Mettler Toledo GPro 500 Manuel utilisateur
PDF
Descarregar
Documento
Mode d’emploi TDLS GPro™ 500 Spectromètre à diode laser accordable pour l’O2 2 Table de matières 1 Introduction..............................................................................................................11 1.1Informations liées à la sécurité............................................................................ 11 1.2Instructions générales......................................................................................... 11 1.3 Consignes de sécurité.........................................................................................12 1.3.1 Pour la série M400 type 3 ; 4 fils...............................................................12 1.3.2Instructions de sécurité relatives à l’installation, au fonctionnement et à la maintenance en environnement dangereux pour la série GPro™ 500 (ATEX)...12 1.3.3Branchement aux blocs d’alimentation........................................................13 1.3.4 Précautions de sécurité relatives à l’installation, au fonctionnement et à la maintenance en environnement dangereux pour la série GPro™ 500.............14 1.4 Principe de mesure............................................................................................15 1.4.1 Charge de poussières................................................................................16 1.4.2 Température.............................................................................................16 1.4.3 Pression..................................................................................................17 1.4.4Interférence croisée...................................................................................17 1.5Description de l’instrument..................................................................................18 1.5.1 Vue d’ensemble du système.......................................................................18 1.5.2 Tête de sonde...........................................................................................22 1.5.3 Sonde à immersion...................................................................................23 1.5.4 Transmetteur M400 type 3.........................................................................23 1.6Logiciel.............................................................................................................23 1.7 Classement laser...............................................................................................23 1.8Données relatives au produit...............................................................................24 2 Préparations............................................................................................................ 28 2.1 Outils et autre matériel........................................................................................28 2.2 Conditions de débit au point de mesure................................................................28 2.3 Mise en place de la tête de mesure......................................................................28 2.4 Critères requis pour les brides et les trous de raccord............................................ 29 2.5 Câbles et branchements électriques.................................................................... 29 3 Installation et démarrage..........................................................................................31 3.1Installation et réglages........................................................................................31 3.1.1Installation mécanique..............................................................................31 3.1.2 Purge du côté procédé...............................................................................31 3.1.3 Purge côté procédé...................................................................................31 3.1.4Réglage du débit de purge.........................................................................32 3.1.5 Purge côté instrument............................................................................... 34 3.1.6Installation de la barrière thermique........................................................... 34 3.2Alignement....................................................................................................... 35 4 Dimensions et schémas........................................................................................... 36 5 Branchements électriques........................................................................................ 43 5.1 Sécurité électrique et mise à la terre.................................................................... 44 5.2Branchements sur la tête de sonde......................................................................47 5.3Branchements sur le M400................................................................................ 56 6 Programme d’entretien............................................................................................. 58 3 Spectromètre à laser pour l’oxygène 6.1 Connexion d’un PC............................................................................................ 58 6.2 Configuration du PC pour se connecter au GPro™ 500 à l’aide du logiciel MT-TDL... 59 6.3Le logiciel MT-TDL............................................................................................. 62 6.3.1La tendance ppm..................................................................................... 62 6.3.2La tendance de transmission..................................................................... 64 6.3.3Enregistrement des données..................................................................... 65 6.3.4 Sondes externes...................................................................................... 66 6.3.5 Sorties analogiques (en option)..................................................................67 6.4La visionneuse.................................................................................................. 69 7 Fonctionnement, maintenance et étalonnage..............................................................70 7.1 M400...............................................................................................................70 7.1.1Démarrage de l’instrument.........................................................................71 7.1.2Arrêt de l’instrument..................................................................................71 7.2 Maintenance......................................................................................................71 7.2.1 Maintenance de routine.............................................................................71 7.2.2Retrait de la sonde du procédé...................................................................71 7.2.3Retrait et nettoyage du cube d’angle............................................................71 7.2.4 Nettoyage de la fenêtre de procédé.............................................................72 7.3 Étalonnage........................................................................................................74 7.3.1 Étalonnage procédé..................................................................................74 7.3.2 Étalonnage à l’aide d’une cellule d’étalonnage..............................................74 7.4Dangers résiduels..............................................................................................74 7.4.1Raccords défectueux.................................................................................74 7.4.2 Panne d’électricité.....................................................................................75 7.4.3 Protection thermique.................................................................................75 7.4.4Influences externes...................................................................................75 8 Protection anti-explosion..........................................................................................76 8.1ATEX.................................................................................................................76 8.2 Homologation FM (version USA)......................................................................... 85 9 Dépannage.............................................................................................................. 89 9.1 Messages d’erreur sur l’unité de commande......................................................... 89 10 Mise hors service, stockage et mise au rebut............................................................ 90 10.1 Mise hors service.............................................................................................. 90 10.2 Stockage.......................................................................................................... 90 10.3 Mise au rebut................................................................................................... 90 4 Appendix Appendix 1 Informations relatives à la conformité et aux normes......................................91 Appendix 2 Pièces détachées et accessoires................................................................... 92 2.1 Options de configuration.......................................................................... 92 2.2 Pièces détachées.................................................................................... 93 2.3Accessoires............................................................................................ 93 Appendix 3 Mise au rebut conformément à la directive relative aux déchets d’équipements électriques et électroniques (DEEE)................................................................................ 94 Appendix 4 Protection de l’équipement............................................................................ 95 4.1Rapport traditionnel entre niveaux de protection du matériel (EPL) et zones.... 95 4.2Rapport entre les niveaux de protection du matériel et les ­catégories ATEX..... 95 Appendix 5 Consignes ESD............................................................................................. 96 5 Figures Spectromètre à laser pour l’oxygène Figure 1Le principe SpectraID™.....................................................................................16 Figure 2 Configuration du GPro™ 500 ............................................................................19 Figure 3 GPro™ 500..................................................................................................... 20 Figure 4La boîte de jonction (GHG 731 de Malux) (EX-e)...................................................21 Figure 5 Transmetteur M400 Type 3.................................................................................21 Figure 6Espace libre minimum sur la bride du procédé......................................................28 Figure 7 Optimisation du débit de purge............................................................................32 Figure 8 Configuration de la purge.................................................................................. 33 Figure 9 Connexion de la conduite de purge au raccord de purge côté procédé.................... 33 Figure 10 Configuration de la purge.................................................................................. 34 Figure 11Dimensions de la sonde de 290 mm.................................................................. 36 Figure 12 Configuration à une bride...................................................................................37 Figure 13 Configuration à deux brides................................................................................37 Figure 14Dimensions de la sonde de 390 mm.................................................................. 38 Figure 15Dimensions de la sonde de 590 mm.................................................................. 39 Figure 16Dimensions de la bride DN50/PN25 du GPro 500................................................ 40 Figure 17Dimensions de la bride ANSI 50,8 mm/300lb du GPro 500.................................. 40 Figure 18Dimensions préconisées pour les brides soudées..................................................41 Figure 19Dimensions de la barrière thermique....................................................................42 Figure 20 Point de mise à la terre externe.......................................................................... 46 Figure 21 Mise à la terre de protection............................................................................... 46 Figure 22Branchements sur la boîte de jonction.................................................................47 Figure 23 Schéma de câblage avec sorties analogiques actives........................................... 48 Figure 24 Schéma de câblage avec entrées analogiques alimentées par boucle..................... 49 Figure 25La boîte de jonction GHG 731.11 (EX-e) . ............................................................ 50 Figure 26Branchements sur le boîtier de raccordement . .....................................................51 Figure 27 Schéma de câblage avec sorties analogiques actives............................................52 6 Figure 28 Schéma de câblage avec entrées analogiques alimentées par boucle..................... 53 Figure 29 Connexions sur la carte mère située dans la tête de sonde.................................... 54 Figure 30 Connexions sur la carte d’E/S située dans la tête de sonde.................................... 54 Figure 31Branchements des câbles sur le M400............................................................... 56 Figure 32 Connexion d’un PC........................................................................................... 58 Figure 33 Connexions réseau........................................................................................... 59 Figure 34 Connexions au réseau local............................................................................... 59 Figure 35 Propriétés de connexion au réseau local............................................................. 60 Figure 36 Propriétés du protocole Internet (TCP/IP)..............................................................61 Figure 37La tendance ppm.............................................................................................. 63 Figure 38La tendance de transmission............................................................................. 64 Figure 39Enregistrement des données.............................................................................. 65 Figure 40 Sondes externes............................................................................................... 66 Figure 41 Sorties analogiques (en option)...........................................................................67 Figure 42 Sélection d’un paramètre................................................................................... 68 Figure 43 Choix des alarmes............................................................................................ 68 Figure 44 Choix du mode Hold......................................................................................... 69 Figure 45La visionneuse................................................................................................. 