- Industriel et équipement de laboratoire
- Mesure, d'essai et de contrôle
- Fisher
- Contrôleur numérique de niveau FIELDVUE DLC3010 de (DLC3010 Digital Level Controller)
- Guide de démarrage rapide
Fisher Contrôleur numérique de niveau FIELDVUE DLC3010 de (DLC3010 Digital Level Controller) Guide de démarrage rapide
Ajouter à Mes manuels36 Des pages
▼
Scroll to page 2
of
36
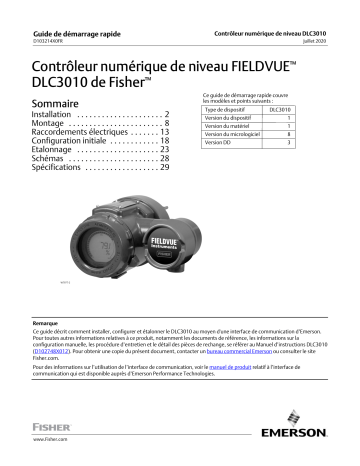
Guide de démarrage rapide Contrôleur numérique de niveau DLC3010 D103214X0FR Juillet 2020 Contrôleur numérique de niveau FIELDVUE™ DLC3010 de Fisher™ Sommaire Installation . . . . . . . . . . . . . . . . . . . . . 2 Montage . . . . . . . . . . . . . . . . . . . . . . . 8 Raccordements électriques . . . . . . . 13 Configuration initiale . . . . . . . . . . . . 18 Etalonnage . . . . . . . . . . . . . . . . . . . . 23 Schémas . . . . . . . . . . . . . . . . . . . . . . 28 Spécifications . . . . . . . . . . . . . . . . . . 29 Ce guide de démarrage rapide couvre les modèles et points suivants : Type de dispositif DLC3010 Version du dispositif 1 Version du matériel 1 Version du micrologiciel 8 Version DD 3 W7977-2 Remarque Ce guide décrit comment installer, configurer et étalonner le DLC3010 au moyen d'une interface de communication d’Emerson. Pour toutes autres informations relatives à ce produit, notamment les documents de référence, les informations sur la configuration manuelle, les procédure d’entretien et le détail des pièces de rechange, se référer au Manuel d’instructions DLC3010 (D102748X012). Pour obtenir une copie du présent document, contacter un bureau commercial Emerson ou consulter le site Fisher.com. Pour des informations sur l’utilisation de l’interface de communication, voir le manuel de produit relatif à l’interface de communication qui est disponible auprès d’Emerson Performance Technologies. www.Fisher.com Contrôleur numérique de niveau DLC3010 Guide de démarrage rapide D103214X0FR Juillet 2020 Installation AVERTISSEMENT Toujours porter des gants, des vêtements et des lunettes de protection lors de toute opération d’installation afin d’éviter les blessures. Des blessures ou dégâts matériels dus à un brusque dégagement de pression, à un contact avec un liquide dangereux, à un incendie ou à une explosion, peuvent résulter de la perforation, du réchauffement ou de la réparation d’un plongeur retenant la pression du procédé ou un fluide. Ce danger n’est peut être pas apparent lors du démontage du capteur ou du retrait du plongeur. Avant de démonter le capteur ou de retirer le plongeur, respecter les consignes appropriées du manuel d’instruction du capteur. Consulter l’ingénieur des procédés ou l’ingénieur responsable de la sécurité pour prendre toutes les mesures de protection supplémentaires contre l’exposition au fluide du procédé. Cette section comprend des informations relatives à l’installation du contrôleur numérique de niveau, y compris un diagramme d’installation (figure 1), les informations de montage et d’installation électrique ainsi qu’une discussion sur les cavaliers en mode de panne. Les personnes effectuant les procédures d’installation, d’exploitation ou de maintenance du contrôleur numérique de niveau DLC3010, doivent être parfaitement formées et qualifiées aux procédures d’installation, d’exploitation et de maintenance de vannes, d’actionneurs et d’accessoires. Pour éviter des blessures ou des dommages matériels, il est important de lire attentivement, d’assimiler et d’observer l’intégralité de ce manuel, y compris les avertissements et les précautions. Pour toute question au sujet de ces instructions, contacter un bureau commercial Emerson avant toute intervention. 2 Guide de démarrage rapide Contrôleur numérique de niveau DLC3010 D103214X0FR Juillet 2020 Figure 1. Organigramme d’installation DEBUTER ICI Contrôle de la position du cavalier d’alarme Câbler le contrôleur numérique de niveau Oui Monté en usine sur capteur 249 ? Allumer le contrôleur numérique de niveau Non Application à températures extrêmes ? 1 Oui Installer l’isolant thermique Non Monter et câbler le contrôleur numérique de niveau Allumer le contrôleur numérique de niveau Saisir l’étiquette, les messages, la date et vérifier ou définir les données de l’application cible 1 Oui Régler la compensation du niveau sur zéro Utiliser l’assistant de configuration pour saisir les données et conditions d’étalonnage du capteur Mesure de densité ? Non Utiliser la correction de température ? Oui Non Définir les unités de température Configurer les tables de densité Définir la densité Etalonner le capteur Oui RTD employé ? Configurer et étalonner le RTD Non Saisir la température de procédé Définir les valeurs de plage REMARQUE : 1 EN CAS D’UTILISATION D’UN RTD POUR LA CORRECTION DE TEMPERATURE, RACCORDER EGALEMENT LE RTD AU CONTROLEUR NUMERIQUE DE NIVEAU 2 LA DESACTIVATION DES ECRITURES N’EST EFFECTIVE QUE SI LE DLC3010 RESTE SOUS TENSION Désactiver les écritures 2 FIN 3 Guide de démarrage rapide Contrôleur numérique de niveau DLC3010 D103214X0FR Juillet 2020 Configuration : sur banc d’essais ou dans la boucle Configurer le contrôleur numérique de niveau avant ou après installation. Il peut être utile de configurer l’instrument sur banc, avant installation, pour s’assurer de son bon fonctionnement et pour se familiariser avec ses fonctionnalités. Protection de l’accouplement et des lames ATTENTION Des lames ou autres pièces endommagées peuvent provoquer des erreurs de mesure. Respecter les étapes suivantes avant de déplacer le capteur et le contrôleur. Verrouillage du levier Le verrouillage du levier est incorporé à la poignée d’accès du manchon. Lorsque la poignée est ouverte, elle place le levier en position neutre de la course pour l’accouplement. Dans certains cas, cette fonctionnalité est utilisée pour protéger le levier d’un mouvement brusque lors du transport. Le contrôleur DLC3010 est dans l’une des configurations mécaniques suivantes lors de sa livraison : 1. Un plongeur en cage couplé et assemblé est livré avec le plongeur ou la tige bloquée, dans la plage de fonctionnement, par un moyen mécanique. Dans ce cas, la poignée d’accès (figure 2) sera en position déverrouillée. Retirer le système de blocage du plongeur avant étalonnage. (Voir le manuel d’instruction approprié du capteur). L’accouplement doit être intact. Figure 2. Compartiment de raccordement du capteur (la bague de l’adaptateur a été retirée pour une lecture plus aisée) TIGES FILETEES DE FIXATION ORIFICE D’ACCES FIXATION DE L’AXE VIS SANS TETE APPUYER ICI POUR DEPLACER LA POIGNEE D’ACCES 4 FAIRE GLISSER LA POIGNEE D’ACCES VERS L’AVANT DE L’UNITE POUR DECOUVRIR L’ORIFICE D’ACCES Guide de démarrage rapide Contrôleur numérique de niveau DLC3010 D103214X0FR Juillet 2020 ATTENTION Lors du transport d’un instrument monté sur un capteur, si l’ensemble du levier est relié à la tringlerie et que celle-ci est gênée par les blocs de plongeur, l’utilisation du verrouillage du levier peut causer des dégâts aux joints à soufflets ou à la lame. 2. Si le plongeur ne peut pas être bloqué en raison de la configuration de la cage, ou pour toute autre raison, le transmetteur est découplé du tube de torsion en desserrant l’écrou de serrage ; la poignée d’accès sera alors en position verrouillée. Avant de mettre un tel équipement en service, suivre la procédure d’accouplement. 3. Pour un système sans cage, lorsque le plongeur n’est pas relié au tube de torsion durant le transport, c’est le tube de torsion lui-même qui stabilise la position du levier couplé en reposant contre une butée placée dans le capteur. La poignée d’accès sera en position déverrouillée. Monter le capteur et accrocher le plongeur. L’accouplement doit être intact. 4. Si le contrôleur a été livré seul, la poignée d’accès sera en position verrouillée. Toutes les procédures de montage, d’accouplement et d’étalonnage doivent être effectuées. La poignée d’accès comporte une vis de fixation sans tête, comme indiqué sur les figures 2 et 6. La vis est placée, avant le transport, de façon à être en contact avec la lame de ressort placée dans l’ensemble de la poignée. Elle permet d’immobiliser la poignée dans la position souhaitée lors du transport et de l’utilisation. Pour mettre la poignée d’accès en position ouverte ou fermée, il faut dévisser cette vis de façon à ce que son sommet soit au ras de la surface de la poignée. Certifications pour utilisation en zone dangereuse et instructions spéciales pour une utilisation et une installation en toute sécurité dans des zones dangereuses Certaines plaques signalétiques peuvent porter plusieurs certifications, chacune d’elles pouvant impliquer des normes d’installation/de câblage et/ou des conditions d’utilisation en toute sécurité spécifiques. Ces instructions spéciales d’utilisation en toute sécurité s’ajoutent aux procédures d’installation standard et peuvent se substituer à ces dernières. Elles sont répertoriées par type de certification. Remarque Ces informations complètent les marquages de la plaque signalétique apposée sur le produit. Toujours se référer à la plaque signalétique pour identifier la certification appropriée. Contacter un bureau commercial Emerson pour obtenir des homologations/certifications spécifiques non mentionnées dans ce document. AVERTISSEMENT Le non-respect de ces conditions d’utilisation en toute sécurité peut entraîner des blessures ou des dégâts matériels par incendie ou explosion, et une reclassification de la zone. CSA Conditions spéciales pour une utilisation en toute sécurité Sécurité intrinsèque, antidéflagrant, Division 2, protection contre les coups de poussière Températures ambiantes nominales : -40 _C ≤ Ta ≤ +80 _C ; -40 _C ≤ Ta ≤ +78 _C ; -40 _C ≤ Ta ≤ +70 _C. Voir le tableau 1 pour des informations relatives aux certifications. 5 Guide de démarrage rapide Contrôleur numérique de niveau DLC3010 D103214X0FR Juillet 2020 Tableau 1. Classifications pour zones dangereuses - CSA (Canada) Organisme de certification CSA Certification obtenue Sécurité intrinsèque Ex ia Classe I, Division 1, 2 Groupes A, B, C, D Classe II, Division 1, 2 Groupes E, F, G Classe III T6 selon schéma 28B5744 (voir figure 13) Antidéflagrant Classe I, Division 1 GP B, C, D T5/T6 Valeur nominale d’entité Vmax = 30 Vcc Imax = 226 mA Ci = 5,5 nF Li = 0,4 mH Code de température T6 (Tamb ≤ 80 °C) --- Classe I Division 2 GP A, B, C, D T5/T6 --- Classe II Division 1, 2 GP E, F, G T5/T6 Classe III T5/T6 --- T5 (Tamb ≤ 80 °C) T6 (Tamb ≤ 78 °C) T5 (Tamb ≤ 80 °C) T6 (Tamb ≤ 70 °C) T5 (Tamb ≤ 80 °C) T6 (Tamb ≤ 78 °C) FM Conditions spéciales pour une utilisation en toute sécurité Sécurité intrinsèque, antidéflagrant, non incendiaire, protection contre les coups de poussière 1. Le boîtier de cet appareil contient de l’aluminium, qui est considéré comme une source potentielle d’inflammation par impact ou friction. Faire preuve de prudence lors de l’installation et de l’utilisation pour éviter tout impact ou toute friction. Voir le Tableau 2 pour des informations relatives aux certifications. Tableau 2. Classifications pour zones dangereuses - FM (Etats-Unis) Organisme de certification Certification obtenue IS Sécurité intrinsèque Classes I, II, III, Division 1 GP A, B, C, D, E, F, G T5 conformément au schéma 28B5745 (voir la figure 14) FM XP Antidéflagrant Classe I Division 1 GP B, C, D T5 NI Non incendiaire, Classe I Division 2 GP A, B, C, D T5 DIP Protection contre les coups de poussière Classe II, Division 1 GP E, F, G T5 S Convient à l’utilisation en Classe II, III Division 2 GP F, G Valeur nominale d’entité Vmax = 30 Vcc Imax = 226 mA Ci = 5,5 nF Li = 0,4 mH Pi = 1,4 W Code de température T5 (Tamb ≤ 80 °C) --- T5 (Tamb ≤ 80 °C) ATEX Conditions