pris pour 2/3 à l’extérieur et 1/3 dans les locaux adjacents à l’atelier, sans pollution spécifique.
Puissance du ventilateur : 18,5 kW.
Débit nominal : 15 000m
3 /h.
D
OSSIER
T
ECHNIQUE
7
Niveau sonore de l’installation : 79 dB(A).
Vitesse de transport de l’air dans les
gaines : 18 à 21 m/s.
Type de conduit : acier galvanisé.
Diamètres des extracteurs : 120, 150,
180, 200 mm suivant le type de machine.
Maintenance et contrôle de l’installation
La maintenance de l’ensemble du système de ventilation et des conduits est effectuée une fois par an par l’installateur (nettoyage à l’eau + air comprimé).
Un contrôle annuel du débit et des vitesses d’air de captage est réalisé par l’entreprise sur l’ensemble de l’installation. Parallèlement, un laboratoire agréé par le ministère de l’écologie
■ ■ ■
21
Photo 22. Les machines sont entièrement encoffrées
(excepté un tour où une ouverture permanente est nécessaire pour le passage de la navette porte-outils). L’accès aux pièces s’effectue par des portes coulissantes.
Photo 23. L’air pollué est filtré, puis rejeté vers l’extérieur. Les éléments filtrants sont constitués de couches de fibres d’acier. Un rinçage automatique du séparateur est effectué toutes les 4 heures à l’eau et avec de l’air comprimé.
22
A
telier d’usinage
(suite)
D
OSSIER
T
ECHNIQUE
7
■ ■ ■ et du développement durable vérifie les mesures d’émission des substances émises dans l’atmosphère.
Résultats des mesures
Sept prélèvements d’atmosphères ont été effectués dont :
■ trois prélèvements d’ambiance à proximité des machines,
■ quatre prélèvements sur les opérateurs.
L’étude de l’évaluation de l’exposition aux aérosols de fluides de coupe a été effectuée lors de l’usinage de pièces en aluminium.
TABLEAU IX
Les résultats sont satisfaisants sur le plan de l’exposition tant aux aérosols qu’aux poussières d’aluminium
(tableau IX)
.
Identification des emplacements
Exposition aux aérosols de fluides de coupe en (mg/m 3 )
(Valeur recommandée 0,5 mg/m 3 )
Ambiance
A proximité du centre d’usinage
A proximité du tour n° 1
A proximité du tour n° 2
Prélèvement sur les opérateurs
Tour (centre d’usinage) prélèvement n°1
Tour (centre d’usinage) prélèvement n°2
Tour n° 1 (commande numérique)
Tour n° 2 (commande numérique)
0,07
0,09
0,06
0,12
0,12
0,28
0,31
Exposition aux poussières d’aluminium en mg/m 3
(VME : 5 mg/m 3 )
< 0,02
0,02
< 0,02
< 0,02
< 0,02
< 0,026
< 0,041
Photo 24. Le fluide est récupéré dans un fût situé sous le séparateur.
Un contrôle du niveau permet d’éviter le débordement du fût et de prévoir son changement.
Photo 25. Bien que les valeurs au tour
à commande numérique soient en deçà de la valeur recommandée, nous constatons lors du démontage de l’outil que l’opérateur doit pénétrer dans la zone d’usinage ce qui entraîne ponctuellement des expositions plus fortes (tour n°2).
11. Glossaire
Aérosol :
On appelle aérosol toute suspension, dans un milieu gazeux, de particules solides ou liquides.
Ces particules sont considérées conventionnellement en suspension si leur vitesse de chute n'excède pas
0,25 m/s (norme NF X 44-001) [40].
Cancérogène :
Classification de la
Communauté européenne :
■
La catégorie 1 correspond aux substances que l'on sait être cancérogènes chez l'homme.
■
La catégorie 2 correspond aux substances devant être assimilées à des substances cancérogènes chez l'homme. On dispose de suffisamment d'éléments pour justifier, avec une forte présomption, que l'exposition de l'homme à de telles substances peut provoquer un cancer.
■
La catégorie 3 correspond aux substances préoccupantes en raison d'effets cancérogènes possibles mais pour lesquelles les informations disponibles ne permettent pas une évaluation satisfaisante (preuves insuffisantes).
Diamètre aérodynamique :
On appelle diamètre aérodynamique, d'une particule de forme et de densité quelconque, le diamètre d'une sphère de densité unité (masse volumique
1 000 kg/m
3
) dont la vitesse de chute limite dans l'air est égale à celle de la particule considérée. Le diamètre aérodynamique est le paramètre essentiel traduisant la taille d'une particule lors de l'étude de ses mouvements dans l'air.