69 Figure 46 M400 vue de face.............................................................................................70 Figure 47 Nettoyage/Remplacement du cube d’angle...........................................................72 Figure 48 Connexion de la conduite de purge au raccord de purge côté procédé.....................72 Figure 49 Nettoyage de la fenêtre de procédé......................................................................73 Figure 50 Cellule d’étalonnage...........................................................................................74 Figure 51 Configuration Ex................................................................................................76 Figure 52L’interface du GPro™ 500 entre la zone 0 et la zone 1...........................................77 Figure 53 Étiquette pour la version ATEX.............................................................................78 Figure 54 Étiquette de note................................................................................................78 7 Figure 55 Étiquette de mise à la terre..................................................................................78 Spectromètre à laser pour l’oxygène Figure 56 Certificat ATEX (page 1/2)...................................................................................79 8 Figure 57 Certificat ATEX (page 2/2).................................................................................. 80 Figure 58Déclaration de conformité CE..............................................................................81 Figure 59 Certificat ICECx (page 1/3).................................................................................82 Figure 60 Certificat ICECx (page 2/3)................................................................................ 83 Figure 61 Certificat ICECx (page 3/3)................................................................................ 84 Figure 62 Étiquette pour la version US............................................................................... 85 Figure 63 Étiquette de note............................................................................................... 86 Figure 64 Étiquettes de mise à la terre............................................................................... 86 Figure 65 Certificat FM. Approbations FM (page 1/2)............................................................87 Figure 66 Certificat FM. Approbations FM (page 2/2)........................................................... 88 Tables Table 1Données relatives à la tête de sonde....................................................................24 Table 2Données relatives à la sonde..............................................................................26 Table 3Données relatives au M-400...............................................................................27 Table 4Brides requises pour certaines configurations types...............................................37 Table 5 Câbles GPro™ 500.......................................................................................... 50 Table 6 Câbles GPro™ 500.......................................................................................... 55 Table 7Bornes d’alimentation secteur............................................................................ 56 Table 8Raccordement du GPro™ 500 sur le M400..........................................................57 Table 9 Connexion des relais sur le M400.......................................................................57 Table 10 Messages d’erreur............................................................................................ 89 Table 11 Clé de produit GPro™ 500................................................................................ 92 Table 12 Pièces détachées.............................................................................................. 93 Table 13Accessoires...................................................................................................... 93 9 10 1 Introduction 1.1 Informations liées à la sécurité Veuillez lire ce manuel et vous assurer de parfaitement comprendre son contenu avant d’essayer d’installer, d’utiliser ou d’entretenir le GPro™ 500. Ce manuel comporte des informations importantes en matière de sécurité, mises en évidence sous les intitulés AVERTISSEMENT et ATTENTION, utilisés de la manière suivante : AVERTISSEMENT Les avertissements soulignent des dangers spécifiques susceptibles d’entraîner des lésions corporelles, voire le décès, s’ils ne sont pas pris en compte. ATTENTION Ces rubriques signalent des dangers à prendre en compte pour éviter d’endommager le TDL ou d’autre matériel ou biens. Ce manuel comporte également des informations visant à attirer votre attention sur un point précis, qui sont signalées de la manière suivante : Elles soulignent des informations utiles dont vous devez avoir connaissance (notamment des conditions de fonctionnement spéciales, par exemple). 1.2 Instructions générales Ce manuel contient des informations relatives à l’installation, au fonctionnement et à la maintenance du GPro™ 500 TDL. Il comprend également une description du GPro™ 500 TDL et de ses caractéristiques élémentaires. Le GPro™ 500 TDL peut être utilisé en environnement explosif, conformément à la définition de la norme EN 60079-14 (ATEX) ou IEC 60079-10 (ATEX). Pour plus de renseignements sur les niveaux de protection du matériel, voir le chapitre 8 « Protection anti-explosion », à la page 76, et voir le chapitre 4.2 « Rapport entre les niveaux de protection du matériel et les ­catégories ATEX », à la page 95. Veuillez lire attentivement le manuel complet avant d’utiliser le GPro™ 500 TDL. Il s’agit d’un instrument sophistiqué qui met en œuvre des technologies électronique et laser sophistiquées. L’installation et la maintenance de l’instrument exigent des soins et une préparation particulière et sont strictement réservés au personnel compétent. Le non-respect de ce critère peut causer des dommages à l’instrument et entraîner l’annulation de la garantie. ATTENTION METTLER TOLEDO recommande vivement d’exécuter l’installation et la mise en service finales sous la supervision d’un représentant METTLER TOLEDO. Veillez à faire vérifier le câblage par du personnel qualifié avant de démarrer le système. Il est fortement conseillé de faire valider le câblage par un technicien de maintenance METTLER TOLEDO. Un câblage inapproprié risque en effet d’endommager la tête de sonde et/ou le transmetteur M400. ATTENTION N’installez pas la sonde dans le procédé avant d’avoir activé la purge. Sans purge, les composants optiques intégrés à la sonde peuvent être contaminés et les performances de mesure du GPro 500 peuvent s’en trouver altérées. METTLER TOLEDO recommande vivement d’exécuter l’installation et la mise en service finales sous la supervision d’un représentant METTLER TOLEDO. 11 1.3 Consignes de sécurité Spectromètre à laser pour l’oxygène 1.3.1 Pour la série M400 type 3 ; 4 fils Avant de brancher le dispositif sur le bloc d’alimentation, vérifiez que sa tension de sortie ne puisse pas dépasser 30 Vcc. N’utilisez pas de courant alternatif ou l’alimentation secteur. AVERTISSEMENT L’installation des raccordements de câbles et l’entretien de ce produit nécessitent l’accès à des niveaux de tensions qui présentent un risque d’électrocution. AVERTISSEMENT Avant l’entretien, il faut débrancher les contacts d’alimentation et les contacts OC ou de relais raccordés sur différentes sources de courant. AVERTISSEMENT L’alimentation doit disposer d’un interrupteur ou d’un disjoncteur comme dispositif de débranchement de l’équipement. AVERTISSEMENT L’installation électrique doit être conforme au Code électrique américain et/ou à toutes les réglementations applicables au niveau local ou national. RELAY RESP. OC CONTROL ACTION : les relais du transmetteur M400 se désactivent toujours en cas de perte d’alimentation, comme en état normal, quel que soit le réglage de l’état du relais pour un fonctionnement sous alimentation. Configurez tout système de contrôle utilisant ces relais en respectant une logique de sécurité absolue. PERTURBATIONS DU PROCÉDÉ : comme les conditions de procédé et de sécurité peuvent dépendre du bon fonctionnement de ce transmetteur, prévoyez des moyens appropriés pour maintenir le fonctionnement pendant le nettoyage et le remplacement de la sonde ou l’étalonnage de l’instrument. 1.3.2 Instructions de sécurité relatives à l’installation, au fonctionnement et à la maintenance en environnement dangereux pour la série GPro™ 500 (ATEX) AVERTISSEMENT Les dispositifs de cette série sont certifiés en vue du fonctionnement en environnement dangereux. AVERTISSEMENT Pendant l’installation, la mise en service et l’utilisation du dispositif, il convient de respecter les stipulations relatives aux installations électriques (CEI EN 60079-14/CEI EN 60079-10) en environnement dangereux. 12 AVERTISSEMENT Lorsque le dispositif est installé en dehors du domaine d’application de la directive 94/CE, il convient de respecter les normes et réglementations appropriées dans le pays où il est utilisé. AVERTISSEMENT Seules les manipulations du dispositif décrites dans le manuel d’instruction sont autorisées. Le GPro™ 500 est fourni avec un câble pré-installé et un presse-étoupe. N’essayez pas de remplacer le câble, car cela annulerait la garantie et constituerait une violation du classement ATEX ! AVERTISSEMENT L’ouverture de la tête de sonde annule la garantie et constitue une violation du classement de zone dangereuse ATEX ! AVERTISSEMENT L’installation doit être réalisée exclusivement par des membres du personnel formés, suivant le manuel d’instruction et conformément aux normes et réglementations applicables. –– Nettoyage : dans les emplacements dangereux, le dispositif doit être nettoyé exclusivement avec un chiffon humide, afin d’éviter toute décharge électrostatique. 1.3.3 Branchement aux blocs d’alimentation Version USA : La version USA doit être installée au moyen d’un système de conduits de câbles approprié, conformément aux réglementations et codes locaux. Pour faciliter la procédure, l’instrument est fourni sans câble raccordé. Les bornes d’alimentation sont conçues pour recevoir des conducteurs simples/fils souples de 0,2 mm2 à 1,5 mm2 (AWG 24–16). AVERTISSEMENT L’installation électrique doit être effectuée conformément au Code électrique national et/ou à tout autre code national ou local applicable. AVERTISSEMENT Après avoir désactivé l’alimentation électrique du système, patientez 2 minutes avant d’ouvrir le boîtier. AVERTISSEMENT Au moment de fixer le couvercle du boîtier sur la tête de la sonde, appliquez aux 8 vis de fixation M5 un couple de serrage de 8 Nm. 13 Spectromètre à laser pour l’oxygène AVERTISSEMENT Pour le groupe de gaz A, la conduite doit être étanche au niveau de l’entrée du boîtier. Pour les groupes de gaz B, C et D, la conduite n’a pas besoin d’être étanche. 1.3.4 Précautions de sécurité relatives à l’installation, au fonctionnement et à la maintenance en environnement dangereux pour la série GPro™ 500 AVERTISSEMENT Les dispositifs de cette série sont certifiés en vue du fonctionnement en environnement dangereux. AVERTISSEMENT Pendant l’installation, la mise en service et l’utilisation du dispositif, il convient de respecter les stipulations relatives aux installations électriques (CEI EN 60079-14/CEI EN 60079-10) en environnement dangereux. AVERTISSEMENT Lorsque le dispositif est installé en dehors du domaine d’application de la directive 94/CE, il convient de respecter les normes et réglementations appropriées dans le pays où il est utilisé. AVERTISSEMENT Seules les manipulations du dispositif décrites dans le manuel d’instruction sont autorisées. AVERTISSEMENT L’installation doit être réalisée exclusivement par des membres du personnel formés, suivant le manuel d’instruction et conformément aux normes et réglementations applicables. –– Nettoyage : dans les emplacements dangereux, le dispositif doit être nettoyé exclusivement avec un chiffon humide, afin d’éviter toute décharge électrostatique. Branchement aux blocs d’alimentation –– Les dispositifs de la série mentionnée ci-dessus doivent être reliés exclusivement à des blocs d’alimentation antidéflagrants (pour les tensions d’entrée, reportez-vous au manuel d’instruction Certificat d’examen de type CE). –– Les bornes d’alimentation sont conçues pour recevoir des conducteurs simples/fils souples de 0,2 mm2 à 1,5 mm2 (AWG 24–16). AVERTISSEMENT Lorsque vous branchez l’alimentation externe directement à la tête de sonde via la boîte de jonction, ne dépassez pas la limite de 24 V, 5 W requise. Mise au rebut adéquate de l’instrument –– Lorsque l’instrument n’est plus utilisé, respectez toutes les réglementations locales en matière d’environnement pour le mettre au rebut comme il convient. 14 1.4 Principe de mesure Le GPro™ 500 TDL est un instrument optique conçu pour contrôler le gaz in-situ dans les raccords, tuyaux et applications semblables. Il est basé sur la spectroscopie d’absorption par diode laser accordable (TDLAS). L’installation du GPro™ 500 TDL s’effectue d’un seul côté et il n’est pas nécessaire d’avoir recours à l’alignement pour mesurer la concentration de gaz moyenne le long de la trajectoire de la ligne de visée de la sonde. Pour que la purge du GPro™ 500 TDL puisse fonctionner correctement, le gaz de procédé doit circuler au point de mesure. Pour en savoir plus à ce sujet, voir le chapitre 2.2 « Conditions de débit au point de mesure », à la page 28, et voir le chapitre 3.1.2 « Purge du côté procédé », à la page 31. Le GPro™ 500 TDL convient pour utilisation en environnement industriel ou dans des environnements où il peut être branché sur le réseau électrique destiné aux locaux domestiques. Le principe de mesure utilisé est la spectroscopie d’absorption infrarouge, qui repose sur le fait que chaque gaz possède des pics d’absorption distincts à des longueurs d’onde données. Dans le cas d’oxygène décrit dans ce manuel, on utilise en fait trois pics. La longueur d’onde du laser est scannée à travers les pics d’absorption choisis du gaz à mesurer. Les pics d’absorption sont soigneusement sélectionnés pour éviter l’interférence croisée d’autres gaz (d’arrière-plan). Grâce à la spectroscopie d’absorption directe, on prend un spectre dans une plage de longueurs d’onde spécifique et on le compare aux données de référence spectrales enregistrées dans la base de données intégrée pour une température et une pression données. La concentration est ensuite calculée. L’incohérence entre les données de référence et les données de mesure déclenche une alarme. Par ailleurs, l’usage de trois pics d’absorption constitue une manière validée de s’assurer de l’utilisation des pics adéquats, puisque leur hauteur et leur position relative constituent leur « empreinte » – SpectraID™ – voir la Figure 1, à la page 16. L’intensité lumineuse détectée varie en fonction de la longueur d’onde du laser, du fait de l’absorption des molécules de gaz ciblées dans le chemin optique entre le laser et le détecteur. La largeur de ligne du laser représente une petite part de la largeur de la ligne d’absorption et le spectre reproduit est donc très précis. L’instrument stocke les données spectrales dans sa mémoire et lorsqu’un scan est obtenu, un ajustage de la courbe sur ces données est effectué pour donner une grandeur de mesure. La température et la pression du gaz de procédé sont également prises en compte. Ces paramètres sont mesurés séparément ou peuvent être fixés manuellement. 15 Puissance de ligne Spectromètre à laser pour l’oxygène SpectraID™ 760,4 760,5 760,6 760,7 Longueur d'onde (nm) Figure 1 Le principe SpectraID™ Le GPro™ 500 TDL mesure uniquement la concentration des molécules LIBRES du gaz spécifique. Il n’est donc pas sensible aux molécules liées à d’autres molécules dans des complexes et aux molécules jointes ou dissoutes dans des particules et des gouttelettes. Il faut faire attention lors de la comparaison des mesures avec les résultats d’autres techniques de mesures. 