Pfeiffer ATH 500 M Mode d'emploi
Vous trouverez ci-dessous de brèves informations sur ATH 500 M, ATH 500 MT. Ces pompes turbomoléculaires à paliers magnétiques actifs sont idéales pour les procédés de dépôt et de gravure plasma, les dépôts sur verre et autres applications de recherche. Elles se distinguent par leur résistance à la corrosion, leur robustesse et leur capacité à pomper de grands débits de gaz à des pressions élevées.
PDF
Télécharger
Document
MANUEL DE L'UTILISATEUR FR Original ATH 500 M - ATH 500 MT Pompe Turbomoléculaire à paliers magnétiques Exclusion de responsabilité Ce manuel d'instructions décrit tous les modèles et variantes de votre produit. Noter que votre produit peut ne pas être équipé de toutes les fonctionnalités décrites dans ce manuel. Pfeiffer Vacuum adapte constamment ses produits sans préavis. Veuillez noter que le manuel d'utilisation en ligne peut différer du document imprimé, fourni avec votre produit. D'autre part, Pfeiffer Vacuum n'assume aucune responsabilité pour les dommages résultant d'une utilisation contraire à l'usage prévu, ou d'une utilisation définie comme mauvaise utilisation prévisible. Droits d’auteur (Copyright) Ce document est la propriété intellectuelle de Pfeiffer Vacuum et tous les contenus de ce document sont protégés par le droit d'auteur. Ils ne peuvent être copiés, modifiés, reproduits ou publiés sans l'autorisation écrite préalable de Pfeiffer Vacuum. Nous nous réservons le droit de modifier les données techniques et les informations contenues dans ce document. 2/84 Table des matières Table des matières 1 A propos de ce manuel 1.1 Validité 1.1.1 Documents applicables 1.1.2 Produits concernés 1.2 Groupe cible 1.3 Conventions 1.3.1 Instructions dans le texte 1.3.2 Pictogrammes 1.3.3 Etiquettes 1.3.4 Abréviations 1.4 Justificatif de marque 8 8 8 8 8 8 8 9 9 10 10 2 Sécurité 2.1 Consignes générales de sécurité 2.2 Consignes de sécurité 2.3 Consignes pour les matériaux pyrophoriques/inflammables 2.4 Précautions 2.5 Usage conforme à la destination 2.6 Utilisation non conforme 11 11 11 14 15 15 15 3 Transport et stockage 3.1 Réception du produit 3.2 Manutention de la pompe 3.3 Stockage 17 17 17 18 4 Description du produit 4.1 Identification du produit 4.1.1 Contenu de la livraison 4.1.2 Les différentes versions du produit 4.2 Interface homme/machine 4.3 Unité de commande électronique 19 19 19 19 20 21 5 Installation 5.1 Conditions d'installation à l'équipement 5.1.1 Spécifications d'installation 5.1.2 Sécurisation de l'équipement et du châssis 5.2 Mise en place de la pompe 5.3 Raccordement à la ligne de pompage 5.3.1 Raccordement côté aspiration 5.3.2 Raccordement côté refoulement 5.4 Raccordement du circuit d'eau 5.4.1 Procédure de montage des raccords 5.4.2 Raccordement de la pompe au circuit d'eau 5.5 Installation de l'accessoire refroidissement air 5.6 Raccordement du circuit d'azote 5.6.1 Purge de gaz neutre 5.6.2 Installation de l'accessoire de purge 5.7 Raccordement de l'électrovanne d'entrée d'air 5.8 Test d'étanchéité de l'installation 5.9 Raccordement électrique 5.9.1 Protection de l'installation électrique du client 5.9.2 Raccordement à l'alimentation électrique externe 23 23 24 25 26 28 29 30 30 31 31 32 33 34 35 36 36 37 38 38 6 Utilisation 6.1 Précautions préalables à l'utilisation 6.2 Démarrage de la pompe 6.2.1 Mise sous tension 41 41 42 42 3/84 Table des matières 6.3 6.4 4/84 6.2.2 Démarrage du pompage 6.2.3 Redémarrage après un arrêt d'urgence de l'équipement Arrêt de la pompe 6.3.1 Arrêt du pompage 6.3.2 Mise hors tension 6.3.3 Arrêt prolongé Surveillance du fonctionnement 42 43 43 43 44 44 44 7 Réglages avancés 7.1 Régulation de la température de la pompe 7.2 Le freinage de la pompe 46 46 46 8 Interfaces de commande 8.1 Différents modes de commande 8.2 Commande via le boîtier HHR 8.2.1 Mise sous tension 8.2.2 Menu DISPLAY 8.2.3 Menu SETUP 8.2.4 Menu SER NUM 8.3 Commande via le connecteur REMOTE 8.3.1 Câblage des entrées logiques 8.3.2 Câblage des sorties logiques 8.4 Commande via la liaison série RS-232/RS-485 8.4.1 Connexions 8.4.2 Protocole de communication 8.4.3 Liste des commandes 8.5 Exploitation avec bus de terrain 47 47 47 48 49 50 50 51 51 52 53 53 54 55 59 9 Maintenance 9.1 Consignes de sécurité pour la maintenance 9.2 Intervalles de maintenance 9.3 Entretien sur site 9.4 Procédure d'échange par un produit de remplacement 9.4.1 Déconnexion de la pompe de l'installation 9.4.2 Vidange du circuit d'eau 9.4.3 Conditionnement de la pompe pour expédition 60 60 61 62 62 63 63 63 10 Mise hors service 10.1 Immobilisation prolongée 10.2 Remise en service 10.3 Mise au rebut 65 65 65 65 11 Dysfonctionnements 11.1 Signalement des mauvais fonctionnements et défauts 11.2 Mauvais fonctionnement 67 67 67 12 Solutions de service de Pfeiffer Vacuum 70 13 Accessoires 72 14 Pièces de rechange 74 15 Caractéristiques techniques et dimensions 15.1 Généralités 15.2 Caractéristiques techniques 15.2.1Caractéristiques environnementales 15.2.2Caractéristiques de l'eau de refroidissement 15.2.3Caractéristiques de l'azote 15.2.4Caractéristiques électriques 15.3 Dimensions 75 75 75 77 77 78 78 79 Table des matières Déclaration de conformité CE 81 Déclaration de Conformité UK 82 5/84 Liste des tableaux Liste des tableaux Tab. 1: Tab. 2: Tab. 3: Tab. 4: Tab. 5: Tab. 6: Tab. 7: Tab. 8: Tab. 9: Tab. 10: Tab. 11: Tab. 12: Tab. 13: Tab. 14: Tab. 15: 6/84 Charges transmises à l'équipement Fixation de la bride de vide élevé (bride d'aspiration) Signification des LED sur l'interface EtherCAT Signification des LED sur l'interface Remote/RS232-RS485/Profibus Description des touches du boîtier HHR Pièces de rechange - ATH500 Tableau de conversion : unités de pression Tableau de conversion : unités de débit de gaz Caractéristiques techniques Caractéristiques environnementales Caractéristiques de l'eau de refroidissement Caractéristiques de l'azote Caractéristiques électriques de la pompe Caractéristiques électriques du réseau client Caractéristiques de l'alimentation externe 48 VDC 25 26 45 45 48 74 75 75 77 77 78 78 78 78 79 Liste des figures Liste des figures Fig. 1: Fig. 2: Fig. 3: Fig. 4: Fig. 5: Fig. 6: Fig. 7: Fig. 8: Fig. 9: Fig. 10: Fig. 11: Fig. 12: Fig. 13: Fig. 14: Fig. 15: Fig. 16: Fig. 17: Fig. 18: Fig. 19: Fig. 20: Fig. 21: Description d'une pompe ATH 500 version M Description d'une pompe ATH 500 version MT Exemple d'interface de commande de l'électronique intégrée Raccordement mécanique de la pompe dans l'équipement Graphe des charges transmises à l'équipement Positions de fonctionnement Installation de la pompe à l'horizontale Installation, aspiration vers le haut Montage de l'accessoire refroidissement air Graphe Débit de purge Lot de purge (accessoire) Connecteur mâle alimentation électrique 48 VDC Câblage du ventilateur sur alimentation externe 48 VDC (accessoire) Schéma de câblage électrique typique Schéma de montage d'une installation de pompage Connecteur Remote : commande par tension continue Connecteur Remote : commande par contacts secs Connecteur Remote : sorties logiques Dimensions ATH 500 M Dimensions ATH 500 M refroidie à l'air Dimensions ATH 500 MT 20 20 21 24 25 27 27 28 33 34 35 39 39 40 42 51 52 52 79 79 80 7/84 A propos de ce manuel 1 A propos de ce manuel IMPORTANT Bien lire avant d'utiliser le produit. Conserver ce manuel pour une future utilisation. 1.1 Validité Ce manuel de l'utilisateur s'adresse aux clients de la société Pfeiffer Vacuum. Il décrit le produit et ses fonctions et présente les informations importantes à connaître pour une utilisation sécurisée de l'appareil. La description est effectuée selon les directives en vigueur. Toutes les informations fournies dans ce manuel de l'utilisateur correspondent au niveau de développement actuel du produit. La documentation est valide dans la mesure où le client n'a pas apporté de modifications au produit. 1.1.1 1.1.2 Documents applicables Document Référence Manuel de l'utilisateur bus de terrain Profibus 004432 Manuel de l'utilisateur bus de terrain EtherCAT 123800 Manuel de l'utilisateur Alimentation 48 VDC 127118 Déclaration de conformité fournie avec ce manuel Produits concernés Ce document s'applique aux produits ayant les références suivantes : Référence Description Vxxxxx00 ATH 500 M : pompes pour applications propres Vxxxxx05 ATH 500 M modèle nickelé : pompes pour applications agressives Vxxxxx03 ATH 500 MT : pompes pour applications agressives Vxxxxx01 ATH 500 MT modèle nickelé : pompes pour applications agressives Option Vanne d'eau en cuivre1) Vanne d'eau en inox1) x x MT V x x x x 2 x 0 3 MT modèle nickelé 2 0 1 MT 3 0 3 MT modèle nickelé 3 0 1 1) voir chapitre « Pièces de rechange » La matrice permet de déchiffrer les références des produits : toutes les combinaisons d'options ne sont pas disponibles en tant que produit. 1.2 Groupe cible Ce manuel de l‘utilisateur est destiné à toutes les personnes en charge du transport, de l'installation, de la mise en service/hors service, de l'utilisation, de la maintenance ou du stockage du produit. Les travaux décrits dans ce document doivent être effectués uniquement par des personnes ayant une formation technique appropriée (personnel spécialisé) ou ayant reçu une formation de Pfeiffer Vacuum. 1.3 Conventions 1.3.1 Instructions dans le texte Les instructions figurant dans ce document sont présentées selon une structure précise. Les actions à réaliser sont soit uniques, soit en plusieurs étapes. 8/84 A propos de ce manuel Action unique Un symbole en forme de triangle signale une activité à effectuer en une seule étape. ► Il s'agit d’une étape unique. Action en plusieurs étapes Une liste numérotée indique une action comportant plusieurs étapes à effectuer dans l'ordre chronologique. 1. Étape 1 2. Étape 2 3. ... 1.3.2 Pictogrammes Les pictogrammes utilisés dans le document représentent des informations utiles. Remarque Conseil 1.3.3 Etiquettes PURGE Dispositif de purge PUMP EXHAUST Refoulement de la pompe WATER MAX Pr 7 bar/101 psi Pression maximum du circuit d'eau WATER IN Raccordement du circuit d'eau : entrée WATER OUT Raccordement du circuit d'eau : sortie Raccordement de la terre fonctionnelle 48 V Alimentation électrique 12 A Verrouillage du connecteur avant utilisation de la pompe. Ne pas débrancher avant arrêt de la pompe LOCK Sens de rotation du rotor de la pompe Plaque signalétique du produit (exemple) 23kg 50000rpm; M:29Vrms 1666HZ 9,5A V2312100 HD3635 2018 ATH500 Cette étiquette indique que certains des composants internes sont sous tension et peuvent entraîner un choc électrique en cas de contact : débrancher la pompe avant toute intervention ou verrouiller/déverrouiller correctement le disjoncteur de l’équipement avant intervention sur la pompe. Cette étiquette indique que le produit ne doit pas être manipulé à la main du fait de son poids : toujours utiliser des appareils de manutention appropriés. Don’t remove the pump connector when the pump is running Cette étiquette signifie que l'utilisateur doit verrouiller le connecteur avant d'utiliser la pompe. Ne pas débrancher avant l'arrêt de celle-ci. 9/84 A propos de ce manuel DO NOT TOUCH WHEN THE PUMP IS RUNNING Cette étiquette informe l’utilisateur des risques d’écrasement ou de coupure liés aux pièces en mouvement : éviter de s’approcher et/ou de mettre les mains à proximité des pièces en mouvement. Toute personne en charge de l’installation ou de l’utilisation doit se référer au manuel de l’utilisateur avant d’intervenir sur le produit. SEE MANUAL BEFORE USE Une planche d’étiquettes comprenant d’autres versions linguistiques est fournie avec le produit. Il est de la responsabilité de l’installateur de positionner ces étiquettes sur le produit, à l’endroit le plus approprié et visible afin de prévenir l’opérateur des risques potentiels. Cette étiquette met en garde l'utilisateur contre le risque de blessure en cas de contact de la main avec une surface chaude : s'équiper de gants de protection avant toute intervention. Exposure may result in severe injury or death. Preventive maintenance must be done by trained personnel only. 1.3.4 Abréviations DC Exh. HHR IN LIE M MT PMA TMS [XXXX] 1.4 Cette étiquette met en garde l’utilisateur contre les gaz pompés qui peuvent être dangereux, toxiques et peuvent entraîner des blessures graves ou la mort. Elle précise que toute opération de maintenance préventive doit être exécutée par un personnel compétent. Courant continu (Direct Current) Refoulement (Exhaust) Boîtier de commande déportable (Hand Held Remote) Aspiration (Inlet flange) Limite inférieure d’explosion Version de pompe sans système de régulation de température Version de pompe équipée d'un système de régulation de température (TMS Temperature Management System) Paliers Magnétiques Actifs Système de régulation de la température (Temperature Management System) Menus et paramètres du boîtier de commande HHR indiqués en gras, entre crochets. Exemple : [DEFINITION][LANGUE] pour choisir la langue d'affichage des messages. Justificatif de marque ● Profibus® est une marque déposée de la société PI (PROFIBUS & PROFINET International). ● EtherCAT® est une marque déposée et une technologie brevetée sous licence par Beckhoff Automation GmbH, Allemagne. 10/84 Sécurité 2 Sécurité 2.1 Consignes générales de sécurité Dans le présent document, 4 niveaux de risques et 1 niveau de consignes sont identifiés comme suit : DANGER Danger direct et imminent Caractérise un danger direct et imminent entraînant un accident grave voire mortel. ► Instruction à suivre pour éviter la situation de danger AVERTISSEMENT Danger potentiellement imminent Caractérise un danger imminent qui peut entraîner un accident grave voire mortel. ► Instruction à suivre pour éviter la situation de danger ATTENTION Danger potentiellement imminent Caractérise un danger imminent qui peut entraîner des blessures légères. ► Instruction à suivre pour éviter la situation de danger AVIS Obligation ou signalement Signale une pratique qui peut occasionner des dégâts matériels sans risque potentiel de blessure physique. ► Instruction à suivre pour éviter les dégâts matériels Consignes, conseils ou exemples désignent des informations importantes concernant le produit ou le présent document. 2.2 Consignes de sécurité Toutes les consignes de sécurité contenues dans ce document sont basées sur les résultats de l’analyse de risque effectuée conformément à la Directive 2006/42/CE Annexe I relative aux machines et à la norme EN ISO 12100 Section 5. Dans la mesure du possible, toutes les phases du cycle de vie du produit ont été prises en compte. AVERTISSEMENT Risque d’écrasement lors de l’élingage du produit Compte tenu du poids du produit, il existe un risque d’écrasement lors de la manutention du produit avec des appareils de levage. Le constructeur dégage toute responsabilité en cas de non-respect des consignes suivantes : ► Seul un personnel habilité et formé aux règles de manutention des objets lourds peut manutentionner le produit. ► Utiliser obligatoirement les dispositifs de levage fournis et respecter les procédures décrites dans ce document. 11/84 Sécurité AVERTISSEMENT Risque d'électrocution lié à une installation électrique non conforme Le produit utilise la tension secteur comme alimentation électrique. Une installation électrique non conforme ou réalisée de manière non professionnelle peut mettre en danger la vie des utilisateurs. ► Seul un personnel qualifié et formé aux règles de sécurité électrique, CEM peut réaliser l'installation électrique. ► Ne procéder à aucune transformation ou modification arbitraire du produit. ► Vérifier que le produit est correctement relié au circuit d'arrêt d'urgence de l'équipement (ou installation de pompage). AVERTISSEMENT Risque d'électrocution par contact lors de l'entretien ou la maintenance Il y a un risque de choc électrique par contact avec un produit sous tension et non isolé électriquement. ► Avant toute intervention, placer l’interrupteur principal sur O. ► Débrancher le câble secteur du réseau électrique. ► Sécuriser correctement l’installation en repérant et condamnant le circuit de puissance pour éviter tout ré-enclenchement non intentionnel (LO/TO procédure de consignation/déconsignation). AVERTISSEMENT Risque de blessures graves provoquées par le détachement de la pompe lors d’un blocage du rotor En cas de fixation incorrecte de la pompe, lors d’un blocage inopiné du rotor, la pompe turbomoléculaire se désolidarise de l’équipement : l'énergie libérée projette la pompe ou des fragments de pompe dans le local, provoquant des blessures très graves voire mortelles, ainsi que des dommages matériels considérables. ► Respecter scrupuleusement les recommandations d'installation décrites dans ce manuel. Pfeiffer Vacuum décline toute garantie et responsabilité en cas de non-respect des instructions d’installation. ► Utiliser exclusivement les pièces d'origine autorisées de Pfeiffer Vacuum (accessoires) pour le raccordement dans l'équipement. AVERTISSEMENT Risque d'empoisonnement en présence de gaz de procédés dans l'atmosphère Le constructeur n’a pas la possibilité de contrôler le type de gaz utilisé avec la pompe. Les gaz de procédés sont fréquemment toxiques, inflammables, corrosifs, explosifs ou réactifs. Il existe un risque d’accident grave voire mortel lorsque ces gaz s’échappent librement dans l’atmosphère. ► Appliquer les consignes de sécurité spécifiques, conformément à la législation locale. Ces informations sont disponibles auprès du service sécurité de l’exploitant. ► Raccorder impérativement le refoulement de la pompe turbomoléculaire à une pompe primaire compatible avec les gaz de procédés : le refoulement de la pompe primaire est raccordé au système d'échappement des gaz dangereux de l'installation. ► Vérifier régulièrement l’absence de fuites au niveau du raccordement de la pompe avec la canalisation d’échappement. 12/84 Sécurité AVERTISSEMENT Risque de blessure au contact de l’azote sous pression Le produit utilise de l’azote sous pression comme gaz de balayage. Une installation non conforme ou réalisée de manière non professionnelle peut mettre en danger la vie de l’utilisateur. ► Installer une vanne manuelle dans le circuit à une distance de 3 m du produit pour verrouiller l’alimentation en azote. ► Respecter la pression d’alimentation recommandée. ► Toujours verrouiller et débrancher le circuit d’azote avant d’intervenir sur le produit. ► Lors de la maintenance, sécuriser correctement l’installation en repérant et condamnant le circuit d’azote sous pression pour éviter tout réenclenchement non intentionnel (LO/TO procédure de consignation/déconsignation). ► Contrôler régulièrement l’état des canalisations et connexions du circuit d’alimentation. AVERTISSEMENT Risque de blessure au contact de l'eau sous pression Le produit utilise de l’eau sous pression comme fluide de refroidissement. Une installation non conforme ou réalisée de manière non professionnelle peut mettre en danger la vie de l’utilisateur. ► Installer une vanne manuelle dans le circuit à une distance de 3 m du produit pour verrouiller l’alimentation en eau. ► Respecter la pression et différence de pressions recommandées. ► Toujours verrouiller et débrancher le circuit d’eau avant d’intervenir sur le produit. ► Lors de la maintenance, sécuriser correctement l’installation en repérant et condamnant le circuit d’eau sous pression pour éviter tout réenclenchement non intentionnel (LO/TO procédure de consignation/déconsignation). ► Contrôler régulièrement l’état des canalisations et connexions du circuit d’alimentation. AVERTISSEMENT Risque de coupure lié aux pièces coupantes en mouvement, accessibles par l'ouverture de la bride de vide élevé L'ouverture de la bride de vide élevé permet le contact avec des pièces aux arêtes vives. Une rotation manuelle du rotor rend la situation encore plus dangereuse : il y a un risque de coupure et de sectionnement de membres (p ex. extrémités des doigts). Les cheveux et les vêtements amples risquent d’être entraînés. Toute chute d’objet dans la pompe turbomoléculaire provoque des dommages lors de la prochaine utilisation. ► L’obturateur d'origine ne doit être retiré qu’au moment de la connexion de la bride de vide élevé. ► Ne jamais approcher les mains de l'intérieur de la bride de vide élevé. ► Porter des gants de protection pendant l'installation. ► Ne jamais démarrer la pompe turbomoléculaire lorsque les brides de vide ne sont pas raccordées. ► L'installation mécanique doit être achevée avant de procéder à l'installation électrique. ► Empêcher l'accès à la bride de vide élevé de la pompe du côté de l'opérateur (p. ex. chambre de vide ouverte). AVERTISSEMENT Risques de brûlure par contact avec des surfaces chaudes Les produits sont conçus de façon à ne procurer aucun risque thermique pour la sécurité de l’opérateur. Selon les applications, les conditions d’utilisations génèrent des températures élevées nécessitant une attention particulière de la part de l’opérateur (surfaces > 65 °C). ► Respecter le signalement des surfaces chaudes repérées par l’étiquette sécurité. ► Attendre le refroidissement complet avant d’intervenir sur le produit. ► Porter des gants de protection conformément à la norme EN ISO 21420. 