Spirax Sarco MFP 14 Manuel utilisateur
Vous trouverez ci-dessous de brèves informations pour MFP14, MFP14S, MFP14SS. Ces pompes automatiques sont principalement utilisées pour le refoulement de condensats ou d'autres fluides à un niveau plus élevé. Elles peuvent également être utilisées pour l'évacuation directe du condensat d'une enceinte vapeur sous vide ou sous pression. L'ajout d'un purgeur à flotteur fermé assure une évacuation efficace du condensat.
MFP14 / MFP14S / MFP14SS
Pompe automatique
IM-P136-03
ST-BEf-11
5.1.3.010
Information générale sur la sécurité
Un fonctionnement sûr de ces appareils ne peut être garanti en condition qu'ils sont installés, mis en service et entretenus par une personne qualifiée ( voir "Instructions de Sécurité" à la fin de ce document), suivant les instructions de montage et d’entretien. On doit également répondre aux instructions générales de montage et de sécurité pour le montage des conduites et la construction des installations. On verra à utiliser des outils et équipements de sécurité appropriés.
1. Généralités
1.1. Description
La pompe automatique Spirax Sarco type MFP est une pompe à refoulement, actionnée par vapeur, air comprimé ou un gaz interte.
Elle est principalement utilisée pour le refoulement de condensats ou d’autres fluides à un niveau plus élevé. Selon les conditions de service, elle peut aussi être utilisée pour l’évacuation directe du condensat d’une enceinte vapeur sous vide ou sous pression.
Avec un échangeur équipé d’un régulateur de température, l’adjonction d’un purgeur à flotteur fermé en aval de la pompe assure, sous toutes conditions de service, une évacuation efficace du condensat.
Types disponibles
Le corps de la pompe MFP est disponible dans les matériaux suivants
Fonte nodulaire
Acier carbone
MFP14
MFP14S
Acier inoxydable
MFP14SS
Normes
Ce produit satisfait complètement aux directives européennes relatives aux réservoirs sous pression 97/23/EG, et aux directives
ATEX 94/9/EC. Le marquage et le marquage
Z
pouvant être apportés.
Certification
MFP14 : Sur demande une certification de matériel EN10204 3.1. est disponible.
MFP14S en MFP14SS : Sur demande une certification de matériel
EN10204 3.1 est disponible. Calcul suivant AD-Merkblatter en
ASME VIII Dir 1 est disponible.
Note: Toutes certifications et exigences d’inspections doivent être demandée lors de la commande.
1.2. Diamètres et connexions
Fonte nodulaire
(MFP14)
Acier
(MFP 14S)
Inox
(MFP14SS)
1”, 1½”, 2” en 3” x 2” taraudées BSP (BS 21 parallèle)
DN25, DN40, DN50 et DN80 x DN50 à brides EN 1092
PN16, ANSI150 B 16.5 et JIS/KS B 2238 10
DN50 à bride EN 1092 PN16, ANSI150 B 16.5 et
JIS/KS B 2238 10.
2” connexions taraudées BSP/NPT disponible sur demande
L’entrée vapeur motrice ½ » et l’évent / équilbrage 1’’ sont disponibles avec des conexions BSP, NPT ou
SW.
DN50 à bride EN 1092 PN16, ANSI150 B 16.5 et
JIS/KS B 2238 10.
2” connexions taraudées BSP/NPT disponible sur demande
L’entrée vapeur motrice ½’’ et l’évent / équilbrage 1’’ sont disponibles avec des connexions BSP, NPT ou
SW.
MONTAGE et ENTRETIEN
Modifications réservées
MFP14 / MFP14S / MFP14SS Montage et Entretien
1.3. Limites d’emploi
(ADM / ASME code vases sous pression version 5.0)
Calcul du corps selon
Pression motrice maximale
(vapeur, air ou gaz)
MFP14 et
MFP14S
MFP14SS
PN16
13.8 bar eff
10.96 bar eff.
PMA
Pression maximale admissible
MFP14
MFP14S
16 bar eff. @ 120°C
16 bar eff. @ 150°C
MFP14SS
MFP14
16 bar eff. @ 93°C
300°C @ 12.8 bar eff.
TMA
Température maximale admissible
MFP14S
MFP14SS
300°C @ 10.8 bar eff.
300°C @ 9.3 bar eff.
Température minimale admissible. Pour des températures basses, veuillez contacter Spirax Sarco.
0°C
PMO
Pression de service maximale vapeur saturée
MFP14
MFP14S
13.8 bar eff. @ 198°C
13.8 bar eff. @ 198°C
MFP14SS 10.96 bar eff. @ 188°C
MFP14 198°C @ 13.8 bar eff.
TMO
Température de service maximale saturée
MFP14S 198°C @ 13.8 bar eff.
MFP14SS 188°C @ 10.96 bar eff.
Température de service minimale admissible. Pour des températures basses, veuillez contacter Spirax Sarco
0°C
Hauteur de relevage ou contre pression ( Hauteur statique + contre pression dans le système de retour ) doit être plus faible que la pression motrice afin d’assurer les débits à relever.
Hauteur (H) en mètres x 0.0981 + pression (bar g) dans le système de retour + pertes de charges ( en barg ) calculées sur base d’un débit équivalent à 6 x le débit de condensats ou 30.000 litres/heure
Hauteur de remplissage au-dessus de la pompe 0.3m
Hauteur minimale acceptable
0.15m
(diminution de la capacité)
1 tot 0.8
Poids spécifiques de fluides pompés:
Débit par cycle
Consommation de vapeur
DN80 x 50
19.3 litres
Max. 20 kg/h
DN50
12.8 litres
Max. 20 kg/h
DN40 & DN25
7 litres
Max.
16 kg/h
Consommation d’air
(air libre)
Limite de température
(
Z
)
5.6 dm³/s maximum
-10°C à
200°C
5.6 dm³/s maximum
-10°C à
200°C
4.4 dm³/s maximum
-10°C à
200°C
Courbe vapeur
Courbe vapeur
Courbe vapeur
Pression bar eff.
Pression bar eff.
Pression bar eff.