1.4.1 Charge de poussières Tant que le faisceau laser est en mesure de générer un signal pour le détecteur, la charge de poussières des gaz de procédé n’influence pas les résultats de l’analyse. En amplifiant automatiquement le signal, les mesures peuvent être réalisées sans impact négatif. L’influence exercée par une forte charge de poussières est complexe et dépend de la longueur du chemin optique (longueur de la sonde), de la taille des particules et de la distribution de la taille des particules. Avec des longueurs de chemin supérieures, l’atténuation optique augmente rapidement. Les particules de taille inférieure ont également un impact important sur l’atténuation optique : plus les particules sont petites, plus la mesure sera difficile. L’impact général sur le résultat de la mesure, en présence d’une charge de poussières élevée est un niveau de bruit accru. Pour les applications à forte charge de poussières, veuillez consulter votre représentant METTLER TOLEDO local et voir le chapitre « Vente et service », à la page 99. 1.4.2 Température Il est indispensable de compenser l’impact de la température sur un pic d’absorption. Il est possible de raccorder une sonde de température externe au GPro™ 500. Le signal est alors utilisé pour corriger les résultats de la mesure. Sans compensation de température, l’erreur de mesure générée par les variations de température du gaz de procédé a une influence considérable sur la mesure. Par conséquent, la plupart du temps, un signal de température externe est recommandé. Le mode manuel, avec des valeurs de température et de pression fixes, est recommandé uniquement pour les procédés dont les valeurs sont constantes et connues. 16 1.4.3 Pression La pression du gaz du procédé influence la forme du pic d’absorption moléculaire et les résultats de la mesure. Il est possible de raccorder une sonde de pression externe au GPro™ 500. Lorsque la pression de gaz du procédé est correcte, le modèle GPro™ 500 utilise un algorithme spécial pour adapter la forme du pic et compenser de manière efficace l’influence de la pression, ainsi que l’effet de la masse volumique. Sans compensation, l’erreur de mesure causée par les variations de pression du gaz de procédé est importante. C’est pourquoi un signal de pression externe est recommandé dans la plupart des cas. Le mode manuel, avec des valeurs de température et de pression fixes, est recommandé uniquement pour les procédés dont les valeurs sont constantes et connues. 1.4.4 Interférence croisée Comme le GPro™ 500 reçoit son signal de trois pics d’absorption moléculaires à résolution complète, il élimine le risque d’interférences croisées avec les autres gaz. Le GPro™ 500 est donc capable de mesurer de manière très sélective le composant de gaz souhaité. ATTENTION Soyez toujours particulièrement prudent au moment de choisir l’emplacement de mesure. Il est recommandé d’opter pour des endroits à faibles particules, où la température est faible et où la pression du procédé est mieux adaptée. Plus l’emplacement de mesure est adapté, plus les performances globales du système sont satisfaisantes. Veuillez consulter votre représentant Mettler Toledo, voir le chapitre « Vente et service », à la page 99. 17 Spectromètre à laser pour l’oxygène 1.5 Description de l’instrument 18 Le GPro™ 500 TDL se compose de 3 unités distinctes : la tête TDL (tête de sonde fixée à l’une des trois sondes d’immersion possibles), un boîtier de raccordement et l’interface utilisateur (M400). Par ailleurs, la purge au N2 et les mesures de pression et de température doivent être disponibles. La configuration au point de mesure est illustrée, voir la Figure 2 « Configuration du GPro™ 500 », à la page 19. 1.5.1 Vue d’ensemble du système Il faut un dispositif de connexion entre le TDL et le transmetteur M400. Pour les applications ATEX, il est possible d’utiliser un boîtier de raccordement existant ou d’en commander un (voir le chapitre 2.3 « Accessoires » de l’annexe, à la page 93). Les signaux 4...20 mA de compensation de la température et de la pression sont reliés à la tête de sonde par le biais du dispositif de connexion. L’interface Ethernet est accessible par le biais du dispositif de connexion également. Pour plus de renseignements sur l’installation en zone dangereuse, voir le chapitre 8 « Protection anti-explosion », à la page 76. En mode d’installation standard, GPro™ 500 est connecté au transmetteur M400, dont l’interface utilisateur conviviale permet de définir les paramètres de l’analyseur requis pour chacune des applications lors de la mise en service, pour la vérification et l’étalonnage du système ainsi que pour l’utilisation des fonctionnalités d’E/S intégrées (4 sorties analogiques actives de 4...20 mA et 6 relais). GPro™ 500 peut également être fourni en tant que version de sortie supplémentaire, auquel cas il est doté, directement sur la tête de la sonde, de 2 sorties analogiques passives de 4...20 mA et représente une solution antidéflagrante Ex d complète. Dans ce cas, aucun transmetteur M400 n’est fourni et ne doit être connecté à la tête de la sonde. Pour configurer les sorties analogiques directes en option, vous devez employer le logiciel MT-TDL lors de la mise en service du GPro™ 500 (via la connexion Ethernet au GPro™ 500: reportez-vous à l’élément 6 de la figure 2, « Configuration du GPro™ 500 », page 19). Pour plus d’informations sur le logiciel MT-TDL, consultez le chapitre 6 « Programme d’entretien », page 58. 15 P 5 T 16 17 4 6 1 2 7 3 9 10 11 8 12 13 14 Figure 2 Configuration du GPro™ 500 1 2 3 4 5 6 7 8 9 10 11 12 13 14 15 16 17 Tête de sonde GPro™ 500 avec sonde d’immersion (ici la sonde de 390 mm) Purge avec du N2, une entrée pour le côté procédé, une entrée et une sortie pour le côté sonde. Bride de procédé (DN50/PN25 ou ANSI 2”/300lb) Boîte de jonction (dispositif de connexion) 2 x 4...20 mA (pression et température) Connexion Ethernet RS 485 Transmetteur M 400 T3 sortie 4...20 mA pour la concentration sortie 4...20 mA pour la pression sortie 4...20 mA pour la température sortie 4...20 mA pour le % de transmission Sorties relais pour les besoins de l’alarme. Les relais sont configurables (6 relais disponibles au total). Alimentation du transmetteur M400. Mise à la terre pour la tête TDL. Source d’alimentation externe de 24 V et 5 W pour la tête de sonde. 2 sorties analogiques directes de 4...20 mA (en option). 19 Spectromètre à laser pour l’oxygène AVERTISSEMENT Lorsque vous branchez l’alimentation externe directement à la tête de sonde via la boîte de jonction, ne dépassez pas la limite de 24 V, 5 W requise. 20 Figure 3 GPro™ 500 Le GPro™ 500 comprend la tête TDL qui contient le module laser avec une diode laser à température stabilisée, les lentilles collimatrices, les composants électroniques et un dispositif de stockage des données. Il est logé dans un boîtier à revêtement aluminium. La sonde de mesure est reliée à la tête TDL. L’indice de protection de la tête TDL est IP65, NEMA 4x. Le GPro™ 500 est installé en assemblant la purge fournie, puis monté sur la bride du procédé DN50 ou ANSI 2“. Vvoir la Figure 16 « Dimensions de la bride DN50/PN25 du GPro 500 », à la page 40, et voir la Figure 17 « Dimensions de la bride ANSI 50,8 mm/300lb du GPro 500 », à la page 40. L’alignement optique est fiable et résistant et n’exige aucun alignement manuel. La purge empêche la poussière et d’autres éléments contaminants de s’incruster sur les surfaces optiques. Figure 4 La boîte de jonction (GHG 731 de Malux) (EX-e). La boîte de jonction permet de connecter la sonde de mesure, la sonde de pression, la sonde de température, Ethernet et le M400. Figure 5 Transmetteur M400 Type 3 21 Spectromètre à laser pour l’oxygène Pour plus d’informations, voir le chapitre 7.1 « M400 », à la page 70, ainsi qu’au manuel M400. L’approbation pour le M400 correspond à la classe 1 Div 2/Zone 2 ATEX. Pour l’installation en zone de type 1, voir le chapitre 2.3 « Accessoires », à la page 93 – Boîtier de purge pour le M400. 1.5.2 Tête de sonde L’ensemble transmetteur-récepteur est désigné sous le nom de tête TDL. Cette partie comprend le laser, le système optique et tous les composants électroniques de la commande laser, du traitement des signaux, du verrouillage de pic, du détecteur, du stockage/de la récupération des données, des sorties actives (en option), etc. La tête de sonde possède une interface Ethernet, accessible via le boîtier de raccordement, pour une maintenance de haut niveau grâce au logiciel propre à METTLER TOLEDO Process Analytics (MT-TDL). Aucune des pièces de la tête de sonde n’est en contact ni avec le milieu, ni avec le procédé. La puissance minimale requise pour la tête de sonde est de 24 V et 5 W. Version ATEX : Dans la version ATEX, la tête de sonde est fournie avec un câble préconfiguré déjà installé. N’ouvrez pas la tête de sonde pour enlever, modifier ou remplacer le câble. AVERTISSEMENT L’ouverture de la tête de sonde annule la garantie et constitue une violation du classement de zone dangereuse ATEX. Version USA : La version USA doit être installée au moyen d’un système de conduits de câbles approprié, conformément aux réglementations et codes locaux. Pour faciliter la procédure, l’instrument est fourni sans câble raccordé. METTLER TOLEDO recommande d’utiliser les câbles répertoriés en tant qu’accessoires dans l’annexe 2 « Pièces détachées et accessoires », page 92. Les bornes d’alimentation sont conçues pour recevoir des conducteurs simples/fils souples de 0,2 mm2 à 1,5 mm2 (AWG 24–16). AVERTISSEMENT L’installation électrique doit être effectuée conformément au Code électrique national et/ou à tout autre code national ou local applicable. AVERTISSEMENT Après avoir désactivé l’alimentation électrique du système, patientez 2 minutes avant d’ouvrir le boîtier. AVERTISSEMENT Au moment de fixer le couvercle du boîtier sur la tête de la sonde, appliquez aux 8 vis de fixation M5 un couple de serrage de 8 Nm. 22 AVERTISSEMENT Pour le groupe de gaz A, la conduite doit être étanche au niveau de l’entrée du boîtier. Pour les groupes de gaz B, C et D, la conduite n’a pas besoin d’être étanche. 1.5.3 Sonde à immersion La sonde existe en plusieurs versions standard, où le matériau de construction (fenêtres, métaux, joints toriques, etc.) et la longueur d’immersion peuvent être adaptés en fonction des besoins. 1.5.4 Transmetteur M400 type 3 C’est l’interface utilisateur de la série GPro. Le M400 permet à l’utilisateur de définir les paramètres nécessaires au fonctionnement, et de contrôler l’alarme et la configuration E/S. Le M400 affiche bien sûr également la concentration de gaz mesurée, la température et la pression du procédé, ainsi que la transmission (qualité/puissance du signal). Il est doté d’une approbation FM de classe 1 div. 2 (zone ATEX 2) et de quatre sorties analogiques 4-20 mA. Assorti d’une approbation FM de classe 1 div. 2 (zone ATEX 2), il est doté de quatre sorties analogiques actives de 4 à 20 mA. Le M400 est également doté de la technologie ISM (diagnostic intelligent), qui comprend les fonctions suivantes : –– Indicateur du délai de maintenance (TTM). Cette fonction assure la prévision dynamique en temps réel sur le prochain cycle de maintenance requis, afin d’améliorer le fonctionnement. Action : Nettoyer l’optique (fenêtre, cube d’angle) –– Indicateur de durée de vie dynamique (DLI). D’après les informations DLI, le transmetteur vous indique lorsqu’il est temps de remplacer le TDL. Action : Remplacer le TDL (Durée de vie prévue >10 ans) 1.6 Logiciel Le logiciel du GPro™ 500 TDL se compose de 2 programmes : • Un programme invisible à l’utilisateur, qui est intégré aux composants électroniques de l’unité centrale (UC), chargé d’exécuter le microcontrôleur sur la carte de l’UC. Le programme réalise tous les calculs et tâches d’autosurveillance nécessaires. • Logiciel MT-TDL : Un programme basé sur Windows fonctionnant sur un PC standard connecté via la connexion Ethernet. Ce programme permet la communication avec l’instrument pendant l’installation, la maintenance, l’étalonnage et le fonctionnement normal, voir le chapitre 6 « Programme d’entretien », à la page 58, pour plus de détails. Le branchement d’un PC n’est requis que pour effectuer des opérations de maintenance avancée ; l’installation normale et le service/étalonnage peuvent se faire via le M400. Les deux ports de communication (Ethernet et RS 485) du M400 peuvent être utilisés en même temps. Toutefois, lors de l’accès via un PC, aucun changement n’est permis sur le M400. 1.7 Classement laser Les diodes lasers utilisées sur le GPro™ 500 TDL fonctionnent avec de la lumière proche infrarouge (NIR), à environ 760 nm. Par son courant de sortie, le GPro™ 500 TDL est classifié, d’après la dernière édition de la norme IEC 60825-1, en tant que produit de la classe laser 1M. AVERTISSEMENT Produit laser de classe 1M Rayonnement laser – ne pas regarder directement avec des instruments optiques. Noter que le laser émet de la lumière invisible ! 23 1.8 Données relatives au produit Table 1 Données relatives à la tête de sonde Spectromètre à laser pour l’oxygène Taille et poids 24 Dimensions 524,5 x Ø175,5 mm Poids 8 kg Matériau de construction Acier 316L Éléments optiques Quartz avec revêtement AR, borosilicate avec revêtement AR Joints Kalrez® 6674, composés graphite Mesure Longueur de chemin optique effective (EPL) 100, 200 et 400 mm fixe, en fonction de la longueur de la sonde. Lors de la configuration du GPro™ 500 avec le M400, la valeur double de la longueur de chemin effective doit être saisie (2 x la longueur de chemin effective). Limite de détection 0,01 % Vol (100 ppmv) avec une longueur de chemin d’1 m et des conditions ambiantes standard (aucune charge de poussières, gaz sec, O2 dans N2) Unités d’affichage ppm-v, % Vol O2 Précision 2 % par rapport à la valeur affichée ou 100 ppm, selon la valeur la plus importante Linéarité Supérieure à 1 % Résolution <0,01 % Vol O2 (100 ppmv) Dérive du zéro Négligeable (< 2 % de la plage de mesure entre les intervalles de maintenance) Taux d’échantillonnage 1s Répétabilité ± 0,25 % de la lecture ou 0,05 % O2, selon la valeur la plus élevée. Temps de réponse (T90) O2 dans N2, 21 % à 0 % dans < 2 s Entrées/sorties électriques Nombre de sorties (analogiques) 2 (en option) Sorties courant Sorties passives de 4...20 mA, avec isolation galvanique, alarmes sur 3,6 mA ou 22 mA conformes aux directives NAMUR NE43 Erreur de mesure due aux sorties analogiques Non-linéarité < ± 0,002 mA sur la plage de 1...20 mA Erreur de décalage < ± 0,004 mA (échelle zéro) Erreur de gain < ± 0,04 mA (pleine échelle) Configuration des sorties analogiques Linéaire Charge 500 Ohms max. Entrée mode Hold Oui, via Ethernet (avec le logiciel) État Hold Automatique (lorsque le port Ethernet est utilisé, pendant l’étalonnage) : dernière valeur, valeur fixe ou valeur actuelle Interface de communication RS 485 (sur le M400) Interface de service Ethernet (vers le PC) en tant qu’interface de service direct pour les mises à jour FW (sans passer par le transmetteur M400), pour les diagnostics hors ligne, ainsi que le chargement en amont et en aval de bases de données de configuration. Interface de la carte mémoire Dispositif de lecture/d’écriture de carte SD pour la récupération des données (mesure et diagnostics), mise à jour FW (via un échange de cartes SD) et diagnostics à distance (chargement/téléchargement des fichiers de configuration) (accessible à l’intérieur du support). Espace de stockage des données : 4 Go. Entrées analogiques 2 x 4...20 mA pour la pression et la température (en option : valeurs calculées) affichage sur le M400. Alimentation 24 V CC, 5 W minimum Étalonnage Étalonnage (usine) Étalonnage complet Étalonnage (utilisateur) Étalonnage à un point et étalonnage procédé Conditions de fonctionnement Plage de température d’utilisation –20 °C … +55 °C en cours de fonctionnement ; –40 °C … +70 °C pendant le transport et le stockage (< 95 % d’humidité sans condensation) Compensation de la température et Utilisation de signaux d’entrée analogiques 4…20 mA ou de la pression définition manuelle de valeurs sur la compensation du M400 (menu de configuration/mesure). Contrôle de plausibilité automatique des entrées