Cela n'est cependant plus le cas pour les particules submicroniques (diamètre
< à 1 μm), dont les mouvements sont liés en partie à des phénomènes de diffusion.
Huile minérale :
Les huiles de base, destinées à la formulation d'huiles de coupe, sont obtenues par distillation sous vide du résidu de distillation atmosphérique du pétrole brut. Ces huiles de base sont ensuite raffinées par différents traitements. Ceux-ci permettent d'améliorer certaines de leurs propriétés et d'abaisser leur teneur en hydrocarbures polycycliques aromatiques
(HPA).
Huile régénérée :
Il s'agit d'huiles industrielles usagées qui ont été récupérées par des sociétés spécialisées et retraitées par un procédé comparable au raffi-
nage, pour fournir des bases lubrifiantes de caractéristiques proches de celles des huiles de base provenant directement du pétrole.
Les traitements sommaires (décantation ou filtration effectuées dans l'atelier par exemple) ne peuvent pas être considérés comme des opérations de régénération.
VLE :
Valeur Limite d'Exposition professionnelle atmosphérique destinée à protéger les salariés des effets immédiats ou à court terme, mesurée ou estimée sur une durée maximale de 15 minutes.
VME :
Valeur limite de Moyenne d'Exposition professionnelle atmosphérique destinée à protéger les salariés des effets à terme, mesurée ou estimée sur la durée d'un poste de travail de 8 heures.
B I BL I OGRAPHI E
[1]
■
NF ISO 6743-7 – Lubrifiants, huiles industrielles et produits connexes (classe L). Classification.
Partie 7 : famille M (travail des métaux). AFNOR,
1987, 8 p.
[2]
■
Guide d'emploi des fluides de coupe. CETIM,
1989, 183 p.
[3]
■
Centre Professionnel des Lubrifiants, 104 av
Albert 1er, 92500 RUEIL MALMAISON.
[4]
■
Solubilisation des métaux dans les fluides
d'usinage. INRS, ND 2148, 2001.
[5]
■
Dermatoses professionnelles aux fluides de
coupe. INRS, Documents pour le médecin du travail,
n° 83, TA61, 2000.
[6]
■
Allergies respiratoires professionnelles aux
brouillards de fluides de coupe. INRS, Documents pour
le médecin du travail, n° 86, TR27, 2001.
[7]
■
Risques liés à l'utilisation des fluides de
coupe. INRS, ND 2164, 2002.
[8]
■
Les maladies professionnelles. Guide d'accès aux tableaux du régime général et du régime agricole de
la sécurité sociale. INRS, ED 835, 2004.
[9]
■
Évaluation des risques professionnels. Aide
au repérage des risques dans les PME-PMI. INRS,
ED 840, 2004.
[10]
■
NF T60-607 – Produits pétroliers et lubrifiants - Détermination de l'indice d'absorption UV de l'extrait DMSO des huiles de coupe entières 1998
[11]
■
Utilisation des huiles de coupe entières.
Recommandation de la CNAM, R 370, 1995.
[12]
■
Criteria for a recommended standard.
Occupational exposure to metal working fluids.
Cincinnati, NIOSH, janvier 1998.
[13]
■
Concentration pondérale sur filtre. INRS,
METROPOL, Fiche 002, 2004.
[14]
■
Metalworking fluids : Method 5524, issue
1, mars 2003. NIOSH Manual of analytical Methods
(NMAM) 4 th Edition.
http://www.cdc.gov/niosh/nmam
[15]
■
NF X 43-257 – Qualité de l'air. Air des lieux de travail. Prélèvement individuel de la fraction inspi-
rable de la pollution particulaire. AFNOR, 1988, 11 p.
[16]
■
NF X 43-261 – Qualité de l'air. Air des lieux de travail. Prélèvement à poste fixe et mesurage de la
pollution particulaire totale. AFNOR, 1988, 9 p.
[17]
■
SEFRIN H. et col. – Evaluation des émissions lors de l’usinage des métaux par enlèvement de
copeaux sous microlubrification. INRS, ND 2215, 2004
(Traduction de : Bestimmung und beurteilung von
Emissionen bei der spanenden metallbearbeitjung mit minimalengendchmierung. In : Gefahrstoffe –
Reinhaltung der Luft, vol. 63, n°10, octobre 2003, p. 417-424)
[18]
■
FORSBERG K., MANSDORF S.-Z. – Quick selection guide to chemical protective clothing.
