Rio Tinto Fer & Titane inc. GS Manuel utilisateur
Gracieuseté de :
édition / 02-2002 e
CIPFGS 10
Rio Tinto Fer & Titane inc.
CONDENSÉ POUR LES INGÉNIEURS DE PROJETS
FONTE À GRAPHITE SPHÉROÏDAL
(FONTE GS)
L’ A L L I A G E C O U L É :
D U P A S S É
D U P R É S E N T
D E L ’ A V E N I R
10
e
édition
CONDENSÉ POUR LES INGÉNIEURS DE PROJETS
FONTE À GRAPHITE SPHÉROÏDAL
(FONTE GS)
Publié par :
Rio Tinto Fer & Titane inc.
770, rue Sherbrooke Ouest
Bureau 1800
Montréal (Québec) Canada
H3A 1G1
Sorelmetal ® est produit par :
QIT - Fer et Titane inc., Canada et Richards Bay Minerals, Afrique du Sud
PRÉFACE
Au cours des dernières années, les producteurs et utilisateurs de pièces en fonte GS ont constaté que beaucoup des utilisateurs potentiels ne sont pas au fait des diverses propriétés offertes par la famille des fontes GS.
Depuis leur entrée dans le domaine commercial en 1948, les pièces en fonte GS se sont révélées être l'alternative au point de vue prix pour les pièces en fonte malléable, en acier coulé, les pièces forgées et assemblées …, ceci pour de multiples raisons dont certaines sont expliquées aux pages suivantes.
On trouve maintenant des pièces en fonte GS dans tous les domaines de mécanique et construction partout dans le monde. On connaît également la fonte GS sous les noms de fonte nodulaire ou fonte ductile. Ce livret utilise l'expression fonte
GS, laquelle est la plus répandue.
Après avoir lu ce livret, nous espérons que l'ingénieur de projets (design) sera suffisamment informé et encouragé à tirer avantage du potentiel performant de la fonte GS en tant que matériau mécanique à prix intéressant. Demandez à votre fonderie de vous donner plus de renseignements sur la fonte GS et de vous apporter le soutien requis.
CHARPENTE DE LIAISON
D'INSTRUMENT DE PRÉCISION
Courtoisie de IBM, Allemagne
3
TABLE DES MATIÈRES
FONTE GS - QUAND ET POURQUOI ? ..........................6
TOUT D'ABORD,
QUELQUES MOTS SUR L'ACIER ET LA FONTE .....8-9
LA FAMILLE DES FONTES GS ……………………… .....10
LA FONTE GS -
PLUS DE RÉSISTANCE POUR MOINS CHER ...........15
LA FONDERIE DE FONTE GS .......................................37
INSPECTION .................................................................38
LA FONTE GS :
UN CHOIX POUR L'INGÉNIEUR ................................39
AUTRES PUBLICATIONS ET SITE WEB .......................40
PRINCIPES
UTILISER LA LIBERTÉ QUE PERMET LE PROCÉDÉ
DE COULÉE .............................................................23
COMPRENDRE LES PRINCIPES FONDAMENTAUX
DU PROCESSUS DE FONDERIE ...............................25
CONCEPTION POUR PRIX DE REVIENT OPTIMAL . .....27
CONCEVOIR EN VUE D’OBTENIR UNE PIÈCE SAINE .....28
NE PAS DEMANDER PLUS DE PRÉCISION
DIMENSIONNELLE QUE NÉCESSAIRE .....................29
EFFET DE L'ÉPAISSEUR DE PAROIS
SUR LES PROPRIÉTÉS MÉCANIQUES .....................30
DESSINER AVEC UN FACTEUR DE SÉCURITÉ
CONVENABLE .................................................................32
FAIRE CONFIANCE À LA FONDERIE ............................34
COMMUNIQUER AVEC LA FONDERIE .........................35
5
CARACTÉRISTIQUE FONTE GS
FONTE
MALLÉABLE
FONTE
GRISE
COULABILITÉ
USINABILITÉ
AMORTISSEMENT
DES VIBRATIONS
TREMPABILITÉ
EN SURFACE
MODULE
D'ÉLASTICITÉ
RÉSILIENCE
RÉSISTANCE
À LA CORROSION
RÉSISTANCE / POIDS
RÉSISTANCE
À L'USURE
COÛT
DE FABRICATION
ACIER
COULÉ
0,3% C
FONTE
BLANCHE
N.D.
N.D.
N.D.
N.D.
N.D.
MEILLEUR PIRE
FONTE GS – QUAND ET POURQUOI
LA PLACE DE LA FONTE GS parmi les matériaux mécaniques est aussi difficile à définir que, par exemple, celle du bois, du plastique ou de l'aluminium. Aucun matériau ne peut être meilleur que tous les autres.
Néanmoins, des milliers d'exemples le prouvent : les pièces en fonte GS peuvent remplacer d'autres matériaux ou procédés de fabrication avec soit une amélioration de performance, soit un coût de production plus bas, ou les deux.
IL EST CONSEILLÉ À L'INGÉNIEUR de faire connaissance avec cette famille d'alliages coulés, la production de pièces coulées et la fonderie. Par exemple, alors que toutes les fonderies ne font pas de la fonte GS, toutes les pièces ou formes coulées peuvent être faites en fonte GS.
La fonte GS sera toujours ductile. Elle est au moins aussi résistante que l'acier doux et on peut l'obtenir avec une limite élastique beaucoup plus élevée. Le choix du matériau ne dépend pas nécessairement de sa résistance.
Ce livret, dans ses limites, essaie de vous familiariser avec les propriétés des fontes GS.
LE CHOIX FINAL peut être la fonte GS ou non. Le but de ce livret est de faire ressortir la combinaison unique des propriétés de ce matériau et, ainsi, aider l'ingénieur à faire un choix sûr et économique. Ce choix est rendu plus facile en raison de l'existence de nombreuses fonderies capables de produire des fontes GS de qualité fiable.
MOULE DE PNEU RADIAL
Courtoisie de Morris Bean & Co., Yellow Springs, Ohio, É.-U.
6
CARTER
Courtoisie de Vulcan Iron Works, É.-U.
Courtoisie de Cast Iron Pipe Research Association, É.-U.
La chute d'un poids de 2 tonnes d'une hauteur de
9 mètres a produit un léger enfoncement de ce tuyau en fonte GS, mais cela n'a pas affecté ses propriétés en service.
7
LES EXEMPLES donnés dans ce livret mettent en lumière la souplesse de conception que la fonte GS offre à l'ingénieur, tout en garantissant l'intégrité interne des pièces. Le turbocompresseur ci-dessus doit être totalement étanche lors d'essais à très haute pression.
Ceci a été obtenu malgré la forme exceptionnellement complexe de ce carter.
TOUT D'ABORD QUELQUES MOTS …
À l'état PUR, sans aucun ajout de carbone, le fer n'est pratiquement jamais utilisé comme métal coulé, car il est mou et faible. Quand la teneur en carbone augmente, la dureté et la résistance mécanique augmentent. L'effet du carbone, bien que créant des problèmes de production, est avantageux jusqu'à une teneur d'environ 0,9%. Ces alliages sont des ACIERS. De nouveaux problèmes apparaissent avec les teneurs allant jusqu'à 2% et ces «demiaciers» sont rarement utilisés. On peut utiliser les FONTES
BLANCHES contenant de 2 à 3% carbone dans des conditions hautement abrasives, mais l'application en est limitée en raison de la nature fragile de l'alliage. C'est une vraie fonte, mais la plus grande partie du carbone est présente sous forme de carbure de fer (cémentite), Fe
3
C, un composé dur et fragile.
Les teneurs en carbone des fontes blanche et MAL-
LÉABLE se recoupent. En fait, la fonte malléable doit se solidifier avec une structure de fonte blanche. (Sa production est donc limitée aux pièces relativement minces). Un traitement thermique prolongé de la fonte blanche permet de décomposer le Fe
3
C en nodules de graphite dans une matrice de fer. Dans cet état, la fonte malléable donne des combinaisons résistance/allongement de 40 000 psi
(200 MPa) avec 18% d'allongement jusqu'à 116 000 psi (800 MPa) et 2% d'allongement.
Fonte grise
8
Fonte GS x50 x50 Fonte blanche x50
A
B
… SUR L'ACIER ET LA FONTE
Dans les fontes grises et GS, le carbone en excédent du pourcentage soluble dans le fer à l'état solide est présent sous forme de graphite finement dispersé, plutôt que sous forme de Fe
3
C (cémentite). Dans LES
FONTES GRISES, les lamelles de graphite agissent comme points de concentration de contraintes et, sous effort, favorisent la propagation de la crique - voir figure (A). Il en résulte que les fontes grises sont peu résistantes, avec des contraintes à la rupture de l'ordre de 20 000 à 58 000 psi (150 à 400 MPa ) et pratiquement aucun allongement. La longueur des lamelles de graphite varie selon les conditions de production et, aussi, avec l'épaisseur de paroi. Normalement la longueur des lamelles varient de 0,1 à 1 mm.
LA FONTE À GRAPHITE SPHÉROÏDAL (c'est-à-dire fonte GS) est devenue une réalité industrielle en 1948. Le graphite précipite sous forme de sphéroïdes plutôt que de lamelles, par un traitement approprié du métal en fusion.
La forme quasi sphérique du graphite supprime l'effet de crique et, en fait, les sphéroïdes deviennent des
«arrêts de criques» comme illustré de manière spectaculaire à la figure ci-contre (B).
9
LA FAMILLE DES FONTES GS
La majorité des pièces en fonte GS sont produites dans l'un des trois types suivants, lesquels peuvent tous
être obtenus bruts de coulée, sans traitement thermique.
• FONTE GS FERRITIQUE (60-40-18)
Sphéroïdes de graphite dans une matrice de ferrite qui est essentiellement du fer pur. Résilience élevée.
Relativement bonne conductibilité thermique. Perméabilité magnétique élevée. Pertes faibles par hystérèse.
Dans certains cas, bonne résistance à la corrosion.
Bonne usinabilité.
• FONTE GS FERRITO-PERLITIQUE (80-55-06)
Sphéroïdes de graphite dans une matrice mixte de ferrite et de perlite. C'est la nuance de fonte GS la plus courante. Ses propriétés se situent entre celles des structures «totalement ferritiques» et «totalement perlitiques». Bonne usinabilité. La moins chère.
• FONTE GS PERLITIQUE (100-70-03)
Sphéroïdes de graphite dans une matrice de perlite.
La perlite est un agrégat fin de lamelles de ferrite et de cémentite (Fe
3
C). Relativement dure. Ductilité moyenne.
Conductivité thermique un peu réduite. Faible perméabilité magnétique. Pertes par hystérèse élevées. Bonne usinabilité.
Ferritique Ferrito-perlitique Perlitique
Nuance 60-40-18 Nuance 80-55-06 Nuance 100-70-03
60 000 psi
(414 MPa)
80 000 psi
(552 MPa)
100 000 psi
(690 MPa)
MATRICE
Martensitique
(avec austenite Martensitique retenue) revenue
* N.D.
115 000 psi
(793 MPa)
ADI ADI
Nuance 150-100-7 Nuance 230-185-
150 000 psi
(1 050 MPa)
230 000 psi
(1 600 MPa)
Austénitique
45 000 psi
(310 MPa)
* Limite élastique approximative : 87 000 psi (600 MPa). Dure, fragile.