analogiques 25 Installation Temps de préchauffage En règle générale, < 1 minute Spectromètre à laser pour l’oxygène Purge Purge côté instrument Oui, débit < 0,5 l/min Enregistreur de données Fonction Enregistrement de l’ensemble des données de la sonde sur une carte SD Intervalle Voir le chapitre 6.3.3 « Enregistrement des données », à la page 65. Format SPC Table 2 Données relatives à la sonde Taille et poids Longueurs des sondes Sonde courte : Longueur physique : 290 mm Longueur effective : 100 mm Sonde moyenne : Longueur physique : 390 mm Longueur effective : 200 mm Sonde longue : Longueur physique : 590 mm Longueur effective : 400 mm Poids 4 kg (sonde de 290 mm) 5 kg (sonde de 390 mm) 6 kg (sonde de 590 mm) Matériau de construction Acier (en contact avec le milieu) 1,4404 (comparable à 316L), C22 Hastelloy Éléments optiques Quartz avec revêtement AR, borosilicate avec revêtement AR Joints Kalrez® 6375, composés graphite D’autres matériaux de construction, ainsi que différentes longueurs de sonde sont disponibles sur demande. Purge Purge côté procédé Azote d’une pureté > 99,7 % (minimum recommandé), 0,5…5 l/min (il est possible d’utiliser tout autre gaz propre et sec sans O2 ; la pureté répond aux exigences de la norme ISO 8573.1 (classe 2–3, analogue à l’air de l’instrument)) AVERTISSEMENT : Le clapet anti-retour est requis (non fourni avec GPro™ 500 – voir le chapitre 2.3 « Accessoires », à la page 93). Purge du cube d’angle 26 Oui, via la purge du côté procédé Conditions de fonctionnement Plage de température 0… +250 °C en option : 0… +600 °C avec barrière thermique et joints plats graphites supplémentaires. Domaine de pression Mesure : 5 bars ; Pression max. : 20 bar Charge max. de poussières @ nom. OPL Selon le contexte d’application Plage de température d’utilisation –20 °C … +55 °C en cours de fonctionnement ; –40 °C … +70 °C pendant le transport et le stockage (< 95 % d’humidité sans condensation) Installation Taille de la bride DN50/PN25 ou ANSI 2”/300lb Dimensions : 82,14 x 3,53 mm Joint plat requis pour assurer l’étanchéité adéquate de la bride (non fourni avec GPro™ 500 - voir le chapitre 2.3 « Accessoires » de l’annexe, à la page 93). Table 3 Données relatives au M-400 Entrées/sorties électriques Interface de communication RS 485 (pour la tête de sonde) Sorties analogiques 4 x 4...20 mA (22 mA) : température, pression, % conc, % transmission du procédé (sur le M400) Relais 6 relais (pour le M400) Alimentation 24 V CC ou 85 à 250 V CA, 50 / 60 Hz à 100 VA Fusible 10 A lent Paramètres des diagnostics ISM % de transmission Disponible en tant que sortie analogique de 4...20 mA Encrassement de la fenêtre Indicateur du délai de maintenance (TTM). Cette fonction assure la prévision dynamique en temps réel sur le prochain cycle de maintenance requis, afin d’améliorer le fonctionnement. Action : Nettoyer l’optique (fenêtre, cube d’angle) Durée de vie du laser Indicateur de durée de vie dynamique (DLI). D’après les informations DLI, le transmetteur vous indique lorsqu’il est temps de remplacer le TDL. Action : Remplacer la sonde TDL (durée de vie prévue de la diode laser >10 ans) Déclencheurs d’alarme Transmission trop faible Valeur de transmission min. à définir dans le menu Config/ISM setup du M400 Autre Toutes les alarmes (y compris. erreurs logicielles/matérielles, etc.) répertoriées au chapitre 8.5.1 du manuel M400. 27 2 Préparations Spectromètre à laser pour l’oxygène 2.1 Outils et autre matériel Les outils suivants sont nécessaires pour installer le GPro™ 500 : • 2 clés plates pour écrou M16 • 1 clé Allen de 5 mm pour les vis de fermeture sur brides et les vis du couvercle Tx • 1 clé Allen de 3 mm pour les vis du couvercle RS 232 • 1 tournevis plat de 2,5 mm pour les branchements électriques • 1 tournevis plat (6 mm) ou cruciforme (Nº 2) pour vis du couvercle Rx • Clé à molette pour les raccords de purge Autre matériel nécessaire, non fourni par METTLER TOLEDO : • Clapet anti-retour • Joint plat côté procédé (99 x 2,62 mm) 2.2 Conditions de débit au point de mesure Lors de la détermination de l’emplacement de la sonde TDL GPro™ 500 dans le procédé, il est conseillé de prévoir une section rectiligne minimale de 5 fois le diamètre de la conduite en amont du point de mesure et de 3 fois ce diamètre en aval. Cela donnera des conditions de débit laminaire qui se prêtent à des conditions de mesure stables. 2.3 Mise en place de la tête de mesure La tête TDL doit être facilement accessible. Une personne doit pouvoir se tenir debout face à celle-ci pour y ajuster les boulons de fixation M16 à l’aide des deux clés standard. Il convient de prévoir au moins 60 cm d’espace libre entre la bride fixée au raccord et l’extérieur comme indiqué ci-dessous. 60 cm (23.6”) 60 cm (23.6”) Figure 6 Espace libre minimum sur la bride du procédé 28 Version USA : Pour une installation en zone de division 1, vous devez disposer d’un conduit ainsi que de presseétoupes homologués pour cette zone. La tête de sonde antidéflagrante devra être soumise à un réglage final, qui suppose son déplacement. Pour simplifier cette opération, vous devez vous procurer une articulation élastique antidéflagrante (par exemple Killark ECF/EKJ) et l’installer tout près de la tête de sonde. L’articulation doit être suffisamment longue et placée à l’intérieur du système de conduits afin de minimiser les vibrations et d’aider au réglage final de la tête de sonde, qui peut impliquer une rotation de ± 90 degrés maximum. Veillez à choisir une articulation de longueur adéquate. 2.4 Critères requis pour les brides et les trous de raccord Pour la sonde, il convient de prévoir un orifice d’au moins 54 mm de diamètre. La bride standard utilisée pour le raccord est DN50/PN25 ou ANSI 2“/300lb. La bride peut être soudée soit directement au procédé, soit en tant que composant d’un système bypass. Les deux brides sont illustrées dans « Dimensions de la bride DN50/PN25 du GPro 500 », page 40 et « Dimensions de la bride ANSI 2“/300lb du GPro 500 », page 40. Lors du montage de la bride, il est important de laisser un espace minimum de 60 cm devant celle-ci, pour faciliter l’installation et la maintenance. Voir la Figure 6 « Espace libre minimum sur la bride du procédé », à la page 28 Le joint plat n’est pas fourni. Voir le Table 1 « Données relatives à la tête de sonde) », à la page 24. Pour obtenir des informations sur les joints plats adaptés. 2.5 Câbles et branchements électriques Le TDL et le M400 sont reliés par un câble RS 485. L’utilisateur doit vérifier que la longueur de câble pour la sortie de courant analogique 4–20 mA du TDL n’ait aucune incidence sur les mesures (à cause de l’induction, par exemple). Si des branchements électriques sont requis à l’installation, voir le chapitre 5 « Branchements électriques », à la page 43. La longueur de câble maximum entre la tête de sonde et la boîte de jonction est de 5 m. Version ATEX : AVERTISSEMENT Le GPro™ 500 est fourni avec un câble préinstallé et un presseétoupe. N’essayez pas de remplacer le câble, car cela annulerait la garantie et constituerait une violation du classement ATEX ! Caractéristiques techniques du câble RS 485 pour la version ATEX : La zone principale doit être au minimum de 0,5 mm2 et la longueur maximum de 100 m. Le câble Ethernet porte la spécification CAT5. 29 Spectromètre à laser pour l’oxygène Version USA : 30 La version FM doit être installée avec un système de conduites de câblage adapté conformément aux réglementations et codes locaux. Pour faciliter l’installation, l’unité est fournie sans câble raccordé. AVERTISSEMENT L’installation électrique doit être effectuée conformément au Code électrique national et/ou à tout autre code national ou local applicable. 3 Installation et démarrage Ce chapitre décrit les étapes et les mesures qui doivent être prises pendant la mise en service du GPro™ 500. 3.1 Installation et réglages 3.1.1 Installation mécanique Le GPro™ 500 est conçu pour faciliter l’installation. Comme le chemin optique est aligné en usine, la procédure d’installation consiste simplement à fixer celui-ci sur la bride du procédé, à installer le tuyau de purge (raccord de tube de 6 mm) et à connecter les câbles. Pour garantir une installation efficace, vous devez veiller à ce que les critères de préinstallation soient remplis avant la visite du technicien Mettler-Toledo. En cours de fonctionnement, il est recommandé d’activer la purge au débit maximum avant d’insérer la sonde dans le procédé, afin d’éviter la contamination instantanée des éléments optiques. 3.1.2 Purge du côté procédé Le GPro™ 500 fonctionne grâce à un laser, par conséquent il doit exposer des surfaces optiques au procédé. Avec le temps, ces surfaces seront contaminées à cause du gaz de procédé (poussière, oxydation, etc.). Normalement, elles seront contaminées très vite si la purge est perdue ou insuffisante. Afin de prolonger l’intervalle de maintenance, les surfaces sont purgées avec un gaz propre. Désormais, comme GPro™ 500 mesure l’oxygène, vous ne pouvez pas effectuer la purge avec l’air instrument puisqu’il contient de l’oxygène. La solution consiste à purger à l’azote ou avec un autre gaz sans O2, propre, nonexplosif et sec. GPro™ 500 est conçu pour consommer le moins d’azote possible, tout en maintenant les surfaces optiques propres. La consommation d’azote pendant le fonctionnement normal est inférieure à 1 l/min. Donc, si vous avez dix bouteilles avec 3 300 litres (litres de gaz à température ambiante et à pression « standard ») remplies à 172 bars (2 500 psi), ce qui correspond généralement aux grandes bouteilles, elles dureront 3 semaines. La consommation d’azote dépasse rarement 5 l / min. 3.1.3 Purge côté procédé Le nettoyage des composants optiques de la sonde est essentiel pour éviter leur contamination lors du procédé. Après l’installation, vérifiez que le nettoyage est opérationnel avant de lancer le procédé. Pour plus de détails, reportez-vous au chapitre 3 du mode d’emploi. AVERTISSEMENT La purge doit toujours démarrer au débit maximum avant le lancement du procédé. AVERTISSEMENT La purge doit toujours être activée afin d’éviter les dépôts de poussière sur les surfaces optiques. Il est aussi possible d’utiliser un générateur d’azote, ce qui évite de devoir se préoccuper des changements de bouteilles. Sur certains sites, de l’azote peut être disponible en grandes quantités, ce qui est bien évidemment l’idéal. Cependant, la pureté, la sécheresse et la teneur en particules de l’azote N2 doivent être conformes aux prescriptions de la norme ISO 8573.1 (classe 2–3, analogue à l’air de l’instrument). Il est aussi possible d’utiliser un générateur d’azote, ce qui évitera d’avoir à s’inquiéter des changements de bouteilles d’azote. Sur certains sites, de l’azote sera disponible en grandes quantités, ce qui est bien évidemment l’idéal. Cependant, la pureté, la sécheresse et la teneur en particules de l’azote N2 doivent être conformes à la spécification indiquée dans les critères de pré-installation. 31 AVERTISSEMENT L’arrivée du gaz de purge pour le côté procédé doit disposer d’un clapet anti-retour, pour éviter la contamination du système de purge par le gaz de procédé. 3.1.4 Réglage du débit de purge Le débit de la purge a une incidence sur la longueur de chemin effective, et par conséquent sur la valeur de mesure. Il faut donc utiliser la procédure suivante. Commencer par un débit très élevé et le réduire progressivement. La grandeur de mesure va donc commencer à une valeur faible et augmenter avec la réduction du débit de purge. À un moment donné, elle va se stabiliser et rester constante pendant quelques instants, puis elle va recommencer à augmenter. Choisir un débit de purge au milieu de la région constante. ATTENTION Si le débit du procédé reste constant, on aura un bon débit de purge, mais n’oubliez pas que la longueur de chemin efficace sera toujours fonction du débit du procédé. 3 Lecture en hausse Spectromètre à laser pour l’oxygène La purge est connectée au raccord de tube de 6 mm. Le gaz de purge sort alors face à la première fenêtre et face au cube d’angle à l’extrémité de la sonde – voir la Figure 7 « Optimisation du débit de purge », à la page 32. 2 4 1 Baisse du débit de purge Figure 7 Optimisation du débit de purge L’axe horizontal représente le débit de purge et l’axe vertical représente la lecture de concentration de l’instrument. 1 Lecture de concentration avec débit de purge élevé. La longueur de chemin est maintenant plus courte que la longueur de chemin effective puisque le tuyau de purge est complètement rempli du gaz de purge et qu’une partie du gaz de purge s’écoule dans le chemin de mesure. 2 Lecture de concentration avec débit de purge optimisé. La longueur de chemin équivaut à présent à la longueur de chemin effective, puisque les tuyaux de purge sont complètement remplis de gaz de purge. Voir l’illustration ci-dessous. 3 Lecture de concentration sans débit de purge. La longueur de chemin équivaut à présent à la longueur de chemin nominale, puisque la sonde est entièrement remplie de gaz de procédé. 4 Débit de purge optimisé. AVERTISSEMENT Le GPro™ 500 ne peut pas fonctionner dans des conditions de procédé où le flux du gaz de procédé est minimal voire nul. En effet, la longueur de chemin effective (voir le chapitre 4 « Dimensions et schémas », à la page 36) serait alors trop variable. 32 2 4 1 6 3 Zone 1 Zone 0 5 Figure 8 Configuration de la purge 1 Arrivée du gaz de purge pour le côté instrument (raccord de tube de 6 mm pour version DIN et ¼” pour versions ANSI) 2 Arrivée du gaz de purge pour le côté procédé (clapet anti-retour requis fourni par l’utilisateur) 3 Sortie du gaz de purge pour le côté instrument (raccord de tube de 6 mm pour version DIN et ¼” pour versions ANSI) 4 Clapet anti-retour obligatoire (fourni par l’utilisateur) 5 Débit du gaz de procédé 6 Zone de découpe : région définissant les limites de la longueur de chemin effective. Voir le chapitre 3.1.4 « Réglage du débit de purge », à la page 32. La connexion de purge côté procédé est munie d’un joint entre le raccord et l’enceinte de purge, conformément aux spécifications de la Directive équipements sous pression (DESP). Pour garantir l’intégrité de ce joint et éviter tout dommage lors du branchement du tuyau de purge sur le raccord, une clé tricoise doit être utilisée afin de maintenir le raccord durant le serrage de l’écrou de la conduite de purge, comme le montre la figure 9 ci-dessous. Figure 9 Connexion de la conduite de purge au raccord de purge côté procédé. AVERTISSEMENT Ne retirez pas et /ou ne démontez pas le tuyau d’admission du gaz de purge du procédé (2). Si vous le démontez, le certificat de pression DESP ne sera plus applicable. 33 3.1.5 Purge côté instrument Spectromètre à laser pour l’oxygène Pour la mesure de l’oxygène, il est indispensable que toutes les régions situées le long du faisceau laser soient exemptes d’oxygène, à l’exception de la zone de mesure. AVERTISSEMENT La purge du côté instrument doit être suffisante pour maintenir la température de la tête de sonde en dessous de la limite maximum acceptable de <55 °C. AVERTISSEMENT Lorsque le flux du gaz de procédé est activé, la purge côté instrument doit toujours être activée, afin d’éviter que le flux de gaz ne pénètre dans la tête de la sonde. 3.1.6 Installation de la barrière thermique Lorsque la température du gaz de procédé est supérieure à 250 °C, il convient de protéger les composants électroniques et le laser encapsulés. Pour cela, il faut utiliser l’accessoire « barrière thermique ». Celui-ci isole les pièces sensibles de la chaleur en ajoutant une protection supplémentaire de gaz de purge entre le support et la bride du procédé. Le gaz de purge doit donc passer tout d’abord par la barrière thermique pour arriver ensuite dans la sonde comme illustré ci-dessous. 