3 rd Edition John Wiley & Sons, INC. 1997.
[19]
■
Guide pratique de ventilation. 0. Principes
généraux de ventilation. INRS, ED 695, 1989.
[20]
■
HAGOPIAN J.-H., BASTRESS E.-K. –
Recommended industrial ventilation guidelines.
Cincinnati, DHEW, 1976, Publication NIOSH n° 76-162.
[21]
■
O'BRIEN D., FREDE J.-C. – Guidelines for the control of exposure to metalworking fluids.
Cincinnati, NIOSH, février 1978.
[22]
■
DALTON A.-J. P. – Oil - A worker's guide to
the health hazards and how to fight them. Londres,
British Society for Social Responsibility in Science,
1975, 93 p.
[23]
■
Guide pratique de ventilation. 1.
L'assainissement de l'air des locaux de travail. INRS,
ED 657, 1989.
[24]
■
Industrial ventilation – A manual of recom-
mended practice. 20
e ed. Lansing, ACGIH, 1989.
[25]
■
EOL : un logiciel de ventilation prévisionnelle applicable à l'assainissement de l'air des locaux
de travail. INRS, ND 2029, 1996.
[26]
■
Validation expérimentale du logiciel de ventilation prévisionnelle EOL-3D en conditions iso-
thermes. INRS, ND 2040, 1997.
[27]
■
Systèmes de compensation d'air.
Contribution à leur conception pour les locaux de tra-
vail. INRS, ND 2118, 1999.
[28]
■
NF EN ISO 7730 Ambiances thermiques modérées. Détermination des indices PMV et PDD et spécifications des conditions de confort thermique.
AFNOR, 1995, 40 p.
[29]
■
La compensation contrôlée d'une installa-
tion de ventilation. INRS, ED 86, 2000.
[30]
■
Note technique du ministère du travail du 5 novembre 1990 relative à l’aération et à l’assainissement des ambiances de travail (non paru au JO )
Bulletin officiel. Travail, emploi et formation professionnelle, 1990, n°90/24, pp 103-109.
[31]
■
NF EN 1822-1 – Filtres à air à très haute efficacité et filtres à air à très faible pénétration (HEPA et ULPA). Partie 1 : classification, essais de perfor-
mance et marquage. AFNOR, octobre 1998, 24 p.
[32]
■
Cooper J.-S., Raynor P.-C., Leith D. –
Evaporation of mineral oil in a mist collector. Appl.
Occup. Environ. Hyg. , 1996, 11(10), pp. 1204-1211.
[33]
■
HOJERDAL P., ALENIUS S.
–
Détermination du rendement d'un séparateur de brouillard d'huile. I - Méthode de mesure et résultats.
Stockholm, Arbetarskyddsverket, 1978, coll. Arbete och hâlsa, Vetenskaplig Skiftserie, vol. 7, 43 p.
(Traduction INRS 530-79).
[34]
■
HOJERDAL P., ALENIUS S. – Mesure du rendement des séparateurs de brouillard d'huile. II -
Résultats des essais pour seize séparateurs en labora-
toire. Stockholm, Arbetarskyddsverket, 1980, coll.
Arbete och hâlsa, Vetenskaplig Skiftserie, vol. 3, 65 p.
(Traduction INRS 544-82).
[35]
■
HOJERDAL P., ALENIUS S. – Mesure du rendement des séparateurs de brouillard d'huile. III -
Résultats des essais pour treize séparateurs testés en
milieu industriel. Stockholm, Arbetarskyddsverket,
1983, coll. Arbete och hâlsa, Vetenskaplig Skiftserie, vol. 5, 63 p. (Traduction INRS 558-83).
[36]
■
Frising T., Thomas D. – Filtration of liquid aerosol. Indoor Air Quality Filtration Conference.
Cincinnati (USA), 2002.
[37]
■
NF X 44-060 – Séparateurs hydrauliques.
Epurateurs de brouillards d'huile avec ventilateur inté-
gré pour l'industrie du décolletage. Méthode d'essai,
AFNOR, 1993, 20 p.
[38]
■
Bémer D., Ginestet A. – Epurateurs de brouillards d’huile. Contribution à l’amélioration de la
méthode d’essai. INRS, ND 2072, 1998, pp. 33
[39]
■
Aération et assainissement des lieux de tra-
vail. Aide-mémoire juridique. INRS, TJ 5, 2004.