Le produit ne doit pas être utilisé dans cette zone
Contacter Spirax-Sarco pour l’utilisation dans cette zone
La version standard ne peut pas être utilisé dans cette zone
A – D: A brides PN16
B – D: A brides JIS/KS 10
C – D: A brides ANSI 150
SPIRAX-SARCO NV
RCG 665 46
Industriepark 5 B 9052 ZWIJNAARDE
Tél. (09) 244 67 10 Fax (09) 244 67 20
2\4\13\00000001 / IM-P136-03 / ST-BEf-11
- 2 / 14 -
Montage et Entretien MFP14 / MFP14S / MFP14SS
1.4. Construction
Nr Description Matériau
1
Couvercle
MFP14
MFP14S
Fonte nodulaire
Acier
MFP14SS Acier inoxydable
(EN JS 1025)
EN-GJS-400-18-LT
DIN GSC 25N
ASTM A216 WCB
BS EN 10213-4
ASTM A351 CF3M
2
Joint de couvercle
3
4
5
6
7
8
9
Fibre synthétique
Boulons de couvercle Acier inox
Corps
Tige
Connecteur
Flotteur/levier
Œillet
10 Ressort
12 Anti retour
MFP14
MFP14S
Fonte nodulaire
Acier
MFP14SS Acier inoxydable
MFP14
MFP14S
Mécanisme levier.
11 Bouchon de vidange
Acier inoxydable
Acier inoxydable
Acier inoxydable
Fonte nodulaire
Acier
MFP14SS Acier inox
Acier inox
Inconel 718
Acier
Acier inox
13 Contre bride
14 Mécanisme
Acier
Acier inox
15 Ecrous de connexion Acier inox
16 Siège d’entrée Acier inox
ISO 3506 Gr. A2-70
(EN JS 1025)
EN-GJS-400-18-LT
DIN GSC 25N
ASTM A216 WCB
1998 – 1.4409
ASTM A351 CF3M
BS 970, 431 S29
BS 1449, 304 S11
AISI 304
(EN JS 1025)
EN-GJS-400-18-LT
DIN GSC 25N
ASTM A216 WCB
1998 – 1.4409
ASTM A351 CF3M
BS 3146 pt.2 ANC 2
ASTM 5962 / ASTM B367
DIN 267 Part III Class 5.8
(non compris)
BS 3146 pt. 2 ANC 4B
BS 6105 Gr. A2-70
BS 970, 431 S29
ASTM A276 440B
17 Clapet d’entrée
18 Joint clapet entrée
19 Siège de sortie
20 Clapet de sortie
21 Joint clapet sortie
Acier inox
Acier inox
Acier inox
Acier inox
Acier inox
BS 1449 409 S19
BS 970 431 S29
BS 3146 pt. 2 ANC 2
BS 1449 409 S19
22 Actuateur EPM ALNICO
23 O-ring EPDM
24* Axe
25* Vis
26* Vis
Inox
Inox
Inox
27* Ecrou de blocage
28 Fixation de ressort
Inox
Acier inox
* Note :
Pour rep. 24, 25, 26 et 27 : voir fig. 8.
BS 970 431 S29
BS 6105 Gr. A2
BS 970 431 S29
Gr. A2
BS 970 431 S29
Event/
équilibre
Fig. 1 DN80 x DN50 MFP14 montré
Fluide motrice
IM-P136-03 / ST-BEf-11 - 3 / 14 -
MFP14 / MFP14S / MFP14SS Montage et Entretien
1.5. Dimensions en mm (approximatives)
DN
25
40
50
A
B C *D E F G H J K
PN ANSI
410 - 305 507 - 68 68 480 13 18 165
∅280
440 - 305 527 - 81 81 480 13 18 165
∅280
637.5
∅321
(kg)
Poids, incl. DCV & brides (kg)
51 58
54 63
72 82
80 X 50
637.5 342 88 98
Note : La dimensions D est valable pour la pompe DN80 x DN50 avec corps oval. Pour les autres pompes, cette dimensions est égale à L.
½” BSP, NPT ou SW. Vapeur, air ou gaz inerte
1” BSP, NPT ou SW échappement
Distance de service
Oeillet de levage
∅ 15 mm
Contre-bride
Contre-bride
Fig. 2 DN80 x DN50 MFP14 montré
SPIRAX-SARCO NV
RCG 665 46
Industriepark 5 B 9052 ZWIJNAARDE
Tél. (09) 244 67 10 Fax (09) 244 67 20
2\4\13\00000001 / IM-P136-03 / ST-BEf-11
- 4 / 14 -
Montage et Entretien
2. Installation
2.1. Système ouvert
Désaération vers atmosphère
Vapeur de révaporisation, air, évent pompe
Désaération de la pompe
Fluide moteur
Retour condensat
Joint d’eau sur le tropplein, min. 305 mm (12”)
Collecteur
Hauteur rempliss.
MFP
Pompe automatique
FT
Purgeur pour vapeur
MFP14 / MFP14S / MFP14SS
Condensat
Hauteur
Attention
Afin de garantir la sécurité du personnel et de l’entourage, s’assurer que toutes les conduites de condensat, de vapeur, d’air comprimé ou de gaz soient isolées avant d’entamer son montage ou entretien. L'œillet de levage sur la pompe est prévu pour soulever la pompe et ne peut être utilisé à d’autres fins. Toujours utiliser des outils adéquats et porter des vêtements de protection.
Si le fluide à pomper est potentiellement explosif, le fluide moteur doit être un gaz inerte sans présence de l'oxigène
1.
Installer la pompe en dessous de l’appareil à purger, l’échappement dirigé verticalement vers le haut. Assurer la hauteur de charge recommandée comme indiqué à la fig. 3
(distance verticale entre le sommet de la pompe et le dessous du collecteur). Pour d’autres hauteurs de charge, consulter l’abaque de débit.
2.
Afin d’éviter que, lors de la phase de refoulement, du condensat soit retenu dans l’enceinte vapeur, un collecteur horizontal, mis à l’atmosphère, sera prévu au dessus de la pompe. Voir ciaprès pour le volume minimal requis. Tous les accessoires dans la conduite d’entrée condensat doivent être du type à
“passage intégral”.
3.
Monter les clapets de non-retour (12) et (12a) sur la pompe en veillant qu’ils soient montés en sens d’écoulement correct. Serrer les boulons des brides jusqu’à 76-84 Nm. Les parties de tuyauterie horizontales, amont et aval des clapets de nonretour doivent être les plus courtes possible. Raccorder la décharge de la pompe au réseau de retour condensat.
4.
Raccorder l’arrivée du fluide moteur au couvercle de la pompe.
Toujours prévoir un filtre en amont de ce raccordement et, en cas de vapeur, un poste de purge. La sortie de ce purgeur peut
être raccordée au collecteur situé au-dessus de la pompe. * Il
est fortement recommandé que la pression de la vapeur motrice ne dépasse pas la contrepression de plus de 2 - 4 bar eff.
5.