10
(Noter que les grossissements sont différents)
Occasionnellement, l'ingénieur rencontrera des situations particulières l'amenant à considérer certaines nuances spécifiques des alliages en fonte GS.
• FONTE GS MARTENSITIQUE (trempée et revenue)
Dans les conditions «brutes de coulée», l'alliage est dur et cassant, et rarement utilisé. Cependant, la MAR-
TENSITE possède de très fortes résistances en traction et à l'usure. Un revenu à 500 o C (930 o F) procure une dureté de 300 HB, un à 600 o C (1 100 o F), 250 HB de dureté.
• FONTE GS AUSTÉNITIQUE
Une fonte GS austénitique n'est jamais choisie uniquement pour sa ténacité. Ses caractéristiques exceptionnelles sont une bonne résistance à la corrosion et à l'oxydation, des propriétés magnétiques supérieures, une ténacité élevée et une bonne stabilité dimensionnelle à températures élevées. (Connue aussi sous le terme GS
Ni-Resist).
Boîte à rebuts
Black Clawson Foundry, Watertown, NY
• FONTE GS À TREMPE BAINITIQUE («ADI»)
C'est la dernière arrivée dans la famille des fontes GS et elle représente un nouveau groupe de fontes GS par elle-même, offrant aux ingénieurs de conception (design) une combinaison remarquable de ténacité, dureté et résistance à l'usure.
L'ADI est presque deux fois plus forte que les nuances
ASTM des fontes GS alors qu'elle garde un bon allongement et une dureté élevée. De plus, l'ADI offre une résistance exceptionnelle à l'usure et à la fatigue, permettant ainsi aux ingénieurs de réduire le poids et le coût des composantes, cela pour une performance équivalente ou améliorée.
240 1660
200
160
1380
Fonte GS «Austempered»
1100
120
80
Fonte grise
Fonte GS trempée et revenue
830
Fonte GS ASTM A-536
550
40 275
11
0 5 10 15
Allongement à la rupture (%)
20
Note : le feuillet orangé inclus dans la pochette de la couverture arrière de cette brochure présente des renseignements additionnels sur les applications et les propriétés.
Les propriétés remarquables de l'ADI sont obtenues par un traitement thermique (trempe étagée) contrôlé de très près, qui permet la formation d'une structure composée de ferrite bainitique et d'austénite résiduelle
(à haut carbone).
L'austénite résiduelle (H.C.) est thermiquement stable; elle est cependant durcissable en service et se transforme même localement en martensite dans les conditions favorables de contrainte. L'avantage de cette caractéristique de l'ADI est que les contraintes de charge durcissent, au travail, les surfaces qui reçoivent l'effort. On peut aussi imposer délibérément, avant service, des tensions de surface, par exemple par
«shot peening» des engrenages ou par galetage des vilebrequins, pour obtenir des améliorations significatives de résistance à l'usure et à la fatigue.
Il n'y a actuellement aucune spécification standard pour l'ADI, mais des propositions couvrant cinq nuances de fonte ADI ont été soumises et servent de base de discussion; elles sont utilisées comme critères de sélection par les concepteurs et les fondeurs.
Résistance en traction
(ksi) (MPa)
125 850
150 1 050
175 1 200
200 1 400
230 1 600
Normes ASTM A897
Spécifications ADI :
Limite
élastique
Allongement Résilience Charpy non entaillée
(ksi) MPa)
80 550
100 700
125 850
155 1 100
185 1 300
(%)
10
7
4
1
-
*Uniquement à titre d’information
(ft-lb) (J)
75 100
60 80
45 60
25 35
-
Dureté Brinell moyenne*
(HB)
269 - 321
302 - 363
341 - 444
388 - 477
444 - 555
Le traitement thermique nécessaire à la production de l'ADI est essentiellement une opération à deux étages :
Stade 1.
Austénisation dans la zone 815 o - 920 o C (1 500 o -
1 700 o F). La température d'austénisation spécifique choisie est liée à la température du second stade et au type d'ADI recherché. Une fois choisie, la température d'austénisation doit être contrôlée de très près (±5 o C) /
(±10 o F).
12
Stade 2.
Transfert rapide des pièces au four (habituellement en bain de sel) dans lequel elles sont maintenues isothermiquement à la température choisie. Les températures de ce 2 ème stade sont dans la zone 230 - 400 o C (450 -
750 o F), selon les propriétés que l'on souhaite obtenir.
Température de trempe bainitique, °F austénisation
ENGRENAGE HYPOÏDE D'ESSIEU EN ADI.
Le passage de l'acier à la fonte GS a entraîné une réduction majeure du coût de production, une meilleure usinabilité, un fonctionnement plus silencieux ainsi qu'un poids plus faible.
Central Foundry Div., Saginaw, Michigan, É.-U.
Courtoisie de General Motors
Température de trempe bainitique, °C
L'ADI est bien connue comme matériau de remplacement de l'acier forgé pour les engrenages avec des réductions majeures des coûts de production, un fonctionnement plus silencieux et un poids plus faible. En usinant les engrenages avant le traitement thermique étagé, on obtient des économies majeures sur les coûts d'usinage.
13
ENGRENAGE EN ADI DES MOTEURS DIESEL CUMMINS
SÉRIE B QUI ONT REMPLACÉ L'ACIER 1022 FORGÉ ET
CÉMENTÉ PROCURANT UNE ÉCONOMIE DE 30%.
ENGRENAGES D'ADI FABRIQUÉS
SELON LES NORMES BREVETÉES K9805.
Courtoisie de Högfors Industries Ltd., Finlande
D'autres exemples d'utilisation de pièces en ADI : supports de ressorts de camions, adapteurs de ressorts de paliers d'essieux, vilebrequins, bielles, socs de charrue, etc.
Pour obtenir avec succès et de manière constante les propriétés et les performances optimales de l'ADI, il faut effectuer un choix et un contrôle judicieux de la fonte de base et des paramètres de traitement thermique.
La fonte GS qui doit subir la trempe étagée doit être de la meilleure qualité qui soit; cela nécessite un compte
élevé de nodules, l'absence de cémentite, d'inclusions et de retassure, et une composition chimique qui minimise les risques de ségrégation.
Les fontes GS bainitiques (aussi appelées fonte GS aciculaires) sont utilisées lorsqu'une résistance mécanique et une dureté très élevées sont requises afin d'assurer une bonne résistance à l'usure de la pièce, tout en affichant une structure usinable. Elles peuvent être produites brutes de coulée par des additions de nickel et de molybdène à la fonte ou par un traitement thermique spécial.
Ce court résumé décrivant la famille des fontes GS est basé sur l'aspect métallurgique de ces matériaux plutôt que sur les spécifications. Un feuillet groupant les propriétés de la plupart des nuances de fontes GS est inséré dans la pochette de la couverture arrière de cette publication. Toutes les propriétés sont déterminées en fonction de la composition chimique, du refroidissement
(solidification et refroidissement en phase solide) et de la structure du matériau.
Vilebrequin en ADI pour un moteur Ford turbocompressé. L'ADI est capable de satisfaire aux impératifs de fatigue à coût beaucoup moins élevé que l'acier forgé.
14
LA FONTE GS – «PLUS DE RÉSISTANCE
POUR MOINS CHER»
Il semble que la fonte GS ait été inventée (1948) avec en tête, l'ingénieur. Les combinaisons de résistance, de limite élastique et d'allongement des fontes GS surpassent celles de tout autre alliage ferreux, y compris l'acier et la fonte malléable.
Depuis sa mise en service, les applications de la fonte
GS ont surpassé tout ce que l'on supposait. La production mondiale était d'environ 16 millions de tonnes en l'an 2000 et on prévoit qu'elle atteindra 20 millions de tonnes en l'an 2006. L'utilisation de la fonte GS est une réalisation technique remarquable de notre époque.
PRODUCTION MONDIALE
DE
FONTE GS
(incluant les tuyaux)
Croissance : 4%
ÉTRIER DE FREIN
Que ce soit dans une pièce automobile, comme cidessus, les tuyaux pour transport d'eau, les charrues, ou les parcmètres inviolables, la fonte GS a effectué des percées majeures dans le marché des pièces de fonderie dans tous les pays développés. La motivation principale ne fait aucun doute : «PLUS DE RÉSISTANCE POUR
MOINS CHER». Ce coût avantageux vient non seulement de ce que les matières premières sont disponibles immédiatement, mais aussi de l'efficacité de la fonderie et des coûts moins élevés des pièces en fonte GS en ce qui concerne l'ébarbage et l'usinage.
Aux pages suivantes on trouvera une diversité de cas vécus provenant du monde entier. On aurait pu en ajouter de nombreux autres. Les fontes GS sont très versatiles et il semble qu'on puisse leur trouver des applications en quantité illimitée.
ANNÉE
15
Le matériau initial de ce bâti de pompe de 1 000 C.V.
était un assemblage en acier. En passant à la fonte GS, on a obtenu une meilleure répartition des efforts, un coût plus bas et un rapport résistance/poids amélioré. Le poids a été réduit de 46%, ce qui est particulièrement important pour les mises en œuvre éloignées lorsque les pièces doivent être transportées par avion.
Courtoisie de Fichtel & Sachs, Allemagne
Cette pièce d'arbre à cames travaille dans un milieu hautement abrasif. On a choisi la fonte GS pour combiner résistance à l'usure et usinabilité. Cette pièce est phosphatée.
Courtoisie de Gardner Denver Co., É.-U.
La fonte GS peut être facilement durcie en surface jusqu'à 55 Rc, ce qui permet une performance améliorée pour cette bague à ergots.
16
Courtoisie de Dana Corp., É.-U.
Dans la conception des cages de roulements, la résistance à la compression est un facteur important. La fonte GS, comme le montre les photos ci-dessous, soutient favorablement la comparaison avec l'acier. Les avantages supplémentaires sont : meilleurs usinabilité et amortissement des vibrations.
Courtoisie de S.K.F., Katrineholm, Suède
Courtoisie de Metallgesellschaft AG, Allemagne
Les raccords d'échafaudage ci-dessus, ayant des
épaisseurs de parois de 2 à 5 mm, illustrent l'excellente coulabilité de la fonte GS.
17
Courtoisie de Ausherman Manufacturing Co. Inc., É.-U.
Ce pignon de chaîne de 2,5 kg (5,5 lb), provient d'un gros cric utilisé pour redresser les châssis de voitures et de camions. Cette pièce, dessinée par Kansas Jack Inc.,
McPherson, Kansas, É.-U. et coulée par Ausherman
Manufacturing Co. Inc., est faite en fonte GS rencontrant les normes américaines ASTM A536 65-45-12 et est utilisée brute de coulée.
Le prix au rayon de Kansans Jack, prêt à l'utilisation, est de 63% inférieur en fonte GS, lorsque comparé à ce qu'il était en assemblage soudé.
Les pistons de compresseurs HP basse vitesse
étaient à l'origine monoblocs en fonte grise avec des parois de 19 mm. Au fur et à mesure que les vitesses ont augmenté le besoin pour des pistons plus légers et plus résistants s'est manifesté; ceci a été obtenu en utilisant la fonte GS, ce qui a permis, en plus, de réduire les
épaisseurs de paroi à 5 ou 6 mm.
Courtoisie de Gardner Denver Co., É.-U.
