KE PL ‘c’ - K7 PL ‘c’ MANUEL UTILISATEUR Le présent document est la propriété de GEFRAN et ne peut être reproduit ni transmis à des tiers sans l’autorisation du fabricant. cod. 80177E Edit. 10/2018 - FRA 80177E_MAN_KE PL’c’ - K7 PL’c’_10-2018_FRA ATTENTION! Le présent manuel doit être considéré comme faisant partie intégrante du produit et il doit toujours être accessible aux personnes qui interagissent avec ce dernier. Le manuel doit toujours accompagner le produit, y compris lors de sa cession à un autre utilisateur. Les installateurs et les agents de maintenance sont tenus de lire le présent manuel et de respecter scrupuleusement les prescriptions contenues dans ce dernier ainsi que dans ses annexes. GEFRAN ne saurait être tenue pour responsable des dommages corporels et/ou matériels résultant du non-respect des prescriptions ci-contenues. Le Client étant tenu au secret industriel, la présente documentation et ses annexes ne peuvent être altérées, modifiées, reproduites ou cédées à des tiers sans l’autorisation de GEFRAN. 1 TABLE DES MATIERES 1. Informations générales pag 3 2. Dimensions mécaniques pag 3 3. Installation et mise en place sur la machine pag 3 3a. Réalisation du logement pag 4 3b. Câblage et étalonnage pag 7 4. Conformité avec les spécifications NE21 et NE43 pag 7 5. Spécifications techniques du capteur pag 8 5a. Série KE niveau de performance “c” pag 8 5b. Série K7 niveau de performance “c” pag 10 6. Transport, stockage et mise au rebut pag 10 7. Sécurité pag 10 8. Manuel de sécurité des capteurs avec niveau de performance “c” pag 10 9. Notes relatives a l’utilisation du relais pag 22 2 80177E_MAN_KE PL’c’ - K7 PL’c’_10-2018_FRA 1. INFORMATIONS GENERALES Le présent Manuel concerne les gammes KE - K7 avec un Niveau de Performances “c”, fabriquées par GEFRAN spa, via Sebina, 74 - 25050 PROVAGLIO D’ISEO - BS - ITALIE. 1.1 Informations générales Le présent Manuel doit être conservé à proximité des installations de travail, dans un endroit accessible qui facilite sa lecture. Le présent Manuel doit être lu, compris et respecté dans son intégralité, afin d’éviter des accidents et/ou des dysfonctionnements. Gefran ne pourra être tenue pour responsable d’éventuels dommages corporels et/ou matériels occasionnés par le non-respect des consignes contenues dans le présent Manuel. 1.2 Copyright Toute reproduction, même partielle ou à usage interne, du présent Manuel requiert l’accord préalable de Gefran. 1.3 Utilisation correcte Les capteurs de pression de Melt Gefran avec sortie électrique amplifiées, sont conçus et réalisés afin de mesurer les variables de pression et de température des matières plastiques fondues à différentes températures, en fonction du fluide de remplissage utilisé. La plage correcte de température atteint 315°C. Si les capteurs sont utilisés en tant que composants de sécurité selon la Directive Machines, lire attentivement le Manuel de Sécurité (chapitre 8, page 10). 2. DIMENSIONS MECANIQUES Pour les dimensions mécaniques, se reporter aux fiches techniques des produits ou visiter le site www.gefran.com 3. INSTALLATION ET MISE EN PLACE SUR LA MACHINE CARACTERISTIQUES TECHNIQUES Les processus d’extrusion sont caractérisés par des températures élevées et le contrôle de la pression d’extrusion peut être obtenu à l’aide de transducteurs spécialement étudiés à cet effet. Cette résistance à de telles températures est le résultat de la construction mécanique du capteur, dont l’élément de mesure est maintenu éloigné de la zone de contact avec le Melt. Le principe de construction se fonde sur la transmission hydraulique de la pression ; le transfert de la contrainte mécanique s’effectue par le biais d’un fluide de transmission incompressible. La technologie extensométrique permet de convertir la grandeur physique de pression en un signal électrique. Voici quelques conseils utiles pour prolonger au maximum la durée de vie des transducteurs. a) Eviter les chocs et les abrasions au niveau de la membrane de contact. Il est recommandé de la protéger à l’aide du cache prévu à cet effet chaque fois qu’on retire le transducteur de son siège. b) Le siège de montage doit être parfaitement réalisé, en utilisant des équipements mécaniques appropriés afin de respecter la profondeur et l’axialité des perçages et du taraudage. Une attention particulière doit être portée à la coaxialité du perçage par rapport au filet, car tout désaxement supérieur à 0,2 mm entraîne la rupture du transducteur dès sa phase de montage. Il est indispensable que la profondeur des perçages garantisse l’absence d’espaces ou d’interstices dans lesquels le matériau en extrusion pourrait stagner. La membrane avant ne doit pas dépasser de la paroi interne de l’extrudeuse, afin d’éviter les contacts avec la vis d’extrusion ou avec les outils de nettoyage de la chambre d’extrusion. c) Avant le montage du transducteur dans des machines qui ont déjà travaillé, s’assurer de l’état de propreté du siège et éliminer les éventuels résidus de matière en utilisant l’outil prévu pour le nettoyage du siège. d) d) Le transducteur ne doit être retiré que dans des conditions de machine vide (sans pression) mais encore chaude. e) Le transducteur doit être nettoyé avec les solvants de la matière usinée. Toute action mécanique sur la membrane de contact en modifie la fonctionnalité et peut en provoquer la rupture. 80177E_MAN_KE PL’c’ - K7 PL’c’_10-2018_FRA 3 3a - Réalisation du logement L’orifice d’installation doit être usiné comme suit: D1 D2 D3 D4 A C .515” [13mm] minimo .790” [20mm] minimo .454 ±.004” [11.53 ±0.1mm] D2 D3 A B C .634 ±.004” [16.10 ±0.1mm] .225” [5.72mm] minimo .240” [6.10mm] minimo .75” [19mm] .99” [25mm] Dimensions de la pointe du capteur D1 M18x1.5 .398 ±.001” [10.10 ±0.02mm] .17” [4.3mm] massimo B Capillaire exposée 1/2-20UNF .313 ±.001” [7.95 ±0.02mm] .16” [4.0mm] massimo Montage dimensions des trous 1/2-20UNF .307/.305” [7.80/7.75mm] .414/.412” [10.52/10.46mm] .125/.120” [3.18/3.05mm] .318/.312” [8.08/7.92mm] 81” [20.6mm] Un orifice d’installation hors spécifications peut entraîner un comportement erroné du capteur ou son endommagement. L’orifice d’installation doit être propre et exempt de résidus di matière. Kit de perçage Pour faciliter la réalisation correcte du siège de montage, un kit de perçage est disponible, avec les outils façonnés pour les perçages, alésages et