L’échappement de la pompe sera mis à l’atmosphère par une conduite sans restriction et de préférence verticale. Si une partie horizontale était inévitable, prévoir alors suffisamment de pente afin d’assurer que toute condensation revienne par gravité vers la pompe ou vers le collecteur.
2.2. Hauteur de charge / d’installation
Une confusion est souvent faite entre la hauteur de charge et la hauteur d'installation. La hauteur de charge est la distance à la verticale entre le point haut de la pompe et le point de purge du collecteur. La hauteur d'installation est la distance à la verticale entre le point de purge du collecteur et le sol.
Hauteur de charge recommandée : 300 mm.
Hauteur de charge minimale : 150 mm (capacité réduite).
Nota : N’utiliser que les clapets de non-retour comme fournis par
Spirax-Sarco afin de pouvoir assurer la capacité spécifiée
Tableau 1 : Volume du collecteur
Le volume du collecteur, au-dessus de la hauteur de charge, doit
être suffisant pour recueillir le condensat qui s’amène pendant la phase de refoulement. Le collecteur peut être constitué soit par un réservoir, soit par une longueur de conduite à grand diamètre. Si nécessaire, le collecteur peut être muni d’un siphon de trop-plein assurant un joint d’eau de 305 mm au minimum (voir fig.3).
DN de la pompe Collecteur
25
40
50
80x50
0,60 m x DN200
0,60 m x DN200
0,65 m x DN250
1,10 m x DN250
Tableau 2 : Tuyauterie d'entrée sans collecteur
Lorsque la pompe MFP sert à refouler le condensat d’un seul utilisateur de vapeur, un collecteur n’est pas absolument nécessaire.
Une longueur de tube éventuellement de diamètre nominal plus grand installée 305 mm au-dessus du couvercle de la pompe suffit pour recueillir le condensat durant la phase de refoulement, ce qui
évite toute retenue de condensat dans l’enceinte vapeur de l’appareil à purger.
Débit de condensat en kg/h jusqu’à 277 jusqu’à 454
Longueur requise en m
DN25 DN40 DN50 DN80x50
1,2
2,0 1,2
jusqu’à 681 jusqu’à 908
3,0 1,5 1,2
4,0 1,8 1,5
3,0 2,1
jusqu’à 1362 jusqu’à 1816 jusqu’à 2270
3,6 3,0
3,6 1,2
jusqu’à 2724 jusqu’à 3178 jusqu’à 3632 jusqu’à 4086 jusqu’à 4540 jusqu’à 9994
1,5
1,8
2,1
2,4
2,7
3,0
IM-P136-03 / ST-BEf-11 - 5 / 14 -
MFP14 / MFP14S / MFP14SS
Tableau 3 : Dimensionnement de l'évent du collecteur
Le collecteur doit être prévu d’un tuyau de désaération avec diamètre minimal selon le tableau ci-dessous:
DN de la pompe
25
DN désaération collecteur
50
40
50
80x50
65
80
100
2.3. Système fermé
Régulation de température
Désaérateur et clapet de non-retour (non dessiné)
Montage et Entretien
Retour condensat
Echangeur
Filtre
Collecteur
Haut. rempl.
Fig.4
Purge d'un échangeur vers un réseau de condensat
à pression supérieure permanente.
P2 toujours supérieure à P1
Pompe automatique
MFP
Tuyau d'équilibrage
Purgeur IFT
Régulation de température
Désaérateur et clapet de non-retour (non dessiné)
Entrée vapeur motrice
Retour condensat
Echangeur
Collecteur
Haut. rempl.
Fig.5
Purge d'un échangeur vers un réseau de condensat
à pression diférentielle variable
P2 pas toujours supérieure à P1
Pompe automatique
MFP
Filtre
Tuyau d'équilibrage
Purgeur IFT
Purgeur FT installé en amont du clapet de non-retour
SPIRAX-SARCO NV
RCG 665 46
Industriepark 5 B 9052 ZWIJNAARDE
Tél. (09) 244 67 10 Fax (09) 244 67 20
2\4\13\00000001 / IM-P136-03 / ST-BEf-11
- 6 / 14 -
Montage et Entretien MFP14 / MFP14S / MFP14SS
Dans l’installation d’une pompe MFP en système fermé, l’échappement de la pompe est raccordé, à l’enceinte vapeur à purger, par un tube d’équilibre.
Attention
Afin de garantir la sécurité du personnel et de l’entourage, s’assurer que toutes les conduites de condensat et de vapeur soient isolées avant de commencer le montage ou l’entretien.
L'œillet de levage sur le couvercle de la pompe est prévu pour soulever la pompe et ne peut être utilisé à d’autres fins. Toujours utiliser des outils adéquats et porter des vêtements de protection. Si le fluide à pomper est potentiellement explosif, le fluide moteur doit être un gaz inerte sans présence de l'oxigène
1.
Installer la pompe en dessous de l’appareil à purger, le tube d’échappement verticalement vers le haut. Prévoir la hauteur de charge recommandée comme indiqué aux fig. 4 et 5 (distance verticale entre le sommet de la pompe et le dessous du collecteur). Pour d’autres hauteurs de charge, consulter l’abaque des capacités.
2.
Afin d’éviter que du condensat soit retenu dans le corps de chauffe pendant la phase de refoulement, un collecteur horizontal sera prévu au-dessus de la pompe. Voir 3.2.1. et/ou
3.2.2. pour le volume minimal requis. Tous les accessoires dans les conduites entrée condensat et échappement de la pompe doivent être du type à passage intégral.
3.
Monter les clapets de non-retour (12et 12a) sur la pompe en veillant qu’ils soient montés en sens d’écoulement correct. Serrer les boulons de brides jusqu’à 76-84 Nm.
Les parties de tuyauterie horizontale, amont et aval des clapets de non-retour, doivent être les plus courtes possible.
Raccorder la décharge de la pompe au réseau de retour condensat.
4.
Raccorder la conduite vapeur motrice (pas d’air comprimé ni gaz) au couvercle de la pompe. Toujours y prévoir un filtre et un purgeur. La sortie du purgeur peut être raccordée au collecteur condensat situé au-dessus de la pompe.
* Il est fortement recommandé que la pression de la vapeur motrice ne dépasse pas la contrepression de plus de 2 - 4
bar eff.
5.
L’échappement de la pompe sera raccordé, sans restriction, au collecteur. (Dans certains cas, l’échappement peut aussi être raccordé à la conduite entre la vanne de régulation et l’échangeur). Monter un purgeur d’air thermostatique au point haut du tube d’équilibre afin d’évacuer les incondensables lors de la mise en route. Toute partie horizontale dans le tube d’équilibre doit être mise en pente de façon à ce que toute condensation revienne vers la pompe.