13/84 Sécurité 2.3 Consignes pour les matériaux pyrophoriques/inflammables L’utilisateur et/ou l’intégrateur du produit a l’entière responsabilité de la sécurité de l’installation de la pompe, de l’équipement mais aussi du système de traitement des gaz. L’utilisateur et/ou l’intégrateur est responsable de l’application qui utilise le produit. Le pompage de gaz pyrophoriques ou inflammables peut présenter des risques. L’utilisateur et/ou l’intégrateur du produit doit respecter les consignes de sécurité ci-dessous et conduire une analyse de risque. DANGER Danger de mort par explosion ou inflammabilité liée aux gaz pyrophoriques/inflammables Les procédés du semi-conducteur, du photovoltaïque, des écrans plats et procédés industriels peuvent utiliser des gaz pyrophoriques ou inflammables. Mélangés à des produits oxydants, ces gaz peuvent s’enflammer spontanément (gaz pyrophoriques) ou suite à un amorçage lors d’une réaction chimique non désirée (gaz inflammables). Dans le pire des cas, cela provoque un incendie, ou une explosion causant la projection de pièces métalliques et pouvant blesser gravement les personnes à proximité. ► Mener une analyse de risques afin d’évaluer les risques avant d’installer la pompe. ► Installer des systèmes de sécurité conformes aux exigences de la norme EN 50495. L’analyse de risques doit prendre en compte les gaz utilisés, les sous-produits du procédé ainsi que les composants constituant l’ensemble de l’installation. Il faut absolument éviter les situations suivantes qui présentent des risques : ● La concentration de gaz pyrophorique ou inflammable dans la plage d’inflammabilité. ● La concentration de gaz pyrophorique ou inflammable au-delà de la plage d’inflammabilité (la concentration pourrait baisser en cas de fuite et atteindre la plage d’inflammabilité). ● Le manque de dilution. ● L’accumulation de matières solides réactives au refoulement. ● L’exposition d’espèces réduites chimiquement ou d’agents réducteurs, à des oxydants. Appliquer les recommandations générales de sécurité suivantes : ● Assurer l’étanchéité sur l’installation complète. ● Éviter le mélange de gaz oxydant (air, autre…) avec les gaz pyrophoriques/inflammables. 1) ● Garantir que la concentration d’oxydant n’excède pas 60 % de la concentration maximum admissible du gaz oxydant (MOC) 2), principalement lorsque la dilution n’est pas suffisante pour atteindre les 25 % de la LIE. ● Réaliser une purge d’azote avant toute maintenance sur la ligne de pompage (ligne d’aspiration, pompe et ligne de refoulement). ● Nettoyer régulièrement la ligne de refoulement des sous-produits de réaction telles que les poussières de silicium pour éviter le colmatage et/ou l’explosion. Pour davantage d’informations concernant la sécurité liée aux gaz pyrophoriques ou inflammables, contacter notre centre de service. Pour toutes ces applications, installer sur la pompe des étiquettes pour identifier les risques (inflammabilité, explosion, toxicité, corrosion,.... etc.) et satisfaire aux exigences de SEMI S1. Ces informations doivent être ajoutées dans le manuel de l'équipement pour l'utilisateur final. 14/84 1) Référence NFPA 69-2019, § 8.3.1 chap.8 Prévention de la déflagration par réduction de la concentration de produit inflammable. 2) Référence NFPA 69-2019, § 7.7.2.5 chap.7 Prévention de la déflagration par réduction de la concentration en oxydant. Sécurité 2.4 Précautions Obligation de fournir des informations sur les dangers potentiels Le propriétaire du produit ou l’utilisateur est dans l’obligation d’informer l’ensemble du personnel opérateur des dangers inhérents à ce produit. Chaque personne en charge de l’installation, du fonctionnement ou de la maintenance du produit doit lire, comprendre et respecter les sections de sécurité de ce document. Violation de la conformité en cas de modifications sur le produit La déclaration de conformité du fabricant n'est plus valide si l'utilisateur modifie le produit d'origine ou installe un équipement supplémentaire ● Après l'installation dans un système, l'exploitant est tenu de vérifier et de réévaluer, le cas échéant, la conformité de l'ensemble du système dans le contexte des directives européennes applicables avant de mettre en service ce système. Seul un personnel qualifié et formé aux règles de sécurité (CEM, sécurité électrique, pollution chimique) peut procéder à l’installation et à la maintenance décrites dans ce manuel. Nos centres de service peuvent dispenser les formations nécessaires. ► Fixer la pompe en respectant impérativement les spécifications d'installation. ► Ne pas exposer une partie du corps humain au vide. ► Respecter les prescriptions en matière de sécurité et de prévention des accidents. ► Vérifier régulièrement que toutes les mesures de précautions sont respectées. ► Ne pas retirer les obturateurs des orifices d’aspiration et de refoulement tant que le produit n’est pas raccordé à la ligne de pompage. ► Ne pas mettre sous tension un produit dont l’aspiration et le refoulement ne sont pas raccordés à la ligne de pompage. ► Avant d'intervenir sur la bride d'aspiration, attendre que le rotor soit immobilisé. ► Les canalisations et les câbles doivent être maintenus à bonne distance des surfaces chaudes (> 70 °C). 2.5 Usage conforme à la destination ● La pompe à vide est utilisée uniquement pour générer du vide en pompant des gaz. ● La pompe turbomoléculaire doit être associée à une pompe primaire appropriée. ● La pompe Version MT peut être utilisée pour le pompage de fluides à risque de condensables sous réserve que les gaz ne se condensent pas dans la pompe. ● La pompe est destinée à être intégrée dans un équipement industriel. Lorsque la pompe est intégrée dans un équipement industriel, elle devient un composant de l’équipement : l'utilisateur et/ou l’intégrateur de ce composant de pompage doit prendre toutes les protections de sécurité vis à vis de l’opérateur, notamment concernant le risque avec les surfaces chaudes. 2.6 Utilisation non conforme Toute utilisation non conforme du produit entraîne l'annulation de la garantie et des droits de réclamations. Toute utilisation, même involontaire, qui diffère de celles précitées est considérée comme non conforme, en particulier : ● ● ● ● ● ● ● ● ● ● ● Le pompage de fluides réactifs Le pompage de fluides corrosifs ou explosifs Le pompage de liquides Le pompage de solides Le pompage de poussières Le pompage de fluides à risque de condensable (Version M) Une utilisation avec débit de gaz élevé non admissible Une utilisation sous une pression de vide primaire élevée non admissible Une utilisation avec apport, par rayonnement, d'une puissance thermique excessive Une remise à l'air avec des débits élevés non admissible L'utilisation d'accessoires ou pièces de rechange qui ne sont pas mentionnés dans ce manuel 15/84 Sécurité ● ● ● ● ● 16/84 L’utilisation dans des zones à risque d'explosion L’utilisation de la pompe à vide pour générer de la pression L’exploitation dans des zones à rayonnements ionisants Une utilisation dans des champs magnétiques non admissibles Une mise en oeuvre des appareils dans des installations qui soumettent la pompe à des contraintes et à des vibrations saccadées ou à des forces périodiques. Transport et stockage 3 Transport et stockage 3.1 Réception du produit Etat de la livraison ● S'assurer que le produit n'a subi aucun dommage pendant le transport. ● Si le produit est endommagé, aviser le transporteur et informer le constructeur. ► Maintenir le produit dans son emballage d’origine pour préserver la propreté que nous lui avons apportée : le déballer uniquement sur son lieu d’utilisation finale. ► Conserver les obturateurs présents sur les orifices d’aspiration, de refoulement et de purge jusqu'à ce que le produit soit raccordé à la ligne de pompage. Conserver l’emballage (matériau recyclable) dans le cas où le produit doit être transporté ou stocké. 3.2 Manutention de la pompe AVERTISSEMENT Risque d'écrasement lors de l'élingage du produit Compte tenu du poids du produit, il existe un risque d’écrasement lors de la manutention du produit. Le constructeur dégage toute responsabilité en cas de non-respect des consignes suivantes : ► Seul un personnel habilité et formé aux règles de manutention des objets lourds peut manutentionner le produit. – Soulever la pompe manuellement : charge < 20 kg. – Utiliser des anneaux de levage appropriés vissés dans les trous prévus à cet effet. ► Porter des chaussures de sécurité avec protection des orteils conformément à la norme EN 347. AVERTISSEMENT Risque d'écrasement lié au basculement du produit Bien que la conformité aux règles de sécurité de la CEE soit assurée, il convient de prendre toutes les précautions nécessaires lors des opérations de manutention, d’installation tant que la pompe n'est pas intégrée dans l'équipement. ► Ne pas positionner la pompe sur un plan incliné. ► Ne pas la pousser latéralement. ► Toujours sécuriser la pompe tant qu’elle n’est pas intégrée dans l’équipement (trous de fixation au niveau de la bride d'aspiration). 17/84 Transport et stockage 1 2 1 Sangle 2 Anneau de levage M8 Manutention avec un dispositif de levage Pour manutentionner la pompe, il est nécessaire de choisir un appareil de levage adapté à la masse du produit. La masse et la position du centre de gravité varient selon le modèle (voir chapitre « Dimensions »). Prévoir 2 anneaux de levage M8 homologués (fourniture du client). 1. Visser les anneaux de levage dans 2 des 3 trous M8 du carter d'aspiration. 2. Utiliser une sangle à plusieurs brins de longueur minimum 230 mm. 3. Fixer la pompe par ses anneaux de levage et la hisser. 4. Transporter toujours la pompe turbomoléculaire à la verticale. 3.3 Stockage Stockage d'une pompe neuve ► Laisser en place l'enveloppe de protection. ► Laisser obligatoirement en place les obturateurs à l'aspiration, au refoulement et sur la bride de purge. ► Laisser obligatoirement les bouchons en plastique en place sur les connecteurs électriques. ► Stocker la pompe selon les températures de stockage autorisées (voir chapitre « Caractéristiques environnementales »). ► Stocker la pompe dans un environnement propre, sec et non pollué, pour une durée maximale de 1 an. Stockage après utilisation ► Pour stocker une pompe qui a été utilisée, voir chapitre « Immobilisation prolongée ». 18/84 Description du produit 4 Description du produit 4.1 Identification du produit Pour identifier le produit de manière sûre et pour communiquer avec notre centre de service, se référer aux informations figurant sur la plaque signalétique du produit (voir chapitre « Etiquettes »). 4.1.1 Contenu de la livraison ● ● ● ● 1 pompe à paliers magnétiques avec unité de commande électronique 1 filtre pare-éclats (installé dans la bride d'aspiration de la pompe) 1 électrovanne d'eau (Version MT) 1 manuel de l'utilisateur et une planche d'étiquettes de sécurité et selon la configuration de commande, les composants suivants sont présents : ● 1 joint cuivre ● 1 lot de visserie ● 1 électrovanne de purge Le boîtier de commande déportable (HHR) et l'alimentation électrique 48 VDC ne font pas partie de la livraison, sauf s'ils ont fait l'objet d'une commande. Pour commander, voir chapitre Accessoires. 4.1.2 Les différentes versions du produit Le constructeur a développé une gamme de pompes turbomoléculaires à paliers magnétiques actifs (PMA), avec étages de compression, de haute performance et fiables, particulièrement adaptées aux procédés de dépôt et gravure plasma, aux procédés de dépôts sur verre et d’autres applications de recherche. Ces pompes disposent d’une électronique intégrée. Ces pompes sont caractérisées par leur résistance à la corrosion, leur robustesse, leur capacité de pompage de grand débit de gaz en hautes pressions, et par leur absence de maintenance. Pour obtenir des informations plus détaillées en fonction des applications, nous contacter. Vitesse de rotation La vitesse de rotation de la pompe à paliers magnétiques peut être sélectionnée et réglée entre une vitesse minimale et la vitesse nominale. Ceci rend possible l’optimisation des caractéristiques de pompage en fonction de chaque application (par exemple, pompage haute pression). Une distinction est faite entre les vitesses suivantes : ● vitesse de rotation sélectionnée (= vitesse de Stand-by) entre la vitesse minimale et la vitesse nominale, ● vitesse nominale définie en usine. Pompe version M La version standard de la pompe correspond à la plupart des applications propres. Cette version de pompe ne dispose pas de système de régulation de température. Cette version est disponible avec refroidissement air ou eau. Pompe version MT Cette version de pompe est recommandée pour toute application nécessitant une température élevée de la pompe et des gaz pour éviter des condensations dans la pompe. Cette version est équipée d’un système de régulation de la température (TMS). La régulation de température est réalisée par l’électronique intégrée. 19/84 Description du produit 4.2 Interface homme/machine 2 1 3 4 5 7 6 Fig. 1: Description d'une pompe ATH 500 version M 1 Bride d'aspiration (vide élevé) 2 Filtre pare-éclats 5 6 3 Raccords d'eau (WATER IN/WATER OUT) (1/8 NPT femelle) 4 Unité de commande électronique 7 Interface de commande Purge de gaz neutre (50 sccm) (1/8 BSPP femelle équipée d'un filtre) Bride de refoulement (PUMP EXHAUST) 2 1 3a 3 8 3b 7 4 5 6 Fig. 2: 1 2 3 3a 3b 20/84 Description d'une pompe ATH 500 version MT Bride d'aspiration (vide élevé) Filtre pare-éclats Electrovanne d'eau Raccord d'eau (WATER IN - 1/4 double bague) Raccord d'eau (Water OUT - 1/4 double bague) 4 5 6 7 8 Unité de commande électronique Interface de commande Purge de gaz neutre (50 sccm) (1/4 VCR) Bride de refoulement (PUMP EXHAUST) Ceinture chauffante Description du produit 4.3 Unité de commande électronique La pompe turbomoléculaire à paliers magnétiques avec unité de commande électronique est destinée à être installée dans un équipement et pilotée par l’équipement. En standard, l'unité de commande électronique comporte une interface de commande type liaison série RS-232/RS-485 et REMOTE. Elle peut également être pilotée avec le boîtier de commande déportable HHR disponible en accessoire (voir chapitre « Accessoires »). Selon la configuration de commande, l'unité de commande électronique intégrée est équipée de l’interface qui permet le pilotage par des réseaux de commande type EtherCAT, Profibus. Dans ce document, seuls les fonctionnements avec les interfaces REMOTE, RS-232/RS-485 et HHR sont décrits. Pour les autres interfaces, se référer au manuel de l'utilisateur de l'interface de commande installée sur la pompe (voir chapitre « Documents applicables »). L'unité de commande électronique n'assure pas l'alimentation électrique de la pompe. L'alimentation électrique est réalisée par un coffret externe 48 VDC. Quelle que soit la configuration du produit, l’interface de commande de l’électronique permet la connexion avec le réseau de commande et l’affichage de l’état de fonctionnement de la pompe. Cette électronique intégrée permet : ● d'alimenter la pompe turbomoléculaire lorsqu'elle est raccordée à l'alimentation électrique externe ● d'alimenter et de piloter l'électrovanne d'eau et le chauffage (Pompe version MT) 1 2 3 4 A 7 6 1 5 2 3 4 B 8 5 4 2 1 C 8 Fig. 3: 5 Exemple d'interface de commande de l'électronique intégrée A Interface type Remote / RS-232/RS-485 B Interface Profibus C Interface EtherCAT 1 Service Connecteur du boîtier de commande déporté (HHR) 2 Liaison série RS-232/ RS-485 La liaison série RS-232/RS-485 est utilisée pour piloter et contrôler la pompe depuis un ordinateur. La liaison série RS-485 permet l’installation et le contrôle de plusieurs pompes en réseau. 21/84 Description du produit 22/84 3 Connecteur REMOTE Le connecteur REMOTE est utilisé pour piloter les fonctions START/STOP/STANDBY, pour permettre la copie du statut de la pompe au travers de contacts secs. 4 Voyants indicateurs Affichage de l'état de fonctionnement de la pompe 5 Connecteur d'alimentation électrique Utilisé pour connecter une alimentation de 48 VDC. 6 Connecteur électrique de la ceinture chauffante Alimentation de la ceinture chauffante 7 Connecteur électrique de l'électrovanne d'eau Alimentation de l'électrovanne d'eau 8 Connexions pour liaison bus de terrain Voir chapitre « Documents applicables » Installation 5 Installation L'installation de la turbopompe et sa fixation sont d'une importance primordiale. Le rotor de la pompe turbomoléculaire tourne à grande vitesse. En pratique, il n’est pas exclu que le rotor entre en contact avec le stator (par ex. en cas de pénétration de corps étrangers dans la bride de vide élevé). En l’espace de quelques fractions de secondes, l'énergie cinétique libérée agit sur le boîtier et sur l'ancrage de la pompe turbomoléculaire. Des calculs et des tests approfondis effectués selon la norme ISO 27892 garantissent la protection de la pompe turbomoléculaire contre la démolition (destruction des pales du rotor) et l'éclatement (rupture de l’arbre du rotor). Les résultats expérimentaux et théoriques se traduisent par des mesures de sécurité et des recommandations à suivre pour une fixation conforme et sûre de la pompe turbomoléculaire. 5.1 Conditions d'installation à l'équipement AVERTISSEMENT Risque de blessures graves provoquées par le détachement de la pompe lors d’un blocage du rotor En cas de fixation incorrecte de la pompe, lors d’un blocage inopiné du rotor, la pompe turbomoléculaire se désolidarise de l’équipement : l'énergie libérée projette la pompe ou des fragments de pompe dans le local, provoquant des blessures très graves voire mortelles, ainsi que des dommages matériels considérables. ► Respecter scrupuleusement les recommandations d'installation décrites dans ce manuel. Pfeiffer Vacuum décline toute garantie et responsabilité en cas de non-respect des instructions d’installation. ► Utiliser exclusivement les pièces d'origine autorisées de Pfeiffer Vacuum (accessoires) pour le raccordement dans l'équipement. Le raccordement de la pompe à l’équipement doit être suffisamment rigide pour absorber l’énergie cinétique libérée par le rotor si la pompe se bloque brutalement. Pour cela, tenir compte : ● Des charges maximum pour dimensionner les dispositifs de fixation. ● De la dimension de la bride d’aspiration. ● De la qualité et du nombre de vis. ● Du type de raccordement entre la bride d’aspiration de la pompe et l’enceinte à pomper. Lorsque la pompe est raccordée selon les recommandations du constructeur, en cas d’incident générant une surpression, l’enveloppe de la pompe est capable de supporter une pression statique de 11 · 103 hPa maximum pendant 1 minute. 