3 1 2 4 Figure 10 Configuration de la purge 1 2 3 4 34 Arrivée du gaz de purge pour la barrière thermique (raccord de tube de 6 mm) Sortie du gaz de purge pour la barrière thermique (raccord de tube de 6 mm) Arrivée du gaz de purge pour le côté procédé (clapet anti-retour requis) Clapet anti-retour obligatoire (fourni par l’utilisateur) 3.2 Alignement Le GPro™ 500 est soigneusement aligné à la sortie d’usine, et normalement aucun alignement n’est requis pendant l’utilisation normale. En cas de doute sur l’alignement, vous devez contacter Mettler Toledo ou votre fournisseur local, voir le chapitre « Vente et service », à la page 99, et renvoyer le GPro™ 500 à l’usine en vue du réalignement. Lors du retrait de la tête du GPro™ 500 de la sonde (ou de la barrière thermique s’il faut installer celle-ci), par exemple pour vérification et/ou inspection, il n’est pas nécessaire de la réaligner pour la remonter sur la sonde (ou sur la barrière thermique). Nous devons toutefois recommander de faire pivoter la tête jusqu’à atteindre la transmission maximale. Consultez le manuel du M400 sur le mode d’affichage de la valeur de transmission actuelle sur l’écran. AVERTISSEMENT Le gaz de purge pour la barrière thermique doit toujours être activé pendant le fonctionnement du procédé, afin d’éviter d’endommager la sonde de façon définitive. AVERTISSEMENT Le dysfonctionnement du système de purge côté instrument et de la barrière thermique doit déclencher une alarme. Celle-ci doit être mise en œuvre dans le DCS par l’utilisateur. 35 Dimensions et schémas GPro™ 500 est proposé avec 3 longueurs de sonde différentes. Il peut aussi être équipé de deux tailles de brides (DN50/PN25 et ANSI 2“/300lb). Ainsi, le nombre d’applications dans lesquelles GPro™ 500 peut s’intégrer facilement est plus important. Les dimensions des têtes TDL, des brides et de la barrière thermique sont indiquées ci-après. Quatre longueurs différentes doivent être observées. La plus importante du point de vue de la mesure des performances est la longueur de chemin effective. 175,5 (6.91") 254 (10") ½" NPT G ¼" 90 (3.54") 307 (12,09") 1 290 (11.42") 2 190 (7.48") 3 100 (3.94") G ¼" 100 (3.94") 4 Spectromètre à laser pour l’oxygène 4 50 (± 0,3 mm) (19.68 [± 0.01"]) Figure 11 Dimensions de la sonde de 290 mm Définition des longueurs : 1 Longueur de chemin nominale : longueur par défaut lorsque GPro™ 500 est fourni. Elle correspond à la longueur de chemin effective sans purge. 2 Longueur de sonde : longueur physique de l’électrode. 3 Longueur d’immersion : partie de la sonde qui doit dépasser dans la conduite pour garantir une purge efficace. 4 Longueur de chemin effective (lors de la configuration du GPro™ 500 avec le M400, il faut saisir la valeur double : 2 x longueur de chemin effective). 36 Table 4 Brides requises pour certaines configurations types Longueur de chemin nominale Longueur de l’électrode Longueur d’immersion Longueur de chemin effective Taille de la conduite DN Taille de la Nbre de conduite SPS brides 307 mm 290 mm 190 mm 100 mm 100 mm 4“ 2 307 mm 290 mm 190 mm 100 mm 150 mm 6“ 2 307 mm 290 mm 190 mm 100 mm 200 mm 8“ 1 407 mm 390 mm 290 mm 200 mm 200 mm 8“ 2 407 mm 390 mm 290 mm 200 mm 250 mm 10“ 2 407 mm 390 mm 290 mm 200 mm 300 mm 12“ 1 607 mm 590 mm 490 mm 400 mm 300 mm 12“ 2 607 mm 590 mm 490 mm 400 mm 400 mm 16“ 2 607 mm 590 mm 490 mm 400 mm 500 mm 20“ 2 607 mm 590 mm 490 mm 400 mm 600 mm 24“ 1 100 mm (4") Figure 12 Configuration à une bride Espace de dégagement min. : 61,5 mm (schedule 40) Espace de dégagement min. : 77,5 mm (schedule 80) 100 mm DIN 50 ou ANSI 50,8 mm DIN 65 ou ANSI 63,5 mm Figure 13 Configuration à deux brides 37 90 (3.54”) 38 Figure 14 Dimensions de la sonde de 390 mm 407 (16.03”) 1 390 (15.35”) 2 290 (11.42”) 3 200 (7.87”) 4 100 (3.94”) Spectromètre à laser pour l’oxygène ½" NPT G ¼" G ¼" 50 (± 0,3 mm) (19.68 [± 0.01"]) ½" NPT G ¼" 607 (23.90”) 1 590 (23.23”) 2 490 (19.29”) 3 90 (3.54”) 400 (15.75”) 4 100 (3.94”) G ¼" 50 (± 0,3 mm) (19.68 [± 0.01"]) Figure 15 Dimensions de la sonde de 590 mm 39 Ø125 (4,92") Ø165 (6,50") Ø165,1 (6 1/2") Figure 16 Dimensions de la bride DN50/PN25 du GPro 500 4 x Ø19 (3/4") (pour écrou de 5/8”) Figure 17 Dimensions de la bride ANSI 50,8 mm/300lb du GPro 500 40 Ø127 (5") Spectromètre à laser pour l’oxygène 8 x Ø18 (0,71") (pour écrou M16) DIN min. Ø 67 mm min. Ø 54 mm DN100 DN65/PN25 DN65 DN 50 DN50/PN25 100 mm 100 mm ANSI ANSI 2.5"/300 lbs 2" 2.5" min. 2.12" min. 2.64" 4" ANSI 2"/300 lbs 4" 4" Figure 18 Dimensions préconisées pour les brides soudées 41 40 (1,57") 42 G ¼" Ø30 (1,18") Ø40 (1,57") Spectromètre à laser pour l’oxygène G ¼" Joint plat ST (voir annexe 2) Joint plat HT (voir annexe 2) 100 (3,94") Figure 19 Dimensions de la barrière thermique. Raccords de tube 6 mm 5 Branchements électriques Version ATEX : La plupart des branchements électriques s’achèvent au niveau du boîtier de raccordement. Tous les potentiels sont flottants et ne doivent pas être mis à la terre par le boîtier. Ce principe est valable pour tous les tableaux de connexion. AVERTISSEMENT Vérifiez que l’installation électrique du TDL est conforme à tous les critères de sécurité électrique requis applicables au niveau local et national. AVERTISSEMENT Lors de l’installation du TDL, observer les consignes de sécurité ci-dessous ; si vous ne le faites pas, cela risque d’annuler la certification TDL, d’empêcher le bon fonctionnement du dispositif ou de l’endommager. AVERTISSEMENT Isolez l’alimentation électrique avant de commencer l’installation. AVERTISSEMENT Vérifiez que l’alimentation est déconnectée ou coupée avant de brancher des câbles. Version USA : La version USA doit être installée au moyen d’un système de conduits de câbles approprié, conformément aux réglementations et codes locaux. Pour faciliter la procédure, l’instrument est fourni sans câble raccordé. Les bornes d’alimentation sont conçues pour recevoir des conducteurs simples/fils souples de 0,2 mm2 à 1,5 mm2 (AWG 16–24). AVERTISSEMENT L’installation électrique doit être effectuée conformément au Code électrique national et/ou à tout autre code national ou local applicable. AVERTISSEMENT Après avoir désactivé l’alimentation électrique du système, patientez 2 minutes avant d’ouvrir le boîtier. 43 Spectromètre à laser pour l’oxygène AVERTISSEMENT Au moment de fixer le couvercle du boîtier sur la tête de la sonde, appliquez aux 8 vis de fixation M5 un couple de serrage de 8 Nm. AVERTISSEMENT Pour le groupe de gaz A, la conduite doit être étanche au niveau de l’entrée du boîtier. Pour les groupes de gaz B, C et D, la conduite n’a pas besoin d’être étanche. Alimentation du GPro 500 et du transmetteur M400 Le GPro 500 et le transmetteur M400 doivent être reliés à des sources d’alimentation distinctes. –– GPro 500 : 24 V CC, 5 W minimum –– Transmetteur M400 : 20–30 V CC ou 100–240 V CA AVERTISSEMENT Vérifiez toujours les câbles entre le transmetteur M400, la tête de la sonde GPro 500, le boîtier de raccordement (si présent) et les sondes de température et de pression externes avant de mettre en marche la sonde. AVERTISSEMENT Contrôlez systématiquement l’ensemble des branchements électriques et mises à la terre avant la mise sous tension. 5.1 Sécurité électrique et mise à la terre Le GPro™ 500 ne comporte pas d’interrupteur on/off intégral. Vous devez prévoir un dispositif pour l’isolation externe entre l’alimentation électrique et le GPro™ 500 : utilisez un interrupteur ou un disjoncteur adapté situé à proximité du GPro™ 500, clairement identifié en tant que dispositif de déconnexion pour le GPro™ 500. –– Le circuit électrique doit comporter un fusible adapté ou un dispositif de protection contre les surintensités, d’une intensité maximale de 10 A. –– Le GPro™ 500 doit être relié à un système de mise à la terre externe par le biais d’une des vis du couvercle de la tête de sonde (voir la Figure 20 « Point de mise à la terre externe », à la page 46). –– Vérifiez que l’installation électrique peut assurer la consommation de puissance maximale nécessaire. Voir le Table 1 « Données relatives à la tête de sonde) », à la page 24. –– L’équipement branché sur l’entrée mA, la sortie mA, la RS 485 et l’Ethernet doit être séparé des tensions secteur au moins par une isolation renforcée. –– Veillez à ce que les câbles que vous raccordez au GPro™ 500 soient bien positionnés afin d’éviter tout risque face à la sécurité. –– Tous les câbles de transmission et câbles électriques doivent être prévus pour des températures minimum de 70 °C. Lorsque vous procédez aux tests d’isolation, débranchez tous les câbles du GPro™ 500. 44 Alimentation du GPro 500 et du transmetteur M400 Le GPro 500 et le transmetteur M400 doivent être reliés à des sources d’alimentation distinctes. –– GPro 500 : 24 V CC, 5 W minimum –– Transmetteur M400 : 20–30 V CC ou 100–240 V CA AVERTISSEMENT Contrôlez systématiquement l’ensemble des branchements électriques et mises à la terre avant la mise sous tension. Mise à la terre de protection de l’instrument AVERTISSEMENT Il est essentiel que le branchement de mise à la terre de protection fourni au niveau du boîtier de l’analyseur soit raccordé à un point de mise à la terre d’instrument adapté sur le site d’installation. Le GPro 500 est fourni avec des branchements interne et externe servant à la mise à la terre de protection. Le branchement externe de mise à la terre de protection est clairement identifié par une étiquette et se compose d’une vis M6 x 12 mm située sur la bride du couvercle de l’instrument. Les branchements internes de mise à la terre de protection se trouvent à l’intérieur du boîtier de l’instrument et sont utilisés pour raccorder le blindage extérieur du câble. Voir le schéma « Mise à la terre de protection », page 46 pour connaître l’emplacement des branchements de mise à la terre de protection. Mise à la terre de protection ATEX Remarque : la version européenne certifiée ATEX est fournie avec un câblage préalable. Le branchement interne de mise à la terre est déjà doté d’une terminaison avec le blindage extérieur du câble. IMPORTANT : le couvercle de l’instrument ne doit EN AUCUN CAS être ouvert car cela annule la certification de sécurité. Pour assurer la mise à la terre de protection externe, un câble de mise à la terre adapté doit être doté d’une terminaison et raccordé correctement au branchement de mise à la terre de protection M6 x12 mm. L’autre extrémité du câble doit être dotée d’une terminaison au niveau du point de mise à la terre de l’instrument sur le site d’installation. Mise à la terre de protection FM La version certifiée FM est fournie sans câble raccordé. Lors de l’installation du câble multiconducteur, le blindage du câble doit être doté d’une terminaison appropriée au niveau de l’un des deux points de mise à la terre de protection interne à l’aide de la vis M4 x 6 mm fournie. Pour assurer la mise à la terre de protection externe, un câble de mise à la terre adapté doit être doté d’une terminaison et raccordé correctement au branchement de mise à la terre de protection M6 x12 mm. L’autre extrémité du câble doit être dotée d’une terminaison au niveau du point de mise à la terre de l’instrument sur le site d’installation. Le câble de mise à la terre doit être conforme aux critères du Code national de l’électricité (NEC). 45 Spectromètre à laser pour l’oxygène Point de mise à la terre externe pour câbles > 4 mm2 (M6 x 12) Figure 20 Point de mise à la terre externe Mise à la terre pour protection Matériau : alliage AISi7Mg0,3 chromé Taille : M6 x 12 mm 2 options de mise à la terre pour protection en intérieur Matériau : 1.4404 (AISI 316L) Taille : M4 x 6 mm Vis à tête hexagonale Raccordement par câble de 4 mm² Figure 21 Mise à la terre de protection. 46 5.2 Branchements sur la tête de sonde Version ATEX : Dans la version ATEX, la tête de sonde est fournie avec un câble préconfiguré déjà installé. N’ouvrez pas la tête de sonde pour enlever, modifier ou remplacer le câble. Le boîtier de raccordement constitue l’interface entre GPro™ 500 et le M400 et également le réseau Ethernet. N’importe quel boîtier de raccordement approprié et certifié pour zones dangereuses peut être utilisé. GPro™ 500 peut être fourni avec l’accessoire GHG 731.11 (en option), boîtier de raccordement conforme vendu par Malux. Ses dimensions sont les suivantes : AVERTISSEMENT L’ouverture de la tête de sonde annule la garantie et constitue une violation de la certification ATEX. 1 2 3 2 4 5 3 6 7 8 4 9 10 11 12 13 14 15 16 5 6 1 7 Figure 22 Branchements sur la boîte de jonction 1 2 3 4 5 6 7 Branchements sur le GPro™ 500 - Voir numéros de câble ci-dessous. Alimentation du GPro 500 depuis une source externe de 24 V et 5 W minimum RS 485 à partir du M400 4…20 mA de la sonde de température 4...20 mA de la sonde de pression 2 sorties analogiques directes de 4...20 mA (en option) Ethernet 47 ACTIVE ANALOG INPUTS – Pressure xT – xT + – + – 24 VDC GND RS-485 A Ethernet Analog Outputs M400 L N 1 24 VDC 2 3 4 5 6 7 8 GND RS-485 A RS-485 B RS-485 GND +Ain 1 4…20 mA –Ain 1 4…20 mA +Ain 2 4…20 mA –Ain 2 4…20 mA 24 VDC Aout 1 Aout 2 TX+ TX– RX+ RX– 9 10 11 12 13 14 15 16 GND 9 8 7 6 5 4 3 2 1 TB4 Power RS-485 20 – 30 VDC or 100 – 230 VAC +/– 10% Figure 23 Schéma de câblage avec sorties analogiques actives. 48 Temperature GND + 24 VDC Junction Box Red Blue Green Yellow Brown Purple Black Pink Grey Red/Blue Grey/Pink White White/Yellow Yellow/Brown White/Green Brown/Green 100 mm (4") 16 15 14 13 12 11 10 9 8 7 6 5 4 3 2 1 Spectromètre à laser pour l’oxygène + GND 24 VDC User-provided 24 VDC Power 0.2 A (5W) M400 TB4 Temperature sensor Pressure sensor 2x 4…20 mA passive analog outputs Ethernet 6 7 8 RS-485 GND RS-485 B RS-485 A User-provided LOOP POWERED ANALOG INPUTS SENSOR IN Pressure 24 VDC GND xT 100 mm (4") Temperature Red Blue Green Yellow Brown Purple Black Pink Grey Red/Blue Grey/Pink White White/Yellow Yellow/Brown White/Green Brown/Green SENSOR IN GND 24 VDC GND 16 15 14 13 12 11 10 9 8 7 6 5 4 3 2 1 Junction Box 24 VDC xT Ethernet Analog Outputs M400 L N RS-485 24 VDC 2 3 4 5 6 7 8 GND RS-485 A RS-485 B RS-485 GND Sensor In GND Sensor In GND 24 VDC Aout 1 Aout 2 TX+ TX– RX+ RX– 9 10 11 12 13 14 15 16 24 VDC Power 0.2 A (5W) M400 TB4 6 7 8 RS-485 GND RS-485 B RS-485 A Temperature sensor Pressure sensor 2x 4…20 mA passive analog outputs Ethernet GND 9 8 7 6 5 4 3 2 1 TB4 Power 1 20 – 30 VDC or 100 – 230 VAC +/– 10% Figure 24 Schéma de câblage avec entrées analogiques alimentées par boucle. 49 Signal Description N° câble Couleur Alimentation +24 V Alimentation 24 V, 5 W 1 Rouge 2 Bleu 3 Vert 4 Jaune 5 Marron 6 Violet 7 Noir 8 Rose 9 Gris 10 Rouge/bleu 11 Gris/rose 12 Blanc 13 Blanc/jaune 14 Jaune/marron RX+ 15 Blanc/vert RX– 16 Marron/vert Terre (alimentation) RS 485 A Interface M400 (RS 485) RS 485 B RS 485 GND 4...20 mA pos Température d’entrée actuelle 4...20 mA nég 4...20 mA pos Pression d’entrée actuelle 4...20 mA nég + 24 V 2 sorties analogiques directes de 4...20 mA (en option) Out 1 Out 2 Interface Ethernet pour communication avec le PC TX+ TX– 120 (4.72”) 140 (5.51”) Spectromètre à laser pour l’oxygène Table 5 Câbles GPro™ 500 1 3 5 2 4 6 Figure 25 La boîte de jonction GHG 731.11 (EX-e) 1 2 3 4 5 6 50 Connexion pour le TDL Connexion pour alimentation externe Connexion Ethernet Connexion pour la sonde de température (4... 20 mA) Connexion pour la sonde de pression (4...20 mA) Connexion pour le M400 (RS 485) Les connexions sont faites selon les mêmes repères sur le GPro™ 500 et sur la boîte de jonction, sauf pour le câble Ethernet. Ce câble doit être équipé d’un connecteur Ethernet côté GPro™ 500 et vissé aux connecteurs à vis appropriés sur la boîte de jonction. Le schéma de connexion est indiqué ci-dessous. Version USA : La version USA doit être installée au moyen d’un système de conduits de câbles approprié, conformément aux réglementations et codes locaux. Pour faciliter la procédure, l’instrument est fourni sans câble raccordé. Pour obtenir la liste des câbles adaptés (par exemple, le Lapp UNITRONIC FD CP [TP] plus), reportez-vous au chapitre 2.3 « Accessoires » de l’annexe 2, page 93. Les bornes d’alimentation sont conçues pour recevoir des conducteurs simples/fils souples de 0,2 mm2 à 1,5 mm2 (AWG 24–16). AVERTISSEMENT L’installation électrique doit être effectuée conformément au Code électrique national et/ou à tout autre code national ou local applicable. 