6.
Au cas où la contrepression dans la conduite de retour serait inférieure à la pression dans l’échangeur, un purgeur approprié
à flotteur fermé et purgeur d’air thermostatique incorporé doit
être installé entre la sortie de la pompe et le clapet de nonretour sur la décharge comme représenté à la fig. 5.
4. Fonctionnement
1.
Lors de la mise en route, le flotteur (7) se trouve normalement au point bas. Le clapet d’admission (17) est fermé et le clapet d’échappement (20) est ouvert (Fig. 1).
2.
Sous l’effet de la gravité, du liquide s’écoule au travers du clapet de non-retour entrée (12) dans la pompe de sorte que le flotteur (7) commence à flotter et s’élève.
3.
Au fur et à mesure que le flotteur (7) monte, le mécanisme à biellettes (9) augmente la tension des ressorts (10). Quand le flotteur (7) atteint sa position la plus élevée, l’énergie accumulée dans les ressorts est libérée instantanément. Cette énergie est alors transmise au mécanisme (9) qui entraîne la tigepoussoir vers le haut, provoquant simultanément l’ouverture du clapet d’admission du fluide moteur (20) et la fermeture de la soupape d’échappement (17) (Fig. 7).
4.
Le fluide moteur (vapeur ou air comprimé) s’écoule au travers du clapet d’admission (17) et crée une pression, dans le corps de la pompe, forçant le liquide à s’écouler au travers du clapet de non-retour de décharge (12a).
5.
Le flotteur s’abaisse en même temps que le niveau de liquide descend dans le corps de la pompe. Avant que le flotteur n’atteigne sa position la plus basse, le mécanisme (9) entre en action et augmente la tension des ressorts (10). Lorsque le flotteur atteint sa position la plus basse, l’énergie des ressorts est restituée instantanément au mécanisme qui entraîne la tige-poussoir vers le bas provoquant instantanément la fermeture du clapet d’admission du fluide moteur (20) et l’ouverture du clapet d’échappement (17).
6.
La pression dans le corps de pompe chute. Dès qu’elle est
égale à la pression dans la tuyauterie d’entrée condensat, le clapet de non-retour s’ouvre, le condensat s’écoule dans la pompe et le cycle recommence
Sortie d’échappement fermée
Arrivée vapeur motrice ouverte
Sortie d’échappement ouverte
Arrivée vapeur motrice fermée
Fig.7 Décharge
3. Mise en route
1.
Ouvrir lentement l’arrivée du fluide moteur (vapeur, air comprimé ou gaz) de façon à ce que la pression motrice soit disponible au niveau du clapet d’admission de la pompe MFP.
S’assurer du bon fonctionnement du purgeur.
2.
Ouvrir lentement l’entrée et la décharge condensat.
3.
Ouvrir lentement l’admission vapeur vers l’échangeur afin que du condensat puisse se former et s’écouler dans la pompe.
Lorsque le condensat y atteint son niveau supérieur, la pompe commencera à refouler.
4.
Vérifier si la pompe fonctionne normalement. Le fonctionnement de la pompe MFP est normalement cyclique avec un
échappement clairement audible en fin de phase de refoulement.
Si des irrégularités sont constatées, vérifier si l’installation est bien conforme aux instructions d’installation. Si nécessaire, consulter Spirax Sarco.
5.
Si un trop-plein est prévu, vérifier la présence du joint d’eau qui
évite que de la vapeur de revaporisation ne s’y échappe. Si nécessaire, remplir d’eau le siphon.
Condensat
Entrée
Clapet de retenue d’entrée
Fig.6 Remplissage
Clapet de retenue de sortie
Sortie condensat
IM-P136-03 / ST-BEf-11 - 7 / 14 -
MFP14 / MFP14S / MFP14SS
5. Entretien
Attention
Afin de garantir la sécurité du personnel et de l’entourage, s’assurer que toutes les conduites condensat, vapeur, air comprimé ou gaz soient isolées et que la pompe soit dépressurisée avant de démonter le couvercle. L'œillet de levage sur la pompe est prévu pour soulever la pompe (+/- 70 kg) et ne peut être utilisé à d’autres fins. Toujours utiliser des outils adéquats et porter des vêtements de protection. Traiter le mécanisme avec précaution afin d'éviter des accidents causés par action des ressorts.
Montage et Entretien
1.
Démonter les raccordements au couvercle. Marquer la position du couvercle. Dévisser les boulons de couvercle et déposer celui-ci avec le mécanisme.
2.
Vérifier si le mécanisme n’est pas encrassé ou entartré, ce qui obstrue son libre mouvement.
Note : Ne pas toucher les vis de réglage (Fig. 8 : 25 et 26).
3.
Vérifier les ressorts (10). Si nécessaire déposer les clips, glisser les ressorts des axes et remplacer les ressorts et les clips.
(voir ref 5 e concernant ressorts)
4.
Vérification des clapets d’admission et d’échappement. a) Déposer l’axe (24) de la tige connecteur et déplacer l’ensemble flotteur avec levier vers l’autre côté de la tige support. b) Déposer les clips et ensuite les ressorts c) Déposer l’écrou de blocage de la tige du clapet d’entrée (qui à
été fixé avec Loctite 620) d) Déposer les boulons du mécanisme et enlever le mécanisme du couvercle. e) Démonter le clapet de désaération (en cas de besoin), déposer les clips sur la tige principale f) Déposer le clapet d’entrée et les sièges du couvercle (marquer les positions respectives). Pour DN25 et DN40, la distinction des sièges peut être faite: rainures doubles sur le siège du clapet de désaération, rainure simple sur le siège de clapet entrée. Sur les DN80x50 et DN50, les sièges sont sans rainures. g) Vérifier l’état des sièges. Nettoyer, ou en cas d’usure,
échanger par des neufs.
Fig 9
5.