[40]
■
NF X 44-001 – Séparateurs aérauliques.
Vocabulaire. AFNOR, 1981, 6 p.
23
Pour commander les films (en prêt), les brochures et les affiches de l’INRS, adressez-vous au service prévention de votre CRAM ou CGSS.
Services prévention des CRAM
ALSACE-MOSELLE
(67 Bas-Rhin)
14 rue Adolphe-Seyboth
BP 10392
67010 Strasbourg cedex tél. 03 88 14 33 00 fax 03 88 23 54 13 www.cram-alsace-moselle.fr
(57 Moselle)
3 place du Roi-George
BP 31062
57036 Metz cedex 1 tél. 03 87 66 86 22 fax 03 87 55 98 65 www.cram-alsace-moselle.fr
(68 Haut-Rhin)
11 avenue De-Lattre-de-Tassigny
BP 70488
68020 Colmar cedex tél. 03 89 21 62 20 fax 03 89 21 62 21 www.cram-alsace-moselle.fr
AQUITAINE
(24 Dordogne, 33 Gironde,
40 Landes, 47 Lot-et-Garonne,
64 Pyrénées-Atlantiques)
80 avenue de la Jallère
33053 Bordeaux cedex tél. 05 56 11 64 00 fax 05 56 39 55 93 [email protected]
AUVERGNE
(03 Allier, 15 Cantal, 43 Haute-Loire,
63 Puy-de-Dôme)
48-50 boulevard Lafayette
63058 Clermont-Ferrand cedex 1 tél. 04 73 42 70 22 fax 04 73 42 70 15 [email protected]
BOURGOGNE et FRANCHE-COMTÉ
(21 Côte-d’Or, 25 Doubs, 39 Jura,
58 Nièvre, 70 Haute-Saône,
71 Saône-et-Loire, 89 Yonne,
90 Territoire de Belfort)
ZAE Cap-Nord
38 rue de Cracovie
21044 Dijon cedex tél. 03 80 70 51 22 fax 03 80 70 51 73 [email protected]
BRETAGNE
(22 Côtes-d’Armor, 29 Finistère,
35 Ille-et-Vilaine, 56 Morbihan)
236 rue de Châteaugiron
35030 Rennes cedex tél. 02 99 26 74 63 fax 02 99 26 70 48 www.cram-bretagne.fr
CENTRE
(18 Cher, 28 Eure-et-Loir, 36 Indre,
37 Indre-et-Loire, 41 Loir-et-Cher, 45 Loiret)
36 rue Xaintrailles
45033 Orléans cedex 1 tél. 02 38 81 50 00 fax 02 38 79 70 30 [email protected]
CENTRE-OUEST
(16 Charente, 17 Charente-Maritime,
19 Corrèze, 23 Creuse, 79 Deux-Sèvres,
86 Vienne, 87 Haute-Vienne)
4 rue de la Reynie
87048 Limoges cedex tél. 05 55 45 39 04 fax 05 55 79 00 64 [email protected]
ÎLE-DE-FRANCE
(75 Paris, 77 Seine-et-Marne,
78 Yvelines, 91 Essonne,
92 Hauts-de-Seine, 93 Seine-Saint-Denis,
94 Val-de-Marne, 95 Val-d’Oise)
17-19 place de l’Argonne
75019 Paris tél. 01 40 05 32 64 fax 01 40 05 38 84 [email protected]
LANGUEDOC-ROUSSILLON
(11 Aude, 30 Gard, 34 Hérault,
48 Lozère, 66 Pyrénées-Orientales)
29 cours Gambetta
34068 Montpellier cedex 2 tél. 04 67 12 95 55 fax 04 67 12 95 56 [email protected]
MIDI-PYRÉNÉES
(09 Ariège, 12 Aveyron, 31 Haute-Garonne,
32 Gers, 46 Lot, 65 Hautes-Pyrénées,
81 Tarn, 82 Tarn-et-Garonne)
2 rue Georges-Vivent
31065 Toulouse cedex 9 tél. 05 62 14 29 30 fax 05 62 14 26 92 [email protected]
Services prévention des CGSS
GUADELOUPE
Immeuble CGRR
Rue Paul-Lacavé
97110 Pointe-à-Pitre tél. 05 90 21 46 00 fax 05 90 21 46 13 [email protected]
GUYANE
Espace Turenne Radamonthe
Route de Raban, BP 7015
97307 Cayenne cedex tél. 05 94 29 83 04 fax 05 94 29 83 01
LA RÉUNION
4 boulevard Doret
97405 Saint-Denis cedex tél. 02 62 90 47 00 fax 02 62 90 47 01 [email protected]
NORD-EST
(08 Ardennes, 10 Aube, 51 Marne,
52 Haute-Marne, 54 Meurthe-et-Moselle,
55 Meuse, 88 Vosges)