Par un changement de conception en faisant un assemblage de 2 pièces, on a simplifié la méthode de coulée et on a encore réduit le poids, ce qui a diminué l'inertie du piston.
Les surfaces d'accouplement et les chanfreins des soudures des demi pistons sont usinés, puis boulonnés et chauffés à 565 o C (1 050 o F). L'ensemble préchauffé est soudé en utilisant un arc à électrodes fer-nickel
(EniFeC1). La soudure est faite en trois passes et l'ensemble traité thermiquement pour atteindre une dureté de 201-260 HB.
18
Courtoisie de C.A. Parsons & Co. Ltd., Angleterre
La couronne d'appui fait partie d'une unité d'engrenage utilisée en milieu marin. En plus d'une haute résistance mécanique, il lui faut une bonne résistance à la corrosion en air salin. Le choix : la fonte GS austénitique répondant aux normes BS3468 - AUS 202A.
Courtoisie de The H.P. Deutscher Co., É.-U.
Ce châssis pour contacteur en surcharge avec parafoudre et dispositif anti-arc de primaire de 4 000 volts
était coulé en acier à l'origine. Une résistance mécanique insuffisante était à l'origine de déformations fréquentes entraînant la panne de tout l'ensemble.
Coulé en fonte GS de résistance mécanique moyenne, on a obtenu une combinaison de résistance mécanique suffisante et une résilience adéquate. Le coût a aussi été diminué.
Courtoisie de Dorr Oliver Long Ltd., Canada
Essieux pour chariots de mines. En passant de l'acier coulé à la fonte GS, la stabilité dimensionnelle en service a augmenté. La principale économie a été obtenue par la réduction des coûts d'usinage.
19
Avant assemblage
Le support ci-dessous doit avoir des dimensions précises et porter de fortes charges. Le matériau de rechange - acier coulé - serait plus cher compte tenu des alliages, de l'usinage et du traitement thermique. La fonte GS est aussi supérieure en précision dimensionnelle. La pièce est utilisée brute de coulée.
Après assemblage
Courtoisie de Ferrovorm, Afrique du Sud
Assemblage pour charrue produit par Fedmech
Holdings Limited. En raison de fréquentes ruptures de la pièce en acier qui comportait de nombreuses soudures, on est passé en fonte GS 72 500 psi (500 MPa).
Les tentatives pour améliorer la conception mécanosoudée requerraient trop de pièces, ce qui entraînait la distorsion et des problèmes dimensionnels pendant le soudage.
Depuis le passage à la fonte GS, il n'y a eu aucune rupture en service.
Courtoisie de Sulzer Bros. Ltd., Winterthur, Suisse
20
QUELQUES PIÈCES EN FONTE GS UTILISÉES DANS L'INDUSTRIE AUTOMOBILE JAPONAISE
Courtoisie de Toyota Motors Corporation, Japon
LES VOITURES UTILISENT BEAUCOUP DE PIÈCES
EN FONTE GS. Compte tenu de ses limites, ce livret ne peut décrire toutes les raisons qui ont fait choisir ce matériau; les principaux avantages sont : coulabilité, usinabilité, fiabilité en service, amortissement des vibrations, trempabilité en surface, possibilités variées de résistance mécanique, etc.
21
De plus, étant donné que le module d'élasticité de la fonte GS est légèrement inférieur à celui de l'acier, les contraintes inévitables reliées à un mauvais alignement sont moindres. Les vilebrequins sont des exemples où on peut prendre avantage de cette caractéristique.
Les écrous usinés à partir d'un manchon en fonte GS coûtent plus chers que les écrous usinés dans une barre en acier. Malgré cela on a choisi la fonte GS. Raison : le graphite dans la structure de la fonte GS affleure à la surface de la pièce, donnant un caractère unique d'auto lubrification en service.
Courtoisie de Von Roll AG, Klus, Suisse
Carters pour dispositifs de contrôle hydraulique utilisés principalement sur les machines à outils lourds. Ces carters usinés dans la fonte GS DIN1693 GGG 60 (standard allemand) - (fonte GS en coulée continue) - doivent supporter jusqu'à 500 atmosphères (7 000 psi) de pression interne.
22
Courtoisie de Metallgesellschaft AG, Allemagne
PRINCIPES POUR DESSINER UNE PIÈCE
EN FONTE GS
On discutera ici de la conception d'une pièce en fonte
GS. Si nous présentions des règles générales, nous serions au-delà du cadre de cette brochure. Il existe plusieurs publications très complètes ayant trait au dessin des pièces en général.
En se familiarisant avec les avantages de la conception de pièces en fonte GS, on réussit non seulement à optimaliser le design (répartition uniforme des contraintes, coût optimal) mais aussi à décider où l'usage de la fonte GS est préférable à celui d'un autre matériau. À cet égard, les caractéristiques de conception de pièces peuvent donc être considérées comme l'une des propriétés technologiques de ce matériau.
La coulée, par opposition à l'estampage, au forgeage ou à la soudure, est la méthode de formage du métal la plus universellement praticable; elle offre une grande liberté dans la création de la forme de la pièce. On peut combiner des courbes complexes, des nervures ou des bosselages avec un minimum de limitations dans l'élaboration. Par exemple, on peut couler les volutes internes de carters de pompe ou de turbine à leur forme définitive et ainsi éliminer une opération d'usinage presque impossible. La combinaison de deux composants ou plus en une seule pièce peut réduire considérablement le coût et améliorer la performance.
Principe 1.
UTILISER LA LIBERTÉ QUE PERMET LE PROCÉDÉ
DE COULÉE
Le but du concepteur est d'obtenir la performance fonctionnelle d'une pièce à un coût minimum de matériau et de fabrication. Un dessin est souvent un compromis entre un concept d'ingénieur satisfaisant des nécessités spécifiques en service et une forme alliant qualité élevée et coût de production faible.
23
Courtoisie de TMF, Afrique du Sud
Roues de tramway en fonte GS pour les mines souterraines présentées après décochage. On a réduit le temps d'usinage à 1/8 de ce qu'il était avec l'acier, tout en augmentant la sécurité en service.
Malgré la facilité de conception, on rencontre quelques fois des difficultés quand on transforme le concept de l'ingénieur en pièce utilisable, surtout quand celle-ci
était, à l'origine, prévue pour la forge, l'estampage ou la soudure.
L'ingénieur étant confronté à un large éventail de produits, il est rarement en liaison avec le procédé de coulée, et il s'ensuit que la pièce est dessinée sans tenir compte de la multitude de variables de fonderie. Ceci ne veut pas dire que l'ingénieur devrait posséder une compréhension totale du procédé de coulée, mais plutôt qu'il devrait comprendre les principes fondamentaux et s'adresser au fondeur pour les questions reliées au procédé de coulée.
L'idéal serait que le fondeur et l'ingénieur soient en contact étroit pendant les premiers stades de la conception de la pièce, afin que le fondeur ait la chance d'utiliser sa connaissance détaillée de la fonderie et de ses propres produits pour leur bénéfice mutuel. À ce stade, on peut faire, avec un minimum d'inconvénients, les commentaires sur les dessins d'ébauche et sur la fabrication des modèles afin de satisfaire aux besoins spécifiques de la fonderie. En conséquence, il n'y aura jamais de modifications majeures et tardives de forme, de tolérances dimensionnelles ou de spécifications de matériel.
Tous ces facteurs se traduisent probablement par un coût plus faible de la pièce coulée car ce dernier ne dépend pas simplement du poids de la pièce mais plutôt de sa complexité et de tout ce qui peut affecter le coût des modèles, des noyaux, des moules, du nettoyage de la pièce et du rendement métallique.
Le processus de décision de concevoir et produire des pièces peut se résumer ainsi :
Préliminaire
Décision d'utiliser une pièce
Dessin détaillé
Demande de prix, remise de prix, commande
Production
Fabrication du modèle
Production du prototype / échantillon
Production de série
Il n'y a souvent qu'un contact très superficiel entre l'ingénieur et le fondeur jusqu'à la production des prototypes ou des pièces types. À l'occasion, l'ingénieur ou le fondeur demandent des changements significatifs à ce niveau. L'ingénieur peut avoir l'impression de ne pas avoir reçu tout à fait ce qu'il avait commandé et le fondeur peut s'apercevoir que quelques changements mineurs de forme peuvent rendre la pièce beaucoup plus simple et donc, meilleur marché sans affecter ses performances. Quelle qu'en soit la raison, les changements à ce stade signifient des retards longs et coûteux.
Il est donc essentiel d'associer le fondeur dès le début aux aspects techniques du dessin de détail, et ainsi minimiser les risques de retards coûteux pendant les étapes de la production.
24
Principe 2.
COMPRENDRE LES PRINCIPES FONDAMENTAUX
DU PROCESSUS DE FONDERIE
De la compréhension du processus de coulée on déduira la plupart des modifications à apporter à la forme de la pièce idéale dans le but de la produire au moindre coût. On peut résumer ainsi cette connaissance nécessaire :
La première étape consiste à fabriquer le modèle, reproduction presque exacte de la pièce complète, habituellement fait en bois ou en métal. Le modèle (a) est ensuite généralement découpé suivant un ou plusieurs plans parallèles. Les parties, l'une après l'autre, sont alors placées dans les châssis qui sont ensuite remplis de sable aggloméré et serré très fermement (b) et (c).
Après retrait du modèle, une cavité est créée (d). On remplira cette cavité avec la fonte liquide pour former la pièce.
On a besoin d'autres cavités dans le moule pour deux raisons : (1) amener le métal liquide du haut du moule assemblé vers la cavité de la pièce (empreinte) et (2) compenser la perte de volume due au retrait du métal liquide entre la température de coulée et la température de solidification. Le premier jeu de cavités ou canaux est appelé «système d'alimentation», alors que les cavités
«nourricières» sont appelées «masselottes». En règle générale, le système de coulée et les masselottes font parties intégrantes du modèle.
La fonte liquide passe d'abord par le système de coulée, puis au travers d'une ou plusieurs ouvertures (les attaques), dans l'empreinte et, enfin, toute l'empreinte, y compris les masselottes, se remplit de fonte liquide.
Pendant qu'elle passe dans les chenaux et qu'elle remplit le moule, la température de la fonte liquide décroît.
Plus les parois de la pièce sont minces, plus grande est la perte de température, d'où l'augmentation marquée du risque de défauts provoqués par un remplissage incomplet.
25
Les cavités de la pièce elle-même sont réalisées en mettant des inserts, nommés «noyaux», habituellement faits en sable aggloméré et placés dans l'empreinte. Le matériau du noyau doit être enlevé par la suite et, par conséquent, la cavité interne de la pièce doit communiquer avec l'extérieur de la pièce. Le noyau doit aussi être bien soutenu et ancré dans le moule pour résister à la poussée d'Archimède ou à la déformation pendant le remplissage en raison de la différence de densité entre le noyau et la fonte liquide. Le minimum théorique est un seul point d'ancrage. Il faut au moins deux points appelés «portées».
Les noyaux sont aussi nécessaires lorsque, compte tenu de la configuration de la pièce, le modèle ne peut
être retiré du moule. De tels noyaux peuvent être fabriqués mais augmentent significativement le coût de production. Pour cette raison, le concepteur devrait savoir que «l'undercut» empêche le retrait du modèle. Les petits noyaux ont une résistance mécanique relativement faible, particulièrement à la température de la fonte. Pour cette raison, si des trous de faible section sont nécessaires dans la pièce, il peut être moins coûteux de les usiner plutôt que de les intégrer lors de la coulée à l'aide de petits noyaux (faibles). Des chenaux de faible section peuvent être coulés directement en plaçant de façon appropriée des tubes d'acier de formes requises dans la cavité du moule comme on fait pour les noyaux. Une partie du mur du tube d'acier se dissoudra dans le fonte
GS liquide.