Montage en ordre inverse. Vérifier que: a) Sièges dans les bourrages corrects (voir 4f) et serrer sur 129-
143Nm. b) Mettre le ressort sur le clapet d’aération. Tenir le ressort sur le fond du bourrage et pousser le clapet sur la tige. Ensuite monter l’écrou sur la tige. c) Serrer les boulons de fixation du mécanisme à 38-42Nm. d) Montage de l’écrou de blocage sur la tige de clapet entrée avec du Loctite 620 ou 272. e) Avant de mettre les ressorts, vérifier que l’ancre des ressorts soit alignée avec le ressort et que, entre les ressort et l’ancre, le jeu soit maximum 0.35mm (Fig. 8). Les embouts du res-
sort peuvent toucher l’ancre mais ne jamais être pliés au-
tour de l’ancre. Toujours monter avec des rondelles et des goupilles neuves.
f) Ajustage du clapet de désaération:
Avec sa tige de commande contre l’arrêt le plus éloigné du couvercle (clapet entrée fermé, sur son siège). Régler le boulon pour qu’il y ait, entre le boulon et la tige, un jeu correct
- voir tableau ci-dessous:
Pompe Nombre de tours
DN80x50 3,75
DN50 3,75
DN40 2,75
DN25 2,75
6.
Remplacement du flotteur Dévisser le flotteur des boulons de montage. Pour cela, déposer le levier. Montage du flotteur neuf avec boulons et rondelles neuves en appliquant une mince couche de pâte de fixation sur le filet. Monter le levier
(si déposé) avec des rondelles et goupilles neuves.
7.
Montage du couvercle Montage du couvercle sur le corps de pompe avec orientation correcte. (voir ci-dessus réf. 1). Toujours utiliser un joint de couvercle neuf. Serrer les boulons à
121-134Nm. Suivre les instructions pour la mise en route.
SPIRAX-SARCO NV
RCG 665 46
Industriepark 5 B 9052 ZWIJNAA RDE
Tél. (09) 244 67 10 Fax (09) 244 67 20
2\4\13\00000001 / IM-P136-03 / ST-BEf-11
- 8 / 14 -
Montage et Entretien MFP14 / MFP14S / MFP14SS
6. Pièces de rechange
Les pièces de rechange disponibles sont représentées ci-dessous. Les autres pièces ne sont pas fournies comme pièces de rechange.
Joint couvercle
Flotteur
Clapet non-retour type DCV
Couvercle complet
2
7
12
1, 2, 7
Ensemble clapet
(entrée et sortie avec siège)
Ensemble ressorts
16, 17, 18, 19, 20, 21
10
Ensemble mechanisme (avec clapet d’entrée et sortie et vis)
(caché)
Fig. 10 MFP14 montré
IM-P136-03 / ST-BEf-11 - 9 / 14 -
MFP14 / MFP14S / MFP14SS Montage et Entretien
7. Dépistage des pannes
Dans le cas où une pompe correctement dimensionnée ne donne pas satisfaction, si l'installation est neuve, un problème d'installation sera suspecté.Lorsqu'il s'agit d'une installation existante où la pompe ne fonctionne qu'occasionnellement ou pas du tout, la cause en est généralement une modifi cation des paramètres d'origine en ce qui concerne les alimentations ou la contre-pression. En comparant les conditions de fonctionnement du système connu et les symptômes décelés, vérifi er les points suivants et procéder aux corrections si nécessaire.
Attention :
Toutes les interventions doivent être effectuées par un personnel qualifié. Avant toutes déposes de canalisation ou, de démontage d'élément de pompe, s'assurer préalablement que ces derniers sont correctement isolés et qu'ils ne subissent pas de pression résiduelle dans ces éléments.
Attention :
Toujours arrêter la pression avant de démonter les joints.
SYMPTÔME 1 : LA POMPE NE FONCTIONNE PAS LORS DU PHASE DE DEMARRAGE.
CAUSE REMEDE
L'alimentation fluide moteur est Ouvrir la vanne d'alimentation sur l'alimentation fluide moteur. coupée
L'arrivée condensat est coupée. Ouvrir toutes les vannes afi n que le condensat puisse atteindre la pompe.
La sortie condensat est fermée.
La pression motrice est insuffi sante pour vaincre la contrepression en aval de la pompe.
Ouvrir toutes les vannes afin de permettre une circulation normale du condensat.
Vérifi er la valeur de la pression motrice et celle de la contre-pression effective totale en aval de la pompe. Ajuster la pression motrice à une valeur minimale supérieure d'environ 0,6 à 1 bar à la contrepression.
Les clapets sont installés à l'envers par rapport au sens d'écoulement
Vérifi er l'installation des clapets et corriger si nécessaire dans le cas d'une installation avec
échappement et collecteur à l'atmosphère. du condensat.
La pompe est bloquée par bouchon S'assurer qu'il n'y a pas de restriction au niveau de l'évent et que de ce dernier le condensat d'air. éventuel peut s'écouler naturellement par gravité vers la pompe ou le collecteur.
SYMPTÔME 2 : LA LIGNE D’ALIMENTATION CONDENSAT S’ENGORGE MAIS LA POMPE CONTINUE DE FONCTIONNER
NORMALEMENT (CYCLE DE FONCTIONNEMENT AUDIBLE).
CAUSE REMEDE
La pompe est sous-dimensionnée. Vérifier les débits condensats (TI-P136-05). Augmenter la dimension des clapets de retenue ou installer une pompe supplémentaire en parallèle si nécessaire.
La hauteur de charge est insuffi sante.
La pression motrice est insuffi sante pour atteindre le débit requis.
Vérifier la hauteur de charge requise paragraphe 3, installer la pompe à un niveau inférieur afin d'obtenir la valeur minimale indiquée.
Vérifi er le réglage de la pression motrice et la valeur de la contrepression durant le fonctionnement.
Comparer les valeurs obtenues avec celles indiquées sur la feuillet technique TI-P136-05. Augmenter
La pression motrice est insuffi sante pour vaincre la contrepression en aval de la pompe. la pression motrice jusqu'à la valeur requise.
Vérifi er la valeur de la pression motrice et celle de la contre-pression effective totale en aval de la pompe. Ajuster la pression motrice à une valeur minimale supérieure d'environ 0,6 à 1 bar à la contrepression.
La perte de charge sur la tuyauterie Vérifi er que les raccords de tuyauterie et la vanne d'isolement sont bien de type à passage intégral. d'alimentation condensat est trop importante.
Le clapet de retenue d'entrée se bloque en ouverture.
Vérifi er le niveau d'encrassement du fi ltre. S'assurer que les vannes d'isolement sont ouvertes à 100
%.
Isoler le clapet de retenue d'entrée de pompe et dépressuriser. Déposer le couvercle du clapet et examiner les éléments internes. Les nettoyer puis les remonter ou procéder au remplacement du clapet si nécessaire.