23/84 Installation 5.1.1 Spécifications d'installation 1 2 Turbo 3 Fig. 4: Raccordement mécanique de la pompe dans l'équipement 1 Chambre à vide 2 Equipement 3 Châssis Point d'ancrage sécurisé Description d’un scénario de blocage brutal L’énergie cinétique du rotor doit être absorbée par l’installation si la pompe se bloque brutalement. Les charges résultantes maximum ont été mesurées sur un banc de test en simulant la cassure du rotor en 2 morceaux, lorsque le pompe tourne à vitesse nominale. L’impact des morceaux de rotor génère les charges transitoires décrites ci-dessous. Force axiale (A) Les morceaux du rotor peuvent être éjectés par l’aspiration de la pompe et endommager la plaque de fixation de la vanne ou de toute autre partie de l’installation. Dans la mesure où l’impact est proche de la pompe, et la surface impactée est rigide, il y a création d’une importante force axiale sur l’installation. En présence d’une vanne pendulaire, ou d’un espace supérieur à 100 mm, on ne constate pas cette force axiale. Moment de flexion (B) L’impact des morceaux de rotor sur le carter de la pompe crée une force radiale sur le carter. Celle-ci engendre un moment de flexion sur l’installation dépendant de la distance du point d’impact par rapport au point d’ancrage sur l’installation. Couple (C) La décélération des morceaux de rotor engendre un couple sur le carter de pompe qui se transmet à l’installation. La valeur maximum de la force axiale et du moment de flexion apparaissent en même temps. Un délai de plusieurs millisecondes s’écoule avant l’apparition du couple maximum. 24/84 Installation 120 10 A C 9 1 100 8 A 2 7 80 B 6 60 5 4 40 3 Force axiale - kN Couple – Flexion kN·m B 2 C 20 1 0 0 0 0.5 1 1.5 2 2.5 Temps ms Fig. 5: Graphe des charges transmises à l'équipement 1 Pompe Turbo 2 Vanne avec plaque pendulaire Caractéristiques Unité Valeur Vitesse nominale min -1 50000 Énergie kN·m 24 Couple (C) Max. kN·m 9 Durée ms 1 Délai ms 1 Max. kN·m 6 Durée ms 0,5 Délai ms 0 Max. kN 0 à 110 Durée ms 0,3 Délai ms 0 Moment de flexion (B) Force axiale (A) 1) 1) La force axiale est maximale lorsque l’aspiration de la pompe est obstruée par des pièces rigides. Il n’y a pas de charge sur l’installation en cas de faible rigidité, par exemple avec une vanne. Tab. 1: 5.1.2 Charges transmises à l'équipement Sécurisation de l'équipement et du châssis Fixation de la pompe à l’équipement Les charges maximum résultant d’un blocage brutal doivent être absorbées par les éléments de fixation de la pompe. ► Concevoir et sécuriser le châssis de la pompe de sorte qu’il supporte les charges maximum. ► Serrer impérativement les vis à la clé dynamométrique selon les couples de serrage du tableau suivant : – si le couple est faible : risque de desserrage des vis. – si le couple est fort : risque de détérioration des vis. Type de bride d'aspiration DN160 ISO-F ou ISO-K DN100 ISO-F ou ISO-K DN160 CFF DN100 CFF Type de vis 1) M 10 M8 M8 M8 Nombre de vis 1) 8 8 20 16 12-9 12-9 12-9 12-9 Qualité des vis 1) 1) Type, nombre, grade et couple de serrage des vis sont imposés et obligatoires. 25/84 Installation Type de bride d'aspiration DN160 ISO-F ou ISO-K DN100 ISO-F ou ISO-K DN160 CFF DN100 CFF Couple de serrage par vis 1) N·m 30 20 20 20 Force de serrage totale N 108000 88500 222000 177000 Longueur des vis mm ≥ 35 - ≥ 40 ≥ 35 1) Type, nombre, grade et couple de serrage des vis sont imposés et obligatoires. Tab. 2: Fixation de la bride de vide élevé (bride d'aspiration) Le constructeur recommande d’utiliser les lots de visserie prévus à cet effet (accessoires). Contacter notre centre de service. Utilisation particulière des brides ISO-K Les brides ISO-K n’empêchent pas la rotation accidentelle de la pompe par rapport à la bride de l’équipement en cas de rupture d’un élément tournant. Cette rotation peut endommager les lignes de prévidage et de purge et présenter un risque vis à vis de l'utilisateur. ● Utiliser exclusivement des brides tournantes. ● En cas d'utilisation de griffes de serrage, installer le même nombre de griffes de serrage (en acier inoxydable) que le nombre de vis recommandé pour la fixation de bride ISO-F (accessoires). Fixation au châssis Si le châssis n’est pas conçu pour absorber les charges maximum en cas de blocage brutal, contacter notre centre de service pour le dimensionnement de votre installation. 5.2 Mise en place de la pompe AVIS Endommagement de la pompe causé par des vibrations externes Les vibrations depuis l’extérieur ou les impacts sur la pompe peuvent surcharger les paliers magnétiques, d’où un stress sur les roulements de secours. ► Évitez les mouvements latéraux et d’inclinaison de la pompe. ► Les turbulences externes doivent être compensées par une conception appropriée du système. ► Sécurisez l’enceinte à vide fournie par le client contre tout mouvement et basculement. ATTENTION Risque de chute due aux câbles ou canalisations mal fixés L’espace autour de la pompe doit être dégagé afin de ne pas encombrer le passage au risque de provoquer des chutes. ► Fixer les câbles électriques et les canalisations de pompage : les acheminer dans des goulottes. Le constructeur garantit le bon fonctionnement de la pompe lorsqu’elle est utilisée dans un champ magnétique uniforme n’excédant pas 0,5 mT. Pour des valeurs comprises entre 0,5 et 5 mT, le bon fonctionnement dépendra du refroidissement et de la charge des gaz. Au-delà de 5 mT de champ magnétique, cela peut provoquer un échauffement du rotor. Prévoir dans ce cas les blindages nécessaires. La pompe seule peut résister à un niveau de radiation inférieur à 103 Gy. La pompe turbomoléculaire ne peut pas refouler à la pression atmosphérique, il faut la connecter à une pompe primaire. Transitoirement, elle peut démarrer sa rotation à la pression atmosphérique. La pompe turbomoléculaire peut fonctionner dans toutes les positions. 26/84 Installation IN IN IN Fig. 6: IN Positions de fonctionnement Mise en place de la pompe 1. Manutentionner la pompe, (voir chapitre « Manutention de la pompe »). 2. Raccorder et sécuriser la fixation de la pompe turbomoléculaire pour garantir la sécurité du personnel et la fiabilité du fonctionnement (voir chapitre « Spécifications d'installation »). 3. Collez les étiquettes de sécurité dans la langue de l'opérateur à l'endroit le plus approprié et le plus visible sur la pompe pour avertir l'opérateur des dangers potentiels. 1 2 IN Fig. 7: Installation de la pompe à l'horizontale 1 Sangle (Qté2) 2 Crochet Mise en place à l'horizontale Pour manutentionner la pompe, il est nécessaire de choisir un appareil de levage adapté à la masse du produit. La masse et la position du centre de gravité varient selon le modèle (voir chapitre « Caractéristiques techniques » et « Dimensions »). 1. Utiliser 2 sangles homologuées EN 1492-1 à plusieurs brins pouvant supporter le poids de la pompe. 2. Utiliser des accessoires homologués pour accrocher la pompe à l'appareil de levage (par exemple, crochet avec verrou de sécurité). 3. Placer les sangles solidement autour de la pompe. 4. Positionner le crochet de l'appareil de levage à la verticale du centre de gravité. 5. Hisser la pompe et la déplacer jusqu'à son emplacement sur le châssis. 6. Maintenir la pompe suspendue tout le temps de l'installation jusqu'à la fixation de la bride de vide élevé. 27/84 Installation IN 1 Fig. 8: Installation, aspiration vers le haut 1 Table de levage (exemple) Mise en place de la pompe avec aspiration vers le haut Pour manutentionner la pompe, il est nécessaire de choisir un appareil de levage adapté à la masse du produit. La masse et la position du centre de gravité varient selon le modèle (voir chapitre « Caractéristiques techniques » et « Dimensions »). 1. Raccorder la pompe au dispositif de manutention en utilisant les trous prévus à cet effet pour éviter tout basculement de la pompe. 2. Maintenir la pompe fixée au dispositif de manutention jusqu'à la fixation de la bride de vide élevé. 5.3 Raccordement à la ligne de pompage Lorsque des matières pyrophoriques, inflammables ou toxiques sont présentes dans la pompe, cela peut engendrer des risques supplémentaires que l’exploitant doit évaluer et gérer au niveau de l’ensemble de l’installation de pompage. L’utilisateur et/ou l’intégrateur du produit a l’entière responsabilité de l’installation et doit appliquer les consignes de sécurité spécifiques, conformément à la législation locale. DANGER Danger de mort par inflammation lors du pompage de gaz inflammables Il y a risque d'incendie provoqué par une réaction chimique non désirée (amorçage) entre des matières inflammables pompées. ► Prévoir un dispositif de détection électromécanique de la LIE dans le système d’extraction (détection possible à 25 % de la LIE) qui arrête l’alimentation de la pompe en produits chimiques lors de la détection de gaz à 25 % de la LIE pour la matière inflammable concernée. AVERTISSEMENT Risque d'écrasement et/ou de coupure au contact de pièces en mouvement La bride d’aspiration est suffisamment grande pour permettre l’introduction d'une partie du corps (un doigt, une main) : il y a risque d’écrasement par contact avec les pièces en mouvement. Les orifices d'aspiration et de refoulement sont toujours fermés à l’aide d’obturateurs. ► Attendre le raccordement à la ligne de pompage pour retirer les obturateurs. ► Attendre que la pompe soit raccordée pour mettre sous tension. 28/84 Installation Consignes générales pour une installation dans la ligne de pompage selon les règles de l'art Les raccordements à l'aspiration et au refoulement de la pompe ne doivent pas engendrer de contraintes pouvant provoquer des fuites sur la ligne de pompage. 1. Utiliser des gants pour raccorder ou retirer la pompe de l'équipement. 2. Effectuer toujours l'installation mécanique avant le raccordement électrique. 3. Eviter d'utiliser une bride de réduction à l'aspiration. Si nécessaire nous consulter. 4. Vérifier la présence du filtre pare-éclats installé dans la bride d'aspiration. 5. Utiliser dans la ligne de pompage, à l’aspiration comme au refoulement, des accessoires dont les matériaux et l’étanchéité sont compatibles avec les gaz pompés. Consulter le catalogue des accessoires de raccordement sur le site pfeiffer-vacuum 6. Prévoir, lors du montage du circuit du vide, des accessoires pour isoler la pompe dans la ligne de pompage et faciliter la maintenance (vannes d’isolement à l’aspiration et au refoulement, purge, …). 7. Les joints toriques situés sous les obturateurs ne sont pas compatibles avec l'ensemble des applications. L'utilisateur ou l'intégrateur du produit a la responsabilité d'installer des joints compatibles avec l'application. 8. Retirer les protections qui obturent les orifices d’aspiration et de refoulement. 9. Garder les obturateurs, vis, rondelles pour les réutiliser lors du transport de la pompe. 10. Veiller à ne pas faire tomber de vis, rondelles ou autres objets dans l’aspiration de la pompe. 11. Réaliser un test d'étanchéité sur l'ensemble de la ligne de pompage après installation de la pompe. 5.3.1 Raccordement côté aspiration AVERTISSEMENT Risques de coupures par contact avec des arêtes vives par la bride de vide élevé L’accès aux pièces ‘coupantes’ est possible par la bride d’aspiration. Les arêtes des ailettes du rotor et du stator des pompes turbomoléculaires sont très tranchantes. ► Attendre l'arrêt complet de la pompe avant d'intervenir sur le produit. ► Toujours maintenir le filtre pare-éclats dans le carter d’aspiration, il atténue le risque de blessures. ► Toujours porter des gants de protection conformément à la norme EN ISO 21420. AVIS Risque de pollution du procédé en cas de non-respect des conditions de propreté Lorsque les pièces en contact avec le vide élevé sont sales, le temps de pompage est augmenté et le procédé est pollué. ► Utiliser des pièces et canalisations propres, sèches et dépourvues de graisse, de poussière. ► Porter des gants pour réaliser les raccordements, principalement côté vide élevé. Veiller à ce que les pièces ou enceintes raccordées à l’aspiration de nos produits supportent une dépression de 1·10-3 hPa absolue. 29/84 Installation 5.3.2 Raccordement côté refoulement AVERTISSEMENT Risque d'empoisonnement en présence de gaz de procédés dans l'atmosphère Le constructeur n’a pas la possibilité de contrôler le type de gaz utilisé avec la pompe. Les gaz de procédés sont fréquemment toxiques, inflammables, corrosifs, explosifs ou réactifs. Il existe un risque d’accident grave voire mortel lorsque ces gaz s’échappent librement dans l’atmosphère. ► Appliquer les consignes de sécurité spécifiques, conformément à la législation locale. Ces informations sont disponibles auprès du service sécurité de l’exploitant. ► Raccorder impérativement le refoulement de la pompe turbomoléculaire à une pompe primaire compatible avec les gaz de procédés : le refoulement de la pompe primaire est raccordé au système d'échappement des gaz dangereux de l'installation. ► Vérifier régulièrement l’absence de fuites au niveau du raccordement de la pompe avec la canalisation d’échappement. ► Raccorder la pompe primaire recommandée (voir chapitre « Caractéristiques techniques »). ► Installer une vanne d’isolement (NF) entre la pompe turbomoléculaire et la pompe primaire. 5.4 Raccordement du circuit d'eau Pour limiter la corrosion et l’encrassement du circuit d’eau, il est recommandé de disposer d’une alimentation en eau douce traitée ou en eau industrielle non agressive ayant les caractéristiques requises (voir chapitre « Caractéristiques de l'eau »). Si les caractéristiques de pollution solides ne sont pas respectées, installer un filtre sur l’arrivée d’eau. AVIS Dégradation du circuit de refroidissement en cas d’utilisation d’un réseau urbain non réglementaire L'utilisation d'un réseau d'eau urbain non réglementaire peut provoquer le colmatage du circuit de refroidissement par des dépôts calcaires. En conséquence le circuit de refroidissement devra être démonté pour nettoyage et maintenance. D'autre part, la présence de micro-organismes (algues), ou substances biologiques (bactéries) dans le réseau d'eau peut générer des problèmes dans le circuit de refroidissement. ► Raccorder le circuit de refroidissement à un réseau d’eau réglementaire. ► Appliquer les traitements nécessaires pour éviter la croissance de micro-organismes. Continuité du refroidissement pour le procédé Si l’arrêt du circuit d’eau génère un risque important pour le procédé, il est conseillé de commander le refroidissement de la pompe par un système externe capable de prendre le relais en cas de défaillance du circuit d’eau. AVERTISSEMENT Risque de blessure au contact de l'eau sous pression Le produit utilise de l’eau sous pression comme fluide de refroidissement. Une installation non conforme ou réalisée de manière non professionnelle peut mettre en danger la vie de l’utilisateur. ► Installer une vanne manuelle dans le circuit à une distance de 3 m du produit pour verrouiller l’alimentation en eau. ► Respecter la pression et différence de pressions recommandées. ► Toujours verrouiller et débrancher le circuit d’eau avant d’intervenir sur le produit. ► Lors de la maintenance, sécuriser correctement l’installation en repérant et condamnant le circuit d’eau sous pression pour éviter tout réenclenchement non intentionnel (LO/TO procédure de consignation/déconsignation). ► Contrôler régulièrement l’état des canalisations et connexions du circuit d’alimentation. 30/84 Installation 5.4.1 Procédure de montage des raccords Raccord fileté Procédure de collage et serrage des raccords filetés 1. Utiliser des raccords 1/8 NPT (fourniture à la charge du client). 2. Coller les raccords avec de la colle oléo-étanche, ou mettre du ruban d'étanchéité PTFE sur le filetage. 3. Serrer le raccord tout en maintenant l’embase côté pompe. Raccord à simple bague Procédure de montage des raccords à simple bague Raccord utilisé pour relier les tuyaux souples entre pompe et électronique (par exemple). 1. Insérer le tuyau en butée au fond du raccord. 2. Approcher manuellement l’écrou. 3. Visser l’écrou à l’aide d’une clé plate, de 1/2 tour, tout en maintenant le corps du raccord immobile. Raccord à double bagues Procédure de montage des raccords à double bagues Raccords utilisés pour relier les tuyaux rigides (acier inox., cuivre nickelé, ...). 1. Insérer le tuyau avec les bagues en butée au fond du raccord. 2. Orienter le raccord en position. 3. Approcher manuellement l’écrou. 4. Visser l’écrou à l’aide d’une clé plate, de 3/4 tour, tout en maintenant le corps du raccord immobile. 5.4.2 Raccordement de la pompe au circuit d'eau Serrage des raccords et sens de circulation de l'eau Respecter la procédure de montage/serrage des raccords pour éviter tout risque de fuites. Pompe version MT : Respecter le sens de circulation de l'eau pour ne pas perturber le fonctionnement de l'électrovanne. 31/84 Installation Raccordement d'un modèle ATH 500 M 1 1 WATER IN / WATER OUT (sens indifférent) Procédure de raccordement d'une pompe ATH 500 M 1. Prévoir une canalisation d'arrivée d'eau et une vanne d'eau pour ajuster le débit. 2. Connecter l'arrivée d'eau sur l'un des raccords et l'autre au circuit d'évacuation. 3. Vérifier qu'il n'y ait aucune fuite au niveau des canalisations et connexions du circuit d'eau. Raccordement d'un modèle ATH 500 MT 1 2 3 1 WATER IN 2 WATER OUT 3 Alimentation électrique de l'électrovanne d'eau Procédure de raccordement d'un modèle ATH 500 MT 1. Prévoir une canalisation d'arrivée d'eau. 2. Connecter le circuit de refroidissement sur les raccords prévus en respectant le sens de circulation : – WATER IN = entrée d'eau sur l'électrovanne – WATER OUT = circuit d'évacuation. 3. Vérifier qu'il n'y ait aucune fuite au niveau des canalisations et connexions du circuit d'eau. 5.5 Installation de l'accessoire refroidissement air Un accessoire « refroidissement air » peut être commandé séparément (voir chapitre « Accessoires »). L’installation est à la charge du client. Selon la configuration de commande (version refroidie à l'air), la pompe est équipée d'un ventilateur au départ usine. Dans ce cas, seul le câblage électrique est à la charge du client. Avec un refroidissement air, le flux maximum de gaz admissible dans la pompe diminue ! L’utilisateur doit contrôler la pression maximale à l’aspiration pour éviter toute surchauffe de la pompe et abaisser la température ambiante. En utilisation continue, la consommation de courant doit être inférieure à 3,8 A : ce paramètre peut être surveillé via interface de commande. 32/84 Installation 5 4 1 2 3 Fig. 9: Montage de l'accessoire refroidissement air 1 Câble d’alimentation du ventilateur (longueur 5 m) - [ 1 ou bleu (-), 2 ou brun (+) ] 2 Rondelle ondulée Diam. 5 3 Vis CHC M5x10 4 5 Connecteur ventilateur [ 1 (-), 2 (+), 3 (non connecté) ] Support Procédure de montage Le lot refroidissement air contient la visserie pour le raccordement mécanique sur la pompe et le câble secteur pour le raccordement électrique. L’alimentation électrique du ventilateur nécessite une alimentation externe de 48 VDC. L'alimentation électrique 48 VDC proposée en accessoire par le constructeur permet d’alimenter la pompe et le ventilateur. ► Serrer les 2 vis sur le support du ventilateur. ► Câbler le ventilateur en respectant le repérage des bornes et fils (voir chapitre « Raccordement à l'alimentation électrique externe »). 5.6 Raccordement du circuit d'azote Selon les applications, la purge de gaz neutre peut consister : ● A injecter de l'air ambiant, ou ● A injecter un gaz neutre dans la pompe. Dans ce manuel, on désignera le gaz neutre par ’azote’ qui correspond au gaz le plus utilisé. Pour davantage d’informations concernant le type de gaz de purge, contacter notre centre de service. DANGER Danger de mort par explosion lors du pompage de gaz chargés de matières pyrophoriques/ inflammables Si des quantités de matières pyrophoriques / inflammables supérieures à la LIE sont envoyées vers la pompe, il y a un risque d'explosion. ► Prévoir un débit d'azote suffisant pour abaisser la concentration en dessous de la LIE. ► Prévoir un verrouillage de l’écoulement des gaz vers la pompe en cas d’arrêt de l’alimentation en azote. 