spéciales pour une utilisation en toute sécurité Sécurité intrinsèque L’appareil DLC3010 est un appareil de sécurité intrinsèque ; il peut être monté dans des zones dangereuses. Cet appareil doit être raccordé uniquement à un équipement de sécurité intrinsèque certifié et l’ensemble doit être en conformité avec les règlements de sécurité intrinsèque. L’électronique de ce produit est isolée du boîtier/de la terre. Température ambiante de fonctionnement : -40 _C à + 80 _C Ignifuge Température ambiante de fonctionnement : - 40 _C à + 80 _C Cet appareil doit être équipé d’un câble d’arrivée homologué Ex d IIC. 6 Guide de démarrage rapide Contrôleur numérique de niveau DLC3010 D103214X0FR Juillet 2020 Type n Cet équipement doit être utilisé avec un câble d’arrivée assurant un indice de protection IP66 au minimum et doit satisfaire aux normes européennes applicables. Température ambiante de fonctionnement : - 40 _C à + 80 _C Voir le Tableau 3 pour plus d’informations relatives à la certification. Tableau 3. Classifications pour zones dangereuses - ATEX Certificat Certification obtenue Sécurité intrinsèque II 1 G D Gaz Ex ia IIC T5 Ga Poussière Ex ia IIIC T83 °C Da IP66 ATEX Valeur nominale d’entité Ui = 30 Vcc Ii = 226 mA Pi = 1,2 W Ci = 5,5 nF Li = 0,4 mH Code de température T5 (Tamb ≤ 80 °C) Ignifuge II 2 G D Gaz Ex d IIC T5 Gb Poussière Ex tb IIIC T83 °C Db IP66 --- T5 (Tamb ≤ 80 °C) Type n II 3 G D Gaz Ex nA IIC T5 Gc Poussière Ex t IIIC T83 °C Dc IP66 --- T5 (Tamb ≤ 80 °C) IECEx Sécurité intrinsèque Cet appareil doit être raccordé uniquement à un équipement de sécurité intrinsèque certifié et l’ensemble doit être en conformité avec les règlements de sécurité intrinsèque. L’électronique de ce produit est isolée du boîtier/de la terre. Température ambiante de fonctionnement : -40 _C à + 80 _C Ignifuge, type n Aucune condition spéciale pour une utilisation en toute sécurité. Voir le Tableau 4 pour des informations relatives aux certifications. Tableau 4. Classifications pour zones dangereuses - IECEx Certificat IECEx Certification obtenue Sécurité intrinsèque Gaz Ex ia IIC T5 Ga Poussière Ex ia IIIC T83 °C Da IP66 Ignifuge Gaz Ex d IIC T5 Gb Poussière Ex t IIIC T83 °C Db IP66 Type n Gaz Ex nA IIC T5 Gc Poussière Ex t IIIC T83 °C Dc IP66 Valeur nominale d’entité Ui = 30 Vcc Ii = 226 mA Pi = 1,2 W Ci = 5,5 nF Li = 0,4 mH Code de température T5 (Tamb ≤ 80 °C) --- T5 (Tamb ≤ 80 °C) --- T5 (Tamb ≤ 80 °C) 7 Contrôleur numérique de niveau DLC3010 Guide de démarrage rapide D103214X0FR Juillet 2020 Montage Montage du capteur 249 Le capteur 249 se monte de l’une des deux méthodes suivantes, selon son type spécifique. Si le capteur comporte un plongeur en cage, il se place sur le côté de la cuve, comme indiqué dans la figure 3. Si le capteur comporte un plongeur sans cage, il se place sur le sommet de la cuve, comme indiqué sur la figure 4. Figure 3. Montage du capteur en cage Figure 4. Montage du capteur sans cage NIVEAU DE LIQUIDE Le contrôleur numérique de niveau de type DLC3010 est habituellement livré avec le capteur. Si ce dernier est commandé à part, il peut être pratique de monter le contrôleur numérique de niveau sur le capteur et d’effectuer la configuration et l’étalonnage initiaux avant d’installer le capteur sur la cuve. Remarque Une bielle et un bloc sont installés à chaque extrémité du capteur avec cage pour protéger le plongeur lors du transport. Retirer ces pièces avant d’installer le capteur pour permettre un fonctionnement correct du plongeur. 8 Guide de démarrage rapide Contrôleur numérique de niveau DLC3010 D103214X0FR Juillet 2020 Orientation du DLC3010 Monter le contrôleur numérique de niveau avec l’orifice d’accès de la fixation de l’axe du tube de torsion (voir figure 2) pointant vers le bas, pour permettre la vidange de l’excès d’humidité. Remarque Si l’utilisateur installe une vidange d’un autre type et qu’une faible perte est acceptable, l’instrument peut être monté autour de l’axe pilote, à des positions séparées de 90 degrés. L’affichage LCD peut être lui aussi tourné par paliers de 90 degrés pour cet usage. Le contrôleur numérique de niveau et le bras du tube de torsion sont fixés au capteur du côté gauche ou droit du plongeur, comme indiqué sur la figure 5. Il est possible de modifier cela sur site pour un capteur 249 (se reporter au manuel d’instruction approprié du capteur). Modifier le montage a une incidence sur l’action efficace, car le sens de rotation du tube de torsion pour un niveau en élévation (quand on est face à l’axe en saillie) est le sens horaire lorsque l’unité est montée sur la droite du plongeur et le sens anti-horaire lorsque l’unité est montée à gauche du plongeur. Tous les capteurs avec cage 249 comportent une tête tournante. Autrement dit, le contrôleur numérique de niveau peut être placé dans huit positions différentes autour de la cage, comme indiqué par les positions numérotées de 1 à 8 sur la figure 5. Pour faire tourner la tête, retirer les boulons et écrous de bride puis placer la tête dans la position souhaitée. Montage du contrôleur numérique de niveau sur un capteur 249 Se reporter à la figure 2, sauf indication contraire. 1. Si la vis sans tête placée dans la poignée d’accès est en contact avec la lame de ressort, utiliser une clé hexagonale de 2 mm pour la faire ressortir jusqu’à ce que sa tête soit au ras de la surface de la poignée (voir figure 6). Faire glisser la poignée d’accès en position verrouillée pour découvrir l’orifice d’accès. Appuyer sur la partie arrière de la poignée, comme indiqué sur la figure 2, puis faire glisser la poignée vers l’avant de l’unité. Veiller à ce que la poignée de blocage se place dans le dispositif de blocage. 2. A l’aide d’une douille creuse de 10 mm de profondeur, introduite par l’orifice d’accès, desserrer la fixation de l’axe (figure 2). Cette fixation sera resserrée au paragraphe Accouplement de la section Configuration initiale. 3. Retirer les écrous hexagonaux des tiges filetées. Ne pas retirer la bague de l’adaptateur. ATTENTION Si le tube de torsion est courbé ou désaligné lors de l’installation, il peut en résulter des erreurs de mesure. 9 Guide de démarrage rapide Contrôleur numérique de niveau DLC3010 D103214X0FR Juillet 2020 Figure 5. Positions de montage typiques pour le contrôleur numérique de niveau FIELDVUE DLC3010 sur le capteur Fisher 249 CAPTEUR GAUCHE DU PLONGEUR DROITE DU PLONGEUR 3 7 1 6 5 8 4 3 1 4 2 1 1 AVEC CAGE 5 2 8 6 7 SANS CAGE 1 Non disponible pour les capteurs 249C et 249K. Figure 6. Gros plan de la vis sans tête VIS SANS TETE 4. Placer le contrôleur numérique de niveau de façon à ce que l’orifice d’accès soit à la base de l’instrument. 5. Faire doucement coulisser les tiges filetées dans les orifices de fixation du capteur, jusqu’à ce que le contrôleur numérique de niveau tienne fermement contre le capteur. 6. Remettre en place les écrous hexagonaux sur les tiges filetées puis les serrer à 10 N.m (88.5 lbf-in.). 10 Guide de démarrage rapide Contrôleur numérique de niveau DLC3010 D103214X0FR Juillet 2020 Montage du contrôleur numérique de niveau pour applications à températures extrêmes Se reporter à la figure 7 pour l’identification des pièces, sauf indication contraire. Le contrôleur numérique de niveau nécessite l’installation d’un isolant lorsque la température dépasse la plage indiquée sur la figure 8. Une extension d’axe du tube de torsion est nécessaire pour le capteur 249 lorsqu’un isolant est employé. Figure 7. Montage du contrôleur numérique de niveau sur le capteur pour des applications à températures extrêmes ISOLANT (NUMERO 57) EXTENSION DE L’AXE (NUMERO 58) VIS SANS TETE (NUMERO 60) RONDELLE (NUMERO 78) ECROUS HEXAGONAUX (NUMERO 34) COUPLAGE DE L’AXE (NUMERO 59) VIS D’ASSEMBLAGE (NUMERO 63) MN28800 20A7423-C B2707 TIGES FILETEES DE FIXATION (NUMERO 33) CAPTEUR CONTROLEUR NUMERIQUE DE NIVEAU TEMPERATURE AMBIANTE (_C) -40 800 -30 -20 -10 0 10 20 30 40 50 60 ISOLANT THERMIQUE NECESSAIRE 400 70 TROP CHAUD 80 425 400 300 200 100 0 ISOLANT THERMIQUE INUTILE 0 -100 1 TROP -325 FROID -40 -20 -200 ISOLANT THERMIQUE NECESSAIRE 0 20 40 60 80 100 120 140 TEMPERATURE AMBIANTE (_F) 160 176 TEMPERATURE DE PROCEDE (_C) TEMPERATURE DE PROCEDE (_F) Figure 8. Recommandations concernant l’utilisation d’un isolant thermique en option TRANSMETTEUR STANDARD NOTES : 1 POUR LES TEMPERATURES DE PROCEDE INFERIEURES A -29 _C (-20 _F) ET SUPERIEURES A 204 _C (400 _F) LE MATERIAU DU CAPTEUR DOIT ETRE CHOISI EN FONCTION DU PROCEDE - VOIR LE TABLEAU 9. 2. SI LE POINT DE ROSEE DE L’AIR AMBIANT SE SITUE AU-DESSUS DE LA TEMPERATURE DE PROCEDE, DU GIVRE RISQUE D’ENTRAINER UN DISFONCTIONNEMENT DE L’INSTRUMENT ET DE REDUIRE L’EFFICACITE DE l’ISOLANT. 39A4070-B A5494-1 ATTENTION Si le tube de torsion est courbé ou désaligné lors de l’installation, il peut en résulter des erreurs de mesure. 11 Contrôleur numérique de niveau DLC3010 Guide de démarrage rapide Juillet 2020 D103214X0FR 1. Pour monter un contrôleur numérique de niveau sur un capteur 249, fixer l’extension de l’axe au tube de torsion du capteur à l’aide du couplage de l’axe et des vis sans tête, le couplage étant centré comme indiqué dans la figure 7. 2. Faire glisser la poignée d’accès en position verrouillée pour découvrir l’orifice d’accès. Appuyer sur la partie arrière de la poignée, comme indiqué sur la figure 2, puis faire glisser la poignée vers l’avant de l’unité. Veiller à ce que la poignée de blocage se place dans le dispositif de blocage. 3. Retirer les écrous hexagonaux des tiges filetées. 4. Placer l’isolant sur le contrôleur numérique de niveau en faisant glisser l’isolant directement sur les tiges filetées. 5. Replacer les quatre écrous hexagonaux sur les tiges filetées et les resserrer. 6. Faire prudemment glisser le contrôleur numérique de niveau, avec l’isolant, sur le couplage de l’axe de façon à ce que l’orifice d’accès soit au fond du contrôleur numérique de niveau. 7. Fixer le contrôleur numérique de niveau et l’isolant au bras du tube de torsion à l’aide des quatre vis d’assemblage. 8. Serrer ces quatre vis d’assemblage à un couple de 10 N.m (88.5 lbf-in.). Accouplement Si le contrôleur numérique de niveau n’est pas encore couplé au capteur, appliquer la procédure suivante pour coupler le contrôleur numérique de niveau au capteur. 1. Faire glisser la poignée d’accès en position verrouillée pour découvrir l’orifice d’accès. Appuyer sur la partie arrière de la poignée, comme indiqué sur la figure 2, puis faire glisser la poignée vers l’avant de l’unité. Veiller à ce que la poignée de blocage se place dans le dispositif de blocage. 2. Placer le plongeur dans la position la plus basse possible du procédé (exemple : le niveau d’eau le plus bas ou la densité minimale) ou remplacer le plongeur par la masse d’étalonnage la plus élevée. Remarque Les applications d’interface ou de densité avec un plongeur/tube de torsion calibré pour de faibles modifications totales de densité sont conçues pour fonctionner avec le plongeur immergé en permanence. Dans ces applications, la bielle de poussée repose parfois sur une butée lorsque le plongeur est à sec. Le tube de torsion ne commencera pas à se mouvoir tant qu’une quantité suffisante de liquide n’a pas recouvert le plongeur. Dans ce cas, procéder à l’accouplement avec le plongeur immergé dans le liquide possédant la densité la plus faible et la température de procédé la plus élevée, ou dans des conditions équivalentes simulées par des poids. Si l’étalonnage du capteur a pour résultat une bande proportionnelle supérieure à 100 % (étendue de rotation totale attendue supérieure à 4,4 degrés), coupler le transmetteur à l’axe pilote en étant à 50 % du procédé, cela pour tirer au maximum partie de la course disponible du transmetteur ($6_). La procédure de saisie du zéro est toujours effectuée à une flottaison nulle (ou flottaison différentielle nulle). 