Les changements de volume qui se produisent pendant le refroidissement et la solidification de la fonte GS sont différents de ceux des autres alliages. Le volume du liquide décroît avec la température jusqu'à une température légèrement au-dessus de la température de solidifi-
26 cation. Après un refroidissement complémentaire la contraction s'arrête et une expansion volumétrique démarre.
Malheureusement cette phase d'expansion ne prévaut que pendant une partie du processus de solidification.
Elle est suivie par une autre phase de contraction, «retrait secondaire», qui continue jusqu'à ce que tout le liquide soit transformé en solide.
L'utilisation de cette séquence de changements de volume en vue d'obtenir des pièces saines fait partie du savoir-faire du fondeur. La température de la fonte liquide doit être assez élevée pour permettre le mélange homogène des courants séparés et éviter l'emprisonnement de petites bulles de gaz. Chaque épaisseur de paroi a sa bande de température optimale de coulée qui permet de réaliser des pièces saines. On peut être amené à couler des pièces de 3 mm d'épaisseur à
1 450 o C (2 640 o F), alors que des pièces de 100 mm d'épaisseur peuvent être coulées entre 1 260 et 1 320 o C
(2 300 et 2 400 o F). Lorsque de fortes différences d'épaisseur existent dans une même pièce, on peut rencontrer des difficultés considérables; on peut quand même faire de telles pièces saines. Le fondeur se fera un plaisir de vous l'expliquer.
Il est de l'intérêt commun du fondeur et de l'utilisateur de concevoir une pièce dont l'épaisseur des murs varie le moins possible. Il peut être économique d'assembler deux (ou plus) pièces coulées plutôt que couler une pièce avec des parois de différentes épaisseurs tout d'un bloc.
Principe 3.
CONCEPTION POUR PRIX DE REVIENT OPTIMAL
Le prix d'une pièce soumis par le fondeur a relativement peu d'importance pour l'utilisateur et pour l'ingénieur. Par contre, la contribution du prix de la pièce au coût total est à considérer. Il comprend des paramètres tels que l'usinage, les coûts d'expédition, la facilité de réparation, la durée de vie, etc.
Chaque étape du processus de fabrication affecte le coût de production total et chacune est influencée par l'ingénieur. Il n'est ni possible, ni nécessaire d'en faire la revue ici. Par contre, on discutera de quatre facteurs majeurs. On parlera plus tard du facteur tolérance dimensionnelle.
FACTEUR 1. - Résistance nécessaire
La nuance de fonte GS choisie aura un effet considérable sur le coût. En se référant au classement de la fiche jointe, la nuance 65-45-12 est la moins chère, en particulier si les coûts d'usinage sont à considérer. La nuance
80-55-06 coûte à peu près aussi chère à couler, mais est moins facile à usiner. La nuance 100-70-03 est encore relativement peu chère et devrait être choisie si l'on doit utiliser sa résistance élevée à l'usure et sa résistance à la traction. Les nuances 60-40-18 et 120-90-02 sont plus coûteuses, mais peuvent aussi être le choix le plus économique si leurs caractéristiques mécaniques particulières sont requises en service. Les qualités austénitiques très chères doivent être envisagées en considérant leur excellente résistance à la corrosion, à l'érosion et à l'oxydation, leur performance à haute température, leurs propriétés mécaniques, leur faible coefficient d’expansion
27 thermique et d'autres caractéristiques qui leur sont uniques.
FACTEUR 2. - Coût d'usinage
Les coûts d'usinage sont fréquemment d'importance majeure. On peut éventuellement déroger aux règles de résistance, poids, durée de vie et autres considérations pour minimiser le coût d'usinage. Les nuances les plus faciles à usiner sont les 3 et 4, suivies de la 5 et de la 2.
La nuance 1 est la moins usinable bien que plus usinable, à dureté égale, que les aciers. L'usinabilité des fontes GS austénitiques est généralement supérieure à celle des aciers inoxydables.
FACTEUR 3. - Vitesse de refroidissement
On montrera comment la vitesse de refroidissement
(épaisseur de paroi) affecte les propriétés de la fonte GS.
Un refroidissement rapide produit une structure dure et fragile, difficile à usiner. En termes d'épaisseur de paroi, des sections de 6 mm ou plus sont relativement faciles à produire sans fragilisation ou dureté anormalement élevée. Les parois plus minces sont plus difficiles à produire sans ces problèmes à l'état brut de coulée. On peut éliminer fragilité et dureté élevées par traitement thermique, mais cela est très coûteux et peut générer des distorsions dans les pièces. Lorsque cela est possible, les parois devraient mesurer au moins 6 mm pour faciliter le brut de coulée. Le traitement thermique augmente le coût des pièces de 10 à 30 %.
FACTEUR 4. - Simplicité de la conception
Il est bien connu que la conception la plus simple est la meilleure. C'est aussi la plus économique. Un compromis acceptable entre simplicité de formes et distribution uniforme des contraintes est celui qui nécessite les modèles les moins chers et peu ou pas de noyaux.
Contribuent au prix du produit final la fabrication et l'entretien des modèles et boîtes à noyaux ainsi que le coût du noyau. Encore une fois parlez avec le fondeur.
On a discuté plus haut de l'effet des grands écarts d'épaisseur sur l'intégrité de la pièce. Les gros bosselages ou les sections épaisses près des sections minces demandent une mise au point particulière de la part du fondeur : masselottes, refroidisseurs. Cela signifie un coût supplémentaire et une mauvaise mise au mille.
L'influence de la mise au mille sur le coût de production par rapport aux autres variables, y compris le matériau choisi et le traitement thermique est la plus significative.
La géométrie du dessin influe aussi sur le mode de solidification et les besoins en alimentation. On en parlera plus loin.
RACCORD D'ÉCHAFAUDAGE
L'un des avantages de l'utilisation des pièces coulées est le marquage clair des noms, sens de rotation, etc. Même la date et l'heure de la fabrication peuvent
être facilement marquées
à la surface.
Courtoisie de Metallgesellschaft AG,
Allemagne
28
Principe 4.
CONCEVOIR EN VUE D'OBTENIR UNE PIÈCE SAINE
Grâce à l'expansion volumétrique qui a lieu pendant une période du processus de solidification, on peut produire plus facilement en fonte GS qu'en tout autre métal ou alliage (à l'exception de la fonte grise), une pièce saine et étanche à la pression. Malgré cela les besoins en masselottage varient avec la forme de la pièce et sa taille, variables qui sont sous le contrôle de l'ingénieur. À la différence de l'acier, du bronze et de la plupart des autres alliages, la conception et les processus de fonderie de fonte GS doivent rechercher une solidification simultanée de toute la pièce. Cet impératif est à l'opposé de la recherche de la solidification directionnelle qui s'applique à l'acier.
Un dessin qui recherche la solidification simultanée minimise et, quelquefois, élimine le besoin de masselottes avec une amélioration correspondante de la mise au mille. À l'inverse, les parties d'une pièce en fonte GS qui se refroidissent beaucoup plus lentement que le reste, peuvent devenir défectueuses, à moins que le fondeur ne fournisse un masselottage supplémentaire et coûteux. Voici quelques exemples de points chauds isolés :
Bosselages importants
Éprouvettes rapportées
Angles internes aigus
Raccordement entre parois de même épaisseur
Raccordements multiples
(2 est mieux que 3, 3 est mieux que 4, etc.)
Raccordements à angles aigus (90 o est le meilleur)
Sections épaisses isolées qui pourraient être allégées sans réduire la résistance aux contraintes
Courtoisie de Hitachi Ltd., Katsura, Japon
Une méthode qualitative simple pour évaluer les chances d'avoir une solidification uniforme consiste à inscrire des cercles dans des sections choisies du plan.
Si les diamètres sont tous les mêmes, comme ce serait le cas dans une paroi à faces parallèles, les conditions seront optimales. Des augmentations soudaines dans le diamètre des cercles (2 fois ou plus dans celui du cercle voisin) nécessitent une attention spéciale de la part de la fonderie.
29
Principe 5.
NE PAS DEMANDER PLUS DE PRÉCISION
DIMENSIONNELLE QUE NÉCESSAIRE
En raison de la nature même de l'élaboration par coulée, la précision dimensionnelle des pièces brutes est plus difficile à contrôler que celle obtenue par usinage, par exemple.
Les principales imprécisions dimensionnelles en fonte GS proviennent des facteurs suivants :
(a) imprécisions inhérentes aux dimensions usinées du modèle et de la boîte à noyaux;
(b) déformation du (des) noyau(x) dans la fonte liquide;
(c) imprécisions dues à la présence des plans de joint;
(d) relâchement des tensions internes, quand il y a traitement thermique.
À l'exception de (a), les imprécisions dépendent de la taille de la pièce. Plus la pièce est grande, plus l'imprécision sera grande. Les imprécisions dimensionnelles dues
à la déformation du moule pendant le retrait du modèle sont minimisées si on utilise une dépouille correcte. Une dépouille de 1% suffit pour des modèles très peu profonds. Les empreintes profondes peuvent demander jusqu'à 5% de dépouille si l'on veut une précision maximale.
Un guide approximatif des tolérances dimensionnelles que l'on peut espérer dans les pièces en fonte GS est présenté ci-dessous :
Tolérances dimensionnelles probables pour les pièces en fonte GS coulées en sable vert
Dimensions demandées
en mm
0 25
25 - 125
125 250
250 - 500
500 - 1 000
1 000 - 2 500
Tolérances ±
en mm
1,0
2,0
2,5
4,0
6,0
8,0
Autres points à considérer : a) Les valeurs données correspondent à des moules de dureté de 80 à 90 (sable vert). Des moules moins serrés donnent une précision dimensionnelle moins bonne.
b) On peut améliorer la précision pour «plus cher», en utilisant des moules très durs : sable étuvé, sable au ciment, etc. On peut obtenir des pièces encore plus précises avec des moulages de précision. Le procédé à cire perdue donne le maximum de précision avec des tolérances approximatives de ± 0,003x dimension spécifiée.
c) La précision dimensionnelle peut être améliorée par un facteur 2 (approximativement) si le nombre de pièces à être coulées permet de produire une première série de pièces expérimentales permettant d'ajuster le modèle avant d'entreprendre la production en série.
30
Principe 6.
EFFET DE L'ÉPAISSEUR DE PAROIS SUR LES
PROPRIÉTÉS MÉCANIQUES
Les données que l'on trouvera dans cette étude, comme la plupart de celles publiées au sujet des propriétés de la fonte GS, sont représentatives de pièces de
20 à 50 mm d'épaisseur. Les normes sont établies pour des éprouvettes usinées dans des «keel blocks» ou des
«Y blocks» de 25 mm. Quelques normes incluent l'effet de l'épaisseur (vitesse de refroidissement) et diminuent les valeurs minimales requises, habituellement l'allongement, pour les éprouvettes plus grosses ou pour les
éprouvettes usinées dans la pièce.