33/84 Installation AVERTISSEMENT Risque de blessure au contact de l’azote sous pression Le produit utilise de l’azote sous pression comme gaz de balayage. Une installation non conforme ou réalisée de manière non professionnelle peut mettre en danger la vie de l’utilisateur. ► Installer une vanne manuelle dans le circuit à une distance de 3 m du produit pour verrouiller l’alimentation en azote. ► Respecter la pression d’alimentation recommandée. ► Toujours verrouiller et débrancher le circuit d’azote avant d’intervenir sur le produit. ► Lors de la maintenance, sécuriser correctement l’installation en repérant et condamnant le circuit d’azote sous pression pour éviter tout réenclenchement non intentionnel (LO/TO procédure de consignation/déconsignation). ► Contrôler régulièrement l’état des canalisations et connexions du circuit d’alimentation. Pour garantir les meilleures performances, il est nécessaire de disposer d’une alimentation en azote sec et filtré, ayant les caractéristiques requises (voir chapitre « Caractéristiques de l'azote »). 5.6.1 Purge de gaz neutre AVIS Rôle de la purge de gaz neutre Lorsque la purge de gaz neutre s’arrête, les gaz de procédé peuvent rétrodiffuser et endommager les paliers internes de la pompe. ► Maintenir la purge de gaz neutre tant que le rotor tourne pour prolonger le balayage. ► Faire débiter la purge sans excéder la valeur maximum de 1 · 103 à 1,5 · 103 hPa absolus. Débit (SCCM) 70 e5 urg 60 CC 0S M P 50 40 30 20 Pression absolue à l’aspiration (hPa) 1000 Fig. 10: 1100 1200 1300 1400 1500 Graphe Débit de purge Dispositif de purge 50 sccm Le fonctionnement de cette purge est continu. Le réducteur de flux intégré garantit un débit de 50 sccm pour une pression de 1,1 · 103 hPa. 1. Raccorder directement l'alimentation de gaz neutre sur l'orifice PURGE en lieu et place du filtre ou du bouchon (raccord 1/8 BSPP-ISO228), ou sur le raccord VCR*. 2. Régler la pression de gaz neutre afin d'obtenir le débit recommandé (voir le graphe Débit de purge). * D'autres raccords sont possibles selon la configuration de commande (voir chapitre « Produits concernés ». Electrovanne équipée d'une purge 50 sccm (seulement pour ATH 500 M) Il s’agit d’une option disponible selon la configuration de la pompe. Cette électrovanne de purge doit être alimentée en 24 VDC : l'alimentation et le pilotage de cette électrovanne sont de la responsabilité du client. 1. Retirer le bouchon ou le filtre à poussières présents sur l'orifice PURGE; 2. Connecter l'électrovanne sur l'orifice repéré PURGE (raccord 1/8 BSPP). 34/84 Installation L'installation et le raccordement d'un accessoire 'lot de purge' sont décrits au chapitre « Installation de l'accessoire de purge ». 5.6.2 Installation de l'accessoire de purge 1 2 A N2 3 4 7 8 6 5 B Fig. 11: A B 1 2 Lot de purge (accessoire) Raccord 1/8'' BSPP (ISO 228) Unité de commande électronique Câble électrovanne Bobine électrovanne 3 4-6 5 7-8 Ecrou H M 4 (Qté 2) Rondelle (Qté 4) Vis CHC M4x30 (Qté 2) Raccord union 1/8'' BSPP Installation de l'accessoire de purge Il s'agit d'un accessoire disponible sur commande. 1. Remplacer les vis M4x16 de l’électronique par les vis CHC M4x30 et les rondelles. 2. Retirer le filtre à poussières ou le bouchon de la purge. 3. Visser le raccord UNION 1/8'' BSPP sur l'orifice de la purge. 4. Placer l’ensemble sur l’électronique en utilisant les vis CHC M4x30 comme guidage dans les trous de la plaque. 5. Aligner les raccords unions 1/8'' BSPP avant de serrer l'écrou. 6. Serrer les écrous avec les rondelles. 7. Tester l'étanchéité du vide. Raccordement de l'accessoire de purge à une alimentation de gaz neutre Cette électrovanne peut être raccordée à une alimentation de gaz neutre. Le flux de purge doit être présent lorsque la pompe est en fonctionnement. Lorsque la pompe est à l'arrêt, l'électrovanne peut être fermée pour faire un test d'étanchéité de l'équipement. Pour raccorder l’électrovanne à une alimentation en gaz neutre, il est nécessaire de disposer d’une alimentation en azote sec et filtré, ayant les caractéristiques requises (voir chapitre « Caractéristiques de l'azote »). 1. Retirer le bouchon sur le raccord de l’électrovanne. 2. Raccorder en lieu et place la canalisation de gaz neutre : raccordement 1/8 BSPP femelle. 3. Coller le raccord avec de la colle oléo-étanche, ou mettre du ruban d'étanchéité PTFE sur le filetage. 4. Serrer le raccord en appliquant un couple de 10 N·m maximum. 5. Régler la pression de gaz neutre afin d'obtenir le débit recommandé (voir le graphe Débit de purge). 35/84 Installation 5.7 Raccordement de l'électrovanne d'entrée d'air Il s'agit d'un accessoire disponible sur commande (voir chapitre « Accessoires »). L’électrovanne d’entrée d’air est calibrée (débit 11 · 103 sccm) pour remettre à la pression atmosphérique le volume interne de la pompe. Son efficacité à ralentir la pompe est améliorée lorsque des vannes d’isolement sont installées à l’aspiration et au refoulement de la pompe. L'alimentation électrique 24 VDC et le pilotage de la vanne d'entrée d'air sont de la responsabilité du client. 1 2 1 Electrovanne d'entrée d'air 2 Filtre à poussières Pilotage de l'électrovanne d'entrée d'air La remise à la pression atmosphérique de la pompe a lieu sur l'arrêt de la pompe ou arrêt sur défaut. La vanne d'entrée d'air doit être alimentée lorsque la vitesse de rotation de la pompe est inférieure < 10000 min-1 et qu'un ordre d'ouverture est envoyé à l'électrovanne. La vanne d'entrée d'air type NO (normalement ouvert) doit être fermée pour redémarrer la pompe. 1. Raccorder l'électrovanne sur le refoulement PUMP EXHAUST de la pompe au moyen d'accessoires de raccordement disponibles au catalogue des produits. 2. Alimenter électriquement l’électrovanne. 3. Câbler le pilotage de l'électrovanne. Raccordement de l'électrovanne d'entrée d'air à une alimentation de gaz neutre Cette électrovanne peut être raccordée à une alimentation de gaz neutre. Pour raccorder l’électrovanne à une alimentation en gaz neutre, il est nécessaire de disposer d’une alimentation en azote sec et filtré, ayant les caractéristiques définies (voir chapitre « Caractéristiques de l'azote »). 1. Retirer le filtre à poussières de l’électrovanne. 2. Raccorder en lieu et place la canalisation de gaz neutre : raccordement 1/8’’ NPT femelle. 3. Coller le raccord avec de la colle oléo-étanche ou mettre du ruban d'étanchéité PTFE sur le filetage. 4. Serrer le raccord en appliquant un couple de 10 N·m maximum. 5.8 Test d'étanchéité de l'installation L'étanchéité du produit est assurée en sortie d'usine pour les conditions normales d'utilisation. L'exploitant doit préserver ce niveau d'étanchéité particulièrement lors du pompage de gaz dangereux. Pour davantage d'information concernant les tests d'étanchéité, contacter notre centre de service. 1. Réaliser un test d'étanchéité sur l'ensemble de la ligne de pompage après installation de la pompe. 2. Vérifier régulièrement l'absence de traces de gaz pompés dans l'environnement ainsi que toute trace d'entrée d'air dans la ligne de pompage pendant le fonctionnement. 36/84 Installation 5.9 Raccordement électrique AVERTISSEMENT Risque d'électrocution lié à une installation électrique non conforme Le produit utilise la tension secteur comme alimentation électrique. Une installation électrique non conforme ou réalisée de manière non professionnelle peut mettre en danger la vie des utilisateurs. ► Seul un personnel qualifié et formé aux règles de sécurité électrique, CEM peut réaliser l'installation électrique. ► Ne procéder à aucune transformation ou modification arbitraire du produit. ► Vérifier que le produit est correctement relié au circuit d'arrêt d'urgence de l'équipement (ou installation de pompage). AVERTISSEMENT Risque d'électrocution par contact lors de l'entretien ou la maintenance Il y a un risque de choc électrique par contact avec un produit sous tension et non isolé électriquement. ► Avant toute intervention, placer l’interrupteur principal sur O. ► Débrancher le câble secteur du réseau électrique. ► Sécuriser correctement l’installation en repérant et condamnant le circuit de puissance pour éviter tout ré-enclenchement non intentionnel (LO/TO procédure de consignation/déconsignation). AVERTISSEMENT Risque de choc électrique au contact du connecteur secteur à la mise hors tension Certains composants comportent des condensateurs chargés à plus de 60 VDC qui restent chargés électriquement à la mise hors tension : des tensions résiduelles dues aux capacités des filtres provoquent des chocs électriques, y compris au niveau de la prise secteur. ► Attendre 5 minutes après la mise hors tension avant d’intervenir sur le produit. AVIS Risque de perturbation électromagnétique Tensions et courants induisent une multitude de champs électromagnétiques et des signaux parasites. Une installation non conforme aux règles CEM perturbe les autres équipements ou plus généralement l’environnement. ► Utiliser des liaisons et raccordements blindés pour les interfaces dans les environnements perturbateurs. La pompe est un produit de classe A. Dans un environnement domestique, ce produit peut provoquer des interférences radio. Dans ce cas, l'utilisateur doit prendre les mesures adéquates. Sécurité électrique Le moteur de la pompe est protégé contre les surcharges par la limitation de courant du variateur de vitesse dans l'électronique (en cas de surcharge la vitesse diminue automatiquement). Lorsqu'il existe un danger lié à un contact accidentel de liquide, de gaz ou d'éléments solides, il est nécessaire d'installer un circuit de verrouillage type arrêt d'urgence pour stopper l'alimentation de l'électronique. ► Ne pas neutraliser ces sécurités pendant l'installation, l'utilisation et la maintenance de la pompe. Lors d’un arrêt de la pompe sur défaut, l’alimentation électrique du variateur est coupée et la pompe est en sécurité. Pour remettre la pompe en service, il faut : ► Attendre l'arrêt complet de la rotation de la pompe avant de couper l’alimentation électrique. – Interrupteur de l'alimentation électrique externe 48 VDC sur O. ► Attendre environ 15 secondes. 37/84 Installation ► Supprimer l'origine du défaut. ► Rétablir l’alimentation électrique. – Interrupteur de l'alimentation électrique externe 48 VDC sur I. 5.9.1 Protection de l'installation électrique du client Disjoncteur différentiel à l’entrée de l’alimentation AC/DC Pour assurer la protection des personnes en cas de défaut d’isolation, il est indispensable d’installer un disjoncteur différentiel (voir chapitre « Caractéristiques électriques »). Le réseau de puissance alimentant l’équipement doit être équipé d’un disjoncteur, courbe D suivant IEC 60947-2, conforme à la législation locale et avoir un pouvoir de coupure en court-circuit d’une valeur minimum de 10 kA. Ce dispositif de protection sera placé de façon visible à une distance maximum de 7 m du produit et identifié comme dispositif de coupure du produit. Ce disjoncteur est de fourniture client : voir chapitre « Caractéristiques électriques » pour le calibre du disjoncteur réseau. Cette alimentation AC/DC de classe 1 doit impérativement être raccordée à la terre. L’installateur doit s'assurer que l’installation comporte un fil de terre correctement relié à la terre. Alimentation via un réseau 48 VDC Pour alimenter la pompe via un réseau 48 VDC, voir chapitre « Caractéristiques électriques ». Mise à la terre Lorsque nécessaire, l'installateur doit prévoir une double protection distincte de la protection en place. Elle est constituée soit d'une tresse non isolée, soit d’un fil vert/jaune isolé de section minimum 3 mm2 (9AWG). L'impédance entre le corps de la pompe et le point de mise à la terre de l'installation doit être < 0,1 Ohm à 25 A). ► Raccorder ce fil au moyen d’une vis M4 x 8 et une rondelle éventail sur le trou prévu à cet effet sur la pompe repéré , puis au point de mise à la terre de l’installation. Absence d'arrêt d'urgence La pompe n'est pas équipée d'un dispositif d'arrêt d'urgence EMS ni de verrouillage électrique. La pompe est conçue pour être intégrée dans un équipement possédant un dispositif d'arrêt d'urgence. ● Ce dispositif d'arrêt d'urgence doit mettre la pompe hors tension lorsqu'il est activé. Signalisation du fonctionnement en mode local Aucune signalisation du fonctionnement en mode local n'est disponible sur la pompe. ● Prévoir un dispositif pour signaler le fonctionnement en mode local lorsque la pompe n'est pas intégrée ni pilotée par l'équipement. 5.9.2 Raccordement à l'alimentation électrique externe AVERTISSEMENT Danger de mort par électrocution en cas de dysfonctionnement En cas de dysfonctionnement, les appareils raccordés au secteur peuvent être sous tension. Danger de mort par électrocution en cas de contact avec des composants sous tension. ► Toujours conserver l’alimentation librement accessible de manière à pouvoir la débrancher à tout moment. La pompe fonctionne avec une alimentation électrique externe 48 VDC. L'alimentation et son câble sont disponibles en accessoires (voir chapitre « Accessoires »). Elle peut également fonctionner avec une alimentation externe et un câble de fourniture client ayant les caractéristiques requises (voir chapitre « Caractéristiques électriques », page 78). Si la pompe est connectée sur un réseau principal 48 VDC (réseau au sens de la norme EN 61000-6), ajouter un filtre et un système d’écrêtage de surtension sur la ligne d’alimentation à l'entrée de la pompe : contacter notre centre de service. En interne, le pôle «-» du 48 VDC est raccordé à la terre. 38/84 Installation 1 2 5 3 6 7 4 Fig. 12: Connecteur mâle alimentation électrique 48 VDC 1 Index 2 Polarité + 48 VDC 5 6 3 Polarité - 48 VDC 4 Potentiel terre 7 Pas connecté Prise de câble alimentation pompe (Réf : UTS6JC104S fournisseur Souriau France) Câble d'alimentation Alimentation électrique de la pompe 1. Repérer l'index principal sur le connecteur électrique mâle de la pompe. 2. Repérer l'index principal sur le connecteur femelle du câble d'alimentation correspondant. 3. Insérer le connecteur femelle en respectant les index puis tourner jusqu'à la position de verrouillage. Version refroidie à l'air ► Si la pompe est équipée d'un ventilateur, le raccorder via le connecteur en face avant de l'alimentation externe. 1 2 3 0V 48V 4 5 Fig. 13: Câblage du ventilateur sur alimentation externe 48 VDC (accessoire) 1 Connecteur pour alimentation ventilateur (version refroidie à l'air) 2 Connecteur pour alimentation pompe 3 Connecteur secteur 4 Câbles alimentation pompe : +++ (48 V), --- (0 V) 5 Câbles alimentation ventilateur [ 1 ou bleu (-) (0 V), 2 ou brun (+) (48 VDC) ] Version ATH 500 M (seulement) ► Alimenter l'électrovanne de purge en 24 VDC (alimentation de fourniture client). Version ATH 500 MT (seulement) ► Alimenter la ceinture chauffante et l’électrovanne d’eau. – les connecteurs HEATER et VALVE en face avant de l'unité de commande électronique sont raccordés. 39/84 Installation V2 V4 Turbo 1 F V1 HEATER V3 2 W VALVE 3 4 Water 24 V DC P N2 48 VDC Fig. 14: Schéma de câblage électrique typique 1 Alimentation ceinture chauffante (Pompe version MT) 2 Electronique intégrée 3 Alimentation électrique externe 4 Alimentation électrique de l'électrovanne eau (Pompe version MT) P Pompe primaire Turbo Pompe turbomoléculaire à paliers magnétiques F Ventilateur (version refroidie à l'air) N2 Entrée gaz neutre V1 Vanne d’isolement vide primaire V2 Vanne d'isolement vide élevé V3 Electrovanne de purge (option) V4 Electrovanne d'entrée d'air (accessoire) W Electrovanne du circuit de refroidissement (Pompe version MT) Raccordement de la terre fonctionnelle 1) Raccordement de la terre de protection 1) Recommandé pour connecter la pompe à la prise de terre dans un environnement perturbé en ondes électromagnétiques. 40/84 Utilisation 6 Utilisation 6.1 Précautions préalables à l'utilisation AVERTISSEMENT Risque d'empoisonnement en présence de gaz de procédés dans l'atmosphère Le constructeur n’a pas la possibilité de contrôler le type de gaz utilisé avec la pompe. Les gaz de procédés sont fréquemment toxiques, inflammables, corrosifs, explosifs ou réactifs. Il existe un risque d’accident grave voire mortel lorsque ces gaz s’échappent librement dans l’atmosphère. ► Appliquer les consignes de sécurité spécifiques, conformément à la législation locale. Ces informations sont disponibles auprès du service sécurité de l’exploitant. ► Raccorder impérativement le refoulement de la pompe turbomoléculaire à une pompe primaire compatible avec les gaz de procédés : le refoulement de la pompe primaire est raccordé au système d'échappement des gaz dangereux de l'installation. ► Vérifier régulièrement l’absence de fuites au niveau du raccordement de la pompe avec la canalisation d’échappement. AVERTISSEMENT Risque de choc électrique en cas de déconnexion électrique pendant la rotation de la pompe La pompe turbomoléculaire et son unité de commande électronique ne peuvent pas être débranchées du réseau électrique avant l'arrêt complet de la rotation du rotor : l'ensemble pompe et électronique doivent être isolés du réseau électrique pour éviter tout choc électrique ! 1. Stopper la rotation de la pompe en envoyant un ordre 'Stop' sur l'interface de commande. 2. Attendre l'arrêt complet de la rotation du rotor (plusieurs minutes). 3. Couper l'alimentation électrique du réseau au niveau de l'équipement. 4. Débrancher le câble secteur. AVERTISSEMENT Risques de coupures par contact avec des arêtes vives par la bride de vide élevé L’accès aux pièces ‘coupantes’ est possible par la bride d’aspiration. Les arêtes des ailettes du rotor et du stator des pompes turbomoléculaires sont très tranchantes. ► Attendre l'arrêt complet de la pompe avant d'intervenir sur le produit. ► Toujours maintenir le filtre pare-éclats dans le carter d’aspiration, il atténue le risque de blessures. ► Toujours porter des gants de protection conformément à la norme EN ISO 21420. Le pompage de gaz pyrophoriques ou inflammables peut présenter des risques. L’utilisateur et/ou l’intégrateur du produit doit respecter les consignes de sécurité (voir chapitre « Consignes pour les matériaux pyrophoriques/inflammables »). Avant chaque mise en service : 1. Vérifier que la fixation de la pompe a bien été réalisée dans le respect des consignes de sécurité (voir chapitre « Conditions d'installation à l'équipement »). 2. Vérifier que l’aspiration de la pompe est bien raccordée à la ligne de pompage. 3. Mettre en service le circuit d’azote et le circuit d’eau. 4. Vérifier que les canalisations de refoulement ne sont pas bloquées et que toutes les vannes du système d’extraction sont ouvertes. 5. Vérifier que les vannes de fourniture client sont bien raccordées et alimentées, y compris la vanne de purge (si présente). 6. Vérifier que la ceinture chauffante et l'électrovanne d'eau sont bien raccordées à l'électronique (Pompe version MT). 7. Vérifier que le ventilateur est bien alimenté (si présent). 41/84 Utilisation 6.2 Démarrage de la pompe 6.2.1 Mise sous tension ► Positionner l'interrupteur de l'alimentation 48 VDC en position I : l'électronique s'initialise. – En fin d'initialisation, la LED jaune s'éteint et la LED verte s'allume. 