3. Insérer une douille creuse de 10 mm de profondeur par l’orifice d’accès, sur l’écrou de serrage de l’axe du tube de torsion. Serrer l’écrou avec un couple maximal de 2,1 N.m (18 lbf-in.). 4. Faire glisser la poignée d’accès en position déverrouillée. (Appuyer sur la partie arrière de la poignée, comme indiqué sur la figure 2, puis faire glisser la poignée vers l’arrière de l’unité.) Veiller à ce que la poignée de blocage se place dans le dispositif de blocage. 12 Guide de démarrage rapide Contrôleur numérique de niveau DLC3010 D103214X0FR Juillet 2020 Raccordements électriques AVERTISSEMENT Sélectionner un câble et/ou des presse-étoupes d’une capacité adaptée à l’environnement d’utilisation (tel que zone dangereuse, indice de protection et température). Un incendie ou une explosion pouvant entraîner des blessures ou des dégâts matériels peuvent survenir si un câblage ou presse-étoupe d’une capacité adaptée ne sont pas utilisés. Les raccordements câblés doivent être conformes aux codes locaux, régionaux et nationaux pour toute certification pour utilisation en zone dangereuse. Le non-respect des codes locaux, régionaux et nationaux peut être à l’origine d’incendies ou d’explosions et provoquer des blessures ou des dommages matériels. Une installation électrique correcte est indispensable pour éviter les erreurs générées par les parasites d’origine électrique. Une résistance de 230 à 600 ohms doit être présente dans la boucle pour permettre la communication avec une interface de communication. Se reporter à la figure 9 pour les connexions de l’entrée de boucle. Figure 9. Raccordement d’une interface de communication à la boucle du contrôleur numérique de niveau 230 RL 600 1 − + + Mesure de référence + pour étalonnage ou contrôle. Un voltmètre présentant une résistance de − 250 ohms ou un ampèremètre fera l’affaire. + Il est possible de connecter une interface de communication en tout point de raccordement de la boucle du signal hormis au niveau de l’alimentation. La boucle du signal doit indiquer une charge de 230 à 600 ohms pour la communication. ALIMENTATION − − La boucle du signal peut être mise à la terre en tout point ou bien laissée sans mise à la terre. REMARQUE : 1 CELA REPRESENTE LA RESISTANCE SERIE TOTALE DE LA BOUCLE. E0363 Alimentation Pour communiquer avec le contrôleur numérique de niveau, il faut une alimentation minimale de 17,75 Vcc. La tension présente aux bornes du transmetteur est déterminée par la tension d’alimentation présente moins la résistance série totale de la boucle multipliée par le courant présent dans la boucle. La tension d’alimentation disponible ne doit pas descendre sous la tension de décollement. (La tension de décollement est la tension d’alimentation disponible minimale nécessaire à la charge totale d’une 13 Guide de démarrage rapide Contrôleur numérique de niveau DLC3010 D103214X0FR Juillet 2020 boucle donnée). Se reporter à la figure 10 pour déterminer la tension de décollement nécessaire. Si la résistance série totale de la boucle est connue, il est possible de déterminer la tension de décollement. Si la tension d’alimentation disponible est connue, il est possible de déterminer la résistance de boucle autorisée. Si la tension d’alimentation tombe sous la tension de décollement alors que le transmetteur est en cours de configuration, il se peut que ce dernier affiche des informations erronées. L’alimentation en courant continu doit délivrer une tension présentant moins de 2 % de fluctuation. La résistance totale est la somme de la résistance des fils du signal et de la résistance de charge d’un contrôleur, d’un indicateur ou d’un quelconque équipement similaire raccordé à la boucle. Il convient de remarquer que la résistance des barrières de sécurité intrinsèque, si elles sont utilisées, doit être incluse. Figure 10. Caractéristiques d’alimentation et résistance de charge Charge maximale = 43,5 x (tension d’alimentation disponible - 12,0) Charge (ohms) 783 Zone de fonctionnement 250 0 10 E0284 12 15 20 25 30 TENSION D’ALIMENTATION DE DECOLLEMENT (Vcc) Câblage sur site AVERTISSEMENT Afin d’éviter des blessures ou dégâts matériels dus à un incendie ou une explosion, couper l’alimentation de l’instrument avant de retirer le couvercle du contrôleur numérique de niveau dans une atmosphère potentiellement explosive ou dans une zone classée dangereuse. Remarque Pour les applications à sécurité intrinsèque, se reporter aux instructions fournies par le fabricant de la barrière. L’alimentation au contrôleur numérique de niveau est entièrement acheminée par le câble du signal. Le câble du signal n’a pas besoin d’être blindé ; utiliser des paires torsadées pour de meilleurs résultats. Ne pas faire passer le câble non blindé du signal dans des conduits ou des chemins de câble ouverts près d’équipements électriques lourds. Si le contrôleur numérique se situe dans une atmosphère explosive, ne pas retirer les couvercles du contrôleur numérique de niveau lorsque le circuit est sous tension, sauf dans le cas d’une installation à sécurité intrinsèque. Eviter le contact avec les fils et bornes. Pour alimenter le contrôleur numérique de niveau, raccorder le fil d’alimentation positif à la borne + et le fil négatif à la borne - comme indiqué dans la figure 11. 14 Guide de démarrage rapide Contrôleur numérique de niveau DLC3010 D103214X0FR Juillet 2020 Figure 11. Boîtier de raccordement du contrôleur numérique de niveau CONNEXIONS DE L’ENTREE DE BOUCLE DE 4 Á 20 mA CONNEXIONS DE TEST ENTREE DE CABLE 1/2 NPT CONNEXIONS RTD CONNEXION DE MASSE INTERNE ENTREE DE CABLE 1/2 NPT VUE AVANT CONNEXION DE MASSE EXTERNE VUE ARRIERE W8041 ATTENTION Ne pas appliquer de tension entre les bornes T et +. Cela peut détruire la résistance de 1 ohm du boîtier de raccordement. Ne pas appliquer de tension de boucle entre les bornes Rs et -. Cela peut détruire la résistance de 50 ohms du module électronique. Lors du câblage sur un bornier à vis, il est recommandé d’utiliser des cosses serties. Serrer les vis du bornier pour établir un contact parfait. Aucun câblage d’alimentation supplémentaire n’est requis. Tous les couvercles du contrôleur numérique de niveau doivent être correctement en place pour se conformer aux exigences antidéflagrantes. Concernant les unités conformes ATEX, la vis du couvercle du boîtier de raccordement doit se placer dans un des enfoncements placés sur le boîtier de raccordement, derrière le couvercle du boîtier de raccordement. Mise à la terre AVERTISSEMENT Des blessures ou dégâts matériels dus à un incendie ou une explosion peuvent être à déplorer lors de la décharge d’électricité statique en présence de gaz inflammables ou dangereux. Relier un ruban de mise à la terre de 2,1 mm2 (14 AWG) entre le contrôleur numérique de niveau et la terre en présence de gaz inflammables ou dangereux. Se reporter aux codes et normes nationaux et locaux pour connaître les exigences de mise à la terre. Le contrôleur numérique de niveau fonctionnera avec la boucle du signal en circuit flottant ou à la terre. Cependant, les parasites supplémentaires générés par les systèmes flottants peuvent affecter de nombreux types d’appareils de lecture. Si le signal paraît brouillé ou irrégulier, le fait de mettre à la terre le circuit en un point peut résoudre le problème. Le meilleur emplacement pour mettre le circuit à la terre est au niveau de la borne négative de l’alimentation. Une autre possibilité est de mettre à la terre au niveau d’une des bornes de l’appareil de lecture. Ne pas mettre le circuit à la terre en plus d’un point. Câble blindé Les techniques de mise à la terre recommandées pour des câbles blindés font généralement appel à un point de mise à la terre unique pour le blindage. Il est possible de relier le blindage soit au niveau de l’alimentation soit aux bornes de mise à la terre, internes ou externes, au niveau du boîtier de raccordement de l’instrument, comme indiqué sur la figure 11. 15 Contrôleur numérique de niveau DLC3010 Juillet 2020 Guide de démarrage rapide D103214X0FR Connexions de l’alimentation/de l’entrée de boucle Utiliser du fil de cuivre d’un calibre suffisant pour que la tension passant par le contrôleur numérique de niveau ne passe pas en dessous de 12,0 Vcc. Raccorder les fils du signal de courant comme indiqué sur la figure 9. Une fois les connexions effectuées, revérifier la polarité et les branchements puis mettre sous tension. Connexions RTD Il est possible de raccorder un RTD, permettant de sonder la température, au contrôleur numérique de niveau. Cela permet à l’instrument d’effectuer automatiquement des corrections de densité en fonction des changements de température. Pour de meilleurs résultats, placer le RTD aussi près que possible du plongeur. Pour des performances optimales en termes de CEM, utiliser des fils blindés d’une longueur maximale de 3 mètres (9.8 ft) pour raccorder le RTD. Raccorder une seule extrémité du blindage. Raccorder le blindage soit à la connexion de masse interne du boîtier de raccordement de l’instrument, soit au puits thermométrique avec sonde RTD. Câbler le RTD au contrôleur numérique de niveau comme indiqué ci-après (voir figure 11) : Connexions RTD bifilaires 1. Connecter un cavalier entre les bornes RS et R1 du boîtier de raccordement. 2. Connecter le RTD aux bornes R1 et R2. Remarque Lors de la configuration manuelle, il est nécessaire de spécifier la résistance du câble de connexion pour une sonde Pt100 2 fils. Un câble 16 AWG de 250 pieds a une résistance de 1 ohm. Connexions RTD trifilaires 1. Connecter les 2 fils se trouvant du même côté que le RTD aux bornes RS et R1 du boîtier de raccordement. Habituellement, ces deux fils sont de la même couleur. 2. Raccorder le troisième fil à la borne R2. (La résistance mesurée entre ce fil et l’un des deux fils connectés aux terminaux RS et R1 doit être une résistance équivalente, pour la température ambiante existante. Se reporter à la table de conversion tension/température fournie par le fabricant du RTD.) Habituellement, ce fil est d’une couleur différente de ceux raccordés aux bornes RS et R1. Connexions de communication AVERTISSEMENT Des blessures ou dégâts matériels dus à un incendie ou une explosion peuvent être à déplorer si cette connexion est tentée dans une atmosphère potentiellement explosive ou dans une zone classée dangereuse. Vérifier que la classification de la zone et les conditions atmosphériques permettent le retrait en toute sécurité du couvercle du boîtier à bornes avant de commencer. L’interface de communication se raccorde au contrôleur numérique de niveau DLC3010 en tout point de raccordement de la boucle 4-20 mA (excepté entre les bornes de l’alimentation). S’il est décidé de raccorder l’interface de communication HART® directement à l’instrument, raccorder l’interface aux bornes + et - de la boucle, bornes placées dans le boîtier de raccordement, et ainsi communiquer avec l’instrument. 