1 2 3 2 4 5 3 6 7 8 4 9 10 11 12 13 14 15 16 5 6 1 7 Figure 26 Branchements sur le boîtier de raccordement 1 2 3 4 5 6 7 Branchements sur le GPro™ 500 - Voir numéros de câble ci-dessous. Alimentation du GPro 500 depuis une source externe de 24 V et 5 W minimum RS 485 à partir du M400 4...20 mA de la sonde de température 4...20 mA de la sonde de pression 2 sorties analogiques directes de 4...20 mA (en option) Ethernet 51 ACTIVE ANALOG INPUTS – Pressure xT – xT + – + – 24 VDC GND RS-485 A Ethernet Analog Outputs M400 L N 1 24 VDC 2 3 4 5 6 7 8 GND RS-485 A RS-485 B RS-485 GND +Ain 1 4…20 mA –Ain 1 4…20 mA +Ain 2 4…20 mA –Ain 2 4…20 mA 24 VDC Aout 1 Aout 2 TX+ TX– RX+ RX– 9 10 11 12 13 14 15 16 GND 9 8 7 6 5 4 3 2 1 TB4 Power RS-485 20 – 30 VDC or 100 – 230 VAC +/– 10% Figure 27 Schéma de câblage avec sorties analogiques actives. 52 Temperature GND + 24 VDC Junction Box Red Blue Green Yellow Brown Purple Black Pink Grey Red/Blue Grey/Pink White White/Yellow Yellow/Brown White/Green Brown/Green 100 mm (4") 16 15 14 13 12 11 10 9 8 7 6 5 4 3 2 1 Spectromètre à laser pour l’oxygène + GND 24 VDC User-provided 24 VDC Power 0.2 A (5W) M400 TB4 Temperature sensor Pressure sensor 2x 4…20 mA passive analog outputs Ethernet 6 7 8 RS-485 GND RS-485 B RS-485 A User-provided LOOP POWERED ANALOG INPUTS SENSOR IN Pressure 24 VDC GND xT 100 mm (4") Temperature Red Blue Green Yellow Brown Purple Black Pink Grey Red/Blue Grey/Pink White White/Yellow Yellow/Brown White/Green Brown/Green SENSOR IN GND 24 VDC GND 16 15 14 13 12 11 10 9 8 7 6 5 4 3 2 1 Junction Box 24 VDC xT Ethernet Analog Outputs M400 L N RS-485 24 VDC 2 3 4 5 6 7 8 GND RS-485 A RS-485 B RS-485 GND Sensor In GND Sensor In GND 24 VDC Aout 1 Aout 2 TX+ TX– RX+ RX– 9 10 11 12 13 14 15 16 24 VDC Power 0.2 A (5W) M400 TB4 6 7 8 RS-485 GND RS-485 B RS-485 A Temperature sensor Pressure sensor 2x 4…20 mA passive analog outputs Ethernet GND 9 8 7 6 5 4 3 2 1 TB4 Power 1 20 – 30 VDC or 100 – 230 VAC +/– 10% Figure 28 Schéma de câblage avec entrées analogiques alimentées par boucle. 53 Spectromètre à laser pour l’oxygène TB1 Pin 1 Pin 4 Figure 29 Connexions sur la carte mère située dans la tête de sonde TB2 Pin 1 Pin 12 Figure 30 Connexions sur la carte d’E/S située dans la tête de sonde 54 Table 6 Câbles GPro™ 500 Signal Description N° câble Couleur Boîtier de raccordement Alimentation +24 V Alimentation 24 V, 5 W 1 Rouge 1 2 Bleu 2 3 Vert 3 RS 485 B 4 Jaune 4 RS 485 GND 5 Marron 5 6 Violet 6 7 Noir 7 Terre (alimentation) RS 485 A 4...20 mA pos Interface M400 (RS 485) Température d’entrée actuelle 4...20 mA nég 4...20 mA pos Pression d’entrée actuelle 4...20 mA nég + 24 V Out 1 2 sorties analogiques directes de 4...20 mA (en option) Out 2 TX+ 8 Rose 8 9 Gris 9 10 Rouge/bleu 10 11 Gris/rose 11 12 Blanc 12 13 Blanc/jaune 1 14 Jaune/marron 2 RX+ 15 Blanc/vert 3 RX– 16 Marron/vert 4 TX– Interface Ethernet pour communication avec le PC TB1 TB2 Broche n° Broche n° Pour toutes les versions. AVERTISSEMENT Toutes les ouvertures doivent être fermées avec des presse-étoupes ou des connecteurs de blocage certifiés répondant au même degré de certification que le GPro 500. AVERTISSEMENT Il est indispensable d’observer toutes les informations et tous les avertissements donnés. Il convient de refermer le système et de le mettre à la terre avant de l’allumer. 55 Spectromètre à laser pour l’oxygène 5.3 Branchements sur le M400 AVERTISSEMENT Pour les versions EX, l’alimentation en courant alternatif doit obligatoirement être branchée via un module de contrôle de purge possédant la certification appropriée. Le câble d’alimentation est attaché à l’intérieur du M400. Il doit s’agir d’un câble doté de conducteurs Actif (L) et Neutre (N). Les bornes d’alimentation du câble sont adaptées aux conducteurs rigides ou multifilaires de 0,205 à 2,5 mm2 (24 to 13 AWG). Branchez le câble secteur de la manière suivante : 1 Passez le câble secteur à travers un presse-étoupe adapté, monté sur la base du compartiment d’alimentation/interface. 2 Branchez les fils du câble d’alimentation sur les bornes d’alimentation correspondantes du M400 de la manière suivante (voir la Figure 31 « Branchements des câbles sur le M400 », à la page 56). Table 7 Bornes d’alimentation secteur Signal Terminal sur l’alimentation secteur Live (actif) L Neutre N USB 1 3 - + N L POWER TB1 1 2 3 4 5 6 7 8 9 1011121314 1 2 3 4 5 6 7 8 9 123456789 TB2 TB3 123456789 TB4 2 Figure 31 Branchements des câbles sur le M400 1 Borne d’alimentation 2 TB4 – borne d’alimentation pour le GPro™ 500 3 TB1 – borne d’alimentation pour les relais. Celles-ci peuvent être configurées avec le M400. 56 Table 8 Raccordement du GPro™ 500 sur le M400 Broche n° Description 1 2 3 4 5 6 GND (Terre) 7 RS 485B 8 RS 485A 9 Table 9 Connexion des relais sur le M400 Broche n° Description 1 NO1 2 COM1 3 INC1 4 NO2 5 COM2 6 NC2 7 COM5 8 NC5 9 COM6 10 NC6 11 NO3 12 COM3 13 NO4 14 COM4 57 6 Programme d’entretien Spectromètre à laser pour l’oxygène 6.1 Connexion d’un PC Le logiciel MT-TDL est l’outil de maintenance du GPro™ 500. Ce logiciel permet d’accéder à tous les paramètres et de modifier tous les réglages possibles. Pour l’exécuter, il faut brancher un PC, équipé du logiciel, sur le port Ethernet de la boîte de jonction, comme illustré ci-dessous. P T 1 Figure 32 Connexion d’un PC 1 Connexion Ethernet Pour l’accès au MT-TDL via PC, il est important de s’assurer qu’aucune tache n’est effectuée en même temps via le M400. AVERTISSEMENT Lors de l’accès au GPro™ 500 à l’aide du logiciel MT-TDL, le travail sur portable ou sur PC doit être conforme aux restrictions établies concernant le travail en zone dangereuse. 58 6.2 Configuration du PC pour se connecter au GPro™ 500 à l’aide du logiciel MT-TDL Cette instruction est valable uniquement pour les utilisateurs de Windows XP. Si vous travaillez sous Windows 7, votre système utilisera automatiquement l’adresse IP correcte. Ouvrez le Panneau de configuration et double cliquez sur Connexions réseau Figure 33 Connexions réseau Double-cliquez sur Connexion au réseau local Figure 34Connexions au réseau local Sélectionnez Protocole Internet (TCP/IP), puis Propriétés 59 Spectromètre à laser pour l’oxygène Figure 35 Propriétés de connexion au réseau local Sélectionnez Utiliser l’adresse suivante et saisissez un numéro IP de la même série que celui de votre GPro™ 500 (ce numéro figure sur le certificat d’étalonnage). Si le numéro IP de votre GPro™ 500 est 192.168.2.16, l’adresse IP de l’ordinateur peut être définie à 192.168.2.1. Si cette option n’est pas définie, sélectionnez Sous-réseau [255.255.0.0] 60 Figure 36 Propriétés du protocole Internet (TCP/IP) Fermez toutes les fenêtres et lancez le logiciel MT-TDL. Il est conseillé d’utiliser un concentrateur Ethernet entre le PC ou l’ordinateur portable et la tête TDL. En cas de conflit avec le port, désactivez manuellement toutes les connexions locales et lancez le logiciel MT-TDL. 61 Spectromètre à laser pour l’oxygène 6.3 Le logiciel MT-TDL Du point de vue du service, les capacités de consignation représentent la fonction la plus importante du logiciel MT-TDL. Lorsque vous êtes relié au GPro™ 500 avec votre PC, il est possible de démarrer un journal des paramètres sélectionnés pour une période donnée. On peut ensuite débrancher le PC du GPro™ 500 et y accéder facilement par la suite avec les données du journal enregistrées sur la carte SD. Un dossier journal est créé sur la carte SD. Il est alors possible d’envoyer les fichiers qu’il contient au personnel formé chez Mettler Toledo pour analyses, ou bien de les afficher sur votre PC avec la visualisation de journaux MT TDL. Les fichiers sont enregistrés dans des dossiers horodatés, à raison d’un dossier par jour. Le logiciel comporte trois niveaux d’accès, mais l’utilisateur courant utilise uniquement le premier (Normal). Les deux autres niveaux d’accès sont réservés au personnel de METTLER TOLEDO. Le niveau d’accès normal permet de réaliser les tâches suivantes : 1 Tendance de la concentration - Vous pouvez suivre ici la valeur de concentration du graphique inférieur. 2 Tendance de la transmission - Vous pouvez suivre ici la valeur de transmission optique du graphique inférieur. 3 Enregistrement des données 4 Sonde ext. 5 Sortie analogique (remarque : disponible uniquement en cas de connexion à une sonde TDL offrant cette option) Différents menus permettent de définir les paramètres d’installation nécessaires. Une fois les paramètres nécessaires définis, il n’y a plus besoin du PC. Tous les paramètres du GPro™ 500 sont enregistrés sur la mémoire interne. Il est donc possible de déconnecter le PC et d’éteindre/allumer le GPro™ 500 sans redéfinir les paramètres. Une fois que le programme commence, un écran comme celui illustré ci-dessous s’affiche. Il est divisé en deux sections. Dans la section supérieure, un graphique représente les pics d’absorption traités par le signal et les pics d’absorption modèles. La version du programme de service est également indiquée à droite (dans notre exemple : V1.0.4.12s), de même que le numéro IP du GPro™ 500. Le contenu de la section inférieure est spécifique à la fonction choisie par l’utilisateur : tendance de la concentration, tendance de la transmission, etc. Leur contenu est traité aux paragraphes suivants. 6.3.1 La tendance ppm Cet écran permet aux utilisateurs de contrôler la valeur de concentration mesurée sur une période donnée : les valeurs actuelles de concentration, transmission, température et pression dans le procédé sont indiquées sur la droite. 62 3 4 5 6 7 8 9 1 2 10 11 12 13 14 15 16 Figure 37 La tendance ppm Voici une description de quelques-uns des paramètres correspondant à cet écran. Notez que les paramètres 3 à 16 sont visibles sur les différents écrans. 1 2 3 4 5 6 7 8 9 10 11 12 13 14 15 16 Nº de scan Unité de concentration Version du logiciel Numéro IP du GPro™ 500 La valeur fixée pour la température La valeur fixée pour la pression Bascule entre les valeurs fixées et mesurées pour la température et pour la pression La longueur de chemin effective Seuil pour l’étalonnage Concentration réelle d’O2 Transmission réelle Lecture de température externe Lecture de pression externe L’analyse est en cours Réinitialiser toutes les tendances Paramètres de flash 63 6.3.2 La tendance de transmission Spectromètre à laser pour l’oxygène Cet écran permet aux utilisateurs de contrôler le niveau de transmission optique dans le chemin de mesure sur une période donnée : les valeurs actuelles de concentration, transmission, température et pression dans le procédé sont indiquées sur la droite. 64 Figure 38 La tendance de transmission 6.3.3 Enregistrement des données Cet écran est utilisé pour administrer les fonctionnalités d’enregistrement des données du logiciel. Figure 39 Enregistrement des données Si vous réglez « Intervalle(s) SPC » sur 1 seconde ou plus, le journal commence. Si l’intervalle du journal est défini à 1 seconde, le système stocke un enregistrement de journal toutes les secondes. Chaque enregistrement fait 8 ko, et l’espace disponible total correspond à 80 % de 4 Go (3,2 Go). Lorsque tout l’espace disponible est utilisé, le système remplace automatiquement l’enregistrement le plus ancien. Si vous redéfinissez « Intervalle(s) SPC » sur 0 seconde, le journal s’arrête. La touche « Get Files » (obtenir les fichiers) permet de télécharger le fichier journal complet sur votre PC. Il est possible de consulter/analyser ultérieurement le journal à l’aide de la visionneuse MT-TDL. 65 6.3.4 Sondes externes Spectromètre à laser pour l’oxygène Pour utiliser des entrées externes pour la température et la pression, il faut configurer les entrées conformément aux spécifications du client. La configuration s’effectue sur cet écran. 66 Figure 40 Sondes externes 6.3.5 Sorties analogiques (en option) Lorsqu’une connexion Ethernet à GPro™ 500 est établie avec l’option des sorties analogiques directes, l’onglet External out apparaît. Cet écran permet de configurer les sorties analogiques passives de 4...20 mA (pour connaître le câblage correct, reportez-vous au chapitre 5 « Branchements électriques », page 43). Il faut savoir que le transmetteur M400 ne propose aucun menu de configuration pour régler les sorties analogiques directes. Figure 41 Sorties analogiques (en option) Pour chaque canal à employer, sélectionnez le paramètre correspondant dans le menu déroulant. Il est possible d’associer à chacun des canaux les valeurs mesurées suivantes : –– Concentration (ppm) –– Concentration (%v) –– Pression (mbar et psi) –– Température (°C et °F) –– Transmission (%) –– DLI (jours) –– TTM (jours) Une fois que vous avez sélectionné le paramètre, entrez la plage qui doit être associée de manière linéaire aux valeurs de 4...20 mA. Les unités doivent être identiques à celles du sélecteur de paramètres du dessus. AVERTISSEMENT Ne raccordez pas simultanément le transmetteur M400 et les sorties analogiques passives directes. 67 Spectromètre à laser pour l’oxygène Figure 42 Sélection d’un paramètre Pour affecter à chaque canal (matériel, logiciel et système) des signaux d’erreur de haut niveau qui seront transmis au système de contrôle, utilisez le menu déroulant correspondant (reportez-vous à l’illustration ci-dessous). Vous avez le choix entre les signaux d’erreur suivants : –– A bsence d’alarme : lorsque l’erreur se produit, les sorties analogiques ne sont pas signalées comme étant en état d’alarme. –– État d’alarme faible (3,6 mA) –– État d’alarme élevée (22 mA) En outre, vous pouvez régler les sorties analogiques sur 3,8 mA ou 21 mA lorsqu’un dépassement de plage doit être détecté par le système. Pour ce faire, cochez la case afférente (sous-rendement/ trop-plein). Figure 43Choix des alarmes Mode Hold (pause) : durant les opérations telles que l’étalonnage ainsi qu’en état d’alarme, les valeurs affichées en mode Hold peuvent être les suivantes : –– Last value ; –– Fixed value. 68 Les valeurs fixes pour la concentration de gaz, la température, la pression et la transmission (exprimée en %) peuvent être définies à l’aide des champs appropriés. Figure 44Choix du mode Hold 6.4 La visionneuse La visionneuse est un outil de diagnostic qui permet de consulter des données enregistrées auparavant par le logiciel MT-TDL et enregistrées sur la carte SIM du GPro™ 500. Figure 45 La visionneuse La visionneuse MT-TDL permet de consulter/analyser des fichiers journaux téléchargés et enregistrés sur votre PC. 69 Spectromètre à laser pour l’oxygène 70 7 Fonctionnement, maintenance et étalonnage 7.1 M400 L’intégration de la technologie ISM et la fonctionnalité d’entrée en mode mixte (qui accepte les sondes conventionnelles ou ISM) sont des caractéristiques essentielles du M400. Figure 46 M400 vue de face 1 8 langues - Anglais - Espagnol - Français - Allemand - Italien - Portugais - Russe - Japonais 2 Écran large rétroéclairé (4 lignes de texte) 3 Protection par mot de passe (5 chiffres) 4 Appareil multiparamètre 5 ISM (la disponibilité de fonctions ISM spécifiques dépend du paramètre mesuré) - Fonctionnalité « Plug and Measure » - Indicateur de durée de vie dynamique (DLI) - Minuteur d’étalonnage adaptatif (ACT) - Indicateur du délai de maintenance (TTM) - Compteur d’autoclavage/NEP/SEP - Historique des étalonnages 6 FM Cl1 Div 2, Zone Atex 2, protection IP 65 /NEMA 4X 7 Mode de configuration rapide 7.1.1 Démarrage de l’instrument En supposant que le TDL soit relié au transmetteur M400, le TDL s’allume automatiquement dès l’activation du M400. Le temps de démarrage est d’environ 1 min. 7.1.2 Arrêt de l’instrument Pour arrêter l’instrument, il suffit de le déconnecter. Il n’y a rien d’autre à faire. 