6.2.2 Démarrage du pompage Les étapes suivantes décrivent l’utilisation de la pompe quelle que soit l’interface de commande. Se référer au chapitre « Interfaces de commande » pour le câblage et le paramétrage des différentes interfaces, ainsi qu'aux chapitres suivants : ● Utilisation via HHR (voir chapitre « Commande via le boîtier HHR ») ● Utilisation via télécommande Remote (voir chapitre « Commande via le connecteur Remote ») ● Utilisation via Liaison série RS-232/RS-485 (voir chapitre « Commande via la liaison série RS-232/RS-485 ») ● Utilisation via Bus de terrain (voir chapitre « Exploitation avec bus de terrain ») IN V2 V4 V1 V3 N2 Exh. Turbo Fig. 15: P Schéma de montage d'une installation de pompage Les composants dans l'installation de pompage V1 1) Vanne d'isolement vide primaire N2 Entrée purge de gaz neutre V2 1) Vanne d'isolement vide élevé Turbo Pompe turbomoléculaire à paliers magnétiques V3 1) Electrovanne de purge (option) P 1) Pompe primaire V4 1) Electrovanne d'entrée d'air (accessoire) 1) La fourniture, l’alimentation et le pilotage de ces composants sont de la responsabilité du client. Procédure de démarrage du pompage Conditions initiales : Les vannes V1, V2, V3, V4 sont raccordées et pilotées par l’équipement (installation client). L’enceinte ainsi que les canalisations sont à la pression atmosphérique, la pompe primaire est arrêtée, les vannes sont fermées. 1. Mettre en service le circuit de refroidissement. 2. Envoyer un ordre ’Start’ pompe via l’interface de commande via l’interface de commande HHR, Remote, liaison série ou bus de terrain. – La pompe primaire démarre et les vannes V1 et V2 s’ouvrent. – La pompe turbomoléculaire démarre pour atteindre la vitesse sélectionnée. 3. Selon l’application, ouvrir l’électrovanne de purge V3 (si installée et câblée). Le pompage s'effectue jusqu'à atteindre la pression d'utilisation pour l'application du client. Vitesse Stand-by La vitesse de Stand-by est sélectionnée pompe arrêtée ou en rotation. ► Envoyer un ordre ’Stand-by’ via l’interface de commande Remote, liaison série ou bus de terrain ou presser la touche STD-BY de l’interface HHR. Régulation de la température (Pompe version MT) ► Sélectionner la température de régulation souhaitée via l’interface de commande HHR, liaison série ou bus de terrain. Pour davantage d’information, voir chapitre « Régulation de la température de la pompe ». 42/84 Utilisation 6.2.3 Redémarrage après un arrêt d'urgence de l'équipement L’arrêt d’urgence est géré par l’équipement dans lequel la pompe est intégrée. Après un arrêt d’urgence, pour redémarrer la pompe, il est nécessaire de : 1. S'assurer que la pompe est arrêtée (toutes les LED sont éteintes). 2. Attendre l'arrêt complet de la rotation du rotor. 3. Corriger le problème. 4. Déverrouiller le bouton d’arrêt d’urgence de l’équipement. 5. Démarrer la pompe en envoyant un ordre ‘Start’ pompe via l’interface de commande : la pompe redémarre à la vitesse sélectionnée. 6.3 Arrêt de la pompe 6.3.1 Arrêt du pompage AVIS Risque d'endommager la pompe en générant un arc électrique La pompe et son unité de commande électronique ne doivent pas être débranchées du réseau électrique avant l'arrêt complet de la rotation du rotor et tant que l'ensemble n'est pas isolé du réseau électrique : un arc électrique est créé lors de l'interruption du circuit qui détériore les composants internes. 1. Stopper la rotation de la pompe en envoyant un ordre ‘Stop’ sur l'interface de commande. 2. Attendre l'arrêt complet de la rotation du rotor (plusieurs minutes). 3. Couper l'alimentation électrique du réseau au niveau de l'équipement. 4. Débrancher le câble secteur. Procédure d'arrêt Les vannes V1, V2, V3, V4 sont raccordées et pilotées par l’équipement (installation client). L’enceinte ainsi que les canalisations sont sous vide, la pompe primaire fonctionne, la vanne de purge V3 est ouverte. 1. Fermer la vanne V2 pour isoler la pompe de l’enceinte à pomper. 2. Envoyer un ordre ’Stop’ pompe via l’interface de commande HHR, Remote, liaison série, ou bus de terrain : – La pompe ralentit. 3. Activer l’électrovanne d’entrée d’air V4 (accessoire). 4. Fermer la vanne V1 et la pompe primaire s’arrête. 5. Arrêter le circuit de refroidissement lorsque la pompe est à l'arrêt (plus de rotation du rotor). 6. Stopper la purge de gaz neutre. AVIS Rôle de la purge de gaz neutre Lorsque la purge de gaz neutre s’arrête, les gaz de procédé peuvent rétrodiffuser et endommager les paliers internes de la pompe. ► Maintenir la purge de gaz neutre tant que le rotor tourne pour prolonger le balayage. ► Faire débiter la purge sans excéder la valeur maximum de 1 · 103 à 1,5 · 103 hPa absolus. AVIS Rôle de l'électrovanne d'entrée d'air L’électrovanne d’entrée d’air est calibrée pour remettre à la pression atmosphérique le volume interne de la pompe. Son efficacité à ralentir la pompe est améliorée lorsque des vannes d’isolement sont installées à l’aspiration et au refoulement de la pompe. ► Si la pompe a été arrêtée par une entrée d’air brutale, limiter le nombre de redémarrage à 2 par heure. ► Si la pompe a été arrêtée sans entrée d’air, le nombre de redémarrage n’est pas limité. ► Nous consulter pour choisir l'électrovanne d'entrée d'air. 43/84 Utilisation Arrêt sur coupure secteur L'arrêt de la pompe par coupure secteur n'est pas un arrêt normal pour la pompe : ● Toujours envoyer un ordre 'Stop' via l'interface de commande et attendre la fin de la rotation de la pompe avant d'intervenir. Lorsqu’une coupure d’alimentation intervient, la suspension du rotor est assurée par l’énergie que délivre la force contre-électromotrice du moteur, ceci jusqu’à ce que la vitesse de rotation du rotor soit suffisamment basse pour qu’il se pose sur les roulements de secours sans dommage. Si l’alimentation revient avant que la vitesse minimum soit atteinte, la pompe reprend alors sa vitesse sans aucune perturbation. Le compteur des roulements de secours ne se décrémente pas. Dans le cas où la vitesse minimum est atteinte avant que l’alimentation secteur ne soit revenue : ● La pompe atterrit sur ses roulements de secours. ● L’unité de commande électronique s’éteint, aucun voyant n’est éclairé. ● Le compteur des roulements de secours se décrémente (voir chapitre « Intervalle de maintenance »). Reprendre ensuite la procédure de démarrage normal après le retour du courant d’alimentation secteur. 6.3.2 Mise hors tension 1. Mettre la pompe hors tension en positionnant l'interrupteur de l'alimentation générale 48 VDC sur O: – Toutes les LED de l'unité de commande électrique sont éteintes. – Attendre l'arrêt complet du rotor. 2. Débrancher le câble d'alimentation de la pompe sur l'unité de commande électronique. 6.3.3 Arrêt prolongé Dans le cas d’un arrêt prolongé de la pompe, appliquer la procédure de mise hors service (voir chapitre « Immobilisation prolongée »). 6.4 Surveillance du fonctionnement Lorsqu'un problème intervient, l'utilisateur est averti par : ● ● ● ● ● ● ● L’éclairage de la LED relative au défaut/alerte L’avertisseur sonore du boîtier HHR (si la fonction est validée) L’activation des contacts défauts sur la prise télécommande REMOTE L’arrêt du pompage alors que l'ordre 'Stop' n’a pas été activé L'affichage d'un message défaut sur le boîtier HHR Un message via la liaison série RS-232 ou RS-485 Un message via la liaison bus de terrain Les messages défauts sont listés au chapitre « Dysfonctionnements ». LED Verte Jaune 44/84 Symbole Etat de la LED Indication Signification éteinte Hors tension. allumée, clignotante 10 % Pompe sous tension. Pompe arrêtée ou vitesse de rotation < 60 min-1. allumée, clignotante 90 % La pompe n’a pas atteint la vitesse sélectionnée. allumée, fixe La pompe a atteint la vitesse sélectionnée. allumée, clignotante 50 % La pompe ralentit, la vitesse est > 60 min-1. éteinte Aucun avertissement. allumée, fixe L'électronique s'initialise ou présence d'une alerte. Utilisation Symbole Rouge Tab. 3: Etat de la LED Signification éteinte Aucun défaut. allumée, fixe La pompe est en défaut. Signification des LED sur l'interface EtherCAT REMOTE PWR Etat de la LED Tab. 4: Indication STBY LED Signification Bleu allumé La pompe est sous tension. Jaune allumé La pompe n’a pas atteint la vitesse sélectionnée. Jaune clignotant La pompe ralentit, la vitesse est > 60 min-1. Jaune STBY allumé Mode Standby sélectionné. Vert allumé La pompe a atteint la vitesse sélectionnée. Vert clignotant La vitesse de rotation est supérieure à la vitesse sélectionnée. Rouge allumé La pompe est en défaut. Rouge clignotant Une alerte est signalée. Signification des LED sur l'interface Remote/RS232-RS485/Profibus 45/84 Réglages avancés 7 Réglages avancés Ce chapitre décrit les fonctions disponibles et leurs fonctionnements respectifs. Ce chapitre aide l'utilisateur et/ou l'intégrateur à paramétrer le produit selon les spécificités d'utilisation en procédé. 7.1 Régulation de la température de la pompe Le système de régulation de température (TMS) qui équipe les pompes version MT est constitué d’une ceinture chauffante et d’une électrovanne d’eau. La ceinture chauffante intégrée permet de chauffer la pompe jusqu’à une température réglable (appelée température de régulation) afin d’éviter les effets de condensation. La température de régulation dépend de l’application pour laquelle la pompe est utilisée. Contacter le service application de Pfeiffer Vacuum pour vous aider à choisir cette température de régulation. La ceinture chauffante et la vanne d’eau permettent de réguler la température de la pompe jusqu’à la température de régulation. L'unité de commande électronique commande la régulation de température. La température de régulation est choisie via l’interface de commande HHR, via la liaison série ou bus de terrain (voir chapitre « Différents modes de commande »). En fonction de la température de régulation choisie pour le chauffage de la pompe et de la température de refroidissement du circuit d’eau, la pompe peut mettre un certain temps pour atteindre sa température de régulation. 7.2 Le freinage de la pompe Freinage avec électrovanne d'entrée d'air Le freinage avec une électrovanne d'entrée d'air permet de diminuer le temps d'arrêt de la pompe dans le cas où le freinage électrique n'est pas suffisant. L’électrovanne d’entrée d’air s'installe sur le refoulement de la pompe. L’électrovanne d’entrée d’air est calibrée (débit 11 · 103 sccm) pour remettre à la pression atmosphérique le volume interne de la pompe. Son efficacité à ralentir la pompe est améliorée lorsque des vannes d’isolement sont installées à l’aspiration et au refoulement de la pompe. L'alimentation électrique 24 VDC et le pilotage de la vanne d'entrée d'air sont de la responsabilité du client (voir chapitre « Raccordement de l'électrovanne d'entrée d'air »). Freinage électrique Le freinage électrique est disponible sur les modèles ATH 500 MT. Le freinage électrique permet de freiner la pompe sur envoi d'un ordre 'Stop' pompe, ou lors d'un arrêt sur défaut après un délai de 15 minutes durant lequel la pompe peut être maintenue sous vide. 46/84 Interfaces de commande 8 Interfaces de commande 8.1 Différents modes de commande Ce chapitre décrit pour chaque mode de commande, les raccordements et protocoles associés. On distingue 4 modes de commande : ● HHR La pompe est pilotée en local à partir d’un boîtier de commande déportable HHR, connecté sur le connecteur SERVICE. ● REMOTE La pompe est commandée à distance par l'ouverture ou la fermeture des différents contacts secs, ou par l'application d'une tension sur le connecteur REMOTE. ● LIAISON SERIE La pompe est pilotée à distance à partir des ordres de commande transmis par la liaison série RS-232/RS-485. ● LIAISON BUS TERRAIN La pompe est pilotée à distance par un système de pilotage (automatisme, régulation, supervision) qui communique avec la pompe selon le protocole de communication du bus terrain. Différentes interfaces de commande pour communication avec bus terrain (Profibus, EtherCAT, ... ) sont disponibles selon le configurateur de commande. Choix du mode de commande C'est le mode sélectionné qui pilote la pompe. Le choix du mode de commande peut être réalisé : ● Soit par le boîtier HHR. ● Soit par la liaison série RS-232/RS-485. 8.2 Commande via le boîtier HHR Description du boîtier HHR Le boîtier de commande HHR connecté à l'unité de commande électronique permet l'affichage et la configuration des paramètres. 1 2 3 1 Afficheur 2 LED 4 3 4 Touches de sélection/configuration des paramètres Touches de pilotage manuel 47/84 Interfaces de commande Touche STATUS PREV. Fonctions Touche ● Accéder à l’affichage des paramètres. ● Sortir des menus et revenir à l’affichage des paramètres. ● Valider le choix d’un menu, d’un paramètre ou d’une valeur. ● Accéder au mode paramétrage. ● Sortir des différents menus sans valider les fonctions. ● Faire fonctionner la pompe en vitesse réduite via HHR lorsque le menu [SET UP][REMOTE CONTROL] est réglé sur [KEYBOARD] (voir chapitre « Menu SETUP »). La LED est allumée quand la pompe fonctionne à vitesse de Stand-by. ● Confirmer une réponse à une question posée. STD-BY ● Accéder au menu suivant ou précédent, au paramètre suivant ou précédent du menu affiché. START ● Choisir ou ajuster la valeur du paramètre. PURGE Fonctions ● Faire fonctionner la purge via HHR lorsque le menu [SET UP] [REMOTE CONTROL] est réglé sur [KEYBOARD] (voir chapitre « Menu SETUP »). La LED est allumée quand la purge est activée. Tab. 5: STOP ● Démarrer la pompe en mode local, via HHR lorsque le menu [SET UP][REMOTE CONTROL] est [KEYBOARD] (voir chapitre « Menu SETUP »). ● Arrêter la pompe en mode local, via HHR lorsque le menu [SET UP][REMOTE CONTROL] est [KEYBOARD] (voir chapitre « Menu SETUP »). Description des touches du boîtier HHR AVIS Risque de détérioration du clavier Un film isolant protège les touches. L'utilisation d'objets durs et pointus tels que stylos, tournevis peut endommager les touches du clavier. ► Activer le clavier manuellement. Description de l'afficheur L'afficheur indique l'état du pompage et des paramètres surveillés. L'appui sur les touches +/- permet le défilement des paramètres surveillés. 1 3 4 2 KEYB xxxx H Pump 24°C 0.00 A 0 rpm Ctrl 27°C ........ Ready to start .......... 1 Interface de commande 2 Heures de fonctionnement 8.2.1 3 4 Paramètres surveillés/défauts Messages état fonctionnement pompe Mise sous tension ► Vérifier avant la mise en service du boîtier HHR que les connexions électriques sont bien réalisées. ► Raccorder le boîtier de commande déportable au connecteur SERVICE. ► Positionner l’interrupteur secteur en position I : le boîtier HHR s'initialise. Le boîtier HHR peut être raccordé alors que la pompe est sous tension et/ou en rotation. Les réglages initiaux A la première mise en service, la pompe fonctionne selon les réglages initiaux réalisés en usine, ces réglages dépendent de la configuration de commande du produit. Les réglages initiaux sont protégés par un code d'accès (valeur usine '0') qui peut être personnalisé. ● L'utilisateur ou l'intégrateur du produit est responsable de la modification des paramètres de la pompe en fonction de l'application. 48/84 Interfaces de commande Le mode de commande HHR est actif lorsque le mode de pilotage ’Keyboard’ est configuré par le boîtier HHR ou par la liaison série RS-232/RS-485. Initialisation de l'affichage 1. L'unité de commande électronique effectue un autotest et identifie la pompe à laquelle elle est raccordée. Le temps d’initialisation est d’environ 15 secondes. ■■■■■■■■■■■■■■■■■■■■■ ■■■■■■■■■■■■■■■■■■■■■ ■■■■■■■■■■■■■■■■■■■■■ ■■■■■■■■■■■■■■■■■■■■■ ■■■■■■■■■■■■■■■■■■■■■ ■■■■■■■■■■■■■■■■■■■■■ 2. 3. L’équipement est identifié, la version du programme est affichée, la communication avec la pompe est testée. HHR V0X.0Y.00 Checking procedure Dans le même temps les voyants sont testés, ils s’allument successivement. HHR V0Z.0X.00 Collecting data ■■■■■■■■■■■■■■■■■■■■■ 4. A la fin du test, l'écran de travail affiche le modèle de pompe connectée ainsi que le message 'Ready to start....'. KEYB 0H CTRL VXX.0Y.0V ATHxxxx ........ Ready to start .......... Accès aux menus 1. Accéder au mode paramétrage par appui sur PREV. Entrer dans le menu [DISPLAY] par appui sur la touche ENTER. 2. Régler les paramètres d'affichage. Passer d'un menu à l'autre avec les touches +/-. Ressortir du menu par appui sur la touche PREV. 3. Accéder au menu [SETUP] avec les touches +/-. Entrer dans le menu par appui sur ENTER. 3. Entrer le code d’accès pour modifier les paramètres et valider par appui sur la touche ENTER. Ressortir du menu par appui sur la touche PREV. 8.2.2 KEYB xxxx H DISPLAY SETUP SER NUM ........ Ready to start .......... KEYB xxxx H STATUS VER FAULT BEARING WARNING ........ Ready to start .......... KEYB xxxx H DISPLAY SETUP SER NUM ........ Ready to start .......... KEYB xxxx H ACCESS CODE 0 ........ Ready to start .......... Menu DISPLAY Sélection Description STATUS Affichage de l’état de la pompe et de l'unité de commande électronique : ● Température pompe ● Courant moteur ● Température de l’électronique ● Vitesse de rotation de la pompe VERSION Affichage de la version de l'unité de commande électronique (dépend du modèle de pompe connectée) : ● Version du boîtier de commande ● Version de la face avant de l’électronique ● Version du variateur intégré ● Version de la pivoterie de la pompe turbomoléculaire FAULT Affichage successif des 10 derniers défauts avec leur intitulé. 49/84 Interfaces de commande Sélection Description WARNING Affichage successif des 10 dernières alertes avec leur intitulé. BEARING Affichage de la durée de vie des roulements de secours en pourcentage et du seuil d’alerte en pourcentage. 8.2.3 Menu SETUP Sélection Choix Description ACCESS CODE 0 à 65535 REMOTE CONTROL Keyboard Remote hard Serial link Profibus EtherCAT Choisir le mode de commande. Selon la configuration de commande STAND-BY SPEED de 15000 min-1 à la vitesse nominale de la pompe Choisir la vitesse de Stand-by (vitesse sélectionnée) de la pompe, réglable entre une valeur minimum et la vitesse nominale (= vitesse réglée en usine). 15000 BUZZER ON OFF Activer l’avertisseur sonore pour signaler un défaut. Pour stopper l’avertisseur, appuyer sur OFF. OFF THERMOSTAT ON = 30 à 65 °C OFF Activer la température de régulation de la pompe. OFF (version M) ON = 65 °C (version MT) RELAY AT SPEED -3 à 50 % de la vitesse nominale Modifier le seuil du contact de vitesse. -3% FIELDBUS PROFILE 2) 0 1 Réservé pour le service 0 RS-232 SPEED 9K6 19K2 38K4 57K6 Choisir la vitesse de transmission sur la liaison série RS-232. 9K6 RS-232 ECHO ON OFF Autoriser ou ne pas autoriser le retour en écho des caractères reçus sur la liaison série RS-232. OFF RS SEPARATOR 0 à 255 Entrer le caractère séparateur en ASCII : exemple “044” correspond à “,”. 44 RS ADDRESS 0 à 255 Affecter une adresse à la pompe. 0 BEARING LIVE Warning limit 0 à 99 % Modifier le seuil d’alerte des roulements de secours. 20 NEW CODING 0 à 65535 Modifier le code d’accès aux paramètres. 0 Réglage initial 1) 0 FIELDBUS ADDRESS 2) 1) Pour des produits spécifiques, les réglages initiaux peuvent être différents (voir chapitre « Produits concernés »). 2) Voir le manuel de l’utilisateur du protocole de communication du bus de terrain qui pilote la pompe. 8.2.4 Menu SER NUM Sélection Affichage Réglage initiaux HHR Affichage du numéro de série du boîtier de commande déportable. XXXXXXXXXX CONTROLLER Affichage du numéro de série de l'interface de commande de l'unité de commande électronique. YYYYYYYYYY CARTRIDGE 1) Affichage du numéro de série de la pivoterie. ZZZZZZZZZZ MMCC06 1) Affichage du numéro de série de la carte électronique. AAAAAAAA 1) Uniquement si HRR connectée à une pompe ATH 500. 