taraudages nécessaires. Aux fins de la fonctionnalité et de la longévité du transducteur, il est nécessaire d’avoir un siège de montage parfait. Les kits de perçage sont disponibles dans les versions suivantes: KF12, KF18. Procédure de perçage 1) 2) 3) 4) 5) 6) Réaliser l’orifice (D4) jusqu’à une distance de la paroi interne égale à la somme (A+B+C) (outil 3). Réaliser l’orifice (D2) traversant à l’aide de la pointe (outil 1). Créer le siège d’étanchéité à une distance de l’orifice égale à (A) (outil 4). Réaliser, avec un taraud de dégrossissage, le filetage 1/2-20UNF-2B (reconnaissable au nombre supérieur de filets arrondis pour l’amorce) (outil 5). Repasser, avec un taraud de finition, le filetage 1/2-20UNF-2B jusqu’à une distance du fond égale à la somme (A+B) (outil 6). Aléser l’orifice (D2) à l’aide de l’alésoir (outil 2). Vérification des dimensions des sièges de montage Les dimensions du siège de montage doivent être vérifiées après son exécution et avant de monter le transducteur. Pour ce faire, l’on peut utiliser la tige de fermeture SC12/SC18, en procédant comme suit : 1) En utilisant une encre appropriée, colorer la partie terminale de la tige. 2) Lubrifier la partie filetée pour éviter tout frottement excessif. 3) Insérer la tige de fermeture et visser jusqu’à la butée. 4) Retirer et examiner la tige. L’encre devra être intacte sur toute la surface, à l’exception des versions à 45°. 4 80177E_MAN_KE PL’c’ - K7 PL’c’_10-2018_FRA KIT OUTILS DE PERÇAGE CORRETTE INSTALLATION CODE VERSIONS KF12 KF18 TYPE FILETAGE 1/2-20UNF-2B M18x1.5 1 Ø 7.6 Ø 9.75 2 Ø 7.95 Ø 10.1 3 Ø 13 Ø 20 4 Ø 11.5 avec guide pilote Ø 16 avec guide pilote 5 6 1/2-20UNF-2B M18x1.5 dégrossissag dégrossissag 1/2-20UNF-2B M18x1.5 finition IMCORRECTE IMCORRECTE IMCORRECTE finition CORRECTE ETANCHEITE CORRECTE surface de contact 80177E_MAN_KE PL’c’ - K7 PL’c’_10-2018_FRA 5 INSTALLATION DU CAPTEUR Procédure d’installation 1) S’assurer que le perçage de montage a correctement été réalisé. Si l’on installe le capteur dans un perçage qui a déjà été utilisé, s’assurer qu’il est parfaitement propre et exempt de résidus de plastique. 2) Oter le cache de protection du bout du capteur. 3) Lubrifier le filet avec de la grasse anti-grippage du type Neverseez (Bostik), C5A (Felpro) ou équivalente. 4) Introduire le capteur dans l’orifice, en le serrant fermement, d’abord à la main puis à l’aide d’une clé à molette, en effectuant des passes de ¼ de tour. Couple de serrage recommandé : 50 Nm. Couple maximum : 56,5 Nm. Dépose (Figure 1) Des tiges de fermeture ayant des dimensions mécaniques identiques sont disponibles pour déposer le transducteur de son siège et poursuivre l’usinage. Les tiges de fermeture se différencient par le type de filetage, tandis que la pression applicable est la même pour toutes, soit 2000 bars. La tige de fermeture est disponible dans les versions suivante: SC12 pour siège 1/2-20UNF - SC18 pour siège M18x1,5. Etrier de fixation (Figure 2) Les modèles avec gaine flexible nécessitent une fixation précise du boîtier de protection. Pour la fixation, il est conseillé d’utiliser l’étrier (SF18), sans oublier que le point de fixation doit être exempt de vibrations (qui se répercutent sur la mesure) et ne pas présenter de températures supérieures à la température maximale du boîtier du pont de jauge, déclarée sur la fiche technique du transducteur. Démarrage de l’extrudeuse Le transducteur installé et sans appliquer de pression, amener le système à sa température de fonctionnement. Attendre jusqu’à ce que toute la matière soit à la même température, afin d’éviter que des parties encore à l’état solide n’endommagent le transducteur. Nettoyage du logement du transducteur Outil de nettoyage du siège Comme rappelé dans les informations d’application, il est nécessaire de procéder au nettoyage du logement avant le montage du transducteur. L’outil de nettoyage est un outil à tranchants en métal dur, expressément réalisé pour éliminer les résidus de matière des usinages précédents. Procédure conseillée (Figure 3) Cette opération doit être exécutée lorsque la matière est à l’état fluide. 1)Introduire l’outil dans le siège, visser la tige porte-fraise avec des passes de ¼ de tour. 2) Tourner la fraise pilote dans le sens des aiguilles d’une montre, jusqu’à ce que toute résistance à la coupe soit annulée. 3) Répéter cette opération jusqu’au nettoyage complet. Pour des raisons de construction, le couple maximum applicable à la fraise pilote est de 15 Nm (1,5 mkg). Si l’occlusion de l’orifice exige des couples supérieurs pour être éliminée, il faudra utiliser le kit de perçage, en suivant la procédure conseillée. L’outil de nettoyage est disponible dans les versions suivantes: CT12 pour siège 1/2-20UNF - CT18 pour siège M18x1,5. Figure 1 Figure 2 Figure 3 REFERENCE DE COMMANDE DES OUTILS ET ACCESSOIRES SF 18 ETRIER DE FIXATION OUTIL DE NETTOYAGE 1/2-20UNF 12 M18x1,5 18 CT TIGE DE FERMETURE 1/2-20UNF 12 M18x1,5 18 KIT DE PERÇAGE 6 1/2-20UNF 12 M18x1,5 18 SC KF 80177E_MAN_KE PL’c’ - K7 PL’c’_10-2018_FRA 3b - Câblage et étalonnage Raccordements Les émetteurs doivent être raccordés selon les schémas présentés aux pages suivantes. Pour un meilleur résultat en termes d’immunité aux perturbations présentes sur le terrain, le blindage du câble devra être raccordé comme suit : le blindage du câble doit être raccordé à la carcasse du connecteur femelle côté capteur. Procédure d’étalonnage L’émetteur installé et relié à l’instrument de mesure, sans appliquer de pression, amener le système à sa température de fonctionnement. L’étalonnage de la chaîne de mesure connectée à l’émetteur s’effectue comme suit: 1) Remettre l’instrument à zéro, en éliminant la dérive thermique du zéro à l’aide de la fonction Autozero. Capteur installé et extrudeuse en température, attendre que celle-ci se stabilise autour de +/- 1°C. Il sera alors possible d’effectuer la fonction Autozero. Cette attente est nécessaire pour que le système reconnaisse et compense toutes les dérives de signal provoquées par le serrage et la température. Les activations successives de la fonction Autozero pourront être effectuées toujours après stabilisation de la température, avec une tolérance de +/- 1°C. 2) Effectuer l’étalonnage de l’instrument et afficher la valeur indiquée sur la plaque signalétique du transducteur, sous « étalonnage » (80% du fond d’échelle). L’étalonnage n’est pas possible avec l’Autozero externe. 