7.2 Maintenance Le GPro™ 500 TDL est conçu pour réduire la maintenance au minimum. L’expérience a démontré qu’un intervalle de maintenance de plus de 3 mois est acceptable pour la plupart des applications. Les opérations de maintenance décrites dans cette section permettent de garantir le fonctionnement continu du moniteur, en toute sécurité. 7.2.1 Maintenance de routine GPro™ 500 ne comporte pas d’éléments mobiles et n’exige aucun consommable. Les fonctions TTM et DLI dans le M400 peuvent générer des demandes de maintenance, par exemple en cas de baisse de la transmission. Toutefois, afin de garantir des performances optimales, nous vous conseillons de réaliser la procédure suivante de manière routinière : –– Contrôler régulièrement la transmission optique (chaque jour). Cela peut se faire automatiquement via les fonctions TTM et DLI ou via le relais d’AVERTISSEMENT ou équivalent. –– Nettoyez les fenêtres lorsque c’est nécessaire (voir ci-dessous). –– Pour les applications où la concentration du gaz mesuré est normalement nulle (application à gaz zéro) : vérifiez la réponse de l’instrument en appliquant un peu de gaz au moins une fois tous les 12 mois. Appliquez des concentrations de gaz suffisamment élevées pour obtenir une réponse durable de l’instrument pendant au moins 10 minutes (au moins 70 minutes après le démarrage). Aucun avertissement ou erreur ne doit s’afficher pendant le test. Contactez votre fournisseur en cas de doutes au sujet de l’instrument. –– Vérifiez l’étalonnage tous les 12 mois (selon la précision requise). Ré-étalonnez si nécessaire (voir le chapitre 7.3 « Étalonnage », à la page 74). –– À chaque contrôle d’étalonnage, enregistrez les paramètres de l’instrument et les données de mesure obtenues avec un gaz (fichiers paramètres et fichiers dump). Cela permet d’assurer le suivi en cas de problèmes de service ultérieurs. 7.2.2 Retrait de la sonde du procédé Pour retirer le GPro™ 500 du procédé, desserrer les quatre boulons de la bride et l’extraire délicatement. Si nécessaire, il faut également retirer la connexion de la purge. AVERTISSEMENT Avant de retirer la sonde du procédé, il est très important de vérifier avec le responsable que cela peut se faire sans danger. Le procédé doit être fermé ou dans un état permettant d’y exposer l’environnement ambiant en toute sécurité. AVERTISSEMENT Ne pas désactiver la purge avant de retirer la sonde. Cela évitera de contaminer les surfaces optiques. 7.2.3 Retrait et nettoyage du cube d’angle Pour retirer le cube d’angle, vous devez dévisser le capuchon d’extrémité de la sonde. Il est ensuite possible de sortir le module contenant le cube d’angle. Nettoyez soigneusement la surface du cube d’angle et remontez-le. La surface optique peut être nettoyée avec des détergents ou des solvants non agressifs et non dangereux. 71 Spectromètre à laser pour l’oxygène 1 2 Figure 47 Nettoyage/Remplacement du cube d’angle. 1 Module du cube d’angle 2 Capuchon final de la sonde 7.2.4 Nettoyage de la fenêtre de procédé Pour nettoyer la fenêtre de procédé, vous devez au préalable retirer la sonde du procédé (voir section 7.2.2 de la page 71). Enlevez la tête de la sonde, dévissez la sonde, puis dévissez le tuyau de purge avec son support. Nettoyez soigneusement la surface de la fenêtre de procédé. La surface optique peut être nettoyée avec des détergents ou des solvants non agressifs et non dangereux. AVERTISSEMENT Ne pas retirer la fenêtre de procédé du module de fenêtres, puisque cela annulerait le certificat de pression. La connexion de purge côté procédé est munie d’un joint entre le raccord et l’enceinte de purge, conformément aux spécifications de la Directive équipements sous pression (DESP). Pour garantir l’intégrité de ce joint et éviter tout dommage lors du branchement du tuyau de purge sur le raccord, une clé tricoise doit être utilisée afin de maintenir le raccord durant le serrage de l’écrou de la conduite de purge, comme le montre la figure 48 ci-dessous. Figure 48 Connexion de la conduite de purge au raccord de purge côté procédé. AVERTISSEMENT Ne retirez pas et /ou ne démontez pas le tuyau d’admission du gaz de purge du procédé (7). Si vous le démontez, le certificat de pression DESP ne sera plus applicable. 72 1 2 3 7 6 4 5 Figure 49 Nettoyage de la fenêtre de procédé. 1 2 3 4 5 6 7 Tête de la sonde Fenêtre de procédé Module de fenêtre Tuyau de purge avec son support Sonde Bride Raccord d’admission du gaz de purge côté procédé AVERTISSEMENT Le verre haute pression de la sonde ne doit pas être soumis à des impacts mécaniques, car ceux-ci pourraient l’endommager (égratignure, entaille, etc.). Le nettoyage du verre doit s’effectuer avec un chiffon doux. Au préalable, assurez-vous que le démontage de la sonde ne présente aucun danger. Si la fenêtre de procédé ne peut pas être nettoyée correctement, l’ensemble module de fenêtres/brides doit être intégralement remplacé. AVERTISSEMENT Le module de fenêtre 3 est bien fixé sur la bride 6 au moyen de vis à tête hexagonale. N’essayez pas d’ôter ou de desserrer les vis ; cela annulerait le certificat de pression DESP. AVERTISSEMENT Lors du réassemblage de la sonde 5, faites doucement glisser le tuyau de purge 4 à l’intérieur, puis vissez la sonde sur la bride 6 jusqu’à ce que le filetage soit entièrement inséré. Cette opération a pour but de garantir l’étanchéité du système de purge dans la sonde. 73 L’étalonnage peut se faire à l’aide du M400. Reportez-vous aux chapitres 7.2.2 et 7.3.1 (pages 44 et 46 respectivement) du manuel correspondant (0150) pour obtenir des informations sur le mode d’étalonnage. L’étalonnage peut se faire de deux façons : directement dans le procédé ou dans une cellule d’étalonnage externe. 7.3.1 Étalonnage procédé Il est possible d’effectuer l’étalonnage directement dans le procédé si la concentration du gaz à mesurer est connue et stable. C’est très pratique et l’étalonnage se fait très rapidement via le menu d’étalonnage du M400. Pour plus de détails, se reporter au manuel M400, page 67. 7.3.2 Étalonnage à l’aide d’une cellule d’étalonnage Pour un étalonnage plus précis, il est possible d’utiliser la cellule d’étalonnage. Dans ce cas-là, il faut retirer le TDL (la tête du module) de la sonde. Il doit ensuite être monté sur la cellule d’étalonnage conformément à l’illustration ci-dessous. Avant de lancer l’étalonnage, il faut saisir de nouvelles valeurs pour la longueur du chemin, la température et la pression sur le M400. Ensuite, le gaz d’étalonnage circule dans la cellule correspondante et l’étalonnage s’effectue dans le menu d’étalonnage du M400. Pendant l’étalonnage avec la cellule d’étalonnage, le procédé reste hermétique et il n’est pas nécessaire de prendre des précautions supplémentaires. 150 (5.91”) EPL 2x100 (3.94”) 104,6 (4.12”) Spectromètre à laser pour l’oxygène 7.3 Étalonnage Figure 50 Cellule d’étalonnage 7.4 Dangers résiduels Malgré toutes les mesures de précaution prises, il reste encore des dangers résiduels. 7.4.1 Raccords défectueux –– Il est possible que les branchements se desserrent sous l’effet des vibrations. –– La liaison entre la sonde de mesure et l’adaptateur du procédé est une source potentielle de fuite. Les raccords entre la sonde de mesure et l’adaptateur du procédé doivent être contrôlés régulièrement par l’utilisateur/opérateur et maintenus en parfait état de fonctionnement. AVERTISSEMENT Les raccords défectueux peuvent provoquer une fuite de produit, et donc présenter un danger pour les personnes et pour l’environnement. 74 7.4.2 Panne d’électricité AVERTISSEMENT En cas de défaillance électrique (faisant sauter le fusible), vérifier que l’alimentation secteur est correctement déconnectée avant de réaliser un dépannage quelconque. 7.4.3 Protection thermique AVERTISSEMENT Le support n’est pas équipé d’une protection thermique. En cours de fonctionnement, la surface du support peut atteindre des températures élevées et causer des brûlures. 7.4.4 Influences externes La chute d’objets sur le support peut endommager ou détruire la tête TDL ou provoquer des fuites, etc. Des forces latérales peuvent endommager ou détruire la tête TDL. 75 8 Protection anti-explosion Spectromètre à laser pour l’oxygène 8.1 ATEX Zone 1 Zone 0 8 P 2 T II 1/2G - Ex op is /[op is T6 Ga] d IIC T6 Ga/Gb II 1/2D - Ex op is /[op is T86°C Da] tb IIIC T86°C Da/Db 5 4 3 1 DN50 / ANSI 2" Zone 2 6 7 Figure 51 Configuration Ex 1 2 3 4 5 6 7 8 76 GPro™ 500 2 x 4...20 mA (pression et température) Boîte de jonction (Ex-e) Ethernet Source d’alimentation externe Boîte de purge pour Zone 1 (en option) M400 Voir la Figure 52 « L’interface du GPro™ 500 entre la zone 0 et la zone 1 », à la page 77, pour consulter la vue détaillée en coupe transversale. 1 2 3 4 5 Figure 52 L’interface du GPro™ 500 entre la zone 0 et la zone 1 1 2 3 4 5 Région de la zone 1 Fenêtre du procédé Clapet anti-retour Zone 0 région Tête de sonde de l’interface - sonde La fenêtre du procédé et le clapet anti-retour garantissent la séparation physique de la zone 0 et de la zone 1. Le tête de la sonde se situe toujours dans la zone 1 et la sonde dans la zone 0. ATTENTION Pour une installation prévue dans une zone classée Ex, veuillez observer les consignes suivantes (ATEX 94/9/CE). Classement Ex :Ex II 1/2G - Ex op is /[op is T6 Ga] d IIC T6 Ga/Gb et Ex II 1/2D - Ex op is /[op is T86°C Da] tb IIIC T86°C Da/Db Désignation et numéro de la déclaration : SEV 12 ATEX 0114 AVERTISSEMENT En configuration normale, la température à la jonction 5 entre la tête de sonde et la sonde ne doit pas dépasser 55 ºC. Si cela se produit à la jonction de la tête de sonde, la température de classe T6 (85 ºC) n’est plus valable et cela constitue une infraction du classement ATEX. AVERTISSEMENT Si la température à la jonction 5 entre la tête de sonde et la sonde dépasse 55 ºC, la barrière thermique (voir le chapitre 2.3 « Accessoires », à la page 93) doit être utilisée de manière à ce que la température à la jonction de la tête de sonde ne dépasse jamais 55 ºC. Si cela se produit à la jonction de la tête de sonde, la température de classe T6 (85 ºC) n’est plus valable et cela constitue une infraction du classement ATEX. 77 Spectromètre à laser pour l’oxygène AVERTISSEMENT Le boîtier métallique de la sonde à oxygène TDL doit être relié au système de mise à la terre du site par le biais d’un câblage conducteur. Figure 53 Étiquette pour la version ATEX. 1 2 3 4 5 6 7 8 9 10 Fabricant Pays d’origine Nom du produit Clé de produit Référence N° de série Limites de température ambiante Marquages ATEX Puissance nominale Classements boîtier 1/2" NPT WARNING DO NOT OPEN THE DEVICE Figure 54Étiquette de note. Veuillez consulter les chapitres suivants de ce mode d’emploi pour lire les consignes supplémentaires en matière de conformité ATEX : –– voir le chapitre 3 « Installation et démarrage », à la page 31 –– voir le chapitre 5 « Branchements électriques », à la page 43 –– voir le chapitre 7 « Fonctionnement, maintenance et étalonnage », à la page 70 M6x12 Figure 55 Étiquette de mise à la terre. 78 Figure 56 Certificat ATEX (page 1/2) 79 Spectromètre à laser pour l’oxygène Figure 57 Certificat ATEX (page 2/2) 80 Figure 58 Déclaration de conformité CE 81 Spectromètre à laser pour l’oxygène Figure 59 Certificat ICECx (page 1/3) 82 Figure 60Certificat ICECx (page 2/3) 83 Spectromètre à laser pour l’oxygène Figure 61 Certificat ICECx (page 3/3) 84 8.2 Homologation FM (version USA) Classement Ex : CP I, Div. 1, Grp. A, B, C, D, T6 CP II, III, Div. 1, Grp. E, F, G, T6 – Désignation et numéro de la déclaration : Projet original nº 3044884 1 2 3 4 10 5 9 6 8 7 Figure 62 Étiquette pour la version US. 1 2 3 4 5 6 7 8 9 10 Fabricant Pays d’origine Nom du produit Clé de produit Référence N° de série Limites de température ambiante Marquages FM Puissance nominale Classements boîtier 85 Spectromètre à laser pour l’oxygène 86 Figure 63Étiquette de note. M6x12 M4x6 Figure 64Étiquettes de mise à la terre Veuillez consulter les chapitres suivants de ce mode d’emploi pour lire les consignes supplémentaires en matière de conformité FM : –– voir le chapitre 3 « Installation et démarrage », à la page 31 –– voir le chapitre 5 « Branchements électriques », à la page 43 –– voir le chapitre 7 « Fonctionnement, maintenance et étalonnage », à la page 70 )0$SSURYDOV %RVWRQ3URYLGHQFH7XUQSLNH 32%R[1RUZRRG0$86$ 7)ZZZIPDSSURYDOVFRP &(57,),&$7(2)&203/,$1&( +$=$5'286&/$66,),('/2&$7,21(/(&75,&$/(48,30(17 7KLVFHUWLILFDWHLVLVVXHGIRUWKHIROORZLQJHTXLSPHQW *3UR86DEFGHI$J*DV6HQVRU ;3,$%&'77D &WR&',3,,,,,()*77D &WR& 7\SH;,3 D 3URFHVV:LQGRZ%RU4 E 3URFHVV2ULQJ0DWHULDO.$RU*5 F :HWWHG0DWHULDOVRU& G 3UREH/HQJWKPPPPRUPP H 3URFHVV&RQQHFWLRQ$RU' I 7KHUPDO%DUULHU67RU+7 J ,QWHUIDFH;RU$ (TXLSPHQW5DWLQJV ([SORVLRQSURRIIRUXVHLQ&ODVV,'LYLVLRQ*URXSV$%&'7DQG'XVWLJQLWLRQSURRIIRU&ODVV,,,,, 'LYLVLRQ*URXSV()*77D &WR&+D]DUGRXV&ODVVLILHG/RFDWLRQVZLWKDQLQGRRURXWGRRU HQYLURQPHQWDOUDWLQJRI7\SH;,3 )0$SSURYHGIRU 0HWWOHU7ROHGR$* 8UGRUI6ZLW]HUODQG )0$SSURYDOV+/& 3DJHRI Figure 65 Certificat FM. Approbations FM (page 1/2). 87 Spectromètre à laser pour l’oxygène 7KLVFHUWLILHVWKDWWKHHTXLSPHQWGHVFULEHGKDVEHHQIRXQGWRFRPSO\ZLWKWKHIROORZLQJ $SSURYDO6WDQGDUGVDQGRWKHUGRFXPHQWV &ODVV &ODVV &ODVV $16,1(0$ $16,,(& 2ULJLQDO3URMHFW,' $SSURYDO*UDQWHG -DQXDU\ 6XEVHTXHQW5HYLVLRQ5HSRUWV'DWH$SSURYDO$PHQGHG 5HSRUW1XPEHU 'DWH 5HSRUW1XPEHU 'DWH )0$SSURYDOV//& -(0DUTXHGDQW *URXS0DQDJHU(OHFWULFDO )0$SSURYDOV+/& 3DJHRI Figure 66Certificat FM. Approbations FM (page 2/2). 88 -DQXDU\ 'DWH 9 Dépannage 9.1 Messages d’erreur sur l’unité de commande En cours de fonctionnement, les informations essentielles relatives à l’état de l’instrument sont affichées sur le M400. Le tableau ci-dessous indique les messages susceptibles d’apparaître sur l’instrument, avec une explication des causes possibles et les mesures à prendre. Table 10 Messages d’erreur Message d’erreur Explications et actions Action Échec de traitement du signal Erreur pendant la procédure d’ajustage DÉFAUT Erreur de la source laser Ligne laser instable DÉFAUT Signal de mauvaise qualité Transmission nulle ou trop faible ; Signal trop bruyant DÉFAUT Erreur sur la carte Flash Erreur base de données DÉFAUT Mode de simulation actif Valeur O2 définie manuellement, non mesurée DÉFAUT Erreur entrée pression Signal 4...20 mA hors limite Entrée pression non valide Pression hors limite MAINTENANCE REQUISE MAINTENANCE REQUISE Erreur d’entrée T Signal 4...20 mA hors limite Entrée T non valide Pression hors limite Diskspace Low Espace disque faible sur carte Flash Erreur de contrôle laser Échec ou mauvais fonctionnement du contrôleur de la température laser Dépassement T interne La température de la carte système dépasse la limite Mode de configuration Connexion Ethernet active Erreur matérielle Incohérence logiciel - matériel ; tension intérieure hors limite Erreur de la source laser Courant laser nul ou hors limites MAINTENANCE REQUISE MAINTENANCE REQUISE MAINTENANCE REQUISE DÉFAUT MAINTENANCE REQUISE MAINTENANCE REQUISE DÉFAUT DÉFAUT 89 Spectromètre à laser pour l’oxygène 10 Mise hors service, stockage et mise au rebut Voir le chapitre 1.1 « Informations liées à la sécurité », à la page 11. La mise hors service est strictement réservée aux personnes bénéficiant de la formation appropriée ou aux techniciens compétents. 10.1 Mise hors service Procédez conformément à la description, voir le chapitre 7.2.2 « Retrait de la sonde du procédé », à la page 71. 