50/84 Interfaces de commande 8.3 Commande via le connecteur REMOTE AVIS Sécurité des circuits très basse tension Les circuits de télécommande sont équipés de sorties à contact sec (24 V - 1 A max.). Toute surtension ou surintensité peut entraîner des dommages électriques internes. L'utilisateur doit respecter les conditions de câblages suivantes : ► Relier ces sorties conformément aux règles et protection des réseaux très basse tension de sécurité (TBTS). ► Alimenter ces contacts avec une tension inférieure à 24 VDC et un courant inférieur à 1 A. Description Le raccordement réalisé via le connecteur REMOTE (HD, Sub-D femelle 15 broches) permet : ● la commande à distance des fonctions démarrage, arrêt ● la recopie de l’état de la pompe sous forme de contacts secs Le mode télécommande est actif lorsque le mode de pilotage ’Remote hard’ est configuré sur la liaison série RS-232/RS-485 ou par le boîtier HHR. Lorsque le mode de pilotage ’Remote hard’ est configuré, le réglage de la vitesse de Stand-by et de la température de régulation sont possibles via la liaison série RS-232/RS-485 ou le boîtier HHR. ► Effectuer le câblage au moyen d’un câble blindé et relier les 2 côtés à la terre. 8.3.1 Câblage des entrées logiques Commande par une tension continue Les entrées sont actives lorsqu'une tension continue comprise entre 10 et 24 VDC est appliquée entre leurs broches (câblage de fourniture client). A B +15 V 5 5 13, 14 (+) (+) 5 4 3 10 9 15 S 1 2 8 7 6 11 (-) (-) 15 15 10 10 10-24 VDC GND - Fig. 16: + + Connecteur Remote : commande par tension continue A Câblage interne B Câblage côté client Tension 10-24 VDC Fonction S3 (13-15) Stand-by 1) Contact fermé : la vitesse de Stand-by est sélectionnée. Contact ouvert : la vitesse de rotation correspond à la vitesse nominale de la pompe. S4 (14-15) Start/Stop pompe 1) Contact fermé : la pompe démarre. Contact ouvert : la pompe s’arrête. 1) Cette fonction est opérationnelle si le mode de pilotage est paramétré sur ’Remote hard’ par la liaison série RS-232/RS-485 (voir chapitre « Liste des commandes ») ou via HHR (voir chapitre « Menu SETUP »). Commande par contacts secs Pour contrôler ces entrées par des contacts externes de l'équipement, relier les broches 10 et 15 et câbler les contacts utilisés (câblage de fourniture client). Les broches 13, 14 sont connectées au + 15 V (broche 5) pour être actives. 51/84 Interfaces de commande A B 5 +15 V 5 4 10 3 9 2 8 7 15 (+) (+) 13, 14 1 5 S 6 11 S4 Fig. 17: S3 (-) (-) 15 15 10 10 GND Connecteur Remote : commande par contacts secs A Câblage interne B Câblage côté client Contact Fonction S3 (13-5) Stand-by 1) Contact fermé : la vitesse de Stand-by est sélectionnée. Contact ouvert : la vitesse de rotation correspond à la vitesse nominale de la pompe. S4 (14-5) Start/Stop pompe 1) Contact fermé : la pompe démarre. Contact ouvert : la pompe s’arrête. 1) Cette fonction est opérationnelle si le mode de pilotage est paramétré sur ’Remote hard’ par la liaison série RS-232/RS-485 (voir chapitre « Liste des commandes ») ou via HHR (voir chapitre « Menu SETUP »). 8.3.2 Câblage des sorties logiques A B 4, 3, 2, 1 5 4 3 2 1 9, 8, 7, 6 10 9 8 15 Fig. 18: 7 6 11 Connecteur Remote : sorties logiques A Câblage interne B Câblage côté client Contact Fonction 1-6 Relay At speed Contact fermé : OK for Process (At speed) ● Version M : vitesse ≥ vitesse nominale (définie par valeur de l’option Relay At speed (Vitesse atteinte) (voir chapitre « Menu SETUP ») ou (voir chapitre « Liste des commandes »). ● Version MT : vitesse ≥ vitesse nominale (définie par valeur de l’option Relay At speed (Vitesse atteinte) (voir chapitre « Menu SETUP ») ou (voir chapitre « Liste des commandes »), et si la température est ≥ à la température de régulation - 3 °C. 2-7 Rotation 1er cas : Rotating mode OPT33 = 0 ● Le contact se ferme quand la vitesse est > 120 min-1. ● Le contact s’ouvre quand la vitesse est < 100 min-1. ème 2 cas : Accelerating mode OPT33 = 1 ● Le contact se ferme quand le moteur est en phase d’accélération. Il reste fermé jusqu’à atteindre la vitesse nominale. ● Le contact s’ouvre quand une commande STOP ou INHIBIT est prise en compte ou si la vitesse nominale est atteinte. Pour éviter toute mauvaise lecture de l’état des contacts, nous conseillons un filtrage d’une seconde sur la lecture des contacts At Speed, Rotation, Fault et Stand-by. 52/84 Interfaces de commande Contact Fonction 3-8 Fault ● Le contact 'Fault' se ferme à l’apparition d’un défaut (externe, température, châssis moteur, etc…). ● Le contact est ouvert en l’absence de défaut. 4-9 Stand-by ● Le contact 'Stand-by' est fermé lorsque le mode stand-by est activé. Pour éviter toute mauvaise lecture de l’état des contacts, nous conseillons un filtrage d’une seconde sur la lecture des contacts At Speed, Rotation, Fault et Stand-by. 8.4 Commande via la liaison série RS-232/RS-485 AVIS Risque de perturbation électromagnétique Tensions et courants induisent une multitude de champs électromagnétiques et des signaux parasites. Une installation non conforme aux règles CEM perturbe les autres équipements ou plus généralement l’environnement. ► Utiliser des liaisons et raccordements blindés pour les interfaces dans les environnements perturbateurs. AVERTISSEMENT Risque de choc électrique par contact avec un produit non isolé électriquement A la mise hors tension _interrupteur secteur sur O_, certains composants situés entre le connecteur électrique et le disjoncteur restent sous tension. Il y risque de choc électrique par contact. ► Veiller à ce que le raccordement au secteur soit toujours visible et accessible pour pouvoir débrancher à tout moment. ► Débrancher le câble secteur du réseau électrique avant d'intervenir sur le produit. 8.4.1 Connexions Le connecteur Sub-D, mâle 9 broches repéré RS-232/RS-485 permet de piloter et de surveiller la pompe connectée à un ordinateur externe. Ce connecteur permet également la mise en réseau de plusieurs pompes. L'ordinateur connecté permet de modifier les paramètres initiaux de la liaison série (voir chapitre « Liste des commandes »). Configuration initiale liaison série Désignation Valeur Interface série RS-232 Vitesse de transmission 9600 bauds Longueur d'un mot de données 8 bits Parité aucune (no parity) Bits de stop 1 Echo non Connecteur RS-232/RS-485 Broche Affectation 2 Réception données (RS-232) 3 Transmission données (RS-232) 53/84 Interfaces de commande Broche Affectation 5 GND 8 RS-485 : V- 9 RS-485 : V+ L'utilisateur doit assurer les blindages extérieurs permettant de satisfaire aux normes C.E.M. et sécurité électrique. Connexion RS-232 Un ordinateur gère une seule pompe (P1) par la liaison RS-232 via le connecteur RS-232/RS-485. P1 Connexion RS-485 Un ordinateur gère plusieurs pompes (P1, P2, Pn,..) par liaison série RS-485 via le connecteur RS-232/ RS-485. Ce type de câblage parallèle permet de maintenir la communication entre les pompes même si une pompe est déconnectée. Le câblage du produit en bout de ligne Pn* ainsi que le câblage d’un seul produit sur le réseau est spécifique. 1,5 kΩ / 1/4 W 120 Ω / 1/4 W RS-485 communication box P1 Pn* P2 Paramétrage Le mode de commande liaison série est actif lorsque le câblage est réalisé et que le mode de pilotage ’Serial link’ est configuré par le boîtier HHR (voir chapitre « Menu SETUP ») ou sur la liaison série RS-232/RS-485 (voir chapitre « Liste des commandes »). ► Positionner l’interrupteur de l'alimentation 48 VDC en position I. ► Envoyer une commande sur la liaison série. 8.4.2 Protocole de communication Les commandes Caractère d'en-tête Le réglage usine est le code décimal 035 du caractère # Adresse Numéro affecté à la pompe sur 3 caractères Ordre Commande envoyée sur la liaison série, sur 3 caractères Paramètre Format et nombre de caractère dépendent de la commande Caractère de fin Caractère de fin de message. Le réglage est le code ASCII 13 <CR> Le caractère <LF> n'est pas pris en compte. Exemple : 54/84 Caractère d'en-tête Adresse de la pompe Commande Paramètre Caractère de fin # ADR ODR XXXX <CR> Interfaces de commande Les réponses Caractère d'en-tête Adresse de la pompe Réponse Caractère de fin # ADR yyyxxxabc <CR> OK Si tout est OK, ou réponse spécifique à l'ordre transmis ERR0 Erreur de réglage ERR1 Erreur d'ordre ERR2 Erreur de paramètre ERR3 Erreur de contexte ERR4 Erreur checksum Exemple de dialogue 8.4.3 Commande #005ECHON<CR> Réponse #005OK<CR> Liste des commandes Ordre Paramètre Description Fonctions Mini Maxi Réglage initial ADR xxx Attribution d'une adresse à une pompe dans le réseau. Exemple : #adrADR,xxx<CR> (RS 232 uniquement) ● adr = adresse de la pompe avant la commande ● xxx = nouvelle adresse 000 255 0 DEF aucun Affichage historique alertes/ défauts Liste les 10 derniers alertes/défauts horodatés au temps de fonctionnement de l’électronique, suivi du nom du défaut. La flèche->indique l’alerte/le défaut en cours Exemple : * 00000:02:20 / Default list ->00000:01:37 / Default in current Yh ->00000:01:37 / PM Default * 00000:02:20 / Warning list ->00000:02:37 / Holweck Temp. sensor 00000:01:30 / Speed controller Hall sensor 00000:00:50 / Holweck Temp. sensor DLI xxx Intervalle de lecture du Data loger Paramétrage de l’intervalle de lecture automatique de l’état de la pompe (STA), en seconde 0 255s 1s DLR aucun Lecture automatique en Data loger Autorisation de lecture automatique de l’état de la pompe (STA) au rythme défini par la commande DLI (RS 232 uniquement) OFF ECH ON ou OFF Renvoi caractère reçu sur la liaison série Activé si ECHON (RS 232 uniquement) Désactivé si ECHOFF (RS 232 uniquement) OFF IDN aucun Identification du produit qui communique avec l’ordinateur Retourne le type de pompe en communication avec l’ordinateur. La version de logiciel (x, yy), l’édition (zz) Exemple : #adr,Pump_name Vx.y.zz,<CR> 55/84 Interfaces de commande Ordre Paramètre Description Fonctions Mini Maxi Réglage initial LEV10 aucun Etat des paramètres de fonctionnement définis avec la commande SET Exemple : #adr,nnnnn,sssss,00000,0,ccccc,eeeee,00000,0000,0000,jj, kk,ll,mmm<CR> nnnnn = vitesse nominale (min-1) sssss = vitesse de standby (min-1) 00000 = non utilisé 0 = non utilisé ccccc = temps de fonctionnement pompe (heures) eeeee = temps de fonctionnement électronique 00000 = non utilisé 0000 = non utilisé jj = consigne du relais ’At speed’ (vitesse atteinte) (3 à 50 %) kk = température régulée (30 à 65° C) ll = seuil alerte roulements de secours (0 à 99 %) mmm = compteur roulements de secours (0 à 100 %) NSP aucun Autorise le passage de la vitesse Stand-by à la vitesse nominale La pompe fonctionne à la vitesse nominale définie en usine OPT XX Choix des options/ commandes par l’utilisateur Exemple : #adrOPTXX,n<CR> ● XX = 25 Commande du freinage n = 1 aucun freinage moteur n = 0 freinage moteur 0 1 0 ● XX = 29 Régulation de température ON/OFF (Pompe version MT) n = 0 régulation de température inactif n = 1 régulation de température actif 0 1 0 ● XX = 33 mode contact n = 0 Rotating (contact fermé si la vitesse > 120 min-1 n = 1 accelerating (contact fermé en phase d'accélération) 0 1 0 15000 50000 15000 ● XX = 14 Mode de pilotage n = 0 pilotage via la HHR (clavier) n = 1 pilotage via la Remote (hard)* n = 2 pilotage via liaison RS-232/RS-485 n = 5 pilotage via Profibus n = 8 pilotage via EtherCAT * pas accessible avec EtherCAT RDI aucun Numéro de série de l’électronique Correspond au numéro de série, codé sur 10 digits et stocké dans EEPROM des numéros de série de la pompe, de la pivoterie, de l'interface de commande. RPM aucun Paramétrage de la vitesse de Stand-by Exemple : #adr,nnnnn<CR> nnnnn = vitesse de Stand-by SBY aucun Autorise le passage de la vitesse de consigne à la vitesse de Stand-by La pompe fonctionne à la dernière vitesse de Stand-by mémorisée. Celle-ci peut être modifiée avec la commande RPM. 56/84 Interfaces de commande Ordre Paramètre Description Fonctions Mini Maxi Réglage initial SEL10 aucun Etat des options/ commandes définies avec la commande OPT Exemple : #adr,0,0,1,0,r<CR> 000 255 044 XX = 30 seuil de relais ’At Speed -Vitesse atteinte’ (%) -3 - 50 -3 XX = 31 température de régulation (°C) (Pompe version MT) 30 65 30 XX = 32 seuil d’alerte des roulements (%) 0 99 20 0 = non utilisé 1 = non utilisé r = retourne le choix du mode de pilotage r = 0 Hand Held Remote (keyboard) r = 1 Remote control r = 2 Serial link r = 5 Profibus r = 8 EtherCAT valeur par défaut en fonction de la référence de la pompe SEL20 aucun Paramètres définis avec la commande OPTXX Retourne l'état des paramètres S25, S29, S33 définis avec la commande OPTXX. Exemple : #000,S25,S29,S33<CR> SEP aucun Caractère séparateur Valable pour les paramètres retournés par les commandes DLR, STA et LEV. Valeur décimale du code ASCII du caractère code 044 correspond à virgule “,” SET XX Réglage des paramètres de fonctionnement de la pompe Exemple : # adrSETXX,ccccc<CR> XX = 10 temps d'utilisation de la pompe (en heures) ccccc = valeur TMP ON ou OFF Démarrer/ arrêter la pompe La pompe fonctionne avec TMPON. La pompe s’arrête si TMPOFF. VER aucun Affichage des versions de logiciel #adr,INTERFACE Vx.yy.zz,CARTRIDGE Vx.yy,TYPE zzzz,FIRMWARE Vx.yy.zz<CR> INTERFACE vx.yy.zz = version du logiciel carte interface CARTRIDGE vx.y = version logiciel du variateur Type zzzz = type de pompe raccordée FIRMWARE Vx.yy.zz = version logiciel Ordre Paramètre Description Fonctions STA aucun Etat de la pompe Exemple : #adr,s1s2s3, rrrrr,vvv, www, xxx, yyy, zzz, aa, bbbbb, ccc, ddd, gggggggggggggggggggggggg<CR> rrrrr = vitesse de la pompe (min-1) aa = tension moteur (V) bbbbb = courant moteur (mA) ccc = Température pompe (° C) ddd = Température électronique (° C) s1s2s3 = nécessite de convertir de ASCII à binaire vvv = Radial Xh www = Radial Yh xxx = Radial Xb yyy = Radial Yb zzz = Axial Z g0 à g24 = bit d’alertes et défauts 57/84 Interfaces de commande Ordre Paramètre STA STA STA 58/84 aucun aucun Description Fonctions s1: état de l’ordre Bit s2: état de la pompe s3: état des électrovannes 7 6 5 4 3 2 1 0 INH Local Fault Serial Fieldbus REM STBY START 0 - 0 OFF OK 0 OFF OFF OFF 1 1 ON ON si HHR a le contrôle Fault si statut Fault actif ON si mode pilotage bus terrain actif ON si mode pilotage Remote hard ON si mode Stand-by actif ON en démarrage, en vitesse ou survitesse Bit 7 6 5 4 3 2 1 0 Fault Warning Temp. Braking (Free) Accelerating Rotating Power (init). 0 - OFF OFF OFF 0 OFF OFF - 1 1 si défaut actif ON si dépassement temp. pompe ON - ON si mode démarrage ON en démarrage, en vitesse ou survitesse ON Bit 7 6 5 4 3 2 1 0 Vitesse (Free) (Free) Vanne d’eau Régulation temp. (Free) (Free) 0 - OFF - - OFF OFF 0 0 1 1 ON si statut ’Vitesse atteinte’ - - ON si vanne d’eau alimentée (MT) ON si TMS actif (MT) - - Interfaces de commande Ordre Paramètre Description Fonctions STA aucun g0 à g24 : bits d’alerte et défaut g 0 0 = ok 1 = alerte 2 = défaut Seized pump Not accelerating 1 Fault (any) 2 3 4 5 Drive fault 6 7 8 Mag. suspens. Power voltage 9 10 Upper radial bearing Yh 11 Upper radial bearing Xh 12 Lower radial bearing Yb 13 Lower radial bearing Xb 14 Axial bearing Z 15 Bearing Bearing change 16 Electronic temperature Electronic temperature 17 Pump temperature, pump sensor Pump temperature 18 19 20 Self check 21 22 23 24 8.5 Internal communication Exploitation avec bus de terrain Le raccordement et l'exploitation de pompes turbomoléculaire Pfeiffer Vacuum par un système bus de terrain est possible lorsque l’interface de commande correspondante est installée sur la pompe (dépend de la configuration de commande). ► Vous référer au manuel de l’utilisateur de l’interface de commande correspondante (voir chapitre « Documents applicables »). 59/84 Maintenance 9 Maintenance 9.1 Consignes de sécurité pour la maintenance DANGER Risque pour la santé lié aux traces résiduelles de gaz de procédés à l'intérieur de la pompe Les gaz de procédés sont toxiques et dangereux pour la santé. Ils peuvent entraîner l’empoisonnement ou la mort. Aussi, avant de déconnecter la pompe, il convient d’éliminer un maximum de traces résiduelles de gaz de procédés. ► Effectuer obligatoirement un balayage de l’équipement (installation de pompage) avec un flux d'azote pendant 30 minutes : la pression et le débit d'azote doivent être identiques aux valeurs programmées pour le procédé. DANGER Risque d'empoisonnement par contact avec des substances toxiques et sous-produits générés par le procédé La pompe à vide, les composants de la ligne de pompage, les fluides d'exploitation sont contaminés par des substances toxiques, corrosives, réactives ou radioactives liées au procédé. Tout contact avec les pièces contaminées ou les sous-produits générés par le procédé présente un risque d’empoisonnement pour la santé. ► Porter les équipements de protection appropriés lors de la déconnexion pour maintenance de la pompe, ainsi que pour le remplissage ou la vidange du fluide d’exploitation. ► Bien aérer le local ou effectuer la maintenance sous hotte ventilée. ► Ne pas jeter les sous-produits/résidus au réseau usuel : faire appel à un organisme compétent pour leur destruction si nécessaire. ► Fermer toutes les ouvertures avec des obturateurs étanches à l’air (obturateurs livrés avec le produit et disponibles en accessoires). AVERTISSEMENT Risques de coupures par contact avec des arêtes vives par la bride de vide élevé L’accès aux pièces ‘coupantes’ est possible par la bride d’aspiration. Les arêtes des ailettes du rotor et du stator des pompes turbomoléculaires sont très tranchantes. ► Attendre l'arrêt complet de la pompe avant d'intervenir sur le produit. ► Toujours maintenir le filtre pare-éclats dans le carter d’aspiration, il atténue le risque de blessures. ► Toujours porter des gants de protection conformément à la norme EN ISO 21420. AVERTISSEMENT Risque d'électrocution par contact lors de l'entretien ou la maintenance Il y a un risque de choc électrique par contact avec un produit sous tension et non isolé électriquement. ► Avant toute intervention, placer l’interrupteur principal sur O. ► Débrancher le câble secteur du réseau électrique. ► Sécuriser correctement l’installation en repérant et condamnant le circuit de puissance pour éviter tout ré-enclenchement non intentionnel (LO/TO procédure de consignation/déconsignation). AVERTISSEMENT Risque de brûlure par contact avec des surfaces chaudes La température des pièces reste élevée même après l’arrêt de la pompe. Il y a risque de brûlure par contact avec les surfaces chaudes, en particulier au niveau du refoulement de la pompe. ► Attendre le refroidissement complet avant d’intervenir sur le produit. ► Porter des gants de protection conformément à la norme EN ISO 21420. 60/84 Maintenance AVERTISSEMENT Risque d'intoxication en cas de fuites de gaz de procédés Lors de la déconnexion/connexion de composants dans la ligne de pompage (pompe, canalisations, vannes....) pour maintenance, l'étanchéité de l'installation est rompue : il y a un risque potentiel de fuites de gaz de procédés. ► Pendant le démontage, toujours protéger les surfaces des brides d'aspiration et de refoulement. ► Après remontage, effectuer un test d'étanchéité sur l'ensemble de la ligne de pompage. AVIS Risque d'endommager la pompe en générant un arc électrique La pompe et son unité de commande électronique ne doivent pas être débranchées du réseau électrique avant l'arrêt complet de la rotation du rotor et tant que l'ensemble n'est pas isolé du réseau électrique : un arc électrique est créé lors de l'interruption du circuit qui détériore les composants internes. 1. Stopper la rotation de la pompe en envoyant un ordre ‘Stop’ sur l'interface de commande. 2. Attendre l'arrêt complet de la rotation du rotor (plusieurs minutes). 3. Couper l'alimentation électrique du réseau au niveau de l'équipement. 4. Débrancher le câble secteur. Recommandations générales pour la maintenance ● S’assurer que le technicien de maintenance est formé aux règles de sécurité qui concernent les gaz pompés. ● Débrancher le câble secteur du produit de toute source d’énergie avant d’intervenir sur le produit. ● Attendre 5 minutes après la mise hors tension avant d’intervenir sur les composants électriques. ● Attendre le refroidissement complet avant d'intervenir sur le produit. ● Les circuits pressurisés - azote et eau - sont des risques énergétiques potentiels : toujours verrouiller ces circuits (LO/TO procédure de consignation/déconsignation) avant d'intervenir sur le produit. ● Fixer les câbles électriques, les canalisations de pompage : les acheminer dans des goulottes pour éviter les chutes. ● Collecter les résidus de procédés et faire appel à un organisme compétent pour leur destruction. ● Toujours protéger les surfaces des brides d’aspiration et de refoulement. 