16 Guide de démarrage rapide Contrôleur numérique de niveau DLC3010 D103214X0FR Juillet 2020 Cavalier d’alarme Chaque contrôleur numérique de niveau surveille en continu ses propres performances en fonctionnement normal. Cette routine de diagnostic automatique consiste en une suite de vérifications répétées continuellement. Si un test détecte une défaillance des composants électroniques, le courant de sortie de l’instrument passe soit en dessous de 3,70 mA, soit au-dessus de 22,5 mA, selon la position du cavalier d’alarme (HI/LO) [HAUT/BAS]. Une condition d’alarme se produit lorsque la routine d’autodiagnostic du contrôleur numérique de niveau détecte une erreur qui rendrait la mesure du procédé inexacte, incorrecte ou non définie, ou si un seuil défini par l’utilisateur est dépassé. A ce moment, la sortie analogique de l’unité passe à un niveau prédéfini, au-dessus ou en-dessous de la plage d’utilisation nominale de 4-20 mA, selon la position du cavalier d’alarme. Sur des composants électroniques 14B5483X042 et antérieurs, si le cavalier n’est pas en place, l’alarme est indéterminée mais se comporte généralement en FAIL LOW (ANOMALIE BAS). Pour des composants électroniques 14B5484X052 et ultérieurs, le comportement par défaut sera FAIL HIGH (ANOMALIE HAUT) lorsque le cavalier est absent. Emplacements du cavalier d’alarme Sans le voltmètre en place : Le cavalier d’alarme est placé à l’avant du module électronique, côté composants électroniques du boîtier du contrôleur numérique de niveau, il est étiqueté FAIL MODE (MODE ANOMALIE). Avec le voltmètre en place : Le cavalier d’alarme est placé sur le panneau LCD du côté du module électronique du boîtier du contrôleur numérique de niveau, il est étiqueté FAIL MODE. Modification de la position du cavalier AVERTISSEMENT Des blessures ou dégâts matériels dus à un incendie ou une explosion peuvent être à déplorer si la procédure suivante est tentée dans une atmosphère potentiellement explosive ou dans une zone classée dangereuse. Vérifier que la classification de la zone et les conditions atmosphériques permettent le retrait en toute sécurité du couvercle de l’instrument avant de commencer. Suivre la procédure ci-après pour modifier la position du cavalier d’alarme : 1. Si le contrôleur numérique de niveau est en place, régler la boucle sur manuel. 2. Retirer le couvercle du boîtier du côté composants. Ne pas retirer le couvercle dans une atmosphère explosive alors que le circuit est sous tension. 3. Placer le cavalier dans la position souhaitée. 4. Remettre le couvercle en place. Tous les couvercles doivent être correctement en place pour se conformer aux exigences antidéflagrantes. Pour des unités conformes ATEX, la vis placée sur le boîtier du transducteur doit se placer dans un des enfoncements situés sur le couvercle. 17 Contrôleur numérique de niveau DLC3010 Guide de démarrage rapide D103214X0FR Juillet 2020 Accès aux procédures de configuration et de l’étalonnage Les procédures qui exigent l’utilisation de l’interface de communication possèdent les zones de texte et la séquence de touches numériques nécessaires pour pouvoir afficher le menu de l’interface de communication souhaité. Par exemple, pour accéder au menu Full Calibration (étalonnage complet) : Interface de communication Configure > Calibration > Primary > Full Calibration (2-5-1-1) Remarque Les séquences d’accès rapide ne s’appliquent qu’à l’interface de communication 475. Elles ne s’appliquent pas à l’interface de communication Trex. Configuration et étalonnage Configuration initiale Si un contrôleur numérique de niveau DLC3010 est livré monté en usine sur un capteur 249, il n’est pas nécessaire d’effectuer la configuration et l’étalonnage initiaux. La saisie des données du capteur, le couplage de l’instrument au capteur et l’étalonnage de la combinaison instrument et capteur sont effectués en usine. Remarque Si le contrôleur numérique de niveau est reçu monté sur le capteur avec le plongeur bloqué, ou si le plongeur n’est pas relié au système, l’instrument sera couplé au capteur et le levier sera déverrouillé. Pour mettre l’unité en service, en cas de plongeur bloqué, retirer la tige et le bloc placé à chaque extrémité du plongeur et vérifier l’étalonnage de l’instrument. (Si l’option factory cal (étalonnage usine) a été demandée, l’instrument sera livré pré-compensé conformément aux conditions de procédé indiquées lors de la commande, il peut donc ne pas paraître étalonné lors d’un contrôle à température ambiante à des niveaux d’eau de 0 et 100 %). Si le plongeur n’est pas connecté, le suspendre au tube de torsion. Si le contrôleur numérique de niveau est reçu monté sur le capteur avec le plongeur non bloqué (par exemple sur des systèmes montés sur plate-forme), l’instrument ne sera pas couplé au capteur et le levier sera verrouillé. Avant de mettre l’unité en service, coupler l’instrument au capteur puis déverrouiller le levier. Lorsque le capteur est correctement connecté et couplé au contrôleur numérique de niveau, régler l’état zéro du procédé et effectuer l’étalonnage du zéro approprié sous le menu Partial calibration (étalonnage partiel). Il ne devrait pas être nécessaire de réétalonner le couple du tube de torsion (Torque Rate). Pour examiner les données de configuration stockées en usine, connecter l’instrument à une alimentation 24 Vcc, comme indiqué sur la figure 9. Raccorder l’interface de communication à l’instrument et l’allumer. Rendez-vous dans Configure (configurer) et eaminez les données de Manual Setup (Configuration manuelle), Alert Setup (Configuration de l’alarme), et Communications. Si vos données d’application ont été modifiées depuis la configuration de l’instrument en usine, reportez-vous à la section Manual Setup (Configuration manuelle) qui contient les instructions de modification des données de configuration. Pour les instruments non montés sur un capteur de niveau ou lors du remplacement d’un instrument, la configuration initiale consiste à entrer les informations du capteur. L’étape suivante consiste à accoupler le capteur au contrôleur numérique de niveau. Une fois le contrôleur numérique de niveau et le capteur couplés, l’ensemble formé par ces deux éléments peut alors être étalonné. 18 Guide de démarrage rapide Contrôleur numérique de niveau DLC3010 D103214X0FR Juillet 2020 Les informations de capteur comprennent les informations relatives au plongeur et au tube de torsion telles que : D Les unités de longueur (mètres, in. ou centimètres) ; D Les unités de volume (po. cubes, millimètres cubes ou millilitres) ; D Les unités de poids (kilogrammes, livres ou onces) ; D Longueur du plongeur D Volume du plongeur D Poids du plongeur D La longueur de la tige du plongeur (bras de moment) (voir tableau 5) ; D Matériau tube de torsion Remarque Le matériau du tube de torsion, pour un capteur possédant un tube de torsion en N05500, sera NiCu sur la plaque signalétique. D Le sens de montage de l’instrument (à gauche ou à droite du plongeur) ; D Le type de mesure (niveau, interface ou densité). Consignes de configuration La configuration guidée (Guided Setup) vous accompagne dans la tâche d’initialisation des données de configuration nécessaires au fonctionnement. Comme l’instrument est livré avec des dimensions par défaut correspondant à la version de Fisher 249 la plus courante, si certaines données ne sont pas connues, il est préférable d’accepter les valeurs par défaut. Le sens de montage de l’instrument (à gauche ou à droite du plongeur) est important pour garantir l’interprétation adéquate du mouvement positif. Le sens de rotation du tube de torsion est horaire avec un niveau en élévation lorsque l’instrument est monté sur la droite du plongeur et le sens anti-horaire lorsque l’instrument est monté à gauche du plongeur. Procédez à la configuration manuelle pour identifier et modifier les paramètres à modifier. Considérations préliminaires Verrouillage en écriture Interface de communication Overview > Device Information > Alarm Type and Security > Security > Write Lock (1-7-3-2-1) Pour configurer et étalonner l’instrument, le verrouillage en écriture doit être réglé sur Writes Enabled (écriture autorisée). Le verrouillage en écriture est réinitialisé par un redémarrage. Si l’instrument vient juste d’être mis sous tension, l’écriture sera autorisée par défaut. 19 Guide de démarrage rapide Contrôleur numérique de niveau DLC3010 D103214X0FR Juillet 2020 Configuration guidée Interface de communication Configure > Guided Setup > Instrument Setup (2-1-1) Remarque Placer la boucle en fonctionnement manuel avant d’effectuer un quelconque changement de configuration ou d’étalonnage. La configuration de l’instrument est disponible pour faciliter la configuration initiale. Suivre les invites sur l’affichage de l’interface de communication pour saisir les informations du plongeur, du tube de torsion et des unités de mesure numérique. La majorité des informations sont inscrites sur la plaque signalétique du capteur. Le bras de moment correspond à la longueur utile de la longueur de la tige du plongeur (entraînement) et varie en fonction du type de capteur. Pour un capteur 249, voir tableau 5 pour déterminer la longueur de la tige du plongeur. Pour des capteurs spéciaux, voir la figure 12. Tableau 5. Longueur du bras de moment (tige)(1) TYPE DE CAPTEUR(2) BRAS DE MOMENT mm In. 249 203 8.01 249B 203 8.01 249BF 203 8.01 249BP 203 8.01 249C 169 6.64 249CP 169 6.64 249K 267 10.5 249L 229 9.01 249N 267 10.5 249P (CL125-CL600) 203 8.01 249P (CL900-CL2500) 229 9.01 249VS (Spécial)(1) Voir carte série Voir carte série 249VS (Std) 343 13.5 249W 203 8.01 1. La longueur de bras de moment (tige) est la distance verticale entre la ligne médiane verticale du plongeur et la ligne médiane horizontale du tube de torsion. Voir la figure 12. S’il n’est pas possible de déterminer la longueur de la tige d'entraînement, prendre contact avec un bureau commercial Emerson et fournir le numéro de série du capteur. 2. Ce tableau est valable uniquement pour les capteurs à plongeur vertical. Pour les types de capteur non répertoriés, ou pour les capteurs à plongeur horizontal, prendre contact avec un bureau commercial Emerson pour connaître la longueur de tige d’entraînement. Pour les capteurs proposés par d’autres fabricants, se reporter aux instructions d’installation correspondantes. 1. Saisir la longueur de la tige du plongeur, le poids, les unités et valeurs volumétriques ainsi que la longueur de la tige d’entraînement (bras de moment) (dans les mêmes unités que celles choisies pour la longueur du plongeur) à l’invite du système. 2. Choisir le sens de montage de l’instrument (à gauche ou à droite du plongeur, voir figure 5). 3. Choisir le matériau du tube de torsion. 20 Guide de démarrage rapide Contrôleur numérique de niveau DLC3010 D103214X0FR Juillet 2020 Figure 12. Méthodes de détermination du bras de moment à partir de mesures externes CUVE LIGNE MÉDIANE VERTICALE CL DU PLONGEUR LONGUEUR DU BRAS DE MOMENT LIGNE MÉDIANE HORIZONTALE CL DU TUBE DE TORSION 4. Sélectionner l’application de mesure (niveau, interface ou densité). Remarque Pour des applications d’interface, si le 249 n’est pas placé sur une cuve ou si la cage peut être isolée, étalonner l’instrument avec des poids, de l’eau ou un fluide test standard, en mode niveau. Une fois l’étalonnage en mode niveau effectué, l’instrument peut être commuté en mode interface. Saisir ensuite la densité du fluide procédé ainsi que la plage de valeurs. Si le capteur 249 est présent et qu’il doit être étalonné pour le ou les fluides de procédé dans les conditions d’exploitation, entrer le mode de mesure définitif et le fluide procédé utilisé maintenant. a. Si Level (Niveau) ou Interface (Interface) est choisi, les unités par défaut des variables du procédé seront les mêmes que les unités choisies pour la longueur du plongeur. Le système vous demande de saisir la compensation de niveau. Les valeurs de plage seront initialisées en fonction de la compensation de niveau et de la taille du plongeur. La borne supérieure par défaut de la plage sera égale à la longueur du plongeur et la borne inférieure est nulle (zéro) lorsque la compensation de niveau est égale à 0. b. Si Density (Densité) est choisi, les unités par défaut des variables du procédé sont définies sur SGU (Specific Gravity Units = unités de densité). La borne supérieure par défaut de la plage sera égale à 1,0 et la borne inférieure à 0,1. 