10.2 Stockage Stocker le GPro™ 500 dans un endroit sec. 10.3 Mise au rebut Il est recommandé de mettre le dispositif au rebut conformément aux réglementations locales. L’opérateur doit déposer le dispositif auprès d’une entreprise publique ou privée agréée pour la collecte des déchets, ou le mettre lui-même au rebut conformément aux réglementations en vigueur. Les déchets doivent être recyclés ou mis au rebut sans occasionner aucun risque pour la santé humaine et sans utiliser de procédures ou de méthodes susceptibles de nuire à l’environnement. Directives européennes 75/442/CEE 91/156/CEE Triage Le tri par groupes de déchets se fait lors du démontage du dispositif. Les groupes sont répertoriés dans le catalogue européen actuel des déchets. Ce catalogue est valable pour tous les déchets, qu’ils soient destinés à l’élimination ou au recyclage. Le conditionnement se compose des matériaux suivants : –– Carton –– Mousse plastique Le support se compose des matériaux suivants : –– Acier –– Polypropylène –– Polymères en contact avec le milieu comme indiqué dans les caractéristiques techniques 90 Appendix 1 Informations relatives à la conformité et aux normes –– Le GPro™ 500 TDL est conforme aux directives de la Communauté européenne en matière de compatibilité électromagnétique et de basse tension. –– Le TDL est classé conformément à la catégorie de surtension II, degré de pollution. –– Le TDL est conforme aux critères requis pour les dispositifs numériques de classe B de la norme canadienne ICES-003 via l’application de la norme EN 55011:2007. –– L’analyseur est conforme aux Conditions B numériques d’appareillage de classe de NMB-003 du Canada par l’application du EN 55011:2007. –– Ce TDL est conforme au point 15 du règlement FCC des États-Unis pour le matériel de classe B. Il convient au fonctionnement sur le réseau électrique général qui alimente également les environnements résidentiels. –– Le TDL a été évalué suivant la norme IEC 61010-1:2001 +Corr 1 : 2002 + Corr 2:2003 en matière de sécurité électrique, y compris tous les critères supplémentaires requis pour les différences nationales entre les États-Unis et le Canada. –– La société Mettler Toledo Ltd est certifiée BS EN ISO 9001 et BS EN ISO 14001. 91 Appendix 2 Pièces détachées et accessoires Spectromètre à laser pour l’oxygène 2.1 Options de configuration Les informations complètes pour la commande du GPro™ 500 peuvent être représentées à partir du tableau ci-dessous. À titre d’exemple, on pourrait avoir le numéro de commande GPro™ 500-ATBGR4404390_D12HT-AX, qui correspondrait à un modèle avec approbation ATEX Ex d, fenêtre standard, joint torique standard, qualité d’acier 316L, longueur de sonde de 390 mm, bride de procédé de dimension DN50/PN25 et barrière thermique. Table 11 Clé de produit GPro™ 500 Analyseur de gaz GPro™ 5 0 0 – Y Y Y Y Y Y Y Y Y Y Y Y Y Y Y Y Y Y – Y Y * Autres configurations sur demande Approbations pour zones dangereuses ATEX Ex d, IECEx FM classe 1 Div 1 Fenêtres de procédé * Standard (Borosilicate) Temp. élevée (Quartz) Joints toriques du procédé * Standard (Kalrez) Haut de gamme (Graphite) Matériaux en contact avec le milieu humide * | | | | | | | | | K A G R | | | | | | | | | | | | | | | | | | | | | | | | | | | | | | | | | | | | | | | | | | | | | | | | 1,4404 (comparable à 316L) 4 4 0 4 Hastelloy C 2 2 _ Longueur de l’électrode * | | | | | | | | | | | | | | | | | | | | | | | | | | | | | | | | | | | | | | | | | | | | | | | | | | | | | | | | | | | | 290 mm 2 9 0 _ 390 mm 3 9 0 _ 590 mm 5 9 0 _ Support * | | | | | | | | | | | | | | | | | | | | | | | | | | | | | | | | | | | | | | | | | | | | | | | | | | | | | | | | | ANSI 2”/300lb A 0 3 DN50/PN25 D 1 2 Barrière thermique * | | | | | | | | | | | | | | | | | | | | | | | | | | | | | | | | | | | | | | | | | | | | Pas de barrière thermique (pour les températures allant jusqu’à 250 °C) S T Avec la barrière thermique (pour les températures allant jusqu’à 600 °C) H T Gaz à mesurer Oxygène Interface 92 |||| |||| |||| A T | | U S | | || B | Q | | || || | | | | | | | | | | | | | | | | | | | | | | | | | | | | | | | | | | | | | | || || || A | | RS 485 (pour M400) X RS 485 et sorties analogiques directes A 2.2 Pièces détachées Table 12 Pièces détachées Pièce détachée Référence Module de fenêtre Q GR 4404 D12 30 032 364 Module de fenêtre Q GR 4404 A03 30 032 365 Module de fenêtre B KA 4404 D12 30 032 366 Module de fenêtre B KA 4404 A03 30 032 367 Module de fenêtre Q GR C22 D12/A03 sur demande Module de fenêtre B KA C22 sur demande D12/A03 O2 Module de cube d’angle B 4404 30 038 091 O2 Module de cube d’angle Q 4404 30 038 092 O2 Module de cube d’angle B C22 sur demande O2 Module de cube d’angle Q C22 sur demande 2.3 Accessoires Table 13 Accessoires Accessoire Référence Barrière thermique 30 034 138 Boîte de jonction 30 034 149 Boîtier de purge pour M400 Ex d 30 034 148 Kit d’étalonnage O2 30 034 139 Joint plat pour la bride du procédé (82,14 x 3,53 mm) À fournir par l’utilisateur Clapet anti-retour À fournir par l’utilisateur Kit joint plat ST 30 080 914 Kit joint plat HT (Graphite) 30 080 915 Câble GPro 500 ATEX, FM 5 m 30 077 735 Câble GPro 500 ATEX, FM 15 m 30 077 736 Câble GPro 500 ATEX, FM 25 m 30 077 737 93 Spectromètre à laser pour l’oxygène 94 Appendix 3 Mise au rebut conformément à la directive relative aux déchets d’équipements électriques et électroniques (DEEE) Le GPro™ 500S TDL n’est pas considéré comme relevant du champ d’application de la directive DEEE (déchets d’équipements électriques et électroniques). Le TDL ne doit pas être jeté dans un flux de déchets municipaux. Il doit être envoyé pour récupération et recyclage du matériel conformément aux réglementations locales appropriées. Pour tout renseignement complémentaire et pour demander conseil au sujet de la mise au rebut du TDL, contactez Mettler Toledo : Mettler-Toledo AG Im Hackacker 15 CH-8902 Urdorf Suisse Tél. : +41 44 729 61 45 Fax : +41 44 729 62 20 E-mail global : [email protected] Si vous envoyez le TDL à Mettler Toledo ou à votre agent Mettler Toledo local (voir le chapitre « Vente et service », à la page 99) pour le mettre au rebut, il doit être accompagné d’un certificat de décontamination dûment rempli. Appendix 4 Protection de l’équipement 4.1 Rapport traditionnel entre niveaux de protection du matériel (EPL) et zones Zone de niveau de protection d’équipement (EPL) Ga Gb Gc Da Db Dc Zone 0 1 2 20 21 22 Lorsqu’ils sont utilisés dans l’installation, il n’y a pas besoin d’évaluation des risques supplémentaire. Lorsqu’une évaluation des risques a été utilisée, il est possible de répartir ce rapport afin d’utiliser un niveau de protection supérieur ou inférieur. Pour plus de renseignements sur les niveaux de protection du matériel (EPL), se reporter à l’Annexe D de la norme IEC 60079-0:2007 ou EN 60079-0:2009. Ga 0 Gb 1 Gc 2 Da 20 Db 21 Dc 22 4.2 Rapport entre les niveaux de protection du matériel et les ­catégories ATEX Zone de niveau de protection d’équipement (EPL) Ga Gb Gc Da Db Dc Catégorie ATEX 1G 2G 3G 1D 2D 3D 95 Appendix 5 Consignes ESD Spectromètre à laser pour l’oxygène ESD (décharge électrostatique) Une décharge électrostatique est un transfert spontané et rapide d’une charge électrostatique induite par un champ électrostatique élevé. Les dégâts causés à des dispositifs électroniques par une charge électrostatique peuvent survenir n’importe quand entre la fabrication et le service sur le terrain. Les dégâts sont dus à la manipulation des dispositifs dans des environnements non contrôlés ou à des pratiques de contrôle ESD peu développées. En général, les dégâts sont classifiés comme défaillance catastrophique ou comme défaut latent. On parle de défaillance catastrophique lorsqu’un dispositif électronique ne fonctionne plus suite à l’exposition à une décharge électrostatique. Ce genre de défaillance est généralement détecté lorsque le dispositif est testé avant expédition. En revanche, un défaut latent est plus difficile à identifier. Cela signifie que l’exposition à une décharge électrostatique a endommagé seulement une partie du dispositif. Il est extrêmement difficile de prouver ou de détecter des défauts latents avec la technologie actuelle, surtout une fois le dispositif assemblé en produit fini. En général, la charge circule via une étincelle entre deux objets à différents potentiels électrostatiques au fur et à mesure qu’ils se rapprochent l’un de l’autre. Il est vital de respecter les procédures de protection contre les décharges électrostatiques pendant l’utilisation sur le terrain. Les composants utilisés dans le GPro™ 500 ont tous été protégés contre les ESD sur l’ensemble de la chaîne de production. Mise à la terre systématique Les protections efficaces contre les décharges électrostatiques revêtent une importance primordiale dans toutes les opérations. La mise à la terre ESD doit être clairement définie et faire l’objet d’une évaluation régulière. Selon la norme ANSI EOS/ESD de l’ESD Association, tous les conducteurs dans l’environnement, y compris le personnel, doivent être rattachés ou connectés électriquement et reliés à un point de terre connu, en mettant tous les matériaux de protection anti-décharge électrostatique et le personnel au même potentiel électrique. Ce potentiel peut se situer au-dessus d’une référence de terre à tension « zéro », tant que tous les éléments du système sont au même potentiel. Il est important de savoir que les composants non-conducteurs en zone EPA (Electrostatic Protected Area) ne peuvent pas perdre leur charge électrostatique par liaison à la terre. Consignes ESD Dans de nombreuses installations, les personnes constituent l’une des principales sources d’électricité statique. Il faut donc utiliser des bracelets antistatiques pour effectuer les tâches de maintenance et de service sur le GPro™ 500, afin de relier les personnes au potentiel de terre. Un bracelet antistatique se compose d’une bandelette qui entoure le poignet de la personne et d’un cordon de terre pour relier le bracelet à la prise de terre commune. Surface de travail Une surface de travail anti-décharge électrostatique correspond à une surface de travail individuelle, construite et équipée de manière à limiter l’endommagement des éléments sensibles aux décharges électrostatiques. La surface de travail contribue à définir un espace spécifique, permettant de manipuler en toute sécurité les dispositifs sensibles aux ESD. Elle est reliée à la prise de terre commune par une résistance à la terre de 106 à 109 ohms. On utilise pour cela un tapis de laboratoire souple, relié à la terre, sur la surface de travail. Tout le matériel doit être relié à des prises de courant mises à la terre et le personnel doit porter systématiquement des bracelets antistatiques reliés au tapis de laboratoire à l’aide d’un cordon. Les tapis de laboratoire, bracelets antistatiques et cordons légers peuvent être fournis par Siemens Laser Analytics dans le kit ESD. 96 97 Organisations du marché de METTLER TOLEDO Vente et service Vente et service après-vente : Allemagne Mettler-Toledo GmbH Prozeßanalytik Ockerweg 3 D - 35396 Gießen Tél. +49 641 507 333 Fax +49 641 507 397 e-mail [email protected] Australie Mettler-Toledo Ltd. 220 Turner Street Port Melbourne AUS - 3207 Melbourne / VIC Tél. +61 300 659 761 Fax +61 3 9645 3935 e-mail [email protected] Autriche Mettler-Toledo Ges.m.b.H. Südrandstraße 17 A -1230 Wien Tél. +43 1 604 19 80 Fax +43 1 604 28 80 e-mail [email protected] Brésil Mettler-Toledo Ind. e Com. Ltda. Avenida Tamboré, 418 Tamboré BR - 06460-000 Barueri / SP Tel. +55 11 4166 7400 Fax +55 11 4166 7401 e-mail [email protected] [email protected] Chine Mettler-Toledo Instruments (Shanghai) Co. Ltd. 589 Gui Ping Road Cao He Jing CN - 200233 Shanghai Tél. +86 21 64 85 04 35 Fax +86 21 64 85 33 51 e-mail [email protected] Corée du Sud Mettler-Toledo (Korea) Ltd. Yeil Building 1 & 2 F 124-5, YangJe-Dong SeCho-Ku KR -137-130 Seoul Tél. +82 2 3498 3500 Fax +82 2 3498 3555 e-mail [email protected] Croatie Mettler-Toledo d.o.o. Mandlova 3 HR -10000 Zagreb Tél. +385 1 292 06 33 Fax +385 1 295 81 40 e-mail [email protected] ISO 9001 certified Danemark Mettler-Toledo A /S Naverland 8 DK - 2600 Glostrup Tél. +45 43 27 08 00 Fax +45 43 27 08 28 e-mail [email protected] Espagne Mettler-Toledo S.A.E. C / Miguel Hernández, 69-71 ES - 08908 L’Hospitalet de Llobregat (Barcelona) Tél. +34 902 32 00 23 Fax +34 902 32 00 24 e-mail [email protected] États-Unis / Canada Mettler-Toledo Ingold, Inc. 36 Middlesex Turnpike Bedford, MA 01730, USA Tél. +1 781 301 8800 Tél. grat. +1 800 352 8763 Fax +1 781 271 0681 e-mail [email protected] France Mettler-Toledo Analyse Industrielle S.A.S. 30, Boulevard de Douaumont F - 75017 Paris Tél. +33 1 47 37 06 00 Fax +33 1 47 37 46 26 e-mail [email protected] Grande Bretagne Mettler-Toledo LTD 64 Boston Road, Beaumont Leys GB - Leicester LE4 1AW Tél. +44 116 235 7070 Fax +44 116 236 5500 e-mail [email protected] Hongrie Mettler-Toledo Kereskedelmi KFT Teve u. 41 HU -1139 Budapest Tél. +36 1 288 40 40 Fax +36 1 288 40 50 e-mail [email protected] Inde Mettler-Toledo India Private Limited Amar Hill, Saki Vihar Road Powai IN - 400 072 Mumbai Tél. +91 22 2857 0808 Fax +91 22 2857 5071 e-mail [email protected] Italie Mettler-Toledo S.p.A. Via Vialba 42 I - 20026 Novate Milanese Tél. +39 02 333 321 Fax +39 02 356 2973 e-mail [email protected] Japon Mettler-Toledo K.K. Process Division 6F Ikenohata Nisshoku Bldg. 2-9-7, Ikenohata Taito-ku JP -110-0008 Tokyo Tel. +81 3 5815 5606 Fax +81 3 5815 5626 e-mail [email protected] Malaisie Mettler-Toledo (M) Sdn Bhd Bangunan Electroscon Holding, U 1-01 Lot 8 Jalan Astaka U8 / 84 Seksyen U8, Bukit Jelutong MY - 40150 Shah Alam Selangor Tél. +60 3 78 44 58 88 Fax +60 3 78 45 87 73 e-mail [email protected] Mexique Mettler-Toledo S.A. de C.V. Ejercito Nacional #340 Col. Chapultepec Morales Del. Miguel Hidalgo MX - 11570 México D.F. Tél. +52 55 1946 0900 e-mail [email protected] Pologne Mettler-Toledo (Poland) Sp.z.o.o. ul. Poleczki 21 PL - 02-822 Warszawa Tél. +48 22 545 06 80 Fax +48 22 545 06 88 e-mail [email protected] République Tchèque Mettler-Toledo s.r.o. Trebohosticka 2283 / 2 CZ -100 00 Praha 10 Tél. +420 2 72 123 150 Fax +420 2 72 123 170 e-mail [email protected] Singapour Mettler-Toledo (S) Pte. Ltd. Block 28 Ayer Rajah Crescent # 05-01 SG -139959 Singapore Tél. +65 6890 00 11 Fax +65 6890 00 12 +65 6890 00 13 e-mail [email protected] Slovaquie Mettler-Toledo s.r.o. Hattalova 12 / A SK - 831 03 Bratislava Tél. +421 2 4444 12 20-2 Fax +421 2 4444 12 23 e-mail [email protected] Slovénie Mettler-Toledo d.o.o. Pot heroja Trtnika 26 SI -1261 Ljubljana-Dobrunje Tél. +386 1 530 80 50 Fax +386 1 562 17 89 e-mail [email protected] Suède Mettler-Toledo AB Virkesvägen 10 Box 92161 SE -12008 Stockholm Tél. +46 8 702 50 00 Fax +46 8 642 45 62 e-mail [email protected] Suisse Mettler-Toledo (Schweiz) GmbH Im Langacher Postfach CH - 8606 Greifensee Tél. +41 44 944 45 45 Fax +41 44 944 45 10 e-mail [email protected] Thaïlande Mettler-Toledo (Thailand) Ltd. 272 Soi Soonvijai 4 Rama 9 Rd., Bangkapi Huay Kwang TH -10320 Bangkok Tél. +66 2 723 03 00 Fax +66 2 719 64 79 e-mail [email protected] Russie Mettler-Toledo Vostok ZAO Sretenskij Bulvar 6/1 – Office 6 RU -101000 Moscow Tél. +7 495 621 56 66 Fax +7 495 621 63 53 e-mail [email protected] ISO 14001 certified Système de gestion certifié selon ISO 9001 / ISO 14001 www.mt.com/pro 99 Spectromètre à laser pour l’oxygène Centre de compétences sur l’oxygène Les toutes dernières informations sur les applications et les produits Consultez notre site Web pour découvrir les documents techniques, les notes d’applications, les vidéos pratiques et la liste des prochains web-séminaires. cwww.mt.com/o2-gas www.mt.com Visitez notre site pour plus d’informations Mettler-Toledo AG Analyse Industrielle Im Hackacker 15, CH-8902 Urdorf Suisse Tél. : +41 729 62 11 Fax : +41 729 66 36 ISO 9001 certified Sous réserve de modifications techniques © 06/2012 Mettler-Toledo AG Imprimé en Suisse 100 ISO 14001 certified Système de gestion selon ISO 9001 / ISO 14001 ">
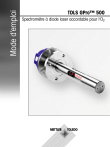
Link público atualizado
O link público para o seu chat foi atualizado.