9.2 Intervalles de maintenance Par conception, la pompe ne comporte pas de pièces d’usure et ne nécessite pas de maintenance préventive. Cependant, les roulements de secours utilisés pour protéger la pompe lors d’entrées d’air brutales, de chocs ou de coupures secteur accidentelles doivent être changés lorsque l’électronique le signale : le pourcentage du temps d’atterrissage déduit dépend du nombre et du type d’incidents. Le seuil d’alerte pour signaler la maintenance des roulements à l’opérateur est paramétrable via l’interface de commande qui pilote la pompe (HHR, liaison série, ou bus de terrain). Un compteur permet d’afficher le niveau d’usure des roulements afin de prévoir la maintenance des roulements de secours. Roulements de secours Les roulements de secours sont conçus pour résister à des atterrissages anormaux à pleine vitesse. L’usure des roulements est gérée par l’électronique qui prend en compte la vitesse de rotation et la durée de l’atterrissage. Le pourcentage initial est de 100 %. Lorsque cette valeur atteint le seuil d’alerte réglé, une alerte se déclenche : les roulements de secours doivent impérativement être remplacés. Si d’autres atterrissages se produisent, le compteur continue de décroître jusqu’à 0 %. Ces roulements doivent être remplacés par un centre de service Pfeiffer Vacuum. Rotor de la pompe La durée de vie du rotor de la pompe varie suivant les conditions de fonctionnement et les applications. Pour garantir les meilleures performances, au-delà de 5 ans de fonctionnement, contrôler l’état du rotor. Nous consulter. 61/84 Maintenance Comment nous contacter ? La révision du produit doit être réalisée par du personnel formé par le constructeur. Contacter notre centre de service le plus proche à l'adresse suivante : [email protected]. 9.3 Entretien sur site La pompe ne nécessite aucune maintenance sur le site client excepté l’entretien courant décrit dans ce manuel. Toute autre maintenance doit être réalisée par notre centre de service. ► Nettoyer les faces externes du produit à l’aide d’un chiffon propre non pelucheux et d’un produit ne détériorant pas les surfaces sérigraphiées et les étiquettes autocollantes. ► Vérifier que la canalisation de refoulement ne soit pas obstruée. ► Vérifier l’état du filtre pare-éclats, le nettoyer ou le remplacer. ► Remplacer le filtre à poussières sur l’électrovanne de purge s’il est obstrué (si vanne présente). ► Procéder au remplacement des bobines d'électrovannes si celles-ci sont défectueuses. ► Procéder au remplacement de l’électrovanne d’eau si elle est défectueuse (si vanne présente). Maintenance du filtre pare-éclats La pompe est livrée avec un filtre pare-éclats installé dans la bride du carter d'aspiration de la pompe. Ce filtre protège la pompe contre l’introduction les corps étrangers provenant des enceintes. Lorsqu’il est pollué ou endommagé, il doit être remplacé. IN 1 2 3 1 Clips 2 Filtre pare-éclats 3 Carter d'aspiration Pour le remontage respecter les instructions suivantes : 1. Positionner le filtre dans la gorge du carter d’aspiration, côté bombé orienté vers l’enceinte à pomper. 2. Positionner le clips et le presser manuellement au fond de sa gorge sur toute la circonférence. 9.4 Procédure d'échange par un produit de remplacement Pour procéder à un échange standard, il est nécessaire de respecter la chronologie des étapes suivantes : 1. Déconnexion de la pompe de l’installation. 2. Vidange du circuit d’eau. 3. Conditionnement de la pompe pour expédition. 4. Déclaration de contamination. 5. Manutention de la nouvelle pompe (voir chapitre « Manutention de la pompe »). 6. Mise en place d’une nouvelle pompe (voir chapitre « Installation»). Pour tout retour d’un produit vers nos centres de service, prendre connaissance de la procédure de demande de Service et remplir la déclaration de contamination (voir chapitre « Solutions de service de Pfeiffer Vacuum », page 70). 62/84 Maintenance 9.4.1 Déconnexion de la pompe de l'installation Rappel des risques et mesures de sécurité ● Observer les consignes de sécurité pour la maintenance. ● Appliquer les consignes de sécurité spécifiques conformément à la législation locale : ces informations sont disponibles auprès du service de sécurité du client. Procédure de déconnexion 1. Arrêter la pompe en envoyant un ordre 'Stop'. 2. Mettre la pompe hors tension en positionnant l'interrupteur de l'alimentation électrique sur O. 3. Déclencher le disjoncteur réseau de l’installation client. 4. Déconnecter le câble secteur au niveau du connecteur électrique. 5. Déconnecter tous les connecteurs au niveau de l'interface de commande. 6. Déconnecter l’alimentation d’azote. 7. Déconnecter le raccord WATER IN puis le raccord WATER OUT. 8. Désolidariser la pompe au niveau de la bride de vide élevé et obturer l’orifice d’aspiration avec les accessoires de raccordement étanches à l'air. 9. Désolidariser le refoulement de la pompe et obturer l’orifice de refoulement avec les accessoires de raccordement étanches à l'air. 10. Mettre en place les dispositifs de manutention (voir chapitre « Manutention de la pompe »). 11. Déconnecter la pompe de l'installation. 9.4.2 Vidange du circuit d'eau L'eau doit être évacuée de la pompe pour éviter le gel dans les canalisations pendant le transport. Pour cela le client doit prévoir des tuyaux flexibles et des raccords ainsi qu'un circuit d'air comprimé (pression de 2 à 5 ·103 hPa). AIR PRESSURE 1 2 3 1 Tuyau d'arrivée air comprimé 2 Tuyau de vidange 3 Récipient (capacité > 1 litre) Procédure de vidange du circuit d'eau 1. Placer un récipient en dessous des raccords. 2. Déconnecter le circuit de refroidissement au niveau des raccords WATER IN et WATER OUT. 3. Raccorder un tuyau de vidange sur l'un des raccords. 4. Raccorder le circuit d’air comprimé sur l'autre raccord. 5. Injecter de l’air comprimé jusqu’à ce que toute l’eau soit évacuée. 9.4.3 Conditionnement de la pompe pour expédition Les pompes qui doivent être expédiées seront grossièrement décontaminées puis pressurisées à l’azote. Pour décontaminer et pressuriser la pompe, il est nécessaire de disposer d’une alimentation en azote ayant les caractéristiques requises (voir chapitre « Caractéristiques de l'azote »). De même, il est re- 63/84 Maintenance commandé de disposer des accessoires de raccordement qui permettent de fermer la pompe de manière étanche (accessoires). Balayage refoulement/aspiration 1. Fermer le raccord de purge à l'aide d'un bouchon. 2. Mettre en place l’obturateur muni de l'injecteur sur la bride de refoulement. 3. Raccorder l'azote sur le raccord gaz prévu à cet effet. 4. Réaliser un balayage à l’azote en injectant une pression relative de 120 à 150 hPa pendant 30 minutes. 5. Stopper le flux d’azote. 30’ N2 Pressurisation de la pompe 1. Obturer l’aspiration avec les accessoires et fermer de manière étanche. 2. Pressuriser la pompe en azote à une pression relative de 120 hPa. 3. Stopper le flux d’azote. N2 Etiquetage de la pompe 1. Coller cette étiquette sur le produit pour informer que la pompe a fonctionné sur des produits dangereux. 2. Remplir la déclaration de contamination et la joindre au produit (voir chapitre « Solutions de service »). 64/84 Exposure may result in severe injury or death. Preventive maintenance must be done by trained personnel only. Mise hors service 10 Mise hors service 10.1 Immobilisation prolongée AVIS Accumulation de gaz de procédés sur un équipement à l'arrêt Toutes les pompes de procédé sont conçues pour fonctionner en continu sur des applications de pompage de gaz de procédés et ne doivent pas être arrêtées. Pfeiffer Vacuum décline toute garantie et responsabilité lorsqu’une pompe de procédé est arrêtée pour une durée prolongée pouvant provoquer la condensation des sous-produits, le dépôt de poudres et la corrosion à l’intérieur de la pompe. ► Réaliser une révision du produit avant de le remettre en service. Contacter Pfeiffer Vacuum. Après utilisation sur applications propres 1. Effectuer un balayage de l’installation avec un flux d'azote durant 30 minutes. La pression et le débit d'azote doivent être identiques aux valeurs programmées pour le procédé. 2. Vidanger le circuit d’eau. 3. Déconnecter la pompe de l’installation. 4. Obturer l’aspiration, le refoulement et l’orifice de purge avec les accessoires fournis. 5. Stocker la pompe dans un environnement propre, sec et non pollué, pour une durée maximale de 6 mois en respectant les températures de stockage. 6. Protéger les connecteurs électriques avec les bouchons de plastique présents sur le produit à la livraison. Après utilisation sur applications agressives ► Ne jamais stocker une pompe qui a été utilisée sur des applications agressives !!. Procéder à un échange standard (voir chapitre « Procédure d'échange par un produit de remplacement ») et retourner le produit auprès du centre de service (voir chapitre « Solutions de service de Pfeiffer Vacuum », page 70). 10.2 Remise en service Pour remettre en service la pompe après un arrêt prolongé, procéder à l’installation complète de la pompe (voir chapitre « Installation », page 23). 10.3 Mise au rebut Conformément à la Directive concernant le traitement des déchets des équipements électriques et électroniques (DEEE), et à la Directive relative à la restriction des matières dangereuses (RoHS), les produits en fin de vie seront retournés au constructeur pour décontamination et valorisation. Toute obligation du constructeur de récupérer de tels équipements s’applique uniquement à des équipements complets, non modifiés, utilisant des pièces détachées d’origine Pfeiffer Vacuum SAS, vendues par Pfeiffer Vacuum et incluant tous leurs ensembles et sous-ensembles. Cette obligation ne comprend pas les frais de transport du produit vers un centre de retraitement, ni la prestation de service qui sera facturée au client. Pour tout retour d’un produit vers nos centres de service, prendre connaissance de la procédure de demande de Service et remplir la déclaration de contamination (voir chapitre « Solutions de service de Pfeiffer Vacuum », page 70). Protection de l'environnement La mise au rebut du produit ou de ses composants doit être réalisée conformément aux réglementations en vigueur pour ce qui concerne la protection de l’environnement et la santé des personnes, ceci afin de réduire le gaspillage des ressources naturelles et prévenir de la pollution. 65/84 Mise hors service Nos produits contiennent différents matériaux qui doivent être recyclés : acier, acier inoxydable, laiton, aluminium, nickel, cuivre, élastomères fluorés, PFPE, FEP, des cartes électroniques. Prendre des précautions particulières pour : ● les élastomères fluorés qui peuvent se décomposer s’ils ont été soumis à de hautes températures, ● les composants en contact avec les produits résultant de procédés qui ont pu être contaminés. 66/84 Dysfonctionnements 11 Dysfonctionnements 11.1 Signalement des mauvais fonctionnements et défauts Prendre connaissance des consignes de sécurité relatives à la maintenance (voir chapitre « Consignes de sécurité pour la maintenance »). Lorsqu'un problème intervient, l'utilisateur est averti par : ● ● ● ● ● ● ● L'activation de la LED relative au défaut/alerte L'avertisseur sonore du boîtier HHR (si la fonction est validée) L’activation des contacts défauts sur la prise télécommande REMOTE L’arrêt du pompage alors que l'ordre 'Stop' n’a pas été activé L'affichage d'un message défaut sur le boîtier HHR Un message via la liaison série RS-232 ou RS-485 Un message via la liaison bus de terrain Signification des LED ● LED jaune allumée/LED rouge clignotante = présence d’une alerte ● LED rouge allumée = présence d’un défaut, arrêt de la pompe Pour la surveillance du fonctionnement (voir chapitre « Surveillance du fonctionnement », page 44). Remise en service après arrêt sur défaut Lors d’un arrêt de la pompe sur défaut, l’alimentation électrique du variateur est coupée et la pompe est en sécurité. Pour remettre la pompe en service, il faut : 1. Couper l'alimentation électrique et attendre l'arrêt complet de la rotation du rotor. – Interrupteur de l'alimentation électrique externe 48 VDC sur O. 2. Attendre environ 15 secondes. 3. Supprimer l'origine du défaut. 4. Rétablir l’alimentation électrique. – Interrupteur de l'alimentation électrique externe 48 VDC sur I. 11.2 Mauvais fonctionnement Problème de démarrage et fonctionnement incorrect Symptôme Cause Remède A la mise sous tension, rien ne se passe et aucun voyant allumé. Absence d'alimentation électrique ● Vérifier que l'alimentation électrique externe 48 VDC est bien raccordée au secteur. ● Vérifier que la pompe est alimentée en 48 VDC. ● Vérifier le chenillard à la mise sous tension. ● Si le problème persiste, contacter notre centre de service. La pompe vibre pendant la montée en vitesse. Problème mécanique ● Vérifier que la pompe est fixée de façon rigide au châssis (voir chapitre « Spécifications d'installation »). ● Vérifier que l’installation n’engendre pas de vibration. ● Vérifier que l’installation est correctement fixée au sol (ce problème peut provenir d’une dalle flottante, par exemple). ● Si le problème persiste, contacter notre centre de service. Le voyant rouge de l'électronique est allumé. La pompe est en défaut. ● Connecter la liaison série. ● Prendre connaissance de la liste des défauts via la liaison RS-232/RS-485 (commande #DEF). 67/84 Dysfonctionnements La pompe fonctionne et signale un défaut Message Symptôme Cause Remède Unbalance fault L’électronique arrête le moteur. L’électrovanne d’entrée d’air est ouverte. La pompe ne peut pas redémarrer. L’électronique n’arrive pas à centrer le rotor. ● Vérifier que la pompe est correctement fixée au châssis (voir chapitre « Spécifications d'installation »). ● Couper l’alimentation de l'unité de commande pendant 15 s puis remettre sous tension. ● Si le message disparaît, redémarrer la pompe. ● Si le problème persiste, contacter notre centre de service. Not Ecc Correcte Le test auto-contrôle Ecc n’est pas terminé. Le contrôleur arrête le moteur. Le contact «START» s’ouvre. La pompe ne peut pas redémarrer. ● Vérifier qu’il n’y a pas de vibrations sur le châssis. ● Vérifier que la pompe est bien fixée. ● Couper l’alimentation de l'unité de commande pendant 15 s puis remettre sous tension. ● Si le message disparaît, essayer de démarrer la pompe. ● Si le problème persiste, contacter notre centre de service. Sur des procédés générant des poussières ou des vapeurs condensables, le rotor peut être bloqué par des sous-produits du procédé. Safety shutdown Problème mécanique ou électrique L'unité de commande électronique arrête le moteur. Le contact “START” s’ouvre. La pompe ne peut pas redémarrer. ● Contacter notre centre de service. Drive fault Surintensité du moteur ou défaut sur les capteurs à effet Hall L'unité de commande électronique arrête le moteur. ● Réduire le flux. ● Couper l’alimentation de l'unité de commande pendant 15 s puis remettre sous tension. ● Si le message disparaît, redémarrer la pompe. ● Si le problème persiste, contacter notre centre de service. Hardware fault Le contact de sécurité apparaît quand un défaut sur l'ensemble pompe/électronique intégrée est détecté. Pas de sustentation magnétique. La pompe ne peut pas redémarrer. ● Contacter notre centre de service. Selfcheck failed Problème mécanique ou électrique Pas de sustentation magnétique. La pompe ne peut pas redémarrer. ● Couper l’alimentation de l'unité de commande pendant 15 s puis remettre sous tension. ● Si le problème persiste, contacter notre centre de service. Electr.Temperature La température de l'électronique dépasse la limite autorisée > 75 - 80 °C La pompe ne peut pas démarrer. ● Vérifier le circuit de refroidissement (voir chapitre « Raccordement de la pompe au circuit d'eau »). Rotate while Powerup La pompe est alimentée, le rotor est toujours en rotation. La pompe ne peut pas démarrer. ● Attendre l’arrêt complet de la rotation du rotor, puis couper l'alimentation électrique. ● Débrancher et rebrancher le câble d'alimentation électrique. ● Si le problème persiste, contacter notre centre de service. Bearing overload Displacement fault Lower Radial Bearing Upper Radial Bearing Axial position Lower Radial current Upper Radial current Axial current No recovery 68/84 Dysfonctionnements La pompe fonctionne et signale un défaut Message Symptôme Cause Remède Magnetic bearing L’unité de commande électronique arrête le moteur. L’électrovanne d’entrée d’air est ouverte. Défaut de sustentation du rotor ● Attendre l’arrêt complet de la rotation du rotor. ● Couper l’alimentation de l'unité de commande pendant 15 s puis remettre sous tension. ● Si le message disparaît, redémarrer la pompe. ● Si le problème persiste, contacter notre centre de service. Pump Temperature La température de la pompe dépasse la limite autorisée : > 105 °C (pompe version MT) > 110 °C (pompe version M) L'unité de commande électronique arrête le moteur jusqu’à ce que la température redescende à 105 ou 110 °C. Alors le moteur redémarre. ● Vérifier le circuit de refroidissement (voir chapitre « Raccordement de la pompe au circuit d'eau »). Bearing Les roulements de secours doivent être maintenus : le seuil d'alerte est atteint. La limite autorisée du nombre d’atterrissage sur les roulements de secours est atteinte. ● Contacter notre centre de service. Seized Pump L’unité de commande électronique cesse d’alimenter le moteur. Blocage du rotor ● Couper l’alimentation de l'unité de commande pendant 15 s et remettre sous tension ● Si le message disparaît, redémarrer la pompe. ● Si le problème persiste, contacter notre centre de service. Not Accelerating L’unité de commande électronique cesse d’alimenter le moteur. La pompe n’arrive pas à accélérer. ● Vérifier le bon fonctionnement du prévidage (niveau de vide primaire). Internal communication La pompe ne démarre pas. Défaut de communication ● Couper l’alimentation de l'unité de commande pendant 15 s puis remettre sous tension. ● Si le message disparaît, redémarrer la pompe. ● Si le problème persiste, contacter notre centre de service. 69/84 Solutions de service de Pfeiffer Vacuum 12 Solutions de service de Pfeiffer Vacuum Nous offrons un service de première classe Une longue durée de vie des composants du vide, associée à des temps d’arrêt réduits, sont ce que vous attendez clairement de nous. Nous répondons à vos besoins par des produits efficaces et un service d’exception. Nous nous efforçons de perfectionner en permanence notre compétence clé, à savoir le service liés aux composants du vide. Et notre service est loin d’être terminé une fois que vous avez acheté votre produit Pfeiffer Vacuum. Il ne démarre souvent qu’à partir de là. Dans la qualité Pfeiffer Vacuum reconnue, bien évidemment. Nos ingénieurs commerciaux et techniciens de service professionnels sont à votre disposition pour vous assurer un soutien pratique dans le monde entier. Pfeiffer Vacuum offre une gamme complète de services, allant des pièces de rechange d’origine aux accords de service. Profitez du service Pfeiffer Vacuum Qu'il s’agisse du service préventif sur place de notre service sur site, du remplacement rapide par des produits de rechange comme neufs ou de la réparation dans un centre de service proche de chez vous ; vous disposez d'une variété d’options pour maintenir la disponibilité de votre équipement. Vous trouverez des informations détaillées ainsi que les adresses sur notre site web dans la section Pfeiffer Vacuum Service. Des conseils sur la solution optimale sont disponibles auprès de votre interlocuteur Pfeiffer Vacuum. Pour un déroulement rapide et efficace de la procédure de service, nous recommandons de suivre les étapes suivantes : 1. Télécharger les modèles de formulaire actuels. ─ Déclaration de demande de service ─ Demande de service ─ Déclaration de contamination a) Démonter tous les accessoires et les conserver (toutes les pièces externes montées telles que la vanne, le filtre d’arrivée, etc.). b) Vidanger le fluide d'exploitation / lubrifiant si nécessaire. c) Vidanger le fluide de refroidissement si nécessaire. 