3) Si, une fois ces opérations terminées, l’instrument n’affiche pas exactement le zéro, répéter les points 1 et 2. Ainsi, l’instrument sera étalonné pour fournir l’indication exacte dans l’unité de mesure choisie. 4. CONFORMITE AVEC LES SPECIFICATIONS NE21 et NE43 Les séries KE et K7 sont pleinement conformes aux recommandations des normes NAMUR NE21 et NE43 (se reporter au tableau 1). Tableau 1 - NAMUR NE21 et NE43 : Valeurs de sortie analogique Panne Câble d’alimentation coupé Capteur non connecté Alimentateur défaillant Débranchement raccordements pont extensométrique Série KE (sortie de courant) Série K7 (sortie de tension) Sortie électrique < 3,6 mA Sortie électrique < 0.25 V Sortie électrique < 3,6 mA Sortie électrique < 3,6 mA Sortie électrique < 0.25 V Sortie électrique < 0.25 V Sortie électrique > 21 mA Sortie électrique > 11.125 V Sortie électrique > 21 mA Sortie électrique > 11.125 V Surtension Sortie électrique < 3,6 mA Sortie électrique < 0.25 V Variations de tension Sortie électrique < 3,6 mA Sortie électrique < 0.25 V Pression dépassant 200% du span par rapport au zéro d’usine à RT Sous-tension Erreur dans la séquence de programme Surtempérature de l’électronique Erreur sur le primaire ou le premier étage d’amplification Sortie électrique < 3,6 mA Sortie électrique < 0.25 V Sortie électrique < 3,6 mA Sortie électrique < 0.25 V Sortie électrique < 3,6 mA Sortie électrique < 0.25 V Sortie électrique < 3,6 mA Sortie électrique < 0.25 V 80177E_MAN_KE PL’c’ - K7 PL’c’_10-2018_FRA 7 5. SPECIFICATIONS TECHNIQUES DU CAPTEUR 5a - Série KE – Niveau de performance “c” – Caractéristiques techniques Précision (1) H <±0.25%FEO (100...1000 bar) M <±0.5%FEO (35...1000 bar) Résolution 16 bit Plages de mesure 0..17 à 0..1000bar 0..250 à 0..15000psi Surpression sans dégradation 2 x FS 1.5 x FS au-dessus de 700bar/10000psi Principe de mesure Extensométrique Tension d'alimentation 13...30Vdc Absorption maximale sur l’alimentation 23mA (40mA avec relais en option) Signal de sortie en fond d’échelle FEO 20mA Signal de sortie à zéro (tolérance ± 0,25% FEO) 4mA Temps de réponse (10…90% FEO) 8ms Bruit de sortie (RMS 10-400Hz) < 0.025% FEO Signal de calibrage 80% FEO Protection inversion de polarité alimentation OUI Plage de température compensée logement 0...+85°C Plage de température de fonctionnement logement -30...+85°C Plage de température de stockage logement -40...+125°C Dérive thermique dans la plage compensée : Zéro/Calibrage/Sensibilité < 0.02% FEO/°C Température maximale membrane 538°C / 1000°F Dérive de tige (zéro) < 3.5 bar/100°C / < 28 psi/100°F Thermocouple (modèle KE2) STD : type “J” (jonction isolée) Degré de protection (connecteur 6 pôles, femelle) IP65 FEO = Sortie en fond d’échelle (1) Méthode BFSL (Best Fit Straight Line) : incluant l’effet combiné de Non-linéarité, Hystérésis et Répétitivité Les capteurs sont réalisés conformément : - à la Directive EMC - à la Directive RoHS - à la Directive Machines Les normes d’installation électrique et le certificat de conformité sont disponibles et peuvent être téléchargés sur le site www.gefran.com 8 80177E_MAN_KE PL’c’ - K7 PL’c’_10-2018_FRA 5b - Série K7 – Niveau de performance “c” – Caractéristiques techniques Précision (1) H <±0.25%FEO (100...1000 bar) M <±0.5%FEO (35...1000 bar) Résolution 16 bit Plages de mesure 0..17 à 0..1000bar 0..250 à 0..15000psi Surpression sans dégradation 2 x FS 1.5 x FS au-dessus de 700bar/10000psi Principe de mesure Extensométrique Tension d'alimentation 18...30Vdc Absorption maximale sur l’alimentation 15mA (30mA avec relais en option) Signal de sortie en fond d’échelle FEO 10,5Vdc Signal de sortie à zéro (tolérance ± 0,25% FEO) 0,5Vdc Temps de réponse (10…90% FEO) 8ms Bruit de sortie (RMS 10-400Hz) < 0.025% FEO Signal de calibrage 80% FEO Protection inversion de polarité alimentation OUI Plage de température compensée logement 0...+85°C Plage de température de fonctionnement logement -30...+85°C Plage de température de stockage logement -40...+125°C Dérive thermique dans la plage compensée : Zéro/Calibrage/Sensibilité < 0.02% FEO/°C Température maximale membrane 538°C / 1000°F Dérive de tige (zéro) < 3.5 bar/100°C / < 28 psi/100°F Thermocouple (modèle K72) STD : type “J” (jonction isolée) Degré de protection (connecteur 6 pôles, femelle) IP65 FEO = Sortie en fond d’échelle (1) Méthode BFSL (Best Fit Straight Line) : incluant l’effet combiné de Non-linéarité, Hystérésis et Répétitivité Les capteurs sont réalisés conformément : - à la Directive EMC - à la Directive RoHS - à la Directive Machines Les normes d’installation électrique et le certificat de conformité sont disponibles et peuvent être téléchargés sur le site www.gefran.com 80177E_MAN_KE PL’c’ - K7 PL’c’_10-2018_FRA 9 6. TRANSPORT, STOCKAGE ET MISE AU REBUT Les capteurs de Melt, réalisés en faisant appel à la technologie « filled », contiennent un liquide de transmission de la pression. A cet effet, l’on utilise des liquides à faible compressibilité, tels l’alliage de sodium et de potassium. Les volumes de liquide dépendent de la structure mécanique du capteur et les fuites ne sont possibles qu’en cas de rupture de la membrane de contact. Aucune autre typologie de rupture n’entraîne de fuites de liquide à l’extérieur. Ne jamais transporter ou stocker les capteurs sans bouchon de protection ou emballage d’origine. Gefran s’occupe de la mise au rebut de ses propres capteurs de Melt, défectueux ou endommagés. 7. SECURITE Le NaK, constitué de sodium et potassium (22 Na / 78 K), est un alliage eutectique (c’est-à-dire un mélange de substances avec un point de fusion plus bas que celui de ses composants), qui possède des propriétés de faible compressibilité et de résistance aux températures élevées (jusqu’à 538°C). Il s’agit notamment un métal liquide atoxique, répertorié parmi les substances GRAS (General Regarded As Safe), qui permet aux capteurs de Melt de la série K de fonctionner en contact avec des matériaux à usage alimentaire (films d’emballage pour aliments, conteneurs pour boissons, etc.) ou pharmaceutique/cosmétique (conteneurs pour médicaments, savons, etc.). Autre caractéristique, le NaK est parfaitement conforme à la Directive européenne RoHS (Restriction of Hazardous Substances), qui restreint l’utilisation de certaines substances dangereuses dans les équipements électriques et électroniques. En cas de rupture de la membrane de contact pour cause d’usure d’application, le NaK a tendance à oxyder ou à enclencher une réaction exothermique avec le milieu de contact (notamment en présence d’eau ou d’humidité). D’où le jaillissement d’une étincelle qui, compte tenu de la faible quantité de matériau (en moyenne 20 à 40mm3), peut durer quelques secondes (jusqu’à un maximum de 5). 