5. Sélectionnez l’action de sortie souhaitée : Action directe ou inverse. Le choix : reverse acting (Action inverse) va permuter les valeurs par défaut des bornes supérieures et inférieures (les valeurs des variables du procédé à 20 mA et 4 mA). En action inverse, le courant de boucle diminuera à mesure que le niveau du fluide augmente. 6. Il est maintenant possible de modifier la valeur par défaut des unités des variables du procédé. 7. Il est alors possible de modifier les valeurs par défaut définies pour la borne supérieure (valeur PV à 20 mA) et la borne inférieure (valeur PV à 4 mA). 21 Guide de démarrage rapide Contrôleur numérique de niveau DLC3010 D103214X0FR Juillet 2020 8. Les valeurs par défaut des variables d’alarme seront définies comme suit : Instrument à action directe (Etendue = Valeur haute d’échelle - Valeur basse d’échelle) Instrument à action inverse (Etendue = Borne inférieure - Borne supérieure) Variable d’alarme Valeur par défaut Variable d’alarme Valeur par défaut Hi-Hi Alarm Valeur haute de l’échelle Hi-Hi Alarm Valeur basse de l’échelle Hi Alarm 95 % de l’étendue de l’échelle + valeur basse de l’échelle Hi Alarm 95 % de l’étendue de l’échelle + valeur haute de l’échelle Lo Alarm 5 % de l’étendue de l’échelle + valeur basse de l’échelle Lo Alarm 5 % de l’étendue de l’échelle + valeur haute de l’échelle Lo-Lo Alarm Valeur basse de l’échelle Lo-Lo Alarm Valeur haute de l’échelle Les seuils d’alarme PV sont initialisés à 100 %, 95 %, 5 % et 0 % de l’étendue de l’échelle. La bande morte de l’alarme PV est initialisée à 0,5 % de l’étendue de l’échelle. Les alarmes PV sont toutes désactivées. Les alarmes de température sont activées. D En mode densité, la configuration est terminée. D En mode interface ou densité, il faut maintenant saisir la densité du fluide procédé (en mode interface, il faudra renseigner les densités des fluides supérieur et inférieur). Remarque En cas d’utilisation d’eau ou de poids à des fins d’étalonnage, saisir une densité de 1,0 SGU. Pour tout autre fluide test, saisir la densité du liquide utilisé. Pour la compensation de la température, aller dans Manual Setup (Configuration manuelle). Dans Process Fluid (Fluides de procédé), sélectionner View Fluid Tables (Tables de fluide). L’activation de la compensation de la température se fait en saisissant des valeurs dans les tables de fluide. Deux tables de données de densité disponibles peuvent être entrées dans l’instrument pour permettre la correction de la densité en fonction de la température (voir la section Configuration manuelle du manuel d’instructions). Pour des applications de niveau d’interface, les deux tables sont utilisées. Pour des applications de mesure de niveau, seule la table de densité inférieure est utilisée. Aucune des deux tables n’est utilisée dans le cas d’application de densité. Il est possible de modifier chacune de ces tables en configuration manuelle. Remarque Il peut être nécessaire d’éditer les tables existantes pour prendre en compte les caractéristiques du fluide de procédé considéré. L’utilisateur peut valider la ou les tables actuelles, modifier une entrée ou saisir manuellement une nouvelle table. Pour une application d’interface, l’utilisateur peut passer de la table du liquide supérieur à celle du liquide inférieur et vice-versa. 22 Guide de démarrage rapide Contrôleur numérique de niveau DLC3010 D103214X0FR Juillet 2020 Etalonnage Guided Calibration (Etalonnage guidé) Interface de communication Configure > Calibration > Primary > Guided Calibration (2-5-1-1) L’étalonnage guidé requiert une procédure d’étalonnage appropriée applicable sur le terrain ou sur banc d’essai en fonction de votre entrée. Répondre aux questions sur le scénario de votre procédé afin d’obtenir les recommandations d’étalonnage. Le cas échéant, la méthode d’étalonnage appropriée sera mise en œuvre à partir de la procédure. Exemples d’étalonnage détaillé Etalonnage du capteur PV Pour pouvoir utiliser les fonctions avancées de transmetteur, il est indispensable d’étalonner le capteur PV. Etalonnage - avec plongeur et tube de torsion standard Procéder à l’étalonnage initial autour de la température ambiante à l’étendue d’échelle programmée pour exploiter pleinement la résolution disponible. Cet étalonnage doit être réalisé en utilisant un fluide test d’une densité (SG) proche de 1. La valeur de SG stockée dans la mémoire de l’instrument lors du processus d’étalonnage doit correspondre à la valeur SG du fluide test utilisé durant l’étalonnage. Une fois l’étalonnage initial terminé, il est possible de configurer l’instrument pour un fluide cible d’une densité donnée, ou pour une application d’interface en modifiant tout simplement les données de configuration. 1. Lancer la configuration guidée et vérifier que toutes les données de capteur sont exactes. Procédure : Régler le mode PV sur Level (Niveau) Si vos observations d’entrée sont faites lorsque le bas du plongeur est réglé au point le plus bas du procédé, régler la valeur de Level Offset (compensation de niveau) sur 0.00 Régler la valeur de Specific Gravity (densité) sur la valeur de SG du fluide test utilisé. Régler le niveau de fluide test sur le point zéro de processus souhaité. Vérifier que le levier DLC3010 a été correctement couplé au tube de torsion (voir procédure d’accouplement, page 12). Pour déverrouiller le levier et lui permettre de suivre librement l’entrée, fermer la trappe d’accès du manchon de l’instrument. Il est souvent possible de savoir quand le fluide entre en contact avec le plongeur en regardant l’écran et/ou la sortie analogique de l’instrument, car la sortie ne commence à monter que lorsque ce point est atteint. Sélectionner l’étalonnage Min/Max dans le menu Full Calibration (étalonnage complet), et confirmer à l’invite que l’état actuel correspond à Min. Après acceptation du point Min, le système vous demande de définir l’état Max. (Pour un fonctionnement adéquat, l’état displacer completely covered (plongeur complètement recouvert) doit être légèrement plus élevé que la marque de niveau 100 %. Ainsi, une hauteur de 15 in. au-dessus de la marque zéro est généralement suffisante pour un plongeur de 14 in. sur un 249B, parce que la distance de montée du plongeur attendue pour cette configuration est d’environ 0,6 in.) Accepter cette valeur pour l’état Max. Régler le niveau de fluide test et vérifier l’affichage de l’instrument ainsi que la sortie actuelle en le comparant à un instrument de mesure externe, cela en différents points, répartis sur toute l’étendue pour vérifier l’étalonnage du niveau. a. Pour corriger les erreurs de biais, procéder à un étalonnage par ajustage du zéro dans un état du procédé connu avec exactitude. b. Pour corriger les erreurs de gain, ajuster le gain à un niveau haut connu avec exactitude. 23 Contrôleur numérique de niveau DLC3010 Juillet 2020 Guide de démarrage rapide D103214X0FR Remarque S’il est possible d’observer précisément les états d’entrée individuels, la méthode d’étalonnage en point double peut être utilisée en lieu et place de l’étalonnage Min/Max. S’il n’est pas possible de réaliser un étalonnage Min/Max ou en point double, régler le procédé au point le plus bas et saisir le zéro. Ajuster le gain à un niveau de procédé d’au moins 5 % supérieur à la valeur basse de l’échelle. Si la sortie mesurée n’atteint pas la valeur de saturation inférieure tant que le niveau n’est pas beaucoup plus élevé que la base du plongeur, il est possible que le plongeur soit en surpoids. Un plongeur en surpoids repose sur la butée de fin de course inférieure tant que la flottaison n’est pas suffisante pour permettre à la tringlerie de se mettre en mouvement. Dans ce cas, utiliser la procédure d’étalonnage réservée aux plongeurs en surpoids indiquée ci-dessous. Une fois l’étalonnage initial terminé : Pour les applications de niveau - Aller dans le menu Sensor Compensation (compensation de capteur) et configurer l’instrument en fonction de la densité du fluide procédé cible en passant par Enter constant SG (saisir SG constante). Pour les applications d’interface - Régler le mode PV sur Interface, vérifier ou régler les valeurs de plage présentées par la procédure Modifier le mode PV, puis configurer l’instrument en fonction des SG de chacun des fluides procédé cibles en passant par Enter constant SG (saisir SG constante). Pour les applications de densité - Régler le mode PV sur Density et définir les valeurs de plage souhaitées en appliquant la procédure Modifier le mode PV. Si la température de l’application cible est extrêmement élevée ou faible par rapport à la température ambiante, se reporter au manuel d’instructions DLC3010 (D102748X012) pour plus d’informations sur la compensation de température. Remarque Des informations concernant la simulation précise de cet effet sont proposées dans le supplément du manuel d’instructions intitulé Simulation des conditions du procédé pour l’étalonnage des contrôleurs de niveau et des transmetteurs Fisher (D103066X012), disponible auprès d’un bureau commercial Emerson ou sur Fisher.com. Etalonnage à l’aide d’un plongeur en surpoids Lorsque l’élément matériel du capteur est dimensionné en vue d’obtenir un gain mécanique important (comme c’est le cas dans certaines applications de mesure d’interface ou de densité), le poids du plongeur sec est souvent supérieur au maximum autorisé sur le tube de torsion. Dans un tel cas, il est impossible de saisir la rotation de flottaison nulle du tube de torsion, parce que, dans cet état, la tringlerie repose sur une buttée de fin de course. La routine de saisie du zéro du groupe de menus Partial Calibration (étalonnage partiel) ne fonctionnera donc pas correctement dans les modes PV cibles d’interface ou de densité lorsque le plongeur est en surpoids. Les routines de Full Calibration (étalonnage complet) : Min/Max, Two­Point (point double), et Weight (poids), fonctionneront toutes correctement en conditions de procédé réelles lorsque le mode choisi est interface ou densité, parce qu’elles effectuent un rétro-calcul de l’angle de flottaison zéro théorique au lieu de le saisir. 24 Guide de démarrage rapide Contrôleur numérique de niveau DLC3010 D103214X0FR Juillet 2020 Lorsque le plongeur est en surpoids, il faut avoir recours aux méthodes d’étalonnage partiel ; on peut alors utiliser la transformation suivante : Une application d’interface ou de densité peut être modélisée mathématiquement comme une application de niveau avec un fluide unique dont la densité est égale à la différence entre les SG réelles du fluide qui recouvre le plongeur aux deux extrêmes du procédé. La procédure d’étalonnage se déroule comme suit : D Régler le mode PV sur Level (Niveau). D Régler la compensation du niveau sur zéro. D Régler les valeurs de Range Values (plage) sur : LRV = 0.0, URV = longueur du plongeur. D Effectuer la procédure de saisie du zéro au niveau de procédé le plus bas (plongeur complètement immergé dans le liquide de la densité la plus faible ­ NON sec). D Définir la Gravity (densité) comme résultant de la différence entre les SG des deux fluides (par exemple, si SG_upper = 0,87 et SG_lower = 1,0, entrer une valeur de densité de 0,13). D Configurer un second niveau de procédé à une valeur de plus de 5 % de l’étendue au-dessus du niveau minimum du procédé, et utiliser la procédure Trim Gain (ajuster le gain) à ce niveau. Le gain sera maintenant initialisé correctement. (L’instrument fonctionnerait parfaitement dans cette configuration avec les applications d’interface. Mais avec les applications de densité, il ne sera pas possible de reporter correctement le PV dans les unités si l’étalonnage de l’instrument est réalisé à ce stade.) Comme le gain est maintenant validé : D Régler le mode PV sur interface ou densité, D reconfigurer les SG du fluide ou les valeurs de plage en fonction des valeurs de fluide réelles ou des extrêmes, et D appliquer la procédure de Trim Zero (ajustage du zéro) du menu Partial Calibration (étalonnage partiel) pour rétrocalculer l’angle de flottaison zéro théorique. La dernière étape ci-dessus alignera la valeur du PV des unités sur l’observation indépendante. Remarque Des informations concernant la simulation des conditions du procédé sont proposées dans le supplément du manuel d’instructions intitulé Simulation des conditions du procédé pour l’étalonnage des contrôleurs de niveau et des transmetteurs Fisher (D103066X012), disponible auprès d’un bureau commercial Emerson ou sur Fisher.com. Les directives suivantes concernent les diverses méthodes d’étalonnage de capteur pour une application avec plongeur en surpoids : Sur la base du poids : Utiliser deux poids connus précisément entre les conditions de flottaison minimale et maximale. L’utilisation du poids total du plongeur n’est pas valide car cela stoppera la tringlerie. Min/Max : Min signifie maintenant que le plongeur est immergé dans le fluide le plus léger et Max dans le fluide le plus lourd. 