L'effet de l'épaisseur sur les propriétés mécaniques est le résultat de modifications de la structure microscopique, puisque cette dernière est influencée par la vitesse de refroidissement. Ces effets se résument comme suit : a) Des taux de refroidissement très élevés ne permettent pas à tout le carbone présent de précipiter sous forme de sphéroïdes. Il se forme alors de la cémentite, Fe
3
C, qui est dure et fragile.
b) Un refroidissement très lent donne des sphéroïdes de graphite très gros, jusqu'à 1,5 mm de diamètre, et de forme irrégulière.
c) En modifiant la vitesse de refroidissement dans la zone 850-250 o C (1 560-480 o F), de très rapide à très lente, on produit différentes structures, allant de la martensite (refroidissement ultra rapide) à la perlite,
à la perlite-ferrite et jusqu'à 100% ferrite (refroidissement lent).
duire des pièces d'essai qui refroidissent à peu près à la même vitesse que la pièce de série. Les essais mécaniques sur ces pièces d'essai donneront la prédiction la plus précise possible pour le produit de série.
La présence ou l'absence de carbures et le type de matrice que l'on obtient dans une section donnée peuvent se contrôler par alliage ou par traitement thermique. Il n'y a pas lieu d'en discuter ici, assumant que les effets en sont connus de l'ingénieur. Par contre, la taille des sphéroïdes de graphite peut être influencée, entre autre chose, par la vitesse de refroidissement de la pièce, qui à son tour peut être déterminée par la forme ou le dessin. Ces effets sont à considérer dans l'élaboration du dessin.
Tant que la forme du sphéroïde est approximativement sphérique, les propriétés technologiques, physiques et chimiques de la fonte GS ne sont que peu affectées. Toutefois, les données publiées ne s'accordent pas toutes. De l'information sur les propriétés mécaniques des pièces en fonte GS sans carbure et de différentes
épaisseurs est disponible. Si pour les calculs de l'ingénieur on doit avoir une connaissance plus précise des propriétés, celui-ci devra demander à la fonderie de pro-
31
Courtoisie de Cleaver Brooks Cony, Division of Aqua-Chem Inc. É.-U.
Ce manufacturier a spécifié le remplacement de la fonte grise par la fonte GS pour certaines sections de vaisseaux pressurisés de sa nouvelle génération de bouilloires. La fonte GS répondant à la norme ASTM-A
395-80 (60-40-18) a été choisie à cause de ses limite
élastique et résistance à la traction élevées et de son excellente réponse à la fatigue thermique. Pour les bouilloires, ces propriétés sont critiques puisqu'elles diminuent les risques de fracture due aux chocs thermiques ou autres. Les résistances supérieures de la fonte GS à la corrosion et à l'usure sont d'autres facteurs justifiant le choix de Cleaver Brooks.
Le besoin de revoir la conception du système de distribution d'ammoniac a donné l'occasion à la société
Henry Valve Co., de l'Illinois, de substituer la fonte GS à la fonte grise, tel que montré ci-dessus. Les réductions de taille (parois plus minces) et de poids (45%) ont été obtenues sans sacrifier la performance de l'équipement.
32
Principe 7.
DESSINER AVEC UN FACTEUR DE SÉCURITÉ
CONVENABLE
On fabrique en fonte GS aussi bien des pivots de direction automobile que des socs de charrue. Il est évident que ces pièces ont des impératifs de sécurité différents, lesquels varient énormément d'une application à l'autre.
L'ingénieur a toutes les informations nécessaires pour obtenir le niveau de sécurité requis. Cependant il faut agir judicieusement, car augmenter la sécurité accroît invariablement les coûts. Les actions disponibles sont : a.
S'approcher de la capacité maximum de charge du matériau à différents niveaux prédéterminés. Sous charge statique, l'effort maximal admissible est la limite élastique. Les efforts habituels pour le dessin varient entre 50 et 75% de la limite élastique à 0,2%.
Les pièces qui subissent des charges variant fréquemment doivent être conçues en fonction de la limite d'endurance en fatigue. Des niveaux de contrainte variant de 50 à 100% de la limite d'endurance du matériau sont habituellement utilisés, ce qui correspond, respectivement, à une marge de sécurité très élevée ou faible.
b.
Estimer l'effet de surcharges potentielles exceptionnelles et déterminer le mécanisme de rupture le plus probable. On peut rarement prévoir les conditions exceptionnelles en service. Cependant il faut y penser.
Des charges dynamiques ou statiques excessives peuvent provoquer la panne, soit par déformation de la pièce soit par rupture. En fonction de l'utilisation, un type de mécanisme de défaillance s'avérera plus
sûr qu'un autre. Par exemple, dans un réservoir
étanche à la pression, une augmentation imprévue de la pression interne peut faire éclater la pièce ou la déformer de manière permanente. La déformation permanente sera probablement le mécanisme de défaillance le plus sûr. Ceci est un exemple des applications relativement peu nombreuses pour lesquelles la ductilité est la propriété critique pour l'ingénieur. Autre exemple : un pignon. Une surcharge soudaine peut casser ou courber une ou plusieurs dents. Dans ce cas, la rupture sera préférable, car la structure sera capable de continuer de fonctionner, bien que médiocrement, jusqu'au remplacement.
L'utilisation généralisée de la fonte GS de ductilité
élevée (nuance 60-40-18) ne peut être considérée, même du point de la sécurité. La nuance 80-55-06 peut supporter des charges de 70 à 80% supérieures. La nuance 120-90-02 peut, quant à elle, supporter une charge deux fois et demie plus élevée, sous condition statique ou dynamique, que la nuance 60-40-18. De plus, les nuances 120-90-02,
100-70-03 et 80-55-06 se rompront franchement alors que la nuance 65-45-12, et encore plus dans le cas de la nuance 60-40-18, se déformera de façon permanente sous l'effet de contraintes beaucoup plus faibles. Selon le critère de sécurité sélectionné, les nuances de grande ductilité et faible résistance mécanique peuvent être choisies mais chaque application doit être évaluée séparément. c.
La spécification d'essais destructifs et non destructifs sur un certain nombre de pièces, ainsi que la fréquence et la rigueur de ces essais, sont directement
33 proportionnelles au niveau de sécurité demandé à la pièce.
Pour les pièces critiques dites de «sécurité», on demande souvent un contrôle à 100%, même si un tel contrôle coûte très cher. Les méthodes radiographique,
à courants de Foucault, magnétique, à fréquences ultrasonique ou sonique sont utilisables pour les contrôles non destructifs.
CARTER POUR UNE SECTION BASSE PRESSION
DE TURBINE 300MW.
Poids total : 48 tonnes. Le succès de la fonte GS dans ce cas est attribué à sa bonne résistance à température élevée et en particulier à sa limite élastique élevée à haute température.
Les pièces coulées permettent à l'ingénieur de créer des contours internes qui sont presque impossibles à usiner.
Courtoise de Salzgitter Hüttenwerk A.G., Salzgitter, Allemagne
Principe 8.
FAIRE CONFIANCE À LA FONDERIE
Les fondeurs qui produisent la fonte GS sont bien au courant des choix à faire vis-à-vis le procédé de fabrication, la composition chimique, le traitement thermique et les contrôles nécessaires en usine pour produire une pièce fonctionnelle.
Lorsque le concepteur spécifie la façon dont la pièce doit être fabriquée, il s'introduit de façon évidente dans le domaine du fondeur. Le concepteur, représentant l'acheteur, pourra faire de telles représentations, mais n'y gagnera rien et, très souvent, finira par payer plus cher les pièces produites selon ses prescriptions que s'il avait laissé le choix du procédé de fabrication au fondeur.
Les instructions superflues les plus souvent données au fondeur sont celles reliées à la composition chimique de la fonte, au traitement thermique et aux méthodes de contrôle de qualité.
Par exemple, il est bien connu que si l'on augmente la teneur en silicium de la fonte, on augmente également la température de transition. Si l'ingénieur décide d'une résilience minimale à une température donnée, il lui suffit de le spécifier sans préciser la teneur en silicium. Une gamme étendue de propriétés peuvent être obtenues par traitement thermique, mais pourvu que l'on exerce des contrôles corrects en production, on peut aussi les obtenir brutes de coulée. Cela doit rester le choix du fondeur de livrer des pièces brutes de coulée ou traitées, tant que les spécifications sont respectées.
Il faut un contrôle de qualité serré pendant tout le processus de coulée, en particulier quand on produit un matériau à haute performance comme la fonte GS.
Le fait de spécifier les propriétés requises n'est pas une indication du manque de confiance de la part du concepteur. Ce n'est non seulement un droit mais aussi le devoir du concepteur d'effectuer ou de demander des essais aussi complets que requis (spécialement pour l'aspect «sécurité»), afin de s'assurer que la pièce possède les propriétés demandées.
Cette roue en fonte GS, en une seule pièce, a remplacé quatre pièces. Redessinée en fonte GS, le coût total est passé de 251 $ à 75 $. Le coût d'usinage a chuté de 189 $ à 38 $, et le nombre d'opérations de production de 7 à 3.
La fonte GS 100-70-03 a été choisie en raison de sa bonne réponse au traitement Tufftride.
Courtoisie de Parten Machinery Co., Minneapolis, MN
34
Principe 9.
COMMUNIQUER AVEC LA FONDERIE
Cela ressemble à du défaitisme de suggérer encore une fois, après avoir décrit tous les principes de conception d'une pièce, que l'ingénieur rencontre le fondeur avant de finaliser ses plans. Cependant, cette suggestion est le dernier principe de la conception de pièces en fonte GS.
Aucun ingénieur ne sera un expert en fonderie après avoir pris connaissance des (brefs) principes fondamentaux du procédé de coulée et des particularités de la fonte GS. Suivre ces principes fondamentaux aidera à
éviter des erreurs majeures. Il faut cependant une connaissance approfondie à la fois du procédé de coulée et de la fonderie pour décider de détails qui peuvent avoir une grande importance vis-à-vis du prix de revient et des performances de la pièce.
Le moment approprié pour discuter avec le fondeur se situe lors de la conception de la pièce «idéale». La fonderie sera impatiente de coopérer pour déterminer si certaines modifications sont nécessaires ou non afin de faciliter la production de la pièce. Les modifications suggérées ne seront peut-être pas acceptables par l'ingénieur, mais les deux parties y gagneront sûrement. Le fondeur sera aussi heureux de vous montrer sa fonderie en service et la capacité de ses lignes de moulage et de noyautage. Vous verrez probablement quelques bons exemples de pièces semblables à celle que vous voulez produire.
Vilebrequin redessiné, utilisé dans le moteur
Pontiac 2,5 litres type L4. D'après les ingénieurs, le vilebrequin en fonte GS est 23% ou 10 livres moins lourd que le précédent. Ceci a été réalisé sans sacrifier la durée de vie ou l'intégrité du vilebrequin.
Courtoisie de Pontiac Motor Division,
General Motors Corp., É-U
35
Courtoisie de Daniel Industries Inc., É.-U.
Cette pièce en fonte GS contient la commande d'une vanne de purge spéciale remplaçant le travail de deux vannes. Ce nouveau carter a été dessiné en une seule pièce de fonte GS au lieu d'un ensemble en acier, économisant ainsi à Daniel Industries 2 300 000 $ par an.
Les coûts de matériel et de fabrication ont chuté de
467 $ à 67 $. Autres avantages : meilleur aspect et problèmes de fabrication diminués.