8. MANUEL DE SECURITE DES CAPTEURS AVEC NIVEAU DE PERFORMANCE ‘C’ (SELON LA NORME EN 13849-1) Catégorie désignée et exclusion des pannes Catégorie désignée à laquelle est limitée l’utilisation des composants liés à la sécurité : Catégorie 2 I im L im O Légende: I L O im dispositif d’entrée (capteur) logique de traitement dispositif de sortie (actionneur) interconnexions La fonction sécurité, assurée par le capteur, est la transduction correcte de la pression à l’intérieur de la chambre de mesure, afin de repérer des surpression dans celle-ci ainsi que le dépassement d’un seul fixe de sécurité. La transduction est considérée comme correcte lorsqu’elle est conforme aux spécifications indiquées dans la fiche technique et le présent manuel utilisateur. Trois exclusions de pannes ont été prises en compte dans l’évaluation: • • • 10 Usure/corrosion des parties mécaniques en contact avec le processus [13849-2:2012 tableau A.4] Rupture des parties mécaniques en contact avec le processus [13849-2:2012 tableau A.4] Déformation des parties mécaniques en contact avec le processus, due à des contraintes excessives [13849-2:2012 tableau A.4] 80177E_MAN_KE PL’c’ - K7 PL’c’_10-2018_FRA Limites d’utilisation et opérations de maintenance Pour pouvoir demeurer dans sa catégorie désignée, le dispositif doit être exclusivement utilisé selon les présentes instructions et les prescriptions du manuel utilisateur relatives à l’installation mécanique, au raccordement électrique, aux conditions ambiantes et d’utilisation maximales. Pour garantir l’exclusion justifiée des pannes, il est nécessaire d’exécuter les opérations périodiques de maintenance suivantes: • Contrôle visuel de l’état de la membrane en contact avec le processus et des filets de la tige, afin de repérer d’éventuelles abrasions anormales ou traces d’usure dues à des conditions incorrectes de montage, prolongées dans le temps. Périodicité : une fois par an. • Vérification du siège d’installation du capteur : exactitude du profil et des dimensions, absence de résidus de matière ou d’occlusions dans le canal de pression. Périodicité : tous les deux ans. • Lors de chaque nouvelle (ré-)installation, appliquer de la pâte anti-grippage sur le filetage de la tige. Effets des écarts de performances sur la fonction sécurité Pour ne pas entraîner la perte de la fonction sécurité, la limite d’acceptabilité des écarts des performances métrologiques est de ± 5% de la valeur de span à température ambiante. Interfaces avec SRP/CS et les dispositifs de protection L’interface avec SRP/CS se compose de connecteurs multipolaires des types VEAM VP07RA10-6PT2 (code GEFRAN CON031), AMPHENOL 62IN-5016-10-7P-4-M (code GEFRAN CON366) et BINDER 8 pôles M18 DIN/ EN 45326 (code GEFRAN CON029), illustrés dans la figure 4, où sont indiquées aussi les connexions en cas de sortie amplifiée en tension (quatre fils : deux d’alimentation et deux de signal) ou en courant (deux fils: le capteur est placé en série sans la boucle de courant). En cas de sortie relais avec sortie retransmise en courant (2 fils) ou tension (4 fils), la signification des broches est illustrée dans la figure 5. 80177E_MAN_KE PL’c’ - K7 PL’c’_10-2018_FRA 11 CONNEXIONS ELECTRIQUES SORTIE DE TENSION AUTOZERO MAGNETIQUE 6-broches AUTOZERO EXTERNE 8-broches 6-broches 8-broches REGULATEUR ALIMENTATION ALIMENTATION AMPLIFICATEUR SORTIE SORTIE ETALONNAGE AUTOZERO La tresse du câble est raccordée au corps di transducteur SORTIE DE COURANT AUTOZERO MAGNETIQUE 6-broches REGULATEUR AMP_CONV AUTOZERO EXTERNE 8-broches 6-broches 8-broches ALIMENTATION ALIMENTATION SORTIE SORTIE AUTOZERO ETALONNAGE AUTOZERO EXTERNE 7-broches REGULATEUR ALIMENTATION F n.c. AMP_CONV SORTIE C ALIMENTATION B n.c. La tresse du câble est raccordée au corps di transducteur AUTOZERO D-G A-E Fig. 4 - Interface SRP/CS 12 80177E_MAN_KE PL’c’ - K7 PL’c’_10-2018_FRA CONNEXIONS ELECTRIQUES SORTIE RELAIS (sortie de tension) AUTOZERO MIT MAGNETSTIFT 6-broches EXTERNES AUTOZERO 8-broches 8-broches REGULATEUR ALIMENTATION ALIMENTATION AMPLIFICATEUR SORTIE SORTIE CONTACT RELAIS CONTACT RELAIS AUTOZERO n.a. La tresse du câble est raccordée au corps di transducteur SORTIE RELAIS (sortie de courant) AUTOZERO MAGNETIQUE 6-broches REGULATEUR AUTOZERO EXTERNE 8-broches 8-broches ALIMENTATION ALIMENTATION n.c. AMP_CONV n.c. SORTIE SORTIE ALIMENTATION ALIMENTATION CONTACT RELAIS CONTACT RELAIS AUTOZERO n.c. AUTOZERO EXTERNE 7-broches REGULATEUR ALIMENTATION F n.c. AMP_CONV SORTIE C ALIMENTATION CONTACT RELAIS La tresse du câble est raccordée au corps di transducteur AUTOZERO B D-G A-E Fig. 5 - Interface SRP/CS Connecteur 6 broches VPT07RA10-6PT2 (PT02A-10-6P) 80177E_MAN_KE PL’c’ - K7 PL’c’_10-2018_FRA Connecteur 7 broches (AMPHENOL) 62IN-5016-10-7P-4-M Connecteur 8 broches(Binder) M16 DIN/EN45326 (09-0173-00-08) 13 Temps de réaction Le temps de réaction à une situation de danger est de 8 ms. Le temps de réaction en cas de panne est égal au temps de réaction de la seule électronique, soit 400 ms. Limites opérationnelles et climatiques Pour pouvoir demeurer dans sa catégorie désignée, le dispositif doit fonctionner dans les limites opérationnelles reprises dans le tableau 2: Limite opérationnelle Sortie tension Sortie courant 2 x FS 1,5 x FS au-dessus de 700 bar 2 x FS 1,5 x FS au-dessus de 700 bar Alimentation 18..30 Vdc Diagramme de charge Température du fluide en contact avec le processus Série K 23..538 °C 23..538 °C Température opérationnelle de l’électronique -30..+85 °C -30..+85 °C Température de stockage -40..+125 °C -40..+125 °C Protection contre la poussière IP 6X (EN 60529) IP 6X (EN 60529) Etanchéité à l’eau IP X5 (EN 60529) IP X5 (EN 60529) EN 60068-2-6 (5g, 10..500 Hz) EN 60068-2-6 (5g, 10..500 Hz) EN 61326-1 EN 61326-2-3 EN61326-3-1 EN 61326-1 EN 61326-2-3 EN61326-3-1 Surpression sans dégradation Niveaux de vibrations Compatibilité électromagnétique - Emissions Compatibilité électromagnétique Immunité EN 61326-1 EN 61326-2-3 EN61326-3-1 EN 61326-1 EN 61326-2-3 EN61326-3-1 Tab. 2 - Limites opérationnelles et climatiques Inhibition et suspension de la fonction sécurité Les capteurs de la série K ne permettent pas de contourner la fonction sécurité, prévue pour la catégorie désignée. 