25 Contrôleur numérique de niveau DLC3010 Juillet 2020 Guide de démarrage rapide D103214X0FR Point double : Utiliser deux points d’interface quelconques, placés sur le plongeur. La précision est d’autant plus élevée que les niveaux sont distants. Le résultat en sera proche même pour un écart de niveau de 10 %. Valeur théorique : S’il n’est pas possible de modifier le niveau, il est possible de saisir manuellement une valeur théorique pour le couple du tube, puis d’effectuer un étalonnage par ajustage du zéro pour régler la sortie sur l’observation indépendante actuelle de l’état du procédé. Des erreurs de gain et des erreurs de biais se produiront avec cette démarche qui peut offrir par ailleurs une capacité de contrôle nominal. Conserver les enregistrements des observations suivantes du procédé actuel par rapport aux résultats de l’instrument et aux différents états, et utiliser les rapports entre les modifications du procédé et de l’instrument pour mesurer la valeur du couple du tube de torsion. Répéter l’étalonnage par ajustage du zéro après chaque modification du gain. Applications de densité avec plongeur et tube de torsion standard Remarque Lorsqu’on fait passer PV is de niveau ou interface à densité, les valeurs de plage sont réinitialisées à 0,1 et 1,0 SGU. Vous avez la possibilité de modifier les valeurs de plage et les unités de densité après cette initialisation. L’initialisation permet d’éliminer les valeurs numériques non pertinentes des dimensions de longueurs qui ne peuvent être raisonnablement converties en dimensions de densités. Il est alors possible d’utiliser l’une des méthodes d’étalonnage complet de capteur (sur la base du poids, Min/Max, et point double) pour le mode densité. Min/Max : L’étalonnage Min/Max commence par demander la valeur de SG du fluide test de densité minimale (qui peut correspondre à zéro si le plongeur n’est pas en surpoids). Il faut ensuite établir une condition d’immersion complète du plongeur avec ce fluide. Le procédé requiert ensuite de communiquer la valeur de SG du fluide test de densité maximale et d’immerger complètement le plongeur dans ce fluide. En cas de réussite, la valeur calculée du couple du tube de torsion et de l’angle de référence du zéro s’affichent pour références. Point double : La méthode d’étalonnage en point double nécessite deux conditions de procédé distinctes, les plus différentes possibles. Il est possible d’utiliser deux fluides standard, aux densités bien connues, et d’immerger le plongeur dans l’un ou dans l’autre de façon alternée. Si le fluide est simulé par une certaine quantité d’eau, il faut se rappeler que c’est la surface immergée du plongeur qui compte, et non la quantité d’eau dans la cage. La quantité dans la cage devra toujours être légèrement supérieure en raison du mouvement du plongeur. En cas de réussite, la valeur calculée du couple du tube de torsion et de l’angle de référence du zéro s’affichent pour références. Sur la base du poids : Cette méthode suppose que l’utilisateur détermine la densité la plus faible et la densité la plus élevée pour les points d’étalonnage. Le système calcule ensuite les valeurs. Il est possible de modifier ces valeurs pour refléter le poids réellement utilisé, au cas où les valeurs exactes ne sont pas disponibles au moment de leur saisie. En cas de réussite, la valeur calculée du couple du tube de torsion et de l’angle de référence du zéro s’affichent pour références. Etalonnage du capteur en conditions de procédé (conversion à chaud) lorsqu’il n’est pas possible de faire varier l’entrée S’il n’est pas possible de faire varier l’entrée du capteur pour l’étalonnage, il est possible de configurer le gain de l’instrument en utilisant des informations théoriques et d’utiliser l’ajustage du zéro pour ajuster la sortie sur la condition de procédé actuelle. Cela permet de rendre le contrôleur opérationnel et de contrôler un niveau autour d’un point de consigne. Il est alors possible de comparer dans le temps les variations d’entrée avec celles de sortie pour affiner l’estimation du gain. Un nouvel ajustage du zéro sera nécessaire après chaque modification du gain. Cette approche n’est pas recommandée pour des applications relatives à la sécurité, car une connaissance exacte du niveau est alors requise pour éviter un débordement ou un carter sec. Cependant, cette approche est adaptée aux applications de niveau courantes, pouvant tolérer des écarts importants depuis un point de consigne médian. L’étalonnage en point double permet d’étalonner le tube de torsion en utilisant deux conditions en entrée, conditions pour lesquelles l’interface mesurée se trouvera n’importe où sur le plongeur. La précision de la méthode augmente à mesure que les deux points sont éloignés, mais un déplacement d’au moins 5 % de l’étendue suffit à effectuer le calcul. La plupart des procédés de niveau tolèrent un petit réglage manuel de cette nature. Si le procédé utilisé ne le permet pas, l’approche théorique est alors la seule possible. 26 Guide de démarrage rapide Contrôleur numérique de niveau DLC3010 D103214X0FR Juillet 2020 1. Déterminer toutes les informations possibles sur la configuration matérielle du 249 : type du 249, sens de montage (contrôleur à droite ou à gauche du plongeur), matériau du tube de torsion et épaisseur de la paroi, volume, poids, longueur du plongeur et longueur de la tige. (La longueur de la tige d’entraînement ne correspond pas à la longueur de la tige de suspension, mais à la distance horizontale entre la ligne médiane du plongeur et la ligne médiane du tube de torsion.) Obtenir également des informations sur le procédé : densités des fluides, température et pression du procédé. (La pression est utilisée à titre de rappel, afin de prendre en considération la densité d’une phase gazeuse supérieure, ce qui est probable à des pressions plus élevées.) 2. Lancer la configuration de l’instrument et renseigner les diverses données aussi précisément que possible. Régler les valeurs de la plage (LRV, URV) sur les valeurs PV pour lesquelles on souhaite une sortie de respectivement 4 mA et 20 mA. Par exemple, 0 et 14 in. sur un plongeur de 14 in. 3. Installer et coupler le procédé actuel. Ne pas effectuer la procédure de saisie du zéro, car elle ne sera pas précise. 4. À l’aide des informations sur le type et le matériau du tube de torsion, trouver la valeur théorique pour le couple composite ou utile du tube (se reporter au supplément Simulation des conditions du procédé pour l’étalonnage des contrôleurs de niveau et des transmetteurs Fisher pour les informations relatives aux valeurs théoriques de couple du tube de torsion), et stocker les valeurs dans la mémoire de l’instrument. Il est possible d’accéder à la valeur en sélectionnant : Configure > Manual Setup > Sensor > Torque Tube > Change Torque Rate (2-2-1-3-2). Si vous sélectionnez l’option Obtenir de l’aide à la place de l’option Modifier la valeur directement, la procédure peut rechercher les valeurs pour les tubes de torsion couramment disponibles. 5. Si la température de procédé dévie de façon significative de la température ambiante, utiliser un facteur de correction interpolé grâce à des tables de module normalisé de rigidité théorique. Multiplier le couple théorique par le facteur de correction avant de saisir les données. Le gain devrait maintenant être exact à 10 % près, tout du moins pour les tubes de torsion courts à paroi standard. (Pour des tubes de torsions de longueur supérieure [249K, L, N] avec une paroi mince et une extension isolant thermique, les valeurs théoriques sont beaucoup moins précises, car les chemins mécaniques dévient considérablement par rapport aux variations linéaires.) Remarque Des tables contenant des informations concernant l’effet de la température sur les tubes de torsion sont proposées dans le supplément du manuel d’instructions intitulé Simulation des conditions du procédé pour l’étalonnage des contrôleurs de niveau et des transmetteurs Fisher (D103066X012), disponible auprès d’un bureau commercial Emerson ou sur Fisher.com. Ce document est également disponible dans les fichiers d’aide relatifs aux appareils liés à certaines applications hôtes avec des interfaces utilisateurs graphiques. 6. Évaluer la condition actuelle du procédé par le hublot de regard ou les orifices de prélèvement. Effectuer un étalonnage par ajustage du zéro et reporter la valeur dans les unités PV choisies pour le procédé. 7. Il devrait maintenant être possible de passer en contrôle automatique. Si, au cours du temps, les observations indiquent que l’instrument affiche une déviation de 1,2 fois la lecture du hublot de regard, à titre d’exemple, il est possible de diviser le couple stocké du tube de torsion par 1,2 et transmettre la nouvelle valeur à l’instrument. Effectuer alors un nouvel étalonnage par ajustage du zéro, et observer les résultats pendant une autre période pour vérifier s’il faut apporter ou non d’autres ajustements. 27 Guide de démarrage rapide Contrôleur numérique de niveau DLC3010 D103214X0FR Juillet 2020 Schémas Cette section comprend des schémas de boucle nécessaire pour le câblage d’installation de sécurité intrinsèque. Pour toute question, contacter un bureau commercial Emerson. Figure 13. Schéma de boucle CSA SCHEMA D’INSTALLATION D’ENTITE DU CSA ZONE DANGEREUSE CLASSE I, GROUPES A, B, C, D CLASSE II, GROUPES E, F, G CLASSE III BARRIERE CERTIFIEE CSA FISHER DLC3010 Vmax = 30 Vcc Imax = 226 mA Ci = 5,5 nF Li = 0,4 mH VOIR REMARQUE 3 REMARQUES : 1. LES BARRIERES DOIVENT ETRE APPROUVEES PAR LE CSA RELATIVEMENT AUX PARAMETRES D’ENTITE ET INSTALLEES CONFORMEMENT AUX INSTRUCTIONS DE SECURITE INTRINSEQUE DU FABRICANT. 2. L’EQUIPEMENT DOIT ETRE INSTALLE CONFORMEMENT AU CODE ELECTRIQUE CANADIEN, PARTIE I. 3. SI UNE INTERFACE DE COMMUNICATION PORTABLE OU UN MULTIPLEXEUR EST UTILISE, L’INSTRUMENT DOIT ETRE CERTIFIE CSA ET INSTALLE CONFORMEMENT AU SCHEMA DE CONTROLE DU FABRICANT. 4. POUR UNE INSTALLATION D’ENTITE : Vmax > Voc, Imax > Isc Ci + Ccable < Ca, Li + Lcable < La 28B5744-B 28 ZONE NON DANGEREUSE Guide de démarrage rapide Contrôleur numérique de niveau DLC3010 D103214X0FR Juillet 2020 Figure 14. Schéma de boucle FM ZONE DANGEREUSE SECURITE INTRINSEQUE CLASSES I, II, III, DIVISION 1, GROUPES A, B, C, D, E, F, G N.I. CLASSE I, DIVISION 2, GROUPES A, B, C, D FISHER DLC3010 Vmax = 30 Vcc Imax = 226 mA Ci = 5,5 nF Li = 0,4 mH Pi = 1,4 W ZONE NON DANGEREUSE BARRIERE APPROUVEE FM 1. L’INSTALLATION DOIT SATISFAIRE AUX NORMES DU CODE NATIONAL DE L’ELECTRICITE (CNE) NFPA 70, ARTICLE 504 ET ANSI/ISA RP12.6. 