Ce support fournit des attaches de ressort horizontales et verticales pour une lame et un bras d'assemblage utilisé sur les charrues. Le nouveau plan composite acier-fonte GS a remplacé un mécanosoudé, diminuant le coût de 37% la première année pour une économie de
167 500 $. Une fiabilité accrue et un aspect amélioré sont les avantages supplémentaires cités par l'ingénieur.
En portant attention au dessin, une pièce en fonte GS est soudée de manière conventionnelle à une plaque d'acier estampée. Au plan, on avait prévu une oreille interne à ajouter à la pièce en vue de placer la soudure en cisaillement côté tension du joint.
La plus grosse pièce au monde réalisée en fonte GS. Bâti pour presse 40MN. Dimensions 11 300 x 3 800 x 3 000 mm.
Courtoisie de Siempelkamp Giesserei GmbH & Co.,
Krefeld, Allemagne
36
Courtoisie de John Deere Plow & Planter Works, É-U
LA FONDERIE DE FONTE GS
La popularité de la famille des alliages de fonte GS vient de leur diversité et de leur prix de revient intéressant. Les observations pratiques et les adaptations par des milliers de fonderies productrices ont fait que la production de la fonte GS est devenue une routine. La fabrication de pièces en fonte GS est semblable à la production de toutes autres pièces en alliage ferreux.
L'expérience et la connaissance sont parties intégrales du métier de fondeur.
Une addition minime mais bien dosée de magnésium, est la base du procédé permettant de changer la forme des particules de graphite de lamellaire à sphéroïdale.
Ce traitement est en général effectué avec un alliage de ferrosilicium-magnésium. L'inoculation de la fonte traitée par addition de ferrosilicium dans la poche de coulée est
également très importante.
Le contrôle de la composition chimique de la fonte
GS s'effectue sur environ une vingtaine d'éléments. La détermination routinière de la teneur de chacun d'entre eux n'est pas nécessaire mais, dans un tel cas, cela requiert l'utilisation de matériaux de charge fiables.
Néanmoins, le suivi des teneurs de carbone et silicium dans le four est requis de façon routinière.
Une fonderie qui réussit, a mis en place des méthodes de fabrication et de contrôle de qualité fiables. Comme nous l'avons dit plus tôt, ce contrôle n'est pas la responsabilité de l'ingénieur. Toutefois, si la fonderie n'a pas mis en place l'équipement de contrôle de base le plus élémentaire, ou encore si elle ne l'utilise pas, on peut douter de l'intégrité des pièces produites.
37
SCHÉMA DE PRODUCTION DES PIÈCES EN FONTE GS
INSPECTION
L'inspection est essentiellement le domaine du client et de l'ingénieur. Cependant le fondeur est impliqué jusqu'à un certain point. Tout d'abord, il contrôle l'aspect extérieur et les dimensions des pièces. L'examen microscopique permettra de vérifier le niveau de sphéroïdisation et la structure de la matrice. Généralement cela suffira si l'échantillon est pris selon les souhaits de l'ingénieur. La fréquence de l'échantillonnage devra également
être établie.
Certains essais de routine peuvent être demandés, si ceux-ci sont justifiés par les conditions prévues lors de la mise en service de la pièce. Ceux-ci sont présentés cidessous.
a) Essais mécaniques.
1.
Détermination de la résistance à rupture, de la limite élastique, de l'allongement et de la dureté.
2.
Détermination de la résilience.
3.
Détermination des tolérances dimensionnelles
(probablement avec gabarits de contrôle).
La vérification des propriétés mécaniques peut se faire à températures élevée, ambiante ou en-dessous de
0°C (32°F), en particulier pour la résilience. La température doit toujours être spécifiée.
On peut en plus évaluer les conditions en surface et sous la surface de la manière suivante : b) Méthodes pour révéler les défauts de surface.
1.
Inspection visuelle.
2.
Contrôle par produit pénétrant.
3.
Contrôle par particules magnétiques (fluorescence).
38 c) Méthodes pour révéler les défauts de sous-surface.
1.
Rayons X (radiographie gamma).
2.
Contrôle ultrasonique.
L'intégrité d'une pièce est déterminée par les paramètres du procédé de fabrication. Aucun des contrôles ci-dessus n'améliorera la qualité de la pièce mais ils en augmenteront le coût. Il est raisonnable de penser que la fonderie effectuera le contrôle de qualité de base par mesure de la dureté, examen de la microstructure et inspection visuelle du fini de surface. Quand ce contrôle est effectué de manière continue, le fondeur est en bonne position pour produire des pièces qui rencontrent constamment les spécifications.
Pièce en fonte GS pesant 85 tonnes utilisée pour le stockage et le transport de barres usagées de combustible nucléaire.
Les contrôles de l'AIEA (Autorité Internationale de l'Énergie
Atomique) sont appliqués à ces pièces et celles-ci ont rencontré ces spécifications extrêmement serrées.
Courtoisie de Siempelkamp, Krefeld, Allemagne
LA FONTE GS : UN CHOIX POUR L'INGÉNIEUR
Les pièces en fonte GS ont remplacé les pièces en fonte grise, en fonte malléable et en acier dans beaucoup de cas, donnant de meilleurs résultats en service et ceci, souvent à moindre coût.
On peut presque toujours remplacer des assemblages lourds mécanosoudés en acier, jusqu'à une taille moyenne, par des pièces en fonte GS. Voici certaines applications :
Automobile et Agriculture
Trompettes et essieux
Traverses de châssis
Cylindres de frein
Étriers de frein
Arbres à cames
Embrayages
Bielles
Vilebrequins
Monoculteurs cultivateurs
Bagues de chemises
Collecteurs d'échappement
Fourches de roues avant
Pignons et engrenages
Supports d'attelage
Composants d'embrayage moto
Segments de piston
Socs de charrue
Boîtiers de direction
Moules à pneus
Accouplements
Moyeux de roues
Joints de cardan
Autres moyens de transport
Ancrages
Paliers de pont
Pièces de bulldozer
Coupleurs de câbles
Cabestans (treuils)
Boîtes d'essieux de voiture
Wagonnets
Plaques de goulottes
Plaques de wagons à coke
Charpentes de convoyeurs
Accouplements
Pignons pour chenilles
Godets d'élévateurs
Glissières de four
Tambours de palans
Pignons libres
Flasques de tuyaux
Hélices
Roues de train
Rouleaux
Drains de piste d'envol
Traverses de rail
Mécanique générale
Cames de commande
Jets (Barres)
Leviers coudés
Éléments de chaudière
Pistons de presse à briqueter
Têtes de poutrelle
Bâtis de machines
Mandrins
Composants de mesure
Conteneurs de combustible nucléaire
Tubulures de pétrole
Commutateurs suspendus
Vérins de serrage
Pignons de broyeurs à charbon
Corps de compresseur
Marteaux de broyeurs
Corps d'amortisseurs
Matrices de presses
Pignons de dragues
Verrouillages d'extensions
Matrices de forge
Bâtis et gabarits
Grilles de fours
Broyeurs giratoires
Bobines de réchauffeurs
Matrices pour formage à chaud
Chapeaux d'isolateurs
Têtes de mouton (sonnette)
Matrices pour former des tuyaux
(formes de cintreuses)
Corps de presses à rouleaux
Corps de pompes
Rochets
Grilles de résistance
Supports de culbuteurs
Rouleaux
Moules à caoutchouc
Berceaux de scies
Arbres
Bâtis de cisailles
Essieux
Supports de suspension
Bâtis et pièces de tondeuses à gazon Couvercles de réservoir
Parafoudres Guides de fil
Tambours de collecteurs
Mèches à bois
Éléments de tunnel
Têtes de tourelles
Bâtis de machines à écrire
Bâtis d'étaux
39
Des informations plus détaillées sur les propriétés et les applications de la fonte GS se trouvent dans la publication «Ductile Iron Data Book» (210 pages) révisée et rééditée en 1998 par Rio Tinto Fer & Titane. Ce volume est disponible par l'entremise du «Ductile Iron
Marketing Group» ou via les bureaux régionaux de Rio
Tinto Fer & Titane. Le volume est aussi disponible sur
Internet, tout comme ce livret et le livret «Conversion to
Ductile Iron»; tous ces documents sont sous forme
«downloadable» sur le site www.ductile.org/dimg. Vous pouvez également nous contacter par courriel à cette adresse ou à l’adresse suivante : www.sorelmetal.com
40
Copyright 2002 Rio Tinto Fer & Titane inc.
Litho Canada Transcontinental, division Métrolitho
Cher représentant de fonderie :
Cette dixième édition a été préparée afin de vous aider à entrer en contact avec les ingénieurs de projets
(design) n’ayant pas encore opté pour la version fonte
GS de leurs pièces.
Cette brochure répond-elle à vos attentes ?
Tous les avantages de la fonte GS n’ont pas forcément été mis en exergue et peut-être, vous même, avez-vous dans vos archives des exemples d’applications méritant d’être portés à la connaissance de la profession. Si tel est le cas, n’hésitez pas à nous contacter à l’adresse ci-dessous.
Services Techniques - Ventes et Marketing
Rio Tinto Fer & Titane Inc.
770 ouest, rue Sherbrooke
Bureau 1800
Montréal (Québec) H3A 1G1
Canada
Concepteur de projets (design)
Ce livret a été conçu afin de vous informer des nombreux avantages que vous offrent la fonte GS et de vous amener à considérer ce matériau pour diverses applications. De plus il suggère des voies de collaboration avec la fonderie afin de rendre celle-ci plus efficace. Cependant, l’espace disponible dans ce livret ne permet d’aborder ces sujets que de façon sommaire.
Vos commentaires sur ce livret, à savoir à quel point ce dernier rencontre vos besoins et quelles sont les modifications que vous souhaitez y voir apportées sont les bienvenus et permettront d’améliorer les éditions futures.
PROPRIÉTÉS PHYSIQUES DE LA FONTE GS ET DE MATÉRIAUX COMPÉTITEURS
PROPRIÉTÉ UNITÉ
120-90-02 100-70-03
FONTE GS
80-55-06 65-45-12 60-40-18
0.3% C
ACIER COULÉ
FONTE
MALLÉABLE
FONTE
GRISE *
Température du solidus
Densité
Coefficient moyen d'expansion linéaire
Capacité d'amortissement
Chaleur de fusion
Chaleur spécifique
Conductivité thermique
(température de la pièce)
PROPRIÉTÉS MAGNÉTIQUES
Perméabilité maximale
à 500 Gauss
Induction de saturation
à 10,000 Oersted
Perte d'hystérèse o F
Lb/in 3 o F 1 x 10 4
-
BTU/lb
BTU/lb/ o F
Cal/cm.s. o C
2 100
0,25
6,0 bon
55
0,15
0,06
2 100
0,25
6,0 bon
55
0,15
0,06
2 100
0,25
6,0 bon
55
0,14
0,08
Oersted
Gauss
Erg/cm 3 /cycle
290
-
-
290
-
30
570
17 600
30
2 100
18 000
5
PROPRIÉTÉS MÉCANIQUES
Contrainte d'écoulement psi (0,62 à 0,75) x Résistance en traction
Module d'élasticité en traction
Résistance en torsion
Module de rigidité psi
X 10 6 psi psi
X 10 6
25,7
108 000
9,6
25,7
90 000
9,6
25,2
72 000
9,6
* Une fonte grise de résistance mécanique moyenne a été utilisée pour les fins de cette comparaison.