14 80177E_MAN_KE PL’c’ - K7 PL’c’_10-2018_FRA Affichages et alarmes Les capteurs de la série melt K peuvent comporter deux typologies de sorties : analogique amplifiée (tension ou courant) et/ou sortie supplémentaire avec relais. La figure 6 indique les intervalles de significativité des sorties en cas de signal analogique: NOMINAL RANGE LOW ALARM ZONE 0 Zero A.L. HIGH ALARM ZONE F.S. L.L. A.H. H.L. Fig. 6 - Niveaux des sorties Tableau des valeurs sorties: L.L . = Low Limit A.L. = Alarm Low H.L. = High Limit A.H. = Alarm High Sortie 4-20 mA Sortie 0,5-10,5 V Sortie Générique = 3,68 mA = 0,300 V = Zero -2,00% Span < 3,600 mA < 0,250 V < Zero -2,50% Span = 20,960 mA = 11,100 V = F.S. + 6,00% Span > 21,000 mA > 11,125 V > F.S. + 6,25% Span Tab. 3 En cas de sortie relais, celui-ci sera normalement fermé sauf en cas : · de conditions d’alarme · de dépassement du % de F.S. programmé en tant que seuil d’alarme 80177E_MAN_KE PL’c’ - K7 PL’c’_10-2018_FRA 15 Le tableau 4 indique les pannes constatées, leurs effets sur les sorties électriques et sur la sortie relais ainsi que les modalités de rétablissement du dispositif. Panne Sortie analogique Câble d’alimentation coupé <3,6 mA < 0,25 V Capteur non connecté Alimentateur défaillant Sortie relais Modalité RAZ OPEN Elimination de la panne <3,6 mA < 0,25 V OPEN Elimination de la panne <3,6 mA < 0,25 V OPEN Elimination de la panne Strain gauge bridge connection detachment >21 mA > 11,125 V OPEN Retour capteur en usine Détachement des broches >21 mA > 11,125 V OPEN Retour capteur en usine Pression dépassant 200% du span par rapport au zéro d’usine à RT >21 mA > 11,125 V OPEN Mise hors tension puis remise sous tension Surtension <3,6 mA < 0,25 V OPEN Mise hors tension puis remise sous tension Sous-tension <3,6 mA < 0,25 V OPEN Mise hors tension puis remise sous tension Variations de tension <3,6 mA < 0,25 V OPEN Mise hors tension puis remise sous tension Erreur dans la séquence de programme <3,6 mA < 0,25 V OPEN Mise hors tension puis remise sous tension Surtempérature de l’électronique <3,6 mA < 0,25 V OPEN Mise hors tension puis remise sous tension Erreur sur le primaire ou le premier étage d’amplification <3,6 mA < 0,25 V OPEN Mise hors tension puis remise sous tension Tab. 4 - Pannes, effets sur les sorties et méthodes RAZ Les valeurs de sortie analogique se rapportent à des capteurs avec sortie 4-20 mA et 0,5-10,5V. Pour d’autres valeurs de sortie électrique, la valeur de la sortie en cas d’alarme est calculée comme suit : Sortie Alarme basse (mA,V)< Valeur zéro (mA,V) – 2,50 % span (mA,V) Sortie Alarme haute (mA,V)> Valeur F.S (mA,V) + 6,25 % span (mA,V) Les sondes de melt serie K ne comportent pas de feedbacks matériels. 16 80177E_MAN_KE PL’c’ - K7 PL’c’_10-2018_FRA Modalités de commande Les modalités de commande sont mises à la disposition de l’utilisateur dans le seul but d’effectuer les recalibrages périodiques du système dans le processus. Elles peuvent être activées de deux manières : √ Broche CAL √ Capteur magnétique Les combinaisons de ces événements réalisent les fonctionnalités suivantes: 1. Autozero 2. Calibrage (CAL) 3. RAZ paramètres Autozero 1) Autozero Modalités d’application La fonction Autozero est activée comme suit : 1) en positionnant l’aimant en contact avec le boîtier, au niveau de la zone délimitée par la plaquette Autozero. 2) En court-circuitant les broches E F, dans la version avec Autozero externe. FEO (bar) Limites ≤ 35 %régulation 100 > 35, < 100 40 > 100, < 200 20 ≥ 200 10 Résultats L’effet d’Autozero sera visible environ 2 secondes après la fin de l’exclusion de la fonction. La sortie analogique de l’émetteur se stabilise sur la valeur de zéro nominale (précision définie par la classe de précision de l’émetteur). Le contact doit être maintenu pendat 2 à 5 secondes. REMARQUE: Pour les émetteurs avec sortie de courant, lors de la phase d’Autozero, la sortie peut augmenter jusqu’à 7mA. Ce comportement est instantané et n’est présent que pendant la phase Autozero ; par conséquent, il n’aura aucun impact sur la RAZ de signal finale 1) Pression machine = 0 bar et capteur alimenté 2) Placer le stylet magnétique en contact avec la plaquette Autozero (2...5 secondes) 3) Retirer le stylet magnétique 4) Lire Stylet magnétique 2...5 secondes Retirer = plaquette Autozero Attention: la procédure de re-calibrage périodique par Autozero doit être exclusivement réalisée dans des conditions de pression nulle et de température stable. 80177E_MAN_KE PL’c’ - K7 PL’c’_10-2018_FRA 17 2) Calibrage (CAL) Modalités d’application Limites Résultats Démarrage CAL : Fermeture des contacts CAL pendant au moins 1 seconde La sortie de l’émetteur avant la fermeture des contacts doit se produire dans ± 20%FE Contacts fermés, la sortie analogique de l’émetteur se déplace en positif de 80%FE. L’effet de calibrage sera visible environ 2 secondes après le début d’activation de la fonction. Arrêt CAL : Relâchement des contacts Si les limites du tableau ne sont pas respectées, la fonction CAL n’aura aucun effet. REMARQUES: La fonction calibrage n’est pas disponible dans les modèles avec Autozero externe. 