2. LES APPLICATIONS DE CLASSE I, DIVISION 2 DOIVENT ETRE INSTALLEES CONFORMEMENT AUX SPECIFICATIONS DE VOIR L’ARTICLE 501-4(B) DU CNE. LE CABLAGE DE L’EQUIPEMENT REMARQUE 7 ET LE CABLAGE SUR SITE SONT NON-INCENDIAIRES LORSQU’ILS SONT RACCORDES A DES BARRIERES APPROUVEES RELATIVEMENT AUX PARAMETRES D’ENTITE. 3. LES BOUCLES DOIVENT ETRE RACCORDEES CONFORMEMENT AUX INSTRUCTIONS DES FABRICANTS DE BARRIERES. 4. LA TENSION MAXIMUM DE ZONE SECURISEE NE DOIT PAS DEPASSER 250 Vrms. 5. LA RESISTANCE ENTRE LA MASSE DE LA BARRIERE ET LA MISE A LA TERRE DOIT ETRE INFERIEURE A UN OHM. 6. LES CONDITIONS D’EXPLOITATION NORMALES SONT LES SUIVANTES : 30 Vcc 20 mADC. 7. SI UNE INTERFACE DE COMMUNICATION PORTABLE OU UN MULTIPLEXEUR EST UTILISE, L’INSTRUMENT DOIT ETRE APPROUVE FM ET INSTALLE CONFORMEMENT AU SCHEMA DE CONTROLE DU FABRICANT. 8. POUR UNE INSTALLATION D’ENTITE (I.S. ET N.I.) ; Vmax > Voc, ou Vt Ci + Ccable < Ca Imax > Isc, ou It Li + Lcable < La Pi > Po, ou Pt 9. LE BOITIER DE L’APPAREIL CONTIENT DE L’ALUMINIUM, QUI EST CONSIDERE COMME UNE SOURCE POTENTIELLE D’INFLAMMATION PAR IMPACT OU FRICTION. EVITER TOUT IMPACT OU TOUTE FRICTION AU COURS DE L’INSTALLATION AFIN D’EVITER LES RISQUES 28B5745-C D’INFLAMMATION. Spécifications Les spécifications des contrôleurs numériques de niveau DLC3010 sont indiquées dans le tableau 6. Les spécifications des capteurs 249 sont indiquées dans le tableau 8. 29 Guide de démarrage rapide Contrôleur numérique de niveau DLC3010 D103214X0FR Juillet 2020 Tableau 6. Spécifications du contrôleur numérique de niveau DLC3010 Configurations disponibles Performance Montage sur capteurs 249 avec ou sans cage. Voir les tableaux 11 et 12 ainsi que la description du capteur. Fonction : Transmetteur Protocole de communication : HART Critères de performance Contrôleur numérique de niveau DLC3010(1) Avec capteur 249W NPS 3 et un plongeur de 14 in. Autres capteurs de la série 249 Linéarité indépendante $0,25 % de l’étendue d’échelle du signal de sortie $0,8 % de l’étendue d’échelle du signal de sortie $0,5 % de l’étendue d’échelle du signal de sortie Hystérésis < 0,2 % de l’étendue d’échelle du signal de sortie --- --- Répétabilité $0,1 % de la sortie de pleine échelle $0,5 % de l’étendue d’échelle du signal de sortie $0,3 % de l’étendue d’échelle du signal de sortie Bande morte < 0,05 % de l’étendue d’échelle du signal d’entrée --- --- --- < 1,0 % de l’étendue d’échelle du signal de sortie < 1,0 % de l’étendue d’échelle du signal de sortie Signal d’entrée Niveau, Interface ou Densité : Le mouvement rotatif de l’axe du tube de torsion est proportionnel à des modifications de niveau de liquide, de niveau d’interface et de densité, modifiant la flottaison d’un plongeur. Température du procédé : Interface pour un thermomètre à résistance en platine RTD de 100 ohm, 2 ou 3 fils, afin de surveiller la température du procédé ou pour une température définie par l’utilisateur, en option, pour compenser les changements de densité. Hystérésis + bande morte REMARQUE : A l’étendue d’échelle maximale programmée, conditions de référence. 1. Pour des rotations du levier en entrée. Signal de sortie Avec une bande proportionnelle utile (PB) < 100 %, la linéarité, la bande morte, la répétabilité, les effets de l’alimentation et l’impact de la température ambiante sont potentiellement réduites par un facteur de (100 %/PB) Analogique : 4 à 20 milliampères en courant continu (J en action directe, une hausse du niveau, de l’interface ou de la densité fait croître la sortie ; ou J en action inverse, une hausse du niveau, de l’interface ou de la densité fait décroître la sortie) Influences sur le fonctionnement Effets de l’alimentation : Variations de sortie de < ± 0,2 % de l’échelle pleine lorsque l’alimentation fluctue entre les tensions minimale et maximale spécifiées. Saturation supérieure : 20,5 mA Saturation inférieure : 3,8 mA Alarme haute : 22,5 mA Alarme basse : 3,7 mA Protection de tension transitoire : Les bornes de la boucle sont protégées par un suppresseur de tension transitoire. Voici ses spécifications : Seule une des définitions d’alarme haute/basse ci-dessus est disponible pour une configuration donnée. Conforme NAMUR NE 43 lorsque l’alarme haute est sélectionnée. Forme d’impulsion Numérique : HART 1 200 Baud FSK (entrée des changements de fréquence). Les exigences d’impédance HART doivent être respectées afin de permettre la communication. L’impédance totale de dérivation aux connexions de l’instrument maître (à l’exception de l’impédance maître et transmetteur) doit se situer entre 230 et 600 ohms. L’impédance de réception HART du transmetteur est définie comme suit : Rx : 42K ohms et Cx : 14 nF Décroissance à 50 % s) Max VCL (Tension de serrage) (V) Max IPP (Courant crête d’impulsion) (A) 10 1 000 93,6 16 8 20 121 83 Remarque : μs = microseconde Température ambiante : L’effet combiné de la température sur le zéro et l’étendue (ou plage), sans le capteur 249, est inférieur à 0,03 % de l’échelle pleine par degré Kelvin au-delà de la plage de fonctionnement de -40 à 80 _C (-40 to 176 _F). Température de procédé : La température de procédé affecte le couple. La densité du procédé est aussi altérée par la température de procédé. Remarquer qu’en configuration point à point, des signaux analogiques et numériques sont disponibles. Il est possible de demander des informations, sous forme numérique, à l’instrument, ou de le placer en mode rafale pour qu’il transmette lui-même des informations sur le procédé, sans avoir été sollicité. En mode multipoint, le courant de sortie est fixé à 4 mA et seule la communication numérique est disponible. Densité de procédé : La sensibilité aux erreurs de connaissance de la densité de procédé est proportionnelle à la différence de densité de l’étalonnage. Si la différence de densité est de 0,2, une erreur de 0,02 en unités de densité, sur la connaissance de la densité du fluide procédé, représente 10 % de l’étendue. - suite - 30 Temps de montée s) Guide de démarrage rapide Contrôleur numérique de niveau DLC3010 D103214X0FR Juillet 2020 Tableau 6. Spécifications du contrôleur numérique de niveau DLC3010 (suite) Compatibilité électromagnétique Conforme aux normes EN 61326‐1:2013 et EN 61326‐2‐3:2006 Immunité - pour les sites industriels, voir Tableau 2 d’EN 61326-1 et Tableau AA.2 d’EN 61326-2-3. La performance est représentée dans le tableau 7 ci-dessous. Emissions - Classe A Classification de l’équipement ISM : Groupe 1, Classe A Indications de l’indicateur LCD L’affichage LCD indique la sortie analogique sur un graphe à barres d’échelle en pourcentage. L’affichage peut également être configuré pour afficher : Unités de mesure des variables de procédé seulement. Plage en pourcentage seulement. Plage en pourcentage alternant avec variable de procédé ou Variable de procédé, alternant avec température de procédé (ainsi que la rotation d’arbre pilote en degrés). Classification électrique Caractéristiques d’alimentation (voir la figure 10) 12 à 30 Vcc ; 22,5 mA L’instrument comporte une protection contre les inversions de polarité. Degré de pollution IV, Catégorie de surtension II conformément aux termes de la norme CEI 61010 clause 5.4.2 d Zone dangereuse : CSA - Sécurité intrinsèque, antidéflagrant, Division 2, protection contre les coups de poussière FM - Sécurité intrinsèque, antidéflagrant, non incendiaire, protection contre les coups de poussière ATEX - Sécurité intrinsèque, type n, ignifuge IECEx - Sécurité intrinsèque, type n, ignifuge Pour de plus amples informations, se reporter aux certifications de zones dangereuses et aux instructions spéciales pour une utilisation en toute sécurité dans les zones dangereuses de la section Installation, qui débutent à la page 5. Boîtier électrique : CSA - Type 4X FM - NEMA 4X ATEX - IP66 IECEx - IP66 Une tension en courant constant minimale de 17,75 V est requise pour garantir la communication HART. Compensation Compensation du convertisseur : à température ambiante Compensation du paramètre densité : pour la température de procédé (nécessite des tables fournies par l’utilisateur) Compensation manuelle : possible pour le couple du tube à la température de procédé cible Moniteurs numériques Lié au signal d’alarme analogique réglable par cavalier Hi (défaut usine) ou Lo : Convertisseur de position du tube de torsion : signal d’entraînement et signal de consigne raisonnable Alarmes configurables par l’utilisateur : alarmes de limites de procédé Hi-Hi et Lo-Lo Via HART uniquement : Signal de consigne raisonnable RTD : RTD en place Moniteur de temps disponible du processeur. Moniteur d’écriture restante en mémoire permanente. Alarmes configurables par l’utilisateur : alarmes de limites Hi et Lo de procédé, alarmes de limites de température de procédé Hi et Lo, et alarmes de limites de température de composants électroniques Hi et Lo Autres homologations/certifications CML - Certification Management Limited (Japon) CUTR - Customs Union Technical Regulations (Règlementation technique de l’Union douanière) (Russie, Kazakhstan, Biélorussie et Arménie) INMETRO - National Institute of Metrology, Standardization, and Industrial Quality (Brésil) KTL - Korea Testing Laboratory (Corée du Sud) NEPSI - National Supervision and Inspection Centre for Explosion Protection and Safety of Instrumentation (Chine) PESO CCOE - Petroleum and Explosives Safety Organisation - Chief Controller of Explosives (Inde) Contacter un bureau commercial Emerson pour obtenir des informations spécifiques sur les classifications/ certifications. Diagnostic Diagnostic de courant de boucle en sortie. Diagnostic d’appareil de mesure LCD. Mesure de densité en un point en mode niveau : utilisé pour mettre à jour le paramètre de densité et améliorer ainsi les mesures de procédé Capacité de traçage du signal numérique : en examinant les variables d’anomalies et la capacité basique d’établir des tendances pour PV, TV et SV. - suite - 31 Guide de démarrage rapide Contrôleur numérique de niveau DLC3010 D103214X0FR Juillet 2020 Tableau 6. Spécifications du contrôleur numérique de niveau DLC3010 (suite) Différence de densité minimale Avec une rotation nominale d’axe du tube de torsion de 4,4 degrés pour un changement de niveau de liquide de 0 à 100 pour cent (densité = 1), le contrôleur numérique de niveau peut être réglé de façon à utiliser toute la plage du signal de sortie pour une plage d’entrée de 5 % de l’étendue nominale du signal d’entrée. Cela est équivalent à une différence de densité minimale de 0,05, avec des plongeurs de volume standard. Voir les spécifications des capteurs 249 pour connaître les volumes des plongeurs standard ainsi que les tubes de torsion à paroi standard. Le volume standard pour 249C et 249CP est de ∼980 cm3 (60 in.3), dans la plupart des autres cas, les volumes standard sont de ∼1 640 cm3 (100 in.3). Un fonctionnement à une bande proportionnelle de 5 % dégrade la précision d’un facteur 20. Utiliser un tube de torsion à paroi mince ou doubler le volume du plongeur, doublera approximativement la bande proportionnelle efficace. Lorsque la bande proportionnelle du système passe en dessous de 50 %, il faut envisager de changer le plongeur ou le tube de torsion si l’on veut préserver une précision élevée. Positions de montage Les contrôleurs numériques de niveau peuvent être montés à droite ou à gauche du plongeur, comme indiqué sur la figure 5. L’orientation de l’instrument est