2. Remplir la demande de service et la déclaration de contamination. ANFORDERUNG SERVICE ERKLÄRUNG KONTAMINIERUNG 3. Envoyer les formulaires par e-mail, fax ou par courrier à votre centre de service local. 4. Vous recevrez une réponse de Pfeiffer Vacuum. Envoi de produits contaminés Aucune unité ne sera acceptée si elle est contaminée par des substances micro-biologiques, explosives ou radioactives. Si les produits sont contaminés ou si la déclaration de contamination est manquante, Pfeiffer Vacuum contactera le client avant de démarrer la maintenance. Par ailleurs, selon le produit et le niveau de contamination, des frais de décontamination supplémentaires peuvent être facturés. 70/84 Solutions de service de Pfeiffer Vacuum 5. Préparer le produit pour le transport conformément aux détails contenus dans la déclaration de contamination. a) Neutraliser le produit avec de l’azote ou de l’air sec. b) Fermer toutes les ouvertures avec des obturateurs étanches à l’air. c) Sceller le produit dans un film de protection approprié. d) Emballer le produit dans des conteneurs de transport stables appropriés uniquement. e) Respecter les conditions de transport en vigueur. ERKLÄRUNG KONTAMINIERUNG 6. Joindre la déclaration de contamination sur l’extérieur de l’emballage. 7. Envoyer ensuite le produit à votre centre de service local. 8. Vous recevrez un message de confirmation / un devis de la part de Pfeiffer Vacuum. Pour toutes les demandes de service, nos Conditions générales de vente et de livraison ainsi que nos Conditions générales de réparation et de maintenance sont appliquées aux équipements et composants du vide. 71/84 Accessoires 13 Accessoires Accessoire Fonction Type Dimension Vanne d’isolement Cette vanne s’utilise pour maintenir le vide dans la pompe et l’isoler de la ligne de pompage. Vanne manuelle voir catalogue constructeur Boîtier de commande déportable Ce boîtier permet l’interface homme/machine pour pilotage de la pompe en mode local. Boîtier avec cordon Joint cuivre pour bride CF-F Filtre pare-éclats Lot de visserie pour fixation pompe 100 CF-F 303291 (Qt 1) 160 CF-F 303292 (Qt 1) DN 100 ISO-F 118001 DN 160 ISO-F 118002 Filtre bombé + clips percé Ce lot comprend les accessoires de fixation de la pompe sur l'équipement par la bride d’aspiration de la pompe. Lot de 12 vis CHc M10x35 DN 160 ISO-F 110676S Lot de 12 goujons CHc M8x35 DN 100/160 CF-F 118690 Acier inoxydable ISO-K PF 300 110 -T (Qt 1) Bouchon de purge Un bouchon peut être installé en lieu et place du filtre à poussières. Alimentation électrique (externe) Entrée : 230V (±15 %) 50-60Hz Sortie : 48 VDC 600 W Câble secteur Ce câble permet le raccordement de l'alimentation externe au secteur (longueur 2 m). Bouchon + joint et rondelle Câble d'alimentation Le câble permet le raccordement de la pompe à l'alimentation électrique 48 VDC. Electrovanne d'entrée d'air L'électrovanne d'entrée d'air est calibrée pour remettre à la pression atmosphérique le volume interne de la pompe. 24 VDC L'électrovanne de purge permet de piloter l'injection de gaz neutre pendant le fonctionnement de la pompe. (uniquement pour pompe version M) Câble de l'électrovanne de purge Lot de fermeture pour pompe polluée 114461 Ce filtre protège la pompe contre l’aspiration de particules solides. Il s’intègre dans le carter d’aspiration. Griffe de serrage pour bride tournante Lot électrovanne de purge (sans câble) Réf. Ce lot de fermeture comprend l’obturateur, joint d'étanchéité et la visserie pour fermer la pompe. 115298S 114866 Norme Europe : 200-240V AC 48 VDC 103566 Norme US : 200-240V AC 48 VDC 103898 3,5 m A331328-035 5m A331328-050 10 m A331328-100 DN 25 ISO-KF (version M) DN 40 ISO-KF (version MT) 200043 24 VDC - 5W 115303S 1m A462403-010 3,5 m A462403-035 5m A462403-050 10 m A462403-100 20 m A462403-200 DN 160 ISO-F 114501 DN 160 ISO-K 114502 voir constructeur Obturateurs, griffes de serrage, colliers de serrage, voir catalogue des accessoires de raccordement sur le site pfeiffervacuum.com. Choisir des matériaux compatibles avec l’application. 72/84 Accessoires Accessoire Fonction Type Dimension Réf. Accessoires de raccordement Pour le refoulement (pressurisation) Obturateur avec piquage pour injecteur DN 25 ISO-KF (version M) 114419 DN 40 ISO-KF (version MT) 065053 Injecteur 106859 Obturateurs, griffes de serrage, colliers de serrage, voir catalogue des accessoires de raccordement sur le site pfeiffervacuum.com. Choisir des matériaux compatibles avec l’application. 73/84 Pièces de rechange 14 Pièces de rechange Remplacement des pièces défectueuses Les conditions initiales de sécurité du produit sont remises en cause si des pièces non d’origine constructeur sont utilisées : ● Utiliser uniquement les pièces de rechange disponibles sur commande auprès de Pfeiffer Vacuum Service. ● Pour identifier le produit et communiquer avec Pfeiffer Vacuum, se référer à la plaque signalétique du produit. Désignation Version de pompe Référence Remarques Bobine 24 VDC Vxxxxx00 (M) Vxxxxx03 (MT) 038066 sur électrovanne de purge et électrovanne d’entrée d’air Filtre à poussières Vxxxxx00 (M) Vxxxxx03 (MT) 106229 sur électrovanne d'entrée d'air Câble ventilateur 48 VDC Vxxxxx00 (M) Vxxxxx05 (M) A464597 Electrovanne d'eau en cuivre 48 VDC (NO) ● Corps de vanne ● Bobine 48 VDC ● Raccord droit 1/8 BSPP ● Raccord droit 1/8 NPT ● Raccord coudé 1/8 NPT Vxxx2xxx (MT) 119110S ● 115062 ● 119079 ● 115304 ● 105559 ● 119077 Electrovanne d'eau en inox 48 VDC (NO) ● Corps de vanne ● Bobine 48 VDC ● Raccord droit 1/8 BSPP ● Raccord droit 1/8 NPT ● Raccord coudé 1/8 NPT Vxxx3xxx (MT) 126753S ● 123192 ● 119079 ● 115304 ● 105559 ● 119077 Tab. 6: 74/84 Pièces de rechange - ATH500 Caractéristiques techniques et dimensions 15 Caractéristiques techniques et dimensions 15.1 Généralités Bases des caractéristiques techniques des pompes turbomoléculaires de Pfeiffer Vacuum : ► Valeurs prédéfinies selon le comité PNEUROP PN5. ► ISO 21360; 2007 : « Technique du vide - Procédé standard pour la mesure des données de puissance de pompes à vide - Description générale ». ► Pression limite : avec dôme de test et après 48 h d'étuvage. ► Débit de gaz : avec refroidissement à l'eau. ► Consommation d'eau froide : avec débit de gaz max., température de l'eau 20 °C. ► Niveau de pression acoustique : distance par rapport à la pompe 1 m. ► Caractéristiques mesurées sans filtre pare-éclats à l’aspiration de la pompe. mbar bar Pa hPa kPa Torr | mm Hg 1 0,1 0,75 1 · 10 1,000 100 mbar 1 1 · 10 bar 1,000 1 100 Pa 0,01 1 · 10 1 0,01 1 · 10 7.5 · 10-3 hPa 1 1 · 10-3 100 1 0,1 0,75 kPa 10 0,01 1,000 10 1 7,5 Torr | mm Hg 1,33 133,32 1,33 0,133 1 -3 5 -5 -3 1,33 · 10 750 -3 1 Pa = 1 N/m2 Tab. 7: Tableau de conversion : unités de pression mbar l/s Pa m3/s sccm Torr l/s atm cm3/s mbar l/s 1 0,1 59,2 0,75 0,987 Pa m3/s 10 1 592 7,5 sccm Torr l/s 3 atm cm /s Tab. 8: 9,87 1.69 · 10 1.69 · 10 1 1,27 · 10 1.67 · 10-2 1,33 0,133 78,9 1 1,32 1,01 0,101 59,8 0,76 1 -2 -3 -2 Tableau de conversion : unités de débit de gaz 15.2 Caractéristiques techniques Caractéristiques ATH 500 M ATH 500 M ATH 500 MT Bride de vide élevé ISO-F DN 100 DN 160 DN 160 Bride de vide primaire ISO-KF DN 25 DN 25 DN 40 1/8 BSPP (ISO228) 1/8 BSPP (ISO228) 1/4 VCR Bride de purge 1) Unités 1) Les produits qui présentent des spécificités client peuvent avoir des caractéristiques différentes. 2) Condition standard de référence : T0 = 273,15 K - P0 = 1013,25 hPa. 3) A vitesse nominale et température eau refroidissement 25 °C. 4) Avec une pression de refoulement < 0,4 hPa, dépend des conditions externes (température, débit d’eau, température ambiante). Pour d’autres conditions, nous consulter. 5) Débit maximum réduit, pression limite au refoulement sans perte de vitesse du débit. Dépend des conditions environnementales. 6) Avec bride ISO-F (meilleure avec bride CF-F). Nous consulter. 7) Cette température maximum influe sur le flux maximum admissible, nous consulter. 8) Accélération jusqu'à 90 % de la vitesse de rotation nominale, avec pression refoulement < 0,1 hPa. 75/84 Caractéristiques techniques et dimensions Caractéristiques Unités Vitesse de pompage N2 Taux de compression Flux maximum 2) 3) 4) Pression maximum à l’aspiration 4) Pression maximum au refoulement 5) ATH 500 M ATH 500 M ATH 500 MT l/s 350 550 550 Ar l/s 320 530 530 He l/s 310 390 390 H2 l/s 170 190 190 N2 > 2 · 10 7 7 > 2 · 10 > 2 · 107 Ar > 8 · 106 > 8 · 106 > 8 · 106 He > 1 · 10 4 4 > 1 · 10 > 1 · 104 H2 > 2 · 102 > 2 · 102 > 2 · 102 N2 hPa l/s 67,6 67,6 8,5 Ar hPa l/s 42,2 42,2 5 He hPa l/s > 169 > 169 > 16,9 H2 hPa l/s > 169 > 169 > 16,9 N2 hPa 1 1 0,04 Ar hPa 1 1 0,02 He hPa 10 10 > 0,1 H2 hPa 10 10 > 0,1 N2 hPa 2,6 2,6 2,6 Ar hPa 3,3 3,3 3,3 He hPa 1 1 1 H2 hPa 0,25 0,25 0,25 hPa < 1 · 10 < 1 · 10 < 1 · 10-8 Vitesse de rotation nominale min-1 (Hz) 50 000 (833) 50 000 (833) 50 000 (833) Vitesse de stand-by min-1 (Hz) 15 000 (250) à 50 000 (833) 15 000 (250) à 50 000 (833) 15 000 (250) à 50 000 (833) Température max. d'étuvage °C 120 120 - Température de régulation maxi. 7) °C - - 65 Taux de fuites hPa l/s < 5 · 10-8 < 5 · 10-8 < 5 · 10-8 Débit de purge recommandé 2) sccm 50 50 50 Tension d’alimentation VDC 48 48 48 Temps de démarrage 8) mn <2 <2 <2 Puissance au démarrage Watt < 560 < 560 < 560 Puissance consommée à pression limite Watt < 100 < 100 < 100 Puissance à vitesse stand-by minimum Watt < 50 < 50 < 50 Niveau de vibration (à vitesse nominale) µm < 0,01 < 0,01 < 0,01 Niveau sonore dB(A) < 42 < 42 < 42 Pression limite 6) -8 -8 1) Les produits qui présentent des spécificités client peuvent avoir des caractéristiques différentes. 2) Condition standard de référence : T0 = 273,15 K - P0 = 1013,25 hPa. 3) A vitesse nominale et température eau refroidissement 25 °C. 4) Avec une pression de refoulement < 0,4 hPa, dépend des conditions externes (température, débit d’eau, température ambiante). Pour d’autres conditions, nous consulter. 5) Débit maximum réduit, pression limite au refoulement sans perte de vitesse du débit. Dépend des conditions environnementales. 6) Avec bride ISO-F (meilleure avec bride CF-F). Nous consulter. 7) Cette température maximum influe sur le flux maximum admissible, nous consulter. 8) Accélération jusqu'à 90 % de la vitesse de rotation nominale, avec pression refoulement < 0,1 hPa. 76/84 Caractéristiques techniques et dimensions Caractéristiques Unités Débit d'eau de refroidissement l/mn Refroidissement (accessoire) ATH 500 M ATH 500 M ATH 500 MT 1 1 1 eau/(air) eau/(air) eau Poids (Version air) Poids (Version eau) kg 19 15 19 15 15 Prévidage recommandé m3/h 15 mini. 15 mini. 15 mini. 1) Les produits qui présentent des spécificités client peuvent avoir des caractéristiques différentes. 2) Condition standard de référence : T0 = 273,15 K - P0 = 1013,25 hPa. 3) A vitesse nominale et température eau refroidissement 25 °C. 4) Avec une pression de refoulement < 0,4 hPa, dépend des conditions externes (température, débit d’eau, température ambiante). Pour d’autres conditions, nous consulter. 5) Débit maximum réduit, pression limite au refoulement sans perte de vitesse du débit. Dépend des conditions environnementales. 6) Avec bride ISO-F (meilleure avec bride CF-F). Nous consulter. 7) Cette température maximum influe sur le flux maximum admissible, nous consulter. 8) Accélération jusqu'à 90 % de la vitesse de rotation nominale, avec pression refoulement < 0,1 hPa. Tab. 9: 15.2.1 Caractéristiques techniques Caractéristiques environnementales Utilisation intérieur Altitude jusqu’à 2000 m Indice de protection (avec refroidissement air) Indice de protection (avec refroidissement eau) IP 20 IP 40 Température ambiante de fonctionnement avec refroidissement eau Modèle M : 5 – 45 °C Modèle MT : 5 – 25 °C Température ambiante de fonctionnement avec refroidissement air Modèle M : 5 – 30 °C Température de stockage -5 – +50 °C Humidité relative maximale 80 % max. avec T ≤ 31 C, à 50 % max. avec T ≤ 40 °C Degré de pollution niveau 2 Protection contre les surtensions transitoires 1) Catégorie II 1) Surtensions transitoires jusqu’aux niveaux de la catégorie de surtension II. Surtensions temporaires survenant sur le réseau d’alimentation. Tab. 10: 15.2.2 Caractéristiques environnementales Caractéristiques de l'eau de refroidissement Les caractéristiques ci-dessous concernent uniquement la pompe turbomoléculaire à paliers magnétiques. Celle-ci est associée à une pompe primaire. Pour le bon fonctionnement de l’application : ► Veiller à respecter les caractéristiques les plus restrictives pour l’installation. ► Veiller à ce que l’eau en provenance de l’équipement ne gèle pas. 77/84 Caractéristiques techniques et dimensions pH Chlorure 5,5 à 9 100 à 20 ppm selon le pH 1) Dureté < 35 °fH (degré français) < 7 milli-équivalent/L < 350 mg/L de CaCO3 (carbonate de calcium) Résidus à sec < 100 mg/L Indice de Langelier LSI = pH - pHs < 0 à 20 °C Taille des particules < 0,2 mm Chlorure (ppm) 100 50 40 20 Résistivité Température d’entrée pH 0 5 6 7 8 9 R > 1 500 Ω·cm 15-35 °C (version M) 15-25 °C (version MT) 2) 10 Pression d’entrée relative < 6·103 hPa Différence de pression entrée/sortie selon débit Débit > 60 l/h 1) L’activité oxydante du chlore dépend du pH (agressivité de l’eau). La teneur en chlorures doit être située dans la zone colorisée du graphique. 2) Selon les conditions d’utilisation, nous contacter. Tab. 11: 15.2.3 Caractéristiques de l'azote Concentration H2O < 10 ppm v Concentration O2 < 5 ppm v Poussière < 1 µm Huile < 0,1 ppm v Pression absolue 1 · 103 à 1,5 · 103 hPa Tab. 12: 15.2.4 Caractéristiques de l'eau de refroidissement Caractéristiques de l'azote Caractéristiques électriques Caractéristiques du moteur Tension entre phases Fréquence d'alimentation Courant par phase 29 Vrms 1666 Hz 9,5 A Fusible interne de protection Fusible soudé sur PCBoard Time-Lag T, L Tab. 13: 16 A Caractéristiques électriques de la pompe Pouvoir de coupure en court-circuit du disjoncteur 10 kA Calibre disjoncteur réseau client 6 A (pour tension 200-240 V 50/60 Hz) Disjoncteur différentiel GFI (ou RCD) type B compatible réseau électrique type T.T) 1) 30 mA 1) pour un réseau de type T.N ou I.T, appliquer une protection adéquate Tab. 14: 78/84 Caractéristiques électriques du réseau client Caractéristiques techniques et dimensions Tension nominale 48 VDC ± 5 % Puissance nominale minimum 550 W Limitation de courant 15 A max. Surtension transitoire réseau Catégorie II mini 1) Pouvoir de coupure 125 A 2) 300 ms En fonction de la puissance de crête délivrable par l’alimentation 48 V ; ajouter un système de protection supplémentaire sur la ligne d’alimentation de la pompe en 48 VDC. 1) doit accepter les surtensions temporaires survenant sur le réseau d'alimentation. 2) si valeur courant supérieure, ajouter un système de protection. Tab. 15: Caractéristiques de l'alimentation externe 48 VDC Le câble d'alimentation utilisé avec cette alimentation doit être compatible avec les tensions et courants d'alimentation de la pompe (48 VDC, 12 A). 15.3 Dimensions Dimensions (mm) L d1 Exh. 90 N x d2 on 3 227 151 10 62 max. K H CG E 4 2° 25° 1 IN 75 .8 90 ° d1 .8 35 55 ° ° 152 180 D CG1 75 3 x M8 J Fig. 19: Dimensions ATH 500 M 1 Trous M4 pour connexion pompe à la terre Centre de gravité 141 IN 40 135 Exh. 93 155 Fig. 20: Dimensions ATH 500 M refroidie à l'air 79/84 Caractéristiques techniques et dimensions IN Exh. 84 162.6 72.5 62 max. L CG1 H J CG J’ E D 182 151 227 42° 25 ° ) ,27 ( +0 ( 0) d1 1 13 90 2 ° 2o n 135 max. 90 152 Ra1.6 d Nx 30° Fig. 21: Dimensions ATH 500 MT 1 Trous M4 pour connexion pompe à la terre Bride aspiration Centre de gravité E H J K L D d1 d2 N CG CG1 DN 160 ISO-F mm 16 159.3 182.5 182.2 254.9 225 200 11 8 112.6 9.7 DN 160 ISO-K mm 12 159.3 182.5 182.2 254.9 180 - - - 128.6 11.3 DN 160 CF-F mm 20 180.3 203.5 203.2 275.9 198 181.1 8.6 20 114.1 10.1 DN 100 ISO-K mm 12 199.3 222.5 222.2 294.5 130 - - - 116.1 10.2 DN 100 CF-F mm 16 209.3 232.5 232.2 304.9 148.5 130.2 8.6 16 109.5 9.8 80/84 Déclaration de conformité CE La présente déclaration de conformité a été délivrée sous la seule responsabilité du fabricant. Déclaration pour produit(s) du type : Pompes turbomoléculaires à paliers magnétiques avec électronique intégrée ATH 500 M ATH 500 MT Par la présente, nous déclarons que le produit cité est conforme aux Directives européennes suivantes. Machines 2006/42/CE (Annexe II, n° 1 A) Compatibilité électromagnétique 2014/30/UE Limitation de l’utilisation de certaines matières dangereuses 2011/65/UE Les objectifs de la Directive Basse Tension 2014/35/UE sont respectés conformément à l'annexe I, n°1.5.1 de la Directive Machines 2006/42/CE. Normes harmonisées et normes nationales appliquées : EN 1012-2/A1 : 2009 EN 61010-1/A1 : 2019 EN IEC 61000-6-2 : 2019 EN IEC 61000-3-2 : 2019 EN 61000-3-3/A1 : 2019 EN IEC 61000-6-4 : 2019 Le responsable de la constitution du dossier technique est M. Varennes Nicolas, Pfeiffer Vacuum SAS, 98, avenue de Brogny B.P. 2069, 74009 Annecy cedex. Signature: Pfeiffer Vacuum SAS 98, avenue de Brogny 74009 Annecy cedex France B.P. 2069 (Guillaume Kreziak) Directeur Général Annecy le 2023/01/31 Déclaration de Conformité UK La présente déclaration de conformité a été délivrée sous la seule responsabilité du fabricant. Déclaration pour produit(s) du type : Pompes turbomoléculaires à paliers magnétiques avec électronique intégrée ATH 500 M ATH 500 MT Nous déclarons par la présente que le produit cité satisfait à toutes les exigences applicables des Directives Britanniques suivantes. Réglementation 2008 (Sécurité) sur la Fourniture de Machines Réglementation 2016 (Sécurité) sur les Equipements Electriques Réglementation 2016 sur la Compatibilité Electromagnétique Réglementation 2012 sur la Limitation de l'Utilisation de Certaines Substances Dangereuses dans les Equipements Electriques et Electroniques Normes harmonisées et normes nationales appliquées : EN 1012-2/A1 : 2009 EN 61010-1/A1 : 2019 EN IEC 61000-6-2 : 2019 EN IEC 61000-3-2 : 2019 EN 61000-3-3/A1 : 2019 EN IEC 61000-6-4 : 2019 Le représentant autorisé du fabricant pour le Royaume-Uni et l'agent chargé de la constitution du dossier technique est Pfeiffer Vacuum Ltd, 16 Plover Close, Interchange Park, MK169PS Newport Pagnell. Signature: Pfeiffer Vacuum SAS 98, avenue de Brogny 74009 Annecy cedex France B.P. 2069 (Guillaume Kreziak) Directeur Général Annecy, 2023/01/31 83/84 *114436* Ed. 09 - Date 2023/03 - P/N:114436OFR ">
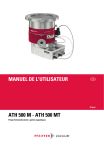
Lien public mis à jour
Le lien public vers votre chat a été mis à jour.
Caractéristiques clés
- Paliers magnétiques actifs (PMA)
- Résistance à la corrosion (versions spécifiques)
- Capacité de pompage de grands débits
- Refroidissement air ou eau
- Système de régulation de la température (TMS) (version MT)
- Interface de commande RS-232/RS-485 et REMOTE
- Conçues pour être intégrées dans des équipements industriels
Questions fréquemment posées
La version M est la version standard pour les applications propres, tandis que la version MT est équipée d'un système de régulation de la température (TMS) pour éviter la condensation des gaz.
La pompe peut être pilotée via la liaison série RS-232/RS-485, le connecteur REMOTE ou avec le boîtier de commande déportable HHR (en option).
Ces pompes sont particulièrement adaptées aux procédés de dépôt et de gravure plasma, aux procédés de dépôts sur verre et à d’autres applications de recherche.