3) Reset parameter Modalités d’application Limites Aimant maintenu en position entre 20 et 25 secondes Résultats L’émetteur est automatiquement ramené dans les conditions d’usine. REMARQUES: Dans les transducteurs de courant, pendant la phase d’application de l’aimant, il est possibile d’observer un déséquilibrage du signal de sortie jusqu’à 7mA. Maintenance et localisation des pannes Pour garantir l’exécution correcte de la fonction sécurité, il est nécessaire de procéder à un certain nombre d’opérations de maintenance : Contrôle visuel de l’état de la membrane en contact avec le processus et des filets de la tige La maintenance doit permettre de repérer d’éventuelles abrasions anormales ou traces d’usure de la membrane, dues à des conditions incorrectes de montage, prolongées dans le temps, ou à une agressivité particulière du matériau traité. Le contrôle des filets doit garantir leur fonctionnement correct, pour éviter de possibles suintements en provenance du processus ou une faible étanchéité du capteur vissé dans son siège. Périodicité : une fois par an. Vérification du siège d’installation du capteur Cette opération de maintenance doit permettre de vérifier l’exactitude du profil et des dimensions du siège, afin d’éviter des pannes ou des dysfonctionnements eu niveau du capteur. Périodicité : tous les deux ans. Vérification du calibrage du capteur Cette opération de maintenance doit permettre de vérifier si la courbe de transduction du capteur est correcte. Elle est exécutée en appliquant des points connus de pression au transducteur et en contrôlant les valeurs affichées par la sonde. Périodicité : tous les deux ans. Vérification de l’éventuelle obstruction du canal sous pression Cette opération de maintenance doit permettre de vérifier l’absence d’occlusions du canal de pression, susceptibles d’entraîner des dysfonctionnements. Périodicité : il convient d’effectuer le contrôle en cas de variations des conditions de fonctionnement (matériau et/ou température), susceptibles de créer des obstructions dans le canal de pression. Vérification du fonctionnement des modalités de commande Cette opération de maintenance doit permettre de vérifier le fonctionnement correct des modalités de commande et leurs effets sur la sonde. Le capteur alimenté hors ligne, l’on doit procéder aux opérations suivantes: RAZ PARAMETRES AUTOZERO, AUTOZERO, CALIBRAGE. Périodicité : tous les deux ans. 18 80177E_MAN_KE PL’c’ - K7 PL’c’_10-2018_FRA Le tableau 5 récapitule les pannes les plus courantes et les solutions adaptées: Panne Causes possibles Solutions Le capteur ne capte pas la pression et n’est pas en alarme • Occlusion du canal de pression • Panne au niveau de l’étage de sortie de l’électronique • Surpression de 106% à 200% du F.S. 1. Mettre le capteur hors tension et le déposer. 2. Vérifier l’éventuelle obstruction du canal sous pression. Eliminer les éventuels résidus et amas de matériau. 3. Alimenter la sonde hors ligne et appuyer légèrement sur la membrane avec le doigt ; si la sonde ne change pas de sortie, l’expédier à son fabricant. 4. Réduire la pression de processus au-dessous de la valeur de P.E. Le capteur affiche une alarme du type “HIGH” • Extensomètre défaillant • Détachement de broches • Erreur du primaire • Valeur de pression mesurée au-dessus du seuil (2 x FS) 1. Mettre le capteur hors tension et le déposer. 2. Une fois la sonde remise sous tension, si le problème persiste, expédier le capteur au fabricant pour les réparations. 3. Une fois la sonde remise sous tension, si le problème paraît résolu, la reposer dans son siège, comme illustré dans le manuel d’instructions Le capteur affiche une alarme du type “LOW” • Câble d’alimentation/connecteur coupé • Capteur non connecté • Capteur non alimenté • Surtension • Sous-tension • Alimentation fluctuante • Erreur de séquence programme • Surtempérature de l’électronique 1. Mettre le capteur hors tension et le déposer. 2. Vérifier que l’alimentateur est branché. Si nécessaire, rétablir l’alimentateur. 3. Vérifier la continuité entre les broches du connecteur femelle et l’alimentateur. Si nécessaire, remplacer le câble et le connecteur. 4. Vérifier si les valeurs d’alimentation sont conformes aux spécifications contenues dans ce manuel. Si nécessaire, remplacer l’alimentateur. 5. Vérifier si les valeurs d’alimentation sont stables ; si nécessaire, remplacer l’alimentateur. 6. Une fois la sonde remise sous tension, si le problème paraît résolu, la reposer dans son siège, comme illustré dans le manuel d’instructions 7 - Si le problème persiste, expédier le capteur au fabricant pour les réparations Opération de CALIBRAGE impossible • Electronique défaillante • Signal de zéro hors seuil d’activation • Connecteur/câble d’alimentation coupé 1 - Arrêter la machine et s’assurer que la pression est égale à zéro 2 - Contrôler le câble et le connecteur et, si nécessaire, les remplacer. 3 - Effectuer dans l’ordre les opérations suivantes : • RAZ PARAMETRES • AUTOZERO • CALIBRAGE 4. Si le problème persiste, expédier la sonde au fabricant pour les réparations. Opération AUTOZERO impossible • Electronique défaillante • Signal de zéro hors seuil d’activation • Connecteur/câble d’alimentation coupé (pour AUTOZERO EXTERNE) • Positionnement incorrect du stylet magnétique 1. Arrêter la machine et s’assurer que la pression est égale à zéro. 2. Veiller à exécuter l’opération avec l’alignement correct entre le stylet et le marquage Autozero. 3. Exécuter l’opération RAZ PARAMETRES; si l’écart entre la valeur de zéro lue et le zéro théorique est, en termes absolus, supérieur à 40 % FS, déposer le capteur, contrôler et nettoyer son logement, reposer le capteur et répéter l’opération AUTOZERO. 4. Si l’écart entre la valeur de zéro lue et le zéro théorique est, en termes absolus, inférieur à 40% FS, contrôler le câble et le connecteur et, si nécessaire, les remplacer. 5. Si le problème persiste, expédier la sonde au fabricant pour les réparations. Tab. 5 - Localisation des pannes 80177E_MAN_KE PL’c’ - K7 PL’c’_10-2018_FRA 19 Applications relatives à la catégorie Les capteurs de Melt de la série W peuvent faire partie d’un système de détection de la pression qui, en cas de dépassement d’une valeur de seuil, désactiverait tous les éléments de génération de la pression à travers un système de commande. Le seuil d’activation du système est défini en usine et il ne peut être reprogrammé par l’utilisateur. Le schéma “A” (fig. 7) illustre une possible application : le capteur mesure la pression et la transforme en un signal électrique analogique proportionnel à la valeur mesurée ; le SRP/CS compare le signal avec celui programmé en tant que seuil d’alarme : en cas de dépassement du seuil, il désactive les éléments de génération de la pression. Sortie de tension V+ V- S+ S- SRP/CS SRP/C S O Sortie de courant à deux fils V+ S+ SRP/CS SRP/C S O Fig. 7 - Schéma d’application A 20 80177E_MAN_KE PL’c’ - K7 PL’c’_10-2018_FRA Le schéma “B” (fig. 8) illustre une deuxième possible application avec la sortie relais. Le capteur mesure la pression et la compare avec un seuil défini lors du calibrage en usine, non modifiable par l’utilisateur ; à cause du dépassement du seuil, le relais passe à l’état NO. Si la sortie est interfacée, comme dans l’exemple avec l’entrée d’habilitation du contrôleur