habituellement telle que la trappe d’accès du manchon est placée au fond, cela afin de permettre une vidange correcte de la chambre du levier et du compartiment de câblage et de limiter l’effet gravitationnel sur le levier. Si l’utilisateur installe une vidange d’un autre type et qu’une faible perte est acceptable, l’instrument peut être monté autour de l’axe pilote, à des positions séparées de 90 degrés. L’affichage LCD peut être lui aussi tourné par paliers de 90 degrés pour cet usage. Matériaux de construction Boîtier et couvercle : alliage aluminium et cuivre basse teneur Intérieur : acier plaqué, aluminium et acier inoxydable ; cartes imprimées encapsulées ; aimants fer bore néodyme Raccordements électriques Deux entrées de câble internes 1/2-14 NPT ; une à la base et l’autre au dos du boîtier à bornes. Adaptateur M20 disponible. Options J Isolant thermique J Supports pour plongeurs Masoneilant, Yamatake et Foxborot/Eckhardt disponibles J Test série de signature de niveau (Rapport de validation des performances) disponible (EMA uniquement) pour les instruments montés en usine sur un capteur de la série 249 J Étalonnage d’usine : disponible pour les instruments montés en usine sur un capteur de la série 249, lorsque l’application, la température de procédé et les densités sont connues J Dispositif compatible avec un indicateur à distance spécifique à l’utilisateur Limites de fonctionnement Température du procédé : Voir le tableau 9 et la figure 8 Température ambiante et humidité : Voir ci-dessous Etats Limites normales(1,2) Température ambiante - 40 à 80 _C (- 40 à 176 _F) Limites de transport et de stockage - 40 à 85 _C (- 40 à 185 _F) 0 à 95 %, (sans 0 à 95 %, (sans condensation) condensation) Humidité relative ambiante Tenue en pression en altitude Jusqu’à 2 000 mètres (6 562 feet) Poids Moins de 2,7 kg (6 lb) REMARQUE : Les conditions spécialisées des instruments sont définis dans la norme ANSI/ISA Standard 51.1 - Terminologie des instruments de procédé. 1. L’affichage LCD ne sera peut être pas lisible en dessous de - 20 _C (-4 _F). 2. Contacter un bureau commercial Emerson ou un ingénieur spécialisé si des températures supérieures à ces limites sont requises. 32 Référence nominale 25 _C (77 _F) 40 % Guide de démarrage rapide Contrôleur numérique de niveau DLC3010 D103214X0FR Juillet 2020 Tableau 7. Synthèse des résultats CEM : Immunité Port Boîtier Phénomène Norme de base Décharge électrostatique (DES) CEI 61000-4-2 Champ électromagnétique rayonné CEI 61000-4-3 Champ magnétique de fréquence industrielle nominale Rafale Signal/contrôle E/S Niveau de test Critères de performances(1)(2) Contact 4 kV Air 8 kV 80 à 1 000 MHz à 10 V/m avec 1 kHz AM à 80 % 1 400 à 2 000 MHz à 3 V/m avec 1 kHz AM à 80 % 2 000 à 2 700 MHz à 1 V/m avec 1 kHz AM à 80 % A A CEI 61000-4-8 60 A/m à 50 Hz A CEI 61000-4-4 1 kV A Ondes de choc CEI 61000-4-5 1 kV (ligne à la masse uniquement, chacune) B Radio-fréquences transmises par conduction CEI 61000-4-6 150 kHz à 80 MHz à 3 Vrms A Remarque : Le câblage RTD doit être d’une longueur inférieure à 3 mètres (9,8 feet) 1. A = Aucune dégradation durant les essais. B = Dégradation temporaire durant les essais, mais rétablissement automatique. Limite de spécification = +/- 1 % de la plage. 2. La communication HART a été considérée comme non adaptée au procédé et elle est utilisée essentiellement à des fins de configuration, d’étalonnage et de diagnostic. Tableau 8. Spécifications du capteur 249 Signal d’entrée Niveau de liquide ou niveau d’interface de liquide à liquide : De 0 à 100 % de la longueur du plongeur Densité : De 0 à 100 % de la modification de la force de déplacement obtenue avec un volume de plongeur donné les volumes standard sont de J 980 cm3 (60 in.3) pour les capteurs 249C et 249CP et de J 1 640 cm3 (100 in.3) pour la plupart des autres capteurs ; autres volumes disponibles en fonction du type de capteur Longueurs des plongeurs de capteur Voir les notes de bas de page des tableaux 11 et 12 Pressions de fonctionnement des capteurs Conformes aux pressions/températures nominales ANSI en vigueur pour les différents types de capteurs indiqués dans les tableaux 11 et 12 Types de raccordement de capteur en cage Les cages sont disponibles avec une large gamme de types de raccordement afin de faciliter l’installation sur des cuves ; les types de raccordement à égalisation sont numérotés et indiqués dans la figure 15. Tableau 9. Températures de procédé autorisées selon les matériaux périphériques 249 de détection de pression courants MATERIAU La plupart des capteurs de niveau en cage comportent une tête tournante. La tête peut être tournée à 360 degrés dans l’une des huit positions, comme indiqué sur la figure 5. Matériaux de construction Voir les tableaux 10, 11 et 12 Température ambiante de fonctionnement Voir le tableau 9 Pour les plages de température ambiante et l’utilisation d’un isolant thermique en option, voir la figure 8. Options J Isolant thermique J Tube de niveau pour des pressions de 29 bar à 232 _C (420 psig à 450 _F), et J Verre réfléchissant pour applications à température et pression élevées Tableau 10. Matériaux du plongeur et du tube de torsion Pièce Matériau standard TEMPERATURE DU PROCEDE Min. Max. Plongeur Inox 304 Inox 316 427 _C (800 _F) Tige du plongeur, support d’entraînement, bielle et entraînement 204 _C (400 _F) Torque Tube (Tube de torsion) N05500(1) Fonte -29 _C (-20 _F) 232 _C (450 _F) Acier -29 _C (-20 _F) 427 _C (800 _F) Acier inoxydable -198 _C (-325 _F) 427 _C (800 _F) N04400 -198 _C (-325 _F) 427 _C (800 _F) -198 _C (-325 _F) -73 _C (-100 _F) Graphite laminé/joints acier inoxydable N04400/Joints PTFE Positions de montage Autres matériaux Acier inoxydable 316, N10276, N04400, plastique et alliages spéciaux N10276, N04400, autres aciers inoxydables austénitiques et alliages spéciaux Acier inoxydable 316, N06600, N10276 1. N05500 n’est pas recommandé pour les applications de torsion au-dessus de 232 _C (450 _F). Contacter un bureau commercial Emerson ou un ingénieur spécialisé si des températures supérieures à ces limites sont requises. 33 Guide de démarrage rapide Contrôleur numérique de niveau DLC3010 D103214X0FR Juillet 2020 Tableau 11. Capteurs en cage à plongeur(1) ORIENTATION DU TUBE DE TORSION CAPTEUR 249(3) 249B, 249BF(4) Bras de tube de torsion rotatif en fonction des raccordements à égalisation MATERIAU DE CAGE, TETE ET BRAS DE TUBE DE TORSION STANDARD Fonte Acier RACCORDEMENT A EGALISATION Type Vissé 1-1/2 ou 2 A brides 2 A vis ou emboîtement soudé en option 1-1/2 ou 2 CL600 1-1/2 CL150, CL300 ou CL600 2 CL150, CL300 ou CL600 1-1/2 ou 2 CL600 1-1/2 CL150, CL300 ou CL600 2 CL150, CL300 ou CL600 Bride à face surélevée ou pour joint annulaire type RTJ en option Vissé 249C(3) Acier inoxydable 316 PRESSION NOMINALE(2) Taille (NPS) Bride à face surélevée CL125 ou CL250 249K Acier Bride à face surélevée ou pour joint annulaire type RTJ en option 1-1/2 ou 2 CL900 ou CL1500 249L Acier Face usinée (joint annulaire) 2(5) CL2500 1. Longueurs standard des plongeurs pour tous les modes (sauf 249) : 14, 32, 48, 60, 72, 84, 96, 108 et 120 in. Le 249 utilise un plongeur d’une longueur de 14 ou 32 in. 2. Raccords à brides EN disponibles en EMA (Europe, Moyen-Orient et Afrique). 3. Non disponibles en EMA. 4. 249BF disponible en EMA uniquement. Disponible également en tailles EN DN 40 avec des tailles de brides PN 10 à PN 100 et DN 50 pour des brides PN 10 à PN 63. 5. La connexion au sommet est une bride pour joint annulaire type NPS 1, pour des modes de raccordement F1 et F2. Tableau 12. Capteurs à plongeur sans cage(1) Montage Montage au sommet de la cuve Capteur Matériau standard de tête(2), de corps de plaquettes(6) et de bras de tube de torsion 249BP(4) Acier 249CP Inox 316 249P(5) Acier ou acier inoxydable Raccordement à brides (Taille) Joint NPS 4, à face surélevée ou annulaire en option CL150, CL300 ou CL600 NPS 6 ou 8, à face surélevée CL150 ou CL300 NPS 3, à face surélevée CL150, CL300 ou CL600 Joint NPS 4, à face surélevée ou annulaire en option CL900 ou CL500 (EN PN 10 à DIN PN 250) CL150, CL300, CL600, CL900, CL1500, ou CL2500 CL125, CL150, CL250, CL300, CL600, CL900, ou CL1500 (EN PN 10 à DIN PN 160) NPS 6 ou 8, à face surélevée Montage sur le côté de la cuve Montage sur sommet de la cuve ou sur une cage fournie par le client 249VS WCC (acier), LCC (acier) ou CF8M (inox 316) Pour NPS 4, à face surélevée ou à face plate WCC, LCC, ou CF8M Pour NPS 4 extrémité soudée bout à bout, XXS CL2500 WCC ou CF8M Pour NPS 3, à face surélevée CL150, CL300 ou CL600 LCC ou CF8M Pour NPS 4, à face surélevée CL150, CL300 ou CL600 249W 1. Longueurs standard des plongeurs : 14, 32, 48, 60, 72, 84, 96, 108 et 120 in. 2. Inutilisé avec des capteurs montés latéralement. 3. Raccords à brides EN disponibles en EMA (Europe, Moyen-Orient et Afrique). 4. Non disponibles en EMA. 5. Type 249P disponible en EMA uniquement. 6. Corps de plaquettes uniquement pour Type 249W. 34 Pression nominale(3) Guide de démarrage rapide Contrôleur numérique de niveau DLC3010 D103214X0FR Juillet 2020 Figure 15. Numéros des modes de raccordement à égalisation TYPE 3 RACCORDEMENTS LATÉRAUX SUPÉRIEUR ET INFÉRIEUR, VISSÉS (S-3) OU À BRIDES (F-3) TYPE 1 RACCORDEMENTS AU SOMMET ET PAR LE FOND, VISSÉS (S-1) OU À BRIDES (F-1) TYPE 4 RACCORDEMENTS LATÉRAL SUPÉRIEUR ET PAR LE FOND, VISSÉS (S-4) OU À BRIDES (F-4) TYPE 2 RACCORDEMENTS AU SOMMET ET LATÉRAL INFÉRIEUR, VISSÉS (S-2) OU À BRIDES (F-2) Pictogrammes apposés sur l’instrument Pictogramme Description Emplacement sur l’instrument Verrouillage du levier Poignée Déverrouillage du levier Poignée Terre Logement de boîtier à bornes National Pipe Thread (NPT) Logement de boîtier à bornes T Test À l’intérieur du boîtier à bornes + Positif À l’intérieur du boîtier à bornes _ Négatif À l’intérieur du boîtier à bornes RS Connexion RTD À l’intérieur du boîtier à bornes R1 Connexion RTD 1 À l’intérieur du boîtier à bornes R2 Connexion RTD 2 À l’intérieur du boîtier à bornes 35 Contrôleur numérique de niveau DLC3010 Juillet 2020 Guide de démarrage rapide D103214X0FR Ni Emerson, ni Emerson Automation Solutions, ni aucune de leurs entités affiliées n’assument quelque responsabilité que ce soit quant au choix, à l’utilisation ou à la maintenance d’un quelconque produit. La responsabilité du choix, de l’utilisation et de la maintenance d’un produit incombe à l’acquéreur et à l’utilisateur final. Fisher et FIELDVUE sont des marques qui appartiennent à l’une des sociétés de l’unité commerciale d’Emerson Automation Solutions d’Emerson Electric Co. Emerson Automation Solutions, Emerson et le logo Emerson sont des marques de commerce et de service d’Emerson Electric Co. HART est une marque déposée appartenant à FieldComm Group. Toutes les autres marques sont la propriété de leurs détenteurs respectifs. Le contenu de cette publication n’est présenté qu’à titre informatif et bien que les efforts aient été faits pour s’assurer de la véracité des informations offertes, celles-ci ne sauraient être considérées comme une ou des garanties, tacites ou expresses, des produits ou services décrits par les présentes, ni une ou des garanties quant à l’utilisation ou à l’applicabilité desdits produits et services. Toutes les ventes sont régies par nos conditions générales, disponibles sur demande. Nous nous réservons le droit de modifier ou d’améliorer la conception ou les spécifications desdits produits à tout moment et sans préavis. Emerson Automation Solutions Marshalltown, Iowa 50158 USA Sorocaba, 18087 Brazil Cernay, 68700 France Dubai, United Arab Emirates Singapore 128461 Singapore www.Fisher.com 36 E 2005, 2020 Fisher Controls International LLC. Tous droits réservés.