SPIRAX-SARCO NV
RCG 665 46
Industriepark 5 B 9052 ZWIJNAARDE
Tél. (09) 244 67 10 Fax (09) 244 67 20
2\4\13\00000001 / IM-P136-03 / ST-BEf-11
- 10 / 14 -
Montage et Entretien MFP14 / MFP14S / MFP14SS
SYMPTÔME 3 : LA LIGNE D’ALIMENTATION CONDENSAT S’ENGORGE ET LA POMPE NE FONCTIONNE PLUS (CYCLE DE
FONCTIONNEMENT NON AUDIBLE).
CAUSE REMEDE
La ligne d'évacuation condensat est fermée ou obstruée.
Le clapet de sortie de pompe est bloqué en fermeture.
La pression motrice est insuffi sante.
Vérifier la pression motrice et la contre-pression en aval de la pompe. Si elles sont identiques, une fermeture ou un blocage de la ligne de décharge peut être suspecté. Vérifi er toutes les vannes situées en aval de la pompe pour s'assurer qu'il n'y a pas d'obstacles ou de frein à la circulation du condensat.
Après avoir effectué les contrôles décrits en 3a, isoler les clapets et dépressuriser. Déposer le couvercle et examiner visuellement les internes. Nettoyer les portées et remonter ou procéder au remplacement si nécessaire.
Si la pression motrice est inférieure à la contre-pression, augmenter sa valeur à une pression supérieure d'environ 0,6 à 1 bar à la contre-pression. Ne pas dépasser la pression maximale admissible de l'équipement.
Pour les étapes suivants, isoler la ligne d'évent ou d'équilibrage (circuit fermé) et dissocier cette ligne de sur l'orifi ce d'échappement de pompe, puis procéder comme décrit ci-après (voir remarque sur consigne de sécurité ci-dessus).
Important : Consigne de sécurité
Pour les étapes suivantes, il est nécessaire de déconnecter la ligne d'évent ou d'équilibrage de l'orifi ce d'échappement de pompe.
Dans le cas d'un système en boucle fermée, on doit impérativement s'assurer avant de procéder à cette opération, que la pompe est correctement isolée (alimentation motrice, entrée condensat et décharge condensat et équilibrage tous fermés) et que la pression résiduelle dans le corps de pompe est évacuée. Dans le cas contraire, il se peut, en cas de défaillance, que du condensat chaud jaillisse par l'orifi ce d'échappement de la pompe lors du démontage. Ceci peut également se produire dans le cas d'un système avec mise à l'atmosphère.
La soupape d'admission fluide moteur n'est pas étanche ou est bloquée en ouverture.
Ouvrir très lentement l'alimentation fl uide moteur tout en maintenant les lignes entrée et sortie condensats fermées. Surveiller l'orifi ce d'échappement afi n de déceler toute fuite de vapeur ou d'air. Si une fuite est observée, cela indique que le problème provient du clapet d'entrée de pompe. Isoler ce dernier et déposer son couvercle. Examiner les éléments internes et les nettoyer ou procéder au remplacement du clapet si nécessaire.
Le mécanisme de pompe est défaillant :
1. Ressorts cassés.
2. Flotteur détérioré.
3. Mécanisme grippé.
Présence d'un bouchon de vapeur lié à la canalisation d'évent ou d'équilibrage (installation en boucle ouverte ou fermée).
Le clapet de retenue d'entrée de pompe est bloqué en fermeture.
L'alimentation en fl uide moteur de la pompe étant ouverte, ouvrir lentement l'arrivée condensat de la pompe pour permettre un remplissage du corps de pompe. Observer l'orifi ce d'échappement. Prendre toutes les précautions pour la protection du personnel. Si du condensat sort par cet orifice, une défaillance du mécanisme est clairement établie. Isoler la pompe puis déposer l'ensemble couvercle et mécanisme et examiner ce dernier. Vérifier l'état des ressorts et rechercher les défauts éventuels sur le fl otteur. Contrôler le mouvement du mécanisme. Remettre en état ou remplacer tout élément défectueux.
Si le fonctionnement du mécanisme est audible et qu'il n'est pas observé de fluide sortant de l'orifice d'échappement ou de l'évent, ouvrir lentement la ligne de sortie condensat et observer le fonctionnement. Prendre toutes les précautions pour la protection du personnel. Si la pompe fonctionne normalement, un problème sur l'évent ou de tuyauterie d'équilibrage est suspecté. Vérifi er la bonne réalisation de cette canalisation (voir chapitre 3 "Installation").
Cette dernière doit se purger automatiquement par gravité afi n d'éviter tout bouchon de vapeur.
Si le fonctionnement du mécanisme n'est pas audible et qu'il n'est pas observé de fluide sortant de l'orifi ce d'échappement ou de l'évent, il est suspecté un problème au niveau de l'alimentation condensat de la pompe. S'assurer que toutes les vannes d'isolement amont sont ouvertes. Si c'est le cas, cela signifi e que le clapet d'alimentation de pompe est bloqué en fermeture. Isoler le clapet et décomprimer. Déposer le clapet et examiner les éléments internes, les nettoyer puis les remonter ou procéder au remplacement du clapet si nécessaire.
Le filtre d'entrée est bloqué. Fermer la vanne d'isolement en amont du fi ltre. Retirer le bouchon de crépine et la crépine.
Nettoyer la crépine ou la remplacer si elle est endommagée. Insérer la crépine dans le bouchon et réinstaller le filtre. Ouvrir la vanne d'isolement.
IM-P136-03 / ST-BEf-11 - 11 / 14 -
MFP14 / MFP14S / MFP14SS Montage et Entretien
SYMPTÔME 4 : CLAQUEMENT DANS LA LIGNE DE RETOUR PRINCIPALE APRES LE CYCLE DE DECHARGE DE LA POMPE.
CAUSE REMEDE
Un vide est crée en sortie de pompe après
évacuation du condensat. (Il est lié à l'accélération/décélération de paquets d'eau dans la ligne de retour principale généralement le résultat de longue section horizontale avec des élévations et abaissements de niveau).
By-pass de la pompe avec passage de vapeur vive.
Installer un case-vide en point haut de la ligne de retour. Dans le cas d'un système en boucle fermée, un éliminateur d'air est alors requis en aval du casse-vide.
Vérifi er la pression d'entrée condensat et la contre-pression effective totale en sortie de la pompe (si installé). Si la pression d'entrée condensat est supérieure ou égale à la contrepression, un problème de by-pass de la pompe avec passage de vapeur vive est suspecté.
Sur un système avec évent de pompe à l'atmosphère, vérifier le fonctionnement des purgeurs en amont car en cas de fuite, la pression d'entrée condensat peut être supérieure à la contrepression sous des conditions normales de fonctionnement, une combinaison pompe/purgeur est nécessaire. La combinaison de ces deux éléments évitera le passage de vapeur vive dans le réseau de retour et permettra un fonctionnement normal de la pompe en présence de condensat.