du moteur des systèmes de génération de la pression, l’état NO entraîne l’inhibition des éléments de génération de la pression dès le dépassement du seuil. + 24V Sortie relais Contrôleur du moteur Systèmes de génération de pression Fig. 8 - Schéma d’application B Catégorie et niveau de performances Les dispositifs, installés, utilisés et entretenus selon les instructions de ce manuel, sont conformes à la norme : EN ISO 13849-1: 2015 Catégorie 2 PL c 80177E_MAN_KE PL’c’ - K7 PL’c’_10-2018_FRA 21 9. NOTES RELATIVES A L’UTILISATION DU RELAIS Contacts Les caractéristiques électriques des contacts, déclarées par les constructeurs, font référence à l’utilisation de charges résistives. Cela signifie que le courant qui passe à travers les contacts est plus ou moins constant. Idéalement, un relais avec une charge purement résistive peut fonctionner sans problème pendant toute sa durée de vie utile, à partir des valeurs de courant et de tension déclarées pour les contacts. Précautions à prendre avec les contacts Les contacts sont les éléments les plus importants dans la construction d’un relais. Leur durée de vie dépend de leur matériau de construction, de leur forme, des valeurs de tension et de courant appliquées, du type de charge, de la fréquence de commutation, de l’atmosphère ambiante, de la température d’exploitation et d’éventuelles fluctuations présentes pendant les phases de commutation. Le transfert de matériau entre les contacts, leur soudure, leur utilisation inappropriée avec des charges non résistives et l’augmentation de leur résistance de fermeture vont rendre inévitablement le relais inutilisable. D’où l’importance de respecter les précautions suivantes d’utilisation des contacts. Charges inductives Il est difficile de commuter des charges inductives, surtout parce que, pendant la phase d’ouverture, le courant cherche à continuer de s’écouler dans l’inducteur. L’énergie stockée dans ce dernier est donc déchargée sur les contacts, ce qui provoque des arcs électriques susceptibles de les endommager. Des circuits de suppression des arcs électriques sont souvent utilisés avec les charges inductives. Lors de l’utilisation de charges inductives, le courant maximum circulant dans les contacts du relais doit être réduit à 40% de la valeur indiquée sur la fiche technique du relais (valeur se rapportant à des charges résistives). Charges capacitives Les capacités, au moment de leur première alimentation, sont assimilables à des courts-circuits. Cela signifie que l’appel de courant (inrush) peut être très important et dépasser de plusieurs fois le courant maximum admissible pour les contacts. Des résistances en série sont souvent utilisées pour limiter le phénomène de l’appel de courant. En l’absence de ces résistances, les contacts peuvent se souder entre eux et rendre ainsi le relais inutilisable. Lors de l’utilisation de charges capacitives, le courant maximum circulant dans les contacts du relais doit être réduit à 75% de la valeur indiquée sur la fiche technique du relais (valeur se rapportant à des charges résistives). Moteurs Le démarrage d’un moteur électrique demande un appel de courant (inrush) très élevé. Pendant sa rotation, le moteur engendre une force contre-électromotrice qui, lors de la phase d’arrêt du moteur, se décharge sur les contacts du relais. Le moteur est donc la pire charge pour les contacts car il demande un appel de courant (inrush) très élevé au démarrage ; par ailleurs, lors de son arrêt, il peut engendrer des arcs électriques dans les contacts. Lors de l’utilisation de moteurs, le courant maximum circulant dans les contacts du relais doit être réduit à 20% de la valeur indiquée sur la fiche technique du relais (valeur se rapportant à des charges résistives). Type de charge et appel de courant Le type de charge, son appel de courant et sa fréquence de commutation sont des facteurs importants, susceptibles de provoquer la soudure des contacts. Le tableau ci-dessous montre la relation qui existe entre des charges typiques et leur appel de courant. Type de charge Appel de courant Charge résistive Courant stationnaire Charge inductive 10 à 20 fois le courant stationnaire Moteur 5 à 10 fois le courant stationnaire Charge lampe à incandescence 10 à 15 fois le courant stationnaire Charge lampe au mercure environ 3 fois le courant stationnaire Charge lampe aux vapeurs de sodium 1 à 3 fois le courant stationnaire Charge capacitive 20 à 40 fois le courant stationnaire Charge transformateur 5 à 15 fois le courant stationnaire 22 80177E_MAN_KE PL’c’ - K7 PL’c’_10-2018_FRA Formes d’onde typiques pour l’appel de courant (1) Charge lampe incandescente (3) Charge lampe fluorescente i/io≈ 5 à 10 (2) Charge lampe au mercure i/io≈ 3 L Contacts C (type avec facteur de puissance élevé) Lampe incandescente 10 secondes ou moins 3à5 minutes Le tube à décharge, le transformateur, l’inductance d’arrêt, le condensateur, etc., sont réunis dans les circuits des lampes à décharge courantes. A noter que l’appel de courant peut être de 20 à 40 fois, notamment en présence d’une faible impédance d’alimentation dans les contacts du type avec facteur de puissance élevé. Env. 1/3 seconde Appel de courant/courant nominal: i/io≈ 10 à 15 (4) Charge moteur i/io≈ 5 à 10 (5) Charge électrovanne i/io≈ 10 à 20 (6) Charge contact électromagnétique i/io≈ 3 à 10 (7) Charge capacitive i/io≈ 20 à 40 Libre Verrouillée Charge 0,2 à 0,5 seconde · Stationnaire Démarrage Freinage Les conditions deviennent plus sévères en cas de freinage ou de marche par à-coups, à cause des transitions d’état répétées. · 0.07 à 0,1 seconde Note: l’inductance étant élevée, les arcs 1 à 2 cycles (1/60 à 1/30 seconde) durent plus longtemps lors de la coupure. Le contact peut facilement brûler 1/2 à 2 cycles (1/120 à 1/30 seconde) Lors de l’utilisation d’un relais pour commander un moteur et un système de freinage CC, l’appel de courant à pleine charge, le courant stationnaire et le courant de freinage à vide varient en fonction de la charge du moteur (libre ou verrouillée). Appel de courant et tension inverse Lorsque des moteurs, des électrovannes ou des lampes sont activés, l’appel de courant engendré peut être beaucoup plus élevé que le courant stationnaire du circuit. Dans une charge inductive – par exemple, une électrovanne, un moteur ou un contacteur – la tension inversa engendrée peut atteindre des