23,8
58 000
9,3
2 100
0,25
6,0 bon
55
0,13
0,09
2 100
0,25
6,0 très bon
55
0,13
0,10
2 100
18 000
5
23,8
50 000
9,1
2 650
0,283
7,0 pauvre
108
0,11
0,11
-
-
100
30 500
30,5
-
11,4
2 050
0,265
6,7 bon
55
0,12
0,14
2 350
-
20
(0,65-0,8) x UTS
25
34 000
11
2 140
0,25
5,8 excellent
55
0,13
0,11
800
16 000
30
-
18,3
60 000
7,1
Rio Tinto Fer & Titane Inc.
770 rue Sherbrooke ouest
Bureau 1800
Montréal (Québec) Canada H3A 1G1
Tél. (514) 288-8400
Fax. (514) 286-9336 www.sorelmetal.com
Rio Tinto Iron & Titanium America
Division of High Purity Iron Inc.
9399 West Higgins Road
Suite 140 West
Rosemont, Illinois 60018 - USA
Tel. (847) 698-4002
Fax. (847) 698-4003
The Ductile Iron Marketing Group
c/o Ductile Iron Society
28938 Lorain Road
North Olmsted, Ohio 44070
Tel. (216) 734-8040
Fax. (216) 734-8112 www.ductile.org/dimg
POURQUOI CONVERTIR UNE PIÈCE À LA FONTE GS?
240
POURQUOI CONVERTIR UNE PIÈCE
À LA FONTE GS ?
Les dessinateurs-concepteurs convertissent de nombreuses pièces coulées ou forgées en acier ainsi que différents assemblages à la fonte GS afin de bénéficier des avantages suivants :
• Rapport résistance/poids amélioré
• Meilleure reproduction des détails de surface et du fini
• Usinabilité supérieure
• Usinage réduit
• Coût moindre des pièces
• Résistance mécanique accrue par dollar investi
• Réduction du poids de la pièce
Plusieurs pièces actuellement coulées, forgées ou assemblages en acier peuvent être convertis à la fonte GS afin de prendre avantage d'un coût de revient moins élevé tout en ayant une performance égale ou supérieure.
CONTACTEZ UN PRODUCTEUR DE FONTE GS AUJOURD'HUI !
CONCEPTION DE PIÈCES COULÉES
DE QUALITÉ
Des pièces coulées de qualité sont le résultat du travail d'équipe du concepteur et du fondeur
* Consultez une fonderie au début du processus de conception
* Discutez des avantages de conception des pièces coulées
* Utilisez la flexibilité de conception et de choix de matériaux qu'offrent les pièces coulées
* Prenez avantage de la conception "near-net shape" qui est offerte
* Dessinez la pièce afin qu'elle soit saine et possède une distribution optimum des contraintes
* Concevez une pièce au plus bas coût possible
* Spécifiez les propriétés et le niveau de qualité requis pour votre application
CONTACTEZ UN PRODUCTEUR DE FONTE GS AUJOURD'HUI !
200
160
Fonte GS «Austempered»
1660
1380
1100
120
Fonte GS trempée et revenue
830
80
Fonte grise
Fonte GS ASTM A-536
550
40 275
0 5 10 15
Allongement à la rupture (%)
20
APPRENEZ-EN PLUS
SUR LES AVANTAGES DE LA FONTE GS
Un livret gratuit de 40 pages «Condensé pour les ingénieurs de projets -
Fonte à graphite sphéroidal (Fonte GS)» est disponible et deux autres publications techniques «Conversions to Ductile Iron» et «The Ductile Iron
Data Book» sont aussi à votre disposition. Pour obtenir ces publications et une liste des producteurs de fonte GS, ou pour discuter de la façon dont vous pouvez prendre avantage de la fonte GS, contacter «Ductile Iron
Marketing Group» ou l'une des compagnies membres.
The Ductile Iron Marketing Group - c/o Ductile Iron Society
28938 Lorain Road, North Olmsted, Ohio 44070
(216) 734-8040 • www.ductile.org/dimg
Le «Ductile Iron Marketing Group» est un organisme à but non lucratif dont la mission est de dissiminer les connaissances reliées aux avantages techniques et économiques des pièces coulées en fonte GS. Les membres de ce groupe sont :
The Ductile Iron Society - Rio Tinto I&T America
SPÉCIFICATIONS - FONTE GS
Organisme de normalisation
ASTM
ASTM
ASME
No.
Spéc.
SOMMAIRE DES SPÉCIFICATIONS DES FONTE GS AUSTÉNITIQUES
Catégorie ou Nuance
Min.Résistance à la traction/psi
Min.Limite
Élastique psi
%
Allongement
Traitement
Thermique
Composition Chimique et Dureté Applications Typiques
D-2 58 000 30 000
D-2B 58 000 30 000
D-2C 58 000 28 000
D-3 55 000 30 000
A439-84
D-3A 55 000 30 000
D-4
D-5
60 000
55 000 30 000
D-5B 55 000 30 000
D-5S 65 000 30 000
A571-71 D-2M 65 000 30 000
(1976)
SA571
8
7
20
6
10
20
6
10
30 recuit
%T.C.
%Si %Mn %P %Ni %Cr BHN
Min 1,50 0,70 18,00 1,75 139 Bagues de tige de valve, corps de valve et
Max 3,00 3,00 1,25 0,08 22,00 2,75 202 de pompe pour service en différents milieux
(pétrole, eau salée, corrosif…), collecteurs, boîtiers de turbocompresseurs, pièces de
Min 1,50 0,70
Max 3,00 3,00 1,25 0,08 22,00 4,00 211 compresseurs à air
18,00 2,75 148 Boîtiers de turbocompresseurs, rouleaux
Min 1,00 1,80 21,00 121 Anneaux de guidage d'électrodes, anneaux
Max 2,90 3,00 2,40 0,08 24,00 0,50 171 de doublage de turbines à vapeur
Min 1,00 28,00 2,50 139 Busettes et boîtiers de turbocompresseurs;
Max 2,60 2,80 1,00 0,08 32,00 3,50 202 diaphragme de turbines à gaz, diffuseurs de
Min 1,00 28,00 1,00 compresseurs à gaz
131 Anneaux de roulement utilisés à haute tem-
Max 2,60 2,80 1,00 0,08 32,00 1,50 193 pérature nécessistant une bonne résistance
Min 5,00 28,00 4,50
à l'écaillage
202 Collecteurs de moteurs diésel,
Max 2,60 6,00 1,00 0,08 32,00 5,50 273 joints de collecteurs
Min 1,00 34,00 131 Boîtiers de système de guidage, anneaux
Max 2,40 2,80 1,00 0,08 36,00 0,10 185 protecteurs de turbines à gaz, "glass rolls"
Min 1,00 34,00 2,00 139 Système de miroir optique et pièces
Max 2,40 2,80 1,00 0,08 36,00 3,00 193 nécessistant une bonne stabilité
Min 4,90 34,00 1,75 dimensionnelle, stator pour compresseurs
131 Collecteurs, boîtiers de turbine,
Max 2,30 5,50 1,00 0,08 37,00 2,25 193 turbocompresseurs opérant à haute température et sous des conditions sévères de cycle thermique
Min 2,20 1,50 3,75 21,00 121 Compresseurs, chambres d'expansion de
Max 2,70 2,50 4,50 0,08 24,00 0,20 171 pompes et autres pièces opérant sous pression demandant une structure austénitique stable à -234 o C (-423 o F)
Organisme de normalisation
ASTM
SOMMAIRE DES SPÉCIFICATIONS DES FONTES GS AUSTÉNITIQUES
No.
Spéc.
Catégorie ou Nuance
Min.Résistance à la traction/psi
Min.Limite
Élastique psi
%
Allongement
60-40-18 60 000 40 000 18
Traitement
Thermique
Autres exigences Utilisations Applications typiques
65-45-12 65 000 45 000 12
A536-80 80-55-06 80 000 55 000
100-70-03 100 000 70 000
120-90-02 120 000 90 000
6
3
2
Peut être recuit
Habituellement normalisé
Trempé et revenu
Pour des pièces nécessistant Pièces travaillant sous une résistance maximum aux pression tels les boîtiers de chocs à basse température valves et de pompes
(<0 o C)
Nuance la plus utilisée pour Pièces de machinerie les pièces travaillant sous des soumises aux chocs et aux conditions normales efforts cycliques (fatigue)
Pour toutes les nuances de Approprié pour traitement de Vilebrequins, engrenages et cette spécification, la compotrempe de surface par flamme rouleaux sition chimique est ajustée ou induction en fonction des propriétés mécaniques requises. Cependant, la teneur de chacun des
éléments peut être spécifiée sur entente entre les parties
Meilleure combinaison de Engrenages de haute résistance mécanique, résistance, pièces d'automorésistance à l'usure et réponse biles et de machineries au durcissement de surface
Meilleures résistances mécanique et à l'usure
Pignons, engrenages, rouleaux, glissoires
SOMMAIRE DE LA SPÉCIFICATION A-897-92/A987M-90 DE LA FONTE GS (ADI)
Nuance
Résistance à la traction (min.) Limite élastique (min.)
%
Allongement
Résilience*
Dureté
HB**
MPa ksi MPa ksi J ft-lb
125/80/10
850/550/10
150/100/7
1050/700/7
175/125/4
1200/850/4
200/155/1
1400/1100/1
230/185/-
1600/1300/-
850
1 050
1 200
1 400
1 600
125
150
175
200
230
550
700
850
1 100
1 300
80
100
125
155
185
1
1
4
4
10
10
7
7
***
***
100
80
60
35
***
75
60
45
25
***
269-321
269-321
302-363
302-363
341-444
341-444
388-477
388-477
444-555
444-555
* Valeurs obtenues avec des échantillons Charpy sans entaille testé à 20 o C (72 o F). Les valeurs présentées dans ce tableau représentent la moyenne des trois valeurs les plus élevées obtenues sur 4 échantillons.
** La dureté n'est pas une spécification formelle et n'est indiquée qu'à titre informatif.
***Les spécifications sur l'allongement et la résilence ne sont pas requises.
Les spécifications détaillées peuvent être obtenues aux adresses suivantes :
American Society for Testing Materials, 1916 Race Street, Philadelphia, PA 19103
Society of Automotive Engineers Inc., 485 Lexington Avenue, New York, NY 10017
American Society of Mechanical Engineers, 345 East 47 th Street, New York, NY 10017
SPÉCIFICATIONS - FONTE GS
Organisme de normalisation
ASTM
ASTM
ASME
No.
Spéc.
SOMMAIRE DES SPÉCIFICATIONS DES FONTE GS AUSTÉNITIQUES
Catégorie ou Nuance
Min.Résistance à la traction/psi
Min.Limite
Élastique psi
%
Allongement
Traitement
Thermique
Composition Chimique et Dureté Applications Typiques
D-2 58 000 30 000
D-2B 58 000 30 000
D-2C 58 000 28 000
D-3 55 000 30 000
A439-84
D-3A 55 000 30 000
D-4
D-5
60 000
55 000 30 000
D-5B 55 000 30 000
D-5S 65 000 30 000
A571-71 D-2M 65 000 30 000
(1976)
SA571
8
7
20
6
10
20
6
10
30 recuit
%T.C.