Pression différentielle trop élevée. Si la pression motrice excède la pression requise pour vaincre la contrepression agissant sur la pompe, la température du condensat pompé sera à une température très élevée par rapport au condensat dans le réseau de retour.
La vapeur de revaporisation provoquée par la
Il est fortement recommandé que la pression de la vapeur motrice ne dépasse pas la contrepression de plus de 2-4 bar eff. température élevée du condensat pompé diminuera lorsqu'elle viendra en contact avec le condensat plus froid dans le réseau de retour, provoquant un claquement audible.
SYMPTÔME 5 : UNE QUANTITE EXCESSIVE DE VAPEUR DE REVAPORISATION EST EVACUEE PAR L’EVENT DE POMPE.
CAUSE REMEDE
Des purgeurs en amont de la pompe sont défaillants et permettent le passage de vapeur vive dans la ligne d'alimentation condensat (voir également 4).
Contrôler le fonctionnement de chaque purgeur et remettre ou remplacer si nécessaire les purgeurs défaillants.
Evacuer ou récuperer la vapeur de révaporisation avant la pompe. Quantité excessive de vapeur de revaporisation (au-dessus de 20 kg/h) se produit dans le corps de la pompe.
La soupape d'échappement n'est pas étanche ou est grippée.
Isoler la pompe puis déposer l'ensemble couvercle et mécanisme. Déposer l'ensemble siège et soupape d'admission. Nettoyer ou remplacer si nécessaire.
ptôme 1 La pompe ne fonctionne pas en phase de démarrage. ment (cycle de fonctionnement audible).
SPIRAX-SARCO NV
RCG 665 46
Industriepark 5 B 9052 ZWIJNAARDE
Tél. (09) 244 67 10 Fax (09) 244 67 20
2\4\13\00000001 / IM-P136-03 / ST-BEf-11
- 12 / 14 -
Montage et Entretien MFP14 / MFP14S / MFP14SS
Instructions de sécurité
L’élimination des risques lors de l’installation et l’entretien des produits Spirax-Sarco
Le fonctionnement sécurisé de ces produits ne peut être garanti que s’ils sont installés, mis en route et entretenus par du personnel qualifié ( voir section “Permis de travail” ci-dessous) en toute concordance avec les instructions de montage et de service. Il faut aussi répondre à toutes les normes de sécurité concernant les installations de tuyauterie. La manipulation correcte des outils de travail et de sécurité doit être connue et suivie
Application
Assurez-vous que le produit est apte à être utilisé dans l’application au moyen des instructions de montage et de service (IM), la plaque signalétique et la fiche technique (TI).
Les produits dans la liste ci-dessous répondent aux exigences de la directive européenne “machines” 97/23/EC et sont pourvus d’un marquage , sauf s'ils ressortent sous les conditions décrits par l'article 3.3 de la directive:
Produit min. max. Gaz Fluides
G2
Appareils conformes à la Directive ATEX 94/9/CE II 2G CT3 i) Les produits ont été conçus spécifiquement pour utilisation avec :
Systèmes sous pression
S’assurer de l’isolation de l’appareil et le dépressuriser en sécurité vers l’atmosphère.
Prévoir si possible une double isolation et munir les vannes d’arrêt fermées d’une étiquette. Ne jamais supposer que le système soit dépressurisé, même lorsque le manomètre indique zéro.
Température
Laisser l’appareil se refroidir afin d’éviter tout risque de brûlure. Portez toujours des vêtements et lunettes de protection.
Outillage et pièces de rechange
S’assurer de la disponibilité des outils et pièces de rechange nécessaires avant d’entamer le travail. N’utiliser que des pièces de rechange d’origine
Spirax Sarco.
- comprimé
Des applications avec d’autres fluides sont possibles, mais uniquement après concertation avec et après accord de Spirax-Sarco. ii) Vérifiez l’aptitude des matériaux et la combinaison pression / température minimale et maximale admissible. Si les limites d’utilisation du produit sont inférieures à celles du système dans lequel il est monté, ou si un dysfonctionnement du produit peut engendrer une surpression ou surtempérature dangereuse, le système doit être pourvu d’une sécurité de température et/ou pression. iii) Suivez ponctuellement les instructions de montage du produit en ce qui concerne direction et sens d’écoulement du fluide. iv) Les produits Spirax-Sarco ne résisteront pas aux contraintes extrêmes induites par le système dans lequel ils ont été montés. Il est de la responsabilité de l’installateur de prendre toutes les précautions afin de minimaliser ces contraintes externes. v) Enlevez les capuchons de protection des bouts de connexions avant montage.
Accès
S’assurer un accès sûr et si nécessaire prévoir une plate-forme de travail sûre, avant d’entamer le travail à l’appareil. Si nécessaire prévoir un appareil de levage adéquat.
Eclairage
Prévoir un éclairage approprié, surtout lors d’un travail fin et complexe comme le câblage électrique.
Conduites de liquides ou gaz dangereux
Toujours tenir compte de ce qui se trouve, ou qui s’est trouvé, dans la conduite : matières inflammables, matières dangereuses pour la santé, températures extrêmes.
Ambiance dangereuse autour de l’appareil
Toujours tenir compte du risque éventuel d’explosion, de manque d’oxygène
(dans un tank ou un puits), gaz dangereux, températures extrêmes, surfaces brûlantes, risque d’incendie (lors de travail de soudure), bruit, machines mobiles.
Le système
Prévoir l’effet du travail prévu sur le système entier. Une action prévue (par exemple la fermeture d’une vanne d’arrêt ou l’interruption de l’électricité) ne constitue-t-elle pas un risque pour une autre partie de l’installation ou pour le personnel ?
Genre de risques possibles : fermeture de l’évent, mise hors service d’alarmes ou d’appareils de sécurité ou de régulation.
Eviter les coups de bélier par la manipulation lente et progressive des vannes d’arrêt.
Vêtements de protection
Vérifier s’il n’y a pas d’exigences de vêtements de protection contre les risques par des produits chimiques, température haute/basse, bruit, objets tombants, blessure d’oeil, autres blessures.
Permis de travail
Tout travail doit être effectué par, ou sous la surveillance, d’un responsable qualifié. Les monteurs et opérateurs doivent être formés dans l’utilisation correcte du produit au moyen des instructions de montage et d’entretien.