centaines, voire des milliers de Volts. Généralement, dans des conditions normales d’atmosphère, de température et de pression, la tension de décharge dans l’air est comprise entre 200 et 300 V. Si la tension inverse dépasse cette valeur, un phénomène de décharge entre les contacts se produira pendant la phase d’ouverture. Tant l’appel de courant que la tension inverse peuvent endommager les contacts et réduire la durée de vie utile du relais. L’utilisation de circuits de protection adaptés peut réduire ces phénomènes. Transfert du matériau des contacts Le transfert de matériau entre les contacts est provoqué par la fusion due à la surchauffe de ces derniers. Cela se produit généralement lors de la formation d’un arc électrique entre les contacts (pendant leur fermeture/ ouverture), provoqué par un courant continu supérieur à la valeur spécifiée, par des charges capacitives engendrant des appels de courant élevés ou par des charges inductives engendrant des tensions inverses élevées. En cas de transfert important de matériau, la déformation des contacts est visible à l’œil nu voir Figure 9. 80177E_MAN_KE PL’c’ - K7 PL’c’_10-2018_FRA 23 Figure 9 Généralement, la partie concave se forme sur la cathode, tandis que la forme convexe se forme sur l’anode. Circuit de protection des contacts L’utilisation de dispositifs ou de circuits de protection des contacts peut ramener les tensions inverses à des niveaux acceptables. A noter toutefois que leur utilisation inappropriée peut avoir des effets néfastes. Le tableau suivant montre des circuits de protection typiques. Circuits de protection des contacts : Charges Inductives Circuit Tension CA CD C* G G C Circuit CR Fonctions/Autres Sélection du dispositif Si la charge est une minuterie, le courant de dispersion (leakage) qui circule dans le circuit CR peut provoquer un dysfonctionnement. * Si utilisé avec une tension CA, s’assurer que l’impédance de la charge est suffisamment inférieure à celle du circuit CR Guide à la sélection de “c” et “r”, c : 0.5 μF à 1μF pour 1A de courant dans les contacts r : 0.5 Ω à 1 Ω pour 1V de tension vers les contacts La variabilité des valeurs dépend de la propriété de la charge et des caractéristiques du relais. La capacité “c” agit pendant la phase d’ouverture et elle sert à supprimer la décharge lorsque les contacts sont ouverts. La résistance “r” agit pendant la phase de fermeture et elle sert à limiter le courant lors de Si la charge est un relais ou l’application suivante de la tension. un solenoid, le temps de re- Utiliser une capacité “c” avec une tension de lachement s’allonge. Surtout rupture (breakdown voltage) comprise entre si l’alimentation est en 24 ou 200 et 300V. 48V. Utiliser des capacités non polarisées avec les circuits à CA. Circuit diode NG G La diode raccordée en parallèle permet à l’énergie stockée dans la bobine de circuler, sous forme de courant, dans la bobine elle-même et d’être ensuite dispersée, par effet Joule, depuis la composante résistive de la bobine. Ce circuit retarde le temps de relâchement de 2 à 5 fois le temps indiqué sur la fiche technique Circuit diode et Zener NG G Efficace lorsque le temps de relâchement avec la seule diode est excessif. Utiliser une diode Zener avec une tension de Zener à peu près égale à la tension d’alimentation. G L’utilisation d’une varistance empêche l’application de tensions excessives sur les contacts du relais. Ce circuit retarde légèrement le temps de relâchement. - Circuit varistance G Utiliser une diode avec une tension de rupture inverse égale au moins à 10 fois la tension d’alimentation et un courant direct égal au moins au courant maximum qui circule dans la charge. Dans les circuits électroniques, où les tensions sont faibles (5V), il est possible d’utiliser des diodes avec une tension inverse de rupture égale à 2 ou 3 fois la tension d’alimentation. (G: Good, NG: No Good, C: Care) 24 80177E_MAN_KE PL’c’ - K7 PL’c’_10-2018_FRA Montage des dispositifs de protection Il est important que les dispositifs de protection (diodes, résistance, capacités, varistances, etc.) soient installés à proximité immédiate de la charge ou des contacts. S’ils sont installés trop loin, leur capacité de protection peut se réduire considérablement. A titre indicatif, la distance maximale entre les dispositifs de protection et la charge ou les contacts doit être de 50 cm. Commutation des charges capacitives L’utilisation d’un relais pour la commutation des charges capacitives demande une attention particulière. Lors de la fermeture des contacts, un appel de courant élevé circule dans le circuit afin de charger le plus rapidement possible la capacité. Cet appel de courant est beaucoup plus élevé que le courant stationnaire (20 à 40 fois, en fonction de la valeur de capacité). Les contacts du relais peuvent fondre à cause de cet appel de courant, et ce même si le courant et la tension à l’état stationnaire sont conformes aux valeurs nominales. Chaque capacité présente dans le système contribue à l’appel de courant, indépendamment du fait qu’elle appartienne à un dispositif réactif, à un câble ou à un blindage. Cet appel de courant peut être limité en interposant une résistance (30 Ω à 50 Ω), entre les contacts eu la capacité à commuter, comme illustré dans la Figure 10. Figure 10 Précautions à prendre en cas d’utilisation de câbles de raccordements longs Si la longueur des câbles de raccordement dépasse 10 m, l’appel de courant, dû à la capacité parasite du câble, peut donner lieu à des appels de courant élevés. Brancher une résistance (10 Ω à 50 Ω) en série sur les contacts, comme illustré dans la Figure 11. 10 Ω à 50 Ω Conducteur (dizaines de mètres) Capacité de stockage de l’énergie Figure 11 Documents de référence : National Instruments: http://www.ni.com/white-paper/4197/en/ Panasonic Corporation: General application Guidelines ASCTB250E 201402-T Hongfa Relay: Explanation of terminology and guidelines of relay Fujitsu Components: Engineering Reference Relays Agilent Technologies Inc: Application Note 1399 80177E_MAN_KE PL’c’ - K7 PL’c’_10-2018_FRA 25 GEFRAN spa via Sebina, 74 25050 PROVAGLIO D’ISEO (BS) - ITALIA tel. 0309888.1 - fax. 0309839063 Internet: http://www.gefran.com 26 80177E_MAN_KE PL’c’ - K7 PL’c’_10-2018_FRA ">
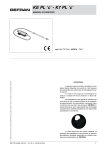
Link público atualizado
O link público para o seu chat foi atualizado.