81 à 85 rue de Metz
54073 Nancy cedex tél. 03 83 34 49 02 fax 03 83 34 48 70 [email protected]
NORD-PICARDIE
(02 Aisne, 59 Nord, 60 Oise,
62 Pas-de-Calais, 80 Somme)
11 allée Vauban
59662 Villeneuve-d’Ascq cedex tél. 03 20 05 60 28 fax 03 20 05 63 40 www.cram-nordpicardie.fr
NORMANDIE
(14 Calvados, 27 Eure, 50 Manche,
61 Orne, 76 Seine-Maritime)
10 avenue du Grand-Cour, 2022X
76028 Rouen cedex tél. 02 35 03 58 21 fax 02 35 03 58 29 [email protected]
PAYS DE LA LOIRE
(44 Loire-Atlantique, 49 Maine-et-Loire,
53 Mayenne, 72 Sarthe, 85 Vendée)
2 place de Bretagne
BP 93405, 44034 Nantes cedex 1 tél. 02 51 72 84 00 fax 02 51 82 31 62 [email protected]
RHÔNE-ALPES
(01 Ain, 07 Ardèche, 26 Drôme,
38 Isère, 42 Loire, 69 Rhône,
73 Savoie, 74 Haute-Savoie)
26 rue d’Aubigny
69436 Lyon cedex 3 tél. 04 72 91 96 96 fax 04 72 91 97 09 [email protected]
SUD-EST
(04 Alpes-de-Haute-Provence,
05 Hautes-Alpes, 06 Alpes-Maritimes,
13 Bouches-du-Rhône, 2A Corse Sud,
2B Haute-Corse, 83 Var, 84 Vaucluse)
35 rue George
13386 Marseille cedex 5 tél. 04 91 85 85 36 fax 04 91 85 75 66 [email protected]
MARTINIQUE
Quartier Place-d’Armes
97210 Le Lamentin cedex 2 tél. 05 96 66 51 31
05 96 66 51 33 fax 05 96 51 81 54 [email protected]
COLLECTION DES GUIDES PRATIQUES DE VENTILATION
0. Principes généraux de ventilation
1. L’assainissement de l’air des locaux de travail
2. Ventilation des cuves et bains de traitement de surface
3. Mise en œuvre manuelle des polyesters stratifiés
4. Ventilation des postes de décochage en fonderie
5. Ventilation des ateliers d’encollage de petits objets
(chaussures)
6. Captage et traitement des aérosols de fluides de coupe
7. Opérations de soudage à l’arc
8. Ventilation des espaces confinés
9. 1. Cabines d’application par pulvérisation de produits liquides
9. 2. Cabines d'application par projection de peintures en poudre
ED
ED
ED
ED
ED
ED
695
ED
657
ED
651
ED
665
ED
662
ED
672
972
668
703
839
928
9. 3. Application par pulvérisation de produits liquides.
Cas particulier des objets lourds ou encombrants
ED
906
11. Sérigraphie
12. Deuxième transformation du bois
ED
711
ED
750
13. Fabrication des accumulateurs au plomb
ED
746
14. Décapage, dessablage, dépolissage au jet libre en cabine ED 768
15. Réparation des radiateurs automobiles
16. Ateliers de fabrication de prothèses dentaires
17. Emploi des matériaux pulvérulents
18. Sorbonnes de laboratoire
19. Usines de dépollution des eaux résiduaires et ouvrages d’assainissement
ED
ED
ED
ED
ED
752
760
767
795
820
Institut national de recherche et de sécurité pour la prévention des accidents du travail et des maladies professionnelles
30, rue Olivier-Noyer 75680 Paris cedex 14
Fax 01 40 44 30 99
•
Internet : www.inrs.fr
•
•
Tél. 01 40 44 30 00 e-mail : [email protected]
Édition INRS ED 972
1 re édition
•
(2005)
• réimpression sept. 2006
•
2 000 ex.
•
ISBN 2-7389-1336-9
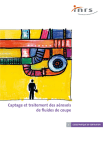
Link pubblico aggiornato
Il link pubblico alla tua chat è stato aggiornato.