Toujours se conformer au règlement formel d’accès et de travail en vigueur.
Si nécessaire, un permis de travail doit être demandé, et les procédures du permis doivent être suivies ponctuellement. Faute d’un règlement formel, il est conseillé de prévenir un responsable du travail à faire et de réclamer la présence d’une personne responsable pour la sécurité. Si nécessaire l’utilisation de panneaux signalétiques est à prévoir.
Manutention
Manutention de produits encombrants et/ou lourds peut être à l’origine de blessures. Soulever, pousser, tirer, porter et/ou supporter un poids avec le corps est très chargeant et donc potentiellement dangereux pour le dos.
Minimalisez le risque de blessures en tenant compte du genre de travail, de l’exécuteur, de l’encombrement de la charge et de l’environnement de travail. Utilisez une méthode de travail adaptée à ces conditions.
Danger résiduel
La surface d’un produit peut, après mise hors service, rester encore longtemps très chaude. Si ces produits sont utilisés à leur tempéraure de fonctionnement maximale, la température de surface peut s’élever juqu’à 200°C.
Sachez qu’il y a des produits qui ne se vident pas complètement après démontage, et qu’il peut y rester une certaine quantité de fluide très chaud
(voir instructions de montage et d’entretien).
Risque de gel
Des précautions contre le risque de gel doivent être prises pour des produits qui ne sont pas complètement vidés lors de périodes d’arrêt ou de charge très basse.
Instructions de sécurité spécifiques au produit
Consultez les sections relevantes dans le manuel d’instruction
Mise à la mitraille
Sauf spécifié dans les instructions de montage et d’entretien, ces produits sont complètement recyclables, et peuvent être repris dans le circuit de recyclage sans aucun risque de pollution de l’environnement.
Renvoi de produits
Suivant la loi de protection de l’environnement, tous les produits qui sont renvoyés à Spirax-Sarco doivent être accompagnés d’informations concernant les résidus potentiellement dangereux qui peuvent y rester, ainsi que les précautions à prendre. Ces informations écrits doivent accompagner les produits, et contenir toutes les données de sécurité et de santé des substances dangereuses ou potentiellement dangereuses.
IM-P136-03 / ST-BEf-11 - 13 / 14 -
MFP14 / MFP14S / MFP14SS
Spirax-Sarco dans le monde
Pays Ville Téléphone
Europe
Autriche
Allemagne
Belgique
Danemark
Espagne
Finlande
France
Grande-Bretagne
Hongrie
Irlande
Italie
Norvège
Pays-Bas
Pologne
Portugal
République Tchèque
Russe
Suède
Suisse
Amérique
Argentine
Brésil
Canada
Mexique
USA
Afrique
Kenya
Afrique de Sud
Asie
Chine
Corée
Emirats Arabes
Hong Kong*
Inde
Indonésie
Japon
Malaisie
Pakistan
Philippines
Singapour
Taiwan
Thaïlande
Australië
Australie
Nouvelle Zélande
* : Office de vente
Vienne
Constance
Zwijnaarde
Copenhague
Barcelone
Helsinki
Trappes
Cheltenham
Budapest
Dublin*
Milan
Oslo
Maarn*
Varsovie
Lisbonne
Prague
St. Petersburg
Stockholm
Zurich - Zollikon
Buenos Aires
Sâo Paulo
Toronto
Monterrey
Columbia S.C.
Nairobi*
Johannesburg
Shanghai
Séoul
Dubai*
Poona
Jakarta*
Tokyo
Kuala Lumpar
Karachi*
Manila*
Taipei
Bangkok
Sydney
Auckland
(43) 1 699 6411
(49) 7531 58060
(32) 9 244 6710
(45) 38 10 4288
(34) 9 3 685 79 29
(358) 9 4136 1611
(33) 1 3066 4343
(44) 01242 521361
(36) 1 222 3708
(045) 876491
(39) 0362 49171
(47) 67 06 7680
(31) 343 442666
(48) 22 843 76 97
(351) 21 417 5093
(420) 2 782 2803
(7) 812 324 4987
(46) 8 556 322 30
(41) 1 396 8000
(54) 11 4741 6100
(55) 11 4615 9000
(1) 905 660 5510
(52) 8 336 3248
(1) 803 714 2000
(254) 2 443340
(27) 11 394 1212-18
(86 21) 6485 4898
(82) 2 525 5755
(971) 4 351 7018
(65) 453 6666
(91) 20 714 5595
(65) 453 6666
(81) 43 274 4811
(60) 3 735 3323
(92) 21 493 7163
(65) 453 6666
(65) 453 6666
(886) 02 2662 6689
(66) 2 379 3211
(61) 2 9621 4100
(64) 9 263 4205
Montage et Entretien
Fax
(43) 1 699 6414
(49) 7531 580622
(32) 9 244 6720
(45) 38 34 3858
(34) 9 3 685 70 11
(358) 9 4136 1640
(33) 1 3066 1122
(44) 01242 573342
(36) 1 223 1110
(045) 875291
(39) 0362 4917317
(47) 67 06 1408
(31) 343 441751
(48) 22 847 63 67
(351) 21 417 5100
(420) 2 781 8051
(7) 812 184 2933
(46) 8 18 29 60
(41) 1 396 8010
(54) 11 4741 7711
(55) 11 4615 9007
(1) 905 660 5503
(52) 8 336 2219
(1) 803 714 2219
(254) 2 444232
(27) 11 394 1219
(86 21) 6485 4899
(82) 2 525 5766
(971) 4 351 9356
(65) 459 6854
(91) 20 714 7413
(65) 459 6854
(81) 43 274 4818
(60) 3 735 7717
(92) 21 454 1768
(65) 459 6854
(65) 459 6854
(886) 02 2662 6715
(66) 2 379 4656
(61) 2 9831 8519
(64) 9 263 8400
SPIRAX-SARCO NV
RCG 665 46
Industriepark 5 B 9052 ZWIJNAARDE
Tél. (09) 244 67 10 Fax (09) 244 67 20
2\4\13\00000001 / IM-P136-03 / ST-BEf-11
- 14 / 14 -
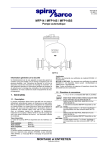
Lien public mis à jour
Le lien public vers votre chat a été mis à jour.
Caractéristiques clés
- Fonctionnement automatique par vapeur, air comprimé ou gaz inerte
- Refoulement de condensats et autres fluides
- Utilisable sous vide ou sous pression
- Disponible en fonte nodulaire, acier carbone et acier inoxydable
- Conforme aux directives européennes 97/23/EG et ATEX 94/9/EC