%Si %Mn %P %Ni %Cr BHN
Min 1,50 0,70 18,00 1,75 139 Bagues de tige de valve, corps de valve et
Max 3,00 3,00 1,25 0,08 22,00 2,75 202 de pompe pour service en différents milieux
(pétrole, eau salée, corrosif…), collecteurs, boîtiers de turbocompresseurs, pièces de
Min 1,50 0,70
Max 3,00 3,00 1,25 0,08 22,00 4,00 211 compresseurs à air
18,00 2,75 148 Boîtiers de turbocompresseurs, rouleaux
Min 1,00 1,80 21,00 121 Anneaux de guidage d'électrodes, anneaux
Max 2,90 3,00 2,40 0,08 24,00 0,50 171 de doublage de turbines à vapeur
Min 1,00 28,00 2,50 139 Busettes et boîtiers de turbocompresseurs;
Max 2,60 2,80 1,00 0,08 32,00 3,50 202 diaphragme de turbines à gaz, diffuseurs de
Min 1,00 28,00 1,00 compresseurs à gaz
131 Anneaux de roulement utilisés à haute tem-
Max 2,60 2,80 1,00 0,08 32,00 1,50 193 pérature nécessistant une bonne résistance
Min 5,00 28,00 4,50
à l'écaillage
202 Collecteurs de moteurs diésel,
Max 2,60 6,00 1,00 0,08 32,00 5,50 273 joints de collecteurs
Min 1,00 34,00 131 Boîtiers de système de guidage, anneaux
Max 2,40 2,80 1,00 0,08 36,00 0,10 185 protecteurs de turbines à gaz, "glass rolls"
Min 1,00 34,00 2,00 139 Système de miroir optique et pièces
Max 2,40 2,80 1,00 0,08 36,00 3,00 193 nécessistant une bonne stabilité
Min 4,90 34,00 1,75 dimensionnelle, stator pour compresseurs
131 Collecteurs, boîtiers de turbine,
Max 2,30 5,50 1,00 0,08 37,00 2,25 193 turbocompresseurs opérant à haute température et sous des conditions sévères de cycle thermique
Min 2,20 1,50 3,75 21,00 121 Compresseurs, chambres d'expansion de
Max 2,70 2,50 4,50 0,08 24,00 0,20 171 pompes et autres pièces opérant sous pression demandant une structure austénitique stable à -234 o C (-423 o F)
Organisme de normalisation
ASTM
SOMMAIRE DES SPÉCIFICATIONS DES FONTES GS AUSTÉNITIQUES
No.
Spéc.
Catégorie ou Nuance
Min.Résistance à la traction/psi
Min.Limite
Élastique psi
%
Allongement
60-40-18 60 000 40 000 18
Traitement
Thermique
Autres exigences Utilisations Applications typiques
65-45-12 65 000 45 000 12
A536-80 80-55-06 80 000 55 000
100-70-03 100 000 70 000
120-90-02 120 000 90 000
6
3
2
Peut être recuit
Habituellement normalisé
Trempé et revenu
Pour des pièces nécessistant Pièces travaillant sous une résistance maximum aux pression tels les boîtiers de chocs à basse température valves et de pompes
(<0 o C)
Nuance la plus utilisée pour Pièces de machinerie les pièces travaillant sous des soumises aux chocs et aux conditions normales efforts cycliques (fatigue)
Pour toutes les nuances de Approprié pour traitement de Vilebrequins, engrenages et cette spécification, la compotrempe de surface par flamme rouleaux sition chimique est ajustée ou induction en fonction des propriétés mécaniques requises. Cependant, la teneur de chacun des
éléments peut être spécifiée sur entente entre les parties
Meilleure combinaison de Engrenages de haute résistance mécanique, résistance, pièces d'automorésistance à l'usure et réponse biles et de machineries au durcissement de surface
Meilleures résistances mécanique et à l'usure
Pignons, engrenages, rouleaux, glissoires
SOMMAIRE DE LA SPÉCIFICATION A-897-92/A987M-90 DE LA FONTE GS (ADI)
Nuance
Résistance à la traction (min.) Limite élastique (min.)
%
Allongement
Résilience*
Dureté
HB**
MPa ksi MPa ksi J ft-lb
125/80/10
850/550/10
150/100/7
1050/700/7
175/125/4
1200/850/4
200/155/1
1400/1100/1
230/185/-
1600/1300/-
850
1 050
1 200
1 400
1 600
125
150
175
200
230
550
700
850
1 100
1 300
80
100
125
155
185
1
1
4
4
10
10
7
7
***
***
100
80
60
35
***
75
60
45
25
***
269-321
269-321
302-363
302-363
341-444
341-444
388-477
388-477
444-555
444-555
* Valeurs obtenues avec des échantillons Charpy sans entaille testé à 20 o C (72 o F). Les valeurs présentées dans ce tableau représentent la moyenne des trois valeurs les plus élevées obtenues sur 4 échantillons.
** La dureté n'est pas une spécification formelle et n'est indiquée qu'à titre informatif.
***Les spécifications sur l'allongement et la résilence ne sont pas requises.
Les spécifications détaillées peuvent être obtenues aux adresses suivantes :
American Society for Testing Materials, 1916 Race Street, Philadelphia, PA 19103
Society of Automotive Engineers Inc., 485 Lexington Avenue, New York, NY 10017
American Society of Mechanical Engineers, 345 East 47 th Street, New York, NY 10017
PROPRIÉTÉS PHYSIQUES DE LA FONTE GS ET DE MATÉRIAUX COMPÉTITEURS
PROPRIÉTÉ UNITÉ
120-90-02 100-70-03
FONTE GS
80-55-06 65-45-12 60-40-18
0.3% C
ACIER COULÉ
FONTE
MALLÉABLE
FONTE
GRISE *
Température du solidus
Densité
Coefficient moyen d'expansion linéaire
Capacité d'amortissement
Chaleur de fusion
Chaleur spécifique
Conductivité thermique
(température de la pièce)
PROPRIÉTÉS MAGNÉTIQUES
Perméabilité maximale
à 500 Gauss
Induction de saturation
à 10,000 Oersted
Perte d'hystérèse o F
Lb/in 3 o F 1 x 10 4
-
BTU/lb
BTU/lb/ o F
Cal/cm.s. o C
2 100
0,25
6,0 bon
55
0,15
0,06
2 100
0,25
6,0 bon
55
0,15
0,06
2 100
0,25
6,0 bon
55
0,14
0,08
Oersted
Gauss
Erg/cm 3 /cycle
290
-
-
290
-
30
570
17 600
30
2 100
18 000
5
PROPRIÉTÉS MÉCANIQUES
Contrainte d'écoulement psi (0,62 à 0,75) x Résistance en traction
Module d'élasticité en traction
Résistance en torsion
Module de rigidité psi
X 10 6 psi psi
X 10 6
25,7
108 000
9,6
25,7
90 000
9,6
25,2
72 000
9,6
* Une fonte grise de résistance mécanique moyenne a été utilisée pour les fins de cette comparaison.
23,8
58 000
9,3
2 100
0,25
6,0 bon
55
0,13
0,09
2 100
0,25
6,0 très bon
55
0,13
0,10
2 100
18 000
5
23,8
50 000
9,1
2 650
0,283
7,0 pauvre
108
0,11
0,11
-
-
100
30 500
30,5
-
11,4
2 050
0,265
6,7 bon
55
0,12
0,14
2 350
-
20
(0,65-0,8) x UTS
25
34 000
11
2 140
0,25
5,8 excellent
55
0,13
0,11
800
16 000
30
-
18,3
60 000
7,1
Rio Tinto Fer & Titane Inc.
770 rue Sherbrooke ouest
Bureau 1800
Montréal (Québec) Canada H3A 1G1
Tél. (514) 288-8400
Fax. (514) 286-9336 www.sorelmetal.com
Rio Tinto Iron & Titanium America
Division of High Purity Iron Inc.
9399 West Higgins Road
Suite 140 West
Rosemont, Illinois 60018 - USA
Tel. (847) 698-4002
Fax. (847) 698-4003
The Ductile Iron Marketing Group
c/o Ductile Iron Society
28938 Lorain Road
North Olmsted, Ohio 44070
Tel. (216) 734-8040
Fax. (216) 734-8112 www.ductile.org/dimg
POURQUOI CONVERTIR UNE PIÈCE À LA FONTE GS?
240
POURQUOI CONVERTIR UNE PIÈCE
À LA FONTE GS ?
Les dessinateurs-concepteurs convertissent de nombreuses pièces coulées ou forgées en acier ainsi que différents assemblages à la fonte GS afin de bénéficier des avantages suivants :
• Rapport résistance/poids amélioré
• Meilleure reproduction des détails de surface et du fini
• Usinabilité supérieure
• Usinage réduit
• Coût moindre des pièces
• Résistance mécanique accrue par dollar investi
• Réduction du poids de la pièce
Plusieurs pièces actuellement coulées, forgées ou assemblages en acier peuvent être convertis à la fonte GS afin de prendre avantage d'un coût de revient moins élevé tout en ayant une performance égale ou supérieure.
CONTACTEZ UN PRODUCTEUR DE FONTE GS AUJOURD'HUI !
CONCEPTION DE PIÈCES COULÉES
DE QUALITÉ
Des pièces coulées de qualité sont le résultat du travail d'équipe du concepteur et du fondeur
* Consultez une fonderie au début du processus de conception
* Discutez des avantages de conception des pièces coulées
* Utilisez la flexibilité de conception et de choix de matériaux qu'offrent les pièces coulées
* Prenez avantage de la conception "near-net shape" qui est offerte
* Dessinez la pièce afin qu'elle soit saine et possède une distribution optimum des contraintes
* Concevez une pièce au plus bas coût possible
* Spécifiez les propriétés et le niveau de qualité requis pour votre application
CONTACTEZ UN PRODUCTEUR DE FONTE GS AUJOURD'HUI !
200
160
Fonte GS «Austempered»
1660
1380
1100
120
Fonte GS trempée et revenue
830
80
Fonte grise
Fonte GS ASTM A-536
550
40 275
0 5 10 15
Allongement à la rupture (%)
20
APPRENEZ-EN PLUS
SUR LES AVANTAGES DE LA FONTE GS
Un livret gratuit de 40 pages «Condensé pour les ingénieurs de projets -
Fonte à graphite sphéroidal (Fonte GS)» est disponible et deux autres publications techniques «Conversions to Ductile Iron» et «The Ductile Iron
Data Book» sont aussi à votre disposition. Pour obtenir ces publications et une liste des producteurs de fonte GS, ou pour discuter de la façon dont vous pouvez prendre avantage de la fonte GS, contacter «Ductile Iron
Marketing Group» ou l'une des compagnies membres.
The Ductile Iron Marketing Group - c/o Ductile Iron Society
28938 Lorain Road, North Olmsted, Ohio 44070
(216) 734-8040 • www.ductile.org/dimg
Le «Ductile Iron Marketing Group» est un organisme à but non lucratif dont la mission est de dissiminer les connaissances reliées aux avantages techniques et économiques des pièces coulées en fonte GS. Les membres de ce groupe sont :
The Ductile Iron Society - Rio Tinto I&T America
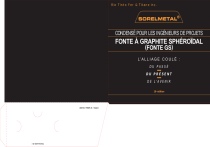
公開リンクが更新されました
あなたのチャットの公開リンクが更新されました。